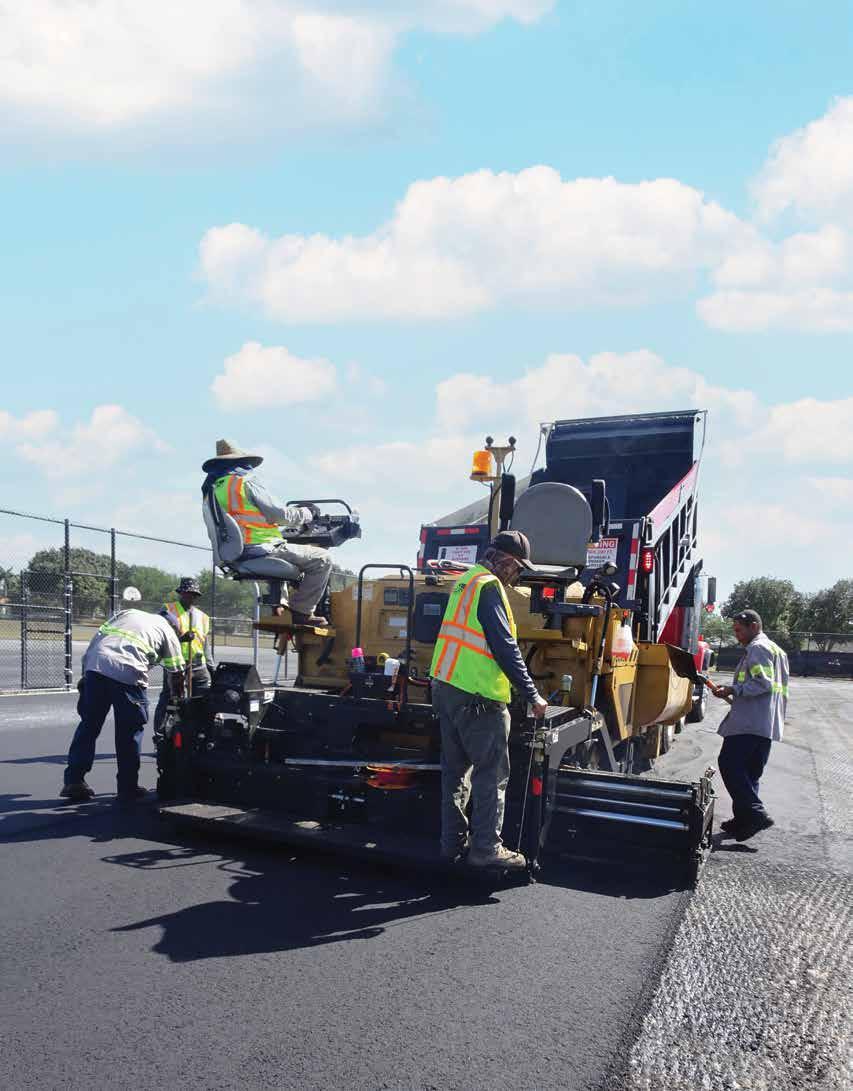
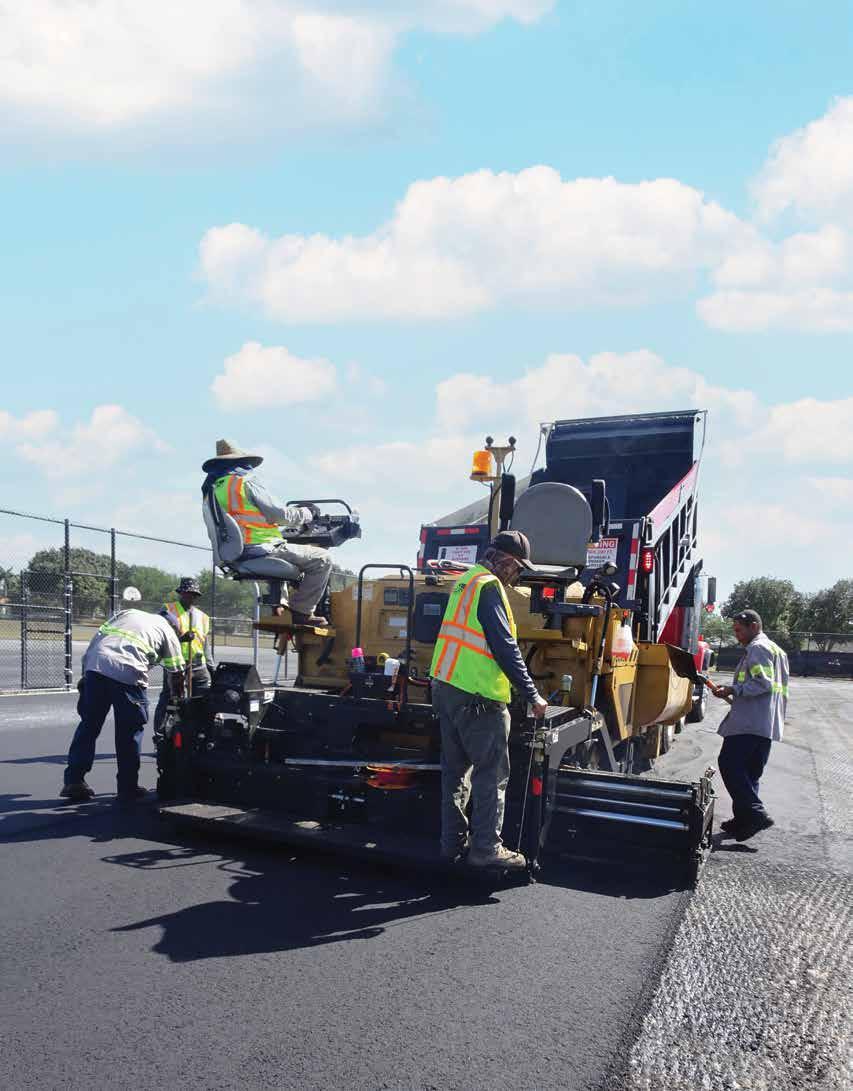
ROCK TO ROAD
Efficiency and Productivity
Designed with safety and operator comfort in mind, the SB-3000 Shuttle Buggy ® material transfer vehicle features adaptive cruise control, bright LED lighting, four-wheel steering for easy transport and ground-level maintenance access for added convenience. Operators can rely on clear sightlines and the ground operator is safely protected inside the structure of the machine. The Roadtec SB-3000 is the perfect blend of traditional craftsmanship and modern technology. Scan to learn more about the SB-3000.
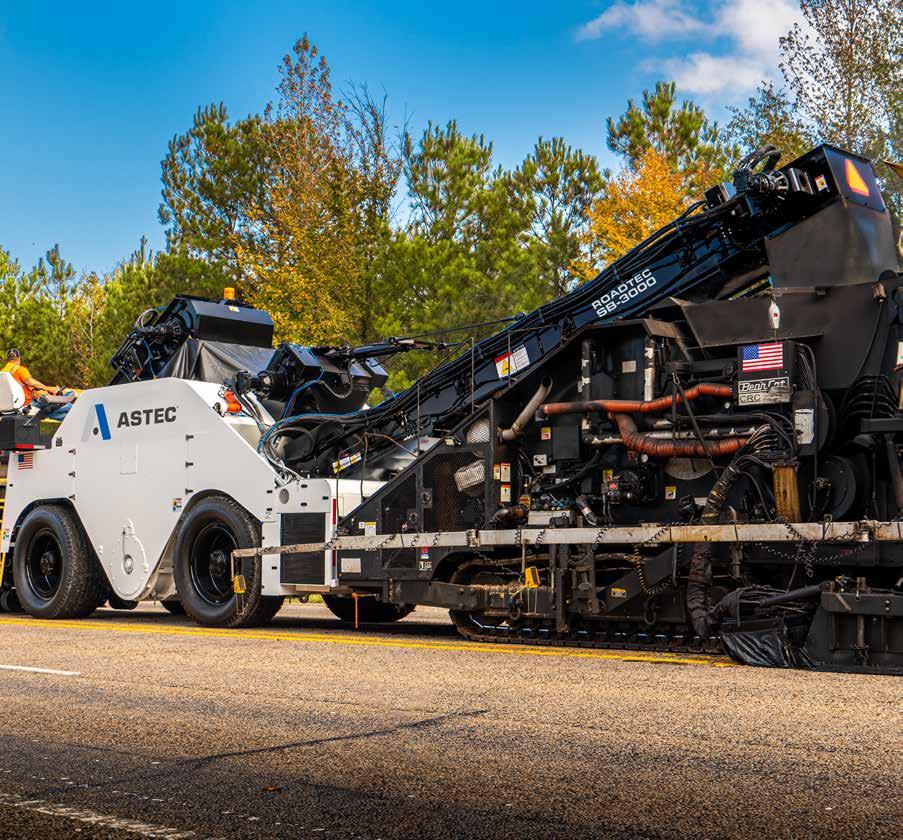
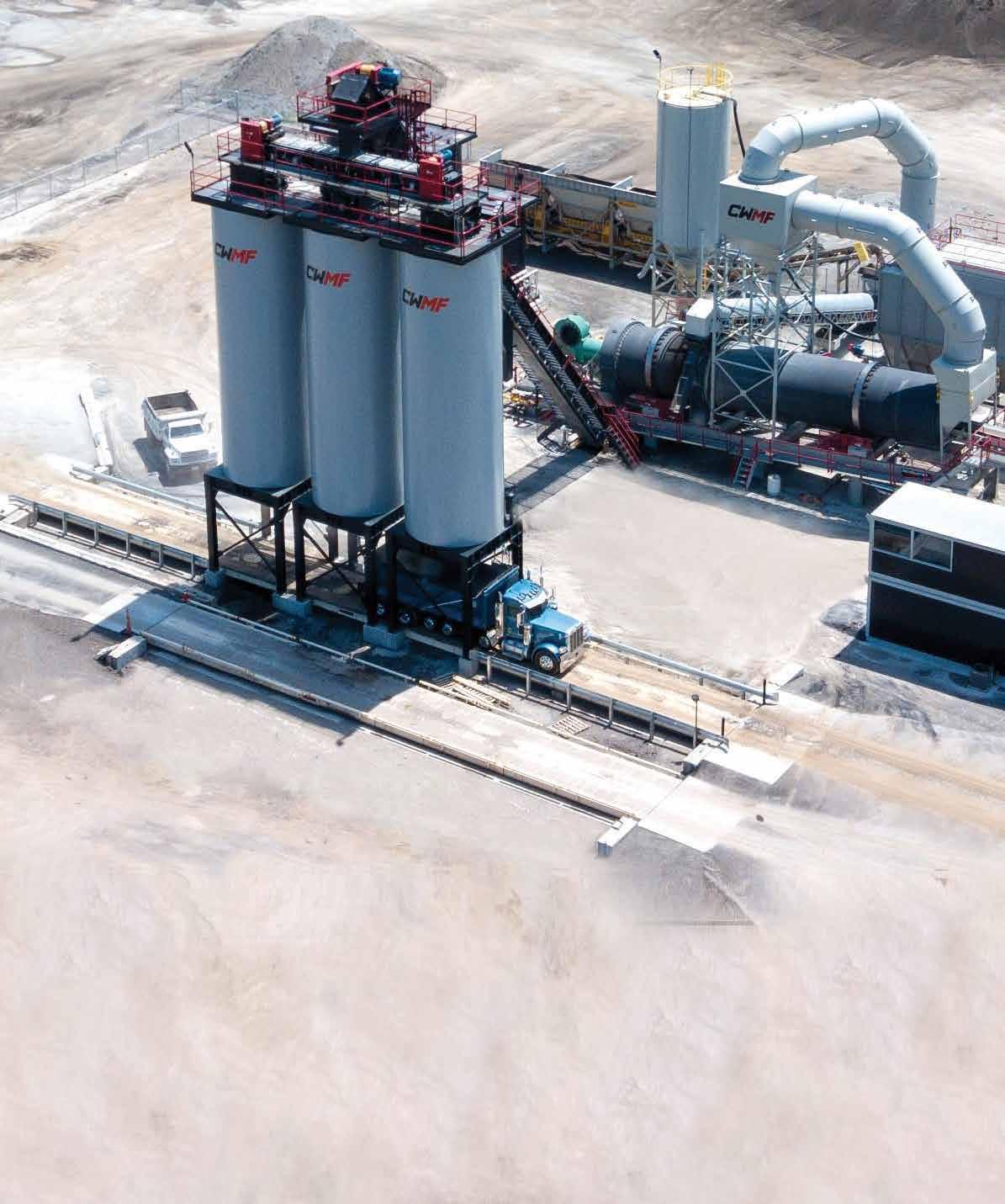
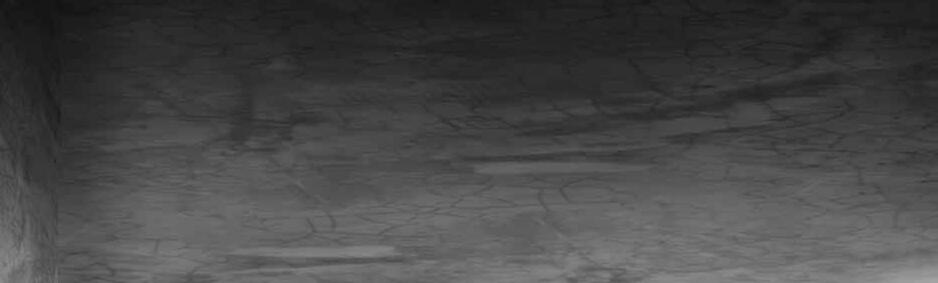
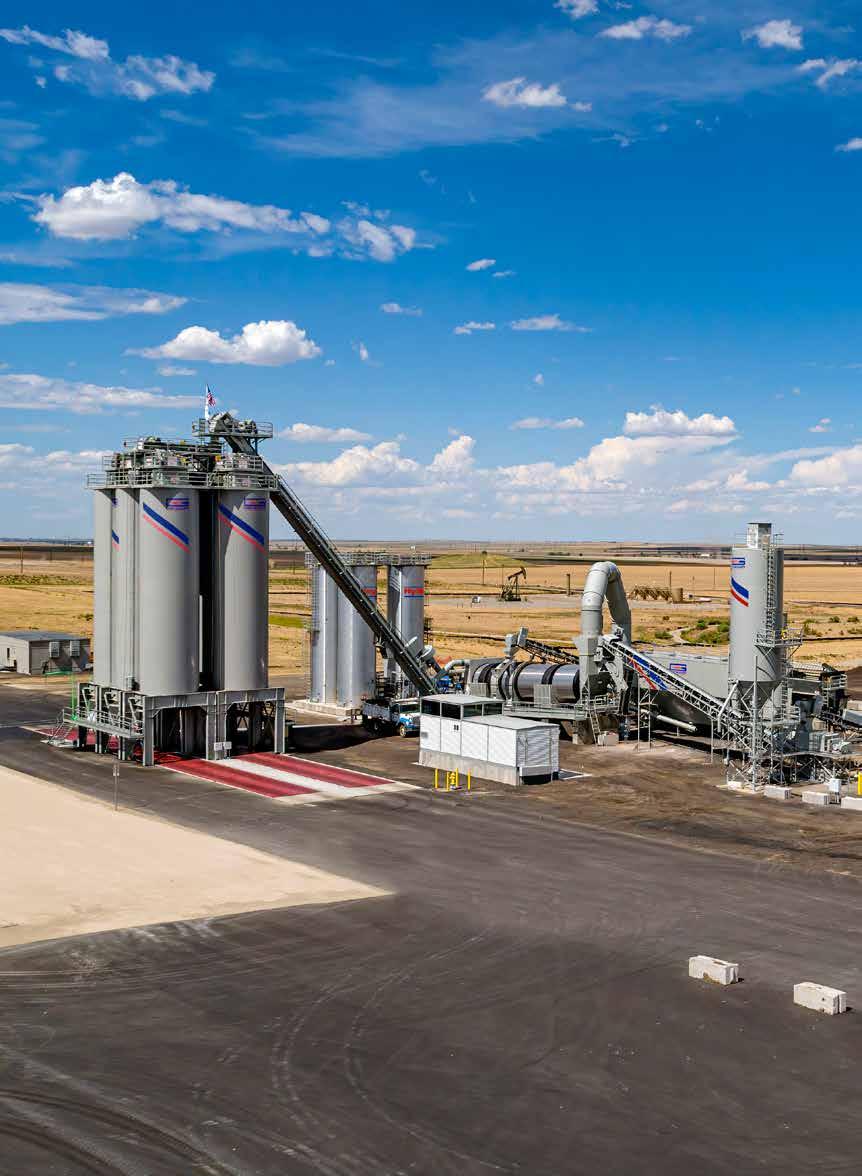
8 – Be Careful Underselling Pavement Treatments SAFETY

10 – Why Emotional Intelligence Matters on the Job Site
Construction workers may not have a reputation for wearing their feelings on their reflective PPE sleeves, but emotional intelligence is an important skill for the job site.
By Sarah Redohl16 – Reduce Risk in Your Lab
By Jayanth Kumar Rayapeddi Kumar, Dave Savage, Paul Matera
18 – All County Shows How to Maintain Courts
By Sandy Lender26 – Train for PC/OA
RMAEC offers certification for process control/owners' acceptance testing
By Tom Clayton WOMEN
ASPHALT 42 – Meet a Woman of Asphalt: Zipp’s Asphalt & Sealcoating’s Brynn Zipp By Sandy Lender
30 – Cherry Point Airfield Project Success Story Crews navigated a rushed start to make a smooth landing for runway, taxiway upgrades By Chris Croom 34 – Indiana Overlays with Aramid Fibers By Jason Martin 36 – How to Get the Best IRI in Florida History By Sandy Lender
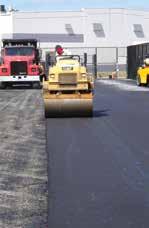
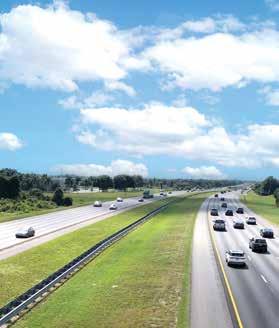
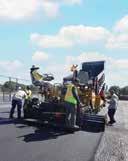
We’ve built our business and reputation through our unparalleled focus on equipment durability, attention to detail, and the ability to customize our products for each customer. We apply these foundations to our complete range of asphalt plants and asphalt plant equipment, designed for producers of all sizes.



Be Careful Underselling Pavement Treatments
During a recent webinar, one of the presenters bemoaned the fact members of the pavement preservation community in his region sold a less-than-adequate treatment for a pavement system. The result was almost immediate reflective cracking and an unhappy owner who saw the asphalt industry as the problem.

In the long run, poor business practices hurt us all. The contractor—whose name I don’t need to know—may have made a quick dollar winning the bid to only seal a damaged pavement. But now he likely has a damaged reputation that won’t win the company any invitations to bid in the future.
Now consider the cost to the industry overall when this kind of poor business practice is happening. If a contractor is consistently underbidding the competition because he’s underselling what the customers need, he’s damaging the industry’s reputation as well.
The thought that came to mind was, “What happens when someone upsells the property owner and does more than the pavement needed? How greedy do we look?” There’s nothing wrong with going above and beyond for the owner. That’s good customer service in anyone’s book. But to go to a property manager and sell him or her a certain dollar amount of infrared patching prior to sealing with two or three coats when a parking lot only needed a few cracks routed and filled before one sealcoat, is to take advantage of people who don’t know any better. That’s not overperforming; that’s fleecing someone.
I’m not saying our industry fleeces customers. I’m saying we should be aware that property managers are watching their nickels and dimes just like the rest of us. The contractor who offers them real solutions to pavement problems with a plan of attack for this season and next
will be the contractor who not only wins the job, but also wins the public relations game for all of us.
Why does that matter?
All ships rise with a rising tide.
If Contractor ABC shows the property manager of High-Quality Estates how to save a few nickels on long-term pavement maintenance plans, then that property manager will talk about Contractor ABC and the asphalt preservation options in positive, glowing terms at the next residential property managers luncheon. It’s better to have the manager of High-Quality Estates beaming about his good experience with the pavement preservation community doing a good job that was matched to his property’s needs than to have him grousing about a contractor taking advantage of him or doing a pricy sealcoating job without addressing the subbase failure in front of his display model office.
This sounds like basic common sense, doesn’t it? Yet it’s something a presenter was complaining about in 2023. We need to remember that a quick buck today could mean the loss of more than one contract tomorrow. Performing the right treatment for the right pavement at the right time applies to the smaller jobs just as it does for the larger, DOT-level projects. Assess what you can do for a property manager and give it to them straight. If that means you spend extra time educating them on a pavement condition index, so be it. If that means you lose the bid to someone else this year, you just might be the one the manager comes to in 2024 or 2025 requesting you bid to repair what didn’t get done properly in 2023.
Stay Safe, Sandy Lender
602 W. Morrison, Box 6a Fayette, MO 65248 (573) 823-6297 • www.theasphaltpro.com
GROUP PUBLISHER

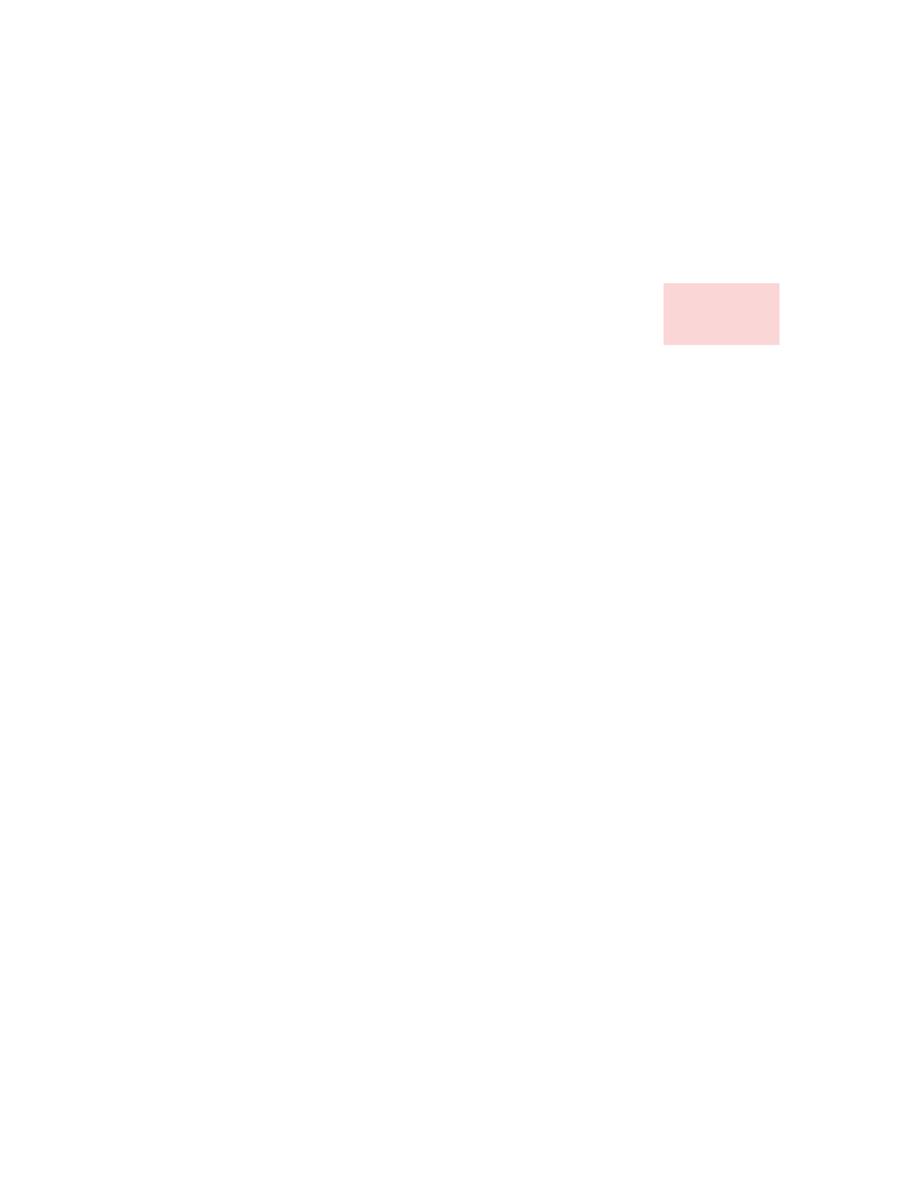
Chris Harrison chris@ theasphaltpro.com
PUBLISHER
Sally Shoemaker sally@theasphaltpro.com (573) 823-6297
EDITOR
Sandy Lender sandy@theasphaltpro.com (239) 272-8613
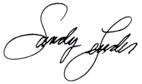
DIGITAL EDITOR
Sarah Redohl
sarah@theasphaltpro.com (573) 355-9775
MEDIA SALES
Cara Owings
cara@theasphaltpro.com (660) 537-0778

ART DIRECTOR
Kristin Branscom
BUSINESS MANAGER
Susan Campbell (660) 728-5007
AsphaltPro is published 11 times per year. Writers expressing views in AsphaltPro Magazine or on the AsphaltPro website are professionals with sound, professional advice. Views expressed herein are not necessarily the same as the views of AsphaltPro, thus producers/contractors are still encouraged to use best practices when implementing new advice.
SUBSCRIPTION POLICY: Individual subscriptions are available without charge in the United Sates, Canada and Mexico to qualified individuals.
One year subscription to non-qualifying Individuals: United States $90, Canada and Mexico $125.00. For the international digital edition, visit theasphaltpro.com/subscribe/

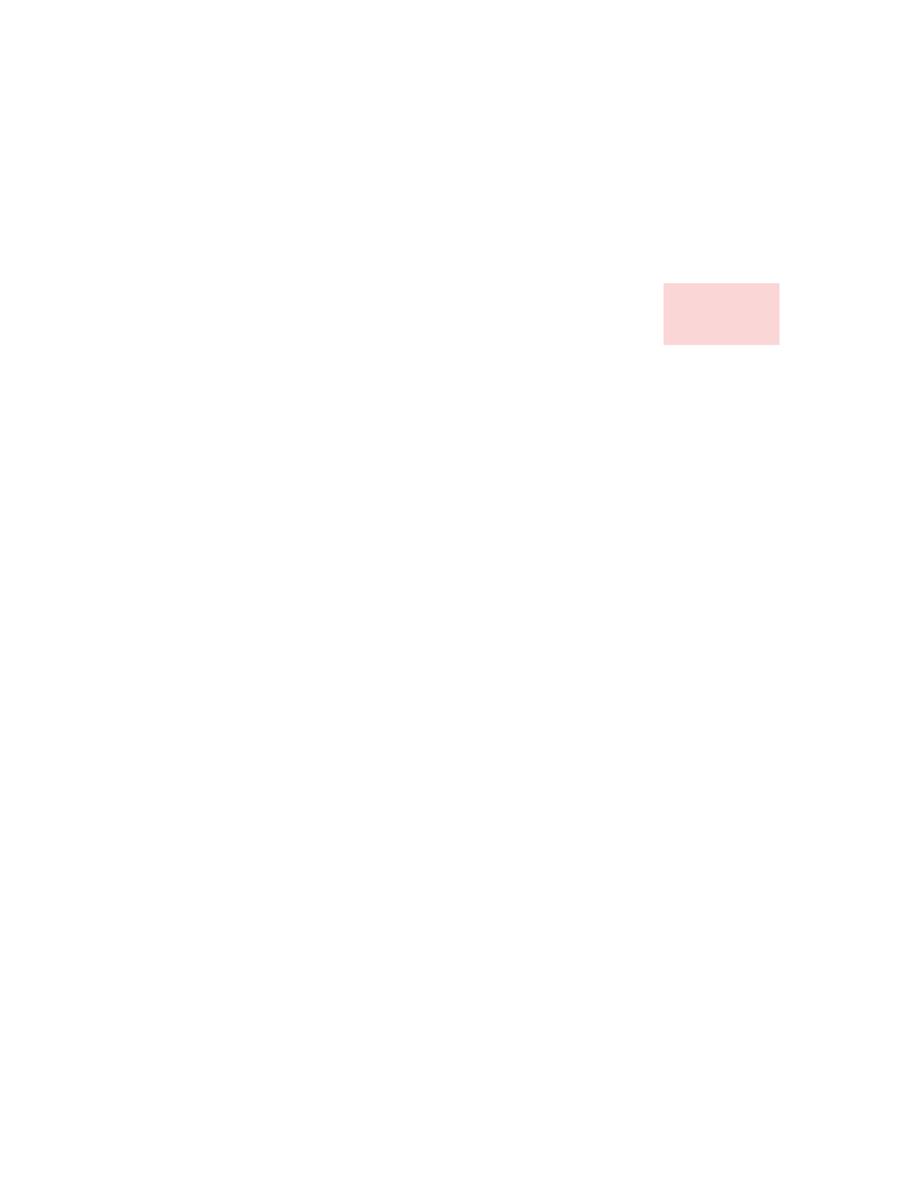
Why Emotional Intelligence Matters on the Job Site
Construction workers may not have a reputation for wearing their feelings on their reflective PPE sleeves, but emotional intelligence is an important skill for the job site.
BY SARAH REDOHLAs Nicholas Pickrel was growing up around the construction industry, he remembers how frequently employees would get yelled at—or even fired on the spot—when something went wrong. When he co-founded asphalt paving company Kingsway Services, Millersburg, Ohio, several years ago, Pickrel knew he wanted his business to operate differently.
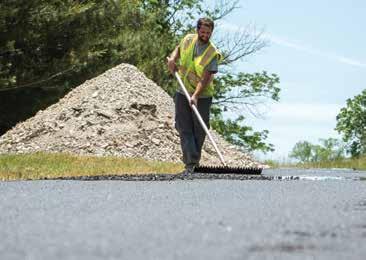
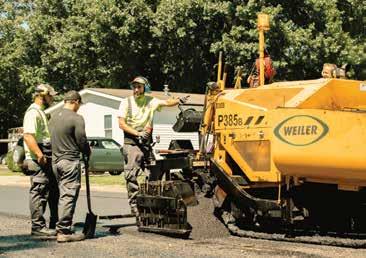
The company, which aims to put its people first, has strived to cultivate a culture of emotional intelligence (EI) among its leadership and its crews. “In the dirt world, there’s often been a lack of EI,” Pickrel said. “There’s this tough-guy mentality where we don’t talk about feelings. But, it’s important to consider how your actions affect others, how they may be feeling and how you’re feeling.”
Last year, Kingsway invested in training from BuildWitt, Nashville, Tennessee, to help them achieve that goal. In addition to helping crews cultivate the hard skills needed to succeed on the construction job site, the training program heavily focuses on effective leadership—which includes EI training.
WHAT IS EI?
EI is frequently defined as the ability to recognize and regulate emotion, and to use social awareness in problem-solving. According to BuildWitt’s CFO Randy Blount, EI comes in two parts: “One is recognizing that people are emotional beings, and that plays a part in the way we communicate. Two, it’s the ability to separate yourself from those emotions when making decisions.”
Blount has recognized the importance of EI on the job site since well before joining BuildWitt three years ago. “When I was young, I’d hear the wisest people in our industry talk about how our industry is all about the people, that the equipment is the easy part,” he said. “I thought they said that because it was what you’re supposed to say.”
During his tenure leading Blount Contracting, growing the company from $3 million in annual revenue to $100 million, Blount quickly realized the importance of understanding and developing EI to better deal with employees, customers and project partners.
“In construction, almost everything you do is as a crew, even a simple patch job,” Blount said. “Recognizing that people are emotional beings and how that influences our interactions every day is the basis of good leadership.”
Blount said that BuildWitt’s initial desire with its training platform was to focus on some of the soft skills the company felt the industry needed to cultivate. For example, leadership, mental health and personal development. “We think those skills are just as important as the technology and safety skills,” Blount said. They also served BuildWitt’s mission, to ‘make the dirt world a better place.’
“We lose an incredible amount of people who join our industry,” Blount said. “We have to recognize that getting them here is one thing;
Although Pickrel and the leadership team want to know when their employees are struggling, they make it clear that employees don’t need to tell them everything and that they’ll handle the situation as the employee wishes. They’ll also attempt to handle the situation as the employee wishes, whether that’s time off or wanting to work to take their mind off the problem they’re facing.
keeping them here is a whole other thing. We need people who are better leaders to attract and retain people in our industry.”
However, BuildWitt recognized that it was the hard skills that brought companies to their training course, “so we started with equipment and
EI can also be a valuable tool to resolve conflict within the crew while maintaining a fun work atmosphere, Blount and Pickrel said.
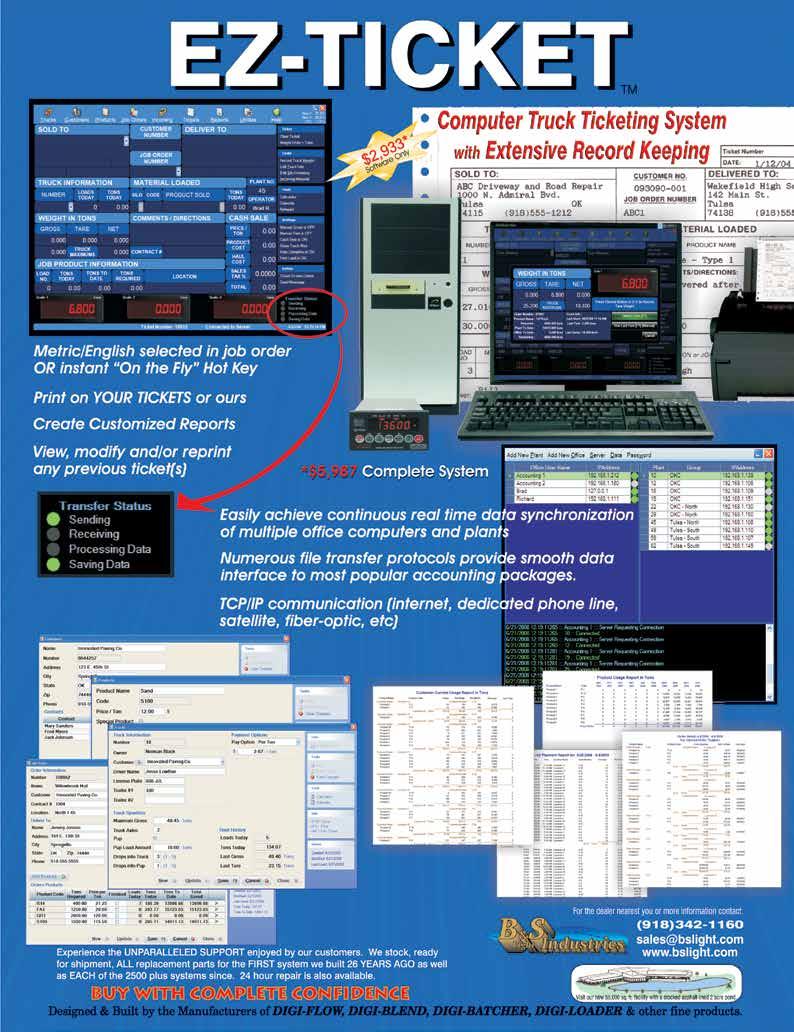
sprinkled in leadership lessons and mental health advice—sort of like putting out a salt lick to draw in wildlife.”
And yet, it was the leadership and personal development training that most appealed to the Kingsway crew. “Recruiting employees is a huge challenge, but we also have to learn how to retain the guys we train,” Pickrel said, adding that operating with EI is a huge part of employee retention. “This stuff sounds wishy-washy, but people make decisions based on emotions more than logic, so it’s very important.”
For those who are new to the concept of EI, here are four common scenarios on a construction job site to illustrate how Blount and Pickrel approach these events with greater EI.
BuildWitt’s training platform includes more than 1400 lessons on topics ranging from leadership and EI to equipment skills and safety best practices. The training can be done in groups or individually, in large chunks of time or as microlearning modules, and companies can select certain videos for certain crews, outline a learning plan based on hire date, or deliver videos at random.
“One of our top methods of training is delivering micro lessons three minutes or shorter for the crew to watch before the daily huddle,” Blount said. “Then, the crew goes around and shares what they learned during the huddle.” By teaching what they’ve just learned, not only is that a refresher course for crew members who may not have yet encountered that tip on the platform, but it also improves the retention of the crewmember teaching the lesson and those hearing it for a second or third time.
WHEN MISTAKES HAPPEN
Imagine you’re on a paving job and the roller operator lets his roller sit still on the newly finished mat before breakdown rolling is complete. “We know that creates a dip in the mat,” Blount said.
“It’s not uncommon for someone to call that person out, saying something like, ‘Hey stupid, I can’t believe you did that!’” Blount said. “How do you expect them to respond to that? That conversation is not going to go well.”
“So often, EI manifests itself in interpersonal communication gone wrong. For example, labeling phrases like ‘You’re dumb,’ or, ‘That was stupid’,” he said. Instead, he recommends avoiding labels and opting for a feelings-based approach. In the above example, Blount would opt for a more constructive reply, such as, “I’m frustrated because I thought you understood doing that would damage the mat. Let’s figure out why it happened and how we can change it for the future.”
Blount’s approach relies on three types of questions. First, searching questions that help him understand why the person made a certain decision. For example: Why did you park the roller on the mat? Next, analyzing questions to establish context. For example: Did you know what parking the roller on the mat does to it? And last, questions that help the employee apply the new lesson he’s learned. For example: When you take a bathroom break tomorrow, what’s your plan going to be to avoid making the mistake of parking on the hot part of the mat?
“It’s unlikely the roller operator thought to himself, ‘I want to suck at work today’,” Blount said. “Most of us want to be good at what we do. We need to recognize that intention when we start that conversation. It’s very unlikely that a person made a mistake because they wanted to make a mistake. Usually it’s because they weren’t trained on it, or they didn’t understand the ‘why’ behind it.”
A common scenario Blount sees on the job site is younger workers making mistakes that surprise the older workers. “The older workers forget how they came to the conclusion that something needs to be done a certain way, which is usually because of the mistakes they’ve made over the years,” he said. “They’ve done that same thing 10,000 times and over the 10,000 times they’ve done it, they’ve come to know the best way. But they don’t communicate the ‘why’ when they’re training the new guy.”
“Usually that young person is looking for a way to do the job faster, easier, with less pain,” Blount said. “These are all good desires, but they may not realize Bob the foreman has already tried every approach they’re going to try, and there’s a reason Bob wants them to do it a certain way. Leaders need to recognize the reason we have our perspective is because we have made mistakes in the past.”
This is the strategy Kingsway has chosen to employ within its crews. “We see mistakes as lessons we’ve paid for,” Pickrel said. “Why not take advantage of them and see them as an investment into that person who more than likely isn’t going to do that again.”
Early on at Kingsway, there was an employee who refused to take a drug test. “Our policy was to let him go, which we did, but we didn’t feel good about that,” Pickrel said. “Maybe we were his last hope. Knowing what we know now, I’d approach that situation differently. I’d offer him a different job if he agreed to a program to get clean and get him back to where he was after he finishes the program and gets clean. I would have offered him a route out of the situation he was in, a route that allowed him to stay if he wanted to stay and to get better.”
WHEN A FELLOW CREW MEMBER SEEMS ‘OFF’
Pickrel defines EI as understanding oneself and those around you. “It’s not just knowing my own emotional state, but also being able to recognize the emotional state of my coworkers,” he said.
For example, if a person is usually chatty and cracking jokes and goes quiet one day, he and his leadership team want to know about it. “Maybe they’re up taking care of someone until 1 a.m. or they’re stressed and they can’t sleep, maybe something is going on with their family,” Pickrel said.
This mentality, he added, starts with leadership. “If leadership starts learning about EI and implementing these strategies, that will trickle down,” he said. “The first time you say, ‘If you see anything off, I want to know about it’, maybe no one says anything. But if you address it two, three, four times, it starts to catch on.”
Blount also stresses the importance of EI among leadership. “We as leaders in industry need to demonstrate behavior we’re expecting from people,” he said. For example, he continued, if a supervisor is going through a personal issue, Blount would hope that they’d mention it in the morning huddle, in whatever level of detail they feel comfortable.
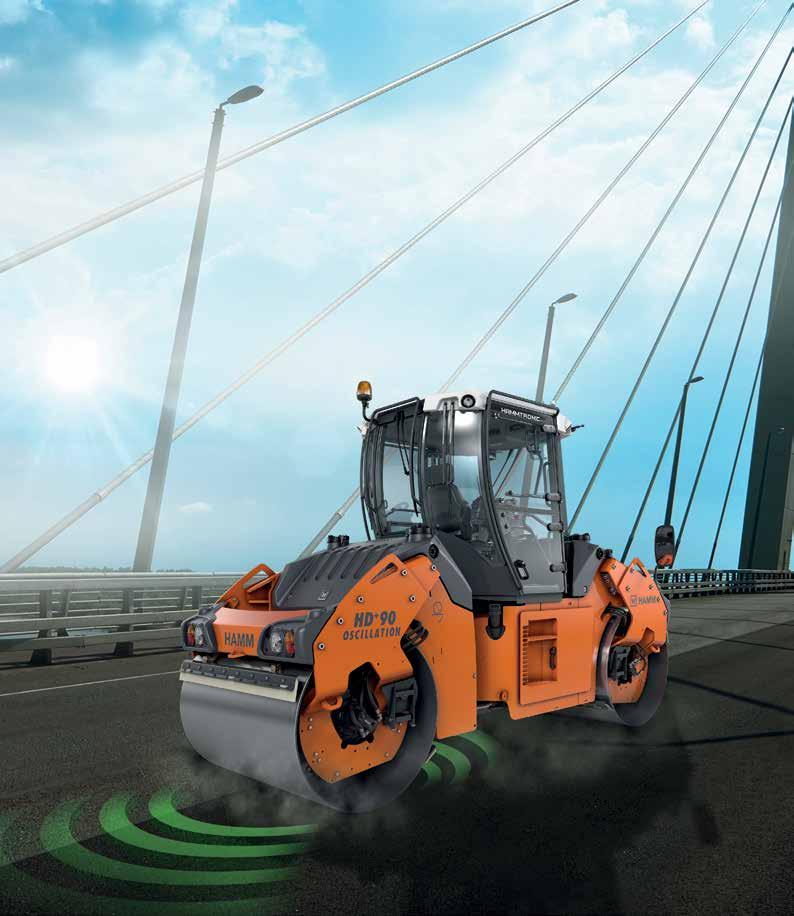
“That could help prevent a potential workmanship issue or safety incident because the crew knows to look out for him a bit more than usual that day. We’re used to having spotters on equipment, but sometimes we also need an emotional spotter on bad days.”
Once leadership effectively exhibited EI, Pickrel said it grew to become a part of Kingsway’s culture. “We recently had a crew member come to us who was worried about one of his coworkers,” Pickrel said. “He said he didn’t think he was in the right headspace for the job site and wasn’t acting like himself. We ended up giving that crew a day off, because it’s not safe to send them out there if someone’s head isn’t in the game. What if he steps out into the road because his mind’s on something else? That day off could have saved someone’s life. And no job is more important than anyone’s wellbeing.”
In another example, one of Kingsway’s employees’ friends was diagnosed with cancer, and the employee was often taking care of their children. “We sat everyone down and explained the situation and told everyone that if he needs extra help, we need to give it to him. If he needs to take off, we need to cover it. If he needs to leave early, we need to do what we can to make that happen.”
Although Pickrel and the leadership team want to know when their employees are struggling, they make it clear that employees don’t need to tell them everything and that they’ll handle the situation as the employee wishes.
“Some people want to throw themselves into their work to deal with their emotions, other people need some time off,” he said. One bit of advice? “If someone says they’re not in the right headspace, asks for the day off, can I go home, and you say no, that erodes trust. If you say yes and pay them for the day, that creates trust.”
Pickrel said EI may be an important tool in suicide prevention. “How many stories have we heard about someone who was ready to take their life and chose not to because one person gave them a call, asked how they were doing, said they’d pray for them,” he said. “If you aren’t aware of how your actions make others feel, you’re not going to notice those small things. If you’re not able to notice someone’s not acting the way they usually do, you’re not going to check on them. We have to pay attention to what’s happening in our teams’ lives.”
WHEN CREW MEMBERS DON’T GET ALONG
Blount said EI can also be a valuable tool to resolve conflict within the crew. For example, when a young operator came up to Blount on a job site to express some trouble he’d been having with his foreman, whom he thought had been extra hard on him, Blount helped him strategize a constructive conversation to resolve the conflict.
“We walked through what that conversation might look like and some productive questions he might ask,” Blount said. For example, instead of asking the foreman, “Why are you such a jerk to me?” and putting him on the defensive, the operator could take radical ownership of the situation and express his desire to improve.
Ultimately, the operator expressed his feelings and his desire to improve, asking the foreman what two or three things he most needed to improve and how he could know in the next 90 days that his improvements have been noticed and made a difference.
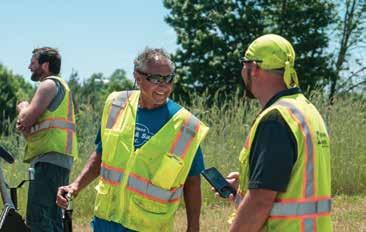
Overall, employees’ responses to Kingsway’s EI initiative have been positive. “Of course, they joke about the feelings stuff, but I know they appreciate knowing we’re looking out for them and they’re looking out for each other,” Pickrel said. “I think part of [our success with EI] is that we [the leadership team] don’t take it overly seriously.”
For example, at the start of the 2023 paving season, Kingsway devoted a week to training, ranging from safety and best practices to addiction prevention. They also had their entire crew take a DISC personality test. “Everyone sort of joked about each others’ results a bit,” he said, even those in leadership positions, but ultimately it was a positive experience. “It was a breath of fresh air, not only in understanding ourselves but also with each other.”
WHEN JOKES GO TOO FAR
One of the challenges to implementing a more emotionally intelligent approach on the job site is a fear that it might change the culture of the crew. “There’s usually this fun banter on a lot of construction crews,” Blount said. “And usually it’s fun to pick on each other a bit, but somebody eventually crosses the line and feelings get hurt.”
This usually happens when someone tries to make a joke that turns out to offend a coworker. In Pickrel’s experience, the way conflicts often end when jokes go too far is with someone quitting. “Then, the company ends up making rules about not joking on the job site,” he said. “Knowing how to resolve the problem when joking goes too far is the key to keep that culture and camaraderie.”
Blount agrees: “If we want to keep that joking culture, we need to know how to have conversations to resolve this type of conflict.” For example, ‘That was hurtful and I don’t believe that was your intention.’
“If we don’t know how to have those conversations, I think that increases the risk that our industry starts creating rules around joking and fun,” he said. “Learning to have conversations to resolve conflict is how we can continue to have a fun industry that can joke around and everyone goes home in better condition when they come in—not just physically, but emotionally.”
Pavement preservation is highly cost-e ective. Every Micro-surfacing study has shown that these types of treatments help extend pavement life.
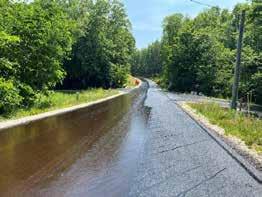
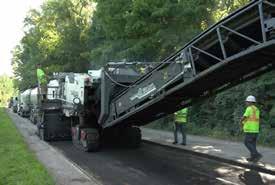
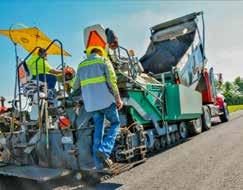
portfolio
intrusion while maintaining the pavement’s
reduce
texture. The penetrating nature of RPE means that the asphalt residue gets “in” the pavement rather than “on” the pavement. RPE is most e ective if applied within the first year of the pavement’s construction.
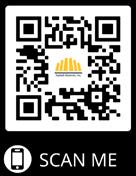
Reduce Risk in Your Lab
Risk-based QMS for Construction Materials Testing Laboratories
BY JAYANTH KUMAR RAYAPEDDI KUMAR, DAVE SAVAGE, PAUL MATERAGood business leaders understand that higher quality generally equates to lower overall risk to the company—lower risk for defective products, associated lawsuits, and the resulting loss of reputation and sales. Let’s look at building a riskbased quality management system (QMS) in your testing lab to meet or exceed a variety of accrediting agency standards, such as the American Association of State Highway and Transportation Officials (AASHTO), ASTM International (ASTM) and International Organization for Standardization/International Electrotechnical Commission (ISO/IEC).
QMS IS REQUIRED

Construction materials testing (CMT) labs that provide testing services on publicly funded projects are required to have an approved QMS to meet the quality requirements of AASHTO R18, ASTM D3666, ASTM C1077, ASTM D3740, ASTM C1093 or ASTM E329. This requirement is typically contract or specification driven and will depend on the scope of work for the project. While most CMT
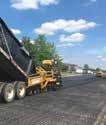
DEPLOYING A RISK-BASED QMS THAT CONFORMS WITH AASHTO, ASTM, AND ISO/IEC QUALITY STANDARDS IS A RIGOROUS TASK.

labs pursue these standards as a framework for developing their QMS, many go above and beyond.
Many labs follow a more robust outline to deploy their QMS to showcase their lab competence and uphold higher standards. Many quality experts consider the ISO/IEC 17025 standard “General Requirements for the Competence of Testing and Calibration Laboratories” one of the most reliable standards for developing a QMS.
When a QMS is developed to meet regulatory requirements or exceed minimum expectations, lab managers often need help to define the scope and extent of policies, procedures, processes, etc. Their challenge is exacerbated by the industry’s continuing evolution and lessening room for error. QMS is always a work in progress.
CONSIDER RISK
Risks, and their associated tolerance, are critical components for any lab operation, but they’re hard to identify. Some are harder to quantify. When risks creep into a QMS, they weaken the system, making it unreliable and prone to manipulation. At the very least, a risk assessment should include risk probability, severity and existing mitigation techniques.
The current version of the ISO/IEC 17025 standard, released in 2017, applies risk-based thinking to developing a QMS. It doesn’t provide any prescriptive solutions to manage risks. Instead, the standard requires the lab to perform a risk assessment and develop a management plan based on the risk’s influence on performance.
The standard gives sufficient discretion to lab managers to assess and manage the risks as they see appropriate. We’ll examine two sections of the ISO/IEC 17025 standard from the risk assessment and management perspective as it applies to CMT labs to demonstrate the risk-based approach to developing a QMS framework. The risk severity and probability for any given section in the ISO/IEC 17025 document will likely differ for different labs; Therefore, consider how the risk assessment and management plan discussed in this article could meet your organization’s needs.
Section 4.1: Impartiality. Risks from perceived bias have always been around, but with the current ISO/IEC 17025 standard, they need to be addressed by assessing and suitably managing them. These risks can range from innocuous to detrimental to any lab’s operation. For example, a personal relationship between a lab staff member and a customer can cause any reasonable person to question the impartiality of the lab finding. If management considers an issue like this harmful to its business, it is in the lab’s interest to establish policy guardrails to curb such problems. To manage the risk described above, the lab can

have a policy that says if the customer and a lab member have a personal relationship, that lab member shall work on the customer’s project under the direct supervision of another lab personnel.
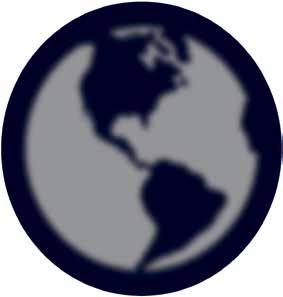
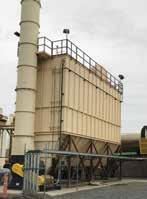
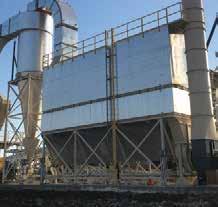
Section 8.7: Corrective action. Nonconformities are inevitable in any lab testing operation. But not all nonconformities rise to the level of requiring a risk-based corrective action. Some are isolated incidents that require a one-time corrective action. If the issues start recurring and become severe, there may be a good case for planning to manage that risk. However, it’s challenging for labs to assess the reason(s) for nonconformities and implement timely and effective corrective action. Let’s look at an example. A lab technician repeatedly failing to follow correct sampling procedures certainly could rise to the level of risk assessment. Managing this risk may include, among other things, retraining the technician to perform their task per the relevant standard methods.
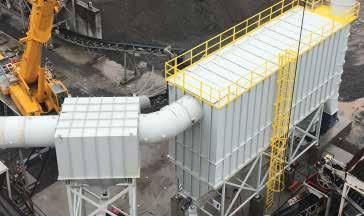
PDCA
The lab should always consider the severity and probability of risks when planning the scope and extent of how to manage them. When planning risk management steps, a good formula is to use the PDCA rule: plan, do, check and act. To elaborate, plan what you will do when there is a risk, do what you planned, check if you accomplished what you wanted, and act on the gap between the plan and accomplishment. The other big part of resolving any issue is to keep all parties in the loop if needed. This will go a long way toward resolving problems and gaining stakeholder credibility.
A QMS is like a musical ensemble, if you will. In a musical ensemble, a group of well-rehearsed musicians plays a piece together in accord. It rarely happens that a change made somewhere or a lack of harmony among musical notes goes unnoticed in the final production. Like a musical ensemble, all it takes is one element of the QMS not to meet its quality objective, potentially reducing its overall effectiveness. Therefore, the lab staff should ensure that all aspects of the QMS are performing optimally. Deploying a risk-based QMS that conforms with AASHTO, ASTM, and ISO/IEC quality standards is a rigorous task. It is common to feel that the QMS is a burdensome requirement for companies to comply with. However, not having a functioning, structured, risk-based QMS could lead to failure for any lab. A reputation for inconsistent or unreliable results does the very opposite of driving sales, especially in the built environment.
Jayanth Kumar Rayapeddi Kumar, PE, ENV SP, currently serves as the quality control engineer for Jas. W. Glover Ltd. in Hawaii, and on the ASTM D04 committee on Road and Paving Materials and the ASTM E36 committee on Accreditation and Certification. Reach him at jayanthk@gloverltd.com.
Dave Savage is the director of accreditation for CMEC Inc. and serves on ASTM Executive Committees E36, Accreditation and Certification, and D04, Road and Paving Materials. Reach him at davesavage@cmec.org.
Paul Matera currently leads the Inspection Body program for the ANSI National Accreditation Board (ANAB). Before joining the ANAB staff as a senior accreditation manager, he provided assessment services to different accreditation bodies and industry groups. Reach him at pmatera@anab.org
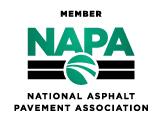
All County Shows How to Maintain Courts
BY SANDY LENDERThe last thing a student athlete wants to see is a cracked or uneven surface when it’s time to practice for a big game. To keep a basketball or tennis court surface smooth and functional, school districts turn to local contractors for expert work. Enter the team of All County Paving— National Pavement Management Solutions, based in Delray Beach, Florida. This company bids on projects ranging from paving, patching, milling, site work, concrete work, striping, ADA and sealcoating. They self-perform projects in the Southeast and reach out
to contractors in their network to accomplish projects farther afield.
“ACP self-performs capital projects nationally and works with local vendors within the pavement network,” a spokesperson explained.
In March 2023, ACP performed a milland-fill for Polo Park Middle School, executing the milling, cleaning, leveling and paving of a basketball court and tennis court situated side by side. They hired a private company to haul mix from a local asphalt plant and brought in a subcontractor to handle the striping. Here’s how they accomplished the project with guidance and
training from Paving Consultant John Ball of Top Quality Paving & Training, Manchester, New Hampshire.
PREP THE EXISTING SURFACE
A spokesperson for ACP said the crew performed milling of the two courts on Monday and Tuesday, March 20 and 21, to a profile of no more than 2%.
To demonstrate preparing the surface for efficient paving, the crew performed additional, detailed cleaning prior to paving on Wednesday and Thursday, March 22 and 23.
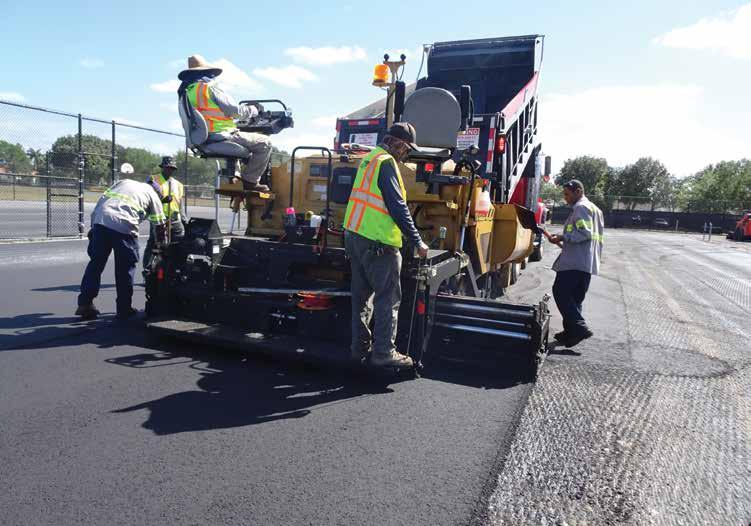
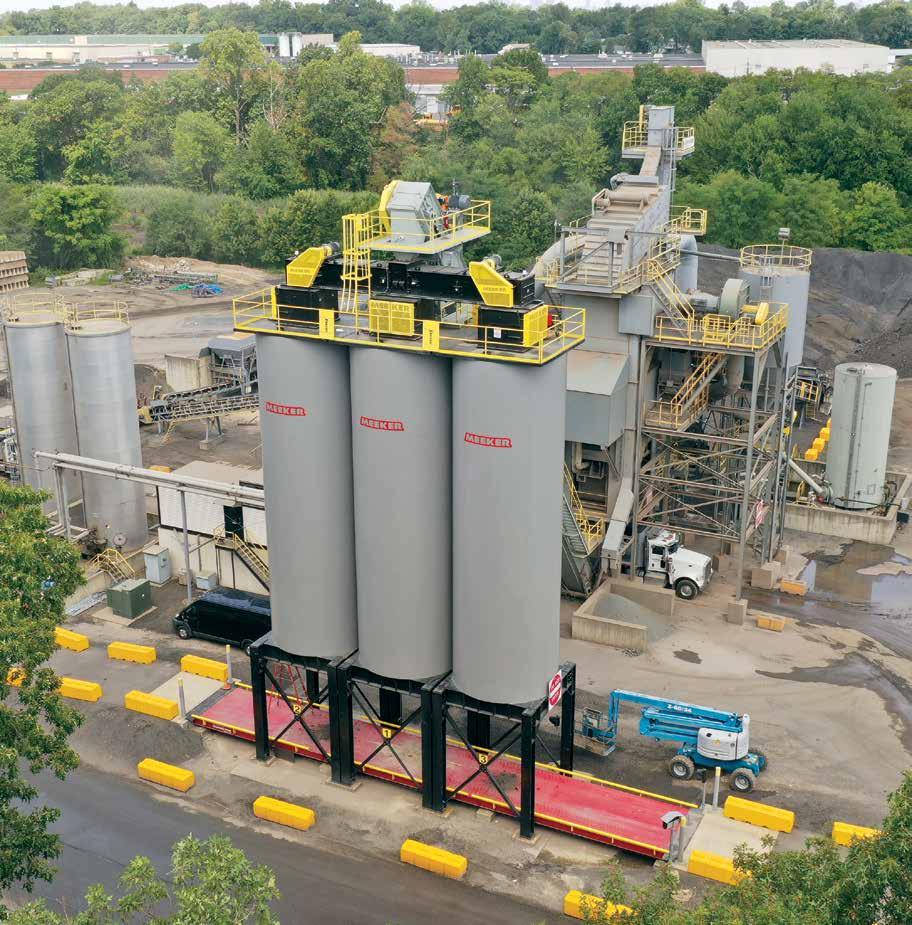





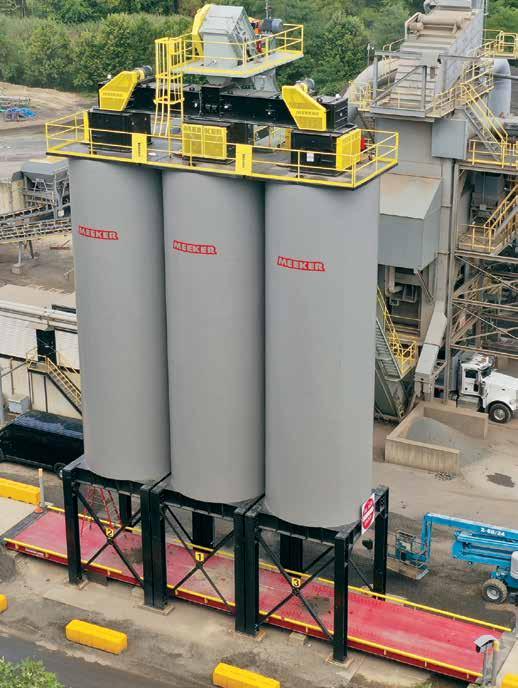
Ball described them using torches to ensure grass and weeds were burned out of cracks and using a leaf blower to get fine dust and stray debris off the surface.
“You want to burn off any weeds you see or they’re going to grow back in a year,” Ball said. “You want to use a blower to get fine dust out of the grooves so the tack can do its job.”
The crew also used a Stihl pavement saw, shovels and Kubota SSV75 skid steer bucket to remove problem areas that required additional work. You can see in the pictures in-
PAVEMENT MAINTENANCE
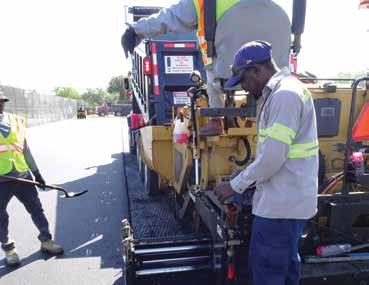
cluded here that the laborers lined out the job and marked the areas that needed additional attention. They came in with the paver to level off these spots.
“There was some scabbing of the old, milled pavement, so the crew leveled it,” Ball said. “To do this, we set the screed down, null it out, then drag it with no angle of attack. This screeds it off, like we’re leveling the foam off a milkshake.” For a primer on nulling out the screed and setting your angle of attack, check out the article “Paving by the Numbers” at TheAsphaltPro.com.
Ball said the 11-person crew—including himself—took the time to get everything right for paving, dedicating about two hours to surface preparation before the mix arrived on each of the paving days.

PAVE THE DETAILS
Because the project required a 1-inch compacted course of S3 mix, the crew had no room for error. They used a Weiler P385B paver with the screed extended to 10 feet to pave 6,900 square yards for both the basketball and tennis court over two days. To
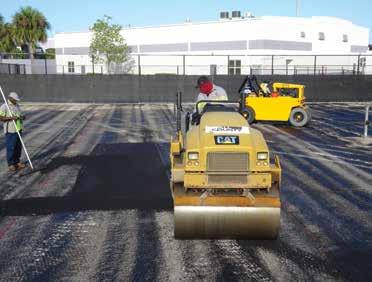

LEADING THE WAY
Weiler Material Transfer Vehicles lead the way with proven innovations to provide the lowest cost per ton of operation.

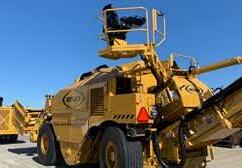
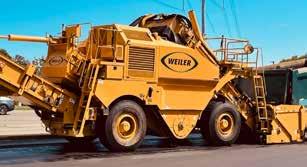

Innovative and reliable operator friendly features such as paver hopper management system with distance to paver, storage hopper management and auto chain tensioning.

Variable speed elevator and conveyors meet production requirements with the minimal amount of wear.
Clam shell doors and full width drop down floors provide unmatched access for cleanout.
The evolution of chains, sprockets and augers are retrofittable to all machines and provide increased wear life.
PAVEMENT MAINTENANCE

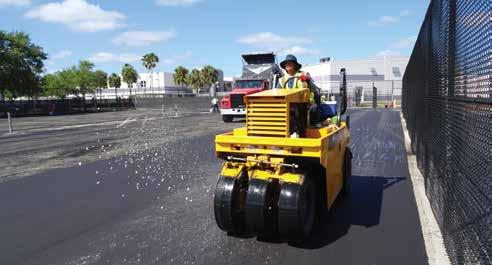
get final compaction, they placed the 1-inch overlay at about 1 1/8 to 1 1/4 inch thick, depending on the leveling required.
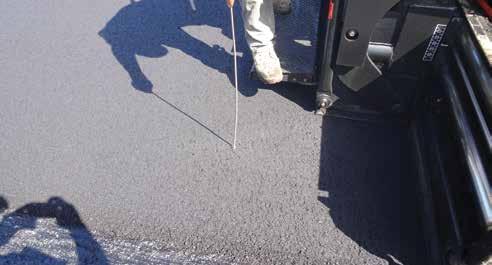
To get compaction, the breakdown roller operator hit the mat with a Cat CB36B small vibratory roller. The intermediate roller operator came along behind with a Basic 700 rubber-tire roller, featuring four tires on the front and three on the back. Not every contractor still uses sand, but this fellow had a very finegrain sand to throw out to help prevent pickup on the tires.
“This crew goes above and beyond for the company and strives for success everyday making sure our customers’ expectations are exceeded,” ACP President Ken Goldberg said. “They all work together well and teach each other new skills that help them grow in the business and help the job run smoothly. Some crew members even stepped into leadership roles. The quality of work they produce is outstanding and we are so proud to have them as members of Team ACP.”
To build up leaders and maintain a knowledgeable crew, ACP prioritizes training. Management brought in Ball for a week of training in March and Goldberg regularly schedules
LEARN MORE
Preparing for a Day’s Success
Just because the milling crew did a good job doesn’t mean you can rest on their laurels. Here’s the way ACP ensures success at the start of the paving day as they pull up to the job.
1. The project manager and foreman will re-measure and line it out.
2. They mark the number of
the surface.
3. They have the tailgate talk to make sure everyone knows exactly what their roles are for the day and for the job.
4. They perform surface prep with cleaning, brooming, blowing and even burning away weeds.
John Ball explained, “They did a lot of finesse work to prepare. That’s the difference between a good job and a great job.”
A torch burns away stubborn weeds so they won’t re-grow through the thin pavement layer and a worker uses a leaf-blower to clear fine dust and debris so the tack can do its job.
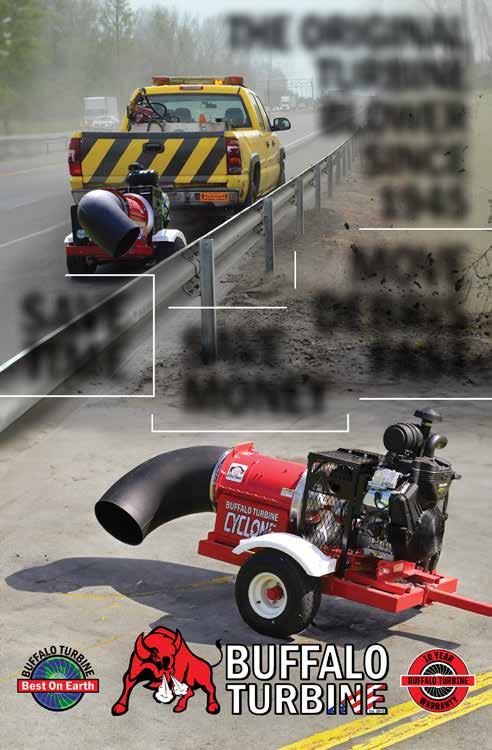

LEARN MORE
Paving by the Numbers
You’ve probably seen this information as a picture and spelled out in great detail in the magazine before. As a quick reminder, here are the steps for paving by the numbers.
1. Heat the screed (while it’s still suspended).
2. Set tow points.
3. Set paving width.
4. Set crown height.
5. Set extender height.
6. Set extender slope.
7. Set screed and remove slack.
8. Null out screed.
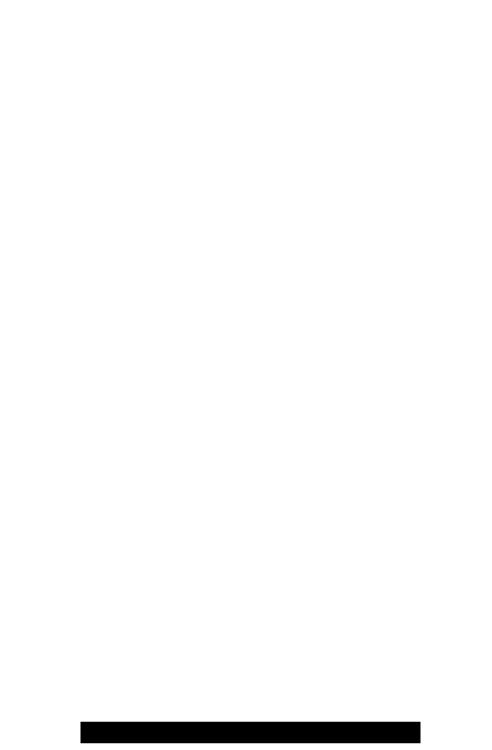
9. Position end gates.
10. Set auger height.
11. Position feed sensors.
12. In low idle, fill auger chamber.
13. Adjust feeder controls.
14. Set accessory functions.
15. Pull off starter plates.
lunch-and-learn sessions with both customers and vendors to spread knowledge on the industry and the company. “He loves doing them,” a spokesperson shared. “Our customers really enjoy them and they learn a lot about us and what we do. We usually do a lunch after the presentation and course, so it really gives us the opportunity to get to know them more and build relationships.”
For the middle school project in March, the crew put their education into practice to deliver a smooth finished surface for the young athletes. “We were paving 20 feet per minute,” Ball said. That gave them about five hours to place about 220 tons on the basketball court. “When you’re only laying an inch, the mat could easily tear or shove, so you want to take your time and do it right.”
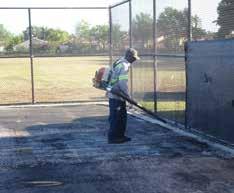
THE POWER
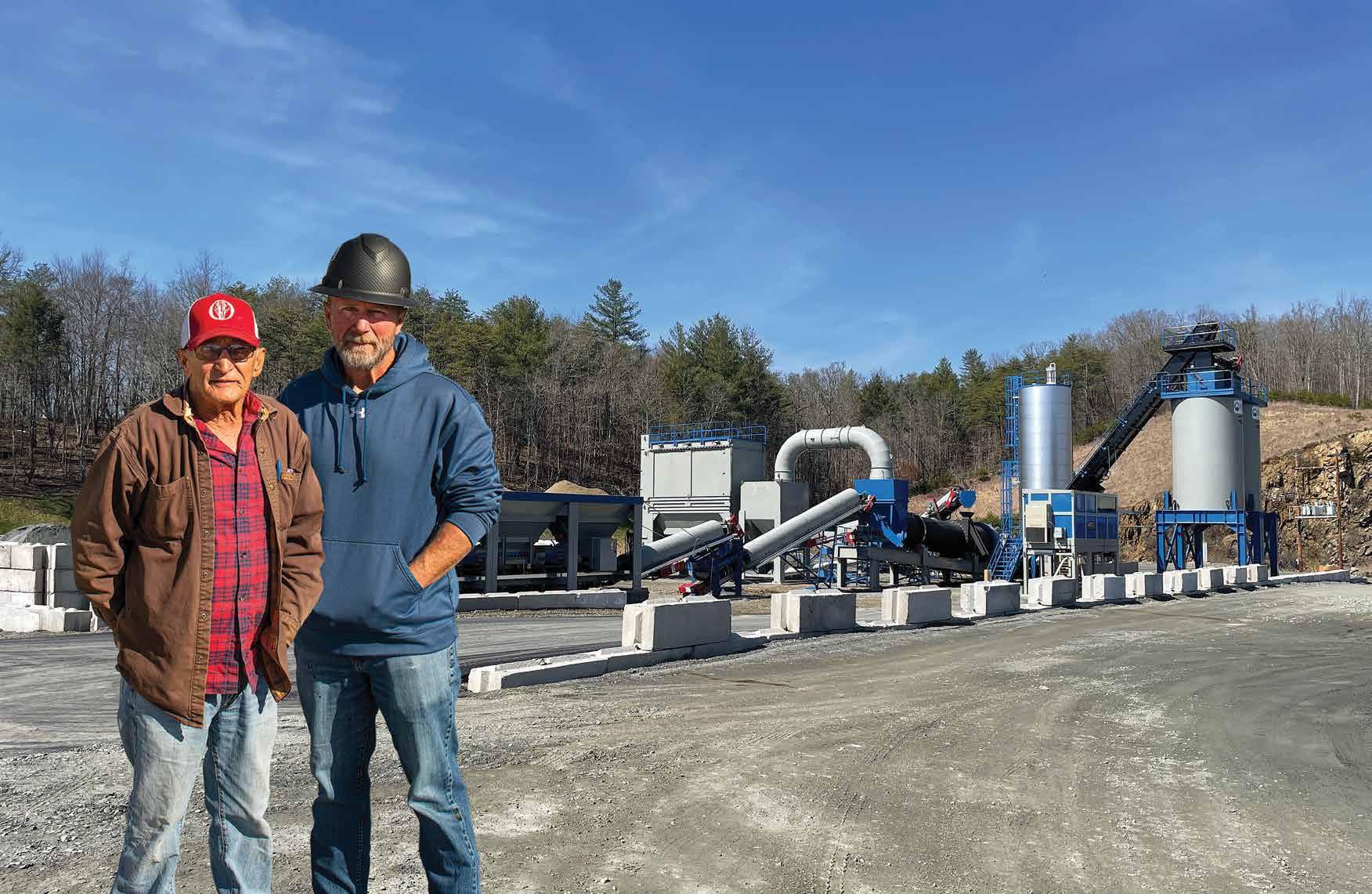
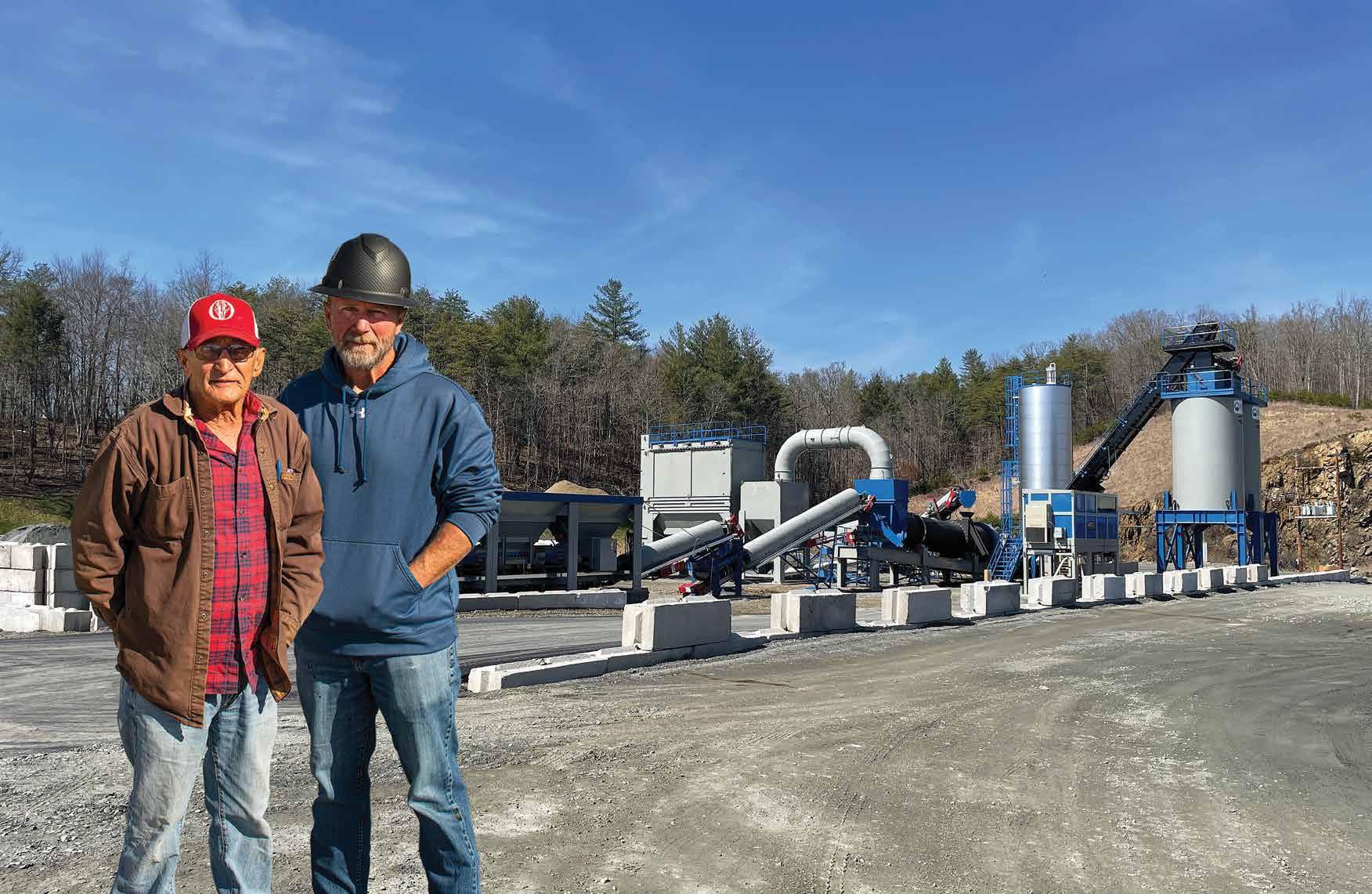

Train for PC/OA
RMAEC offers certification for process control/owners' acceptance testing
BY TOM CLAYTONAsphalt construction plays a vital role in building and maintaining our transportation infrastructure. To ensure high-quality results and long-lasting roads, it is essential to emphasize the significance of proper training for process control and owners’ acceptance (PC/OA) testing.
Process control refers to the systematic management of construction processes to ensure compliance with specifications, industry standards, and best practices. In the context of asphalt construction, process control involves monitoring and optimizing various stages, such as material selection, mixing, paving, and compaction. Adequate training for personnel involved in these processes is crucial for the following reasons:
• Quality assurance;
• Efficiency and cost reduction; and
• Safety and environmental considerations.
Owners’ acceptance testing is a crucial step in asphalt construction, where the completed pavement is evaluated against predetermined criteria and specifications. This testing phase involves collaboration between the construction team and the project owners. The significance of owners’ acceptance testing can be understood through the following points:
• Quality assurance and compliance;
• Performance assessment;
• Accountability and warranty; and
• Public perception and trust.
To achieve the desired outcomes in asphalt construction, it is crucial to invest in comprehensive training programs for personnel involved in process control and owners’ acceptance testing. These training programs should cover the following aspects:
• Technical knowledge;
• Equipment and technology;
• Safety and environmental awareness; and
• Collaboration and communication.
The training arm of the Colorado Asphalt Pavement Association (CAPA)—the Rocky Mountain Asphalt Education Center (RMAEC)— is poised to help with such training by offering a session titled “Introduction to PC/OA Testing.” CAPA established the RMAEC in the mid1980s when the Federal requirement to have certified technicians was being implemented. CAPA worked with the Colorado Department of Transportation (CDOT) to develop the certification program (LabCAT) to be operated by CAPA under the watch of a board of directors made up of CDOT, FHWA, consultants and contractors.
They also established a technical committee to create the instruction materials for the certification program. The technical group is constantly monitoring and updating the materials being instructed.
A need was determined to get technicians prepared to sit for certification as it was a new program and requirement so the Introduction to PC/OA class was developed.
The RMAEC facilities are located adjacent to the CAPA offices in Centennial, Colorado. The facility has a training/certification room capable of seating about 20 people for a session. In the facility there are
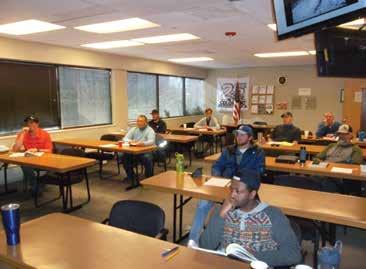
six individual rooms, which are the laboratory procedure room. The rooms will host one or more of the required lab procedures to be performed during the introduction or certification sessions. The RMAEC laboratory is a fully functioning lab for training purposes only. It is equipped with the most modern and relative equipment used in the asphalt testing industry.
TEST IT OUT
“Introduction to PC/OA Testing” is an introductory course designed to help technicians new to the industry understand and perform current CDOT/AASHTO test procedures used in the process control and owners’ acceptance testing of asphalt paving materials (APM), and in the placement of asphalt pavements. The training includes classroom instruction and hands-on experience in the laboratory. During the week, the attendees work with the RMAEC instructor each day. If they return for certification at a later date, the same instructor will be the person leading those as well.
Attendance at the sessions is limited to allow the necessary time and attention while in the learning session. The sessions are limited to no more than 12 people in each of the four days of training. The usual makeup of a session is the first day will be the most participants with the numbers declining each of the following days as the procedures become more technical and complex.
Within the class session, each of the attendees is provided with a guidebook, which contains a PowerPoint presentation for each of the procedures that will be taught over the four days. Those are for attendees to keep as detailed notes or comments as they feel necessary to get the most from the instruction. The RMAEC provides the attendees with any other materials they would need, such as gloves or other safety equipment when in the laboratory rooms.
YOUR PARTNER ON THE ROAD AHEAD

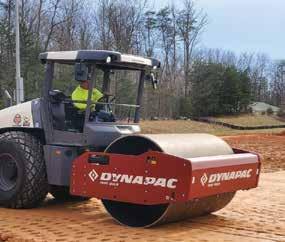
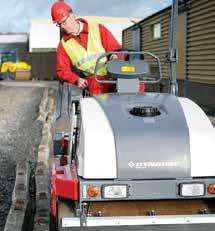
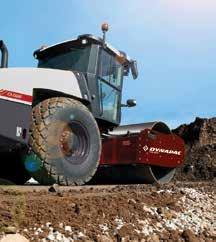
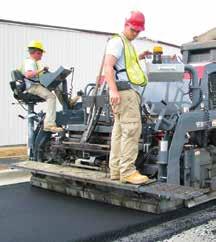
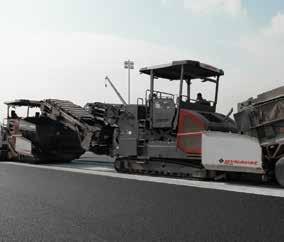

What does that mean? It means that we are determined to support you in your journey towards greater profitability, safety and environmental stewardship. It means that we will help you forge new paths, shape key trends and offer new solutions to support you on that journey. And it means we will be with you for every step of that journey through application consultancy, personalized trainings; across numerous geographic territories and around the clock.
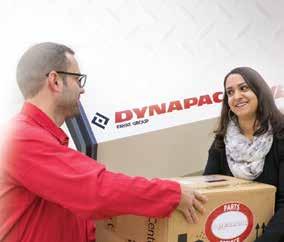
Tell us where you’re going and we will help you get there.
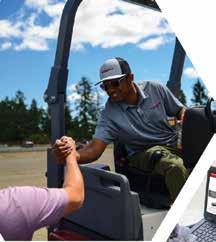
The instructor starts in the training room with a detailed presentation of each of the individual procedures that are used in the LabCAT certification program. These are presented one or two at a time depending on the different procedures. When the classroom portion is completed, the instructor will have the attendees move into one of six lab rooms to see a demonstration of how the procedure or test is executed.
After the demonstration, each of the attendees is provided the opportunity, under the supervision of the instructor, to do firsthand performance of the various testing procedures. The attendees may run the procedure as many times as they feel necessary to have a decent grasp of the test procedure. While they are in the process the instructor will provide guidance and correct any errors in running the different procedures. After the lab portion is completed, the students return to the training room to begin preparation for the next procedure or test process. This continues throughout the day until each of the level’s procedures have been completed.
The course format is divided into four separate one-day sessions. Participants may register for any combination of the days, depending on the information desired and needed to perform their duties for a contractor or consultant.
THE FIRST DAY
geared for those who are new and performing the most basic testing in the field during laydown operations such as sampling of asphalt mixes, sampling aggregate and performing nuclear density testing, observing and documenting a compaction test section (CTS), and random sampling plans
→ Participants will perform aggregate sampling from a miniature stockpile using the plate and shovel method and from a stopped conveyer belt using the belt cut template.
→ Participants will perform testing using the Troxler or Instrotek nuclear gauges—without sources in the machines.
THE SECOND DAY
focused on testing procedures in the lab such as Maximum Theoretical Density (RICE)
→ Participants will split out a sample of the appropriate size, get weights on the flasks, introduce the materials into the flask, cover it with water, place it on the shaker rack and apply vacuum following all the necessary times, temperatures and vacuum.
→ Participants will perform Bulk Specific Gravity.
→ Participants will reduce samples to testing size.
→ Participants will find binder content by ignition and nuclear oven methods.
→ Participants will perform gradation analysis and splitting aggregate.
THE THIRD DAY
focused on volumetric testing and compaction of samples using the gyratory compactor
→ Participants will use a sample they split out the day before, which was placed in the oven to heat.
→ They will remove the sample and mold, place the materials into the mold following the test procedure, place the heated mold into the gyratory compactor and then extract the specimen at the completion. Participants will also learn moisture damage testing by performing the Lottman Test.
THE FINAL DAY
focused on testing of aggregate properties for materials used in the design and production of asphalt paving materials including coarse and fine aggregates
→ Participants will learn Toughness and Tenacity, Micro Deval utilizing the equipment in our laboratory introducing a sample into the drum, adding the water and charges. Setting the equipment for the required number of rotations and extracting the materials at the end of the test.
→ Participants will learn Fine Aggregate Angularity testing by placing the graded materials into the cylinder without causing vibration; this becomes a challenge for new people and sometimes for experienced lab personnel. And more.
This training is useful for both entry level technicians who are preparing for asphalt technician certification (LabCAT), as well as for more seasoned technicians who may be re-entering the testing arena or changing levels of knowledge. There could be great benefit to inspectors and engineers who desire more knowledge about testing procedures, how they are to be conducted during a paving project, and basic information on how the test results may affect the quality of the pavement.
Proper training for PC/OA testing is indispensable for ensuring high-quality asphalt construction. By equipping personnel with the necessary knowledge and skills, PC can enhance the overall quality, efficiency and safety of asphalt construction. Similarly, OA testing provides a comprehensive evaluation of the constructed pavement, ensuring compliance with specifications, assessing performance and promoting accountability. Investing in comprehensive training programs for PC/OA testing is a key step toward building durable, functional and trusted road infrastructure. The final PC/OA introduction course for 2023 is Oct. 10-13 and CAPA requests you email rmaec@co-asphalt. com to express your interest.
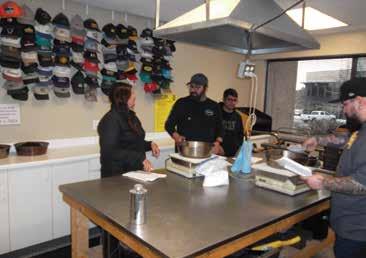
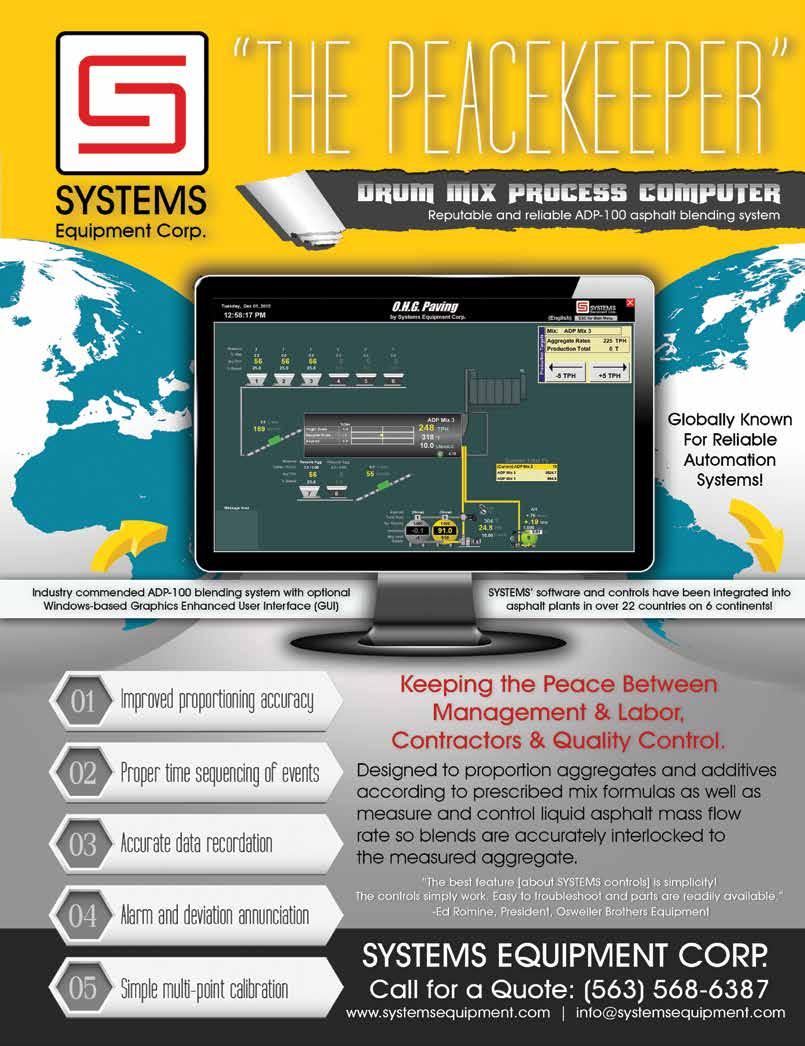
CHERRY POINT AIRFIELD PROJECT SUCCESS STORY
Crews navigated a rushed start to make a smooth landing for runway, taxiway upgrades
BY CHRIS CROOMTTeamwork was the recipe for success on S.T. Wooten’s paving project at the Marine Corps Air Station (MCAS) Cherry Point in Havelock, North Carolina. Tasked with repaving several runways and taxiways at the airfield, crews collaborated closely to execute in the short turnaround between departure and arrival time for the finished job.
Crews from S.T. Wooten’s asphalt and commercial divisions along with various subcontractors worked together to ensure a smooth landing for the project. Thanks to their hard work, the project was recognized with a national honor for excellence in airport paving— the National Asphalt Pavement Association’s (NAPA) 2022 Ray Brown Asphalt Pavement Award.
S.T. Wooten was hired as the turnkey contractor to manage and execute all construction activities for the Cherry Point job. While
the project was given a tight timeline, the company’s previous experience on runway mill and overlay projects at the same airfield was beneficial on this project.
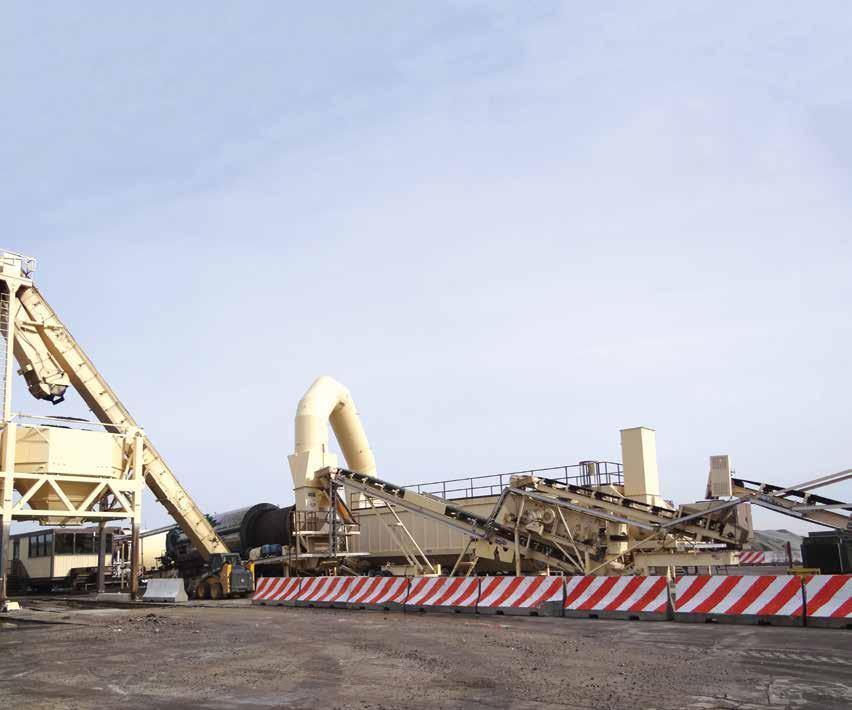
BUILDING THE ITINERARY
The military hires construction companies through a Multiple Award Construction Contract (MACC) process which calls upon larger, pre-qualified general contractors to submit for and oversee projects. This system helps streamline the paperwork and increase efficiency. Historically, it could be a tedious process to ensure contractors align with all the federal requirements to work on a military base.
Daniels and Daniels Construction was selected as the prime contractor to oversee the Cherry Point project and S.T. Wooten was hired as the turnkey subcontractor to manage and execute all
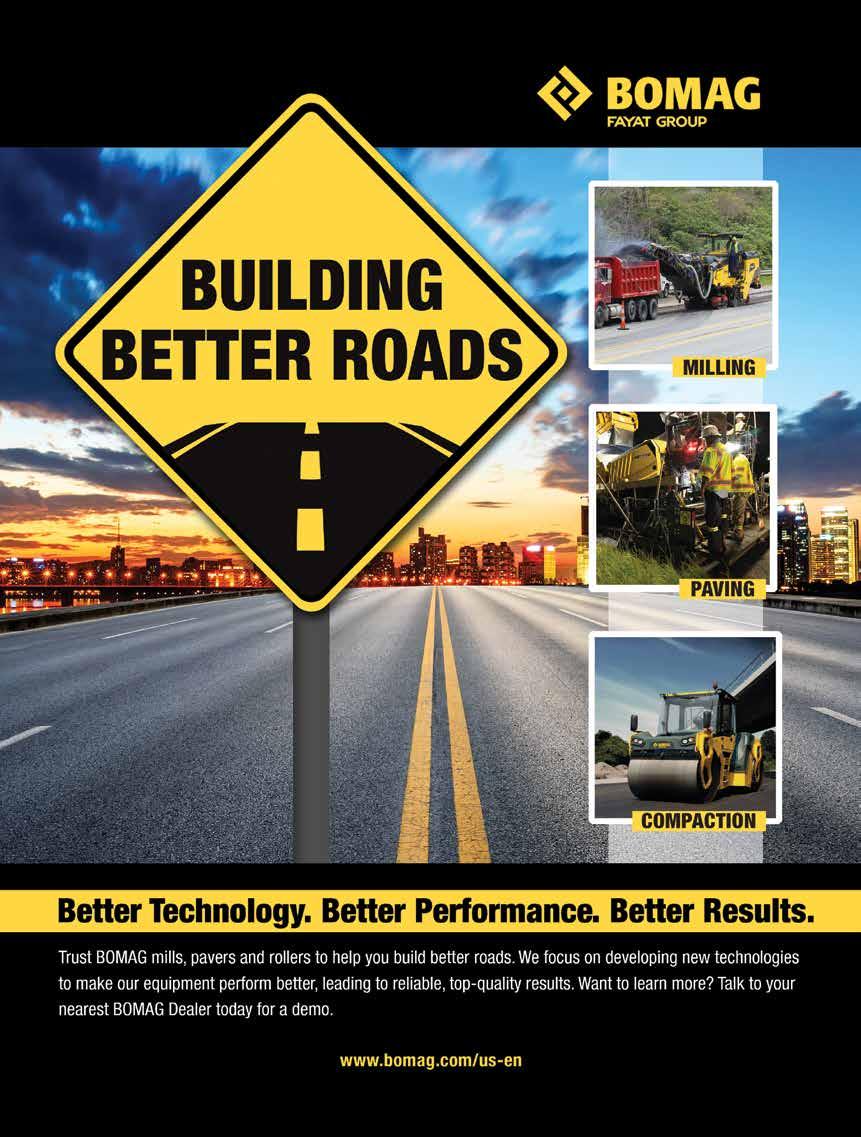
construction activities. While the project was given a tight 570-day timeline, S.T. Wooten’s experience having previously worked on resurfacing projects at the same airfield came in handy.
READYING FOR TAKEOFF
Crews understood that there was pressure to put the Cherry Point job on a fast track given the short timeframe to complete the project. Contracts were not finalized until mid-September 2021 and the base’s leaders wanted to get some paving done before the end of the year. Managers had to begin strategically developing schedules for not only milling and paving but also other subcontractors.
To expedite the process, S.T. Wooten moved a portable plant onto the base so crews could deliver asphalt as quickly as possible to the runways. A total of 53,470 tons of hot-mix asphalt was placed for the project. The asphalt plant came from the company’s Garner, North Carolina, location and was returned to that same site at the completion of the project. The same plant has been used to support the I-40 road widening project that is in the works between nearby Raleigh and Clayton.
GAINING ALTITUDE
Paving work is always done with precise measurements in mind, but being exact is even more important for runways and airplanes. For

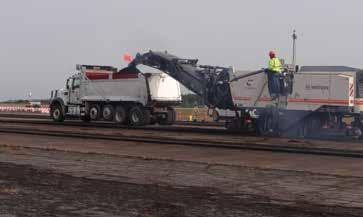
Cherry Point, the military required that the finished pavement had to be within 3/100s of an inch of the plan’s elevations.
To help achieve such an exact standard, S.T. Wooten utilized a Wirtgen milling machine with 3D machine control. This is the same approach used in GPS-controlled grading and earthmoving equipment; here, those same 3D models were used for machine-controlled milling to both the exact grade and slope needed.
S.T. Wooten started by surveying the existing elevation on each runway.
• The measurements were compared to the project plans, which proposed a new finished elevation. The crews couldn’t simply mill and replace the pavement in the exact same way; the entire runway needed to be reprofiled.
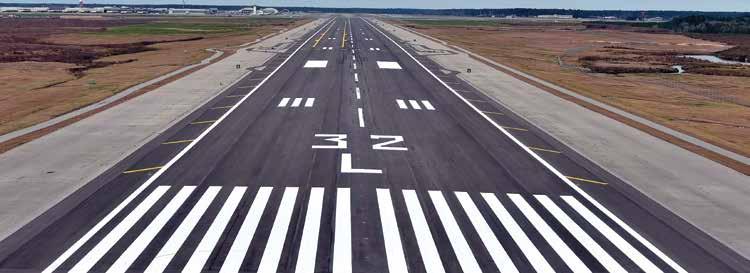
• Senior GPS Engineer Danny Wrench used the project plan to create a 3D model of those new elevations.
• The Wirtgen machine-control technology used the 3D model to mill and cut to the proposed grade. This helped ensure the milled surface matched both the new grade as well as milling down to the level required. In this case, that was two inches below the proposed finished elevation.
A second elevation survey was done to ensure the newly profiled and milled surface matched the project specs. This post-mill survey had to be submitted for approval by the government or architect/engineer before the next step.
Crews then paved the 2-inch surface course. A third and final survey confirmed that the final surface elevations were within the 3/100s of an inch of the plan’s specifications.
PREPARED FOR TURBULENCE
While 3D modeling helped crews ensure accuracy, the unexpected realities of a work zone can always throw a wrench into plans. One obstacle with the Cherry Point job emerged when it came time to change out the existing pavement profile, which consisted of an old layer of paving fabric that was installed between asphalt lifts. The fabric was not always in the exact location it was supposed to be, which caused milling and paving to take longer than expected.
The team took some troubleshooting measures to help clear the hurdle. Crews performed additional milling in locations of the runway where uncertainty existed to ensure any fabric they encountered was completely removed. Then they placed a new leveling layer of asphalt and re-milled the leveling course to the required pre-pave elevation per the 3D model.
CHANGES IN FLIGHT PATH
In addition to some execution challenges, there were changes in the project plans that called for crews to pivot. For paving, a Michigan Wedge technique had traditionally been used for runway construction at the base—involving the creation of a 45-degree slope on the asphalt edge and joining lanes with a joint heater. The Cherry Point project had initially called for a similar strategy, but specs were updated to require a saw-cutting technique.
A subcontractor was hired to perform the saw cutting, which helps ensure a tight connection between lanes. However, the process—combining saw cutting and milling—was one that crews also had to monitor stringently as it can be somewhat messy. Crews were constantly cleaning up foreign object debris (FOD), which is airfield jargon for dust, bits of pavement and rocks. While these small bits might not seem like a big deal, they are especially important to manage on airfield projects where too much dust can cause costly problems for jet engines.
A SUCCESSFUL LANDING
Despite a rushed start and some changes to the project specs, roughly half of the work was completed before Christmas 2021. That gave crews a long runway to finish the paving when the weather was warmer in the spring and summer 2022. It also meant that crews mostly had to deal with reinstalling the lights and finishing the lane markings toward the end of the project.
Having runway experience helped the team successfully fasttrack this project and ensure they safely and successfully met each milestone along the way. Collaboration and hard work also propelled the project to its scheduled completion date. The results will allow a smoother landing for aircraft in the years to come at Cherry Point airfield.
And thanks to the great work conducted by all the crews involved with the project, S.T. Wooten was proud to put some new hardware in the trophy room with its NAPA Ray Brown Award recognition.
ON THE ROAD TO NET ZERO EMISSIONS, WE CAN HELP YOU FIND YOUR WAY.
Are you exploring NAPA’s climate challenge, but unsure of your navigation? We can help you take at least one step forward — by replacing your tank heaters, hot oil heaters, fuel oil preheaters, and distributor truck heaters with our zero-emission, 100% efficient, Lo-Density® drywell-style electric heat.
Check out our new operating cost calculator at processheating.com!
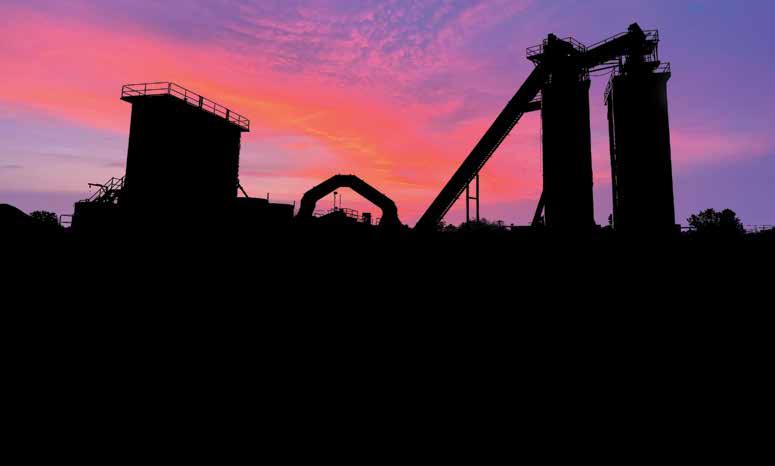
A INDIANA OVERLAYS WITH ARAMID FIBERS
BY JASON MARTINApproximately half of all infrastructure dollars are invested in pavements with more than half of that investment in overlays of existing pavements, according to the Targeted Overlay Pavement Solutions (TOPS) program from the Federal Highway Administration. One approach to enhancing overlay performance is using aramid fibers. This targeted overlay pavement solution can allow state and local highway agencies to maximize their investment to provide safer roads and to help ensure longer-lasting roadways for the traveling public. Aramid fiber has been proven to enhance properties of the asphalt mix like thermal cracking, block crocking, rutting, fatigue and modulus/structural number without changing the job mix formula, in studies performed at the National Center for Asphalt Testing (NCAT), Blankenship Asphalt Tech and Training (BATT), Oregon State University, and others.
In 2018, the Town of Plainfield, Indiana, collaborated with Milestone Contractors LP, Indianapolis, and Surface Tech LLC, Solana Beach, California, to provide an overlay pavement solution to improve the performance of the overlay with the objective of extending the pavement life. The Town of Plainfield wanted to control cracking on an industrial service road near the Indianapolis airport.
Milestone’s crew milled and placed a 2-inch overlay on June 27-28, 2018, on Stafford Road. The control section consisted of a PG76-22 in the passing lane while the ACE XP aramid fiber section with a PG7622 was placed in the truck lane.
INITIAL OVERLAY PERFORMANCE
To evaluate the consistency of each mix, plant produced samples of mix with and without fibers were collected from Milestone’s HMA plant on each night of production to check asphalt binder content and aggregate gradation. Asphalt binder content was tested from a sample each night of paving following AASHTO T164 while the recovered aggregates were tested for gradation following AASHTO T30. The results indicated that the asphalt content from the paving production was consistent at 5.35%. The aggregate gradation of the dense-graded mix from the plant produced mixes was also consistent for both nights of paving. One can conclude that the only difference between the two mixes is with and without ACE XP fibers.
Volumetrics alone is not enough to quantify performance differences. Most roads look great when they are paved, but owners want to know how they will perform after the first few years. They want to know if aramid fiber will add to the life of the pavement, delaying maintenance or reconstruction. Just adding one year to a pavement saves valuable construction dollars that can be spent by the owner to improve other pavements in the area.
Site Supply conducted a field survey on the project in 2019 after one year of service. The control mix in the passing lane exhibited 124 feet of lineal cracking, which translates to 37.6 feet of cracking per 1,000 lineal feet (normalized to project length). The ACE XP aramid fiber mix exhibited 15 feet of lineal cracking over the project length, which translates to 4.5 feet of cracking per 1,000 lineal feet (normalized to project length).
LONG-TERM OVERLAY PERFORMANCE
For the next five years, both pavement sections were surveyed manually by Site Supply and then a detailed site survey was performed in May 2023 by BATT to quantify the long-term performance. The figure below shows the transverse cracking in feet per 1,000 lineal feet from 2018 to 2023. One can see an immediate improvement after the first year of in-service life and that improvement in pavement life follows for the next four years. The ACE XP fiber section has extended the life of the overlay by more than four years. The control section cracking in 2019 is comparable to the ACE XP cracking in 2023. The rate of cracking over five years for the control section is 128.2 feet/1,000 lineal feet per year while the ACE XP section is 10.7 feet/1,000 lineal feet per year.
BATT performed the most recent manual crack count and video Pavement Condition Index (PCI) survey in May 2023. Not only was the transverse cracking impressive, but the PCI also showed an improvement of 5 points after five years of service, where the control was a PCI of 84 and the ACE XP section was 89.
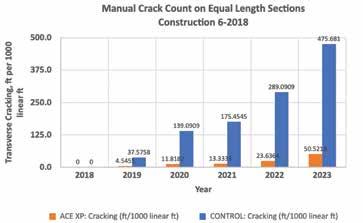
“The reduction in transverse cracking is some of the most outstanding that I have seen,” said Phillip Blankenship, owner of BATT.
The ACE XP section has improved the cracking resistance of the overlay for the Town of Plainfield. Using a targeted overlay solution (an innovative material such as ACE XP), the overlay life has been extended, which will allow the Town of Plainfield to pave more roads in the future.
Recently, ASTM has standardized the use of aramid fibers in asphalt mixes with the adoption of ASTM D8395-23. This standard calls out key properties such as length, density, strength, modulus and decomposition of the fiber. This is to ensure that customers are receiving high performance aramid fiber for their asphalt mixes, which is designed to improve the mix’s resistance to rutting, cracking and fatigue.
A 4 - day training and technical conference
Join us for Hotmix University in Louisville, Kentucky. During the focused exchange sessions, participants enjoy a combination of lectures and hands - on workshops on actual equipment.
PLANT MANAGERS are interested in making their plants run better while maintaining maximum profitability. Other topics include:

Industry changes and trends which require Plant Response/Modifications.
Tuning Plant Asphalt Automation to achieve 100% End Results and Project Bonus Pay.
Importance of Combustion and Air Systems to Achieve Production Rates.
Benchmarking and Measuring Plant Performance.
PLANT OPERATORS will invest half of their course time with hands - on demonstrations of asphalt equipment. The other half of the course time will be invested in learning via classroom-style presentations. Topics include:


Specifies where the Hotmix Asphalt Plant fits into the entire business operation including the management of aggregates, liquid A.C., paving, and quality control.
Dr ying Systems: Alignments, flighting, and troubleshooting.
Slat s & Silo System monitoring and wear-reduction. Plant Automation and Multiple Liquid Blending.
Call today to book a spot. 800 - 826 - 0223
Or register online at: hotmixu.com
HOW TO GET THE BEST IRI IN FLORIDA HISTORY
BY SANDY LENDERPPreferred Materials Inc., a CRH company based in Tampa, has a host of quality in construction (QIC) project wins to its name, but there’s a pair of projects along Interstate 75 (I-75) in Florida that deserves extra attention. Let’s start with the one you can find between exits 254 and 256, which crews returned to traffic Oct. 12, 2021.

The company took home a QIC award from the National Asphalt Pavement Association (NAPA) in January 2022 for this project of over 50,000 tons. The mill-and-fill encompassed eight total lanes north of CR672 to south of Progress Blvd. on SR93A/I-75 where the company placed a surface mix of FC5 Superpave mix design. The crew first milled and replaced 2 inches compacted of structural course, then placed the open-graded friction course (OGFC) at a mere ¾ of an inch, yet they achieved something remarkable—an average international roughness index (IRI) on the project of 25.
What’s more remarkable than that? The same crew performed the same mill-and-fill work with the same mixes immediately south of the 8-mile project in 2020 with an average IRI of only 24.
Farhad Zafaranian, E.I., M.S., is the construction manager for Florida Department of Transportation (FDOT), Tampa Operations Center, and shared this represents the “[s]moothest pavement in the history of FDOT since IRI has been recorded. It is important to note that the low IRI number would reflect consistency in production as well as placement procedures, which is the ideal goal of FDOT’s quality control process.”
“As both the state construction pavement engineer and a road user, I’m very happy to see our roads getting smoother than ever before,” said
FDOT’s Richard M. Hewitt, P.E. “I believe it is a direct result of the department’s incentive/disincentive smoothness specifications and a contractor who has put effort into trying to pave smoother than ever before. I’m very proud of the work Preferred Materials achieved on their two I-75 projects, as well as the majority of our asphalt paving contractors who have been paving significantly smoother in recent years.”
That pride is shared. Richard Crocker, operations manager of Preferred Materials Asphalt Division Tampa, wore his commemorative “24-IRI Club” polo shirt during our interview at CONEXPO-CON/ AGG and spoke readily of his team’s accomplishments. He proudly named the foremen and roller operators who contributed to the success of the 24-IRI project and easily spoke about their skills, not only on the I-75 projects, but also on a recent racetrack project that took all hands on deck.
“A year-and-a-half later, we went up and did another project just north of it and repeated the same,” Crocker said. “That same crew with the same rollers, with the same operators. And this is why you must take care of your people. You don’t want your people coming and going and losing their expertise.”
The secret to success is working with skilled operators who know their best practices and know their equipment. “Try to keep people on the same piece of equipment as often as you can,” Crocker said. He advised the successful companies out there will crosstrain crewmembers and have multiple workers who can perform the vital tasks on the paving train, but you’re building a team of experts.
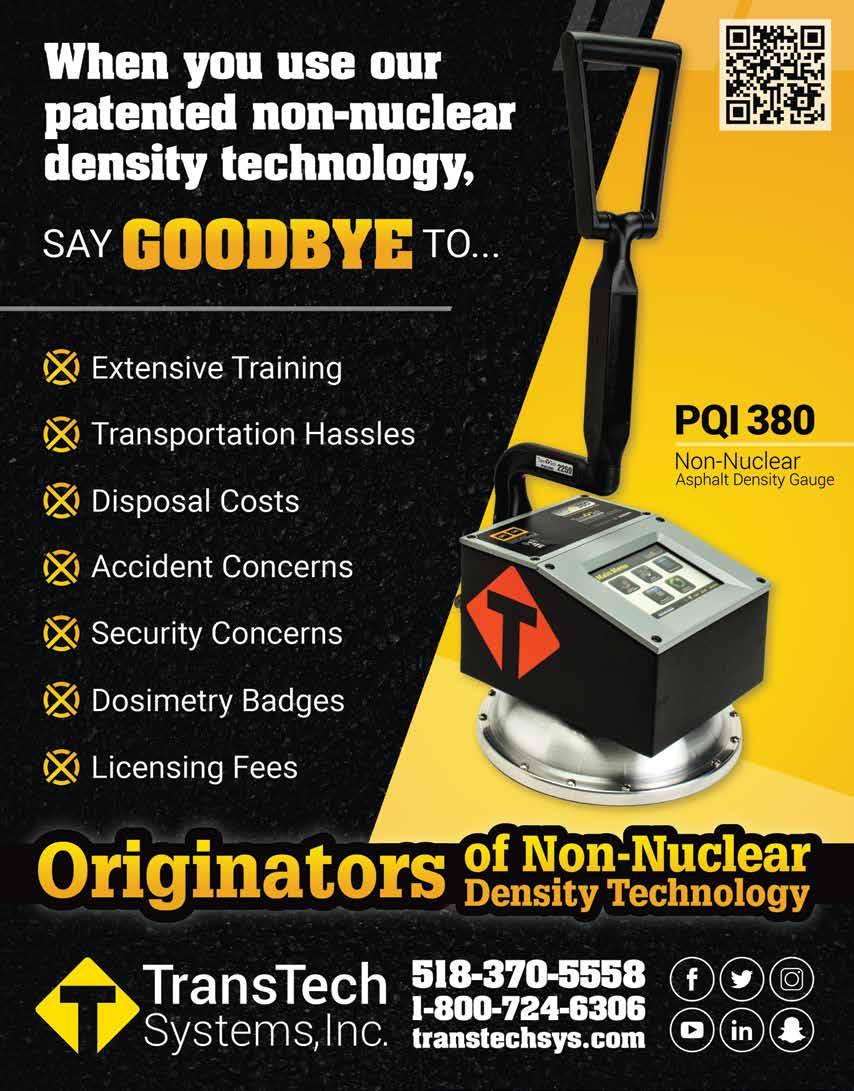
Pat Longstreet is the foreman for the crew that handled the I-75 project and his breakdown roller operator is Javier Gonzalez, who has 14 years with Preferred Materials. He runs a Sakai GW850 in the breakdown position and typically runs it with both drums in oscillation mode.
“For I-75, for the structural mix, we were putting down about 900 to 1,000 tons per shift due to lane closure restrictions,” Crocker said. The team performed layout and milling, so they had about six hours of paving before they had to turn things over to striping and open it up to traffic. “We were paving at about 28 to 32 feet per minute on the structural on 75 at 12 feet wide, 2 inches compacted.”
COLLABORATION ACROSS THE BOARD
Charles Holzschuher, P.E., is the state pavement materials engineer for FDOT. He spoke of attaining smoothness as a collaboration: “Based on collaboration with industry and the department, roadway construction and implementation of these smoothness specifications has improved the quality of paving resulting in smoother IRI. Ultimately, the goal of
smoother pavements and utilizing industry leading construction techniques is to embrace innovation, technology, and competition which has resulted in smoother pavements on a statewide level.”
While FDOT isn’t going to dictate a specific technology, the one Crocker spoke of as integral to smoothness success during our time at CONEXPO was oscillation for compaction.
The crews use rollers from Sakai, as mentioned above, and they typically have them set in oscillation mode, according to Crocker. It’s a feature of Sakai rollers that the front and back drums can be set in either vibratory or oscillation mode, or be switched from one mode to the other, or be both in oscillation mode.
“I like the capabilities of both drums being able to oscillate,” Crocker said. “Very seldom do we oscillate with only one drum. 99% of the time, we are oscillating with both drums. We do use the vibration on the 750 pneumatics, too. That’s usually on a #3 or #4 setting, whether we’re putting out a poly mix or not, we use them. And, again, that’s training roller operators and setting expectations and knowing what to do.”
SMOOTHNESS MATTERS
The Florida Department of Transportation (FDOT) has put time and energy into its smoothness specifications to encourage and reward those contractors who take on state projects. One of the measurements of smoothness is the International Roughness Index (IRI), which members of FDOT discuss here.
Farhad Zafaranian, E.I., M.S., Construction Manager, Tampa Operations Center: “IRI describes how much total vertical movement a standard passenger vehicle’s body would experience if driven over a 1-mile segment of the subject pavement at 50 mph. IRI is useful for assessing overall pavement ride quality; a higher IRI value indicates a rougher road surface. It is used by highway professionals throughout the world as a standard to quantify road surface roughness. A continuous profile along the road is measured and analyzed to summarize qualities of pavement surface deviations that impact vehicle suspension movement.
“Lower IRI equates to a smoother pavement surface which equates to increased pavement life and it will create a more pleasurable driving experience for the travelling public. Ultimately it would contribute to lower number of accidents, and decreased maintenance cost.”
Charles Holzschuher, P.E., State Pavement Materials Engineer: “Pavement smoothness is a key performance indicator and top priority for road users. Smooth-riding pavements provide comfort, raise optimum travel speeds, maintain traffic flow, reduce safety hazards, and increase fuel efficiency. Pavement smoothness also imparts a positive reflection on the construction and maintenance proficiency of the owner agency. Furthermore, research has shown that over time, smooth roads cost the owner/ agency and users less in maintenance and lead to longer pavement service lives.
“To better achieve smooth pavements and increase the service life of our roads, FDOT in partnership with the paving industry has formed smoothnessbased specifications to promote good construction practices and to develop and implement profile-based construction smoothness specifications. The long-term success of profiler-based specifications relies in part on the implementation of an FDOT profiler certification program to verify the accuracy and repeatability of test equipment to measure a longitudinal surface elevation profile.
“To realize this goal, a certification test track was constructed at Williston Municipal Airport. The test track meets the reference and inertial profile requirements set forth in AASHTO R-56. This certification program will ensure profiler operators have the ability to collect profile data and evaluate the quality of the acquired data.”
Richard M. Hewitt, P.E., State Construction Pavement Engineer: “Smoother pavements are not only more enjoyable to ride on, but they last longer and can help reduce some vehicle maintenance costs. Since smoother pavements last longer, the cost is spread out over a greater number of years resulting in a lower annual cost for pavement.
“The IRI provides a rating of the quality of a pavement’s ride with lower numbers representing smoother pavements and higher numbers representing rougher pavements. Lower IRI, i.e., smoother pavements, last longer and result in less maintenance costs for the state and for road users’ vehicles.
“Most drivers are not familiar with asphalt content, aggregate gradation, air voids, or density, but they do know if a pavement is smooth or not. As such, smoothness is the measure by which road users evaluate pavements.”
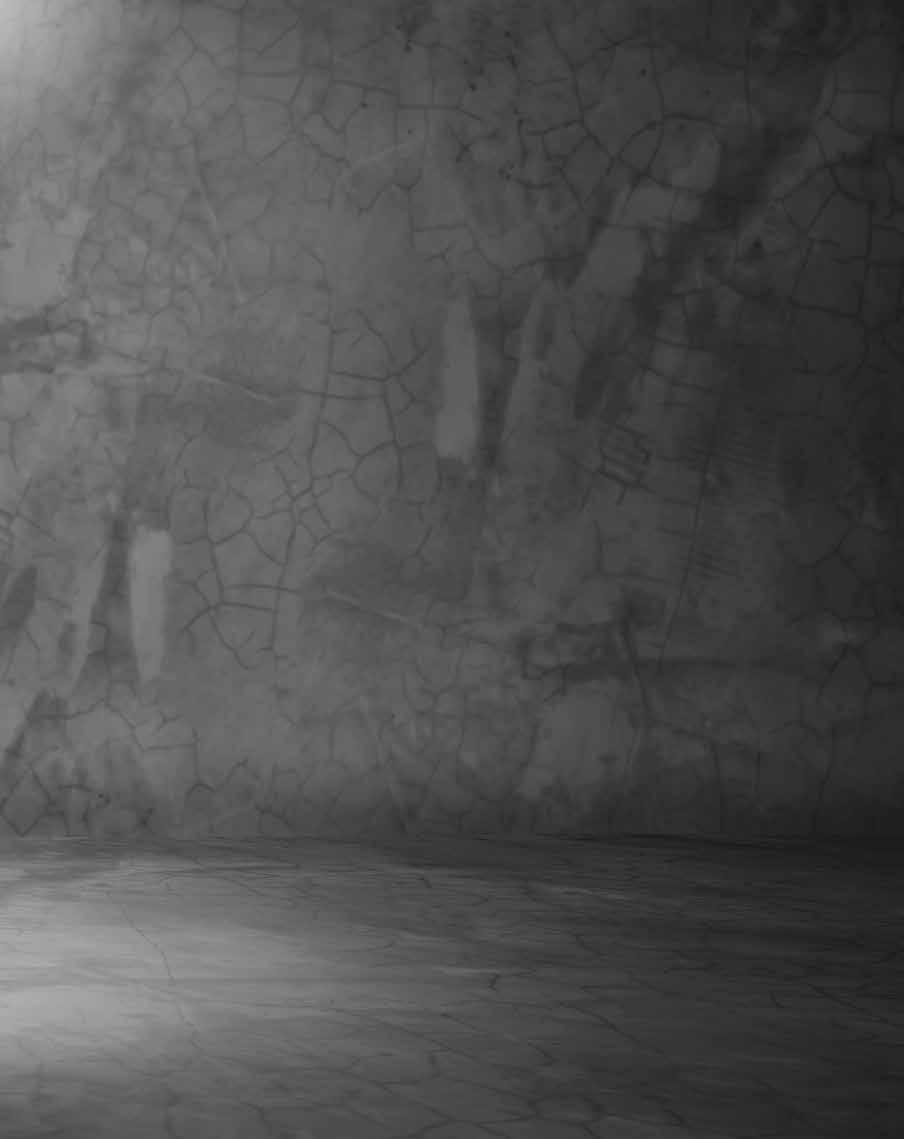
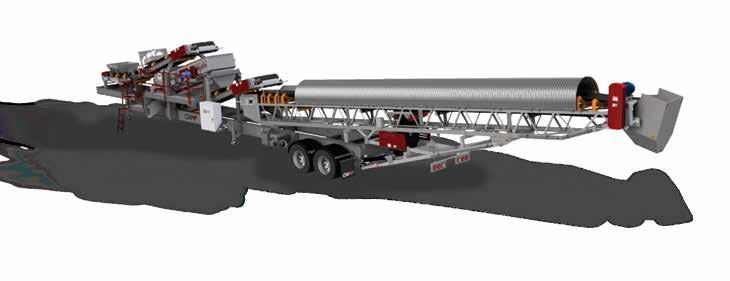
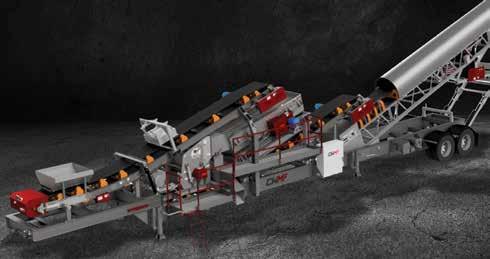
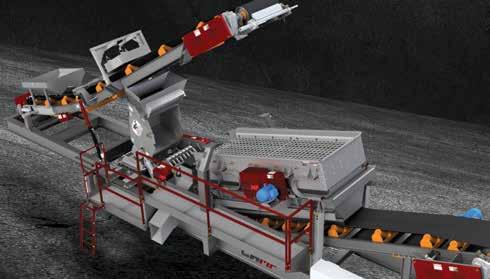
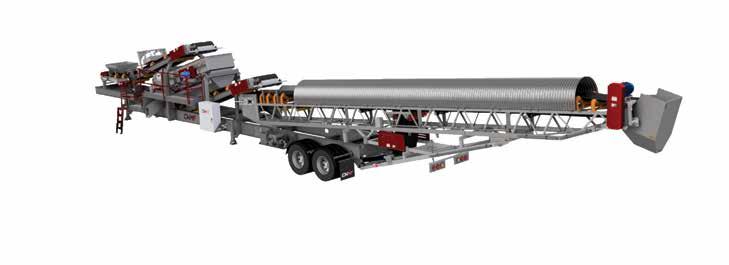
While at the booth at CONEXPO, attendees could gather information about the benefits of mixing and matching technologies. Studies showed using both drums in oscillation mode offered bonus potential; check out the sidebar below for that information.
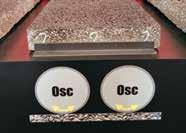
Crocker also spoke of the importance of collaboration and cooperation with all the partners and owners. By communicating needs and requests up front, contractors increase their opportunities to use best practices. They increase their chances to achieve the smooth results the asphalt industry can offer the taxpayers.
“We try to do a lot of continuous paving and that’s why we get the IRI result numbers we do,” Crocker said. “We coordinate, we plan, and we execute. There are a lot of partners that go along with that. Trucking, traffic control, the plant, QC, milling, cleanup.”
Crocker explained that the plant might be producing 4,000 tons of FOB mix on a given day, but his crew needs to pull 1,000 tons of structural. That takes coordination. Planning. A dedicated group of silos and one lane of the scales that the truckers know they’re to access.
LEARN MORE
SMOOTHNESS TRACK RECORD
The team from Sakai set up an educational section of their booth at CONEXPO-CON/AGG 2023 where they displayed three slabs of SMA pavement, constructed using six passes of a breakdown roller moving at 3.4 miles per hour.
The first sample showed results of a Sakai SW994ND roller with both drums in vibratory mode at 3,000 VPM. The objective results showed an IRI of 99 (inch/ mile), a theoretical maximum specific gravity (TMD) of 95.9% and MPD of 0.39. The summary suggested fair rideability and that “Vibe may reduce surface air void due to downward pressure.”
The second sample showed results of a Sakai SW994ND roller with both drums in oscillation mode. The objective results showed an IRI of 50, a TMD of 97% and MPD of 0.61. The summary suggested this one’s IRI value fell in the FHWA’s “very good” rideability category; its highest MPD value of the three tested offered better draining and the quietest, safest ride; and that “Dual drum oscillation with reduced amplitude reduces scoring of binder content.”
The third sample showed results of a conventional roller with one drum in oscillation mode and one in static. The objective results showed an IRI of 174, a TMD of 97% and MPD of 0.42. The summary suggested this one’s IRI value fell in the FHWA’s “very poor” rideability category and that “Excessive oscillation amplitude in single drum scores aggregate/binder, reducing life.”
The second sample on display at the Sakai CONEXPO-CON/AGG 2023 booth showed results of a Sakai SW994ND with both drums in oscillation mode. Photo courtesy of AsphaltPro
“It’s all relative,” Crocker said. “If we can continuously pave, then we can continuously roll.”
One way to increase the time spent paving is to ask for it. If you have a good reputation, you might get that time. For example, he said the I-75 projects had clear start times at 10 p.m. and stop times before rush hour traffic kicked in. “You had to be off the road, and that’s painted, everything’s off the road by 6, some spots of the road was by 5.”
What Crocker shared is how to wisely extend that time. “If you can go out and show, hey listen, over this 12 miles, I can eliminate four sets of transverse joints,” you could gain “an hour or an hour and a half at the beginning of the shift.”
He explained that you can approach the project owner, even if that’s a DOT with set specs for the project, and show them what you can do with the extended time. By eliminating transverse joints, you eliminate the potential for bumps in the road. By extending time on the northbound lanes while most traffic is building up southbound, you’re using time wisely.
“You gain an hour, hour and a half at the beginning of the shift going northbound because all the traffic then is trying to go south,” Crocker said. “Then when you go the other way, you get it on the other end.”
Crocker said you must then execute what you say you will, or the agencies won’t be eager to grant requests in the future. That means instilling pride in workmanship in your crewmembers and getting quality results that back up what you say you’ll do.
“We try to empower all of our people from the guy putting out the cones all the way up to our VP,” Crocker said. “We try to empower our people to take pride. Our reputation has got to get us something. And it has. We have a great safety record, and we have the smoothest road in the history of Florida DOT.
“And this is worth talking about; you have to back up what you say. With our equipment, with our rollers, I was confident we were going to get joint density, I was confident we were going to get mat density, and I was confident we were going to get ride.”
Channel Your Inner Kenny Rogers
Preferred Materials’ Richard “Rick” Crocker said to figure out what you need to get the quality job done right and ask for it. If you have a good reputation and a good working relationship with the owner/agency, you might be successful in getting the leeway you need to adjust a timeframe or a parameter of the job. “You have to know when to hold ’em and when to fold ’em. I look at it like a card game. How can the project win? How can the owner win?” When he’s able to work out an extended timeframe with the project owner, he can put additional best practices into motion. And that’s a win for his crew, the project owner and the end user.
Asking for what your crew needs helped Preferred Materials get the recent racetrack paved in an efficient manner as well. Crocker explained they worked with the owner to gain access to the site for continuous paving. “We had to talk to the (track) owner about access, about ingress and egress because they had the guardrail up. There’s only so much opportunity to get in on a racetrack.”
As Crocker said above, the team coordinates, plans and executes the plan. For the racetrack project, they wanted to eliminate any centerline joint, so they made a plan to build up, staggering and layering with eche-
lon paving in mind. “We figured out which crew should be wider and which narrower to stagger the center joint.”
They placed the base with one paver and material transfer vehicle paving 17 feet wide; the other coming alongside at 13 feet wide to total the 30-foot width. When it was time to place the surface, they staggered differently. “For the friction course, the joint was right down the center.”
The racetrack crew also faced a temperature challenge with a high-polymer mix. It was produced at about 340 degrees but lost temperature in a hurry once it left the haul truck. “We had a 15-minute haul. By the time it was coming out the back of the screed, it was already down to 285, 290 degrees and that’s with 80-degree ambient temperatures in Florida.”
“We were only paving 18 to 20 feet per minute,” Crocker said. “We’re using automation on the paver. We’re using two non-contact skis. It’s a MOBA-based system. Your rollers are trying to roll this joint. The first roller has to stay off the joint. The second roller has to roll it over and push it down. The rollers are the key. We had to look at when do you start the breakdown process? In this case, immediately.” And the rollers had to come right up to the screed. “We had to communicate that in the pre-construction meeting.”
Best practices came into play. “When the roller starts to approach, he has to come right up to the screed. We can’t stop 20 feet away, and we can’t stop straight. He has to always stop at an angle. And when we come onto the mat; we have transverse joints, we can’t come onto the mat straight, we have to come on at an angle.”
Pat Longstreet and his crew had Gonzalez as the breakdown roller operator on the racetrack project. Chris Longstreet and his crew were the second crew on the project. They had two breakdown roller operators during the project: Ceasar Jimenez, who has been with the company for eight years, and Mytara “Nubs” McCray, who has been with the company for 22 years.
That longevity, coupled with the skill and pride in workmanship so evident in the Preferred Materials ethos, lends itself to a set of low-IRI, high-quality pavements that our industry can point to as examples of exemplary asphalt construction. As the team at FDOT pointed out, getting high quality translates to long lasting pavements for the taxpayers, and that’s a win we can all be proud of.
LEARN MORE
SMOOTHNESS TRACK RECORD
• The 2021 project on I-75 totaled 56,543 tons of HMA, opened to traffic Oct. 12, 2021, and achieved an IRI of 25. (That average was later adjusted at the state level to 24 when data was reviewed.)
• The 2020 project on I-75 totaled 107,400 tons of HMA, opened to traffic Dec. 16, 2020, and achieved an IRI of 24.
• The racetrack project totaled 11,459 tons of HMA and saw an IRI go from exceeding 400 on the subgrade to ranging between 40 and 70 on the finish with a joint density average of 93.4 and a mat density average of 93.7.
Meet a Woman of Asphalt: Zipp’s Asphalt & Sealcoating’s Brynn Zipp
BY SANDY LENDERBrynn Zipp saw a need for high quality sealcoating services in her region of Indiana back in 2016. True to her proactive nature, she dove into the market and saw almost immediate growth of her company, Zipp’s Sealcoating. It didn’t take long to expand into crack filling and then commercial paving, taking on the projects she knew her company and crew could handle to build into the Zipp’s Asphalt & Sealcoating LLC we see today.
She took some time out of a busy schedule to share with us her experience as not just a woman of asphalt, but the owner of a growing asphalt paving company.
AsphaltPro: What did you find interesting or fulfilling about the sealcoating and then crack filling activities as you were building the Zipp’s Sealcoating business the first two years? What do you think about those roles or activities would be attractive to other women joining our industry?
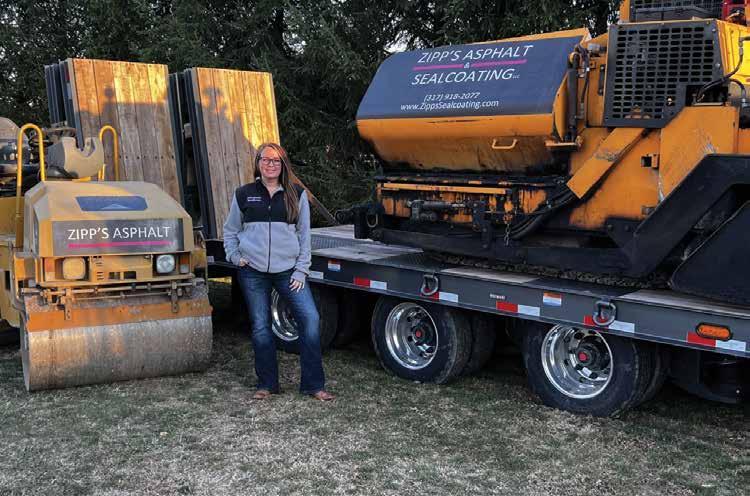
Brynn Zipp: Truly the instant gratification of our work is what is most fulfilling about what we do. It’s work where you see the final result immediately. Even as you’re progressing through it, seeing that hard work instantly is so rewarding.
Our goal was always to get into paving, but from a new business startup perspective, sealcoating and/or crack sealing has a lower start-up cost associated with it, which allows you to start becoming a staple and building a reputation on your skill sets quickly. So, the low start-up cost aspect is definitely appealing.
Sealcoating may not be for everyone. I recognize it’s a stinky job, but for us, it’s what launched our business, drove us to expand and become Zipp’s Asphalt, and really got us to where we are today. Other than that, I’m not sure that sealcoating/crack sealing is necessarily “attractive” to both men and women, but for someone who is self-motivated and appreciates instant feedback on their daily work, plus the low start-up costs, it’s great for filling that!
AsphaltPro: Could you share with the readers how your education in business administration prepared you for the ups-anddowns or day-to-day growth of an asphalt business? (And what courses would you recommend to women who want to join an asphalt sealing or paving company as a manager or co-owner?)
Brynn Zipp: I received a certificate in Business Administration, but I really feel that owning and running a business cannot be taught by a book. This helped me prepare for the behind the scenes work that needs completed every day, in terms of bookkeeping, communication, office skills, etc. I feel that my self-motivation, my ambition to succeed and my eagerness to be a staple in Indianapolis in the asphalt industry has been what has helped me with the upsand-downs and ins-and-outs. The ups can be very high and satisfactory, but the lows can be really hard. Without the support and teamwork of my husband and my crew I wouldn’t have the business I have today.
Speaking about formal education: I truly feel that you don’t need a degree to join this industry. The construction industry has a lot of room to start straight from high school and work your way up based on skills, work ethic, etc. College isn’t for everyone, and I want women, and men, to keep in mind that these industries are hurting for labor and it’s a great way to grow. I would personally recommend working on certifications with areas like OSHA, your state and/or city. Those are going to take you so much further, I think.
AsphaltPro: Could you share with the readers what your job as the owner for Zipp’s Asphalt requires of you these days?
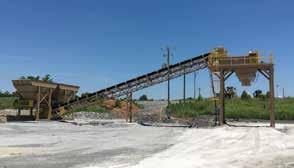
Brynn Zipp: As the owner of Zipp’s Asphalt, I carry most of the primary duties. I communicate with all the customers. I am walking potential jobs and completing and submitting bids. I am the HR, accounts receivable and payable, and I handle ensuring we’re up to date on the insurance, bonds and licenses required of us.
Daily, I am checking in with the crew, setting up jobs to fill the days, and communicating with our suppliers. It’s definitely not all fun and games, but again, it’s extremely rewarding.
There are days that I am on the job site, running the paver or hauling material—you name it, I’ll do it. Being the owner requires me to be readily available for any and all things. Especially with
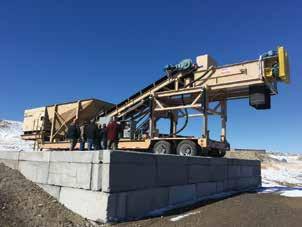
PUGM I L L SYST EM S
We’ve been designing and manufacturing custom mixing solutions in Tennessee for nearly 40
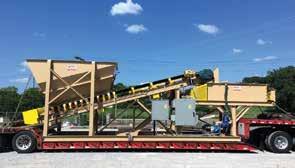
the current job market we’re in, I find myself doing the manual labor more and more while it can be hard to find crew members. There are days we’re a short a lute man, so here I come to pick it up and lute for the day!
I’m here for whatever is needed, what it takes to meet the needs of the day-to-day.
AsphaltPro: What about your “job” with Zipp’s Asphalt is “most cool” to you?
Brynn Zipp: I can’t even call what I do a job. This is my life. Every day I am doing something for our business. I stay up to the early hours of the mornings working on bids at times so that I can also be Mom and Wife in between all else.
I think the coolest part of all this is simply that this is my company! I played a huge role in starting this and continue to play that role carrying us into the new phases of business. I dream that we can build something great and that our hard work will allow us to have something for our kids to join one day.
AsphaltPro: What do you think is the most important skill you’ve brought to your position in the industry? (And how would you encourage other women entering the industry to hone a similar skill to be any kind of asphalt leader they want to become?)

Brynn Zipp: I think the most important skill I’ve brought is communication. I’m a people person. I could talk all day about the right subjects, and I’m truly passionate about our work and this industry that I’ll continue to sell our work as long as there’s someone there to listen.
I know that local colleges, the state, maybe even local governments, offer classes that you can sign up for in relation to communications
and relationship building. I’d really recommend that if that isn’t a strong point. Sign up for one and just take it all in.
I’m lucky enough to have been raised by two parents who are also excellent in communications, so I owe my appreciation for that skill to them, but it shows that it is a teachable side of business and it’s very important.
AsphaltPro: What would you say was the most challenging “obstacle” you, as a female in the industry, had to overcome in the past six or seven years, and how did you overcome that obstacle? How do you think other women in the industry can incorporate that skill or habit into their workdays?
Brynn Zipp: My perception was that it would be hard to earn respect from vendors, supplies and prime contractors in a male dominant industry, but I’ve quickly learned that they’re all very welcoming and supportive. I am fortunate to work with some of the leading industry vendors and suppliers, and they’re always willing to tell me about products, why we use them, how to use them, etc. “Teamwork makes the Dream Work” is very evident, and I really see them as part of my team.
Now, with that being said, I feel that my biggest obstacle has been earning the respect of customers. I think in general, we as a public see these trades as a male job, so to have a woman standing there selling it, can be sort of shocking. As I’ve become more comfortable in my knowledge of products and gotten the experience in estimating to get me to solely handling that, most customers would look and ask questions directly to my husband rather than to myself. I really feel that we need to all work together to overcome this stereotype of men in the manual labor industry, and support that women can do this too.
I will say, my husband is a great example of supporting women in asphalt, or other trade work. He’s never been one to just take over speaking when I was learning the estimation process, but he was always willing to teach me all areas and aspects of the backend information to support why we do this. I would encourage others in the field to do the same: teach and mentor, help women grow and expand their knowledge.
J.K. Rowling said, “We are only as strong as we are united, as weak as we are divided.”
AsphaltPro: Let’s talk about teamwork. What is an example of a project you were able to help your company bid successfully or a challenging project you were able to help your team complete smoothly because you all worked together/as a team?
Brynn Zipp: We were very fortunate to earn business with a leading financial corporation here in Indianapolis, and it brought a large project requiring multi-step business: mill and pave, crack seal, and line stipe. With the tight labor market, we found ourselves short on crew members. I found myself having to step up and be present for the job entirely. Like I’ve said before, communication is vital. If it weren’t for the constant communication between my crew, we could have had ugly seams, or a wavy mat, and those are things you cannot have. Instead, because of our strong communication as a team, our cross-training effectiveness, and willingness from all to step in where we needed it, we were able to get this project completed, and done well, which helped us to win continued business from them.
AsphaltPro: Let’s talk about perceptions. What do you think is an incorrect perception that we, as an industry, can re-educate young people about to encourage more women to consider a career in the asphalt business? What is something you would tell a young lady to encourage her in this industry?
Brynn Zipp: There is a huge opportunity for women right now. There’s a push for increasing diversity in the construction industry and it’s an awesome time for women to get into trade work, especially with the increasing demand for labor. Getting into this industry: Yes, it’s hard work, but women can do it all too. There’s a lot of room for growth, to move up and be recognized. Get through the nitty-gritty, you could run a crew, be a project manager, maybe even one day have your own business related to the industry. But everyone has to learn the skills, and you have to start somewhere.
AsphaltPro: What is the most rewarding aspect for you of being in the asphalt industry?
Brynn Zipp: The most rewarding aspect is knowing that I’m making a difference. I have the satisfaction of knowing that my customers are taken care of and they’re getting topof-the-line service. I get a huge smile on my face knowing that I am building a business where we can be a competitor in Indianapolis as a start-to-finish asphalt contractor. Not to mention, the before and after of these projects can be jaw dropping!
AsphaltPro: Will you tell us about a person who served as a mentor for you? How did this person encourage you?

Brynn Zipp: My husband, Andrew Zipp, has never let me think that I can’t do this. He’s always been an advocate for me to learn the industry, teach me the skills, grow my skill sets. He always has my back, and I’m lucky enough to have him to manage jobsites and ensure that our work is nothing but the best.
AsphaltPro: What piece of advice from Andrew would you share with other women in the industry/other leaders?
Brynn Zipp: He is a man of few words, but he’s always said and will say to anyone, “No excuses. Get it done.” He pushes me to be the best version of myself and to give everything I have to everything I do.
Women of Asphalt (WofA) will have its first national event
“ Women of Asphalt Day ,” taking place on March 27, 2024, in Nashville, Tennessee, in conjunction with the World of Asphalt. This conference is set to be a landmark event in the asphalt industry, bringing together women from all corners of the country to learn, network, and grow. Mark your calendars and plan to join us! Check out WofA’s website for updates on the event!
“I DREAM THAT WE CAN BUILD SOMETHING GREAT AND THAT OUR HARD WORK WILL ALLOW US TO HAVE SOMETHING FOR OUR KIDS TO JOIN ONE DAY.”—BRYNN ZIPP, OWNER OF ZIPP’S ASPHALT & SEALCOATING LLC
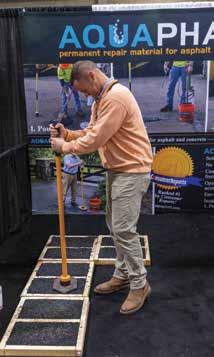


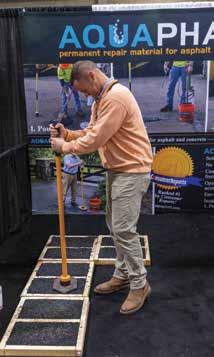
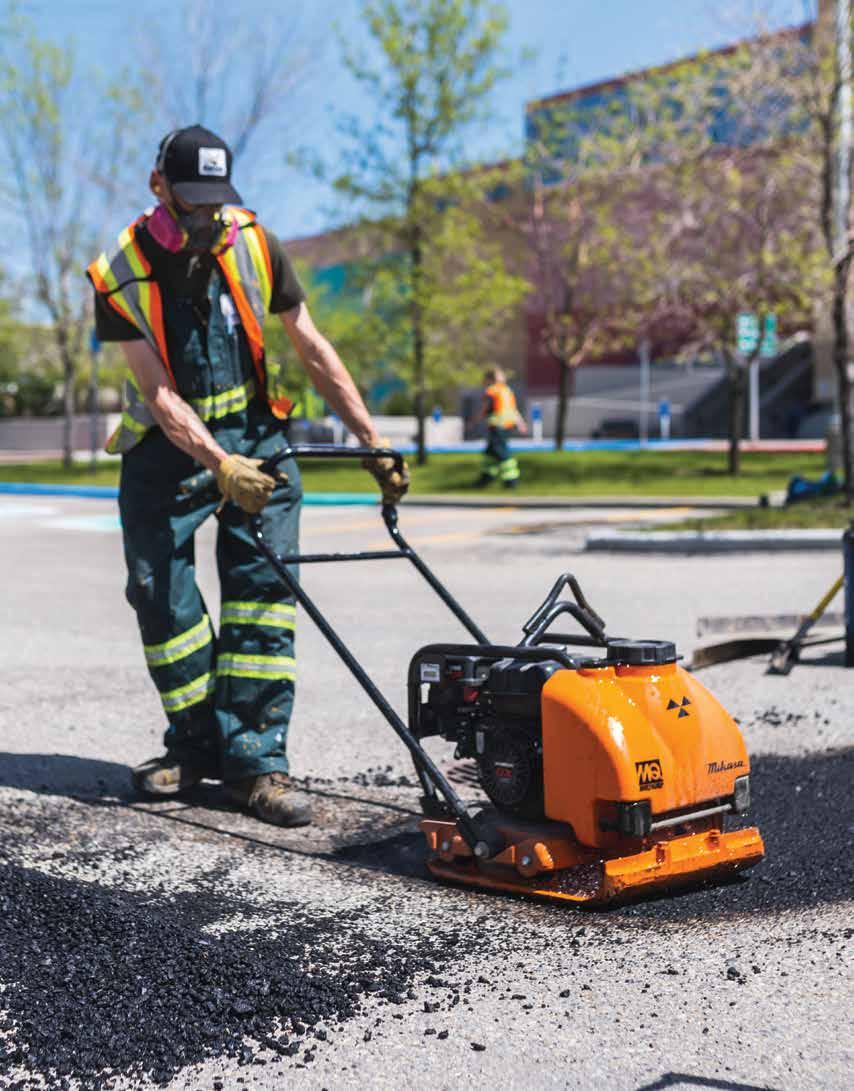
Revive the Client’s Driveway with Infrared Patching

How to use infrared patching to fix failing asphalt spots
By Rudy CurtlerEEverLine Coatings, Twin Cities, Minnesota, is a parking lot line striping and pavement maintenance service that handles projects for the long-term preservation of asphalt. One of our customers was looking to have his driveway repaired after years of wear and tear. He had taken good care of it and maintained it for over 20 years, but it had really begun to wear down recently. Part of the problem had been a recently purchased, large, heavy pickup truck regularly parked in the driveway. The weight of the vehicle caused two noticeable “ponding” areas at the front of the driveway near the garage. There was also some noticeable asphalt beginning to fail along the side of the driveway, which was causing some concerns.
When we first arrived at the home to assess his driveway, we knew that a conventional approach would not suffice. Simply repairing the damaged areas would only offer a temporary fix, and replacing the entire driveway would be costly and unnecessary. As experts in asphalt maintenance, we suggested a more sustainable and cost-effective solution: infrared patching.
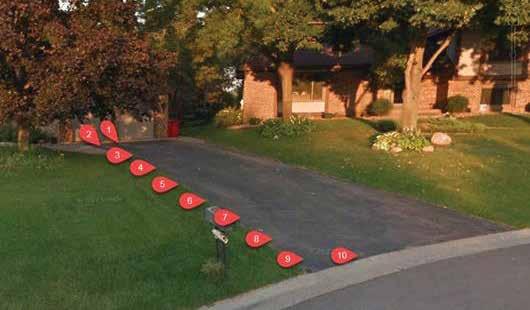
Infrared patching is a technique that is one of the most effective ways asphalt can be repaired. This method uses infrared rays to heat the damaged asphalt, softening it to a workable state. We then add fresh asphalt, seamlessly blending it with the existing surface to create a smooth, durable patch. Unlike traditional methods that require cutting out damaged areas, infrared patching eliminates the need for a full excavation, making the whole project and overall product more stable. Our client was intrigued by this solution, and after explaining the process and its advantages, we moved forward with the process.
We performed 10 infrared patches, each measuring 6 feet by 3 feet, targeting the area most in need of attention. The result was remarkable, with the once troublesome spots now smooth and level, allowing rainwater to drain away effectively. Furthermore, the failing asphalt on the side of the driveway was effectively restored, eliminating any safety hazards and preserving the overall integrity of the driveway.
The benefits of infrared patching were twofold for the client. Not only did it resolve the “ponding” areas caused by the weight of the heavy pickup truck, but it also addressed the failing asphalt along the side of the driveway. But we didn’t stop there. To ensure the longevity of the repairs and give our client’s driveway a fresh, polished appearance, we applied three coats of sealcoat. Sealcoating provides an additional protective layer, shielding the asphalt from the damaging effects of UV rays, water and chemicals. Not only does it improve the aesthetics of the driveway, but
Women in the Asphalt Business
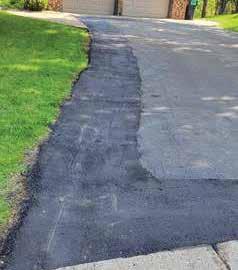
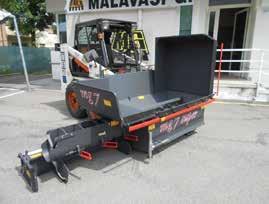
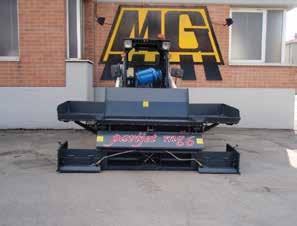
Earlier this summer, EverLine Coatings added to its senior leadership team when it brought aboard Bridgette Morgan as vice president of market development, bringing her years of experience in overseeing sales and product marketing operations and cultivating customer relationships to drive business growth.
In her new role, Morgan will define and execute comprehensive market development strategies, ensuring alignment with overall business objectives. She will oversee sales quotas and assign strategic account objectives for the national accounts team, fostering revenue growth and client retention, plus track key performance metrics for the executive team, highlighting progress and recommending actionable insights. Other initiatives include identifying market trends, customer needs, and competitive landscape to guide product development and market positioning and spearhead efforts to position the company as an industry leader in brand image, presence, and thought leadership.
“I am excited to join the EverLine team at this time of growth and expansion,” Morgan said. “This role is critical to enhancing the overall EverLine brand experience, and I’m enthusiastic about the opportunity to focus on sales and marketing initiatives that will support our ever-growing franchise organization.”
For information on becoming a franchisee, visit https://everlinefranchise.com/us/

it also significantly extends its lifespan, saving the client unnecessary expenses in the long run.
Our client was delighted with the results. Not only did the driveway regain its former glory, but it also received a boost in resilience and is better equipped to handle the demands of the regular wear and tear the asphalt takes. The combination of infrared patching and sealcoating offered the perfect solution, and the client was amazed at how this approach surpassed initial expectations and is now built to stand demanding weather conditions for years to come.

Looking at the benefits of infrared repair, the overall process is an effective solution to some of the most deteriorating asphalt problems. For contractors working in this space, this process also helps save time and money by eliminating the need to cut and jackhammer, and decreases the manpower needed for the repair job. The results are also longer lasting compared to just filling a spot with asphalt. Leaving joints and seams in the asphalt opens the door to water infiltration, which will reverse all the work that has been put into a project.
Using state-of-the-art technologies like infrared repair can really make the life of a contractor or repair company a lot easier by saving time and resources, plus the customer money in the long run with an effective solution.
Rudy Curtler is the owner and principal operator of EverLine Coatings, Twin Cities, Minnesota, a parking lot line striping and pavement maintenance service for commercial and residential property owners.
How to Patch with Infrared Tech
If the pavement structure doesn’t require repairs to the subbase to resolve a rutted, alligatored or other problem area, you may be able to complete a repair with infrared patching, rather than sawcut and fill. Here are the steps to make it a successful job.
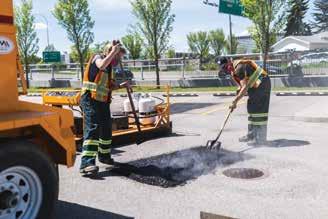
• Step 1. Heat the area to be repaired.
• Step 2. Scarify (or rake) the now-malleable section.
• Step 3. Add and blend in fresh pavement mix so you have a fluff factor for rolling. You’ll select hotmix asphalt, a cold patch material or other mix based on the needs of the client, pavement, traffic loading and so on.
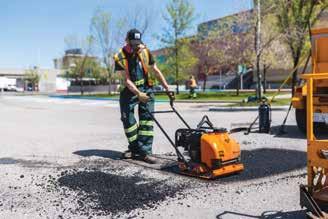
• Step 4. Compact the repair flush to the surface of the surrounding pavement.
• Step 5. Stand back and admire your handiwork. If you’ll be sealing over the pavement, assess the project to see if repairs need a day (or longer) to cure. By spraying or squeegeeing sealant over an oxidized pavement with a number of fresh patches, you risk uneven application and absorption rates. Giving the new spots a minimum of 24 hours helps maximize sealing success.
Teach Your
Crew What it Takes to Pave a Bonus-Worthy Mat
AsphaltPro magazine joined forces with hall-of-fame paving consultant John S. Ball III of Top Quality Paving & Training to bring you the newest online training resource for your crew: Asphalt Paving 101.
The course is available on any device, anytime, anywhere to train your entire crew. Your single subscription to the best curriculum of all time gives you access to train all of your employees, each time you bring in a new hire.
Asphalt Paving 101

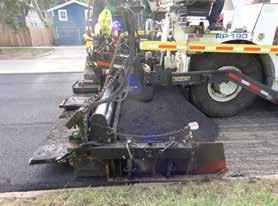
In this course, your crew will learn:
• How to stay safe on the job site
• How to build a takeoff ramp
• How to determine fluff factor
• How to determine yield
• How to prep for real paving in the real world

• How to maintain equipment the right way
• Job responsibilities for each paving crew member
• and so much more…
Purchase your access to the course at: training.theasphaltpro.com
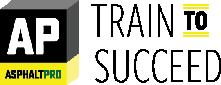
Maximize Milling with these Best Practices
By Sarah RedohlTTom Chastain has learned a thing or two about quality milling in his 29 years in the milling industry. Currently the milling product manager at Wirtgen America, Antioch, Tennessee, he regularly conducts application training on milling machines for dealers, contractors, unions and municipalities and has assisted with projects and conducted training on four continents. At CONEXPO-CON/AGG 2023, Chastain shared some of his advice for maximizing milling quality.
“The job of a milling crew is to give the paving crew a clean palette to paint a masterpiece on,” he said. With each passing year, Chastain said the standards for milling crews have risen. “With asphalt paving, they’re using big skis and more technology to get a smoother ride. With rolling, they’ve got intelligent compaction, oscillation, etc. to get a smoother ride. Now, the focus is on [milling to get a smoother ride].”
Of course, achieving a smoother milled surface involves technological improvements, but Chastain said milling quality is mostly about getting the basics right. “I hear all the time, ‘We’ve been through basic milling training. We want advanced milling training,’” he said. “But advanced milling training is the basics.”
Here are eight best practices any milling crew should know based on Chastain’s nearly three decades of experience.
1. Know the details of the job.
Chastain shared a story from a project he was on in Missouri many years ago on I-55 southbound. “The milling crew was already there
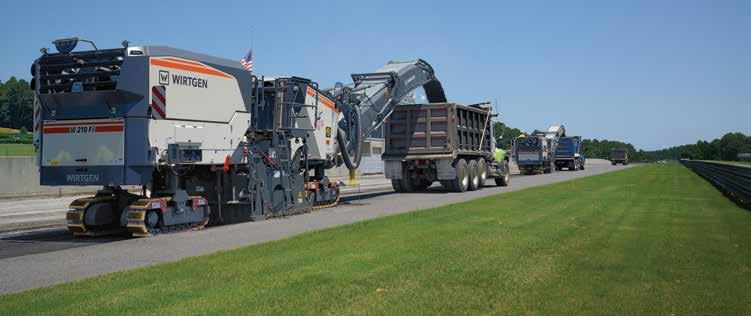
when I showed up to the job site,” he said. “I asked them where the machine was and they said they didn’t know. I asked where we’re going to start milling and they said they didn’t know. Eventually, the machine shows up and we start rolling down I-55 southbound. The DOT shows up an hour later and says, ‘What are you doing? You’re supposed to be going northbound.’”
His example stresses the importance of quality communication. “If you communicate with your team regarding the job, the better chances you have to achieve quality,” he said. Chastain stresses the importance of the information in the office making its way to the superintendent, foreman and milling crew. “But it doesn’t stop there.”
“We also need our safety personnel—our flaggers and anyone else involved—to be on the same page,” Chastain said. He also recommends discussing with the truck drivers how you want them to maneuver in front of the machine, how to leave the job site, and the importance of operating safely in the work zone. “If we’re working for a prime on a project, we need to have an understanding of what we’re going to do on that project.”
“Everything we do starts with communication,” Chastain said.
2. Know the right machine for the job.
Choosing the right machine for the job is key to a project’s success and efficiency. “We’ve got to understand what machines we need for the project,” Chastain said.
“Maybe we think we can get away with a small machine because we think we’re just doing some patchwork,” he said. “So, you take out the
compact machine, knock those out, then you find out you need to mill three lane miles. We can do it with that [compact] machine, but it’s not going to be the most time efficient.”
However, small milling machines are handy to have in one’s fleet. “The reason is they can flush cut around manhole covers,” he said. One issue he’s noticed with using a skid steer with a milling head attachment is that they are challenging to operate well. “That manhole cover often ends up looking like a great white shark’s been gnawing at it and we have to go in with a pickaxe or a jackhammer to clean it up. Having a small milling machine makes it that much easier.”

3. Know your milling modes.
These days, Chastain said most manufacturers offer milling machines with several operating modes. For example, eco mode for fuel efficiency and power mode when “you want everything the machine’s got,” he said.
Many machines also have a pattern mode for optimal milling quality, Chastain said. “With the way milling used to be, when we hit a hard section of asphalt the machine slows down because of the load against the machine drum, and that would tighten up our pattern,” he said. “With new machines, you can put them in pattern mode, tell the machine what drum you’ve got, what teeth you’re running, and what pattern quality you want it to maintain. If you hit that same hard section of asphalt, not only is that machine going to slow down but now the drum is going to slow down as well. That way, we keep a consistent pattern, curb to curb.”
Like 3D grade control, Chastain said, this is another way to “make it easier for inexperienced operators to get us to a higher quality of milling.”
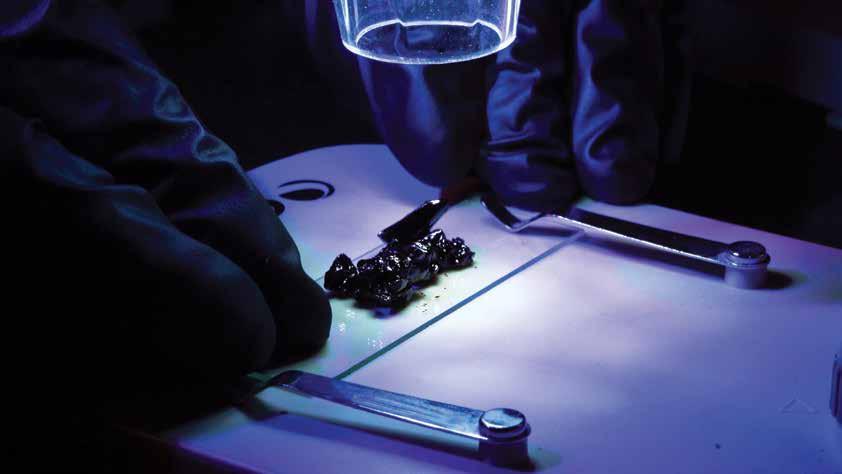
4. Know your drum types.
“You’ve got standard drums, then you have fine drums, then you have micro drums,” Chastain said. “A standard drum is made to mill to the machine’s maximum cutting depth. If the machine’s maximum cutting depth is 14 inches, it’s made to cut 14 inches. Fine or micro drums are for thin lifts or profiling.”
Sometimes, Chastain said, a milling crew will get the idea that they can use a fine drum to mill faster while maintaining pattern quality. For example, on a job in the Midwest, an operator planned to cut 7 inches with a fine textured drum. “He put the machine in the ground, one track
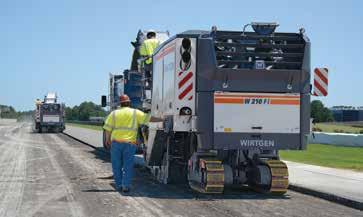
Why? “Because the material couldn’t get out of the housing,” Chastain said. He explained that with a standard drum, there’s space between the material and the teeth. With a fine drum, “there’s not much space. If you pick that machine, you’re going to have to do a bunch of 1 ½-inch passes all day.”
Another thing to keep in mind if using a fine or micro drum is its implications on reclaimed asphalt pavement (RAP). “If we’re going to use a finer micro drum, we need to understand we’re going to lose 10 to 12% of that material,” Chastain said. “We’re turning it into dust because we hit it with so many teeth.”
However, the worst thing about a micro drum, according to Chastain? “Somebody’s got to change all 1,100 teeth on that drum.”
5. Know how your grade technology works.
Chastain said these days there is a wide variety of grade controls available for milling machines.
“We need to understand what grade controls we need,” he said. “There’s a big difference between copying the road and profiling it.”
“If you’re copying the road, basically what you see is what you get,” Chastain said. “If there’s a bump in the road, unless you’re really good at using your grade controls, there’s still going to be a bump in the road.” Although the road may look all right after milling and immediately behind the paver, Chastain said once it’s compacted, “you’re back to exactly what you had.”
When a crew is simply copying the profile of the road, Chastain said they may even risk making bumps worse if they’re milling at a high feet-per-minute rate. “If you’re milling faster, you didn’t do anything to that bump except lengthen the size of that bump because the hydraulics need enough time to react.”
“With profiling, like with a sonic averaging system, you can take a big bump and turn it into three smaller ones,” he said. “Is it perfectly flat? No. But it’s a whole lot smoother than it was before.” Depending on the road conditions, Chastain said a crew may need to cut the road two or three times with an averaging system to get it perfectly flat. “It all depends on that road.”
Although 3D technology has been a “big topic in dirt,” Chastain said, “it’s coming over to the asphalt side.” He said there are a variety of 3D systems out there. “The big thing now is doing road scans. They’ll drive the job, get their plotting, make a 3D plan, then plug the plan into the street and go.”
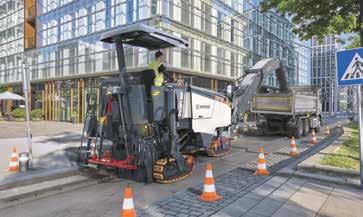
“[3D] takes the guesswork out of milling,” Chastain said, while achieving a quality milled surface. “This also helps less experienced operators to get acclimated to the machine quickly.”
6. Know your teeth options.
“[Manufacturers] make different teeth for different applications,” Chastain said. “When you have soft asphalt, it’s going to wear out the body, but not really the carbide. Hard asphalt is going to wear the carbide, but not really the body.”
In addition to carbide teeth, diamond teeth may be a good alternative depending on the application. “Say you’re in the middle of nowhere, diamond teeth can be the way to go because they’re rated for 400,000 tons,” he said. “You can get a whole season on a set of teeth.”
The higher-wear teeth aren’t the solution for every application. “Someone who’s been milling a while might think, ‘I don’t have to change teeth anymore? Yeah, I’ll do that’,” Chastain said. But you have to understand the application. “I once saw a guy put a diamond drum on a machine, it goes 50 yards and hits a manhole cover.” Chastain shared that the operator wasn’t experienced enough to know what to do. “The whole time, that manhole cover is inside the housing bouncing around.”
“Your standard carbide milling tooth is $7, whereas a diamond tooth is $275 a tooth,” Chastain said. “That mistake cost 38 teeth. You do the math.”
7. Know how to start—and how to stop. “My philosophy of starting off is this: start slow, stop slow,” Chastain said.
“The hydraulics need time to react, so when we start off we have to go slow to let those rear tracks walk into the cut,” he said. Otherwise, the machine will put a dip in the road about 3 feet from where it started. “Once the tracks get into the cut, then ramp up speed.”
The same applies when it’s time to stop the machine. “With older machines, everybody used to think that it would leave a dip in the road because the machine settled when it came to a stop,” Chastain said. However, that isn’t the case.
Let’s take a closer look at how the teeth of the mill work. “Some people think that the teeth rotate while they’re in the cut,” Chastain said, but that’s not the case. “When the tooth is in the cut, it’s actually flexed. There’s pressure working against that tooth. Once the tooth releases from the cut, that’s where we’re actually getting the tooth rotation, and that’s what we’re wanting to see between that flex release and material flying around inside that housing, we want to get that tooth rotation.”
When the mill comes to a stop, it isn’t that the mill settles. “It’s actually that you didn’t have pressure working on that tooth, so it relaxed from the holding about ¼ inch,” he said. “Now, when good operators come to a stop, they bump their grade controls up about ¼ of an inch. When they get going again, they bump it back down.”
8. Know how fast to mill.
“The three magic words to a milling crew are production, production, production,” Chastain said. “We’re production oriented. We’ve got to go, go, go.”
Is it possible to get quality and quantity? Chastain said it’s possible, but that he sees one of these “unicorn projects” about once a decade. “The last one I had was shutting down a major interstate outside New York City where we had six full lane machines, each with their own wa-
ter trucks, and thirty trucks,” he said. “We went 2 ½ miles down and 2 ½ miles back without stopping.”
However, on a normal job where a milling crew might only be running half an hour out of every hour, going 30% faster in order to wait longer isn’t worth the potentially reduced quality, Chastain said. “Instead of milling at 150 feet per minute and then sitting there 40 minutes [instead of 30], slow down your feet per minute,” he said. “Work more out of an hour and get better quality while still getting your production. Unless we have trucks to burn, that should be sufficient.”
Milling at high speeds, Chastain said, can result in a number of issues. First, “You’re not actually cutting at the depth you set,” he said. “The machine starts to water ski a bit when you go that fast.”
Having a poor pattern also reduces the interlocking capability between the milled surface and the asphalt to be paved. “We have to remember we’re making ½ of VELCRO®,” he said. “The paver is coming in with the other half.”
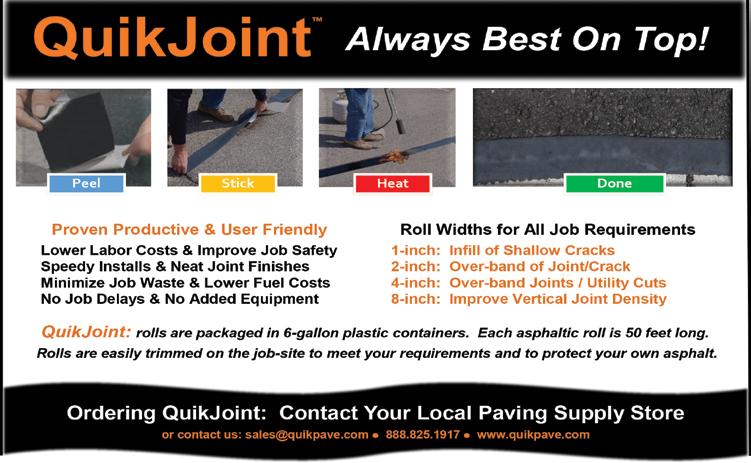
Because milling at high speed can result in erratic milling depth, the tonnage may be off. Although Chastain said this might not matter much on a small project, it can have a significant impact on an interstate project.
Furthermore, poor milling quality is going to cause compaction numbers to fluctuate. “Say we’re doing a thin lift mill-and-fill at full speed,” he said. “The paver paves it, then the breakdown roller comes by and hits one of our high spots. We could break the aggregate. It’s not the roller’s fault. It’s our fault.”
Milling quickly can also put an unnecessary amount of wear on the machine. “These machines are beating themselves to death and
we’re trying to put one foot in the grave by running them that hard,” Chastain said.
Lastly, milling at high speeds can cause issues with sizing material. “We’re trying to use that RAP material,” Chastain said. “The slower feet-per-minute we go, the tighter the pattern, the smaller the RAP material. The faster we go, the more coarse the pattern, the larger the RAP material. We have to screen that RAP, we may even have to crush it, too. So, we’ve added a process simply because we like to mill fast.”
Those chunks can also present a risk to safety. “It’s possible that a chunk could find its way toward live traffic,” Chastain said.
According to Chastain, 30 feet per minute is a tight pattern; 60 to 80 feet per minute is still a good pattern, “but you can see that the drum is no longer [pulling] that material toward the center.”
“When we get to 85 to 90 feet per minute, we’re starting to get a little coarse and stretching out that pattern,” he said. “When you get over 170 feet per minute…the machine’s actually walking faster than the drum is turning.”
He gives milling machine operators the following bit of homework: “If you’re used to running fast and you don’t believe me, slow down by 20 to 30 feet per minute and look at what happens to the pattern quality and the RAP going into the truck.”
“[Milling too quickly] equals lower quality, a waste of material and loss of money,” Chastain said. He reiterates that advanced milling best practices are, in fact, the basics. “Milling in a nutshell is this: common sense and simple math. I can teach simple math, but I cannot teach common sense.”
Keyword New for NPE’s Offerings
By AsphaltPro StaffWWith the annual event right around the corner, National Pavement Expo (NPE) staff are putting the final touches on the education programming for the paving and pavement maintenance audience gathering in Tampa Jan. 23-25, 2024. While some speakers and topics are in such high demand from attendees that they can’t be left off the agenda, the programming team went all out to bring a host of new sessions to the 2024 show. The upcoming event will present 80% new content to help attendees put real-world information into practice when they go back to the field, office or estimator’s seat. Let’s take a look at an enticing example or two.
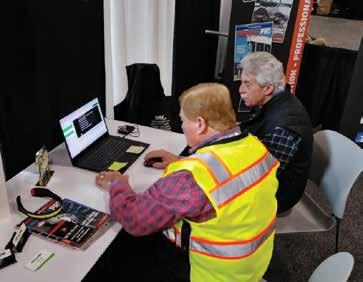
While the programming includes important topics for decision-makers in the C-suite—about two dozen in the employee management, leadership, business operations, and sales and marketing tracks—speakers are bringing their A game to topics in the how-to realm of paving, sealcoating, striping and technology.
New for 2024, a technology track features presentations from Austin Rabine, president of The Rabine Group; Chelsea Ellis-Hogan, president, and Samuel Ellis, co-owner, of Jim Reynolds Asphalt Contractor Inc.; Shane Farlin, owner of Quality Asphalt & Maintenance LLC; and others still being confirmed.

What attendees will find unique to the programming at NPE is the high level of expertise of the presenters. Knowledgeable members of the asphalt paving industry such as Tanya Nash and Steve McReynolds of Duval Asphalt, Vince Hafeli of Ajax Paving of Florida, returning speaker Wayne Jones of the Asphalt Institute, Mark Roberts of the Kansas Turnpike Authority, returning speaker John Ball of Top Quality Paving & Training, among a host of others, will offer actionable information.
Take the team of Gary Stapleton and Dejah Anderson as merely one example. Stapleton is the operations manager at Anderson Striping & Construction Inc. Anderson is the COO there. Not only can they talk shop with anyone who has a striping question, they’re presenting on the heart of an issue our industry faces day in and day out: building up and retaining our workforce. Their topic, “Building Striping Teams for the Next Generation,” will be held Tuesday, Jan. 23, from 1 to 2:30 p.m., giving the audience 90 minutes to learn how to navigate the transitioning workforce, while attracting and engaging young talent; how to design a plan for a structure of team building and cross training within striping crews; and how to develop actionable strategies to mentor, train and retain the crucial striping work force.
A spokesperson for the show shared, “We’ve got an awesome line up of speakers for NPE 2024—including 20+ new speakers—and an equally impressive collection of session topics, 80% of them being new to the 2024 conference agenda, never presented at our show.”
Something the team has brought back is a structured opportunity to network for those folks who might not be comfortable walking up and starting a conversation on their own.
Wednesday, Jan. 24, from 11 a.m. to noon, four rooms will be set up with industry topics for a “morning huddle.” Pick the one you want to participate in and let the conversational atmosphere of industry pals helping one another put you at ease.
Another opportunity to network with ease is being arranged through the clever and thoughtful guidance of Elle O’Flaherty, CEO of Interlace Solutions. She’ll give the presentation “Conference Connect” in the leadership track from 3:00 to 4:30 Tuesday, Jan. 23, and then all attendees are welcome to put their new skills into practice at the following networking event, “Conference Connect: In Action,” from 4:30 to 6 p.m.
If you’re looking for big inspiration at this year’s NPE, arrive early for the “Iron-Sharpened Leadership” session Tuesday morning, presented by Major General John L. Gronski (U.S. Army Retired). He’s the founder and CEO of the consulting firm Leader Grove LLC. Gronski is not only an international speaker, leadership trainer and executive coach, but is also a graduate of Penn State with a Master of Strategic Studies from the US Army War College. He’s a decorated combat veteran and his impressive bio at https://nationalpavementexpo.com/conference/speakers/ should attract a standing room only crowd.
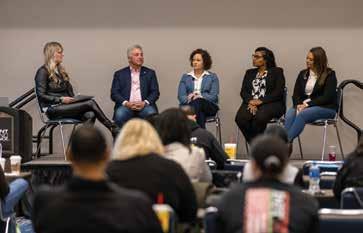
Whether your interest at NPE is in leadership training, paving advice, employee management ideas, sealcoating tips and tricks, educating a few members of your core crew, or some other aspect of growing your business, the knowledge you’ll be exposed to in the 2024 agenda will put you on the right path. The AsphaltPro magazine staff looks forward to seeing you and your crews in the education sessions and on the tradeshow floor, learning and networking alongside us. Make your travel plans early and register all your top operators with the “register now” button at this link: https:// nationalpavementexpo.com/. We’ll see you in Tampa in January.
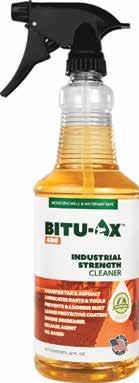

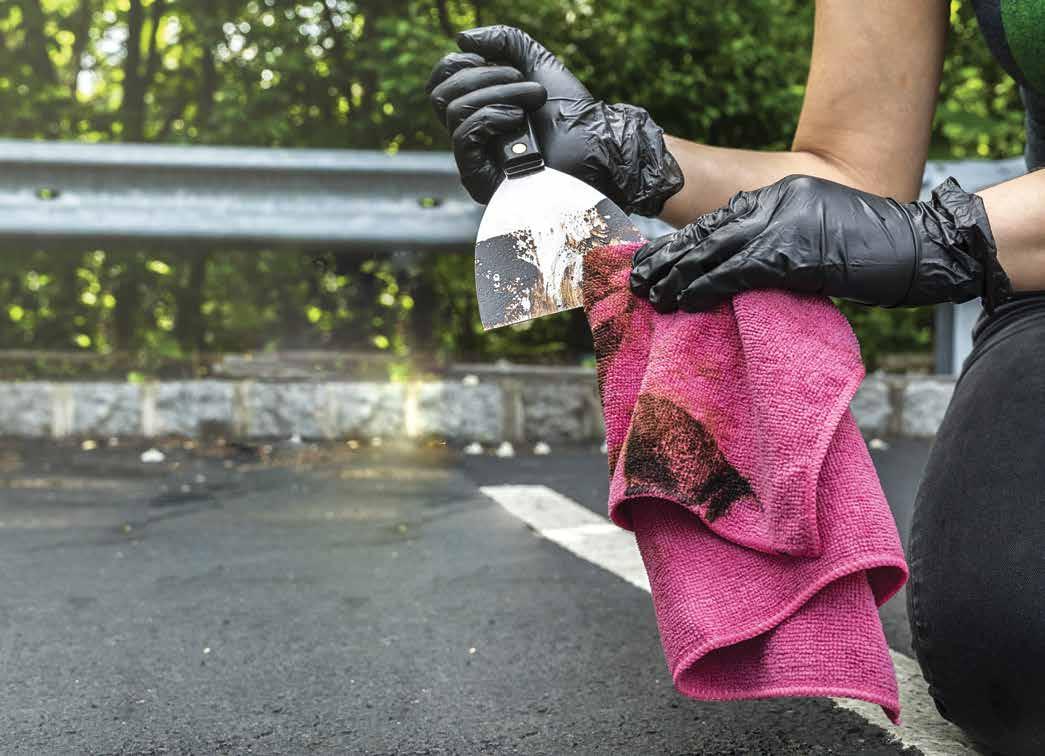
NPE 2024 will present 80% new content to help attendees put realworld information into practice when they go back to the field. Visit nationalpavementexpo.com for details!
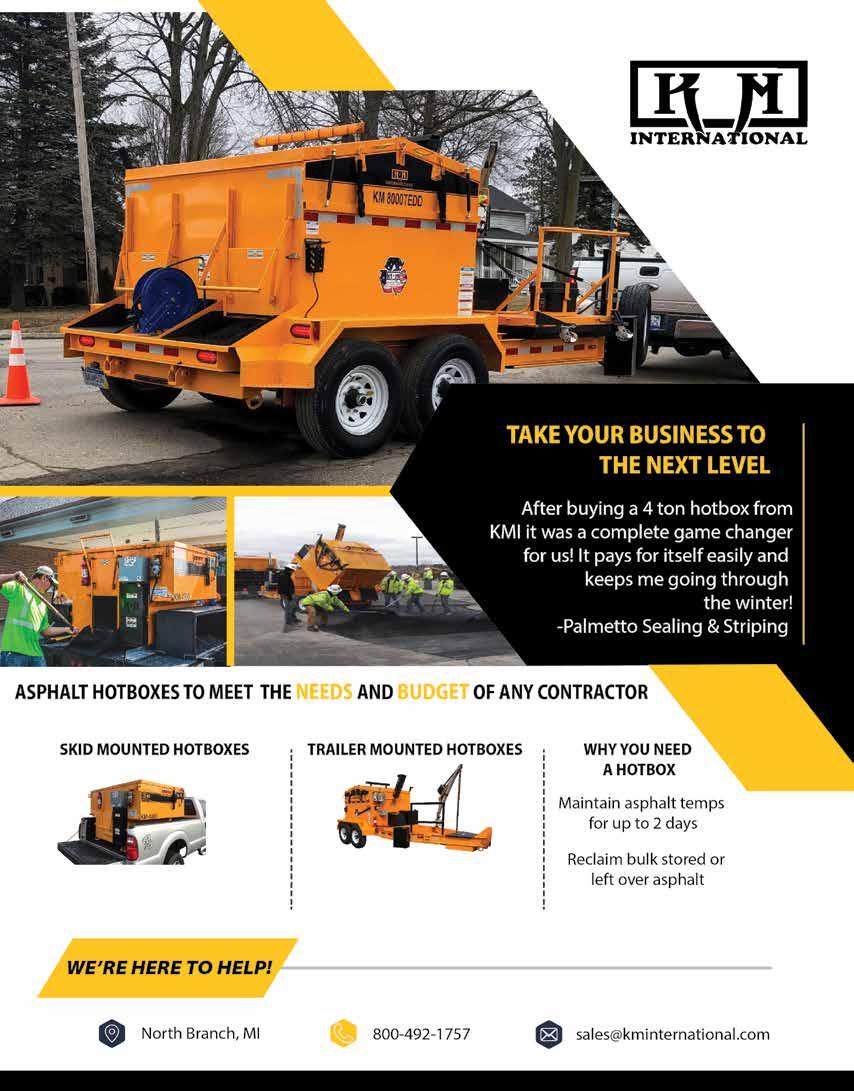
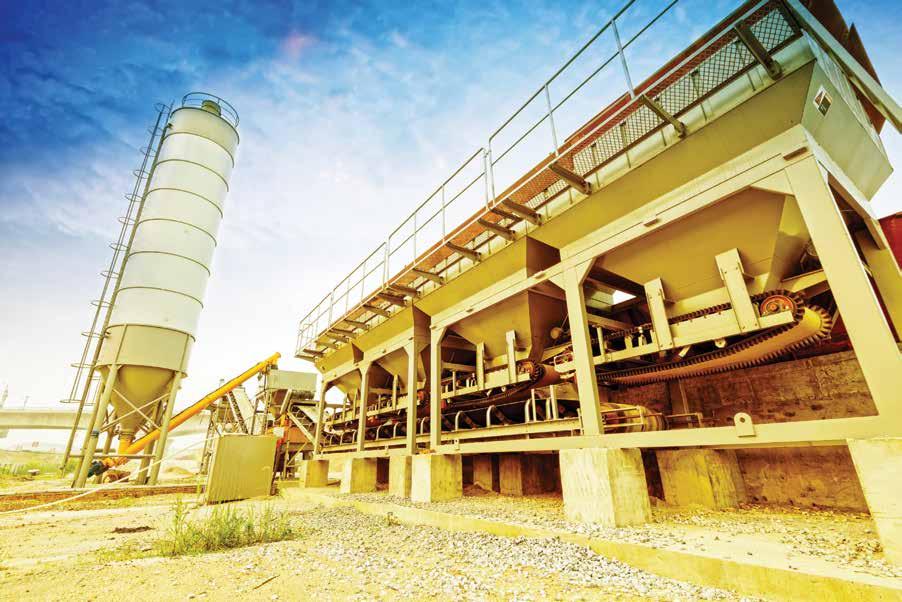
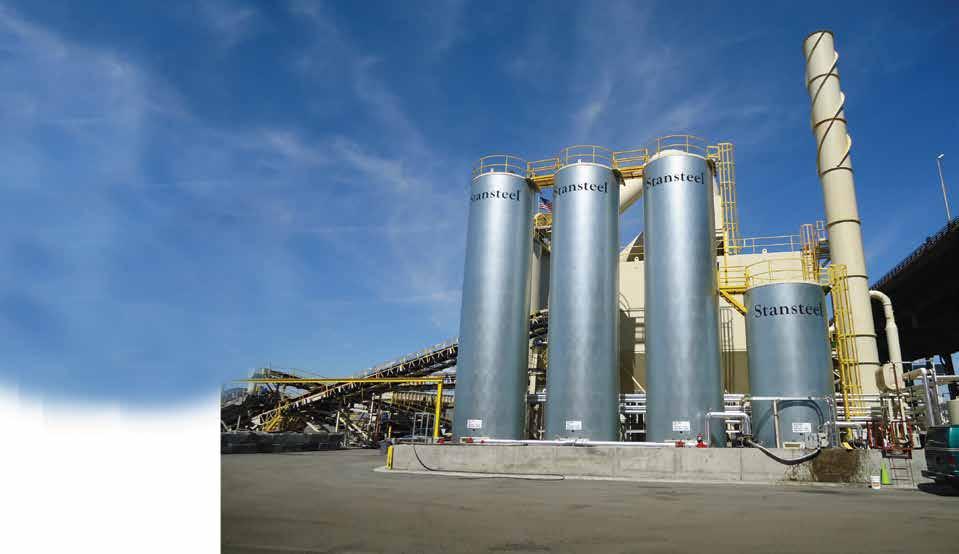
Responding to Private Equity Solicitations

If you’re one of the asphalt contractors and producers who has received an email from a private equity firm wanting to “connect,” you’ve probably been left with a lot of questions. Aside from wondering what exactly private equity is, you might contemplate what type of firm fits your needs and how partnering with one would affect your business. With our 35-plus years of experience, we can demystify this increasingly complex world.
WHAT IS A PRIVATE EQUITY FIRM?

These firms are set up to invest in businesses. Typically, they manage pools of capital contributed by pension funds, endowments, insurance companies, high net worth individuals and the like.
Each firm will have its own style of investing, some focused on certain ownership structures and others on specific industries. If you are receiving an e-mail or call, it is likely that the firm has identified asphalt and paving as an industry of interest.

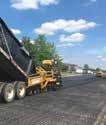

These firms will typically invest in one of two ways. The first is a majority transaction (also called a “buyout”) where the firm will look at buying greater than 50% of your business. This provides liquidity for owners, who may continue as employees in the company with some equity ownership or may decide to exit the business altogether. However, this also means the private equity firm will have operational control of the business and drive its future growth plans.

On the other hand, some firms take a minority investment approach, where they buy less than 50% of the business. The existing owner and management team continue to run the business and are responsible for day-to-day decisions.
PARTNERING
The reasons for taking on a private equity firm as a partner can vary. For some, nearing retirement can prompt business owners to consider succession planning; if the next step is not clear, a majority exit might be a preferred way to enter retirement.
For others, they may feel that growth has plateaued, and the business needs the professionalism and capital backing of a larger partner. In these circumstances, a minority equity partnership can be beneficial as the existing owners continue to own a large portion of the business, which may eventually lead to a more lucrative sale in the future.
Private equity firms may also inject cash into the business to fund purchases of equipment or support mergers and acquisitions (M&A). Aside from financial backing, private equity firms can bring qualitative benefits to your business. As you grow, having access to a broad rolodex of advisors, board members and executives can be a value-add. Furthermore, access to a pipeline of M&A targets can be helpful if you are looking to grow through acquisition—these firms often speak to many players in the industry and have a pulse on potential targets for acquisition. Additionally, if the firm has the right experience, its personnel can help guide or build critical functions as your business scales. For example, this could include a business development team, sophisticated finance function or in-house M&A group.
Banking relationships are often an area where asphalt contractors can benefit from private equity firms. This can open better access to financial products, including loans and asset-backed lending facilities, which are particularly important for producers with significant fixed assets. Private equity firms open these doors through the success of their prior investments and longstanding lender relationships. Overall, a great first question to ask a prospective private equity partner is exactly what value they will provide when the deal is done.
NEXT STEPS
It never hurts to have an initial conversation to understand what the firm has to offer and what a partnership could look like. However, it is important to enter every conversation with an understanding of your needs and wants to make the conversation productive. Some example questions for the representative contacting you could include:
• Why are you interested in my business?
• What experience do you have in the industry?
• What is your role in the private equity firm?
• Do you undertake minority or majority transactions?
• What would it be like post-investment—who would be involved, how would important decisions be made?
The list goes on. We encourage you to take the time and learn about the private equity firm before jumping into a transaction.
In the end, there is no one-size-fits-all answer but given the growth of private equity across all sectors, it’s important to understand if it’s right for you, and if not, how it may be impacting others—including competitors in your industry.
Mohit Kansal is the managing director of Clairvest Group. For more information, contact him at mohitk@clairvest.com or (416) 4136017. Alexander Carbone is a senior associate for Clairvest Group. For more information, contact him at acarbone@clarivest.com (416) 413-6005. Clairvest has been partnering with entrepreneurs for over 35 years and is actively seeking opportunities to partner with asphalt and paving businesses.
ASPHALT BINDER TESTING
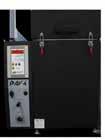
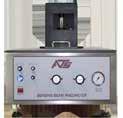

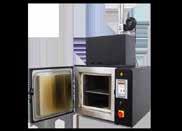
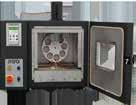
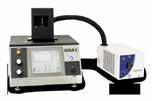
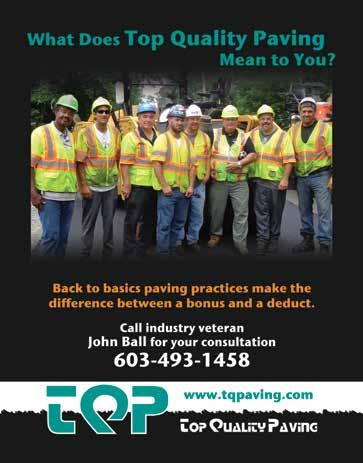

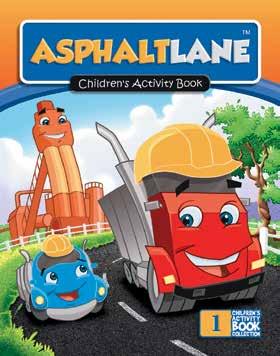
AD INDEX
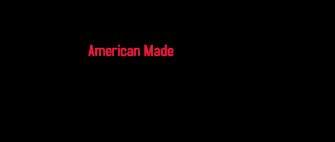

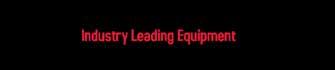
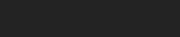


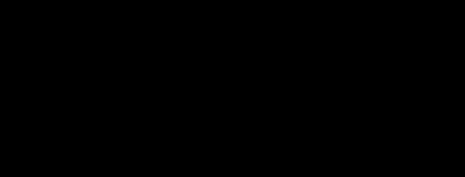

AsphaltPro’s advertiser index is designed for you to have quick access to the manufacturers that can get you the information you need to run your business efficiently. Please support the advertisers that support this magazine and tell them you saw them in AsphaltPro magazine.

FEATURES & BENEFITS:
• Concentrated
• High Flashpoint or No Flashpoint
• Effective on Asphalt, Tar, Oil & Grease
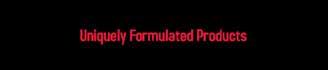
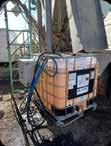
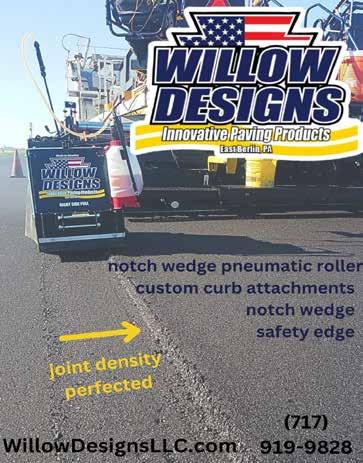
• No SARA Section 313 Reportables on drag slat conveyors, g drums, material handling ment, pavers and .
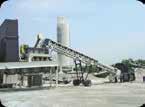
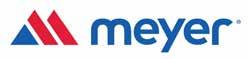

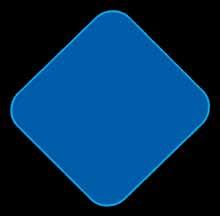
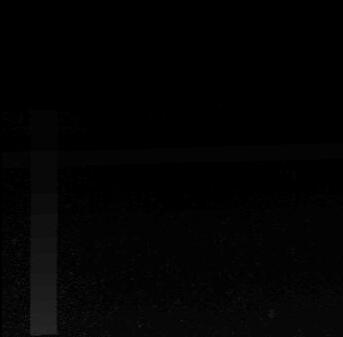
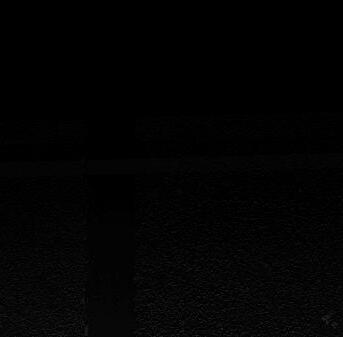

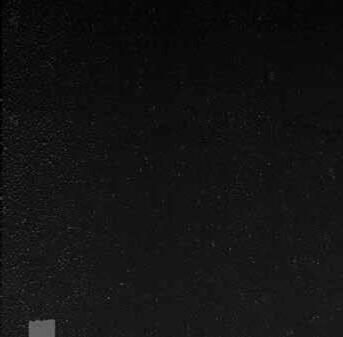
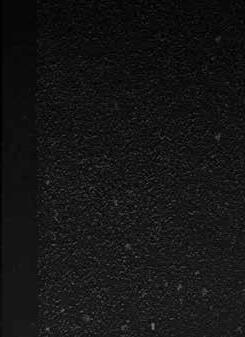
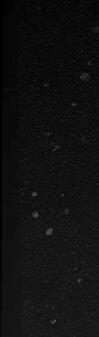
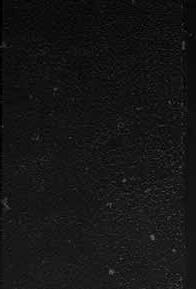
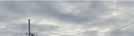

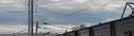

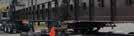


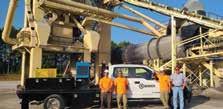
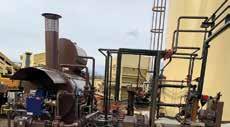
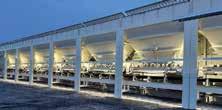

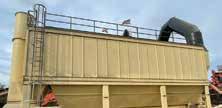
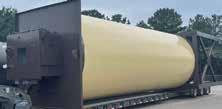
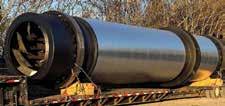
Brigade Backsense Solutions Make Job Sites Safer
BY SARAH REDOHLBBetween 2011 and 2020, 63% of fatal injuries to workers at road construction sites were caused by the worker being struck by a vehicle, according to the Centers for Disease Control and Prevention. This includes construction equipment operating within the work zone.
That’s why Brigade Electronics, Portland, Indiana, has spent decades developing technology to eliminate blind spots and provide real-time alerts to drivers and equipment operators when there is potential for a collision.
“While passive systems, such as mirrors and cameras, do help the driver to spot people and objects in blind spots, utilizing proactive technology that site managers can rely on to provide reliable alerts, no matter the conditions, are key to protecting the lives of road construction workers,” said Brigade CEO Corey Heniser.
Brigade offers a number of passive and active systems, including individual, multiple and 360-degree camera solutions; ultrasonic and radar obstacle detection; wearable RFID devices for crew members; and video recording solutions. The company also launched its first 360-degree artificial intelligence (AI) camera, SidescanPredict, in November 2021.
SEVERAL CAMERA SYSTEMS
With a Backsense® radar or ultrasonic obstacle detection system, paired with Backeye®360 or other heavy-duty camera monitoring system, Brigade’s line of safety solutions can identify people and objects, whether stationary or moving, and provide the operator with in-cab visual and audible alerts.
With one or multiple cameras, the operator will be able to see the view from each camera. With Backsense®360, the operator will see on the screen in the cab both an overhead view of their vehicle and surroundings and one of four camera
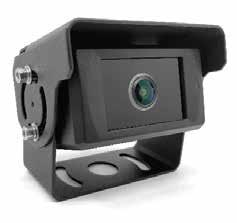
angles, based on direction of travel or use of turn signals.
Back when Brigade first began offering a 360-degree solution eight years ago, Heniser said it was too expensive to justify its use on anything but the most expensive equipment. However, technological advancements have made the solution comparable in price and ease of use to Brigade’s multi-camera setup. With the 360-degree solution, Heniser said, “You get the best of both worlds.”
AUDIBLE ALERTS
Brigade’s approach to audible alerts differs from the usual backup alarms, instead relying on multi-frequency alarms using a broadband sound (BBS) backup alarm, also known as a white sound backup alarm.
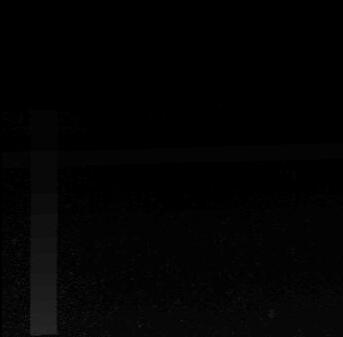
Rather than the traditional ‘beep’ of tonal alarms, these alarms create a ‘ssh-ssh’ sound that is loudest in the direction of vehicle travel and dissipates quickly. “The result is that when a vehicle is coming toward you, you know it’s coming toward you,” Heniser said. “If it’s moving away from you, it’s not nearly as noticeable. But, you’re not in the danger area so no action is required.”
Heniser said this can reduce worker desensitization to backup alarms, since they are hearing them less frequently and usually only in situations in which they should take action. This type of system can also
help reduce noise complaints related to backup alarms, for example, if you’re paving in a residential neighborhood early in the morning.
However, the white sound still meets all alarm volume requirements. “Our solutions have a microphone built in that will make sure the alarm adjusts itself automatically to be 5 decibels louder than the ambient noise,” Heniser said.
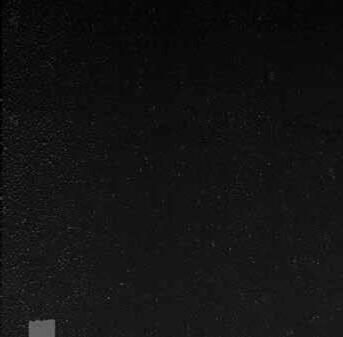
CHOOSE THE RIGHT SOLUTION
Heniser said the right Brigade solution depends on the vehicle and its applications. “It would be nice to have one solution that fits all,” he said, “but every customer type and vehicle type has different problems.”
For example, the ultrasonic solution is common for on-road vehicles where it’s only used at low speeds as a parking assistant. For vehicles moving at higher speeds or those with larger tires (therefore covering more ground per tire rotation), Heniser recommends the radar solution.
“The faster a vehicle moves, the longer the range needs to be to predict and stop an accident from occurring,” he said. Brigade’s radar solution offers a range of 1520 feet off the shelf, with a programmable version that can operate at ranges 30-50 feet out, versus 10-12 feet for the ultrasonic solution.
“IDENTIFYING HUMANS IS ALWAYS THE BIGGEST CONCERN. YOU CAN ALWAYS REPAIR A BENT FENDER, BUT YOU CAN’T ALWAYS REPAIR AN INJURED HUMAN.”— COREY HENISERAI Intelligent Cam
Other factors to consider when selecting a solution include the direction of movement, how frequently a vehicle turns, and what else is operating nearby. “All those factors come into play,” Heniser said, both in terms of camera systems and obstacle detection.
“If backing is the only problem, then we can have a single camera application and tie a ra-
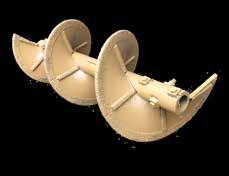
dar to that,” he said. Or, if a haul truck carrying asphalt only needs extra help when backing to the paver, the ultrasonic sensors may suffice. “It really depends on the customer’s needs.”
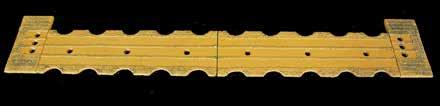
THE NEXT FRONTIER(S)
Brigade’s latest safety innovation is its AI camera solution, Sidescan® Predict.
“If an individual’s crossing [between the backing haul truck and the paver] trying to beat the two coming together, we can actually put a box around that individual [on the monitor in the haul truck] and give a different warning to the driver,” Heniser said. “We have three ranges programmed behind the camera, so [the system] will give you a green, yellow or red warning along with the corresponding audio frequency change.”
It’s also possible to add a mobile digital recorder to any Brigade camera system. “We can record all the footage coming across the monitor, with a timestamp, and that’s admissible in court,” Heniser said. The system also tracks triggered events, saving a short clip leading up to and following an event—for example, a hard G-force braking event. When a triggered event occurs, the customer can set it up for certain employees to be notified.
Not only does this elevate the most significant obstacle to avoid (people), but it also eliminates the need for a sensor at all.
Brigade is also working on a system that uses sensor fusion technology to combine Brigade’s range of safety devices to predict collisions and alert operators. “[Fusion] takes a lot of these individual components and networks them together so it can go one step further to offer vehicle-to-vehicle communication to prevent collisions,” Heniser said.
The company is also working on autonomous features, such as active warnings that take action automatically. For example, applying the brakes to prevent a collision if needed. “Those [technologies] will eventually filter down into everyday onroad and off-road vehicles,” Heniser said.
Although the technology may advance over time, Brigade’s goal remains the same, whether a customer deploys a single camera or an entire vehicle-to-vehicle networked solution: making the road construction job site safer.
ROCK TO ROAD
What’s Next In Cold Planers
Introducing the nimble and powerful Roadtec RX-405 cold planer. A hinged cutter housing door makes for easy drum changes, while maintenance mode, with the drum indexer and belt lifter, simplifies regular tooling changes. Bring the same level of productivity you expect from Astec mills to compact spaces with ease.
See the new RX-405.
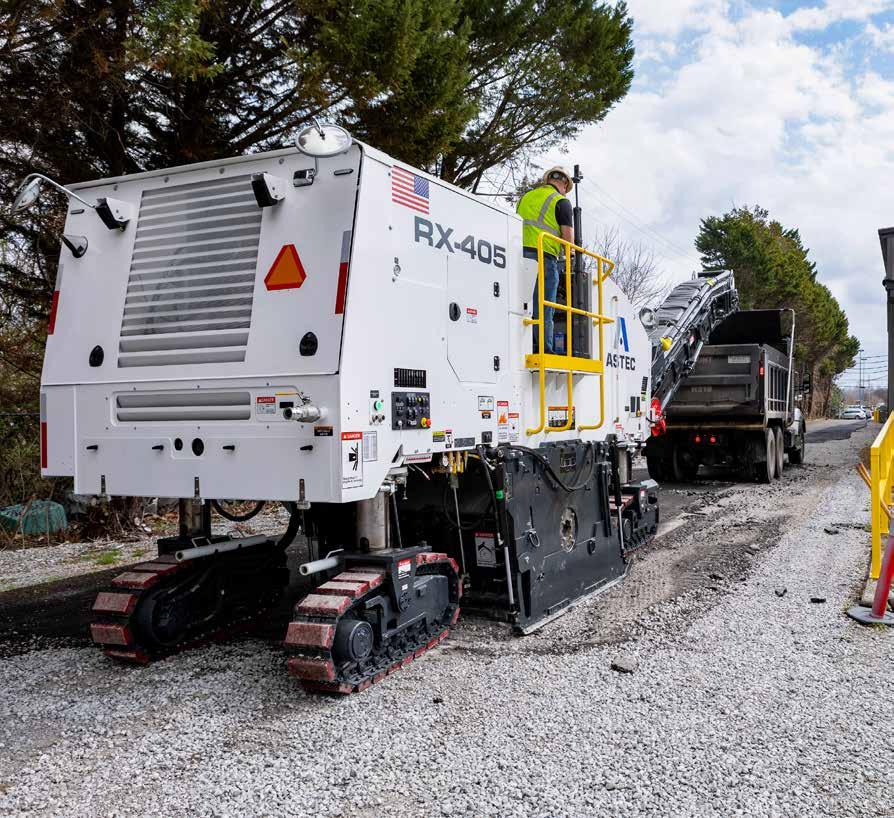
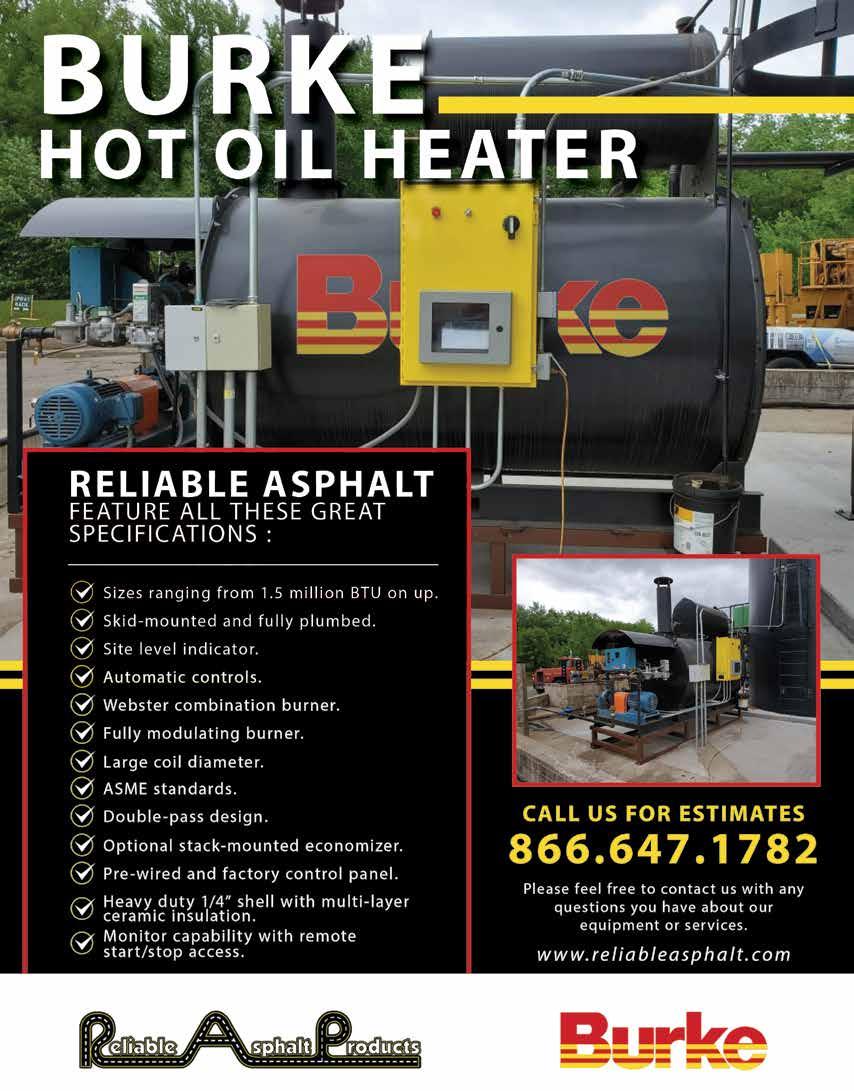