
13 minute read
Family Connections
JM Fahey celebrates 50 years with CWMF’s stationary full plant build
RBY SANDY LENDER Replacing the original plant at its Holliday Drive, Kansas City, Kansas, location represented the icing on the cake for the 50-year anniversary of JM Fahey Construction Company, Grandview, Missouri. Joseph M. Fahey founded the company in 1971 with his son Kevin Fahey and grandson Andrew Fahey at the helm today. They’re not only celebrating five decades of quality workmanship from the early days of cold milling to acquisition of land and facilities for quarrying and asphalt production, but also celebrating growing a family-oriented company that takes its commitment to employee, community and vendor relationships seriously.
Read the history of J.M. Fahey on the company website at https://www.jmfahey.com/history.
A TEAM BUILD
Andrew Fahey, president of the company, spoke proudly of the team at JM Fahey when describing the new plant now in service for them. He also spoke of the team and family atmosphere of the vendors his company elected to work with for the build. Those vendors, CWMF Corp., Waite Park, Minnesota, and Motion Engineering Inc., Kenosha, Wisconsin, also have family histories as their backbones.

The robust control house is centrally located where the operator has a bird’s eye view of loadout and production. All photos courtesy of CWMF The Revolution drum from CWMF for JM Fahey’s new plant is 10.5 feet in diameter, 54 feet long and includes a RAP collar.
“This is our first experience with CWMF and we’re looking forward to that relationship moving forward,” Fahey said. The company’s management team was able to meet with the ownership of CWMF before design conversations or permitting applications began.
“CWMF is a family-owned business, which was important to us,” Fahey said. “That was meaningful to us on the front side of this. You don’t see enough of that anymore, but you can learn a lot about somebody by sitting down with them for a while and learning their values. We had that opportunity with CWMF. They’ve got a lot of skin in the game, and we understand that better than anybody.”
Wally Olson, regional sales manager for CWMF, explained he and owners Travis Mick and Carmie Mick were about to meet with Fahey’s management team before design and engineering conversations got started. “We went to Kansas City, and I thought I’d need to present all the ways we could help them, build a plant for them. All they wanted to do at that time was meet, get to know us. We were building a relationship between a family-owned group and a family-owned business.”
The custom-build conversations began around December 2019.
By December 2020, CWMF had a commitment from the Fahey company to bring the build to fruition. “It took all of a year for the permitting,” Olson explained. “What CWMF was providing was good to help in the permitting process, but more information was needed from our engineering department due to the nature of a custom-built design to facilitate permitting and for management to come to final decisions.”
The physical on-site build began when the first truckload arrived at Holliday Drive Feb. 15, 2022. Over 30 truckloads would be delivered over the next 20 days, complete with some weather interruptions. The CWMF and Fahey teams didn’t have to go it alone, though. CWMF hired its trusted subcontractor, Motion Engineering, to erect the plant.
“My dad had a long-standing relationship with CWMF,” Mike Petrie, owner/operator of Motion Engineering said. “Travis [Mick] calls us up, we bid the project, and go from there.” After winning the JM Fahey job, Petrie went over the project with their project manager. “They had made the decision on the placement for the plant, provided drawings and layout.”
Because the new plant would ultimately rest upon the old plant’s foundation, the Motion Engineering crew arrived and set the components in place. “On this project, there was no electrical for us to perform,” Petrie said. “Motion Engineering does electrical, builds control houses, motor control centers, but this project didn’t require that of the crew.”
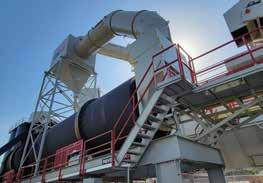
Motion Engineering does everything from smaller repairs to full plant installs and teardowns. The company erects silos, handles retrofits and is a Honeywell/Eclipse/Maxon Channel Partner. “I ran an asphalt plant for seven years,” Mike Petrie explained. “We get involved in almost any project for any brand.”
What the Fahey project did require of all crewmembers was flexibility. “We had snow that threw us off course a little bit,” Petrie said. “Pretty heavy snow conditions. You just have to roll with it
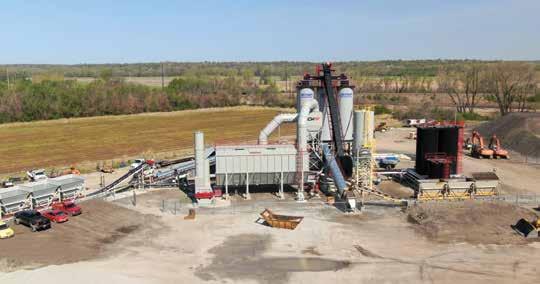
When the plant started operation May 1, the set-up personnel vehicles were gone and the sloped ground leading up to the cold feed bins and recycle bins was complete. By creating a ramp up to the bins, the Fahey team gives loader operators a better opportunity to maximize fuel efficiency and optimize feeding the plant during production. Also notice the covered conveyors and covered and skirted transfer points for material to assist in controlling dust during production.
With the moon setting in the background, the team of JM Fahey, CWMF and Motion Engineering worked through record snowfall to stay on schedule with the new plant build. and do what you can get done, then get up the next day and just keep going.”
Olson and CWMF’s engineering manager, Luke Vossen, commented on the efficiency of the Motion Engineering team members staying on task despite weather or other delays. It was the kind of energy needed in an industry like construction, and Fahey attributed everyone’s success on the project in part to industry knowledge.
“In this business, you better be ready to pivot,” Fahey said. “This team did an amazing job of adapting and making every day count. Not every day is perfect and you have to do what you can on the imperfect days.”
Asphalt Plants Manager Britt Jaudon described one imperfect day as starting with about an inch of snow on the ground at 7 a.m. By 10 a.m., they had 8 inches of snow on the ground and near-blizzard conditions. “We were on a deadline, so we kept one eye on safety and kept pushing forward,” Jaudon said. “We had a good group of guys who knew we were on a deadline.”
“We did have some extreme weather conditions that our team had to fight through during the set-up of the plant,” Petrie shared. “There was a record snowfall during that timeframe, but our team was able to communicate and plan ahead to meet the deadlines that CWMF and Fahey had for the project. We received excellent feedback about our team on that project by CWMF as all were pleased with the outcome of the project.
“If you’re waiting on trucks or a delayed delivery of equipment, my guys are jumping on putting up handrails and other miscellaneous stuff to keep the project moving forward,” Petrie continued. “You keep identifying what needs to be done next and tackle that.”
Sara Petrie explained, “Our guys are away from their families four to six weeks at a time, so they’re a cohesive team that works together well. And it’s a team driven to get a job done in a timely manner.”
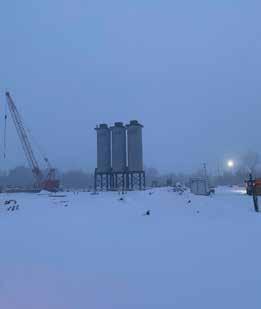
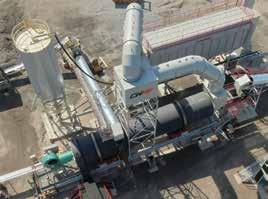
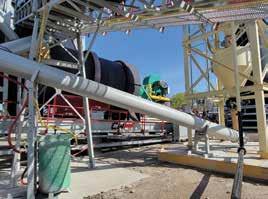
LEFT: Included in this image above the plant, you can see the hose leading from the mineral silo to the Dust-Eater 90,000-CFM pulse-jet baghouse. Rather than build and maintain a mini baghouse atop the mineral silo, the team lets stray dust carry to the baghouse, which serves as the filter. RIGHT: At the bottom right of this picture, the black pipe delivers air into the adaptor flange on the mineral silo’s weigh pod.
TOP: Along with the metering, unloading and pumping packages, CWMF provided two 30,000-gallon and one 15,000-gallon AC tanks for JM Fahey’s new tank farm. BOTTOM: The team held a ribbon-cutting ceremony May 2.
By March 5, 2022, JM Fahey had its plant in place. As of May 1, the plant was in production. “It was a mutual process with CWMF and the customer throughout the design and build phases,” Vossen said. “We had countless virtual meetings to ensure we were building what they wanted.”
Olson and Vossen said that included: • 10.5- x 54-foot drum with RAP collar • 90,000 CFM pulse-jet baghouse • Three 250-ton silos • Drag slat and transfer conveyors • A tank farm with two 30,000-gallon and one 15,000-gallon AC tanks, plus the metering, unloading & pumping packages • Feed bins and scale conveyors • A two-story control house discussed below • Systems Equipment controls • A complete auger package (driven by the customer) to feed dust return to the drum and to the existing mineral silo
BUILDING A WORK ENVIRONMENT
Along with building a new asphalt mix production facility, JM Fahey Construction was building a new work environment for its team at the Kansas City, Kansas, site. To that end, Fahey, put much consideration into the workspaces. One of those spaces is the control house.
“The control house had a separate permit for inhabited structures,” Olson said, not hiding how impressed he was with the planning Fahey put into the building. “You should see how cool this thing is. It’s state of the art. It’s the biggest control house I’ve seen.”
Fahey explained the separate permit was a building permit ensuring the structural integrity of the control house and showing inspections of the foundation work they poured. “We took that in stride,” Fahey said. “CWMF did a great job getting all the necessary engineering approvals.”
The new control house offers more than a central location for plant controls and ticketing. Garage doors on the ground floor open to reveal an electrical hub, easy for maintenance personnel to access. The garage bay doubles as tool and equipment storage, providing a secure and dry place to lock pricy and “easily mobile” items when the crew is
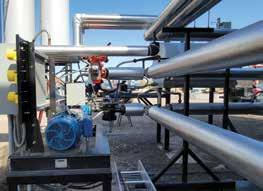
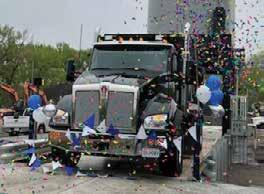
away. The building also offers a comfortable environment with breakroom and office space.
The control house now offers the team—and new members to the team—a pleasing environment to conduct business. “People who aren’t familiar with an asphalt plant don’t realize how much business takes place inside the control house and how busy it can be,” Fahey said. “This larger structure allows an office with a door that allows a little more business to take place and lets Britt [Jaudon] or any of the plant managers stay in one spot to get work done and handle the logistical challenges of the plant. Getting all of that scheduled down to extreme detail is an enormous task; having a place to accomplish those tasks is important.”
Providing the best for the workforce is important to Fahey. “With anything you do today as it relates to your employees, you want to make coming to work a better experience,” Fahey said. “That’s low-hanging fruit. That’s not only benefiting the individual worker, but it’s also benefiting the company as well.”
To prove the point, both Jaudon and Fahey remarked on the current workforce’s contributions to the plant build’s possibility.
“JM Fahey Construction employees need to understand, their efforts are what made this all possible,” Fahey said. “Britt and his team, there are too many to list all the workers who had a hand in making this happen. Forming the relationships with CWMF and Motion Engineering is part of it, but this wouldn’t have happened without our team.”
“It took all those guys to make this come together,” Jaudon said.
BUILDING DUST CONTROL
Another aspect of the build that took a team effort was the dust return. Jaudon explained the system they created was an amalgamation of technologies seen around the industry. No matter which brand of plant or baghouse you look at, he said, there are different aspects of the dust-return systems that are excellent. “All these systems are different, and we designed our own as a combination from multiple plants we’ve been around over the years. With it, we have the way to pull dust out and add dust in simultaneously.”
With material fed via augers, the plant operator can move air locks to feed dust from the baghouse to the drum collar or to the mineral silo, from the baghouse to both the drum and silo, or to feed dust from the mineral silo to the drum. The concept is an example of Jaudon’s ingenuity, nurtured in an environment like JM Fahey and encouraged by the engineering camaraderie with CWMF.
“The customer one hundred percent drove that design,” Olson said. “It’s a custom reverse auger.”
“It’s all driven by the industry’s higher specs,” Fahey said. He explained that the asphalt industry must still meet stringent specifications that incorporate fines and changing designs while maintaining the ability to modify and experiment with materials. “How do we meet those requirements and still have some flexibility?” he asked. Being able to auger fines to the location they’re needed, as they’re needed, gives JM Fahey plant operators that flexibility.
Other dust control around the plant is less technical, but just as important. Visitors to the new plant may notice the site isn’t fully paved, and that’s by design. In the city, stormwater run-off regulations depend on one’s square footage of paved property. “The more you pave, the more run-off you create,” Fahey explained. “If we did decide to pave the lot, we would have been required to put in a retention pond, which we don’t have the space for in our footprint.”
Instead of having a completely paved lot, Fahey has a water truck almost full-time on the site to keep dust down and the drive leading into and out of the site is paved to keep traffic from kicking up too much dust.
From creating a comfortable environment for workers to forming lasting relationships with similar family-oriented businesses, the team at JM Fahey has shown workforce-building and quality-minded growth since 1971. Now the 2022 construction season has launched with a state-of-the-art facility built to attract business, quality and workers for the future.

Move Dust for Quality Control
The team at JM Fahey had been brainstorming ways to improve mix quality for their customers, according to CWMF’s Wally Olson. During the plant designing process from 2019 to 2021, they came up with the ideas for CWMF to design. The result is the system in these images. It may look complex at first with enclosed augers crisscrossing this flat image, but the design contained within the space of the pertinent components allows the plant operator to physically meter fines to his mix.
In the photo below, you can see a forward auger (the base of which is indicated by the letter B) to move dust from the baghouse (indicated by the letter A) to the drum. The system gives the plant operator the ability to block the rotary airlock and reverse the auger (indicated by the letter C) to move dust up to the mineral fill silo.
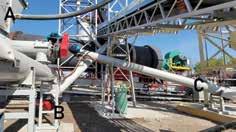
The hose leading from the top of the mineral silo to a flange on the baghouse (indicated by the letter A) represents another innovation from JM Fahey and CWMF. Olson said this idea not only reduced maintenance by eliminating the need for a “mini baghouse” atop the mineral silo, but also lets the Dust-Eater from CWMF serve as a filtration for the dust silo.