BuildingsCostConstructionofTimber
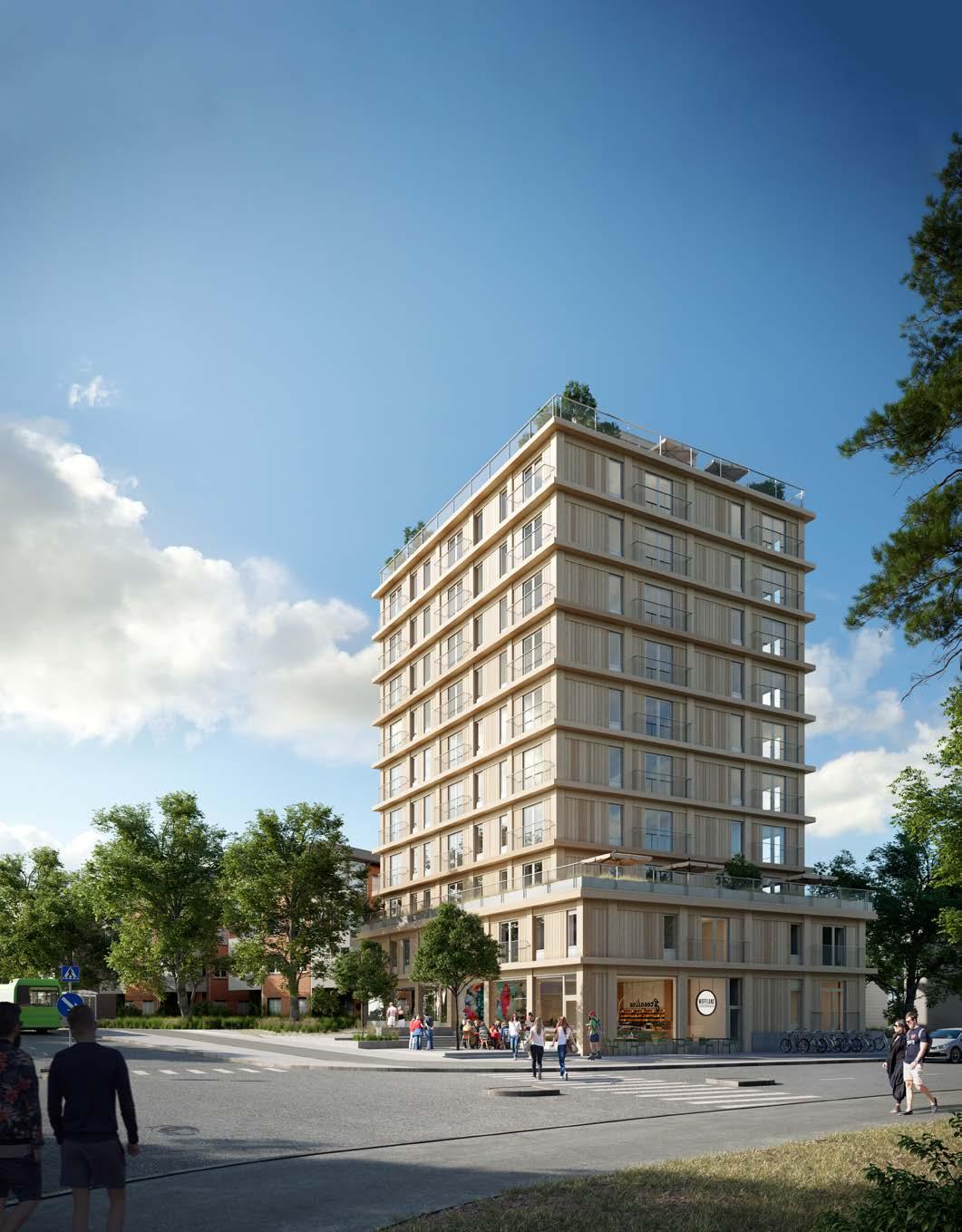
This related
to engineering.
study was conducted by: Henning Johansen Chief Project Manager COWI Norway Julie Hansted Andersen Sustainability Specialist Arkitema Denmark Ketil Armann Hansen Senior Project Manager COWI Norway Michael Englund Competence Leader of Sustainability Arkitema Sweden Yutaka Goto Researcher, Department of Architecture and Civil Engineering, Chalmers Funding came from the COWIfoundation, whose objective is to support research and development
3 Content 1095715
CaseConclusionsMethodStudyProjects
WoodPreludeas a material
4
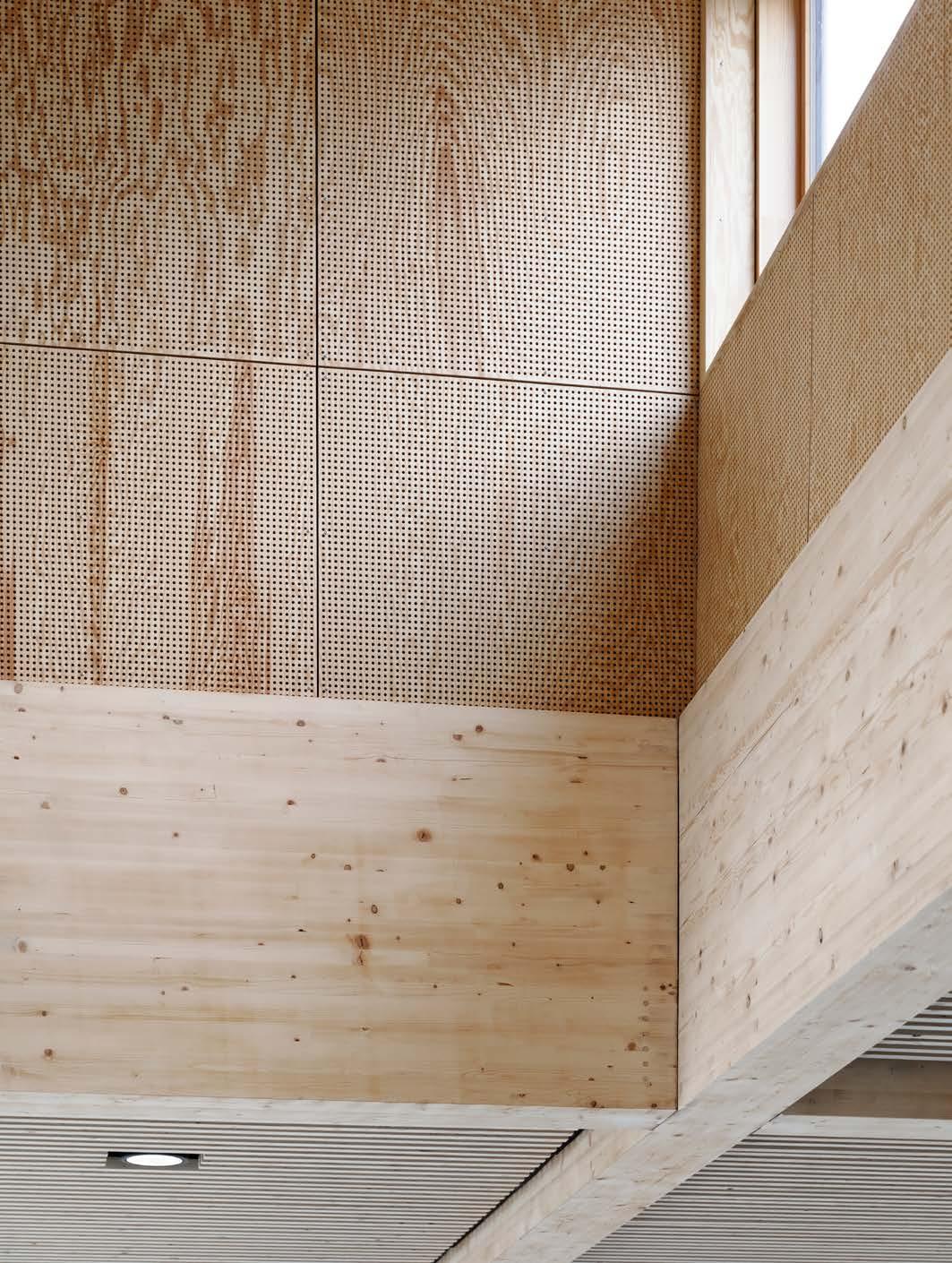
Although there are increasing interest and practices in modern large timber constructions, many stakeholders feel uncertain on how to carry out construction projects with timber. One major concern is the economic aspect of the projects. The common notion is that timber con structions would become more costly than a conventional alternative such as concrete. It is important that we make decisions based on facts, not feelings or even experiences that are no longer valid – innovation moves quickly. Therefore, we have conducted a study to find out if these notions are true. We hope that you'll find this material useful.
5 Prelude
The construction industry is responsible for 37% of GHG emissions. If we truly want to be part of a sustainable future, we need to rethink "business as usual". To build in wood is one of the ways to lower GHG emissions.
industrytheRethinkingconstruction
6 Although there is an increasing interest in timber constructions, many stakeholders feel uncertain on how to carry out construction projects with timber.

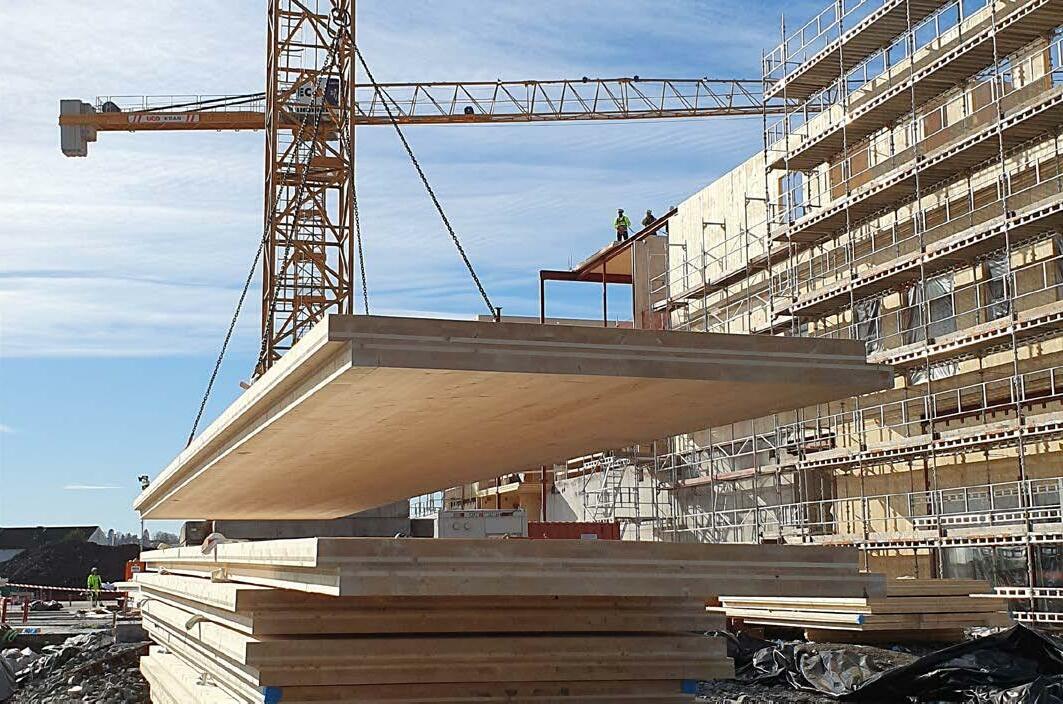
7
Wood as a material
Furthermore, the current market situation does not economically favour a less carbon intensive material unless it is less costly than other common materials.
Wood is a natural and renewable material that sequesters carbon from the atmosphere and stores it in the wood material for a long time when used in buildings, up until the wood is burned or composted. If a timber construc tion is fully protected against weather, the lifespan of the construction will be the same as for a conventional concrete construction. Reuse of materials will of course delay the return of carbon to the atmosphere. In the practices of construction projects, decisions are very often made based on the priority on the economic performance among all viable technical alternatives.
One major concern for many stakeholder regarding construction projects in timber is the economic aspect of the projects. The common notion is that timber con structions would become more costly than a conventional alternative such as concrete.
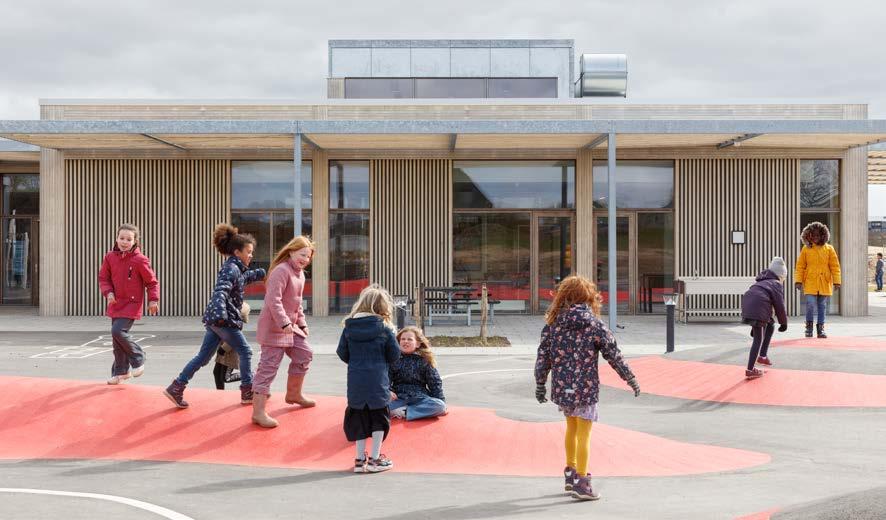
— Jens Hagelberg, Calculation manager, SJB bygg b b b
If we were to do a similar project again using CLT, the project time would be approx. 10-20% shorter.
— Erlend Dragesæt, Project manager, Veidekke byg
— Jakob Kock, Technical director, Adserballe & Knudsen
8
CLT manufacturers have both come closer to us, so transport costs take up less space. But there has also been increased competition, which means we are able to buy the CLT elements cheaper today than when we bought our first CLT elements three years ago.
The shorter construction time is beneficial for the developer of the project, since the occupancies can move into the apartments earlier and start paying rent, which means that the developer will save interest rate for the earlier incoming money.
CLT is a multi-layered glued timber panel. Each layer consists of timber lamellaes laid in the same direction, and each neighboring layer is glued crosswise. It has a high loadbearing capacity, the structural planning is similar to concrete structure, and it has a higher dimensional stability under varying humidity conditions compared to solid wood.
The study investigated the actual construction cost of multi-story residential buildings whose primary loadbearing structure is made of CLT in Norway and Sweden. A specific typology of building (multi-story residential) with a specific material (CLT) was chosen to make the collected data more comparable to each other. The cost data analysis and comparison were carried out in a simplified manner, not applying a full life cycle cost (LCC) analysis. The investigation was limited to the cost of the design and construction stage (A1-A5 module, according to the Life Cycle Stages of EN 15978:20116) until the project is handed over to the occupants. Only the actual construction cost was investigated, and the sales price and other sales-associated factors of the apartments is not included. The cost has been evaluated pr. GTA (Gross total area) and converted to euro (2021 rate).
What is CLT?
9 Method
There is a tendency that the CLT buildings has a higher construction cost compared with the concrete buildings for the Norwegian case
Thebuildings.material
10 Conclusions
The cost of a CLT building does not necessarily need to become higher compared to a concrete building. It depends on the type of project and how it is executed.
CLT buildings are lighter than concrete ones and in many cases that presents an advantage on foundation costs. The more experience one has with CLT buildings, from cost calculation to designing and constructing, the more likely the building becomes more cost efficient.
cost is often higher for CLT buildings compared with concrete buildings.
Conclusions
The prefabrication of CLT modules most often result in a shorter construction time as well as better working conditions in the factory and on site. In order to optimize timber construction in both structural system with realistic dimensioning and material cost, it is important to engage an engineer in the early phase of the project planning.
Want to know more?
Read the full report by clicking here or scan the QR code with your phone

11
The logistics of a CLT building is different than for a concrete building and most be considered carefully to lower the cost. None of the case studies used a tent as weather protection, but it is stated that it possible to save money when applying a tent, due to a more continuous workflow.
cost
Total pr. Norwegian case projects regulated)
If the apartment building is a student building or care homes the building will consist of many small apartments and therefore more fire sections, internal walls, and more bathrooms. These extra materials might result in a higher construction cost compared with a family apartment building with larger rooms. Two out of the three CLT case buildings in Norway are care homes but none of the con crete case buildings in Norway are care homes.
GTA for the
(index
Total cost pr. GTA for the Swedish case projects (index regulated) 0 € 500 € 1 000 € 1 500 € 2 000 € 2 500 € 3 000 € 3 500 € 0 € 500 € 1 000 € 1 500 € 2 000 € 2 500 € 3 000 € 3 500 € Concrete 1 Concrete 4 CLT 4 CLT 5 CLT 3CCLT 2CLT 1 Concrete 2 Concrete 3
12 ConclusionsNote:
— Erlend Dragesæt, Project manager, Veidekke byg
13
— Jakob Kock, Technical director, Adserballe & Knudsen
— Erlend Dragesæt, Project manager, Veidekke byg b b b
We can also see that it gets cheaper because we become faster and more skilled. It gives us some security in relation to the fact that we can afford to be ambitious in the logistics and put the processes close together, because the elements will fit together when they arrive.
The biggest savings for us as a contractor is clearly the construction time. If you shorten the construction time you will reduce financing costs considerably for the client.
CLT is a lighter construction that can help to avoid costly measures for foundation if there are poor ground conditions.
14
CO 2 will become a currency in the building sector alongside cost of money as there will be limits to how high CO 2 emissions can be when commissioning a contractor.
- Daniela Grotenfelt, Head of Sustainability, Arkitema
15 Case StudyBergheimProjectsboaktivitetssenterog CLT 1, Norway - p. 16 Solhøy CLT 2, Norway - p. 16 St. Olavsvej 18 CLT 3, Norway - p. 16 Ski BB1 Magasinparken Concrete 1, Norway - p. 17 Trelasttomta Concrete 2, Norway - p. 17 Fagertun Panorama Concrete 3, Norway - p. 17 Arken CLT 4, Sweden - p. 18 Björkdungen 5 CLT 5, Sweden - p. 18 Tingstorget Concrete 4, Sweden - p. 18
16 CLT 1 (NO)
Solhøy has four storeys and is a care home for 67 residents. The basement is constructed in concrete and steel, and the above three storeys are in CLT.
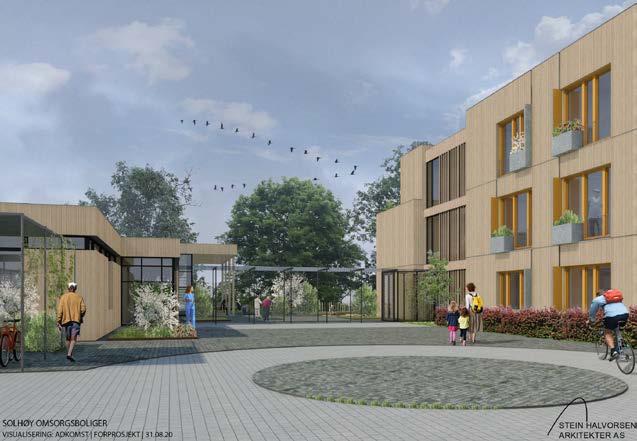
© EntreprenörVEF © EntreprenörVEF © EntreprenörSolid
CLT 2 (NO) CLT 3 (NO)
Year:Size:Year:Size:Year:Size: 11.700 m² 2021-20221.657Under22.5362017-2019GTAm²GTAconstructionm²GTA Bergheim boSt.SolhøyaktivitetssenterogOlavsvej18
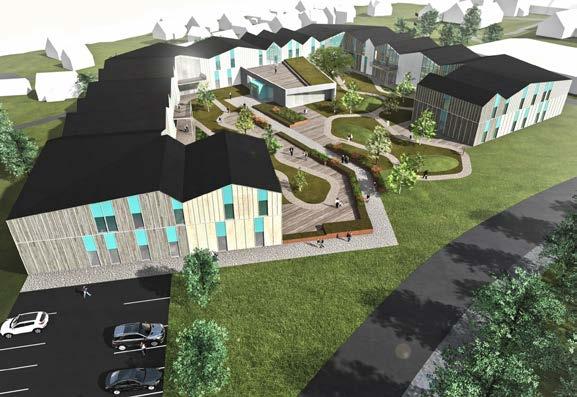
St. Olavsvej 18 is an apartment build ing in five storeys (incl. basement) located in Kristiansand in the south of Norway. The basement is con structed in concrete and the upper storeys are constructed in CLT.
Bergheim bo- og aktivitetssenter is a three storeys care home for 96 residents.The upper two storeys were constructed in CLT and the ground floor in concrete. The build ing is shaped in a horseshoe form with a yard in the middle.
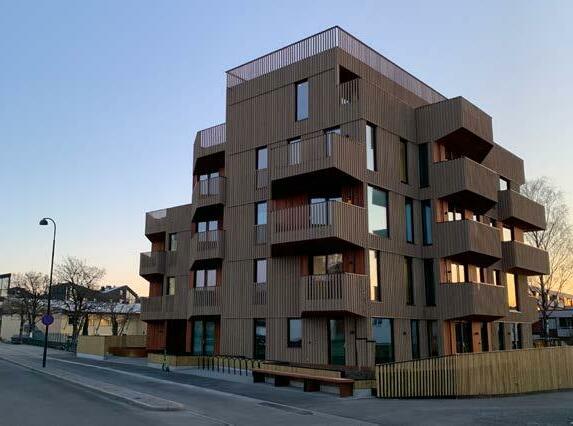
17 Concrete 1 (NO)
2019-20213.5592019-20209.9502019-2020m²GTAm²GTA Ski BB1 FagertunTrelasttomtaMagasinparkenPanorama© EntreprenörSolid©EntreprenörSolid © EntreprenörVEF

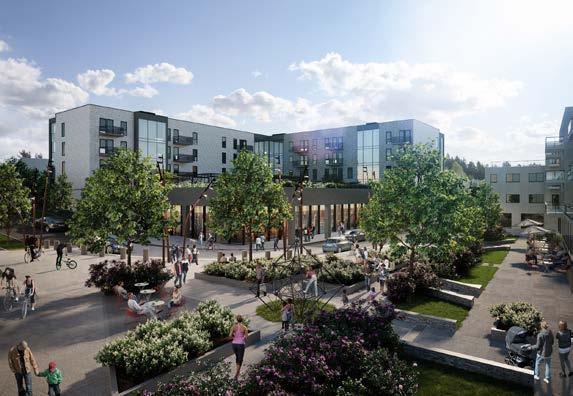
The project Trelasttomta consists of four apartment buildings varying from four to seven storeys and one shared basement underneath all the four buildings. The buildings are mainly constructed in concrete and steel, with concrete slabs and load bearing system in steel.
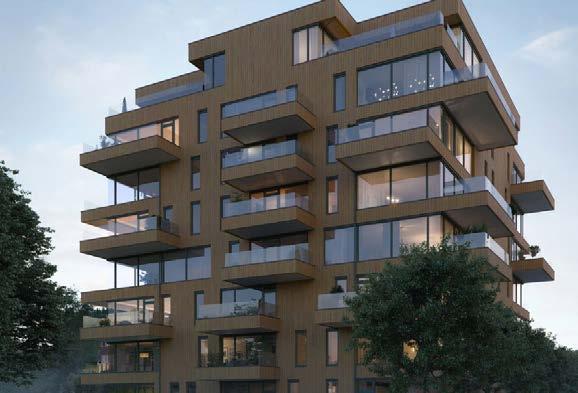
Concrete 2 (NO)
Concrete 3 (NO)
Ski BB1 Magasinparken is an apartment complex, (7 buildings with 183 apartments in total). The number of storeys varies for each building. The buildings are constructed with slabs in concrete and steel columns as the loadbearing system. The foun dation was made as pile foundation, which often has a higher cost.
Fagertun Panorama consists of four apartment buildings with two or three storeys and a basement. The buildings were constructed as conventional apartment buildings with a loadbearing system in con crete and steel. 24.805 GTA
Year:Size:Year:Size:Year:Size:
m²
Tingstorget offers 729 apartments distributed in 14 buildings varying from rowhouses in 3 storeys to multi-story buildings with 6-8 storeys. Tingstorget has a load-bearing sys tem in concrete, load bearing inner walls, elevator shaft, staircase and joist constructed in steel and massive concrete. The exterior wall is made of concrete sandwich elements.
© Arkitema
18 CLT 4 (SE)
Year:Size: 43.007 m² GTA 2016-2019 Tingstorget
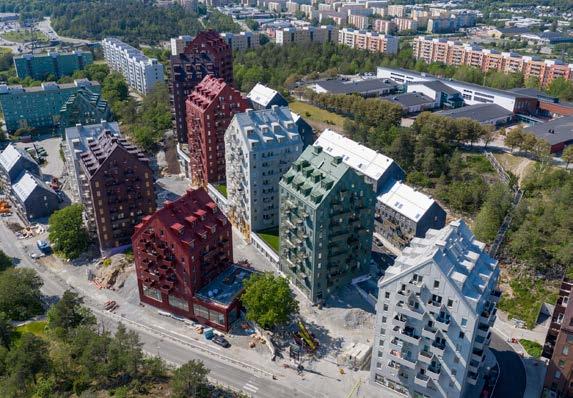
BjörkdungenArken 5 © Arkitema © Växjöbostäder Concrete
Arken consists of three buildings with total of 85 rental apartments. The buildings were constructed with a CLT frame, with slabs, outer walls, load bearing inner walls, joist, balconies, elevator shafts, beams and columns in CLT and glue laminated timber. The basement and ground floor was made from concrete. The load bearing structure in the two storeys above was made from CLT including half of the facade walls. The other half of the facade was made from SJB byggs own light weight system in wood. The inner load bearing walls of the smaller top floor was from CLT. The facade walls were made from their own light weight system.
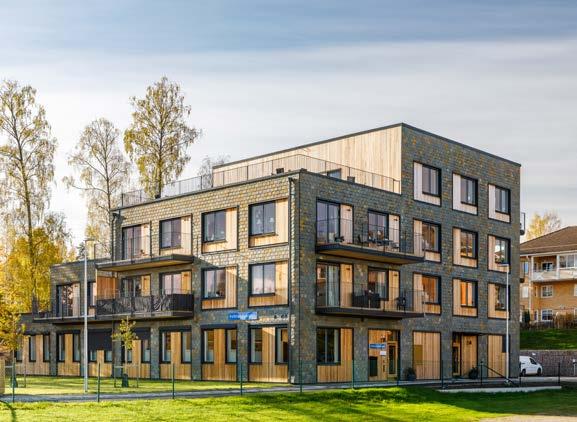
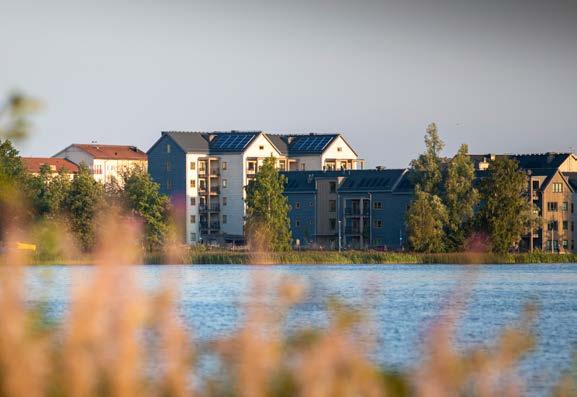
Year:Size:Year:Size: 8.327 m² 2020-20211.5362019-2021GTAm²GTA4 (SE)
CLT 5 (SE)
19
— Olivia Thim, business developer, Växjö municipality
In the beginning the CLT projects in Växjö municipality had a 20-30% higher project cost than concrete. As more CLT projects were built in Växjö, the cost difference decreased to 10% between CLT and concrete. There was the wood shock during the pandemic period, and the construction cost was heavily influenced by it.
It is important that the building is designed with solid wood in mind. Solid wood has a number of limitations in relation to span, and it is important to get an engineer involved quite early on to look at how the load-bearing system should be designed in relation to the use of the building.
— Erlend Dragesæt, Project manager, Veidekke byg b b
Bengtsforshus - Pär Nilsson Chief Executive Officer
Solid - Richard Hansen
20Contributed
VEF - Petter Pallesen Project- and property manager City of Växjö - Olivia Thim Business Developer
Technical director Red Fire Engineer Sweden AB - Carl Petterson Fire engineer
Calculation/Project/purchase manager
SJB Bygg - Jens Hagelberg
to studied buildings
Växjöbostäder - Carina Herbertsson, Maria Dahl Project managers Business Developer
Structural Specialist, Buildings West COWI - Flemming Kristensen, Leading specialist, cost management Adserballe & Knudsen - Jakob Kock
Veidekke byg - Erlend Dragesæt Project manager
Other valuable contributions COWI - Erik Asplund
This study would not have been possible without the generous contribution of entrepreneurs, project leaders and specialists willing to share their knowledge and experience:
Calculation manager Titania - Wojciech Wondell Project manager
21
www.arkitema.comwww.cowi.com