PRODUCTION – PROFESSIONALS – PRODUCTS • Fall PreservationPro • 3 Performance Tests • Fishing for Plastic Mixes • How to Stripe an Airfield • How Your Peers Keep Workers QC/QA Issue SEPTEMBER WWW.THEASPHALTPRO.COM2022 asphaltasphaltPROPRO Parts Ship Out for Plant Build
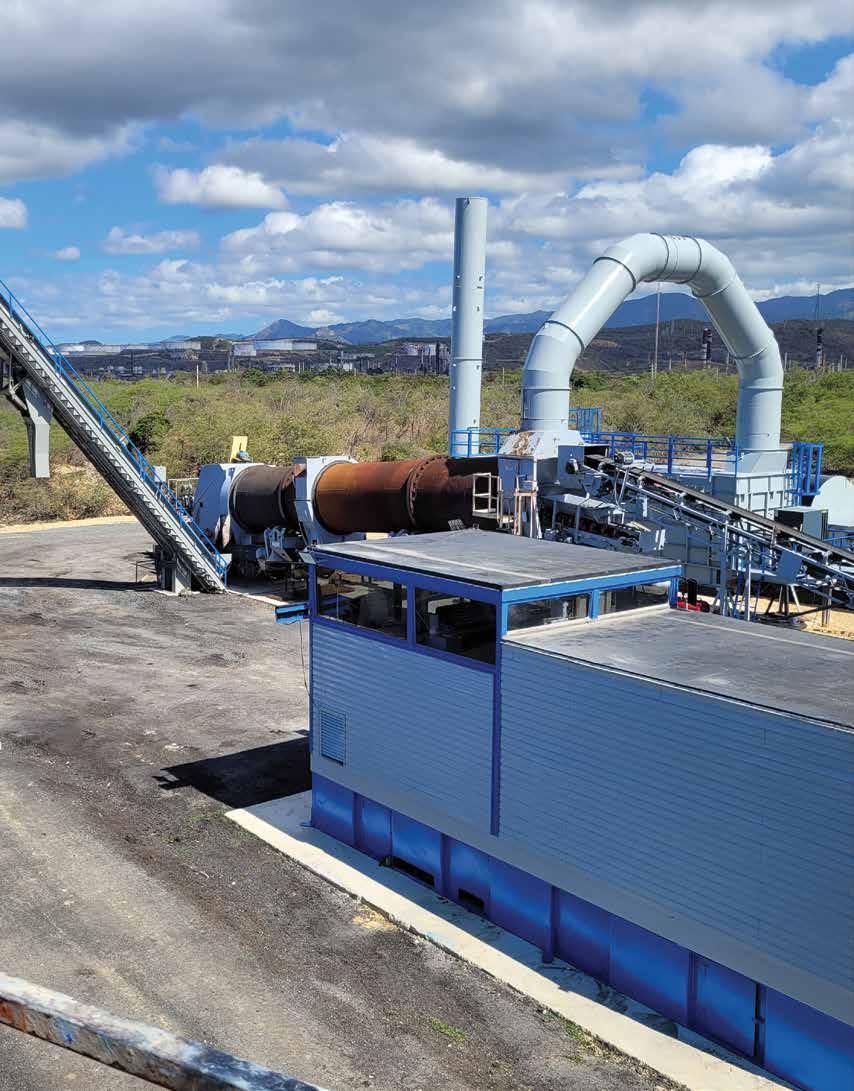
Single-Source Supplier Advantage
BUILT TO CONNECT
Astec provides a significant advantage as a single-source supplier for the diverse products and services involved in building and maintaining an asphalt mixing plant.
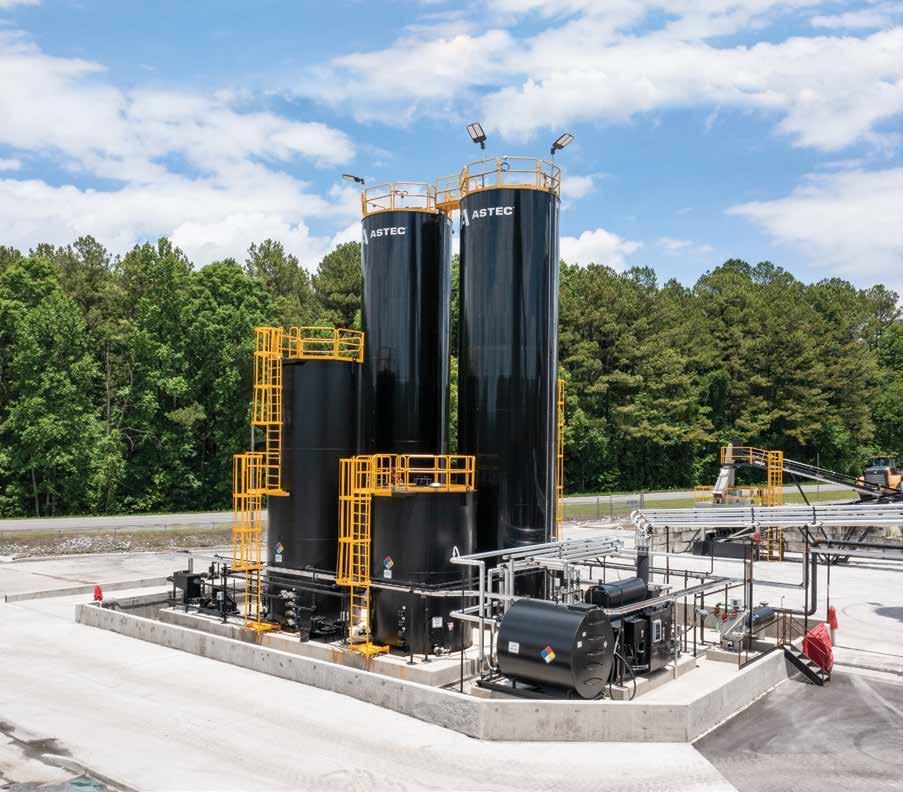
Astec liquid AC storage tanks, tank farms, and heating system controls feature high quality construction and unmatched efficiency. We offer a variety of sizes and configurations that can be fully customized. Optimize your asphalt storage tanks and hot oil heaters with the addition of the Recon® mobile monitoring system to receive status updates on a smart phone, tablet or PC.
Scan QR code to see Astec’s full line of Tank Farm Components.

cwmfcorp 877.457.3938.com sales@cwmfcorp.com FAMILY CUSTOMEROWNED,DRIVEN. As a family-owned and operated business offering state-of-the art portable and stationary asphalt plant equipment, having a personal touch with our customers is important to us. People always come first. When you call, you can speak to an owner. We are large enough to supply your equipment needs, while still being flexible and responsive. Contact us today to learn more about how CWMF Corporation goes the extra mile. We build long-term relationships by earning the trust of our customers. Customer-Driven Equipment & Solutions Unparalleled Service After the Sale Complete Product Line Designed & Built In-House
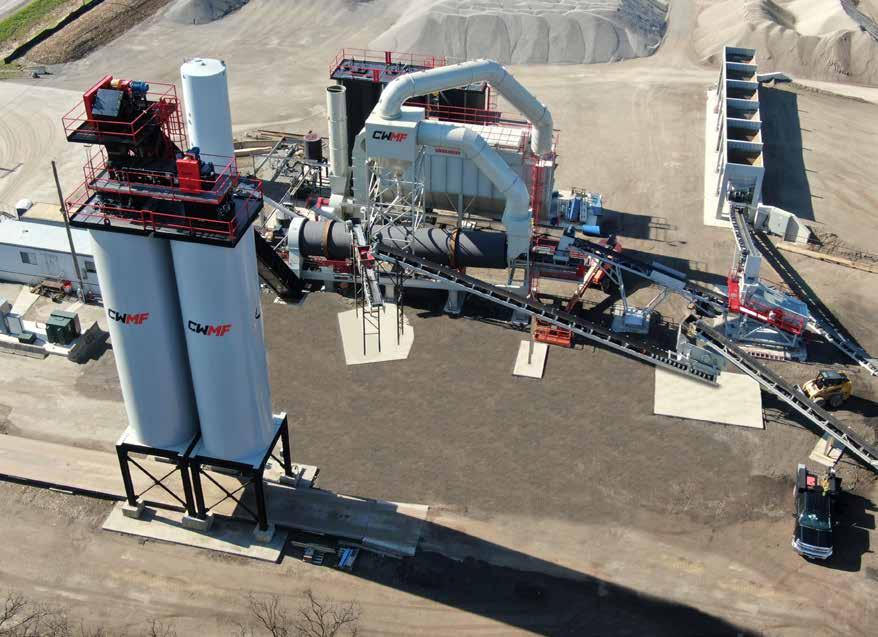
experts
2023 DATES • Week 1: January 16 - 19 • Week 2: January 23 - 26 • Week 3: January 30 - February 2 • Week 4: February 6 - 9 REGISTRATION CLASS SIZE IS LIMITED ! To secure your seat, please register before November 15, 2022 DETAILS Details can be found at www.gencor.com/ training or call us at 407-290-6000 ext. 342. 5201 N. Orange Blossom Trail Orlando Florida 32810
Improving overall plant production are all common concerns plant Having a well-trained technical crew is vital to maintaining plant and Gencorefficiency.and its training staff the biggest concentration of knowledge and expertise in all the sciences and technologies involved in the production of asphalt plants. Customers who attend these seminars benefit by having the support and focused attention of the best specialists in the asphalt industry. Using Gencor’s state-of-the-art control simulators and actual equipment, our take stepby-step through a comprehensive intensive concentrated hands-on providing the latest techniques on optimizing production efficiency.
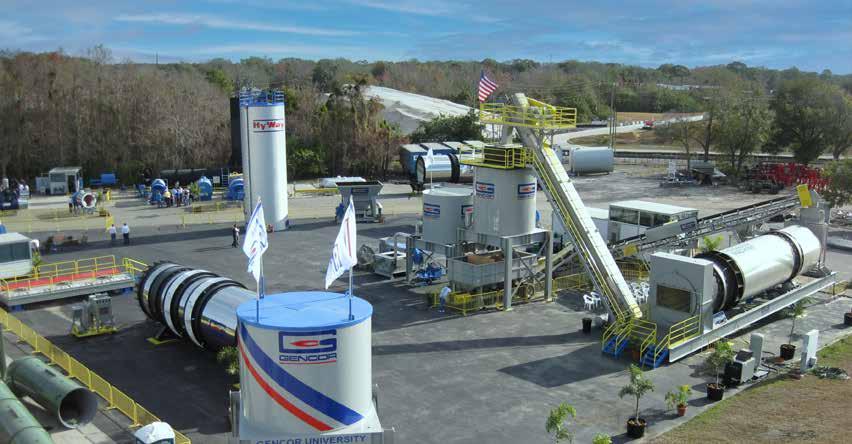
for
&
you
and efficiency
performance
owners and operators.
represent
GENCOR 2023TRAININGADVANCEDSCHOOL BE PART OF THE GENCOR EXPERIENCE
training program
CONTENTS EDITOR’S LETTER 8 – Risk in the Time of Suicide SAFETY SPOTLIGHT 10 – Generational Differences Influence Safety Culture By the Association of Equipment Manufacturers MIX IT UP 12 – Three Tests to Perform By Sina Varamini, PhD, PE 14 – Fishnets Capture Plastic Discussion By Sandy Lender TRAINING 18 – There’s More to Cleaning the Equipment By John Ball PRODUCER PROFILE 20 – Journey Group Diversifies for Growth By Sarah Redohl WOMEN OF ASPHALT 26 – Meet a Woman of Asphalt: Lehman-Roberts’ Maria Bennett By Sandy Lender INTERNATIONAL SNAPSHOT 34 – International Combo From Reliable Asphalt Products PRODUCT GALLERY 50 – Protect Parts for Sustainable Asphalt Production By Martin Kirchgassner OFF THE MAT 56 – 13 Strategies to Retain Asphalt Workers By AsphaltPro Staff 60 – Digital Disruption for Aggs By Nick Grandy NEW TECH 62 – Know Where You're Working With OnStation By Sarah Redohl HHIW 66 – CWMF’s Fines Metering System asphaltPRO September 2022 ON THE COVER Super Asphalt of Puerto Rico worked with Reliable Asphalt Products of Kentucky to piece together a plant with two labs and MINDS controls this season. See related article on page 34. Photo courtesy of Reliable Asphalt Parts Ship Out for Plant Build PRODUCTION – PROFESSIONALS – PRODUCTS HowHowFishingPerformancePreservationProTestsforPlasticMixestoStripeanAirfieldYourPeersKeepWorkers QC/QA Issue asphaltasphaltPROPRO Parts Ship Out for Plant Build DEPARTMENTS 2012 PRESERVATIONPRO 38 – Overcome Recycled Asphalt Anxiety By Sarah Redohl 40 – The Warehouse Revolution is Built on Relationships By Sarah Redohl 44 – How to Stripe an Airfield By Sarah Redohl 48 – SealMaster’s CrackPro RMV SPECIAL SECTION40



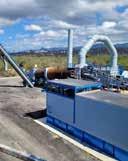
DESIGN, DETAILS, AND DURABILITY.
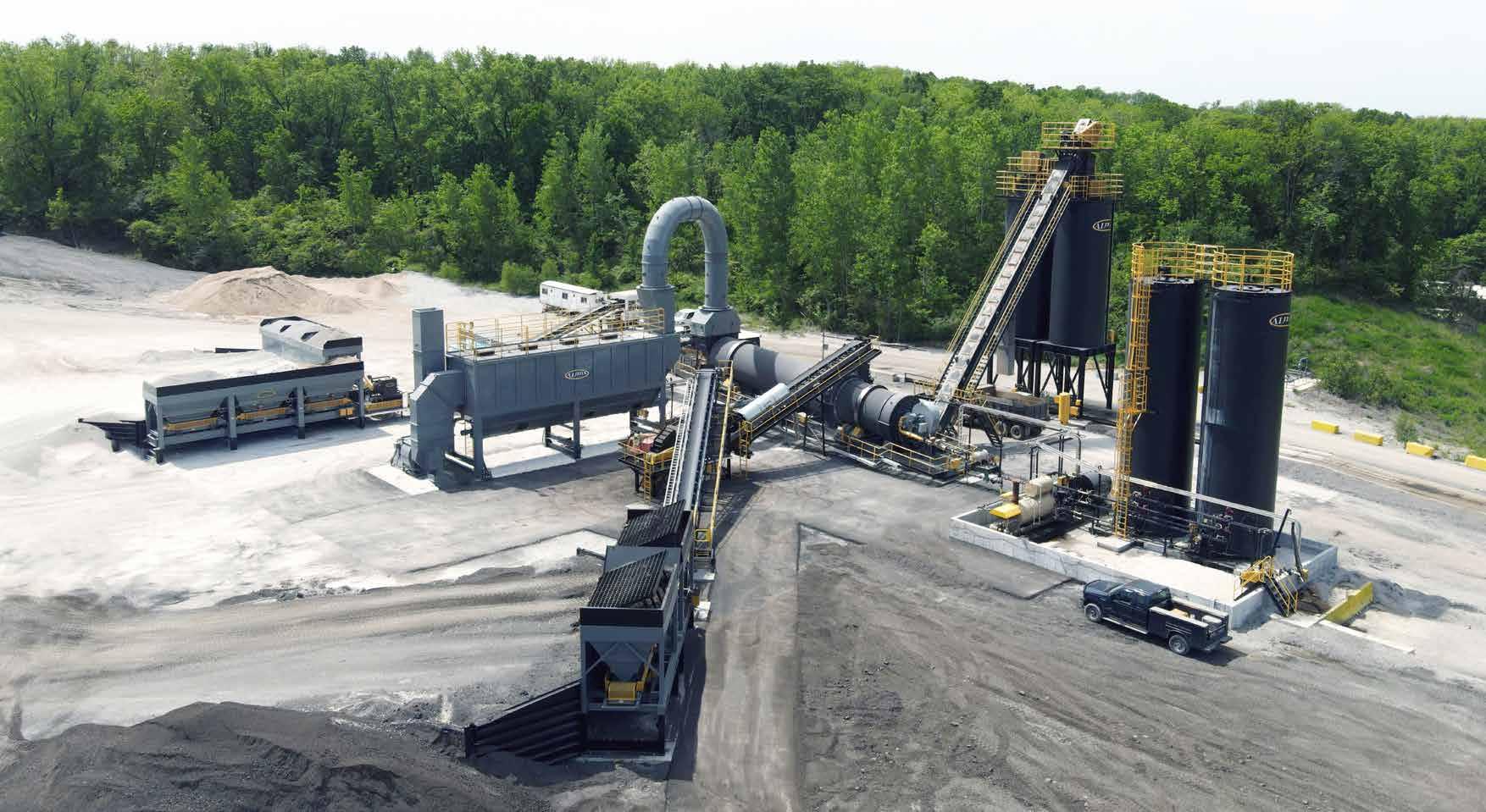
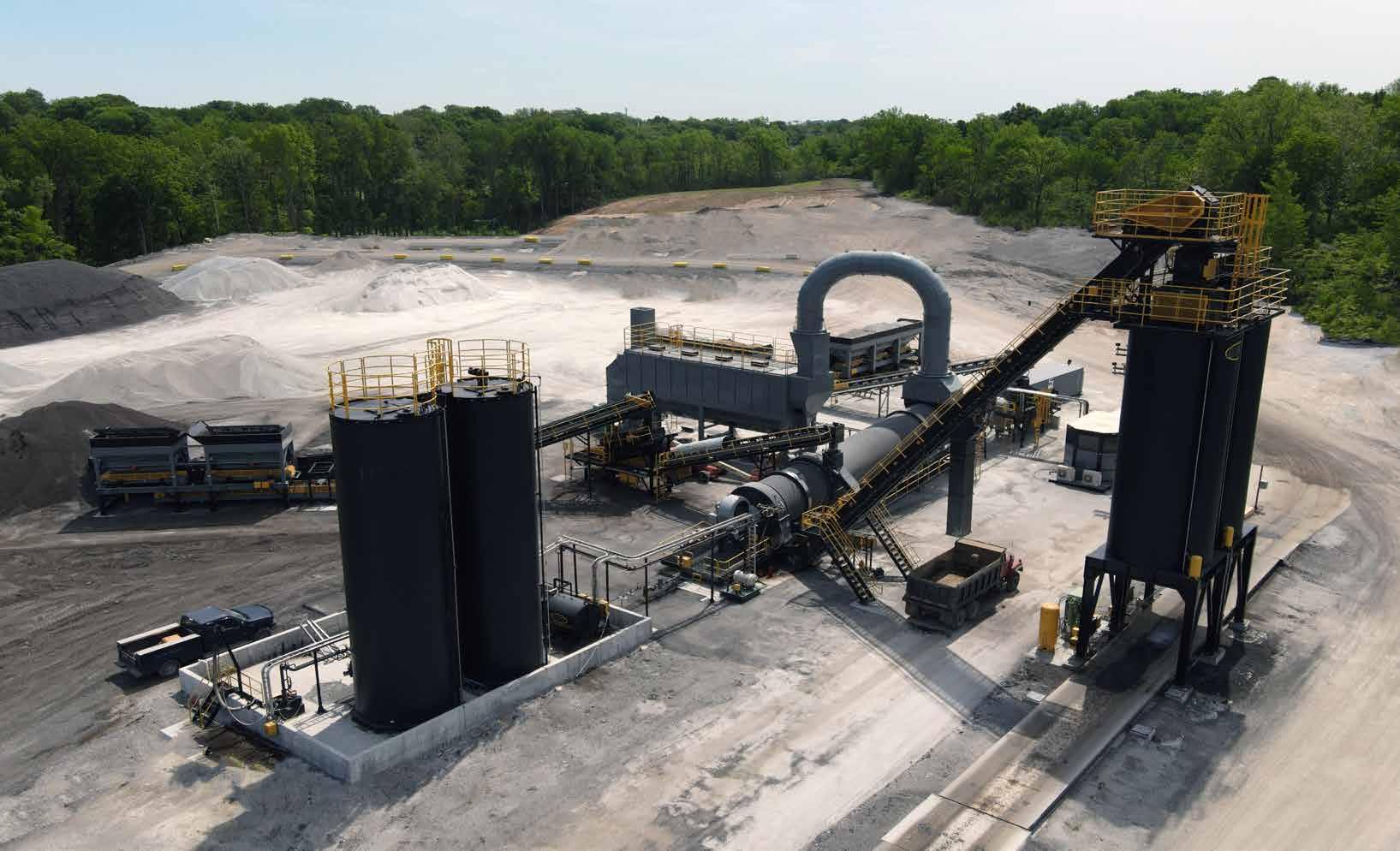
10106 SMITH ROAD, FORT WAYNE, IN 46809 | (260) 672-3004 | ALmix.com
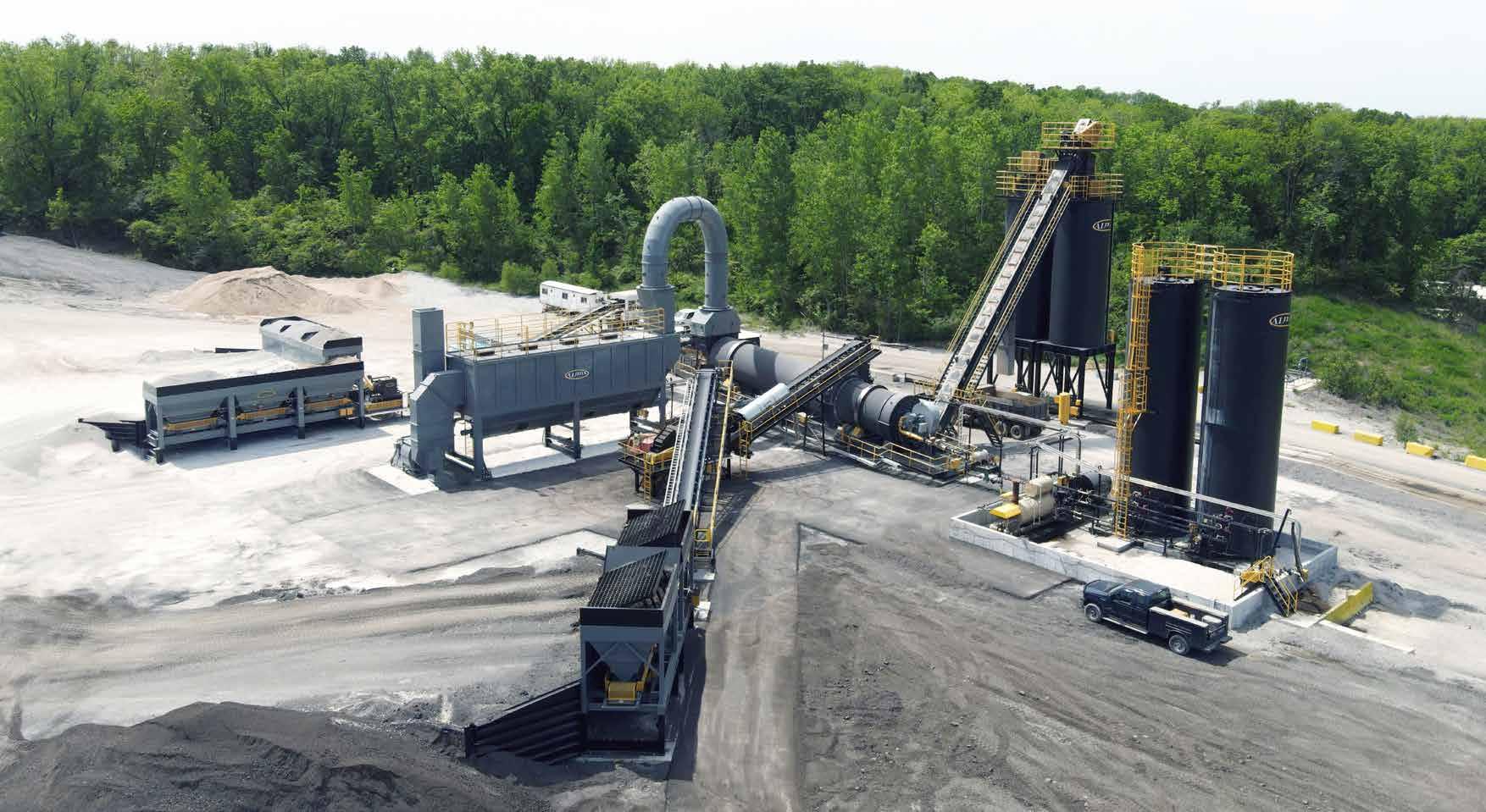

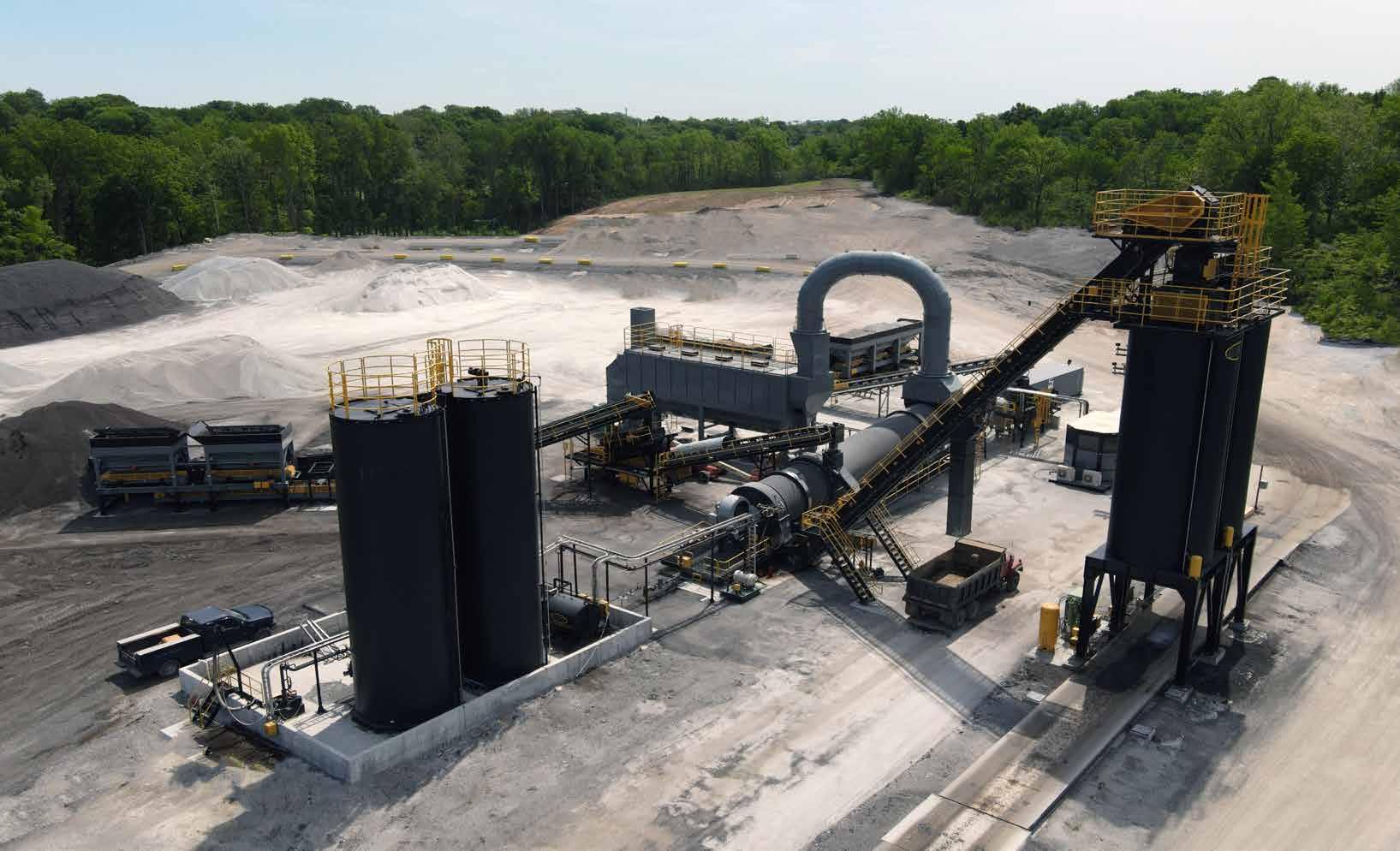
The problem of ignoring mental health wellness in macho industries like ours is real. Seeing members of the construction com munity rally around solving the problem has been heartening; therefore, I don’t want to present my worries in too flippant a manner.
SUBSCRIPTION POLICY: Individual subscriptions are available without charge in the United Sates, Canada and Mexico to qualified individuals. One year subscription to non-qualifying Individuals: United States $90, Canada and Mexico $125.00. For the international digital edition, visit theasphaltpro.com/subscribe/
But have I oversimplified the problem? Have I made it too cut and dry? Let me know your thoughts, because I’m working with a safety-oriented entity to prepare for NAPA’s website a course that will train your work force (for free) to recognize the signs and help one another. If that isn’t desired—if that will expose you to litigation you don’t want—then now is the time to re-think the training. Stay SandySafe,Lender 602 W. Morrison, Box 6a Fayette, MO 65248 (573) 823-6297 • www.theasphaltpro.com
While preparing information for the Na tional Asphalt Pavement Association’s safe ty and health committee’s push for mental health wellness and suicide prevention in the construction industry, I have had the opportunity to take courses for certification in suicide prevention. These courses have afforded me a better understanding of the risk factors to watch for in colleagues, fam ily, friends, myself, and others. Now I know acceptable, non-judgmental language to use to approach and visit with those persons in a helpful manner. This is an underlying skill set that I believe every person in our indus try should have.
Let me ask this favor of you: Tell me what youWouldthink.you rather have members of your crews trained to notice suicide risk factor behavior in one another and to approach one another to assist, or would you rath er have your safety director and/or upper management be the ones trained in inter vention for the purpose of protecting your company from any perceived health infor mation violations?
DIGITAL EDITOR Sarah sarah@theasphaltpro.comRedohl(573)355-9775
GROUP PUBLISHER Chris Harrison chris@ theasphaltpro.com
Just because some folks who have en dured the litigious side of society are being cautious doesn’t mean they’re being callous. It means they’re being careful and looking at multiple sides of the issue for us. I’d like to hear more opinions on this. I want to learn alongside you as we develop plans to help the workers who may be struggling with any of the suicide risk factors we’re being trained to pick up on.
8 | SEPTEMBER 2022 asphaltPRO September 2022 • Vol. 15 No. 11 EDITOR'S LETTER D
I know that I would rather each member of the crew be able to approach any person he or she is most comfortable approaching to say, “Hey, I’m having some mental anguish and I can’t concentrate on this 16,000-pound machine I’m supposed to be operating next to high-speed traffic.” I would prefer the po tential for someone to misunderstand moti vations and feel their health privacy has been shared incorrectly, than to having the per son zoning out and trying to power through his or her shift until he or she can get back to the shop to walk into the office of the compa ny-approved crisis management officer, with everyone watching.
ART DIRECTOR Kristin Branscom BUSINESS MANAGER Susan Campbell (660) 728-5007

uring a recent interview, a compa ny spokesperson suggested I rethink my idea of encouraging crewmem bers within construction companies be em powered to talk to one another about the po tential for suicide. The spokesperson’s fear— which I understand—was company liability considering HIPAA violations inherent in such conversations. I also understand we’re talking about a potentially lifesaving conver sation to inquire of a colleague if he or she is in crisis or if he or she is considering an act of violence against himself or herself.
EDITOR Sandy sandy@theasphaltpro.comLender(239)272-8613
MEDIA SALES Cara cara@theasphaltpro.comOwings(660)537-0778

Personally, I’d be more unhappy if a co-work er went to HR and tattled about perceptions of me rather than walking up to me and saying, “Hey, Sandy, it looks like you’re about to break down. How can I help prevent that?”
AsphaltPro is published 11 times per year. Writers expressing views in AsphaltPro Magazine or on the AsphaltPro website are professionals with sound, professional advice. Views expressed herein are not necessarily the same as the views of AsphaltPro, thus producers/contractors are still encouraged to use best practices when implementing new advice.
If that makes human resources direc tors nervous about potential litigation, then I believe the companies for which they work should purchase additional legal insurance and get a lawyer on retainer. Because the con struction industry overall has a significant problem: Many of our workers are in crisis. To solve that problem, we must all be willing to help one another. I refuse to recognize a friend in the industry is suffering and walk away to find the nearest HR manager—who my friend may or may not be as willing to open up to— because someone else thinks I’m exposing the company to invasion-of-privacy concerns.
Perhaps it’s time to have an editorial note about the goals of a safety culture that consid ers the whole person. And timing that note with September’s Suicide Prevention Month works for me.
PUBLISHER Sally sally@theasphaltpro.comShoemaker(573)823-6297
Risk in the Time of Suicide
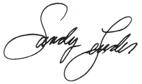
The BLAW-KNOX University2023 PAVER OPERATION AND MAINTENANCE The Blaw-Knox University, now in its 58th season, is dedicated to training paver operators and foreman on proper Paver Operation and Maintenance and applied Best Paving Practices through classroom-style and hands-on application Forcourses.over a half a decade Blaw-Knox has earned its reputation as the go to source of training and instruction on hot mix paving. Blaw-Knox provides improved technical and problem-solving skills on a variety of paver operations and maintenance topics. Course instructors share decades of field and teaching experience with attendees, including training on the latest DOT requirements. Blaw-Knox offers multiple dates to satisfy the demand for its popular courses. 2023 DATES • January 16 - January 19 • January 23 - January 26 • January 30 - February 2 • February 6 - February 9 CLASSREGISTRATIONSIZE is limited, register today! DETAILS All details can be found at www.blawknox.com/ training or contact at (407)290-6000 ext. 342 or training@blawknox.com COME BE PART OF THE EXPERIENCE 5201 N. Orange Blossom Trail Orlando, Florida 32810
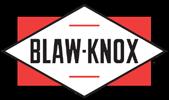
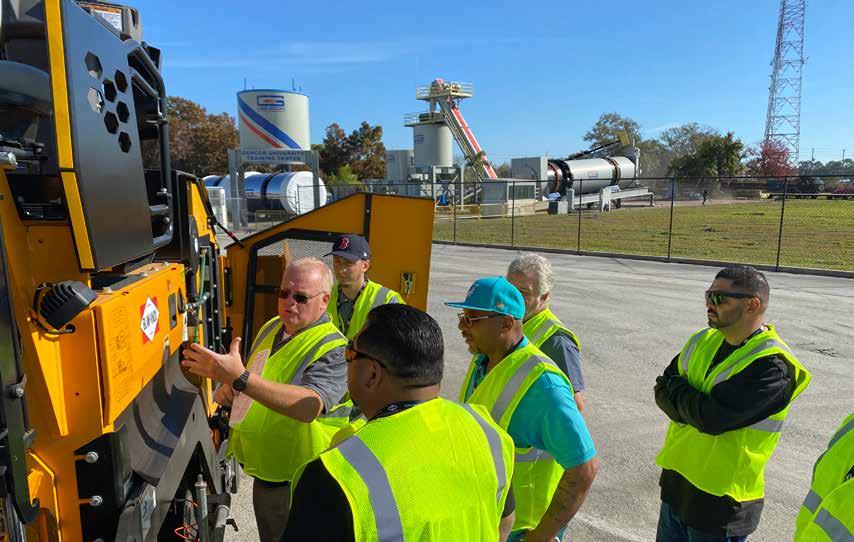
And it all comes down to people themselves, Vandervert said, and how they’re managed. With so many generations in the work force right now, managing them effectively is a task that’s easier said than done.
in that work environment. And if you step into a workplace with all five generations, you will see conflict.”
“Culture is what we learn from our people, and it’s specific to the group you belong to, and, as I said, it’s all learned,” Elaine Cullen Vandervert, PhD, said. She’s the president of Prima Con sulting, and a presenter at AEM’s recently held Product Safety and Compliance seminar. “Culture tells you what is going on, how you should feel, what you should do, and how you should go about doing it. It tells you how to operate in that group we are talking about.”
• Baby Boomers—Born between 1946 and 1964, Baby Boomers, once upon a time and not all that long ago, dominated the work force. Known as the optimistic and loyal generation, Boomers committed themselves to changing the world. On the other hand, they tend to be workaholics who were perhaps too often willing to make personal sacrifices in exchange for success.
All of this is to say when members of these five groups come together in the workforce, things can become complicated. That’s because, in many cases, people tend to operate very differently within professional environments based on the rituals, behaviors and norms associated with the generation from which they come.
The Association of Equipment Manufacturers (AEM) is an international trade group based in North America representing offroad equipment manufacturers and suppliers.
Unfortunately, there’s a significant consequence to Boom ers leaving the workforce: They are taking with them a wealth of knowledge, skills and wisdom that only comes from signifi cant experience. A study cited by Vandervert found it takes 8-10 years on average for an employee to be able to develop a cer tain level of experience that allows them to administer on-thejob teaching and training. It’s a sobering statistic, especially when considering what it takes to establish an effective safety culture within an organization.
C
• Generation Xers—Born between 1964 and 1980, members of Generation X are known as the first “latchkey kids.” Skeptical and independent-minded, Gen Xers tend to value work-life bal ance more so than any other generation in the workforce.
• Millennials—Born between 1981 and 1994, millennials can best be described as competitive, open-minded and very open to personal opportunities. In addition, they are known for their desire to be part of a team, having fun at work, and for their ten dency to seek out (and embrace) new professional opportunities as they become available.
“Because, ultimately, culture is the glue that holds everyone and everything together,” Vandervert said.
HERE ARE THOSE FIVE GENERATIONS, AS DESCRIBED BY VANDERVERT:
Culture is an incredibly important consideration when looking to establish a safe and productive workplace, because employers must be able to determine exactly what will make workers choose to act safely and productively and, perhaps more importantly, find a way to make all those widely varying factors work within the confines of their own organizational structures.
Generational Differences Influence Safety Culture
It's obvious everyone belongs to, and participates in, a variety of cultures. A person’s nationality, gender and religious belief (or lack thereof) all contribute to how they present themselves. In her presentation to Product Safety & Compliance seminar attendees, Vandervert emphasized the impact of culture in determining how employers can and should go about creating a safe and productive workplace.Onecomponent of organizational culture that employers can not afford to overlook is the wide range of ages of their respective workforces and its impact on the development and refinement of safety culture. For the first time ever, there are five generations that can currently be found in the workforce. Baby Boomers used to comprise the largest section of the workforce by a fairly comfort able margin. That’s starting to change, however, as they continue to retire in greater numbers.
“You need to be able to know what to do when things go wrong from a safety perspective,” Vandervert said.
10 | SEPTEMBER 2022 SAFETY SPOTLIGHT BY THE ASSOCIATION OF EQUIPMENT MANUFACTURERS
It’s impossible for a person or group to participate within an or ganization’s culture if they are unwilling, or unable, to embrace its norms. Cultures change slowly, however, and patience is required.
“A study we conducted showed there are five variables related to work that are different across generations,” she continued. “How they approach it, what motivators they have, how they view pro fessional growth, and the attitudes they have about learning with
• Traditionalists—Born between 1927 and 1946, traditionalists are quite obviously no longer very prevalent in the workforce. However, those who remain are best described as dependable, respectable and loyal. More than anything else, however, tra ditionalists believe they have earned the right to be respected largely based on their lengthy track record of experience.
reating an effective safety culture in the workplace when you have a diverse employee base takes a better under standing of what “culture” refers to and how it impacts or ganizational goals and priorities.
• Generation Zers—Born between 1995 and 2010, Gen Z mem bers tend to think more in global terms than many of those who came before them. They are dependent on digital devices and, thus far, have been—generally speaking—more apt to experi ence mental health issues. (The source for this stat is the We Level Up Florida Mental Health Center.)
BUILT TO CONNECT
Efficiency and Productivity
Designed with safety and operator comfort in mind, the SB-3000 Shuttle Buggy ® material transfer vehicle features adaptive cruise control, bright LED lighting, four-wheel steering for easy transport and ground-level maintenance access for added convenience. Operators can rely on clear sightlines and the ground operator is safely protected inside the structure of the machine. The Roadtec SB-3000 is the perfect blend of traditional craftsmanship and modern technology. Scan to learn more about our SB-3000

The SCB device positions a semi circular specimen on top of two roll ers and then applies a load along the vertical diameter to determine the fracture energy and tough ness of the mix. Other fatigue-predicting tests are available, some that apply cyclic loadings, but the SCB is the most wide ly known and accepted by government agencies due to its sim plicity of operation as well as providing enough information to understand the limits of the mix. This makes it an indispensable tool in your arsenal of testing.
The DCT test measures the fracture energy of asphalt pavements. Gyratory-compacted samples of mix designs are tested at various temperatures and loading rates. The test has the capability to capture the transition of as phalt concrete from a brittle material at low temperatures to a more ductile material at higher temperatures.
TO SKIP OR NOT TO SKIP?
LEARN MORE
BENDINGSEMI-CIRCULAR(SCB)
Three Tests to Perform
When it comes to asphalt pavements, balance is key. You don’t want to go the total bodybuilder route and concentrate only on thick layers and strength. At the same time, you don’t want to install the equiva lent of the skinny marathoner with limited strength.
The HWTT helps you predict strength, and the SCB reveals a lev el of long-term flexibility. As an important follow-up, the DCT shows how the road layers will relax under extremely cold weather. To adequately predict a pavement’s chances of success, you should consider these three tests when developing a new mix de sign. And since strength and flexibility largely determine the over all life and performance of asphalt pavements, the answer is clear: Don’t skip them. Sina Varamini is a professional engineer and the director, pavement and materials group, for Engtec Consulting Inc., Toronto, Canada. For more information, visit https://www.linkedin.com/company/ engtec-consulting-inc.
HAMBURG WHEEL TRACKING TEST (HWTT)

Asphalt mix designers widely use the HWTT to evaluate rutting re sistance and moisture susceptibility. The HWTT subjects the asphalt mix to torturous loading and water-submerged conditions under con trolled lab conditions. It performs well in raising red flags that should not be ignored. The HWTT can pinpoint uncertainties or risks relat ed to ultimate field performance, or unforeseen changes in summer temperatures, thus qualifying it as one test you shouldn’t skip.
The SCB is another load-simulating test; it calculates the fracture energy of as phalt mixes from a load-displacement curve. It’s often referred to as a “flexibili ty index test.” It can predict whether the material is resilient enough to meet its intended longevity.
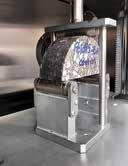
12 | SEPTEMBER 2022 MIX IT UP BY SINA VARAMINI, PHD, PE A sphalt professionals want the pavements they design and in stall to perform up to expectations. Pre-testing provides one method to foretell the road’s future performance under ev er-increasing traffic and weather changes. Here are three tests to in clude when attempting to predict the future. Two simulate the com bined effect of traffic loadings and climate stresses on asphalt layers, and one tests the resiliency of top road layers in cold weather. Each per forms an important role in determining how well your asphalt mix, and eventually your road, will perform under real-world conditions.
The HWTT is designed to pinpoint uncertainties or risks related to ultimate field performance. Photos courtesy of Engtec Consulting Inc. What these 3 Critical Asphalt Tests Can Do for Your Next Mix Design: 1. Increase understanding of how your mix design will behave 2. Provide a benchmark for making improvements 3. Deliver cost savings in the long run 4. Improve pavement performance 5. Offer performance results in as little as three to four days
TEST
This index test helps mix designers deter mine how the pavement will perform under the extreme cold of Canadian winters.
DISC SHAPED COMPACT TENSION (DCT) TEST
The SCB simplicityoffersofoperation. Skipping the DCT could mean you miss signs of potential for coldweather cracking.
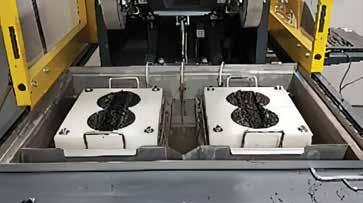
The Meeker Family
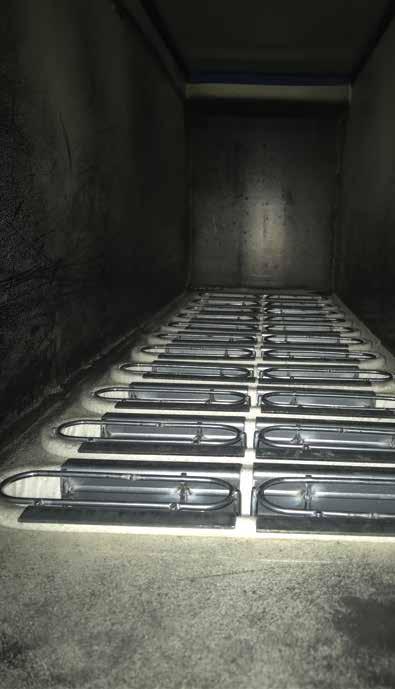
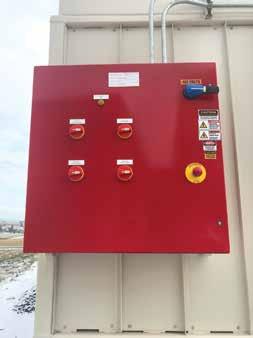
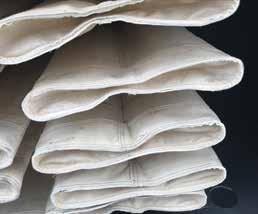
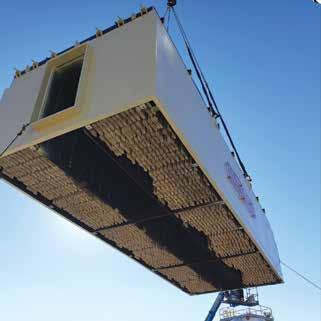
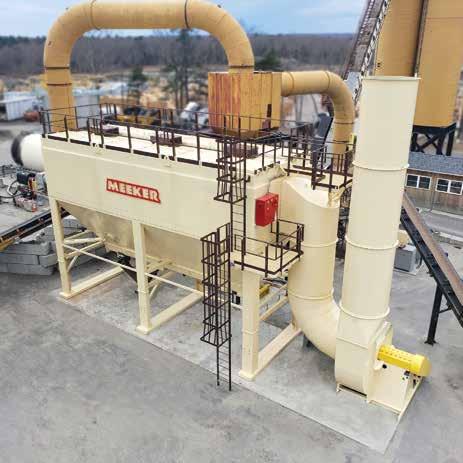



• AltiSora, of Houston, Texas, where Michael Smith, PhD, is a senior engineering fellow • University of Hawaii at Manoa’s College of Engineering, where Adrián Ricardo Archilla, PhD, is a professor of Civil and Environ mental Engineering and the director of the college’s pavement mate rials lab (PML).
Volunteers and members of CMDR pull derelict fishing gear out of the water for next steps. Photo courtesy of Lynch and CMDR
• Hawaii Department of Transportation (HDOT)
Lynch shipped samples of the nets to AltiSora in Houston. “Jennifer Lynch sent us several different types of nets, which we have converted into our high-performance additive formulation for asphalt,” Smith said. He explained that the nets arrived in the condition they were col lected from the beach. “Jennifer’s team may have cleaned some of the net samples to some extent, but we believe we have used the nets as
14 | SEPTEMBER 2022
MIX IT UP
BY SANDY LENDER s anyone in the asphalt industry will tell you, testing and prov ing a theory is slow, tedious and often costly. Luckily, there’s a team centered in Hawaii willing to take on the arduous pro cess to pull foreign derelict fishing gear from our oceans and prepare it for positive use in careful asphalt mix design. The members of that team currently include:
This is an example of the cleaned fishnet sample at AltiSora’s lab. Photo courtesy of AltiSora

PROOF IS IN THE LABS
Fishnets Capture Plastic Discussion
• Hawaii Pacific University’s Center for Marine Debris Research (CMDR), led by Jennifer Lynch, PhD. She’s a research biologist with the U.S. Department of Commerce’s National Institute of Standards and Technology (NIST) and the co-director of the CMDR.
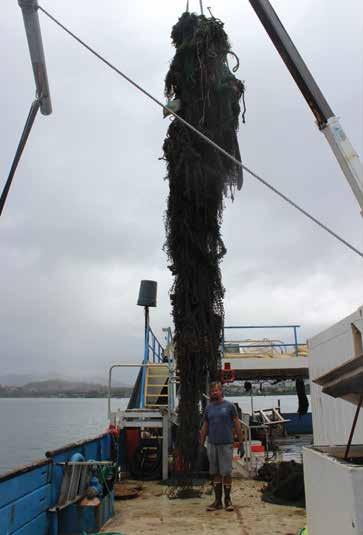
A
• Additional companies—such as Grace Pacific LLC, headquartered in Kapolei, performing mix design with Marshall testing—are con tributing to a field test of roadway sections with a plastic product by ThisNewRoad.article will focus on the concept of fishnets for feedstock and lab testing thereof. As Lynch pointed out in a presentation to the Hawaii Asphalt Pav ing Industry (HAPI) audience June 8, “The feedstock is totally different from soda bottles. They have totally different chemical structures.” That means the CMDR team is working to prove the viability of using the plastic waste found within this foreign derelict fishing gear. Lynch shared that 80% of the net is made of high-density polyeth ylene (HDPE), making that a good starting point. Getting to the HDPE takes a few steps. Thus far, the CMDR derelict fishing gear project has been finding and removing from the ocean these large, tangled masses of nets manual ly. Teams then measure, disentangle and sample the conglomerate. They test the samples for at least 100 different forensic metrics. They archive the information and reuse the plastic waste. One example of the reuse is their “nets to energy” program where the nets are burned to produce electricity for the city and county of Honolulu. The team has surmised the HDPE nets are a sizeable feedstock for plastic repurposing into Ha waii’s infrastructure, as well.
Proving this feedstock of HDPE is worthy of asphalt mix design takes a few steps as well. It requires processing, partnership and plenty of Summertesting.2021,
For Archilla, his focus will be mechanical testing. “We have sufficient plastic from AltiSora to produce multiple batches,” he shared. “We will add these plastic pellets to an unmodified PG64-16 and a polymer mod ified PG76-22 (or PG64E-22) at 1% by weight of binder. We will also measure the viscosity of those binders on samples with and without the addition of plastics; and for those with plastics, we will take samples from the top and bottom of the container after stopping the blending to see if there are significant differences.”
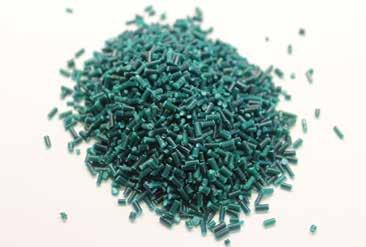

Archilla also shared temperature information, in the event pro ducers or DOTs would like to consider the use of this recycled waste plastic within the warm-mix asphalt (WMA) discussion. “The mix es with AltiBinder will be tested in the lab only. We plan to use mix ing temperatures that Grace Pacific has used in their mix designs for the actual field mixes that will be used in the pilot project. We will double-check their adequacy for the binder with AltiBinder plas tics based on the viscosity measurements we will perform on the Brookfield viscometer. The temperatures used in the mix designs are 295°F for the PG64-16 and 325°F for the PMA....Given that the melting point of the HDPE is around 131°C, or 267°F, there seems to be some room, but not a lot of wiggle room, to lower the tempera ture for WMA.”
The product in the picture is called AltiBinder, made from high-density polyethylene fishing nets that washed up on the shore in Hawaii. CMDR provided AltiSora with different types of nets, which the lab converted into the high-performance modifier formulation for asphalt. An amount typically around 1% of the asphalt binder is designed to provide improvements in paving performance and durability. Photos courtesy of AltiSora
WWW.THEASPHALTPRO.COM | 15 found and collected from the beach. We shredded and prepared the nets for compounding and pelletization.” AltiSora blends modifiers with the recovered fishing nets to ho mogenize the plastic with the asphalt binder and enhance pavement performance. AltiSora’s objective is to improve road performance through the addition of recovered fishing nets, according to Smith. Then AltiSora’s lab shipped two baggies of pellets, 1 kg each, back to Hawaii for testing in the next lab—Archilla’s PML.
For additional information on a recent leaching study regarding reclaimed asphalt pavement (RAP), see the study posted Feb. 10, 2021, from the Department of Environmental Engineering Sciences at University of Florida, Gainesville. of-leaching-and-environmental-risk-assessment.pdfwp-content/uploads/sites/210/2022/06/A-critical-analysis-https://faculty.eng.ufl.edu/timothy-townsend/
“They were prepared in October 2021 and we received them in November or December,” Archilla recalled. HPU took some sam ples for chemical analysis and Archilla will perform the Hamburg wheel test for rutting, dynamic modulus testing and the IDEAL-CT. “Some testing will be done with and without MIST testing with the dual purpose of collecting water for testing for microplastics and testing for moisture sensitivity effects on the mechanical response,” Archilla shared. “We will also be working with Jennifer to collect water from the Hamburg to test for microplastics and she will also be collecting water in the field.” Lynch’s research focuses on understanding marine pollution and its impact on the environment, including the identification and quantification of plastic marine debris and microplastics. Lynch’s team will test the water samples from Archilla’s PML to determine the extent of microplastic and plastic additive leaching from the as phalt test samples. “Our goal at CMDR is to help find solutions to repurpose plas tic into infrastructure, to promote a circular economy, but we do not want these solutions to lead to unintended environmental consequences. Many people are concerned that the roads paved with a tiny percentage of plastic may release microplastics or oth er chemicals into the environment through stormwater runoff or dust,” Lynch emphasized. She explained that, “Plastic additives are chemicals that were intentionally added to the fish nets to provide them durability, flexibility or flame resistance. Some plastic additive chemicals have been shown to be toxic.” Lynch’s team will help de termine if modifying roads with discarded fishing nets will generate additional pollutants in the environment. Her team has found polycyclic aromatic hydrocarbons (PAHs) in tire particles and road paint in the past and is looking for microplas tics from any source. She shared: “PAHs may not come from the as phalt itself but will be found at high levels in roadway runoff because of gasoline and oil leaks on the road. The large concern is that PAHs are carcinogenic, more toxic than the plastic additives. I’m trying to put the compounds that might leach out of the small amount of plas tics in the road in context to the other more toxic compounds found in roadway stormwater runoff (regardless of source).”
MIX IT UP PROTECTING PERFORMANCE

16 | SEPTEMBER 2022
Photo courtesy of InstroTek
For more information on the CMDR’s efforts, please reach out to Jennifer Lynch at cmdr@hpu.edu.
“Our #1 goal is road performance,” Smith said. “The road’s prop erties must improve when adding the recovered nets or any waste plastic. We are looking for a win-win. We want to improve our nation’s roads and help the environment. Adding plastic like the high-density polyethylene found in nets can improve some road properties, but not all. The objective of our modifier is to help the waste plastic improve roads. The modifier helps with homogenization and processing, but one of its key objectives is to help the plastic further improve binder properties like rutting and cracking.”
Hawaii as an island is challenged, so this is a great opportunity. Landfilling nets, importation of raw materials and road construc tion are exceptionally costly in Hawaii. We believe our solution is an elegant one to address waste management, raw materials and paving durability.”
SCALE UP Lynch’s presentation to HAPI showed the multiple challenges CMDR is up against. As mentioned early on, proving a hypoth esis can be costly and that can factor into a timeline for even the most motivated of partnerships. Archilla shared that HDOT is the source of funding for performing the tests via his lab, “though it is actually 80% FHWA and 20% state funds.”
“Jenn and beach clean-up volunteers have done a lot of work collecting and sorting the nets,” Smith pointed out. “There have been a lot of hours spent doing this. In the long term, a more ef ficient automated processing system is needed. Additionally, the long-term solution needs to ensure the product design accommo dates net mixture types.”
Funding is only half the battle. Not only is derelict fishing gear choking the ocean, presenting enormous conglomerates of sea turtle and coral reef killing messes, but it is also difficult to move once it’s found. The CMDR team is developing a program to detect and remove marine debris that involves satellite monitoring, ves sels with towing and crane capabilities, and people willing to help.
The team is also developing a network to transport, store, dis entangle, polymer-identify and sort marine debris that involves trucks, containers, warehouses, hoists, forklifts, shredders, chem istry equipment, and, again, people willing to help.
The team is looking for a way to fund a facility on Hawaii that can convert material to product for improving road performance.
“Economies of scale have a significant role in plastic recycling,” Smith said. “Today’s typical recycling equipment is extensive. It either requires a lot of manual labor or automation that increas es cost. Standard full-scale recycling equipment should be able to meet Hawaii’s needs. There will be excess shredding and manufac turing capacity. Ideally, I would like to see an additional recycling application developed for Hawaii to fill out that excess capacity.
And as you’ve seen in this article, the CMDR team is in the process of testing and proving this specific marine debris can be turned into a product for use in pavement designs. That involves all the moving pieces discussed herein.
Using a portion of a $75,000 donation from Hawaii Asphalt Paving Industry member, Bowers + Kubota, Adrián Ricardo Archilla, PhD, purchased the moisture induced stress tester (MIST) from InstroTek for the pavement materials lab at the University of Hawaii College of Engineering. This instrument is designed to facilitate testing for moisture sensitivity by producing stresses and pore pressure in an asphalt sample at elevated temperatures to accelerate the effects that a mix would experience from traffic at normal temperatures and conditions.
Better Increaseddata.control. Higher profits. A decidedly human touch to plant automation.
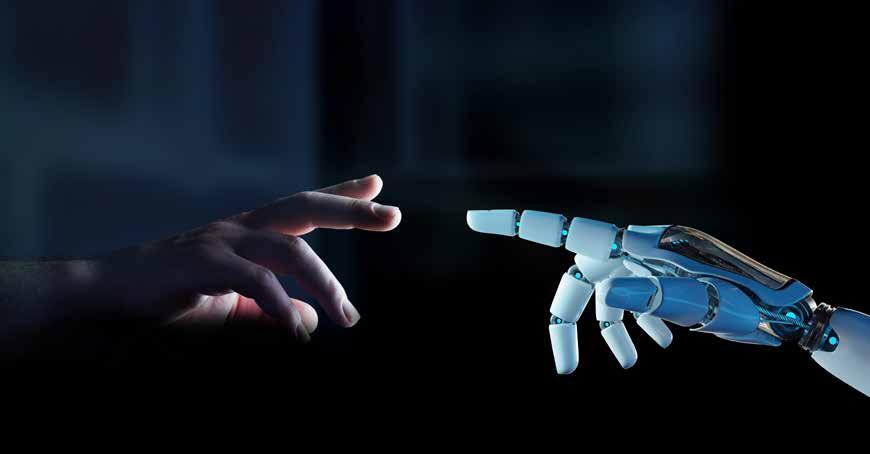
For the past 25 years, MINDS has built a reputation for user-friendly, advanced, customizable plant automation control systems. As of April 2022, we became part of the Astec family to add to their Rock to Road solution for asphalt road building. MINDS provides award-winning desktop software, mobile apps, and hardware for many applications: Drums, Batches, Combo/hybrid hot mix plants, Emulsion plants, Liquid Terminals. Silo load-out, Ticketing, and Cloud-based data management for the Rock to Road industry. Designed around real people. “The plant control system that MINDS designed for us has worked very well. The graphics depict the plant almost identically as built and are very easy to follow from the control room. Each value is shown with its position indicated by colours that make identifying issues, such as a stuck valve, extremely easy. The materials that we have produced with the system have been very consistent from the first production run.”

SALES INQUIRIES: 866-971-2980 contact@mindsusa.com mindsusa.com
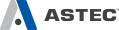
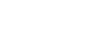
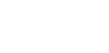
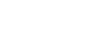
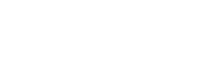
Blythe
Allen Hendricks, Vise President, Asphalt Divisions Manager Construction, Inc.
18 | SEPTEMBER 2022 TRAINING
On the top deck, you can see the hose leading into the 5-gallon bucket of soapy water. They’re using this setup because there’s no hose hookup nearby.
IBYCleaningMoreThere’stotheEquipmentJOHNBALL
John Ball is the proprietor of Top Quality Paving & Training, Manchester, New Hampshire. He provides personal, on-site paving consulting services around the United States and into Canada. For more information, contact him at (603) 493-1458 or tqpaving@yahoo.com.
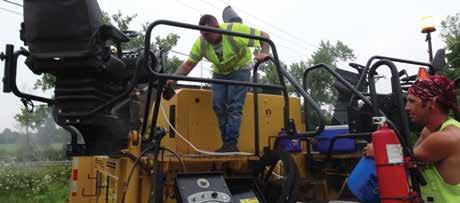
t’s a sad state of affairs when laborers go on social media and mock a company’s desire to have clean equipment on their job sites. Workers should take pride in their work and in their equipment. That’s why I was so happy to ar rive at a job site one Friday afternoon to find two members of the Barrett Paving crew cleaning the paver on their own. This is something they do ev ery Friday, of their own volition. The workers in these photos weren’t told to do this; they just have a good attitude and clean their own equipment because they care about the image they’re presenting to the public and to the inspec tors who show up to check out their projects. They go above and beyond and have taken the initiative to make this machine safe. They’re cleaning the areas where workers climb and walk and cleaning the reflective safety tape that catches drivers’ eyes. This is all part of making the machine part of a safer working environment for the team. They understand the need to see their instru mentation clearly and easily when paving, and that’s easier to do when asphalt and dirt isn’t built up on the equipment. Making instruments and markings visible means they’re giving the paver and screed operator a fighting chance at achieving quality paving results. They understand that you won’t know some thing’s wearing out if you can’t see it and moni tor it, and that’s a cost item companies need to be tracking.These workers aren’t just keeping the pav er safe and better maintained, they’re keeping it looking good for the company image. That paver is out front showing the public a high standard of quality.
LEFT: Getting the bogies clean so they don’t laminate with asphalt. RIGHT: This is a portable, battery-powered car wash sprayer.
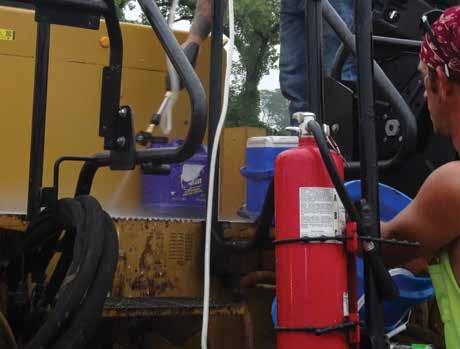
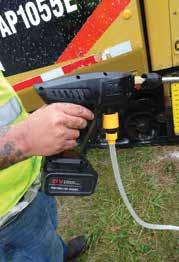
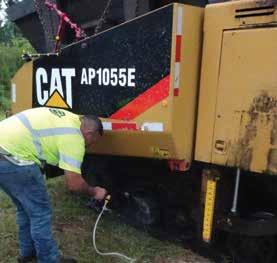
800 826 0223 Stansteel.com HotmixPar ts.com For more information In Plant Automation and Technology. LEADING THE WAY Chain - conveyor, elevator and drive Sprockets and Traction wheels Bearings - Dodge, Rex, SKF & more Air Cylinders for all applications Motors - LINCOLN, Baldor, Toshiba Slats and Elevator BUCKETS Rotary Airlocks - MEYER & SMOOT Cone Liners for ANY Size Liquid AC Handling Fuel Efficient Flighting Systems Pumping Systems - VIKING BRAND Dust Systems - DURAFLOW Blowers Warm Mix Systems - 3 or more options Dryer Shell Replacements Conveyor Flooring - Ni Hard or Chrome AC Metering Skids Gearboxes - Dodge, Foote & Rexnord DUFF NORTON Actuators Smart Heaters™ Plant Controls - Batching/Blending and Silo Loadout with tech support! Plant Alert System - NiteOwl® HOMESTEAD TrunnionsLiquidThermocouplesvalvesIn-LineBlendingandThrustRollers A SOLUTIONS PROVIDER We offer engineering, new and used components, parts and repairs for all brands, and excellent customer service. That’s why the only call you need to make is to Stansteel/Hotmix Parts & Service. TM STOP OVERFILLINGSMARTTOTALTANKS.PLANTCONROL.
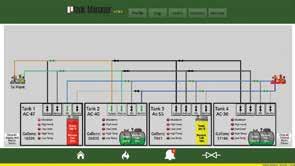
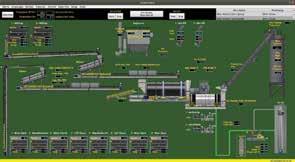


PRODUCER
20 | SEPTEMBER 2022
he history of the Journey Group, Sioux Falls, South Dakota, dates all the way back to 1910 when the company was known as Sioux Falls Construction.
PROFILE
BY SARAH REDOHL
In 2014, the company changed its name to Journey Group, which encompases a vertical construction division, Journey Group Con struction; a civil construction division, Sioux Falls Civil Constructors; a division based in Spearfish, South Dakota, that performs ver tical and civil construction, Ainsworth-Ben ning Construction; and Black-Top Paving, Journey Group’s asphalt division that also performs grading, asphalt maintenance and concrete work. Despite the name change, Journey Group continues to self-perform a wide variety of work in and around the city of Sioux Falls. “Not only is our company diversified with the construction sectors we serve, but we’re also diversified in the services each sec tor provides,” Kerkvliet said. Prior to 2014, Black-Top Paving only performed grading and asphalt paving, but has since expanded to offer pavement maintenance and concrete work in order to meet the demands of the market. The division frequently found itself on jobs that required a small amount of con crete work that often needed to be complet ed before its crews could do their work.
“Sometimes we struggled to find a con crete contractor willing to come in and do that work,” Kerkvliet said, “especially if the job was small.” And so, Black-Top Journey Group Diversifies for Growth Black-Top Paving’s asphalt crews run two Caterpillar pavers, a newer AP1055 paver and an AP655F purchased this year.
“For a company to succeed back in the day it had to self-perform all kinds of work,” said Ryan Kerkvliet, Journey Group’s vice presi dent of asphalt paving. When the company launched its asphalt paving division in 1950, that division of the company became the first paving contractor based in Sioux Falls.
T

WWW.THEASPHALTPRO.COM | 21
Paving expanded its services. “That gave us better control over our asphalt jobs, al lowing us to get our work done in a time ly fashion without having to wait for other contractors.”Thedivision also discovered similar ben efits when it expanded into pavement main tenance. “A lot of the large property manag ers prefer to deal with just one contractor versus having to find and schedule sever al contractors,” Kerkvliet said. “Ultimately, expanding into pavement maintenance and concrete work has allowed us to get more asphalt paving work.” Projects that involve every scope of work that Black-Top Paving offers are near and dear to Kerkvliet, such as a recent project at Sioux Falls Federal Credit Union. BlackTop Paving’s crews placed new concrete curb and gutter and sidewalks, but they also had to address several parking lots on the site, each of which with its own needs. Some of them required removal and re placement, some were overlaid, and others just required crack sealing. “It’s always neat to be on those types of projects,” Kerkvliet said. “Not a lot of companies can self per form that work.” It’s an illustration of how far the division has come. When Kerkvliet started at Journey Group in 2010, the asphalt division consist ed of one crew that performed grading and paving. Today, 62 of Journey Group’s 300 employees are in the asphalt division. This includes a team of six office staff, in cluding Kerkvliet and five estimators and project managers. Black-Top Paving also has two crews devoted to grading, prep work and milling. “We’d love to have three of those crews, but it’s been hard to find employees,” Kerkvliet said. It also has three concrete crews, one focusing on curb and gutter install, one handset crew, and a box crew for inlets, storm sewers, etc. Its maintenance crew performs crack sealing, sealcoating and striping and its two asphalt paving crews perform a va riety of work ranging from $500 asphalt patches to $8 million state jobs. Howev er, Kerkvliet estimates that around 75% of its paving jobs are asphalt parking lots and cityJourneystreets.Group also has close relation ships with several large entities in the Sioux Falls area, including Avera Health, South Dakota’s largest private employer, and the University of Sioux Falls. “With Journey as a whole, we’re able to be their go-to, whetherBlack-Top Paving also has two crews devoted to grading, prep work and milling.



Kerkvliet is originally from South Dakota, and returned to the state after living in Colorado for several years to be closer to his family and his wife’s family. “Although Sioux Falls is South Dakota’s most populous city, it still isn’t a big city,” Kerkvliet said, adding that it’s easy to take a quick weekend trip back to the farm where he grew up to hunt and spend time on the lake with family and friends. “And it still has a hometown feel.”
22 | SEPTEMBER 2022 they need site work, new building construc tion, or parking lot maintenance.”
Additionally, Journey Group expects to benefit from Infrastructure Investment and Jobs Act (IIJA) funding in the coming years. Kerkvliet anticipates the company’s bridge division will see the greatest impact from IIJA, but that the asphalt paving division will also benefit. “We do bid for DOT jobs,” he said. “And if we don’t get it, we’re usually able to pick up additional work in the market that our competitors busy doing DOT work aren’t able to take on.”
CITY COMPANYGROWS,GROWS
According to the U.S. Census Bureau, South Dakota ranked 10th nationwide in terms of population growth between 2020 and 2021. The state also experienced popu lation growth above the U.S. average between 2010 and 2020, the most significant chang es of which occurred in South Dakota’s cit ies. For example, Lincoln County, which contains parts of Sioux Falls, experienced the state’s fastest population growth of 45% be tween 2010 and 2020.
“South Dakota was pretty progressive in its handling of COVID-19, in terms of keeping people safe while also allowing businesses to remain open so our market could continue to thrive,” Kerkvliet said. “We’ve seen a lot of people and businesses move into our state.”
Black-Top’s two asphalt paving crews perform a variety of work ranging from $500 asphalt patches to $8 million state jobs.
PRODUCER PROFILE
Black-Top has a team of six office staff; two crews for grading, prep work and milling; one pavement maintenance crew; three concrete crews; and two asphalt paving crews.
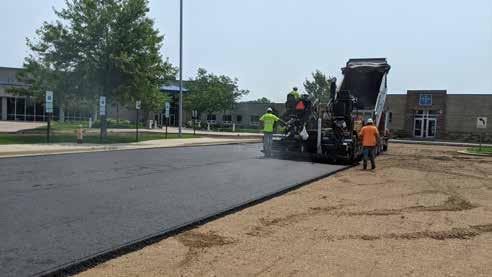
In fact, Kerkvliet said, with the strength of the Sioux Falls market, the limiting factor
Black-Top Paving is Journey Group’s asphalt division, which also performs grading, asphalt maintenance and concrete work.

At least some of the company’s growth can be attributed to the growth of Sioux Falls. “The market has been outstanding here, especial ly after the COVID-19 pandemic,” Kerkvliet said. “There’s a lot of work to be had out here.”

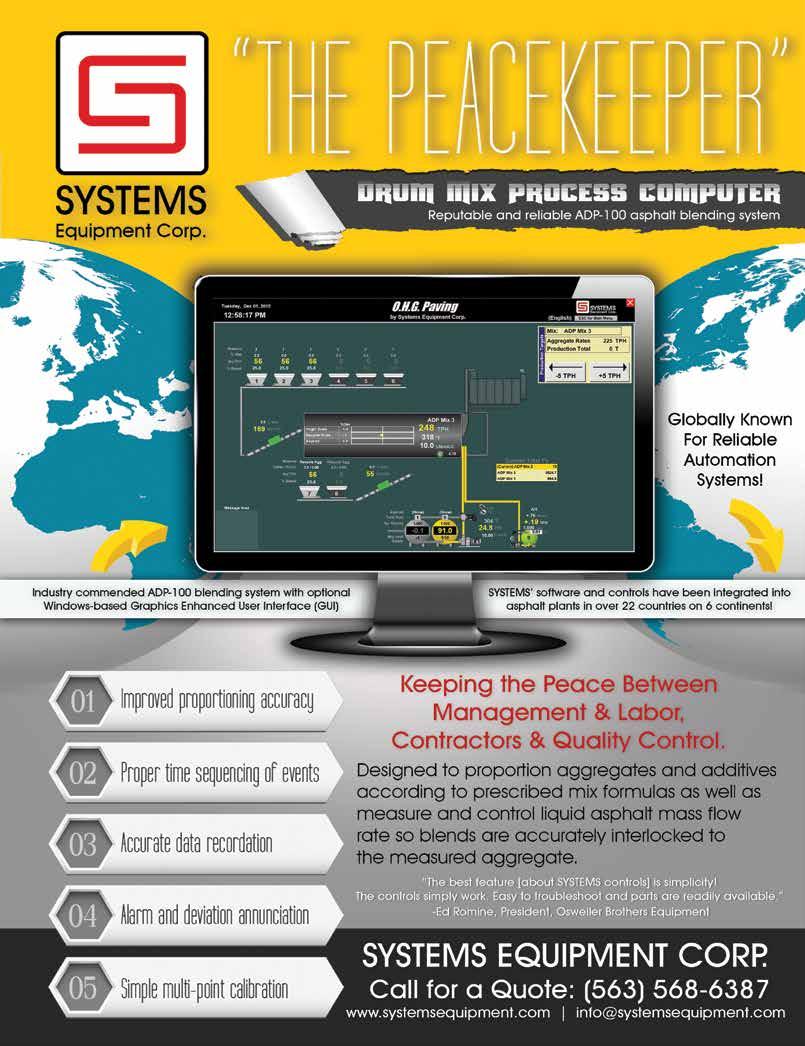
PRODUCER PROFILE You spent big money on your equipment... 800 www.kencoengineering.com363-9859 MAKE IT LAST! Kenco Engineering, Inc Protect the investment in your production equipment with Kenco longer life wear parts. Kenco offers innovative products for the aggregates, road building, and biomass industries. Spend more time making money and less time on maintenance!
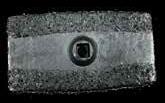
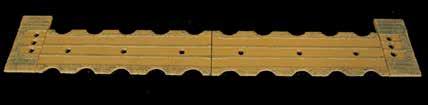
To maximize employee engagement and retain quality employees, Journey Group im plemented career pathing last year.
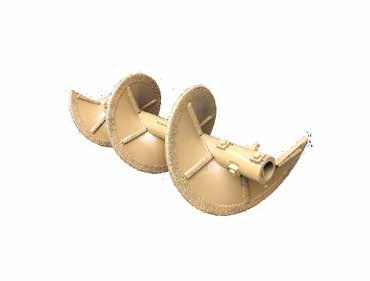
24 |
“We started with our asphalt paving crews, laying out every position and what is required for each role, the tasks performed by that po sition, and how to move up to the next posi tion,” Kerkvliet said. For example, if an em ployee starts as a laborer, they have a clear path of what they need to do to move up to a skid steer operator or roller operator, on up to the paver operator and screed operator, and into management roles. “If you don’t commu nicate what’s next, there’s nothing to look for ward to. We want to show they have some thing to work toward.”
Already, this strategy has helped a couple laborers from the 2021 paving season prog ress more quickly. “One of our laborers did so well he moved up to a screed operator,” Kerkvliet said. “Not everyone will be able to move through the positions that quickly, but this individual has been very successful. The people who are interested in improving, who want to continue to train, are the types of people who could be foremen for us down At least in the Sioux Falls market, that will be key to the continued growth of Black-Top Paving. “If we didn’t have the team we have, we couldn’t grow,” Kerkvliet said. “The qual ity of the work they put in is a reflection of work to come.”
SEPTEMBER 2022 for growth is often finding skilled employ ees. “Every company here is struggling with that. When we have good people, the work is there for us.” In order to attract quality employees, Jour ney Group offered walk-in interviews every Monday evening throughout March 2022. They also invested in radio and billboard ad vertising, an employee referral bonus pro gram, and increased wages during the last two years. “We want to pay at the top of the market and are trying to set the bar high here at Black-Top Paving,” Kerkvliet said. Another aspect that Kerkvliet believes sets Black-Top Paving apart is its workplace cul ture. “It’s hard enough doing this work, deal ing with 90-degree heat, traffic, and the trav eling public honking at you, so we try to make our work environment as good as we can,” he said. “We have a high standard for our leaders to treat people the way they’d like to be treat ed and give feedback constructively.” Kerkvliet also tries to make himself visible and accessible to Black-Top’s employees, of ten showing up to foremen and crew meet ings in the morning or heading out into the field during the day. “Our project managers and superintendents aren’t above going out and helping shovel if need be,” Kerkvliet said. “Illustrating that this is a team and we’re all in this together starts from the top.” Engaging the whole crew in the plan for the day is another way to demonstrate the division’s commitment to teamwork. Kerkvliet has seen work cultures where a foreman gives one instruction, the employ ee completes the task, and waits for the next instruction. “That’s not our way. We put a lot of effort into communicating the plan for each project and give employees a chance to offer input, address safety concerns, and get involved in the process.”
CRUSH RAP COSTS with the HONEY BADGER STATIONARY PORTABLE 877.457.3938 cwmfcorp.com Reduce or ReducedcrushingeliminatecostsRAPmoisture = lower fuel consumptions Typical 6 month ROI (300,000 ton/season plant) Minimizehandlingmaterial From replaceable abrasion-resistant steel wear liners to a 1/2" steel pulverizing hopper, this machine is ready for wear and tear. And by reducing material handling and minimizing moisture, the Honey Badger increases production and saves on fuel costs. Average return on investment is 1/8 the cost of other crushing operations. Fully-equipped with max power, reliable operation, and easy maintenance, the Honey Badger is ready to crush your costs!
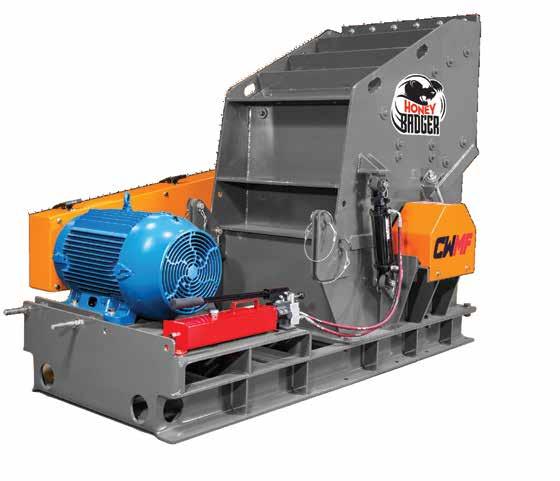


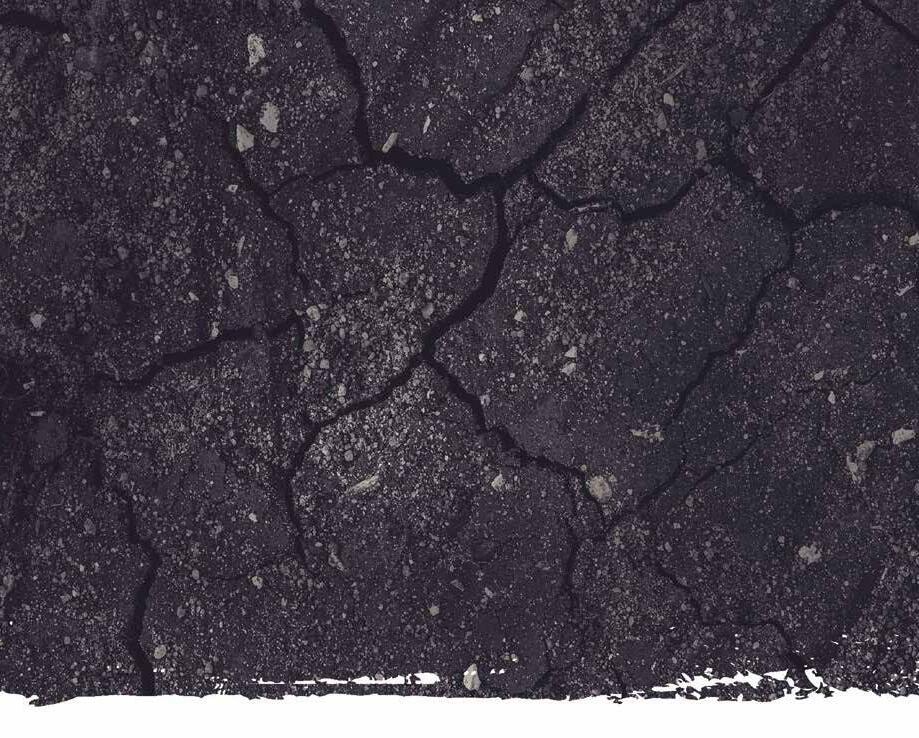
With the extra expense of school behind them, Bennett had the freedom to look for “something else.” Her aunt, who had been work ing in construction for over 20 years, suggested a company that was looking for a contract administrator. Bennett took the plunge and applied to Lehman-Roberts.
Meet a Woman of Asphalt:
AsphaltPro: What do you find most rewarding about your role as contract administrator for Lehman-Roberts?
Lehman-Roberts’ Maria Bennett
Once her husband graduated and landed his dream job as a flight paramedic, Benett saw him excited to go to work each day. “He was happier and really loved what he was doing. It was then that I real ized I was envious of his excitement and love of his job. The bank ex perience had been really good to me and had helped me grow pro fessionally, but just because I was good at it didn’t mean I was happy doing it. The atmosphere was very corporate, and I never felt like I could just be me, like I always had to walk a line to be what every one expected me to be.”
I was able to bring my computer knowledge, management skills, and system knowledge I had learned from banking and found ways to apply it to my job here at Lehman-Roberts.
Maria Bennett: There are so many wonderful areas to get in volved in within this industry, whether you are just graduating high school or hold a master’s degree.
Maria Bennett: The appreciation I get from my peers and my management team makes me feel like the hard work and all the ef fort I put into my job is absolutely worth it. I love the feeling of get ting everything ready for a new project because it’s always some thing different. The processes may be similar, but the jobs always have their own “flavor.” I feel like I will be doing this job for another 25 years and will still be learning new things every day. There are so many people and pieces involved with a project (The subcontractors, the plants, the haulers, the project managers, the administration, HR, the crews, etc.) that when a project is complete, you can’t help but sit back and say to yourself, “Wow! That’s incred ible! All those cogs in the wheel worked out perfectly!” That always amazes me.
Bennett took some time out to share her experience as a woman of asphalt.
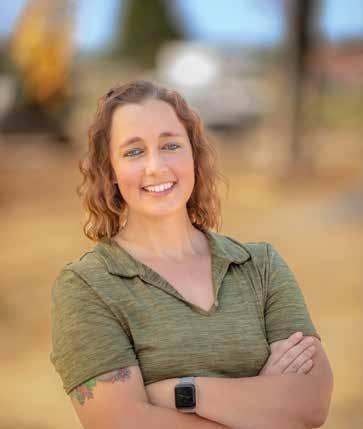
There are people that I work with that never went to college who simply started out with a shovel and determination. They’ve since worked their way up to foremen, managers and the top “go to” peo ple in our field. That’s what I believe makes this industry so amaz ing. There is a place for everyone.
26 | SEPTEMBER 2022 WOMEN OF ASPHALT
“It was one of the best things to ever happen to me. I am at a place that is professional yet does have that genuine family feel.”
aria Bennett joined the asphalt industry and Leh man-Roberts Company, Memphis, Tennessee, in 2018 and works for the company as its contract administrator. She switched careers from a local bank in Memphis, where she’d worked her way up from an insurance processor to vice president of collections and special assets. “My move up the ladder was a six teen-year journey that I was very proud of and the promotions, as well as my husband’s time in the National Guard, helped to pay for the education my husband needed to complete his schooling.”
Maria Bennett
BY SANDY LENDER M
AsphaltPro: What part of your education would you recommend or “highlight” to others wishing to join this segment of the con struction industry?
AsphaltPro: Could you share with the readers what your job as a contract administrator for Lehman-Roberts requires of you?
AsphaltPro: What do you think is the most important skill you’ve brought to your position as a contract admin istrator in the asphalt/construction industry? (And how would you encourage other women entering the industry to hone a similar skill?)
Maria Bennett: My main duty is processing all the paper work with the project owners and any subcontractors we may use for a project. I handle the contracts and subcontracts to make sure that we are in compliance with the required pa perwork like the monthly payment and progress forms for the different states and counties. I also post the state and city estimates and process the quantities for the subcontractors for payment. I work directly with seven project managers, so the proj ects and workload can add up quickly. There’s never a dull day. From processing accounts receivable (AR) and accounts payable (AP), ordering bonds, ordering plans and specs, managing vendors, posting estimates and contracts, I am never bored.
Maria Bennett: I am very detail oriented and the paper work that is involved in a project can be overwhelming, es pecially if you have 10 or more subcontractors on a proj ect! So, I loved the challenge of making this role organized and the process smooth. I was given free rein to set up my position as I saw fit. I’ve really been able to make my po sition transparent and easy to follow up on. Thanks to the faith my team had in me, I was able to really make this po sition my own. I have it so organized now that anyone can see what step we’re on at any given time. I love being busy and there is never a dull moment. I thrive when I’m busy, it helps me focus and the day flies by. This position is a mul titasker’s dream.
AsphaltPro: Would you like to share a skill you’ve learned on the job since joining Lehman-Roberts that surprised you OR one that you think other women entering the industry would find beneficial?
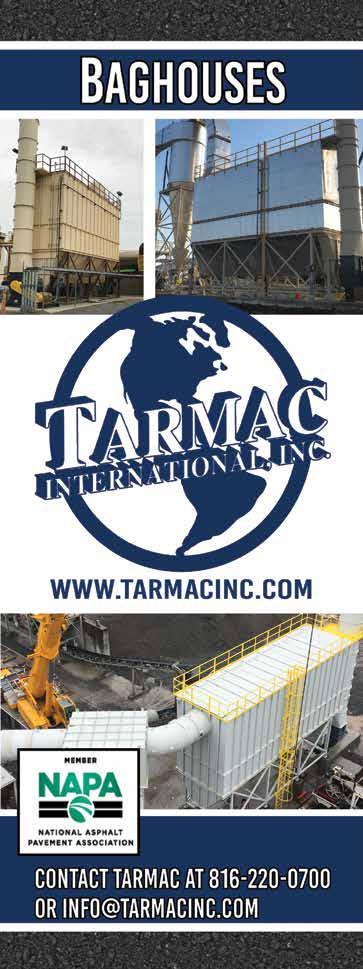
Maria Bennett: Organization! I think that women in general have superior organization al skills. I believe that women have always had to be the ones to organize not only their lives, but everyone else’s too. I see so many working women juggling their jobs, their family’s schedules, outings, and vacations, and these women do it with such grace. They are the ones making sure everyone is on the same page and that the world is on track. I think those natural skills give women the advantage because they are able to look at something and have the ability to communicate clearly what needs to be done.
WWW.THEASPHALTPRO.COM | 27
AsphaltPro: Why did you choose to become a contract ad ministrator? What about that position is “most cool” to you?
Maria Bennett: Honestly, I have taken my skills from my previous job and have been able to apply a lot of them here. I think women may be nervous about joining this industry because they believe it will be so for eign to them. But it isn’t. Trust me when I tell you that I never imagined that I would use all my Microsoft Excel skills in construction!
I was surprised to realize it is not as male-dominated as I thought! I find myself surrounded by hard working and fully supportive women. Some as new as myself, and some with tons of years under their belt. Every one of them has been open and welcoming and eager to share their knowledge, which really helped me to find my place in this com pany/industry.
AsphaltPro: What would you say was the most challenging “obsta cle” you, as a female in the construction/asphalt industry, had to over come in the past four years, and how DID you overcome that obstacle?
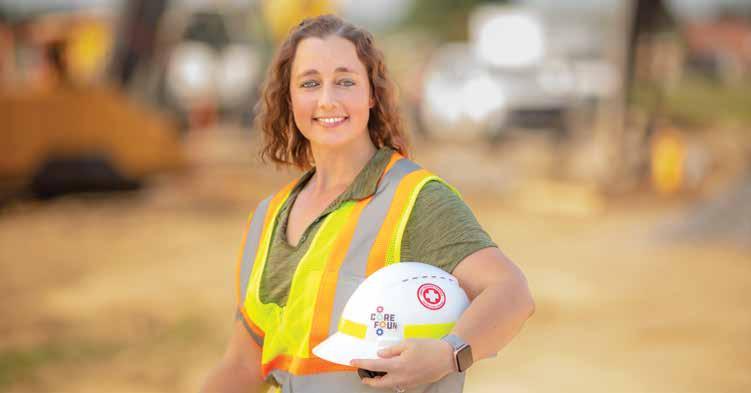
It’s just like any other business environment that needs a million hands in it to run smoothly. You get to learn about estimates and bid ding, and a lot of other things that make paving new roads work. But it’s also comforting to know that it’s just like any other job where you have to learn their systems and their procedures.
For example, in banking you must learn about many different laws and compliance regulations. It’s the same in the construction industry. There are laws and compliance regs that you must follow here as well. So, once you get into this industry, you will find it’s not as scary, intim idating, or as foreign as you may think it is. That was a very pleasant surprise for me personally.
AsphaltPro: Let’s talk about teamwork. What is the most challeng ing project you’ve been a part of and how did you and the team over come the challenge?
Maria Bennett: We had a project where one of our subcontractors was having a hard time reconciling their quantities with the project owner. I wound up building a spreadsheet of the quantities that were turned in by the subs versus what was paid by the owner. (Lovely reg ular office skills!) After sitting down and working with the subs, the project manager, and the owner, we were able to find the issues and fix them to where everyone was happy and felt that they had all been treated fairly. I take that as a feather in my cap, since I had never dealt with the subcontractor quantities before that (other than just pulling them in from what the estimate stated). So, this was a whole new perspective
Maria Bennett: I initially had two reservations about going into this industry. The first was being a woman in what I thought was a male-dominated field. The second was being super novice. I knew nothing about asphalt or what it took to do what we do.
In addition, I also deal with subcontractors every day, and the ma jority of those contacts are women. So many wonderful women that are contributing to this industry from payroll to estimates to project management and I had no idea. The whole feeling I had about being an outsider in this industry did not last long. The second obstacle I had to overcome was really one that could be for anyone starting a whole new career, no matter what industry they may be going into. I went from knowing everything to not knowing a thing and having to learn all over again. I’ll be trying to overcome that obstacle for years to come, I’m sure, but I am absolutely looking for ward to it. I left banking when I was 38 years old. The fear of going to a whole new career path was almost too daunting, but I wanted to have a job that fit me and I wasn’t going to find it by not getting myself out there. With a good company, you will find the training needed to be the best at your position.
28 | SEPTEMBER 2022 WOMEN OF ASPHALT
From innovative designs to Caterpillar dealer service and support, Weiler is paving the way to success for contractors across North America. Weiler’s material transfer vehicles, commercial pavers, road wideners, windrow elevators, static compactors, soil stabilizers, rock drills, tack distributors and front mount screeds are engineered with innovative features to increase productivity while reducing operating costs. Weiler equipment is sold and serviced exclusively at Caterpillar dealers throughout North America.
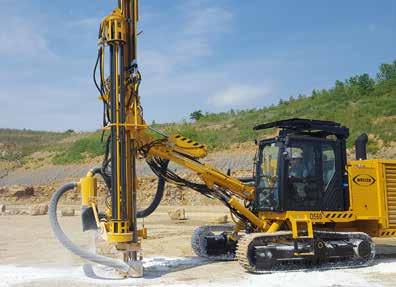
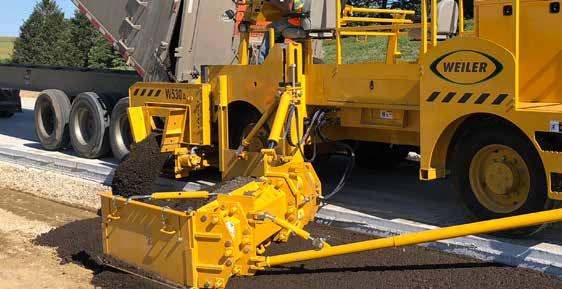
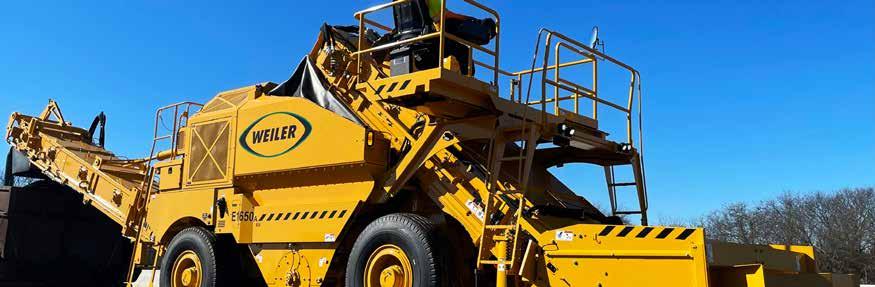
weilerproducts.com
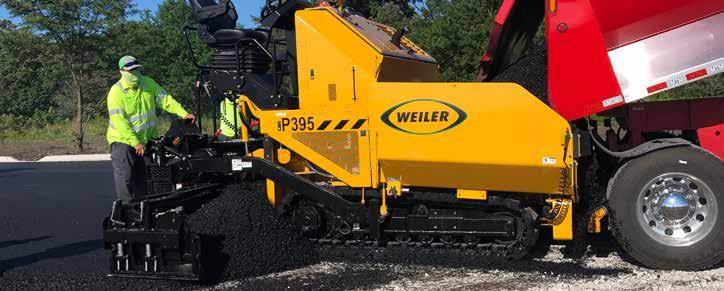
Women are capable of so much and there is so much this indus try can offer us. It is also a field that is needed no matter where you move in this world. The world will always need roads and a strong infrastructure. It’s an industry that isn’t a fad or the current new thing. It’s job security in a field that you could grow in, learn so much, and never get bored with it because it’s always changing.
One thing all the women in my life have told me without fail is that you miss 100% of the shots you don’t make.
AsphaltPro: Let’s talk about perceptions. It’s a fact that asphalt paving or construction in general can be hot and dusty. How do you respond to people who say it’s a “dirty job?”
Maria Bennett: Being able to see the end result. To see a com pleted project and know that I had a hand in it. That is a good feeling. Nothing beats riding in to work with a cup of coffee on a road I helped get completed and it’s smooth as butter. I’m always so proud of our teams.
AsphaltPro: Will you tell us about a person who served as a mentor for you and is there a piece of advice from this person that you would share with other women in the industry?
WOMEN OF ASPHALT “WITH A GOOD COMPANY, YOU WILL FIND THE TRAINING NEEDED TO BE THE BEST AT YOUR POSITION.”—MARIA BENNETT
Maria Bennett: They are right. There are a lot of positions in this industry that make you go home craving a shower as soon as you walk in the door. But that’s because they are hard working men and women putting that labor out there to give society that smooth road to work, to school, and to home. It’s an honorable job and one that we as a so ciety desperately need. It takes a VERY strong person to stand in MidSouth humidity next to an asphalt machine spouting out 300-degree asphalt. That is something that should be respected. There is a lot that goes into paving a road. There is so much pap werwork, teamwork, administrative work, and a million other du ties—yet not all of it is outdoor labor. You can find anything from driving, mining, payroll, accounts payable, accounts receivable, lo gistics, surveying, IT, programming, communications, and so much more. A woman can absolutely find her place here and rock it.
Maria Bennett: This is not just a man’s industry anymore. More and more women are joining the workforce in this field and this field needs us. It is an industry that you can grow with and absolutely shine in.
AsphaltPro: What is the most challenging aspect for you of being in the asphalt/construction business?
Maria Bennett: I like to get things done, but with this type of work, I found that I had to really work on patience. I can’t do every thing myself because so many hands are in a project. Sometimes it can be challenging to deal with that because you’re waiting for ev eryone to do their part in order for you to continue yours.
AsphaltPro: What is the most rewarding aspect for you of being in the asphalt/construction business?
I am very blessed to be able to say that these women are still very much a part of my life. They teach me so much by how they live their own lives. To see my Aunt Bonnie working as a construction manager for the city and how many glass ceilings she shattered to get to where she is today is both humbling and awe inspiring. To see my mother work so hard at her job and then come home and work hard to make her house a home for her family. To see my Bubbi fight cancer for over 20 years and still live life to the fullest. To see my Nana caring for all the wild animals and plants in her yard and how she is always going out of her way to make sure we all have food to eat and that we still make time together as a family. To see my Aunt Joni working hard at her successful career and still making time to be a kid whenever Star Wars is mentioned and not caring what any one else thinks because she is happy. All these things have molded me into the well-rounded person I believe myself to be today.
I didn’t know anything about the asphalt industry when I ap plied four years ago and as scary as that was to make such a huge change in my life, I am so glad I did. I made my shot, despite my fear, and now I work for an excellent company that truly cares about their people and community. I encourage women to take that shot and realize that we are all powerhouses in our own right and that we can do anything together, even take over the asphalt industry.
30 | SEPTEMBER 2022 for me. It took three groups to get those quantities agreed upon and thanks to the reputation that Lehman-Roberts had with the subcon tractor, we were able to work everything out respectfully and still have a wonderful relationship with them.
For example, I will complete the subcontract packages and send those out to the subs. Then, I have to wait for their paperwork to come back. Then, I submit those subcontracts and required docu mentation to the DOT for their approval and have to wait for them to get approved. I find myself moving forward with momentum and then in the blink of an eye, I can shift to waiting on DOT, the subs, or the proj ect managers to do their part to move the process forward. It’s part of really learning how to be a team and how everyone has a hand in all the projects.
Maria Bennett: I have been incredibly fortunate to have many mentors in my life. I have spent my 42 years surrounded by strong women. It’s very hard to list just one. There have been so many women to influence who I am today from my mother, my aunts and my grandmothers. My mother taught me the value of being a hard worker and responsible. My aunts taught me how to have fun and be nerdy while at the same time being strong and confident. My grand mothers taught me kindness, empathy and to appreciate every day I’m given on this earth because tomorrow is never promised.
AsphaltPro: What do you think is an incorrect perception that we, as an industry, can re-educate young people about to encourage more women to consider a career in the asphalt business?


IMAGINE YOUR
YOUR BUSINESS STARTED AS A DREAM, TO GROW AND PROFIT. To get the personalized attention you want to help you on your way. The customization you need to meet your business’s specific production goals. Consult with one of our specialists today to help configure just the right asphalt plant for you. Start your custom plant design today.
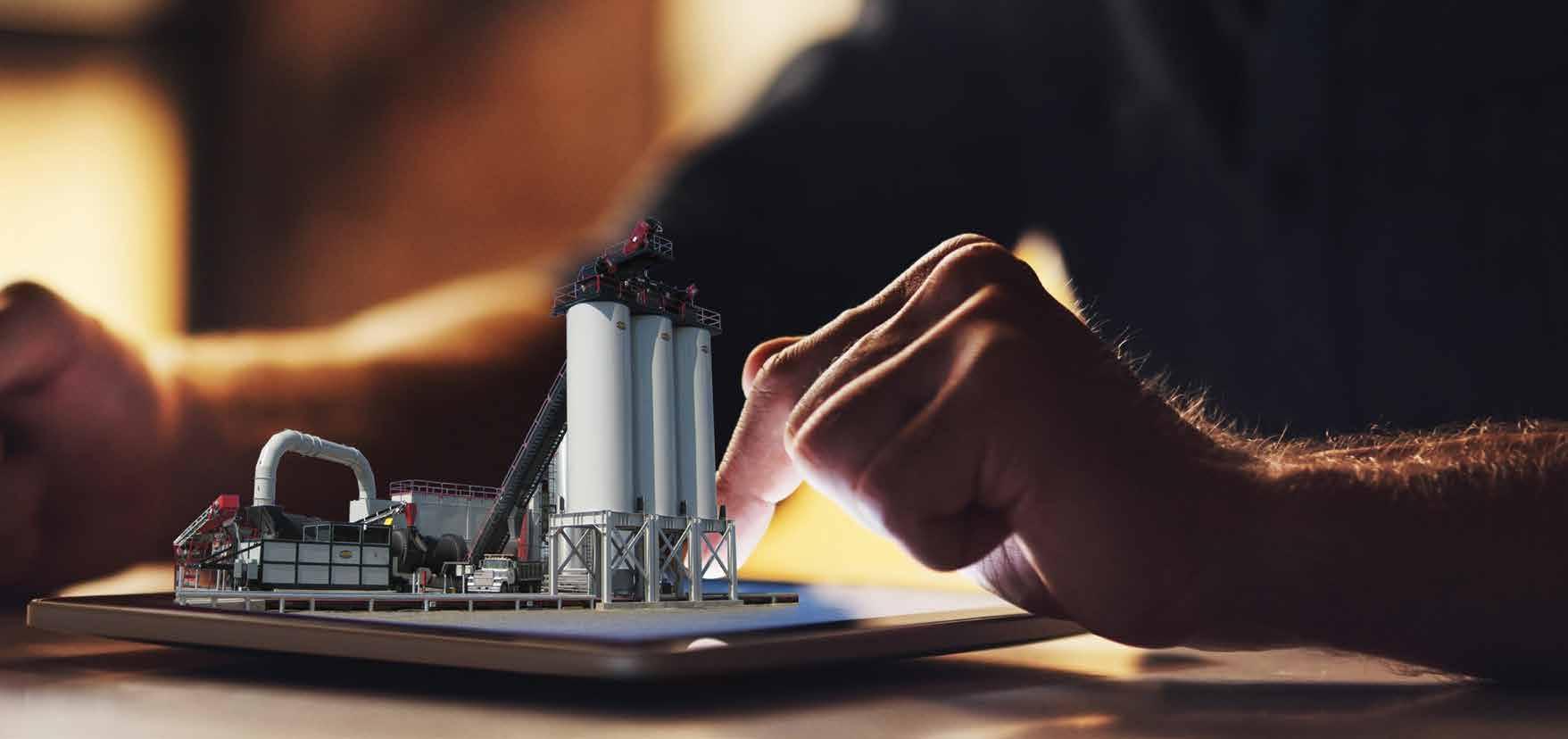
YOUR DREAMFULFILLYOURDREAM 260-637-5729 • admasphaltplants.com
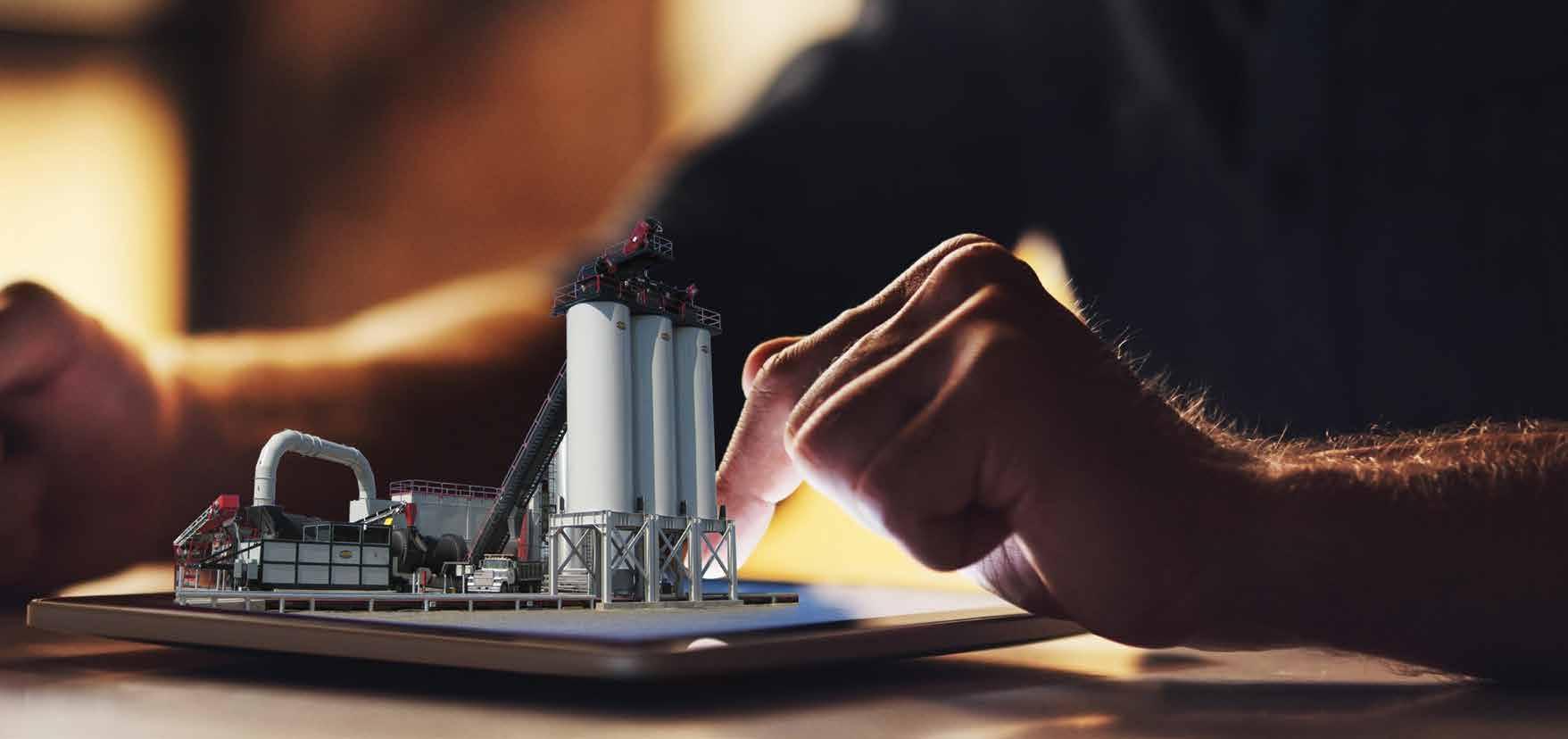
The plant combined components from several manufacturers. It was equipped with a Cedarapids E-300 counterflow drum, a portable Mad sen baghouse, a set of portable cold feed bins and a portable HyWay tank. The plant also had a silo system with more storage than Super Asphalt required.
INTERNATIONAL SNAPSHOT

Miguel Suria is proud of the latest Super Asphalt plant. Photos courtesy of Reliable Asphalt Products
FROM RELIABLE ASPHALT PRODUCTS B y combining used and new plant equipment, Super Asphalt has expanded its Puerto Rican asphalt production business to the southernmost part of the island.
Suria mentioned, “We didn’t need more than one silo, so we bought a new silo system instead of paying for the freight to move the system to Puerto Rico.” Even though this plant was not complete, the components that were available met the needs of Super Asphalt. Suria travelled to inspect the equipment shortly after Mauzy sent him the pictures and information. “The equipment was good, and the price was good,” so Super Asphalt proceeded to purchase it.
Although the plant was nearly complete and in Puerto Rico, the fa cility still needed a control house with motor control center, a hot oil heater and plant automation. Super Asphalt and Mauzy worked to gether to complete the plant.
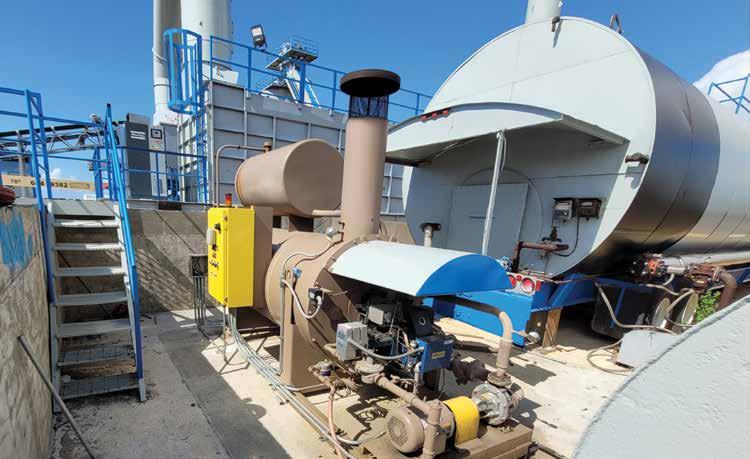
Reliable assisted Super Asphalt by getting the equipment to the Port of Jacksonsville. From there, Super Asphalt utilized its in-house ocean bound freight specialist to get the equipment shipped to the island. When Suria was asked how hard it is to get equipment from the states to the island, he responded, “It’s not difficult at all, but expensive.”
Miguel Suria, Super Asphalt’s operation manager, has been with the company from the beginning in 1999. Under his guidance, the is land-based asphalt producer has grown to seven plants in the past 23 years. Suria came to Super Asphalt with a wealth of plant knowledge and experience. Over the years, he has often recommended that Super Asphalt purchase gently used equipment to meet their needs. For this plant project, Reliable Asphalt Products had a plant that met Super As phalt’sMikerequirements.Mauzy,co-owner of Reliable Asphalt Products, has worked with Super Asphalt in the past so he was familiar with their require ments. “As I was seeing customers, I had in the back of my mind the need for a plant to go to Puerto Rico. Once I saw this plant, I felt like Super Asphalt would like it too.”
Reliable Asphalt Products worked with the previous owner to dis mantle the equipment and prepare it for shipment. Reliable also ac quired another plant nearby and when Suria was in the states inspect ing the equipment, he also inspected the other site and utilized some of that equipment for this plant.
International Combo
34 | SEPTEMBER 2022
The plant was installed very close to Super Asphalts’ liquid AC sup plier and close to the job site that justified this plant purchase. After a cross country plant move, ocean bound shipping and a lengthy per mitting process, Super Asphalt’s latest plant is in full operation. “Even though this is partly used, with the controls and the hard work of all those involved, we have something that we can be very proud of,” stat ed Suria.
Once the plant arrived in Puerto Rico, Super Asphalt began the permitting process. As is the case many times, this took longer than expected. Their site was prepared; however, the plant was not al lowed to be erected until the permit was secured. Upon securing the permit, Suria, along with the team of Eduardo Enchautegui, plant superintendent, and Rawand Perez, plant operator, began the pro cess of erecting the plant at the Penuelas, Puerto Rico, site.
WWW.THEASPHALTPRO.COM | 35
Among his many talents, Suria is an electrical engineer. He installed the MINDS plant automation. Once he completed the plant and au tomation installation, Len Newton, Reliable Asphalt Products’ leading automation technician, arrived to commission the plant. According to Newton, “Miguel did an excellent job installing the MINDS system. Because of his good work, we were able to commission the plant in a very short time.”
TOP: From left to right, Miguel Suria, Eduardo Enchautegui, Rawand Perez BOTTOM: Super Asphalt has two complete labs on site. According to Suria, one is for his company, and the other is for the Puerto Rico Highway Authority’s use. Reliable Asphalt Products located the used control house with a complete motor control center for the team. Miguel Suria is an electrical engineer and took care of installing the MINDS plant automation for the plant.
Reliable Asphalt Products located a used control house with a complete motor control center shortly after the rest of the compo nents were shipped to the island.
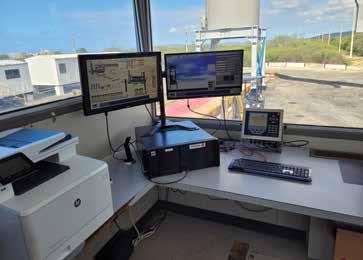
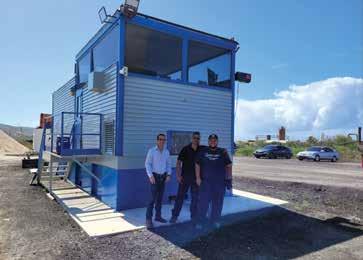
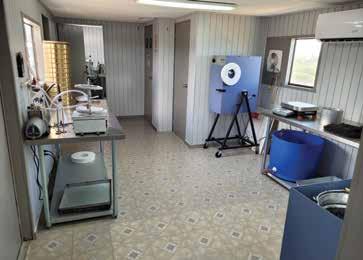
“The used control house that Reliable found for us was an ex cellent option. I did not inspect it myself but got a good report from Reliable and this has worked out really well,” Suria said.
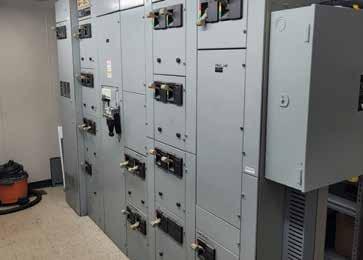
Upon Reliable’s recommendation, Super Asphalt elected to pur chase a MINDS automation system for this plant. Reliable also supplied Super Asphalt with a reconditioned hot oil heater to complete the plant. Although it is not currently equipped with a RAP system, there are plans to install a RAP system in the future, according to Suria.
Because these components were sourced from several locations and included some new components, installation of a plant like this can be tricky. In order to meet the permit requirements, Super Asphalt had to install two complete labs on site. According to Suria, “One is for us, and the other is for the Puerto Rico Highway Authority.”
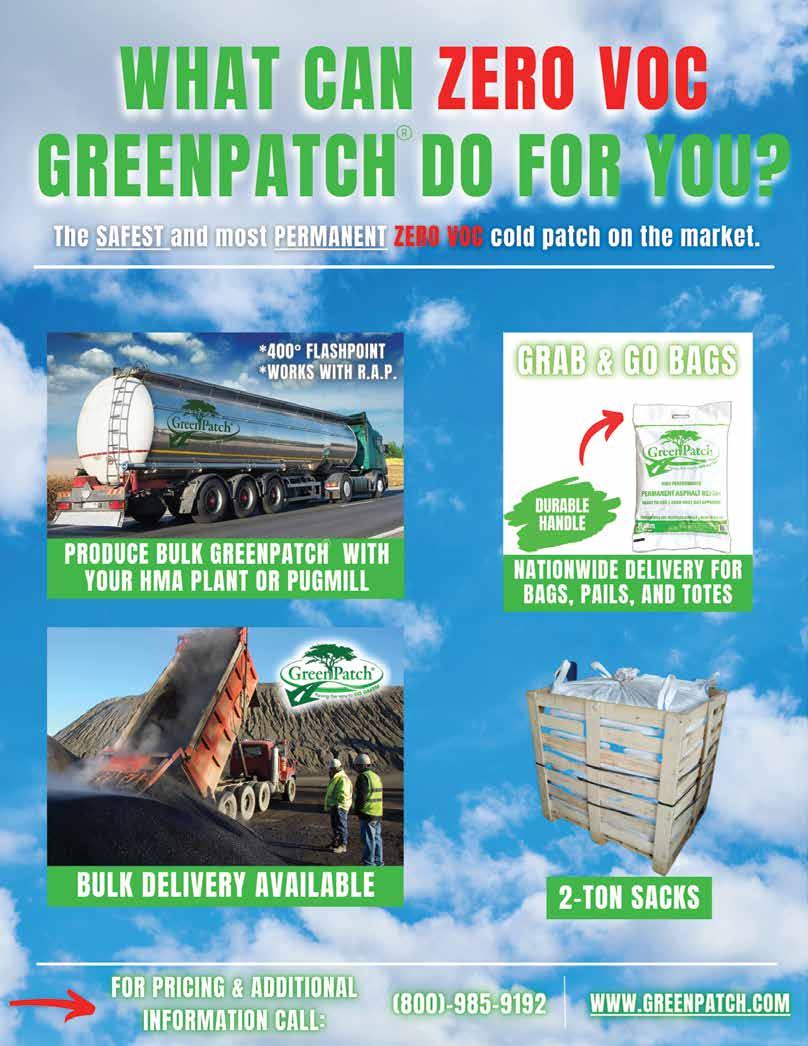
Warehouse Depth Veteran Striping Robotic Cracksealing Fall www.TheAsphaltPro.com2022 ATS Shares Tips for Best RAP Practices for All Manner of Preservation, Maintenance, Paving a supplement to AsphaltPro magazine
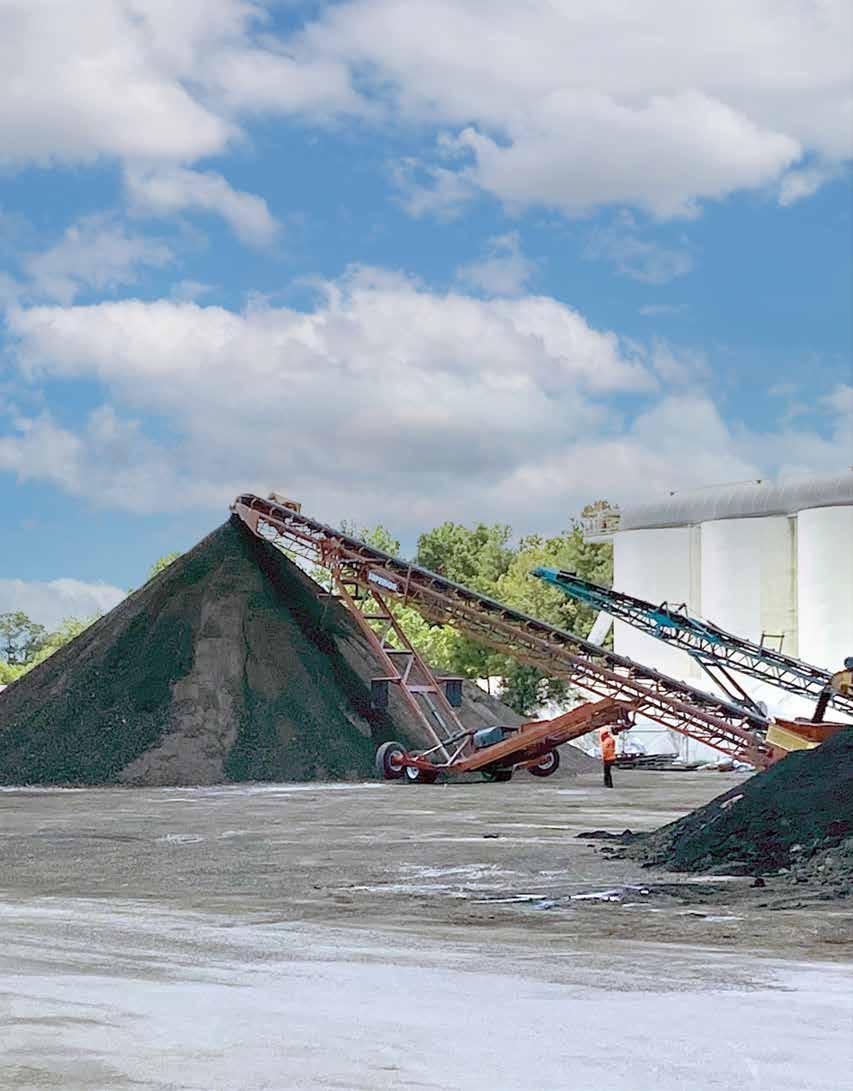
The Ohio Department of Transportation (ODOT) contract ed with RAP Management, Columbus, Ohio, on its first offi cial balanced mix design (BMD) project in August 2021. With its new Ammann high recycling technology (HRT) batch plant, RAP Management would produce a 55% RAP mix for the southbound lanes along 4.6 miles of State Road 664 to compare against a normal medium traffic mix with 20% RAP placed on the highway’s northbound lanes. According to ODOT’s State Asphalt Materials Engineer Eric Biehl, “The production volumetrics [of the 55% RAP mix] were all spot-on.” Ultimately, the high-RAP mix performed as well as the control mix, if not better. During a recent webinar put on by Asphalt Testing Solu tions & Engineering (ATS), Jacksonville, Florida, Biehl said he thinks BMD will open the door to increased RAP use in the future. RAP Limits Biehl said RAP caps for ODOT jobs range from 15 to 25% for the surface mix and up to 40% for intermediate mix. There are also caps based on traffic load of 55% for light and medium trafficked roads and 40% for heavily trafficked roads. “We don’t technically hit those points, but we do see pretty high RAP,” Biehl said. Instead, the limitations to RAP use in Ohio relate to the requirement that producers perform binder test ing and that anything above 25% RAP requires PG -28 or -22 Binder testing is also a limitation contractors experience in Texas, said Corey Pelletier, director of special projects at Anderson Colum bia in Texas. “Texas requires binder testing if a project uses more than 20% RAP in the mix,” Pelletier said, adding that the Texas Department of Transportation (TXDOT) doesn’t have a limit on the amount of RAP other than the binder testing requirement above 20%. “If there’s a large stockpile [of RAP] at a permanent plant facility, they already know what’s in that pile and have time to do the testing and are able to put in the maximum amount of RAP,” Pelletier said. However, projects in more rural areas rely heavily on the use of portable plants and are primarily using RAP coming off that project. Furthermore, mill-andfills are common across the state. In those scenarios, the binder testing requirement creates a timing issue, and so those jobs often opt for less than 20% RAP. “That’s what’s hindering our use of RAP in Texas.”
Overcome Recycled Asphalt Anxiety
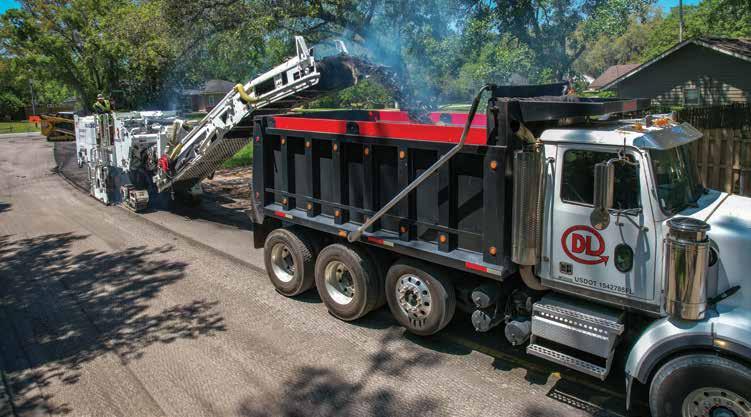
During a recent webinar put on by Asphalt Testing Solutions & Engineering (ATS), industry experts shared insights on the state of RAP usage.
Increasing the use of RAP continues to face limitations across the country. However, experts from Ohio, Texas and Michigan offer a message of hope with the advent of BMD.
All photos courtesy of ATS
T
By Sarah Redohl
38 SEPTEMBER 2022
Otherwise, he added, there’s a risk that some producers could shoot for a certain RAP percentage that meets all specs while not achieving the performance one can expect of an asphalt pavement. Pelletier cited an example from Texas where contractors overused recycled asphalt shingles in mixes to realize cost savings to the det riment of pavement performance.
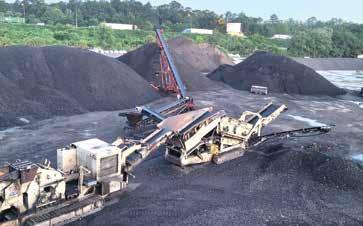
BMD Offers Opportunities
Brett Stanton, executive director of the Asphalt Pavement Associa tion of Michigan (APAM), said the Michigan DOT (MDOT) has tried to simplify binder replacement criteria for RAP into three tiers. “Tier 1 includes mixes up to 17% binder replacement where there are no ad ditional binder grade requirements,” he said. “Tier 2, 18 to 27%, often requires a binder dump on the low end with an option to drop the top grade as well or do a blending chart to show you have not impacted the final grade, and Tier 3, anything above 27%, requires a full binder grad ing to show what the virgin binder grade must be to meet the planned grade on the lower end with the top end contractor-optioned.”
BMD may be the answer to several of those limitations to increasing the use of RAP and it’s one state DOTs are watching closely.
Stanton said there is a possibility, with increased work to come, that it may be possible to run low on RAP. “It depends on how much RAP you’ve got stockpiled in the yard now,” he said, “but we’ve seen in certain areas around our state that have gone to full reconstruct—brand new pavements were removing concrete and putting back asphalt, there’s no RAP coming off the job and putting back 10 or 12 inches of asphalt and you’ve got 25 or 30% RAP in there, you’re starting to burn through RAP faster than you’re bringing it back in. We haven’t hit that yet, but have talked to a few members that are concerned what will be the future for RAP and hedge bets to figure out where to haul it from and where in the state there’s excess to make sure there’s enough supply, because it’s a very big bargaining chip when it comes to bidding work; you’ve got to have it in order to be competitive.”
Pelletier believes a better approach would be one based on mate rials available. That is the common denominator limiting RAP us age he’s seen in the nine states he’s worked (Florida, Texas, Missou ri, Kansas, Iowa, North Carolina, South Carolina, Alabama and Geor gia). “The mix is only going to be as good as what you put in it, and material deviates so much within a state, let alone state to state,” Pelletier said. He doesn’t think specifications pertaining to RAP per centage should be the same, regardless of the materials. “Being stuck with the standard spec is one of the big problems we run into. I think it needs to be more relaxed so long as you can prove you’re achieving the end results.”
“We’ve come a long way as an industry on how to better process, utilize and design with RAP,” Stanton said, citing the breadth of re search showing that medium- to high-RAP mixes can perform. To take advantage of that expertise, he hopes to see Michigan use some sort of BMD approach with performance metrics during design and checked during field production. “If we tell the industry how we want the pavement to perform and let the contractor use the tools in their toolbox, whether that’s warm mix, RAP, etc., that’s how in novation will come.”
However, producers in Michigan face other types of limitations, in cluding Department of Environmental limits on RAP usage in order to get a plant approved. “We have a lot of plants bumping right up against [theAnotherlimits].”challenge producers face in Michigan is a stigma related to past failures perceived to be the result of RAP. “We need to educate people who saw, or thought they saw, a failure and capped RAP at low er percentages,” Stanton said, adding that some of Michigan’s coun ties cap RAP at 10 or 15%. Other counties use MDOT’s specification, which results in counties bordering one another having very different RAP specifications. Not only does that add cost to the counties as con tractors must produce different mix designs, but it’s also arbitrary, he said. A certain percentage of RAP might be fine in one county, but deemed unacceptable one foot into the next county over.
WWW.THEASPHALTPRO.COM 39
As RAP percentages increase, that’s the benefit of a perfor mance-focused BMD approach rather than the process-oriented approaches of the past. “We have the tools to properly engineer these mixes, but we need to be able to test and adjust on the fly like any other QC adjustment. If you see air voids starting to tick down, you know you need to make a void adjustment. We need to be doing the same thing [in regards to RAP],” Stanton said.
On the DOT side of the equation, Biehl said the limiting factor to in creased RAP use is DOTs “having the confidence in [their] performance index limits.” ODOT only began searching for its first official BMD proj ect once it was fully confident in its cracking test (IDEAL-CT). “The cri teria is what’s holding [DOTs] back right now. If you can get those figured out and relate them to some sort of performance, it be comes a matter of opening up the specs.” Although there is some progress yet to be made before that can happen, with the recent success on Ohio’s State Road 664, Biehl’s parting message is a positive one: “Don’t let recycling scare the RAP out of you!”
Another limitation in Texas is that many regional engineers prefer RAP from state-owned projects, which means RAP from local roads and parking lots often cannot be used. This requires producers to have separate piles to keep state RAP separate from other RAP sources.
“We have a lot of repeat customers in the warehouse industry, since there’s a relatively small pool of players in that market,” Powell said. There are the Walmarts, Amazons, UPSs and FedExs, but also a small handful of warehouse developers, like Prologis and North point, who build warehouses and lease them to the Walmarts, Am azons, UPSs and FedExs. “The companies are national in nature, but there aren’t many of them.”
Warehouses account for around 40% of Schlouch Inc.’s book of work. But being a part of this warehouse revolution, Schlouch says, is still a relationship game.
The Warehouse Revolution is Built on Relationships
Schlouch is a heavy civil site work contractor that employs 285 peo ple. The company, founded in 1983 by Barry and Deborah Schlouch, performs heavy civil services ranging from excavation to utility instal lation, drilling and blasting, design build services, concrete work, and asphalt paving, with asphalt paving accounting for roughly one-fifth of the company’s annual sales.
However, Schlouch has been involved in warehouse work since the 1990s. That history in the industry, and the relationships it’s cultivated over the years, is integral to the company’s success in this niche.
“Since a lot of these companies are national players, they don't neces sarily have the intimate relationship with local governments, town ships, the state DOT, inspectors and such that we do,” Powell said.
“Plus, this is prime real estate along the Interstate 78/81 corridor in this section of Pennsylvania to further distribute goods around the northeast,” added Schlouch Site Superintendent Derek Bainbridge.

Powell estimates warehouses account for around 40% of Schlouch’s work and its biggest market outside of residential subdivision work.
F By Sarah Redohl
“Geographically, eastern Pennsylvania is in a sweet spot for ware houses,” said Glen Powell, Schlouch’s paving department coordinator and project manager. “This area is considered an inland port, with a lot of goods coming off of ships in the New York and Newark, New Jersey, areas coming into this region for warehousing.”
40 SEPTEMBER 2022 For many of us, the days of face-to-face shopping are gone; we no longer have a close relationship with sales clerks or ask for their recommendations on our purchases. Many online shop pers have noticed algorithms now rule their recommendations; after ward, anonymous warehouse workers fulfill the orders. However, ac cording to Schlouch Incorporated, Blandon, Pennsylvania, the con struction of those warehouses is still a relationship game.
“In this market, relationships are everything,” Bainbridge said.
Powell estimates warehouses account for around 40% of Schlouch’s work and its biggest market outside of residential subdivision work. “We’ve seen the warehouse market more than double in this region in the last five years,” Powell said, adding that it grew even more in the wake of the COVID-19 pandemic. Bainbridge estimates they do five or six warehouse jobs per year.
Design-Built, Value-Engineered
Powell said proper planning and communication with the asphalt plant is also key. Demand for asphalt paving is high in Schlouch’s region of Pennsylvania, which makes planning ahead all the more important on the material side of things, Powell said, “especially given the quantities of material involved in warehouse jobs.”
Powell said it’s quite common for the state DOT to require improvements to the existing road network around the warehouse to accommodate the increased traffic.
“Since these jobs are usually done under such tight timelines, we’re often coordinating with other trades working on the building itself,” said Paving Field Coordinator Rob King. “A higher level of coordination is re quired when you’re paving at a warehouse than if you’re shutting down one road. There’s a lot of internal traffic control and sequencing that has to take place.”
“Our relationships with local entities help them through the construc tionAlsoprocess.”important are the relationships Schlouch has with its warehouse clients, since they’re often working closely with the property owner and general contractor. “Design-build is big for larger warehouse projects,” Bainbridge said, adding that it’s a bit of a niche for Schlouch. This also helps Schlouch value engineer potential alternatives for its clients. “Since we’re often doing design-build, we have a firsthand op portunity to provide the best value for the client,” Powell said. “With our warehouse projects, we may look at the materials specified and the pavement design and present value engineering to clients that could im prove service life or give them the same service life while reducing up frontOften,costs.”this is a result of changes in material. “Engineers are limited to what they know and their past experiences,” Bainbridge said, “whereas we have a broader horizon of understanding with materials and may be able to recommend alternatives that can be equal to or better than what was designed while also saving the customer money.”
Improvements to existing roads might include widening to accommodate turn lanes, deceleration and acceleration lanes; reconstruction; and/or installation of traffic signals.
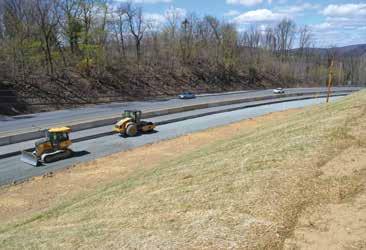

Bainbridge estimates that the average warehouse job requires between 20,000 and 40,000 tons of asphalt.
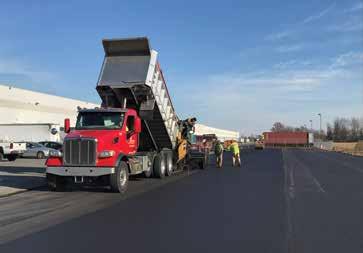
This is made a bit easier, because Schlouch can perform such a broad variety of work common on warehouse jobs. “We only have to rely on a small number of subcontractors on these types of jobs,” Powell said.
For example, at a warehouse in Bethel, Schlouch was able to recom mend the use of a geogrid between the soil and the aggregate subbase to reduce subbase thickness. “That gave them the same strength while saving a substantial amount of money,” Bainbridge said. Powell added that they were also able to reduce the paving cross section thickness by an inch or two, “which resulted in a sizable savings on a 40,000-squareyardOnjob.”another job, the soil conditions weren’t great, so Schlouch rec ommended cement stabilization. “Through that process, we built more strength into the subgrade and were able to reduce 1 inch of paving thick ness on the project while giving the client a job that would last them as long as the original design,” Powell said.
Bainbridge estimates that the average warehouse job requires be tween 20,000 and 40,000 tons of asphalt. “If you wait until a couple days before a warehouse job to order that much material, you’re not going to be able to get the amount of material you need,” Powell add ed. “Advanced planning and scheduling with the selected supplier is paramount.”
“That means we can schedule and coordinate seamlessly and smoothly to perform in a tight time frame.”
Schlouch also must have good working relationships with the other trades working on the project.
WWW.THEASPHALTPRO.COM 41
“I think that value engineering shows our investment in the project and our willingness to help the customer and the GC get the job done,” Bainbridge said. “We’re fully invested in the success of the project and are willing to come up with ideas to help them achieve their end goals.”
As part of the Hamburg project, Schlouch’s crews did some ma jor improvements to PA Route 61, adding a half-mile of acceleration and deceleration lanes at the entrance to the industrial park.
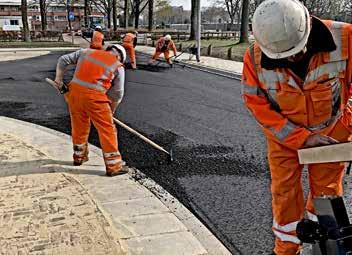
The asphalt pavement at the industrial park in Hamburg had between 6 and 8 inches of 2A aggregate subbase in the light and heavy duty sections of the project, respectively. The light duty section was topped with 2.5 inches of binder course HMA and a 1.5-inch wearing course, while the heavy duty section was topped with 4 inches of base course HMA and a 1.5-inch wearing course, for a total of 30,000 tons of asphalt.
42 SEPTEMBER 2022 Having a good relationship with the asphalt plant isn’t only im portant in terms of material quantity, but also material quality.
Powell said it’s quite common for the state DOT to require im provements to the existing road network around the warehouse to accommodate the increased traffic.
“With the increased truck traffic to the warehouse, the surround ing roads may need to be reconstructed or reconfigured for addi tional traffic,” he said. This might also include widening to accom modate turn lanes, deceleration and acceleration lanes; recon struction; and/or installation of traffic signals.
To widen Route 61 near the Hamburg industrial park, Powell said the crews encountered some deposits of rock they were able to ul timately use as general fill on the job site. “It wasn’t suitable for our subbase, but it was structurally sound to help resolve the topo graphical issues,” he said.
“If during laydown the crew placing the product sees any chang es in the material, visually or in how it behaves, they need to be in constant contact with the material supplier,” Powell said. “It’s not uncommon to see issues throughout the day where the ven dor will send a lab tech out to understand what’s going on. Having a good relationship with the vendor is important so they can sup port you if you start to see any quality issues.” Materials Matter Among the largest warehouse jobs Schlouch has ever performed is one the crew is currently paving at an industrial park in Ham burg, Pennsylvania. “We designed the entire industrial park from day one,” Bainbridge said, adding that they’ve been work ing on various phases of the park for around five years. They’re currently working on the fourth building, a 1.2-mil lion-square-foot warehouse.“The biggest challenge on that job was the topography of the existing land,” Bainbridge said. “The topography wasn’t ideal for a warehouse at all because it was on the side of a giant hill we had to carve up to make it as flat as weThecould.”jobrequired extensive earthmoving, amounting to more than 800,000 cubic yards of material, as well as extensive blast ing, storm sewer and underground utilities installation, curb paving, topsoil work, and 30,000 tons of asphalt paving.

He stresses the importance of heated end gates to achieve quality joints. They also follow state DOT methods on their warehouse jobs to maximize joint quality. “The other thing is training,” he said, adding that Schlouch trains constantly. From when and how to rake the joint to how to compact the job, Powell said everyone has a role to play in quality. Where the asphalt ties into the many concrete aprons located around warehouse jobs is also important. “The rollers have to get right up to the edge of the concrete,” King said, adding that it’s also import ant to keep the concrete free of track marks and material.
“It’s common to come across rock on warehouse jobs that can be crushed on site to use as a subbase,” Powell said, “but the aggregates you use have to be quality aggregates.” “You have to go through the quality control process to make sure what you’re using is suitable for the conditions you have and the in tended use,” he said. “It’s not as simple as taking any old rock and using it. Sometimes crushed concrete with proper testing could be an alter native to just using aggregates specified from a quarry, but that QC part of it is so important to ensure you’re delivering something of equal or better value to the customer long term.”
Bainbridge reminds us to watch for segregation as the subbase material is delivered and placed. “If the stone doesn’t have enough fines, or has too many, you won’t achieve the stability you need,” he said.
WWW.THEASPHALTPRO.COM 43
“At the end of the day, the client wants to look across their property and wants their blacktop to be black and their concrete to be white,” Powell said, highlighting the importance of meticulous cleaning and attention to detail. That, too, is a matter of teamwork. “We’re all one team,” Powell said. “Our whole company rallies behind one another to make sure we deliv er what we promised by the end of every day.”

Where the asphalt ties into the many concrete aprons located around warehouse jobs is also important. “The rollers have to get right up to the edge of the concrete,” King said.
Another thing to watch out for on warehouse jobs is joint construc tion. “The team also needs to be very good at asphalt joint construc tion,” Powell said. “Because of the size of these paving areas, you’re talking about thousands of feet of joints.”
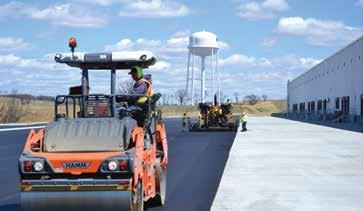
44 SEPTEMBER 2022
G-FORCE sent three of its franchise owners to Sightline’s Air field Marking Professional Symposium in the fall of 2021. “They en joyed the class so much, we sent several more owners to the follow ing course,” Child said, adding that they’ll be sending a handful more to Sightline’s symposium in October. “Soon, more than one-third of our owners will be trained and certified for airfield markings.”
When northeastern Alabama’s Anniston Regional Airport reached out to G-FORCE’s North Alabama franchise to ask if they performed airfield markings, the owner was able to leverage G-FORCE’s recently trained team out of Baltimore.

Ultimately, G-FORCE hopes to certify at least two-thirds of their franchise owners with airfield marking training. “That would give us very broad, local coverage around the country.”
Child began investigating airfield marking training courses and came across an offering from Sightline, Culpeper, Virginia, a con sulting company specializing in airfield markings that has worked with some of the United States’ busiest airports and pre-eminent airfield marking contractors.
Although the ability to send staff around the country when needed is a benefit for G-FORCE’s airfield marking operations, Child said it’s a strategy they use on projects of all kinds. “We send folks all over the country to help each other,” he said. “No franchise partner is ever alone and there’s never a project so big they have to turn it down.” For example, a large warehouse in Upstate New York, which required crews from Tampa and New Hampshire to travel to assist.
J By Sarah Redohl
“I spent a lot of time looking at airfield markings (and unknow ingly doing my best to wear them down), so I’ve come to know the difference between quality workmanship and sloppy workmanship quite well,” Child said. When the company decided to break into airport markings, he wanted to make sure the crews were equipped with the training they’d need to succeed.
In one of those rare but happy accidents, just as G-FORCE’s first batch of franchise partners had completed the training course, northeastern Alabama’s Anniston Regional Airport reached out to G-FORCE’s North Alabama franchise to ask if they performed air field“Themarkings.owner of our North Alabama franchise, Rob Young, hadn’t been trained on airfield markings yet, but he was able to collaborate with one of our other owners, Steven Hull of G-FORCE Baltimore, who had been through the course and was able to travel to Alabama to oversee the project,” Child said. “The timing worked out perfectly.”
Jack Child understands the importance of quality and pre cision when it comes to airfield markings. He was a military and airline pilot for 39 years before founding G-FORCE, a pavement marking company with franchises in 37 locations around the country, as its CEO in 2017.
How to Stripe an Airfield
The job also just happened to be in the niche G-FORCE was hoping to carve for itself in airport markings of private and regional airfields. “We see a real opportunity in that particular space because the proj ects are often too small to attract the large companies specializing in airfield markings,” Child said. That leaves a gap in the market that an organization like G-FORCE can fill using much of the same equipment and crews for its existing book of work, under the guidance of its new ly trained certified airfield professional franchise partners. “This is a great growth opportunity for our brand because of our large geograph ic reach and our ability to bring together multiple teams of trained pro fessionals to complete these jobs.”
WWW.THEASPHALTPRO.COM 45 QuikJointProvenProductiveandUserFriendlyLessLabor,LessWaste&LessFuelSpeedyInstallations&NeaterFinishesPromotesJobSafety&SkillNoDelays,NoStaging&NoTowing Peel Stick Heat Done To Order Best Top Roll Asphaltic Joint Tape - Visit Your Local Paving Supply Store or contact: sales@quikpave.com ⚫ 888.825.1917 ⚫ www.quikpave.com ™ Always On Top ! QuikJoint: rolls come in 4 widths and each roll is 50 feet long. Packaged in 6 gallon plastic containers. Rolls are easily trimmed on the job-site to meet your requirements and to protect your own asphalt. Widths for a Variety of Job Applications 1 inch: Infill of Narrow/Shallow Cracks 2 inch: Over-banding of Joint/Crack 4 inch: Utility Cuts, Comply Govt Specs. 8 inch: Adds to Vertical Joint Density
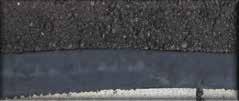
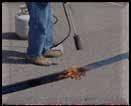
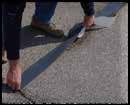

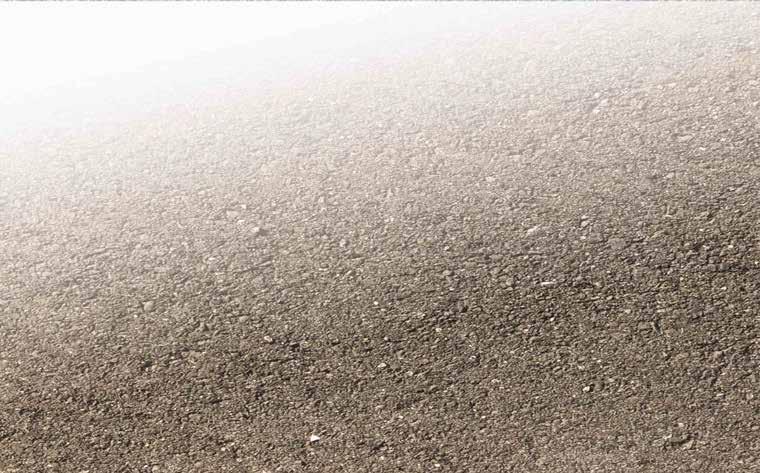
All the owners of G-FORCE’s 37 core locations are military veterans, several with aviation backgrounds. “Our team understands the impact of their workmanship in something as critical as a runway operation,” Child said. “When we expanded into this market, we wanted to make sure our team had the knowledge to perform these critical jobs the right way. And, frankly, we’ve found the FAA inspectors and field managers like working with veterans.”
Child said G-FORCE will always have a certified professional on its airfield marking projects, while also utilizing the projects as an oppor tunity to share those skills with other franchise owners and their local crews. “We have the crews in place who already know how to perform most of these tasks and just need a supervisor and project manager to make sure they’re performing the work in compliance with the specifi cations for that particular project,” he said.
The specifications are the most challenging aspect of airfield markings, Child said.
According to Mike Speidel, vice president at Sightline, the FAA came out with guidance in 2019 that said those performing mainte nance activity surrounding airport markings should be trained. In government terms, he added, “should is a recommendation, while shall is a “Airportsrequirement.”withcommercial passenger traffic coming through have very high standards,” Speidel said. “Just because you can paint a 4-inch line or a 6-inch line, doesn’t mean you can paint airfields.”
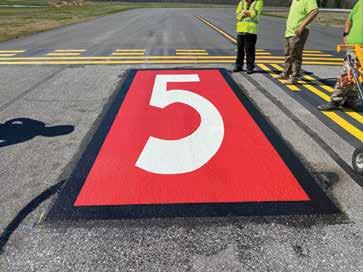

Train to Gain A Competitive Edge
As G-FORCE’s interest in the airfield marking niche grew, Child was surprised to learn the Federal Aviation Authority (FAA) does not re quire airfield marking training. “As an airline captain I often joked that my real job was ‘aviation attorney’ since so much of each flight involved legalities as much as engine thrust to get my jet legally and safely off the ground,” Child said. “I was very surprised to learn you don’t need to be certified to be awarded a project on an airport. But, your work does have to meet the specifications of installation, which are very rigid, and that’s why we chose the path of getting properly trained from the beginning.”
According to Child, the markings on the taxiways are more detailed than the runways. “The runways primarily have rectangular bars with numbers, but taxiways have turns, curves, checkerboard patterns, skip lines and other markings that require much more skill,” he said, adding that the specific designs are outlined in the project specifications.
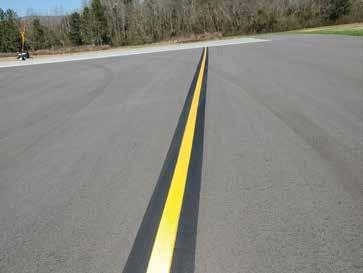
An Alabama Airport
46 SEPTEMBER 2022
Understanding how to apply the beads so the project passes the FAA’s retro-reflectivity test was a top takeaway for Hull from the Sightline training.
An emerging trend for the company is what Speidel calls semi-private training, where smaller airports hire Sightline to train their staff and then invite nearby airports, consulting engineers and area contractors to attend for a fee. Speidel just put on a training of this kind at Colorado Springs Municipal Airport, where 10 state airports were in attendance, and has also performed this type of training for Nashville International Airport and Palm Beach International Airport, among others. “Semi-private training helps them include all the people who contribute to the quality of that airport’s airfield markings.” Sightline also plans to launch an online version of its airfield marking training course in 2023.
One of the lessons Speidel sees as most valuable from Sightline’s course relates to calibration of the equipment using a test strip. “It’s key to identify all the variables—how fast you can go, what’s the pressure of the machine, the tip size to be used, the pavement you’re working with— to get the right paint thickness and to apply the right number of beads in a given time frame,” he said. “That calibration process is one thing that most contractors attending our course haven’t done much, if at all.”
If there is a single runway, as was the case in Anniston, the airport will shut down and publicize a Notice to Air Mission (NOTAM) of the air port’s closure, which pilots check for when plotting their flights. Then, the airport puts a large x-shaped sign on the runway and broadcasts the airport’s closure from the tower to approaching aircraft. The signage and broadcast would also apply if certain runways of a multiple-runway air port were closed for marking.
Traffic control was another area in which the training was particular ly useful, since it is so different from traffic control for G-FORCE’s other types of work.
Once it was safe to begin performing the work on Anniston’s airfield, the G-FORCE crew set to work removing the old thermoplastic with its Smith rotary grinders and collecting the dust debris to prevent Foreign Object Damage (FOD), a real threat to all aircraft and particularly jets. After properly preparing the surface to maximize adhesion, it was time to apply new thermoplastic and re-stripe the taxiway.
Understanding how to apply the beads so the project passes the FAA’s retro-reflectivity test was a top takeaway for Hull from the Sightline training.
The FAA regulates paint color codes and G-FORCE was able to use their standard Graco line striping equipment with on-board computers and lasers, but the use of reflective beads was something new to this crew.
Ensuring the project passes the retro-reflectivity test is also a con cern for the thermoplastic markings. “You have to be extra cautious to heat the thermoplastic markings to the proper temperature and no higher, so the glass beads adhere but don’t sink in too far that you
That’s exactly what happened when Hull and business partner Harry Rowan joined Young for the airfield marking job at Anniston Regional Airport in March 2022. The airport services regional passenger traffic and airborne firefighting units, and is a major hub for visitors to the Tal ladegaYoungSpeedway.hadperformed work for the city of Anniston in the past when the airport reached out to him to see if he was interested in doing their airfield markings. “Rob wasn’t certified yet, so he asked if we’d be inter ested in helping,” Hull said. “We were excited to help him, but also to get our feet wet since it was our first airfield job.”
Sightline has been offering airfield marking training for 15 years, but launched its Airfield Marking Professional Symposium in 2018. Since then, roughly 2000 people have participated in the symposium. The symposium is held two or three times per year, usually in different locations to make it more convenient for contractors and airports around the country. Sightline also performs around 20 private trainings per year, for example, a recent training Speidel put on at Dallas/Fort Worth International Airport. The benefit of private training, Speidel said, is the opportunity for hands-on training using the crew’s own equipment. “That’s something 95% of our private customers opt for, so we can put into practice what they’ve learned in class.” Besides the hands-on training, the public and private training covers the same subjects, ranging from traffic management and specifications to surface preparation, calibration, achieving reflectivity and the inspection process.
Hull said one of the most valuable aspects of the training program was the manuals and reference materials he was able to return to as needed and the ability to contact Sightline with questions should any arise.
Setting Sights on Airfield Marking Training
The specifications are the most challenging aspect of airfield mark ings, Child said. “These projects can be fraught with peril,” he said. “If you don’t apply it to spec, you’ve opened up a can of worms that might require additional applications or even removal, which is both costly and not a good look.”
One common issue they experienced was that the airport had some areas where the pavement was cracked, which they filled with a rubber type crack filler. “In order to ensure proper aesthetics on the final mark ings, the crack filler was heated to level out inside the crack and the crew scraped away any excess protruding filler,” Wacha said. “The outcome was a pristine marking without the interference from the filler beneath it.” Otherwise, the job went perfectly. “The city was very happy with it and we passed the FAA inspection, so I’d consider that a big win for our first time,” Hull said. Next for the Niche Already, G-FORCE has fielded quite a few calls about their expansion into airfield marking, and has performed two additional projects in 2022.
“Now that we’re doing airfield markings, I have a whole new perspec tive when I’m looking down at an airport,” he said, finding that he often makes note of thermoplastic that needs to be replaced or dirty hold bars. “I’m taking pictures from the sky of any deficiencies I see as I approach these airports and then calling them to offer an estimate.” With each airfield job, G-FORCE strives to pursue this new niche strategically. “We aren’t going after O’Hare International,” Child said. “We’re taking baby steps, making sure we can perform smaller region al airports to a high standard. As we do, I think this niche is going to take off for us (pun intended) and open up new opportunities for our teams around the country.”
“When you have such a high profile job, you want your finest work out there. If we can be trusted to mark an airport, we can be trusted to do a strip mall.”—Jack Child

As G-FORCE’s airfield marking operations increase, Child said they anticipate needing bigger, more advanced striping equipment for strip ing and dispensing reflective beads and larger heaters for applying ther moplastics. Several of its franchises are uniting together to make those investments. For example, Hull and Young plan to team up to buy air port-specific equipment to share between their franchises. Hull is also taking action to attract more of this work. Since he is currently working toward his private pilot’s license, Hull frequently finds himself at the types of airports for which G-FORCE is hoping to perform work.

WWW.THEASPHALTPRO.COM 47 won’t pass the reflectivity test,” Hull said. He stresses the importance of keeping the heater moving to avoid overheating the thermoplastic and checking on the bead depth as you go. Since the Anniston Regional Airport was G-FORCE’s first airfield marking job, they brought in technical support from their preformed thermoplastic supplier, Preform LLC, St. Augustine, Florida. “Two of Preform LLC’s owners, Susan Wacha and Steve Makosch, walked us through the job to make sure we were applying the thermoplastic cor rectly,” Hull said.
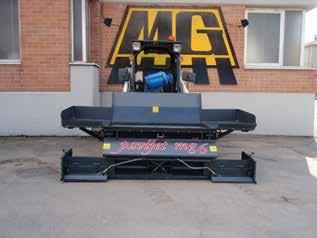
First, a worker pre-heats the crack sealant onboard the unit so the material is ready to use upon arrival at the job site.
The integrated blow-off system cleans the road surface and cracks for sealing. Step 4
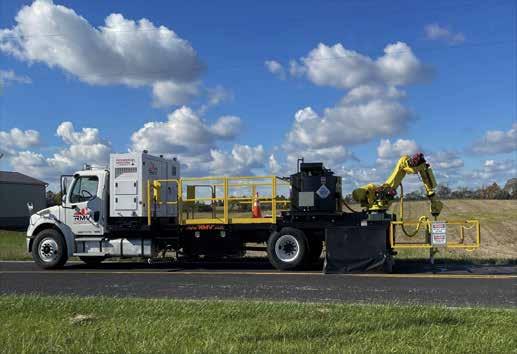
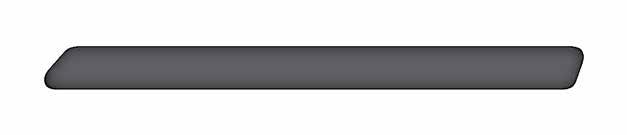
Step 3 how it works
2022 Keeping maintenance crewmem bers out of harm’s way is easier to do if you can automate the labor-inten sive portions of pavement maintenance or turn those activities over to a machine. After seeing a crack sealing crew working along side traffic during his commute to work one day in 2019, Todd Hendricks of Pioneer In dustrial Systems, headquartered in Alvord ton, Ohio, came up with the concept of a robotic maintenance vehicle, developed a RMV division of his company and partnered with SealMaster to make the vehicle a reality. Engineers integrated an R2000 onto a truck chassis and equipped it with components to create an efficient form of work. Here’s how this award-winning system works:
Next, the safety cage is expanded hydrauli cally from the cab of the truck to accommodate the FANUC R2000 robot’s range of motion.
The CrackPro RMV’s advanced AI vision system measures and scans cracks in the area where maintenance is to be performed.
A driver pulls the CrackPro RMV—which is a full truck chassis equipped with a FANUC R2000 robot, generator, integrated blow-off system, custom Crack Pro 260, LED safety lights, and rear safety cage—to the work zone where crack sealing is to be performed.
SealMaster’s CrackPro RMV
48 SEPTEMBER
The robotic arm guides the wand and shoe of the heated hose to fill cracks.
Step 5
At the job site, the driver expands the safety cage to accommodate the robotic armʼs range of motion. Step 2
WEB EXTRA
Watch a video of the CrackPro RMV in action on YouTube https:// youtu.be/lO5A2BR79OE
SafetyExpandableCage K Here’s
The advanced AI vision system measures and scans the cracks to be filled.
With this gathered data, the system guides the automated blower system in cleaning the cracks for sealing. The system communi cates with the robotic arm, guiding the wand and shoe of the heated hose to dispense crack sealant. It controls material flow. A second worker stays on the back of the unit to monitor application and replenish the crack sealant as needed throughout the shift. For more information, visit sealmaster.net.
The driver pre-heats the crack sealant material before driving Step 3
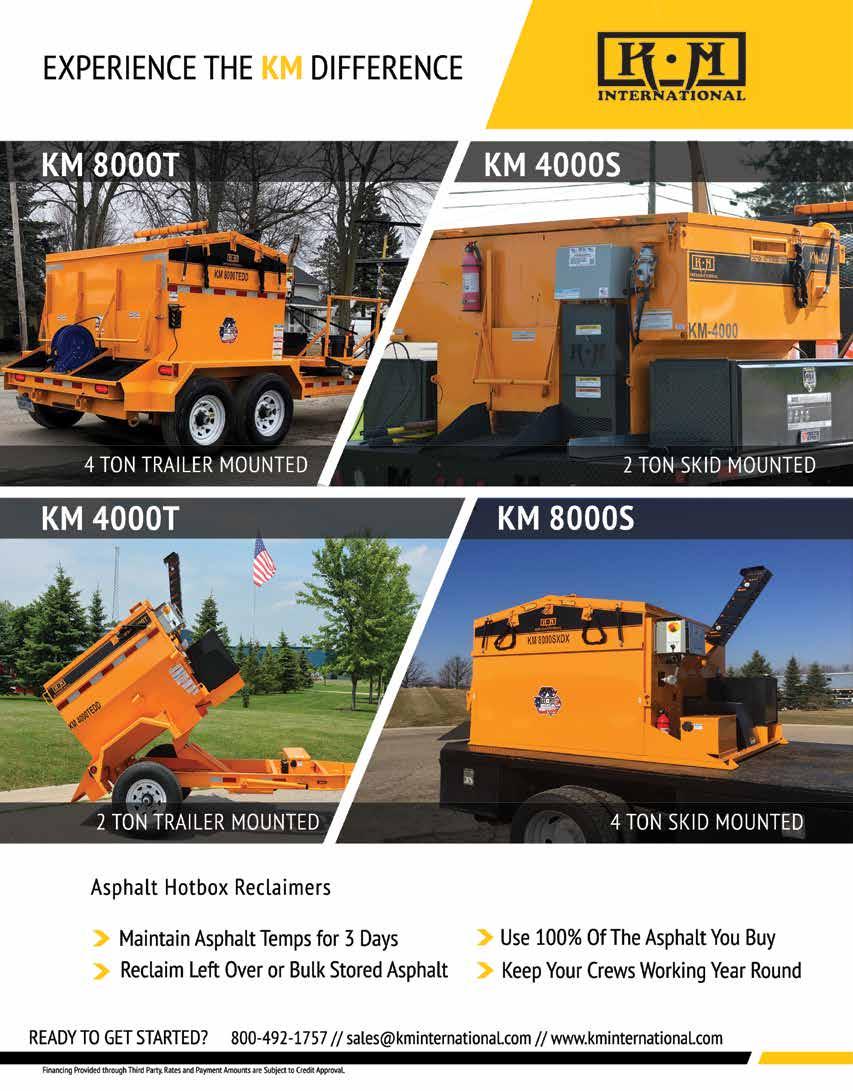
BY MARTIN KIRCHGASSNER O
DIAMOND PLATES FOR ACTIVE PROTECTION
To assist asphalt producers with their bottom lines, original equipment manufacturers (OEMs), component manufacturers and service providers are releasing a host of new offerings to the mar ketplace. Check out a sampling over the next few pages of what’s new to help you with production. THESE TREATMENTS CAN BE APPLIED TO ASPHALT PROCESSING EQUIPMENT AT ANY STAGE, FROM ORIGINAL MANUFACTURE OR AS PART OF A REPAIR AND RESTORATION PROCESS.
PROTECTIVE COATINGS
Wear facing can help address these challenges by protecting equip ment against wear. In addition to extending the life of components, it can help maintain their original shape and dimensions, so they con tinue to offer optimal performance and energy-efficiency. These treat ments can be applied to asphalt processing equipment at any stage, from original manufacture or as part of a repair and restoration pro cess. Not only does wear facing give components a second life, but it of ten results in better-than-new performance. This article looks at Casto dur Diamond Plates® (CDP®) specifically.
CDPs are designed to provide the basis for comprehensive and cost-ef fective wear protection. They feature a composite structure made by arc-welding, vacuum-fusing or laser-powder-coating of abrasion-ero sion-resistant alloys onto a weldable steel plate. The production process is based on advanced material science to ensure premium quality and consistent properties across the entire surface.
Tests have shown that CDP plates can offer up to five times longer service life when compared with previous solutions such as hardened steel, polyurethane and cast iron. They provide a high level of pro tection for equipment both while asphalt is being mixed and during cleaning and maintenance. In addition, the plates are highly resistant to chipping and are available in different alloys and thicknesses, designed for specific wear scenarios.
CDP plates can be cut—using standard methods such as plasma arc, water jet or laser—and shaped and fitted to protect almost any sur face in an asphalt production plant or to construct components like the tubes for filler transport, chutes, grates and screw flights. Retrofitting the plates to existing equipment is straightforward, with attachment by screws, rivets or spot welding. (It should be noted that the robust na ture of asphalt equipment means that it can change shape over its long life. Therefore, to maintain the best possible fit and function, new mea surements should be taken each time an engineer returns to check for wear and plan liner replacements.)
pera tors of asphalt plant and paving equipment can re duce maintenance costs and downtime by taking advantage of the latest wear facing technologies. When critical equip ment functions optimally, it consumes less energy; therefore, asphalt plants can benefit from both improved energy efficiency and a lower CO2Asphaltfootprint.production and paving subjects heavy equipment to an abrasive mix of aggregates, binder and filler. Where aggregates used to be mainly crushed rock, sand, gravel or slags, they are now being sup plemented or replaced with construction and demolition debris. The main binder used is liquid asphalt cement (AC); however, bio-based binders are also under development. Whatever its constitution, asphalt can cause intensive wear and tear that left unchecked will cause early failure of components. The deterioration of key components will lower energy efficiency and performance. It may also affect the quality of the asphalt, increasing the risk of rejection by the final customer.
Protect Parts for Sustainable Asphalt Production
REINFORCE PAVING EQUIPMENT
Wear facing can be usefully applied to asphalt paving equipment such as road scrapers and pavers. On road scrapers, CDP has been used to protect the rail, the rotor and the casing. On pavers, CDP is an ideal solution for lining the chain conveyor. In one example, a chain conveyor liner manufactured from specialized heat-treat ed steel plate with a Brinell hardness of 400 HB was replaced by CDP. The result was a fivefold increase in component life.
50 | SEPTEMBER 2022 PRODUCT GALLERY
There are some components where CDP plates may not be suit able due to the nature of the surface that needs to be protected, such as mixer blades or finisher screws. In this case a protective coating may be applied using techniques including wire coating, arc wire spraying and powder coating.
The hardness value (HV) of the CDP material is 1,500 to 3,000. Its durability owes much to the presence of ultra-hard phases anchored in a robust matrix.
Whatever the maintenance or wear-related challenge in asphalt plant or paving equipment, Castolin Eutectic has a well-proven answer. The aim is to help customers build key components back to better-than-new performance over significantly extended life times. A network of 700 technicians and specialists is ready to provide on-site wear detection, analysis and advice, before rec ommending the ideal solution. Repairs and wear protection can be applied either at the customer’s own site or in specialized workshops. Martin Kirchgassner is the chief technology officer of Castolin Eutectic. For more information, visit the company’s website.
And a world of experience to build that road. As the global leader in road construction and minerals processing technology, we‘ve seen just about everything there is to see. In every climate, every condition, every twist, turn and terrain. And we put that world of experience in your hands, so you can experience exceptional performance and results at every phase of the road construction cycle. A JOHN DEERE COMPANY CLOSE TO OUR CUSTOMERS It takes a road to get there. WIRTGEN VÖGELE HAMM KLEEMANN




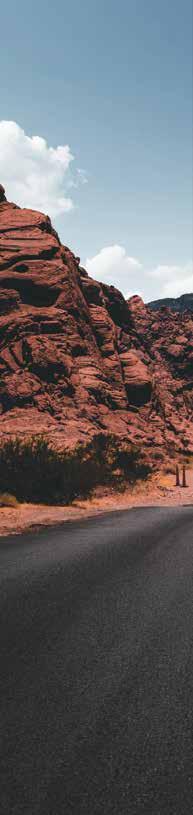
For more information, contact socialmarketing@astecindustries.com.
52 | SEPTEMBER 2022 PRODUCT GALLERY ASTEC The Materials Solutions Group of Astec Industries, Chattanooga, has designed and launched its newest portable high frequency screen plant, the PTSC2818VM. The plant’s innovative design features an 8-foot-wide high frequency screen. Astec’s newest PTSC plant is equipped with an 8-foot x 18-foot top deck and an 8-foot x 12-foot bottom deck. The patent-pending screen design features externally mounted vibrators at the ends of the tappets for a more aggressive screening action. This unique design creates a high G-force and re duces heat load from material to motors as compared to single, cen ter-mounted vibrators. The screen is equipped with hydraulic operat ing angle adjustment, a fines collection hopper, top- and bottom-deck discharge chutes and an aggregate spreader.
For more information, contact Travis Sneed at (423) 476-9900.
Commenting on the announcement, Ben Brock, President and CEO of BROCK, said, “Nothing we do at BROCK is possible without support from our customers. We thank our customers for our growth. The new paint booth and main office are already helping us be more efficient in providing quality products and outstanding service to our customers.”
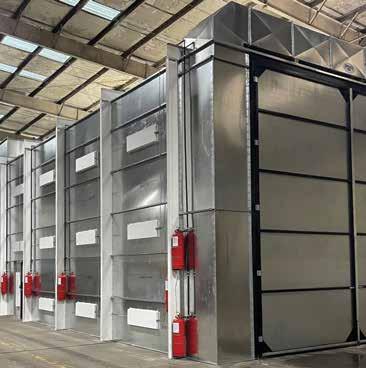
The new portable plant is available with a variety of options, in cluding: steel screen cloth, vinyl dust cover, hydraulic leveling jacks, immersion heaters for hydraulic reservoirs, starters for three offplant conveyors and more.
H&B Haver & Boecker Niagara, St. Catharines, Ontario, announced the next-generation Niagara T-Class vibrating screen. Its new de sign retains the original concentric technology while improving screening uptime and performance with new features, according to the manufacturer. For example, the T-Class deck frame is now primarily lock bolted, rather than welded. The machine also per mits cross beams to be positioned and lock bolted every 4 feet, allowing for better clearance and easier maintenance, according to theThemanufacturer.newvibrating screen includes Haver & Boecker Niagara’s new Drop Guard system. Innovative liners are designed to provide 100% cross beam protection. The system drops over the cross beam with no adhesive or tools required. The manufacturer also redesigned the flat deck frames of the new T-Class vibrating screen for simplified maintenance. The pin & an chor deck frame is adaptable to virtually any pin-style modular screen media. It features polyurethane anchors that are designed to The new portable screen plant from Astec features an 8-foot-wide high frequency screen. Brock’s new paint booth is now in operation.
BROCK BROCK, Chattanooga, a manufacturer and supplier of equipment, parts and on-site services to the hot-mix asphalt (HMA) plant in dustry, announces the opening of a new paint booth and new main office. The new paint booth is inside the company’s existing manu facturing facility, and was custom built to allow for painting of any size HMA plant component. As for the new main office, company personnel have already moved into the 6,000-square-foot build ing. The office is connected to Brock’s main manufacturing facili ty, which is located on the company’s 23-acre site in Chattanooga.
Similar to other PTSC plants, the 2818VM features a nominal 54-inch x 38-foot delivery conveyor with hydraulic drive and full-length skirt boards. The chassis is fitted with manually operating support legs, outrig gers for additional support and folding walkways along the screen.
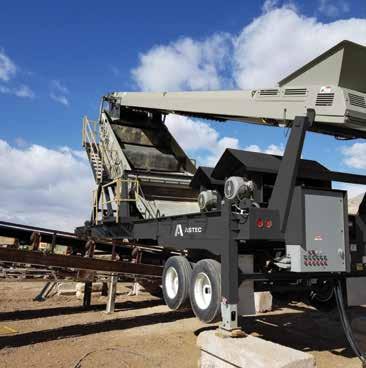
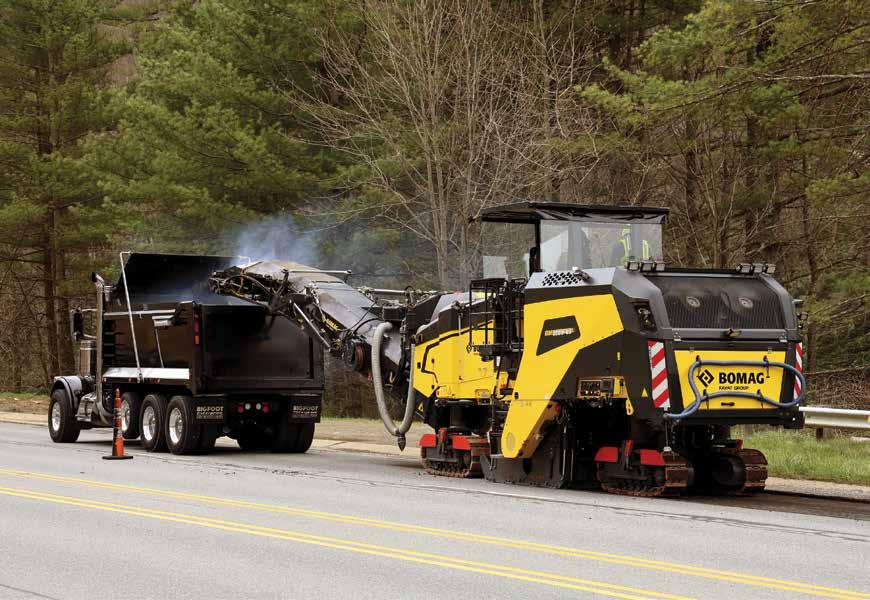
• SriCote: An amine-free anti-stripping agent, providing moisture and fuel resistance. For more information, visit Sripath.com
• ReLIXER: a green asphalt recycling agent or rejuvenator used to restore properties of aged bitumen in RAP;
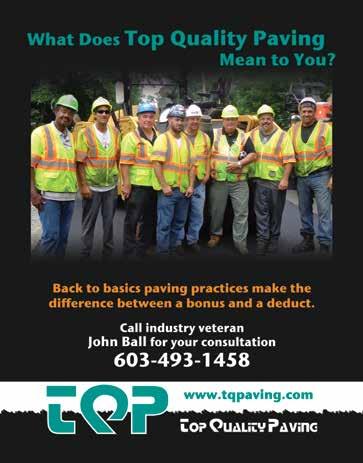
The T-Class can also be manufactured for side-tensioned or bot tom deck end-tensioned screen media. Each new side-tensioned machine comes with Haver & Boecker Niagara’s signature Ty-Rail™ quick-tensioning system. For more information, contact Duncan High or visit the H&B website. MAJOR Major, Candiac, Quebec, a global manufacturer of high-perfor mance wire screen media, introduces its FLEX-MAT Modular PLUS screen media. This screen media offers a high open area, efficient stratification, no blinding or pegging, and new and im proved wear life comparable to polyurethane screen media, ac cording to the manufacturer. The efficiency-enhancing characteristics of all FLEX-MAT screen media, including the modular PLUS series, are created by bonding with distinctive lime-green polyure thane strips rather than weaving them. This allows wires to vi brate independently from end to end under material contact. The high frequency of the wires—8,000 to 10,000 cycles per minute— adds to the vibration of the screen box to speed up material sep aration and passing. The increased screening action is designed to improve material throughput while virtually eliminating nearsize pegging on the top decks and fine material blinding and clog ging on the bottom decks. The new PLUS series is available in a variety of patterns, includ ing the D, S and T series. The D series features a standard square pattern, which is ideal for precise sizing. FLEX-MAT Modular PLUS screen media panels are available in either the patented OP TIMUMWIRE or 304 stainless steel wire. In addition to modular panels, MAJOR’s signature FLEX-MAT Modular PLUS media is available in tensioned sections for use on crown decks. For more information, visit the Major website.
OPTIMUMWIRE®
“Alan and Jonathan bring decades of technical and marketing ex pertise to our team and provide us with a valuable leverage to pur sue and develop new opportunities within Africa. We are thrilled to have them on our team,” said Deepak Madan, chief marketing & business development officer of Sripath.
• PGXpand: a unique polymer designed to improve high tem perature performance of bitumen and rutting resistance, fatigue properties, and roadway durability;
AW&A markets a variety of products to the bitumen and asphalt industries in Africa. AW&A effectively uses its technical expertise and commercial know-how to provide innovative solutions for a wide range of challenges faced by its customers in the industry.
54 | SEPTEMBER 2022
SRIPATH Sripath Technologies®, Mahwah, New Jersey, recently finalized an agreement with Alan Wills & Associates, establishing AW&A as its distributor and marketing partner in South Africa and various oth er countries in Africa.
Sripath develops, manufactures and markets a range of addi tives used to enhance performance of bitumen and asphalt mix es. Sripath is a global company, with offices, affiliates and agents in USA, India, Australia, UK, Brazil, and now in South Africa.
Alan Wills, owner & CEO of AW&A said: “We are enjoying our co-operation with Krishna and Deepak, who have a very clear idea of the value Sripath products offer to road industries around the world. Sripath’s drive to reach and gain traction in all major geog raphies and understand the unique requirements of each market, is unsurpassed by any principal we have worked with. We look for ward to bringing the benefits of Sripath products to road builders in South Africa and other African countries.”
Key products offered by Sripath® include:
“We are excited to formalize our arrangement with Alan Wills to market Sripath products in Africa. We welcome both Alan and Jonathan Wills to the Sripath team,” said Krishna Srinivasan, pres ident of Sripath.
• ReNUBIT and NuMIXER: modifier oils used to manage viscosi ty and improve polymer and crumb rubber compatibility; and
PRODUCT GALLERY prevent premature wear on the deck frame. Additionally, the open design of the modular deck prevents material build-up on the bar rails. The cap & slide deck frame is adaptable to virtually any groove style modular screen media and features full rail protection.
geophysical.com800.524.3011sales@geophysical.com REDUCE CORING PaveScan® by GSSI GSSI’s revolutionary PaveScan RDM 2.0 is a full-coverage asphalt density measurement system that accurately identifies variations in road quality in real-time. IMPROVE QUALITY Quickly assess the quality of pavement during the paving process. Finally, you can fix low density issues related to cold mix, paver stops and breakdowns. IMPROVE LIFE SPAN Detect problems to help avoid such premature failures as road raveling, cracking and deterioration along longitudinal joints. IMPROVE SAFETY Reduce the need to core and expose fewer workers to the dangers of work zones. MORE INFO
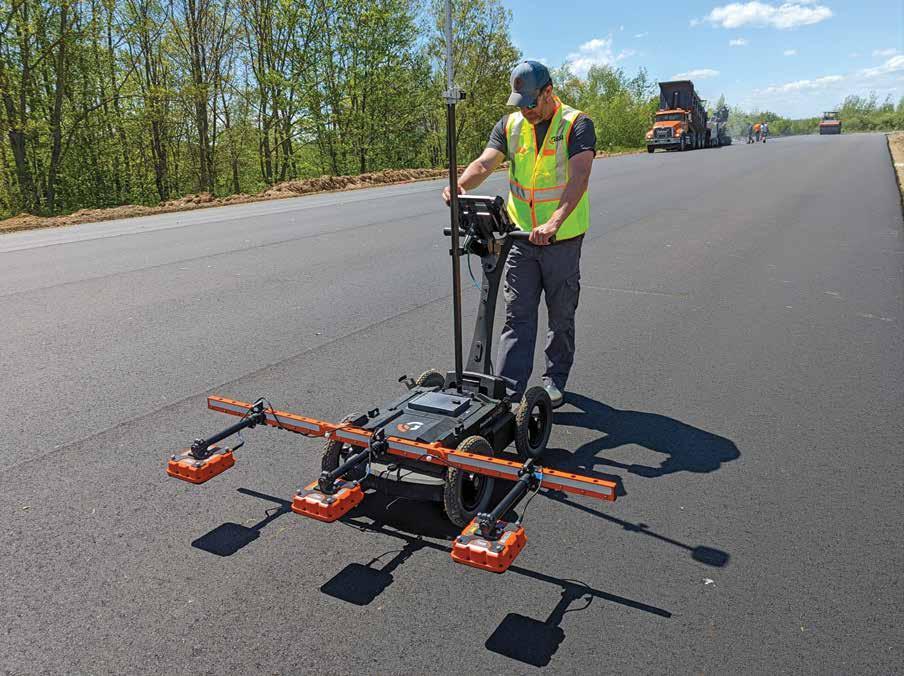
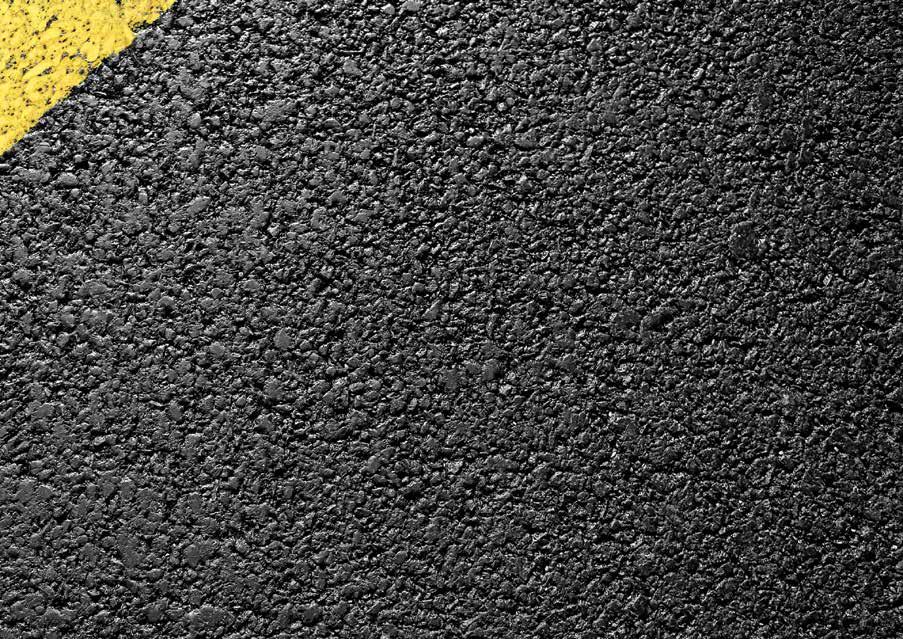
5. EQUIP THE CREW PROPERLY.
lthough many industries currently face labor shortages, the asphalt industry has unique factors that make worker reten tion more challenging. Not only does it often involve hard, hot work, but it takes crews across the city, state, or region. Work is frequently performed at night, and it can also be more dangerous than other professions. Add to that list the fact that asphalt paving is seasonal in much of the United States, and you have a perfect storm to lose members of the workforce. With a few weeks left in the 2022 paving season, AsphaltPro crowd sourced some strategies to retain this summer’s top talent for 2023.
One tip to retain asphalt workers is to remind them how their work positively impacts our communities. Photo courtesy of James Kelly
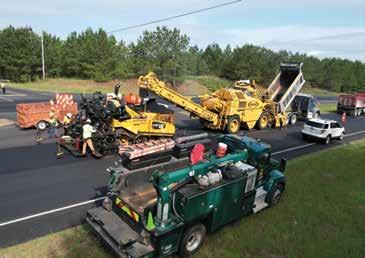
2. BENEFITS MATTER ALL YEAR.
Pat Ferry, estimator and project manager at Aztec Paving Inc., San Diego, said their number one retention strategy is to offer employees roughly 5 to 8% more than their competition. He said it’s easy to find out what other companies offer through the grapevine, adding that some companies have called Aztec directly to ask what they pay em ployees. “It’s a small industry in San Diego, so it’s easy to keep abreast of what other companies offer so we can offer a fair and competitive wage based on our market.”
A
3. TAKE CARE OF THE WHOLE EMPLOYEE.
Glen Powell, paving department coordinator and project manager at Schlouch Incorporated, Blandon, Pennsylvania, said the company strives to promote the overall well-being of its employees. Not only does Schlouch offer numerous wellness activities as part of its health care package, including things like webinars on various health topics and free health screenings, but it also provides access to other ser vices like legal and financial planning advice.
13 Strategies to Retain Asphalt Workers
One asphalt industry professional on LinkedIn stressed the differ ence between employees during training and a company’s skilled workers. “My number one is I do not tell [my skilled workers] what to do,” she said. “The training process is a different chapter [com pared to] skilled workers.”
Adrian Alblas, president at Burnaby Blacktop Ltd., Vancouver, sum marized it well: “Trust in people. Do not micromanage.”
It may sound obvious, but paying a fair and competitive wage goes a long way. As one asphalt professional put it on AsphaltPro’s Facebook page, “I don’t do it for a pat on the back.” Or, as another put it, “If you have good help, you have to pay them [well].”
4. DEVELOP A SOLID ONBOARDING EXPERIENCE.
“If people are constantly performing tasks that leave them exhaust ed at the end of the day, day after day, that reduces the longevity of that person’s working career,” said Alex Berg, CEO of Cratos Equip ment. “If they’re exhausted and have to move into another role, now you have to train someone else. That really affects your turnover rate.”
“We look at the well-being of the employee and their families as a whole,” Powell said. Some examples of employees using Employ ee Assistance Programs (EAP) include writing a will and financial planning for retirement and other goals. “We offer assistance to help our employees achieve their personal goals because we as a compa ny care about them and their families. If we can reduce some worries for our team members, we believe they will be happier and more fo cused at work.”
1. PAY EMPLOYEES WELL.
Not only does this apply to having the equipment the crew needs to perform the job safely and successfully, but asphalt pros on social media suggested taking it one step further. For example, they sug gested investing in better fitting and cooling safety gear and putting canopies on machines where possible.
6. DON’T MICROMANAGE SKILLED WORKERS.
BY ASPHALTPRO STAFF
Asphalt professional Lance Rickenberg on Facebook commented on the importance of compensation, but also health care (also during the offseason). “Most of the bigger asphalt companies offer year ’round [health] coverage, or some version of it,” he said. This includes his em ployer, Continental Paving, Hudson, New Hampshire, a family-owned business of roughly 400 employees. “It’s a great company to work for.”
“Starting a new job can be stressful for many people,” Powell said. “We make a concerted effort to make every new employee feel wel come and connected with the team. Just doing a simple once-perweek check-in to see how things are going and if they need help with anything shows leadership is committed to helping the new employ ee succeed.”
56 | SEPTEMBER 2022 OFF THE MAT
For more information on the items above and more, call or visit our website. Our trusted and knowledgeable asphalt experts will come to your site and appraise your equipment or plant. All you will have to do is sit back and let us bring approved buyers to you! Turn your surplus asphalt plant equipment into much needed plant upgrades. F E A T U R E D E Q U I P M E N T GTB-5516D Astec® 200 TPH Double Barrel Stationary Counterflow Drum GTB-5489 Astec® 400 TPH Partial Portable Counterflow Drum Plant GTB-5513 Astec® 300 TPH Portable Counterflow Drum Plant Availability, price and condition subject to change by Stansteel®. Specifications are accurate to our knowledge, however; they are not guaranteed. All prices are in U.S. dollars unless otherwise noted. Equipment is sold on the basis of as is, where is, therefore, Stansteel® recommends inspection by buyer of any used equipment to determine suitability to their requirements. GTB-5543E Hauck® StarJet 580 Burner with TBA-36-100 Blower GTB-5542 Dillman® 400 TPH Highly Por table Parallel Flow Drum Plant GTB-5540I Cedarapids®/Standard Havens® Nominal 60,000 CFM Portable Baghouse Inspection Marketing Showing Sales
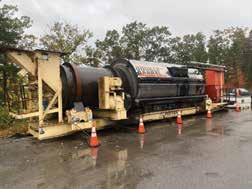
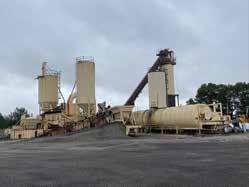



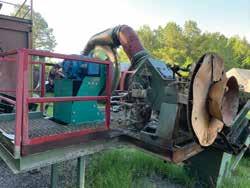
Ferry said Aztec strives to create a professional but fun work environment. “We are here to work and get the job done, but we also like to laugh and joke around,” he said.
PUGM I L L SYST EM S We’ve been designing and manufacturing custom mixing solutions in Tennessee for nearly 40 RCC • CTB • Pugmix • Stabilized Sand Coldmix • Fly Ash • Salt Treatment Rental Plants Available Check out additional projects at: PU GMILLS YSTEMS .C O M or give us a call at: 9 3 1 -388- 06 2 6
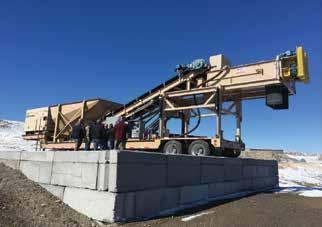
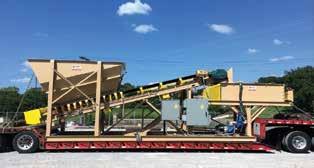
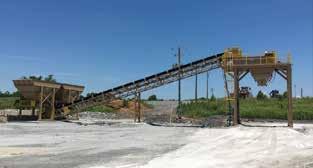
58 | SEPTEMBER 2022
“If you take care of your employees every year, they will work hard for you and will be there for life,” commented another as phalt professional.
10. SCHEDULE EMPLOYEES THE WAY THEY PREFER, WHEN YOU CAN. Although the exact project schedule will likely be subject to the owner, agency, or customer’s calendar, remember that dif ferent employees/crews may prefer to work different sched ules. For example, one asphalt professional shared with As phaltPro his experience of quitting after 33 years with the same asphalt contractor when a change in company policy meant he was no longer able to work the hours and days he had become accustomed to.
“Respect your people, because without your employees, you are nothing,” said Glenn Pye, a professional in the asphalt/ heavy civil industry. “If you’re a supervisor or manager, you are supposed to be a leader.”
8. FUN HELPS, TOO. Jacob Weins, senior project manager at North Star Contracting Inc., Calgary, Alberta, said management often brings the crew cold drinks on hot days or coffee and donuts to the job site. He also likes to hand out swag to the employees, like hats, shirts andJeffsweatshirts.Wilsteinof Tuscon Asphalt Contractors, Tuscon, Arizo na, recommended keeping treats like a freezer full of ice cream on hand, a refreshing treat after a hot day’s work.
OFF THE MAT
7. TREAT PEOPLE RIGHT. Although good pay is important, wrote Juan Sebastian Sarto rio Nuñez, an asphalt plant operator for Grinor S.A., Uruguay, treating employees well and making it clear to them that you value their work is extremely important. “Wherever you are treated well, you will return,” he said.
9. SHOW EMPLOYEES A CAREER PATH FORWARD. Another tip from Kerkvliet is to show employees opportuni ties for growth. At Journey Group, this takes the form of ca reer pathing. “So many times, an employee starts in a role and doesn’t get communicated to on how to take the next step,” he said. “We want to show them there is an opportunity to ad vance if they so choose, and what is expected in order to do that.” Journey Group has several current foremen and superin tendents who began with the company as laborers.
“We have a high standard for our leaders to treat people the way they’d like to be treated and give feedback constructively,” said Ryan Kerkvliet, vice president of asphalt paving at Jour ney Group, Sioux Falls, South Dakota. “It’s hard enough doing this work, dealing with 90-degree heat, traffic, and the travel ing public honking at you, so we try to make our work environ ment as good as we can.”
WWW.THEASPHALTPRO.COM | 59
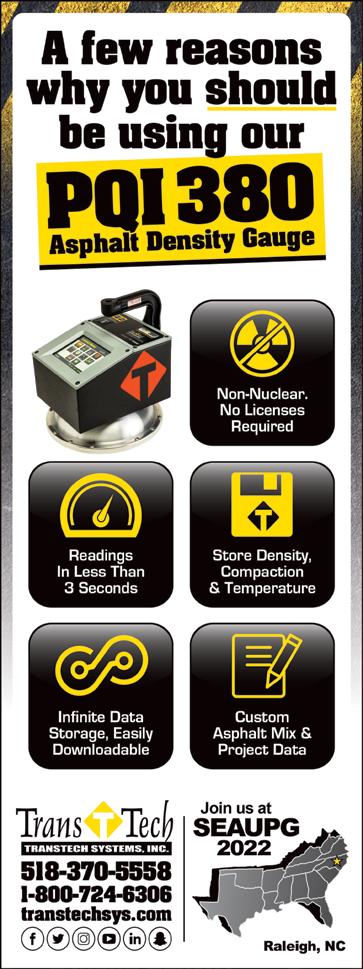
13. HELP EMPLOYEES SEE THE FRUITS OF THEIR LABOR.
“The feeling that our crew was a family and we stuck together [through] good and bad kept me coming back,” said one retired as phalt professional on LinkedIn.
At C.W. Matthews Contracting, Marietta, Georgia, superinten dent of the asphalt construction division James Kelly likes to show the crew any drone photos and videos he’s taken. “Getting that bird’s eye view of what they’ve done gives them that buy-in and helps them see what we’ve accomplished as a team,” he said. “There’s more to it than just work; there’s pride to it.”
THERE’S
After paying employees at the top of the market and illustrating that Journey Group values employees’ opinions, Kerkvliet’s final tip was to do what he can to cultivate a work culture employees enjoy.
12. CULTIVATE A CREW THAT FEELS LIKE FAMILY.
“THERE’S MORE TO IT THAN JUST WORK; PRIDE TO IT.”—JAMES KELLY
“Do they enjoy working here? Do they like the team they’re working with?” he said. “That’s the next biggest thing.”
If a worker’s schedule cannot fit into a new project schedule, being flexible enough to move that worker to a different crew or to a different role, when possible, goes a long way in prov ing to that worker how much you value his or her skill in your company. Conversely, if a worker is a caregiver in his or her family, or encounters a change in circumstance that requires a change in scheduling for a month or a season, consider care fully whether you can modify work schedules or crewmember roles rather than lose a valued worker for the long-term over a short-term problem.
11. SHOW YOUR EMPLOYEES YOU VALUE THEIR OPINIONS.
Ferry also recommended sharing compliments and feedback from customers on a job well done. “As the project manager, I am usually the only contact with the customer while the work is performed,” he said. “Rarely do the customers actually communicate with my fore men or workers, so when they are satisfied with the work, I always pass it along to my employees. It is very gratifying to know someone is happy with your workmanship.”
“We try to keep [our employees] informed on the plans for the day/ week,” Kerkvliet said. “We want their input on how the plan could be affected/improved. We want them to feel like a part of the plan and to have buy-in on making the plan happen.” Powell said Schlouch also maintains an open-door policy. “If an employee has an issue that can’t be resolved with their supervisor, they always have an opportunity to elevate it to the next level for further resolution,” he said. “This is built into our company culture. When employees feel like they have a voice and they are treated fair ly, they feel valued.”
BY NICK GRANDY O
And as the company grows, the integration of IoT-connected de vices into smart mobility management solutions provides even more valuable telemetry outside the onboard data generated by your assets. These types of devices include wearables, drones, cameras, various types of sensors, and other positioning systems.
1. LEVERAGE THE CLOUD TO WRANGLE DATA AND PROVIDE REAL-TIME ANALYTICS. Modern fleet management solutions greatly reduce the time-con suming process of manually collecting, transferring, and storing data from disparate sources. Connected, smart mobility technologies such as the cloud make this possible, effectively un-siloing and wrangling data from various job sites and assets into a consolidated view, while ensuring the data is safe. An additional benefit that aggregate companies gain from the adoption of cloud and connected technologies is that many process es become automated thanks to software. This is not meant to replace jobs, but instead to augment the skills and expertise of humans on the job, letting them devote more time to making strategic decisions, and less time to mundane, manual tasks.
DigitalForDisruptionAggs
2. DIGITALIZE MAINTENANCE TOOLS TO LIMIT PREVENTABLE VIOLATIONS. With modern technologies, such as artificial intelligence and ma chine learning, maintenance becomes less reactive and more predic tive and preventive, by providing operators with forward-thinking insight into diagnostic information that can be easily understood as a digital health score.
3. MODERNIZE INSPECTIONS AND IMPROVE COMMUNICATION WITH CONNECTED DEVICES. Connected tablets and devices enable operators to manage tasks by the hour with full visibility into the operation, at their fingertips. Incab tablets allow drivers to complete time, date, and location-verified pre- and post-trip inspections, while receiving detailed directions for each route. They are also a powerful communication tool for the co ordination of unexpected changes.
ut of necessity, the construction aggregate industry operates like a well-oiled machine. A one-minute delay in cycle time can easily cost fleet managers more than six figures. As fed eral infrastructure funding starts to pour into the aggregate industry over the coming years, so will the demand to produce more material, faster. We can no longer track cycle times—along with any violations noticed in the quarry yard—with old-fashioned pen-and-paper and stopwatches. Now we have connected technologies that dramatically streamline these processes in real-time.
Today, major equipment manufacturers and modern AEMP 2.0 standards provide a wealth of data on how equipment is being oper ated and maintained. As the number and OEM variety of fleet assets increase across a growing number of work sites, so does the volume and complexity of this data—leaving fleet managers and manufactur ers with mountains of data. The more quickly companies can understand this data, the more efficient they will be. One solution is to undergo a company-wide dig ital transformation effort that replaces outdated processes, tools, and technologies with more modern and connected data-driven solu tions. Here are three first steps that aggregate companies can take in their digital transformation journey:
The future of construction and aggregate site operations is in le veraging better data trends and technologies that are designed to im prove the speed of production and growth of the business—while en suring best practice safety and environmental conditions are met.
Nick Grandy is the GM, Vocational—Industrial Services at Zonar.
60 | SEPTEMBER 2022 OFF THE MAT


The app’s Flag & Chat features enable re altime chat to record work-related notes and communication on the project. For ex ample, users can drop a flag on any point of interest and collect notes with text or loca tion-stamped pictures and video.
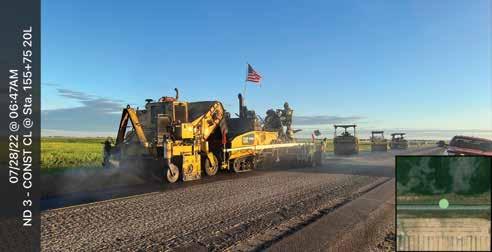
BY SARAH REDOHL T he idea of OnStation was created in the living room of former Ohio Department of Transportation’s (ODOT) Transportation Engineer, Jake Bailosky, in 2014. He’d just finished read ing “iOS App Development for Dummies” and wanted to put his skills to the test to re solve the all-too-common jobsite question, “Where are you?” Several years later, the roadway location solution was officially launched on the Ap ple and Google Play app stores. Geared to ward highway/road construction, OnStation has been used on more than 600 projects to date, totaling more than $12 billion in project value, and is used by more than 10 DOTs and more than 200 contractors.
OnStation’s Automatic Station Finder fea ture delivers accurate project location infor mation within 2 to 4 feet of accuracy, and lo cation options include stationing, LRS, mile marker, and OnStationlatitude/longitude.AccountExecutive
“Instead of taking pictures, adding them to a Word document, entering notes and lo cation information, and saving it as PDF to drop into the project folder, the crew can take photos with auto-stamped date, time and lo cation within OnStation and save them to the project folder in 15 seconds,” Thomas said, adding that they’ve strived to make the app easy. According to Thomas, the average user opens OnStation six times a day but for a very short period of time, to get their station, ac cess plans or take a photo.
And the team behind OnStation isn’t done yet. In July, OnStation released a Stationing API feature to integrate with several leading e-ticketing systems, including FleetWatcher, with others to come. “Currently, for projects using e-tickets, only a lat/lon is auto applied when that ma terial is laid,” Russo said. “Since lat/lon is not an easily referenceable location, the contrac tor or DOT must manually enter the project’s specific station to know where that material
62 | SEPTEMBER 2022 NEW TECH
For example, on a recent project in Indiana, the contractor created flags within OnSta tion for each core location along with notes and“Sayphotos.there was a problem with the paver at that location that caused an area of low den sity, that information can be noted in OnSta tion and available for reference next month or next year,” Russo said. “If there’s a failure, it’s possible to go back to that conversation and get a quick bead on what happened.”
Dave Thom as reminds us that not all projects reference stationing. “Occasionally, the DOT will re lease a project that references mile-markers or mile posts and we’ve adapted the app to match those projects, too.” Although jobsite locationing is the heart of OnStation, the app is also a centralized com munication tool that can be used to corre spond with others on a project across organi zations and “Knowingcontractors/subcontractors.whereyouareontheproject is the core of what we do,” Russo said. “Once OnStation solves that problem, there are a lot more advanced tools our users gain access to.” The app can also be used to instantly access and view current project plans, specifications, and design drawings. Users can overlay any detailed linework, represented in the plans, onto the project map, simplifying the difficult task of matching PDF plans to live observa tion on site. “If [the contractor] were using paper plans in the field, it would be much harder to fig ure out where they’re looking at on the road,” Russo said. “With OnStation, they can open the app and see their location immediate ly and compare it to whatever design layer they’d like to see. Any design elements includ ed when the project was created can be over laid on the map.” For example, the president of a paving con tracting company in Indiana woke up in the middle of the night with a fear that the loca tion of a pipe might impact their work. “He was able to log into OnStation at 2:30 a.m. to find out that his worry was true and was then able to plan accordingly,” Thomas said.
Know Where You‘re Working With OnStation
OnStation is a roadway location solution that can be used to access stationing, design layers and plans in one place.
OnStation can also be used to mark the locations of density tests and core samples.
“There’s no faster way to get your location when you’re out in the field,” said CEO Patrick Russo. “There’s no need to keep asking ‘Where are you?’ ‘What are you doing?’ ‘Where do I park?’ ‘Am I in the right location?’ ‘Where are the stakes?’ or ‘Are there any utilities where I’m at?’ If you know where you’re working on a project, the whole crew is able to be more pro ductive, efficient, and safer.”
“IF YOU KNOW WHERE YOU’RE WORKING ON A PROJECT, THE WHOLE CREW IS ABLE TO BE MORE PRODUCTIVE, EFFICIENT, AND SAFER.”—PATRICK RUSSO is on the road. With OnStation, the e-ticket is automatically updated with the station in formation when the truck meets the paver.” In July, OnStation also introduced a mea suring tool within the app to allow users to capture linear and shape measurements. “If I know I'm supposed to get ‘x’ feet on a 2-inch compacted fill with a particular truck and I see with OnStation that it got me an extra 100 or 150 feet, that information is money in the bank to the paving contractor,” Rus so Accordingsaid. to Thomas, new features for the app are heavily driven by users’ expe riences and feedback. “We have a very en gaged community of users ranging from road workers to engineers managing multi ple projects to construction company CEOs who tell us what they like and don’t like,” he said. “We put in a lot of effort to make the app even Currently,better.”OnStation is working to inte grate with major industry software provid ers to automate the daily diary process on the job site. “With the old system, the dai ly diary process is usually done at the end of the week or the month and you’re having to try to remember what happened and when,” Russo said. “If you’re already gathering that information with OnStation and it’s time stamped, that can be your project record.”
OnStation’s Automatic Station Finder feature delivers accurate project location information within 2 to 4 feet of accuracy, and location options include stationing, LRS, mile marker, and latitude/longitude.
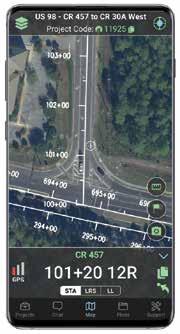
For more than 40 years, we’ve partnered with our clients to build customer-focused solutions that empower users like you to take control of your production and operations. For our team to continually improve, we need to know about your experience with our company, products, and services – both the positive and negative. Please take a moment to provide some feedback that will help us to understand what steps we need to take to become a better partner to you.
Command Alkon Wants Your Feedback.
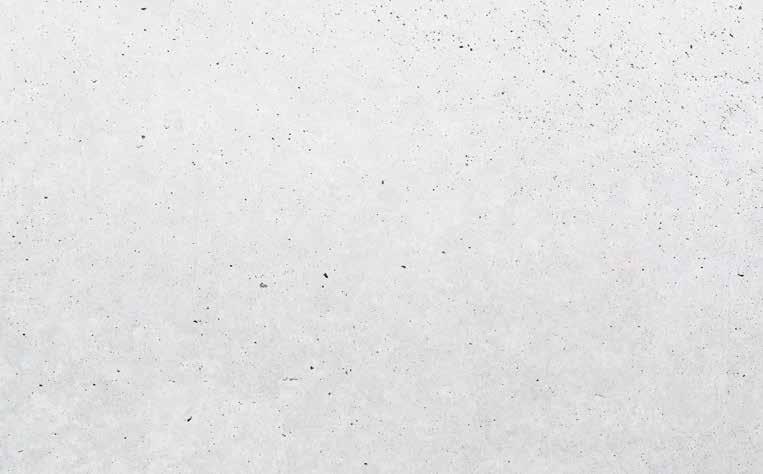
OnStation is available for Apple and An droid, smartphone or tablet, and offers both online and offline access modes. For more information, visit onstationapp.com.
Partnership is Key.
WWW.THEASPHALTPRO.COM | 63
“Some of our users may not go deeper than using OnStation as a roadway location solution, while others will want to use ev ery feature we make available,” Russo said. Either way, he added, “OnStation gives you a more informed workforce on the job site.”
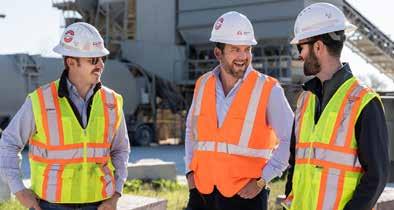
64 | SEPTEMBER 2022 781.738.5805 Elise Posillico Peter Brickman 516.353.9177 AsphaltPro’s advertiser index is designed for you to have quick access to the manufacturers that can get you the information you need to run your business efficiently. Please support the advertisers that support this magazine and tell them you saw them in AsphaltPro magazine. AD INDEX ALmix 6, 7 Asphalt Drum Mixers, Inc 32, 33 Astec Industries Inside Front Cover, Inside Back Cover, 11 B&S Light 61 Blaw-Knox 9 Bomag 53 BROCK 65 Cargill 31, 42 Command Alkon 63 CWMF 3, 25 Fast Measure 60 Forta 43 Gencor Industries, Inc 4 Greenpatch 36 GSSI 55 HiTek 47 Kenco 24 KM International 49 Meeker 13 Minds, Inc 17 National Credit Card Processing 64 Pugmill 58 Quickpave 45 Reliable ProductsAsphalt Back Cover Stansteel 19, 57 Systems Equipment 23 Tarmac International 27 Top Quality Paving 54 Transtech 59 Weiler 29 Willow 64 Wirtgen 51
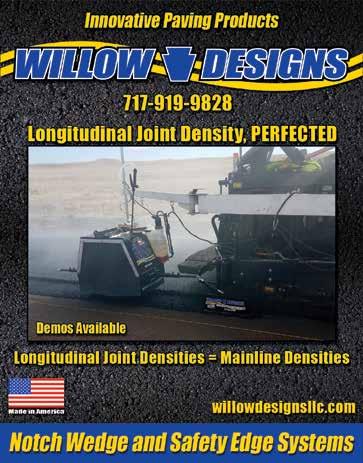


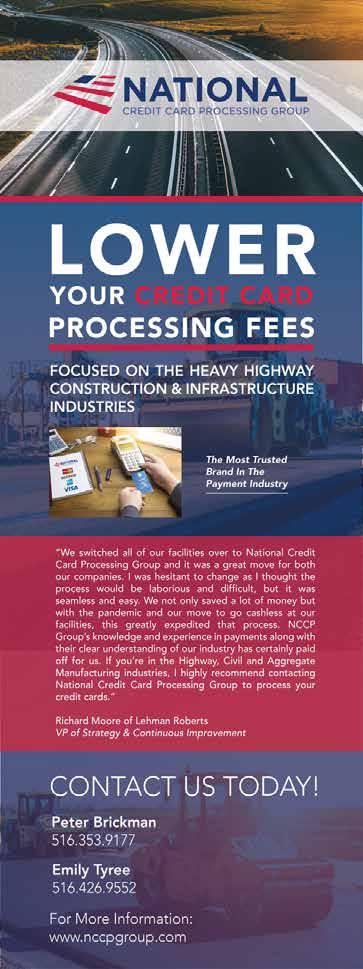
We’re on it. BROCK is proudly manufacturing equipment and supplying parts for hot mix asphalt plants. www.brock.llc | 2011 West Polymer Drive, Chattanooga, TN 37421 | 1.800.441.9528 | 1.423.476.9900
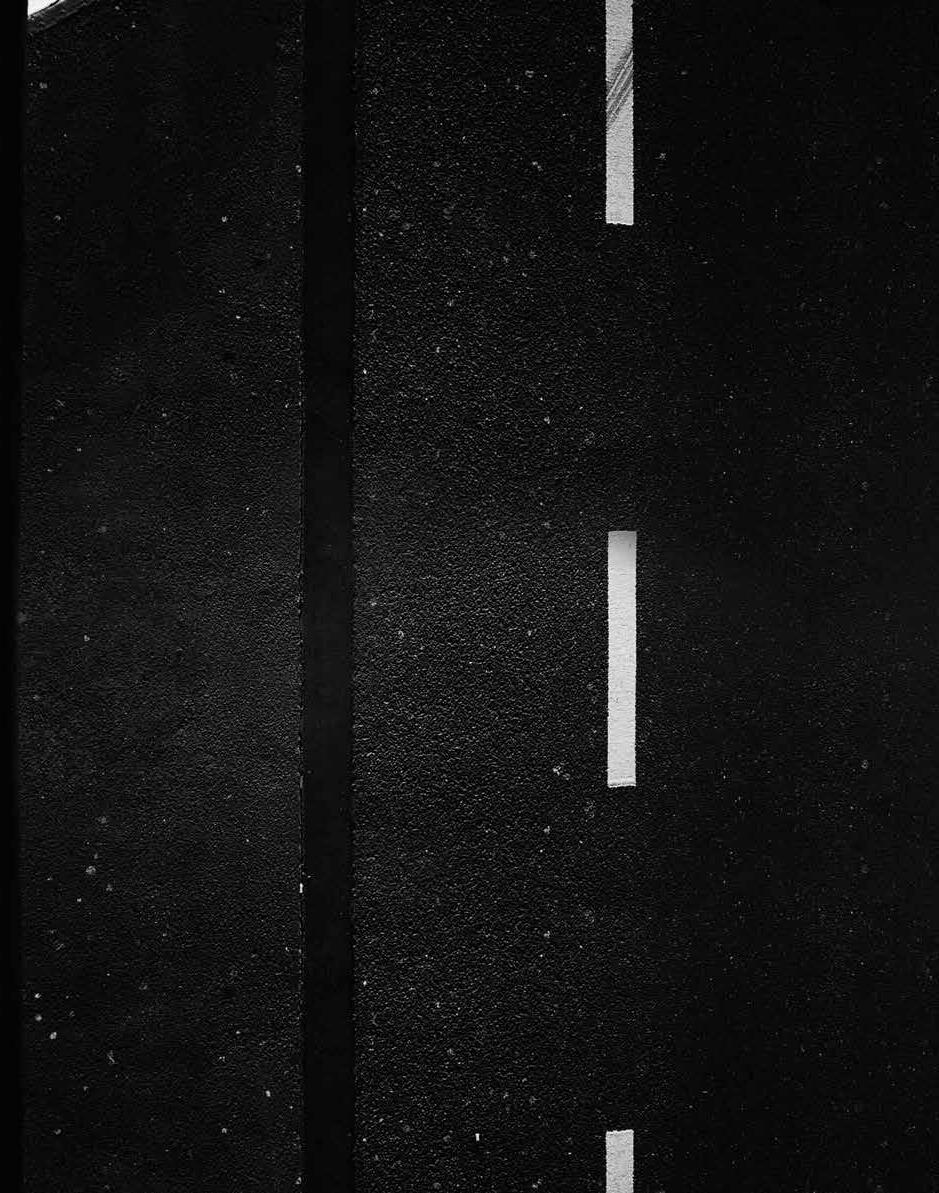
CWMF’s Fines Metering System
66 | SEPTEMBER 2022 HERE ’ S HOW IT WORKS
If you are producing more fines than you are returning, the fines in the auger will by pass the dust pod, traveling up to a second drop-out point where it will be discharged to a wet auger. At this point, water will be blended with the fines and the slurry will be rejected. For more information, contact a member of the CWMF sales team at travis@ cwmfcorp.com.
Fines drop to the pod. Step 2 Additional fines bypass the dust pod to the wet auger discharge. Step 4 The discharge auger carries the fines from the baghouse to the fines metering system. Step 1 Step 3
BY ASPHALTPRO STAFF
Bypass to Wet Auger To Baghouse
A rotary vane feeder at the dust pod would meter the dust being returned to the drum via a return auger.
Fines—or dust—are carried up the dis charge auger, which has a drop-out point where dust will flow into a small pod. Not pictured, a rotary vane feeder will attach to the pod to meter and control the amount of fines—or dust—being returned to the drum via a return auger. The vane feeder is the regulating device controlling the amount of dust return.
ToDrum

As mix designs evolve, controlling the fines being fed to the mixing drum is imperative to producing the qual ity product that will meet spec. To address this need, the team at CWMF Corp., Waite Park, Minnesota, developed a fines metering system for its portable Dust-Eater® baghous es. The device is designed to consolidate a re motely located dust pod and additional au gers. Here’s how it works:
First, the baghouse fines are conveyed to the discharge auger on the baghouse.
Power and Portability Our portable plant configurations feature a variety of components including jaw crushers, cone crushers, impact crushers and a variety of screening plants. Without sacrificing power or productivity, portable options deliver efficient and reliable performance with extra portability and adaptability. BUILT TO CONNECT Scan to see all our portable products
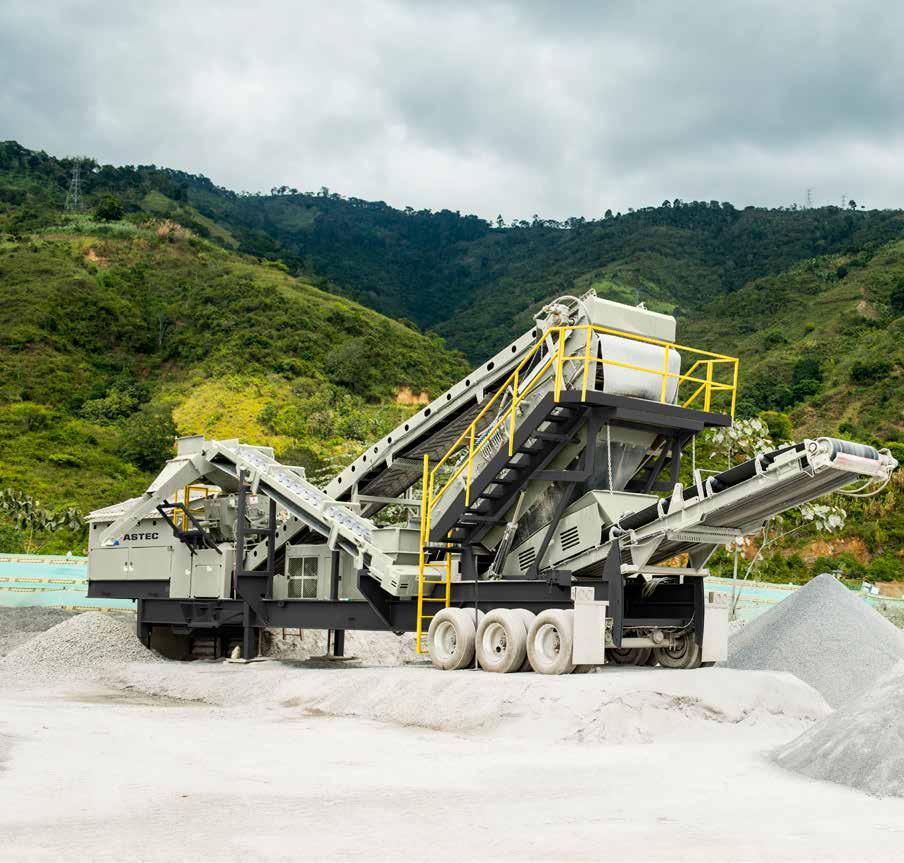
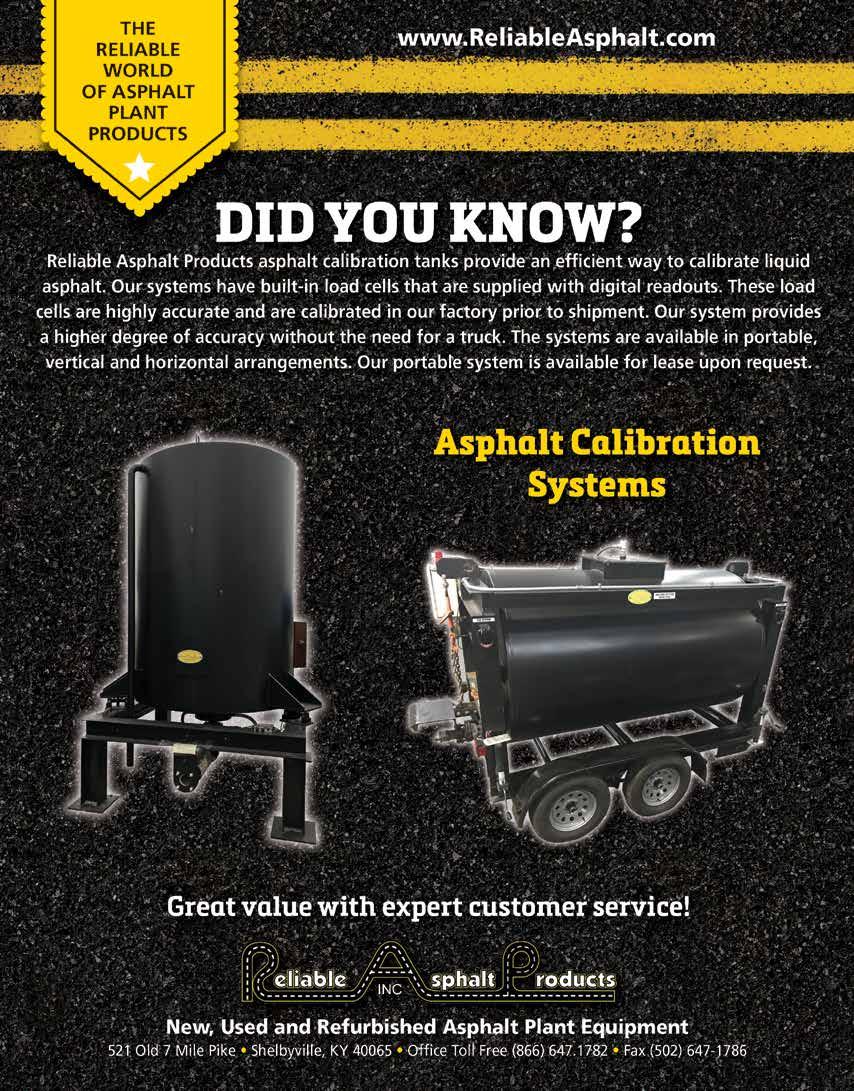