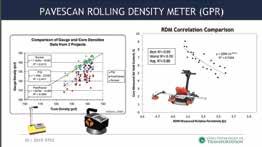
15 minute read
PaveScan MDM Offers Real-Time Density Data
BY SARAH REDOHL
Imagine being able to know the density of the entire pavement without having to take a single core. That’s the ultimate goal behind the new PaveScan MDM (Mixed Design Module) from Geophysical Survey Systems Inc. (GSSI), Nashua, New Hampshire.
When used along with GSSI’s PaveScan RDM (Rolling Density Meter) or RDM 2.0 systems, PaveScan MDM is used to correlate dielectric values with the known densities from gyrotory pucks directly from the asphalt plant to the PaveScan RDM system.
In layman's terms, dielectrics refers to how permeable/permitive the substance is. The dielectric constant of a surface (for our purposes) is the ratio of how permeable it is compared to the permeability of free space—and this is expressed by how much electric flux is involved. For a scientific, in-depth explanation of dielectrics, visit www.vedantu.com/physics/dielectric-constant.
Paving Consultant Bryce Wuori of Wuori Consulting has used PaveScan RDM 2.0 since 2019 and has tested out the MDM system on more than 30 projects in 15 states since 2020. “I use PaveScan RDM 2.0 as a real-time quality control tool, whereas the MDM system is the calibration kit from dielectric to density. I consider it the link between PaveScan RDM and the asphalt mix being produced.”
FROM DIELECTRIC TO DENSITY
Since the launch of GSSI’s first PaveScan RDM model in 2016, the RDM system can be used to calculate the asphalt dielectric values for the entire pavement in real time.
The dielectric values are based on the pavement’s void content, a relative indication of density. Visit theasphaltpro.com/articles/ gssis-pavescan-rdm-asphalt-density-assessment-tool/ for a full explanation of how PaveScan RDM works.
“The dielectric maps can help show pavement uniformity and areas that are lower or higher in density,” said GSSI Business Development Manager Rob Sommerfeldt, “but alone it can’t tell you density values.”
In the past, it was possible to convert dielectric data into density only after the job was cored. Only after the density of the cores was matched to the dielectric values that PaveScan RDM collected at the coring locations could a calibration curve be created, which converts the dielectric map to a density map.
Since the launch of GSSI’s PaveScan MDM calibration system in January 2022, it is possible to use the RDM system to map the density of the entire pavement while there is still time to resolve potential issues.
PaveScan MDM can be used to convert dielectric to density using pucks instead of cores. “Then, instead of seeing the dielectrics when using the RDM on the job site, the crew and DOT will be able to see the density displayed on the RDM’s screen from day one of the job,” Sommerfeldt said.
It’s even possible for this calibration to be done during the winter for a variety of common mix designs, so long as the same mix from the same plant gets used.
Although Wuori has been using ground penetrating radar (GPR) technology for many years and has grown familiar with dielectric data, he said being able to see density data on the RDM’s screen, when used alongside MDM, is useful for those with less familiarity with dielectric data. “Dielectric doesn’t mean anything to many people in the asphalt industry,” he said. “Converting dielectric into a term they’re more familiar with helps the user better understand what’s happening with the asphalt.”
QUALITY CONTROL, QUALITY ASSURANCE
Not only can PaveScan RDM and MDM be used as quality assurance tools by agencies, the systems can also be used as quality control tools by contractors. “Contractors are making tons of decisions every day,” Sommerfeldt said. “This is a tool that can help them evaluate the job immediately.”
For example, PaveScan RDM was used on a recent job in Texas where the crew realized they were seeing a pattern of low density. They were able to stop the job to diagnose and resolve the issue (the temperature on the auger of the paver wasn’t hot enough).
This is how Wuori prefers to use the PaveScan RDM system. In fact, he uses RDM to set up roller patterns for all his projects, but also to adjust roller patterns as needed.
“Since it produces real time data, we can walk behind the intermediate roller and look at rolling consistency in real time, to see density from the centerline to the shoulder in real time,” he said. If an area isn’t achieving the density required to satisfy a percent within limits (PWL) specification, Wuori and his contractor client can change the rolling pattern immediately to ensure uniform compaction.
These charts from the Ohio Department of Transportation shows how PaveScan RDM’s results correlate with nuclear and non-nuclear density gauges. Courtesy of GSSI
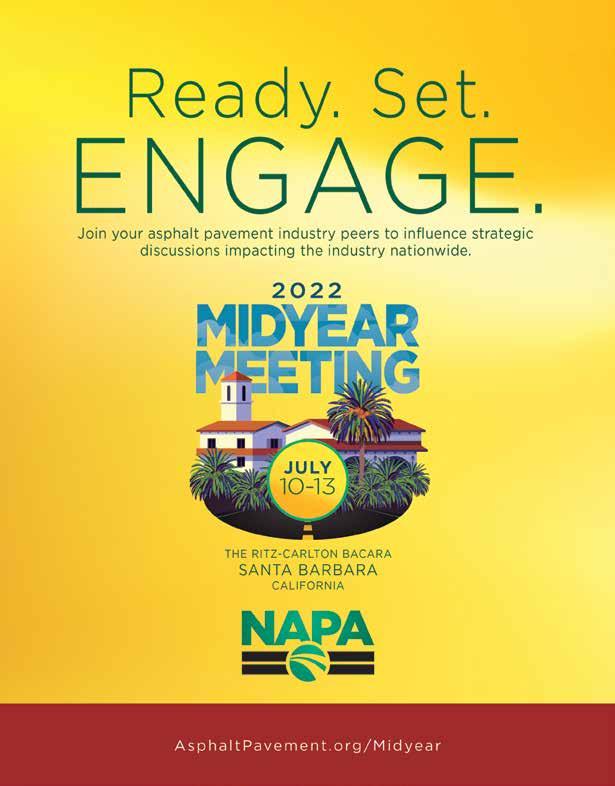
“With a nuclear gauge, I can’t collect enough data to identify issues and make adjustments in real time,” Wuori said. However, he still uses a non-nuclear gauge; for example, if Wuori identifies an area with low density using PaveScan, he’ll use the non-nuclear gauge to verify those results.
Although those benefits could already be realized with the PaveScan RDM, MDM makes it possible for contractors to know the density numbers right away. “If they’re just using the RDM, they can see the pavement’s uniformity via the dielectric data, but not many people are familiar with the term dielectric,” Sommerfeldt said. “MDM can be a complement to the RDM system to help a contractor use numbers they’re used to.”
FULL COVERAGE DENSITY DATA
Sommerfeldt said PaveScan’s most significant benefit beyond its instantaneous feedback (dielectric with RDM, and density with RDM and MDM) is that it offers full-coverage density data. “Instead of spot-checking, PaveScan RDM can tell you what percentage of the total pavement meets density specs and show exactly where there are areas of low density.”
“Whether you’re coring or using a nuclear gauge, you don’t always know how large an area of low density might be,” Sommerfeldt said. When in doubt, he added, contractors usually end up repairing a large area, perhaps larger than the actual area experiencing low density. “Forensics like what we offer with our PaveScan RDM system helps agencies know how large of an area contractors need to repair.”
Although Wuori sees the value of the PaveScan system as a QA tool, he prefers to use the system proactively. “I use the system to fix any issues before they show up during QA,” he said. “That’s my hope for how this technology will be used in the industry.”
Wuori does see the benefits of full-coverage density data: “I can find things with PaveScan RDM that I’d never find with other QC procedures, simply because other methods don’t gather enough data to identify trends. With this, I can identify ways for the contractors I work with to improve their quality in ways that weren’t possible in the past.”
And, he sees the benefits of being able to identify exactly where to start and stop any repairs that may be required. However, Wuori believes there will be a transition phase among contractors who may be hesitant about the capture of so much data.
“This technology will show flaws anywhere on the road, which is very different from coring here and there,” Wuori said. “What I stress to contractors is that this is an identification tool that will help them get better and give them a chance to fix issues before they become a problem.”
CORE NO MORE?
So far, GSSI’s RDM and MDM systems have been tested by several DOTs alongside nuclear gauges to see how the density numbers it measures compare to density numbers measured by the nuclear gauge.
“It isn’t that we can get better data, but that we have better data because we collect more data since we have full coverage of the area,” Sommerfeldt said. “We know 10 cores can’t represent 20 miles of road.”
Although coring continues to be the method most states measure (and pay for) density, Sommerfeldt said he hopes the PaveScan RDM system paired with the MDM system will eventually be another option—and perhaps one that reduces or eliminates the need for coring.
“When you core, you’re putting holes in the road you’ve just paved and those spots are often where potholes start,” Sommerfeldt said. Furthermore, he added, a reduction in coring can result in improved safety.
“Coring is by far one of the most dangerous aspects of an asphalt paving project,” Wuori said. Not only are these operations not accompanied by the lights and visibility of the paving train, but they also often happen during low-visibility hours—at night or early morning before sunrise—so the pavement has had time to cool. This is particularly relevant as longitudinal joint density specifications become more common, requiring coring at a particularly dangerous location, he added.
FUTURE-FOCUSED TECH
Wuori is currently working to develop a specification for the use of this technology in Alaska, adding that Minnesota and North Dakota aren’t far behind.
“I think we are going to see less coring in the near future as a result of this technology,” Wuori said, especially with dielectric-to-density conversion tools like the PaveScan MDM. As the technology gains traction, he anticipates destruction coring could be a thing of the past in the next five to seven years.
“I think this is the future of QC/QA in the asphalt paving industry,” Wuori said. “It’s just a matter of time before it gains traction. Once it does, it’s something that’s going to improve our infrastructure because it’s pushing the industry to be better. Anything that can improve the quality of our roads will be beneficial to the whole industry.”
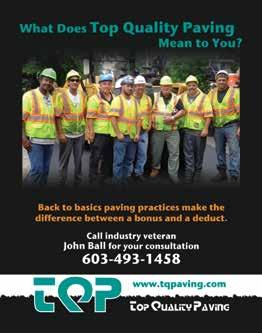
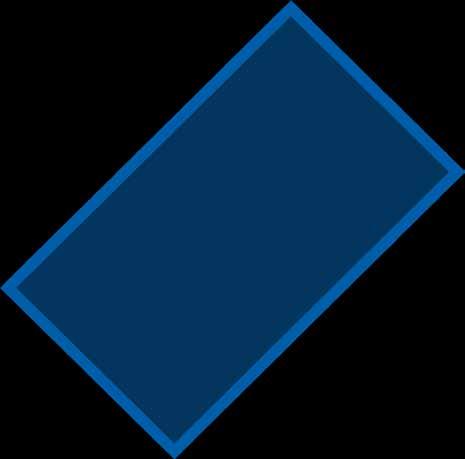
ALmix . . . . . . . . . . . . . . . . . . . . . . . . . . . . . . . . . . . . . . . . . . . . . . 7 Asphalt Drum Mixers, Inc . . . . . . . . . . . . . . . . . . . . . . . . . . . . . . . . 24, 25 Astec Industries . . . . . . . . . . . . . . . . .Inside Front Cover, Inside Back Cover, 11 Blaw-Knox . . . . . . . . . . . . . . . . . . . . . . . . . . . . . . . . . . . . . . . . . . . 9 Bomag. . . . . . . . . . . . . . . . . . . . . . . . . . . . . . . . . . . . . . . . . . . . . 13 BROCK . . . . . . . . . . . . . . . . . . . . . . . . . . . . . . . . . . . . . . . . . . . . . 48 CWMF . . . . . . . . . . . . . . . . . . . . . . . . . . . . . . . . . . . . . . . . . . . . 3, 19 Fast Measure . . . . . . . . . . . . . . . . . . . . . . . . . . . . . . . . . . . . . . . . . 47 Gencor Industries, Inc. . . . . . . . . . . . . . . . . . . . . . . . . . . . . . . . . . . . . 4 Greenpatch. . . . . . . . . . . . . . . . . . . . . . . . . . . . . . . . . . . . . . . . . . 37 Meeker . . . . . . . . . . . . . . . . . . . . . . . . . . . . . . . . . . . . . . . . . . . . 41 Meyer Labs . . . . . . . . . . . . . . . . . . . . . . . . . . . . . . . . . . . . . . . . . . 49 Minds, Inc. . . . . . . . . . . . . . . . . . . . . . . . . . . . . . . . . . . . . . . . . . . 43 NAPA. . . . . . . . . . . . . . . . . . . . . . . . . . . . . . . . . . . . . . . . . . . . . . 45 NCCP. . . . . . . . . . . . . . . . . . . . . . . . . . . . . . . . . . . . . . . . . . . . . . 47 PetroCanada . . . . . . . . . . . . . . . . . . . . . . . . . . . . . . . . . . . . . . . . . 33 Reliable Asphalt Products . . . . . . . . . . . . . . . . . . . . . . . . . . . . Back Cover Stansteel . . . . . . . . . . . . . . . . . . . . . . . . . . . . . . . . . . . . . . . . . 35, 39 Systems Equipment . . . . . . . . . . . . . . . . . . . . . . . . . . . . . . . . . . . . . 23 Tarmac, Inc. . . . . . . . . . . . . . . . . . . . . . . . . . . . . . . . . . . . . . . . . . 21 Top Quality Paving. . . . . . . . . . . . . . . . . . . . . . . . . . . . . . . . . . . . . . 46 Weiler . . . . . . . . . . . . . . . . . . . . . . . . . . . . . . . . . . . . . . . . . . . . . 17 Willow . . . . . . . . . . . . . . . . . . . . . . . . . . . . . . . . . . . . . . . . . . . . . 47 Wirtgen . . . . . . . . . . . . . . . . . . . . . . . . . . . . . . . . . . . . . . . . . . . . 15 Women of Asphalt . . . . . . . . . . . . . . . . . . . . . . . . . . . . . . . . . . . . . . 27 Wuori Consulting. . . . . . . . . . . . . . . . . . . . . . . . . . . . . . . . . . . . . . . 49
AsphaltPro’s advertiser index is designed for you to have quick access to the manufacturers that can get you the information you need to run your business efficiently. Please support the advertisers that support this magazine and tell them you saw them in AsphaltPro magazine.
Integrating technology for quality.
QUALITY CONTROL
Field Density Management Longitudinal Joint Density Management Paving Plan Development Ground Penetrating Radar Services TECHNOLOGY CONSULTING
Intelligent Compaction Paver Mounted Thermal Profiler 3D Asphalt Paving EQUIPMENT CONSULTING
Paver and Distribution Setup Compactor Pattern Development
WUORI CONSULTING, LCC (701)426-7873 wuoriconsultingllc@gmail.com
GREAT PEOPLE. GREAT WORK.
Specially formulated temporary and semi-permanent release agents and coatings, drag slat cleaners, and extraction solvents. Designed to work on all asphalt mix designs, including on all PG grade asphalt mix designs such as PG-76-22 and 70-22.
Our asphalt release agents are state DOT-approved and NTPEP tested and listed.
All our proprietary asphalt products and equipment are proudly formulated and manufactured in the United States.
"Since making the switch to Meyer Laboratory’s asphalt release agents and drag slat cleaners at all the All States Materials Group plants throughout New England more than 2 plus years ago, we are extremely pleased with the performance of the products and customer service provided. I have also received positive feedback from our paving superintendent that Meyer’s products have performed much better than our previous products used on the tools, transfer machines, rubber tire rollers and pavers in the field. Thank you again for everything - Todd Jarvis, Plant Operations Manager - Trew Stone, LLC a division of All States Material Group
We custom build our dispensing systems to meet each customers unique needs.
Meyer is a full-service supplier with more than 75 service reps and numerous warehouses located across the United States. We can serve any customer, anywhere and anytime.
Arrange for an appointment today:
sales@meyerlab.com
800-580-7677
www.meyerlab.com
Discover our SERVICES Scan the
We are family owned and operated for over 40 years. Our focus is meeting the needs of our customers. Our service reps are always available for installation, repairs, and product delivery. In short, we provide service where and when you need it - every time.
QR
CODE