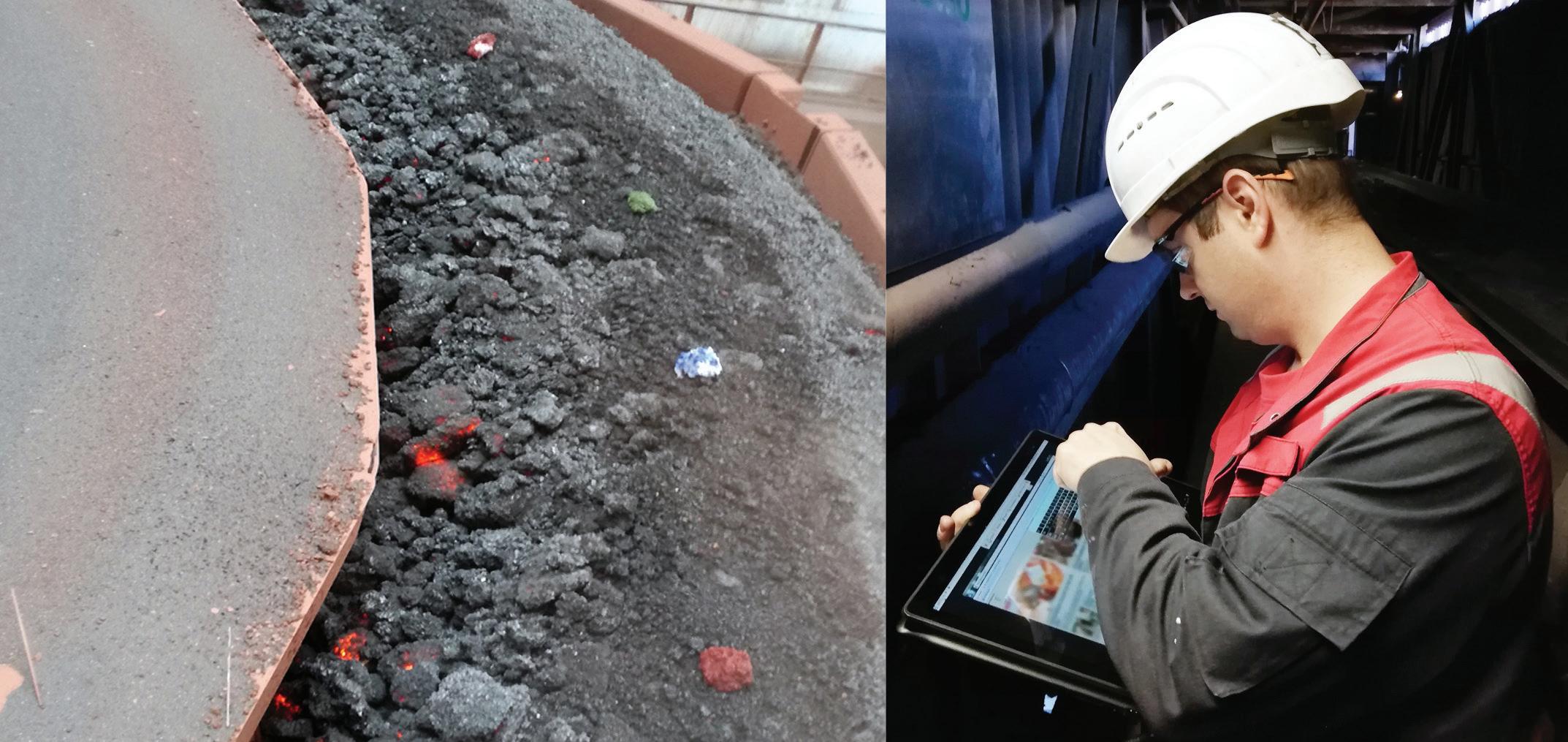
10 minute read
SmartSinter – Materialverfolgung von Schüttgut und deren Eigenschaften
from WINGbusiness Heft 01 2022
by WING
Bildquelle: © voestalpine Stahl Donawitz GmbH
Christian Weichbold
Advertisement
SmartSinter – Materialverfolgung von Schüttgut und dessen Eigenschaften
In modernen Lager-, Förder- und Produktionsanlage wird der Einsatz von Identifikationssystemen gefordert. Die Kopplung des Informationsflusses mit dem Materialfluss ist dabei ein wesentlicher Bestandteil neuer Produktionskonzepte. Dabei ist die Zielsetzung, in Echtzeit den Zustand des Produktes, bei gleichzeitiger Überwachung der Prozesse zu verfolgen. Die grundlegende Aufgabe stellt dabei die Initiierung, Steuerung, Überwachung und Dokumentation des Informationsflusses dar.
Für die Verfolgung und Steuerung von diskreten, standardisierten, eindeutig beschreib- und identifizierbaren Gütern bzw. Materialflüssen gibt es eine Vielzahl von Verfahren und Technologien. Durch automatisierte Identifikation (AutoID), Lokalisierungstechnologien, Sensorik und entsprechender Software können Objekte nahezu lückenlos und in Echtzeit verfolgt werden und sind somit nach Typ, Lokation und Qualität jederzeit bestimmbar. Nach eindeutiger Identifikation können Guteigenschaften wie Farbe, Gewicht, Werkstoff, Geometrie, Temperatur, Volumen, usw. letztlich referenziert werden.
In vielen Branchen wie dem Bergbau, dem Tunnelbau (Ausbruchmaterial), der Landwirtschaft und der Hüttenindustrie (Sinter) sind gewohnte Merkmale von Materialflüssen jedoch häufig nicht vorhanden.
In diesen Branchen handelt es sich vielfach um Stoffströme, die zwar kontinuierlich anfallen, aber bezogen auf ihre Eigenschaften inhomogen, unregelmäßig und daher in ihrer Qualität und physischen Beschaffenheit durch die verfügbaren Messverfahren nicht lückenlos bestimmbar sind und diese vor allem nicht eindeutig dem Gutstrom zuordenbar sind Die Qualitätseigenschaften dieser Stoffströme in Echtzeit jederzeit bestimmen zu können, ist für die Produktionsplanung und –steuerung wesentlich. Die bessere Informationsbasis könnte in Folge in einer effizienten Prozesssteuerung umgesetzt werden, welche über verbesserte Materialeffizienz auch positive Einflüsse auf die Energiebilanz, Umweltbeeinflussung und Wirtschaftlichkeit hätte.
Im Unterschied zu diskreten Strömen, bei denen in ununterbrochener Folge diskrete Mengeneinheiten einzeln oder bulkweise ankommen, ist dies bei kontinuierlichen Strömen von polydispersem Schüttgut nicht der Fall. Die Durchflussgesetze diskreter Ströme unterscheiden sich grundlegend von den Strömungsgesetzen inhomogener Schüttgüter. Es existieren keine offensichtlichen Anhaltspunkte zur Definition von konkreten Losen. Bisweilen eingesetzte Bewegungsstrategien wie FIFO (first in – first out), LIFO (last in – first out) usw. versagen spätestens dann, wann das zu verfolgende Gut aufgrund seiner Korngrößenverteilung zur lokalen Entmischung neigt und zufallsabhängige Staueffekte in betriebsbedingten Puffern eine Vermischung der Abschnitte des Stoffstromes bewirken.
Die spezifischen Eigenschaften des Gutes inhomogener Stoffströme können dabei nur mit großer Zeitverzögerung gemessen werden, wodurch die durch die Summe der Materialeigenschaften definierte Produktqualität im Extremfall erst posthum bekannt ist.
Daraus resultiert, dass die Einflussnahme auf den Prozess nur in unbefriedigendem Ausmaß gegeben ist. Indirekt eingesetzte rasch verfügbare Qualitätsindikatoren liefern hingegen sehr unscharfe Aussagen. Um diese mit den exakt, aber zu spät gemessenen Guteigenschaften verknüpfen und früher konkrete Aussagen hinsichtlich Qualität und Eigenschaften des Stoffstromes treffen zu können, bedarf einer zuverlässigeren Materialverfolgung des Schüttgutes.
Die existierenden intralogistischen Verfahren der Materialidentifikation, Steuerungsstrategien, Kommunikationstechniken und Informationsflüsse sind aber nur für Stückgüter und zum Teil für diskretisier- und eindeutig bestimmbarer Schüttgüter anwendbar.
Die konkrete Problemstellung, der Verfolgung des kontinuierlichen, inhomogenen Gutstromes sowie der Zuordenbarkeit von dessen gemessenen Eigenschaften, wird in der Literatur nicht beschrieben.
In den letzten Jahren wurden in unterschiedlichen Branchen versucht, inhomogene, kontinuierliche Gutströme durch verschiedene technologische Ansätze verfolgbarer zu machen. Beispielsweise wurde versucht, das Schüttgut durch das Einbringen von sogenannten Markern, welche idente Flusseigenschaften wie das Schüttgut aber mindestens ein leicht unterscheidbares Merkmal aufweist, zu erfassen. Um eine zuverlässige Identifizierung des Materials zu erreichen, können physikalische Eigenschaften (Farbe, Magnetismus, Radioaktivität), chemische Parameter (Tracer) oder auch Auto-ID Methoden (Codes, RFID) verwendet werden.
Einige Methoden, welche in kurzer Zeit (online) Ergebnisse liefern, können sowohl zur Materialverfolgung als auch zur Bestimmung von Guteigenschaften, herangezogen werden. Ihre Anwendbarkeit auf Gutströme mit komplexem Eigenschaftsprofil – wie z.B. dem Sintergut in der Stahlherstellung - ist jedoch kaum möglich.
Zur detaillierten Bestimmung der Guteigenschaften stehen Mess- und Prüfmethoden zur Verfügung, welche punktuell und zeitverzögert Daten auf Basis dem Gutstrom entnommener Stichproben liefern. Sie liefern bei Einhaltung der Regeln der Probenahme zwar gute Ergebnisse, sind aber sehr (zeit)aufwändig und limitieren die Dynamik einer Prozessoptimierung.
Durch prozessbedingte Trennschnitte, Segregation und Vermischungen eignen sich solche Messverfahren für inhomogene, kontinuierliche Gutströme – wie dem Sinter in der Stahlherstellung – nur bedingt.
Um die qualitätsrelevanten Eigenschaftsparameter in Echtzeit dem richtigen Material zuordnen zu können, müssen Messwerte prompt zur Verfügung stehen und der richtigen Losgröße zu geordnet werden können. Für Schüttgut - vor allem Fertigsinter - stellt dies eine besondere Herausforderungen dar und verlangt nach neuen Messmethoden.
Vorgehensweise zur Beantwortung der Problemstellung
Am Beispiel der Sinteranlage der voestalpine Stahl Donawitz GmbH wurde ein Modellkonzept für die Verfolgung eines kontinuierlichen, inhomogenen Materialflusses entwickelt. Die Herstellung von Stahl aus Eisenerz basiert am Standort der voestalpine Stahl Donawitz GmbH auf der Hochofen – LD (Linz-Donawitz Verfahren) Route. Das Eisenerz wird als Stückerz, Pellets oder Sinter zusammen mit weiteren Zuschlagsstoffen als sogenannter Möller und dem Koks als Reduktionsmittel in den Hochofen chargiert. Der Sinter ist ein dominierender Einsatzstoff im Hochofen. Sinter wird am Standort selbst erzeugt. Dabei werden Feinerze und Zuschlagstoffe durch partielles Aufschmelzen gesintert und damit „stückig“ gemacht.
Das Sintermaterial stellt einen kontinuierlichen, inhomogenen Gutstrom dar. Je nach Prozessschritt verändert sich seine Zusammensetzung und seine Qualitätseigenschaften sind nicht in Echtzeit über den gesamten Prozess nach verfolgbar. Modellbasierte Qualitätsvorhersagesysteme unterstützen an manchen Stellen den Bediener der Anlage. Diese Systeme bilden jedoch nur Teilprozesse ab, weshalb das implizite Erfahrungswissen der Mitarbeiter eine wichtige Rolle spielt, um eine bestimmte Prozessqualität zu erreichen.
Die wenigen verfügbaren Echtzeitdaten wie Bandgeschwindigkeiten, Massenströme, Temperaturen, Bunkerfüllstände usw. unterliegen gewissen Toleranzen bzw. Ungenauigkeiten. Auswirkungen von durch den Mitarbeiter vorgenommene Parameterveränderungen werden erst mehrere Stunden später im Prozess messtechnisch erfasst. Wichtige Prozessparameter können - bedingt durch die großen Totzeiten im gesamten Prozessverlauf - nicht in Echtzeit bzw. online überwacht werden. Zusätzlich kommt es durch die derzeitige Manipulation des Sinters in den Anlagen zur Segregation bzw. Degradation des Schüttgutes. Das lässt vermuten, dass Potential zur Verbesserung der Prozesseffizienz durch eine kontinuierliche Materialverfolgung des Sinterstromes und Erfassung seiner Qualitätseigenschaften in Echtzeit besteht, um Ausschussraten (Rückgutanteile) zu minimieren, Energie- und Ressourceneinsatz zu optimieren, Umweltbelastungen zu reduzieren sowie Qualitätsschwankungen besser beherrschen zu können.
Für die Verfolgung und Sichtbarmachen der Eigenschaften des Stoffstromes wurden im Sinter- und Hochofenbereich zur Charakterisierung des Sinterstromes die Systemgrenzen für den Untersuchungsbereich definiert und vorhandene Datenquellen analysiert und ausgewertet. Für die Diskretisierung des Materialstromes wurde im definierten Untersuchungsbereich der Transport- und Informationsfluss erhoben und visualisiert. Der Stand der Technik der Stückgutlogistik ist weitgehend anwendbar, stößt aber beim Thema der Schüttgutverfolgung an Grenzen. Während ein Stückgutstrom natürliche Abgrenzungen aufweist, müssen diese bei einem kontinuierlichen Schüttgutstrom neu gebildet werden. Für die Bildung dieser Abschnitte können unterschiedlichste Diskretisierungsstrategien angewendet werden, abhängig vom Typ des jeweiligen Prozessschrittes bzw. -teilschrittes. Aufeinanderfolgende Schritte können dabei verschiedene Strategien aufweisen, solange sich diese ineinander überführen lassen. In bestimmten Bereichen, wie z.B. Materialspeicher, müssen die Methoden aus der Stückgutlogistik erweitert werden.
Das Ergebnis waren mögliche Strategien für die Bildung von homogenen, diskreten Abschnitten im Gutstrom. In den einzelnen Verfahrensschritten bzw. Aggregaten erfolgte die Modellierung der Flusscharakteristik des Stoffstromes. Dabei sollten die Durchlauf- und Verweilzeiten des Materials erfasst und ausgewertet werden. Das Flussverhalten wurde auf Basis einer Modellierung, in welche die identifizierten Fluss- und Materialeigenschaftsdaten einflossen, dargestellt. Siebe und Förderstrecken lassen sich in Bezug auf den Materialfluss verhältnismäßig leicht beobachten und beschreiben. Der Sinterkühler und Bunkeranlagen (Möllerbunker) stellen eine Herausforderung dar, da sich ihr Inneres der Beobachtung entzieht. Um die Flusscharakteristik dieser Teilbereiche zu untersuchen wurde ein physisches Bunkerschnittmodell, Bunkersimulationen (DEM – Diskrete Elemente Simulation), sowie Traceruntersuchungen (RFID- & Farbtracer) in den Betriebsanlagen angewendet. Aus diesen durchge-
führten Untersuchungen wurde für den Kühler eine Übergangsfunktion für den Gutstrom gefunden. Diese Funktion beschreibt die Antwort des Systems bei sprunghafter Änderung einer Guteigenschaft am Eingang. Durch die im Gegensatz zum Sinterkühler moderat vorherrschenden Guttemperaturen in den Möllerbunkern wurde die Anwendung der RFID-Technologie in diesem Bereich untersucht. Der Einsatz der Technologie verlief positiv und lieferte wichtige Erkenntnisse über das Flussverhalten in diesem Teilbereich. In den Möllerbunkern herrscht ein ausgeprägter Kernfluss vor, was mit allen drei angewendeten Methoden bestätigt wurde. Die DEM-Simulation konnte diesen quantifizieren und lieferte darüber hinaus wichtige Aussagen über Entmischungsvorgänge beim Befüllen und Entleeren des Möllerbunkers. Grobstückiges Material sammelt sich nahe der Bunkerwand wogegen sich feinere Anteile im Kern (Zentrum) konzentriert. Daraus resultiert, dass in der ersten Phase bei der Bunkerentleerung der Feinanteil überwiegt und in der Schlussphase der Grobanteil ausgetragen wird. Somit wurde nachgewiesen, dass eine ursprünglich gleichmäßige Kornverteilung nach der Bunkeranlage stark schwanken muss. Das lässt ich in den betrieblichen Messdaten eindeutig nachvollziehen. Aus dem breiten Spektrum der Möglichkeiten unterschiedliche Guteigenschaften zu messen, konzentrierte sich diese Arbeit auf die Festigkeitsindikatoren, Korngrößenverteilungen, Massen und Volumina und chemische Zusammensetzungen. Während Massen gut online über Bandwaagen verfolgbar sind, können qualifizierte chemische Analysen des Gutstromes nur über Probenahmen realisiert werden.
Das Ziehen einer repräsentativen Stichprobe aus einem kontinuierlichen Gutstrom stellt durchaus eine Herausforderung dar. Die Probemenge wird durch das Material (Korngrößenverteilung, Inhomogenität) bestimmt, die Probenfrequenz durch den Prozess. In Summe kann der Aufwand (Zeit, bewegte Massen, Personalaufwand) erheblich werden. In der Regel werden für die Probenahme selbst automatisierte bzw. teilautomatisierte Vorrichtungen eingesetzt, um zufällige Fehler zu vermeiden. Auch bei idealer Gestaltung des Probenahmeprozesses sind Ergebnisse nicht sofort verfügbar und weder für Prozesssteuerung bzw. Qualitätsverfolgung einsetzbar. Eventuelle systematische Fehler in der Probenahme sind durch eine unabhängige Überprüfung (z.B. Probenahme vom stehenden Band) zu quantifizieren. Für die Stichproben gilt daher, dass diese genau gezogen und ermittelbar sein müssen. In der betrieblichen Praxis werden oft größere Probenmengen (bis 200 kg) gezogen und verarbeitet. Für bestimmte Analysen, wie etwa Bestimmung der Kornverteilung oder der chemischen Eigenschaften, muss die Probe aufbereitet werden. Die richtige Wahl der Teilung bzw. des Teilaggregates hängt von der anfallenden Probenmenge und deren Kornverteilung ab. Zur Bestimmung der Korngrößenverteilung wird standardmäßig ein Siebturm eingesetzt.
Alternativ wurden online-Messtechniken zur Bestimmung der Korngrößenverteilung untersucht und die Herausforderungen dieser Systeme erläutert. Die Vorteile liegen darin, dass
sie nahezu in Echtzeit Informationen liefern, die Grundgesamtheit betrachten und daher Probenahmefehler vermeiden. Dem steht gegenüber, dass die Genauigkeit teilweise begrenzt ist und sie nur als Indikatoren gelten können. Die Herausforderung für den Einsatz solcher VisionSysteme liegt daran, wie das Material dem System präsentiert werden kann. Abhängig von den Gegebenheiten kann direkt am laufenden Band oder im Bereich von Abwurfstellen wo eine Vereinzelung des Materials stattfindet das Schüttgut analysiert werden. Am laufenden Band neigt inhomogenes Schüttgut auf Förderbändern dazu sich zu entmischen, d.h. Feinkorn liegt unter dem Grob- und Mittelkorn und kann messtechnisch über das System nicht erfasst werden. Wesentlich für den Einsatz dieser Systeme ist ihre Kalibrierung und die Notwendigkeit, sie regelmäßig durch Stichproben zu überprüfen. Die Erkenntnisse aus den
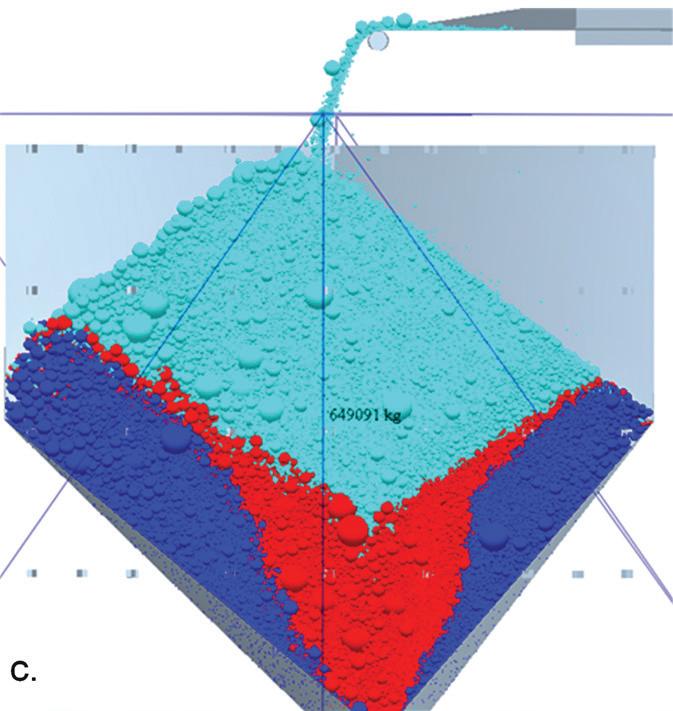
Abbildung 1: DEM-Simulation – Bunkerbefüllung und –entleerung Abbildung 2: VisioRock – online Korngrößenmesssystem
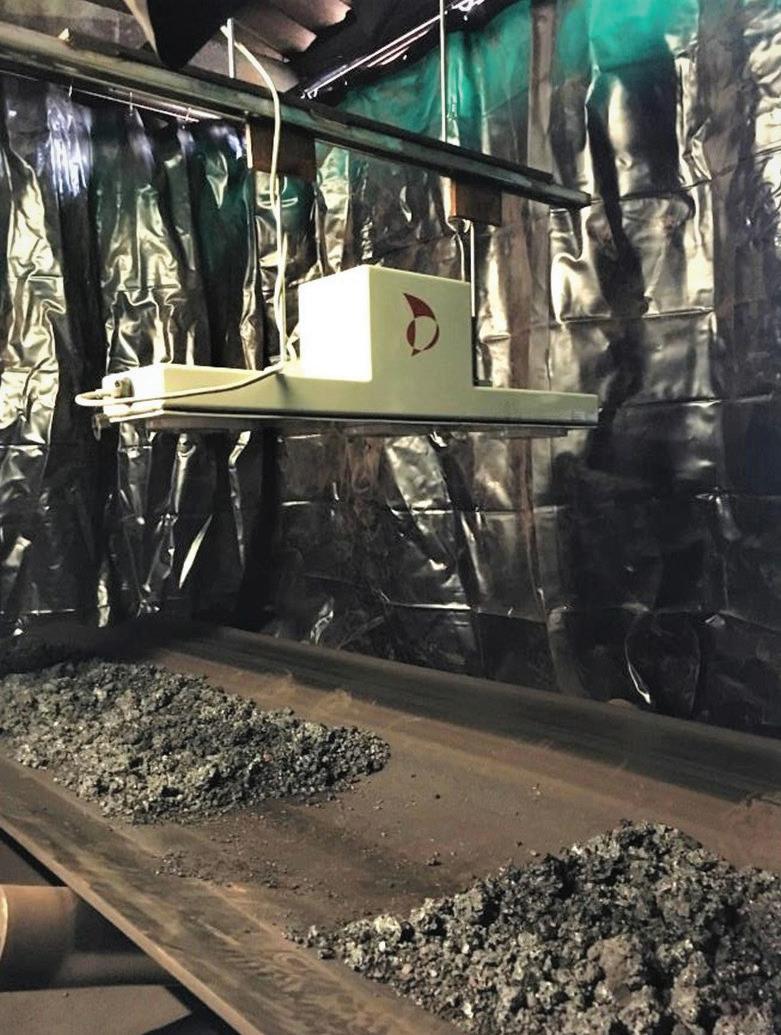
Betriebsversuchen zeigten das Potential dieser Systeme zur Bestimmung der Korngrößenverteilung auf und werden auch weiterverfolgt.
Die Herangehensweise zur Verfolgung eines kontinuierlichen, polydispersen Gutstroms und dessen Eigenschaften von der Materialflusserhebung über die Entwicklung von Methoden zur Bestimmung der physikalischen und chemischen Eigenschaften bis hin zur Erstellung eines Konzeptes wurde beschrieben und hat sich in der Praxis der Sinteranlage (voestalpine Stahl Donawitz GmbH) bewährt.
Der Sinter- und der Hochofenprozess wurden jeder für sich über Jahrzehnte betrieben und weiterentwickelt und haben eine gewisse Reife erreicht. Größere Schritte der Weiterentwicklung sind bei Betrachtung von Gesamtsystemen unter Einbeziehung der Materiallogistik zu erzielen. Bessere Kenntnis der Guteigenschaften von Einsatzstoffen erlauben eine effizientere Prozesssteuerung. Verlässlich gemessene und zuordenbare Produkteigenschaften eröffnet trotz großer prozessbedingter Totzeiten die Möglichkeit, einen zumindest modellbasierten Qualitätsregelkreis zu schließen. In Branchen, in denen Schüttgut ver- und weiterverarbeitet wird, liegen die Potentiale nicht im einzelnen Prozessschritt, sondern im gesamten System.

Autor:
Dipl.-Ing. Dr.mont Christian Weich-
bold ist seit Jänner 2020 als Projektmanager in der K1-MET GmbH für die Weiterentwicklung des Sinter- und Hochofenbetriebes der voestalpine Stahl Donawitz GmbH tätig. Im Fokus seiner Arbeit liegen das RFCSProjekt MinSiDeg (Minimise Sinter Degregation), online Messungen der Sintereigenschaften, sowie Umsetzungen der Erkenntnisse aus seiner
Dipl.-Ing. Dr.mont Christian Weichbold
Projektmanager in der K1-MET GmbH
Dissertation SmartSinter. Er hat die HTL-Leoben für Maschinenbau mit Ausbildungsschwerpunkt Metallurgie absolviert und vor Beginn seines Studiums Industrielogistik an der Montanuniversität Leoben vier Jahre in der Privatwirtschaft verbracht. Nach Abschluss seines Masterstudiums 2015 war er 3,5 Jahre für die voestalpine Stahl Donawitz GmbH im Bereich Forschung und Entwicklung Abteilung Reduktionsmetallurgie tätig. Dort beschäftigte er sich mit dem Thema seiner Dissertation, nämlich der Materialverfolgung von Sinter und deren Eigenschaften
WING-REGIONAL WIEN, NIEDERÖSTERREICH, BURGENLAND

Sehr geehrtes WING-Mitglied,
der Regionalkreis in Wien, NÖ und Burgenland erhält weitere Unterstützung. Herr Dipl.-Ing. Martin Atassi, MBA verstärkt ab sofort das bestehende Team. Martin Atassi hat in Wien Wirtschaftsingenieurwesen-Maschinenbau studiert und seither einige Stationen in Industrie und Politik hinter sich gebracht. Aktuell ist er als Head of Business Development & Marketing bei ITSDONE tätig.
“Es gibt wohl kaum einen klassischen Werdegang für einen Wirtschaftsingenieur. Auch mein persönlicher Karriereverlauf war geprägt von Abwechslung. Nach vielen Jahren in der Telekommunikationsbranche, habe ich einige Jahre die Digitalisierungspolitik begleitet, um nun in der IT-Branche zu landen. Ich freue mich den Regionalkreis WING Wien, Niederösterreich und Burgenland in seiner weiteren Entwicklung begleiten zu können und hoffe auf neue inspirierenden Austausch mit vielen Absolvent_innen“, fasst Atassi sein Engagement zusammen.
Wir freuen uns auf die Zusammenarbeit!