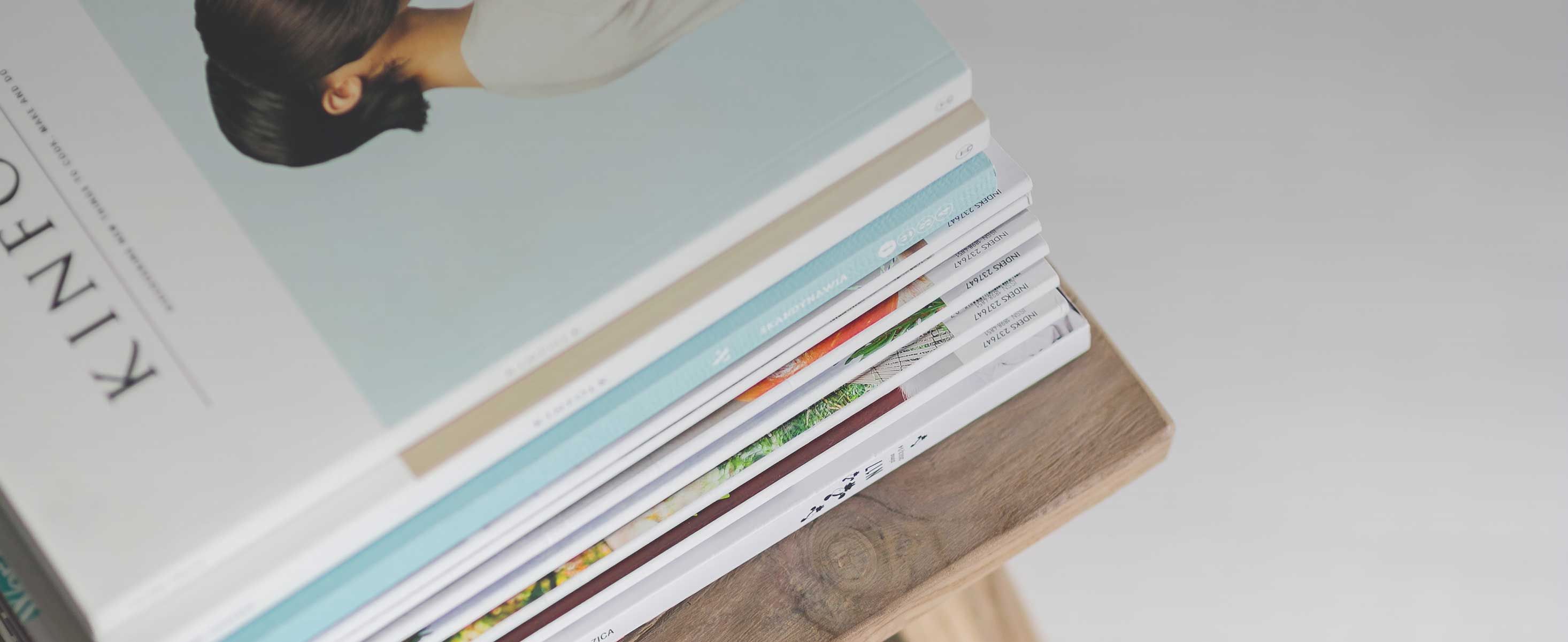
4 minute read
Raise the Resilient RAP Bar
A discussion of one plant-based rejuvenator to facilitate higher RAP in the BMD paradigm
BY SANDY LENDER
Members of the asphalt industry want to do all they can to encourage higher percentages of recycled asphalt pavement (RAP) in mix designs while maintaining or improving performance of the resulting pavement. Let’s look at one additive that’s designed to accomplish a number of goals—such as retaining the effective contributing RAP binder—and is doing so within the balanced mix design (BMD) conversation.
Hassan Tabatabaee is the global technical manager—asphalt solutions at Cargill, Wayzata, Minnesota, and he shared how the company’s Anova rejuvenator can assist agencies and producers in realizing a long-lasting, resilient pavement with the best of both worlds: enhanced cracking resistance and low rutting.
He explained that the Superpave design method optimized mixes to where they were generally lower in asphalt cement (AC) content than they had been prior to the 1990s. “However, the industry found issues with durability in some regions,” he said. When it came to performance of the mix, “not everyone saw a positive trend on the cracking or durability side.”
With the BMD movement taking place around the United States— and abroad—agencies have an opportunity to address additional performance needs, and many are looking to a performance test in the mix design phase where they can raise the bar for optimum pavement performance. Tabatabaee said many agencies are finding the BMD-optimized binder content of an existing mix volumetric/Superpave mix design may need to increase by as much as half a percent, in many cases. If everything else in the mix design remains constant, the 0.5% increase in AC means a more expensive design.
Enter innovative materials.
With ambitious environmental targets set by industry associations, it behooves all stakeholders to find innovative ways to incorporate more RAP, including adding material to rejuvenate oxidized binder within the RAP. As Tabatabaee said: “Our mission is to responsibly push RAP contents higher. Producers should be able to change their recipes as long as the mix meets that higher performance bar.” He believes BMD takes us part of the way there and Cargill’s engineered, plant-based additive is designed to assist.
“Not all of the binder in the RAP is acting as contributing binder,” he explained. “You need to do something to make it effectively contribute to durability, to meet the higher bar.”
One method is, of course, to add virgin AC. Along with the additional cost and environmental product declaration (EPD) a producer may wish to avoid1, there comes a performance thought to keep in mind.
“When trying to offset the impact of increased RAP content on cracking performance, softening the virgin AC or increasing the virgin AC content can only take you so far,” Tabatabaee reminded readers. “Before you run the risk of over-softening the mix and creating potential rutting problems,” which puts the balanced-mix designer back to square one. “Without an additional tool, your only dial to adjust mix durability will be the virgin binder, which has a limited range in terms of either AC contents and grade. A good rejuvenator will increase the amount of effective contribution of the recycle binder, giving you a much wider window of opportunity for balancing the rutting and cracking performance of the mix.”
Selecting a rejuvenator that can help enhance your mix’s overall EPD makes sense given NAPA’s initiative to move the industry toward net-zero. The offering of Anova rejuvenator has EPDs for some of the company’s European markets where standards for calculating EPDs for asphalt additives have been defined. “These are done by a third party designated by the state. However, we do not have an EPD for North America, pending a defined framework and standard practice for calculating EPDs for asphalt additives.”
Cargill shared that it is actively involved with sustainable pavements groups across the industry to develop an EPD for its asphalt additives. “Because these types of technologies are innovative, industry groups are working on developing a framework and standard practices for calculating EPDs for asphalt additives.”
What Anova currently offers producers is a measurable unit of green savings. The product can work simultaneously as a warm-mix additive and RAP binder rejuvenator to lower production temperatures at the asphalt plant and enhance contributing binder availability, as discussed above. The company has learned from the National Asphalt Pavement Association (NAPA): “The estimated reduction of GHG emissions from production of WMA at a reduced temperature can be up to 0.21 million metric tons of CO2e (which is the equivalent to the annual emissions of 46,000 passenger vehicles.)”
NAPA further reported “the use of RAP in new asphalt mixtures reduced greenhouse gas emissions in 2019 by 2.4 million metric tons of CO2e, which is equivalent to the annual emissions of 520,000 passenger vehicles.”
By incorporating bio-based rejuvenators that pull double duty in balanced design, the asphalt industry can increase its environmental stewardship while improving a mix’s chances for long-lasting pavement resilience.
1 The author does not wish to imply virgin AC is a negative; merely, when contrasting the virgin AC with the RAP binder, one is going to see a more positive environmental credit score for the recycled product.