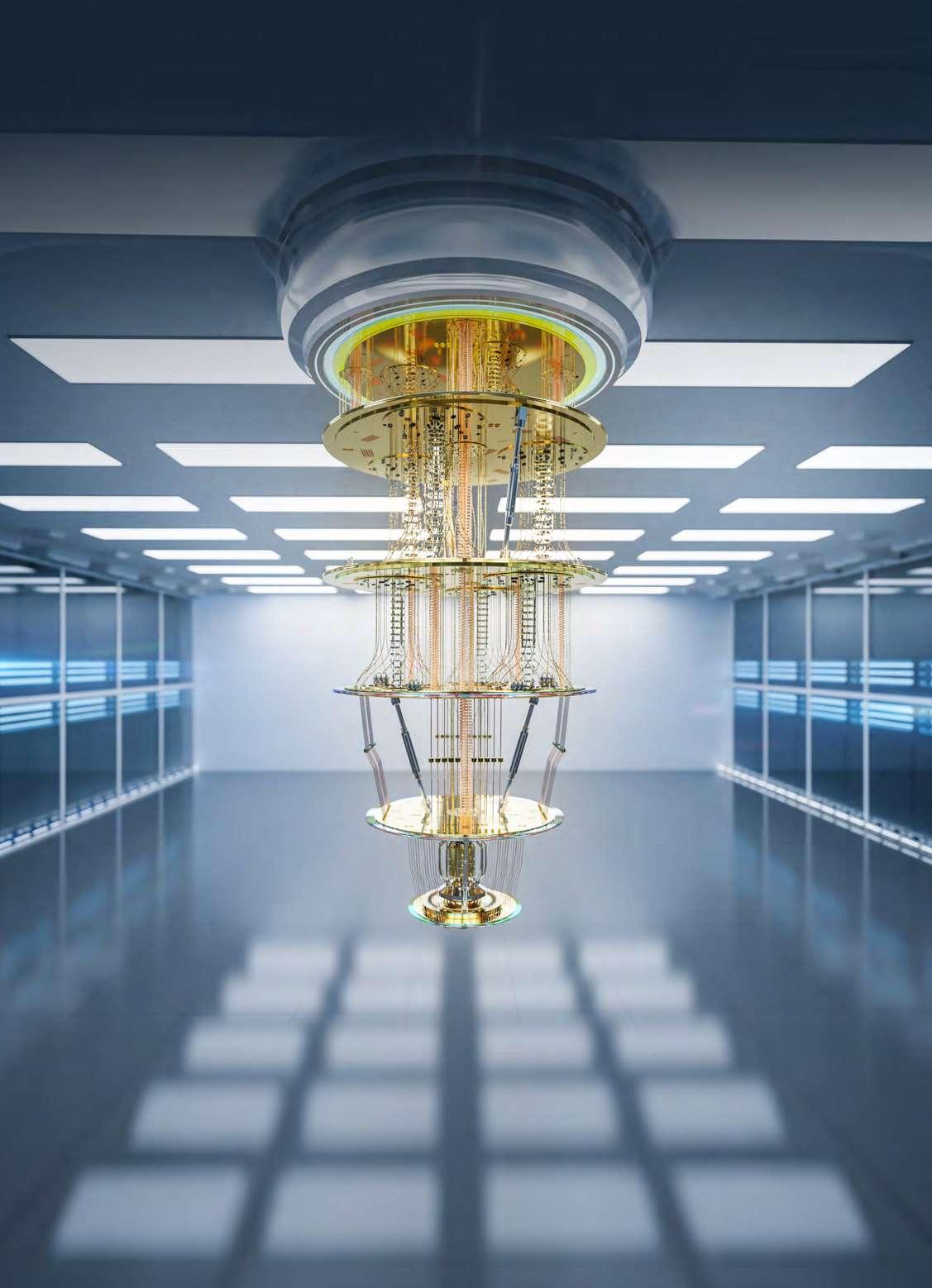
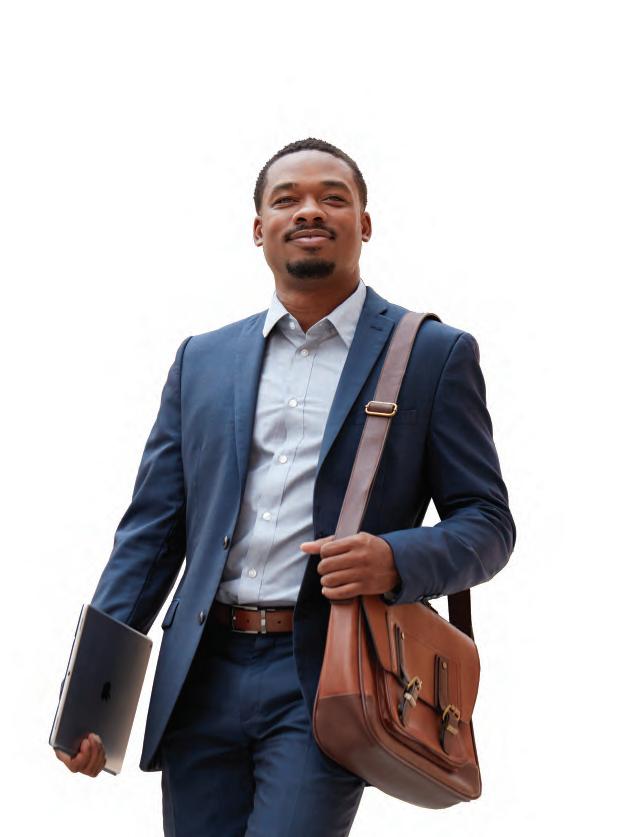
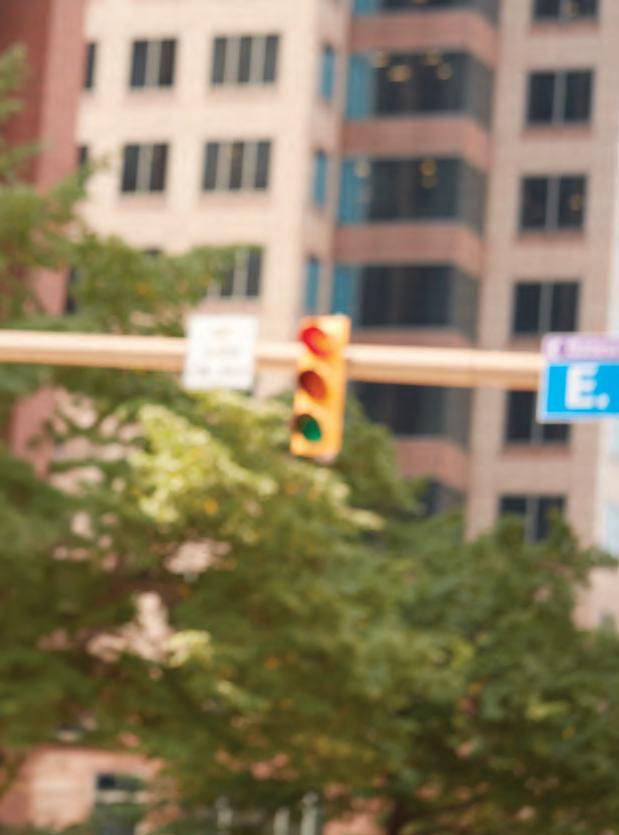
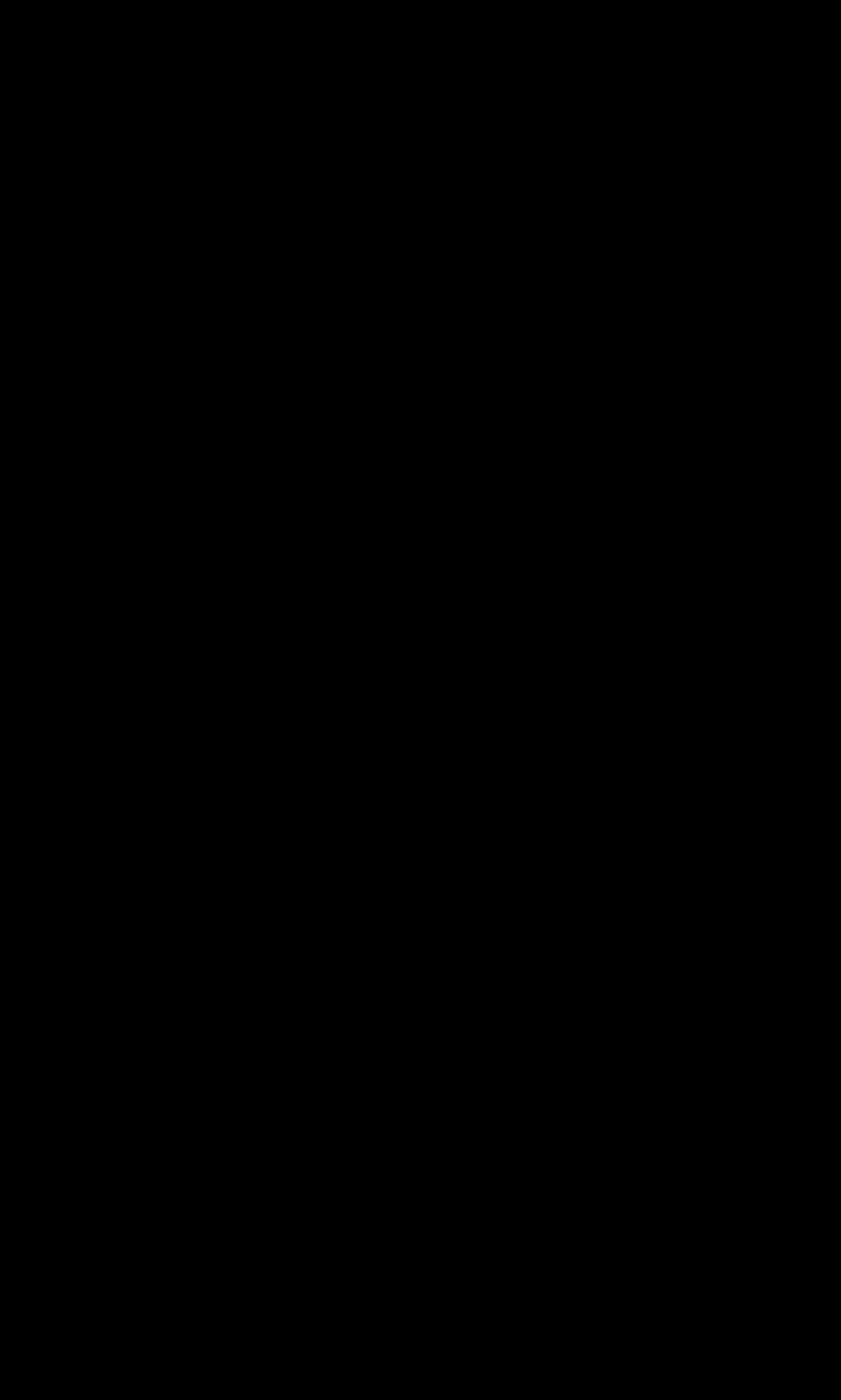
By Ermengarde Jabir, Director of Economic Research, Moody’s
As oil and gas giants consolidate, their real estate footprints shrink—but their office demands rise. Discover why premium locations and top-tier amenities matter more than ever.
Shifting supply chains and evolving policies are transforming industrial real estate. Find out where that investment is heading and what it means for businesses.
Explore how geography, subsidies, and economic impact are shaping the future of nuclear development— and where the next big projects will emerge.
As energy demand surges, companies must secure
With trade tensions rising, new tariffs could reshape supply chains. We break down key indicators for China, the EU, Mexico, and Canada.
From securing approvals to aligning infrastructure, strategic collaboration can mean the difference between smooth progress and costly delays.
If there’s one lesson we’ve learned in the past few years, it’s that uncertainty is no longer a passing storm—it’s the climate we operate in. From shifting trade policies to the rapid emergence of quantum computing as a practical tool, today’s business leaders must navigate an environment where the fundamentals of competitiveness are being rewritten in real time.
In this issue, we explore the levers executives need to pull to stay ahead. Our feature on quantum computing infrastructure examines the coming wave of investment and site selection strategies that will support this next technological frontier. As industries from pharmaceuticals to finance begin integrating quantum capabilities, the question is no longer if this technology will be transformative, but where and how companies should prepare for it.
At the same time, our piece on tariff planning – expertly written by guest editor Charlie Smith -- reminds us that while technology reshapes operations, policy still defines the playing field. With trade landscapes shifting yet again, smart tariff strategy isn’t just a compliance matter—it’s a core component of supply chain resilience.
Of course, no issue of Area Development would be complete without a data-driven look at the state of corporate expansion. This year’s Corporate and Consultant Surveys offer critical insights into the priorities and challenges that are shaping site selection decisions today.
Taken together, these stories highlight a common thread: Proactive leaders don’t wait for change to dictate their strategy—they position themselves to capitalize on it. The companies that will thrive in this era of transformation are the ones thinking ahead, balancing risk with opportunity, and making investment decisions with both precision and agility.
As always, we’re here to provide the analysis and insights that help you do just that.
Editor Andy Greiner
2025 EDITORIAL ADVISORY BOARD
Scott Kupperman Founder KUPPERMAN LOCATION SOLUTIONS
Eric Stavriotis Vice Chairman, Advisory & Transaction Services CBRE
Brian Corde Managing Partner ATLAS INSIGHT
Amy Gerber Executive Managing Director, Business Incentives Practice CUSHMAN & WAKEFIELD
Alexandra Segers General Manager TOCHI ADVISORS
Dennis Cuneo Owner DC STRATEGIC ADVISORS
Publisher Dennis J. Shea dshea@areadevelopment.com
Sydney Russell,
Publisher 1965-1986
Events / Business Development Director
Matthew Shea (ext. 231) mshea@areadevelopment.com
Media / Accounts Director
Justin Shea (ext. 220) jshea@areadevelopment.com
Courtney Dunbar Site Selection & Economic Development Leader BURNS & MCDONNELL
Stephen Gray President & CEO GRAY, INC.
Bradley Migdal Executive Managing Director, Business Incentives Practice CUSHMAN & WAKEFIELD, INC.
Brian Gallagher Vice President, Corporate Development GRAYCOR
Marc Beauchamp President SCI GLOBAL
David Hickey Managing Director HICKEY & ASSOCIATES
Chris Schwinden Partner SITE SELECTION GROUP
Chris Volney Managing Director, Americas Consulting CBRE
Matthew R. Powers, Lead Site Selection Consultant REDI SITE SELECTION
Scott J. Ziance Partner and Economic Incentives Practice Leader VORYS, SATER, SEYMOUR AND PEASE LLP
Chris Chmura, Ph.D. CEO & Founder CHMURA ECONOMICS & ANALYTICS
Alan Reeves Senior Managing Director NEWMARK
Lauren Berry Senior Manager, Location Analysis and Incentives MAXIS ADVISORS
Courtland Robinson Director of Business Development BRASFIELD & GORRIE
Dianne Jones Managing Director, Business and Economic Incentives JLL
Joe Dunlap Chief Supply Chain Officer, LEGACY INVESTING
Editor Andy Greiner editor@areadevelopment.com
Staff and Contributing Editors
Mark Crawford
Kimberly Graulein
Jim Richardson
Brian Eddow
Garrison Partridge
Katy McElroy
Circulation/Subscriptions circ@areadevelopment.com
Production Manager Jessica Whitebook jessica@areadevelopment.com
Web Designer Carmela Emerson
Print Designer
Victoria Corish
Business/Finance Assistant Barbara Olsen (ext. 225) olsen@areadevelopment.com finance@areadevelopment.com
Halcyon Business Publications, Inc.
President Dennis J. Shea
Correspondence to: Area Development Magazine
30 Jericho Executive Plaza Suite 400 W Jericho, NY 11753
Phone: 516.338.0900
Toll Free: 800.735.2732 Fax: 516.338.0100
Newmark – Managing Director
Charlie advises clients on geopolitical strategy, analyzing international locations and U.S. markets to assess risk, manage challenges, and uncover opportunities. Page 60
Ken Biberaj
Executive Managing Director – Savills
Ken focuses on site selection and incentives for advanced manufacturing, drawing on two decades of real estate and public policy expertise. Page 88
Brasfield & Gorrie – Director of Business Development
Courtland specializes in power-intensive site selection and economic development, supporting industrial and commercial projects across local, regional, state, and Fortune 500 utility sectors. Page 67
Jeff Troan
Partner and Managing Director – Vista Site Selection
Jeff specializes in site selection, incentives, and real estate, drawing on decades of experience at Lockheed Martin and aerospace consulting. Page 74
Tyler Keel
Burns & McDonnell – Engineering Project Manager
Tyler is a design-build project manager at Burns & McDonnell, specializing in aerospace, space, and defense facility development. Page 78
Site Selection Practice Leader – Burns & McDonnell
Courtney leads Burns & McDonnell’s site selection practice, advising on industrial growth, infrastructure planning, and economic development strategies for manufacturing and mission-critical projects. Page 78
Project Management Advisors – Project Director
Myung specializes in life sciences facilities, corporate interiors, and workplace strategy, with extensive experience in design and project management. Page 86
Travis Sayler
Senior Civil Engineer – Gresham Smith
Travis is a senior civil engineer at Gresham Smith, specializing in transportation engineering, highway design, and industrial park development for economic growth. Page 72
Sarah Carnes
Deloitte Consulting LLC – Senior Consultant
Sarah specializes in site selection, workforce analytics, and footprint optimization, with expertise in energyintensive manufacturing and investment strategy. Page 50
Brian Gallagher
Vice President – Graycor Construction
Brian leads business development, marketing, and communications. With 30+ years of experience, he drives strategic growth, brand stewardship, and project alignment. Page 80
You might not need a certified site for your next facility project
By Kimberly Graulein Area Development Staff
You might not need a certified site for your next facility project. Certified sites provide a level of due diligence that can be valuable in site selection, but many certification programs take an all-or-nothing approach.
A site either meets rigid certification standards, or it doesn’t qualify—leaving potentially viable properties out of the running. A better approach might be tiered site readiness.
Rather than labeling a site as either certified or uncertified, tiered readiness categorizes sites based on their level of preparation. This approach acknowledges that different industries have different needs and allows site selectors to evaluate sites on a continuum rather than an arbitrary pass/fail basis. A rigid certification program might require that a site has natural gas access, but if the end user doesn’t need natural gas, that requirement could unnecessarily disqualify a great location. A tiered system instead provides information about what’s in place and what would require additional investment, letting companies make the best decision for their specific needs.
“The value is in the information obtained and made available, not the certification ‘stamp,’” said Scott Kuppermann, the owner of Kupperman Location Solutions. “Certified sites are useful if they provide detailed, reasonably
current, and transparent data, but certification alone doesn’t necessarily mean a site is the best fit for a project.”
This approach benefits both communities and companies by ensuring more sites remain in consideration rather than being dismissed over criteria that may not be relevant to a particular user. It also speeds up decisionmaking by offering a clear picture of a site’s existing infrastructure, entitlement/ approval, and due diligence status, as well as any gaps that would need to be addressed. If multiple sites in a region are missing the same key asset, such as rail access, economic developers can use this information to prioritize infrastructure investments.
Beyond that, tiered readiness provides much-needed flexibility in an environment where shovel-ready industrial land is in short supply. Many communities are already struggling to keep up with demand, particularly for midsized sites that fall between small industrial parks and mega-sites. A rigid certification process can shrink the pool of available properties even further, inadvertently discouraging viable development.
For communities looking to implement a tiered readiness system, a good starting point is to focus on gathering and documenting site data, rather than aiming for a certification label. Decisionmakers should also consider
industry-specific readiness factors. For example, a food processing plant will have vastly different water, wastewater, and power requirements than an automotive supplier. Instead of a onesize-fits-all checklist, a more nuanced readiness framework allows site selectors to match properties to industry needs without unnecessary disqualifications.
Providing clear information about infrastructure, transportation access, environmental conditions, and permitting history makes a site more attractive to companies evaluating their options. Some economic development groups have begun labeling sites by readiness level, such as shovel-ready, due diligence completed, or infrastructure in progress, rather than enforcing rigid certification criteria.
“I’ve never had a client specifically request we only look
at certified sites,” said Amy Gerber of Cushman & Wakefield. “What they want is to know that due diligence has been done, that the site can support our requirements, and that they won’t run into any surprises. Tiered readiness allows for that transparency without unnecessary exclusions.”
The takeaway for businesses and economic developers alike is clear: more information, not more rigid designations, leads to better site selection decisions. By asking for site transparency and flexibility rather than rigid certification requirements, businesses can ensure that more viable locations remain in the mix. A tiered approach allows companies to assess sites based on their own priorities while giving communities a framework for continuous improvement in site readiness.
Mississippi is breaking new ground for business with record-setting speed to market. Shovel-ready sites and smoother processes coupled with collaborative communities and leadership help you turn the corner from investment to revenue faster.
Let’s break new ground together.
mississippi.org
By Brian Eddow Area Development Staff
For decades, the people of Lincoln, Maine, lived with the pungent reality of the paper industry. The town’s mill, once a vital economic engine, left behind more than just memories when it shut down—it also saddled Lincoln with a contaminated 400-acre site and a lingering nickname: “Stinkin’ Lincoln.”
But the town refused to let its industrial past define its future. In a remarkable turnaround, Lincoln is now home to one of the most significant battery storage projects in the country, a $300 million investment by Form Energy that will house the largest battery storage facility on the East Coast.
“This project is a game changer,” said Ruth Birtz, Lincoln’s economic development leader, who has spent more than three decades working to transform the town. “To go from being a paper mill town, written off after the industry collapsed, to attracting cutting-edge technology—this is exactly what we envisioned.”
Lincoln’s road to securing Form Energy wasn’t accidental. The town had methodically positioned itself for redevelopment, purchasing the shuttered mill site from bankruptcy proceedings and
initiating a cleanup process that included removing an estimated $60 million in asbestos contamination.
“We weren’t going to just let the site rot,” Birtz said. “We knew we had to be proactive.”
The town’s strategy centered on leveraging its natural assets and existing infrastructure. Lincoln sits on the edge of what’s known as Maine’s wood basket, a dense forest region full of untapped potential for new industries. But the real selling point? The town’s proximity to one of the most critical electrical grid hubs in New England.
“Just across the river in Chester is one of the largest circuit breakers in the entire regional grid,” Birtz explained. “Form Energy needed an ideal interconnection point, and we had it. That was a huge advantage.”
The Deal Behind the Scenes
When Form Energy began scouting locations for its novel iron-air battery technology, Lincoln was on the list. The company needed a large site, environmental clearance, and access to the grid. The town had all three.
The conversations were quiet at first. Lincoln had a strict policy of keeping negotiations under wraps until contracts were signed—partly to avoid raising community expectations too soon, partly to prevent unnecessary scrutiny before deals were secured.
“We didn’t even know how serious they were,” Birtz admitted. “Then, all of a sudden, they were awarded a federal grant for 50 percent of the project cost, and it was announced through our senators’ offices. Everyone was looking at us like, ‘Why didn’t you say anything?’ But that’s just how we operate.”
Form Energy was drawn
to Lincoln’s Opportunity Zone designation, which made the project eligible for tax incentives. However, local incentives weren’t the primary driver—federal support played the biggest role in making the deal financially viable.
The technology itself is what sets the project apart. Unlike traditional lithiumion batteries, Form Energy’s system stores electricity by rusting and de-rusting iron—a safer, more sustainable alternative that could revolutionize grid storage.
“This isn’t just another battery facility,” Birtz said. “This is about making green energy actually work at scale.”
For a town of just over 5,000 people, the economic impact is enormous. The project promises jobs, investment, and a role in shaping the energy future.
“This investment will play an important role in revitalizing Lincoln, including the site of the former paper mill, providing new opportunities for rural Maine. I thank the Biden-Harris Administration for this investment and for its support of our work to build a more resilient, clean electrical grid that can withstand the impacts of a changing climate,” said Governor Janet Mills when the project was announced in August.
For Birtz, it’s also a redemption story.
“No more Stinkin’ Lincoln,” she said with a smile. “Now, we’re leading the way.”
By Jim Richardson Area Development Staff
When Tyson Foods set out to build a $355 million bacon facility, it evaluated 100 locations before choosing Bowling Green, Kentucky. What tipped the scales in Warren County’s favor? A community willing to go the extra mile—literally
One decisive moment came when a local company under Houchens Industries voluntarily cut a road to improve site access—at no cost to the city or county.
“That’s the kind of teamwork that makes a difference,” said Ron Bunch, CEO of the Bowling Green Area Chamber of Commerce. “It signaled to Tyson that this community was all-in.”, we’re leading the way.”
Bunch recalls that the project, initially operating under a code name, started in the summer of 2021.
“Tyson had evaluated 100 sites before selecting Bowling Green. We found out on the day of the public announcement,” he said.
Bowling Green didn’t just offer available land—it offered solutions. The Chamber proposed eight site configurations before landing on one that met Tyson’s needs. When it became clear the project required more land, local officials acted fast, purchasing 200 additional acres. “The city and county split the cost 50-50 and even dipped into reserves,” Bunch said.
In addition to the land, infrastructure was a priority. The Chamber had secured $46.5 million in bond funding, but additional investment was needed. “The road Scotty cut was invaluable. It allowed Tyson’s team to see the full potential of the site immediately,” Bunch said.
Beyond infrastructure, Bowling Green’s workforce
strategy played a major role. “We’ve spent over a decade building a career pipeline with our local schools,” Bunch said. The program provides realtime workforce demand data, five- and ten-year projections, and aligns training programs with employer needs.
Tyson’s facility, employing over 450 people, benefits from this workforce preparation. “Every company we meet is blown away by how comprehensive our workforce programs are,” Bunch noted.
The 430,000-square-foot plant represents a major leap in automation. Tyson integrated high-tech robotics, driverless forklifts, and autonomous guided vehicles to increase efficiency and reduce strain on workers. The technology eliminates ergonomically stressful tasks like moving large pork bellies and stacking boxes.
Tyson’s investment will generate $2.7 billion in local economic activity over the next decade. “This isn’t a generic estimate. We had an economist update our local variables to reflect Bowling Green’s economy,” Bunch said.
Tyson already employs nearly 4,000 people statewide, and this project cements its long-term commitment to Kentucky.
“We’ve hosted economic development teams from Louisville, Savannah, and Indiana studying our approach,” Bunch said. “This deal proves that when a community works together before a client arrives, it makes all the difference.”
For site selectors and corporate executives, Bowling Green’s success highlights the
importance of adaptability, investment, and collaboration in securing major projects.
By Garrison Partridge Area Development Staff
Colorado isn’t just a player in the aerospace industry—it’s a launchpad for the future of space. With over 2,000 aerospace companies, a workforce exceeding 200,000, and half of the nation’s Space Force based there, the state has become a backbone of U.S. space innovation. Now, fresh investment is reinforcing its leadership.
Among the marquee projects fueling this growth is Sierra Space’s Orbital Reef, a private space station set to redefine space tourism, research, and manufacturing. Developed in partnership with Blue Origin, Boeing, and Redwire Space, the platform will be built and tested largely in Colorado.
Meanwhile, industry heavyweights like United Launch Alliance (ULA) and Lockheed Martin are scaling up operations, solidifying Colorado’s status as an aerospace powerhouse.
Robert Beletic, Aerospace and Defense Industry Manager for the Colorado Office of Economic Development and International Trade (OEDIT), sees the momentum firsthand.
“When projects like Orbital Reef choose Colorado, they benefit from a full-spectrum aerospace ecosystem—returning Americans to the moon, supporting the James Webb Space Telescope, and enabling private space projects.”
While Sierra Space’s partnerships with Blue Origin and Boeing are critical to Orbital Reef, the heart of the project beats in Colorado. The company has expanded its testing and manufacturing footprint throughout the DenverBoulder region, including over 100,000 square feet of high-precision space hardware production.
“There’s a reason we see this kind of expansion here,” Beletic explains. “Colorado attracts and retains aerospace talent. Companies know they’ll find a highly skilled workforce and an established aerospace supply chain that accelerates innovation.”
That talent pipeline runs through top institutions like the University of Colorado Boulder, Colorado State University, and the U.S. Air Force Academy. Beletic also highlights the unique mix of legacy aerospace giants and startups. “From Lockheed Martin to Sierra Space, from Maxar to ULA—there’s a density of expertise here that’s unmatched.”
Orbital Reef’s logistics depend on another Coloradobuilt innovation: the Dream Chaser. Sierra Space’s winged, reusable spaceplane will deliver cargo—and eventually people—to the private space station.
“This is a game-changer,” Beletic says. “Two of the four planned manned spacecraft will be built in Colorado— Lockheed Martin’s Orion and Sierra Space’s Dream Chaser. That speaks volumes about the state’s central role in space exploration.”
Dream Chaser’s first cargo flight to the Internation-
al Space Station is expected this spring. Meanwhile, Sierra Space is developing additional versions, including a crewed model and a Department of Defense variant.
“What’s happening in Colorado is a full-spectrum aerospace revolution,” says Beletic.
United Launch Alliance recently debuted its Vulcan Rocket, which is expected to receive National Security Space Launch certification, further cementing Colorado’s role in military and commercial space. Lockheed Martin is preparing to deliver Orion II, the next-generation spacecraft that will take astronauts around the moon and back. And roughly 200 Colorado-based companies are contributing to NASA’s Artemis program, which aims to return humans—including the first woman and first person of color—to the lunar surface.
“Colorado is putting Americans back on the moon,” Beletic says. “We’re not just contributing—we’re leading.”
With aerospace growth of 26.3 percent in the past five years, Colorado’s trajectory is clear. A mix of cutting-edge projects, a robust workforce, and strategic state incentives ensures companies like Sierra Space continue pushing the boundaries of space exploration.
“This isn’t just about one project,” Beletic emphasizes. “It’s about an ecosystem driving innovation for decades to come. From Dream Chaser to Orion, from the James Webb Space Telescope to Artemis— the future of space isn’t just happening in Colorado. It’s being built here.”
Port congestion has significantly reduced since mid-2022, with wait times dropping across major coastal regions
West Coast Recovery: Long Beach and Los Angeles, previously notorious for long delays, have now stabilized.
Wait Time Trends (2023-2024): 2.5 days.
Gulf Coast Resilience: Houston remains a volatile but crucial port, showing mixed impacts on wait times.
Wait Time Trends (2023-2024): Varied, with Houston peaking at 17 days but averaging lower.
East Coast Gains: Ports like Virginia and New York/New Jersey have seen steady improvements due to infrastructure investments.
Wait Time Trends (2023-2024): 3.5 days.
Outliers: Savannah and Oakland continue to experience fluctuations, with occasional spikes in delays.
By Georgia Power
Georgia has established itself as the number one state in the nation in which to do business, growing steadily for decades in large part due to its investment in infrastructure, education, and workforce development that help foster innovation and business growth across the state. Another important factor in Georgia’s continued economic success becoming more apparent as customers increasingly seek to locate high power use projects to the state is Georgia Power’s diverse mix of clean, safe, reliable, and affordable energy which ensures dependable power to businesses and residents alike and will position the Peach State as a competitive destination for decades to come.
The state’s business-friendly environment has supported the rapid growth of a wide variety of businesses within the state. Industries like electric transportation (ET), data and technology, manufacturing, entertainment, and more have continued to pour their resources into Georgia not only because of the state’s commitment to innovation and growth, but increasingly because of availability of clean, safe, reliable, and affordable energy made possible thanks to a constructive regulatory environment and forward-looking energy policies.
With major players like Hyundai, Kia, and Rivian investing billions in new facilities and creating thousands of skilled jobs, Georgia has become a hub for ET manufacturing. Meanwhile, an influx of data centers and other technology firms have chosen to call Georgia home as well – not only bringing an influx of new jobs to the state but also signaling a broader shift toward industries which depend on a clean and stable energy supply. Beyond technology, Georgia’s entertainment industry also benefits from Georgia Power’s reliable power supply. With a growing number of sound stages, production facilities, and recording studios requiring reliable uninterrupted power, Georgia Power’s commitment to providing reliable energy to Georgia ensures that the state remains a preferred destination for major and independent productions alike.
None of this would be possible without Georgia Power’s diverse mix of energy generation.
Throughout its more than 140-year history, Georgia Power has built, maintained, and improved power plants across the state to reliably and affordably serve both its current customers and a growing Georgia. The company’s generation mix has evolved to include cleaner and more efficient forms of energy generation as technology has advanced and it continues to be an industry leader in the research and development of emerging energy technologies, while maintaining a commitment to providing safe, reliable, and affordable energy to the state.
In 2024, the fourth nuclear reactor at Plant Vogtle entered commercial operation making Plant Vogtle the largest generator of clean energy in the United States, capable of generating enough electricity to power over 2 million homes and businesses. While traditional fuels like natural gas and coal remain an important part of Georgia’s reliable and affordable energy strategy, renewable energy sources are also a key and growing part of the mix. Georgia Power has invested strategically and substantially in cost-effective renewable energy, making Georgia a top 10 state for solar, and leverages modernized hydropower and other renewable sources to further diversify its emission-free energy portfolio.
Georgia Power’s diverse energy mix is no coincidence; it is an intentional cornerstone of both the company and the state’s success. By balancing reliability, affordability, and sustainability, the company ensures that Georgia remains a top destination for business and innovation.
As Georgia’s economy continues to grow and evolve, so too must its energy strategy. Working with state leaders and with the oversight of the Georgia Public Service Commission, Georgia Power is ensuring it remains ready to meet the needs of a rapidly growing state by making significant investments in the state’s power grid to increase reliability, add resilience and accommodate the growing demand for energy. From deploying technologies like smart devices and investing in advanced energy storage solutions, Georgia Power is continually improving reliability and efficiency.
As Georgia continues to welcome newcomers, Georgia Power is ready to serve them all with clean, safe, reliable, and affordable energy today and for generations to come.
To learn more, visit SelectGeorgia.com (selectgeorgia.com/about-us/ our-approach/).
This
Charlie Smith, managing director of geopolitical strategy at Newmark, filled in as guest editor of Area Development for Q1 2025. He sat down with fellow experts in site selection, foreign direct investment, incentives, and economic development from Newmark to discuss the current trade tensions across North America and their implications. Below is an edited excerpt of his discussion with managing director Carlos Sanchez (based in Mexico) and senior managing director Gregg Wassmansdorf (based in Canada).
Charlie Smith:
Gregg Wassmansdorf: There’s significant disappointment that the U.S. is treating Canada—its closest ally and trading partner—almost as an adversary. The administration’s 25 percent tariff proposal is viewed as an existential threat. Foreign Affairs Minister Mélanie Joly recently stated at the Munich Security Conference that if the U.S. is coming for Canada, other nations should take note. There’s concern this is about more than just trade—it’s a geopolitical shift that undermines Canadian sovereignty.
Charlie Smith: Carlos, what’s the perspective from Mexico?
Carlos Sanchez: It’s similar. There’s massive uncertainty, given that 80 percent of Mexico’s exports go to the U.S. This has triggered a nationalistic response, which could be problematic. Our president remains extremely popular and has overwhelming legislative power. If the U.S. escalates tariffs, Mexico could retaliate, which would disrupt business on both sides of the border. The bigger issue is trust—if the U.S. is no longer a stable trade partner, companies will seek alternatives.
Gregg Wassmansdorf : The biggest risk is recession. A 25 percent tariff could shrink Canada’s GDP by 6 percent, according to the Bank of Canada. We’re already seeing companies freeze investments. Retaliatory tariffs will also raise costs for U.S. consumers—from aluminum cans to housing materials.
Charlie Smith: Carlos, what are the risks for Mexico?
Carlos Sanchez: The biggest immediate risk is supply chain disruption. The auto industry, which relies on cross-border production, would be severely affected. Auto parts cross the U.S.Mexico border multiple times before final assembly, meaning a 25 percent tariff compounds costs at every crossing. Agribusiness is also vulnerable—much of the fresh produce in U.S. grocery stores comes from Mexico. If that trade is disrupted, supply chains will be in disarray.
Charlie Smith: Are there any opportunities amid these challenges?
Gregg Wassmansdorf : Canada can address U.S. concerns in ways that also benefit us—like increasing military spending and improving border security. Beyond that, we’re working to reduce reliance on the U.S. We have a free trade agreement with the E.U. that the U.S. does not, and we’re strengthening trade ties with Mexico.
Charlie Smith: Carlos, is Mexico diversifying as well?
Carlos Sanchez: Absolutely. Mexico has started strengthening ties with the E.U. and Latin America. If North America pulls apart, other markets will step in. Southeast Asian countries, for example, have already gained market share from China in the U.S. If the U.S. and Mexico disengage, those countries will be the biggest winners.
Charlie Smith: How does this impact the upcoming USMCA renegotiations in 2026?
Gregg Wassmansdorf : It’s uncertain. The U.S. could even withdraw entirely, shifting to bilateral agreements and a tariff-based trade model. That would be disruptive, especially for industries like automotive, aluminum, and steel. The current trade dispute resolution mechanism is also at risk, which would make it harder for smaller countries to challenge unfair trade practices.
Carlos Sanchez: From Mexico’s perspective, the U.S. has already undermined the credibility of USMCA. Businesses need stability, but with a six-year sunset clause in the agreement, long-term planning becomes difficult. If tariffs are used as leverage in negotiations, Mexico and Canada may pivot more aggressively toward Europe and Asia.
Charlie Smith: What should we be watching for in the months ahead?
Gregg Wassmansdorf : The administration has indicated it will move beyond tariffs to non-monetary trade barriers—like labeling environmental regulations or food safety standards as unfair trade practices. That could lead to further economic fragmentation. If supply chains become too costly, companies will rethink their North American footprint.
Carlos Sanchez: The big question is how isolated the U.S. wants to become. If it moves away from North American trade, countries like Canada and Mexico will double down on new partnerships. The unintended consequence could be a weaker North American bloc overall.
Charlie Smith: This is an evolving situation, and it will take time to see the full impact. Thanks to you both for sharing your insights.
talk,
The EVP for Government Affairs at GlobalWafers discusses the thinking behind the company’s $3.5 billion Sherman, Texas investment, workforce strategy for wafer and chip makers, and how record-low power costs and CHIPS Act funding are reshaping U.S. semiconductor manufacturing
Area Development: Brent, thank you for joining us. Can you begin by giving an overview of GlobalWafers and your role in the semiconductor supply chain?
Brent Omdahl: Certainly. GlobalWafers is one of only five companies globally producing semiconductor wafers. We currently hold about an 18 percent market share, making us the third-largest player. Our annual sales are between $2.2 and $2.5 billion. Semiconductors begin with wafers, and the properties we engineer into them—flatness, resistivity, defect tolerance—are critical to the performance of our customers’ chips. To put it into perspective, we sell wafers for about $100 each, but our customers turn them into products worth $10,000 to $12,000. This demonstrates the high value-add downstream in the semiconductor supply chain.
Let’s talk about your new $3.5 billion facility in Sherman, Texas. Why did GlobalWafers choose Sherman over other locations?
Omdahl: It was a highly competitive process. Ohio made a compelling case,
offering significant incentives and leveraging Intel’s recent foundry investments in the state. However, Sherman had several key advantages. First, there’s a legacy of semiconductor talent in the area, dating back to the MEMC days (Editor’s note: Monsanto Electric Materials Company was a semiconductor wafer manufacturer from about 1959 to 2006; it’s now called SunEdison and it makes solar technology). MEMC pioneered wafer manufacturing, and many experienced engineers are still in the region. Second, Sherman’s economic development organization provided strong tax abatements and other incentives. Texas’ decentralized economic development structure and low energy costs sealed the deal. For instance, our power costs in Sherman are by far the lowest across our global operations, giving us a critical competitive edge.
Workforce development is often a significant factor in site selection. How is GlobalWafers approaching this?
Omdahl: Workforce development is a major focus for us. In Sherman, we’re leveraging partnerships with
local institutions like Grayson College, which runs an Advanced Manufacturing Program developed in collaboration with Texas Instruments. This program trains semiconductor technicians with the exact skills we need. We’ve also joined workforce consortia such as the North Texas Semiconductor Workforce Consortium and the Texoma Tech Hub. These initiatives allow us to expand our recruitment efforts across the DallasFort Worth area and even into nearby states like Oklahoma. Additionally, while automation will reduce operator roles, it increases the demand for skilled technicians, so we’re concentrating our efforts on two-year degree programs that train manufacturing, repair, and maintenance technicians.
What challenges have you faced in bringing this project to life?
Omdahl: One of the biggest challenges has been the cost of construction, which is 40 to 50 percent higher in the U.S. than in East Asia. Additionally, this facility marks a strategic shift for us. Historically, we’ve grown through acquisitions, but
this greenfield investment was driven by customer demand for local supply. Another key challenge was ensuring we remain competitive on costs. Texas’ infrastructure, particularly its low energy costs, was a major factor in overcoming this. We’ve even built a substation on-site to secure reliable and affordable power.
Sustainability has become increasingly important in manufacturing. How is this reflected in your Sherman facility?
Omdahl: Sustainability is one of our top priorities. Our facility is already connected to the Texas grid, which is 34 percent renewable, but we’ve committed to transitioning to 100 percent renew-
able energy by 2030. We’re exploring options such as investing in solar farms to achieve this. In Denmark, we built a solar park to power one of our facilities, and we’re considering similar initiatives here in Texas. These efforts align with our broader corporate goals and reflect the environmental values of our leadership.
How do you view U.S. industrial policy, particularly the CHIPS Act, in shaping the semiconductor industry?
Omdahl: U.S. industrial policy, including the CHIPS Act, has been instrumental. Programs like these help level the playing field, especially for companies like ours that face high capital expenditures and
thinner margins. Whether through tax incentives or direct grants, these subsidies are critical for driving manufacturing back to the U.S. Additionally, our customers have been pushing for more regionalized supply chains, and policies like the CHIPS Act support this trend. Our investment in Sherman is a direct response to these market and policy shifts.
Thank you, Brent, for sharing these insights. Is there anything else you’d like to add?
Omdahl: Just that I appreciate the opportunity to speak with you. If you’re ever in Sherman, feel free to visit our facility and see what we’re working on.
By Juan Escudero, Managing Director, Energy and Logistics & Louis I. Rosenthal, Executive Managing Director, Brokerage at JLL
Following years of technological change and a record-setting volume of mergers and acquisitions (M&A), the oil and gas industry is transforming. While major enterprises are growing larger, their real estate footprints are becoming more compact and centralized as companies consolidate staff and property portfolios, increasingly relying on technology rather than people
Almost every major integrated energy company has engaged in M&A activity, but the recent surge has been exceptional. Between mid-2023 and July 2024, M&A among oil and gas exploration and production companies totaled an unprecedented $250 billion, according to Enverus Intelligence Research. All this activity is reshaping the way oil and gas companies acquire space, manage their properties and facilities, and reduce real estate costs.
Industry consolidation is being driven by the maturation of domestic shale deposits in the Lower 48, including the Permian Basin and Eagle Ford Group in Texas, the Bakken Formation in North Dakota, and the Marcellus Formation on the East Coast. As vast as these resources are, every oil and gas field is finite, and fracking sites deplete much faster than conventional oil fields.
Now, companies are turning to M&A to replenish assets and boost shareholder returns more quickly and cost-effectively than through organic growth. Consolidation also strengthens companies against the rise of alternative energy sources and stakeholder interest in zero-carbon emissions while mitigating market volatility and regulatory risks.
Consolidation often leads to administrative streamlining and layoffs, reducing the need for office space. This provides oil and gas companies with an incentive to unload outdated, underutilized, or poorly located facilities. The ConocoPhillips-Marathon Oil transaction, for example, merges two Houston-based companies that will no longer need separate headquarters.
However, industry footprints were shrinking even before this latest wave of consolidation. Oil and gas exploration is now increasingly driven by geographic information systems and other sophisticated technology, reducing the need for manpower in the field.
With headcounts declining by as much as 30% and little projected workforce growth in the near future, many energy companies face space underutilization and excess real estate. The continuation of hybrid work policies, albeit with some in-office requirements, also contributes to
underused space. Some companies are actively shedding space, while others continue to carry excess real estate.
JLL Research shows that in Q4 2024:
Technip Energies vacated its approximately 300,000-square-foot U.S. headquarters in Houston’s Energy Tower II and is relocating to a 171,600-square-foot space at West Memorial Place II.
OneSubsea downsized a 212,000-square-foot office at 4646 W. Sam Houston Parkway North to 99,400 square feet at Energy Center V.
Modec reduced its footprint from 168,800 square feet at Energy Crossing II to 116,200 square feet at West Memorial Place I.
Some companies have been actively shedding space, while others continue to carry excess real estate. The oil and gas industry’s response to hybrid work policies has varied, with many firms enforcing some level of in-office attendance while still allowing for flexibility. Companies that do retain space are increasingly focused on optimizing it for collaboration, innovation, and employee well-being.
Many energy companies are not only looking to optimize their real estate portfolios but also to secure high-quality office space that supports talent recruitment and retention. Oil and gas companies compete with many other sectors for tech-savvy workers who expect modern workplaces, short commutes, and hybrid work options. HR executives are increasingly involved in real estate decisions to align office space with workforce strategies.
Today’s office market dynamics enable energy companies to secure space in premium buildings at rents significantly lower than pre-pandemic levels. With Houston’s office vacancy rate at 26.4% in Q3 2024, companies have opportunities to lease high-quality, amenity-rich properties in desirable locations near dining, retail, and transit options.
Hybrid work policies are likely to continue, though with some limitations, as many employees prefer flexibility. Yet, most energy companies recognize that in-person work fosters collaboration and innovation. Many are consolidating into premium buildings with generous on-site and neighborhood amenities. They seek workplaces
Continued on p. 84
By Andy Greiner Editor
As businesses evaluate expansion strategies and site selection priorities in 2025, both corporate executives and site selection consultants emphasize the critical importance of energy, skilled labor, and regulatory considerations. The findings from Area Development’s annual surveys provide a comprehensive look at how decision-makers are navigating the current landscape and what factors are shaping their investment plans.
The corporate site selection process has grown increasingly complex in recent years, as businesses face rising costs, evolving regulatory pressures, and shifting workforce dynamics. The 39th Annual Corporate Survey and 21st Annual Consultants Survey highlight key trends shaping location and expansion decisions for 2025. Corporate leaders and site selection consultants alike report that economic conditions, labor availability, and incentive programs remain at the forefront of their decision-making processes.
Let’s take a look at the results of both surveys.
Consultants report that economic factors, workforce constraints, and sustainability goals are shaping location decisions, with companies focusing on the South and Midwest for new projects.
For site selection consultants, helping businesses expand and establish new locations is a daily responsibility. Their insights provide a unique perspective on the evolving priorities and challenges companies face when choosing where to invest. The 21st Annual Consultants Survey sheds light on how consultants are dealing with economic uncertainty, labor shortages, and shifting corporate priorities to secure optimal locations for their clients.
The consultants responding to this year’s survey represent a wide range of industries. Nearly all (92 percent) are working on manufacturing projects, underscoring the continued strength of industrial investment. Distribution and warehousing projects rank second, with more than 60 percent of consultants assisting clients in logistics and supply chain expansion.
Which types of facilities are you currently working location or expansion projects?
In terms of new job creation, the new facilities and/or facility expansions will create:
What’s one word that sums up site selection in 2025?
Formidable. I believe in 2025 economic development will be a series of tough decisions to be made both by economic development and corporate decision makers.
Compared to the last year’s Consultants Survey, headquarters (41-->48) and data centers (30-->40) have seen a noticeable increase, perhaps indicating renewed investment in corporate expansion beyond industrial facilities.
The scale of projects varies widely, with threequarters of consultants working on projects involving 500 or more employees. Notably, more than half of the respondents are working on deals that will create over 1,000 jobs, a slight increase from last year’s sur vey, suggesting larger-scale investments despite economic caution.
Most projects remain on a six-to-18-month timeline, though a growing number of consultants report even shorter turnaround times as companies seek to fasttrack their expansions to capitalize on incentives and favorable economic conditions.
The South and Midwest continue to dominate site selection activity. Nearly all consultants are actively working on projects in the South Atlantic and Southwest regions, citing business-friendly policies, strong labor markets, and available land. However, the Midwest has seen an increase in consultant-led projects compared to last year, reflecting the region’s competitive workforce programs and growing investment in advanced manufacturing and battery production.
2025 will have a high level of uncertainty from consumer demand, construction costs and federal funding support. Companies will be faced with tough decisions on how and if they are going to continue moving forward with their projects; we have started to see some large projects in the EV industry that have decided not to move or have reduced their scope.
For economic development, when there is a shortage of quality real estate (with infrastructure) and a high demand, it creates a cost structure that only the largest projects, such as a data center, can absorb because the land is such a small percentage of the total project costs. Projects that are small to mid-sized have a far greater sensitivity to these costs, especially since they are upfront costs. The challenge for economic development, what type of project best supports the community's goals and how do you get political alignment and strengthen the tools to support those projects.
Amy Gerber, Executive Managing Director, Business Incentives Practice at Cushman & Wakefield
The expected timeline for these new facilities and/or facility expansions is:
What’s one word that sums up site selection in 2025?
Uncertainty is maybe the best word I could pick because there's so much change going on. You know, as an example, 2024, you know, 40 developed countries around the world elected new leaders, one of the highest number in any year we've seen, and that, along with geopolitical events going on, what's happening the Middle East, Russia, Ukraine, obviously, new President of the United States, who talking about tariffs related to different countries around the world, the impact on the global economy.
Larry Gigerich, Executive Managing Director at Ginovus
Where are your clients considering new facilities or facility expansions (physical footprint)?
Upheaval. We will see an influx of international companies that have already been doing business in the US, now need a domestic presence to avoid tariffs in their supply chain. We will see a pause, then a likely readjustment, of the EV battery and EV/hybrid automotive world as continuing federal support flounders. Growing NIMBY-ism on the community level will crescendo as emboldened activists and politically astute residents rally to limit local development across nearly all industrial sectors.”
Ford Graham, Senior Vice PresidentInfrastructure & Economic Development at McGuireWoods Consulting
For yet another year, the availability of skilled labor remains the number one site selection factor, rated “very important” or “important” by nearly all respondents. This aligns with corporate executives’ priorities and reflects ongoing labor shortages across multiple industries.
However, state and local incentives have declined in importance, with 50 percent of consultants rating them as a very important factor—a noticeable decrease from the previous year’s 66 percent. This shift suggests that companies are relying less on incentive packages to offset rising operating costs and capital expenditures.
Another notable shift in this year’s rankings is the increased concern over energy costs and availability as a chief concern. In last year’s survey, energy availability and cost (20%) ranked behind economic pressures (46%) and workforce (26%) as a concern. This mirrors broader concerns about grid reliability, industrial power demand, and the rising costs of energy in high-consumption sectors.
Available land continues to be a huge concern for consultants. Fast-track permitting and the availability of shovel-ready sites continue to rank higher in the Consultants Survey than in the Corporate Survey, demonstrating the importance of speed-to-market considerations when selecting locations.
Which of the following will most affect your client’s expansion/investment plans in 2025?
Bold and exciting advancements are happening in the Grand Canyon state. Cutting-edge companies are launching, testing and scaling new technologies in Arizona. Our culture of innovation, highly skilled talent, lean regulatory environment, and affordable operating costs provide an ideal platform for business growth and success. The state has announced investment from industry leaders including Benchmark Electronics, JA Solar, LG Energy Solution, Lucid, Virgin Galactic, TSMC and more. Ranked top five for largest growing state, it’s clear why people are flocking here. Beyond being a place where you can achieve your professional goals, Arizona provides an unmatched lifestyle that allows you to achieve your personal goals. It’s this perfect balance that makes life better here.
Half of the consultants surveyed report that environmental, social, and governance (ESG) factors are now a consideration in site selection decisions, a significant jump from last year’s survey. While sustainability has long been a talking point in corporate strategy, it is increasingly becoming a hard requirement for many companies looking to meet carbon neutrality and emissions reduction goals.
Similarly, environmental regulations have climbed in the rankings, reflecting growing scrutiny over permitting, emissions standards, and compliance with state and federal sustainability mandates.
To what extent are sustainability goals of importance to your clients?
Direct Investment and International Influence
Global economic trends continue to shape site selection. Four out of five consultants are currently working on projects involving foreign direct investment (FDI), a percentage that has remained stable over the past three years. The CHIPS and Science Act and Inflation Reduction Act have driven renewed international interest in U.S. site selection, particularly in semiconductor, clean energy, and EV battery production, but questions about those programs loom under the Trump administration regime. To
What are some site selection trends to look out for in 2025?
The trend right now is that there is no trend. From active projects to prospects, it's all over the board right now.
Lindsey Cannon, Managing Director at Quest Site Solutions
Expecting some amount of tariff-riskmanagement driven onshoring. Clients are extremely concerned about the fate of the IRA and whether incentives may be clawed back. Craving more certainty from the Trump administration.
Joe Carpenter, Director, Location Strategy and Analytics at PwC
Are you currently working with any international companies / foreign direct investment (into U.S.)?
With prime sites and industrial parks across eight counties and the City of Columbia, the Central SC Region offers businesses the space, access and infrastructure to scale for success.
AVAILABLE SF: 57,394
AVAILABLE ACRES: 260
Scan QR to view drone footage and available properties at the center of South Carolina’s thriving business landscape.
wit, consultants are generally worried about new administration policies.
Nearshoring and reshoring are also key themes in 2025. Many consultants reported assisting clients in relocating supply chain operations from Asia to Mexico, Canada, or the U.S., reflecting continued supply chain diversification efforts.
Consultants widely agree that economic conditions continue to be the biggest variable influencing site selection. More than 85 percent report that inflation, interest rates, and recession concerns are either greatly or moderately affecting their clients’ expansion plans.
Yet, despite these concerns, the volume of projects has remained steady, with a growing focus on strategic investments in manufacturing, logistics, and corporate headquarters.
As companies navigate cost pressures, workforce constraints, and shifting regulations, consultants remain focused on identifying competitive locations that offer the right mix of talent, incentives, and infrastructure to support long-term success.
What are some site selection trends to look out for in 2025?
How much do you expect policies from the new U.S. administration to impact your clients’ expansion or investment plans?
How much are current economic conditions affecting your clients’ expansion or investment plans?
A key trend shaping site selection in the battery sector (which supports energy storage, EVs, military equipment, and electronics) is the evolving policy landscape around critical minerals. While the Trump administration has rolled back policies supporting EVs, it announced a new DOE funding round for battery materials and issued executive orders aimed at bolstering domestic critical mineral supply chains. This could accelerate existing projects and create new opportunities. However, ongoing trade tensions with Canada could complicate projects—Canada currently ships $24B a year in critical minerals to the U.S., a number that was set to grow. If tensions escalate, the U.S. may find it more difficult to secure these minerals, hindering domestic project expansion.
Isabel Cyr, Public Affairs & Communications Director at Lithion Technologies
Pramod Raheja CEO and Co-founder Airgility
Finding STEM talent doesn’t have to be difficult. In Maryland, it’s not. For Airgility, only the best and brightest STEM workers will do. That’s why we built our business here.
The past few years have presented an evolving economic landscape for corporate decision-makers. From inflationary pressures and supply chain disruptions to federal legislative incentives and shifting workforce expectations, businesses are continuously recalibrating their expansion and investment strategies. The 39th Annual Corporate Survey provides an in-depth look at how corporate leaders are adapting to these changes and what priorities are shaping their site selection decisions heading into 2025.
Which category best describes your company’s business?
What are some site selection trends to look out for in 2025?
A lot of interest from many in the marketplace right now about whether new cost-cutting efforts may significantly impact federal programs important to their business objectives. Also, many are monitoring the geopolitical tensions around the globe and considering how ongoing (or expanded) regional conflicts may impact their supply chain(s).
Steve Tozier, Executive Director, Indirect Tax at EY
Power capacity and timeline to serve are leading most major industrial and data center projects with the others coming in far second because it is such a dynamic time.
Kim Moore, Executive Managing Director at Newmark
The composition of survey respondents reflects a strong manufacturing presence, with nearly half of all corporate executives representing manufacturing firms. This continues a trend observed in prior surveys, where industrial sectors dominated site selection and expansion activities. Additionally, business ser vices, transportation, and food processing companies represent significant portions of the respondents, underscoring the broad industry reach of this survey.
Ownership and decision-making authority remain consistent with past results: nearly 60 percent of respondents are either CEOs, presidents, or partners, giving weight to the insights captured in this year’s survey.
How many people does your company employ worldwide? (all facilities)
Corporate leaders remain measured in their approach to expansion. Only about one out 10 of our respondents plan to open a new domestic facility in 2025, a big change from last year when 1/3 of respondents planned to open a new facility.
This cautious stance aligns with the economic pressures that continue to weigh on investment decisions. However, companies that are expanding are primarily focusing on manufacturing, distribution, and warehousing operations—a trend that has held steady over the past three years.
The state’s advanced manufacturing sector is driving innovation, improving efficiency, and strengthening critical supply chains
By VEDP
Speed, efficiency, and reliability are essential competitive edges for any manufacturing operation. Companies are finding that new types of manufacturing technology can deliver levels of precision never before possible, creating safer, more secure, more sustainable, and higher-performing products. The growing adoption of advanced manufacturing techniques isn’t just boosting the efficiency with how goods are produced — it’s changing the types of goods that can be made and where they are produced.
Along the Interstate 95 corridor in central Virginia, innovative manufacturing techniques have helped create a pharmaceutical manufacturing hotspot in the cities of Richmond and Petersburg. Biopharma companies are seeking to put much-needed medicines in the hands of consumers faster and cheaper through advanced manufacturing.
Phlow Corp., a Certified B Corporation based in Richmond with a manufacturing facility in Petersburg, is focused on leveraging advanced manufacturing processes to reimagine the domestic production of key starting materials and active pharmaceutical ingredients (API), an area of particular vulnerability for the United States. The company leverages continuous manufacturing processes developed at Virginia Commonwealth University’s Medicines for All Institute that involve sustained processing of raw ingredients and completion of medicines instead of manufacturing in smaller batches.
Continuous manufacturing can come with high upfront equipment costs, but increases yield while decreasing the waste of traditional batch manufacturing, which makes it more economically competitive. In continuous manufacturing, testing occurs intermittently throughout more automated processes, allowing for product quality issues to be addressed in real time and prior to becoming a finished product.
As Robby Demeria, Phlow’s chief corporate affairs officer, put it, “We’re not just creating advanced processes, we’re relooking at chemistry that hasn’t been looked at in decades. We can reduce needed steps exponentially.”
Elsewhere in Virginia, advanced and additive manufacturing companies are leveraging automation, data collection, and advanced analysis to identify opportunities to enhance production capacity. In 2023, the Additive Manufacturing & Advanced Materials (AM2) Tech Hub was launched to formalize collaboration across companies. Headquartered in Radford and funded through a federal Tech Hubs Strategy Development Grant, this consortium of more than 50 partners has set its sights on accelerating the growth of manufacturing in the New River Valley and across the southern part of Virginia.
Major institutions have taken notice of the advanced manufacturing capabilities found in Virginia. The U.S. Department of Defense engaged MELD Manufacturing in Christiansburg to create seamless components for tanks and other vehicles, looking to reduce the vehicles’ vulnerability to explosive devices.
To remove this weakness, the U.S. Army contracted with MELD to deliver a custom machine capable of printing metal components 20 feet by 30 feet by 12 feet in size. The resulting “Jointless Hull” machine, the world’s largest additive manufacturing apparatus, was designed to print massive metal sheets to serve as seamless tank hulls.
Emerging technologies are making it possible to work with advanced materials and even produce parts on the go. Imagine, for example, the tactical advantage of a naval vessel printing replacement parts onboard and on demand. Creating these innovative components requires innovative equipment, and this is where MELD Manufacturing delivers. The company’s machinery uses additive friction stir deposition, a technique that allows for the printing of metal without melting it to a liquid state, allowing the company to print in metals like copper and titanium that would otherwise be unprintable. Many of these materials are particularly valuable to the aerospace and space industries due to their improved performance of wear, corrosion, and heat resistance characteristics. These properties, alongside the scale of parts that MELD equipment can deliver, have prompted clients as varied as NASA, SpaceX, and Blue Origin to adopt MELD’s additive manufacturing technology for use producing spacecraft components.
Virginia has become a hotbed for advanced manufacturing techniques with the potential to solve key issues for the United States and the world. Companies in the Commonwealth are innovating throughout the process to stabilize essential supply chains and improve lives in the U.S. and beyond.
This article was paid for and written by the Virginia Economic Development Partnership and approved by Area Development.
The Port of Virginia recently wrapped up $1.4 billion in upgrades to its Hampton Roads facilities, opening a new, wider shipping channel that allows two-way traffic of ultra-large container vessels, saving an estimated 15% of time on berth. The port continues to work on its dredging initiative, which will create the deepest, widest channels on the East Coast. It’s upgrades like those, in addition to targeted investment in site development, that led CNBC to name the Commonwealth its No. 3 state for infrastructure in its Top States for Business rankings (and the top state overall).
Does your company plan to open a new U.S. facility in 2025?
For yet another consecutive year, economic pressures and labor costs rank as the most critical site selection factors.
More than percent of respondents rated economic pressures as “very important” reflecting the ongoing struggle to attract and retain skilled workers in an increasingly competitive labor market. Energy availability and cost, while not as big of a concern as for the consultants, is notably higher among the corporate respondents this year, too.
Construction costs have business leaders giving pause, too. It’s the number one real estate factor for corporate respondents in terms of making a site selection decision.
In terms of infrastructure requirements, it’s all about energy and energy cost, like last year. Projects nowadays require enormous amounts of power.
Property taxes are top of mind for corporate respondents this year. Interest in tax exemptions and state/local incentives remained high as well. Companies are placing greater emphasis on incentives that can offset capital expenditures and long-term operating costs.
What site selection factors have changed most?
Certified sites, while helping you gather the requisite information for one site, are not as important as having a site that is pad ready for development. In manufacturing site selection most sites do not have a solution for delivering the utilities, solving the utility equation right now appears to be the most critical location factor.
Bradley Midgal, Executive Managing Director, Business Incentives Practice at Cushman & Wakefield
Due to the current lead time of 36 months for transformers, the available power capacity is a big advantage. Also worth noting that water shortages are a major concern to my FDI clients.
Alexandra Segers, General Manager at Tochi Advisers
Which of the following will most affect your company’s real estate expansion/investment plans in 2025?
Policies
Contrary to the results of the Consultants Survey, corporate leaders don’t seem to think the election of Donald Trump will have too much of an effect on their site selection decisions. More than 30 percent of those surveyed said it would have no impact at all.
Perhaps surprisingly, the same cohort is leaning into the importance of environmental regulations. This increase suggests that businesses are growing more aware of sustainability mandates, emissions reduction requirements, and the impact of evolving government
* All figures are percentages and are the total of the “very important” and “important” ratings of the Area Development Corporate Survey and are rounded to the nearest tenth of a percent.
At the nexus of access and influence exists a place where the frontiers of the future are being reimagined. Here in Fairfax, businesses from rising startups to Fortune 500s find fertile ground to put down roots and scale to new heights. A community grounded in diversity of thought, we are the center of gravity where purpose and progress intertwine. In this place, icons come to reinvent, and the workforce of the future is being built today. From here, you can dent the universe.
www.fairfaxcountyeda.org
Flint and Genesee County, Michigan is
Leveraging workforce programs and military partnerships to fill job gaps and retain skilled veterans in high-demand industries
By Kansas Department of Commerce
Like most other states, Kansas has a worker shortage. And, as the number of international companies locating here and existing businesses expanding operations continues to soar, Kansas has more opportunities for lucrative careers than ever before. Almost 60,000 brand-new jobs have been created since 2019 alone.
One of the strategic approaches Kansas employs to find potential talent for a wide range of available positions is to work collaboratively with private-sector employers and military members about to transition out of the service. With three military installations, the Sunflower State is home to a large number of military families. Approximately 3,000 members of the armed forces rejoin the civilian sector each year in Kansas. Research reveals only about 10% of these veterans decide to remain here.
The state does not see that as a deficit. Instead, it is committed to bridge workforce gaps, assist military transitions, and
retain this highly motivated, trained talent in Kansas — and fill critical roles in all industries.
By investing in programs that focus on post-military education and employment, Kansas has created an environment where veterans can plant roots and thrive. Kansas’ state-level support for military families through initiatives such as military articula-
tion agreements with education institutions, workforce engagement and services, and occupational licensure reciprocity.
In 2021, Governor Laura Kelly signed the bipartisan Occupational License Reciprocity bill — recognizing that a license obtained in one state by military spouses also is valid in Kansas. By expanding on the existing law, it’s now easier for military spouses to utilize their professional licenses and find fulfilling careers in Kansas.
KANSASWORKS is another Department of Commerce workforce initiative that assists jobseekers find reliable employment in any region of the state. Qualified veterans are granted priority in employment offerings through KANSASWORKS, as well as assistance with referrals to specific job openings, training or related services.
With the goal of retaining and growing the state’s workforce, Kansas is committed to being a leader in the SkillBridge program offered through the U.S. Department of Defense (DoD). The state’s laser focus on growing and retaining workforce and partnership with the SkillBridge program will bring opportunities for transitioning service members – and provide a viable solution for companies with critical vacancies in Kansas.
The DoD’s SkillBridge program assists veterans with postmilitary employment opportunities such as training, apprenticeships and internships that prepare them for permanent employment at the conclusion of their service. Participating service members are granted up to 180 days of permissive duty to focus solely on training and gaining in-demand work experience.
The shared values and goals at the federal and state level make for great partnerships to elevate the work being done by both entities.
Economic opportunities are booming in the Sunflower State, and there are no signs of the momentum slowing down. With innovative programs such as SkillBridge — and dedicated workforce development professionals at KANSASWORKS — there is no doubt that Kansas will be a strong player in assisting and placing veterans and their families into promising careers.
For more information on doing business in Kansas – The State of Unexpected, please visit kansascommerce.gov.
Kansas provides bridges for military members transitioning to civilian duty.
Do you have a company that prioritizes hiring veterans?
policies on their site selection choices. Similarly, these same respondents said that sustainability goals were more important this year than last year.
In terms of labor, corporate leaders still prioritize labor costs and access to skilled labor above all. But they continue to show a strong preference for right-towork areas and low union profiles.
Overall, economic pressures remain at the forefront of corporate leaders’ minds. More than half of respondents cite economic uncertainty as the biggest factor influencing their 2025 expansion plans, mirroring sentiments from previous surveys.
Rising interest rates, supply chain realignments, and geopolitical concerns all contribute to a landscape of cautious investment.
However, there are also signals of optimism. Consumer confidence has rebounded, business sentiment is improving, and companies continue to explore opportunities for expansion.
With government incentives like the CHIPS and Science Act and the Inflation Reduction Act still shaping investment decisions, many businesses are leveraging federal support to move forward with strategic growth plans.
As 2025 unfolds, companies will need to balance cost efficiency, workforce availability, and sustainability priorities to remain competitive in an evolving business environment.
The 39th Annual Corporate Survey provides a snapshot of these priorities, reinforcing the enduring significance of labor access, incentives, and regulatory clarity in site selection strategies.
How much are current economic conditions affecting your company’s real estate expansion/investment plans?
How much do you expect policies from the new U.S. administration to impact your company’s real estate expansion/investment plans?
How companies should think about evolving utility policies to secure reliable power and mitigate risks in a shifting electric landscape
By Sarah Carnes, Senior Consultant, Enterprise Services and Location Strategy practice at Deloitte Consulting LLP
Think the recent surge in electric demand is a thing of the past? Think again.
Despite relatively flat demand since the early 2000s, advanced economies are experiencing a resurgence in electric demand. In the United States, domestic electric demand is projected to increase approximately 2 percent annually over the next three years—adding the total electric demand of California to the nation’s grid during this period.
This uptick—driven by increased data center activity, the electrification of the automotive and household appliance sectors, and a revival in domestic manufacturing, particularly among energy-intensive users like chip manufacturers—means that energizing large-load projects on expedited timelines will remain a challenge in the immediate future.
The evolving energy landscape is prompting electric service providers to rethink how upgrade costs for new customers are covered. While utilities have a duty to serve, service now comes at a higher upfront cost for select users. Understanding cost variations across markets, industries, and among service providers is crucial; upfront contributions may otherwise impact a company’s business case in a particular location.
In some regions, capital- and energy-intensive investors have often avoided paying for transmission line upgrades and other system improvements required to service their projects, instead paying facilities charges for dedicated assets like substations. But expectations are shifting as utilities grapple with mounting interconnection requests, which in some instances represent cumulative loads that exceed their current peak demands.
For example, the Georgia Public Service Commission approved a new provision in January allowing Georgia Power, the state’s largest investor-owned utility, to modify standard terms and conditions for new customers with demands of 100 megawatts or more. This change aims to insulate existing residential, industrial, and commercial customers from risks associated with larger projects. Eligible costs for recovery include upstream generation, transmission, and distribution improvements required to service the new customers’ facilities. Additionally, all contracts meeting this megawatt threshold must now be approved by the Public Service Commission.
Other jurisdictions are considering upfront payments for energy usage. The Public Utilities Commission of Ohio is expected to rule in the
coming months on a new pricing scheme for data center users. Under the current proposal, a data center customer may be required to purchase up to 85 percent of its projected power demand in advance of consumption—regardless of actual electricity usage. Other specifics on how the potential provision would apply are yet to be determined. Regulators in other states, including California, Indiana, Texas, and Virginia, are also considering how to allocate upgrade costs required to serve data centers.
Electric utilities and their regulators seem most occupied by managing load growth spurred by data centers. But leaders contemplating any energy-intensive deployment should be prepared to actively engage with utilities to understand current practices and future expectations on cost recovery, including the level of support from regulatory bodies for economic development projects.
Asking about the weather is no longer just small talk. Executives must now consider the immediate and long-term impacts of power supply interruptions on their operations, especially as extreme weather events become more frequent and the adequacy of reserve margins is tested. Energy-intensive operations are particularly susceptible when these weather events coincide with increased electric demand, often leading to supply disruptions.
Weather-related outages in the United States nearly doubled from 2014 to 2023 compared to 2000 to 2009. Severe weather—such as high winds and thunderstorms—and winter storms accounted for more than 80 percent of outages, with the South, Southeast, and Northeast experiencing the most impacts. The North American Electric Reliability Corporation (NERC) reports that maintaining reliability during winter is increasingly complex, raising questions about how utilities are incorporating resiliency and reliability measures into their system planning activities.
System reliability is challenged by more than just the weather. The pace of new resource additions and grid improvements is outstripped by asset retirements and growth in power demand. In December 2024, NERC released its long-term reliability assessment on 20 geographic regions across the United States and Canada, reporting that more than half of analyzed regions are at a “high” or “elevated risk” of electric supply shortfalls over the next five years. The Midcontinent Independent System Operator (MISO)—the electric grid operator for 15 states and one Canadian province—appears to be at the greatest risk, with supply shortfalls anticipated as early as this summer due to delayed resource additions and generation asset retirements.
To maintain operations and avoid financial losses, executives exploring expansions or new deployments should consider implementing electric supply security measures, such as:
• Behind-the-Meter (BTM) Solutions – Energy that can be generated or provided onsite and used directly by the end user. BTM energy systems do not require power from the grid to remain energized. Examples include onsite generation (such as solar), energy storage (such as commercial-scale batteries), and microgrids.
• Demand-Side Management (DSM) Solutions – Energy reduction and load management strategies that aim to increase operational efficiency and reduce energy costs, typically through shifts in the timing of energy usage. Many utilities offer demand response programs, which may provide financial incentives for achieving energy reduction targets at certain periods.
Corporate executives should rigorously evaluate electric service providers during the site selection process; doing so is critical for operational planning and risk mitigation. Multiple rounds of technical discussions and due diligence are required to adequately assess service providers’ capabilities and potential blind spots—which could otherwise leave companies in the dark.
Immediately following his inauguration in January 2025, President Donald Trump declared a national energy emergency, issuing an executive order directing federal agencies to develop “a reliable, diversified, and affordable [national] supply of energy.”
The National Energy Dominance Council is now tasked with delivering a set of recommendations to the president by late May on how the administration can expand domestic energy production, expedite permitting and regulatory requirements for energy projects, and lower energy costs. The council is also advising on incentives for private-sector energy production investments. Given the immediate directive to address supply constraints and emphasize baseload resources like fossil fuels, nuclear, geothermal, and hydropower, the scale, timing, and federal support of clean energy projects remain unclear.
At the same time, the National Governors Association is pushing for bipartisan support to accelerate infrastructure investments and permitting for the siting, approval, and construction of new energy assets, acknowledging tightening supply and the need for more firm capacity.
Corporate executives preparing for future projects should consider the potential impacts of federal energy policy shifts on their operations, including:
• How will changes in federal energy policy influence the availability, procurement, and cost of renewable energy?
• W hat are the financial implications of potential policy changes on operations?
• How will shifts in federal policy impact state-level regulations and influence utilities’ priorities, such as generation asset retirements?
As power supply becomes more constrained in some regions, corporate executives planning facility deployments or expansions should explore behind-the-meter and demand-side management solutions to mitigate potential operational disruptions. Companies should also assess variations in upfront cost contributions across utilities and monitor pending regulatory changes affecting large-load users.
By Ermengarde Jabir, Director of Economic Research at Moody’s
The industrial sector has undergone a seismic shift over the past five years, transforming from a stable yet unremarkable sector into a high-growth, frenetic superstar sector. Nonetheless, exponential growth is not forever, nor should it be, and as the industrial sector stabilizes, new opportunities and challenges emerge for the property type.
Nearshoring and reshoring have been top-of-mind for manufacturing and industrial commercial real estate investors alike. While globalization led to manufacturing in concentrated locations where there was a competitive advantage – think production in the lowest cost location – the global shut down of trade brought on by the pandemic revealed the need for more domestic manufacturing of critical intermediate and final goods.
A key example of this is semiconductors. Supply chain stress skyrocketed as countries shut down production and shipping during the pandemic. Although conditions have vastly improved in the five years since the start of the pandemic, the supply chain stress index remains elevated, 12.4 percent higher than its long-term prior average.
In response to these challenges, the CHIPS Act was passed in 2022 with the primary goal of reshoring semiconductor supply chains, along with other science-focused manufacturing sectors. The implications for industrial properties were clear: a buoying effect across various industrial property subtypes, including manufacturing, warehousing, and cold storage to name a few. This policy support
encouraged the private sector to invest in reshoring and nearshoring initiatives. Manufacturing investment in the United States has since soared due a desire to avoid the supply chain constraints and manufacturing limitations that contributed to decades-high inflation. While the growth rate of total construction spending on manufacturing has leveled off and remained flat for the last five months of available data (ending December 2024), monthly spending more than tripled from its most recent trough-to-peak cycle between November 2020 and June 2024, growing by 227 percent.
Focusing on reshoring, there has been tremendous activity in the industrial sector in the U.S., leading to outsized growth in property types and propelling the sector to a new higher-growth path. Nonetheless, there has been a pullback in recent industrial demand drivers, particularly from e-commerce growth, which is back on its original growth path. Many retailers have switched to just-in-time inventory management systems, reducing the need for warehousing goods for extended periods and instead focusing on storing and shipping items to customers directly from retail points of sale.
Nearshoring has also become a significant focus in recent years. Free trade agreements like the current United States-Mexico-Canada Agreement (USMCA) and the North American Free Trade Agreement (NAFTA) before it, combined with the competitive advantage of less expensive and well- established manufacturing processes, have incentivized manufacturers to relocate to Canada and Mexico over
Source: Federal Reserve Bank of St. Louis (FRED)
Source: Moody’s
Source: Moody’s
the past three decades as globalization has expanded to be in close proximity to final consumers in the U.S. The ability to engage in free trade across North America without tariffs for 30 years has resulted in numerous industrial hubs flourishing in border cities, performing remarkably well compared to the national figure in recent years in the effective rent growth category as overall growth in the asset type across the country has slowed. Border cities in the south with land crossings, like El Paso and San Diego, and in the north, with quasi-land crossings
in the form of a bridge, like Buffalo and Detroit, have had consistently lower vacancy rates than the national figure, regardless of the timing of the industrial market cycle. Additionally, other markets, including McAllen and Laredo, both in Texas, have burgeoned as the flow of goods from Mexico has expanded.
However, proposed and implemented policy actions in the form of tariffs present a headwind for nearshoring. Manufacturers, concerned about the duration and severity of tariffs might weigh the cost of domestic manufacturing against the cost of manufacturing abroad with a tariff fee structure in place. This comparison could influence their decisions, potentially favoring free trade scenarios over those with tariffs.
Employment metrics serve as a useful indicator in determining investor interest in reshoring and consequently, demand for industrial properties. In a May 2023 report, the Reshoring Initiative estimated that approximately 400,000 new jobs would be added that year for domestic manufacturing, a peak forecast for annual job growth. Such an optimistic forecast was based on the fact that in 2022, the number of observed reshoring and foreign direct investment job announcements peaked at 343,304. However, for that same metric, the observed number of jobs announced in 2023 only reached 287,299. While still the second highest figure on record dating back to 2010, the figure was nonetheless 16 percent lower than the prior year, highlighting that the strength and perseverance of reshoring waned slightly due to the time-intensive nature of the process. This slowdown in job growth coincided with a slowdown in the industrial sector, as both absorption and rent growth began to normalize.
Another example of changing policy targets related to manufacturing that have a strong impact on industrial demand relates to electric vehicle battery production. Growth in demand for this product was tied not only to changing consumer tastes for vehicles but also to an executive order passed in 2021 that required all new vehicles sold in the U.S. to be electric. However, this has since been reversed. Renewable energy in the form of solar was also supported by policy, but once again, the changing tides of policy priorities have pivoted away from renewables and toward natural gas extraction.
Although the positive impacts of reshoring and nearshoring initiatives have lessened over the course of the past two years, as policy focuses shift in 2025 and geopolitical risk endures, renewed investment interest in this industrial tailwind can be expected on one hand, while on the other, the site selection decisions may move away from border cities to manufacturing heartlands.
It’s looking like a question of when, not if. A look ahead at this emerging technology — and what it means for economic development
By Lee Walker Helland Area Development Staff
ardly a day goes by that we’re not absorbed in artificial intelligence news. Unprecedented product launches, enormous data center projects, and concerns around the tech’s energy consumption and sustainability dominate tech headlines. But meanwhile, a smaller and quieter narrative about the future of data processing is quickly gaining volume and momentum.
Tech giants like IBM, Google, and Microsoft, along with academic, healthcare, and government institutions around the world, are racing to develop quantum computers, a completely different information technology that has the potential to increase A.I.’s speed and power. Scaling quantum computing would mean rethinking data centers as we know them, but the payoff could be huge: thousands of profitable businesses, geopolitical dominance, and solutions to some of humanity’s biggest challenges, like cancer and climate change.
So while quantum headlines only make a tiny ripple compared to the giant splash of showy announcements like Stargate, OpenAI’s $500 billion A.I. infrastructure endeavor, or the $60 billion that Meta has committed to investing in A.I. this year alone — folks in economic development are already preparing for a quantum computing wave. While some experts assert that we’re still 20 years away from reliable, practical, profitable applications of quantum, others say this could happen much sooner.
“The timing is not what people think it is; I don’t think it’s two decades,” says Victor Hoskins, President and CEO of Fairfax County Economic Development Authority (FCEDA), a local government funded organization in Virginia, the largest data center market in the world according to a 2024 report from the Joint Legislative Audit and Review Commission (JLARC). “I think a decade from now there will already be a lot of practical
The estimated economic value quantum computing could generate by 2040 (Boston Consulting Group).
applications [of quantum computing].”
Indeed, just in the past 12 months large-scale quantum data centers have opened in Israel and Germany, and IBM completed a major expansion of its Quantum Data Center in Poughkeepsie, NY. Colorado recently won a $40.5 million federal grant to establish a quantum computing hub in the state, and Illinois has committed $500 million to develop the National Quantum Algorithm Center, a partnership among IBM, the University of Chicago, and the University of Illinois Urbana-Champaign.
Here’s a look at the state of quantum computing, its growth trajectory, its unique data center requirements, and how business and civic leaders can start preparing today.
A unique information technology with distinct capabilities and needs
Since the 1980s, scientists have been experimenting with quantum computers and their potential to process vast amounts of data much more quickly and accurately than the classical computing systems we use today.
Unlike classical computers, which process information in binary bits (0s and 1s), quantum computers leverage qubits, data units that are capable of existing in multiple states simultaneously—a phenomenon known as superposition. This flexibility allows quantum computers to perform extremely complex calculations at speeds unimaginable with traditional systems, including A.I. Additionally, a quantum phenomenon called entanglement enables qubits to be interconnected, further enhancing these new computers’ potential to process unprecedented data loads with accuracy and efficiency.
Quantum computing is still in early stages, and it’s a small world — last year’s third annual Quantum World Congress, a conference co-sponsored by FCEDA, had about a thousand in attendance, representing 30 countries. But that’s double the crowd compared to the conference’s debut in 2022.
Plenty of money has been directed toward this research. Since 2020, the U.S. government has invested between $3 and $4 billion into quantum technology (which includes quantum sensing, communication, and materials in addition to computing). And venture capital investors have also coughed up roughly $3 billion for quantum computing in recent years.
Increasing investments yield new advancements every year as scientists work to prove and scale “quantum advantage” — a problem or class of problems that quantum computers can solve better than classical machines.
“We believe that before the end of 2026, we’ll reach advantage in a real problem,” says Antonio Córcoles, PhD, Head of Quantum and HPC and Principal Research Scientist at IBM. Córcoles leads a group of several dozen developers who are building user-friendly software architecture around IBM’s evolving offerings
and capabilities — part of the company’s extensive and ambitious quantum computing roadman.
Experts say the earliest practical applications of quantum computing are likely to be in cybersecurity in addition to chemistry, opening doors in fields like life science and drug development. According to a 2024 report from Boston Consulting Group quantum computing could create up to $850 billion in economic value by 2040.
Unlike the simpler bits used in classical computing, qubits require extreme stability in order to maintain their quantum state. This poses significant challenges for data center facility planners.
First, qubits need to be kept extremely cold — near absolute zero, or −459.67° F — to eliminate thermal vibrations that can disturb calculations. IBM has already built a special helium-based cryogenic fridge, which is in use at its Quantum Computation Center in Poughkeepsie. Dubbed “Project Goldeneye,” the device is intended to help them develop a scaled-up cooling method to pave the way for quantum data centers in the future.
Others are experimenting with alternative cooling techniques. Researchers at the University of Rochester, for example, recently won a $1.25 million grant to explore how quantum mechanics itself, specifically quantum “dots” that trap electrons, might facilitate an ultra-cold environment that costs less and uses less energy — music to any data center operator’s ears.
Similarly, qubits must be insulated from electromagnetic disturbances and noise, something that will require a considerable pivot from the loud roar of today’s data centers.
How the solutions to these problems will be implemented into facility design remains to be seen. Fred Miller, Project Executive at Gresham Smith, a Nashville-based architecture firm that designs and plans “mission-critical” facilities including many data centers, says he’s not getting requests for quantum data center projects — yet.
But many in the economic development space are confident that these quantum data center challenges will be surfaced, solved, and scaled. “It’s just [a question of] when the science is ready,” says George Thomas, President and CEO of Connected DMV, a nonprofit dedicated to solving economic development challenges across Washington DC, Maryland, and Virginia, and host of Quantum World Congress. “I’m never worried about engineering because we as creatures are optimization engines.”
Like many countries, the United States likes to maintain leadership in new technologies just for the prestige and bragging rights. When it comes to quantum computing,
there is an even greater incentive to arrive first. That’s because, as quantum computers continue to advance, they could easily surpass the cybersecurity threshold of today’s most sophisticated encryption and threat detection programs. Banking, retail, and national security data could be at risk in the future, or perhaps even now with a method called “harvest now, decrypt later,” in which bad actors steal information to decode later, once quantum has evolved enough.
Despite these potentially looming threats, some feel the U.S. government is not moving fast enough on quantum computing.
“When I consider the focus of some of the national labs in the U.S., they are at the moment so excited about AI that it’s hard to bring the quantum story,” Córcoles says, speculating that achieving quantum advantage could
Since quantum computers have been shown to complete calculations almost inconceivably faster than classical computers, some folks have suggested that they could be an answer to today’s energy crisis, which has been exacerbated by the colossal energy demands of A.I. Couldn’t we just replace power-hungry classical computers with sleek, efficient quantum processing?
The reality is more complicated. Córcoles says that while quantum will be more energy-efficient than classical computing eventually, achieving that is still some distance in the future. In the nearer term, it’s more likely that quantum computers will be deployed to solve problems that classical computers can’t even attempt. “In this way, the energy problem is a little bit different because we are talking about being able to compute something
“The timing is not what people think it is; I don’t think it’s two decades. I think a decade from now there will already be a lot of practical applications of quantum computing.”
— Victor Hoskins, President & CEO, FCEDA
be the type of breakthrough that prompts a sudden, drastic increase in quantum computing investments.
Another motivating factor: China may be outpacing the U.S. and allies in quantum computing, having published more research papers on the topic annually than any other country since 2022, according to the Mercator Institute for China Studies, the leading European think tank on China.
The U.S. government is perhaps unlikely to allow its main adversary to have a leg up on quantum for long, considering the implications for national security. “And that government money — once it starts coming, it flows,” Hoskins says.
“The barrier right now is that the [U.S.] government has to be more courageous and lean in,” Hoskins says. “The Netherlands is investing — what is it, $600 million in quantum? That’s a little country. We need to think about on a per capita basis what we need to invest. Breakthroughs don’t happen by accident, they happen by investment and intellectual prowess.”
versus not,” he says.
Further, the first large-scale quantum-friendly data centers will likely be hybrid, handling classical computations, too — similar to the task switching that’s now standard between central processing units (CPUs) and powerful graphic processing units (GPUs).
“You will [use quantum] for very complex correlation kind of functions and have the output sent to the classical [components] to handle whatever workflow you have,” Córcoles says. “So every quantum computation is going to be surrounded by classical processing but without quantum, you won’t have the access to very important problems.”
Therefore, it’s quite possible that quantum computing will hit some level of mainstream before it becomes the answer to our sustainability problems. This means that data center owners’ and tech leaders’ current endeavors to source more power and/or right-size tech stacks are more necessary than ever.
“Utilities and power availability is a driving factor right now, because computing density keeps going
up, and more and more power is required,” Miller says. “People are already scouring the United States looking for any utility that might have a few hundred megawatts of available power that they could put to work or a data center project.” Some tech companies are exploring nuclear energy, though this is not expected to be a quick fix, as the up-front cost and time commitment for new nuclear power plants are significant.
“Perhaps there could be a 100,000-qubit machine that can replace a hundred A.I. data centers, in which case the footprint would be smaller,” Thomas speculates. “But we just don’t know those answers.”
Córcoles asserts that collaboration with traditional data center partners sooner rather than later is crucial. “When we get to the end of this decade, when data centers are going to really be benefiting from these quantum computers, if we have standardized things enough [by then], it won’t be a lot of effort structurally or infrastructurally.”
The projects involved in necessitating and developing the quantum data centers of tomorrow could be significantly slowed by labor shortages.
First, this industry would have to create the demand for quantum data centers in the first place — meaning, enough businesses, academic institutions, organizations, and government agencies have to be leveraging quantum computing to even have a need for large-scale data centers. Here, the advancement of quantum computer science may be ahead of the available workforce. A 2022 McKinsey report revealed a major gap between available quantum computing jobs and people to fill them.
Connected DMV runs quantum programs for area high schoolers — workforce development for 10 years on (and beyond). “Many of them have entered Ivy League schools in physics and quantum to build this [field] up,” Thomas says.
Thomas explains that this year, his organization is focused on supporting middle schoolers’ interest in quantum, too. “By the time they get into the seventh grade, kids [are having to make choices that] restrict them.”
Part of his organization’s strategy even involves raising awareness of quantum computing among middle school teachers, who could have considerable influence on their students’ academic paths and the quantum computing worker pipeline.
Then there’s the question of designing, permitting, and building a scaled-up quantum data center. With classical data center development already soaring today, Miller says, credentialed contractors and their skilled crews are in high demand. Depending on where a data center is being built or modified, there may be a wait.
Tying quantum into existing data centers may minimize snags. The classical computing folks already did the
hard work of finding spots with energy, water, reasonable bureaucratic pathways, and amenable local communities where local energy and safety requirements have been met — and where not-in-my-backyard (NIMBY) responses have been avoided or overcome.
Is there any way to predict when quantum data centers will be needed?
Guesses vary widely, but Thomas suggests one reliable way to follow quantum computing’s trajectory and be ready to meet data center demand: Watch quantum computing enterprise activity.
“If I am a generic data center owner in Northern Virginia, I don’t need to be thinking about whether I’ll have a full-scale quantum-only center today because there’s 50 different business opportunities between now and then.”
Eventually, Thomas says, there is likely to be a tipping point at which there are enough quantum-related businesses, which attract enough users, to warrant a ramp-up in data centers that can accommodate quantum calculations. “I would estimate dozens if not hundreds of companies are going to start popping up,” Thomas says — enterprises in finance and biotech, either building quantum machines or quantum-reliant software that runs on the cloud. We’re just not there… yet.
Córcoles also seems confident. “Within my career, I will see… important developments that are held by quantum, and that excites me a lot,” Córcoles says. “Let’s say that quantum helps make progress in developing a vaccine an order of magnitude faster — that’s a huge impact on everything. That’s an easy example, but there are many more.”
What leaders in the data center space can do now: Spend the next few years paying attention to big tech’s quantum teams, and to the academic institutions they’re partnering with, to get a sense for advancements, timelines, and breakthroughs in infrastructure design. And if you’ve got friends in cryogenics, it may not hurt to start sending them holiday cards.
How economic developers, manufacturers, and policymakers can prepare for potential trade shifts
By Charlie Smith, Managing Director, Geopolitical Strategy at Newmark
Tariffs are rising in prominence as a key variable and economic tool in the global macroeconomic conversation, creating a new era in global trade.
At the core of this conversation are ongoing trade dynamics between the U.S. and China. China’s economic position continues to be driven by broad-based export growth and global dominance in manufacturing, spotlighting U.S. competitiveness in key strategic sectors. China’s strength in advanced manufacturing and security-relevant sectors is a large focus for U.S. officials, and U.S. politicians maintain a cautious stance toward the country. Indeed, the tariffs laid out in the first Trump administration were expanded during the Biden administration, reflecting the bipartisan appeal of this economic tool.
In recent months, the discussion of tariffs has extended to countries and regions such as E.U., Mexico and Canada – the latter two of which are members of the U.S.-Mexico-Canada Agreement (USMCA), a free trade agreement, and are the United States’ top two trading partners (followed, of course, by China).
Given that tariffs are already being deployed in the early days of the new U.S. administration, keeping an eye out for directional signals can indicate which way tariffs are moving in the near-term and help economic developers, governments and businesses prepare.
To that end, this piece reviews some major U.S. trade partners and signs that may signal reduced or increased tariff pressure for them.
Increased Tariff Pressure
China
• Status quo persists
• Weighted media attention
• Negotiation complications
• Ear ly trade talks
Reduced Tariff Pressure
• U.S. Administration offers reprieve
• L ower Chinese export volumes
Tensions between the U.S. and China are high and the new administration continues to focus much attention on economic competition between the two countries. The bilateral relationship eased a bit in 2024, because of internal dynamics in each country. Otherwise, the trend has persisted
If this status quo continiues, both countries are under pressure to respond to the other, creating a likely scenario for tariffs and offering fewer opportunities for de-escalatory paths.
Relations between the U.S. and China continue to be a leading discussion in the media. With the possibility of
The current U.S. tariff rate on Chinese electric vehicles, a major barrier to entry for Chinese automakers.
security, social or economic incidents hitting the front pages, as has occurred in the media over the past several years, tariffs and other policies would be a natural tool – among others – for a response.
For example, the spotting of a high-altitude balloon originating from China held wide attention in the U.S. for an extended period, but also directly led to state-level laws across the U.S. restricting or prohibiting the purchase of land by firms or citizens linked to China, as well as other investment restrictions.
Tariffs are generally not an end in-and-of-themselves but serve a desired end goal and deal. In the instance of U.S.China tariffs, the stakes are higher than trade conflicts of the past. Wrapped up in their complexity are matters of not only economic, but also political, military and social importance. The perceptions of tariff negotiations among the U.S. and Chinese populations are a key component. Negotiations would be a tool of communication by one or both sides that the tariff threat is real and, perhaps, imminent. Odds for tariffs would rise in this scenario.
As its trade balance is heavily weighted toward exports rather than imports, it is likely that China would favor more trade and fewer tariffs. The reverse is the case for the U.S., whose trade balance is more heavily weighted toward imports. As such, this signal is most meaningful if initiated by the U.S. Indications by the U.S. that there is interest in talks opens a window for discussion. Should these talks continue with positive framing by both sides, then a lower/no tariff outcome could be more likely. But it would take sustained, tangible progress for the lower/no tariff outcome to extend into a longer-term scenario.
China has already taken more proactive measures toward potential tariffs than when they were initially introduced in 2018. These include economic measures (including tariffs of their own) and non-economic measures to bolster of their position, reducing the likelihood of China being the first to offer a trade-oriented reprieve. The U.S., then, may be in a better position to offer a tariff or trade reprieve. By making a gesture of reprieve, the U.S. offers goodwill to China in the hopes of reciprocal extractions. If that does take place, then a more collaborative dynamic could emerge, ranging from a postponement of possible tariffs to firmer agreements.
Underscoring its economic position, China’s trade of global exports continued to grow in the past few years, stimulating
calls for economic responses domestically. However, should China’s export volumes decrease, it could provide less incentive for U.S. tariffs on China.
This export decrease could come about from either Chinese government efforts or reduced demand from the market. China has long provided support to domestic industries, so if this stops or slows then it could be either a short-term or long-term solution, depending on the government’s appetite. Reduced market demand may well entail a global economic slowdown given the cost competitiveness of Chinese exports, a scenario that is longer-term in nature.
As mentioned, the U.S. trade imbalance with the E.U. drives the discussion around tariffs and how best to manage the imbalance. E.U. exports are weighted heavily toward a few sectors, such as pharmaceuticals, machinery, chemicals and vehicles. These are not the low-cost items that China exports in more volumes, but high value-added products that play sensitive roles in U.S. consumption and supply chains. That reason may have provided some tariff deterrent up to now.
• Election results align with U.S. administration E.U.
Increased Tariff Pressure
Reduced Tariff Pressure
• Trade imbalance increases
• Posturing by E.U. leaders
• E.U. corporate champions struggle
• U.S. energy purchase commitments
• Stronger actions to scale back relations with China
Should trade dynamics increasingly favor of E.U. exports, though, there may be more support for tariffs. This dynamic could suggest that structural factors are driving the imbalance, prompting suggestions for structural tools – including tariffs – that can address them. One consideration here may be an effort to attract more foreign direct investment (FDI) to the U.S., encouraging local manufacturing rather
than exporting. Discussion of this facet on the heels of an increasing trade imbalance may heighten tariff likelihood.
On the flipside of election results aligning with the U.S. administration, E.U. leaders and governments could choose alternative postures toward the U.S. Local officials may see domestic political benefits to this posturing to encourage support. Looming elections possibly provide a more fertile environment for this approach.
Doubling down on a defensive political posture may incentivize the U.S. to respond assertively, leading to an escalatory environment for both sides. There could be a pathway where firm responses lead to more considerate negotiations, so more a matter of posturing rather than implementation. However, this escalation comes with the risk of higher tariffs along with the opportunity of quicker resolution.
The E.U. is home to iconic industrial champions, such as VW, Siemens, and Telefonica, which bring both economic impact and social visibility. Dynamic changes in the global economy offer new opportunities and risks for these firms. There are good reasons for countries to support their globally leading companies; think of U.S. support for the automotive industry after the global financial crisis.
Should E.U. corporate champions have publicized challenges, local governments may be interested in protectionist measures to better protect them. These may include tariffs, but even if not, the political and economic moods could be less inclined to negotiate with the U.S. for better tariff terms, instead seeking to prioritize national champions.
The E.U. holds a significant positive trade balance with the U.S., which is a point of attention for the U.S. administration. Addressing a trade imbalance is not a simple proposition since trade is made up of countless decisions made by businesses and consumers on either end. That said, the U.S. administration has called out U.S. energy exports as a top area of opportunity for increased E.U. purchases.
The U.S. is the largest oil and gas producer in the world, so the scale needed to make an impact on the trade balance is there. The E.U. is already shifting its energy supply chain away from Russia, including higher purchases from the U.S. Announcing additional energy purchases by the E.U. would be a public show of its desire to collaborate with the U.S. to head off or mitigate a possible tariff situation.
In its attempt to establish stronger economic footing globally, the U.S. has worked with partner countries to align on related policies. Notably, U.S. restrictions on the sale of
advanced semiconductors to China have been adopted by other countries such as the Netherlands and Japan.
Should the U.S. continue to prioritize this global positioning, it would likely welcome similar acts by other countries. As one example, the E.U. is currently more open to Chinese electric vehicles than the U.S. Changing this, or other policies, in favor of a more restrictive stance toward imports from China would be a signal of support for U.S. positions, possibly as an attempt to avoid tariffs.
The E.U. is set to hold several major elections this year. Germany, Poland, Romania and others are holding national elections, setting the tone for near-term policy in those countries. This includes the prospect of wins by political parties and candidates whose views more closely align with the U.S. administration. Indeed, some politicians in Europe are selling themselves as more effective interlocutors with the U.S. administration due to shared goals.
This political alignment could lead to more constructive negotiations around new tariffs, including outcomes where they are reduced or avoided. Moving closer to the U.S. on any range of issues – China, security, technology, corporate taxation, etc. – could preclude the reasons for implementing tariffs in the first place.
A Mexican manufacturing plant for Chinese automaker BYD has been floated, with U.S. responses suggesting that this could affect the entire U.S. automotive industry. With a low cost and competitive quality of Chinese EVs compared with U.S. counterparts, BYD’s entry into the U.S. via Mexico may destabilize long-time U.S. electric automakers. With U.S. tariffs on Chinese EVs already at 100 percent, the intent to shift vehicle manufacturing to North America is clear.
Should the BYD plant, or other Chinese EV manufacturing facility, come to fruition, there may be less willingness to accede on other U.S. interests and increase the odds of tariffs as a result. It is worth noting that an opposite decision, to more visibly reduce or eliminate the possibility of Chinese EV manufacturing in Mexico, would reduce tariff tensions and fall under the “scaling back ties to China” category.
Migration into the U.S. via the border with Mexico is, as noted, an issue tied to potential tariffs. In 2024, efforts by Mexican authorities to limit the ability of migrants to reach the U.S. border lowered the number of apprehensions tallied by the U.S. Border Patrol. This suggests that the ability to control migration is partly administrative, although patterns could shift if the numbers change.
A surge in migrants may come down to two explanations. Either the Mexican government chooses to have more
Direction of Policy Mexico
• Chinese EV production occurs in Mexico
Increased Tariff Pressure
Reduced Tariff Pressure
• Migration surge
• Security concerns escalate
• Publicized actions on migration, narcotics
• Mexican President remains popular
• Stronger actions to scale back ties with China
• Ear ly renegotiation of the USMCA
migrating people reach the U.S. border, or Mexico becomes less able to control the flow, likely due to an increase in numbers. Given that Mexico has taken actions already on the former, the latter may be more possible. Rising political and climate issues in the Western Hemisphere (political repression in Venezuela, erratic growing conditions in Central America, etc.) are motivating factors for people to immigrate to the U.S., and a spike in migration would heighten tensions in the tariff negotiating context.
There are issues on both sides of the border regarding the security situation. For Mexico, these can be around U.S. demand for narcotics and a flow of firearms from U.S. sources to drug cartels. For the U.S., there are concerns around violence stemming from the drug trade. These are not new issues, but their persistence despite mitigating efforts over the years can increase tensions and prompt the use of escalatory measures, such as tariffs. The possibility of using U.S. military force, for example, could create a backlash in Mexico, leading the country to consider tariffs or other economic tools to change U.S. policy. Since security is a core function of any government, a deterioration on this angle may incentivize strong responses.
The U.S. administration’s focus on migration and the illegal narcotics trade continue to be relevant in in tariff discussions. It is not a new topic, and potential tariffs were
US Trade Deficits (in billions of dollars)
averted in both 2019 and already in 2025 after the Mexican government announced actions to boost security personnel on their borders.
Border actions may re-emerge as a negotiating point for potential tariffs, which has already proved productive for both sides. Previous instances had the Mexican government publicly announcing about these activities, clearly communicating their actions and intent. Any new public statements by Mexico to address U.S. concerns on the border or narcotics issues would also likely be intended as signals to avoid tariff issues.
The current Mexican President, Claudia Sheinbaum, won her election in late 2024 with the highest margin since 1982, and she retains over 70 percent support in recent polls. This comes on the heels of her predecessor, Andrés Manuel López Obrador (or AMLO), who hailed from the same political party and enjoyed similar popularity.
Possessing this level of popularity provides buffer room for more difficult and possibly unpopular decisions. These may include mirrored tariff actions, agreeing to terms sought by the U.S. over the course of tariff negotiations, which could
weaken a less popular official with claims of relenting to foreign pressure or similar arguments.
China’s investment in Mexico has risen in recent years, leading to claims that Chinese firms are violating the spirit of the USMCA to avoid tariffs, potentially running counter to the intended purpose of the agreement.
Should Mexico take visible actions to reduce ties with China, there may be less fuel for a tariff argument. Mexico could institute its own tariffs on Chinese goods, restricting the kinds of investment open to China, or publicly cancel more salient projects. At the very least, tariffs on Chinese goods would likely reflect a willingness by the Mexican government to take steps to ease U.S. concerns and potential tariffs.
It is not lost on Mexico or the U.S. (or Canada, for that matter) that the USMCA is up for review and renewal in 2026. Tariffs among these countries come into conflict with the agreement, setting the stage for a competitive renegotiation process.
To that end, one possible pathway may be an early renegotiation, even as soon as 2025. An earlier revision to the USMCA would signal a willingness to compromise by Mexico, as well as Canada, potentially bypassing tariffs as a negotiating tactic. Moving up the date would address trade uncertainty sooner rather than later, so it could be an attractive option.
Because the U.S. and Canada conduct such a high volume of bilateral trade, a flat tariff would affect many sectors on both sides. The U.S. Trade Representative reported over $900 billion in cross-border trade in 2022. Intermediate goods can cross the border several times before final assembly, compounding the tariff impact each time. All of this can disincentivize flat tariffs and reduce their utility.
What could be more plausible are targeted tariffs, such as the steel and aluminum sectors that have already been announced. Specific sectors for tariff application may be selected by the U.S. administration for having fewer side effects for U.S. industry. They could otherwise have a symbolic, but less material, impact. As such, a declaration of targeted tariffs on Canada, rather than a flat tariff rate, could have more credibility and chance for implementation.
Canadian oil imports are a critical piece of the current energy mix in the U.S. The Congressional Research Service notes that Canada provided nearly 60 percent of all U.S. crude oil imports in 2023. The specific kind of crude oil sent from
Reduced Tariff Pressure
Increased Tariff Pressure
• Specific U.S. tariff targets emerge
• Canadian oil becomes less attractive
• Election results align with U.S. admin
• Commitments on migration, illegal drug, and military collaboration
• “No news is good news”
Canada requires a particular refining process (as well as pipelines to transport it), but the U.S. has that infrastructure set up. Changing this arrangement would be costly, given the pieces that are already in place to change it.
However, the dynamic nature of energy markets over time could shift the underlying fundamentals. More U.S. oil could emerge, renewable energy sources could continue to gain market adoption, and new import sources may become more attractive. Guyana, for example, is only beginning to tap the 11 billion barrels discovered there. If Canadian oil becomes less attractive for U.S. buyers, which would be a medium- to long-term proposition, then the U.S. would have less of a pain point deterring it from using tariffs.
The current Canadian administration has taken a robust response to tariff announcements so far. The current Prime Minister stated in response to proposed U.S. tariffs that, “We didn’t ask for this but we will not back down.” What could change this posture is that Canada is headed for a federal election this year.
As with Mexico and the E.U., election results in Canada may change leadership in the federal government to the Conservative party that is more aligned with the U.S. administration. Indeed, Canadian polls have indicated this as a likely outcome for several months now. Pushback in Canada to tariff announcements came from across the political spectrum, though, so this result would not be a cureall. Stephen Harper, former prime minister of Canada and
leader of the country’s Conservative Party, stated recently that if he were still in office he would “accept any level of damage” to preserve Canadian independence.
The U.S. border with Mexico has taken up more airtime as a political issue, but, famously, the border with Canada is the longest one in the world. Reported numbers of migrants and drug seizures on the U.S.-Canada border are relatively low, but the broader context of heightened security tensions persists.
With that in mind, Canadian announcements of new border and narcotics control efforts may improve the rhetorical environment and reduce chances for tariffs, which would address a top concern for U.S. officials, provide action and offer a near-term offramp for tariff tensions. So, too, are recent Canadian federal commitments to increasing overall military spending and more ambitiously address North American joint security objectives. Such announcements are an open signal by the Canadian government to work proactively on U.S. concerns and deescalate the use of tariffs as negotiating leverage.
Canada and the U.S. have long shared a close and critical relationship, being among the top trading partners for each other and having aligned on strategic concerns for many years. Relatively smooth ties mean fewer dynamic headlines about bilateral ties, contributing to a context of steady collaboration.
To that end, simply avoiding being part of headlines associated with tariffs could extend this collaborative dynamic. Tariff discussions shifting focus away from Canada and toward with other countries could signal a reduced desire for a U.S.-Canada dispute and a lower likelihood of tariff implementation.
How can economic developers, governments and businesses respond in this environment? As President Eisenhower famously put it, “plans are useless, but planning is indispensable.”
Scenario planning is one critical tool that can be used for a key set of pathways, ranging from high likelihood/low impact to low likelihood/high impact. The past several years show that the only certainty is uncertainty, but even going through the thought exercise of what that can look like will build more flexibility and resilience.
Communities can also prepare themselves now by both mitigating potential risks and positioning for new opportunities. The recent experience of inflation is instructive in showing what sectors may be vulnerable should it return – one possible consequence of higher tariffs. Export-reliant industries will be on the front lines, as well, and may need collaboration with local partners to ride out market tur-
Tariffs are rising in prominence as a key variable and economic tool in the global macroeconomic conversation, creating a new era in global trade.
bulence and reorient toward new markets. Advocating for beneficial trade relationships at the state and federal levels also offers the chance for leaders to show where economic value is real and growing.
Close coordination and communication between economic developers and their local industries will help prepare everyone for what might come next. All players in the economic development ecosystem will benefit from understanding strengths, weaknesses and opportunities. Even arranging scenario planning events can reveal ways that partners can work better together.
Many possible scenarios may emerge in the coming months and years, including a combination of some of the ones mentioned here. Also critical will be the timeline of any tariffs; will they arrive immediately, over several months, or take a few years to roll out?
Regardless of how the tariff situation evolves, the most effective responses will rest on some of the greatest strengths the U.S. possesses: innovative ecosystems, workforce development, and cost-effective power generation
1 While BYD has a production facility in California, it only manufactures buses and at relatively low scale.
Technology gains traction as a strategic investment, with evolving reactor designs, streamlined site selection, and regional incentives shaping the future of clean, reliable power
By Courtland Robinson, Director of Business Development at Brasfield & Gorrie
As the U.S. works to alleviate national security concerns and prime the country’s future with clean, reliable power, utilities and influential private industry leaders are collaborating to develop next-generation nuclear energy. While it is difficult to forecast exactly which reactor technology will dominate the market in the coming decades, investors increasingly view advanced nuclear technology as a path to maintaining economic leadership on the world stage.
First commercialized in the late 1950s, nuclear power has long served as a clean, scalable source of baseload energy to support regional growth strategies. With more than 50 nuclear power plants and nearly 100 nuclear reactors, the U.S. remains one of the world’s largest producers of nuclear energy.
Today, the nuclear industry is closely monitoring government support for advanced nuclear technology, including further guidance from the U.S. Department of the Treasury and the IRS. Meanwhile, clean energy subsidies and electricity credits are fueling interest in new zero-emission technologies. As power delays and regional
electricity shortages highlight the potential of nuclear energy as a reliable alternative, the case for investment grows stronger.
Developing nuclear energy projects is a major undertaking that requires weighing a complex and unique set of location determinants. New reactor designs offer improved safeguards, modular construction techniques, advanced fuels, improved waste management strategies, and other modern features that meet regulatory requirements and reshape the traditional site selection model.
Evolved from their large reactor predecessors, modern designs require smaller sites, reduced water needs, and, in some cases, relaxed geotechnical conditions. Notably, most advanced reactor designs have a lower likelihood of accidents and can tolerate closer proximity to population centers, opening the door to previously ineligible locations. Last year, the Nuclear Regulatory Commission published a set of alternative approaches to the population-density criterion for both non-light-water and light-water small modular reactors (SMRs),
suggesting that safety features associated with advanced reactor designs warrant specific provisions in the siting process.
Still, most advanced nuclear projects announced to date are evaluating land on or near existing energy assets or brownfield locations with supporting infrastructure. An analysis last year from the Department of Energy showed the potential to install 60-95 gigawatts of additional nuclear capacity at existing and retired nuclear sites. Siting nuclear assets under these conditions creates a foundation for public acceptance and political feasibility—valuable factors given the high costs of due diligence. Additionally, siting multiple advanced nuclear reactors in one location offers significant economies of scale, allowing for reduced infrastructure development and workforce efficiencies.
Subsidy-eligible census tracts outlined in the Inflation Reduction Act—including brownfield sites, former coal mine communities, and energy-dependent employment areas—help bridge funding gaps. Other factors influencing levelized costs include cooling sources, surrounding land uses, hazardous weather conditions, transportation logistics, and water availability.
Conservative estimates from the National Renewable Energy Laboratory (NREL) suggest SMR construction timelines are 54 months shorter than those of large reactors. Their heat applications, enhanced safety features, and reduced land needs are reshaping nuclear site selection. Land requirements range from 25 to 200 acres for the plant itself—potentially doubling in size when buffer areas are included. However, SMR site selection depends on reactor technology, future phases, and site characteristics, and big challenges remain. Despite a more standardized design, upfront costs are steep. In many cases, the levelized costs of SMR energy—the average cost of producing one unit of energy over the asset’s lifetime—remain two to five times higher per megawatt-hour than other energy types, including renewables.
W hile many critical systems are factory-assembled (modular) and offer significant economies of scale, these projects are not “plug-and-play.” Their feasibility often hinges on leveraging existing infrastructure. Under a stringent and often unpredictable regulatory environment, many reactor designs face an uphill climb toward profitability.
“Energy infrastructure investments often serve as a bellwether for economic change, with capital and innovation riding on the winds of strong energy policies.”
A study released last year by the Southeast Nuclear Advisory Council found that the nuclear energy industry in the Southeast—encompassing Georgia, North Carolina, South Carolina, Tennessee, and Virginia—has the largest nuclear workforce in the U.S., generating an annual economic impact of $42.9 billion. The average employment multiplier across the five-state region is 2.8, meaning for every 10 jobs directly created by the nuclear industry, an additional 18 jobs are generated elsewhere—a significantly higher multiplier than the regional average across industries.
Moreover, the study found that nuclear projects frequently source raw materials from local vendors, reinforcing the economic benefits for surrounding communities.
W ith an established regulatory framework, skilled workforce, supporting infrastructure, and access to potential subsidies, the Southeast continues to lead in advanced nuclear innovation.
• Tennessee: Kairos Power is developing an NRC-approved non-lightwater demonstration reactor near TVA’s 1,200-acre Clinch River Site, where an early site permit for an SMR has already been obtained.
• V irginia: Amazon is partnering with Dominion Energy to develop an SMR at the North Anna Power Station to support its growing cloud computing operations. Commonwealth Fusion Systems plans to build a commercial fusion power plant in Chesterfield County, marking a notable development in the emerging fusion energy sector.
Across the country, announcements like these signal that advanced nuclear investments will be prioritized in areas with regulatory and licensing advantages, modernized grids, and skilled workforces.
W hile estimates vary, analysts project that U.S. advanced nuclear capacity will expand rapidly over the next decade. The DOE forecasts that U.S. nuclear capacity could triple to 300 gigawatts by 2050, signaling a major transformation in the nation’s energy landscape.
For those involved in industrial real estate and site selection, the siting of advanced nuclear projects should be of particular interest. History shows that energy infrastructure investments often serve as a bellwether for economic change, with capital and innovation following strong energy policies. As both a catalyst and predictor of transformational economic development, nuclear energy remains a key factor in shaping the future of industrial site selection.
IMPOSSIBILITY BECAME REALITY when Oak Ridge, Tennessee, became a nuclear frontier, pioneering the creation of the war-ending atomic bomb of World War II. Today, this “Secret City” works with visionary industries looking to transform the world through nuclear innovation—creating safe, reliable, and sustainable energy. The next generation of nuclear will power future generations and redefine possibility, once again. Will you join us? Learn about our nuclear-friendly community at: www.oakridgeedi.org
By Mark Crawford, Area Development Staff
Tennessee has long played a critical role in America’s nuclear industry. From Oak Ridge’s roots in the Manhattan Project to today’s cutting-edge research at Oak Ridge National Laboratory (ORNL), the state has been at the forefront of nuclear innovation. Now, with a strategic focus on workforce development and industry expansion, Tennessee is doubling down on its nuclear future.
Nestled just outside Knoxville, Oak Ridge is home to the largest Department of Energy and Science laboratory in the country. While the city’s history is well known, its future is turning heads. Recent investments in workforce training and infrastructure are positioning Tennessee as the place where nuclear companies can not only manufacture but also design, engineer, and innovate.
A prime example of this momentum is the Nuclear Energy Fund, established through Governor Bill Lee’s Executive Order 101. Originally backed with $50 million in 2023, the fund provides financial incentives to nuclear-related companies expanding in Tennessee while also strengthening higher education programs that are training the next generation of nuclear workers. An additional $10 million was approved in 2024 to further advance the initiative with another $10 million recently proposed in Gov. Bill Lee’s FY2026 budget, which is currently under review.
With energy at the center of nearly every business expansion conversation, Tennessee’s economic development team and its partners at the Tennessee Valley Authority (TVA) have made nuclear a priority. The Tennessee Nuclear Energy Advisory Council, a 22-member body, is guiding investment strategies to support nuclear businesses and ensure the state remains a leader in clean, reliable energy.
Since its launch, the Nuclear Energy Fund has already helped two companies and three educational institutions accelerate nuclear development in Tennessee. Type One Energy is bringing a total of 330 new jobs to East Tennessee, where it will establish its headquarters in the Greater Knoxville region and build its Infinity One stellarator fusion prototype at TVA’s Bull Run Fossil Plant site in Anderson County. Orano USA has selected Oak Ridge as the site for a multi-billion-dollar uranium enrichment facility, expected to create more than 300 jobs and become Tennessee’s largest private investment to date. In addition to corporate investment, the University of Tennessee, Knoxville, Roane State Community College, and Tennessee
Tech University are all expanding nuclear education programs, preparing students for careers in engineering, reactor systems, and nuclear safety.
A key reason companies like Orano are choosing Tennessee is the state’s uniquely supportive nuclear ecosystem. The combination of top-tier R&D at ORNL, TVA’s energy infrastructure, a pro-nuclear regulatory environment, and a skilled workforce pipeline creates an unbeatable advantage.
“When you go to a community, you want to be welcomed. You want to see your place in that community,” said Curtis Roberts from Orano USA. “When you’ve got other nuclear energy companies around you—General Fusion, X-energy—it’s like you’re with your people. The whole package Oak Ridge put together was unmatched by anywhere else in the nation for our particular facility.”
Tennessee’s investment in nuclear is not just about jobs—it’s about securing the nation’s energy future. By fostering a probusiness environment, supporting next-generation reactor and fusion development, and investing in a world-class workforce, the state is ensuring that the companies shaping the future of energy are doing so right here.
For businesses looking to be part of the next wave of nuclear innovation, Tennessee is more than a great location— it’s the nuclear capital of the future.
This article was paid for by the Tennessee Department of Economic and Community Development and approved and written by Area Development.
By Travis Sayler, Senior Civil Engineer at Gresham Smith
Effective collaboration with local governments is essential for success when planning large industrial developments. These partnerships often determine whether a project moves smoothly through approvals and into operation or encounters delays, budget overruns, and community opposition. For decision-makers overseeing site selection or expansion, building and maintaining strong relationships with local authorities is no easy task. Balancing regulations, infrastructure requirements, and stakeholder expectations calls for more than just technical expertise—it requires strategic communication and collaboration.
Consideration No. 1:
Strong communication is the foundation of any successful collaboration. Ensuring that the right stakeholders engage at the right levels can help align expectations, reduce misunderstandings, and, perhaps most importantly, build trust.
Match Stakeholders Thoughtfully — Developers/real estate teams should connect with economic development leaders and local politicians who influence incentives and permitting processes. Simultaneously, project engineers should coordinate directly with municipal engineers on technical matters like utilities and regulatory compliance.
Bridge Communication Gaps — Professionals such as engineers, politicians, and business leaders often use industry-specific jargon. Translating needs and priorities into plain language can prevent confusion and foster better collaboration. Although we share a common language, we don’t always speak the same dialect. Having the right technical team to translate the project needs into clear, actionable information for local utilities and regulators is key.
Discuss Timelines Transparently — Early-stage conversations must include candid discussions about what’s known and unknown. While a project’s full scope and needs might not yet be defined, flexibility and proactive updates can build trust with local stakeholders.
By prioritizing transparent, aligned communication from the outset, project leaders can ensure a smoother path to completion and foster goodwill that may prove critical when unexpected challenges arise.
Consideration No. 2:
Utility access—electricity, water, gas, and telecommunications—is critical to any industrial development. Misalignment between a project’s utility demands and a municipality’s capacity can cause costly delays.
Connect Engineers with Engineers — Project and municipal engineers should meet regularly to review utility requirements, infrastructure capacity, and potential improvements. These tec hnical discussions ensure feasibility and alignment.
Leadership Focus on Incentives — While engineers tackle technical issues, leadership teams should focus on securing commitments and incentives from local government decision-makers. Encouraging municipal governments to think creatively—such as leveraging stormwater grant funding to achieve cutting-edge water quality improvements while also reducing infrastructure cost burdens on cities and end users—can lead to mutually beneficial outcomes.
Plan Logistics Early — Early discussions about infrastructure improvements can mitigate potential bottlenecks. For example, if a municipality needs to upgrade water lines or power grids, clear milestones can be set to ensure these upgrades align with the project’s construction schedule.
By aligning technical details and leadership priorities, teams can avoid utility-related roadblocks and maintain project momentum.
Consideration No. 3:
Infrastructure improvements are a critical component of industrial developments, directly impacting construction schedules, production start dates, and even workforce accessibility.
Impact on Construction and Access — Local roadway improvements could hinder the delivery of equipment and materials to the site or prevent tradespeople from accessing the location. Assessing how infrastructure changes might affect the contractor’s ability to meet deadlines is essential.
Work Closely with Local Officials — Establishing a positive relationship with local permitting authorities can streamline the review process. Regular communication ensures that all requirements are met in a timely fashion.
By addressing zoning and permitting considerations early and maintaining ongoing communication with local officials, developers can navigate regulatory hurdles with minimal disruption.
Legacy Business Park in Lexington, Kentucky, is a 200-acre site resulting from a historic land swap between the University of Kentucky and the Lexington-Fayette Urban County Government. As the largest contiguous lot within the city’s urban service boundary, the site offers opportunities for economic growth while preserving community and ecological assets.
Establishing Power Sources — Permanent power is often necessary for commissioning equipment, but temporary power may suffice during earlier phases. Understanding when and how power can be established—both temporary and permanent—is a key milestone for the project timeline.
Phased Improvements — Some infrastructure upgrades may need to occur in phases to align with the construction sequence. Clear coordination with government entities ensures that these phases support, rather than hinder, overall project goals.
Proactive planning around infrastructure timelines not only helps meet construction deadlines but also strengthens the collaborative relationship between developers and local authorities.
Regulatory requirements can make or break a project. Understanding the local ordinances and zoning laws governing a site is critical in avoiding unexpected roadblocks during the development process.
Monitor Ordinance and Zoning Changes — Local governments may have pending changes to ordinances or zoning regulations that could impact your project’s design or feasibility. Staying informed about these potential changes helps avoid costly redesigns or permitting delays.
Understand Review Timelines — Permitting processes often include review periods that vary by jurisdiction. Identifying key dates and factors that could impact these reviews, such as public hearings or holiday-related delays, is essential.
By applying the four considerations outlined above, our multidisciplinary team of landscape architects, civil engineers, and architects successfully laid the groundwork for development:
Clear Communication: Early engagement with local politicians and community stakeholders secured financial incentives and community support, while engineers collaborated c losely with utility providers to resolve technical challenges.
Infrastructure Collaboration: Temporary utility connections supported construction, allowing the project to progress without delays.
Flexible Timelines: Construction schedules were adjusted to account for delays in road improvements and environmental factors.
Proactive Zoning & Permitting Engagement: The team worked with city planners to address zoning concerns and secure approvals before breaking ground.
From clear communication to aligning utility demands, managing infrastructure timelines, and navigating local regulations, these four considerations provide a comprehensive framework for fostering successful collaboration with local governments. By investing in these relationships early and maintaining them throughout the project lifecycle, decision-makers can set the stage for projects that are not only operationally successful but also align with the long-term goals of the local community.
Ultimately, industrial developments are more than just physical structures—they represent partnerships that create lasting value for all stakeholders.
By Jeff Troan, Partner & Managing Director at Vista Site Selection
Ispent 30 years at Lockheed Martin, 20 of which were in site selection, workforce development, and real estate disciplines, followed by the last 11 years consulting in the tech sector. Site selection has come a long way in the last four decades, driven by increased investment requirements, heightened investor scrutiny, and deteriorating workforce demographics.
Forty years ago, touch labor training requirements were relatively rudimentary, most of the population was mechanically adept, and workers were willing to move for a job in the tech sector. In those days, you could locate a new facility at the whims of management with little investor scrutiny.
Today, workforce development and pipelining criteria play the primary role in developing a site selection profile that ensures the ability to hire, train, and perpetuate an affordable workforce.
Until we develop a K-12 system that teaches higherlevel math and science in the elementary grades and begin profiling a student’s curriculum to their likely profession early, we will continue to graduate generations of entrylevel workers with very few job skills.
Forty years ago, it took 35 man-hours to assemble a television set. Today, that can be done in less than three. Advanced manufacturing facilities using seven to 10 varieties of additive manufacturing systems, composite robotic lay-up and weaving, robotic subtractive manufacturing processes, and robotic blacksmithing (sheet metal forming) are highly complex technologies requiring a few highly skilled workers instead of armies of low-skilled laborers from Henry Ford’s era.
Turbine, produced from a bed of titanium powder by focusing a laser at selective areas to bond molecules together. (Courtesy: DMG Mori)
program to train them to meet the higher specifications of aerospace coatings work.
Modern, effective site selection starts with an analysis of the proposed new facility’s labor requirements at the Standard Occupational Classification (SOC) code level. This can be aided by looking at both the company’s existing facilities or its primary competitors using cell phone tracking and various financial databases.
With the labor requirements in hand, artificial intelligence and conventional software algorithms are used to scan the country or globe to locate workforce enclaves that match the company’s requirements at a significant cost savings. As shown in the example above, certain disciplines aren’t reasonably available anywhere, so the model has to be adjusted to look for ancillary skills.
That’s the starting efficiency rate of a new worker before on-the-job training
Worse, many of the entry-level K-12 jobs can be blended into skilled operators’ downtime (waiting on machines) or eliminated with a variety of automated, tailorable manufacturing systems.
The exponential increase in technology innovation that began in the mid-20th century also plays a factor, creating new professions for which there is no heritage workforce. For example, “aerospace coaters” are people who can apply special ablative and stealth coatings to aerospace hardware. A recent Vista analysis of this market showed that there were 5,000 people in this field in the entire United States, all of them employed by Pratt & Whitney in Connecticut or Lockheed Martin in Texas.
If you need 200 of these people to support your new facility, you quickly conclude that you will have to train them up from an ancillary profession, like robotic automotive painting. You then look for clusters of robotic automotive painters and develop a workforce development
The training program for the new facility can no longer be delayed until the new facility is nearing completion. It should be instituted the day after the site selection decision is announced.
Phase One is a short-duration pre-employment program to assess the applicant’s dedication (will they show up for work?) and mechanical aptitude (do they know a torque wrench from a set of slip-joint pliers?). Most of the people you will be hiring will already be employed, so the Phase One sessions are held in the evening for three to four hours per night. If the applicant shows up for all the sessions on time, they pass the dedication criteria. Interestingly, a state training director recently told me they lose a third of applicants in this phase. During their classes, applicants are asked to perform simple tasks on rudimentary machinery and identify tools and their use.
Get actionable talent benchmarks, competitive intelligence, and firmographic data with JobsEQ technology or by working with our team of economic consultants.
Chmura’s consulting team, including Ph.D. and Blue Chip economists, can provide economic and fiscal impact studies, industry & labor market analyses, competitor benchmarking, and economic development & strategic planning. They can also help you draw your own insights through our powerful JobsEQ software platform. Learn more at www.chmura.com.
Access JobsEQ from anywhere, at any time.
Answer your research questions with guided prompts from JobsEQ.
Chat live with economists and get responses in under a minute.
Create custom regions, industry groups, occupation groups, forecasts, and more.
Tell your region’s story with clear maps and charts.
Forecast which industries and skills will be in demand in the future.
The company generally defines the tasks they want to see demonstrated. The cost of recruiting applicants for the Phase One program and its execution should be covered by regional government as part of a comprehensive incentives package.
Phase Two training can run from a few weeks to a twoyear associate degree or certification. This level of training can generally be carried out by the community college and trade school systems and is aimed at building the general skills necessary for productive employment. In the aerospace coaters example above, this training would consist of a generic robotic automotive painting program. The costs for these programs should be covered by regional government as part of a comprehensive incentives package, and most states have special funds available for this type of program. If possible, this training should also be pre-employment, with the promise of an interview upon successful completion of the curriculum. Many candidates voluntarily enter Phase Two training outside of the Phase One system by simply selecting the major as part of their post-K-12 study.
Having completed generic training for the job skills needed, we now need to train the workforce in specific job skills. In our aerospace coater example, this entails training the successful robotic automotive painter to spray advanced aerospace coatings to much higher specifications than the automotive industry. These processes are either company proprietary or classified for much of the aerospace industry and therefore can’t be taught through the community college and trade school systems. They require a company training center and production equipment and are done post-employment using shop queen, sample, and scrap hardware. Finding public-sector incentives funds to establish the training center and teach the skills is a large hole in the U.S. business incentives infrastructure. If you want this level of training paid for, you need to be cautious about which states you select as prospective sites for the new facility.
With formal training complete, the new employee is now first exposed to production hardware under the supervision of an experienced operator. The cost of this training is somewhat latent and often materially underestimated by the company. For example, if we assume a new employee enters the system 35 percent efficient and improves along an 86 percent learning curve to reach 100 percent competency over the first six months of employment, the company will incur 580 hours of unproductive time during the on-the-job training process. If we assume a burdened manufacturing rate of $100 per hour, the cost of on-the-job training is $58,000. Once again, public-sector
incentives to cover this cost in the form of a wage subsidy are a challenge, and you have to be particular about which states you consider in site selection to maximize this level of workforce development support.
When we implement these strategies with client companies, we generally get pushback from two sources: economic development officials and corporate training professionals.
I’ve heard from more than a few economic development professionals, “Why isn’t the company paying for all this? Fifty years ago, companies paid for this.” The answer is clear from the earlier discussion: The manufacturing that’s financially feasible to do in the United States is much more complicated than it used to be, and the candidates the country is delivering are devoid of most of the skill sets necessary. Further, the world has become a very competitive place and other countries do a much better job providing pre-employment skills.
So far, everything I’ve covered would be categorized as workforce development, which gets an initial workforce in place to operate the new facility. Workforce pipelining is a twin discipline, extending workforce development efforts to ensure a perpetual pipeline of new employees to cover growth, attrition, and retirements. There’s no room to discuss those constructs here, so I’ll save them for a follow-up article.
So, what should your son or daughter study to ensure a financially rewarding career in aerospace and tech? First, don’t opt out of those higher math and science classes in the K-12 system because it is easier. Then augment that education with shop classes in wood, metal, automotive, and robotics from 7th to 12th grades. Don’t spend your retirement on expensive private universities, there are lots of good public university engineering programs that will get you a job without half a million dollars in debt.
Then let the company pay for an expensive master’s degree at a prestigious university. It’s no crime not to be able to make the engineering hurdle, but that’s not a reason to switch to a major that doesn’t offer any reasonable job opportunities.
Go to trade school instead and learn a skillset industry is desperate for. Here are a few: Airframe and Powerplant Mechanic, Robotic Welder (including exotic metals), NC Machinist, Robotic Painter, Additive Manufacturing Technician, Engineering Technician, etc. Thanks for your time, and as they say in the military, “Good Luck and Good Hunting” in all your business endeavors.
Ohio’s big cities and small towns thrive with a mix of economic development initiatives that drive momentum.
By JobsOhio
Since 2019, Ohio has seen a surge in economic vitality. New project wins have increased by 47% to 2,155, creating over 126,000 jobs. New payroll climbed 27% to $6.6 billion, putting more money in Ohioans’ pockets. Ohio is the only U.S. state in the top five for economic development projects and projects per capita for five consecutive years (2019-2024). This success stems from a best-in-class business climate.
From attracting global giants like Amazon Web Services, Intel, and Joby Aviation to investing in more than 550 small businesses, Ohio’s inclusive approach is spearheaded by JobsOhio, the state’s private economic development corporation. “We are private, which means less red tape,” said JobsOhio President and CEO J.P. Nauseef. “We help companies avoid gamechanging surprises with a proven process that protects their confidential information. We don’t just see company growth as a metric – we want Ohio to be their competitive advantage. And we’re willing to work as hard as it takes to make it happen.”
JobsOhio recently secured the largest job-generating megaproject in state history: Anduril’s $910 million investment in a military drone aircraft facility near Rickenbacker International Airport, creating 4,000 jobs over ten years. The company cited Ohio’s advanced manufacturing prowess, ideal site options, aerospace supply chain, and ease of working with JobsOhio as key factors in their decision.
JobsOhio provides companies with a competitive advantage through best-in-class industrial sites. The SiteOhio program and Ohio Site Inventory Program (OSIP) proactively prepare and authenticate shovel-ready locations for business expansion. SiteOhio ensures all utilities are at property boundaries, due diligence is complete, and relevant state and federal entity approvals. Of the 32 sites authenticated, 10 have already been developed, attracting companies like Google, MAGNA, and Nestlé Purina.
OSIP accelerates site readiness, turning $148 million in investment since 2020 into nearly $1.8 billion in private development, adding over 18 million square feet of industrial space. The state’s All Ohio Future Fund, a $750 million investment, will further prepare sites for the next wave of megaprojects.
Ohio is experiencing significant domestic migration. From 20192023, a net of 97,000 people moved to the state for jobs. A 2024 Bloomberg analysis shows Ohio’s 25-44-year-old workforce is
Partner with
and see how your business and life work better together.
stable or growing in most counties. Newcomers cite proximity to family, affordability, and quality jobs as key advantages.
To sustain this workforce, Ohio invests in programs like TechCred, which has awarded over 100,000 credentials, equipping workers with skills for advanced industries. Additionally, Ohio’s universities graduate 21,000 engineers and scientists annually, ensuring a strong talent pipeline.
With the conclusion of JobsOhio’s five-year strategic plan, its next phase, JobsOhio 2030, aims to elevate the state’s economic impact under the banner “Let’s Grow, Together.”
“Our aspiration is for Ohio to be the #1 state in the Midwest and top five in the U.S. for high-quality jobs, a resilient economy, and increased prosperity,” said Nauseef. Six strategic pillars will drive progress:
• Silicon Heartland: Building on Intel’s investment, JobsOhio aims to position Ohio as a semiconductor innovation hub
• AI Integration: Leveraging artificial intelligence to enhance Ohio’s industrial base.
• Skilled Technical Workforce: Strengthening workforce development through Talent Acquisition Services and upskilling programs.
• Innovation: Uniting JobsOhio’s Innovation Districts under the Ohio Discovery Corridor to attract research, investment, and talent.
• Energy Production: Capitalizing on Ohio’s natural resources, projected to supply nearly half of America’s natural gas by 2040.
• Competitive Brand: Promoting Ohio’s appeal as a destination for companies and talent through its “Heart of It All” brand.
Ohio’s dynamic economic strategy, bolstered by JobsOhio, continues to drive inclusive growth, attracting investment and talent while ensuring long-term prosperity.
This article was paid for and written by JobsOhio and approved by Area Development.
Site selectors and engineers must be extra cautious dealing with energetics, like ammunition and explosives
By Tyler Keel, Engineering Project Manager & Courtney Dunbar, Director of Site Selection at Burns & McDonnell
rojects involving the manufacturing, processing, handling, or storage of explosives, ammunition, or other energetic materials are among the most demanding for any engineering or construction firm.
Unique challenges arise at every turn, requiring a meticulous approach, a deep understanding of safety protocols, and the ability to navigate complex regulatory frameworks. These projects demand extraordinary attention to detail, as success is defined by an uncompromising focus on the safety of all personnel working within and near these facilities.
A detailed understanding of the Department of Defense Contractor’s Safety Manual for Ammunition and Explosives (DOD 4145.26) is fundamental to the success of these projects. This manual serves as a comprehensive safety framework that requires more than simple compliance; it demands a rigorous process for assessing how explosives impact buildings, equipment, and personnel from initial planning through construction and final facility turnover.
Before engineering design can begin, a thorough understanding of the specific energetics involved is required. Evaluating explosive properties includes calculating net explosive weight (NEW) and modeling maximum credible event (MCE) scenarios. Storage, handling protocols, and historical incident data must be examined to establish a strong foundation for safety and design decisions.
One critical tool in this phase is a quantitative risk assessment (QRA), also referred to as a process hazard analysis (PHA) on some
sites. This process involves detailed hazard assessments and blast modeling, providing critical insights for design decisions.
Proper categorization and classification of materials are foundational to safety evaluations in chemical and explosive handling. Chemists may be needed to classify materials and assess volatility if properties are not well established. Material tests may be necessary to determine the precise properties of ordnance.
Developed processes can rely more heavily on published Safety Data Sheets (SDS) or a history of field tests. Evaluating materials, total quantities, usage, and potential interactions significantly impacts facility criteria. Some ingredients, when packaged, may be treated as inert but can create explosive dust particulates upon processing. Exposed energetics drive the highest safety concerns, requiring the most stringent facility requirements.
Selecting the right site and obtaining necessary approvals are pivotal. Site layout must balance operational needs with safety, achieved through one of three approaches:emissions while mitigating market volatility and regulatory risks.
Avoidance: Using quantity distance (QD) arcs to separate hazardous areas.
Prescriptive Design: Relying on preapproved designs.
Custom Protective Construction: Creating tailored designs based on detailed analysis.
Each approach requires rigorous documentation and coordination with the Department of Defense’s Procurement Contracting Officer (PCO) to maintain compliance.
Advanced blast-resistant technologies are critical for protecting personnel and assets. These include fire- and blast-resistant materials for structural components, specialized wall materials to minimize debris, and innovative solutions such as liquid body armor and carbon nanotubes. High-performance laminated glass and layered concrete further enhance safety by dispersing blast energy.
Several key principles contribute to effective explosives facility design, such as using convex building exteriors to deflect shock waves, employing strategic ventilation systems to reduce pressure buildup, and avoiding reentrant corners to prevent amplification of shock waves.
These measures, combined with advanced materials, create resilient structures capable of withstanding potential blast impacts.
A proactive approach to identifying hazards is essential. This includes evaluating flammable materials, high-risk processes, and proximity to other industrial facilities containing similar explosive
materials. Lessons from past incidents help inform design and operational protocols.
Compliance with industry standards from the American Petroleum Institute (API), American Society of Civil Engineers (ASCE), National Fire Protection Association (NFPA), and International Organization for Standardization (ISO) ensures alignment with best practices and regulatory requirements.
Modern computational tools enhance design efficiency. AI and machine learning optimize designs by simulating various scenarios, while additive manufacturing enables rapid prototyping. Computational modeling provides precise blast effect predictions, allowing designers to refine protective measures.
Setback distances for explosive storage and handling are critical for safety and regulatory compliance. The impact of explosives decreases exponentially as distance increases. Key principles include reducing explosive quantities and minimizing exposed populations.
Allowable activities vary by distance type. Land use considerations are significant, often requiring extensive safety buffers. A single building with 450 pounds of explosives may need 150 acres. Efficient land use strategies include grouping similar hazard operations and utilizing agricultural or natural areas as buffer zones.
Despite the complexity of explosives facility design, common pitfalls are vast, and can include things like overlooking fragmentation hazards; misapplying inhabited building distance (IBD) or intraline distance (ILD) standards; ignoring the compatibility of mixed substances; failing to account for backup power needs, such as diesel tanks; failing to document distances to utility needs (power, water, sewer); locating sensitive areas near off-campus operations.
Navigating the complexities of explosives facility design requires an experienced, multidisciplinary team. From calculating blast effects to maintaining regulatory compliance, a team with the right expertise provides balanced designs that prioritize safety without compromising functionality.
Designing facilities for explosives is a high-stakes endeavor. Every element, from site selection to material choice, plays a crucial role in safeguarding lives and assets. By embracing a methodical approach and leveraging the latest technologies, operators can manage risks, avoid common pitfalls, and deliver projects on time and within budget. In this field, thorough preparation and an unwavering commitment to safety are not just best practices—they are nonnegotiable.
By Brian Gallagher, Vice President, Corporate Development, & John Denbo, Project Executive at Graycor
s global initiatives place increased emphasis on sustainable construction and built environments, emerging priorities for building projects in nearly every industry are focused on resilience, embodied carbon reduction and achieving net-zero energy. For building owners, the challenge lies in effectively integrating sustainability and environmental, social and governance (ESG) strategies into their construction projects and long-term building operations. This integration is vital for maintaining a competitive edge, complying with evolving regulations and meeting the increasing demands of investors and stakeholders. Successfully incorporating these principles begins with defining clear sustainability scopes and objectives right from the start of a project. Renewable energy, electrification and efficient water usage are critical focus areas for sustaining operations long after construction ends.
A collaborative approach helps to bridge the gap between lofty
goals and practical outcomes. Architects, designers, contractors and vendors can play a pivotal role in helping owners define realistic and achievable sustainability requirements during the design phase. Early contractor involvement, which leverages the expertise of experienced teams as early as concept development and preconstruction, is vital for aligning goals, understanding costs and addressing material and equipment availability—minimizing surprises and supply chain issues down the line.
For instance, integrated design workshops that bring all parties together can be instrumental in considering the implications of design choices on both sustainability and budget. These strategic workshops often last a day or more and involve project owners, architects, engineers/designers, general contractors, subcontractors and vendors, who share their expertise and input in developing goals and specifying sustainable options as the basis of design. These strategic workshops can result in realistic, actionable objectives that spur
meaningful progress. Product research should be conducted at this stage, especially for engaging supply chains to identify the right low embodied carbon materials.
Some owners and developers are even working with governmental entities as they revise and create new building and energy codes. These companies engage decision-makers early, hosting open discussions, to learn what is driving the code requirements and understand how implementation will affect project delivery. Such discussions should be approached as a partnership opportunity to improve the effectiveness not only of the design and construction process, but of the built product.
Constraints related to power and water are among the most important considerations when aiming to build a netzero building. Electrification, power grid and capacity, and water supply should be thoroughly researched during site selection. Renewable energy sources are often part of the solution and may qualify for
funding or incentive packages. Design teams can also identify ways of conserving water, such as modifying equipment and outfitting it with leak detection, or configuring systems to use less water for cooling.
Environmental impacts that flow from project activities should be examined as early as possible—and from as many angles as possible. The team should identify ways to reduce emissions during construction, such as by using hybrid or electric construction equipment. Supporting local economies by sourcing local materials wherever possible further enhances the environmental sustainability of a project.
Looking into supply chain logistics in conjunction with exploring design alternatives is key to managing jobsite resources, especially given current supply chain challenges. On one project, a design team explored options to replace steel elements with mass timber—a design alternative that is only available during a project’s early stages. In this example, having players across the design team involved achieved efficien -
cies because while contractors were performing take offs for wood from a cost perspective, the design team was able to simultaneously provide data on quantities to calculate carbon reduction.
There is increasing transparency into the embodied carbon of various materials, especially now that product category rules (PCRs) and environmental product declarations (EPDs) are being widely adopted. One development company was able to greatly reduce embodied carbon on their industrial project by switching to a different type of steel than what was originally considered.
Jobsite waste is another area receiving attention, with target numbers for reuse and waste reduction climbing higher. This makes tracking all waste generated on site important. Consistent waste tracking and landfill diversion options are often lacking, especially in rural areas, but working with haulers and recyclers can help overcome these challenges to achieve true zero waste. Designing for modular construction and reusing surplus materials are other ways to minimize waste.
Increasing the energy efficiency of finished buildings is fundamental to improving life cycle costs, especially given the potential future increase in cooling needs due to climate change. Therefore, building envelope commissioning and air-tightness testing are becoming more common practices. Another end-use consideration that should be addressed during early planning is how to restore the ecosystem surrounding a finished building to original conditions, to whatever extent possible.
The project planning phase is also the right time to focus on social responsibility.
Tracking and reporting on local hiring practices and using minority businesses is a part of social governance. Additionally, health and safety considerations must be prioritized when selecting materials and construction practices.
Increasingly, ESG reporting requirements are being driven by investors. In fact, investors are making decisions to finance projects based on ESG-related criteria.
Tracking data is essential for driving improvements— and the task should not be left up to the busy site team.
With advanced software solutions, project owners can automate the tracking of carbon emissions and other critical metrics. It’s important to note that there’s not likely to be one single tool that can scale the tracking of all sustainability metrics; a coordinated suite of solutions will be necessary. Useful tools provide the flexibility needed to adapt as reporting requirements evolve, ensuring that sustainability efforts are both effective and transparent.
While automation can reduce barriers to data collection and processing, it is nevertheless important to establish a sitewide culture of valuing sustainability. This allows the
project team to take advantage of bottom-up insights and not just top-down ones.
The future of sustainability in construction lies in innovation. By adopting innovative approaches and leveraging tools for tracking and reporting, building owners can ensure their projects are sustainable and compliant. While the tools don’t have to be perfect to provide value, they should be embraced wherever possible. Ultimately, fostering a culture of sustainability— where tracking, reporting and improvement are ingrained in the project workflow—is what will improve resilience, reduce embodied carbon and achieve net-zero energy.
Green Badger ESG reporting in construction
Cobuilder Collaborate
Sustainability data management
Sustaira Carbon accounting and ESG KPI tracking
Tracks metrics like carbon, energy, water, waste, and wellness; intuitive dashboards
Your Carbon Report
Carbon footprint reporting
Manages environmental, technical, and safety data, including Environmental Product Declarations (EPDs)
Scalable solution for both individual projects and organizational reporting; simplifies ESG data management Green Badge
Streamlines compliance with Corporate Sustainability Reporting Directive (CSRD) requirements; enhances data transparency BuildTech Solutions
Tracks carbon emissions, waste management, water usage, materials, and jobsite wellness
Offers detailed visibility into the carbon footprint of construction products used in projects
Provides customizable applications; fosters sustainability transparency; co-created solutions with industry leaders
Fully customizable reports; aids in accurate carbon accounting and reduction strategies Aggregate Industries
By Garrison Partridge, Area Development Staff
Anew Space Race is unfolding, but this time, it’s not just about exploring the stars — it’s also about fueling economic growth and redefining industrial landscapes. Space launch pads are big business.
In 2024, there were 259 orbital launch attempts globally — a record-breaking figure that marked a 17 percent increase over the previous year. SpaceX led the charge with 134 missions launched from sites in the United States, underscoring the growing influence of private enterprise in astronautics.
This rapid pace of activity isn’t confined to the U.S. China expanded its own space ambitions, unveiling the Wenchang Commercial Space Launch Site, while countries like Norway, the U.K., and Peru began building new spaceports to join the growing market. Yet, for the U.S. to maintain its leadership in the “second Space Race,” significant investments in infrastructure and site selection are required.
Most American launches take place at three key sites: Kennedy Space Center, Cape Canaveral Space Force Station, and Vandenberg Space Force Base. Cape Canaveral alone handled 93 launches in 2024 — a dramatic increase from 30 launches in 2020. While these record-breaking numbers inspire national pride, they also highlight the challenges posed by aging infrastructure. Kennedy Space Center, built in the 1960s, is struggling to keep up with modern demands, with overburdened roads and an underpowered electrical grid raising concerns about the sustainability of current growth.
“Capacity constraints at the federal ranges are an increasing concern. The near-term solution will likely involve expansions at existing facilities like Wallops Flight Facility in Virginia and the Pacific Spaceport Complex in Alaska, alongside investments in new public and private spaceports,” said Tom Taylor, Managing Director and Head of Aerospace and Defense at JLL.
The emergence of private spaceports such as SpaceX’s Starbase in Texas and Spaceport America in New Mexico signals a shift in how spaceport site selection is approached. Traditionally, ideal locations were near the equator to optimize orbital access and near large bodies of water to safely manage falling debris. However, innovations like SpaceX’s recoverable boosters may allow for a broader range of site options in the future.
Taylor notes that “site selection must still account for factors such as land availability, environmental impact, access to infrastructure, and community support.” With these considerations in mind, spaceports have the potential to become economic development drivers, creating high-tech jobs, attracting advanced manufacturing, and catalyzing regional investment.
The development of spaceports presents a transformative opportunity for communities. Beyond their core function as launch sites,
spaceports generate jobs in engineering, logistics, and manufacturing while also attracting ancillary businesses. For example:
• Job Creation: New Mexico’s Spaceport America has been instrumental in creating jobs across the aerospace supply chain, from rocket assembly to tourism.
• Regional Hubs: The Pacific Spaceport Complex in Alaska supports defense and commercial launches while serving as an anchor for regional economic growth.
• Advanced Manufacturing: SpaceX’s Starbase has driven significant investment in local infrastructure and supply chains, proving the value of private-public partnerships.
In addition, smaller launch facilities could proliferate to meet the needs of specialized industries, further diversifying economic opportunities. Virginia and Alaska, for instance, are gaining popularity among
“Managing launch traffic across all ranges remains a critical task for space access. Coordinated efforts are essential to provide safe and efficient operations.” — Richard Pruss, Space Facilities Lead at Burns & McDonnell
newer space companies due to their perceived less congested launch schedules, leading to the development of new facilities in these areas.
Building a modern spaceport requires significant investment in infrastructure and power capabilities. Launch pads, ground support equipment, communication networks, and safety systems demand resilient and sustainable power sources to support operations. “Power solutions for modern spaceports will likely focus on resiliency and sustainability to minimize operational disruptions and environmental impacts,” Taylor said. As such, regions with robust energy grids and access to renewable energy sources may hold a competitive edge in site selection.
Meanwhile, Cape Canaveral and Kennedy Space Center are actively modernizing, renovating and repurposing several launch pads to accommodate increased launch frequencies. However, managing launch traffic across all ranges remains a critical task for space access. “Coordinated efforts are essential to provide safe and efficient operations,” said Richard Pruss, Space Facilities Lead at Burns & McDonnell. The expansion of launch capabilities across multiple sites reflects the growing demand for space access — with each location offering distinct advantages.
W hile the Department of Defense historically dominated the U.S. space industry, the commercial sector is increasingly taking the lead.
Private companies are not only building rockets but also developing the infrastructure to support them. This shift represents a new model of economic development, with private-public partnerships enabling innovation and reducing the financial burden on taxpayers.
“Commercial launches will soon exceed DoD launches at the next generation of spaceports,” Taylor predicts. This trend opens the door for regions across the U.S. to position themselves as leaders in the burgeoning space economy, provided they can offer the right mix of incentives, infrastructure, and expertise.
For corporate site selectors, the rise of spaceports presents a unique challenge and opportunity. Decisions about where to build or expand these facilities require balancing technical, regulatory and community considerations. Regions that proactively invest in workforce development, streamline regulatory processes, and strengthen infrastructure will have a distinct advantage.
As global launch rates continue to climb and new technologies redefine traditional limitations, the second Space Race is not just about exploring new frontiers in space — it’s about driving economic growth here on Earth. Whether through public investments in legacy facilities or private sector innovations, the U.S. has a chance to maintain its leadership — if it’s willing to invest in the infrastructure of the future.
California
Vandenberg Space Force Base
Alaska
Colorado
Colorado Air & Space Port
Oklahoma
Oklahoma Spaceport Alabama
New Mexico
Spaceport America
Pacific Spaceport Complex – Alaska
Virginia
• Mid-Atlantic Regional Spaceport
• Wallops Flight Facility
Huntsville International Air and Space Port
Georgia Spaceport Camden
Texas
• Launch Site One West
Texas | Blue Origin
• Boca Chica | SpaceX
• Houston Spaceport (Ellington Airport)
• Midland Spaceport
• Kennedy Space Center (NASA)
• Cape Canaveral Space Force Station
• Space Florida Launch Complex 46
• Space Florida Launch and Landing Facility
• Cecil Air and Space Port
• Space Coast Regional Airport
designed for productivity and engagement, featuring natural light, green space, fitness centers, and modern HVAC systems. Flexible workspaces, meeting rooms, and informal collaboration areas also provide adaptability.
In the United States, energy companies have been consolidating into Houston, the long-standing hub of the oil and gas industry. Denver has also become a notable energy sector center, offering a high quality of life and urban amenities. Both cities provide access to talent, capital, and industry resources. For instance, in 2024, Chevron Corporation announced its headquarters relocation from San Ramon, Calif., to Houston. Senior leadership is also moving to Houston to enhance collaboration with executives, employees, and business partners. Chevron plans to transition all corporate functions to Houston over the next five years while maintaining crude oil fields, technical facilities, and refineries in California. The company will also continue supplying over 1,800 retail stations in the state.
In addition to Houston and Denver, energy companies continue to establish operations in other Texas markets, as well as in oil and gas centers such as Greeley, Colo.; Oklahoma City and Tulsa, Okla.; Pittsburgh; and New Orleans.
Total oil and gas M&A activity between mid-2023 and July 2024
W ith energy demand expected to rise in the coming years, the industry will require space to manage growth efficiently. As oil and gas companies consolidate, they aim to optimize their workforce and real estate strategies. However, expectations for quality office environments remain high, particularly in sought-after energy corridors.
Companies are also placing a greater emphasis on environmental, social, and governance (ESG) factors when selecting office space. Many are seeking buildings with improved energy efficiency, sustainability certifications, and enhanced wellness features. Modern office design is playing a key role in retention strategies, particularly as companies aim to attract younger generations of workers who prioritize workplace experience.
By understanding industry consolidation trends and market dynamics, executives can better determine ideal locations to manage their property and facilities while reducing real estate costs—all while ensuring continued energy supply nationwide.
From maintaining the bottom line for small businesses to keeping the assembly line moving for our major industries, NV Energy is powering Nevada’s future.
Our economic development experts work strategically to facilitate business location and expansion within Nevada. We can assist with pricing and renewable tariffs, site visits and provide the data critical to making an informed decision for business investment in Nevada.
We know there’s a lot on the line. That’s why we’re always there to power it.
Learn more at nvenergy.com/econdev.
By Myung Kim, Project Director at Project Management Advisors, Inc.
There was a time not long ago when the concept of using the body’s immune system to kill cancer cells was considered fringe. That all changed in 2017, when the U.S. Food & Drug Administration (FDA) took the historic action of approving the first cell and gene therapy (CGT) treatment. Since then, 37 additional CGT products have been approved by the FDA, and there are more than 4,000 cell and gene therapies in clinical or pre-clinical development, according to McKinsey.
CGT involves drawing blood from a patient or universal donor, altering genes in specific types of cells in the blood, then reinfusing those cells into the patient. Ideally, upon reintroduction into the patient’s body, the altered cells attack the malignant cells with-
Like all drug and biologic products, CGTs must comply with FDA regulations that ensure the products’ purity, quality, contents and strength. Unlike most other medicines, however, the process of manufacturing CGTs is largely manual, carried out by scientists in cleanrooms rather than equipment on an assembly line. Because CGTs involve live cells that are extremely sensitive to changes in temperature, a cold chain process must be maintained from the moment blood is drawn to the moment the patient receives the treatment. For these reasons, CGT biomanufacturing facilities require a reliable supply of power, specialized HVAC systems, cold rooms and process chemicals. These facilities range in size from under 20,000 square feet to more than 100,000 square feet.
out causing the unpleasant and life-altering side effects of chemo or radiation. In recent years, interest in CGT has exploded, both from hospitals hoping to offer it to their patients and companies interested in researching new applications for the approach. As the number of players in the CGT space has grown, so has the demand for the highly specialized biomanufacturing facilities needed to produce these therapies. This presents an enormous opportunity for stakeholders in the life sciences real estate sector, but it also comes with some challenges.
While CGT industry is growing, the unique requirements of designing and building these bespoke facilities has concentrated demand in two key bicoastal locations: the Northeast and the Bay Area.
A CGT research lab is not much different from other types of labs where tissue cultures and blood samples are handled. Work can continue to be carried out in a lab-scale cleanroom environment even as it progresses through the first phase of clinical trials. But, after that, things get complicated.
Once blood is drawn for a treatment, the altered cells must be reinfused into the patient within 24 hours for select therapies. This “vein-to-vein” limit has been a determining factor in where CGT manufacturing has developed.
The first cell and gene therapy approved by the FDA was developed at the University of Pennsylvania’s Abramson Cancer Center, while clinical trials were conducted in patients at the nearby Children’s Hospital of Philadelphia (CHOP). This symbiosis is characteristic of other cities where CGT manufacturing has emerged, including Boston – where researchers from Harvard and the Massachusetts Institute of Technology partner with the Mass General Brigham healthcare system – and San Francisco, where the University of California San Francisco uses its own network of hospitals to conduct trials of therapies developed in its labs
For start-up companies hoping to jump on the CGT bandwagon, decisions around real estate can be a big obstacle to entry. While it’s
true that CGT research can be carried out in a lab space that’s not especially difficult to source or equip, making the jump from research to production can be a leap of faith. Contract development and manufacturing organizations (CDMOs) exist for CGT, but limited capacity is likely to make them cost-prohibitive over the long term.
In the Bay Area, for example, the hindrances to building new biomanufacturing facilities may outweigh the cost and headaches of relying on CDMOs. Site selection is the biggest constraint, as the supply of available land zoned and appropriate for biomanufacturing is low, driving the cost of available sites higher. Another strike against new construction is that procuring new electricity service from Pacific Gas & Electric is a lengthy and difficult process, and water scarcity is also an issue. For ground-up construction, regardless of where you’re building, CGT manufacturing facilities must not only go through local permitting processes, but also entitlement approvals, including a potential environmental impact report process, that can take months to receive. Finally, new biomanufacturing facilities must be validated by the FDA, a process that can take six to eight months.
Altogether, the process of building a new ground-up facility can take up to four to five years. For that reason, many companies
Index
establishing themselves in the Bay Area are focusing on Berkeley, Emeryville, Hayward and Fremont, former industrial areas with available single-story buildings that can be modified for CGT manufacturing. Companies are also opting for shell buildings that can be customized to fit their needs, or leases or adaptive reuse of existing spaces.
Arguably the world’s center of innovation, as well as the epicenter of venture capital funding in the U.S., the Bay Area is a place where we expect more opportunity to present itself as CGT becomes more ubiquitous, treatment costs decrease, and manufacturing processes improve.
At this point, even the skeptics of a quarter-century ago would have to admit that CGT will play a big role in the future of medicine. But whether you’re an established biotech/pharma company or a new kid on the block, figuring out how to approach the real estate side of research and manufacturing is a challenge. The best course of action is to connect with experts who understand the state of play in both the CGT and life sciences real estate sectors nationwide and can advise you on a way forward that fits your needs, budget and timeline.
By Ken Biberaj, Executive Managing Director at Savills
We are at the dawn of America’s next Industrial Revolution, and it will be shaped in large part by the convergence of technological innovation, climate change and geopolitical pressures.
Over the past decade, advanced manufacturing in the U.S. has grown from niche sectors into vital industries with farreaching implications. Companies like Tesla have revolutionized the automotive sector, SpaceX is spearheading a new era in space exploration, and Anduril Industries is pushing the boundaries of defense technology.
These companies are not just manufacturing products; they are transforming entire industries, creating thousands of jobs, and attracting billions of dollars in venturebacked investment. However, their success is, in no small part, a result of federal policies that align with their technological ambitions.
The role of the federal government supporting these growing sectors is more pronounced than ever before. Whether through federal contracts, loans or grants, industrial policy coming out of Washington is shaping this growth. However, navigating Washington can be daunting and this new wave of companies will need to be clear eyed about the need to build relationships in D.C. and learn how best to navigate the halls of government. Innovators move fast and innovation is flowing across the country, but the learning curve is steep in the halls of Washington and in state capitals across America.
As we crisscross the country on behalf of advanced manufacturing companies for site selection, we prioritize our understanding of D.C. and national strategic objectives in our process to ensure we find the best location for our clients to select. The competition from within the government is more exciting than ever.
Companies must navigate multiple avenues for potential manufacturing support in D.C., from the Loan Program Office of the Department of Energy and the Office of Strategic Capital at the Department of Defense to the CHIP’s office at the Department of Commerce and the Export-Import Bank, the commitment to bolster domestic
Understanding D.C. is not just about meeting politicians—it’s about finding the right thought partners to amplify your story.
bridge and El Segundo or Santa Clara and Princeton, the geographic map for where to build factories is wide open. Companies now have the opportunity to build anywhere, and part of the challenge on the site selection front is to develop drivers and a process to select the top states for the client based on talent, access to power and supply chain considerations.
Once top states are identified, a process-driven approach is needed to compete states and municipalities against each other for the best incentive package, often prioritizing speed to market based on power and talent access, and less around getting the largest dollar package.
With a new administration taking office, reshoring, bolstering energy production, expanding AI investment, strengthening national security, pushing for permitting reform and accelerating infrastructure projects are all on the horizon and likely to further incentivize manufacturing.
Sitting in D.C., I have been thrilled to see a growth in advocacy, innovation and thought leadership from new organizations like the Special Competitive Studies Process and the New American Industrial Alliance as well as from the Institute for Progress and Station D.C.. Understanding D.C. is not just about meeting politicians—it’s about finding the right thought partners to amplify your story.
manufacturing and job creation is a whole of government objective. That commitment is equally matched by the competition from states to not only offer large incentive packages, potentially including free land and commitments to power, but also in developing industrial ecosystems to attract talent and sector-specific industries.
While technological innovation continues to be developed in places like Cam -
The support from the Federal Government is stronger than ever, there are more Michelin-Star restaurants than ever before, so our advice to the new innovators across America is to prioritize a Washington strategy as you explore how and where to site your next project. Looking ahead, the future of American manufacturing is bright—but it will require sustained collaboration between the federal government, state and local governments, and the private sector.
By continuing to prioritize innovation, national security, and economic resilience, Washington can lay the groundwork for a new generation of manufacturers that will drive America’s economic strength for decades to come.
“
Thanks to the great vision and support of the State of Tennessee and Gallatin Economic Development Agency, who welcomed and supported us along the way, this has been a story of continuous growth.”
Franco Gussalli Beretta President & CEO, Beretta
SUPERIOR-SIZE YOUR SUPPLY CHAIN.
PURE OPPORTUNITY ®
Only Michigan has a supply chain that includes four Great Lakes with an extensive network of marine highways and 33 deep-water ports. It’s how the world’s top manufacturing, engineering and mobility businesses get the upper hand in global logistics. Seize your opportunity at MICHIGANBUSINESS.ORG