
6 minute read
PROJECT DESCRIPTIONS
The LightBrush Team 23013
Project Goal
Improve oral health and surface appearance of the oral cavity using LEDs.
For those who have mental or physical limitations or aversions to traditional toothbrush use, photodynamic therapy can improve overall oral health and decrease plaque bacterial colonization. This project presents a waterless, bristleless alternative to traditional mouth cleaning devices. It allows the user to select a light mode for three individual LED treatments using blue light, red light or a combination of the two.
The LightBrush design uses an Arduino Nano Every microcontroller to power the high-wattage LEDs, which are located on a custom-designed printed circuit board in the head of the brush. Custom code controls the LEDs according to the selected light mode, and it delivers a specific lux dosage amount over a set treatment time. For safety, an accelerometer ensures the user or caregiver is properly holding the LightBrush and automatically shuts off the device when the LEDs are shining upwards, preventing ocular damage. A piezo buzzer notifies the user when the treatment begins and is completed to prevent light exposure outside of the mouth. The lithium polymer battery can be recharged when voltage is low. The team 3D printed a prototype of the LightBrush to verify functionality of the complete system. Further research into potential environmentally sustainable materials for large-scale production of the device was also completed, and instructions for use were developed for customers.
Feeding the Future: Student-led Design at the Nexus of Food, Energy and Water
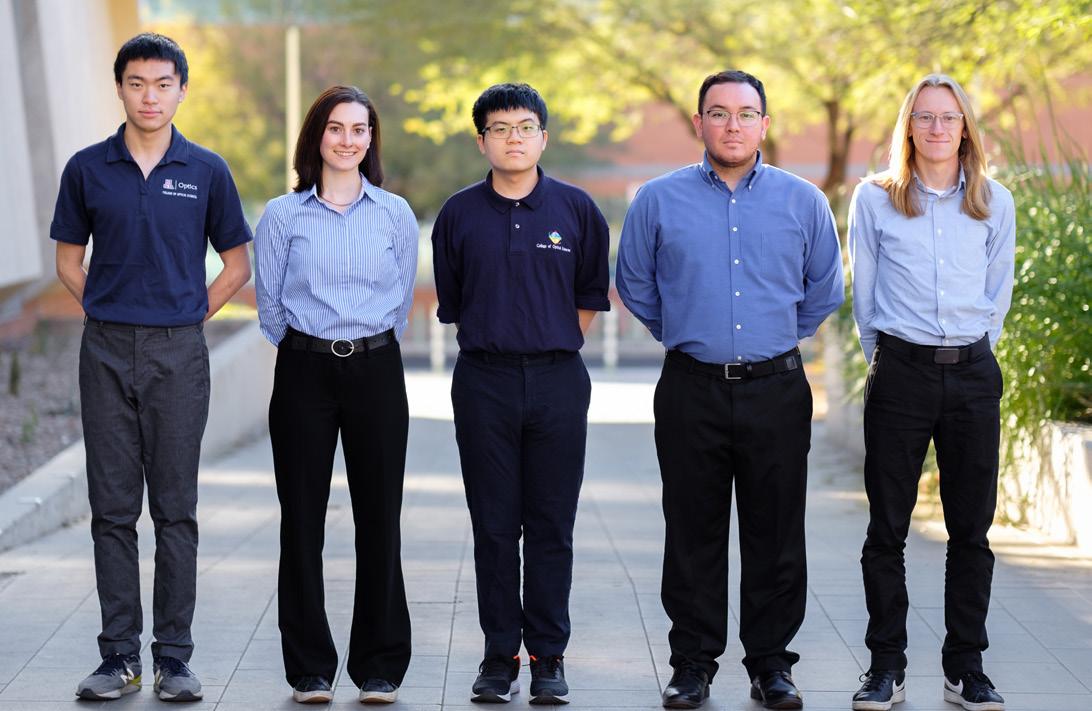
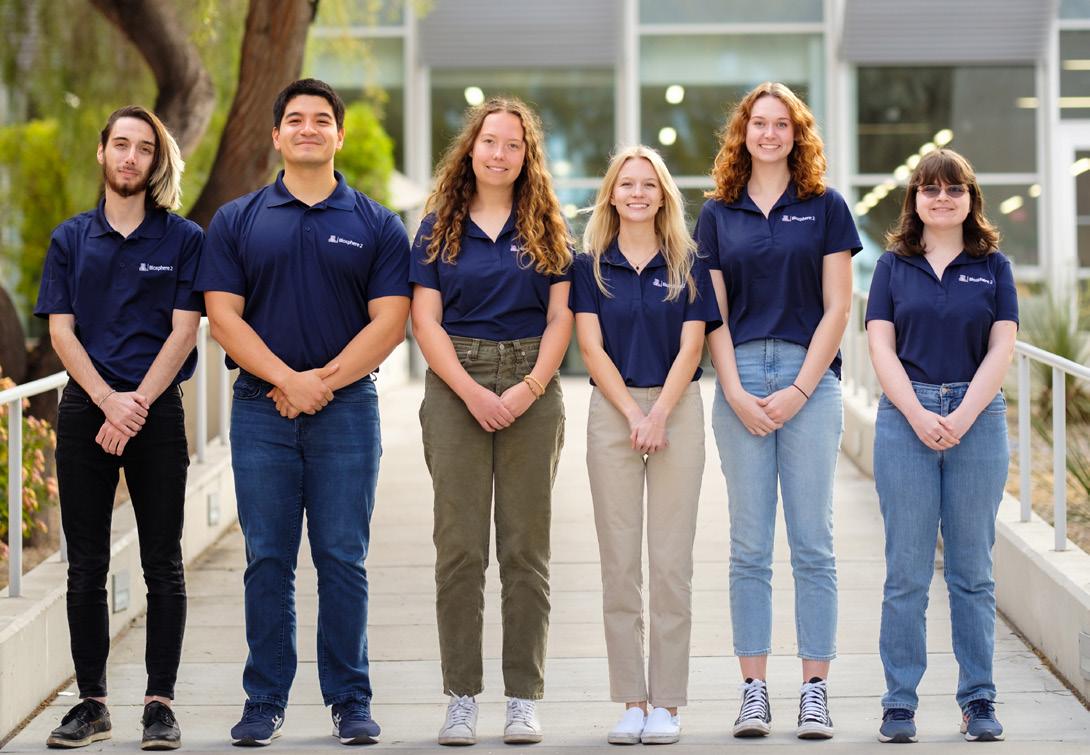
Team 23014
Project Goal
Design an agrivoltaic system to provide power to the Greenery S Freight Farm at Biosphere 2 and create a functional demonstration model.
The project team developed an agrivoltaic system design and established solar production estimates to determine the renewable energy off-set for the Freight Farm located at Biosphere 2. Additional goals included structural design, operational guidelines, design of a secondary freight container to house electronics for the solar components, and a functional model. The design can work in any offgrid system located in arid regions where there is no or limited electrical grid connectivity.
The agrivoltaic system consists of 61 solar panels, a structural support system for the panels and an electrical system that controls the flow and storage of energy. While the team built a functional, smaller-scale prototype, they also created various models and electrical diagrams, worked with structural applications, and performed calculations to verify the full-scale design. The demonstration model incorporates the key components of the Freight Farm-Agrivoltaic System, including a structural assembly, electrical and solar components, and system monitoring.
TEAM MEMBERS
Ismael Ballesteros, Electrical & Computer Engineering
Jazmine Barraza, Engineering Management
Natalie Hall, Biomedical Engineering
Haley Renee Johnson, Biomedical Engineering
Fernando Romero, Industrial Engineering
Sovenna Emily Thorn, Systems Engineering
COLLEGE MENTOR
Mike Nofziger
SPONSOR ADVISORS
Shoshi Almog, Judith Macias-Harris
TEAM MEMBERS
Brooke Elizabeth Bykowski, Engineering Management
Lynn Carroll, Biosystems Engineering
Logan Eaton, Electrical & Computer Engineering
Stephanie Beatrice Orchard, Biosystems Engineering
Alejandro Quijada, Mechanical Engineering
Hailey R Schleining, Biosystems Engineering
COLLEGE MENTOR
Michael Madjerec
SPONSOR ADVISOR
John Adams
TEAM MEMBERS
John Roger Allen, Aerospace Engineering
Charles James Fischer, Aerospace Engineering
Keegan Kelaher, Aerospace Engineering
Kyle Ryan Peabody, Aerospace Engineering
Aidan Petrie, Electrical & Computer Engineering
Will Wong, Aerospace Engineering
COLLEGE MENTOR
Sergey Shkarayev
SPONSOR ADVISOR
Adrien Bouskela
AIAA Design/Build/Fly Competition
Team 23015
The Simpson Family
PROJECT GOAL
Create a unique radio control aircraft that will compete in the American Institute of Aeronautics and Astronautics (AIAA) international Design/Build/Fly (DBF) competition.
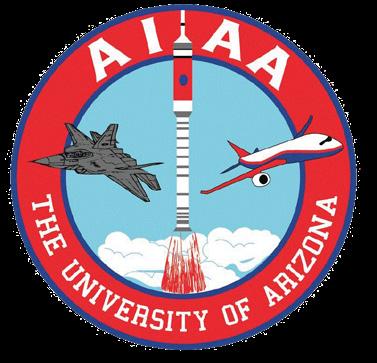
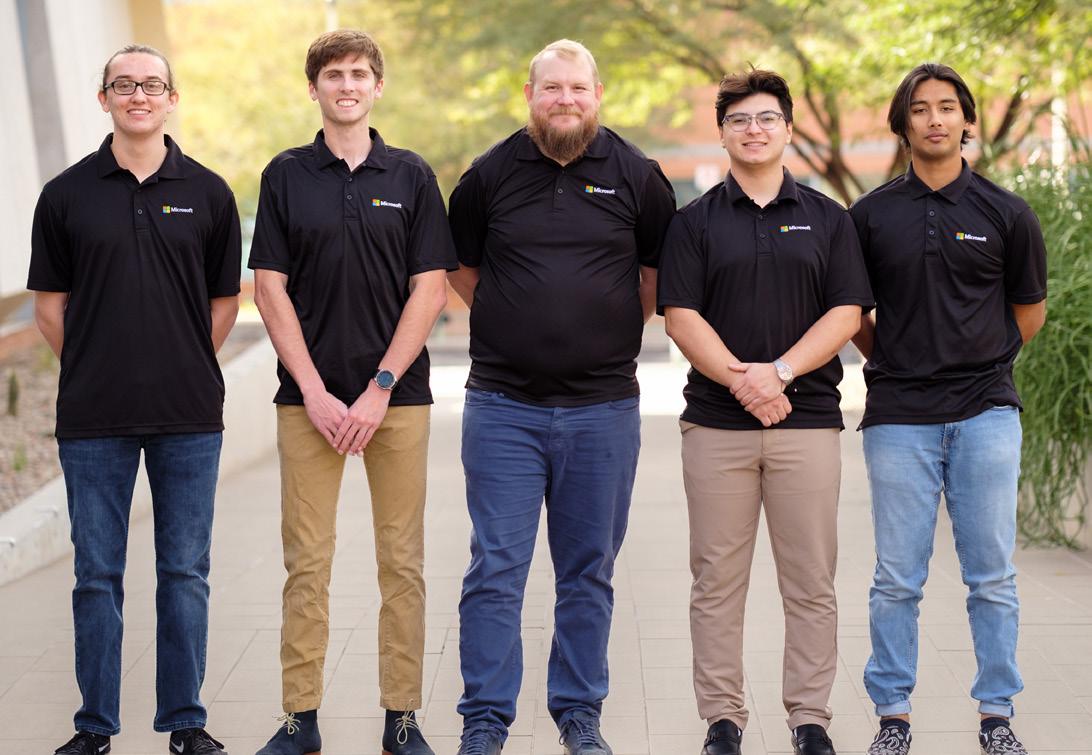
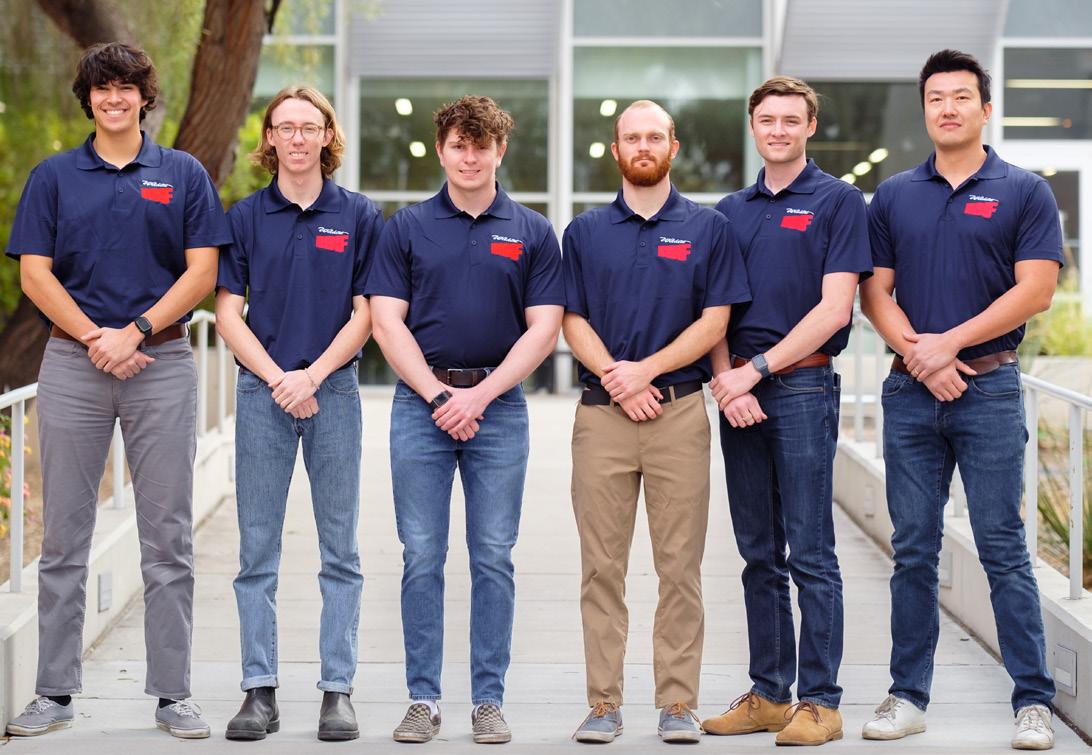
The annual AIAA DBF competition is an international event, hosted in Tucson and Wichita, Kansas, that invites schools from all over the world to design, build and fly an aircraft according to the design requirements that are set each year. Each team must attempt to maximize their possible points earned via scoring guidelines set by the competition. Flight envelope attributes such as endurance, speed and payload weight must be balanced accordingly to create an aircraft that will obtain the highest score.
This year, the schools were tasked with designing an aircraft that is capable of flying three missions, each with their own stipulations. Based on the scoring and competition guidelines, this design must be able to carry a heavy internal payload, mount a vertical antenna to one wingtip and have an endurance of around eight minutes. In addition, the aircraft must be able to disassemble and fit into a box that is compliant with FAA carry-on regulations, limiting battery size and aircraft dimensions. By employing computational fluid dynamics, advanced composite building techniques and rigorous aerodynamic design processes, the University of Arizona team developed a competitive aircraft to represent the school on the international stage.
Let’s Boil a Computer Again!
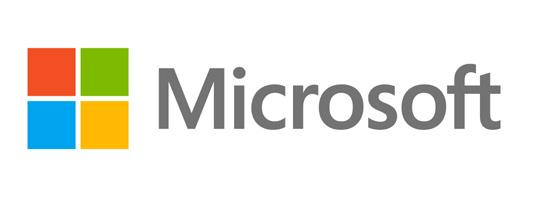
Team 23016
TEAM MEMBERS
Jesus Arias, Electrical & Computer Engineering
Chris William Bremser, Electrical & Computer Engineering
Sean Brown, Systems Engineering
Prasanna Raut, Mechanical Engineering
Rusty D Rinehart, Electrical & Computer Engineering
COLLEGE MENTOR
Bob Messenger
SPONSOR ADVISOR
Nicholas Keehn
PROJECT GOAL
Create a two-phase immersion cooling and filtration system with Fluorinert to significantly reduce computer server farm power and water usage.
The rapid growth in smartphone usage has led to a surge in demand for cloud services. Major data centers, which store information for cloud service providers, have replaced traditional local computer storage with large data storage facilities. These facilities require a huge amount of energy to power and drinkable water is used to keep them cool.
To address these issues, the team designed hardware and software to cool the computer servers using FC-72 Fluorinert as an alternative to current swamp cooling forced air systems. Flourinert was selected for its low boiling point of 132.8 degrees Fahrenheit. They also designed a custom filtration system to reduce and mitigate dendritic salt growth, which can lead to electrical shorting. This system eliminates vulcanizers and plasticizers that cause the damaging growth.
The team built a test system for data center applications, which required finding a suitable pump that handles the low boiling point and low viscosity of Fluorinert. Finally, they created an interactive graphical user interface to allow technicians to monitor cooling system efficiency. The team then measured progress toward the goal of reducing power and water consumption.
Automated Universal Part Singulator (AUPS)
Team 23017
Project Goal
Design and build a flexible part feeder with a cartesian robot and high-resolution camera for use in automated assembly lines.
With millions of dollars being spent on tooling for automated assembly lines, companies are relying more on reconfigurable part feeding and sorting mechanisms to save costs. This project provides a solution by being easily adaptable to any assembly process without compromising effectiveness or reliability.
The AUPS consists of a cartesian robot, a high resolution camera, a gripping mechanism and a vibrating table. The robot is controlled using the CtrlX Machine Controller developed by Rexroth and an Arduino is used for controlling the sensors and gripper. Parts are fed manually onto the vibrating table, where the camera identifies and locates them, allowing the robot to travel, pick up and sort them correctly. If no parts are detected, the system uses the vibratory table to disperse parts until the camera can locate one. The gripping mechanism is attached to the end of the Z-axis of the robot and is capable of handling parts between 2-10 cm3 with a weight limit of 0.5 kg.
The system can automatically sort parts based on their shape and size. It is designed to operate in an enclosed factory floor environment and is therefore shielded from external interference with a metal frame and acrylic walls.
Throw Phone for UAPD/FBI Crisis Negotiation Team
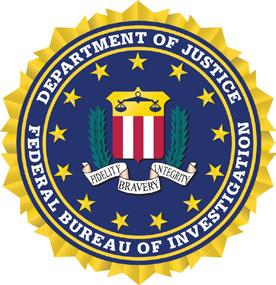

Team 23018 supported by Craig M. Berge Dean’s Fund

Project Goal
Deliver a rugged, reliable and secure audio-visual communication system for law enforcement to negotiate with hostage-takers and de-escalate situations.
During hostage situations, SWAT teams toss “throw phones” into buildings and encourage hostage-takers to initiate communication with a negotiator at a remote command center. These phones must be rugged, reliable and provide clear communication. However, the current 20-year-old system is hard-wired, cumbersome and intimidating to hostage-takers.
The team has advanced the technology to a more robust, reliable and friendly wireless solution. The solution consists of two major components, the throw phone and the command module. The design utilizes a 4G cellular network to ensure wireless connectivity and full-duplex communication across long distances. Low-light cameras controlled by a multiplexor provide video surveillance of the phone’s surroundings. Audio and video data is wirelessly sent over antennas, processed by a Raspberry Pi microcontroller and recorded onto a micro SD card capable of storing over six hours of audio and video footage. The data can then be quickly uploaded to an external thumb drive. All the components are contained in hard and soft plastic casing that is rugged enough to withstand throwing through windows.
Results of the project have shown the system provides real-time audio and video and a clear line of communication from as far as 300 feet for up to six hours. The device has proven to be nonintimidating to focus groups, which invites users to pick up and handle the phone without worry.
TEAM MEMBERS
Abdullah Albar, Systems Engineering
Kevin Dennis Gilman, Electrical & Computer Engineering
Nafisul Huq Khondaker, Electrical & Computer Engineering
Daniel Mack, Mechanical Engineering
Anthony Phillips, Optical Sciences & Engineering
Esmeralda Pimentel Enriquez, Mechanical Engineering
COLLEGE MENTOR
Pat Caldwell
SPONSOR ADVISOR
Brett Dooley
TEAM MEMBERS
Tanner Birecki, Optical Sciences & Engineering
Reid Clark, Industrial Engineering
John Paul LaRue, Electrical & Computer Engineering, Mechanical Engineering
Thaddeus Propper, Mechanical Engineering
Marcus Tal Wieser, Mechanical Engineering
COLLEGE MENTOR
Jeff Scott Wolske
SPONSOR ADVISOR
Joseph Berriman