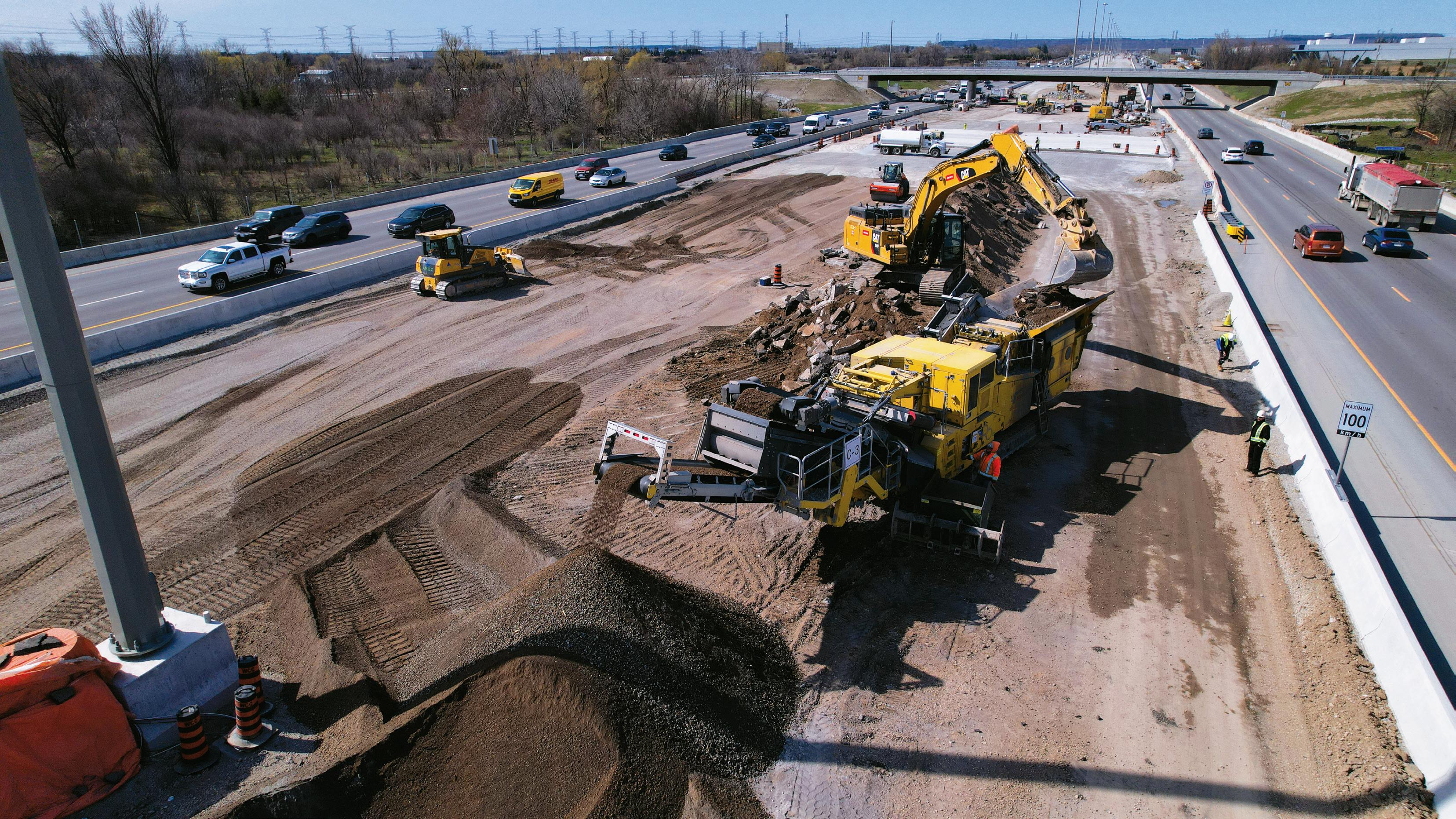
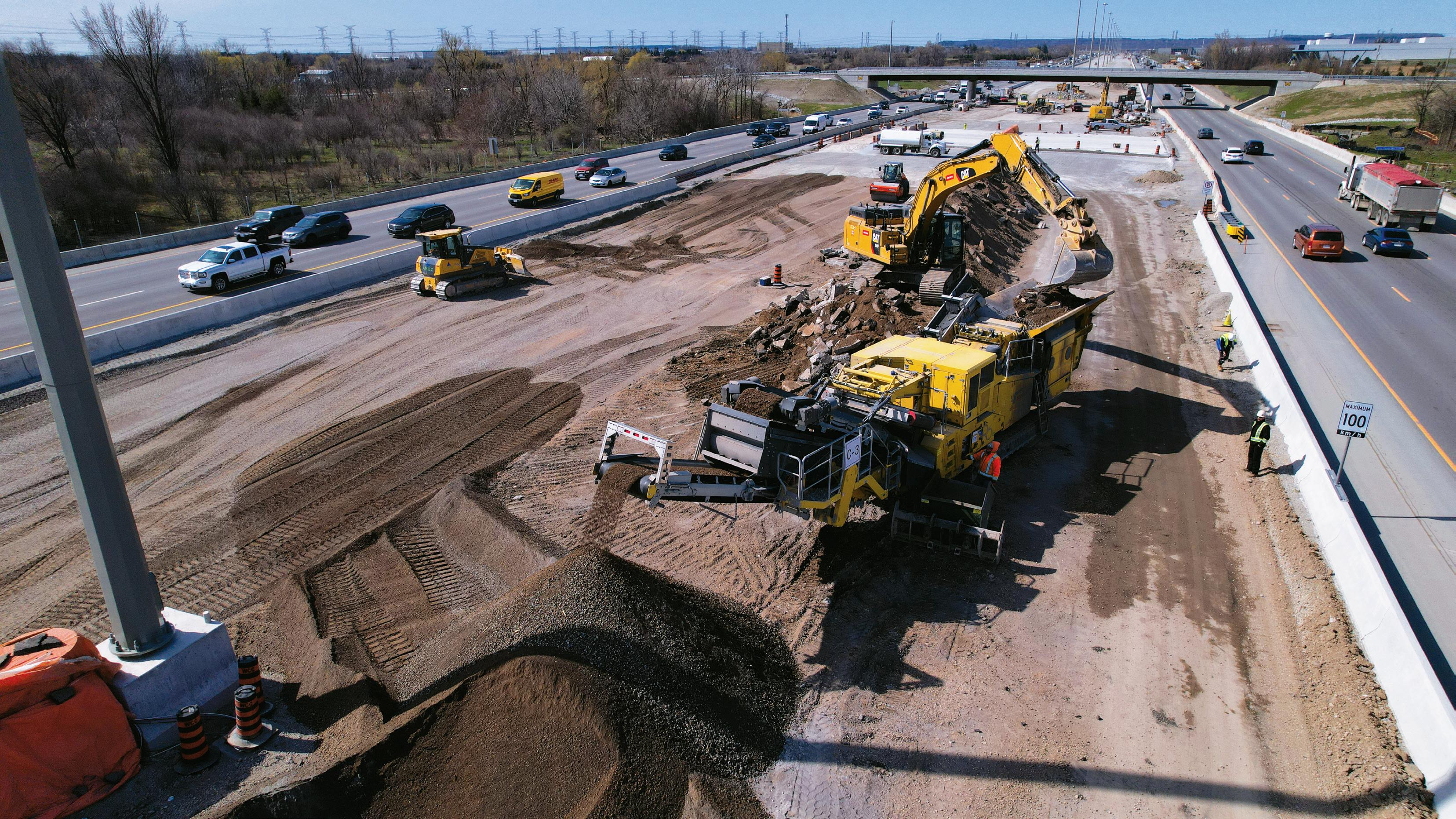
LOADS OF OPTIONS. ZERO COMPROMISE.

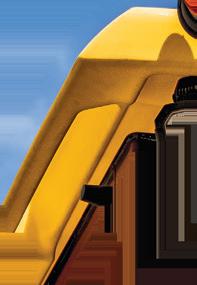


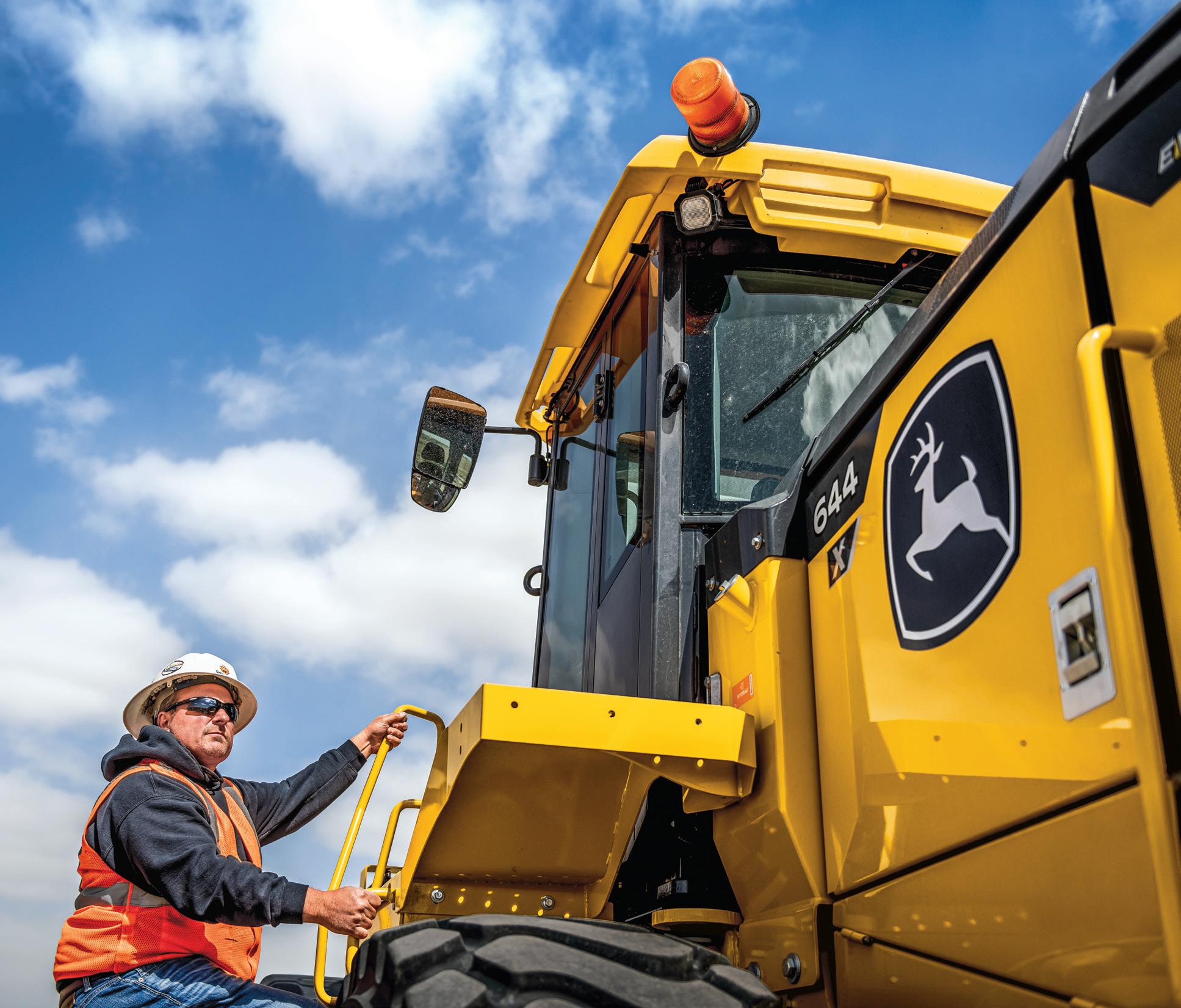
You can’t always choose the deadline. But you can choose how you get the job done. That’s why we offer distinct levels of innovation, comfort, and performance to help you get done faster, more efficiently, and on budget.



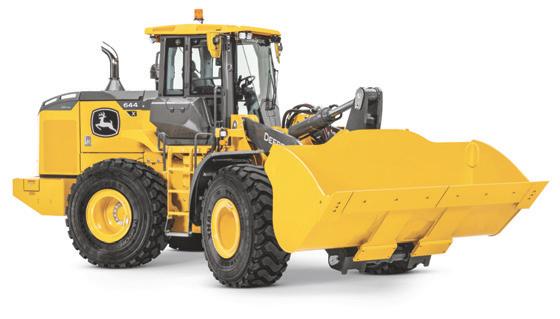

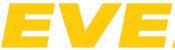






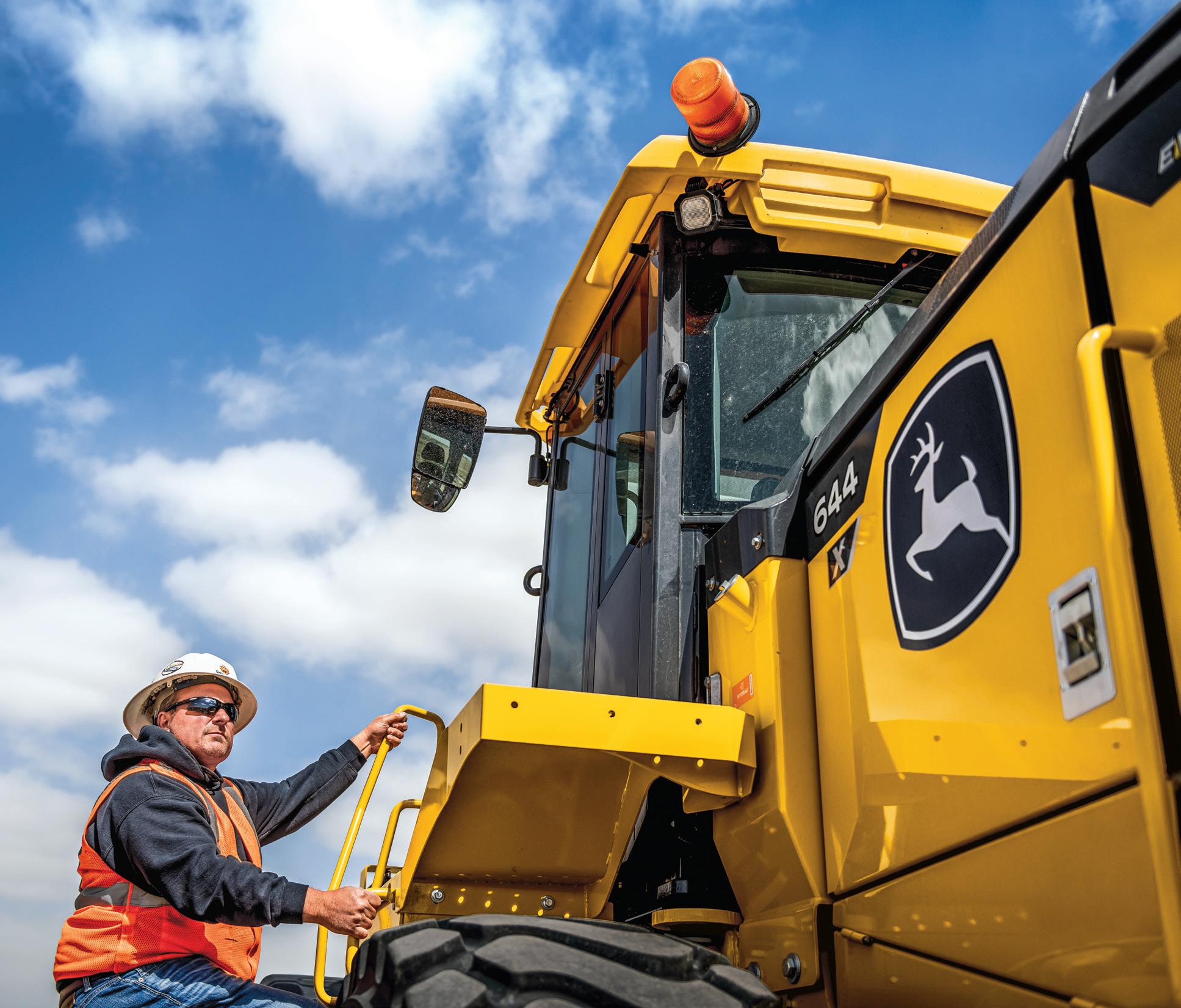
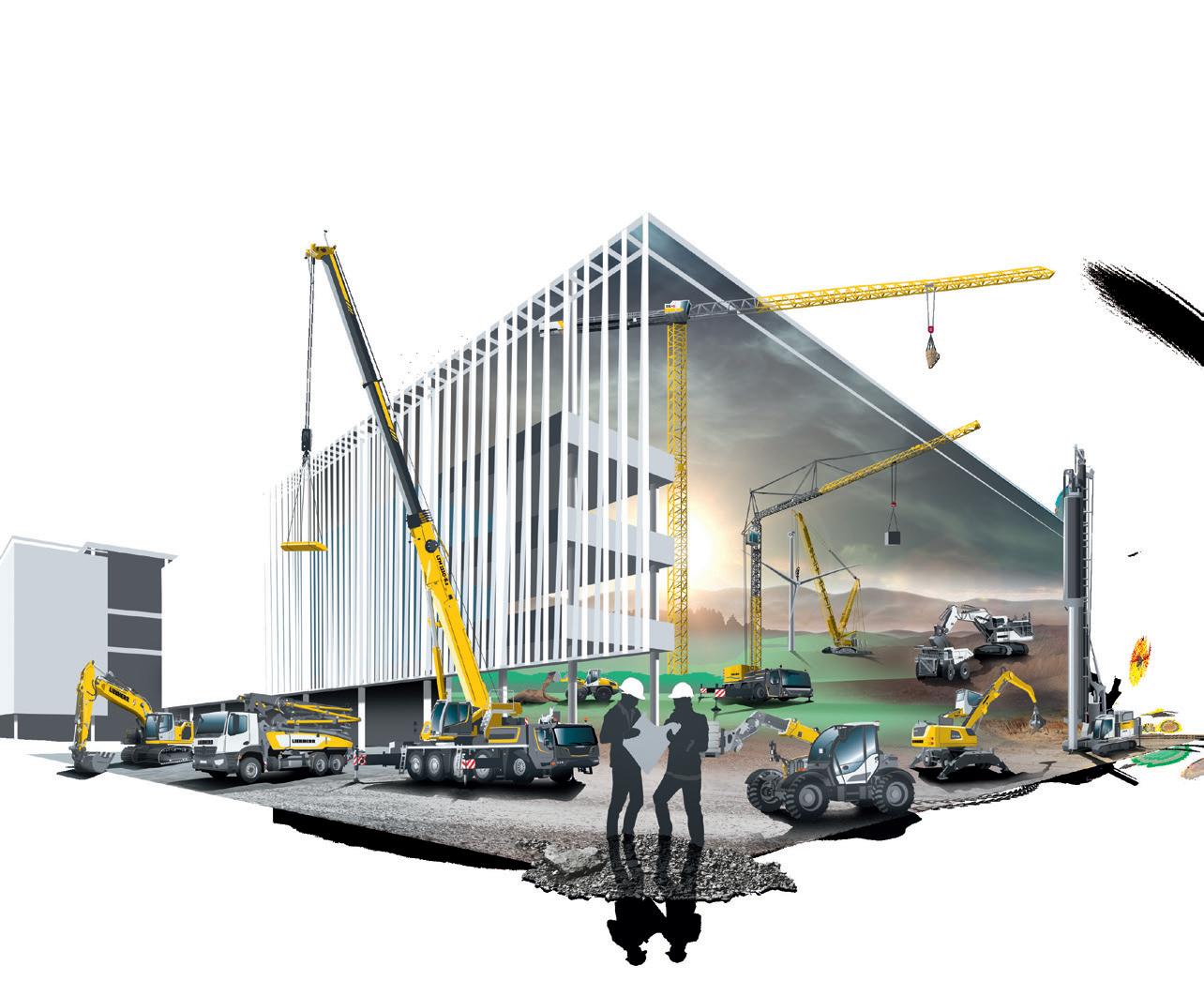
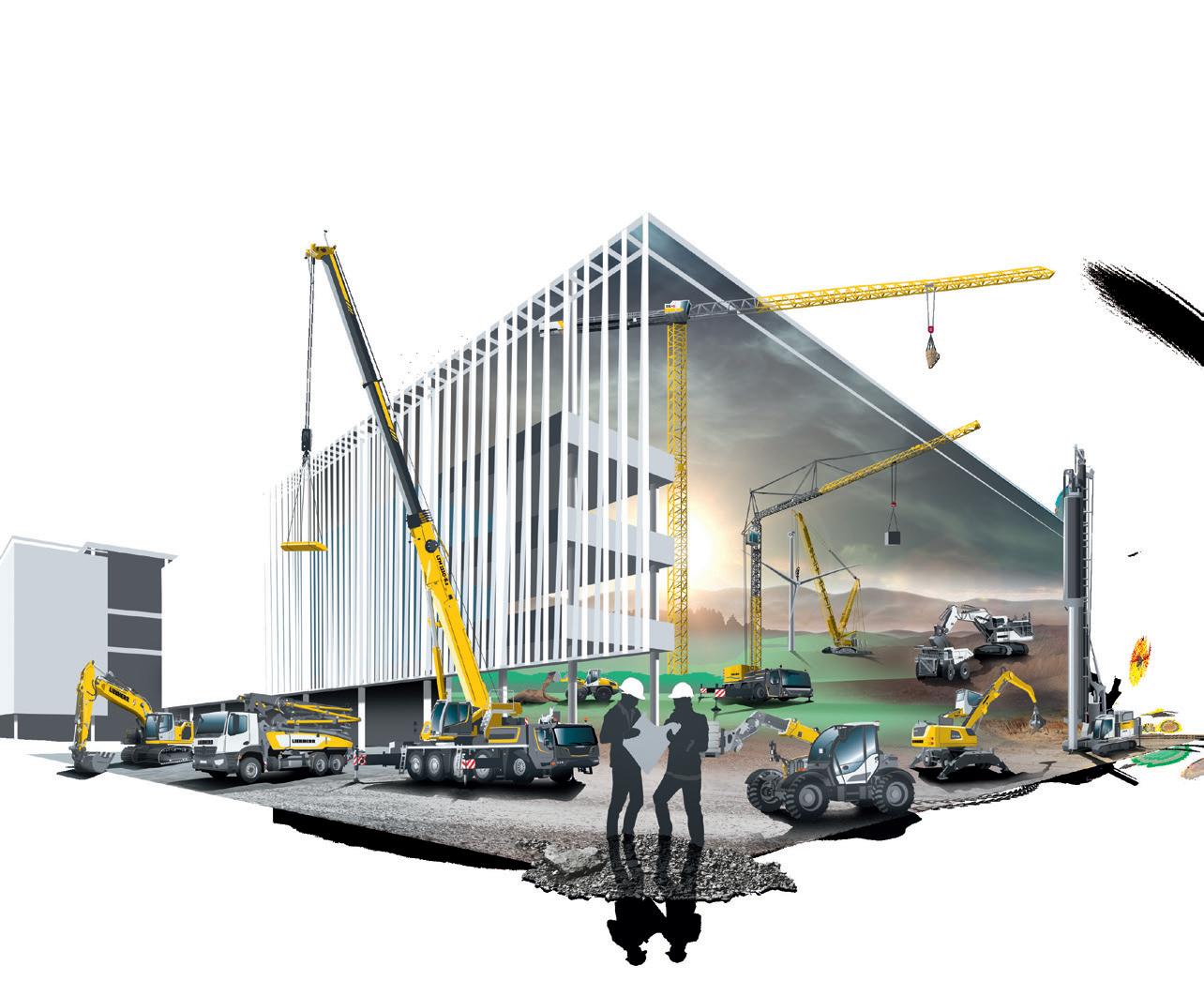
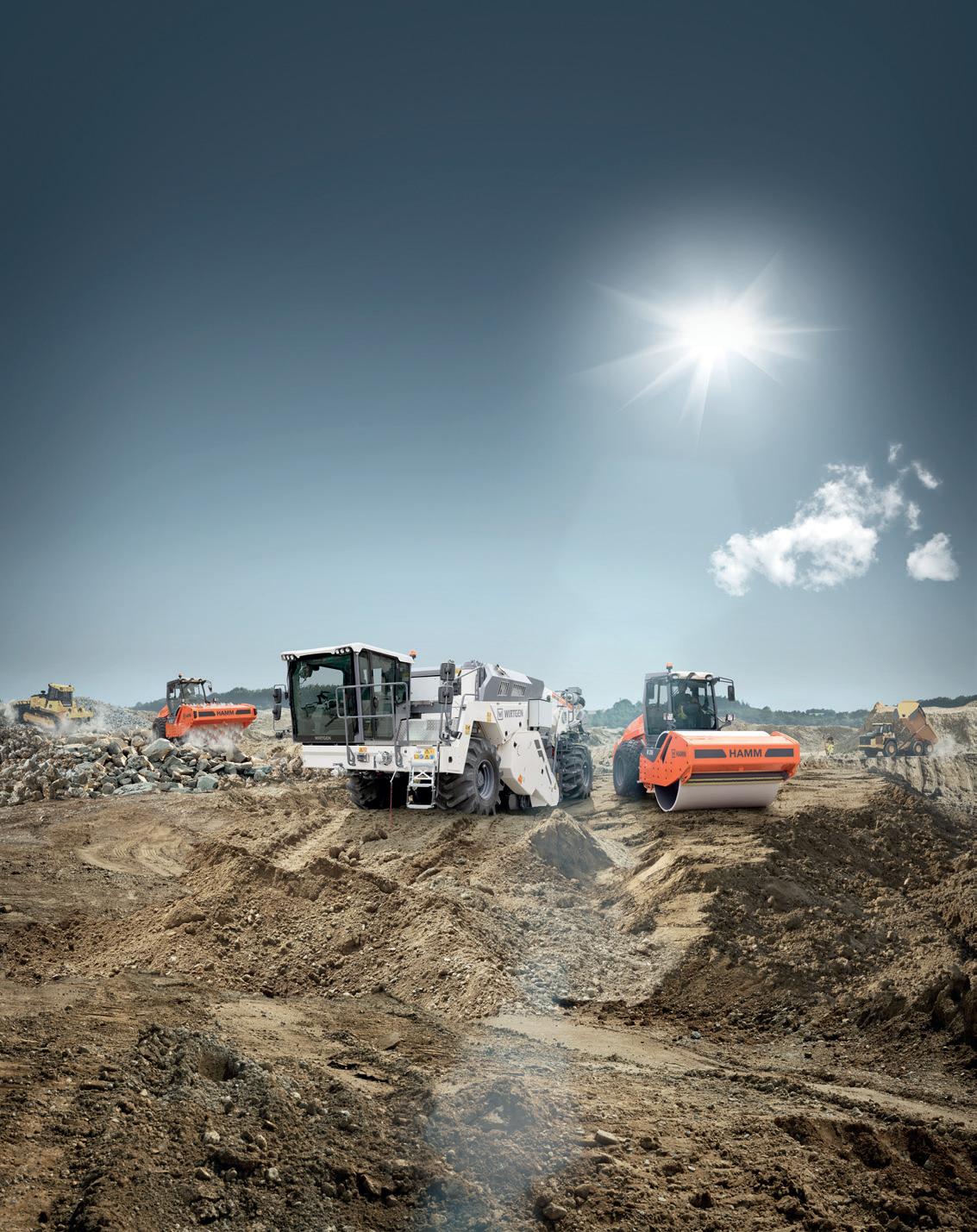



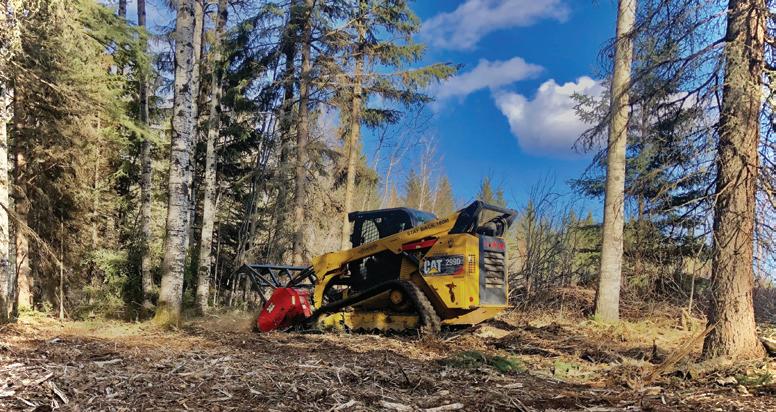

COVER PHOTO: A KEESTRACK R6 IMPACT CRUSHER AND S5 STACKER AT WORK ON HIGHWAY 401.
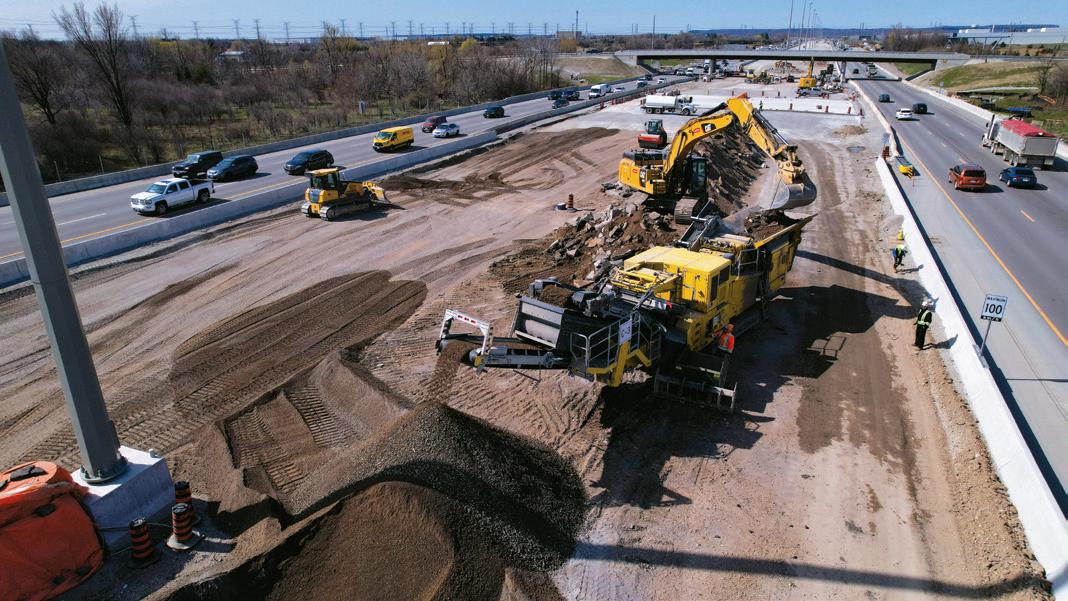
Highway expansion keeps moving with mobile crushing strategy
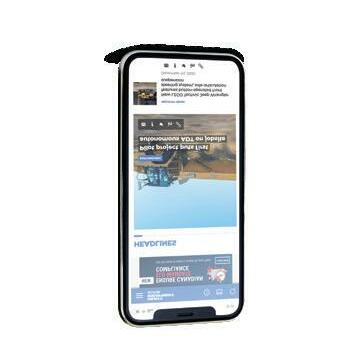
Turn to page 36 .
WE’D LIKE TO HEAR FROM YOU
Do you have a job site story, innovation, or industry concern that our readers should know about? We’d like to hear from you.
Contact: Editor in Chief Kaitlyn Till at ktill@baumpub.com or 604-291-9900 ext. 330
EDITOR IN CHIEF
Kaitlyn Till ktill@baumpub.com 604-291-9900 ext. 330
EDITORIAL DIRECTOR
Arturo Santiago asantiago@baumpub.com 604-291-9900 ext. 310
EDITOR
Lee Toop ltoop@baumpub.com 604-291-9900 ext. 315
ASSOCIATE PUBLISHER
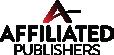
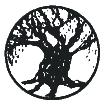
Sam Esmaili sam@baumpub.com 604-291-9900 ext. 110
FOUNDER Engelbert J. Baum
ADVERTISING
PRODUCTION MANAGER
Tina Anderson tanderson@baumpub.com 604-291-9900 ext. 222
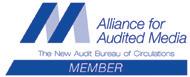
DESIGN & PRODUCTION
Morena Zanotto morena@baumpub.com 604-291-9900 ext. 325
PRESIDENT/PUBLISHER
Ken Singer ksinger@baumpub.com 604-291-9900 ext. 226
VICE PRESIDENT/CONTROLLER
Melvin Date Chong mdatechong@baumpub.com
Published by: Baum Publications Ltd. 124 - 2323 Boundary Road Vancouver, BC, Canada V5M 4V8 Tel: 604-291-9900 Toll-free: 1-888-286-3630 Fax: 604-291-1906 www.baumpub.com www.heavyequipmentguide.ca @HeavyEquipGuide
FOR ALL CIRCULATION INQUIRIES
Toll-free: 1-866-764-0227 email: heg@mysubscription.ca
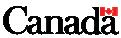
Subscription: To subscribe, renew your subscription, or change your address or other information, go to: http://mysubscription.ca/heg/
Heavy Equipment Guide serves the Canadian engineered construction industry including: roadbuilding and maintenance; highways, bridges, tunnels; grading and excavating; earthmoving; crushing; trucking and hauling; underground utilities; trenching; concrete paving; asphalt paving; demolition; aggregates production; fleet maintenance; and asset security and management. The magazine is distributed to key industry personnel involved in these sectors.
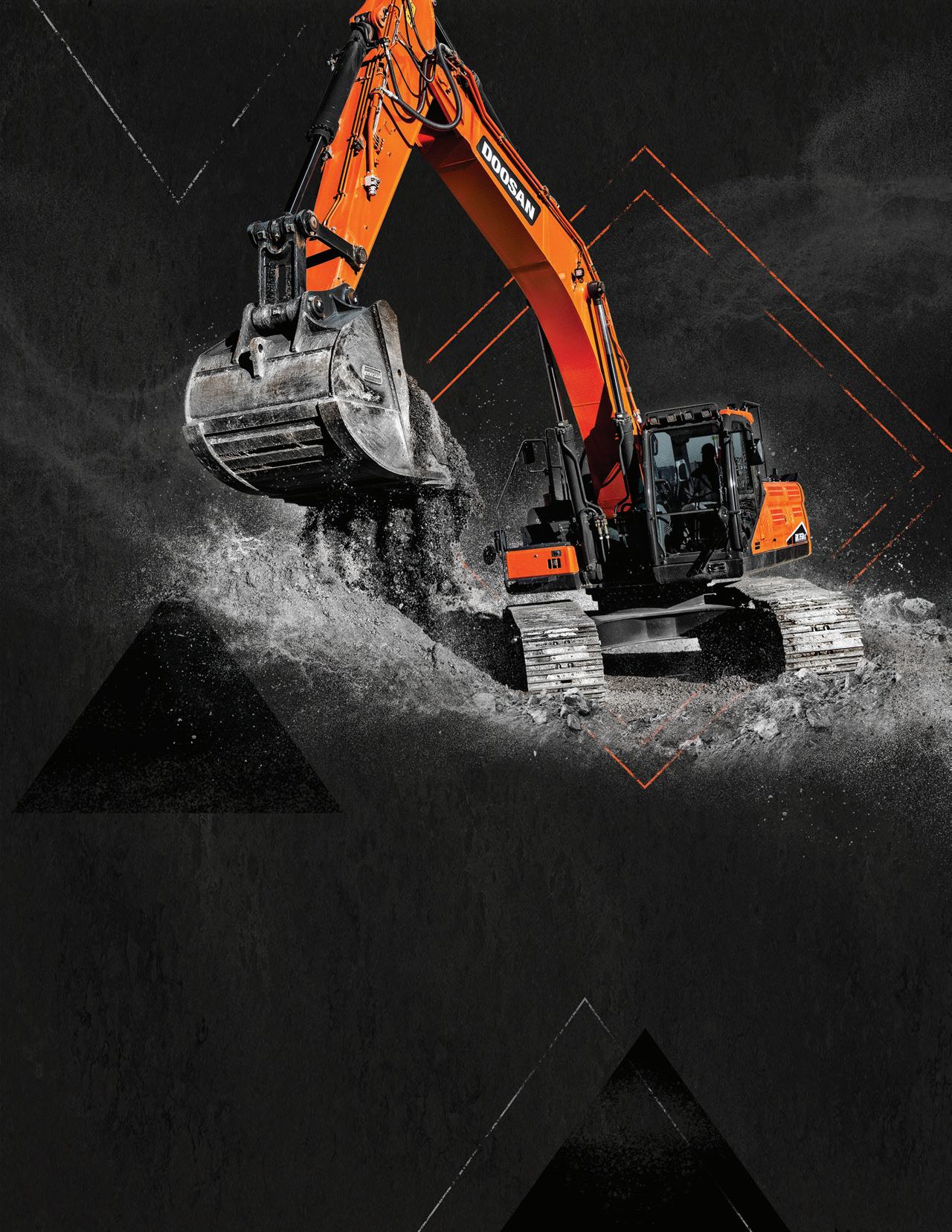
Subscription Price: In Canada, CDN $91.00; Outside Canada, US$149. Heavy Equipment Guide is published ten times a year in January, February, March, April, May, June, July/August, September, October and November/December.
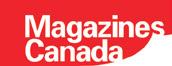
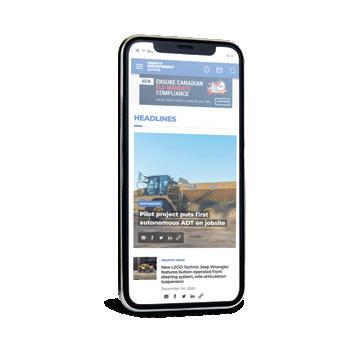
Heavy Equipment Guide accepts no responsibility or liability for reported claims made by manufacturers and/or distributors for products or services; the views and opinions expressed are those of the authors and not necessarily those of Baum Publications Ltd.

Copyright 2022, Baum Publications Ltd. No portion of this publication may be reproduced without permission of the publishers.
We acknowledge the financial support of the Government of Canada.
Printed in Canada on recycled paper by Mitchell Press Ltd. ISSN 1485-6085
PUBLICATIONS MAIL AGREEMENT NO. 40069270
Return undeliverable Canadian addresses to: Circulation Dept., 124-2323 Boundary Road, Vancouver, BC V5M 4V8 email: heg@mysubscription.ca Toll-free: 1-866-764-0227
SCAN THE
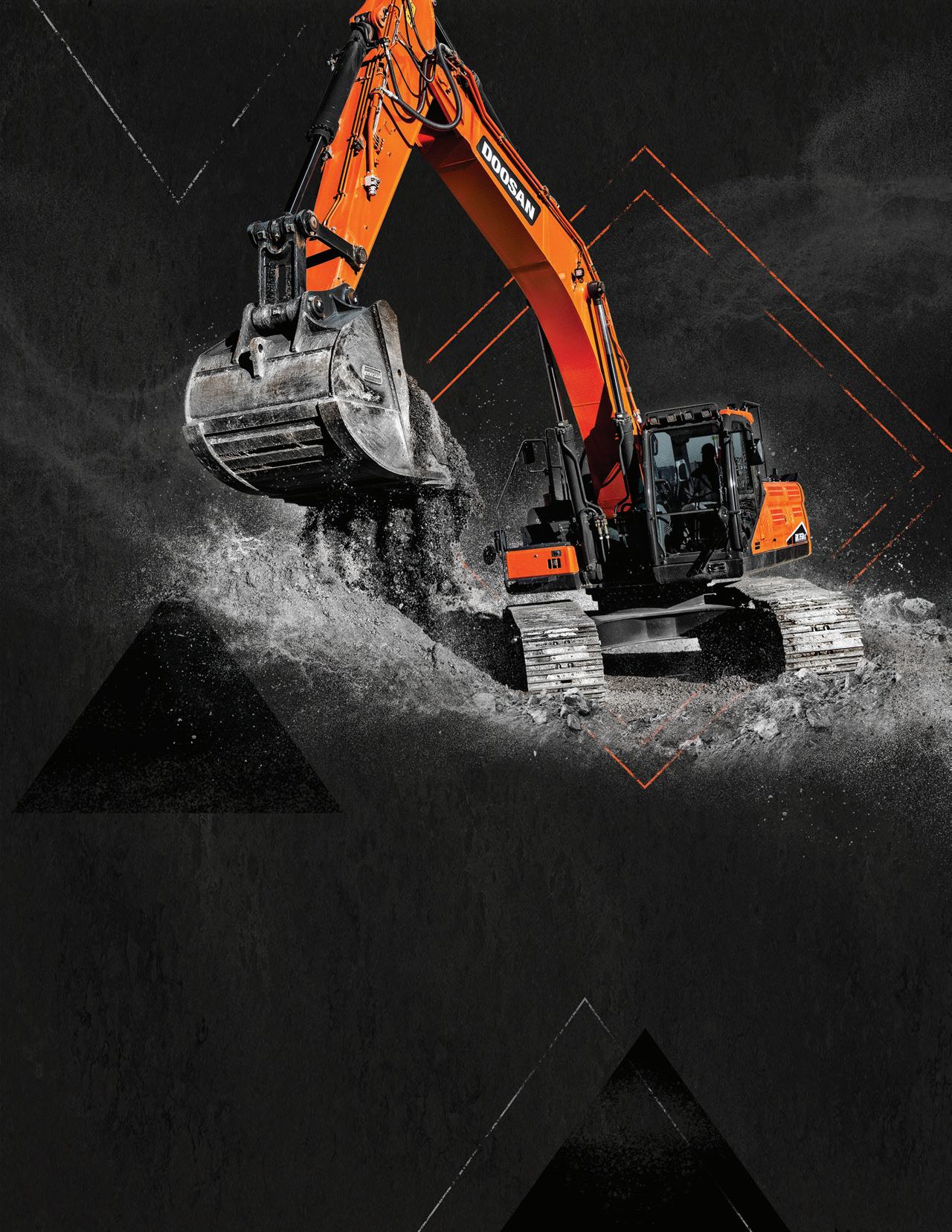
FROM THE EDITOR
CONEXPO-CON/AGG PODCAST OFFERS VALUABLE INSIGHTS FROM CONSTRUCTION INSIDERS
Taylor White is a busy guy these days. I spoke with him earlier this year about Ken White Construction, and we discussed the way in which he has used popular social media sites like TikTok, Instagram, and YouTube to build knowledge and spread the word about his company. Through those outlets, the message has reached not only people in construction, but beyond, and provides a new way of recruiting employees.
Now, White has taken on a new role: host of the revived CONEXPO-CON/AGG podcast, another platform through which he hopes to connect with a broader audience, sharing stories about the construction industry from the professionals who are part of it.
When I connected with White about his new role, he ex plained that the concept of the podcast is to speak with leaders in the industry who have insights that can be beneficial to peo ple both in construction and those who are considering it, or listeners who are just interested in construction. The goal, he says, is to draw valuable information from his guests that can make his listeners more successful in their own lives.
Shows like the CONEXPO-CON/AGG podcast are excellent ways to learn in what feels like an intimate setting – it’s a con versation that you, the listener, can be part of, learn from, and use in your own ways. White expressly told me that he doesn’t like thinking of his shows as interviews – they really are just a chat with an industry expert that covers topics applicable to construction as a whole.
As I write, four episodes are out, and the guest list has covered both large companies and individuals who cover the industry online. For example, White’s third episode featured Ryan Priestly, president of Ontario’s Priestly Demolition, for a conversation that covered everything from the challenges and benefits of being featured on the Salvage Kings television show to ways that Priestly manages the stress of a busy industry.
Another episode featured Nick Drew, who produces the Digger Man blog and writes for construction magazines in the United Kingdom. This conversation covered some topics that have always been of interest to me, such as the ways in which Europeans use their machines that haven’t made it across to North America. Jeff Cavanagh, of Cavanagh Construction – a 1,200-employee-strong firm in the Ontario region – discussed

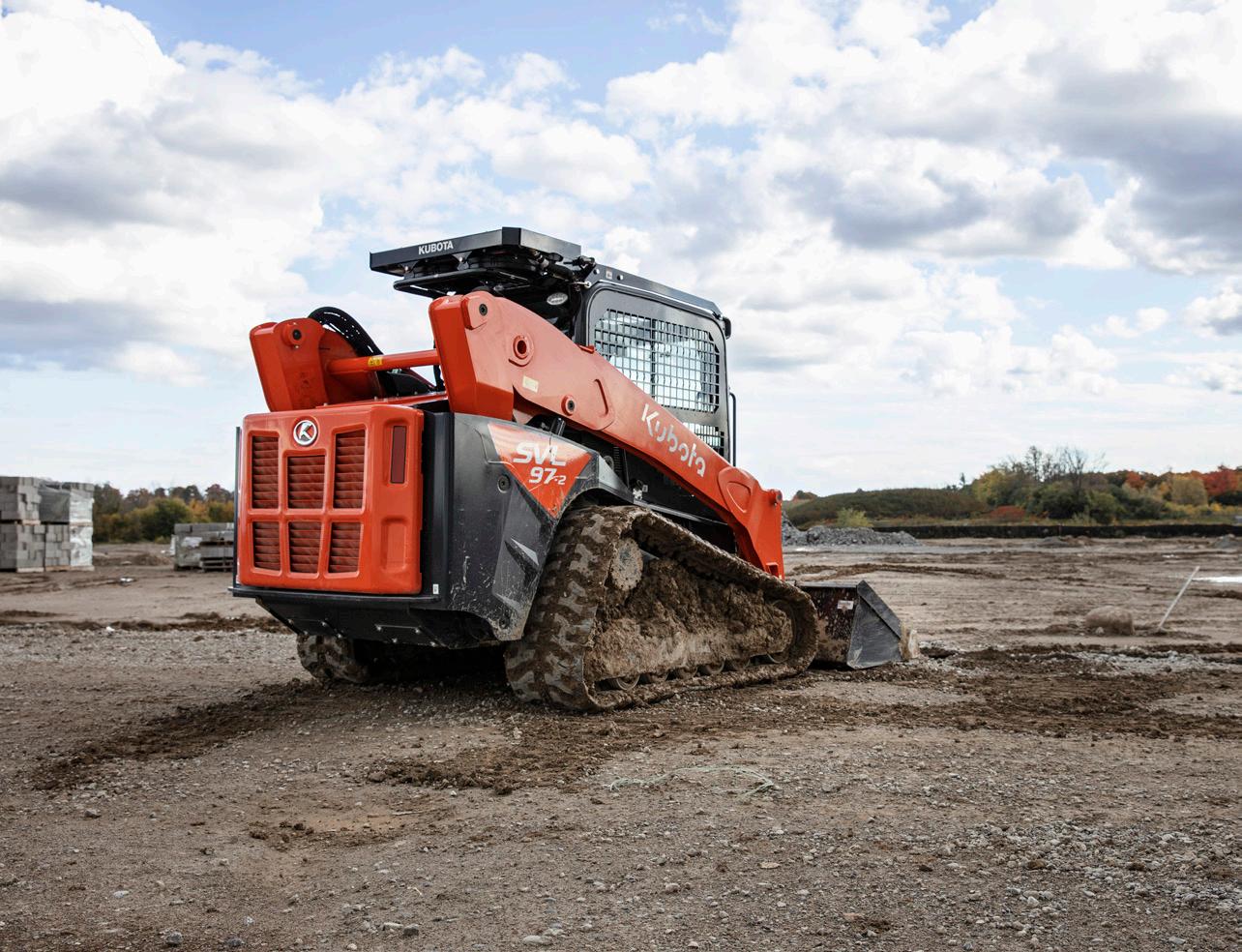
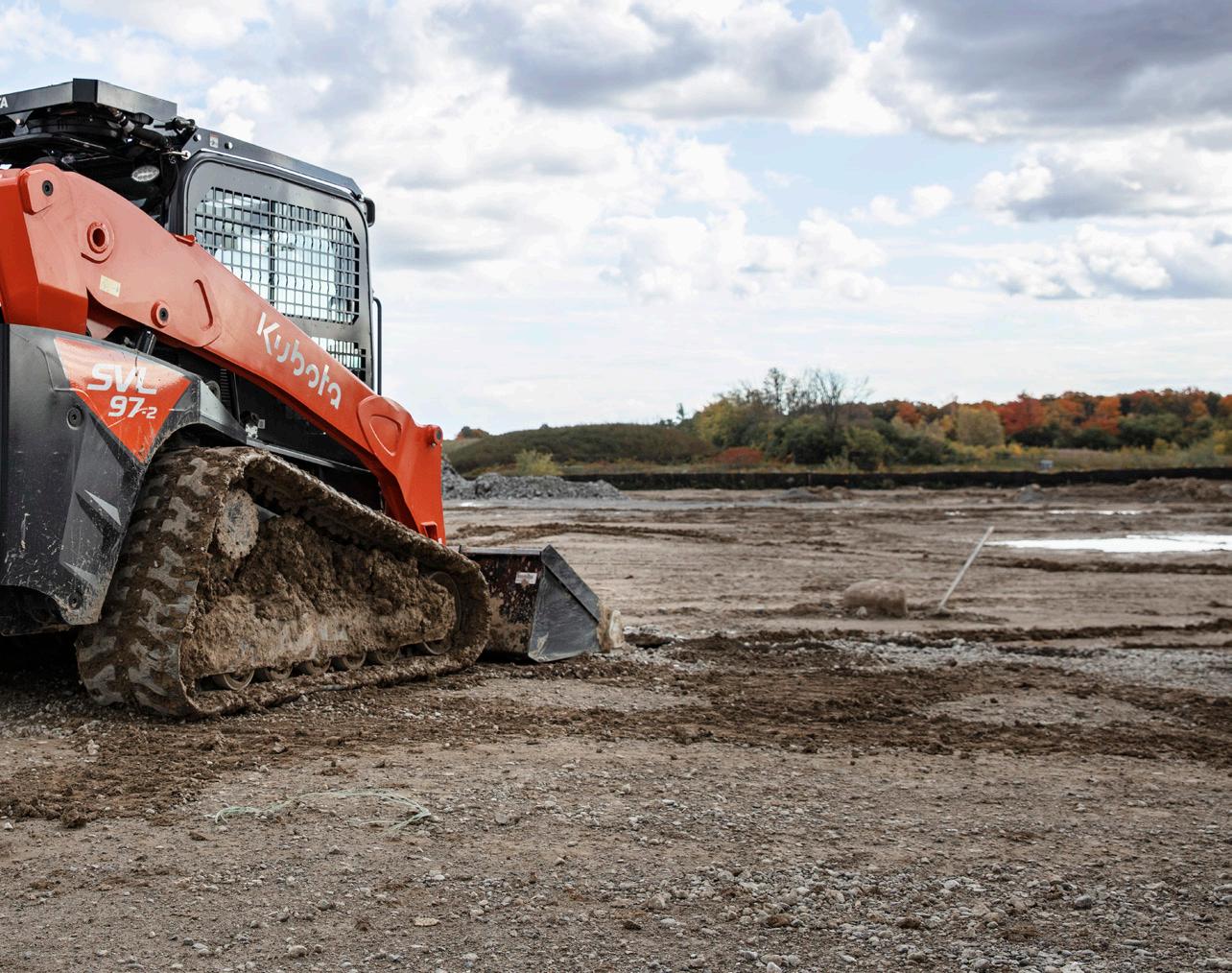
Shows like the CONEXPOCON/AGG podcast are excellent ways to learn in what feels like an intimate setting – it’s a conversation that you, the listener, can be part of, learn from, and use in your own ways.
the challenges of running a business of that size, finding the right people to fill the right positions, and building a strong corporate culture.
Those are just a few of the topics that have come up and the unique perspectives that have been shared. There are sure to be many more as the CONEXPO-CON/AGG podcast releases new episodes twice monthly leading up to the show in March. And, White emphasized that many of his guests will be at the show in 2023 as well.
The CONEXPO-CON/AGG podcast is an excellent opportunity to gain insight on key topics for the industry and connect with construction through the knowledge and experiences of these fascinating guests.
Lee Toop Editor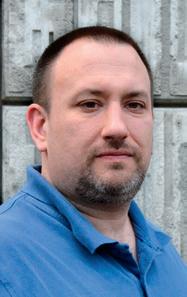
MADE FOR CANADIANS
BUILT FOR ALL KINDS OF CANADA.

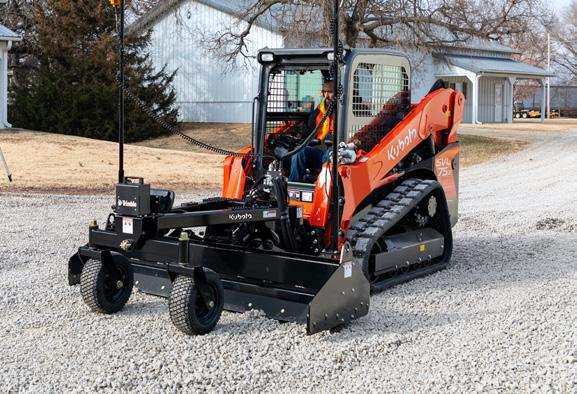
Building in Canada has its own challenges. What you need for downtown is different from what you need out-of-town. It’s why our equipment is cold weather tested. It’s also why we offer compact sizes for flexibility, versatile attachments for multitasking, and comfort for long days on the job. Best of all, with a range of financing and extended warranty options, you can get started and keep working from dawn until deadline.

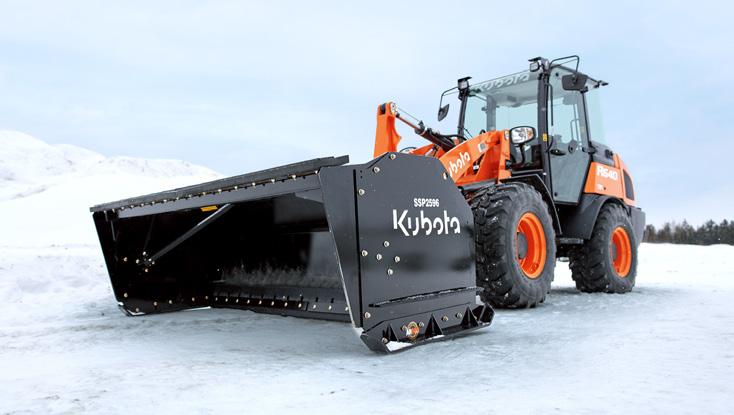
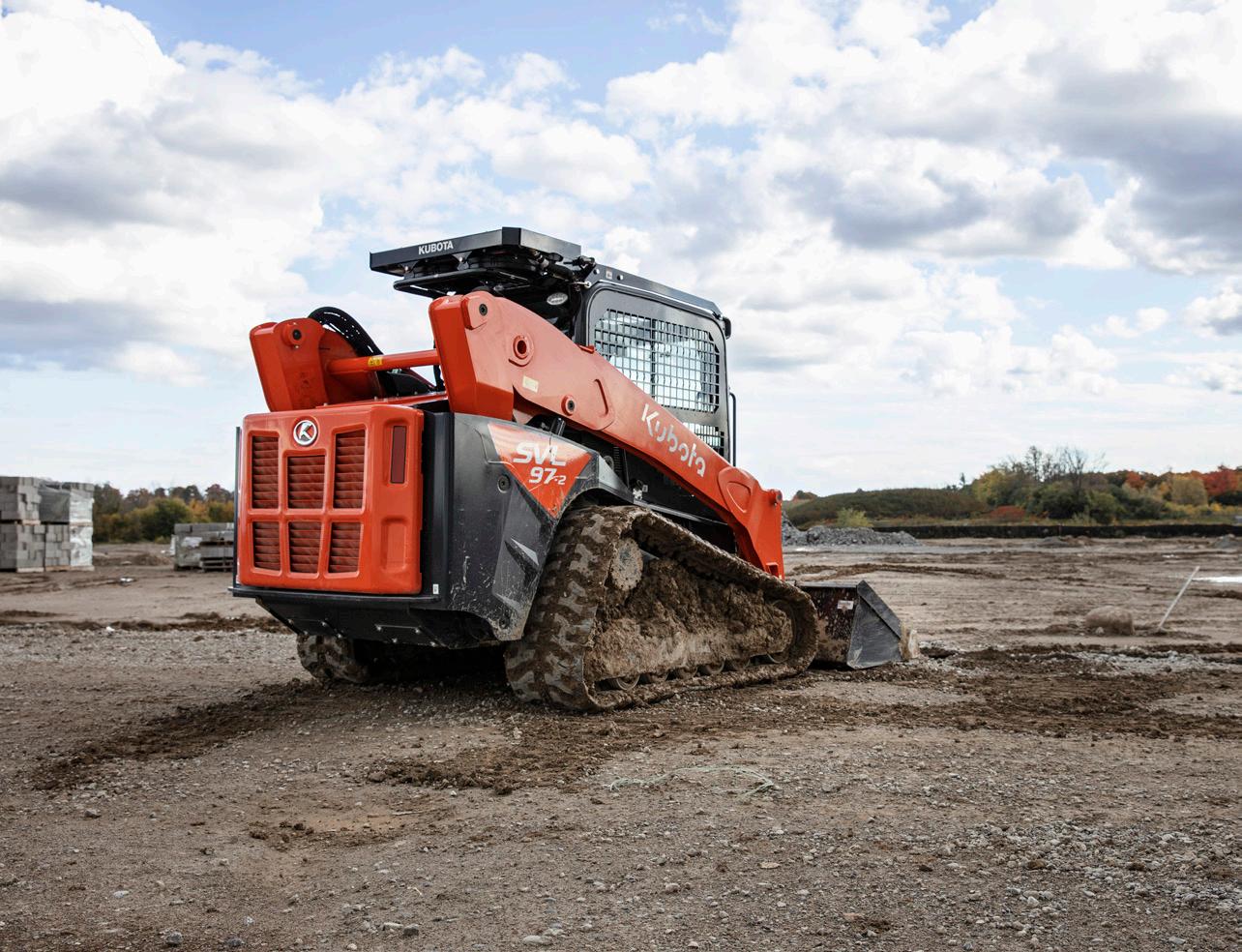
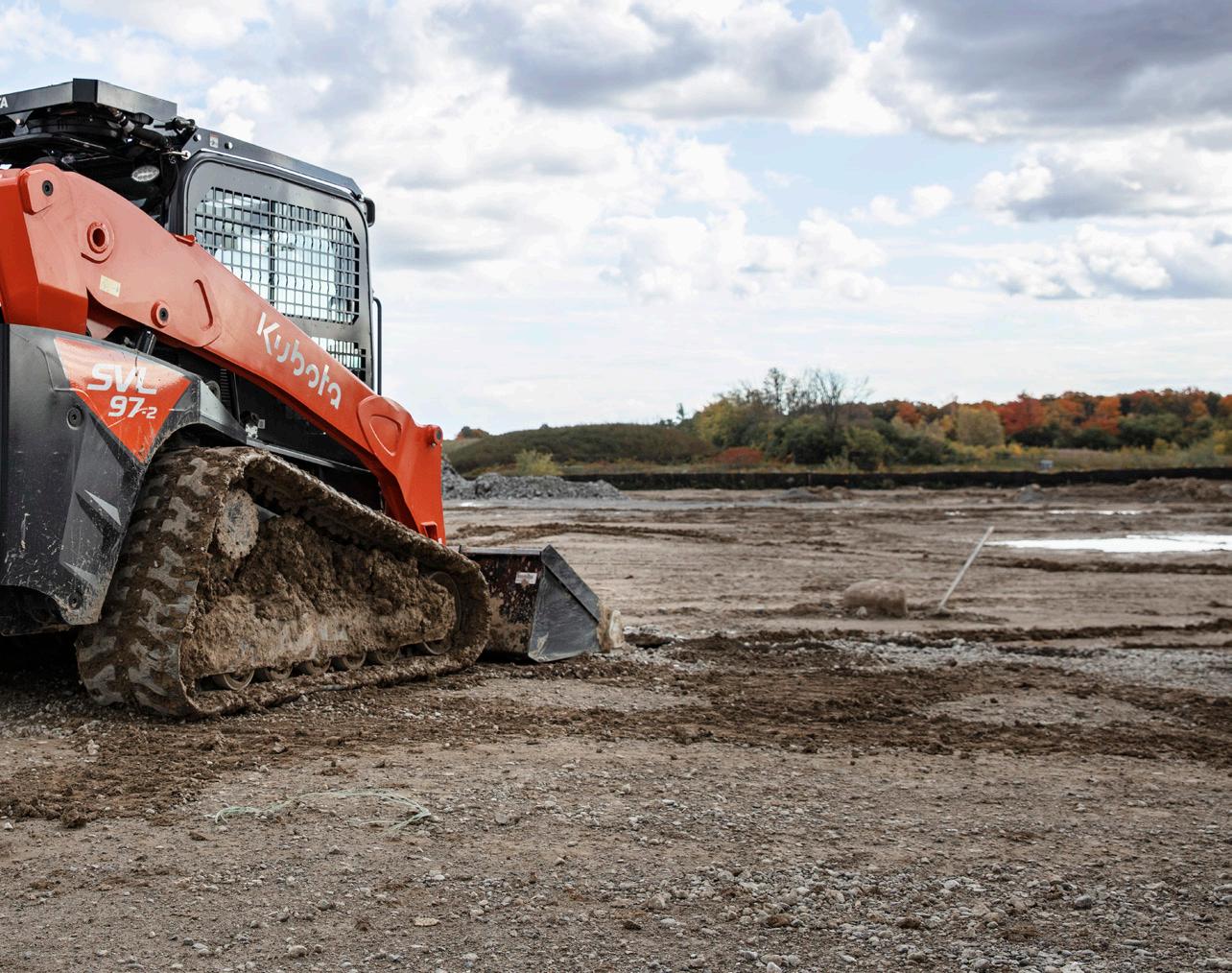
OWhite Construction brand through social media. Now,
CONEXPO-CON/AGG 2023 next March, and White will be on the Equipment Manufacturers (AEM) builds toward the big show. White, a third-generation member of the industry, has built Ken White Construction to nearly 85,000 followers on TikTok and 75,000 on YouTube and Instagram, among others. That experience is coming in handy for hosting the podcast, he said.

The goal of the CONEXPO-CON/AGG podcast is to share sto ries from those in the construction industry and provide insight to their peers – just like the trade show does for attendees.
“We talk to leaders in the construction industry that are do ing things maybe a little different, or that stand out. They may be a person who is able to provide value to others doing the same thing within the industry, whether they own a business, or work in construction, or are just interested,” White said.
Through its first few episodes, the podcast has featured a mix of guests, including Scott Colclough, better known as “Pushy six” on social media, and Nick Drew, the British creator of the “Digger Man” blog, along with Ryan Priestly, owner of Priestly Demolition. The diversity of guests is key for White, who wants to share as many perspectives as possible.
Viewers can expect a lot of different topics to be touched on by White and his various guests, but three that he suggests are key leading into CONEXPO-CON/AGG 2023 are technology, labour shortage challenges, and handling the current inflation issues on both sides of the border.
TO BUILD
FACILITY IN ONTARIO
Toromont Industries Ltd. will construct a new 137,000-square-foot remanufacturing facility in Bradford West Gwillimbury, Ontario. This investment will support the growing needs of users while creating opportunities for Toromont employees and the surrounding community.
The facility is scheduled to open in early 2024 and will employ 150 skilled tradespeople at the time of opening, with an ultimate capacity of 200. The remanufacturing facility has incorporated design and equipment solutions to ensure ideal standards of safety, quality, and production efficiency, says Toromont. Remanufacturing of components is a critical ele ment of the circular economy and helps lower life cycle cost of users’ equipment. It also complements Toromont’s sustainabili ty and environmental, social, and governance (ESG) objectives.
This added capacity combines with the Reman operations in Quebec City, Pointe-Claire, and Thunder Bay to support Torom ont’s customers.
DOUGLAS LAKE EQUIPMENT AND AVENUE MACHINERY COMPLETE MERGER
Douglas Lake Equipment (DLE) and Avenue Machinery Corp. (AMC) have completed a merger agreement. Both AMC and DLE have built strong reputations in supporting farmers, contractors, homeowners, and other users throughout British Columbia and Alberta.
DLE says that this merger will provide additional choice of service locations and an expanded selection of available machines at its locations. Further, DLE expects the merger to help increase the service available to contractors who buy their equipment through DLE.
Avenue Machinery and Douglas Lake Equipment will contin ue operations under their respective names. Additionally, to en sure continuity, all company locations will continue operations, and all user and vendor contacts will remain the same.
CUMMINS TO DELIVER 300,000 ENGINES TO HYUNDAI CONSTRUCTION EQUIPMENT IN 2022
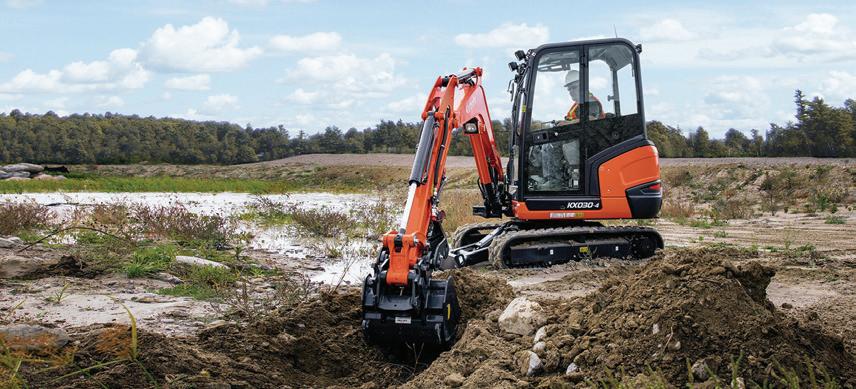
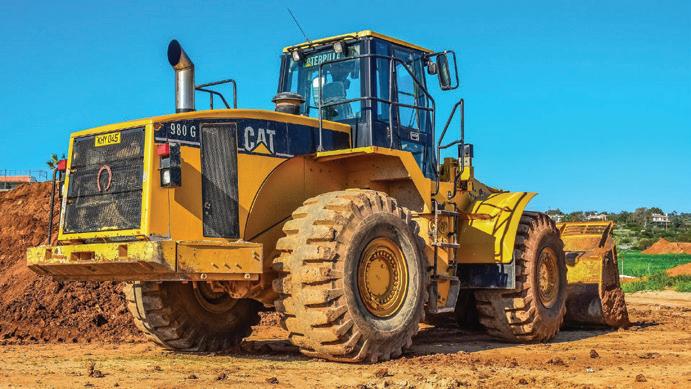
Cummins Inc. will deliver 300,000 engines to Hyundai Construction Equipment (HCE) in 2022. Cummins has been supplying engines to HCE since 1990, hitting 10,000 engines supplied in 1996 and 200,000 in 2016. Earlier this year Hyundai Construction Equipment received the 1.5 millionth mid-range engine produced from Cummins’ Darling ton, U.K., plant.
GET READY FOR SNOW SEASON
How to select and prepare equipment for snow and ice clearing operations. Turn to page 56.
addition of B2W’s
expand
One. B2W’s suite of

more.
operations
UNITED RENTALS ADDS JCB ALLELECTRIC DUMPSTERS TO NORTH AMERICAN RENTAL FLEET
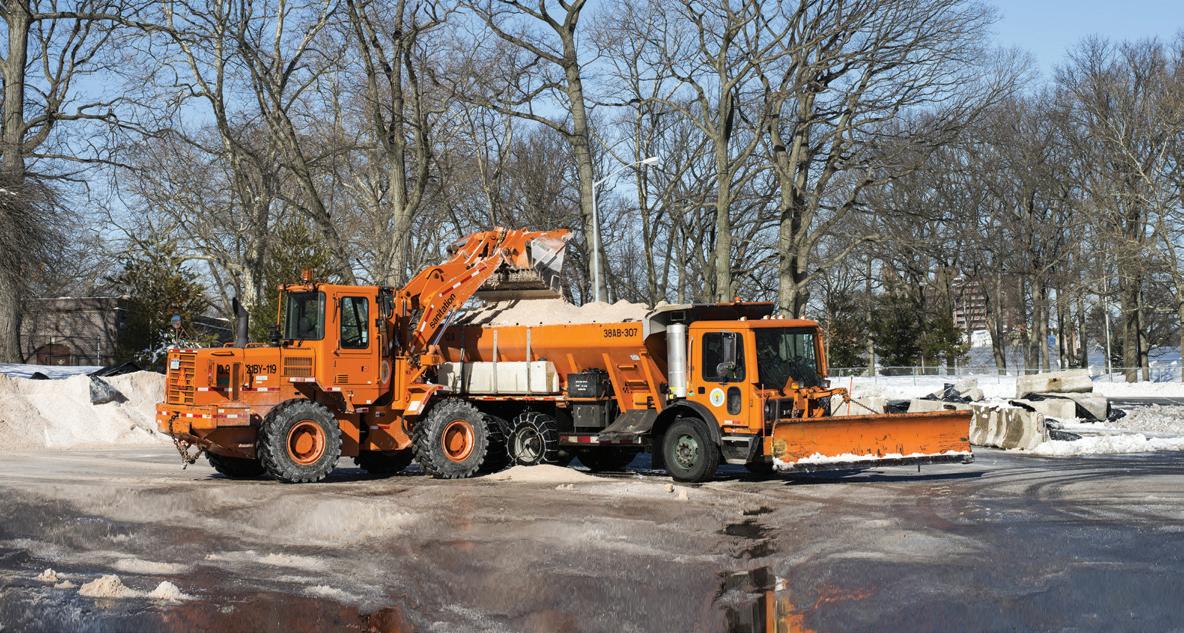
Trimble
esti
Rentals has agreed to purchase fully electric dumpsters from JCB for its rental fleet. United Rentals is the first equipment rental company to offer JCB’s HTD-5E electric dumpsters to North American contractors. The tracked electric dumpster is offered as a ride-on model capable of carrying up to 1,102 pounds.
combining
Trimble’s field data, civil contractors
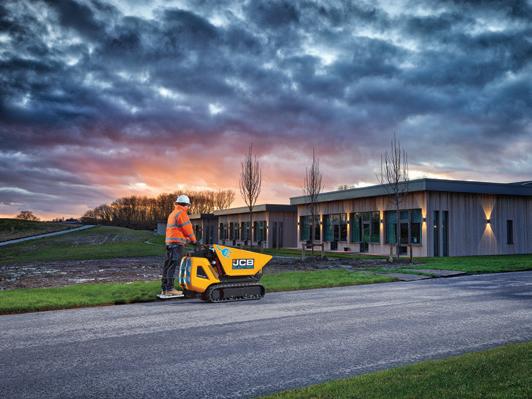
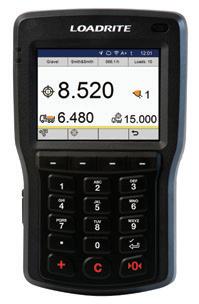
between office and field
be able to bridge
new
HELPS
WORKERS GAIN CAREER
The B.C. Construction Association’s Building Builders program will start connecting under- and unemployed workers with experienced mentors across all disci plines in B.C.’s construction industry. Building Builders is a province-wide mentorship program serving B.C.’s construction industry, filling an important gap that often does not adequately encourage skilled trades as a career path.
Personal guidance can be difficult to access for job seekers without connections inside the industry, and it can take years for talent to get on an accelerated path. The B.C. Construction Association hopes that the Building Builders program will help first-year apprentices get started earlier and stay in the system by providing personalized, ongoing career guidance.
Three hundred mentee positions are available. Building Build ers will carefully match each mentee with a successful profession al in construction who aligns with their goals and life experience.
FPT INDUSTRIAL’S HYDROGEN COMBUSTION ENGINE POWERS PRINOTH’S NEW SNOW GROOMER
FPT Industrial has launched a concept application of the XC13 hydrogen combustion engine through a collab oration with Prinoth on the LEITWOLF h2MOTIO, a hydrogen-powered snow groomer. The concept vehicle uses the 13-litre, six-cylinder FPT XC13 hydrogen version engine deliver ing 460 hp (338 kW) and 2,000 Nm of torque.
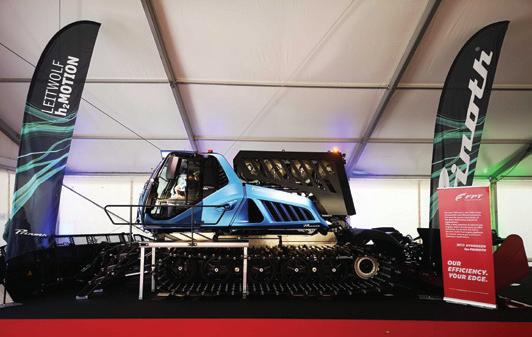
The FPT XC13 multi-fuel single-base engine is able to use diesel, natural gas, hydrogen, and renewable fuels. The hydrogen fuel on the Prinoth LEITWOLF h2MOTION is stored in five tanks for a running time of over three hours.
Your experts in road construction service and support
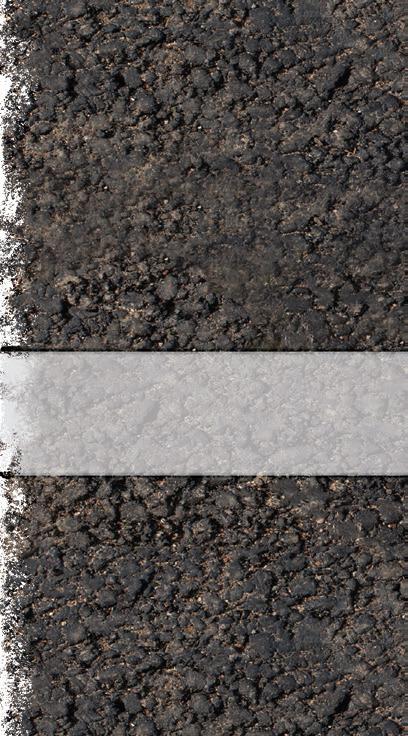

FIVE REASONS EQUIPMENT DISTRIBUTORS SHOULD ATTEND THE 2023 AED SUMMIT IN CHICAGO
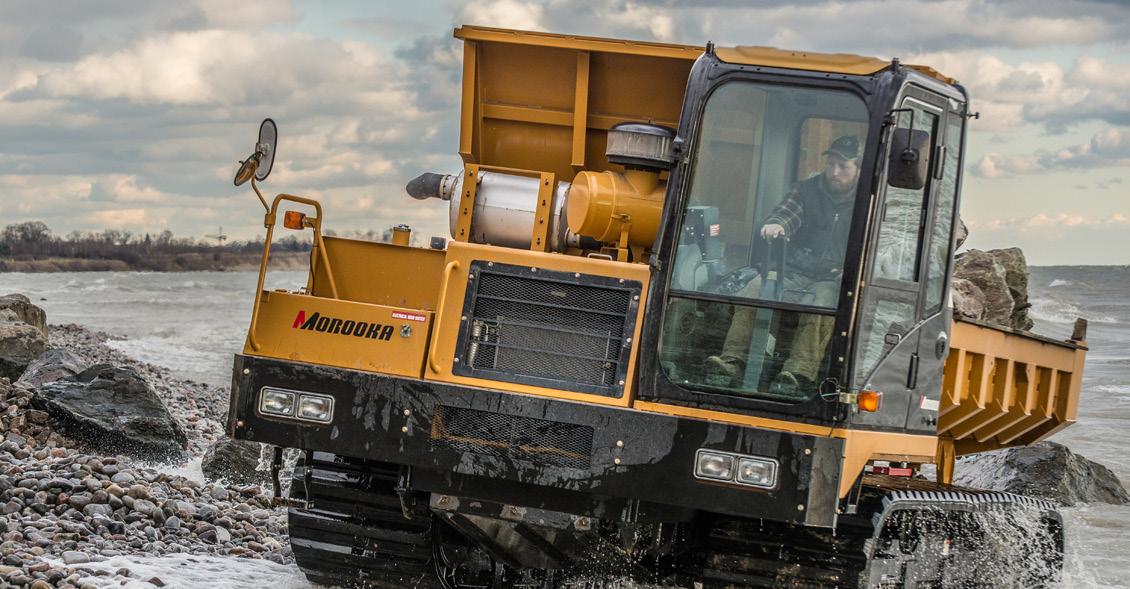
Each year, equipment distributors across North America attend the AED Summit for three days of networking, education, and industry leadership. Now in its 104th year, Associated Equipment Distributors (AED) continues to bring together equipment distribu tors at Summit along with manufacturers that equip the industry and service providers that offer a wide variety of services for distributors. This dynamic combination of equipment-focused enterprises makes the AED Summit a one-of-a-kind, industry-leading event.
Throughout the three days of AED Summit, attendees will gain crucial insights into today’s most pressing is sues in the industry that will guide their success for the rest of the year. Attendees will also partake in an optimal environment to network with peers, connect with sup pliers, and learn ways to improve their businesses today and into the future.
The 2023 AED Summit will take place January 10–12
at the Hyatt Regency Chicago, located in the heart of downtown Chicago. With its long history, the AED Summit is the symbolic kickoff for each business year within the equipment distribution industry. Here are five reasons to attend:
Industry-specific education
With over 40 breakout education sessions that have been curated and developed by AED, attendees will learn about industry trends, tips, and gain insight though sev eral tracks including Leadership, Management, Product Support, Technology, Rental, and Sales. Session topics in each track cross a variety of industries represented by equipment distributors including Agriculture, Construc tion, Material Handling, Cranes, Municipal, and more. The breadth of topics covered ensures that all members of your team will benefit from attending. Visit www.aed summit.com for more details on the education sessions.
Hospitality/meeting room suites
One of the most unique aspects of AED Summit is the hospitality/meeting room suites. These suites are an ex clusive feature of the event. During Summit, distributors can privately meet one-on-one with executives from leading manufacturers and service providers to discuss business. Planning for the year, planning for a change, and discussing the year ahead are all on the table for attendees in these private sessions. You can meet with your existing suppliers and providers and/or meet with
Networking events
Networking events throughout Summit offer a great opportunity to reconnect with industry colleagues and make new connections for your business. With several receptions and networking events included in the con ference registration, these social gatherings offer a great opportunity for attendees to build and continue the lifelong connections that are the foundation of the equip ment distribution industry. Visit www.aedsummit.com to view the schedule and add the networking events to
IMPACT CRUSHER
R6
Converting waste products and virgin materials into high-quality aggregates, requires equipment that is engineered to perform. Unrivaled in performance, the Keestrack R6 mobile impact crushing plant is designed with state-of-the-art technologies, innovative controls, and a heavy-duty mobile design. This is where portability meets performance.
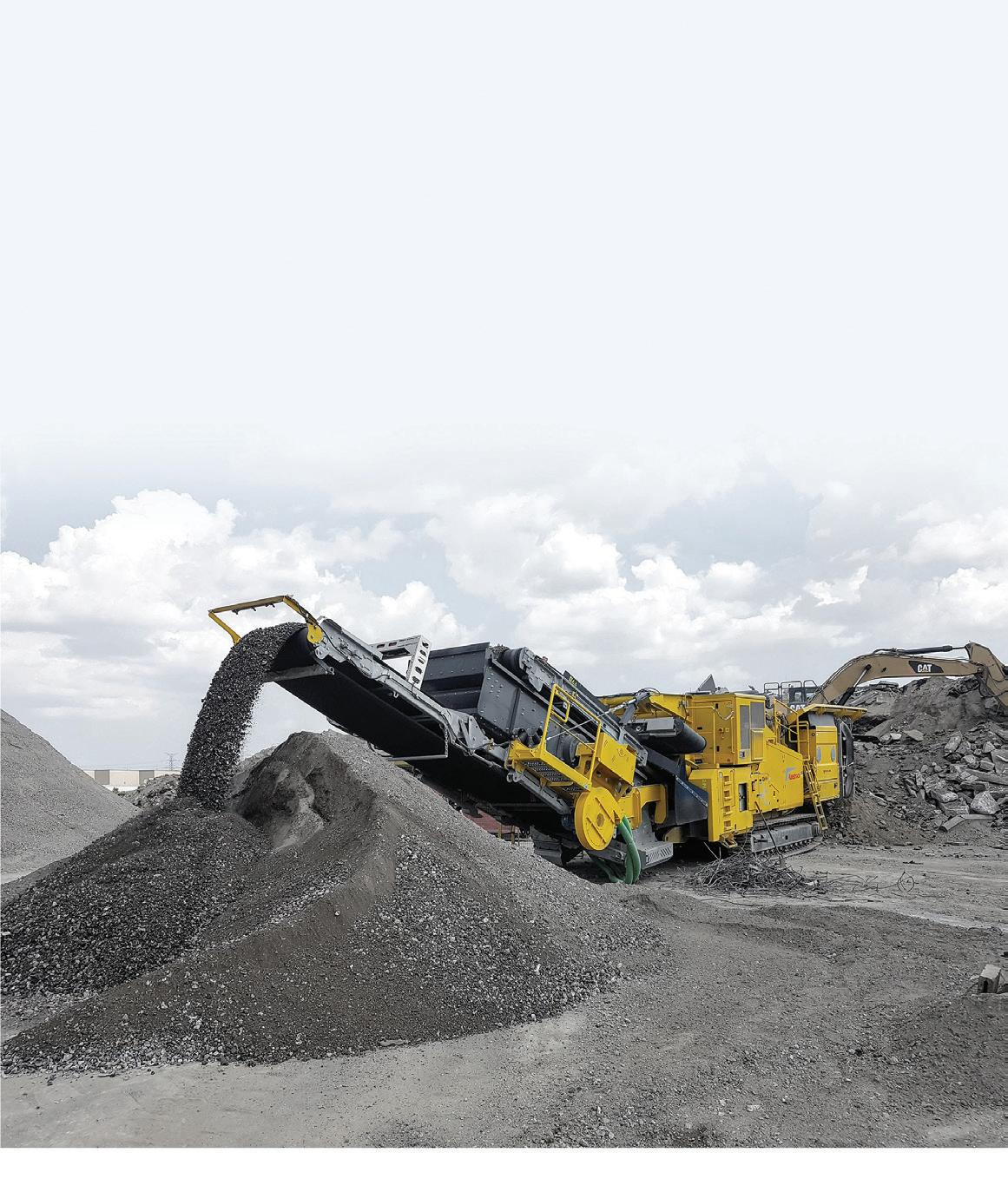
SPOTLIGHT
Caterpillar Hydraulic excavator
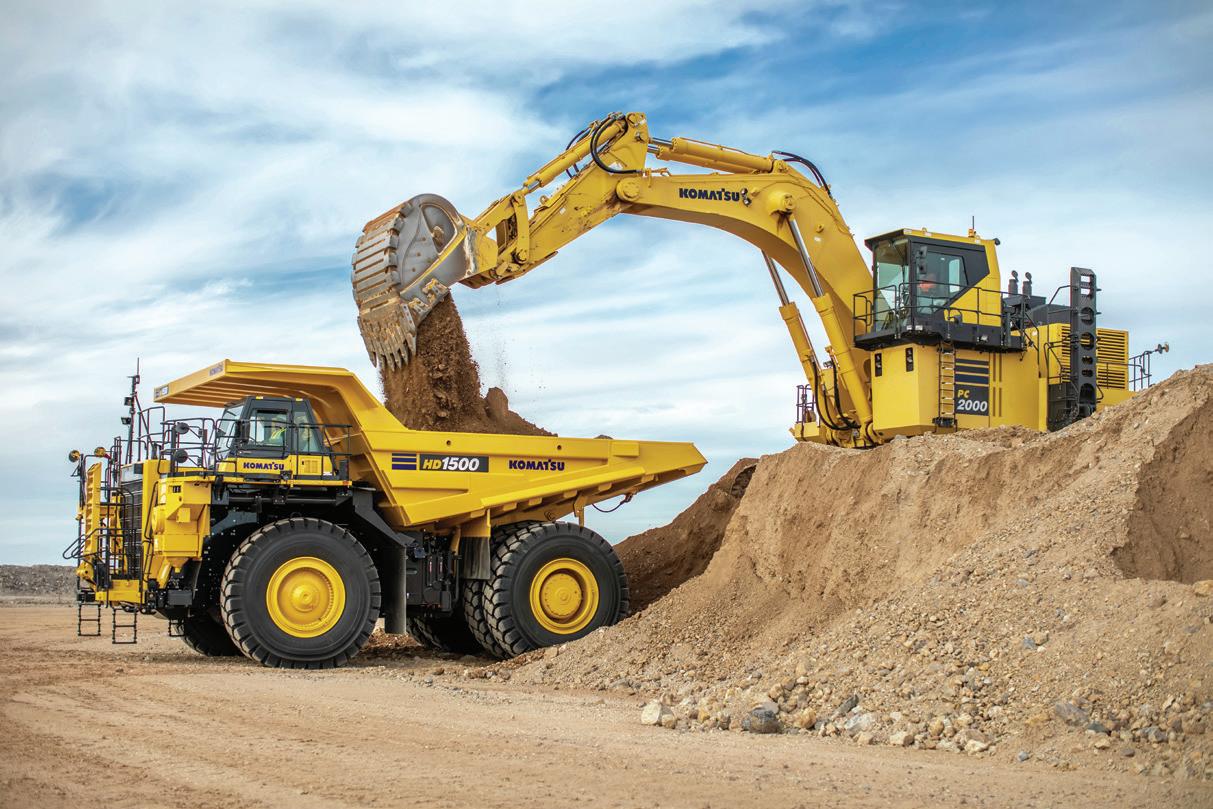

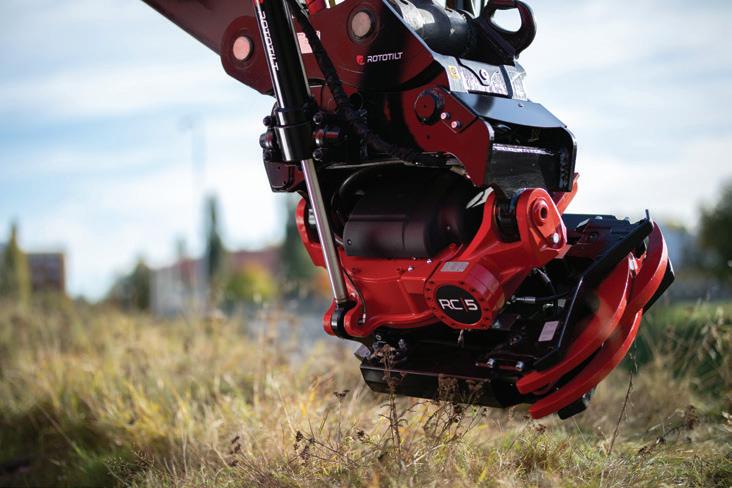
The new Cat 336 hydraulic excavator features three engine modes that match excavator power to the demands of the job while saving fuel. Power mode delivers power to meet tougher tasks and Smart mode automatically matches engine and hydraulic power to digging conditions to lower fuel consumption. Reducing engine speed to a constant 1,500 rpm, Eco mode minimizes fuel consumption. High-ambient temperature capability of 52 degrees Celsius (125 degrees F), cold-start capability at -18 degrees C (0 degrees F), and the ability to work at up to 4,500 metres (14,764 feet) above sea level enables the 336 to work in various climates. Optional Cat Stick Steer makes travel and turning easier, and standard technologies include Cat Payload on-board weighing, Grade Assist for maintaining grade, and 2D Grade with depth and slope indication.
Ammann 3D vibratory compactor
Ammann says that the battery-powered eAPX 68/95 3D vibrato ry compactor is the first vibratory plate on the market that can go in an arc, circle, or turn on the spot. It has a low operating height of 700 mm and is ideal for trench applications – includ ing those with support systems and cross braces. A remote-con trol unit provides the eAPX 68/95’s precise movements and the operator can easily steer the eAPX 68/95 along straight lines or in hard-to-reach spots from a distance. Four battery-powered electric motors enable the machine to work in applications off-limits to combustible engines, including indoors and in en closed spaces. The plate can run continuously for approximate ly 80 minutes before a 30-minute recharging is needed. The drive requires minimal maintenance as it has no hydraulics, operating fluids, or gears.
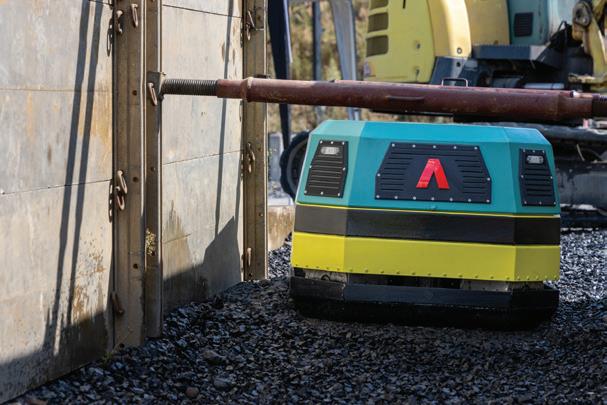
Rototilt
Tiltrotators and control system
Rototilt Control is a new series of tiltrotators, control system, and app for remote support. The display for the RC system has been redesigned with a new touchscreen that allows the user to oper ate the SecureLock safety lock directly in the display with just two presses of a button. The upgraded tiltrotators will be available for owners of excavators weighing between 10 and 43 tonnes. Rototilt has improved energy and fuel efficiency with pressure-compen sating hydraulics in the tiltrotators and these tiltrotators meet the Open-S hydraulic interface standard. Customers who choose an RC tiltrotator without the QuickChange fully automatic quick coupler system will now have the ability to retrofit at a later date.
Takeuchi
Compact excavator
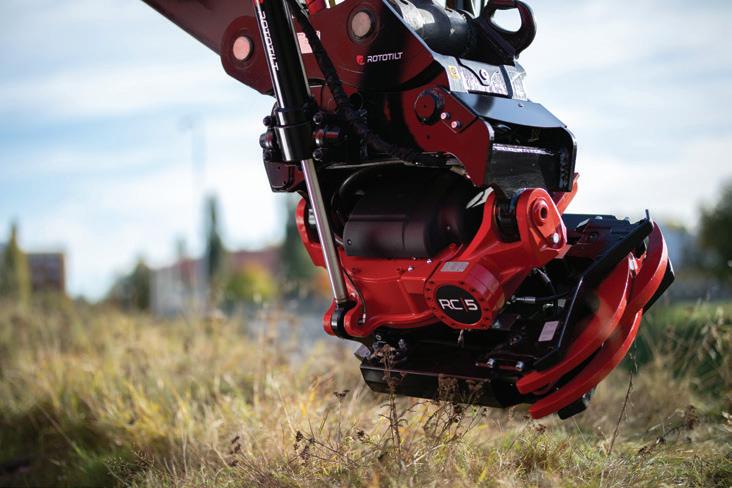
Takeuchi new-generation TB335R short tail swing compact exca vator delivers a rear overhang of only 3.1 inches over the tracks, making it ideal for working in tight or confined spaces. The cab model has an operating weight of 8,310 pounds (3,770 kgs.), a maximum bucket breakout force of 9,127 pounds (40.6 kN), and a maximum arm digging force of 4,290 pounds (19.1 kN). The exca vator is powered by an EPA Tier 4 Final engine delivering 24.4 hp (18.2 kW) and a maximum torque of 70.6 ft.-lbs. (95.8 Nm). Two work modes – Standard and ECO – allow operators to match the mode to the task at hand, choosing more power or fuel savings as desired. The TB335R’s cab includes a 7.0-inch touchscreen, multi-function colour display. Canopy models offer a 4.3-inch, high-definition, multi-function display. Both cab and canopy models have low-effort, pilot-operated joystick controls.
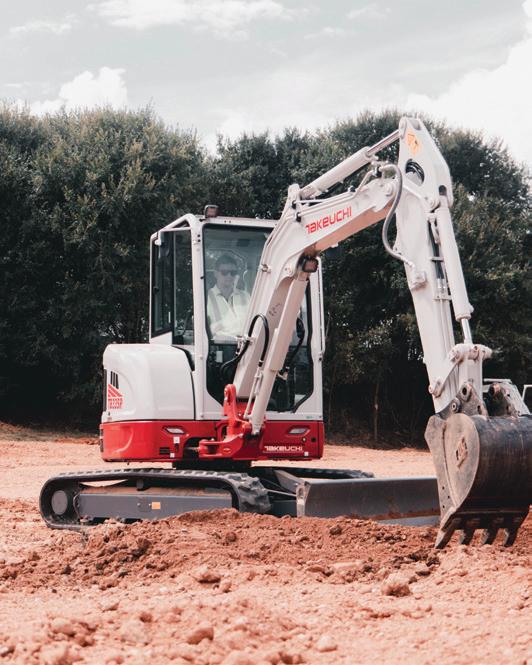
Komatsu
Haul truck
Komatsu’s rigid frame off-highway haul truck, the HD15008E0, is built for mining, quarry, and aggregate applications. The machine can handle 150 U.S. tons of material and features a 1,580 gross horsepower (1,180 kW), Tier 4 Final Komatsu SDA16V159E-3 engine. The redesigned cab, combined with a MacPherson strut-type and hydropneumatic suspension, gives operators a smooth ride. It is equipped with hydraulic, wet mul tiple-disc brakes on all four corners. The continuously cooled, large-capacity brakes also act as a responsive retarder. Downhill descent can also be controlled by setting a desired travel speed with the automatic retard speed control. With a tight turning radius (36 feet 9 inches), operators can maneuver in and out of close quarters. The truck has a seven-speed, fully automatic transmission with two configurable reverse speeds. Komatsu’s advanced transmission with an ideal modulation control system provides electronic shift control with automatic clutch modula tion, delivering optimized clutch engagement at every gear.
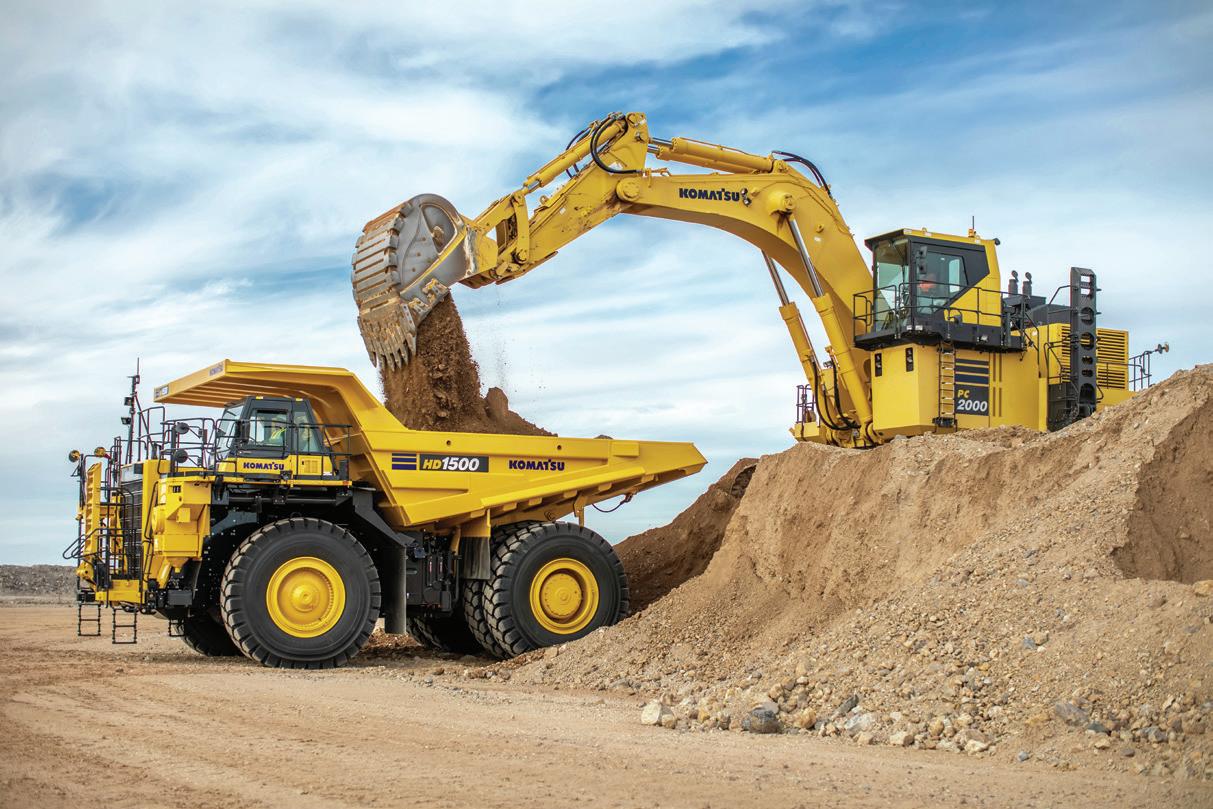
IN-DEPTH REPORT FULL-SIZE EXCAVATORS
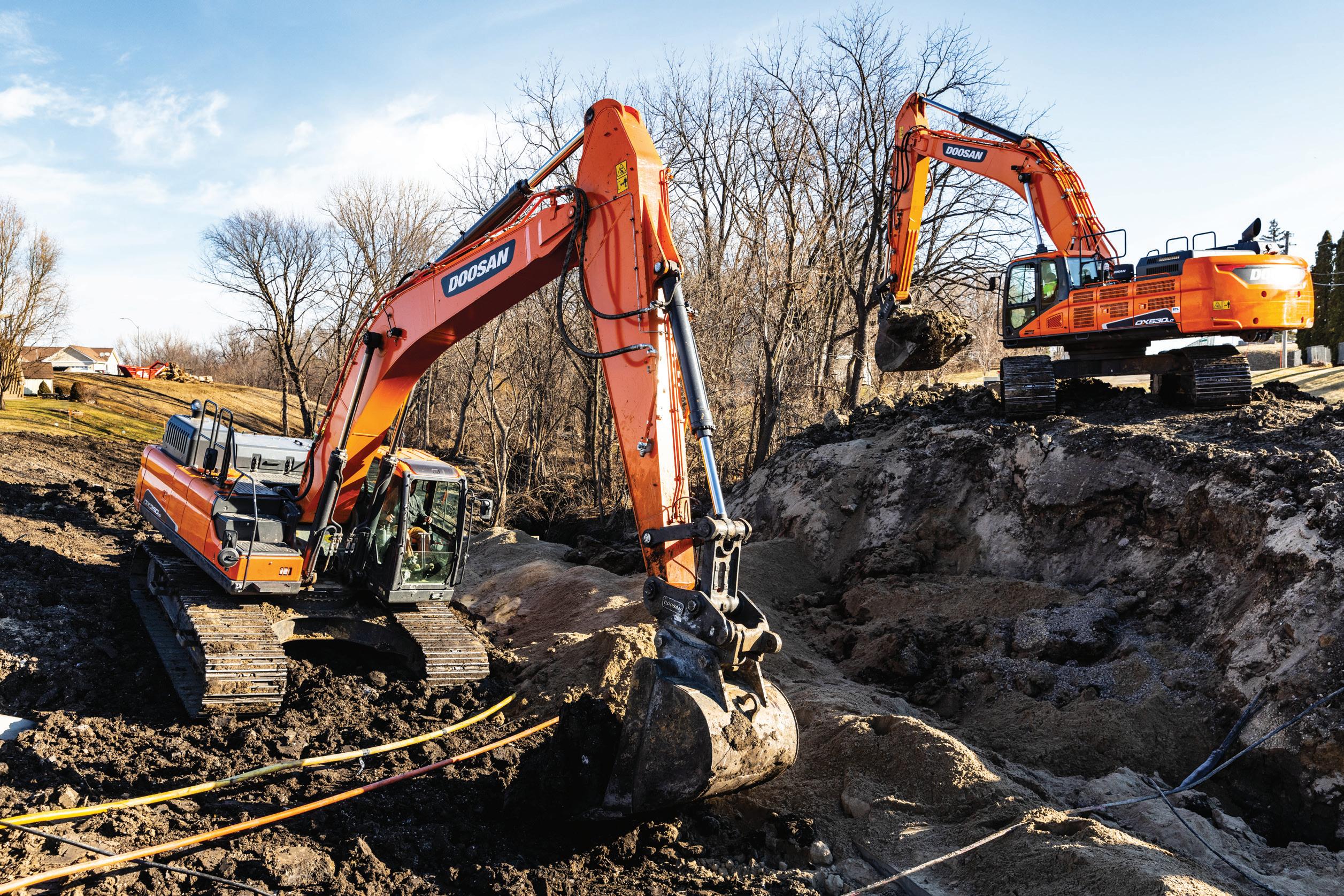
CHOOSING EXCAVATORS FOR SEWER & WATER PROJECTS
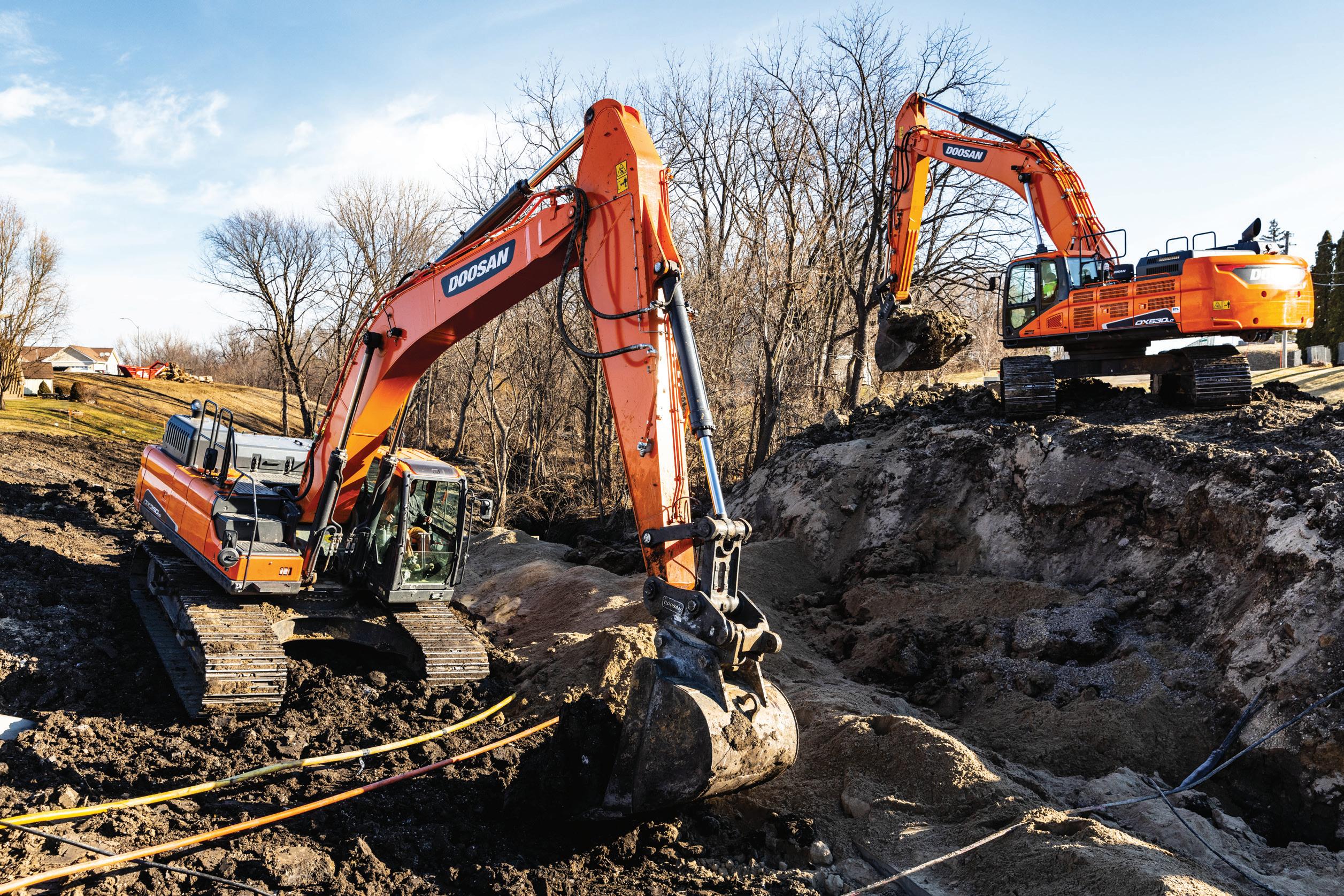
Sewer and water infrastructure, handled by municipalities and contractors alike, requires the right machinery to en sure that installation or repair is done quickly, efficiently, and in the safest possible manner. Trenching, lifting, grading –all of these applications are handled by excavators.
Heavy Equipment Guide spoke to a panel of industry experts to find out what buyers should think about when they are select ing an excavator for sewer and water work.
MATCH SIZE TO THE REQUIRED ROLE
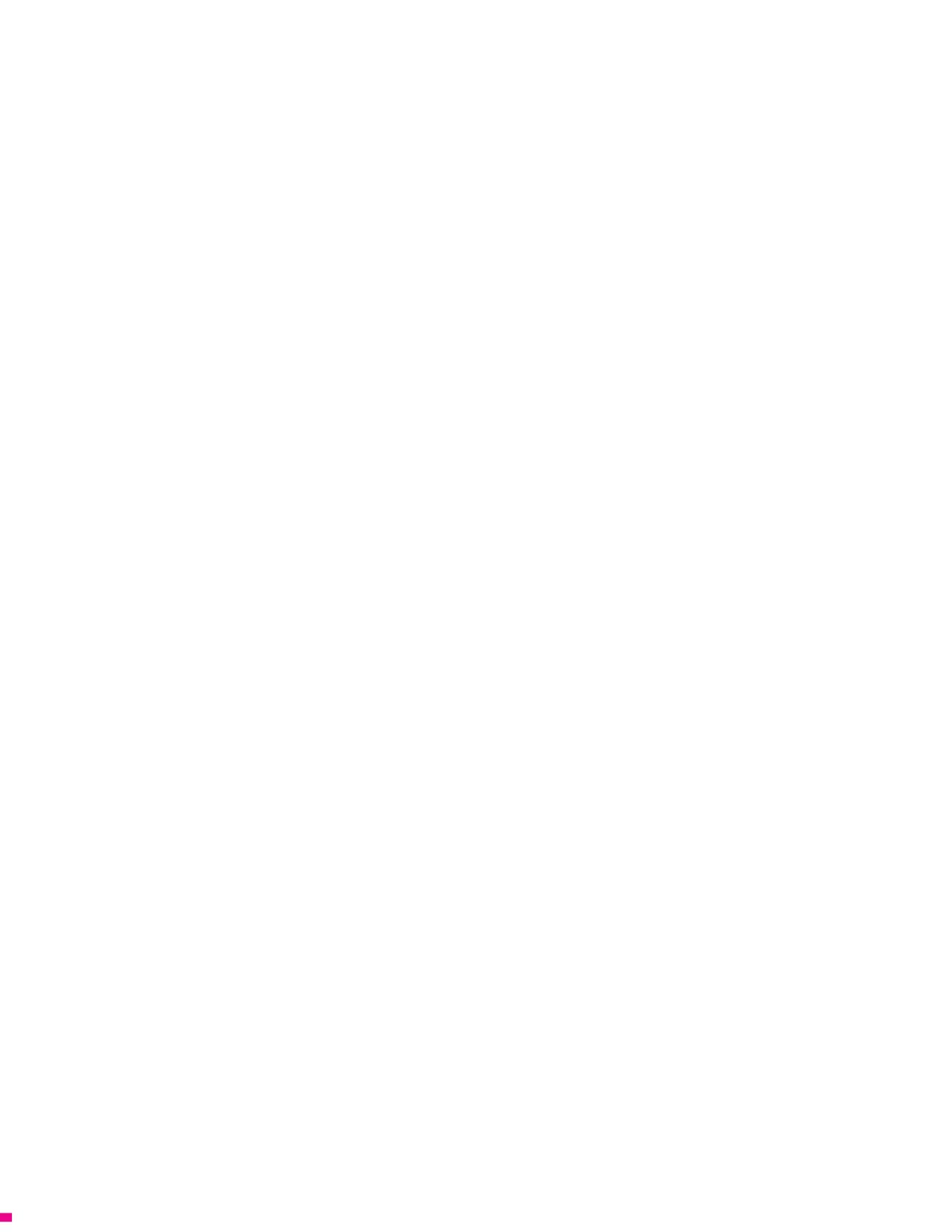
Of the many things to consider when picking an excavator, size is a key point for our experts – though the right size of ma chine will change depending on the overall needs of the buyer and their projects.
“Size can be dictated by a number of things,” says Kurt Mon cini, senior product manager with Komatsu. “For example, the size of pipe . . . or lifting capacity. Am I dealing with manhole risers? Am I dealing with concrete pipe, steel pipe, large pipe, small pipe – all those kinds of things.”
Depth of digging, size of pipe, and operational considerations all come to mind when choosing an excavator size, advises Sam Wagstaff, JCB product sales manager. Municipalities especially are likely to be purchasing machines for multiple uses, while keeping sewer and water work top of mind.
“If you’ve got to put so many feet into the ground per day, that could dictate the difference between a 50,000-pound and an 80,000-pound machine. I think that’s part of the reason you
spec’ing a machine.
Some contractors may go larger to dig more in less time where speed is a factor, according to our experts. Bigger ma chines can move a lot of dirt in many different situations, says Brett Mitchell, product sales support manager at Headwater Equipment, a Sany dealer in B.C. and Alberta. He finds that buyers in the utility pipeline sector are buying machines in the 50-ton range or larger because they prove more economical on many projects. Bigger machines moving dirt at a lower cost per yard also lend themselves to different approaches to trenching, such as benches that allow smaller machines to dig deeper.
In the end, the choice of configuration comes down to evalu ating the jobs to be done, advises Ryan Neal, market profession al with Caterpillar.
“I was with a customer using one of our 374 Next Gen ma chines with our longer fronts, and they’re digging 30 feet deep – they need one of the larger excavators to move the amount of dirt, the depth, and the size of the trench box needed,” Neal says.
Manufacturers offer a variety of stick and boom lengths, notes Trevor Hoff, Liebherr-Canada Alberta sales representa tive. Liebherr, for example, offers five different stick lengths and four boom options for a six-metre spread in dig depth.
Longer reaches, however, can cause issues with weight, says Doosan Infracore North America Senior Product Specialist Joel Escalante. Buyers should be aware that the addition of specialized attachments and universal quick couplers can weigh down the arm and unbalance the ma chine when that longer reach is used.
If you’ve got to put so many feet into the ground per day, that could dictate the difference between a 50,000-pound and an 80,000-pound machine. I think that’s part of the reason you see contractors doing these bigger pipeline jobs jump into the bigger excavators.
Sam Wagstaff Product Sales Manager, JCBsee contractors doing these bigger pipeline jobs jump into the bigger excavators – they’re going to get more feet in the ground per day,” he adds.
“The name of the game is always keeping the excavator as small as possible, while still being able to do the work that it needs to do,” says John Deere Solutions Marketing Manager Justin Steger. Utility contractors tend to buy 21- to 35-metric-ton machines, in Steger’s experience, though that changes depend ing on how deep the pipes are buried.
Review the machine’s geometry and determine how deep it can dig a level bottom to ensure it will work for the jobs it will perform. Moncini, for example, advises that an eight-foot trench bottom is often an ideal dig depth to keep in mind when
A shorter tail swing machine can also be a benefit for buyers in this sector, but again its capacity must be reviewed to ensure it fits the needs of the job. Patrick Baker, product manager, large excavators with Hitachi Con struction Machinery Americas, says shorter tail swings work well along roads or highways, as well as in new construction where there are many machines in a small space.
QUICK RESPONSE, LIFT, AND DIGGING ALL IMPORTANT
Beyond size and general configuration, there are some important capabilities that can be considered for excavators being tasked with water and sewer work.
Hoff says buyers should keep several things in mind: machines should be quick and re sponsive, while providing the lift and digging capability that best fit the job. Hydraulic systems are key, and Hoff notes that the Liebherr machines encourage multifunction capability with a three-pump system for fast operation.
Wagstaff agrees, noting that all excavators can dig holes, but finding the right mix of weight, features, and capacity is what makes the difference on the bottom line.
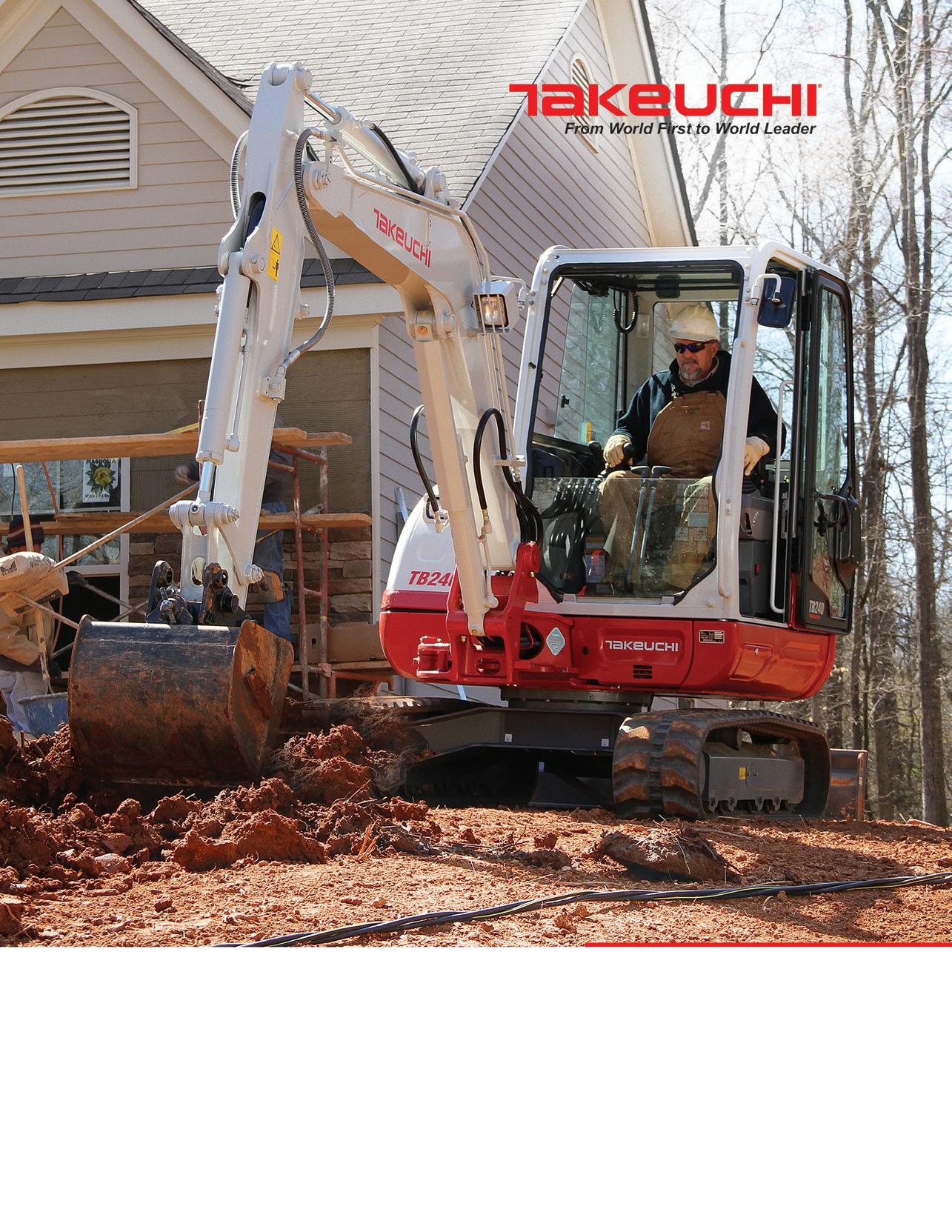
The type of soil to be moved and the general location where it will be operating can also be a deciding factor in picking size and features of an excavator for underground work, Neal sug gests. Digging in a city, for example, means avoiding existing infrastructure, requiring a nimble machine.
For Steger, power is important, not just for digging and mov ing material but for manipulating other items.
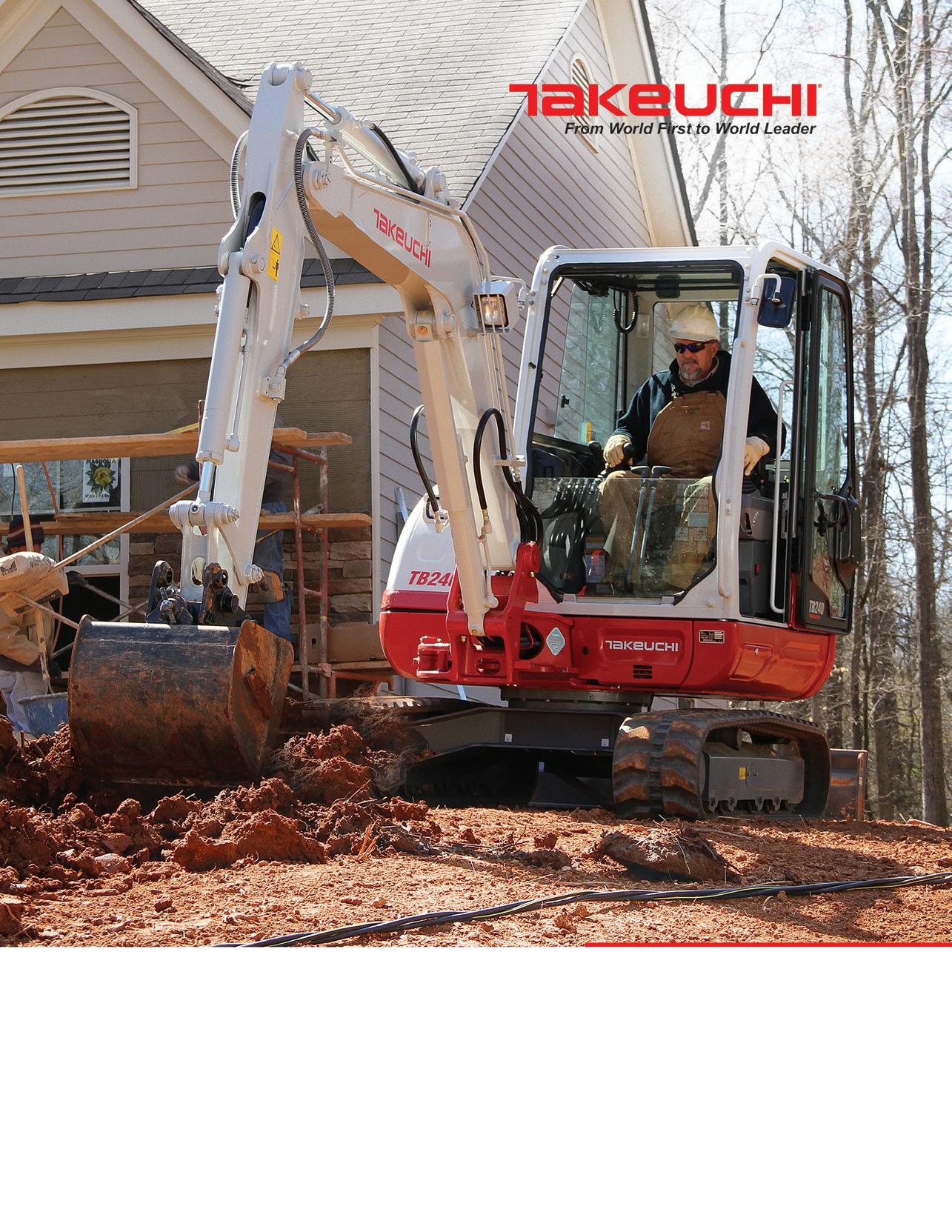
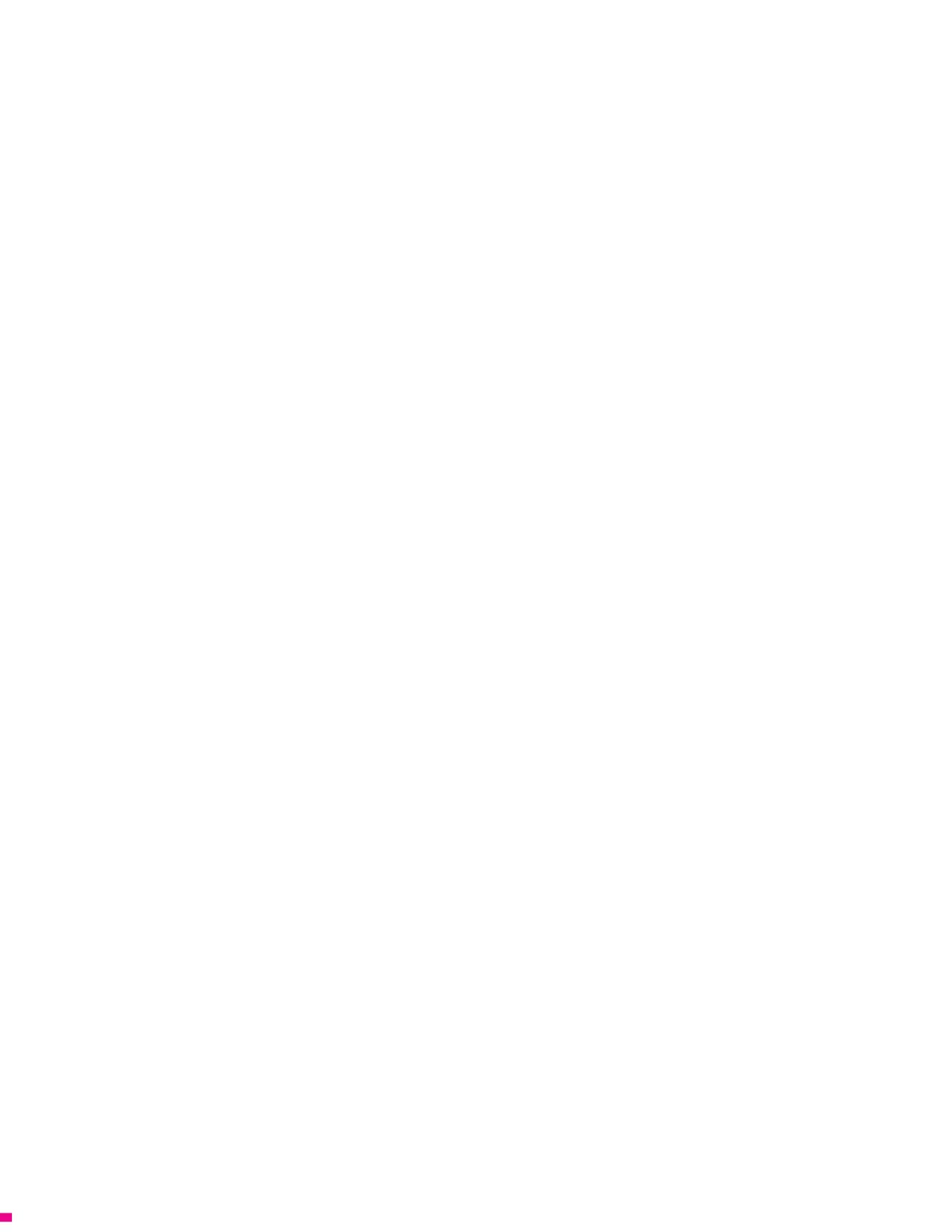
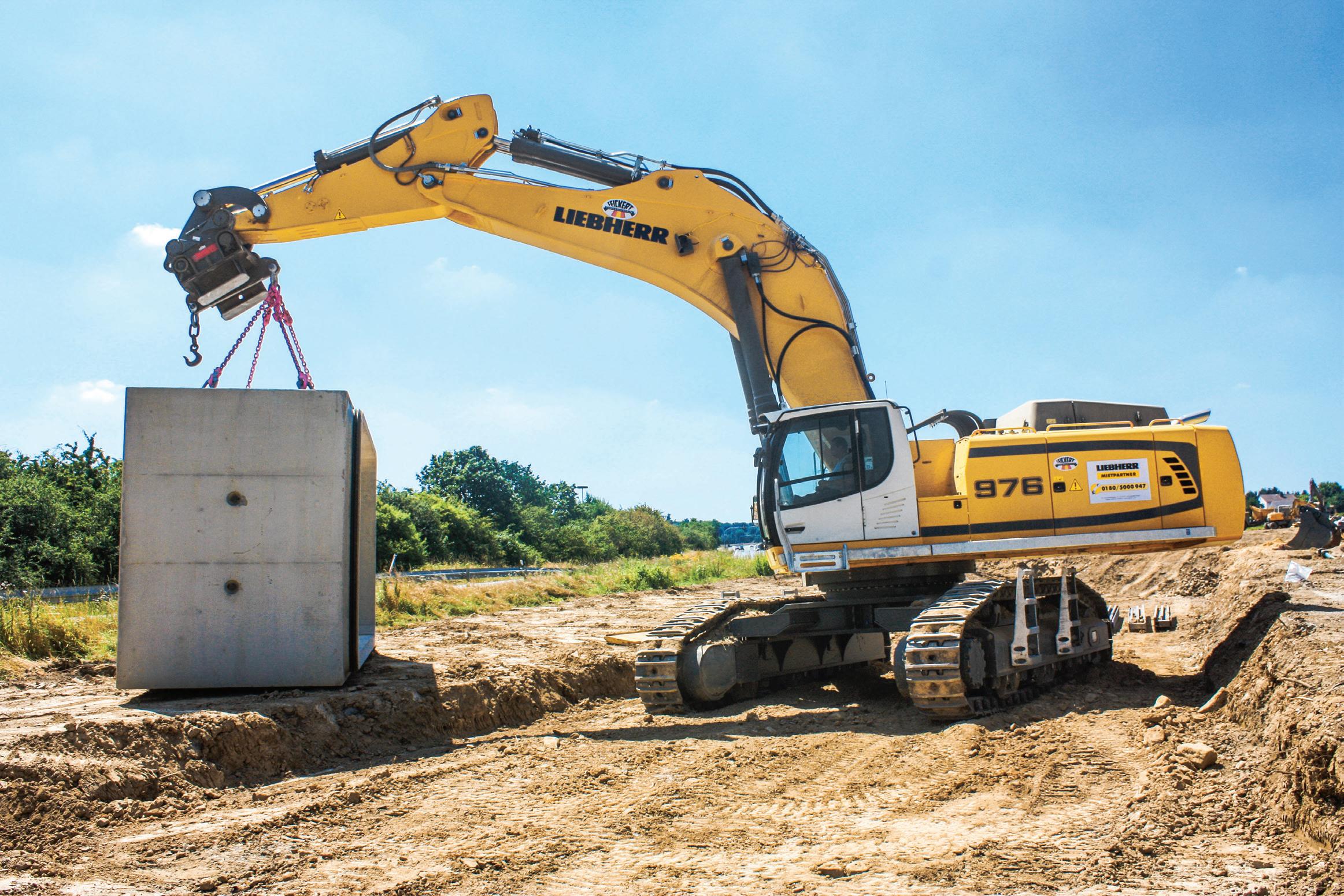
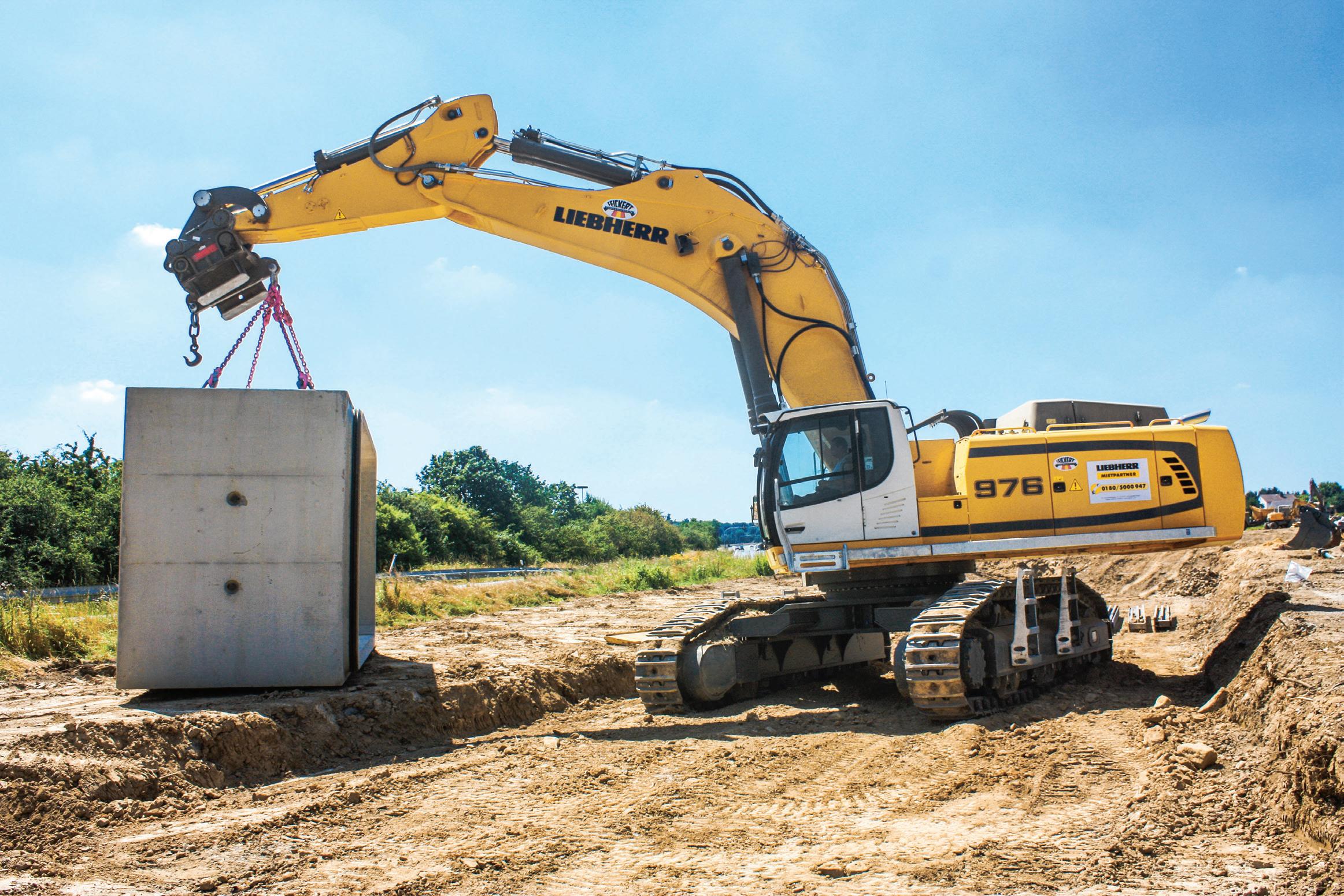
“Typically trench boxes are going to be set up at roughly 48 inches or narrower, and your bucket’s going to be sized accordingly if you’re digging the narrowest possible trench to eliminate extra digging,” he notes. “Think about pulling that trench box through the tight, not exactly perfect walls of that trench . . . Sometimes it can take quite a bit of power to pull through.”
Attachment versatility should be considered, and Escalante points to the growing use of tiltrotators.
“With a tiltrotator, it allows the machine to do much more because you don’t have to move the machine around. If you’re doing, for example, a manhole, because you want to reach down to the sewer or water, with a standard machine you would have to move the machine around, but with a tiltrotator you don’t have to reposition,” he explains. Mid-sized excavators pair well with tiltrotators, but buyers need to keep hydraulic capacity in mind.
As an underground utility contractor, I get paid for the amount of feet of pipe I lay in a day – if I can lower my cost per foot of pipe, I can potentially make a better margin, I can reduce my bid, I can do a lot of things.
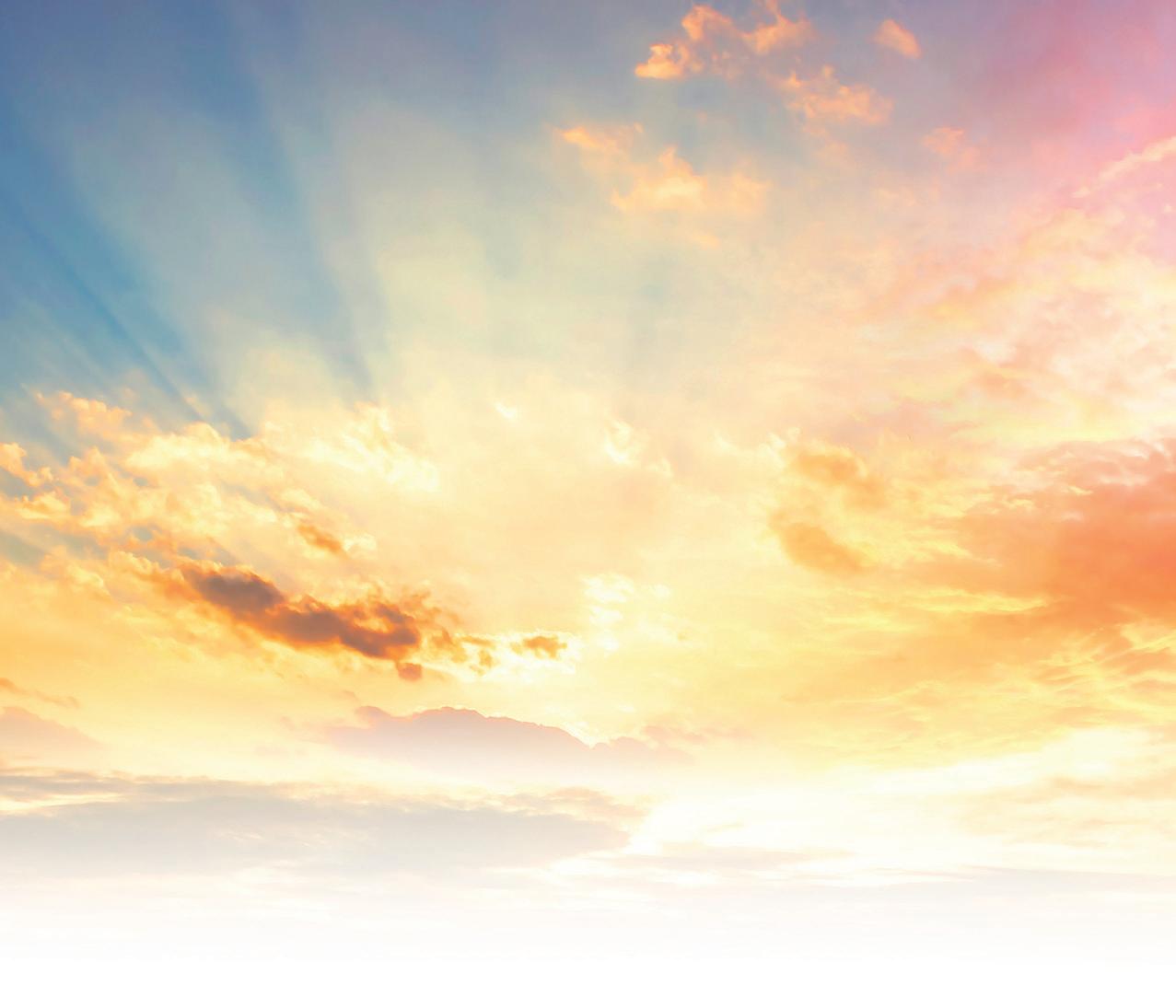
Hydraulic quick couplers should also be part of the consider ation. Mitchell and others note that being able to switch from one bucket to another quickly adds efficiency and also plays into the machine’s overall lifting capacity.
LIFTING PIPES, TOOLS, AND MORE IS PART OF THE JOB
Using excavators in place of a crane requires precise knowl edge of the weights involved, the lift chart of the machine, and many other factors.
Moncini emphasizes that buyers need to know the over-theside lift capacity of any excavator they are considering, as it is often a limiting factor on the job site when moving material or equipment – a lift may be successful over the front of the machine, but then if the operator needs to swing it to the side,
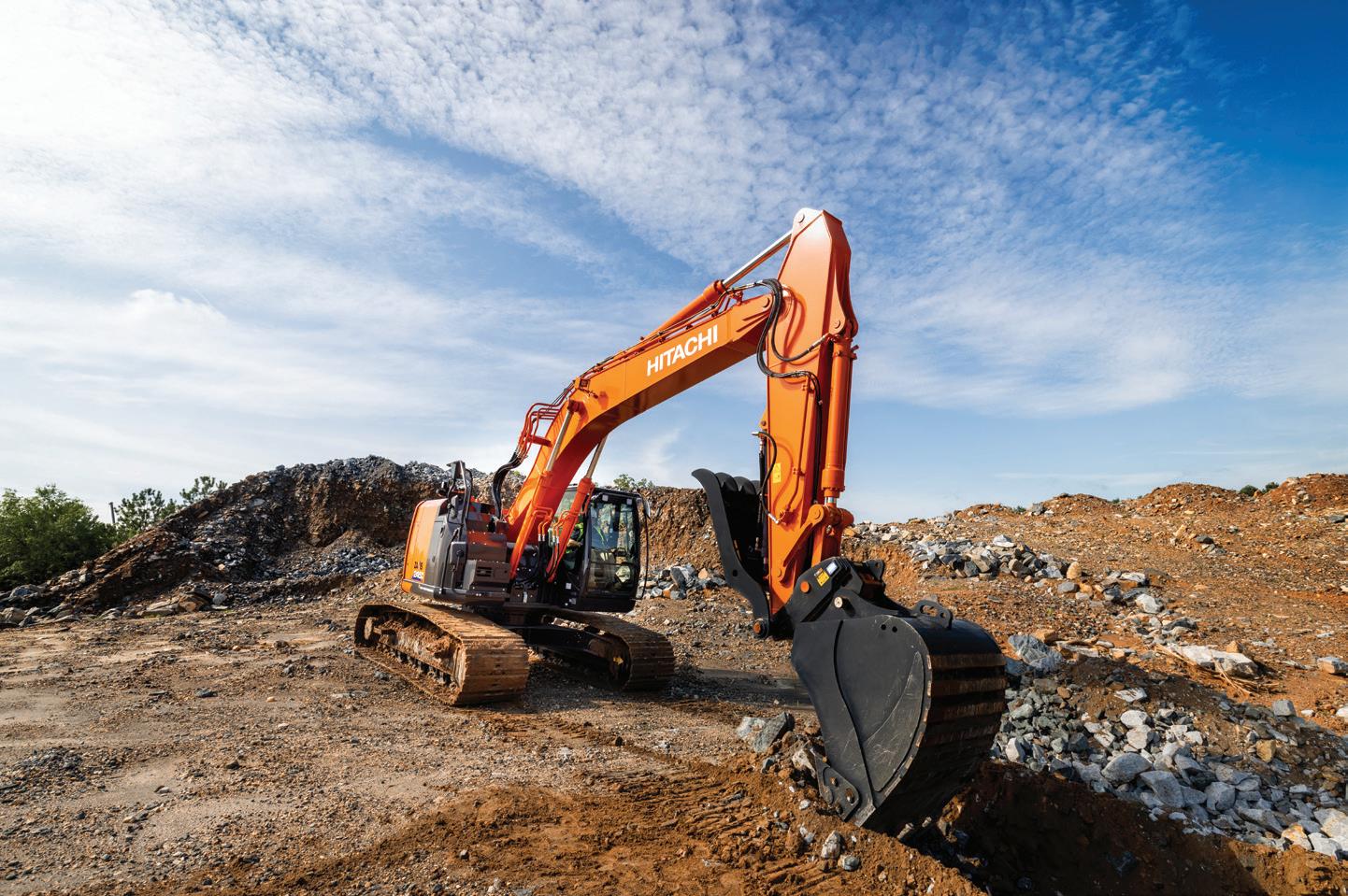
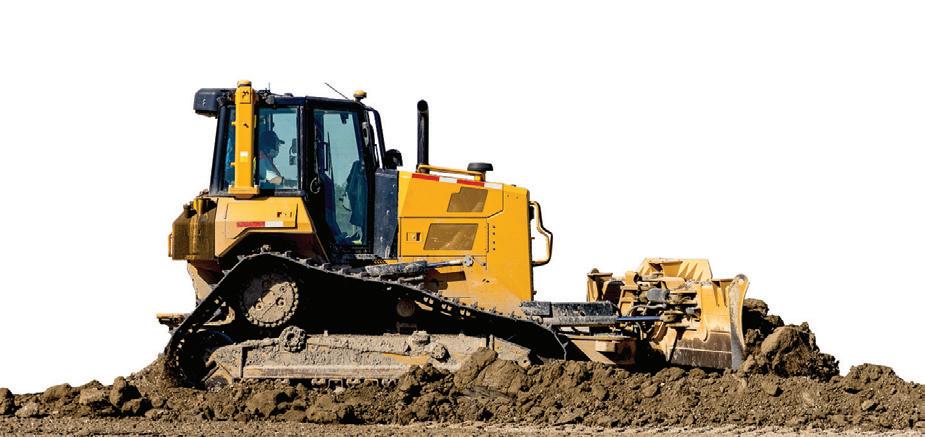
EASY LIKE MONDAY MORNING
SCAN HERE
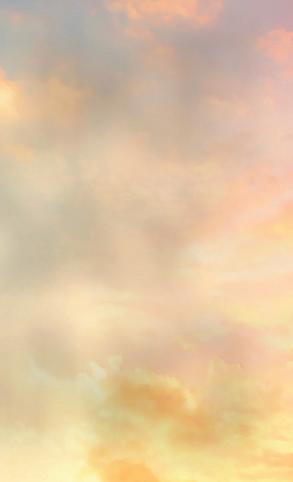

We make machine control that easy. MC-Max simplifies earthmoving and ensures a common operator experience regardless of make or machine. Every day of the week.
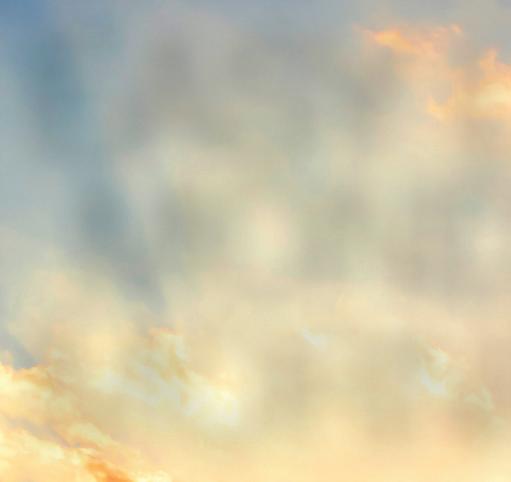



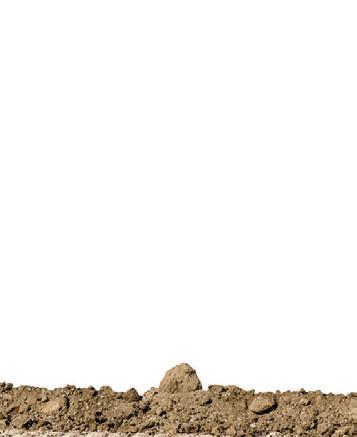
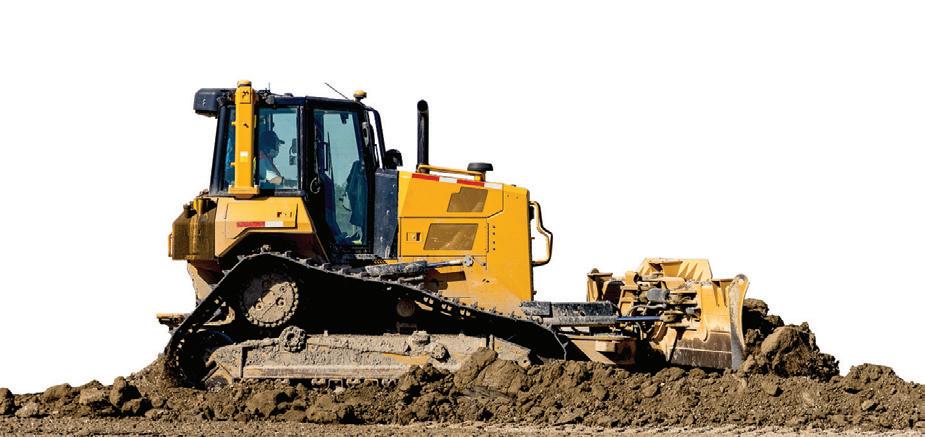
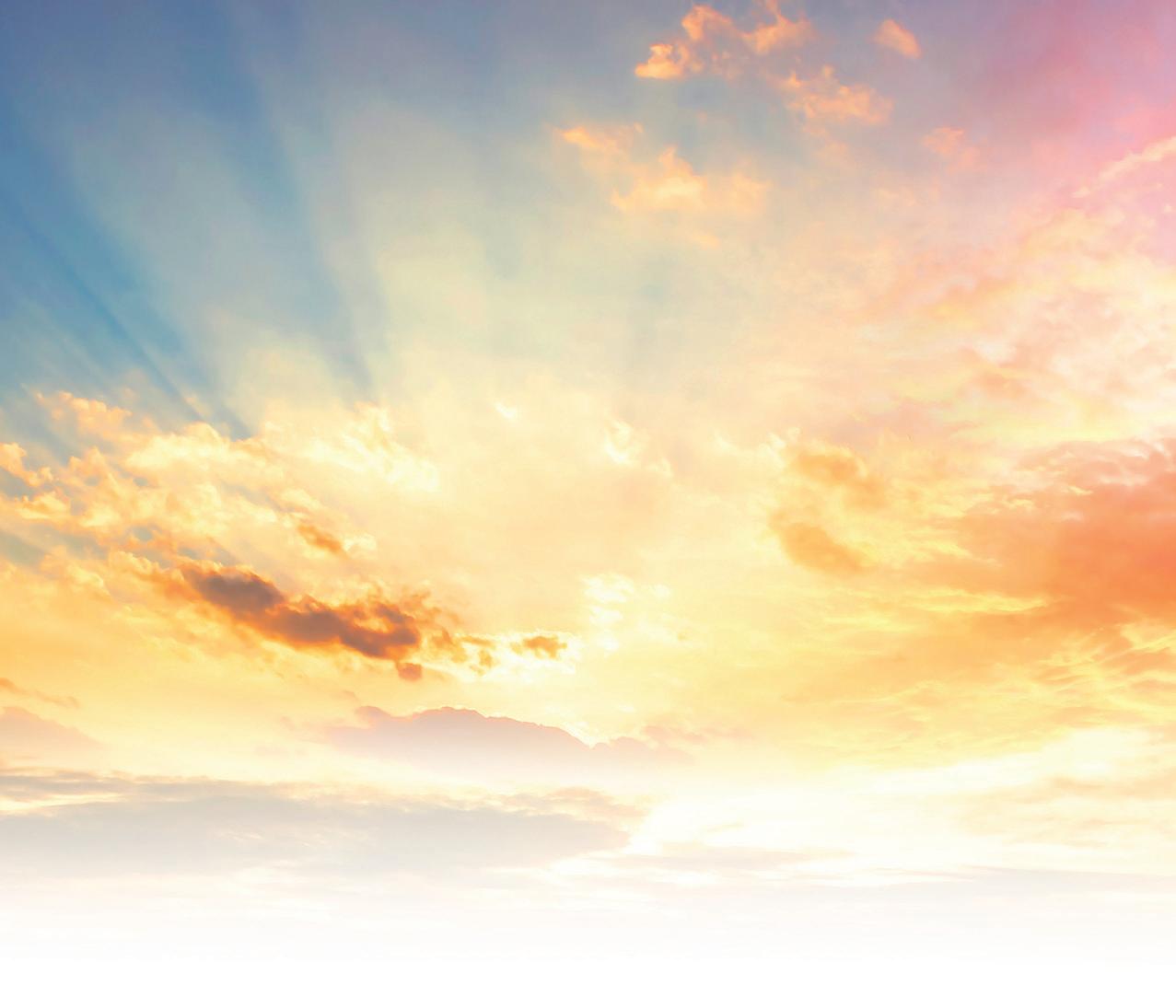
they may find it exceeds the side stability.
It’s also important to understand the proper use of the lift chart and how to adjust it based on the attachments being used on the excavator. If the bucket is not taken into account, users need to calculate that into the weight being moved. In addition, things like quick couplers change the capacity and must be calculated in – but also allow the bucket to be dropped quickly to save that additional weight at the end of the arm.
“This is why quick couplers are so predominant . . . I can easily drop my bucket, perform my lift, then get my bucket and go digging,” Steger points out.
How to lift is as important as how much to lift when it comes to rigging out an excavator, he also points out, and buyers need to ensure that the rigging they intend to use is also certified for the weights that it will be called on to handle.
A knowledge of what the excavator will be moving is neces sary to ensure it can handle the job, Neal advises.
“If you have a heavy concrete structure, a large manhole, or whatever it may be, if the excavator can’t lift it, it’s not going to do you any good,” he said. Weight can differ depending on the type of pipe, whether it’s steel ductile pipe or concrete, and the width of the pipe to be placed – these are all aspects that need to be kept in mind when calculating lifting capacity.
From a power perspective, excavators that have specific operating modes for lifting work are beneficial for this type of work. Wagstaff says JCB’s dedicated lifting mode provides added power for the lift while managing a number of other actions.
“You’re doing very delicate precision work – you don’t want auto engine shutdown engaging, you don’t want auto idle to en
gage. Sometimes you have to sit there and wait while the guys are in the trench,” he says. “When you do need to move that pipe, you want the power exactly where you left it.”
Buyers should look for machines with hydraulic systems that are able to handle the pressures of lifting, Baker points out. High-performance hydraulics such as Hitachi’s TRIAS 2, which features three pumps that serve individual actuators, help put more power into heavier lifts and aid in multitasking during lifts.
Even when the operator is aware of the load and lift chart, overloads may happen. Overload warnings, an option on Lieb herr excavators, can help, Hoff notes. “You can set the excava tor to lifting mode, and it will reach 75 percent lifting capacity, then sound an alarm and let the operator know, so you aren’t putting anyone in danger in the trench.”
KEEPING WORKERS SAFE IN THE TRENCH
Safety considerations on excavators can encompass ev erything from the overall design concept of the machine to optional technology additions that aim to protect operators and others nearby.
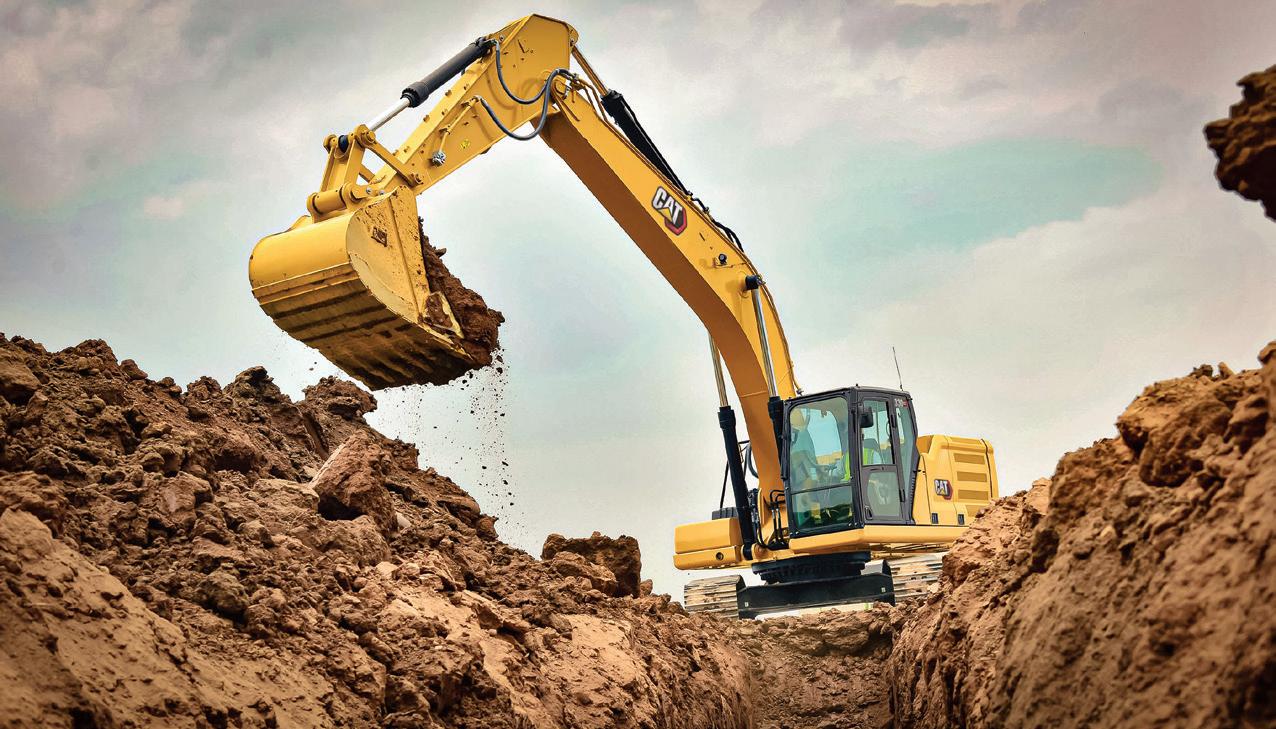
“There’s always at least one person in the trench at any given time . . . maintaining eye contact on the job site is really, really critical. If they can’t see you, you can’t see them,” Steger points out. Hand signals are used frequently on trenching jobs, so it’s important to have that visibility. In many cases the operator will want the front windows of the machine or the door open when working closely with a crew.

WHEN YOU WANT TO IMPROVE PRODUCTIVITY
Choose ESCO® Buckets with Nemisys®

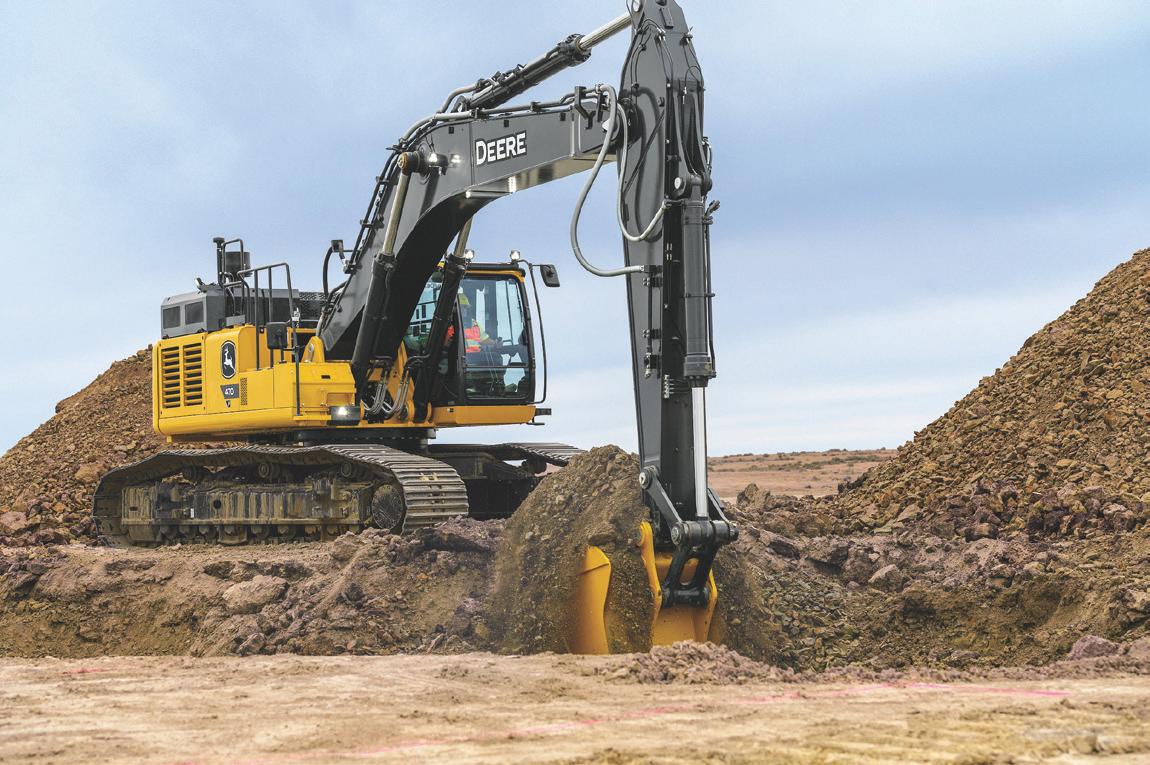

Design for visibility encompasses more than just window size – it includes small things, like window screening
protect against rock chips being thrown up during hammering, or sun shades to block glare. Lighting packages are also import ant, and today’s LED lights are becoming key to added safety around operating equipment.
“The LED light systems now are fantastic – we do different lighting packages, and you can go all the way up to one that gives you 20-odd lights on the machine,” Wagstaff says.
Cameras are also an important part of safety precautions, and for infrastructure projects the newest options that provide a broad field of view around the excavator are ideal. Bird’s-eyeview cameras are becoming popular, as they give the operator much broader awareness of where other workers and machines might be around them. Moncini describes the Komatsu system as providing indicators on its bird’s-eye views showing the swing of the counterweight, as well as a cautionary area, giving the operator a better indication of where potential hazards might be in relation to their excavator.
BETTER MANAGE
LOADERS SCALES


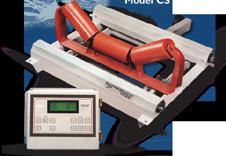

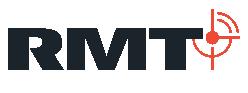


Doosan adds an ultrasound sensor system that comple ments its area view, Escalante says. “If the operator is getting too close to a structure or someone comes in toward the machine, the system will beep an alarm to let him know.”
There are a number of mechanical features that improve ex cavator safety in operating areas especially useful for sewer and water work. Hydraulic hose rupture prevention systems can be beneficial in reducing potential dangers.
“If you blow a hose or a hydraulic line, it locks that system so you don’t lose control of your stick or boom,” Hoff explains. “If there’s a rupture, you’re not going to have anything fall to the ground or into a hole – it will hold its place.”
Technology has its own role to play in improving safety, with many manufacturers including Caterpillar offering features such as e-fences that keep excavators in a specific location and operating area, important when working in tight spaces.
“We can prevent the machine from swinging too far to the left, or too far to the right, booming up or down too far, or even sticking out too far,” Neal explains. “If we can prevent an exca vator from getting close to a power line by physically stopping it, that is a great safety aspect keeping the machine, and most importantly people, out of harm’s way.”
ONBOARD TRUCKS SCALES
[Machine control is] going to be the way of the future – we have young operators who are inexperienced, but now are responsible for these high-dollar jobs. Anything you can do to take the human error out of it is increasing profitability.
GRADE CONTROL AND OTHER TECHNOLOGIES ADD EFFICIENCY
Technology has brought great advances to the industry in the form of grade control systems, which our experts agree are ideal for pairing with excavators in the sewer and water sector.
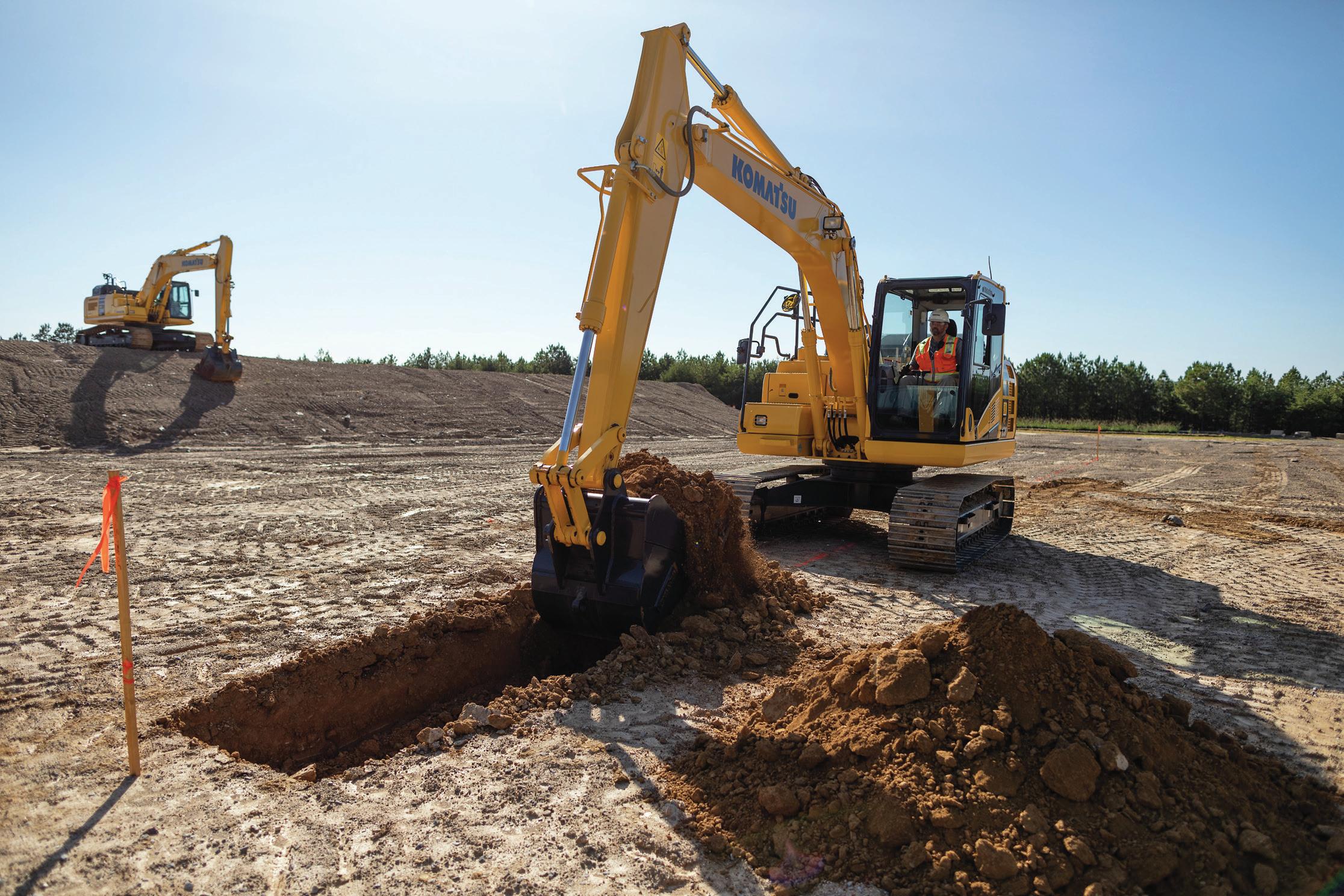
“It’s becoming really key in underground utility to have machine control. I want to minimize any overages on bedding materials or aggregates, and the best way to do that is exca vate to the correct depth and grade the first time,” Moncini describes.
Overwork and reworking on an infrastructure job can be costly and time consuming. The use of grade control in these jobs not only reduces the number of workers on the ground near the machine by eliminating the need for the grade check er, but also reduces potential errors.
“As an underground utility contractor, I get paid for the amount of feet of pipe I lay in a day – if I can lower my cost per foot of pipe, I can potentially make a better margin, I can reduce my bid, I can do a lot of things,” Steger describes. “Eliminating that over-excavation saves time, it saves rework, and it reduces the amount of bedding material. Every penny counts.”
Long, gradual slopes such as those needed for sewer work call for the growing use of grade control, Escalante notes, to improve efficiency overall on the job. Allowing the machine to handle much of the work rather than relying on survey stakes and ground workers to get the slope right makes life easier and reduces the potential for errors and rework.
Advanced grade control systems that can import digital job site maps and plans also add a level of safety, especially when they incorporate municipal data to identify potential problem spots below ground; it’s now possible to set bound aries for machines to dig within and prevent those potential conflicts.
Mitchell says that he expects to see continued growth in the use of grade control systems as newer operators move in, especially with a growing number of OEM and aftermarket op tions. “That’s going to be the way of the future – we have young operators who are inexperienced, but now are responsible for these high-dollar jobs. Anything you can do to take the human error out of it is increasing profitability.”
If you have a heavy concrete structure, a large manhole, or whatever it may be, if the excavator can’t lift it, it’s not going to do you any good.
Ryan Neal Market Professional, Caterpillar
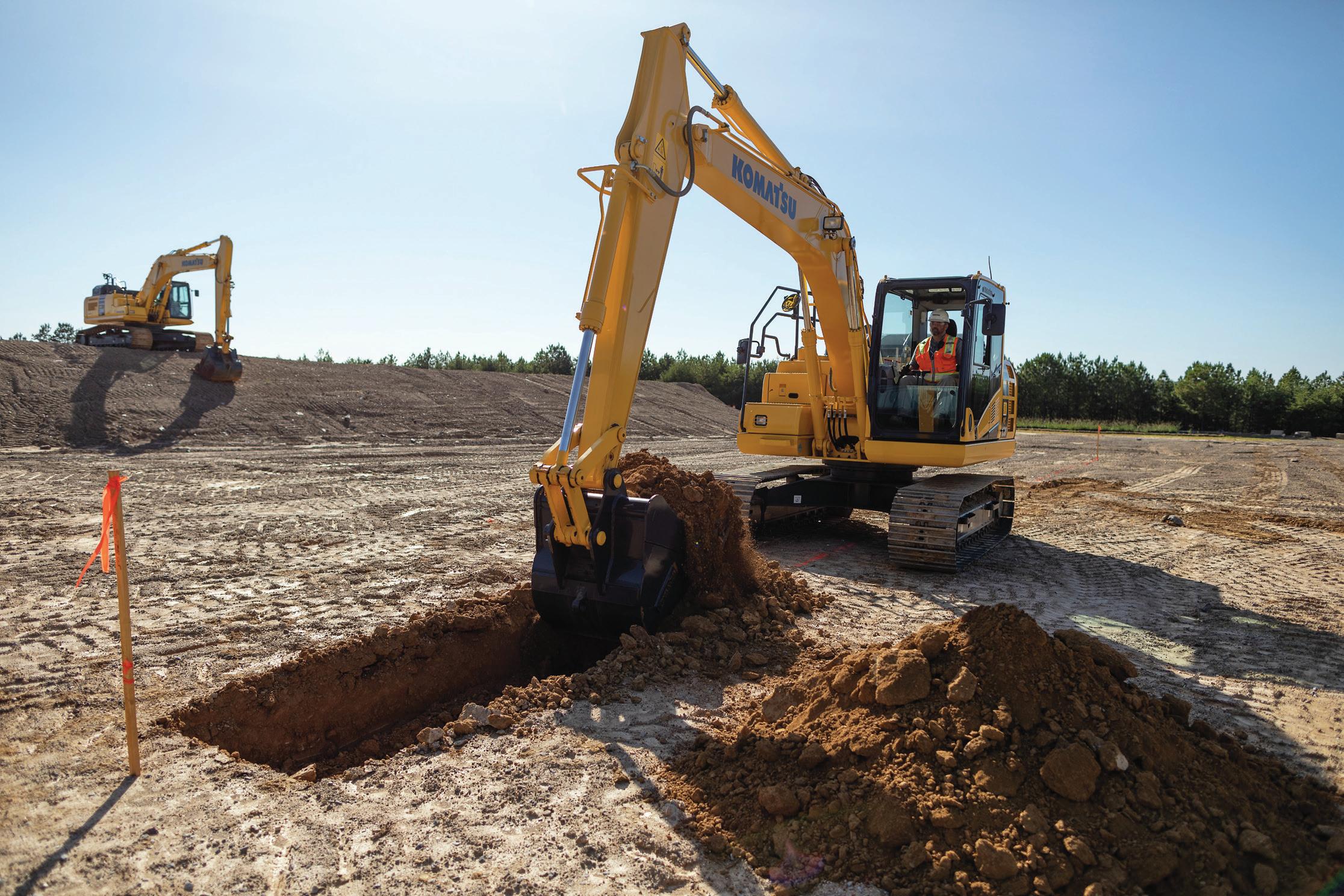
Technology reaches beyond grade control in excavators, however, with engines, hydraulics, and other systems adding efficiency. Hoff notes that improved engine technologies have helped Liebherr meet Tier 4 Final emissions requirements without the use of DPF or EGR systems on its equipment, as well as expanding oil change intervals to reduce maintenance time and costs.
Telematics systems can monitor a variety of machine condi tions, and are beneficial for sewer and water as well as other operations. Hitachi machines feature ConSite OIL, Baker says, which tracks the oil and hydraulic systems. “You get a monthly report to see how efficient the machine is, so it’s a great way for the owner to sit down and analyze the report to see what they could be doing better,” he notes.
Finally, payload systems are also beneficial for infrastructure work, especially when excavated dirt must be moved off site in trucks, Neal says. Tracking the material that is moved into trucks means less likelihood of overloads that can end up being ticketed, while also adding data that can be used for improving efficiency over time.
Underground utility installation and maintenance requires machines that are quick, efficient, and capable. When buying an excavator that will be used on sewer and water projects, it’s
important to know the requirements of the job, consider the machine size needed, the dig depth and lifting capacity, the technology that will make it more efficient, and safety options to keep operators and others on the job site safe. HEG
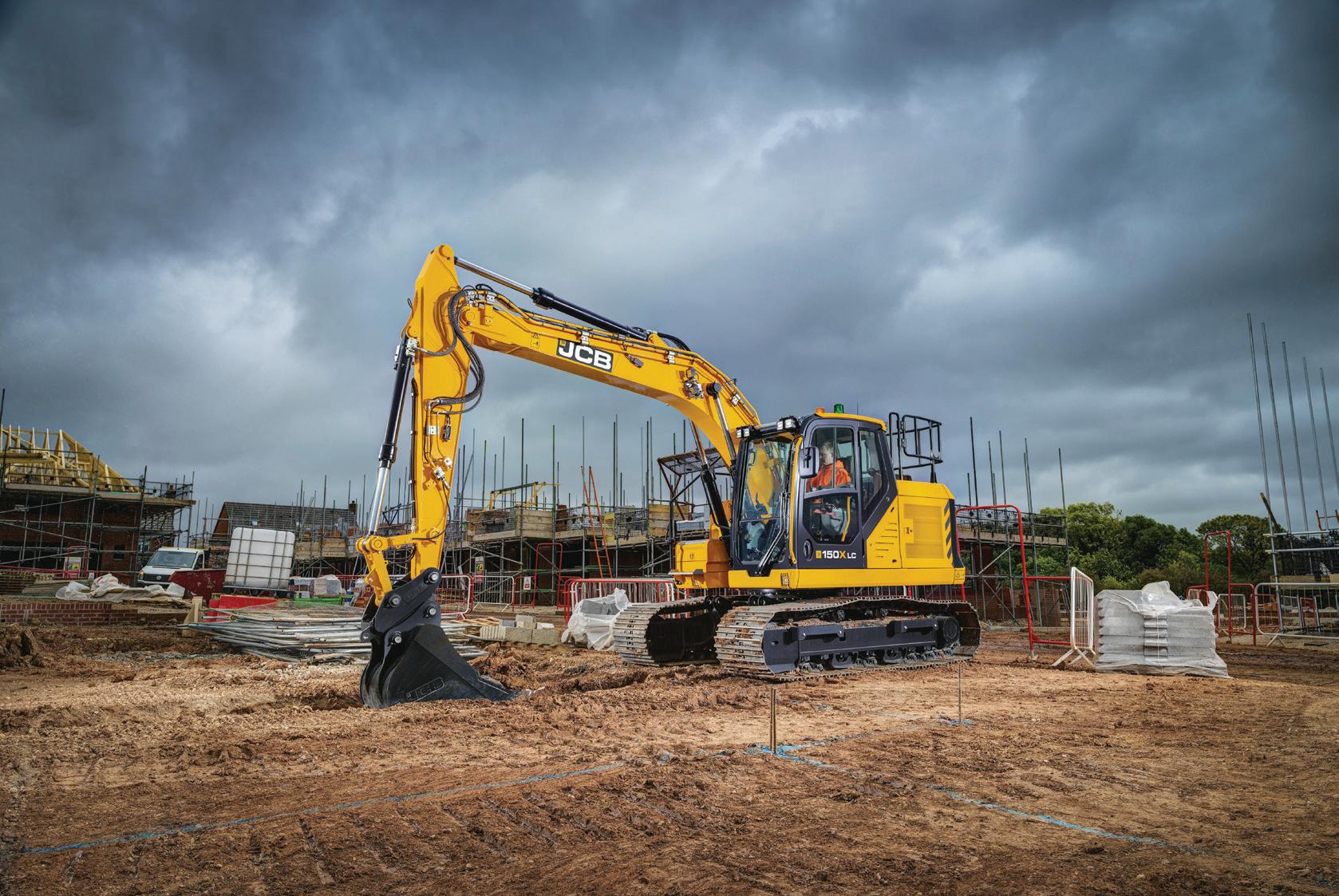
It’s becoming really key in underground utility to have machine control. I want to minimize any overages on bedding materials or aggregates, and the best way to do that is excavate to the correct depth and grade the first time.
Kurt Moncini Senior Product Manager, Komatsu
Tougher made smarter
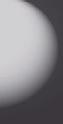
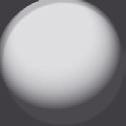
On the jobsite you need a truck that’s tough, safe, and smart. So, we built the new Volvo VHD to be the best-looking, most rugged vocational vehicle in the industry, packed with innovative ideas like Volvo Active Driver Assist and the revolutionary Volvo Dynamic Steering. Your toughest jobs just got easier.
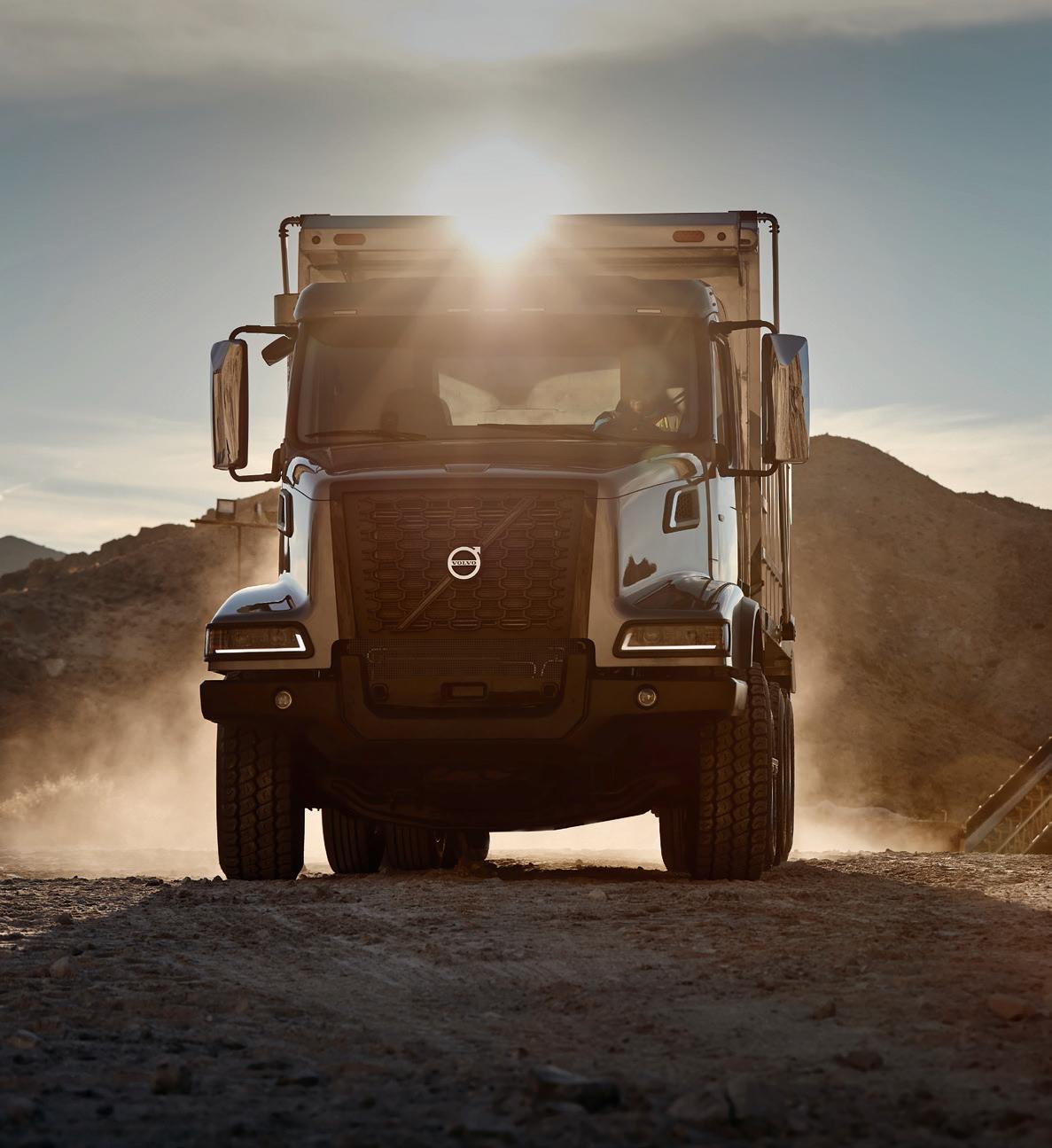
Learn more

HIGHWAY EXPANSION KEEPS MOVING WITH MOBILE CRUSHING STRATEGY
UPGRADES TO ONTARIO’S HIGHWAY 401 ARE BENEFITTING FROM ON-SITE AGGREGATE RECYCLING AND CRUSHING
BY LEE TOOP, EDITORThe stretch of Ontario Highway 401 running through the Greater Toronto Area is the busiest piece of highway in North America and has been an ongoing point of con gestion for drivers. An expansion project currently underway will add lanes and capacity to the highway, focusing on 18 km through Mississauga and Milton. In that segment of the high way, the six-lane road will be replaced by 10 to 12 lanes, plus HOV lanes, support facilities, and more features.
West Corridor Constructors, a consortium of Aecon, Parsons, and Amico, is the contractor overseeing the expansion work. Part of its goal was to ensure efficient construction and a re duced impact on the environment; to meet this goal, WCC has taken a unique approach to aggregate supply and reuse by opt ing to use on-site crushing and recycling with equipment that, instead of being placed in one location and served by trucks, moved along with the project as construction continued.
WCC worked with the Ontario branch of Frontline Machin ery, a Canadian dealer specializing in mobile and portable ag gregate processing equipment, to select the right crushing and screening equipment for the project, and then collaborated on training and maintenance to ensure the successful completion of aggregate crushing and supply for the project.
EXTENSIVE PLANNING RESULTS IN EFFICIENTLY PRODUCED IN-SPEC PRODUCT
For this large-scale highway project, it was obvious that WCC would need vast amounts of material to support the con
Harrie Van Dyk Construction Manager, Amico Infrastructures Inc.
struction. According to Harrie Van Dyk, construction manager with Amico Infrastructures Inc. – West Corridor Constructors, the decision to consider on-site crushing was reached early and set off a lengthy planning process.
“The project, from a design and construction perspective,
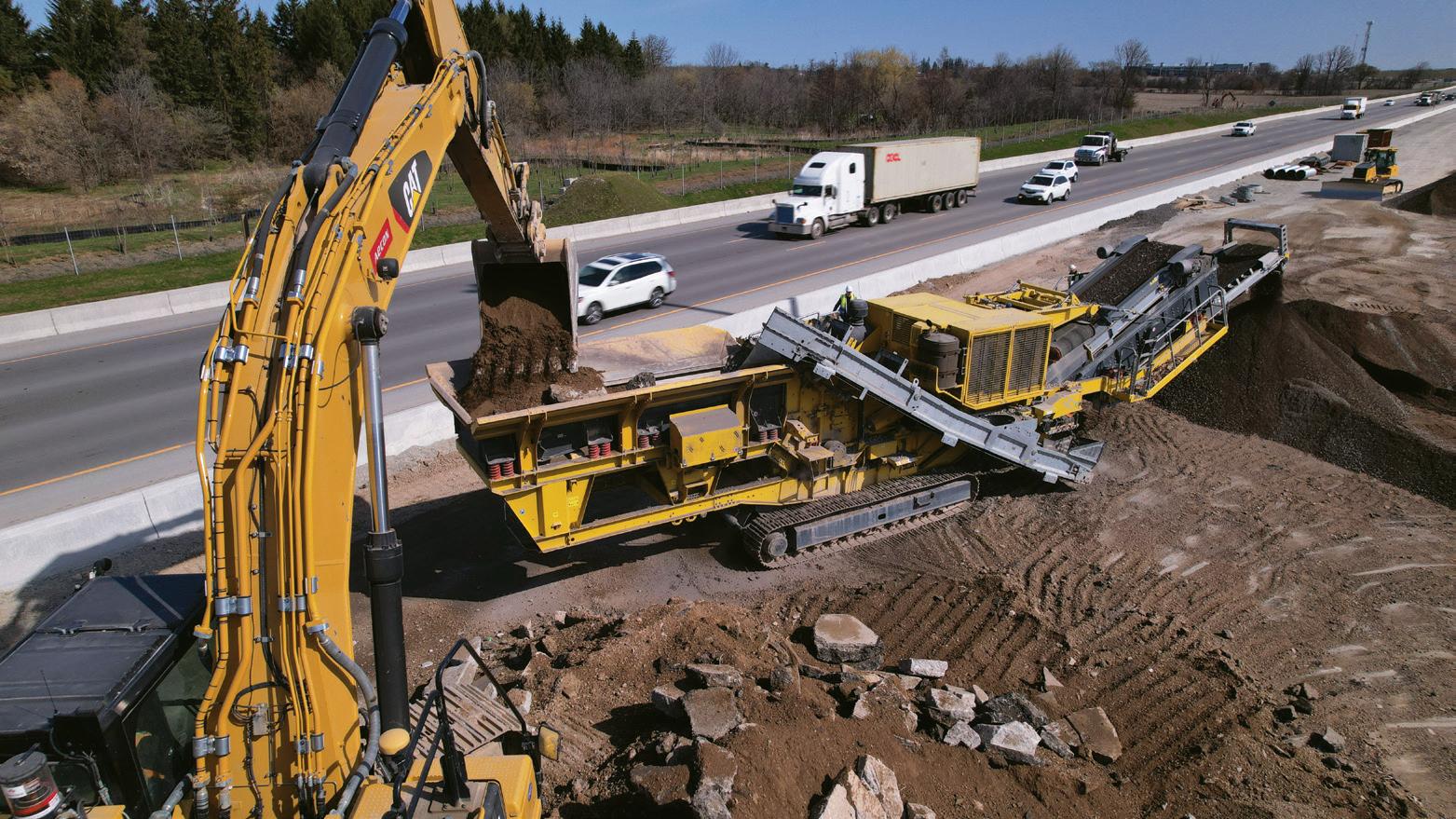
The last thing we wanted to do was start filling quarries and landfills with asphalt, concrete, and rebar. One thing we demonstrated early through our demos with Frontline is that we could produce a product and that the output product was going to meet the needed specification.
THE HIGHWAY 401 EXPANSION PROJECT REQUIRED MONTHS OF CRUSHING WORK DONE WITHIN THE MEDIAN OF THE ACTIVE ROADWAY.
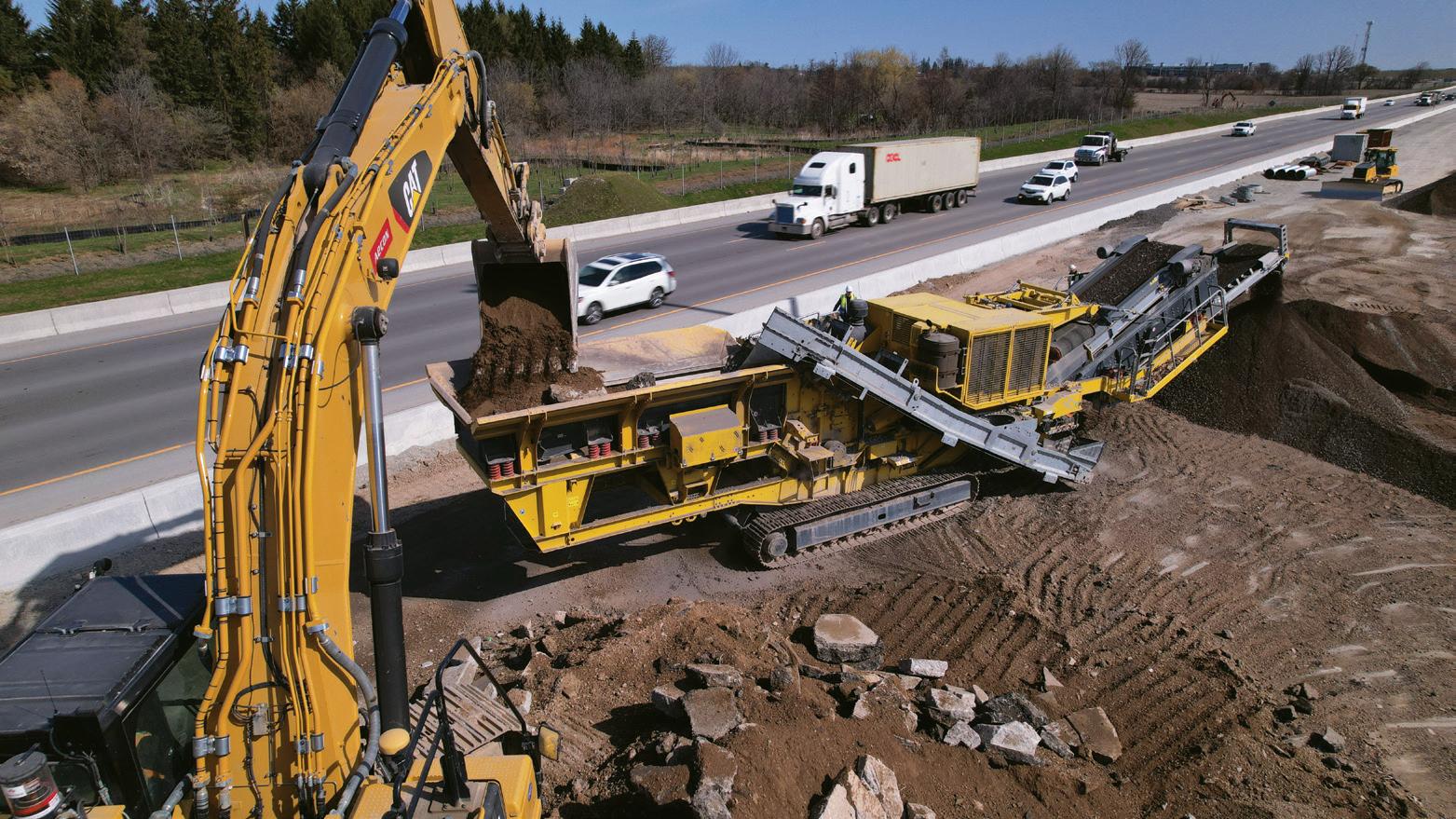
was four years. One year to design, with three years to build eighteen kilometres of full reconstruction and widening,” Van Dyk said. “So, we needed to look at opportunities to help our schedule and work within our budget. The recy cling process development itself was almost nine months in the making. WCC looked at numerous scenarios we had in our project associated with varying widths and material composition.”
Traditionally, projects would remove old road surface, haul it to a yard, crush it, then return it back to the site when needed. However, the time taken to truck material away and eventually bring it back is significant because of road capacity, storage space issues, and other factors.
“The last thing we wanted to do was start filling quarries and landfills with asphalt, concrete, and rebar. One thing we demonstrated early through our demos with Frontline is that we could produce a product that was going to meet the required output specifications,” Van Dyk described. “We were able to recycle the old concrete road, existing aggregate, and we were able to introduce asphalt RAP into the granular mix. That helped WCC avoid disposing of this material.”
That led the project managers to a different approach: in stead of taking material to the crusher, bringing the crusher to the material.
With an estimated 800,000 tons of material that could po tentially be reused through the project, having crushers that could keep up the pace was a big need, and took some time to nail down.
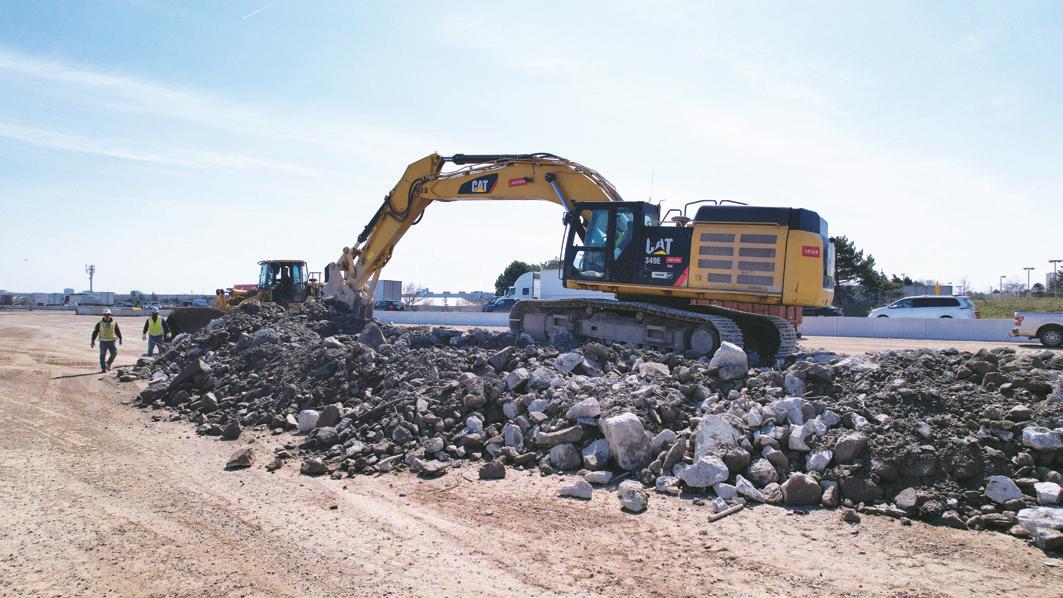
DEMONSTRATIONS OF PERFORMANCE WITH FRONTLINE MACHINERY PROVED CRUSHER CAPABILITIES
WCC took a cautious approach to its aggregate management, Van Dyk said.
“The challenge was that no one had actually done this before on this scale, so there were a lot of trials and demonstration of equipment, but we also had to consider logistics. How we were going to get this all to fit in a hundred-foot-wide corridor while maintaining our other operations around the clock,” he explained.
For Frontline Machinery, the trials with WCC were an op portunity to show the qualifications of Keestrack’s R6 impact crushers and S5 stackers. Frontline Regional Manager Martin Anderton said the goal for his team was to go into the demon strations and show exactly how effective Keestrack machines could be in demanding circumstances.
“They replicated what they expected the job to be, so they built a 100-metre-long by 15- to 20-metre-wide berm. Each machine had two days, and what we had to do was crush the material as efficiently as possible,” he explained. “They mea sured everything that went through the crusher using Optical Belt Scales so they could average it for all the machines.”
Van Dyk said the demos were an opportunity to achieve several goals: evaluate the feasibility of on-site crushing, deter mine which crushers were able to handle the role, and sort out many potential logistical challenges that might crop up during the project.
MATERIAL TO BE RECYCLED WAS WINDROWED IN FRONT OF THE MOVING EXCAVATORS, READY TO BE REUSED AS THE HIGHWAY WAS EXPANDED.“The demonstrations we did with Frontline early on in the process re ally allowed us to try a lot of different things, to figure out what would and wouldn’t work, and refine things a lot faster,” he said.
WCC even got a little old-school with its planning – it used scale drawings and even 1:50 scale models of crushers and other equipment to determine the best placement and configuration of ma chines, piles, access routes, and all the
other aspects of the project.
“The job is so large that you get lost in the magnitude of the project – it’s chal lenging to see what a 2,000-ton pile looks like when you have 30 or 40 of them,” Van Dyk said.
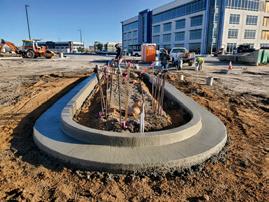
In the end, WCC rented multiple Keestrack R6 impact crushers and S5 stackers from Frontline to deploy on the project. In addition, Frontline continued to be heavily involved, starting with oper ator training.
New iSlip Control System
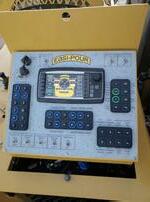
“Frontline was responsible for training all six crews that were working on these machines – we trained them on every thing from equipment maintenance, operation, and troubleshooting to be able to work with these machines in different situations,” Anderton said. “Frontline was right there from the beginning throughout the project, making sure their operators had the skills necessary to run the machines.”
CRUSHERS KEEP UP WITH CONSTRUCTION
Once the crushing equipment was on the job, the plan was to keep it moving constantly as the road construction continued around it. Van Dyk said WCC’s intention was to move the material as little as possible – so the crushers moved instead.
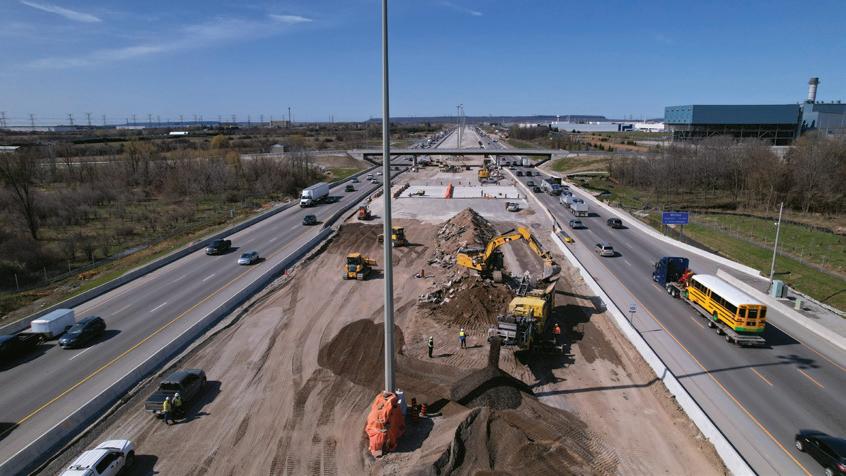
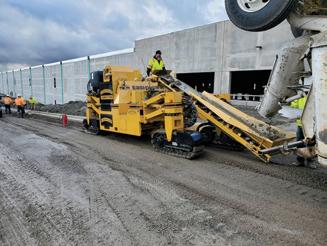

“They were moving probably every half hour to 45 minutes – they would process an area by running it through the crusher, then move. We were bringing the crusher to the material in a wind row,” he described. “The crushers were very easy to move.”
With multiple operators trained to run each unit, WCC was able to run the crushers steadily, including some stretches of round-the-clock work, with minimal downtime between shifts for ba sic maintenance, Van Dyk related. More extensive maintenance was handled quickly and easily by both Frontline and on-site service teams.
“We worked with Frontline and had some of our guys work with their folks to do some of the maintenance – it was a good strategy for us to help understand the equipment better, and it allowed us to do some of the maintenance, rather than Frontline, as part of the rental agreement. We were able to mitigate some of our costs by taking on some of
the maintenance,” he said.
Frontline’s team handled much of the routine maintenance, working with WCC to find convenient times to reduce the impact on progress. A unique aspect of the agreement was Frontline’s on-site provision of a 20-foot container custom stocked with wear components and other parts that allowed for quick response by the WCC teams when needed.
“It was important to be able to pro vide parts so that if something did hap pen, a bar breaks or a wear component gets worn out, that they would be easily accessible and immediately available. By working with the customer, we real ized that the amount of time that might be used up having to send someone to pick up parts or have a tech go on-site was cost prohibitive,” Anderton said. “The on-site parts support was definite ly unique to this job and unique to the scale of parts that were supplied to the project. We have done it in the past on a small scale, but this was the largest and most detailed parts support we’ve ever provided.”
CRUSHING PHASE PROVES SUCCESSFUL
With a targeted end date of Novem ber 2022 for the expansion project, the crushing component wrapped up in July and, according to Van Dyk, the Keestrack equipment has fit the bill when it comes to production and overall expectations. The crushed material has met speci fications, the innovative approach to recycling has proven to be impressive in its results, and the machines themselves worked well throughout the project.
“Our downtime was very minimal in the grand scheme of things. We wanted something that was going to work, and when it worked, it worked hard,” Van Dyk said. “We pushed these machines,
and we were getting some pretty high production numbers out of them. They had some really hard days, a lot of easier days, but for the most part they stood up to our demanding schedule and the production targets we set.”
From Frontline Machinery’s perspec tive, the project proved to be a winner as well.
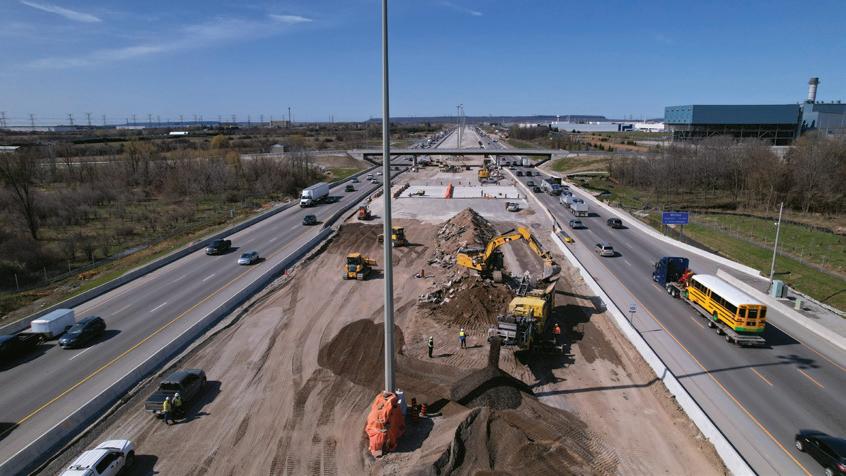
“The project was a complete success – that’s the overall feeling based on the open communication we had with the
WCC team, from the boots on the ground doing the crushing on a daily basis up to the team overseeing the project in the office,” Anderton said. “We were able to show different efficiencies in the way we do business, and also that for construc tion companies, not having to remove material from the site is a huge cost savings from being able to recycle that amount of material and reuse it on the site. I think this is a template for tons of future generational projects.”
HEG
Frustrated with long lead times? UNDERHOODTM air compressors ship in 10 days.
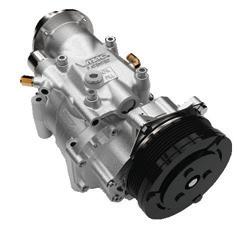
Supply chain shortages are causing significant deck mounted air compressor delays. We have a solution: The UNDERHOODTM is available today with options for your entire fleet.
Learn more at: VMACAIR.com/underhood
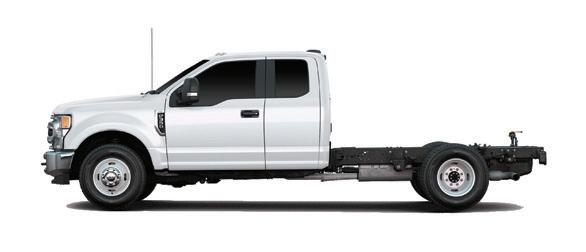
NEW SCREENS ARE THE LATEST INNOVATIONS FROM ASTEC
COMPANY CELEBRATES 50 YEARS OF PRODUCT DEVELOPMENT FOR VARIETY OF INDUSTRIES
Astec Industries has marked its fiftieth anniversary with the release of several new products for the aggregates industry.

PORTABLE SCREEN PLANT WITH UNIQUE VIBRATOR MOUNTING
The PTSC2818VM portable high-frequency screen plant has an innovative design for a unit with an 8-foot-wide screen. Rather than using a single, centre-mounted vibrator, this new PTSC plant has a patent-pending design featuring externally mount

ed vibrators at the end of the tappets. This design provides a more aggressive screening action, with higher G-forces, while reducing the heat load from material to motors, As tec says. This motor location also makes for easier main tenance and adjustments.
The plant has an 8- by 18-foot (2.4 x 5.5 m) top deck and an 8- by 12-foot (2.4 x 3.7 m) bottom deck and is equipped with features like a hydraulic operating angle adjustment, fines collection hopper, top and bottom deck discharge chutes, and an ag gregate spreader. It features a nominal 54-inch by 38-foot delivery conveyor with hy draulic drive and full-length skirtboards.
SCREEN PLANT TENSIONING SYSTEM SPEEDS MAINTENANCE
The GT2612V screen plant has incorporated its own innovations – in this case one that speeds up maintenance times. The plant, which features a 2612V Vari-Vibe
high-frequency screen, uses a unique rotary tension ing system which makes screen mesh changes faster and reduces maintenance downtime. It also features remote grease lubrication for ground-level access and a walkway around the screen as additional maintenance features.
ASTEC GT2612V SCREEN PLANTTwo new screen plants continue the innovation that has been a hallmark of Astec for 50 years.
THE COMPACT ALL-PRO
Experience the ultimate in snow clearing visibility, control and performance with CASE B Series skid steers and compact track loaders. Extremely agile, capable of working on accounts of all sizes — and giving each operator the control they want with simple electro-hydraulic controls, easy pattern selection and an intuitive eight-inch LCD operator screen with integrated backup camera.
Outperform the storm. With CASE. CaseCE.com/Snow

The GT2612V is a twodeck, 6- by 12-foot (1.8 x 3.7 m) screen, which has deck-mounted, vari able-speed hydraulic vibra tors; a hydraulic mechanism to change operating angles; a fines collecting hopper; top and bottom deck discharge chutes; and an aggregate spreader. An 8-cubic-yard hopper is equipped with 6-inch sloped grizzly open ings and a remote tipping grid. The variable-speed, 48-inch-wide belt feeder has a high-torque hydraulic drive, full-length impact bed, rub ber lagged head pulley, and self-cleaning wing tail pulley.
Four conveyors are includ ed with the plant – a delivery conveyor, two side conveyors, and a fines conveyor, all with variable-speed hydraulic drives and the ability to easily fold for transport.
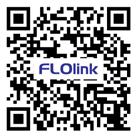
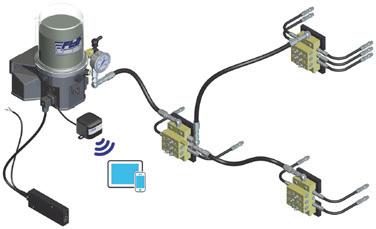
The GT2612V plant is avail able with a range of options. While it is powered standard by a Caterpillar Tier 4 Final engine providing 136 hp, there are other engines avail able as well. Other options include a larger hopper/feed er, heavier grizzly section, a vibrating grid, bridge break er, vinyl dust cover, telemat
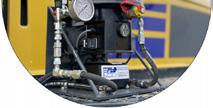
ASTEC CELEBRATES 50 YEARS OF INNOVATION
In August 1972, Dr. J. Don
Brock led the way in creat ing Astec Industries which focused on the development of new, high-tech equipment for a variety of industries. Fifty years later, the company that Brock helped to found continues to develop new products for asphalt road
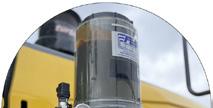
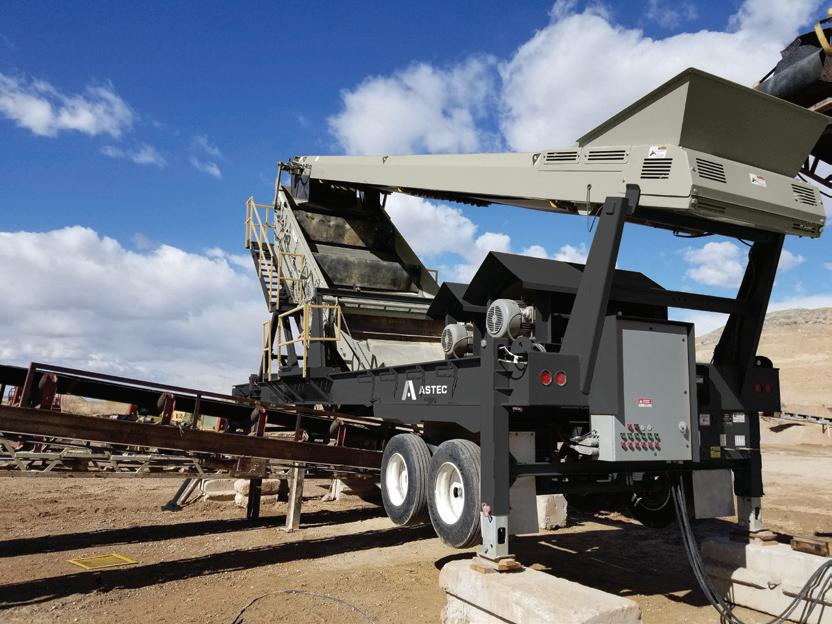
building, aggregates, and more.
Over the past five decades, Astec has continued Brock’s legacy, according to Barry Ruffalo, Astec president and CEO, through continued inno vation and customer-focused commitment in its more than 100 products.

To celebrate the fiftieth anniversary, Astec has com mitted $1 million to the Dr. J. Don Brock Astec Industries Inc. Memorial Scholarship Endowment at the University of Tennessee Foundation, Inc. The scholarship endow ment will be available to children and grandchildren of Astec employees and will encourage study in science, technology, engineering, and math.
“Dr. Brock had more than 100 patents to his name. He had a passion for learning, but he also had a reputation for being a great teacher,” says Ruffalo. “I can’t think of a better way to honour his legacy than encouraging the next generation of innovators at Astec.”
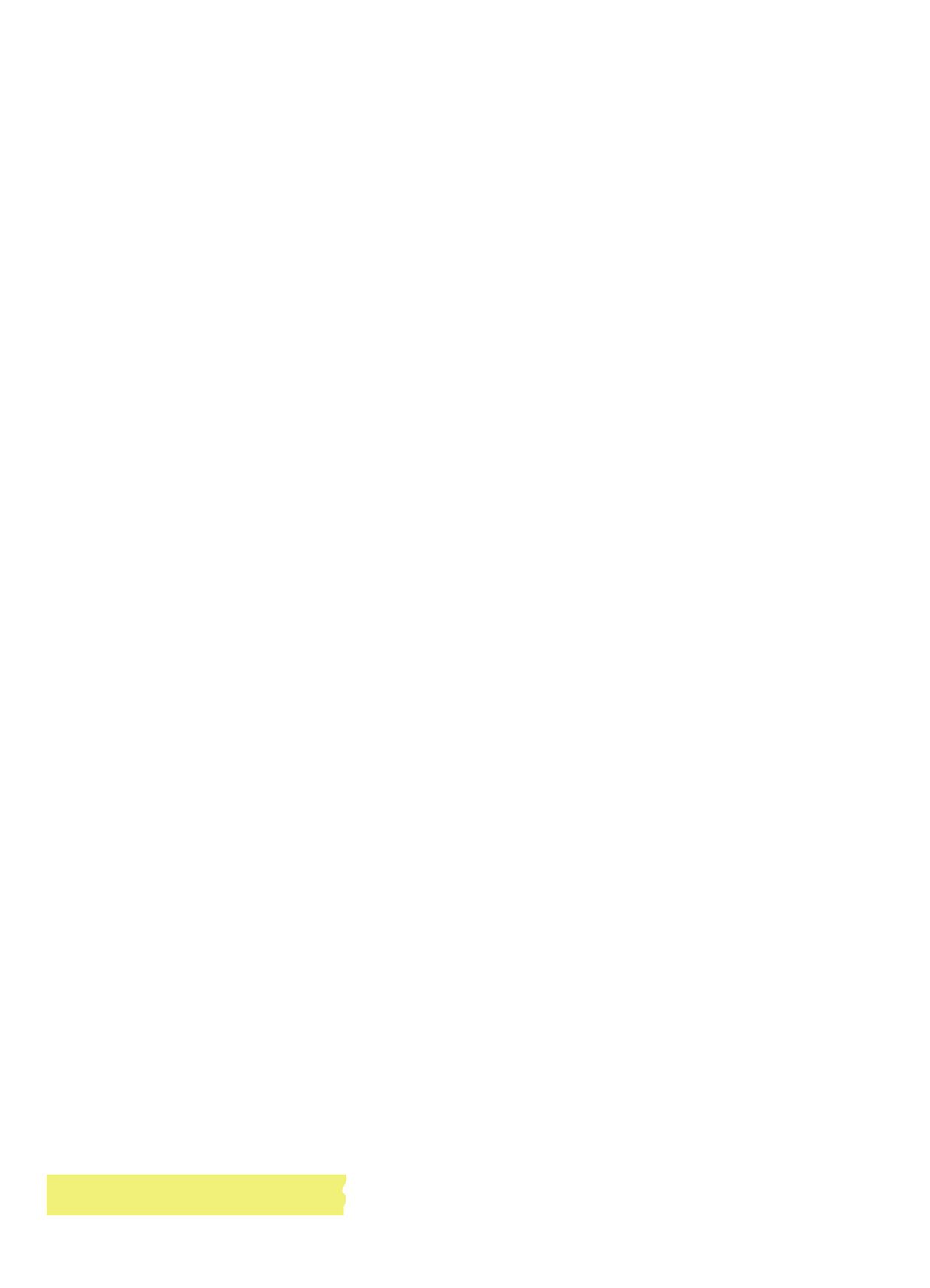
CANADIAN CONTRACTOR CONQUERS SWAMPY GROUND WITH CTL AND MULCHER PAIRING

Vinnie’s Bobcat and Mulch Master, Ltd., more com monly known as Vinnie’s Mulching, performs a lot of FireSmart clearing work from its Drayton Valley, Al berta, location. And while some folks have adopted the mantra “go big or go home,” owner/operator Vinnie Holmes gets big mulcher results from more nimble compact equipment. Oper ating two high-flow Cat 299D XHP compact track loaders with Fecon BH74SS Bull Hog Forestry Mulchers, Vinnie’s Mulching tackles FireSmart mulching projects over diverse terrain popu lated with an interesting array of vegetation.
SWAMPY CONDITIONS CHALLENGE
MULCHING OPERATIONS
One of the company’s FireSmart jobs covered a three-year span, working only in wintertime to avoid swampy, unworkable conditions. “We were actually cutting existing pipeline rightsof-way to clean them up so they can access them,” says Holmes. “Over a three-year span, we did 300 kilometres with two ma chines 10 metres wide, so 300 hectares of land we cut. We only worked in February and March, so in six months, we cut 300 kilometres [for] pipelines.”
These FireSmart jobs are very important to limit the damage fires cause. The black spruce, or swamp spruce as it’s called locally, acts as ladder fuel, allowing fire to build momentum, climb to the canopy, and leap from tree to tree.
“We want to eliminate a percentage of the fuel. In areas where it’s really heavy black spruce, we go and wipe out 90
percent of it, just put it on the ground,” explains Holmes. “Then when we get into the bigger trees, they want to maintain a 12foot crown spacing in the trees so that the fire doesn’t get the momentum to hop from tree to tree.” They also limb the trees up about six feet high and pull the limbs out and mulch them. Any dead-standing trees are taken out, any trees that are laying on the ground are allowed to stay. “We leave some standing bigger broken off ones for owls and other wildlife, but we try to eliminate as much of the fuel as we can.”
The foliage encountered on these projects was anything from grass to eight-inch trees. Primarily encountering spruce, pine, poplar, and willow, the only really hard wood that he saw was tamarack. Most of the trees were 10-year-old growths. Holmes enjoyed the variety of foliage, and how each day would present unique challenges for him and his Fecon mulchers.
The terrain for these projects can also be rather challenging. “We had some pretty good hills we had to climb, and some pretty ugly swamps where we could’ve lost a machine,” he re called. At one point, when his daughter was helping on another machine, she noticed a spot of dirt that didn’t feel quite right. “I went over there, and we took about a six-foot long stick, and we shoved it right out of sight.” With up to 26-degree slopes, and perilously swampy ground, Vinnie’s Mulching relies on the Fecon mulcher head for help. “If it wasn’t for the Fecon head tickling the ground as you’re going, we’d be in trouble. It’s not pulling you up but it’s stirring enough tread up as you’re going up the hill to give you a little bit of traction.”
OBSTACLES TEST MULCHER
ATTACHMENT DURABILITY
This swampy ground can also hide other problems.
“I’ve hit lots of metal, blocks, wire, cable, phone boxes, ev erything. You name it, I’ve hit it. Rims – I’ve split rims with my Fecon heads and had them jammed in there so bad you have to use a chain to get them out, but then we just carry on.” Holmes is very impressed with the Fecon mulching head’s durability. Recalling his experience with early mulchers, he said, “If I hit something on my old ones, I broke something. Then, as Fecon evolved, they’ve definitely given me a more superior product. I can go out and roll over a three-foot rock thinking it’s an anthill or something and come out of it unscathed doing 2,200 rpm on the drum.”
The rugged build of the Fecon mulcher heads is compounded by the strength of the teeth used. Holmes prefers the double carbides, saying “I’ve tried the sharp ones in the past, and I just prefer the durability of the double carbides.”

Double carbides are the standard teeth offered with the FGT rotor that Holmes has on his mulcher heads, and he’s averag ing 1,000 hours of life per set. The balance, performance, and durability of these teeth complement the durability of the FGT drum rotor, and the lacing pattern of the teeth maximize ener gy transfer into the material, optimizing tool life and ensuring that Holmes can get the most use out of his mulcher head. The mulcher and the teeth are tough, but the durability of them really comes from simple continual maintenance.
Over a three-year span, we did 300 kilometres with two machines 10 metres wide, so 300 hectares of land we cut. We only worked in February and March, so in six months, we cut 300 kilometres [for] pipelines.”
“They’re so durable now, as long as you keep up on mak ing sure they’re balanced and keeping your teeth good and your skid shoes all maintained, you won’t have problems. I’ve never had a motor fail, never changed a bearing yet, only had one spline failure, and that was on an older head, which was off warranty.”
Holmes greases once a day, balances his mulcher head when
Vinnie Holmes Owner/Operator, Vinnie’s Bobcat and Mulch MasterA HIGH-FLOW CAT 299D XHP COMPACT TRACK LOADER OUTFITTED WITH A FECON BH74SS BULL HOG FORESTRY MULCHER.
he needs to, and has had very few problems. When he does have problems, Fecon has been very helpful in solving them. When the off-warranty spline failed, he explained that he hadn’t used the head much recently, and that it shouldn’t have failed. Fecon shipped him the parts free of charge to get him up and running again.
Fecon also takes feedback on their products very well. Holmes used to have to gouge off the skid shoes to balance the head and bring in a welder to put them back on. Other contractors had faced the same dilemma, and when Holmes brought up the issue to Fecon, they said that a fix was in the works, and soon followed up with bolt-on skid shoes.
On a separate occasion, Holmes had a problem with a head that didn’t free-spool. He ran over a cable which then wrapped itself around the rotor. With the power off attempting to remove the cable was challenging because Holmes could not roll the rotor backward by hand. After mentioning this to Fecon service personnel, they came up with a solution and shipped him the parts. He was able to get back up and running very quickly. “They just continuously give a better product, and they take good feedback and criticism,” comments Holmes. “I’ve had some issues, and I phoned them up, and they come through and fix whatever the problem is.”
All his mulching equipment was purchased through SMS Equipment in Edmonton, and Holmes doesn’t foresee ever switching from Fecon. “I've never run anything but Fecon, and I have no reason to change.”
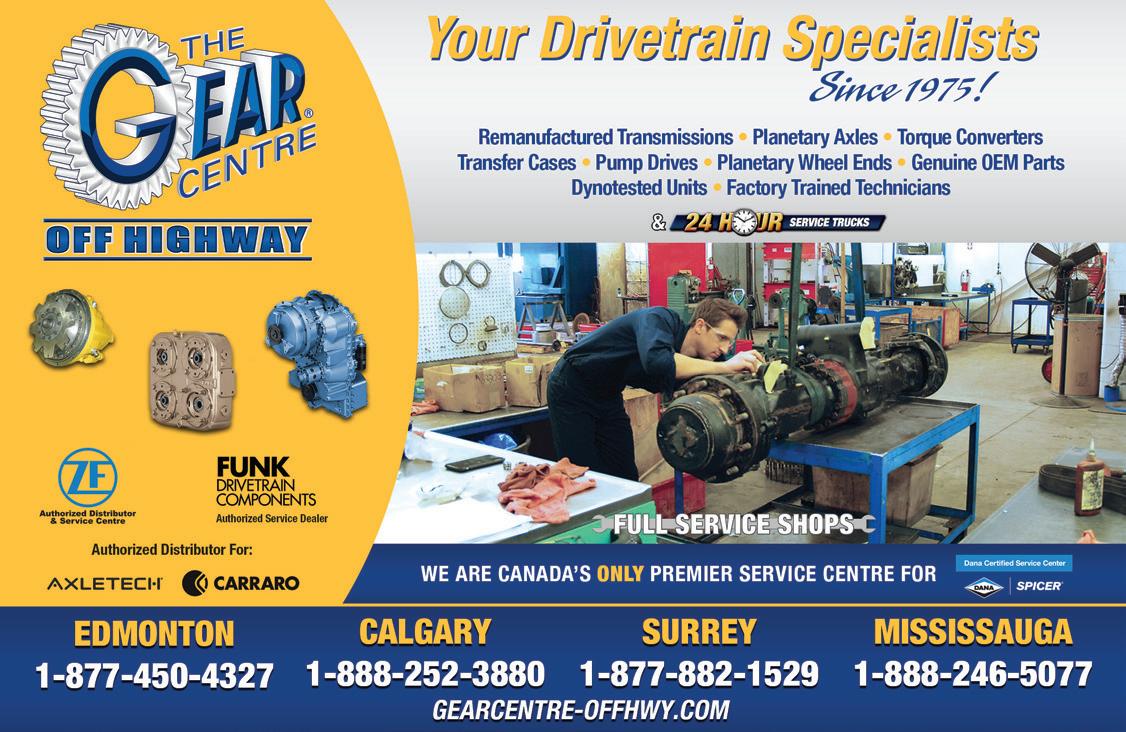
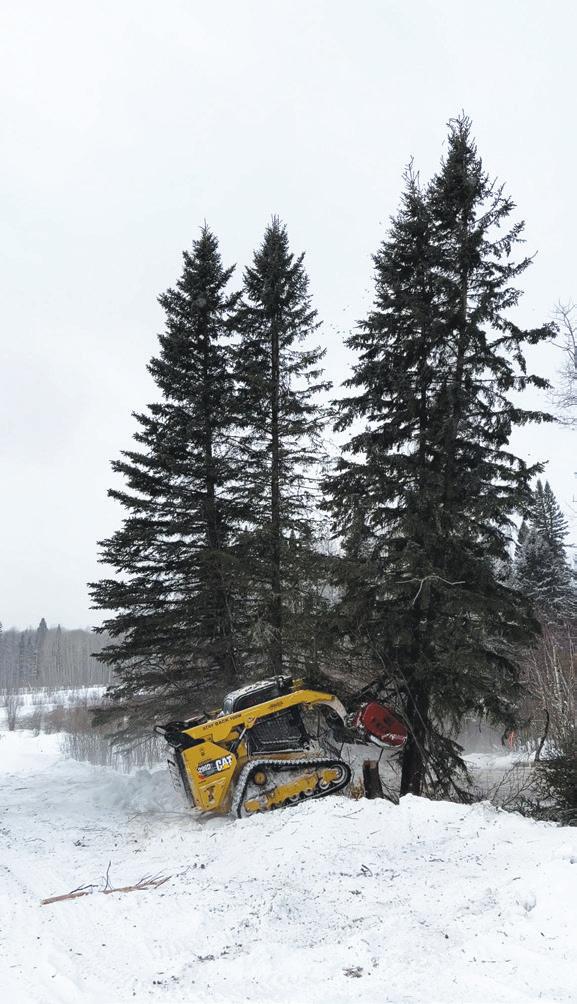
KNOW ABOUT CATERPILLAR SMART CREEP
Caterpillar has intro duced a new technolo gy for operating a cold planer or wheel saw attach ments on the Caterpillar D3 skid-steer loaders and CTLs – Smart Creep. With Smart Creep, operators no longer need to guess the right creep speed for operating these attachments. It is, essentially, adaptive cruise control for creeping.
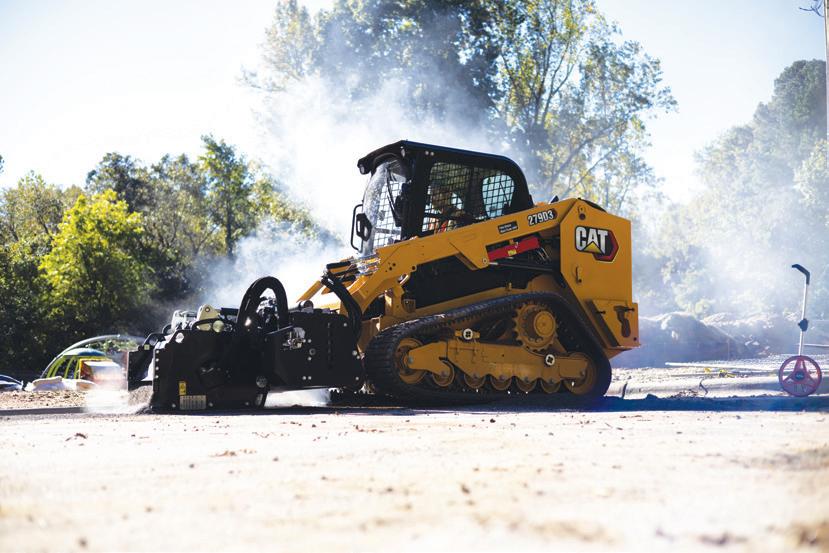
HERE ARE FIVE THINGS TO KNOW
drive command automatically as cutting begins.
2
1
The standard creep control system is activated and is set to the maximum creep speed. Smart Creep kicks in once the tool engages the cut. It measures load on the attachment and adjusts the
Smart Creep continually senses the load on the attachment using sensors and software to balance the load on the attachment with the machine speed. It will increase machine speed when there is less resistance and automatically slow down the machine when there is a higher load. The machine monitors what the attachment is doing via pressure sensor feedback. An algorithm in the machine uses the data to do the finessing for the operator.
changes the machine’s direc tion momentarily and allows the tool to clear the jam or free the stall. It then starts itself back up again to re-engage.
productivity while getting up to speed on the use of the ma chine and its attachments.
5
4

3
If the attachment head has stalled or the cutter jams, Smart Creep’s auto reverse
Smart Creep is useful to the expert operator as it eases the stress of maintain ing maximum productivity by taking over some of the tasks involved in monitoring per formance. The inexperienced operator using Smart Creep will be able to rely on the technology to achieve greater

For existing fleet loaders and attachments, a field installation kit with sensors and machine software will be made available. New cold planer and wheel saw pur chases will have the required hardware already installed from the factory. New Cater pillar D3 skid-steer loaders and CTLs will come Smart Creep ready from the factory.
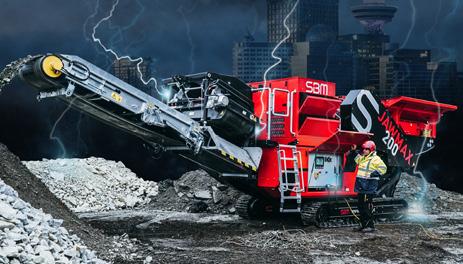
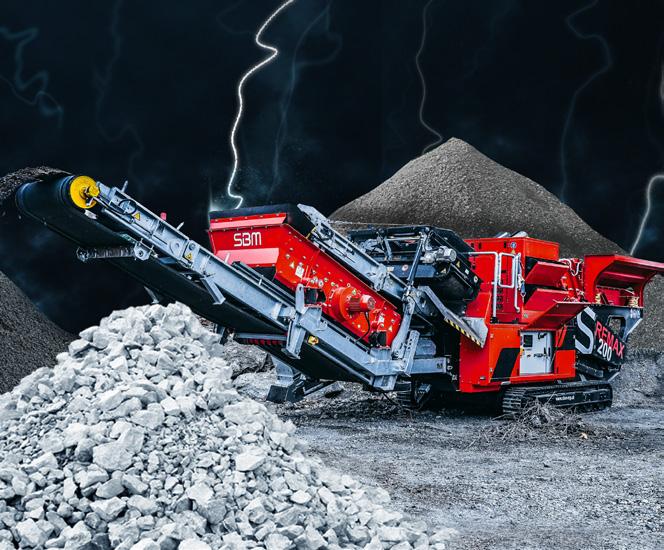
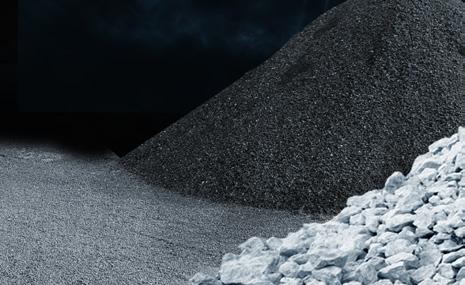
NIMBLE AND EFFICIENT SITE DUMPERS FIND SPACE ON GROWING NUMBER OF JOB SITES
BY LEE TOOP, EDITORMoving lots of dirt around on a job site usually calls for the use of a truck of some kind, depending on the vol ume to be moved. However, for smaller jobs with lower volume, a smaller solution may be needed.
Small and nimble, site dumpers are becoming more popular for a variety of job sites, taking advantage of their ability to access smaller spaces with ease. Contractors are finding that these machines can move all kinds of material and increase their overall efficiency.
Site dumpers feature a large dump box and a control station, allowing an operator to pick up material and move it easily before dumping in the necessary location. According to Sam Shimwell, equipment rental specialist with Conquest Equip ment, the flexibility of these small units makes them useful for a broad range of contractors.
“These little site dumpers’ main purpose is for projects and applications where there is confined space or rough terrain . . . for transportation of material. It could be topsoil, it could be bark chips – there’s a whole list of material that they can haul,” Shimwell related.
SITE DUMPERS IDEAL FOR URBAN JOB SITES
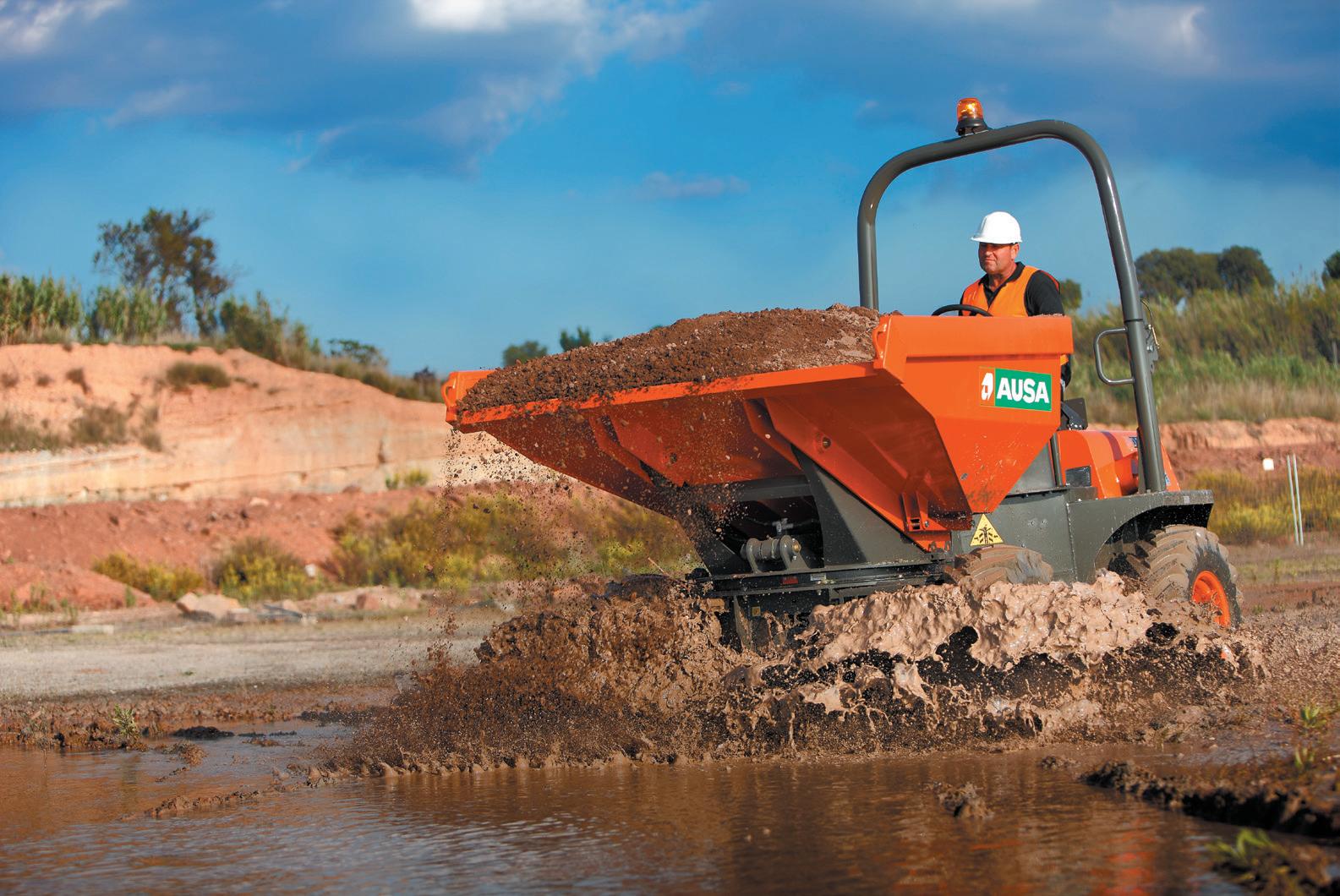
A very popular piece of equipment in Europe and the United Kingdom, it’s common to see several site dumpers working on most any job site, said Shimwell, and especially in urban spaces where it might be difficult to place a larger machine for moving material. Conquest Equipment, which offers AUSA site dump ers through its western Canada locations, has seen interest in the region growing as people become more aware of the ben efits that site dumpers provide.
These little site dumpers’ main purpose is for projects and applications where there is confined space or rough terrain . . . for transportation of material. It could be topsoil, it could be bark chips – there’s a whole list of material that they can haul.
Sam ShimwellEquipment Rental Specialist, Conquest Equipment
“We have a location in Abbotsford, B.C., and they are very popular out there just due to confined space on job sites,” Shimwell noted. “A lot of cities in western Canada have received government grants for building paths and cycle pathways, and most of these projects are in steep terrain or hard-to-get-to lo cations. You can’t just back a tandem dump truck or a full-sized loader in there.”
Larger units are capable of working on more rugged jobs, such as pipeline work and in the oil fields, as well, thanks to their ability to manage challenging terrain.
Trinda Jocelyn, Conquest Equipment’s marketing coordi nator, said that it’s often a case of having contractors see the machines at work to give them a better idea of how they can be used to improve efficiency.
“We have a lot of conversations with people who are out and about, asking what they are and what they’re for, and they always say ‘oh, that’s really cool.’ Then they start think ing about how they could be using that on their job site as well,” Jocelyn said. “The market is definitely there, we just have to get it out there and let people know what they are, how they’re used and how they can be useful for them.”
FOUR DUMPER SIZE OPTIONS DELIVER

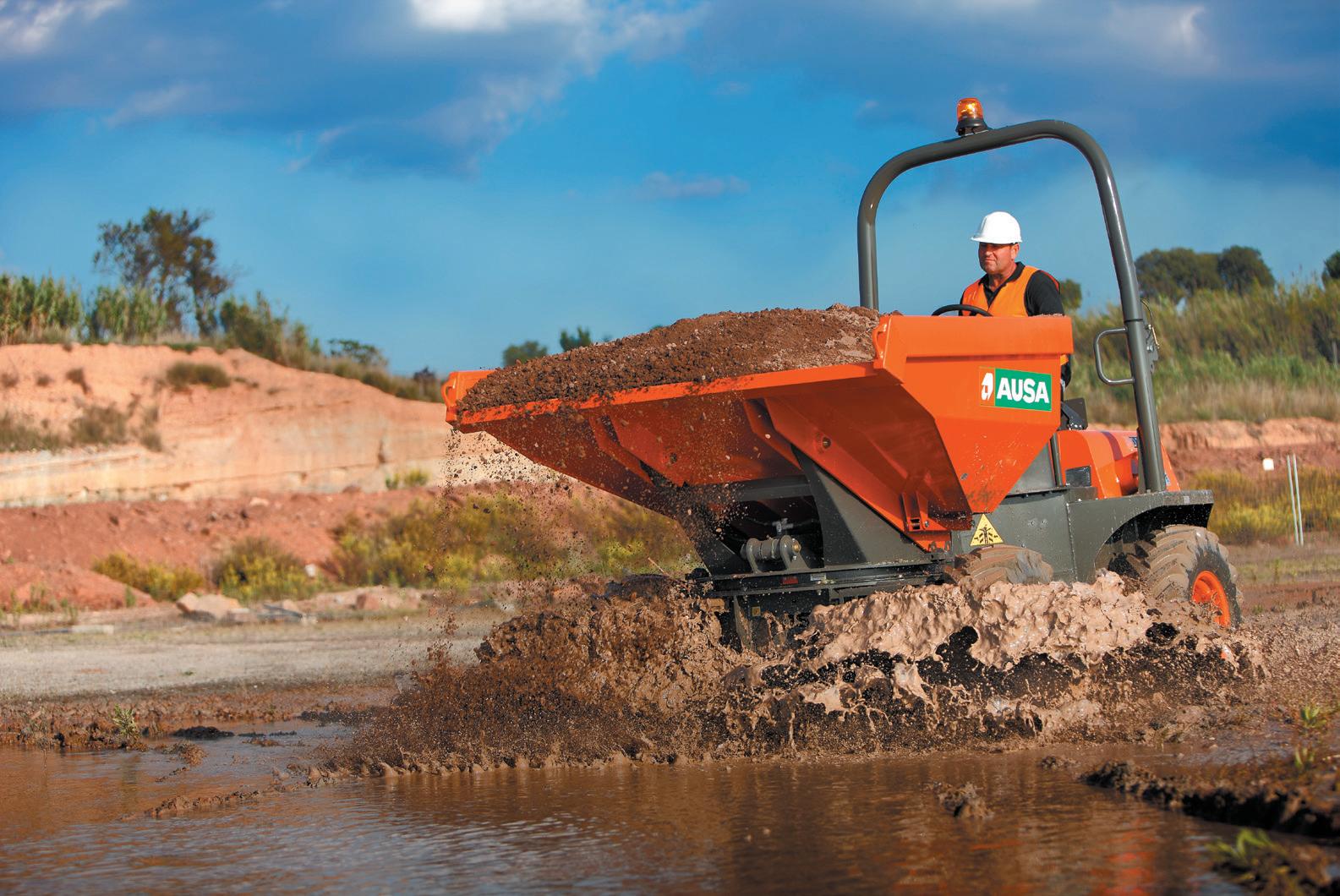
RANGE OF CARRYING CAPACITY
In the case of AUSA dumpers, four different models are available, at 1.5, 3.5, 6, and 11 tons, giving owners a significant carrying capacity for their job site. All of the machines are four-wheel-drive and articulated and, according to Shimwell, offer a popular feature: a swiveling dump box.
All the units can swivel the box 90 degrees to the left and right of centre, and once swiveled can move forward while dumping, allowing them to spread material easily while re ducing the need to move around and adjusting the backfilling where needed. The two largest units are built with enclosed cabs, which feature a rotating operator station – the chair, levers, gearshift, and all other necessary controls are able to swing around as needed.
Cabs are designed with a workstation that rotates 180 degrees, allowing the dumper to drive forward, drop mate rial, then swivel fully around to avoid the need for backing
up with the operator looking over their shoulder, Shimwell noted. “That’s a huge safety feature, but also provides more ease of operation for the driver as well.
Powered by Kubota and Deutz engines, the AUSA dumpers feature hydrostatic transmissions that are robust and respon sive; some are available with a Hill Holder system for added protection on slopes. Jocelyn noted that the machines are designed with hoses and cables protected to reduce poten tial downtime on the job site. Maintenance operations are designed for ease of access.
Other available features, depending on model, include Smart Stop, which shuts down the engine when not in use, and the Full Visibility System, which combines cameras and proximity sensors to give drivers a greater view of the sur rounding area for increased safety.
While Conquest is based in Estevan, Saskatchewan, it is capable of providing service for AUSA dumpers across western Canada, Shimwell said.
“We have a fleet of our own equipment as well, so we have a full shop with service bays and a full crew of certified mechanics. Plus, we stock all the parts – filters, tires, backup alarms, seat belts, anything that could possibly go wrong,” he noted.
For buyers in B.C. and Alberta, there are service locations available as well, and if those aren’t feasible, Conquest has third-party mechanic partners to assist.
With interest in site dumpers growing, AUSA machines have been picking up new fans across the region. B.C. con tractors have shown quite a lot of interest, and that is spread ing across the Prairies, Shimwell said. “As a new product to Canada, It’s the education part that we’re working on – telling people how they work and where.”
HEG
SITE DUMPERS ARE BECOMING MORE POPULAR ON A VARIETY OF JOB SITES FOR THEIR CAPABILITY IN MANY SITUATIONS. FOUR SIZES OF AUSA DUMPERS ARE AVAILABLE, WITH A NUMBER OF DIFFERENT CONFIGURATIONS.Contractor embraces technology to expand and succeed
Earthmoving and construction have changed a lot in recent years, and it can be challenging for contractors to keep up with that pace of change. In some cases, though, that change is embraced and becomes part of a company’s identity.
That is how Dig It Contracting has handled change – by jumping in willingly and taking advantage of advancing tech nology to improve its ability to service local clientele in British Columbia’s busy Okanagan Valley.
Based in Kelowna, B.C., Dig It has been in business for around 15 years and, according to owner Dwayne Flett, had been a plan he’d conceived in childhood when he had a passion for heavy equipment and trucks.
“Dig It started, I guess ultimately, when I was a little boy playing in the sandbox, and I just never really got out,” Flett de scribed. “Something I’ve always been passionate about is equip ment – I love equipment, and I just took it to the next step.”
Since its inception, Flett has grown Dig It Contracting and moved into a variety of construction segments. Today the com pany has a mixed fleet of heavy equipment and prides itself as a one-call solution for water and sewer work, power and cable installation, curb and gutter work, and more.
TECHNOLOGY A KEY APPROACH TODAY
As the company grew, Flett started to recognize that the adoption of technology was key to expansion in today’s mar kets. The availability of these new approaches, combined with the overall labour landscape in construction, made technology an important way to meet the requirements of more and larger contracts.
“In the paradigm that we’re in at this point with labour short ages, I believe that technology is going to be the only way that we’re going to be able to move forward,” Flett described. “Our labour pool is shrinking. I think technology is going to help fill that gap.”
That knowledge has driven Flett’s decisions on equipment
purchases for Dig It Contracting in the past few years, and a strong partnership with his dealer, SMS Equipment, combined with a desire for more technology has led to Komatsu machines becoming a central part of Dig It’s fleet.
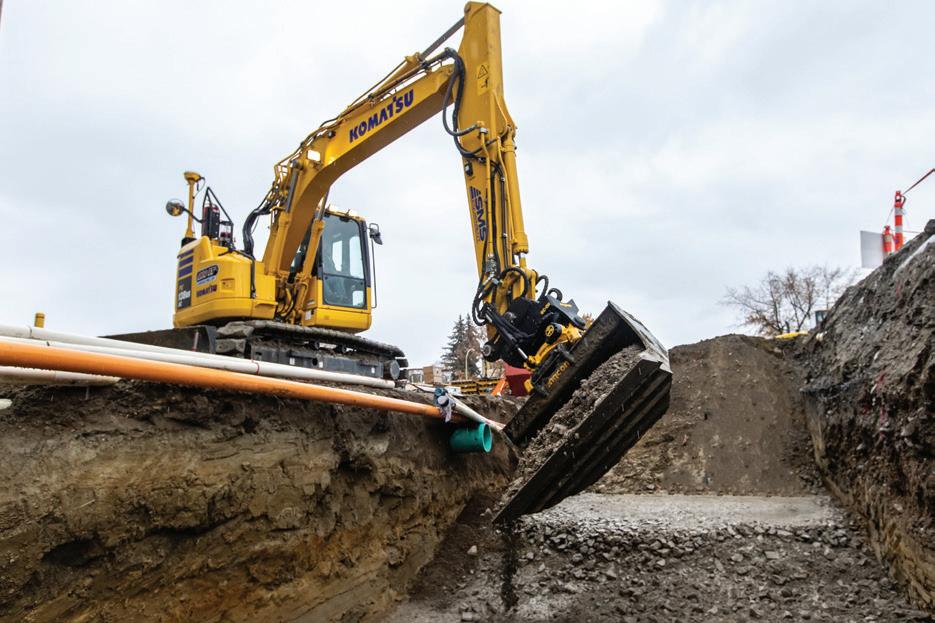
Flett was facing challenges with aftermarket technology on an excavator when Jeff Martin, Smart Construction represen tative, and Steve Ten Veen, sales representative, dropped by for an SMS Equipment site visit.
“Steve and I were coming by doing some customer visits, and [Flett] was running technology on one of his excavators. They were struggling with a [modelling] application,” Martin said. “We suggested a different way of utilizing the technology he was using.”
Dig It was working on a highly technical project at the time, much of it slope work that could be done only once – there were no opportunities to go back, so the model had to be per fect. SMS Equipment suggested a unique package involving an Engcon tiltrotator with grade beam, pallet forks, and sorting grapple, and aftermarket technology. It worked, the job got done, and Dig It started looking more closely at how it used
In the paradigm that we’re in at this point with labour shortages, I believe that technology is going to be the only way that we’re going to be able to move forward.
Dwayne Flett Owner, Dig It Contracting
technology, such as machine control, on its jobs.
“A lot of our customers are repeat customers because they see the benefits of technology,” Flett noted.
One such client had Dig It handle a large commercial project and then, knowing the quality of the work and the benefits of Flett’s technology approach, brought them in for a large home build.
“It’s a big project, complete with a basketball court, detailed footing package – it’s a very complicated technical dig,” he related.
Flett’s decision to expand his fleet of more than a dozen ma chines with Komatsu equipment has helped with the growth of Dig It’s technology focus – a trio of Komatsu purchases have taken advantage of the company’s intelligent Machine Control system. The contractor has added a PC290LCi-11 excavator, a PC360LCi-11, and a D51PXi-24 dozer, all with integrated technology.
MACHINE CONTROL MAKES A BIG DIFFERENCE
Having machine control included on the machines makes a huge difference, Flett noted. On the house job, for example, the Komatsu PC290LCi is able to load all of the data for footings, loading pads, and other details into the system and present it on the operator’s screen, making it much easier to hit the nec essary design grades every time.
Komatsu’s iMC machines integrate 3D design data fully into the machine, allowing operators to work more efficiently on every pass. That gets to finished grade much faster, and assists operators for both training and getting the job done.
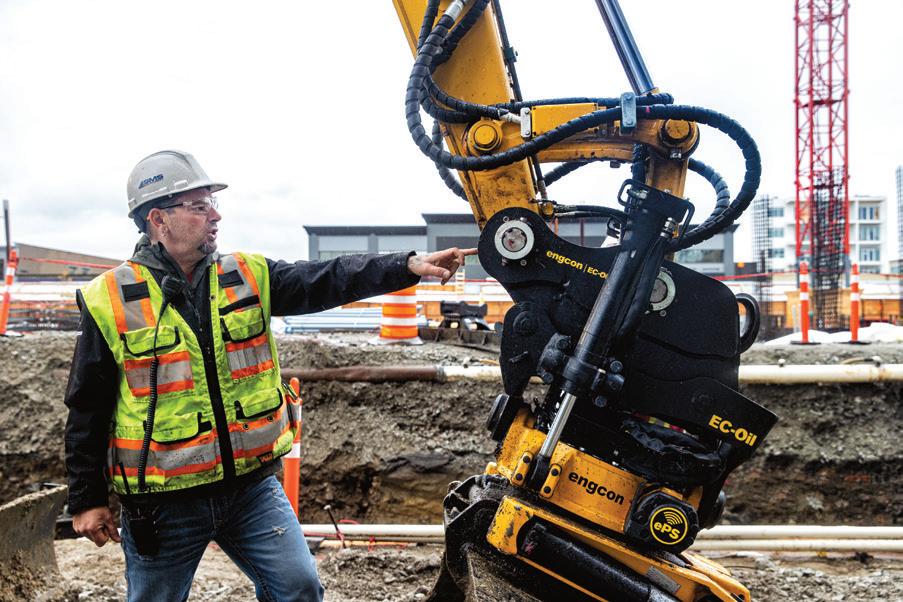
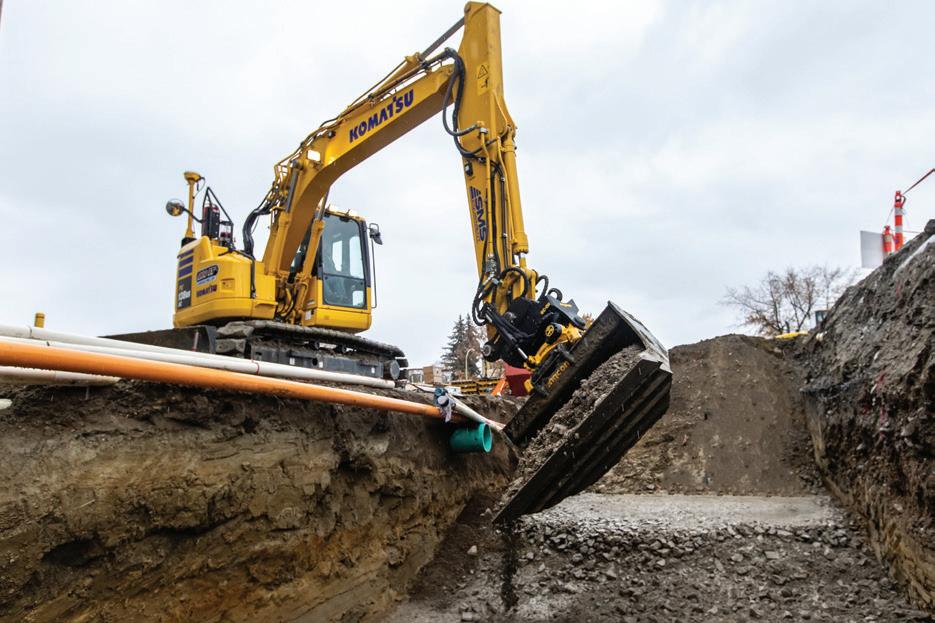
“It’s right in the machine, so I don’t have to go out of my ma chine to look at my blueprints or talk to the general manager on site. It’s all there. It’s a one-stop-shop, and it’s exactly what I’m looking for,” added Cole Kendall, general manager for Dig It Contracting.
It was important having a strong dealer partner to make the transition to greater technology use, and working with SMS Equipment made that much easier, Flett said.
“SMS has solutions, and Dig It is all about solutions, so when I look at another company that’s like-minded in being able to have solutions, that means a lot,” he described. ”SMS really did tailor a solution for the technology that we needed to move forward.”
Having higher levels of integrated technology on his ma chines adds a variety of benefits for Dig It and its employees, Flett noted.
“Costs are creeping up all the time . . . being able to be on grade all the time, you aren’t moving material twice unneces sarily. You know where you are all the time,” he said. “You may be the best operator in the world, but you can’t see where the corner of the building is or what grade you’re at. A lot of old timers will say ‘a good operator can hit grade.’ If he’s got a grade stake – but when the grade stake got knocked over by the truck driver, where are you at?”
TIME SAVINGS KEEPS DIG IT ON SCHEDULE
Time savings are also a big part of the benefits of adding ma chine control technology to Dig It’s inventory of offerings, Flett added. “The schedule is always important, so to be able to stay on that schedule, I feel technology helps us with that because we’re not waiting for stakes . . . we don’t need layout, we don’t have to wait for the surveyor to come in. We’ve got proper setup from the get-go and we’re ready to roll from start to finish.”
Looking forward, Flett said that Dig It’s experience and em bracing of new approaches to construction will help it along in a continually challenging sector.
“As the industry slows down, we’re going to be the guys that are cutting edge,” he said. “There’s nobody who’s going to be able to compete with us, I feel.”
SMS EQUIPMENT PAIRED ENGCON TILTROTATORS WITH DIG IT’S MACHINES FOR THE BEST EFFICIENCY. GRADE CONTROL AND OTHER TECHNOLOGY INSTALLED ON KOMATSU EXCAVATORS HAVE HELPED DIG IT CONTRACTING SUCCEED.

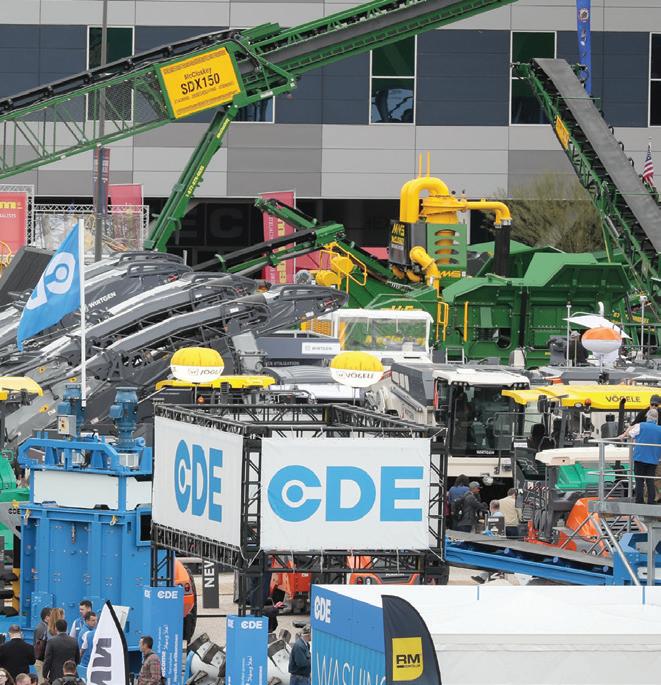
COMPACT MACHINES GAIN PRECISION AND PERFORMANCE FROM MACHINE CONTROL
Already a popular addition to larger earthmoving equip ment, machine control is continuing to evolve with solutions for more machine types and sizes. Compact equipment is the next step for machine control adoption, with a number of options now available to give versatile compact machines greater precision.
Machine control systems for compact equipment are smaller and easier to install, and some are designed to be portable so that they can be moved from machine to machine with ease. These systems may not have all of the same features as their larger cousins, but they allow owners to incorporate machine control at a lower price point and improve efficiency.
PORTABLE AND MODULAR THE FOCUS FOR TOPCON
Topcon Positioning Systems has built a broad range of ma chine control systems across a variety of machines through its
MC-X platform and recently introduced the same capabilities to compact equipment with the launch of MC-Mobile. Porta bility is a big draw for owners of smaller machines, as it allows them to use one system on multiple pieces of equipment while benefitting from the same features as a full-size machine con trol guidance system.
MC-Mobile is designed for mini excavators, compact track loaders, and skid-steer loaders. These machines combine with the system and software to add design, build, and check func tionality to small equipment.
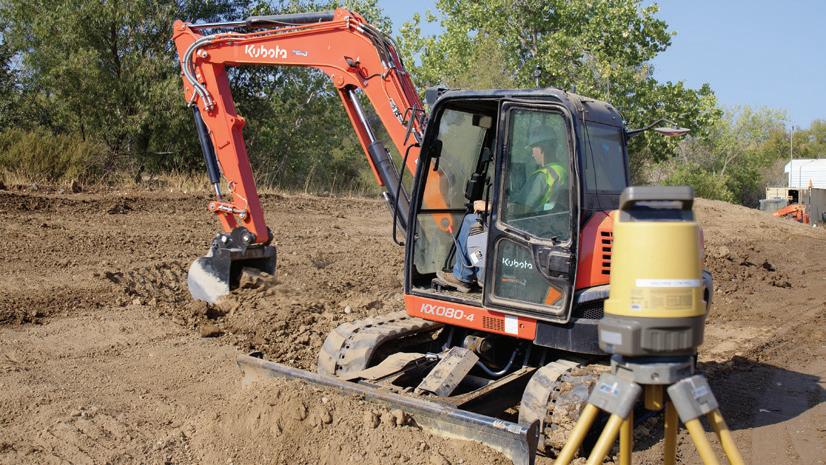
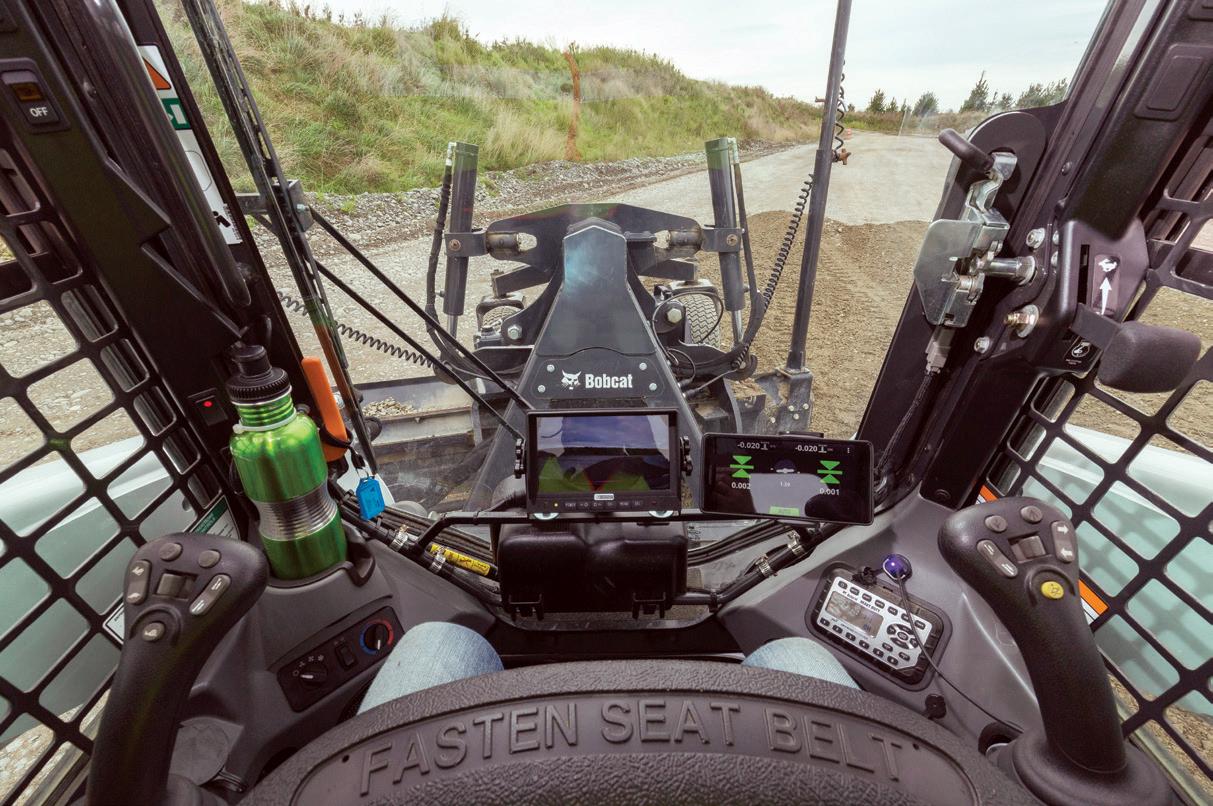
“It’s easy to set up and use, it’s affordable, and it offers the same competitive benefits of machine control solutions de signed for larger equipment,” commented Jamie Williamson, executive vice president of Topcon. “MC-Mobile enables con tractors to get jobs done faster and more accurately, eliminat ing costly rework and allowing them to reallocate resources to other tasks on the job site.”
MC-Mobile can be used for applications like grade checking, working through designs on the job site, and site layout with no need for staking. As a modular system, displays and com ponents can be shared across machines, and it is simple for operators to pick up, allowing contractors to shift resources to other areas of the job site.
COMPACT MACHINERY A PRIME TARGET FOR GNSS MACHINE CONTROL
Hemisphere GNSS has made compact machinery a prime target for its machine control technology. Smaller excavators can take advantage of Hemisphere’s GradeMetrix and SiteMet rix products.
GradeMetrix allows compact excavators up to 8.5 tons to
work in 2D, 2.5D, or 3D operation, all of which are standard. For compact machines, the system includes the VR500 smart antenna and IRONONE 8-inch colour touchscreen display, both of which are ruggedized to protect against the shock, vibration, and environmental conditions of job sites.
Using those components, or paired with a laser receiver for higher-accuracy elevation demands, the operator can switch between a variety of views and stake points, input flat or sloped designs, and more.
Hemisphere GNSS has focused on making its equipment work well in mixed fleets using multiple brands of machine control systems and tools, which helps companies that have already embraced machine control as well as those just starting out with technology.
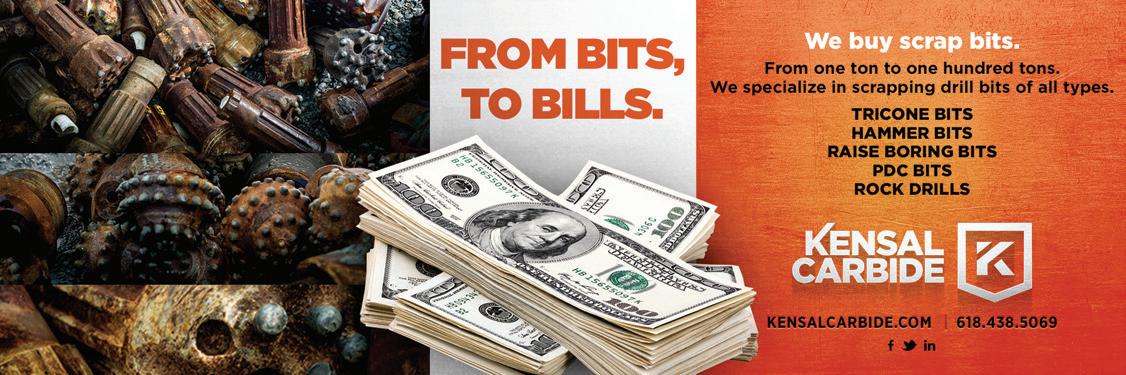
TRIMBLE MACHINE CONTROL THROUGH YOUR SMARTPHONE
Trimble’s Earthworks GO! machine control system for com pact equipment makes use of mobile computing to expand the accessibility of grade control technology.
The system pairs with grading attachments for skid-steer and compact track loaders and leverages the operator’s smart phone as the interface. It is compatible with both Android and iOS devices. Contractors performing earthmoving, site prep, and other jobs that require precision grading can make use of Earthworks GO! to grade flat or simple slopes, Trimble says. The system ties in to laser technology to provide real-time po sitioning, making it easier for the operator to remain on grade and quickly reach the targeted profile.
Most of the system components are included in Trimble’s GO! Box, which affixes to the machine without the need for mounting equipment. This makes it easy to move the system from machine to machine. For each piece of equipment the operator can use their own smartphone as the display and control of the unit.
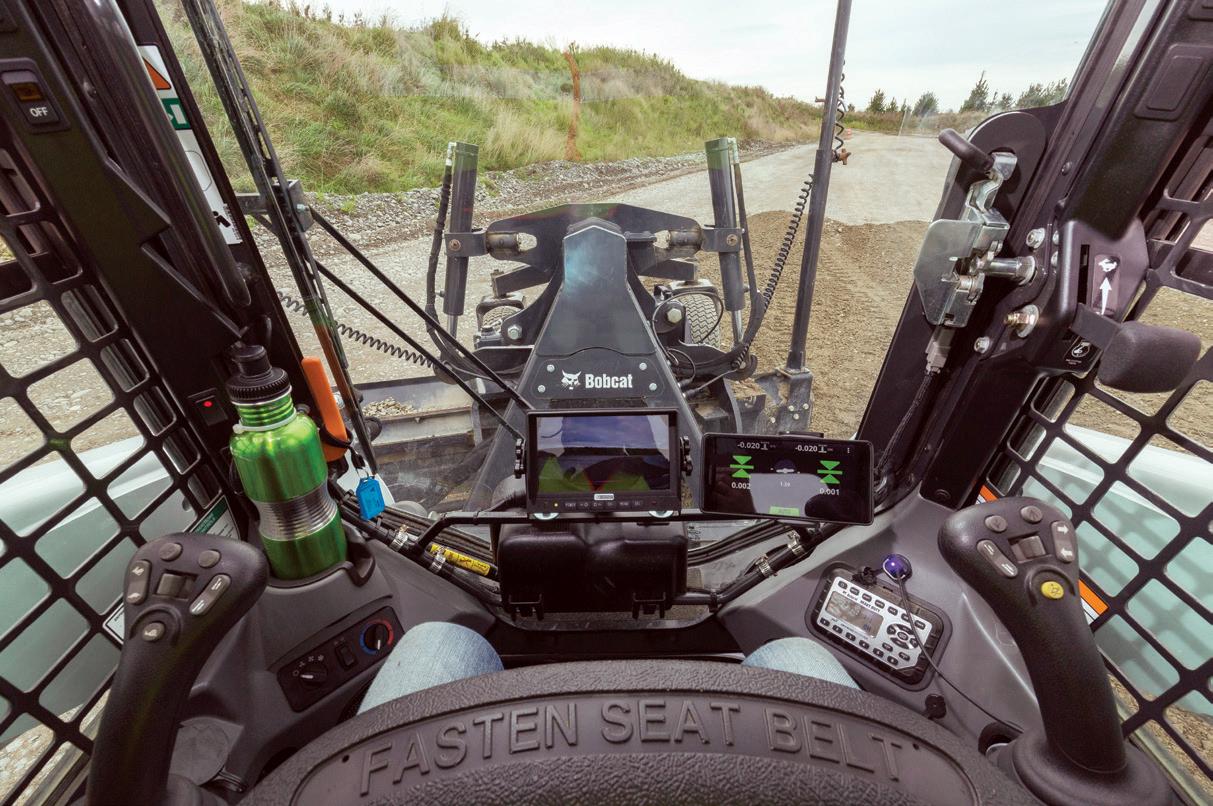
It’s easy to set up and use, it’s affordable, and it offers the same competitive benefits of machine control solutions designed for larger equipment.
Jamie Williamson Executive Vice President, Topcon Positioning Systems
How to select construction equipment for snow removal

When hard winter months hit, utilizing your dirt fleet for snow removal operations can keep your assets generating income for your business. Commonality of attachments across compact wheel loaders and skid-steer loaders, as well as versatility with quick couplers and auxiliary hydraulics, make switching between sectional snow pushers, salting devices, and snow blowers easy. Agility and clear sight lines to the work tool and around the machine make construc tion equipment safe and efficient for snow removal. Here are nine features to look for when selecting construction equip ment for snow removal operations, as recommended by CASE Construction Equipment.
HYDRAULIC COUPLERS AND ATTACHMENTS
Look for hydraulic attachment capabilities that minimize how often the operator has to get in and out of the cab to change attachments. These hydraulic couplers are available on almost every piece of equipment and compact wheel loaders are compatible with the same attachments as skid steers and CTLs. One of the things that makes construction equipment so versatile for snow removal is the ability to op erate a range of attachments including plows, boxes, brooms, blowers, and salt spreaders.
AUXILIARY HYDRAULICS AND ELECTRICAL CAPABILITIES
You’ll want to make sure that your machine is outfitted with auxiliary hydraulics and electrical capabilities. CASE recom
mends you get a 14 pin connection for attachments such as snow blowers and brooms that require electrical input and that you outfit your machine with high-flow hydraulics for operating snow blowers to their full capability.
Some attachments may require a secondary hydraulic circuit for performing a secondary hydraulic function such as posi tioning the chute of the snow blower. If you’re just running boxes and snow blades, you may not need these features. Or, if you’re just running a hydraulic angle blade, you may be able to use standard auxiliary hydraulics.
CREEP SPEED
Creep speed is a particularly valuable feature if you're run ning snow blowers or brooms. Creep speed is available across equipment platforms and this functionality allows you to set the maximum continuous ground speed for the machine while independently controlling hydraulic power to the attachment. This allows you to operate your skid steer or compact wheel loader at a consistent 3.2 mph, for example, while delivering varying throttle to the attachment.
TIRES OR TRACKS?
Both skid-steer and compact track loaders can be effec tively deployed for work in snow removal. CTLs can get the job done and there are special snow tracks that can improve performance, but in a head-to-head comparison for this ap plication skid-steer loaders are slightly better suited for snow and ice removal. While snow and ice can provide a buffer with the ground, this application is entirely about running on improved surfaces and rubber tracks will experience greater
wear and abrasion rates than rubber tires – and are more expensive to replace. The initial purchase price of a CTL is also higher and the undercarriage costs more to own and maintain over the life of the machine, so when purchasing a machine for snow removal a skid-steer loader is recommend ed. For skid steers, wheel loaders, and backhoes, radial tires are recommended for snow and ice removal – they provide greater traction and generally more surface contact. Another important element to consider for improved traction, be sides tires, is axle configurations. When it comes to wheeled machines, all-wheel drive is recommended for providing the best traction and performance. Reduced slippage will slow tire wear replacement schedules.
ELECTRO-HYDRAULIC CONTROLS
Electro-hydraulic controls let you either set total machine responsiveness or to independently set different factors includ ing drive speed. Depending on the conditions of the pavement, you can set the drive speed to smooth, moderate, or aggressive, and then adjust tilt, lift, and motor arm speed as well based on performance and the site.
LIGHTING
Lighting is critically important in a snow removal applica tion – both for the machine to be seen and for the operator to see the job site. Talk to your dealer about lighting options available, as they may have specific packages ideal for snow removal.

A good rule of thumb, between lights, strobes, and bea cons, is to outfit your equipment with as much as you can.
CAB FEATURES
In-cab features, such as air ride seats where available, provide a smoother ride for the operator. A heated air seat will provide added comfort, and a rear-view camera in the cab is ideal for optimal visibility.
COLD WEATHER OPTIONS
Make sure to talk to your equipment dealer about available cold weather options including block heaters, air intake grid heaters, heavy-duty batteries, and the fluids you should be using in cold weather applications. These options will improve uptime. Some snow packages come with other features such as lighting, rear-view camera, and heated mirrors.

TELEMATICS
CASE recommends using telematics on your snow fleet. While telematics provides fleet management benefits when you have numerous machines spread out and provides oper ational data, such as hours of use and service needs, it also provides a security advantage. Snow removal equipment is often parked in unsecured public spaces. Telematics, whether utilizing geo-fencing or simple location tracking, can help identify unauthorized use and even recover equipment after it has been stolen.
COLD WEATHER PREP FOR COMPACT UTILITY LOADERS
BY DAN ROBERTSFor many contractors, winter is one of the most challenging seasons. Dropping tem peratures, frozen ground, plus snow and ice cover all translate to extra steps on the job site. Compact Utility Loaders (CULs) are versatile machines increasingly found on many job sites, and when equipped with the right at tachments, CULs can be par ticularly useful in the winter. CULs can use blades and buckets to quickly remove snow or easily spread salt, and the machines’ maneu verability and compact size prove particularly helpful for these applications.
However, cold weath er can cause issues with starting equipment, ma chine performance, and more. But, with a little bit of know-how, many of these potential problems can be avoided.
HOW TO OPTIMIZE THE OPERATION OF YOUR CUL IN WINTER CONDITIONS
Start well When starting an engine in cold conditions, running at mid-throttle for two to five minutes before increasing to high throttle can be helpful. If the outdoor temperature is below freez ing and there is access to a garage or other building, store the machine there to keep it warmer and aid in starting. Never run an engine in an enclosed area.
Run at the right speed When a hydraulic system is cold – meaning the air temperature is at or below freezing – running the engine at high speeds could damage the hydraulic system.
Use the correct fuel
Using an improper fuel grade in the machine may result in engine failure, or the engine may start but not continue
running. Using clean, fresh (within 180 days of purchase) diesel and biodiesel fuel is important for optimal perfor mance. Most machines also benefit from ultra-low sulfur content and cetane ratings of 50 and higher. Around mid-September, winter-blend gasoline and diesel fuels are delivered to fuel stations. When temperatures reach around 32 degrees Fahrenheit and colder, diesel fuel is sus ceptible to gel. Additionally, there are options for fuel ad ditives for diesel fuel to lower the fuel gel point and raise the cetane to improve the ignition point for enhanced cold start ing. At lower temperatures, winter-grade fuel provides a lower flash point and cold flow characteristics which aid in starting and reduce filter plugging.
Protect your charge Keeping the CUL’s battery fully charged is especially
important to prevent battery damage when the tempera ture is below freezing. It’s also recommended to ensure the charger doesn’t get wet and keep it protected from rain and snow. With lithium-ion batteries, electric machines can discharge at a quicker rate in temperatures around 32 degrees Fahrenheit, and it can lower the runtime. Additionally, there are tem perature sensors in electric CULs that may prevent the motor from starting until the temperature is above the threshold or above 0 degrees Fahrenheit.
Become familiar with all controls By understand ing the controls before start ing the machine, operator errors are minimized – as is time spent in the cold.
DAN ROBERTS is a senior technical representative with Toro.
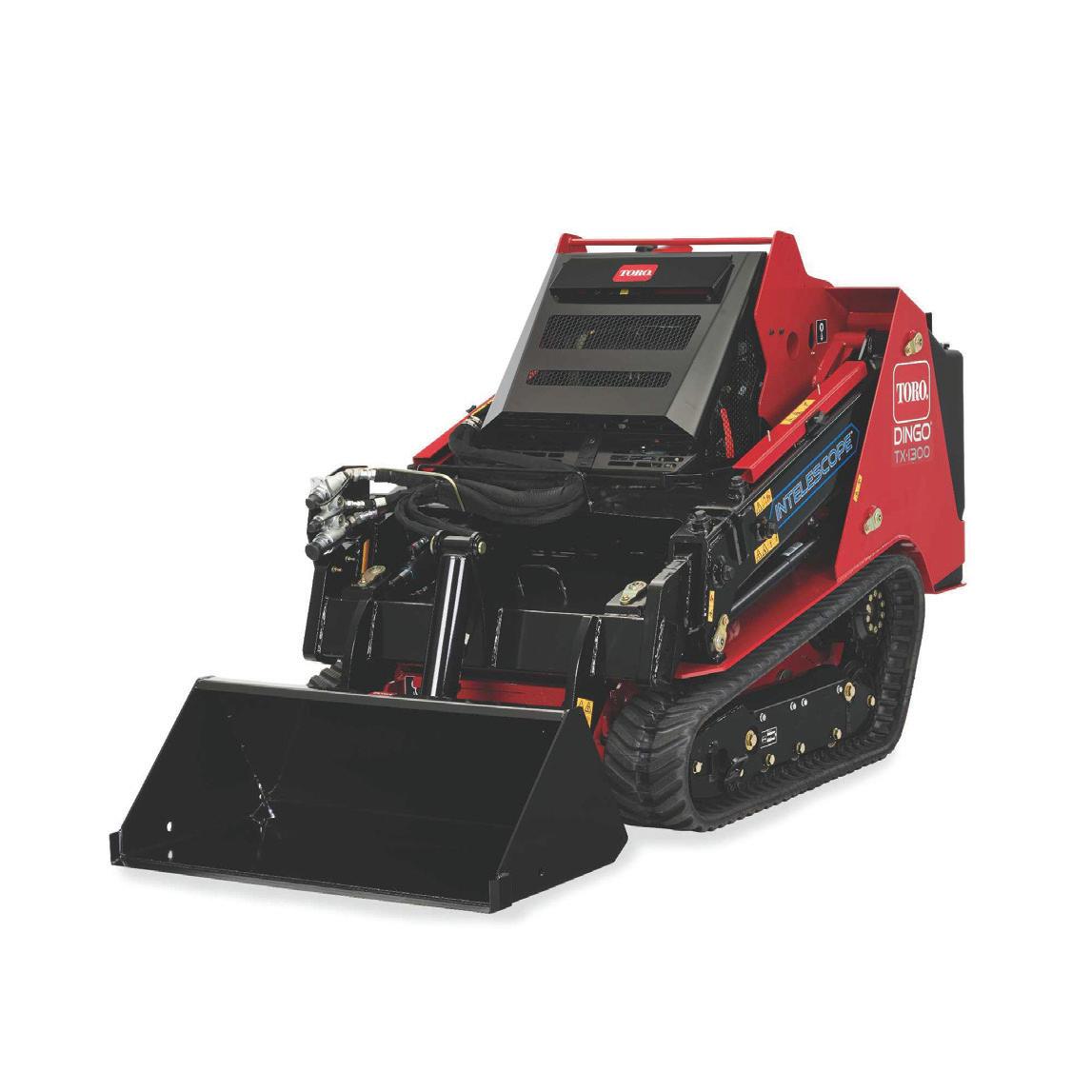
BOBCAT SNOW BLOWER ATTACHMENT FOR COMPACT LOADERS
The snowblower features an ultra-durable direct-drive, sprocket-style chute rotation, which improves the performance, durability, and ease of maintenance. It enables operators to point snow in virtually any direction and place it wherever the job requires – even in hard-to-reach places such as the middle of lawns, in ditches, or inside wooded areas along a path. It is pow erful enough to break through ice buildup and eliminates chains, which can rust, loosen, or break. The chute delivers 270 degrees of rotation for a wide range of accurate snow placement possibili ty, which is a 15-degree increase over previous designs.
Bobcat’s ultra-durable snowblower attachment makes quick work of winter drifts. With an increased intake height and bigger auger to draw more snow into the blower, operators can clear snow quickly.
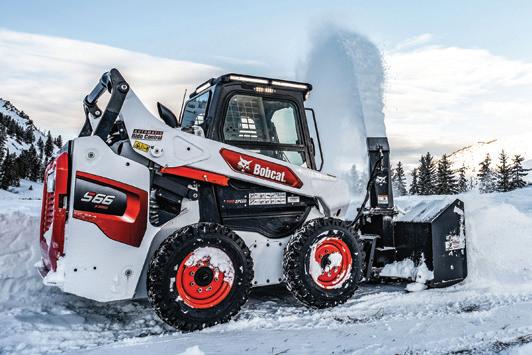
Equipped with nine different width options and numerous motor packages, the Bobcat snowblower attachments can be matched to the carrier and the application – from wide-open sites like driveways and parking lots, to narrow spaces like sidewalks.
The chute’s rounded intake provides a smoother surface to roll the snow into the feed impeller, rather than pushing it. This design minimizes clogging and reduces resistance for improved snow flow through the attachment and better productivity. The optional truck-loading chute allows the operator to place snow high into a truck and simplify hauling. High-flow models capture extra available hydraulic horsepower from the carrier, which en ables clearing through the deepest drifts and heaviest snow while throwing it farther.
Easily adjustable skid shoes are mounted to the sides of the snowblower, allowing operators to raise or lower the clearing depth to match the surface of the job site. They not only make it easy to maintain ground alignment, but they can also help guide operators along curbs or walls – while preventing contact with the snowblower itself.
ROTARY BROOM ATTACHMENTS
Hilltip’s SweepAway rotary brooms for use on pickups, tractors, and other equipment are available in 59- to 86-inch widths and feature a 20-inch-diameter brush for high performance in a variety of applications including snow removal.
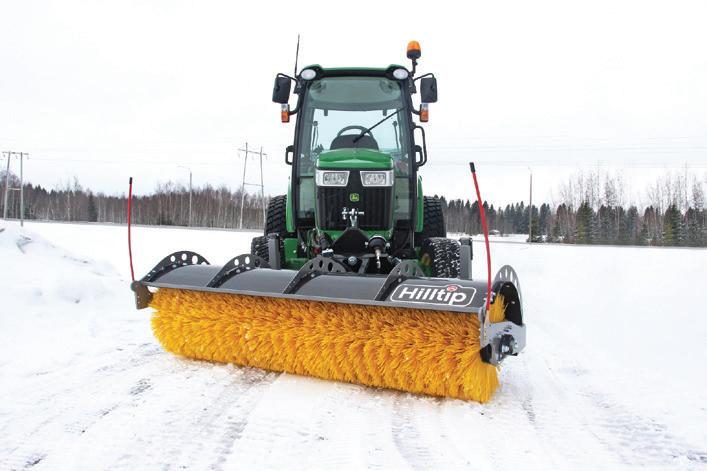
The SweepAway rotary brooms mount on pickups using Hilltip’s Quick Hitch mounting frame. They can also be used on tractors with the company’s STR and VTR mounting frames. Other mounting frames are available for attaching to different types of equipment, such as loaders or forklifts. The mounts allow the brooms to be angled up to 25 degrees for controlling the direction of swept material.
The brooms require a hydraulic system with a minimum flow of 11 gpm. If the vehicle does not meet the hydraulic system requirements, then a Hilltip Power Unit can be added. Featuring a heavy-duty design, the power unit has a KOHLER engine that provides up to 12 gpm of hydraulic flow to operate the SweepAway rotary brooms, as well as other machines.
A variety of other options and accessories are available for the SweepAway rotary brooms, including a deflector, a sprin kler kit with a 132-gallon tank, and an electrical oil-flow valve.
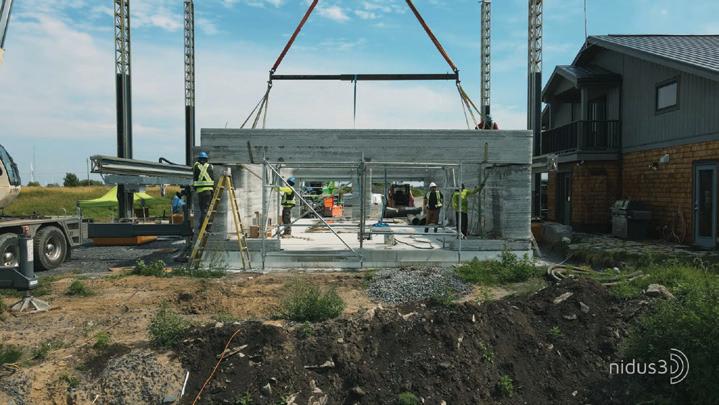

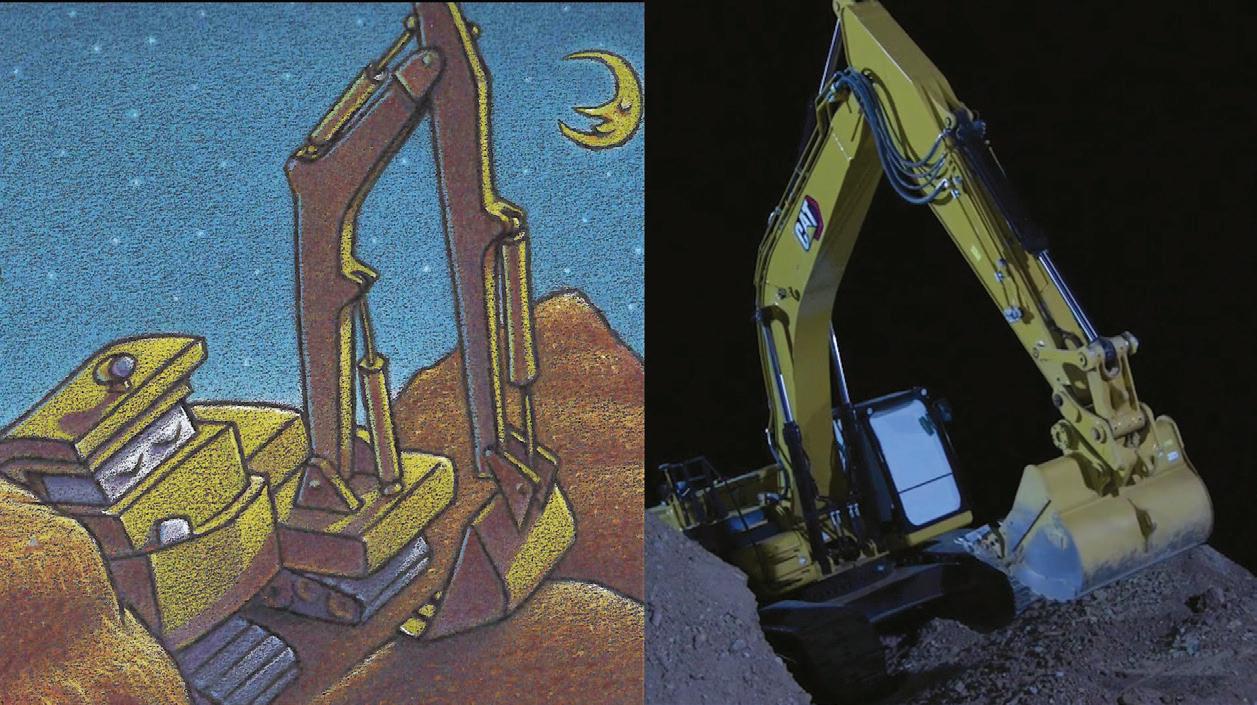
SUBSCRIBE
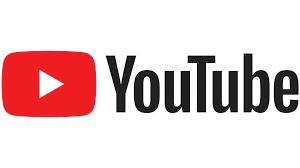
Big advantages for your smaller machines
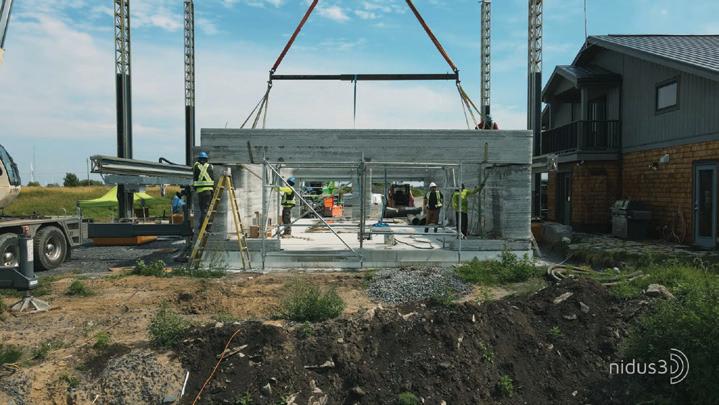
Choosing a compact machine doesn’t mean that you have to compromise size over power. Our compact tiltrotators turn even your small machines into powerful do-it-all tool carriers for precision and capacity in small spaces. rototilt.com/tiltrotators
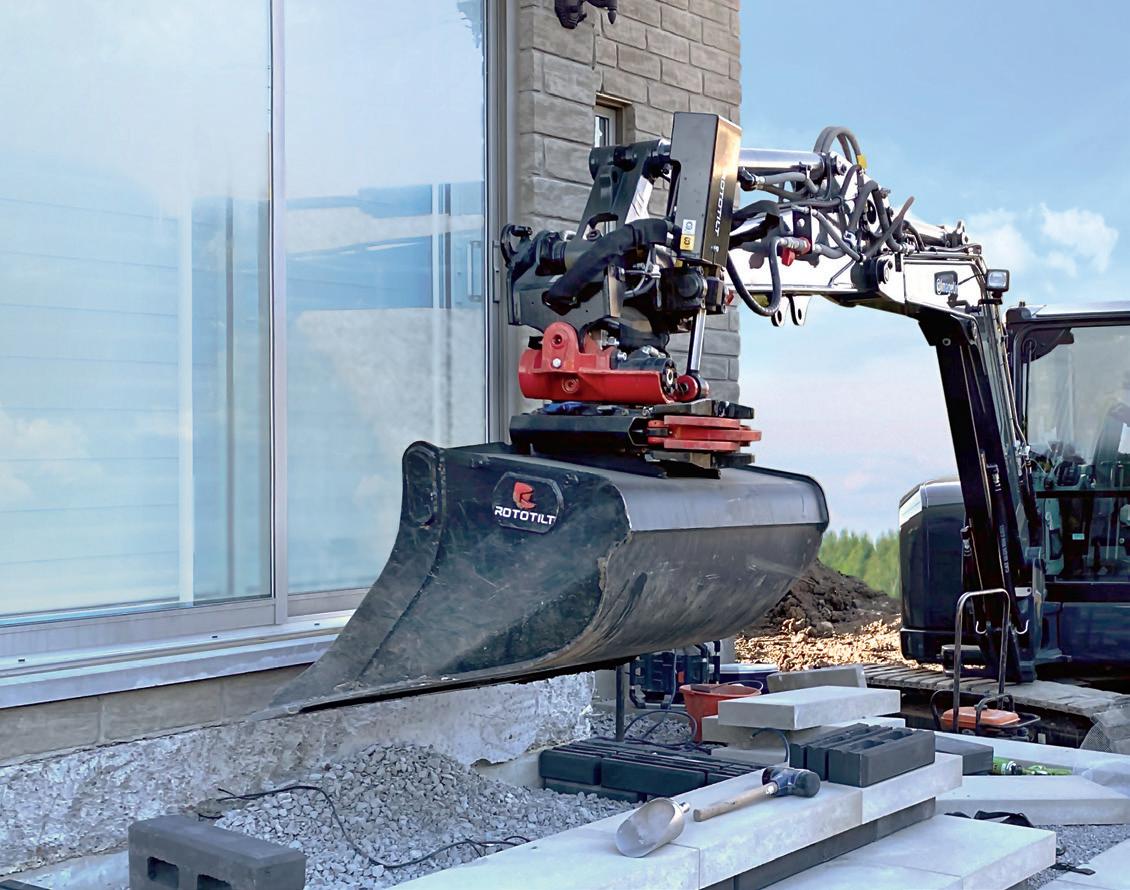

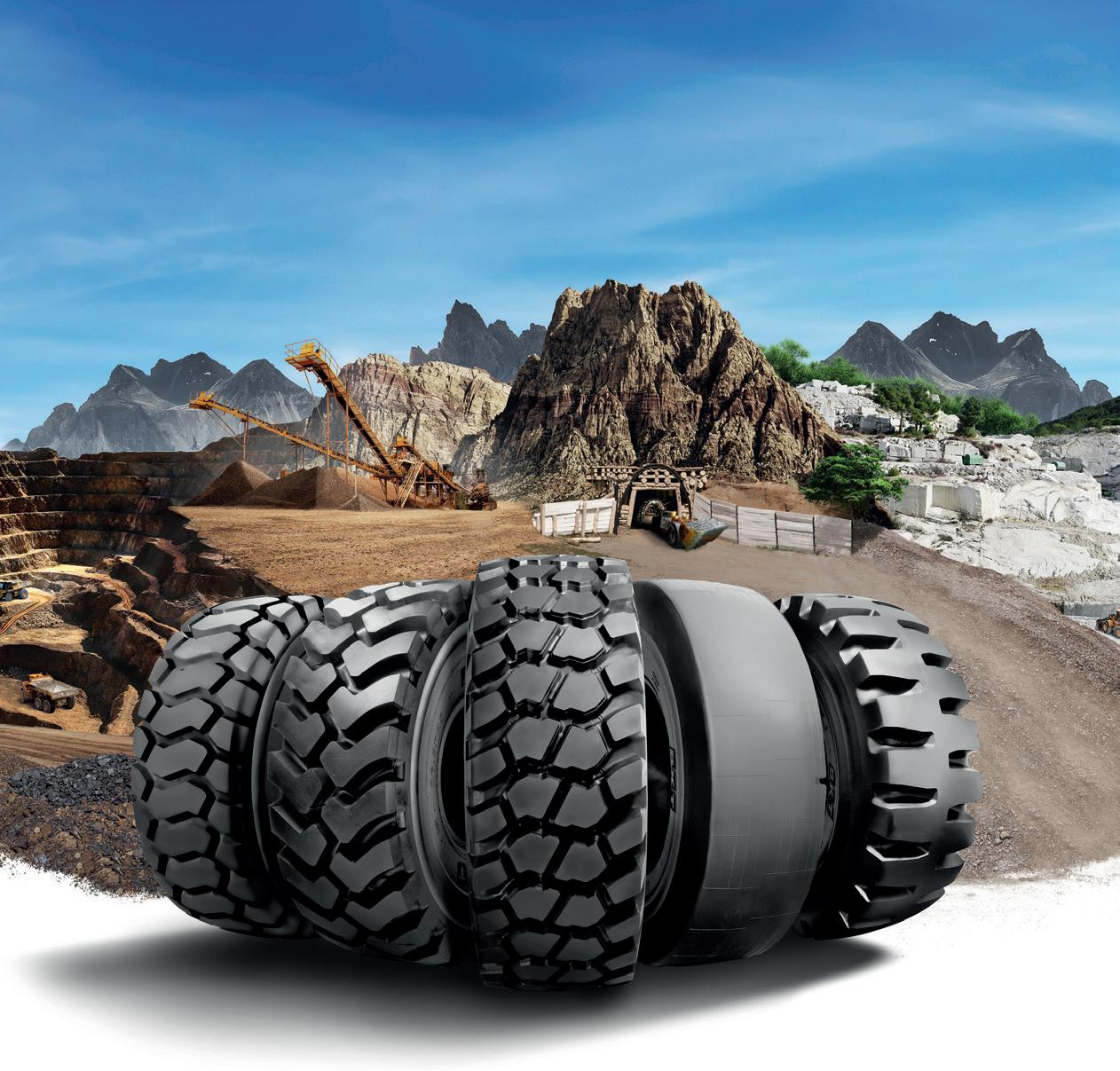

No
A LONG WAY
WHEREVER YOU ARE, BKT IS WITH YOU
BKT
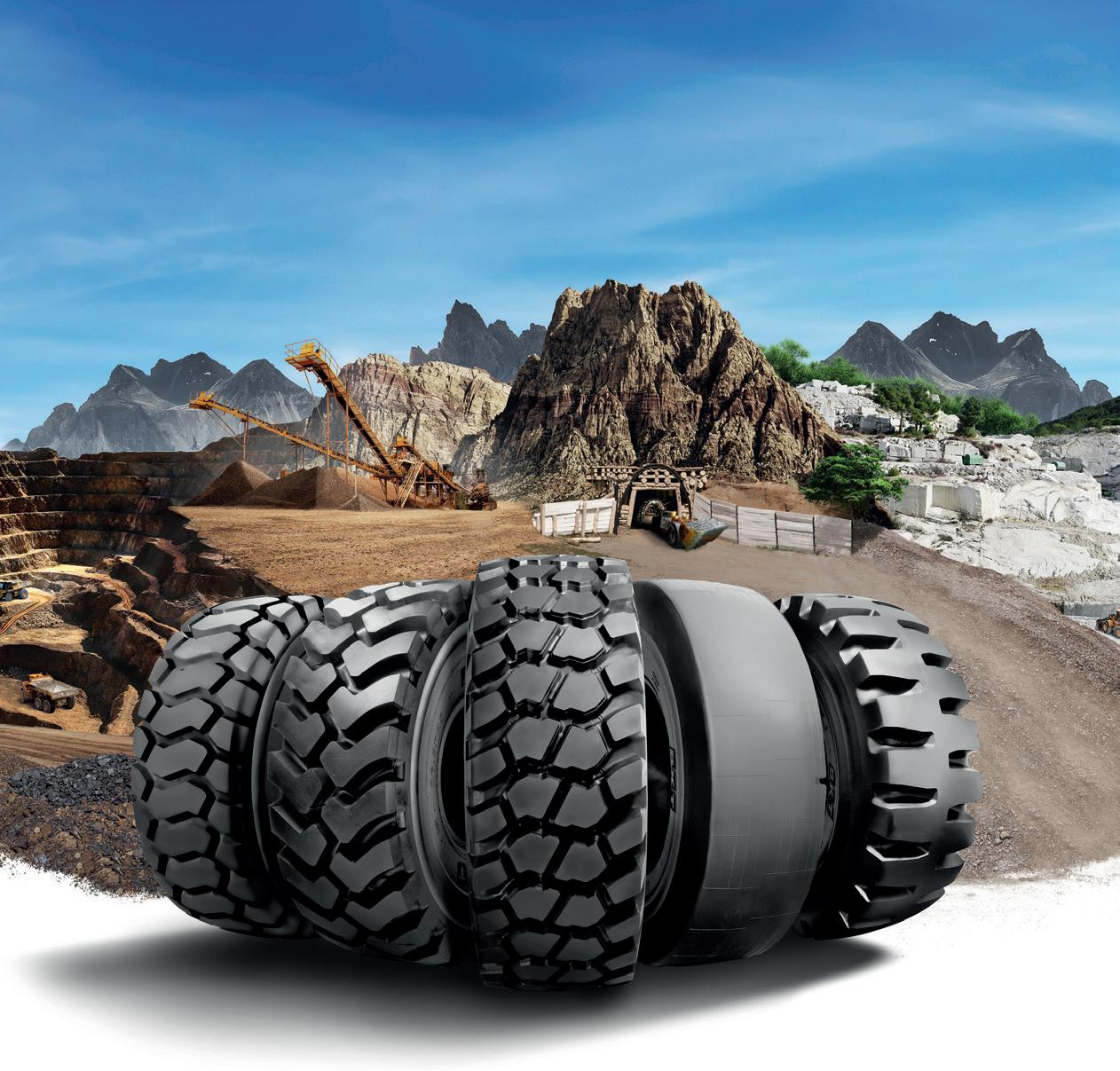
The Worldwide Leader in Concrete Paving Technology
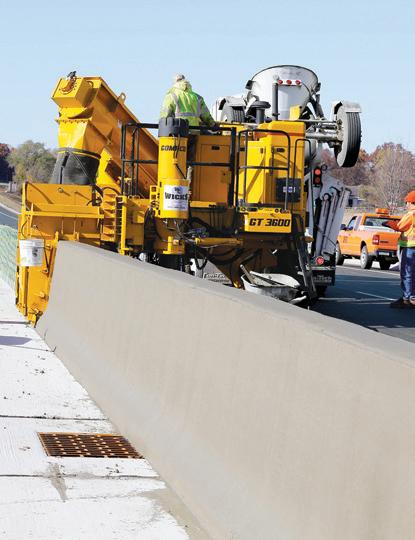
control system, created in-house by

exclusive and proprietary
software
and
in the field. At the heart of GOMACO equipment is our passion for concrete and our commitment to our customers. We look forward to visiting with you about your upcoming paving projects and your concrete paving equipment needs. Our worldwide distributor network and our corporate team always stand ready to serve and assist you.
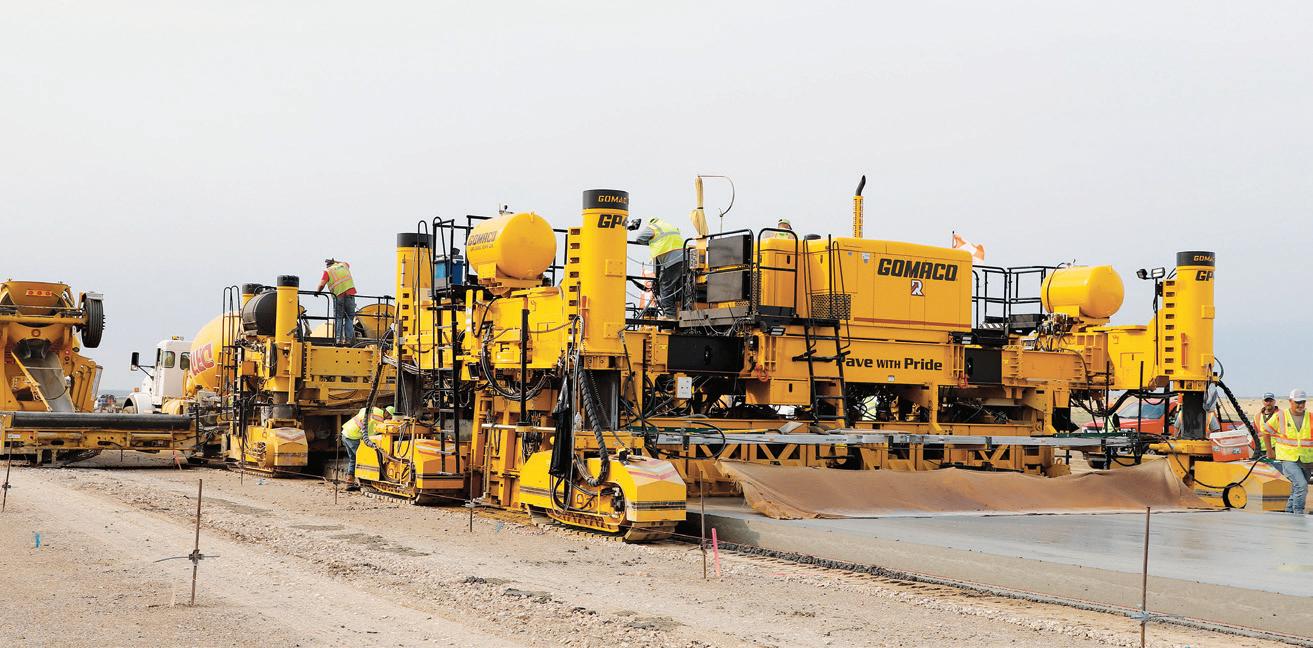
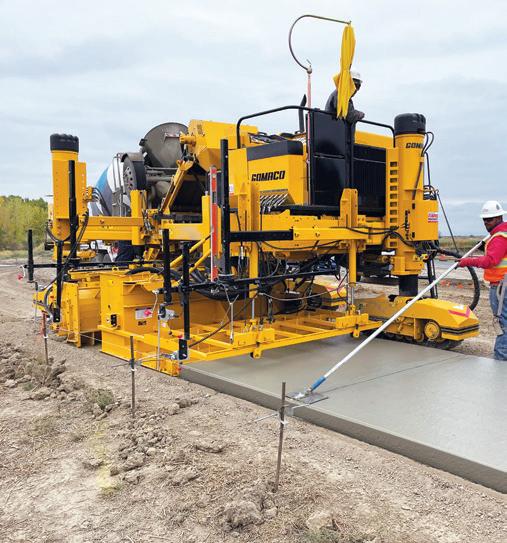
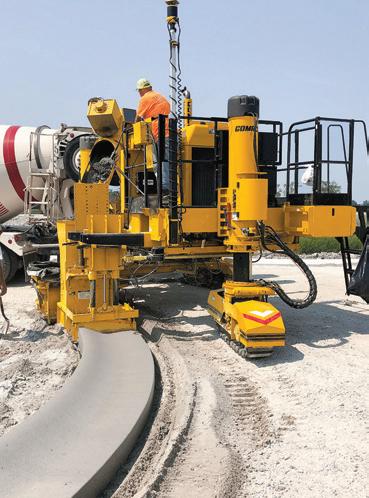