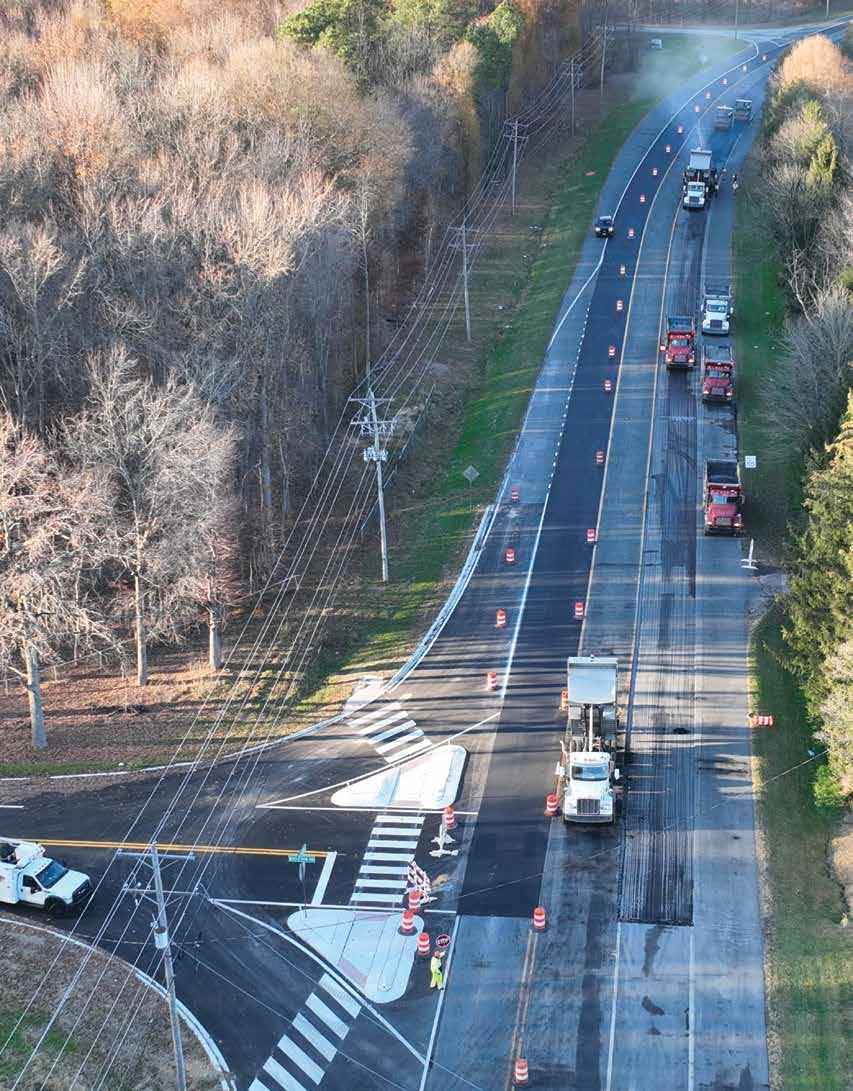
• WOA/AGG1 Wrap in Nashville
• BMD, GTR, RAP Win on Route 63
• Expand Your Operation to Paving
• How Does AI Affect Efficiency?
• Spring 2024 PreservationPro
• WOA/AGG1 Wrap in Nashville
• BMD, GTR, RAP Win on Route 63
• Expand Your Operation to Paving
• How Does AI Affect Efficiency?
• Spring 2024 PreservationPro
From the beginning, our service team has provided construction services for the equipment we build. Astec construction and relocation services for asphalt plants include plant and equipment installs, plant tear-downs and moves, silo repairs, and industrial piping and tank farm installs.
Efficient planning minimizes downtime, local regulations and permits also play a key role. Astec has an extensive history and experience with permitting and regulations. Safety, efficiency, and compliance are paramount throughout the process.
Let me begin with something obvious today. One of the ways to increase the use of recycled asphalt pavement (RAP) and thus decrease the perceived horror of using virgin materials in pavement construction is to remind—or convince— state departments of transportation (DOTs) that using RAP is a positive. We, as an industry, would like to share the message with our DOTs and other agencies that increasing RAP percentages in various lifts, including substantive surface courses and thinlays, yields a long-lasting and environmentally responsible product for taxpayers.
but also their potential to perform or fail two, three or four years down the road. You can bet the engineers at the DOT are considering it.
Agencies typically wish to reuse and recycle these days. But state DOTs are notoriously cautious when it comes to throwing “used materials” into their mix designs. And they should be. Asphalt pavements are not and should not be landfills.
Let me reiterate for absolute clarity. It is the opinion of the editor of AsphaltPro magazine that asphalt pavement systems are not and should not be modern day landfills.
While asphalt mix designs of course have room to incorporate novel materials, with additives to enhance adhesion, blending, viscosity or what have you, the industry works to maintain high quality of performance. A smooth, long-lasting roadway is truly environmentally responsible in that its smoothness leads to improved gas mileage (and less wear) for the vehicles traveling upon it and its longevity leads to fewer materials (and funds) required to preserve and maintain it.
By paying attention to the inputs’ potential for performance, we get a better outcome. Isn’t there an adage about garbage in, garbage out? Then let us turn to the materials going into the mix design and consider carefully not only their carbon footprint(s)
If we, as an industry, continue to show good faith in building quality pavements with excellent materials as inputs in our environmental product declarations (EPDs) and use of best production and paving practices, we win the confidence of the DOTs who may have seen less than stellar results in experimental products of the past. It’s no secret that some DOTs still look askance at high-RAP in surface courses. There are entities who have had negative experiences with crumb rubber, various additives for rejuvenation and so on. These unfortunate moments don’t have to hinder the use of high percentages of RAP.
As an industry, we know how to increase RAP content in mix design and pave a long-lasting roadway for taxpayers. We can prove to agencies that we have the integrity to use quality materials that are both environmentally friendly and high performing in a low-bid system. For this month’s “Paving For Bonus” issue, I encourage thinking along the lines of how to incorporate higher RAP mixes in upcoming paving projects, but doing so with highest quality for longest lasting pavements in mind. All eyes are on the carbon footprint these days, but I can guarantee all eyes will be on performance two, three or four years from now. Let’s make sure we’re still giving agencies the best pavement choice with best material inputs.
Stay Safe,
602 W. Morrison, Box 6a Fayette, MO 65248 (573) 823-6297 • www.theasphaltpro.com
GROUP PUBLISHER
Chris Harrison chris@ theasphaltpro.com
PUBLISHER
Sally Shoemaker sally@theasphaltpro.com (573) 823-6297
EDITOR
Sandy Lender sandy@theasphaltpro.com (239) 272-8613
DIGITAL EDITOR
Sarah Redohl sarah@theasphaltpro.com (573) 355-9775
MEDIA SALES
Cara Owings cara@theasphaltpro.com (660) 537-0778
ART DIRECTOR Kristin Branscom
BUSINESS MANAGER
Susan Campbell (660) 728-5007
AsphaltPro is published 11 times per year. Writers expressing views in AsphaltPro Magazine or on the AsphaltPro website are professionals with sound, professional advice. Views expressed herein are not necessarily the same as the views of AsphaltPro, thus producers/contractors are still encouraged to use best practices when implementing new advice.
SUBSCRIPTION POLICY: Individual subscriptions are available without charge in the United Sates, Canada and Mexico to qualified individuals.
One year subscription to non-qualifying Individuals: United States $90, Canada and Mexico $125.00. For the international digital edition, visit theasphaltpro.com/subscribe/
The future is connected. That’s why we’ve designed the ALmix Insignia Control System (ICS) around the power of high-speed Ethernet communication. An ethernetconnected facility means our team of programmers have complete visibility into your plant equipment and motor control center for diagnostics and remote troubleshooting. View and control data from your asphalt plants like never before. The Insignia Cloud Platform provides access while you are at the plant, in the office, or on the go. Critical, real-time, plant information is at your fingertips when you need it.
DON’T LET YOUR EXISTING ASPHALT PLANT CONTROLS KEEP YOU GUESSING:
The Insignia Control System is available on all new ALmix Asphalt Plants and is also available for existing plant control upgrades.
SCAN HERE TO LEARN MORE OR TO SCHEDULE A DEMO
On April 16, 2019, 26-year-old Christopher Ramirez and 41-year-old Jorge Valadez were working in a 15-foot-deep trench installing utilities for a new neighborhood in Windsor, Colorado, when the trench suddenly collapsed. Beneath 8 tons of dirt, Ramirez was somehow able to breathe for hours, speaking to rescue workers through PVC pipe and later a microphone. Before Ramirez passed away, he was also able to say goodbye to his wife, who shortly afterward gave birth to their son.
“[That story] drives us to this day,” said Perry Silvey during a recent webinar about trench safety presented by the Center for Construction Research and Training (CPWR). Silvey is the safety manager of BT Construction, Henderson, Colorado, and also an active member of the Trenching and Excavation Safety Task Force (TEST), an organization founded one week after the event occurred.
Last year, the Occupational Safety and Health Administration (OSHA) announced that there would be enhanced enforcement initiatives and outreach programs focused on trench safety following an increase in trench collapse fatalities to 39 people in 2022.
According to Nicholas DeJesse, assistant regional administrator of OSHA’s Philadelphia regional office, the increase in trench collapse fatalities may be a result of an overall increase in work being performed as a result of infrastructure spending and age-related wear on underground utilities. “We’ve also seen a lack of education, a lack of training, and a lack of having a person [on-site] who understands soil analysis, protective systems, spoil piles and things of that nature,” DeJesse said.
That’s why the CPWR webinar dug into some best practices for staying safe while digging, inviting Douglas Trout, a medical officer with the Office of Construction, Safety and Health at the National Institute for Occupational Safety and Health (NIOSH), and Phillippe Falkner, safety director at Ed Bell Construction Company, to highlight the following best practices.
It’s important for employers to train and designate a competent person to ensure safety measures are in place. “A competent person is one who understands OSHA regulations, can recognize hazards, and is authorized to correct them,” Trout said. There should also be a competent person to evaluate the soil to determine its stability.
OSHA also requires that all excavations 5 feet deep or greater make use of protective system options, which can include sloping or benching the ground, shoring the trench with supports, or shielding the trench, for example using a trench box. “Employers should have a competent person to determine what type of protective system will be used for the job and schedule the steps needed to have the system complete and in place before workers enter,” Trout said.
“A lot of contractors focus on getting a handful of people trained well enough that they can serve as competent persons,” Falkner said. However, he prefers training as many people as possible and encouraging dis-
cussion on the job site. “Even on a small job site where the designated competent person is there all the time and focused 100% of the time, he still can’t see every angle of that excavation.”
It’s also the employer’s responsibility to ensure workers involved in the job are properly trained, Trout said.
Of course, employers should use processes to determine the exact location and depth of utilities before digging, Trout said (811 is the national Call-Before-You-Dig number). They should also plan the job layout to identify safe locations away from the trench for spoil piles and heavy equipment routes.
However, Falkner also stresses the importance of planning when it comes to determining soil classification and appropriate protection systems before digging begins. “Having this done well in advance is part of the critical planning process,” he said.
It’s also important to develop a trench emergency action plan outlining steps to be taken and appropriate emergency contact information. “OSHA also requires employers to provide ladders, steps, ramps or other safe means of egress for workers working in trench excavations 4 feet deep or deeper,” Trout said.
Think Outside the Box—Sometimes: Falkner said that while trench boxes are the most common protection system, there are some conditions where they aren’t ideal. But, because of familiarity with trench boxes, contractors will try to make them work in suboptimal conditions. “You have to figure out what systems are available for which conditions,” he said. “Talk to your competent person, talk to people experienced with engineering plans, seek the help of a registered engineer if that’s what it takes. Talk to your vendors that deal in trench protection.”
“Planning is not just in-house; you have to communicate with everyone else on the job site,” Falkner said. “Your operation may have haul routes designated and stockpiles planned and fall protection in place, but if you’re not the only contractor on site, you need to be planning and coordinating with the other people on that site to make sure they don’t get hurt by your excavation or they don’t hurt your people and your excavation.”
“There are a number of people that will come to see what’s going on with the excavation or play a role [in the job] that doesn’t have them down [in the trench],” Falkner said. The edge of a trench is no different than working near any other fall hazard. “You need to make sure the people up top are also protected.”
Another way to prevent trench collapses and therefore fatalities is to use alternative methods where feasible, Trout said. This may include directional boring, relining the pipe (including cured-in-place pipe), pipe ramming, utility tunneling and pipe jacking.
Falkner stresses the importance of keeping the big picture in sight. “It’s easy to get tunnel vision with collapse prevention that we forget about other risks,” Falkner said. “Especially if you’re on a complex trench set up that’s taking a lot of engineering, planning and teamwork.”
“I’ve seen it happen one too many times where a team has done everything correctly [to prevent trench collapse],” Falkner said, but they might overlook atmospheric hazards such as gas. These hazards need to be checked at the start of shift and monitored throughout the day.
It’s also important to be mindful of critical load plans. “We’re building these trenches generally to put things in the ground or take them out,” Falkner said. “Oftentimes equipment is a bit further back from the trench than what would normally be done to ensure a safe excavation, so you may have to account for things that aren’t normally a critical lift.”
He also reminds us that workers in the trench will have more limited escape routes. “It’s not as easy to get away from problems with the lifted load as it is on even ground,” he said. “And make sure you’re still placing your fall protection where applicable.”
Trout stresses the importance of having your designated competent person inspect the excavation, adjacent areas and protective systems each day before work, but also as needed throughout a shift, and specifically after every rain storm.
In Falkner’s experience, most contractors pay attention to these aspects of trench safety at the start of the job, but this wanes as the job continues. For the crew that moves protection systems “as they go,” they could be moving through changing soil conditions and changing construction sites, Falkner reminds us.
“There’s never a point where we get to check that box and say, ‘Okay, I’m done with that step for today,’” Falkner said.
“Make sure your employees have the right and the expectation to stop work if something doesn’t look right,” Falkner said. “Maybe something was working this morning and now the job is a whole different ball game. It’s okay to stop and reevaluate.”
He’s heard employees time and again say they didn’t feel like they had time to follow best practices because they were behind schedule. “You need to express that if something’s not right, it’s absolutely okay to take a knee until it is,” Falkner said. “Make sure you’re preaching to them that production takes that backseat to safety.”
“Instead of approaching things with an attitude of ‘What’s the minimum I can do that meets the OSHA guidelines,’” Falkner said, “you absolutely
need to go to the other end of that spectrum and say, ‘What’s absolutely the maximum I can do to protect my people and protect the workplace?’”
“We all have to keep in mind that there’s almost no excavation we do where you’re not at some risk for injury or death,” Falkner said. However, Trout said, the hazards associated with trench work and excavation are defined and preventable.
According to Silvey, one aspect of the trench collapse in Colorado that stood out to him was that there had been a trench box on site that had not been in use. “Of course, our question is always ‘Why?,’” he said. “We continue to ask that question and we continue to try to find solutions and try to find creative ways to help folks make the right decisions.”
“We’re here [at this webinar] because construction workers are at risk of death or serious injury if they enter an unprotected trench,” Trout said. That’s why it’s so important to take a maximalist attitude to trench safety. “If you’re just trying to get by, it may not be a problem today or tomorrow,” Falkner said, “but eventually it will catch up with you.”
Get Involved: Silvey encourages anyone interested in trench safety to join the Trenching and Excavation Safety Task Force, use the hashtag #thinkinsidethebox to join the conversation on social media, reach out at thinkinsidethebox@gmail.com, or learn more at thinkinsidethebox.info/.
At the end of the webinar, one attendee asked about the effects of extreme drought on soil conditions, as Texas experienced in 2023. Falkner said the extreme drought and extreme temperatures fractured the soil, adding that there’s likely more instability and variability of soil conditions.
“When soils dry, they start to pull away from each other and create fissures and cracks,” Silvey said, “and you can’t see through the dirt to know where those are.” Falkner said those fractures can run 10 to 15 feet deep, “especially when you get these expansive clay soils down here.”
Falkner said Ed Bell Construction is taking a more cautionary approach in light of these events. “If you’re on the fence between A and B or B and C, you just need to be more cautionary,” he added.
Silvey seconds that approach. “You should look at it like everything is a Type C soil,” he said. “It’s not a matter of if it will collapse, it’s a matter of when it will collapse.” He added freeze/thaw cycles can have a similar effect. “The soil expands when it freezes and starts to break apart as it thaws, creating those large fissures that could cause collapse as well,” Silvey said. “Be a little more conservative. Take the extra precaution.”
The construction industry has the second-highest suicide rate in the United States. While the industry loses two to three workers each day to job-related accidents, they lose ten to fifteen workers each day to suicide. Listen as the author tells his story about his phenomenal life until he attempts to end it. He shares twelve individual stories from those who lost someone to suicide.
Based on his qualitative interviews, conversations, and lived experiences, he will educate leaders that once they begin addressing mental health and suicide in their organizations, they will have a resilient, loyal workforce and a competitive advantage.
The book scared the hell out of me and is a mustread for any human.”—Wally Adamchik, CMC, CSP, MBA
With the Federal Highway Administration’s (FHWA’s) Every Day Counts eTicketing initiative, contractors, suppliers and departments of transportation (DOTs) across the country were introduced at a broad scale to technology in a way our industry hadn’t seen before. In digitizing material tickets, we have made work zones safer, have made information easier to track down, have made payment quicker and have freed up space in our construction trailers, but our work is not complete. As eTicketing matures and becomes more standardized, the onus falls upon all of us to seize the momentum that was created and continue to advance digital construction.
At the Delaware Department of Transportation (DelDOT), we have taken that step, and are incrementally working toward our goal of a completely connected work zone. A work zone that doesn’t just provide an electronic version of a paper ticket, but one where the equipment itself provides estimated quantities, reports on quality control metrics, reports its emissions for inclusion in Environmental Product Decla-
rations (EPDs), provides information for asset management, and most importantly, provides its status to the traveling public to make the work zone itself even safer.
In fall 2023, DelDOT and its partners, Greggo & Ferrara Inc. (G&F), HaulHub Technologies and iCone Products, completed two trials of a connected work zone. G&F, the contractor and supplier, volunteered to connect its Caterpillar paver and Hamm rollers, as well as iCone’s Temporary Traffic Control devices, to HaulHub’s EDOT portal for two separate weekend partial road closures. In doing so, we collected some of the first information on what we hope will become a standard practice across the industry.
Regarding the smart work zone aspect, many DOT projects can have multiple locations under a single contract, so having just the eTicket information is not sufficient to determine what location may be active on a given day. Recognizing this was one of the impetuses to connect the contractor’s equipment to HaulHub’s portal. In doing so, we gained the GPS location of the equipment and knew exactly which work zone on that
multi-location project was active. We then harnessed this “active” status and provided it to Waze in a dynamic manner, giving Waze reliable information that workers were present in the work zone. Waze, in turn, was able to broadcast that information to its users.
To use the equipment’s GPS data, we first needed to define the work zone within HaulHub’s EDOT app. This, in turn, created a geofence for the contractor’s connected equipment to broadcast as active.
While the work zone definition is currently an intuitive process, it is still entirely manual. However, we are investigating ways to get the work zones defined automatically based upon the digital plan information, and our own publicly available linear reference system, eliminating the need for multiple points and further reducing the burden on the inspection staff.
Creating and activating a work zone is not the only consideration when it comes to traffic safety implementation. We must also consider the deactivation of the work zone notification, for both the planned duration and unplanned events such as weather interruptions.
In fact, on our second trial weekend, we experienced a weather interruption.
At this early stage in our trial, the work zone deactivation within Waze was operating based upon a planned duration. With the weather interruption, the team had to manually deactivate the work zone. Subsequently, HaulHub made quick adjustments within the platform to introduce automation into the deactivation of the work zone based upon both the equipment status and eTickets.
While DelDOT’s own traffic notification showed the site as still active, the equipment was no longer operating, and material was no longer being shipped. By all accounts, it was clear in the portal that the site was no longer active, but DelDOT’s current process is dependent on a manual process with multiple layers. With a connected work zone, we are one step closer to harnessing available information to automatically prompt staff to deactivate the public notification, which doesn’t just aid traffic flows, but also improves trust in work zone notifications.
While notifications to the public for active work zones are a significant focus of our early efforts, we do not intend to stop there. DelDOT has partnered with Iowa, Nebraska, Louisiana, HaulHub, Iowa State University, WSP, and WAP Consulting and was recently awarded $4 Million grant from FHWA. Collectively, we intend to use this grant to begin connecting various pieces of equipment throughout our states. Because
we are only in the initial phases of this effort, we focused on simple information— where is the equipment, is the equipment operating, when is the data being sent, which is all that is relevant for a safety feed. As our efforts become more mature, we intend to gather more equipment information like the width of the screed, the depth of the screed, the depth of the mill, the slopes, etc.
Connected Machinery Special Provision
ORIGINAL DATA ELEMENT
OEM Name Model Equipment ID
Location Datetime
Latitude
Longitude
Engine Status Datetime Running?
ADDITIONAL DATA ELEMENTS
Cumulative Engine Hours
Cumulative Fuel Consumption
Heading (if available)
Speed (if available)
Width (if available)
Depth (if available)
Drum RPM (if available)
This chart shows the data requirements in the original connected machinery special provision and the additional data requirements in the updated special provision, as provided by DelDOT.
This type of information can provide, at the very least, a check against calculated numbers or perhaps even replace information collected by inspection staff once we build confidence in those systems. The goal though, is to give the department another way to verify that 3,046 tons of mix were placed on DE-72 on our first trial date, or that 14,350 SY-IN of bituminous concrete were milled on our second trial date.
To this point, we have engaged with equipment manufacturers to understand what is currently available on their equipment, what sensors can be easily added to their equipment and what else we can do as we move forward. Can we add a thermal sensor on the pavers or rollers? Can we get theoretical densities off the roller? With the next version of our Connected Machinery Special Provision, DelDOT will be asking for some of those additional data points (See the Sidebar).
As we build this database of information, we will grow our efforts to start getting information on quantities directly from the equipment itself. We will have geolocation data on where that work was done to feed into our asset management systems. We can use run times to determine the A5 component of EPDs on a project-wide or material-focused basis. These are no longer theoretical goals to obtain far in the future. In many cases the information is there today; it exists. We simply need to join together and capture it in a standardized manner.
That is the goal of our project.
Personally, I feel the next five years in construction will be as transformative as the preceding 15 years, as we see various technologies finally begin to come together. From eTickets, to digital as-builts, to building information management (BIM) and beyond. Connected machinery and a connected work zone are where all these things come together. Construction is the final link in the lifecycle of information for infrastructure, and connected machinery is the key to that link. We encourage all our partners in highway construction, from equipment manufacturers to contractors to suppliers to fellow agencies, to reach out to our ADCMS team and join us in bringing these innovations to fruition.
If you’d like to read more about DelDOT’s first trial project and view the information in an interactive way, please visit https://bit.ly/ AsphaltProDelDOT
Jackson isn’t the only person noticing the hard work of his crew. “Somebody sent us an email about how they’ve never seen that many people in a work zone all working. Another lady called and said, ‘that group out there, they’re all working, there’s nobody standing around.’” All photos courtesy of West Contracting
Balancing GTR, RAP, WMA over failing concrete proves successful for Missouri taxpayers
EEarly June 2023, the team at NB West Contracting, headquartered in Pacific, Missouri, began work on a complex overlay. The main goal was to cover up a 15.3-lane-mile, potholed, concrete section of Route 63 in Maries County and make it a smooth, safe driving surface for the taxpayers. The Missouri Department of Transportation (MoDOT), Ingevity, National Center for Asphalt Technology (NCAT) and NB West partnered to exceed that goal.
Steve Jackson, the vice president of asphalt plant operations and sustainability for NB West spoke of combining ground tire rubber (GTR) and 20% recycled asphalt pavement (RAP) as one aspect of the warm-mix asphalt (WMA) project.
“It was a balanced mix design, performance spec, SP095C (9.5-millimeter,) Superpave with ground tire rubber and RAP, warm mix, placed through a spray paver, and bonding to a concrete pavement,” he said. He listed off all those moving parts of the project like it was business-as-usual for the production and paving personnel. For a team that’s been on the scene since 1956, it almost is a walk in the park, yet they pulled out the quality control/quality assurance (QC/QA) and safety best practices to make sure everything flowed smoothly for an award-worthy project. In the end, they garnered the Missouri Asphalt Pavement Association (MAPA) 2023 award for a primary route under 50,000 tons. Here’s how they accomplished it.
In 2012, NB West had successfully performed a project bonding an asphalt layer to concrete with the company’s Roadtec spray paver, and saw an opportunity to apply that technology again. Jackson explained
the DOT originally was letting the project with the 19.0 mm mix and a 12.5 mm mix for the surface layer, but his team wasn’t excited about that because both layers would have been placed at less than four times the nominal maximum aggregate size.
“The thickness of the layer didn’t allow for the 12.5 mm to work smoothly,” he said. “In 2012, we’d done something similar bonding concrete with the spray paver, so after we were awarded the [Maries County] job, we did a value engineering proposal to bond to the concrete. We suggested two lifts of 9.5 mm Superpave with an overall reduction of 1 inch in the overlay. We’ve been trying to get back to realistic lift thicknesses that can get good compaction and DOT agreed with that.
“We also proposed using ground tire rubber to delay the cracking coming back through the mix. The other reason for the GTR is we were doing our performance tests, and when we’re using the GTR in those mixes, our IDEAL-CT numbers have just been off the charts. Our performance tests are the IDEAL-CT and the IDEAL-RT.”
For the Maries County project, the team saw an average CTIndex of 168, an average RT-Index of 77 and Hamburg rutting result of 7.0 mm.
Jackson credits the elasticity of the GTR for aiding in pavement performance. “We’re putting the ingredients back in that gives it a little flexibility.”
The unconfined joints were on the outer edge of a concrete roadway that had a rock shoulder. The NB West crew paved the mainline and used a nonSuperpave asphalt layer over the rock to cover up the shoulder.
To add the GTR, NB West uses the dry process, adding Elastiko® engineered crumb rubber asphalt (ECR) manufactured by Envirotx and supplied by Asphalt Plus. N.B. West’s Joe Schroer, P.E., materials and support engineer, explained the dry process is considered mixture modification. Performance testing measures the interaction of GTR, aggregates and binder as a system, and allows a more innovative
approach to designing asphalt mixtures, he shared. Additional enhancements to mixture performance can be made by adjusting the grade of the binder.
A groundman brings the 2,000-pound tote of Elastiko material to the feed bin of a modified Hi-Tech Fiber machine with a forklift. From the bin, the machine feeds the material to a 6-inch-diameter flexible hose and to the portable Astec Double Barrel.
“We blow it right into the drum,” Jackson explained. “The control unit’s inside the control house and it’s tied into the tons per hour you’re producing.” In this manner, the plant controls the addition of the GTR product as it would cellulose fibers being fed in.
This project ended up with a variety of additives in the production process, but Jackson said it was business as usual for the team. “We had the normal challenges. This still had our normal Superpave testing in it; we were still running volumetric testing and adding in the performance testing. So, it was a lot of testing.”
Jackson shared a testing tip for working with GTR. “When you’re making pucks up, if you put a weight on your mold top (with the GTR in there), it keeps the GTR from rebounding while cooling. If you don’t do that, you get some kinda strange results.”
In the field, the crew worked with temperatures below 300 degrees F. Even with the Evotherm WMA additive in play, they elected to have temperatures closer to HMA to accommodate the Elastiko. “The
One of the reasons NB West uses a warm-mix additive in every mix they can is to get the compaction aid assistance.
“We run Evotherm in every mix that we have to get density on,” Jackson said. “We don’t run it on Novachip, but every other mix, we’re putting it in there.”
One of the factors that changes when developing a balanced mix design (BMD) and doing your performance testing is the number of gyrations.
“You’re dropping your gyrations,” Jackson said. “You’re making a mix that’s got more AC in it. So, you can take advantage of some of those mixes then of making them more compactible in the lab so when you go to the field, it’s easier to get compaction.”
Take a typical interstate mix as an example.
“We started off at 125 gyrations on interstate mixes. When you’re trying to compact that, you’re breaking rock trying to get density. Then we backed off to 100 gyrations, then to 80. I think we’re at 60 with BMD.
“To keep your voids in mineral aggregate (VMA), you end up putting some more AC in it. So, you have a mix that will compact, and it’s got binder to hold it together. Now instead of breaking rock to get to 92%, you’re rolling this and getting 96%. That’s what FHWA wanted: higher density. We get higher density by going to balanced mix design.”
manufacturer told us not to go below 280 with the GTR,” Jackson said. “We went down to 270 and didn’t have any problems.” A longer haul—approximately 40 minutes from the plant—for this project allowed a longer dwell time for interaction of the GTR with the binder at the reduced temperature, according to Schroer.
Jackson took infrared images of the project to double-check consistency of mat temperatures and confirmed that consistency coming from the plant to the jobsite. “I took my FLIR camera out there... the good thing is I think the ground tire rubber holds the heat in the mixes. It was about 40 minutes to the job, and we were on a two-lane road where we had to flag the traffic, so it was challenging getting the trucks in and out. But we didn’t lose a lot of heat in the mixes.”
One of the best practices Jackson recommended was staying on top of the rolling pattern. “We were keeping our rollers right up on the screed. Because we were already dropping our temps below 300.”
The mix design used all the moving parts. “We used 20% RAP in this mix and 10% by weight of AC was the asphalt plus Elastiko product. The idea was that we had our baseline AC, which was a 6422 and 10% of the Elastiko was in there to bump it up to a 76-22. It was the same mix on both lifts.”
The Missouri DOT allows whatever percentage of RAP the contractor wishes to use and still meet performance specs. “Technically, there’s no limit,” Jackson said. “Our problem is availability. We can’t
run maximum RAP in our mixes because we don’t have it. There was nothing to mill on this project, so we had to bring RAP from other locations to put in this mix.”
For the NB West team, that’s just one more solvable problem. Jackson spoke of the “can do” willingness to put a puzzle together when it comes to the crew, starting with Plant Operator Clay Pitts.
“Number One is just the general attitude of not saying ‘we can’t do that.’ Yeah, we’ll try that. That’s huge. Clay’s great about that. Always willing to try something new and make it work.
“Dustin Hollis was the foreman and Juan Marquez was the general superintendent; they manage several jobs at a time.”
Jackson also described the effort the quality control/quality assurance (QC/QA) team had to put forth, given the changes to the contract after it was bid.
“Our quality control dept came up with these mixes and tried new things and really kind of pushed the envelope. The performance testing, the way we did this, that wasn’t set up in the contract, so we still had to do all the volumetrics testing and add the performance on top in a BMD situation. We’ve never run this mix so we were going live on the road with what looked in the lab like it would run well and do its performance testing. We had to go behind the spray paver and dig a sample behind the screed in a mat that has a polymer in it. It was a monumental challenge for our QC team.
“We have our plant people and our QC people coming up with this crazy stuff and then we go execute it and we still have to make money at it. I think we did a slight tweak to the mix after the first day or two to take advantage of the performance test because we could reduce our air voids using the performance test.”
The final result gave an average international roughness index (IRI) of 32.
“On concrete pavement that they didn’t have enough pavement repairs for, to come out like that, I think it was great,” Jackson said.
Not only did the project win a MAPA award, the traveling public noticed the good work. Jackson has received unsolicited comments about the work. “I’ve had somebody call and say, ‘that rides real good.’ People see that [kind of result] and they’re more likely to support the gas tax.”
A snapshot of the millions of dollars of our asphalt
If the part you are looking for is not listed, please call. Chances are, we will have what you need.
We carry parts for every make and model of asphalt equipment.
Motors
Baghouse Parts
Silo Parts
Replacement Flighting
Sprockets for Slat Conveyors
Thrust Rollers to Retrofit
Rotary Airlocks
Baghouse Valves
Baghouse Valve Repair Kits
Burner Safety Switches
Trunnions
Hot Oil Heaters
Electronic Parts
Electronic Safety Switches
Thermocouples
Used Plant Components
RAP Gator Recycling Breakers
Air Cylinders
AC Metering Pumps
NiteOwl Plant Alert System
Dryer Seal Systems
Gear Reducers
AC Valves & Seals
Warm Mix Systems
Inline Liquid Blending Systems
Wear Plates
Custom Shafts
Bearings
Idler Wheels
Variable Frequency Drives
Actuators
Used Asphalt Plants
Hotmix Parts is located within minutes of the UPS world air hub. Many parts can be delivered within hours!
A&A has been growing ever since investing in its first mill. The W 150 has been such a benefit to his company that Eichholz is now running the math to invest in a second mill
Editor’s Note: For 2024, AsphaltPro Magazine allows experts in the industry to share how to expand your operations to the next phase of business. Are you ready to take the plunge and add more services to your arsenal? Let’s turn to some professionals who have equipment, services, software and tenure to help you expand to bigger, broader, more lucrative projects. This month’s paving installment looks specifically at milling technologies and applications for different sized projects.
hen Todd Eichholz first joined the asphalt industry, it wasn’t an obvious decision. He was a commercial real estate developer with no ties to asphalt when Bob Olson approached him about buying into A&A Paving, Roselle, Illinois, 10 years ago.
“A&A was my paving supplier,” Eichholz said. Olson was 72, without an exit strategy for his company. “His kids didn’t want to take it over and he knew if he sold it to a large national company that they’d likely fire [Olson’s] employees. He wanted to find somebody who would take over
the company, keep his employees, and grow the business into something even better.”
That person turned out to be Eichholz, then 32. “We had a deal within three weeks of him approaching me,” Eichholz said. Although it was a risk to take on a new venture, it was the type of risk that paid off. “We started scaling the company very quickly from the moment I joined.” Five years later, Eichholz bought the remaining half of the company and decided it was time to take another calculated risk. In 2020, he bought the company’s first milling machine.
“A lot of smaller contractors struggle with the idea of buying a milling machine,” Eichholz said. “It’s the most expensive piece of equipment they’ve ever bought, plus there’s the issue of the additional needs for a semi, lowboy, water truck, etc.”
Although those factors tend to scare smaller contractors away from taking that risk, Eichholz said the decision has been key to scaling A&A to where it is today. “We’ve doubled our production by bring-
ing milling in-house,” he said. “By investing in that machine, training our crew, and dialing up our production, we’re doing jobs I never thought possible.”
Located in the suburbs of Chicago, A&A is in a somewhat unique position. “In our area, there are non-union, smaller contractors in one sandbox and there are large union companies in the other sandbox,” Eichholz said. “We had one foot in both sandboxes, because we were smaller size-wise but we were union competing against non-union companies for smaller jobs. And when we tried to compete in the bigger sandbox, we didn’t have the production capabilities they had. We realized we had to figure out which sandbox we wanted to play in, and it was pretty obvious we should be playing in the bigger sandbox.”
The key to playing in the bigger sandbox? “We had to invest in our own milling machine,” Eichholz said.
Prior to 2020, A&A had very little trouble subcontracting milling services. “I could usually have our milling sub on a parking lot within 48 hours,” Eichholz said. “I felt that as long as I got good service from my milling subs that there was no need to buy a milling machine of my own.”
Then, at the end of 2019, their larger milling sub companies began gearing toward municipal work. “They started needing two weeks’ notice, and if it rained on that day, we’d go to the back of the line,” Eichholz said. “We were at the mercy of their schedule and production rates. That’s when we started investigating what it would cost to buy a milling machine and its ancillary pieces, so we could control our own schedule.”
After running the math with help from NPE instructor Tom Eosso from Eosso Brothers Paving, Eichholz decided investing in the milling machine of his dreams was a no-brainer. He purchased a Wirtgen W 150 mill in May 2020.
Investing in its own mill gave A&A control over more than its schedule; the decision gave them control over material and yields. “Sometimes our subs wouldn’t mill at a consistent depth,” Eichholz said. “Say it was a 2-inch mill, they might mill 2 ½ here or 2 ¼ there, which meant we’d have to put back more material than we bid, making it hard to make our margins. Once we started doing the milling ourselves, we noticed we were never going over on tonnage. We were also able to control the grades better so we’re leaving our customers with a better product while also improving our margins.”
Eichholz said the decision to invest in a milling machine has been key to scaling A&A to where it is today, adding that the company has doubled its production by bringing milling in-house.
The Math to Mill
It was in 2020 that Eichholz finally decided to buy his first milling machine. “I took a class at the National Pavement Expo (NPE) in 2019 that was all about learning how to buy your first milling machine,” Eichholz said. He became good friends with the instructor, Tom Eosso from Eosso Brothers Paving. “I told him how I was scared to death to buy a mill, that if it didn’t work out such a decision would sink us for years.”
Eichholz had run the numbers and nearly purchased a milling machine three times in the past, but was afraid of the ‘unknown unknowns’—costs he wouldn’t be able to anticipate without expertise in milling. “No matter how much due diligence I put into budgeting out that machine, I was always afraid my math wasn’t accurate,” he said. “That’s the beauty of events like NPE—building relationships with people you can ask these sorts of questions.”
“I’m not sure I’d own a milling machine today if I hadn’t been able to ask those questions to someone who knows,” Eichholz said. “I think I’d still be too scared about spending half a million on a single machine, plus $150,000 on the rig, $80,000 on the trailer and $80,000 on the water truck to support it.”
Eosso helped assuage these fears by sitting down with Eichholz over dinner to break down the costs of the milling machine into simple math. Together, they calculated the cost of continuing to subcontract milling operations compared to purchasing a machine of one’s own. They factored in the monthly payment of the machine, the cost to own (both when the machine was and was not in use), as well as the ancillary equipment required. They even calculated how many months the machine could sit dormant (six to 12) without a single day of work before becoming a financial risk—all done on the back of a napkin at the restaurant.
“Once we’d calculated everything, the math spoke for itself,” Eichholz said, concluding the machine would pay for itself if A&A used it at least four days a month—a number the company could easily achieve. “Running the math proved that it was a calculated risk rather than a drastic risk.”
In fact, Eichholz felt so confident about purchasing his own milling machine that he went through with the purchase in May of 2020— during the most tumultuous period of the Covid-19 pandemic. He was no longer afraid, even if there was less work available than usual. This confidence enabled him to get the machine he had long had his eye on—the Wirtgen W150—at a 15% “Covid-19 discount.”
Eichholz also had a partner in his equipment dealership, Roland Machinery, and manufacturer, Wirtgen America. “We had John Kroger [from Roland] and a rep from Wirtgen walk us through what we could expect—the good, the bad and the ugly—as well as the process to transition into performing our own milling,” Eichholz said.
Kroger also helped guide A&A to the right machine for their particular needs. “I was between the Wirtgen W 120 and W 150—the primary difference being the size of the drum,” Eichholz said. “He wasn’t trying to upsell us or anything, he really made sure the machine we bought was the best fit for us.”
The 150 was a better fit not only because the wider drum enabled 20% more production per pass, but also because the location of the cutter drum in the middle of the machine offered a better turn radius—particularly important for parking lot islands and light poles on many of A&A’s jobs.
Eichholz has no regrets about his choice. “It’s the most amazing machine I’ve ever owned,” he said. “It has completely changed the face of our company. We grew 30% in 2020—despite Covid-19—because of that machine.”
If the ancillary equipment required for a milling machine is a concern to contractors, Eichholz recommends buying the minimal required equipment or contracting out those services until feeling confident to buy one’s own. For example, he bought a 500-gallon water tank with a pull-cord pump for the back of A&A’s box truck instead of a water truck and hired out transport of the milling machine at first. “As we made money with the mill, we invested in the semi and a used lowboy. Then, as we saved more money, we bought a new lowboy and eventually a water truck,” he said. “You don’t have to go all in, all at once. All you need to do is figure out a way to move and maintain the machine as you go along.”
Purchasing the machine was only half the equation; once A&A received the Wirtgen W 150, the crews had to learn how to use it. A Wirtgen trainer was on the first milling job A&A took its 150 out on, training several of A&A’s employees on the job.
“I was nervous about learning on an actual job, but it turned out perfect and went exactly as planned,” Eichholz said. By learning on an actual job, the training the crew received was very real to the types of situations they’d face on future jobs. For example, there were many manholes on that particular job. “The trainer was like, ‘Hey, you didn’t spray the manholes,’ and we didn’t even know what he meant,” Eichholz said. “He talked us through that, through walking the site, marking the site, all that prep work.”
“One of the most important steps that has to be taken prior to starting a milling project, is to walk the entire site to locate and spray paint any manholes, clean outs or buffalo boxes,” Eichholz said. “This step will help alert your milling operator of when to stop milling and where to pick back up without damaging the teeth on your drum or your customers‘ property.”
Eichholz also learned the importance of having a ground operator for each mill. “I know a lot of contractors don’t do that, but we think the ground guy is just as important as the mill operator because he’s the one watching the grades, marking things out, stopping issues before they arise.”
Ultimately, the two A&A employees who would be operating the mill picked it up quickly. “Hugo and Octavio are both phenomenal operators,” Eichholz said. “They’ve used other types of machinery, they understand depth and pitch, etc., so even though they had never used a milling machine, they had it down right away.”
After a few more milling jobs with A&A’s new machine, Eichholz decided the machine was too important for only two employees to know how to operate it. “We started training additional employees with each milling job from that point forward,” he said. “It took a bit off the margin of the job, but cross training others on the mill was our insurance policy if ever someone else needs to jump on that machine to keep the job going.”
To keep the job going, Eichholz also had to be prepared in terms of maintaining the milling machine. “The mill is unlike any other piece of equipment in that it’s almost self-imploding because of the type of job it performs,” he said. “It is guaranteed to go down on occasion, so you have to have a backup plan.”
A&A’s plan is to immediately call the service department at Roland, keep the client informed, and keep the skid steers moving on the tight areas the 150 can’t mill so the job site is as ready as possible once the mill is operational again. “Roland’s mobile service truck is out there almost immediately to get it back up and running,” Eichholz said.
It was also important for Eichholz to educate the sales department about the new machine. “Instead of just stumbling across milling jobs, we needed to target those types of jobs and keep that machine busy,” he said. This turned out to be an easy task. “We very quickly went from being fearful about keeping the machine busy to using it 20 times a month, minimum.”
Eichholz also learned the importance of having a ground operator for each mill. “I know a lot of contractors don’t do that, but we think the ground guy is just as important as the mill operator because he’s the one watching the grades, marking things out, stopping issues before they arise.”
If the ancillary equipment required for a milling machine is a concern to contractors, Eichholz recommends buying the minimal required equipment or contracting out those services until feeling confident to buy one’s own.
Since buying its own milling machine, roughly 60% of A&A’s work has been commercial, the other 40% residential—primarily for homeowners’ associations. Even before purchasing its own milling machine, the company had begun to aim for larger commercial projects, and focusing on private roads within HOA communities.
Since investing in its own mill, private roads have become quite a niche for A&A. “The guys in the big sandbox don’t want to deal with 150 homeowners, and the smaller guys don’t have the equipment for such a job,” Eichholz said. “We’ve really tried to illustrate that we have both the production capabilities of a large company and the ‘white glove’ service of a small company.”
That mentality served A&A well with its homeowners’ association and private road customers, but it has also been a game-changer for the company’s commercial clients as well. For example, in 2022 A&A was able to win a large 2-inch mill-and-fill project on the Bass Pro parking lots at one of the largest malls in the Chicago suburbs—a job Eichholz said would never have been possible without a mill of its own.
“The size of the job caught my eye,” Eichholz said. “Plus, I’m a hunter and spend a lot of money at Bass Pro, so I thought it might be nice if I went there and they actually paid me instead,” he joked.
The project was also a shining opportunity to show what A&A could do with its new mill. First, the client owns many similar properties and could become a repeat customer if A&A did a good job. Second, the mall itself is a high profile property in A&A’s community. “It’s one of the busiest shopping centers in our area,” Eichholz said. “It was something to beat our chest about, to share on social media that we could handle jobs that large.”
At the time of that project, A&A had its mill for roughly 1.5 years, so the company was very confident in its capabilities in terms of both production rates and customer service.
The project was complex because entrances couldn’t be shut down and A&A had to strive to ensure shoppers weren’t inconvenienced. “We also had to shave off a day for an event Bass Pro was having in the parking lot called Camper Days,” Eichholz said. They achieve this by adding a couple extra hours to each of the other days they were on the job to achieve 60,000 square feet per day. “Doing that showed them we were willing to do whatever they needed. I think that’s why they chose us for the project at that mall the following year in front of Macy’s.”
“With our milling machine, we can do a much larger square footage with a much tighter turn around, and we’re able to work around scheduling conflicts like we never could before,” Eichholz said. “If we were still subcontracting milling, we never would have the capability to meet their schedule. If we couldn’t commit to the type of turnaround time we did, we wouldn’t have been awarded that project (or many others like it). We wouldn’t even be playing in that sandbox without our mill.”
The ability to control the milling schedule has been key to any work A&A has done, both residential and commercial. “Our customer experience has improved because we don’t have to delay projects by a couple weeks anytime it rains,” Eichholz said. “We’re trying to be the most relational paving company in our market and we can’t do that if we’re rescheduling jobs non-stop. Once we had control of our equipment, we had control of our schedule. And once we had control of our schedule, we realized how much more we could be doing.”
At the beginning, Eichholz estimated they’d be able to mill 20,00025,000 square feet a day because that’s often what the milling subs could achieve. Furthermore, a project of that size would require two days—one for milling and one for paving. Once the company got its milling machine, Eichholz realized they could mill and repave up to 50,000-60,000 square feet in a single day.
“As we figured that out, our margins went way up,” Eichholz said. “It seemed like every month, we were breaking a new production record.”
Another lesson Eichholz learned is the permitting required to move such a heavy piece of machinery in Illinois. “I didn’t know how many permits I’d need to move this machine every single day,” Eichholz said, adding that the fine to cross a bridge over weight is $5,000. “That was a bit of an unknown unknown I wish I’d learned sooner.”
A&A has been growing ever since investing in its first mill. “The mill put us firmly into the big contractor sandbox,” Eichholz said, adding that the company now competes with companies with $40-60 million in revenue. “We went from the biggest of the small guys to the smallest of the big guys.”
The W 150 has been such a benefit to his company that Eichholz is now running the math to invest in a second mill—potentially the W 120 so he can have the ability to back up to buildings and curbs and because it’s lighter and will require fewer permits to transport.
“When I bought the first one, I was told the big changes really start to happen when you buy your second and third mills,” Eichholz said. “I have so much respect for the companies running five, six, 10 milling machines. I’d love to see what that could do for A&A.”
Despite the many benefits the mill has brought to A&A, Eichholz said the company’s white glove approach to customer service has been equally important to its success. “I can do the same production as the big guys, I’ve got the same equipment, but my sales team and our company is more relational,” Eichholz said. “We always try to put ourselves in the customer’s shoes.”
Perhaps this is easier for him, since he spent so many years as an A&A customer before investing in the company. Regardless of the reason, Eichholz said this mentality is as key to the company’s growth as its new milling machine. “If you can wow the customer on every single job—if you can make white glove service your standard operating procedure—you’re going to stand out in your marketplace.”
Eichholz is now coaching and consulting asphalt companies who are trying to get from one sandbox to the next. “I’ve always had the thought process of trying to learn from somebody two stages bigger than me,” he said, attributing that as a key factor of his success in real estate and in the asphalt industry. “Because of all the things I’ve learned from the people who have coached me, my companies now run 70% without me.”
That gives Eichholz the time and space to build his consulting company and bring what he’s learned to companies one or two stages behind A&A. “I’d speak at events like NPE and I noticed people were coming up to me asking for help nonstop,” he said. “And I realized how much I enjoyed teaching them. I realized maybe coaching others is what God created me to do, more than real estate, more than asphalt.”
Since starting his consulting company in early 2023, Eichholz has coached companies in Texas, New York, Philadelphia, South Carolina and Wisconsin. “I’ve never felt so fulfilled, like I’m living God’s calling,” Eichholz said. “If anyone is ready to work through the math on milling, I’d be more than happy to help them just as others have helped me.”
reserve can be defined as to keep in good condition or to keep safe from harm; to prevent decay and maintain. Think about preserving or upkeeping your home’s exterior. Rather than tearing everything down and starting over, properly timed preservation techniques can help to keep your house looking like new and functioning properly and efficiently. Some of these techniques include painting or replacing the windows or the roof. Applying these treatments at the right time prevents costly repairs and even complete reconstruction.
Maintaining an asphalt pavement is like preserving your house. There are times you don’t have to do full reconstruction of the road or even mill off the surface of the pavement. There are treatments to extend the lifespan of the pavement, keeping it in good condition and safe for the driving public. Not only does this extend the life of the pavement, but it also benefits the bottom line. Roads are a capital investment. Maintaining them properly can save money and stretch a tight budget.
Simply stated, pavement preservation is applying the right treatment to the right place at the right time. An asphalt deterioration curve can help determine timing and treatment.
Surface preservation treatments are meant to delay the need for rehabilitation or milling of the structural asphalt. As the pavement moves from fair to poor condition, the treatments available to you must be more structural in nature. Figure 1 shows an asphalt deterioration curve with different treatments applied to the pavement as the condition deteriorates.
Pavement preservation treatments can be divided into four categories:
• Surface treatments
• Pre-treatments
• Recycling and reclamation
• Base treatments
Some common surface treatments are crack seal, rejuvenating fog seal, micro surfacing and thin lift HMA overlay. Let’s discuss those in some depth.
Placement of material into existing cracks.
Crack filling is the placement of modified asphalt material into non-working cracks to prevent the infiltration of water and incompressible materials like gravel and sand. Routing and sawing is performed as needed to create a more uniform area for the filler allowing for better control and ensuring a proper seal to the existing pavement.
There are certain conditions that should exist for a pavement to be a good crack sealing candidate:
• New or recently rehabilitated surface
• Limited linear cracking
• Little or no secondary cracking
• Little or no raveling at crack face
• Good base support
• Limited structural deterioration
Cracks must be cleaned and dried prior to applying the filler or sealant. Having a dry road is even more important than the air or pavement temperature. It’s also important to keep the meter tank no less than ¾ full to maximize the effective melting point.
Process of restoring chemical properties of the aged asphalt binder.
A rejuvenating fog seal or asphalt rejuvenation does not provide any structural improvement, rather it’s an emulsion that penetrates the top 3/8" of pavement restoring the aged asphalt binder. The effectiveness of the treatment is typically determined by the reduction of the binder viscosity. It is a “top of the curve” preventative maintenance and extends a typical pavement life by 3-5 years per treatment when applied at the right time.
Asphalt rejuvenation works by re-proportioning the aged fractions (asphaltenes) to the fluid portion (maltenes) of the asphalt binder. The maltene fraction gives the asphalt binder its flexibility. Asphaltenes effects the viscosity of the asphalt; as this fraction increases with age, the viscosity also increases making the pavement less pliable and prone to cracking. Thus, by restoring the maltene to asphaltene ratio like that of a new binder, the life of the pavement is extended. This process is not unlike a bowl of spaghetti (asphaltenes) with sauce (maltenes).
Over time the water in the sauce evaporates causing the sauce to dry out or age making it difficult to move or separate the spaghetti. Refreshing (rejuvenating) the sauce brings the bowl of pasta back to life, making it easier to separate the spaghetti noodles and move them
around. Rejuvenation aims to restore the pavement’s flexibility and resistance to cracking.
Surface treatment mixture of polymer-modified asphalt emulsion, mineral aggregate, water, and additives. The mixture is made and placed on a continuous basis by mixing the ingredients using specialized equipment
The micro surfacing formulation is based on mix design parameters: resistance to raveling, lateral displacement and resistance to moisture damage. The emulsion plays a key part in micro surfacing. The wrong emulsion or an emulsion that doesn’t work well with the other components can cause issues such as long set times, durability, and delamination.
Remember that temperature, humidity, and wind conditions all affect emulsion break and cure times. If using a micro surface in combination with crack sealing, ensure crack sealing material is not excessive where it can be picked up by the paver tires and spreader box runners. Screen the material immediately prior to loading the mobile support unit so there is no possibility of contamination when re-handling the material. Treat vegetation with herbicide early to prevent it from returning after the project is completed.
Many agencies have reported ten years or more of service life when micro surfacing is installed on newer asphalt pavements in good condition. However, when used as a “band aid” or as a stop-gap measure on an asphalt pavement in marginal condition in order to delay rehabilitation/reconstruction, surface treatments including micro surfacing will have a shorter service life. Having the proper mix design for the micro
While the materials for HMA and pavement preservation treatments are the same, the equipment varies, and the material testing is different. In efforts to standardize the testing and material selection, AASHTO created an emulsion task force in 2008.
While the materials for HMA and pavement preservation treatments are the same (aggregates, liquid binder, emulsions), the equipment varies, and the material testing is different. In efforts to standardize the testing and material selection, the American Association of Highway and Transportation Officials (AASHTO) created an emulsion task force (ETF) in 2008. Material standards, design standards and construction guides have since been developed, and in a 2012 passage from the Moving Ahead for Progress in the 21st Century (MAP-21), state DOTs could begin to use federal funds for pavement preservation. This high level of confidence was only one benefit to the on-going AASHTO standardization efforts. Other benefits include educating the next generation of DOT staff and preservation crews and offering a consistent way to select materials, test and design. Constant collaboration and education will only further enhance the quality of the pavement preservation techniques, ultimately extending the life of our pavements.
The team at Asphalt Testing Solutions & Engineering LLC, Jacksonville, Florida, prepared this back-to-basics article for the AsphaltPro and
BITU-OX-Ad-3.625x4.625.pdf 1 12/8/2023 9:44:30 AM
ason Gomez, owner of Ontario Parking Lot Services Ltd., Ontario, is the world’s best line striper. Or, at least that’s what his children, 6 and 9, have been telling their friends and teachers ever since Gomez won the line striping competition held at the National Pavement Expo (NPE) in January 2024 in Tampa.
Alongside the trade show and education sessions for which NPE is known, the 2024 show saw the start of a new tradition where attendees were invited to put their line striping skills to the test. The competition, sponsored by Graco and Pavement Stencil, saw more than 100 individuals use a Graco LineLazer ES 500 to stripe and stencil an American flag for a chance to win a Graco LineLazer of their own (first place) or a Graco ES 500 Stencil rig (second place).
“I decided to compete when I saw that the winner was going to win a Graco LineLazer ES 500, for one,” Gomez said, adding that he uses an identical machine on many of Ontario Parking Lot Services’ jobs. “I love those machines.”
His existing electric LineLazer striper has been handy since it runs on the same battery as all of Gomez’s DeWalt tools. “I have a whole bunch of those batteries, which is more than enough for a day of painting,” he said. “Because the machine is electric, it’s so quiet and there are no fumes, so it’s great to use indoors.”
The chance to win his favorite striper was certainly a motivating factor, but Gomez had a second reason, too: “The competition is just a fun idea.”
Gomez started Ontario Parking Lot Services in 2010. “I went to school to become an architect, but over time realized I didn’t enjoy it at all,” he said. “With architecture, you’re working at a desk all day and there’s a very long time scale to see the fruits of your labor.”
In his early 20s, Gomez approached his father, who owned a fairly large building maintenance and landscaping company and was performing some striping and sweeping for his customers, with a
proposition. “I asked if I could spin off the parking lot services he was doing into a separate company.”
“With striping, I get to work outside most days and I can see the results of my efforts every single day,” Gomez said. With his father’s support, some equipment and a few dozen existing customers, Ontario Parking Lot Services was born.
“When I took over, [our book of work] was very small,” Gomez said. He began learning how to use Google Ads to get the business’s name out there. “It took some time to learn the hang of Google Ads, but once we did, it was a night-and-day difference for the business.”
Prior to advertising, he said it was rare to receive a call inquiring about the company’s services outside of referrals. “Then, all of a sudden, we were fielding several calls a day during the busy season, so it was a major turning point for us,” Gomez said.
“When I first started the business, I thought I wanted to grow the company into a very large operation because that’s what I saw my dad do with his business,” Gomez said. Then, a few years ago, Gomez had a change of heart. “I realized I enjoy the smaller size of the business, at least while my kids are still young. Summer weekends are busy, but I have the flexibility to make my own schedule and I get to spend a lot of time with my kids without being stressed out about work. This is really a job that affords me the type of life I want.”
“Maybe I’ll grow the business into something larger when my kids are older and I’ll be looking for something else to fill my time, but for now, I enjoy the size of the business and the type of work we do,” Gomez said.
Since incorporating Ontario Parking Lot Services, Gomez has focused more on the striping side of the business rather than the cleaning. “With cleaning, there’s significantly more investment in equipment and labor, so it really comes down to the economics of it,” he said, estimating three quarters of the company’s work is striping.
As a result of the decision to remain smaller, Gomez said Ontario Parking Lot Services has found an interesting niche that larger companies aren’t as well-equipped to handle: custom painted markings, such as company logos or playground games for local schools.
“With custom markings, there’s a lot more office work to get the design and stencils just right whereas the time spent painting isn’t very time consuming,” Gomez said, “so it’s not a very good niche for larger companies who have a lot of employees and need to keep multiple crews busy.”
Gomez estimates roughly half of the company’s line striping work is custom markings while the other half is parking lot striping. “The work that pays the bills is the line striping, but the work I most enjoy is the custom markings,” he said. “I like that there’s a way to be artistic when it comes to line striping.”
When local school districts in need of parking lot striping reach out to the company, Gomez sets up appointments with the principals to discuss not only their parking lot services but also to show them the types of games they’ve painted for other schools in the past, ranging from mini hockey rinks or soccer field striping to foursquare and hopscotch. One time, the company even painted a “floor is lava” obstacle course game.
“We talk about which games would be best for the space and the age of the kids,” Gomez said. “When I went to school, we just had a pole with a ball attached to it and a couple of basketball nets. It’s nice to do these colorful, artistic games for the kids. We paint them over the summer and when the kids come back in the fall, they have a bunch of new games to play.”
In fact, Gomez also painted several games for his own children’s school for free. Although he doesn’t usually get to see the children play with the games they paint, he’s enjoyed seeing his own children and their friends play the games he painted at their playground.
“This can sometimes be a thankless business,” Gomez said. “Few people outside of our industry care about the striping in the parking lot, or even notice it, but at schools there’s always so much fanfare for the work we do.”
Gomez believes his experience with custom markings came in handy when competing in the line striping competition at NPE. “When you’re doing that custom work versus a large shopping center, the attention to detail required is much higher,” Gomez said. “For example, if you’re painting a company logo right at the entrance to the company headquarters, people are going to be paying a lot of attention to that.”
Secondly, Gomez said he was well-positioned to win the competition because he uses an identical machine on many of his jobs. “In fact, I used my [LineLazer] a few days before the competition to paint some custom markings in a warehouse, so I guess you could say I was already ‘warmed up.’”
It was actually because of a past NPE show that Gomez chose to invest in a LineLazer of his own. The 2024 show was his fourth time attending NPE. “I try to go every year or at least every other year,” he said, adding that it’s a great opportunity to catch up with indus-
When Gomez first started the business, he wanted to grow the company into a very large operation, “because that’s what I saw my dad do with his business,” he said. Then, a few years ago, Gomez had a change of heart when he realized the smaller size of the business gave him more time to spend with his kids and also enabled him to serve a niche with custom markings.
try friends and colleagues as well as to learn new information to take his business to the next level.
For example, utilizing the automatic layout feature on his striping machines. “I had a Graco machine with the automatic layout feature, but I never used that feature because I wasn’t familiar with how to do it,” Gomez said. Then he attended a class taught by Chad Jung about the use of technology in striping at NPE to learn how the automatic layout feature could make him more efficient.
The automatic layout feature allows users to set the width of each parking stall. Then, as they push the striper across the lot, it drops a dot of paint at the preset intervals. “All you have to do then is stripe at each dot and make sure each line is straight, which is easy to do because of the laser system,” Gomez said. “Seeing that technology in action at NPE was a real lightbulb moment for me. I’d probably still be out there with
1-inch: Infill of Shallow Cracks
2-inch: Over-band of Joint / Filled Crack
4-inch: Over-band Joints / Utility Cuts
8-inch: Increase Vertical Joint Density
“The work that pays the bills is the line striping, but the work I most enjoy is the custom markings. I like that there’s a way to be artistic when it comes to line striping.”—Jason Gomez
a tape measure without that show. That class alone and the skills it taught me have been enough to pay for the cost of attending NPE 100 times over at this point.”
“The people who teach the classes at NPE are out there doing this work day in and day out every summer, so they really know their stuff,” Gomez said. “The show is also just full of little hints that are invaluable that there’s no other way to easily learn besides trial and error, trial and error.”
Throughout the 2024 show, Gomez kept returning to the competition area to see how his striped-and-stenciled flag stacked up against the competition. “Before I competed, I watched a few others to see what types of mistakes and issues they were having,” he said. “Most were struggling with starting/stopping the stripes neatly, so I paid extra attention to that.”
“I just tried to do the nicest job I could possibly do,” Gomez said. It’s a level of effort and attention that he tries to bring with him to every job. “Sometimes, line striping can get tedious doing the same thing over and over. The way I keep it interesting is I’m always trying to make each line better than the last.”
“The technology on some of these new striping machines has made the learning curve to stripe well a bit easier, but at the end of the day, I think it still comes down to practice, having a steady hand and attention to detail,” Gomez said. “I also think I got lucky a bit, too.”
Luck aside, Gomez’s experience, steady hand and attention to detail paid off for him. At the end of the show, his flag took first place. “I’m still shocked I won,” Gomez said, adding that he’s very excited for his new Graco LineLazer ES 500. “I was probably going to buy another one this year anyway, so it was really nice to win one instead.”
Gomez said the second machine is going to come in handy throughout the 2024 season, not only for the company’s parking lot jobs but also its custom work. “These machines are great for our custom jobs where we aren’t running our machines constantly because of the intricacy of the stencil we’re painting,” he said. “Instead of having them run the whole time or pulling a cord to restart the machine every time, we can just pull the trigger when we’re ready to paint again.”
Having two electric machines will also make it easier for Gomez to offer more colors for his custom work. Last year the company offered 12 colors; this year, with the second machine available, Gomez plans to add orange and pink to the mix.
The machine was delivered to Gomez in Ontario three weeks after the show, once Gomez’s family had returned home from a post-show road trip around Florida. “When my family found out the show was in Florida this year, they jumped at the chance to go,” Gomez said. Although the trip was planned well in advance of Gomez’s victory, it’s only fitting that after winning “the Super Bowl of line striping” that Gomez and his family would end their trip at Disney World.
Gomez estimates roughly half of the company’s line striping work is custom markings while the other half is parking lot striping. Although the line striping work is more profitable, Gomez most enjoys the custom marking.
NPE 2025 will also take place in Tampa. If Gomez chooses to attend next year’s show, he’ll have a chance to defend the title his kids have given him as “the best line striper in the whole world.” “That’s probably been the best part of winning [the competition],” Gomez said. “I feel like a hero in their eyes.”
t the 51st annual meeting of the Asphalt Emulsion Manufacturers Association (AEMA), held Feb. 19-23, 2014, in Palm Harbor, Florida, the association recognized the 2023-2024 Leadership Education for Asphalt Preservation (LEAP) class.
The 14 individuals that were part of this LEAP class included: Alejandro Rosales, Idaho Asphalt Supply; Emmanuel Delgado, Kao Chemicals; Josh Guidice, Ergon Asphalt & Emulsions; James Schoger, Ergon Asphalt & Emulsions; Crystal Castillo, Arkema; Brody Young, Idaho Asphalt Supply; Gia Carbonara, Russell Standard; Shawn Bryam, Russell Standard; Nate Jenkins, Asphalt Materials Inc; Campbell Higbie, Heritage Research Group; Shafer Soars, Arkema; Charles Taylor, Ergon Asphalt & Emulsions; Matthew Gutkaiss, Asphalt Emulsion Industries; and Bobby Behrens, Terry Asphalt Materials.
Charity Cook, Paragon Technical Services, was also recognized as the 2023-2024 LEAP class dean.
The LEAP program is a 12-month immersive experience for developing members of the asphalt emulsion industry by engaging participants and building confidence and understanding in areas they may never get a chance to see.
The Asphalt Emulsion Manufacturers Association (AEMA), founded in 1973, is an international non-profit trade association of asphalt emulsion producers and sellers, suppliers, users, research personnel,
public officials, consulting engineers, and contractors working together to promote the increased and more efficient use of asphalt emulsions. AEMA is a founding member of the Pavement Preservation & Recycling Alliance along with the Asphalt Recycling & Reclaiming Association and the International Slurry Surfacing Association. To learn more, visit www.aema.org.
At the recent World of Asphalt (WOA) and AGG1 Aggregates Academy and Expo held in Nashville, original equipment manufacturers (OEMs) and service providers brought equipment, technology and information to the tradeshow floors. You can visit the WOA website to see the basic wrap-up of the show, including the good industry barometer of record attendance this year. When over 15,800 people descend upon 207,000 square feet of sold-out trade center space at the Music City Center, you can bet there’s a lot of “participation” in the industry going on. Let’s take a closer look at some facts about the iron and info that matter to your bottom line.
Some quick facts about WOA/AGG1 2024
• The show ran from March 25-27, 2024
• Attendance was up 38% over 2022’s previous record-setting numbers
• The 207,000 square feet of show floor space was a 14,000-foot increase over 2022’s floorplan
• The WOA’s People, Plants & Paving Conference and the AGG1 Academy totaled more than 120 learning sessions
• Raised on Blacktop co-hosted a sold-out kick-off party and the show featured a sold-out Women of Asphalt Day on the last day of the show
To kick off the show, the team from Raised on Blacktop collaborated with WOA to host a party at Kid Rock’s Big Honky Tonk and Rock ’n Roll Steakhouse. A number of manufacturers stepped up to help out with that Sunday evening, including AsphaltPro advertisers Dynapac and Wirtgen Group. A variety of company parties lured attendees out after the show each evening, including the first
BOMAG Live! event, which attracted nearly 1,100 to the Walk of Fame Park just down the street from the convention center for food, live entertainment and chances to win one of four all-expenses-paid trips to Bomag’s upcoming Innovation Days in Boppard, Germany.
Other events included the inaugural Women of Asphalt Day, held Wednesday, March 27, with guest presenters speaking to a sold-out audience on topics relevant to women in the industry, and the 2024 National Stone, Sand & Gravel Association (NSSGA) annual convention.
Jim Nickolas, executive vice president and chief financial officer of Martin Marietta, will be the next chair of NSSGA. Outgoing Chair Seth Hankowski, All States Materials Group, handed off the gavel during a ceremony at the convention, where Nickolas said: “It’s an exciting time to be in aggregates. The stone, sand and gravel industry is the foundation for so many products we use every day. The nation’s infrastructure, including roads, dams and pipelines, depends on the materials we provide.”
Nickolas spoke about the importance of working together as one group to continue the momentum the aggregates industry has experienced in recent years. Acknowledging that the country’s political environment is often divided, he said he would strive, as NSSGA’s leader, to further the view that infrastructure investment is a non-partisan issue that affects every American. Nickolas further said he would work to unite all material providers around the NSSGA’s important mission.
“My goal is to work across the industry until 100% of producers are active members of NSSGA. No matter our size, we face many of the same challenges. We must seek solutions as one,” he said. “Among our many shared tasks is to make our value clear. The most effective way to do this is to share our recent successes while emphasizing that we are stronger together.”
The National Asphalt Pavement Association (NAPA) had a presence at the co-located event, giving away hardcover copies of the 2005 Paving the Way: Asphalt in America by Dan McNichol from both the association’s booth and publication bins near the doors.
See You in Cardinals Country! World of Asphalt and AGG1 will be held in St. Louis, Missouri, March 2527, 2025.
The AsphaltPro staff noticed an overwhelming sense of positivity and optimism while at WOA/AGG1 2024. More than one exhibitor indicated the traffic at the booths included decision-makers making purchasing decisions. Original equipment manufacturers (OEMs) could—and did—point to machines that were headed to new homes from the show floor. One OEM spoke of silo orders in production through November of this year. Another spoke of taking orders for 2025. (This sign of health in the industry also reminds contractors to plan for expansion and stocking parts.)
While the WOA/AGG1 information is almost “old news” at this point, there were elements of the show and conferences that will continue to help the asphalt contractor’s bottom line. For example, many of the People, Plants and Paving Conference learning sessions, press conferences and booth conversations held a common theme of incorporating more technology and automated processes to make the contractor’s job easier. Whether the product or service was targeted for the owner, equipment operator, safety director, estimator or other member of the team, data gathering, monitoring and use is being incorporated beyond mere telematics.
In fact, the winner of the iPad giveaway from AsphaltPro magazine also received a year’s access to the Pavewise software solution on the iPad. Bryce Wuori, CEO of Pavewise Inc., Bismarck, North Dakota, and Brittany Wuori, COO, pulled the name of Brenton Young of Mountain Companies, Van Lear, Kentucky, to receive the iPad, year of Pavewise service and swag from Raised on Blacktop. And of course, there was iron on the tradeshow floor.
This month, we shine the product gallery spotlight on the products and services that assist the asphalt and aggregate pro-
LEFT: The team at Asphalt Materials Inc., Indianapolis, discussed the use of void reducing asphalt membrane (VRAM) under rumble strips to protect an agency’s investment. Check out the March 2021 article Innovate at Centerline Rumble Strips for more information. https:// theasphaltpro.com/articles/innovate-at-centerline-rumble-strips/ RIGHT: From left, Brittany Wuori, COO, and Bryce Wuori, CEO, of Pavewise Inc., Bismarck, North Dakota, pulled the name of Brenton Young, Mountain Companies, Van Lear, Kentucky, to win an iPad with a year’s subscription to Pavewise and a bag of Raised on Blacktop swag on the final day of WOA.
LEFT: The RPL/SSL cold planer attachment from FAE Group, Flowery Branch, Georgia, was on display connected here to the RCU-75 remote control skid steer, which the company unveiled at CONEXPO in 2023. RIGHT: You probably know Weiler for pavers and material transfer vehicles but check out this sporty CT3A rubber-tired roller the OEM had on display at the show.
ducer’s bottom line. Let’s dive into offerings from WOA/AGG1 and from entities who were unable to exhibit at the Nashville event. Be sure to scroll through the AsphaltPro Instagram and Facebook pages to see a host of quick videos from the tradeshow floor posted both during and
after the March 25-27 program. (Next month, we’ll shine the product gallery spotlight on the paving and pavement maintenance sector of the industry, bringing you a look at updates to tried and true equipment as well as new pieces to enhance job performance.)
Ammann America Inc., Orlando, announced its newest counterflow drum mix plant specifically designed for high production and high-capacity recycling technology. The Ammann ACC Alpine drum mix plant is available in stationary and portable configurations ranging from 300 to 600 tons per hour.
The Alpine series enables HMA producers to maximize high total production and amount of recycled asphalt pavement (RAP) content without sacrificing mix quality utilizing Ammann’s controls and technologies, according to the manufacturer. The Alpine series control system is intuitive and allows tracking and analyzing plant operating data in real time.
The manufacturer states the benefits of the new plant include:
• Single drum, multi-zone drying and mixing system with VFD;
• Modular and scalable designed components;
• High RAP capabilities up to 60%;
• Warm-mix asphalt capability with the proven Ammann foam system;
• Easy customization of plant arrangements;
• Easy retrofit to existing facilities;
• Extreme wear packages for extended operating life; and
• 24/7 local support with a hands-on project management team.
Ammann’s HMA storage silos have capacities ranging up to 300 tons with extended mix storage options available. Silos are engineered with expansion in mind.
Ammann’s aggregate feed systems include troughing feed belts, steep, sloped bin walls, and variable frequency drives.
The reverse-air baghouse system is the newest version of a broad range of existing Ammann dust control products with a reduced length and increased width of the Alpine series baghouse.
For more information, visit www. ammann.com.
Astec Industries, Chattanooga, released the Astec ReMix™ cold central plant recycling (CCPR) system prior to World of Asphalt. The system is designed to address the industry's growing need for sustainable road construction practices by using reclaimed asphalt pavement (RAP) stockpiles. The Astec ReMix™ CCPR has a rated capacity of 300 tons per hour. Its modular design—which includes pugmill, foaming system and controls—can be configured to exact needs and translates to reduced upfront costs and enhanced adaptability.
According to the manufacturer, the key benefits of Astec ReMix CCPR include:
• It employs cold recycling technology. By reusing RAP materials and mixing them at ambient temperatures, the system reduces the need for both virgin aggregate and energy for heating the mix. This conserves natural resources and lowers carbon emissions.
• One of the primary advantages of system is its ability to consume ever-growing RAP stockpiles. With this system, road construction projects can contribute to the circular economy by incorporating recycled materials, thereby reducing the overall environmental footprint.
• The Astec ReMix system offers a range of modular configurations, providing flexibility to asphalt mixing operations. From highly portable setups suitable for changing locations to maximum production configurations capable of handling largescale road construction, Astec ReMix CCPR provides producers with the options to meet diverse requirements.
• The system features an intuitive user interface. This user-friendly design enhances productivity and reduces the learning curve for operators, according to the manufacturer.
Astec also introduced its IntelliPac™ Moisture System, which offers visibility into virgin aggregate moisture levels. This system is equipped with advanced features that empower operators with real-time data and insights, which are designed to allow for precise adjustments to result in significant cost savings. At the heart of the Astec IntelliPac™
Moisture System is its carefully vetted moisture measurement methods. The system employs a state-of-the-art approach to gauge virgin aggregate composite moisture levels. This measurement forms the foundation for the system’s capability to deliver real-time moisture values, providing operators with immediate visibility into crucial data.
One of the standout features of the Astec IntelliPac™ Moisture System is its comprehensive data logging functionality. The system records virgin aggregate composite moisture levels, enabling operators to track and analyze historical trends. This historical data serves as a resource for optimizing processes and making informed decisions to enhance overall efficiency. The real-time moisture values offered by the IntelliPac™ Moisture System are fully integrated into the plant control system, empowering operators to make on-the-fly adjustments, fostering a dynamic and responsive asphalt production environment.
This level of visibility into virgin aggregate moisture allows for more precise addition of liquid asphalt cement. Additionally, operators can fine-tune burner operations based on real-time moisture values, maximizing energy efficiency and reducing operational costs.
For more information, visit astecindustries.com.
Cardinal Scale Manufacturing Co., Webb City, Missouri, offers the ARMOR steel deck digital truck scales, which are optimized for cold climate operations and manufactured with a variety of features to benefit all-season weighing needs. They have no moving parts below the scale deck, which means snow or ice accumulation along the foundation won’t
create binding to affect the scale. The checkered steel decks are constructed of tread plate for optimized vehicle traction and there’s no external checking for ice to accumulate and affect weighing.
The scales incorporate SmartCell digital load cells, which are completely encapsulated. The SmartCell SCBD load cells are mounted up high within the load cell pocket to keep them away from accumulating snow and ice.
You might be running an asphalt plant that would never load out during a snow event, but the ARMORs are built with a wide-open bottom weighbridge with I-beam construction and no interior spaces, which prevents water collecting that can change to ice, according to the manufacturer. The weighbridge’s I-beams run the complete length from end plate to end plate and surround the load cell pocket, protecting it from stress fractures, according to the manufacturer.
The scales work with iSite remote monitoring, where e-mail/text alerts to your scale service company notify them about any potential issues before they affect your truck scale’s performance. This means maximum uptime for your weighing operation. In the rare event of a load cell issue, SCBD load cells can be replaced in five minutes, according to the manufacturer.
In addition to introducing attendees to a genuine American Bald Eagle in their booth on the first day of the show, the team from Eagle Crusher, Galion, Ohio, introduced everyone to two new plants in one with the Eagle Crusher MaxRap® 25 Portable. When you remove the actuated diverter chutework of the MaxRap 25 Portable, the plant becomes an
UltraMax 1200-OCSS, open-circuit secondary system.
The manufacturer explained: “The MaxRap 25 Portable provides the same precision crushing of the stationary MaxRap, enabling operators to crush RAP at multiple locations with ease. Actuated diverter chutework allows multi-feature deck selection, blending, and bypass and the calibration chute for sampling verifies that the mix-design spec requirement is correct. The plant’s side-discharge conveyor may be used for stockpiling or returned to another conveyor for re-circulating back to the plant for resizing. The system may also be used for screening only, conveying all material to the stockpile. MaxRap 25 Portable plant produces highly uniform, cubicle spec product with a minimum of white rock and a minimum of fines. Remove the actuated diverter chutework, and the plant becomes a 1200OCSS. Recycled concrete and aggregate producers will benefit from the greater flexibility the newly-redesigned 1200-OCSS provides. Operators now have a choice whether the top and middle deck material both go to the impactor, or the middle deck material goes directly to stockpiling so only the oversized material is crushed.”
The 1200-OCSS includes a 6 by 20 triple-deck horizontal screen for screening before crushing, along with screening options for multiple spec products. It includes discharge conveyors for second and third decks, as well as for fines. The side-discharge conveyor transports the crushed material to other equipment for further processing, stockpiling, or to another conveyor for re-circulating back to the plant screen for sizing.
For more information, visit https:// eaglecrusher.com/
Weiler Material Transfer Vehicles lead the way with proven innovations to provide the lowest cost per ton of operation.
Innovative and reliable operator friendly features such as paver hopper management system with distance to paver, storage hopper management and auto chain tensioning.
Variable speed elevator and conveyors meet production requirements with the minimal amount of wear.
Clam shell doors and full width drop down floors provide unmatched access for cleanout.
The evolution of chains, sprockets and augers are retrofittable to all machines and provide increased wear life.
Finlay® introduced its TR-80 radial conveyor (TR-80), which has been engineered to be integrated into static operations or as part of a mobile crushing and screening set up in a diverse range of applications, from heavy duty primary crushing to light duty applications. A key feature of the TR-80 radial conveyor is the automated stockpile program that allows operators to stockpile materials in set patterns to suit their operations and site configuration. Adding to its adaptability, the radial functionality allows for flexible stockpile configurations, catering to various material types and site layouts.
When operated in conical mode, the TR-80 has a maximum discharge height of 10.18m (33 feet, 5 inches (10.18 meters) and can stockpile (2,369 cubic yards (1,811 cubic meters) of material. When configured to operate at 120° Kidney Bean mode, the machine will stockpile 9,897 cubic yards (7,566 cubic meters) of material.
Safety measures engineered into the machine include hydraulic feed height adjustment of the feedboot and pinless deployment of the main conveyor to assist in creating a safer working environment and enable rapid onsite setup and teardown.
Alan Witherow, product & applications manager, Finlay said, “The launch of our new TR-80 radial conveyor demonstrates our commitment to delivering solutions that our customers can rely upon. The TR-80 reduces segregation, degradation, compaction and contamination of material in the stockpile. By enhancing site efficiency and streamlining material handling processes, the TR-80 demonstrates Finlay’s commitment to delivering high-performance solutions that enable cost-savings across our customer operations while providing a consistent quality product.”
Haver & Boecker Niagara, St. Catharines, Ontario, now presents Rhino Hyde liners to enhance the wear life of a full range of equipment. The company’s custom-blend liners are strategically formulated and installed on key wear, material handling and impact areas of chutes, hoppers, vibrating screens and more. Rhino Hyde, constructed from thermoset polyurethane, boasts superior abrasion resistance, durability and chemical resistance compared to alternatives like thermoplastic polyurethane, rubber or metal, according
to the manufacturer. Rhino Hyde liners offer a simple fix to seal worn spots. Polyurethane liners are a cost-effective solution and have the unique characteristic of being higher wear but are also a lighter-weight product with reduced maintenance and replacement costs, according to the manufacturer.
Rhino Hyde liners are designed for applications such as screening, material handling and hauling. They can be fully customized to the required size and are available in multiple styles and attachment systems including the classic Rhino Hyde Blue, magnetic, urethane-backed ceramic, polyurethane blades, belt skirting and weldable liners.
• Rhino Hyde Blue: These liners boast high abrasion and impact resistance, along with reduced noise and vibration. Additionally, they are designed to not expand or contract in environments with fluctuating temperatures. Rhino Hyde Blue liners can be custom-made with several different backings, including solid steel, plain, expanded metal, fabric and ceramic chip embedded.
• Magnetic Liners: These liners feature rare-earth magnets that fasten to steel without welding or bolting. Users can simply place the liner and remove as needed, saving both time and labor. They are designed to reduce material sticking, lessen noise and provide protection in even the most demanding applications. Magnets stay secure regardless of climate and withstand high levels of vibration and impact, according to the manufacturer.
• Urethane-Backed Ceramic Liners: These liners are installed where severe abrasion is an issue. The highly abrasion-resistant panels have replaced plain or weldable ceramic tile for decades in aggregate, coal, fly ash, glass, grain, gravel, cement and other industries. They combine the cut and abrasion resistance of ceramic, and the impact resistance and resiliency of Rhino Hyde polyurethane.
• Weldable Liners: These standard Rhino Hyde weld-in liners are installed with tack welding and have weld plates every 6 to 8 inches (15 to 20 centimeters). Rhino Armor weldable liners feature backing made entirely of perforated steel plate. These liners are designed to excel in heavy-duty applications, particularly those with heavy load drops.
Haver & Boecker Niagara offers Rhino Hyde liners through its partnership with Tandem Products Inc. Together, Haver & Boecker Niagara and Rhino Hyde develop tailored solutions for customers in a wide range of applications and industries.
HCSS, Sugar Land, Texas, announced its partnership with Bulk Exchange, San Rafael, California, stating the collaboration will enable contractors to seamlessly access bulk construction materials and streamline the bidding process. Bulk Exchange is an online marketplace where contractors and construction professionals can find bulk construction materials and dumpsites. Bulk Exchange will integrate with HCSS’s HeavyBid, enabling customers to conduct more accurate bidding around the materials sourcing process and get instant materials pricing estimates.
John Deere of Moline, Illinois, introduced the 444 G-Tier wheel loader in January as part of its performance tiering strategy, offering customers a model without the extras that they would find in a P-Tier or X-Tier machine. The 444 G-Tier is similar to the previously introduced 544 and 644 G-Tier machines, but at a lower operating weight and smaller size. This latest addition to the wheel loader lineup aims to cater to the segment of the construction market that values simplicity and reliability and serves as a response to the demand for more economically priced wheel loader options that don’t compromise on quality and durability.
Among its standout features, the 444 G-Tier can be equipped with optional high-lift, expanding the reach of the machine. The optional debris package, which comes equipped with a centrifugal air pre-cleaner and an auto reversing fan, helps reduce downtime by enabling the operator to stay up and running on the job without pausing to remove job site debris. This model also boasts protective transmission and bottom guards, which are specifically designed to fend off debris and ensure the machine’s longevity.
The stacked cooling package, with the hinged door for cleanout, can be set to automatically reverse at regular intervals, making for simplified maintenance. Additionally, it offers ground-level access on the machine’s left side, making refills of major
A comprehensive assembly custom engineered to offer the advantages of accurately injecting water, other liquid additives or a combination of these materials.
PLANT INTEGRATION FLEXIBILITY: Ability to retrofit on any continuous mix or batch plant.
COMPETITIVE MARKET ADVANTAGE: Ability to blend multiple liquid products: Warm Mix, Anti-Strip, Rejuvenators, Cold Mix Products and #2 Fuel Oil.
FINANCIAL SAVINGS: Lower expenses from reduced fuel consumption.
IMPROVES ENVIRONMENTAL IMPACT: Elimination of blue smoke emissions from plant, silos and from behind paver.
REDUCES PAVING CREW STRESS: From increased workability, reduction in roller passes and patterns, increased, longitudinal joint densities.
INCREASES PROFITABILITY: From increased RAP usage, silo storage time, and haul times in truck bed.
EXPAND PLANT MARKET REACH: Superior coating of the mix and haul-time performance allows expansion of your plant’s geographic reach.
ENHANCES REPUTATION: Improves company reputation from reduction of road degradation.
SAVES MONEY: Reduces the number of required AC tanks and grades to be stored.
IMPROVED MIX WORKABILITY: Example: Grade-bumping (with latex). Grade-bumping custom design.
A MUST FOR PARALLEL FLOW DRUMS: Increases RAP, less blue smoke.
BUDGET RELIEF: No monthly service/subscription charge.
fluids, fuel and DEF straightforward. This loader also boasts clear visibility for both transmission and hydraulic sight gauges, enhancing access to important components when needed. Further enhancing its user-friendly design, there is dedicated right-side access to the machine’s engine, after-treatment systems and the cooling system.
For more information, contact your local John Deere dealer.
MAJOR, Candiac, Quebec, offers the FLEX-MAT Modular PLUS advanced screen media to heighten screening performance and wear life. The product is specially designed to withstand harsh screening conditions with abrasive materials, such as granite and basalt.
“We’re always looking at ways to help producers get the best end product,” MAJOR President Bernard Betts said. “What better way than to optimize the design of our efficient FLEX-MAT product for even better performance.”
The efficiency-enhancing characteristics of all FLEX-MAT screen media, including the modular PLUS series, are created by bonding OPTIMUMWIRE® with distinctive lime-green polyurethane strips rather than weaving them. This allows wires to vibrate independently from end to end under material contact. The high frequency of the wires—8,000 to 10,000 cycles per minute—adds to the vibration of the screen box—800 to 900 cycles per minute—to speed up material separation and passing. The increased screening action improves material throughput while virtually eliminating near-size pegging on the top decks and fine material blinding and clogging on the bottom decks, resulting in a lower cost of production per ton, according to the manufacturer.
During World of Asphalt/AGG1, Masaba Inc., Vermillion, South Dakota, displayed a model of its drive-over truck unloaders to increase efficiency and safety, while reducing fuel costs. With the costs of transport and handling on the rise, any time a producer can reduce rehandling of aggregate material, the savings will add up.
Truck unloading systems can help eliminate material rehandling and traffic congestion, and in turn, they will help to minimize fuel costs, improve cycle times and increase worker safety. Low-profile, drive-over truck unloaders, from Masaba are designed to allow quick unloading of material from belly- or end-dump trucks in a matter of minutes, without the need for the truck or a loader to drive onto or even approach the stockpile.
Available in portable or stationary models, with 48-inch or 72-inch discharge conveyors, Masaba Truck Unloaders feature heavy-duty steel frames. Self-cleaning onboard hydraulic ramps allow for fast setup onsite, eliminating the need for earthen ramps. Hydraulically adjustable discharge conveyors feature an AR-lined discharge hood, making them ideal for feeding stackers, telescoping conveyors or other equipment in the operation.
Masaba Truck Unloader features include:
• Self-cleaning hydraulic ramps
• Hydraulically adjustable discharge height
• Heavy-duty steel ramps to grade
• Nema 4 control panel
• 20 hp electric auxiliary hydraulic pump
• Removable drive-over grizzly bars
• Class II dual drives
• Gen-set (optional)
For more information, call (605) 624-9555.
Metso Corporation, Espoo, Finland, now offers a new software application called Metso Remote IC. The new Metso Remote IC is used for remote control and monitoring of the crushing and screening process, and it connects wirelessly all the Lokotrack® crushers and screens at the site.
With the Metso Remote IC app, the operator can view all the Lokotrack train machines and their main process parameters using a single dashboard. The feeder and crusher settings can be adjusted from the excavator cabin, and the overall visibility of the process allows the operator to adjust the feeding for an optimal production level. In problem situations, the Remote IC automatically stops the feeder. It also instantly alerts and provides a reason for the stoppage.
The Remote IC app can be operated by one person and viewed by many. Everyone at the site can view the main process parameters and alarms. For example, the wheel loader driver can acknowledge the alarm and fix the problem.
OMI Industries (OMI), Palatine, Illinois, introduced the Ecosorb® 1300 series at World of Asphalt in Nashville. The latest 1300 series is designed to provide manufacturers and contractors in the asphalt and paving industry with an improved response to strong odors associated with operations.
Over the last five years, the Ecosorb 1300 series has undergone testing on asphalt cement (AC) blends, evolving through evaluations across North America. Under research and development, OMI identified new asphalt mix odor profile trends and crafted this latest line of products to offer a broader spectrum of odor control in the asphalt and petrochemical industries.
The 1300 series distinguishes itself by incorporating plant oils, effectively addressing hundreds of odor-generating compounds, such as hydrogen sulfide and mercaptans. Simple to apply by directly blending into hot mixes, or distributing in the air via vapor phase systems, these new formulations neutralize airborne chemical compounds that cause offensive odors. Complementing OMI's broader Ecosorb product line, the 1300 formulation stands out for its exceptional ability to reduce unpleasant sulfurous and malodorous compounds.
As the industrial odor control market has evolved, OMI has developed an entire family of plant-based Ecosorb products that maintain a philosophy of environmental and worker friendliness, while avoiding the concept of odor masking. Instead, these innovative products chemically react with odor-causing molecules in the air, neutralizing malodors on contact, according to the manufacturer.
For more information, contact Brian Duffy at bduffy@omi-industrial.com.
Rubble Master Americas Corp., headquartered in Ennis, Texas, exhibited at the co-located shows despite a state of flux in the organization. The company released a statement saying: “After four years as managing
director of Rubble Master Americas Corp., Jackson McAdam will return to Europe to take on a new role within the RM Group... The new managing director will be appointed by June this year at the latest. In the management of the RM Group, the founder and owner of Rubble Master, Gerald Hanisch, will withdraw from the day-today business and concentrate on the stra-
tegic role of ownership.” Even with these disruptions, the company plans for the upcoming managing director to introduce the new RM J110X to the North American market with its first demo event in the United States in Q2/2024. The RM J110X will be a 44-inch by 28-inch jaw crusher and will be launched globally, starting with its international launch in Austria in April.
Editor’s Note: For 2024, AsphaltPro Magazine allows experts in the industry to share how to expand your operations to the next phase of business. Are you ready to take the plunge and add more services to your arsenal? Let’s turn to some professionals who have equipment, services, software and tenure to help you expand to paving bigger, broader, more lucrative projects. This month’s installment from Astec Industries looks specifically at paving technologies and applications for different sized projects.
WWhen it comes to building roads, finding the right paver for the job is critical to your success. Paving encompasses a wide spectrum of applications, ranging from the establishment of smallscale pedestrian walkways and residential projects like driveways and parking lots, to highly regulated endeavors such as interstates and racetracks. Choosing the right paver for your project can make a substantial difference in terms of efficiency, quality and cost-effectiveness. When you’re ready to invest in your first paver or considering an upgrade, there are questions to answer before making a final decision.
To help answer these questions, we called on Tom Travers, director of technical sales at Astec Industries. Tom has been with Astec for nearly 20 years.
“When deciding what paver to purchase, I recommend you keep three key factors in mind,” Travers said. “You need to know what class of machine best suits your project needs, the material throughput required for the job and the level of technical support you will need over the course of the project.”
The class of machine encompasses the width and weight of the machine. Pavers are typically categorized as commercial or highway class. The class you choose should align with the scope of your work. Commercial class pavers are suitable for projects with a daily production volume of a few hundred tons. They are often preferred for smaller-scale work due to their lower weight and size, which makes them more maneuverable. They can handle a wide range of projects, including parking lots and smaller roadways.
If you are working on larger projects with higher daily production volumes, highway class pavers are the better choice. These machines are designed to handle the demands of highway construction, with larger sizes, more horsepower and greater material throughput.
In some instances, commercial and highway class pavers may be interchangeable, depending on the requirements of your project. Always consider factors like the scope of work, production volume, speed, size of trucks and the expected lifecycle of the paver.
2. Material Throughput
Material throughput refers to the paver’s capacity to handle and lay down material effectively. This feature will directly impact the paver’s efficiency and productivity. When assessing material throughput, consider both the rate of throughput and grade conditions.
“Too much or too little throughput can lead to subpar results,” Travers said. “The weight of the paver directly affects its ability to handle different grade conditions. Your machine should maintain stability and quality in varying terrains and slopes.”
3.
Technical support from the dealer or manufacturer can have lasting impacts. Reliable technical support and availability of parts can make a significant difference in your overall experience with the machine.
Asking the right questions on your hunt will help you choose the right paver for the job. For example, proper width and height clearances influence the paver’s functionality and the quality of the final product. The paver’s ability to handle the required material throughput helps keep the project on schedule, while using a paver that cannot handle the grade conditions of a project may result in an unstable paving process and subpar results.
To choose the right paver, begin by evaluating your current projects. What type of work are you doing, and what are your shortterm goals? This will help you choose a paver that matches your immediate requirements.
Then consider where you aspire to be in the future. If you plan to take on larger projects or expand your services, it’s important to invest in a paver that can accommodate your growth.
Another important decision you will need to make in your pursuit of the best paver for the job is between wheeled and tracked pavers. Where and how you plan to use the machine, along with the overall cost, come into play when deciding between the two. In certain scenarios, a combination of both types may be required to achieve the best results.
Wheeled pavers are well-suited for road construction or resurfacing projects that are relatively short in duration or need to be interspersed
with other jobs. These machines are ideal for scenarios where you have multiple projects ongoing and require a paving machine that can be swiftly and seamlessly moved from one job site to another because of their speed of mobilization and setup. These machines often have a lower initial purchase price, and their maintenance and operational costs are also generally more affordable compared to tracked pavers.
Tracked pavers are more suited for specific scenarios that demand enhanced traction and stability. These machines are indispensable when working on soft sub-base conditions that require maximum flotation to prevent the paver from sinking. They provide excellent stability, especially when paving wide and deep lifts, resulting in a uniform and consistent finish. In situations where the terrain is steeper or uneven, tracked pavers offer enhanced operation. Their tighter turning radius offers an advantage in confined spaces.
These are just some of the considerations to keep in mind when shopping for your first paver. Make sure to give yourself the time you need to make the right call. By taking the time to learn more about your options before making an informed decision, you can set the stage for success.
When assessing paver options, it’s essential to understand the key components of the machine that impact the quality and efficiency of the paving process. These components include:
Conveyors: The conveyor system is responsible for moving materials to the screed. Look for one that minimizes material segregation while promoting a uniform head of material through the flow gate to achieve a smooth surface.
Augers: Augers play a crucial role in preventing material segregation and ensuring even distribution. A well-designed auger focuses on reducing material shearing, which can lead to segregation.
Flow Gates: Flow gates are metering plates that allow you to adjust the amount of material without changing the conveyor speed. This feature helps reduce material shearing, prevent segregation and maintain an even and consistent mat.
Screeds: The screed is responsible for shaping and smoothing the material. An ideal taper design will allow material to move from the center to the edges, improving material fluidity and reducing the chances of cold material in the mix.
Delta Plate: Positioned under the conveyors at a 45-degree angle, the delta plate directs material toward the screed instead of allowing it to fall forward. This adds uniformity to the material and prevents segregation.
Sight Lines: Good visibility from the operator’s seat is vital for safety and achieving precise results. Well-designed sight lines make it easier for the operator to maintain control and accuracy during the paving process.
Finlay®, global manufacturer of mobile crushing, screening and conveying equipment, has supported OPS Screening and Crushing, based in Australia, in the manufacture of a vividly pink machine built with purpose: to support Australia’s National Breast Cancer Foundation in the fight against cancer. As part of their commitment to social responsibility, OPS commissioned a Finlay 883+ heavy duty screen in breast cancer’s worldly recognizable pink color, destined to join its rental fleet. Partnering with the National Breast Cancer Foundation (NBCF) in Australia, aiming to raise $100,000 for breast cancer research, a portion of the revenue generated from the rental of this unique machine will be contributed to the foundation, aiding in the critical vision of Zero Deaths from breast cancer.
“At OPS we have long aspired to undertake a project of this nature and seeing it come to fruition fills us with immense sense of pride,” said Shane Czerkasow, director at OPS. “Our objective is to align with NBCF’s mission by contributing to breast cancer research, working towards their 5-year vision of zero deaths from breast cancer.
“As we worked on the project with our business partners and suppliers around the world, it was evident the widespread effect
of breast cancer—the room was constantly filled with individuals sharing stories of ‘My mum,’ ‘My best friend,’ ‘My sister’ and even ‘Me’ as people shared their stories of being affected. With the machine now arriving in Australia we look forward to working with our customers to further raise awareness and for the NBCF foundation.”
Joe Donnelly, regional sales director for Finlay added, “When OPS approached me with this idea, I was more than happy to support it. Cancer has impacted the lives of countless individuals in one way or another, and this initiative provides us with a great opportunity to make a positive difference. A big, bright, pink machine is not something you’d often see in our industry so I’ve no doubt it will be a talking point on the various rental projects it will be involved in. We hope this awareness will highlight the importance of early detection and provide a positive ripple effect on the lives it touches.”
Manufacturing of such a distinctive machine would not have been possible without the dedication and collaboration of all parties involved. The collaboration included securing parts in the distinctive pink color to ensure on-time delivery for production.
Donnell and Ellis transport carriers provided a specially branded truck for the journey to Southampton, where Terex global RoRo partner Wallenius Wilhelmsen facilitated its
sea voyage to Western Australia.
Matt Dickson, business line director for Finlay concluded, “I would like to thank OPS Screening and Crushing Equipment for coming to Finlay with such an innovative approach to citizenship. Finlay is not just a team that excels in business, but a team that cares about making a meaningful impact in the lives of others. From the initial planning stages to today, where we see the pink 883+ standing in all its glory, our team poured their enthusiasm and hard work into making this vision a reality.
“Meaningful change happens when organizations come together with a shared vision. Collaborating with OPS on this initiative has been a wonderful experience—we wish them all the best with the machine and congratulate them on this inspiring initiative.”
Increase production and efficiency without the investment of a new drum. A leader in the retrofit market, we’ll work with you to come up with the best solution at a competitive price.
· HIGHER RAP PERCENTAGES
· SINGLE POINT ADJUSTMENT
TRUNNION DESIGN WITH HEAVY
DUTY TIMKEN RAIL CAR BEARINGS
· WEDGE-LOK™ TIRE SUSPENSION
· IMPROVED FLIGHTING DESIGN
· PARALLEL TO COUNTER FLOW CONVERSIONS
· PORTABLE AND STATIONARY
AsphaltPro’s advertiser index is
Artificial intelligence affects heavy equipment performance, maintenance, safety
BY LOUISA DIAZEditor’s Note: As the asphalt industry collectively understands, you can’t manage what you don’t measure. In this article, the lines between telematics systems and artificial intelligence systems tend to blur, but the reader is encouraged to recognize AI uses and learns from the data telematics captures. This article offers some benefits of using copious amounts of data to enhance procedures, either through telematics or telematics-plus-AI.
Imagine a work zone of immense proportions, populated with equipment that functions like clockwork, calibrated to execute specific tasks yet adaptable to unforeseen on-site challenges. This vision is no longer science fiction, but a reality unfolding with the aid of artificial intelligence (AI), enhancing the efficiency of heavy equipment.
The influence of AI on machinery such as cranes, bulldozers and excavators underscores a profound shift in the sector. The inception of AI-enabled monitoring systems has led to a 25% improvement in fuel efficiency and substantial reduction in maintenance downtime, according to industry statistics.
AI can be used to improve the efficiency of heavy equipment by optimizing fuel use, predicting maintenance needs and increasing operational accuracy. The real-time data provided by data-sharing technologies enables you to better manage your equipment, resulting in reduced downtime and cost savings.
AI can assist with managing your heavy equipment fleet. Let’s look at predictive maintenance first. Beyond telematics “telling” your mechanic when it’s time for routine maintenance, AI can predict when machines need extra care. This translates to better planning. You can see less unscheduled downtime and lower costs when you can fix small problems before they become catastrophic.
Equipment tethered to communicate can efficiently load aggregate in fewer passes for fuel savings and other benefits. Photo courtesy of Boom & Bucket
Real-time diagnostics from AI-powered tools keep machines healthy. Think of it like a doctor's check-up for your equipment.
• Alerts pop up if something looks wrong.
• Sensors check all parts, making sure they run smoothly.
• Errors are caught quickly, before they can cause trouble.
AI takes control with autonomous operation when robots and drones do the work. Here’s what this means for equipment:
• Machines work day and night.
• No breaks needed means more production.
• Tasks can be accomplished with incredible precision if machines are tethered to “talk” to each other.
Obviously, working with and around heavy equipment in industries like construction or mining comes with a level of risk. AI can boost safety for workers through sensing danger. One example is collision avoidance systems, which use AI to keep an eye on surroundings. These systems detect objects and give warnings to prevent struck-bys.
Remote monitoring—watching operations with a computer or smartphone—lets a manager or super check in on machine health and worker safety from anywhere.
One area where AI can help an organization is in optimizing workflows. Enhanced by smart algorithms, back-office tasks that once consumed hours can now be streamlined, making operations swifter and more cost-effective.
AI-powered tools can take over repetitive tasks such as scheduling or allocating resources for projects or maintenance, freeing employees for complex jobs. Here are a few examples.
• Automated Scheduling: Machines decide when work starts, ensuring no downtime.
• Self-operating Machinery: Equipment operates independently, reducing manual errors.
• Real-time Adjustments: AI instantly tweaks tasks to suit changing conditions.
As AI becomes more common in heavy equipment management, it also presents unique challenges and considerations. It’s essential to address these concerns to fully harness AI’s potential. Ensuring data security and providing adequate training are crucial for the successful implementation of AI. Protecting sensitive information amidst the adoption of AI is vital. Heavy equipment often contains critical operational data, which becomes susceptible to cyber threats when connected to AI systems.
• Encryption: Vital for data in transit and at rest
• Access Control: Ensures only authorized personnel can interact with AI systems
• Regular Audits: Identifies and addresses potential security vulnerabilities Companies must prioritize these areas to safeguard data from unauthorized access and breaches. Management must train personnel effectively in the use of AI-powered equipment and programs to reduce the risk of operational errors, safety hazards and data breaches. A strategic approach to training can significantly impact the success of AI integration in heavy equipment operations. The integration of AI in heavy machinery heralds a new efficiency era. Advanced algorithms can enhance operational precision, minimize downtime and cut costs. Adopting smart technology is key to staying competitive in a fast-evolving sector. But such adoption requires training and smart implementation for safe, efficient, productive use in the heavy equipment landscape.
Louisa Diaz is the market operations manager at Boom & Bucket.
Astec water clarification systems effectively remove fine particles from dirty water, eliminating the need for costly settling ponds. With a water recovery rate of up to 95%, these innovative solutions can reduce your overall water consumption and operating costs.
See our water clarification solutions.