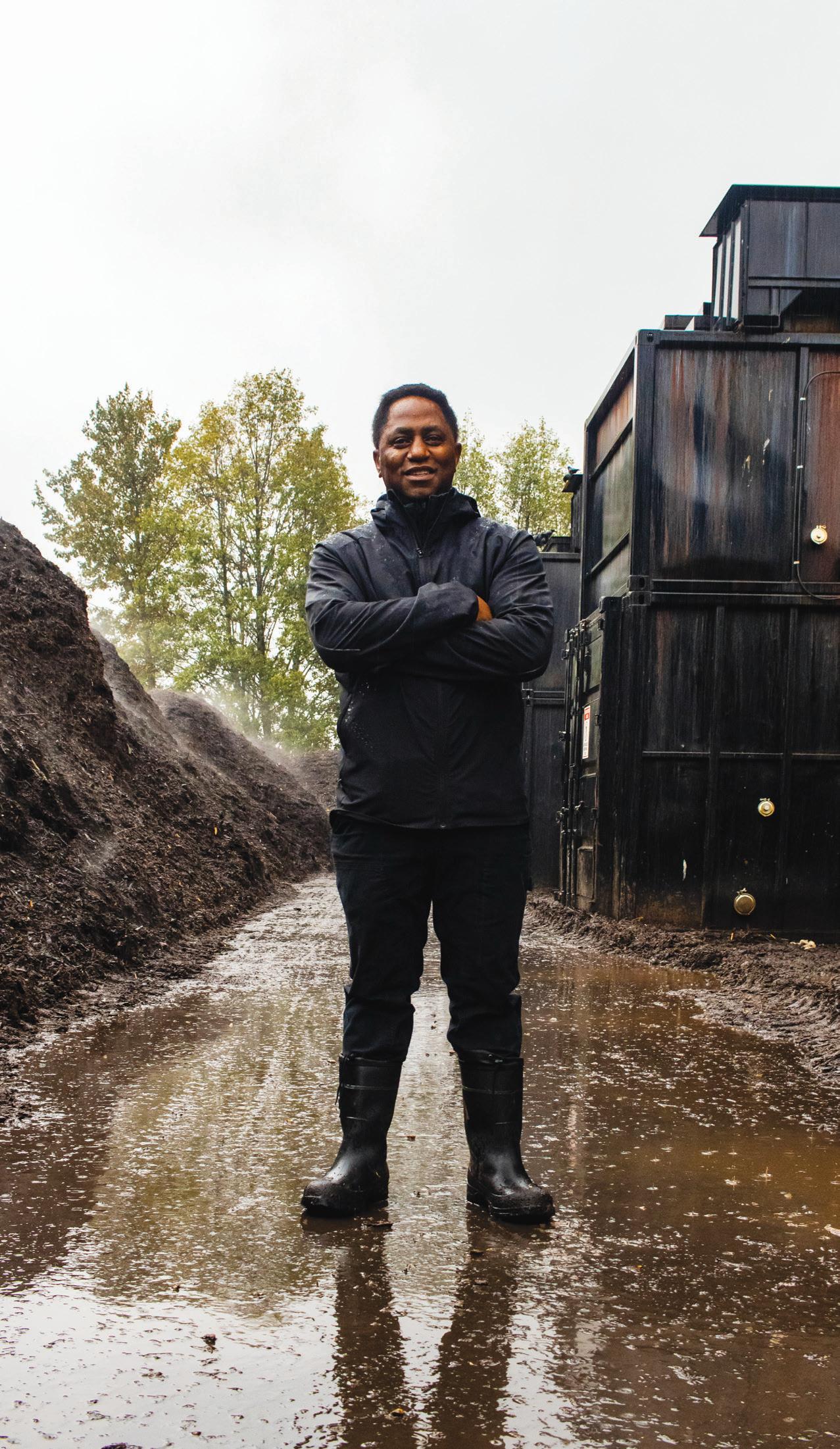
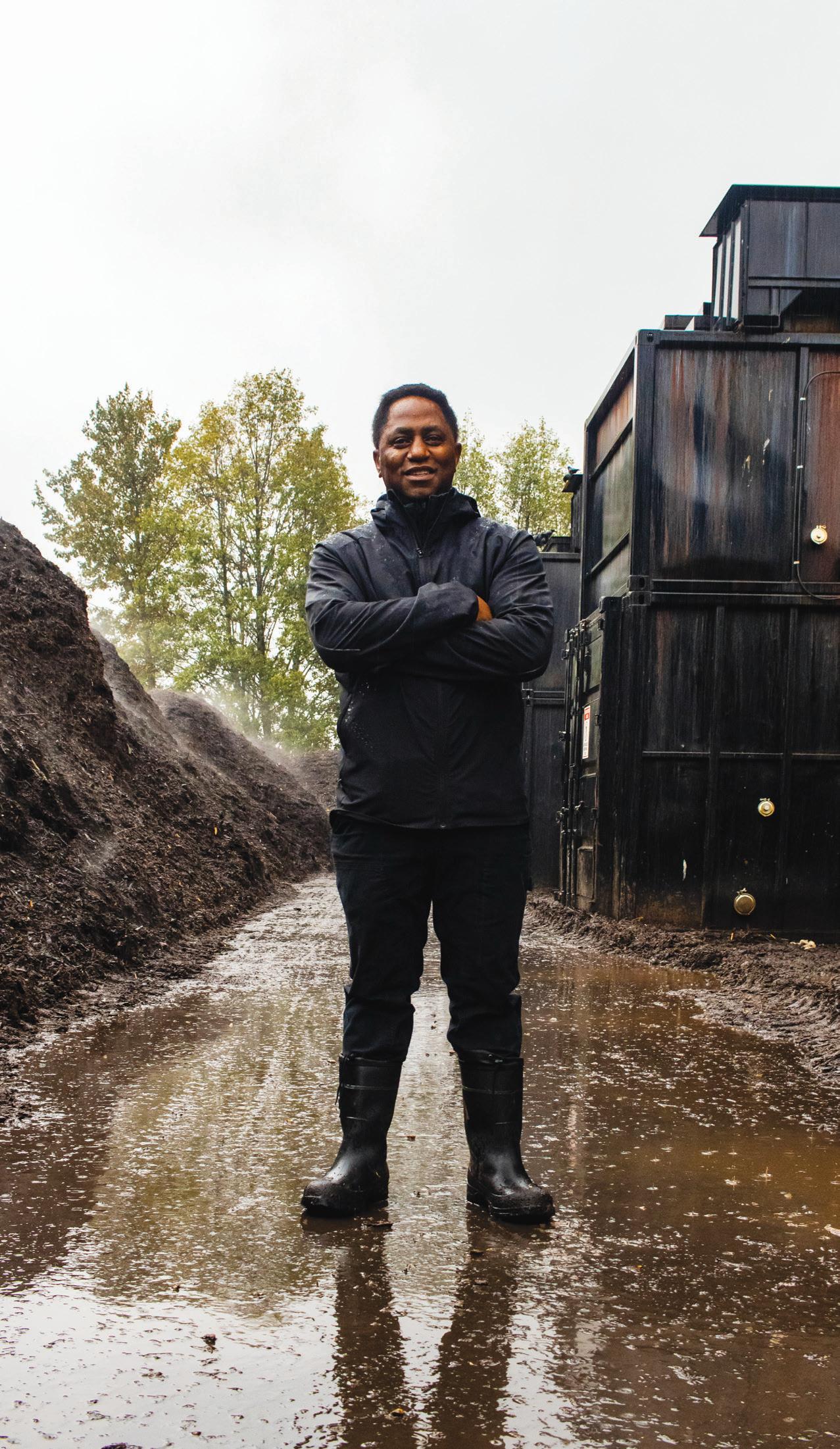
MERRY XMAS!
We are looking back on a year that has been both eventful and gratifying. LINDEMANN has officially become a separate and independent company again since June – more modern, more digital, and with a clear focus on the values of quality, performance and innovation. We would like to extend our sincere thanks for your trust during these turbulent times and are proud to be able to walk the new and exciting path alongside you.
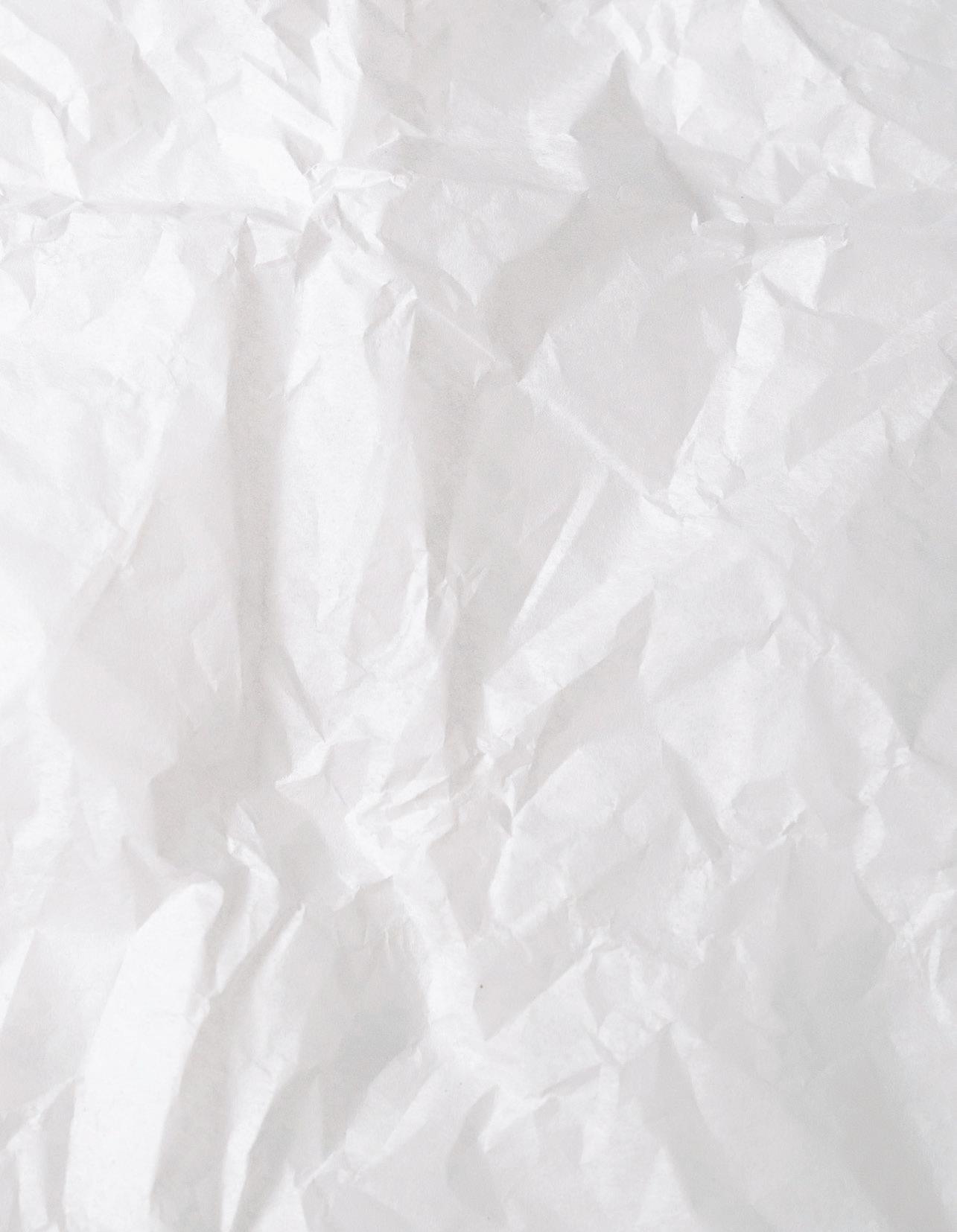
May you enjoy the festive season and have a good start into the new year!
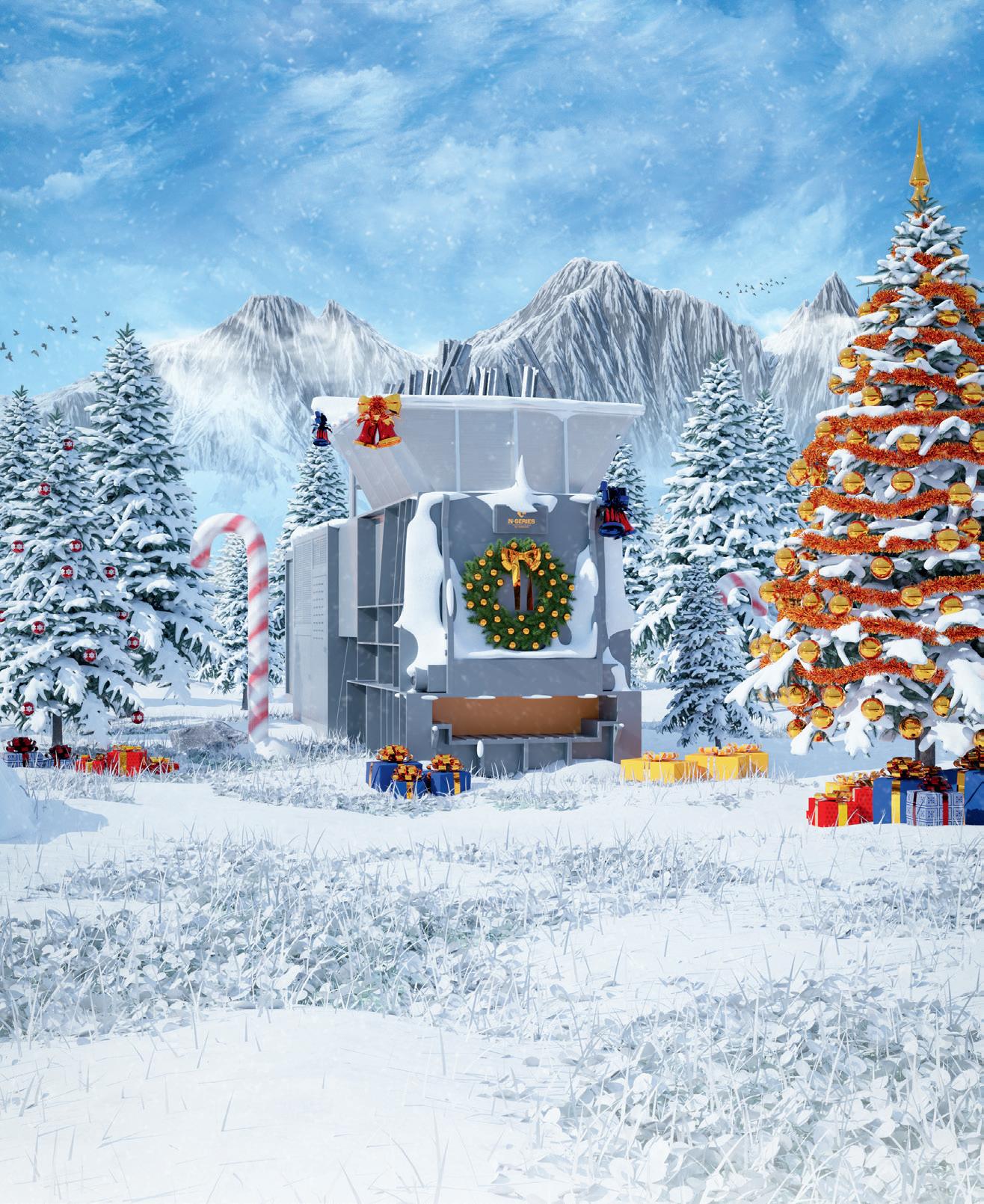
With the lowest minimum quantity requirement in industry for ceramic, foil, DPF and aftermarket converters, we assist scrap metal recyclers, automotive recyclers, and core buyers in getting the best potential value for all material types.

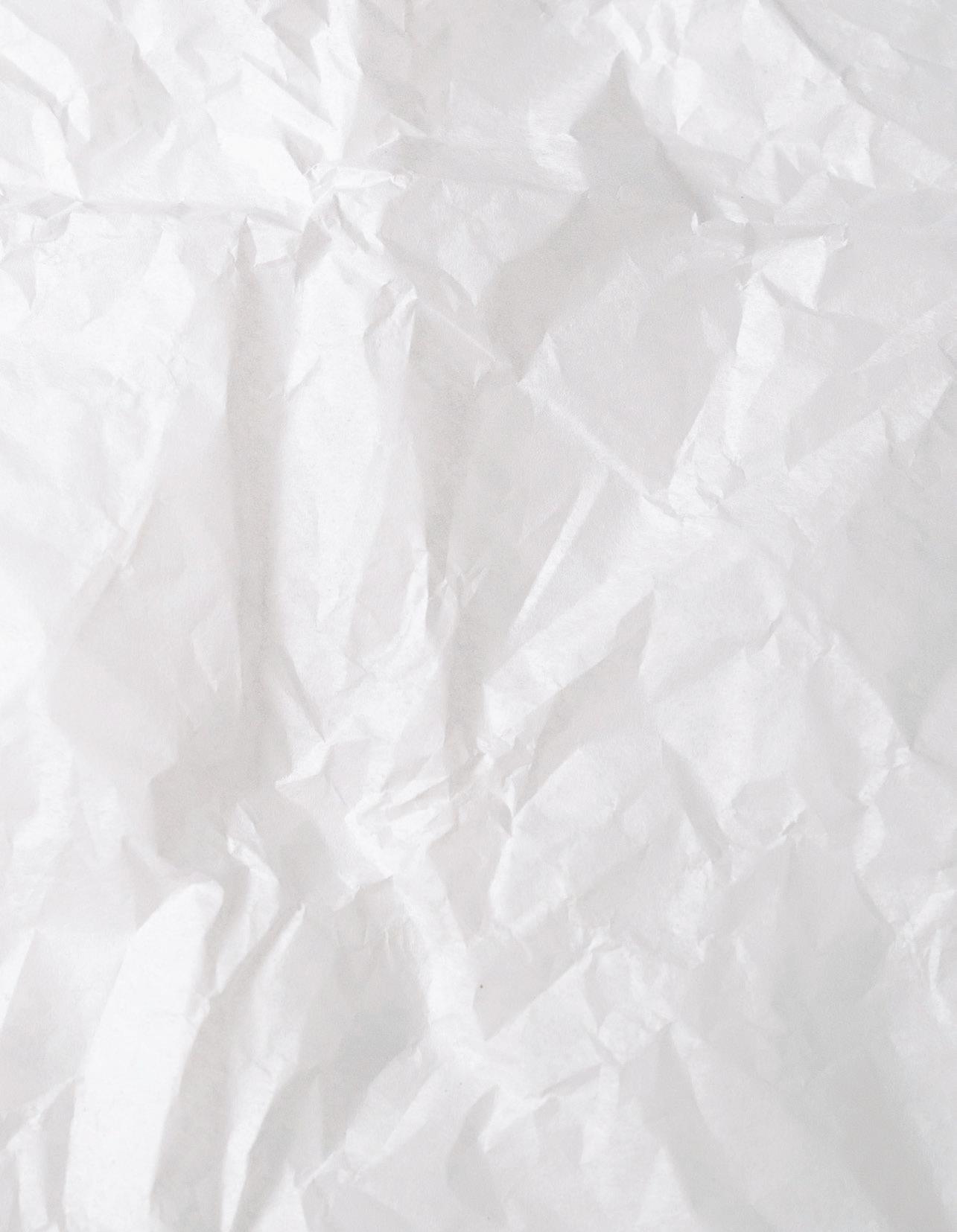
PMR’s state of the art PGM laboratory provides suppliers with the most accurate and precise precious metal returns 6x faster than competitors, allowing businesses to react quickly to market changes with detailed and transparent results; diminishing the risks associated with a naturally volatile market.

Through multiple and exclusive data insight tools, such as an online database that assigns converter count and value to vehicle VIN number, PMR helps businesses be more aggressive in obtaining market share while elevating their competitive edge.
PMR focusses on providing attentive and consultative support to each recycler looking to not only maintain but gain in the years to come.
Working with PMR means working with a company that adapts to your needs.
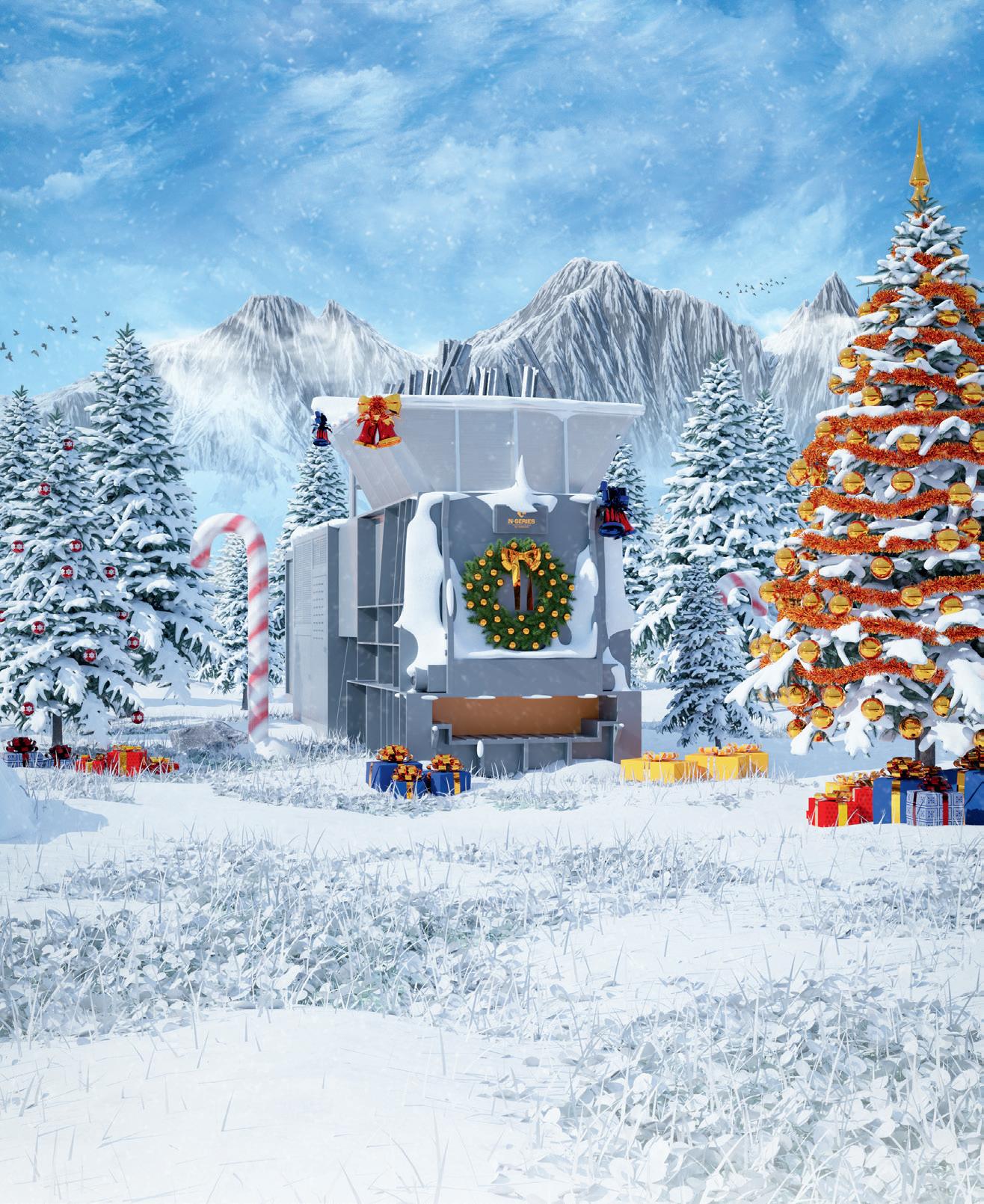
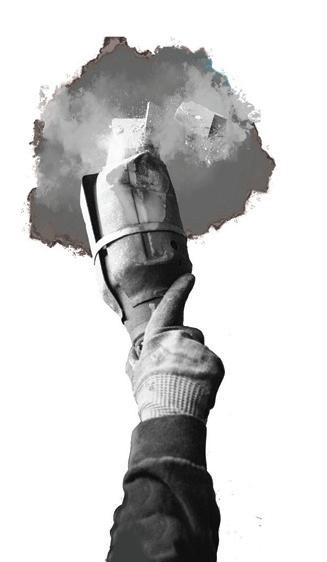
PMR is an industry leading expert in the recovery of Platinum, Palladium and Rhodium from scrap catalytic converters.
The ARMOR® Digital Truck Scale is not like other truck scales. It is an advanced digital system that is top-to-bottom different (and superior) to your grandfather’s truck scale.
From the manufacturer of the very first all-steel truck scale comes the all-new, state-of-the art ARMOR® digital truck scale with SmartCell® load cells.
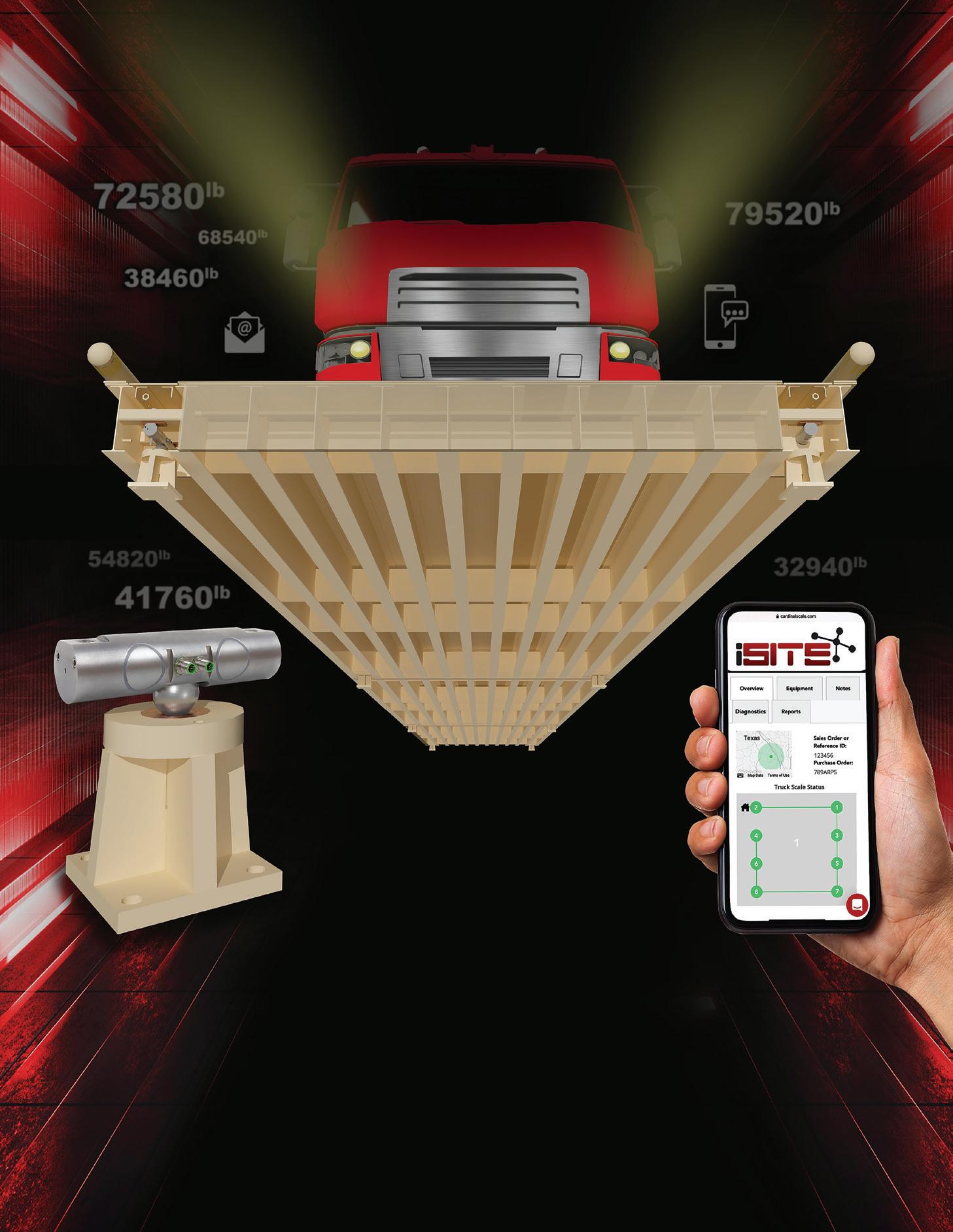
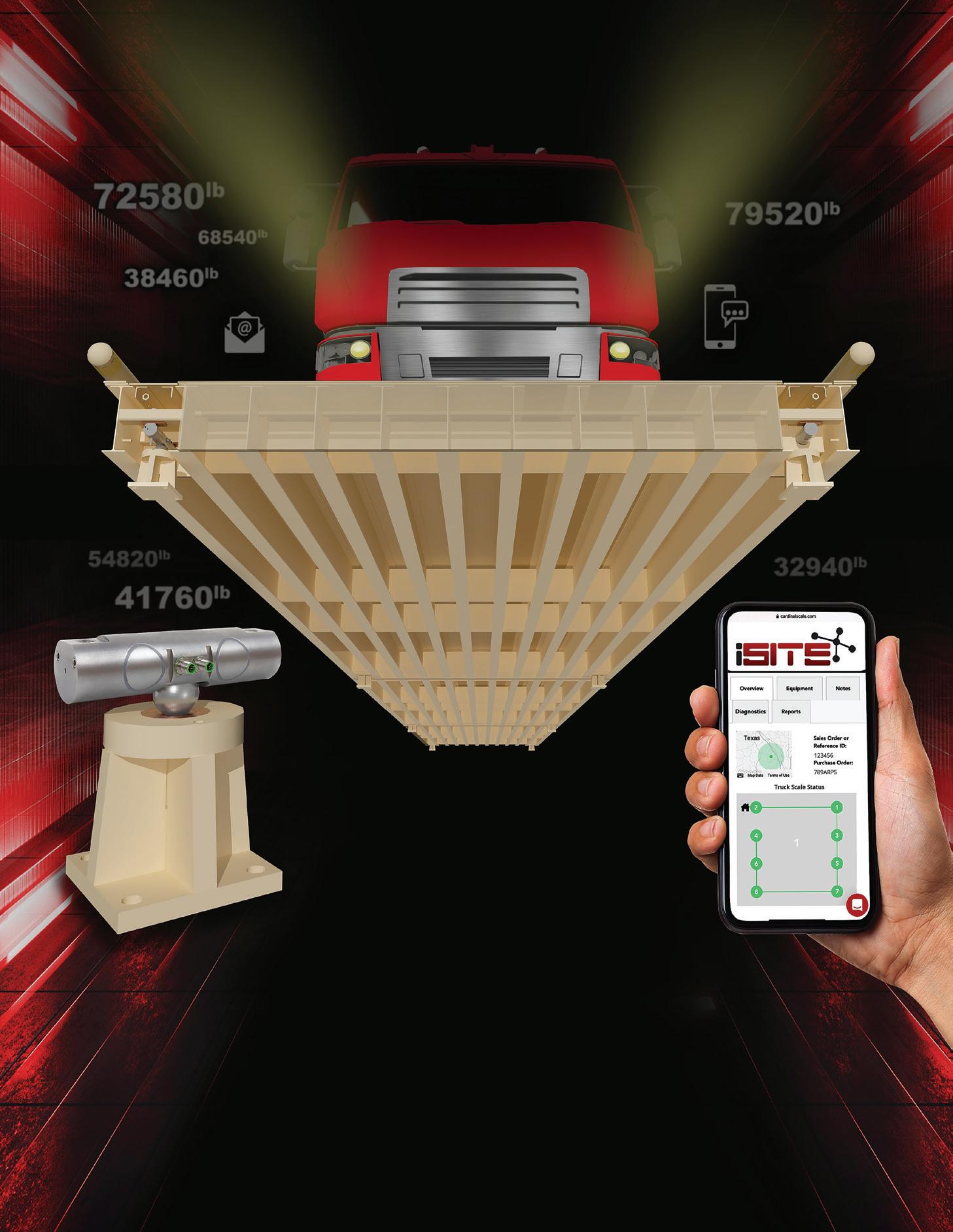

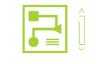


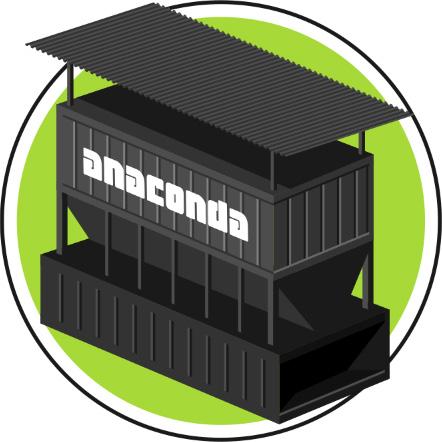

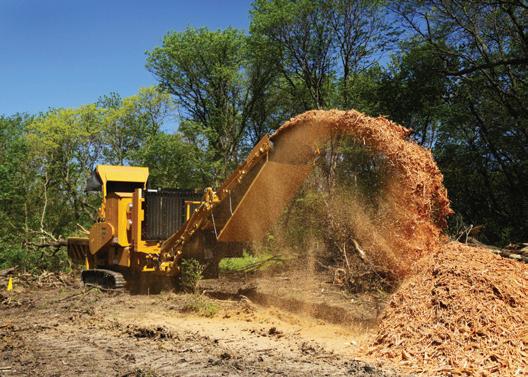
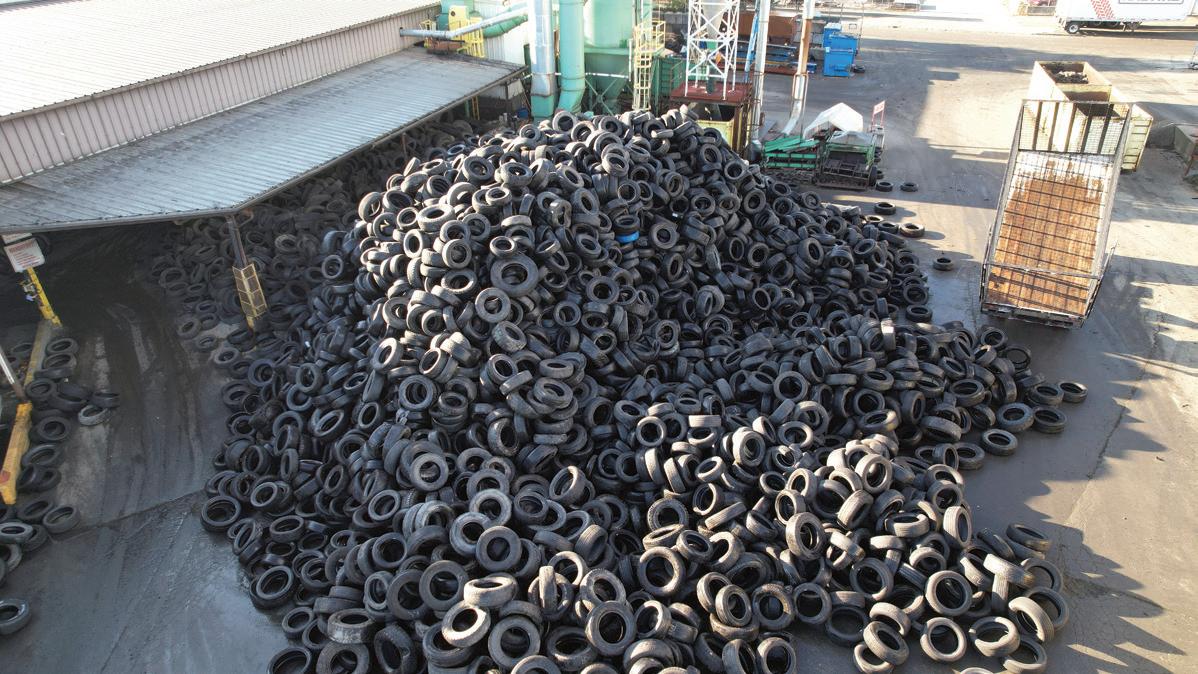
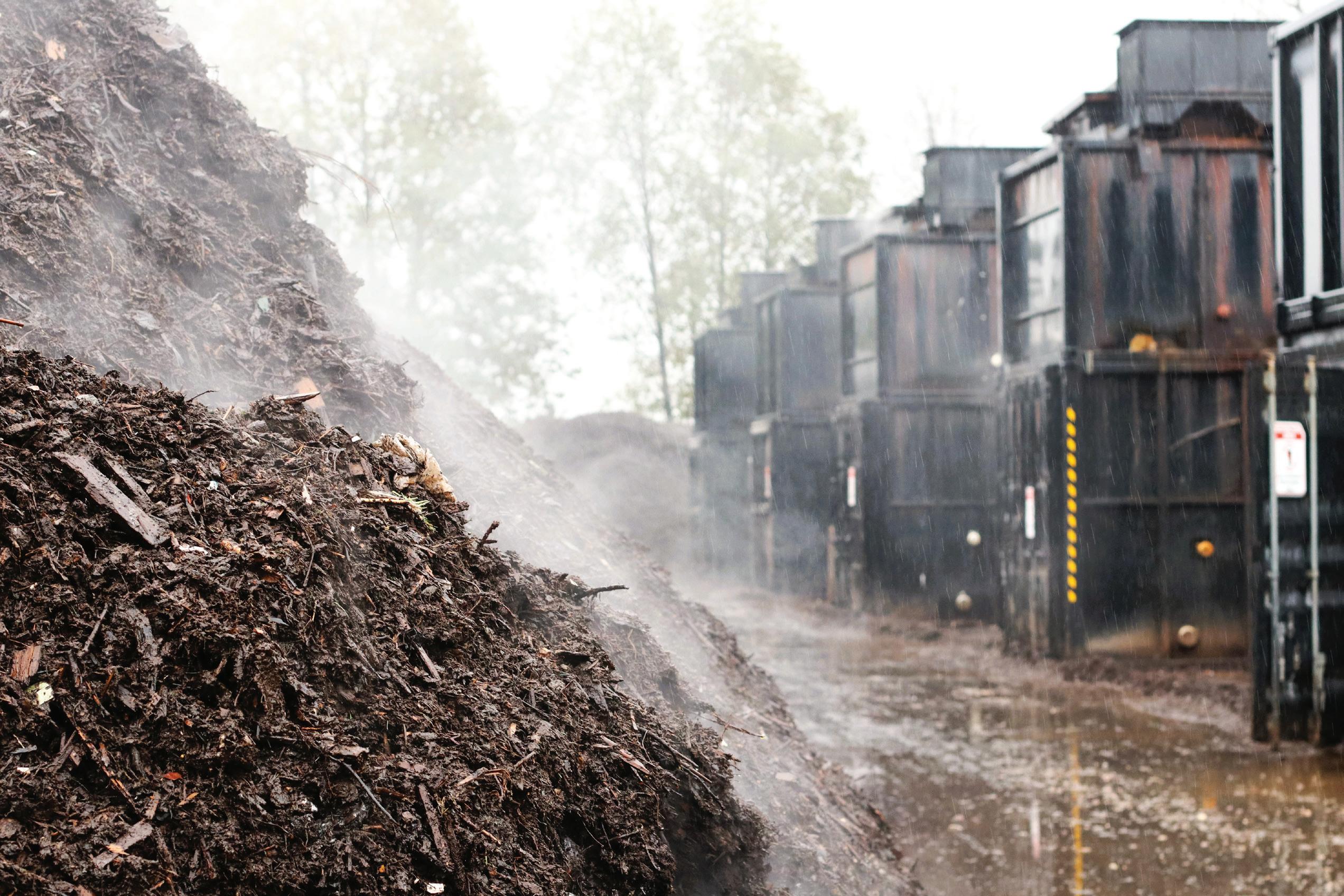
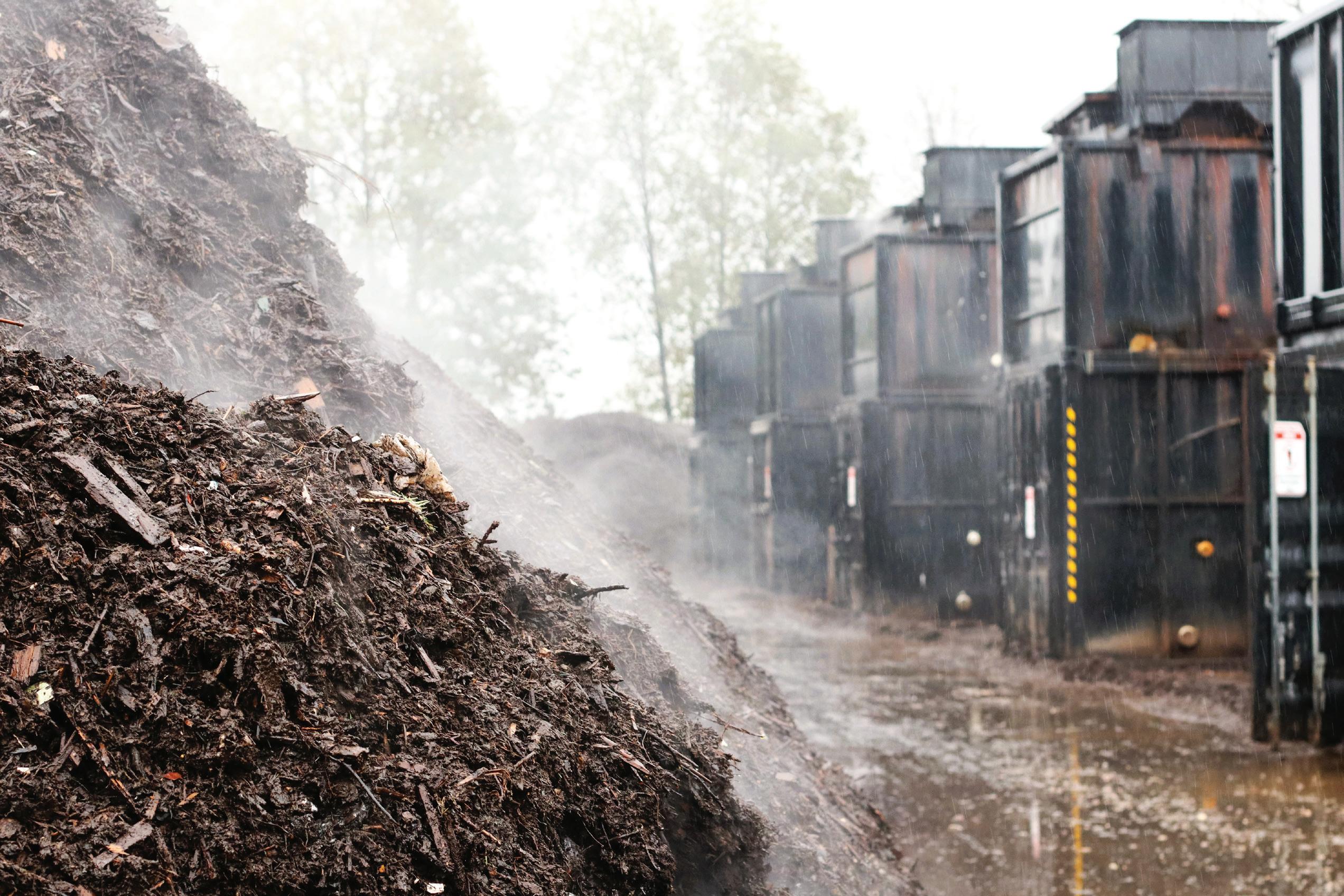
Anaconda Systems addresses the factors that have historically prevented organics facilities from existing within city limits, allowing processing to happen closer to home and cut down on commutes and costs for haulers.
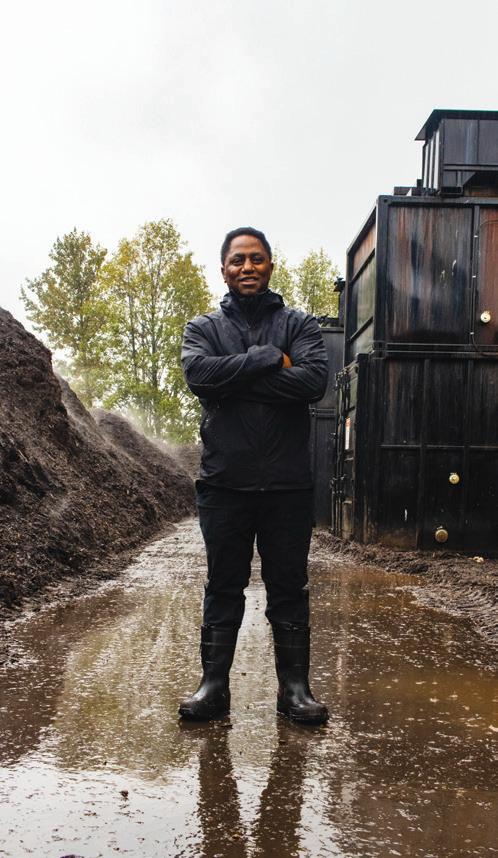
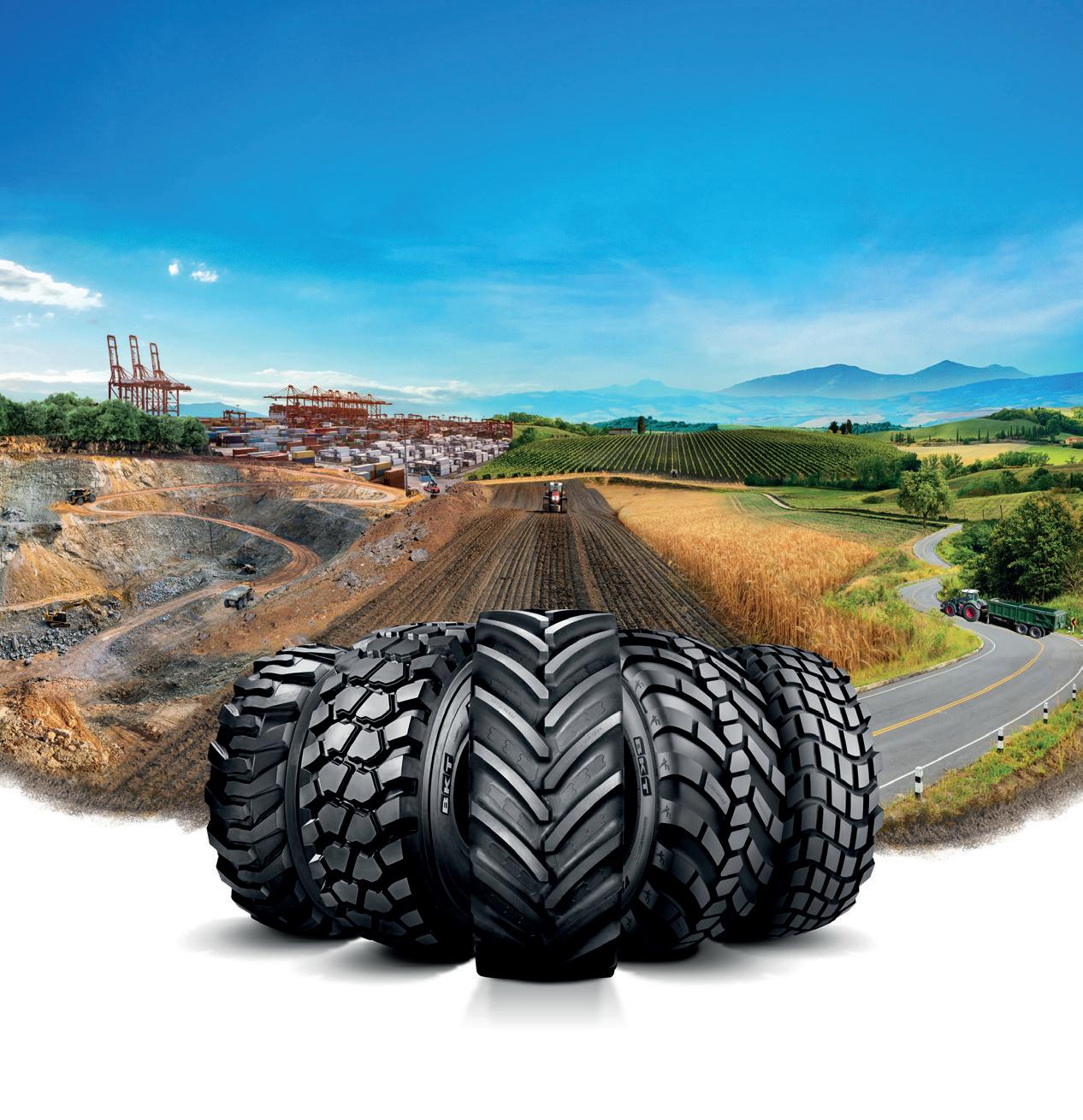
See more on page 20.
WE’D LIKE TO HEAR FROM YOU
Do you have a story, equipment, or technology innovation, commentary, or news that our readers in the recycling industry should know about? Drop us a line any time.


Contact: Editor Slone Fox at sfox@baumpub.com or 604-291-9900 ext. 335
NOVEMBER/DECEMBER
EDITOR IN CHIEF Kaitlyn Till ktill@baumpub.com 604-291-9900 ext. 330
EDITORIAL DIRECTOR
Arturo Santiago asantiago@baumpub.com 604-291-9900 ext. 310
EDITOR Slone Fox sfox@baumpub.com 604-291-9900 ext. 335
ASSOCIATE PUBLISHER/ VICE PRESIDENT OF SALES Sam Esmaili sam@baumpub.com 604-291-9900 ext. 110

ADVERTISING PRODUCTION MANAGER
Tina Anderson production@baumpub.com 604-291-9900 ext. 222
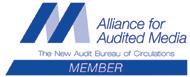
DESIGN & PRODUCTION
Morena Zanotto morena@baumpub.com 604-291-9900 ext. 325
PRESIDENT/PUBLISHER Ken Singer ksinger@baumpub.com 604-291-9900 ext. 226
VICE PRESIDENT/CONTROLLER
Melvin Date Chong mdatechong@baumpub.com
FOUNDER Engelbert J. Baum
Published by: Baum Publications Ltd.
124 - 2323 Boundary Road Vancouver, BC, Canada V5M 4V8
Tel: 604-291-9900 Toll-free: 1-888-286-3630 Fax: 604-291-1906 www.baumpub.com www.recyclingproductnews.com @RecyclingPN
FOR ALL CIRCULATION INQUIRIES
Toll-free: 1-866-764-0227 email: rpn@mysubscription.ca
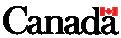
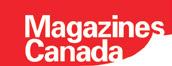
Subscription: To subscribe, renew your subscription, or change your address or other information, go to: https://www.recyclingproductnews.com/ mysubscription/subscribe
Recycling Product News is published eight times yearly: January/February, March, April, May/June, July/August, September, October, November/ December. Advertising closes at the beginning of the issue month.
One year subscription rates for others: Canada $33.50 + 1.68 GST = $35.18; U.S.A. $40; other countries $63.50. Single copies $6.00 + 0.30 GST = $6.30; outside Canada $7.00. All prices are in Canadian funds.
Recycling Product News accepts no responsibility or liability for reported claims made by manufacturers and/or distributors for products or services; the views and opinions expressed are those of the authors and not necessarily those of Baum Publications Ltd.

We acknowledge the financial support of the Government of Canada.
Copyright 2022 Baum Publications Ltd. No portion of this publication may be reproduced without permission of the publishers.
Printed in Canada on FSC®-certified paper by Mitchell Press Ltd. ISSN 1715-7013. PUBLICATIONS MAIL AGREEMENT NO. 40069270.
Return undeliverable Canadian addresses to: Circulation Dept., 124-2323 Boundary Road, Vancouver, BC V5M 4V8 email: rpn@mysubscription.ca Toll-free: 1-866-764-0227
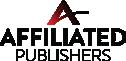
A LONG WAY TOGETHER
WHEREVER YOU ARE, BKT IS WITH YOU
No matter how challenging your needs, BKT is with you offering an extensive product portfolio for every field such as agriculture, OTR and industrial applications.
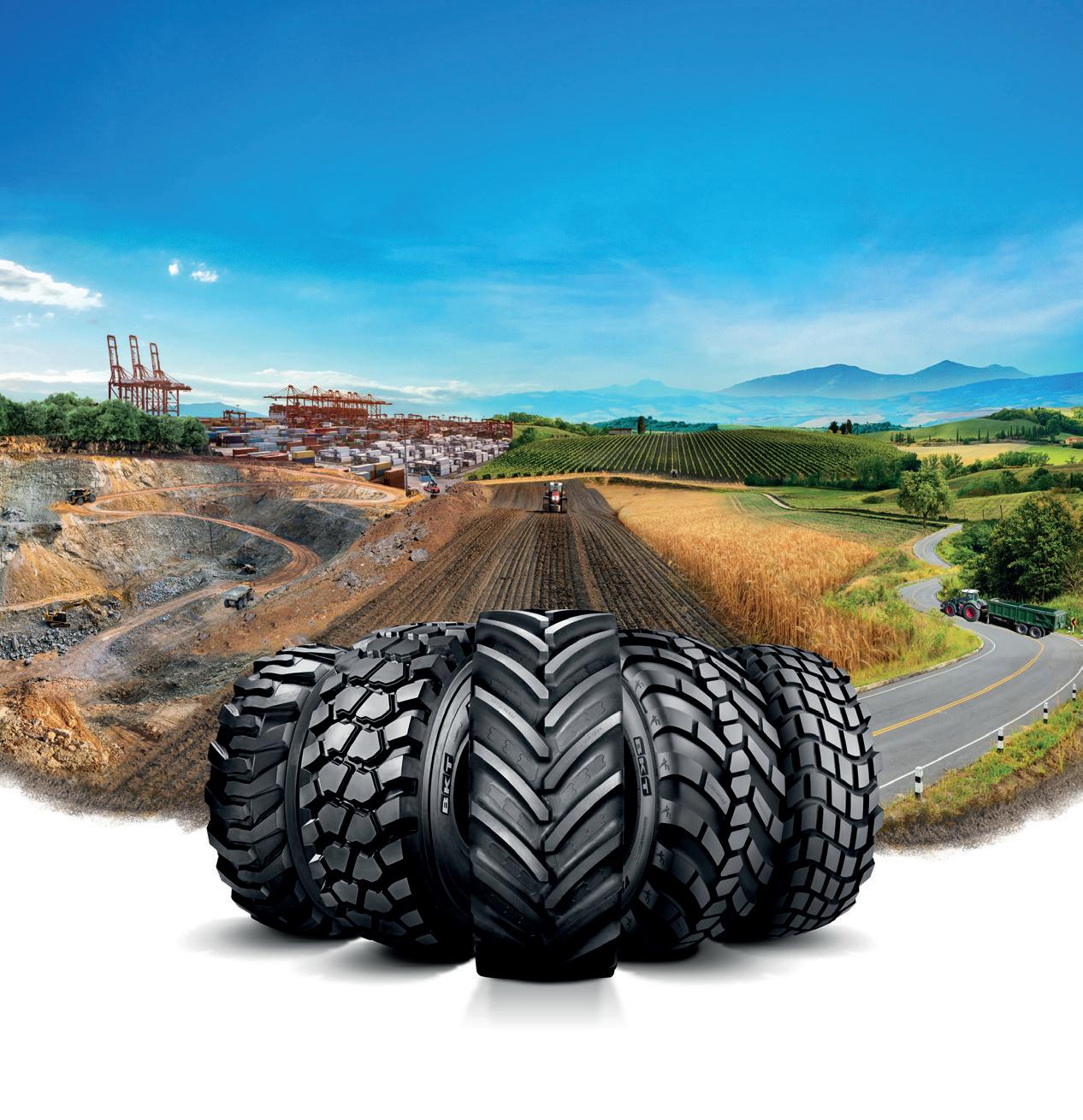
BKT provides concrete, reliable and high-quality solutions to your requests and working needs.
Wherever you are, BKT is with you.
This year was undoubtedly one of innovation and change. After countless postponements and cancellations, there was a tangible excitement and renewed enthusiasm at trade shows this year as the industry was brought together again for the first time in a long while. I was lucky enough to attend many of these events, where I finally got the chance to meet members of the industry face-to-face and get an up-close look at some of this year’s most innovative technologies.
One of the most prevalent themes from this year was un doubtedly the ongoing shift toward electrification and alter native fuels. It’s a topic that we covered in one way or another in almost every issue, whether it was taking an in-depth look at the facilities that produce alternative fuels (like 2Point0’s carbon negative waste-to-energy facility from our July/August cover story), or the companies and jurisdictions that leverage these technologies to create more sustainable operations (such as Emterra Group’s regenerative take on waste management as featured on the cover of our October issue).
The implementation of zero-emission equipment and the adoption of alternative fuels will undoubtedly continue to accelerate in 2023 as we creep closer toward the deadlines laid out by the Paris Agreement – reducing emissions by 45 percent by 2030, and reaching net zero by 2050.
Regional legislation and policy changes aimed at creating a more sustainable waste and recycling industry were also plentiful in 2022. One of the most notable was California’s new organic waste mandates which require jurisdictions to reduce the amount of green waste sent to landfills by 75 percent of 2014 levels by 2025. In New Jersey, it was announced that there will be minimum recycled content requirements for certain plastic, glass, and paper packaging by 2024.
Here in Canada, it was announced that Ontario’s Blue Box recycling program will be overhauled into a fully producer-led model starting in 2023. According to the new plan, a common collection system will be run by a single entity for the entire province, replacing the current system which leaves municipal ities in charge of setting up their own collection systems.
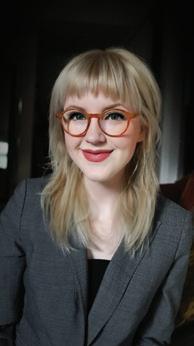
With so much change that has occurred this year and so much more on the horizon, I’m excited to see how the recycling
industry will continue to adapt to new sustainability goals and changing policies through innovative technologies, smarter equipment, and increased collaboration. As my first year as editor of Recycling Product News comes to a close, I also want to extend a whole-hearted thank you to an industry that has shown me an exceptional welcome over the last few months. On behalf of the entire Recycling Product News team, I look for ward to continuing to bring you vital news and in-depth articles in 2023!
With so much change that has occurred this year and so much more on the horizon, I’m excited to see how the recycling industry will continue to adapt to new sustainability goals and changing policies through innovative technologies, smarter equipment, and increased collaboration.
The new model 4 E-Z log Baler is just what mid size scrap yards have been asking for! Priced right for any yard — small, mid size, or large!
Like the Model 3, the NEW Model 4 has no set up time and a very low cost to operate. The one man operations are all handled from the newly designed cab. With the 400º rotation crane and a reach of 27’ adding the continuous rotation grapple, it makes loading the larger chamber a breeze.
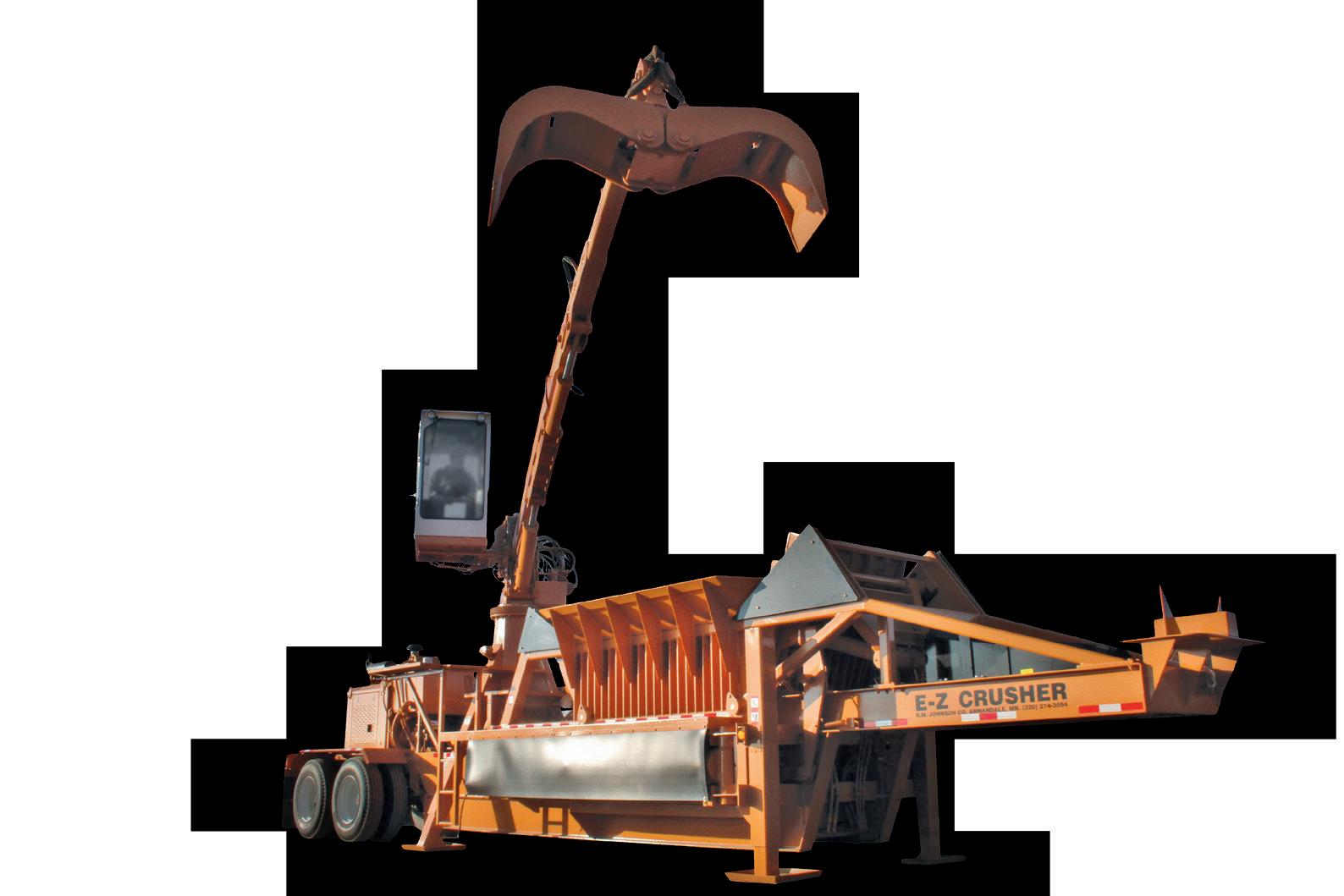
Taking your loose scrap to a highly sought after shreddable log.
— Cycles in under 2 minutes!
— Produces up to 70 tons per day.
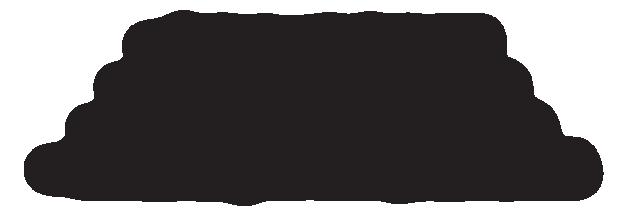

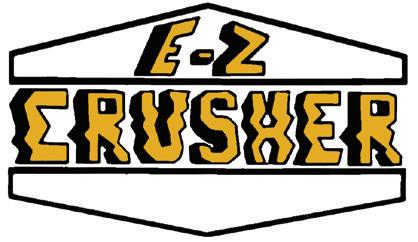
— Fully portable in the closed position.
— New seat design for more operator comfort.
EVERESTLABS RAISES $16.1 MILLION TO FURTHER AI-ENABLED OPERATING SYSTEMS
EverestLabs has raised $16.1 million in Series A funding led by Translink Capital and joined by NEC Orches trating Future Fund and existing investors BGV, Sierra Ventures, Morado Ventures, and Xplorer Capital. The funding enables the company to invest in its scaling and go-to-market capabilities, including further commercialization activities that build on its AI-powered RecycleOS operating system, robotics, and end-of-arm tools.
“The materials recovery facility industry represents a major market with a $9 billion opportunity in the U.S. alone, yet MRFs are losing billions in missed revenue from recyclables that end up in landfills or that could have been sold in bales to man ufacturers,” says Kaz Kikuchi, principal of Translink Capital. “EverestLabs’ AI-enabled RecycleOS solution has proven that it is uniquely positioned to solve this challenge, significantly improving MRFs’ operational efficiency and cost savings, and alleviating labour shortage issues – all of which are critical as the recycling industry continues to evolve and play a key role in the future of global sustainability and the circular economy.”
Recent socioeconomic issues are further driving investments in AI and robotics to enable better material recovery within MRFs, including international policies such as China’s National Sword policy that mandates minimal contamination in recycla bles, changing U.S. national and state policies, high turnover in sorting jobs amplified by COVID-related issues, and commit ments to minimum recycled content goals.
EverestLabs’ value proposition has been validated by public companies, private companies, and local cities in the U.S., including one of North America’s largest MRFs, Sims Municipal Recycling Sunset Park in Brooklyn, New York.
“EverestLabs’ mission to improve performance in our indus try is welcome, and we are excited to see what the company will achieve,” says Tom Outerbridge, president of Sims Municipal Recycling. “Since installing four EverestLabs robotic cells in our commingled recycling facility in spring 2022, we’ve seen cost savings and improved materials recovery within a short period. We look forward to continuing work with EverestLabs to expand our investments in the coming months.”

GLOBAL COMMITMENT TO SUSTAINABLE PACKAGING IS FAILING TO MEET TARGET
The commitment made by many of the world’s largest consumer brands to use only reusable, recyclable, or compostable plastic packaging by 2025 will likely not be met, according to the latest New Plastics Economy Global Com mitment progress report. The report was issued by the Ellen MacArthur Foundation, which in collaboration with the UN Environment Programme, united more than 500 organizations including brands, retailers, and major packaging manufactur ers to reduce plastic waste.
Measurable progress is being made toward reaching the glob al commitment, but the use of flexible packaging and a lack of investment in collection and recycling infrastructure means the 100 percent reusable, recyclable, or compostable plastic packag ing by 2025 target is becoming unattainable for most businesses.
Four years after launching the New Plastics Economy Global Commitment, the 2022 annual report shows progress varies across the signatory group.
Brands and retailers must continue to exponentially increase their use of recycled content if they are to hit the aggregate target of 26 percent by 2025. Whilst some businesses appear on course to exceed their goal, others will need to significantly accelerate their use to achieve theirs.
Since 2018, more than half – 59 percent – of brands and retailers have reduced their use of virgin plastics. However, in 2021 increases by some of the biggest users of plastic packaging resulted in an overall rise of 2.5 percent, reversing the reduc tions seen in 2019 and 2020.
In 2021, the first few global brands announced quantitative targets to increase the adoption of reusable packaging. How ever, 42 percent of signatories have yet to introduce any reuse models into their packaging strategies.
Many businesses have been investing in ways to achieve 100 percent technical recyclability for rigid plastic packaging, but the benefit of this investment is being stifled by inadequate collection and sorting infrastructure around the world.
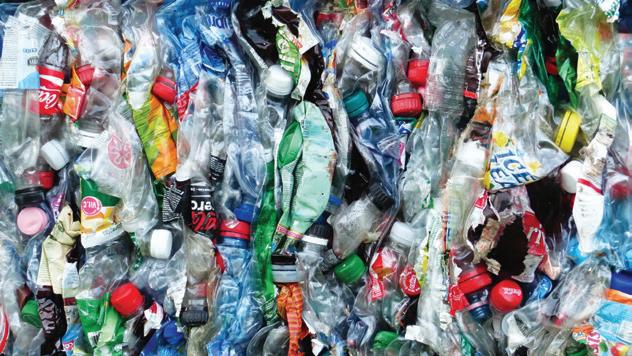
Flexible plastic packaging, such as sachets and films, poses a significant problem. The difficulty of recycling these plas tics – in practice as well as at scale – is a key reason why most businesses will miss the 2025 target.
BALCONES RESOURCES PARTNERS WITH CP GROUP TO BUILD NEW MRF IN SAN
ANTONIO
Balcones Resources has selected CP Group as the equip ment provider of its materials recovery facility in San Antonio, Texas, set to open in 2024. The MRF will have a processing capacity of 50 tons per hour and will service both residential and commercial recycling streams for the City of San Antonio. It will be integrated with the ability to receive and bale high volumes of post-commercial, post-industrial paper and plastic waste for the region’s growing distribution infra structure, and will employ only five to ten manual sorters.
The Balcones MRF will be able to process significant vol umes of high-quality recycled materials, allowing more quality feedstock to enter the circular economy. The site and building design is focused on rapid turnaround time for city collec tions, haulers, outbound recipients of baled commodities, and businesses.

TOP NEWS OF 2022
This year saw in surge in news related to electrification, alternative fuels, robotics, and artificial intelligence, in addition to an increased focus on the shift toward a fully circular economy.
Turn to page 34 for our roundup of this year’s most notable stories.
JOINT VENTURE WILL BUILD AND OPERATE 10 NEW ADVANCED RECYCLING FACILITIES IN
THE U.K.
Clean Planet Energy has agreed to a new joint venture with private equity firm Crossroads Real Estate to fund Clean Planet Energy’s flagship ecoPlant currently under construction in Teesside in North East England. This will be the first of 10 new ecoPlants that Crossroads Real Es tate and Clean Planet Energy are jointly seeking to build and operate across the U.K.
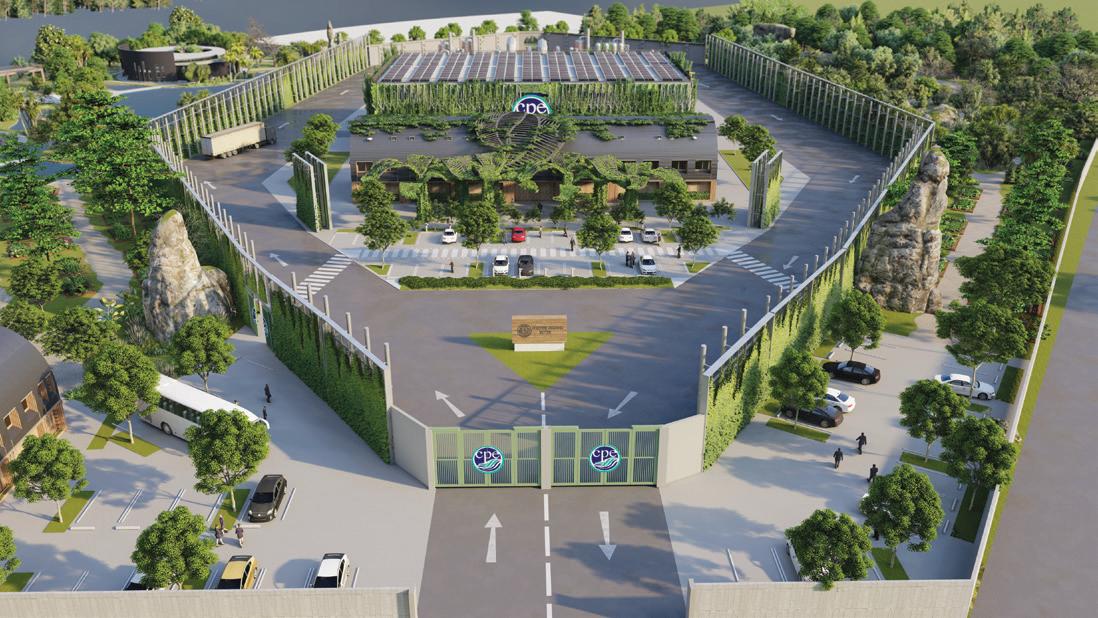
The new joint venture could see over £400 million of new U.K. investment deployed for the future construction of these facilities to tackle the plastic waste crisis. Potential sites have already been identified in Lincolnshire, Gloucestershire, Lancashire, and South Wales, with further locations to be added.
Clean Planet Energy’s ecoPlant is an advanced recycling fa cility intended to process non-recyclable and hard-to-recycle waste plastics that would otherwise be sent to landfill. Each ecoPlant is designed to accept 20,000 tonnes of plastics each year and to convert this waste into ultra-low-sulphur fuels which can reduce greenhouse gas emissions by 75 percent compared to the use of traditional diesel.
MENTOS TRAINS TEAM OF RACCOONS TO FIND AND RECYCLE PAPERBOARD GUM BOTTLES
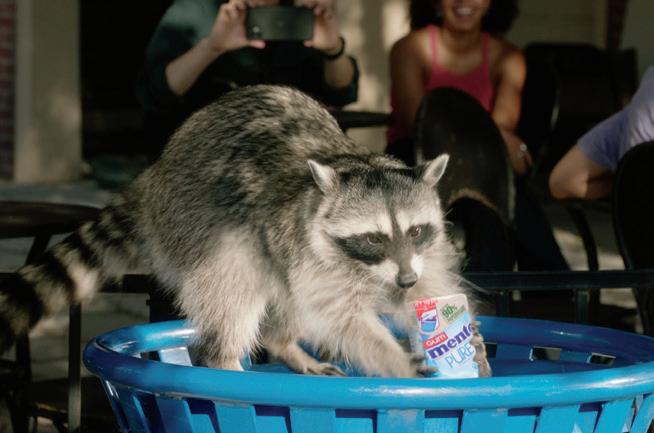
The Mentos paperboard gum bottle was made to be recycled, yet only 32 percent of Americans actually re cycle. Mentos is tackling that problem head-on with the only logical solution: raccoons. Dubbed the Mentos Raccoon Recycling Force, these raccoons just completed a successful mission on the streets of Simi Valley, California, by digging through trash cans and placing the paperboard gum bottles in the recycling.
More than 40 hours of expert training were given to four raccoons to help them learn the difference between a recycling bin and a trash bin, and they took it from there.
After conducting several real-world tests with the raccoon task force, the results are in: the Mentos Raccoon Recycling Force can recycle 75 percent of the time.
BRANDT TRACTOR NAMED AUTHORIZED DEALER FOR MORBARK, RAYCO, AND MORE
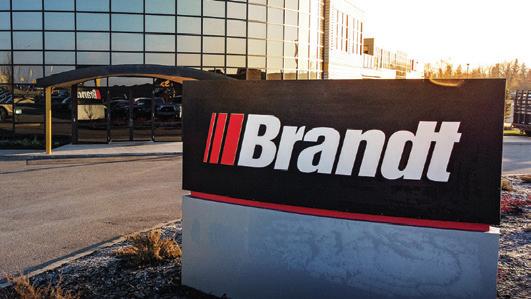
Morbark and its affiliated brands Rayco and Denis Cimaf have selected Brandt Tractor as the exclusive, autho rized dealer for the company’s tree care, forestry and biomass, recycling, and Rayco Forestry/Denis Cimaf equipment lines in Canada. The lines include equipment like brush cut ters, stump cutters, articulated wheel loaders, horizontal and tub grinders, forestry mulchers, mulching attachments, whole tree drum chippers, and flails.
“For Morbark, it was an easy choice to sign Brandt as our ex clusive dealer in Canada,” says Michael Stanton, vice president of sales and marketing. “Their 56 full-service locations will provide our Canadian customers with the complete support they need and deserve.”
REPUBLIC SERVICES AND ARCHAEA ENERGY TO BUILD NEW RNG FACILITY
Republic Services and Archaea Energy will build an re newable natural gas facility at Middle Point Landfill that will be developed through both companies’ Lightning Renewables, LLC joint venture. The project will convert the gas that naturally occurs as the waste at Middle Point Landfill decomposes into pipeline-quality RNG that can be used as a low-carbon alternative to fossil fuels.
The Middle Point Landfill gas-to-RNG project will create clean energy resources, further control the potential for off-site odour, and help reduce greenhouse gas emissions while con tributing directly to Republic Services’ long-term sustainability goal to beneficially reuse 50 percent more biogas by 2030. RNG projects bring meaningful local and global environmental ben efits with little to no negative impacts on the local community.
SURVEY FINDS CONSUMERS STRUGGLE TO UNDERSTAND PLASTICS RECYCLING
According to a new survey from Republic Services, despite high confidence levels in their knowledge, most consum ers lack an understanding of proper recycling practices, particularly for plastics. In fact, confusion about which plastics should be recycled is leading some to forgo it completely.
The survey analyzed the recycling knowledge and habits of more than 2,000 U.S. consumers. While nearly two-thirds (64 percent) of respondents said they know what types of plastics can be recycled, 61 percent incorrectly believe flexible plastics, including grocery bags and bubble wrap, are recyclable in their curbside bins.
As for recycling habits, water bottles, milk jugs, and laundry detergent jugs are some of the most widely acceptable recycla bles, yet consumers aren’t always recycling them. When asked about which items they consistently recycle:
• 62 percent of consumers recycle water bottles
• 51 percent recycle milk jugs
• 43 percent recycle laundry detergent jugs
As brands set ambitious targets for recycled content in their packaging and jurisdictions begin to adopt minimum recycled content standards, the demand for high-quality recycled plas tics will only grow – but the current supply of the right types of recycled plastics falls short.
Using EPA estimates, the projected total annual environ mental benefits from the project will be equivalent to the carbon sequestered by more than 800,000 acres of U.S. forests in one year.
The Lightning Renewables, LLC joint venture includes plans to develop 39 new RNG projects at landfills owned or operated by Republic Services across the U.S. The Middle Point project is part of the first phase of development for the joint venture. This RNG partnership builds on a growing slate of environmental commitments by Republic Services, includ ing fleet electrification and investments in plastics circularity.
Republic Services is involved with 77 renewable energy projects at its landfills across the U.S., which generate electric ity as well as RNG and help users and communities meet their own sustainability goals. RNG powers 21 percent of Republic Services’ fleet, and when used as a transportation fuel, RNG can reduce emissions by up to 70 percent.

NOVELIS OPENS $35 MILLION FACILITY FOR DEVELOPMENT OF ALUMINUM SOLUTIONS
Novelis has celebrated the opening of its Customer Solu tion Center (CSC) for the automotive market in Novi, Michigan. The $35 million facility is part of Novelis’ global network of CSCs, which are designed to speed up the development of aluminum solutions.
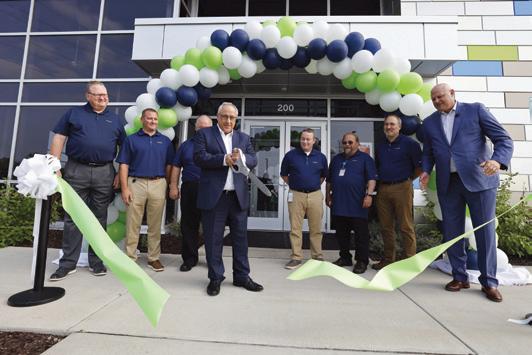
The centre’s high-tech equipment ranges from a hot stamp ing press to computer-aided design software to visualization technologies that model vehicle safety scenarios. These
capabilities enable Novelis to develop new aluminum solutions and demonstrate their benefits for current and future vehicle applications. Manufacturers and suppliers are using the centre to see these technologies firsthand, which includes greener life cycles and more cost-effective solutions.
Since launching the Customer Solution Centers in 2018, Novelis has made several advancements in automotive innova tion. In addition, Novelis has worked to increase the amount of recycled aluminum in automotive alloys and expanded closed-loop recycling systems, which recovers aluminum scrap generated during the stamping process and recycle it back into the same product.
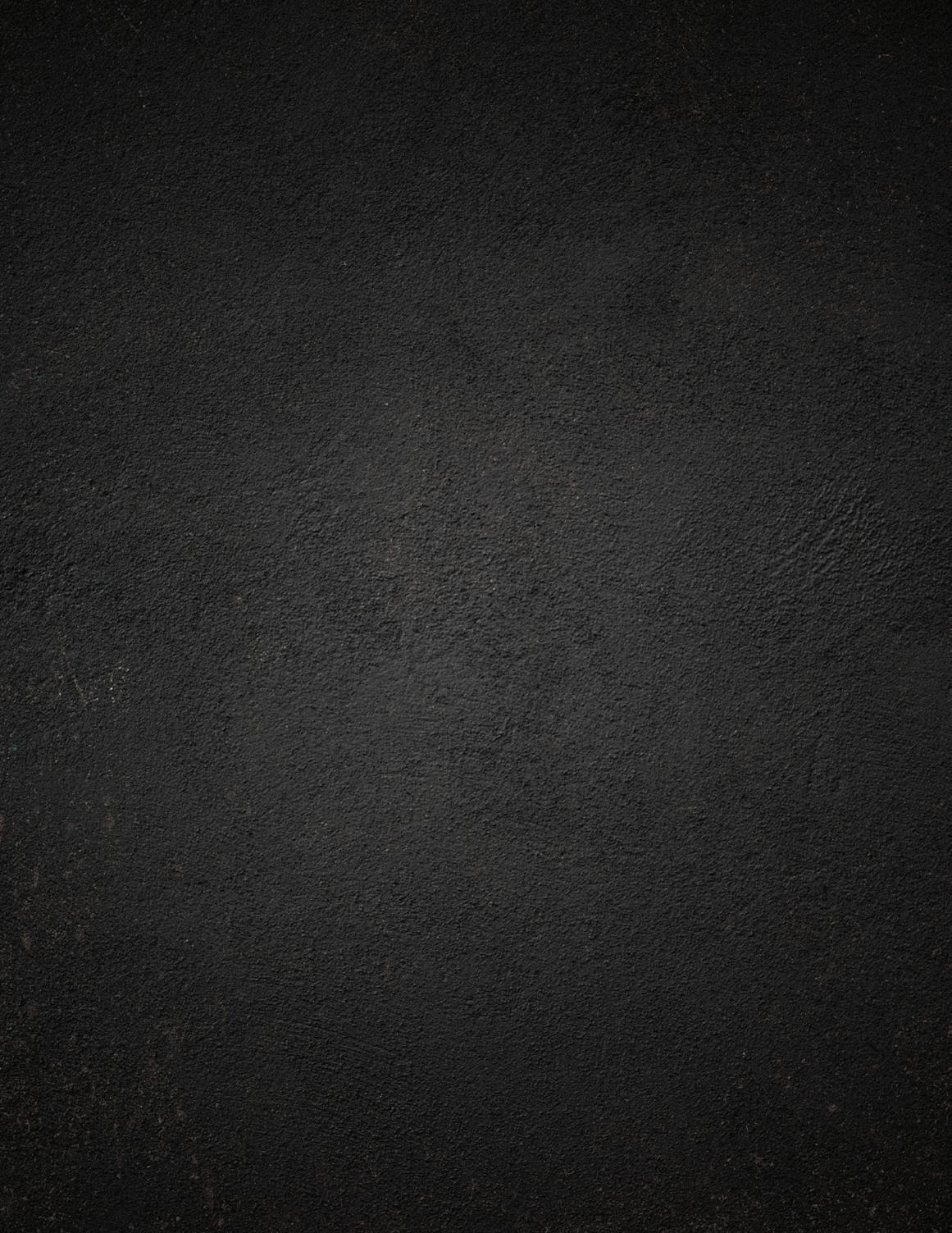
PELLENC ST AMERICA INAUGURATES NEW TEST CENTRE IN NORTH CAROLINA
Pellenc ST has opened a new test centre in Pineville, North Carolina. Pellenc ST will also be moving and upgrading its Japanese test centre and opening two new test centres in Australia and the U.K.
With this new test centre, Pellenc ST will provide its users with a 560-cubic-metre industrial demonstrator site with the latest intelligent sorting equipment. Two Pellenc ST sorting ma chines are available to study sorting strategies and ensure the quality of the sorted flows. A machine from Bühler was added to the process in order to carry out tests on plastic flakes.
ELV Select Equipment is the authorized North American Distributor for Ecohog Waste Processing Equipment.

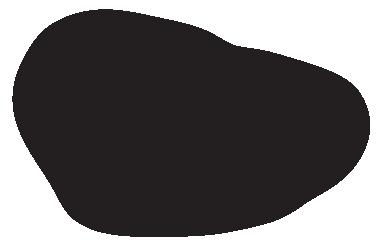
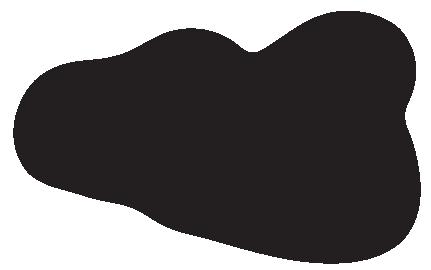
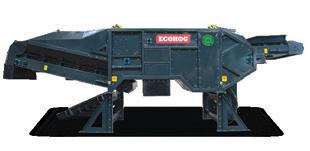
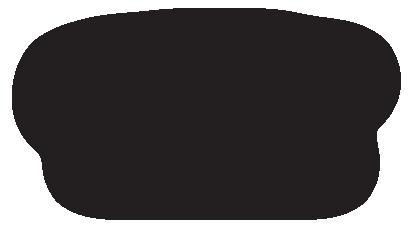
There is a machine for a variety of waste applications, including: C&D, Compost, Scrap Metal and Biomass.
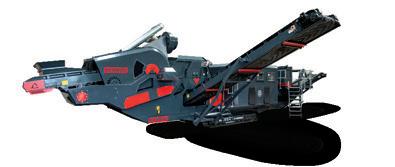
TEXTILES RECYCLING OPERATION FOLLOWING
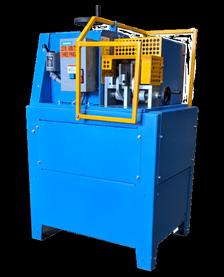
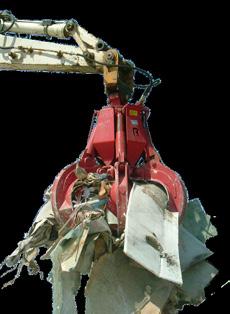

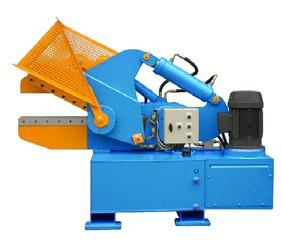

WM INVESTMENT
Debrand, a reverse logistics textile solutions provider, has received a strategic investment from WM, the first investment made by WM in textile recycling. Lever aging Debrand’s technology, WM expects to offer new textile recycling capabilities and provide circular solutions across North America.
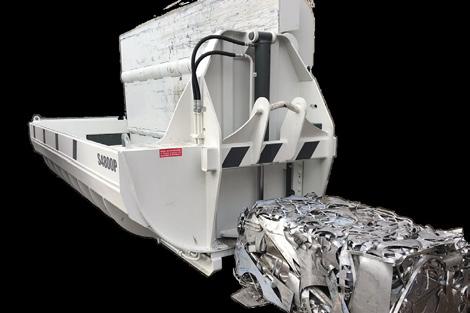
This year, Debrand is projected to divert nearly 1,000 tons of used textiles from landfills through resale, recycling, and repurposing. The investment from WM will accelerate Deb rand’s plans to grow its operations, capabilities, customer network, and team.

“Our customers are looking for ways to reduce waste from their operations, enhance their sustainability reporting, and accelerate the transition to a circular economy,” says Eric Dixon, vice president of sustainability and environmental solutions at WM. “WM, in turn, is continuing to adapt to meet these needs and become a true sustainability partner to our customers.”
Significant demand and growth are expected for Debrand’s solutions as the industry moves toward a circular economy. The fashion industry is one of the highest producers of greenhouse gas emissions globally, and a growing number of brands have committed to adopting circular strategies to reduce emissions that derive from producing fibres and raw materials.
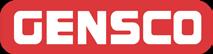

SPOTLIGHT INTRODUCTIONS & UPDATES
Lindner
SHREDDER FOR PLASTIC FILM
Lindner’s Jupiter BW series of shredders are specially tailored to film recycling, allowing for enhanced optimization right from the first step in the process. After opening a bale, the films are cut to a size of A4/A3. Due to the continuous film size, downstream NIR systems are able to work within the optimum operating point to detect materials in a more targeted manner and assign them to the correct material stream. According to the company, the new line of shredders successfully reduces the proportion of fines that are unusable by 44 percent which is achieved through a slow-running but powerful shredding operation with unique control parameters.
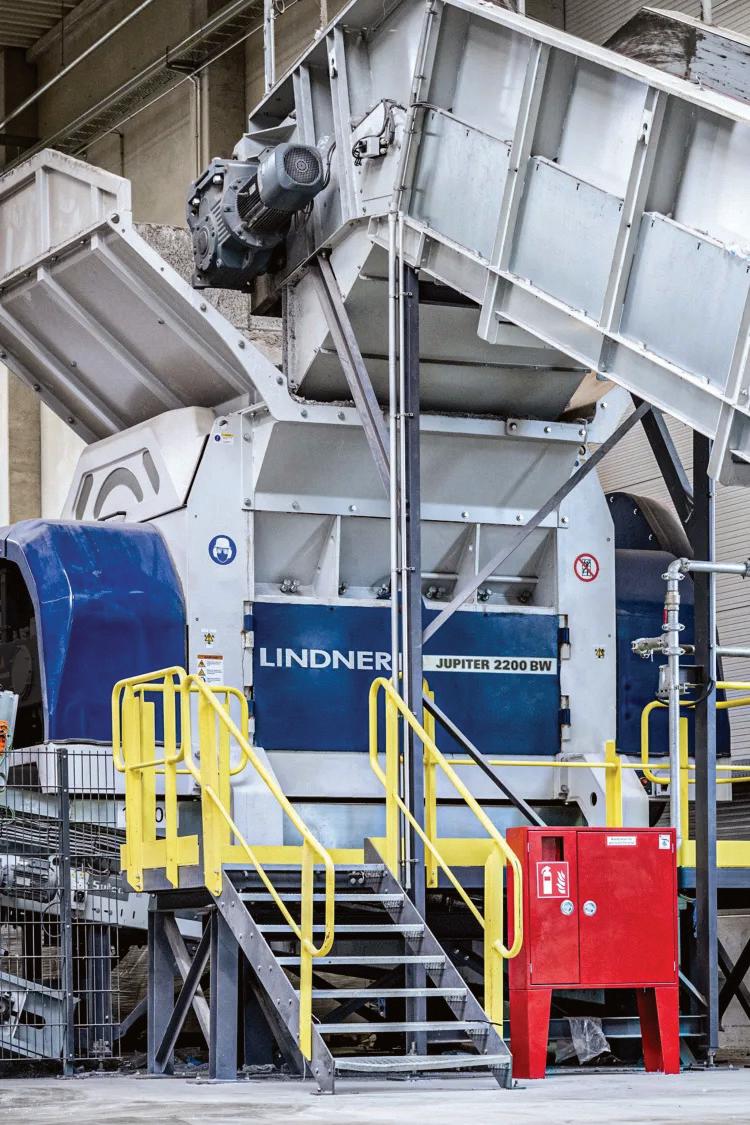
Vermeer GRINDER TIPS
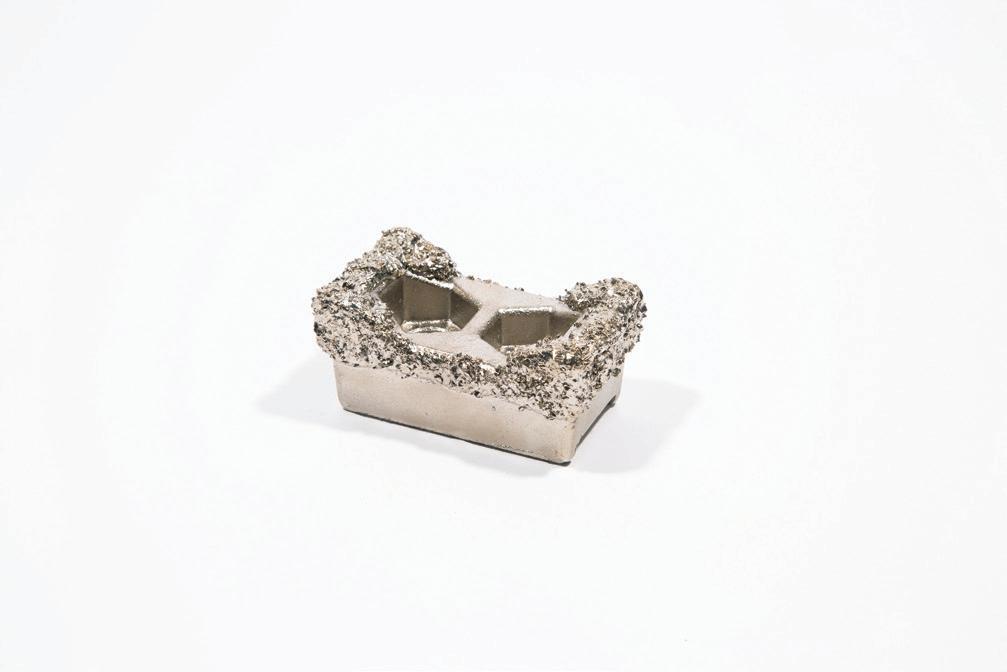
Vermeer’s long-lasting grinder tips contain a large amount of car bide to provide durability that results in less downtime and less time spent changing tips. The durable grinder tips are designed for a precise fit, eliminating the time required for modifying tips to fit your grinder. The types of grinder tips offered include three grit, wide block, abrasion resistant, wing, impact resistant, nar row block, and sharp. With the addition of the max grinder tips, there are now more options to match cutting tips to the specific application while extending the time between changeouts.
McCloskey International JAW CRUSHER
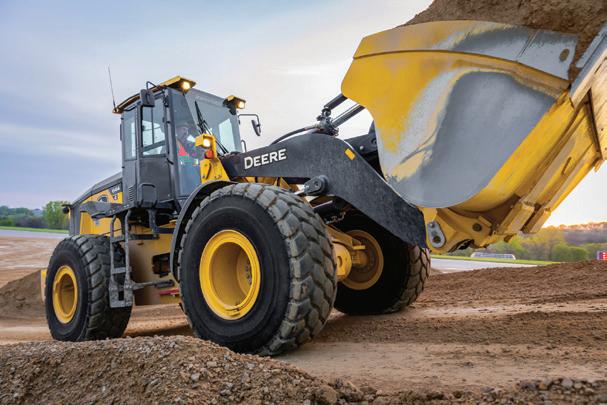
McCloskey International’s J4 jaw crusher builds on the robust fea tures of the existing design, while adding new productivity with features and options aimed at boosting productivity and offering enhanced durability across applications. Designed for applica tions such as aggregates, construction and demolition recycling, and site preparation, the J4 delivers high production due to its innovative jaw chamber design and enhanced material flow. The large 1,060- x 700-mm (42- x 28-inch) jaw opening accommodates large feed sizes, contributing to higher production. The material path is enhanced with the 1,064- x 4,247-mm (41.9- x 167.2-inch) grizzly pan feeder under the hopper that allows for better sizing of material with a variety of mesh options.
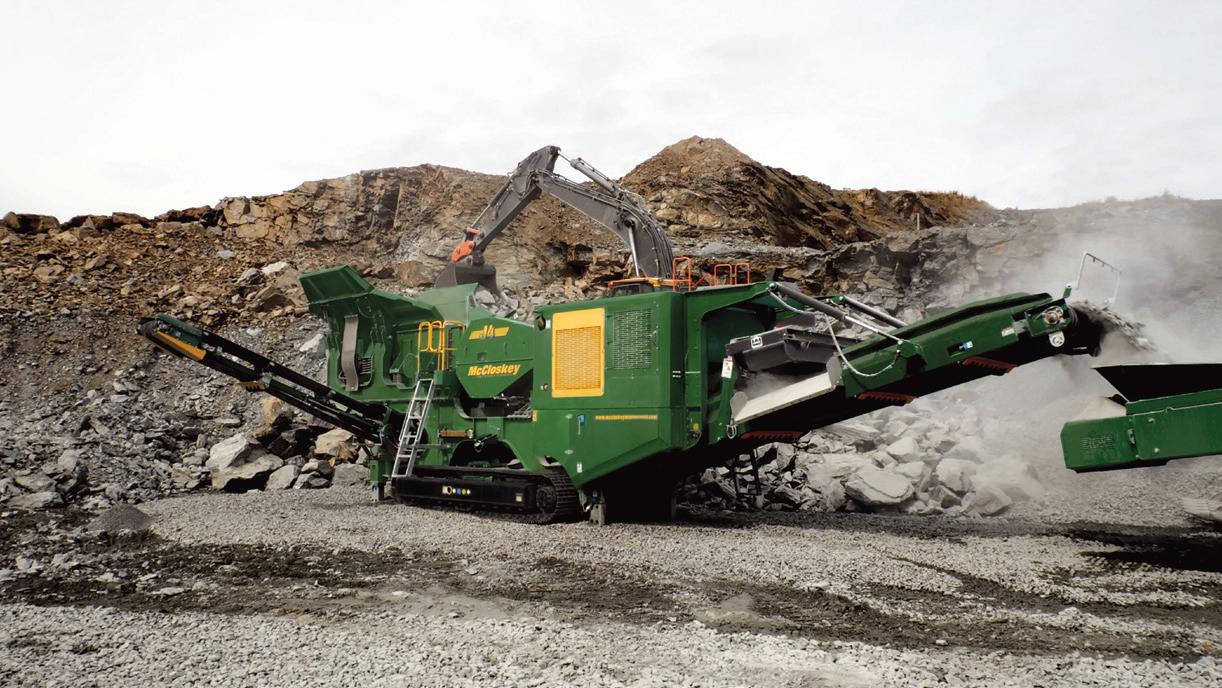
John Deere Construction & Forestry WHEEL LOADERS
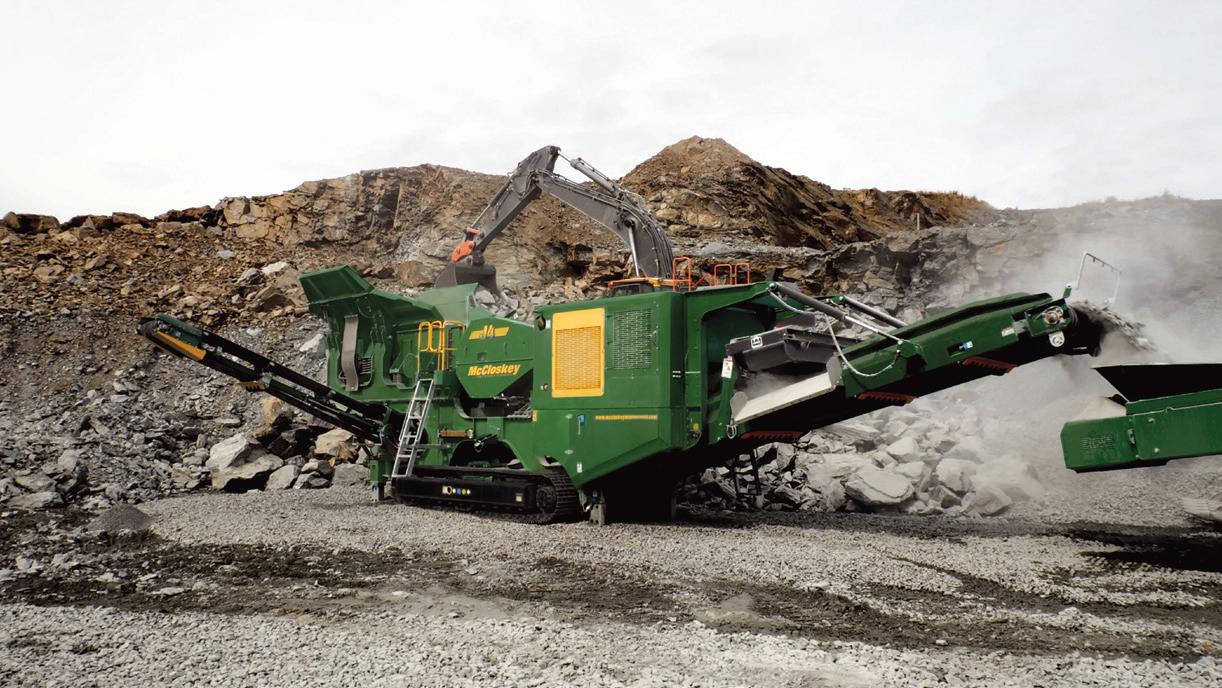
John Deere has expanded its G-tier wheel loader series with the 544 and 644 G-tier wheel loaders. The 644 G-tier is equipped with a John Deere 6.8L engine and can be customized through a variety of base-level packages, including options related to lock ing differentials, ride control, and rear chassis work lights. The 544 G-tier wheel loader is designed to provide a more economi cal solution in the three-cubic-yard loader size class. Promoting ease of operation, the in-cab controls include adjustable boomheight kick out, return to carry, and return to dig, which can all be activated from inside the cab, speeding up production times during repetitive applications.
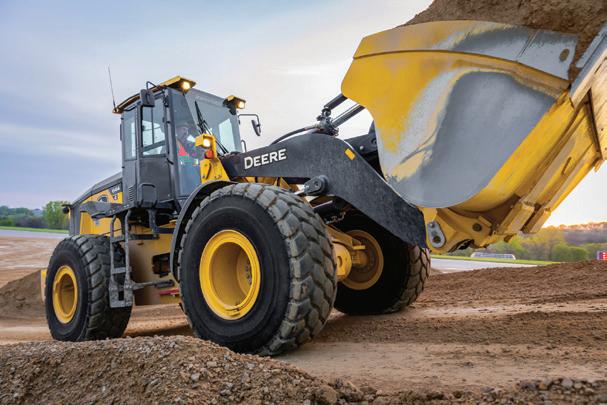
Rapid Granulator SHREDDER FOR PLASTICS
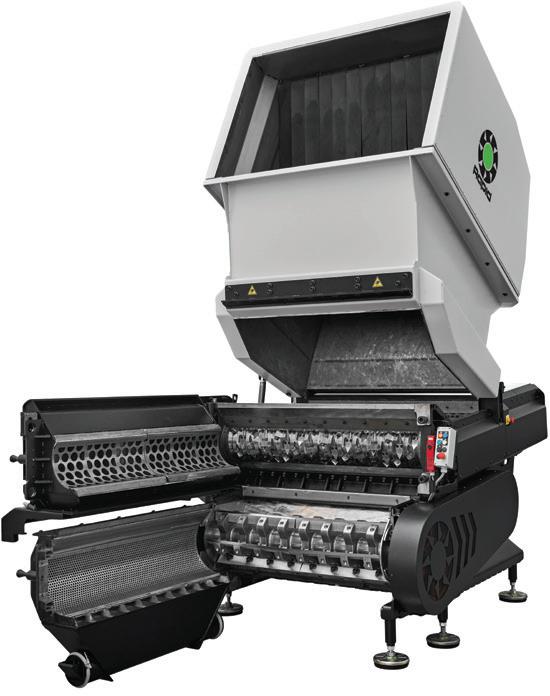
Rapid Granulator’s next-generation Raptor DUO series for plastics granulation now features an integrated grinder. Rapid Granulator’s focus on modular units enables the company to integrate the DUO solution in multiple configurations. The Raptor series features both pneumatic and hydraulic pusher systems with a third pusher system available for bulky items to increase capacity and feed large products directly into the hop per of the shredder. Rapid Granulator offers 36 base configu rations of the Raptor to accommodate a wide range of applica tions, as well as three different cutting systems: quad cut, claw, and power wedge. The modular systems feature two widths of 31.5 inches and 53 inches (800 mm and 1,350 mm).
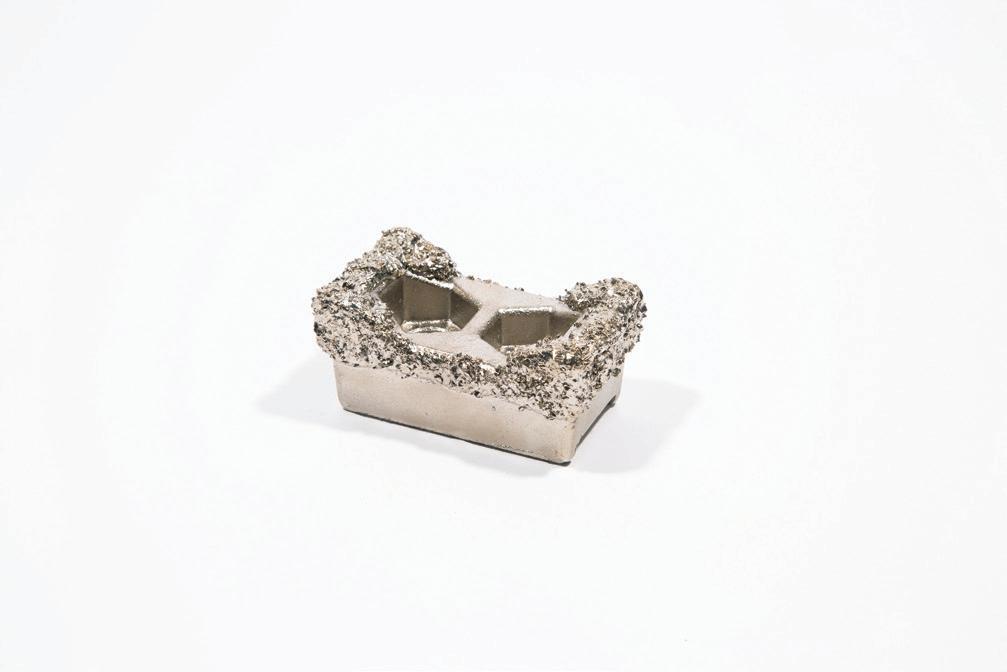
ANACONDA SYSTEMS CUTS COSTS AND COMMUTES WITH URBAN COMPOSTING
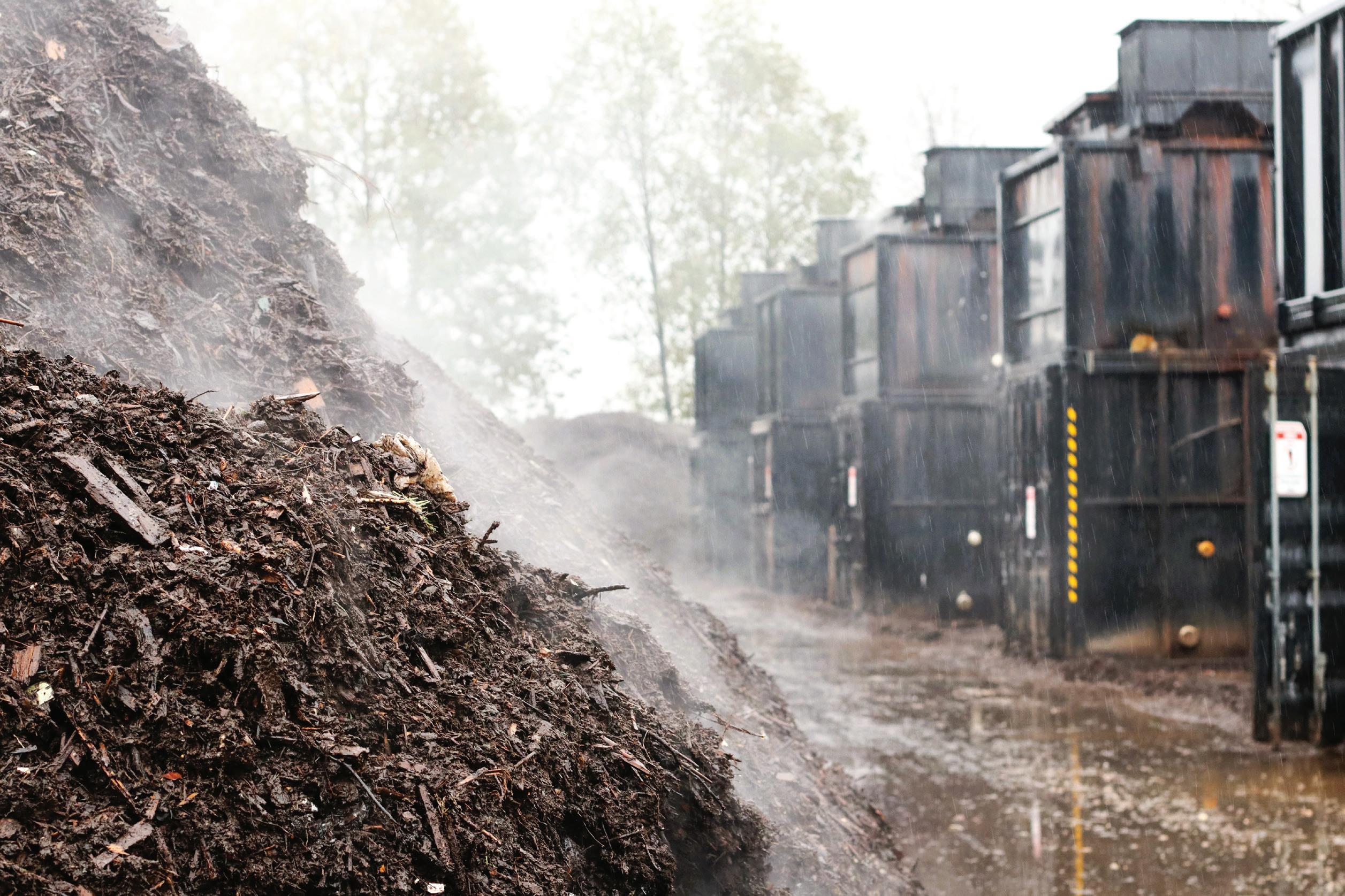
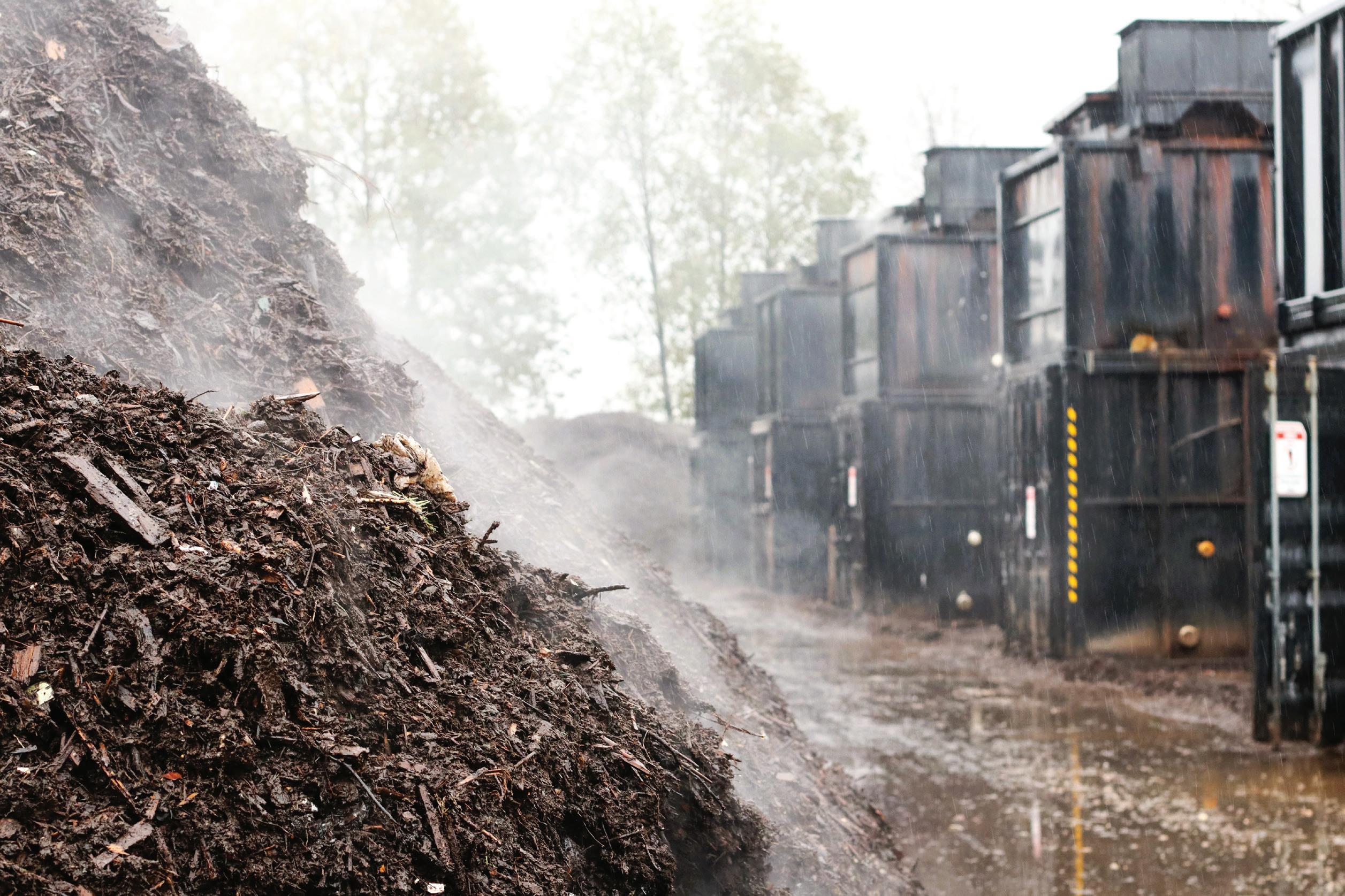
Russell Zishiri has always had an entrepreneurial mind set. He first got his start in the recycling industry over a decade ago while operating his own hauling business in Vancouver, British Columbia. Each day after collecting a box truck’s worth of organic materials, he would make the bumperto-bumper, two-and-a-half-hour round trip commute to the rural processing facility. He wasn’t the only hauler making this trek.
Experiencing this frustration day in and day out sparked an important realization for Zishiri: if the lengthy drive is such a widespread issue, why not bring the processing facility closer to the city? By addressing the factors that have historically prevented organics facilities from existing within city limits –odour, land costs, and permitting – processing could exist clos er to home and cut down on commutes and costs for haulers.
This led Zishiri to embark on a research project supported by the National Research Council of Canada’s Industrial Research Assistance Program. After analyzing close to a hundred existing technologies currently in the marketplace, he decided that there was still more that needed to be done.
“There was nothing that could do what we wanted, which was something with a high throughput, low footprint, low capital expenditure, and the ability to be permitted in the city,” says Zishiri.
mercial haulers. And ultimately, for them, it’s an effective way to be able to increase productivity with short trips,” says Zishiri. “Our facility is centrally located, so if you’re in downtown Vancouver you can empty your truck within 15 minutes. That’s a valuable option for companies, allowing them to double productivity with their trucks by collecting more material and competing more effectively in the marketplace since they need less equipment to do the same work.”
URBAN WASTE MANAGEMENT PRESENTS UNIQUE HURDLES
Processing organic waste in urban areas comes with plenty of challenges. There are capacity issues, tricky permitting pro cesses, strong odours, and the large amount of land required for processing which can be extremely costly in the city. And since most cities generate more organic waste than they can process, this leaves two options: shipping it out of the region, or leaving it to rot in a landfill where it will generate methane, producing significant greenhouse gases.
Faced with these two undesirable options, Anaconda Systems created an alternative choice: a proprietary, in-vessel compost ing system capable of turning organic waste into high-quality fertilizer supplements in 96 hours, about 1/9 of the standard processing time. The enclosed design and assembly line process uses aerobic digestion with no mechanical agita tion, allowing for high-speed throughput and processing that reduces odours and maintenance.
“From end-to-end, our materials go through an en closed system, even the pre-treatment,” says Zishiri. “It’s enclosed, it has a low footprint, and we can rapidly move through the materials and have no adverse effects on the surrounding community and environment. And obvi ously, being in Vancouver, acquiring the permits that are required to do this kind of work in the city is a demon stration of the ability to be able to process these materials within the region.”
AEROBIC VERSUS ANAEROBIC DIGESTION FOR URBAN WASTE STREAMS
At the most basic level, the differences between anaer obic and aerobic digestion are simple: aerobic systems require oxygen, and anaerobic systems do not. While anaerobic digesters take organic waste and transform it into biogas, urban organic waste is volatile, and often too contaminated with materials such as yard waste, plastics, and metals to be a viable feedstock for that process. There are other challenges as well.
Drawing upon his expertise and existing relationships in the commercial waste industry, Zishiri established organic waste processing company Anaconda Systems to help solve some of these common pain points within the industry, successfully opening a pilot facility in Vancouver in 2017. The facility’s con venient location allows haulers to tip waste mid-route without leaving the city, helping municipalities and private waste com panies increase efficiency and reduce costs.
“We have customers that are institutional, industrial, and commercial. So the waste comes from any sort of food produc tion, from restaurants to hotels, and that’s through the com
“The costs of anaerobic digestion can be prohibitive, especially for smaller municipalities. And the permitting around anaerobic systems is much more complex and lengthy because of the gas and all of the extra risks that come with that,” says Zishiri.
Due to the complications and challenges associated with anaerobic processing, aerobic digestion was the natural choice for Anaconda Systems. With technology specifically designed to work around the contamination challenges of urban waste streams, Anaconda Systems utilizes aerobic digestion in its operations to simplify the process and cut costs, making its technology affordable for most municipalities and private waste services. Utilizing an aerobic system also has the added benefit
Our facility is centrally located, so if you’re in downtown Vancouver you can empty your truck within 15 minutes. That’s a valuable option for companies, allowing them to double productivity with their trucks by collecting more material and competing more effectively in the marketplace since they need less equipment to do the same work.
Russell Zishiri Founder & CEO, Anaconda Systems
of producing a high-quality end product that is suitable to sell on the market, further increasing revenue streams for the company.
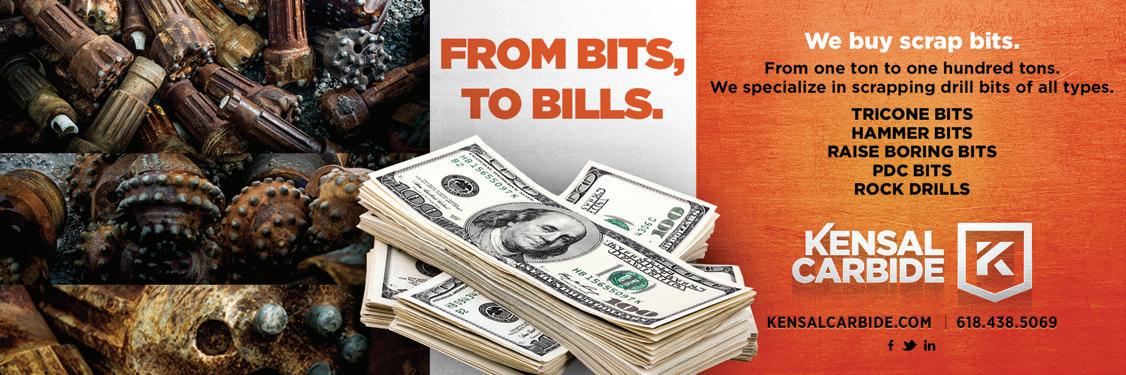
Most traditional processing methods can only operate outside of populated areas due to the smell, something that has proved to be a key pain point when it comes to processing waste within city limits. Located just a few blocks away from residential areas on only 3.5 acres of land, Anaconda Systems’ facility is also 87 percent smaller than most facilities, allowing it to fit almost anywhere and scale to meet customer needs, while also reducing the odours that are traditionally associated with organic waste.
“Being able to process the material rapidly in less than 10 days is what allows you to save space and cut costs. Each unit has 90 tonnes of static capacity, so the longer the materials are in the vessel, the more containers that you need. Ultimately, in order to take up less space, you need to be able to process mate
rials in short cycle times,” says Zishiri.
“In terms of developing our technology, a key focus was to maximize the biological reaction that’s happening inside the vessel so that material is digested and pasteurized in the shortest time possible. This allows us to move through organic waste with less vessels and land. The sweet spot for us is 30 to 60 kilotonnes of organic waste per annum, and we only need three to five acres of land to build a facility. For larger municipalities, multiple facilities can be built and be distributed throughout a region.”
A PROPRIETARY PROCESS
Anaconda Systems’ pre-treatment process separates contami nants and inorganic materials from organic waste. After adding its own unique formula to the treated waste, the company is left with a homogenous material ideally suited for rapid digestion using Anaconda’s proprietary aerobic system.
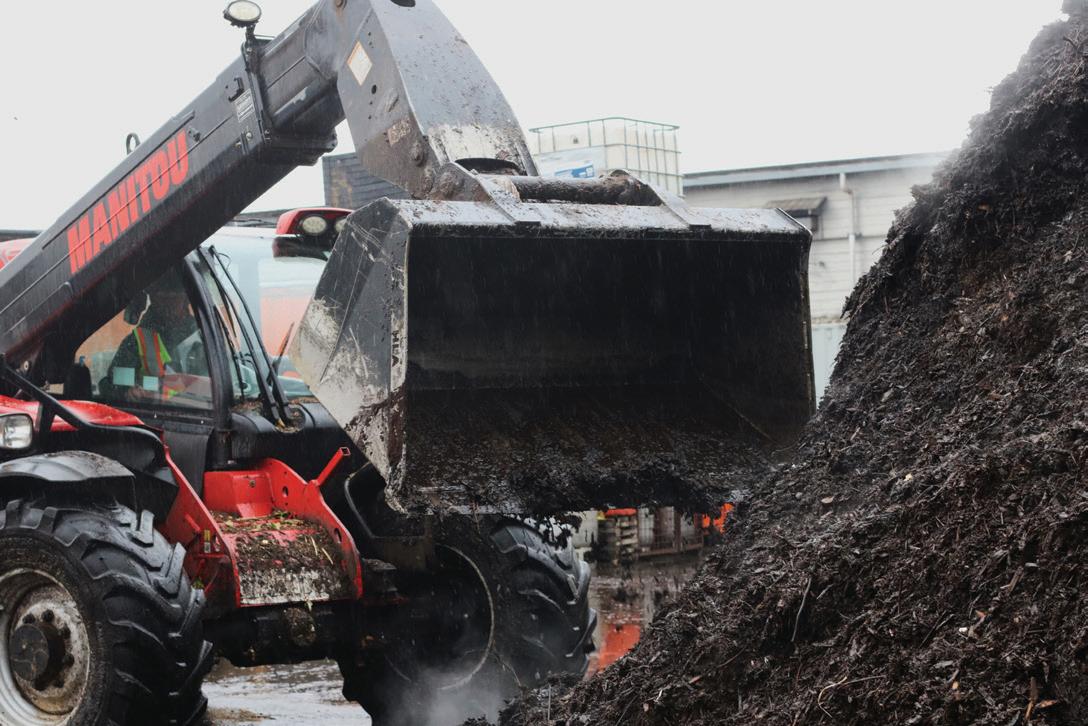
“The key is our pre-treatment process and recipe that creates the substrate that we need before it goes into the pro cessing unit,” says Zishiri. “Our recipe
degrees Celsius, and that temperature is maintained for three consecutive days to meet regulations. Each vessel is fitted with a biofilter to take care of any odours
any resulting food waste back into usable fertilizer to start the process over again.

“Ultimately, our NPK [nitrogen, phospho rus, and potassium] ratio is actually higher than regular output. We’ve tested it against regular composted material and it’s about 50 to 60 percent more potent. We have some commercial farmers that we’ve been working with over the last few years that are looking at it as a replacement for syn thetic fertilizer. It’s not just the nitrogen, phosphorus, and potassium that is in there, but all the other minerals, too. Outside of the nutrients, our output also increases the water retention of the soil, allowing for healthier root growth. And because of our pre-treatment process, we have basically no contamination in the output product which is important to farmers.”
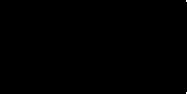


GROWTH ON THE HORIZON
What began as one man searching for a solution to a prevalent problem within the collection industry has now grown into an operation that processes over one million pounds of organic waste each month with the potential to reach over four million pounds in just one facility alone. Although investing in organic waste treatment can be complex and costly, Anaconda Systems has found a way to treat materials close to home in a viable way, eliminating virtually all pain points that previously prevented such facilities from operating within city limits.
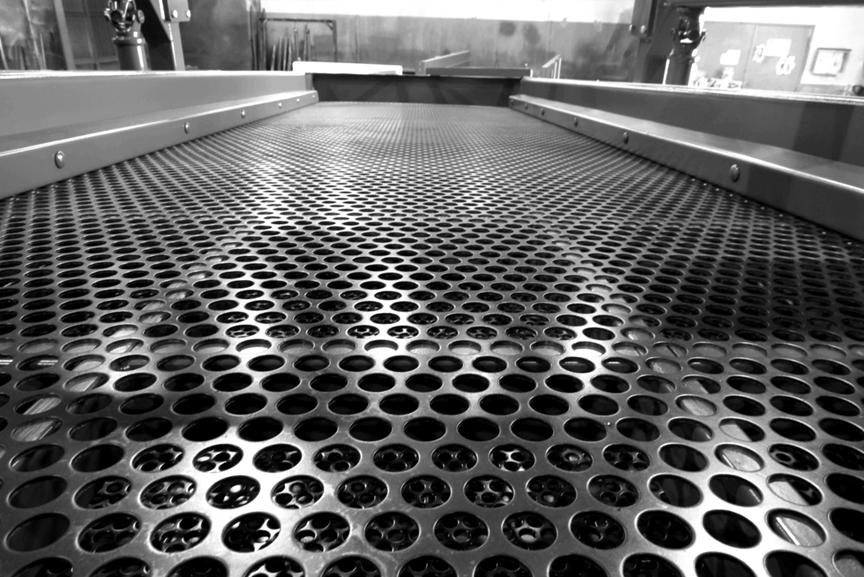
By demonstrating the facility’s ability to process waste within the city while also producing a valuable end product, Zishiri anticipates Anaconda Systems’ technology will continue to expand in the waste industry, allowing for more in-city tipping and process ing with very little greenhouse gas emissions, benefitting both compa nies and the environment.
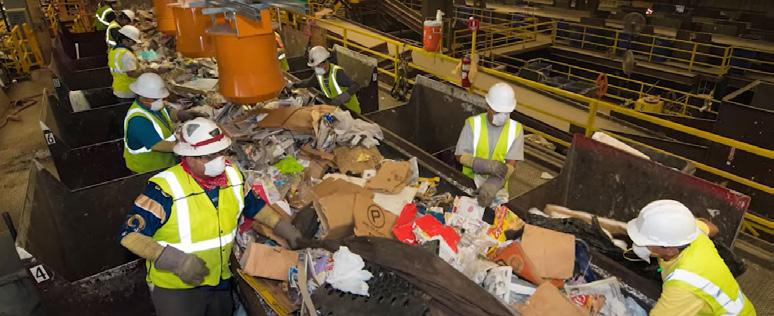
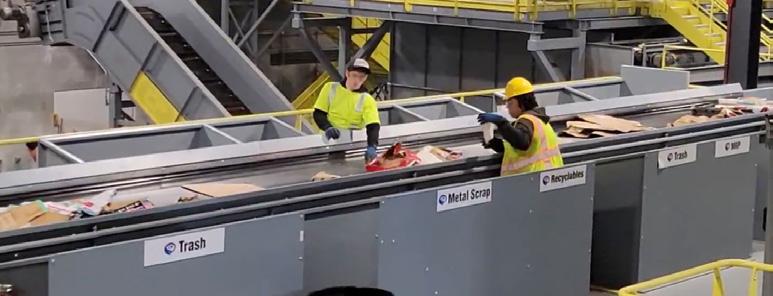

“We weren’t after disruption,” says Zishiri. “What we were after was find ing a solution for when I was trucking it. That’s how it came about.”
As the years progressed, Zishiri and the Anaconda Systems’ team knew they needed new infrastructure to be able to process organic waste in the way that they envisioned. And while larger municipalities didn’t want to pay hundreds of millions of dollars to build new facilities, many small er municipalities hit the sweet spot of between 30 and 60 kilotonnes of organic waste per year, making them the perfect candidates for Anaconda Systems’ technology. Following the success of the Vancouver pilot facility, Anaconda Systems has plans to expand its solutions to other municipalities by commissioning and installing both small- and large-scale facilities.
“Where there’s no land and con sumption abounds, there’s an oppor tunity for us to be able to create a circular system,” says Zishiri. RPN
THIS? THAT?
OR
Learn more at cpgrp.com/occ-auger-screen
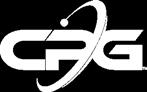
Why have an over-burdened presort when you can eliminate it all together?
CP Auger Screens revolutionized MRF process flows by eliminating the presort, prioritizing worker safety and increasing system efficiencies.
From end-to-end, our materials go through an enclosed system, even the pre-treatment.
It’s enclosed, it has a low footprint, and we can rapidly move through the materials and have no adverse effects on the surrounding community and environment.Russell Zishiri
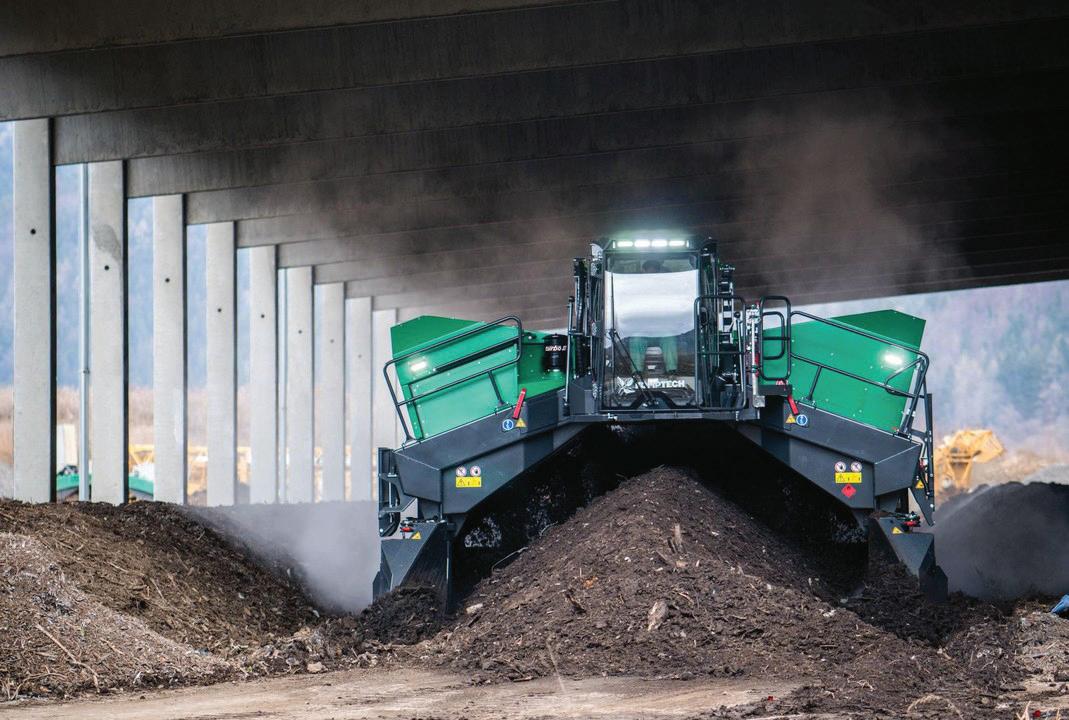

1is a self-propelled wind row turner designed for the medium- to high-through put range. The Topturn X5000 is ideal for windrows that are approximately 5 m wide by 2 m tall, as used at many larger facilities. It can turn up to 4,000 cubic metres of compost in an hour and is available with two different engine options. The X5000’s large 1.2-m-diameter drum features 180-degree turning teeth and ensures high throughput for thorough windrow mixing. The one-piece clearing blades allow for faster and more con venient changes from work to transport, making transporta tion more economical.
2towable, self-powered unit that is able to turn a windrow 6 feet (1.8 m) high by 16 feet (4.9 m) wide. It features a 40-inch (101.6-cm) tip-to-tip drum diameter, and its 275-hp (205-kW) engine offers a maximum turning capacity of 3,000 tons (2,721.6 mT) per hour. Heavy-duty construction and added features, like a hydraulic ac tuated clutch, allows for years of service, while an aggressive flail design assures complete aeration and mixing. A slow speed transport kit also allows the CT616 to be hauled from site-to-site, making it a more mobile machine.
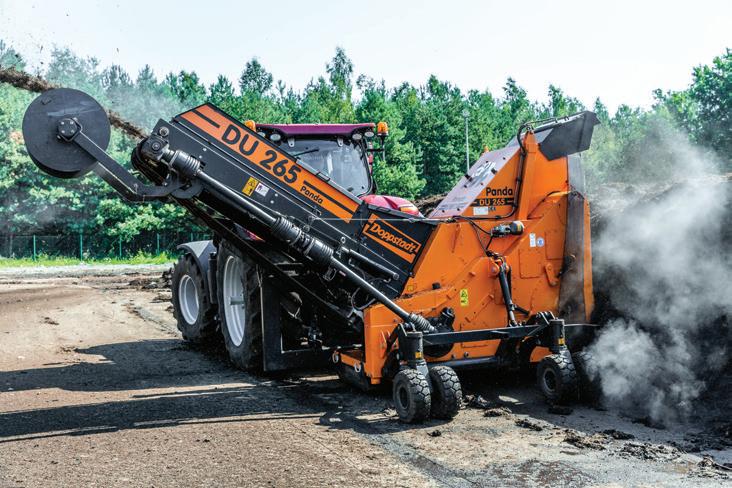
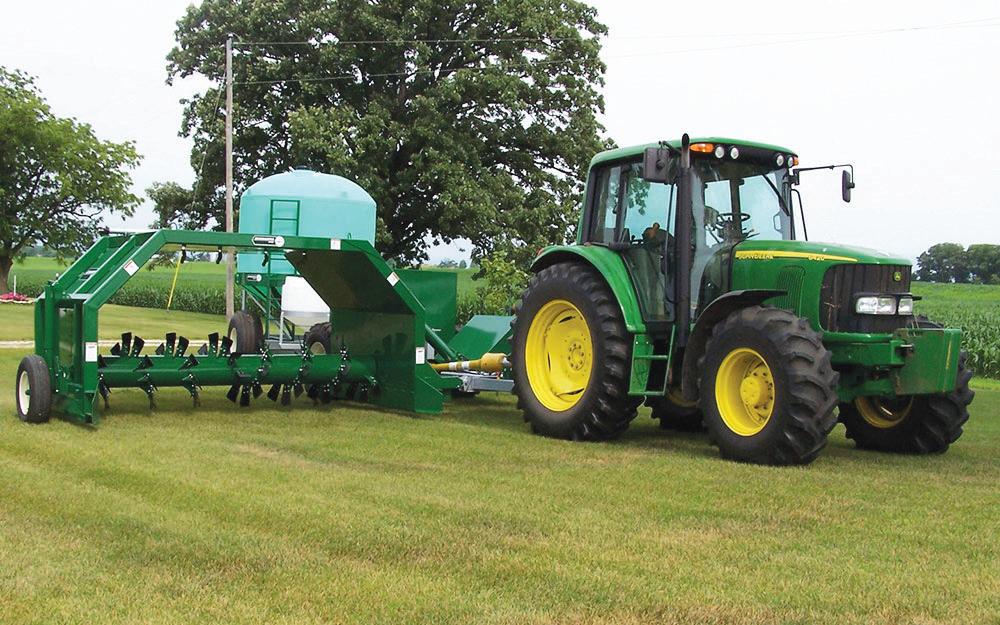
3Doppstadt’s DU 265 mobile windrow turner achieves throughput rates of up to 600 cubic me tres per hour. The machine features a short set-up time, and the windrow turner can be seamlessly adapted to different requirements by using different tool shapes. The hydraulically driven drum ensures variable dis charge which enables exact, individual windrow building. The machine is able to turn trapezoidal, flat-top, or static pile windrows by moving alongside the pile and throw ing the material to the side. Controlled pile building while utilizing an existing tractor saves space and enhances ease of use.
4Midwest Bio-Systems’ Aeromaster PT-130 pull-type compost windrow turner is ideal for sites producing up to 9,000 tons of finished compost per season. Its design allows a single operator to aerate, blend, and add water and inoculants in a single turn ing pass. Driveline safety is provided by an auto trip PTO driveline that disengages if it encounters excess stress. When the drivetrain stops turning, the clutch resets, and turning can restart immedi ately. The retractable drum hydraulically lifts out of the windrow in seconds to allow for inspection of the wind row’s inside profile or to exit the windrow.
Q & A AMY BRACKIN, LIBERTY TIRE RECYCLING

As the recycling industry continues to push toward the adoption of a more circular economy, waste that was once viewed as a bur den is now being recognized as a resource. This is especially true with end-of-life (EOL) tires, which have become one of the most recycled materials on the planet, according to a report by the U.S. Tire Manufacturers Association.
Liberty Tire Recycling is at the forefront of ongoing efforts to turn these scrap tires into usable materials, and has been for decades. Through collaborative partnerships, remediation efforts, and extensive R&D, Liberty Tire manages the collection of nearly 200 million tires each year with more growth on the horizon. I caught up with Amy Brackin, senior vice president of sustainabil ity at Liberty Tire, to discuss supply chains, market challenges, recycling program efficacy, and more.
BY SLONE FOX, EDITORLiberty Tire is North America’s largest network of tire recycling facilities with op erations across the U.S. and in both British Columbia and Alberta. We have a vast and complex supply chain, accepting and pro cessing virtually any kind of tire – passen ger car, truck, agricultural, commercial, and even large mining tires that are 13 feet in diameter. We have over 400 trucks in our transportation fleet, and we’re able to effectively manage the collection of nearly 200 million tires from over 39,000 retail and customer locations every year.
From these collection locations, the tires are transported by our truck fleet to Liber ty Tires’ various recycling facilities, where they’re shredded, ground, and go through multiple material removal processes. The resulting products then move to secondary manufacturers, and finally, are transport ed to an area for end product use.
In addition to our typical collection ef forts, we support tire cleanup efforts both through the remediation of illegal dump sites and local and regional amnesty pro grams that encourage the public to dispose of end-of-life tires.
SF ABA major portion of our remediation evolves from companies that start a business or idea without understanding the challenge of bal ancing inbound EOL tires with outbound mar kets. Over time, these companies build a large stockpile of used tires with no outlet and are forced to walk away, leaving the pile for state, municipal, or other levels of local or regional governments to clean up.
Liberty Tire works in conjunction with various levels of government, individuals, businesses, and customers to seek out and participate in cleanup efforts of both relatively small and very large waste tire piles. These projects include a range of different activities, such as providing workforces to facilitate mul tiple shoreline and roadside cleanups; direct ing personnel and equipment at local amnesty events which encourage individuals to drop off higher than usual numbers of EOL tires; and the mobilization of heavy equipment and specialized transportation methods for larger scale collection activities. Over the past 20 years, we’ve remediated more than 50 million tires from several hundred project sites.
Can you describe your supply chain for these end-of-life tires?
Can you explain the tire remediation side of the business in a bit more depth?
SF AB
Depending on the ultimate end market for the material, we use a variety of shredders, magnets, air systems, granulation equipment, screens, and bagging stations to produce quality products.
As a tire comes into our facility, it’s unloaded from a transport truck where it’s placed on a con veyor belt that leads into a sequence of shredders. Along the way, wire is removed using a series of magnets, and fibre is separated using sophisti cated air systems. To achieve the highest quality end products, oftentimes various grades and sizes of materials will be passed through a series of screens to ensure they consistently meet customer specifications.
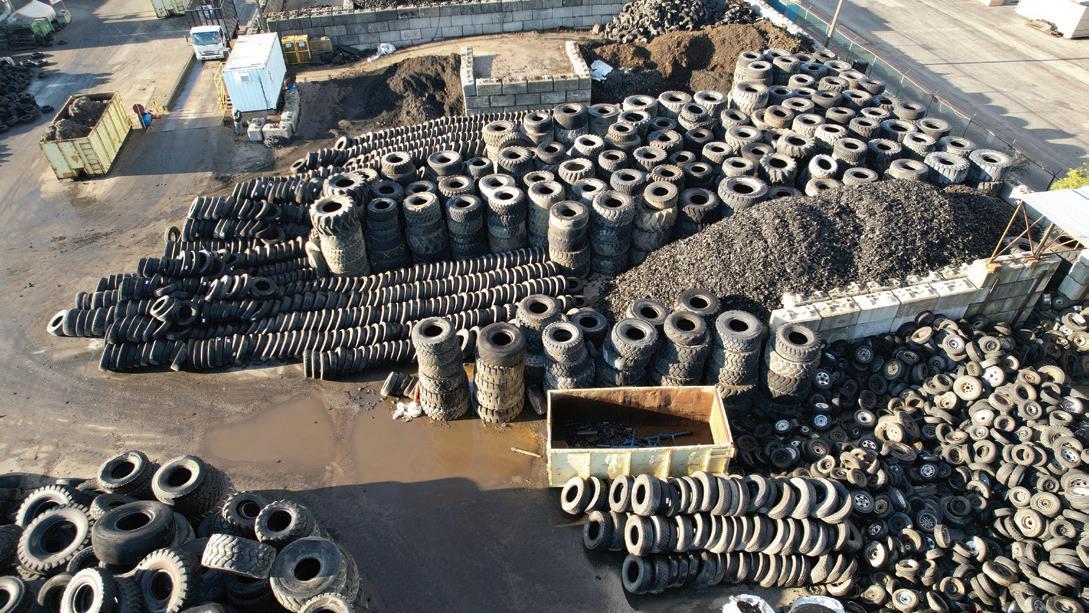
mulch for your flower beds. Items you may not even realize are sourced from recycled rubber include the base of an orange traffic cone at a road construction project where crews may even be paving with rubberized asphalt. Our products could also form part of the splash block at the end of your rain gutter, or the landscape edging used around your garden. Even the rubber floor ing you see in your local gyms – and the weights you use while you’re there – are being made from recycled tire rubber every day. When we engage in EOL tire conversion, we recycle all parts of that tire including the metal, which is sent back to smelters and repurposed in the manufacturing of new steel.
There are exciting new emerging technolo gies such as devulcanization, gasification, and pyrolysis that are opening the doors to many new market opportunities because these technolo gies produce net new raw materials. We also see a growing market in the use of finely ground recycled rubber going back into the manufacture of new tires. Rubber is becoming more preva lent in extrusion applications where it may be blended with plastics and compounding efforts. We’ve even seen early research regarding the use of recycled tire rubber in graphene – a highly technical and sophisticated application.
many well-developed
In order to create a sustainable future for endof-life tires, there is no silver bullet that is going to get us there. We need all of these markets and more to eliminate the disposal of tires and continue to move product offerings up the value chain to more renewable solutions. It will take time and requires the innovation and contri bution from all segments of the industry to get there, but we firmly believe we’re headed in the right direction.
What types of machines and equipment are used during the tire recycling process in terms of sorting and separa tion, steel removal, etc.?
What are the current end markets for the materials produced during this process? Are there any emerging end markets on the horizon?
There are
markets for theSF AB

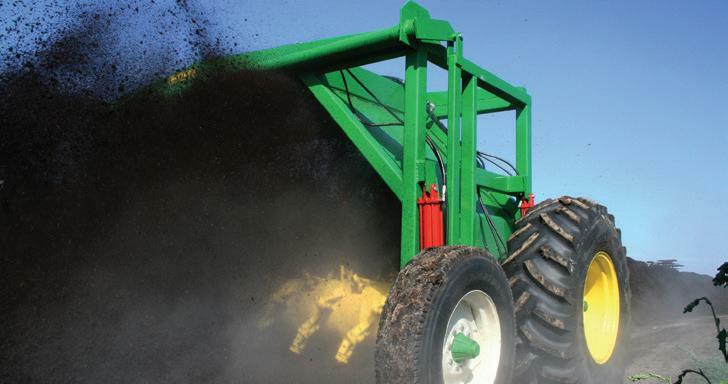

Across our operating landscape, there are a variety of ways end-of-life tires are managed in the U.S. and Canada, and we view all of them as successful. For decades, we’ve been committed to supporting a more circular economy by finding new and better ways to not only collect and recycle end-of-life tires, but to support innovation and new market development for recycled rubber products. Our focus is on ensur ing a high recycling rate and responsible management of end-of-life tires, and we’ve been able to effectively operate in a variety of different environments and regulatory structures.
The biggest challenge for any of these programs is that in general, we do not believe that the mere introduction of a program such as extended producer re sponsibility (EPR) or individual producer responsibility (IPR) necessarily drives market growth or development, which is the ultimate desired outcome. We’ve also found that in some cases, entities use EPR and IPR programs as marketing tools for their business which misinterprets its true intent. The intent is to ensure that EOL solutions continue to improve, and we’re pleased to see that happening in most jurisdictions across the U.S. and Canada.
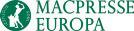
While the industry has its challenges, the reality is that tires are one of the most recy cled materials on the planet and one of the most widely studied.

Liberty Tire is investing capital and ener gy into a range of opportunities, including the development and growth of new prod ucts and new markets. This requires col laboration across the industry and honest conversations about options for end-of-life tires. Interestingly, the growth of the elec
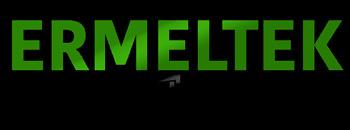

tric vehicle [EV] market will actually increase the number of tires being recycled every year. An April 2022 study from Clean Fleet Report shows that for a variety of reasons, including increased weight and higher torque, tires are proven to wear out roughly 20 percent faster on an EV than on an internal combustion engine vehicle.
Where do you see the tire recycling market heading in the future?
We’re very excited about the future and be lieve that looking at ways to vertically inte grate will strengthen our ability to establish new markets. As the focus on sustainability continues to grow in the minds of the con sumer, and companies increase efforts to provide solutions for a truly circular economy, innovation will pave the way to creative new uses for a material that has so many valuable properties. RPN
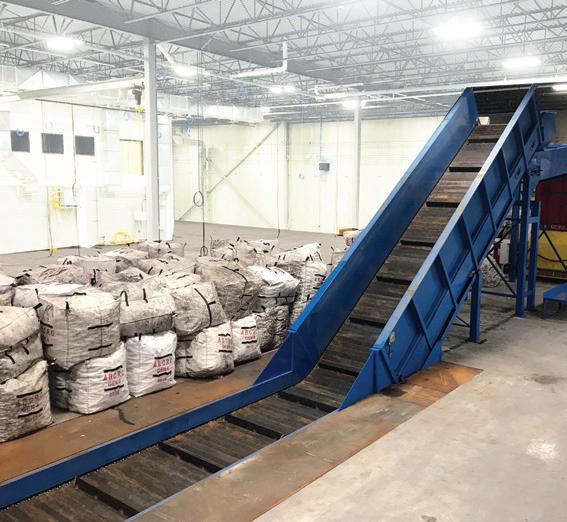
From your perspec tive, how effective are current end-of-life tire programs and what are some of the challenges and opportunities that they present?
What are some of the main challenges that the tire recycling indus try is currently facing?
WHAT’S THE RIGHT GRINDER FOR YOUR OPERATION? A
When it comes time to add or replace a grinder in your equipment fleet, one of the first questions you should consider is, “Do I need a tub grinder or a horizontal grinder?”
It is important to compare the two grinder designs and features for yourself and then determine which is right for your operation. Here is a brief overview of what to consider during the selection process.
SAFETY
According to David Steege, recycling account manager at RDO Equipment, properly trained and experienced operators know that if they are working with material that may contain non-organic contaminants (i.e. metal), they need to spend a bit of time sorting and paying close attention to every load they feed into the grinder. This step will help mitigate the risk of thrown objects.
“With tub grinders, features like the patented thrown object restrain system (TORS) found on Vermeer models, can help reduce the amount and distance of thrown objects,” explained Steege. “The TORS system has a deflector plate positioned across from the hammer mill to help redirect loose material back inside the tub. Making sure the tub grinder’s bowl is filled to proper capacity per your operator’s manual also can help reduce the risk of the grinder throwing material. Since tub grinders use gravity to feed the hammer mill, a full tub can provide an additional layer of protection to help keep material where it belongs.”
To mitigate the risk of metal contaminants cycling through with organic material, Vermeer grinders (tub and horizontal) can be outfitted with the optional Vermeer Damage Defense System. When a metal contaminant is detected during opera tions, the Damage Defense System will alert the grinder control and automatically initiate the shutdown process.
SPACE AVAILABLE
You may have heard that tub grinders need a lot more room to operate. This is due to the distance thrown objects can travel, but Steege explained that there is more you need to consider in the working area.
“Tub grinders will often be used to process a lot of different types of wood waste, and possibly in a setting where the incom ing material may not be the cleanest. Tubs can handle that type of material, but it’s always advisable to have more open area surrounding the machine. Otherwise, the operational space needs for horizontal and tub grinders are similar.”
MATERIAL SIZING
Next to assess is which machine will size your material more consistently. There are several factors to consider beyond the basic tub or horizontal grinder design.
“Consistency of material sizing can be more related to the qual ity of the machine and how all of the moving parts work together than whether it’s a tub or horizontal grinder,” said Steege. “The Vermeer duplex drum system and screen configuration optimize the grinders’ performance to produce a quality end product.”
According to Steege, taking a look at the size of the incoming material is a more important consideration.
“When I’m in the field talking to contractors and facility man agers about grinders, one of the first things I ask them about is the type and size of material they are going to be grinding. Horizontal grinders are more efficient than tubs at handling longer material because less cutting is required before it can be fed through the machine. So, if they are going to be running long branches and tree trunks, a horizontal grinder will likely be their more efficient machine. However, if they are running a bunch of stumps and odd sizes of material, they are going to want a tub grinder.”
For loose green waste, Steege said either grinder is fine, but tub grinders may be more efficient for their operation. “With horizontal grinders, the material is being force-fed into the drum, but tubs use gravity, so there are fewer moving parts involved with the process.”
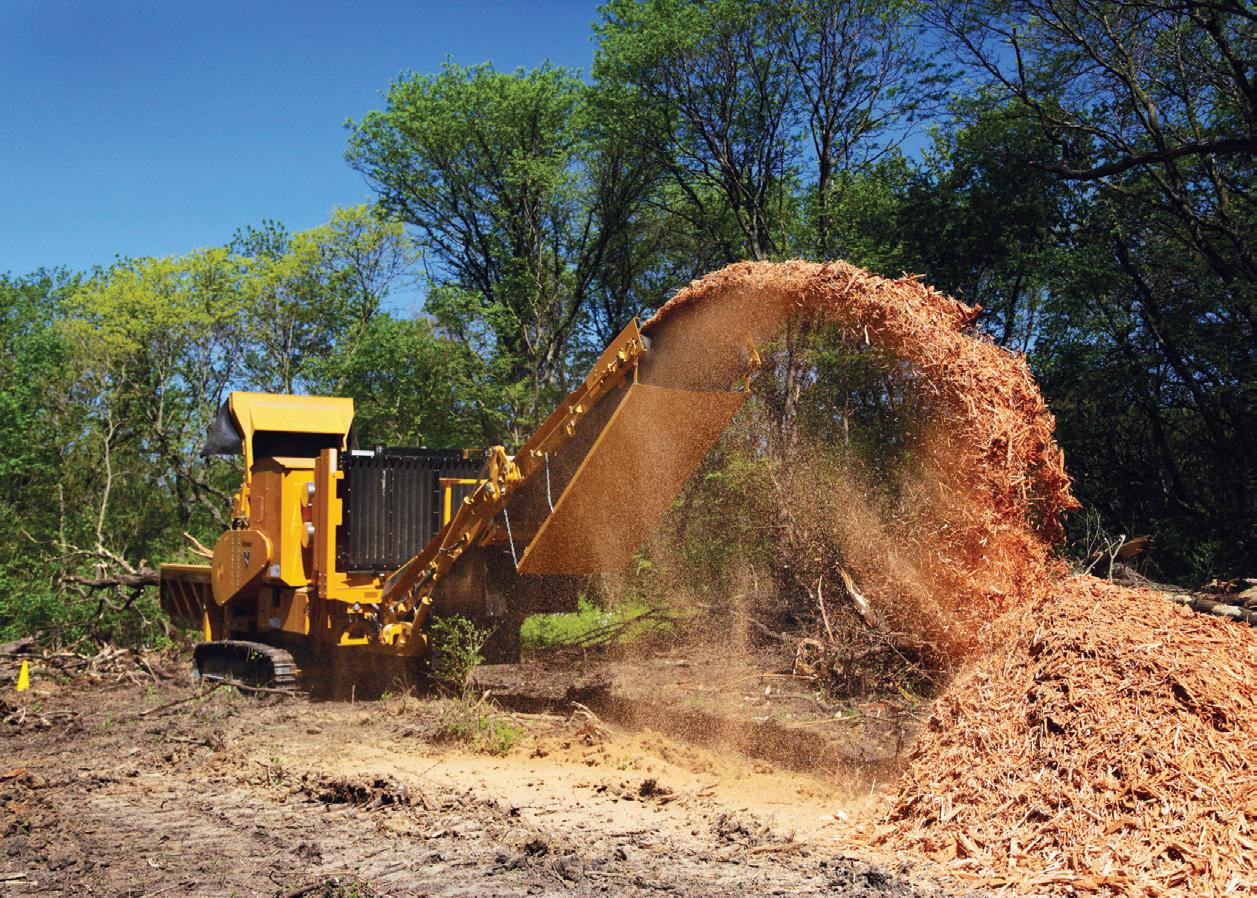
TRANSPORTABILITY
Depending on your line of work, hauling and moving a grinder around your facility is another factor to consider. If you’re working on a big job or you fre quently need to reposition the grinder, you’re going to want to look at a grinder with tracks.

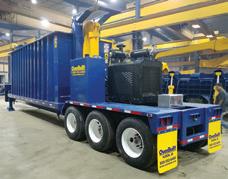
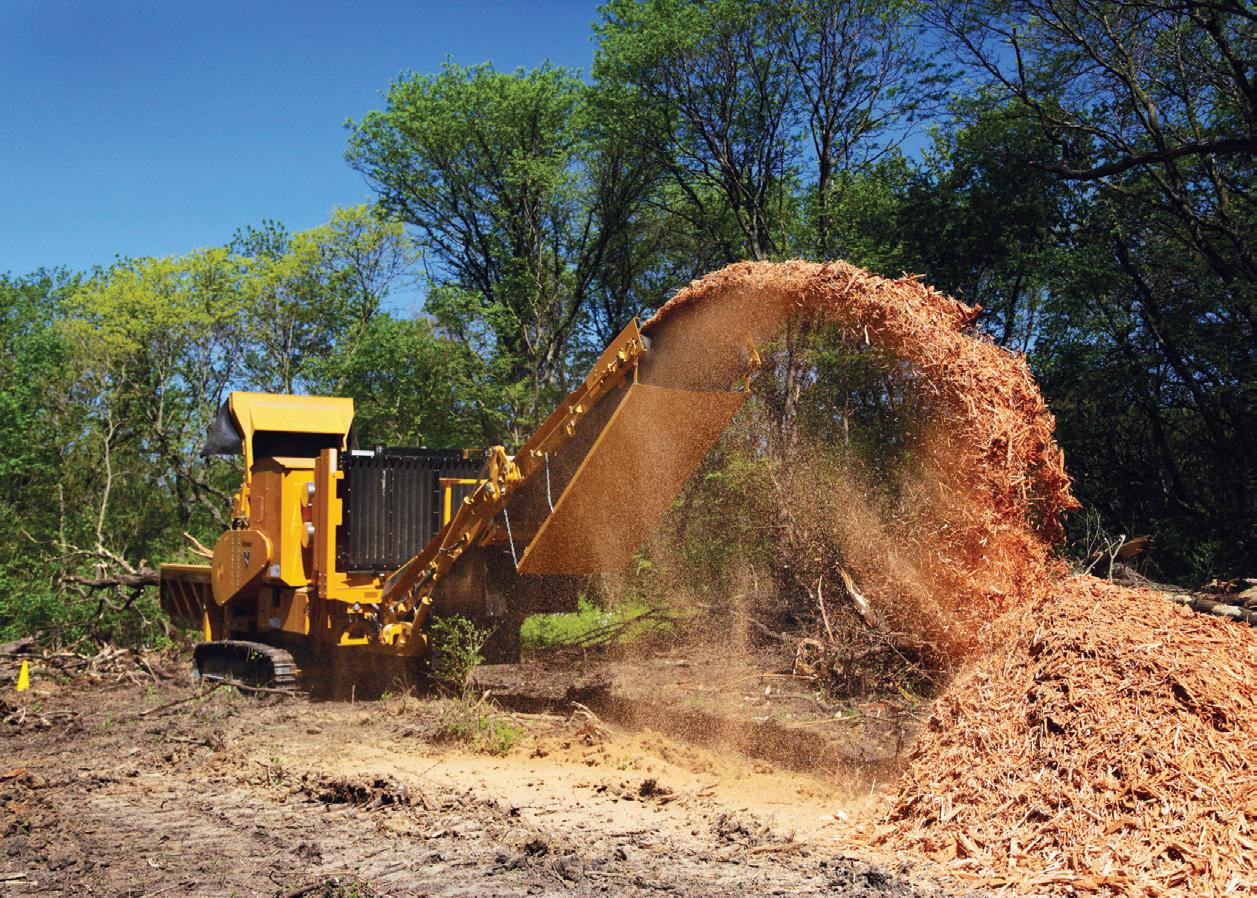
If you’re moving from one site to another, you may want to review any size and weight restrictions in your area to see which unit will be more efficient to haul.
“The sides on Vermeer tub grinders fold in for transporting, which gives them a similar travel width to a compa rably sized horizontal grinder,” Steege explained. “However, tub grinders without a loader are considerably light er than that same horizontal grinder, which can help reduce transportation expenses.”
WEIGHING THE PROS AND CONS
As you can see, both tub grinders and horizontal grinders have helpful qualities to offer. So, when it’s time to add or replace a grinder in your fleet, it’s important to think about your needs and what type of grinder will deliver the best results for your organization.
Making sure the tub grinder’s bowl is filled to proper capacity per your operator’s manual also can help reduce
risk of the grinder throwing material. Since tub grinders use gravity to feed the hammer mill, a full tub can provide an additional layer of protection to help keep material where it belongs.
Steege Recycling Account Manager, RDO Equipment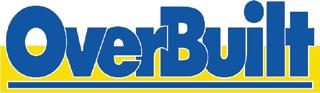
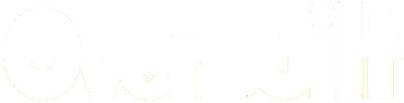
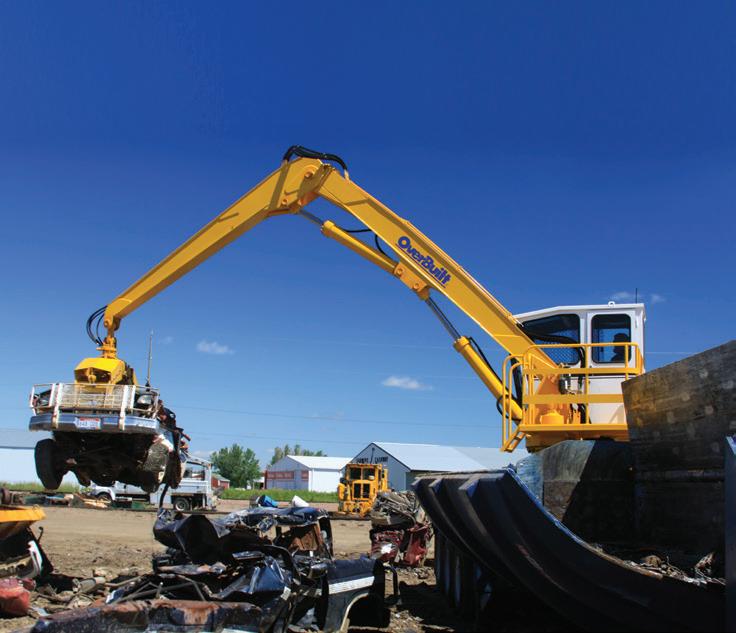
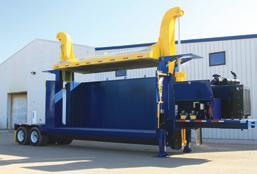
theDavid
OF THE YEAR
2022 TOP NEWS NEWSMAKERS
BY SLONE FOX, EDITORWhile the circular economy has been an important focus in the industry for years now, 2022 saw an even bigger push toward circularity in light of changing regional regulations and increased sustainability goals, such as bans on single-use products and increased extended producer responsibility programs. This year saw many companies teaming up through partnerships, joint ventures, and acquisitions to leverage each other’s strengths in the hope of closing the loop and developing more sustainable solutions for the recycling industry. Other popular themes from this year include the advancement of electrification and other alternative fuels, the continued development of robotics and artificial intelligence, as well the increased use of recycled feedstocks. Read on for our roundup of this year’s most notable stories that have set the stage for what will undoubtedly be an even more innovative and collaborative 2023.
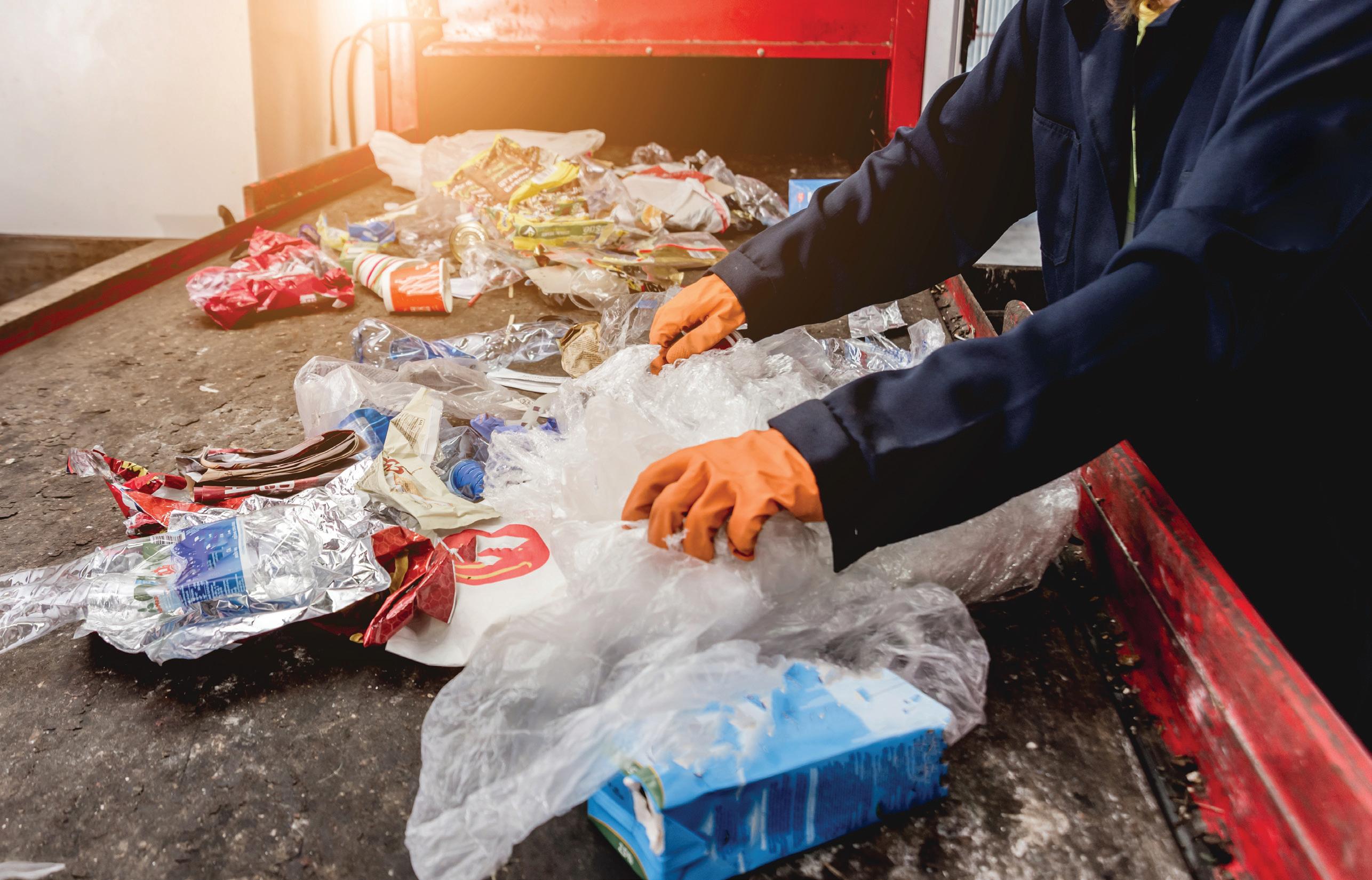
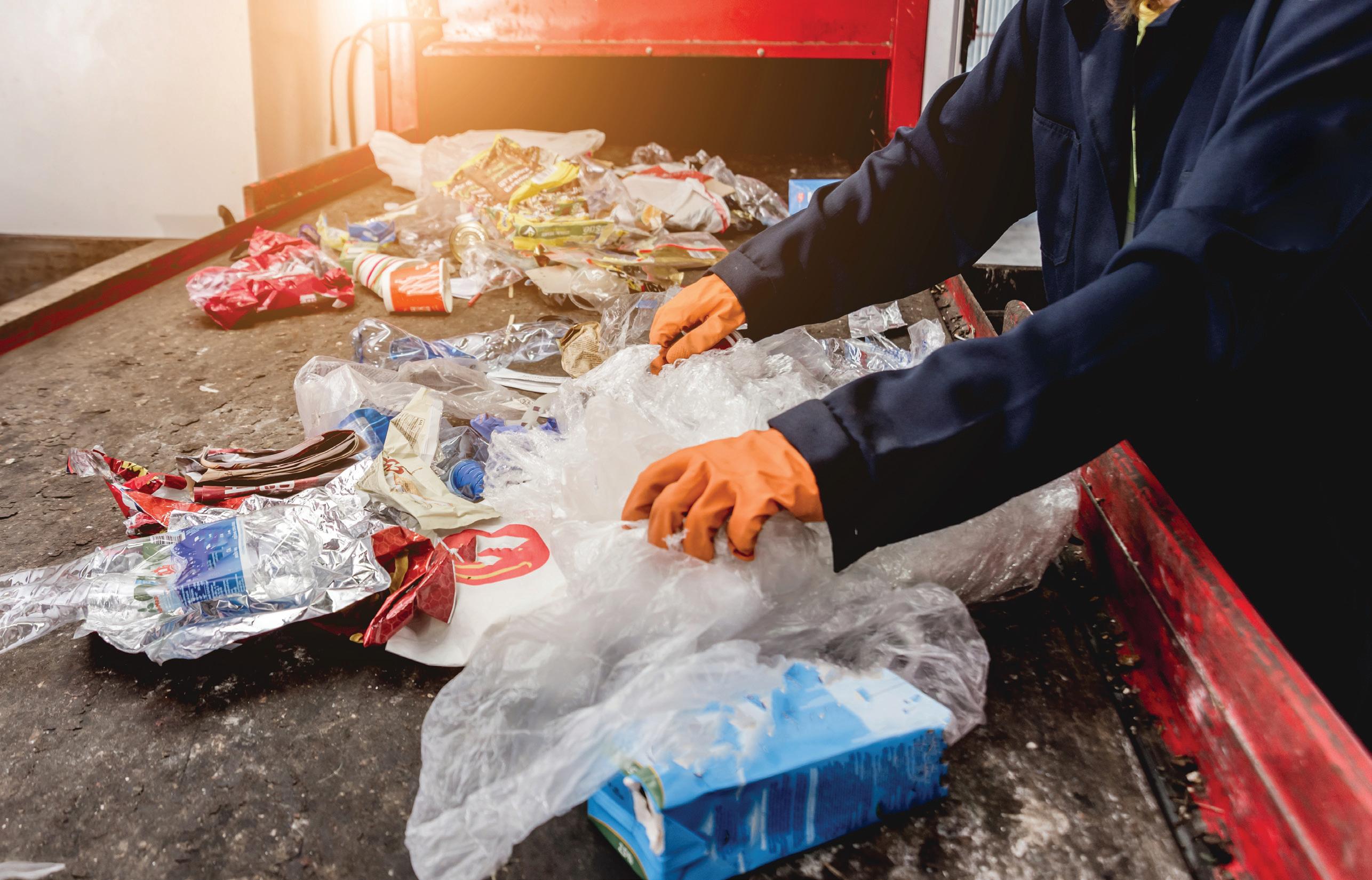
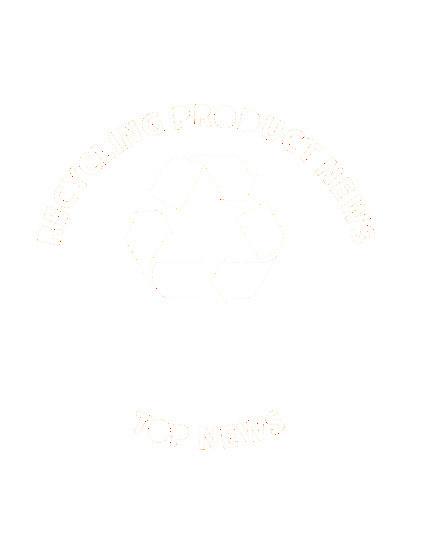
2022 TOP NEWS NEWSMAKERS OF THE YEAR
TEREX MP ACQUIRES ZENROBOTICS
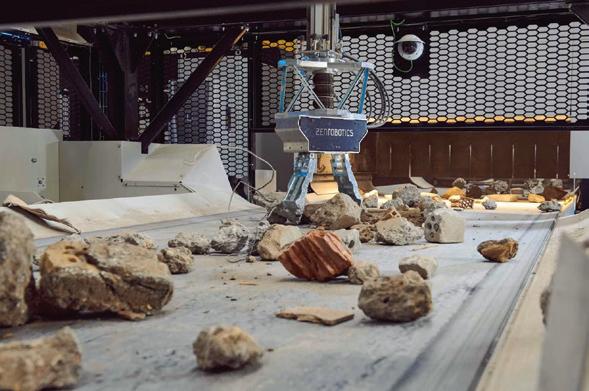
In one of the most notable acquisitions this year, Terex Materials Processing acquired the assets of ZenRobotics, a company that designs and creates robots that pick, sort, and recycle waste material. With the acquisition, Terex MP aimed to make the circular economy a reality by turning global waste into clean raw materials. Zen Robotics added to the Terex portfolio in global waste, where it continues to be operated as a standalone business while also benefiting from Terex MP’s broader market presence.
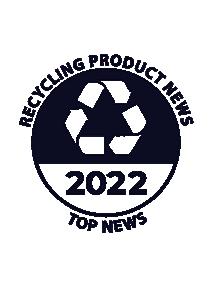
MCCLOSKEY INTRODUCES ENVIRONMENTAL EQUIPMENT DIVISION
Due to expansion and the realignment of its recycling capabilities, McCloskey International introduced a new environmental division earlier this year to support the company’s overall evolution and commitment to the waste recy cling sector. The new division moves forward under McCloskey Environmental brand. The strategy for the new division is built on partnerships with companies that have the expertise to deliver enhanced solutions, and together with these companies, McClo skey Environmental will design and manufacture a full range of environmental products including shredders, trommels, and stackers.

WM INVESTS $56
TO UPGRADE MRFS
WM announced its plan to invest $56 million to advance recycling technology at three materials recovery facilities in Washington state as well as North Idaho. The projects are part of WM’s goal to invest $800 million in recycling infrastructure through 2025, including au tomating existing facilities and developing new facilities. With the demand for recycled content products expected to rise, the investment will enable WM to capture more recycled materials and increase access to recycling.
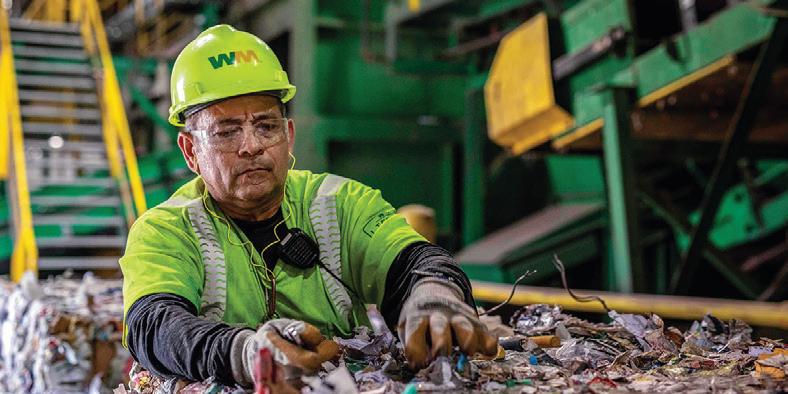
MILLION
ASCEND ELEMENTS RECOVERS
99.9 PERCENT PURE GRAPHITE FROM EV BATTERIES
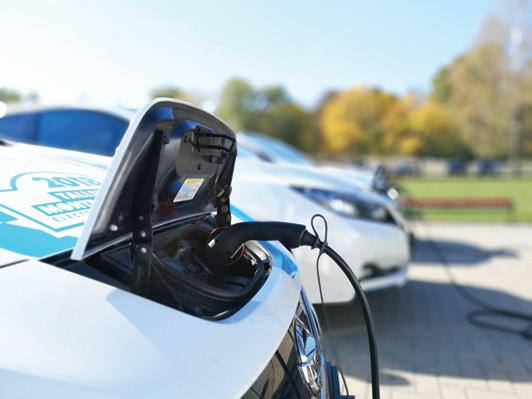
Ascend Elements and Koura launched a proprietary process technology earlier this year that yields battery-grade graphite material from spent lithi um-ion batteries. With consistent yields of over 99.9 per cent pure graphite and with energy capacity and cycle life on par with virgin battery-grade graphite anode material, Ascend Elements’ Hydro-to-Anode process technology has the additional benefit of extending recycling and manufac turing throughput beyond cathode active materials to anode materials as well. This technology increases the value of lithium-ion batteries recycled using the Ascend Elements process.
AVANGARD INNOVATE FIRST TO USE HONEYWELL TECHNOLOGY FOR PLASTICS RECYCLING
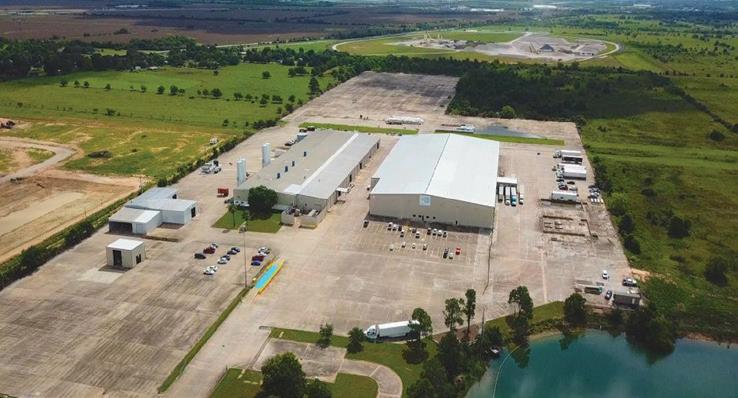
This year saw many joint ventures that all centred around advancing the circular economy. One notable joint venture saw Honeywell and Avangard Innovative team up to co-own and operate a facility within Avangard’s Natu raPCR complex in Waller, Texas. The facility will be the first in North America to use Honeywell’s UpCycle Process Technology to transform end-of-life plastic waste into recycled polymer feedstock that can be used to create new plastics. The planned advanced recycling plant is expected to have the capacity to transform 30,000 metric tons of mixed waste plastics into Honeywell recycled polymer feedstock per year. Production is anticipated to begin in 2023.
RECYCLING PRODUCT NEWS JOINS YOUTUBE
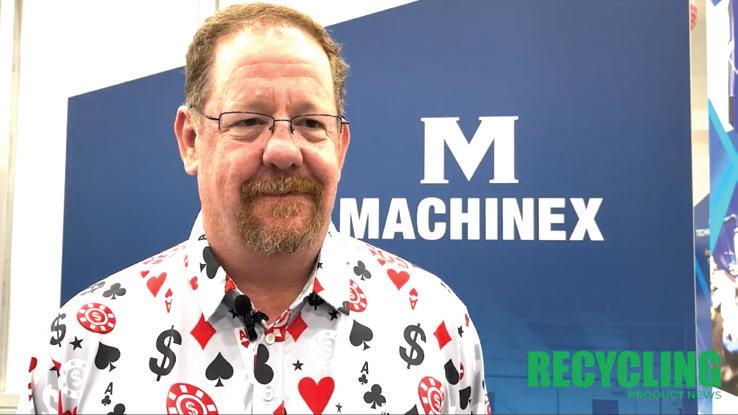
This year, we met with in dustry leaders to gain their unique perspectives on topics ranging from how the use of AI in recycling now includes data gathering and analysis, to the growing use of auto mated technologies.
Check out our YouTube channel for these videos, in addition to facility tours, exclusive interviews, and indepth coverage of innovative technology.
Connect with us by searching for Recycling Product News on YouTube.
2022 TOP NEWS NEWSMAKERS OF THE YEAR
CIRCULAR POLYCARBONATE
PRODUCED FROM POSTCONSUMER MIXED PLASTIC
SABIC launched its certified circular polycarbonate resin and blends made from the upcycling of post-consumer mixed plastic, a first in the industry according to the company. This solution, based on advanced recycling, aims to drive a circular economy for plastics by increasing the avail ability of more sustainable products.
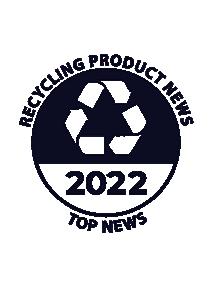
Through a process called pyrolysis, difficult-to-recycle used plastic is broken down into a liquid called pyrolysis oil. This is then used as a feedstock to create certified circular building blocks for high-performance plastics with the same properties as the virgin material – in this case, polycarbonate.
MATERIAL RECOVERY DOUBLES AFTER ROBOTIC SORTER INSTALLATION
Back in July, the Sunnyvale Materials Recovery and Transfer Station completed the installation of multiple EverestLabs RecycleOS SM-powered robotics to aid in quality control. The facility accepts garbage and recycling materials from 235,000 residents and all businesses in the area, processing 7,500 tons of recyclables annually. The installation of the sorting robots is expected to increase material recovery rates by two to three times compared to human sorters, as well as to help alleviate labour shortages. RecycleOS also enabled the Sunnyvale facility to track data for real-time continuous improvement and reporting.
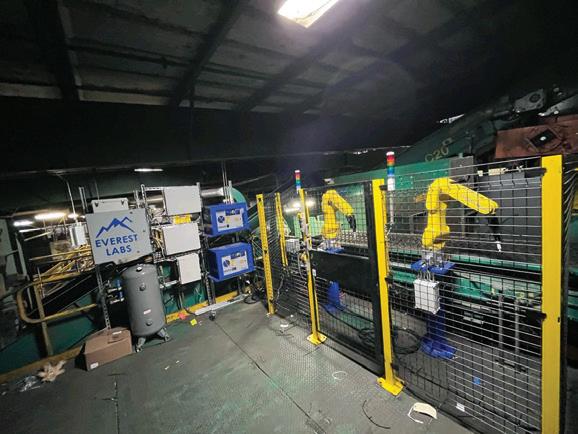
YOUNGER GENERATIONS LEAST CONFIDENT ABOUT RECYCLING

Astudy released this year by DS Smith showed that the generational gap in recycling has gone global with older people more than any other generation holding themselves accountable for recycling responsibly. While Gen Z is often considered to be the most environmentally conscious, they have the least confidence among all age groups in knowing how to recycle. Two-thirds of Gen Z respondents (those born from 1997 to 2012) blame barriers to recycling, including con fusion over what items can be recycled, a shortage of recycling bins, and a lack of clear disposal instructions on products. Only 41 percent of those over age 55 see such obstacles. Plus, twice as many in the Gen Z group compared to older generations say they don’t know where to find advice on recycling.
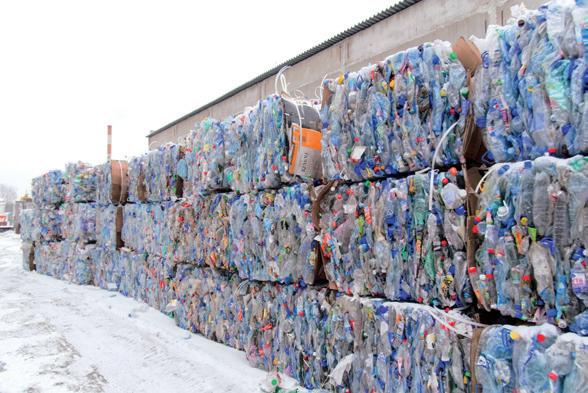
Prevent
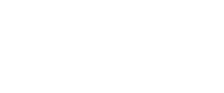

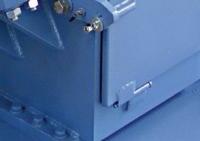
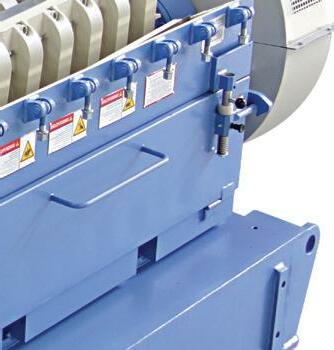
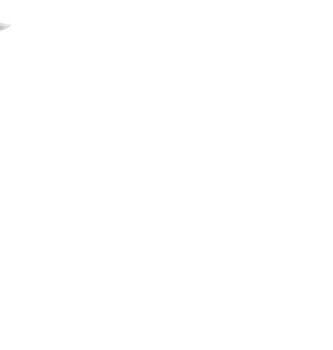
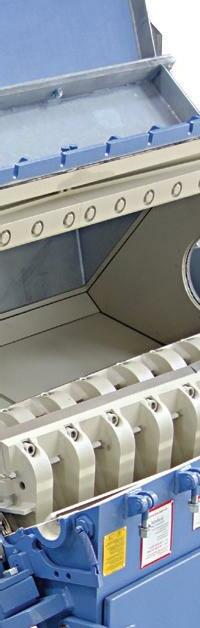
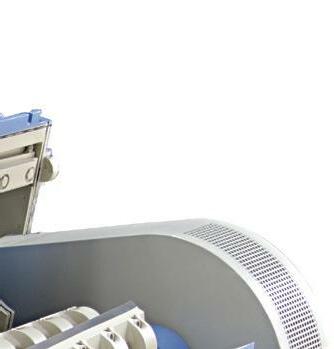
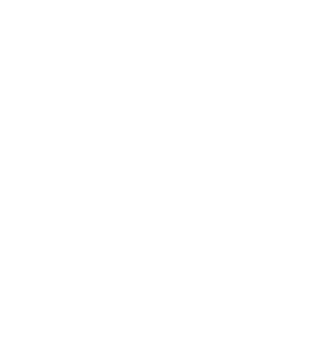
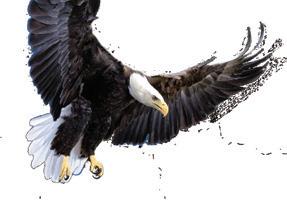
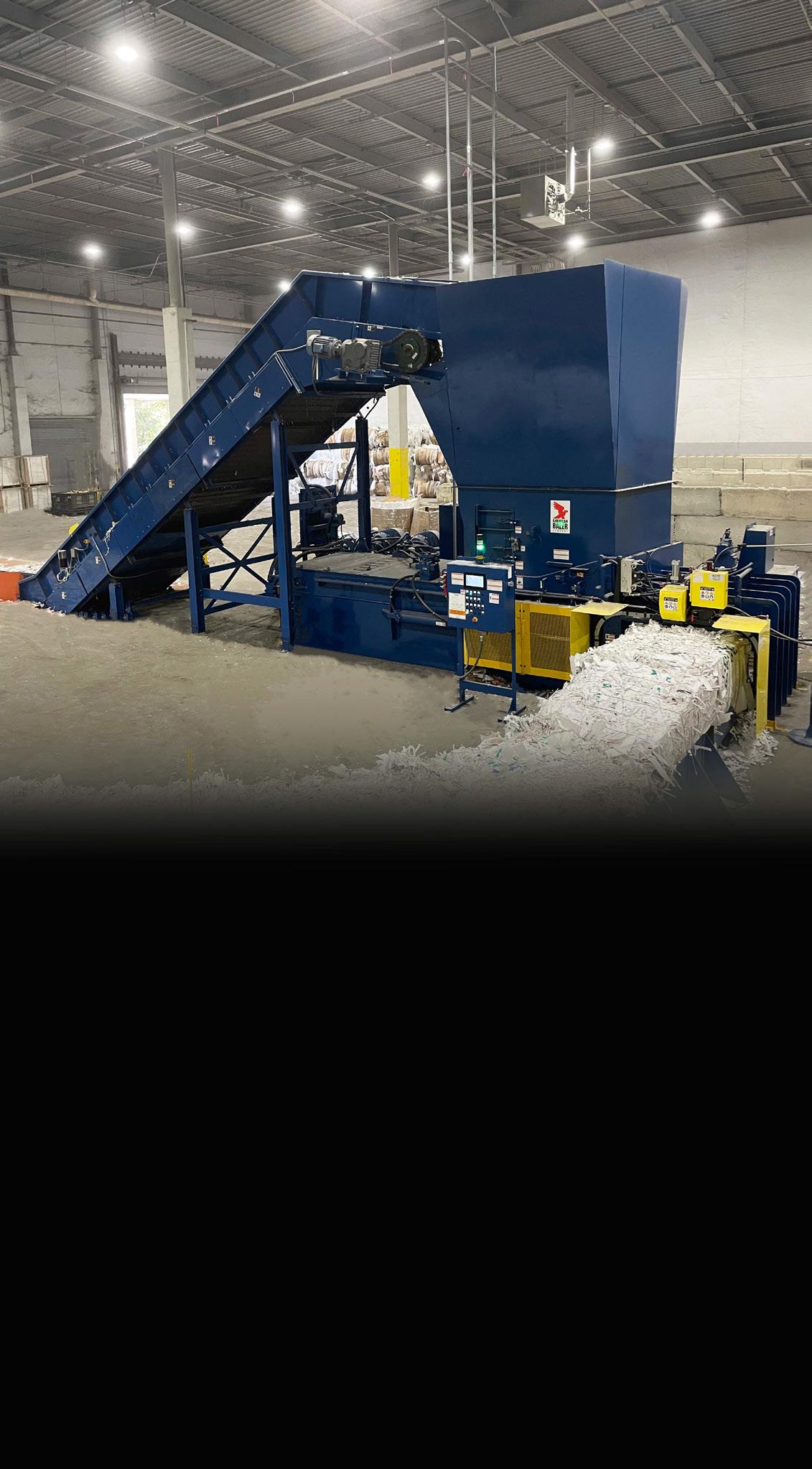
FL’s first fully electric automated side loader has begun operation in Squamish, British Columbia. This came as part of GFL’s plan to reduce greenhouse gas emissions from its operations and increase the use of alter native and low-carbon fuels in its fleet. Approximately 15 percent of GFL’s collection fleet is fuelled with compressed natural gas, and the introduction of the electric truck will contribute to the company’s low-carbon goal.
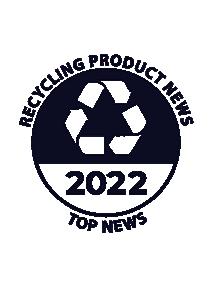
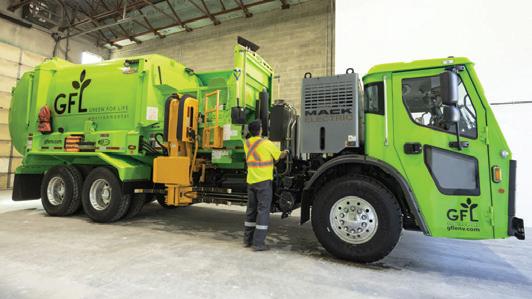
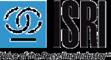

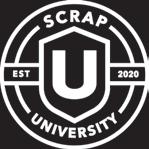
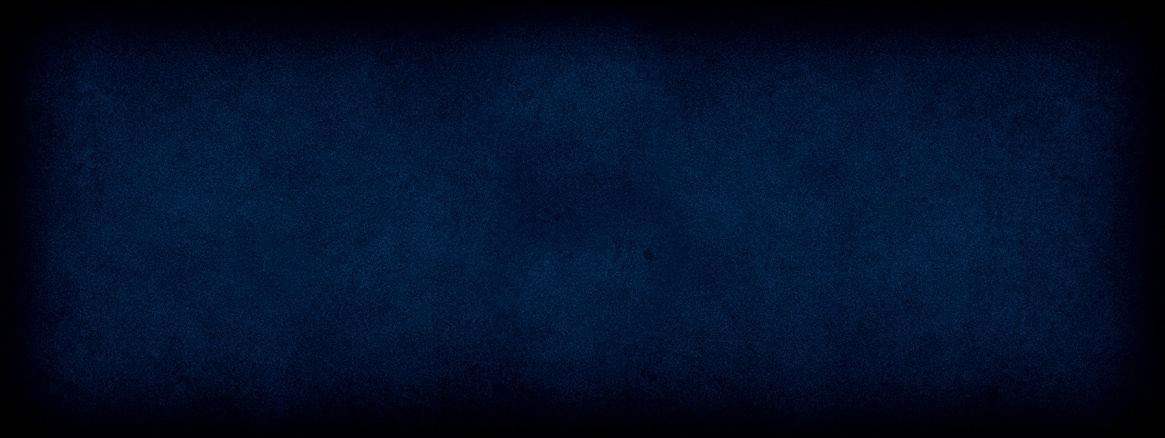
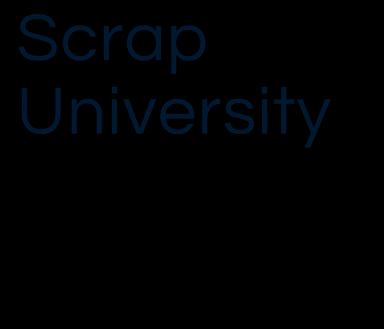
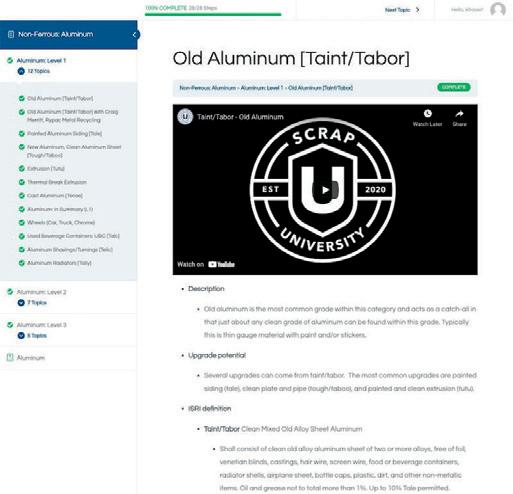
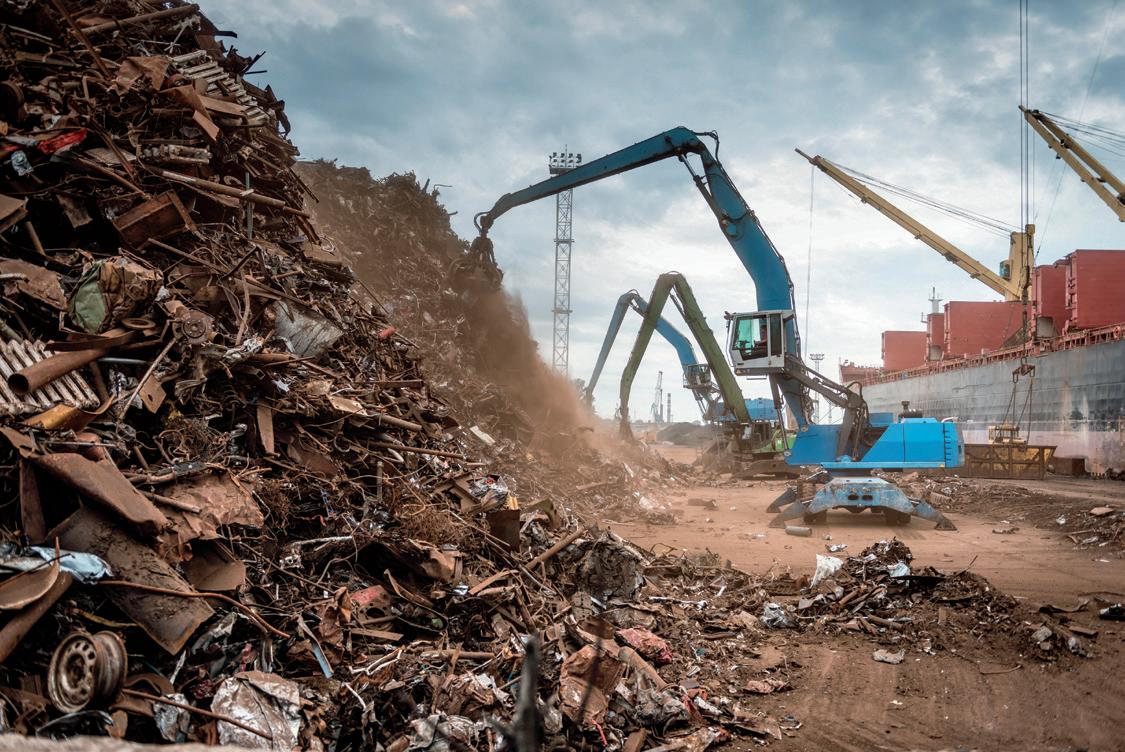
ALUMINUM CANS BETTER SUPPORT CIRCULAR ECONOMY THAN OTHER CONTAINERS
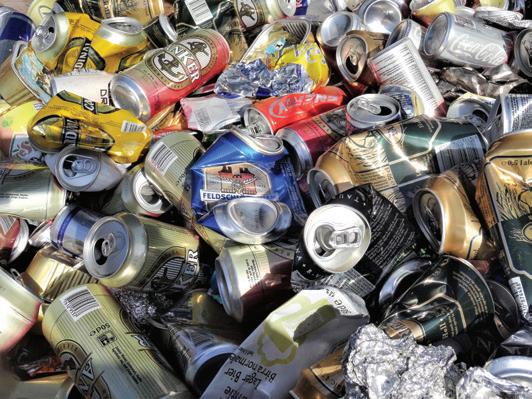
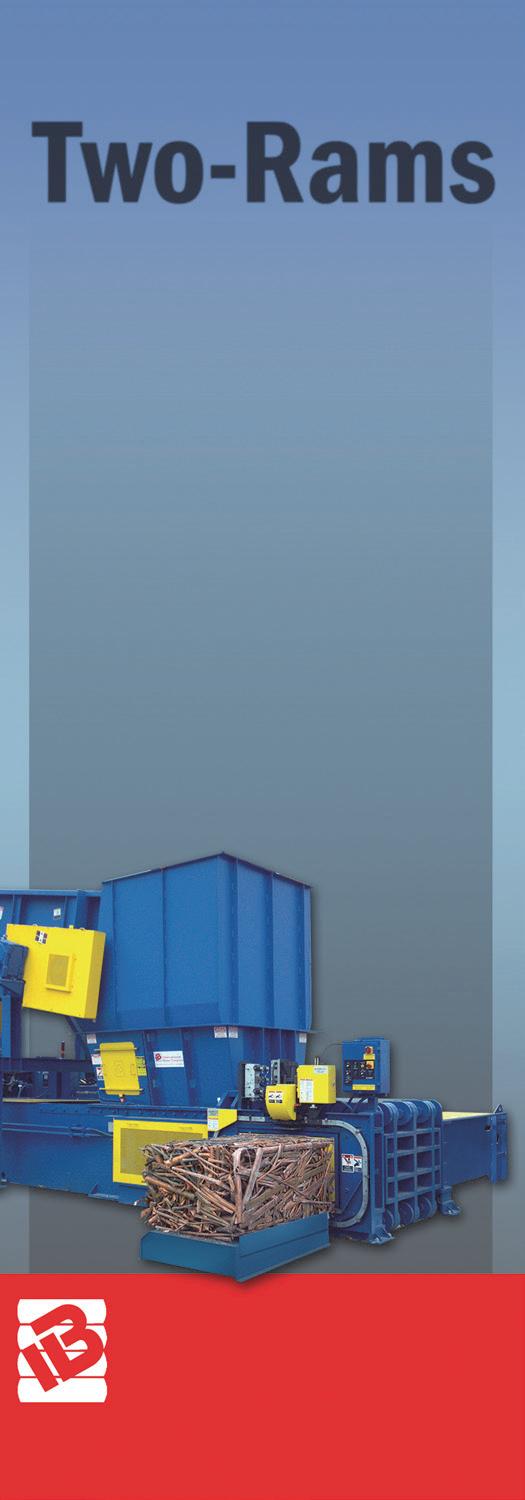
Research commissioned by the International Aluminium Institute into the recycling of three beverage container ma terials – aluminum, glass, and plastic – has shown that alu minum cans best support a circular economy. The study showed that compared with aluminum cans, more glass and plastic bottles end up in landfills because they are not collected. In addition, the losses in the recycling system, once collected, is three times high er for plastic and glass bottles than for aluminum cans.
JOHN DEERE AND FORDCOLLABORATION
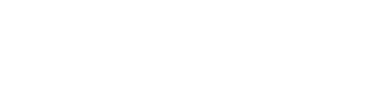

Earlier this year, Ford and John Deere teamed up to produce a new sustainable concept Gator, a machine prototype built in collaboration with Ford Motor Com pany’s sustainable materials team to examine ways of taking waste streams, like plastic bottles, and turning them into viable machine components. The machine featured a hood made of plastic bottles pulled from the Mississippi River and a storage bin made of coconut filler. Other materials used in the produc tion of the prototype included soybeans, flax fibre, sugar cane, hemp fibre, and fishing nets.
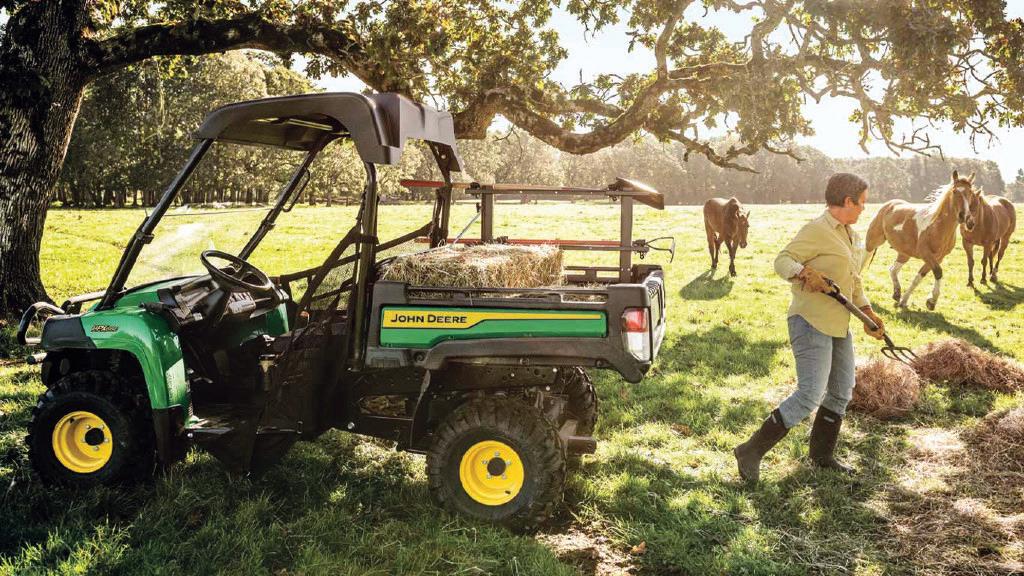
THE BIPARTISAN APPEAL OF COMPOST
BY FRANK FRANCIOSIs I write this article, we are watching the results of Americans going to the polls in a highly partisan era of
Partisanship becomes a real factor in achieving sensible economic, environmental, and health decisions in our country. Those of us affected by it find ourselves working to navigate the very different priorities of two parties.
But compost makes our job easier. Compost itself, and the commercial composting industry at all scales, has so many benefits, appeals, and arguments for people to support and adopt it that we find in our meetings with regulators and legislators in the past year that the idea is quick to catch on. It shows as our membership continues to grow, surpassing 850 organizations and businesses plus an increasing number of individual advocates for the first time since our formation three decades ago. The support we’ve received in the past few years for the product, the process, and the businesses created by our industry has been phenomenal and has enabled us to expand our reach in many ways.
NEW TRAINING INITIATIVE GROWS EXPERTISE ACROSS THE INDUSTRY
Last June, we launched Compost University – not a building of brick and mortar, but an online study hall (officially called a learning management system in the industry). Compost Uni versity delivers training covering the full range of composting issues (safety, feedstocks, odour, regulations, contamination, and more) to people where they are – regardless of level of business, geography, or time of day – through their computer.
This is a game changer for our industry, and will allow our Compost Research and Education Foundation to vastly improve its training reach. In the past, Compost Operations Training Courses – the standard in the industry – have required learners to be away from the loader/truck/turner for five days, limiting the numbers of people who could take the course. Now, we’re able to reach frontline operators who couldn’t come to training to help them develop better systems, and for diversity/equity/ inclusion/access purposes, to advance further along the ladder of their career than they were previously able.
Since mid-summer when Compost University opened its doors, 182 courses have already been completed by members and 32 non-members who have enrolled as Compost U Schol ars. Regulators are already passing the link to people applying for permits and composting products because they see value in the education.
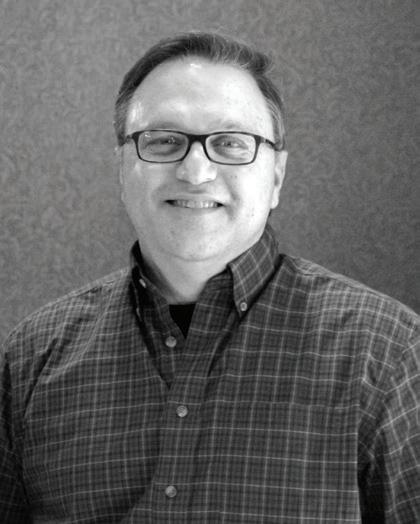
We continue to watch our community of certified compost operators and compost professionals grow and thrive. With the expansion of compost access across North America, profes sionals who know how to run compost facilities of all sizes in ways that benefit their communities are in high demand.
THE ON-THE-GROUND NETWORK IS GROWING
Composting is growing in awareness through more boots on the ground, and it’s a critical element with the federal govern ment turning its attention to organics diversion and compost ing to have advocates and businesses in the field to demon strate and promote understanding of what the industry does, the benefits of using compost, and the community and climate connection of diverting inedible food waste.
There has been a surge of cities, counties, and states writ ing Climate Action Plans (CAPs) – comprehensive documents laying out a foundation for how communities will approach reducing methane, finding alternative energy sources, and se questering carbon. Writers of CAPs are increasingly turning to the place compost fits in the food waste hierarchy to find local, scalable ways to handle inedible food waste in their commu nities, adding CAPs to the traditional government solid waste plans that have governed recycling and composting resources in the past.
Thanks to USCC’s growing number of chapters, the growth of composting at small scales thanks to the Institute of Local Self-Reliance’s Community Composter Coalition, and the outpouring of interest by individuals in USCC’s advocacy com munity, there are voices ready to speak for expanding com posting at the ready. Chapters were key to raising the profile of composting and gaining co-sponsors for the Compost Act through direct meetings with their congressional staff over the past year, and the Community Composter Coalition continues (along with municipal recycling and composting managers) to serve as frontline educators about the benefits and rules for community composting.
INROADS AND CHALLENGES
The industry is making inroads with both state and federal legislation and grant programs that are directing unprece dented funding to the industry because of the growth of our resources and programs. Along with the Compost Act, our attention is now on the Farm Bill, which funds farm, food, and resource programs; the Natural Resource Conservation
Service’s addition of compost to farm conservation practices; and an updated compostable labelling bill, which USCC and its partner the Biodegradable Products Industry will be producing from a stakeholder process.

Challenges loom that divert our attention from our prog ress in solving these fundamental challenges. Perfluoroalkyl Substances (PFAS) and their related chemicals are under standably alarming citizens after stories of water and soil con tamination, and the U.S. EPA has been slow to fund research for updated health effects of PFAS in soil. This has left state regulators, under pressure by their communities, to place non-standardized, non-researched PFAS limits on PFAS in soil that could lead to devastating consequences for the industry. Ours is an industry that offers so many benefits, such as car bon sequestration, water retention, lower greenhouse gases, and soil benefits to the planet.
USCC, on behalf of the industry, is working with coalitions of other groups who, like us, are passive receivers of PFAS products. (BPI and the Compost Manufacturing Alliance do not allow PFAS in items that they certify, so any entry via foodservice ware is coming through contamination of “look alike” non-compostable products, and the ubiquitous sourc es of PFAS throughout the consumer supply chain.) We are also planning aggressive lobbying and public information campaigns to alert the public to the danger these regulations and legislation pose to an industry formed to do good for the globe, such as Maine’s successful bill forbidding biosolids use. We are also pressuring the USDA to fund research studying the plant uptake of PFAS in soils using compost so there is an
equivocal answer to this question.
We will continue, even in a divided Congress and U.S. state houses that run the gamut of the political spectrum, to bring forward the benefits of compost and compost businesses to the planet, as well as green jobs and local economies. That’s something everyone can agree on.
FRANK FRANCIOSI is the Executive Director of the US Composting Council, the trade organization represent ing commercial composting at all scales in the U.S.Compost itself, and the commercial composting industry at all of its scales, has so many benefits, appeals, and arguments for people to support and adopt it that we find in our meetings with regulators and legislators in the past year that the idea is quick to catch on.
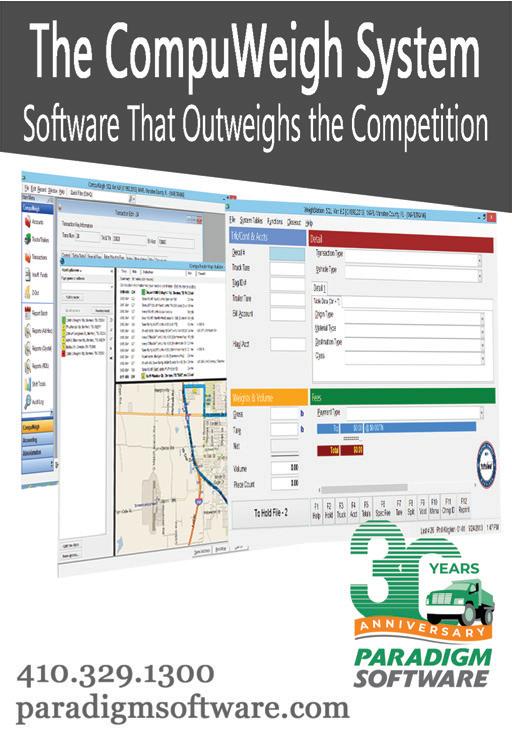
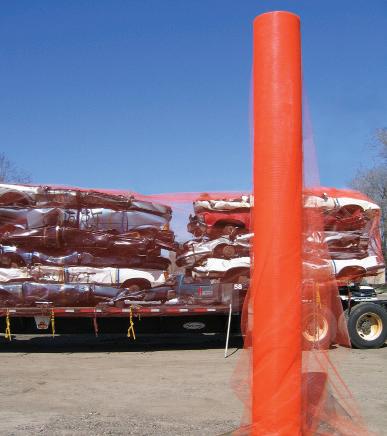
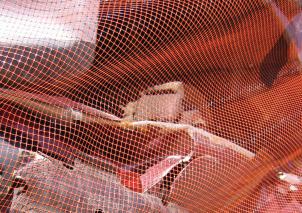
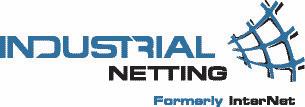
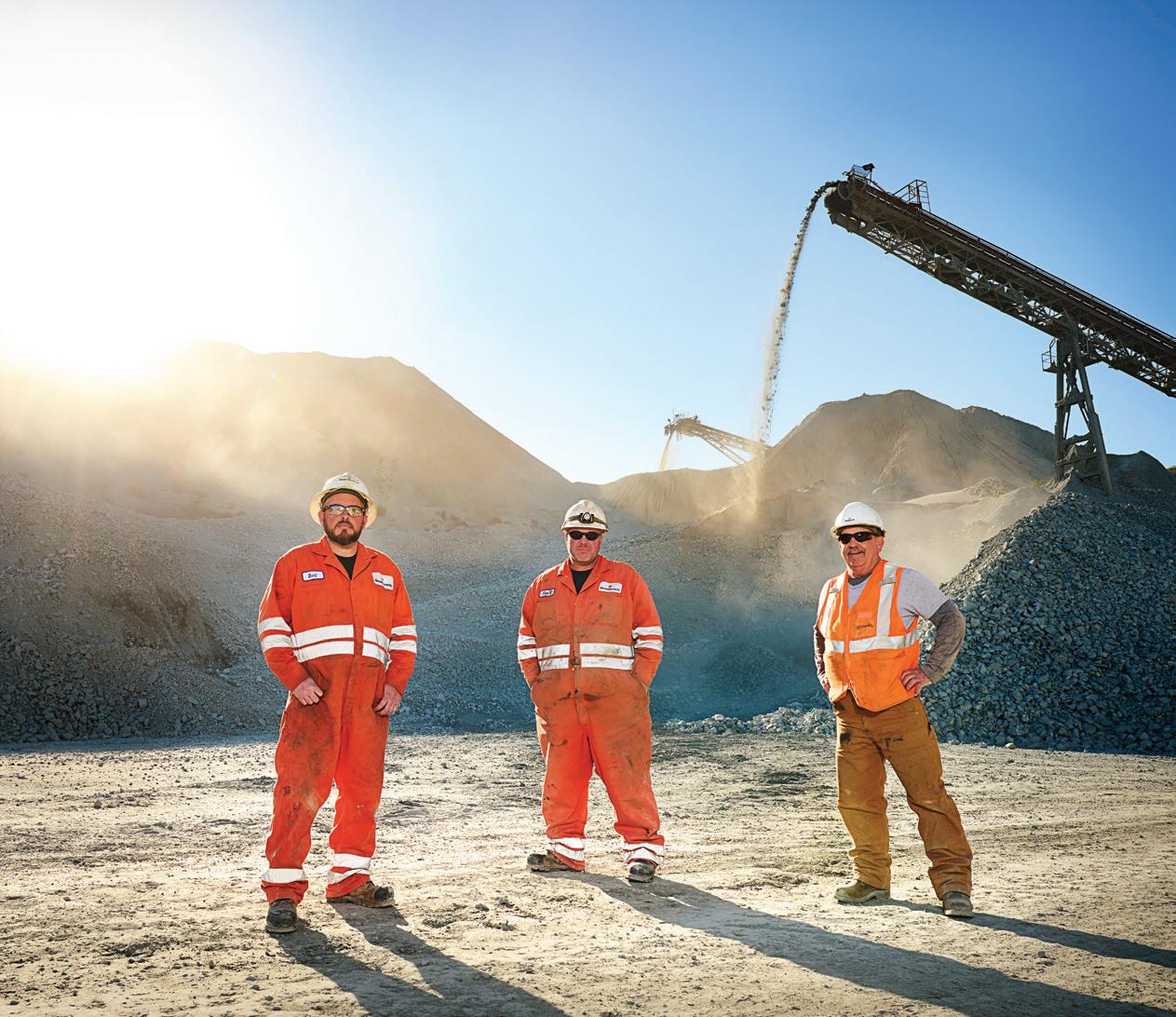
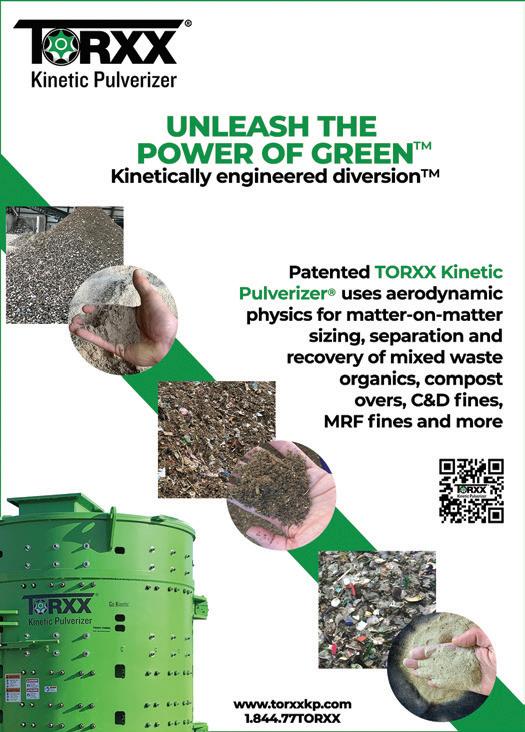
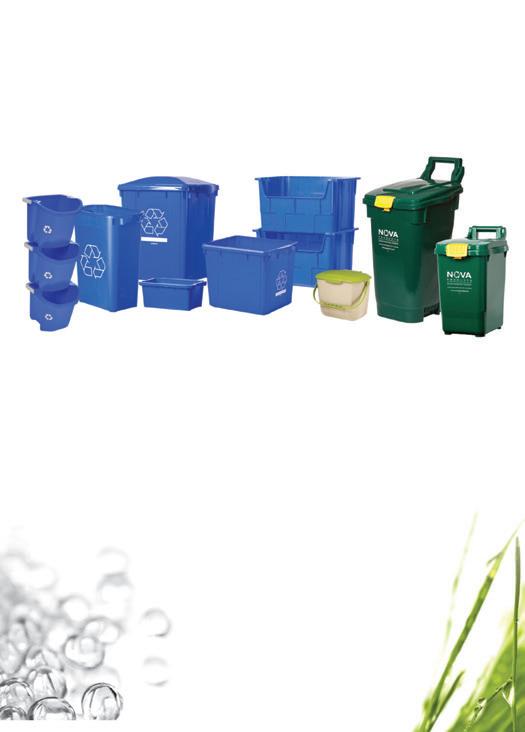

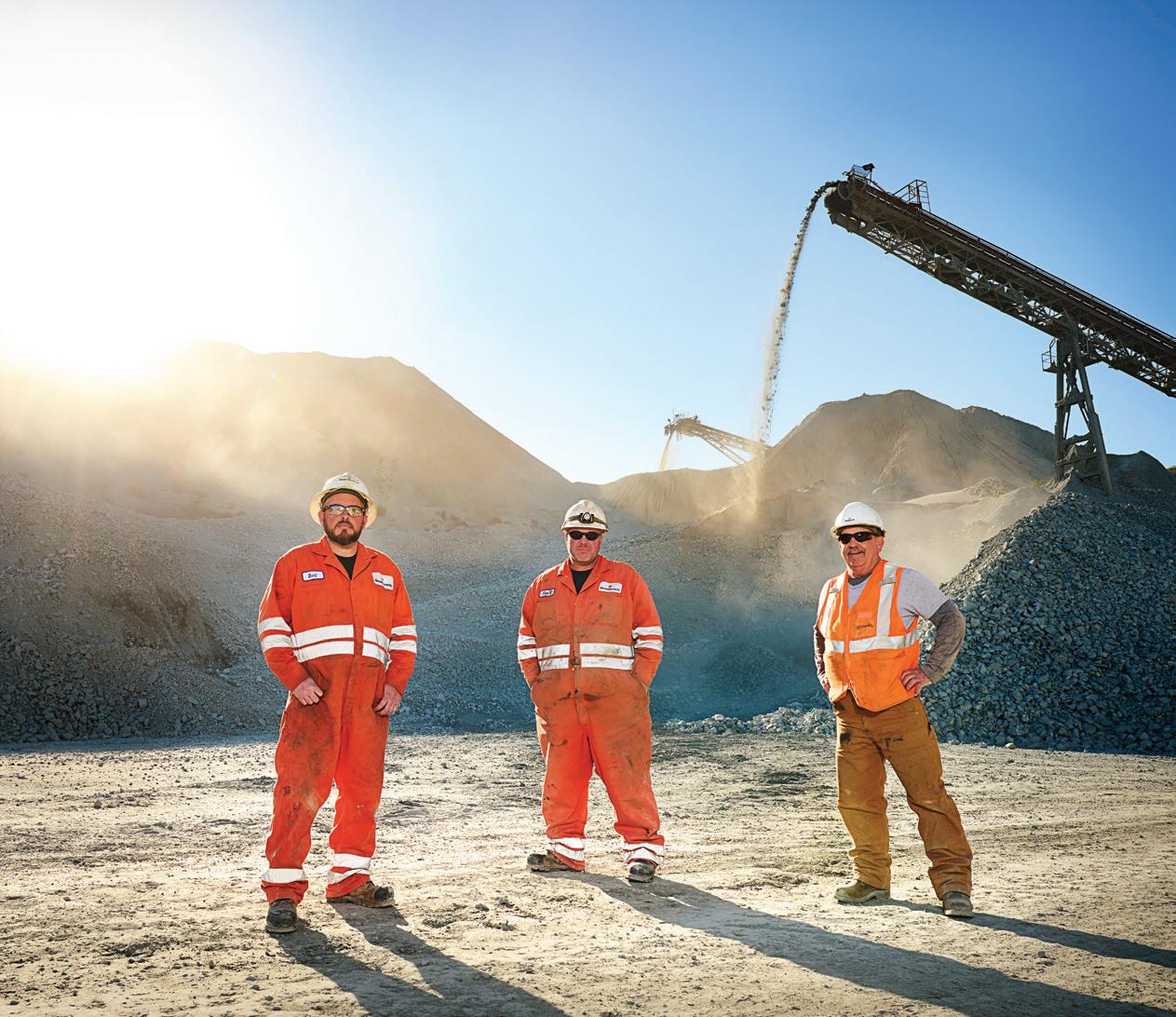
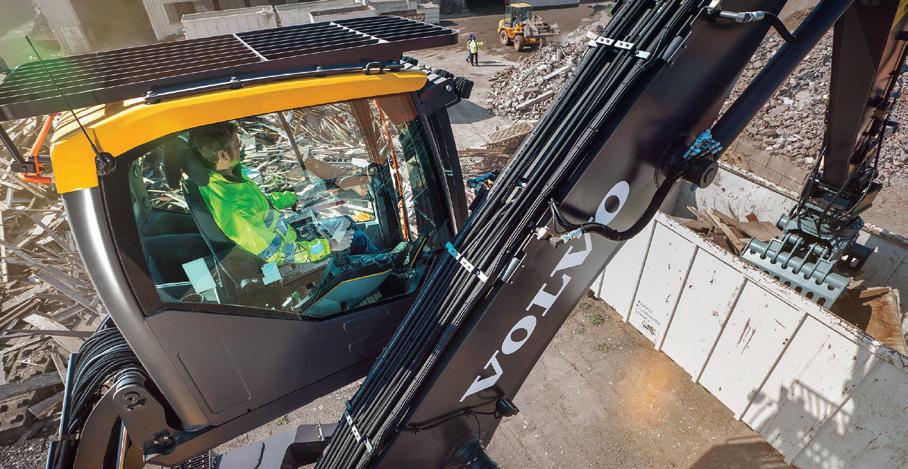
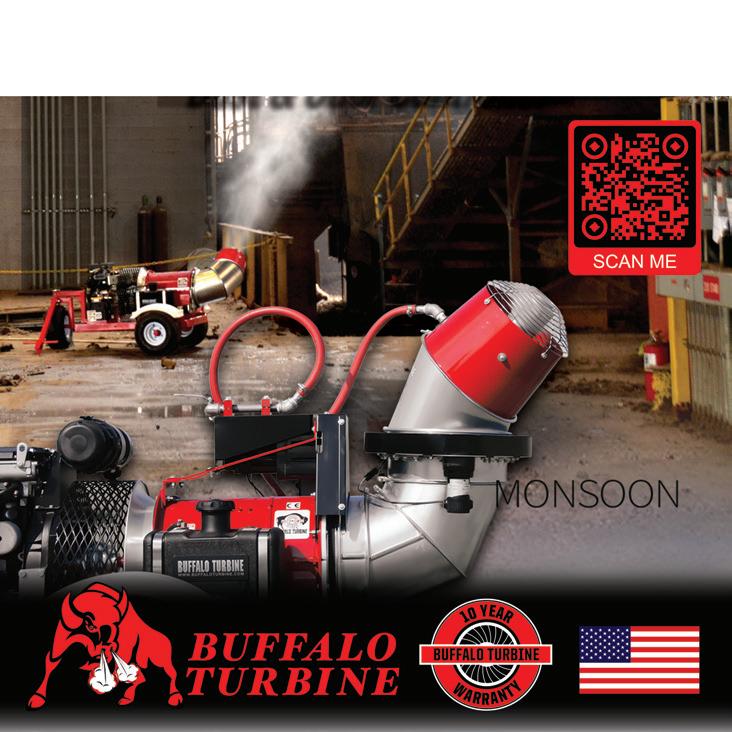
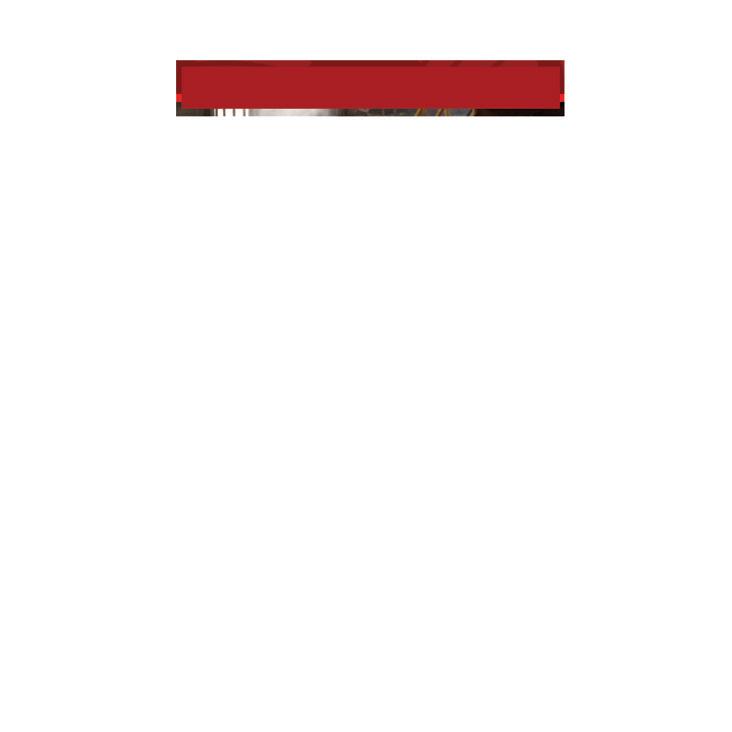
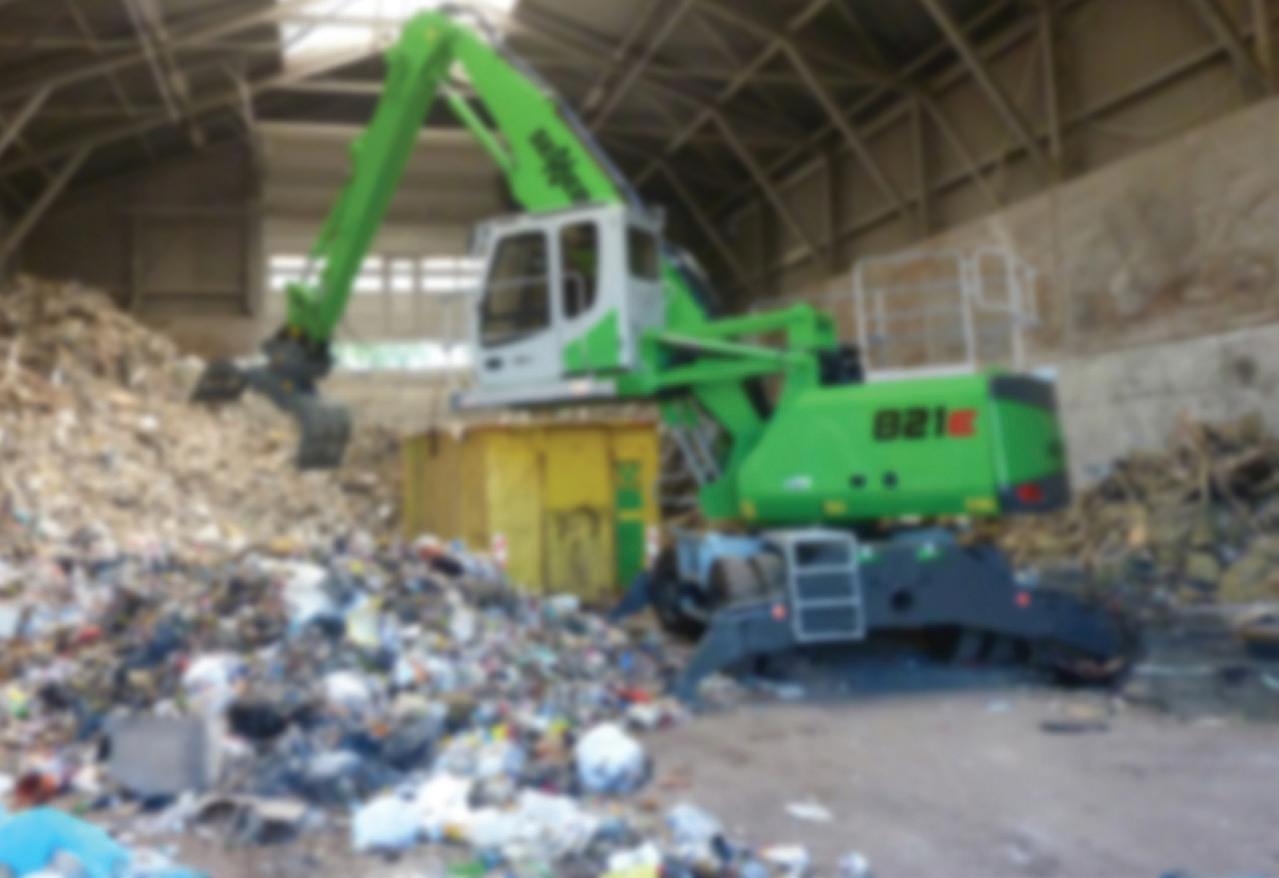
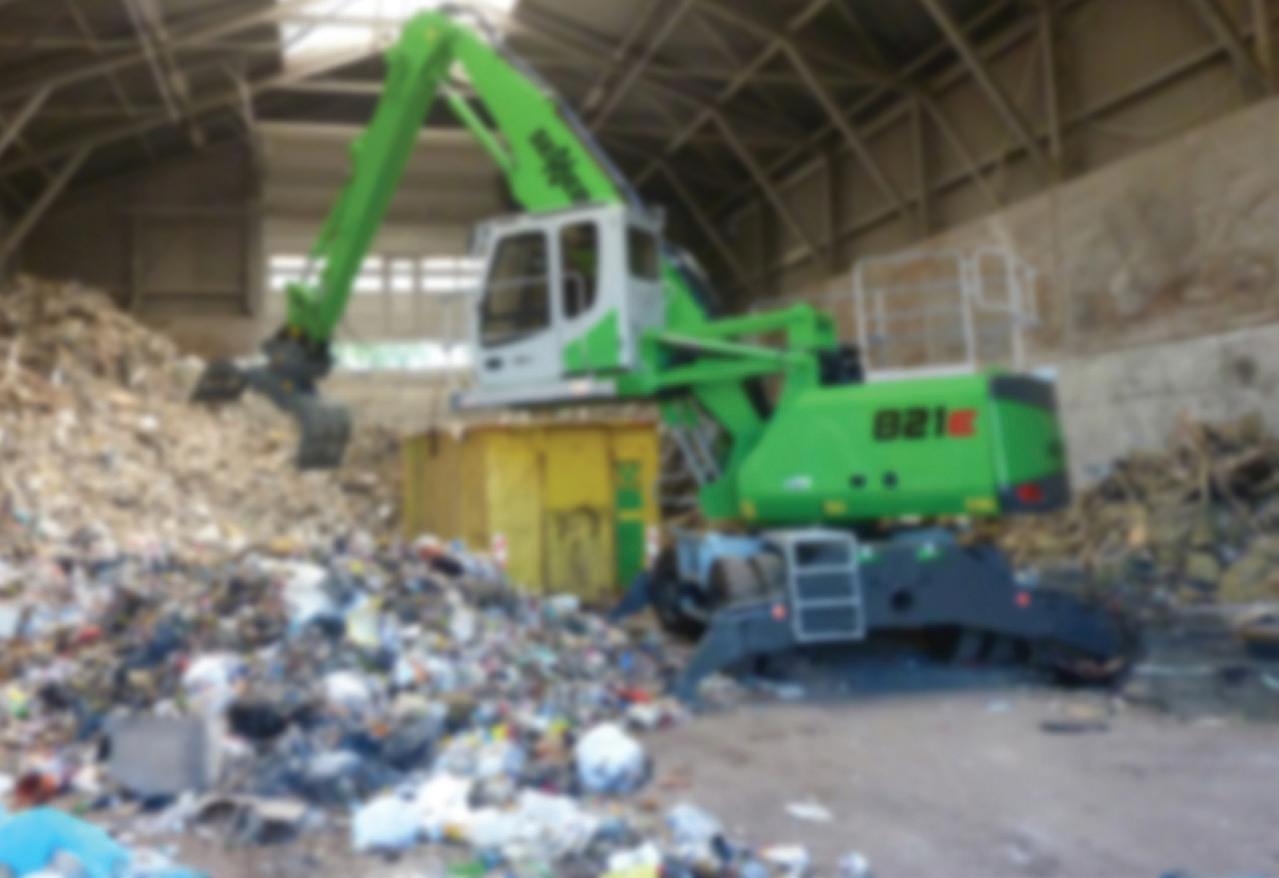
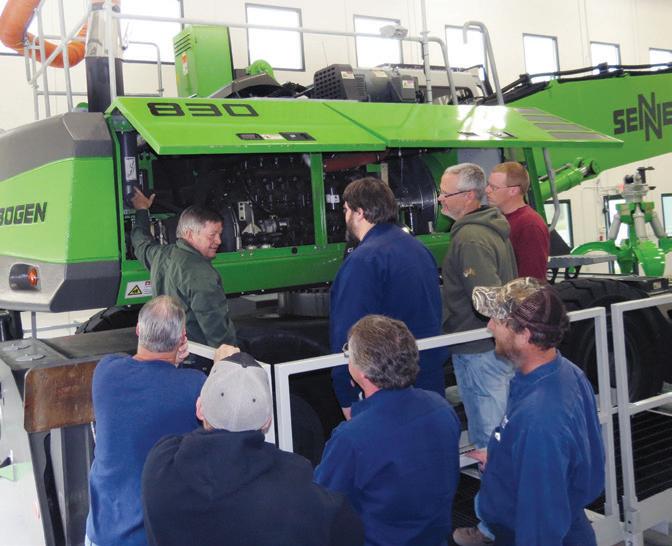
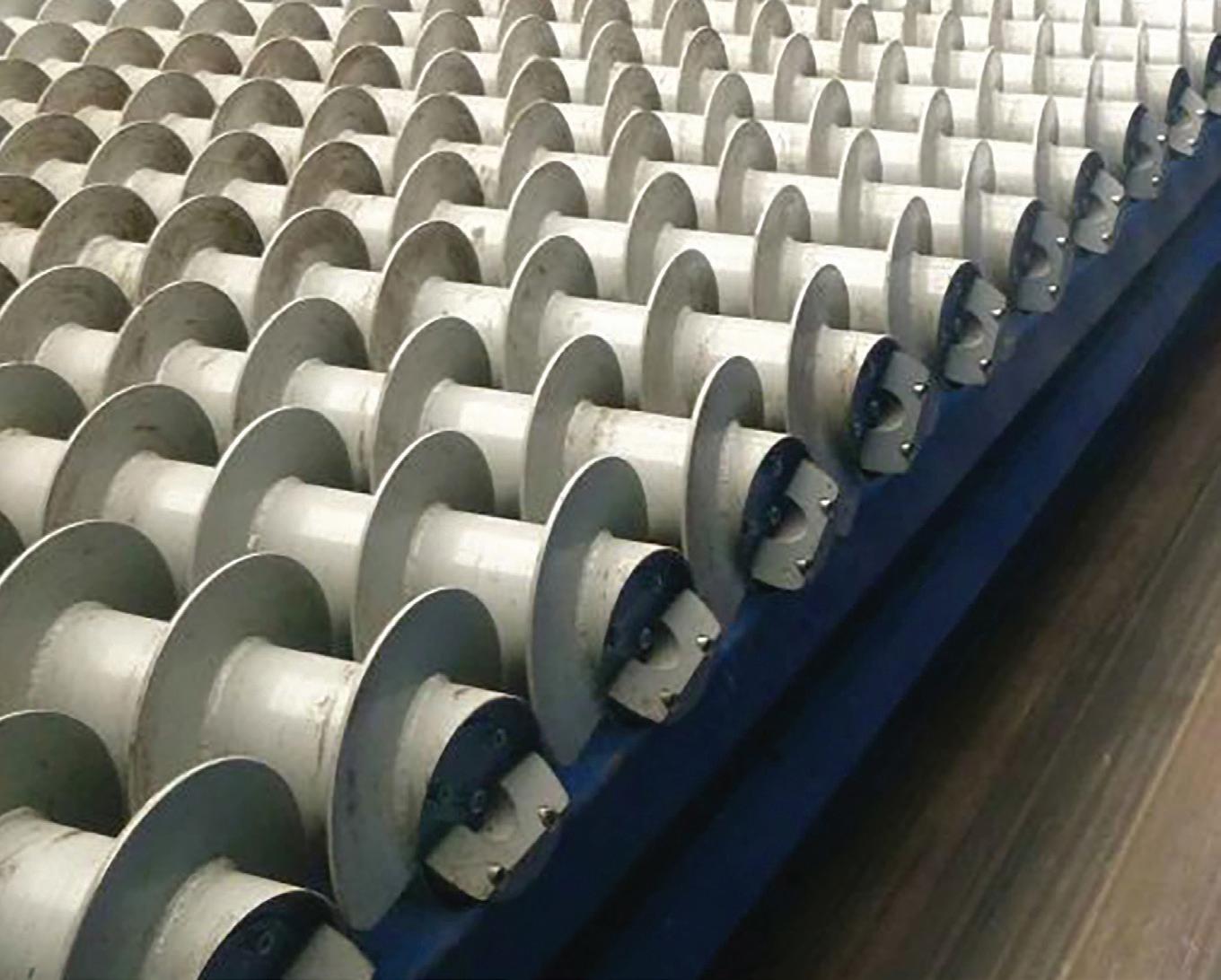
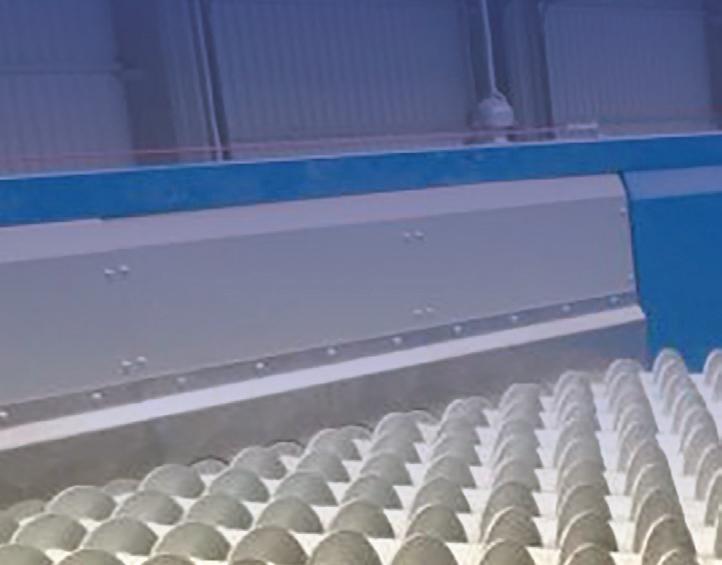
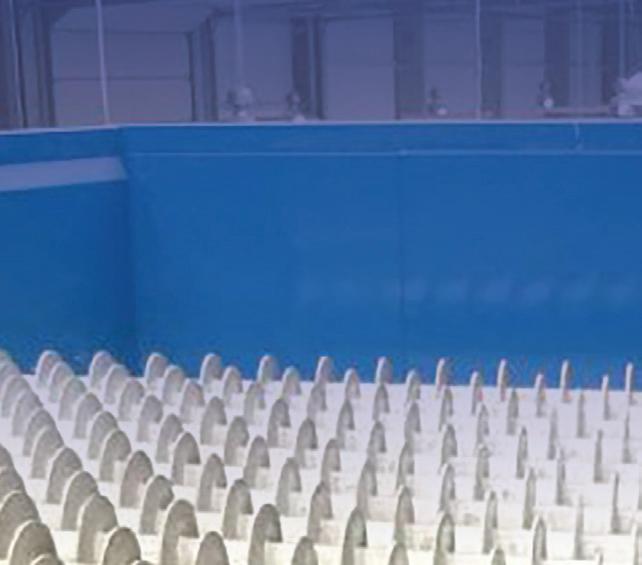
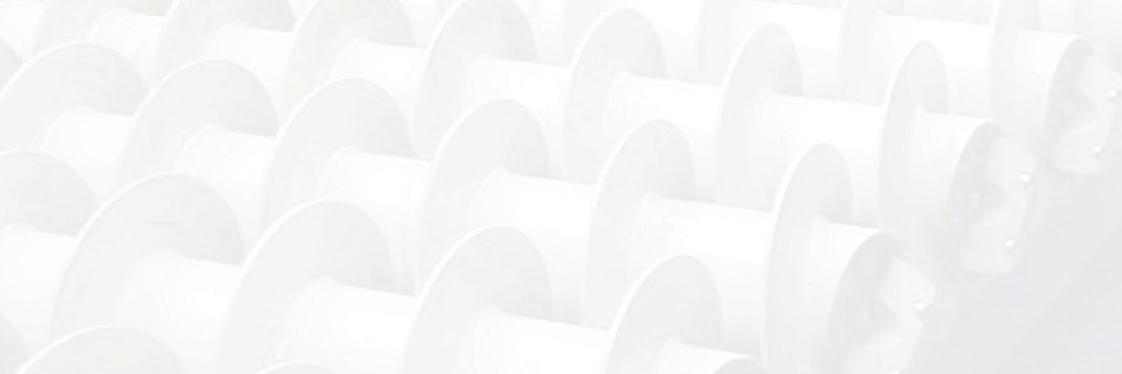
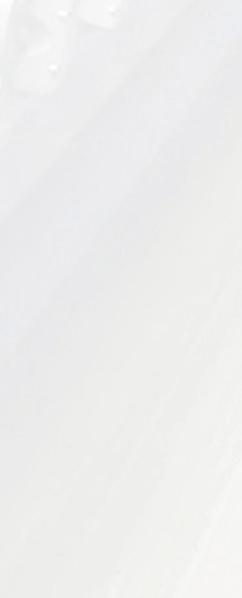


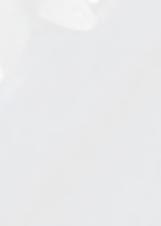
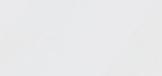

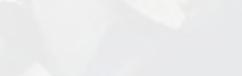
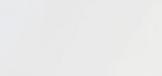
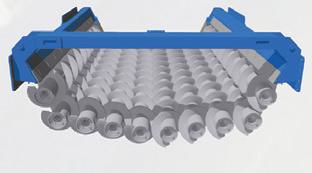
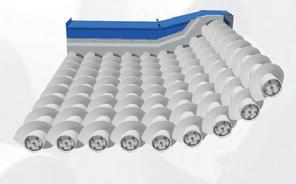
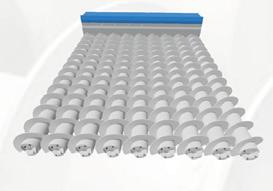