DARTMOUTH METALS MAXIMIZES RECOVERY RATES
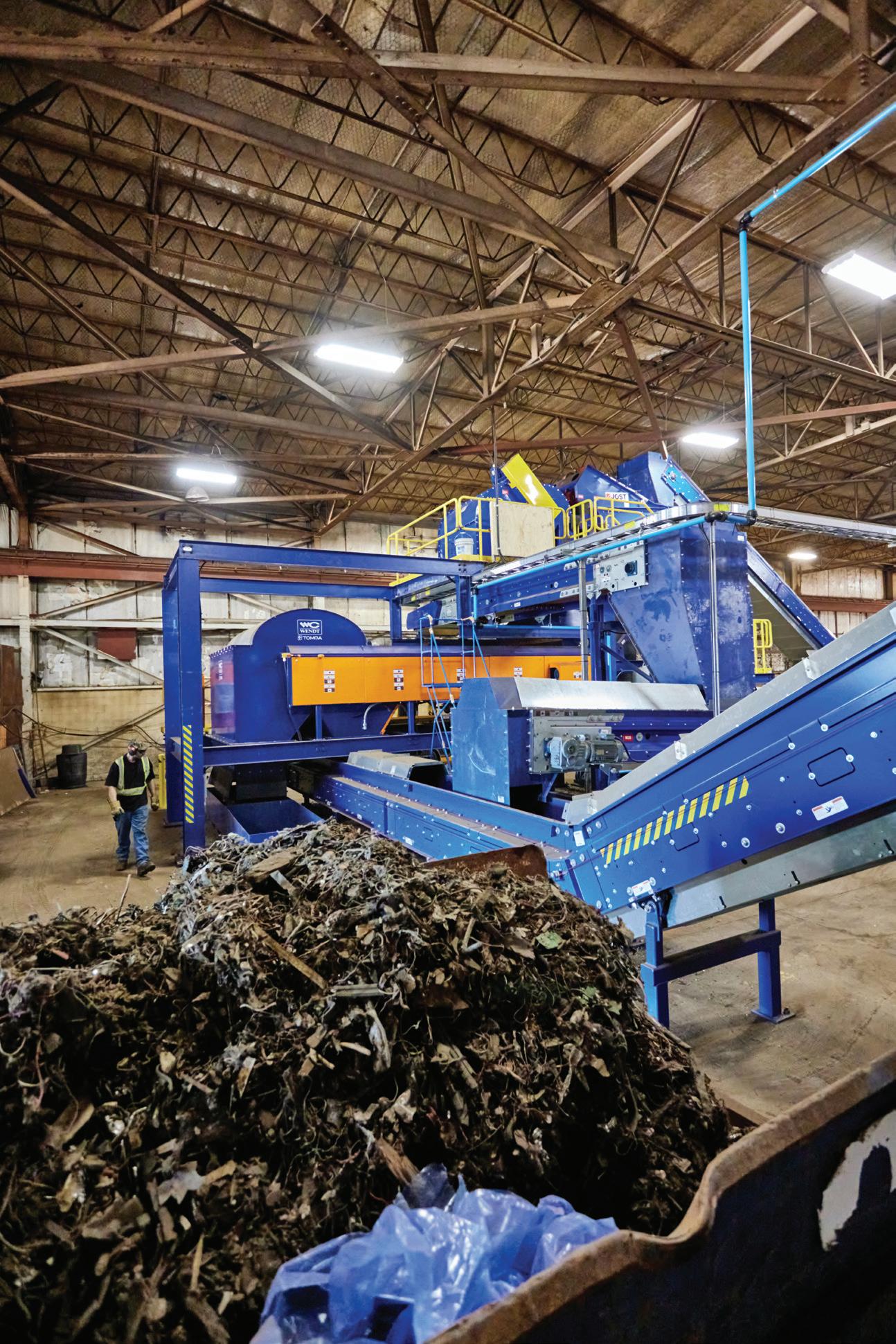
ALUMINUM’S YEAR OF TRANSITION
THE DRIVE FOR GREATER PLASTICS CIRCULARITY
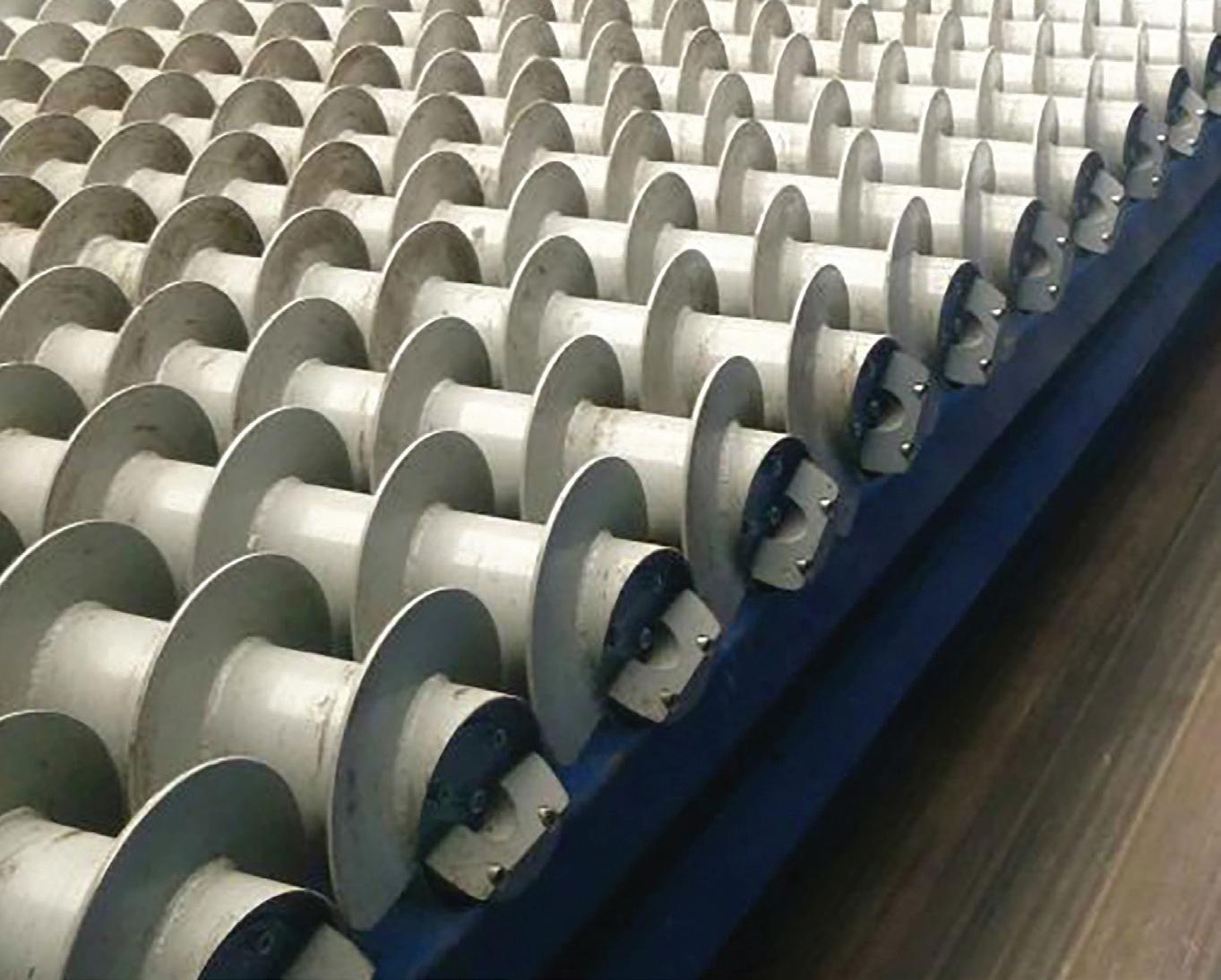
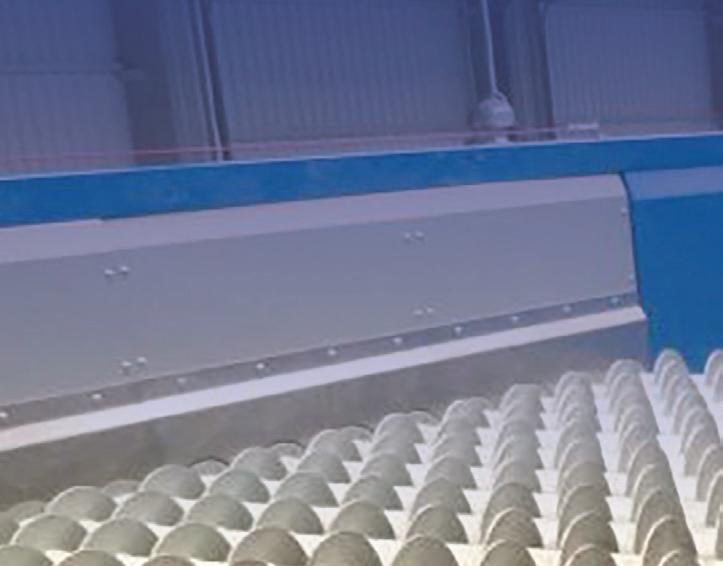
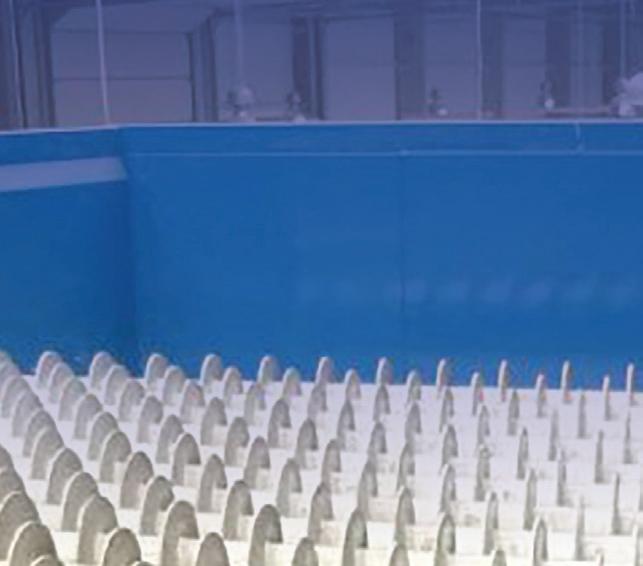
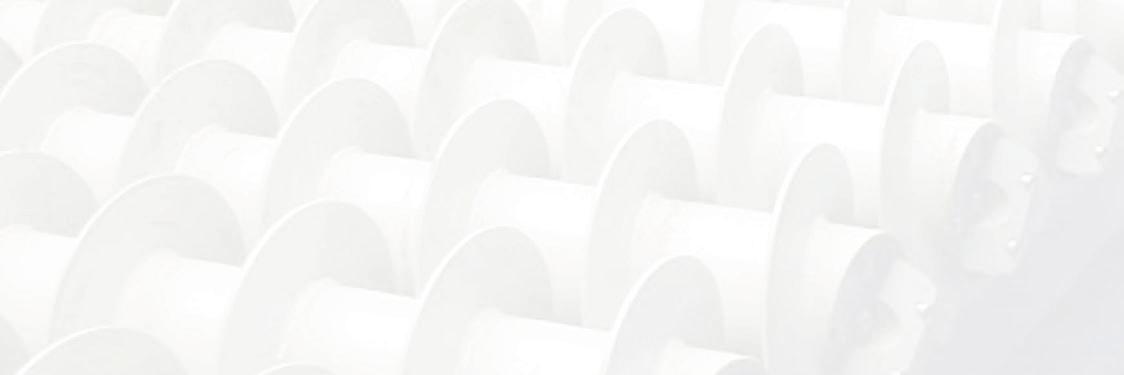

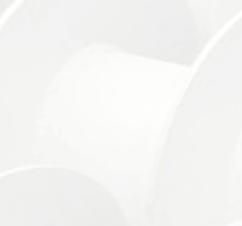
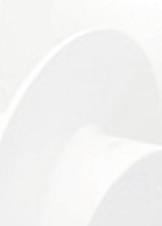

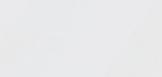
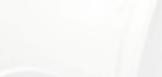
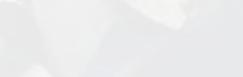

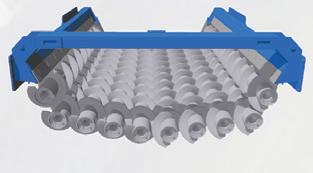
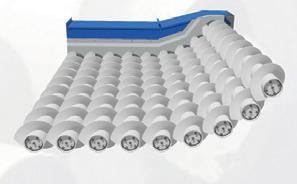
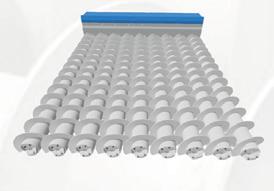
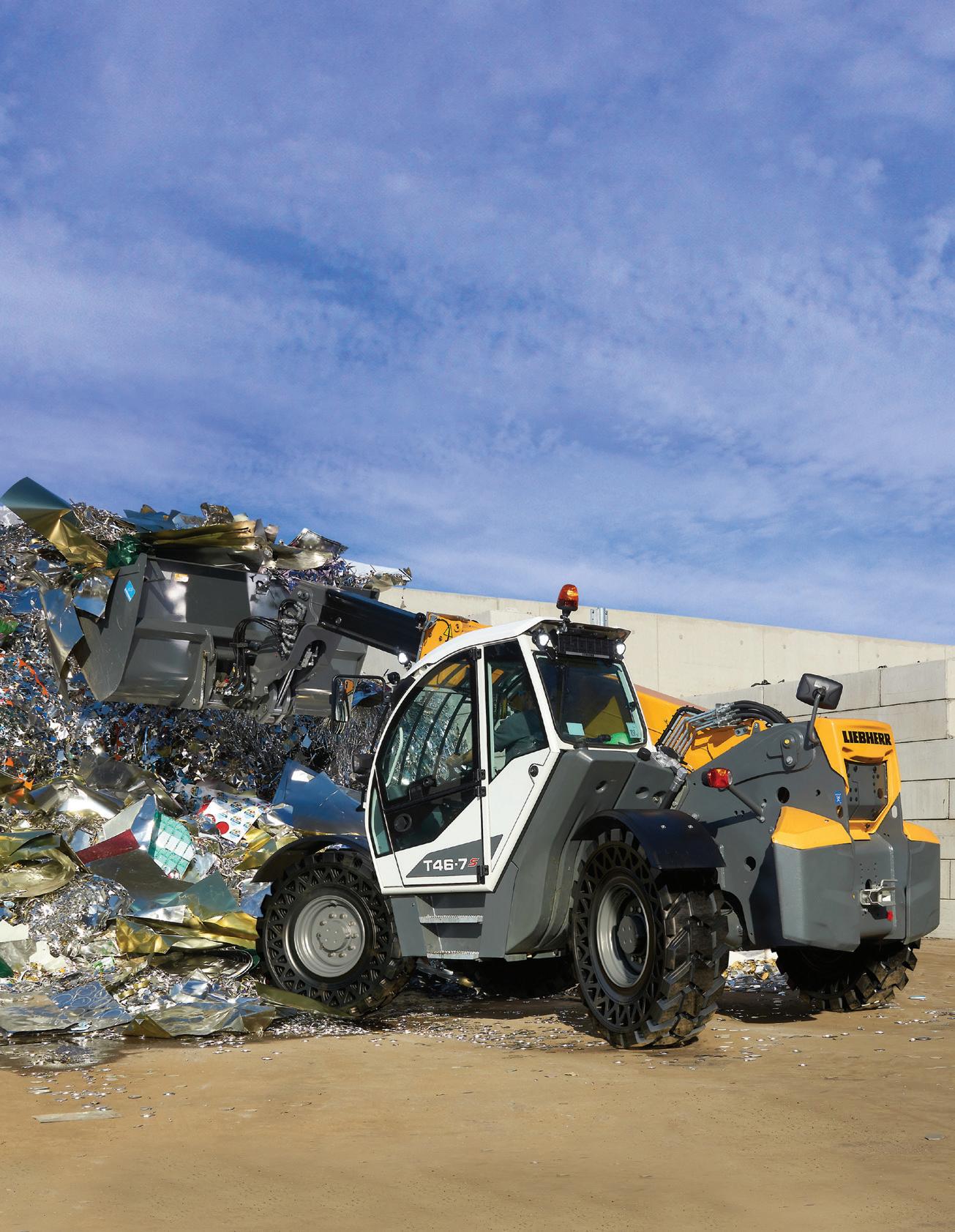
ALUMINUM’S YEAR OF TRANSITION
THE DRIVE FOR GREATER PLASTICS CIRCULARITY
The Telescopic Handler T 46-7s shows its strength as highperformance do-it-all machine: swift and nimble, equipped with strong work hydraulics and capable of lifting large material loads up to even the tallest storage shelves. www.liebherr.ca
Harris, American Baler and International Baler have come together under the Recycling & Waste Equipment Division of Avis Industrial.
While Avis began building its ownership position back in 1979, the new structure creates an exciting path forward.
The three companies have been in business for 289 years combined and offer unmatched breadth of baling solutions, operate four manufactur-
ing locations and have the largest global installed base of recycling and scrap compaction equipment. Each company will operate individually, but customers will benefit from increased flexibility in machine choice, enhanced field support and parts availability.
With a shared heritage of performance, reliability and support we’re proud of our past. Knowing that we are better together, we’re excited about our future.
20 COVER STORY DARTMOUTH METALS MAXIMIZES RECOVERY WITH NEW WENDT SYSTEM
52 ALUMINUM’S YEAR OF TRANSITION
28 NAVIGATING HEADWINDS AND TAILWINDS IN THE AUTO RECYCLING INDUSTRY
54
THE DRIVE FOR GREATER PLASTICS CIRCULARITY
EDITOR IN CHIEF
Kaitlyn Till ktill@baumpub.com
604-291-9900 ext. 330
EDITOR
Slone Fox sfox@baumpub.com
604-291-9900 ext. 335
ASSOCIATE PUBLISHER/ VICE PRESIDENT OF SALES
Sam Esmaili sam@baumpub.com
604-291-9900 ext. 110
ADVERTISING PRODUCTION MANAGER
Tina Anderson production@baumpub.com
604-291-9900 ext. 222
THE NEWLY INSTALLED WENDT NONFERROUS SYSTEM AT DARTMOUTH METALS
Dartmouth Metals expects to increase purity rates and recover higher volumes of Zorba, Zurik, and copper wire with its new system.
See more on page 20.
DESIGN & PRODUCTION
Morena Zanotto morena@baumpub.com
604-291-9900 ext. 325
PRESIDENT/PUBLISHER
Ken Singer ksinger@baumpub.com
604-291-9900 ext. 226
VICE PRESIDENT/CONTROLLER
Melvin Date Chong mdatechong@baumpub.com
FOUNDER Engelbert J. Baum
or 604-291-9900 ext. 335
CONNECT WITH US @RecyclingPN
Published by: Baum Publications Ltd.
124 - 2323 Boundary Road Vancouver, BC, Canada V5M 4V8
Tel: 604-291-9900
Toll-free: 1-888-286-3630
Fax: 604-291-1906
www.baumpub.com
www.recyclingproductnews.com @RecyclingPN
FOR ALL CIRCULATION INQUIRIES
Toll-free: 1-866-764-0227
email: rpn@mysubscription.ca
Subscription: To subscribe, renew your subscription, or change your address or other information, go to: https://www.recyclingproductnews.com/ mysubscription/subscribe
Recycling Product News is published eight times yearly: January/February, March, April, May/June, July/August, September, October, November/ December. Advertising closes at the beginning of the issue month.
One year subscription rates for others: Canada $33.50 + 1.68 GST = $35.18; U.S.A. $40; other countries $63.50. Single copies $6.00 + 0.30 GST = $6.30; outside Canada $7.00. All prices are in Canadian funds.
Recycling Product News accepts no responsibility or liability for reported claims made by manufacturers and/or distributors for products or services; the views and opinions expressed are those of the authors and not necessarily those of Baum Publications Ltd.
Copyright 2023 Baum Publications Ltd. No portion of this publication may be reproduced without permission of the publishers.
LINDEMANNs NxtCut is the new generation of hydraulic scrap shears with side compression bed. The machine is specially designed for processing various light to medium-heavy scrap materials of medium volumes. Small, fast, strong and flexible, with original LINDEMANN quality made in Germany, and equipped with an energy-efficient and sustainable 400 bar hydraulic power unit, up to 1,000 t shearing force and improved maintainability.
Exactly what you are looking for? Give us a call: +1 210-491-9521
→ Real LINDEMANN side compression shear with generous overstroke of side ram and lid
→ Unique: hydraulic 400 bar system for highest efficiency through minimized losses
→ Improved wear plate concept for cost-effective and sustainable operation with maximum operational reliability
→ Blade slide with well-known LINDEMANN bending bar for improved shearing performance with long materials
→ Compact design of the hydraulic power unit and control cabinet optimized for maximum ease of maintenance
→ Charge box length of 20.3 ft – 26.2 ft
With a new year upon us (and new budgets) many metals recyclers are taking stock of their current equipment and seeing what can be added to streamline efficiency, what needs to be replaced entirely, and what might be worth investing in down the road.
While the right equipment can improve your yard’s productivity, capacity, and bottom line, these kinds of investments can be a massive financial undertaking and, as such, shouldn’t be rushed. It’s vital to weigh factors such as short- and longterm needs, current resources, and industry trends before making any major decisions. Ask yourself if you need new equipment, or if you can upgrade what you already have on hand. If you do need new equipment, look for the most versatile machine possible to get the most bang for your buck. It’s a lot to consider, but making the right choice can open the door for new revenue streams, increased sustainability, and enhanced efficiency overall.
The 2023 ISRI Convention & Exposition in April is ideal for potential buyers who will be able to weigh all of their options under one roof. With over 275 exhibitors and live demonstrations, having multiple manufacturers and equipment types in one place can simplify the decision-making process and alleviate much of the stress that comes along with investing in new equipment.
For other metals recyclers, it’s less about investing in the equipment they know they need, and instead finding supplementary equipment that can help boost profits. Many recycling operations produce waste that can be turned into cash with the right machine, a prime example of which can be found in this month’s cover story. Dartmouth Metals, a Nova Scotia-based metal processor, recently invested in a non-ferrous plant that’s doubling recovery rates for the yard and capturing previously missed insulated copper wire. Where the company used to recover 1,000 pounds of wire per month, its now capturing 20,000 pounds. And, as the first metal recycling company in the Atlantic provinces to purchase a copper and aluminum granulator, Dartmouth Metals has been able to nearly double the value of its insulated wire by processing it into clean copper.
With such a substantial focus on metals in this month’s issue, I look forward to carrying this momentum into ISRI 2023 and meeting even more industry professionals. Swing by our booth to say hello, and on behalf of the Recycling Product News team, I look forward to another great convention!
Ask yourself if you need new equipment, or if you can upgrade what you already have on hand. If you do need new equipment, look for the most versatile machine possible to get the most bang for your buck. It’s a lot to consider, but making the right choice will open the door for new revenue streams, increased sustainability, and enhanced efficiency overall.
With shifting catalytic converter legislation, recyclers feel confident partnering with PMR for their processing needs. As a company committed to supporting a lawful and ethical industry, no converter shipment is accepted without a seller’s legal business documentation and registration validating their right to purchase and acquire catalytic converters.
PMR’s suppliers have access to a detailed history of their operations through online lot tracking and photo grading, helping them keep a record of the material type and origin of the converters they’ve
sent to processing. Through extensive invoicing, with precise material returns and assay results, suppliers create an accountable record of their finances.
PMR is committed to the long run, helping you get to your business goals while providing the peace of mind of doing things the right way, without taking any shortcuts.
The Composting Consortium has launched a compostable packaging degradation pilot to study real-world compostable packaging disintegration in the U.S. The project marks a milestone for the Consortium, as it aims to improve available data on how certified, food-contact compostable foodware and packaging are currently breaking down at various types of composting facilities – from static piles, to worms, to GORE covers.
Working with composting facilities across the U.S., the pilot will evaluate the disintegration of more than 30 types of certified compostable products and packaging across facilities operating with varying climates, composting methods, and equipment. Data gathered from the assessment will inform work to align the rapid growth of compostable packaging with the needs of industrial composters.
Data collected from this pilot will be provided to the Compostable Field Testing Program (CFTP), a non-profit international research platform which facilitates field testing across North America. The CFTP is designed to develop comprehensive baseline data that correlates composting conditions with the disintegration of common compostable products and packaging.
The EPA estimates that around four percent of food waste is composted in the U.S., and as the composting landscape in the U.S. evolves, new materials are flowing through the organics stream. With these changes comes increasing pressure to successfully recover and process food scraps and food-contact compostable packaging. Many cities across the U.S. are setting ambitious zero waste goals and, in some cases, mandating organics diversion.
Among these efforts, the compostable packaging market is poised to grow 17 percent annually between 2020 and 2027, adding complexity to the challenge. With lookalike and imposter materials contaminating composting and recycling facilities, composters face challenges in efficiently processing inputs and maximizing valuable outputs.
The degradation pilot is critical to the Composting Consortium’s goal to identify best practices in areas including consumer understanding of compostable packaging labelling and collection, sortation and sensing technologies, and policy.
The U.S. Department of Energy (DOE) has committed a conditional loan of $2 billion to Redwood Materials for the construction and expansion of a battery materials campus in McCarren, Nevada, that will support the growing electric vehicle market in the U.S.
According to the company, once fully operational, the project would be the first U.S. domestic facility to support the production of anode copper foil and cathode active materials in a fully closed-loop lithium-ion battery manufacturing process by recycling end-of-life batteries and production scrap and remanufacturing that feedstock into critical materials.
Redwood Materials will use both new and recycled feedstocks to produce approximately 36,000 metric tons per year of thin, battery-grade copper foil for use as the anode current collector, and approximately 100,000 metric tons per year of cathode active materials.
To date, nearly all anode and cathode production supporting U.S. battery cell manufacturers occurs in Asia. With this conditional commitment, Redwood Materials will lead one of the first domestic projects that produces cathode materials at scale for battery cell manufacturing. The project will also support a domestic, sustainable supply of anode copper foil, onshoring a key part of the critical materials supply chain as U.S. EV adoption grows exponentially.
To meet the increased demand for lithium-ion batteries, recycling will play an increasingly important role in battery materials production. On average, Redwood can recover greater than 95 percent of the critical battery elements in an end-of-life battery and then use those metals to manufacture anode and cathode components domestically for U.S. battery cell manufacturers.
Redwood Materials’ Nevada operation recycles end-of-life batteries from consumer electronics like cellphones, laptops, power tools, and other electronic waste, remanufacturing these feedstocks into critical components that help support the domestic lithium-ion battery supply chain.
While this conditional commitment demonstrates the intent to finance the project, several steps remain for the project to reach critical milestones, and certain conditions must be satisfied before the final loan is issued.
U.S. states can expect significant increases in recycling rates for packaging and printed paper with the adoption of Extended Producer Responsibility (EPR) programs, a new study from The Recycling Partnership finds.
Increasing Recycling Rates with EPR Policy explores the impact of EPR programs in seven jurisdictions worldwide and in six U.S. states to assess the effect on state-level recycling rates and other key metrics.
The research examined the impact of EPR policies on seven paper and packaging recycling programs around the world. The findings showed that across the board, EPR policy drove the collection and recycling of target materials to over 75 percent in British Columbia, Belgium, Spain, South Korea, and the Netherlands, with Portugal and Quebec at over 60 percent. Across all materials, U.S. state programs performed far lower.
Under EPR policy, companies that produce packaging materials are required to fund local recycling programs by paying fees, shifting the financial burden away from local governments and taxpayers. EPR fees can also incentivize companies to make packaging more recyclable.
The Recycling Partnership’s study explored the prospective impacts of the policy on a sample of U.S. states. The research showed that implementing EPR programs in U.S. states would:
• Increase overall residential recycling rates by as much as 48 percent.
• Create nearly universal recycling access.
• Increase overall participation in recycling.
• Boost the amount of recycled content by millions of tons.
• Recapture between $13 million and $91 million in lost material economic value in EPR states.
“With this research, we can see that these international programs drive dramatic improvement in recycling rates and that EPR policy has a significant impact. It’s clear that well-designed EPR policy is key to growing and improving recycling and achieving a circular economy,” says Dylan de Thomas, vice president of public policy and government affairs at The Recycling Partnership. “EPR has the potential to close gaps in recycling rates for all materials, create jobs, reduce greenhouse gas emissions, and deliver even more benefits to support people and the planet.”
Call2Recycle Canada and GFL Environmental Services Inc. have agreed to expand the sorting capacity of endof-life batteries in Western Canada. This agreement will bring GFL’s experience and waste management centre in Delta, British Columbia, to support Call2Recycle’s existing battery collection and recycling network, bolstering British Columbia’s circular economy sector and reducing the carbon footprint of the recycling supply chain in Western Canada.
This new partnership will effectively double the used battery sorting capacity and significantly enhance the battery recycling
ecosystem, offering new opportunities to increase battery collection volume throughout the entire Western Canada region.
“We are excited to expand our relationship with GFL Environmental Services and leverage their considerable expertise and presence in British Columbia. We share a common vision of offering efficient and sustainable battery disposal solutions to all Canadians,” says Joe Zenobio, president of Call2Recycle Canada. “Access to the Delta waste management centre means that we will be able to better fulfill our mission of safely collecting and recycling as many batteries as possible, supporting B.C.’s local economy and environmental commitment.”
Sierra International Machinery has released its documentary series Repurposed. Sierra’s president and co-owner, John Sacco, narrates this multi-episode series to highlight various American metal and paper processors and recyclers to show how recycled materials are vital to manufacturing and the production of everyday goods.
Repurposed will take viewers behind the scenes to witness how the items utilized on a day-to-day basis rely on recycled materials facilities, steel mills, foundries, and paper mills.
The familiar brand of orange construction equipment known as Doosan will now be called DEVELON throughout the world. Work began to identify a new brand name to replace Doosan following the August 2021 sale of Doosan Infracore to HD Hyundai.
The new name is the first of many steps to launch the new brand. Visitors to CONEXPO-CON/AGG 2023 will see the next phase of the launch with newly branded equipment including the latest developments in the Concept-X autonomous equipment solution.
After CONEXPO, continued efforts will be made to advance the brand at the local dealer level through updates to signage and machine decals. Contractors are likely to begin to see newly branded
machines at their local DEVELON dealerships and on job sites as early as the end of Q2 2023.
DEVELON will continue as a subsidiary in the Hyundai Genuine group alongside Hyundai Construction Equipment. These two subsidiaries will remain independent construction equipment companies under HD Hyundai.
Tassimo has partnered with TerraCycle to recycle all varieties of used single-serve Tassimo brand T-Disc coffee capsules.
“More than 1.5 billion plastic coffee pods end up in Canadian landfills each year, making it critical that the industry take steps to reduce packaging waste and move to a more circular economy,” says Steven Tschirhart, associate director of marketing for Tassimo coffee in Canada.
Through the Tassimo Free Recycling Envelope Program, users can request a free envelope using the order form provided. Once the envelope arrives, they can remove the prepaid return label from inside the envelope, affix it to the outside, and fill it with used Tassimo T-Disc coffee capsules. When full, they can seal the envelope and drop it at their nearest UPS store, where it will be delivered to TerraCycle for recycling.
• PERFECT MIX OF PRESSURE (UP TO 4000 PSI) AND SPEED (UP TO 225 HP)
• HOPPER SIZED FOR THE LARGEST OF OCC AND TO MINIMIZE OVER FEEDING HIGH GRADES
• MANIFOLD BLOCK DESIGNED WITH REPLACEMENT CARTRIDGE VALVES THAT KEEP THE POWER UNIT COOLER AND QUIETER
• OPTIONAL STAMPER - TO MAXIMIZE RUNNING IN AUTOMATIC WITH BULKY GRADES
Rip Curl has launched a program to recycle used wetsuits which will operate in partnership with TerraCycle. The Recycle Your Wetsuit program will recycle old and unusable surfing wetsuits so that the collected material can be recycled to make soft rubber playground matting.
The program was first launched in Australia in 2021 and has since been announced in the U.S., France, Portugal, and Spain. The program offers surfers the opportunity to recycle any surfing wetsuit at participating stores across Australia via in-store dropoff or mail. Now, the Recycle Your Wetsuit program has expanded in an effort to reduce the impact of wetsuit waste.
“Most surfing wetsuits are made from synthetic rubber, a com-
WEIMA offers a range of size reduction machinery for the scrap and recycling industries, including shredding and compressing technology.
Metal scrap is valuable, and shredding it allows for easy recycling. Transforming this often bulky material from large to small is an important first step in the recycling process. WEIMA machinery can shred light metals such as aluminum, magnesium, copper, brass, bronze, and steel milling waste to a homogenous size. WEIMA will have a WMS 60 metal shredder on display at its ISRI booth for attendees to view.
Compressing metal has many benefits. Loose chips and turnings can be bulky, sharp, and hard to manage. WEIMA briquette presses compress these loose materials into a compact, stackable size and shape. This increases safety, optimizes storage space, and makes the material easier to
Visit
plex material that isn’t accepted in curbside recycling,” says Tom Szaky, founder and CEO of TerraCycle. “But through the Recycle Your Wetsuit recycling program we are providing a new use for this material and offering consumers the opportunity to think twice about what can be repurposed and what truly is garbage.”
Surfers can drop their old wetsuits, booties, gloves, and hoods off at their nearest participating store or mail them in directly to Rip Curl. Old wetsuits are then gathered and shipped to TerraCycle. TerraCycle processes and crumbles the wetsuits into new raw materials which can be used to create the soft rubber matting found on playgrounds.
Multiple recycled materials companies have been recognized as among the world’s most sustainable – including Schnitzer Steel Industries, which was named the most sustainable company in the world. Corporate Knights, a global research company, released the Global 100 Most Sustainable Corporations in the World. Ranking nearly 7,000 publicly held companies with more than $1 billion in revenue, companies are evaluated across numerous metrics, including water, energy and carbon productivity, safety performance, diversity, and sustainable revenues and investments.
handle. Compressed metal briquettes can decrease burn off during the smelting process, thus increasing the value of the reclaimed metal. Expensive cutting fluid is also reclaimed through this process. The WEIMA team will have the matrix portion of a TH 1500 M briquette press on display in its booth at ISRI. Destroy Responsibly™ with WEIMA!
Electra Battery Materials Corporation has launched a demonstration plant designed to recover and recycle high-value elements found in lithium-ion batteries like nickel, cobalt, lithium, copper, and graphite at its refinery complex north of Toronto.
Electra will process up to 75 tonnes of black mass material in a batch mode using its hydrometallurgical process in the demonstration plant. Electra expects to complete the demonstration plant in Q1 2023. When the demonstration plant is completed, Electra will assess whether to continue processing
black mass throughout 2023 with material supplied by partners or from third parties.
In advance of the launch of the black mass demonstration plant, Electra completed process development and engineering on recycling black mass material. Electra previously sourced black mass samples from suppliers in North America, Europe, and Asia; studied the feed characteristics; and developed a hydrometallurgical process to recover contained lithium, nickel, cobalt, manganese, copper, and graphite.
Electra’s battery recycling strategy is the second of a phased development plan for an integrated battery materials park in Ontario that will recycle lithium batteries, produce cobalt, nickel, and manganese sulphates from primary feeds and before supplying the battery-grade material to third-party cathode precursor manufacturers. In 2023, Electra will commission a North American cobalt sulphate refinery that will have an initial production capacity of 5,000 tonnes of contained cobalt per annum.
Brandt
Brandt’s all-new BMH40A material handler is built on John Deere components. Features include rapid cycle times that allow operators to get the job done faster, and an energy recovery system with auto-idle/shutdown that maximizes fuel efficiency, contributing to reduced cost of operation and wear of machine components. The BMH40A is North American-designed, -built, and -supported through Brandt’s collaborative product design process, which involves extensive consultations with contractors and operators.
Vermeer
Ideal for wood waste recycling applications, Vermeer’s redesigned HG4000 horizontal grinder is equipped with a 536-hp (399.7-kW) CAT C13B Tier 4 Final/Stage V diesel engine, a Series III duplex drum, an aggressive infeed to accommodate a variety of materials, and many performance and durability features. The HG4000 has a feed table capacity of 4.6 cubic yards (3.5 cubic metres) and features a patented Series III duplex drum with reversible hammers and tips for extended wear life compared to single-sided designs. The hard-faced anvil on the HG4000 delivers enhanced cutting action with the drum, and a redesigned robust anvil-mount structure helps ease the hard-faced wear edge replacement process.
Cedarapids’ CRC1350 portable cone plant implements the enhanced TC1300X cone crusher which features 400 hp, a significant increase in power over the previous version. The complete configuration increases stroke from 45 to 70 mm which results in an increased throughput and an improved quality product shape. The portable plant includes an oversize quick-release cone feed hopper extension with an overflow chute, a 42-inch (1,070 mm) rugged straight-line product conveyor, a metal detector for offplant feed conveyor, and service platforms with an elevated deck. Maintenance and safety features include conveniently located grease banks, a ground-access cone lubrication module, and manual crank-style landing jacks.
Superior Industries’ portable Sentry HSI closed circuit plant is equipped with the ability to process recycled concrete, reclaimed asphalt, and pit run materials into salable products. From a single feed, operators will be able to produce up to four unique products. The closed-circuit crushing and screening arrangement includes a 4250 Sentry horizontal shaft impactor that is fed by a 4- x 18-foot Intrepid vibrating grizzly feeder, equipped with interchangeable grizzly cassettes to accommodate multiple applications. Additionally, a 2-deck Anthem inclined screen screens up to three material sizes. Returning material is fed back to the HSI via a recirculating conveyor.
The compact DustBoss DB-10 is the latest addition to BossTek’s line of atomized mist cannons. Engineered for enclosed working environments, the easily maneuverable unit provides enhanced suppression in a compact, portable design for industries such as demolition and raw material handling. A ¾-hp fan delivers 3,335 CFM of airflow, powered by 120-volt current. Mounted on the front of the cannon is a circular manifold with 12 atomizing nozzles that fracture pressurized water into a fine mist. About as loud as a handheld hair dryer, the fan forces air through the barrel then pushes millions of tiny droplets in a cone-shaped pattern up to 30 feet (10 metres).
The company processes a diverse range of materials each year, consisting mainly of electronic components and ferrous and non-ferrous metals.
Dartmouth Metals got its start in the metals processing game back in the 1960s when Linwood Giberson began buying and selling metals in Dartmouth, Nova Scotia. His son Peter joined the family business in 1979, followed by Peter’s son, David, a few decades later. After working part-time at the yard throughout high school and university, David Giberson was able to learn the intricacies of the family business before eventually taking over the company in 2009.
Fast forward to present day, and Dartmouth Metals processes metal from all over the Maritimes to sell locally, provincially, and internationally. As a third-generation family-owned metal recovery and recycling business, Dartmouth Metals credits its longevity to staying ahead of a constantly evolving industry by cultivating a unique mix of services, equipment, and lasting customer relationships.
With services including demolition and interior dismantling for structures such as refineries, mines, bridges, and boats, Dartmouth Metals is no stranger to complex waste streams. The company processes a diverse range of materials each year, consisting mainly of electronic components and ferrous and non-ferrous metals sourced from auto parts salvage yards, demolition sites, industrial applications, and the general public. In order to offer such a sizable portfolio of services, Dartmouth Metals maintains an extensive fleet of specialized equipment to demolish, clean up, and recycle projects of all sizes.
turing many of the residual non-ferrous metals from the automotive shredder, leaving the company no option but to ship the materials to a local competitor. Where they should have been achieving a recovery rate of between 11 and 14 percent, Dartmouth Metals was instead hitting closer to six percent. With the new system, the company now expects to raise these numbers and recover a substantially higher percentage of materials.
“That system has made a big difference here, just being able to sort all that material where we couldn’t before, plus reducing the landfill costs,” says Giberson. “There were valuable metals that you would have to send to the landfill knowing full well what you were losing.”
The new system will recover the previously missed Zurik, copper wire, and Zorba fines from the auto recycling process by incorporating the company’s two previously existing eddy current separators with a WENDT Tumbleback Feeder, fines eddy current separator, J-Box, trommel, and a WENDT/TOMRA FINDER.
After shredding the cars, the ferrous materials are separated out via magnets, and everything else is sorted into a separate pile consisting of non-ferrous metals and waste components such as vehicle upholstery. The pile then enters into a single-line downstream plant containing three eddy current separators and a trommel which produces three sizes of aluminum: one inch and less, one to four inches, and a four-inch-plus size.
“If you think of the car with an aluminum motor, when that goes through the shredder, it gets smashed into a thousand pieces,” says Giberson. “We’re able to get every piece of aluminum from that motor, even if it’s the size of a dime.”
After all of the aluminum has been removed, the remaining pile drops down onto a different sorting line where it passes through the J-Box to screen out any remaining waste before entering the x-ray sorting machine where it is then sorted based on metal.
“With [the WENDT] plant, we’re able to separate the metal better from the shredder, and also reduce our landfill costs,” says Giberson. “The amount of material that’s now going to the landfill from the shredder, we’ve probably been able to reduce it by I’d say 10 to 15 percent as a result of this machine. It’s probably because we’re recovering more metal, but another huge benefit was reducing our landfill costs. Obviously, as a result, it’s better for the environment overall since we’re able to keep that out of the landfill and recycle the metal at the end of the day.”
After over six decades in the recycling business and faced with an ever-increasing volume of incoming materials, Dartmouth Metals was in need of an upgrade. Fortunately for the company, its 10-acre yard allowed for the flexibility to accommodate new equipment and system expansions. Utilizing an existing building on the property, Dartmouth Metals recently installed a WENDT non-ferrous plant that was specially engineered and customized to work within the space restraints of the building.
Previously, Dartmouth Metals’ system was incapable of cap-
When it comes to output, recyclers have two main options: sell it as-is, or invest in equipment that will increase the quality of the yield and boost profits. As the first metal recycling company in the Atlantic provinces to purchase a copper and aluminum granulator, Dartmouth Metals has been able to nearly double the value of its insulated wire by processing it into clean copper.
Our whole business is predicated on recycling metal and trying to educate people that, yes, it looks like a pile of metal, or maybe it’s not the most sightly thing in the world, but that pile of metal is going back into the supply chain and reducing a lot of energy costs in the process of making new steel aluminum or copper.
David Giberson Owner, Dartmouth Metals
The new system incorporates the company’s two previously existing eddy current separators with a WENDT Tumbleback Feeder, fines eddy current separator, J-Box, trommel, and a WENDT/TOMRA FINDER.
The new system will recover the previously missed Zurik, copper wire, and Zorba fines.
“The new WENDT system produces a lot of insulated copper wire,” says Giberson. “Before, that wire would just go into the landfill since it was so small that we couldn’t manually sort it. Now, you can take a little piece of wire the size of a pen, for example, and we’re able to capture that in our downstream plant. Before, we would get maybe 1,000 pounds of wire. Now, we’re getting 20,000 pounds a month that we can run through the copper granulator and create pure copper. That’s a huge benefit.”
Choosing the right equipment can benefit more than just a company’s bottom line, though. Safety in any recycling operation is a huge priority, and equipment is one major way that Dartmouth Metals is tackling occupational hazards.
“We have these stationary inclined shears that we use to pre-cut any vehicles that enter our shredding process,” says Giberson. “We do that basically for two reasons, to increase the production of the shredder, but also safety-wise, we’re able to eliminate any chance of an explosion in the shredder. The idea is that if something in there is combustible, like a propane tank or a gas tank, it’s fully decompressed before it enters the shredder. In the metal recycling industry, the shredders are the biggest risk of having an explosion. We haven’t had one in three years now with this machine.”
David GibersonWhen it comes to safety, Dartmouth Metals has done more than just eliminate shredder explosions. Following a car pile fire last year, the company made substantial investments in fire prevention technology to protect its employees and assets from any future incidents. However, even with fire prevention technologies becoming more advanced and accessible than ever, fires remain one of the top challenges for recyclers. According to the most recent fire safety report from Fire Rover, 2022 was the worst year yet when it came to recycling facility fires in the U.S. and Canada.
“It’s an awful thing when it happens,” says Giberson. “We’ve invested a lot into firefighting equipment, and also into our employees and educating them on what to look for. We recently purchased a piece of equipment that will monitor the pile 24/7, and it has the ability to sense anything that’s going to heat up. If it reaches a certain level, it’ll deploy fire retardant material and notify the fire department. It’ll hopefully put the fire out before it starts, but can also keep it at bay until the fire department gets there. We’ve invested a lot of money in that.”
According to Giberson, the rise of lithium-ion batteries has
Before, we would get maybe 1,000 pounds of wire. Now, we’re getting 20,000 pounds a month that we can run through the copper granulator and create pure copper. That’s a huge benefit.
Where Dartmouth Metals used to recover 1,000 pounds of wire per month, they’re now recovering nearly 20,000 pounds.
also exacerbated an already challenging landscape. And with the increased adoption of electric vehicles, this hazard won’t be subsiding any time soon.
“There are no real guidelines on how to handle lithium-ion batteries or put out a fire that ignites from them. That’s something operationally that is a concern right now,” says Giberson. “You could have a bale of steel come into the yard that you bought from a customer. You can inspect it the best you can. You can talk with your suppliers. But all it takes is one bale to come in this yard, and overnight that bale could ignite. We’re pretty vigilant, but there’s still only so much you can do. It’s a constant worry.”
Metal recycling facilities are, at their core, built on sustainability. By melting down metals for reuse in the production of new metals, Dartmouth Metals is playing an important role in the move toward a more circular economy.
“Our whole business is predicated on recycling metal and try ing to educate people that, yes, it looks like a pile of metal, or maybe it’s not the most sightly thing in the world, but that pile of metal is going back into the supply chain and reducing a lot of energy costs in the process of making new steel aluminum or copper,” says Giberson.
With a cradle-to-grave approach and decades of success behind it, Dartmouth Metals is gearing up for an even brighter and greener future. With long-term goals to eliminate fossil fuels from the yard, Dartmouth Metals’ next step is to incorporate electrification into every aspect of its operations, from the trucks delivering the materials to the excavators loading the containers and rail cars.
“Everything I’m doing, I’m trying to convert over to a sustainable aspect of the business,” says Giberson. “Whether it’s converting diesel machines to the electrical grid here in Nova Scotia, we’re always looking at new ways to process the metals in a sustainable fashion. That’s where we’re headed in the future.” RPN
At WENDT , we have always been an equipment supplier, but at our core, we are a solutions provider. Our company value stems from 45 years of experience, continuous innovation of our product lines, and the ability to deliver quality and performance. Our reliable and efficient shredders, that span multiple applications, combined with our proven processes and most intelligent and advanced downstreams provide you with a turnkey solution tailored to your application. From the smallest to the largest recycling facility, WENDT is committed to building fully integrated systems that are more environmentallyfriendly than ever before – closing the recycling loop for a cleaner, low carbon, and sustainable metal recycling industry.
Will auto recycling survive? If you want to jump to the end and miss some insights into what’s happening in the world of auto recycling, the short answer is yes. But the headwinds and tailwinds that are buffeting the industry are the interesting part. The better question would be ‘what do auto recyclers need to do to survive?’
At its heart, the question of the auto recycling sector surviving is moot – it’s a necessary part of society, sometimes hidden, that needs to exist otherwise our landscape would be littered with dead vehicle carcasses, and the cost of everything metal would increase. That’s the economic power of the auto and metal recycling industries.
So why is it rare to see derelict vehicles in Canada? They’re worth money at end-of-life, both in terms of the parts that can be harvested for reuse and for the metals that still make up over 75 percent of a modern car. That value helps offset the cost of acquiring the vehicle, moving the vehicle to a centralized location for treatment, and undertaking proper environmental de-pollution of the vehicle to prevent pollution from escaping from the vehicle or processing facility.
Let’s turn to the headwinds that the industry is facing today, as they are numerous and pervasive. Like most industries, auto recyclers suffer from serious staffing issues. Auto recycling, and specifically auto dismantling which focuses on parts resale and harvesting higher value metals, has a high labour requirement. Most recyclers process all years, makes, and models of cars, making it difficult to standardize. Each car needs some level of hands-on work to properly de-pollute a vehicle, catalogue it, and remove the reusable parts. Technology and automation help to increase productivity, but in the
end, processing more vehicles requires more people. There’s no easy path into auto recycling – no apprentice programs, no degrees, and very limited training, not to mention that the pool of readily available workers is limited since every sector is also clamoring for workers.
The auto recycling industry grew up spontaneously over 100 years ago as vehicle production and ownership grew. People figured out early on that the best way to find parts for the few models on the road was to keep a few wrecked versions around and harvest their parts as needed. That still happens today, but as model choices exploded and environmental regulations kicked in, the need for a professional industry blossomed. Most regulation of the industry was old, outdated, and virtually devoid of enforcement. The regulations have begun to modernize, thanks to things like the introduction of the Canadian Auto Recyclers Environmental Code, but enforcement and even recognition of auto recycling as a profession by the public, officials, and those in the overall automotive sector is lacking.
The slump in new car sales due to product availability, cost of ownership, and economic uncertainty saw another sales drop of 10 percent that has a cascading effect through the industry.
While vehicle fleets are generally expanding as new vehicles enter the system, eventually older vehicles will need recycling. Fewer new cars sold – or even available to be sold – means fewer end-of-life vehicles (ELVs) available to process, and that either drives up the cost to acquire those vehicles or pushes recyclers farther out of their local trading zone to find vehicles. Oftentimes, these price increases prevent the profitable acquisition of ELVs, resulting in lower inventory levels of parts and materials.
You could argue that lower throughput of vehicles requires less staff – but not many are interested in a drive to the bottom. Fewer cars or fewer resources recovered per vehicle starts the negative downward cycle of sustainability that could prevent the proper education and investment from staying in the industry that so many love.
There are some tailwinds affecting the industry – not many, but they are there.
The parts supply chain disruptions facing the auto sector are making used parts more desirable. If you can’t find or can’t wait for a new part, a locally available used part looks a lot more attractive. Auto dismantlers across Canada are seeing record part requests, and sometimes record sales if they have that part in inventory and the staff to dismantle, inventory, sell, and deliver.
The new car sales slump introduced as a headwind means that some drivers are holding on to their vehicles longer. While that reduces the number of ELVs available for dismantling, the
aging vehicle fleet oftentimes turns to used auto parts to keep their vehicles on the road. That has translated into a boon for auto dismantlers.
ESG data reporting requirements are driving insurers to adopt strategies to increase their use of recycled parts in the vehicles they repair for policyholders. Not only do they want to minimize the number of vehicles needed to declare a total loss, but insurers are recognizing that recycled parts play a big role in helping them meet their net-zero and climate change commitments.
The future of aluminum recycling has met its match: a robust, high throughput XRT sorting system capable of detecting overlapping objects and composite materials. Proven to outperform, X-TRACT™ goes above and beyond to deliver high purity aluminum fractions.
Fewer new cars sold – or even available to be sold –means fewer ELVs available to process, and that either drives up the cost to acquire those vehicles or pushes recyclers farther out of their local trading zone to find vehicles.
Sometimes, a trend has both positive and negative consequences. One such trend is the sustained rise in platinum group metals (PGMs) prices, which include platinum, palladium, and rhodium – the key metals in catalytic converters. You would think that the increase in prices for catalytic converters would be a good thing for auto recyclers. It is. Cats have become a steady revenue source for ELVs, and as big cat buyers partner with auto recyclers to provide better data and better valuation technology, those recyclers who pay more attention to cats are seeing steady returns.
But who hasn’t heard of catalytic converter theft? Criminals are stealing these units at record levels and ELVs are showing up at recycling centres without their catalytic converters. That is a big revenue loss for the auto recycler. As well, illicit buyers of ELVs within the underground economy are helping to fence these stolen cats. A quick web search shows these two types of buyers are one and the same.
The coming proliferation of electric vehicles (EVs) reaching end-of-life is a generational change coming head-on at auto recyclers. The biggest issue with EVs right now and for the near future is the uncertainty of almost every facet of the business. We simply do not have the experience with these vehicles and their new part types to understand what parts of the EV are good, bad, great, or frightening for auto recyclers. The Automotive Recyclers of Canada (ARC) has created an EV Roadmap for the industry, with the support of Natural Resources Canada, and is also hosting an upcoming multi-sectoral roundtable on the effect of electrification on auto recyclers. We won’t solve many issues directly there, but it’ll get the ball rolling and bring together important stakeholders.
One main issue with EVs is trying to get everyone involved to talk about the whole car, not just the battery, since the industry
deals in whole cars and not just pieces of them. I can’t tell you how many times I start talking EVs to someone and they immediately jump to the battery. Keeping the battery and the car together helps to keep the economics of processing together, and that could help keep EVs in the positive column.
Auto recycling is a unique industry in that it needs to spend an inordinate amount of time and money locating vehicles to recover and recycle. What isn’t unique about auto recycling is change. Everyone is undergoing an extraordinary revolution in their business as new products, consumers, and channels emerge and change. Auto recyclers have not always been at the table when decisions are being made about the overall auto recovery sector. They are not policymakers. They have existed for over a century by reacting to the vehicles automakers put on the road and consumers want to keep on the road. But that is changing as calls grow for the development of a more circular economy. Auto recyclers play a pivotal role in the proper endof-life management of vehicles – something they are experts at.
A wise person in the industry once told me: “You can’t have a world of doctors and midwives without some undertakers.”
So I do believe that the answer is a resounding “yes!” to the question of the auto recycling sector surviving. Not everyone will evolve, pivot, and transition to new realities. Those who invest, train, educate, collaborate, and keep searching for new ways to extract and create value for ELVs will survive and thrive.
Your old vehicle will have a proper retirement at end-oflife, and even contribute to a circular society – but only if you choose a professional auto recycler that is living for the future.
THE PILOT PLANT WILL BE INSTALLED IN WOLFSBURG, GERMANY, IN JULY 2023
In 2030, the batteries of an estimated four million electric vehicles will reach the end of their useful life. These lithium-ion batteries contain valuable raw materials and recycling them has both ecological and economic benefits. Up until now, however, the disassembly of the battery system has been complex and expensive as the separation of the components is usually done manually. To combat this, Liebherr-Verzahntechnik
GmbH is developing strategies and processes for the automated disassembly of battery packs in partnership with the government-funded research project ZIRKEL, which investigates the entire circular economy of electric vehicle batteries.
Lithium-ion vehicle batteries are taken out of circulation once their overall capacity has reached about 70 to 80 percent of their original capacity. The majority of these batteries are recycled and the raw materials are reused for the production of new batteries. Depending on their condition, a small proportion of the old batteries are reused in battery-electric vehicles or in second-life applications such as stationary battery storage systems.
When they have finally reached the end of their useful life, the new EU Battery Regulation stipulates recycling quotas and minimum quantities of reused raw materials in new production. The industry must find the most efficient solutions possible for returning them to the material cycle, especially since the volumes of batteries returned will increase significantly in the future. The aim is to achieve a sustainable, CO₂ neutral battery production along the entire process chain with unlimited reuse of materials in a closed product life cycle. This is intended to minimize waste products and dependence on important primary materials.
Due to the relatively low quantities of batteries and large number of manufacturers and product generations, many disassembly and remanufacturing processes still take place manually today.
“We are almost talking about a batch size of one in the return flow of battery packs,” explains Jan Pollmann, development en-
I
virtually lose NO downtime
They have a technician come through once a month to go over every machine, front to back. If I have a situation, [they] just bring in another machine and I virtually lose no downtime… Since they have the repair parts in stock. I get the unit back quickly.
Demolition Contractor, Bloomfield Hills, MI
factory-trained technicians
gineer for automation systems at Liebherr. In order to achieve a high recycling rate and to be able to process the increasing return volumes economically, it is necessary to automate the processes.
Another aspect is occupational health and safety: automated disassembly ensures the health and safety of employees by eliminating their exposure to high voltages, hazardous substances, and fire risks.
The ZIRKEL research project, funded by the German Federal Ministry of Education and Research (BMBF), involves an interdisciplinary consortium of research and industry to investigate the entire recycling management of batteries.
As part of this project, Liebherr is developing strategies and processes for the automated disassembly of battery packs. The aim is to recover and recycle the highest possible proportion of raw materials by mechanically disassembling and sorting the components. By removing valuable components or those containing pollutants at an early stage, the cost- and energy-intensive pyrometallurgical and hydrometallurgical processing of the black mass is reduced.
ous substances must be taken into account. And finally, the disassembly of flexible parts such as cables or cooling hoses is difficult to automate.
“In principle, the established assembly process runs backwards here, but it is many times more complex,” explains Viktor
Harris is excited to announce that the Harris GPS Series Predator scrap baler/car logger will be on display at ISRI 2023! This game-changing machine delivers industry-leading operational speed, compression force, and bale density with its innovative three-lid design and double-hydraulic circuit design. Please stop by Harris’ booth #C4 to see the Predator in person and our team will walk you through the productivity and bottom line gains you can expect to realize.
In principle, the established assembly process runs backwards here, but it is many times more complex.
Viktor Bayrhof Product Manager of Automation Systems, Liebherr
WM and Dow are collaborating to improve residential recycling for hard-to-recycle plastic films by allowing consumers in select markets to recycle these materials directly in their curbside recycling. According to The Recycling Partnership, currently, only 1.9 percent of U.S. households have access to curbside plastic film recycling, which is the plastic material with the lowest overall recycling rate. Once operating at full capacity, this program is expected to help WM divert more than 120,000 metric tons of plastic film from landfills annually.
The initiative has kicked off with an initial pilot program in the Chicago-area community of Hickory Hills, Illinois,
reaching approximately 3,500 households, with more cities to follow across the country. Consumers in the program’s pilot cities will be able to recycle film plastics like bread bags, cling wrap, and dry-cleaning bags directly in their curbside recycling.
WM expects to invest over $800 million through 2025 to improve and enhance recycling infrastructure, including specialized technology that will allow WM to sort plastic films. WM will lead the collection and processing for the film recycling pilots and continue to identify film recycling opportunities across the U.S. By 2025, film recycling through WM is expected to reach 8 percent of U.S. households.
The Government of Canada released the next steps in its ban on harmful single-use plastics. Moving forward, checkout bags, cutlery, food service containers, and wares made from, or containing, hard-to-recycle plastics such as stir sticks and straws will be prohibited from being manufactured or imported into Canada. The ban on the manufacturing and importation of ring carriers will begin in June 2023.
Over the next decade, this ban on harmful single-use plastics will result in the estimated elimination of over 1.3 million tonnes of hard-to-recycle plastics and more than 22,000 tonnes of plastic pollution, which is equivalent to over one million full garbage bags.
The federal government is working with provinces, territories, and industries to set an ambitious collection target of 90 percent for recycling plastic beverage bottles. It is also developing regulations to require that certain plastic packaging contain at least 50 percent recycled content and to establish clear rules for labelling recyclable and compostable plastics. Draft regulations are targeted for publication as early as fall 2023. In addition, the government is developing a plastic registry to hold plastic producers accountable for their plastic waste.
Canada is currently working with countries and stakeholders globally to develop an ambitious legally binding treaty to end plastic pollution, and these measures will help Canada meet the commitments of the Ocean Plastics Charter.
The new model 4 E-Z log Baler is just what mid size scrap yards have been asking for! Priced right for any yard — small, mid size, or large!
Like the Model 3, the NEW Model 4 has no set up time and a very low cost to operate. The one man operations are all handled from the newly designed cab. With the 400º rotation crane and a reach of 27’ adding the continuous rotation grapple, it makes loading the larger chamber a breeze. Taking your loose scrap to a highly sought after shreddable log.
— Cycles in under 2 minutes!
— Produces up to 70 tons per day.
— Fully portable in the closed position.
— New seat design for more operator comfort.
Pyrowave technology has successfully passed Michelin Group’s quality tests with the first 99.8 percent pure recycled styrene monomer produced from polystyrene waste.
The recycled monomer can now be integrated into industrial elastomer batches. For the first time, a finished product will incorporate fully traceable and segregated recycled styrene, where all the styrene will be physically present in the product rather than credit-based content.
A container with approximately three tons of recycled styrene has left Montreal for the Michelin plant in France. Following years of testing, Michelin will be in a position to manufacture batches of industrial styrene-butadiene rubber products with Pyrowave recycled styrene, which would represent over 1,000 passenger car tires.
Pyrowave’s microwave technology returns waste polystyrene plastics to their original form, i.e. styrene monomers. This high-value raw material, which is identical to virgin material, but with a 45 percent reduced carbon footprint, can then be reused in the production of items made from recycled materials and share the same applications as virgin materials used in transportation, packaging, electronics, and construction.
Why have an over-burdened presort when you can eliminate it all together?
CP Auger Screens revolutionized MRF process flows by eliminating the presort, prioritizing worker safety and increasing system efficiencies.
Learn more at cpgrp.com/occ-auger-screen
Ocean Legacy has produced Legacy Plastic, a commercially available plastic pellet in North America. Legacy Plastic is made from 100 percent post-consumer processed recycled plastic recovered during ocean, shoreline, and marine equipment cleanups.
Legacy Plastic consists of recovered marine gear such as fishing ropes, buoys, floats, oyster trays, and other anthropogenic plastic debris collected from cleanup activities and reprocessed for use in the manufacturing of new durable products. Legacy Plastic is sourced from used marine gear from fishing and aquaculture operations along the Pacific Coast, as well as plastic recovered from shoreline cleanups.
WasteExpo has always been a moving experience. WE move products, people, tech—and the needle.
Need proof? Take look at these numbers: 97% of attendees recommend WasteExpo to a colleague, 50% influence or recommend buying decisions, 37% make final purchase decisions and nearly a quarter ask for a price quotation.
So make your move to WasteExpo and join over 14,000 of the best minds in the business. LET’S
Back in the 1930s and 1940s, long before recycling technology was even a consideration, aerosols were introduced commercially to consumers. Since then, the production and use of spray cans has seen tremendous growth, reaching over 15 billion units per year. With this growth, however, comes a significant waste stream that is hazardous and potentially explosive.
At the time, landfilling and incineration were the best practices, but these methods did not allow the aluminum containers to be reused or recycled in any way. Understandably, sustainability and the circular economy were not commonly considered back then.
Fortunately, things have changed for
the better. One example can be found within the UK Aerosol Recycling Initiative, a program headed by Alupro, that aims to increase public awareness surrounding aerosol recycling and drive increased recycling rates across the U.K. The program is supported by major players in the aerosol industry, including Ball Cans, Despray Environmental, Trivium Packaging, and the British Aerosol Manufacturers Association. This initiative brings industry players together and paves the way for a new way of thinking when it comes to aerosol and aluminum can recycling.
All of the waste types within the body of an aerosol can must be considered to access the valuable aluminum and
meet all environmental responsibilities. This was previously a formidable technical task, but it is now possible. The opportunity for the recovery and recycling of over 15 billion cans per year not only saves valuable resources, but also reduces the carbon footprint of the propellants and liquid contents that contribute to greenhouse gas production and climate change.
The aerosol filler industry already has an impressive sustainability report card when it comes to manufacturing and its corporate environmental footprint. We now have the opportunity to advance those gains to include complete waste-to-energy solutions and recover up to 100 percent of the aluminum. This is
an example of a circular economy that can be expanded worldwide.
The aerosol industry has come a long way in terms of sustainability and corporate responsibility, driven by pressure from health and safety concerns, global environmental awareness, and corporate image. While 100 percent recycling technology exists, the future of aerosol recycling still has many hurdles to overcome, including corporate practices, public awareness, and appropriate price levels for aerosol recycling.
The good news is that these obstacles are achievable in the near future with the continued focus and support of all parties involved. With modern day recycling and sustainability expectations, best practices, and a new way of thinking, we can continue to meet environmental responsibilities and move toward a more sustainable future while reclaiming otherwise lost metals and valuable fuel sources.
The opportunity for the recovery and recycling of over 15 billion cans per year not only saves valuable resources, but also reduces the carbon footprint of the propellants and liquid contents that contribute to greenhouse gas production and climate change.
•
•
The opportunity for the recovery and recycling of over 15 billion cans per year saves valuable resources. MIKE MACKAY is the co-owner and managing director of Despray Environment which offers recycling technology for aerosols.Our WALKER™ and JAVELIN™ brands of durable and powerful industrial scrap and separator magnets are capable of handling scrap and recycling operations of any size and capacity.
Recycling metals saves precious resources and is also cheaper compared to mining new minerals since less energy is required. However, this approach would not be feasible without efficient ways to determine the composition of the materials earmarked for recycling.
There are a number of non-destructive methods available that can do this – including X-ray fluorescence (XRF) and laser induced breakdown spectroscopy (LIBS) – that are commonly used for positive material identification (PMI) across many different industries to rapidly identify metals and alloys, including sorting and classification of alloys in bulk scrap. Both XRF and LIBS have their advantages and drawbacks, and choosing which of these two technologies is most appropriate for any one application is not straightforward.
Scrap recycling is a growing industry, driven by environmental concerns and an increasing scarcity of raw materials. However, it is extremely important that the exact chemical composition of any material for recycling is known, and that it has been checked for contaminants and hazardous elements to ensure quality, safety, and regulatory compliance when selling scrap metal to industrial consumers. Quickly pinpointing the most valuable materials in scrap can also be very profitable and soon provides a return on investment on analytical equipment.
Handheld devices such as XRF and LIBS analyzers offer recyclers tools to rapidly and accurately determine the composition and grade of incoming scrap. This eliminates the need to send samples away for analysis or rely on the old ways of verification – using spark or chemical tests – that require material grinding, as well as the storage and handling of hazardous materials. In contrast, XRF and LIBS analyzers can rapidly verify high-value elements in virtually all types of metal alloys, from trace levels to commercially pure metals. These latest analyzers are even capable of distinguishing alloy
grades that are nearly identical in composition to one another such as 304 and 321 stainless steels, or L grade versus H grade 316. Both offer different benefits when performing sorting, particularly in terms of their accuracy for analyzing different types of materials. So, how do they work, and what’s the difference between what they can achieve?
Accurate scrap metal sorting helps to ensure industrial customers receive materials that meet their production needs, as well as increasing the recycler’s profits and ensuring product safety.
Handheld XRF analyzers produce X-rays that are directed at the surface of a sample. The X-ray energy displaces electrons in the sample atoms, causing each element in the sample to produce a set of characteristic fluorescent X-rays which can be used like a unique fingerprint to identify it. The detector collects the characteristic X-rays and converts them into electronic pulses, which are sent to the central processing unit (CPU). The CPU produces a detailed compositional analysis and grade identification of the material. This is a non-destructive process that has no impact on the sample being inspected with results available in seconds.
Handheld XRF analyzers are tried and tested in the world of scrap metal recycling, and are well established in many organizations as the best-known method for operators aiming to sort scrap quickly and accurately. The technology is very useful for distinguishing between different grades of mate-
OverBuilt has been building the fastest and largest car crusher since 1992. With our 10’ opening and available 20’, 22’ and 24’ charge boxes, we can custom build a crusher to fit your individual needs. Our baler logger has 225 tons per door and 175 tons per ram of baling and logging force.
Call us today for more information at 605-352-6469 or email sales@overbuilt.com. Visit
rial, such as determining different stainless steels within a container. However, XRF is unable to identify lighter elements – generally below magnesium in the periodic table – as the energy released by these low atomic number elements is too low to be detected.
Handheld LIBS analyzers use a high-focused laser to ablate the surface of a material, forming a plasma made up of electronically excited atoms and ions on the surface. As the atoms decay back into their ground states, they emit characteristic wavelengths of light, which act as a unique fingerprint for each element in the sample. The emitted light is transferred through fibre-optics, and enters the spectrometer, where it interacts with a diffraction grating, splitting it into component wavelengths before it passes on to the detector. The resulting spectral data is processed by the CPU to provide a detailed composition analysis of the material. Although this technology is minimally destructive, the impact on the sample can be considered very small.
LIBS analyzers are still the new kid on the block when it comes to scrap metal analysis, with XRF having been the technology of choice for many years. But LIBS has some significant advantages that mean it should be seriously considered.
Since it is an optical method that measures light in the NIR, visible, and the UV spectrums, it can analyze a broader range
of elements compared to portable XRF, which cannot measure those lower atomic number elements. This is particularly rel evant when it comes to measuring carbon, because customers need to be aware of the carbon content of alloys as this has a direct impact on welding properties, hardness, and toughness of the material. Aluminum is also easier to sort with LIBS technology, but is not as effective when it comes to sorting heavy metals, high-temperature alloys, and stainless steel.
XRF analyzers are often still the technology of choice in scrap recycling centres, but handheld LIBS and XRF should be considered complementary rather than competing tech nologies. When used together, they can measure a greater range of elements across the periodic table. Both types of analyzer are portable and can identify a material in just a few seconds. LIBS has the advantage of requiring minimal safety training or special storage, since it does not use X-ray radia tion. Overall, they are both very useful tools for identifying the most valuable scrap and also ensure that recyclers can provide customers with safe, correctly identified products.
FOLLOW THESE TIPS TO GET THE MOST OUT OF YOUR INVESTMENT
Shear/baler/loggers offer the versatility of three machines in one, making them a popular choice for scrap recyclers looking to process both heavy and light metal materials. These machines work by taking metals and compacting them into a log that is then either compressed into a bale or cut to length by a shear to prepare them for transport.
When it comes to selecting the right shear/baler/logger for your facility, there are many factors to take into consideration, such as machine capacity, manufacturer support, type of metal processed, and material volumes, to name a few. All shear/baler/loggers are not created equal, so make sure you consider these tips to ensure you invest in the best possible fit for your application.
Primary processing grades for scrapyards are steel #1 and #2, although the majority of facilities today process a high percentage of lighter, bulkier materials than were previously found in facilities decades ago. Stationary units with higher forces can handle heavier, bulkier materials and provide higher production rates.
Portable shear/baler/loggers typically are lower force machines and are limited to lighter material than a stationary unit. The unit’s charge box may be shorter and have less side forces to handle heavier, bulkier materials.
Shear throat size is also a limiting factor in some of these units. Again, bale density can be a concession in a portable unit. Stationary shears generally have larger charge box openings, larger shear throat openings, and higher forces. Stationary shears are typically available in 800- to 2,200-ton models, and there are usually a variety of charge box configurations (clamshell, tuck and fold, and side squeeze) available to fit particular applications.
Stationary balers are available in multi-ram compression under higher forces and will achieve high-density bales. A stationary unit will be a higher production unit compared to a portable unit.
When comparing portable balers, you should know what your markets are, what current production requirements are, and what future production requirements will be.
When comparing various models, look at:
• Chargebox size (width and length).
• Chargebox configuration (for trapping larger bulky material).
• Chargebox forces.
• Baling force.
• Bale eject door versus moving bales with a grapple or magnet.
• Type of engine (name brand).
• Type of programmable logic controller (name brand).
• Manufacturer support options.
• Resale/trade-in value (name brands will hold higher values).
Investing in equipment is no small decision, and it’s important to evaluate not only your present needs, but any future needs that may arise as a result of changing markets and increased volumes. Buying a machine that is too small for possible future demand is a common mistake made during the buying process based on current capital or cash constraints. To avoid this, carefully consider:
• Current and future projections of tons per day and tons per month.
• The useful life expectancy of the machine.
• Buying new versus used equipment.
• Ease of maintenance.
• Initial purchase price versus ongoing operating costs.
• Installation costs, including possible permitting requirements.
• Electrical service requirements for non-diesel units.
• Foundation design and construction.
• Conveyor systems or material handling equipment to feed or remove material.
Size reduction is tough work that can push equipment to the extreme. At Herbold, we know that granulator performance and durability is critical to your success. That’s why we build our equipment to deliver maximum throughput and require minimal maintenance and downtime.
Here’s how:
• Double Cross Cutting Action – Reduces Jams and Material Fines
• Adjustable Bed and Rotor Knives – Maintain Constant Cutting Circle
• Safe, Easy Access to the Grinding Chamber – for Improved Maintenance, Screen Changes and Machine Cleanout
• Replaceable Armor Plating Inside the Cutting Chamber
• Faster and Safer Knife Changes – Adjustments are Made in Jig Outside of Granulator
• Available Force Feeders – Increase Throughput by 50% - 80%, Reducing Power Consumption
888.612.7774
www.herboldusa.com info@herboldusa.com
THREE MACHINES IN ONE
SIERRA INTERNATIONAL MACHINERY SLK-SERIES
LEFORT TRAX
2
1
Sierra International Machinery’s SLK-Series of shear/baler/loggers provides recycling facilities with optimal strength, speed, and efficiency. Available for diesel or electric power, the SLK-Series doesn’t require a special foundation and is ready to work after a two-day assembly process. The machines are also easily transportable, allowing the SLK-Series to be taken from yard to yard with ease. The machines come fully equipped with remote-control operation, eliminating the need for an operator. As with all Sierra machines, the SLK-Series is manufactured with an L-Boxshaped design, 11/16th-inch replaceable abrasion-resistant steel Hardox 450 liner plates, and outer honeycomb construction creating greater box integrity.
2TRAX self-propelled shear/baler/loggers are engineered to offer enhanced mobility on site. A flip of a switch on a remote control converts the machine into a crawler model, allowing the operator to easily bring the machine to the piles of scrap, as opposed to losing valuable time moving the scrap to the shear. With cutting forces ranging from 660 to 1,375 tons, Lefort TRAX are robust shears, engineered for extreme conditions, and capable of processing most metals and demolition scrap with low operating costs.
Lefort TRAX shear/baler/loggers are equipped with quality hydraulic components, as well as a high-performance engine, making them powerful and productive machines.
3The Harris GPS Destroyer shear/baler/ logger represents a combination of strength, productivity, and efficiency for recyclers. The three-lid design of the charging box optimizes distribution forces (440 to 880 tons) and gives the operator an advantage in the processing of bulky scrap through the machine. Features like the stroke economizer, cycle economizer, and full auto cycle maximize production efficiency at a reduced costper-ton ratio. The Destroyer is sold in configurations ranging from 900 to 1,350 ton shear forces and 20- to 30-foot box lengths. Remote-control operation, diesel and/or electric versions, flat slab/plinth installations, load hopper, and operator cabin are all available configurations.
THE AUTOMATIC BRAKING FEATURE REDUCES THE RISK OF COLLISION WHEN WORKING IN REVERSE
As part of its vision for zero accidents, Volvo CE has developed its collision mitigation system for Volvo wheel loaders – an automatic braking feature that supports operator response and helps reduce the risk or consequences of collision when working in reverse.
According to the company, this marks the first system of its kind from any original equipment manufacturer. The system assists operators while working in reverse and automatically applies service brakes when the wheel loader
approaches any obstacle, alerting the operator to take further action. With wheel loaders spending an average of 40–50 percent of their time driven in reverse, the collision mitigation system is a valuable solution for operators and site managers.
Lars Eriksson, global product manager for wheel loaders at Volvo CE, says “We at Volvo CE continue to proactively develop intelligent solutions which not only mitigate the consequences of accidents but strive to avoid them altogether. This new colli-
sion mitigation system is one important part of our work to reduce the risk of accidents and help fulfill our commitment toward zero accidents.”
With this new system, operators are moving a step closer to not only eliminating accidents – and therefore improving job site safety for everyone – but also reducing any unplanned interruptions that can be incurred during avoidable knocks and bumps.
It works by identifying when there is a risk of collision and responding by automatically activating the brakes for two to three seconds to slow the machine down prior to impact or bring it to a stop to avoid it. This initiation of the braking alerts the operator to intervene. And for seamless stockpiling operations, the system will remember the last slope the machine climbed, allowing operators to reverse down a pile without activating it. It can
also be temporarily deactivated for specific site conditions.
Functioning only when the wheel loader is in reverse and driving at speeds of between 3 and 15 kph (1.86 – 9.32 mph), no matter what gear it is in, it serves as a facilitator to job site safety.
Developed in-house by Volvo CE, the collision mitigation system for Volvo wheel loaders is a factory-fit option currently available on the L110H/L120H equipped with OptiShift, L150H, L180H, L220H, L260H, and L200H High Lift wheel loaders.
Requiring a Radar Detect System to be fitted, it works as an additional system to the existing range of features, options, and site services provided by Volvo CE for its line of wheel loaders, all of which have been designed to promote job site safety and minimize unplanned interruptions. The collision mitigation system is available in all markets around the world.
This new collision mitigation system is one important part of our work to reduce the risk of accidents and help fulfill our commitment toward zero accidents.
Lars Eriksson
Global Product Manager for Wheel Loaders, Volvo CEThe system automatically applies brakes when the wheel loader approaches obstacles.
Demand for aluminum in the U.S. is expected to grow by 0.5 to 2 percent in 2023, largely unchanged from the previous year as mills and scrap processors remain wary of inventory due to an anticipated change in scrap consumption patterns.
Since January 2023, recycled LME aluminum material prices have witnessed a 20 percent swing, finding a floor at $2,150 to 2,200/mt (metric tons). These prices are expected to average around $2,300 to 2,600/mt during the year. However, in the short term, prices could spike to $3,000 to 3,200/mt before settling down to the average levels. But what has led to this outlook?
In 2022, an energy crisis in the EU, Russia’s invasion of Ukraine, and China’s COVID-19 lockdowns were just some of the factors that impacted the primary and secondary aluminum markets. Last year, global primary aluminum production climbed by 2 percent to 68.4 million mt, mostly led by increases in Asia, according to the International Aluminium Institute (IAI). Smelter shutdowns across Europe were reflected in the 12 percent decline in primary output to 2.9 million mt. In North America, production dropped by 4 percent to 3.7 million mt while Russia’s output declined by 1 percent.
Aluminum companies in the EU mothballed 1 to 1.3 million mt or 25 to 30 percent of the approximately 4.5 million mt primary aluminum capacity in the region due to the energy crisis. Companies in the U.S. also curtailed more than 500,000 mt per year in capacities.
This provided an opportunity for the secondary aluminum market. In the U.S., secondary production increased by more than 10 percent annually and constituted about 78 percent of the total production in 2022, the latest U.S. Geological Survey (USGS) data indicated.
However, the secondary aluminum and scrap market will likely bear the brunt of weak demand this year as the market grapples with many uncertainties.
Uncertainties over an economic slowdown and its extent have also kept the market guessing. However, according to a recent World Economic Outlook by the International Monetary Fund (IMF), global economic growth has been revised to 2.9 percent for 2023 from 2.7 percent earlier. The U.S. slowdown is also not expected to be as severe.
The Federal Reserve has not shown any signs of lowering interest rates despite encouraging trends that reflect a deceleration in inflation along with improved employment. Demand for consumer durables, housing, and automotive is expected to trend flat in 2023 due to the high interest rate regime. Thus, the risk of a demand downside is higher, and markets anticipate a decline without support from credit.
Transportation accounts for 35 percent of total aluminum consumption in the U.S., with automotive constituting the lion’s share. According to the latest analysis released by Moody’s Analytics, 9.3 percent of loans have been more than 30 days late in payment for the first time since 2010.
Loan defaults in automotive can be a significant deterrent to new car production. Scrap availability is also likely to increase, and that, along with declining demand, could have catastrophic effects on secondary scrap prices – both alloy and non-alloy grades.
Demand in the aluminum packaging segment, which con-
stitutes 23 percent of the U.S. aluminum consumption and is dominated by aluminum beverage cans, is expected to be flat in 2023, which could impact the grade’s supply-demand dynamics. Still, the national implementation of bottle bills could potentially improve recycling rates. Aluminum demand is also expected to remain tepid in the U.S. housing market, which comprises around 16 percent of the country’s total aluminum usage. Loan defaults are inching up and higher interest rates will prevent any significant improvement in the year.
COVID-19 restrictions slowed down the Chinese economy in 2022. In 2023, the country’s economic activity is expected to recover in the post-new-year market. Expected production and demand of bauxite is also expected on par.
However, Chinese primary aluminum production could be capped at 45 million mt, the same levels as the previous year. Secondary production capacity in China of 2.3 million mt could increase with government focus on reducing emissions. Demand from China and other Asian countries will also rise in 2023 especially for twitch, taint tabor, extrusions, and ADC.
Any changes in China’s stance, which may boost its production, can result in a spike in bauxite prices, eventually snowballing to scrap price increases in 2023.
In September 2022, the LME released a statement about considering a ban on Russian aluminum from LME-approved stockyards. The exchange has since abetted all thoughts of Russian stock ban, as the markets reacted with a $200/mt-plus increase in prices within a week.
However, with the worsening condition of the war on Ukraine, the calls for Russian stock ban are expected to rise. Prices could soar in that case, going back to $3,000/mt according to some participants. U.S. aluminum premiums are also expected to rise in tandem, as already witnessed in January.
New capacities are likely to improve primary aluminum supply in 2024 as well as the demand for recycled aluminum raw material. Novelis’ 600,000 mt per year flat rolled mill and 100,000 mt per year rolling unit is expected to be online in Q1 2024. Moreover, a 650,000 mt per year aluminum mill by Steel Dynamics is also expected to come online in early 2025. Demand for grades like UBCs will soar due to raw material demand with the UBC balance, which has been in excess since 2013, expected to turn to a deficit next year as mills plan for the new mix.
Mills have started working on scrap grade replacement to improve efficiency and tackle high energy cost and availability. In 2024, the industry is expected to see changes in grade consumption and availability of feedstock, having far-reaching consequences on the aluminum scrap supply segment. Combined with high export demand, scrap supply for specific grades will witness a shortage in the domestic market.
SOVIT BISWAL is a reporter with Davis Index, a market intelligence platform for the ferrous and non-ferrous metals and recycling industry. He covers the U.S. aluminum markets and can be reached at sovit.biswal@ davisindex.com.
BRIDGING THE GAP OF MATERIAL SHORTAGES STARTS WITH THE EFFECTIVE COLLECTION OF RECYCLABLES
Brand owners and packaging converters in the plastics industry are facing major bottlenecks in recycled content availability. To overcome this challenge and meet ambitious recycling targets, recyclers and material recovery facilities (MRFs) are using advanced technologies to produce feedstock for high-grade applications, expanding their business opportunities.
As legislation continues to push for a reduction in plastic waste, the drive for greater plastics circularity and maximizing resource use is a topic of global concern. Plastics are durable, efficient, and convenient, which makes them beneficial to consumers and businesses alike.
Making consumer products and packaging more sustainable is a major challenge of our time. As brand owners look to increase the share of recycled content used to reduce their production emissions and meet consumer demands, they are met with a new set of challenges. High-grade applications like automotive and packaging require high-quality recycling processes and advanced sorting technologies to effectively source feedstock from post-consumer and post-industrial plastic waste.
Over a 50-year period from 1966 to 2016, global plastic production increased nearly 20-fold, from 20 million metric tons (mmt) to 381 mmt. In 2019, 19 percent of global plastic production occurred in North America, and plastic production is projected to increase by 200 percent and 350 percent by 2035
Improving recyclability and increasing the quantity of recycled content demands that the industry go upstream because highquality recycling begins in the design phase.
and 2050 respectively. In the quest to create a circular economy for plastics, the share of virgin material in manufacturing should be reduced and replaced by secondary raw materials.
Plastic recycling has certainly had its share of bad publicity, not least due to downcycling – after all, there is a limited demand for items such as park benches, flowerpots, and speed bumps. The recycling industry, working in collaboration with members of plastic value chains, has now made it possible to create virgin-like recycled content with advanced mechanical recycling. Not only does this prove to be an economically feasible and practical alternative to primary materials, but it gives recyclers and MRFs the opportunity to create new revenue streams. Even in the case of highly contaminated plastic waste streams, like municipal solid waste (MSW), it is now possible to source quality feedstock that can be used to create new products.
The S&P Global Platts Analytics predicts that by 2030, more than 1.7 mmt of virgin polymers will be replaced by mechanically recycled plastics – compared to 688,000 metric tons in 2020. To date, less than 10 percent of recyclates have found their way into the production of new materials. Most of the recyclates are used for lower-grade applications. So, how can industries such as automotive, food and beverage, and cosmetics ensure a reliable supply of high-quality recycled feedstock? Bridging the gap of material shortages starts with the effective collection of recyclables and continues by deploying the latest sorting technologies in modern processes and configurations.
On the front end, deposit return systems (DRS), for instance, are a global best practice for the recycling of beverage containers in a closed-loop system. Mid-recycling supply chain, innovative optical sorting, and other separation technologies maintain yield and quality. On the tail end, advancements in flake sorting have significantly contributed to closing the remaining quality gaps for many plastics.
However, there is no singular solution. To achieve circularity, complementary solutions are needed to capture and recover various packaging materials. Mitigating contamination and increasing the quantities of recovered recyclates across all waste streams is crucial to the future of plastics.
In addition to conserving valuable natural resources, recycling is a key economic driver in the United States. Released in 2019, the EPA’s National Framework for Advancing the U.S. Recycling System mentions that recycling and reuse activities in the United States account for 757,000 jobs, $36.6 billion in wages, and $6.7 billion in tax revenues. Astoundingly, recyclable materials with a commodity value of approximately $8.9 billion are still sent to landfills each year.
A regenerative approach is required to increase material recycling and reuse efforts, drive greater plastics circularity, and provide a long-term supply of recycled content for the market to reduce dependency on primary materials. For this reason, many countries around the world and several U.S. states are considering or have already introduced Extended Producer Responsibility schemes (EPR), which give producers significant responsibility for the product’s life cycle – from design to the post-consumer stage. These policies incentivize producers to consider environmental factors when manufacturing packag-
ing and to contribute to a reduction of the product’s environmental impact.
Aligned with companies creating a profitable business model, legislation plays a fundamental role in supporting infrastructure investment, including effective collection, sorting, and recycling of plastic waste. Plastic directives and mandatory minimum recycled content targets can establish the proper framework for prioritizing circularity and breaking the bottleneck of feedstock recovery.
Binding frameworks constitute a necessary intervention in the market. They support sustainable waste management and stimulate the industry to increase the use of recyclates while securing demand and infrastructure investment. The EPA’s National Recycling Strategy focuses on enhancing and advancing the national MSW recycling system and supports the implementation of the National Recycling Goal to increase the recycling rate to 50 percent by 2030.
In July 2022, California enacted the country’s most sweeping restrictions on single-use plastics and packaging. The law requires single-use packaging and plastic single-use food service items to be recyclable or compostable by 2032, and it requires a 25 percent reduction in the sales of plastic packaging plus 65 percent of all single-use plastic packaging to be recycled within the same time period.
The Last Beach Clean Up and Beyond Plastics report, “The Real Truth About the U.S. Plastics Recycling Rate,” documents a recycling rate of just five to six percent for post-consumer
You begin each day before dawn with the drive and determination to do more than the day before. When you move at this pace, you know to do more, you need equipment that is Made for More. That’s why our horizontal and tub grinders are built from the ground up to meet your needs, delivering:
More Power and Production • Consistent, Quality End Product
Lower Operating Costs • Ease of Maintenance
Greater Longevity and Resale Value
Find complete information about all our equipment brands at morbark.com or call us toll free at 1-800-831-0042
Brandt is the Authorized Dealer for Morbark recycling and forestry equipment for all Canadian Provinces. To find the Brandt location nearest you, scan the QR Code with the camera on your mobile phone.
plastic waste for the United States in 2021. Juxtaposed against declining recycling rates for plastics, the per capita generation of plastic waste has increased by 263 percent since 1980.
In sharp contrast to abysmal plastic recycling rates, paper enjoyed a recycling rate of 65.7 percent in 2020, according to the American Forest & Paper Association. Post-consumer paper, cardboard, and metals all enjoy high recycling rates in the United States, proving that recycling works to reclaim and save valuable natural resources. It is plastic recycling that has been the failure point, never reaching 10 percent, even before China enacted its National Sword policy.
While directives are a decisive step forward, there is still room for improvement. For instance, there is little legislation specifying the use of post-consumer recycled content (PCR) that could fill the gap between demand and supply. The state of California leads the most ambitious targets for PCR in beverage bottles. The recently established California Recycled Content Laws set PCR targets at 15 percent by 2022, 25 percent by 2025, and 50 percent by 2030.
Increasing the use of recycled content requires the entire industry to act, design recyclable packaging, and improve the supply of quality recyclates with both new and existing instruments. Applying the Holistic Resource Systems approach to waste management combines DRS, separate collections for selected material streams and mixed waste sorting to recover plastics for advanced mechanical recycling.
Beyond dedicated collection streams, the addition of mixed waste sorting is also proving to deliver high-quality plastic for recycling. In California, Santa Barbara County’s new ReSource Center recovers recyclable materials from commercial and residential waste, pushing the region’s landfill diversion rate above 85 percent and reducing greenhouse gas emissions equivalent to those generated by 28,668 cars. A case study with AVR, a residual waste sorting plant in the Netherlands, demonstrated that mixed waste sorting with high-performing technologies can capture 12 times more plastics for recycling, cutting down on carbon dioxide emissions.
Today, recyclers and sorting plant operators are faced with the task of cleaning contaminated waste to a level suitable for further processing or local trading. At the same time, brand owners and converters that buy PCR are demanding high-purity mono fractions, sorted by polymer type and colours. By adopting new sensor-based sorting technology, plant operators can effectively sort and purify high-value plastics from waste streams to supply PET or PO fractions to the market. To create more valuable products, a combination of pre-sorting and flake sorting solutions is needed.
First, near-infrared (NIR) sorters separate targeted plastics from contaminants such as unwanted polymers and foreign materials. The purified plastics are then shredded, washed, and dried. The resulting plastic flakes are then processed in a secondary step with a high-precision flake sorting system that can sort flakes as small as 0.80 inches (2 mm). These ultra-flexible systems enable operators to define whether they’d like to sort materials by polymer type and/or colour, creating products specifically tailored to even the most demanding requirements. The sorting technology featured in these systems can sort a vast range of colours, including the highly demanded
natural, clear, and light blue flakes, as well as all bright colours while ensuring maximum polymer purity. Thus, operators are given the means to minimize contamination levels and supply the industry with high-quality materials they can process into virgin-like recyclates.
While most recyclers prefer plastics coming from single material streams with lower contamination levels, operators can source more materials to meet demand by cleaning plastics of impurities. Post-consumer packaging waste, for instance, can be an excellent source of recyclable polymers and is available in large quantities. Although more contaminated compared to post-industrial plastic waste, sophisticated sorting systems can automatically recover and purify the materials by utilizing advanced mechanical recycling processes. This too would increase the availability of PCR material on the market.
Collaboration is key in plastic recycling. Improving recyclability and increasing the quantity of recycled content demands that the industry go upstream because high-quality recycling begins in the design phase. Brand owners are incentivized to implement design-for-recycling to help facilitate the sorting process. The more complex and colourful the product’s design, the more difficult it is to sort and recycle. Thus, to maximize resource recovery, product design, sorting technology, and the overall process must complement each other. With all methods, from the product’s design to its end-of-life management going hand in hand, it is evident that change does not come from a single actor in the value chain. To innovate and transform the industry, everyone must play their part, and we all must come together in new ways.
The recycling sector offers tremendous potential, but limited recycled content availability, low-quality recyclates, and a lack of financial incentives seemingly impair its evolution. Consumer values and purchasing behaviour, legislation, and supply chain vulnerabilities signal that it is time to reduce waste and make recycling a priority. Highly efficient sorting processes that enable MRFs and recyclers to create high-purity mono fractions from even the most contaminated waste streams will ensure a long-term supply of recycled content. As part of the road map to the circularity of plastics, the capability to create virgin-like recycled content opens new revenue streams for sorting facilities and recyclers while reinforcing local trading. Using sensor-based sorting technologies provides an economic advantage to the entire plastics value chain.
ERIC OLSSON is the area segment manager of plastics at TOMRA Recycling Sorting.In the quest to create a circular economy for plastics, the share of virgin material in manufacturing should be reduced and replaced by secondary raw materials.
No matter how challenging your needs, BKT is with you offering an extensive product portfolio for every field such as agriculture, OTR and industrial applications.
BKT provides concrete, reliable and high-quality solutions to your requests and working needs. Wherever you are, BKT is with you.