ELEKTRISCH VERZÖGERN
Die Rekuperation ist eine tolle Sache. Aber es ist nicht ganz einfach zu entscheiden, wann die E-Maschinen Verzögerungshilfe von den Radbremsen kriegen sollen und wer dann den dazu nötigen korrekten Druck aufbaut. Der von der E-Maschine gelieferte Strom muss noch gleichgerichtet und auf das Spannungsniveau der Batterie gebracht werden. Ausserdem muss die Batterie diesen Strom verarbeiten und aufnehmen können. Text: Andreas
Lerch | Bilder: Bosch, Volkswagen, Lerch
Bild 1. Klar und deutlich zeigt dieses Bild, was Rekuperation ist. Aber auch hier liegt der Teufel im Detail. Welche elektrische Verzögerung liegt wie lange elektrisch und thermisch drin?
Dass elektrisch betriebene Fahrzeuge an einer Steckdose oder einer Wallbox aufgeladen werden, ist klar und bekannt. Die Plug-in-HybridFahrzeuge, welche auch mit Netzstrom aufgeladen werden können, sind auch verbreitet. Es ist natürlich sinnvoll, die Batterien am Netz zu laden (auch ohne eigene Photovoltaikanlage), denn im Moment ist die elektrische Energie – trotz der ständigen Preisaufschläge – immer noch günstiger als die chemische Energie in Form von Benzin oder Diesel. Hybridfahrzeuge ohne Plugin-Möglichkeit müssen ihre Batterien aber auch irgendwie laden. Das geschieht über Lastpunktverschiebungen und über rekuperatives oder regeneratives Bremsen. Beim Rekuperieren wird ganz einfach die Traktionsmaschine (Elektromotor) des batterieelektrisch betriebenen Fahrzeuges (BEV) oder des Hybridfahrzeuges (HV) als Generator eingesetzt. Wenn der Generator mechanische Energie in elektrische
Energie umwandelt, kann er auf diese Art und Weise das Fahrzeug abbremsen und die Batterie aufladen. Wunder lassen sich damit nicht erreichen, aber ein Teil der Bremsenergie geht nicht als Wärme in die Umwelt, sondern als elektrische Energie in die Batterie. Was so gespart und wieder eingesetzt werden kann, ist für das Portemonnaie des Fahrers, aber auch für die Umwelt positiv. Und da gilt natürlich das alte Sprichwort: «Wer den Rappen nicht ehrt …».
Kinetische Energie
Bewegt sich ein Körper mit einer bestimmten Masse, so entwickelt sich in ihm eine Wucht. Das kann die Faust eines Boxers oder der Fussball im Flug oder beim Rollen sein. Auch das Auto hat eine Wucht. Diese ist bei einer Vollbremsung oder gar bei einem Crash nur allzu gut spür- und hörbar. Diese Wucht ist eine spezielle Energie. Sie wird Bewegungsenergie oder auch kinetische Energie genannt. In der Physik berechnet man sie nach der Formel:
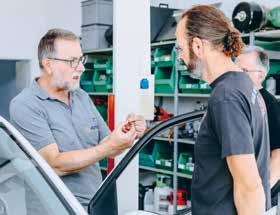
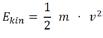
m steht für die Fahrzeugmasse und v für die Geschwindigkeit. Da gerade Elektrofahrzeuge sehr schwer und häufig auch stark motorisiert sind, können die Annahmen im Bild 2 als realistisch angeschaut werden. Die blaue Kurve symbolisiert ein Fahrzeug mit einer Masse von 1000 kg. Die oberen Kurven symbolisieren Fahrzeuge, welche immer um 500 kg schwerer werden. Die graue Kurve entspricht demzufolge einem Fahrzeug, welches doppelt so schwer ist wie das Fahrzeug der blauen Kurve. Doppelte Masse bedeutet, dass auch die kinetische Energie bei gleicher Geschwindigkeit doppelt so hoch ist. Die gelbe Kurve steht für ein Fahrzeug mit 2.5 t. Seine kinetische Energie beträgt bei 100 km/h 965 kJ und bei 200 km/h 3860 kJ. Das sind genau viermal mehr. Da die Geschwindigkeit doppelt so hoch ist und diese auch noch im Quadrat in der Formel steht, bedeutet das «doppelt im Quadrat» oder vierfach. Damit wirkt sich die Geschwindigkeit viel aggressiver auf die kinetische Energie aus als die Masse.
Beim Bremsen muss diese Energie wieder in eine andere Energieform umgewandelt werden (Wärme oder elektrische Energie). Aufgrund der doppelten Energie ist auch der Bremsweg bei doppelter Geschwindigkeit gegenüber der einfachen Geschwindigkeit viermal länger. Bei elektrisch betriebenen oder unterstützten Fahrzeugen kann ein Teil dieser Energie in elektrische Energie umgewandelt und in der Batterie erneut gespeichert werden.
Wie soll gebremst werden?
Mit welcher Intensität elektrisch verzögert werden kann, hängt von verschiedenen Aspekten ab. Sicher ist die Leistungsfähigkeit der EMaschine ein wesentlicher Faktor. Dabei geht es aber auch darum, mit welcher Drehzahl die Drehstrommaschine gerade bewegt wird. Da Elektrofahrzeuge in den meisten Fällen über ein nicht schaltbares Einganggetriebe verfügen, ist die Motordrehzahl direkt proportional zur Fahrgeschwindigkeit. Bei hohen Drehzahlen kann die Leistungsgrenze der E-Maschine schnell erreicht werden (Feldschwächbereich – Bild 3, Bereich 3). Bei mittleren Drehzahlen (Grunddrehzahlbereich – Bild 3, Bereich 2) weist die E-Maschine ein konstantes Drehmoment auf, und da kann es häufiger vorkommen, dass rein elektrisch verzögert werden kann. Bei geringen Drehzahlen wird dann die Induktion schwächer und die Reibungsbremsen müssen eingeschaltet werden (Bild 3, Bereich 1). Wenn die Leistungsgrenzen der E-Maschine überschritten werden, überhitzt diese. So muss also über die Regelung des Thermomanagements dafür gesorgt werden, dass die Motorkühlung möglichst effizient verläuft. Sonst muss die Bremsleistung
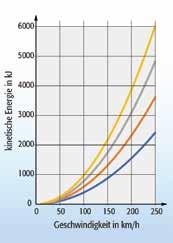
Bild 2. Die kinetische Energie ist abhängig von der Fahrzeugmasse und der Geschwindigkeit. Fahrzeugmassen: blau: 1000 kg, orange: 1500 kg, grau: 2000 kg, gelb: 2500 kg.
Bild 3. Das grundsätzliche Diagramm einer EMaschine für Vorwärtsfahrt. Das orange Feld zeigt die Betriebspunkte der EMaschine, das blaue Feld jene der Betriebsbremse. 1 Kleine Geschwindigkeit, die Reibungsbremse übernimmt –
2 Mittlere Geschwindigkeit, die EMaschine ist im optimalen Bremsmomentbereich –
3 Hohe Geschwindigkeit, die Leistung der EMaschine begrenzt die Rekuperation.
am Motor gedrosselt werden. Auch die Batterie muss sich bei einer Bremsung in einem SOC-Bereich befinden, in dem sie Energie aufnehmen kann. Ist ihr Ladezustand zu hoch, darf ebenfalls nicht rekuperiert werden. Ist der Ladezustand jedoch im richtigen Bereich, muss auch hier wieder beachtet werden, dass die Batterie ob dem grossen zugeführten Strom nicht überhitzt. Also ist auch hier das Thermomanagement gefordert. So wird auch klar, warum heute von Thermomanagement gesprochen wird und nicht mehr einfach von Kühlung.
Wer bestimmt aber nun, ob rekuperiert werden darf oder nicht? Das sind die Steuergeräte des Motors und der Batterie, welche sich verständigen müssen, wo die Betriebstemperaturen gerade liegen und welchen Ladezustand die Batterie gerade aufweist. Dann muss das Steuergerät des Motors bestimmen, wie viel Energie die E-Maschine gerade abliefern könnte. Wenn alle diese Kontrollen zu einem positiven Ergebnis geführt haben, kann mit der Verzögerung begonnen werden.
Rekuperationsmodell
Im Bild 4 sind einige Zusammenhänge zwischen dem mechanischen und dem elektrischen Bremsen dargestellt. Zunächst muss das System klar erkennen, dass der Fahrer bremsen will und wie stark er bremsen will. Diese Information liefert das Bremspedal bzw. die Sensorik, welche in der Bremsbetätigungseinheit verbaut ist.
Das Bremssystemmodul verarbeitet diesen Wunsch, vergleicht ihn auch mit den Fahrzustandsvariablen, z. B. mit den ABS-Sensoren, um zu ermitteln, ob die gewünschte Verzögerung physikalisch überhaupt darstellbar wäre. Gleichzeitig stellt das Bremssystemmodul an das elektronische Fahrzeugmodul die Anfrage, wie viel Bremsmoment in diesem Moment gerade elektrisch geleistet werden könnte. Das Fahrzeugmodul verarbeitet die Sensorinformationen der E-Maschine und weiss, wie diese ausgelastet ist und wie stark sie thermisch belastet ist. Das Fahrzeugmodul fragt auch beim Batteriemodul nach, wie es mit der Batterie aussieht. Die Antworten werden verknüpft und als Rekuperationspotenzial wei-
tergeleitet. Daraufhin wird dieses Potenzial als Generatormoment angesteuert und das Bremssystemmodul steuert – falls erforderlich – den hydraulischen Druck für das restliche Bremsmoment zu den Radbremsen.
Rekuperationsarten
In der Umsetzung der Bremsrekuperation gibt es verschiedenste Ausführungsmöglichkeiten. Natürlich geht es da auch wieder um die Qualität und um den Preis der Ausführung. Im Bild 5a ist eine einfache Version für Hybridfahrzeuge dargestellt. Das Bremspedalspiel wird vergrössert, ein Wegsensor misst den Pedalweg und gibt diesen Weg als Sensorgrösse weiter. In dieser Ausführung wird zuerst nur elektrisch verzögert und erst wenn das Pedalspiel überdrückt ist, wird im Hauptbremszylinder Druck aufgebaut und die Reibungsbremsen rund um das Fahrzeug werden betätigt. Da die E-Maschine aber keine gleichbleibende Verzögerung realisieren kann (vgl. Bild 3), muss
der Fahrer mit dem Pedalweg das zusätzliche Reibungsbremsmoment immer mit seinem Bremsfuss neu einregeln.
Das zweite System (Bild 5b) verfügt immer noch über einen Unterdruckbremskraftverstärker, da aber das Fahrzeug offenbar auch elektrisch betrieben werden kann, wird zusätzlich eine Unterdruckpumpe zur Evakuierung des Bremskraftverstärkers benötigt. Das vergrösserte Pedalspiel ist hier durch eine aufwendigere elektronische Regelung mit dem Pedalwegsensor ersetzt worden. Dazu gehören auch ein Pedalwegsimulator und vor allem ein Gegenkraftsimulator. Je nachdem, wie viel vom Bremsmoment elektrisch aufgenommen wird, ist die Gegenkraft am Pedal sehr gering und muss mit dem Simulator ergänzt werden, damit der Fahrer ein vernünftiges Bremspedalgefühl kriegen kann.
Bei den Systemen c und d sind die Betätigungen und die Drucksteuereinheiten nicht mehr mechanisch miteinander verbunden. Das heisst,
Bild 4. Die gesamte (vereinfachte) Rekuperationseinrichtung besteht aus der elektrischen Antriebseinheit und der Reibungsbremse des Fahrzeuges. Der Schnittpunkt zwischen den beiden Einrichtungen wird von einem oder mehreren Steuergeräten übernommen.
Bild 5. Vier unterschiedliche Ansteuerungen der hydraulisch betätigten Radbremsen. 1 Pedalkraft – 2 Pedalwegsensor – 3 vergrössertes Pedalspiel –4 Bremsweg und Gegenkraftsimulator –5 Hauptbremszylinder – 6 Unterdruckpumpe – 7 Druckleitung zur Lenkhilfepumpe – 8 Hydraulikpumpe.
die mechanische Verbindung ist bei normaler Fahrt nicht aktiv und kommt nur bei Systemausfällen in Aktion. Die beiden Systeme unterscheiden sich im Wesentlichen durch die hydraulische Energieerzeugung. Beide Systeme sind in ein Steuermodul mit Bremspedal, Sensor und Simulator bzw. ein Aktormodul mit hydraulischem Bremskraftverstärker, Ventilblock und Hauptbremszylinder aufgeteilt. Die Ansteuerung der Magnetventile erfolgt über das Steuergerät. Im Bild c erfolgt der Druckaufbau durch die Lenkhilfepumpe und im Bild d ist eine spezielle Druckpumpe eingebaut.
Drehstrommaschinen
Drehstrommaschinen sind Wechselstrommaschinen, welche mit drei-
phasigem Wechselstrom funktionieren. Der dreiphasige Wechselstrom umfasst drei sinusförmige, aber um 120° versetzte Schwingungen. Wird mit jeder Phase je ein Lämpchen bestromt, so leuchten die Lämpchen nacheinander auf. Sind sie im Kreis angeordnet, so scheint es als würden sich die Lichtimpulse drehen. Werden die Lämpchen mit Spulen ersetzt, so dreht sich nicht Licht, sondern ein Magnetfeld und es wird von einem Drehfeld gesprochen. Befindet sich ein gelagerter Permanentmagnet im Innern der Spulen (Bild 7), so wird der Magnet vom sich drehenden Feld mitgezogen, es handelt sich um einen permanenterregten Synchronmotor (PSM). Beim elektrisch erregten Synchronmotor (ESM), werden die beiden Pole des Rotors von einer gleichstromdurchflossenen Wicklung erzeugt.
Die Asynchronmaschine (ASM) verfügt im Rotor über leitende, aber an den Rotorenden kurzgeschlossene Stäbe. Durch das Drehfeld wird Spannung in diese induziert, und wenn ein Strom fliesst, baut sich ein Magnetfeld um die Stäbe auf, welches mit dem Statorfeld reagiert. Damit die Induktion funktioniert, braucht es eine Drehzahldifferenz zwischen Rotordrehzahl und Drehfelddrehzahl (Schlupf). Je grösser der Schlupf, desto grösser das Drehmoment. Ein konstruktionsabhängiger Maximalschlupf darf jedoch nicht überschritten werden.
Die Synchronmaschinen weisen keinen Schlupf auf, aber auch bei ihnen hängt im motorischen Betrieb der Rotor etwas hinter dem Drehfeld zurück. Wenn dieser positive Lastwinkel (Bild 7) zu gross werden sollte, kommt der Motor aus dem Takt und bleibt stehen. So ist auch sein maximales Drehmoment bestimmt.
Vier-Quadranten-Diagramm
E-Maschinen können grundsätzlich in vier Quadranten arbeiten (Bild 6). Im ersten Quadranten ist der «normale» Antrieb dargestellt: Die Maschine läuft als Motor und treibt
Bild 6. Das VierQuadrantenDiagramm von Drehstrommaschinen. Diese EMaschinen können vorwärts und rückwärts antreiben und verzögern, deshalb werden ihre Kennlinien in die vier Quadranten eines Diagramms verteilt.
das Fahrzeug vorwärts an. In diesem Quadranten werden die meisten Diagramme, auch die LeistungsDrehmoment-Diagramme von Verbrennungsmotoren dargestellt. Bei E-Maschinen liegt bei null Drehzahl das Drehmomentmaximum an. Dieses kann durch Spannungssteigerung bis zur Grunddrehzahl konstant gehalten werden; danach wird durch die Selbstinduktion das magnetische Feld schwächer, und das Drehmoment fällt ab. Man spricht vom Feldschwächbereich.
Da aber gleichzeitig die Drehzahl weiter ansteigt, bleibt die Leistung im Feldschwächbereich ziemlich konstant.
Bei E-Maschinen ist speziell, dass sie kurzzeitig stark überlastet werden dürfen. Das heisst, dass sie bis zu 20 Sekunden (je nach Maschine und Konstruktion) lang das doppelte bis dreifache Drehmoment zur Verfügung stellen. Danach besteht Überhitzungsgefahr. Da dieser Überlastbereich in der Regel nur selten gebraucht wird, wäre es sinnlos, viel stärkere und damit schwerere und teurere Motoren zu bauen. Die gleichen Eigenschaften weist der Motor beim Rückwärtsfahren auf. Im Diagramm ist die Rückwärtsfahrt im 3. Quadranten dargestellt.
Wird die E-Maschine angetrieben und gibt sie dabei elektrische Energie ab, so kann man sich das als Bremsvorgang vorstellen – sowohl bei Vorwärtsfahrt (4. Quadrant) wie auch bei Rückwärtsfahrt (2. Quadrant). Wir bewegen uns jetzt hauptsächlich im 1. und im 4. Quadranten, weil wir uns Situationen bei Vorwärtsfahrt vorstellen wollen.
Lastwinkel kontra Schlupf Bei motorischen Aktivitäten weisen PSM positive Lastwinkel (Bild 7) auf, da die Rotoren etwas hinter dem Drehfeld hängen. Stellt man sich die Feldlinien als elastische Riemen vor, dehnen sich diese Riemen mit zunehmendem Drehmoment immer mehr. Es kann somit eine Beziehung zwischen dem Lastwinkel und dem Drehmoment dargestellt werden. Ähnlich beim Bremsen: Der Rotor läuft jetzt vor, und die Feldlinien halten ihn zurück. In dieser Situation wird Energie durch Induktion in die Statorwicklungen zurückgespiesen. Je mehr gebremst werden soll, desto weiter muss das Drehfeld hinter dem Rotor definiert werden. Die genaue Rotorposition ist durch die Resolver-Sensoren (AUTO&Technik 5/2022) dem Steuergerät bekannt, und das Drehfeld wird ja im

Steuergerät erzeugt, also ist dessen Frequenz auch sehr genau bekannt. Damit kann das Steuergerät nun mit der Frequenzlage etwas spielen. Sie muss natürlich in jedem Moment der Rotordrehzahl entsprechen, aber sie muss in der Phasenlage eben etwas hinterherkommen, damit die «elastischen Riemen» den Rotor bremsen können.
Ähnlich funktioniert die Geschichte bei der ASM. Diese weist nun einen Schlupf auf, also sind die Drehzahlen zwischen Rotor und dem Drehfeld leicht verschieden. Der positive Schlupf beim Beschleunigen berechnet sich nach der folgenden Formel:
Bild 7. Die permanenterregte Synchronmaschine (PSM) im Leerlauf (oben), beim Beschleunigen (Mitte) und beim Rekuperieren (unten).
Bild 8. Der vereinfachte Hochvoltkreislauf eines BEV oder HV. Von links nach rechts: Hochvoltbatterie, DCDCWandler, Zwischenkreiskondensator, Leistungsendstufe (Wechselrichter) und Drehstrommaschine.
nFeld steht für die theoretische Drehzahl, welche der Feldfrequenz entsprechen würde, und nRotor steht für die gemessene Rotordrehzahl. Soll der Schlupf in Prozenten angegeben werden, muss das Resultat noch mal 100 % gerechnet werden. Beim Bremsen erfolgt auch hier eine Verminderung der Frequenz, dass der Rotor schneller dreht als das Erregerfeld. Durch die Induktion, welche jetzt passiert, entsteht eine Spannung und die dazugehörende Energie kann der Batterie zugeführt werden. Je mehr Bremsenergie verlangt wird, desto kleiner wird die Frequenz, und mit dem negativen Schlupf steigt auch das Bremsmoment an.
Über den Schlupfwert oder den Lastwinkel kann nun die Elektronik das elektrisch zu erzeugende Bremsmoment bestimmen und einstellen. Wird eine kleinere Verzögerung verlangt, können Schlupf oder Lastwinkel etwas zurückgefahren werden. Sind aber grössere Verzögerungen gefragt, müssen die elektromagnetischen Ventile für die Radbremsen geschaltet werden. Dies funktioniert bei den Rekuperationssystemen nach Bild 5c und 5d so. Bei 5b ist es schwieriger, weil das Bremspedal direkt mit dem Hauptbremszylinder verbunden ist. Da könnte höchstens über den Unterdruck im
Bremskraftverstärker die Wirkung etwas beeinflusst werden. Das System nach 5a ist sehr einfach und der elektronische Aufwand bescheiden.
Rekuperationsstrom
Es ist bekannt, dass sich der Strom in einem Leiter nicht gleichzeitig in beide Richtungen bewegen kann. Dies ist jedenfalls in der Gleichstromtechnik so. Beim Wechselstrom gibt es aber verschiedene Widerstände, welche die Spannungs- und die Stromkurve etwas verschieben können.
Kapazitive Widerstände: Ist ein Kondensator in einen widerstandslosen Stromkreis eingebaut, so werden die Kondensatorplatten im Einschaltmoment des Stromes von Elektronen überflutet, es sieht wie ein Kurzschluss aus und die Spannung bricht auf null zusammen. Je mehr sich der Kondensator lädt, desto kleiner wird der Strom und desto grösser der Spannungsabfall. Wird der Kondensator mit Wechselstrom bedient, passiert dieser Effekt ständig wieder, es scheint, als würde der Strom der Spannung um 90° voreilen.
Induktive Widerstände: Durch die hohe Selbstinduktion wird der Strom am Anfang unterdrückt und erholt sich erst allmählich. Die Spannung eilt dem Strom um 90° vor.
Phasenverschobene Ströme werden auch Blindströme genannt. Wie blinde Passagiere mogeln sich diese durch das Leitersystem. Diese Phasenverschiebungen ermöglichen es nun, die Ströme zu ungleichen Zeiten durch die Leiter zu schieben. Im Bild 8 kommt der Strom aus der Phase v, fliesst über die Freilaufdioden, den Zwischenkreiskondensator zum DC-DC-Wandler. Dort wird die Gleichspannung auf das Niveau der Ladespannung gelegt und der Batterie zugeführt. Auf der Minusseite verfolgen die Elektronen den entsprechenden Weg, aber im Beispiel zur Phase u. Das Beispiel zeigt den Zeitpunkt im Drehstromverlauf, in welchem die Phase v positiv ist, die Phase u negativ und die Phase w sich im Nulldurchgang befindet.
1. Welche kinetischen Energien speichert ein Fahrzeug mit einer Tonne Masse und eines mit zwei Tonnen Masse bei einer Geschwindigkeit von 150 km/h?
2. Wer entscheidet aufgrund welcher Informationen, welche Bremse zum Einsatz kommt?
3. Welcher Drehstrommaschinentyp arbeitet mit Schlupf?
LÖSUNG ZUR AUSGABE 11/2024
1. Die Batterie trägt ihre ganze Energiereserve bei sich, die Brennstoffzelle ist nach aussen offen und der Energiespeicher ist örtlich getrennt vom Energiewandler.
2. Anode: Wasserstoff, Elektronenüberschuss, Oxidation, Abspaltung von Elektronen, Minuspol.
Kathode: Sauerstoff, Elektronenmangel, Reduktion, Aufnahme von Elektronen, Pluspol.
3. Weil dort im Verhältnis mehr Wasserstoff verbraucht wird als bei kleineren Lasten bzw. Leistungen.
FRAGEN
Leistungselektronik
EFFIZIENTER LADEN
Im Projekt «EnerConnect» wird mit Hilfe bidirektional sperrender Transistoren aus Galliumnitrid eine Schaltung entwickelt, die in aktiven Wechsel- und Gleichrichtern der nächsten Generation zum Einsatz kommen und effizientes Schnellladen an der Haus- bzw. Garagensteckdose ermöglichen soll. Text: Stefan Gfeller | Bilder: Volkswagen, Fraunhofer IZM
Das Laden von Elektroautos an der heimischen Steckdose soll dereinst effizienter werden und schneller vonstattengehen. Dazu arbeiten Forschende des Fraunhofer-Instituts für Zuverlässigkeit und Mikrointegration IZM und der Technischen Universität Berlin mit Unterstützung von Delta Electronics Inc., der BIT GmbH und Infineon Technologies AG zusammen im Projekt «EnerConnect». Sie erproben eine Schaltung mit neuartigen, bidirektional sperrenden GaN-Transistoren, um deren Vorteile hinsichtlich Leistungsdichte und Effizienz zu nutzen und damit eben den Ladeprozess am Hausstrom effektiver zu gestalten.
Halbleiter aus Galliumnitrid (GaN) oder Siliziumcarbid (SiC), die hohe Schaltfrequenzen und damit kleinere, günstigere passive Bauteile ermöglichen, kommen zwar bereits in aktiven Gleichrichtern für Elektrofahrzeuge zum Einsatz, können die Spannung jedoch nur in einer Richtung sperren. Dies trifft, wie der Name schon sagt, nicht auf die bidirektional sperrenden GaN-Transistoren zu: Hier können
durch zwei Gatestrukturen positive und negative Spannungen gesperrt werden. Das macht neue Schaltungstopologien für Wechsel- und Gleichrichter, die am öffentlichen Versorgungsnetz betrieben werden, interessant.
Einsparung einer Wandlerstufe
In der Leistungselektronik spielte die Schaltung, an der die Forschenden arbeiten, bisher keine Rolle, weil die Realisierung mit konventionellen Bauteilen zu aufwendig wäre. Es handelt sich um eine sogenannte Buck-Boost-Schaltungstopologie, mit der die Eingangsspannung sowohl höher als auch niedriger gesetzt werden kann. Durch die Verwendung von bidirektional sperrenden Transistoren lassen sich die Vorteile dieser Schaltung nutzen: Konventionell werden aktive Gleichrichter in E-Autos mit hohen Spannungen geschaltet. Mit der neuartigen Schaltung kann die Spannung aber eben auch tiefer gesetzt werden – und durch die dadurch niedrigere Schaltspannung verringern sich die Schaltverluste im Stromrichter.
benötigte Batteriespannung herabgesetzt werden. Durch den Einsatz von bidirektional sperrenden GaNTransistoren lassen sich diese beiden Schritte in einer Wandlerstufe vereinen, wodurch die Effizienz weiter gesteigert wird, während der Materialaufwand und die Kosten sinken.
Hohe Leistungsdichte
Durch diese beiden Effekte kann der Wirkungsgrad des Wandlers auf bis zu 99 % erhöht werden. Mit der neuen Schaltung wird auch eine weitere Erhöhung der Schaltfrequenz und der Leistungsdichte denkbar. So wird eine Schaltfrequenz von 300 kHz angestrebt, was das Potenzial birgt, die Leistungsdichte auf 15 kW/l zu erhöhen – das entspräche dann dem 8-Fachen von derzeit handelsüblichen Ladegeräten.
Zudem kann mit der Schaltung eine Wandlerstufe eingespart werden. Denn für gewöhnlich muss in einem Gleichrichter die Eingangsspannung in zwei separaten Komponenten erst einmal hochund anschliessend wieder auf die
Die Technologie bietet sich insbesondere für den Einsatz in Elektrofahrzeugen an, weil der Wandler fest im Fahrzeug installiert ist und somit sehr kompakt sein muss. Das Ziel für das Projekt «EnerConnect» ist es, die Schaltung für den Betrieb am öffentlichen Versorgungsnetz zu optimieren, was zum Beispiel das Schnellladen von E-Autos am Hausstrom ermöglichen soll. Da der Energietransfer des Wandlers in beide Richtungen erfolgen kann, ist diese Technologie sowohl bei Nutzung der Fahrzeugbatterie als Energiespeicher (bidirektionales Laden) als auch für den Einsatz in Photovoltaikanlagen prädestiniert.
Schematischer Vergleich eines unidirektionalen und eines bidirektionalen GaNTransistors. Durch die Eigenschaft, die Spannung in beide Richtungen zu sperren, ergeben sich neue Einsatzmöglichkeiten.
Das Projekt «EnerConnect» möchte das Laden von EAutos am Hausstrom energieeffizienter und schneller machen.
Recycling
BATTERIE-KREISLAUF GESCHLOSSEN
Eine neue Batterie-Recyclingfabrik von Mercedes-Benz soll mit ihrem integrierten mechanischhydrometallurgischen Verfahren wiedergewonnene Wertstoffe zur Produktion von jährlich mehr als 50’000 neuen Batteriemodulen für die Elektrofahrzeuge des Automobilherstellers generieren. Text: Stefan Gfeller | Bilder: MercedesBenz
Mercedes-Benz hat im Oktober im süddeutschen Kuppenheim die erste Batterie-Recyclingfabrik Europas mit integriertem mechanisch-hydrometallurgischem Verfahren eröffnet. Das Unternehmen schliesst damit – als nach eigenen Angaben erster Automobilhersteller weltweit – den Batterie-Wertstoffkreislauf mit einer eigenen Anlage und kooperiert dazu mit dem Technologiepartner Primobius, der ein Joint-Venture des deutschen Unternehmens für Anlagen- und Maschinenbau SMS Group und des australischen Prozesstechnologieentwicklers Neometals ist.
Die Batterie-Recyclingfabrik deckt erstmalig in Europa alle Schritte von der Zerkleinerung der Batteriemodule bis hin zur Trocknung und Aufbereitung der batterieaktiven
Wertstoffe ab. Dabei beträgt die erwartete Rückgewinnungsquote der mechanisch-hydrometallurgischen Recyclinganlage, anders als bei heute etablierten Prozessen, mehr als 96 %. Während das mechanische Verfahren in einem komplexen, mehrstufigen Prozess Kunststoffe, Kupfer, Aluminium und Eisen sortenrein sortiert, widmet sich das nachgelagerte hydrometallurgische Verfahren der sogenannten schwarzen Masse, also der aktiven Materialien, aus denen die Elektroden der Batteriezellen bestehen.
Integriertes mechanisch-hydrometallurgisches Recyclingkonzept
Der Prozess startet nach der Prüfung des Ladezustands mit dem Auflegen der Batteriemodule auf ein
Förderband. Anschliessend werden die Akkus mechanisch zerkleinert, gewaschen und in eine Grob- und Feinfraktion getrennt. Mittels schwerkraftbasierter Luftsysteme, Magnetabscheider, Mühle und verschiedener Siebe werden Kunststoffe, Kupfer, Aluminium und Eisen getrennt und sortenrein abgefüllt. Gleichzeitig wird die in der getrockneten groben Fraktion enthaltene schwarze Masse separiert.
Chemisches Trennverfahren
Die zuvor abgetrennte feine Fraktion enthält den grössten Anteil an schwarzer Masse. Diese wird gefiltert und zusammen mit der Masse aus der groben Fraktion in der Hydrometallurgie weiterbearbeitet. Hier erfolgt zunächst im Leaching
die Auflösung der Metalle in eine flüssige Lösung. Das nicht gelöste Graphit wird mittels Filter separiert und abgefüllt. Ebenso wird mit dem ausgefällten Eisen und den Aluminiumanteilen verfahren. In einem mehrstufigen chemischen Trennverfahren werden die wertvollen Rohstoffe wie Kupfer, Kobalt, Mangan, Nickel und Lithium nacheinander zurückgewonnen. Kobalt und Nickel werden abschliessend kristallisiert.
Weniger Energieeinsatz, weniger Abfall
Die Batterie-Recyclingfabrik in Kuppenheim hat eine Jahreskapazität von 2500 t. Der Fahrzeughersteller betont, dass die wiedergewonnenen Wertstoffe in die Produktion von mehr als 50’000 Batteriemodulen für neue vollelektrische MercedesBenz-Modelle einfliessen: Somit ist der Wertstoffkreislauf geschlossen. Das hydrometallurgische Verfahren bietet zudem weitere Vorteile. So ist es im Vergleich zur heute in Europa etablierten Pyrometallurgie weniger energieintensiv, da es mit niedrigen Prozesstemperaturen von bis zu 80 °C arbeitet, und erzeugt geringere Abfallmengen. Darüber hinaus wird die Recyclingfabrik, die zu 100 % mit Grünstrom versorgt wird, wie alle Mercedes-Benz-Produktionswerke bilanziell CO2-neutral betrieben: Nicht vermiedene oder reduzierte CO2-Emissionen werden durch zertifizierte Ausgleichsprojekte kompensiert. Und dann kommt noch die Photovoltaikanlage auf der Dachfläche des 6800 m2 grossen Gebäudes hinzu, die über eine Leistung von mehr als 350 kWp verfügt.
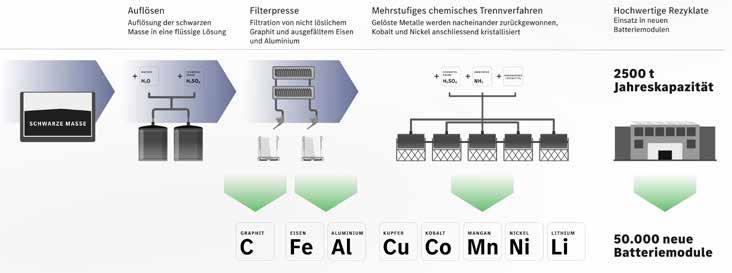
Stufe 1: mechanisches Verfahren zur Zerkleinerung und Vorsortierung.
Stufe 2: hydrometallurgisches Verfahren zur Rückgewinnung der Rohstoffe.
Auf das Fahrzeug abgestimmte Bremsbeläge bzw. Reibmaterialmischungen sind eine wesentliche Voraussetzung für leises Bremsen.
Bremsgeräusche
AUF DEN BELAG KOMMT ES AN
Bremsgeräusche führen häufig zu Reklamationen in der Werkstatt. Bei der Ursachensuche ist auch auf die Bremsbeläge zu achten, denn eine auf den Punkt genau auf das Fahrzeug abgestimmte Reibbelagrezeptur ist eine wesentliche Voraussetzung für leises Bremsen. Bilder: TMD Friction
Beim Bremsen können aufgrund der Trockenreibung Geräusche von bis zu 100 dB entstehen, was ungefähr der Lautstärke eines Presslufthammers entspricht. Je nach Geräuschphänomen hat man es zum Beispiel mit Quietschen, Muhen oder Knarzen zu tun. Das ist bekanntlich kein neues Problem, solche störenden Geräusche zählen lange schon zu den Hauptursachen für Reklamationen in der Werkstatt. Doch die Ansprüche an das Komfortverhalten – kurz NVH (Noise, Vibration, Harshness bzw. «Geräusch, Vibration, Rauigkeit») –der Bremse steigen kontinuierlich: Die Elektrifizierung und das fehlende Motorengeräusch fordern ohnehin leisere Bremsen. Unabhängig vom Antrieb begünstigen gleichzeitig Leichtbaukonzepte Quietschen und Rubbeln. Und die beliebten SUV haben ebenfalls ihre Tücken: Sie verfügen über längere Querlenker mit höherer Empfindlichkeit gegenüber
niederfrequenten Schwingungen wie Knarzen. Aber auch Automatikgetriebe, Fahrerassistenzsysteme wie Parkassistenten und Berganfahrassistenten können zu NVH-Problemen führen.
Abgestimmte Belagrezepturen
Die Geräusch- und Reklamationsvermeidung fange schon mit der Wahl des Bremsbelags beim Wechsel an, betonen etwa die Bremsenexperten von Textar. Denn während Standardmischungen, die für viele unterschiedliche Fahrzeuge funktionieren sollen, zur Geräuschentwicklung neigen, schaffen Werkstätten mit Belägen von Erstausrüstern die nötigen Voraussetzungen für leise Bremsen. Dank entsprechender Expertise aus der Serienfertigung und umfangreichen Testkapazitäten lässt sich das Risiko für spätere NVHProbleme von Anfang an minimieren: durch individuelle Reibmaterialmischungen, die für ein bestimmtes
niedriges Eigenschwingungsverhalten und gute Dämpfungseigenschaften aufweisen sollten. Neben abgestimmten Belagrezepturen helfen umfangreiche sogenannte Sekundärmassnahmen, die Schwingungsübertragung vom Belag auf andere Komponenten zu dämpfen. Die Textar-Entwickler beispielsweise nutzen 350 verschiedene Dämpfungsblechmaterialien, Zwischenschichten, Laufrichtungsbindung, Schrägen, Nuten oder Ausgleichsgewichte.
Fahrzeug, sein Bremssystem und seinen Einsatzzweck auf den Punkt genau entwickelt werden. Entscheidend sind die Mischung und die verwendeten Materialien, die ein
Hochkomplexe Geräuschursachen «Um NVH-Phänomenen auf den Grund zu gehen, leisten wir mit einem Spezialisten-Team, das sich ausschliesslich NVH-Phänomenen widmet, schon bei der Entwicklung der Bremsbeläge wahre Detektivarbeit», erklärt Wolfgang Hoffrichter, Senior NVH Engineer bei TMD Friction. «Wir analysieren in ausführlichen Tests jedes kleinste Geräusch. Die Ursachen sind oft hochkomplex; die Reproduzierbarkeit und Vorhersage von Bremsgeräuschen auf dem Prüfstand oder im Rahmen von Simulationen ist nicht garantiert. Um solche Probleme zu lösen, müssen wir die Komponenten im Einzelnen, ihre Rolle im Gesamtsystem Bremse sowie ihre Eigenschaften verstehen. Mit Hilfe von eigenen Analyse- und Simulationstools sowie sieben Geräuschprüfständen, aber auch eigenen Fahrversuchen, sorgen wir dafür, dass Textar-Beläge auch im freien Ersatzteilmarkt den steigenden Anforderungen in Sachen NVH genügen.» (pd/sag)
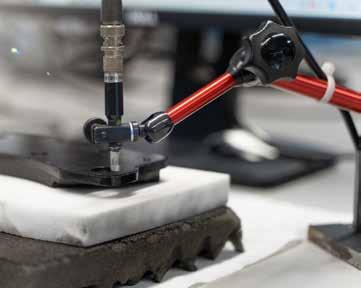
In der TextarEntwicklungsabteilung widmet sich ein SpezialistenTeam ausschliesslich NVHPhänomenen.
Komplettlösung für Garagen und Werkstätten
Komplettlösung für Garagen und Werkstätten
Altola AG | Gösgerstrasse 154 | 4600 Olten | Tel. 0800 258 652 www.altola.ch | mail@altola.ch
Komplettlösung für Garagen und Werkstätten
Altola AG | Gösgerstrasse 154 | 4600 Olten | Tel. 0800 258 652 www.altola.ch | mail@altola.ch
Altola AG | Gösgerstrasse 154 | 4600 Olten | Tel. 0800 258 652 www.altola.ch | mail@altola.ch
Altola AG | Gösgerstrasse 154 | 4600 Olten | Tel. 0800 258 652 www.altola.ch | mail@altola.ch
Ifangstrasse
&Technik
TITELTHEMA
Schmierstoffe/Öl
Motorenöl für moderne Verbrenner und E-Fluids zur Schmierung/Kühlung von Getriebe, E-Maschine respektive Batterie in E-Autos: A&W stellt die Neuheiten vor.
WIRTSCHAFT
Prognosen 2025
Marktprognosen, Fahrzeughandel, Händlernetze und Aftermarket: Wir bieten einen Ausblick auf das neue Jahr.
Zu den weiteren Themen der Januar-/FebruarAusgabe zählen Entsorgung/Recycling, Berufsbekleidung, Sicherheit in der Werkstatt sowie Weiterbildung.
AUTO-EVENTS 2024/2025
FACHWISSEN
Drehmoment und Energie
Ist von Kraft und von Weg die Rede, denkt man häufig zunächst an ein Drehmoment. Dieses ist bei der automobilen Antriebstechnik sehr wichtig, muss doch die Kolbenkraft im Motor zunächst in ein Drehmoment und im Rad wieder zurück in eine Antriebskraft verwandelt werden. Aber die Beziehung zwischen Kraft und Weg kann auch Arbeit oder Energie bedeuten. Dabei ist die Energie die gespeicherte Arbeit. So stellt der Tank den Energiespeicher im Auto dar und speichert chemische Energie in Form von Benzin/Diesel. Im BEV ist es die Batterie, welche elektrische Energie speichert. Die Energie wird beim Fahren in Arbeit, Drehmoment und am Schluss in Kraft umgewandelt.
Termin Veranstaltung Ort Internet
14.12.24 EAutoMeet Derendingen enter.ch
21.12.24 4x4Meet Derendingen enter.ch
29.12.24 Classic Car Auction Gstaad oldtimergalerie.ch
18.01.25 Züriring GP Zürich zueriring.ch
21.01.25 Tag der Schweizer Garagen Bern agvs.ch
23.01.2525.01.25 Winter Raid St. Moritz raid.ch
29.01.2505.02.25 Rallye Monte Carlo Monaco acm.mc
30.01.25 A&W Branchenanlass Safenwil autowirtschaft.ch
05.02.2509.02.25 Retromobile Paris retromobile.com
21.02.2522.02.25 The Ice St. Moritz theicestmoritz.ch
27.02.2502.03.25 Retro Classics Stuttgart retroclassics.ch
01.03.25 Sam's OTM Brunegg samsotm.ch
20.05.25 Driving Day Experience Brunegg aboutfleet.ch
IMPRESSUM
Ein Unternehmen der ZT Medien AG
Herausgeber/Verlag
A&W Verlag AG
Riedstrasse 10
CH8953 Dietikon
Telefon: 043 499 18 60 info@awverlag.ch www.autowirtschaft.ch www.awverlag.ch
MARKEN VON A&W
Geschäftsführer Giuseppe Cucchiara gcu@awverlag.ch
Verkaufsleiterin / Mitglied der Geschäftsleitung
Jasmin Eichner je@awverlag.ch
Chefredaktor Mario Borri (mb) mborri@awverlag.ch
Redaktion
Michael Lusk (ml)
Fabio Simeon (fs)
Isabelle Riederer (ir)
Felix Stockar (fst) Andreas Lerch (ale)
Stefan Gfeller (sag) Leitender Redaktor AUTO&Technik redaktion@awverlag.ch
Anzeigenverkauf Juan Doval jd@awverlag.ch Mobile: 076 364 38 41
SCHWERPUNKT
Lackieranlagen und Lacktrends 2025 In der ersten Ausgabe des neuen Jahres setzt AUTO&Carrosserie den Schwerpunkt auf Lackieranlagen und Lacktrends. Zum einen spüren wir die neusten Trends bei den Lacken auf. Einer davon ist, dass die Produkte laufend verbessert werden und noch schneller zu applizieren sind. Zum anderen stellen wir die neusten Lackierkabinen, Multiarbeitsplätze sowie innovative Technologien bei der Lackaufbringung vor. Schlagworte dabei sind schnellere Trocknung und weniger Energieaufwand.
Die AUTO&Carrosserie-Ausgabe 1/2025 erscheint Mitte März.
DER AGVS LÄDT ZUM TAG DER SCHWEIZER GARAGEN 2025 NACH BERN EIN
Der Tag der Schweizer Garagen findet am 21. Januar 2025 statt und wird über 800 Teilnehmende aus der Branche, Politik, von Zulieferanten und weiteren Stakeholdern anziehen. Der Event wird im Kursaal Bern bei wunderschöner Kulisse mit Blick auf die Berner Altstadt abgehalten.
www.agvs-upsa.ch
Leiterin Marketing & Events Arzu Cucchiara ac@awverlag.ch
Leiterin Administration / Assistentin der GL Amra Putinja ap@awverlag.ch
Telefon: 043 499 18 60
Buchhaltung / Administration Natalie Amrein na@awverlag.ch
Telefon: 043 499 18 91
Berufslernende
Mariam Nasrat
Abo/Leserservice
Telefon: 043 499 18 60 info@awverlag.ch
Abonnementpreis
Inland CHF 95.–/Jahr (inkl. MwSt.)
Erscheint 10mal jährlich
Layout
Simon Eymold info@awverlag.ch
Druck
Printi Pronto AG
Riedstrasse 10 / CH–8953 Dietikon
Gründer
Helmuth H. Lederer (2004 – 2014, † 2014)
© 2024 A&W Verlag AG. Alle Eigentums, Verlagsund Nachdruckrechte bei A&W Verlag AG. Der Vertrieb sowie die Wiederverwendung des Inhalts sind nur mit schriftlicher Genehmigung des Verlags erlaubt. Für unverlangt eingesandte Manuskripte und Fotos wird keine Haftung übernommen.