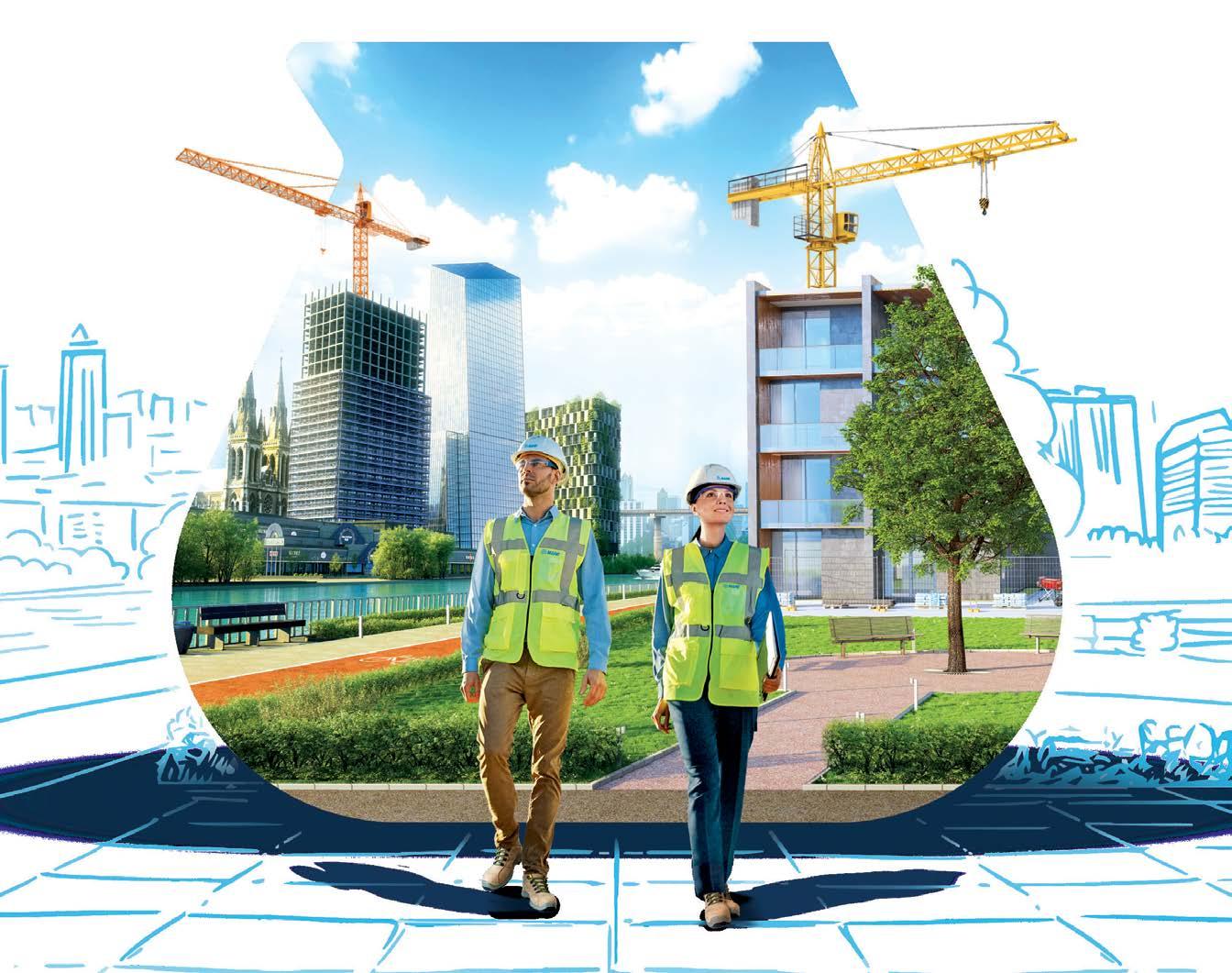
HANSEN YUNCKEN
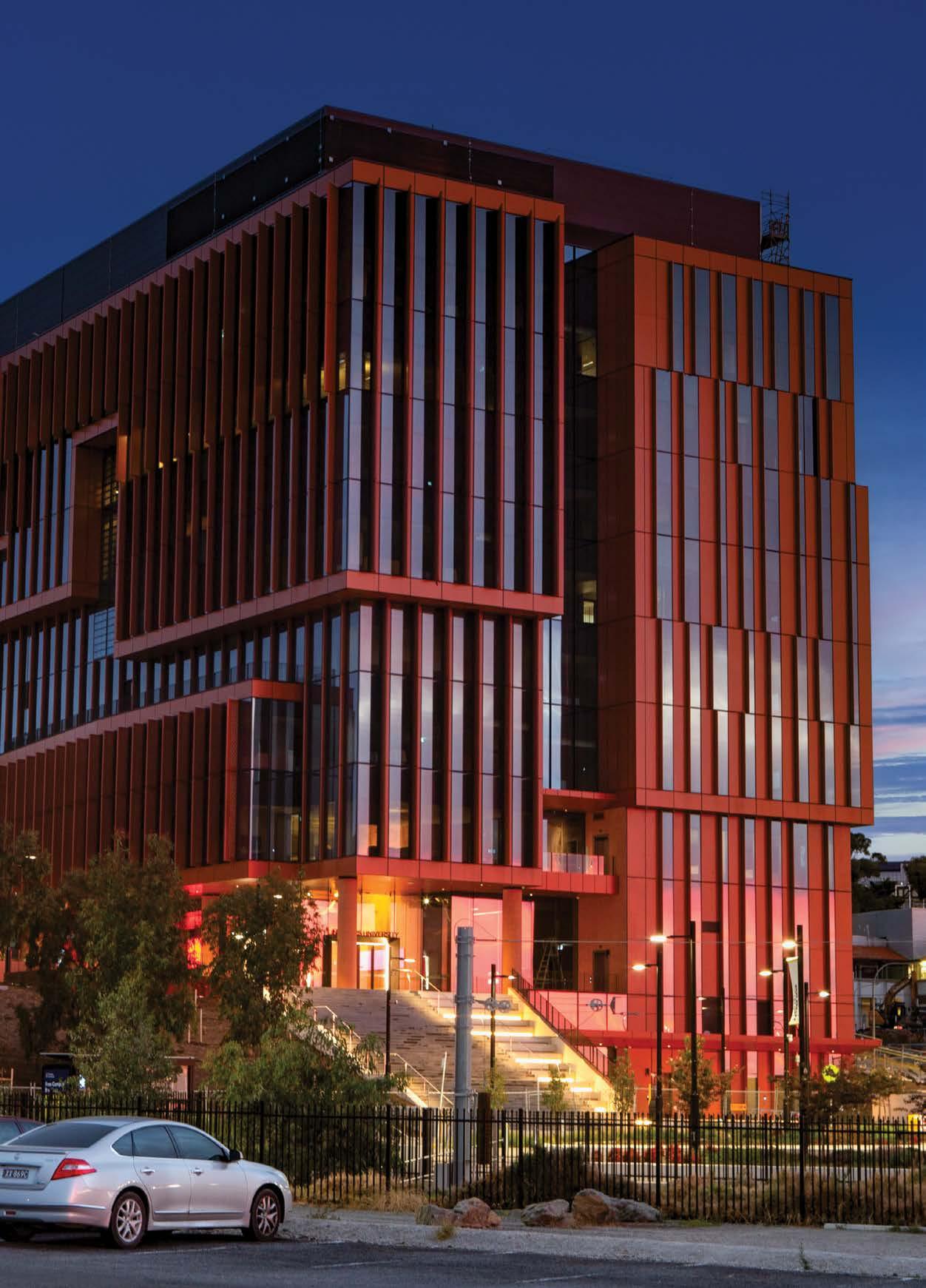
UNVEILING THE POTENTIAL OF MEDICAL RESEARCH
MIRVAC
TOGA GROUP
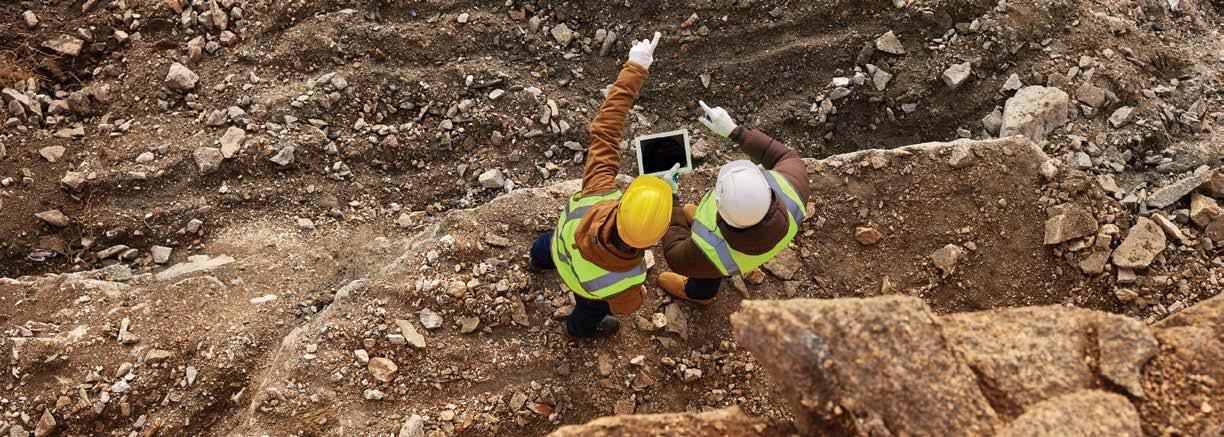
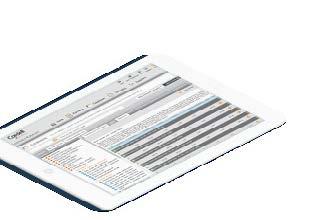
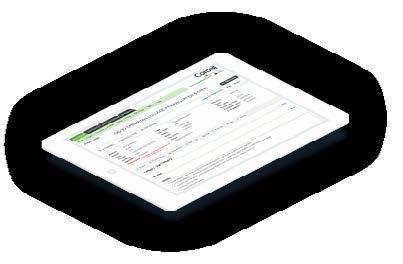
Find out more about how Cordell Connect and Cordell Estimator Platinum can help your business grow
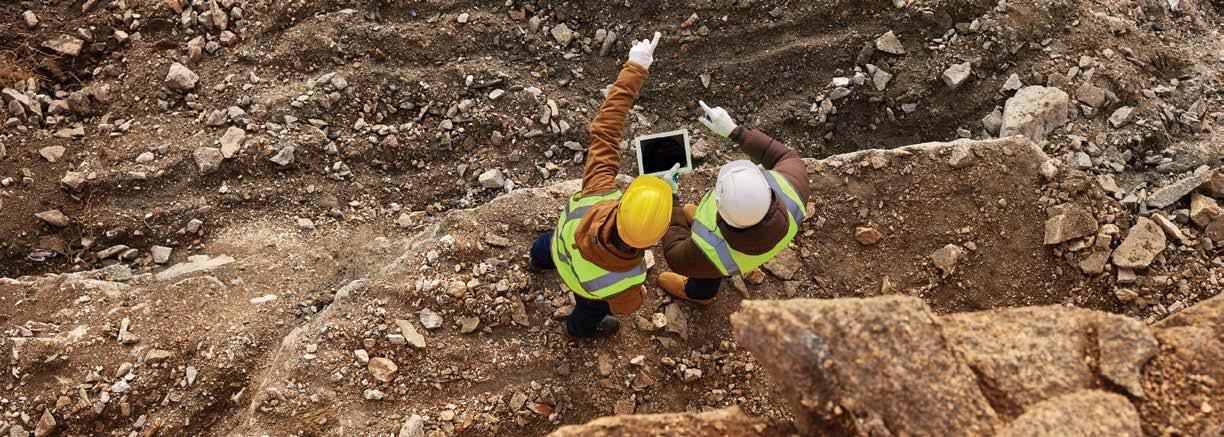
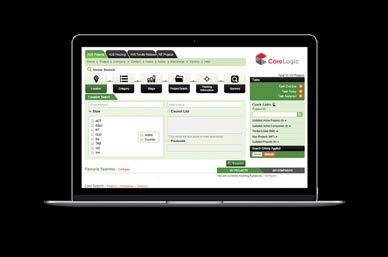
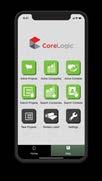
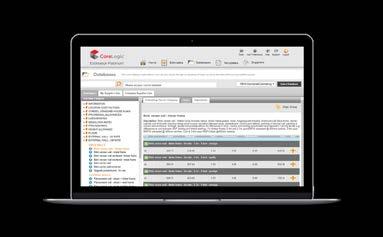
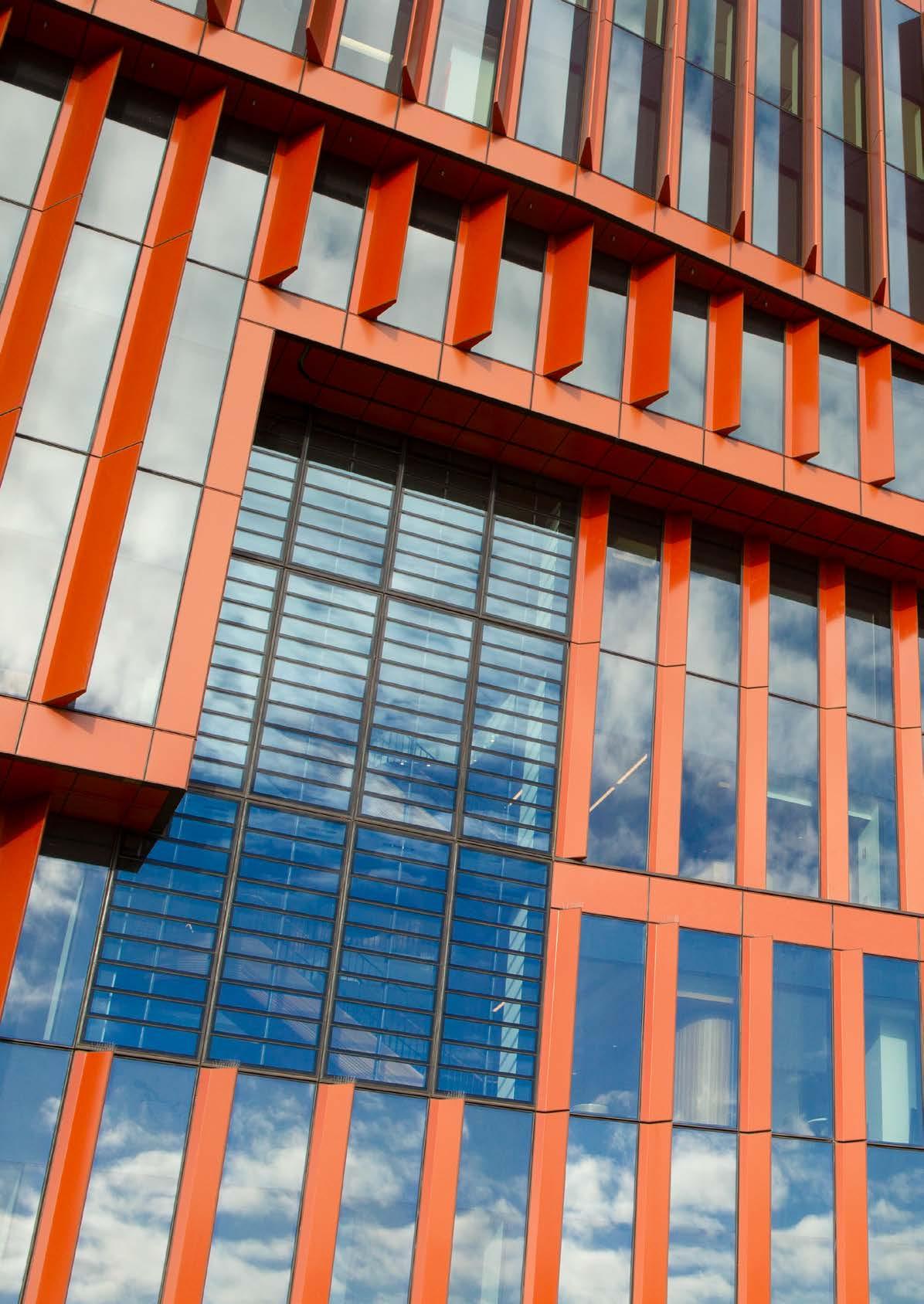
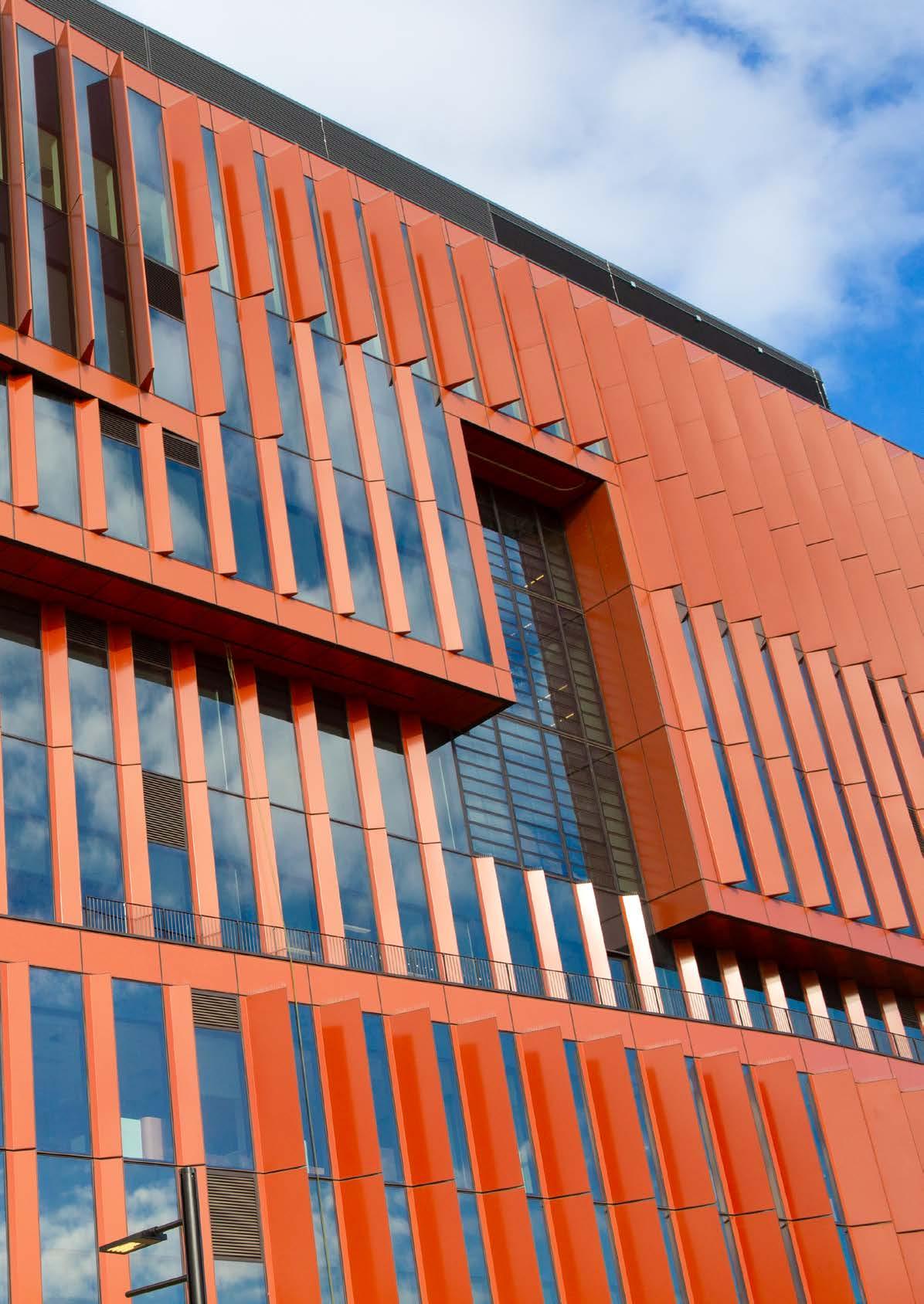
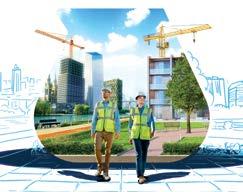


UNVEILING THE POTENTIAL OF MEDICAL RESEARCH
Find out more about how Cordell Connect and Cordell Estimator Platinum can help your business grow
Medium and large-scale construction projects will have a better chance of success if they are able to adhere to a set of success criteria, new research from Edith Cowan University (ECU) found.
ECU Lecturer Dr Neda Kiani Mavi has developed a system that could help builders take the guess work out of the feasibility of construction projects. The machine learning-based decision support system is able to forecast the success of mid- and large-scale construction projects based on their identified critical success factors and criteria.
“There is a need to clearly define and determine success factors and success criteria for construction projects to make project success measurement possible,” said Dr Kiani Mavi. In her research, Dr Kiani Mavi has identified 19 success criteria, which have been grouped into five clusters: project efficiency, business success, impacts on end-users, impacts on stakeholders, and impacts on the project team.
“Our findings reveal that project efficiency holds the highest importance, followed by impacts on the project team and stakeholders. Within project efficiency, effective risk management is ranked as the most crucial criterion. This enables organisations to manage and monitor risks effectively by employing strategies such as resource reallocation.
“Research revealed that large construction projects exceeding $200 million often surpassed their budgets by over 30%, with 77% of them lagging behind schedule by more than 40%, partly due to ineffective risk management practices. However, efficient, and effective operations management can enable construction companies to achieve margins ranging from 20% to 30%.”
The construction industry plays a pivotal role in the development of economies worldwide. In Australia, this sector contributes approximately 20% to the nation’s gross domestic product, which totals over $2.85 trillion.
The Australian Construction Industry Forum (ACIF) recently forecast that the building and construction industry would grow by 5% in 2023-24, raising the value of work
currently under way to $298 billion. However, as the ACIF points out, the industry has been grappling with a difficult economic environment, which included rising inflation, high interest rates and industrial relation changes.
“Despite its vital role in the economy, the construction industry faces numerous challenges that significantly impact its success. The inherent complexity and uncertainty of construction projects make them difficult to manage, even for experienced project managers,” said Dr Kiani Mavi.
“The Australian construction sector is particularly affected by issues such as stagnant productivity growth and increasing pressures related to risk management. Over the past three decades, Australia’s productivity in this sector has been
We offer unique, cost effective and high quality professional aerial and site time lapse photography, along with video from drone, plane and helicopter for the construction and property industry.
SKYview has been in business for nearly 20 years servicing the construction industry, with over 25 years of onsite construction experience.
We can service everything from small residential projects to the largest of government projects, throughout NSW and ACT.
We are unconditionally certified, insured and operate from planes, helicopters and drones as required.
On 6 May, the Queensland Government confirmed engineered stone will be banned across the state from 1 July this year.
This follows the agreement by the nation’s Work Health and Safety Ministers to prohibit the use, supply, and manufacture of engineered stone benchtops, panels and slabs containing crystalline silica across the nation. Several other products will be excluded from the prohibitions.
The safety of our building and construction workers is of course, paramount – and without compromising that safety, but against the backdrop of the dual crises of cost of living and housing shortages, there are other considerations.
Master Builders had written to Minister Grace Grace twice after the national ban was announced, seeking clarity on whether
persistently poor, resulting in an estimated $47 billion in lost opportunities.”
The 2023 KPMG Global Construction Survey showed that an overwhelming 87% of project managers continue to struggle with project performance, often dealing with schedule delays and cost overruns. Additionally, only 50% of project owners are successfully meeting completion deadlines, mainly due to effective risk management strategies.
Dr. Kiani Mavi’s decision support system analyses the interrelationships among critical success factors and critical success criteria of construction projects, to forecast project success.
She noted that the early introduction of the application would allow for early intervention in a project, which could mitigate potential delays, cost overruns or other issues.
“When contractors, sponsors, owners, and project managers understand whether a project is more or less successful than previous similar projects, they then can address the weaknesses and improve the strengths to enhance the success of their own project in terms of project efficiency,
a transition period would apply for contracts entered into before 13 December, as Work Health Safety Queensland had previously flagged.
The state government has now belatedly confirmed there will be no transition period. We acknowledge the decision not to adopt a transition period was due to the government’s view that there was an unacceptable risk to workers’ safety.
However, many small businesses had relied on these commitments. During what is already a tough time in economic terms, it remains to be seen how many of them are caught short and suffer a financial impact.
We urge government to make the appropriate regulatory changes as quickly as possible, to ensure builders with contracts on foot can obtain agreement with their clients on a variation, allowing them to find alternative products, and complete their works as seamlessly as they can.
addressing things like schedule, budget, scope, quality, and project effectiveness, addressing issues of business success, and stakeholder satisfaction,” Dr Kiani Mavi added.
“Successful projects lead to satisfied clients, enhanced reputations for companies, and increased profitability. On the other hand, project failures can result in financial losses, legal issues, and damage to a company’s reputation. Given this, understanding and achieving project success is crucial for project sponsors who aim to control both current
and future projects. So, forecasting project success is not just beneficial but essential for the industry.”
Scan to read
Dr Kiani Mavi’s research, as it appeared in the International Journal of Construction Management
Scan to read
Dr Kiani Mavi’s research in Engineering, Construction and Architectural Management.
The refrigeration industry will be among 30+ trades represented at the 47th WorldSkills International tournament, a global movement dedicated to promoting the skills excellence of young tradespeople playing a crucial role in the visibility, development, and empowerment of tomorrow’s experts.
WorldSkills Australia competitor, Bailey Loenneker, a fourth-year refrigeration apprentice from the Sunshine Coast, and his Expert Carl Balke will represent Australia in the Refrigeration and Air Conditioning
category on the global stage in Lyon, France in September to compete against the best young apprentices in the world.
The contingent of apprentices, trainees, and students, known as the Skillaroos, is the largest delegation of competitors, trainers, officials, and team management ever sent to an International Competition.
Scan to Read the full article
INDUSTRY COMMENT
TITLE
NAME title and company
The Civil Contractors Federation NSW welcomed the $119 billion essential infrastructure investment outlined in today’s [18th June, 2024] NSW Budget but warned it will not be delivered unless the NSW government removes the red-tape that cuts out local contractors and makes construction slow and unaffordable.
“We have the opportunity to build more houses, schools and hospitals for NSW, but only if we overhaul the pipeline which is deathly slow and clogged by bureaucratic road blocks,” said CEO of the state’s peak body for civil construction industry, Ms Kylie Yates.
“Despite the opportunities, local contractors are currently locked out of 1 in 2 state government projects due to costly red tape, and lack of suitable projects coming to market.”
“We commend the Minns Government for this year’s State Budget in difficult circumstances, and look forward to working with them to help improve infrastructure delivery in NSW.”
Budget highlights welcomed by the NSW civil construction industry include the:
• $119.4 billion Essential Infrastructure Plan to 2027-28 which includes:
• $62.9 billion in transport Infrastructure
• $17.6 billion in water infrastructure, including $362.3 million for regional water security (co-funded by the Australian government)
• $6.1 billion in social housing
• $9.5 billion in schools and education
“It’s great to see new road projects announced including a $661 million upgrade to Elizabeth Drive to provide access to Western Sydney Airport and the widening of Mamre Road between Erskine Park Road and Kerrs Road,” Ms Yates said.
“We support the funding committed to plan further improvements to regional roads including the Golden Highway from Dubbo to Newcastle, Hume Highway and Mount Ousley.
“Infrastructure investment creates local jobs and keeps our local economy thriving, so we applaud the Minns Government’s continued commitment to a strong pipeline,” Ms Yates said.
“In rolling out this budget over the next four years, civil contractors urge the Minns Government to deliver on its promise to support local industry.
“Building a better NSW means releasing construction tender packages of all sizes and cutting red tape so that local businesses can win head contract opportunities in their own state.”
Your Subscription to the Australian National Construction Review ensures you receive our premium hard copy publication, featuring stunning Project Showcases, Case Studies, Product Information and Commentary from within the industry and associated disciplines.
OR if digital is more your speed, subscribe to our e-newsletter, released monthly for a snapshot of new products, innovations and services that can benefit your next project.
BESIX Watpac has been appointed as the Principal Contractor for the modernisation, upgrade, and life extension of Airservices Australia’s (Airservices) Sydney Kingsford Smith Airport Air Traffic Control Tower.
The commencement of construction marks a significant milestone for the air traffic control tower which originally began operations in 1996. Upgrade works will progress in stages through to 2025, adding two decades to the lifespan of the facility.
Under the purview of the Airservices Sydney Kingsford Smith Airport Air Traffic Control Tower Life Extension (LEX) project, BESIX Watpac will undertake infrastructure upgrades to enhance the condition and longevity of the facility which houses critical air traffic management services for one of Australia’s busiest airports.
Key elements of the project include the upgrade of existing building systems, construction of a new services building, enhancement of security infrastructure, civil works, amenities, and landscaping.
Sydney’s original home of sport and entertainment is poised for a transformational chapter in its history through a partnership between BESIX Watpac and Venues NSW that will deliver new community and recreational facilities, increased public space and a new
underground car park in the Moore Park Precinct Village project.
BESIX Watpac CEO Mark Baker said the project win is testament to BESIX Watpac’s ability to add value coupled with the breadth of experience in the NSW team.
Award-winning developer Billbergia has reached a major construction milestone on Stage Two of Rhodes Central, ‘topping out’ Peake Tower - a 48-level residential high-rise apartment building. Peake Tower is now the tallest building in Rhodes - part of the $2.5 billion Rhodes Central, Billbergia’s ambitious three-stage master-planned precinct in Sydney’s inner-west.
Delivering critically-needed new homes for over 3,500 people, Rhodes Central is a multistage five-tower development at Rhodes Rail Station, overlooking the Canada Bay foreshore.
Stage Two comprises a combined total of 674 apartments across two residential high-rise buildings, Peake Tower and Oasis. It will also see the delivery of $70 million in new community infrastructure – including a 9,100m2 multipurpose community recreation and childcare centre – built in the precinct’s three-level podium through a planning agreement with City of Canada Bay.
“We are delighted to have reached this exciting milestone on Peake Tower, a critical step towards the completion of this new waterfront precinct at Rhodes. Our vision of creating a highly-connected new community is fast becoming a reality,” said Rick Graf, Development Director at Billbergia.
Located at 34 Walker Street, Peake Tower and Oasis were designed by high-profile architects SJB.
Peake Tower stands an impressive 162m above street level, and over 1.7 million hours of labour have been worked to date on Stage Two of Rhodes Central. Interestingly, some 200,000m3 of bulk excavation and 85,000m3 of concrete has been used to get the Peake and Oasis towers to their highest point.
Rhodes Central’s Stage One comprises a total of 568 apartments across two buildings of 25 and 39 storeys, the tallest of which features an iconic heliostat. The towers sit above the award-winning, >13,000m2 Rhodes Central super neighbourhood shopping centre, delivered by Billbergia in 2021.
A significant employment generator, some 10,000 direct and indirect jobs have been created to date by the construction of Rhodes
“BESIX Watpac is thrilled to be entrusted with this high-profile project that will enhance both the SCG and Allianz Stadium’s appeal as a recreational destination,” Mr Baker said.
“The project will benefit from our team’s commitment to delivering innovative solutions that meet the needs of our clients as well as enrich the surrounding community – these include proposing alternative design solutions to optimise functionality, mitigate risks and save time while retaining quality.”
The project will see an existing parking area near Allianz Stadium and Sydney Cricket Ground (SCG) transformed into a vibrant ‘village precinct’ featuring accessible open green spaces, a children's play area, food and beverage offerings and the creation of a car park with up to 1500 spaces available.
Central, with at least a further 450 permanent jobs within the completed precinct.
Progressive completion of Peake Tower is due in Q3 2024.
Do you have a project, media release, product or news item you would like to feature with the Australian National Construction Review?
Get in touch with our submissions team by scanning the code or at submissions@ancr.com.au to find out more.
oceaniaglass.com.au
The NSW Government Women in Construction Program has launched a survey to deepen the understanding of women’s experiences in the construction industry and shed light on the cultural and diversity challenges across the sector.
As one of the most male dominated industries in Australia, women make up just 13% of the construction sector and 2% trade roles. With construction facing severe skills shortages, particularly in trade roles, the need to take steps aimed at making the sector more diverse and inclusive is critical to deliver the State’s infrastructure pipeline.
The survey, targeting construction businesses and workforce, builds on baseline data collected in last year’s inaugural survey. In addition to providing insights into the experiences of women in construction, the findings enable Government to make data driven decisions on allocating resources
to shift the dial and improve women’s participation in the construction sector.
Results from last year’s survey revealed a lack of work-life balance and flexible working hours as the top issue for both men and women, as well as insights into the working conditions and policy implementation across businesses.
These results have informed policy changes aimed at improving workplace practices and
highlight the importance of the continued partnership between Government and industry to deliver change.
The survey is being delivered as part of the Women in Construction Program alongside a range of initiatives aimed at increasing and retaining women in construction trade and non-traditional roles
Scan to take the Survey
Construction is the second most maledominated workplace in Australia. The scale of construction needed to support the housing and infrastructure transition for our growing population requires an increase in the workforce that should be met by increasing women’s participation. Improving women’s participation in the industry doesn’t have a single fix, we need a multifaceted approach. We need to make the industry a safer and more equitable place to work and come together to understand the factors that many women experience causing them to leave.
At NAWIC, we are dedicated to increasing the number of women entering the construction industry to 40% by 2030. If we want to reach this target, we need more girls and women to see the industry as a place for them to thrive. Our advocacy focuses on their attraction, retention and career development. NAWIC’s Five Priorities aims to close these gaps and create an equitable construction industry where women fully participate.
The lack of women within senior leadership positions directly relates to the lack of women who see themselves in them. Providing
leadership training, mentoring programs, scholarships, KPI and addressing bias will support their growth. We want to see 30% of women in leadership positions in top 20 construction companies by 2030.
We need to see better representation of women in the trades. Tradies are well paid and have real economic growth. Let’s promote the trades to young women and girls and show university pathways. Our goal is to increase the current statistics of women only representing 3% of those working in trades.
We need to focus on prevention and enforcement on zero tolerance policies for sexual harassment. This includes education, anonymous reporting, legal aid for complainants, mandating induction topics and enforcing workplace termination policies for perpetrators.
Safe and Appropriate Facilities on all Worksites
There are often no safe or close toilets for women on remote worksites. Our latest
campaign highlights the right of workers in remote and mobile settings, and how you can advocate for appropriate facilities that meet Government standards.
Women are paid 20% less than their male counterparts. We need to close the gender pay gap in construction by auditing businesses, advancing women into leadership roles and reconsidering renumeration of female roles.
No single measure is going to fix the issue of not enough women in construction. Government, membership organisations and construction firms need to work together. The National Association of Women in Construction (NAWIC) is a not-for-profit organisation led by a team of employees and volunteers who all strive to champion and empower women to reach their full potential through membership. Our mission is to drive changes that will aid in the increased recruitment, retention and further development of women in the construction industry.
You can join the conversation on our socials @nawicau and keep up with our advocacy, events and opportunities at nawic.com.au.
As we celebrate the 20th anniversary of the Australian National Construction Review, we want to extend our deepest gratitude for your unwavering support. For two decades, you have been at the heart of our journey, helping us grow and evolve into a trusted source of industry news and insights.
Your loyalty and trust have been the driving force behind our continued success. We are immensely proud to serve such a dedicated and passionate community. Thank you for being an integral part of our story, and we look forward to many more years of partnership.
futuro. infrastrutturali, ai globale. Nel segno sostenibile. global residential name industry.
rivolto al futuro. infrastrutturali, ai globale. Nel segno più sostenibile. contributes at a global works, residential in the name building industry.
Richard Crookes Constructions (RCC) recently completed Lot 1 CEVA Warehouse, a 35,000m² flagship project within Mirvac’s Aspect Industrial Estate in Western Sydney. This state-of-the-art facility features diverse storage options and modern office space with a focus on flexibility, functionality, sustainability, and cutting-edge technology.
Lot 1 CEVA Warehouse is a cutting-edge facility, designed to meet the diverse and every-changing needs of modern logistics operations. The first warehouse delivered within the Aspect Industrial Estate, Lot 1 CEVA offers exceptional industrial facilities that put the focus on flexibility, functionality, and sustainability for the needs of logistic handling.
Designed to accommodate client needs, Lot 1 CEVA Warehouse features multiple storage solutions including 20,000m2 of ambient
storage, 12,7000m2 of temperature-controlled storage (between 15-2C5C) and modern office spaces including three dock offices.
This advanced industrial facility includes 1,510 solar panels, generating an 830kW photovoltaic system with a 500kW battery to maximise self sufficient energy consumption and generation. This is complemented by translucent roof sheeting, LED lighting, electric vehicle charging points, and rainwater harvesting systems. These features align with CEVA Logistics’ commitment to achieving net zero by 2050.
The strategic location of the warehouse, close to the Western Sydney Airport and major transportation routes such as the M4 and M7 motorways, makes it a crucial hub for logistics in the region. This positioning allows CEVA Logistics to efficiently serve the growing demands of the technology and healthcare sectors in New South Wales, reinforcing the importance of this development for the local economy.
The successful delivery of the CEVA warehouse is a testament to Richard Crookes Constructions’ commitment to excellence
and their ability to meet the evolving needs of their clients. With a focus on quality, sustainability, and strategic partnerships, Richard Crookes Constructions continues to be a driving force in the delivery of industrial facilities that support economic growth and sustainability.
The completion of the CEVA warehouse was celebrated with a formal event attended by New South Wales Premier Chris Minns, Minister for Roads John Graham, and representatives from Mirvac, the Australian Retirement Fund, and CEVA Logistics. Premier Minns highlighted the importance of this development, stating,
“The brand-new facilities at the Mamre Road Precinct are cutting edge and will form the backbone of an expanding growth in the economy out here in Western Sydney.”
This complex facility came to life as a result of close collaboration between Mirvac, Australian Retirement Fund, CEVA Logistics and Richard Crookes Constructions. This project forms part of a broader initiative to develop Aspect Industrial Estate, which is expected to create over 500 jobs during construction and 1,200 operational jobs, further contributing to Western Sydney’s economic growth.
For more information visit Richard Crookes Constructions, Levels 13/14, 558 Pacific Highway, St Leonards, NSW 2065, phone 02 9902 4700, email reception@richardcrookes.com.au, website www.richardcrookes.com.au
Founded in 2010, Trio Sign Group has evolved into one of Adelaide's leading signage and project management companies. The company’s inception is rooted in the combined expertise of its founders, Ryan Westley and Andrew Baohm, who brought together their unique skills to create a dynamic and innovative signage company.
Today, Trio Sign Group is renowned for its comprehensive signage solutions, its track record speaks volumes for the quality, workmanship and attention to detail that goes into every one of their projects, something that owners Ryan and Andrew are very proud of.
Ryan Westley, a qualified industrial designer with over 20 years of experience in the signage industry, began his journey at the University of Johannesburg, graduating with a qualification in Industrial Design. He initially designed and built exhibition displays at a small signage company, later managing the prototype department at Kitemark in South Africa, where he gained extensive experience in quality workmanship and design. Ryan’s career spanned various industries and countries, including construction, building, manufacturing, and demolition. In 2001, he moved to Australia and worked as a Graphic and 3D Exhibition Designer at the Museum and Art Gallery of the Northern Territory, enriching his skill set and preparing him to co-found Trio Sign Group.
Andrew Baohm brings over 35 years of experience in the visual communication industry. His background as a professional photographer and marketing manager paved the way for his transition into the signage industry. Andrew’s journey in signage began working for 20 years with one of Adelaide’s most successful photographic laboratories and 15 years as Director of Business Development in a former successful signage company he was a partner in. Andrew’s extensive experience and network in the digital printing and signage industry have been instrumental in helping Trio Sign Group establish itself as a trusted brand in the Construction and Architectural Signage industry.
Ryan Westley
The idea for Trio Sign Solutions was born when Ryan approached Andrew with intention to start his own signage business, together they recognised the potential of joining forces to leverage their combined expertise to create a new venture that could tackle a broader scope of projects. The duo set an ambitious goal: to expand their market from small-scale signage to large corporate and architectural projects. The challenge was met with resounding success, leading to the rapid growth of Trio Sign Solutions.
In 2018, the company bolstered its market position by acquiring Signscope, a major competitor and one of Adelaide’s most successful signage companies. This strategic acquisition further established Trio Sign Solutions as a leader in corporate and architectural signage in South Australia.
By 2023, Trio Sign Solutions continued growth necessitated a move to larger premises. The company purchased J&J Signs and relocated to Mile End, just outside Adelaide's CBD. The new location provided a much larger facility providing the necessary space for continued growth and expansion, not just for production but also their expanding project management and design team.
With the acquisition of J&J Signs, Trio Sign Solutions had now acquired two of its competitors, each with over 40 years of experience and history in the signage industry in South Australia.
It was now only fitting that Trio Sign Solutions would simply become Trio Sign Group and continue on with its increased knowledge, expertise and experience producing the highest possible standard of signage for the architectural & construction projects they work on.
Trio Sign Group specialises in providing a complete signage solution. The company’s capabilities include industrial and graphic design, project management, signage manufacture and installation for corporate and architectural projects. Their focus on communication and collaboration sets them apart from competitors. Clients work directly with dedicated project managers through every stage of the process, ensuring streamlined communication and successful project completion. Trio Sign Group works at all levels of the construction industry up to tier one. It works regularly on State Government, Commonwealth Government and Classified Defence Projects with its clients and is adaptable to providing signage solutions for any industry.
Trio Sign Group has worked on numerous high-profile projects, recently they have been particularly active in the growing healthcare sector. The Queen Elizabeth Hospital redevelopment is the largest single project the company has undertaken, involving extensive internal wayfinding signage. Other notable healthcare projects include the Mount Barker Hospital Emergency Department, Gawler Hospital Emergency Department and they are currently working on the new Playford Health Hub.
Beyond healthcare, Trio Sign Group has a diverse range of clients, working regularly in industries such as Defence, Education, Aged Care, Architecture, Construction and Property Development.
They have collaborated with Australian Naval Infrastructure on the Signage at the Osborne Ship and Submarine Building Facility and Walker Corporation on the Riverlea Development, the largest housing development project in South Australia. Their client list includes major builders such as Lendlease, Built Environs, Sarah Construction, Built, Schiavello just to name a few.
Trio Sign Group is committed to continuing its growth and innovation in the signage industry. With a focus on collaboration, quality, and client satisfaction, the company aims to remain at the forefront of corporate and architectural signage in South Australia.
For more information on Trio Sign Group contact Andrew Baohm, mobile 0418 500 778, email andrew@triosigngroup.com.au
PROJECT : Frankston High School
LOCATION : Frankston, Melbourne, VIC
COMPLETION DATE : November 2023
CONTRACTOR : Mechflow Air-Conditioning
Located in Melbourne South, Frankston High School underwent a transformative journey with the refurbishment and expansion of the campus. Mitsubishi Heavy Industries Australia with trusted contractors Mechflow Air-Conditioning, collaborated to provide energy-effieicent ceiling cassette and wall-mounted system to service the developments multiple areas.
Frankston High School, a renowned public school in Melbourne’s South, is marking a significant milestone in 2024 as it turns 100 years old.
To meet the needs of its nearly 2,000 current student enrolments and provide top-notch facilities, the school embarked on a large-scale, multi-million dollar redevelopment project.
The redevelopment included the construction of new buildings, in addition to extensions to existing structures, to support the ongoing needs of the student population and staff. Facilities included the
upgrade or addition of 34 rooms, ranging from purpose-built classrooms, learning spaces, common rooms, amenities, server rooms and office space.
Research has indicated a direct correlation between student comfort and their learning abilities. To ensure the student’s environment was optimised for learning, the climate control system was required to be reliable, energy-efficient, and applied to all spaces of the new builds, and the retrofit applications.
Furthermore, it was necessary for the system to run quietly to reduce disturbances and save energy. Centralised control and monitoring were also crucial for facility managers to effectively oversee the school’s climate control systems.
After careful consideration and discussions with trusted contractors Mechflow Air-Conditioning, a selection of ceiling cassette systems and wall-mounted systems from Mitsubishi Heavy Industries AirConditioning Australia were chosen for the project.
The FDT ceiling cassette systems were selected for classrooms and common areas, offering high airflow yet quiet operation. Due to the small amount of space in between levels, this proposed a design challenge for indoor unit selection.
Indoor Units Installed
24 X FDT**KX Ceiling Cassette Systems
41 x FDK**KXZ Wall Mounted Split Systems
Outdoor Units Installed
7 X FDC***KXZE2 VRF Systems
1 X FDC**KXZEN1-W VRF Systems
With two plant rooms, one located in the basement and one on the roof – both being quite small in size, it was important that all condensing units were compact and allowed for flexibility to ensure installation, commission and ongoing maintenance would be as easy as possible.
The FDT series features a draught prevention panel which utilises four specially designed louvres to direct airflow horizontally along the ceiling, eliminating uncomfortable draughts for students and staff. These systems also incorporate a built-in drain pump which discharges up to 850mm, allowing for easy installation and flexibility regarding pipe design.
For spaces with limited ceiling space, the FDK series of wall-mounted systems were chosen. These systems offer a flexible solution and are connected to a mix of KXZRE2 VRF systems and KX Micro VRF systems. The KXZRE2 series of outdoor units provide high energy efficiencies, while the KX Micro systems offer easy installation due to their compact size.
All systems were installed with wall-mounted RC-EXZ3A’s wired controllers for ease of use for occupants. These controllers also allow the systems to be connected to central controllers, providing staff with
day-to-day control and facility management with advanced control and monitoring capabilities.
The completion of this project ensures that Frankston High School can continue to offer a comfortable and conducive learning environment for its students, setting them up for success for the next 100 years and beyond.
Delivering engineering excellence for over 130 years, the Mitsubishi Heavy Industries brand has a rich history of superior air conditioning products. Japanese-engineered technologies enable the design and delivery of world class air conditioning systems that go the distance within the tough Australian climates.
Standing behind the quality of MIHAAA’s products is their commitment to their customers and after sales service guarantees.
For more information contact Mitsubushi Heavy Industries Air-Conditioning Australia, Pty. Ltd., Block E, 391 Park Road, Regents Park NSW 2143, phone 1300 130 007, info@mhiaa.com.au, www.mhiaa.com.au
Scan the QR Code to discover more on Frankston High School and MHIAA's solution.
The Ashfield Polish Club’s recent $72 million renovation is a testament to the club’s commitment to providing top-tier facilities while preserving its rich heritage.
Opening its doors to the public in June 2023, the club’s transformation is remarkable, featuring an expansion to 1,800m2 and the addition of 80 residential apartments.
This renovation also introduced new restaurants, a café and deli, function rooms, pokies, and a reception area, making it a comprehensive upgrade. The project was led by Deicorp, a renowned developer who also recently upgraded the Petersham RSL.
For such a significant project, selecting the right window and door systems was crucial. Style Windows & Doors, the appointed fabricator, chose Darley Aluminium’s commercial framing and CityView window and door systems to meet the multi-functional needs of the club. These systems provided the perfect balance of modern aesthetics and respect for the club’s Polish heritage.
Darley Aluminium, an Australian-owned family business, has been at the forefront of the aluminium industry for over 26 years. Known for their wide range of aluminium
extrusions, Darley has built a reputation for delivering high-quality solutions across various sectors, including residential, commercial, aged-care, and education. Their extensive experience and commitment to excellence make them a trusted partner for large-scale projects like the Ashfield Polish Club.
The renovation required a comprehensive solution that could cater to diverse areas within the club, including the main restaurant, dining area, café, and outdoor courtyard.
The choice of Darley’s 100mm x 50mm Front Glazed commercial framing system
Fabricator: Style Windows & Doors
Darley Systems Installed:
• 100m x 50mm Front Double Glazed Commercial Framing
• 45mm Commercial Hinged Doors
• 45mm Commercial Sliding Doors
• Cityview Sliding Windows
• Cityview Apartment Doors
• 100mm x 50mm Centre Commercial Glazed Framing
and 45mm commercial hinged doors ensured that each space is highly functional and durable and gave the outdoor courtyard area a chic Parisian feel.
In the main restaurant, dining, and café areas, the commercial framing system provided panoramic views and an abundance of natural light, enhancing the overall ambiance. The CityView 45mm commercial hinged doors, installed in a French door configuration,
allowed for easy sectioning of spaces for privacy and were ideal for high-traffic areas due to their durability and ability to withstand frequent use.
Automatic sliding doors and 45mm commercial doors were installed at the club’s front entrance. These door systems were not only functional but also enhanced the building’s overall modern and contemporary appearance.
Darley Aluminium’s involvement in the Ashfield Polish Club project is a reflection of their versatility and capability to handle large-scale projects across various sectors.
Their products are not only compliant with the latest Australian standards but also designed to integrate seamlessly into
both contemporary and heritage settings. This flexibility makes Darley a popular choice for RSLs and social clubs, among other sectors.
The aluminium framing systems installed at the Ashfield Polish Club have been tested to meet and exceed the latest Australian Standard AS2047: Windows and external glazed doors in buildings. This ensures that the installations are robust, weather-resistant, and built to last. High-quality commercial hardware, including Briton door closer and Austral stainless steel Verta door handles, were used throughout the club to ensure longevity and reliability.
Hansen Yuncken is spearheading groundbreaking advancements in healthcare with the Flinders University Health and Medical Research Building (HMRB) in Adelaide. This architectural marvel, designed by Architectus, will be the focal point of Flinders Village, adjacent to the university’s medical facilities. Boasting cutting-edge amenities, the HMRB aims to revolutionise collaborative health research, exemplifying Hansen Yuncken’s dedication to excellence and sustainability.
Drawing from over 50 years of exemplary health and medical teaching, the HMRB offers a creative space for collaboration to enable researchers, practitioners and industry partners to work together more closely than ever before.
The HMRB will house over 600 researchers, clinicians and support staff. The 10-storey building will provide state-of-the-art facilities for collaborative research, aiming to make a significant impact on the health and wellbeing of people worldwide.
“Innovation has always been at the core of Hansen Yuncken’s projects,” said Senior Project Manager, Luke Crouch. “We are constantly seeking better, more efficient ways to deliver our projects, using tools like our award-winning management system HYway.”
Health and wellbeing are central to the new Health and Medical Research Building’s mission, reflected in its design and location. Its proximity to Flinders railway station is an incentive to use public transport and provides easy access to the Tonsley and CBD campuses. For those who prefer to travel under their own steam, dedicated end-of-trip facilities and a bike store make commuting or a lunchtime walk a breeze.
The HMRB has achieved a Platinum rating under WiredScore certification, making it the
CLIENT : Flinders University
BUILDER : Hansen Yuncken
ARCHITECT : Architectus
CONSTRUCTION VALUE : $280 million
FEATURE IMAGE : Mark Zed Photography (supplied by Hansen Yuncken)
PROJECT IMAGES : Cameron Longshaw (ANCR photographer)
first medical research institute in the world to receive this rating.
The building is also on schedule to achieve Gold WELL and LEED certification for sustainability and wellbeing. Achieving these three certifications together will make the HMRB unique in Australia, and the world.
One of the major challenges of the Flinders University project was integrating the new building with the surrounding landscape and existing facilities.
The design, informed by a cultural narrative and guided by the Indigenous Art and Design Advisory Panel, features colours and elements that reference Rainbow Sands, the natural pigments of the Kaurna Yarta coastline, as well as significant Indigenous landmarks.
The landscaping will connect the University and Flinders Station to the HMRB, creating a new gateway entrance to Flinders and a walking environment that is streamlined, safe and engaging. Lifts at both ends of the building will allow people to move easily from the Village to University Drive, and green spaces will encourage time outside the building.
“The Flinders University Health and Medical Research Building is a testament to our commitment to innovation and excellence in construction,” said Luke. “We are proud to be part of a project that will have such a positive impact on healthcare and research in South Australia.”
For more information contact Hansen Yuncken, Level 1, 191 Fullarton Road, Dulwich SA 5065, phone 08 8229 7300, email adelaide@hansenyuncken.com.au, website www.hansenyuncken.com.au
JFloors, a dynamic and rapidly growing business, is making waves in the commercial flooring industry with its commitment to excellence and customer satisfaction.
Specialising in a wide range of flooring options, including carpet, vinyl, timber, laminate, and more, JFloors has established a reputation for delivering high-quality, innovative solutions for commercial spaces of all sizes.
Their work on the Flinders University Health and Medical Research Building highlights the company’s expertise and dedication to superior craftsmanship. The scope of work for this project included floor preparation, grinding, moisture barrier and screeding, as well as the supply and installation of coved floor vinyl and wall vinyl.
Thanks to the efficient collaboration between JFloors’ team and the builder’s team, the job ran extremely smoothly, showcasing JFloors’ ability to deliver exceptional results through effective teamwork.
“We are a relatively young business experiencing consistent growth. We value our reputation for on-time delivery and our ‘above and beyond’ approach,” said Jesse Roberts, General Manager of JFloors.
In addition to Flinders University, JFloors is also working on several other projects, including Resthaven Aged Care, NCIS Sub-Corp, Harpers Field Community Sports Club, and Deloitte Festival One Tower.
These projects showcase the diversity of JFloors’ capabilities and their ability to handle a wide range of commercial flooring needs.
“Our flooring options cater for all types of commercial buildings from small retail through to large office spaces, high rise projects, and everything in between,” said Jesse.
At JFloors, customer satisfaction is paramount. The team is dedicated to working closely with clients to achieve the right flooring for their needs, ensuring that every project is completed to the highest standards.
“Attention to every detail is what sets us apart – from the subfloor to the finished product,” said Jesse. “Our highly skilled team of managers, project co-ordinators and installers ensure you will receive an exceptional job. We are proud of our reputation and go above and beyond to maintain it.”
The team at JFloors are invested in your project from start to finish. They have a vast selection of flooring available for all applications.
“With decades of experience in every imaginable commercial project and delivering within deadlines, our team can handle anything you throw at them. We’ve become the go-to place for people who want everything done in one place, from start to finish,” said Jesse.
With a rich history and a passion for flooring, JFloors is setting the standard for commercial flooring solutions. With many years of combined experience in the industry, the team at JFloors has the knowledge and expertise to handle projects of any size and complexity.
“Our team of industry-leading trade professionals work tirelessly to stay at the forefront of the commercial flooring industry. There is no job too big, and no solution we can’t provide,” said Jesse.
For more information contact JFloors, Unit 1, 20 Adam Street, Hindmarsh SA 5007, phone 0492 972 228, email projects@jfloors.com.au, website www.jfloors.com.au
Below JP Drafting Services created Structural Steel Shop Fabrication Drawings for Gant and Sons Engineering, for the in Flinders University’s Health and Medical Research Building.
JP Drafting Services provided Structural Steel Shop Fabrication Drawings for Gant and Sons Engineering, the contractor responsible for supplying and installing structural steel for the Flinders University Health and Medical Research Building.
The scope of work for this project was extensive, requiring JP Drafting to deliver accurate steel models and coordinate with various services such as mechanical, fire, and plumbing to avoid clashes with the structural steel. Utilising Tekla Structure, they created a Structural Steel 3D Model and shop fabrication drawings, employing BIM modelling to aid in coordination efforts.
“The Flinders University Health and Medical Research Building stands as an iconic project for South Australia, featuring architectural features supported by approximately 250 tonnes of structural steel,” said Managing Director, Jigar Patel.
Despite short lead times and the complex design requirements, JP Drafting worked meticulous coordination with architects, engineers, and builders to create high quality models. “It was a great experience to work on this project and we are proud to be part of it. It was great to work with the Hansen Yuncken team, and their support and extensive
knowledge on the project always always provided a collaborative platform for problem-solving,” said Jigar.
JP Drafting Services specialise in architectural, electrical, structural, mechanical, and electronics drafting, utilising cuttingedge technological expertise to meet client requirements. With a commitment to understanding clients’ precise needs and delivering sound and affordable solutions, JP Drafting Services ensures projects are completed within proposed budgets and timelines without compromising quality.
By partnering with JP Drafting Services, clients can focus on their core business activities while receiving CAD services that meet international standards. With a dedication to excellence and efficiency, JP Drafting Services is ready to provide solutions for design, drafting, and imaging projects of any scale.
For more information contact JP Drafting Services, 191 Philip Highway, Elizabeth South, SA-5112, phone 0433 366 435, email jpatel@jpdrafting.com.au, website www.jpdrafting.com.au
Below Dorma Hüppe’s movable walls provided flexibility needed for HRMB’s needed adaptable room setups for conferences, offices, and exhibitions.
Dorma Hüeppe, a global provider of high-quality operable partition systems, played a crucial role in the Flinders University Health and Medical Research Building Project.
With a legacy of 130 years in the industry, Dorma Hüeppe is renowned for its innovative solutions that maximise space and functionality with movable walls.
The Flinders University Health and Medical Research Building Project required versatile room configurations to accommodate various functions such as conference facilities, conventions, offices, and exhibitions. Dorma Hüeppe’s movable wall systems offered the perfect solution, allowing the university to efficiently manage its rooms and spaces.
One of the major challenges faced during the project was the installation of a 4m high Glass Operable Wall. Dorma Hüeppe worked closely with the architect to design and install the specified operable walls on-site, ensuring seamless integration with the building’s layout and design.
The MOVEO Glass Operable Wall provided both flexibility and transparency, creating a modern and open environment.
The successful supply and installation of operable walls, contributing to the multifunctional room configuration of the building, is a highlight of the project. The VARIFLEX Solid and MOVEO Glass systems offered a harmonious blend of daylight-flooded and soundinsulated room concepts, meeting the university's requirements for versatility and openness.
Dorma Hüeppe’s commitment to delivering the highest quality custom wall solutions was evident throughout the project. The company’s operable partitions and glass wall systems not only met but exceeded the expectations of the university, providing endless possibilities for the building’s environment.
With a focus on trust, reliability, and customer satisfaction, Dorma Hüeppe continues to be a leader in the global movable walls market, offering smart and easy space solutions for various industries worldwide.
For more information contact Dorma Hüeppe, Unit 10, Block R, 391 Park Road, Regents Park NSW 2143, phone 0455 321 035, email salesmovablewalls.au@dormakaba.com, website www.dorma-hueppe.com.au
Below PGS undertook a comprehensive role, supplying and installing vital power infrastructure, including standby generators, fuel systems, and a tailored control system.
Power Generator Systems (PGS) ensured the Flinders University Health and Medical Research Building’s power infrastructure met the demanding requirements of the facility.
PGS’s scope of work for the project was extensive and intricate, encompassing the supply and installation of essential power infrastructure. This included the installation of two 2400kVA standby rated generators, equipped with remote radiators and super low-noise stainless-steel exhaust systems, as well as fuel systems with approximately 50,000L of on-site fuel capacity, along with a unique tailored control system designed to prioritize power to critical areas.
One of the primary challenges faced by PGS was meeting the client’s critical requirement for robust and reliable power to support extensive research and facilities. This necessitated advanced design solutions and close collaboration with stakeholders to ensure seamless integration of power systems.
Additionally, the installation of super low-noise exhaust systems posed unique constraints, which PGS addressed through in-house fabrication capabilities, ensuring compliance with noise regulations while maintaining optimal performance.
A standout feature of PGS’s work on this project was the customdesigned fully integrated control systems. These systems constantly monitor and control building loads, ensuring critical site operations are supported at all times.
“The final commissioning with all stakeholders was a project highlight,” said Managing Director, Andrew Frost. “It was great to see so many integrated components and aspects of this project assembled by numerous trades, and co-ordinated and supported by Hansen Yuncken – coming together to provide a valuable asset for the future of medical research and training.”
PGS specialises in diesel and gas generator systems for critical infrastructure, offering a range of commercial and industrial generators for standby, prime, or base load applications. With access to leading generator brands and a highly experienced team, PGS delivers adaptive design solutions, compliance maintenance, and responsive 24/7 emergency services.
For more information contact Power Generator Systems, 3 O’Connor Court, Gepps Cross SA 5094, phone 08 8349 7854, webstie www.pgsys.com.au
Below JRCM Commercial Joinery created and installed proportional workstations, panelling, and seating solutions for the project.
JRCM Commercial Joinery played a crucial role in the construction of the Flinders University Health and Medical Research Building, focusing on the installation of joinery items including wall paneling, booth seating, and workstations.
“This project was particularly challenging due to the unique requirements of the staircase areas, as well as the need to achieve a woodgrain finish and scale the joinery items to fit the space,” said Project Manager, Leigh Pedrick.
Equipped with modern machinery and a team of skilled craftsmen, JRCM Commercial Joinery has established a reputation for delivering high-quality joinery solutions for a diverse range of clients. Their ability to work with various materials, including timber, veneers, laminates, concrete, stainless steel, upholstery, stone, and glass, allows them to meet the unique needs of each project.
With a team of 35 staff dedicated to the project, JRCM Commercial Joinery worked diligently to ensure the joinery elements were completed to the highest standards. Despite the challenges faced, the team’s expertise and commitment to excellence allowed them to overcome obstacles and deliver exceptional results.
Founded in 1993 by John Reuther, JRCM Commercial Joinery has grown significantly over the past 30 years. Starting from a small workshop in Edwardstown, the company has expanded its operations and relocated to a larger facility in Thebarton, and later to an even larger workshop in Dudley Park, boasting 4,000m2 of floor space.
With a focus on quality, integrity, and customer satisfaction, JRCM Commercial Joinery continues to be a trusted partner for joinery solutions in South Australia.
Some of the notable projects completed by JRCM Commercial Joinery include Her Majesty’s Theatre, Adelaide Oval & Oval Hotel, Skycity, Calvary Adelaide Hospital, 60 King William Street, Adelaide Botanic School, Walker Tower and many more.
For more information contact JRCM Commercial Joinery, 88 Exeter Terrace, Dudley Park SA 5008, phone 08 8234 9600, email admin@jrcm.com.au, website www.jrcm.com.au
Below PLG Painting efficiently finished interior surfaces at the HRMB including painting walls, ceilings, doors, frames, and steel stair balustrades.
Since 1985, PLG Painting Services has been a trusted name in the painting industry, offering superior workmanship and expertise in large-scale projects throughout South Australia. As a family-owned and operated business, PLG has built a reputation for excellence, specialising in high-end residential homes to multi-storey commercial and industrial buildings.
At the Flinders University Health and Medical Research Building, PLG Painting effectively completed interior surface finishes, encompassing painting walls, ceilings, doors, frames, and steel stair balustrades, tailored for their intended purposes and to the highest possible standard.
“We used Dulux Professional® SteriGuard® inside all the laboratories,” said PLG’s Lisa Giamarelos. “Dulux Professional® SteriGuard® is a range of premium specialty paint products designed to support internal environments in clinical settings, ensuring a healthy and sterile state.”
Led by founder and Director, Peter Giamarelos, along with his sons Sotiri Giamarelos and Apostoli Giamarelos, PLG Painting Services has the experience and skills to handle a wide range of projects,
working closely with South Australia’s largest building companies to ensure projects are completed on time and to the highest standards.
One of PLG’s key strengths is its specialisation in commercial and industrial painting. With a focus on projects in Adelaide, PLG has successfully completed painting projects for schools, shopping centers, office fit-outs, new multi-storey apartment blocks, retail fit-outs, government defense projects, and more.
PLG Painting Services stands out as a leading painting contractor in South Australia. With a focus on quality, expertise, and customer service, PLG remains a trusted choice for painting projects of all sizes and complexities.
For more information contact PLG Painting Services, 26 Lysle Street, Brooklyn Park SA 5032, phone 08 8352 8180, email info@plgpainting. com.au, website www.plgpainting.com.au
Below Capella Science installed advanced STATEBOURNE Cryogenics systems at Flinders University Health and Medical Building.
The STATEBOURNE Cryogenics solutions implemented at Flinders University represents cutting-edge advancements in cryogenic storage, with enhanced efficiency, safety, and reliability. Supplied and installed by Capella Science, the project is a testament to the company's ability to deliver high-quality scientific solutions, for a variety of purposes.
Capella Science commenced on-site work in February 2024, and drew on the collective experience of their team, which included a STATEBOURNE Cryogenics UK engineer, local service technician and Director, Paul Doyle.
The Flinders University project is unique, reflecting Capella Science's adaptability to complex requirements. “We’ve installed an entire system including external supply tanks, super-insulated pipelines, and automatic refrigerators with integrated temperature logging and alarm systems,” Doyle said. “Our solutions are designed to be economical on LN2 and avoid triggering oxygen alarms unnecessarily.”
In total, Capella science installed four STATEBOURNE Cryogenics Biosystem Access 24 Automatic LN2 storage tanks, three STATEBOURNE Cryogenics Biosystem 24 Vapour Phase racking with
Daisy Chain Connections, 1.5m insulated hoses, 2m insulated Hot-Gas Bypass Hoses, and Biosystem Access 24 Liquid Phase Racking.
The STATEBOURNE Cryogenics Biosystem Series is capable of handling up to 98,000 vials. “These units offer automatic liquid nitrogen top-up, dual fill solenoids for extra security, and a self-diagnostic data logging processor,” Director, Paul Doyle said. “They are compliant with MDD93/42/EEC standards and can be integrated into a pipeline system or operate as standalone units.”
What sets these products apart is their versatility and robust features. The Biosystem Access units, available in models 12, 24, and 50, provide rapid specimen storage and retrieval, crucial for frequent-access users.
“Each unit can be configured for liquid or vapour phase storage, featuring full-width openings for easy access, quick chill functions, and a vapour guard option,” Paul said. “They also come with enhanced control via PC connections, and robust construction, ensuring durability and security.”
For more information contact Capella Science, phone 02 9575 7512, email enquiries@capellascience.com.au, website capellascience.com.au
Below Ecept managed detailed design, engineering, production, installation, and project management for internal and external branding, wayfinding, and Sky signage
Ecept, a South Australian owned and operated Design and Construct Signage Company, is making waves in the signage industry with its innovative approach and commitment to excellence.
Ecept provided detailed design, engineering, production, installation, and project management for all internal and external branding, statutory, wayfinding and Sky signage for the Flinders University Health and Medical Research Building project.
“This project was the largest to date for Ecept,” said Director, Ian Widdop. “We produced over 2,000 signs over a 10-month program.”
Ecept embraced new technologies and utilised non-specific signage materials to help create a unique look and feel for the building. The team also employed problem-solving and prototyping techniques to create bespoke signage solutions that met the project’s requirements.
One of the highlights of this project was Ecept’s recent acquisition of a tactile/braille printer from the US, the only one of its kind in South Australia. This investment in new technology enabled Ecept to expand
its capabilities and deliver high-quality tactile and braille signage for the project.
“Our personal goal as a company is to constantly challenge our abilities by developing and implementing new ideas that stand out from the crowd and provide recognition for our clients,” said Ian.
This commitment to innovation and excellence has earned Ecept multiple national awards and recognition as a leader in the signage industry.
As a proud partner for Hansen Yuncken, Ecept continues to provide outstanding services in graphic design, industrial design, interpretive and corporate signage, wayfinding, exhibitions, and creative fitouts. With a broad base of skills and experience, Ecept is well-equipped to handle projects of any size and complexity, delivering exceptional results for clients across South Australia and beyond.
For more information contact Ecept, 236 Richmond Road, Marleston SA 5039, phone 0435 844 779, email ian@ecept.com.au, website www.ecept.com.au
Below SA Commercial Blinds enhanced the functionality and aesthetics of rooms with the installation of motorised and manual roller blinds, and curtains.
SA Commercial Blinds demonstrated their expertise in providing quality window furnishings for commercial spaces at the Flinders University Health and Medical Research Building.
The project involved installing motorised and manual roller blinds, as well as curtains, to enhance the functionality and aesthetics of the building. The scope of work for this project was extensive, including the installation of motorised and manual roller blinds to most perimeter windows, as well as curtains to wet areas and the prayer room.
One of the major challenges faced during the project was the installation of high-level 5.5m blinds on Level 2. To overcome this challenge, the team installed wire guides to ensure the blinds were securely in place.
Despite facing challenges on site at times, SA Commercial Blinds successfully completed the project to the highest standard. Their expertise in the industry, coupled with their commitment to delivering quality products and services, ensured the project was a success.
SA Commercial Blinds is a South Australian owned business. They specialise in providing innovative window covering solutions for
commercial projects, no matter the size. Their partnership with leading brands in the industry allows them to offer a wide range of products to suit any project requirements.
Current projects include SAAB at Mawson Lakes, CMI at Cristies beach, and SASI at Mile End.
For more information contact SA Commercial Blinds, phone 08 8347 8700, email sales@sacommercialblinds.com.au, website www.sacommercialblinds.com.au
Below GMR Interiors installed Siniat Createx Perforated Plasterboard and Soundshield for partitions and ceilings.
GMR Interiors completed all of the internal ceilings and partitions as well as aluminium and glazing work for the Flinders University Health and Medical Research Building.
GMR Interiors specialise in commercial ceilings, partitions, aluminium and glazing. All the aluminum is manufactured in their workshop. The scope of work for this project was extensive, with GMR Interiors tasked with installing Siniat 13mm Createx Perforated Plasterboard in the stair voids, as well as 13mm Soundshield and Siniat framing for partitions and ceilings.
A notable accomplishment was the full framing, sheeting, and flushing of the Level 3 Stairwell utilising Siniat products, underscoring the expertise of the GMR team. Moreover, GMR Interiors demonstrated their dedication to quality and precision by installing Alspec’s Aluminium Suites in both the wet and dry labs.
“Despite facing challenges related to the complicated build and specifications outlined for the project, in collaboration with the Hansen Yuncken team, we successfully overcame them by coming up with innovative solutions on a day-to-day basis,” said Project Managers, Seth Powell and Alby Kenney. “The close relationship
formed between GMR Interiors and Hansen Yuncken was a key factor in navigating these challenges and ensuring the project’s success.”
One of the major highlights for GMR was seeing the finished product come together, with the contributions from the GMR team highlighted within the design. Their dedication to delivering high-quality workmanship and their ability to overcome challenges are a testament to their professionalism and expertise in the field.
GMR Interiors’ contribution to the Flinders University Health and Medical Research Building project was instrumental in achieving the high standards of construction and finishing expected for such a prestigious project. Their commitment to excellence and collaborative approach ensured the successful completion of this iconic building.
For more information contact GMR Interiors Pty Ltd, 18-20 Richard Street, Hindmarsh SA 5007, phone 08 8363 3636, email gmr@gmrinteriors.com.au
PRINCIPLE : The Department For Infrastructure And Transport
MANAGING CONTRACTOR : Built Environs Pty Ltd
CONSULTING TEAM: Cheesman Architects (Lead), STH, Aurecon, Bestec, BCA, Oxigen, Rider Levett Bucknall and dsquared
CONSTRUCTION VALUE : $314 million
The Queen Elizabeth Hospital (TQEH) redevelopment will modernise and increase the emergency, critical care and surgical capabilities of the hospital. The project includes the construction of a 46-bay emergency department, 12 operating theatres, 14 bed intensive care unit, and 52 bed rehabilitation unit, along with medical imaging department, catheterisation lab, and pathology lab.
Built Environs provided the SA Department of Infrastructure and Transport and SA Health with procurement, construction coordination, testing and commissioning services for the new $314 million redevelopment of The Queen Elizabeth Hospital (TQEH) New Clinical Services building.
The project created around 400 jobs each year, with 90 – 95% of those jobs directly employing South Australian residents.
Built Environs General Manager (SA), Tony Jachmann, reflected on the challenges and highlights of this ambitious project.
“With the construction site located adjacent to the existing hospital and associated health services, our delivery approach has been developed to minimise disruption and keep TQEH operational throughout construction.
The project, which began in December 2021, has faced numerous challenges familiar to all in the construction industry including global supply chain disruptions, inflation and industry skill shortages.”
“Inflation resulted in a significant amount of value management needing to be done to pull the project back into budget without compromising any of clinical function,” said Tony.
Despite these challenges, Built Environs managed to keep the project on track, ensuring that it remained within budget and achieved on-time completion in May 2024.
“One of the key highlights of the project has been the high level of stakeholder engagement and collaboration at all levels,” said Tony.
“I attribute the high degree of collaboration to the passion and pride of the project members, who share a common vision and are dedicated to delivering a facility that will benefit the community.”
Built Environs has worked closely with the Department for Infrastructure and Transport and SA Health to ensure that the project meets the needs of the state. The project highlights the collaborative efforts of all parties involved
“The building is an all electric facility with significant environmental initiatives incorporated into the services design and thermal performance of the façade. Carbon reduction initiatives and responsible building materials were incorporated from the project outset such as green concrete and structural LVL in wall timbers reducing project steel content. Over 40 environmental initiatives were incorporated across design, construction and as-built performance verification. The TQEH Redevelopment project has been awarded an IGRAT 6-Star Design and Construction Rating.”
Additionally, the Built Environs delivery team included in-house biomedical specialists who procured and coordinated the integration of over $25 million of complex medical equipment and fixtures in close collaboration with CALHN / SA Health.
The project represents a significant investment in the healthcare infrastructure of Adelaide’s western suburbs. Built Environs’ commitment to delivering a high-quality facility that meets the needs of the community is evident in its approach to the project with staged handovers.
Built Environs is a full service construction company that provides a range of building services, from design consultation and management, right through to construction and fit out.
Built Environs invest in clever people, innovative methods, and smart technologies to deliver what they promise, able to provide services to local, state and federal governments, health providers, universities and education providers, commercial, residential and industrial property developers.
For more information contact Built Environs, Level 12, 99 Gawler Place, Adelaide SA 5000, phone 08 8232 1882, email builtenvirons@ builtenvirons.com.au, website www.builtenvirons.com.au
Arjo Australia, a global supplier of medical devices, believes empowering movement within healthcare environments is essential to quality care.
Their products and solutions are designed to promote a safe and dignified experience through patient and resident medical beds, hygiene care, disinfection, diagnostics, and the prevention of pressure injuries and venous thromboembolism.
For The Queen Elizabeth Hospital Redevelopment, Arjo was involved in the design and project management, working closely with the builders and architects. Arjo supplied and installed ceiling hoists (Portable Maxi Sky 440, Maxi Sky 2, and Maxi Sky 2 Plus Bariatric hoist system) and a range of medical products including, medical beds, stretchers, slings, and foam & air mattresses.
“For the early stages of a project, we provide practical advice on planning and designing care facilities, and design inspiration for different types of rooms,” said Sales Director, James Blieschke.
The project also marks the first installation in a South Australian Hospital of the Maxi Sky 2 Plus Bariatric unit.
“Patients of larger size have the right to be treated with comfort and dignity. Maxi Sky 2 Plus makes it possible to transfer non-ambulatory bariatric patients (up to 454kg),” said Ivan Molina, State Manager.
“Three Bariatric rooms were installed with the Maxi Sky 2 Plus Bariatric ceiling hoist system, which has been a real highlight of the work at the Queen Elizabeth Hospital.”
Research shows that there is a clear connection between mobility and people’s physical and mental well-being.
Creating the best opportunities for mobility is therefore at the very core of providing high-quality care. Arjo has seen how empowering movement can quickly improve both clinical and financial outcomes to facilities. As a leading specialist in the field, they work continuously to promote mobility – with the aim of contributing to better healthcare.
The Queen Elizabeth Hospital project is also one of Arjo’s largest installations of Ceiling Hoists in South Australia with installations in the gym, general wards, ICU, patient bays, emergency department, changing places and bariatric rooms. Arjo is currently finalising installation of ceiling hoists at Eldercare Goodwood in South Australia.
Consolidating their place as leaders in mobility solutions and quality care, Arjo, your mobility outcome partner, has created the Arjo Portal for Architects and Planners.
The Arjo Portal for Architects and Planners
Scan the QR Code to learn more.
Users of the portal will find layout drawings with dimensions that allow sufficient space for caregivers, patients/residents and maneuvering of equipment; a collection of articles on bestpractices and design requirements when planning different care environments; and a CAD library (2D and 3D) of individual products, complete room solutions and space requirements.
“We have a long history of collaborating closely with architects, safe patient handling experts, hospital and aged care executives,” said James Blieschke
“Our experience has taught us that to create efficient care facilities and to obtain a good working environment, the right combination of environment, equipment and care skills are needed. Therefore, it
is key to design for sufficient space early in the planning of a new facility.”
Founded in 1957 by Arne Johansson, in Eslöv, Sweden, Arjo has over 6500 people worldwide and 65 years of caring for patients and healthcare professionals. The company is committed to driving healthier outcomes for people facing mobility challenges around the world.
For more information contact Arjo Australia, Level 3 Building B, 11 Talavera Road, Macquarie Park NSW 2113, phone 1800 072 040, email insidesales.au@arjo.com, website www.arjo.com.au
In the transformative redevelopment of the TQEH (The Queen Elizabeth Hospital), Square Ceilings’ wall and ceiling played a pivotal role in elevating the structural and aesthetic aspects of the project. Their comprehensive involvement encompassed the supply and installation of various critical elements, contributing to the seamless integration of both old and new structures.
Central to Square Ceilings’ contribution was the provision and installation of essential materials, including Plasterboard, Trurock, Fireshield, and ceiling tiles. These materials were strategically applied to create ceilings and partitions throughout the hospital, addressing a diverse range of requirements such as firewalls, smoke walls, acoustic walls, shaft walls, and T-bar ceilings. The team’s meticulous approach ensured the adherence to stringent safety and functionality standards crucial in a healthcare environment.
A notable aspect of Square Ceilings’ work involved the installation of lead-lining in sensitive areas like the CT, X-Ray, and MRI rooms. This specialised application was undertaken with precision and attention to detail, reflecting their commitment to creating spaces that meet the highest standards of safety and functionality in medical imaging.
One of the standout challenges encountered during the project was the construction of feature ceilings. Given the demanding schedule of the redevelopment, Square Ceilings faced the unique task of building the frame based on shop drawings, as the feature ceiling panels had not been manufactured at that stage. Despite this challenge, the team demonstrated resilience and expertise, successfully executing the construction of intricate feature ceilings within the tight timeframe.
Square Ceilings’ commitment to quality craftsmanship and their ability to adapt to evolving project requirements were instrumental in overcoming the complexities inherent in hospital construction.
Through their diverse capabilities, Square Ceilings contributed significantly to the success of the TQEH redevelopment, ensuring that the hospital now stands as a testament to both functionality and aesthetic excellence.
For more information contact Square Ceilings, 33 Hutt Street, Adelaide SA 5000, phone 0451 779 828, email admin@squareceilings.com, website www.squareceilings.com
Below A&M Passive Fire Systems fireproofed structural beams with PROMAT Vermiculite, using INTERNATIONAL primers and intumescent paint on exposed steel.
A & M Passive Fire Systems delivered structural steel fire protection systems for the Queen Elizabeth Hospital Stage 3 Redevelopment Project.
The scope of works included the application of PROMAT CAFCO 300 Vermiculite to concealed and internally exposed structural beams and pre-cast connections, Fendolite cementitious and INTERNATIONAL (AksoNobel) intumescent paint systems on externally exposed structural steel beams and columns, and the installation of PROMAT fireboard to structural columns.
“One of the major challenges faced by the team was the coordination with numerous contractors on site,” said Business Development Manager, Andrew Nelson. “With structural steel present throughout the building, interfacing with contractors required clear communication and coordination of project deliverables with the appropriate stakeholders.
The team at A & M Passive Fire Systems demonstrated their expertise in the project, by working closely with the builder creating a zoned-based approach to delivery, enabling safer and faster application.
The project’s success was facilitated by the builder’s readiness to collaborate to achieve delivery.
Andrew and business partner, Milo Terzic, showcased their synergy between corporate and fire protection experience, ensuring that systems were compliant and aligned with delivery requirements. Project walkthroughs with manufacturers were carried out to ensure adherence to tested systems and fire resistance levels FRLs. Commitment to quality and safety was evident throughout the project.
A & M Passive Fire Systems’ specialises in providing Passive Fire Protection systems which include the application of Vermiculite, Fendolite (cementitious), fireproof boards, and fire-stopping penetrations. A team of experienced and certified professionals dedicated to delivering quality and compliant fire systems.
For more information contact A & M Passive Fire Systems, phone (Andrew) 0412 799 335, website www.ampassivefiresystems.com.au
Below Adelaide Passive Fire Solutions certified fire penetrations at The Queen Elizabeth Hospital, ensuring compliance with standards.
Adelaide Passive Fire Solutions were contracted to inspect and certify the sealing of all fire penetrations at The Queen Elizabeth Hospital and document them on a register.
Specialists in the Passive Fire Protection of structural assets, Adelaide Passive Fire Solutions are committed to offering practical, compliant solutions that meet all relevant standards including the BCA.
“Being a health facility with a multitude of systems in a multitude of locations, it is imperative that each and every one of those systems are sealed and compliant,” said Kyle Smith, Director of Adelaide Passive Fire Solutions.
“As with any project of this size on a tight time frame, we needed to coordinate with the builder and subcontractors to access areas once they’d been completed,” said Kyle. “This meant multiple returns after services have been rewired or penetrated by another service needing to complete their work in the same location.”
Passive fire protection is a barrier or shield, stopping the spread of fire from one area to another. Unlike active fire protection products such as sprinkler systems, fire alarms, fire extinguishers, and fire hoses
which become active in the event of fire, passive fire products remain non-active.
“The end-user needs to be confident that all penetrations have been sealed and have been done compliantly,” said Kyle. “They need to be able to refer to the register if unsealed penetrations are found when future contractors are brought in.”
Adelaide Passive Fire Solutions offers a vast range of services in Passive Fire Protection including inspection, installation, repair, and compliance in all fire protection systems. Including the supply and install of Fire doors, Barriers, penetrations, and building work rectification involving these areas. The company has experience in all types of working environments including aged care, hospitals, offices, education, retail, hospitality, residential, and manufacturing in Adelaide and regional South Australia.
For more information contact Adelaide Passive Fire Solutions, Unit 10a 41-47 O’Sullivan Beach Road, Lonsdale SA 5160, phone 0437 372 319, email kyle@apfsol.com.au, website www.apfsolutions.com.au
Below Paint Machine unitilised mineral silicate paint to created the façades vibrant colour finish, and allowing substrates to breathe.
In a world where modern architecture often gleams with glass façades and metallic finishes, The Queen Elizabeth Hospital stands as a striking departure from the norm, instead embracing a more enduring and distinctive aesthetic.
The brief to paint the entire exterior of the hospital presented a unique challenge and an opportunity for Paint Machine, a South Australian commercial painting contractor, to showcase their expertise and elevate the standard for quality and longevity in architectural coatings.
The project brief was to use mineral silicate paint that bonds chemically with concrete and stone. Where traditional acrylic paint seals and traps moisture, mineral silicate paint allows substrates to breathe, making it ideal for the Queen Elizabeth Hospital. The paint is also highly resistant to UV damage, ensuring that the building will maintain its colour for years to come.
“We used three separate brands of mineral silicate paint to ensure warranty coverage on the various surfaces,” said Managing Director, Steve De Luca. “Specialised equipment such as EWPs and Dog Box lifts were employed to navigate challenging areas, ensuring coverage and precision.”
“Unique challenges posed by a hospital environment and a tight program required exceptional planning and execution,” said Steve. “The whole team pulled off a remarkable project, delivering results that exceeded expectations.”
Paint Machine specialises in a range of services, including venetian plastering, lime-wash paints, and protective coatings for steel. Their expertise in these areas, along with their dedication to quality and customer satisfaction, has earned them a reputation for excellence in the industry.
As a family business, Paint Machine takes pride in its close-knit team, consisting of Chris, Anthony, Daniel, George, Sahil and Steve. Despite scaling back from 15 to 7 team members, they continue to take on challenging projects across South Australia, including government jobs, High Schools, custom homes, and institutions like Adelaide University.
For more information contact Paint Machine, phone 0412 112 663, email office@paintmachine.com.au
Below Schneider Electric installed their IoT-enabled EcoStruxure platform, ensuring efficiency, sustainability, and innovation for the hospital.
Schneider Electric played a key role in realizing SA Health’s ambitious vision for the cutting-edge redevelopment of The Queen Elizabeth Hospital by installing their IoT-enabled EcoStruxure for Healthcare platform.
The EcoStruxure for Healthcare platform is an innovative facility management tool that combines the Building Management System (BMS) and the Energy Monitoring System (EMS) into one digital platform. It seamlessly connects to existing campus infrastructures and integrates various facility systems such as HVAC, metering, electrical, hydraulics, lighting control, fire safety, and medical gas systems. This comprehensive integration enhances building performance and resilience, significantly improves operational efficiency, and promotes smart energy management. As a result, the platform optimises resource use, reduces costs, and contributes to a safer, more reliable, and environmentally friendly healthcare environment.
Schneider Electric also supplied a range of essential products through the electrical contractor, which adhered to the company’s rigorous Green Premium product label standards. This ensured compliance with the strictest environmental regulations and underscored the company’s commitment to transparency in environmental disclosures
and end-of-life instructions. By providing these environmentally conscious products Schneider Electric played a vital role in supporting SA Health’s sustainability objectives for the project.
With a proven track record in delivering large-scale, fully integrated solutions—including the Australian Bragg Centre, Lyell McEwin Hospital Expansion, and Festival Tower 1, which were executed concurrently with the clinical services project—the team showcased their expertise in project delivery. Their specialist approach was bolstered by the use of their innovative digital delivery platform, IMPACT. This secure platform provided live updates on installation and commissioning status, facilitated issues tracking, and offered convenient consolidation of current drawings, points lists, and datasheets for all trades.
As a result, Schneider Electric’s EcoStruxure solutions, coupled with their expert team and digital platforms, significantly contributed to the successful completion of this transformative healthcare project. Their commitment to innovation, sustainability, and project delivery excellence was pivotal in delivering a state-of-the-art, all-electric facility.
For more information contact Schnieder Electric Australia, phone 13 73 28, website www.se.com/au/en/
DEVELOPER : TOGA Group
ARCHITECT : Turners
INTERIOR DESIGN : Richards Stanisich
LANDSCAPE ARCHITECTURE : Black Beetle
Wicks Place stands as a breathtaking mixed residential urban village, boasting a vibrant new retail and dining precinct alongside 270 apartments spread across five buildings. These residences offer a unique blend of urban living and serene green spaces, providing a homely ambiance.
Wicks Place, a joint development by TOGA and Danias Group, represents a transformative endeavor poised to redefine contemporary urban living.
Standing tall on Victoria Road, this $130 million luxury development is architecturally designed to maximise space and light. The project features a standard of luxury rarely seen in Marrickville, with apartments embodying home-like amenities that provide maximum comfort and storage for an easy, uncluttered lifestyle. The selection of one, two, and three-bedroom apartments comes with generous-sized balconies offering views of the surrounding district and parklands.
Homes on the upper floors provide uninterrupted views of the city skyline and airport runway, while those closer to ground level enjoy a vivid green backdrop of communal gardens and Wicks Park. The European oak flooring, Fisher & Paykel appliances, natural stone splashbacks, and close attention to detail demonstrates TOGA’s commitment to delivering highquality products.”
During the construction phase of Wicks Place, TOGA used 15,000m3 of concrete and 2,300 tonnes of steel across 14 levels, with
a total of 84 pours. The ground floor and Level One transfer slabs consisted of transfer beams up to 1.3m deep and widths of 5.2m. The total reinforcement used for these two slabs accounted for 40% of the total tonnage of steel and 30% of the total concrete, which is enough to fill one and a half Olympic swimming pools. At the peak of the project, TOGA had more than 300 workers onsite.
The site presented some unique challenges including installation of bespoke single pane windows up to 39mm thick, which required specialist handling, to achieve an acoustic rating not yet seen in the industry, and as the site is located beneath active flight paths, the last three floors of the structure required to be stick-built without a tower crane. Despite these challenges, TOGA’s construction team carefully managed site operations to ensure the smooth and successful delivery on the project.
TOGA has built a reputation for creating high-quality properties and offering services that exceed customers’ expectations. They have been developing, building and enriching communities for over 60 years, establishing themselves as one of Australia’s most experienced, fully integrated property developers.
TOGA partners with their customers throughout the entire property journey, fostering open and transparent relationships. Their committed and dedicated team of property professionals are there from the very first moment a customer considers a TOGA property to the day the keys are handed over and beyond.”
Wicks Place reached practical completion in June 2024.
For more information contact TOGA Group, Level 5, 45 Jones Street, Ultimo NSW 2007, phone 02 9356 1000, email info@toga.com.au, website www.toga.com.au
Below Soldier Tower Cranes & Labour Services offers comprehensive construction solutions, serving builders of any scale, committed to local infrastructure development.
Soldier Tower Cranes & Labour Services (Soldier), a highly experienced operator in Australia’s construction industry, provides a comprehensive service for builders and construction companies of any scale. Soldier offer a large fleet of cranes, hoists and labour division including crane operators, riggers, hoist operators, RTA Certified traffic control division and skilled labour.
At a time when Sydney’s Inner West local government area is forecast to grow by approximately 32,600 residents and 14,000 workers between 2022 to 2036, Soldier Tower Cranes & Labour Services is committed to the development of Inner West’s infrastructure.
Soldier recently joined forces with one of Australia’s most experienced, fully integrated property developers, Toga Group. Toga Group, which has 60 years of experience in the building industry, is leading the way in the Marrickville community with its new development, Wicks Place, a hub of premium apartments combining luxury living and eclectic retail space.
Soldier commenced working on this Project in 2022 taking note that this Project would involve an intricate tower crane and construction methodology. This Project is very complex due to its close proximity to the airport; the cranes provided are limited in height and can only be erected and dismantled between the hours of 11pm and 5am.
The restrictions created a significant level of complexity for Soldier to overcome, who have installed, and recently dismantled two tower cranes for this project.
Soldier executed a jib reduction from 35m down to 25m on TC1, preventing structural cycle time delays and enabling crane operation to continue, given the restrictions faced on the project.
Soldier is now providing crane, hoist and crew, skilled labour, and machine operators, for Toga’s Made Marrikville, an industrial commercial project, offering premium adaptive space for a range of business ventures.
Soldier is proud to be a part of Toga’s Marrickville development.
For more information contact Soldier Tower Cranes & Labour Services, phone 1300 SOLDIER, email admin@soldiertowercranes.com.au, website www.soldiertowercranes.com.au
Backed by an experienced team and global purchasing prowess, Rexel Electrical Supplies are the foremost wholesale electrical supply distributor renown for delivering compliant products tailored to the needs of Industrial, Commercial, and Residential sectors.
For over three decades, Rexel Alexandria has been a trusted name in electrical wholesaling, providing top-quality supplies and unmatched service. Backed by a team of 35 seasoned professionals and a fleet of vehicles facilitating twice-daily deliveries from our expansive 5,000m2 warehouse, we ensure prompt and reliable service that exceeds industry standards.
Our Specialist Projects team excels in creating bespoke lighting designs, while our dedicated Data Division provides expert data solutions, enhancing our comprehensive service offerings. Our commitment to excellence is evident through our ISO standard certification, showcasing our dedication to quality and efficiency. As a proud member of the global sustainability charter, we priorities environmentally responsible practices in all our operations.
Additionally, our support for Beyond Blue underscores our commitment to mental health awareness and community welfare.
Choose Rexel Alexandria for a seamless experience and access to a comprehensive range of electrical solutions tailored to meet your needs.
Irongate Solutions successfully implemented advanced security measures for the Wicks Place Project, delivering a facial recognition access control system to ensure secure site access and smooth site operations .
“We provided access control, including a facial recognition system with a turnstile and pedestrian gate on the site. Our team managed site security, ensuring that only authorised workers were allowed through,” explained CEO Tim Dickeson
The project presented some unique challenges, particularly due to the site’s heritage walls that needed to remain intact.
“It was a slightly more complex site layout,” Tim explained.
“We had to deliver and install the gates and access controls system in a location that was not easily accessible.
To overcome this, we worked closely with the Wicks Place site team.”
“We utilised our facial recognition access control system, which validates people very fast and therefore allows for quick ingress and egress of workers and prevents bottlenecks. This newer technology is unique to Irongate; we are one of the few that deliver facial recognition systems specifically for construction sites. Additionally, we integrated with HammerTech, the safety management platform, ensuring seamless management of data and security.”
The solution provided by Irongate Solutions significantly increased the efficiencies of on-bording new workers and eased the operations for the Wicks Place site team.
“Our system made the lives of the site team easier by administering workers and managing who should and shouldn't get through the gates and access the site,” Tim said. “This smooth management and reporting on the number of workers on-site each day allowed the site team to
focus more on the project rather than worker management and site access.”
Irongate Solutions was set up on-site for the duration of the project, making this their second collaboration with Toga. Their comprehensive approach includes providing full end-to-end access control solutions tailored for construction sites, integrating with safety platforms, like HammerTech and Vanguard, to keep all information centralised, and offering full setup, installation and support.
Below Fastform expertly completed Wicks Place, overcoming crane restrictions to complete the Wicks Place project.
Partnering with TOGA, Fastform played a crucial role in realising the transformative, community-focused addition to the Wicks Park area.
The Wicks Place development was completed with a slightly different construction method then expected for high rise developments of this size. The projects proximity to the airport and beneath flight paths, resulted in the last 3-levels of the project being completed without the advantage of a crane.
“We had to form up the last three levels, including steel fixers, form workers and scaffolders, materials, material handling up and down for three floors, concreting with no crane. That was a great achievement by all involved,” Tarek Massri, Chief Operating Officer of Fastform.
The complexity of relocating a crane due to stringent airport regulations and continuing construction without it was a formidable challenge. However, the Fastform team rose to the occasion, showcasing their expertise in formwork, steel fixing, and concrete placement across a sprawling 2,000m2. This dedication ensured that the project proceeded smoothly and met its high standards.
With a proven track record and a commitment to safety and quality, Fastform has established itself as a leading provider of formwork services in Sydney. For over 20 years, Fastform has been synonymous with excellence, continually pushing the boundaries of what is possible in construction, delivering quality projects on time and within budget.
Fastform’s contributions to projects like Wicks Place highlight their unwavering commitment to creating spaces that serve the community while showcasing their industry leadership. This project not only enhances the local landscape but also stands as a milestone of collective effort and ingenuity.
For more information contact Fastform, 14 Enterprise Circuit, Prestons NSW 2170, phone 02 8783 0400, email enquiries@fastform.net.au, website www.fastform.net.au
The $50 million Gosford RSL showcases architectural excellence, capitalising on North Construction & Building’s expertise and local trades, to deliver the striking 3-story club. Featuring a RSL museum, cafe, lounge, and event spaces, the project has transformed the existing RSL club into a premier destination for the local community.
In a landmark project for the Central Coast, North Construction & Building has played a pivotal role in the transformation of Gosford RSL into a modern superclub. Engaged as the Design and Construct partner after a competitive tender process, North worked closely with Gosford RSL to deliver a $50 million redevelopment that has redefined the club as a beacon of community.
The new Gosford RSL is a striking 3-storey ultra-modern club featuring a distinctive porte cochere entry, RSL museum, and reception servicing both the RSL and the adjoining motel, on the ground floor.
The first floor boasts a cafe, lounge, bar, multiple indoor and outdoor dining options, a kids’ play area, and a teenage retreat. The second floor showcases sophisticated conference and event spaces, a sports bar, and a brewery.
The building itself is supported by a nest of 156 concrete piles to a depth of 25m – 30m. A detailed methane extraction mattress is installed under the ground floor. The remainder of the structure consists of typical reinforced footings, columns, post tensioned slabs, concrete plant deck and structural steel roof structure.
The external fabric of the building consists of significant glazed elevations, detailed masonry work, glazed curtain walls to the foyer,
dispersed with Monoclad panels and fascia. A traditional metal deck roof completes the building.
An additional 154 car parking spaces will be added on site to accommodate the expected increase in patron numbers.
One of the specific challenges faced by North was the proximity of the building footprint to adjacent Sydney Trains power lines. “This challenge emerged after construction had commenced and required significant redesign, including a reduced footprint for the club, changes to the internal layout, and alternate construction methodology,” said Matthew Cook, Managing Director at North Construction & Building.
North worked diligently and collaboratively with the client and consultant team to overcome all challenges, ensuring the project was delivered on time and to the highest standard.
“The Gosford RSL Club deserves recognition and acclaim for several compelling reasons,” said Matthew. “The new club stands as a beacon
CLIENT : Gosford RSL
MAIN CONSTRUCTION COMPANY : North Construction & Building
ARCHITECT : WMK Architecture
CONSTRUCTION VALUE : $50 million
of heritage and honors its rich history spanning over six decades. The club’s design, meticulously crafted by our team, exemplifies architectural brilliance, and it provides a space for social interaction, camaraderie, and shared experiences.”
“As a regional construction company founded on the Central Coast over 37 years ago, it’s very special to us to have delivered a project like the Gosford RSL Club,” said Matthew. “Not only does the development transform this gateway into Gosford, but as a venue doing so much for the local community and Central Coast broadly it is rewarding for us to play our part.”
A key highlight of the project is the positive impact it has had on the local community. By purposefully engaging local trade contractors and suppliers, North provided a boost in local employment and minimised the need for workers to commute from Sydney or Newcastle.
“Being the largest project North has delivered to date, it has enabled us to demonstrate our expertise as a trusted building partner. With our focus on local engagement and with great thanks to a team of supportive and skilled trade contractors,” said Matthew.
North Construction & Building was founded in 1987 and has grown to become a trusted regional construction company with an awardwinning reputation for excellence. With offices in Tuggerah, Newcastle,
Dubbo, Orange, Mudgee and Tamworth NSW, and most recently Brisbane QLD, North works across a diverse range of projects within the commercial, education, aged care, health, industrial, infrastructure, retail, and hospitality sectors.
For more information contact North Construction & Building, Level 5, Suite 501, 1 Bryant Drive, Tuggerah NSW 2259, phone 1300 667 840, website www.north.com.au
Innavate provided high-quality audio and IPTV systems in the comprehensive refurbishment of Gosford RSL
“Our goal was to deliver a club-wide system consisting of highquality audio and IPTV systems that are easy to use yet capable of being scalable. We were brought in to assist North Construction & Building in taking the original design from 70% completion to a fully functioning system,” said Director, Anthony Finlay.
The club needed an efficient way to select TV channels or signage for specific displays at any given time. They also desired a prominent feature screen in the Sports Bar and a robust audio system in the Terrace area for events, including DJ performances.
A slight redesign was needed to accommodate the LED wall in the Sports Bar, as the overall width of the wall increased. However, the most significant hurdle was the programming.
“A venue of this size, with numerous displays, audio zones, and function rooms, required extensive detail and coordination between our design and programming teams,” said Anthony. “It took months of development and custom coding to create a seamless user experience.”
Several key products were integral to the project’s success:
• QSC Platform: Used for both audio and control, its flexibility and iPad compatibility made it ideal. Innavate developed a 3D rendered user interface for easy TV content selection and control.
• Exterity IPTV Platform: Chosen for intuitive TV to signage selection, it provided a user-friendly backend that the RSL staff quickly adapted to.
• Samsung Displays: Used throughout the venue for signage and IPTV displays, known for their reliability.
• Unilumin LED Display: Selected for the Sports Bar, featuring a 1.8mm pixel pitch and measuring 5m by 3m, it offered excellent quality within budget.
“Having the Club CEO and COO get their hands on the iPads and really turn up the volume in the Terrace and Sports Bar was the icing on the cake,” said Anthony.
For more information contact Innavate, 2/80 Somersby Falls Road, Somersby NSW 2250, phone 0438 469 042, email sales@innavate.com.au, website www.innavate.com.au
Below Broad Windows and Façades Sydney created intricate gyprock, wall and ceiling framing designs for the Gosford RSL
The renovation of Gosford RSL proved to be a particularly intricate and rewarding endeavor for Broad Windows and Façades Sydney Pty Ltd.
“Our primary focus for the Gosford RSL was gyprock, wall and ceiling framing,” said Managing Director, Jiawei Lin. “However, what set this project apart was the intricate and advanced designs specified by the architect and client. Each area and floor required unique effects, challenging us to deliver precision and perfection in our work.”
To overcome this dilemma, the team collaborated closely with North Construction & Building’s on-site management team, ensuring that every curved wall and spiral stair was meticulously constructed to bring the architect’s vision to life.
“The project is filled with highlights that showcase the skill and craftsmanship of our team. The spiral stair, in particular, stands out as a testament to our ability to execute complex designs with precision,” said Lin.
“Additionally, the Level 1 kids area and function room are not only aesthetically pleasing but also functional and practical.”
Broad specialises in linings subcontract work, including gyprock, cladding, and windows installation. Based in Sydney, the company’s services extend to the northwest of New South Wales, with projects reaching as far as Broken Hill. With a commitment to quality and precision, Broad Windows and Façades has earned a reputation for excellence in the construction industry.
“As Managing Director, I’ve had the privilege of overseeing a project that pushed the boundaries of our capabilities and showcased our commitment to excellence in construction,” said Lin. “I am incredibly proud of what we have accomplished and look forward to taking on the next challenge with confidence and determination.”
For more information contact Broad Windows and Façades Sydney Pty Ltd, phone 0452 211 064, website www.broadwindows.net
DEVELOPER : MIRVAC
CONSTRUCTION VALUE : $230 million
Mirvac’s latest Green Square development features three high rise apartment buildings – The Frederick, Portman on the Park, Portman House, along with Portman Street Terraces. In total, the project includes 318 luxury apartments homes and retail spaces, more than 13,500 shrubs, trees and grasses 490 bathroom pods, Wellness Studio, and for residents a Business Studio and Sky Lounge – a private dining space.
Mirvac, a leading Australian property group, has set out on a mission to reimagine urban life with its latest project Green Square.
Green Square by Mirvac is more than just a development; it’s a thriving community hub that prioritises sustainability, diversity, and social inclusion. With amenities such as parks, schools, and recreational facilities, Green Square offers residents a high quality of life in close proximity to essential services and public transportation.
This mixed-use development represents a harmonious blend of luxury residential spaces, cutting-edge office facilities, and vibrant retail offerings, all thoughtfully designed to foster a sense of community and well-being.
Standing as the tallest among its trio, The Frederick building stands at an impressive 23-storeys, in the heart of Green Square.
This residential tower offers a luxurious living experience with 151 apartments, each boasting breathtaking vistas of the Sydney CBD. Within The Frederick, residents are treated to amenities including a Business Studio, Wellness Studio, and Sky Lounge – a secluded space for private dining, reserved solely for residents of The Frederick and their guests.
The Portman Collection includes Portman on the Park and Portman House and completes the trio of buildings. Portman on the Park presents 116 luxury apartments, many featuring dual-aspect views of Sydney’s CBD and the scenic Drying Green, optimising natural airflow and daylight. On the other hand, Portman House offers a boutique living experience, with 44 apartments spread across 12-storeys, boasting just four residences per floor for a heightened sense of exclusivity and privacy.
All buildings in Green Square offers residents a contemporary lifestyle experience of sophistication and convenience. Boasting meticulously crafted apartments with stunning views of the Sydney CBD, residents are treated to a sanctuary of comfort and style.
Each residence is thoughtfully designed to maximize natural light and space, with premium finishes and fixtures ensuring both luxury and functionality.
Green Square features an increasingly diverse array of retail offerings, providing residents and visitors alike with access to an eclectic mix of shops, cafes, and restaurants. The retail precinct adds vibrancy to the community, creating the perfect destination for socialising and leisure.
Beyond its architectural brilliance and contemporary design, Green Square is rooted in sustainable and environmentally focused practices. Mirvac’s commitment to sustainability is evident throughout the development, with features such as energyefficient appliances, water-saving fixtures, and green spaces contributing to a healthier and more sustainable way of life.
Established in 1972, Mirvac boasts over five decades of experience in shaping Australia’s urban landscape. From its early beginnings as a small joint venture, the company has evolved into a thriving ASX-listed property group, renowned for its commitment to innovation, sustainability, and placemaking.
Mirvac’s portfolio encompasses residential, office, industrial, retail, and build-to-rent properties. Each development is carefully curated with a focus on sustainability, social connection, and community engagement.
With over 800 industry awards to its name, Mirvac stands as a testament to excellence in the development and construction industry.
For more information contact Mirvac, Level 28, 200 George Street Sydney, NSW 2000 Australia, phone 02 9080 8000, website www.mirvac.com
Below Macquarie Rendering utilised colour-match tilt-up panels including an exposed stone look using STO render system.
New South Wales-based Macquarie Renderers is renowned for its expertise in plaster and render applications. Recently, the company completed the acrylic render work and remedial tilt-up panels on the prestigious Green Square by Mirvac development in inner Sydney. According to Cillian McManus, Director of Macquarie Renderers, “We leverage our deep experience across a wide range of finishes and partner closely with clients to achieve their vision.”
Macquarie Renderers has contributed its unparalleled craftsmanship to some of New South Wales’ most prestigious and award-winning projects. Notable achievements include the centrepiece swimming pool at One Sydney Harbour and the complete office fit-out, including key furniture, at the Microsoft Head Office. The company is also gearing up for the upcoming Powerhouse Museum project in Parramatta.
The firm’s strong partnerships with both local and international suppliers provide clients access to a diverse range of premium products. Options include hand-made clay plaster by an Australian-owned bespoke render/plaster supplier and products from the German global leader Sto. The selection of finishes includes: Traditional sand and cement; White set; Clay and lime plasters; Micro cement; Venetian plaster; and Acoustic ceilings
“As a company committed to sustainability and innovation,” McManus emphasises. “We collaborate closely with clients to deliver thermal-efficient substrates, cement-free render systems, and even carbon sequestration solutions, contributing to the drive for net zero in construction.”
Over the past decade, Macquarie Renderers has developed a customised onsite management system that enhances efficiency across large-scale commercial projects and high-end residential builds alike. This system ensures seamless project execution, delivering exceptional results on time and within budget.
Each project undertaken by Macquarie Renderers is executed to the highest standards, producing beautiful, durable, and functional finishes. Their team of skilled tradesmen, renowned for their local and international expertise, specialises in crafting unique surfaces and Level 5 finishes.
For more information contact Macquarie Renderers, email info@ macquarierenderers.com.au, website www.macquarierenderers.com.au
macquarierenders barebymqr
Below Embelton installed engineered timber flooring across the Green Square development including AB Grade, straight plank and herringbone flooring.
Building a world-class residential complex like the Green Square project requires the highest quality finishes and attention to detail, an ethos that Embelton, a leading Australian flooring and carpet contractor is no stranger to.
For over 50 years, Embelton has specialised in the design and manufacture of flooring, providing a broad range of quality timber, hybrid, laminate, vinyl flooring and carpet solutions to commercial and residential properties.
“This is a truly brilliant project that will be a standout once completed and we’re excited to be a part of its construction,” said Peter Gremos, Embelton Commercial Flooring Manager for New South Wales. “We have been contracted to supply and install Embelton Engineered Timber Flooring. This included AB Grade, straight plank and herringbone flooring as well as timber stairs in four colour schemes through 124 apartments and 7 townhouses across buildings A, B and C.”
“The curved kitchen island joinery was installed prior to the flooring, making it technically challenging for our team, particularly when installing herringbone flooring around this interface,” said Peter.
“This meant ensuring that all flooring installed was millimetre perfect, to fit around the existing island.”
Across the project, the Embelton team will supply and dual bond install approximately 7,000m2 of flooring including a traditional, durable Engineered European Oak Timber flooring in both straight plank and herringbone pattern.
The team involved two senior members of staff and several professional installers who commenced on-site in April 2023 with final installation projected for April 2024.
Current projects include Nine by Mirvac in New South Wales, and Victorian projects Flinder West by Mirvac, Greystar by Icon, The Eighth by Crema, Metro Tunnel Project, and Awaken Resisdences by McNab.
For more information contact Embelton, 147-149 Bakers Road Coburg, VIC 3058, phone 1800 339 638, email gpevic@embelton.com, website www.embelton.com
Below Fytogreen carried out green installations across the development, such as planter boxes, suspended planter boxes, roof gardens, green façades, and green walls.
Fytogreen as Australia’s leading full-service green infrastructure specialist, was responsible for designing, supplying and installing 600 custom aluminium planters, numerous green walls and roof gardens to create lush green infrastructure across the five buildings of the Green Square development.
“The coordinated design and response process with the developer and the engineers to deliver this project has been an extremely constructive process. The outcome has met all our expectations with a veil of greenery on the building,” said Geoff Heard, Fytogreen Managing Director.
Fytogreen is a multi-award-winning innovator of sustainable green solutions supplying over 900,000m2 of green infrastructure Australia wide. Incorporating roof gardens, green walls, planter boxes, 3D gardening, green facades, floating wetlands and ongoing maintenance for their elevated greening installations since 2002.
Current Sydney projects include Nine by Mirvac and One Circular Quay.
For more information contact Fytogreen Australia. ph. 1300 182 341, e. info@fytogreen.com.au, www.fytogreen.com.au
CLIENT : Alfred Health
MAIN CONSTRUCTION COMPANY : Kane Constructions
ARCHITECT : Lyons Architecture
Spanning 6-stories, the state-of-the-art Paula Fox Melanoma and Cancer Center integrates advanced clinical care with cutting-edge research. Equipped with telehealth-capable meeting rooms, a dedicated wellness center, a clinical trial hub, and top-tier medical imaging and research facilities, it's poised to revolutionise melanoma treatment.
Delivered under an AS4300 1995 amended Design & Construct contract by Kane Constructions, the Paula Fox Melanoma and Cancer Centre marks a significant leap forward in healthcare infrastructure, consolidating lifesaving clinical trials, cutting-edge research, and compassionate care under one roof.
The Paula Fox Melanoma and Cancer Centre project encompassed a comprehensive scope of work, including the construction of state-of-the-art laboratory facilities such as the GMO Pharmacy, Car-T Cell laboratories, PC2 labs, Cellular therapy labs, clinical trial labs, and Monash University Tenancy labs.
Additionally, the project involved seamless integration with the existing Alfred Health Hospital, implementation of an ICT backbone, installation of pneumatic tube systems, construction of a two-level basement carpark, and provision of shell spaces for future development at basement level, and Level 3.
Designed by Lyons Architecture, the building’s distinctive façade draws inspiration from a skin graft—a common treatment for skin cancer.
“One of the major challenges we faced was the procurement of the façade, which included
a curved curtain wall with a ceramic Frit pattern combined with GRC feature panels,” said Project Manager, Tom Chambers. “This required several coordination meetings between various stakeholders to achieve the design intent while ensuring structural adequacy and meeting OH&S standards. Through collaboration with stakeholders, we were able to overcome this challenge and deliver a stunning façade.”
Another challenge was the completion of the Level 04 PC2 labs, particularly the GMO Pharmacy and CAR-T Cell lab clean room facilities. Stringent QA was required to meet the strict PC2 guidelines, and Kane Constructions worked closely with their PC2 lab consultant and trades to ensure compliance.
A further challenge experienced by the team was the loss of several key trades along the journey namely our fire detection contractor, concretors and electrician. Kane were able to react quickly to these unfortunate situations to ensure impact to program was reasonably contained.
The development of this centre was driven by Alfred Health patient and philanthropist Paula Fox and is the result of significant support from the Victorian Government
and Australian government, the Fox Family Foundation, Minderoo Foundation and Monash University, along with many other donors and supporters.
“One of the most rewarding aspects of the project was the opportunity to work closely with Paula Fox herself, who attended the site regularly to talk to Kane management and workers,” said Tom. “We always love it when we are able to put a face behind who we are building our project for and her and the Alfred Hospital delivery team’s support along the journey was fantastic.”
Kane Constructions has delivered a worldclass facility that will make a significant impact in the fight against melanoma. “Being able to be a part of such a landmark project, not only for Alfred Hospital, but the Victorian Healthcare system is a real highlight,” said Tom. “This facility will provide an elevated standard of care for people in our community who need it and we are proud to be involved in that.”
For more information contact Kane Constructions, Level 9, 510 Church Street, Cremore VIC 3121, phone 03 8420 1200, email viccontact@kane.com.au, website www.kane.com.au
HOF Electrical, a trusted name in the electrical services industry, has been instrumental in the construction of the Paula Fox Melanoma and Cancer Centre. Known for its innovative approach and commitment to quality, HOF Electrical has rapidly established itself as a reliable provider of top-tier electrical solutions across various sectors, including but not limited to healthcare, industrial, commercial, and residential.
The company’s involvement in the Paula Fox Melanoma and Cancer Centre underscores its capacity to handle complex projects. HOF Electrical undertook the comprehensive electrical design and construct package for the centre, which involved the installation of advanced systems and infrastructure to support the facility’s diverse and specialised zones.
The scope of work included a 1675kVA generator and fuel system, nurse call systems, comprehensive communications and security packages, a Dali Dynalite lighting control system, a 250kVA UPS system, and extensive EMF shielding to protect both personnel and sensitive medical equipment.
Additionally, the project featured the installation of a 100kW solar
system, lightning protection, and a monitored emergency and exit system. Coordination with CitiPower for a new high voltage underground supply and indoor sub-station was also a key part of the HOF Electrical team’s scope.
One of the challenges HOF Electrical faced was the complexity involved due to the diverse range of spaces integrated within the facility’s design. The centre features numerous specialised zones, including PC2 and PC4 laboratories, body-protected patient treatment areas, imaging facilities, multi-disciplinary meeting rooms, and offices. Each of these areas adheres to distinct electrical regulations and standards, further complicating the project's execution.
To address these challenges, HOF Electrical employed innovative solutions and drew upon their extensive experience in the healthcare sector. “Despite the unique challenges inherent in this project, our team leveraged their collective knowledge and specialised expertise to manage and successfully deliver this multifaceted project,” Managing Director, Heath O’Farrell explained.
Collaboration with multiple trades and stakeholders was essential to the project’s success. “Working closely with architects, consultants,
Below HOF Electrical designed and installed advanced electrical systems for the Paula Fox Melanoma and Cancer Centre, ensuring regulatory compliance and innovative solutions.
suppliers, Kane Constructions, and CitiPower fostered a dynamic team environment that was critical in completing the project,” Heath noted.
“It was a privilege to be part of this project, contributing to the development of such an impactful facility that will make a tangible difference in healthcare delivery,” said Heath.
HOF Electrical, based in Richmond, Victoria, is dedicated to delivering reliable and professional electrical solutions. As a recently established entity, the company brings a fresh perspective and approach, leveraging the teams dynamic mix of experience with non-traditional methodologies and cutting-edge industry knowledge. This enables innovative solutions, agile adaptation to market demands, and strategic guidance with technical insights for clients across various industries.
With a rapidly growing team and a diverse portfolio of projects across various sectors, HOF Electrical continues to set new standards in the industry.
The company offers a comprehensive range of services, including end-to-end design and construct, electrical
engineering consulting, service and preventative maintenance, and data and communications solutions.
From minor works to large-scale undertakings, HOF Electrical ensures seamless integration from concept to completion, providing clients with expedited project delivery and meticulous attention to detail. Their commitment to exceeding client expectations through tailored, cost-effective solutions has established HOF Electrical as a trusted partner in the industry.
For more information contact HOF Electrical, 28 Blazey Street, Richmond VIC 3121, phone 1300 92 73 74, email admin@hofelectrical. com.au, website hofelectrical.com.au
Central Communications and Electrical Contractors (CCE) were instrumental in providing flawless cellular connectivity throughout the Paula Fox Melanoma and Cancer Centre project, with the installation of a Distributed Antenna System (DAS).
“Our scope was to build the DAS that can provide 100% cellular coverage within Alfred Melanoma as per the specs,” explained CCE Director, Jonathan Cornford. “Being able to provide a great user experience when it comes to using cellular services to the wider community is truly rewarding. We are pleased with the performance of the DAS as shown in our testing results.”
The team encountered a significant obstacle in running 7/8” coax cables along intricate routes with bends and obstacles obstructing other services. CCE effectively navigated the complexities by fostering collaboration with other trades, ultimately ensuring the successful installation for all services.
Electrical and communications contractors were required to work with minimal allowance on cable tray runs, resulting in an opportunity for creative problem-solving and collaboration, between teams to effectively manage available resources. “We were able to overcome
issues with labs, clean areas, and pressurised areas and install to suffice the builder’s expectations and standards.”
Since 1997, CCE has been serving clients throughout Australia, offering premium products and turnkey solutions for wireless enhancement needs. CCE specialises exclusively in building DAS systems to Australian cellular operators standards. With skilled and experienced resources available for the design, drafting, installation, testing, and commissioning of any in-building system, CCE delivers projects from beginning to end with seamless and trouble-free consultation with both builders and carriers to give a satisfactory result. We are Supply Nation registered which helps with indigenous procurement required on many projects.
“We are an established company in which the directors and employees all work together as a team dedicated to providing a quality installation on time,” said Jonathan.
For more information contact Central Communications and Electrical Contractors, Factory 2 & 3, 188 Centre Road, Narre Warren VIC 3805, phone Directors Sean McGarrigle 0418 384 629 or Jonathan Cornford 0407 432 853, email projects@cce.com.au, website cce.com.au
Below Fangda Australia created a stunning curved glass facade with specialised printed fritted glass to create the unique pattern design.
Behind the striking façade of the Paula Fox Melanoma and Cancer Center lies the meticulous work of award-winning façade specialist, Fangda Australia.
“Fangda supplied the external façade components for this project, including unitised curtain wall, glazing, perforated aluminium cladding, and featured shroud for the Level 5 terrace,” said Project Manager, James Gong. “The scope of work was extensive, requiring precision and attention to detail to meet the architect’s vision.”
One of the major challenges faced by Fangda was the fritted glass, which required a digital print to create the pattern and meet the architect’s expectations.
Additionally, the concave and convex glass, as well as the top curved fair-shaped glazing, posed design and production challenges for the unitised panel. To overcome these challenges, Fangda used special extruded profiles to achieve the desired aesthetic without compromising the overall performance of the curtain wall.
Another notable challenge was the removable curtain wall panel on the east elevation, which required careful planning to allow for the
construction of a link bridge between PFMCC and the existing old hospital building.
“A big highlight of this project was that all curtain wall production supply was completed within three months,” said James.
Fangda Australia, part of the China Fangda Group, delivers high-end facade solutions for curtain walls and window walls. Since its founding in 2016, Fangda Australia has built a reputation for excellence in workmanship, competitive pricing and outstanding results. The company offers a one-stop solution for all facade needs, including design, engineering, production, logistics, site installation and aftersales services.
“We provide clients with high-class boutique curtain walls to meet all their needs. No matter what your project might be, our team of professionals is ready to bring your ideas to life,” said James.
For more information contact Fangda Australia, 3B/990 Toorak Road, Camberwell VIC 3124, email overseas@fangda.com, phone 03 8685 8432, website www.fangda.com.au
Below Arctic Constructions created PC2 labs crucial for the Paula Fox Melanoma and Cancer Center, within tight space and access limitations.
Arctic Constructions has showcased their expertise in the construction of PC2 level laboratory rooms crucial for the Paula Fox Melanoma and Cancer Center’s clinical trials, demonstrating Arctic Constructions’ capability in delivering high-quality healthcare facilities.
“The Paula Fox Melanoma and Cancer Centre project presented us with several challenges that required innovative solutions and meticulous planning,” said Arctic Constructions Director, James Lawless. “One of the major challenges was the spatial restrictions on Level 4, where the laboratory rooms were to be constructed. We had to work closely with service trades to ensure that all penetrations through the panels were sealed appropriately, while also designing alternative wall-to-ceiling connection methods to accommodate the services.”
Access to the construction site also posed a significant challenge. “With all materials needing to be craned up onto the loading dock and 9m long panels being maneuvered with precision, the project required careful coordination and skillful execution,” said James.
Arctic Constructions also had to meet stringent design requirements. The walls, ceilings, doors, and windows had to be PC2 compliant
and withstand significant pressure. This necessitated custom design work in-house, working closely with Kane’s design team to develop solutions that met the project's unique demands.
Despite these challenges, Arctic Constructions successfully delivered a project that not only met but exceeded expectations.
“I am incredibly proud of the Arctic Constructions team for their professionalism, patience, and resilience throughout this project. Their dedication to delivering exceptional quality despite the challenges is commendable,” said James.
Arctic Construction specialises in all aspects of insulated panel construction including Clean Room, Cold Storage and Pharmaceutical. Services include insulated panel construction, all types of controlled atmosphere environments, coolroom/ freezer facilities, food processing areas, controlled clean and dust proof rooms, portable structures, architectural façade systems, and insulated panel roofing systems.
For more information contact Arctic Constructions, Factory 2/12 Access Way, Carrum Downs VIC 3201, email sales@arcticipc.com.au, phone 03 9708 2750, website www.arcticipc.com.au
DEVELOPER :
MAIN
ARCHITECT :
PROJECT MANAGER :
ENGINEER
CONSTRUCTION
Benevolent Living Rockhampton comprises two buildings; ‘The Terraces’, a 4-storey aged care building with one-bedroom apartments and private suites, and ‘Benevolent on West’, a 5-storey boutique retirement village with 40 two and three-bedroom apartments and basement parking. The project includes ‘The Town Hub Precinct’, offering amenities such as a chapel, theatre, coffee shop, gym, day spa, and learning hub.
Founded in 1866, Benevolent Living is a regional stand-alone provider in Central Queensland and is one of Australia’s oldest not-for-profit organisations.
Their mission was to transform their existing traditional residential aged care facility from a gated nursing home operating on a medical model into a vibrant and connected senior living community.
“Our vision was to inspire and enable people to live a happy life based on health, wellness, purpose and meaning. Not only is this the first vertical retirement village in Central Queensland, but Benevolent Living is also the first aged care provider in Australia with a working art gallery onsite that has a creative arts strategy that focuses on community connection and integration,” said Alison Moss, CEO of Benevolent Living.
Benevolent Living collaborated with architects to help redesign the master plan for the diversification and refurbishment of the current Benevolent Living site, with alleviating social isolation, loneliness, anxiety and depression in the elderly as the central focus.
Other key objectives of the re-design included increasing density on-site, diversifying revenue streams through retirement village accommodation and creating a beautiful inspiring community where people want to live, work and play. The result was a new masterplan that emphasised the importance of greenspace, filtering community engagement, holistic health and wellness and the arts.
The design features a fully functional art gallery and arts workshops, as well as other spaces for community events. A creative arts strategy was specifically developed for this site, and an Exhibition Programmer/Arts Coordinator was employed to activate the site and run programs.
Project works included the development of two multi-storey buildings and refurbishment of existing spaces within the Benevolent Living facilities. Building A consists of 36 residential care suites and apartments, and
associated support spaces including lounge, dining, servery, and treatment spaces. Building B features 40 two- or three-bedroom units as well as communal spaces, including a kitchen, dining, library, lounge, bar, consult spaces, and gym.
“This is the largest project that Benevolent Living has committed to, with a total of $47 million spent across both Stages 1 and 2,” said Alison.
“This project presented some unique challenges due to the size and scale of the development within an operating aged care community. This project creates its own complex issues in terms of access, maneuverability, separation and ensuring that the construction works do not interrupt or significantly impact the residents,” said Alison.
Works commenced onsite in 2021 with Building A and in September 2022 for Building B. The works for Building B included some demolition and service relocation works prior to the basement works being undertaken and the slab being poured in November 2022.
Stage 1, which includes the residential care building, art gallery, coffee shop, art workshop and cinema/chapel, has been completed, with work on stage two now complete in April of 2024.
With over 35 subcontractors engaged on this project, the daily site attendance averaged around 70, reaching 350 during peak times.
Throughout its two-year construction programme, the project faced numerous challenges, specifically, COVID and working within the grounds and alongside a highrisk health setting, coordinating works and trades within a live facility whilst minimising the impact on the facility operators and its residents, and the flow on effects of COVID within building industry such as significant price rises.
For more information contact Benevolent Living, phone 07 4837 0300, email communications@benevolent.com.au, website www.benevolent.com.au
Established in 2003, Boland Cranes is now a second-generation family-owned and operated business servicing Queensland and northern New South Wales. Boland Cranes were contracted to supply and install a tower crane for the Benevolent Living site in Rockhampton. Additionally, Boland Cranes supplied a qualified three-man crew, including an operator and two dogmen, for the duration of the project.
The team transported the tower crane on 10 semi-trailers from their Caboolture site in SEQ to Rockhampton in late 2022 and installed, tested and commissioned the crane all within one day. The base of the tower crane was specifically engineered to suit the ground conditions of the site, and the crane was strategically placed on site to ensure it was in the most economical location to best service the entire site.
“Since 2003, we have been providing professional crane hire for projects of 3-storeys and up, and with lifting capacities between 4 tonnes to 24 tonnes,” said Director, Ciaran Boland. “Our crane hire fleet has grown to 20 cranes plus multiple personnel/material hoists, loading bays and lifting equipment. We also provide qualified and trained operators and dogmen to ensure any lifting project is carried out professionally and safely.”
“To provide the safest, fastest and most economical solutions to our clients with smaller projects, we have recently added two spiering mobile cranes, the only two of their kind in Australia, to our fleet. These cranes are perfect for three to 4-storey walk-up projects,” said Ciaran.
To name a few current projects include retirement villages in Ascot and Carindale in Queensland, health care facilities and high-rise residential buildings in Brisbane and an 8-storey high-rise residential building on the Sunshine Coast.
For more information, contact Boland Cranes, 310 Old Toorbul Point Road, Caboolture QLD, phone 0417 619 140, email admin@bolandcranes.com.au, website www.bolandcranes.com.au
One of Australia’s leading building services engineers, JHA Consulting Engineers were engaged to provide building services design on the Benevolent Living Rhythm of Life Retirement Village project.
“It has been an exciting project to be a part of. We’ve loved the challenge that comes with an operational site that is also regionally situated,” said JHA Director, Tian Song. “It’s an impressive large-scale project that really stands out from other retirement villages.”
“We provided engineering and documentation, including drawings, reports and specifications for the project’s mechanical, electrical, hydraulic, fire, and ESD and Sustainability components during the course of the project,” explained Tian.
“We experienced complex constraints for this site. Works had to be undertaken in stages as the site is still operational, and we had to address upgrading the infrastructure, including power for new buildings, while considering the existing buildings. It meant we needed to be highly detailed and strategic with our design construction sequencing.”
The JHA team began working with the builder and architects during the initial design stages in early June 2020. The team provided support, documentation, and consultancy through to project completion in late 2023, aiding a smooth transition between construction and occupation.
JHA is a boutique, privately owned and multidisciplinary group of building services engineers who provide a comprehensive technical service offering for all facets of the built environment industry. They team pride themselves on their grassroots approach and deep understanding of local requirements.
Current projects include healthcare facilities in Queensland, including the Logan, Princess Alexandra and Prince Charles hospitals. While nationwide projects include correctional centres, private and public education facilities including tertiary universities, and residential and BTR developments.
For more information contact JHA Engineers, Level 1, 100 Brunswick Street, Fortitude Valley QLD 4006, phone 07 3257 4890, email brisbane@jhaengineers.com.au, website www.jhaservices.com
McAlister & Burford are the commercial paint, waterproofing and resin flooring specialists trusted with the interior/ exterior painting, wallpapering and exterior rendering for the Benevolent Living Retirement Village.
The team have been the site’s painting and rendering specialists of choice for the last 20 years.
“This project is very special to us as we have been lucky enough to have worked on every building of this site throughout the last two decades,” said McAlister & Burford Managing Director, Matt McAlister.
“It really is a marquee project for us. Not only is this a project that is going up within
our own community, it’s one of the largest projects to go up in the region in many years.”
Between the two buildings, we have painted over 27,500m2 of walls and ceilings, rendered over 2,800m2 and painted 3,500m2 of cladding. During peak times, McAlister & Burford had up to 15 Trade Painters, Solid Plasterers and Apprentices on-site working on the various elements of the project.
The team began work on the first of two buildings in November 2020 and were faced with the impact of COVID-19 and the particularly heavy restrictions of working within an aged care facility. The team completed work on the building in mid-2021 before beginning six months of painting and rendering on the second building in June 2023.
Servicing central Queensland, the team pride themselves on their expert knowledge, unparalleled experience and dedication to excellence and quality craftsmanship.
McAlister & Burford recently completed a three-year-long project installing epoxy flooring and painting 22 buildings within the Capricorn Correctional Centre.
Current projects include waterproofing 30 live fire buildings in Shoal Water Bay, multiple residential and NDIS apartment buildings and the Fitzroy Community Hospice project.
For more information contact Directors Matt or Dan McAlister, McAlister & Burford, phone 07 4921 3895, email admin@mcab. com.au, website www.mcab.com.au
ACCESS CONTROLS
Irongate Solutions
Page 58 | 1300 986 371
AIR CONDITIONING, (HVAC, REFRIGERATION & MECHANICAL SERVICES)
Mitsubushi Heavy Industries
Air-Conditioning Australia, Pty. Ltd
Page 8, 22 | 1300 130 007
AERIAL PHOTOGRAPHY
Skyview Aerial Photography
Page 4 | 0431 931 910
AUDIO/VISUAL & IT EQUIPMENT
Innavate
Page 62 | 0438 469 042
BUILDING MANAGEMENT SYSTEMS
Schnieder Electric Australia
Page 51 | 13 73 28
CEILINGS & WALLS
GMR Interiors Pty Ltd
Page 41 | 08 8363 3636
Square Ceilings
Page 46 | 0451 779 828
CELLULAR CONNECTIVITY (DISTRIBUTED
ANTENNA SYSTEM - DAS)
Central Communications and Electrical Contractors
Page 76 | 0418 384 629
CONSTRUCTION COMPANIES & ALLIANCES
Built Environs
Page 42 | 08 8232 1882
Hansen Yuncken
Page 26 | 08 8229 7300
Kane Constructions
Page 73 | 03 8420 1200
North Construction & Building
Page 60| 1300 667 840
Richard Crookes Constructions
Page 18 | 02 9902 4700
TOGA Group
Page 52 | 02 9356 1000
CONSTRUCTION SOFTWARE / DOCUMENT/PERSONNEL MANAGEMENT
CoreLogic
Page 1 | 1300 734 318
CRANES/HOISTS & RIGGING (ALL CRANE PRODUCTS & SERVICES)
Boland Cranes
Page 84 | 0417 619 140
Soldier Tower Cranes & Labour Services
Page 54 | 1300 Soldier ( 1300 7659 497)
DEVELOPERS
Mirvac
Page 66 | 02 9080 8000
DRAFTING (SHOP FABRICATION
DRAWINGS)
JP Drafting Services
Page 30 | 0433 366 435
ELECTRICAL DESIGN AND FITOUT
HOF Electrical
Page 74 | 1300 92 73 74
ELECTRICAL PRODUCTS
Rexel
Page 56 | www.rexel.com.au
ENGINEERING CONSULTANTS
JHA Engineers
Page 85 | 07 3257 4890
FAÇADES
Fangda Australia
Page 77 | 03 8685 8432
FIRE SAFETY (PASSIVE FIRE)
A & M Passive Fire Systems
Page 47 | 0412 799 335
Adelaide Passive Fire Solutions
Page 48 | 0437 372 319
FLOORING
JFloors
Page 28 | 0492 972 228
FLOORING (TIMBER)
Embelton
Page 69 | 1800 339 638
FORMWORK
Fastform
Page 59 | 02 8783 0400
FRAMING SYSTEMS ( ALUMINIUM
WINDOWS AND DOORS)
Darley Aluminium
Page 24 | darleyaluminium.com.au
Innovative Window Solutions
Page 62 | 03 5278 7655
GLASS & GLAZING
Oceania Glass
Page 10 | oceaniaglass.com.au
GREEN FAÇADES / GREEN WALLS
Fytogreen Australia
Page 71 | 1300 182 341
HEALTHCARE EQUIPMENT
Arjo Australia
Page 44 | 1800 072 040
HEALTHCARE & AGED CARE PROVIDERS
Benevolent Living
Page 80 | 07 4837 0300
INSULATION
Arctic Construction
Page 79 | 03 9708 2750
INTERIOR FINISHES
McAlister & Burford
Page 87 | 07 4921 3895
JOINERY & FITOUTS
JRCM Commercial Joinery
Page 33 | 08 8234 9600
LAB EQUIPMENT (CRYOGENICS
SOLUTIONS)
Capella Science
Page 37 | 02 9575 7512
PARTITION SYSTEMS
Dorma Hüeppe
Page 31 | 0455 321 035
PAINTERS
Paint Machine
Page 49 | 0412 112 663
PLG Painting Services
Page 36 | 08 8352 8180
PLASTERBOARD (GYPROCK AND FIBRE CEMENT)
Broad Windows and Façades Sydney Pty Ltd
Page 63 | 0452 211 064
POWER GENERATORS & SYSTEMS
Power Generator Systems
Page 32 | 08 8349 7854
PRODUCTS
Fosroc
Page 6 | 1800 812 864
RENDERING
Macquarie Renderers
Page 68 | www.macquarierenderers.com.au
SIGNAGE / WAYFINDING
Ecept
Page 38 | 0435 844 779
Trio Sign Group
Page 20 | 0418 500 778
WINDOW FURNISHINGS
SA Commercial Blinds
Page 39 | 08 8347 8700
We make the brands you know and trust for the community we live in.
Passion, team spirit and a constant eye on the future. Mapei contributes at a global level to the most important architectural and infrastructure works, residential projects and restoration work on historic buildings. Each and every day, in the name of innovation, we are committed to an increasingly sustainable building industry. BUILDING A PRESENT
Passion, team spirit and a constant eye on the future. Mapei contributes at a global level to the most important architectural and infrastructure works, residential projects and restoration work on historic buildings. Each and every day, in the name of innovation, we are committed to an increasingly sustainable building industry.
Passione, spirito di squadra e uno sguardo sempre rivolto al futuro. Mapei contribuisce alle più importanti opere architettoniche e infrastrutturali, ai progetti in ambito residenziale, al restauro di edifici storici a livello globale. Nel segno dell’innovazione, ci impegniamo ogni giorno per un’edilizia sempre più sostenibile.
Passione, spirito di squadra e uno sguardo sempre rivolto al futuro. Mapei contribuisce alle più importanti opere architettoniche e infrastrutturali, progetti in ambito residenziale, al restauro di edifici storici a livello globale. Nel segno dell’innovazione, ci impegniamo ogni giorno per un’edilizia sempre più sostenibile.