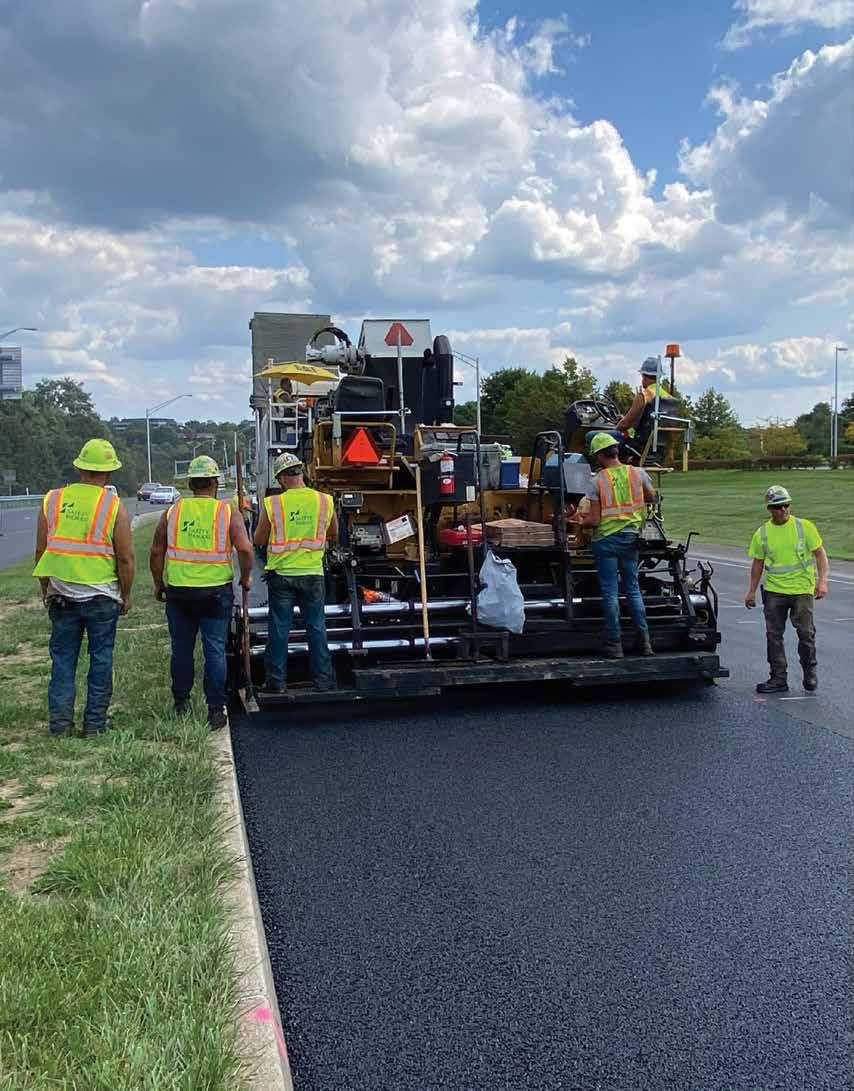
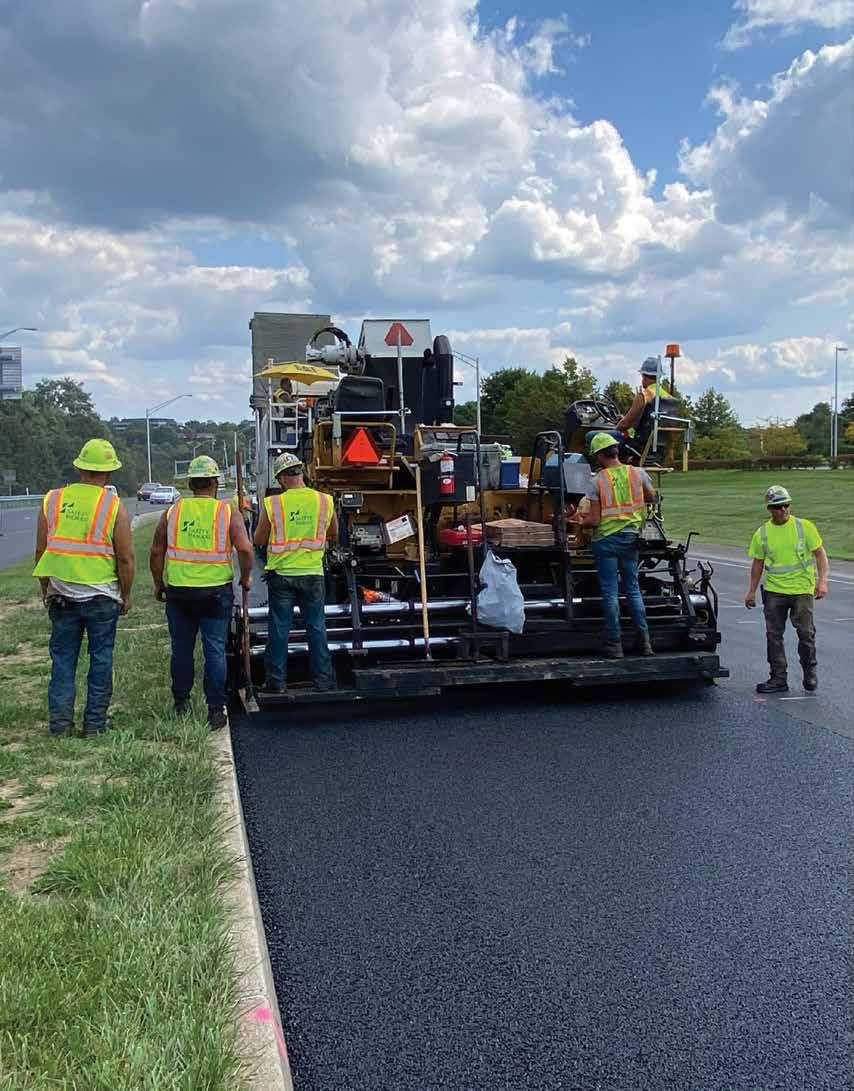
BUILT TO CONNECT
Single-Source Supplier Advantage
Astec provides a significant advantage as a single-source supplier for the diverse products and services involved in building and maintaining an asphalt mixing plant. Astec liquid AC storage tanks, tank farms, and heating system controls feature high quality construction and unmatched efficiency. We offer a variety of sizes and configurations that can be fully customized. Optimize your asphalt storage tanks and hot oil heaters with the addition of the Recon® mobile monitoring system to receive status updates on a smart phone, tablet or PC.
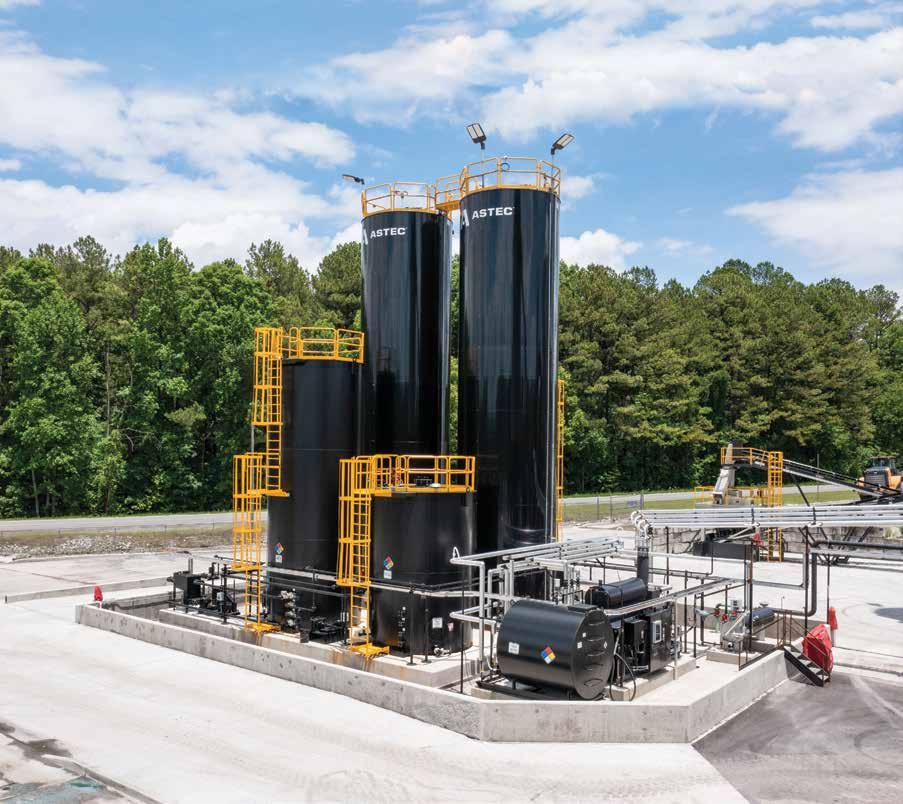
COME VISIT BOOTH C30235
MARCH 14-18, 2023 • LAS VEGAS, NV
Scan QR code to see Astec’s full line of Tank Farm Components.


Improving overall plant production and efficiency are all common concerns for plant owners and operators. Having a well-trained technical crew is vital to maintaining plant performance and efficiency.
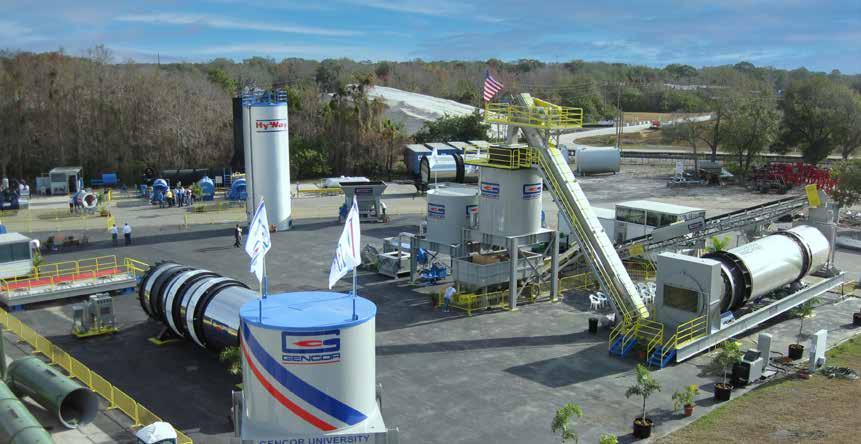
Gencor and its training staff represent the biggest concentration of knowledge and expertise in all the sciences and technologies involved in the production of asphalt plants. Customers who attend these seminars benefit by having the support and focused attention of the best specialists in the asphalt industry.
Using Gencor’s state-of-the-art control simulators and actual equipment, our experts take you stepby-step through a comprehensive & intensive concentrated hands-on training program providing the latest techniques on optimizing production efficiency.
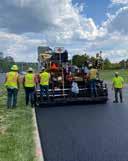

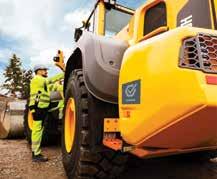
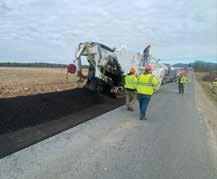
Pave Resiliently
The asphalt industry comprises more than a few exemplary contractors who pave with best practices day in and day out. They train new workers to do the same and they take home bonuses, awards and renewed contracts from sat isfied customers for their hard work. The traveling public receives long-lasting pave ments as a result of this hard work.
Along comes a bureaucrat who says, “Hey, I think you should pave a different way, so the pavement is resilient.”
I’d argue that the pavement is resilient, but, for argument’s sake, let’s get a defini tion on that. According to the “New Col lege Edition of The American Heritage Dictionary of The English Language,” re silience, a noun, is, “The ability to recover quickly from illness, change, or misfortune; buoyancy.” It can also be, “The property of a material that enables it to resume its original shape or position after being bent, stretched, or compressed; elasticity.”
Last I checked, the Asphalt Pavement Al liance (APA) was handing out awards for as phalt pavements that have been able to re cover quickly from minor misfortunes that don’t require more than 3 inches of structur al assistance over their lifetimes of 50 years and longer. Visit driveasphalt.org/awards for more information on that. For this note’s purposes, we’re gonna call that resilient.
Of course, a pavement built before 1972 was designed with an earlier set of stan dards and codes than the structures we’re engineering today. As an industry, collec tively, we’ve advanced in technology and understanding. Even though our pave ments are lasting “a long time,” we can— and do—build them even better now, to last even longer under new and more de manding stressors.
Codes and standards change over time as engineers learn more and the materials they work with or have access to advance. I’ll bring up the original Sunshine Skyway Bridge, opened to traffic over the intra coastal waters of Tampa Bay 1954, as an ex ample. On the morning of May 9, 1980, the Summit Venture encountered rough waters and near-zero visibility as it approached the bridge and, tragically, impacted Pier 2S. The west span of the cantilever bridge collapsed and 35 people died in the water below. Did
engineers prior to 1954 realize a ship to be commissioned in 1976 would weigh 33,912 tons without cargo and would, at a reduced speed of 6 nautical mph, ram into an inef fective support?
A larger question: should the engineers prior to 1954 have consulted a crystal ball and foreseen the types of vessels and ear ly morning weather conditions 1980 Tam pa Bay would collude to present? Could the engineers prior to 1954 have guessed that two vessels would strike the southbound bridge Feb. 5 and the southwest support Feb. 16 of that year, potentially compound ing structural weaknesses of the supports?
What I’d like to suggest is engineers, de signers, mathematicians, bridge builders and paving contractors in today’s world work with ever-evolving codes and regula tions that result in incredibly strong—dare I say resilient—elements of infrastructure. Sometimes, natural disasters or un foreseen accidents plow through best in tentions and the most up-to-date codes. Sometimes, you can’t guess what the future will bring.
What the asphalt industry can do is build long-lasting structures for the future with lower carbon and low-emission materials available today. This edition of AsphaltPro focuses on best paving practices, but it’s sprinkled with environmentally friendly practices as well. Check out Sarah Redohl’s reporting on page 28 where Prairie State Trucking and Bowes Construction raised the grade of I-81 on a 100-year floodplain. Check out Peckham Industries Inc.’s efforts to raise awareness of best practices for cold in-place recycling in the northeast on page 18. Check out the use of a soybean-based additive to fortify reclaimed asphalt pave ment (RAP) millings in Iowa on page 34. These are not isolated incidents of our in dustry’s work toward increasing the life of pavement structures, thus offering en hanced resiliency of roads for anyone who’s paying attention.
Stay Safe, Sandy Lender
asphaltPRO
602 W. Morrison, Box 6a Fayette, MO 65248 (573) 823-6297 • www.theasphaltpro.com
GROUP PUBLISHER Chris Harrison chris@ theasphaltpro.com
PUBLISHER Sally Shoemaker sally@theasphaltpro.com (573) 823-6297
EDITOR Sandy Lender sandy@theasphaltpro.com (239) 272-8613
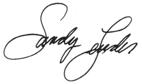
DIGITAL EDITOR Sarah Redohl sarah@theasphaltpro.com (573) 355-9775
MEDIA SALES

Cara Owings cara@theasphaltpro.com (660) 537-0778
ART DIRECTOR Kristin Branscom

BUSINESS MANAGER Susan Campbell (660) 728-5007
AsphaltPro is published 11 times per year. Writers expressing views in AsphaltPro Magazine or on the AsphaltPro website are professionals with sound, professional advice. Views expressed herein are not necessarily the same as the views of AsphaltPro, thus producers/contractors are still encouraged to use best practices when implementing new advice.
SUBSCRIPTION POLICY: Individual subscriptions are available without charge in the United Sates, Canada and Mexico to qualified individuals.
One year subscription to non-qualifying Individuals: United States $90, Canada and Mexico $125.00. For the international digital edition, visit theasphaltpro.com/subscribe/
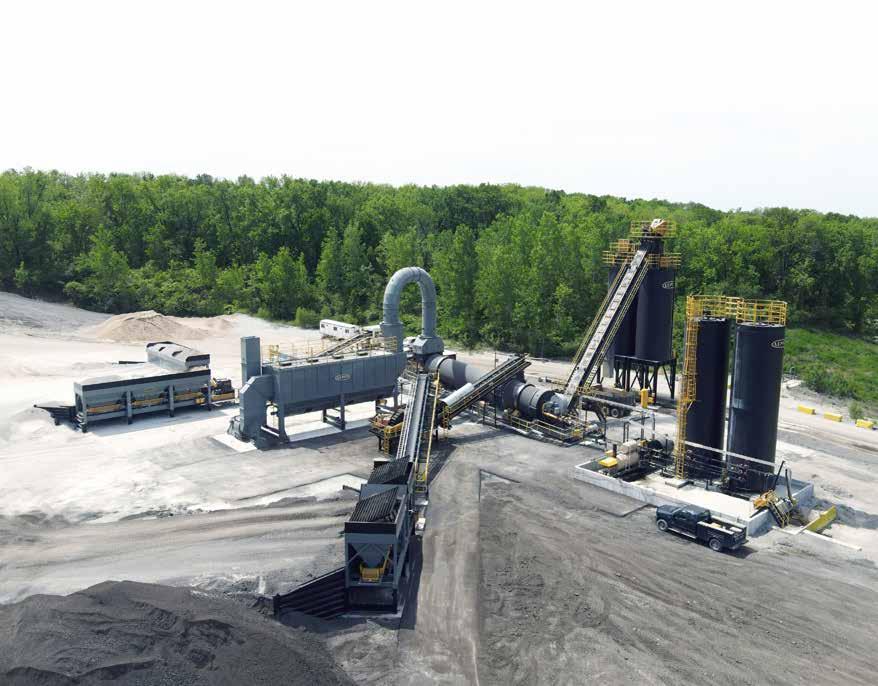
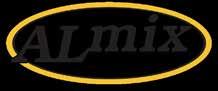

FHWA’s Minimum Retroreflectivity Standards Now In Place
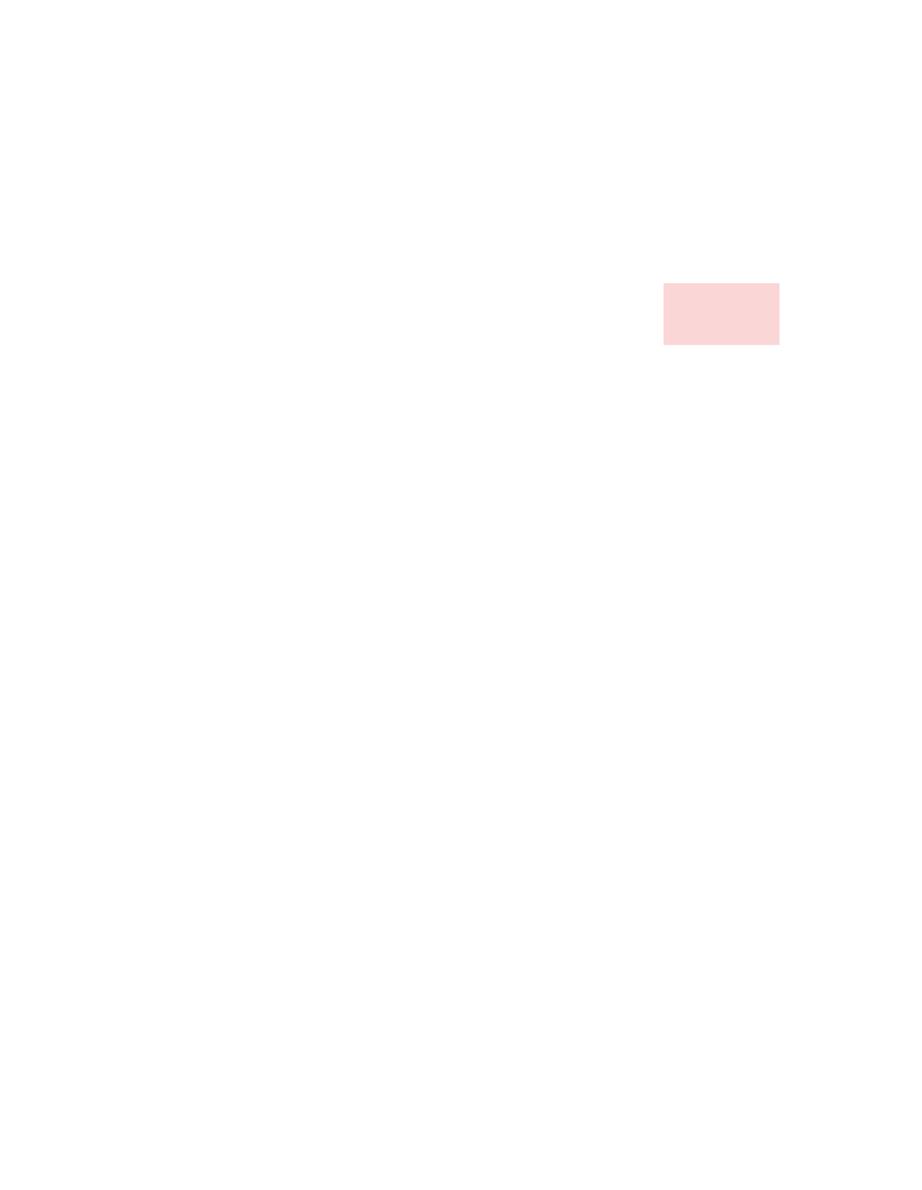
The U.S. Department of Transporta tion’s Federal Highway Administra tion (FHWA) has enacted a new rule to improve road safety by ensuring pave ment markings are more visible in dark and low light conditions. The final rule, an nounced August 2022, is the first federal minimum standard for retroreflectivity of pavement markings.
“This rule will save lives by helping those traveling see pavement markings more clearly and know what lies ahead, especially in darkness and other instances when visi bility is critical,” said Acting Federal High way Administrator Stephanie Pollack in a press release.
The Manual on Uniform Traffic Control Devices for Streets and Highways (MUTCD) currently requires that pavement markings be visible at night and that all markings on interstate highways be retroreflective. How ever, it does not set a minimum level of ret roreflectivity. The new standard, outlined in the MUTCD, establishes two minimum tar gets for reflectivity:
• Longitudinal pavement markings for roads with speed limits of 35 miles per hour or greater with an average annual daily traffic of 6,000 vehicles per day must meet a min imum retroreflectivity of 50 millicandelas per square meter per lux; and
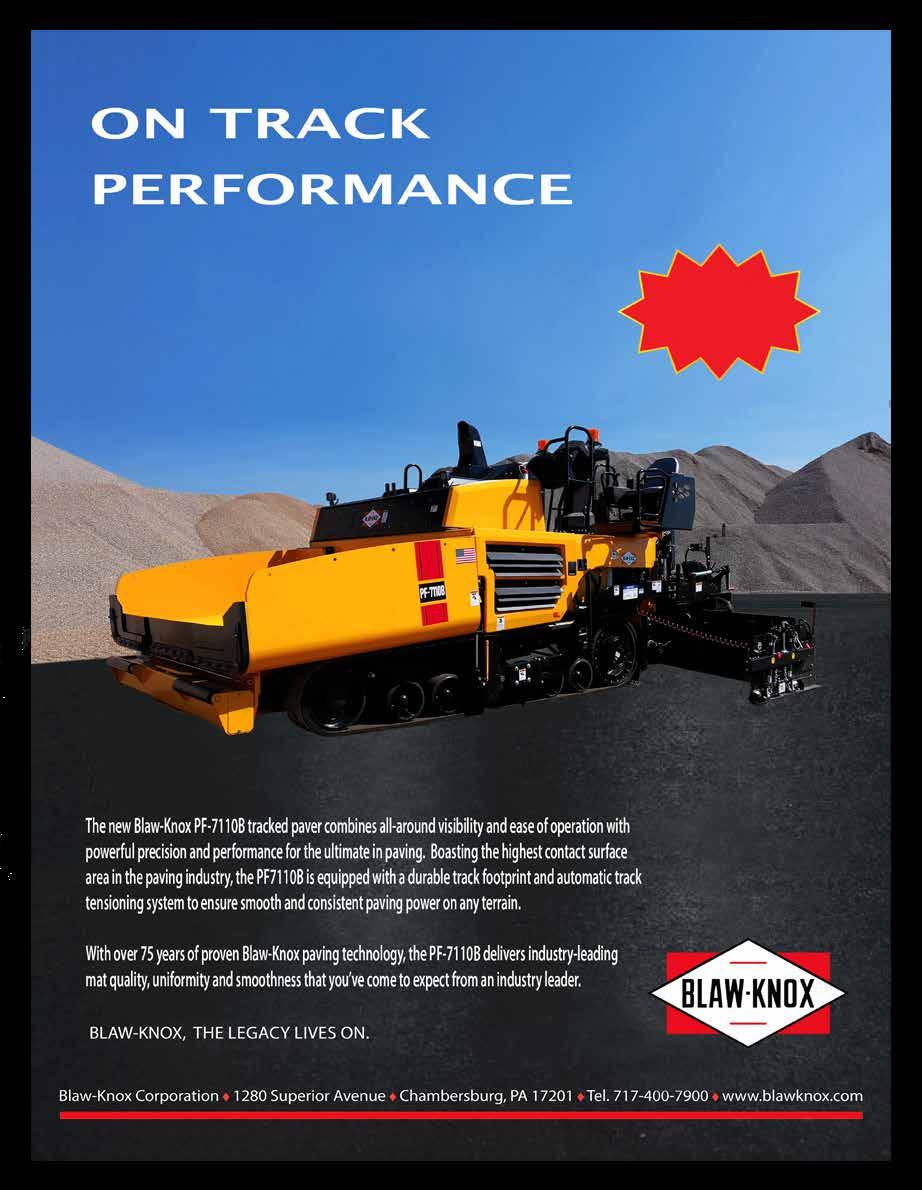
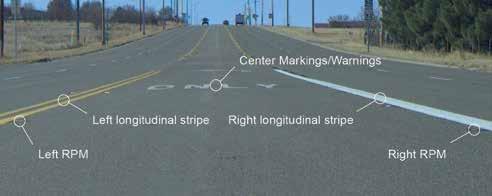
• Longitudinal pavement markings for roads with speed limits of 70 miles per hour or greater must meet a minimum retroreflectivity of 100 millicandelas per square meter per lux.
The rule also aims to make pavement markings clearer for Autonomous Driver Assisted Systems (ADAS).
Roads with fewer than 6,000 vehicles per day and those that are sufficiently lit are exempt from the minimums. The stan dard also does not apply to other pavement markings, such as center symbols, arrows,
chevrons, words and crosshatch markings. Transverse markings and crosswalks are also excluded.
Although some state and local agencies already have standards that meet or exceed the new requirements, those that don’t will have four years to establish a method for maintaining pavement marking retroreflec tivity at those minimums.
The methods for maintaining pavement markings, detailed in FHWA-SA-14-017, include visual inspections, measured ret roreflectivity, expected service life replace ment and blanket replacement. Accord ing to the FHWA, pavement marking im provements are eligible for up to 100% federal aid funding.
“We would highly recommend that U.S. road agencies start the planning process now to address how they will monitor and maintain pavement markings to the new standards for minimum retroreflectivity levels,” said Joe Turley, CEO of pavement marking supplier RetroTek, Dublin, Ire land, in a press release.
Omar Smadi at the Institute for Trans portation at Iowa State University told Bloomberg News that the new standard may propel cities to “invest in higher-per forming pavement paint to reduce the need to redraw lane markings.” The standard may also increase the use of new pavement marking materials and technologies.
Solutions that maximize data collec tion and minimize traffic disruptions, like RetroTek-D mobile retroreflectometer sys tem, could help road authorities get accurate retroreflectivity measurements across the full lane width in one pass. “The ability to com pare survey results over different years within our survey software helps authorities to plan and predict pavement marking maintenance requirements and budgets,” Turley said.
The Retroreflective Pavement Markings fi nal rule will be included in the 11th Edition of the MUTCD and is effective as of Sept. 6, 2022. Read the final rule published in the Federal Register Aug. 5.
ALTHOUGH SOME STATE AND LOCAL AGENCIES ALREADY HAVE STANDARDS THAT MEET OR EXCEED THE NEW REQUIREMENTS, THOSE THAT DON’T WILL HAVE FOUR YEARS TO ESTABLISH A METHOD FOR MAINTAINING PAVEMENT MARKING RETROREFLECTIVITY AT THOSE MINIMUMS.
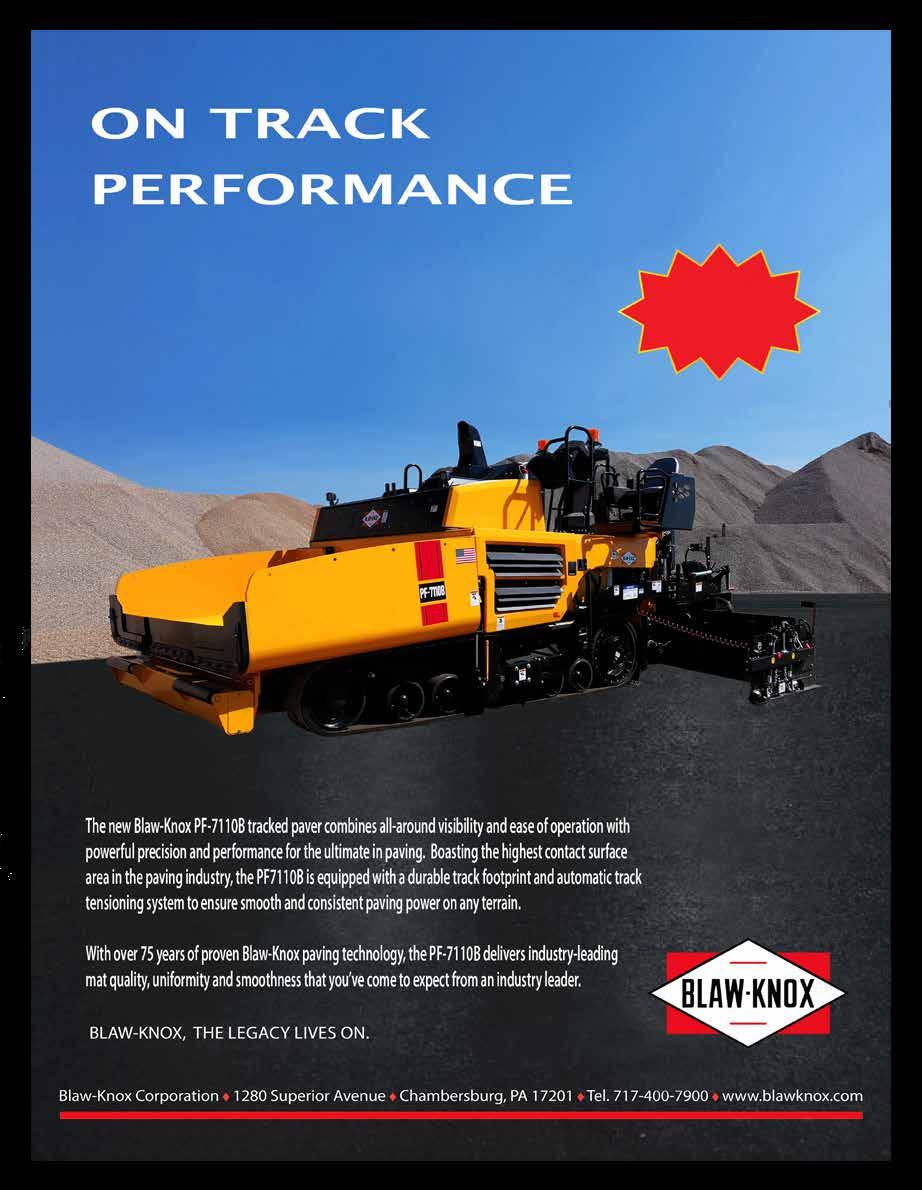
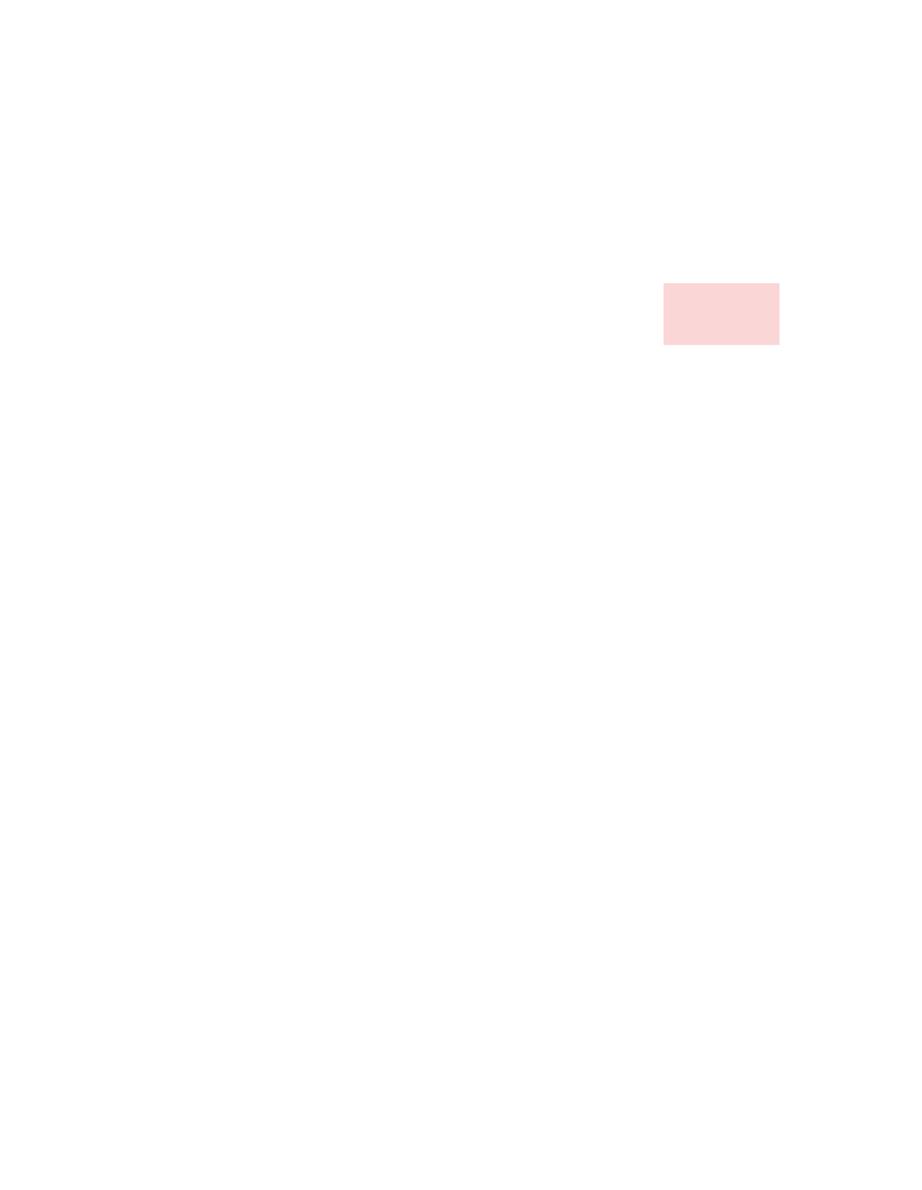
Comparing CTIndex Devices
BY NATHAN MOOREImagine a scenario where a contractor works on a balanced mix design (BMD) and finally gets that mix to pass an agen cy’s IDEAL-CT criteria. Then, after submit ting specimens to the agency for approval, the agency’s results fail the mix design crite ria. What happened? When the contractor and agency discuss the results, they realize both sets of specimens were tested with machines from different manufacturers.
Could using different devices be the reason for the discrepancy between the two labs? How can we ensure that different machines will provide equivalent results? A recent National Center for Asphalt Technology (NCAT) study could help resolve this situation. In the study, six different devices were evaluated to assess how much they could affect the overall vari ability of IDEAL-CT results.
Variability in IDEAL-CT test results can come from many sources: operator, materi als, specimen preparation, equipment differ ences, etc. Specimen preparation is known to have a large effect on IDEAL-CT results. For this study, careful attention to detail was giv en to making the specimens by using a single technician, using the same specimen prepara tion equipment and oven heating times, and by randomizing the specimens to be tested among the six devices.
When investigating differences in test re sults due to devices, analysis should include data from a variety of mixtures with results ranging from low to high. In this study, eight replicates from seven different mixtures were tested on each device by the same technician. Due to natural variability, results for each mix ture will differ from device to device. Although replicates from a mix may be repeatable with in the specific devices, there still may be differ ences when comparing results between devic es. The concern is when one device consistent ly yields results that are higher or lower than another device. We want to know how much of a difference can be tolerated.
Statistical equivalence is not a term used of ten in materials testing. This is the idea that re sults are considered equivalent when the dif
ferences between them are practically irrel evant. For example, if Sample A has an aver age CTIndex of 95 and Sample B has an average CTIndex of 93, is this two-unit difference large enough to be considered important given the test’s variability? To establish a limit for accept able difference, the analysis used the average within-lab variability—measured in percent coefficient of variation (COV)—from the 2018 NCAT Round Robin Study, where the average within-lab COV was 18%. Therefore, when two devices can consistently produce mean re sults less than or equal to 18%, they should be considered equivalent.
Two key findings came from this study. First: Some devices had average loading rates faster than the 50 ± 2 mm/min currently specified in ASTM D8225. All the measured speeds from over 300 IDEAL-CT tests fell be tween 49 and 53 mm/min. Thus, although all the rates do not meet the standard’s specified range of 48-52 mm/min, the devices are still operating within the maximum allowable 4 mm/ min tolerance window. There was no discernable effect of speed on the final CTIndex results for each mix because the devices were operating similarly.
Second: Using the Two One-Sided Test (TOST) equivalence test, all but one of the de vices were found to provide equivalent results. When the specific manufacturer was made aware of this issue, a flaw in the data collection system was found and the issue was correct ed. Although there were differences up to 5 CTIndex units present in the final comparisons, these differences were not large enough to be considered relevant given the variability of the test. Thus, the study indicates that different de vices can be trusted to yield equivalent results.
The findings of the current study do not mean that differences won’t occur, and it’s im portant to investigate large variances between comparison testing results. Following prepara tion and testing best practices will greatly re duce the chances of having a wide range be tween specimens from the same mix sample. It is highly recommended that when specimens are to be tested between two different devices, they should be prepared at the same time and under the same conditions to reduce variabili ty between the split samples.
A deeper study at NCAT is planned to bet ter quantify some of the effects of improper specimen preparation or specimen ambient aging—among other unintended errors—on the variability of the test. At this time, the big gest differences in test results stem from spec imen preparation. By the time the specimens have been made and are ready for testing, the variability from specimen preparation has al ready been introduced and can’t be removed. This is not to say ambient aging or time after compaction before the test is run has no role in variability. It would be prudent to test all por tions of a split sample as close as possible to the same day. This, too, is a variable that hopefully will be assessed in a future study. It would be useful to the industry to know if testing three days after splitting will yield equivalent results to testing “next-day.”
The best way to avoid the problem posited in the first two paragraphs above is to make all the specimens from the same mix sample at the same time, then randomly split them, then test them at the same time to avoid any “ambient aging.” This does not suggest match ing testing time to the nearest minute, but in stead suggests performing tests within a few hours of each other. By eliminating as much of the sample prep differences as possible, the contractor and agency set themselves up for matching test parameters.
Nathan Moore is an assistant research engineer at the National Center for Asphalt Technology. For more information, contact him at nathan.moore@auburn.edu. This article is reprinted, with additions and with kind permission, from the Spring 2022 NCAT Asphalt Technology News.
IT WOULD BE PRUDENT TO TEST ALL PORTIONS OF A SPLIT SAMPLE AS CLOSE AS POSSIBLE TO THE SAME DAY.
Specimen preparation matters more than device selection for results to meet mix design criteria
BUILT TO CONNECT
Efficiency and Productivity
Designed with safety and operator comfort in mind, the SB-3000 Shuttle Buggy ® material transfer vehicle features adaptive cruise control, bright LED lighting, four-wheel steering for easy transport and ground-level maintenance access for added convenience. Operators can rely on clear sightlines and the ground operator is safely protected inside the structure of the machine. The Roadtec SB-3000 is the perfect blend of traditional craftsmanship and modern technology.
Scan to learn more about the SB-3000.
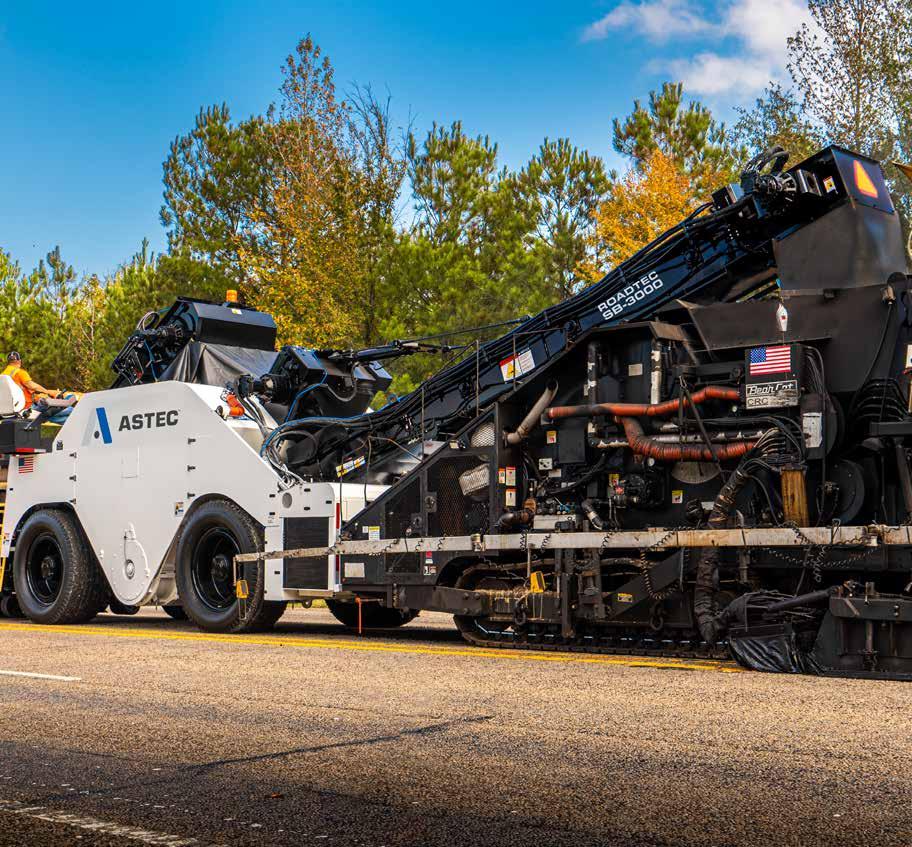
How to Pave a Complex Lot
BY JOHN BALLIn 2021, a paving crew for Pawtucket Paving out of New Hampshire tackled a commercial project that only needed about 400 tons of as phalt mix but required a great deal of expertise. The team started by mapping out a plan of action to work around the following:

• the new convenience store;
• a drive-thru lane with stanchions;
• gas pumps;
• raised, decorative curbing;
• multiple grates and utility covers;
• fenced dumpster areas; and
• parking areas.
They needed to accomplish this single lift of top course while building the proper pitch to allow water drainage within the curbed property. At
the end of the day, their hard work left a smooth and beautiful mat for the customer. Let’s take a look at how they did it.
STARTER PADS, PLATES
During the year prior to this sunny day, sitework included drain and util ity installation, and the base course and extensive curb work you see in these pictures. When it came time to pave the lot, the crew began with a starter pad for the first lane across the front part of the property. Even though they needed to build a starter pad, they had starter plates on hand, too. You’ll notice that the property is surrounded by curbs and full of decorative, raised curbs. Because of the curbs closing in the lanes, they couldn’t set starter plates down to begin each pass. In fact, this project required copious amounts of handwork and building pavement around curves and structures.
The first two passes along the front of the store were about 100 feet long. Notice the laborers are keeping up with cleanliness and aesthetics throughout the project.
The
operator is compacting the front passes while the crew pulls the first lane down the side and already begins attending to the utility covers.
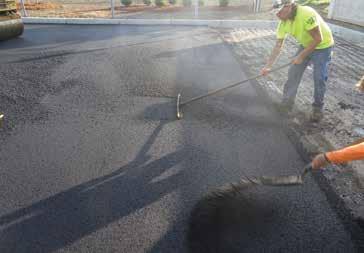
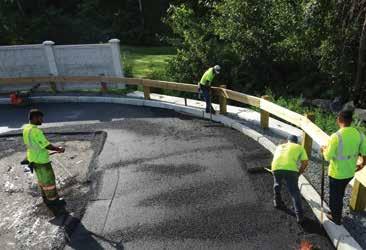
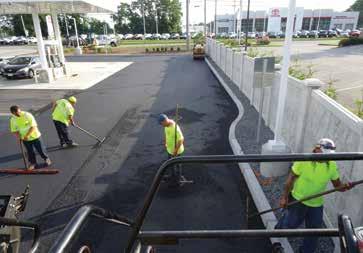

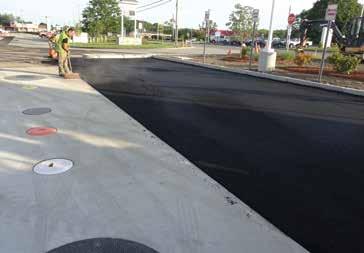
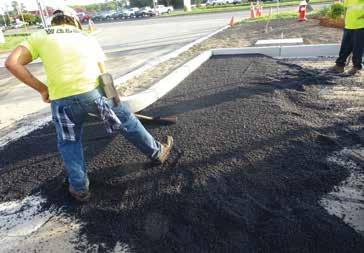
It took teamwork and expertise to make this project a success. One of the elements to consider on such a project is who will run the plate compactor? For this project, the fellows working the plate compactor were professional and skilled. They took their responsibilities seriously and monitored their equipment closely throughout the day, keeping it lubricated and moving correctly. I never saw them pick up material once.
THIS PROJECT REQUIRED COPIOUS AMOUNTS OF HANDWORK AND BUILDING PAVEMENT AROUND CURVES AND STRUCTURES.
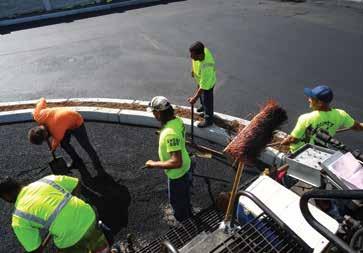

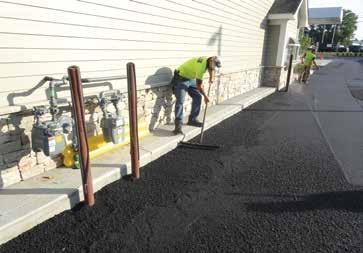
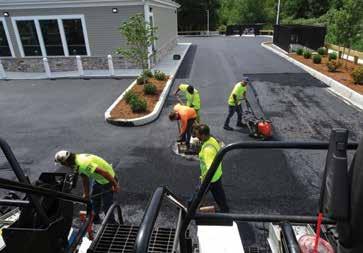
There’s only one way in and out of this gas station. Picture it as a square with a store in the middle. We needed to get the trucks in and out with out running all over the mat, so we planned it out with that in mind.
To begin, we built the starter pads for two passes. Those were sealed up with a plate compactor. Then we set the paver back for the first pass of
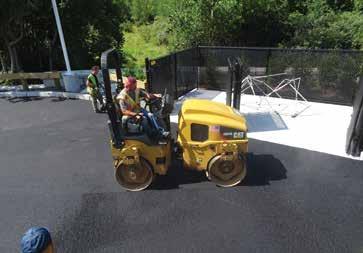
A decidedly human touch to plant automation.
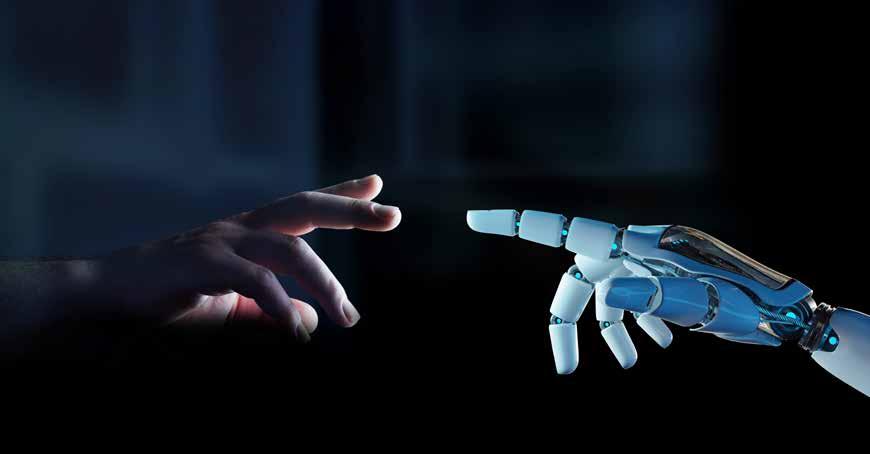
Designed around real people.
“The plant control system that MINDS designed for us has worked very well. The graphics depict the plant almost identically as built and are very easy to follow from the control room. Each value is shown with its position indicated by colours that make identifying issues, such as a stuck valve, extremely easy. The materials that we have produced with the system have been very consistent from the first production run.”

Allen
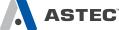

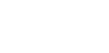
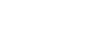
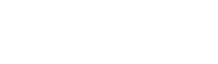
For the past 25 years, MINDS has built a reputation for user-friendly, advanced, customizable plant automation control systems. As of April 2022, we became part of the Astec family to add to their Rock to Road solution for asphalt road building. MINDS provides award-winning desktop software, mobile apps, and hardware for many applications:
Drums, Batches, Combo/hybrid hot mix plants, Emulsion plants, Liquid Terminals.
Silo load-out, Ticketing, and Cloud-based data management for the Rock to Road industry.
Better data. Increased control. Higher profits.
Because the crew would pave various widths throughout the project, they manually shoveled material to the endgate rather than install and remove auger extensions repeatedly throughout the day.
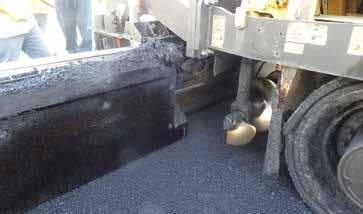
about 100 feet in front of the store. You’ll see that the paver has an 8-foot screed, but we had extensions on it going out to 10 and 12 feet as need ed. Because we had to keep moving the extensions in and out, we didn’t affix the auger extensions. That would have been a nightmare to stop and change out as often as we needed to move the extensions. Instead, we monitored the head of material closely and used shovels to manually keep the mix moving all the way to the endgate when necessary.
With the first two passes in front of the store complete, we picked up and pulled two passes down the side of the building. This involved a ton of handwork and plate compaction around the stanchions that protect the utility meters and drive-up window.
You’ll see the workers completing another significant amount of hand work inside a curve. They had to build a large enough starter pad to ac commodate the screed and that took about 30 square feet of handwork to make room for the screed to get in that curve. That section between the building and fancy curb-work took two 15-foot passes and the third pass of 10 feet.
TEAMWORK
One of the highlights of this complex project was the communication and teamwork of the crew. Getting a quality job out of something with this many moving parts boils down to the fine tuning, and this crew paid attention to the fine tuning. It took a lot of time to line it all out, measur ing and figuring depth. There’s a lot of finesse getting the right height on the curb and matching all the joints. These crewmembers all worked to gether and helped one another to get the final top quality product.

John Ball is the proprietor of Top Quality Paving & Training, Manchester, New Hampshire. He provides personal, on-site paving consulting services around the United States and into Canada. For more information, contact him at (603) 493-1458 or tqpaving@yahoo.com.
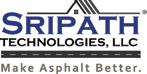
Hotmix Parts & Service supplies and upgrades any plant, any brand, any time.
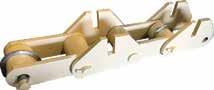



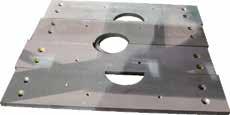

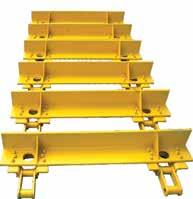
Recognized as the world’s leading producer of quality asphalt plant products, Stansteel has nearly a century of experience in the design and manufacturing of all types of operations.
Our state-of-the-art reconditioning facilities can upgrade any asphalt plant into the 21st Century for significant cost savings and increased efficiency
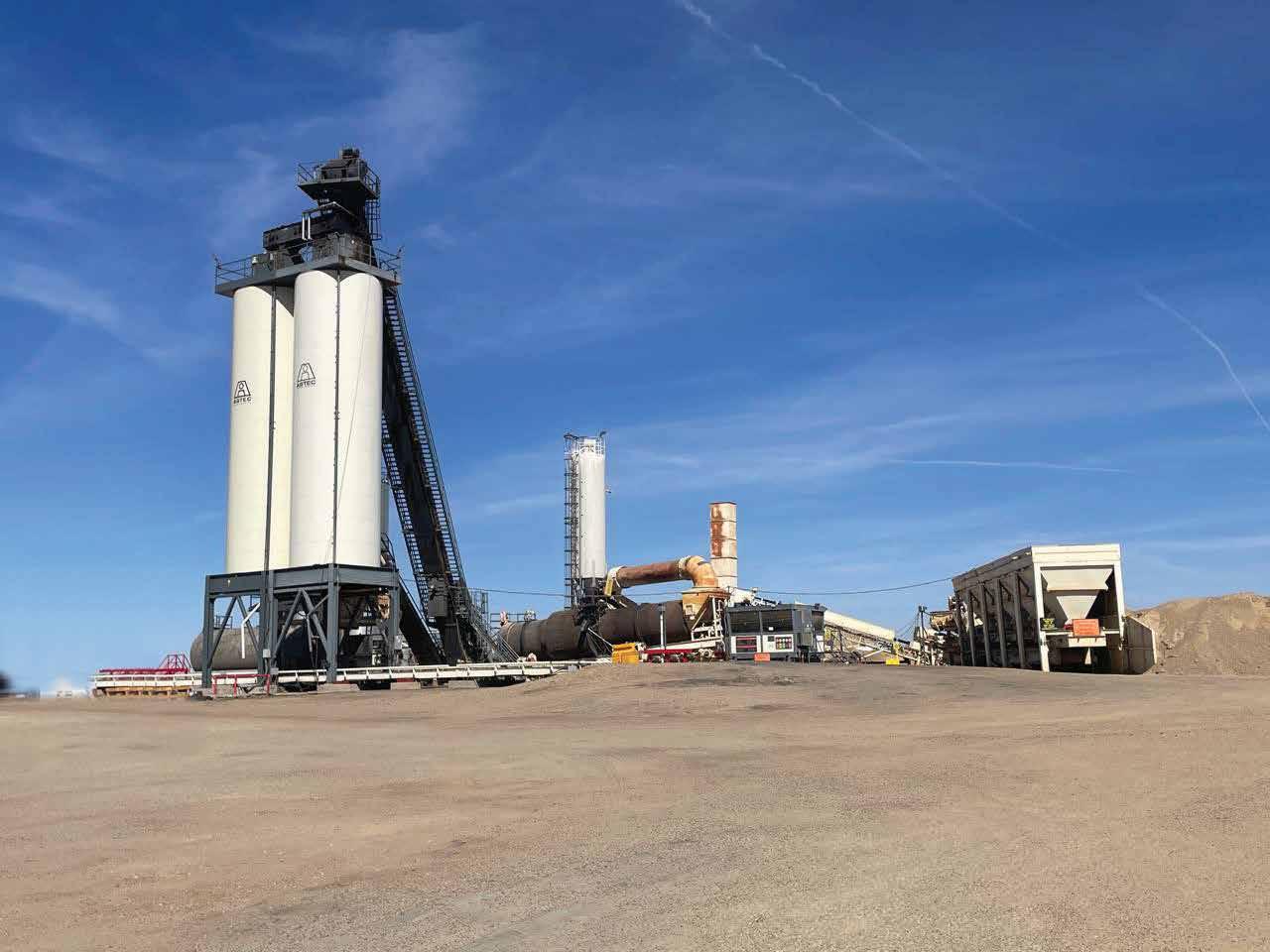
CIR Project Sets Northeast Standard
BY SANDY LENDERManagement at Peckham Industries Inc. (PII), headquartered in Brewster, New York, has given the asphalt industry a blue print on how to showcase an environmentally friendly pave ment maintenance method to multiple state agencies. Upon winning the bid for a cold in-place recycling (CIR) project for the Town of Kingsbury to rehabilitate Mattison Road, PII teamed up with indus try partners and vendors to put on more than a demonstration. They wanted to educate and inform with two days of classroom sessions and field demos on the intricacies of CIR.
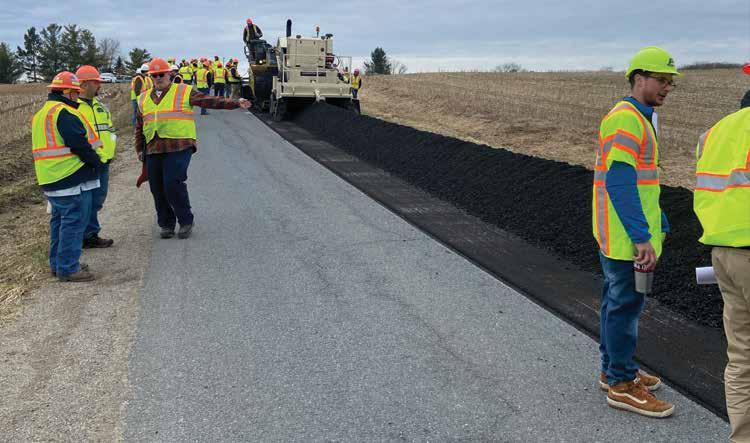
Gregory Peckham, general manager of Peckham Road Corporation (PRC), a PII subsidiary, explained they reached out to Astec Indus tries, Chattanooga; The Gorman Group, Albany, New York; and SuitKote Corporation, Cortland, New York, to bring the parties together not only for the coordination of the event but also to expand the reach of the learning experience across multiple geographies. That expan sion began almost immediately when Eric Baker and Kyle Hammon at Astec reached out to Stephen Cross, Ph.D., P.E., who is the current technical director of the Asphalt Recycling and Reclaiming Associa tion (ARRA) and professor emeritus at Oklahoma State University’s College of Engineering, Architecture, and Technology, to participate as
well. Tracey Road Equipment in East Syracuse, a distributor for Astec, also participated and provided lunch between the field demo the morn ing of April 5 and final informational sessions that afternoon.
Astec’s Hammon explained that attendees benefiting from the edu cational event included engineers from state departments of transpor tation (DOT) throughout the northeast, including Maine, New Hamp shire and Vermont. The education itself was geared toward all facets of the CIR process.
“The contractor members of the seminar wanted to ensure a por tion of it was devoted to lab testing,” Hammon said. He spoke highly of PII’s initiative.
“I give credit to the contractors,” Hammon said. “They did the heavy lifting. Gary Foux at Suit-Kote got the venue.”
The venue used for the classes prior to the outdoor demo was the Kingsbury Firehouse, located near the job. The team from Suit-Kote was unavailable for comment on the project, but Hammon described the venue as perfectly located and ideal for their needs.
Peckham explained the project was quoted using a New York State Of fice of General Services (NYS OGS) contract. This system allows state agencies, public authorities, local governments or political subdivisions, and volunteer organizations, among others, to procure work as autho
rized users in three contract types or categories—commodity, service, and technology. With an authorized user identification number in this system, entities can provide assurances to com panies that they are eligible to use state contracts and stream line projects with a purchase order rather than filing copious amounts of paperwork. (Source: https://ogs.ny.gov/procure ment/ogs-centralized-contracts)
The CIR project fit nicely in the technology category and the education began with informational sessions. The presentations April 4 and 5 included key components of the process but were not limited to:
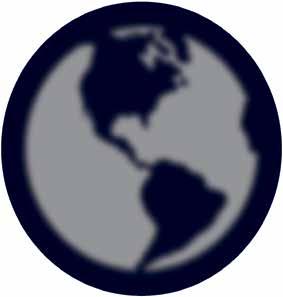
• Depth(s) of recycling
• Metering of materials
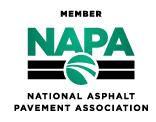
• Material sizing, plus the effects of add stone and the effects of cement
• Production speeds
• Temperature limits
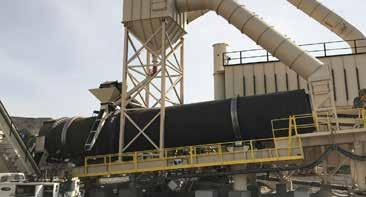
• How terrain and road conditions influence the process and how sensors can assist, plus the ideal project size and terrain
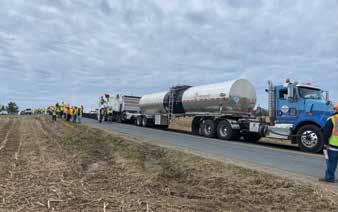

• Accounting for fluff factor in CIR
• Cross slope

• Performing shoulder repairs
• Drainage and water considerations for the CIR project
• Performing CIR at night
Peckham explained that much of the quality control/quality assurance (QC/QA) discussions during the seminar portions of the event were handled by ARRA’s Cross.
“My first presentation covered the basics, such as sustainability, cost effectiveness, project selection and assessment, and a few topics of in terest to New York—weather, fog seals, slope and grade corrections, and smoothness,” Cross shared. “My second presentation covered mix design and the use of add stone plus an overview of performance studies and current research activities.”
Cross’s presentation explained—among other things—to the audi ence that CIR is meant to treat non-load associated distresses, also called functional failures, and most structural distresses that occur in the top 2 to 5 inches of the pavement structure. That means, it can be used to mit igate transverse or reflective cracking if the agency selects the road in need of this treatment at the correct stage in its life cycle.
In other words, follow the mantra of selecting the right method for the right road at the right time. Considering Hudson Falls had the right road with the right underlying conditions, the team was on track to perform the right treatment with CIR.
Let’s take a look at the mix design, with guidance from Cross, and the recycling train, with guidance from both Astec and the Federal Highway Administration’s (FHWA) “CIR Application Checklist.”
That’s right: Even though CIR requires an in-place recycling and pav ing train, it incorporates a mix design. This is required to determine the optimum recycling agent rate and the optimum dosage of additive to be used, whether that’s a corrective aggregate, hydrated lime, Portland ce ment, and so on.
Cross presented, if a contractor will be using an emulsion as the re cycling agent, they will follow AASHTO PP 86 & MP 31 for emulsified asphalt. If using a foamed asphalt as the recycling agent, they will follow AASHTO PP 94 & MP 38 for foamed asphalt. Tests to perform include, but won’t necessarily be limited to, the indirect tensile strength, tensile strength ratio (TSR), Marshall stability, and retained stability. If using the emulsion method, you’ll want to perform a raveling test and possibly a high temperature evaluation. Again, the point is to optimize your results with the design.
Cross’s presentation showed the contractor wants the mix design to establish four things:
• An acceptable range of binder contents with expected changes in RAP gradation;
• The need for additives for dry strength;
• The need for additives to improve moisture resistance; and
• The need for high early strength.
For the demonstration on Mattison Road, the PRC crew used the foamed method. “We used a foam process for the demo supplied by our Athens, New York, terminal,” Peckham shared.
The team from Astec presented information on the CIR “train,” which can be as simplistic as a single-unit train or as robust as a multi-unit train, which incorporates the following:
1. A water truck, which feeds into
2. A cold planer/milling machine, which feeds millings onto
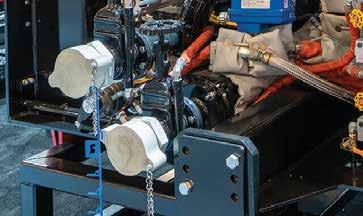
3. A screen deck, which sifts material into
4. The pugmill, where a nurse truck delivers emulsion and where mixing occurs before material is delivered to
5. Either a windrow for a pickup device or directly to a paver to be placed under the screed.
When placing and compacting cold-recycled material, the focus will be on achieving density, not on measuring air voids. PRC’s Greg Peckham shared, “The average density is typically about 132 pounds per cubic foot.” To achieve this goal to rehabilitate Mattison Road, the crew used two 12-ton steel rollers and a 20ton pneumatic roller in the compaction train behind the Cat paver, which was fed by an MS2 pickup machine.
The RX-900e cold planer from Astec Industries can be equipped with a skid-mounted additive package, which includes an integrated pump/meter package, automated flush system, and electric over hot oil heating system to facilitate delivering additive materials to the blending chamber.
Both trains will be followed by a steel drum breakdown roller and pneumatic roller (or two).
As you can see in the pictures on these pages, the PRC team used a wa ter truck and nurse truck to deliver additives to the mixing chamber of the RX-900e from Astec, which milled a depth of 4 inches.
The RX-900e cold planer can be equipped with a skid-mounted addi tive package, which is mounted to the rear of the milling machine and in cludes an integrated pump/meter package, automated flush system, and electric over hot oil heating system to facilitate delivering additive mate rials to the blending chamber. The system includes additive system con trols within a control panel allowing the operator to meter up to three additive materials.
The recycled material was placed behind the RX-900e in a windrow for PRC’s Cedarapids’ MS2 pickup machine to feed it to a Caterpillar AP-
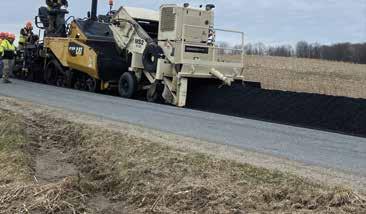
1055F paver for laydown. “The average density is typically about 132 pounds per cubic foot, and we use two 12-ton steel rollers and a 20-ton pneumatic roller to achieve it,” Peckham shared.
For CIR projects, density is the focus rather than air voids. The agency and inspectors will be interested in density achieved and time for curing to ensure moisture is removed. For this suc cessful demonstration project, Peckham explained the road was paved two weeks later with no issues.
“They did a fantastic job,” Peckham said of his team. “We real ly lucked out with temperatures on that day of construction and the crew performed beautifully for a season start-up job.”
With a host of state and agency materials engineers on hand to learn from two days of classroom presentations and outdoor demonstrations, the Peckham family brought about an example of industry cooperation for training. Not only did the contrac tors in the region come together to showcase an environmentally friendly asphalt recycling practice, but they also did it in a spirit of industry advancement.
LEARN MORE
Peckham Industries Goes First with More Green Ideas
The Road Forward initiative of the National Asphalt Pavement Association (NAPA) welcomed its first two funding partners in May. The inaugural sponsors are producer member Peckham Industries Inc. (PII) and associate member Cargill Asphalt Solutions.
A NAPA member since 1973, PII produces hot-, warm-, and cold-mix asphalt in New York, Vermont, and Massachusetts. A NAPA member since 2016, Cargill offers a line of asphalt additives including rejuvenators, warm- and cold-mix additives, and anti-strip to help producers increase performance and profits.
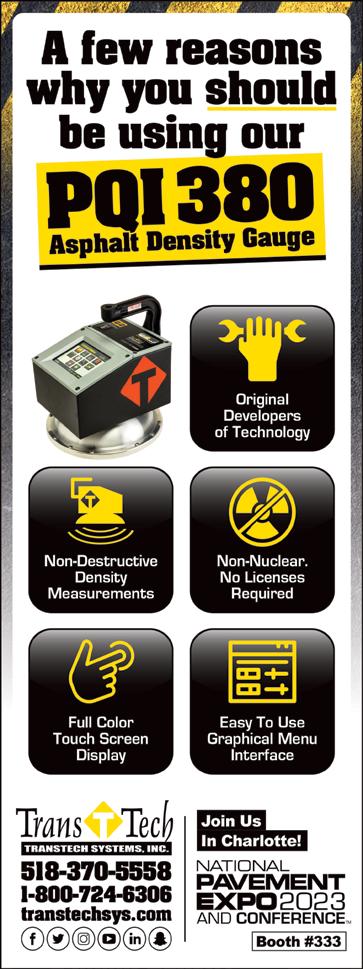
“Peckham Industries is excited to take part in The Road Forward and join NAPA on their journey to a net zero future,” said Will Hadeka, sustainability lead for PII. “Since 1924, our company’s foundation has been built on family values, and we are committed to building a sustainable future for our employees, customers, and communities for generations to come. The Road Forward allows us to unite across the country to help move our industry forward as we pave the way to a sustainable future.”
"Cargill provides sustainable asphalt technologies and solutions around the world, and we are on board with NAPA to help advance environmental stewardship in the asphalt industry through The Road Forward initiative,” said Justin Black, Cargill Asphalt Solutions category leader.
“Cargill and Peckham’s foresight in sustainability is an example for our industry and our customers— DOTs and road owners,” remarked NAPA President & CEO Audrey Copeland, PhD, PE.
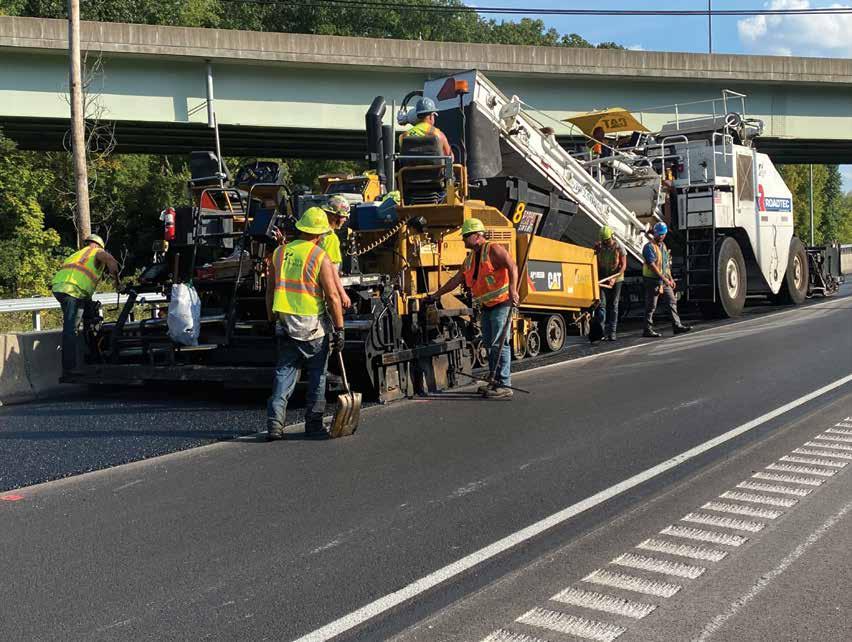
TTo offer contractors options when building stone matrix asphalt (SMA) pavement systems in the state, the Pennsylvania Depart ment of Transportation (PennDOT) let a 3.9-mile mill-and-fill project on Business State Route 376 (SR376) in Allegheny Coun ty as a pilot project. The option was to design the mix without fi bers and the team from Lindy Paving Inc., New Galilee, not only took on the challenge, but also lowered fuel consumption via lowered production temperatures while enhancing performance test results.
Plant Quality Control Manager Martin Libertini, who has been with Lindy Paving for seven years, said the company’s Neville Is land plant is set up to introduce fibers or other additives into mixes during production, but the concept of making a fibreless SMA for the state also gave them the opportunity to inject innovation. And that’s something the team at Lindy Paving is known for.
Pennsylvania Asphalt Pavement Association (PAPA) Execu tive Director Charles C. Goodhart reminded us that Lindy Pav ing has been awarded five National Asphalt Pavement Associa tion Sheldon G. Hayes awards for highest quality paving projects. “Without a doubt, Lindy Paving is one of the premiere asphalt mix producers and laydown contractors in the United States,” Goodhart said. “Lindy leads the way with quality and innovation because their president, Vince Tutino, sets the example of push ing forward to ever improve their operations and organization. Lindy focuses on the customer and encourages innovation and risk-taking from their staff. If you want to move the state of the possible forward, get Lindy Paving involved and they will make it happen.”
The state of the possible in this case was, as Libertini shared, to modify the state’s spec to allow contractors the option to use fibers when placing an SMA pavement. The end user benefits when industry is allowed to innovate and make choices concern ing the right materials and right methods on the right road at the right time. The industry partners who came together to develop the pilot project workplan for assessing this innovative idea were PennDOT, PAPA, Lindy Paving, and Ingevity Pavement Technol ogies, headquartered in North Charleston, South Carolina.
“One of the roles of the PAPA is to bring innovations in asphalt pavement technology to the highway owners for their consider ation,” Goodhart shared. “If we don’t try it, they won’t buy it. So, a pilot project is normally necessary to prove that a material, ad
ditive, technology, equipment, test, etc. works as well as or better than the product it is replacing. This project, completed by Lindy Paving, with technical assistance by Ingevity, proves that you can produce SMA without the use of fibers.”
Let’s start by looking at the mix design options on the table.
MAKE THE MIX
Libertini said, “The key to making the fibreless SMA work is to go with a true warm-mix asphalt so you’re producing at cooler temperatures. You want to produce it around 280 degrees instead of 320 to 330 degrees, where you’d normally run that material.”
Making the fibreless SMA as a WMA offers the obvious bene fit of lowering fuel consumption, thus lowering emissions, but it also offered the Lindy Paving team an opportunity to reduce the traditional 6.7% liquid asphalt cement (AC) content of an SMA by 0.3%, thus lowering production costs. The WMA paradigm also saw positive index testing results, according to Libertini. “We’re saving on cost a little bit, but we’re gaining performance,” he said. “It was amazing how much better the testing got.”
He explained, “We performed Index testing in 2021 using three different labs. We performed testing at our Zelienople Central Lab and Ingevity ran samples at their lab and Rutgers University. The IDEAL-CT Index test for cracking resistance is where we saw the increased performance on the fibreless SMA.”
As he explained, the traditional SMA contains cellulose fibers that exist in an incredibly fine, almost dust-like state. “The fibers are used to make the liquid binder stable,” Libertini said. “Tra ditional SMA uses cellulose fibers to prevent the liquid asphalt binder from draining out of the mixture. You have to use warmmix technology, producing the mix between 260 to 285 to pre vent drain down.”
When the team removed the cellulose fiber content from the equation, it was necessary to counteract the potential for drain down. They raised the film thickness of the liquid with warm-mix temperatures, facilitated by the use of Evotherm J1 from Ingevity.
“We wanted to establish limits for drain down, so we ran tests from 275 to 295 with 295 being our limit,” Libertini said. “How ever, we produced this mix and never exceeded 285 and our av erage temperatures were between 275 and 280.”
Let’s look at the production for the Sept. 17-18, 2022, pilot project.
PRODUCE IT AT THE PLANT
The traditional SMA and two fibreless mixes—one using the addi tive Sonnegreenas by Sonneborn LLC at a 0.25% dosage rate and one using the additive Evotherm J1 at a dosage rate of 0.5%—were pro duced at the Neville Island Gencor 600-ton-per-hour drum plant.
Lindy Paving produced the traditional SMA on Saturday and paved the fibreless SMA on Sunday. With a target temperature in the 320-degree range, the plant hit a production between 350 and 400 TPH, according to Barilla. He shared that the natural gas con sumption on Saturday/with the traditional SMA was 60 MCF/hour, taking readings every 10 minutes for an hour.
Libertini confirmed his team injected the Evotherm J1 into the asphalt cement at the plant, adding it at a rate of half a percent. Sun day’s production of fibreless SMA mix was between 300 and 350 TPH and the natural gas consumption showed 45 MCF/hour, tak ing readings every 10 minutes for an hour.
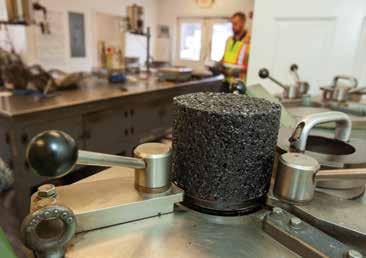
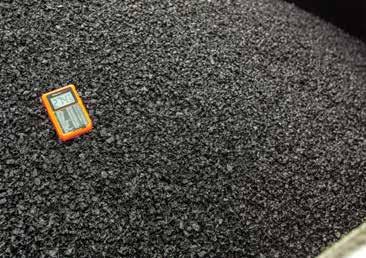
Let’s look at how these mixes arrived and performed in the field.
PAVE IT IN THE FIELD
The job began with the cold planing portion of the mill-n-fill. Lin dy Paving’s crew handled milling operations, using two Wirtgen 210
cold planers and a Wirtgen 150 cold planer to remove 1.5 inches of existing pavement. Greg Tomon, the field quality control manag er for Lindy Paving, has been with the company for 22 years, and shared how the milling crew adapted to a quick challenge on the roadway.
“After milling 1.5 inches off concrete, some areas began to ravel. We took the mill back out and took the remaining asphalt down to concrete in a few areas in the passing lane.”
They paved the 9.5-mm SMA at a width of 13 feet and at a depth of 1.5 inches, using a CAT AP1055D tracked paver with an ExtendA-Mat 10-20B screed. A Shuttle Buggy SB2500 from Astec Indus tries took delivery from the haul trucks at consistent temperatures.
The temperatures ranged from 245 to 265 at the paver for the fi breless SMA, according to Libertini and Tomon. They observed temperatures, “Cooler than we normally would see from fibered SMA with little to no problem being fed through the MTV/paver.”
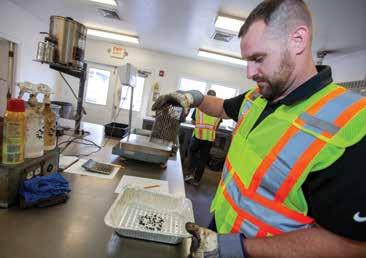
Five rollers made up the compaction train. Tomon listed the Sakai SW774 in the breakdown position. Barilla listed the other rollers as the SW800, two SW770HF compactors, and a tandem Hamm com pactor “for rolling against the curb and barrier wall.”
For the fibreless mix, the compactors averaged 94.8% density, ac cording to Libertini and Tomon. They observed, “The mat did move around more than fibered SMA,” but “It stayed workable all the way down to 120 degrees.”

Let’s grow the future of asphalt.
At Colorbiotics, our soybean-based science is changing the asphalt industry just as much as it changes the molecules inside recycled asphalt. But having the best science in the business only makes a difference if we have the best people, too.
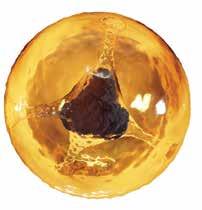
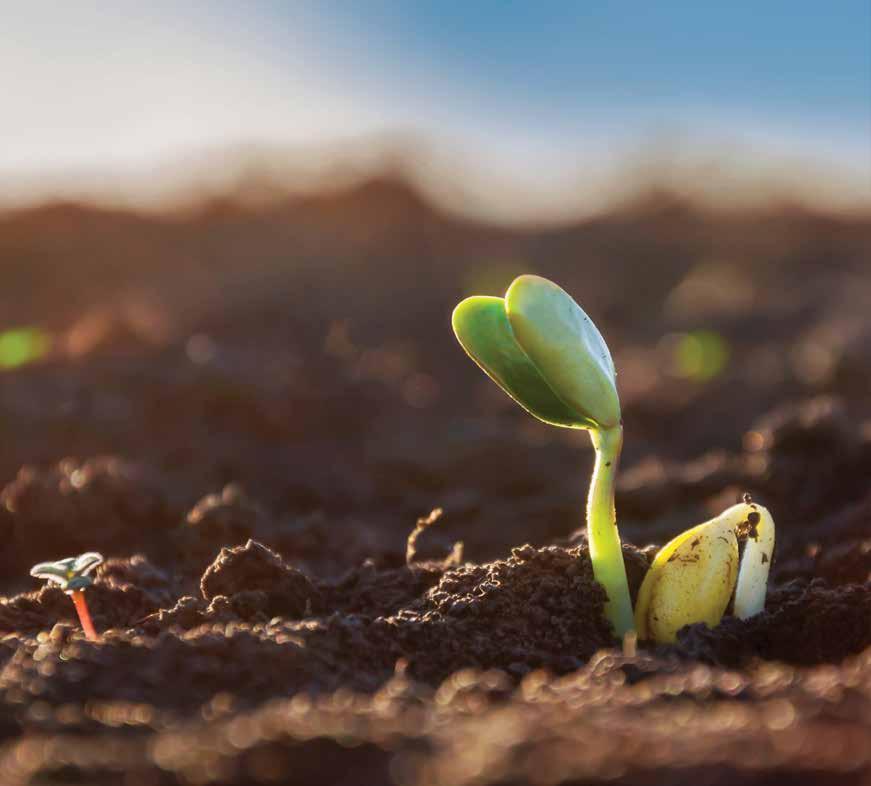
We are looking for sales people to join our team — so let’s talk about your future and get to growing together.
Give us a call: 888-663-6980 | Apply today: invigorateasphalt.com
Colorbiotics is a registered trademark of MBCC Group. © 2022 MBCC Group. All Rights Reserved.
LEARN MORE
They used the same compaction train for the traditional SMA, which they said saw temperatures between 290-305 degrees at the paver and achieved an average density of 95.8%.
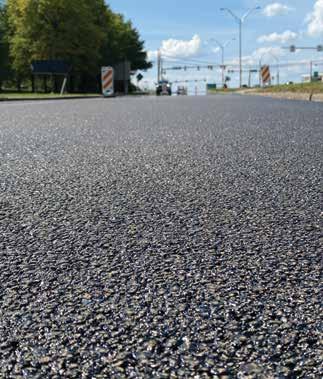
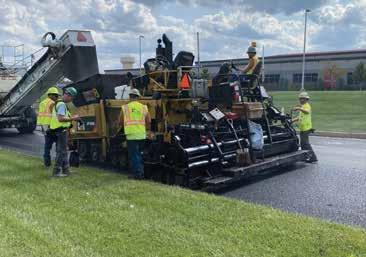
PROVE IT
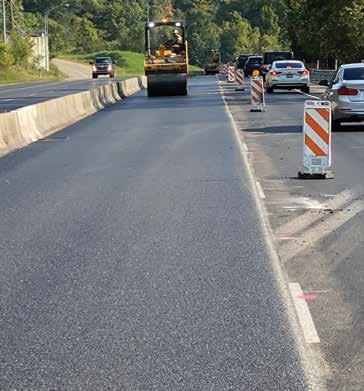
With PennDOT districts continuing to use more 9.5-mm and 12.5mm SMA mix designs on interstates and other high traffic volume roadways, giving contractors options to enhance the designs’ per formance is in the agency’s best interest. As Libertini said, “If we can lay down mix at cooler temperatures and still get good performance, that’s a good end result. It’s lowering emissions and getting perfor mance. It’s all good for the state.”
Barilla shared that the team took eight 5-gallon samples of mix during production Saturday and another eight 5-gallon samples during production Sunday. These samples have gone to Ingevity’s lab for volumetric and balance mix design testing as well as binder aging assessment. Those results, along with highlights learned from the weekend’s project, will be shared at the 63rd Annual PAPA Con ference in Hershey, Jan. 16-18, 2023.
“Again, our members are always open to trying new products,” Goodhart said. “Doing demonstration projects such as this shows not only the ways and means of how you can make a fibreless SMA, but also what the ancillary benefit will be, like lower carbon footprint, re duced asphalt mix costs, etc. We plan to have Lindy and Ingevity make a presentation at our annual conference to preview the pilot project and highlight the production, delivery, laydown, and testing required for the pilot. We think PennDOT will see the viability of allowing fi breless SMA and we intend to suggest that we change the specification to allow producers to supply either fibreless or SMA with fibers. A per missive spec would seem like the way to go for now.”
WMA in SMA
The team from Ingevity shared, “Using a lowtemperature warm-mix asphalt (WMA) additive like Evotherm is a proven way to eliminate drain down without the use of fibers” in a stone matrix asphalt (SMA) mix. “Almost 2 million mix tons of fibreless SMA with Evotherm have been paved across the United States. Three hallmark benefits of these mixtures are improved drain down, remarkable cost savings, and increased density and workability,” according to the manufacturer.
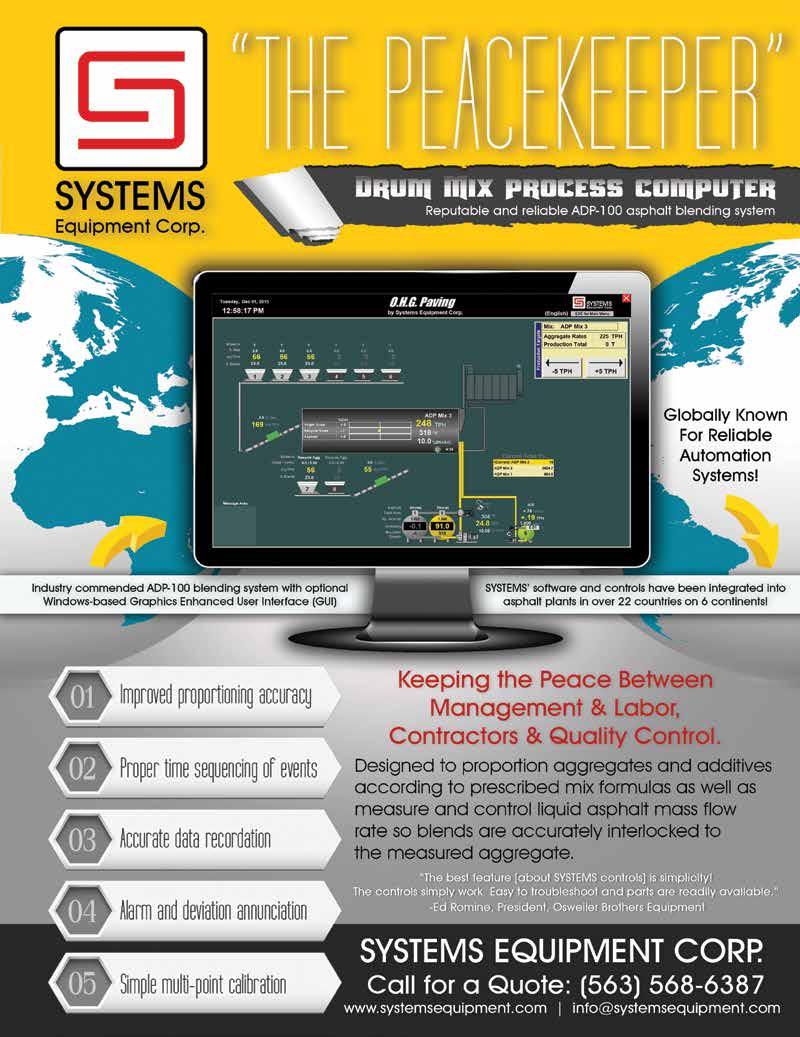
RESILIENT INFRASTRUCTURE RAISES THE GRADE
BY SARAH REDOHLUU.S. Highway 81 (US-81) is a major northsouth highway extending 1,220 miles from northern Texas to the Canadian border. Just south of where U.S. Highway 14 crosses US81 is the Twin Lakes region of South Dako ta, known for its popular public grounds for hunting waterfowl. However, when South Dakota was inundated with heavy rain throughout 2019, this stretch of highway found itself in the cross hairs.
“We were facing one rain event after anoth er and the water level just kept rising,” said Joe
Gilsdorf, project estimator for Bowes Con struction, Brookings, South Dakota, which worked on both the temporary and perma nent grade raise on US-81 in August 2019 and July 2022, respectively. “US-81 ended up under a foot of water.”
According to Wayne Lloyd, vice president of Prairie State Trucking Inc., Sioux Falls, South Dakota, the prime contractor for both projects, the highway is an important route through the state. “Agriculture is the main in dustry in South Dakota, and US-81 is a main connector to several [grain] elevators and eth
anol plants in the area,” Lloyd said. The area is also home to many dairies and other agricul ture facilities.
Located 15 miles west of Interstate 35, US-81 is also a major thoroughfare connect ing smaller towns in the region, added Gils dorf. Bowes Construction also served as the asphalt contractor on the permanent grade raise on US-81.
RAPID EMERGENCY GRADE RAISE
When the highway found itself under water in the summer of 2019, it was no small inconve nience. In order to open the highway to traffic, SDDOT aimed to raise the grade immediately. Shortly after the highway flooded, it tendered a bid for an emergency grade raise.

“The project was bid in July, but it had to be done by the fall,” Lloyd said. “Many con tractors didn’t think it could be done in that amount of time, given the volume of material that had to be hauled out there. But, we knew with the amount of trucks we had available and our ability to innovate that we’d be able to get it done in time.”
Construction on the temporary grade raise began in August 2019. “The road was still un der a foot of water when we first went in there,”
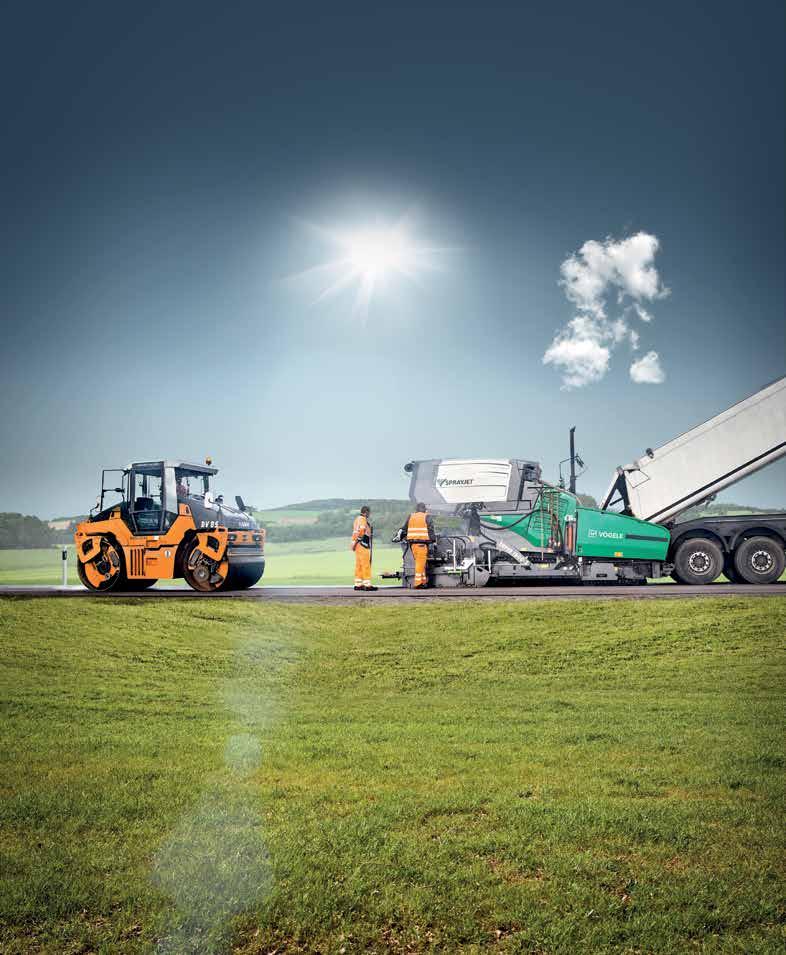
Lloyd said. Over the existing concrete pave ment, Prairie State’s crews placed four lay ers of geogrid and separator fabric, 46 inches of surge rock, pit run, and base course, fol lowed by three 2-inch lifts of asphalt. “The fabric had to be wrapped around the outside of the base course to keep it in place because we built up the aggregate sections vertically.”
“I’ve never done a project like that,” Lloyd said, referencing placing the base course atop the existing pavement. Also unique to the project was beginning work while the road was still underwater. Even after the initial flooding had subsided, an 8-inch rain event during the construction process flooded the road once more. To solve this, Prairie State raised the surge rock section above the new water level. “We were sup posed to remove the cable rail but convinced
the SDDOT to leave it in place to help con tain the aggregate sections,” Lloyd said.
A PERMANENT SOLUTION
When SDDOT looked for a permanent solu tion, Prairie State once again won the bid. The $8.5 million project would raise the grade on 2.5 miles of US-81 by approximately 2 feet.
First, in four locations along the project, Prairie State removed everything down to the original road’s subbase in order to place four 48-inch equalizer pipes across the road.
Then, they began trucking in 100,000 tons of riprap from a quarry in Spencer, South Da kota, 120 miles from the project. The riprap along both sides of the existing road would be the base for expanding the width of the road by 5 feet on each bound for a total of 12-foot-wide driving lanes and 7-foot-wide shoulders.
“We began hauling that in over the winter and dumping it over the existing guardrail,” Lloyd said, adding that they had placed most of the riprap by spring. They were then able to place a 1- to 3-inch quartzite aggregate to fill the voids in the riprap before placing the base course of 1 foot of class 5 gravel.
Atop the existing lanes paved after Prairie State's emergency grade raise from 2019, the company placed 20 inches of granular aggre gate. “I’ve been doing this for 30 years and that’s the first time I’ve ever done that,” Lloyd said.
By July 2022, Bowes’ crew could begin pav ing. “It certainly felt like new construction pav ing [rather] than a reconstruction or mainte nance project,” Gilsdorf said, adding that it otherwise seemed like a fairly standard paving job. “It went very smoothly.”
In two weeks, the crew paved three 2-inch lifts of standard Q3 state virgin hot-mix as phalt with PG64-34 and 1% hydrated lime as an anti-stripping agent along the 5 lane-miles
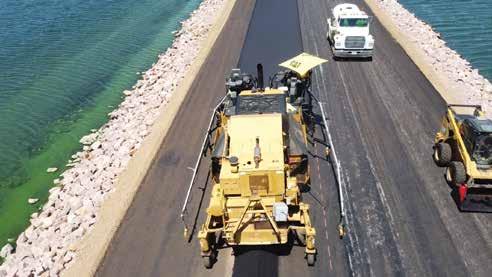
LEARN MORE
Timeline to Resiliency
Summer 2019 = Multiple rain events lead to flooding, putting a section of U.S. Highway 81 under a foot of water.
August 2019 = Prairie State performs an emergency grade raise while the roadway is under water, placing multiple layers of geogrid, aggregate, and 6 total inches of asphalt.
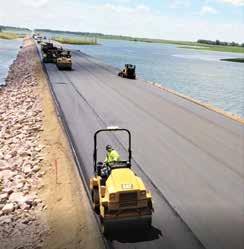
Spring 2022 = Prairie State wins the bid to build a new, permanent, raised grade for 2.5 miles of the roadway.

Summer 2022 = Prairie State removes the structure down to its subbase in some areas to place equalizer pipes across the road, brings in riprap to widen the road, and places 20 inches of granular aggregate atop the existing roadway.
July 2022 = Bowes Construction paves a total of 6 inches of HMA along the 5 lane miles.
Fall 2022 = Prairie State installs new guard rails designed to minimize snow drifting onto the roadway.
Bowes trucked the material with belly dump trucks and used its Barber Green pickup machine to feed the mix into its Cat AP1055 paver.
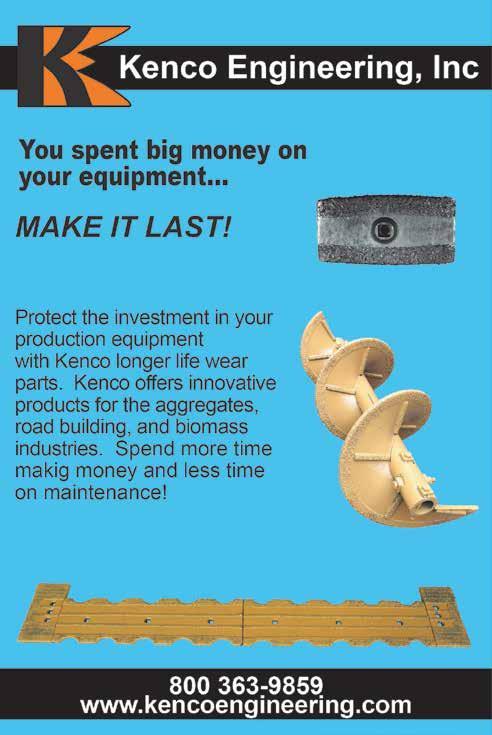
of the project. The 20,000 tons of mix was pro duced at Bowes’ Barber Green asphalt plant in Brookings, 25 miles from the project.
They trucked the material with belly dump trucks and used its Barber Green pickup ma chine to feed the mix into its Cat AP1055 paver, followed by several rollers (Caterpillar CB36, Caterpillar CB54XW).
Then, Prairie State was able to put up the 3-cable guardrail that replaced the exist ing W-beam guardrail, which SDDOT said should eliminate some of the snow drifting that has been known to occur through this stretch of road.
Bowes Construction is a veteran/ family-owned business. Lyle Bowes served in the Army during Vietnam, his son Jason Bowes served in the Marines on Okinawa in the 1990s, and Jason’s son Logan Bowes is currently serving in the Marines. Bowes’ Head of Marketing and Public Relations Kesmond Willert said the company strives to hire veterans and works closely with the local Veterans Affairs office to recruit them. “Our veteran employees are decisive, dependable and great with thinking on their feet as a result of the training they’ve gone through with the U.S. Military,” he said. “They treat their workplace with the same attention and respect as they did their service.”
will have a new road upon which to haul their corn and grain this fall.
“When we were out on 81, I heard our crew talking about how well the road was riding af ter each and every lift,” Gilsdorf said.
Although the new pavement was the re sult of a natural disaster, Gilsdorf, who fre quently drives this section of US-81 to get to the lake where he camps, said it was only a matter of time before the road needed some repairs. “It wasn’t a terrible drive, but it was getting to the point that it was due for some maintenance,” he said.
One of the next big projects in the area is the repaving of a stretch of US-81 a few miles south of the recently completed project, from the border of Brookings County to Madison.
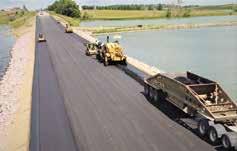
Lloyd, who grew up in the area and still hunts near the project site, said that flooding has occasionally been a problem in the past. Now, he added, the road is above a 100-year flood event. “The road is high enough that the water won’t come across it,” he said. “In stead, it’ll drain to the southeast toward Big Sioux River.”
OPEN FOR HARVEST SEASON
Ultimately, US-81 opened to traffic Sept. 6, 2022, approximately two weeks ahead of schedule. “By getting the road open [right at] Labor Day, it will be open for the entire harvest season,” Lloyd said, adding that area farmers
THE POWER
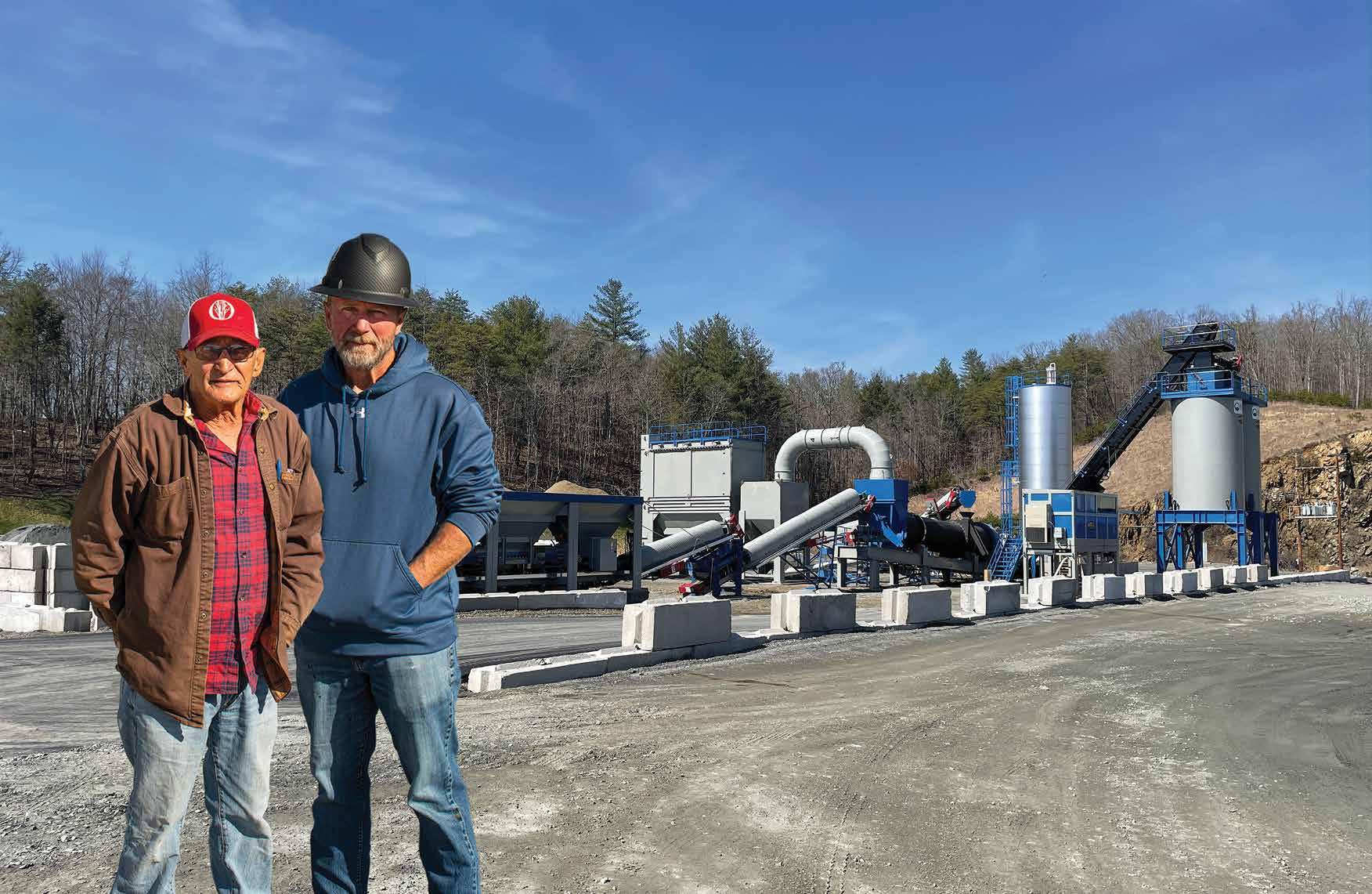

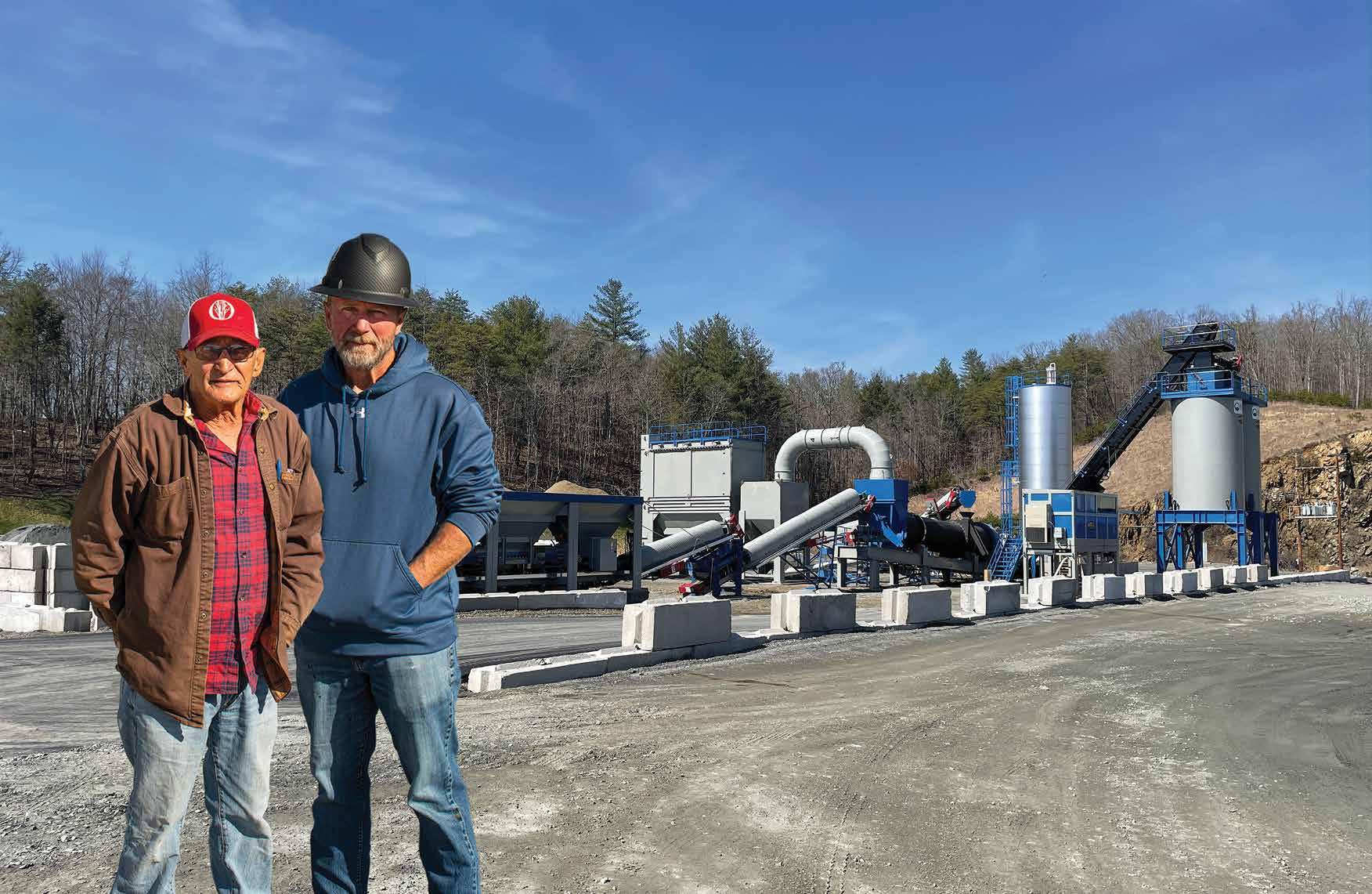
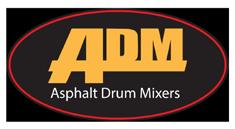
The process to incorporate Biomag Easy Pave from Colorbiotics atop asphalt millings involves spray-applying the topical solution. This image shows the process on a parking area in Columbus, Ohio, after the crew first loosened 2 to 3 inches of gravel. All photos courtesy of Colorbiotics
BY ALEXANDRA ZAHNTThe rising cost of crude oil, mixed with changing environmental regulations, is making asphalt applications less profitable for con tractors. Within the past two years, asphalt pavement has doubled in price from $45 per ton to $80–$90 per ton, as of early Septem ber 2022.
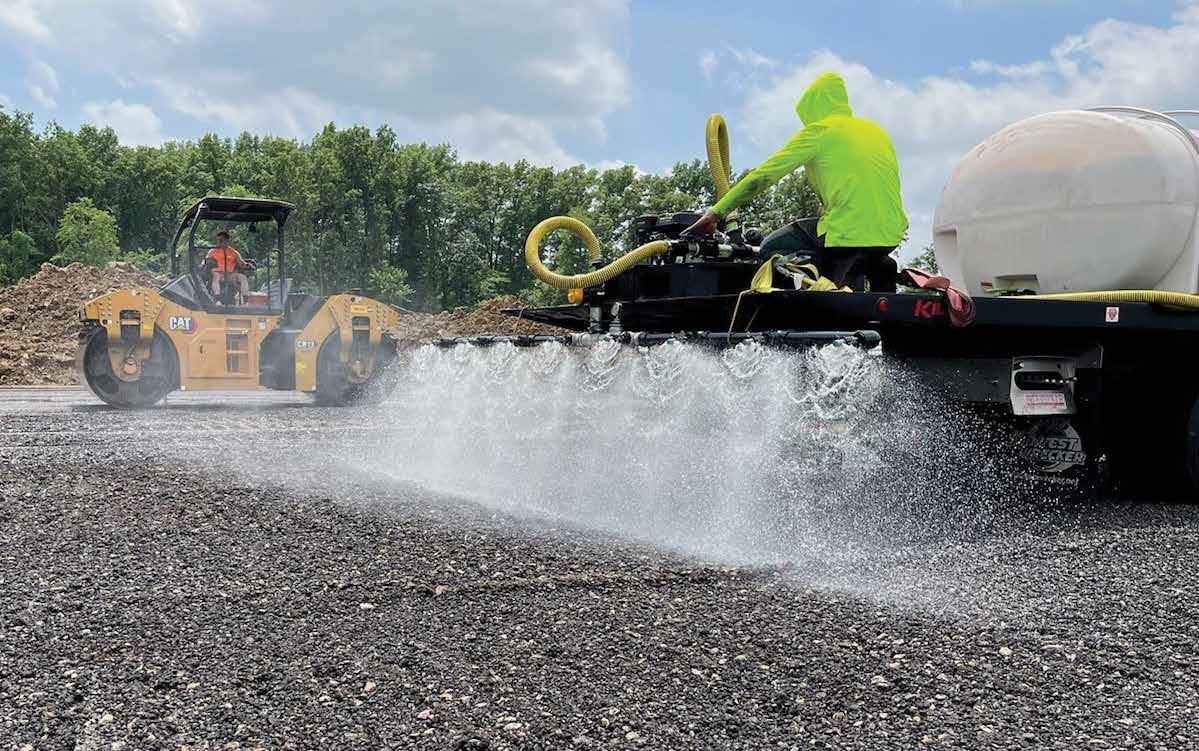
One solution to this problem is reducing the percentage of vir gin liquid asphalt cement (AC) needed in asphalt applications by increasing the use of reclaimed asphalt pavement (RAP). Accord ing to the National Center for Asphalt Technology (NCAT), there are many benefits to using RAP in asphalt mixes—including mate rials cost savings, conserving natural resources, and reducing en ergy consumption and the associated greenhouse gas emissions. However, increasing the amount of RAP used in asphalt mixes can increase its susceptibility to cracking and may cause durability is sues if the contractor doesn’t consider its age or a restorative agent.
There are now new solutions on the market in the cold-in-place space that address these concerns. Colorbiotics has introduced Biomag™ Easy Pave, a soybean-based topical additive.
“We’re excited to offer a solution that allows contractors to in crease cost efficiency in such a unique way,” said Austin Hohmann, product manager at Colorbiotics. “Hot mix can run about $4 per square foot, but this product paired with using RAP will cost only $0.60 per square foot. And this could easily go up by a dollar as the price of RAP varies dramatically.”
While still new to the market, Biomag Easy Pave has already been put to work in the real world. “We are always interested in gathering more data about our products and their performance,” Hohmann said. One of the first applications of Easy Pave was to help prepare the site for the largest U.S. outdoor farm event: the Farm Progress Show in Boone, Iowa.
Before the show is hosted in Boone every other year, the orga nizers survey the Central Iowa Expo showgrounds and determine what improvements need to be made. This can include anything from grounds maintenance to building upgrades. This year, the dirt area reserved for the varied industries tent was due for a facelift.
“In the past, we would put down wood chips to control the dust and mud inside the tent area,” said Matt Jungmann, events director
WE ARE A UL-142, ASME SECTION VIII AND API APPROVED TANK MANUFACTURER. Our facility is quality control inspected by Underwriter’s Laboratories four times per year. WE ARE A LICENSED MANUFACTURER FOR THE STEEL TANK INSTITUTE (STI). We are the recipient of STI’s Quality Award 16 consecutive years and inspected two times annually. ALL ASPHALT TANKS ARE BUILT TO THE UL-142 CONSTRUCTION CODE. We keep records of the steel purchases, welding practices, pressure tests and other quality control measures. WE USE 6” INSULATION ON TOP AND SIDEWALLS OF OUR TANKS. The bottom of our tanks are insulated with foam glass block. ALL OF OUR SHELL JOINTS ARE DOUBLE BUTT WELDED AND NOZZLE JOINTS SEAL WELDED INSIDE AND OUT. 100% Welded - The strongest union of two pieces of steel possible.




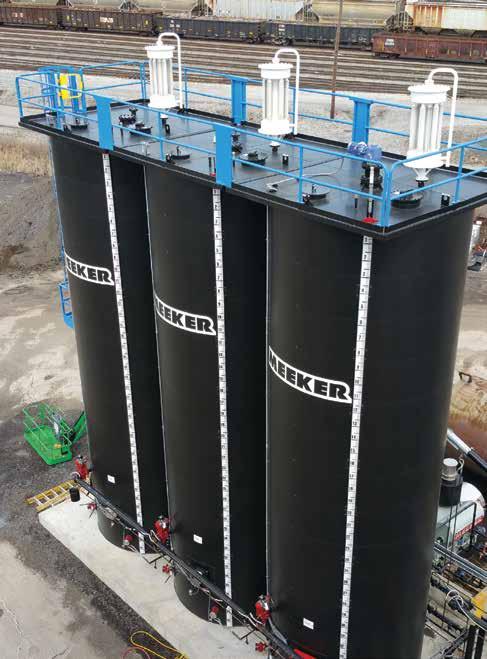

WE ARE CONSTANTLY IMPROVING OUR TANK DESIGNS. The only way to keep our tanks better than any other tank on the market!

for Farm Progress. “When the idea of paving at the showgrounds was presented to us, we immediately thought that the varied indus tries tent would be the perfect place. We knew we’d get maximum value out of improving that spot.”

Simply having a paved area would improve the guests’ experi ences and allow for more engagement within the space. “We would have continued to put down wood chips and scrape them up after the show. This is a much better alternative,” Jungmann said.
Biomag Easy Pave is recommended for use on low-volume road ways, including parking lots, gravel roads and driveways. This makes it an ideal solution for the showgrounds, as it can easily with stand foot traffic.
The application process for Biomag Easy Pave includes three steps.
1. Spread a layer of asphalt millings.
2. Spray the area with the topical solution.
3. Compact the treated millings.
“The topical agent we apply uses water as a transport vehicle to get the material down,” Hohmann explained. “It is almost like a tack weld, binding the points at which the millings connect.”
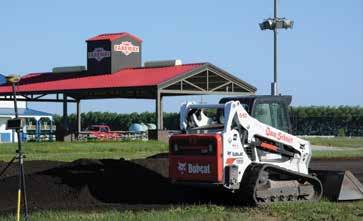
For the Farm Progress Show project, crews put down a 6-inch layer of asphalt millings at the site and then spray-applied the Easy Pave solution followed closely by an asphalt compactor.

The millings used for this project were a mixture of excess RAP from a variety of road types like old, low-volume roads, sections of an interstate, and even main roadways in a city. Traditionally, RAP from high-volume roads is more desirable due to the added poly mers that strengthen the asphalt. But this high-volume RAP is also more expensive.
“Fortunately, Easy Pave not only seals the surface of aging as phalt, it also penetrates deeper to help restore the micro-fractures,” Hohmann said. “Because of this, we’re able to use the ‘less desirable’ RAP from low-volume projects for this application, which is more cost-efficient.”
After testing the application, the Farm Progress site showed a com paction of 4-5% air voids, meaning it has the same density as a typical roadway. The ability to use recycled materials while still achieving the same end result is key for widespread industry adoption.
While using renewable materials benefits asphalt applications, us ing soy-based ingredients in Biomag Easy Pave benefits more than one industry. Finding innovative ways to use crops also benefits the agriculture sector and helps reduce waste.
Easy Pave’s soy-based formulation is an alternative to petroleum or formaldehyde-based products because it is considered safe for the environment and more carbon neutral. This is especially im portant when applying to roads that can have run-off into nearby ditches or grassy areas.
Renewable products are a growing preference in the pavement industry, especially as technology continues to advance and new breakthroughs are achieved. Colorbiotics has developed multiple asphalt products using soy, including Biomag Easy Pave, Invigorate™ Additive and Invigorate™ Topical, that are designed to provide im provements to the molecular makeup of asphalt.
“We take pride in developing products that push the boundaries of what’s been done traditionally,” Hohmann said. “With solutions like these, contractors can make pavement that is good for the plan et and even better for their bottom line.”
LEARN MORE
Discover the strength of the most versatile, durable, and reliable crushing equipment on the market today. Take on even the toughest applications with confidence. Experience unparalleled parts and service support, 24/7. Let Eagle Crusher keep you up and crushing, year in and year out.

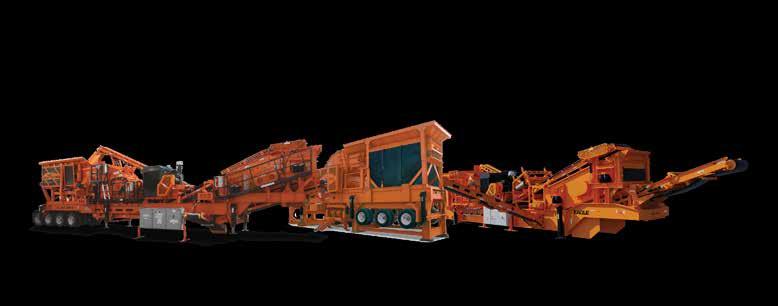
TRUST THE STRENGTH OF EAGLE CRUSHER

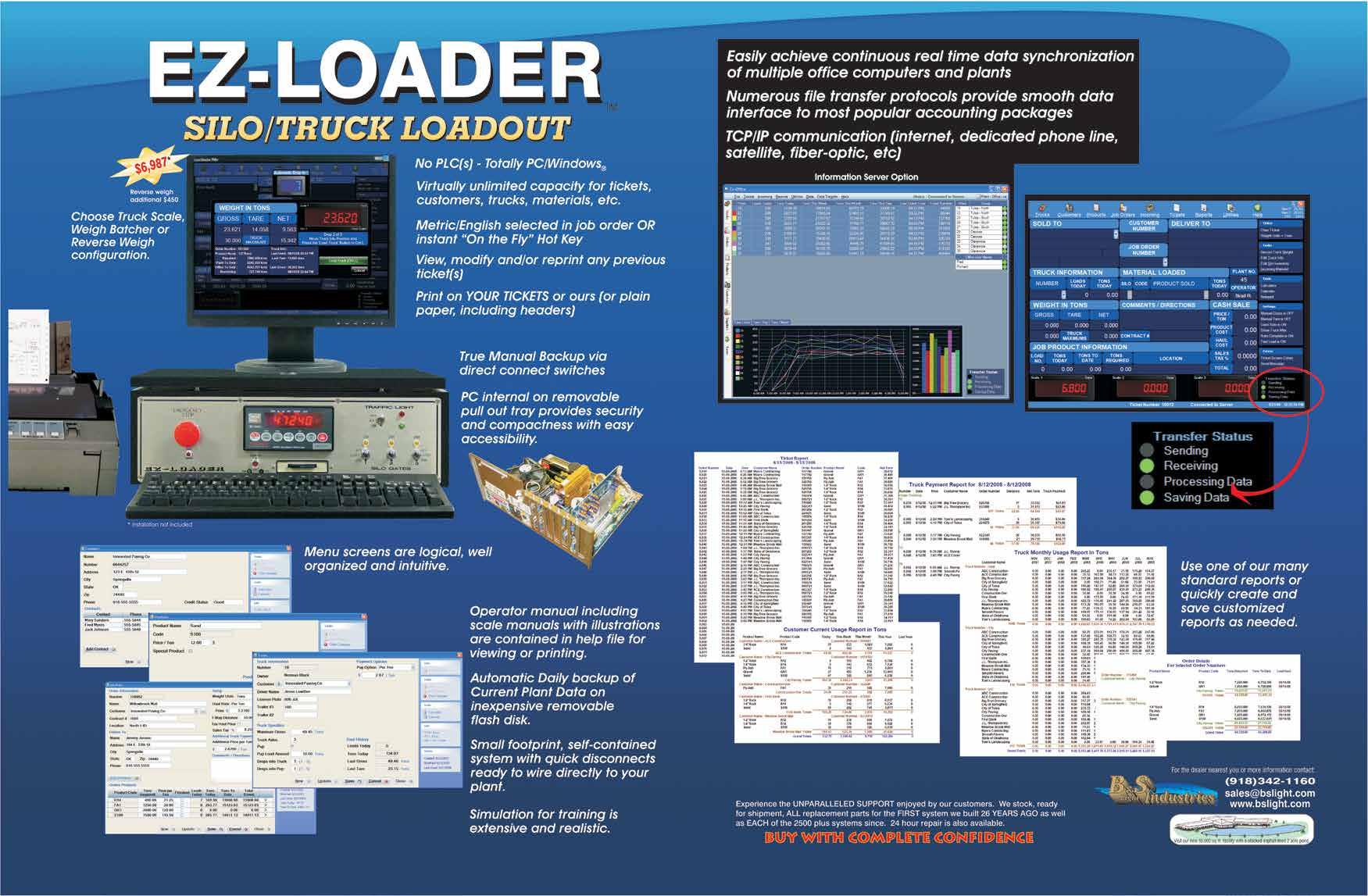
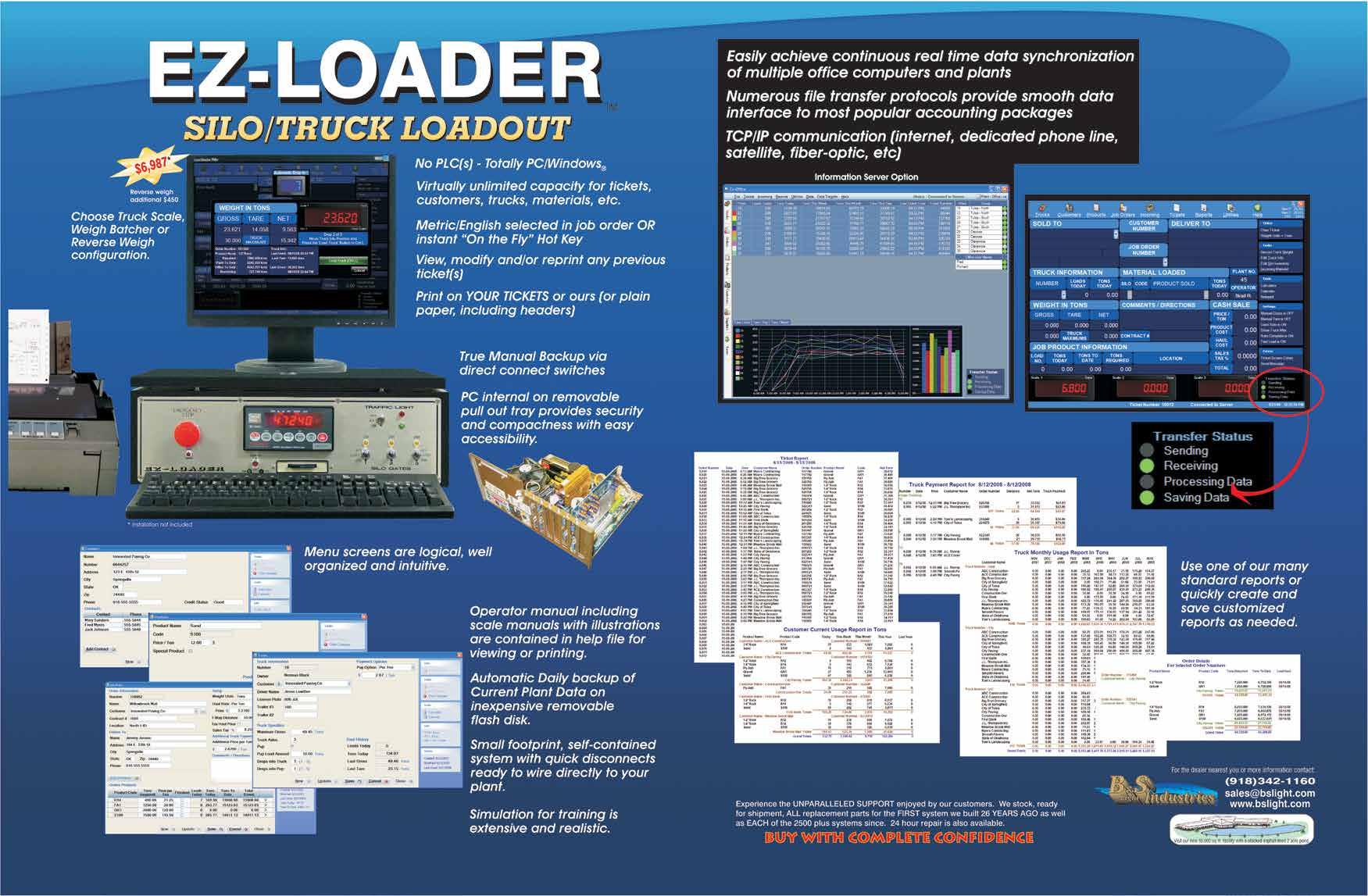
Learn How to Write a Grant
BY SANDY LENDERIt may catch asphalt professionals off guard to find a plant-relat ed product and services gallery introduced by an article about grant-writing. Your average asphalt company owner or CFO may be hesitant to go through the effort of learning how to write a grant, but the skill could take on great importance in the next few months for the for-profit entities in the industrial sector.
Specifically, if your asphalt plant still has room to reduce green house gas (GHG) emissions, you may be eligible to receive a De partment of Energy (DOE) rebate of up to 50% of your costs for engineering and installing advanced technologies that assist in decarbonizing industries within the United States. Within the In flation Reduction Act (IRA), the National Asphalt Pavement As sociation (NAPA) has identified seven sections where the asphalt industry may take advantage of such grant funding opportunities.
This list is sourced from the NAPA document “Key Asphalt Provisions in the Inflation Reduction Act,” which you can read in its entirety on the NAPA website under the Advocacy link. I’ll list the section that involves our topic of grant-writing last and re mind readers, while its program hasn’t gone into effect yet, pre paring for it involves steps that will take some time.
• Section 60112, Environmental Product Declaration Assistance, under which the Environmental Protection Agency (EPA) has up to $250 million in grants for contractors available until Sept. 30, 2031.
• Section 60116, Low-Embodied Carbon Labeling for Construc tion Materials, under which EPA—in consultation with the Federal Highway Administration (FHWA) and the General Service Administration (GSA)—has up to $100 million avail able to it until Sept. 30, 2026.
• Section 60503, Use of Low-Carbon Materials, under which GSA has up to $2.15 billion available until Sept. 30, 2026.
• Section 60504, General Services Administration Emerging Technologies, under which GSA has up to $975 million avail able until Sept. 30, 2026.
• Section 60506, Low-Carbon Transportation Materials Grants, under which FHWA has $2 billion available until Sept. 30, 2026.
• Section 70006, FEMA Build Materials Program, under which the Federal Emergency Management Agency (FEMA) has its existing budget with no new funding.
• Section 50161, Advanced Industrial Facilities Deployment Pro gram, under which the Department of Energy’s (DOE) Office of Clean Energy Demonstration (OCED) has up to $5.812 bil lion available through Sept. 30, 2026.
Looking at the third bullet point above, consider the opportunity to comment on the current availability of your materials that have lower levels of embodied carbon as compared to industry averages, or other estimates of similar materials.
As of Oct. 4, GSA had completed seven paving projects funded by the Bipartisan Infrastructure Law (BIL) using new asphalt standards, according to a GSA press release. The administration is seeking input from industry to learn more about the availability of domestically man ufactured, locally sourced, low-carbon construction materials.
The press release stated, “The Buy Clean Task Force is prioritizing low-carbon selections for the most carbon intensive materials (con crete, steel, glass, and asphalt) for construction and building proj ects, which account for 98% of what the federal government spends on construction materials.” To comment, visit the GSA’s Federal Buy Clean Request page or email embodiedcarbon@gsa.gov by Thurs day, Nov. 3.
Obviously, the asphalt industry has been implementing environ mentally sustainable practices and upgrading systems with advanced “green” technology over the past few decades. As articles in this publi cation have pointed out, FHWA and various government entities don’t want to see any sector of industry rest on its laurels, but now are willing to, as NAPA’s current vice president of advocacy Jay Hansen repeated ly tells us, incentivize companies to adopt even more environmentally friendly manufacturing processes. Section 50161 is a prime example of that incentivization, complete with some government bureaucracy to work through. We’ll look at how to make it work over the next few is sues of AsphaltPro, and we’ll start with writing grants.
To take advantage of the provisions in Section 50161, you must apply to the DOE for a grant. While the DOE hasn’t put out guidance on the program yet, the equipment manufacturers, additive suppliers and as phalt mix producers need to be ready for when this program takes off in the next few months. The grant money would reimburse the entity up to 50% of the cost to design and/or install advanced technology that is designed to reduce GHG emissions. To apply for a grant, your com pany must have a unique identifier at SAM.gov and planned unique entity identifier (UEI) at grants.gov. To get the unique identifiers, you must go through an approval process, but the use of these sites is free.
Don’t let this idea of red tape dissuade you from participation. If I may interject a personal anecdote, I’ve participated in non-prof it grant-application seminars and in-person round-table discussions to assist sea turtle groups and parrot rescue organizations in finding scraps to keep their doors open. I understand there’s a science to facili tating the application process and an art to writing the grant. It takes a team with different skill sets. It takes time to put it all together. Starting early is one key to success.
Here are some resources for getting that early start rolling:
• Your local community college (The director of my local bird sanc tuary took a course from Central Florida University alongside an online course from nonprofitready.org. Such local and online re sources are easily searchable.)
• The home page of Grants.gov (There's a button leading to “Grant Writing Tips.”)
• The EPA’s grant’s page (The slide deck, helpful links, FAQs and recording of the Sept. 13 webinar on Competition Process are available at https://www.epa.gov/grants/competition-pro cess-webinar-september-13-2022.)
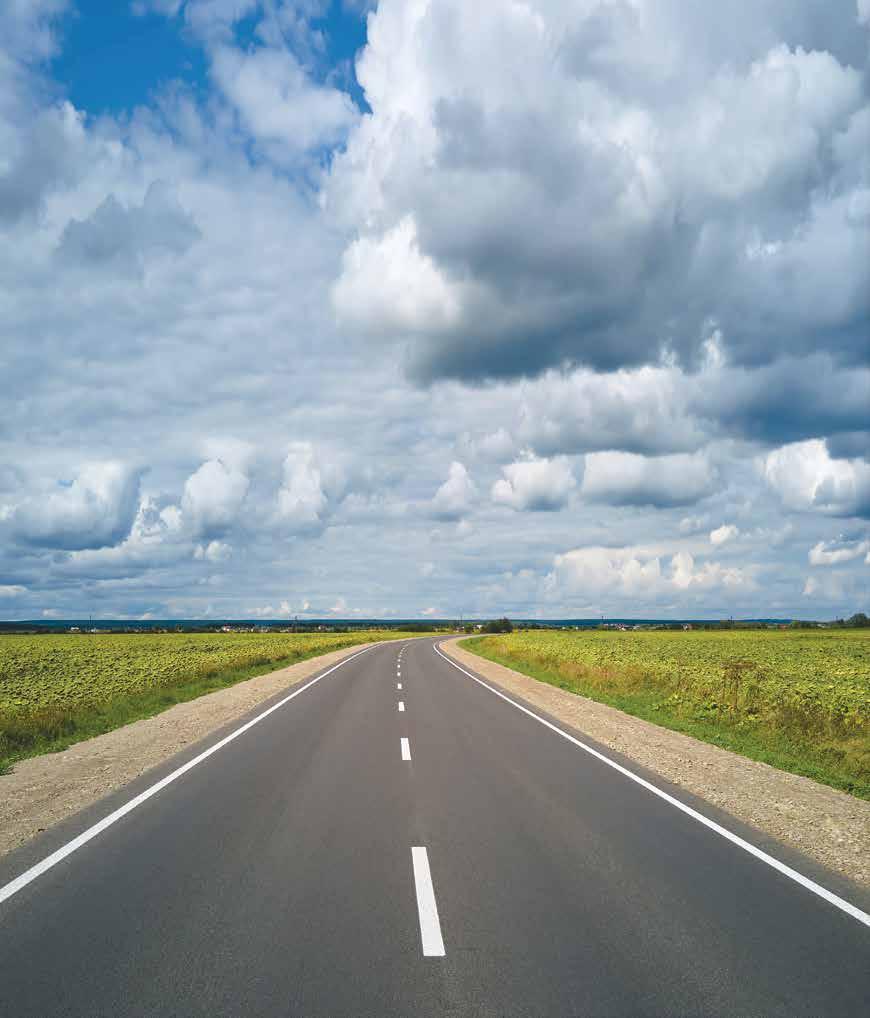
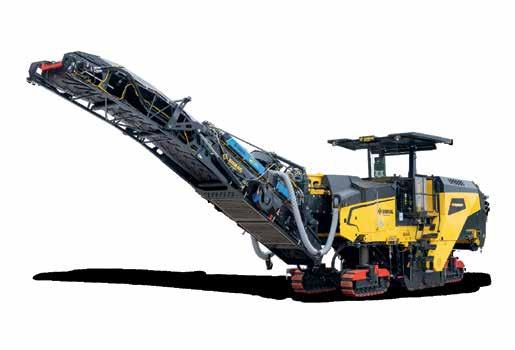
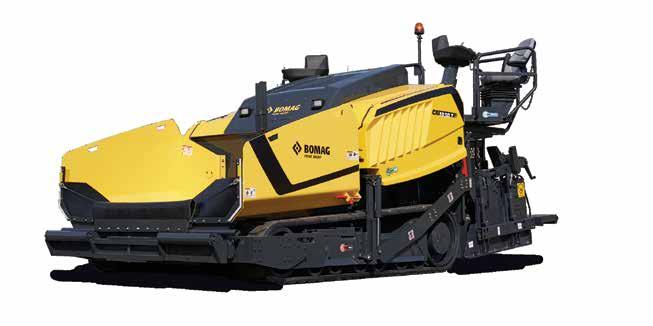
Of course, companies aren’t required to apply for reimbursement to implement green technology. As mentioned above, members of the as phalt industry have been upgrading systems and components for de cades. But if the government is handing out $5.8 billion for something we already know how to do, why not take the time to jump through the hoops to get some of your monetary investment back as you march ahead on The Road Forward?
In the next few issues of AsphaltPro, we’ll look at how industry might influence what technologies qualify more easily for reimbursement un der this grant program, and which might need more explanation in the grant-writing exercise. We’ll also look at which OEMs are on board with assisting you in greening up your facility. Stay tuned.
In the meantime, this month’s product gallery focuses on the plant and production products and services that enhance your bottom line with ef ficiency and positive sustainability.
ASPHALT SOLUTIONS
Asphalt Solutions Inc., headquartered in Florida, is proud to an nounce a partnership with AlGol Chemicals in Finland to distribute its time-tested odor suppressant Asphalt Solutions Additive. AlGol Chemicals is leading the way in Europe, developing innovative and high-performance asphalt products for road construction and main tenance. AlGol first used Asphalt Solutions Additive in their facilities in Finland, Denmark, Sweden and Estonia in 2020 with successful results, leading the way to offer other countries the opportunity to solve odor control issues they may be having associated with the as phalt paving and roofing industries. Asphalt Solutions Additive was first patented in 2002 for use in paving asphalt production, followed by the Roof Odor Additive for roofing asphalt applications, which was granted its patent in 2006. Asphalt Solutions looks forward to a successful future with AlGol Chemicals in the markets they serve.
For more information, contact AJ Ronyak at (623) 853-2273.
ASTEC
Astec Industries’ Materials Solutions Group has launched its newest mobile high frequency screening plant, the GT2612V. The plant fea tures a 2612V Vari-Vibe™ high frequency screen. The two-deck, 6-foot by 12-foot screen uses a unique rotary tensioning system. The 2612V also has deck-mounted, variable-speed hydraulic vibrators, a hydrau lic mechanism for varying operating angles, a fines collecting hopper, top and bottom deck discharge chutes, and an aggregate spreader. The high frequency screen is designed to size crushed stone, recycled as phalt pavement, sand, gravel, coal and a variety of other materials.
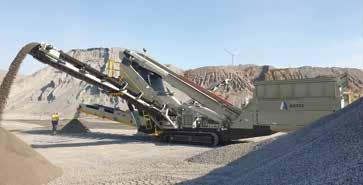
The mobile GT2612V is manufactured on a heavy-duty, welded steel main frame with a channel cross section. A walkway around the screen and remote grease lubrication for ground-level access are designed to make maintenance simple.
The plant includes a large hopper with a capacity of 8 cubic yards that is equipped with 6-inch sloped grizzly openings and a remote tipping grid. The hopper also includes foldable wings and hydraulic support legs. The variable-speed, 48-inch-wide belt feeder features a high-torque hydraulic drive, full length impact bed, rubber lagged head pulley and self-cleaning wing tail pulley. The screen plant is equipped with four con veyors: a delivery conveyor, two side conveyors and a fines conveyor. All conveyors feature a variable-speed hydraulic drive and fold for transport.
The GT2612V is powered by a Caterpillar Tier 4 Final, 136-horse power (101.4 kW) engine, while engine-mounted hydraulic pumps operate all plant functions. The plant includes a PLC control system with pendant remote controls for the tracks. Additional options for the GT2612V mobile plant include: engine alternatives (Caterpillar Tier 3 and Stage V), 15-foot hopper/feeder in lieu of standard for additional capacity, heavier-duty grizzly section with replaceable grouser bar car tridge, vibrating grid, bridge breaker, vinyl dust cover, standard steel screen cloth, engine enclosure filter kit, engine block heater, immer sion heater, wireless track remote, telematics system, auto-grease sys tem and more.
For more information, email socialmarketing@astecindustries.com.
CLARENCE RICHARD
The Clarence Richard Company, Minnetonka, Minnesota, offers the asphalt level tank gauge, which includes fluid level indicator and alarms. The programmable system is designed to decrease labor, down time, tank coil damage, and material waste by eliminating the need to stick the tank and by transmitting vital tank data, via signal, to a small computer.
The manufacturer shows the asphalt level tank gauge assists in meeting environmental protection agency (EPA) 40 CFR Part 112 rules and regulations, which require tanks have good engineering practices to avoid discharges.
For more information, visit ezfloweighing.com/.
DEERE
John Deere, Moline, Illinois, expands its G-tier wheel loader offerings to the United States with the 644 G-tier wheel loader, continuing the transition to performance tiering. The expansion of this lineup also includes the new 544 G-tier wheel loader now available in Canada.
“Not every customer is looking for the most technology in a ma chine. By introducing the 544 G-tier in Canada and expanding the availability of the 644 G-tier into the United States, we are providing our customers with options to help meet their diverse needs,” said Luke Gribble, solutions marketing manager, John Deere. “The G-ti er models support customers looking for reliability, without the add ed extras that they would find in a P-tier or X-tier machine, and that fit their investment levels as well. With the G-tier models, customers are getting the versatility and ruggedness in a machine, without any compromises.”
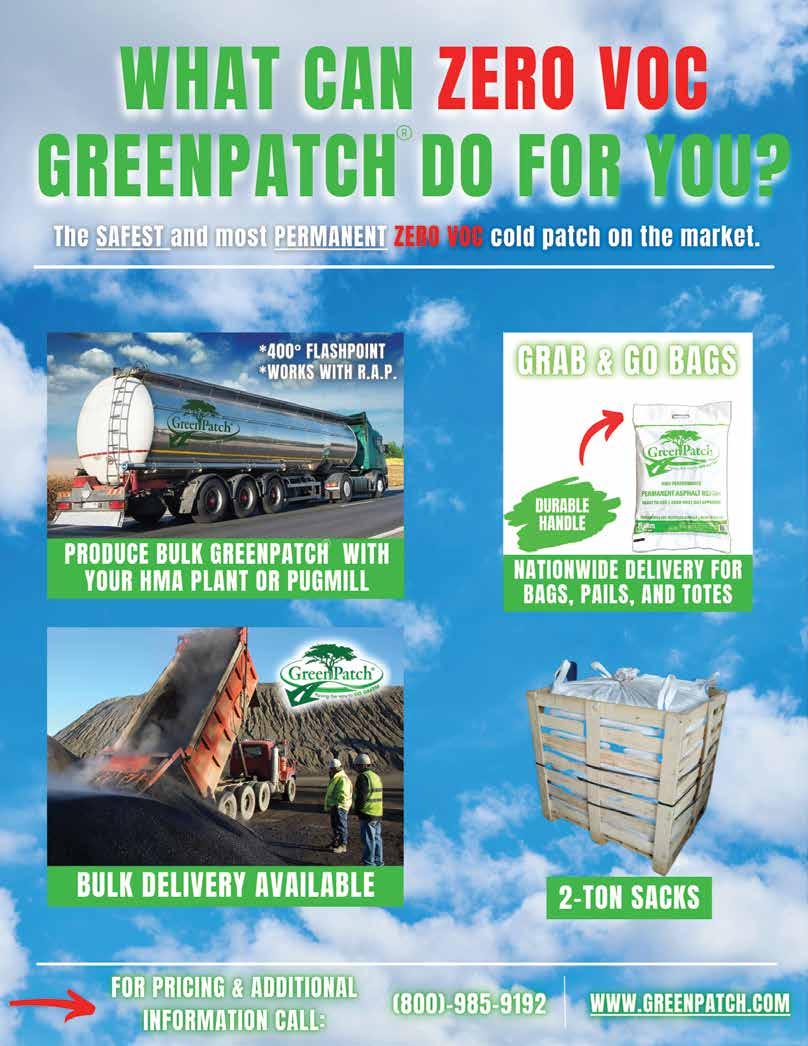
Now available in the United States, the 644 G-tier leverages indus try-proven components for customers in the governmental, rental, site development and asphalt industries. The 644 G-tier wheel load ers include a John Deere 6.8L engine and feature John Deere Team mate axles. Customers can customize the machine through a variety of base-level packages, including options related to locking differen tials, ride control, seats, radio and rear chassis work-lights.
Making its debut in the Canadian market, the 544 G-tier is de signed to provide a more economical solution in the 3-yard loader size class. The 544 G-tier controls were designed with operators of all skillsets and productivity in mind. Promoting ease of operation, the in-cab controls include adjustable boom-height kickout, return to carry, and return to dig, which can be activated from inside the cab.
All G-tier machines are backed by JDLink™ Connectivity and Con nected Support. Both the 544 G-tier and the 644 G-tier machines are eligible for the John Deere Protect™ Service Plan. With the John Deere Protect™ Service Plan, routine maintenance is performed at ev ery 500-hour interval by an experienced John Deere dealer. In addi tion, the John Deere Protect™ Parts & Fluids Plan provides customers with options to conduct maintenance services and inspection while utilizing their own technicians.
EAGLE
Eagle Crusher Co. Inc., Galion, Ohio, an nounced in August that Mike Tinkey has been promoted to president of the compa ny. Tinkey previously served as CFO since joining Eagle Crusher in 2002. Susanne Co bey, who previously served as president, will remain as CEO of the company. Previously Tinkey served as CEO, Holbrook & Manter Inc.; CFO, Ohio Industries Inc.; and account ing and audit manager, Ciuni & Panichi Inc.
In naming Tinkey president, Cobey stated, “I have been with Eagle Crusher Co. for nearly 48 years, 32 as president and CEO. I have worked closely with Mike for the past 20 years. As someone who shares a similar company vision, tru ly understands the industry, and exemplifies a leadership style that recognizes the value of the entire Eagle Crusher team of employ ees to accomplish goals, I can think of no better person to see Eagle Crusher through its continual growth and take the company to the next level. Already handling many of the responsibilities that the role of president entails, Mike is well positioned for his new role.”
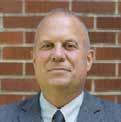
Tinkey said he initially joined Eagle Crusher because of the unique business model Cobey created, capitalizing on the ev er-changing crushing industry while always keeping the needs of customers paramount. Of his new position, Tinkey stated, “It is a privilege to be a part of a company that delivers the highest qual ity crushing and screening equipment, innovative solutions, and phenomenal service and support to all our customers. We have an exceptionally talented team at Eagle Crusher, focused on the con tinued expansion of our product line to provide the best customer solutions in the industry. I look forward to working closely with Su sanne and our entire team to usher in Eagle Crusher’s next chapter of growth and success.”
For more information, visit https://eaglecrusher.com/
HONEYWELL
Producers interested in their upstream scope 3 emissions will also be interested in the latest from Honeywell, headquartered in Hous ton. The company has unveiled the ECOMAX® LE burner with a me tallic recuperator for indirect radiant tube heating applications such as tempering, hardening, continuous lines and annealing. Developed for furnace original equipment manufacturers (OEMs) that need to meet tightening global nitrogen oxide emissions requirements and end users who want to increase fuel gas savings, Honeywell’s latest ECOMAX family member features low emissions, process efficiency and low operating costs.
ECOMAX LE offers both flame and flameless operation, with a switching temperature of 850°C (1560°F). The burner operates in flame mode until the switching temperature is reached, then switches to flame less mode for the best nitrogen oxide performance, delivering an aver age of 30% fuel gas savings compared to a typical cold air burner and enabling compliance with the latest emissions regulations. In addition, ECOMAX LE burners can run on up to 100% hydrogen without a sig nificant increase in nitrogen oxide emissions, when compared to firing natural gas.
For more information, visit the Honeywell website.
METSO
Metso Outotec Corporation announced at the end of August it has con solidated its minerals testing services in the United States into a single 5,500-square-meter facility located in York, Pennsylvania. The test cen ter capabilities will be continuously developed with the goal of covering the full minerals value chain to support the mining industry worldwide.
“The volume of testing activity has increased significantly during the last year,” explained Alan Boylston, director of process engineering at Metso Outotec. “With more space and operations in one place, we can do a lot more linked and pilot-scale testing. The test center in York spe cializes in standard and proprietary grinding tests in both laboratory and pilot scale, focusing also on grinding R&D in close co-operation with our office in York. The addition of pyro testing capabilities allows us to run calcining, induration and drying tests, too. Currently, we are also build ing new capabilities for bench and laboratory scale thickening and filtra tion tests.”
The Metso Outotec global network of minerals test facilities includes main test centers in the United States, Brazil, Chile, Peru, Finland and Australia.
POWERSCREEN
Powerscreen®, a Terex Brand, has attended the rescheduled Bauma 2022 in Munich alongside its German distributors Kölsch and Christophel. The machine line-up at Booth FN. 1024/1 included the Powerscreen Premiertrak 330 Jaw Crusher and the Chieftain 1700X 3 Deck Incline Screen. The Premiertrak 330 has a two-piece grizzly feeder that sends material flow toward the chamber. User benefits include track mobili ty for a quick set-up time, and variable crusher speed, according to the manufacturer. The Powerscreen® Chieftain 1700X is a mid-sized tracked mobile screen to allow high volumes of finished products. User benefits include a quick set-up time, drop down tail conveyor ad the patented four-bearing screenbox with the ability to switch to a two-bearing set up in less than three hours, according to the manufacturer.
For more information, visit the Powerscreen website.
From innovative designs to Caterpillar dealer service and support, Weiler is paving the way to success for contractors across North America. Weiler’s material transfer vehicles, commercial pavers, road wideners, windrow elevators, static compactors, soil stabilizers, rock drills, tack distributors and front mount screeds are engineered with innovative features to increase productivity while reducing operating costs.
Weiler equipment is sold and serviced exclusively at Caterpillar dealers throughout North America.
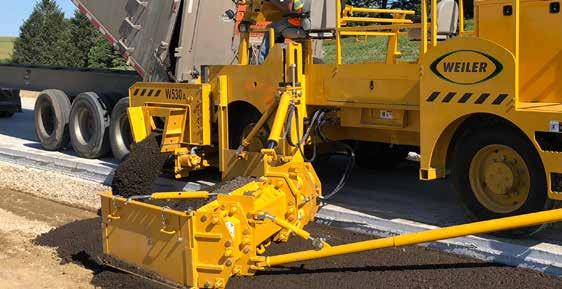
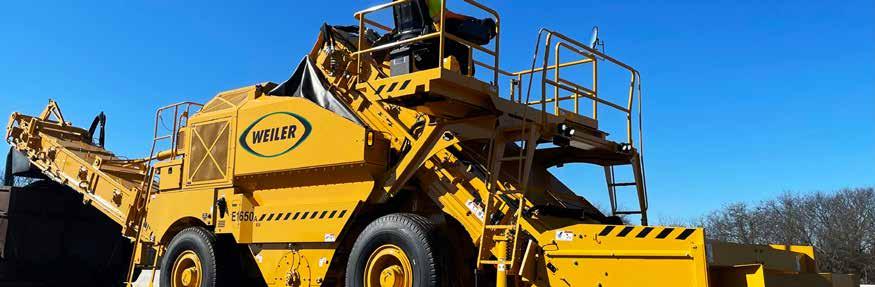
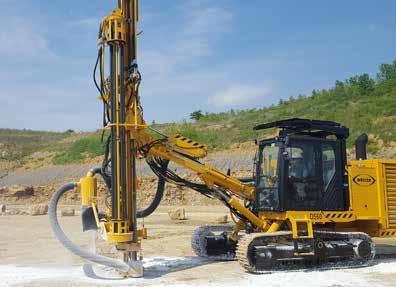
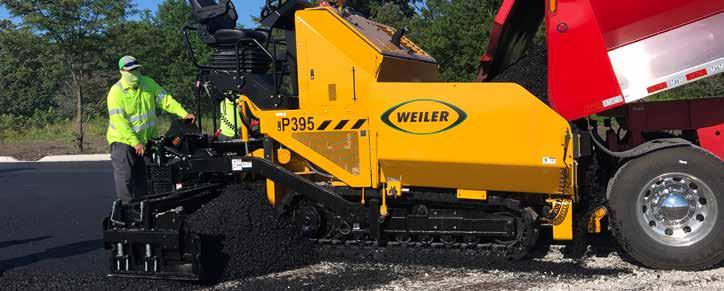
The Precision Pin Pusher from Stansteel-Hotmix Parts & Service is designed to press chain’s pins out with ease.
STANSTEEL

The Precision Pin PusherTM is available from Stansteel-Hotmix Parts & Service®, Lexington, Kentucky. The Precision Pin Push er pushes pins out on 4-inch and 6-inch pitch chains, which means users will only need this one tool for multiple chain siz es. Additional features and benefits include:

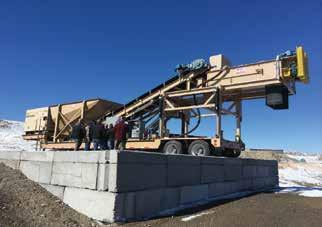
• This one tool fits most chain sizes.
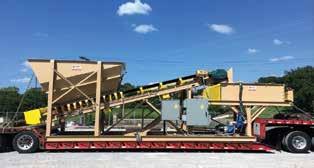
• It has a pushing power of 30 tons.
• No more hammers or torches.
• Includes a Hard case for storage and security.
For more information, visit https://hotmixparts.com/pinpusher.
YOKOHAMA
The new Galaxy AT Grip Steel steel-belted skid steer radial tire is available from Yokohama Off-Highway Tires, Wakefield, Massachusetts, for skid steers.
Dhananjay Bisht, product manager—Earthmoving, Con struction and Industrial Tires for Yokohama Off-Highway Tires America Inc., said the feature customers were most inter ested in was “a strong sidewall. The feature they admired most about their old bias-ply tires was the stability and durability of the sidewalls. So, we developed a radial tire that delivers the footprint and ride benefits of radial construction as well as a much sturdier, reinforced sidewall.”
The Galaxy AT Grip Steel also features a non-directional block tread design. The blocks are optimized for wear and trac tion, Bisht noted.
The Galaxy AT Grip Steel steel-belted radial is available in 260/70R16.5, 300/70R16.5 and 360/70R17.5 sizes.
For more information, call (800) 343-3276.
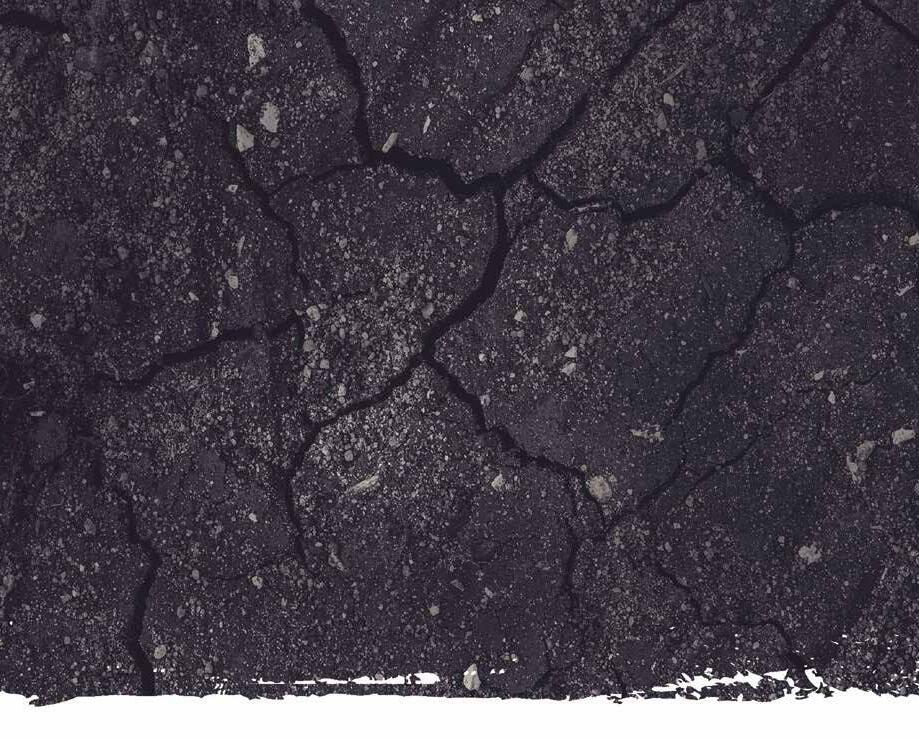

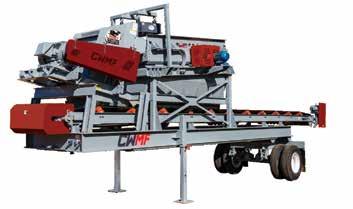
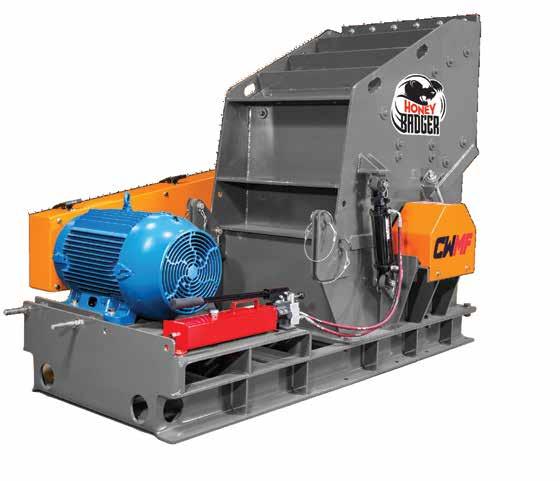
Rebuild & Reman for Savings, Sustainability, Supply Chain
BY SARAH REDOHLThe concept of rebuilding machinery, or remanufacturing parts, is nothing new. However, the supply chain crisis contractors are facing across the country has increased interest in making the most out of a contractor’s existing fleet for as long as possible. Pair that with the ever-expanding offerings from original equipment manufac turers (OEMs) and growing interest in operating more sustainably, and this may be a perfect time to weigh the benefits of a rebuild.
1. OVERCOME (SOME) SUPPLY CHAIN ISSUES
CNH Industrial Reman, Springfield, Missouri, has been remanufactur ing parts since 2009 and offers more than 3,000 part numbers. Chan dler Dalenberg, CNH Industrial Reman dealer development manag er, has seen interest in remanufactured parts grow as the United States continues to face supply chain challenges, as new parts are less easily available, and as there is higher used machine utilization in the mar ket. “The supply chain crisis has had a significant impact on our abili ty to leverage our remanufactured product lines to fulfill our custom ers’ needs.”
This is also true of certified rebuilt machinery, said Jared Haughton, certified used sales manager in North America for Volvo Construction Equipment, Shippensburg, Pennsylvania. “It’s becoming increasingly dif ficult to get new equipment, so a certified machine might be as close to new as you can get.”
Simultaneously, there are also fewer certified rebuilt machines avail able. Under normal circumstances, Haughton said around half of all Volvo CE rebuilds have historically been articulated trucks (with the other half mostly composed of excavators and wheel loaders), but that’s dropped to around 30% in the past couple years.

“As a result of the supply chain shortages, the demand for new trucks has outpaced the supply in North America,” he said. Volvo CE’s cer tified rebuild program is primarily fed by its lease portfolio in North America, and its lease customers are now extending their leases as they wait for new trucks to become available, “which prevents them from entering our certified rebuild program.”
“We haven’t seen the same level of supply chain issues as new equip ment, but parts availability is an ongoing issue and probably will be for the foreseeable future,” Haughton said, adding that certified rebuilds are currently delayed by around two weeks from their usual 30-day turnaround. “It’s not so much parts availability, but shipping challeng es to get parts in from Sweden, China, South Korea, South America.”
Haughton said he expects the backlog for certified rebuilds to con tinue for a while after the market normalizes, as contractors can once more get their hands on new equipment and send leased equipment back in for certified rebuilds.
For those interested in buying certified rebuilt equipment, he recom mends ordering well in advance. “Our certified rebuilds are normally available for sale after they’ve been certified, but customers are plac ing orders to secure them 60 days ahead of them becoming available.”
Jaco Nolte, services development manager at Caterpillar, Peoria, Il linois, also expressed the importance of planning ahead in the current climate. “When planning a rebuild, it is critical to work with the Cat dealer to schedule the rebuild and execute a plan to ensure the parts will be available at the time of the rebuild to ensure the machine can be re turned to work as quickly as possible,” he added.
2. COST SAVINGS
“Every customer is looking to lower their total cost of ownership,” said Tara Stryker, head of used equipment for Volvo CE in North America. “Certified used machines give them the reliability of a new machine at a lower acquisition cost, which will reduce the total cost of ownership over the lifetime of that asset.”
Nolte said the machines in Cat’s certified rebuild program are de signed for multiple lives. “If customers took care of their machines through good maintenance and operating practices, they would lose out on economic value left in that machine if they don’t rebuild,” he said, adding that certified dealer technicians can evaluate which parts of the machine can be reused according to Caterpillar reuse and sal vage guidelines, leading to cost benefits versus buying new. Cater pillar also uses remanufactured components in its certified rebuilds when possible, which also lowers the total rebuild cost.
Dalenberg at CNH said its remanufactured parts are priced at a fraction of the cost of new parts (roughly 25 to 30% less).
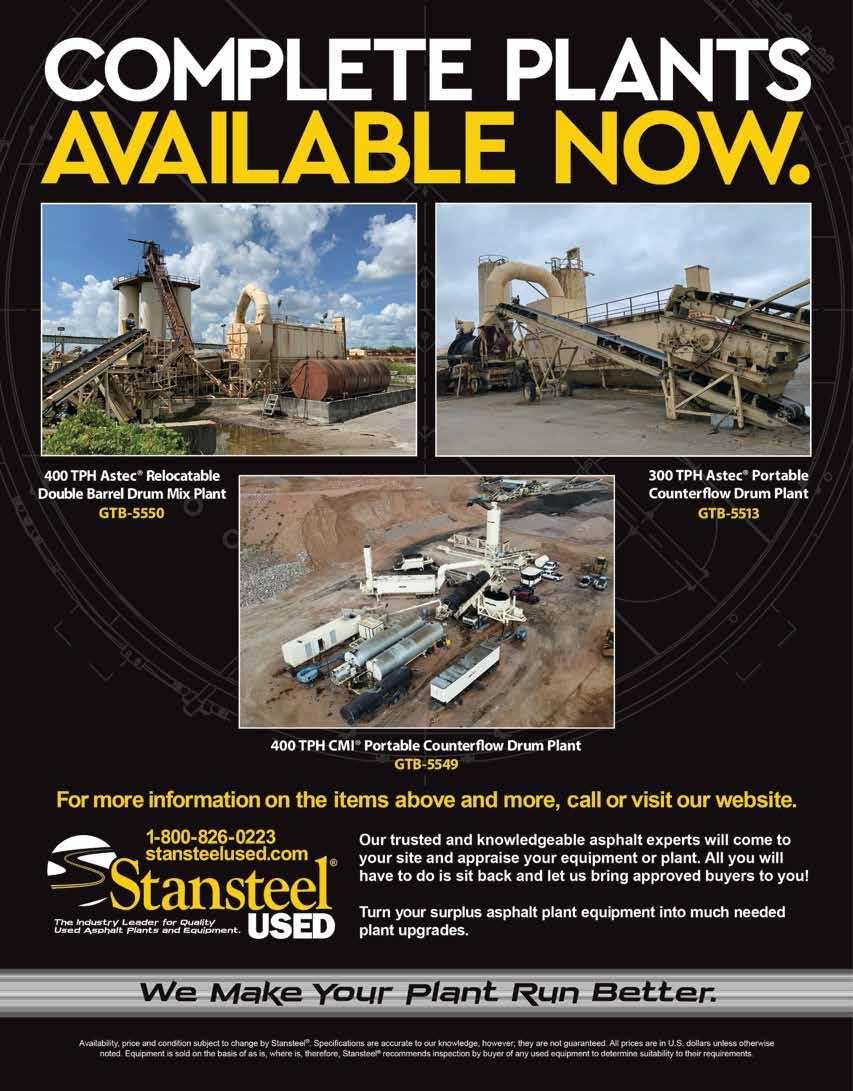
3. SUSTAINABILITY
Nolte said customers may favor rebuilding over buying a new ma chine for sustainability reasons, as well. “The Cat certified rebuild program has been practicing sustainability since it was launched in 1985,” he said. “[Caterpillar’s] rebuild guidelines for reuse or salvage criteria encourages reusability of parts on a machine and/or compo nent without sacrificing reliability or durability and provide a com plete second life for the customer.”
During the Caterpillar Executive Sustainability Forum Sept. 15, Ja son L. Conklin, vice president of global construction & infrastruc ture, said, “Cat machines are built to be rebuilt” as part of a core sus tainability strategy for the company. In 2021, the Cat certified rebuild program kept “127 million pounds from going to the landfill,” Conk lin said.
This strategy of reusing existing iron lets customers leverage today’s technology updates. The Cat team members participating in the Fo rum that day made it clear how smart it is to drop new-and-improved tech into well-maintained iron to keep an existing fleet agile.
According to Jamie Collins, director of sales and marketing, CNH Industrial Reman was also able to keep 8.4 million pounds of raw ma terials out of landfills through core parts and remanufacturing com ponents back to OEM specifications in 2021.
4. FLEET MANAGEMENT
Nolte said rebuilding an existing machine versus buying new can also offer some benefits in terms of fleet management and mainte nance. “The customers’ operators and technicians may be very fa miliar with that machine or they may own a fleet of them, which would make sense to return [that asset] to original performance and productivity levels,” he said. “This could even simplify parts stock ing for the customer.”
When the first Cat certified rebuild was performed in 1985, the program only covered one machine and one product offering - a complete machine rebuild. Today, the Cat certified program covers over 1,000 machine serial number prefixes and has rebuild offerings from full machine rebuilds to certified machine component rebuilds.
5. UPGRADE AND RETROFIT
Another benefit of the rebuild process, Nolte said, is that customers can choose upgrades and retrofits available for their machine to en hance its features or capabilities. This might include ergonomic im provements; safety, visibility and security enhancements; emissions and performance upgrades; or telematics, to name only a few. For ex ample, LED work lights, Cat Work Area Vision System (WAVS), Cat Stand Alone Tire Monitoring System, Product Link Elite and Pro Se ries Cellular and Satellite Kits (PL631, PL641 and Elite Upgrade).
6. IMPROVE NEXT-GEN EQUIPMENT
For Volvo CE, upgrades and enhancements might include ActiveCare Direct, Haul Assist for articulated trucks, or Load Assist for loaders. However, Stryker added, another benefit of OEM rebuilds is that the
process helps Volvo CE develop a better product in the long-run. “We learn so much more about our machines when we get them back to rebuild them,” she said. “The longer the OEM stays engaged with its machines throughout their life cycles, that helps us make better design and production decisions.”
In June, Volvo CE opened its fifth certified rebuild center, in Shippensburg, Pennsylvania. “Our customers see we aren’t just investing in new machines, but also in our used machines,” Stryker said, adding that Volvo CE eventually plans to remanufacture components as well.
7. UPGRADE PARTS WHILE INCREASING WARRANTIES
According to Collins, not only are remanufactured parts “virtual ly indistinguishable from new parts,” but CNH is also able to bet ter understand failure modes of parts and correct them. “This gives end-customers the opportunity to upgrade parts at a lower cost while reducing their liability with an increased warranty.” CNH of fers a 24-month warranty on remanufactured parts.
Dalenberg said a significant piece of the growing popularity of remanufactured parts is educating dealers and customers about the process. To do so, CNH has a field sales team that handles various training opportunities at its plant and dealership locations across North America. CNH also established a Reman Technical Center that answers 30,000 calls annually from its dealership network. “These combined resources have led to great strides in the perception of quality around our parts,” Dalenberg said.
8. IMPROVED BUYING EXPERIENCE
In the past couple of years, Volvo CE has also made some chang es to the way it sells its certified rebuilt equipment. For example, it overhauled its inspection process to make it easier for customers to inspect the equipment they’re interested in buying.
They also have a 360-degree walkaround video of each machine like you see on car dealerships’ websites, “so it really feels like you’re there,” Stryker said. “Some of our customers still want to come see the equipment they’re buying, but with our 360-degree walkaround videos, many are buying used equipment sight unseen. I think that would have happened eventually, but the COVID-19 pandemic definitely accelerated that trend.”
“There are a lot of old wives tales, like you have to go see a ma chine before you buy it or if you paint something you’re hiding something,” Stryker said, but added that Volvo CE is striving to change those conceptions. For example, although painting certified rebuilt machines remains optional, Haughton said Volvo CE has aimed to increase transparency by providing before and after pho tos and explaining what’s been painted and why. “Having transpar ency about the equipment’s history and the OEM standing behind the condition of the machine makes a big difference.”
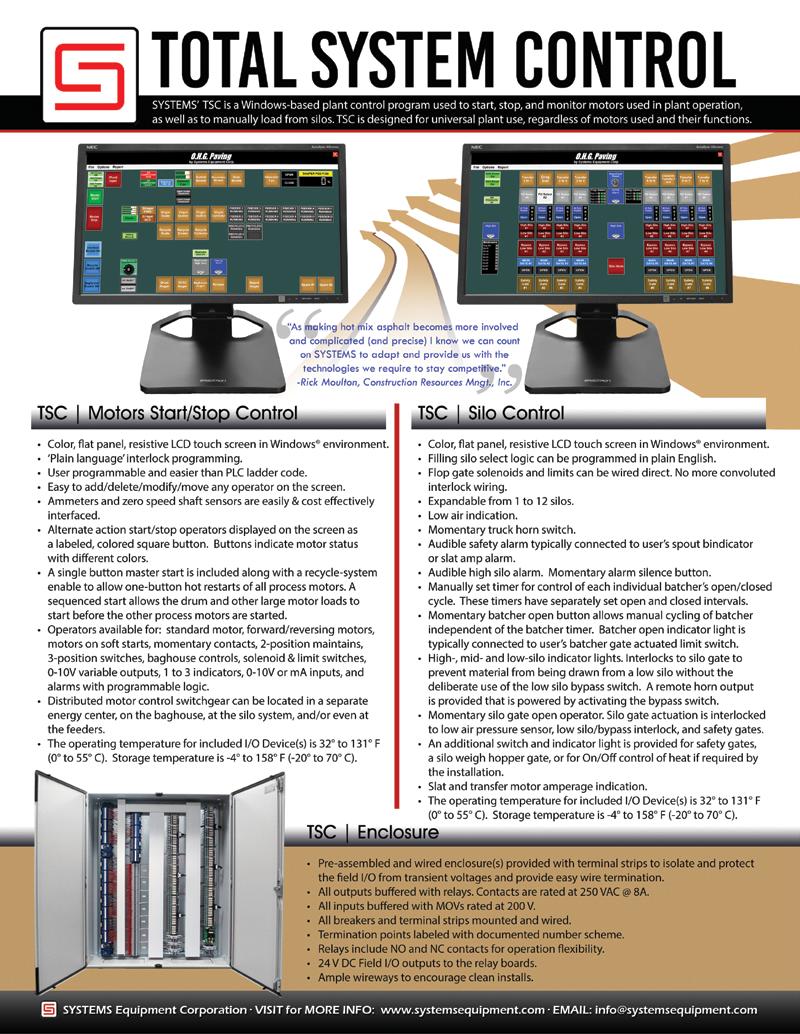
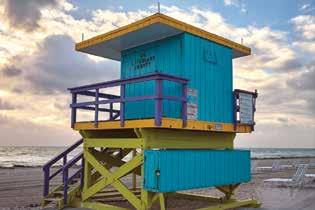
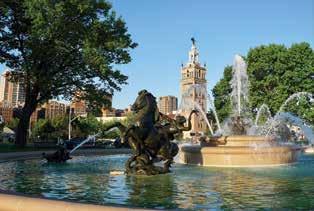
Cashflow Management Tips for Paving Seasonality
BY JEFF HEYBRUCKAsphalt businesses face the challenge of a short busy season dependent on regional climate, day-to-day forecasts and large fixed asset requirements. Without accurate forecast ing and proper cashflow management, this short window to complete jobs, and the resources needed to ramp back up quickly in the spring, can lead to cashflow challenges.
As a CFO, I’ve had the privilege of helping construction businesses successfully manage cashflow through seasonality. Based on this ex perience, here are some financial best practices to survive the paving offseason and to maximize revenues during the spring and summer.
TRACK CASHFLOW
The current and projected timing of the industry cycle where the as phalt business operates will determine the cashflow management strategy. Understanding and forecasting cashflow based on this cycle is the first step to healthy financial management.
Consider keeping a rolling 12-month forecast and analyze year over year data. Use this data to predict the cash reserves or financing that will be needed for the next offseason and at the beginning of the next busy season, when the business is paying out more than it is pull ing in. During the winter months, most paving businesses must sur vive on the cash they generated during the warmer months. However, it’s also important to factor in the “ramp-up” period where produc tion takes off quickly but A/R collections lag by 30-45 days. Month over month this can have a catastrophic impact to cashflow.
Also compare year-to-date progress and forecasted expectations to determine if this year’s seasonality is consistent with the prior year. If the result shows a shortfall (possibly due to growth or a large asset purchase), recognizing that fact quickly and taking proactive steps to increase collections or cut expenditures can help to offset what was not planned for in terms of seasonal fluctuations.
In some cases, cashflow projections may show building cash re serves as an impossibility. If financing will be needed, knowing in ad vance will allow the time needed to apply for and secure a loan. A bet ter option, if the business can qualify, is to be prepared with a line of credit that is properly matched to the size of the business.
RIGHT SIZE THE FLEET
Equipment and its maintenance are large expenses, making fleet right-sizing a good place to start when optimizing cashflow. Use the off months to perform a year-in-review, evaluating how often you use your equipment and vehicles, weighed against repair costs and useful life of the equipment.
Is it a good time to sell any existing equipment? If equipment is underutilized, selling it can be a great way to access cash quickly, pay down debt, and cut future cashflow needs by eliminating the monthly payment. In some cases, it might make more sense to subcontract out (especially when a specialized laborer is needed to operate the equip ment) or rent the equipment per job.
Is it the right time to purchase new equipment? While new pur chases might not seem like the place to start for improving cashflow, replacing equipment that could break down at the peak of the busy season can prevent future cashflow woes. Make sure to ask your tax professional about any benefits of purchasing equipment that might help to make the business case.
With buying equipment in the slow season, it’s important to bal ance the discount against having to make payments on the asset for 4-6 months before it starts producing significant revenue. For exam ple, a client decided not to buy a paver in November, despite being offered a considerable discount, because they knew there wouldn’t be the demand for it until Spring. The client felt it would sit in the yard and our analysis showed over half of the savings would be taken up by the monthly payments. Instead, this client put in an order for de livery in April/May when it would immediately be put to work and generate revenue.
Tip: Take the time to perform a cost-benefit analysis per equipment purchase.
Simply making the right choice of buying versus renting can make a considerable impact on monthly cashflow. We had one paving cus tomer considering purchasing a new skid-steer rather than continu ing to rent the equipment whenever the extra machine was needed. The full cost-benefit analysis, when considering maintenance, useful life, and residual, showed that purchasing the new skid-steer would save them almost $8,000 per year when compared with renting—and that was before considering increased revenue or more efficient oper ations from having the new equipment in the fleet.
In most cases, buying versus renting will be the more cost-effec tive option. The exceptions are for short-term jobs, where the equip ment would sit unused after, or specialized jobs, where renting both the specialized labor and the equipment together versus finding tem porary specialized labor will reduce headache. While this serves as a good rule of thumb, it is still worth it to complete the cost-benefit analysis.
BEWARE OF GIMMICKS
Leasing versus buying equipment to ease cashflow stress with lower monthly payments can be a good option in some cases. Make sure to consult your tax professional about the impacts of leasing versus buy ing equipment, as you may be able to write off the monthly payments. Many times equipment companies will offer seasonal payment plans for relief during the slow season, but this may come with a high er interest rate. We’ve also seen “equipment finance plans” wherein the buyer makes X number of payments of Y dollars and the equip ment is paid off. In the couple examples of this we’ve seen, the ser vicing company claims there is no interest or principal balance. The
18 WofA Branches & Counting!
The
Jersey
By becoming a member of WofA you are joining an organization which strives to advance and support women in the asphalt industry.
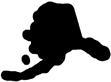

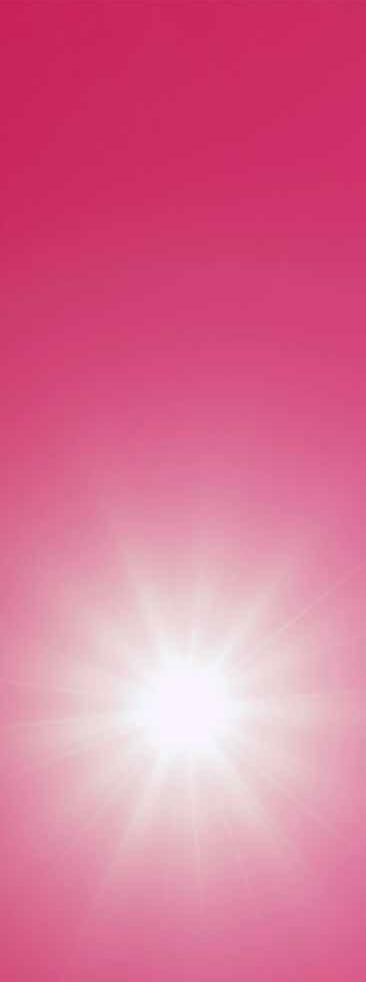
Membership is FREE and open to all.
balance they told us was the number of months left on the “fi nance plan” multiplied by the monthly payment. We backed into the interest rate and got something like 7-8% when market rates were half that figure.
DIVERSIFY SERVICES
Offering additional services to anchor clients (e.g. winter ice and snow removal) is a strategy to keep revenues coming in during the offseason. For paving businesses, the viability of offering these services depends on whether the region gets frequent enough snow and ice fall to warrant keeping on the staff needed to operate the equipment.
Paving businesses may already have much of the most expen sive equipment needed for snow plowing. In general, it is not rec ommended to make significant purchases to offer services not core to the business. It is important to weigh the cost of the at tachments or snow packages that might be needed to outfit ex isting equipment to be able to perform snow and ice removal against the forecasted revenue from offering the services.
In addition to improving cashflow, offseason services also help with another seasonal challenge—the ability to continue to offer hours to talented crews that will be essential when the pav ing season wakes back up.
INVOICING
While most content around paving industry seasonality focuses on how to survive the offseason, our experience is that securing the financial resources needed to support the intense ramp-up at the beginning of the busy season can be equally as challenging. During this period, the paving business is often paying out more than it is taking in. Prompt and smart invoicing policies can help to ease cashflow strain during this period. We encour age our clients to include payment terms in their contracts and enforce them. Proactively bring them up to the customer during the quote process and if not followed, it should be discussed with the customer before the next project.
For example, rather than billing at the completion of a large project, consider invoicing in smaller amounts at each point in the project. In most cases, this will prompt faster payment from the customer and keep at least some cash coming in to help with the subcontractor and supplier invoices already due as well as the upcoming payroll.
Cashflow is a topic of improvement for most businesses, re gardless of seasonality. For paving businesses that do experience the challenges of seasonality, it’s especially worth securing an outsourced CFO or strategic financial resource to audit and pro vide recommendations for improving cashflow. These resources can also help to establish with confidence the tracking and re porting needed to change processes to improve cashflow and better prepare for seasonal ups and downs.
womenofasphalt.org
Jeff Heybruck is the founder and CFO of Lucrum Consulting, where he brings more than 15 years of accounting experience and strategic financial expertise in the construction industry. Jeff holds a Master of Accounting degree from UNC-Charlotte. You can reach him at jheybruck@lucrumconsulting.com.
Women of Asphalt (WofA) would like to welcome Iowa and New
to its growing list of Branches!
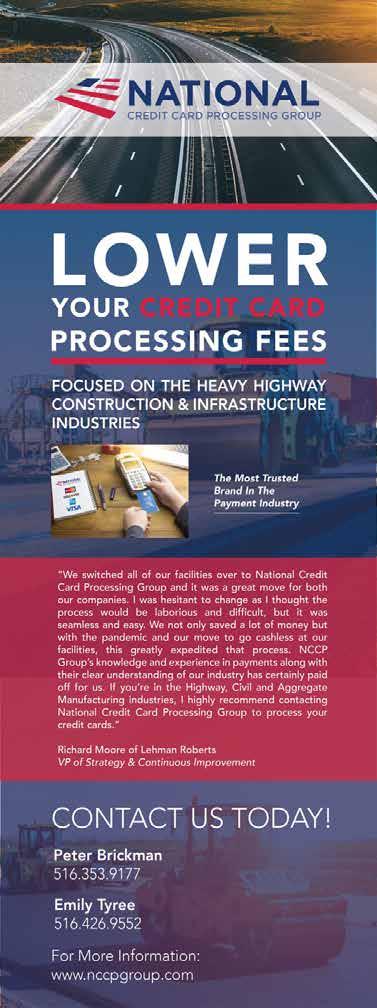
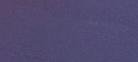

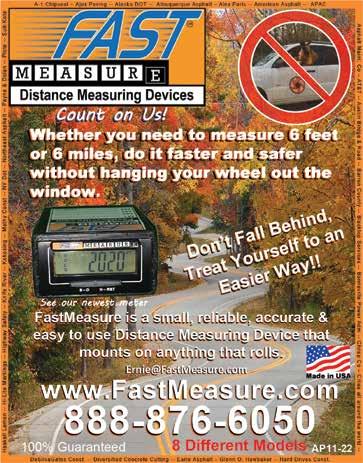
ALmix 7
Asphalt Drum Mixers, Inc 32, 33
Astec Industries Inside Front Cover, Inside Back Cover, 11
B&S Light 38,39
Blaw-Knox 9
Bomag 41
BROCK 57
Clarence Richard Company 56
Colorbiotics 25
CWMF 3, 47
D&H Equipment 56 Eagle Crusher 37
Fast Measure 55
Gencor Industries, Inc 4 Greenpatch 43
Kenco 31
Meeker 35
Minds, Inc 15
National Asphalt Paving Assoc 52
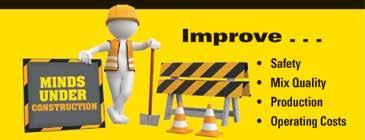
National Credit Card Processing 55
Pugmill Systems 46
Reliable Asphalt Products Back Cover
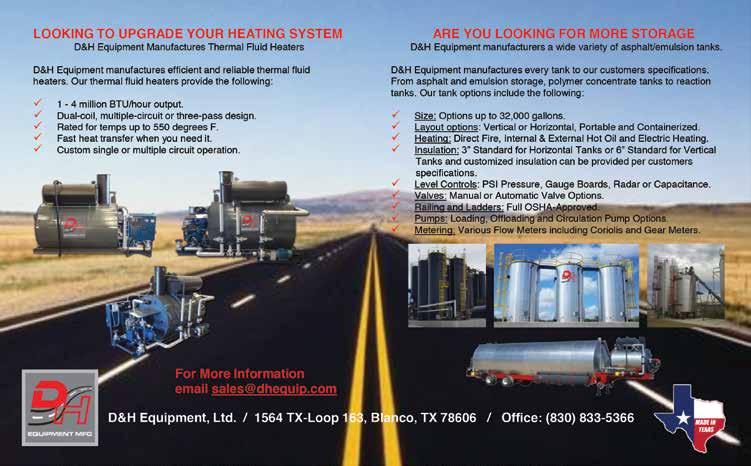
Sripath Technologies 16 Stansteel 17, 49
Systems Equipment 27, 51
Tarmac International 19
Top Quality Paving 58
TransTech Systems, Inc 21 Weiler 45 Wirtgen 29 Willow 55 Women of Asphalt 54
AsphaltPro’s advertiser index is designed for you to have quick access to the manufacturers that can get you the information you need to run your business efficiently. Please support the advertisers that support this magazine and tell them you saw them in AsphaltPro magazine.
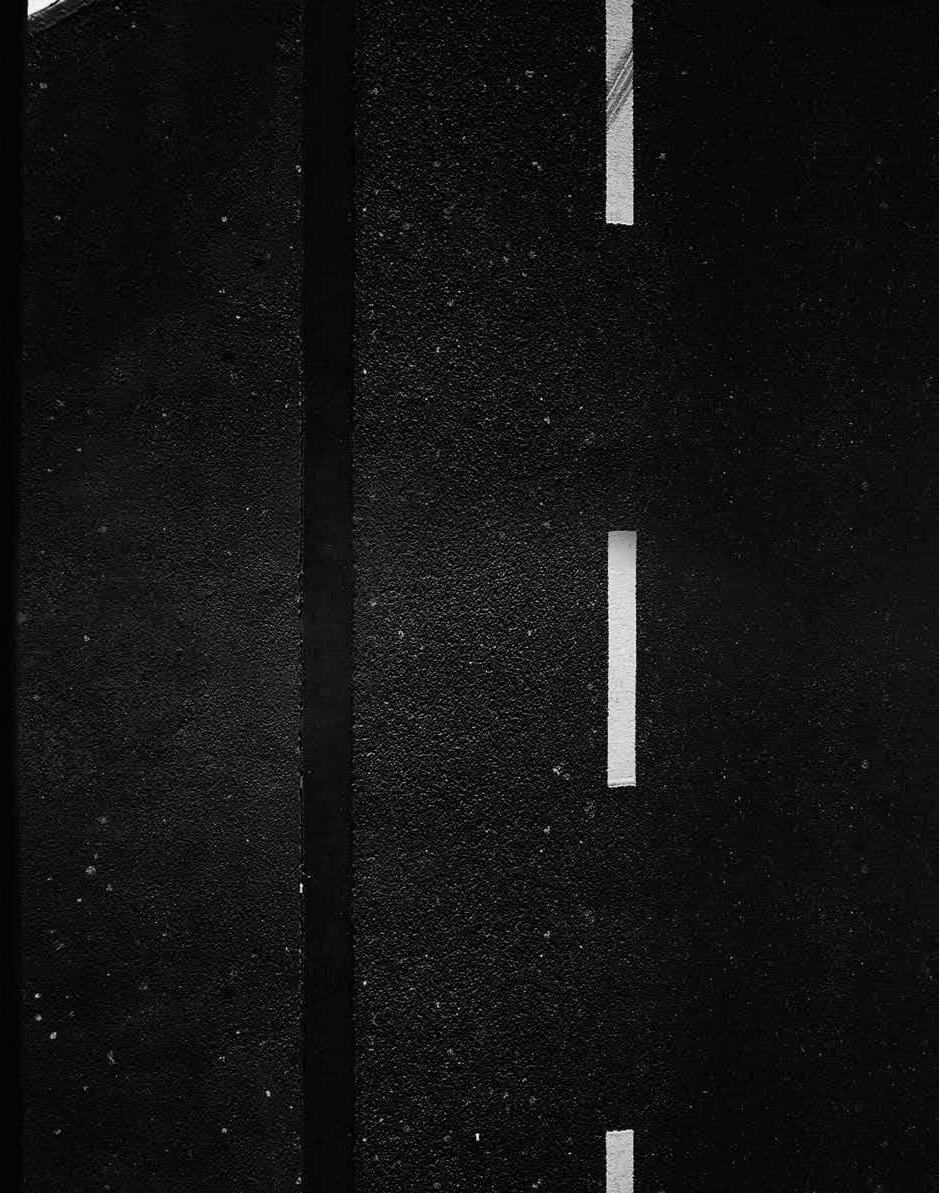
FDOT Launches Statewide Lane Closure Notification System Pilot
BY SARAH REDOHLIn August 2022, the Florida Department of Transportation launched a one-year statewide technology pilot program with a new Lane Closure Notification System (LCNS)—the first of its kind in North America, according to FDOT—in partnership with the Florida Transportation Builders Association and one.network.
The LCNS aims to notify the traveling public of work zones through leading GPS apps and services in the same way they receive other alerts, like accidents ahead and upcoming congestion.
A soft launch of the LCNS technology was successfully kicked off in June, and there were several construction projects entered into the system upon launch. FDOT Executive Director of Trans portation Technology Trey Tillander said the number of construc tion lane closures entered and reported in the LCNS will increase each month.
In the next few months, the LCNS will be rolled out to include more than 500 construction projects and, ultimately, the one-year pilot will cover all planned construction sites across more than 12,000 miles of state roads in FDOT’s seven regional districts and Florida’s Turnpike Enterprise.
“Improving work zone safety and mobility is a critical focus area for FDOT,” Tillander said. “One way to improve work zone safety is to alert drivers of closed lanes, reduced speed limit, and presence of workers in work zones so that drivers can prepare to slow down before entering work zones and drive more carefully as they navigate through the work zone.” He said the notifications may also increase safety within work zones by making drivers aware of expected delays, which might encour age them to choose an alternative route.
According to Tillander, construction supervisors on the road worksite input the lane closure information into one.network’s LiveLink smart phone application, including the number of lanes closed (direction and specific lane numbers), reduced speed limit (if implemented), worker presence, and detour information (if implemented).
“The contractor activates the lane closure when the cones or barrels are placed,” he said.
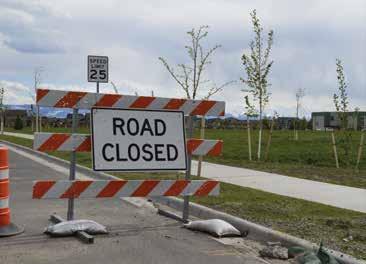
The information is then shared with third-party navigation app pro viders like Google Maps, Waze, TomTom and Apple Maps, which pub lish the data to motorists via their smartphone or in-vehicle devices. Waze was currently sharing notifications with their users as of press time while other providers were expected to begin sharing in the near future.
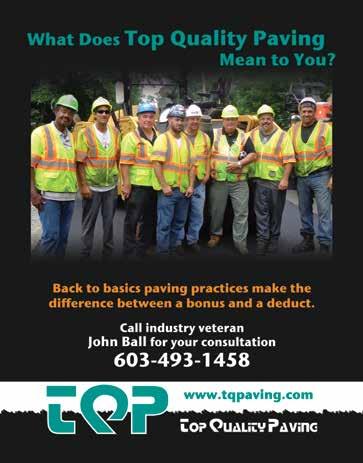
“There is no significant change in the way contractors work on roads in the state of Florida due to this project,” Tillander said, except inputting the data into LiveLink as they close or open lanes. However, before su pervisors are allowed to do so, they are required to complete a one-time training and pass a short quiz. FDOT has already initiated this training for the staff and contractors who will use the LiveLink application.
Although Florida is the first state in the United States to introduce this safety technology, it is unlikely to be the last. Already, the State of Texas has requested information about this initiative, Tillander said.
Power and Portability
Our portable plant configurations feature a variety of components including jaw crushers, cone crushers, impact crushers and a variety of screening plants. Without sacrificing power or productivity, portable options deliver efficient and reliable performance with extra portability and adaptability.
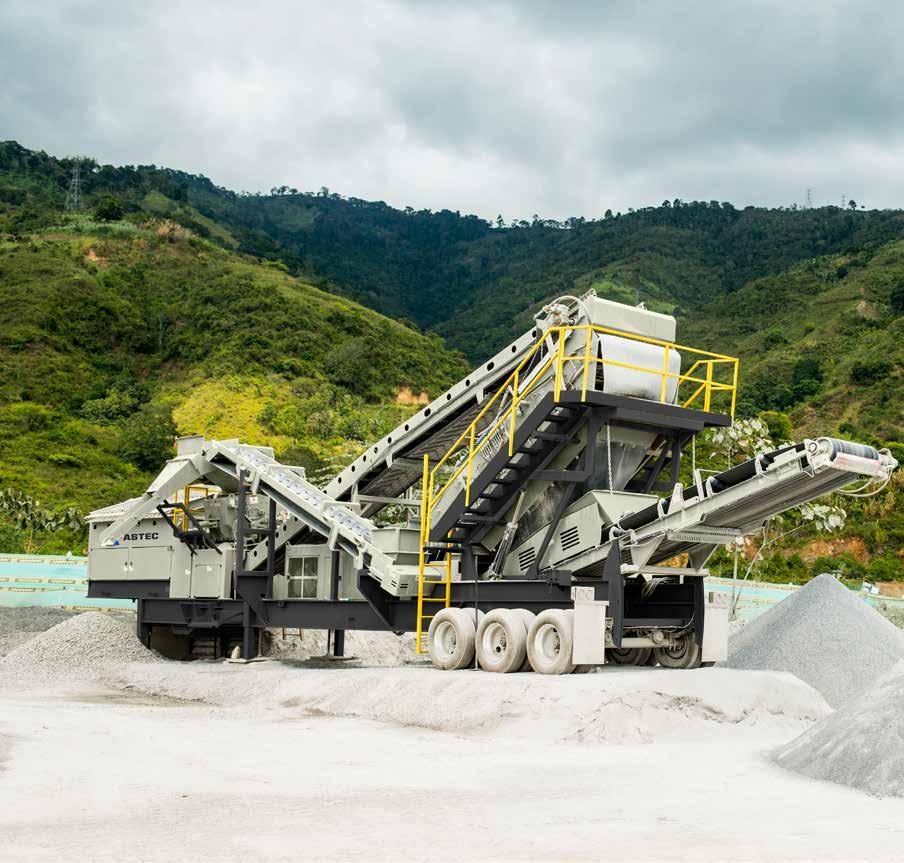
BUILT TO CONNECT
Scan to see the full line of portable products.
