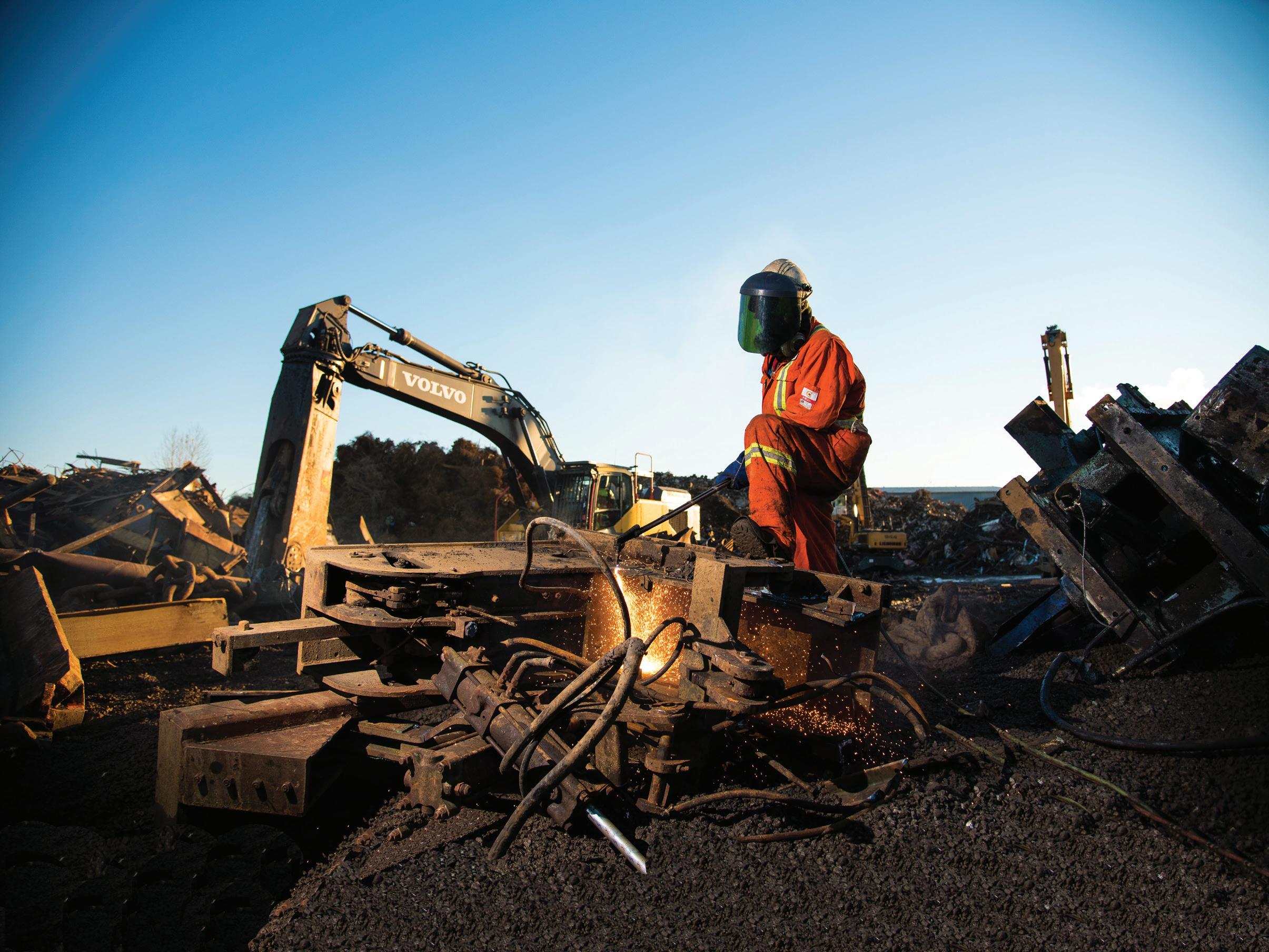

FOOD WASTE INTO > 99.5% PURE
Horizontal depackers offer multiple bulk feed options to process a wide variety of materials and contaminants. Our robust design and unique screening chamber achieves the market’s highest purity organics.
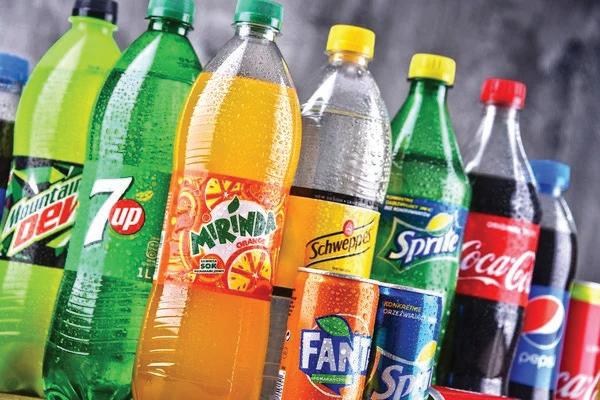



FOOD WASTE INTO > 99.5% PURE
Horizontal depackers offer multiple bulk feed options to process a wide variety of materials and contaminants. Our robust design and unique screening chamber achieves the market’s highest purity organics.
No matter how challenging your needs, BKT is with you offering a wide range of OTR tires specifically designed for the toughest operating conditions: from mining to construction sites.
Sturdy and resistant, reliable and safe, able to combine comfort and high performance. BKT is with you, even when work gets tough.
For info: 514 -792-9220
24 COVER STORY RICHMOND STEEL CRUSHES THE COMPETITION WITH B.C.’S ONLY LARGE-SCALE AUTO SHREDDER
30
REBUILD PROGRAM GIVES SECOND LIFE TO AGING EQUIPMENT
42 TECHNOLOGY INNOVATIONS MAKE FOR SAFER WHEEL LOADER OPERATION
48 PROTECT LIVES AND PROPERTY WITH AUTOMATED FIRE SUPPRESSION
36 The race for
38 New plastic baler boosts Canada’s
40 C&D
42
Richmond Steel handles both ferrous and nonferrous scrap metals, household items such as cars and appliances, and heavy items like structural steel, beams, plates, and rebar. The company also offers decommissioning and industrial demolition services, focusing on specialized projects such as mines, oil and gas pipelines, railroads, and sawmills. See more on page 24.
LIKE TO HEAR FROM YOU
Do you have a story, equipment, or technology innovation, commentary, or news that our readers in the recycling industry should know about? Drop us a line any time.
Contact: Editor Slone Fox at sfox@baumpub.com or 604-291-9900 ext. 335
ASSOCIATE PUBLISHER/ VICE PRESIDENT OF SALES
ADVERTISING PRODUCTION production@baumpub.com
DESIGN & PRODUCTION
Morena Zanotto morena@baumpub.com 604-291-9900 ext. 325
PRESIDENT/PUBLISHER Ken Singer ksinger@baumpub.com 604-291-9900 ext. 226
VICE PRESIDENT/CONTROLLER Melvin Date Chong mdatechong@baumpub.com
FOUNDER Engelbert J. Baum
Published by: Baum Publications Ltd. 124 - 2323 Boundary Road Vancouver, BC, Canada V5M 4V8
Tel: 604-291-9900
Toll-free: 1-888-286-3630 Fax: 604-291-1906 www.baumpub.com www.recyclingproductnews.com
@RecyclingPN
FOR ALL CIRCULATION INQUIRIES
Toll-free: 1-866-764-0227 email: rpn@mysubscription.ca
Subscription: To subscribe, renew your subscription, or change your address or other information, go to: https://www.recyclingproductnews.com/ mysubscription/subscribe
Recycling Product News is published seven times yearly: January/February, March, April, May/June, July/August, September/October, November/ December. Advertising closes at the beginning of the issue month. One year subscription
Recycling Product News accepts no responsibility or liability for reported claims made by manufacturers and/or distributors for products or services; the views and opinions expressed are those of the authors and not necessarily those of Baum Publications Ltd.
We acknowledge the financial support of the Government of Canada.
Copyright 2024 Baum Publications Ltd. No portion of this publication may be reproduced without permission of the publishers.
Printed on paper made of FSC®-certified and other controlled material. ISSN 1715-7013. PUBLICATIONS MAIL AGREEMENT NO. 40069270.
Return undeliverable Canadian addresses to: Circulation Dept., 124-2323 Boundary Road, Vancouver, BC V5M 4V8 email: rpn@mysubscription.ca Toll-free: 1-866-764-0227
SENNEBOGEN’S ELECTRIC EGREEN MACHINES HAVE BEEN PROVEN TO REDUCE COSTS UP TO 50% COMPARED TO DIESEL. ELECTRIC SERIES MACHINES CAN ALSO REDUCE YOUR CARBON FOOTPRINT, OPERATING COSTS, AND DOWNTIME.
Qualified technical support network
Optional pony motor in counterweight
Electric motor - no battery
Proven cable system
Easy to service and support
FEDERAL GRANTS AVAILABLE FOR ELECTRIC MACHINES
In the recycling industry, every word we use makes a significant impact on how those outside of the industry perceive and approach recycling. One term that often comes under scrutiny is “scrap.” While it accurately refers to discarded materials, its connotations don’t necessarily align with the value these materials hold in the context of recycling. The word “scrap” often conjures images of something useless or of little value, contributing to a negative perception of recycled materials. In reality, these materials are valuable resources waiting to be transformed into something new through recycling. This is where the power of language comes into play.
The choice of words extends beyond semantics; it influences public perception and attitudes toward recycling. By framing recycled materials positively, people are more likely to participate in recycling efforts. It becomes a narrative of environmental stewardship rather than simply discarding waste.
Emphasizing the environmental benefits of recycling is also crucial. Terms like “closed-loop” and “circular economy” convey the idea of a sustainable system where resources are continuously reused, minimizing waste and environmental impact. These terms resonate with individuals seeking eco-friendly alternatives, driving demand for recycled materials and sustainable practices.
Additionally, initiatives aimed at changing the language surrounding recycling are gaining traction. Companies and organizations are adopting terms like “upcycled,” “reclaimed,” and “remanufactured” to emphasize the quality and value of recycled products. These terms not only educate consumers but also encourage them to make sustainable choices by supporting products made from recycled materials.
One of the most notable initiatives for changing the industry’s language took place back in April at the ISRI2024 Convention’s closing session when the Institute of Scrap Recycling Industries introduced its rebrand. After more than 35 years as ISRI, the association announced that it is now the Recycled Materials Association (ReMA), dropping the word “scrap” in exchange for the more favourable term “recycled materials,” further proving the power of words.
“From everyday items to our essential infrastructure, recycled materials power the manufacturing supply chain that makes our economy stronger, our planet more sustainable, and
The word “scrap” often conjures images of something useless or of little value, contributing to a negative perception of recycled materials. In reality, these materials are valuable resources waiting to be transformed into something new through recycling.
our lives better,” said Robin Wiener, president of the Recycled Materials Association. “Our new name, the Recycled Materials Association, clearly and accurately describes who we are as an organization and who we represent.”
As advocates for recycling and sustainability, it’s essential to be mindful of the language we use. By using positive and empowering terms, we can reshape the narrative around recycling, turning it into a compelling story of innovation, conservation, and responsible consumption. When we use positive and empowering terms to describe recycling and sustainability efforts, we not only educate but also motivate others to join the cause.
The new model 4 E-Z log Baler is just what mid size scrap yards have been asking for! Priced right for any yard — small, mid size, or large!
Like the Model 3, the NEW Model 4 has no set up time and a very low cost to operate. The one man operations are all handled from the newly designed cab. With the 400º rotation crane and a reach of 27’ adding the continuous rotation grapple, it makes loading the larger chamber a breeze.
Taking your loose scrap to a highly sought after shreddable log.
— Cycles in under 2 minutes!
— Produces up to 70 tons per day.
— Fully portable in the closed position.
— New seat design for more operator comfort.
After more than 35 years as the Institute of Scrap Recycling Industries, ISRI is now the Recycled Materials Association (ReMA). The new name and logo were unveiled during the closing general session of the ISRI2024 Convention and Exhibition in Las Vegas.
“From everyday items to our essential infrastructure, recycled materials power the manufacturing supply chain that makes our economy stronger, our planet more sustainable, and our lives better,” said Robin Wiener, president of the Recycled Materials Association. “Our new name, the Recycled Materials Association, clearly and accurately describes who we are as an organization and who we represent. I am excited to unveil our dynamic new name and logo to stakeholders around the world.”
The organization’s new identity includes a new tagline – Sustainable. Resilient. Essential. – which emphasizes the industry’s core benefits to society. The recycled materials industry is sustainable – helping protect the environment. It is resilient – providing materials that strengthen the economy. It is also essential – to ensure the things we need are there to make everyday life better.
In the lead-up to the new name and logo reveal, the association celebrated its history with several initiatives. In April, the organization launched an online timeline featuring milestones from the recycled materials industry, as well as memorable moments from across the organization’s more than 30-year history. There are interviews, videos, and museum-grade images that tell the story of the recycled materials industry.
The association also launched a digital mosaic where members shared memories of ISRI and various events over the years in the lead-up to ISRI2024. A full-scale physical installation was then part of the ISRI Hub during the convention to bring members’ memories to life on-site.
The Paris 2024 Olympics’ circular economy strategy is based on three key principles: organizing the games with fewer resources, making better use of these resources by promoting eco-design, and ensuring the second life of resources after the games.
Paris 2024 wanted to calculate its “material footprint” in advance of the event, meaning the sum of the weight of all the resources mobilized. Venue by venue, Paris 2024 produced a detailed map of the resources needed to organize the event to reduce and pool resources and control their life cycle before, during, and after the event.
To obtain supplies, the event organizers applied a responsible purchasing strategy of which the circular economy is one of the pillars. Paris 2024 has given preference to suppliers who:
• Adopt an eco-design approach to their products and services;
• Give priority to equipment hire and long-life products;
• Use lower-impact raw materials such as recycled materials or production offcuts;
• Are committed to certification processes;
• Offer solutions for the second and end-of-life of products; and
• Minimize the use of packaging and promote reusable or recyclable packaging.
At the time of the bid, Paris 2024 proposed a concept for a more responsible Olympic Games that capitalized on 95 percent of existing infrastructure or temporary venues to build less and mobilize fewer resources.
In addition to reducing its needs, Paris 2024 has given preference to renting rather than buying from event organizers. Of the two million items of sports equipment, three-quarters will be rented or made available by sports federations. Seventy-five percent of electronic equipment, such as televisions, computers, and printers, are also rented rather than purchased. All of the stands, tents, and bungalows used will also be rented.
Heavy investment from the private sector and the U.S. government has led to plans for battery recycling outpacing demand. According to new research from global technology intelligence firm ABI Research, U.S. electric vehicle (EV) battery recycling plants plan to have the capacity to recycle 1.3 million EV-equivalents of batteries annually, but only 341,000 will be available by 2030.
“There are concerns about a lack of capacity for EV battery recycling, but the opposite is true. Current plans for recycling plants see capacity greatly outstripping the supplies of waste batteries. This will lead to uneconomic utilization rates or, more likely, a delay or scaling down in recycling projects,” says Dylan Khoo, electric vehicles industry analyst at ABI Research.
In 2030, around one-third of waste EV batteries will be end-of-life batteries from cars that have reached the end of use and are ready for recycling. The rest will come from factory scrap: batteries that do not pass quality control on production lines and go directly to recycling. For the planned battery recycling plants to reach a viable utilization rate, there must either be a massive reduction in EV battery lifespans or a gigafactory yield rate, neither of which is likely.
“We expect to see a revision of recycling plant plans to account for the shortage of waste EV batteries and an increase in demand for these batteries, which will put pressure on recyclers. This will have knock-on effects, further weakening the business case for second-life applications, as used batteries are more likely to go directly to recycling rather than be reused,” says Khoo.
These findings are from ABI Research’s Securing the EV Supply Chain: Battery Recycling in the United States application analysis report which is part of the company’s electric vehicle research service.
The Glass Recycling Coalition (GRC) has named Murphy Road Recycling as a recipient of a gold-level certification for its U.S. material recovery facility in Berlin, Connecticut. The approximately $40 million single-stream MRF started operations in 2022 and features a processing system that includes optical sorters, artificial intelligence, and robotics supplied by Van Dyk Recycling Solutions.
The MRF utilizes glass cleaning equipment including a glass breaker, vibrating table screen, secondary fines screen, and vacuum system. The MRF sends its clean glass to processors that convert the material into a cullet used for manufacturing glass containers, fine powders used in fibreglass insulation, and ground glass used as a cement binder.
The GRC MRF Glass Certification program launched in the fall of 2019. In 2022, the glass certification criteria were updated to prioritize end-market consistency and more thorough glass cleaning prior to beneficiation. Eligible applications are judged on their current MRF infrastructure and the results of a glass purity test that is aligned with the Recycled Materials Association’s Three-Mix Specification. An independent committee scores applications and awards MRFs with either gold, silver, or bronze certification.
Frontline Machinery has acquired Lonetrack Equipment, a dealer of specialized machinery for the aggregate, mining, and road construction industries in British Columbia and the Yukon.
Lonetrack Equipment’s range of heavy equipment, including crushers, screeners, conveyors, and concrete construction equipment from brands such as Astec, Sandvik, Vale, BTI, Gomaco, and more, complements Frontline Machinery’s existing portfolio.
Effective May 1, 2024, the combined entity will operate under the Frontline Machinery brand, leveraging shared resources, product options, and expertise to maximize value for contractors and stakeholders. Frontline Machinery will retain the personnel of Lonetrack Equipment.
The California Carpet Stewardship Program has surpassed its annual carpet recycling goal for the second year in a row. The data released by the Carpet America Recovery Effort shows the program achieved a 35.1 percent recycling rate in 2023, surpassing its target goal of 31 percent. The accomplishments of the Carpet Stewardship Program result from expanding awareness among all stakeholders to increase knowledge of drop-off sites, ultimately enhancing accessibility for California residents and encouraging proper disposal practices.
Two years of investment, transformation, and growth have led waste-to-energy provider Covanta to a new milestone: the introduction of its new identity, Reworld.
Reworld has become a multifaceted entity, expanding its geographic footprint, showcasing solutions for waste management and adopting a fully regionalized approach focused on enhancing customer experience.
The launch of the Reworld identity brings a number of new introductions as well, with a focus on ReDirect360 (zero-wasteto-landfill), ReDrop (wastewater treatment), ReKiln (alternative fuel engineering), ReMove (transportation and logistics), and ReCredit (sustainable carbon offsets). These solutions provide customers with a fast way to meet sustainability objectives by minimizing carbon footprints, preserving resources, and introducing new revenue streams.
The U.S. Department of Energy has released a new report that shows that the U.S. could sustainably triple its production of biomass to more than 1 billion tons per year. The report – the fourth in a series of assessments of potential biomass resources in the United States since 2005 – finds that 1 billion tons of biomass could satisfy over 100 percent of the projected demand for airplane fuel in the U.S., allowing the U.S. to fully decarbonize the aviation industry
with sustainable aviation fuel.
Other highlights from the report include:
• The U.S. currently uses about 342 million tons of biomass, including corn grain for ethanol and wood/wood waste for heat and power, to meet roughly five percent of America’s annual energy demand.
• The U.S. can triple the production of biomass, producing an estimated 60 billion gallons of low greenhouse gas liquid fuels, while still meeting the projected demand for food, feed, fibre, conventional forest products, and exports.
• Currently available but unused biomass resources can add around 350 million tons of additional biomass per year above current uses and double the U.S. bioeconomy.
• Biomass resources, like energy crops, in a future mature market, can provide more than 400 million tons of biomass per year above current uses.
• Further technological innovations could lead to evolving and emerging resources that represent additional biomass potential.
The report analyzed the biomass production capacity of approximately 60 resources. These include winter oilseed crops; trees and brush harvested from forests to prevent wildfires; macroalgae, such as seaweed cultivated in ocean farms; and carbon dioxide from industrial plants. The report finds that the wide dispersion and variety of these resources will ensure that the benefits of expanded biomass production extend to both rural and urban areas.
•
•Lowfuelcosts»averageof10-15gal/h •Lessfines»betterproductquality •Resistantagainstcontaminants(steel,etc.)
Therearesomeapplicationswhereahigh-torqueshredderisthebetterchoicethanahigh-speedgrinder!Withtheoptionalscreenbaskets (single-shaftshredders)orbreakerbars/screenbaskets(dual-shaftshredders)theseshreddersareabletomakeasizedandconsistentproduct. Checkusoutformoreinformationonshredders,trommelscreensandstarscreensorgetintouchwithoneofourdealersinyourregion.
tim@timberridgeequip.com
EggersmannNorthAmericaInc.|Contactdetails:ChristopherPickhardt|(646)-391-3177|sales@eggersmann-na.com|www.eggersmann-na.com
ROCSYS
Autocar is collaborating with Rocsys to enable hands-free charging for Autocar’s electric terminal tractors.
“Providing hands-free charging for Autocar customers means they won’t have to piecemeal charging solutions together when they purchase EV trucks from us. All they need will come in one package – ‘always up’ EV trucks combined with non-manual charging set up for them on-site. By elimi-
nating the need for manual intervention, hands-free charging ensures uninterrupted and efficient charging operations round the clock, enhancing fleet productivity and sustainability,” says Andrew Taitz, chairman of Autocar.
Rocsys chargers are compatible with any high-power DC charging station utilizing a CCS-1 charging connector. Rocsys utilizes a combination of soft robotics, computer vision technology, and advanced AI to create an ideal charging process. Throughout the pilot, Rocsys will capture hundreds of images that its system will then use to work toward a 99 percent successful plug-in rate before deployment.
Glencore has invested $75 million in Li-Cycle, marking the second investment that Glencore has made in the company.
Glencore has designated Li-Cycle as one of its preferred recycling partners, and Li-Cycle and Glencore entered into a strategic commercial partnership aimed at creating an integrated platform to supply a global base with both primary and recycled critical battery materials. As part of the partnership, Glencore previously made a $200 million investment in Li-Cycle in June 2022 by purchasing a convertible note.
CONFERENCE: NOVEMBER 5 - 6, 2024
EXHIBITION: NOVEMBER 6 - 7, 2024
INTERNATIONAL CENTRE, TORONTO, ON
Demonstrations Inspiration Canada‘s ONLY event serving the waste, recycling and public works markets — under one roof!
See the latest from Machinex, Durabac, Nova Products, Frontline, Accent Wire, Keith Mfg. and many more. cwre.ca Follow us online:
Electra has commissioned its pilot plant in Boulder, Colorado. The pilot demonstrates Electra’s technology to produce metallic iron from already mined, high-impurity, commercially stranded ores to help accelerate decarbonization, sustainability, and circularity efforts across the ore-to-steel value chain. With 90 percent of steel production’s CO2 emissions coming from ironmaking, Electra’s process operates at 140 degrees
Fahrenheit, enabling the integration of intermittent renewable energy resources, making emissions-free iron possible at temperatures colder than coffee. The process intakes a wide range of ores and the principal iron ore impurities like alumina and silica are selectively refined as co-products. Electra’s clean iron, combined with recycled scrap steel, offers high value-in-use for electric arc furnace steelmakers, while also reducing the capital intensity, cost, and waste across the value chain.
American Baler Company will expand its Bellevue, Ohio, manufacturing facility by 20 percent. Started in April of this year, the project is expected to be completed by the fall of 2025, coinciding with American Baler’s 80th anniversary.
The expansion will increase the physical size of the facility as well as its available capacity for fabrication, production, and assembly with an eye on the reduction of equipment and parts lead times. The initial phase will include site and utility preparation, construction of the new addition, and installation of overhead cranes. Subsequent phases will include the installation of steel processing equipment along with workflow enhancements to improve material movement throughout the plant.
PET collection and recycling accelerated in 2022 ahead of the new EU Single-Use Plastic Directive targets. The collection rate of PET in 2022 was 60 percent, showing an increase from the 45 percent achieved in 2020. Furthermore, the recycling rate for PET beverage bottles alone was estimated to be 75 percent, compared to 61 percent in 2020. Packaging was the dominant end-use for rPET in 2022, with 48 percent used in bottles. This shows an increase in bottle-to-bottle recycling in Europe. For rPET, 25 percent was used in sheets (trays), and the remainder was used in non-packaging applications including polyester fibres (15 percent), strapping (six percent), and others (six percent).
Eastman’s second U.S. molecular recycling project has been selected by the Department of Energy (DOE) to begin award negotiations for up to $375 million in Bipartisan Infrastructure Law and Inflation Reduction Act funding as part of the Industrial Demonstrations Program. As a result, Eastman will build a second U.S. molecular recycling facility at its location in Longview, Texas.
Eastman selected the Longview site due to synergies with existing infrastructure and operations, favourable energy supply and footprint, and access to western and central U.S. feedstock pools. The location also provides enough space for on-site renewable energy.
The investment includes operations that will prepare mixed plastic waste for processing, Eastman’s molecular recycling unit to depolymerize waste, and a polymer facility to create virgin-quality materials for packaging and textiles. The Longview molecular recycling facility will have the capacity to recycle approximately 110,000 metric tonnes of hard-to-recycle plastic waste.
The investment is expected to bring over 200 full-time jobs to the Longview community in addition to approximately 1,000 temporary construction jobs during site development and building of the facility.
Size reduction is tough work that can push equipment to the extreme. At Herbold, we know that granulator performance and durability is critical to your success. That’s why we build our equipment to deliver maximum throughput and require minimal maintenance and downtime.
Here’s how:
• Double Cross Cutting Action – Reduces Jams and Material Fines
• Adjustable Bed and Rotor Knives – Maintain Constant Cutting Circle
• Safe, Easy Access to the Grinding Chamber – for Improved Maintenance, Screen Changes and Machine Cleanout
• Replaceable Armor Plating Inside the Cutting Chamber
• Faster and Safer Knife Changes – Adjustments are Made in Jig Outside of Granulator
• Available Force Feeders – Increase Throughput by 50% - 80%, Reducing Power Consumption
888.612.7774
www.herboldusa.com info@herboldusa.com
Volvo Construction Equipment took its L180H wheel loader, swapped in larger 875/65 R29 tires, a long boom, and a rehandling counterweight to create a new truck-loading variation called the L180 3-Pass Rehandler. The machine is designed for rehandling applications – such as C&D and scrap – with a higher tipping load, better fuel efficiency, and longer reach to fill a truck in three passes.
The larger tires provide lateral traction and flotation, durability, and resistance to cuts and impacts. The long boom brings an additional 675 lbf in breakout force and two feet of dump clearance. The longer reach also allows the wheel loader to stay farther from the truck while still dumping material into the centre of it. Cycle times are also improved by the higher reach because the operator doesn’t have to roll the bucket back to move away from the truck, especially when dumping the last bucket.
Genesis Attachments
Designed to fit remote-controlled demolition robots and mini excavators, Genesis Attachments’ M7 concrete cracker is ideally sized for concrete processing and recycling. The M7 efficiently processes concrete with a hydraulic booster, that increases power and speed, and a fully guarded cylinder rod that’s protected from debris. Fitting up to 25,000-pound carriers, the M7 weighs 1,400 pounds and features a 27-inch jaw opening with a 19-inch jaw depth. The solid Strenx 900 steel jaws provide durability while the replaceable teeth and blades simplify maintenance. A knock-around rotation option makes it easy for operators to position the M7 for picking up material.
The STADLER WireX automated bale wire remover measures bales and removes wires from single- and cross-wired bales in one pass without double feeding. The bales are fed onto the machine by a conveyor, and then guided by a moving push plate onto the floor plate which keeps the bale in position. Sensors located above the input conveyor, inside the chamber, and on the flap ensure the bale is positioned correctly before combs are pushed into the bale to fix the wire for cutting. When the cutting is done, the combs pull out and the wires are coiled up and discharged by a small integrated conveyor into a separate bin, ready for recycling.
Concrete crackerSorting technology
TOMRA Recycling’s GAINnext deep-learning-based AI technology solution features five sorting applications, including PET cleaner for higher purity PET bottle streams, paper deinking for cleaner paper streams, and three food-grade from nonfood-grade plastics sorting applications. GAINnext enhances the sorting performance of TOMRA’s existing AUTOSORT units by combining traditional near-infrared, visual spectrometry, or other sensors with deep learning technology, making the machines capable of identifying objects that are hard or even impossible to classify using traditional optical waste sensors. According to TOMRA, the machine can achieve a purity rate upwards of 95 percent in packaging applications.
Finlay’s 890 is a heavy-duty, two-deck scalping screener with a variety of screen box media options and a variable screen angle. The Finlay 890 can process a high tonnage throughput of up to 700 tph / 771 US tph, depending on mesh sizes and material type. The screen box is engineered to deliver a high-quality screened product in secondary screening applications such as aggregates, C&D waste, biomass, compost materials, and foundry waste. The Finlay 890 is available with hybrid technology consisting of on-board electrical motors which give users the flexibility to run the plant from an outside power supply or standard on-board engine.
Scalping screenerRICHMOND STEEL DRIVES INNOVATION AND EFFICIENCY WITH B.C.’S ONLY LARGE-SCALE AUTO SHREDDER
BY SLONE FOX, EDITORDuring the late sixties and early seventies, winds of change were blowing through the recycling industry. The environmental movement was gaining momentum, causing a significant shift as more people began to advocate for sustainable waste management practices. Recognizing this growing need, British Columbia–based Richmond Steel Recycling adapted to the changing landscape of recycling by installing a shredder and making sustainability a cornerstone of its operations.
At the time, B.C. faced a shortage of options for recycling end-of-life vehicles, raising concerns about automotive waste ending up in landfills or scattered across auto wreckers’ yards. To address this issue, the government initiated the Scrap Auto Management (SAM) program, purchasing mobile car crushers to assist recyclers in crushing cars throughout the province. Richmond Steel and its shredder played a crucial role in this initiative, providing a final destination for the materials. The government’s efforts during Richmond Steel’s formative years enabled widespread car crushing and facilitated efficient recycling through the company’s facilities.
ventured into decommissioning and industrial demolition services, focusing on specialized projects such as mines, oil and gas pipelines, railroads, and sawmills. By diversifying its operations, the company has tapped into new markets and opportunities, underscoring Richmond Steel’s commitment to innovation and growth.
Central to its success is not just its facilities, but also the continuous development of its employees. Throughout its evolution, Richmond Steel has prioritized training, recognizing the crucial role of ongoing education and skill enhancement in its operations. Maintaining a comprehensive set of standard operating procedures for all tasks is essential to ensure consistent training across locations. “A standard operating procedure for a material handler in Edmonton would be the same as if you’re operating that material handler in Richmond,” says Rai. “We can pluck an employee from our Fort St. John Yard, for example, and parachute him into the Kamloops yard and he’s good to go. There’s site-specific training since every site is obviously a little bit different, but the training is pretty well standardized to our standard operating procedures.”
The pandemic has greatly affected the metals recycling industry, as it did all industries. We went through shortages of consumer items throughout the latter half of 2020 and throughout 2021, and into 2022 there was a shortage of microchips that affected all these consumer products, including automobiles that we shred.
John Rai VP of Business Development, Richmond Steel
“Once the province was caught up with crushing the cars, Richmond Steel purchased those original crushers from the province, and we were still operating them when I started at Richmond Steel back in 1998,” says John Rai, vice president of business development. “Obviously they’d been repaired and welded and rebuilt along the way, but they were in operation right up until about 2005.”
Today, Richmond Steel runs as a joint venture between Sims Metal Management and Nucor Corporation, operating from five key locations strategically situated across Western Canada, including its B.C. yards in Fort St. John, Prince George, Kamloops, and Richmond, and a yard in Edmonton, Alberta. With the province’s only large-scale auto shredder situated in its main yard in Richmond, the company has established a significant presence in the Canadian recycling industry.
Richmond Steel handles both ferrous and non-ferrous scrap metals, household items such as cars and appliances, and heavy items like structural steel, beams, plates, and rebar. Expanding beyond traditional recycling, Richmond Steel has
Continuous education and consistent training have played a key role in safety at Richmond Steel. Rai notes that the company’s safety standards often surpass government requirements, meeting or exceeding the standards set by both WorkSafeBC in British Columbia and the Workers’ Compensation Board in Alberta, highlighting their proactive approach to ensuring a safe work environment.
Richmond Steel actively showcases its employees on its blog, recognizing their achievements, skills, and contributions. This practice not only celebrates individual and team successes but also plays a crucial role in employee retention. By featuring employee stories and accomplishments, Richmond Steel fosters a culture of recognition which in turn enhances job satisfaction and motivation. This visibility encourages skill building and development, as employees see firsthand the value of their work and the opportunities for growth within the company.
Richmond Steel’s comprehensive training programs also ensure that employees are well-equipped to handle the complexities of recycling operations safely and efficiently. By fostering a culture of continuous learning, Richmond Steel has built a workforce capable of navigating the evolving industry landscape.
The impact of industry trends and external factors also underscores the importance of adaptable and well-trained teams. The pandemic in particular highlighted the need for agile training strategies to navigate disruptions and ensure business as usual.
“The pandemic has greatly affected the metals recycling industry, as it did all industries,” says Rai. “We went through shortages of consumer items throughout the latter half of 2020 and throughout 2021, and into 2022 there was a shortage of microchips that affected all these consumer products, including automobiles that we shred.”
Richmond Steel’s commitment to employee development is evident in its ongoing training initiatives.
Recyclers rely on people buying new vehicles to obtain the old ones as feedstock. A shortage of new cars – as well as higher costs for them – emerged during the pandemic, causing many people to keep and repair their older vehicles far longer than usual. According to Rai, it became common to see people investing in substantial repairs for older vehicles which would typically have been scrapped. However, as new car prices have started to taper off, Rai says this pattern may change.
“Typically, those kinds of vehicles come off the road because people won’t put a transmission into a 2002 Honda Accord, for example. But during the pandemic, we saw that people would put that $3,000 repair on a 2002 Honda Accord because the rest of the car was fine, and that would extend the life of that 2002 Honda for another 10 years,” says Rai. “That was partly because of the shortage of cars, and the price spike for a while. People also didn’t know what was going to happen. It was a way of saving money because $3,000 put into a car is still cheaper than $40,000 for a new Accord to replace it.”
Rai notes a similar trend with people holding onto their appliances and household goods longer, leading to a decrease in the volume of materials brought to the yard. Over the past four years since the pandemic began, Rai says that significant changes have also occurred in related industries that supply materials to the yard.
“There’s been other shifts as well that have happened in what I call ancillary industries, or industries that feed our shredder. Auto wrecking, for example,” says Rai. “There’s been a shift in that. We see a lot more vehicles or parts from vehicles – engines, etc. – going in containers offshore. It’s just been a different type of market since the pandemic for sure. I don’t think we’ve returned to what the market was pre-pandemic.”
As a key player in British Columbia’s recycling sector, Richmond Steel has adapted to market challenges and changing trends through innovation and a steadfast commitment to its employees. By leveraging its strengths in training and innovation, the company has not only weathered the storm, but emerged stronger.
The lessons learned during the pandemic have reinforced the importance of agility, innovation, and a strong focus on employee development. As the market gradually recovers, Richmond Steel’s strategic initiatives and strong foundation will enable it to capitalize on new opportunities and navigate future challenges effectively. Through trends and challenges, its commitment to continuous learning, operational efficiency, and collaboration remains steadfast – a testament to its legacy and vision for a sustainable future. RPN
A C C E N T ® 4 7 0
DESIGNED FOR TWO-RAM BALERS
S T RONG PE OPLE .
S T RONG PR ODU C TS . S T RONG T IE S .
Accent W ire Tie is the largest supplier of baling wire and wire tier technology in the recycling and waste industry. Our leading line of bale packaging equipment includes the Accent 470® W ire Tier, featured on balers around the world and the Envirobale® bagging system for solid waste containment.
Accent W ire Ties’ sales and service technicians teams have hands-on experience and stay up-to-date on the latest industry trends. Accent W ire Tie has forged the strongest ties in the industry since 1986.
Four-wheel drive design for exceptional performance and reliability
Pivot-out or removable parts cartridge cutting maintenance time from hours to minutes
No mechanical or hydraulic adjustments needed, allowing for trouble-free operation
Meets ANSI, CSA standards and is CE compliant
Carrying out repairs and maintenance within the normal life cycle of shredders and compactors enables them to work as efficiently as possible during their planned service life. Rebuilding, on the other hand, aims to give the equipment a second life.
TANA is currently testing how to sustainably and profitably double the life of machines. In solid waste processing, there is a growing need to rebuild machines – Tana Second Life is a program that addresses that need. The program aims to extend the life cycle of machines while at the same time reducing the consumption of materials needed to manufacture new machines, cutting waste, and minimizing emissions.
The timely refurbishment, rebuild, or upgrade of the main components of a compactor or shredder, mainly the powertrain, offers both financial and environmental benefits. When the diesel engine and the main hydraulic components reach the end of their intended service life after 10,000 operating hours, they must either be completely refurbished or replaced.
Based on a condition assessment, it is possible to calculate in advance when a rebuild is feasible. Using data to predict maintenance is already a reality since today’s machines are compatible with remote diagnostics. By knowing all the pressures and fault warnings, the need for refurbishments can be assessed in advance.
Remote monitoring produces data not only about operating hours, but also about how hard the machine has been used. When a sufficient amount of data is accumulated, the estimate of the need for refurbishing and the costs becomes more precise.
TANA’s product development and production have always focused on a long service life and easy maintenance. Making it easier to replace components and anticipate maintenance needs means fewer materials that need to be replaced at once. In this way, the downtime can be as short as possible.
The modular design of TANA machines also simplifies rebuilds as entire units can be changed. In the future, it will even be possible to replace the diesel engine with an electric powertrain.
In practice, rebuilds are carried out by partners certified by TANA according to a common operating model. Components and certified processes ensure that rebuilt machines retain their original performance.
The first partner, Humdinger Equipment in the U.S., has already completed several rebuild projects with TANA. In North America, machines undergo up to two full-scale rebuilds during their lifetime, so they even get a third life after their second life.
New network partners are starting to be certified in Europe as well. TANA has done rebuilds together with its network partners, and several projects are currently in progress.
Although the proportions of recyclable components vary, rebuilding is a significantly cheaper option than purchasing a new machine. The difference compared to a new purchase can be in the range of 30 to 70 percent, depending on the age of the machine and the level of refurbishment.
During the rebuild, the machine’s chassis structures are preserved. The owner of the machine gets guarantees for the
main components that are replaced, as well as the opportunity to purchase an extended warranty.
When the need for a rebuild is anticipated and the rebuild is carried out as planned, significant savings can be made in investment costs. The contractor’s productivity also increases when there are fewer disruptions in production or they are kept short.
TANA has a separate recycling and refurbishment program for main components, such as diesel engines. End-of-life machines consist mostly of steel components that can be sold for metal recycling, while some components can also be recovered as spare parts. This provides a way to handle the final phase of a machine’s life cycle while putting a much smaller burden on the environment.
The difference compared to a new purchase can be in the range of 30 to 70 percent, depending on the age of the machine and the level of refurbishment.
The recycling industry depends on machinery that can process a wide variety of materials, from traditional waste like tires and plastics to more complex items like mattresses and construction debris. The Z 60 high-torque single-shaft shredder from Eggersmann streamlines recycling operations by providing a single-machine solution for diverse waste streams, minimizing the need for multiple specialized machines and reducing costs and space requirements.
The Z 60 also tackles one of the major challenges in recycling: producing consistent and specified end products. Its design enables precise control over the final particle size, ensuring the uniformity and consistency that is crucial for meeting industry standards and user requirements. By processing diverse materials and delivering consistent outputs, the Z 60 increases recycling efficiency across a variety of applications.
The high-torque single-shaft Z 60 shredder can shred C&D waste, commercial waste, MSW, wood waste, tires, plastic, mattresses, and even railroad ties with its standard Multigrip teeth, making it suitable for a wide range of applications. Optional Rootgrip teeth are specially designed to shred green waste and roots, adding to the machine’s versatility. The Z 60 shredder is capable of producing a specified and consistent end product in a single pass, allowing for both pre-shredding and the creation of sellable products using just one machine.
The Eggersmann Z 60 features a 10-foot-long shredding rotor with 30 mounted tools (optionally 20 or 40 teeth) and a counter comb equipped with 19 teeth. After passing through the counter comb, the material either falls onto the discharge conveyor or an optional screen basket enclosing the rotor’s lower half. The cutting clearance can be varied depending on contamination and the requested particle size, up to a minimum size of 2-inch minus. The machine also includes a neodymium cross belt magnet for metal discharge, a radio remote control for easy operation, a 600-hp Cummins diesel engine, and an oversized cooling system with a reversible fan.
Operating the Eggersmann Z 60 is straightforward. It offers tool-free adjustment of the cutting gap between the shaft and comb sections, allowing for quick changes in product size. The hopper capacity can be increased with double-sided hopper extensions, maximizing productivity. The machine’s large and wide conveyor belts enable maximum material discharge, while the rear conveyor offers adjustable height and speed for precise control. The Minimum Maintenance System and Eggersmann Telematics System simplify maintenance and monitoring tasks.
Over the last few years, the carton recycling landscape in Canada has undergone significant change. The Carton Council of Canada (CCC) has provided a summary of notable updates to the regulations and operating systems in various provinces and territories in both 2022 and 2023.
The recap below provides an update on this extended producer responsibility (EPR) evolution with a focus on recent changes and those anticipated in 2024.
Ontario’s Blue Box Regulation sets out a three-year transition to full producer-led EPR for residential paper and packaging materials that began on July 1, 2023.
As of March of this year, 130 communities have completed their transition, including Toronto, Ottawa, and London. One hundred and thirty-two communities, including Peel Region, are expected to transition in 2024; 187 will follow suit in 2025.
Under the new framework, Circular Materials (CM) has a dual role as both the administrator of the common collection system for Blue Box materials and a producer responsibility organization (PRO) responsible for operating a post-collection system for Blue Box material on behalf of its producers. The other PROs in Ontario are Ryse Solutions and H2 Compliance, with RLG acting as the day-to-day operator for the common collection system.
CM recently shared some updates regarding the common collection system. Specifically, 265 collection contracts and 27 receiving facility contracts are now in place. Likewise, CM will soon announce the successful proponents for three greenfield MRFs that it recently put out for tender. On a national front, CM’s chief executive officer indicated that a consistent material list across Canada should be a reality by 2027. This would be no small feat and a significant advancement for recycling in our nation.
On the broader policy front, industry observers have reported that the province is contemplating changes to both the Blue Box Regulation and the Resource Recovery and Circular Economy Act. Reportedly, the changes being considered pertain to the current framework’s outcome-based and competitive PRO features. Lastly, as reported in CCC’s winter newsletter, Ontario is con-
In preparation for the transition to a full producer responsibility framework on January 1, 2025, ÉEQ is in the process of signing partnership agreements with municipal organizations. To date, more than 50 of these agreements have been signed, representing over 60 percent of Quebec’s population.
sulting with representatives of the beverage and waste management industries on the creation of a deposit return system (DRS) for non-alcoholic beverages. The initial time frame announced for those consultations to wrap up (February 2024) is delayed.
PEI is currently conducting a review of its DRS, exploring the pros and cons of moving to a producer-led model. The current system is operated by the province. In parallel, earlier in March, Environment Minister Steven Myers said his department is looking at doubling the deposit on beverage containers to 20 cents in order to triple the payout on returned containers to 15 cents and encourage more returns. No details on timing have been shared.
In PEI, juice and water cartons are included in the DRS, while dairy and food cartons are collected in the publicly funded residential recycling program.
In May 2023, Circular Materials’ New Brunswick Stewardship Plan for Packaging and Paper was approved by Recycle
cents, the program will transition to a full-back deposit refund structure. A container recycling fee (CRF) will also be applied to each container material type, like what is in place in British Columbia and Alberta’s DRS. CRF values are available on Encorp Atlantic’s website.
The approved stewardship plan for the modernized DRS lays out the material-specific targets to be achieved over the next five years. The goal for the carton category (which also includes wine boxes) is 34 percent, versus today’s 32 percent performance. Likewise, the overall recovery performance target is 75 percent by unit and 79 percent by weight, up from the current 73 percent and 77 percent, respectively.
Nova Scotia’s new EPR for Packaging, Paper Products, and Packaging-like Products Regulations were enacted on August 2, 2023. The target materials are those from residential sources, including schools. The regulations are expected to be fully in force by December 1, 2025.
Under the new model, producers – via their PRO(s) – must implement a province-wide common collection system and must provide, at a minimum, the same service level as currently provided for garbage collection.
The province has also outlined material management requirements by designated material type. Targets for 2026 and 2027 range from 30 percent for flexible plastics to 80 percent for paper.
Quebec’s population. Cartons holding non-beverages such as soup and cream will be managed under this new framework.
As we reported one year ago, one aspect that differentiates Quebec’s new EPR framework from the other provinces is its scope, as it includes all generators, not just the residential, public space, and school sectors. To prepare for this, starting in 2025, producers will have to report materials destined for the industrial, commercial, and institutional (IC&I) sectors. This major change will require adjustments for businesses generating these materials.
New EPR regulations for packaging and paper products in the Yukon went into effect on January 25, 2024, and will come into force no later than October 1, 2025.
Beverage, dairy, and creamers are already included in the territory’s DRS, so the regulations only target food cartons (e.g., soup, broth).
In conclusion, it continues to be a dynamic environment for recycling in general and cartons in particular in Canada. CCC will continue to monitor these developments and looks forward to continued improvement in the collection and recycling performance of food and beverage cartons across the country.
ISABELLE FAUCHER is the managing director for the Carton Council of Canada.
RECOVERED PAPER OR RECYCLED PLASTIC PACKAGING – WHICH ONE CARRIES MORE WEIGHT?
BY HUBAN KASIMISustainable packaging solutions have gained popularity in a worldwide shift to reduce carbon emissions and raise the consumption of “greener” products. As more consumer-focused companies lay out their climate goals, the demand for materials like recovered paper and recycled plastic has strengthened.
According to a November 2023 report by consulting firm Statista, paper and cardboard (paperboard) were the most widely used packaging materials at 33 percent in 2019. Flexible and rigid plastics followed at 25.5 percent and 18.7 percent, respectively. Moreover, cartonboard consumption for packaging is likely to reach 66 million net tons (59.87 million metric tons) by 2032 and was estimated at 53 million nt in 2021.
So, how do you relate the above data realistically? The best place to begin is by observing trends in the consumer goods sector. Food and beverage manufacturers are at the forefront of this global shift toward environment-friendly options. PepsiCo and its subsidiary Quaker Oats, Coca-Cola, Pringles, and Unilever are all launching or testing paper-based technology to replace plastic wrapping and containers. These companies have partnered with packaging solution providers like DS Smith, Mondi, Graphic Packaging, and WestRock to overhaul the plastic rings, clips, or cartons with corrugated or kraft paper that can mirror the qualities of plastic.
To understand the depth of recent demand trends, it is necessary to study a few technologies or products available to companies that want to overhaul their packaging process.
Massachusetts-headquartered Seaman Paper has launched an alternative flexible stretch film for storage and shipping loads. The company’s trademark SeaStretch is compatible with handwrapped or automated pallets and is completely recyclable.
Global conglomerate DS Smith, through its Greencoat technology, has unveiled Shop.able Carriers and DryPack in North America. The former are sustainably produced moisture-resistant corrugated boxes meant for supermarkets. Any store chain can replace almost 100,000 plastic bags per year. The latter are boxes (also made from corrugated fibre) that can store and ship fresh fish.
Visy International has launched Visy Tread in Australia, a retail surface protection product suitable for home decorators, renovators, and similar requirements. The company has also introduced plastic bag alternatives.
We believe that our products are 100 percent recyclable, but will we be rewarded for it? It’s a chicken and egg conundrum. Our material is sustainable, but because it isn’t yet accepted at facilities we are at zero percent compared to the FTC’s accepted rate of 60 percent.
Will Lorenzi President and CEO, SmartPlanetSmartPlanet Technologies, a California-based startup, has developed EarthCoating and Hyperbarrier. The former is a resin coating that can be used on cups/containers, bottle labels, or cartons. The latter is a “green” flexible packaging solution that can be used to make bags, sacks, or pouches.
Most of the paper-based products are already in various stages of market scalability. There are a few innovations that are yet to be commercially accepted. SmartPlanet’s EarthCoating cuts plastic usage in packaging by 51 percent and is compatible with all conventional paper recycling systems; however, its popularity is lagging in some parts of the world. According to Will Lorenzi, president and CEO of SmartPlanet, the U.S. Federal Trade Commission’s (FTC) Green Guides have defined a 60 percent acceptance rate at facilities for any material to be deemed recyclable. This, among other factors, is proving difficult for his company to widely launch EarthCoating in the U.S. On the other hand, SmartPlanet’s HyperBarrier is more successful.
The transition from plastic to paper comes with its own obstacles. Let us look at the significant ones.
One would think that a better and cleaner product or technology would be a crowd-puller, but that may not be the case
“The word ‘recyclable’ is a reward. It motivates change. However, it has to be used for materials that are recyclable,” notes Lorenzi. Authorities must give the word to products that
“We believe that our products are 100 percent recyclable, but will we be rewarded for it?” Lorenzi continues. “It’s a chicken and egg conundrum. Our material is sustainable, but because it isn’t yet accepted at facilities we are at zero percent compared to the FTC’s accepted rate of 60 percent.”
Moreover, when converting a product from plastic to paper, you must add a heat seal or barrier to infuse the same qualities and performance. This makes the process counterintuitive since packagers may lose the recyclable mark because most product coatings aren’t sustainable. “It makes you wonder if you innovated a ‘greener’ product or will it still end up in a landfill even if it is made from paper?” asks Lorenzi.
To overcome the loss of recycling claims, SmartPlanet advocates for a solution similar to the Holy Grail 2.0, an initiative by the European Brands Association (AIM). The association is pushing for a digital watermark that can be detected in optical sorters across recycling facilities. This mark is invisible to the naked eye, but if implemented worldwide, it can save millions of tons of sustainable material from being landfilled.
The current legislation framework appears to be more placative than supportive of innovation. A convenient stance that limits scientifically proven solutions and wastage of tonnages. Still, one U.S. state has taken the lead to roll out a practical framework to lift the recycling rate of single-use plastic and packaging to 65 percent. “I am a fan of California’s Plastic Pollution Prevention and Packaging Producer Responsibility Act SB 54. The only drawback is that it will be effective in 2032,” says Lorenzi. He adds that if implemented correctly, SB 54 will be pivotal in bringing about the change the recycling industry needs. If the law is successful in California, Lorenzi hopes that other states will follow, making it easier for innovators like SmartPlanet to contribute with more groundbreaking technology.
There are other challenges, like the cost-effectiveness of scaling a process whose outcome is unknown, or, as many believe, the resultant energy consumption. A recent media report citing a Rabobank survey highlights that replacing plastic with paper might be more expensive and increase global carbon emissions.
Lorenzi concludes that the recycling industry needs to be more proactive in identifying processes or technologies that are “greener” and viable. “When you are a disruptor, there is some level of discomfort. You have to keep pushing for the ideal change you are looking for.”
HUBAN KASIMI is the recycled materials editor at Davis Index and can be reached at huban.kasimi@davisindex.com.
TRANSPORTATION SPACE AND CUT BACK ON TRAVEL TIME AND COSTS
Safety-Kleen has installed a new plastic baler in Delta, British Columbia, as part of an industry partnership with Interchange Recycling, a not-for-profit organization dedicated to the collection and recycling of used oil, antifreeze, and automotive containers in B.C. The new plastic baler will help improve automotive container recycling rates across B.C. and Canada and will process over half a million kilograms of automotive plastic annually. According to the company, it’s the first of its kind in B.C. capable of facilitating increased consolidation with other automotive and industrial liquid packaging from across the country.
“We have been working with Safety-Kleen Canada Inc. for two decades to help close the loop on the life cycle of oil in the auto industry by diverting used oil, oil filters, and used antifreeze from landfills,” says David Lawes, CEO of Interchange Recycling. “With this new infrastructure, our partnership with them has deepened as they have expanded their operation to include the collection of automotive containers. Currently in B.C., 1.7 million kilograms of automotive plastic containers are recycled every year, but I expect that will grow with the new plastic baler. Most of the recycled containers will end up being used again in industrial sectors or in landscaping, and the plastic collected will circle back into the North American economy.”
Part of Canada’s zero plastic waste agenda includes retaining the value of products and facilitating the transition to a circular economy. The new plastic baler in Delta supports Canada’s shift from a linear “take-make-dispose” method by handling automotive containers at the end of their anticipated life, extending their use, and sending them back into the production chain to create new and useful products.
“We needed brand-new infrastructure to help process plastic locally,” says Sam Glofcheskie, regional vice president of bulk product and services for Safety-Kleen Canada. “Right now, only around nine percent of plastic waste is recycled in Canada. We
Currently in B.C., 1.7 million kilograms of automotive plastic containers are recycled every year, but I expect that will grow with the new plastic baler. Most of the recycled containers will end up being used again in industrial sectors or in landscaping, and the plastic collected will circle back into the North American economy.
David Lawes CEO, Interchange Recyclingwant to help fix that. The new baler has allowed us to create jobs in the province, has expanded our partnership with Interchange Recycling, and will help British Columbia move a step closer to a circular system in the auto space. The plastic we encounter and bale at our facility in Delta will go to the RPM eco processing facility in Quebec where it will be recycled and eventually re-used as a new product.”
“RPM eco has years of operational experience in collecting contaminated plastics in New Brunswick, Prince Edward Island, Quebec, Ontario, and Alberta. We’re grateful that they have now entered the market in British Columbia and will be helping us collect plastic in the Lower Mainland before it is baled in Delta, and then processed at their facility in Quebec,” adds Glofcheskie.
“ BOOST YOUR PRODUCTIVITY WITH THE GENUINE PATENTED TRAX ”
✅ From 720 to 1,375 T of cutting force
✅ The utmost in scrapyard mobility
✅ Patented jam resistant hold down
✅ Full automatic lubrication system
German company Manfred Woitzel GmbH & Co. started in 1956 as a quarry operation and today specializes in groundworks, demolition, recycling, and disposal services. One of the streams that the company handles is construction and demolition waste, which it processes on-site in its holding yard.
Today’s third generation of the Woitzel family is always looking for ways to improve efficiency and profitability, and it has turned to Keestrack for new solutions to improve the bottom line.
Previously, Woitzel used two crushers – one jaw crusher at their holding and C&D recycling site, and an impact crusher that travelled between demolition sites. Woitzel also has two Keestrack K4 screens and an S5 stacker which drove interest in exploring new crushers from the brand.
Woitzel selected a Keestrack R3 impact crusher with a double deck afterscreen and wind sifter. Fuel savings compared to the previous crushers were part of the decision-making process, says Jannik Woitzel.
“The two-deck afterscreen with return conveyor saves space, is easy to detach, and is easy to transport to demolition sites without a permit,” says Woitzel. “This way the impactor is used both on the holding and recycling site, as well as the actual demolition site. The fully equipped machine is in fact two machines in one, saving a lot of cost in our operations.”
At the holding and recycling site, Woitzel produces RC-1 certified 0/8 mm and 8/45 mm used as crushing sand, and the bigger fraction is used as a stable base for applications such as road construction with high drainage capacities. The R3 runs up
to six hours a day, producing about 160 tph. When the S5 stacker is added to the production process, more savings can be realized due to reduced wheel loader use and personnel costs.
The R3 impact crusher has unique safety features including a safety key system, and is compact for easy transport. It is also available in a fully electric plug-in drive version with a capacity of up to 250 tph.
A vibrating feeder has a prescreen of 1,200 x 920 mm to optimize crushing results and minimize wear. An asymmetric opening facilitates longer material turning into the 770 x 960 mm inlet. A high inertia rotor with a diameter of 1,100 mm and width of 920 mm produces high-quality end products with low wear.
The crusher is equipped in a closed circuit with a recirculation conveyor and a two-deck precision screen measuring 3,100 x 1,400 mm. It produces a defined aggregate product size. The installed wind sifter eliminates contaminants like plastics, wood, or paper, and an overband magnet separates valuable materials. The total weight of the R3, with all options included, is approximately 33 tonnes.
The Keestrack-er UMTS/GPS telematics system provides real-time data and analytics and the exact location of the machine. All aspects can be checked from a distance and, if necessary, remote software updates can be made. Owners and dealers can take advantage of data from the system for planning maintenance. Diagnostic tests for all components, including the feeder, crusher, afterscreen, and conveyors, can be run through Keestrack-er.
TRANSPARENT BUCKETS AND OTHER TECHNOLOGIES ARE ENHANCING EMPLOYEE SAFETY AT RECYCLING FACILITIES
BY RYAN JOHNSONAwheel loader paired with a bucket carries materials at a recycling centre. A distracted employee walks in front of the machine. Thankfully, the operator is using a new technology to see through the attachment and stops before causing a serious injury.
Situations like this one – and other hazards associated with construction equipment at recycling centres – can pose significant risks to both equipment operators and workers in the area. Additional risks may include collisions, limited visibility, overturning and rollover, falling objects, and entanglements.
To help minimize or avoid these dangers at recycling centres, the industry is stepping up its efforts to promote safety. Safety at recycling facilities remains a top priority for company owners and operators as well as manufacturers. Equipment companies are taking steps to implement new technologies that make it safer for their operators to work, especially in areas where other machines or people are working.
Wheel loaders and attachments are staple products for the
recycling industry, according to Bill Zak, wheel loader product manager at DEVELON. They’re critical to the continued success of many recycling facilities today because of their versatility and productivity.
“Wheel loaders rack up countless hours every day at recycling centres across the country,” Zak says. “They’re often put in situations where they’re required to work more than 12 hours a day, performing repetitive tasks in busy environments. That’s why our product management team, using input from our customers, has made it a priority to enhance the safety of our equipment.”
Manufacturers like DEVELON are increasingly incorporating new technologies in their construction equipment. These advanced safety features, coupled with machine design changes, enhance your operators’ safety and those around them. One of the recent technologies is DEVELON’s Transparent Bucket, which helps minimize blind spots for wheel loader operators when the bucket is raised.
“Available as a standard feature for our -7 Series wheel loaders, the Transparent Bucket technology offers a supplemental view from a monitor inside the wheel loader cab,” Zak says. “Using two cameras and stitching together the video feeds, operators can ‘see through’ the bucket to the area in front of them.”
Rear-view cameras for wheel loaders are common in today’s recycling industry. Wheel loader operators can easily activate the rear-view camera and see what’s behind the machine before backing up. Manufacturers are expanding their offerings with features such as around-view monitor (AVM) camera systems.
“AVM camera systems can provide up to 270 degrees of enhanced visibility,” Zak says. “Our optional AVM camera system uses three cameras and several sensors mounted on the rear of our wheel loaders. When activated, the system significantly increases the operator’s visibility around the machine.”
Another feature of the AVM camera system is notifications or alerts from an object detection system.
“Ultrasonic proximity sensors installed on wheel loaders notify operators when an object is within a certain distance from the machine,” Zak says.
A flashing green caution box will appear if there’s an object 8 to 12 feet behind the wheel loader, notifying the operator. A yellow caution box will appear if the object is 4 to 8 feet away, and the system will emit a beeping sound to provide an audio alert to operators. A red triangle and red border notification are visible if the object is closer than 4 feet.
“When wheel loader operators combine an AVM camera system with our Transparent Bucket technology, it can give them nearly 360 degrees of visibility,” Zak says.
This technology complements updated wheel loader cab designs which feature increased glass area in the front windows and the side windows for enhanced operator visibility.
Additional safety features available for the recycling industry include a standard rollover protective system for the cab and
The Transparent Bucket from DEVELON helps minimize blind spots for wheel loader operators when the bucket is raised.A feature of the AVM camera system is notifications or alerts from an object detection system.
What operators see when using the Transparent Bucket.
an optional backup alarm system, rotating beacon, and smart load weighing system. The weighing system tells operators the weight of the material in the bucket and helps minimize overloading the attachment.
None of these technologies are intended to substitute for operator training. Before employees operate a wheel loader, it’s important that they have a good understanding of how the wheel loader works. Operators should familiarize themselves with the machine’s operation and maintenance manual and the basic operating procedures before getting in the machine.
Available as
a
standard feature for our -7 Series wheel loaders, the Transparent Bucket technology offers a supplemental view from a monitor inside the wheel loader cab. Using two cameras and stitching together the video feeds, operators can ‘see through’ the bucket to the area in front of them.Bill Zak Wheel Loader Product Manager, DEVELON
“We strongly recommend that all operators, particularly new ones, receive proper training before using wheel loaders,” Zak says. “In addition to the manual, there are in-person training opportunities with our dealers, providing detailed instructions for how to properly operate and maintain our machines. We encourage recycling facilities to routinely coach even seasoned operators on machine operation and safety features.”
At recycling facilities where operators regularly change attachments, Zak recommends that they have a clear understanding of how the attachment mounting system works. For example, when changing from a bucket to a grapple attachment, operators should know how to correctly engage the hydraulic connections and ensure that the hoses are routed correctly to minimize getting caught or snagged on the material.
From a practical standpoint, some recycling facilities equip their wheel loaders with fire extinguishers as a standard safety protocol. If your wheel loaders have fire extinguishers in them, be sure to check them regularly to make sure they are working properly. Also, be sure that your operators know how to use fire extinguishers to promptly address and contain fires if they occur.
Although not directly related to safety, manufacturers are adding new features to their wheel loaders to further increase operator productivity. For example, DEVELON offers its Smart Guidance System for -7 Series wheel loaders. The system analyzes operator driving habits and provides tips during operation on the Smart Touch display to improve efficiency. Operators are rated or scored on operational efficiency, fuel economy, and equipment durability. “The Smart Guidance System gives operators a report card, so to speak, on how they are using the machine,” says Bill Zak. “This real-time feedback can improve operator productivity and reduce the machine’s fuel consumption.”
The Association of Equipment Manufacturers (AEM) recently introduced a free online safety toolkit to promote safety awareness, education, and training for equipment users in a variety of industries, including recycling. According to AEM, the safety toolkit provides valuable reference materials, including articles, safety education action plans, and PDF resources for toolbox talks. AEM is also providing its new safety materials in a digital format. Visit the AEM website (www.aem.org) to find these helpful safety materials.
New wheel loader technologies are making it safer for operators and workers at recycling facilities. Contact your local dealer to learn more about these technologies and how they can benefit your company.
RYAN JOHNSON is a public relations and content strategy manager at Two Rivers Marketing in Des Moines, Iowa.
sion, multiple power modes, a Z-bar lift arm, return to dig, and limited slip differentials. The reinforced box frame is designed to endure harsh working environments while the improved cooling system features wider radiator fin spacing and a reversible fan to clear debris and reduce clogging. The Transparent Bucket option provides a supplemental visual perspective by allowing operators to “see through” the bucket from an in-cab display. Situation Awareness Technology saves fuel by automatically adjusting the engine output in real time to the needs of the drivetrain and hydraulics.
lenge. The L 550 XPower is equipped with a power-split travel drive, installed as standard on all Liebherr XPower wheel loaders. By increasing the engine power, the travel drive is more effective with consistently low fuel consumption, such as when accelerating or penetrating into materials. Liebherr offers four lift arm versions in the form of Z-bar kinematics and industrial kinematics both in standard and high-lift configurations, providing strength in the lower lifting range and higher breakout forces. 4
increased productivity. Compared to previous models in the series, the Cat 950 provides up to 30 percent lower maintenance costs. This reduction is achieved through features like remote troubleshooting and flash capability, which save time and money. Integrated Cat technologies, such as Cat Payload with Assist and onboard job aids, make machine operation more straightforward, contributing to a more efficient job site. The new Autodig with Auto Set Tires automates loading, ensuring consistent high fill factors and reduced tire wear, which together contribute to up to 10 percent more productivity.
stability during loading and carrying and allows easy filling of the buckets. A full line of dedicated attachments and machine configurations are designed specifically for waste handling, ensuring efficient and productive operation. The engine automatically regenerates while working, eliminating the need to stop and park up. Operator Coaching helps to ensure operators are using the machine to its full potential by providing real-time guidance, helping them understand how their actions influence machine efficiency, as well as identifying areas for improvement or changes in their technique.
It’s a hot day inside a transfer station where various machines are moving recycling and waste materials into their proper places for processing. A wheel loader pushes into a pile to fill its bucket. In the engine compartment, bunched piles of paper and plastic that have gathered unnoticed near hot components start to smolder, then burst into flames.
This scenario might go a couple of different ways. One: The fire intensifies, starts burning more materials, and before the operator realizes it there’s a serious – and potentially life-threatening – problem right behind them. It’s too big to use a hand extinguisher, if there’s one available. The operator abandons the machine and calls for help. They are safe, but the loader continues to burn and so does the waste pile it is next to. Within minutes the fire has spread, and the entire building is now in danger.
Or, two: The flame is detected by an automated system. The fire melts a detection wire or is picked up by a heat sensor, and tanks filled with fire suppressant spray into the affected area. The fire is knocked down, giving the operator more time to get clear. Damage to the machine and the job site is minimized.
On-board fire suppression systems are a regular sight on large mining equipment, popular on forestry machines, and are becoming more commonly required in waste and recycling. With equipment running at higher temperatures and working in hotter climates, automated fire suppression provides a level of insurance that protects against injury and damage.
AFEX Fire Suppression Systems has more than 50 years of experience manufacturing automated fire suppression systems designed specifically for heavy equipment. It has partnered with FLO Components, a Canadian supplier of auto-lubrication systems for heavy equipment, to supply automated fire suppression in Ontario and Manitoba.
The detection wire melts at 356 degrees F, and once that melts the controller alerts the operator that the system has been activated. If the operator sees flames before that, they can hit the manual button, or if a machine is parked and someone sees a fire, they can trigger the system from outside.
Mike Deckert Vice President, FLO ComponentsFor FLO Vice President Mike Deckert, a veteran of four decades of dealing with heavy equipment, automated fire suppression is a lot like buying insurance – it protects lives and property if the need arises.
“They want to protect their employees and the surrounding area – a mine, a forest, a garbage dump, a recycling centre,” Deckert says. “For customers in construction and recycling, automated fire suppression is increasing.”
Deckert says there have been incidents in which waste and recycling facilities have been damaged after equipment catches fire within them. It may not be an everyday occurrence, but the possibility is always there.
Equipment fires tend to be caused by several factors. Tier 4 diesel engines feature turbochargers that run hotter than previous engine types, and the associated aftertreatment systems emit more heat than before, Deckert explains.
Machines working in sectors like recycling, where a lot of debris can collect unnoticed in various spots, are at higher risk of fires.
“I was on site at a dealer location where they had a loader compactor that needed work on the rear axle. They pulled the rims off and had to clean all the material that was packed in there from the landfill – they actually filled up a dumpster and a half,” Deckert says.
C&D waste may include materials that are flammable or capable of throwing sparks. Even something as small as a frayed wire in the engine compartment can, in the right conditions, start a blaze.
Those factors become part of a fire risk assessment for fleet owners who are considering automated fire suppression. The assessment ensures that any unique challenges an operation might face – ignition sources, types of fuel, and insurance or regulation requirements – are addressed and the correct fire protection system is designed. From there, it is very similar to the process for installing the auto-lubrication systems FLO provides, Deckert notes.
“We look at the specific machine so that we obtain information about the proper size of tanks, the number of nozzles, and installation routing,” he adds.
FLO Components’ teams handle individual design of the system, which includes a controller in the cab, tanks for the required fire suppression agent, piping, wires or sensors for detecting a fire, and the nozzles covering areas where potential fires may occur – turbochargers, transmissions, and batteries being the most common sites.
When a fire breaks out, an auto-detection wire in the area melts, or a temperature sensor activates, triggering the system. Nitrogen bottles release into the tank and shoot dry or liquid chemicals through a distribution network for quick knockdown of the fire.
There are also manual releases for when the operator or another worker spots a fire before the automated system is triggered. Up to three manual buttons are installed on machines, with one in the cab and others at ground level along the path of egress.
“The detection wire melts at 356 degrees F, and once that melts the controller alerts the operator that the system has been activated,” Deckert says. “If the operator sees flames before that, they can hit the manual button, or if a machine is parked and someone sees a fire, they can trigger the system from outside.”
Most fires on heavy equipment can’t be handled by handheld fire extinguishers and need a bigger response, Deckert adds. AFEX systems installed by FLO Components technicians offer three different types of chemical response to suppress the fire and give time for operators to get clear and emergency crews to react if needed.
“Dry chemical is like a fog for fast knockdown of flames and suppressing the fire. It covers Class A [ordinary combustibles], B [burning liquids], and C [electrical] type fires. The liquid type removes the heat so it eliminates the chance of flare-ups afterward – it cools the hot surfaces. It handles A and B class fires, but not C,” Deckert says. “The dual agent provides a dry and liquid system together.”
Fire safety can’t be trivialized, even if equipment fires aren’t an everyday occurrence. When a fire does happen, it threatens lives, equipment, surrounding materials, and the greater environment. Automated fire suppression systems provide fleet owners with added peace of mind knowing that their equipment and people have an extra level of protection if the unexpected occurs. RPN
The Battery and Critical Metals Recycling Conference explores the topics and ideas surrounding the battery and critical metals recovery and recycling industries. The 2024 show features plenty of educational sessions to provide key insights, strategies, and concepts. The event prioritizes its speaker lineup and available networking opportunities. batteryrecyclingconference.com
The Plastics Recycling Show Europe is a two-day event showcasing developments and current trends in the industry. The event will feature over 450 exhibitors and attendees from over 80 countries. Visitors can expect numerous opportunities to learn from industry veterans, network with other visitors, and see the latest equipment. prseventeurope.com
Visitors to the International Automotive Recycling Congress 2024 can expect to actively participate in debates while networking with decision makers from various industries. The event hosts five keynote speakers and 26 additional speakers to lead discussions. The significant transformation of the automotive recycling industry will be a key topic. events.icm.ch/event/e4909c12-3f60-4d16-a470-08db11965647
RECYCLING CONFERENCE & EXPO 2024
FRANKFURT, GERMANY | JUNE 26 – 27
METALRECYCLING-EXPO.COM
E-WASTE WORLD CONFERENCE & EXPO 2024
FRANKFURT, GERMANY | JUNE 26 – 27
EWASTE-EXPO.COM
No matter how challenging your needs, BKT is with you offering a wide range of OTR tires specifically designed for the toughest operating conditions: from mining to construction sites.
Sturdy and resistant, reliable and safe, able to combine comfort and high performance. BKT is with you, even when work gets tough.
21st Century Programming
Accent Wire Tie
BKT Tires ...............................................................................
Cardinal Scale Manufacturing Co.
CARI-ACIR .......................................................................................
CP Group
CWRE 2024 ....................................................................................
Eggersmann North America GmbH
Fagus–GreCon US ....................................................................
Gensco Equipment Co. Ltd.
Harris Inc. .......................................................................................
Herbold USA
Hillhead ............................................................................................
Industrial Netting
LEFORT America
Machinex Industries Inc.
MB S.p.A. (MB Crusher)
SORTING TECHNOLOGIES EXPERT
The MACH Hyspec® s o r t i ng solu t ion extracting organic valuables from Municipal Solid Waste