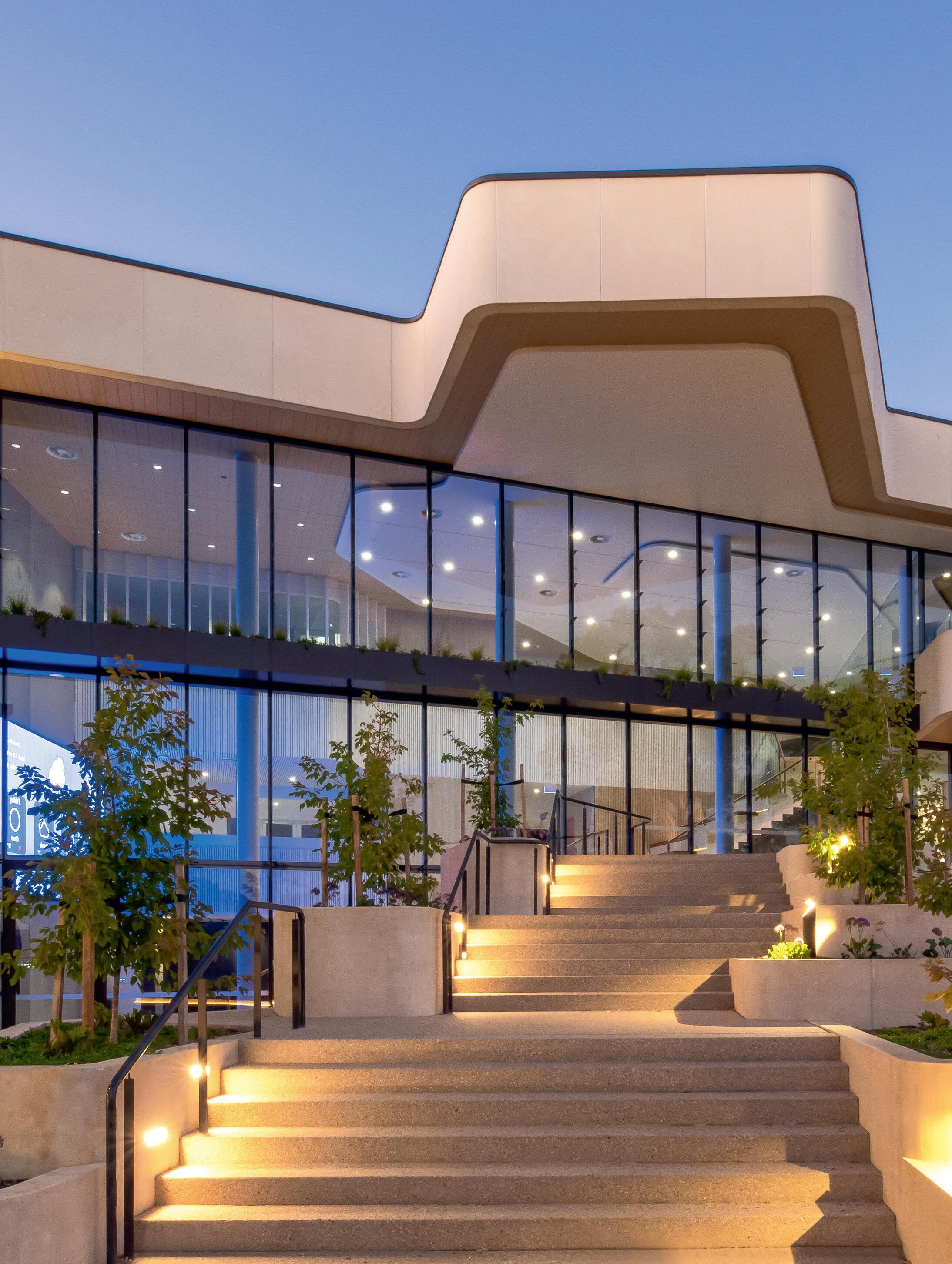

Parkwood’s aluminium front doors are made-to-order, fnished in any powder coat colour and supplied to window fabricators nationwide. Add Parkwood’s premium aluminium front doors to your product range to complete your offer.
BuiltView Magazine is a quarterly publication of the Australian Glass & Window Association.
EDITORS
Melissa Baker
Ingrid Pagura
SUB EDITOR
Helen Dawes
DESIGN
Webqem Pty Ltd
EDITORIAL & ADVERTISING ENQUIRIES
Helen Dawes
+61 2 9498 2768 marketing@agwa.com.au
PUBLISHED BY
AWA-AGGA LIMITED
ABN 57 629 335 208
Suite 101B, Level 1, Building 1, 20 Bridge Street, Pymble NSW 2073 +61 2 9498 2768 admin@agwa.com.au www.agwa.com.au
COVER IMAGE & CONTENTS PAGE IMAGE
Scotch College
Carruth Rd, Torrens Park, SA
Architect: Hames Sharley
Builder: Badge Constructions Group
Glazier: Packers
Fabricator: Chevron
Photographer: Dan Trimboli
CONTRIBUTORS
Clinton Skeoch, Lars Meuter, Steve Lygris, Jelena Ninkovic, Lucy Kendall, Maria Babic, Mark Giles, Tony Vella, Maurice Tapang, Deborah Deeth, Ingrid Pagura, James Whitehouse, Adam Davies, Tim Johnston, Russell Harris, Vivienne Munter, Angela Farrell, Mari Lehtinen, Elizabeth Dimabuyu, Samara Davis, Roger Bishop, George Karabinas, Tarek Mostafa, Helen Dawes, Melissa Baker, Kerrie Henderson, Tyler Gonzales and Dominique Macartney.
PRINTED BY
SOUTHERN IMPACT southernimpact.com.au
Our printer conforms to the ISO-14001 environmental management standard and the ISO-9001 quality management standard.
DISTRIBUTED BY
D & D MAILING SERVICES
www.ddmail.com.au BuiltView Magazine is proudly packaged in Biowrap, 100% degradable plastic wrapping.
DISCLAIMER
Copyright © 2024. All rights reserved. Reproduction in whole or part without written permission from AWA-AGGA Limited is strictly prohibited. It is impossible for the publisher to ensure that the advertisements and other material herein comply with the Australian Consumer Law Competition and Consumer Act 2010. Readers should make their own inquiries in making decisions and where necessary, seek professional advice.
Dear Members,
Clinton Skeoch Executive Director and CEO AGWAAs this year continues to pass by so quickly, it was great to see so many of you at our recent state member forums. These forums provided an invaluable platform to discuss the latest developments in Standards and the NCC, as well as to update you on our continually expanding member services on ofer with AGWA. If you haven’t already, I would encourage you to look for the QR code in the ad from Standards Australia in this issue of BuiltView as after consultation with Standards Australia, we have secured a member discount package for AGWA members purchasing Glass and Window small business sets. This is another way we are showing our ongoing commitment to enhancing your membership experience and delivering a more knowledgeable and compliant industry.
In May this year, we have actively engaged with members to cover the emergent NCC2025 changes and highlighting the areas to be aware of. This is an ideal time for members to engage with our tech team and have your perspective heard as we seek to provide a voice for our industry on these important changes. Feedback will be open until 1 July so make sure your voice is heard.
Looking ahead, I am thrilled to announce the upcoming 2024 Design Awards nights around the country. It will be a fantastic opportunity to come together once again and celebrate the new, innovative, and excellent contributions within our industry. Your presence at these events will be greatly anticipated, as we honour the remarkable achievements of our members and industry.
I am also pleased to share that the AGWA Board recently held a strategy day in Sydney this April. Our directors dedicated the day to discussing the challenges, opportunities, and future direction of our Association. While it was a big day, it was great to come away with an aligned view of our future project priorities and I look forward to providing a detailed update to you later this year.
As always, your support and active engagement are the driving forces behind our Association’s success. Together, we will continue to elevate and champion the glass and window industry in Australia.
Clinton Skeoch Executive Director & CEOScotch College, Torrens Park, SA SA State Winner 2023 Design Award for Commercial Window and Glass Project Over $750,000
Packers fabricated all aluminium windows and doors for the new Scotch College gymnasium, well-being centre and swimming centre. The project included 1250 sqm of glass, which was locally manufactured in South Australia by Chevron Glass.
The showcase is a large 5.5 m high feature window that protrudes from the façade, overlooking the Adelaide CBD. On the same building, there is a complex multi-storey foorto-ceiling double-glazed facade window that follows the contour of the external steps, featuring a hidden custom-designed frame-locking system. This enables the window to support laser cut aluminium plates, and stainless-steel cabling for a vertical vine garden. To ensure that Packers met the multiple energy and impact requirements on the project, they used 15 diferent glass types, including high-performance, impact-resistant and structurally glazed options.
INDUSTRY DEVELOPMENT COORDINATOR, AGWA
Ingrid began her role with AGWA in May 2021 looking after the training needs of members. Her role soon progressed to include working on Safety, BuiltView, the AGWA Design Awards, the website and other marketingrelated activities.
Prior to AGWA, Ingrid worked for a legal publishing company as an editor, a publishing manager and then an editorial trainer. Her time at Butterworths saw her work on their building and local government and environment suite of products and with the CSIRO and ABCB on other BCA projects. She also previously worked for many years as a part time teacher at TAFE teaching law, business, communications and work health and safety across multiple faculties.
COPYWRITER, TRADE ADVERTISING AGENCY, AUSTRALIAN OLYMPIAN
Angela is an advertising copywriter and business content writer with over 15 years, advertising agency experience. She loves the challenge of working across industries and genres; writing radio ads for snack brands, websites for SaaS, articles for AGWA, and everything in between!
Having represented Australia in the sport of sailing, Angela is passionate about the teamwork and hard work that goes into success — be it in sport or business.
Deb has been in the glass industry for 20 years since the inception of Greater Glass, of which she is the proud founder and the driving force.
For the past decade, Deb has held prominent positions within the glass industry and currently serves as a Director on the AGWA Board, contributing to the advancement of the glass industry and glazing as a competitive and lucrative trade and profession. She actively campaigns to entice young apprentices into the feld and to elevate safety, compliance, and quality standards.
A frm believer in the power of shared knowledge and learning, she is committed to advancing our industry through awareness programs around reduced energy consumption and emission targets.
James Whitehouse graduated in Structural Engineering in the UK before discovering building facades, working initially for systems’ companies before becoming a Facade Engineer at LendLease. Over the last decade working in Australia, he has worked for two of the largest WA commercial fabricators and then Capral Aluminium before joining AGWA in 2022.
He is a cricket fanatic and former state longbow champion.
Adam holds a degree in Materials Engineering and started his glass career as a part-time employee at the Viridian Ingleburn foat line in his fnal year of study. After graduation, he moved into a full-time role as a Process Engineer and later to Technical Manager at Viridian.
Adam has seen most aspects of the industry. Adam’s role supports and participates in extensive technical enquires, technical documentation development, dispute resolution, non-conformance investigation and independent technical inspections and reporting, concurrently advancing and promoting AGWA and the Insulating Glass Manufacturers Alliance (IGMA).
Tim joined AGWA in July 2023. With a degree in Architecture from the University of New South Wales, as well as postgraduate qualifcations in environmental management and economics, Tim has more than 25 years’ experience working in the built and natural environment, not for proft industry associations, private and government sectors.
Maurice graduated with a Bachelor of Economics from the University of Sydney in 2021, majoring in Financial Economics and Econometrics. He led two collaborative projects, one analysing of the efects of COVID on the stock prices of commercial property companies and the second, collaborating with ANZ Banking involving recommendations to improve their data analytics for the approval of home loans in disadvantaged postcodes. He joined the HIA in 2023, and his responsibilities involve contributing to HIA’s suite of publications and articles.
The easiest way to a 7-Star Home
At Kommerling, we build excellence every day, through our modern and innovative production facilities and the strict quality controls along the entire production line, to ensure the creation of superior high-performance windows and doors. Our continuous research and development leads to ofering unique solutions with many innovative features, which cover completely the needs of our customers.
Recent trends in home renovations suggest that the ‘lofty’ levels of activity achieved during the pandemic are being replaced by less ambitious home improvements in 2024, as the full impact of higher interest rates hits household expenditure.
People have spent more time at home in the past 4 years. Working from home replaced commuting to the ofce. Lockdowns coincided with families preparing food in their kitchens as opposed to dining out. What would otherwise have been spent on entertainment, and especially travel, was redirected to better home appliances, furniture, and fxtures, as evidenced by retail trade fgures.
Consumers spent $64.7 billion on household goods in 2020, which was $9.5 billion more compared to the previous year, while spending in supermarkets and grocery stores increased by $11.0 billion. These more than ofset the $7.2 billion decline in spending on cafes, restaurants, and takeaway services.
Australians spent more on hardware, building and garden supplies, electrical goods, and furniture, consistent with the shift in households spending more time at home and improving many aspects of it. Data from HIA’s Survey of Builders in 2022 indicated that new homes, on average, had around 3 bathrooms installed, up from 2 pre-pandemic.
These changes in trends have been material in producing a structural transformation in the demand for housing. Whether it is through moving into larger houses with fewer family members or roommates, or through expanding the footprint, quality or number of kitchens, bathrooms, home ofces, entertainment rooms and backyards, there was clearly pent-up demand for greater space and amenity.
This mellowed out as supply chain constraints saw prices of goods and services sharply spike. The Reserve Bank of Australia hiked rates rapidly in response, which increased the cost of borrowing. Consumers responded to these developments by tightening their belts and spending less where they could.
The home building industry continues to be adversely afected by these changing consumer habits. Elevated borrowing costs forced households to delay their decision to purchase a home. It also forced many to wind back their home improvement plans for their existing dwelling.
The results of the most recent HIA Survey on the Kitchens and Bathrooms Segment show that home buyers and renovators are winding back on some of the extras where they can. A majority of new home builds in 2023 had 2 or less bathrooms installed. The trend of having an extra bathroom installed during the pandemic was notably absent in these results. Kitchens are also being built or renovated with fewer of the higher-end fnishes and appliances of the previous year.
This trend can also be observed as a fall in the volume of renovation projects across Australia. Renovations activity has moderated from pandemic heights to levels that are more consistent with underlying demand, measured using the age of Australia’s dwelling stock.
There are still several factors supporting renovations activity. Data on renovation lending and approvals indicates that some households are still undertaking large home improvement projects. Approvals for renovations nationally are still up by around 40% on pre-pandemic levels, while lending for renovations is more than double pre-pandemic levels.
This is likely driven by the ‘wealth efect’ of rising house values and the desire to increase the potential selling price of one’s home, should one ever wish to trade up or downsize. Many wealthier households also accumulated a war chest of savings and assets during the pandemic. In practice, this means that because household expenditure is increasingly constrained and there is a limited volume of established homes for sale, households are increasingly deciding to borrow and renovate, rather than to relocate.
But for many, their aspirations are likely constrained by tighter budgets.
The Fair Work Legislation Amendment (Closing Loopholes) Act 2023 (Cth) has brought in several changes to workplace law in Australia. In the Autumn issue of BuiltView, I outlined some changes to the National Employment Standards. In this issue I will review another change that will impact your workplace, Workplace Delegate’s rights and protections.
The law protects the right of every worker to participate in, or not to participate in, industrial activities. These can range from joining a union, attending meetings, participating in lawful industrial activity (for example, over WHS breaches) and complying with legal requests (obey lawful requests).
Workplace delegates are those people who are appointed to represent members of an organisation (union) in their workplace. This legislation has increased their rights and protections in several ways from 15 December 2023 and 1 July 2024.
From 1 July 2024
• All Modern Awards must include a Delegates Rights’ Term. A Delegates Rights’ Term is defned in section 12 as meaning ‘a term in a fair work instrument that provides for the exercise of the rights of workplace delegates’.
• Enterprise Agreements negotiated after this date must also include a Delegates’ Rights Term.
From 15 December 2023
• New protections for Workplace Delegates
A new section 350A (Protection for workplace delegates) outlines these as follows:
‘(1) The employer of a workplace delegate must not:
(a) unreasonably fail or refuse to deal with the workplace delegate; or
(b) knowingly or recklessly make a false or misleading representation to the workplace delegate; or
(c) unreasonably hinder, obstruct or prevent the exercise of the rights of the workplace delegate under this Act or a fair work instrument …
‘(3) The burden of proving that the conduct of the employer is not unreasonable as mentioned in subsection (1) lies on the employer.’
This new section strengthens the language as previously it referred to reasonable communication and reasonable access to the workplace. As an employer you must ensure that are aware of
this new increased requirement on you.
• New Rights for Workplace Delegates
A new section 350C (Workplace delegates and their rights) outlines their strengthened rights in representing the industrial interests of their members as follows:
‘(3) The workplace delegate is entitled to:
(a) reasonable communication with those members, and any other persons eligible to be such members, in relation to their industrial interests; and
(b) for the purpose of representing those interests: (i)reasonable access to the workplace and workplace facilities where the enterprise is being carried on; and (ii) unless the employer of the workplace delegate is a small business employer—reasonable access to paid time, during normal working hours, for the purposes of related training.’
• Taking adverse action
You are prohibited under the Fair Work Act 2009 (Cth) from taking adverse action against workers who have workplace rights. This has now been expanded to include Workplace Delegates’ rights. This means that you can’t dismiss an employee, demote them to a lower job, treat them diferently or cut their shift hours for example.
What
First, make sure that you are familiar with your responsibilities towards Workplace Delegates. You must be aware of these entitlements and ensure that you comply with all reasonable requests made of you. Don’t ignore requests for meetings or information as the onus is now on you, the employer, to prove that you weren’t being unreasonable.
From 1 July 2024, if you are negotiating a new Enterprise Agreement with your employees, you must include a Delegates’ Rights term in it.
For help and guidance on workplace delegates please see the Fair Work Ombudsman at: www.fairwork.gov.au/employmentconditions/protections-at-work.
For help and guidance on negotiating enterprise agreements please see Fair Work Ombudsman at: https://www.fairwork.gov.au/ tools-and-resources/fact-sheets/rights-and-obligations/enterprisebargaining
A common topic across recent AGWA Member Fora, the growing interest and regulatory oversight of environmental performance, especially embodied carbon, continues to evolve with the Federal Government’s recent policy announcement on reporting climate-related risks.
As many of AGWA’s larger members are already aware, the Federal Government will soon be requiring climate-related fnancial disclosures, with information about an entity’s exposure to climaterelated fnancial risks and opportunities, as well climate-related plans and strategies (refer Treasury’s Mandatory climaterelated fnancial disclosures - Policy position statement). Disclosures will be mandated through amendments to the Corporations Act 2001 (Cth) (Corporations Act) and related legislation. Disclosures will be mandated through amendments to the Corporations Act and related legislation. Detailed sustainability and assurance standards will be made and maintained by the Australian Accounting Standards Board (AASB) and the Australian Auditing and Assurance Standards Board (AUASB).
Who will be included?
Large entities required to prepare and lodge annual reports under Chapter 2M of the Corporations Act must disclose information about climate-related risks and opportunities. This includes listed and unlisted companies and fnancial institutions, registrable superannuation entities and registered investment schemes.
Asset owners (such as registrable superannuation entities and registered schemes) will be considered large, if funds under management are more than $5 billion.
Where entities are subject to both the Corporations Act’s annual reporting requirements and emissions reporting obligations under the National Greenhouse
and Energy Reporting Act 2007 (Cth) they will be required to disclose regardless of their size.
Exemptions will apply for:
• Small and medium businesses, below the relevant size thresholds.
• Entities that are exempt from lodging fnancial reports under Chapter 2M of the Corporations Act, including where exemptions have been made through ASIC class orders or where the entity is registered with the Australian Charities and Not-forProfts Commission.
Entities subject to mandatory disclosure would be phased in 3 groups, over a 4-year period.
Reporting content
Disclosures will include information about an entity’s climate-related risks and opportunities, as required by Australian Climate Disclosure Standards, relating to:
• Information relating to governance, strategy, risk management and metrics and targets (including Scope 1 and Scope 2 greenhouse gas emissions) will be required from the frst year of reporting.
• Scope 3 emissions (ie, emissions occurring up or down the supply chain and emissions associated with the fnancing or investment activities) will be required from the second year of reporting. Scope 3 disclosures would represent information available at the reporting date without undue cost or efort.
Group 3 materiality exemption
Group 3 entities (entities that are inscope for reporting but do not meet the thresholds for Group 2) would only be required to make disclosures in line with the climate disclosure standards, if they face material climate-related risks or opportunities for the fnancial reporting period. Where Group 3 entities assess that they do not have material risks or opportunities, they would only be required to disclose a statement to that efect.
Reporting framework
Climate-related fnancial disclosures will sit within a sustainability report, forming the fourth report required as part of annual fnancial reporting obligations and be contained in an entity’s annual report. Entities should include an index table within their annual report enabling users to easily navigate climate disclosures. The timing of annual report lodgement, including for those required to lodge with ASIC, will stay consistent with current requirements under section 319 of the Corporations Act.
Assurance requirements
Climate disclosures will be subject to similar assurance requirements to those currently in the Corporations Act for fnancial reports and will require entities to obtain an assurance report from their fnancial auditors who will use technical climate and sustainability experts where required. These requirements will be set out in Australian Assurance Standards for Climate Disclosures.
Liability framework
Climate disclosures will be subject to the existing liability framework under the Corporations Act and Australian Securities and Investments Commission Act 2001 (Cth), including director’s duties, misleading and deceptive conduct provisions, and general disclosure obligations. This is appropriate to ensure directors fully engage with climate disclosure obligations and to support investor confdence in the information disclosed.
Modifed liability for climate disclosure
Entities will be provided relief for a fxed 3-year period for disclosures relating to Scope 3 emissions and certain climaterelated forward-looking statements. Only the regulator will be able to bring actions relating to breaches of relevant provisions made in these disclosures for reports issued between 1 July 2025 and 30 June 2028, with injunctions and declarations the limited remedies available to the regulator. Beyond this period, the existing liability arrangements will apply.
The Government will review climate disclosure requirements in 2028-29. While AGWA will continue to monitor government policy decisions, it is reasonable to expect that over time the requirement to report will be extended beyond large entities.
As we are now in the colder months, we have all seen an increase in fu, colds and viruses. We’ve also seen those workers who like to soldier on, coming into work sick and then spreading it to everyone. Since COVID, this has become more frowned on, as people being of sick impacts the ability of the business to function efectively. It now even has a name: Presenteeism. So how can we prevent this? My Business has published an article by Catherine Ngo (31 January 2024) with some tips on how to prevent this, which we’ve extracted for members.
An innocent cough here and there may seem innocent at frst, but did you know that the cost of presenteeism to organisations is almost 10 times higher than that of absenteeism? Harvard Business Review estimates it costs more than $150 billion annually in lost productivity.
With this in mind, what preventative measures can employers implement to protect workers and reinforce a culture of care?
Train leaders to be aware of warning signs
One way to reduce presenteeism is to coach managers on identifying the early warning signs of burnout and other health conditions so they can intervene as early as possible. Have wellbeing conversations and empower people to make good choices.
Remind team members about the personal leave policy
As part of the National Employee Standards (NES), permanent employees are entitled to 10 sick days (prorated for part-time employees) per year. To ensure employees’ well-being, leaders should encourage them to use their paid sick leave and take the necessary time to recover.
Also, fostering a workplace culture prioritising a healthy work-life balance is essential. Encourage employees, especially those who are keen and highly motivated, to take time of without feeling guilty.
If leaders notice a trend in employees presenting to work sick, leaders should address this in team meetings to remind employees not to come to work while sick. This serves as a reminder of expectations, helping create a culture of health and well-being …
speak louder than words
If your corporate policy emphasises work-life balance as a priority and leaders present to work visually unwell, that will convey mixed messages. To efectively communicate your commitment to employees’ well-being, demonstrate it through your actions …
Prevent presenteeism by ensuring adequate staf
Ensuring sufcient stafng levels is another efective strategy to combat presenteeism in businesses. This involves maintaining
an adequate number of employees to manage the workload efectively, even in situations where some employees are absent due to illness. Contingent staf can play a valuable role by providing temporary or fexible support during peak times or unexpected absences.
When businesses are understafed, employees may feel pressure to come to work even when sick because they worry their work will not get done. Adequate stafng levels also allow businesses to manage unexpected absences more efectively. When an employee calls in sick, their work can be easily redistributed to other team members, which helps to minimise the impact on the business.
Is remote working an option?
Today’s employees have the tools to work from home when needed … If the role allows for working remotely, leaders should encourage employees to stay home if they feel unwell.
Encourage a results-only work environment
In a results-only work culture, the emphasis is on outcomes rather than the specifcs of where and when employees work. It means employees have increased autonomy over their workload, as goals are collaboratively determined from the bottom up. This approach shifts the focus away from the number of hours worked or physical presence; instead, employers hold employees accountable for delivering tangible results. As a result, employees are no longer pressured to be physically present when they are physically or mentally unwell.
Over to you
Presenteeism negatively impacts productivity despite its perceived benefts in showing up. It has become more prevalent since stay-at-home mandates were lifted … By implementing these strategies, employers can work towards reducing presenteeism and its associated costs, improve employee wellbeing, and maintain high productivity levels.
‘In today’s construction industry, balancing sustainability with cost efciency is a pressing concern’, says Craig Palmer, Managing Director at AJ Aluminium.
The Sydney FC Centre of Excellence emerges as a shining example of how innovative technologies can be seamlessly integrated to achieve both objectives. This article delves into the implementation of thermally broken window frames versus non-thermally broken frames, showcasing the tangible benefts.
Ofcially opening in August 2023, The Sydney FC Centre of Excellence is colloquially known as Sky Park. It is the training and administration headquarters of Sydney FC soccer club and located in the sporting precinct of Macquarie University in Sydney.
During the initial design stage of The Sydney FC Centre of Excellence project, AJ Aluminium was approached to help incorporate thermally broken window frames. This choice was driven by a dual aim: to enhance energy efciency and to mitigate long-term operational costs, all while ensuring optimal comfort for athletes and staf.
Energy consumption and its associated costs in commercial buildings were meticulously analysed, factoring in variables such as climate conditions, building orientation, and energy prices. The results consistently favoured thermally broken window frames, demonstrating potential energy savings of up to 40% compared to non-thermally broken frames. These savings translated into substantial reductions in operational expenses, reinforcing the economic viability of sustainable design choices.
Moreover, the enhanced insulation provided by thermally broken frames signifcantly improved indoor comfort levels year-round. This not only optimised the training environment within The Sydney FC Centre of Excellence but also contributed to a more sustainable operational model.
As The Sydney FC Centre of Excellence reached completion, it stands as a beacon of inspiration for future construction projects across Australia. ‘We at AJ Aluminium are proud in our commitment to embracing innovative manufacturing technologies and sustainable design principles that will set a new standard in the industry’. The project exemplifes the harmonious integration of sustainability and performance, debunking old misconceptions on thermally broken windows and paving the way for future developments here in Sydney.
In conclusion, The Sydney FC Centre of Excellence serves as a testament to the transformative power of sustainable construction practices. By prioritising energy efciency and optimal performance, this landmark project not only elevates the standard for sports facilities but also underscores the importance of sustainability in modern construction endeavours.
For more information, please contact www.ajaluminium.com.au
Protect your family and home from the life-threatening effects of cyclones with the new ScreenGuard Extreme stainless steel mesh security system.
Specifcally designed for cyclone regions to provide protection against cyclones, tropical storms, and fying debris. It has been rigorously tested to AS1170.2 Structural Design Actions and achieved a cyclone rating of 44m per second! Made from 1.2mm high tensile 304 stainless steel mesh and 6036 T6 aluminium frame, ScreenGuard Extreme has been tested to the latest Australian security standard AS5039-2023.
ScreenGuard Extreme is manufactured using our unique two-part wedge and seat technology, making it one of the strongest security systems available in the market.
Features and Benefts
Tested to AS5039 and AS1170.2
Corrosion Resistant
Compatible with a range of hardware
Backed by a 10-year warranty
Cyclone Rated to 44m / sec
To fnd out more, scan the QR code or contact your local Darley branch on
. NSW (02) 8887 2888 . sales@darleyaluminium.com.au
. VIC (03) 9238 3888 . salesvic@darleyaluminium.com.au
. QLD (07) 3287 1888 . salesqld@darleyaluminium.com.au
. WA (08) 9437 2999 . saleswa@darleyaluminium.com.au
Let’s face it, most of the population doesn’t really know what a glazier is, right? At least, I didn’t know until I started dating one back in 1997. I was completely unaware that glazing could be a lucrative and wellpaid trade qualifcation. Herein lies our challenge.
Having spent 20 years immersed in construction environments, I’ve gained a deep understanding of the multitude of nuances and specialised aspects. When trying to explain the unique and diverse nature of installing glass and related products, I often use the following teacher analogy ‘put simply, you wouldn’t want your kids being taught Maths by the PE teacher’. In other words, you wouldn’t engage a window installer to install your frameless shower screen.
The breadth of hands-on skills within the glass industry is super diverse. You have your trade-qualifed glaziers, aka the ‘hack out guys’/glass replacement professionals, which speaking from experience, can be divided into 2 groups. The frst, I call the BIG hack out guys, ie, façade and large shopfront glaziers, with loads of experience needed for large replacements in crazy hard-to-reach places with extra safety considerations, often lifting equipment and a prerequisite of no fear. These work environments are not for the faint hearted.
The second, EVERY OTHER hack out job. These guys can perform a multitude of glass replacement jobs in a day, are traditionally trained and can run putty. Yes putty, increasingly difcult to fnd tradespeople with this skill!
As architecture evolves with a demand for minimalist frameless applications, we have seen the emergence of the Frameless Glass Specialists for all those frameless showers, balustrades, pool fences and various architectural elements, necessitating precision down to the millimetre.
Last, but not least, the more well-known, the window installers, with various trade types and labourers dedicated to this line of work. Within this domain, labour is also specialised from fabrication to remedial work to the never as straight forward as it should be removal and replacement of residential windows.
Is our broad, unique, yet essential, evergrowing product range a blessing or a curse? There is huge opportunity for career diversity and specialisation just in the labour component alone, and surely this puts construction, especially complex glazing and window installations and related subtrades, as a future-proof career option. So why do many in our industry feel like the odds are stacked against us? Well, the average age of a glazier is 37 years, the second oldest to bricklaying at age 38. Will the obvious career progression to get of the tools and up the career ladder into estimating and project management not be as lucrative? As the ‘on the tools’ labour pool ages and replacement rates fall, will the demand for the everelusive tradie result in them becoming the highest paid in the company? Will the design, project management, estimating and engineering jobs be halved with the introduction of AI?
for employers and consumers, however, also ofering potential advantages for school leavers who pursue this career path and remain committed to it. Initially, they need awareness that this career path exists! So how are we attracting people to glazing? We need to brainstorm to create positive solutions which will future proof the industry we love.
As leaders and caretakers of our industry, it’s our obligation and our duty to engage with our youth and unveil the thrilling prospects awaiting them: the burgeoning demand, the lucrative opportunities for those bold enough to diverge from the prevailing trends of the IT and AI sectors. While I’m no PR expert, I have to ask, ‘do we have an identity problem?’ ‘Is an all-out rebrand of our industry and required trades overdue?’ ‘Do the fundamentals of how we structure our businesses, work and study have to change?’
Maybe we should consider crafting the perception of 5 distinct careers within a single industry, forging a pathway that intertwines and aligns with both the industry’s needs and the aspirations of the next generation. This roadmap could ofer enhanced fexibility, immediate rewards and a genuinely fulflling career with a sustainable focus. Many glaziers and window installers will deliver same-day results, fostering high job satisfaction and leaving behind contented customers. Tick for the instant gratifcation!
‘As leaders and caretakers of our industry, it’s our obligation and our duty to engage with our youth and unveil the thrilling prospects awaiting them’
While AI might help write this article, create better software to manage our projects and people, and even develop higher performing glass and automate assembly lines, I have found it quite astonishing that discussions about the construction industry have mostly consisted of broad statements on AI’s potential to revolutionise construction processes and of the growing use of robotics and automation on construction sites for tasks requiring repetitive precision and speed, surpassing human labourers in efciency.
Call me shortsighted but, at this point, I haven’t seen any evidence that AI will be able to address the complex challenges facing the installation shortage in construction, particularly with our diverse, aging building stocks and fragile product such as glass. So which AI platform is working on the robots to complete these complex installations?
As the classic dynamics of supply and demand persist, the cost of labour for tradespeople continues to rise, presenting challenges
Let’s bring sexy back! Anyone in our industry knows glass is a sexy product and a clean trade, apart from a bit of silicone here and there (yes, I have had the pleasure of trying to get black silicone of clothing for 20 years, but hey it’s not grease!!) Where are we showing up? Clearly not where our next generation of glaziers are. Hell, let’s all jump on Tik Tok, that’s where our next generation of glaziers are.
Talk to your local member and ask them why aren’t we building trade schools and flling them with every child who’s not heading to the education space? What about all those kids who can’t sit still in class and will never cut it in a computer or retail environment? Is it simply a contest of the trades?
While advancements in technology may shape various aspects of the construction industry, the role of skilled glaziers remains irreplaceable. By embracing the opportunities within the trade, investing in a campaign that shows our industry as a viable profession, and coupled with ongoing investment in training and education, we can ensure that our aging professionals will have young blood to pass on their knowledge to, allowing our industry to thrive in the years to come.
But frst our youth and their parents need to know who we are and what’s on ofer? So, what small part are you going to commit to that will help our industry thrive into the future? I’d love to hear your thoughts. Please reach out to an AGWA team member or email me at deb@greaterglass.com.au.
‘Our management team has some of the best fabrication experience in the industry, and you’ll often see those guys reaching for the tools if needed, helping the team get through a busy day or some complexities.’
Born out of Palmer Aluminium, a successful commercial window business through the 1990s and early millennium, PCW Commercial Windows, led by Leigh Spinks and his partners Ross Farrelly and Jay Atkins, is nestled in Somersby, NSW and stands as a testament to the power of dedication, innovation, and strategic partnerships.
Over the years, PCW has witnessed substantial growth, evolving from a team of 8-9 to a workforce of more than 40 at its peak. The company’s move to a larger facility in Somersby in 2023, underscores its commitment to expansion and excellence, and its resilience through challenging times.
PCW Commercial Windows has carved a niche in the commercial building sector, ofering various customised window, door and glazing solutions from hospitals and schools to car showrooms and industrial complexes. Their expertise extends to high-end residential projects and multistorey apartments, showcasing their versatility and reliability in delivering quality outcomes.
Managing Director Leigh Spinks comments ‘we service builders from anywhere, from south of Sydney all the way through to the Central Coast and the north of Newcastle, where I would probably think we would be one of the preferred suppliers of commercial windows and doors throughout the region’.
If you ask Leigh what sets PCW apart, he is quick to tell you it is its early engagement approach with clients. From the tender stage to project completion, PCW’s team provides invaluable support ofering clarity, problem-solving, and technical expertise. This proactive stance has earned them a reputation as a trusted partner among builders, leading to long-term relationships and repeat business.
‘We get a lot of compliments about how we construct our quotations and tenders; they’re very clear. The builders often use those to pass on to their clients. Being involved early makes the whole project run better, and builders recognise and value that’, comments Leigh.
If client engagement is its diferentiator, a skilled and dedicated team is certainly PCW’s backbone. Leigh proudly admits that the heart of PCW’s success lies in its meticulously selected, nurtured and skilled team. From management to fabrication and installation, PCW boasts a roster of qualifed tradespeople, while its commitment to apprenticeship programs ensures a continuous infux of talent, bolstering its workforce and fostering a culture of growth and expertise.
Leigh explains, ‘we’ve been quite focused on bringing qualifed tradespeople into our management structure. So, we’ve got glaziers, joiners, draughtsmen, and carpenters — they’re all involved in our management team.
‘Through installation, we ensure we have good leading hands or good installation qualifcations, including qualifed carpenters. We have proactively brought apprentices through over the last few years, and we’ve currently got 3 apprentices on the team completing various qualifcations in glazing or joinery. You really can’t beat experience.
‘Our management team has some of the best fabrication experience in the industry, and you’ll often see those guys reaching for the tools if needed, helping the team get through a busy day or some complexities.’ PCW’s strategic partnership with Capral Aluminium, spanning over 2 decades, is central to its success. Capral’s commitment to innovation, quality, and environmental sustainability aligns seamlessly with PCW’s values and objectives.
‘I’ve been in business myself for over 20 years, and I can tell you now, Capral has been my mainstay. I can’t recommend them enough; they’re innovators and continue to stay on trend. They’re very open to feedback and constructive communication’, says Leigh.
PCW manufactures products that are designed, tested and extruded locally by Capral. Boasting one of Australia’s most experienced fenestration technical design departments, Capral works alongside manufacturers like the PCW team, providing a suite of commercial window
and door systems ft for purpose for the Australian market and suitable for the wide range of applications that PCW services. With all of this and warehousing and inhouse fnishing options, Capral can provide a full-service solution for independent manufacturers like PCW.
All Capral window and door systems are rigorously tested to meet and exceed Australian Standards and supplied to manufacturers with comprehensive technical manuals, round-the-clock support and state-of-the-art manufacturing tooling and equipment.
In addition to fabricating Capral’s commercial window systems, PCW is also a licenced distributor of the Amplimesh range of security screens, widely used on residential and commercial projects to deliver security, cyclone impact resistance and fre attenuation outcomes. Leigh comments, ‘the Amplimesh product has a really good reputation. It’s a fantasticlooking product, and it covers all the Australian Standards, so it made sense’.
Capral’s LocAl initiative, aimed at reducing the carbon footprint of the primary aluminium used to create the aluminium windows, has been enthusiastically embraced by Leigh and the PCW team, refecting a shared commitment to ethical environmental practices and showcasing PCW’s dedication to sustainability and responsible manufacturing. Leigh explains, ‘we’ve got an agreement with Capral that all of our aluminium is sourced from LocAl and at no extra cost to our client’. This provides it with an additional diferentiator, ensuring PCW is taking positive steps towards carbon reduction and sustainability, while still being highly competitive.
As PCW continues to grow and innovate, it remains steadfast in its mission to deliver unparalleled quality and service to its clients. With landmark projects like the Gosford Library and an 11-storey apartment complex on the horizon, PCW is poised to leave an indelible mark on the built environment sector. It also leaves an indelible mark on its Managing Director, who beams with pride when he talks about the business and his skilled, loyal team.
‘It’s nice to see the product go out the door. You can sit back out there and look at the building and say, “we did that”. But more than that, running PCW is like having a second family that you come to work with every day. Watching how hard everybody works, I think, people are proud to work for PCW commercial windows, and that makes me really proud’.
As they continue to forge ahead, PCW remains committed to its core values of integrity, quality, and customer satisfaction, ensuring a future flled with growth, prosperity, and groundbreaking achievements.
For more information, please contact www.pcw.net.au or (02) 4340 1100 or Kellie Moore on kellie.moore@capral.com.au
Mention the name Kömmerling and people think of more than just windows and doors. Kömmerling is one of the most recognised brands in the German manufacturing industry, known not only for reliability and luxury, but also for innovations that improve its customers’ quality of life. This recognition was not easily earned, and with more than 125 years of experience, the brand has cultivated a reputation for its outstanding designs, innovation and sustainability and established a rich history.
Kömmerling’s story began in 1897 in Pirmasens, Germany, with the profne’s Kömmerling brand marking its 127th birthday this year. International production and market expansion started in 1954, and since then, the company has established production facilities at 29 locations across 23 countries, distributing products to over 100 countries all around the world. Even in its early days, a key success factor was using modern materials produced by high quality and advanced technologies. Today, the company has led the development of the most advanced high-performance windows and doors across the globe.
Compared to around 80% of residential properties in Europe and the United States, only less than 10% of Australian homes have high performance windows. The most common type of windows in Australian households are aluminium single glazed. While aluminium is known as a highly conductive material where heat can easily pass through, these type of doors and windows are also not thermally broken, resulting in about 40% of heat loss and up to 85% of heat gain.
With its commitment to excellence and an ambitious goal of transforming its manufacturing operations and products to net zero emissions, Kömmerling proudly acquired state-of-the-art technology in its R&D, manufacturing and testing processes to deliver unparalleled energy-efcient windows and doors. This will enable Australian homes to be cooler in summer and warmer in winter, while optimising the free natural energy of the sun all year round. By helping to reduce heating and air conditioning costs, overall energy consumption is also reduced, contributing to a much more sustainable environment. In addition, every product has been tested in accredited facilities to ensure they not only adhere to Australian Standards, but also meet the rigorous challenges of Australia’s harsh weather conditions, even in cyclonic zones.
‘With a global footprint and a track record of success, Kömmerling will play a pivotal role in propelling Australian houses towards safer, happier, and healthier homes.’
Embarking on 2024 with the rising cost of living, alongside people’s environmental concerns and renewable imperatives, Kömmerling has seen a big shift towards the higher performing windows and doors on a global scale. With the attitude of not only making a diference towards a happier and less wasteful planet, but also making a house a home, it was the time to embrace new recourses and technologies. Driven by TODAY FOR TOMORROW, Kömmerling’s key focus is on putting the future frst by using sustainable technologies, sourcing biodegradable and raw materials, and designing and manufacturing products entirely from recycled resources. This has not been easy but was necessary.
This revolutionary approach symbolises the transformation of traditional production equipment into new simulation practices by reducing its carbon footprint and contributing positively to the planet’s wellbeing. Operating in an environmentally friendly manner for years, Kömmerling exclusively uses eco-friendly calcium-zinc based stabilisers in the production of profles, alongside recycled materials in fresh PVC. Millions of old uPVC profles
are replaced and ground into pellets, that are then reused to make attractive new windows and doors. With this initiative, it is one of the pioneers of substance-free products in the construction and building sector.
Kommerling’s objectives are very clear. It intends to continue to be a leading window and door manufacturer with every action revolving around the customer.
Consumer behaviour is changing due to technological innovation and the adoption of digitalisation, directly contributing to how we interact, make decisions and shop across all industries, including the building and construction. Not only do over 80% of customer interactions begin online, but customer service expectations have grown too, expecting the same level of service in the digital worlds as in the real world.
In alignment with a commitment to digitalisation and customer-centric policy, Kömmerling’s aim to redefne efciency, reliability and adaptability in window and door applications is helping achieve this. As the brand expands its presence in the
ever-growing Australian market, the new digital approach stands as a testament to Kömmerling’s commitment to delivering efcient and high-quality solutions to the industry.
Since early 2023, Kömmerling has been developing core improvements to existing applications and developing new tools to boost efciency. These include global eStores for faster and more accurate ordering, ePlanners for architects and fabricators, and 3D virtual frameworks for homeowners. Navigating the complexities of developing and delivering digital projects is no small step, but it is well-equipped and ready to handle the challenge by leveraging proven technologies and fostering open and transparent relationships with customers ensuring Kömmerling meets customer expectations and timelines.
Let Kömmerling’s family look after yours. With a global footprint and a track record of success, Kömmerling will play a pivotal role in propelling Australian houses towards safer, happier, and healthier homes. As the nation embraces a future powered by clean, sustainable sources, the brand is leading the charge towards a greener, more
With the number of workplace fatalities increasing across Australia, employers and business owners need to be aware of Industrial Manslaughter ofences that have been introduced across Australia and take them seriously.
This was highlighted in late February when the frst case was prosecuted in Victoria imposing a record fne of $1.3 million on a stone masonry business, after a 25-year-old was crushed by a forklift at a warehouse in Somerton. The business owner was attempting to move an A-frame rack when the forklift rolled on a slope, then tilted and pinned the worker under it, killing him. The crucial point of the judgement against the owner was that his behaviour was a ‘very signifcant departure’ from normal forklift practices by operating the load 2 m above the ground and with people in an unsafe proximity.
Refecting on this decision, it is important to understand what the ofence of Industrial Manslaughter is and where each state stands at present.
Generally, the defnition means that a PCBU (Business Owner/Employer) commits Industrial Manslaughter if they engage in conduct that breaches their duty of care and that conduct causes the death of an individual. There is an element of recklessness or negligence in failing to ensure the safety of workers or others and this leads to a death. The test is slightly diferent in each state and territory, but they all revolve around the words ‘negligent’ and ‘reckless’.
Commonwealth
The ofence will commence on 1 July 2024 with the introduction of the new section 30A of the Work Health and Safety Act 2011 (Cth) but applies only to the Commonwealth Public Sector.
Penalty: Maximum for a PCBU (individual) is 25 years’ imprisonment and for a PCBU (body corporate) is a fne of $18 million.
Australian Capital Territory
Industrial Manslaughter has been an ofence since 2004. Originally part of the Crimes Act 1900 (ACT) it was transferred to the Work Health and Safety Act 2011 (ACT) as section 34A from 5 November 2021.
Penalty: Maximum for a PCBU (individual) is 20 years’ imprisonment, and for a PCBU (corporate) is a fne of $16.5 million.
Northern Territory
Industrial manslaughter has been an ofence since 1 February 2020 when section 34B was added to the Work Health and Safety (National Uniform Legislation) Act 2011 (NT).
Penalty: Maximum for a PCBU (individual) is imprisonment for life, and for a PCBU (corporate) is 65,000 penalty units ($11,440,000 as at February 2024).
Two charges for this ofence have been laid, though one against a construction company was later withdrawn. The second charge is currently being prosecuted in the Supreme Court at the time of writing this article.
New South Wales
Industrial Manslaughter is currently not an ofence in NSW though it was previously under the Occupational Health and Safety Act 2000 (NSW).
The NSW Government announced that it would introduce a Bill enacting the ofence of Industrial Manslaughter but had not at the time of the writing of this article.
Victoria
The Victorian Government introduced the ofence of Industrial Manslaughter on 1 July 2020 with the new section 39G of the Occupational Health and Safety Act 2004 (Vic).
Penalty: Maximum for an individual is 25 years’ imprisonment, and for a body corporate 100,000 penalty units ($19,231,000 as at February 2024).
As outlined above there has been a conviction under this section in February 2024. There have been another 3 charges laid.
Queensland
Queensland introduced the ofence of Industrial Manslaughter on 23 October 2017 under section 34C of the Work Health and Safety Act 2011 (Qld).
Penalty: Maximum for a PCBU (individual) is 20 years’ imprisonment and for a PCBU (corporate) is 100,000 penalty units ($15,480,000 as at February 2024).
Queensland was the frst state to convict an individual and a body corporate. In
2020 a company was fned $3 million and 2 directors were convicted to 10 months’ imprisonment (suspended) and in 2022 an individual was sentenced to 5 years’ imprisonment (suspended after 18 months).
South Australia
One of the more recent states to enact this legislation, SA added section 30A of the Work Health and Safety Act 2012 (SA) and will be in force on 1 July 2024.
Penalty: Maximum for a PCBU (individual) is 20 years’ imprisonment, and for a PCBU (corporate) is a fne of $18 million.
On 31 March 2022, Industrial Manslaughter became an ofence under section 30A of the Work Health and Safety Act 2020 (WA).
Penalty: Maximum for a PCBU (individual) is 20 years’ imprisonment and a fne of $5 million, while the penalty for a PCBU (corporate) is a fne of $10 million.
Tasmania
Industrial Manslaughter is not an ofence in Tasmania. The Tasmanian Government has not committed to legislating against it.
This is a reminder that you should thoroughly assess your safety systems including your risk management processes and injury reporting mechanisms, especially those for near misses. A near miss can often predict a real incident just waiting to happen.
This is not the time to think that the Regulators will only go after bigger businesses, these penalties apply to all businesses.
While it might cost money to set up and maintain efective safety systems, the cost of not doing so far outweighs this. Regularly review your risk management plan and make sure that it is practical and understood by everyone in your workplace.
For help on setting up your safety systems, please see the AGWA Member Portal/ Technical Resources where you will fnd many Safety Documents for you to use in your business.
For an easy way to stay up to date, check out AGWA’s Safety Round Up published in the News section of the Member Portal and on LinkedIn and Social Media.
It’s a homeowner’s worst nightmare to discover that the builder they’ve engaged (and paid) has not lived up to their expectations and they’ve been forced to terminate the contract. Even worse, they’re left with an empty and incomplete new home that nobody will certify because of its many defects.
This is the nightmare that Sydney homeowner Jenny* has been living for over 4 years, after she terminated her builder’s contact, having discovered several aspects of her home were not as they should have been. Jenny has been slowly sorting through the mess of obtaining all the relevant documents so that she can have the house certifed and fnally move in. Some of these have been impossible to obtain from the original contractors as they are still owed money by the builder.
Jenny needed to gain a compliance certifcate for a balustrade on the internal stairway and landing of her home, installed by a non-member of AGWA. She reached out to an AGWA member glazier, asking them to have a look at the balustrade with a view to providing a glazing certifcate. The member had a look at the balustrade and quickly had doubts about its compliance.
The member then reached out for our technical help. The team discussed the installation with the member, quickly realising that there were some signifcant concerns with the installation, especially after viewing a photo. AGWA advised the member that it would be unwise to provide a certifcate and
they agreed. The member then informed Jenny of this and, at our request, asked if he could also pass on her contact details, so that AGWA could investigate the possible noncompliance for the installation. She agreed.
AGWA called Jenny and discussed the situation with her. During this conversation, she explained the nightmare she had had with the builder and the signifcant fnancial impact on her. We explained that although AGWA was not able to certify the balustrade or provide engineering, we could ofer to do an independent assessment, as one of our core focus areas was to actively investigate non-compliance in our industry to ensure a compliant and level playing feld. The inspection could be used to determine the extent of non-compliance and as evidence should any legal action be commenced. Additionally, we could recommend local member businesses who could, depending on the nature of any non-compliance, remediate or re-install and certify.
Jenny engaged AGWA to complete the inspection and Adam Davies, AGWA Glass Technical Manager and Siddharth Kumaran, AGWA Graduate Structural Engineer, attended the site to conduct the independent assessment. It was immediately clear that the installation had several areas of concern. The obvious one was the lack of sufcient standof fxings supporting the panels. Further, the standof fxings installed into the end of the stair treads, which were not thick enough to attach a fxing, were already showing signs of splitting. The installation
also lacked sufcient rigidity and was quite easy to rock back and forward. This was done before they also discovered the lack of isolators present on the treads of the standof fttings. This resulted in direct metal to glass contact and thus a high chance of panel failure.
Jenny received the fndings report from AGWA stating that the installation had signifcant areas of concern and would require replacement as, due to the use of toughened panels, the installation would not be able to be modifed to make it compliant. Additionally, if the new installation were to again be fxed to the side of the timber treads, these would require replacement to a thicker tread to comply with the end grain fxings requirements contained in AS 1720.1.
AGWA provided Jenny with a list of all local glazing members that she could contact. We advised her that as members they could reach out to us directly for technical help.
Jenny has now engaged an AGWA member to redo the balustrades, but the work has not yet been started, as unfortunately, there are still unresolved legal issues holding back the commencement of the works.
Members can contact AGWA for technical support by emailing Technical@AGWA.com.au or contacting us on (02) 9498 2768
*Jenny’s name has been changed due to ongoing legal action.
‘If I had my time again’ says Jenny ‘I would have used an AGWA member glazier from the start, because there’s no recourse if they’re not a member, plus, members can seek technical advice from AGWA when they need it. I feel like that’s a no-brainer for homeowners and builders to use AGWA members.’
•
During the audit process, we have found some confusion around the requirements for Window Rating Labels, both in when they need to be used and what they should contain.
Section 8 of AS 2047: 2014 describes how all Class 1 buildings (houses) must have a Window Rating Label applied to each window or door. Only timber windows can ofer a Certifcate as an alternative. Missing the rating labels on your windows and doors may cause the refusal of issue of an Occupancy Certifcate by Certifers.
AGWA has been collaborating with the team at Guru Labels to put together the following guidance.
An example of this would be:
The label must contain the following information:
A ― Manufacture’s identifcation mark: can be just your business name or your company logo.
B ― Serviceability limit state wind pressure: also referred to as SLS and is a value in kilopascals (kPa) or Pascals (Pa).
C
― Ultimate limit state wind pressure: also referred to as ULS and is a value in kilopascals (kPa) or Pascals (Pa).
D ― Water penetration resistance: also referred to as WPR and is a value in pascals (Pa).
As you can see, the WPR rating for non-exposed has been crossed out so this window/door is being used on an N3 rated project with an exposed site location.
To further assist members AGWA has created a multiple rating label that you can order. As you can see on the following example the project is N3 non-exposed.
150200 N1 4006009001300150200 N2 60080014002000150300 N3
Appendix C of AS 2047: 2014 states that it is the purchaser’s responsibility to provide you with this AS 4055 rating. AGWA is aware that sometimes this is not provided. To assist members, AGWA has developed the AS 4055 Calculation Tool which is free to use for members after completing a short course.
Here are some handy tips on what to include on your label for all Class 1 Buildings:
• Ratings will either be N or C (from AS 4055) or for very large homes refer to AS 1170.2 actual pressures.
• Do not use the values from the test reports. These do not refect the project-specifc size or pressures as they are just from a set size.
• Always allow for corner pressures in the calculation of your frames/glass.
• Always follow this up with the Compliance Certifcate giving the full project performance data.
• Remember Safety Glass labels where required.
• Include manifestation strips where required.
• Take photos all these labels when the project is completed as evidence you were compliant.
• Labels from other sources are compliant as long as they have the required information and are non-transferrable.
For a frst time audit any missing or incorrect labels would be noted as a minor, but for following audits this would become a Non-compliant.
For more information on labels please contact Guru Labels on sales@gurulabels.com.au
For more information on AS 4055 Tool training please contact training@agwa.com.au.
Service. Service. Service. These are Overseas Glass Agencies’ 3 principal values. We sat down with OGA business owner Neil Searle to fnd out about this service-based approach that has helped OGA transform from a substantial raw glass importer to a major glass processing machinery import agency.
Neil’s father, Jim Searle, sold his small glass business in Fitzroy, Victoria, in 1975 and established OGA to represent two major Japanese architectural glass manufacturers. Neil joined the business in 1976, and his passion for machinery saw the company gradually move away from glass importation and into supply of processing machinery over the subsequent decades.
OGA has been an active participant within the glass industry associations during this time, being a foundation member of AGGA (now AGWA) and IGMA, with Neil also chairing both Associations at various times.
The industry’s growth over recent decades has been exceptional, especially in the electronics areas. Neil recalls one of the very early highlights was being the frst to ofer a small optimising system in the late 1980s. Neil explains that ‘the system was a small 8-bit desktop box with a print roll on the back. You had to manually enter all the stock sizes and the required cut sizes, then after a very long wait, it would print out an optimised cutting plan ofering minimal glass waste. It was a substantial glass processing breakthrough in the 80s! The units cost around $2000 each and we sold over a hundred in the next few years!’.
Today, the team at OGA is one of the largest suppliers of glass processing systems in Australia and New Zealand, including supply and installation of glass storage, handling, edge processing, CNC processing, double glazing, Shuttle Storage systems, tempering, laminating and even water treatment systems. ‘Our success is directly attributed to the level of service we seek to provide, together
with excellent support from our suppliers’, begins Neil.
‘Because we are not a manufacturer, our success relies on supplying the best possible service in the selection, installation and after-sales support of the best, highly respected Italian machinery manufacturers’ products, ofering the latest glass processing advances and solutions. We have been truly fortunate to have been selected to represent many highly respected world-leading, principally Italian, machinery suppliers. This allows us to achieve our goal of ofering our customers the best possible solutions to improve and grow their businesses.’
As well as ofering a complete range of machinery solutions for their clients, OGA’s extensive worldwide experience allows them to ofer expert advice in developing complete production layouts for both existing and new, partial or complete, processing facilities.
This service includes the development of suggested layouts, including CAD drawings, for optimal processing solutions. Neil explains ‘a client asked us to do a complete reorganisation of their existing factory. We had prepared and submitted some suggested layouts and during a meeting with the client, and together with our Sales Manager Steve Lygris, we were able to present and modify the initial CAD layouts “live”, allowing us to develop a fnal agreed layout within a matter of hours. The client was impressed with this value-added service’, says Neil.
Self-professed machinery buf Neil has attended the biennial Glasstec Trade Show in Dusseldorf since 1978. That’s around 22 times! Glasstec is the industry’s largest glass processing machinery exhibition, featuring hundreds of the latest versions of operational machinery on show. It has always been the best opportunity for Neil and his team to mingle with suppliers and customers and to stay at the forefront of the latest developments in glass processing machinery.
‘20 years ago, as more and more Australian and New Zealand glass industry visitors were attending, we began losing touch with who was attending. Together with some of our industry competitors, we established the “Aus/NZ Happy Hour” networking event, held on the frst evening of the Exhibition. With free drinks on ofer it has become a very popular event attracting Aus/NZ attendees, as well as many of the European suppliers. It’s now recognised as a benefcial networking opportunity within our industry!’
Having processes and resources in place ensures that OGA minimises any downtime and the associated challenges that considerable time diferences present. Neil explains, ‘if our customers have an issue with their machinery, by the time we contact the manufacturers in Europe, that’s potentially 7-11 hours of downtime for the businesses here’. To overcome this substantial challenge, OGA engages independent technicians around Australia and New Zealand, as well as arranging regular Manufacturers’ Technicians service visits, to ensure clients maximise their machinery uptime.
‘Our team is the real value of this company, allowing OGA to professionally represent our respected machinery suppliers.’
An experienced and close-knit team of people are critical to the service and success of OGA. ‘It gets extremely busy at times, but experience has shown us what is manageable through the typical industry-cyclic peaks and troughs. This allows us to retain a stable, longstanding workforce. Our team is the real value of this company, allowing OGA to professionally represent our respected machinery suppliers. I am proud of their skills and the resultant exceptional service that they provide’, ends Neil.
TNT Towers, nestled in Redfern’s (Sydney) vibrant centre, stands as a beacon of luxury and innovation with its 162 luxury apartments, commercial spaces, and retail outlets, all ofering breathtaking city panoramas. This project is a testament to collaborative excellence, brought to life by the renowned architect Angelo Candalepas & Associates alongside the eminent Sydney developer Deicorp, marrying aesthetic appeal with functional design through high-end SMEG appliances, stone and marble countertops, and bespoke foor-to-ceiling windows and doors framed in aluminium.
The project’s window and door solutions, crafted by NSW Fabricator Style Windows and Doors, incorporated Darley’s commercial framing systems and CityView products, ensuring each of the building’s eighteen foors radiated with style, functionality, and strict adherence to Australian Standards. The ground foor welcomed a Woolworths Metro, adorned with Darley’s robust 150 mm x 50 mm commercial framing system, optimising visibility and light infow, essential for the bustling retail environment.
For the commercial ofces and the lobby, Style Windows selected systems that enhanced the spaces with unobstructed city views and natural lighting, adding to the workspace’s ambiance. The ofce spaces featured 100 mm front glazed framing and CityView sliding doors, known for their durability and acoustic properties, fnished in a soothing Dulux Duratec Surfmist to complement the interior’s neutral tones. Similarly, the
lobby showcased the 100 mm framing in Dulux Duratec White, paired with sleek, automatic sliding doors.
The residential quarters are no less impressive, with apartments boasting top-tier appliances and fnishes. Key to merging the indoors with the scenic exteriors are the CityView Architectural sliding doors, ofering soundproofng — a necessity given the proximity to Redfern train station — and the capability to support large, foor-to-ceiling confgurations, enhancing the residents’ living experience. The soundproof CityView Architectural Sliding doors, with an acoustic rating of Rw 35, are particularly noteworthy, addressing the challenge of noise while enabling expansive panel designs.
Additionally, the bedrooms feature CityView 50 mm heavy-duty awning windows, chosen for their superior noise reduction, ventilation, and compliance with safety standards, refecting the project’s commitment to comfort and quality.
TNT Towers is a landmark development that skilfully integrated luxury living with functional commercial spaces, thanks to the visionary design by Angelo Candalepas & Associates, Deicorp’s development expertise, and the cuttingedge window and door solutions provided by Darley and Style Windows. This blend of style, innovation and quality ensured that TNT Towers was perfectly poised to cater to the needs of both residential and commercial occupants, now and into the future.
Location: TNT Towers, 1 Lawson Square Redfern NSW 2016
Developer: Deicorp
Architect: Candalepas & Associates
Fabricator: Style Windows & Doors
Darley Systems: 150 mm x 50 mm front single-glazed commercial framing systems
100 mm x 50 mm front singleglazed commercial framing systems
CityView Awning Windows
CityView Architectural Sliding Doors
A full range of options available, including High Performing Softcoat LowE
Proven certifed full frame performance data available in WERS
Australian Glass Group also understands the vital importance of certifcation and compliance of glass products. Our products are manufactured and certifed to Australian Standards by an international certifcation body and compliance is certifed and available on request in key areas including;
It has been great seeing you all at our member forums over the last few months. AGWA held forums in all major cities to update members on AGWA activities and changes to Regulations afecting our industry.
Perched in Victoria’s Yarra Valley, the Gruyere Farmhouse, afectionately known as ‘Hilltop Hood’, is a testament to a 5-year journey, which overcame a pandemic, planning challenges and harsh weather. The journey also saw close collaboration between architects, builders, suppliers and the owners. The design process considered the challenging topography and climate of the 100-acre hilltop property.
Architect: Rachcof Vella
Builder: BD Projects
Fabricator: European Window Co
Supplier: Thermeco
Photographer: Tatjana Plitt
The Gruyere Farmhouse features 3 distinct wings, enclosing a sheltered courtyard and a unique cantilevered hood roofine, which optimised the structures’ relationship with the surroundings. The main pavilion’s unique roofine earned the project the nickname ‘Hilltop Hood’ and boasts a pitched roof that cantilevers 3 metres at both ends, providing weather protection as a ‘hood’ or ‘hoodie’ over the glazed and delicately ribbed pavilion.
The large foor to ceiling windows serve as a frame to the panoramic views, to the West capturing Melbourne’s skyline, to the North overlooking the Yarra Ranges, and a morning view over the Warramate Ranges from the master bedroom.
The Thermeco 115 series was used for their minimal frames and ability to be integrated into the fabric of the architecture. Their performance as a double-glazed thermally broken system meant the maximum amount of glass could be expressed, increasing the experience from within the dwelling.
The large sliding panels served as both doors and windows, meaning that no horizontal elements interrupted view lines.
These days winning a project is tough and delivering a project is equally challenging, while getting paid at the end often feels like being Tom Cruise in a Mission Impossible flm. However, getting all the information to allow you to price a project in full, at the very start, is a task even Hercules would be nervous at tackling.
Over recent years AGWA has reviewed disputes, the reasons behind technical queries, misinterpretation of Standards, and court cases, with projects often becoming embroiled in issues and legal challenges. Many of these issues can be linked all the way back to when the people pricing the project are not supplied with the full and accurate reports, drawings and relevant information they needed to do their job.
AGWA has developed two new Technical Fact Sheets called:
• Estimator’s Checklist for AS 4055 Houses
• Estimator’s Checklist for All Other Buildings
The Checklists highlight the missing or incomplete information which can then be followed up with the client. The Checklists also include a brief explanation of possible outcomes should the information not be provided.
AGWA’s aim with the Checklists is to help our members price on an informed and level playing feld. This is done by ensuring the person making the price request (builder or homeowner) is fully aware of all the relevant information required to provide a complete quotation, and ultimately a fully compliant product.
The frst Checklist is for homes within the geometric limits of a Class 1 or 10 building (ie, a house) as defned in AS 4055.
Class 1 and 10a buildings that fall outside these geometric limits and buildings from other categories (Class 2-9) must use the Estimator’s Checklist For All Other Buildings as this covers wind ratings covered under AS 1170.2.
The estimator can have this document open as they review a request for pricing, tick the boxes according to Yes it was supplied or No it is outstanding and then simply email the client wanting a price, showcasing what is missing, but most importantly, what the potential issue (ie, extra cost) would be for not having this information.
Some examples of issues that could arise:
Acoustics ― a project next to a major road/rail line might have a high acoustic requirement. Not having that report would mean the cost uplift to suitable acoustic glass and seals could be missed but also if the extra thick glass weighed more than the system could safety carry, there may be a need to redesign the window/door arrangements accordingly.
Sections ― a project requires a fush threshold from inside to outside but, without the sections, the strip drain is not allowed for.
Sections ordered would be wrong and the cost per metre for a strip drain (material, waterproofng, formwork etc) would have to be argued over.
Floor Plans ― AS 4055 has a rating for general and for corner locations, with the corners being a higher requirement than the main elevation. Corner windows and doors are defned as having 25% or more of any panel or pane within 1200 mm of an external corner of the building. Without the foor plan to work out if a sliding door is on a corner the light/light interlock might rate with 5 mm toughened glass yet on the corner it might require light/heavy with 6 mm toughened glass. The cost and potential non-conforming products would have to be argued over.
Façade Engineers Report ― a separate project report from a façade engineer might state that all products supplied must be tested to AS 4284, which is an above and beyond level of testing to AS 2047 compliance. This may disqualify some products from being used but after the contracts are signed, the cost to do additional testing could run to tens of thousands of dollars.
AS 1428.1 Disability requirements ― while the NCC 2022 still calls up the 2009 edition of this Standard, it might be that the specifcation or a stand-alone report requires the 2021 edition to be used. Signifcant diferences between these could lead to cost variations and the building certifer refusing a Certifcate of Occupancy.
Contract ― some contracts have onerous penalty clauses attached to them; indeed, some could state that variations due to information not requested will not be paid.
In conclusion, AGWA is always here to help you ― don’t get caught out by missing something; using our Estimator’s Checklist could save you a world of pain down the line.
For a copy of the Estimator’s Checklists and other Technical Fact Sheets please go to the Member’s portal of the AGWA website and then to the Technical Resources section.
In accordance with global imperatives for sustainable development and thoughtful resource management, Alspec is pleased to formally announce a transformative leap in our product portfolio: the GreenCore® range of low-carbon aluminium. This innovation underpins our strategic commitment to environmental, social, and governance (ESG) excellence, while maintaining our premium standards of quality and performance.
GreenCore® is not merely an aluminium product; it is a testament to Alspec’s dedication to eco-efcient solutions. ‘Green’ signifes an all-encompassing embrace of environmentally conscious practices and state-of-the-art technologies. ‘Core’ refers to the billet, signalling that the material’s reduced carbon footprint is inherent, extending throughout its entire composition. We are proud to confrm that GreenCore® specifcations are available across our comprehensive range of commercial window and door systems,
providing customers with sustainable options that do not compromise on technical excellence.
The GreenCore® range boasts a carbon intensity of just 8 kg CO2 e per kg of aluminium. The metric, expressed as carbon dioxide equivalent (CO2 e), is a universally recognised measure for assessing the global warming potential engendered during the production process. This value sets a new industry standard, showcasing our commitment to advance the frontiers of sustainable aluminium production. Our focus on reducing CO2 e in the GreenCore® range not only advances our ESG objectives, but also ofers our customers a quantifably greener choice. We invite you stakeholders to join us in pioneering a sustainable future for our industry.
Max. 800Kg. Lif Capacity
• Six degrees of movement (with Wireless Remote):
▪ 360° rotaton
▪ 300mm side shif
▪ 300mm Vertcal lif
▪ 100° forward tlt to horizontal
▪ 300mm forward extension
• Two wireless remote controls
• Dual vacuum pump system
• Installaton at elevated heights using a telehandler or of road forklif
• Fully integrated and independent power supply to drive electric actuators and vacuum pumps
• 4 x 300mm and 2 x 400mm adjustable vacuum cups
• Easy to maintain
• Patents pending
Cyber criminals do not target small businesses! This is a dangerous misconception in 2024. In the early 2000s, it was quite rare for small businesses to be targeted, but now they are considered low hanging fruit, at risk due to having inadequate resources devoted to cyber security. On average, 71% of cyber security breaches target small business with a breach being reported every 10 minutes to the Australian Cyber Security Centre.
Some examples of how businesses can be targeted are:
• Phishing attacks ― Where a cyber criminal poses as a trusted person and/or entity to gain sensitive information from their victim.
• Outdated software ― Can leave businesses open to ransomware, malware and data breaches.
• Weak passwords ― Using the same password for multiple logins or using number sequences that are easy to guess, eg, 123456 or your birthday is never recommended.
Even if you are well protected with great anti-virus or Endpoint detection and response, mail and web fltering and a next generation frewall, security is a multi-layered process and is not a set and forget system. It requires constant management and monitoring.
There are 3 areas where we see many small businesses fall short:
• Staf education with cyber security training.
• Inadequate company policies, which often even if you have them, you can’t be sure that staf have read and follow them.
• Not understanding how to complete their annual Cyber insurance questionnaire. Getting this important step wrong may lead to the insurance company refusing any claims made.
So, in this fast-paced digital landscape, what are steps businesses can take to keep their data safe?
• Ask your IT provider about scanning and monitoring the dark web for breached company email addresses and passwords.
• Run employee security training courses which can measure the risk of each employee.
• Make available continuous training, incorporating shortfocused learning sessions on cybersecurity.
• Have regular simulated phishing campaigns.
• Create strong company security policies and procedures acknowledgement.
• Consider the option of a pre-employment assessment so you can qualify a candidates cybersecurity knowledge before employment.
Ongoing cyber security training is considered the last line of defence and a breach from just one employee can afect the whole business. The repercussions of a breach are increasing your insurance premiums, efecting your reputation locally, reducing revenue due to loss of customers and time and money during downtime, paying high remediation costs and losing the trust of customers with their data.
Many organisations ask their IT company to complete their insurance forms for them. Most IT Companies will refuse to do so as it is important for the Business Owner/Director to complete them. The IT company may assist with answering the questions, but it is the Business Owner or Director’s responsibility to do their own risk assessment and due diligence, and to know what they are and aren’t covered for.
Some of the most common questions you should be able to answer are:
• Is any part of your IT infrastructure outsourced to third party technology providers, including application service providers? For example, Xero, MYOB, Microsoft 365, Shopify, NAB, CBA, Salesforce, etc
• Data type and state the number of Unique Individuals: Sensitive data (eg, medical records, passport details, TFNs etc) and non-sensitive data (eg, full names, addresses, email addresses and phone numbers)
• Access Controls: Is MFA (multi factor authentication) in force for all staf who access company resources and sensitive information?
• Do you have a disaster recovery or incident response plan?
• Do you use an endpoint detection and response (EDR) product on your network?
• How frequently do you conduct the following training for all employees:
• Cyber Risk Awareness Training?
• Phishing email simulations?
• Describe your patch management and monitoring process for operating systems and applications updates.
• Do staf have local administrative rights on their laptops/ desktops?
• Do you have any end of life or end of support hardware or software?
• Describe your data backup system and is it immutable or air gapped?
• Do you have a Cyber Security ofcer assigned in the organisation?
• If you use Microsoft 365, what is your Microsoft Secure score percentage?
To create a strong cyber security workplace culture, business leaders must make a commitment to prioritising the importance of cyber security through planning, goals and strategies as well as encouraging employees to work together to identify and address potential threats.
Phrixus Technologies is a small Managed IT Services provider and have been supporting and protecting Australian Small Businesses for 25 years. For more information, please see www.phrixus.com
The AGWA NSW Chapter enjoyed another great day on the greens at the annual Golf Day, held at Bankstown Golf Course on Friday 22 March.
Many thanks to our Major Sponsors AGG, Viridian Glass and Railsafe Balustrading. And thanks to our Hole Sponsors Express Glass, Hogans Wholesale, LiSEC, AWS, Stegbar Lansvale and Glasscorp.
Thanks for your support and we look forward to seeing you all again next year!
IGUs are the manufactured glass unit forming the glass component in a double-glazed window.
As Australia moves towards an efcient use of electricity, the energy compliance of buildings is becoming more important and insulating the entire house paramount, as windows and doors form a large part of most building envelopes.
Normal clear monolithic glass ofers very little insulation value, allowing the heat or chilly weather to afect the internal environment of a building. This means that the occupants need air conditioning or heating to ensure comfort levels inside the building, driving up energy usage.
How do you know if you have compliant IGUs that will offer long-term clear vision and good insulation value?
Azuma Design type tests IGUs to the long-term requirements of AS 4666 Insulating Glass Units. This testing ensures good manufacturing practices have been used to produce good IGUs that will last for many years, providing great insulation. The sample IGUs are placed in an accelerated weathering cabinet for 15 weeks. Azuma Design then tests the moisture content of sample products provided both before weathering and post weathering. A failure will result if the moisture content has increased signifcantly post testing, also indicating to the manufacturer that they will need to correct their manufacturing practices before they are issued a compliance certifcate.
Great IGUs need to have both their primary and secondary seals applied correctly for longevity, ensuring that no moisture can penetrate the internal gap between the windows. If these seals fail, moisture will penetrate, ruining the integrity of the IGU, decreasing the insulation value of the IGU and possibly the visual aspect, allowing fogging in the internal gap. Many IGUs have argon gas flling in the gap between the two glass panels providing a 10%15% insulation improvement. If the seals fail then this gas escapes, reducing the insulation value the IGU provides, meaning the building envelope is compromised.
Azuma Design’s testing capabilities ensures that the IGUs presented for type testing have been manufactured correctly from a supplier are of great quality. If the IGUs pass the long-term testing requirements of AS 4666, then the product is ft for purpose and installation. This means that the product then is ideal for meeting the comfort levels we expect over the useful life expectancy, while installed in the building.
Manufacturers are required to type test there IGUs every 2 years when purchasing double-glazed windows, ensuring that the product purchase has been accredited.
For more information, please contact www.azumadesign.com.au.
LiSEC Australia is excited to announce the recent expansion of its team with the addition of 8 new members since September 2023. This growth will enhance our capacity to support our valued customers in areas of machinery, software, spare parts, project delivery, customer service, sales, fnance, and administration. Strengthening the footprint of the service department has been an area of focus, achieved through the recruitment of technicians to support New South Wales, Western Australia, and Victoria.
LiSEC operates globally and has ofered innovative individual and complete solutions in the feld of fat glass processing and fnishing for more than 60 years. The performance portfolio includes machines, software solutions and services.
When LiSEC frst entered Australia, it was a humble beginning. The Sydney branch, established in 2006, operated with a team of just three. Angela De Maina, Projects and Service Coordinator and a long-term employee, recalls in the early days they processed only a handful of orders and responded to a couple of queries in a day.
Since then, the subsidiary has experienced remarkable growth, a testament to its commitment to excellence and innovation. LiSEC holds an impressive share of glass machinery and software in the region. With such a substantial presence, efective collaboration within the team of 29 is essential.
Meeting customer demands requires a synchronised efort and shared vision. The vision for LiSEC Australia is to be the partner of choice for glass processors’ automation requirements and their digital transformation journey. Twain Drewett, Head of HUB Region COS-Oceania/SEA, says about his plans for the future: ‘Our key focus is to increase LiSEC’s value proposition to existing and new customers by providing “all.in.one:solutions” that combine top-tier machinery and software with quality end-to-end support services, with customer success central to all that LiSEC do every day.’
Darley Aluminium completes Fenestration Essentials course
AGWA ran its frst Instructor Led training course for 2024 with a face-to-face course with Darley Aluminium on 21 and 22 February. The 2-day course was held in Parramatta and covered glass and framing materials, Standards, hardware and installation, and energy, among other things. Every attendee submitted
their assessment on time and passed, an amazing achievement. It was a pleasure meeting everyone and being able to facilitate this training event. A big thank you to Ray Kwan for organising the attendees. Congratulations to all the following staf who attended:
Maria Babic, Mark Lee, Joshuah Leigh, Sarah Joass, Luke Wicks, Fred Kwan, Alyce Martinuzzo, Gemma Morrison, Rebecca
Li, Daniel Turner, Seho Kim, Joe Su, Alistair Foss, Mike Roe, Harshad Kulkarni, Harrison Blair, Matt Scott, Tammy Banabakis, Cindy Scriven and Prashanth Danam.
If you are interested in exploring AGWA running a custom course for your business, please contact training@agwa.com.au
Congratulations to recent course graduates February-March 2024
Upcoming Training July and August 2024
• AS 1288 Human Impact and Wind Loadings, 3/7/24, 1.00–4.00 pm, via Zoom
• Fenestration Essentials, 9/7/24 (then 11/7, 16/7, 18/7, 23/7), 1.00 -3.30, pm via Zoom
• AS 1288 Overhead, Barriers and Structural, 24/7/24, 1.00–4.30 pm, via Zoom
• Window Essentials Azuma ,7/8/24, 8.30 am-4.00 pm, face-to-face.
The National Construction Code is revised on a triennial basis, meaning a new edition is published every 3 years. The Australian Building Codes Board (ABCB) published a preview version of NCC 2025 on the 1 May with a public comment period extending until the 1 July.
Key changes which afect our industry include:
• Section A Governing Requirements ― new provisions and requirements for new provisions to improve how updated Standards can be used. Currently, the edition of a referenced document listed in NCC Schedule 2 must be used, even if a newer revision exists, however the new ‘register of alternative referenced documents’ will provide that newer revisions can be used much sooner.
• Section F Health and Amenity ― Part F1 includes the expansion of provisions for surface water management, including new
Objectives, Functional Statements, Performance Requirements and DTS provisions designed to minimise the risk of water leaking into or accumulating within a building and causing unhealthy conditions or damaging building elements.
• Section J Energy Efciency requirements ― including DTS external envelope provisions for wallglazing (clause J4D6) for commercial buildings (Class 3-9 and Class 2 common areas) intended to reduce greenhouse gas emissions, reduce commercial building running costs, make commercial buildings more resilient to heatwaves, and assist with the decarbonisation of the electricity grid.
A copy of the NCC 2025 preview version can be downloaded from the ABCB website from 1 May 2024.
The Australian Glass & Window Association is working closely with members to understand the likely impact of these amendments on our industry and provide appropriate feedback to the ABCB and the Government. We encourage members to familiarise themselves with the proposed measures and provide feedback to technical@agwa.com.au by the 24 June to inform our response.
AGWA and Standards Australia Store have curated the Windows & Glazing Set, available with 2 user licenses* for only $192.34 per year incl. GST.
AGWA members save 10% on access to the Windows & Glazing Set, as well as over 20 other unique content sets covering a wide range of trades. (Eligibility criteria and T&Cs apply)
Use voucher code: tLrSxjNK
Scan the QR code or visit store.standards.org.au/curated-subscription/windows-glazing
Designed for glaziers and building professionals involved in the installation of glass windows and doors in buildings. Included documents in the Windows and Glazing Set:
*For small businesses with less than 20 employees only
AS 1288 SUPP 1-2006, Glass in buildings — Selection and installation (Supplement to AS 1288-2006)
AS 3959:2018, Construction of buildings in bush-fre prone areas
AS 4666:2012, Insulating glass units
AS/NZS 4667:2000, Quality requirements for cut-to-size and processed glass
AS 2047-2014, Windows and external glazed doors in buildings
AS 1428.1:2021, Design for access and mobility, Part 1: General requirements for access — New building work
AS 4055:2021, Wind loads for housing
AS 1288:2021, Glass in buildings — Selection and installation
Rencraft® is a revolutionary polycarbonate product that will change the perception of transparent glazing forever with the following features and benefts:
• Virtually unbreakable ― Tested to AS 3555.1: 2003 Building Elements Testing and Rating for Intruder Resistance.
• Virtually Flawless ― Superior optics and light transmission compared to any transparent glazing material.
• Surface abrasion resistance as good as glass ― windscreen wiper resistant for heavy equipment and mass transit applications.
• Supplied in fat sheets or can be supplied in 3D shapes with compound curves and black frit printing.
• Half the weight of glass and available from stock in fat sheet in gauges of 6 mm, 9.5 mm and 12.7 mm and other gauges on request.
• Can be digitally printed direct to surface.
• It has 15 Year Warranty
The applications for Rencraft® are virtually limitless for both residential and commercial applications and it can be cut, drilled and fabricated on or of-site. It is currently used for windows in safety and security applications such as correctional facilities,
holding cells, mental health facilities, automotive, mass transit, mining and rail and has the following ISO accreditations, local and international safety glass compliance and certifcations:
ISO 9001:2015 and ISO 14001:2015
AS 2080: 2019 ― Australian Safety Glazing for Land Vehicles
ECE 43R ― European Safety Glazing Materials and Installation in Vehicles
ANSIZ 26.1 ― US Safety Glazing Motor Vehicles
AS 2, AS 4, AS 5 ― US Safety Glass Standard
JIS R 3211 ― Japan Safety Glass Materials for Road Vehicles
GAT Technologies is the exclusive distributor of the Rencraft® product range and we look forward to working with the market to identify applications that would beneft from this new technology.
For more information please contact www.gat.com.au
Making life easier for their OEM customers was high on the priority list at ASSA ABLOY when they designed the new Lockwood Induro 2-point lock because they really have thought about making life easier for their customers with this new product.
Part of a full refresh of their Euro Profle Mortice Lock range, the Induro series replaces the Optimum series locks. The solutions-focused redesign thinking led to the unique applications, the Induro 2-point and 4-point locks, which are signifcantly diferent in their functionality, despite being under the same Induro banner.
The Induro 2-point lock has customer experience highest on the agenda. Listening to customers who found the lock-status indicator of the Optimum added complications to installation, they removed this feature for the Induro.
Long-throw vs short-throw bolts were also changed to better suit customers. Previous products had specifc locks for each of these confgurations, but the Induro 2-point made this a selectable feature, so
the one lock can do both! While the more commonly desired long-throw is the default setting, it is easy to limit it to short-throw. The upgrade means SKU reductions, easier order forecasting, less stock on shelves, and more fexibility in inventory consumption. This seemingly small change, with big advantages, really highlights the considerations made by the ASSA ABLOY bofns in this new product design. Make sure to check it out.
For more information on the Induro 2-point lock, visit www.lockweb.com.au
A major problem for glass, window and panel installers is to install units above ground level. Whenever a glazing robot is designed to reach a greater height, there is always a cost.
Invariably the mobile base must grow in weight and outriggers to support the extra forces making it a less nimble mobile machine for use in restricted spaces.
The OMNI 800 has overcome this problem by becoming a specialised Glazing robot for working at heights. The OMNI 800 glazes multi-storey buildings and houses using a telehandler or of-road forklift, which can be used inside and outside a building envelope to allow for safe and efcient glazing of glass, windows, panels and stone weighing up to 800 kg.
Accurately controlled by wireless remote controls, one remote is used by the forklift driver outside the building envelope and the second remote is used by the operator on the inside of the building.
There are 6 degrees of precise speed adjustable movement, allowing for precision movement for installation, controlled by the operator inside the building with the remote including:
• 300 mm forward movement;
• 300 mm side shift;
• 300 mm vertical shift;
• 95 degrees forward tilt to horizontal;
• 360 degrees rotation; and
• 30 degrees side pivot.
The OMNI 800 has a fully integrated and independent power supply to drive electric actuators and vacuum pumps. All components and batteries are housed under the OMNI’s distinctive blue hood.
The OMNI 800 has a genuine Dual Vacuum System including 2 vacuum pumps, vacuum sensors and alarms. Six spring-loaded adjustable vacuum cups (2 x 400 mm and 4 x 300 mm) deliver greater safety while handling the panel.
For more information, please contact Quattrolifts at martin@quattrolifts.com
Glaston, a pioneer in cutting-edge glass processing technologies, continues to advance automation solutions that improve the quality, efciency, and proftability of glass tempering.
Efortless glass tempering with Autopilot Glaston Autopilot is the company’s newest technology in the feld of tempering automation. This groundbreaking system provides fully automated glass tempering, taking care of all necessary settings and process adjustments. By minimising manual input, the solution guarantees repeatable quality ― regardless of operator or shift.
With its outstanding features, Glaston Autopilot contributes to the lowest operating costs ― and highest proftability. It enables unmatched output and yield by bringing simplicity and ease to glass tempering and especially facilitating mixed production.
Additionally, the system empowers glass processors to attain up to 50% in energy savings. As it eliminates downtime between product transitions and optimises bed loading and utilisation, maximised efciency is ensured. By fostering precision throughout the entire production line, it efectively minimises waste.
Glaston tempering line with its solid design, automation and the highest uptime supported by services ofers a
reliable solution for a lifetime. Plus, system upgrades allow glass processors to easily keep pace with industry developments, maintaining a competitive edge.
Enhanced safety with OSC Glaston Online Stress Calculation (OSC) solution calculates glass surface stress, middle-pane tension, and estimated fragmentation amount for all processed glasses. This tool automates quality monitoring, replacing inefective conventional approaches. By increasing automation, we can be more certain that the safety standards required for tempered glass are met.
The system issues automatic alerts when any variations in stress levels are detected. The results are based on real-time measurements of critical process variables during the tempering process.
Autopilot and OSC mark a signifcant leap forward in redefning the glass tempering industry and increasing glass processors’ proftability. These innovative solutions not only elevate quality and safety in glass processing but also guarantee heightened efciency, directly translating into increased profts.
Both are available as an optional feature for new Glaston tempering lines or as an upgrade for Glaston’s existing lines.
For more information please contact www.glaston.net
The architectural landscape has witnessed a transformative shift towards a more open and functional living environment, with window louvres emerging as one of the preferred choices among homes, commercial, and industrial settings. This growing trend is driven by the myriad benefts that louvres ofer, making them an ideal solution for those seeking both aesthetic appeal and practical functionality.
One of the key advantages of window louvre galleries lies in their ability to provide a 100% opening advantage. Unlike traditional windows, louvres enable an unrestricted fow of air and natural light into living and working spaces, creating an atmosphere of openness and healthy living attributes. This unique feature not only enhances the overall living experience, but also promotes energy efciency by reducing the reliance on artifcial lighting and ventilation systems. Louvres are a versatile window type used in everything from hot climates with high airfow, to winter gardens in the colder climates.
Ventus Louvre Galleries have been in the market in Australia for many years now, and recently Doric undertook a redevelopment and expansion of the Ventus Louvre Galleries facility at its Wetherill Park (Sydney) operations centre to meet growing demand. Taking pride in being Australian owned and moving to be locally manufactured, this strategic move not only ensures a greater supply to meet the growing market needs but also brings home control over the quality of products. As a result of the implemented changes rolling out, our customers can expect to see better support, increased responsiveness with orders, and enhanced colour choices.
What has set Doric’s Ventus Louvre Galleries apart from the rest of the market over time has been the attractive streamlined blade clip design with integrated strong clips, providing functional architectural aesthetics, durability, and longevity. Furthermore, meeting and going beyond compliance requirements as proven through rigorous tests to meet the standards set by AS 4420 and AS 2047. This commitment to adherence underscores the reliability and performance of louvres, making them a trustworthy choice for architects, developers, builders, and window fabricators.
Doric’s Ventus Louvre Galleries are manufactured with a High Mar resistance powder coat, providing protection against the elements while maintaining a fawless appearance and a range of blade sizes and handle options.
For more information about Doric’s capabilities for projects and sales inquiries, contact us at at www.doric.com.au/ventus/ or 1300 132 389
At Smartech, crafting personalised solutions that resonate with the individual style and requirements of our clients is our forte. In a bespoke residential project located in Perth, Western Australia, we’ve designed a Tilt Glazed Garage Door that perfectly marries functionality with elegance, thus enhancing the home’s curb appeal.
In tune with our client’s desire for a glazing solution that ofers both privacy and soft, natural light, we’ve selected acid-etched frosted glass for the Tilt Garage Door. This choice not only fulfls the need for difused lighting but also adds a layer of aesthetic elegance. The satin fnish, known for its low maintenance, greatly diminishes the visibility of dirt and fngerprints. Additionally, the glass’s thermal properties ensure a consistent, comfortable temperature within the garage throughout the year.
Our Glazed Tilt Garage Doors, with their sleek, refective design, perfectly complement modern architectural styles, integrating the garage as a natural extension of the home’s elegance. They illuminate the garage with sunlight during the day and subtly display the vehicle at night, hinting at the luxury within.
Opt for the efortless convenience of our motorised system for easy access with just a push of a button, or choose the rewarding feel of manual operation, enhanced by our precisely engineered counterweight system. This system ensures smooth, efortless motion, improving your daily interactions with the door.
Elevate your home’s elegance today with Smartech Tilt Glazed Garage Doors.
For further information about any Smartech products or services, please visit www.smartechdoorsystems.com.au or email sales@ smartechdoorsystems.com.au
‘Sustainability’, ‘energy efciency’ and ‘environmentally friendly’ are not just buzz words to help make sales but real issues for our generation to tackle, which need to be chipped away at from every angle.
Induro 4-point lock is ASSA ABLOY’s latest contribution towards shifting the needle and helping its customers to achieve their targets too. The additional points of locking in the older 4-points were always there to not only add security, but also help achieve better door sealing and meet higher standards. With the increasing focus on sealing requirements, ASSA ABLOY focussed on improving these even further.
The Induro 4-point lock’s bolt has lever compression as its locking function, with a lift-bolt replacing the more common throw-bolt. The design of the bolt incorporates a taper-out so that as the bolt is engaged and lifted, the taper pulls the door tighter closed against the seals. Using a lift-to-lock cleverly utilises the handle lever to provide the lever force required to pull the whole door in, a load which would be difcult for users to apply with a key.
By having better compression locking, the Induro 4-point helps achieve better sealing efciency on those doors that are hardest to seal and that are growing in demand, such as large aluminium framed doors, especially when used in French and bi-folding confgurations.
The time is right to start thinking about better ways to achieve our collective environmental targets, so it is defnitely worth considering upgrading from 2-point to 4-point locking with the new Induro.
For more information on Induro 4-point lock, visit www.lockweb.com.au
Looking to reach the highest quality for all types of tempered glass?
Here are three reasons why Glaston tempering technology is your best choice:
1. #1 for quality with any product or glass type
2. Lowest production costs with high energy effciency
3. Highest automation level
How to avoid common mistakes and succeed in the glass tempering business — Download THE TEMPERING LINE BUYER'S GUIDE here www.glastory.net
Machinery, services and solutions designed with the future in mind for the architectural, mobility, display, solar and appliance industries. info@glaston.net | www.glaston.net | www.glastory.net | www.gpd.f
CK Facade Pty Ltd, Auburn, NSW
DGU Manufacturing, Condell Park, NSW
GAT Technologies, Williamstown, VIC
Harbour Glass, Langwarrin, VIC
Hustle Installations, Tullamarine, VIC
Ozwest Group, Wangara, WA
Premier Windows (WA) Pty Ltd, Balcatta, WA
SAL Commercial, Revesby, NSW
Vision Solutions Glass and Aluminium, Kuluin, QLD
Wizard Glass & Windows Pty Ltd, Clontarf, QLD
In March, AGWA’s Victorian auditor Michael Spencer met with Windoor Joinery’s General Manager, Ryan Cumming, at their premises in Sydney to undertake their frst compliance audit. Michael was extremely impressed, not only with the quality of their timber craftsmanship, but their commitment to the 3 ‘Pillars’ of AGWA’s Accredited Companies Program (ACP).
Established in 1985 as a family-run business, Windoor Joinery joined AGWA in 2022. From small beginnings manufacturing timber windows and doors from a garage in Liverpool, they now operate a 5000 sq metre factory at St Marys with the most up-to-date machinery and tooling and employing over 40 staf.
From a compliance perspective, Michael was able to access a range of test reports on site to support the timber window and door products being fabricated including sliding doors, awning and sliding windows. Products are typically glazed to meet the standards set by the N2 wind classifcation system where a house must stand up in winds of 26 m/sec (93.6 kmph) and gusts of 40 m/sec (144 kmph). This classifcation is relevant to most of NSW.
Windoor Joinery’s commitment to maintaining skills and currency in training goes well beyond the minimum requirements of AS 1288 and AS 2047
currency needed to satisfy Pillar 2. Both Ryan and Sales Manager, Stuart Neilsen, completed AGWA’s Fenestration Diploma Program, with other colleagues currently enrolled as well. Numerous staf have also accessed courses such as the AS 1288 Human Impact and Wind loadings, AS 2047, Acoustics and Windows in Bushfre-Prone Areas.
Commitment to workplace safety is also front of mind. Michael was able to sight numerous safety documents that met and/or exceeded the legal minimum requirements as well as see their practical day to day implementation on the factory foor.
Overall, Michael felt the calibre of this frsttime audit was noteworthy and enjoyed the opportunity to see frsthand the sheer size and scope of Windoor Joinery’s range and operations and their commitment to sustainability.
If you would like any information regarding AGWA’s audit program including training options for your next audit, please contact: accred@agwa.com.au.
AGWA welcomes the following Accredited Members
A K&R Windows and Doors, Campbellfeld, VIC
A1 Screens & Maintenance, Scoresby, VIC
Aluming Pty Ltd, Rydalmere, NSW
BetaView Aluminium Windows & Doors, St Marys, NSW
BGS Aluminium Pty Ltd, Horsley Park, NSW
CVD Commercial Glass & Aluminium
Windows P/L, St Marys, NSW
Distinct Aluminium Solutions, Lidcombe, NSW
ODS Windows, Btraeside, VIC
Oracle Windows, South Windsor, NSW
PG Windows, Gnangara, WA
RJS Aluminium Group Pty Ltd, Bankstown, NSW
Rylock Pty Ltd – Geelong, VIC
Starglazing Pty Ltd/ Red Crab Windows & Aluminium, South Geelong, VIC
Stegbar Pty. Limited, Lansvale, NSW
Trend Windows & Doors, Girraween, NSW
Trenda Window and Door Pty Ltd, Punchbowl, NSW
Weatherall Windows, Campbellfeld, VIC
Windoor Joinery, St Marys, NSW
Windows for Life, Campbellfeld, VIC
High performance double glazing.
The ideal residential solution for 7 Star compliance.
LightBridge™ o ers exceptional insulation, reduces energy consumption and limits heat conduction between inside and outside temperatures.
Locally stocked and manufactured for short lead times and reliable supply.
Australian Certified Compliance & Performance
UV Protection
Australian Manufactured