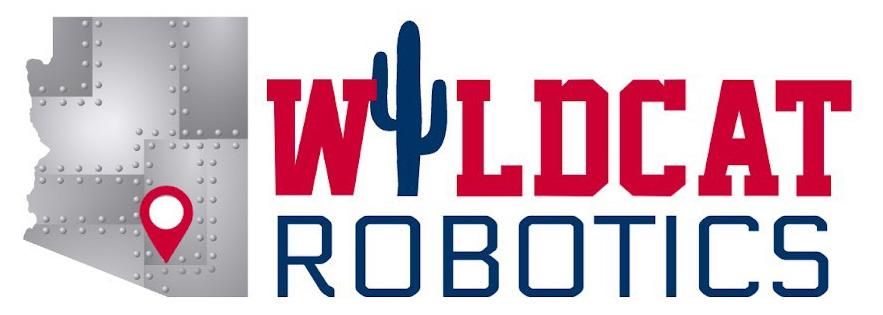
7 minute read
Telemetry and Data Logging System for the Wildcat Formula Racing Car
Team 23036
Project Goal
Develop a modular system to sense, transmit and display real-time racecar data.
In motorsports, data is paramount. Having the ability to gather information about the track, environment and car allows a team to better tune a vehicle optimally for a race. Technology that helps gather this data is available, but it is expensive and not compatible with all configurations of vehicles. To tackle these issues, the team created a modular system that is configurable with multiple sensors and usable in a wide variety of scenarios and environments. It provides critical real-time data for the Wildcat Formula Team.
The system has two Raspberry Pi computers that communicate with each other. One of them is onboard the race car for the driver, and the other is at the team’s chosen position, typically the pit lane. The onboard Raspberry Pi is connected to GPS, accelerometers and strain gauges, all gathering information on the car during a race. The remote subsystem has a Grafahan data plotting suite that converts the data into easily read figures. Use of this telemetry system allows setup of the car on race days to improve performance and safeguard against critical issues becoming safety hazards.
BattleBots
Team 23037
Project Goal
Design, build and verify a 250 lb. combat robot with active telemetry sensors capable of competing on the BattleBots TV show.
The BattleBots competition provides a space for builders to forge robots of destruction. As long as robots are under the weight limit and adhere to the BattleBots rules, they can fight. High achieving combat robots deal damage, survive deadly blows and look good while doing it. This project is a leap in the University of Arizona’s robotic community involvement and creates a space for future students to learn and have fun.
The team’s robot design integrates over 400 parts in six major subsystems – drive, weapon, armor, electronics, frame and telemetry sensors. The drive system uses four brushed motors to propel the robot to 20 mph. The weapon spins 45 lb. over 250 mph in eight seconds with a belt system. The stingray exterior is made of ultra high molecular weight plastic and AR400 ballistic steel for defense. The design includes an electronic system with kill switches, safety fuses and critical part protection. Holding it all together, the frame interlaces steel, aluminum and neoprene rubber to absorb impacts. Lastly, the combat robot houses speed, temperature and current sensors to ensure the driver is as informed as the robot is tough.
TEAM MEMBERS
Shayan N Afzal, Biosystems Engineering
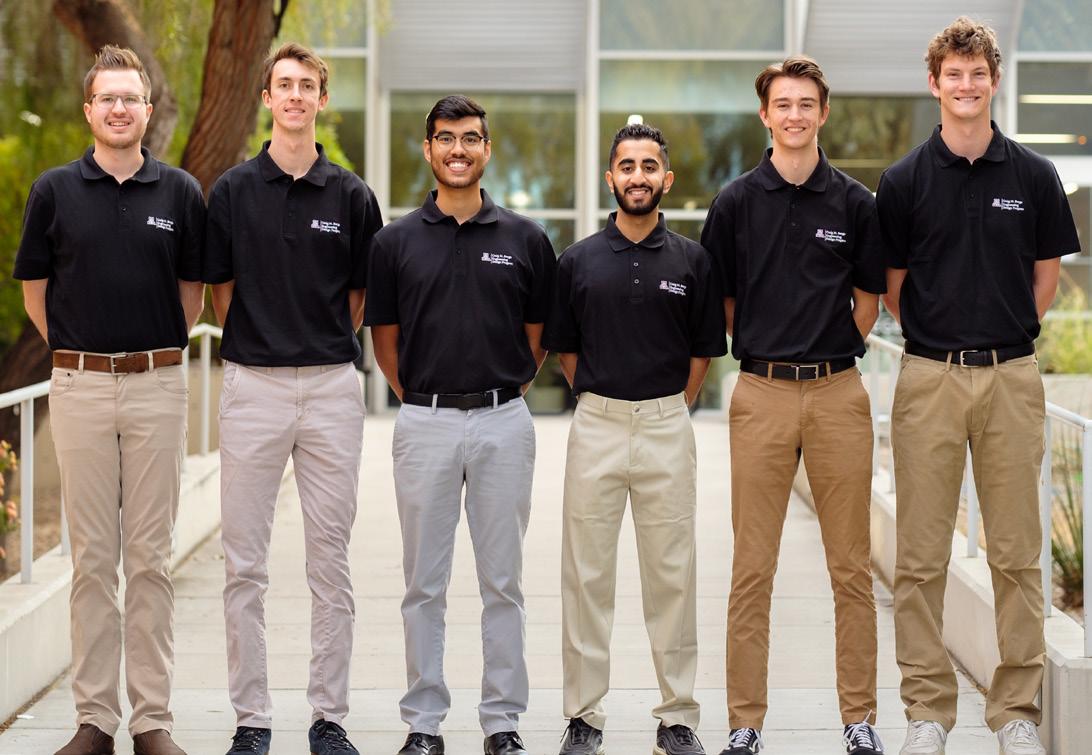
Lukas Matthew Baker, Mechanical Engineering
Christian Copic, Electrical & Computer Engineering
Isaac Carlos Gloistein, Mechanical Engineering
Luke Kobran, Mechanical Engineering
Nicholas J Smith, Electrical & Computer Engineering
COLLEGE MENTOR
Doug May
SPONSOR ADVISOR
Michael W Marcellin
TEAM MEMBERS
Yousuf Choudhary, Electrical & Computer Engineering
Al Hurworth, Mechanical Engineering
Knudson Karson, Electrical & Computer Engineering

Mathias Micah Ramirez, Aerospace Engineering
Nick Scott Sivertson, Mechanical Engineering
Alex Tynan Wait, Mechanical Engineering
COLLEGE MENTOR
Steve Larimore
SPONSOR ADVISOR
Michael W Marcellin
TEAM MEMBERS
Dylan Etson, Electrical & Computer Engineering
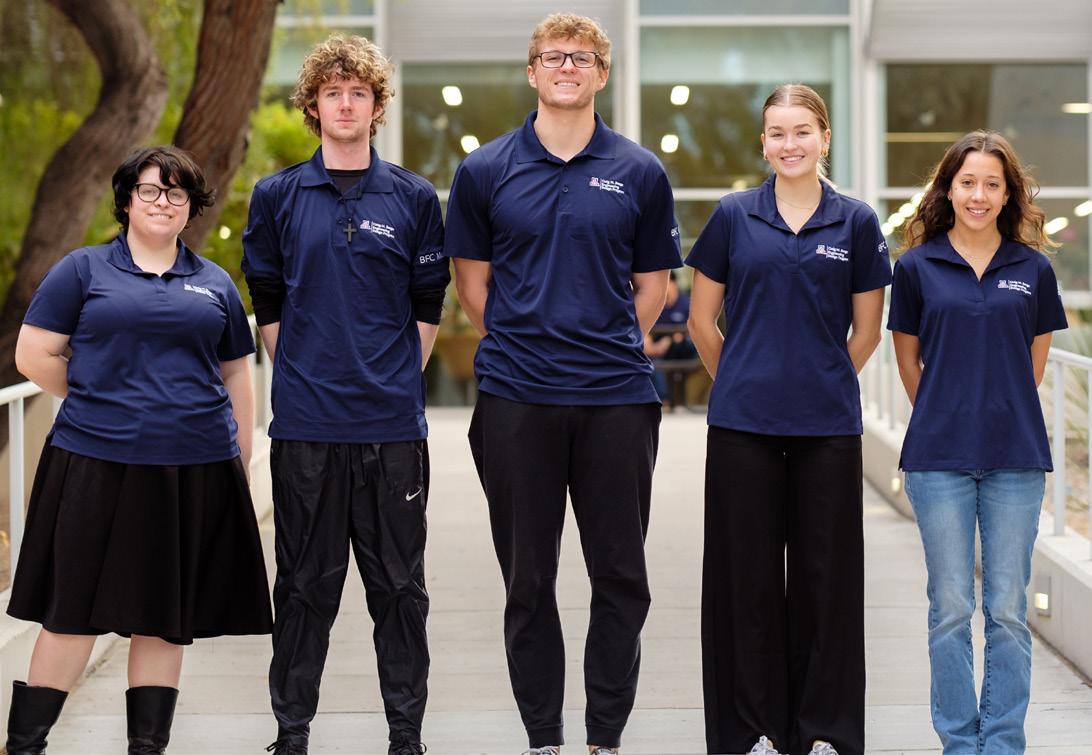
Jerry Klosterman, Electrical & Computer Engineering
Brandon Kron, Biomedical Engineering
Isabella Martinez, Systems Engineering
Lauren Meloche, Biomedical Engineering
Nathan Owens, Systems Engineering
COLLEGE MENTOR
Elmer Grubbs
SPONSOR ADVISORS
Arun Rao, Lacey Rao
My Health Navigator
Team 23038
Bfc Medical
PROJECT GOAL
Develop a mobile phone application to improve outcomes and experience during inpatient hospital stays.
Many hospitals still rely on outdated communication techniques, ultimately leaving patients in the dark. The team designed My Health Navigator to improve the inpatient experience. It consists of two interacting systems, a database and an internet application. The database acts as the central storage of all information passing through the hospital system, while the application is responsible for the major functionality.
The application incorporates three distinct views, for patients, doctors and administration. Patients can see their care team members, schedule and rounding alerts, while physicians control that data using the doctor view. All functionalities are supported by the admin view, where accounts are created and patients are assigned their doctors and care team.
The team began with in-depth stakeholder analysis, operational concept development and requirements engineering. Then they created graphical user interface wireframes along with UML model components to map out the design for future development. The system information and files are securely hosted on a Liquid Web server. Stored HTML and CSS files direct the application front end, while Javascript and routing files dictate all backend functionality.
Mechanical Energy Storage System
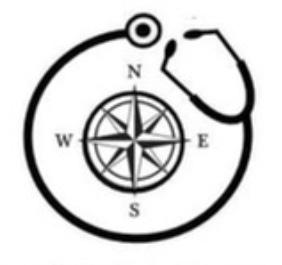
Team 23039
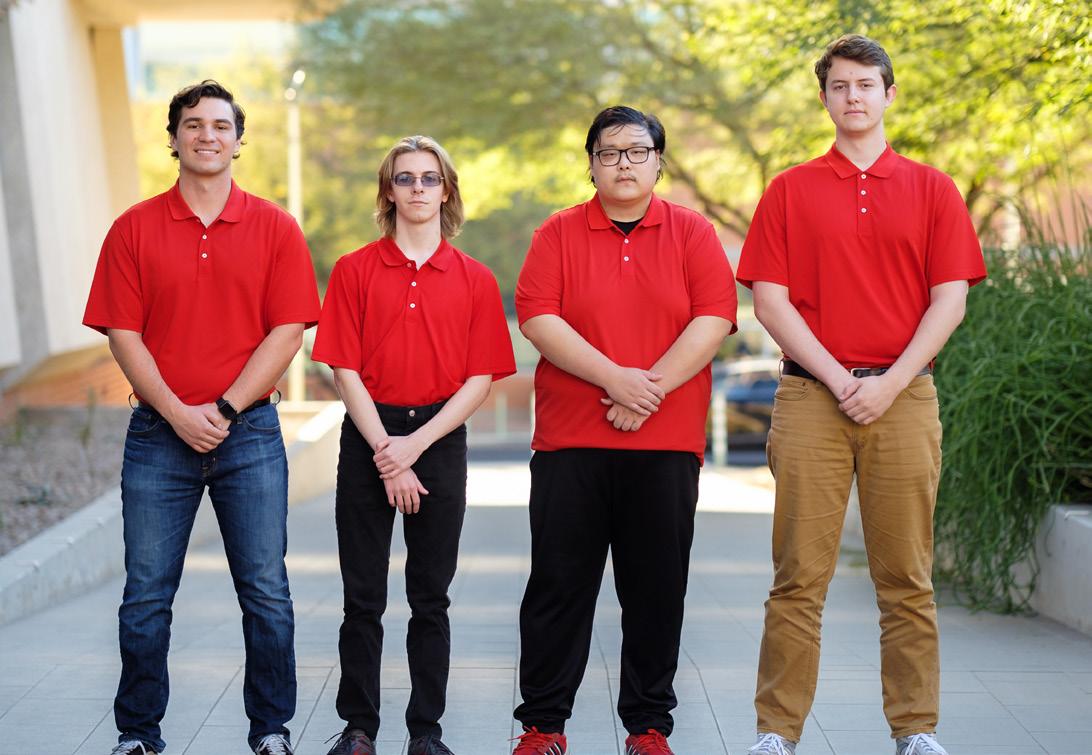
TEAM MEMBERS
Thomas Carroll, Electrical & Computer Engineering
Jesse Koontz, Electrical & Computer Engineering
Yudong Liang, Mechanical Engineering
Keegan Michael Pierson, Engineering Management
COLLEGE MENTOR
Michael Madjerec
SPONSOR ADVISOR
Michael Hemphill
Project Goal
Design a gravity battery, and characterize the efficiency of such a system for applications in existing vertical mineshafts.
When using renewable energies, storage is essential due to the significant variance in power produced throughout the day. Resolution Copper is evaluating alternatives to battery arrays for on-site power in their facilities. The solution must be cheaper and have less environmental impact, while still being reliable. To answer this need, the team designed a gravity battery that uses Resolution Copper’s existing vertical mine shafts.
The proof of concept is a tower-like structure that uses a brushless motor, a permanent magnet generator and a belt system. It turns electrical energy into potential energy by suspending a mass, which can then be converted back into electrical energy when gravity pulls the mass and drives the generator. Push-button user inputs relay commands to an Arduino microcontroller that interfaces with the motor and braking systems. The design uses proximity sensors to detect the position of the mass and terminate cycles automatically. Additionally, the system uses AC voltage and current sensors to calculate the total energy and efficiency produced by the system.
Automated Oil Dispenser
Team 23040
Competitive Engineering
Project Goal
Design and build an automated oil dispenser to eliminate cross contamination, reduce waste and notify the user of low fluid level for a standard 55-gallon drum.
Machine shops use devices such as computer numerical control (CNC) machines to cut all types of material. These CNC machines can require a variety of lubricant types in different amounts for their operations. They are often filled by the operator manually pumping from a 55-gallon oil drum. This regularly leads to spillage, wasted oil, cross contamination and safety hazards within the workshop.
The team designed the Automated Oil Dispenser to decrease the amount of spillage, time and work required due to manual pumping. This will result in a cleaner, safer and more efficient work environment. The design uses a color-coded categorization system to minimize cross contamination and ensure each machine gets the correct oil. A sink basin filters the oil to eliminate spillage, reduce waste and prevent contamination, while a microcontroller and electric pump fill the oil safe containers. This microcontroller is programmed to detect the amount of oil dispensed and alerts the user when the drum reaches a low level.
Pulsed Detonator Ignition System Optimization
Team 23041
Project Goal
Design and optimize a pulsed detonation tube as an igniter for a Rotating Detonation Engine (RDE).
Innovations in propulsion presently are focused on supersonic combustion of propellants to increase the useful energy yield in the cycle of an engine. In contrast, this technology adapts supersonic combustion in an RDE.
Traditional engines and nozzles have subsonic combustion called deflagration, and shock waves travel around a ring-shaped chamber to combust propellants. To successfully start an RDE, a shock wave must propagate within the combustion chamber itself.
This project focused on creating and inserting supersonic combustion waves into an RDE. Geometric and chemical factors dramatically impact the efficiency and reliability of the detonation process. The team designed and fabricated a modular system to conduct an extensive test campaign varying numerous factors, including internal geometry, fuel-oxidizer ratio, pressure, and timing of spark plug ignition.
The result was enhanced supersonic wave velocity measured at the outlet of the system, yielding an optimized design with favorable shock wave generation, reliability and velocity.
TEAM MEMBERS
Harry Chhieu, Mechanical Engineering
Marco Andres Lopez, Mechanical Engineering
Cameron John Frost Meehan, Electrical & Computer Engineering
Tania Mitnasala, Electrical & Computer Engineering
Mandeep Singh, Mechanical Engineering
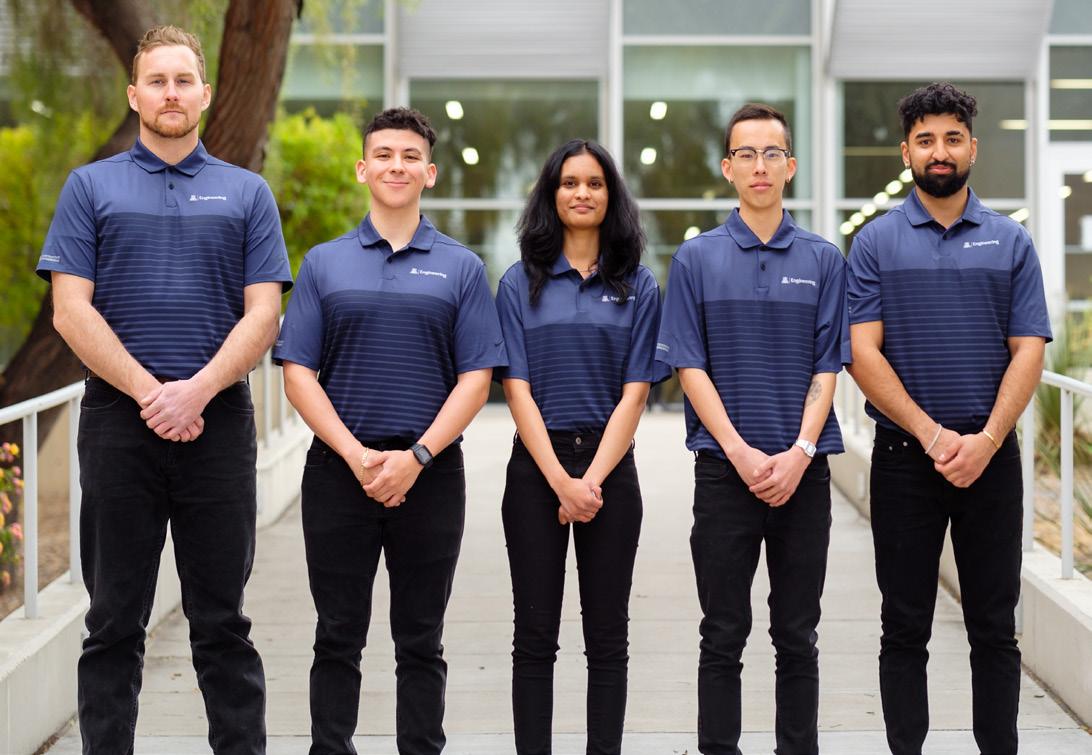
COLLEGE MENTOR
Michael Madjerec
SPONSOR ADVISOR
David Saucedo
TEAM MEMBERS
Chad Aykroyd, Mechanical Engineering
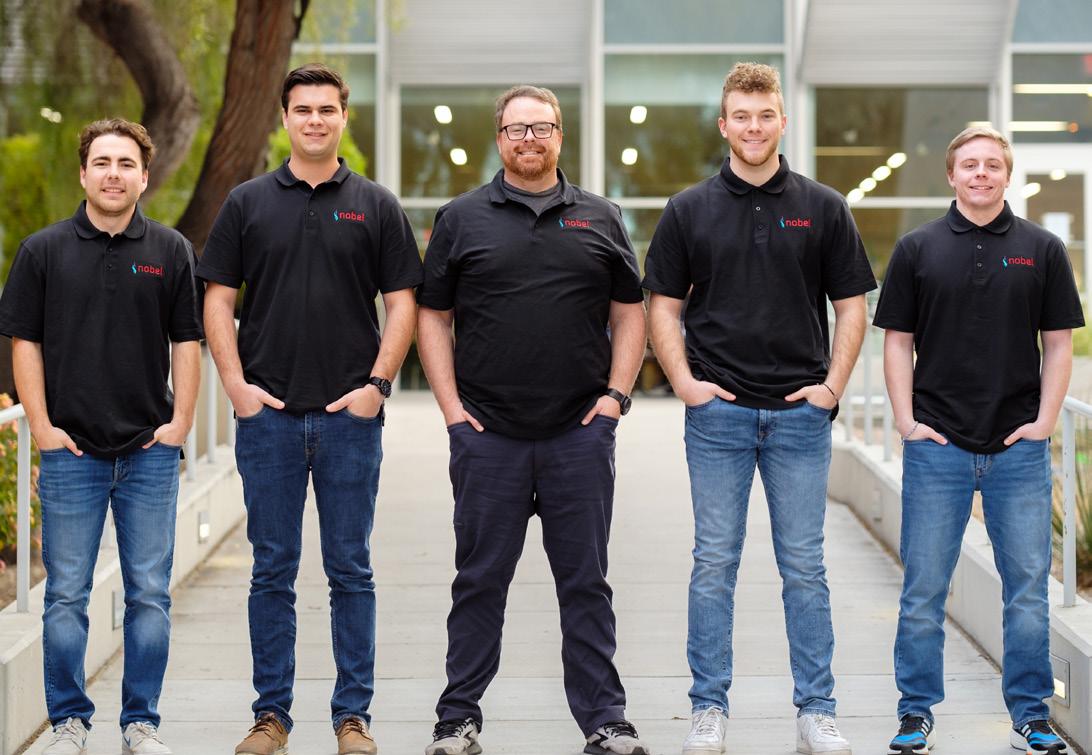
Ryan Curtis-Sanchez, Aerospace Engineering
Curtis Dodd Goldin, Aerospace Engineering
Weston Cole Meyers, Aerospace Engineering
Jacob Thomas Roschak, Aerospace Engineering
COLLEGE MENTOR
Doug May
SPONSOR ADVISOR
James Villarreal
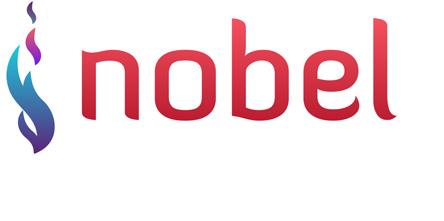
TEAM MEMBERS
Fahad Mohammad Alrashed, Electrical & Computer Engineering
Martin Calderon, Mechanical Engineering
Canyon Charles Cooke, Mechanical Engineering
Erick F Dzeketey, Biosystems Engineering
Alex J Hillman, Electrical & Computer Engineering
COLLEGE MENTOR
Michael Madjerec
SPONSOR ADVISORS
Duarte Diaz, Brian Little
Live Silage Analyzer and Mini-Fermenter
Team 23042
TEAM MEMBERS
Sebo Diaz, Biomedical Engineering
Vinamra Kumar, Biomedical Engineering
Kenzi Marie McNeil, Biomedical Engineering
Aaron A Ramos, Materials Science & Engineering
Alex Joseph Sciortino, Mechanical Engineering
COLLEGE MENTOR
Justin James Hyatt
SPONSOR ADVISOR
Dan Latt
Project Goal
Build a better research tool for silage analysis.
Silage is a long-storage-life cattle feed created through the fermentation of various agricultural products. The study of silage fermentation and additive processes affects commercial enterprises, such as dairies and feedlots, including the environmental impact of these enterprises. This project redefines silage research.
The current method of silage study wastes large quantities of disposable bags and silage. This team set out to build a research tool to replace the existing wasteful method of analyzing silage as well as simplify the data collection and analysis process.
The team’s design builds on an off-the-shelf pressure cooker modified to collect scientific data. The pressure cooker base is ideal, as it already facilitates successful fermentation with little modification. Students installed several sensors integrated into the lid of the pressure vessel to analyze trends in pH, temperature, humidity, oxygen and volatile organic compound (VOC) content. This information is then processed by an onboard Raspberry Pi before being uploaded to a GitHub repository for ease of access.
Arch Reactivator Brace
Team 23043
Project Goal
Using an energy return mechanism to support normal human gait while maintaining adequate range of motion in the affected foot, design and build a comfortable, wellfitting, brace that corrects Adult Acquired Flat Foot (AAFD).
AAFD is a potentially debilitating condition that affects up to 5 million people in the United States. Left untreated, AAFD can cause limiting pain and arthritis. Mild to moderate AAFD can be addressed using braces and orthotic supports. However, the design of available products to treat AAFD may be impeding their effectiveness.
This team designed a novel brace to address common complaints about available products: high temperatures within the brace, discomfort, poor fit in readily available footwear, inadequate correction of the deformity, and reduced range of foot motion.
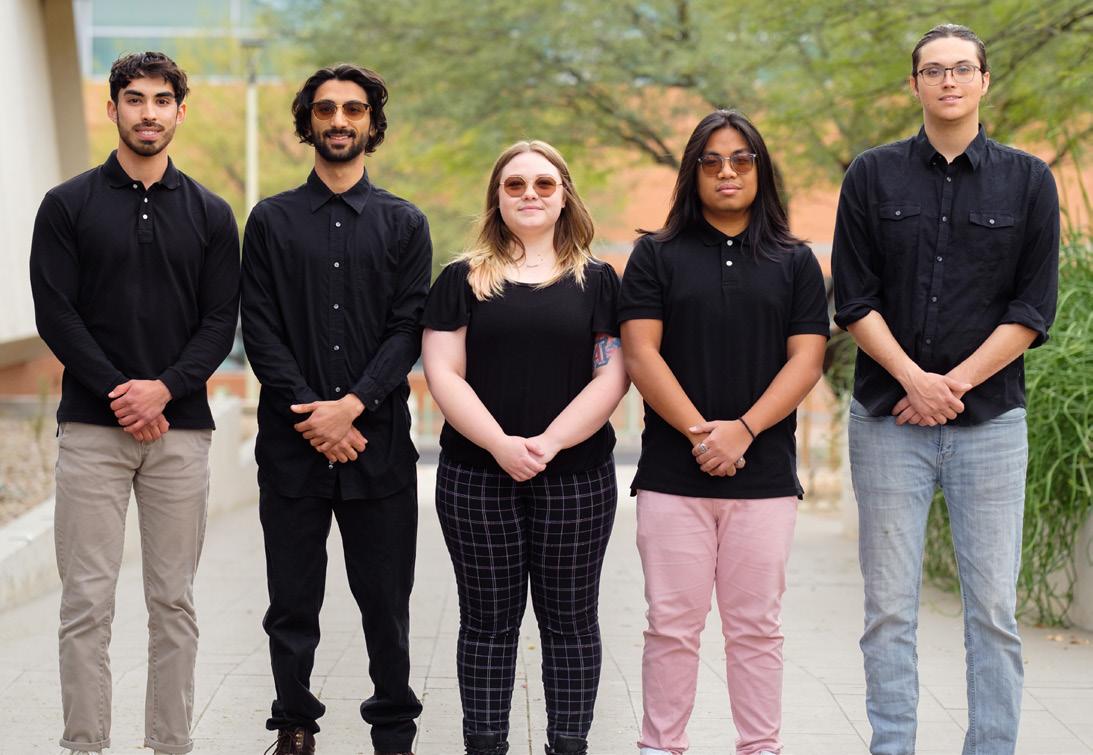
Combining previously proven static archplate geometry with an adjustable springpack system, the Arch Reactivator allows a user to step down naturally then get dynamic support via the lifting of a springpack system at the upper portion of the brace. All of this is contained within a sleek, comfortable sleeve that is easy to put on.
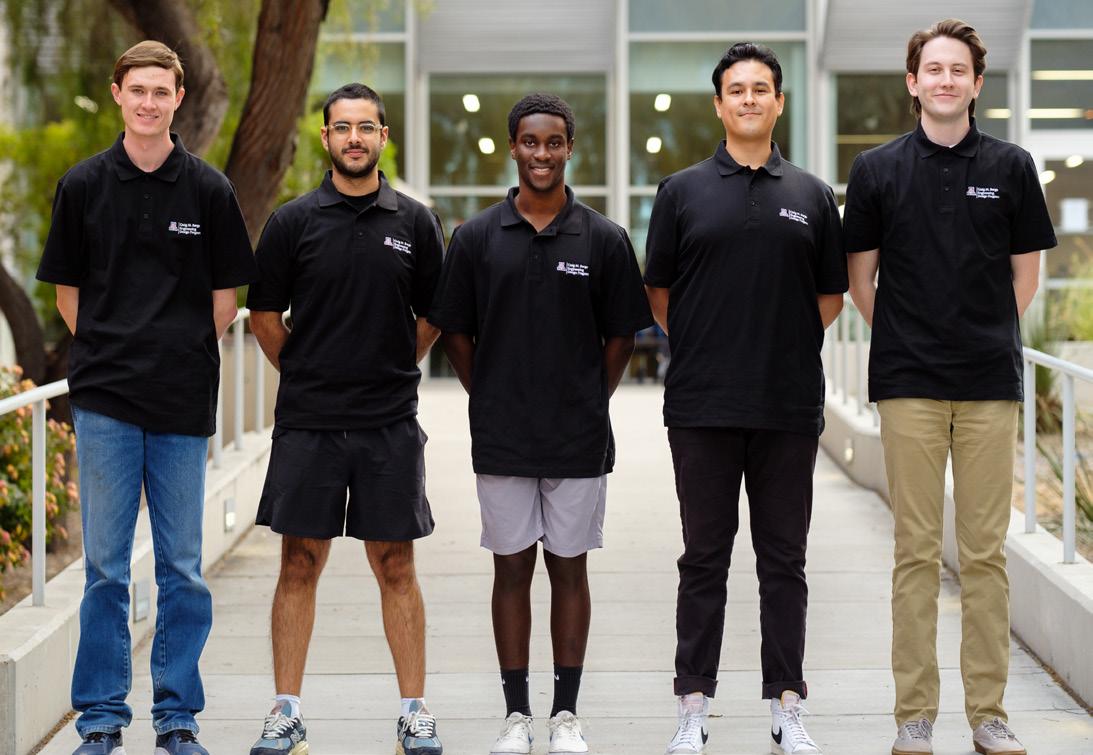