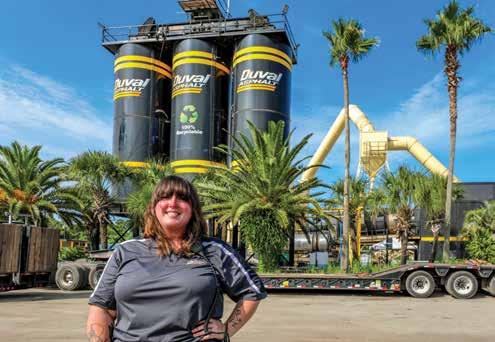
6 minute read
Meet a Woman of Asphalt Duval Asphalt’s Rena Deihl
SShe officially joined the asphalt industry in 2020 at the urging of her father, an employee of Duval Asphalt, Jacksonville, Florida, and has already taken her education at the scale house to a larger role at the company. Rena Deihl is now a plant operator for Duval Asphalt working among all three asphalt plants in Jacksonville and learning new aspects of the job that endears the industry to her more each day.
Duval Asphalt’s West 12th Street plant has been featured on AsphaltPro’s front cover to highlight environmental excellence. A spokesperson for the company shared that both the 12th Street plant and the Philips Highway plant Deihl operates have garnered National Asphalt Pavement Association (NAPA) environmental diamond achievement commendations over the years. The 12th Street plant is an Astec 400 Double Barrel. The Philips Highway plant is a Gencor 400 Ultradrum, rated at 300 TPH. Deihl shared that her top production day so far at the Gencor plant was 1,400 tons.
She took some time to share her insight as a fairly new woman of asphalt.
AsphaltPro: What did you find most rewarding or most interesting about your job at the scale house when you started out? Rena Deihl: Most interesting was finding out all of the different materials that came into our plant. Understanding what the different aggregates were and learning how “milling” can be recycled.
AsphaltPro: Would you say “jumping into” the asphalt industry with the job at the scale house was a good fit for you, and how would you advise or encourage other women who are interested in plant operations for entering the industry? Rena Deihl: Most definitely. It allows other departments within the business to see what you’re capable of. Apply for the job, work hard and be open to learn new things.
AsphaltPro: Could you share with the readers how the scale house and materials work prepared you to transition to plant operation? Rena Deihl: Learning the basic knowledge of how to do customer/job tickets, and learning the difference in the aggregates we receive that get fed into our plant to make our asphalt.
AsphaltPro: What part of your education relates best to the career track you’re on?
She might be relatively new to the asphalt industry, but she already knows how to keep the asphalt plant clean and dust-free. Here she smiles proudly in front of the facility she operates.
Rena Deihl: I really did not need a degree for what I am doing now as a plant operator. Although, I would really like to take some production courses to further my education.
A spokesperson for Duval Asphalt shared the company suggests both industry consultants—such as TJ Young of T2ASCO LLC—and the original equipment manufacturers (OEMs) around the country that offer training for continuing education for workers on the production side of our industry. For example: “Classes are offered by Astec, Gencor, Stansteel. Clarence Richard Company offers online classes.”

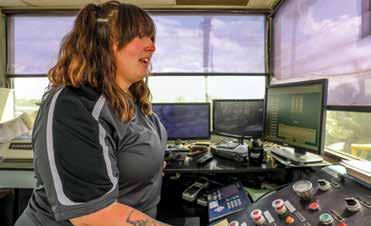
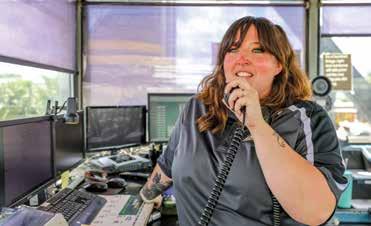
LEFT: Lonnie Couch has served as a mentor for Rena Deihl. His advice: “The only way you will learn is to just do it, literally. If you want to run a piece of equipment, run a plant, jump on it and do it.” RIGHT: Rena Deihl is the plant operator for Duval Asphalt’s Gencor 400 Ultradrum, rated at 300 TPH.
AsphaltPro: Could you share with the readers what your job as a plant operator for Duval Asphalt requires of you? Rena Deihl: To make a good quality asphalt mix that paves our roads. Ensure the safety of my crew and to make sure our equipment/plant is in working condition to run.
AsphaltPro: Why did you choose to become a plant operator? What about that position is “most cool” to you? Rena Deihl: I wanted to be a part of something big, making something that is used every day, all across the world. Watching my mentors operating our plants and observing what is done to make the asphalt, just seemed very awesome. Honestly, making asphalt is the coolest thing.
AsphaltPro: What would you say was the most challenging “obstacle” you, as a female at the asphalt facility, had to overcome in the past 8 months, and how did you overcome that obstacle? Rena Deihl: I have not come across one person that felt I could not do the job. I am not sure what skill could help others other than to prove to the men on the job you can do anything they do.
AsphaltPro: Let’s talk about Teamwork. What is the most challenging project you’ve been a part of and how did you and the plant team overcome the challenge? Rena Deihl: When I was on nights in our Green Cove plant, we had run on two separate occasions, we got a call to fire up a third time to send out another 120 tons. I started everything up, the belts, the drum, the drag, exhaust fan. When I’d get ready to ignite the burner, our exhaust fan would kick out. Took us a bit to figure it out but after inspecting my controls, my ground lead and I went to our breaker room and discovered the breaker had tripped. After resetting the breaker, we were finally able to run. AsphaltPro: It’s a fact that asphalt paving can be hot and dusty. How do you respond to people who say it’s a “dirty job?” Rena Deihl: It’s only dirty if you make it dirty. When making our mix, it can get dusty but as long as you run your waste auger/dust screws, it pulls the dust from the initial fire up and at time of shut down to eliminate “the dusty air.”
AsphaltPro: What is the most rewarding aspect for you of being in the asphalt business? Rena Deihl: Truthfully, making the asphalt and seeing that our test grades come back good. Both for the AC target and air voids.
AsphaltPro: Will you tell us about a person who served as a mentor for you? Rena Deihl: Lonnie Couch. He pushed me out of my comfort zone and allowed me to see my potential.
– BY SANDY LENDER
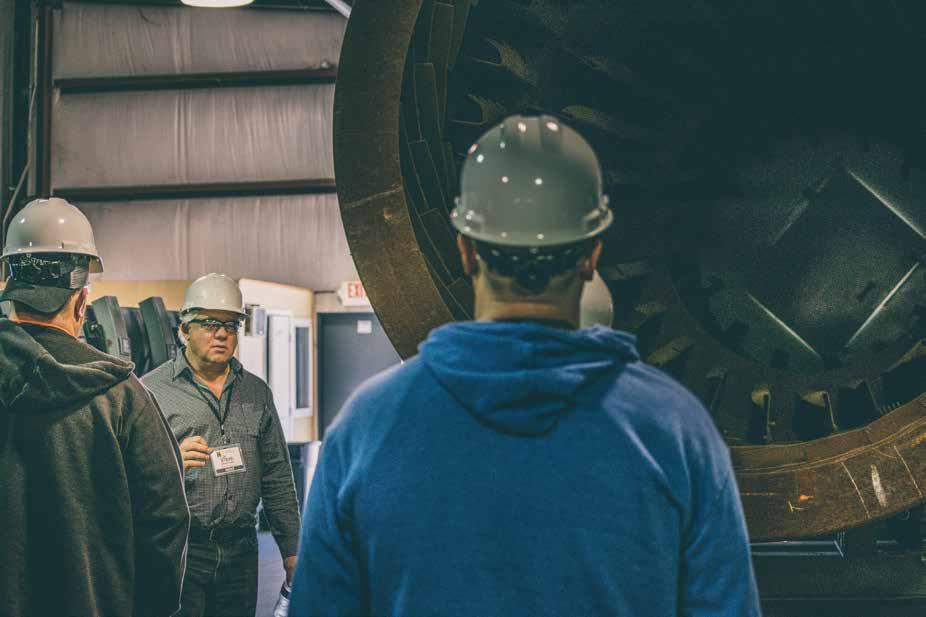
Managers Exchange
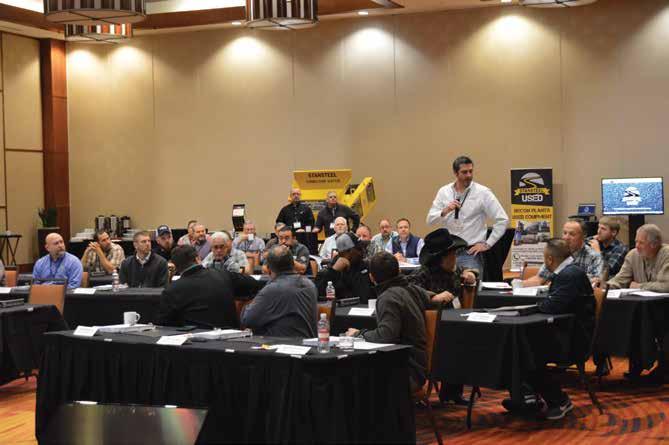
January 16-19, 2022
Operators Course
February 6-9, 2022 February 20-23, 2022
Book Early!
Space is limited.
Call your rep to book a spot. 800-826-0223
A 4-day training and technical conference o ered by
R
Join us for Hotmix University in Louisville, Kentucky. During the intense exchange sessions, participants enjoy a combination of lectures, hands-on workshops on actual equipment, break-out sessions and discussions, as well as fun times to facilitate networking among industry peers.
We limit our class size so we may allow productive interaction with instructors and among asphalt producers and operators. Those who have graduated from HU have raved about the practical benefits received during their time spent learning with us.
Our staff of instructors boasts over 1,500 years of combined experience in the asphalt industry but also in the broader rotary processing equipment world. This makes our agenda unique to any other training event. Here are just some of the topics covered:
Performance measures Best practices and how to improve Establish FACTS about your plant Specific plant components review Design and operation practices Heating and drying: burners and dryer/drums Baghouse and air systems Silo systems Recycle - RAP & RAS Electronic controls Preventive Maintenance and Minimizing Downtime Productivity Reliability Engineering Much more!