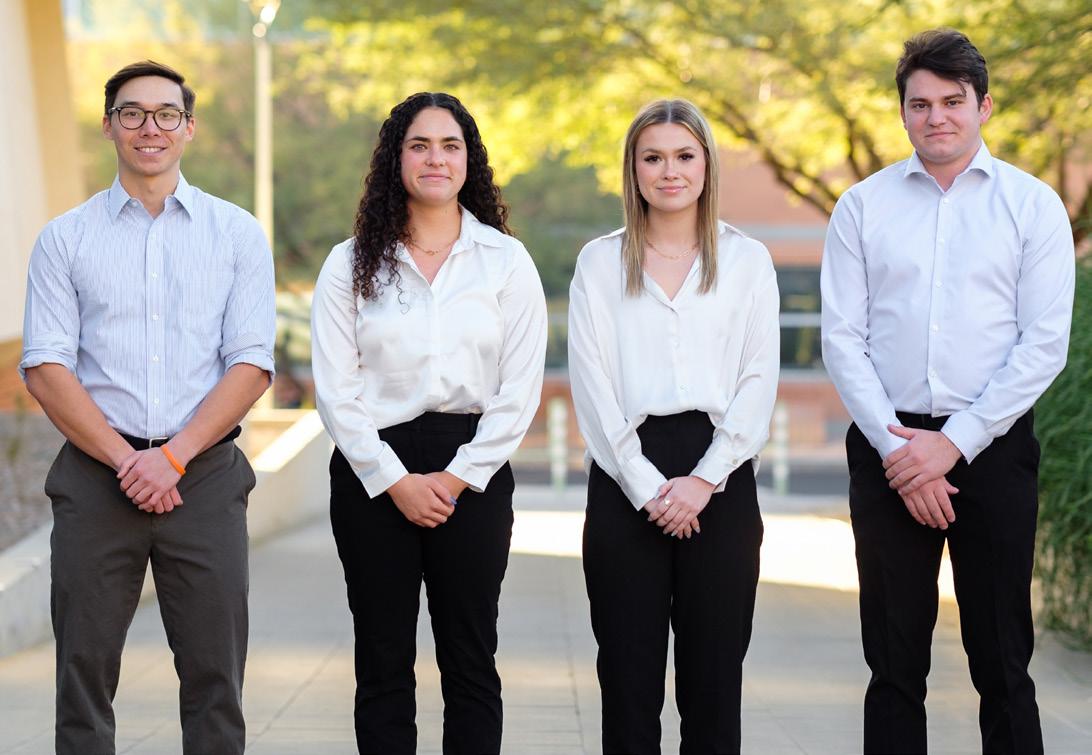
3 minute read
Perfume Manufacturing Process
Team 23116
Project Goal
Create a perfume with a popular scent that will produce profits while minimizing carbonbased energy. Optimization should increase efficiency, decrease energy requirements, and power the process with sustainable energy sources.
The first step is using steam distillation to extract the essential oils of orange peels and cinnamon bark in a semi-batch process. The product from steam distillation is cooled by a refrigeration cycle. The condensed exit stream is then pumped into two decanter centrifuge separators: one for orange and one for cinnamon. The oil and water mixtures separate due to differences in polarity. The floral water from each separator is pumped into a single floral water holding tank, while the essential oils are pumped into surge tanks, where they are held until needed for perfume formulation.
The perfume formulation process starts when the essential oils are combined with all other required ingredients: vanilla essential oil, water, ethanol, and the UV filter (ethylmexyl methoxycinnamate). From there, the final mixture goes into a chiller for 25 minutes before being pumped into a filter. The vibratory filter separates the final product from the precipitate wax that forms during the chilling process. The filter waste is transported into the previously mentioned waste tank. The final product leaves the filter and is pumped into the product holding tank to be held until transportation to be packaged.
The process will be powered by solar panels.
Re-injection & Extraction Process for Simulated Crude Oil Plant
Team 23117
Project Goal
Design a vapor reinjection system that utilizes the separation of liquids and gases from the production well to increase the well’s oil and natural gas production.
In enhanced oil recovery, liquid and/or gas is reinjected into an oil reservoir to re-establish lost pressure and extract additional oil. This project focuses on the reinjection of gas into the oil well using the tertiary reinjection of methane, specifically in an Alaskan oil field. Before being reinjected into the reservoir, the methane must be separated from the oil and water that is entrained in it. This is done using a series of heat exchangers, separators and compressors to safely and efficiently separate out the different components for use in their own streams.
The safety of this process is of utmost importance, since many pieces of equipment are operating at high pressure and high temperature. To reduce operator injuries and prevent the need for maintenance, misters and control valves will be used to maintain safe operations at all times. Optimal operations for this process will yield an increased separation and recovery of oil and natural gas as well as increase safety and decrease the need for maintenance.
TEAM MEMBERS
John Siruzie Bergin, Chemical Engineering
Kale Teagan Burke, Chemical Engineering
Chloe Elizabeth Sarocka, Chemical Engineering
Makayla Marie Schilling, Chemical Engineering
COLLEGE MENTOR
Adrianna Brush
SPONSOR ADVISOR
Rodney Keith
TEAM MEMBERS
Hayden A Borden, Chemical Engineering
Alena Isabel Hermosillo, Chemical Engineering
Abby Regan Long, Chemical Engineering
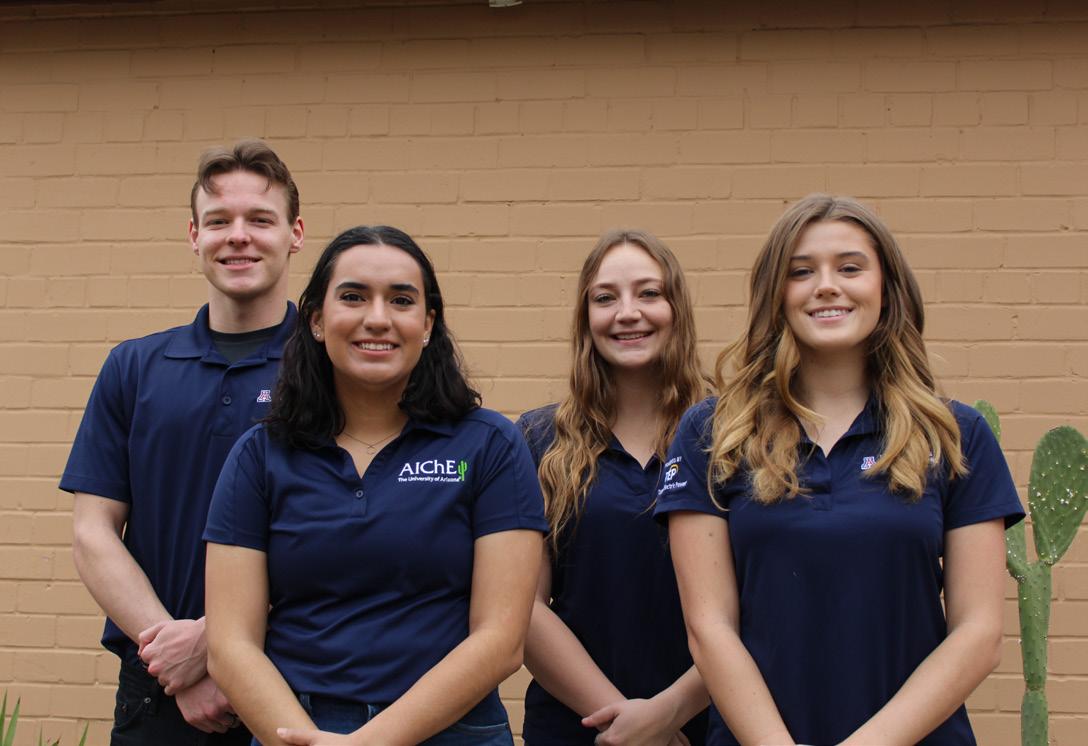
Regan M Wagner, Chemical Engineering
COLLEGE MENTOR
Adrianna Brush
SPONSOR ADVISOR
Robert Siml
TEAM MEMBERS
Chandler Arden Canant, Chemical Engineering
Dallan D Graybill, Chemical Engineering
Sophia Mischke, Chemical Engineering
Jamie Nicole Scott, Chemical Engineering
COLLEGE MENTOR
Kimberly L Ogden
SPONSOR ADVISOR
Jared Gardner
In-House Foam Part Production
Team 23118
TEAM MEMBERS
Kyle Thomas Churchman, Chemical Engineering
Morgan P Habkirk, Chemical Engineering
Ismael Q Hernandez, Chemical Engineering
Alejandra Hinojosa, Chemical Engineering
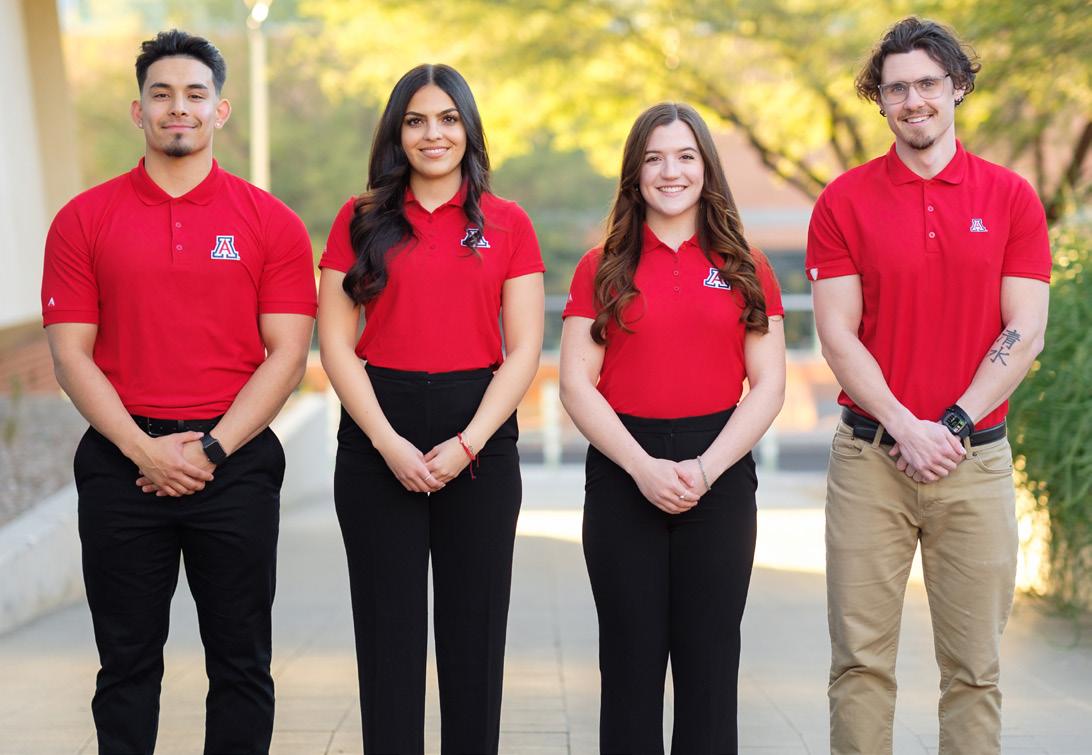
COLLEGE MENTOR
Adrianna Brush
SPONSOR ADVISOR
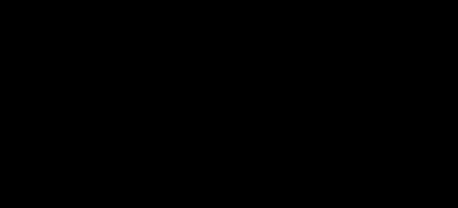
Thomas Olden
PROJECT GOAL
Create a foam for marine applications with desirable material physical properties.
The team began by conducting research to identify foam candidates, then selecting and ordering raw materials. Next, they created a test plan; conducted safety analysis; and began test apparatus building, including CAD drawing and 3D printing. Finally, they began creating foam samples in the lab, testing the physical properties of the material, analyzing the data, and creating a theoretical scale-up process.
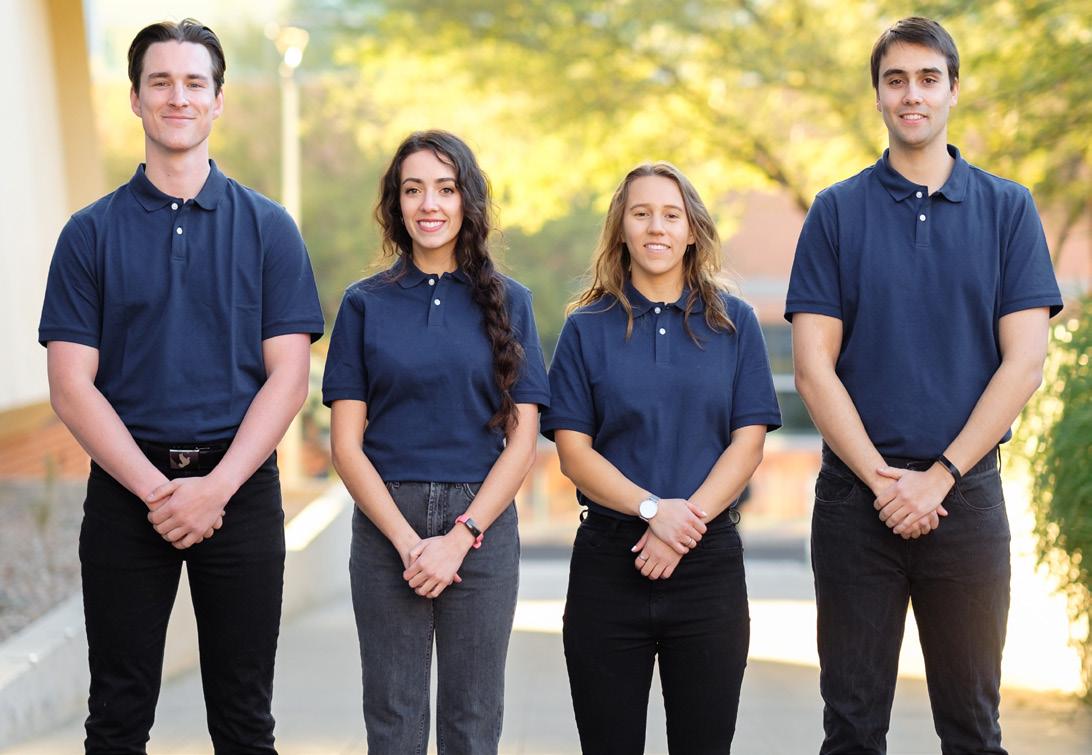
AZ Water Competition: Rainbow Valley Water Reclamation Facility Expansion Project
Team 23119
PROJECT GOAL
Provide a detailed expansion design recommendation for the Rainbow Valley Water Reclamation Facility located in Goodyear, AZ.
This project consisted of upgrading the Rainbow Valley Water Reclamation Facility’s water treatment capacity from 0.75 to 1.25 million gallons per day. Additional deliverables included expanding and upgrading the biosolids treatment to produce Class B biosolids for land applications, implementing an efficient odor control strategy to reduce odorous hydrogen sulfide emissions, providing an economic analysis on capital costs, and providing a plant layout that includes a hydraulic profile and construction sequencing plan.