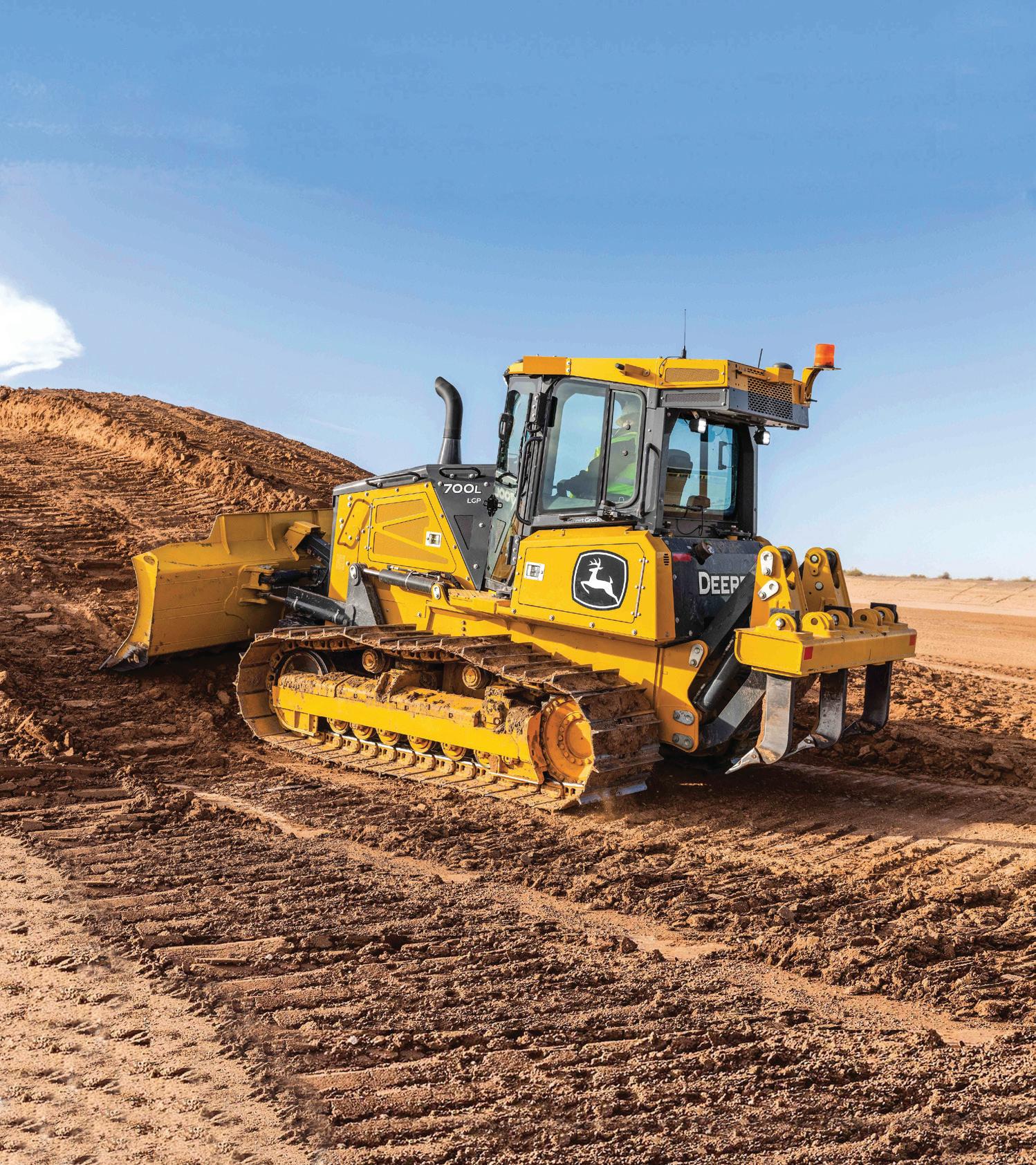

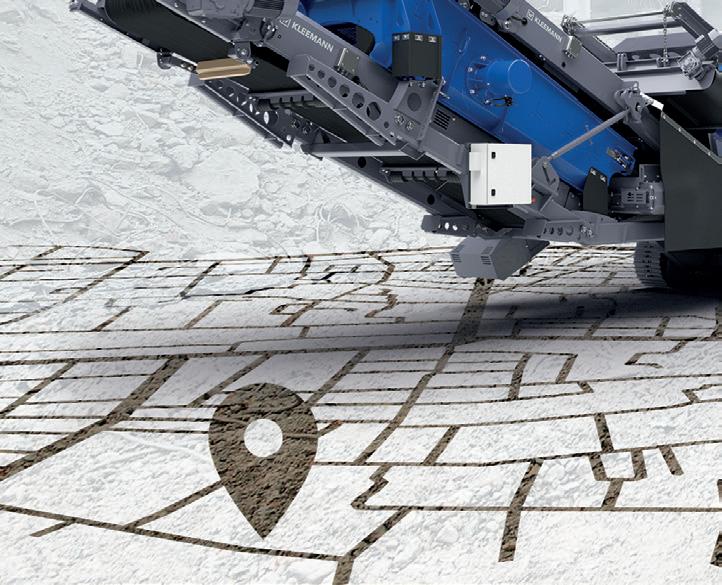

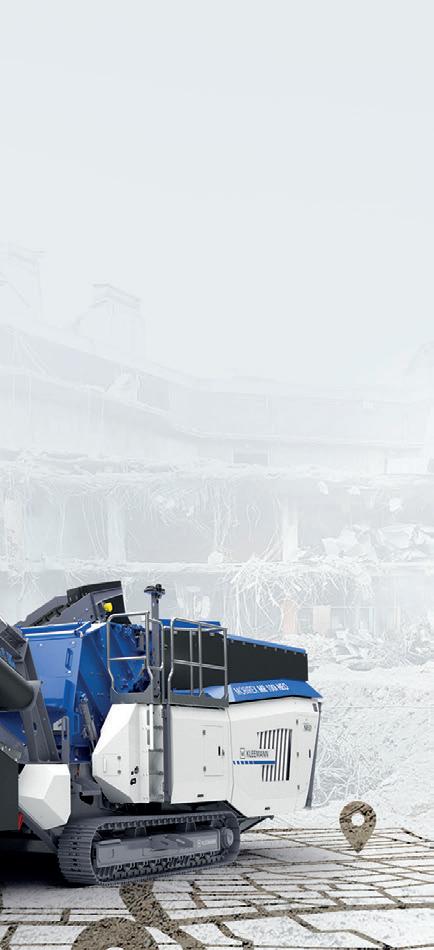
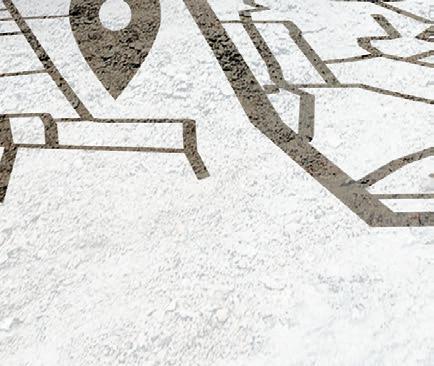
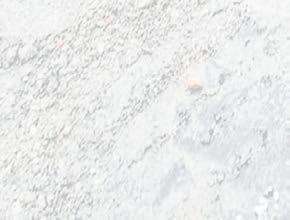




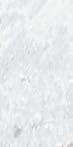
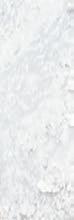
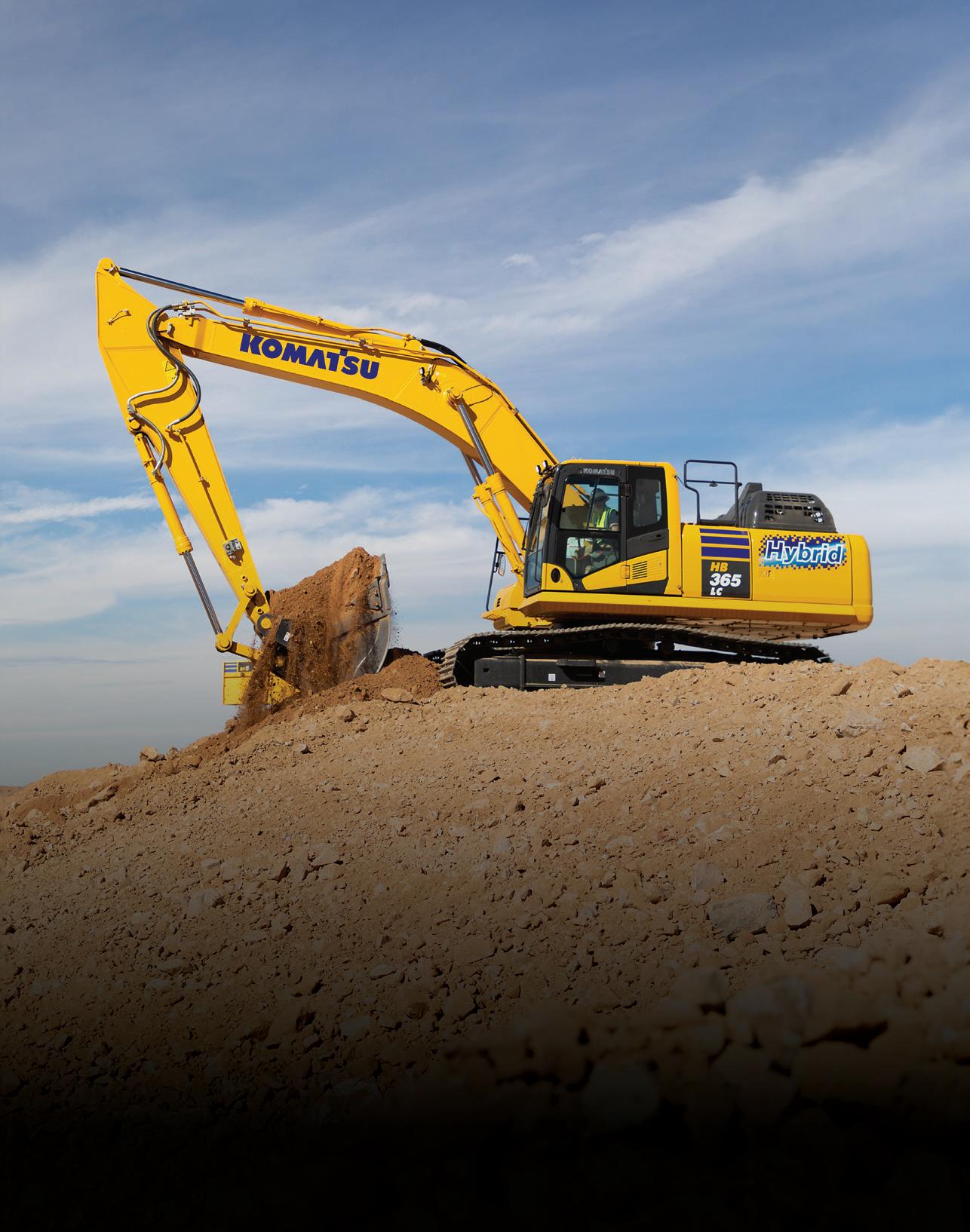
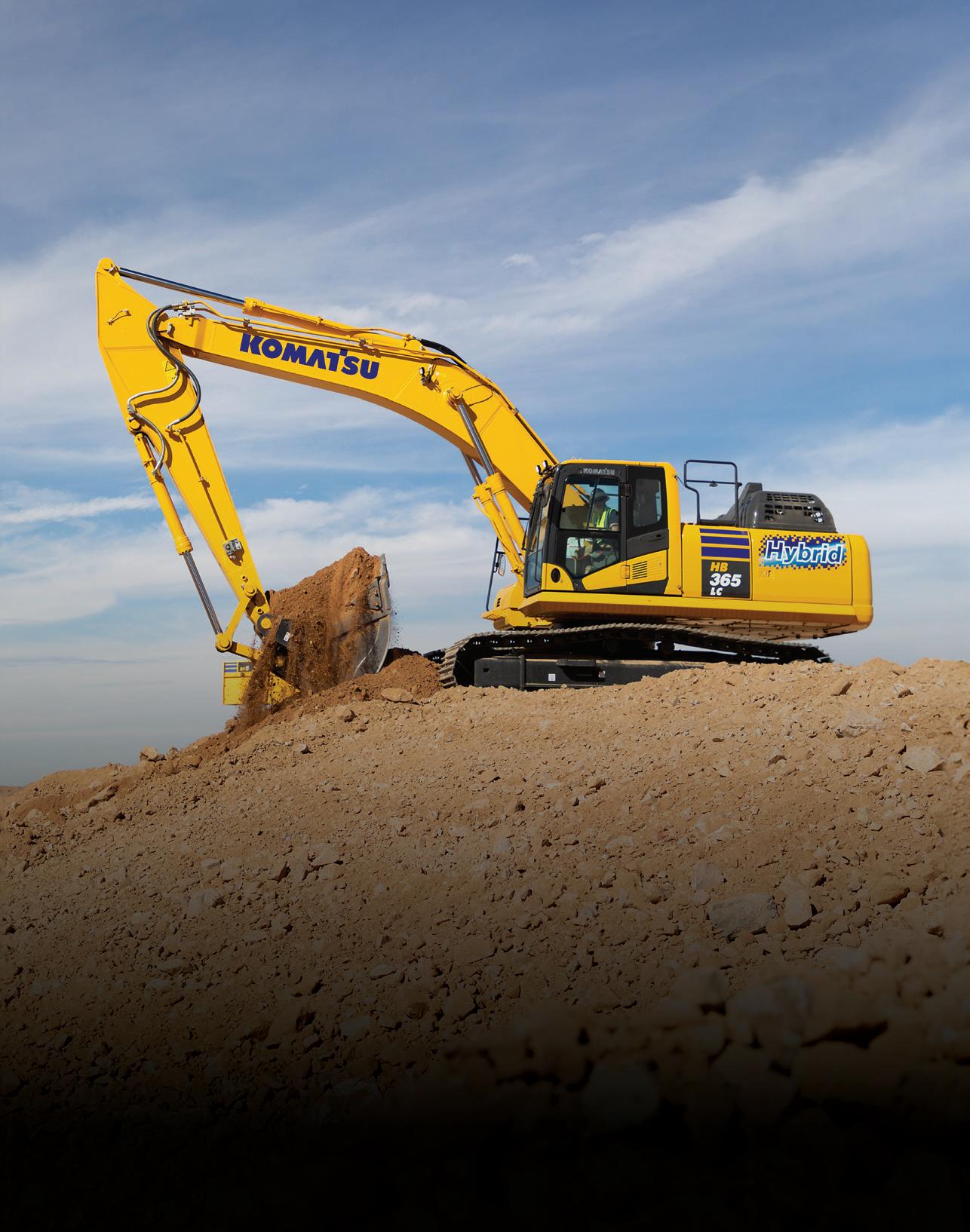
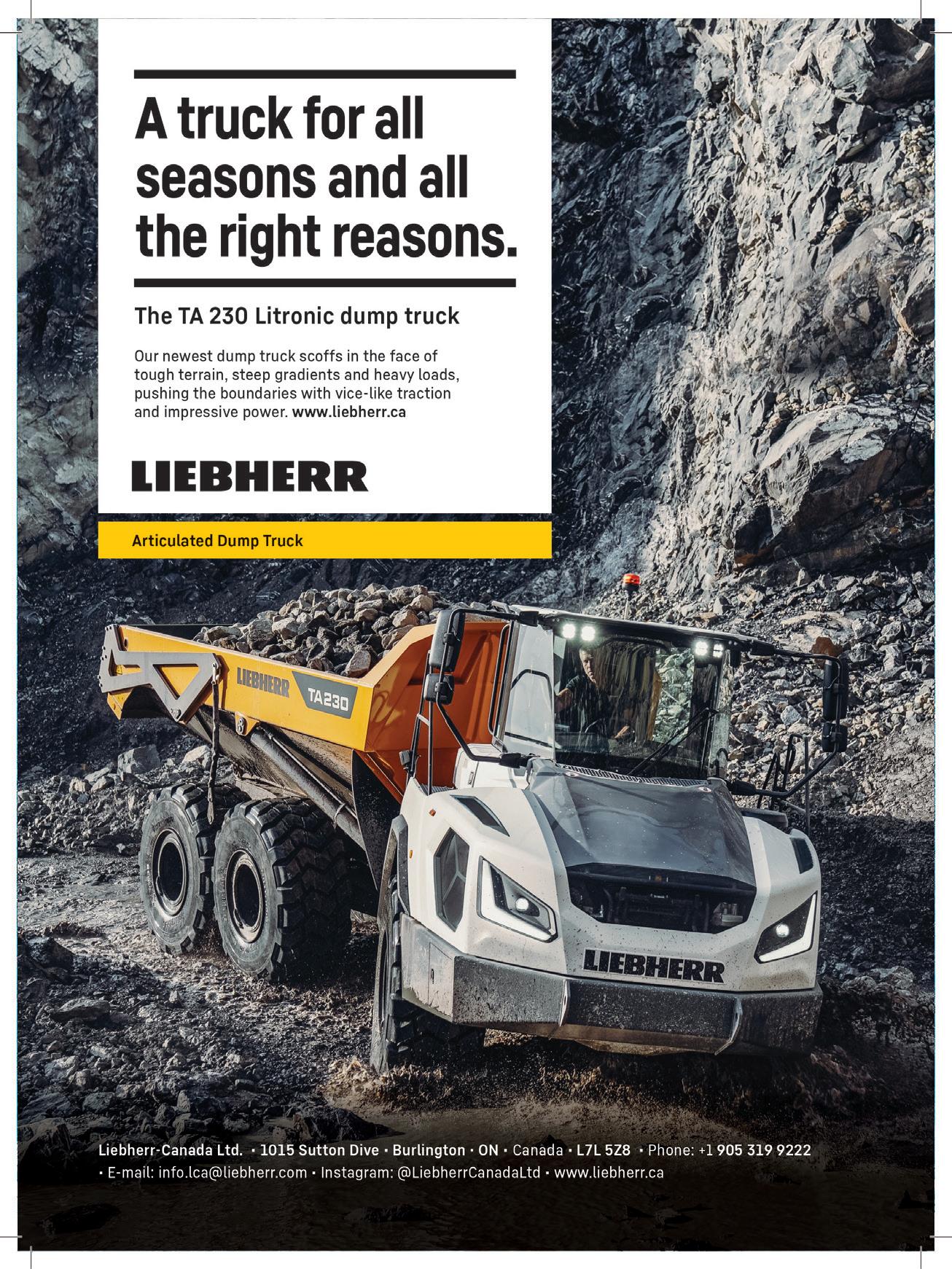
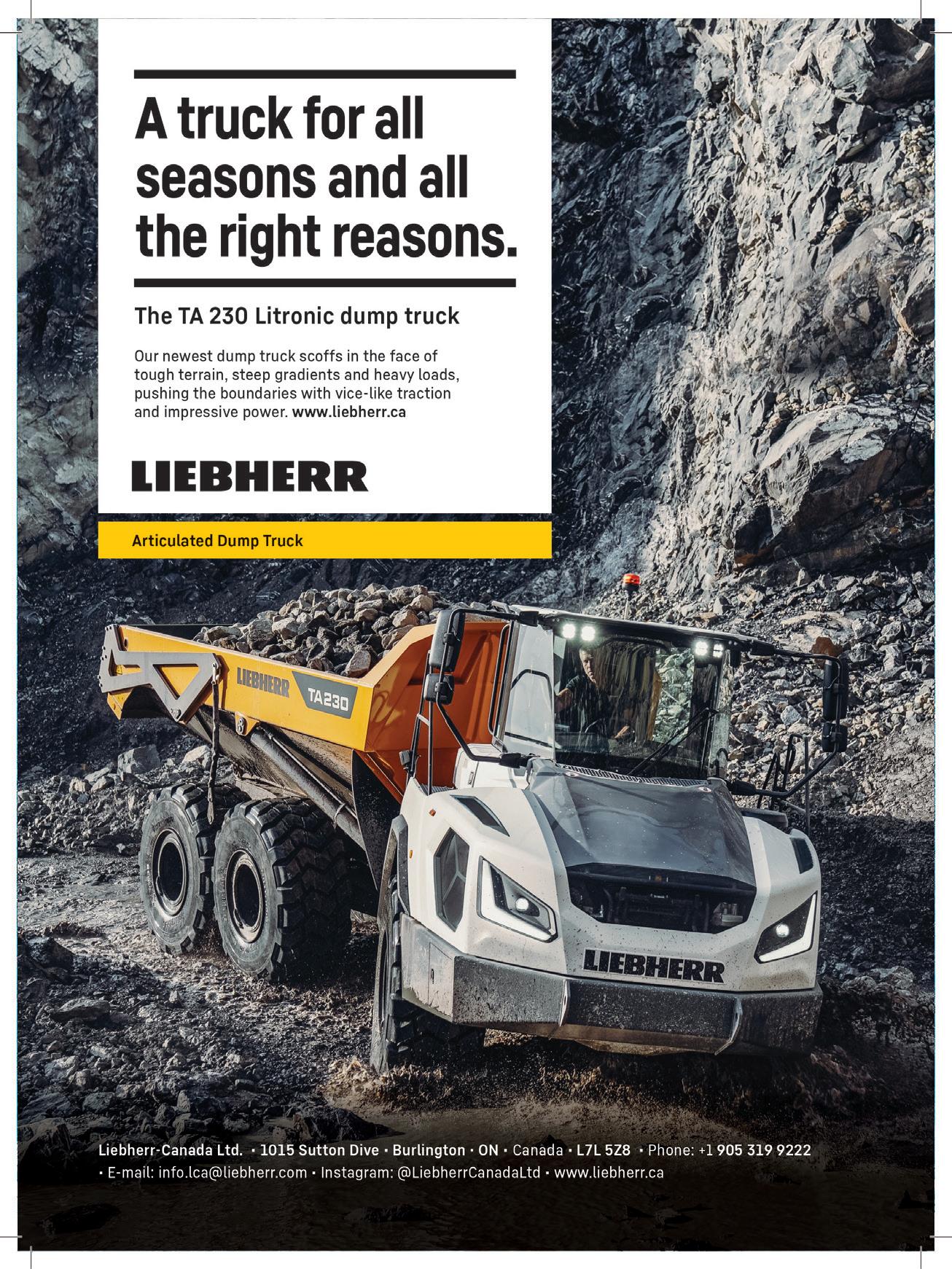
Introducing the new VHD
On the jobsite you need a truck that’s tough, safe, and smart. So, we built the new Volvo VHD to be the best-looking, most rugged vocational vehicle in the industry, packed with innovative ideas like Volvo Active Driver Assist and the revolutionary Volvo Dynamic Steering. Your toughest jobs just got easier. Learn more at volvotrucks.ca/en-ca/trucks/vhd/
FEATURE STORY
INVESTMENT IN TECHNOLOGY SETS UP B.C. CONTRACTOR FOR SUCCESS
SPEC GUIDE: DOZERS
COVER PHOTO: JOHN DEERE 700L
DOZER
Spec Guide: Dozers
Turn to page 18 . JULY/AUGUST 2024 | VOLUME 39 • NUMBER 5
WE’D LIKE TO HEAR FROM YOU
Do you have a job site story, innovation, or industry concern that our readers should know about? We’d like to hear from you.
Contact: Editor in Chief Kaitlyn Till at ktill@baumpub.com or 604-291-9900 ext. 330
EDITOR IN CHIEF Kaitlyn Till ktill@baumpub.com 604-291-9900 ext. 330
EDITOR Lee Toop ltoop@baumpub.com 604-291-9900 ext. 315
ASSOCIATE PUBLISHER Sam Esmaili sam@baumpub.com 604-291-9900 ext. 110
ADVERTISING
PRODUCTION MANAGER Tina Anderson tanderson@baumpub.com 604-291-9900 ext. 222
DESIGN & PRODUCTION
Morena Zanotto morena@baumpub.com
604-291-9900 ext. 325
PRESIDENT/PUBLISHER Ken Singer ksinger@baumpub.com 604-291-9900 ext. 226
VICE PRESIDENT/CONTROLLER
Melvin Date Chong mdatechong@baumpub.com
FOUNDER
Engelbert J. Baum
Published by: Baum Publications Ltd.
124 - 2323 Boundary Road Vancouver, BC, Canada V5M 4V8
Tel: 604-291-9900
Toll-free: 1-888-286-3630
Fax: 604-291-1906 www.baumpub.com www.heavyequipmentguide.ca @HeavyEquipGuide
FOR ALL CIRCULATION INQUIRIES
Toll-free: 1-866-764-0227 email: heg@mysubscription.ca
Subscription: To subscribe, renew your subscription, or change your address or other information, go to: http://mysubscription.ca/heg/
Heavy Equipment Guide serves the Canadian engineered construction industry including: roadbuilding and maintenance; highways, bridges, tunnels; grading and excavating; earthmoving; crushing; trucking and hauling; underground utilities; trenching; concrete paving; asphalt paving; demolition; aggregates production; fleet maintenance; and asset security and management. The magazine is distributed to key industry personnel involved in these sectors.
Subscription Price: In Canada, CDN $91.00; Outside Canada, US$149. Heavy Equipment Guide is published eight times a year in January/ February, March, April, May/June, July/August, September, October, and November/December.
Heavy Equipment Guide accepts no responsibility or liability for reported claims made by manufacturers and/or distributors for products or services; the views and opinions expressed are those of the authors and not necessarily those of Baum Publications Ltd.
Copyright 2024, Baum Publications Ltd. No portion of this publication may be reproduced without permission of the publishers.
We acknowledge the financial support of the Government of Canada.
Printed on paper made of FSC®-certified and other controlled material. ISSN 1715-7013.
PUBLICATIONS MAIL AGREEMENT NO. 40069270
Return undeliverable Canadian addresses to:
Circulation Dept., 124-2323 Boundary Road, Vancouver, BC V5M 4V8 email: heg@mysubscription.ca Toll-free: 1-866-764-0227
BIG BROTHER IS NOT WATCHING – BUT DO YOUR EMPLOYEES KNOW THAT?
Irecently attended a technology-focused event where contractors were invited to share some of the roadblocks and concerns around adopting new technology for their businesses. The biggest concern was, unsurprisingly, price, and the significant up-front outlay that can be required to set up a digitally connected job site before the benefits and savings from that technology are realized.
But another concern that repeatedly came up was that employees would think that “Big Brother” was watching if management introduced camera systems or other operator behaviour tracking and intervention tools on the equipment.
This is a completely understandable concern, and organizations need to address it with employees before introducing something that looks like a surveillance tool into what is effectively their office.
When introducing any new technology on the job site, the first mistake that management can make is adding that technology without explaining how it benefits the workers using it. This problem can arise with the introduction of any new productivity boosting tool, but the point of introducing the new tool is defeated if workers don’t know how to use it effectively or understand the value. When the new technology involves cameras and data collection the additional risk is the erosion of trust between employee and employer. Employers already strapped for skilled labour can’t risk the degradation of those relationships.
It is essential to have transparent conversations with employees because camera-based safety alert systems, in particular, can save lives and protect assets. Obstacle detection systems on heavy equipment alert operators to the presence of people and objects within dangerous proximity of working machinery. Cameras in the cab on haul trucks alert operators if their attention is diverted from the road. Sensors and cameras on trucks can detect hard braking and speeding and record these incidents for review.
No one wants to admit that they have lapses in attention or make mistakes – but we all do. When operating heavy equipment or driving a truck the consequences of not seeing a pedestrian or falling asleep behind the wheel can be
When introducing any new technology on the job site, the first mistake that management can make is adding that technology without explaining how it benefits the workers using it.
catastrophic. The case for introducing camera technology on the job site has to start there. These are not tools used to judge or police every behaviour. They are teaching tools used to improve performance, and they prevent accidents when mistakes are made so that everyone can go home safely at the end of the day.
Before introducing this technology into your workplace, sit down with your employees and listen to their concerns. New technology needs buy-in at all levels of the organization to maintain morale and trust, but that can only happen once the operator in the cab understands that Big Brother is not watching. Once that trust is established, everyone in the organization can experience the benefits of a safer, more efficient job site.
Kaitlyn Till Editor In Chief
ktill@baumpub.com
heavyequipmentguide.ca
From the original compaction brand comes a full line of construction equipment designed to help you get the job done with efficiency, quality and comfort. Whether your challenge is to load, move or place material, compact soil and asphalt, or to provide light, heat, power or pumping on your job site, Wacker Neuson has the machines to get it done right. This includes zero-emission, battery-powered solutions to meet the demands of the construction environment today, as well as tomorrow.
Contact your local Wacker Neuson dealer today. All it takes for
HD Hyundai Construction Equipment North America has opened a parts distribution centre in Mississauga, Ontario. Representatives from HD Hyundai Construction Equipment North America and HD Hyundai Construction Equipment were in attendance for the opening event along with Maninder Sidhu, a Canadian Member of Parliament who serves as the Parliamentary Secretary to the Minister of Export Promotion, International Trade and Economic Development.
“This is an important first step toward establishing an HD Hyundai Construction Equipment corporate presence in Canada,” said Stan Park, president of HD Hyundai Construction Equipment North America. “Canada accounts for a significant share of our North American construction equipment business. This centre will provide important efficiencies and cost savings to further strengthen our Canadian presence.”
The new facility is located at 2450 Hogan Drive, Unit 3, Mississauga, Ontario. Mahmoud Jamii, Canada parts sales representative at HD Hyundai Construction Equipment North America, will lead the operation, with initial staffing through Expeditors Canada.
“Our first goal in adding this centre to our global integrated supply chain is to provide faster, more comprehensive parts availability to Hyundai customers and dealers across Canada,” said Park. “Working with an established partner like Expeditors allows us to grow our presence and infrastructure in Canada more quickly.”
HD Hyundai Construction Equipment North America currently serves its Canadian customers through its network of 17 dealers with 33 locations across Canada.
SMS Equipment has unveiled the expansion of its Timmins branch at a grand opening celebration. The $30M development bolsters the company’s support to Northern Ontario’s mining, construction, and forestry sectors.
“We’re thrilled to open our incredible new SMS Equipment Timmins branch and serve our customers with equipment, technology, service, and support right where it’s needed in Northern Ontario,” said Robin Heard, SMS Equipment president and CEO.
“The demand for heavy equipment has steadily increased alongside explosive growth of the province’s mining sector and its related service industries,” he continued. “We wanted to invest in a facility and the personnel that could fulfill that demand with a broad range of solutions to keep our customers’ operations running smoothly.”
Spanning 37,000 square feet, the Timmins branch houses the company’s new and used equipment sales. The expansion also increases its service and maintenance capabilities in the region. The new building is designed to hold large mining equipment. It includes two heavy-duty welding bays, five service bays, and a 100-ton heavy-lift capacity, which together accommodate new remanufacturing, welding, painting, and large equipment rebuilds in-house. Environmental sustainability was top-of-mind in its design. Among many water and energy-saving features, its solar generation system is expected to supply nearly 70 percent of the administrative offices’ power.
“With this expansion, we’re building on our 30-year foundation in the region,” added Heard. “SMS Equipment is proudly investing in Northern Ontario through our facility, local community initiatives, and job creation.”
Along with jobs created through the expansion, the branch employs a growing staff, including skilled heavy equipment technicians and apprentices.
“Timmins is the city with a heart of gold and having a worldclass supply and service company like SMS Equipment is important for our local economy,” said George Pirie, Member of Provincial Parliament for Timmins. “I want to congratulate SMS Equipment on this terrific expansion that will create over 100 good-paying jobs and benefit the people and businesses in our region. This brand-new facility will help mining operations get machines back up and running faster, while also ensuring Timmins will be the supply and service hub of the Northeast.”
STERLING CRANE NAMED ONE OF SAMSARA’S
ACanadian crane services company has been recognized for its leading use of technology in reducing costs and improving safety and efficiency with one of Samsara’s 2024 Connected Operations Awards.
Sterling Crane is a Marmon Crane Services/Berkshire Hathaway company that provides crane services across Canada, the U.S., and Australia. It has more than 16 branches and 650 employees in Canada, and has a reputation of trusted and reliable service for customers in infrastructure, industrial, power, and commercial sectors.
Since implementing Samsara, Sterling Crane has achieved an estimated annual savings of $2.5 million from major maintenance costs for its on-road and off-road fleet by using Samsara to inform its proactive maintenance program. Samsara has also helped improve driver productivity, saving more than $1.2 million, and technician time and maintenance costs have been reduced by saving more than $500,000.
“At Samsara, we understand the pivotal role that physical operations play in running our world’s economy. Technology is a critical component to ensure that operations run smoothly, efficiently, and safely,” said Lara Caimi, president of worldwide field operations at Samsara. “Our Connected Operations Award winners are leading the way in transforming their organizations and industries with a combination of technology, strategy, and creativity. We are honoured to be part of their story and celebrate their impact on the world’s foundational industries.”
Samsara recognized 16 companies in all from North America and Europe. They represent a broad range of segments including infrastructure, logistics, specialty contracting, communications, and more.
United Group’s investment in technology sets the company up for success in B.C.
Turn to page 28.
EPIROC ACQUIRES CANADIAN
DIGITAL GEOTECHNICAL
INSTRUMENT MANUFACTURER
YIELDPOINT
Epiroc has agreed to acquire Yieldpoint Inc., a Canadian company that provides ground support solutions that strengthen safety for mining and civil engineering applications. Yieldpoint is based in Kingston, Ontario, and has about 10 employees. The company designs, manufactures, and sells digital geotechnical instruments worldwide. The products, which include ground movement sensors and telemetry solutions, are primarily used for underground mining, tunnelling, and civil construction applications. Yieldpoint’s solutions help digitalize ground support and create a safer working environment.
K-TEC TO BECOME FIRST SCRAPER MANUFACTURER TO BUILD ITS MACHINES USING FOSSIL-FREE STEEL
K-Tec has partnered with SSAB to source pilot deliveries of its fossil-free steel for manufacturing heavy-duty scrapers. The collaboration will reduce emissions and improve sustainability for scraper customers. K-Tec currently designs and manufactures earthmoving equipment using SSAB’s Hardox and Strenx performance steel. Pilot deliveries of SSAB Fossil-free steel use HYBRIT technology. It replaces the coking coal traditionally used for iron ore-based steelmaking with fossil-free electricity and green hydrogen. The byproduct remaining is water, rather than carbon dioxide emissions.
Manitou North America has named Quebec’s J.-Rene Lafond as its first Canadian partner dealer. Partner dealer is a designation given to Manitou dealers who exhibit quantifiable excellence in product sales, parts support, and service in its territory. This includes commitments to training, parts inventory, brand support, and overall sales of Manitou equipment.
“Our first partner dealers represent both American and Canadian excellence in serving their customers with the right mix of products, service and support to succeed,” said Ilmars Nartish, vice president of Manitou North America. “Both Ste-
venson Crane and J.-Rene Lafond have demonstrated excellence in listening to the needs of their markets and building their businesses intelligently – and representing Manitou to the industry with great pride and customer service proven to make a difference.”
Bird Construction Inc. will acquire Jacob Bros Construction for an estimated $135 million. Headquartered in Surrey, British Columbia, Jacob Bros is a privately owned civil infrastructure construction business with a workforce of over 350 personnel. Scott Jacob, CEO of Jacob Bros, and Todd Jacob, COO of Jacob Bros, will join Bird to lead the combination of Bird’s western infrastructure business and their existing business. Jacob Bros specializes in civil infrastructure construction across a wide array of projects, such as airports, seaports, railways, bridges and structures, earthworks, energy projects, and utilities.
Get the best of both worlds with the TCi 920 dozer.
Power and durability for tough applications. Finesse and response for fine grading.
H Series rough-terrain forklifts handle heavy loads off-road and now available with the option of a factory-installed, enclosed cab to provide a more comfortable operating environment. These forklifts can travel at up to 24 mph, and have mast options that lift up to 8,000 pounds as high as 22 feet. Cabs include heat and air conditioning, Bluetooth radio, and USB charging ports, giving operators the ability to work in any temperature and weather conditions. Wide doors secure completely open for easy communication with crew on the ground as well as increased air flow. An overhead roof window gives visibility to overhead loads.
The Woodcracker tree saw with grapple is available for three Manitou rotating telehandlers, the MRT 2260, MRT 2660, and MRT 3060 Vision+. Designed for tree and limb removal work, the saw paired with a rotating telehandler can reach up to 98 feet in height and more than 84 feet out, depending on the model. The saw rotates into position to cut, hold, and deliver each limb. Maximum lifting capacity with the tree saw attachment is 8,000 pounds. Telehandlers equipped with the tree saw are fitted with a specialized forestry package including a windshield guard, boom covers and guards, hydraulic and electrical system covers, and a second return-to-tank line.
The SUPER 1800-5(i) is a compact machine capable of paving widths between 2.55 and 10 metres on city streets and highways. Vögele Dash 5 technologies feature the ErgoPlus 5 operating design that provides more visibility and comfort, an ergonomic design, and simplified use of individual functions for operators. Fine-tuning can be accomplished easier using a smartwheel. A new four-cylinder motor uses less fuel than previous models while maintaining output with its the EcoPlus low-emissions package. The auger and conveyors communicate to ensure material feed is consistent and coordinated, which reduces load peaks and saves more fuel while ensuring an optimum head of mix.
operator comfort, ergonomics, and visibility. The ZB21 bolter has intuitive operator controls and integrated patented screen handling. An optional pumpable resin system allows resin to be pumped into the hole prior to bolt installation. The ZJ21 jumbo drill is a single-boom development drill with innovative drilling feeds and advanced pilot hydraulics. Both feature Montabert drifters. Battery-electric versions are available for both machines, fusing Komatsu’s on-board charging system which offers compatibility with mine infrastructure.
hydrostatic transmission, advanced controls, electric-over-hydraulic joystick are highlights of the SkyTrak 8042 telehandler. The machine has a maximum lift height of 42 feet 4 inches, a maximum reach of 29 feet 6 inches, and a 21,200-pound operating weight. The enclosed cab has optional air conditioning and a larger LCD display plus single-page load charts. The hydrostatic transmission provides greater comfort, ease of operation, and inching – running the boom at high speeds without shifting into neutral – for faster material delivery. A 74-hp Deutz diesel engine does not require diesel exhaust fluid, reducing maintenance costs.
Dozers are a perennial favourite among equipment enthusiasts young and old. The simple raw pushing power of these earthmoving elder statesmen holds an appeal for both kids in the sandbox and operators in the field. Dozers, however, have evolved beyond the simplicity of merely pushing material with the level of precision totally reliant on the skill and experience of the operator in the cab. Today’s dozers can no longer be separated from the technology that now often comes standard. These technologies make it easier and faster for novice operating talent to run the machine with the finesse of a grizzled veteran. Turn the page for our 2024 spec guide, and explore dozers up to 100,000 pounds for earthmoving applications.
The Liebherr PR 726 XL and LGP crawler dozers offer excellent efficiency and versatility, making them ideal for medium-duty tasks such as site preparation, road construction, and moderate earthmoving. Both versions of the PR 726 have advanced Liebherr diesel engines that deliver high performance and low fuel consumption. Equipped with operator assistance systems such as Free Grade and Definition Grade, along with an innovative hydrostatic drive, these dozers ensure precision and ease of use. The PR 726 XL handles demanding tasks, while the LGP model’s low ground pressure undercarriage is perfect for soft, sensitive terrain.
Liebherr Crawler Dozers ensure that full power is on-call at all times, regardless of weather conditions or material grades. Designed for heavy dozing and precision grading, the hydrostatic drive system provides optimal pushing speed, ensuring consistent power and efficiency. Operator Assistance Systems enhance grading quality and operational efficiency, maximizing productivity on the job site. Whether tackling tough terrain or intricate grading tasks, Liebherr Crawler Dozers are designed to meet high standards with robust performance and innovative technology.
*Models available in XL and LGP configurations.
John Deere currently offers eight dozer models – three small P-Tier dozers, three midsize dozers, and two large P-Tier dozers. Enhancing operator performance and safety, the P-Tier small dozers feature a variety of strategic design choices aimed to increase visibility and comfort. The mid-size dozer models offer exceptional performance, reliability, and ease of operation in a mid-size design. Lastly, the 950 P-Tier and 1050 P-Tier large dozer models have been upgraded with versatility and efficiency in mind, equipped to optimize productivity and fuel savings.
The John Deere 1050 P-Tier Dozer offers extreme durability to tackle even the most rough and rugged job sites. Customers looking to move large amounts of material efficiently will benefit from the standard 168-inch semi-U blade. Along with a wider blade, the 1050 P-Tier is now configured with a redesigned blade linkage which moves the blade rearward and reduces the overall length of the machine, improving balance and grading performance. Also, several changes have been made to enhance visibility to the blade corners, ensuring operators have optimum visibility on the job. Lastly, the redesigned suspended double-bogie undercarriage reduces vibrations throughout the machine, improving ride quality and component durability.
The D71PXi-24 is Komatsu’s largest and most powerful hydrostatic transmission (HST) dozer. This voice-ofcustomer-designed dozer performs in all grass to grade applications. From stripping, rough dozing, and spreading to finish grading, the D71PXi-24 utilizes iMC 2.0 automatics to maximize efficiency and productivity throughout the entire process. It is equipped with a power angle tilt (PAT) blade and 36-inch shoes providing a 5-psi ground pressure for maximum flotation and pushing ability. Komatsu’s super-slant nose cabforward design on HST dozers helps provide outstanding visibility to the cutting edges while enhancing operator comfort for a balanced ride and increased field of view.
Komatsu offers a diverse lineup of dozers ranging from small to large models designed for various applications and available in AX standard track; EX extended track for flat, rocky, or high-impact work; and PX for lowest ground pressure. Configurations can be tailored to meet specific applications, providing operators with performance, efficiency, and durability. Komatsu dozers are equipped with Komatsu’s Parallel Link Undercarriage System (PLUS), which offers a unique rotating bushing design, durable longer-wearing links, and self-adjusting idler support with recoil spring. iMC 2.0, offered on Komatsu dozers, gives inexperienced operators the ability to run a dozer like a pro. iMC 2.0 allows operators to use automatics nearly 100 percent of the time with proactive dozing, lift layer control, and tilt steering.
The DEVELON DD100 dozer competes in the 140-hp and under category. Standard premium features for the DD100 include MY DEVELON Fleet Management telematics for remote monitoring, ECO mode for reduced fuel consumption, rearview camera for enhanced visibility, blade shake for removing material stuck to the blade, and an easy-to-read, user-friendly touchscreen display for access to the dozer’s functions and machine settings.
DEVELON introduced its first dozer in 2022 and currently offers two models: the DD100 and DD130. Both dozers provide exceptional visibility from the cab to the front and sides of the machine. A standard rear-view (backup) camera enhances operator visibility. A sixway power-tilt angle blade moves and grades dirt, clay, and other materials. Operators can activate the blade float function for back grading or fine finishing. A blade shake button is available to quickly remove stuck-on materials. Operators can reduce the dozer’s fuel consumption using an ECO mode, saving up to 5 percent without sacrificing grading performance when working in lower tractive conditions. Additional fuel-saving technologies include auto idle and auto engine shutdown. Optional features available for DEVELON dozers include 2D blade assist and 3D machine guidance and 3D machine control.
*Operating weight is for low ground pressure dozer blade configurations.
CASE Construction Equipment’s M Series dozers deliver contractors more precision, reliability, and control than ever before. Electro-hydraulic blade control, which reduces overall operator fatigue while increasing productivity, comes as a standard feature on most models, along with customizable blade, shuttle, and steering controls.
When equipped with CASE Universal Machine Control, the M Series dozers can be outfitted with machine control solutions from any of the three major suppliers of precision construction technology. Each dozer also features maintenance-free, Tier 4 Final emission solutions, excellent serviceability access, spacious floor-to-ceiling glass, and positive-pressure cabs that offer ample elbow room while keeping dirt out.
CASE Construction Equipment’s 850M dozer offers drawbar pull of 41,010 pounds and features a 120-hp (90 kW) engine. A hydrostatic transmission ensures constant power transfer under load and allows for on-the-spot counter rotation, while electro-hydraulic blade and customizable steering and shuttle sensitivity controls, along with a load management system that adjusts the track speed based on the amount of dirt being moved, enable ease of use. The electrical and hydraulic routings enhance serviceability and durability while LED lights, Bluetooth radio, a rear-view camera, and undercarriage spade holder provide convenience and accessibility.
The D6 XE is the world’s first high-drive electricdrive dozer. The electric drive makes this the most fuel efficient dozer in Caterpillar’s lineup and with fewer moving parts and longer service intervals, there is opportunity to save on maintenance time and money as well. The D6 XE powertrain provides up to 45 percent steering radius reduction compared to the D6. The D6 XE offers ingear counter rotation for increased maneuverability. Cat dozers are designed with grouped service points and easy-to-access fluids and filters for an easy owning and operating experience. The cab features integrated ROPS (rollover protective structure) that provides more visibility to the work and comfortable seats with adjustments to personalize the work environment.
Caterpillar’s D4 to D8 dozers offer a range of technology features to help operators of varied experience levels get work done quickly and accurately. Cat Assist with ARO (attachment ready option) is a suite of features that is standard on every model. This technology package includes the following features: ARO Sensors (IMUs) on machine for GPS capability; Cat Grade with Slope Assist which holds blade angles with no GPS; Steer Assist which automatically keeps dozing straight; and Stable Blade, which makes finish dozing easier, as well as Slope Indicate, Blade Load Monitor, Traction Control, and AutoCarry. AutoRip, on the D7 and D8 only, automates ripper raise/lower and shank in/out.
*D4 shares more common features with D1–D3, and D5–D8 (high-drive machines) are more similar to each other. †The D6 is also available with XE Electric Drive (D6 XE). ‡Transmission with Lock Up Clutch (LUC) torque divider.
Cardinal Scale’s ARMOR® digital truck scale with included free iSite remote monitoring means you can say goodbye to downtime with high-tech Cloud-based diagnostics.
BY MACK PLOVIE
United Group has an extensive history of helping build British Columbia over the past 80+ years, working on key infrastructure projects like the original Sea to Sky Highway. With recent investment in Topcon technology and John Deere equipment, the company is primed for growth into new regions and is well-equipped to tackle larger construction projects.
United Group’s history is deeply rooted in British Columbia, dating back to November 1939 when A.B. (Tony) Cicozzi incorporated ‘United Cartage Co Ltd’, a hauling and trucking company servicing the region with a fleet of tandem axle dump trucks. United Cartage Co continued to grow with the acquisition of Hassell Bros Contracting in 1954, later renamed to United Contractors Ltd. United Contractors worked on numerous infrastructure projects throughout B.C., including the original construction of the Sea to Sky Highway in the 1960s – a challenging thread of highway skirting steep rocky terrain alongside the ocean, connecting North Vancouver to Whistler and beyond. The company also became actively involved in the BC Road Builders Association with founder Cicozzi, as the first President of the association and on the Board of Directors from 1966 to 1968.
Technology is an up-front investment. A lot of companies don’t see the benefit of it right away, but we have a long-term focus. It has given us an advantage and ability to tackle projects at a rapid pace.
Dave Kleszewski President, United Group
The company continued to work on projects throughout British Columbia’s lower mainland, and when Cicozzi passed in the 1990s his brother and son took over the company, changing the name in July 1998 to United Earth Contractors Corp. In 2023, the name was updated to United Group, a change that reflects the company’s growth in service offerings.
Today, United Group is a full-service company and has grown to over 100 employees with 200 pieces of equipment across three main divisions: United Earth, United Civil, and United Equipment, which specialize in earthworks, civil construction, and equipment rentals respectively. The company has done residential development, commercial development, major highway infrastructure, landfill closure and reclamation, land clearing, and grading.
“Construction of Highway 17 was when we really grew as a company,” says Dave Kleszewski, president of United Group. The four-year highway construction project involved building a 34km four-lane highway between Surrey and Delta.
In 2023, Corporate Vision named United Group the Best Com-
Development & Landfill Restoration Company – British Columbia, highlighting its accomplishment in reclaiming and closing a portion of a landfill in Richmond.
Since its beginnings in 1939 with a fleet of tandem axle dump trucks, United Group’s fleet has grown drastically to over 200 pieces of equipment today. The modern fleet primarily consists of John Deere equipment, including rock trucks, excavators, dozers, backhoes, skid steers, wheel loaders, and more, all supplied by Brandt Tractor Ltd.
“We are big on relationships here at United Group, and have built a great relationship with Brandt over the years to where we are now their biggest buyer in the lower mainland. They have always been able to get us equipment when we need it,” says Kleszewski. Although United didn’t start with all John
“TECHNOLOGY HAS REALLY SPED UP THE GRADING PROCESS TO WHERE EVERY PASS I MAKE IS ACCURATE TO A FEW MM,” SAYS KARL TASCHNER, HEAVY EQUIPMENT OPERATOR WITH UNITED GROUP.
UNITED GROUP RECENTLY USED MC-MOBILE ON A WAREHOUSE GRADING PROJECT IN SURREY TO INSTALL UNDERGROUND UTILITIES AND COMPLETE FINAL GRADING FOR CONCRETE SLAB TO MM ACCURACY INSIDE THE BUILDING.
Deere equipment, the company has focused on investing in the John Deere product in recent years, including an investment in K and L series dozers to modernize the fleet and streamline maintenance, operator training, and dealer support.
United Group remains focused on staying at the leading edge of its business, constantly updating the fleet with newer equipment once machines reach roughly the 5,000 hour mark. Not only does new equipment appeal to and attract operators, but the technology offerings, fuel savings, and performance offers United Group a competitive edge in a market saturated with contractors competing for work.
Early adoption of Topcon Positioning Systems technology for both heavy equipment and surveying has underpinned United Group’s growth. The contractor bought its first piece of Topcon technology in 2015, an indicate-only system for a Caterpillar D6T dozer. Today over 50 percent of United Group’s large equipment is outfitted with Topcon machine control.
UNITED GROUP’S FLEET HAS GROWN TO OVER 200 PIECES OF EQUIPMENT, INCLUDING JOHN DEERE ROCK TRUCKS, EXCAVATORS, DOZERS, BACKHOES, SKID STEERS, WHEEL LOADERS, AND MORE.
United Group’s fleet of Topcon-equipped machines now includes two 850 Deere dozers, two 700 dozers, and two each of the 245, 345, and 470 John Deere excavator models all equipped with 3D MC-Max machine control systems. The 245 size excavator and up is where United Group really notices production gains from 3D MC-Max grade control technology. In addition, United Group recently acquired the first MC-Mobile system installed on a Level Best box blade in Canada, which is currently fitted to a 333G John Deere skid steer. Alongside machine control, United Group invested heavily in base and rover kits for its in-house survey team. Multiple base stations allow for strategic setup of permanent bases to reduce any errors from daily setup. While rover kits enable accurate regular surveying for project take offs, design builds, and survey pickups on the job.
“Technology is an up-front investment. A lot of companies don’t see the benefit of it right away, but we have a long-term focus. It has given us an advantage and ability to tackle projects at a rapid pace,” explains Kleszewski.
United Group has also invested in drone surveying technology including Propellor software. This technology unlocks potential for their survey team to perform design builds, and more importantly enables quantity tracking in a marketplace where being accountable for materials on a project is important.
“We used to send out surveyors to get quantities on projects. With drone surveying, we get cost accountability with materials and accuracy on projects,” says Kevin Jones, operations manager.
With an industry-wide workforce shortage, experienced operators are hard to find, resulting in a pool of less experienced operators entering the industry. Technology is helping address this issue by enabling operators with little experience to achieve a baseline of productivity on machines equipped with Topcon machine control. United Group’s 3D MC-Max–equipped John Deere dozer fleet is a fine example.
“It’s very user friendly, we can honestly put anyone in the machine. If they know how to operate a machine, they can be taught how to operate GPS,” explains Rusty Hodge, site superintendent.
[Kleszewski] has been a great supporter of Brandt and has become one of our biggest customers in the span of about a year and a half. They’ve been really good to deal with,” says Jake Buskell, sales manager for Brandt Tractor’s Positioning Technology Division.
Brandt supports United Group from start to end, including acquisition and delivery of heavy equipment, performing installations of Topcon machine control on their fleet, supplying parts, and repairs. They are a full-service dealer for all United Group’s needs and have grown alongside United Group, adding more field technicians to the team.
“We started adding all machines to the remote support desk within Sitelink. Our technicians can dial into machines to diagnose problems, view error codes, and determine what parts are needed before we even send them out into the field,” explains Joseph Bradley, regional service manager with Brandt Tractor’s Positioning Technology Division.
“We really haven’t had to call Brandt much, and if we have, they have been great with warranty,” notes Hodge.
Now
we are putting experienced operators in machines equipped with machine control and getting two to three times the production. We have since changed our opinion of ‘it’s expensive’ to ‘everything needs it.’
Dave Kleszewski
“Now we are putting experienced operators in machines equipped with machine control and getting two to three times the production. We have since changed our opinion of ‘it’s expensive’ to ‘everything needs it,’” says Kleszewski.
United Group’s landfill closure and reclamation project proved that point during construction of a mechanically stabilized earth (MSE) wall using Topcon-equipped dozers. Operators of all skill levels were achieving tight tolerances on fills, minimizing rework and reducing waste of materials, all of which translates to a healthier bottom line for United Group and the client.
From United Group’s first purchase of John Deere equipment and Topcon technology to the numerous pieces of equipment and technology in their fleet today, Brandt Tractor has been right alongside supporting the company’s growth. “Dave
United Group certainly isn’t afraid of technology. In early 2024 they again took initiative and added a new Topcon product: MC-Mobile. Currently fitted on a Deere 333G skid steer, MC-Mobile functions as both a rover kit and machine control package, with the ability to create designs as a rover kit, then use the same design in Pocket 3D software on an Android tablet for grading. The system really gives one operator the ability to be self-sufficient, creating designs on the fly and then using them in the machine to build to.
United Group recently used MC-Mobile on a warehouse grading project in Surrey when partnering with a builder from Alberta. This project was different because the builder constructed the walls and roof before installing underground utilities and grading for a concrete slab – an approach that has proven successful in Alberta’s harsh weather conditions.
The United Group team had to install underground utilities and complete final grading for concrete slab to mm accuracy inside the building. Using a Local Positioning System (LPS) comprised of Total Station, MC-Mobile system, and Prism in place of GR-I3 GNSS receivers, United Group deployed a John Deere 700L dozer and the 333G skid steer to complete the final slab prep.
“We are ahead of schedule on this project thanks to our team, the machines, and the technology. That total station has mm accuracy, moving the dozer blade up to 100 times per second,” says Ryan Morrison, general superintendent. Having the ability to complete precise grading for a concrete slab indoors where conventional GNSS from a base station or network may not have proven reliable was a real advantage on this project.
“Technology has really sped up the grading process to where every pass I make is accurate to a few mm,” says Karl Taschner, heavy equipment operator with United Group. Once complete indoors, both the skid steer with Level Best box blade and dozer can easily convert back to using GNSS receivers operating off a local base station or Brandtnet, a service developed by Brandt Tractor’s Positioning Technology Division. This RTK GNSS network service allows contractors using Topcon technology on their machines to connect and start receiving GPS corrections without the need for base station setups.
United Group certainly isn’t done growing yet, and plans to expand in the Lower Mainland. The company also aims to add four more locations within the next five years, expanding into Edmonton, Squamish, Vancouver Island, and the Interior of B.C.
“Dave [Kleszewski] sets goals for the year, and we make it our goal to beat those goals,” says Terry Traynor, project manager with United Group.
United Group’s ambitious growth is underpinned by quality work and its track record of infrastructure projects in the Lower Mainland. The team is tuned into replicating that success in new regions.
“We are one giant team here at United Group. Nothing gets done without each other – I really have to applaud everyone’s effort,” says Kleszewski. With ambitions to be one of the top 5 construction companies in the region, United Group plans to purchase more John Deere equipment and Topcon technology. “We are already looking at more Deere 245 and 345 zero-swing machines with technology,” says Morrison. The zero-swing machines really shine on road work projects where space is limited and work is often conducted adjacent to live traffic.
With an early and continued investment in Topcon technology, United Group has gotten ahead of the curve and plans to stay there.
MACK PLOVIE is the president and chief dirt enthusiast of Earthmovers Media Group.
A LOCAL POSITIONING SYSTEM (LPS) COMPRISED OF TOTAL STATION, MC-MOBILE SYSTEM, AND PRISM IN PLACE OF GR-I3 GNSS RECEIVERS WAS USED TO COMPLETE THE FINAL SLAB PREP INDOORS.
Volvo has begun the rollout of a complete reintroduc tion of its crawler excavator line starting with multiple medium and large models: the ECR145 short swing, EC210, EC230, EC370, EC400, and EC500. More models will be announced in the coming months.
“This new excavator series is the realization of our commit ment to our customers. Every design change, innovation, and weld were made with our customers’ needs top of mind,” says Scott Young, head of Region North America, Volvo CE. ”All together, these updates will substantially impact their produc tivity, uptime, employee satisfaction, and, ultimately, their success.”
Volvo has optimized the electro-hydraulic system and in troduced a smart cooling system and engine speed regulation at higher engine RPM to increase fuel efficiency by up to 15 percent compared to the previous generation – all while outper forming those models.
These excavators now have 10 work modes, including two specific to power and four specific to automatic ECO modes.
According to Volvo, enhanced hydraulics enable better machine control and the smooth, precise movement of the boom, bucket, and other hydraulic components. These excavators now have 10 work modes, including two specific to power and four specific to automatic ECO modes. A new creep travel mode combined with boom and arm shock reduction reduces spillage.
“Our customers are looking for ways to increase productivity and reduce expenses, and we deliver on that with these new excavators,” says Sejong Ko, product manager – large excavators at Volvo CE. “Fuel in particular is a major expense, and the improved fuel efficiency will reduce costs with the added benefit of lowering the environmental impact.”
job site.
Volvo Smart View with Obstacle Detection gives operators 360-degree visibility of the machine’s surroundings by combining cameras with radar detection to distinguish between objects and humans on the job site. Volvo has also added more lights to the cab, boom, and arm.
Hiring and retaining skilled operators is essential in a tight labour market, and Volvo has made the new excavators an attractive work environment for the operators who make them their office. Volvo has improved the human–machine interface and the automation of boom and bucket movement with the Volvo Active Machine Control system, and an advanced electric control joystick also helps operators increase productivity.
Other new and upgraded features include: updated seat design, improved ventilation, new footrest support for working on slopes, keyless engine start with ability to store multiple operator preference settings, larger cab side mirror with heater, in-cab wireless phone charger, built-in cooler/ heater compartment for food or drinks, more sunscreens and storage areas, additional safety railings and relocated steps, and new DEF sight gauges and splash guard.
Volvo has included the newest generation Co-Pilot in these excavators. The in-cab tablet’s larger, high-resolution screen will display Dig Assist applications, such as on-board weighing, in-field design, and more.
Volvo Smart View with Obstacle Detection gives operators a 360-degree view of the machine’s surroundings by using the camera and the new radar detection system.
Smart View with Obstacle Detection can identify obstacles as either an object or a human being, allowing the operator to take appropriate action.
Volvo used deep learning technology to develop Smart View with Obstacle Detection – a person crouching, moving, or leaning can be detected. Every human is visible to the system, no matter what colour of clothes they’re wearing.
The operator can set how far they want the radar to reach. For example, when working in a confined space the operator can set a smaller radar area. The operator can also customize which sectors they want to see via the touchscreen.
When it comes to your work, having the right features is a BIG advantage. It’s nice to have an ace up your sleeve when taking on the toughest tasks on the jobsite. From accessible technology and rear view visibility to a quiet and comfortable cab, plus roll-up front door and easy maintenance - all these features and more come together in the Kubota SVL75-3.
CANADA.
#1 in overall satisfaction in product quality in parts availability and parts quality in manufacturer response to dealer needs and concerns Kubota Canada was recently named the top full line manufacturer in multiple categories by the North American Equipment Dealers Association*, including: EXPERIENCE THE DIFFERENCE WITH KUBOTA
*2023 Dealer-Manufacturer Relations Survey, North American Equipment Dealers Association.
Purchasing your first piece of equipment is a big investment when you run your own small business and Jason Rottier was intent on getting it right.
“It was a giant, and I mean giant, step for a small company less than three years old,” explains the owner of Rottier Excavating in Wallaceburg, Ontario. “I looked at used and new machines, I looked at horsepower, hydraulic output, high flow capability, user comfort, I looked at everything.”
Jason’s exhaustive research led him 45 minutes up the road to nearby Wyoming, ON, where he met Eric Vanderlinde, a sales representative at SouthPoint Equipment, an official full line Kubota dealer.
“Once I talked to Eric, it was seamless - he kind of put me at ease,” says Rottier. “He said, “We’ll figure it out. We’ll get you in the machine you want to be in.”
That machine was the Kubota SVL65-2 compact track loader. Rottier made the purchase in early 2022 but with his company rapidly expanding, he found himself back at SouthPoint less than two years later ready to purchase the new SVL75-3.
“Jason was very confident in the Kubota brand,” explains Vanderlinde. “After experiencing zero issues and minimal downtime with the SVL65-2, and excellent support from our service department, he knew the SVL75-3 would prove to be just as reliable and durable for his business.”
“I wanted to upgrade to something with a little more horsepower and ergonomics,” says Rottier, who measures in at over six feet tall. “When you have big boots, you need a big area and there’s a lot of leg room in the SVL75-3. The Air Ride seat is nice. I have lower-back issues and I can sit in that thing for 10 hours a day.”
“Jason is a bigger guy, so having a roll-up door and the widest cab in the market is huge,” says Vanderlinde. “Getting in and out of the machine is very easy for him now.”
“I use it for everything - landscaping, bush removal, loading dump trucks, cutting wood, and I’m not easy on things, says Rottier. “If it lasts for what I do, then it’s a solid piece of equipment.”
“The pushing power of the SVL75-3 is great - it’s like a small dozer. Now I have the horsepower and weight to run a forestry mulcher and do more kinds of jobs.”
Thanks to its compatibility with all types of attachments, Rottier says his new machine has opened the door to additional opportunities.
“The SVL75-3 is a Swiss Army Knife for my business. I have a grapple bucket. I do a lot of brushing and moving material. I have a trencher for putting in hydro, gas and waterline trenching. I have a soil conditioner. I have a Kubota land plane, which is one of the most useful things I own. Forks, buckets, an HLA SnowBlade, you name it!”
“It’s nice when you can get your arms in and see the hydraulics and not have to dismantle everything and take all the panels off,” explains Rottier. “With the SVL75-3, you open the door and flip the hatch up and the whole thing’s open.”
“I had to change my hydraulic filter at 50 hours. It was the first service thing that popped up and I was dreading it. But when I pulled the cab up, it was two bolts and I lifted it by hand. I got my partner to put a lock on the hydraulic and I crawled into the belly of that machine and grabbed the filter, gave it a wrench, and we had it done in like ten minutes.”
“One thing that is very big, not only for our dealership but also for Kubota Canada, is training,” explains Vanderlinde. “We invest a lot of money into getting to know our products and competitor products, and Kubota has dedicated field product specialists to teach both our salesmen and our customers about the equipment.”
“Everybody at SouthPoint has extensive knowledge of the machines and the equipment,” says Rottier. “Parts are always in stock and I’m never shutdown or left waiting for service. When I call, someone answers the phone, and if Eric’s busy with a customer, he always calls me right back.”
“The Kubota KX080-5 series is a beautiful machine - it’s next on my wish list,” says Rottier. “I really want one bad, but I have to convince my wife and business partner, Sarah, that we need it and it’s going to pay for itself. Kubota machines always do.”
“ I USE IT FOR EVERYTHINGLANDSCAPING, BUSH REMOVAL, LOADING DUMP TRUCKS, CUTTING WOOD... ”
TRACK DESIGN – What an upgrade, I love it! It doesn’t plug up. It floats beautifully across the ground. In terms of comfort, it makes a 10-hour day a lot nicer.
VERTICAL LIFT – I think I gained eight-to-ten inches in reach height. That doesn’t sound like a lot until you’re loading over the side of a dump truck all day.
FULL-COLOUR REAR-VIEW CAMERA – The clarity of the integrated backup camera is phenomenal. I can maneuver it to see in those blind spots, which from a safety standpoint, is huge for me.
BY KEN SINGER, PUBLISHER
This April, 2,700 guests from more than 100 countries attended Wirtgen Group Technology Days 2024 in Göppingen, Germany. The overarching themes of the two-day event at the headquarters site of Kleemann were digitalization and sustainability, inspired by the motto “Smarter. Safer. More Sustainable.” At Göppingen, the Wirtgen Group demonstrated machines and technologies developed to enable maximum versatility and productivity to meet today’s changing, demanding expectations.
The Wirtgen Group impressed the attendees with numerous innovative systems and solutions, including 11 new machine world premieres and a clear vision for the future of road construction.
“Innovation is in our genes. As we are aware from the feedback we receive from our customers, there is increasing demand for smarter, safer, and more sustainable solutions in markets around the globe. We have concentrated our efforts on this and can now present state-of-the-art machine technologies and digital systems with which we provide support and assistance to our customers in all aspects of the digital transformation. At the same time, we attach great importance to holistic solutions for their construction projects – from the planning phase through to documentation and statistical analysis,” says Dr. Volker Knickel, CEO of the Wirtgen Group.
With around 70 exhibits for a range of different application scenarios, Wirtgen, Vögele, Hamm, and Kleemann, as well as the Benninghoven and Ciber brands not currently offered in North America, showed the solutions which will propel the industry to more integrated digitalization and automation in road construction and materials processing.
Interest in the world premieres was particularly strong. These included a SUPER 1800-5(i) “Dash 5” generation asphalt paver from Vögele, which offers smart automatic functions, improved comfort, and an optimized drive system. The SUPER 1800 is considered Vögele’s most popular paver, and attendees were impressed by the updated ergoPlus 5 operating system and the optional “Premium Touch” display screen which allows users to easily monitor and control existing and future digital solutions. Hamm presented a total of four new machines, including an HC series compactor with the innovative VA (variable amplitude) drum. The Smart Compact compaction assistant enables automatic compaction to a specified target value with VA-compactors. With its satellite-based AutoTrac system, the latest addition to the portfolio of wheeled soil stabilizers from Wirtgen, the Rock Crusher WRC 240i, demonstrated how preparation of the ground for road and highway construction can be realized
more quickly and with fewer resources.
For the materials processing sector, Kleemann, the host of the event, presented the new MSS 502(i) EVO scalping screen with an alternative, fully electric drive option. With its compactness, the MSS 502(i) EVO is optimized for the lower feed capacity range of up to 350 tph. A generously dimensioned feed hopper, a screening surface of 5.4 square metres, and a wide main discharge conveyor guarantee excellent material guidance. For high flexibility in the application, the speed of all conveyor belts is steplessly adjustable and a simple conversion from two to three final grain sizes is possible.
Asphalt production offers the greatest potential for reducing CO₂ emissions. In response to this, the Wirtgen Group also presented the new generation of burners from Benninghoven, which supports the simultaneous use of up to four different fuels. This means, for example, that an asphalt mixing plant can be flexibly operated with the most appropriate energy source –including, for the first time, exclusively with green hydrogen.
Internationally recognized experts and specialists from the Wirtgen Group provided first-hand insights into the technologies of the future. On the subject of sustainability, they shared
THE WIRTGEN GROUP IMPRESSED THE ATTENDEES WITH NUMEROUS INNOVATIVE SYSTEMS AND SOLUTIONS, INCLUDING 11 NEW MACHINE WORLD PREMIERES AND A CLEAR VISION FOR THE FUTURE OF ROAD CONSTRUCTION.
their experiences and knowledge of sustainable construction, the potential for CO2 reduction offered by the recycling of hotmixed asphalt and cold recycling, and new electrically powered drive solutions for crushers and screening plants.
In the thematic complex of digitalization, presentations by specialists from the Wirtgen Group showed how the company can support and assist its customers in the course of the digital transformation. The John Deere Operations Center for construction equipment will become the central platform for providing digital solutions for the management of entire construction sites – at any time and from anywhere, including planning, monitoring, analysis, and maintenance. The Operations Center will act here as an interface between operators and machines on the construction site, the offices of site and resource managers, and the workshop manager.
But what does this mean in practical terms? Thanks to plannable machine availability, customers will, for instance, enjoy the benefits of reliable equipment utilization. The immediate availability of comprehensive information will enable project managers and machine operators to make the right decisions. A higher degree of process automation and the use of machine assistance systems will not only lead to higher productivity due to operators being able to concentrate fully on the work in progress, but also to a more efficient and effective deployment of human resources. The precision and, consequently, the quality of the work will
also increase, which will in turn avoid the necessity of reworking and will help reduce material and operating costs.
The broad spectrum and informational depth of the presentations underscored a clear road map that lays out how customers can be fully supported on today’s evolving job site. Wirtgen Group Production Systems provides end-to-end process solutions that address a wide range of project requirements aiming to decisively accelerate the digital transformation and connectivity of the industry with the ultimate goal of increasing profitability and maintaining the highest machine utilization rate
The greatest ecological and economic potential lies in the totality of the construction process. Various live demonstrations showed how the Production System solutions from the Wirtgen Group play a role in this – for instance the use of low-temperature asphalt, concrete and asphalt recycling, or soil stabilization – and illustrated how the target-oriented utilization of technologies leads to greater precision, higher quality of results, and the consumption of fewer resources. Or, in other words: how to “Do More with Less” – and be “Smarter, Safer, and More Sustainable.”
As Knickel explains, “This enables our customers to realize more construction projects with fewer resources, build and rehabilitate more infrastructure, and simultaneously increase their profitability.”
At the same time, he emphasizes that digital assistance systems and process automation also contribute to offsetting the shortage of qualified personnel throughout the industry. “This also means that less experienced machine operators will be in a position to deliver qualitatively identical results to those a skilled specialist would achieve,” he says.
On top of this, telematics solutions will deliver greater transparency about the operational status of customers’ fleets and enable them to carry out proactive and even more precisely targeted servicing and maintenance of their machines.
On a guided tour through the Kleemann production facilities, the host of the event gave the professional audience fascinat-
ing insights into the manufacturing process. Since the opening of the new plant in 2009, the highly specialized facility has been successively extended and, like all other Wirtgen Group factories, has been constantly upgraded for sustainable operation in line with the Group’s sustainability strategy. Today, the Kleemann plant is one of the world’s most modern facilities for the production of crushers and screening plants. Many of the visitors were particularly impressed, not least by the highly complex prefabrication centres in which the core components of the Kleemann plants are produced with exceptional precision.
“In past years, we concentrated our efforts on target-oriented expansion of our product portfolio and now offer suitable solutions for every application, no matter whether for recycling or natural stone processing. To achieve this, we invested in areas such as expanding our production capacities and improving our assembly or logistics processes,” says Kleemann CEO Alexander Knam, describing the development of the company’s headquarters site in Göppingen. He believes that the specialist for materials processing equipment is ideally positioned for the future. “With these investments, we have laid the foundation for the ongoing production of our products and technologies under ideal conditions, sustainably and efficiently.” HEG
MILLS, PAVERS, MACHINE CONTROL & MORE
Three cold planers in the Caterpillar PM300 series have been updated with new designs and features that improve peak torque, gross power, and the operating environment. The PM310, PM312, and PM313 are compact and maneuverable, good for smaller or mid-sized road repairs where high capacity is needed.
New models are fitted with the Cat C9.3B engine generating an increased 343 hp along with increased torque. Performance upgrades on the PM300 series include a redesign of transition flashing between the primary and loading conveyors, which improves material containment and cuts down buildup on the front of the machine. The right-hand side plate, chamber-to-conveyor sealing, and loading conveyor belt sealing have all been enhanced as well. Front track deflectors in front of the drive motors also provide more debris
protection for increased service life.
An adjustable on-screen guidance line added to the left-hand camera now gives operators the ability to track the cutting edge from either side of the machine.
Ground personnel can also control the obstacle jump capability from rear ground controls. LED lighting options provide better visibility and safety around the machines.
FAE road planers use cold planer technology to turn skid-steer and compact track loaders into road maintenance machines capable of resurfacing in preparation for new asphalt or concrete, or simplifying excavation work.
The RPL/SSL is compatible with loaders from 60 to 120 hp. It can mill up to 7 inches deep in three widths – 18, 24, or 30 inches. The RPM/SSL, for loaders between 75 and 120 hp, mills up to 10 inches deep and up to 24 inches wide. Both heads have self-levelling skids and tilt to ensure good results on uneven surfaces. A hydraulic drive system helps the attachments mill precisely. A high-visibility design makes these planers easy to view from the cab. Attachments are plug-and-play with most SSLs and CTLs.
The 8-ton CC2200 VI tandem asphalt roller is part of a new series of rollers ranging from 8 to 10 tons with drum widths of 59 to 66 inches. Dynapac says it has taken cues from larger rollers to improve paving results and operating efficiency on the CC2200 VI, such as 180-degree seat rotation, an efficient eccentric system that combines with ECO mode to cut down on fuel use and emissions, and full backup sprinkler water systems.
A new operator interface is part of the roller’s ergonomic interior and includes
a full-colour 7-inch touch display along with easy access to all controls. An optional 360-degree pedestrian detection camera is available and provides a continuous bird’s-eye view around the machine while working.
Dynapac’s SEISMIC asphalt technology is standard on the CC2200 VI. It automatically determines the optimal frequency for any compacted material, monitoring the variations of the asphalt layer and automatically adjusting to temperature conditions. The optional Dyn@Lyzer is a
compaction control and documentation system that records and maps stiffness and compaction progress of the compacted asphalt layer in real time. It also tracks asphalt temperature and the number of completed passes and can be used as a quality control and assurance device.
Five roller models will be available in the range, with three articulated machines, including the CC2200 VI, joined by two fixed-frame pivot-steer split-drum models. Combination versions of select models will also be available.
BOMAG is taking on segregation to improve mat quality with its updated CR 1030 10-foot paver. Available in 2025, the CR 1030 Series includes new interface features, multiple control options, and a new independent auger/conveyor system. Also new is the versatile Versa 20 front-mount screed.
The independent auger/conveyor system has an outboard auger drive system and a design that lets the conveyors and auger run independently with a two- or optional four-sensor control system. A raisable or fixed outboard-driven auger system allows better visibility into the conveyor discharge area, and eliminates segregation in that area for better mat quality.
New interface features grouped on the tractor console, and a new screed control system with integrated automation features, help operators run their machines more efficiently. On the console, similar functions are grouped together for quick identification and adjustment. A 7-inch multifunction colour screen display has multiple configurable detailed screens that accommodate multiple operators and working conditions. With both a touchscreen and remote dial control, operators are able to navigate and adjust settings in whichever way is more convenient. A new sloped hood improves visibility into the hopper.
The Versa 20 front-mount electric screed offers variable paving widths from 10 to 19 feet at paving thicknesses to 12 inches. Bolt-on left- and right-hand extensions add more width up to 23 feet. Quick connections provide heat and vibration for increased mat quality.
A 10-foot catwalk and foldable walkway extensions for the operator are standard.
The 11-inch-deep hydraulic extensions, with manually adjustable angle of attack, allow for better density and mat quality, and the hydraulically powered crown can be adjusted from 3-inch positive to 1-inch negative. New controls and remotes allow for a better operator experience and accommodate special features like integrated MOBA automation.
Modular, simplified configurations and advanced features are highlights of the MC-Max Asphalt Paving and MC-Max Milling solutions from Topcon Positioning Systems. Made up of GNSS receivers, total stations, displays, and other high-precision sensors, these solutions are built on the MC-X machine control platform which includes highly customized systems and upgradeability for growth.
Choices range from entry-level 2D systems that follow a
Apair of new highway-class pavers provide versatility and choice for contractors who want efficient asphalt machines.
The PF-5170C paver is powered by a 188-hp Cummins Tier 4 Final engine with DPF and active, semi-automatic regeneration, reducing engine emissions while increasing fuel efficiency. On the larger PF-7110C paver, a 225hp Cummins Tier 4 Final engine provides the power.
A four-sensor feed system matches proper delivery and flow of material to the speed of these pavers for smooth and even paving. Both the driver and the screed operator have a button on the control panel to hydraulically extend two-stage tunnels that give better material control and a consistent head in front of the screed. Flow gates can also be used.
reference, such as a curb or string, to automated solutions that track the paver or mill in 3D. Users can pave and mill at variable depths to meet smoothness requirements. Solutions also include MC-X licensing options that provide users with further flexibility to meet project and budget requirements.
expands on Topcon’s SmoothRide road resurfacing solution to create 3D models of existing road surfaces.
Operators have 360-degree visibility from Blaw-Knox’s single-level platform. Dual rotating, tiltable consoles make the machines more versatile – the operator can work from either side. An adjustable seat extends beyond the edge of the paver for even more visibility.
The SmokEater fume extraction system removes fumes at 83 percent efficiency without blocking the view into the auger channel.
The newest member of the Wirtgen milling machine lineup is the W 150 XFi. A compact unit that mills up to 6 feet wide, the machine is a good choice for use on construction projects taking place in tight spaces, such as downtown cores. New engine technology from John Deere is environmentally friendly and fuel efficient, and performance is boosted by digital assistance and levelling systems.
The front loading design delivers high performance on restricted job sites.
The Level Pro Plus levelling system combines with an intuitive operating system to ensure the machine can be run by a single person while achieving precise results.
Wirtgen’s Flexible Cutter System permits the use of different milling drums offering maximum working widths of up to 6 feet, making the compact milling machine flexible and allowing it to be used on more contracts.
The low weight and milling drum unit mounted in the centre of the milling machine provide ideal weight distribution.
Flexible adjustment of the extra-large slewing angles and speed of the front-loading conveyor ensure efficient material loading.
include small milling jobs, such as spot road repairs, up to the removal of complete road surfaces.
BY LEE TOOP, EDITOR
Roadbuilding job sites are busy places, with workers and machinery moving constantly to ensure trucks, pavers, and rollers work together effectively. This can lead to increased risk of machines colliding with workers or other equipment. New technology and design features on tandem rollers are intended to reduce the risk of collisions.
Roller operators need to keep an eye on everyone around them when working, but that is easier said than done, explains Brad Belvin, sales and marketing manager with Sakai America.
“There are so many people on that job site, from dump truck operators to the people on the paving crew, to the rake people, people with a shovel, inspectors coming through – everyone has to be aware of everyone else at all points and times,” he says. “From a roller standpoint, you’re out there for eight hours a day going forward and backward – you have to pay attention. Awareness has to be the number one concern.”
Visibility is the top safety concern for roller design, Belvin says. It is important that workers on the ground and the roller operator can see one another clearly while the machine is working, no matter the angle the operator’s seat is at.
To determine the quality of visibility, Sakai uses what Belvin describes as a one-by-one system – if a one-metre by one-metre cube is placed against the machine on the front, side, or rear, the operator should be able to see it from their station. If not, the design must be adjusted.
Operator comfort is a close second to visibility for safety-focused design. If the operator is comfortable on the machine, they will be more vigilant throughout the day.
Operators of large Sakai double-drum
asphalt rollers are provided with a 180-degree swivel seat that has a number of different locking points. A lever the operator can control with their heel unlocks the seat for rotation, removing the need to bend over which reduces another stress point.
“If it’s easier to move with less obstruction and less torquing on your body, it’s going to be less stress on the person,” Belvin says. “If you are more stressed and more tired . . . you’re less aware because you’re focused on other things. Taking out that uncomfortable element and making it as easy to operate as possible increases overall awareness.”
A third area to consider is ease of control – the easier it is to understand and use the roller controls, the better for operator awareness. If a machine is difficult to run, the operator is going to spend more time focused on the controls and less on the surroundings. Sakai’s controls are kept very simple to reduce the operator’s stress, Belvin says.
QUICKLY BUT SMOOTHLY
The ability to brake quickly and smoothly is important for a machine as large as a roller.
“On our 79- or 84-inch double-drum rollers, you’re talking about 30,000-pound machines going at a general operating speed of around four and a half miles per hour. Stopping 30,000 pounds at that speed is not something you can immediately do,” Belvin says.
Sakai Guardman is integrated into the machine hydraulics to slow and stop the machine if an obstruction is detected.
“It’s essentially a rear proximity detection system but takes it a step further, where it actually brakes the machine before making contact with someone or something,” Belvin explains.
Guardman is available on a number of Sakai rollers, including the SW884ND, the first roller models to be produced
in and specifically for North America. It uses either a millimetre-Hertz wave radar system or 3D LIDAR depending on the machine, which detects objects behind the roller and moves through three stages of response.
When an obstacle is first detected, the system sounds an audio alert to the operator. If the machine moves closer, the audio alerts become more aggressive. Within a certain distance, the system engages through the hydraulics and brings the roller to a safe and smooth stop.
“If you’re going full speed, the machine does not come to a shaky, abrupt stop . . . it will slow the machine down just enough so it doesn’t skid,” Belvin says. “Obviously, the last thing you care about is the asphalt at that point in time, but if it can still protect that job, that is a nice thing.”
In addition to protecting those around the machine, Guardman also collects data about incidents that activate the system, providing greater awareness for owners and operators about the job site safety culture.
Operator comfort is a close second to visibility for safetyfocused design. If the operator is comfortable on the machine, they will be more vigilant throughout the day.
“Calculating near misses or stopping a general injury – it’s anything you can do to protect your workers. Did it go off and engage? How many times does that happen?” Belvin says. “Any time it does go off completely, you now have a time where you can sit down before a shift and say ‘maybe we need to do more coaching here, and raise more awareness of the people that are on our job site.’” HEG
SAFETY SUITE STANDARD ON ALL DRIVETRAINS OF ITS VOCATIONAL TRUCKS
BY LEE TOOP, EDITOR
More than any other type of truck, vocational trucks are at risk of accidents involving vehicles and pedestrians – on the road, around the job site, or at the terminal. Drivers must constantly watch for people, equipment, and other vehicles around them as they do their work.
Daimler Truck North America (DTNA), the parent company of Western Star, has developed the Detroit Assurance suite of active safety tools to promote more road and job site safety. Detroit Assurance was previously only available on Western Star trucks with Detroit Diesel powertrains, but is now standard on all X-Series vocational trucks.
Detroit Assurance helps drivers respond to potential accidents more quickly and, in some cases, provides direct action to mitigate or lessen the severity of collisions. Assurance includes features like Active Brake Assist (ABA5), Side Guard Assist (SGA), Lane Departure Warning, Intelligent High-Beam, and Automatic Wipers and Headlamps.
All X-Series trucks can also now be fitted with a factory-installed backup alert system.
Heavy Equipment Guide caught up to Aaron Scates, vice president, Vocational & Medium Duty Market Development with DTNA, to talk about Western Star’s expanded safety options for vocational trucks.
“The operator is the person who creates the safety of a truck or job site, so we want systems that make that operator better at being safe,” says Scates. “Safety is embedded everywhere in the design of the truck, and then we look at technologies that enhance the operator’s ability to get their job done efficiently and safely.”
Owners of truck fleets of different sizes and makeups have different approaches to technology, especially when it comes to active safety systems. On-highway fleet owners have come to recognize the benefits of such systems over time, but vocational owners tend to be more conservative, Scates explains.
Larger fleets are frequently driven by corporate values to emphasize safe operation as much as possible. For them, the cost of active safety is often non-negotiable. The adoption rate among smaller fleets tends to be slower – they want to see the value before they spend money on technology.
Broader availability of technology on new trucks helps improve that uptake rate and can also improve driver hiring and retention, especially with the ongoing skills shortage.
Scates points out that driving a truck has
always been a difficult job, but technology has consistently made it easier by allowing the driver to focus more on the road. For example, the shift from manual to automatic transmissions has made it easier for drivers with less experience, and newer safety tools will have the same effect.
“Drivers can focus on the road and their equipment, and they have a system there that helps them be better at what they do – it’s not taking their place, but it’s making them better,” Scates says.
DTNA has previously offered Detroit Assurance on Detroit Diesel–powered Western Star trucks, and has now expanded that availability to units with third-party powertrains.
“Our customers know that if they have a mixed fleet of vehicles, they can get that feature with similar functionality –there will be no difference in terms of
how they operate,” Scates says.
A combination of radar and camera technology makes up the Active Brake Assist feature (ABA 5), which provides a series of supports to the driver in the case of a potential collision. It calculates the truck’s speed and determines distance to obstacles such as pedestrians or vehicles, and if a collision is possible, begins to issue warnings in a four-stage process. A visual and audible alert is first, followed by a more insistent alert tone and partial automated braking. If there is no driver input, stage 3 initiates full braking along with alerts. Stage 4 is after the full braking event has completed, with the brakes held at a full stop.
Scates says ABA 5 is intended to provide safety as needed, without being too intrusive for drivers who may be uncomfortable with automation.
“Operators need to have control of the vehicle at all times, and unexpected intervention is something that some folks would say they don’t want. We heard a similar sentiment a few years ago when we were going from manual transmissions to AMTs and automatics,” he relates. “Once an operator experiences it and sees the
value, there’s a shift in mindset. I think the first time you have an active brake event that helps keep you out of trouble, it’s like ‘oh my gosh, I really want that.’”
In addition to the expansion of Detroit Assurance, Western Star’s X-Series trucks can now be fitted with a factory-installed backup alert system, adding a camera, reverse proximity sensor, and 7-inch touchscreen display. Cameras are used on most trucks today, and factory fit makes more sense for buyers than having an upfitter tear apart the dash, run wiring, and work other camera needs in around the body.
Two backup camera choices are available – an end-of-frame mounted camera, or a fully prepped camera with added harness length that will allow buyers or truck equipment manufacturers to relocate it based on body needs. All components will be provided from the factory.
The factory-installed backup alert system is just one more tool that empowers drivers to be safe and productive in
The operator is the person who creates the safety of a truck or job site, so we want systems that make that operator better at being safe.
Aaron Scates Vice President, Vocational & Medium Duty Market Development, Daimler Truck North America
X-Series trucks.
“When we designed the X-Series, comfort and operator productivity was a huge focus. It’s about comfort, about visibility, about access to controls, the safety aspect – all those little things add to the operator being able to do better,” Scates says. HEG
Both Volvo Trucks North America and Mack Trucks now use hydrogenated vegetable oil (HVO) to move completed vehicles off the production line as they depart from the Volvo Trucks New River Valley Assembly Operations in Dublin, Virginia, and Mack Trucks’ Lehigh Valley Operations (LVO) in Macungie, Pennsylvania.
“The utilization of HVO will help Mack in its journey to promote the decarbonization of the transportation industry,” said Jonathan Randall, president of Mack Trucks North America. “Whether it’s through the use of HVO, or through the development of Mack battery-electric vehicles (BEVs), such as the Mack LR Electric refuse and Mack MD Electric models, Mack is committed to reducing its carbon footprint and achieving our sustainability goals.”
All Mack Class 8 models for North America and export are produced at LVO. It is estimated that by utilizing HVO, LVO was able to reduce carbon emissions by about 18 percent. The Mack MD Series is produced at Roanoke Valley Operations (RVO) in Salem, Virginia. RVO has plans to begin utilizing HVO this year.
All Volvo trucks for the North American market are produced at the NRV plant, including the Volvo VNL which will begin production later in 2024. This initiative is part of several strategies that will help decarbonize Volvo Trucks’ operations. Other strategies include enhancing internal combustion engine efficiency and drop-in renewable fuels, scaling the Class 8 Volvo VNR Electric, and developing hydrogen fuel cell trucks.
“Today and for the foreseeable future there will not be a
one-size-fits-all approach to decarbonizing transportation,” said Peter Voorhoeve, president of Volvo Trucks North America.
“That is why, at Volvo Trucks, we are focused on the three-pillar strategy with battery electric, hydrogen fuel cell, and renewable fuels in the internal combustion engine. With the all-new Volvo VNL and by utilizing HVO, we can make the most substantial and immediate impact today. There is a future for the ICE and we’re happy to be doing all factory fills with renewable fuel, an important step toward walking the talk in our sustainability journey.”
Volvo Trucks is fuelling new trucks leaving the NRV plant with 20 to 25 gallons of HVO per tank, with full tanks provided for trucks destined directly to operators. This initiative is expected to replace 1,125,000 gallons of fossil-based diesel annually, achieving an estimated 75 to 85 percent reduction in CO2 emissions for Volvo Trucks’ operations in North America.
“The internal combustion engine has more than 100 years of research and development and established support in the industry. It must be part of the decarbonization journey and major, immediate decarbonization possibilities exist by using renewable fuels, including HVO and hydrogen,” said Johan Agebrand, director of product marketing at Volvo Trucks North America. “Volvo Trucks continues to work with the industry to broaden the use of renewable fuels. Fuels produced using hydrotreatment processes such as HVO and RD100 can be interchangeable with diesel and is a viable fuel to decarbonize transportation truck operators can start using today.”
The new XL Knight 80 MFG has an updated and improved mechanical, full-width gooseneck trailer design. The 48-foot-long detachable gooseneck lowboy has an overall capacity of 80,000 pounds and a concentrated capacity of 70,000 pounds in 16 feet. The trailer offers 29 feet of main deck loading space and a loaded deck height of 18 inches.
The mechanical, full-width gooseneck – also known as the double drop – is a version of a staple product in the lowboy industry. The Knight is an ideal model for versatile hauling across the U.S. and Canada, encompassing what XL Specialized Trailers says are the most popular specs and options possible into a competitive offering.
The XL Knight 80 MFG offers many new standard features. The detachable goose-
a half inches, for a total of a three-inch variance. The raise and lower valve in the rear allows for an adjustment of one and a half inches. The Colas-plus raise and lower valve is especially user-friendly with its large and durable handle.
The Knight trailer has MicroNova clearance lights. A battery backup with
storage area to stow chains or other materials. Swingout outriggers can be added to the main deck for hauling over-width loads. A two-foot by two-foot cutout in the rear transition provides additional space for equipment such as drawbars on tractors. The two-axle wheel area is prepped to accommodate a third axle if needed.
BY LEE TOOP, EDITOR
It’s nearing the end of a hot day at work on an industrial construction site. An excavator operator moves their machine across a dry, grassy field to park for the evening. Grass and debris that has collected unnoticed in the engine compartment heats up and catches fire.
This scenario might go a couple of different ways. One: The fire intensifies, starts burning more materials and, before the operator realizes it, there’s a serious – and potentially life-threatening – problem right behind them. It’s too big to use a hand extinguisher, if there’s one available. The operator abandons the machine and calls for help while the excavator burns. The operator is safe, this time, but the excavator is badly damaged, and there’s potential for a grass fire to start and cause even more harm to the surrounding area.
Or, two: The flame is detected by an automated system. The fire melts a detection wire or is picked up by a heat sensor, and tanks filled with fire suppressant spray into the affected area. The fire is knocked down, giving the operator more time to get clear. Damage to the machine and the job site is minimized.
On-board fire suppression systems are a regular sight on large mining equipment, popular on forestry machines, and becoming more commonly required in waste and recycling. Fire damage may not be the first problem that comes to mind for a construction fleet owner, but with equipment running at higher temperatures and working in hotter climates, automated fire suppression provides a level of insurance that protects against injury and damage.
AFEX Fire Suppression Systems has more than 50 years experience manufacturing automated fire suppression systems designed specifically for heavy equipment. It has partnered with FLO Components, a Canadian supplier of auto-lubrication systems for heavy equipment, to supply automated fire suppression systems in Ontario and Manitoba.
For FLO Vice-President Mike Deckert, a veteran of four decades of dealing with heavy equipment, automated fire suppression is a lot like buying insurance – it protects lives and property if the need arises.
“They want to protect their employees and the surrounding area – a mine, a forest, a garbage dump, a recycling centre,” Deckert says. “For customers in construction and recycling, automated fire suppression is increasing.”
Deckert says machines parked in a maintenance shop overnight have experienced an electrical short, caught fire, and destroyed the shop. News reports talk about equipment catching fire in log yards, on construction sites, inside buildings – it may not be an everyday occurrence, but the possibility is always there.
Equipment fires tend to be caused by several factors. Tier 4 diesel engines feature turbochargers that run hotter than previous engine types, and the associated aftertreatment systems emit more heat than before, Deckert explains. Machines working in sectors with a lot of debris collecting in body panels and engine compartments – woody debris in forestry, for example, and general waste in recycling uses – are at higher risk of fires. Demolition work takes place in and around a lot of potentially flammable debris, as well as materials that can easily throw sparks. Even something as small as a frayed wire in the engine compartment can, in the right conditions, start a blaze.
Those factors become part of a fire risk assessment for fleet owners who are considering automated fire suppression. The assessment ensures that any unique challenges an operation might face – ignition sources, types of fuel, and insurance or regulation requirements – are addressed and the correct fire protection system is designed. From there, it is very similar to the process for installing the auto-lubrication systems FLO provides, Deckert notes.
“We look at the specific machine so that we obtain information about the proper size of tanks, the number of nozzles, and installation routing,” he adds.
FLO Components teams handle individual design of the system, which includes a controller in the cab, tanks for the required fire suppression agent, piping, wires or sensors for detecting a fire, and the nozzles covering areas where potential fires may occur – turbochargers, transmissions, and batteries being the most common sites.
When a fire breaks out, an auto-detection wire in the area melts, or a temperature sensor activates, triggering the system. Nitrogen bottles release into the tank and shoot dry or liquid chemical through a distribution network for quick knock-down of the fire.
There are also manual releases for when the operator or another worker spots a fire before the automated system is triggered.
Up to three manual buttons are installed on machines, with one in the cab and others at ground level along the path of egress.
“The detection wire melts at 356 degrees F, and once that melts the controller alerts the operator that the system has activated,” Deckert says. “If the operator sees flames before that, they can hit the manual button, or if a machine is parked and someone sees a fire, they can trigger the system from outside.”
Most fires on heavy equipment can’t be handled by handheld fire extinguishers and need a bigger response, Deckert adds. AFEX systems installed by FLO Components technicians offer three different types of chemical response to suppress the fire and give time for operators to get clear and emergency crews to react if needed.
“Dry chemical is like a fog, for fast knock-down of flames and suppressing the fire. It covers Class A [ordinary combustibles], B [burning liquids], and C [electrical] type fires. The liquid type removes the heat so it eliminates the chance of flare-ups afterward – it cools the hot surfaces. It handles A and B class fires, but not C,” Deckert says. “The dual agent provides a dry and liquid system together.”
Fire safety can’t be trivialized, even if equipment fires aren’t an everyday occurrence. When a fire does happen, it threatens lives, equipment, surrounding natural resources, and the greater environment. Automated fire suppression systems provide fleet owners with added peace of mind knowing that their equipment and people have an extra level of protection if the unexpected occurs. HEG
BY NELSON ABELHA
equipment for a specific period, paying relatively lower monthly installments. At the end of the lease term, the lessee has the flexibility to return the equipment, purchase it at its fair market value, or extend the lease. This empowers businesses to align equipment usage with evolving needs, making FMV leases a practical and versatile option.
Capital leases, also known as finance leases, are more akin to a loan. The lessee essentially finances the equipment purchase, typically with higher monthly payments, and owns the equipment at the end of the lease term. With this type of lease, there are higher monthly payments when compared to an FMV lease, but at the end of the lease term, the lessee purchases the equipment for $1. This is like an equipment loan and is ideal if you plan to keep the equipment for a long time, or when equipment obsolescence isn’t a concern.
Cost per hour is a crucial metric that measures the total cost of owning and operating equipment; it’s calculated by dividing the total payments for the initial lease term by the number of hours the equipment is used.
FMV leases can provide several cost per hour advantages: Lower monthly payments Since FMV leases do not require the lessee to pay the full equipment cost over the lease term, the monthly financial burden is significantly reduced compared to capital leases. Lower payments mean better cash flow, allowing businesses to allocate funds to other critical areas, such as labour, materials, and project
Maintenance and repair costs FMV leases often include maintenance and repair services as part of the lease agreement. This can equate to substantial savings in equipment operation cost per hour. With maintenance covered, businesses can dodge unexpected repair costs, reduce downtime, and ensure equipment is always in optimal working condition. In contrast, with a capital lease, the lessee is typically responsible for maintenance and repairs, which can be unpredictable and costly.
The choice between Fair Market Value (FMV) and capital leases can significantly impact operational efficiency and financial health.
Technological advancements Heavy construction equipment technology is constantly evolving. With an FMV lease, companies can upgrade to newer, more efficient models at the end of the lease term without the financial burden of owning outdated equipment. This ensures ongoing access to the latest technology, for greater productivity and reduced operational costs. Capital leases could lock companies into long-term ownership of equipment that may become obsolete, leading to higher costs due to less efficiency.
Flexibility and scalability FMV leases offer greater flexibility compared to capital leases. Projects vary in scope and duration, and it’s critical to adjust equipment needs accordingly. With FMV leases, companies can scale equipment fleets up or down based on project requirements without long-term ownership commitment. This ensures equipment costs align with actual usage, optimizing cost per hour.
Tax advantages FMV leases can offer tax benefits not available with capital leases. Lease payments under an FMV lease are often fully deductible as business expenses, reducing taxable income which can provide significant tax savings, lowering overall equipment operation cost per hour. Capital leases typically allow for depreciation deductions, which may not be as advantageous depending on a company’s tax scenario.
FMV leases offer several advantages over capital leases for heavy construction equipment, especially in cost per hour, making FMV leases an appealing option for construction companies seeking to improve their operations and financial well-being.
NELSON
ABELHA is the regional vice president of First Financial Canadian Leasing.
XYZ Construction Company is evaluating leasing options for a $705,000 articulated dump truck:
XYZ opts for an FMV lease with a monthly payment of $18,437.19 over two years. Maintenance and repairs are included in the lease. At the end of the term, XYZ can return the equipment and lease a new model.
Alternatively, XYZ could choose a capital lease with a monthly payment of $31,177.70 over two years, and be responsible for all maintenance and repair costs, estimated at $15,000 annually.
Top-line cost analysis:
• Total lease payments:
$18,437.19 x 24 months = $442,492.56
• Maintenance and repair costs: $0 (included)
• Total cost: $442,492.56
Cost per hour breakdown (if XYZ uses the excavator for 1,500 hours per year):
$442,492.56 / (1,500 hours x 2 years) = $147.50 cost per hour
• Total lease payments:
$31,177.70 x 24 months = $748,264.80
• Maintenance and repair costs: $15,000 x 2 years = $30,000
• Total cost: $778,264.80
$778,264.80 / (1,500 hours x 2 years) = $259.42 cost per hour
In this scenario, the FMV lease provides a significantly lower cost per hour – a savings of $111.92 per hour – which would cover the costs of more than two unionized machine operators.
Held every four years, DEMO International is a unique event that takes place on an active forestry site near Ottawa/Gatineau. Attendees can get up close to see the latest tools for forestry in a working environment. demointernational.com
NV | SEPT. 24 – 26
MINEXPO takes place every four years and is hosted by the National Mining Association in Las Vegas. It draws members of the mining sector from around the world to learn more about solutions and products for safety, drilling, engineering, and more. minexpo.com
VEGAS, NV | NOV. 11 – 13
Trimble’s yearly user conference provides attendees in construction, mining, infrastructure, and other industries with educational sessions on the latest in construction software and technology. The off-site demo area offers a first-hand look at new tools and solutions in real-world situations. trimble.com/en/our-company/events/dimensions/overview
FL | JAN. 15 – 17, 2025
| JAN. 21 – 23,
Mammoet assembles world’s strongest land-based crane
Liebherr mining truck prototype takes first drive powered by hydrogen
Kleemann crusher plays central role in C&D recycling and emissions management
iSlip allows more accurate, intelligent placement of concrete for your paving applications. With remote access, machine monitoring capabilities and so much more. The iSlip Control System sets a new standard for automated concrete placement.
Curb & Gutter | Sidewalk | Recreational Trails | Special Projects
1-800-368-8920 | www.easipour.com | sales@easipour.com
No matter how challenging your needs, EARTHMAX SR 41 is your best ally when it comes to operations that require extraordinary traction. Thanks to its All Steel radial structure and the special block pattern, EARTHMAX SR 41 provides excellent resistance against punctures and an extended service life. In addition to long working hours without downtime, the tire ensures extraordinary comfort.
EARTHMAX SR 41 is BKT’s response to withstand the toughest operating conditions in haulage, loading and dozing applications.
GOMACO offers the full range of concrete slipform pavers, curb and gutter machines, trimmers, placer/spreaders, texture/cure machines and bridge/canal finishing equipment. GOMACO equipment features our exclusive and proprietary G+® control system, created in-house by our software engineers from the wants and needs of contractors paving in the field. At the heart of GOMACO equipment is our passion for concrete and our commitment to our customers. We look forward to visiting with you about your upcoming paving projects and your concrete paving equipment needs. Our worldwide distributor network and our corporate team always stand ready to serve and assist you.