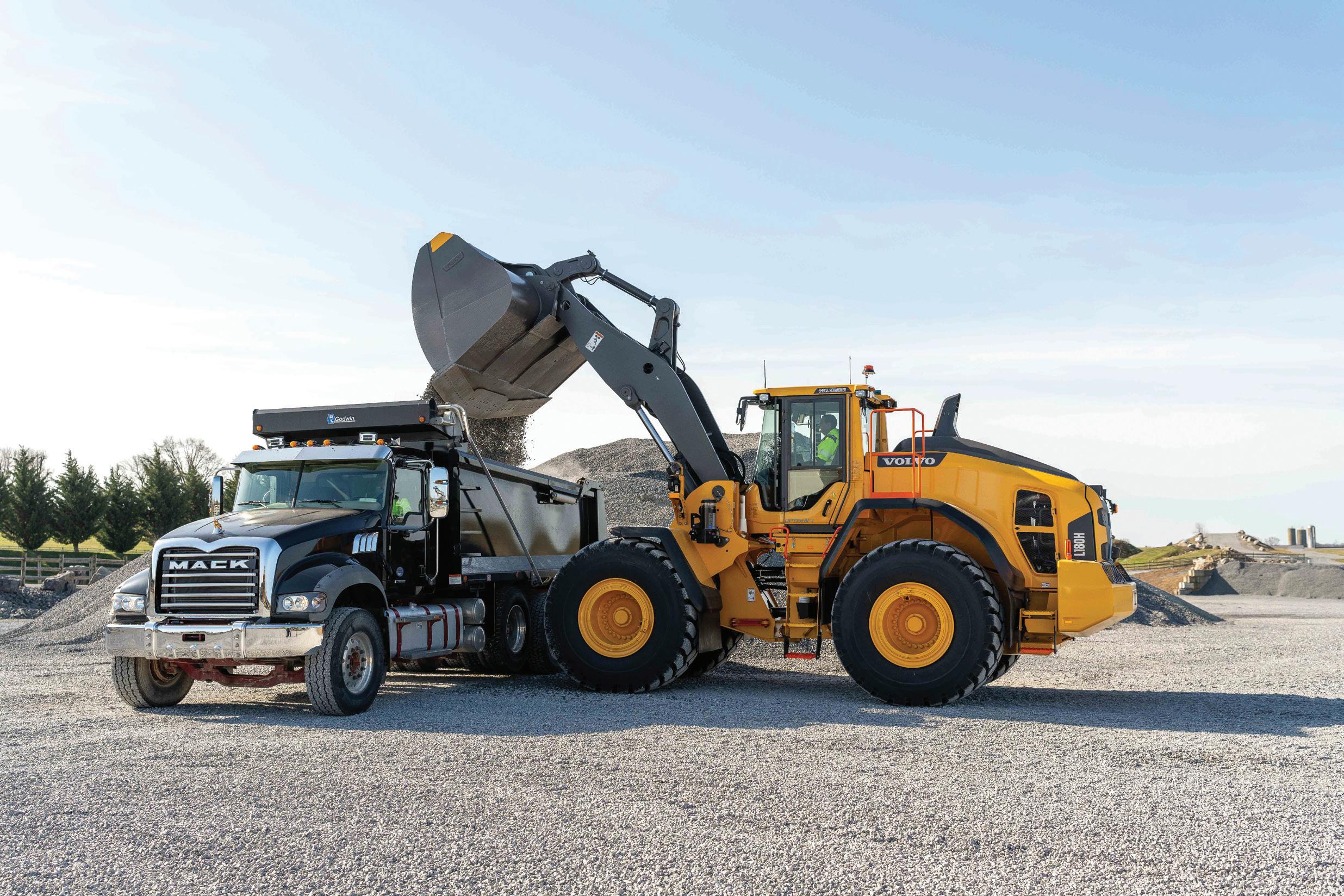

BUILD A BID AROUND IT. START BEFORE DAWN ROLLS OUT OF BED. USE 30 TONS OF IRON TO MOVE 30 TONS OF ANYTHING. RUN FOR HOURS. MAKE THAT A DECADE. THIS EXCAVATOR KEEPS THE JOB MOVING FORWARD.
SCAN FOR CURRENT EXCAVATOR OFFERS.


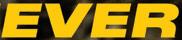

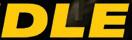

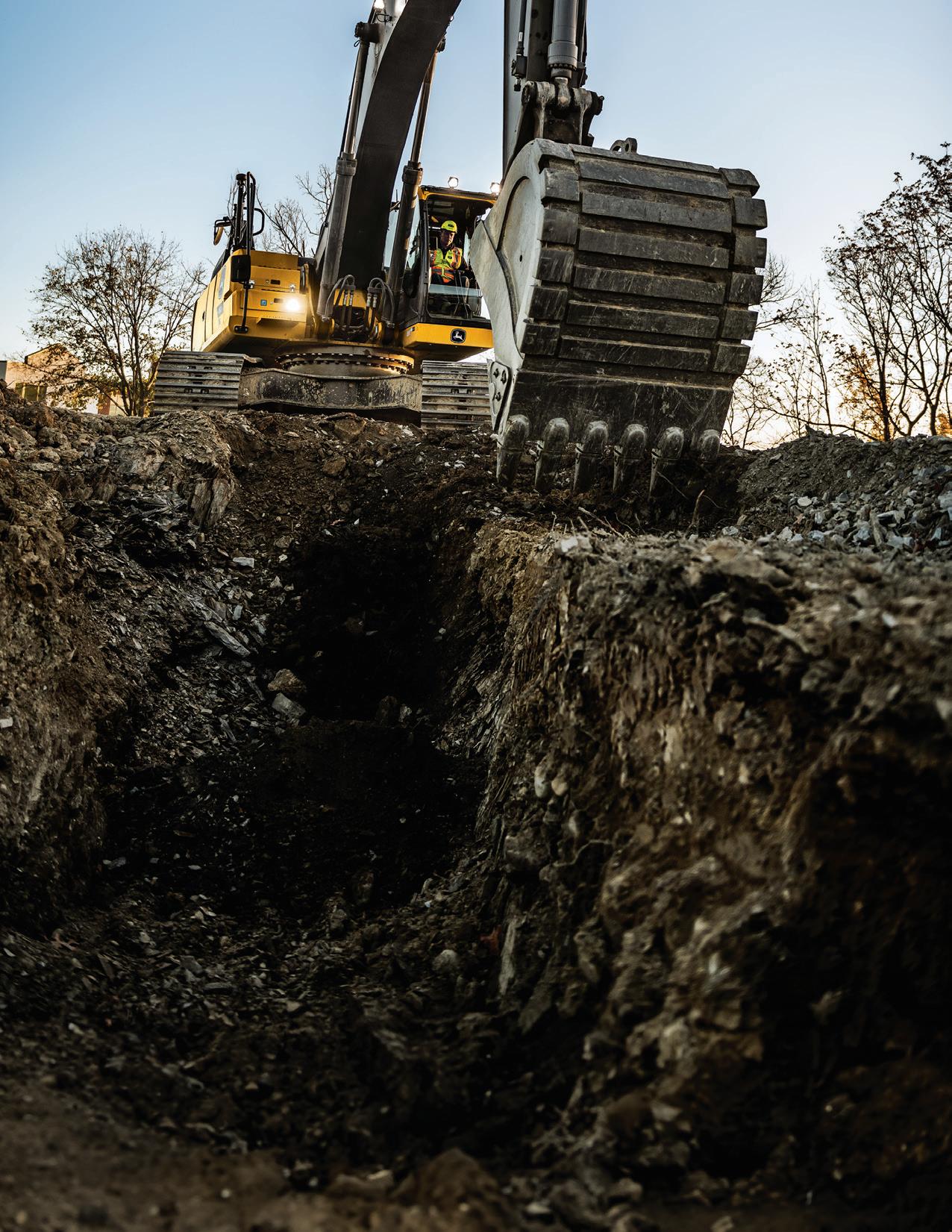
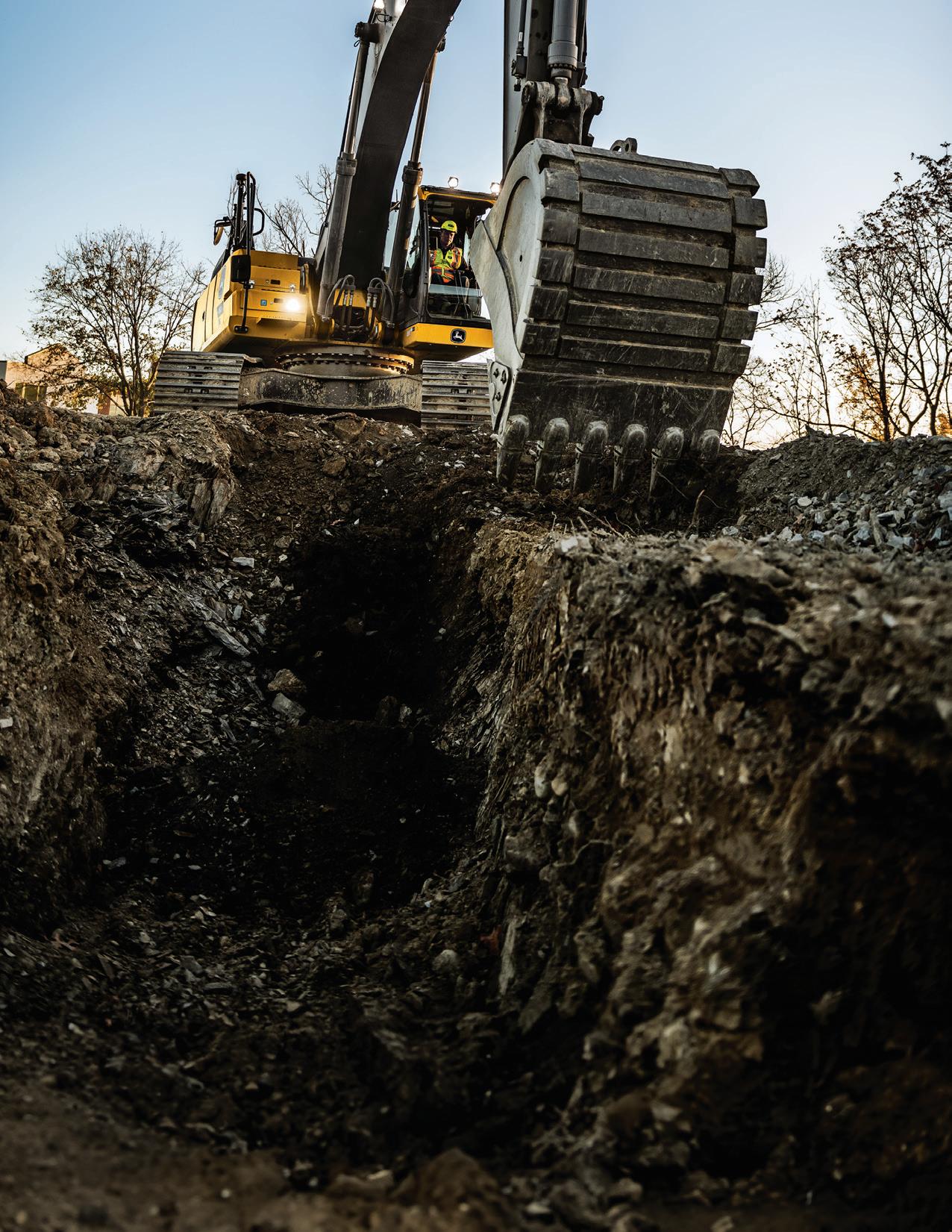

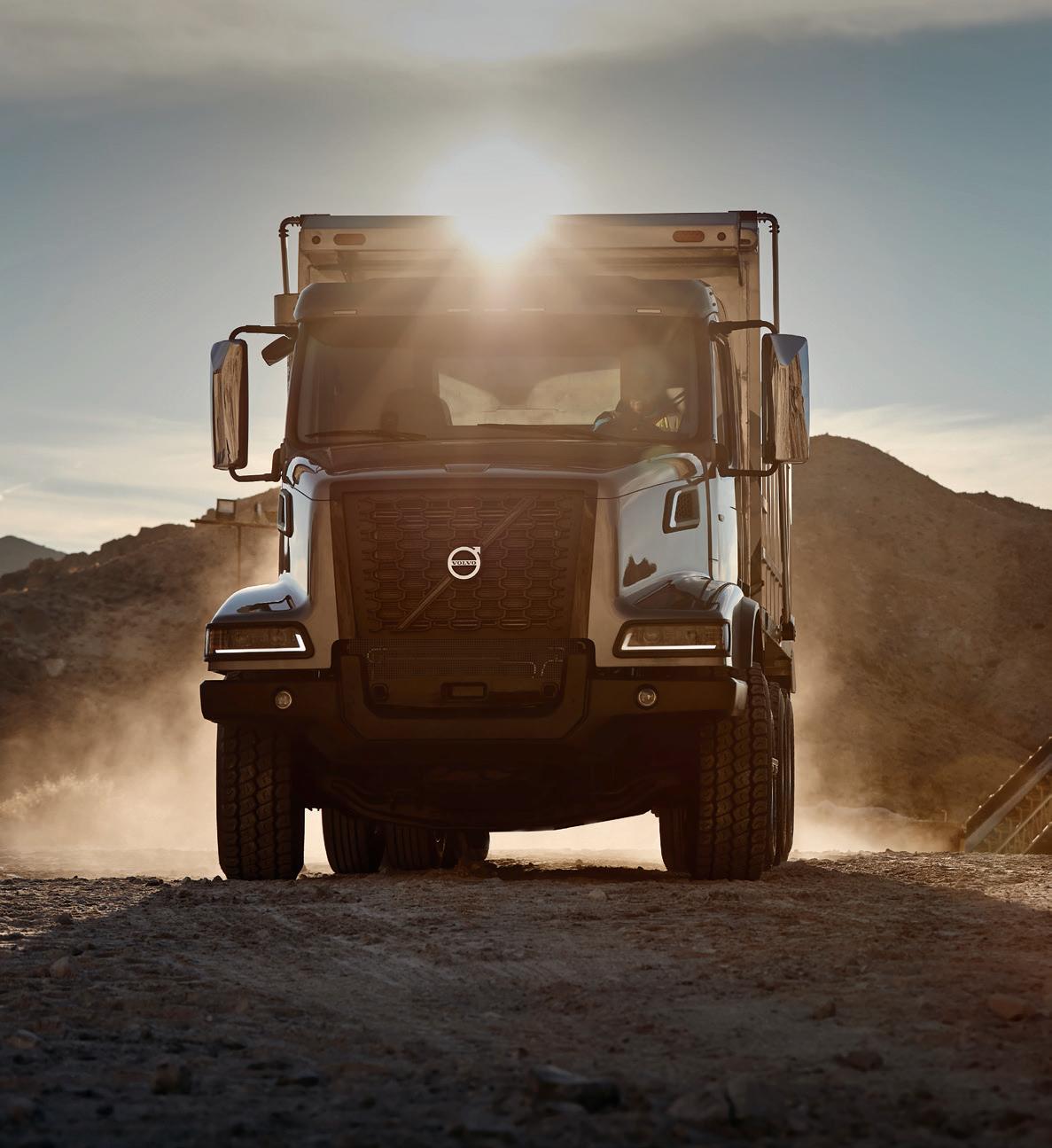
BUILD A BID AROUND IT. START BEFORE DAWN ROLLS OUT OF BED. USE 30 TONS OF IRON TO MOVE 30 TONS OF ANYTHING. RUN FOR HOURS. MAKE THAT A DECADE. THIS EXCAVATOR KEEPS THE JOB MOVING FORWARD.
SCAN FOR CURRENT EXCAVATOR OFFERS.
Introducing the new VHD
On the jobsite you need a truck that’s tough, safe, and smart. So, we built the new Volvo VHD to be the best-looking, most rugged vocational vehicle in the industry, packed with innovative ideas like Volvo Active Driver Assist and the revolutionary Volvo Dynamic Steering. Your toughest jobs just got easier. Learn more at volvotrucks.ca/en-ca/trucks/vhd/
Cloud-based remote monitoring
Heavy-duty digital truck scales
Cardinal Scale’s ARMOR® digital truck scale with included free iSite remote monitoring means you can say goodbye to downtime with high-tech Cloud-based diagnostics.
FEATURE
LINK-BELT EXCAVATORS READY FOR MACHINE CONTROL
Equipment & technology highlights from AGG1
Turn to page 42 .
Do you have a job site story, innovation, or industry concern that our readers should know about? We’d like to hear from you.
Contact: Editor in Chief Kaitlyn Till at ktill@baumpub.com or 604-291-9900 ext. 330
EDITOR IN CHIEF Kaitlyn Till ktill@baumpub.com 604-291-9900 ext. 330
ltoop@baumpub.com 604-291-9900 ext. 315
ASSOCIATE PUBLISHER
Sam Esmaili sam@baumpub.com 604-291-9900 ext. 110
ADVERTISING
PRODUCTION MANAGER Tina Anderson tanderson@baumpub.com 604-291-9900 ext. 222
DESIGN & PRODUCTION
Morena Zanotto morena@baumpub.com 604-291-9900 ext. 325
PRESIDENT/PUBLISHER
Ken Singer ksinger@baumpub.com 604-291-9900 ext. 226
VICE PRESIDENT/CONTROLLER
Melvin Date Chong mdatechong@baumpub.com
FOUNDER
Engelbert J. Baum
Published by: Baum Publications Ltd.
124 - 2323 Boundary Road Vancouver, BC, Canada V5M 4V8
Tel: 604-291-9900
Toll-free: 1-888-286-3630
Fax: 604-291-1906 www.baumpub.com www.heavyequipmentguide.ca @HeavyEquipGuide
FOR ALL CIRCULATION INQUIRIES
Toll-free: 1-866-764-0227 email: heg@mysubscription.ca
Subscription: To subscribe, renew your subscription, or change your address or other information, go to: http://mysubscription.ca/heg/
Heavy Equipment Guide serves the Canadian engineered construction industry including: roadbuilding and maintenance; highways, bridges, tunnels; grading and excavating; earthmoving; crushing; trucking and hauling; underground utilities; trenching; concrete paving; asphalt paving; demolition; aggregates production; fleet maintenance; and asset security and management. The magazine is distributed to key industry personnel involved in these sectors.
Subscription Price: In Canada, CDN $91.00; Outside Canada, US$149. Heavy Equipment Guide is published eight times a year in January/ February, March, April, May/June, July/August, September, October, and November/December.
Heavy Equipment Guide accepts no responsibility or liability for reported claims made by manufacturers and/or distributors for products or services; the views and opinions expressed are those of the authors and not necessarily those of Baum Publications Ltd.
Copyright 2024, Baum Publications Ltd. No portion of this publication may be reproduced without permission of the publishers.
We acknowledge the financial support of the Government of Canada.
Printed on paper made of FSC®-certified and other controlled material. ISSN 1715-7013.
PUBLICATIONS MAIL AGREEMENT NO. 40069270
Return undeliverable Canadian addresses to:
Circulation Dept., 124-2323 Boundary Road, Vancouver, BC V5M 4V8 email: heg@mysubscription.ca Toll-free: 1-866-764-0227
THERE’S MORE THAN ONE WAY TO DECARBONIZE CONSTRUCTION
Ihad the pleasure of attending Intermat 2024 in Paris in April, and a central theme of this year’s show was decarbonization in the construction industry.
Battery-electric construction equipment was certainly a substantial part of the decarbonization conversation at Intermat, but battery-electric equipment is far from the only way to reduce emissions in construction. There are a number of factors that make widespread adoption of electric equipment unlikely for the time being. They include current battery technology and the perception of run times, lack of economic incentives for equipment buyers in both Europe and North America, access to zero-emissions power sources for charging, and the high acquisition cost of the machines that are currently on the market.
Even with all these challenges to overcome, we remain excited about battery-electric construction equipment – the wider adoption of it will come, if not quickly. However, there is more than one approach to reducing carbon emissions in your construction operations.
Another hot topic of conversation at Intermat, particularly with engine OEMs, was hydrogen combustion. Several OEMs now have hydrogen combustion engine solutions ready to meet the demand when it comes, but similar to battery-electric equipment, there are significant barriers to fast adoption – the big one, globally, is the lack of infrastructure to deliver hydrogen fuel to where it’s needed. Hydrogen combustion is a promising solution, but it isn’t yet practical.
Today, you can reduce carbon emissions through looking at your job site holistically to make a series of changes that can deliver not only substantial emissions reduction, but time savings as well. These changes can include adopting biofuels; hybrid equipment; newer, more efficient equipment; and technology. In this issue we explore how technology can save time and reduce emissions on road resurfacing projects. Turn to page 24 to learn how a paving contractor uses Topcon scanning
There is more than one approach to reducing carbon emissions in your construction operations.
technology to get insight into the roads it resurfaces. The contractor is able to significantly reduce the number of days that it takes to complete a job and the number of passes that the equipment has to do. This lowers the emissions on a given project and reduces the amount of time that paving crews have to spend in work zones adjacent to active roadways. Finally, for a peek at a future battery-electric job site solution and some more examples of innovation in the industry today, turn to page 58 to see the Bobcat electric telehandler concept that was revealed at Intermat 2024 and to find out who won Gold at the Intermat Innovation Awards.
ktill@baumpub.com
heavyequipmentguide.ca
Liebherr has a rich history of daring to take new approaches and by redefining what is possible. We invite you to embrace our spirit of innovation and ambition. Shaping the world of tomorrow, today.
Hitachi Construction Truck Manufacturing, a wholly owned subsidiary of Hitachi Construction Machinery, headquartered in Ontario, will produce and remanufacture dump truck maintenance and service parts. This decision will establish a production and service framework for dump trucks in the Americas market.
Hitachi says that this decision is in response to strong market demand in the Americas. Hitachi can meet market needs faster by developing a local production and service framework for dump trucks. Hitachi hopes to accelerate independent business expansion while increasing the local procurement rate.
The Americas (North, Central, and South America) account for approximately 40 percent of the global dump trucks over 150 tons market. South America sees a lot of copper, iron ore, and gold hard rock mining operations. Mining for these minerals is also expected to keep rising in the future. Hitachi has been producing dump trucks at the Hitachinaka-Rinko Works in Hitachinaka, Ibaraki Prefecture, and delivering them to the world. Now, with the local production of dump trucks in Canada, transportation time for Hitachi dump trucks will be shortened.
For dump trucks produced in Canada, mainframes, welding structures, and components such as engines and radiators will be locally sourced to improve the local procurement rate. Other key components will be imported from Japan so that Hitachi can keep the same level of reliability as dump trucks produced in Japan. Engineers, including designers, will be present to deal with specification changes on individual dump trucks.
Hitachi Construction Truck Manufacturing’s predecessor, Euclid-Hitachi Heavy Equipment Ltd., was acquired by Hitachi Construction Machinery in 1988. It halted the production of dump trucks in 2018 to focus on producing service parts for delivered dump trucks and remanufacturing parts for ultra-large hydraulic excavators and dump trucks. Toward the start of fullscale production of dump trucks in 2026, the staff is expected to double the current size as part of efforts to strengthen the production system.
The Brandt Group of Companies will expand its material handling equipment dealer network, adding up to 300 new jobs over the next three years.
The company’s acquisition of Cervus Equipment in 2021 included material handling operations from Alberta through Manitoba. Brandt aims to deepen and expand its commitment to the material handling industry in Canada. The company will expand its material handling business nationwide, creating a new and separate division that will deliver solutions and aftersales support from coast to coast.
“We believe that the material handling sector is primed for growth and in need of a nationwide alternative to the existing patchwork of small dealer groups,” says Shaun Semple, CEO of Brandt. “That is why we’re using the lessons we have learned from growing the agriculture, construction & forestry, and transportation pillars of our business to create a fourth pillar to serve the material handling industry.”
Canada depends on its material handling operations – from ports and transportation hubs to warehouses and distribution centres. Lift trucks and other material handling equipment and related infrastructure are essential to support the flow of goods to Canadians and support the country’s ongoing national growth every single day.
As part of this expansion, Brandt plans to grow its network of material-handling-focused stores into new territories with aims to deliver forklift brands backed by a rental fleet, parts network, and dedicated service network prepared to provide repair work and preventive maintenance.
Strongco has launched a dedicated rental fleet featuring Volvo Construction Equipment machinery. With this addition, Strongco looks to provide contractors with more options to help lower downtime and complete projects on time.
The rental fleet has an inventory of Volvo heavy equipment, including medium- to large-sized crawler excavators, articulated haulers, and soil compaction rollers. This range of equipment ensures that contractors have access to the right tools for their specific needs, whether it’s excavation, material transport, or compaction.
“Our commitment at Strongco has always been to support our customers in achieving their project goals efficiently and cost-effectively,” says Stephen George, vice president of rental equipment at Strongco. “With the introduction of our dedicated rental fleet featuring the latest Volvo equipment, we are furthering that commitment by offering more options to manage cash flow and minimize project delays.”
One of the advantages of Strongco’s rental fleet is its availability, ensuring that contractors can access the equipment they need. This eliminates the need for large capital investments in purchasing equipment outright, allowing businesses to allocate resources more strategically. In addition, Strongco’s rental fleet is designed to help contractors avoid delays and downtime on their projects.
“We understand the importance of keeping projects on track and within budget,” says Oliver Nachevski, president and chief executive officer at Strongco. “That’s why we’ve curated our rental fleet to feature the latest Volvo equipment, ensuring that our customers have access to dependable machinery that can withstand the rigours of the job site.”
Turn to page 42 to learn about equipment and technology highlights from the show.
Oshkosh Corporation, the parent company of telehandler manufacturer JLG, is expanding its equipment portfolio with the acquisition of AUSA. AUSA, which builds wheeled dumpers, rough terrain forklifts, and telehandlers for construction, material handling, agriculture, and other industries, will become part of the Oshkosh Access segment after the acquisition.
AUSA has been working with JLG since 2020 through a partner agreement, manufacturing the SkyTrak 3013 compact telehandler.
Frontline Machinery has acquired Lonetrack Equipment, a dealer of specialized machinery for the aggregate, mining, and road construction industries in British Columbia and the Yukon.
Frontline says that Lonetrack Equipment has built a reputation of trust and a commitment to support. The company’s range of heavy equipment includes crushers, screeners, conveyors, and concrete construction equipment from Astec, Sandvik, Vale, BTI, Gomaco, and more.
As of May 1, 2024, the combined entity operates under the Frontline Machinery brand.
Cooper Equipment Rentals has acquired Action Equipment Rentals. Action was formed in 1991 in Sundre, Alberta, to serve the Central Alberta market. The company opened a second location in Red Deer about a year later. Action joins the Cooper family as the Red Deer branch.
HBC-radiomatic, which produces radio systems for the wireless control of cranes and other construction machinery, has a new Canadian subsidiary, HBC-radiomatic Canada, based in the GTA. This latest expansion of HBC’s network enables the company to offer its solutions to Canadian users. HBC has more than 75 years of experience in the industry, in-house R&D, and engineering capabilities at its German headquarters, and domestic production capabilities in North America. Until HBC-radiomatic Canada is up and running, Canadians can utilize HBC’s production and service teams in the United States.
CZM Foundation Drilling Equipment has entered a dealer partnership with RTI Equipment Solutions, a heavy equipment provider in Innisfil, Ontario. RTI Equipment Solutions provides sales, rentals, parts, and services for a range of solutions to meet project needs.
Liebherr has launched a new portal for the sale of used machines. On this platform, contractors can find used construction and material handling machines, used attachments and accessories, and used spare parts from certified Liebherr sales and service partners. The Used Equipment Marketplace is available both as a website and as an app.
future of the industry.
The solution is women.
And yes, compared to a decade ago things have changed, but women are still under-represented in the construction sector. Let’s look at the stats. In Ontario, just 8 percent of trades, transport,
and equipment operators are female according to Statistics Canada. The Commission de la Construction du Québec recently reported that just 3 percent of Quebec’s construction workforce is female. Numbers are equally low in other provinces.
What happens when we get more women into the construction industry? To start, we increase profitability. According to McKinsey research, companies in the top-quartile for gender diversity on executive teams
were 21 percent more likely to outperform their national industry median on operating earnings margins. The same report shows that gender-diverse construction companies are 25 percent more likely to achieve above-average profitability compared to less diverse companies.
If that isn’t enough, how about the unique perspectives women bring? Or the skill sets you access when you diversify your recruitment? This isn’t going to happen on its own – it takes work. So it’s
time to ask the question: Are you willing to put in the effort needed to bring more women into your workforce? It means committing to an inclusive organization and helping build a diverse workforce that fosters innovation, better decision-making, and teams where everyone feels safe and supported. Who wouldn’t want that?
Where would we be if schools were providing the resources and encouragement for young women to learn about opportunities in the construction and rental industry? Both have so much to offer: competitive salaries, flexible work hours, safety training, mental health benefits, and mentorship.
I joined the equipment rental industry in 2020 with no prior experience and I have never experienced more support in my career development. It can be intimidating entering a new industry where there’s a lot of technical knowledge to acquire, but with a supportive learning environment and the right motivation, anyone can develop new skills and knowledge. Even if they have no prior industry experience, leadership teams should be fully invested
in attracting, retaining, and developing more women in our industry – not just for business performance, but because it opens up a whole new pool of talent.
For Lana Frank, a mom of two and the only female outside sales rep in Cooper Equipment Rentals’ Trench Safety division in Canada, a career in construction was never something she imagined. She says working in the industry has had a real impact on her career and her family life. The flexibility, support, and ability to spend time with her family has allowed her to flourish both professionally and personally. It’s not all perfect of course; she faces some real challenges on site. Some male customers doubt her ability and knowledge, looking past her when she arrives. What’s her advice to women wanting to join the industry? “Be the ‘calm in the storm’ and focus on the unique
attributes you can bring to the table,” she says. For Lana that’s empathy, understanding, and patience.
Updated recruitment efforts can help pave the way for tapping into a new talent pool and, as a result, increase retention too. To start, it might be time to have a long hard look at the language you use in your recruitment, like reviewing interviewing processes and removing biases from job descriptions. We recently went through all our job descriptions to identify underlying biases, words, and descriptions that weren’t gender neutral. At one point, a role might have required an employee to be able to lift 50 pounds, but the requirement is now irrelevant. Updating language and requirements removes barriers for female applicants.
It can be intimidating entering a new industry where there’s a lot of technical knowledge to acquire, but with a supportive learning environment and the right motivation, anyone can develop new skills and knowledge.
For organizations committed to measuring and improving diversity efforts, certifications can add credibility and rigour to your practices. We’ve pursued the parity certification by Women in Governance, and it’s a point of pride that we’ve improved our level of certification over the last year. It’s a lot of work but it’s also a great opportunity to not only measure your diversity efforts but also see what other companies are doing to attract and retain more women.
Consider for a moment the potential outcomes when workers, especially women, do not feel safe to speak up. How many accidents could have been prevented? How many innovative solutions were never voiced? Developing an open culture of communication between workers and managers is critical. Companies with high levels of emotional intelligence
EVEN
are able to foster more trust with workers. This is key for establishing a safe work environment both physically and psychologically, especially on construction sites. How likely is an employee to speak up about a potentially dangerous move if they don’t feel safe to do so? In an industry that doesn’t typically lend itself to open discussions about mental health, this can be a game changer.
When we are open to different perspectives we bring better solutions to the table when it comes to employees’ wellbeing. So if your focus is not just on hiring women, but retaining them, your teams should feel comfortable reporting unsafe behaviours or concerns to their managers.
Young women want to see workers who look like them
and have experiences they can relate to. But that’s hard when there are still so few women on most job sites.
Emily Henderson is an apprentice mechanic based in Calgary and cannot recall learning about skilled trades opportunities in high school. After a family member told her about their experience as a heavy-duty equipment mechanic, she decided to go for it. Emily’s now finishing her second year as an apprentice and isn’t looking back. When she applied for her role she had no relevant experience and didn’t know heavy equipment.
“They could tell I wanted to learn and that I was determined. They took a chance on me,” she recalls. From there she earned her various safety certifications and started heading out on service calls. She gets a lot of double takes and sometimes feels uncomfortable as the only woman on site but stays focused on
the job. And that’s her advice to young women entering the industry. “I would say 100 percent go for it. You need to minimize the background noise of people saying you belong in the office and not in the field. Realize that these people aren’t part of your career path, chase what you want to do.”
So how do we improve culture on job sites when female representation is still so rare? There are a few organizations leading the charge on this –Canadian Women in Construction actively supports the training and development of young professionals entering or considering the construction industry. Their goal is to increase employment, awareness, and development for all women during various stages of their career journey. Providing hands-on experience and an engaging learning environment to young women as a way to introduce them to a possible career in the trades
is key. I also encourage younger women to attend Jill of All Trades events to see first hand what employment opportunities are available.
Seeing a clear path to career advancement is the most important factor for women. While challenges still exist, diversity stands as a proven asset and plays a key role in addressing the industry’s labour shortage.
There are incredibly accomplished women already working in the construction and rental industries who are challenging gender norms and inspiring younger generations to follow them. We just need to keep going!
ANTONIAEDWARDS is the director of marketing at Cooper Equipment Rentals Limited.
The 973, which is the largest of Caterpillar’s three track loaders, is powered by a 275-hp engine and has an operating weight of 65,901 pounds. With its Cat C9.3B engine, the 973 consumes 10 percent less fuel than its predecessor due to an Auto Mode that adapts engine speed to the load. Eco Mode uses lower speeds for better fuel consumption in lighter duty applications, and Power Mode keeps engine speed high when
power is needed the most. Joystick or V-lever and pedal steering are available for transmission control, and either joystick or two-lever systems for implement control. Implement response can be set to fine, normal, or coarse to match a particular use or the operator’s preferences. Presets make repetitive actions, such as lift, lower, rack, dump, and float, easier. An updated cab includes a suspension seat, adjustable armrests and controls, and an intuitive 10-inch touchscreen dash display with a standard high-definition rear-view camera.
Contact your local Wacker Neuson dealer today. All it takes for the
From the original compaction brand comes a full line of construction equipment designed to help you get the job done with efficiency, quality and comfort. Whether your challenge is to load, move or place material, compact soil and asphalt, or to provide light, heat, power or pumping on your job site, Wacker Neuson has the machines to get it done right. This includes zero-emission, battery-powered solutions to meet the demands of the construction environment today, as well as tomorrow.
The 24SG stump grinder attachment has a 24-inch cutting wheel and is designed for use on low-flow skid steers and excavators. It has a rigid mount that allows operators to work quickly by repositioning the power unit rather than articulating the attachment itself. An angled hitch and forward-reaching boom provide visibility and control. Leonardi’s Phantom stump grinder wheel further improves visibility with its cutouts, which create a see-through effect during operation. Powered by a 110cc high-torque radial piston motor, the new Stump Ax is compatible with 17- to 35.9-gpm flow ranges.
Liebherr
Available in conventional or unplugged (battery-electric) versions, the LBX 600 carrier machine for slurry wall construction is compact for urban job sites. Standard height is 17.8 metres, but a modular design allows use of an 11-m Low Head boom or the Ultra Low Head boom at just 5.8 m. A slim design and telescoping carriage make the machine easier to transport. It is designed for work with a hydraulic grab and also with a mechanical grab and chisel, thanks to two free-fall winches with a line pull of 300 kN each. Multiple grabs are available for different excavating needs.
The TH 3.6 compact telehandler has a maximum load capacity of 6,613 pounds and a maximum lifting height of 19 feet. It can lift its maximum load to a height of 17.7 feet, and can lift 5,511 pounds to its maximum height. It can lift 2,425 pounds to a horizontal reach of more than 3 metres. A low-level design gives it room to move in tight spaces while retaining ground clearance for uneven terrain. The telehandler reaches a top speed of 21 mph, has four-wheel drive and steering with hydrostatic transmission for stability and maneuverability, and features a compact cab with a new dashboard that optimizes user experience through ergonomic control placement.
The CX50D mini excavator is a 5-metric-ton machine that provides a comfortable work space, including auto climate control with heat and AC, Bluetooth radio, five-way adjustable seat, and a customizable LCD screen. This mini excavator comes with multi-functional hydraulics and a second auxiliary circuit. An optional third auxiliary circuit powers advanced attachments like tiltrotators and grapples. Another optional dedicated circuit is available for mulchers. Users can increase safety and efficiency of material handling with the optional Object Handling Kit that includes check valves on the boom and arm.
TelehandlerPAVING SPECIALIST REALIZES COST, TIME, SAFETY & ENVIRONMENTAL BENEFITS OF USING TOPCON SMOOTHRIDE ON HIGHWAY PROJECTS
BY LARRY TROJAKBanks Construction is no stranger to recognition for its paving excellence. The Charleston, South Carolina, company is a regular presence on the South Carolina Asphalt Paving Association’s (SCAPA) list of award-winning projects and is one of the region’s most in-demand asphalt paving specialists. However, when it was recently lauded for its 2023 performance on a major interstate resurfacing project, it felt particularly good for them, more for the sense of accomplishment it represented than for the accolades. On that project, Banks, never one to balk at new technology, utilized a paving solution that is touted as being “intelligent.” With some key team members somewhat skeptical at the outset, the company nevertheless put the solution to the test on one of Charleston’s highest-profile thoroughfares. By project’s end, they became a true believer in the new paving approach, shared some impressive benefits in cost savings, saw undeniable safety enhancements – and won an award to boot.
The project was a 32-lane/mile resurfacing that included a series of seven bridges and took place on an 8-mile portion of the heavily travelled I-526 loop around Charleston. According to Trey Cox, P.L.S., Banks Construction’s survey manager, even before securing the bid for the job, a serious concern was staring them down.
hance the entire workflow of their asphalt operation, from highway-speed road scanning to variable-depth milling to 3D paving (and more), Banks Construction management felt the solution, called SmoothRide, was the answer they needed.
Cox was initially skeptical about the viability of SmoothRide, specifically its ability to provide a profitable result on their project. But Banks Construction management felt it was the right move to make. With their blessing, Cox and his team set to proving it out.
“We had Justin Thompson, one of Topcon’s intelligent paving specialists, come to our office where we talked a bit about the system, used the Topcon RD-M1 to scan a portion of I-26, and set a time for demonstration,” says Cox. “In typical Banks Construction fashion, we did not hold back. We had 25 trucks lined up, two mills and a full paving crew and I said, ‘Alright, let’s see what happens.’ Even though we did a very basic scanning session and job set-up, it worked to perfection. At that point, I was all in for the 526 job.”
With that peace of mind, Banks Construction went back to the DOT with a bid number which was now substantially lower because of the savings they knew could be realized by streamlining the workflow.
Because the full milling operation can now be done at the same time as the paving, the cost savings are substantial.
Trey Cox, Survey Manager Banks Construction
“We’d done a job similar to this for the DOT a while back and, because of the way we had to do it, it proved a disappointment for everyone involved,” he says. “That was a two-stage milling operation which called for the surface to be milled, then surveyed to get the design needed for correction, then milled again to match that correction. The problem in this part of the country is that, once you mill a surface – even when you micro-mill it – between the moisture and the cold temperatures we can get, the milled surface tends to crumble. That increases the risk of motorist claims, which we always want to avoid. We knew we could not tackle the I-526 job using the same techniques.”
The alternative to which Banks Construction turned was a revolutionary solution from Topcon Positioning Systems they’d seen at CONEXPO-CON/AGG. Because it would en-
“Because the full milling operation can now be done at the same time as the paving, the cost savings are substantial,” says Cox. “You’ve reduced milling time, minimized the need for traffic control trucks, etc. And less time on the interstate reduces our safety exposures. So, we had DOT engineers come down, showed them the technology, and laid out what we planned for the project. One point of contention was that some of the specs called for actual true elevations rather than relative ones. However, with a simple update to SmoothRide’s software, we were able to pull that info directly from either a control file or the Geoid file. They walked away happy knowing they were saving money and we would get the job done quickly.”
While Cox values every facet of the SmoothRide process, he finds particular appeal in the scanning aspect of the solution. It is there, he feels, that Banks Construction has found –and will continue to find – the most benefits moving forward.
“SmoothRide provides what the paving industry has been wanting for years and never had: the ability to see what we are going to get into before getting into it,” he says. “A company like ours can get a milling job or a slope correction project and survey it, giving us a pretty good idea of what’s needed, but we can never really know exactly what is going to happen until we get out there. This technology changes all that. We were able to go in, and once we set up our parameters – max mill of 4 inches, minimum mill of 1 inch – we could go through the design and see areas where we were either going to be deep or ‘daylighting,’ then modify those areas to fix them. It’s just what we need.”
He added that, while SmoothRide has already proven itself as an outstanding milling and paving solution, that hardly scratches the surface of what can be done with it.
THE SAVINGS REALIZED THROUGH THE ELIMINATION OF ONE COMPLETE MILLING RUN ON AN EIGHT-MILE, FOUR-LANE PROJECT CAN BE SUBSTANTIAL.
“With the RD-M1 scanner, which is the initial step in the SmoothRide process, we see a real benefit in scanning roads for as-built information,” he says. “We regularly bid on jobs that were surveyed and designed five or six years ago. Well, in that five or six years, that road’s already been overlaid –maybe a couple times – but needs to be resurveyed because the design says, ‘Match Existing.’ Using the RD-M1 to do that, not only does it eliminate the cost of lane closures, it keeps a survey crew out of the road. The safety factor it provides was almost as important in our decision-making process as streamlining the workflow. At Banks Construction, safety cannot be overstated.”
The savings realized through the elimination of one complete milling run on an eight-mile, four-lane project can be substantial – a fact that was proven out on the I-526 resurfacing. Though exact numbers weren’t readily available, Cox did present some fascinating figures for consideration.
“First and foremost, you have to look at the fact that we cut 20 shifts out of the job by not having to mill ahead of time,” he says. “That’s a significant savings in per night
costs. Being able to gather as-built data while out there rather than at the end of the project was also huge. And there’s simply not a way to put a number on the safety and liability. Unlike the project I mentioned earlier, I don’t believe we had a single claim on this job, which is almost unheard of on an Interstate project. All of that together is the reason our owners believe that the SmoothRide solution was well worth the investment.”
Though it’s sometimes easy to overlook, the reduction in environmental impact that can be realized by streamlining a project’s workflow can be quite compelling. According to Cox, those savings were literally across the board on the I-526 project.
“Each one of the 20 triaxle trucks working for us probably burns 25 gallons of diesel fuel per night – and that was with a shorter discharge run,” he said. “So, that’s easily 10,000 gallons of fuel that wasn’t used – and didn’t create emissions. And I can tell you now that a Wirtgen 220 mill uses its share of diesel as well, which would add to that consumption total. When you can cut days – or shifts – off of a job, the impacts in so many areas can be just staggering.
BANKS CONSTRUCTION’S UTILIZATION OF NEW TECHNOLOGY RESULTED IN SIGNIFICANT SAVINGS TO THE DOT AND MINIMIZED IMPACT TO THE TRAVELLING PUBLIC.
Banks Construction’s SCAPA award cites that, by the time the I-526 Resurfacing Project was completed in October 2023, a total of 42,826 tons of asphalt had been placed over the 8-mile span of the project. Its continuation reads like a laundry list of SmoothRide benefits, saying that the Banks Construction team utilized new technology that allowed for all of this to be performed in one operation, resulting in significant savings to the DOT. In addition, it mentions that the scope change significantly reduced the duration of the project and also eliminated any exposure to a milled surface, both of which minimized the overall impact to the travelling public. The final results were an average rideability improvement of approximately 30 percent.
“What the award doesn’t call it out is the fact that we had to meet some very stringent cross-slope correction specifications – and we did,” says Cox. “I’m extremely proud of the work our team did on the I-526 job and am glad that they were able to share in this award. We, as a company, are also very grateful for the support we get from Randall Brown at Georgia Surveyors Exchange, our Topcon dealer, and can’t say enough about Topcon and the solutions they continue to provide. Performing a job in 300 days – when it was bid for 360 days – significantly enhances the safety of our employees and the travelling public. That’s another reason we’ve partnered with Topcon for some 16 years now.
With the RD-M1 scanner, which is the initial step in the SmoothRide process, we see a real benefit in scanning roads for as-built information.
Trey Cox, Survey Manager Banks Construction
“As to who was the real winner of this award though, I’d have to say it was the Charleston-area residents who travel I-526 regularly – or daily. They’ve gotten something they’ve missed for some time now: a truly smooth ride.”
Backhoe loaders are natural multitaskers, handling a variety of tasks in construction and utility work. A backhoe feature found on many machines outside North America makes these versatile machines a better fit for digging in increasingly tight urban job sites.
When CASE Construction Equipment announced an expansion of its backhoe line with the 580SV, 695SV, and Utility Plus models in 2023, it also included two models featuring side shift booms.
I caught up with George MacIntyre, who has been product manager for backhoe loaders with CASE since 2022, to discuss the new models and the addition of side shift. He says the goal behind the backhoe loader line expansion is to give contractors more choice in machine sizes and features.
“We know the CASE customer is very happy with the backhoes we’ve offered, such as the N Series which we launched around 2010, but we were looking for ways to appeal to customers that have not bought CASE in the past,” MacIntyre says.
Contractors often find themselves in tight spots – working within a road lane next to active traffic, for example, or up against the side of a building. CASE has introduced two backhoe models with side shift to provide options that work for close-quarters digging.
Side shift backhoes are popular in Europe where they are regularly used in narrow streets and alleys. Side shift has historically been less popular in North America, but the benefits
of a machine that can set up and dig quickly in small urban spaces have led CASE to introduce side shift versions of both the 580SV and 695SV.
On centre-pivot models, the backhoe is equipped with outrigger stabilizers that fold out from the sides of the machine to provide a sturdy platform for digging. Side shift machines have vertical stabilizers that move up and down within the footprint of the machine, reducing the overall width and making it easier to operate in tight spaces, MacIntyre explains. Side shift is best for close-in work. For example, digging up against buildings and foundations, as well as trenching.
Once in position, the press of a button in the cab moves the boom from side to side, which allows the operator to precisely position the bucket where it can dig the most efficiently. That might mean digging straight trenches along either side of a buried utility or excavating a rectangle, both of which can be done by shifting the boom, rather than repositioning the machine. This pairs well with CASE ProControl anti-damping, which allows higher precision placement over the trench and reduces spillage from the bucket thanks to smoother movements.
In addition, shifting the boom provides better visibility into the excavation, MacIntyre notes. It also allows the boom to be stowed more closely to the machine for a smaller footprint when roading.
The new models carry a familiar branding: Construction King. CASE previously sold backhoes, tractor loaders, and
SIDE SHIFT GIVES OPERATORS THE ABILITY TO WORK CLOSER TO OBSTACLES WITH BETTER VISIBILITY.
rough-terrain forklifts under the Construction King name starting in the 1960s, and carried on through the 1990s, so the brand has history and name recognition, MacIntyre says. Moving forward, as N Series backhoes are updated, they too will take on the Construction King brand.
The new models carry forward many N Series features, but the 695SV is unique in its design compared to the other machines. It features large, equally sized tires all around and is fitted with four-wheel steering, making it drive much like another construction site stalwart, the wheel loader. In fact, MacIntyre says, it can replace a wheel loader on the job site.
“It has the capabilities of a wheel loader, but the great thing is you have the backhoe on the rear end. So, you have a machine that has the ability to do stockpiling or truck loading, and at the same time you’re able to do trenching work,” MacIntyre says. “From a utility standpoint this will be a great machine for larger projects . . . where you need to move a lot of dirt, whether for backfilling or stockpiling.”
Four-wheel steer on the 695SV adds maneuverability and three different steering styles. Traditional two-wheel front steer is joined by crab steer, allowing the backhoe to move parallel with four tires in the same direction at an angle. In circle steer, the operator is able to reduce the turning radius of the machine by nearly 50 percent, making it more efficient for loading.
The Utility Plus is a backhoe aimed at users who need a basic, high-performance machine. A 74-hp machine with a large cab, good visibility, and easy operation, the Utility Plus provides a base on which buyers can expand through various options if they desire.
The 580SV Construction King centre pivot and Utility Plus
THE 695SV CONSTRUCTION KING FEATURES FOUR EQUALLY SIZED TIRES AND HAS THE STEERING CAPABILITIES OF A WHEEL LOADER.
Side shift has historically been less popular in North America, but the benefits of a machine that can set up and dig quickly in small urban spaces have led CASE to introduce side shift versions of both the 580SV and 695SV.
models have been available since 2023, and are now joined by the 580SV side shift and both versions of the 695SV.
While it may not be a familiar sight on North American job sites yet, the side shift boom is an addition that gives backhoe loaders the ability to take on new roles on various job sites. The Construction King side shift models give buyers one more choice that can make their multi-purpose machine even more versatile. HEG
X4S LINEUP INCLUDES NEW MACHINE SIZES WITH UPDATES THAT AID OPERATION AND PRODUCTIVITY
BY LEE TOOP, EDITORLink-Belt has made machine control readiness a design feature of its newest excavators. The X4S line is technology-ready, making it easier for owners to incorporate machine control into their operation.
Contractors are facing tighter timelines for completing jobs and are being called on to improve productivity. This, combined with the assistance that technology can provide newer operators as experienced ones retire, is driving greater interest in machine control.
Installing machine control on an excavator that isn’t prepped for it can be tedious and expensive. Systems require multiple brackets for sensors, radios, receivers, and other components –plus the wiring to go with it.
Darren Hoskins, manager, product and innovation with LBX Company, told me that Link-Belt has made it easier for users to add machine control to their new excavators by preparing the machines for technology right from the factory, whether that means Link-Belt’s own Precision Grade 2D machine guidance
When we designed the X4S models, we looked at preparing the machine for Precision Grade and combined it with the new monitor and options in the cab for greater operator comfort.
Darren Hoskins Manager, Product and Innovation, LBX Companyand machine control offerings, or third-party systems.
“When we designed the X4S models, we looked at preparing the machine for Precision Grade and combined it with the new monitor and options in the cab for greater operator comfort,” Hoskins says.
Brackets on the bucket dog bone, the boom, and the stick are already welded in place to hold components, reducing costly
control systems.
Inside the cab, an updated 10-inch touchscreen monitor provides operators with the necessary machine control features and settings and can be customized. A new joystick has repro grammable controls to match up with individual preferences and needs.
Machine control, combined with a comfortable and more customizable operator experience, means that owners facing skills shortages can put newer operators into the excavator with good results, Hoskins adds.
Along with making the X4S series ready for machine con trol, Link-Belt has added other new technology. A new feature, Custom Flow Balance, allows the operator to customize the way the hydraulics react from the monitor. The system priori tizes hydraulic flow for specific tasks, improving productivity.
“If the operator is going to be trenching, for example, you can set your flow more to the boom and arm, or if you’re load ing trucks you can prioritize the flow so you have more swing,” Hoskins explains.
A tilt feature allows the controls and seat to angle downward, providing better visibility down into the trench for safer work
around the machine.
Operators can also use Link-Belt’s WAVES, or Wide Angle Visual Enhancement System, which is standard on the X4S excavators, to spot potential danger. “Operators want to see everything they possibly can to improve safety,” Hoskins says. “WAVES gives you a 270-degree view of what’s around you and object detection as well.”
Continuing the technology theme, Link-Belt has added new modems to the X4S series for improved access to its RemoteCare telematics system.
The six models in the X4S series run the gamut from 39,500 to 78,700 pounds in operating weight. The two smallest models, the 170 and 190 X4S, are equipped with Yanmar engines producing 120 hp. The 190 is a new size for Link-Belt and features an upsized undercarriage compared to the 170 for increased lifting and stability. Multiple counterweight options give customers the ability to customize the 170 for their digging needs.
Isuzu engines power the 220, 260, 300, and 355 X4S models, which range from 160 to 205 hp. Added technology features are available on the 220 X4S, including payload, height, and depth alarms, a digital level, and dynamic stability control. The 355 X4S is Link-Belt’s largest minimum swing radius machine.
All of the X4S machines are built with durability in mind. High-quality metals, from the undercarriage to the sheet metal, are used to ensure the machines are capable of operating in rugged conditions.
With a year of operation since release, the X4S series has received good reviews from buyers. Hoskins says that customers report better fuel consumption and productivity, as well as satisfaction with the machines’ balance and digging power.
“Everything we’re hearing out there, around the Precision Grade technology, the mountings for machine control systems – it’s all been very positive.” HEG
1CASE’s 651G wheel loader takes on challenging jobs with breakout force of nearly 24,000 pounds and lifting capacity of more than 16,000 pounds. A large hydraulic pump helps speed up cycle times, while a curved bucket provides better material retention. The loader is designed with a higher hinge pin for better dump clearance. In the cab, a touchscreen display and adjustable, intuitive electro-hydraulic controls make setting boom and bucket responsiveness for each operator’s needs easier. An integrated on-board scale allows for weighing and tracking of material while working.
John Deere says that the 444 G-Tier is an economically priced, reliable wheel loader with similar productivity to other models in its size class. It can be equipped with optional high-lift, expanding its reach. The 444 G-Tier can work with a variety of attachments, making it suitable for multiple tasks and applications. The ergonomic cab has adjustable controls, added floor storage space, and a joystick with integrated forward, neutral, and reverse controls for easy operation. A stacked cooling package can be set to reverse at regular intervals, reducing maintenance. An optional debris package also helps cut downtime.
3
Volvo has upgraded the L110H and L120H mid-size wheel loaders with new D8M 8-litre engines producing 256 and 272 horsepower respectively. The D8M automatically regenerates while working, a technology found on Volvo’s larger wheel loaders. Upgraded electronics include a new ignition strategy that powers the machine without use of a ground-level main switch. These loaders will have the new generation of Volvo Co-Pilot tablet. The larger tablet displays Load Assist applications including standard on-board weighing, operator coaching, and tire pressure monitoring. Bucket sizes run from 3.2 to 12.4 cubic yards.
CLEAR BRUSH, GRADE, MOVE MATERIALS & MORE WITH ONE MACHINE
BY KAITLYN TILL, EDITOR IN CHIEFa vertical lift configuration. In the past, radial lift machines
KUBOTA SVL75-3 COMPACT TRACK LOADER WITH TRENCHER.
COMPACT TRACK LOADERS ARE READY TO REMOVE BRUSH, UNLOAD AND LOAD MATERIALS, GRADE, CLEAR SNOW, AND MORE.
offered more breakout force in ground engaging applications, but Gardner says that for larger machines the height provided by a vertical lift configuration is essential and advances in engineering have closed the gap between radial and vertical machines in breakout force.
The footprint that you have to move those materials in could matter as well. Often the length of the machine is overlooked when selecting a CTL for size, says Gardner. But if you’re doing a lot of spinning, the length of the CTL could matter, and he notes that Kubota has customers who choose a smaller machine, even if its length is shorter by only three inches, because they’re doing a lot of turning and those three inches make a big difference.
CTLs can be outfitted with a variety of track widths as well. While a wider track will offer greater flotation, if your CTL is going to be used in the winter to clean up snow on the job site, you will want narrower tracks to increase the ground pressure for better pushing power and traction.
The acquisition of new attachments can save you time and diversify the capability of your CTL, but proper care is essential, not only for ensuring the longevity of your investment, but also the safety of your operators and other ground crew on the job site. These maintenance tips can help you get the most out of your attachments while avoiding downtime and promoting job site safety.
Look for cracks in attachment frames or worn out teeth on buckets
Motor graders and dozers are too big for many grading applications, but a CTL can come into a job site, such as a new housing development, with a box blade and grading system to get that work done.
If you’re grading for a long pathway a lot of material can build up. Smaller horsepower CTLs will have less power to push all that material than their higher horsepower counterparts – the operator will have to feather the material out more.
“A 65-hp machine might only be able to handle anywhere from a 72- to 84-inch-width box blade, while a 95-hp machine can handle an 8-foot-wide box blade. Even though you’re doing fine grading, the 65 just doesn’t have the power to keep going,” says Gardner.
However, he adds that a lot of customers want to avoid larger engines that need diesel exhaust fluid and opt to buy machines that are 75 hp or under. “A lot of people went with the SVL 75 instead of the 97 because they didn’t want to have to add diesel exhaust fluid, so they gave up more horsepower for that reason,” Gardner says.
But there’s another tradeoff if you select the smaller machine. “A 75-hp machine won’t run a 40-gpm attachment,” warns Gardner. “There’s a formula where horsepower and flow gives you the output of what horsepower is left. So if you’re running 40 gpm and you have a 95-hp machine, you’re not left with much horsepower because you’re using most of that horsepower to run the attachment.”
Higher horsepower is essential if your machine is going to be clearing brush or snow with powered attachments such as mulchers and snowblowers.
Gardner says you can prolong your bucket life by replacing the cutting edge more, and damaged attachments are dangerous on the job site. If your pallet forks are damaged, for example, and you drop a load, workers on the ground can be seriously injured. Operators should take a few seconds to visually inspect attachments before starting work – it’s a small task for essential peace of mind.
Any powered attachment with moving parts should be greased on a regular basis. This will significantly increase the life of your attachment.
Visually check your hydraulic lines. Broken lines can put the attachment out of commission, but more importantly are very dangerous on the job site. If a line bursts during operation, hot hydraulic fluid can spray on workers, so line inspection should always be taken seriously.
Operators need to know their hydraulic attachments. Gardner says that Kubota’s high-flow machines are very popular, but there aren’t too many high-flow attachments. Operators need to know which of their hydraulic attachments require high-flow and which ones require standard flow. It is essential that high-flow hydraulics aren’t used with the standard flow attachments – the attachment can break and require a repair.
CTLs working in land clearing and site prep applications can be outfitted with forestry attachments, pallet forks, ground clean-up tools, grading attachments, and more. Choosing the right hydraulics option for the attachments that you want to use can make a big difference to that attachment’s productivity.
There are two hydraulic flow configurations to choose from when selecting a CTL: open centre and closed centre hydrau-
lics. Gardner says that simultaneous function is better on machines with closed centre hydraulics, as the loader arms have their own circuit. On a closed centre machine, the attachment and the arms use the same circuit which prioritizes loader arms, then the bucket, then auxiliary functions.
To demonstrate the advantage of closed centre hydraulics, Gardner offers up the example of a mulcher – an attachment that is going to be functioning as the operator moves the loader arms up and down. The operator is going to have much better function if that machine has closed centre hydraulics. Open centre will work, but it won’t be as efficient.
Closed centre hydraulics also give the operator more flexibility for adjusting the attachment. On a machine with open centre hydraulics, the options are either high flow or standard flow. With closed centre hydraulics, the operator can adjust the machine hydraulics to match the attachment flow for optimal performance of that attachment.
Bigger CTLs tend to be configured with closed centre hydraulics, but Gardner adds that some smaller machines are starting to get them too.
A box blade with grade control gives a CTL precision capability
The range of attachments for use in site preparation and land clearing is extensive, but there’s one in particular that Gardner is excited about – pairing a box blade attachment with grade control technology. He doesn’t believe that this attachment/technology is given enough consideration by CTL owners. Motor graders and dozers are too big for many grading applications, but a CTL can come into a job site, such as a new housing development, with a box blade and grading system to get that work done. And, as housing developments in urban areas get tighter, Gardner expects contractors will take more advantage of their CTLs’ grading capability.
Kubota Canada offers the BB30 Series box blades for skid-steer and compact track loaders, which is compatible with third party laser/2D or GPS/3D control systems.
Kubota Canada offers the Trimble Earthworks GO! attachment system for high-accuracy 2D grading that improves operator performance and reduces rework. The operator just brings their own device, iOS or Android, to interface with the Trimble system in the cab.
“I’m a firm believer in grade control and how it can take that novice operator and make them an expert. In the past, grade control was so expensive and it was either the price of the machine or three-quarters the price of the machine and people couldn’t make that justification,” Gardner says. “You don’t need the 3D systems to build roads and housing developments, and to do tennis courts, sports facilities, and pathways all you need is 2D.” HEG
Take a Volvo L180H wheel loader, give it bigger tires, a longer boom, and more counterweight, and what do you get? A dedicated machine that can turn truck loading around faster for aggregate operations.
The L180 3-Pass Rehandler is equipped with 875/65 R29 tires, normally used on larger Volvo loaders, and a long boom plus a rehandling counterweight. The result is a loader that has a higher tipping load, longer reach, and the capability to load a truck in three passes.
Larger tires are more fuel efficient, improve lateral traction and flotation, and improve stability. They are more resistant to cut and impact damage. With the long boom in place, the adapted machine has an additional 675 lb.-ft. of breakout force and two
more feet of dump clearance. The wheel loader can stay farther from the truck while still dumping into the centre to avoid too much pileup at the side which can become spilled material. Cycle
times are improved by the high reach since the bucket doesn’t need to roll back before moving away from the truck. A longer reach cuts down wheel spin and damage caused when driving into
the less stable material at the edge of the pile. Adding the rehandling counterweight allows for a bucket 0.25 cubic yards larger than on the standard L180H. Four different buckets are available.
CDE SmartTech is a performance app that connects with plants to provide an inside look at operations and maintenance needs. Here are six ways that this app works with users, plants, and CDE experts:
Real-time data captured by sensors on the plant is analyzed to keep track of overall health and note any trends that indicate potential issues.
RubbleCrusher’s new compact screen allows for screening of material on site to complement its tracked mobile jaw crusher. The RSC48T is just under 8,000 pounds in weight but has a large, 4-foot by 8-foot top deck and 4-foot by 6-foot bottom deck. A good choice for hard-to-access areas due to its compact size, the RSC48T can be fed directly with an excavator or skid steer and can produce up to three material sizes.
Quick to deploy, the RC150T track-mounted jaw crusher is designed for on-site recycling of C&D waste material which can cut costs associated with material removal or new aggregate purchases.
The RC150T also weighs in at just under 8,000 pounds and can be easily transported between job sites, reducing hauling costs.
Flow rates and the tonnage of material moving through the plant are tracked and reviewed. This information can be used to optimize operations.
Use of water, energy, and chemicals is tracked. This pro vides opportunities to review and adjust for more efficient operation.
SmartTech data is analyzed by CDE process engineers who then provide details to the customer and CDE CustomCare team, enabling proactive maintenance and plant optimization.
An interactive 3D view of the user’s plant expands to provide a view of individual parts – right down to the smallest nuts and bolts. Users can identify the parts they need for a specific repair or maintenance task and order directly from the app.
Checklists created and assigned through the app can be used to track maintenance activities. As work is completed, users can input notes and photographs, generate reports, and log any issues.
Montabert Variable-Speed Breakers handle harsh conditions, sensing changes in material hardness and adjusting impact energy and striking rate as needed. This approach cuts down on blank firing and, depending on the application, can increase productivity. Variable-speed technology also reduces the amount of energy transferring back to the machine and breaker, which saves maintenance and wear.
Premium Heavy Breakers are available for carriers of 18 to 120 tons, and along with variable-speed technology have features like an energy chamber that acts as a shock absorber to provide consistent energy to the breaker, a progressive start system, and automatic lubrication. Heavy-Range 2-Speed breakers fit on 20- to 80-ton excavators and have a
simpler design than the premium line, reducing costs but maintaining productivity.
Montabert breakers can work in tandem with TRA-
The Bridgestone V-STEEL Z TRACTION (VZT) is a 25-inch construction tire for loader and grader applications, which Bridgestone says is designed for longer tire life and reduced cost. Advanced tread compounds improve heat, cut, and tear, adding up to 15 percent total tire life compared to previous products. A new tread pattern offers improved traction, with low-angle centre block and self-cleaning wide shoulder groovers for wet, muddy surfaces as well as challenging terrain. The sidewall shape is optimized, and protectors help minimize damage, defending against tears and cuts.
MAC stationary boom systems that are available with horizontal reach from 14 to 65 feet and can handle hammers from 1,098 to 9,920 pounds.
The Nordberg HP350e cone crusher has joined Metso’s Nordberg HPe crusher series, which are engineered to meet evolving and increasing performance needs in aggregates and mining.
Performance is improved up to 10 percent in secondary and tertiary applications due to enhanced kinematics and more efficient chambers, Metso states.
It has no backing liners for quick, easier, and safer liner changes, and a head anti-spin brake extends liner wear life. Optional ring bounce monitoring provides active overload protection, and a new feed cone lifting tool makes for safe lifting and handling.
Three alternative kinematics are available to choose from, as are alternative speeds. Ten application-specific no-backing chamber designs can be selected depending on need for secondary, tertiary, and quaternary stages. Most parts are common with the previous HP300 and others are either interchangeable or upgradeable. Metso is making upgrade kits available for owners of HP300 crushers to access new features economically.
Rubble Master’s new RM J110X jaw crusher is the heaviest in the industry, according to the company, and is capable of handling hard rock or heavily reinforced concrete. With a 44-inch by 28-inch opening and a 10 percent deeper jaw box combined with high-efficiency drive and a range of other updates, the RM J110X has plenty of crushing capacity.
The RM J110X processes 496 tph. In diesel-hydraulic configuration it is powered by a 335-hp Cat Tier 4 Final engine paired with hydraulic degassing and return technology intended to extend the lifetime of the hydraulic oil. The crusher is available with an optional diesel-electric drive.
An 11-inch information display provides clear information about the machine’s condition, allowing operators to make adjustments as required. A remote radio control lets operators start, stop, or adjust the feeder speed, adjust the closed side setting while crushing, and lower the main conveyor.
Liebherr’s improved LICCON3 control system is at the centre of updates to the LTM series of mobile cranes.
The LTM 1300-6.4 is the latest crane to receive the new system, along with new cabs and components that tie into the controls.
The 300-tonne, six-axle 1300-6.4 has a 90-metre telescopic boom and is designed to be fast-erecting with high capacity. It retains the same performance capabilities as its predecessor, the 1300-6.3.
LICCON3 is the third generation of the LICCON (Liebherr Computed Control) control system. It includes entirely new software and programming language to make it easier to use and understand. The update includes a faster data bus, significantly more memory, and higher computing power. Operators who are familiar with the previous control system will be able to pick up the new one quickly.
On the hardware side, the 1300-6.4 includes the BTT mobile
operating and display unit, with a touchscreen function that makes it easy and comfortable to operate, along with simplified displays. LICCON3 cranes are also prepared for fleet management and telemetry. In the future, Liebherr says contractors will be able to use the MyLiebherr customer portal to view data.
A new driver’s cabin includes a multifunction steering wheel, side roller blind on the driver’s door, improved instruments and modules, and new displays. Liebherr has also updated the heating and air conditioning systems in both the driver’s and operator’s cab. Sun sensors detect strong sunshine and adjust the system to match.
Lighting packages for the crane cab, superstructure, rear of the vehicle, front headlights, telescopic boom, and lattice fly jib have been optimized and can be used with LEDs for better performance and longer life.
The LTM 1300-6.4 is currently unavailable in Canada, but Liebherr–Canada plans to offer it in the future.
Mammoet is testing a new safety system to protect the operators of mobile cranes and the road users around them. Working with Rietveld, a specialist in fleet management, vehicle, and machine safety systems, Mammoet has combined three different safety technologies for testing on a Liebherr LTM 1070-4.2 70-tonne mobile crane.
“By combining these three systems, Mammoet will improve safety, minimize accidents and damage, and give greater confidence to crane operators to create safer working environments,” says Ferdi Kivanc, project coordinator EMD at Mammoet. “We see this as a comprehensive system that will not only enhance crane safety, but also operator training in the future. Initial tests are promising, and I am very proud of the results.”
Rietvelt’s OmniVue uses a combination of cameras on the crane’s chassis for 360-degree real-time views. The driver can take advantage of first- and third-person images of the vehicle, enabling them to see what pedestrians and other road users can see.
A second level of technology uses sensors that detect people and obstacles within a specific adjustable radius around the crane. If a hazard is detected, an acoustic signal alerts the driver, and an LED warning panel indicates the section of the crane where the motion was detected.
Finally, a visual indicator, the “halo,” draws a light boundary on the floor around the crane, which provides a clear indicator
of the safe zone. This helps protect workers around the machine, especially on sites where hearing protection is required. The boundary can be switched off and on manually, and it shuts off automatically when a certain speed is reached.
THE GROUND BEARING CAPACITY IS DEFINED BY THE SUPPORTING SURFACE’S ABILITY TO WITHSTAND THE FORCES THAT THE EQUIPMENT WILL APPLY.
Understanding the ground conditions of the supporting surface before setting up a crane or other equipment with outriggers is essential. This includes a combination of ground bearing capacity and an understanding of suitable set-up areas, limitations, and hazards that would affect the support of the equipment into the job site, during operations, and out of the job site.
The ground bearing capacity is defined by the supporting surface’s ability to withstand the forces that the equipment will apply. The responsibility for the ground and its capability and suitability to support equipment is assigned to the controlling entity for the project by OSHA 1926.1402(c)(1).* If there is no controlling entity for the project, the responsibility for providing adequate ground conditions rests on the employer that has authority at the site to make or arrange for ground preparations. Whether you are the contractor responsible for the site or the operator communicating with the controlling entity about ground conditions and set-up needs, understanding the factors that affect safe equipment set-up is essential for safe and successful operations.
The controlling entity must supply the contractor with the permissible ground-bearing pressure for every set-up location. If any uncertainties arise, it’s important for contractors to initiate a dialogue about the permissible ground-bearing pressure and to understand the extent of the controlling entity’s knowledge and acknowledgment of their duties. Should the controlling entity be unfamiliar with its obligations, the contractor is advised to direct them toward the relevant regulations for clarification.
Equipment operators should perform their own visual site evaluations. Visual inspections should be focused on any presence of standing water, excavations, and indicators of underground structures such as manhole lids, utility access points, and catch basins. The intent is to ensure that all observable conditions match the information given by the controlling entity. If inconsistencies or contradictions are found, they should be immediately discussed and reconciled before operations begin.
To aid in these important communications about ground conditions, here are two of the most important terms to know. Ultimate Ground Bearing Capacity is the maximum amount of vertical pressure the ground can withstand before failing. This value must be determined by a civil engineer, who is trained and experienced in the science of determining the strength and stiffness of the ground.
*Canadians should refer to OHS Regulations, CSA Standards for Crane Safety, and provincial and territorial legislation.
Equipment operators should perform their own visual site evaluations. Visual inspections should be focused on any presence of standing water, excavations, and indicators of underground structures such as manhole lids, utility access points, and catch basins.
Allowable Ground Bearing Pressure (AGBP) is to be specified by the controlling entity to help ensure pressures imposed on the ground stay below the levels the ground is able to support. The AGBP is calculated by dividing the Ultimate Ground Bearing Capacity by a factor of safety. The generally accepted factor of safety for temporary loading is two.
When planning to operate equipment at a site, knowing just how much weight the ground can support can be a challenging question to answer. Methods used to identify and understand the ground bearing capacity include a geotechnical report, previously documented information, and in-the-field testing and observations. A report from a geotechnical engineer will provide ground classification information and provide detailed ultimate ground bearing capacity data on the site.
In the field, physical assessments, such as plate or roll tests, and performing a visual inspection can be helpful to assess the current state. However, they should only serve as a substitute of last resort. These investigations should help operators determine if the ground should be improved, if the equipment needs to be relocated, and what type of supporting materials, such as outrigger pads, mats, dunnage, or cribbing, is needed.
DICA offers a resource page, Determining Your Ground Bearing Capacity (dicausa.com/soil-bearing-capacity), to help clarify some of the terms discussed in this article. A Ground Bearing Capacity Chart is included to aid in the difference between the ultimate ground bearing capacity of the supporting surface and the allowable ground bearing capacity that is used for operational purposes.
UNDERSTANDING AND PREPARING FOR GROUND CONDITIONS IS NOT JUST A SAFETY PROCEDURE, IT’S A FOUNDATIONAL ASPECT OF SUCCESSFUL EQUIPMENT OPERATION.
There are many choices of supporting materials. Fundamentally the basic area sizing evaluation is the same for all. To determine the minimum pad area, you must know the outrigger load, also known as the Outrigger Reaction Force, and the Allowable Ground Bearing Pressure (AGBP).
The Outrigger Reaction Force is the amount of load a crane will apply to the supporting surface during operations (typically expressed as a unit of weight, such as pounds). To calculate the supporting material minimum bearing area, divide the Outrigger Reaction Force (ORF) by the Allowable Ground Bearing Pressure (AGBP); (ORF/ABGP = Pad Area).
Equipment Outrigger Reaction Force = 100,000 lbs.
Allowable Ground Bearing Pressure = 3,500 psf.
100,000 lbs / 3,500 psf = 29 sf
In this example, supporting material with the strength to withstand the imposed 100,000 lbs. outrigger reaction force and the stiffness to distribute the load over a minimum bearing area of 29 sf. is required. Therefore, an outrigger pad such as a 6- x 5-foot (30 sf) is a viable solution.
Additional information on this topic can be found on the resource page dicausa.com/stiffness-vs-strength.
Understanding and preparing for ground conditions is not just a safety procedure, it’s a foundational aspect of successful equipment operation. Contractors and equipment operators alike must ensure that the ground can sustain the forces exerted by heavy machinery. Initiating clear communication with the controlling entity about ground-bearing pressures and set-up locations is imperative.
Visual site inspections by operators act as a final, crucial checkpoint to confirm site conditions align with reported data, ensuring a secure operational environment. With the availability of resources like DICA’s Ground Bearing Capacity Chart, determining the appropriate supporting materials such as outrigger pads becomes a precise, calculated decision – not guesswork. Adhering to these practices will not only uphold safety standards but also enhance the efficiency and reliability of project operations.
KRIS KOBERG is the CEO of DICA.Contractors are under pressure to tackle the rising demand for underground construction projects amidst a slew of challenges such as compact job sites, complex underground networks, and a persistent labour shortage. Ensuring operators are well versed in their equipment is more crucial than ever for safe and efficient project completion.
Original equipment manufacturers (OEMs) know this and are taking actions like developing innovative and adaptable training solutions that engage the next generation of workers. With flexible training options already in place – such as online training platforms, simulators, instructor-led courses, and hands-on job training – OEMs are turning to technology to help prepare operators for the demands of the job site. One technology in particular is bringing training into a new era: virtual reality (VR).
VR provides an innovative way to engage and upskill new workers. By simulating 3D underground environments, VR allows trainees to gain hands-on experience safely and efficiently. Using VR, trainees can apply textbook knowledge in lifelike scenarios before ever stepping foot on a job site and operating expensive and often intricate machinery.
From operating HDD equipment to navigating complex job site conditions, operators can use VR to gain the skills, muscle memory, and confidence they need for real-world jobs.
OEMs like Ditch Witch and Subsite have been using simulation in training for years. For example, Ditch Witch has a 2D HDD simulator curriculum that is divided into three progressive lessons. The first lesson introduces the basics of operating a directional drill in an open space, focusing on pipe handling and drilling. The second lesson focuses on navigating tighter spaces in residential areas, emphasizing utility awareness. The third lesson simulates drilling under a bustling four-lane highway and teaches trainees back-reaming best practices.
However, the underground construction industry, with its diverse skill requirements and demanding backlog of work, today needs a more comprehensive training solution that equips contractors with the necessary expertise to operate a safe job site.
Operating HDD equipment and their guidance systems can be daunting and intimidating for beginners. Incorporating VR into training adds a heightened sense of realism and immer-
VR is not a catch-all solution. Instructor-led courses bridge the gap between virtual learning and practical application, helping get VR-trained operators ready for the job site.
sion, allowing trainees to practice complex tasks while eliminating the fear of costly mistakes. This can save contractors from potentially significant equipment downtime and project delays. And it can give workers a broad range of machine and tool experiences that they would typically encounter day-to-day on the job site.
Additionally, with safety top of mind, VR training alleviates worries about injuries or damaging valuable machinery and existing underground infrastructure during initial attempts. In the virtual world, mistakes become learning opportunities instead of costly equipment damage or job site catastrophes. Trainees can hone their skills in precise machine operation and techniques within a safe, simulated environment before they transition to real-world tasks.
VR gives the underground construction industry a powerful tool to engage with and appeal to the highly sought after next generation of workers.
Immersive and interactive, VR resonates with young professionals who grew up in a world of video games, including VR video games. The technology also offers digital-first experiences that appeal to tech-savvy professionals. This modern approach to training can help attract new operators to help fill the talent pipeline.
Gamification transforms training from routine to revolutionary. Trainees are immersed in 3D underground environments
where they can see firsthand the interplay of utilities and drilling operations. Through VR training with Subsite’s Marksman Guidance System, operators can virtually see beneath the ground to assist navigation through utility-laden areas in today’s neighborhood rights of way. This not only equips them with practical skills but also adds fun into their learning journey.
However, VR is not a catch-all solution. Instructor-led courses bridge the gap between virtual learning and practical application, helping get VR-trained operators ready for the job site. The optimal use of VR lies within a blended training approach, which complements traditional methods, preparing a new generation of professionals for the demands of the real world.
Additionally, VR is not just for the novice. Ongoing employee development also benefits from VR’s versatility. Seasoned operators can leverage VR to refresh their skills or cross-train on new equipment, maximizing job site efficiencies.
In the virtual world, mistakes become learning opportunities instead of costly equipment damage or job site catastrophes.
Ditch Witch introduced its latest training platform for HDD guidance in 2022 and has developed multiple lessons for it. Designed in a trailer to make VR training accessible and mobile for the OEM, the lessons mimic the hands-on work of underground construction. The Subsite Marksman VR lessons coupled with Ditch Witch's HDD simulator — featuring actual drilling console controls — provide operators with a diverse skill set.
While drilling is traditionally easier to teach, tracking the drill head and helping guide the driller presents a unique set of challenges. The Subsite Marksman VR tackles this by visualizing underground utilities and equipment working in tandem, enhancing training effectiveness.
HDD guidance training is split into two lessons: the first covers equipment set-up and calibration of a tracker, which has proven to be one of the most difficult job site tasks. The second focuses on beacon tracking and its critical role in underground construction and directional drilling. An upcoming third lesson will teach operators how to run a drill and tracker simultaneously, mimicking a real-world application to set up trainees for success.
The training blends text instruction and audio instructions and is currently available in Spanish, English, and German. Operators can learn more about these trainings by reaching out to their local Ditch Witch dealer.
Today, VR is bringing tremendous value to underground construction by serving as a compelling recruitment tool and a means for operators to build and refine their skills. Still, this is only scratching the surface in terms of what the technology can do.
OEMs will continue to broaden VR’s applications, integrating diverse equipment to streamline training, attract new talent, and improve job site safety. As VR becomes more prevalent, it has the potential to bridge the skills gap, mitigate workforce shortages, and shape the underground construction industry of the future.
NICHOLAS SMITH is a product trainer with Ditch Witch.
VR PROVIDES AN INNOVATIVE WAY TO ENGAGE AND UPSKILL NEW WORKERS.Bteries, Bobcat says its TL25.60e telehandler with a 2.5-tonne ROC delivers performance equivalent to its diesel counterpart. Three separated electric motors are designed to maximize efficiency, a hydrostatic transmission boosts performance, and maximum travel speed is 25 kph. This concept delivers low noise levels, minimal operating costs, and compact versatility which makes it suited to work on confined job sites and in urban centres.
Bobcat has been demonstrating the machine with customers to gain feedback and is already working on the next generation of its design, but don’t expect to see an electric telehandler from Bobcat available to buy just yet. There are still many
of zero-emission machines are also a barrier to adoption in Europe and North America.
Serge Boyer, product manager for telehandlers, Bobcat EMEA, was excited to share the new concept on the show floor.
“We are building for the future,” Boyer says. “We know this is going to be the next generation and the next trend but it will take time to ramp up.”
For now, Bobcat will learn from this machine and get input from customers and dealers to better understand the market.
“The key word for me is agility,” says Boyer. “We want to be an agile company. We want to be able to build progressively by iterations until we get to the best we can.”
Intermat 2024 was heavily focused on decarbonization efforts and electric equipment on the show floor was just one element of industry’s focus on reducing carbon emissions and promoting sustainable construction solutions. The 2024 Intermat Innovation Awards showcased a range of sustainable construction solutions promoting emissions reduction, recycling, and safety.
In the category of Earthmoving, Demolition and Transport, the Gold medal winner was Dynaset for its HRVB hydraulic recycling vacuum bucket, an all-in-one attachment for gathering, recycling, and sorting material and scrap from construction sites, parks, roads, and railways.
BOMAG won a Gold award in the Roads, Materials and Foundation Industries category for Emergency Brake Assist which prevents collisions while protecting the asphalt surface from damage. Lidar technology on the roller continuously scans the surroundings to detect people and objects and applies the brakes early to prevent accidents and protect the surface.
In the New Technologies category, the Gold medal winner was Tenstar Technologies for its VTS – Virtual Training Space which enables users to train together in a virtual sandbox environment for construction, agriculture, and the transport sector.
The Gold medal winner in the category of Low Carbon and Energy Transition was Moog Construction for its electric TerraTech Ecosystem, which combines control software; hardware, including electric cylinders, vehicle control modules, motors, controllers, and energy management; and digital insight via IoT connectivity. This system enables OEMs to design electric equipment that is as efficient as equivalent diesel machines.
tion companies to postpone the acquisition of new equipment and continue “making the best of it” with older existing machinery.
Equipment procurement is critical for construction projects but is a costly proposition – and even more so without credit – making it difficult for businesses to find the necessary funds without straining their budgets or disrupting cash flow.
This is where equipment leasing, as part of a well-executed construction equipment acquisition plan, can increase profitability, accommodate growth, and reduce the risks of maintaining outdated assets.
Whether you’re broadening the scope of your existing company or contracting a major project, having the right equipment to get the job done is a necessity. However, purchasing equipment outright is not always the best option.
Purchasing your construction equipment comes at a much higher upfront cost, and the ownership of equipment can be a significant liability for your company. This could be worthwhile if your company uses the equipment regularly.
Many companies choose to finance equipment by offering a down payment and monthly payments (including interest) until it is paid off. Equipment ownership offers financial advantages, such as tax benefits/tax write-offs and asset value. While these benefits are significant, the ultimate question to ask before purchasing is: Will I get my money’s worth?
Other advantages of purchasing equipment include the ability to customize the equipment to your needs, no usage re-
strictions, adding value to your company with a new asset, and generally being more cost-effective in the long run.
However, there are also disadvantages of purchasing equipment that must be considered. These include paying a high initial cost, even when financing, being responsible for maintenance and associated costs, acquiring some depreciation costs, paying monthly interest on your loan, getting stuck with outdated equipment that still needs paying off, being responsible for equipment storage and transport, and having to pay equipment insurance costs.
Alternatively, leasing enables equipment acquisition with little or no money, making replacing outdated equipment more manageable and cost-effective.
A lease is a contractual agreement between two parties where one owns the property or equipment and rents it to the other for an extended period in exchange for periodic payments. A lessor would rent construction equipment to the lessee for a set time while the latter makes payments throughout the lease term. Leasing equipment can be ideal for business owners who are not yet ready to purchase equipment but need the machine for longer than a few months.
Leasing equipment is dissimilar to renting because it typically covers a longer period of time, such as 24–48 months. A lease also differs from renting because there is more flexibility in options outside of returning the equipment at the end of the contract.
When a lease expires, you can choose to return the equipment, renew the lease, or, in some cases, purchase the equipment outright. The benefits of leasing equipment include avoiding the upfront cost of a down payment, the option to buy if you like the model, the ability to regularly upgrade your equipment at the end of each contract, and reduced maintenance costs. You also have the option to extend your contract, if desired.
Leasing rather than buying equipment can offer some compelling benefits for businesses. By choosing to lease, you don’t have to make a cash purchase, as 100 percent of the costs are
Plus, you can spread the sales tax (GST, HST, and/or PST) out over your lease term, allowing you to apply tax write-offs over several years.
Financing is a necessity, particularly for enterprisegrade production-class equipment. As the top five banks restrict their lending, businesses must find a way to sustain and grow; this is where equipment leasing can be a timely and savvy strategy.
covered and no down payment is required. This can help preserve your business’ credit line, allowing you to borrow money for other business needs.
Another advantage of leasing is that it allows you to bundle soft costs, such as engineering, software, freight, installation, and service, into one unified payment. In this way, you don’t have to make expensive up-front investments, sparing business cash reserves.
With leasing you avoid large upfront costs and instead pay for the equipment as you benefit from its use. This means your equipment can be used to start generating income for your business right away – often greater than the cash outlay for your lease payment. Additionally, lease payments can be lower than traditional debt payments or direct cash outlay, which can increase your purchasing power.
Leasing also offers tax benefits, as your lease payments are an expense that can be used as a write-off on your financials.
Finally, leasing offers super flexible terms, which means that your lease can accommodate your business’s unique circumstances. For example, you may be able to get flexible payment terms for seasonal businesses, skip payments, or stick with standard low monthly payments. A well-structured lease should align with current needs and budgets while preparing for future upgrades and business fluctuations.
To properly secure your business’s future, you must focus on where your company is headed and ask: Have I secured contracts? What does my work-in-progress report look like? Have I budgeted for income projections based on work I’ve secured for the coming year?
Acquiring the right equipment at the right price enables businesses to take on more significant projects and build a solid foundation for future expansion – crucial in a challenging economy.
Financing is a necessity, particularly for enterprise-grade production-class equipment. As the top five banks restrict their lending, businesses must find a way to sustain and grow; this is where equipment leasing can be a timely and savvy strategy.
Given Canada’s tightened lending environment, it’s prudent to consider alternative financing sources such as leasing. Short-term equipment leasing conserves capital and provides 100 percent financing with no down payment required. It is a hassle-free financing option for specialized industries that are unable to secure flexible funding through traditional lenders.
NELSON ABELHA is the regional vice president of First Financial Canadian Leasing.
BUXTON, UK | JUNE 25 – 27
Set in a former working quarry, aggregates professionals visit Hillhead for live demonstrations and displays of new crushing and screening equipment. Demos focus on working areas including Quarry Face, Rock Processing, and Recycling. hillhead.com
19 – 21
Held every four years, DEMO International is a unique event that takes place on an active forestry site near Ottawa/Gatineau. Attendees can get up close to see the latest tools for forestry in a working environment. demointernational.com
VEGAS, NV | SEPT. 24 – 26
MINEXPO takes place every four years and is hosted by the National Mining Association in Las Vegas. It draws members of the mining sector from around the world to learn more about solutions and products for safety, drilling, engineering, and more. minexpo.com
LAS VEGAS, NV | NOV. 11 – 13 TRIMBLE.COM/EN/OUR-COMPANY/EVENTS/ DIMENSIONS/OVERVIEW
LAS VEGAS, NV | JAN. 21 – 23, 2025 WORLDOFCONCRETE.COM
First Liebherr mining excavator in eastern Canada goes to work at Quebec lithium mine
Close quarters and tight timing no challenge for Wirtgen slipform paver on interstate project
Watch Teleo autonomous equipment clear land for a new community
iSlip allows more accurate, intelligent placement of concrete for your paving applications. With remote access, machine monitoring capabilities and so much more. The iSlip Control System sets a new standard for automated concrete placement.
Curb & Gutter | Sidewalk | Recreational Trails | Special Projects
No matter how challenging your needs, BKT is with you offering a wide range of OTR tires specifically designed for the toughest operating conditions: from mining to construction sites.
Sturdy and resistant, reliable and safe, able to combine comfort and high performance. BKT is with you, even when work gets tough.
GOMACO offers the full range of concrete slipform pavers, curb and gutter machines, trimmers, placer/spreaders, texture/cure machines and bridge/canal finishing equipment. GOMACO equipment features our exclusive and proprietary G+® control system, created in-house by our software engineers from the wants and needs of contractors paving in the field. At the heart of GOMACO equipment is our passion for concrete and our commitment to our customers. We look forward to visiting with you about your upcoming paving projects and your concrete paving equipment needs. Our worldwide distributor network and our corporate team always stand ready to serve and assist you.