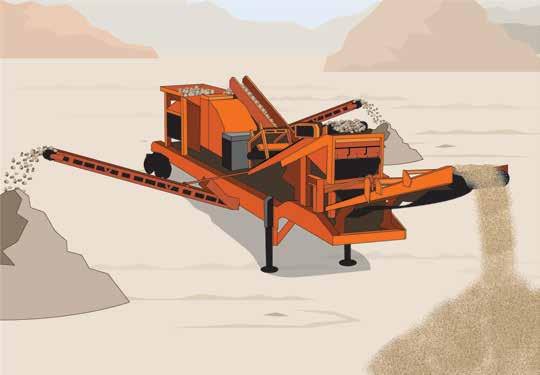
2 minute read
Eagle Crusher’s RapiDeploy 1000
Step 1
The operator lowers the run-on legs and extends the plant’s conveyors to prepare for operation. Step 2
A loader or excavator feeds material to the 11-cubic-yard capacity hopper.
Step 3
Material is screened via the 2-step, 5-foot grizzly deck to remove smaller material and bypass the impactor. Step 4
Material that has bypassed the impactor, and material from the crusher, are deposited on the crusher discharge conveyor, and then transported to the two-deck screen with third reliever deck for sizing.
Step 6
The return conveyor transports oversized material from the screen to the hopper, where it is introduced directly into the impactor for re-crushing.
Step 5
Material that meets intermediate or final spec product is discharged onto the side discharge conveyor or fines conveyor, respectively, for stockpiling.
The team from Eagle Crusher, Galion, Ohio, offers the RapiDeploy® 1000, which includes the features of the original RapiDeploy (now called the RapiDeploy 500®), plus the Eagle Crusher UltraMax 15 impactor. The RapiDeploy 1000 is designed to crush, screen, separate and stockpile—all in one pull. Here's how it works:
Material is dumped into the vibrating hopper. At the end of the hopper, material flows across the two-step, 5-foot grizzly deck. Smaller material slips between the bars, allowing it to bypass the crusher and be screened first, reducing wear on the impactor.
Material that bypasses the impactor is deposited on the crusher discharge conveyor where it rejoins material crushed in the impactor and is transported to the two-deck screen with third reliever deck. The third reliever deck is two-thirds the length of the full screen decks to help bypass the close-tosize material through the screen to the absolute decks, while retaining the larger, oversized material. This gives the screen more opportunity to size the close-to-size material without blinding itself with too much oversize material.
Oversize material is returned via the return conveyor to the hopper, where it is introduced directly into the impactor for re-crushing.
Material that meets the producer’s intermediate or final specs is discharged off the side discharge or fines discharge conveyors, respectively, for stockpiling.
Optionally, smaller material that falls through the grizzly bars can be removed by the throw of a lever onto the optional grizzly discharge conveyor.
For more information, contact (800) 2532453 or sales@eaglecrusher.com.
SHOW US HOW IT WORKS
If you’re an original equipment manufacturer with a complex product, let us help you explain its inner workings to asphalt professionals. There’s no charge for this news department, but our editorial staff reserves the right to decide what equipment fits the parameters of a HHIW feature. Contact our editor at sandy@theasphaltpro.com.
BUILT TO CONNECT
Power and Portability
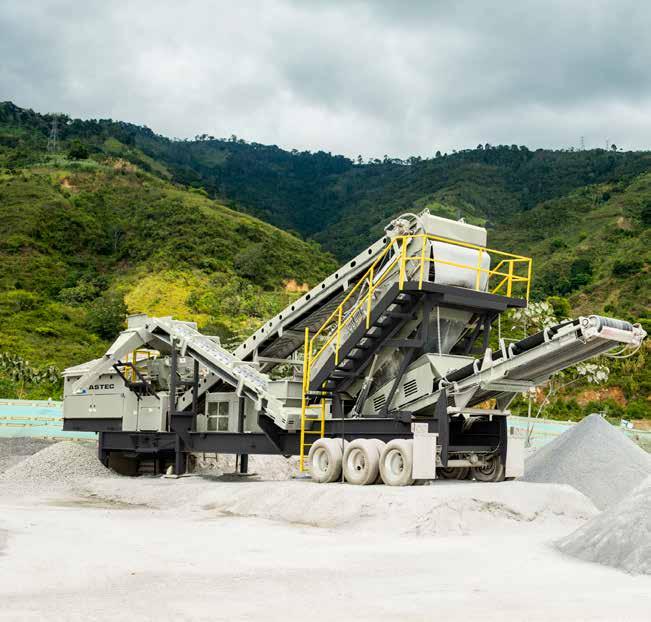
Our portable plant configurations feature a variety of components including jaw crushers, cone crushers, impact crushers and a variety of screening plants. Without sacrificing power or productivity, portable options deliver efficient and reliable performance with extra portability and adaptability.
Scan to see all our portable products
