
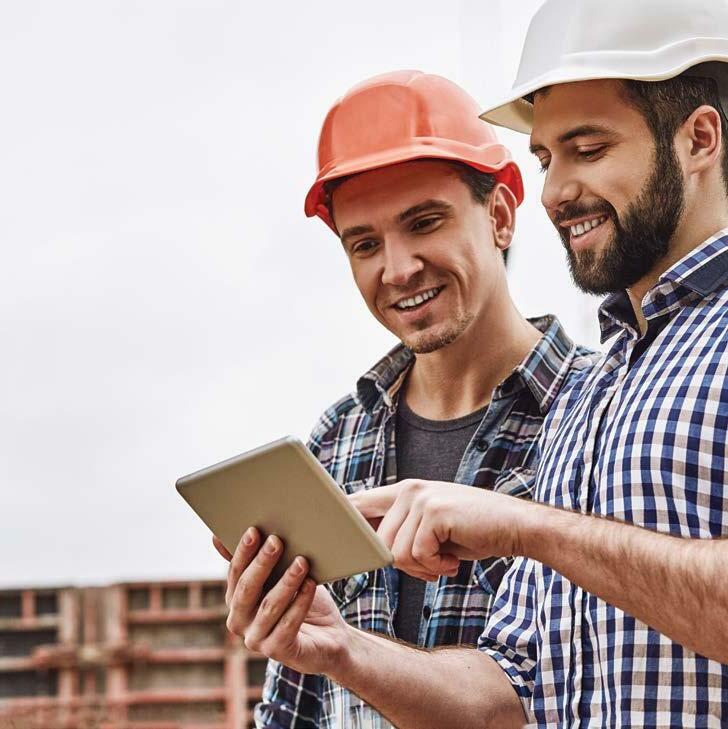
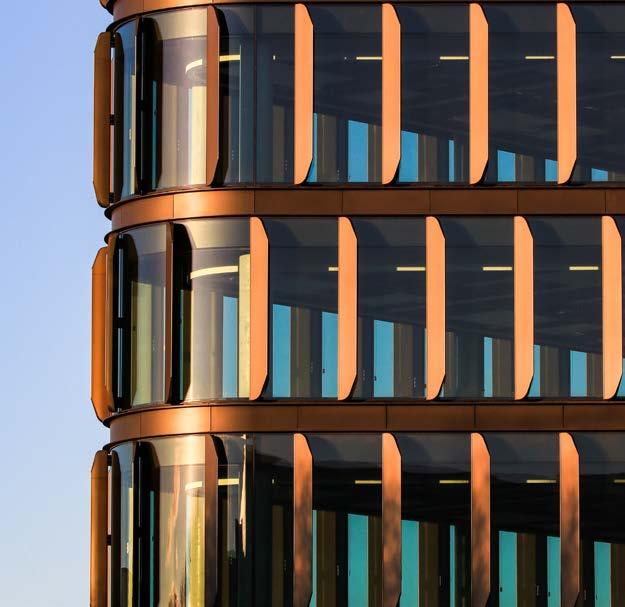

Find out more about how Cordell Connect and Cordell Estimator Platinum can help your business grow
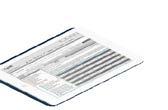
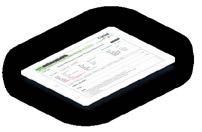
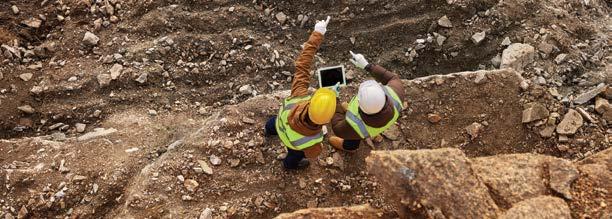
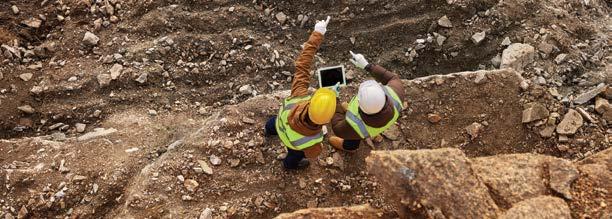
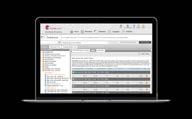
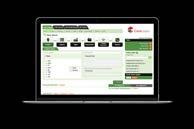

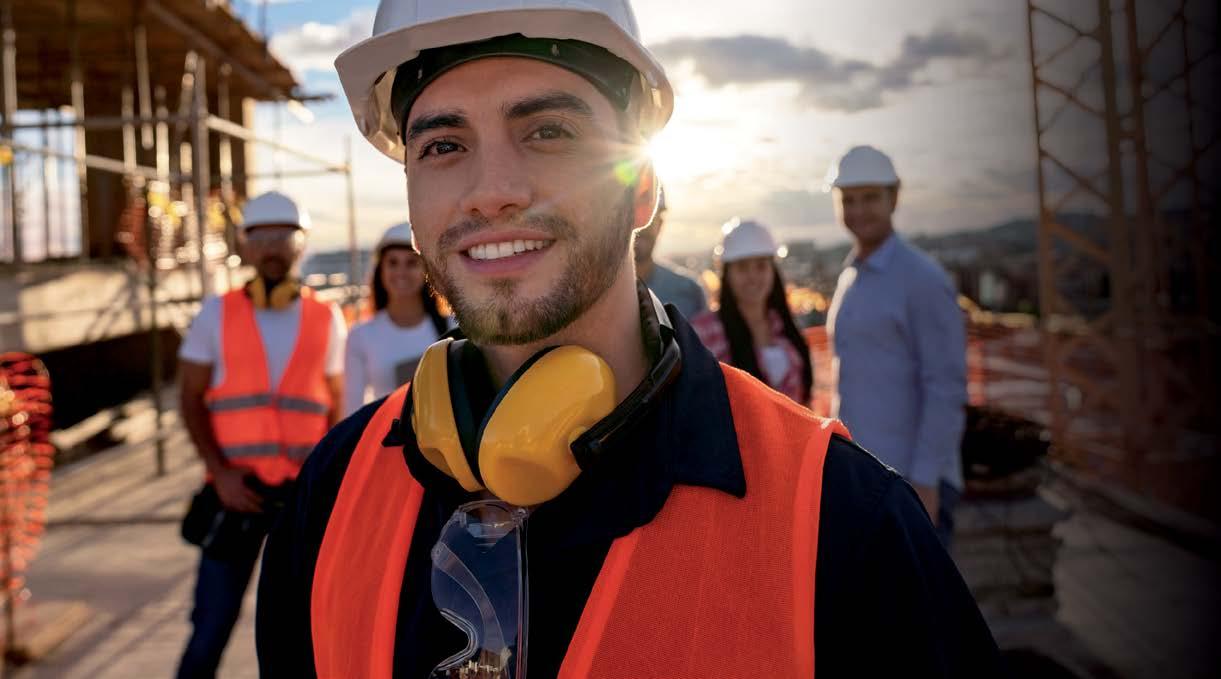
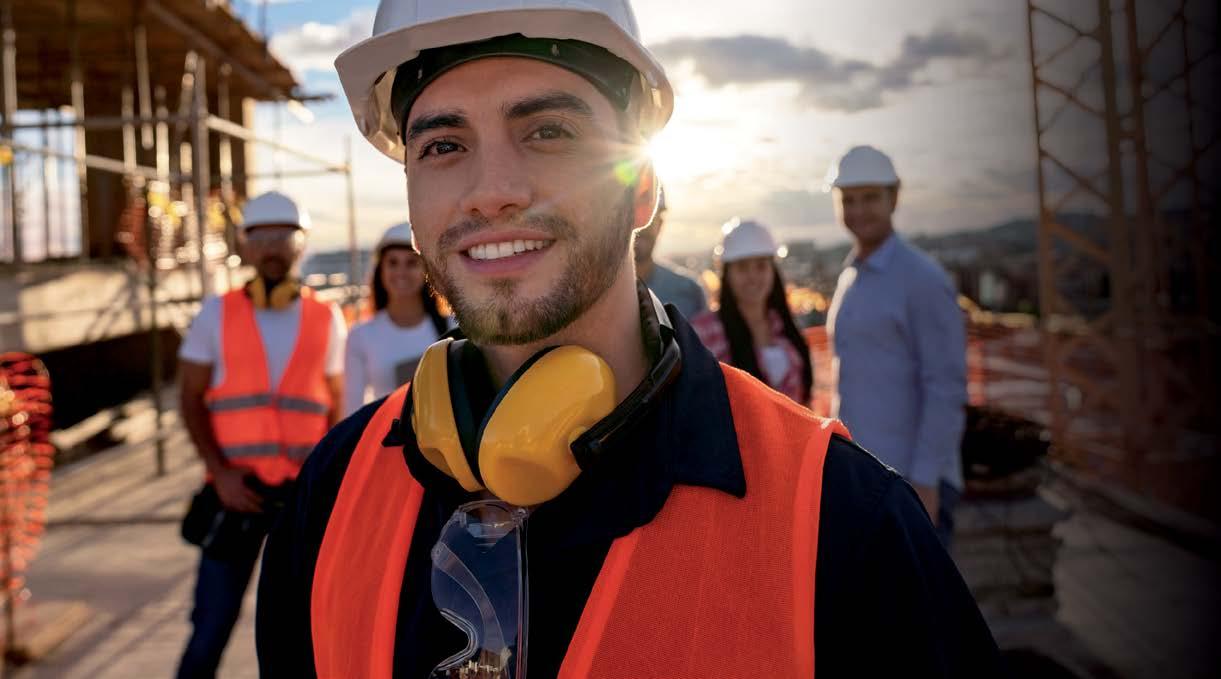

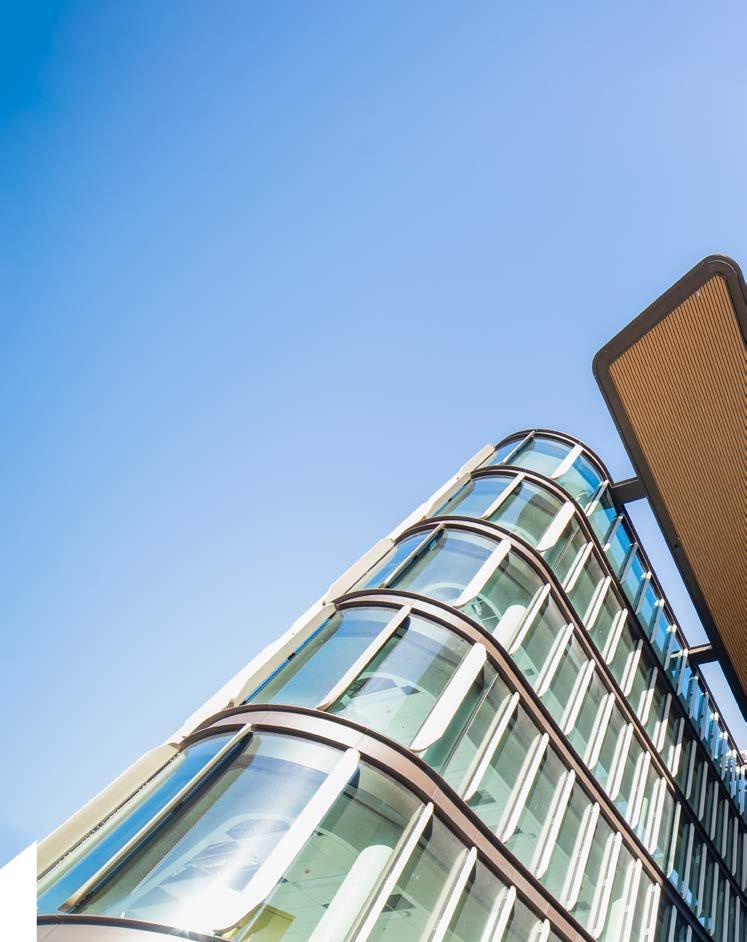

Find out more about how Cordell Connect and Cordell Estimator Platinum can help your business grow
The transformation of Darlinghurst’s Oxford Street made further progress today [12 October, 2022] as development partners, AsheMorgan and TOGA, together with construction firm, Growthbuilt, hosted the Lord Mayor of Sydney Clover Moore, to celebrate the progress at its heritage re-development, Oxford & Foley.
The Lord Mayor joined the Aboriginal Smoking Ceremony and general celebrations which marked the next phase of development of this landmark offering along Oxford Street, with the workplace, retail, creative, and dining destination set to reinvigorate the cultural and creative heart of Darlinghurst when it opens in 2023.
The ceremony follows the recent announcements from joint-venture partners TOGA Group and AsheMorgan, about the first major commercial office and retail tenants for the precinct. It will become the Sydney home of Melbourne’s worldfamous croissanterie, Lune, and fast-growing Australian customer research start-up, Dovetail. Joining them are multinational music companies, Sony Music Entertainment, Sony Music Publishing and The Orchard, who will relocate their Australian head offices and recording studios to Oxford & Foley.
Mendy Moss, Principal at AsheMorgan said: “We are extremely pleased with the strong commercial and retail leasing interest surrounding this new development and look forward to welcoming further tenants, as we
curate the limited remaining spaces in what will be Sydney’s latest hub for a dynamic and diverse set of businesses.”
“Separately, preparations for WorldPride 2023 and our alignment with the City of Sydney’s LGBTQIA+ Cultural and Social Place Strategy for the neighbourhood allows Oxford & Foley to become a focal point for LGBTQIA+ community life and culture.”
Allan Vidor, Managing Director of TOGA Group said the ceremony celebrates the hard work and dedication that has already gone into this three-building development on Sydney’s iconic Oxford Street - the first under the City of Sydney’s new Cultural & Creative precinct plan.
“The Oxford Street precinct is one of Sydney’s best-known neighbourhoods. The
transformation of these buildings is expected to be the catalyst to other developments along the street. We are honoured to deliver this project alongside our partners, restoring this iconic area,” Vidor said.
“The site will combine the rich heritage of Oxford Street with a modern feel, helping to reinvigorate an area that is close to the hearts of so many locals. We’re excited to be part of the journey that will shape the future of Oxford Street and deliver a bustling hub for local Sydneysiders and visitors to enjoy for decades to come.”
“Oxford Street is one of our great and bestknown streets and we’re committed to building on its reputation as an iconic gay and lesbian and creative precinct and a centre of buzzing activity both day and night,” Lord Mayor Clover Moore said.
Six months after opening, Greater Shepparton Secondary College (GSSC) is demonstrating the educational power of purpose-built, modern schools. With over 2,000 students enrolled, the award-winning ‘super school’ is a glimpse into the future of Australian education.
GSSC was built to amalgamate four separate secondary schools. The project’s impressive construction was completed in less than two years and earned building firm Hansen Yuncken two Regional Building Awards from Master Builders Victoria. GSSC was awarded for Excellence in Construction of Commercial Buildings, while Hansen
Yuncken took out the title of North East Commercial Regional Builder of the Year.
The school is custom-designed to support more pathways for students, featuring a careers hub and an Enterprise and Innovation Centre providing specialist teaching and learning areas for science, music, arts, drama, robotics and material technology. The new gymnasium is a sports education hub with two Netball Australia compliant courts, learning spaces, a dedicated weights and movement room and change facilities.
Traditional classrooms have been replaced by a new ‘school within a school’ model. The contemporary design features a series of smaller school buildings which form three ‘neighbourhoods’. The house-like buildings provide smaller, inclusive and flexible environments for students to foster a closer sense of community.
Another highlight of the construction was the upgrade of the one remaining Shepparton High School building, involving a complete fit-out to transform the space into a health and wellbeing centre.
Burning fossil fuels has been the go-to solution for heat generation and cooking since the industrial revolution, with natural gas boilers and cookers at the pinnacle of this old technology in buildings. But we are seeing a new revolution unfold, with clean energy addressing the challenges of health, climate change, air quality and energy affordability. Electrifying buildings is part of this revolution and the technologies to make it happen exist and are being used today, in new and existing buildings.
Here’s why more buildings are electrifying:
Climate change: all-electric buildings powered by renewables are the preferred pathway to decarbonise our built environment. Removing fossil fuels reduces climate change impacts and electrification enables buildings to be fully powered by renewables.
The construction industry is suffering from a gender gap significantly more extensive that any other industry with a representation of only 13% women.
The National Association of Women in Construction (NAWIC) responded with a goal for women to make up 25% of the industry by 2025. Can this goal be achieved or, more to the point – do women want to make up these numbers simply to serve public approval?
“Can we please stop with the quota hiring!” says Janet McCulloch, Strategic Consultant at Lysander, who is a strong advocate for increasing the presence, impact and effectiveness of women in the industry and has successfully improved the mental health of construction workers. Janet believes that this is a critical issue that won’t be solved with quotas. Ask almost any woman in construction, and she’ll tell you she doesn’t want to be a ‛quota hire’, she wants to be the best (wo)man for the job. Women need
to be able to succeed, not because of how well they act like men, but because they bring recognised skills and behaviours to the industry.”
Ellie Brown, also a Strategic Consultant with Lysander agrees “The construction industry needs to start looking at and owning why women don’t want to work in construction first.” According to Janet, “It’s not as easy as just finding and employing more women. There are systemic issues associated with culture that must be addressed first like flexibility, attitudes, behaviours.”
Lysander and Ellie Brown have created a ‛Women in Construction’ program that provides leadership development centred around emotional intelligence and skills to lead a strong inclusive team, with the confidence and capacity to thrive within the infrastructure and construction industry. Ellie concludes by saying, “my goal is that we will not need a program targeting ‛women in construction’ but we are not there yet”.
Investor benefits: Assets on a clear decarbonisation pathway are in high demand. All-electric buildings using renewable energy can also access sustainable finance, potentially at lower interest rates.
Resilience and risk reduction: as we decarbonise the economy, the need to retrofit assets and remove equipment using fossil fuels will become more important. An all-electric building is a step ahead and a valuable, futureready asset.
Health: Cooking with natural gas in buildings generates toxic air pollutants, increasing asthma and exacerbating respiratory illnesses. All-electric services eliminate pollutants and boost indoor air quality.
Tenant and consumer preferences: Natural gas and fossil fuels are incompatible with net zero targets of and do not meet the health and environmental expectations of today’s consumers and tenants.
The NATURA project is recognised as the most luxurious and uniquely designed apartment, which is now located and available in Macquarie Park. The NATURA was developed by Romeciti, a developer known for its ‛green’ and ‛technology’ residential concepts; designed by Architectus—Australia’s first 6 Star residential designer; and built by BESIXWatpac, which is a division of BESIX, the world-class architectural magnate that built the Burj Dubai.
public space and greenery, including 3,000m2 of functional space. This includes a swimming pool, gym, library, business lounge and more. The whole community can experience a star-level resort with flawless facilities and can truly sense the idea that “community is an extension of home.”
Information silos are detrimental to today’s construction jobsite, leading to inefficiencies, miscommunication and mistakes, which can cause projects to go over budget and past their deadlines, leaving clients unhappy and employees frustrated. Silos are typically caused by disparate systems that don’t talk to one another, and by data that isn’t connected across an organisation or between teams. In fact, according to a recent Trimble Viewpoint survey, 48% of project managers said their project management software had basic or no data and didn’t connect well to other software systems.
That’s why contractors should invest in cloudbased, connected construction management software since it enables all project stakeholders to all work off of the same data in realtime. With connected data and workflows, the barriers to true construction collaboration are broken down, and the complexities of modern construction processes are simplified and automated, allowing every role in construction work smarter, rather than harder.
Having data in the cloud means that data is even more accessible and secure. Backups are virtually automatic and information is protected via encrypted user-level permission controls, single sign-on and multi-factor authentication, all of which help block unauthorized access.
Contractors can also expect to have lower costs as new efficiencies can lead to cost savings, while implementations are typically done quickly, bringing contractors up to speed to compete with their more advanced competitors in a matter of weeks.
At a time when margins are already razor thin, contractors can’t afford to be behind schedule or over budget. Connected construction management software is the key to disconnecting silos and fast tracking your business for future success.
This project was completed and delivered by the end of 2021 and was designed and built with the concept of a ‛green environment’ and ‛technology’ at its core. The whole project has reserved about 10,000m2 of land for community
Another important keyword of NATURA is ‛technology’. The integration of technological elements such as solar power panels, Samsung intelligent door locks, water-cooled central air conditioning, Jalousie safetyline louvered windows and more, not only improves the living experience of residents, but it also makes the buildings more energy-saving and environmentally friendly.
The Energy Efficiency Council (EEC) welcomed the Albanese Government’s adoption of regulations allowing the Australian Renewable Energy Agency (ARENA) to invest in research, development and demonstration of energy efficiency and electrification technologies.
Energy efficiency and electrification are key strategies to enable the clean energy transformation needed to achieve Australia’s emissions reduction targets and make the most of Australia’s abundant renewable energy resources.
EEC CEO Luke Menzel, said that a focus on energy efficiency and electrification would complement ARENA’s existing activities.
“Energy efficiency and electrification bring the smart flexibility needed in a 21st century energy system and lets Australian households and businesses unlock Australia’s clean energy advantage,” Mr Menzel said.
“Harnessing efficient electric technologies is a key strategy to reduce energy use and bills, which is front of mind for households and businesses during the energy crisis,” he said.
The Australian Renewable Energy Agency Amendment (Powering Australia) Regulations 2022 are currently before Parliament, and Mr Menzel encouraged the new Parliament to support them.
“Energy efficiency and electrification supports and enhances the outstanding work done by ARENA over the past decade and helps extract the most value from investment in renewable energy. We must ensure that ARENA can give proper attention to its new functions, and we urge the Government to consider extra funding for ARENA in the upcoming Budget.
The role of electrification and energy efficiency is particularly important for business and industry, as high gas prices are creating havoc amongst Australia’s manufacturing sector.
Charter Hall Group (Charter Hall or the Group) is pleased to announce its Charter Hall Prime Office Fund (CPOF) has ranked as a Global Sector Leader in the 2022 Global Real Estate Sustainability Benchmark (GRESB) for leadership in integrating environmental, social and governance (ESG) considerations.
This year, 24 Charter Hall funds participated in the GRESB Assessment with 17 of these achieving scores within the top 20% of the GRESB universe. Our unlisted Retail funds are also credited as Regional Sector Leaders for Oceania.
Established in 2009, GRESB is today used by more than 170 institutional investors and is considered to be the largest and leading assessment of the sustainability performance of real estate assets and portfolios. In 2022, more than 1,820 listed and unlisted portfolios participated in the assessment, representing USD $6.9 trillion in gross asset value under
management across 74 countries.
Charter Hall’s performance in ESG benchmarks, including GRESB, is underpinned by our long-term commitment to integrating ESG into our business. This reflects our Groupwide approach to actively partnering with customers to drive mutual success, including environmental and social outcomes, alongside financial.
Marking another milestone in its commitment to innovation, Hansen Yuncken has signed on to be an Autodesk lighthouse customer for another three years. As one of the first Asia-Pacific adopters of Autodesk BIM 360 technology across the business, Hansen Yuncken has played a critical role in providing insights back to Autodesk to drive continuous improvement.
Hansen Yuncken has worked with Autodesk over the past decade, using its construction software across the business including in the current build of the Meadowbank TAFE Multi-Trades and Digital Technology Hub in New South Wales and the recently completed Sydney Coliseum Theatre.
The real-time technology centralises the design, modelling, documentation and data of projects. This has led to a multitude of advantages for collaboration, efficiency and decision-making – and Hansen Yuncken believes these learnings can be applied across the wider industry.
Daniel Smith, Building Information Modelling (BIM) Manager at Hansen Yuncken, said that cloud-based technology has saved hundreds
of hours in the build phase of major projects. “Meadowbank TAFE is a complicated project due to limited site accessibility and an intricate design. On top of that, we were completing a lot of the construction during the height of COVID disruptions over the last couple of years,” said Smith.
“One of our site managers estimated that, using Autodesk, an extra 50 hours invested in the planning stages saved us 200-300 hours of construction work, plus the flow-on costs.
“Team members, contractors and the client have visibility to a central hub of data, creating greater trust and more informed decisionmaking. We can better model and plan the entire construction process, mitigating potential risks before they occur. The current market has reinforced the need to achieve every possible efficiency.”
Autodesk cloud-based software has enabled Hansen Yuncken to go from 3D modelling of the design, to 5D modelling which considers time and cost information. Looking ahead, Hansen Yuncken and Autodesk are working toward 6D modelling to also factor in management.
Romilly Madew CEO Engineers AustraliaAs the world continues to embrace technology, systems will become more complex making the skills engineers possess critical to the construction industry. Australia is currently experiencing a significant shortage of engineering skills affecting most disciplines and sectors.
Infrastructure Australia predicts 41,000 further engineers will be needed to meet the pipeline of public infrastructure work. With private construction also booming nationwide, the need to look to increase productivity in the sector and develop the skills of tomorrow is more important than ever.
The uptake of technology can provide benefits to all phases of the construction and maintenance of assets. Digital twins, smart sensors, building information modeling (BIM) systems, digital engineering, and digital asset management tools can all help to reduce costs, increase productivity, and improve construction quality. The use of these technologies has numerous benefits, including increased collaboration and communication between teams and enhancing innovation through data capture.
Developing the skills to utilise these technologies within the existing workforce and in the next generation is critical for the construction industry to experience the gains possible from technological advancement. The construction industry needs to consider how to support the engineering workforce to up-skill. Mechanisms such as microcredentialing and career mentors can be a good start.
In addition, offering supportive internships and graduate programs for new engineers entering the sector can help to develop the next generation while also capitalising on their digital savviness.
Western Sydney University, Charter Hall and UNSW Sydney have celebrated the official opening of the $300 million world-class ‘Engineering Innovation Hub’ at 6 Hassall Street – a world-leading engineering and industry innovation precinct in the heart of Parramatta designed to blend state-of-the-art commercial and education facilities and deliver the next generation of engineers, architects and entrepreneurial leaders for Western Sydney and the nation.
A major investment in the Western Sydney region, the 21-storey Engineering Innovation Hub is firmly embedded in the civic centre of the Parramatta CBD. Featuring state-of-theart, digitally infused education, commercial, retail, and co-working facilities, the building has been specifically designed to promote knowledge sharing and to create meaningful connections between universities, industry, and the community.
Teaching programs offered at the new campus include a collaborative joint engineering degree, developed and delivered in partnership with UNSW, as well as courses in architecture, industrial design, and entrepreneurship. It is home to Western Sydney University’s worldleading research programs such as the Urban Transformation Research Centre and the University’s tech start-up incubator, LaunchPad.
Western Sydney University Vice-Chancellor, Professor Barney Glover AO, said the Engineering Innovation Hub is a milestone achievement – truly transformative infrastructure for Parramatta that fosters all-important innovation in the engineering sector and delivers positive outcomes for the whole community.
“The Engineering Innovation Hub is creating unparalleled opportunities to collaborate across disciplines and across industries –a world-class innovation precinct that is driving academic excellence and promoting economic growth across the whole western Sydney region,” said Professor Glover.
“This campus provides an exceptional teaching and work-integrated learning environment for our students, with the chance to leverage knowledge-jobs and research and development opportunities arising from the large-scale infrastructure and engineering investments across the region, including the new airport at Bradfield, the Sydney West Metro, and the Parramatta Light Rail. It is also fostering important research collaborations with business and industry and developing an
Architecture, engineering and planning firm, HDR, has appointed Simon Dormer as Sustainability Leader in a move that cements the company’s commitment to sustainable business practices and project delivery, and underpins HDR’s future trajectory towards truly regenerative design.
At HDR, Simon Dormer will be responsible for leading sustainable design across the business and mentoring and coaching design teams to drive a sustainable design culture. He will also work closely with HDR Architecture’s Health, Education, Science, Civic, Justice and Defence
innovation ecosystem for Western Sydney.”
Charter Hall Managing Director & Group CEO, Mr David Harrison, said, “We are proud of this outstanding investment in the heart of Parramatta, which Charter Hall will own long term after a successful joint venture development with Western Sydney University.”
“In addition to expanding our continued partnership with Western Sydney University, we are pleased to welcome valued tenant customers in CBHS Health Fund, Pepper Money and Hitachi Construction Machinery Australia who will play a vital role in creating a future-ready and resilient precinct where commerce and learning collide to create the next generation of industry leaders in Western Sydney,” said Mr Harrison.
sector leads to design and deliver buildings that regenerate people, places and nature.
In his role, Dormer will champion HDR’s global Regenerative Design Framework to support designers in moving beyond basic high-performance design goals towards netpositive impacts which consider buildings in a broader context. Winner of a Fast Company Innovation by Design award, the framework reinforces the importance of renewal-focused impacts and metric-driven targets for carbon, water, nutrients, air, biodiversity, social and health categories.
Photo © Sally TsoutasLeading designer, manufacturer and supplier of composite products Dura Composites has announced that its d2 product range of performance-improving composite walkway products is now available in Australia and New Zealand for the first time.
Following the successful deployment of the company’s award-winning Dura Platform train station platform overlay solution at Victoria Street station in New South Wales in 2018, Dura Composites has continued to innovate, launching a range of patented solutions including d2 Dura Grating – a GRP flooring and walkway product that offers the best performance-to-weight ratio in the industry and is up to 35% lighter than other GRP grating and around 45% lighter than a steel grating equivalent.
Dura Composites is an expert in the design, manufacture and supply of Glass Reinforced Polymer (GRP) products which are widely acknowledged to have major advantages over
more conventional material options as they are less energy-intensive in development and have an extremely long lifecycle.
However, not all GRP composites are created equal, and with a strong reputation for innovation, Dura Composites has continued to invest in its design, technology and manufacturing techniques to create a unique range of solutions known as d2, which redefine what customers should expect from their composite products.
With the d2 range, Dura Composites is able to solve real-world challenges for clients and customers, helping to reduce costs whilst improving safety and performance.
In many cases, the safer, stronger, faster and proven d2 products replace more traditionally accepted materials such as steel, wood and concrete and are faster and easier to deploy, reducing time and costs whilst also improving safety and sustainability.
Much has been said about the lack of housing across Australia, and there is no doubt we are facing a critical housing shortage. Supply is being routinely constrained due to increasingly difficult and slow planning systems.
Planning and approval systems across Australia have seen orders of magnitude increases in complexity compared with a decade ago, sometimes with questionable benefit. These are coupled with often conflicting policies, diverging interests, duplication and lack of consistency.
The capacity of planning assessments also hasn’t kept up with the growth in complexity, which means processes that might have taken six or 12 months, now take two or three years or more, adding cost and uncertainty.
NHFIC has identified it takes a minimum of six years from identification of new land for potential development to the first delivery of a new dwelling. This stymies delivery capability and capacity, even before adding on the recent shortages of labour and materials.
Fixing supply requires a holistic review of planning systems across Australia, from zoning, infrastructure planning and delivery, to planning and building approvals and most critically, bringing existing communities on the journey and recognising that we need to keep building new homes to keep our communities vibrant and accessible.
(CONTINUED)
New Housing: It’s about supply, actually! - Maxwell Shifman
Continued from this page of an incredibly complex system to deliver an important community need – new homes.
more responsive to both where and when demand is there.
Housing development is a highly complex and risky business, involving enormous investments and capital risk, and navigation
Part of the solution is to increase trust of our industry, recognising developers not as opponents, but actually as partners of Councils, authorities and the broader community in delivering new housing supply.
Planning systems need to be flexible and allow faster processing. We collectively need to be focused on the desired outcome – meeting the housing needs of current and future Australians – and ultimately enable housing supply to be
The construction industry is currently under immense pressure, facing a number of challenges, including rising commodity prices, supply chain disruptions, and a protracted labour shortage. More than 30% of construction businesses reported job vacancies in May 2022, according to the Australian Bureau of Statistics. Further, a February 2022 Procore survey found that 46% of Australian construction leaders believe the industry is suffering from a ‛brain drain’, and it is hard to compete with other industries for good employees. There is a clear imperative to ensure there is a pipeline of young talent entering the struggling sector.
Traditionally male-dominated and manual labour-oriented, the construction industry is quickly transforming due to the influence of climate change and the impact of accelerated technological development. New roles and career opportunities are being created in the industry all the time – due to an increased focus on sustainability and with robotics and automation replacing a lot of physical and administrative tasks. In fact, 47% of respondents in Procore’s How We Build Now 2022 report expect some future construction functions won’t require human labour and 36% think builders will need a broader skill set.
As this transformation continues, we’ll see construction professionals focusing more on problem solving, strategy, technology and even ethics, both onsite and in the office. We must continue to educate the market about what it's really like to work in construction, and in particular, ensuring young women are aware of the exciting opportunities in sectors they may have previously discounted. Just 39% of APAC construction leaders believe that women will form a key part of the construction workforce over the next 10 years – a number that must improve.
iStock, a leading e-commerce platform providing premium content to SMBs, SMEs, creatives, and students everywhere, and Tradeswomen Australia, a not-for-profit organisation dedicated to increasing the representation of women in skilled trade roles, have released new images of real Australian female tradies.
These images, taken by Australian Photographer Louise Beaumont, feature five real female tradies, selected from Tradeswomen Australia’s community, instead of models in an effort to prevent tokenism, and will feature in Project #ShowUs the world’s largest stock photo library created in partnership with Dove by women and non-binary individuals to shatter beauty stereotypes by showing women as they are, not as others believe they should be.
“Tradies are quintessentially Australian, making up almost a third of the workforce. But the visual representation of tradies
hasn’t kept up with Australia’s richly diverse population,” said Kate Rourke, Getty Images and iStock Head of Creative, APAC.
“By tapping into Tradeswomen Australia’s community to find real female tradies from different backgrounds, working across a range of industries, we hope to foster not only a more meaningful, authentic and inclusive representation of tradies in visual storytelling, but to raise reflection on how other underrepresented groups are being visualised in media and advertising.”
The Federal Government’s Budget recognition of infrastructure as a great enabler of social, economic and environmental benefits has been welcomed by Infrastructure Sustainability Council CEO Ainsley Simpson.
Ms Simpson said it was pleasing to see key election commitments honoured, in particular over $8 billion investment in infrastructure, the first $7 billion in commitments made through the Rewiring the Nation Fund, $42.6 million for the Climate Change Authority, $500 million to reduce transport emissions, and a total of $1.2 billion to 2030 to protect and manage and restore the Great Barrier Reef.
“This Budget represents a sensible first step in addressing climate change, but with only seven years to 2030 and the need to reduce our emissions by at least 43%, its time to make every dollar count,” she said. “We don’t have any more time to lose.”
While integrated climate, industry and infrastructure policy work is underway, immediate action is needed to deliver wider
benefits from the $248 billion infrastructure pipeline and avoid locking-in decades-worth of harmful emissions.
“One immediate action would be ensuring wider outcomes and whole-of-life carbon are considered at the business case stage, a step made easier by the inclusion of national targets in the Infrastructure Australia Act in September.”
The Council also called for accountability for all government infrastructure investment to credibly measure what matters. The Infrastructure Sustainability (IS) Rating Scheme was seed-funded and launched in 2012 by the then Minster of Infrastructure & Transport, Anthony Albanese, and is designed to create a common and harmonised approach to advancing the sustainability performance of infrastructure.
The evidence of progress is the 55% reduction of lifecycle energy CO2e emissions in 60 projects certified under the IS Rating Scheme over the past five years.
Investors are having to ‛look laterally’ to find opportunities for growth in the current market but can still successfully deploy capital, experts say, as ongoing uncertainty in the macroeconomic environment slows early-year momentum.
Speaking at a recent Cushman & Wakefield webinar, panelists from leading investment houses said rising interest rates and an inflationary environment had caused a ‘pause’ in the market as investors re-weighted their portfolios within the current conditions.
Despite the slowdown, investor sentiment was leaning towards a cautious resumption of deal flow to Asia Pacific later in 2022 once global
players from the United States and Europe had adjusted to the current conditions, said Regional Director, APAC Capital Markets at Cushman & Wakefield and webinar moderator Gordon Marsden.
“It is true that there are a large number of different economic circumstances ahead of us and trying to work out what that means for growth, interest rates and inflation is quite difficult right now,” Marsden said.
“But our panelists took the view that if the choices at each end of the scale are either to pause, or to invest in everything right now, then neither of those decisions is smart. Instead, we need to average-in over time.”
NAWIC has a bold mission to achieve 25% female participation in construction by 2025.
A key pillar of NAWIC’s strategic advocacy is to grow awareness of construction career options for high school girls. Across the nation our passionate team and volunteers give their time to visit local schools and share their insights and passion for the industry.
We had an incredible time at the Canberra Institute of Technology Try a Trade Day this month. It's amazing to see initiatives such as the Understanding Building and Construction Pilot Program from the ACT Government bringing together over 100 young women that are interested in a career in construction.
HDrive (a subsidiary of Australian specialist vehicle manufacturer BLK Auto) announced its entry into the hydrogen fuel cell vehicle (HFCV) truck market, with a range of trucks now in production after a successful design and engineering period.
HDrive has already taken several orders for its HFCV trucks, including for a dual control side lifter waste truck and a 6x4 prime mover recently purchased by fuel provider Pure Hydrogen for use by their clients.
HDrive’s HFCV trucks have been designed and engineered in Australia, using high-quality components sourced from its trusted network of suppliers to develop the company’s fuel cell and other market-leading technology. In a joint venture, HDrive trucks will initially be built at Wisdom (Fujian) Motor Company premises using the proven Ballard Fuel Cells. Wisdom majority shareholders are Ballard
and Hong Kong based investment company Templewater.
The range of trucks will sit alongside BLK Auto’s existing hydrogen coach and electric truck, & bus options. They are suitable for a variety of heavy-duty industries and with several drivetrain options available, including:
• Prime mover hydrogen trucks: 4x2 drivetrain, 24 tonne gross vehicle weight. 6x4, 18T to 70T GVW. 8x4, 49T GVW
• Refuelling trucks – 6x4
• Dual control waste trucks – 6x4
• Cement mixer trucks – 8x4, 10x4
HDrive is working with its customers to define requirements for other HFCV trucks to suit demand and improve its already comprehensive aftersales support, cementing partnerships and supply agreements with world-leading companies.
The UBCPP is aimed at boosting women’s participation in the construction industry through education pathways such as early learning about the building and construction industry in schools, which will be piloted in four schools around the ACT.
NAWIC is also supporting Inspiring the Future to facilitate discussions about career opportunities. Our General Manager, Lauren Fahey visited Blacktown Girls High for a speed careering event earlier this month.
Similar events have also been held in New South Wales, Queensland and Western Australia and partnerships growing across the country with apprenticeship providers, employers and schools.
We rise together.
Australia needs to think smarter about skills at the upcoming Jobs and Skills Summit to address the current crisis, according to Consult Australia which represents an industry that directly employs over 285,000 people in architectural, engineering and technical services and many more in advisory and business support.
CEO, Kristy Eulenstein discussed at the Infrastructure Roundtable hosted by the federal government in the lead up to the Summit.
To achieve Net Zero carbon by 2035, it is imperative for the Australian construction industry to develop and adopt AustralianBased Embodied Carbon Standards which are independent, transparent, and meet international standards. As noted by Slattery in their Upfront Embodied Carbon Benchmarks report, at present there are no industry agreed frameworks in Australia and, as a result, there are inconsistencies in methodology, scope and data sources that deliver inconsistent results. Additionally, not all professionals use the same methods or data sources. This makes comparisons and benchmarking across different businesses/projects problematic.
AIQS therefore, is working with MECLA, NABERS, GBCA and others to assist in the development of a national framework for measuring, certifying, and benchmarking emissions from construction and building materials. The main goal is to create a transparent benchmark which can stand up to external scrutiny and get to a point where the industry can be on a level playing field and communicating to clients/stakeholders in a common language.
Once this comprehensive framework for measuring and benchmarking emissions has been developed, the next step will be in ensuring emissions are correctly quantified on each and every future project.
The NSW Government has taken a lead through its Discussion Paper ‛Decarbonising Infrastructure Delivery’ which identifies a number of principles to account for a reduction of embodied carbon in infrastructure projects. Any meaningful quantification of embodied carbon prior to construction can only be undertaken with the provision of comprehensive project design and documentation.
Here the engagement of the quantity surveyor at project inception will prove critical in quantifying embodied carbon.
The acute shortage of around 52,100 engineers, scientists and architects required to deliver Australia’s burgeoning pipeline of public infrastructure projects is threatening economic growth and must be urgently addressed. The skills need is higher when you add other sectors, such as private sector building projects.
Consult Australia outlined its concerns and proposed solutions in its recent Thinking Smarter About Skills report, which interim
“We can’t keep doing the same thing and expecting different results. We need to start thinking smarter about skills to address the current shortage, which has been years in the making. That means strengthening STEM education, increasing skilled immigration and prioritising over-due procurement reform,” Ms Eulenstein commented.
Consult Australia’s contribution to the Roundtable supported role-modelling a collaborative education strategy that prioritises STEM, with focus on the participation of women. Bridging the gap of skills shortages would also mean employing tertiary educated engineers as well as paraprofessionals.
Wyndham Destinations Asia Pacific has wrapped up an almost $3 million refurbishment of rooms and common areas at Ramada Resort by Wyndham Shoal Bay, located beachfront at Port Stephens.
The refurbishment, which was completed in stages between May and September, included retiling of the indoor and outdoor pools, a refreshed reception area and updating 56 studio, one, two and three-bedroom apartments, including standard, Grand, Deluxe and Presidential categories.
“We used the resort’s incredible position right on the beach and the vibrancy of the Shoal Bay community as inspiration for this refurbishment of the apartments and reception areas,” said Senior Vice President of Acquisitions, Procurement, Property Development and Technical Services, David Wray.
“As part of our refresh, the apartments were repainted and we replaced most of the furniture, bedding and window furnishings and replaced the flooring with high-quality vinyl in the living areas. We conduct these refurbishments on a cycle in order to continually raise the standard of our properties, improve the experience members and guests enjoy, and show our commitment to the Port Stephens region.”
Ramada Shoal Bay is a mixed-use property providing accommodation to both the general public and members of Club Wyndham South Pacific, one of Asia Pacific’s leading timeshare clubs. Adjacent is the independently owned Shoal Bay Country Club, iconic home of Mermaids Café, lunch and dinner restaurant The Kitchen & Patio and Greek restaurant Atmos, along with event spaces.
The property is one of Club Wyndham South Pacific’s most popular resorts, with the refurbished rooms enjoying an average occupancy of 92% currently, and forecast to hit similar levels for the next eight months.
Leading Indigenous workwear company, Bunji Workwear has teamed up with one of Australia’s largest and most trusted PPE brands, TRu Workwear to release the first Bunji Indigenous Range.
As a teaser, Bunji Workwear has unveiled a first look at the TRu Workwear Hivis Indigenous Shirt and Trouser displaying the artwork of award-winning artist and co-designer of the first Indigenous Queensland Maroons jersey, Jyi Lawton.
Bunji Business Development Manager, Darrin Cross said they were proud to be launching a range that directly impacts and shapes the new generation of Australia’s Indigenous businesses. “The Bunji Indigenous Range is more than just a beacon of awareness or a conversation starter, it’s making a physical impact in Indigenous communities,” Cross said.
“From the garment artwork through to the distribution and sales, we are engaging indigenous talent and businesses however we can and will inject a portion of the profits back into these communities by donating a portion of the profits to Dreaming Futures.
“It’s been fantastic to have support and collaboration from other forward-thinking businesses like TRu Workwear to make this range and the resulting positive impact, possible.”
Managing Director at TRu Brands, Tony Urquhart said as Australia’s first certified range of workwear they were pleased to be able to offer their quality garments as the foundation of the new range.
“TRu Workwear has been developed to combat Australia’s harsh environment and conditions to ensure the utmost safety, comfort and reliability, over the years the business has really solidified its position as an innovative force in the development of unique and task specific Workwear and PPE,” Urquhart said.
“So, when Bunji Workwear reached out with the idea for the new Indigenous range, we had to be involved and together, we were able to turn this around in less than six weeks.”
Already, the Bunji Indigenous Range is flying off the shelves with large orders being placed by Indigenous-owned property services company, Multhana Property Services to supply their entire workforce with the new uniform.
In the coming months, Bunji Workwear plan to expand the range and launch additional items such as winter wear, Hi-Vis jackets and fleece jumpers, PPE gear from gloves and glasses through to hard hats, as well as corporate wear for project and site managers.
Russell Martin Group Water Sector Lead Wallbridge Gilbert Aztec (WGA)It seems incongruous to be commenting on water shortages and drought when so many of the eastern states are suffering major flooding events. Most climate analysts predict that many parts of Australia will experience more severe and prolonged droughts and rainfall will generally be lower resulting in significant water scarcity. Coupled with the threat of drought, is the growing tension between population, energy, agricultural and environmental demand for the available water.
Many of the States and Territories have plans in place to address water security and climate resilience but the timing to implement various initiatives are often at the tail end, that is, 2050 of the current planning horizon. To avoid reactive solutions initiatives such as stormwater harvesting and water recycling need to be brought forward.
California have taken up the challenge of water security by investing USD $8 billion over three years to modernise water infrastructure and water management. Initiatives include recycling and reusing up to 1,000gl (two times the annual water consumption for Sydney) of treated wastewater, creating storages in aquifers for a further 5,000gl of stormwater and freeing up a further 600gl through more efficient use and water conservation measures.
Closer to home, WA is front footing water security and climate resilience by investing $320 million as part of the Stage 2 Beenyup groundwater replenishment scheme which utilises high quality recycled water to deliver 28gl of potable water (approximately 10% of current potable demand).
We have plenty of warning that future droughts will be more severe and prolonged. Therefore, to match the pace of climate change, scientists and engineers across the water sector must be smarter and move faster to develop new responses to improve water infrastructure and water security.
For 25 years, the NAWIC Queensland Awards for Excellence in Construction have been the state’s premier event recognising outstanding achievements in architecture, engineering, and construction.
Every year, projects are evaluated by a panel of distinguished judges who bestow awards to those they deem most deserving. It is through these awards that we recognise and celebrate excellence in collaboration, innovation, leadership, and project management. It is also an opportunity for us to honour the individuals, teams and companies that have contributed substantially to our industry.
In October, NAWIC QLD hosted a gala dinner ceremony at the Royal International Convention Centre to celebrate these successes with our industry peers. Managed by the National Association of Women in Construction (NAWIC), the annual Queensland Awards for Excellence is one of the most prestigious diversity awards programs in Queensland.
Showcasing the achievements and industry advancements of women, men and organisations in the industry. A panel of industry experts selected the winners and highly commended, of each of the 13 categories, based on strict criteria. These and many more women have been involved in projects that are shaping the built environment and the construction industry.
NAWIC is a not-for-profit organisation, formed in 1995, that seeks to promote and improve the construction industry through the advancement of women. NAWIC is led
by a team of passionate volunteers who all strive to help champion and empower women in the construction and related industries to reach their full potential. With Chapters in every state and territory, we are also part of a global network of NAWIC organisations, including those in the United States, New Zealand and Canada. NAWIC provides a forum for its members to meet and exchange information, ideas and solutions.
NAWIC also offers its members an opportunity to expand personal and business networks, maintain awareness of industry developments, improve skills and knowledge, and contribute to other women in the construction industry.
Collaboration is the key to the construction industry. It is the process by which we work together to create innovative solutions to complex problems. The industry’s constant state of change is a result of the need to respond to an ever-increasing demand for new infrastructure, as well as advances in technology. Collaboration is the means by which these advances are incorporated across all levels of the industry.
Technology is constantly evolving, and this is driving innovation. Advances in technology are fuelling growth in the construction sector, which will see the industry generate an additional $470 billion in business by 2025. At the same time, labour shortages are causing the construction industry to struggle to keep up with growing demand. The solution, however, is innovation.
As such, NAWIC gathered together to recognise leadership, a critical aspect of
construction. We must all strive for excellence in everything we do, and this includes leadership practices.
At the same time, the construction industry is unique in its reliance on project-based contract work. This means that a high turnover of workers means little opportunities for leadership development. The key is in fostering leadership development at all levels.
The 2022 NAWIC QLD Awards for Excellence in Construction was a celebration of excellence in collaboration, innovation, leadership, project management, and much more. It was an opportunity to honour the contributions of those who have helped shape our industry.
NAWIC would like to say a very big thank you to their sponsors and look forward to continuing the success of breaking the bias for women in construction.
QLD Government Award for Outstanding Achievement of a Woman in Environment & Sustainability within the Construction Industry
Winner: Abigail Heywood
National Crystal Vision Award Winner: Dominque Gill
BESWIX Watpac Award for Achievement in Health & Safety Winner: Amanda Nicolo
TAFE QLD Trainee, Apprentice or Student of the Year Winner: Allyson Burrows
Construction Skills QLD Tradie of the Year Winner: Emma de Roia
Multiplex Award for Achievement in Construction (General Building) Winner: Rebecca Wood
QUT Award for Achievement in Design Winner: Holly Ramsey
Seymour Whyte Achievement in Construction (Civil Works) Winner: Yasmine Edlin
QBCC Award to a Young Achiever Winner: Holley Morton
Acciona Emerging Leader Award Winner: Yasmin Edlin
ADCO Constructions Award for Achievement as a Businesswoman Winner: Rachel Turner
John Holland Crystal Vision Award –for Advancing Women in Construction Winner: Protech
Established in 1995, the National Association of Women in Construction (NAWIC) champions and empowers women in the construction and related industries to reach their full potential. NAWIC hosts networking events and education seminars, runs annual awards programs, funds scholarships, and works with both government and industry to advance opportunities for women in Australia’s construction industry.
Climate change is the most critical issue of our time. Urgent action is needed now if we are to protect our future. The construction industry generates 23% of global carbon emissions with 5.5% of that coming from the fossil fuels used to power construction machinery and commitment.
As industry leaders, Lendlease is committed to leading the way in decarbonising construction and has embarked on ‛Mission Zero’, their plan to achieve net zero carbon emissions by 2025 and absolute zero by 2040.
Lendlease partnered with the University of Queensland (UQ) to investigate ways to reduce emissions by electrifying construction machinery and utilising alternative fuels. UQ prepared an evidencebased research report, ‛Planning a Transition to Low and Zero Emission Construction Machinery’. Lendlease’s companion report ‛Stepping up the Pace: Fossil Fuel Free Construction’ presents an action plan drawing on UQ’s research to create fossil fuel free construction sites.
The transition will be challenging however there are promising signs. Based on current policies and plans, UQ has projected that 40% of construction machinery and equipment (by energy use) can be electrified by 2030, growing to 60% by 2040. While the ownership costs of electric vehicles are more upfront initially, they are significantly cheaper to maintain over their lifetime, so the overall cost of ownership is less.
Currently not all construction equipment has a suitable battery-electric option. However UQ’s research has shown that renewable diesel, once established, can plug the gaps. A two-step approach prioritising
electrification and supported by renewable diesel has the potential to remove a large portion of a construction site’s fossil fuel consumption.
Thanks to pioneers like Lendlease many of the green building features that were once considered leading edge are now business as usual. Now ‛Stepping up the Pace: Fossil Fuel Free Construction’ is set to be another area where Australia’s largest construction company will lead the entire market.
Continues over page
Austin, Head of Sustainability at Lendlease, elaborates on Lendlease’s initiative and the critical importance of achieving the goal of fossil fuel free construction sites.
Why has Lendlease embarked on this initiative and how does it link back to the ‛Mission Zero’ approach?
We’re absolutely committed to climate action and the challenge to achieve our Mission Zero targets has now begun in earnest. This report is part of that journey. It zeroes in on a single action within our Mission Zero Roadmap: ‘Zero Use of Fossil Fuels in Construction’. With the help of the University of Queensland we explored how quickly we can electrify construction machinery and what alternative low carbon fuels are viable.
How does this initiative build on Lendlease’s previous work on sustainability?
As a global industry leader, Lendlease takes its responsibility to the planet seriously. Our Mission Zero targets are among the industry’s most ambitious and will only be achieved if our construction sites are fossil fuel free. We have been exploring ways to reduce emissions in construction for a number of years, mandating the use of 5% biodiesel in diesel in 2020 and trialling a 20% biodiesel blend (B20) on some of our sites. Renewable diesel and electrification take this work to a whole other level and much closer to zero.
Do you see Lendlease as having a social responsibility to promote a low-carbon approach and how does this initiative respond to that?
Absolutely. We have a responsibility and obligation to take an industryleading position. Lendlease has set ambitious targets of reaching
‘absolute zero carbon’ by 2040 and to do that, we must find a way to eliminate all emissions from construction sites – without the use of carbon offsets. We’re also cognisant that not one party can fix it, it needs to be a team effort that involves all players: clients need to request zero emissions, contractors need to assess their supply chain, suppliers need to be able to innovate, while designers need to test and try new things.
Does Lendlease perceive an increasing market demand for more sustainable projects?
Yes. We have seen a steady increase in sustainability expectations from customers and investors that has significantly spiked in the last two years.
Sustainability excellence and particularly carbon neutrality is already critical to attract both capital partners and quality tenants. Buildings that integrate the physical risks of climate change will increasingly contribute to investment performance and provide a competitive advantage.
The signposts are all pointing Australia in one clear direction. The question is how quickly we can introduce policies that support an orderly transition towards the inevitable fossil fuel free future.
What are the main barriers preventing fossil fuel free construction?
The main barriers to fossil fuel construction in Australia relate to the limited local availability of two essential fossil fuel free construction ingredients: renewable diesel and electric equipment and machinery.
Renewable diesel is a critical transition fuel made from animal fats, vegetable oils and agricultural waste. It is chemically identical to conventional diesel and is being used across several of our construction projects in the UK, including Google’s headquarters in London.
Currently renewable diesel is not manufactured in Australia and can only be imported at a significant cost. However two renewable diesel
Ann joined Lendlease in 1992 and has worked in a variety of project and people management roles. She established Lendlease’s first suite of sustainability metrics, guided by the Global Reporting Initiative framework, and is passionate about nurturing a culture that supports a consistent approach to sustainability excellence across all aspects of it’s business.
Ann chaired the award-winning Miller’s Point Youth and Employment Partnership, was the 2003 National Association of Women in Construction NSW Vision Award winner, the 2005 National Crystal Vision Award runnerup and the 2011 Contribution to Sustainability winner. Ann currently sits on the leadership group for MECLA, the Materials and Embodied Carbon Leaders Alliance.
refineries in Australia are expected to be in production by 2025, one in Queensland and one in Westerm Australia.
Electrification is the surest path to decarbonising construction but there is still limited availability of electric construction equipment and machinery in Australia. There are no battery-electric models currently available for a significant amount of construction equipment within typical trades such as civil, demolition and piling.
Added to this electrification challenge are grid constraints including a lack of capacity and the inability to manage ‘peak loads’ from individual construction machines such as cranes. Urgent upgrades to grid infrastructure are required to meet Australia’s transition to a low carbon economy.
Australia has no policies currently to support either electrification or renewable diesel, no national biofuel programme and no government subsidies. If we are to take a serious step change towards decarbonising construction, renewable diesel must be manufactured locally and electrification must be supported and accelerated.
Does fossil fuel free construction increase costs? Is this changing over time?
Electric construction equipment and machinery is expensive to buy but the total cost of ownership is less. The high upfront costs can be mitigated by low-interest green financing and significant ongoing operational savings. Imported renewable diesel is also expensive but local manufacturing will provide a clean fuel option that is commercially competitive with mineral diesel.
How urgent is it for the construction industry to become more sustainable? Do we have time for gradual change or do we need a step change now?
We have learned that gradual change is insufficient to meet decarbonisation pathways that keep us on target to achieve 1.5 degrees. We need to significantly accelerate the electrification of construction machinery and equipment. This is a challenge that can only be solved systemically – it’s one of those wicked problems no single party can ‘fix’.
However, rather than let this deter us, understanding the nature of our challenge can give us direction. Now, with UQ’s help, we know we are a 'hard to abate sector' and what change is needed.
With this initiative, do you see Lendlease as setting an example for the wider construction industry to follow?
Our hope in publishing this paper is firstly to allow the issues to be understood and secondly inspire collective action to decarbonise construction. There’s a sense of urgency about the work our sector needs to do around fossil free fuels and we need to shift our focus now.
For more information visit: www.lendlease.com/au/better-places/ stepping-up-the-pace-fossil-fuel-freeconstruction/
or Scan the QR code
For the fifth consecutive year in a row, Mitsubishi Heavy Industries Air-Conditioners Australia have been awarded the CHOICE® 2022, ‘Best Brand of Air Conditioners’ award and is the only Australian air conditioner brand to have achieved this accolade consecutively.
To be considered for the ‘Best Brand’ award, an air conditioner brand must have had at least a minimum of five different models tested by CHOICE® and a minimum of 50 consumer responses. An award-winning brand also requires an above average test, reliability, and satisfaction score.
In the 2022 review, MHIAA outperformed all other brands of air conditioners to receive an overall ‘Best Brand’ Score of 74% and was also rated highly in both reliability and customer satisfaction, achieving a 90% and 94% respective rating.
Demonstrating the highly rated consumer responses regarding their air-conditioning product range, the independent review and award, highlights not only the quality of their products, but also MHIAA’s superiority in the market, stemming from their 130 years of industry know-how.
Additionally, MHIAA were also awarded the Canstar Blue, 2022, ‘Most Satisfied Customer’ award, for the fourth consecutive year. Within these awards, MHIAA outperformed every other Australian air-conditioner brand and achieved a 5-Star rating in five of the six rated categories in the survey and customer feedback cited product quality, value and efficiency as being the reasons for rating MHIAA air conditioners as their preferred product.
Winning this accolade highlights MHIAA’s on-going dedication to Australian consumers and also means they are now in the top 15 percentile of multi-year award winners, with an incredible four consecutive wins across the air conditioning category.
Recognising brand sentient, resulting from customer feedback on different retail product categories, nearly 20,000 Australians rated
brands across 200 categories, MHIAA were also rated the ‘Best Split System Air Conditioner Brand’ in the 2022 Finder Awards.
Having taken out the same award in 2021, MHIAA once again reclaimed the ‘Best Split System Air Conditioner Brand’ award this year, outperforming all other brands and receiving an overall rating of 4.5 out of 5 and a 100% recommendation rating. MHIAA also outperformed in the categories of ‘Features and Functions’ and ‘Heating and Cooling Performance’, with an outstanding rating of 4.7 out of 5 in each category.
In terms of ‘Quietness’ and ‘Value for Money’, MHIAA was also rated highly with respective ratings of 4.4 and 4.5 out of 5 in each category.
MHIAA took their award winning products to this years Air Conditioning, Refrigeration and Building Services (ARBS) trade exhibition. In its’ 24th year and returning after a four year hiatus due to COIVD-19, ARBS is one of Australia’s most respected business events on the trade show calendar, was back earlier this year, bigger and better than ever before.
MHIAA boasted an elegant, sophisticated and functional brand space, which showcased some of their latest and soon to be released products. Yet the team from MHIAA went one step further and incorporated a ‘Taste of Japan’ experience. This unique experience not only highlighted their extensive Japanese history, but also included traditional Japanese Yakitori being cooked over coals, as well as Japanese whisky beer tasting throughout the week. It also saw them being awarded the ‘Best Large Custom Stand’, highlighting and recognising the hard work of the team, as well as the innovative ideas they showcased at the exhibition.
These recent accolades reflect MHIAA’s position as one of Australia’s most trusted air conditioner brands. With a focus on innovation and technological leadership, delivering reliable and high-quality air conditioners to Australian consumers is what clearly makes MHIAA the ‘Experts in Air’.
For more information contact Mitsubushi Heavy Industries Air-Conditioning Australia, Pty. Ltd., Block E, 391 Park Road, Regents Park NSW 2143, phone 1300 130 007, email info@mhiaa.com.au, website www.mhiaa.com.au
Australian owned and customer focused, SAYFA design and manufacture access and fall protection systems that offer trusted solutions which ensure the safety of workers throughout Australia. Recently engaged on the The Park, Maquari e Park, SAYFA utilised their RAPTOR Rope Access Davits and AP118 XPLORA Concrete Mount Anchors to provide effective rope access to the project ’ s façade.
SAYFA specialises in the design and manufacture of access and fall protection systems that are slimline and lightweight with low visual impact for commercial and industrial structures.
“Founded in 2002 SAYFA began as installers of access and fall protection equipment, however, there were very few proprietary systems available and we began designing and manufacturing our own,” said Technical Manager, Murray Voss. “Due to increased demand, from 2008 we’ve concentrated on producing our own specialist access and fall protection products.”
SAYFA’s Approved Installer, Sky5, was contracted to design and install access and safety equipment to The Park, a 5-storey warehouse and office space development in Macquarie Park, with façades comprising over 260 linear metres of glazing.
“The client required a system that took the rope access loads off the parapet and extended them out past sunshades. We also had to deal with a foam and gravel rooftop which meant a traditional system wouldn’t work. Our davit base solved these problems, installed on the rooftop slab, extending out and ensuring safe façade access,” said Murray.
“The design had to be a lightweight system that could withstand the rope access loads. Most importantly systems had to comply with Australian Standards. We are proud to say that the RAPTOR Rope Access Davits do just this, as do all of our products,” said Murray.
“The manufacturing challenge included creating a system that allowed rope access technicians to easily manoeuvre and reposition themselves between the davit bases. Many systems are too heavy and difficult to handle without mechanical assistance, but these davit arms can be lifted by one or two workers and this is the ideal scenario.”
“Our installer, Sky5, are a trusted SAYFA Approved Installer and they carried out the design and installation at The Park. The products installed were RAPTOR Rope Access Davits, designed and manufactured at our facility in Boronia; and AP118 XPLORA Concrete Mount Anchors, which we imported and then assembled.”
Sky5 were able to design, and install an appropriate access and safety system at The Park largely due to their early involvement in the design, ensuring an access system that is user friendly, aesthetically pleasing and satisfies the legal requirements for
working at heights. The SAYFA team provided a slim modern and lightweight system with low visual impact that was appropriate for the medium-rise buildings.
SAYFA has over 20 years experience in the height safety industry and are Gold Members of the Working at Height Association (WAHA). All SAYFA products are designed and manufactured to conform with the requirements of Australian Standards, the Work Health and Safety Act and relevant Industry Codes and Regulations.
Australian owned and operated, SAYFA offer a one-stop-shop experience for all fall protection and access equipment, ranging from anchors, static lines, rigid rails, rope access davits and needles as well as modular access and safety systems. They offer design and consultation services to installers, building designers and architects providing fit for purpose solutions using standard stock products or customised systems.
Recently SAYFA introduced three new products to expand their versatility and cater to the ever changing needs for access and fall protection:
• RAPTOR Rope Access Needles, especially suited to metal deck roofs spreading the load to avoid any damage, with low visual impact, can be extended out past facades for maintenance work.
• RAPTOR 80 Rigid Rail. This has a more compact design to provide increased load capabilities and can be mounted easily and quickly using SAYFA’s patented RAPTOR T-Bolt fastener.
• 3SIXTY Rapid Fall Arrest Anchor. Lightweight construction and fast installation using only eight rivets, connection to two roof sheets with a powder coated finish.
For a full suite of documentation available for SAYFA’s products, including brochures, operation and installation manuals, technical drawings, videos, Revit files for designers and architects, warranties and certifications visit LIBRARY at the SAYFA website.
For more information contact SAYFA, phone 1300 301 755, email sales@sayfa.com.au, website www.sayfa.com.au
Australia's best air conditioner brand five years in a row
Australia's most satisfied customers four years in a row
Australia’s best rated split system air conditioner brand two years in a row
25 years ago, in November of 1996, Darley Aluminium started as a small family owned business fabricating and installing security windows and doors from a suburban home in Sydney. The business started with four employees and has transformed during the 25 years that followed.
It wasn’t long before Darley expanded their capabilities which led to the need for a bigger workspace. The team moved from their home office to a spacious warehouse in Wetherill Park.
By the year 2000, the team had evolved to 25 staff which included drivers and warehouse employees, however this wasn’t where the expansion ends.
Fast forward to 2021 and the company has grown to become a national distributor with four branches positioned throughout Australia and employing more than 230 staff. Darley has become one of the largest distributors of aluminium extrusions in the country and provides complete systems and services for all types of residential, commercial and industrial projects.
2006 was a milestone year for Darley following the acquisition of land in Erskine Park which saw the construction of a much needed new head office. Spanning over 12,000m2, the NSW branch is now the main hub for distribution and is home to the business operations.
Darley offers a number of value added services in addition to the distribution of aluminium extrusions, which includes powder coating, light fabrication and packaging.
In 2008, Darley developed a new suite of window and door systems. The CityView system for the commercial sector and the KlassicView for residential window fabricators.
More recently in 2019, ClimateGuard was launched. Along with building their capabilities, Darley have established a solid and experienced team leading to the company being recognised as a trusted, and highly regarded brand.
Darley value their people. They understand that they could not have achieved the longevity and continued growth without the hard work, dedication, and support of their employees. The company’s success is
also attributed to their loyal customer base, who continually provide repeat business and referrals.
Darley are excited to celebrate their 25th anniversary this year and are looking forward to another 25 years of success.
The management and staff are committed to the ongoing growth of Darley and will continue to stay at the top of their game with the latest technology and systems.
Ray Kwan, National Sales Manager at Darley Aluminium said, “We started as a small family business providing aluminium extrusions to window and door fabricators.”
Over the last 25 years, the business has grown into more than just an aluminium distributor and into a full service solutions provider, offering customers everything from locally designed and tested thermally broken windows and doors, customised extrusions and fully glazed windows and doors via our partnership with Alucity Architectural Product Supply. Darley are committed to building a sustainable future by investing in developing their window and door systems, digital infrastructure and investing in their branch facilities and people.
If one of the 3,000 aluminium extrusion products on offer at Darley isn’t what you need for your next building project, then the team at Darley are there to help. Darley is your one-stop-shop for all your aluminium window and door needs and can cater for small-scale fabricators to large construction companies buildings multi-level apartments.
DARLEY ALUMINIUM
NSW (02) 8887 2888
VIC (03) 9238 3888
QLD (07) 3287 1888 WA (08) 9437 2999
Heritage Lanes at 80 Ann Street Brisbane is a 35-level world-class office tower with over 60,000m2 of premium-grade office space. The project blends heritage with contemporary aesthetics, while embracing leading technology, sustainability, and design which will set a new benchmark for Brisbane’s premium office market and for workplaces all over the country.
Heritage Lanes is an exciting development that sets a new benchmark in both style and sustainability for commercial office space. On completion the new tower will integrate seamlessly with the heritage structures, retaining the spirit of the past within a contemporary environment.
“Built on the site of the 1906 Brisbane Fruit and Produce Exchange, Heritage Lanes has incorporated features and materials from the past,” explained Head of Integrated Investment Portfolio at Mirvac, Campbell Hanan. “The podium reflects the pitched roof design of the old marketplace, while a Heritage Market zone on the ground plane incorporates original shed formwork into a new energetic retail space. Timbers from the original buildings are reused in the modern tower foyer on Level 1, which is designed to speak to the traditional ‘Queenslander’ veranda.”
Elevating the tower lobby meant the entire ground plane could be public space with three new laneways, exciting art installations, retail stores and event facilities. Native sub-tropical planting and water features make a gorgeous urban garden setting, suited to contemporary hybrid working expectations where the office transforms into a hub of community and collaboration.
Mirvac formed an Art Committee for the development, appointing art curator, Simon Koger from iAM Projects, to work with architects Woods Bagot and representatives from the Mirvac Development and Mirvac Asset Management teams, as well as coowners, M&G and Suncorp. The committee
commissioned artworks that celebrate Brisbane’s environment including a digital display on the foyer ceiling and a fully integrated BIM system was used to facilitate full 3D modelling.
“From a sustainability perspective we have achieved net carbon in operations, and we are on track to be the first building in Australia to achieve 6 Star certification for Green Star Buildings.”
The 6 Star Rating represents ‘World Leadership’ in environmentally sustainable building practices and we’re extremely proud of that achievement. Heritage Lanes targets some of the highest standards across NABERS, WELL and additional Green Star ratings, and is one of the most intelligent buildings in Australia.
“The comfort of employees and visitors was emphasised throughout the design, with several permeable and breathable floors with openable façades that reflect a quintessentially Queensland ‘life lived outdoors’ experience.”
“We also have a best-in-class IT infrastructure with a fully Integrated Building Platform and Integrated Communications Network. The project also included the delivery of nearly 50,000m² of integrated fitout across Suncorp and IWG Co-working.”
“Beyond constraints due to COVID, the challenges included the introduction of jump steel to address programme pressures. Structural steel was built to span from the lower ground to Level 5, enabling us to get
into building our typical office floor plates from Level 5 and above much quicker. It was extremely important that we were able to deliver the project without any disruption to our anchor tenant Suncorp, with them having early occupation from October 2021.”
Mirvac is actively pursuing other opportunities in the Brisbane CBD as we look to further expand our commercial and mixed-use portfolio in the thriving Brisbane marketplace and across other cities in Australia.
“We are also one of Australia’s leading developers of Built to Rent (BTR) which arrives in Brisbane with LIV Anura, a pilot project delivered in partnership with State government. Located in the inner-city suburb of Newstead, LIV Anura sits within our broader Waterfront Newstead masterplanned development.”
“Waterfront Newstead also includes the Build to Sell (BTS) projects, Quay and Isle, luxury residential apartment buildings with an innovative green ‘biophilic’ focussed design that will deliver more than 50% of the ground level for public use and open space to create an even bigger Waterfront Park.”
“On the back of a very strong sales response we’ve also recently commenced construction of the next stage of our Ascot Green masterplan, further expanding supply in the highly sought-after Ascot suburb.”
For more information contact Mirvac, Level 14, 80 Ann Street, Brisbane QLD 4000, phone 07 3859 5888, website www.mirvac.com
Below Fredon designed, supplied, installed, commissioned and certified the electrical, communications and security systems, on the project.
Fredon is the leading provider of electrical, HVAC, technology, security and asset services to suit a variety of commercial and industrial needs. The company was contracted to design, supply, install, commission and certify the electrical, communications and security systems.
“Fredon won this project due to our inhouse design engineering capabilities and project team structure, which enabled us to provide a competitive bid that included value engineering,” explained Project Manager, James Jones. “Fredon re-engineered the entire project during the bid phase and presented the new design with costings at a meeting with the client.”
Over 95% of the re-engineered design was approved and this demonstrated significant savings for the client. The client later advised Fredon senior management that it was awarded the project because of our innovations and design changes that improved the overall lifecycle of the development.
“The project consisted of a $21 million base building works package followed by a $21 million integrated fitout. A ream of 60 from Fredon worked on the project designing and detailing for the installation of:
• The distribution system from the onsite Energex substation
• Diesel generators
• A 130kW solar system on the roof
• A 160kVA UPS for the base building
• Two 250kVA UPS for integrated fitout
• Communications throughout the building including an N+1 ICN network
• The security system including access control and CCTV
• Lighting including specialty architectural lighting and lighting control
• DAS (distributed antenna system) throughout.
• MATV (digital master antenna television) – a technology used to service multiple use facilities with a number of television outlets from one antenna system
“We designed and deployed one of the largest solar systems in the Brisbane CBD for a commercial tower totalling a 130kW of renewable energy. This powers the entire
building’s base build lighting load including all carparks, lift lobbies, amenities, lobbies, the market hall and all terrace and façade lighting. Early occupation by Suncorp required the major infrastructure and building systems be commissioned and operational almost a year before the building was finished.
“We were also required to demonstrate a WELLS compliant building, and introduced a new uniformity test that was recognised by the builder and the peer review consultant as unique and innovative. The building has also achieved a 6 Star Green Star as built rating, a 5 Star NABERS energy rating, a 4 Star NABERS water rating and Platinum Core Certification.
“Heritage Lanes is considered to be a next generation workplace setting a new benchmark for office space in Brisbane and across Australia. Fredon is extremely proud to have been able to work on this project. The client will now work with us to target future projects that will make use of our internal engineering capabilities. Our new innovation in light testing and modelling with whole of lifecycle readiness deployment of systems will offer future advantages for the business.
“In business for 54 years Fredon employ 340 people across Queensland. We are a multidisciplinary team with years of experience in the design and implementation of complete integrated solutions. At Fredon each division employs specialists in their respective fields, who draw on each other’s expertise to achieve result-driven outcomes.”
Currently Fredon are at work providing their electrical and communications expertise to the Southern Queensland Correctional Precinct Stage Two, due for completion in late 2023; and at Melbourne Quarter, Fredon is the mechanical contractor for the 36-storey premium grade commercial tower, Sky Park. The works will target 6 Star GreenStar and 5.5 Star NABERS energy ratings and will be completed in 2024.
For more information contact Fredon QLD, 7 Welch Street, Underwood QLD 4119, phone 07 3340 7300, website www.fredon.com.au
Below Ellis Air Conditioning designed, supplied and installed the HVAC system into the new and heritage sections of the project.
Ellis Air Conditioning is expert in the design, supply and installation of heating, ventilation and air conditioning solutions for commercial properties across Queensland and Victoria.
In May 2019, Ellis Air Conditioning was awarded the D&C contract by Mirvac for the HVAC services at Heritage Lanes. The project involved the design, supply and installation of contemporary air conditioning equipment to the new tower, as well as a more complex installation in the heritage component.
“The major challenge involved fitting the ductwork and AC equipment into the existing structure. Ellis Air’s engineers designed the HVAC to fit within the existing constraints of the building with the goal of limiting the affect the new work would have on the existing structure and the ceiling space,” explained Project Director, Joshua Daley. “At Heritage Lanes we had a large timber truss to work around and we had to thread the ductwork through what was available. Often the building fabric is compromised in older buildings and the challenge includes ensuring that fire ratings are achieved.”
“We had a team of 10 installing at the heritage part of the build, however the HVAC system for the tower was a much larger job, at $35 million. Our inhouse engineers modelled the design using BIM and we then installed HVAC equipment across all 32-storeys, a plant room on Level 6 and five cooling towers to the roof. At peak periods we had many different trades at work including 30 sheet metal workers and 20 electricians. Other challenges included restrictions due to COVID, volatile prices and long lead times.”
Founded in 1964, Ellis Air Conditioning boosted its staff and capabilities in 2011 to serve a wider range of commercial applications with a Queensland office opening in 2014. Ellis Air Conditioning designs and installs HVAC systems across a range of commercial sectors from offices, apartments, factories and sports complexes to laboratories, hospitals and clean room facilities. In Melbourne a large portion of their work involves HVAC installations for luxury residences with Ellis Air Conditioning’s own inhouse design team providing tailor-made solutions.
Ellis Air Conditioning provide a comprehensive service from design and product specification, sourcing, installation and commissioning. The company focus on achieving and maintaining ongoing working relationships with clients that add value to both businesses, provide a 24-hour emergency service, and a preventative and essential services maintenance programs.
Ellis Air Conditioning are up-to-date with changing environmental regulations and the achievement of contemporary building standards. Understanding that current legislation requires property owners and tenants to have an essential services maintenance program in place for air conditioning and ventilation systems, Ellis Air offer a free site visit to enable preparation of a detailed maintenance plan for air conditioning and ventilation equipment. They offer NEBB Certified Air and water balancing, upgrades for energy efficiency, BMS integration and condition reports on HVAC and gas appliances.
In February 2022 Ellis Air Conditioning was awarded the mechanical services package at the Logan Hospital Expansion Project in Brisbane. The project involved the installation of air conditioning equipment to serve specialist laboratories and air-tight rooms. Ellis Air Conditioning will continue at Logan Hospital till mid-2023.
At the University of Queensland, Ellis Air Conditioning installed their own prefabricated structural steel risers comprising 16 sections installed into the central shafts of the new Andrew N. Liveris Building. For the Thomas Dixon Centre, Ellis Air Conditioning’s mechanical services involvement included a combination of concealed and exposed ductwork to the heritage structure.
Recently Ellis Air Conditioning started major HVAC installation works for the Cross River Rail Project in Brisbane, winning contracts for mechanical services at Woolloongabba and at Albert Street stations.
For more information contact Ellis Air Conditioning, 54 Alexandra Place, Murarrie QLD 4172, phone 07 3213 9700, email ellis@ellisair.com.au, website www.ellisair.com.au
Building Experts Australia (BExA) is Queensland’s leading independent provider of building and engineering consultancy services specialising in defect assessments and quality control management. In July 2021 BExA started onsite at Heritage Lanes ensuring compliance with contract documentation and quality control.
“We undertook quality assurance of finishes throughout the interior and exterior of the building, including the sound insulation compliance and the functionality of the lift security communications system,” explained BExA CEO, Bruce Haines:
“Onsite we worked with Mirvac engineers to identify and resolve some commonly occurring defects, for instance we had an issue with tiles and grout cracking on curved sections of wall in the amenities area. We assisted Mirvac in changing construction details and it has been successful in preventing recurring damage.
“A first for us was the use of Zutec Defect Management software. Mirvac dictated our use of this software and provided our access to it. The system had each area of the building uploaded into it and this made it easier to identify defect locations; and we could photograph
defects, upload them into the numbered defect description item and track its repair.”
Established in Brisbane in 2018 BExA operate throughout north and east Australia providing building and engineering consultancy services, project management, and design drafting. They also carry out forensic damage investigations and write reports for expert witness services, to assist clients succeed in building industry tribunals or in court. BExA offer defect and maintenance inspections, as well as strata property condition reports.
“Recently we wrote an insurance repair scope and assisted in the remediation design for a $40 million fire damage claim at a rendering plant near Beaudesert. That remediation scope incurred extensive fire, mechanical, structural and electrical engineering works, plus extensive chemical analysis works undertaken to determine the extent of heat and soot damage,” added Bruce.
For more information contact Building Experts Australia, 2 Brookvale Close, Kenmore Hills QLD 4069, phone 0475 454 350, email admin@bexa.net.au, website www.bexa.net.au
Micos designed, manufactured and installed the curtain wall and window wall to the podium and tower at Heritage Lanes. “A special feature of the façade is the vertical and horizontal decorative fins and the Micos design team worked to allow the fins to be folded, with a pivot connection, so they wouldn’t clash with the builders’ screen,” said Design Manager, Poppy Veerasawmy.
“Manufacture took 12 months, and included extrusion die trials, procuring glass and the fabrication of powder coated aluminium frames, steel, galvanized sheeting and insulation for all the panel components,” said Project Manager, Brendan Booth. “We also carried out machining and assembly of the aluminium frames and structural glazing of the panels ready for installation in August 2020.”
“The biggest challenge onsite involved installing the curtain wall panels behind the builders’ screens. The curtain wall panels arrive onsite with the glass facing upwards and we flip the panels so the glass is facing down. The distance between the slab and the screen was so tight we were unable to launch the panels in the conventional way and a machine was specifically made to flip the panels and then we attached the fins. After removal of the builders’ screen, an abseiling team unfolded the fins to their intended position.”
The Micos installation team of 19 worked as two crews installing simultaneously on multiple floors to complete the installation by January 2020.
Established in 1958, Micos offer a comprehensive service of design and detailing, sourcing and fabrication, project management, and a quality installation. Heritage Lanes is a testament to Micos’ ability to manage entire projects and rise to the challenge of today’s unique design and construct demands.
Previous successful projects for Mirvac include the Pavillions at Sydney Olympic Park and St Leonards Square, two stylish tall towers on Sydney’s north shore.
For more information contact Micos Group, Suite 1.02, Unit 16B, Discovery Cove Estate, 1801 Botany Road, Banksmeadow NSW 2019, phone 02 8058 3000, website www.micos.com.au
Zenith designs, manufactures and distributes high-performance furniture solutions that inspire people and organisations to thrive. “Our furniture brands include products designed and manufactured by Zenith, along with prominent local and international designers,” explained Queensland Manager for Zenith, Chadd Burdon.
“At Heritage Lanes, Zenith was contracted to complete the internal fitout for the Suncorp workspaces and the Queensland team supplied and installed contemporary workstations and loose furniture items. As a response to the demand for more flexible workspaces, Zenith supplied a Floorsense desk booking solution, allowing employees to pre-book their deskspace, choosing a setting suitable to their day’s tasks. We also installed a fully customised Smartalock locker solution, and both of these systems were integrated with Suncorp’s IT infrastructure.”
Established in 1956 as a humble partitions and joinery company, Zenith Interiors have grown into one of APAC’s leading design and experience-centric furniture solutions companies. Zenith is built around the core belief that people should be inspired and motivated by their work environment, so they can focus, collaborate, socialise, and feel part of a community.
“With a growing network of 13 showrooms across Australia, New Zealand and Asia, our clients and partners have local customer service and support teams on hand,” said Chadd.
“We also have manufacturing plants in Sydney, Melbourne, Auckland, and Shanghai, which are supported by our digital production platforms. This vertically-integrated business model allows us to be agile and versatile in our design, manufacturing and delivery operations, enabling us to deliver affordable luxury and exceptional quality at scale. This is how we curate modern, dynamic and inspirational workspaces for all our clients. By partnering with local and international designers, architects, interior designers and builders, we curate modern working environments for our clients that reflect their core values and culture.”
For more information contact Zenith, Level 2, 11 Commercial Road, Newstead QLD 4006, phone 07 3170 0000, email info@zenithinteriors.com, website www.zenithinteriors.com
Established in Brisbane in July 2000, Arden Architectural Staircases design, manufacture and install functional and elegant staircases to commercial developments. For Heritage Lanes the ARDEN design team of six spent three months detailing and producing shop drawings for the manufacture of the structural steel staircases.
“We took the architectural vision and the engineering input to design the staircases and balustrades,” explained CEO, Jim Browne. “For the Suncorp fitout on the upper storeys, we installed three triple storey helical staircases assembled one above the other, they are very impressive. A further 17 flights of steel helical staircases were put throughout the building. The scope of the work was challenging and we had to ensure our installation method was efficient and safe. It was our biggest project to date.”
ARDEN has developed strong working relationships with leading architectural firms and construction companies and has previously completed contracts with Mirvac.
“The Mirvac team is very good to work with,” said Jim. “We prefer to be involved early in the design process and we were able to do this at Heritage Lanes and ensure a quality outcome.”
ARDEN employ CAD operators and 3D modelling professionals to produce quality designs, skilled fabricators in manufacturing and an experienced onsite installation team. They also offer well designed associated structures such as contemporary tiered seating arrangements, and all their products are manufactured in compliance with Green Star, WELL and LEED ratings.
In 2018 ARDEN won the QLD MBA award, Commercial Trade Contractor of the Year, for second year running, for its work at the Aurizon building in Brisbane. Other successful projects for ARDEN include the design, manufacture and installation of a 5-tonne staircase craned four storeys into the Midtown Centre for a Rio Tinto fitout. The team were again awarded Commercial Trade Contractor of the year, for their exceptional delivery on the project.
ARDEN also designed the beautiful flowing staircases installed at 200 George Street, Sydney, in 2016.
For more information contact Arden Architectural Staircases, 46 Radley Street, Virginia QLD 4014, phone 07 3267 6100, email admin@arden.net.au, website www.arden.net.au
Below Tilecorp installed floor and wall tiling throughout the apartments and common areas of Heritage Lanes.
Tilecorp is one of Queensland’s largest commercial tiling contractors carrying out the supply and installation of a vast range of wall and floor tiling including ceramic, stone, marble and granite. Tilecorp started onsite at Heritage Lanes in November 2020.
“We installed floor and wall tiling throughout the apartments and common areas from the basement to Level 31, as well as stone cladding to the ground floor and Level 1. This included tiling the lobby and main staircase as well as exterior works to the street entrance,” explained Tilecorp’s Project Manager, Rod Walls. “The stone cladding was challenging as the pieces were huge, measuring 600mm x 1500mm. We also installed terrazzo benchtops on Level 23, in the Suncorp offices.”
Due to COVID restrictions, the company needed to carefully manage labourers to ensure all aspects of the project were met. “We also spent time implementing the new laws concerning dust and silicosis, however it was a good project for us and the job went very well,” said Rod.
Tilecorp is a family operated business with over 29 years experience in the commercial market with contracts completed for highrise
apartments and office blocks, shops, fitouts, hospitals and railway stations. Brisbane based, Tilecorp work across the CBD and along the Gold and Sunshine Coasts.
With an installation team of 35, Tilecorp provides quality tiling and cladding solutions for large scale and complex projects. “We take on the jobs that other tiling companies won’t tackle, and we’ve achieved a reputation for reliability and a timely, quality outcome,” added Rod.
In 2017 Tilecorp completed the tiling contract for the two towers, Unison Apartments in Brisbane and in 2018 they finished a high quality supply and installation job to the kitchens and common areas of Brisbane Racing Club.
Currently Tilecorp is at work on some major developments including Queens Wharf Apartments in Brisbane and the Gold Coast Airport.
For more information contact Tilecorp, 108 Stradbroke Street, Heathwood QLD 4110, phone 07 3279 9009, email kelsey@tilecorp.com.au, website www.tilecorp.com.au
The Ci Group is a national technology and AV company working within the contemporary discipline of media architecture, the idea of enlivening a building’s static surfaces with LED screens to creatively communicate and stimulate.
“The reason we do practically all the major project examples in Australia is that they all need what our inhouse team provides. Without it, a builder risks an unhappy client and they would rather enjoy a risk-free turnkey success instead,” said Director, Chris Gauci
“Our design and construct team includes R&D people, project managers, AV engineers, specialist installers and fabricators, software programmers, and more. This provides the necessary skill-set to collaborate with the client and content provider. Control and content need to cooperate for success, and on Ann Street we again worked closely with Spacesuit & Co from Bengar Films to help them realise their creative vision.”
“The project features two LED ceilings: one on the first level where we installed the largest indoor LED screen in the southern hemisphere measuring 232m², made up of 4,240 individual LED tiles and powered by a custom-built PC. Its content aligns with the building’s wellness
aspiration. Above the rooftop terrace, we added an outdoor screen of 384m². 23m wide, it can be seen from street level and displays real-time digitally rendered art. A macro bubble system is generated by BOM wind direction and velocity data.”
The Ci Group successfully met technical challenges of construction at Heritage Lanes that other installation companies would have found difficult, such as accommodating HVAC items or screens needing sweeping curves. Most of the complex LED projects throughout Australia are Ci projects. There is no other technical facilitator in the country as committed to the cause, and they also provide the ongoing support LED demands.
A special 40-minute presentation of The Ci Group’s project capabilities at your premises can be requested.
For more information contact The Ci Group, phone 1300 242 742, email contact@thecigroup.com.au, website www.thecigroup.com.au
Most buildings present a data ecosystem that very few tenants have the opportunity to engage with. 80 Ann Street provides a platform that delivers information and value from hundreds of thousands of data points throughout the building, which enables access to data for Mirvac, their chosen third party stakeholders and tenants with the appropriate access credentials.
VAE Group’s Technology department were contracted by Mirvac to provide an Integrated Building Platform (IBP) and Integrated Communications Network (ICN) for 80 Ann Street which enables all the building’s data sources to be integrated into one platform.
The interactive displays showcase the advanced technological capabilities built into 80 Ann Street. The scalable, future-proofed infrastructure and data capacity in the base build makes 80 Ann one of Australia’s most advanced data rich buildings, projected to collect over 16 million data points daily.
• Responsive action-based insights: The buildings integration also helps to ensure a swift and supportive response to any building issues.
For example, if an escalator outage notification is received, real-time CCTV is available on your device (i.e., mobile phone) to instantly understand whether there are people in need of assistance. With real-time data securely captured across every building system, any problem can be analysed based on the data record to ensure clear and transparent answers are available.
• Leading security: Every sensor and device installed in 80 Ann was meticulously qualified to ensure they met the highest possible cyber security standards, including on-going live monitoring for any irregularities or network traffic anomalies, where devices are disabled, or shutdown should suspicious activity occur.
• Ongoing enhancements: Building data is stored and analysed to explore improvements in existing assets as well as refine the design of future projects.
• Customised Tenant Smart Platform: A collaborative design approach was undertaken for Suncorp’s specific operational requirements within their space offering lighting, blind control, air conditioning and security control through mobile apps and integrated AV systems. This means a meeting room booking will prepare all smart systems in the space automatically, responding to the environmental conditions on the day, and ensuring it’s ready for any meeting or event taking place within.
• Designed to seamlessly enable connectivity to Mirvac’s Enterprise Cloud ecosystem
• Over 2,350 connected operational technology devices
• Over 150,000 hardware and software points with over 170,000 history extensions
• Customized user interfaces and branded tenant graphics and systems which eliminates the need for an independent user interface for each service, providing one unified system for the building managers, this reduces training and increases productivity.
Mulherin Rigging & Cranes Australia (MCRA) specialise in the installation of structural steel with a range of cranes, qualified operators, riggers and installers. At Heritage Lanes MCRA completed the craning and installation of 600 tons of structural steel for the Jump Start construction process. The steel frame was installed to Level 5 and, working up and down the building, a rapid construction programme followed.
“The Jump Start steel exceeded our expectations and allowed us deliver high quality end product,” said Project Supervisor, Liam Liddell. “We completed the job safely and quickly and continued onsite with mechanical rigging, assisting Mirvac, and number of trade’s with complex rigging installation including methodologies and high risk workshops.”
MCRA installed the stunning steel veil façade on Ann Street and the strong steel arches at roof level, as well as manufacturing and installing precast concrete panels and elegant curved seating.
“We made a design change to the roof to include roof sheeting, façade cladding and solar panels to minimise the risks of working at heights, improve utilisation of the tower crane and keep to the programme.
We used new product, Hilti X-HVB shear connectors, as an efficient replacement for welded shear connectors. Also new for us was the Bimtek 3D laser scanning which gave us a schematic representation of existing works and easy access to information about the structure in real time,” said Liam.
Mulherin Rigging & Cranes Australia were founded in Queensland in 1995 and by 2013 had established a precast concrete facility to support their construction services, offering design, fabrication and installation in one package. Their portfolio includes 1 William Street in Brisbane, which features interesting steel work installed by MCRA, they installed the huge spire, finishing the building at 259.8m. At the beachfront at Surfers Paradise, MCRA installed the gold patterned crown steel to the stunning slimline 78 storey residential tower, Ocean Apartments.
“We focus on designing the way to erect and install steel and concrete with safety and efficiency. To achieve this it’s best to be involved early in the construction planning,” added Liam,
For more information contact Mulherin Rigging & Cranes Australia, phone 07 3807 0222, email admin@mulrig.com.au, website www.mulrig.com.au
The Thomas Dixon Centre Refurbishment and Performing Arts Expansion will provide new world class facilities, enabling the Queensland Ballet to accommodate more dancers, expand their training programs and enhance community initiatives.
The refurbishment of the Thomas Dixon Centre will provide world class contemporary performance and rehearsal spaces for the Queensland Ballet.
Renovations to the existing building included the provision of new offices, boardrooms and back-of-house areas, soft and hard landscaping to the perimeter of the site and the conversion of five historic air raid shelters into the Bunker Bar. New facilities include a wellness centre, expanded dressing and fitting rooms, wardrobe space and a dancers lounge.
The design includes a roofed promenade that links the new four storey structure and the heritage building with the two buildings connected by an elevated walkway at level 1. The new building has a performance venue with seating for 330, a rehearsal studio, performance spaces and a public studio, all over two levels of basement car parking for 66 vehicles.
“Hansen Yuncken worked in close liaison with the heritage architect to ensure that the works were being undertaken in strict accordance with the Department of Environment and Science Queensland
“The existing windows needed upgrading as well as the installation of the new dance floors, mechanical services, and audio visual equipment to the four performance studios on level 1. The ground floor now houses administration areas and offices, the gym, rehabilitation facilities, a cold spa and the staff kitchen.”
“We installed floors of hollowcore panels and Bondek slabs with structural steel walls and floors to the main performance studio. External cladding is a combination of Colorbond, precast concrete
Heritage Act,” explained Hansen Yuncken Project Manager, Justin McGrath.and glass, the eastern elevation has a coloured sand-blasted concrete finish and the perimeter walls of the performance studio are also precast concrete clad with Hebel wall panels.”
“Asbestos was also discovered in the ceilings and the old concrete floor slabs, as well as lead paint on most of the timber. This required the introduction of detailed work method statements to enable safe removal and remediation while the rest of the build continued. An especially challenging aspect of the project was the interface between the heritage building and the new construction and we had weekly site inspections with consultants to ensure the work was in accordance with the design intent.”
“The building is entirely unique: the overall fit and finish throughout the project is of a very high standard due to the numerous types of finishes and different interfaces. With projects where new work has to marry with existing heritage materials, we focus on detailing how the new materials dovetail with the old.”
The site was very restricted with buildings taking up the full footprint and materials handling required meticulous planning. COVID-19
restrictions had an impact and then floods slowed the final stages of the project, yet with up to 130 workers onsite during peak periods, the project was completed by May 2022.
Hansen Yuncken have recently completed several performing arts projects in other states, Her Majesty’s Theatre Redevelopment in South Australia, completed in 2020 was another major project requiring renovation of heritage listed structures. New builds include the stunning Sydney Coliseum Theatre in Rooty Hill, completed in 2019 and The Hedberg, in Tasmania, delivered in 2018.
“At Hansen Yuncken we are proud of taking on projects that other contractors steer away from. That’s what sets us apart, Hansen Yuncken has a successful history of innovation, performance, and collaboration, with a review process to help clients find alternatives, adding value and reducing costs. Projects such as the Thomas Dixon Centre may bring challenges, however, the Hansen Yuncken team excel in the delivery of more complex, bespoke and technical jobs. We see them as an opportunity to step outside the box with creative and innovative thinking,” added Justin.
For more information contact Hansen Yuncken, Level 1, 639 Wickham Street, Fortitude Valley QLD 4006, phone 07 3872 4000, email brisbane@hansenyuncken.com.au, website www.hansenyuncken.com.au
Fitout Glass and Aluminium is the leading provider of high quality internal and external glazing packages including the installation of spectacular high performance façades for the commercial construction industry.
In January 2020 Fitout Glass and Aluminium commenced the $1.5 million contract for a full glazing package comprising internal and external works at the Thomas Dixon Centre.
In the existing heritage listed structure, timber frames were rectified and new glass fit. New work included a complete internal fitout with partitions, timber linings and skylights as well as the construction of the walkway roof and glazing to the new four-storey structure.
“We had a lot of design input on this job, we detailed some of the drawings and consulted often with the designers and the builders,” said Owner, Micah Woods.
“We installed a structural glazed window wall façade on the new building and used a new product for the glass units – a custom made brass mesh interlayered between the panes. The material helps with thermal and acoustic insulation and gives a rustic appearance,
matching the old structure with the new. It was challenging fixing the large mirrors in the rehearsal space, the substrate had to be perfectly flat so the mirrors could give a true reflection, a critical requirement for the dancers, and we spent a lot of time getting it right.”
“The new building and walkway component required a focus on fitting new members to the existing work, and with a team of 20 on the job, the façade and the internal works were completed by the end of April 2021,” said Project Manager, Simon Inns.
Established in 2015 Fitout Glass and Aluminium began fabricating and installing glass and aluminium partitions, doors and windows, frameless glazing systems and balustrades for internal fitouts.
Fitout Glass and Aluminium has grown in its expertise in external façade installation and has a list of successful commercial projects under its belt, including previous work with Hansen Yuncken.
The $140 million, University of Queensland Andrew N. Liveris Building boasts a unique and spectacular multi-coloured façade, highly articulated with balcony pods and a dual skin façade to the lower levels, a complex project completed in early 2020.
Also for Hansen Yuncken, at the University of the Sunshine Coast, Fitout Glass and Aluminium completed a total internal fitout package of glazing and aluminium framing for the four Levels of the Foundation Building in 2020.
Fitout Glass and Aluminium offer an extensive design, manufacture and install service. With years of experience and established industry relationships, they are able to source unique products, develop the design, and assist in creating solutions to challenging issues.
They operate a 2,000m² manufacturing facility in Eagle Farm, currently employing 10 people working on over 100 projects. The large scale and organisation of the factory allows the quick turnaround of high quality product.
Brisbane based, Fitout Glass and Aluminium serve south east Queensland and into northern New South Wales. They work across a range of commercial sectors including offices, retail and health facilities, cinemas, shopping centres and schools.
Successful projects for Fitout Glass and Aluminium include Aurizon, the 5 Star Green Star rated office block in Brisbane where they
provided a $2 million integrated internal fitout package comprising 14,500m² of glazing to 12 Levels.
The job included aluminium framed partition glazing, doors and frames, frameless automatic sliding doors, frameless glass pivot doors and custom fabricated aluminium portals and planters.
The stylish bespoke façade at The Complex is another fine example of Fitout Glass and Aluminium’s work. Completed in 2021, the $4 million façade redevelopment included the installation of a frameless assembly and a massive glass atrium roof with individual glass panels weighing up to 250kg.
For more information contact Fitout Glass and Aluminium, 185 Lavarack Avenue, Eagle Farm QLD 4009, phone 07 3393 9033, email info@fitoutglass.com.au, website www.fitoutglass.com.au
Builders Hansen Yuncken called on HME Services, Australia’s premier entertainment industry engineers for over 29 years, to deliver innovative stage engineering designs for the Thomas Dixon Centre’s new Performance Studio and Rehearsal Studios.
HME Services has recently completed Sydney Theatre Company’s Wharf Theatres, new venues for the Australian Chamber Orchestra, the Australian Theatre for Young People, Brisbane’s Princess Theatre and Christchurch Convention Centre. HME Services is currently engaged in the Sydney Opera House Concert Hall refurbishment.
You cannot have a functioning theatre without appropriate design and safety measures and that’s where HME Services stepped up.
“Our scope of work for the Thomas Dixon Centre entails the design, manufacture, supply and installation of theatre equipment including theatre rigging, curtains, tracks, motors, lighting bars and ladders, cyclorama, DMX/data infrastructure, power and control outlets plus a Tension Wire Grid. All of this is completed in accordance with the project documentation and Australian Standards, Codes and Legislation” said Kiran Musharraf, HME Service’s Project Manager.
“It is our job to ensure that the theatre equipment works well and contributes to the functionality of the space,” commented Kiran. “It also needs to be user friendly and most importantly, safe.”
One of the most interesting aspects of the Thomas Dixon Performance Studio is the Tension Wire Grid that we installed beneath all of the hung theatrical equipment. This creates a permanent overstage floor strong enough to carry the weight of theatre technicians so they can have permanent access to moveable equipment such as lights, speakers and stage rigging.
“The Tension Wire Grid has to be strong enough to take two people standing within a 1m2 space with each carrying a 25kg load,” said Jonathan Yeoman, HME Service’s Head of Sales. “By negating the need for moveable scaffolding or ladders – and also catwalks –the Tension Wire Grid makes any performance space much safer for everybody.”
The Tension Wire Grid is strong, safe and virtually invisible whilst not interfering with the light beams – even the house lights are hidden from view!
HME Services set out to provide an extremely configurable space and so above the Tension Wire Grid is a custom-designed system that allows the lighting bars to be easily moved forwards and backwards giving complete flexibility to where the lights can be positioned. This is achieved by placing the 10 lighting bars, two FOH and eight over the stage, on roller trollies. Cable management to the trolley beams in the grid ensures no entanglement.
Dance companies rely a lot on side lighting using lighting ladders and so we installed six lighting ladders that are also on roller trollies, again delivering the ultimate flexibility. Clearly, on a roll, we designed the masking legs to roll on track too!
HME Services designed, manufactured and installed four 500kg capacity drum hoists to enable scenery to fly in and out at a variable speed. Each drum hoist has its own controller for simple operation by the crew.
The Performance Space features a motorised house curtain that can be operated either from the side of the stage or from the control booth. There are also rear stage traverse curtains, rear stage crossover curtains and masking legs, along with a large white cyclorama.
HME Services ensured lighting and power distribution throughout the Performance Space and Rehearsal Rooms including a Stage Lighting Dimmer System, DMX/ Data Racks and DMX Splitters, Socapex and DMX/Data Outlet Boxes. Curtains and masking drapes were also supplied throughout.
HME Services are proud to assist the Queensland Ballet to reach its goal of becoming a leader on the world stage by redeveloping the Thomas Dixon Centre to be a state-of-the-art ballet centre.
For more information contact HME Services, phone 1300 873 463, website www.hmeservices.com.au
Arden Architectural Staircases designed, manufactured and installed eight magnificent staircases, eight balustrade systems, seven structural steel portals and up to 2km of stainless steel and brass handrails at the Thomas Dixon Centre.
In early 2020, four designers from the Arden team worked collaboratively to complete design development and produce the workshop drawings as CEO, Jim Browne explained:
“We integrate the architectural intent with the engineering whilst combining our own vast experience to present the best possible design outcomes. What we provide is all about buildability while satisfying the consultants’ wishes and ensuring code compliance. We strive towards not making any changes to the aesthetic, although, where required, it is done sympathetically and in close consultation with the architect and other stakeholders.”
“The architects, Conrad Gargett, had conceptualised traditional style stairs in the old building and dramatic minimalist stairs for the new. Brass handrails with LED puck lights featured throughout. The feature staircase, running from the basement to top level, comprises about 10 tons of steel plate with overlay timbers of Silvertop Stringybark.
The feature balustrade bounding the ‛Catwalk’, has micaceous iron oxide painted steel frames, woven brass mesh infills and brass handrails,” said Director of Sales and Design, Scott Nicholas.
Fabrication of all components took six months in Arden’s 2,500m² facility ready for onsite work to commence in March 2021 and, with a team of 12 installers, the job was completed within 13 months.
“We have offices in Brisbane, Sydney and Melbourne, and we have worked into Adelaide, Darwin, Perth, Fiji, and the Solomon Islands. We recently completed the 80 Ann project in the Brisbane CBD including 20 structural steel helical stairs while simultaneously undertaking the Rio Tinto Project at Midtown Centre installing six staircases and multiple levels of balustrades and planter boxes featuring Corten Steel which exhibits a rusty look.”
“We pride ourselves on quality of finish, professionalism, and a dedication to preserving design intent. This we do whilst delivering on time and on budget,” added Scott.
For more information contact Arden Architectural Staircases, phone 07 3267 6100, email admin@arden.net.au, website www.arden.net.au
In May 2021 Schiavello started the D&C contract to manufacture, supply and install functional and well crafted workstations and boardroom tables, as well as sourcing and connecting high quality whitegoods to the Thomas Dixon Centre.
The 110 workstations were located throughout the ground and first floor levels, with a range of whitegoods being installed, including fridges and microwaves in the kitchens and washing machines in the wardrobe and dressing areas.
Manufacture of the office furniture with metal bases and laminated desktops started in 2021 and took a full six weeks at Schiavello’s 90,000m² facility. Onsite work began in December 2021 and with a team of eight installers the job was completed within four months.
“We have a good working relationship with Hansen Yuncken,” said Operations Manager, Fabio Colonico.
“We started work with them on the Liveris building in August 2021, where we manufactured and installed contemporary workstations and loose furniture items, finishing the job within seven months.”
Established in 1966 Schiavello is a 100% Australian own manufacturing company. The Schiavello story begins with Tony Schiavello, an Italian furniture maker who came to Australia in the 1950s, bringing with him a can-do attitude that drove him to set up shop providing partitions and internal carpentry services.
With younger brother Joe, Tony established Schiavello with the mantra ‘anything is possible’. The company has grown into a global organisation that employs over 1,100 people, with two manufacturing plants and 10 showrooms, operating from award-winning headquarters in Melbourne.
“We are a company that remains true to the strong work ethic and family values on which we were built. Quality and service excellence is ingrained in our people, and a vision to lead and innovate is at our core,” said Fabio. “From humble beginnings, Schiavello has grown to become one of Australia’s top 100 privately owned companies, proving time and time again that ‘anything is possible’ some 52 years later.”
For more information contact Schiavello, 265 Coronation Drive, Milton QLD 4064, phone 07 3368 3388, website www.schiavello.com
Safeguard Scaffold is a professionally run scaffold company serving Brisbane, Toowoomba, Gold and Sunshine coasts and far north New South Wales. In June 2020, Safeguard Scaffold started delivery of scaffold to the Thomas Dixon Centre. “We wrapped scaffolding around the perimeter of the old building to enable restoration of the heritage façade and provided scaffold for constructing the new buildings inside and out,” said Owner, Adam Young. “We had 400 tons onsite at the peak of construction.”
There were many design changes throughout the build due to the complexity of the architecture, Safeguard Scaffold were able to maintain supply, quality and safety standards throughout the project, solidifying their reputation for reliability. With 40 men onsite at peak periods the scaffolding was managed extremely well onsite by team leader, James O’Neill, supported by the inhouse design and engineering team.
“We worked well with Hansen Yuncken and have become one of their trusted contractors, based on this work at Thomas Dixon Centre, and our previous project at RACF Caboolture. We have just started the early works on the $30 million Plant Growth Facility at the University of Queensland and look forward to the continued association with one of the country’s most reputable building brands,” continued Adam.
Established 2004, Safeguard Scaffold is a family owned and operated company with Adam and designer/estimator Nick Brooker working as the engine room of the business, supported well by a raft of long serving staff.
“We are big enough to serve large scale projects, yet we provide quite a personalised style of service. We pride ourselves on managing all aspects of our operation inhouse, using our own scaffolding equipment, trucks/ transport, and preferred scaffold subcontractors,” Adam concluded.
“In addition to scaffold equipment, we have recently secured exclusive rights to import and distribute Green Formwork in QLD/NT. It will become known as the safest and most labour efficient formwork system in the market,” said Adam.
A new patented product, not seen before in Australia, Green Formwork allows Safeguard the opportunity to take advantage of its current market position, and continue its rise up the ranks of one of the most trusted names in the industry for the discerning builder.
For more information contact Safeguard Scaffold, 19 Cairns Street, Loganholme QLD 4129, phone 1300 971 603, email estimating@ safeguardscaffold.com.au, website www.safeguardscaffold.com.au
Mozbiz (Potrzeba heritage) are the leading brick and masonry restoration specialists, a family company of five generations with years of experience working with the fabric of older structures. In August 2020, Mozbiz were contracted to renovate the existing Thomas Dixon Centre with both external and internal works.
“The job involved the careful disassembly and cleaning of the bricks and rebuilding. The early works involved taking apart the WWII bunkers. The brick walls were 350mm and 460mm thick and required a strategy for removal. There was also some graffiti to be saved and that required some planning however the main challenge was the boiler room where we had to remove 20,000 bricks,” explained Owner, Maurice Potrzeba.
“There was also a number of walls that required special treatment and we lined them with paper to draw the salts out of the bricks, washed and vacuumed the surfaces and repointed. Restoring the heritage listed masonry fence was the last part of the project and with a team of nine onsite we finished up at the Dixon Centre in April 2022.”
“We always use traditional methods with lime putty mortar and we use hand tools to avoid damage to any existing work. I have enormous respect for the people who built the old structures. In 2010, we were
awarded a Churchill Fellowship and I went to the UK to study with a master mason.”
Mozbiz are expert bricklayers for new work and for restoration projects. They offer a consultancy service or will inspect, provide a quote and a report on the condition of the building fabric. A string of National Trust Heritage Awards is testament to the quality and authenticity of their restoration work.
They have recently moved a small brick building at Ravenswood a distance of 5km and undertook the separation of three historic chimneys of 18m, separating them every 3m and moving them to storage for later re-building.
“My son, Alek works with me and he has learnt the trade working for me over the past 18 years. When he left school he spent two years on Brisbane’s Saint John’s Cathedral and its unique vaulted masonry ceiling. He is an expert problem-solver and my right-hand-man,” added Maurice.
For more information contact Mozbiz, 68 Lillian Avenue, Salisbury QLD 4107, phone 0418 882 126, email maurie@mozbiz.com.au, website www.mozbiz.com.au, PotrzebaHeritageMasonry
CONSTRUCTION VALUE : $105 million
GemLife Maroochy Quays is a lifestyle resort with meticulously-designed two and three-bedroom homes with high ceilings within a private gated estate, including a 2-storey country club with indoor pool and spa, tennis court, bowling green, bowling alley, cinema, library and more.
GemLife develops exceptional lifestyle resorts designed for today’s over-50s. When GemLife launched its first resort in late 2016, the company set out to redefine the retirement living sector by emphasising a dynamic lifestyle, high quality homes and a huge offering of facilities for fitness and fun. GemLife Maroochy Quays is one of GemLife’s newest additions to its highly successful resorts.
Located on the Sunshine Coast, GemLife Maroochy Quays is a gated estate, a lush and private oasis, secure and environmentally sustainable. The 20 hectare site was acquired in April 2018, and as with all GemLife locations, it was chosen for convenient access to shops and restaurants, the beauty of nature and vibrant local communities.
“During master planning we focus on providing positive solutions for home owners and the broader community into the future,” explained
Director and CEO, Adrian Puljich. “Our resorts have large scale solar installations with energy storage systems, reducing reliance on the grid and promoting renewable energy. GemLife resorts have modern stormwater retention and treatment systems, reducing potential waste discharge into natural waterways. Our floating wetlands at Bribie Island, for example are designed to remove nutrients from stormwater, enabling natural ecosystems to flourish,”
Gold Coast architectural firm, Jared Poole Design, designed the communal facilities at GemLife Maroochy Quays with the homes the work of GemLife’s inhouse drafting and interior design teams. The homes are exceptionally low maintenance, highly energy efficient and designed for optimal thermal comfort with reduced energy use. Inside are 2.7m ceilings, stone benchtops throughout the kitchens and bathrooms, high quality stainless-steel appliances and are 6 Star energy rated.
“GemLife operates under the ‘Land Lease Community’ model, and government legislation stipulates homes must be ‘movable’. GemLife meets these requirements by using a fully customised, engineered steel chassis frame, constructed over a footing and slab system, designed for each site. The roof framing truss is integrated into the structure, a clever design to eliminate potentially complicated internal loads on the frame, thereby simplifying lifting, if the home is moved.
“At the heart of the resort is the country club, a contemporary 2-storey structure full of light due to an abundance of glass. There is exceptional workmanship inclusive of custom joinery, premium fittings, fine soft furnishings, custom lighting and cabinetry,” continued Adrian.
“Its features include a heated indoor swimming pool, 10-pin bowling alley, cinema, hair salon, library and creative arts studio to encourage connectedness and build positive physical and mental health outcomes.
“The country club overlooks a semi-tidal lake, the proximity to salt water and the high water-table levels were a consideration in the design and selection of materials used for the substructure. Galvanised screw piers were used to found the lake-front footing beams associated with the clubhouse retaining walls and ‛Xypex’,
a concrete core-filled blockwork was used for the wall construction, providing construction flexibility and an additional level of waterproofing.
“The outdoor deck structure, reaching out over the water, was founded on an epoxy coated hollow steel pile, installed from a barge in the lake. The deck superstructure was constructed from galvanised steel bearers and timber joists. Decking and a laminated glass and polished stainless-steel balustrade were then installed.”
“The Summer House is built upon a concrete slab with block and timber walls, timber trusses and steel roofing,” said Adrian. “There is a sleek modern pool house with outdoor pool, croquet lawn, floodlit tennis courts and a shaded 2km boardwalk. Due to the dominance of marine clay the boardwalk and viewing platform structures were founded on small diameter timber piles installed by vibration. The superstructure was constructed from best quality hardwood sections, all with stainless steel fixings.”
GemLife has future developments in the pipeline across Australia including Queensland, New South Wales and regional Victoria. Across Australia GemLife homes are consistently selling faster than competitors.
For more information contact GemLife, phone 1800 317 393
OSKA Hydraulic Consultants specialise in the design and documentation of plumbing and fire services design for commercial and large-scale developments. OSKA have been working with GemLife since 2016 supplying hydraulic designs for their resort lifestyle communities across Queensland and Victoria as well as Tweed Heads in New South Wales.
At GemLife Maroochy Quays, OSKA were contracted to carry out the design and documentation of plumbing services for the unique country club and the vast range of common areas as well as all 256 residences. Design work started in late 2018.
“We spent eight months working with the architect on the hydraulics design for the country club, the whole job ran very smoothly and our negotiations with council went well. As the residences are classified as relocatable homes, we had to provide design drawings for each villa and that took time,” company Director, Cameron Maxwell explained.
From concept design through to construction management and certification, OSKA Hydraulic Consultants can deliver comprehensive and contemporary hydraulic and fire services engineering. They provide a range of services including the design and engineering
of sanitary plumbing and drainage, water storage harvesting and re-use, stormwater and roof water services as well as pre-treatment and drainage of waste. They also provide designs for natural and LPG gas installations, fire hydrant and hose reel systems, risk management investigations and reports and safety design.
“Our design teams’ practical approach to each project along with our knowledge of current regulations and standards means that our hydraulic designs always meet expectations,” said Cameron. “We maintain strong working relationships with local and statutory authorities, architectural and engineering firms, to deliver outstanding customer service.”
OSKA Hydraulic Consultants work for corporate, government and private sector clients on a vast range of projects including highrise residential towers, hotels and international resorts, schools and municipal projects and infrastructure to the more complex engineering for hospitals and industrial developments.
Locally owned and operated OSKA Hydraulic Consultants are Gold Coast based with offices in Brisbane employing drafters, designers and engineers using the most advanced technologies for design and
modelling. New levels of accuracy and understanding can be achieved with 3D drawings of hydraulic services within a virtual structure with the ability for sharing in real time.
OSKA also provide professional Building Information Modelling (BIM) Services through the implementation of Autodesk Revit and Navisworks. This technology allows the automatic generation of bill of quantities, fixture and fitting schedules as well as timetables. OSKA have an internal BIM management plan which is compatible with the Australian and New Zealand Revit Standard.
In 2016 OSKA Hydraulic Consultants completed the design of the hydraulic services for new 1,700 bed Grafton Correctional Facility where they provided three personnel onsite to oversee the hydraulic services installation. They also provided hydraulic engineering services for massive projects in Perth including the $820 million Optus Stadium and the $700 million Karrinyup Shopping Centre.
“Currently we’re engineering the hydraulic services design for the Southern Queensland Correctional Precinct, Stage 2 at Gatton in the Lockyer Valley. We started this job 12 months ago and are still at work there,” added Cameron. “Over the last 12 months we’ve been working
on the new Tweed Hospital and we look forward to a future modular building project with GemLife.”
OSKA Hydraulic Consultants operate under the OSKA Consulting Group, established in 2019. OSKA Consulting Group is an alliance of professional Engineers, combining the services of three leading engineering practices - civil and hydraulic and structural services.
For more information contact OSKA Consulting Group, 4/155 Varsity Parade, Varsity Lakes QLD 4227, phone 07 5557 0509, email hydraulic@oska.net.au, website www.oska.net.au
White Light Electrical carried out the electrical installation, including a PV solar system, on all the 252 villas at GemLife Maroochy Quays. They also completed the electrical installation to the common areas and country club including the gym, cinema, golfing simulator, indoor pool and commercial kitchen, emergency and exterior lighting as well as floodlighting for the outdoor activity areas.
“For the country club and the summer house we were working to specifications, however we also worked closely with the GemLife team to make changes as the works progressed. We modified the lighting design and added improvements with LED strips to the balustrades and to the front of the country club,” explained Production Manager, Shaun McCormack.
“In the country club we installed Control4 automation to operate the AV system and the televisions via touch screens, a more user-friendly method for the residents. We maintained constant communication with the GemLife team and the project ran very smoothly and was completed on time.”
“In 1993, White Light Electrical Contractors started a small business with a couple of electricians on the Sunshine Coast. The company
has grown to employ over 40 people specialising in residential, commercial, and civil work.
“Our major client is GemLife, we have been with them since 2016 and have established a good working relationship. We continue to work on their sites in Queensland, New South Wales and Victoria.”
“We also carry out residential installations for a project builder on the Sunshine Coast completing over 100 homes per year. We’ve worked on several Brisbane child care centres and some large architectural homes including installing home automation. Last year we upgraded the field lighting at the Gold Coast Knights sports field to 500 lux and it is now suitable for TV coverage.”
“At White Light we provide a reliable, consistently high standard of service and workmanship. Our culture is one where our employees care for our clients, have integrity, accountability, and reliability,” added Shaun.
For more information contact White Light Electrical, Unit 1/15 Premier Circuit, Warana QLD 4575, phone 07 5493 2835, email info@whitelightelectrical.com, website www.whitelightelectrical.com
Engenuity Solutions is a multi-disciplinary engineering company focused on the design of power distribution, control and management across large sites.
“In 2019 Engenuity was introduced to GemLife to achieve compliance for four Queensland sites, one of which was GemLife Maroochy Quays,” said Business Development Manager, Tom Lawson.
“At Maroochy there are two connections to the Energex grid each an Embedded Network through a single electricity meter. GemLife’s original electrical design didn’t meet the solar generation compliance requirements and Engenuity Solutions stepped in, designing a system for over 850kW, a Virtual Power Plant connected to the grid.”
“The electrical infrastructure already installed was limited and Engenuity had to meet Energex compliance requirements and maximise production for residents from each villa’s 3kW PV system. The design challenge was to meet all of these requirements in a simple, retrofit solution.”
“Design work was completed by late 2020 and we were further engaged to supply the Energy Maestro system, a central computer measuring voltage, power and frequency at the connection to Energex and also
communicating with the more than 250 individual solar inverters around the site. We expect to be involved until completion, into 2023. GemLife is keen to add a central battery to store excess daytime solar production at Maroochy.”
Founded in 2013, Engenuity Solutions serve a range of sectors including local government, water and power utilities, heavy industry, ports and mining, oil and gas and defence. They also provide civil, structural and mechanical process design with experience designing power systems for water authorities, mineral processing plants, mine sites and theme parks.
“Engenuity Solutions provides designs for managing the solar generation, meeting compliance and maximising production. We’ve worked on many GemLife sites including Bribie, Highfields, Palmwoods, Lake Cathie and Tweed Heads. We also provide solar control systems for RACV solar, who are supplying and installing the systems at a Victorian embedded network,” added Tom.
For more information contact Engenuity Solutions, 8/249 Scottsdale Drive, Robina QLD 4226, phone 07 5559 2892, email engenuity@ engenuitysolutions.com, website www.engenuitysolutions.com
Computer Score installed the state-of-the-art scoring equipment at the 10-pin bowling alley at the GemLife Maroochy Quays country club. They installed their DUOHD system that includes hardware and software to automatically keep score, allowing the residents to relax and enjoy their game.
“For Maroochy we designed and installed a system that was especially easy to operate,” explained Director Engineer, Ross Biggs. “Our scoring system can be adapted for various styles of installations, from private residences to dedicated Bowling Centres.
“The job went smoothly, we co-ordinate with the lane installer and the trades at fitout, it’s best to be involved early in the design process. We’ve completed a few installations for GemLife including resorts at Toowoomba, Bribie Island, Woodend and Caboolture and we look forward to working with them in the future.
“We are excited to launch a new product: ‘Darts for the modern age’, a fully automatic enhancement to the game of darts that accurately detects the darts and offers a range of traditional and fun games. It’s ideal for similar locations.”
Computer Score is an Australian owned, family run company operating out of Tweed Heads servicing Australia wide and overseas. Computer Score has equipped a significant majority of all Bowling Centres in Australia, including many ZONE Bowling locations around the country.
Computer Score has many installations in the USA, from private homes to large bowling centres. Computer Score Scoring Equipment has recently been installed at Martis Camp Club in Lake Tahoe (an upmarket community).
“We’re continuing development with automated gaming systems suitable for the modern community clubhouse market,” said Ross. “We also serve the commercial sector as well as exporting our products.”
For more information contact Computer Score, 1/40 Machinery Drive, Tweed Heads South NSW 2486, phone 07 5524 4786, email darts@computerscore.com.au, websites darts.computerscore.com.au and www.computerscore.com.au
Arrow Interior Linings (AIL) are expert at the installation of plasterboard linings and all aspects of plasterboard linings and finishes.
Starting in February 2021 with a team of 11, AIL installed up to 6,000m² of wall and ceiling linings including plasterboard, moisture resistant plasterboard for wet areas and fibre cement sheeting. The installation also comprised an intricate coffered ceiling of perforated plasterboard to the clubhouse and Fyrchek board, with a glass fibre-reinforced core, for fire rating and acoustic insulation.
“The GemLife Maroochy Quays country club has been our largest project so far, it went very well and we are looking forward to the next one,” said Director, Dale Lawson.
Successful projects for AIL include work at GemLife’s other retirement developments in Queensland.
“In June 2021 we completed all the plastering works for the summer house at Pacific Paradise. In April 2022 we completed the supply of a plastering and carpentry package to the new summer house and the managers workshop at Palmwoods. The work included the installation
of trusses, timber and steel frames, walls and ceilings, insulation, external cladding, soffits and doors. Continued work at Palmwoods includes starting on the next clubhouse towards the end of this year,” Dale explained.
Established in 2019, AIL is a family owned company operated by brothers James and Dale Lawson. AIL’s services include the installation of steel, and timber framing and aluminium partition systems. AIL specialise in the quality installation of partitions, suspended ceilings, passive fire protection as well as acoustic and thermal systems for walls and ceilings. The team focus on efficient delivery of outstanding work across high rise residential buildings, commercial office fit outs, schools and hospitals.
“At AIL we pride ourselves on our work ethic of reliability and safety and especially our ability to integrate with other trades and services,” added Dale.
For more information contact Arrow Interior Linings, phone 0430 328 382, email admin@arrowinteriorlinings.com.au, website www.arrowinteriorlinings.com.au
Air Smart specialises in the design, supply and installation of modern and efficient commercial and residential Air Conditioning systems. At GemLife Maroochy Quays Air Smart completed the Air Conditioning for the clubhouse and all the residential villas.
“Air Smart were involved in the design process, working collaboratively with the engineer discussing opportunities to improve the design and create optimal cooling solutions for our client,” said Sales Manager, Danica Vucic.
“We were able to provide practical design feedback on the best application of heat load and design principles to produce the most efficient conditioning system. Air Smart installed multiple VRF Fujitsu system’s to the clubhouse and the extraction system for the commercial kitchen. One of the more common design challenges for us involves negotiating on ceiling heights as this has an impact on air flow and system effectiveness.”
The Air Smart inhouse designers and engineers started work in March 2021, revising mechanical plans and procuring Fujitsu equipment. With a team of six the project was completed within four months including the supply and installation of an ARMCOR Pool Pack, a humidity control system.
“Air Smart is a Fujitsu Authorised Partner and we have enjoyed a long relationship with Fujitsu, working with them to deliver a number of successful projects to GemLife,” added Danica.
“Air Smart has enjoyed a 10 year relationship with GemLife, we’ve successfully delivered air conditioning solutions across eight GemLife sites including the Bribie Island Club House and the Summer Houses at Pacific Paradise and Palmwoods. Over the past five years we have designed and delivered air conditioning solutions to 10 gyms including the Fitness Cartel and World Gym franchises.”
In business for 15 years Air Smart is distinguished by its experience of complex high end home airflow design, dedication and attention to detail. Servicing Queensland, the north Gold Coast and interstate, Air Smart offer full mechanical estimation and tendering services for new work and also provide maintenance and repairs to existing installations.
For more information contact Air Smart, Unit 13, 14-28 Ivan Street, Arundel QLD 4214, phone 07 5563 8530, email info@airsmart.com.au, website www.airsmart.com.au
Australasia Stone Group (ASG) are the experts in the supply of quality architectural, commercial and residential stone and porcelain surfaces.
“Australian owned and operating on the Sunshine Coast the ASG family was created from a desire to introduce and supply a large range of high quality, distinctive stone that complements and enhances Australia’s unique design and lifestyle trends,” says Sheree Mengel.
“We offer three exclusive collections of engineered stone: Technistone, the highly translucent Aurea Stone and Lumina Stone with finishes so beautiful, they are a work of art.”
At GemLife Maroochy Quays, ASG supplied Technistone benchtops throughout the villas as well as Aurea Stone for the light-filled interior spaces of the country club.
“We have been working with GemLife since 2017 and have a wonderful working relationship with them,” continued Sheree. “We’ve supplied stone to a vast majority of GemLife’s Queensland resorts, catering to their needs by supplying different options for the stone used to create
the unique look for their country clubs. Their whole team is amazing to work with.”
“Recently we supplied our Lumina stone to Newport, large residential apartment in Brisbane; and Aurea and Lumina stone for the interiors of Seanna Apartments in Bokarina on the Sunshine Coast.”
ASG source their raw materials overseas, observing the manufacturing and quality control processes to create the best products. They supply a vast collection of natural and engineered stone, large format porcelain slabs and tiles.
“We invite you to book an appointment to visit our Sunshine Coast showroom where you can view our range and we can discuss your individual or project needs,” added Sheree.
For more information contact Australasia Stone Group, 20 Hitech Drive, Kunda Park QLD 4556, phone 07 5445 5183, email sales@australasiastone.com.au, website www.australasiastone.com.au
Tile City specialises in the supply of floor and wall tiles for domestic and commercial applications. In business for 39 years, the team at Tile City are expert at sourcing the appropriate tile for any project.
“At GemLife Maroochy Quays, Tile City liaised with GemLife’s design team leading up to finalisation of the tile selection and design specifications. We supplied all the floor, wall and special feature tiles and associated tile products,” said Director, Michael Hutchinson. “We are direct importers of quality tiles and flooring materials from around the globe. With all the projects we have worked on for GemLife we’ve supplied them with the latest and most up to date tiling products to create an extremely lavish and stylish interior with a high quality finish.
“Tile City has been the preferred supplier of tiles and tiling products for GemLife since they commenced operations, completing work on a number of their lifestyle community developments in Queensland and New South Wales, including Palmwoods, Pacific Paradise, Toowoomba, Bribie Island and Tweed Heads. We are very pleased to be associated with GemLife and look forward to continuing our working relationship with them.”
Tile City invite you to visit their showrooms at Stafford, Browns Plains and Ipswich where a stunning range of wall and floor tiles are available including tiles for special features, splashbacks, bathroom, kitchen and laundry as well as non-slip flooring for outdoor areas, including pools and patios.
Tile City stock ceramic, glass, marble, natural stone and timber look tiles available in a range of finishes from high gloss, polished, matt and external surfaces along with the necessary accessories, adhesives and tools. Visit Tile City’s website for access to their virtual showroom – an easy tool to see the enormous range of product offered.
Currently Tile City are busy fulfilling contracts for the supply of tiles to a string of domestic, multi-residential and commercial projects throughout Queensland and New South Wales.
For more information contact Tile City, 27 Babarra Street, Stafford QLD 4053, phone 07 3856 4415, email sales@tilecity.com.au, website www.tilecity.com.au
K&F Fabrications specialise in the manufacture and installation of quality aluminium and stainless steel building elements.
For GemLife Maroochy Quays K&F Fabrication worked to specifications to produce stylish architectural features including balustrades and handrails, screens, fencing and gates.
“We worked closely with the GemLife team, modifying the design for many of the items we fabricated. This included aluminium awnings and pergola frames as well as screens, fencing, handrails and gates to the lawn bowls area, the tennis courts and the summer house. We also manufactured, supplied and installed stainless steel balustrades and this was a challenge, achieving a quality job with the stainless steel was time consuming,” said Director, Noel Rogers
K&F Fabrications have been manufacturing and installing contemporary aluminium and stainless steel products for GemLife’s over 50s resorts for the past 5 years.
“In late 2021 we completed an installation of privacy screens as well as toughened glass and aluminium balustrades around the pool,” continued Noel. “Currently we are finishing off at Palmwoods fitting balustrades to the pool and summer house as well as aluminium
pergolas and screens. The GemLife team are great to work with and over the years we’ve established a good working relationship with them. We look forward to future contracts with them.”
Established in 2004, K&F Fabrication have the capacity to manufacture and install for large scale projects. They focus on commercial developments and residential complexes as well as the highrise residential and retail sectors. They serve the Sunshine Coast from as far south as Brisbane and north to Gympie.
K&F Fabrication also manufacture, supply and install all styles of awnings and architectural sun shades, fixed and adjustable louvered screens and gates as well as providing powder coating.
A successful project for K&F Fabrication, completed in 2020, involved the installation of vertical aluminium elements as a feature of the façade at the Sippy Downs Medical Centre.
For more information contact K&F Fabrications, 1/9 Charlston Place, Kuluin-Maroochydore QLD 4558, phone 07 5479 4064, email info@kandffab.biz, website www.kandffab.biz
STRUCTURAL ENGINEER : Wallbridge Gilbert Aztec (WGA)
CONSTRUCTION VALUE : $150 million
83 Pirie Street is a state-of-the-art business destination with a stunning façade, over 20-levels of commercial office space, and includes an opulent fitout, intelligent interior design, floor-to-ceiling windows, expansive panoramic views, hybrid communal spaces, a wellness centre, and a 3-storey car park.
83 Pirie Street, Adelaide is set to become the benchmark in workplace evolution where innovation and productivity are a way of life. Cbus Property has overseen the development for a future Adelaide workforce with a focus on sustainability, wellness, connection to the public community, nature and productivity.
“It’s an incredibly exciting project that has optimised the site’s potential and created a new landmark for the city, as well as reinvigorating the city’s office precinct,” said Cbus Property CEO, Adrian Pozzo.
The key features of the Woods Bagot designed 20 level, A grade office tower includes approximately 30,000m2 of commercial office space, a stunning triple height foyer, ground floor retail, a roof top terrace, exceptional connectivity to public transport, amenity and parklands, a 3-storey car park, a wellness centre and premium end-of-trip facilities, and a vibrant retail laneway to adjoining streets and Adelaide's premier mix of eateries and nightlife.
The modern, flexible and dynamic floor plates transform multiple floor spaces into vertical communities. A stunning façade design, the likes of which have never been seen before in Adelaide, will compliment the current Pirie Street street-scape while setting a new standard for architectural design and visual impact.
Vertical communities are fast becoming the optimal development solution where working, shopping, socialising and relaxing all under one roof. The design of 83 Pirie lends
itself well to adaptations for even greater wellbeing, including increased ventilation, expanding the end-of-trip facilities for active transport choices, and spaces in the lobby for greater work flexibility.
The project’s construction began at the onset of the second year of the COVID-19 pandemic. Practical completion was achieved approximately three months ahead of schedule.
“This has been a fantastically well coordinated project with everyone meeting their timelines,” said Adrian. “The team has been on top of all of the COVID implications. We’ve had close to 2,000 workers involved in this project at various intervals and we’ve been really fortunate with our workforce availability.”
The building will capture several firsts for Adelaide including the first all-electric, carbonneutral-ready Grade-A commercial building to come online, the first development to be delivered with WiredScore and SmartScore ratings and the first Platinum WELL v2 pilotcertified office tower.
“The development will also have a 6 Star Green Star (Design Review) rating and is an integral part of Cbus Property’s sustainabilityleading, net zero carbon (in operation) office investment portfolio,” said Adrian.
Cbus Property acquired the site in February 2018 and specifically targeted government tenants, resulting in the South Australian Department of Infrastructure and Transport (DIT) leasing office accommodation on a 10 year term.
“This creates a sustainable revenue stream for Cbus Superannuation Fund members,” said Adrian. “And bolsters the company’s diverse investment portfolio, which is currently more than 40% occupied by long-term government tenants.”
Cbus Property is a national award-winning property investor and developer responsible for the performance and management of all aspects of the Cbus direct property investment business, with offices in Sydney, Melbourne and Brisbane.
Cbus Property has the expertise to meet the end-to-end requirements of all their diverse clients. Their specialist teams of professionals have the skills to manage every stage of a property project and investment, from acquisition, finance, investment and portfolio management, contracts and planning, right through to architectural design, development management and asset management.
“Our team of professionals has a proven track record for establishing and maintaining harmonious relationships with builders and all other suppliers, ensuring that every project is seamlessly delivered,” said Adrian. “We achieve the best commercial outcome for everyone involved, from our future tenants to the members of the Cbus Superannuation Fund.”
For more information contact Cbus Property, Level 14, 447 Collins Street, Melbourne VIC 3000, phone 1300 319 890, email reception@cbusproperty.com.au, website www.cbusproperty.com.au
Below WGA delivered structural, civil and geotechnical engineering solutions for 83 Pirie Street.
Adelaide’s central business district has been enhanced with a new, state-of-theart office development, 83 Pirie Street — delivered by local multi-disciplinary engineering and project management team Wallbridge Gilbert Aztec (WGA). Completed three months ahead of schedule, this unique mixed-use development will enrich the lives of its tenants to offer a modern, flexible, and sustainable work environment.
Collaborating with client Cbus Property, Woods Bagot and Multiplex, the $150 million project involved WGA’s cross discipline expertise, with its Adelaide-based team delivering structural, civil and geotechnical engineering solutions for the multi-storey office building that also encompassed the design of carparks and met the brief of achieving Green Star sustainability certification.
83 Pirie Street is a 21-level office tower with 30,000m2 of commercial office space with large flexible floor plates of 1,780m2 and 360m2 of ground floor and laneway lettable retail space. The building also includes a much-coveted three-storey carpark with 120 spaces, a triple height foyer, a wellness centre, end-of-trip facilities and a rooftop terrace with panoramic city views.
The building was very much designed with sustainability in mind, looking ahead to what the ideal workplace of the future will look like. This includes incorporation of sustainable design features including electric car charging stations, considerable natural light from the building’s three street frontages, and drought-
resistant landscaping on the rooftop terrace. The building has achieved energy approvals, including 5.5 Star NABERS Energy 6 Star Green Star Base Building rating and a Gold WELL rating.
Notable features and design elements of 83 Pirie Street
A number of interesting features and facets have been incorporated, including:
• Raking or vertically-inclined columns from ground up to Level 4 – an architectural feature that allows for increased floor area at higher elevations.
• An integrated building maintenance unit – essentially a crane on a rail – to allow for safer façade and window cleaning.
• Ability to withstand a 1-in-1000-year extreme wind or earthquake event, meeting the National Construction Code’s Building Importance Level 3 criteria.
Integrated design and construct team led to rapid build efficiencies
The collaborative working relationship between WGA and architects Woods Bagot led to various initiatives that aided in the rapid construction of the commercial building:
• A column grid for the structure worked across the various competing retail, carpark, and office floor types, and allowed for the columns to run continuously through the building. This resulted in the following benefits:
• Transfer structures could be excluded from the building, which resulted in significant cost, material and time gains to the construction works
• A consistent column grid resulted in efficient and cost-effective floor plate design, which was replicated throughout the building
• By incorporating car parking levels above ground floor, this offered significant cost and time savings to the project while also mitigating the risk of encountering contaminated material during the excavation of the basement levels if underground car parking had been required.
Early in the design and construct phase of the project, Multiplex identified concrete elements that could be precast offsite, rather than being poured onsite. This allowed for both time savings to the overall program of works and reduced manual handling onsite, reducing occupational health and safety risks during construction.
The architectural design called for multiple façade types throughout the building. Each façade required unique structural responses from the base building, however, WGA’s design team could meet façade load requirements without requiring significant changes to the overall structural design.
Combined, these initiatives assisted Multiplex to achieve its fastest rate of constructability ever achieved on a multi-storey building project and in it completing the build three months ahead of the original contracted schedule.
The anchor tenant for the building is South Australia’s Department for Infrastructure and Transport, consolidating the department’s seven city locations into one when the lease agreement for 10 floors begins in 2023.
A prime location, high end facilities and smart approach to office design, 83 Pirie Street is forecast to be one of the most coveted commercial properties in Adelaide’s central business district.
With offices located across Australia and New Zealand, WGA’s buildings portfolio is ever expanding, with major projects currently underway for public and private sector clients across health and aged care, education, commercial, retail and justice.
For more information contact WGA, 60 Wyatt Street, Adelaide SA 5000, phone 08 8223 7433, email adelaide@wga.com.au, website www.wga.com.au
Below Ceiling and Wall Contractors installed the ceilings and partitions, feature timber ceilings and more at 83 Pirie Street.
Ceiling and Wall Contractors are a specialist contractor operating in the supply and installation of ceilings and walls. The company was contracted to install the ceilings and partitions, feature timber ceilings, Blackbutt framed windows and doors and carpentry for 83 Pirie Street.
Over 12 months, they had a team of 104 staff who worked on the project, along with Key Partners Knauf Gypsum, Rondo Building Services and Atkar.
Ceiling and Wall Contractors are a proud Australian owned company who have be in operation since February 1992, with a full time office in South Australia and Western Australia. Ceiling and Wall Contractors are able to provide, supply and install suspended ceilings, steel stud partitions, fire-rated systems, acoustic systems, insulation, Barrisol ceilings, internal aluminium windows and doors and general fitouts in the commercial construction market.
With a team of 120 staff, they take pride in constructing high quality facilities in a timely and economical manner. Ceiling and Wall Contractors have extensive experience and a wide range of clientele. They are able to tailor various procurement strategies to meet the specific needs of their clients and their projects.
The company is committed to a corporate philosophy of quality, integrity, hard work, and teamwork, collaborating closely with their partners, keeping high standards in quality, efficiency, responsibility and sustainability.
Projects include the award winning Flinders Student Hub, South Australia Health & Medical Research Institute (SAHMRI), Adelaide Botanic High School, Adelaide Convention Centre, Adelaide Oval Western Grandstand, Australian Tax Office, Bendigo and Adelaide Bank, Crown Hotel, CMAX, Colonnades Precinct, David Jones, Fort Largs Police Academy, Lyell McEwin Hospital, Rundle Place, Sage Hotel, University of South Australia, and the Youth Training Centre.
Projects Ceiling and Wall Contractors are currently working on are the Australian Bragg Centre and AIR 555.
For more information contact Ceiling and Wall Contractors, 55 Hampton Road, Keswick SA 5035, phone 08 8292 6600, email luke@ceilingandwall.com, website www.ceilingandwall.com
Echuca-Moama Bridge Project was the largest infrastructure project in northern Victoria. Stage 3 of the project featured the construction of two new bridges over the Campaspe and Murray rivers. This means locals and visitors to the region can now enjoy safer and easier travel between Echuca and Moama. The project was jointly funded by the Australian, Victorian and New South Wales governments.
CLIENT : Major Road Projects Victoria
STAGE 3 CONSTRUCTION PARTNER : McConnell Dowell
PROJECT VALUE TOTAL : $324 million
McConnell Dowell (MCD) was awarded the project’s Stage 3 contract by Major Road Projects Victoria (MRPV) in 2019, for works including new bridges over the Campaspe and Murray rivers, two flood relief bridges and a new shared walking and cycling path along the route.
For the design of the new Murray River crossing, named the Dhungala Bridge, McConnell Dowell presented a balanced cantilevered box-girder bridge solution with a 115m main span to avoid permanent piers in the river. The bridge construction methodology, which was built from supports on both banks of the river, minimised the need to access the waterways during project works. It also lessened the environmental impacts of building piers in the river, and added the advantage of ongoing river-wide water access for local boats including the region’s iconic paddle steamers.
The new Dhungala Bridge is the third longest in Victoria and one of few in Australia to be built using this balanced cantilever method which required careful coordination between construction and engineering teams.
Another major challenge for Stage 3 of the project was the impact of COVID-19 which was especially pronounced for the project team, as works spanned an interstate border which was intermittently impacted by closures and restrictions. “We had different work crews in Victoria and New South Wales to keep the project moving,” said Matt Boyd, MCD Project Director. “Even when we could get travel permits, simple matters like trucking materials across the state border on the existing bridge were made complicated and needed careful management.”
The need for a new river crossing between the twin-towns of Echuca and Moama was originally identified in the 1970s and is today delivering benefits to the community, providing an alternative to the previous bridge built in 1878, originally designed for trains and road traffic. The new Dhungala Bridge also provides greater connectivity between the towns where the community’s work, study and other activities often span the border.
“The local community couldn’t be happier to finally see this project delivered,” said Matt. “The construction process created a lot of
interest and excitement culminating in 8,000 people crossing the bridge on foot during the project’s open day celebrations.”
Sustainability, cultural heritage, stakeholder management and social benefit procurement initiatives were all considerations for this regionally-based project. The project’s reduction in water use and carbon emissions, plus ecological improvements such as the installation of squirrel glider crossings, weed control and revegetation to improve habitiat for wildlife, were all impressive factors in the project's overall success.
Indigenous cultural heritage was protected on site with the Yorta Yorta Nation Aboriginal Corporation (YYNAC) closely engaged with during the project. Indigenous artwork was incorporated along the new shared walking and cycling path and the region’s Traditional Ownership is also reflected in the naming of both the Dhungala Bridge and the Yakoa Bridge which cross the Murray and Campaspe rivers respectively. The naming of the Dhungala Bridge included consultations with the YYNAC and the Cummeragunja and Moama Local Land Councils.
Social procurement was also a priority with traineeship and Indigenous employment outcomes exceeding expectations during the project, partly due to MCD’s partnership with local disability support service, We Are Vivid and social enterprise, Vivid Work Crew.
“At McConnell Dowell we really wanted to leave a legacy through this project,” explained Matt. “By working with Vivid we were able to offer employment to a lot of people who had never really worked before. It’s had a positive impact on a lot of families and we are proud of that.”
According to the MCD Project Director, the project was successfully completed on time and under budget, with no major defects at completion and no safety incidents. “It was great to have such a positive delivery experience with a young team,” Matt said. “It has been a memorable achievement.”
For more information contact McConnell Dowell, Level 3, 109 Burwood Road, Hawthorn VIC 3122, phone 03 9816 2400, email mcdgroup@ mcdgroup.com, website www.mcconnelldowell.com
Chief Group is a leading provider of plant, people and services in the civil contracting space. It provides cutting edge and innovative solutions to cater for all civil scope requirements with a large focus on program, budget, and safety. Chief has been involved in the successful delivery of some of Victoria’s most recent major projects.
Chief Group provided plant and equipment along with engineering and supervision resources to the Stage 3 construction partner, McConnell Dowell, for the recent Echuca-Moama Bridge Project that included the construction of a second river crossing over the Murray River, between Echuca and Moama.
The scope of work undertaken by Chief Group on the project encompassed work sites on both sides of the Murray River in Echuca, Victoria and Moama, New South Wales. The group’s scope included enabling works as well as permanent earthworks, pavements, substructure and rehabilitation work. Included were the construction of abutments on both bridges for the Campaspe and Murray river spans as well as carriageway and intersection builds.
“Our work on the Echuca-Moama Bridge Project was both diverse and challenging,” said Ben Cook, Chief Group Business Development
Manager. “The COVID-19 lockdowns, particularly with the everchanging conditions such as the metro ‘ring of steel’, created challenges when allocating our workforce. The situation was compounded with the added pressure of interstate border closures, which were managed differently depending on the state enforcing them. All of these factors contributed to making the management of this project unique.”
“We worked closely with the project team throughout the delivery phases to provide the best solutions for the job, as the build went on,” said Ben. “We had sound job knowledge coupled with collaborative planning, ensuring the provision of the right people and plant combination. Our plant list covered everything from graders, scrapers, excavators, rollers and almost everything in between.”
“We worked hard to exceed the project’s expectations which were challenged with constraints such as managing earthworks in winter and working with the complexities presented by the pandemic setting. We were able to rise to the challenge of providing the best equipment and most trusted operators to deliver the job,” Ben said. “We are very experienced working with McConnell Dowell (MCD) systems and admire its commitment to safety. This culture of cooperation, created a solid partnership on the project. We delivered
McConnell Dowell with the quality and flexibility it needed and that’s due to our high level of capability to serve all regional areas, as well as metropolitan.”
From its home base near Melbourne, Chief Group delivers road, rail and infrastructure projects across Victoria as well as interstate. The group has extensive experience with road and rail projects as well as renewable energy such as wind and battery farms.
Established over 15 years ago, Chief Group has grown into a family-owned business with more than 100 employees. “We started as an owner-operator grader hire business working on earthworks and pavement construction. We began to price and deliver scopes of work
and grew the business from there,” Ben said. “We have a great team and a strong client base with a high percentage of repeat business which shows the trust our clients’ place in us, for our ability to deliver.”
Chief Group’s strong reputation is built on its ability to think ‛outside the box’ and create innovative solutions that deliver results for clients on time and on budget, no matter what the challenge.
The company’s service offering is tailored for every project, and the group works as a ‛one-stop-shop’ offering in-house surveying, consulting, and lump sum delivery, as well as people and plant on demand. It is Chief’s fresh approach to civil construction combed with its depth of experience and energetic, friendly service that produces outstanding results, time and time again.
“It all comes down to teamwork,” said Ben. “We work with the contractor’s delivery team, understand their KPIs and combine it with our services and expertise to get the job done.”
For more information contact Chief Group, PO Box 592, Bacchus Marsh VIC 3340, phone 1800 4CHIEF (1800 424 433), email info@chiefgroup.com.au, website www.chiefgroup.com.au
The positive aspects of the Echuca-Moama Bridge Project haven’t just been about delivering major infrastructure. The project has brought about major changes in the lives of young people living with a disability, engendering long-lasting local benefits.
By listening to the close-knit community of Echuca-Moama, the project team became aware of disability support service, We Are Vivid (Vivid), and its social enterprise, Vivid Work Crew.
The Work Crew presents a way of providing people, living with a disability, an opportunity to explore employment pathways. Vivid’s support workers help facilitate this experience by being mentors to the ‘crew’ in the workplace setting.
While the project prepared for construction activity in 2020, the MCD commercial team confirmed that the Work Crew’s capability could fulfil specific project needs across its worksites, such as office and vehicle cleaning, and site maintenance. A procurement partnership was formed, which correspondingly aimed to align with the project’s overarching goal, to leave a positive, lasting legacy for this region and its community.
During the life of the project, 23 young people, living with a disability, were employed on the project. They successfully fulfilled all site induction requirements, which included mandatory ‘white card’, safety and cultural heritage training.
On their individual personal journeys, having managed setbacks throughout their young lives, the Work Crew cohort became very much part of the project, joining the rest of the workforce for site barbeques, special days, and milestones. They learned skills, guided by the project team and support workers, undertaking tasks such as water quality monitoring and weed management.
The project also partnered with Vivid to provide a learning opportunity for nine of these supported employees. This initiative enabled them to embark on a vocational, education pathway for the first time, which saw all nine students graduate with flying colours, attaining a Certificate II in Cleaning Operations, through TAFE. This accomplishment has been instrumental in opening up permanent employment and traineeship pathways for this group.
According to MCD Project Director, Matt Boyd, building a bridge with these young people has been a highlight for the whole project team.
“We’ve seen friendships form with the Vivid crew and our team; we’ve seen their confidence grow and their skills develop. We were continually impressed by the Work Crew’s high degree of dedication and commitment, and collectively they contributed 36,000 work hours to the project, an outstanding achievement,” Matt said.
worked on a project of this magnitude. It has propelled us to work in different ways.”
While Vivid was growing from the project experience, families and carers also noticed growth in the form of positive change occurring in the lives of the young people they nurtured.
For local mother, Susan Ryan, her daughter Sophie’s opportunity to be part of ‛something big’ has developed a greater ‛sense of self’, and she’s grasped a much stronger understanding
He added that MCD’s social procurement strategy focuses on realising positive community impacts through a project’s purchasing power. “Our team created procurement packages to suit local businesses in Echuca-Moama. Our partnership with Vivid is a great example, innovating and building relationships that support the local economy and generate social benefits.”
According to Vivid CEO, Scott Alexander, the Work Crew supported employees have gained huge amounts of confidence. “They’ve developed a real purpose to their working day and (on the project) they felt ‘included’ and respected … that doesn’t always happen in the world of people with a disability.”
He said Vivid has also changed the way it looks at its business, stretching expectations and “stepping up to the plate” due to its experience with the project. “We had never
of what it means to be part of a team. “She’s has learned about the value the Work Crew brings to a workplace. She’s also observed how a busy project operates, and she’s learned about the benefits of teamwork.”
Susan summed up the experience by saying, “Sophie’s enthusiasm for being in the workforce has grown, and for all of the Vivid Work Crew supported employees, working on the Echuca-Moama Bridge Project has been a confidence-building experience. It has been truly great for everyone involved, including our community.”
Vivid Work Crew is an Australian Disability Enterprise, that offers that offers paid, meaningful employment in a supported environment.
Echuca-Moama Bridge Project feature continues over page
Below The site’s Indigenious Dreamtime heritage was displayed through the Corten perforated weathered steel artwork screens.
The Echuca-Moama Bridge Project has delivered much needed new vehicular and pedestrian links between Echuca and Moama on the Victorian and New South Wales border. The project forms a new river crossing and has been carefully integrated into its natural setting by urban design and landscape firms CM+ and Tract.
Based in Sydney and operating nationally, CM+ are industry leaders in highly crafted, sustainable architecture and urban design. Tract are multidisciplinary planners, urban designers and landscape architects with decades of experience delivering sustainable and memorable places and five offices around the country.
Both CM+ and Tract were involved in the project from the early stages of the tender process, developing the urban design and landscape concept based on the masterplan. The design intent of the masterplan was preserved and developed to a point where it could be delivered incorporating new dedicated pedestrian crossings and input from community stakeholders including the Yorta Yorta Nation Aboriginal Corportion (YYNAC).
“One of our key initiatives was to ensure the project was conducive to its setting,” explained Kash Rangan, Director of Infrastructure at CM+. “We treated the new infrastructure as sculptural elements respectfully sited in a parkland environment with public use right up to the road embankments. Our idea was to create a simple, low-key bridge in the bush.”
“The site is quite ecologically sensitive,” added Deiter Lim, Managing Director of Tract. “There are middens and other Aboriginal artefacts across the whole area along with flora and fauna biodiversity. We made a big effort to ensure those connections were preserved with interpretive elements and artwork incorporating Dreamtime stories from the local community.”
The sculptural artwork is built into the retaining wall along the shared user path following the road embankment and was constructed from Corten perforated weathered steel. Other interventions include new handrails along the river foreshore with irregularly spaced uprights reflecting the arrangement of riverside trees.
“Community involvement was immense during the whole project,” Kash said.
“Around 7,000 to 10,000 people attended the open day event which was very exciting. The development will be a real asset for the community with greatly improved access to the riverside including new recreation facilities for people to really enjoy the space.”
Tract and CM+ took a shared approach for the Echuca-Moama Bridge Project although CM+ led the design in the precinct around the Murray River crossing while Tract were more involved with the bridge over the Campaspe River and overall soft landscaping concept. Both parties have previous experience working with Stage 3 lead contractor McConnell Dowell and the whole team maintained a close-knit working relationship during the works.
“We worked hand in hand with CM+ to develop our shared vision,” explained Deiter. “We looked together at how the design should respond to its context, built a shared understanding and worked towards that vision. We really enjoy working together and sharing that joy that comes from good design on a worthwhile project.”
“Excellence in urban design is a common goal for both CM+ and Tract,” Kash added. “We have complementary capabilities and know-how which really allows us to work well together.”
The project is now complete and the new river crossing is operational. The project delivers benefits every day to the towns of Echuca and Moama.
“We’re proud of how much we were able to achieve with simple, uncomplicated interventions in this landscape,” Deiter said. “The project allows the site to shine both ecologically and culturally. It celebrates its natural setting and sits in harmony with it. The whole project team collaborated so well together and the community involvement was fantastic. This has been a very successful project and it was a pleasure to be a part of it.”
For more information contact CM+, Level 1, 52-58 William Street, East Sydney NSW 2011, phone 02 8244 8888, email enquiries@ cmplus.com.au, website www.cmplus.com.au
For more information contact Tract, phone 03 9429 6133, email melbourne@tract.com.au, website www.tract.com.au
The towns of Echuca and Moama are enjoying greater connectivity with a new bridge connection following the completion of the Echuca-Moama Bridge Project.
Centre State Asphalting was appointed by Stage 3 contractor McConnell Dowell to lay multiple layers of asphalt across the project including the main bridge decks, approach roads and new shared walking and cycling path.
The main bridge spans the Murray River, crossing the Victorian New South Wales border which caused some minor challenges for the works, as asphalt requirements differ between the states. McConnell Dowell’s client, Major Road Projects Victoria (MRPV), was instrumental in managing Stage 3 of the project across work sites in Victoria and New South Wales.
“MRPV oversaw (stage 3 of) the project really well and worked hard to find a solution to make the asphalt mix consistent between the states,” said John Bell-Andrews, General Manager. “It’s unusual for us to have such close engagement with the ultimate client but in this case MRPV was onsite every day, with the MCD team, carrying out inspections which was very helpful and ensured the job ran smoothly for us.”
Centre State Asphalting established a very good working relationship with McConnell Dowell and closely collaborated with the project team to find innovative ways to improve productivity.
“We were always on the lookout for alternative solutions to improve productivity and quality, tailoring our approach for each part of the project as required,” John said. “For this project there were some big time constraints, so we developed a method of moving the asphalt mix by shuttle buggy, reducing installation time for key areas of the project from weeks to days.”
The road surface needed to be formed with very tight tolerances for the consistency of surface levels in order to achieve a highquality ride. Centre State Asphalting deployed an automated pavement level control system, incorporating a levelling beam, to create a smooth road surface.
The COVID-19 pandemic created particular challenges on this job as work was conducted
in both states, and an interstate border that was intermittently restricted during the works. “We had massive issues moving manpower and vehicles across the border,” said John. “We ended up bringing in additional people and undertaking weekend work to keep the job moving forward. To deliver the project on time and to a high standard, it is testament to the hard work everyone put in and the co-operative support offered by McConnell Dowell. It was a great team effort and a job well done.”
The asphalt for the project was produced at Centre State’s plant near Maryborough, Victoria. Special insulated ‛Trout River’ trucks were mostly used to transport the asphalt to work sites and all waste materials were taken back to the plant for recycling, improving the overall sustainability of the project.
Following the completion of the EchucaMoama Bridge Project, Centre State’s project team attended the community open day and had the opportunity to ‛test out’ the road surface first-hand. “We are very proud of the quality of the surface,” said John. “The road rides really well and the new shared walking and cycling path is also beautifully smooth.”
“The project is a great community asset incorporating not just the new bridge over the Murray River, but also all the associated infrastructure and paths. It has been great to be able to deliver such a positive project for the local community in association with MCD and MRPV.”
Centre State provides innovative and sustainable products that lower its carbon footprint without sacrificing its quality standards, utilising the latest equipment and technologies. The company is committed to closing the loop on waste to protect the environment.
Since 2003, Centre State Asphalting has grown to become central Victoria’s leading asphalt manufacturer and contractor. Supported by being part of Colas Group and VSA Roads, Centre State Asphalting has the local knowledge and global expertise to deliver on the most challenging asphalt projects.
For more information contact Centre State Asphalting, PO Box 1240, Castlemaine VIC 3450, phone 03 5470 5028, email admin@csasphalt.com.au, website www.vsagroup.com.au/our-brands/
Based in Echuca-Moama, Australasian Fencing is a familyowned and operated business with over 15 years’ experience supplying and installing all types of steel fencing to major construction projects for Tier 1 builders nationwide.
For the recent Echuca-Moama Bridge Project across the Murray River, Australasian Fencing supplied and installed multiple products including chain wire corridor fencing and pedestrian/bike rails. The company also upgraded the fencing of the Echuca Lawn Tennis Club to achieve a regulation fence height of 5m, as part of the project’s contribution to local stakeholders.
A contributor to the success of the project was Australasian Fencing’s good working relationship with the whole project team. “It was clear sailing for us,” explained Neville Barnes, Director. “(Lead contractor) McConnell Dowell was fantastic to work with, as was everyone else.”
In addition to major roads, Australasian Fencing serves other project types including rural properties, military installations and solar farms. Australasian Fencing has also expanded its field of expertise to cover high security projects specialising in palisade, pressed form spear, chain wire, razor wire and 358 mesh products.
Other current major projects include the Winneke Solar Farm, Yarram Aerodrome and the Puckapunyal Army Base where Australasian Fencing is installing a total of 115km of fencing.
With the resources and expertise to serve multiple projects and a wide range of quality products available, Australasian Fencing is committed to safely and sustainably delivering projects on time, on budget and to the highest standard.
The company is backed by comprehensive quality standards and policies reflecting their commitment to the environment, employee and public safety. The company has an in-house Occupational Health and Safety Management System and can also comply with clients’ specific requirements.
“Our focus is on delivery,” Neville said. “Our clients trust us to always deliver on time according to the programme. It was a pleasure to be able to achieve that same outcome on this fantastic project.”
For more information contact Australasian Fencing, PO Box 562, Moama NSW 2731, phone 0418 176 178, email info@ australasianfencing.com.au, website www.australasianfencing.com.au
Flatout Surveying is an expert provider of surveying services in Melbourne, across Victoria and interstate. With over 10 years’ experience in the construction and engineering industry the company provides quick, reliable and cost-effective surveying solutions on projects of all sizes.
Flatout Surveying completed all survey tasks for Stage 3 of the recent Echuca-Moama Bridge Project including measuring the balanced cantilever bridge segments. This was a challenging undertaking which required onsite monitoring and corrections over a two-year period.
“The bridge installation was complex and the sequence of site works depended on the actual deflections that we recorded each day,” explained Rob Toller-Bond, Senior Surveyor. “Comparing expected deflections with the actual values we recorded onsite each day enabled the project team to plan the next steps.”
Many factors had an impact on the bridge deflection including daily temperature fluctuations which required values to be frequently checked. This meant Flatout Surveying maintained a constant presence onsite throughout the works.
Flatout Surveying is a specialist in infrastructure projects and other current projects including Stage 2 of the Monash Freeway and various Level Crossing Removal projects in Melbourne. Along with its separate commercial and domestic team, the company offers most facets of construction site surveying.
With a strong reputation for quality and technological innovation at competitive rates, Flatout Surveying is dedicated to meeting its clients’ specific requirements with safety and integrity first and foremost.
With client MRPV, Stage 3 of the Echuca-Moama Bridge Project was Flatout Surveying’s first project with lead contractor MCD, and with this success Flatout Surveying has started another project with MCD, a testament to the great result achieved.
“Our team did an amazing job on the Echuca-Moama Bridge Project,” said Rob. “We are all good mates and work well together, that makes all the difference on a long and complex job, such as it was. We’re very happy with the end result.”
For more information contact Flatout Surveying, phone 03 9068 6043, website www.flatoutsurveying.com.au
Walker Grader Hire is an earthmoving plant hire company based in Victoria. The company provides grader and water cart services in Melbourne and regional Victoria and specialises in major road and rail projects in the civil construction sector.
For the recently completed Echuca-Moama Bridge Project across the Murray River in northern Victoria, Walker Grader Hire was appointed by Stage 3 lead contractor, McConnell Dowell to supply grader and water cart equipment and operators for placement of fill and final trim operations.
“Once the surfaces were built up to subgrade, we placed all the verges and cement-treated crushed rock in accordance with the required specifications,” said Brad Walker, Construction Director.
“We worked on both sides of the Murray River, with permits in place to allow us to cross the New South Wales and Victorian border during COVID-19 related shutdowns.”
Despite the challenging timescales, the Walker Grader Hire team worked efficiently to get the job done. “There was a considerable amount of ‛fill’ to be placed within limited areas and timeframes,
and our operators were able to work collaboratively with McConnell Dowell’s project team to achieve a great result”
Walker Grader Hire had the experience to deliver an excellent outcome on the Echuca-Moama Bridge Project as roads and rail projects are a specialty of the business. Other recent and current major projects include the West Gate Tunnel Project, Monash Freeway Upgrade, Barwon Heads Road Upgrade and the Mount Beauty Airport Upgrade.
Walker Grader Hire combines industry experience with a commitment to customer satisfaction. “Our goal is to get the job done at a productive rate and to the highest quality,” Brad said. “We understand our clients want the work done quickly and to an exceptional standard and we focus on ensuring we exceed our customer expectations and get the best result every time.”
For more information contact Walker Grader Hire, phone 0418 210 543, website www.walkergraderhire.com.au
VSL Australia is a specialist civil works contractor established in Australia in 1966. Part of the VSL International Group, its capabilities include constructing long-span bridges, lifting large and complex loads, rehabilitating and repairing buildings and structures, and the design, supply and installation of specialist post-tensioning products and high tensile stress bars (manufactured in Australia).
VSL’s sister company Intrafor operating under VSL Australia also constructs complex deep foundations and specialist ground engineering works, further expanding VSL’s capability to provide specialist construction techniques for a wide range of challenging projects.
VSL constructed the bridge deck of the new Dhungala Bridge across the Murray River between Victoria and NSW. The construction technique was developed by VSL and used a balanced cantilever method for the 115m main span with a specialised VSL modular form traveller system.
The type of VSL modular form traveller used on the project had previously been successfully used on the Pimlico to Tevan Project in NSW and was further adapted by VSL for Stage 3 of the Echuca-Moama Bridge Project to include an entirely new and ergonomic access system.
The strong relationship between VSL and main contractor McConnell Dowell was key to the project’s success. The two firms collaborated in an exclusive relationship starting at the tender stage when the methodology was developed and extending right through to the project’s completion.
“Early collaborative involvement of specialist organisations like VSL from bid stage to delivery improves risk and cost management of these complex structures and is simply essential to the success of such projects in the challenging landscapes we find ourselves,” explained Stephen Knox, Business Development Manager – Civil Projects.
As Australia’s foremost specialist in long bridge construction, VSL has built a reputation for quality, innovation and expert service on complex projects nationwide. Other recently completed and current projects under delivery include Batemans Bay Bridge in New South Wales, Bridgewater Bridge in Tasmania MCD, Sydney Metro West and the Queen’s Wharf Skydeck in Queensland.
For more information contact VSL Australia, phone 02 9484 5944, website www.vsl.com
Permadec is an innovative permanent formwork solution for bridges and other civil structures. Made from GRP (glass-reinforced plastic), Permadec panels are lightweight, versatile and easy to handle and install. They can span from 1m to over 5m and are installed using a simple sealing solution. Once installed, Permadec panels can support concrete decks up to 700mm and have a 120-year lifespan.
The Permadec system was originally developed in the UK and has become a common approach to bridge building due to the many benefits it brings to projects. Now the use of Permadec is rapidly growing in Australia and it was used by Stage 3 lead contractor McConnell Dowell, on the new Echuca-Moama Bridge Project and its crossing spanning the Murray River between Victoria and New South Wales.
“The beauty of Permadec is that being permanent formwork there are no temporary elements to remove, and it still provides that safe working platform for site operatives to lay reinforcement,” explained Iain Baron, Regional Director for Asia-Pacific.
Permadec panels are custom manufactured to site-specific sizes and delivered ready for installation and use. On Stage 3 of the
Echuca-Moama Bridge Project this minimised on-site cutting and helped realise savings in onsite labour costs. Being lightweight the panels had simplified craneage requirements while still delivering the robustness and durability needed on this major project.
EMJ Plastics, the UK-based manufacturer of Permadec, has supplied panels to over 5,500 projects worldwide and the product has been helping projects in Australia save time and money since 2018. Permadec panels are fully designed and produced in the UK and can be cost-effectively and sustainably shipped worldwide due to their slim and stackable profile.
The Permadec panel range includes various types to suit individual project requirements. With in-house design capability and over 50 years experience, Permadec is the formwork option of choice for the world’s leading engineers and contractors.
For more information contact Permadec, Level 16, Tower 2, Darling Park, 201 Sussex Street, Sydney NSW 2000, phone 02 9052 4975, email sales@permadec.com.au, website www.permadec.com.au
InEight integrated construction management software is transforming the way the world builds with advanced program and project controls. The software offers a complete solution for design and construction teams, improving stakeholder collaboration and confidence at all project stages.
For the recent Echuca-Moama Bridge Project, InEight provided the core application supporting seamless communication of critical project documentation between Stage 3 lead contractor McConnell Dowell, its project partners and client, Major Road Projects Victoria.
The platform used on the project was InEight Document, a well known and highly capable solution for major projects. InEight Document is configurable for both up and downstream activities and multiple stakeholders while preserving privacy requirements. Key functions include document control, design review, variation management, progress reporting, quality and handover activities.
Stage 3 of the Echuca-Moama Bridge Project was complex with the project’s workforce, located both on site and in offices hundreds of kilometers apart. Reliable access to current information was critical for the project to be delivered on time and on budget. InEight ensured
that the latest document revisions were always used with appropriate approvals in place to support governance and compliance.
The project leveraged one core capability of the overall InEight Connected Data Platform, a complete solution spanning the overall asset lifecycle from design through handover to operation.
With the ability to support a multitude of core business processes, the InEight platform is benefiting hundreds of projects globally. In addition to road and rail infrastructure projects, InEight is increasingly being adopted across the energy and resources sectors as the world transitions towards renewables and carbon neutrality.
Headquartered in the USA, InEight serves customers in more than 60 countries around the world providing real-time insights to manage risk and keep projects on schedule and under budget. The team at InEight are driven by a passion to deliver a brighter future for the construction industry.
For more information contact InEight, Level 6, 700 Swanston Street, Carlton VIC 3053, phone 03 9291 0800, email sales@ineight.com, website www.ineight.com
Ivers Civil is a dynamic mid-tier construction company serving large civil infrastructure projects. Founded by Director, Sean Ivers in 2017, the company is focused on providing complex solutions for concrete structures in Victoria, New South Wales and ACT.
For the recently completed Echuca-Moama Bridge Project, Ivers Civil completed the construction of the new eight-span crossing over the Campaspe River. The company also completed the construction of the Murray River crossing approach spans on the New South Wales side, including a particularly complex transition pier between the super-tee beam and box girder sections of the bridge.
Ivers Civil completed all formwork, steel-fixing and concrete placement works for the full bridge structure including pile caps, bridge piers, blade walls, decks and barriers. The company was responsible for most of the project’s Stage 3 concrete works and associated temporary works in a challenging location extending across rivers.
Another challenge was the fact that the project spanned an interstate border, which at the time of the project was subject to constantly changing pandemic restrictions requiring careful workforce management to ensure appropriate permits were in place
Ivers Civil had a good relationship with main Stage 3 lead contractor McConnell Dowell and the other trades onsite which helped with coordinating the works.
One major strength of Ivers Civil is its diverse group of people including site workers, supervisors, engineers, project managers and professional staff, all of whom are committed to delivering the best service to clients. “Thanks are due to our staff for their dedication working away from home for extended periods in a very challenging pandemic period,” said Sean.
Ivers Civil is a specialist in bridge projects as well as concrete structures for roads, tunnels, marine and general civil projects. The company is involved in other major projects in Victoria including Melbourne’s West Gate Tunnel Project and Port Rail Transformation Project.
Ivers Civil’s expertise across the whole project lifecycle, from design to delivery of the technical solution, ensures its ability to maximise value on the most challenging projects.
For more information contact Ivers Civil Contractors, Unit 21, 830 Princes Highway, Springvale VIC 3172, phone 0415 250 852, email info@iverscc.com.au, website www.iverscivil.com.au
The largest transport infrastructure project in northern Victoria, the $323 million Echuca-Moama Bridge Project now provides a second river crossing in this growing region. Local business, Sweeping the Murray provided industrial sweeping and pressure washing services for various areas onsite for Stage 3 lead constractor, McConnell Dowell, including the roadway, bridge decks and the new shared walking and cycling path.
Sweeping the Murray was involved in many aspects of Stage 3 of the project, first cleaning up the base layer of the road prior to asphalting then cleaning the new surfaces as well as final touch-ups. Some aspects of the work required great care and precision, for example cleaning the expansion joints on the new bridge.
To deliver a better result on the project Sweeping the Murray invested in new equipment. “We purchased a truck-mounted sweeper with a built-in pressure washer to help us provide a more cost-effective service,” said Justin Wills, Director.
On such a large and complex project, Sweeping the Murray’s expertise made a big difference. “We had a good understanding of what was required and the standard we needed to meet,” Justin explained.
“Communication was also important and we had a good rapport with others on site.”
Based in Echuca, Sweeping the Murray are a family-run small business. “We set up the company because we saw a gap in the market,” Justin said. “We provide a service to northern Victoria and southern New South Wales that wasn’t really available in the past.”
The Echuca-Moama Bridge Project is the company’s first major project. “The McConnell Dowell team has been brilliant,” Justin said. “We really appreciate that they gave us a go and look forward to doing more projects with them.”
Sweeping the Murray’s vision is to keep the local community, river systems and environment clean for the next generation. The company offers commercial, industrial, carpark, factory and warehouse sweeping and is committed to providing exceptional and friendly service to ensure customer satisfaction.
For more information contact Sweeping the Murray, 47 Woodlands Circuit, Echuca VIC 3564, phone 0428 524 127, email justin@ sweepingthemurray.com.au, website www.sweepingthemurray.com.au
Moddex is a leading supplier of low-risk modular handrail and balustrade systems serving Australia and New Zealand. Its no-weld solutions eliminate design and engineering costs while reducing installation costs and onsite issues.
Moddex had two separate contracts as part of the Echuca-Moama Bridge Project. For the Stage 3 lead contractor McConnell Dowell, the company supplied 900 linear metres of galvanised steel barrier fencing to either side of the project’s new shared walking and cycle path, using a proprietary system.
The system was pre-engineered to require minimal site assembly. “We were able to give our client peace of mind with a tested, compliant system,” said Joe Stead, State Manager. “We had all the stock in hand already and it went in seamlessly. McConnell Dowell raved about how easy the product was to install.”
Moddex also designed and supplied a handrail system to specialist subcontractor Macfab for access stairs and maintenance benches under the bridge abutments. “We used our proprietary product that complies with AS1657 (Australian Standard) for maintenance access handrails and all Transport for NSW and VicRoads requirements,”said
Terry Sargeant, Project Consultant. In addition to supplying the products, Moddex provided a modelling, drafting and design service as well as warranties and customer support.
“One major reason we get repeat business from our customers is the consistency of service and support they get from us,” Joe explained. “We work with customers to find the best solution for their project.”
Moddex provides a wide range of handrail and balustrade products covering diverse sectors. Large-scale road and rail infrastructure is a particular speciality but they also cover education, sporting facilities, industrial projects and more.
With its unique expertise and processes and the widest range of proprietary modular designs, Moddex is the number one choice for innovative barrier systems.
For more information contact Moddex, located Australia-wide and New Zealand, phone 1800 663 339, email info@moddex.com.au, website www.moddex.com
The Green Pipe is manufactured by Circle P, a Moama-based business that manufactures a range of 100% recycled plastic pipes for use in low pressure water transfer applications including stormwater, irrigation and drainage. The company is a nationally recognised sustainable pipe supplier to rural, forestry, maritime and major infrastructure projects, such as the Tullamarine Freeway and Calder Highway projects in Victoria.
The Green Pipe produces standard 6m lengths of pipe with six different diameters ranging from 250mm to 600mm, they have a bell and spigot joint incorporating a rubber o-ring. The company’s unique product was developed with testing by CSIRO and Swinburne University and uses 100% recycled plastic bottled sourced primarily from kerbside collections.
The locally developed, patented, low energy manufacturing process gives The Green Pipe a carbon footprint 50% smaller than alternative virgin products. The product is lightweight, easy to transport and possesses stiffness and tensile toughness in line with the strongest alternative High Density Polyethylene (HDPE) pipes.
Due to the high performance, sustainability benefits and competitive price, The Green Pipe was contracted to supply stormwater pipes
along the road kerbs on Stage 3 of the new Echuca-Moama Bridge Project for lead contractor McConnell Dowell. The project includes a second river crossing over the Murray River, a bridge over the Campase River and link road approaches between Echuca and Moama along with a new shared walking and cycling path.
As a local Moama-based business, The Green Pipe saw firsthand the benefits the project has brought to the community. “It was great to have been a local supplier on this project that has improved travel times between Echuca and Moama so much,” said Managing Director, Nick Hogan. “The project team was a pleasure to work with and the new bridge is just fantastic.”
As a 100% Australian product made from 100% recycled plastics, the benefits of The Green Pipe are clear with proven performance on civil, agricultural and forestry projects and a nationwide distribution network. More and more clients are asking ‛Why aren’t we using The Green Pipe?’
For more information contact Circle P, PO Box 214, Moama NSW 2731, phone 03 5480 7060, mobile 0483 181 514, email sales@thegreenpipe.com.au, website www.thegreenpipe.com.au
The new crossing over the Murray River, the Dhungala Bridge, is now complete and open to traffic. Fastsec Security was involved on Stage 3 of the project from the start right up to completion. The company provided site security and monitoring including managing the receipt of equipment and deliveries, running perimeter patrol vehicles day and night, and maintaining guards onsite at all times.
“We had a constant presence,” said Director, Gary Sidhu. “Even during Christmas and New Year we were onsite 24/7. It was tricky to manage resources at times, especially due to COVID-19 but we managed it and happily with no major security incidents.”
One challenge was the impact of state border closures as the site spanned the New South Wales/Victoria interstate border. From its home base in Shepparton, Fastsec covers northern Victoria and southern New South Wales with a two-state operating licence. This meant they could service the whole site without major difficulties.
Maintaining a constant presence on site meant that a good relationship with the wider project team was critical. “We had a really good experience with everyone on this job,” Gary said. “They were a fantastic team to work with.”
Many of the personnel provided by Fastsec were local to the Echuca area. Fastsec also provides security services to the hospitality sector in Echuca as well as serving larger projects in the region, including Victoria’s largest solar farm which was recently completed in Numurkah.
Fastsec was founded seven years ago, and has grown steadily with a recent expansion into New South Wales indicating expansion means is set to continue. The company’s contingent of highly trained, licensed and accredited security officers are constantly undergoing training in systems and procedures to stay up to date with security standards.
Fastsec’s dedication and professionalism has gained it a strong reputation. “For us it’s all about trust,” said Gary. “Our customers know they can count on our security services.”
For more information contact Fastsec Security, phone 0452 525 117, email fastsec@hotmail.com, website www.fastsecsecurity.com.au
ARCHITECT : Bates Smart
CONSTRUCTION VALUE : $58.8 million
Iglu Flagstaff Gardens is a 17-level student accommodation building located at 7 Batman Street, West Melbourne.
The new tower rises through the centre of an existing heritage listed office building - Flagstaff House. Once the home of renowned Melbourne architects Yuncken Freeman, the existing modernist facade was retained and incorporated into the new development.
The project features a biophilic façade, high performance envelope and glazing, generous communal and recreation facilities, bicycle storage and views over the adjacent Flagstaff Gardens.
The new student accommodation development offers secure inner-city living and opened to students in late 2022. The project was built by Kane Constructions and incorporates 362 beds in single and twin rooms (including 12 accessible apartments) and a range of communal spaces.
The building has been designed to achieve a 5 Star Green Star rating and incorporates sustainability features such as a rainwater collection system, a biophilic façade and photovoltaic panels.
“The new tower was designed to be sympathetic and complementary to the existing heritage façade,” explained Jamie Rigg, Project Manager. “The tower is stepped back to allow the heritage elements to retain their prominence but it still makes the most of this great site with views across Flagstaff Gardens.”
Kane took possession of the site after strip out and façade retention works had been completed and installed the new tower structure within the Flagstaff House footprint. The site is constrained and required careful planning and management of the construction process to avoid negative impacts on the heritage features and the surrounding environment.
Containment and safety works were required to remove lead paint from the existing façade which was tied back to the new structure. Adding further complexity, the new façade has an integrated planter requiring all associated plumbing and landscaping works
to be undertaken during the façade install, behind captive permitter safety screens. “We established a strong working relationship with all of our consultants particularly Bates Smart and TTW who all worked collaboratively to complete the design for the project,” said Jamie.
Our trades were instrumental in the delivery of this challenging project,” said Jamie. “It was a delicate operation with multiple trades working together during COVIDrelated labour restrictions. Maintaining the construction cycle took careful planning and the successful result is testament to the entire project team.”
Kane’s innovative approach included the use of off-site prefabricated elements including precision manufactured bathroom pods that were produced in Melbourne. Components of the tower façade were also manufactured locally avoiding delays associated with importing materials.
The strong technical capability and engineering expertise within Kane’s team made them well suited to deliver this complex project. Having completed Iglu Flagstaff Gardens, Kane is currently delivering a second student accommodation project for Iglu – a 28 storey, 374 bed development located on Russell Street, in the heart of Melbourne’s CBD.
“We couldn’t be happier to have a client like Iglu,” Jamie said. “They are very
knowledgeable about their product and take a pragmatic and fair approach. They have been very involved throughout the process, supporting us every step of the way and it was terrific to work with them.”
Kane Constructions is a multi-award winning, privately owned commercial construction company with a diverse portfolio of projects active in all sectors of the industry. With a turnover in excess of $1 billion and over 450 full time employees, Kane operates throughout the east coast of Australia and overseas from offices in Melbourne, Sydney, Brisbane, Sunshine Coast and Canberra.
With over 450 full-time employees, Kane Constructions greatest asset are their people. They have a strong culture of collaboration, professionalism and integrity which runs through all aspects of their business and is reflected in the successful outcomes achieved on Iglu Flagstaff Gardens.
“This has been a great opportunity for Kane to showcase what we can do across two projects for a single client,” said Jamie. “It has been fantastic to have such strong support from Iglu and we are proud of what we have delivered for them on this project.”
For more information contact Kane Constructions, phone 03 8420 1200, email viccontact@kane.com.au, website www.kane.com.au
Capture Point Media are Australia’s industry leaders in infrastructure and construction video production. Servicing Melbourne, Sydney, and Brisbane, they document some of the nation’s most iconic large-scale projects.
As part of the featured article on the Flagstaff Gardens project, main contractor Kane Constructions appointed Capture Point Media to document site progress with two high resolution time-lapse cameras from sod turn to top out.
The talented photography and video production team at Capture Point Media have many years’ experience in providing professional still images and video content to clients. They have a successful track record of repeat business with some of Australia’s leading Tier 1 and 2 contractors delivering construction projects across many sectors.
“A key feature of Capture Point Media is the fact that we offer a fully inhouse service,” said Ben Johnson, Creative Director. “We plan the camera positioning, obtain any necessary approvals, complete the installation, and do all the back-end production ourselves. Every image goes across my desk which ensures we keep our quality standards high.”
Capture Point Media utilise the latest digital photography techniques and streamlined editing systems. They provide an online portal for clients to access a library of still images from their time-lapse cameras and all their cameras are monitored twice daily to avoid any issues that may arise. Safety is of paramount importance with a full suite of safety measures in place for all installers.
With a track record of providing Australia’s most compelling construction photography, Capture Point Media have built a strong reputation within the industry. “We pride ourselves on our commitment to maintaining the highest standards of communication and customer service,” Ben explained. “Our clients trust us to deliver on our promises when it comes to capturing their projects.”
SYNC is an Australian pioneer advancing manufacturing to change the way the world builds by fabricating cleaner, integrated, and more intelligent construction solutions.
Utilising innovative digital design and manufacturing processes, SYNC pods are a faster, simpler and more sustainable alternative to conventional construction and fitout.
SYNC was appointed by main contractor Kane Constructions to provide 306 smart pod bathrooms for the new 17-storey Flagstaff Gardens Student Accommodation in central Melbourne. The new development rises through the centre of an existing heritage listed building, Flagstaff Melbourne on King Street.
The pods supplied by SYNC featured gloss white wall tiles with terracotta floor finishes and chrome sanitary fixtures. Made in Melbourne at SYNC’s purpose-built manufacturing facility, the pods are simply installed and connected on arrival to site, by removing multiple trades from the projects critical path, enable a more sustainable and streamlined construction solution. SYNC worked closely with the project builder, designer and architect to provide a modern approach to student accommodation.
Prefab and off-site manufacture is a way in which clients can mitigate risks while improving safety and sustainability. The success of prefabricated pods is reflected in their exclusive five-year partnership with Metlifecare involving the exportation of pods to New Zealand. Providing intelligent integrated solutions, the pods contain under tile heating mats helping prevent mould, SYNC’s focus on precision quality allows for innovation and opportunity.
SYNC is leading the way in manufacturing change to future proof the construction industry. Their focus on continual innovation keeps them in SYNC with their clients.
For more information contact SYNC, 55 Leakes Road, Laverton North VIC 3026, phone 03 8329 4111, email info@sync.industries, website www.sync.industries
Positioned prominently along Melbourne’s iconic Kings Way, the Melbourne BMW Dealership and Showroom has been completely transformed. Consolidating Melbourne BMW’s operations into one central location, the ‘ultimate redevelopment’ has been unveiled – completely reimagining the customer experience into a world class retail destination.
Spanning across 13,305m2, the project team worked rapidly and efficiently to deliver this exclusive, high quality project involving the design and construction of a new two-level building adjoining the original dealership location. Integrating with the existing building tower, the site was transformed into a single, impressive retail and commercial hub for Melbourne BMW at 209 Kings Way in South Melbourne.The two-storey extension and a reconfiguration of the existing showroom space included upgrading the existing showroom, improving vehicle service circulation, and expanding the workshop capabilities, while enhancing Kings Way as a commercial precinct.
“This is one of five dealerships worldwide, and the first to be completed, to rollout BMW’s new global corporate identity developed to enhance the overall customer experience,” said Hansen Yuncken’s Senior Project Manager, Tom Cumming. “With client expectations front and centre, we carefully considered all aspects of the build to
ensure the project delivered the sought-after premium and luxurious feel to the showroom.”
At the peak of the project, Hansen Yuncken had 150 employees onsite and like the rest of the industry, weathered the many challenges endured through the COVID-19 pandemic and additional pressures felt through shipping, supply chain and labour shortages. “We commenced construction in August 2021, and despite the many challenges experienced across the construction sector, the project team have worked diligently to overcome them, ensuring we met all client expectations,” said Tom.
“The redevelopment has a high spec finish,” said Tom. “We worked closely with the client, the consultants and other stakeholders recommending an alternate ceiling design throughout the showroom spaces – this ultimately worked out exceptionally well with the final
outcome resulting in 6m high ceilings with zero reverberation, over polished concrete floors.” Working collaboratively with Autex, this innovative acoustic ceiling system designed for targeted sound absorption for today’s ever changing open plan workspaces, retail, education and hospitality environments, ensured best for project outcomes could be achieved.
Working with the best consultants and subcontractors in the industry has ensured Hansen Yuncken has always been at the forefront of change and innovation in the building industry. In 1929, Hansen Yuncken invented a suspended scaffold to replaster the domed ceiling at Melbourne’s State Library. In 1985, they converted Adelaide Railway Station into a casino while the trains were still running below. In 2011 Hansen Yuncken managed to etch their way into the side of a peninsula on the banks of the picturesque Derwent River, giving life to the globally iconic MONA – Museum of Old and New Art.
Founded in 1918, Hansen Yuncken is one of Australia’s leading, privately owned construction companies delivering some of the nation’s most iconic buildings such as the recently completed
Victorian Pride Centre, Thomas Dixon Centre Redevelopment for the Queensland Ballet Company, and the Eos By SkyCity Adelaide Casino Expansion. With over 650 staff and an annual turnover exceeding $1 billion, the company operates nationally across nine offices in Victoria, New South Wales, South Australia, Tasmania and Queensland. Behind their success is their reimagination of construction as a service industry. It’s about how they can help, not just what they can build. The company is always evolving their delivery procedures to suit each client’s specific requirements.
The company is an enduring and dedicated supporter of the construction industry. Being long term players in most Australian sectors, they are not just affiliated with professional bodies, they are actively involved. Hansen Yuncken recently celebrated 104 years of continuous membership of the Victorian Chamber of Commerce and Industry, a remarkable feat.
For more information contact Hansen Yuncken, Level 10, 412 St Kilda Road, VIC 3004, phone 03 9831 6500, email melbourne@ hansenyuncken.com.au, website www.hansenyuncken.com.au
Kelvin Way is the solid plaster and rendering contractor who is responsible for the magnificent high end polished plaster finish at the Melbourne BMW Dealership. Specifically, Kelvin Way delivered the application of Novacolor Marmarino KS to numerous walls throughout the dealership.
Marmorino KS is a lime-based plaster coat used for smoothing and finishing with a satin effect for interiors and exteriors; it is made of well seasoned hydrated lime putty, fine marble powders, and rheologic modifiers which guarantee a perfect workability.
Manufactured in Italy, Marmorino KS is able to achieve ‛cloudy’ esthetic effects with soft and vibrant shades or totally even and uniform surfaces reminiscent of the traditional and historical ‛Marmorino Veneziano’.
“This type of polished plaster has become the finish of choice for architects in apartment complexes and public buildings,” said Kelvin Way Director, Joe Forcadell.
The Marmorino KS plaster is a central feature of the architect’s vision for the BMW dealership. “We had to complete a huge feature wall in the main showroom that extends into the next level,” said Joe. “The architect requested a raked finish and because of the sheer size of the wall we completed the work using scissor lifts.”
“With the lights and televisions in place, the whole wall has really come together to be something quite spectacular,” said Jo. “The number of high end finishes makes this project quite unique.”
Kelvin Way was founded in 1986 by Sicilian immigrant John Maugeri. Initially the company worked in the residential space, but over the ensuing decades moved into the commercial arena. Kelvin Way will take on high end residential projects in certain instances however they have become known as specialists in the commercial building industry.
“We’re a family owned and run business,” said Joe. “John is my father-in-law and my wife Lisa runs the office.” Kelvin Way has serviced most of the Tier 1, 2, and 3 commercial builders in Melbourne through repeat business.
“Being a family run business, our clients deal directly with me as the Director,” said Jo. “Our clients have high expectations and we pride ourselves on always meeting their requirements and delivering a high end product.”
The Kelvin Way team are all solid plasterers and their workmanship and attention to detail sets them apart from other businesses. The company’s extensive exposure to the commercial arena means they know how to work with builders and understand how everything flows on commercial worksites.
“We’ve done some pretty special projects over the years including the terminals 2, 3, and 4 at Tullamarine airport, the elephant enclosure at Melbourne Zoo, and Hamer Hall at the Victorian Arts Centre,” said Joe. “But the BMW project is one of those rare unicorn projects and it was great to work with Hansen Yuncken once again.”
“The precision and detail of the BMW Dealership is next level. It’s full of sharp lines and immaculate finishes,” said Joe. “Now the cars are in it and the architect’s intention has been brought to life. It looks magnificent.”
Kelvin Way has a first class team of staff and is based in the eastern suburbs of Melbourne with most of their work in the city and regional Victoria.
For more information contact Kelvin Way, 21/125 Rooks Road, Nunawading VIC 3131, phone 0418 334 564, email sales@kelvinway.com.au
Below Boswen supplied and installed high quality expanded sheet cladding, balustrades and mesh screening, for the project.
Boswen supplied and installed the expanded sheet cladding, balustrade and mesh screening, louvers and a number of staircases including the main staircase, Mottorad stair and the showroom entry staircase at the BMW’s Flagship Dealership in Melbourne.
“The job itself was straightforward, however we didn’t have a lot of lead time. What would usually take 2.5 months we got done in 1.5 months,” said Boswen Project Manager, Moose. “I put all of our resources into this job as a priority and we delivered a high quality product that is in keeping with the rest of the dealership,” said Moose.
Boswen is the market leader in providing Melbourne’s best louvers installation services. Louvers provide maximum airflow along with 100% direct visual screening. The aesthetic appeal of louvers is their modern and contemporary finish.
“With our metal balustrades, you get a material made of toughened glass and even one for a more minimal look, structural glass that needs no posts for support,” said Moose.
Unlike other metal balustrades, Boswen’s handrails, balustrades, stairs, and balconies keep the best quality in mind. For outdoor installations they use high quality marine-grade stainless steel to provide maximum resistance to the elements.
“Most importantly, our balustrades are created to last for a long time,” said Moose. “We often weld the joints rather than glue them for maximum strength and quality in terms of finish.”
Established in 2008, Boswen is one of Melbourne’s finest industrial fencing and gates companies, providing perimeter security solutions to Australian businesses. Including security fences, automatic gates, security systems, safety railing and balustrades, façades, and much more. Their mission is providing a safe environment for Australian businesses to grow.
“Our design and materials provide a high standard of safety and maximise sunlight and natural airflow,” said Marketing and Design Manager, Tuff Yu. “High quality, security and reliability are the number one criteria.”
Boswen’s gates and security fencing solutions keep Melbourne’s homes and business safe by employing the latest technology and high grade, locally acquired materials. Their range of long-lasting products and versatile solutions coupled with their dedicated customer service has earned them the trust and appreciation of many happy clients.
“We have a team of over 100 staff that specialise in installing automatic gates and security fencing for industrial, commercial and domestic locations,” said Tuff.
Boswen’s wide range of products with automation features include heavy-duty sliding automatic gates for industrial applications with higher security requirements. They also have lighter-duty everyday gateways that can be custom made to suit and blend with any existing environment.
“Our range of remote-operated automatic gates means you no longer deal with the inconvenience of having to get in and out of your car every time you exit or enter the building,” said Senior Project Engineer, Max.
The company’s adherence to stringent quality standards coupled with their continual investment in product development ensures that Boswen consistently delivers effective solutions. Their pretreatment techniques and modern powder-coating fights corrosion and ensures Boswen gates and security fencing can stand up to all kinds of conditions.
“Working in conjunction with our long term partners, including suppliers and subcontractors, gives us the flexibility to offer our customers a wide range of options for automatic gates and security fencing in Melbourne,” said Max.
“Boswen is a hassle free, one-stop-shop for manufacturing, design, project management and service for all commercial and industrial applications across many industries.”
For more information contact Boswen, 44-48 Ordish Road, Dandenong South VIC 3175, phone 1300 849 800, email info@ boswen.com.au, website www.boswen.com.au
Tesla Constructions was contracted to complete the plastering, walls and ceilings, doors and door furnishings for the Melbourne BMW Dealership redevelopment.
“The work we do is fairly specialised,” said Tesla Constructions Director, Zoran Gvozdenac. “It’s niche and architectural and often challenging. But we roll our sleeves up and get the job done.”
Commencing onsite in March 2022, Zoran had up to 30 staff working on the project which finished in August 2022. “All jobs have their unique aspects, but this one had quite a few,” said Zoran. “We installed the Autex Axis acoustic ceilings which reduces echo in any space and was perfect for the open plan showroom where reverberated noise can be problematic.”
Other acoustic systems used in this build were the Armstrong Ceiling Aluminium Baffles which provides a balance of high sound absorption and high sound attenuation, and the Rimex ceiling panels that have a sheet metal-look finish.
“This job had a really tight schedule,” said Zoran. “But onsite it was a real team effort with all trades working well together. We’ve been
working with the Hansen Yuncken team to get the project over the line and it's always a great experience to see the end product. I’m looking forward to many more jobs like this one in the future.”
Tesla Constructions has been in business for 25 years and specialises in interior fitouts, plastering, walls, ceilings, paneling and cladding. Zoran runs a small but quality crew and is very involved with every project.
“We have a great bunch of toadies we call upon and we always produce a quality job,” said Zoran. “We do the architectural stuff that demands attention to detail and a high level of skill.”
Tesla Constructions works mainly in Victoria and is accredited to do government jobs. Other projects have included Melbourne Central, The Emporium ACMI, and the State Library.
For more information contact Tesla Constructions, 9/53 Dingley Avenue, Dandenong VIC 3175, phone 0419 301 735, email zoran@teslaconstructions.com, website www.teslaconstructions.com
Heritage Glass Products in Victoria completed the glass façade and all the internal office partitioning for the Melbourne BMW dealership. Eight staff worked on the project from April to August 2022.
“There was an enormous amount of glass used in this project,” said Heritage Glass Project Manager, Craig Cannavo. “The façade of this build is huge and has minimal aluminium structures. It was a highlight to be able to source all of the glass and materials locally from Australia, and mainly Melbourne.”
Heritage Glass specialise in the design, supply, installation and certification of glass and aluminium for commercial and residential building projects throughout Victoria. Since 1983, Heritage Glass has worked closely with architects, designers, builders and developers to realise their visions, including bringing some of Australia’s iconic buildings and glass features to reality.
As an established glass specialist, Heritage Glass offers a unique service to clients providing both the source and supply of glass for projects that require expert knowledge and experience as well as the ability to deliver high risk and complex projects.
“All jobs present a challenge but it was pleasing that the Melbourne BMW dealership threw up nothing out of the ordinary,” said Craig.
Heritage Glass has been part of the Schiavello Group since 2005, internationally renowned for providing intelligent products and services for commercial, healthcare, hospitality, education, retail and living environments.
The company has the capability to provide end-to-end service, from design and construct,through sourcing and installing for a wide array of architectural and building requirements. With inhouse drafting capabilities, the Heritage Glass design and technical centre can supply engineering drawings, computations, certification and shop drawings, to ensure that what has been designed can be built, installed and complied to Australian standards.
Other projects include University Hill, Bundoora, Medibank and ANZ Docklands and Melbourne Park Eastern Plaza.
For more information contact Heritage Glass Products, 9/504 Fullarton Road, Airport West VIC 3042, phone 03 9251 2888, email info@heritageglass.com.au, website www.heritageglass.com.au
MAIN CONSTRUCTION COMPANY : Hutchison Builders
ARCHITECT : Candalepas Associates CIVIL & STRUCTURAL ENGINEER : BG&E
CONSTRUCTION VALUE : $170 million
Castle Residences combines modern high end living with the opulence of a heritage hotel. Spread over 37-storeys, the residential tower features Manhatten-style living spaces, designer kitchens and chic bathrooms. The development boasts a gym and rooftop pool, along with ground floor retail.
Hutchinson Builders is Australia’s largest privately-owned construction company and for more than 100 years and five generations, has placed family values at the core of every structure and every task. Hutchinson’s latest contribution to the industry does not disappoint – a 37-storey tower boasting 131 luxurious, Manhattan style residences and an opulent, heritage hotel in the heart of Sydney.
The $170 million landmark development stands tall on Bathurst and Castlereagh Streets and fuses high end apartment living with luxury, 5 Star hotel services in an enviable location in the CBD, which has emerged as a distinctive offering in the Australian market.
“Hutchinson’s is well known for delivering projects in relation to major heritage restoration, high quality details and complexity in busy, inner-city environments across Australia,” said Timothy Ferguson, Project Manager at Hutchinson Builders. “We were approached by United Development Sydney to design and construct the Castle Residences, which is their flagship, mixed-use luxury development and both residents and hotel guests will enjoy a range of first-class amenities between the two buildings.”
Sitting above an 8-level basement, Castle Residences is home to 131 stunning apartments which are dripping in sophisticated features and modern finishes. There is a selection of one, two, three and four bedroom apartments, meticulously designed with a private balcony, soaring windows to maximise the city views, European oak and pale Limestone finishes and Miele appliances.
Beautifully crafted, off-form concrete domes on the lower floors are a standout and perfectly complement the repetitive moulded sandstone veneer of the Porter House. Beyond Level 11, the building cantilevers 12m off the site and continues 27-levels up, suspended gracefully over the Porter House.
“The building has various areas of operation and so the design and features on offer are also
varied,” Timothy explained. “For example, the Automated Guided Vehicle carparking system (AGV) is the first of its kind in Australia, there is a pool on Level 11 and the very top of the tower offers five levels of stunning, stepped sky gardens for residents.”
The scope for Hutchinson Builders also included the highly anticipated refurbishment of the historically significant, 142 year old, heritage listed Porter House building next door with 121, 5 Star guest rooms.
The building, formerly known as the Dixson & Sons Tobacco Factory, is a rare surviving example of a Victorian factory and warehouse in this part of the city. Originally constructed in 1876, it has a significant presence on the Castlereagh streetscape and has certainly added a special element to this project and one where the expertise of the team at Hutchinson’s has proven essential.
The internal finishes appointed in the hotel meet the M Gallery standards and hotel guests and residents are privy to an all-day café and wine bar, restaurants, gym, pool, business centre and dedicated 24-hour security.
The concrete arches of the Porter House externally highlight the exposed concrete and also provide acoustic treatment to the hotel rooms based on their cylindrical shape. Hutchinson’s also worked with artists, MariaFernanda Cardoso and Amanda Sharrad to bring to life the concept of concentric circles and spirals like ripples on a pond and the silky thread of a spider web which is nestled off the side of the 11-storey hotel façade under the main building’s cantilever.
“The Porter House provided many challenges during its redevelopment,” Timothy said. “The external sandstone façade was refurbished and the entire ground floor was replaced to bring back the original façade as constructed some 100 years ago.”
“Added to this, all columns were clad with fire-rated structural steel and the existing floor bearers and rafters were in a fairly good
condition with only minor timber repairs and termite removal required.”
Hutchinson’s was awarded the contract for Castle Residences on 31 May 2018 and the development was completed in four stages. Project Manager, Timothy Ferguson, alongside the site management team led a team of more than 200 management staff, labourers and subcontractors each day and the sheer size of the scope and the heritage aspect of the site did prove challenging at times.
“The unique development of Castle Residences has incorporated the past with the present and has been a successful project for all parties involved,” Timothy said. “It’s been a long time in the making but we couldn’t be happier with the results, achieving a quality build for the client and an equally impressive hotel facility with a huge range of amenities.”
Hutchinson Builders has an impressive portfolio of projects all around Australia and is one of the most recognised builders in the construction industry. Most recently, the company has completed at 194 unit residential development alongside R&F Property in Box Hill, Victoria.
For more information contact Hutchinson Builders, phone 07 4038 9000, email Timothy. Ferguson@hutchinsonbuilders.com.au, website www.hutchinsonbuilders.com.au
MTI Stone has been supplying and installing stone and tiles to the construction industry in New South Wales for more than 12 years, and has shown time and again that a meticulous eye for detail and dedication to their clients, is achieving superior results every time.
Working alongside Hutchinson Builders at Castle Residences, the two companies share a similar work ethic and passion for delivering a quality finish with no compromise.
MTI Stone’s well-earned reputation on high end developments made them the natural choice at Castle Residences, to supply and install the tiling finishes throughout the 36-storey residential tower and the historic Porter House Hotel which has also been restored.
“Our brief was to provide high quality tiling finishes to complement the overall design of the development and included all bathroom and balcony wet areas, living areas, lobbies, the pool and pool deck, the sandstone façade and the cobblestone driveway,” said Memo Ibrahim, Director at MTI Stone.
“The Porter House was particularly challenging with a host of stone works including three bars, commercial kitchens, bathrooms and mosaic tiling and other areas such as the display cabinets which house the historical artefact's found onsite.”
A team of 25 were onsite at Castle Residences for around eighteen months and the location in the heart of the city, as desirable as it is, presented a few challenges along the way, including the handling of material in limited space.
“There was a great amount of stone specified for this project which contained detailed and intricate design details, which in turn required special fabrication works using modern cutting methods such as our water jetting cutting machines,” Memo said.
“The end result at Castle Residences is a high quality, detailed finish which has complemented the designer’s intent and it’s a project we are very proud to have been part of.”
Established in Sydney in 2010, MTI Stone began as a small group that was passionate about making a difference in the tile and stone industry. The company’s Directors, with combined industry experience of more than 70 years, had a vision to build a trusted and well-respected team.
Today, the team at MTI Stone (including it's fabrication and supply partner companies), comprises more than 50 dedicated industry professionals who strive to deliver quality projects which satisfy and exceed the expectations of their clients.
“We specialise in both luxury residences and commercial, multi-storey buildings and over the years, our team has gained extensive experience across all sectors of the industry,” said Memo. “We have built relationships with some major suppliers around the globe, enabling us to import and supply only the finest materials for our projects.”
For more information contact MTI Stone, 2 Prime Drive, Seven Hills NSW 2147, phone 02 9620 8330, email info@mtistone.com.au, website www.mtistone.com.au
Feature Stone Pty Ltd is a Sydney-based company specialising in detailed stonework and has been fabricating natural stone, terrazzo, porcelain, and engineered stone since 2002. The family owned business has created a lasting impression at Castle Residences, the luxurious 36-storey tower which is unlike any other in the heart of Sydney.
Director of Feature Stone, George Nohra, has been in the stone industry for more than 30 years and his hands-on approach to every project ensures both quality and service which is second to none. Over the last two decades, Feature Stone has gained a reputation for delivering quality workmanship and friendly customer service, all using the best quality stone.
“We have undertaken many projects involving complicated detail and we pride ourselves on our quick problem solving methods and dedication to achieving the best possible outcome for our clients,” George Nohra.
A team of a dozen stonemasons, fabricators and installers from Feature Stone were onsite at Castle Residences for more than six months where they installed the kitchen benchtops, splashbacks and islands, bathroom vanities and laundry tops in all 131 apartments. The interiors needed to match the stunning external façade of the building and so Caesarstone features heavily throughout the apartments. A main feature in this project are the large, curved islands
which feature a coloured inlay and a laminated 40mm edge, a perfect combination of external and internal elements.
“The main challenge on this project were the delays onsite during COVID restrictions in 2021, which in turn pushed our works back, and the effects are still being felt now,” George Nohra said. “As one of the last trades to be onsite, we are always working to a tight timeframe, so the restrictions really put our team to the test. I’m happy to say though, that the end result is sleek and sophisticated, and we’ve delivered an ultimately clean and fresh look at Castle Residences.”
Whilst most of Feature Stone’s work can be seen primarily in Sydney, the team is also working on developments across regional New South Wales and Canberra and is currently completing another exciting project for Hutchinson Builders, Whitton Lane in Bondi Junction. Feature Stone is also working on several other commercial projects in Waverton, Bellevue Hill and Edgecliff.
For more information contact Feature Stone, phone 02 9757 3121, email info@featurestone.net.au, website www.featurestone.net.au
CONSTRUCTION VALUE : $77 million
The $77M Ace Hotel Sydney is an incredible 19-storey tower with 264 beautifully designed guest rooms, ground floor lobby with bar & cafe, Level 18 dining and cocktail bar. This project consolidates two separate sites while retaining the ‛Tyne House’ heritage-listed façade, roof plant, kitchen and back-of-house facilities.
Hickory has completed construction the Ace Hotel in Surry Hills, an iconic project seeped in local history.
Australia's first Ace Hotel is an incredible 19-storey tower with 264 beautifully designed guest rooms, ground floor lobby with bar and café, with a sophisticated dining room and cocktail bar at level 18. The existing basement has been refurbished to include a commercial kitchen and backof-house staff facilities.
The development involved the consolidation of two separate sites, one with a threestorey building that was demolished and the other, an adjoining nine-storey federation warehouse, Tyne House with its heritagelisted façade.
The Bates Smart design for the Ace Hotel retains the Tyne House façade and adds nine new floors with contemporary services and modern roof plant. The new structure is of in situ concrete with precast and prefabricated elements manufactured by Hickory.
Prior to demolition, archaeologists investigated the site and carefully removed any artefacts, discovering the oldest known kiln in Australia during the process.
In collaboration with Mann Group, Hickory undertook a complex demolition of the existing structure, which involved adding 100 tonnes of additional structural steel to retain the early 20th-century heritage façade.
During the demolition, Hickory was also required to undertake replacement works for one of Sydney Water's oldest oviform drain assets. The historic brickwork stormwater channel was built in the 1860s, with the stormwater line entirely below ground and preceding through the foundations of Ace Hotel.
The complex installation required Hickory to work around the structural steel bracing
system to retain the façade, before installing a new drain channel that was constructed from glass-reinforced plastic and encased in reinforced concrete.
Throughout the build, Hickory worked hard to preserve heritage elements such as an original oriel bay timber window, and pressed metal cladding and cornices.
With Hickory putting the final touches on Ace Hotel Sydney earlier this year, the hotel officially opened to the public in May 2022 to a warm reception.
Established in 1991, Hickory has an unwavering focus on innovation, , striving to create better places for future communities. The building and development company uses its unique Hickory Building Systems (HBS) methodology to streamline the construction process of high-rise builds.
Constructing the majority of the building elements offsite, this technology enables Hickory to fast-track projects by up to 30%, whilst reducing construction waste, build defects, noise pollution, and traffic congestion at the same time.
With a team of over 1,000, Hickory has delivered more than 150 projects across Australia and is currently involved in a several developments across the commercial, hospitality and high-rise residential sectors.
Hickory is quickly expanding its portfolio of buildings and development projects in Sydney, and was recently contracted for the design and construction of the façade for Parkline Place, a 39-storey office block with a podium above the new Pitt Street station.
Hickory’s in-house façade team have designed a tower façade with 7m high sandstone fins and a podium clad with double-height curved glazing. Hickory is currently working through the procurement, manufacturing and installation to complete the job by mid-2023.
In conjunction with Time & Place, Hickory will also build and develop Bourke & Bowden, a contemporary office precinct located in the up-and-coming Sydney suburb of Alexandria, set for completion in June 2023.
Another Hickory venture is Flex, a premium flexible workspace service that has been incorporated into Hickory’s Market Lane headquarters, with plans for further expansion across several of Hickory’s upcoming development projects.
For more information contact Hickory, Level 5, 68 Clarke Street, Southbank VIC 3006, phone 03 9429 7411, website www.hickory.com.au
Mann Group demolition are subject matter experts, specialising in structural demolition, internal strip-out, hazardous material removal and excavation. Mann Group were awarded the contract for demolition services at the Ace Hotel site in June 2019.
Building 1, a 3-storey brick warehouse was to be totally demolished, and Building 2 Tyne House built in 1915, a 11 story heritage brick building, where perimeter façade was to remain and all internal slabs, columns, and beams to be demolished.
“Mann Group had to design a way to demolish the interior of the building, whilst leaving the very old 10-storey high, perimeter brick walls” said, James Manassa. “We designed a system of steel members bolted to the brick façade bracing the structure from the basement to level 10. We then worked downwards, removing the slabs, columns and beams, in and around the temporary steel bracing.”
Each steel member had to be strategically placed, both in a RL, and in a North/South, East/West configuration. This temporary structural design allowed Hickory to install structural concrete precast pods without fouling. Precast building components are part of the Hickory Building System (HBS) and each level had 12 to 14 precast pods installed inside the building and the temporary steel had to allow for this.
“Despite the many constraints and intricacies of the job, it was undertaken with the paramount focus being the safety for our workers and the general public. There was comprehensive, R&D and much liaising with clients and engineers to deliver this project completely injury and incident free. It was a major achievement on everyone’s part,” said James.
“We’ve worked with Hickory before at the Chadstone Link in Melbourne (2019), demolishing a 4-level post-tensioned carpark and a large commercial building at Toorak Road, South Yarra in (2020).
Hickory approached us to provide a D&C demolition solution for their first Sydney project, the Ace Hotel. They were a great team to work for and we look forward to working with them more often as they expand into Sydney.”
Mann Group was established in 1949 by Anthony Manassa, delivering major projects throughout Sydney. Today Mann Group fulfil many D&C contracts for demolition services nationwide. This family run business has grown over 70 years and now engages in demolition work and HAZMAT removal across a broad range of industry sectors.
Mann Group are passionate in bidding, winning and completing projects that are complex, large scale and unique. In particular, the demolition of the heritage silos project in Cremorne, Melbourne where Mann Group became the first Australian contractor to be awarded first place at the ‘World Demolition Awards 2021’ in Chicago. The demolition of the silos was completed utilising custom built platforms and remote-controlled robot excavators.
“In the future we hope to improve project methodologies to cater for complex projects. It’s a high-risk industry and we hope to introduce robots to keep staff out of dangerous situations. Safety is a priority for us at Mann Group and we are going to use more robotic unmanned excavators in demolition. We are also constantly monitoring our operations to improve safety and legal standards,” added James.
Mann Group has a management team of engineers, project managers and site supervisors with years of experience working in construction, oil and gas, maritime and critical infrastructure sectors.
In both NSW & VIC Mann Group has successfully completed many infrastructure projects, non-exhaustive: NorthConnex, WestConnex, Northwest Rail Link, Gateway, Sydney Metro, NSRU, Western Sydney Airport, Melbourne Metro, Sparks Alliance, Railway Level Crossings, Marvel Stadium, Bushfire Recovery Victoria and over 40 other railway station projects.
For more information contact Mann Group, (NSW) 02 9890 3335, (VIC) 1300 626 647, www.manngroup.com.au
Lusso Venetian Finishes are expert in the application of traditional hand crafted finishes producing beautiful timeless surfaces for walls and floors. Lusso Venetian Finishes started at the Ace Hotel in February 2021 working on the interior of the new construction as well as restoring the façade of Tyne House.
“We applied over 750m² of finishes to the interior spaces of the hotel using a mix of resin, lime and sand, for the lobby and conference room. The mix was made especially for the Ace Hotel,” explained Owner, Eric Moroney. “We put a stippled finish to the lobby and made the corridor floors of raw concrete. For the Level 18 bar area we used different layers of rammed earth. The restoration was a painstaking job involving the complete stripping back of the façade along with research into aesthetics and materials,”
With seven tradesmen on the job Lusso Venetian Finishes completed onsite by the end of 2021.
“Our work is highly detailed restoration for heritage listed buildings as well as applying beautiful venetian finishes to new buildings,” said Eric. “We bring the old back to life as well as using old techniques and materials in different contexts.”
Lusso Venetian Finishes enjoy collaboration with architects, designers and builders to achieve the perfect artisan finish, to give spaces a unique feeling. “This was our first job with Hickory Group and we worked really well with them, they were very good to deal with,” said Eric.
In 2018, Lusso were engaged on the Indigo Slam project in Chippendale, to provide a whole interior and full resurface faclift to the project. Over six weeks Eric, designed and developed a new methodology through strenuous testing and modifications to allow for the structure to move without cracking the stucco. Layers of a German material, mesh from Spain and American gypsum created a shock-absorber to leave a smooth surface. “We completed 1,350m² of wall, primed, applied with stucco and waxed, in 16 weeks,” said Eric.
The Indigo Slam project received the 2017 Best of State Award, Residential Award and Premier Award for Australian Interior Design.
For more information contact Lusso Venetian Finishes, Eastgate Bondi Junction, 83-85 Spring Street 1010, Bondi Junction NSW 2022, phone 0477 773 264, email info@lussovenetianfinishes.com, website www.lussovenetianfinishes.com
IJF Australia specialises in high-volume commercial joinery across high rise apartments, hotels and hospitals, Australia wide, and were engaged by Hickory to supply and install joinery across all 264 guest rooms and common areas of the Ace Hotel.
Working to architect’s specifications IJF manufactured prototypes to ensure the items met with the designer’s and client’s approval and also to streamline fabrication and installation.
There was considerable collaboration between IJF, the builder and the architect to complete the design. This was seamlessly managed by IJF Australia through logistical and geographical challenges with COVID in a professional and experienced manner to achieve the desirable outcome of the project.
IJF Australia’s admin and project headquarters is based in Adelaide, but have extensive site resources in New South Wales, built over 25 years in the New South Wales market, and this complimented and supported Hickory’s first hotel project in New South Wales.
In the hotel rooms, the joinery items included American oak veneer bedhead panels and curved timber veneer vanity units with natural
stone benchtops and solid timber mirror surrounds. IJF also supplied and installed kitchenettes in the six suites. The reception and retail areas included a number of unique metal finishes, integrated with artworks commissioned by the client.
For the gym, bar and dining areas the joinery was of an especially high quality, with a variety of leather and steel finishes used throughout.
IJF Australia’s parent company, the IJF Group, also has other business divisions which specialise in private residential joinery and custom projects on a smaller scale.
For more information contact IJF Australia, 41-43 Cormack Road, Wingfield SA 5013, phone 08 8349 7400, webstie www.ijf.com.au
Beyond Solar, established in 2015 is a locally owned company providing high-quality customer service to their clients with tailored solutions for residential and commercial projects.
At the Ace Hotel, Beyond Solar designed and installed a solar system comprising 47 solar panels and inverter. The system is to meet the energy needs for servicing all the common areas including the air conditioning, lighting, lifts and access doors.
Initial design discussions took place toward the end of 2020 with the rooftop panel installation completed within a few days by a team of six.
Beyond Solar worked with Hickory to design the rooftop structure that would hold the panels which weighed 20kg each. It was important for the team to achieve structural integrity in the framing, especially in regards to the wind loads.
“The Ace project was quite complex with changes to the layout as the work progressed. We had to be flexible and respond in a timely manner. Once the electricians had completed their work we were able to connect, run safety checks and commission the system in late November 2021,” said General Manager, Steve Tabbah.
Beyond Solar work in Sydney, Canberra and across New South Wales serving the residential, commercial, industrial and government sectors. They are especially proud to be contributing to ‘Turning Schools Green’ by installing solar systems to government schools across Sydney.
“We like to make our installation a learning opportunity for students, giving teachers tools for teaching about the collection and monitoring of solar energy,” said Steve. “We’ve installed systems at Strathfield and Port Hacking and are currently involved in the design and installation for solar energy at five public schools on Sydney’s northern beaches.”
“At Beyond Solar we focus on customer education,” added Steve. “We look at our clients’ needs and explain what is available to them, they can then make an informed decision about the type of system that is appropriate.”
For more information contact Beyond Solar, 2/79 Williamson Road, Ingleburn NSW 2565, phone 02 8074 0759, email info@beyondsolar.com.au, website www.beyondsolar.com.au
Winfix Façades install sparkling glazed façades to high rise structures in Sydney.
They started at the Ace Hotel in late January 2021 installing a window wall and a curtain wall to the 19-storey structure. Winfix Façades also installed shop fronts and steel-framed windows to the heritage-listed Tyne House.
“A challenge within this project was marrying the existing lower facade, together with the new façade at Level 9 as they become continuous glazing up the structure,” said Director, Frank Stournaras.
“The curtain wall is a double glazed unitised system of prefabricated panels. Each unit was 2.4m x 3.1m and we had terracotta panels 800mm x 3m as well as copper cladding,” Director, Chris Pattison explained. “The main challenge was the logistics, moving such large pieces around the site and as with all CBD jobs, deliveries. We made up six weeks lost due to stop and start COVID-19 restrictions affecting both materials supply and onsite workers.”
Established 2005, Winfix Façades is a family owned and operated company, industry leaders in the installation of glass and aluminium
facades as well as double-glazed windows and doors, awning windows, sliding and bi-fold doors, fixed and operable louvre screens.
“We focus on the best outcome,” explained Frank. “Our work is of a high standard thanks to our great team of 40 permanent installers and the pro-active approach by the directors, we are onsite and often on the tools.”
Winfix Façades recently completed project the high profile luxury development Blue Apartments at Lavender Bay where the team installed a curved glass façade, balustrades, windows and doors, as well as a window wall and a curtain wall, finishing in April 2021.
They have also recently completed The Langston at Epping, which saw the team install 23,000m² of glazing. across three towers of residential apartments.
For more information contact Winfix Façades, 2/3 Pat Devlin Close, Chipping Norton NSW 2170, email info@winfix.com.au, website www.winfix.com.au
Sky Residences is a two building development comprising a 19-storey building with 113 apartments and a private residents only roof-top Sky Lounge, and a nine-storey tower with 73 apartments joined by a podium level on Level 3.
Constructed by GWH, the company has over 25 years of experience in commercial, industrial and residential construction and development. Located in Newcastle, New South Wales they have delivered over 600 new homes in the region, since 2017.
SKY Residences, GWH’s latest residential development, comprises two residential apartment towers of one, two and three bedroom apartments featuring a range of communal facilities, built over two stages. Onsite works for stage 1, the largest structure standing 19-storeys tall, began in October 2019.
Fronting Hunter Street, one of Newcastle’s busiest arterial roads, stage one of the development comprises 113 apartments, a gym, heated pool and a beautifully landscaped rooftop area, the SKY Lounge, offering uninterrupted views over the city. At 66m tall this tower truly epitomises the name Sky Residences. Three ground floor suites are also available for business tenants, ideally located in close proximity to public transport, retail and hospitality venues.
Construction of the second structure fronting King Street began in March 2021. The 9-storey building features 73 apartments with its architectural design complementing the taller tower through consistent use of façade materials.
As the largest residential project undertaken by GWH, the construction and project teams implemented a range of innovative engineering feats throughout the buildings development.
“A 1m thick raft slab comprising 2,000m³ of concrete and 600 tonnes of steel was
developed to support both the Stage 1 and 2 towers, whilst excavation of the shared basement saw the removal of 30,000 tonnes of sand. For construction of the 11m deep basement retaining wall, we used a specialist basement construction technique known as Cutter Soil Mix (CSM), 300 steel beams and 1,800m³ of bespoke concrete mix,” explained Project Manager, Brad Aldous.
This was the first time the CSM construction method had been utilised outside of an Australian capital city. A more expensive option, the CSM method was selected for its premium waterproofness and durability, amongst other advantages in comparison to traditional retaining wall construction methods.
“The building contains a number of precast elements all supplied by our partners at Hunter Precast. The Stage 1 tower alone featured 1,360 precast elements, as well as 850 windows and frames manufactured by Hunter Windows,” explained Mr Aldous.
The project was successfully delivered through extremely difficult operating conditions, with GWH and many others forced to adapt to the continually evolving COVID-19 restrictions placed on the construction industry across the country. At the projects peak there would have been approximately 140 people onsite including subcontractors. To deal with COVID restrictions, GWH implemented a number of measures above and beyond the Public Health Order guidelines onsite, with these measures enabling GWH to maintain site continuity and ensure progression of the project and delivery by the end of July 2022.
Another key to the company’s ability to maintain continuity through a period that saw many other operators struggle to do
so is the strategic partnerships established with companies within Hunter Construction Group. Consisting of seven companies in total offering a range of services that span the construction industry, these integrated partnerships provide GWH unparalleled visibility into the supply and quality of key materials required to construct their developments.
“Access to such a high quality specialist construction network allows us to enjoy unprecedented transparency across all our projects, providing us with: end-to-end visibility of projects, extraordinary architectural and structural solutions, complete transparency of costs and timelines, and the ability to plan, implement and maintain control of projects efficiently and cost-effectively while managing risk,” said Marketing and Communications Manager, Shannon Hutton
“In addition to our strategic partnership with Hunter Construction Group, we also have a network of preferred partners whom we utilise for all of our projects, ensuring consistency in results for our clients.”
“The opportunity to routinely work with our established network of preferred partners from project to project is one of our greatest advantages. The consistency and continuity that this approach provides ultimately flows through to the quality of the finished product.”
“When combined with our long standing strategic partnership with businesses within the Hunter Construction Group, we believe we have the proven formula to deliver exceptional projects on time and within budget, without compromising on quality,” continued Shannon.
Successful developments for GWH include AERO, awarded Apartment Development of the Year, 2018 by the Master Builders Association; and Highpoint, a 17-storey apartment building with a ground floor commercial suite located in Charlestown, Lake Macquarie. Recently completed is Darby Plaza, a 7-storey state-of-the-art A-grade office space in the heart of the Newcastle CBD.
For more information contact GWH, Suite 301, Level 3, 352 Hunter Street, Newcastle NSW 2300, phone 02 4966 3766, email admin@ gwh.com.au, website www.gwh.com.au
Below BG&E designed the structure
BG&E is a leading global engineering consultancy which has been enhancing the built environment for over 50 years.
From structural engineering to façade design, civil engineering to materials testing, and beyond to transport planning, hydrology, flood modelling, digital engineering, asset management and geotechnical – BG&E’s expertise is characterised by technical brilliance, innovation and buildability.
New development solutions add value to client projects and enable communities to thrive, including BG&E’s structural engineering innovation for Sky Residences, Newcastle’s newest skyline tower, comprised of over 19-storeys of luxury apartments.
To construct the foundation of the two reinforced concrete residential towers of Sky Residences, the need to drill 40m into the ground was eliminated, along with the associated time and cost implications.
“To enable GWH to start laying the foundations straight away, we designed a raft slab along with temporary anchors to be used during construction for the complex site, which is prone to movement due to coal mining, has a deep compressible clay layer and a high water table. The anchors held the hydrostatic slab down against the pressure of the groundwater and GWH were able to stop dewatering the site much earlier than usual,” explained Structural Designer, Peter Shrewsbury:
As another win for sustainability, and a first for Newcastle, the Sky Residences project also used Cutter Soil Mixing (CSM), which means existing soil was used as an aggregate for concrete instead of importing new materials.
“CSM entails a process where sand from the foundations is mixed with cement to make a retaining wall, which speeds up the construction process and provides a better finish with walls that resembled sandstone aesthetically. We also used slabs of post tensioned in-situ concrete and precast concrete panels for the walls, including the lift core, which is a cost-effective and environmentally friendly foundation method.”
The walls are further strengthened with stitched steel plates to ensure they are earthquake resistant – a system BG&E first
designed for GWH at Aero Apartments in 2016.
BG&E’s structural engineering services for Sky Residences encompassed the design and analysis of both buildings, including the 2-level basement, for vertical and lateral loads, in addition to working with a CSM consultant for better materials outcomes.
Founded in 1970, BG&E established a solid reputation for the design of tall towers with its engineering of the award-winning 226m high commercial development Central Park in Perth.
By 1989 BG&E were operating in Sydney and soon after that opened offices in Brisbane and Melbourne. Today BG&E has a team of over 800 highly skilled people in 14 offices across Australia, New Zealand, Singapore, the United Kingdom and the Middle East.
“We opened the Newcastle office in 2014 and have been growing in the local market, currently working as far as Gosford, Armidale and Dubbo. We hope to continue to expand the company, especially in our emerging disciplines such as resources, flood modelling and façades,” said Peter.
All BG&E offices leverage global experience, which includes groundbreaking high rise developments and hallmarks of ingenuity, including AMP’s Quay Quarter Tower.
BG&E worked closely with Multiplex for the 216m tall redevelopment project, which entailed partial demolition of the existing commercial tower at 50 Bridge Street in the heart of Sydney, while retaining over 60% of the core. Australia’s first large scale example of upcycling was underpinned by innovative structural and construction engineering, in addition to materials services by BG&E.
Working for clients in the property, transport, marine, defence, renewables and resources sectors, BG&E’s clients benefit from multi-disciplinary services from specialist inhouse teams.
They work collaboratively with leading contractors, developers, architects and government agencies to create projects that make a difference in people’s lives.
For more information contact BG&E, phone 08 6364 3300, email info@bgeeng.com, website www.bgeeng.com
CF Group is a geotechnical contracting company offering a wide range of engineering techniques facilitated by state-ofthe-art installation equipment and an innovative approach to the construction of structural foundations, ground improvements and retaining structures. For Sky residence, CF Groups experienced personnel delivered and successfully installed CSM perimeter shoring wall, capping beam, and temporary ground anchors. On this project, they utilised their innovative piling rigs for the installation of the shoring wall. The system used, Cutter Soil Mix (CSM) wall, is an advanced deep soil mixing method with sophisticated CSM equipment which allows the mixing of natural ground with a cementitious material to provide high quality retaining wall for deep basements solutions.
At CF Group, their skilled, dedicated and vastly experienced team will bring you the results that you need. For over 15 years, CF Group has specialised in design and construction of a wide range of shoring walls, foundation pile and excavation projects. They are piling and complete basement specialists using state-of-the-art machinery owned by CF Group
They own and operate a comprehensive fleet of piling & earthmoving equipment. The wide range of fleet gives CF Group the advantage to manage and deliver projects for all types of ground conditions and
complexities. The company specialises in shoring walls (CSM, Secant, contiguous, soldier and sheet piles), Foundation piles (CFA, Bored, driven), Ground anchors, structural bracing, excavation, remediation. They also offers others services such as demolition, capping beam, de-watering, shotcrete, underpinning.
CF Group prides itself on its inhouse ability to deliver all of the services necessary to provide the complete basement solution. Commencing with detailed design, the engineers will develop a competitive and comprehensive certified design basements solutions. CF Group was appointed as the main contractor for the Cranbrook School Redevelopment project for Richard Crookes Constructions. The scope included, turn-key package with cased secant wall, capping beam, permanent & temporary anchors, bulk & detail excavation and foundation piles.
Other projects CF Group have worked on are, Pagewood Re-development for MERITON, Barangaroo Re-development for VENTIA and Rockdale Central.
For more information contact CF Group, 154 Euston Road, Alexandria NSW 2015, phone 02 9316 4012, email admin@cfgroup.net.au, website www.cfgroup.net.au
Founded in 2004, All Floors Commercial is a family run business operated by partners Brian Russel and Mel Bower. Following success across Canberra, All Floors Commercial opened an office in Newcastle in 2016 and has been expanding its business in the region.
At Sky Residences, All Floors Commercial installed all the flooring including sub floor preparation, in all the apartments and common areas across both towers.
“We started on the first building in November 2020 laying 15mm thick timber boards with acoustic underlay in the 140 apartments and high quality carpet tiles in the common areas,” explained Brian. “We laid the carpet planks in a herringbone pattern and we were very pleased with the result. In the gym we put down a Regupol flooring system with rubber and foam for acoustic insulation. Stage 1 took 9 months and we then finished the apartments in the second tower in late June 2022. Altogether we installed 9,000m² of timber floorboards.”
“The challenge involved co-ordinating with other trades however the work went very well. This was our first job with GWH and the whole team was very good to work with.”
All Floors Commercial work across the commercial and high rise residential sectors with experience in the completion of large scale developments. They also supply and install flooring to the health care industry, residential aged care facilities, education and hospitality.
All Floors Commercial employ local labour and support local suppliers to install a range of flooring products including laminates and vinyl sheet, Axminster carpet and rugs, rubber and synthetic grass. They also offer a range of hybrid flooring, a contemporary water and stain resistant timber look-alike option.
A special feature used by All Floors Commercial is an application developed by a colleague called Dash Pivot. The app allows photo and data inputs to be uploaded in real time and it can then be accessed by builders, project managers and subcontractors for updated information.
For more information contact All Floors Commercial, phone 0478 680 646, email brian@allfloorscommercial.com.au, website www.allfloorscommercial.com.au
Euroform is an Australian owned and operated manufacturer specialising in providing cabinetry, stone benchtops and high quality polyurethane finish doors and panels to the wholesale market. For Sky Residence, Euroform manufactured and installed cabinetry and joinery items as well as stone benchtops across all apartments as well as the Sky Lounge on Level 19 and the ground floor commercial tenancy.
Working to the designer’s specifications, Director, David Galea worked closely with GWH to choose the best finish, colour and style for the kitchens, laundries, bathroom shaver cabinets, linen and storage. Coordinating with the other interior fixtures, the team created apartments that are both functional and visually striking. Utilising polyurethane painted kickboards and channel handles in Evic Dusty Gold or Evic Graphite, the design team brought a beautiful modern silhouette to the kitchen to compliment the Smartstone™ bench tops.
The fitout of the SkyLounge is one that David is particularly proud of. “Incorporating three Bars, a wall fireplace, firepit with surround bench seating and table areas, the stunning entertaining area is finished off with over 150m2 of Smartstone™ Atlas Plan Porcelain and we were able to install it all in just over two weeks”.
“Euroform have partnered with GWH for over 10 years” said HR Manager, Janene Liddell. “We manufactured and installed cabinetry, joinery and stone benchtops for their eight-storey luxury residential development Milhorn Apartments in 2018. Recently we completed the cabinetry at their 6,000m2 commercial development Macquarie Tower in Charlestown and we are currently working with them to fitout ‘One’ –a twin tower highrise residential development in Newcastle West. We are looking forward to continuing our business relationship with GWH and are excited to see what new projects they have in the pipeline.”
As a GHW preferred contractor Euroform are featured in their display unit at Sky Residences showcasing future projects and capabilities. Operating for over 19 years with 140 employees, the business has the capacity to manufacture and install one off designs through to multilevel apartments. With the three divisions of the business – Cabinetry, Painted Doors/Panels and Stone Benchtops, Euroform are able to offer builders a one-stop-shop for creating kitchens, bathrooms and laundries that will become the hero of any home.
For more information contact Euroform, 20 Kennington Drive Tomago NSW 2322, phone 02 4964 8333, email reception@euroform.com.au, website www.euroform.com.au
3D Splash is Newcastle’s leading pool designer with a team specialising in the design and construction of swimming pools of the highest quality and with the lowest maintenance in mind.
In April 2020, 3D Splash started onsite to construct the beautiful sparkling blue swimming pool for Sky Residences.
“As soon as GWH got to Level 5 we were able to start,” explained Owner, George Rejtano. “We spent five weeks concreting followed by two weeks installing the plumbing. We then left the job for seven months and returned to spend 10 weeks tiling and finishing off with completion by Christmas 2021. A feature of this pool is a 40mm thick glass wall, at the end of the pool, that fits into the exterior wall of the building. At 1.4m high by 4.2m wide, the wall gives an underwater view.”
3D Splash also installed cleaning equipment and heating controls to keep the water at a constant temperature of 27ºC.
“Working to install a pool at Level 5 meant that the biggest challenge was access, GWH craned all the materials and equipment including our tools. GWH are a great company, they really are good people to
work with. The weather didn’t help either, we had some high winds and it rained on the day planned for concreting,” said George.
3D Splash have over 30 years experience in the design and construction of swimming pools for the domestic and commercial sectors across Newcastle, Port Stephens and the Hunter Valley.
“Prior to Sky Residences we were with GWH at their retirement village development at Soldiers Point. We travel around New South Wales installing commercial pools however we prefer to focus on the construction of quality rather than quantity,” said George.
“Just before Christmas 2020 we finished a contract for the Australian Government at HMAS Albatross, refurbishing a very old pool, as well as the hydraulics and installing a new sanitation system.
For more information contact 3D Splash, phone 02 4006 5998, email admin@3dsplash.com.au, website www.3dsplash.com.au
DEVELOPER : Cricket NSW / MostynCopper
PARTNERS : Buildcorp, Evergreen and Ford Civil STRUCTURAL & CIVIL ENGINEER : Taylor Thomson Whitting ARCHITECT : Cox Architecture CONSTRUCTION VALUE : $50 million
In partnership with the Australian Government, NSW State Government, Sydney Olympic Park Authority and Cricket Australia, Cricket NSW has moved to a new home, built for the needs of current and future generation cricketers at every level, coaches, umpires, administrators and volunteers.
“Our overriding vision was to find a permanent home base for cricket in NSW,” said Cricket NSW General Manager for Venues and Development, David McDonald. “We were running out of facilities for training because we play and train 12 months of the year. We landed on Sydney Olympic Park as the perfect location.”
The key features of the new facility include an International Cricket Council compliant sized cricket oval, outdoor practice nets, an indoor training facility, a 2-storey cricket centre including an internal atrium, gym, community facilities, sports science and sports medicine facilities and sport administration offices, car parking and a single storey grounds-keeping shed.
MostynCopper specialises in complete project management services for the construction industry. They were appointed as the Project
Manager and Superintendent entrusted to deliver Cricket NSW’s vision for Cricket Central.
MostynCopper were responsible for all aspects of the project from master planning, concept design, authority approvals and construction delivery. This included engaging and coordinating multiple contractors concurrently onsite. “The site itself (Wilson Park, Sydney Olympic Park) was a former gas works plant, and while it has been previously remediated, the complexity of managing the risks associated with in ground works was significant,” said Senior Project Manager for MostynCopper, Kael Williams.
“This was overcome by partnering with a knowledgeable civil contractor (Ford Civil Contracting) with experience in remediating such sites and consultation with Sydney Olympic Park’s Environmental Team and the EPA.”
To ensure the integrity of the existing capping layer, the entire site was raised utilising 60,000 tonnes of imported material sourced from the Rozelle Interchange. Given its location within the Sydney Olympic Park Parklands and its proximity to the Parramatta River, the site also
had sensitive ecology and biodiversity which needed to be monitored and protected for the duration of works, which was undertaken with consultation from Sydney Olympic Park’s ecology team.
Cricket NSW and Cox Architects created an amazing design that has resulted in a world-class cricket facility. “The facilities are second to none, an ICC oval with 15 centre wickets (the largest in the southern hemisphere) and 43 outdoor turf training wickets with soil from New South Wales, Queensland and Western Australia,” said Kael. “It really is an unrivalled world class sporting facility that will further enhance cricket in New South Wales and Australia.”
Cricket Central was originally designed for elite performance, however there is a huge focus on integrating community use. It is anticipated 35,000 people will utilise these facilities every year. “We have 15 indoor lanes and nine are for community use,” said David. “Anyone can hire a lane and be training beside Australian Test stars. We’ve created the Disneyland of cricket.”
There are 16 meeting rooms in the administration area and Cricket NSW have chosen to acknowledge the contribution of volunteers to the game by naming each room after someone who has given their time and commitment to coaching, indigenous development, female development, scorers, umpires and so on.
“The internal graphics of the admin area reflect the spirit of cricket – how cricket has changed someone’s life for the better,” said David. “For example, a group of Afghan refugees who found a sense of community and belonging in Australia through getting involved in a local cricket team.”
For more information contact NSW Cricket Centre, 161 Silverwater Road, Sydney Olympic Park NSW 2127, phone 02 8302 6000, email info@cricketnsw.com.au, website www.cricketnsw.com.au/about/ cricket-central
For more information contact MostynCopper, Suite 1 Level 8, 9 Hunter Street, Sydney NSW 2000, phone 02 9241 1699, email info@mostyncopper.com.au, website mostyncopper.com.au
Rider Levett Bucknall (RLB) is an independent global construction and property consultancy providing management and advice throughout the built environment. RLB are the cost managers for the Cricket Central and have been involved with the project from inception through to construction for the last three years. Cricket NSW moved into the facility in June earlier this year.
RLB’s role included cost planning of masterplan options and cost management throughout the design and into construction.
There were three construction contracts for this project – early civil works, main building, and the field of play for the oval and training wickets. RLB also played a role in the tender review process that selected each contractor. During construction, RLB authorised payments for the contractor’s monthly progress claims and provided assessments for variations and scope changes.
Sean Fry, Senior Associate, led the RLB team, and we asked Sean what was RLB’s key success in this project. “It was always going to be a challenge to meet all functional requirements and aspirations of the client while balancing these against time and cost. COVID-19, a spike in building prices and extreme weather were unforeseeable
events that created problems for all involved. Despite this, the project was delivered on budget to a high standard and prudent cost management during the design phase was a fundamental driver in achieving this result.”
RLB are delighted to be part of a great outcome for Cricket NSW who now have an ICC rated oval and World Class cricket training facility. The success of this project centred around a strong delivery team, excellent communication, and collaboration between everyone involved.
RLB is committed to creating value for their clients, achieving commercial certainty, project and programme success and optimising assets to projects across the world.
For more information contact Rider Levett Bucknall, website www.rlb.com
Douglas Partners is an Australian employee-owned professional engineering consulting firm, specialising in Geotechnics, Environment, Groundwater, Rock Mechanics, Geophysics, Occupational Hygiene, Hazardous Materials and Earthworks testing. Douglas Partners is also affiliated with Ground Test for the provision of drilling services and cone penetration testing (CPT).
Douglas Partners was commissioned by Cricket NSW as the geotechnical and environmental consultant for the proposed Centre of Excellence development at Wilson Park. Douglas Partners developed and implemented an investigation program comprising a review of historical information, field investigations, testing and reports pertaining to the site.
Historical information, supported by the investigations by Douglas Partners, showed that the site was affected by a number of constraints requiring a degree of mitigation or management. These included the landfill management infrastructure, uncontrolled fill, sporadic waste fill (including buried tar residue), variable capping thicknesses, shallow perched groundwater, landfill gas, and acid sulphate soils (ASS).
Douglas Partners produced a contaminated land management/ remediation action plan (CLM/RAP) which was implemented during
the development to manage known or then unidentified contamination in soil, groundwater (leachate) and landfill gas. The CLM/RAP had key procedures including the verification of imported materials, the monitoring and management of ground gases, the assessment of ASS, the provision and verification of a gas proof membrane beneath new buildings, and waste classification of materials to be removed from the site.
Douglas Partners had a continued role during the construction works, including the verification and approval of imported materials, analysis of settlement and slope stability, pile inspections, compaction control, monitoring of excavations, waste classification of soils, construction quality control during the laying and testing of the vapour membrane, indoor air monitoring, footing inspections, validation sampling and testing. Douglas Partners will be preparing a final site validation report at the completion of the project supporting the suitability of the site for the intended land use as a community and cricket facility.
For more information contact Douglas Partners, 96 Hermitage Road, West Ryde NSW 2114, email sydney@douglaspartners.com.au, website www.douglaspartners.com.au
In elite sporting environments, the strength and conditioning spaces are often the heartbeat of the facility. Energy, enthusiasm and the hard work that goes on within these spaces can set the tone of the wider organisation and perform a critical role in team morale and connection.
With an unrivalled record of designing and delivering such spaces in elite sporting environments, PLAE International were able to collaborate closely with Cricket NSW to bring the high performance training areas of the Cricket Central facility to life.
“PLAE had successfully worked with Cricket NSW previously, and were engaged early in the process of this new facility to put together some layout and design options” said Jarrod Reid, APAC Head of Sales for PLAE International. “This early involvement, to align the needs of the coaches with the ideal training surfaces and equipment, ultimately results in the best possible result for the client, the architect and the builders during design, construction and once the doors open”.
“Each facility PLAE are involved in has a different shape, parameters, characteristics and demands,” adds Jarrod. “By working in step with the coaches, project managers and all involved throughout the process, PLAE can ensure that we deliver a facility that takes everything into account and is going to be a functional training space for many years.”
Specifically in the Cricket Central project, a 40m x 3m Attack Turf track (the largest in elite sport within Australia) sits just outside the doors of the gym, is easily accessible and adds training versatility and connection to the strength areas. The performance turf surface aids in providing variety in training running mechanics, plyometrics, sled push/
pulls and other cricket-specific work. This track is complemented with a turf warm-up space within the gym in the same grey colour, adding lightness and comfort to the room.
Within the gym, eight inlaid rubber lifting platforms sit in front of the racks, complete with custom Cricket NSW logos. These provide designated zones for barbell work without any dangerous trip hazards or surface inconsistency, and assists in making the space flow well and feel very open, even with large groups of athletes training at once. PLAE even provided rubber surfacing for the throwing wall, adding further dynamic training options to the space.
The majority of the strength equipment within the gym was also completed by PLAE, with the centrepiece being four linked Double Half Racks, maximising the programming options. With customised racks, bumper plates and dumbbells, in conjunction with the platform logos, there is a strong Cricket NSW feel which further strengthens the ownership and sense of place within the gym.
PLAE’s in-house design and project management team were heavily involved before, during and after installation, with render and shop drawing documentation, on-site management and flexibility within the program to meet the needs and variations of the job.
Brittany Royds, PLAE International Head of Design, reiterates how this helps the project run smoothly “The collaboration on this project from all of the stakeholders was instrumental in allowing the design team to help design, develop and document this facility. Utilising the latest in BIM technology PLAE International was able to seamlessly integrate their designs within this elite performance space.”
“PLAE’s involvement in the Cricket Central project aligns with our mission to continually innovate and delivery high-performance solutions and world-class experiences,” summarises Jarrod. “Our entire team is very proud to have been involved in this facility.”
For more information on PLAE and how they can assist your next project, please contact, Jarrod Reid (Jarrod.reid@plae.global) or visit www.plae.global
Vari Group is a privately-owned labour hire, traffic management company with an operating platform structured to ensure excellence in quality standards, competence, and compliance.
Our values and philosophies are based on respect and integrity, safety and wellbeing, communication, efficient responsiveness and service delivery through sustainability, continuous improvement, and innovation with evidence through our policies and procedures.
Vari Group worked with Buildcorp for over a year on the Cricket Central project, delivering competent and trustworthy labourers and traffic controllers who seamlessly blended with
the Buildcorp team and are proud to have contributed to the creation of the centre.
Vari Group has worked on some of Australia’s largest projects and can meet any staffing requirements with immediate access to suitably skilled personnel. Projects include Sydney Football Stadium Redevelopment (John Holland), Campbelltown Hospital Redevelopment (CPB Contractors) and Waterloo Integrated Station Development (John Holland).
Vari Group have been in operation for eight years and have 180 employees who we utilise across a range of projects, including Cricket Central, drawing on their talents and experience as highly skilled Labourers and Traffic Controllers.
Eastwood Air Conditioning installed all of the air conditioning and mechanical ventilation systems for Cricket Central.
“To meet the complex heating and cooling requirements of the Cricket Centre we installed Daikin’s VRV heat recovery systems,” said Eastwood Air Conditioning Director, Dean Nowland. “These systems can simultaneously heat and cool different parts of the building.”
The Daikin VRV provides superior comfort levels due to the heat recovery process that allows waste heat from one part of the building to be redirected to another that requires heating. The result is significant energy efficiency gains compared to conventional HVAC systems. In conjunction Daikin VRV also has improved energy performance over its predecessors with the introduction of VRT Smart technology.
The company worked on the job for 12 months including COVID delays, with an average of eight staff onsite.
Eastwood Air Conditioning is a well established commercial and residential air conditioning and ventilation company servicing the Greater Sydney region. Whether your needs are small or large, Eastwood Air Conditioning has the resources to provide a quality
designed, fabricated, installed, commissioned and maintained air conditioning and/or mechanical ventilation project.
“We employ highly qualified estimating, project and mechanical engineers who are able to tender and install fully designed, or design and construct projects,” said Dean.
Eastwood Air Conditioning supplies residential air conditioning and maintenance. The team can step you through the type of air conditioning equipment, zoning/supply air registers, ductwork/fittings and electrical controls to help you choose the right system for your home.
Upcoming projects include the Sydney FC Centre of Excellence, Mirvac Industrial at Homebush and a number of logistics office warehouse facilities including the new Harvey Norman Logistics Centre in Casula.
For more information contact Eastwood Air conditioning, PO Box 123 , Winston Hills NSW 2153, phone 02 9674 9944, website www.eastwoodair.com.au
Cre8tive Roofing Services was contracted to deliver all of the roofworks, box gutters, flashing and Danpalon cladding for Cricket Central.
“It was a big job with some architectural elements we don’t usually see in residential or factory roofs,” said Cre8tive Roofing Services Director, Michael Gulino. “It was a great experience to work on such a high profile project.”
Cricket Central gave Michael and his team an opportunity to work with the Danpalon daylighting system. Danpalon is manufactured from the highest quality polycarbonate and is a complete daylighting solution offering exceptional quality of light, thermal insulation and UV protection.
“The entire assembly uses no caulking or adhesives, eliminating the difficulties of sealant and adhesive bond failure common to traditional systems,” said Michael. “The system also has windows that open, to help with air circulation.”
The welded stainless steel guttering was another specialised item Cre8tive Roofing Services were able to accommodate.
COVID restrictions and extreme weather were the only real challenges Cre8tive Roofing Services faced on this project. Approximately 10-15 staff worked on Cricket Central over a four month period.
Based in Narellan, Cre8tive Roofing Services Sydney has over 20 years industry experience and is a successful, family-run business. They offer a multitude of roofing services including roof repairs and replacement, guttering and downpipes, metal roofs, and skylights.
“At Cre8tive Roofing Services, we care about customer satisfaction and provide an honest, reliable and friendly service,” said Michael. “We always aim to deliver the highest standard of workmanship every time and with minimal interruption.”
Their current projects include reroofing crematoriums at Matraville and Sutherland, Bankstown Airport, a heritage refurbishment at Camden Airport and a number of schools and nursing homes.
For more information contact Cre8tive Roofing Services, 4/4 Forge Place, Narellan NSW 2567, phone 02 9790 6177, email info@cre8tiveroof.com.au, website www.cre8tiveroof.com.au
A NEW KID ON THE BLOCK
CLIENT
: Catholic Education Diocese of Bathurst
North Construction & Building (North) was awarded the D&C contract for the new St Matthews Catholic School Mudgee – Secondary Campus in early 2021, initially engaged as the ECI partner working to progress the development. “The new secondary campus spans nine hectares and includes a multipurpose hall, sporting facilities, state-of-the-art music and drama facilities and chapel as well as purpose-built spaces for vocational education and training (VET). The new spaces are designed to provide a flexible and unique schooling environment with the opportunity for future expansion to include subjects such as agriculture, construction and primary industries,” explained Managing Director, Matthew Cook.
“The challenge involved the civil works due to an unseasonably high rainfall and flood management issues. We designed and constructed a levee bank and this included the installation and compaction of several thousand cubic meters of engineers’ fill to the southern and western boundaries of the site,” said Nick.
“North has worked across a wide range of iconic commercial construction projects throughout regional New South Wales from key infrastructure and commercial projects such as the Newcastle Light Rail depot and stops, multiple ambulance stations, Maitland Mutual Head Office and the Mariners Centre for Excellence, through to more unique developments like the Port Stephens Koala Sanctuary and the Line of Lode Miner’s Memorial in Broken Hill,”
said Matthew. “Key to our ongoing success is our relational approach founded on mutual trust. We have multiple long time repeat clients, the Catholic Diocese of Maitland-Newcastle being one.”
“Currently we’re delivering Stages 3, 4, and 5 at Catherine McAuley Catholic College, Medowie after completion of Stages 1 and 2. Traditionally we have focused on commercial projects, yet we’ve begun to enter the residential sector, most notably through affordable housing developments. Recently we completed a new 7-storey building of 56 units for Home in Place in Gosford. We’ve since gone on to build another development for Home in Place in Newcastle, a $7.5 million apartment building.”
“North is proud to be celebrating 35 years of operation this year. With Company Shareholder and Construction Manager, Richard Telfer, relocating in early 2021, it was the time and opportunity for North to open a Brisbane office and we are proud to have now established a presence in Queensland. Richard’s leadership, together with his great connections and significant construction experience of over 20 years across Brisbane and regional Queensland, sees us now delivering multiple projects between Brisbane and the Sunshine Coast.”
North has further cemented its reputation of being a trusted building partner by receiving a 4.0 Gold Star rating under the new independent Construction Industry Rating Tool, iCIRT. “We’re proud to be the first purely commercial construction company to be given a 4.0 Gold Star rating and listed on the iCIRT register. Trust is the foundation of our business and has always differentiated us from most other builders. Undergoing this independent, rigorous review process and receiving this outcome confirms that we have a proven track record of quality and integrity, fundamentally bolstering our reputation of building with trust,” added Matthew.
“As a long-time player in the construction landscape, we have worked hard to build confidence back into our industry. This public register brings more transparency and certainty, it is much needed and hopefully will encourage improved outcomes across the board.”
For more information contact North Construction & Building, Level 5, 1 Bryant Drive, Tuggerah NSW 2259, phone 1300 667 840, email mail@north.com.au, website www.north.com.au
Civiq designs, manufactures, installs and maintains a vast range of products to support indoor and outdoor activities, specialising in the production and installation of drinking fountains and water bottle refill stations for schools.
Customer Care Executive, Kim Butler and Sales and Marketing Manager, Brittany Thompson worked on the St Matthew’s School project.
“The school chose our new school drinking trough for use by their teachers and students. The product specified for this project was our Hydrobank. Schools love this hybrid drinking water station as it packs a lot into a compact, robust and durable solution. The station combines three fountains with three bottle refill outlets. It’s specifically suited to areas where lots of people are looking to access water at the same time,” said Brittany.
“We’ve been specialising in the production of drinking fountains and water bottle filling stations for over 15 years now,” said Brittany, “We have a range of high quality products to suit any project scope and budget. We work with clients to ensure the drinking stations suit their location – we have often incorporated student’s artwork into the units, making the fountains unique and fun.”
In business for over 20 years, Civiq have a team of inhouse designers and a manufacturing facility in Sydney, producing Australian made drinking stations within a four-week turnaround. Civiq are the preferred supplier Australia wide for Schools that wish to upgrade old infrastructure or install new drinking water fountains and bottle refill stations.
“We also work with Architects and builders on new school projects. For example, our product range was chosen to hydrate students at the new Riverbanks B-12 College and Aldinga Payinthi College in South Australia. Fortitude Valley State Secondary College in Queensland. Inner City High School, Arthur Phillip High School and Fort Street Public School in Sydney just to name a few,” said Brittany.
Civiq also work in many other market segments. For example they have recently supplied product to the New Waves Aquatic and Fitness Centre in Baulkham Hills as well as Sydney Olympic Park Cricket Central.
For more information contact Civiq, 8-10 Giffard Street, Silverwater NSW 2128, phone 1300 600 300, email sales@civiq.com.au, website www.civiq.com.au
Established in 2001, Smyth Structural Steel Fabrication Pty Ltd offer a comprehensive service from initial consultation and the production of shop drawings to fabrication and installation of structural steel members. Starting the St Matthews job in May 2021, Smyth Structural Steel worked according to engineer’s specifications and initial drawings to fabricate the structural steel members for Block E, a two-storey classroom building.
“North Constructions & Building awarded us the contract for Block E which altogether amounted to 52 tonnes of steel in the project. We also fabricated and installed walkway Steel work to the school. North then awarded us the contract to Block B, the chapel, where we supplied and installed 11.5 tonnes of structural steel columns and roofing members,” explained Manager, Bill Hicks.
“We had some difficulties with labour supply due to COVID restrictions, however with our team of erectors, we finished both buildings within 11 months. St Matthews was our first job with North and it all went really well, the site personnel were very easy to work with.”
Smyth Structural Steel specialise in the fabrication and installation of structural steel for industrial and commercial construction including
high strength steel, structural beams, columns and frames as well as canopies and stairs. They offer customised steel fabrication services and include blasting, priming, galvanising and powder-coating as well as onsite welding and erection services.
Locally owned and operated, Smyth Structural Steel operate from premises in Dubbo including their large workshop. Smyth Steel own and maintain their own fleet of trucks and cranes to manage transport as well as forklifts, telehandlers and EWPs to support construction. Smyth Structural Steel operate across regional Australia serving the industrial and commercial, education and infrastructure sectors, with successful contracts ranging from small commercial jobs to large scale developments.
Recent projects for Smyth Structural Steel include the fabrication and installation of structural steel for a large scale renovation to Red Bend Catholic College in Forbes. In September 2022 they completed a supply and construct contract to the Condobolin Visitors Centre.
For more information contact Smyth Structural Steel, PO. Box 4862, Dubbo NSW 2830, phone 02 6885 3366, email admin@smythstructural.com, website www.smythstructural.com
CDE Structures is a team of four professionals, specialists at Building Information Modelling including 3D construction modelling, visualisation, drafting and structural steel detailing. CDE Structures started work on St Matthews Catholic School in early 2022.
“We were engaged directly by North Construction & Building, early in the design process, to work alongside architects and engineers to develop the structural steel model. We started detailing before completion of the design and were able to issue shop drawings on the award of tender, so fabrication could start much sooner,” Managing Director, Phillip Bird explained.
“To meet the tight deadlines North awarded the steel contracts to a number of different fabricators, one for each of the five buildings, with manufacturing starting when early onsite works commenced. This ‘Detail Direct’ method is a new way of working for us, promoted by Nick Windsor at North Construction & Building. It’s challenging detailing a developing design however it was also an opportunity to have valuable input at that level. We established a good working relationship with the architect, engineer and with North Construction & Building”
“For our modelling and shop drawings we use industry leading software, Tekla Structures, which allows online sharing, commenting and collaboration through Trimble Connect. With 3D Modelling technology we are able to move quickly through design and construction decisions giving construction projects a real boost in terms of time and cost savings.”
CDES has the experience and commitment to bring concepts into reality. They serve the commercial, industrial, mining and health sectors as well as infrastructure across transport and energy. Previous work for North Construction & Building includes 3D modelling and structural steel detailing for the tourist attraction Line of Load at Broken Hill.
Successful projects include long term modelling work for the tunnels at the West Connex and Western Sydney Airport project and in 2009 CDES were contracted to complete the structural modelling and detailing for the $214 million Orange Base Hospital.
For more information contact CDE Structures, 2/32 Sale Street, Orange NSW 2800, phone 02 6362 5066, email pbird@cdestructures.com.au, website www.cdestructures.com.au
Zahra Formwork work hard and fast to deliver the rapid installation of all types of formwork for in-situ concrete placement. Starting in June 2021 Zahra Formwork were contracted by North Construction & Building to supply and install formwork to the 2-storey classroom building at St Matthews, Block E.
“We put up the formwork for the rammed columns, round and square, working on the building in the separate sections. We had a team of 10 formworkers onsite and completed the job in time for Christmas,” said Owner Director, Ahmad Jamil. “COVID restrictions gave us some difficulty with labour supply but we were easily able to subcontract extra workers. It wasn’t a big job for us and it went really well. North Construction & Building are an extremely good building company and really good to work with.”
Zahra Formwork were established in 2015 working across Canberra and regional New South Wales, including Newcastle and the Central Coast, to serve the residential and commercial sectors.
“We supply and install all types of formwork, marine ply, timber and brands of plastic formwork such as Dincel and AFS Rediwall. At Zahra Formwork we focus on getting a quality job done in a timely
manner. We care for our customers and work quickly and efficiently, with absolutely no delays,” added Ahmad.
Zahra Formwork also offer a comprehensive service that includes steel fixing, concrete pumping and placing. Currently they are at work at installing formwork for an on ground slab and a suspended slab, each 1,300m², for an apartment block at Wickham in Newcastle.
They are also at work installing formwork, over the next six months, for a large new building, the Gosford RSL Club.
“We are a family owned and operated company based in Sydney. Our work covers formwork installations to small buildings as well as installations for large scale concrete structures,” said Ahmad.
For more information contact Zahra Formwork, 479 Bringelly Road, Rossmore NSW 2557, phone (Ouday) 0426 268 892, (Ahmad) 0420 424 003, (Obada) 0450 447 044, email zahraform@hotmail.com, website www.zahraform.com.au
In Australia Broad Windows & Façades specialise in internal lining and cladding solutions. Known as Broad, they are a dedicated team producing quality work, quickly and cleanly with experience across a range of cladding and lining materials.
“We put up a Rondo internal and external metal stud frame wall with an exposed ceiling grid and a suspended ceiling system. We used square perforated plasterboard for all walls and ceilings, Aquacheck for wet areas, Soundcheck acoustic ceiling tiles and Commercial ExpressPanel for external cladding. In the chapel and hall we installed special Supawood acoustic slotted timber panels and Supaline solid panels and these two installations really look very good,” explained Australian Manager Director, Jiawei Lin.
Sydney based, a Broad team of 12 started onsite in July 2021, with lockdowns they couldn’t travel, so Lin encouraged workers to stay in Mudgee to keep the job moving. The internal and external cladding of all five new buildings was completed according to programme by June 2022.
“The shortage of materials, especially cladding and insulation, gave me concerns for the project’s progress, and I spent time and money
reserving materials as well as sourcing them from a number of different places. It was important to us to overcome the challenges and avoid delays,” said Lin.
“Broad have been with North Construction & Building since we began. For our first job with them we installed the exterior cladding to a 7-storey apartment building, a public housing project in West Gosford. We enjoy working with North and hope to continue with them into the future.”
Established in April 2020, Broad employs hard working and dedicated installers and has quickly established a reputation for professional service and delivery.
“Our main business scope is now in regional New South Wales, and we pursue quality and efficiency in our work and trust in relationships. We hope to leave our Broad works in every town across New South Wales,” added Lin.
For more information contact Broad Windows & Façades, 16 Chapel Lane, Baulkham Hills NSW 2153, phone 0452 211 064, email Lin@broadwindows.net, website www.broadwindows.net
JLE Electrical is an expert in engineering, design and construction of electrical infrastructure provides specialised services to the Australian construction industry. Including school, hospital and largescale infrastructure projects. JLE started onsite work as the principal electrical contractor at St Matthews Catholic School in April 2022.
“We provided the electrical and data services, automated lighting control, security and CCTV across all five new buildings. This included some specialised areas, such as the science laboratories, performing arts space and the multi-purpose hall. We also completed the external lighting throughout the school grounds and the high voltage network upgrade,” said Operations Manager, Damian Rootes. “This was JLE’s first job with North Construction & Building, and by working in close partnership, we navigated a challenging period, including managing COVID restrictions and protocols, labour and material supply issues and wet weather.”
With 12 staff on the job, JLE was able to complete the project in July 2022, which was within the delivery programme.
Having been in business for over 18 years, JLE employs inhouse designers to provide a comprehensive service from the first estimation
through to delivery. Bringing experience in complex underground infrastructure projects across the commercial, industrial and mining sectors, JLE can service projects of all sizes and complexity.
“Our core work and experience in complex high voltage cable installation, civil construction and tunnel boring means we can deliver projects of all sizes efficiently and cost effectively,” added Damian.
JLE has also worked on the Mindyarra Rail Maintenance Facility in Dubbo, integrating the low and high voltage electrical services. They are also providing Trunk Services to the Future Generation Joint Venture on the Snowy 2.0 Project, including Installation & terminations of the 33kV temporary underground infrastructure for the construction of a new power station.
JLE is part of Maas Group – an integrated property, construction and infrastructure company specialising in construction materials, civil construction and hire, manufacturing and real estate.
For more information contact JLE Electrical, 17R Yarrandale Road, Dubbo NSW 2830, phone 02 6884 5973, email admin@jlegroup.net.au, website www.jleelectrical.com.au
Chill-Rite Refrigeration & Air Conditioning have years of experience providing Mechanical Services – air conditioning and refrigeration for residential and commercial projects. They are an experienced team specialising in the project delivery methods of D&C along with prescriptive client and consultant HVAC designs.
“We worked on the design for 12 weeks and this included all aspects of the mechanically and naturally ventilated systems including exhaust and extraction. Onsite works started in June 2021 and we increased our number of onsite workers to support North’s timeline, completing the job by May 2022,” explained Commercial Projects Manager, Drew Irvine
“There were several revisions to the design to achieve a high level of operating efficiency, now and into the future, as well as Green Star compliance. We installed enormous fans as well as automatically actuating smoke louvres in the hall and Chill-Rite provided high level specialised EWPs to avoid damaging the newly installed floor.
“Onsite challenges included the large number of trades working simultaneously and frequent wet weather that made access very difficult at times. However, North’s experienced team, in particular
“Chill-Rite have completed several projects for North including the Dubbo Courthouse extension, finished in June 2021. This project was particularly challenging as we installed a modern HVAC system into a heritage listed building. Recently we completed a HVAC design and installation for the Wildlife Hospital at Taronga Western Plains Zoo in Dubbo for staffrooms, animal surgical and recovery facilities and specialist veterinary medical equipment, all integrated with the Building Management System. This project was completed for one of our foundation clients – David Payne Constructions, who we have a long-standing relationship with.”
“The future for Chill-Rite is very promising. With continued growth and investment across our branches in Dubbo, Tamworth, Orange and Mudgee we continue with our unwavering commitment to exceed clients’ expectations.”
For more information contact Chill-Rite Refrigeration & Air Conditioning, 52 Depot Road, Mudgee NSW 2850, phone 02 6885 2254, email reception@chill-rite.com.au, website www.chill-rite.com.au
The Siding is Stage 2 of Deicorp’s Petersham Precinct and comprises 199 stylish ultra-modern residences, across three buildings with contemporary styling, sophisticated architecture and open plan living spaces.
Perfectly positioned in Petersham, close to transport and within a vibrant dining precinct, The Siding offers the charm of village life, yet is just 6km from Sydney’s CBD.
With construction commencing in February 2020, the Occupation Certificate was issued at the end of June, 2022. Within this time, Deicorp delivered 249 apartments and a 3,500m2 RSL Club, as well as basement parking over two sites.
Robert Furolo, Head of Corporate Communications at Deicorp, said that one of the biggest challenges they faced throughout the development and construction phase was the impact of the COVID pandemic and unusually wet weather.
“From construction industry shutdowns, restrictions and ‘areas of concern’, limited availability of labour and supply chain issues and materials shortages, there have been many challenges to overcome,” Robert said.
“On top of this, the first six months of 2022 have been the wettest on record, and this has also added to the difficulty for the project. Fortunately, our experienced team were able to navigate these issues and minimise the impacts on the project,” he said.
With over 20 years in the industry, award-winning and Australian owned and operated developer-builder, The Siding is just another example of Deicorp’s commitment to selecting the best position for their projects.
Committed to providing confidence and peace of mind to every purchaser through the delivery of their end-to-end services, Deicorp understands that the purchase of a home is a significant life investment and want to ensure the journey, from sales, through to post-settlement, is as seamless as possible.
As a result, throughout construction on The Siding, the astute team from Deicorp liaised with the construction crew to produce update videos, ensuring purchasers were informed of the progress on their apartments throughout the entire process.
Furthermore, the Deicorp team is committed to delivering the highest standards, from
site selection to design and construction, sales and customer care, delivering significant residential development to areas of growth across Sydney.
“The Siding is another example of Deicorp’s commitment to selecting the best position for our projects. Located just moments from Petersham station and minutes by train to the CBD, The Siding also enjoys being on the doorstep of the vibrant and trendy inner west eateries and venues that make the area so popular. Together with the facilities of the new Petersham RSL Club, The Siding offers a great lifestyle in a fantastic location,” Robert said.
Given their outstanding and trustworthy reputation throughout the building and construction industry, as well as their commitment to giving back to the communities in which they build, 2022 is proving to be yet another significant year for the team. As well as working on the 3,000 apartments they currently have under construction, Deicorp are also expanding their community programmes and sponsorships to include the Parramatta PCYC and the Hurricanes Cricket Club in Sydney’s Northwest.
Deicorp were also the first developer in New South Wales to be rated under the new Independent Construction Industry Rating Tool (iCIRT). Introduced by the government to assist purchasers in recognising which companies are trustworthy and have been independently assessed, this new tool will be an important new tool within the development industry.
“We were really proud to have led the industry on this important new initiative and will continue to take responsibility for every aspect of our projects,” Robert said. “As we say, at Deicorp, we Design, Develop and Deliver the homes Sydney wants and loves and will continue to do so well into the future,”
For more information contact Deicorp, Suite 301, Level 3, 161 Redfern Street, Redfern NSW 2016, phone 02 8665 4100, email admin@deicorp.com.au, website www.deicorp.com.au
With an experienced and innovative team, dedicated to completing even the most challenging fabrication and structural projects, Tenze Engineering are specialists in mild steel, stainless steel and metal work supply, fabrication and erection for the building and construction industry.
Recently involved on The Siding residential project in Petersham, Tenze Engineering were responsible for the supply and installation of all the structural steelworks and specialised architectural requirements, access staircases, as well as steel works to the façade and roof of the building.
Working closely with engineers, architects and surveyors on all projects, Tenze Engineering pride themselves on the fact that despite the difficulty or scale of a project, they always deliver their outstanding structural works, in both a time and cost-efficient manner. As a result, they maintain a strong rapport with all their clients, who in turn, use them time and time again.
With 40 years of experience under their belt, Tenze Engineering continue to lead the steel fabrication and erection industry, delivering quality and professional workmanship every time.
For more information contact Tenze Engineering, 55 Christian Road, Punchbowl NSW 2196, phone 02 9758 2677, email info@ tenzeengineering.com.au, website www.tenzeengineering.com.au
Laser etched mural screen at ground level on Trafalga Street. Part of the Petersham RSL development on the site.
With more than 30 plus years of industry experience, award-winning Nordon Jago Architects create intelligent, cutting-edge designs, offering their clients strategic advice and solutions in all things architecture.
Nordon Jago Architects have worked on a range of building typologies, from domestic to large-scale commercial projects. Given their problem solving expertise and ability to oversee projects from the initial conception phase, right through to construction, Nordon Jago were also recently engaged on the Siding development, in Petersham.
With a small, yet astute team, consisting of Mark Richards, Anthony Payne and Andy Twine, Nordon Jago were engaged from the initial sketch analysis of the site, including liaising with council over the master planning of all three sites of the development, through to the DA design and full construction documentation of Site Three of the Siding project.
“Initially, one of the main challenges we came up against was developing a residential design, in conjunction with providing a space large enough for the new RSL also located at ground level,” said Mark Richards, Director of Nordon Jago Architects.
“However, we pride ourselves on our problem solving abilities, and our designs are always able to evolve to match the vision our clients have for their projects,” he said.
In fact, given such experience and creative response to every job, Nordon Jago Architects have also been involved on a bunch of other projects for a range of sectors, such as the childcare, aged care, government, industrial, medical and retail sectors. “We strongly believe that communication with our clients is paramount to great design, understanding the vision the client has of their project is one of the most integral parts to delivering a stand-out result,” Mark said.
Following the new Building Design Practitioners Act, which came into effect last year, Nordon Jago Architects have been using their existing skill sets to further develop a strong set of design and documentation procedures. Not only does this provide their clients with a sense of surety and peace of mind, but it also highlights their commitment to evolving with the times and providing only the best client oriented services.
For more information contact Nordon Jago Architects, Level 4, 111-117 Devonshirt Street, Surry Hills NSW 2010, phone 02 9318 8416, email mrichards@nordonjago.com, website www.nordonjago.com
Renowned for their innovation techniques, SYNC advances manufacturing to change the way the world builds by fabricating cleaner, integrated, and more intelligent construction solutions. The precision made, mass customised, smart rooms seamlessly connect into building projects, delivering quality and reliability at scale.
Given their unique approach, whereby the bathroom pods are made in Melbourne, delivered across Australia and New Zealand and then connected on-site, SYNC are able to seamlessly integrate the smart rooms without waste due to the decrease in trades on-site.
As a result of their high quality outcomes and products, repeat customer, Deicorp, recently contracted SYNC to manufacture 245 bathroom pods, with six different designs, for the Siding Project in Petersham. Minimally styled for maximum impact, the apartments all feature luxurious bathrooms that SYNC’s experienced team were able to meet the brief and deliver in their usual innovative and collaborative fashion.
Featuring light and dark colour schemes, with white wall subway tiles, all of the shower and sanitary fixtures manufactured by SYNC have a matte black finish. In addition, the bespoke bathrooms feature Carrara marble hexagonal mosaic floor tiles, mirrored shaving cabinets and an open shelf, with LED lighting.
Since 2013, SYNC has been supplying bathroom pods to residential, government, commercial and aged care projects. Powered by a team of in-house design, engineering and manufacturing experts, SYNC’s end-to-end solution follows a seven-step process to deliver quality and reliability at scale for your next project
For more information contact SYNC Industries, 55 Leakes Road, Laverton North VIC 3026, phone 03 8329 4111, email info@sync.industries, website www.sync.industries
Melrose Park – Pulse & Pavilion is a luxury residential development with a range of technologydriven initiatives including electric vehicle charging stations, NBN node-to-residence connections, environmental monitoring systems, sensor street lighting, an indoor activities centre, BBQ area, gym, sauna, and yoga studio.
The latest project by leading residential developer Sekisui House is nearing completion. Pulse and Pavilion together included 156 apartments across two separate buildings, rising up to 9-storeys on a combined ground floor podium above a 2-storey basement carpark. Surrounding the new buildings are extensive landscaped areas including play and barbecue facilities.
Pulse and Pavilion feature superior internal finishes, amenities and technology along with a striking external design. The development comprises Stage 3 of the multi-stage Melrose Park residential district in Sydney and new roadworks are also well underway to connect the area to the wider district.
Across the entire Melrose Park master plan there will be 6,000 apartments, creating a vibrant new community located centrally near Sydney’s Parramatta River. Pulse and Pavilion is the first stage to be delivered by main contractor Parkview Constructions.
Parkview is an industry-leading property company with a 25-year history of delivering outstanding project outcomes for diverse clients.
In addition to residential, Parkview specialises in sectors such as aged care and social housing, commercial, industrial, education, sport and recreation, public facilities, retail and hospitality.
Parkview has an internal team of over 200 skilled personnel managing projects across the complete value chain from strategic planning through to concept design, construction and post-completion. The company is accustomed to working alongside project stakeholders to achieve the best project outcomes.
During the project Parkview deepened its strong working relationship with Sekisui House. “It was great to have a very involved client working alongside us,” said Steve Desho, Project Manager.
“This is Parkview’s seventh project with Sekisui House and we have built over 1,500 apartments for them so we have a longstanding relationship based on mutual trust.
“It means we understand Sekisui's needs and have proven our ability to consistently deliver their vision ahead of time and within their
budget,” he continued. “They know that our team will always deliver what they need.”
The Pulse and Pavilion project was not without challenges. Inclement weather in the early stages of construction made excavation works tricky. Later in the project the impacts of COVID were felt with labour shortages and material delays exacerbated by the fact the local council area, the City of Parramatta, was affected by extended lockdowns.
“There were definitely challenges but we had a strategy for dealing with them,” Steve explained. “Early procurement was a key factor for us. One of our main priorities was to accelerate the design on long lead items and get the procurement organised. It’s a strategy that worked really well for us and we managed to get the project completed with no delays to the overall programme.”
The smooth delivery of the project was helped by the close working relationship between Parkview and its subcontractors.
“Most of our subcontractors have done extensive work for Parkview before so they already have a good understanding of our processes and methodologies,” Steve said. “That made communication a lot easier and helped us achieve the best outcome on the project in terms of quality, time, cost and safety.”
Project quality is a cornerstone of the Parkview way. The company’s three stage design management process of Early Planning, Construction and Completion/Handover enables the project team to find best value designs that ensure the smooth delivery of projects within budget and without delays.
The on time delivery of the Pulse and Pavilion project despite the external challenges has been a major accomplishment. “We’re proud of getting such a high quality result on this project,” said Steve. “The aesthetic of the finished building is even better than the architectural renders. It’s a great achievement to have exceeded expectations on a project like this.”
For more information contact Parkview Constructions, PO Box R1779, Royal Exchange NSW 1225, phone 02 9506 1500, email enquiries@ parkview.com.au, website www.parkview.com.au
As part of the project, Power Distribution Australia (PDA) installed a new 1000kVA Endeavour Energy substation along with a high voltage (HV) line extension and earthing grid to supply energy for the entire Melrose Park precinct.
As a Level 1 accredited services provider, PDA had the capability and experience to coordinate the works which involved multiple stakeholders. “The project was complex but everyone worked well together,” said Emily Rossi. “Communication is key on a project like this. The main contractor, Parkview, is a well-established client and we have a long working relationship with them which meant we knew what to expect.”
The project had a tight construction programme and the limited availability of materials during the COVID pandemic made the works even more challenging. “Lead times can be an issue especially for internationally-built equipment,” Emily said. “However we have good relationships with all our suppliers which helped us achieve our milestones.”
Established eight years ago, PDA is a family owned and operated business founded by Tony Rossi, who brings over 25 years of industry
experience and his daughter, Emily Rossi. “The family-oriented mentality influences every aspect of how our business is run,” Emily said. “We are passionate about our work and treat every client and project as an extended part of our family. We strive to form strong partnerships with developers, consultants and builders to achieve the best results.”
The passion PDA brings to every project large and small is the key to their success, with an established track record of completing projects on time and budget. Covering Level 1 construction works, private network installation and earthing design and installation, PDA are electrical infrastructure experts with the insurances and management systems in place to cover any project.
For more information contact Power Distribution Australia, 57 Argyle Street, South Windsor NSW 2756, phone 02 8880 3514, email emily@pdas.com.au, website www.pdas.com.au
The third stage of the landmark Melrose Park urban smart community comprising of two new residential developments, Pulse and Pavilion, is breathing new life into this area of Sydney.
On the project, leading civil engineering and construction contractor Chalouhi provided site remediation services for main contractor Parkview Constructions including the removal and remediation of around 20,000m3 of contaminated material and the temporary diversion of existing utilities.
To accelerate the overall programme, Chalouhi also constructed basement retaining shoring systems concurrently with the remediation works. Chalouhi designed an innovative retaining system for the future road easement to avoid impacts on upcoming stages of the development, ensuring future construction and road infrastructure can be delivered more smoothly.
Managing the remediation of an EPA audited site while also constructing shoring walls was a challenging approach. “We had to work hard to achieve an EPA registered site audit statement,” said Jordan, Project Manager. “This was achieved through close collaboration with multiple stakeholders and transparent delivery of works using technology such as GPS survey tools.”
On the project Chalouhi continued their strong working relationship with Parkview, having recently completed the bulk excavation of a 20m deep five-Level basement for Parkview’s 48-storey mixed-use development in Parramatta, utilising telescopic arms to improve project efficiency.
Over the past decade Chalouhi have grown into a dynamic company with a strong reputation based on innovation, quality and excellence. They provide a wide range of services including coordination, engineering and site preparation, working closely with Sydney’s leading consultants, architects and developers.
Chalouhi’s reputation in the industry is built on their track record of project completion on time and on budget. Their diverse team of hardworking professionals make them a leading choice for builders. Their award-winning approach is founded on their commitment to health and safety, environmental protection and quality management.
For more information contact Chalouhi, 2/22 Centenary Avenue, Moorebank NSW 2170, phone 02 9790 3799, email estimating@chalouhi.com.au, website www.chalouhi.com.au
Renyi is a sustainable building engineering and design firm based in Sydney and offering a comprehensive range of environmental building design solutions. They help leading builders nationwide achieve optimised design solutions that meet the highest standards of environmental performance.
Renyi were appointed by main contractor Parkview Constructions to complete a thermal performance analysis of Stage 3 (Pulse and Pavilion) of the Melrose Park integrated urban development in Sydney.
Renyi conducted an AFRC (Australian Fenestration Rating Council) thermal analysis of the building to predict the thermal performance of the façade systems. Based on the output of this analysis, they then made recommendations to Parkview about how to achieve a compliant design that also met the architectural and aesthetic requirements of the design.
“Our recommendations were based on a number of factors including cost, aesthetics and availability in the market,” explained Allan Ang, Director. “We have a streamlined process to identify solutions that are cost effective and perform in the real world.”
Based on Renyi’s recommendations Parkview were able to procure and install the specified products to achieve a compliant design. Renyi reviewed the installation to verify compliance and produced a final design statement. The whole process was smooth and efficient from start to finish thanks to the strong collaborative relationship between all the parties.
“Parkview are a fantastic client to work with,” said Allan. “We’ve done many jobs with them and they always know what they are doing. We are proud of our unique methodology and the successful outcome of the process we introduced to Parkview and all our construction clients.”
Renyi’s expertise covers many industry sectors from highrise residential to large scale commercial developments. On all their projects, Renyi are dedicated to leading the way in sustainable building to reduce the Australian construction industry’s carbon footprint and achieve cleaner, greener cities.
For more information contact Renyi, Suite 2404 Level 23, 520 Oxford Street, Bondi Junction NSW 2022, phone 02 9316 8882, email info@renyi.com.au, website www.renyi.com.au
The Pulse and Pavilion residential developments in Sydney’s Melrose Park North urban renewal project represent a milestone in the transformation of the area into a world-class smart community. Specialist contractor Premium Fire Services provided the design, supply and installation of the wet and dry fire services and passive fire services within the developments including sprinklers, hydrants and smoke detectors.
“We’ve worked with the main contractor Parkview before and it was great to be appointed for this project,” said Jimmy Zheng, Construction Manager. “The project went very smoothly for us. The project team put heavy and diligent effort to satisfy latest regulation under Fair Trading Class 2 Building Act and reflected high professional standards to implement the process.”
Premium Fire Services applied their extensive experience on residential projects to deliver their works. They designed the fire systems based on the project’s fire engineering strategy and completed the full installation and commissioning. To enable accelerated works completion, some commissioning was completed using special pumping system methodology in advance to facilitate the process and completion ahead of programme.
“As with all our projects, at Melrose Park we did everything we could to take care of the client,” Jimmy explained. “We always try to deliver a premium service, communicating and working with the project team to get occupancy certificates in place as smoothly and efficiently as possible.”
In addition to residential projects Premium Fire Services have satisfied customers in sectors such as offices, schools, aged care, medical centres and government buildings. They maintain the highest quality assurance standards along with one of the industry’s highest inspection pass rates. Their services span wet and dry system design and construction, passive fire protection, preparation of tactical fire plans, testing, maintenance and certification.
With years of experience providing innovative, cost-effective and high quality fire protection solutions to diverse customers, Premium Fire Services has you covered with the latest in testing and certification and an emphasis on ongoing preventative maintenance to protect what you value most.
For more information contact Premium Fire Services, Suite 67, 89 Jones Street, Ultimo NSW 2007, phone 02 8880 9930, email contact@premiumfire.com.au, website www.premiumfire.com.au
Sydney based cladding subcontractor Australian Cladding Specialists were appointed by main contractor Parkview Constructions to supply and install the cladding to the third stage of the Melrose Park residential development in Sydney, including the Pulse and Pavilion buildings. The cladding used on the development was primarily Colorbond by Lysaght.
“We have worked with Parkview on several jobs before so we know them well and know what they expect from us,” said Claus Maarschalk, Managing Director. “This was a challenging project with very tight timescales made even more difficult by inclement weather. However, we were able to increase our resources to meet the deadlines.”
“We always try to collaborate with the builder to understand their requirements and deliver a good result,” Claus said. “Whether it’s a big job or a small job we treat it the same. We always strive for reliability and on time completion.”
Australian Cladding Specialists are experienced with most commercial cladding systems including aluminium composite panels, terracotta and sandwich panels as well as Colorbond. They have a highly skilled
team of tradespeople with experience in commercial, industrial, residential and infrastructure projects in Sydney and interstate.
Australian Cladding Specialists offer a broad range of services including cladding installation, production and fabrication, and façade renewal. They have a well equipped and modern production facility with a range of specialist equipment covering many aspects of cladding manufacture.
Safety and professionalism is paramount at Australian Cladding Specialists and they always strive for zero incidents onsite. They are also proud members of the Master Builders Association reflecting their commitment to the highest standards of quality.
“Our focus is delivering a complete service that exceeds our clients’ expectations,” said Claus. “We are cost-effective, smart and we have a reputation of performing on even the most challenging projects to finish jobs on time and within budget.”
For more information contact Australian Cladding Specialists, 122 Lang Road, Moore Park NSW 2021, phone 1300 930 889, email claus@aucs.com.au, website www.aucs.com.au
Part of Brindabella Business Park, BB6 – 6 Brindabella Circuit consists of two 6-storey commercial office buildings, North and South and feature stunning curved façades.
“Everything is curved in this build,” said Project Manager for Construction Control, Boris Hahn. “That in itself was a challenge, but it’s also what makes this building so unique and impressive.”
Award-winning architects Bates Smart, were responsible for conceptualising this project, utilising their expertise in creating transformative designs to reflect the way people use and inhabit urban spaces and built environments. “Bates Smart is one of the best in the business and pleasing these guys is not easy – but this building has impressed them,” said Boris.
Each building has a central atrium space housing three glass lifts. The typical layout of each level is open plan office space with a core area housing wet area facilities, mechanical plant space and a service lift.
The north building differs from the south as it has a single level basement car park and end-of-trip facilities on the ground floor. At the northern end of the project is a Central Services Building housing several essential building services for the two office buildings.
Construction commenced in July 2020. “The Capital Airport Group (CAG) launched this project just as COVID-19 struck,” said Boris. “And it has complicated the build all the way along in terms of material and labor shortages.”
“Our focus has always been on careful consideration and planning on all projects, and the forming of close, strategic collaborations with clients, consultants and contractors,” said Boris.
“We have consistently proven that complexity is only a challenge to be overcome. Our team thrives on solving complex problems in construction. This project is the perfect example of our ability to achieve the improbable.”
The company’s reputation for dedicated and methodical services that are focused on each client’s specific needs has grown their list of clients to include Commonwealth, State and Territory Governments, Australia’s top ranked educational institutions, some of Australia’s largest retail centres, publicly listed corporations and privately owned companies.
“The long term relationships we have forged within the Canberra, Sydney and Brisbane business community and government sectors are testament to the excellence of our quality product, our people, client focus and attention to detail,” said Boris.
Construction Control is more than just a builder. Their service model is built on strong relationships and collaboration, an approach that defines the Construction Control difference. No matter where you are in the project development cycle, the company can match the service offering to your needs.
The builder was an early adopter of the Early Contractor Involvement (ECI) model of project delivery, supporting clients to work through key feasibility questions and adding value from the beginning of a project.
As a design manager, Construction Control believes outstanding projects are conceived via a collaborative, creative and disciplined design management process. This process establishes a culture of innovation, listening and teamwork. The company also specialises in Fit Out Management and Delivery, as well as refurbishment projects.
Construction Control remains 100% Australian owned and operated, employing construction professionals who are the best and brightest in the game. They deliver projects in the Australian Capital Territory, New South Wales, and Queensland.
For more information contact Construction Control, phone 02 6257 4775, website www.ccontrol.com.au
Eifer is a team of experimental makers, balancing form and function to build high end architectural features within commercial spaces. They were awarded the special finishes contract for 6 Brindabella Circuit in the Australian Capitol Territory.
“This project is very much a portfolio piece,” said Eifer Director, Jackson Roberts. “Every item is challenging to create in terms of its intricacies in the way it interfaces with the other finishes. But that’s also what makes the finished product stunning.”
Eifer created the complex work around the central atrium which involves curved glass, mirrored Rimex and 20mm thick solid aluminium reveals. There are many other curved finishes made of timber veneer and rolled solid aluminium pieces. Eifer also completed the structural café awnings.
The solid aluminium work features a custom die developed exclusively for this job. A team of 15 worked on this project for 10 months.
Based in Fyshwick, Australian Capitol Territory, Eifer are creative builders who do things that others can’t. Their work is bold in concept, powerful in approach, and forged through seamless collaboration. Eifer is where design gets built.
“The scale of the team and projects have increased but the enjoyment of putting our skills to the test has never changed,” said Jackson. “The quality of our team is our greatest asset as we attract and retain top performers. This results in high performance under pressure and meeting commercial deadlines when it matters. For me, the work
becomes impressive when there’s constraints to overcome.”
Eifer was established in 2015 and considers themselves three parts innovative construction and one part careful execution. Eifer is drawn to challenging concepts that come alive with nuance and tactility. Through commitment, experience and the relentless pursuit of new challenges, their projects aim to elevate the spaces and places within commercial environments.
Striking the fine balance between understanding and creative problem solving, every vision Eifer builds comes to life as something exceptionally inventive and entirely something you won’t find anywhere else. From concept and ideation to prototyping and refining, each project is a true exploration of possibility.
“We are creative builders who do things that others can’t. We use our hands to merge ambitious elements with singular design and make every process an improvement on the last,” said Jackson.
Every fabrication solution interweaves the kind of practical considerations and technical innovation that’s constructed to stand the test of time. Big picture thinking and small detail focus are the cornerstones of Eifer’s developmental research, guided by their first principle methodology and informed by their keen experimentation with materials.
“By exploring new concepts and effectively constructing them, we work meticulously to help you create landmark spaces with timeless appeal,” said Jackson.
Eifer is invested in every element of their projects and takes an integrated approach to their installation. Simplicity, continuity, and ease define their onsite (and offsite) process as their highly skilled network gives tangible shape to ideas and turns excellence into form.
The company has a number of high profile tenders in the pipeline. Recent projects include the rebuild of Mt Selwen Ski Resort in New South Wales which was destroyed in the 2019/2020 bushfires. Eifer is a working Civic Quarter 2 in Canberra, another project collaboration with Construction Control.
For more information contact Eifer, website eifer.com.au, eifer_projects
Phase 4 Electrical & Data were contracted to provide a wide range of electrical and data solutions for 6 Brindabella Circuit, Canberra. This included the overall electrical design and installation, Building Services Network, Distributed Antenna System, CCTV access and security system, solar services and the emergency generator backup system.
“It was certainly a challenge to coordinate all of the components and trades and integrate them into a working system,” said Phase 4 Director, Jeremy Fooks. “But that is also the highlight of this job. Once it’s finished and it all comes together as one, it will be really fantastic and I am pleased we are on track to meet all of the challenges for a successful outcome.”
The company is responsible for the coordination of multiple sub-contractors at work from the rooftop PV System to the emergency backup generator on the ground. Once you add in things like the security system, building data network and Distributed Antenna System it demonstrates just how comprehensive the build is.
“Phase 4 is systematic in their approach to all projects and works on clear timelines and project plans,” said Jeremy. “This ensures a smooth-running job for all involved.”
During this project a new standard for electrical fittings was introduced that required all fittings to be able to withstand earthquakes. Australia sits on the Indo-Australian plate which is being pushed towards the north-east, colliding with the Philippine and Pacific plates and leading to a severe build-up of stress. It is this stress that causes the earthquakes we feel all over the country. According to research by Geoscience Australia, there has been about one earthquake measuring 2.0 or greater every day in Australia for the past decade.
Phase 4 were trained in the correct installation of seismic fittings and applied this new knowledge and technology to the build, ensuring essential services can remain operational in the aftermath of an earthquake or seismic event.
Another feature of 6 Brindabella Circuit is the installation of EV charging stations. The ACT has Australia’s most generous financial incentives for the purchase and
registration of Electric Vehicles and the market is growing which means cheap and affordable EVs will be available on the Australian market in the years to come.
“EV charging stations are fast becoming a must-have product to accommodate drivers as they change over to Electric Vehicles,” said Jeremy. “EVs aren’t going anywhere, they’re going everywhere.”
“Other highlights for BB6 include the location of the 40ft long generator and the installation of the L3 linear feature lighting.”
The L3 concept is designed for the integration of LED indirect lighting in angular and sharp lines, breaking with traditions and conventions and focusing on the interaction between architecture and aesthetics.
Jeremy Fooks and fellow Phase 4 Director Tony Polak worked with each other for another employer for 10 years before they decided to go into business together. They started out with a ute and a van and over the next 20 years the company went from strength to strength. Based in Mitchell in the ACT, they currently have a staff of 25.
“Phase 4 always has a keen eye on the local builders and developers and we look forward to the next project we can get involved in,” said Jeremy.
The company is currently working on the Yarra Rossa Retirement Village and Section 96 Canberra Centre along with BB6.
For more information contact Phase 4 Electrical & Data, PO Box 414, Mitchell ACT 2911, phone 02 6262 3500, email electrical@phase4.com.au
Parliament Constructions possess a vast knowledge and experience in Canberra’s commercial building industry, making them the perfect choice for the supply and installation of the partitions, ceilings, doors, frames and door hardware. This has been demonstrated once again across both buildings at 6 Brindabella Circuit (BB6).
The unique layout of BB6 called for numerous curves throughout the building. This is not something new for Parliament who have undertaken many intricate and complex projects with curved walls and ceilings in the past. However, the project brief at BB6 included the design input and construction of curved structure which had not been attempted before.
“The biggest challenge in this project was the large, curved gyprock features at the top of the atrium,” said Director, Anthony Bailie. “This required custom designed and engineered framing, along with masterful sheeting and plastering works. A lot of hours were taken in slowly bending and curving the gyprock to create this eye-catching centrepiece.” Only the experience of Parliament constructions
and their hard-working employees allowed this architectural idea to become reality.
Another challenge to overcome for Parliament Constructions at BB6 was the use of a new perforated Gyprock product from Decor Systems. This required our employees to learn a few new techniques for installation. The time and diligence put into fully understanding the product allowed for a high-quality finish throughout.
Founded by award-winning builders, Anthony Bailie and Michael Wood in 2009, Parliament Constructions is located in Fyshwick ACT. They specialise in partitions, ceilings, fitouts of offices and retail outlets, glazed partitions, doors and door hardware, high security/zone requirements, demolition, lightweight façades and cladding. Their sister company, Performance Windows and Doors is also based in Fyshwick and offers high performance, exceptional quality custom products at the best possible price with outstanding after-sales service.
“Our approach is quality work with outstanding service,” “We achieve this with a hands-on management team that is actively involved in every aspect of planning and execution of all our projects” said Anthony. “The diverse skills of our highly expert and enthusiastic team enables us to offer an extensive scope of works in commercial environments.”
For more information contact Parliament Constructions, phone 02 6297 4480, website www.parliamentconstructions.com.au
UTJ Interiors is one of Australia’s premier manufacturers of custom joinery and detailed veneering, specialising in hotels, universities, schools and commercial facilities.
UTJ Interiors brief on 6 Brindabella Circuit was to provide joinery for the end-of-trip facilities and vanities and overhead mirrors for all the wet areas on every level. The contract included managing subcontractors specialising in lockers and toilet partitions. “Our Site Managers manage our subbies well and they quickly become a seamless part of our team. We make sure everything from WHS compliance to Quality is 100% on point” said Managing Director, Paul Van de Haar.
We have 70 years of experience working with the full range of products available to be specified by architects and designers. Pictured above, the vanity tops are a stone look Corian and lockers are Polytecs Natural Oak Ravine. “Corian is perfect for public bathrooms, scratches just buff right out and Polytecs timber look laminates are incredible these days, very true to natural timber and extremely durable. Both products are a perfect choice in this application”.
UTJ Interiors is a third generation, family-owned and run business based in Unanderra, Wollongong. Paul’s grandfather Johannes Van de Haar immigrated with his young family from Holland after World War II. Seeing an opportunity in Wollongong to establish his own business, Johannes bought land and worked as a carpenter
while he built his factory. In 1951, UTJ opened its doors and began building joinery for housing commission properties and windows for local schools.
In order to overcome the building supplies shortage (materials were rationed at the time) Johannes opened his own hardware store in the main street of Unanderra. This commitment to hard work and a focus on quality and customer relations has helped UTJ become one of Australia’s leading manufacturers of custom joinery and detailed veneering.
Johannes passed the company down to his son Hans, and from Hans to his son Paul.“We are the joinery manufacturer of choice for Australia's largest builders for a reason,” said Paul. “Our experience, and professionalism have cemented our place in the industry.”
UTJ Interiors current commercial projects in Sydney include; Sandstones Hotel, Polycentre, and the Reserve Bank in Martin Place.
For more information contact UTJ Interiors, 234 Berkeley Road, Unanderra NSW 2526, phone 02 4271 5522, email reception@ utjinteriors.com.au, website www.utjinteriors.com.au
Belconnen Concrete has been providing quality concrete pumping, placing and finishing services in the Canberra region for over 50 years. In their latest project at 6 Brindabella Circuit, Belconnen were contracted to complete the concrete pump, place and finish.
“We actually started on the Canberra Airport group site with Construction Control some 30 years ago,” said Belconnen Director, Andrew Spinelli. “It was terrific to continue our excellent working relationship on this job.”
Belconnen Concrete has the only hydrostatic water washout system in Canberra and utilised it on this project. This has resulted in considerable savings to the client and developer.
“A highlight of the project was the speed at which the concrete pours and consistency was achieved,” said Andrew. “Especially with the delays we all experienced with COVID lockdowns and considering we were working in and around an operational airport precinct.”
“At the same time we were working on BB6 we were also completing work on a similar sized project at 25 Catalina for Construction Control,” said Andrew. “Which means we were effectively working
on the equivalent of a 30 storey highrise, as well as a number of other projects in the ACT.”
As Canberra’s only operator of seven mobile concrete placing boom pumps, including a 20m, 28m, 34m, 36m, 39m detachable, 42m, 61m, City Pumps, BPL 3,500 HP trailer mounted Schwing mobile concrete pumps, and 39m Separate Placing Tower Booms (five off) and directly employed concrete finishers, Belconnen believe they can provide your company with the necessary skills and support to complete any project safely, efficiently and to the required quality.
For more information contact Belconnen Concrete, PO Box 1002, Fyshwick ACT 2609, phone 02 6280 2700, website www.belconnenconcrete.com.au
The Griffin is a stunning residential development for Parkes in the ACT which includes spacious one, two and three bedroom apartments and penthouses with open-plan living areas, private terraces, elegant kitchens, stylish bathrooms, large podium gardens, indoor pool and sauna, gym, wellness centre and concierge.
Inspired by the holistic design philosophy of Walter Burley Griffin, The Griffin is a residential development like no other. Engaging with its surrounding natural landscape and only minutes to the city, the development is a refreshing architectural delight, that truly envelops the natural surroundings of Canberra.
Amalgamated Property Group began the planning and conceptual phases of The Griffin over five years ago. The site was first acquired in November 2017 and Amalgamated Property Group listed the luxury residences on the market in late 2019, with more than 95% sold by the end 2021. By May 2022, well before the construction process was complete, it had completely sold out. Unlike other mainstream developments, The Griffin is unique in the fact it is the first residential development to be built inside the Parliamentary Triangle, meaning it is blessed with extremely unique location features that have never been seen before.
With 254 luxury apartments and penthouses across three buildings, each 8-levels, a mix of one, two or three bedrooms, up to 278m2 and over 50 plan types, The Griffin caters for all demographics. The site also encompasses an underpass to the park and the lake, creating three minute access to the water’s edge and a stunning pathway rejuvenation, the entire Canberra community can enjoy.
In addition, there are also six retail units on the ground floor, facing Constitution Avenue and the heritage-listed Pavilion building, which is being repurposed into a premium dining destination. At The Griffin, every unit feels like a penthouse as the standard inclusions are of the utmost quality, and include engineered timber flooring, ducted heating and cooling, meticulously considered colour schemes, 30mm stone bench tops, internally ducted range hoods and bespoke joinery features that give the apartment interiors a luxurious and sumptuous feel.
In addition, in keeping with the principles and values of Amalgamated Property Group, the floor plans are efficient for liveability and energy consumption, designed to minimise wasted space, yet maximise natural light, storage and usable spaces. Michael D’Elboux, Development Manager, has been involved on The Griffin since conception and is passionate about its success, for both home owners and the community as a whole.
“The Griffin is a new addition to the prestigious and much loved ‘Parliamentary Triangle’, so throughout the development, we’ve ensured the project will stand the test of time, regarding both the design and aesthetics of the building,” explained Michael.
“Every building enjoys views of something special, be it Lake Burley Griffin, Commonwealth Park, Mount Ainslie, the Brindabella’s, Black Mountain Tower or the large podium gardens. It’s also in a highly connected location, meaning commuting for work, education or social events, can be done so with ease.”
“With respect to the Pavilion and The Griffin, we needed to ensure a successful harmony between old and new, particularly given the significance of the Pavilion in regards to Canberra’s early history. The unique result is a brand-new premium development, in a 60-year old landscape setting,” explained Michael.
Operating akin to a family, Amalgamated Property Group has fostered a work environment that enables precision and agility, giving buyers both reassurance and confidence. With numerous other projects in the pipeline, such as the prestigious development of ANZAC Park East on ANZAC Parade, Amalgamated Property Group continue to deliver outstanding products to the property development industry, time and time again.
Boasting a team of honest, approachable perfectionists, who go above and beyond on every project they work on, as well as 40 years of industry experience by their founder, Graham Potts, Amalgamated Property Group take pride in being accountable at every step of the design and construction processes. Furthermore, their level of care and commitment to quality extends deep within their team and processes. As a result, they’ve implemented an internal structure and unique approach to the development cycle, leading to consistent, reliable results and a lowly-geared balance sheet.
For more information contact Amalgamated Property Group, Civic Quarter, Level 12, 68 Northbourne Avenue, Canberra City ACT 2601, 02 6162 8888, info@apg-act.com.au, www.amalgamatedpropertygroup.com.au
Below Pacific Stone supplied and installed the milestone kitchen bench tops, splash backs and all of the bathroom vanity tops.
With 70 employees and more than 20 years experience, Pacific Stone is a company that knows and understands the stone, tiling and waterproofing industry inside out.
Specialising in the supply of stone bench tops, Ceasarstone, Quantum Quartz, Essa Stone, Sile Stone, marble and sandstone throughout the Canberra region, Pacific Stone are at the forefront of smart and renewable manufacturing and are able to handle a variety of projects, ranging from small, domestic installations through to largescale, residential or commercial projects.
As a result of their renowned reputation and their team of highly experienced and astute stone masons and tilers, Pacific Stone also recently worked on The Griffin. Consisting of 254 units, shared between three buildings, over eight residential levels, the team of 10 were responsible for the supply and installation of milestone kitchen bench tops, splash backs and all of the bathroom vanity tops.
Throughout the extensive installation process, a range of new materials and colours were supplied and utilised by Pacific Stone. Using Cosentino Silestone, 30mm, and three unique colour combinations, including Calcutta Gold, Pearl Jasmine and Charcoal Soap, the team worked quickly and efficiently to ensure the installation of both the bench and vanity tops was completed in a time and cost-effective manner, and that the outcome was one of excellence and first class quality.
In addition, the penthouse apartment (made up of two traditional units) included a range of new stone products. Some of these were the Quantam Quartz Carrara Quartz kitchen, laundry and pantry, as well as Pantheon and Rosso Lavendo Marble used throughout the bathrooms. A Scheme Grande Max Capraia Marble porcelain was also used for the kitchen’s splash back, which once complete, created an outstanding and unique finished product.
The Pacific Stone team were also responsible for the installation of several stone features throughout the Lobby and the Omega Black Quartzite Leather finish, on the landing of the main entry stairwell in the foyer. Finally, eight columns, made from Chambered Grey Limestone, within the building’s lobby,
were additional stand-out features the team installed.
Understanding the importance of quality installation as part of the building or renovation process, Pacific Stone worked closely together with Chase Group throughout the project, to ensure there were minimal challenges or disruptions throughout and that the job was completed in their usual professional manner. In addition, their close relationship with stone and tile suppliers means that despite the extensiveness of The Griffin project, their top quality products were delivered in a timely manner, without delays or issues. Furthermore, their attention to detail across the work they completed resulted in outstanding workmanship and a formidable finished product.
Given the fact each project differs from the next and has its’ own unique sets of challenges, Pacific Stone advise the best possible way to undertake the job, ensuring a tailored, quality result that gives any project they complete an edge over their competitors.
Currently working on the installation of both kitchens and bathrooms for DKSN Tiling Package and the installation of the kitchen and bathroom tiles, on the Huntington Waterfront Residential Apartments in Newcastle, Pacific Stone continues to forge their path in the industry as one of the nation’s go-to suppliers for all kitchen bench top and bathroom vanity needs and products.
For more information contact Pacific Stone, 8 Spongolite Street, Beard ACT 2620, phone 02 6297 7304, email sales@pacificstone.com.au, website www.pacificstone.com.au
With more than 20 years of experience, Diverse Concreting is Canberra’s premiere provider of concrete pumping and concreting services. With their strong knowledge of concrete pumping, placing and finishing, as well as rectification, clean-up and project closure, their extensive services were recently used for The Griffin Parkes residential project in Canberra.
With an astute team of 20, Diverse Concreting was responsible for the installation and completion of the structural concrete pumping, placing and finishing all of the concrete, as well as a range of landscaping works for the project.
Diverse Concreting undertook larger than normal pour sizes, drawing on their expertise within the industry, the team were able to handle the load, with minimal patching and fixing required, maintaining compliance with health and safety and upholding their commitment to safe environmental practices.
Tony Sergi, General Manager of Diverse Concreting, said that their standards of work are always above and beyond other commercial Pump, Place and Finish companies, both in Canberra and interstate.
“We stand out from our competitors on every level, from management of our staff, through to how we conduct our daily operations, the service and maintenance of our gear and finally, to our post pour servicing and rectification,” Tony said. “We have processes in place for all aspects of pumping, placing and finishing concrete and our clients are never left with any issues that were associated with the project before commencing work.”
Diverse Concreting also have the ability to run multiple projects, regardless of associated project challenges, including geographical location and human resources availability, and their highly experienced team ensures that the best quality workmanship is delivered time and time again.
Currently working on a range of projects, such as the Canberra Hospital expansion project, (Multiplex) and Molonglo Falls and Del Ray (Chase), Diverse Concreting continue to bring their expert team and know-how to every job.
For more information contact Diverse Concreting, phone 02 6281 2002, email tony.sergi@diverseconcreting.com.au, website www.diverseconcreting.com.au
Given their comprehensive 28 years of experience and understanding of the engineering industry, ACT Geotechnical Engineers have earned a solid reputation within the Australian construction industry. Providing a range of engineering solutions that benefit residential, commercial and industrial developments, they were recently involved on The Griffin, Parkes, residential development.
Throughout the various stages of development, a small team was responsible for the geotechnical investigation of the site, prior to construction, as well as various inspections and certification of piles and footings of the building during the construction phase.
Jeremy Murray, Director and Senior Geotechnical Engineer, said the geotechnical investigation on The Griffin, Parkes, project comprised drilling deep cored boreholes across the site, which enabled them to develop a comprehensive geotechnical model.
“We were able to use the geotechnical model to provide accurate geotechnical parameters that would allow optimal design for structural aspects of the project, including footings, shoring walls, excavation costs, and dewatering. This allowed the builder to have a smooth
earthworks operation and save time and money on substructure design and excavation.
“ACT Geotech were also responsible for supervising and certifying substructure elements during construction and were able to provide quick, accurate, and practical recommendations to any issues that arose during the earthworks phase of the project,” Jeremy explained.
Given ACT Geotech’s vast experience of similar projects in Canberra, as well as an astute team of 13 geotechnical engineers and engineering geologists, they have the largest and most experienced geotechnical consultancy in the ACT and southern New South Wales, as well as having a Sydney office to service the Sydney metro area. This allows them to service their clients needs in a timely and professional manner, swiftly dealing with any geotechnical issues that arise, to ensure the smooth-running operation of any project. “Our role is to not just tick boxes, but to actually give advice that is practical, efficient, and costeffective for any project,” Jeremy said.
For more information contact ACT Geotechnical Engineers, phone 02 6285 1547, email admin@actgeoeng.com.au, website www.actgeoeng.com.au
Family owned and operated since 2008, JSC Concreting is a Canberra-based company, with a plethora of experience and ‘can-do’ attitude. Renowned throughout the ACT for their excellent service and quality assurance, JSC specialises in concrete pavements, including kerb and gutters. They also provide concrete slabs, driveways, paths, vehicle entries and cross overs, and their specialist equipment provide the logistical back-up every project deserves.
Recently involved on The Griffin Parkes project, the team from JSC provided all of the external concrete works, such as concrete pavements, in and around the building.
“Our job at The Griffin ran really smoothly for two reasons,” explained Josh Small, Company Director. “Firstly, we do this type of work on a daily basis and have a plethora of experience and secondly, we have a reliable team of staff that are always capable of the work, no matter how big or small the project size.”
In fact, due to the extensive growth of the company, JSC are now able to provide bulk haulage services, with their truck and dogs, as well as earth moving, with a number of bobcats and excavators, ranging from 1.5 to 14 tonne.
With their attention to detail and deliverance of quality services every time, JSC have worked on a range of iconic developments and ACT government projects, and are looking forward to their next challenge.
“It was an absolute pleasure to work alongside Chase Group and have the opportunity to build our ever-growing portfolio on such a prestigious residential development,” Josh said. “We’re looking forward to continuing our participation in building Canberra’s future.”
For more information contact JSC Concreting, Unit 5/35 Essington Street, Mitchell ACT 2911, phone 02 6174 1280, email accts.jsc@ outlook.com
Central West Waterproofing have over 23 years of extensive industry experience, high quality workmanship, premium products and outstanding customer service. Servicing the Central West of New South Wales, the Hunter region, the Central Coast and the ACT, their professional team are able to service all of your waterproofing needs, ranging from Commercial, Industrial and Civil
Given the fact they tailor their approach to specifically suit a particular project, using only the highest quality products and applications, they were recently involved on The Griffin, Parkes project.
Joseph Harlan, Estimator and Contract Administrator from Central West Waterproofing, said that their team were responsible for the supply and installation of external waterproofing to all areas, ranging from podium slabs, balconies and the roof. “This project was unique in that the three buildings share a single basement and as a result, the entire 3,000m2 podium slab had to be waterproofed to avoid leakage,” Joseph said.
“It also included all types of waterproofing applications, such as ‘spray applied’ to the podium, ‘liquid applied’ to other areas and ‘torch applied sheet membranes’ to the roof areas,” he said.
“It all ran smoothly though as Chase Group, not only had a great management system, but also went the extra mile and specifically requested items that increase the lifetime of the waterproofing product applied for the work we undertook,” he said.
Taking pride in the professional outcomes Central West Waterproofing deliver across the construction, building and architectural sectors, they have also worked on a range of renowned projects, such as ‘W2’ from Chase, DKSN Cape Apartments from BLOC, Pacific Cape Residence by Richard Crookes Construction and Oaks Crown Stage Two, from Milin Builders.
With their outstanding reputation and commitment to maintaining the highest quality of work, at a competitive price, Central West Waterproofing are the number one waterproofing solutions provider.
For more information contact Central West Waterproofing, 7/98 Sawmill Circiut, Hume ACT 2610, phone 02 6179 7009
non-compliance issues.
Formed in 1997, Fire Safety Science provides a comprehensive range of specialised activities, such as Fire Engineering and Building Surveying, to the building and property industry.
Using a performance based building code, Fire Safety Science are continually researching the application of this cutting-edge technology, across all projects they work on. As a result, they provide outstanding customer service and business development skills, initiating new building development opportunities and building on existing facilities.
Given their expertise and know-how within the industry, Fire Safety Science also carried out the fire engineering report, assessment and identification of non-compliance issues associated with The Griffin.
Brian Lucas, (M.App.Sc. Fire Safety Design) Director of Fire Safety Science, said within their extensive fire engineering report, they performed a range of assessments on the residential building.
“Some of these assessments included a report on the buildings fire control systems position, the requirement for smoke doors in residential corridors, an assessment of the basement levels egress distances and the distance between alternative exits in basement
levels,” Brian explained. “Throughout the thorough assessment process, we also identified a number of non-compliance issues that needed to be remedied.”
However, given Fire Safety Science’s fundamental understanding of the factors and physical processes that govern the growth and spread of fire, as well as the performance of active and passive fire systems, Brian was able to provide The Chase Group with innovative, cost-effective solutions to ensure fire safety requirements were met.
“There were a total of eight non-compliance issues identified in the Executive Summary, however, with the assistance from ACT Fire and Rescue, these were all resolved and the proposed methodologies I put forward were all approved,” Brian said. “As a result, our ‘can do’ attitude has resulted in the implementation of performance based design and a successful result overall.”
For more information contact Fire Safety Science, 32 Conyers Street, Hughes ACT 2605, phone 02 6162 0167, email firessci@fss.com.au
With an emphasis on exemplary product quality and outstanding customer service, SEM Windows are the leading experts in the provision of residential and commercial windows and doors.
SEM Windows’ solid management team, who have been together since the company first began, as well as their years of industry expertise, is the reason the company is continuing to grow to meet growing market demands and their ever-expanding clientele.
“We adhere to a 40% product and 60% service rule, so basically, whenever a client calls, we are always first onsite,” said Ben Chen, Operations Manager of SEM Windows. “We specialise in both residential and commercial windows and doors, across a broad range of budgets. Some of our products include timber revealed residential windows, subhead and subsill commercial windows, thermally broken systems, shopfronts and curtain walls.”
“We also design, manufacture and install aluminium windows and doors across a range of commercial and domestic projects,” Ben said.
Given their integrity and dependability, SEM Windows were responsible for the glazing of all windows and doors, including all decoration fins
and ground floor windows. Redesigning the standard system of typical fins, SEM Windows delivered an architecturally enhanced range for The Griffin at a low cost rate. Additionally, the team fulfilled their extensive responsibilities within the required timeframe, despite the challenges they faced throughout the scope of the project.
“Unfortunately, this project was smack-bang in the middle of COVID, where we faced country-wide lockdowns, shipping import increases and material shortages. Although we had to pay extra for delivery and materials, our positive attitude and commitment to the project meant that we were still able to deliver our services and products on time for CHASE,” Ben said.
“Just knowing that we continued to persevere through these hard times for CHASE was enough to see us through and reinforced our strongly held belief that the customer always comes first,” Ben concluded.
For more information contact SEM Windows, 67 Assembly Drive, Dandenong South VIC 3175, phone 03 9793 2888, email sales@semwindows.com.au, website www.semwindows.com.au
Since 1977, Morgans Group have been providing solution oriented outcomes to their range of clients, delivering meticulous results and quality assurance. Specialising in commercial flooring supply and installation, post construction cleaning, labour hire, carpet and general office cleaning.
Given their decades of experience in the provision of quality carpet and flooring installation, the Morgan’s Group were the ideal company to complete The Griffin. Understanding all flooring needs from the inside out, the Morgans Group were engaged to supply and install flooring to all units, corridors and gym for the project.
The astute team from Morgans Group were able to complete the job in a timely and efficient manner. If challenges arose with product or supply, the team were able to provide solutions quickly with a ‛can-do-attitude’, to ensure everything ran smoothly. Their strong, long-term relationships with their suppliers, allows Morgan’s Group to continually meet any client’s projects deadlines and demands.
Morgans Group also completed an initial post construction clean, involving industrial vacuum to all floor area surfaces, extensive dusting and wet dusting of all horizontal surfaces, shelving, cabinetry, fixtures
and fittings, scrub and mop all tired floors, and cleaning of all toilets, showers, and kitchens. Upon conclusion of work from all trades, Morgans Group completed a final ‘sparkle’ clean, so the property is ready to hand over to the new purchaser pre-settlement in perfect condition.
“We pride ourselves on the close relationships we have forged with all our clients and suppliers. The work we completed at The Griffin was just another example of why we stand out from the competitors and have a high retention rate of clients – we have the expertise, capacity and capability to deliver any project, regardless of the size,” said Damien Murphy, Managing Director of Morgan’s Group.
For more information contact Morgans Group, 18 Lyell Street, Fyshwick ACT 2609, phone 1300 362 911, email installs@ morgansgroup.com.au, website www.morgansgroup.com.au
With a wealth of knowledge in civil, infrastructure, structural, and traffic design, Indesco deliver quality design solutions to every project they manage. Integrating a range of industry knowledge and technical skills, the team at Indesco work closely with stakeholders, partners and contractors to overcome complex issues that often arise throughout the development stages, effectively managing risks and achieving outcomes that exceed client expectations.
With expertise across a range of fields, such as project and risk management, feasibility studies and project evaluation, Indesco believe that collaboration with the client is the key to quality engineering outcomes. Given their reliability and reputation across industries, Indesco also recently carried out structural engineering services for The Griffin.
Consisting of 254 residential units, along with commercial tenancies, The Griffin building is comprised of three, 8-storey towers, each with a common podium and three levels of basement.
From the initial stages of development, Indesco’s engagement involved driving a concept, with efficient post-tensioned slab spans, whilst maintaining vertical alignment and eliminating structural transfers.
As a result, an efficient and economical structure, with proven buildability, was created and experienced during construction.
Given their integrated knowledge across various aspects of construction and infrastructure, Indesco’s scope of works included a range of other services for Chase Group, such as structural feasibility studies, value engineering, lateral analysis and stability design. In addition, they carried out pre-cast design, pre-cast shop drawing documentation, foundation and shoring design. Understanding the importance of clear consultation and communication, Indesco were able to deliver their services in both a timely and effective manner that not only met the client brief, but also ensured the construction stages of the development ran smoothly.
Priding themselves on their core values of transparency and integrity, Indesco continue to strive for design excellence and a culture of innovation, delivering quality outcomes and professional services to every project they complete.
For more information contact Indesco, Level 5, 68 Northbourne Avenue, Canberra ACT 2601, phone 02 6285 1022, email indesco@ indesco.com.au, website www.indesco.com.au
Steve Pattrick Electrical (SPE) is one of ACTs most experienced electrical companies. With more than three decades of success and growth, Steve Pattrick Electrical is focussed on the innovative delivery of electrical, mechanical, civil, security and access control services throughout ACT and New South Wales.
With extensive experience across various trades, and inhouse engineering team, SPE is well positioned to undertake highly technical and secure projects, including the capacity to manage works from design to execution.
SPE were Recently engaged by Chase Construction on The Griffin Apartments.
Made up of a collection of residences inspired by the holistic design philosophy of Walter Burley Griffin, the extensive development consists of 254 units, shared between three buildings, over eight residential levels and overlooks the renowned Lake Burley Griffin.
As one of the only companies who specialise in Electrical and Mechanical services in developments such as The Griffin, Matt Parker,
from SPE, said that from late 2019, up until the recent handover, SPE were involved across all aspects of this iconic project.
“With a focus on high quality products, fixtures and fittings, we designed and constructed all of the electrical, access control and CCTV systems. In addition, we carried out all of the mechanical services for the project, including Basement and Pool HVAC systems,” Matthew said. “This was a significant project for SPE because of the iconic nature of the development.”
SPE were faced with a number of challenges throughout the project. “Given the scale and bespoke nature of the development, a high level of management and documentation was required to execute our works,” said Matthew.
“However the biggest challenge we faced was the COVID-19 pandemic, which significantly affected our productivity and material procurement.”
For more information contact SPE, 3/82 Townsville Street, Fyshwick ACT 2609, email info@speact.com.au, website www.speact.com.au
One Star Group is a leading commercial painting contractor based in Canberra, who have been delivering a full range of painting services to high density residential and commercial projects since 2013.
Given their renowned reputation for getting the job done, in both a time and cost effective manner, as well as their commitment to listening to their clients in order to provide the best quality outcomes, One Star Group was also recently involved on The Griffin, project in Canberra.
Responsible for painting 250 of the residential units, including the corridors, gallery and lobby of The Griffin, the team of 20 painters worked efficiently within the apartments, creating optimal and aesthetically pleasing outcomes.
In addition, a polished venetian plaster finish was used throughout the gallery and lobby, which created not only a stunning, smooth surface and look, but also an eco-friendly and highly durable result.
Steve Cho, Managing Director of One Star, said that although The Griffin project was an extensive undertaking, they managed to attain
the necessary resources and supplies, to ensure the project was delivered on time.
“COVID presented us with a few challenges, such as minor supply issues and labour shortages and unfortunately, the painting industry is completely reliant upon labour resources. However, we were able to work around all of these issues and managed to complete the project in a timely fashion,” Steve said.
“Although this was one of the largest projects we’ve worked on to date, it was our third time working alongside and coordinating with the Chase site team, so it was a highly enjoyable 10 months,” he said.
Currently also working on the 82W Apartment for BLOC and the Hume Data Centre for Hindmarsh, One Star Group are continuing to grow and expand their business, bringing their painting know-how and expertise to the forefront of commercial and residential projects throughout the Australian Capital Territory.
For more information contact One Star Group, PO Box 347, Mitchell ACT 2911, phone 02 6262 0408, email steve.cho@onestargroup.com.au, website www.onestargroup.com.au
Amara City Gardens is a residential development comprising 124 luxury apartments over 15 levels including a sauna, tai chi deck, fully equipped gym, dining lounge with wine cellar, open-air BBQ and sunset verandah, solar power to common areas, car-charging bay, and central solar hot water systems.
Iris Residential is a family-owned apartment developer with a long track record of more than 1,500 apartment homes across Western Australian and Victoria. The company was established in 2001 and behind the well-known name is a dedicated local team that is working hard to achieve the best quality and design outcomes with family-sized living, clever storage solutions and generous practical amenities.
The proud Western Australian company places focus on local projects for owneroccupiers and every site is chosen for its unique and life changing characteristics in highly-regarded suburbs. Connectivity and convenience for every owner and resident is key and there is no better example of this than Amara City Gardens.
The unrivalled location connects residents to well-lit walkways to Perth’s premium fashion, dining and entertainment destination that is Westfield Booragoon, which is situated in the heart of this well-established and highly sought after suburb.
“The location of this development is what truly sets it apart,” said Simon Trevisan, Managing Director at Iris Development.
“The building is connected to Westfield Booragoon, which means our residents will have shopping, dining, entertainment, medical and health services, fitness centres and public transport right on their doorstep.”
The $50 million luxury residential development stands tall on Davy Street and is the result of Iris Residential joining forces once again with BGC, one of Perth’s leading building companies. The 15-storey building and all that it encompasses, is the answer to the growing demand for apartment-style living and with 70% of apartments sold prior to completion, this further demonstrates Iris Residential’s flair for delivering liveable homes in premium locations.
The project features 124 one, two and threebedroom apartments, each one designed with
owner-occupiers in mind. They are spacious, inviting and the carefully considered interiors are without a doubt the major drawcard for buyers.
“Each apartment boasts 2.7m high ceilings, expansive windows which let natural light flood in, premium materials such as 100% wool carpet and engineered oak floorboards and designer fixtures including reconstituted stone benchtops, gas cooktops and quality Smeg appliances,” Simon Trevisan explained.
“Amara City Gardens also offers impressive inhouse amenities including a yoga deck, gym, sauna, wine cellar and a dining pavilion for residents.”
Generous sized balconies offer views of the surrounding gardens and some even provide sweeping views of the Perth skyline and the Swan River. Double-glazed windows, a boosted solar gas hot water system and photovoltaic cells which provide solar power to the common areas, have catapulted Amara City Gardens to an average Nationwide House Energy Rating of 7 Stars, proving that sustainable living and premium finishes really do go hand-in-hand.
BGC Constructions’ Stephen Barr was the Project Manager at Amara City Gardens and in his 11 years with the company, the relationship between the two companies continues to flourish.
“BGC and Iris Residential enjoy a professional and productive relationship and whilst COVID restrictions were our biggest challenge on this project, by working as a team, we were able to stick to the schedule and safety was the number one priority,” Stephen Barr said.
“Not only is Amara City Gardens the highest building in the area, it is the most distinguished and we are proud to have been part of this quality development.
Stephen managed more than 140 workers onsite over a period of around 18 months and
from a construction perspective, Amara City Gardens has met all the expectations and more. “All parties that have been involved with this project couldn’t be happier with the results, including the builders, developers and buyers,” Stephen said.
“The development was on schedule and incident free which is largely thanks to the great team of subcontractors and we are really looking forward to our next project with Iris Residential.”
Iris Residential is currently developing a new residential property, Shenton Quarter, which will feature 157 one, two and threebedroom apartments in one of Perth’s most sought-after suburbs, Shenton Park. The company is also set to announce the appointment of a builder to The Terraces, Claremont which has been designed to reach new heights in sustainable living and design innovation. Featuring 137 premium apartments, The Terraces achieves an outstanding 8.05 Star Average NatHERS rating and a ‘best practise’ 35% reduction in energy use and a 40% reduction in internal lighting energy consumption.
For more information contact Iris Residential, Level 14, 225 St Georges Terrace, Perth WA, phone 08 9424 9340, email mstokes@tribis. com.au, website www.amaracitygardens.com.au
For more information contact BGC, Level 6, 22 Mount Street, Perth WA 6000, phone 08 6220 4800, email corporate@bgc.com.au, website www.bgc.com.au
Steel Reinforcement Company Malaga (SRCM) is a major supplier for all steel reinforcing requirements in the construction industry and has a wellearned reputation for quality and service that is second-to-none spanning 15 years.
SRCM covers all aspects of steel reinforcement including scheduling, estimating, reinforcing bar and specialised bending, to mesh and fixing accessories. The company is also an approved distributor of Danley and Ancon Products and to further demonstrate its commitment to its client base, SRCM is now an on-seller for an exciting new product in Australia. GFRP Bar is a trailblazing solution to concrete reinforcement – a glass fibre reinforced polymer composite bar that is strong, lightweight, sustainable and doesn’t corrode.
A family run business that started in 2007, SRCM Owner/Director, Russell Williams has more than four decades of handson experience in the building industry, completing major formwork projects throughout Perth, before pivoting the business to steel reinforcement. Seven of the 13 employees are part of the family, joined by two staff members, who have been with SRCM since the very beginning.
“Our customers are the foundation of our business and we are always committed to providing the highest level of professionalism, service response and quality workmanship,” said Jane Tilley, Manager at SRCM. “Being a smaller operation, customer service is by far our best selling point and our focus has always been to rectify any issue that may arise in less than 24-48 hours where possible.”
At Amara City Gardens, SRCM was appointed by BGC Construction for the fabrication and supply of the reinforcing bars (reo), which are manufactured in the company’s state-of-the-art
Below SCRM delivered 1,290 tonnes of reo over a 12-month period for Amara City Gardens.
facility in Malaga before being transported out to site. The project saw the team deliver 1,290 tonnes of reo over a 12-month period, meeting the engineers’ requirements and the overall deadline for this build.
“There is a significant history between our company and BGC and over the years, we’ve worked on several projects together, forging a very good relationship,” Jane said.
“They are so easy to deal with and our two companies share the same work ethic and Project Manager, Stephen Barr’s approach to the coordination of this development made everyone’s life easier.”
Amara City Gardens is a 14-storey residential development and SRCM’s streamlined process from the initial scheduling and estimation stage through to completion, has ensured a great result for all stakeholders. It’s a company that continues to evolve by offering new products and always striving to improve on what is already a reputable operation.
“Our Sales Manager, Gunther Werner has been with us since 2016 and has brought years of experience and customer service to our team, visiting sites and offices to ensure we’re meeting all requirements,” Jane explained.
“All of our staff and contractors are highly skilled to undertake the supply of our product and we are proud to comply with ISO 9001 and Australian Steel Standards, which provide a framework for setting our goals and continual improvement.”
SRCM is providing quality service and reinforcement to projects all across Western Australia in the civil, residential and commercial sectors. The company is currently working on a residential development with BGC Construction called H20 which is set to re-shape the skyline on Hastings Street in Scarborough. SRCM has recently completed works on Hilton Garden Inn Busselton, RAAF Base Pearce and Coles Hilton with current works on Perth Hub, Melvista on Broadway and Clydesdale Apartments to name just a few.
For more information contact Steel Reinforcement Company Malaga, 186 Beringarra Avenue, Malaga WA 6090, phone 08 9248 1105, email enquiries@srcm.com.au, website www.srcm.com.au
WestOz Fire Protection is a trusted provider in the industry, specialising in wet fire systems including fire sprinklers, hydrants and hose reels, detection systems, extinguishers, fire pumps and tanks. The company, which was established in 2012, is proudly Western Australian owned and operated and boasts a team of fire protection professionals with extensive industry knowledge and experience.
WestOz has a reputation for delivering a high level of service to the construction industry in a timely and professional manner, where reliability is key. The company has a systematic approach to compliance and workmanship and their inhouse design team, together with experienced installers, is well known for implementing fire protection systems designed to meet their clients’ requirements.
“Our dedication to customer service and excellent in the construction industry has led to the successful delivery of many commercial projects,” said Tim Jakovich, Director at WestOz Fire Protection.
“At Amara City Gardens, we were engaged by BGC Construction to design, supply and install the wet fire system and we enjoyed a
great working relationship right throughout the project and wouldn’t hesitate to join forces with BGC again in the future.”
Tim managed a team of six employees onsite at Amara City Gardens over a period of around 17 months, where they designed, supplied and installed the fire sprinklers, fire hydrants, hose reels, fire extinguishers, fire pumps and tanks across the development which spans 14-levels and includes residential apartments as well as a sauna and gym, commercial tenancies and common areas.
WestOz Fire Protection’s portfolio boasts several large scale projects and residential developments and the company is currently working on the Amazon Logistics Warehouse, the Australia Post Distribution Centre and the Hello Fresh Warehouse in Western Australia to name a few. For more information contact WestOz Fire Protection, Unit 6, 11 Weedon Road, Forrestdale WA 6112, phone 0419 936 048, email tim@westozfire.com.au, website www.westozfire.com.au
Sez Painting service spent one year onsite at Amara City Gardens, where they took the appropriate steps to prepare all of the different surfaces and areas for painting, including the concrete floors throughout the building. The painting scope included 124 apartments and all internal areas, the exterior of the 14-storey building, as well as common areas and the stairs.
Sez Painting Service has worked to the specifications provided by the interior designers for Amara City Gardens, where three contemporary colour schemes feature throughout the apartments.
“Amara City Gardens is a beautifully designed project and is in such a good location,” Director, Sez James Greenhill said. “I enjoyed being part of this development because BGC is a great company to work with and their managers and supervisors are very experienced, which made the process very easy for us. All of the contractors were able to safely do their jobs at the same time and to schedule.”
Since 2012, Sez Painting Service has been transforming residential apartments, warehouses, aged care facilities and schools around Perth, with a professional team of painters and customised solutions for every client.
Sez has extensive experience in the industry and leads a team of professional painters which has gained a reputation for high quality workmanship in the construction industry using only premium quality products.
Over the last decade, Sez has continued to increase the capacity of his company, quoting projects of all shapes and sizes and streamlining his processes to achieve the very best outcome for his clients, the most recent transformation occurring at Amara City Gardens.
Sez’s brushwork can be found all around Perth’s centre at various large scale projects and residential developments and looks forward to continuing the partnership on BGC’s projects in the future.
For more information contact Sez Painting Service, P.O Box 208, Morley WA 6062, phone 0417 360 083 email sezpaintingservice@ hotmail.com
AIR CONDITIONING, (HVAC, REFRIGERATION & MECHANICAL SERVICES)
Air Smart
Page 64 | 07 5563 8530
Chill-Rite Refrigeration & Air Conditioning
Page 151 | 02 6885 2254
Eastwood Air conditioning Page 139 | 02 9674 9944
Mitsubushi Heavy Industries Air- Conditioning Australia, Pty Ltd.
Page 24, 28| 1300 130 007
AERIAL PHOTOGRAPHY
Skyview Aerial Photography
Page 8 | 0431 931 910
AGE CARE PROVIDERS
GemLife
Page 56| 1800 317 393
ARCHITECTS
Nordon Jago Architects
Page 157 | 02 9318 8416
ARCHITECTURAL FINISHES
Eifer
Page 170 | eifer.com.au
ASPHALT
Centre State Asphalting Page 82 | 03 5470 5028
AUDIO/VISUAL DISPLAYS
The Ci Group
Page 43 | 1300 242 742
BALUSTRADES AND HANDRAILS
K&F Fabrications
Page 67 | 07 5479 4064
Moddex Page 93 | 1800 663 339
BRICK RESTORATION
Mozbiz
Page 55 | 0418 882 126
BRIDGE CONSTRUCTION
VSL Australia
Page 87 | 02 9484 5944
Building Experts Australia
Page 38 | 0475 454 350
BUILDING INFORMATION
MODELLING (BIM) & DIGITAL ENGINEERING
CDE Structures
Page 147 | 02 6362 5066
BUILDING MANAGEMENT SYSTEMS
(INTEGRATED BUILDING PLATFORM (IBP) & INTEGRATED COMMUNICATIONS NETWORK (ICN))
VAE Group Page 44 | 1300 829 829
CEILINGS (ACOUSTIC)
Tesla Constructions
Page 106 | 0419 301 735
CEILINGS & WALLS
Ceiling and Wall Contractors
Page 72 | 08 8292 6600
CLADDING
Australian Cladding Specialists Page 167 | 1300 930 889
CONCRETE, CONCRETE SERVICES & CONCRETE PRODUCTS
Belconnen Concrete Page 177 | 02 6280 2700
Ivers Civil Contractors Page 91 | 0415 250 852
Diverse Concreting Page 182 | 02 6281 2002
JSC Concreting Page 184 | 02 6174 1280
CONSTRUCTION COMPANIES & ALLIANCES
BGC
Page 192 | 08 6220 4800
Construction Control Page 168 | 02 6257 4775
Deicorp
Page 154 | 02 8665 4100
Hansen Yuncken (VIC)
Page 100 | 03 9831 6500
Hansen Yuncken (QLD)
Page 46 | 07 3872 4000
Hickory
Page 116 | 03 9429 7411
Hutchinson Builders Page 110 | 07 4038 9000
Kane Constructions Page 96 | 03 8420 1200
LendLease
Page 20 | lendlease.com/au McConnell Dowell Page 74 | 03 9816 2400 Mirvac Page 32 | 07 3859 5888
North Construction & Building Page 142 | 1300 667 840 Parkview Page 160 | 02 9506 1500
CONSTRUCTION SOFTWARE / DOCUMENT/PERSONNEL MANAGEMENT
CoreLogic Page 2 | 1300 734 318
Viewpoint Construction Software Back cover | www.viewpoint.com
InEight Page 90 | 03 9291 0800
CONSTRUCTION SERVICES
Parliament Constructions Page 174 | 02 6297 4480
CONSULTANTS (PROPERTY MANAGEMENT AND QUANTITY SURVEYING) Rider Levett Bucknall Page 134 | www.rlb.com
CRANES/HOISTS & RIGGING (ALL CRANE PRODUCTS & SERVICES) Mulherin Rigging & Cranes Australia
Page 45| 07 3807 0222
DEMOLITION
Chalouhi Page 163 | 02 9790 3799 Mann Group Page 118 | www.manngroup.com.au
DEVELOPERS
Amalgamated Property Group Page 178 | 02 6162 8888
Cbus Property Page 68 | 1300 319 890 GWH Page 124 | 02 4966 3766
Iris Residential Page 192 | 08 9424 9340 MostynCopper Page 132| 02 9241 1699
DRINKING FOUNTAIN (BUBBLERS) Civiq Page 144 | 1300 600 300
EARTH MOVING (EQUIPMENT HIRE) Walker Grader Hire Page 86 | 0418 210 543
EARTHWORKS/CIVIL CONTRACTING
Chief Group Page 76| 1800 4CHIEF (1800 424 433)
ELECTRICAL DESIGN AND FITOUT SPE Page 190 | www.speact.com.au White Light Electrical Page 60 | 07 5493 2835
ELECTRICAL SERVICES JLE Electrical Page 150 | 02 6884 5973 Phase 4 Electrical & Data Page 172 | 02 6262 3500
ELECTRICAL INFRASTRUCTURE Engenuity Solutions Page 61 | 07 5559 2892 Power Distribution Australia Page 162 | 02 8880 3514
ENGINEERS (CONSULTING) WGA Page 70| 08 8223 7433 BG&E Page 126 | 08 6364 3300
ENGINEERS (GEOTECHNICAL) ACT Geotechnical Engineers Page 183 | 02 6285 1547 CF Group Page 128 | phone 02 9316 4012 Douglas Partners Page 135 | www.douglaspartners.com.au
ENGINEERS (METAL)
Tenze Engineering
Page 156 | 02 9758 2677
ENGINEERING CONSULTING
Indesco
Page 189 | 02 6285 1022
ENVIRONMENTAL ENGINEERING
Renyi Page 164 | 02 9316 8882
FAÇADES
Micos Group Page 39 | 02 8058 3000
FENCING
Australasian Fencing Page 84 | 0418 176 178
FIRE SAFETY (ALL FIRE PRODUCTS & SERVICES)
Fire Safety Science Page 186 | 02 6162 0167
Premium Fire Services Page 165 | 02 8880 9930
WestOz Fire Protection Page 196 | 0419 936 048
FLOORING
All Floors Commercial Page 129 | 0478 680 646
Morgans Group Page 188 | 1300 362 911
PLAE Page 136 | www.plae.global
FORMWORK
Permadec Page 89 | 02 9052 4975
Zahra Formwork Page 148 | www.zahraform.com.au
FORMWORK & SCAFFOLDING
Safeguard Scaffold Page 54 | 1300 971 603
GLASS & GLAZING
Fitout Glass and Aluminium Page 48 | 07 3393 9033
SEM Windows Page 187 | 03 9793 2888
GLASS FACADES
Heritage Glass Products Page 107 | 03 9251 2888
Winfix Façades Page 123 | www.winfix.com.au
HVAC
Ellis Air Conditioning Page 36 | 07 3213 9700
Fredon QLD Page 34 | 07 3340 7300
SAYFA Page 26| 1300 301 755
HYDRAULIC SERVICES
OSKA Consulting Group Page 58| 07 5557 0509
INDUSTRIAL SUPPLIES
Winc Page 4 | winc.com.au/safety
JOINERY & FITOUTS
Euroform
Page 130 | 02 4964 8333
IJF Australia Page 121 | 08 8349 7400
UTJ Interiors Page 175 | 02 4271 5522
LOUVRES & SCREENS Boswen Page 104 | 1300 849 800
MODULAR BATHROOMS (INSTALLATION)
SYNC Page 99,159 | 03 8329 4111
PAINTERS
One Star Group Page 191 | 02 6262 0408
Sez Painting Service Page 197 | 0417 360 083
PHOTOGRAPHY (TIMELAPSE)
Capture Point Media Page 98 | 1300 853 514
PIPES (RECYCLED)
Circle P Page 94 | 03 5480 7060
PLASTER & INTERNAL CLADDING
Arrow Interior Linings Page 63 | 0430 328 382
Broad Windows & Façades Page 149 | 0452 211 064
PLASTERING SERVICES
Kelvin Way Page 102 | 0418 334 564 Lusso Venetian Finishes Page 120 | 0477 773 264
POOLS
3D Splash Page 131 | 02 4006 5998
ROOFING
Cre8tive Roofing Services Page 141 | 02 9790 6177
SCORING SYSTEMS
Computer Score Page 62 | 07 5524 4786
SCREENS (CORTEN WEATHERED STEEL)
CM+ Page 80 | 02 8244 8888 Tract Page 80 | 03 9429 6133
SECURITY Fastsec Security Page 95| 0452 525 117
SOLAR ENERGY Beyond Solar Page 122 | 02 8074 0759
SPORTS INSTITUTIONS NSW Cricket Centre Page 132 | 02 8302 6000
STAGING AND RIGGING HME Services Page 50| 1300 873 463
STAIRCASE MANAFACTURER
Arden Architectural Staircases Page 41, 52 | 07 3267 6100
STEEL REINFORCING
Steel Reinforcement Company
Malaga
Page 194 | 08 9248 1105
STEEL (STRUCTURAL/ FABRICATION)
Smyth Structural Steel Page 145 | 02 6885 3366
STONE AND TILE
Australasia Stone Group Page 65 | 07 5445 5183
MTI Stone Page 112 | 02 9620 8330
Pacific Stone Page 180 | 02 6297 7304
Tile City Page 66 | 07 3856 4415
Tilecorp Page 42 | 07 3279 9009
STONE MASONRY Feature Stone Page 115 | 02 9757 3121
SURVEYORS
Flatout Surveying Page 85| 03 9068 6043
SWEEPERS/SWEEPER HIRE Sweeping the Murray Page 92 | 0428 524 127
TRAFFIC CONTROL/ MANAGEMENT
Vari Group Page 138 | 1300 008 274
WATERPROOFING & WATERPROOFING SERVICES Central West Waterproofing Page 185 | 02 6179 7009
WINDOWS AND DOORS (ALUMINIUM)
Darley Aluminium Page 29 | www.darleyaluminium.com.au
WORKSTATIONS
Schiavello
Page 53 | 07 3368 3388 Zenith Page 40 | 07 3170 0000
All material in this publication is copyrighted to the publisher and/or its advertisers and contributors. No material or portion of this publication may be reproduced in whole or part without the express written permission of the publisher.
The Australian National Construction Major Project Review and the publisher Trade Media Group Pty Ltd reserve the right to alter or omit any advertisement, editorial, or advertorial. Advertisers and/or their representatives indemnify the Australian National Construction Major Project Review and the publisher in relation to defamation, slander, breach of copyright, infringements of trademarks of name of publication titles, unfair competitor or trade practices, royalties or violation of rights and privacy and warrant that their material complies with all the relevant laws and regulations and that its publication will not give rise to any rights against or liabilities against the Australian National Construction Major Project Review, its publisher, its servants or agents. The Australian National Construction Major Project Review and the publisher are not liable for inaccuracy in any advertisement or editorial and do not accept responsibility for any claims made by advertisers. Any material supplied to the Australian National Construction Major Project Review or the publisher are at the contributors risk. No responsibility will be taken by the Australian National Construction Major Project Review, its publisher, its servants or agents. Opinions published in The Australian National Construction Major Project Review are not necessarily those of the publisher or staff of The Australian National Construction Major Project Review.
The Australian National Construction Major Project Review is not related to any other publication.