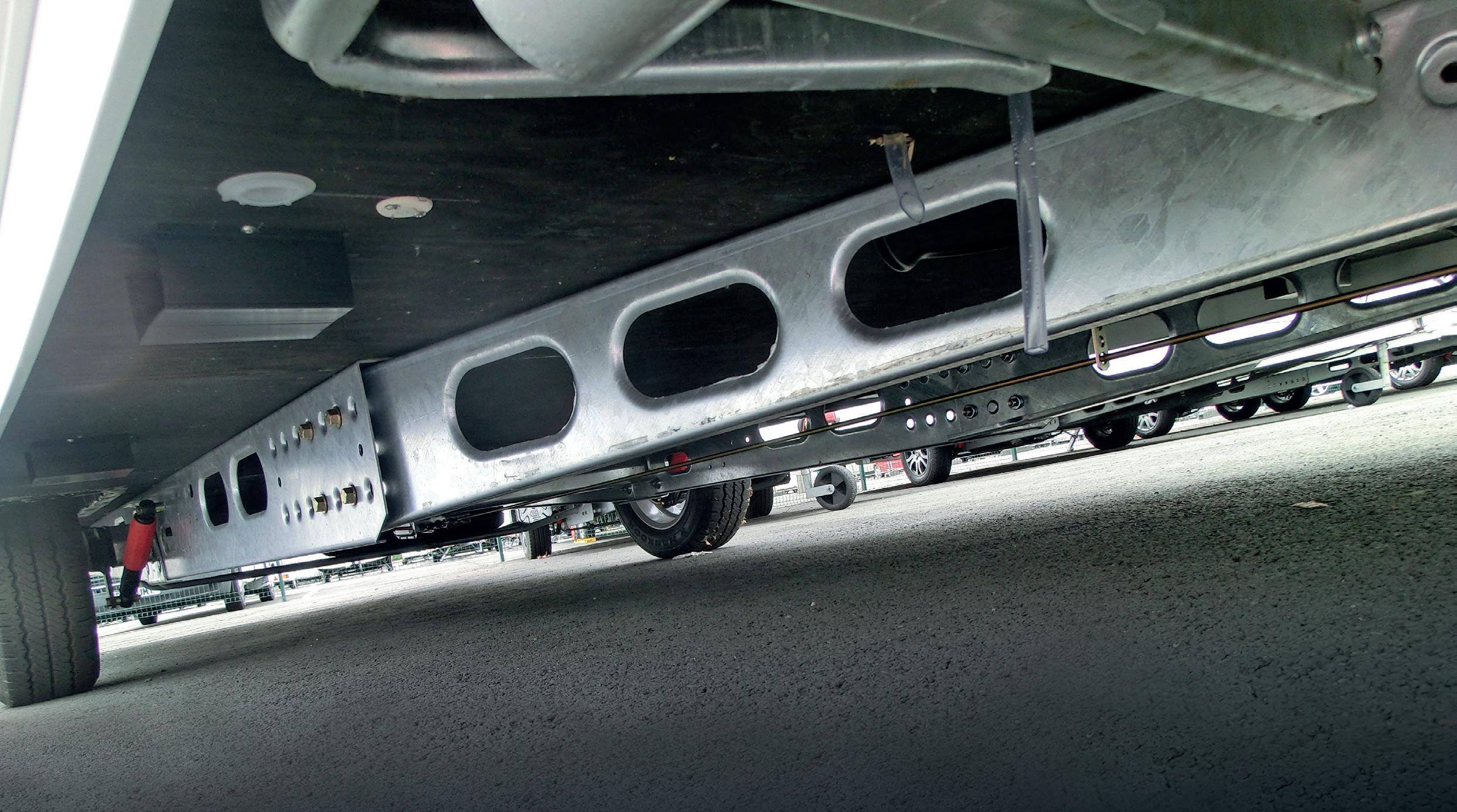
11 minute read
Focus: Invenzioni di successo
Chassis per caravan e sistemi di ausilio alla marcia
In questo articolo sulle invenzioni che hanno cambiato il nostro mondo, esaminiamo i giunti a sfera, le barre di torsione in gomma, il telaio alleggerito e i sistemi di frenata a inerzia. Nella prossima puntata esamineremo altre quattro invenzioni relative allo chassis
Testo di Terry Owen
Itelai delle caravan e i loro organi di movimento hanno fatto segnare un’evoluzione sorprendente sin dai primi tempi del 20° secolo. Il risultato è stato una completa trasformazione nel modo in cui produciamo e utilizziamo le nostre caravan da turismo, soprattutto in Europa. È interessante notare che la maggior parte di queste innovazioni si registra negli ultimi 40 anni circa. Prima di allora la produzione di una caravan da turismo sarebbe iniziata con la costruzione di un telaio in acciaio, probabilmente saldato, e proseguita con sospensioni a balestra o molle elicoidali. Gli ammortizzatori non sarebbero presenti, così come qualsiasi mezzo di controllo della stabilità. I freni, se montati, sarebbero probabilmente elettromeccanici e soggetti ad ogni genere di problema. Cominciamo la nostra analisi da un dispositivo le cui origini risalgono a oltre 100 anni fa.
Il giunto a sfera
Praticamente tutte le caravan e i rimorchi da turismo oggi in produzione utilizzano il giunto a sfera come mezzo di collegamento al veicolo di traino. Un tale dispositivo di accoppiamento apparve per la prima volta in un brevetto statunitense (n. 1.147.844) nel luglio del 1915. I signori Milton e Alfred Brice descrissero quello che chiamarono il loro “accoppiamento dell’asta d’attacco” come un “accoppiatore estremamente semplice e altamente efficiente, particolarmente

Un giunto AL-KO con stabilizzatore adatto al collegamento dell’asta d’attacco di un carrello a rimorchio con la parte posteriore di un’automobile.” Come si può vedere, è un sistema straordinariamente simile ai giunti sferici che usiamo oggi. Naturalmente, nei 100 anni circa che sono passati da allora, sono stati apportati miglioramenti. Il primo è stato un meccanismo di bloccaggio, introdotto dai signori Brice un paio di anni dopo, seguito da una varietà di dimensioni del sistema per soddisfare un’ampia gamma di esi-
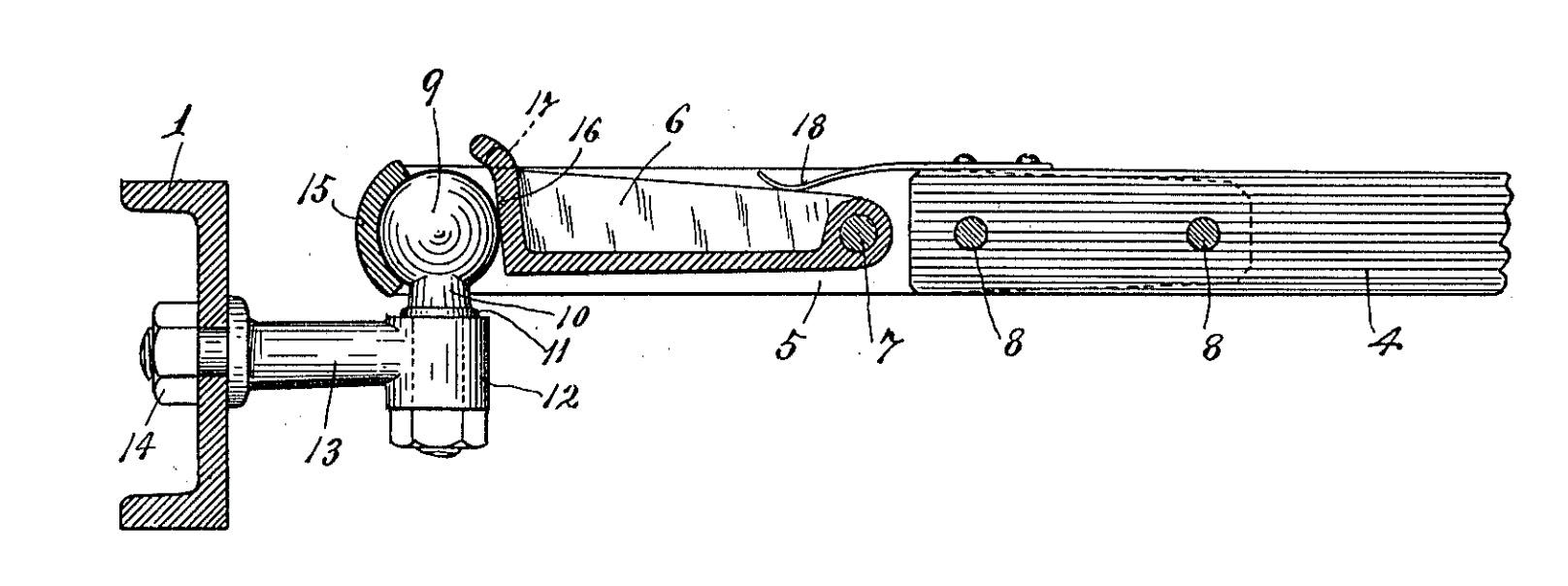
Brevetto americano del 1915
genze di traino. Nel 1934 Franz Knobel, un membro della famiglia fondatrice di Westfalia Automotive, ottenne un brevetto tedesco per un dispositivo simile. Un aggiornamento è stato concesso a Westfalia nel 1985 dall’ufficio brevetti europeo (EP0176825A1) e descrive l’alloggiamento dell’accoppiamento come “parte di una sfera cava... agganciabile con una testa a sfera fissata a un veicolo trainante”. La cavità della sfera può essere bloccata nella sua posizione di innesto rispetto allo spazio cavo della scatola della frizione.» È giusto dire che molti brevetti per dispositivi simili sono stati depositati negli anni, ma il principio del giunto a sfera è rimasto lo stesso. Oggi le dimensioni degli accoppiamenti variano in base ai paesi. Negli Stati Uniti, la misura standard del giunto è di 2” (50,8 mm), mentre in Europa e in Australia la norma è l’accoppiamento standard ISO da 50 mm. Tuttavia, alcuni paesi come la Nuova Zelanda utilizzano 1-7/8” (47,6 mm) come standard per i loro rimorchi. Prima dell’accoppiamento a sfera, quello più comune era il semplice tipo a “perno e occhiello” ancora in uso oggi. È semplice ed efficace ma non fornisce la connessione solida e priva di gioco di un giunto a sfera.
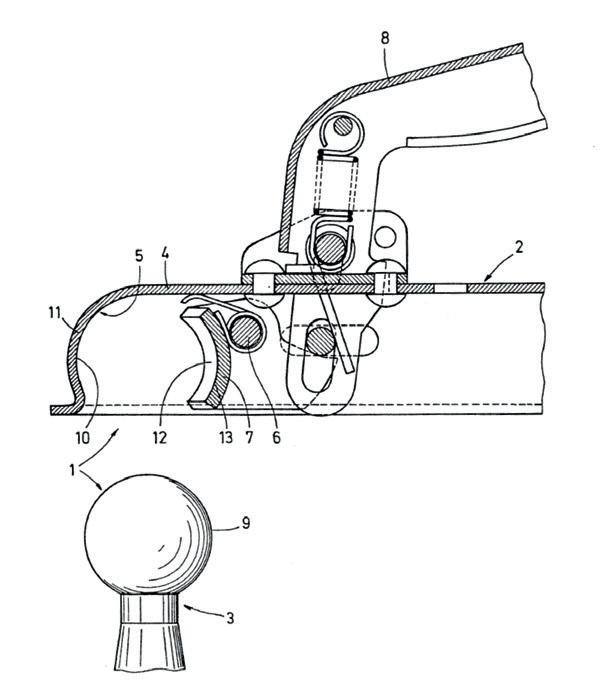
Sopra: il brevetto tedesco del 1934
A destra: giunto a sfera B&B del 1976 Sopra: un moderno giunto a sfera di AL-KO


A destra: un vecchio sistema a perno e occhiello
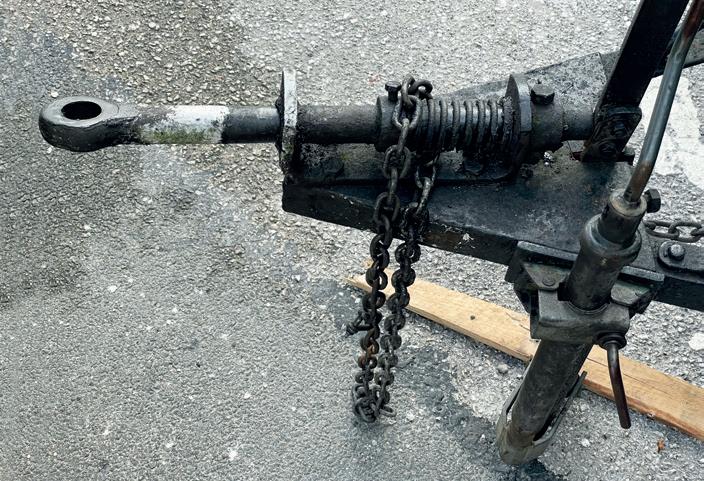
Barra di torsione in gomma
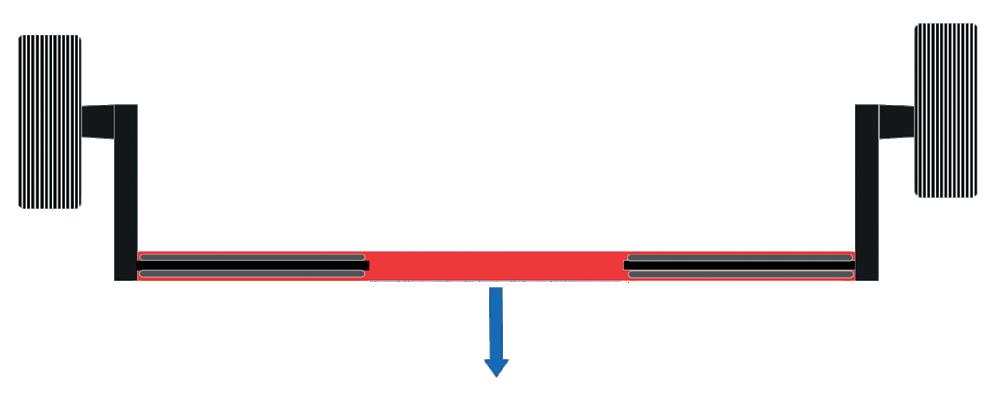
Le barre di torsione in gomma contengono inserti elastici in gomma all’interno dell’assale quadrato o esagonale. L’estremità esterna dell’assale comprende un braccio oscillante e un supporto che regge il tamburo del freno e la ruota. Quando le ruote si muovono su e giù, la barra di torsione ruota in senso contrario agli inserti elastici in gomma. Ciò fornisce resistenza al movimento, come potrebbe fare una molla. La disposizione permette alle ruote di muoversi indipendentemente l’una dall’altra, assorbendo gli urti e offrendo una guida migliore rispetto a un assale intero (dove le ruote sono collegate da un unico asse). La gomma fornisce anche un certo grado di assorbimento delle asperità, quindi non sempre sono necessari ammortizzatori opzionali. Non è noto (almeno all’autore) quando sia stata inventata la barra di torsione in gomma, ma il dispositivo ha rivoluzionato il mondo dei rimorchi. Uno dei primi utilizzatori fu Airstream che, nel 1961, passò dalle sospensioni a balestra a un assale che incorporava la tecnologia di torsione della gomma. L’assale era noto come Dura Torque, prodotto da un’azienda chiamata Henschen Axle, ora parte di GKN. Nel 1967, AL-KO sviluppò il proprio assale con ammortizzazione in gomma, basato su un unico tubo asse esagonale anziché sul tubo quadrato che era diventato comune, che ha segnato l’inizio della produzione di assali ALKO, con una produzione, nel primo anno, di soli 520 assali. Tuttavia, nel 1973 il totale di assali prodotti è salito a 100.000 e nel 2015, con impianti di produzione in tutto il mondo,
Tubi quadrati concentrici e quattro inserti in gomma, come quelli usati da Dexter Axle, BPW e molti altri
L’esclusiva sospensione a tubo esagonale di AL-KO
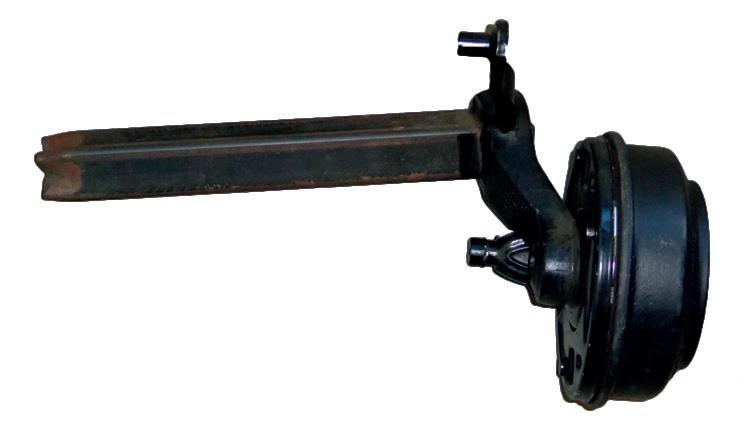
Un braccio radiale BPW con barra di torsione e tamburo del freno, pronto per l’inserimento nell’assale Barra di torsione in gomma
Direzione di marcia
A destra: spaccato di un tubo dell’assale BPW
Sotto: un tubo dell’assale ALKO in attesa di inserimento del tubo centrale con braccio radiale e tamburo freno
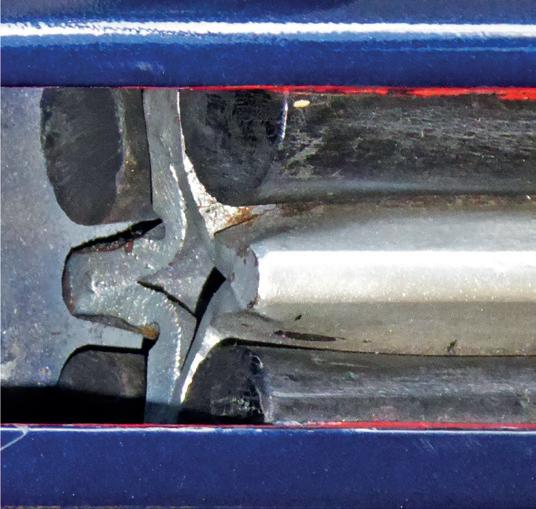
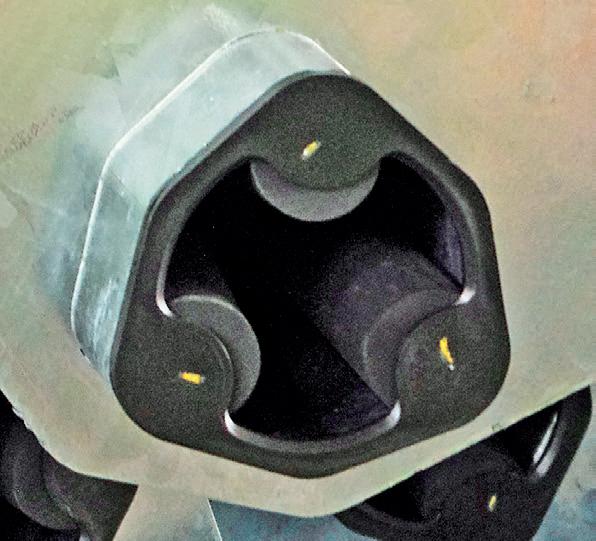
AL-KO aveva raggiunto 25 milioni di assali prodotti. Nel 1984 la Dexter produsse la propria versione, con il marchio “Torflex”. Utilizzava un tubo quadrato e si è rivelato uno dei prodotti di maggior successo mai progettati e lanciati da Dexter. Airstream, infatti, è passata a Torflex verso la fine del 2005. Per i produttori di caravan, i vantaggi delle barre di torsione in gomma, rispetto agli assali e alle sospensioni convenzionali, sono considerevoli: peso leggero, basso costo, assorbimento delle asperità integrato, funzionamento silenzioso e lunga durata. Normalmente la gomma perde elasticità, ma questo processo può richiedere fino a 25 anni di tempo.

Assali in produzione presso lo stabilimento AL-KO di Kötz, in Germania
Innovazioni nel telaio della caravan
Nel 1957 una pubblicità per una caravan Paladin Commodore nel Regno Unito vantava un “telaio in acciaio saldato rinforzato a croce per una maggiore resistenza”. Il risultato fu indubbiamente robusto, ma quei poveri progettisti di caravan dovettero affrontare una notevole penalizzazione dal punto di vista del peso.
A quel tempo i pavimenti erano fatti di fogli di compensato o talvolta anche di assi a incastro. Naturalmente, questo tipo di pavimentazione necessitava di un buon supporto. Il primo significativo passo avanti è stato compiuto negli anni ‘70 con lo sviluppo di pavimenti incollati realizzati con una struttura a sandwich, che si sono dimostrati più forti e hanno permesso di ridurre le guide di supporto del telaio. All’inizio degli anni ‘80 i pavimenti venivano incollati utilizzando un sandwich di compensato con schiuma ad alta densità (Styrofoam) all’interno e listelli di rinforzo in legno attorno al bordo e da un lato all’altro. Il risultato è un pavimento robusto e relativamente rigido con uno spessore standard di 44 mm. Questa soluzione richiedeva un intervento minore in termini di supporto del telaio, fornendo anche un buon isolamento termico. Tutto questo ha consentito di ridurre il telaio a due longheroni principali con timone, più una o due traverse. Il telaio e il pavimento sono diventati effettivamente un’unità integrale e ciascuno ha guadagnato forza dall’altro. Con il progredire degli anni ‘80, l’alluminio venne spesso utilizzato al posto dell’acciaio per risparmiare peso. Tuttavia, il problema con l’alluminio è che non è robusto come l’acciaio, quindi ne serve di più, perdendo un po’ di vantaggio riguardo al peso. Tuttavia, il peso restava minore e poi l’alluminio resiste alla corrosione, quindi non era necessaria alcuna verniciatura o zincatura, a compensare in qualche modo anche il costo aggiuntivo dell’alluminio che, all’epoca, costava circa il doppio. Oltre al costo, un altro svantaggio dell’alluminio è la corrosione galvanica che può verificarsi quando le parti in acciaio, come la testa dell’attacco e gli assi, sono imbullonate ad esso. Sebbene questi non fossero problemi cruciali, fu presto evidente che l’alluminio non era la soluzione migliore. Perciò all’inizio degli anni ‘90 si ebbe l’introduzione di elementi leggeri in acciaio zincato da parte di AL-KO e BPW: robusto, leggero e resistente alla corrosione, questo sistema ha presto sostituito l’alluminio per i longheroni del telaio. Un vantaggio dell’acciaio è che si presta ad essere imbullonato: quindi, utilizzando una serie di fori, la lunghezza complessiva del
1957 Paladin Commodore Questa Swift del 1987 era equipaggiata con un telaio in alluminio del produttore specializzato Syspal
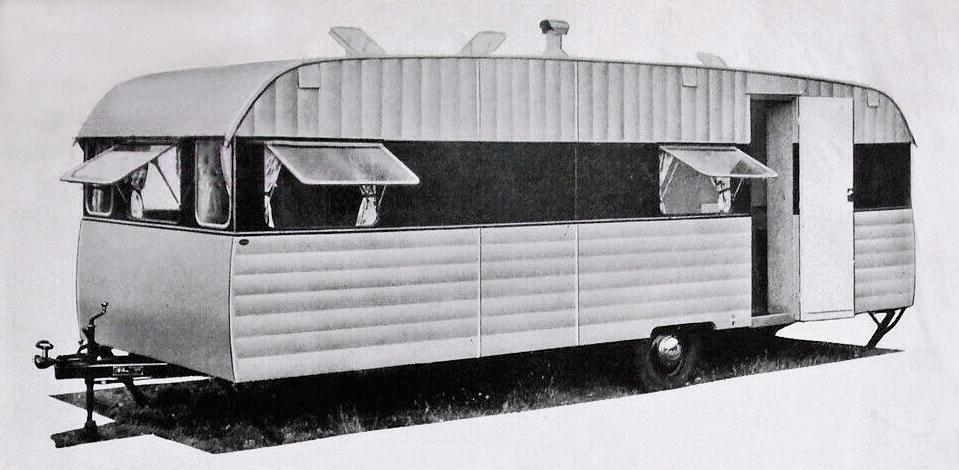
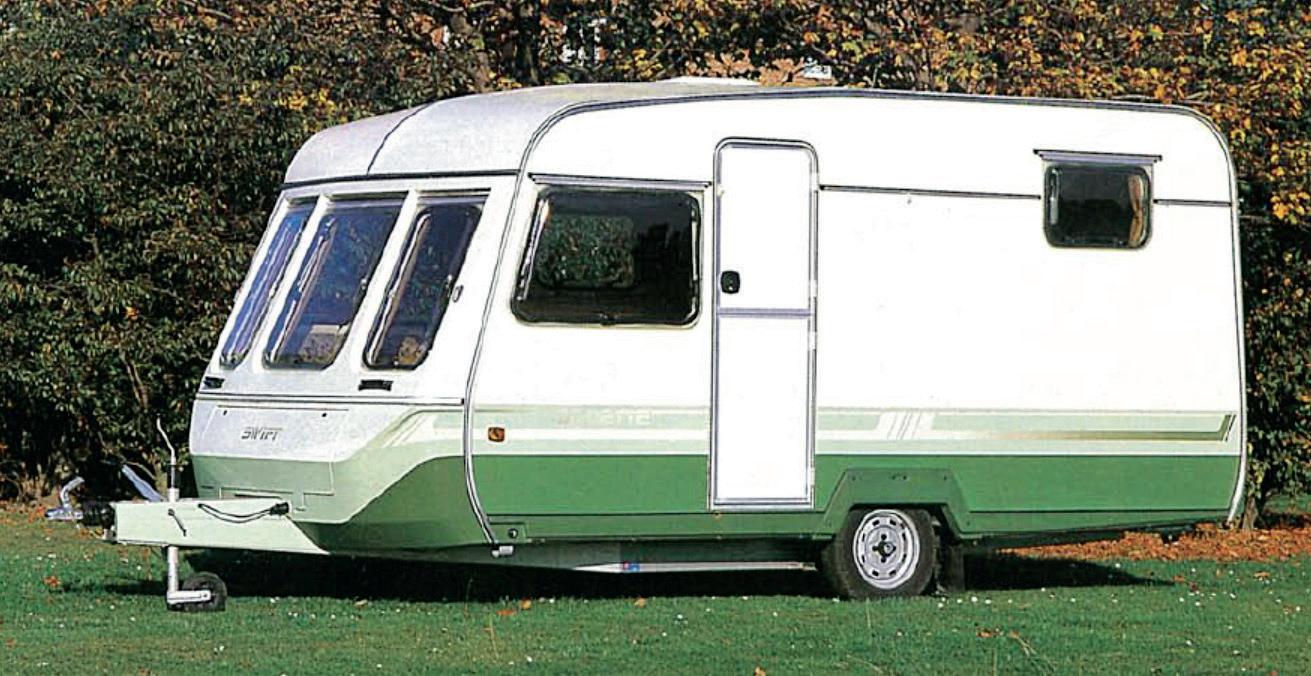
Telaio leggero AL-KO con asse Delta e mover MammutQuesto telaio B&B risale ai primi anni ‘70 ma è rimasto in uso fino agli anni ‘80

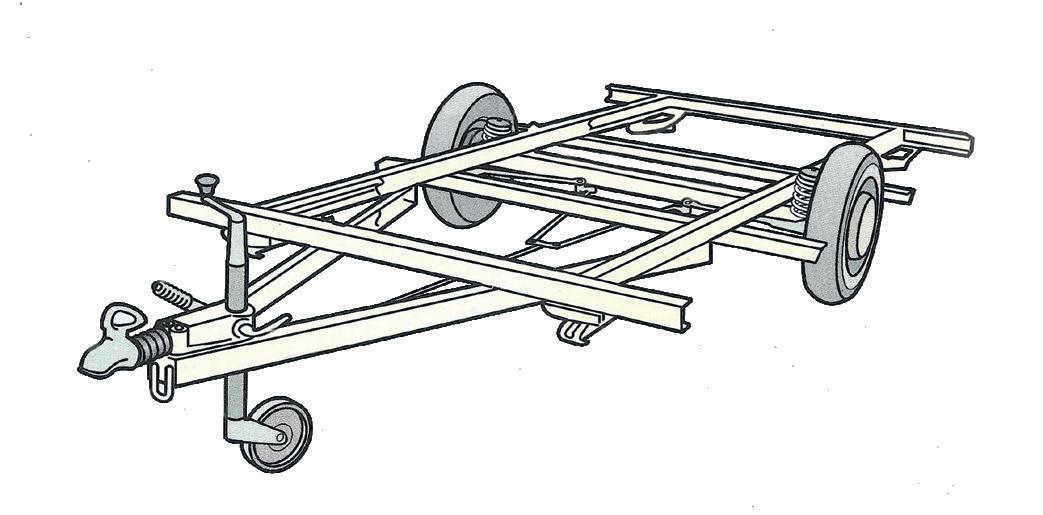
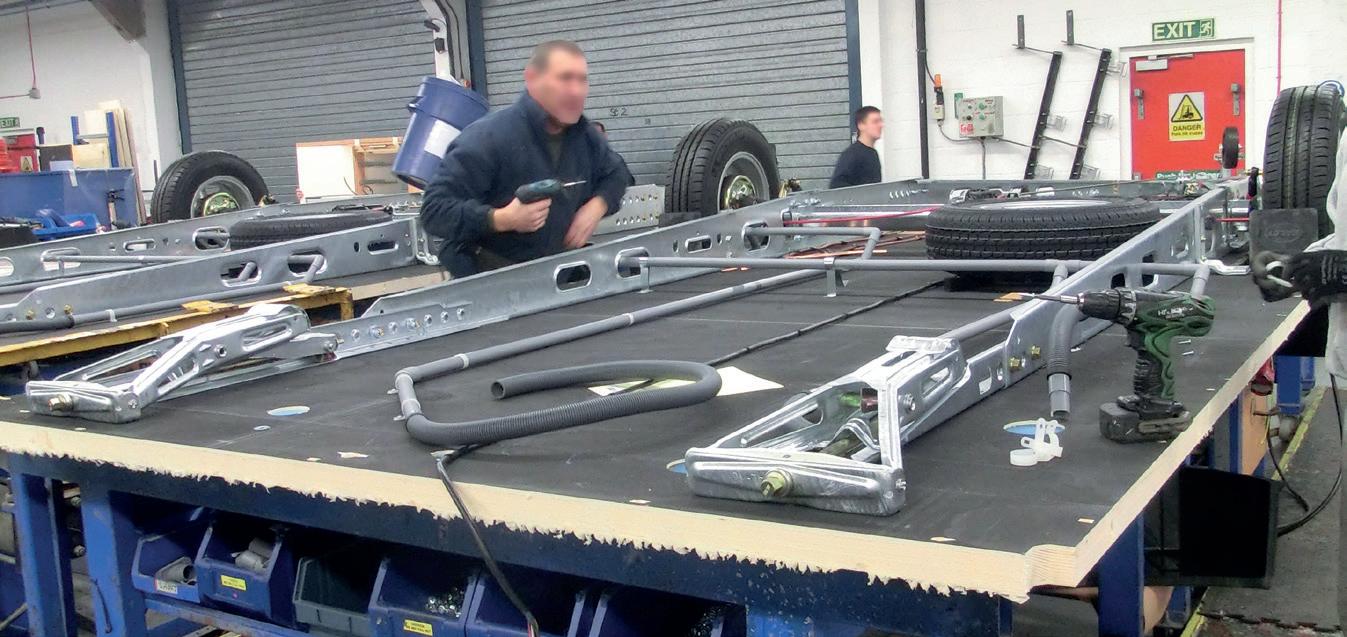
Quando sono fissati insieme, il telaio e il pavimento formano una solida base per l’allestimento
telaio può essere variata in base alla lunghezza della caravan. AL-KO chiama questa soluzione Vario Chassis. Se combinato con un pavimento adeguatamente incollato, il risultato è una piattaforma robusta e leggera per il resto del corpo della caravan e per l’equipaggiamento. Questo design ha avuto un tale successo che è arrivato quasi invariato fino ad oggi. Il risultato è che i produttori di caravan sono stati in grado di arricchire i propri con attrezzature sempre più allettanti per i clienti. Al Caravan Salon del 2016, BPW ha presentato un nuovo telaio leggero con ampi tagli triangolari lungo i due longheroni principali. Tre anni dopo, in seguito all’acquisizione di BPW Fahrzeugtechnik da parte di AL-KO avvenuta nel 2017, AL-KO ha lanciato la propria versione: il Vario X. Riduce il peso del telaio fino al 30% grazie all’utilizzo di una struttura a nido d’ape. AL-KO afferma di non scendere a compromessi sulla rigidità, e il prodotto è già utilizzato su alcune caravan entrate in produzione. Vale la pena sottolineare che, sebbene la disposizione a due longheroni sia perfetta per le strade relativamente lisce che si trovano nella maggior parte dell’Europa, non è l’ideale per aree come l’entroterra australiano, dove prevalgono condizioni molto più accidentate. In questi tipi di mercato prevalgono soluzioni più tradizionali.
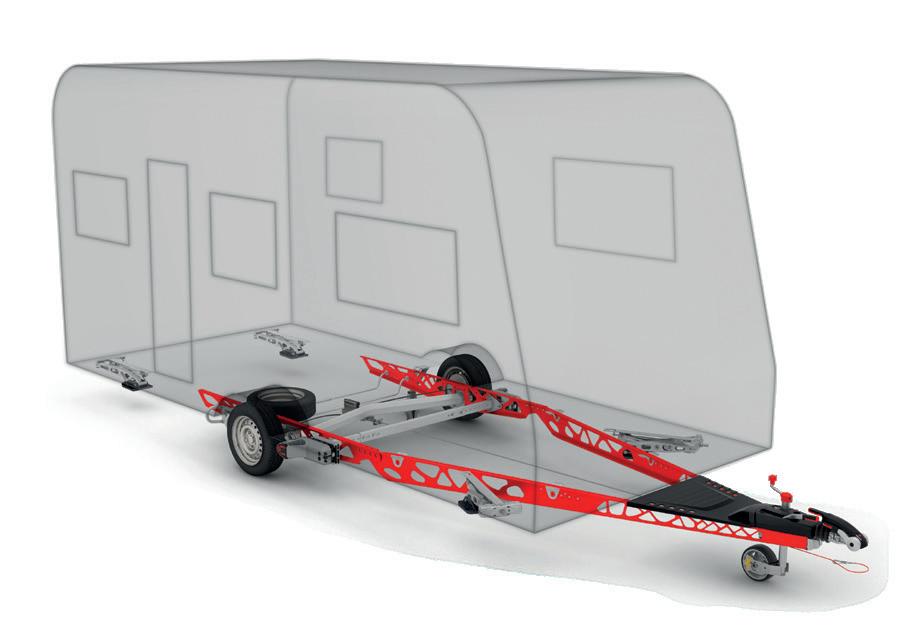
A sinistra e sotto: il telaio Vario X super leggero di AL-KO
BPW ha presentato questo telaio ultraleggero a Dusseldorf nel 2016
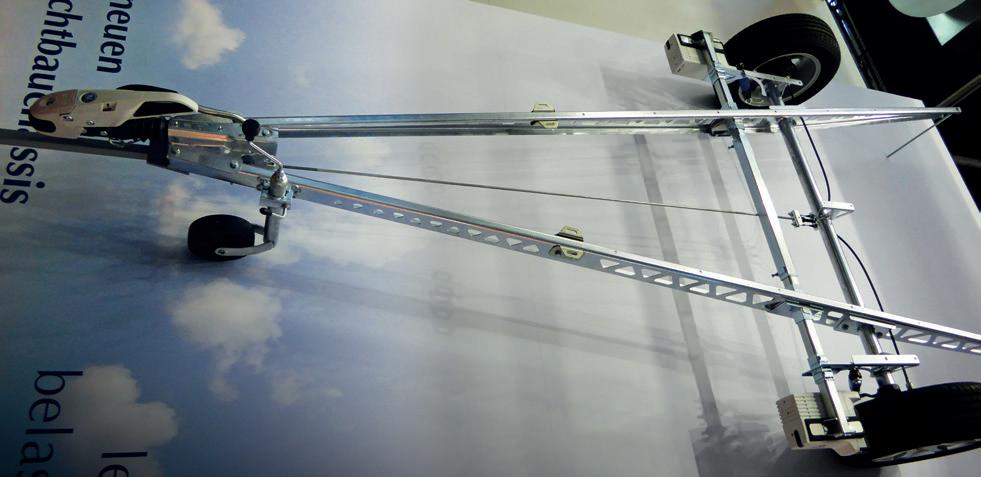
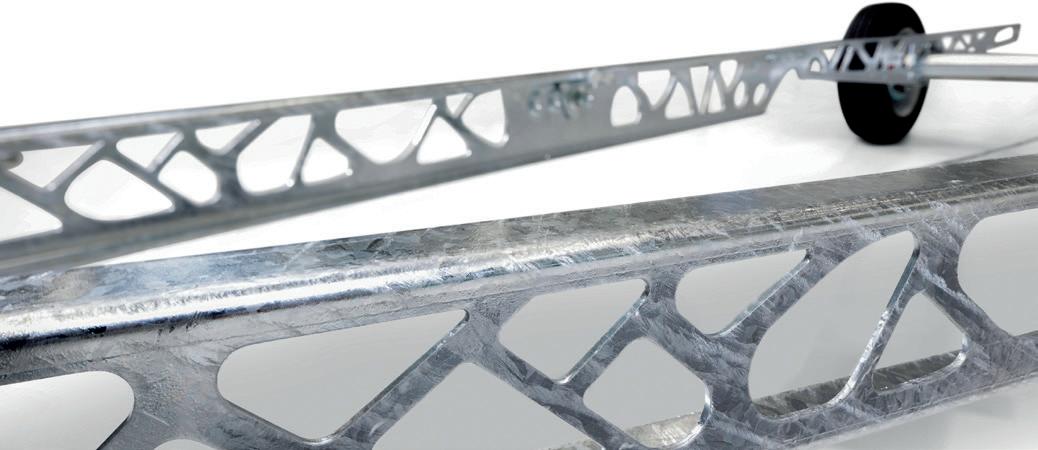
Sistemi di frenata a inerzia
L’impianto frenante a inerzia è un altro esempio di invenzione le cui origini si perdono nella notte dei tempi. In sostanza, è un sistema in cui, quando la motrice frena, i freni del rimorchio vengono automaticamente azionati senza la necessità di alcun collegamento speciale tra i due. Funziona sfruttando lo slancio in avanti del rimorchio che viene spinto contro il veicolo trainante in frenata, creando una forza contraria che viene utilizzata per respingere un ammortizzatore a molla (1 - albero). Il movimento all’indietro dell’ammortizzatore viene quindi utilizzato per azionare i freni del rimorchio tramite una leva (2 - leva di rinvio) e un’asta (3 - tiranteria del freno). In questo modo i freni del rimorchio (4) vengono azionati automaticamente. Quando il rimorchio rallenta, la forza sull’ammortizzatore a molla si riduce, riducendo così il livello di frenata. I primi sistemi si basavano su una semplice molla senza alcuna forma di smorzamento, e questo potrebbe avere risultati indesiderati, come un forte “martellamento” del rimorchio contro il veicolo trainante e una riduzione dell’efficienza frenante. Il fondatore di AL-KO Alois Kober e suo figlio Herbert, dopo un brutto incidente d’auto nel 1952, passarono molti mesi in convalescenza: durante quel periodo iniziarono a progettare un sistema di freno a repulsione migliorato, che rispondesse alla minima pressione piuttosto che speronare il veicolo trainante. I primi test sono stati effettuati utilizzando vecchie Jeep residuati bellici e hanno introdotto AL-KO alla progettazione e produzione di sistemi frenanti: i nuovi freni AL-KO AAA BRAKE, per esempio, hanno il notevole pregio, per un freno ad inerzia, di recuperare i giochi che si formano con l’usura dei ferodi e garantire quindi una frenata sempre al massimo dell’efficienza. Oggi tutti i sistemi utilizzano qualche forma di smorzamento per prevenire colpi indesiderati; tali sistemi sono di solito integrati nel gruppo timone per fornire una frenata regolare e affidabile. Assumono spesso la forma di un ammortizzatore a molla riempito di gas.
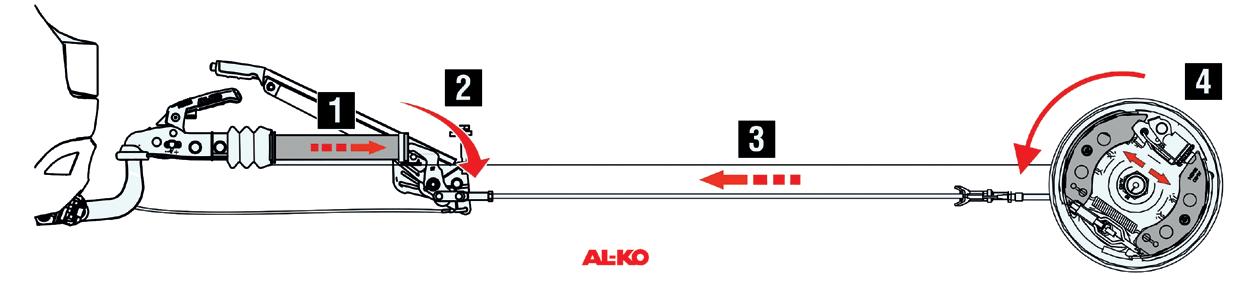
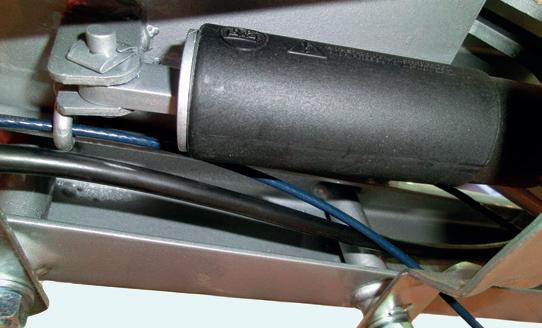
L’ammortizzatore a molla / gas su un attacco BPW
Le ganasce dei freni vengono spinte contro il tamburo per rallentare il veicolo