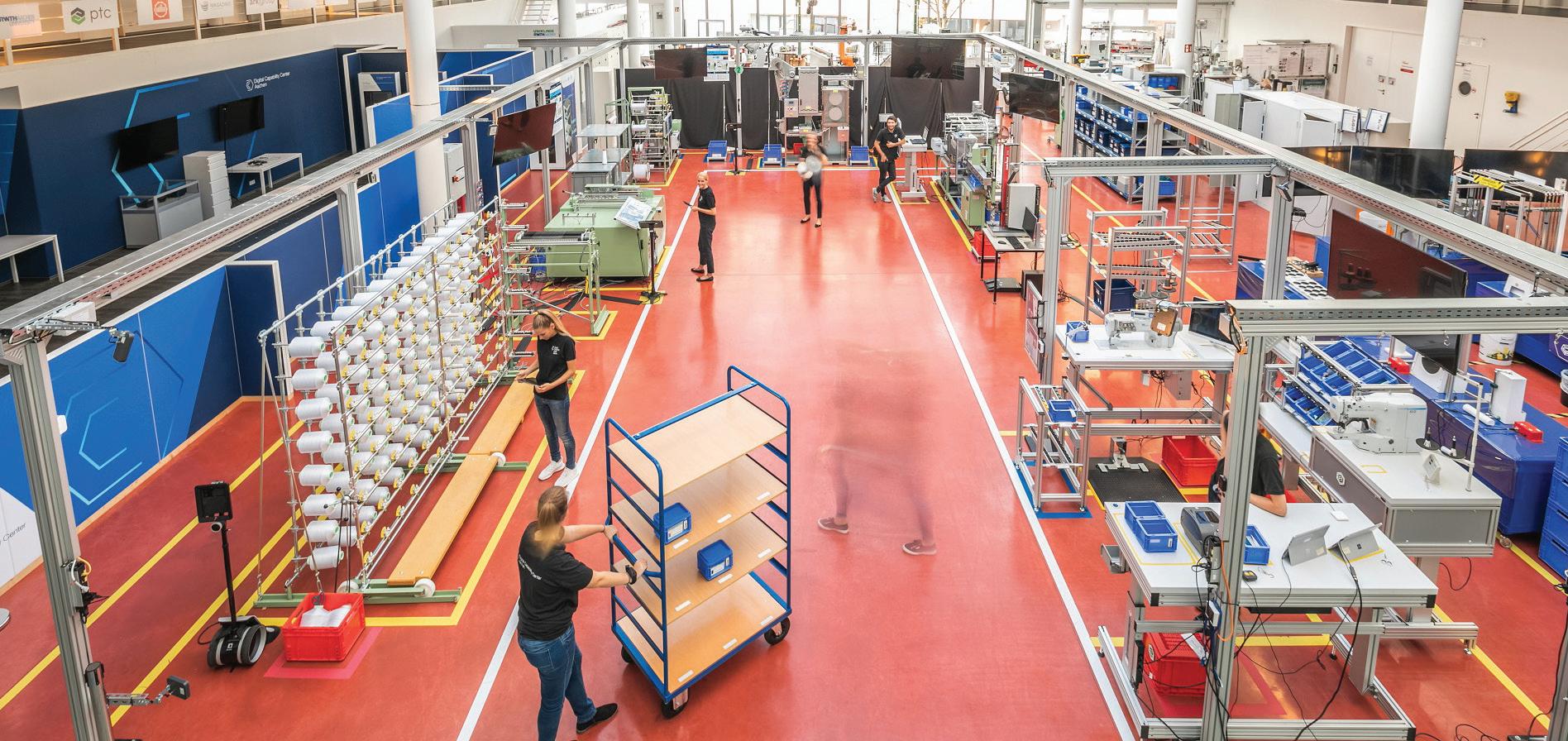
13 minute read
Rethinking Supply Chains – Industry 4.0 and Circular Economy
from WINGbusiness Heft 03 2021
by WING
Foto: Digital Capability Center Aachen (Quelle: ITA Academy GmbH)
Sven Gores, Gesine Köppe, Nicolina Praß, Thomas Gries
Advertisement
Das Digital Capability Center in Aachen, ist die erste und einzigartige textile Lernfabrik mit einer realgetreuen Produktionsumgebung. Durch einen intensiven Austausch mit etablierten Lernfabriken von europäischen Universitäten wird die Kooperation gestärkt.
Industrie 4.0
Um sich in der Zukunft auf rasant wachsenden Märkten behaupten zu können, müssen Unternehmen vor allem ihre Effizienz steigern. Ein oft thematisierter Lösungsansatz bietet die Digitalisierung der Industrie. Doch die voranschreitende digitale Transformation stellt Unternehmen vor eine große Herausforderung.
Durch erhöhte Qualifizierungsbedarfe und veränderte Kompetenzprofile vermehren sich Unsicherheiten und Unwissen. Zudem gilt es besonders bei kleineren und mittelständischen Unternehmen, eine erste Basis und das nötige Grundlagenwissen für den Start einer erfolgreichen digitalen Transformation zu schaffen.
Hier findet die ITA Academy GmbH mit dem 2017 gegründeten Digital Capability Center (DCC) in Aachen ihre Aufgabe. Sie unterstützt die digitale Transformation der produzierenden Industrie durch Forschungs- und Entwicklungsprojekte sowie ausgewählte Weiterbildungsprogramme. Das DCC ist eine Modell- und Lernfabrik, die in Partnerschaft der ITA Academy GmbH mit McKinsey & Company Inc. und weiteren Technologiepartnern – sowohl internationalen Konzernen als auch Start-Ups – ins Leben gerufen wurde. In der Lernfabrik wird an acht Arbeitsstationen eine durchgängige Produktionslinie eines Textilbetriebes realgetreu dargestellt. Diese acht Stationen sind: Arbeitsvorbereitung, Additive Fertigung, thermische und chemische Oberflächenbehandlung, Montage, Qualitätsprüfung und Verpackung, ergänzt durch ein Logistiklager für die interne Materialversorgung.
Das hergestellte Produkt ist ein smartes Armband, welches aus einem elastischen Bandgewebe sowie einem eingenähten RFID-Chip besteht. Dieser kann mit individuellen Daten beschrieben werden. Im Falle des DCC Aachens, dient der Chip dem Mitarbeitenden als persönlicher Login sowie der personenspezifischen Maschinenrechtevergabe an den jeweiligen Arbeitsstationen.
Die Lernfabrik zeigt einen Produktionsablauf im Lean-Status, wie er heutzutage in der Industrie üblich ist. Innerhalb weniger Minuten kann dieser in einen digitalisierten Zukunftsstatus umgebaut werden. So werden an den acht Arbeitsstationen mittlerweile mehr als 40 digitale Industrie 4.0 Use-Cases präsentiert. Diese erstrecken sich beispielsweise von Maschinenkonnektivität, Zustandsüberwachung und prädiktiver Instandhaltung über adaptive Arbeitsplätze, digitale Assistenzsysteme, virtuelle und erweiterte Realität (VR/AR) bis hin zu maschinellem Lernen und künstlicher Intelligenz.
In einer an der Produktionslinie angrenzenden „Innovation Area“, werden Entwicklungen an weiteren Arbeitsstationen vorangetrieben, welche nicht in den vollstufigen Prozess zu integrieren sind. Dabei handelt es sich beispielsweise um Montagestationen mit kollaborativen MenschMaschine Interaktionen oder um
Augmented- und Virtual Reality UseCases für die Produktionsplanung einer Produktionslinie.
Ziel der Trainingsangebote der ITA Academy GmbH ist es, die digitale Transformation für Unternehmen erlebbar zu machen, sowie mit der Komplexität des Begriffes „Industrie 4.0“ aufzuräumen. Die Workshops in der Lernfabrik sollen Mitarbeitenden und Management ein Grundverständnis geben, von dem ausgehend die digitale Transformation im eigenen Unternehmen geplant und entwickelt werden kann. Dabei geht es nicht um die exakte Übernahme der hier implementierten Lösungen. Vielmehr sollen Unternehmen lernen, die für sich gesuchte Lösung daraus abzuleiten. In den meisten Fällen begleitet die ITA Academy GmbH diese Entwicklungsprozesse in Form von Pilotprojekten und hilft bei der Wahl der passenden Technologiepartner.
Automation Logistik
Die Logistikbranche steht in den nächsten Jahren vor großen Herausforderungen: CO2-Abgaben, Personalmangel, Handelsbeziehungen die noch vor kurzem als stabil galten und der „Aufbruch zur letzten Meile“. Wer hier seinen Platz in der Branche festigen möchte, muss sich den neuen Herausforderungen annehmen und Lösungen entwickeln, welche die Prozesse effektiver und kosteneffizienter gestalten[1].
Seit der Wirtschaftskrise im Jahr 2008 gewinnt die Branche jährlich mehrere Prozent Zuwachs [2], und gerade in der Corona-Krise konnte sich eines stark abbilden: die letzte Meile bis zur Haustüre wird immer wichtiger. Dies schlägt sich aber auch auf steigende Logistikkosten nieder, wodurch der Druck für die Umsetzung von kosteneffizienten Prozessen erhöht wird. Ansätze gibt es zuhauf, sei es zum einen die Idee des autonomen Logistikzentrums, welches durch künstliche Intelligenz ohne menschliche Hilfe auskommt, bis hin zur Paketauslieferung via Drohne. Die Robotik ist in vielen Bereichen schon jetzt nicht mehr wegzudenken, ist aber auch wegen seiner größten Hürde, der menschlichen Akzeptanz, noch nicht vollumfänglich integriert. Dabei gibt es für jeden Anwendungsfall schon jetzt eine bestehende Lösung. Automated Guided Vehicles, kurz AGVs, unterstützen bei der Intralogistik die Mitarbeitenden immer zur rechten Zeit, mit ausreichend Materialien ausgestattet zu sein. Diese AGVs können sich durch ihre Umgebungssensoren jegliches Hindernis, ob beweglich oder nicht, umfahren und ihr angestrebtes Ziel selbständig erreichen. Zusätzlich zu der hinzukommenden Schwarmtechnik solcher Vehicles, können deutlich schnellere und zum Teil auch kürzere Lieferwege angepeilt werden. Als weiteres Beispiel sind skalierbare und flexible Goods-to-Person-Kommissionierungssysteme mit sehr hohen Lagerdichten zu nennen, welche ebenfalls Lösungen der Modellfabrik am DCC Aachen sind. Vorteil solcher Systeme ist zum einen die erstrebte Lageroptimierung, aber auch die Energieeffizienz, sowie die Sicherheit, entsprechend dem eigenen Unternehmenswachstum weiter mühelos anbauen und erweitern zu können.
Dennoch oft ist gar nicht der Wille das Problem, sondern der Mangel an qualifizierten Fachkräften im Unternehmen. Daher durchläuft gerade die Logistikbranche einen millionenschweren Boom in der Start-upSzene, welche sich teilweise darauf spezialisiert hat, einen schnellen und einfachen Einstieg in die Industrie 4.0 im Logistikbereich zu gewährleisten. Gerade die künstliche Intelligenz und deren Möglichkeit, große Datenmengen (Big Data) auswerten zu können, kann den entscheidenden Vorteil bringen [3]. Mit dem zusätzlichen Echtzeittracking via RFID-Chips und der Aufnahme von Echtzeitdaten aus der Umgebung, wie zum Bespiel Verkehrsmeldungen, können aus den vorhandenen Daten zu einer gewissen Wahrscheinlichkeit das Eintreffen bestimmter Ereignisse vorhergesehen werden und das Supply Chain Management effizient umgestaltet und verbessert werden.
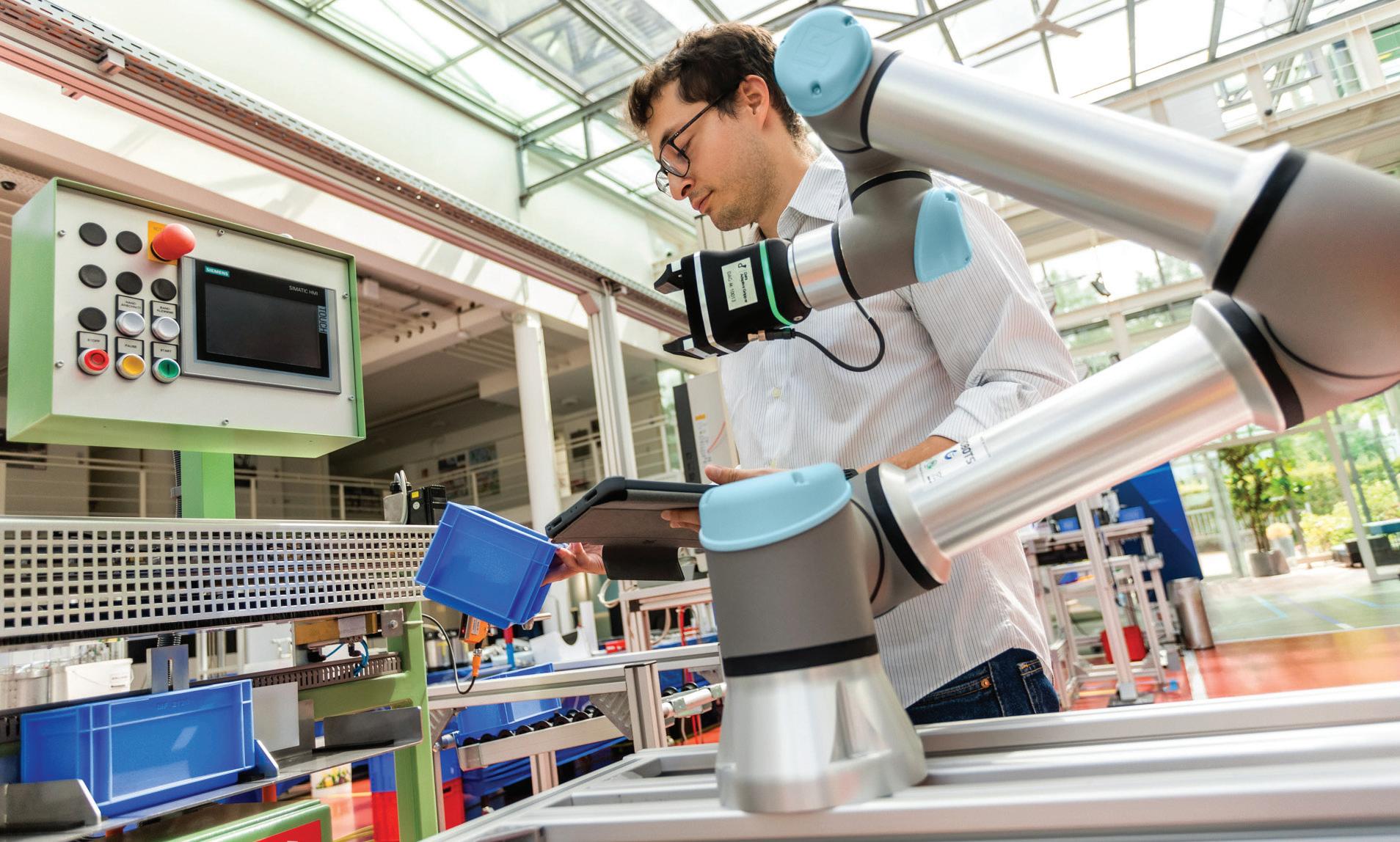
Abbildung 1: Automated Guided Vehicles für die Intra-Logistik am DCC Aachen“. (Quelle: ITA Academy GmbH)
Energieoptimierung durch künstliche Intelligenz
Wettbewerbsfähigkeit ist ein Teil der menschlichen Natur. Dieser ständige Wunsch, immer mehr und bessere Ergebnisse liefern zu wollen, treibt die Menschen dazu an, nach neuen Methoden und Werkzeugen zu suchen, die das Erreichen solcher Ziele ermöglichen. Dieser Verbesserungsbedarf ist in vielen Bereichen vorhanden, in denen sich der Mensch entwickelt. Die Fertigung in der Industrie bildet da keine Ausnahme. Das Ziel jeder Produktionslinie, unabhängig von der Art der Industrie, ist es, die Nachfrage zu decken und die Qualitätsstandards zu erfüllen, die der Markt verlangt.
Eines der Instrumente, die es den Unternehmen ermöglichen wettbewerbsfähig zu bleiben, ist die Optimierung. Sei es die Suche nach einer optimalen Konfiguration der Stationen einer Produktionslinie, um einen optimalen schlanken Zustand zu erreichen oder die Optimierung von Fertigungsprozessen, um ihren
Durchsatz und ihre Qualität zu erhöhen oder ihren Ressourcenverbrauch zu reduzieren.
Die Notwendigkeit, Industrieprozesse mit Software zu optimieren, ergibt sich aus den meist langen Zeiten, die das Personal in der Produktion benötigt, um die Maschine optimal zu bedienen. Der Betrieb einer Maschine mit optimalen Parametern erfordert erfahrenes Personal, welches weiß, wie die Betriebsparameter modifiziert werden müssen, sodass die Qualität des Produktes die geforderten Standards erreicht. Basierend auf den Erfahrungen und dem Qualifikationsniveau der Maschinenbediener, kann das effiziente und schnelle Bedienen variieren.
Nicht zu vernachlässigen ist die Fluktuation in den Unternehmen. Neue Mitarbeiter müssen schnell eingearbeitet werden, um die Standards zu erfüllen. Auch wenn die Einweisungen in die Bedienbarkeit gut geschult werden, sind es meist Erfahrungswerte, auf die die Bediener zurückgreifen, um die Maschinen optimal zu betreiben.
Die künstliche Intelligenz und insbesondere das maschinelle Lernen, bietet eine Möglichkeit, das Lernen erheblich zu beschleunigen, indem die Hardware- und Software-Technologien große Datenmengen mit Algorithmen des maschinellen Lernens antrainieren. Die von den Industrieprozessen geforderten hohen Genauigkeitsraten können somit erreicht werden. Der Grund für die Anwendung von Algorithmen des maschinellen Lernens zur Regelung industrieller Prozesse liegt in ihrer Fähigkeit, komplexe Muster zu erkennen, wie sie von erfahrenen Maschinenbedienern aus sich ändernden Variablen wie der Umgebung oder dem Materialtyp erkannt werden. Künstliche Intelligenz und Optimierungsalgorithmen sind Hauptbestandteile der vierten industriellen Revolution und erobern allmählich den breiten Markt. Die Vielfalt an grafischer Software zum Trainieren von Machine-LearningModellen und zur Optimierung von Prozessen wird von Tag zu Tag größer, welche die Unternehmen nutzen können, ohne spezielle Programmierkenntnisse aufzuzeigen.
Im Rahmen eines Projektes am DCC Aachen wird künstliche Intelligenz (KI) für die Entwicklung und Anwendung von Methoden eingesetzt, die es dem Computer ermöglicht, Aufgaben in der Produktion zu lösen [4]. Ziel des Optimierungsprojektes ist die Reduzierung des Energieverbrauchs der Veredlungsmaschine, die aufgrund der Thermofixierung einen hohen Energieverbrauch aufweist. Der hohe Energieverbrauch wird durch eingesetzte Infrarotlampen, welches das Textil auf 900 °C erwärmt sowie durch die Thermofixierung von zwei Zylindern mit 180 °C im Prozess erzeugt.
Um sich den Grund dieses Ziels vor Augen zu führen: In der deutschen Textilindustrie entspricht der Energieverbrauch mit einem durchschnittlichen Verbrauch von ca. 11,5 TJ [5] dem zweitgrößten Bedarf nach Gas. Im Bereich der Beschichtungs- und Thermofixieranlagen für Textilien werden üblicherweise 1,1 kWh/ kg Gewebe [6] verbraucht. Aus diesen Zahlen entstand der Bedarf der Senkung notwendiger Energie für Veredlungsprozesse, ohne die Qualität oder die Produktionsgeschwindigkeit zu verringern. Der angewendete Lösungsansatz der Energieoptimierung an der Veredlungsmaschine kann in 4 Schritte unterteilt werden. Im Folgenden wird darauf näher eingegangen:
1. Verständnis des Prozesses:
Alle prozessbezogenen Variablen werden aufgelistet und mit Einheiten, Physikalischen- und Betriebsgrenzen beschrieben. Eine möglichst umfangreiche Aufklärung der Variablen erfolgt durch Gespräche mit Maschinenbedienern, Prozessingenieuren und Betriebsleitern, in denen Variablen wie beispielweise Maschinenparameter und Umgebungsvariablen erkannt und beschrieben werden.
Die Variablen, die trotz hoher Wichtigkeit nicht digital erfasst werden, müssen mit einbezogen und die Anlage dementsprechend nachgerüstet werden. Bei diesem Schritt muss eine Netzwerkverbindung zwischen der Anlage und einer Datenbank bestehen, um erfassende Sensordaten abzuspeichern. 2. Erfassung von Maschinendaten:
Nachdem alle benötigten Variablen erkannt und durch Sensoren aufgenommen wurden, müssen Maschinendaten während der Produktion erfasst werden, um einen Datensatz für das Anlernen der KI-Modelle aufzubauen. Der aufgenommene Datensatz wird anschließend bereinigt, da unnötige Daten, die bei der Erfassung ebenfalls aufgenommen werden, bei der Genauigkeit der Modelle ein Senkungsrisiko darstellen. Die Bereinigung der Datenpunkte kann mittels einer Auswertung vereinfacht werden, da ein erster Einblick in die Daten hilft, unnötige Daten und mögliche Abhängigkeiten zwischen den Variablen zu finden. Die Abhängigkeiten können ebenfalls dazu führen, mögliche Netzwerkarchitekturen für die KI-Modelle zu definieren.
3. Erstellung einer Optimierungsstrategie:
Auf Basis der Auswertung kann eine Hypothese erzeugt werden, die die Zielfunktion, die Einschränkungen, die Anzahl an neuronalen Netzen und deren Ein- und Ausgänge definiert. Zur Erstellung der Optimierungsstrategie gehört auch das Training der KI-Modelle, welches in Trainingsiterationen stattfindet. In jeder Trainingsschleife wird eine andere Architektur des neuronalen Netzes getestet, sodass diejenige ausgewählt wird, die die Werte vorhersagt, die dem realen Verhalten der Maschine am nächsten kommen. Das Training de Modelle kann ebenfalls zu einer Modifikation der ursprünglichen Optimierungsstrategie führen, da Architekturen, die unterschiedliche Ein- und Ausgabeparameter berücksichtigen, dass Verhalten der Maschine besser als die ursprünglich gewählten, darstellen können.
4. Optimierung und Integration:
Mit den angelernten Modellen berechnet der Optimierungsalgorithmus basierend auf der zuvor definierten Optimierungsstrategie die optimalen Werte für die Prozessparameter. Dieser Schritt ist ein iterativer Prozess, in dem die Sinnhaftigkeit der Ergebnisse der optimierten Strategie
bei jeder Schleife überprüft wird, um beispielsweise die KI-Modelle oder die Einschränkungen dementsprechend anzupassen. 4.1. Offener Regelkreis: Sobald die von der optimierten Strategie ausgegebenen Werte realistisch und ausreichend sind, wird die optimierte Strategie in die Produktion integriert. Dafür wird die Hardware, worauf die Regelungssoftware läuft, in dem Produktionswerk integriert. Die Strategie wird zuerst im Leerlauf angewendet, sodass die Werte, die die Software zur Prozessoptimierung empfiehlt, vom Maschinenbediener geprüft werden. Der Bediener kann im Nachgang an der Anlage die empfohlenen Werte schrittweise eingeben, während er die Produktion überwacht und überprüft. 4.2. Geschlossener Regelkreis: Der Regelungskreis der Software wird geschlossen, sodass die Prozessoptimierung in Echtzeit im Prozess läuft. Sowohl im offenen als auch im geschlossenen Regelkreis kann der Benutzer das automatische Weiteranlernen der Modelle starten, damit die Modelle während der Produktion mit neuen Informationen weiter angelernt werden.
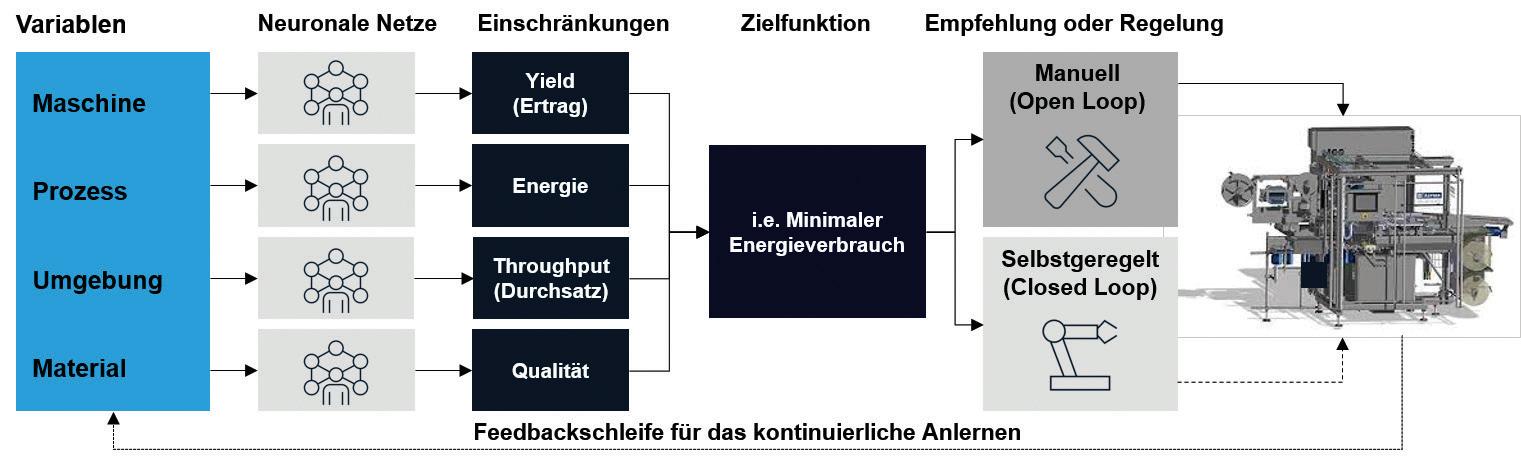
Abbildung 2: Schematische Darstellung der am DCC Aachen entwickelten Optimierungsstrategie eines Wärmebehandlungsprozesses (Quelle: ITA Academy GmbH)
Kreislaufwirtschaft
Optimierungsmöglichkeiten erstrecken sich über weite Gebiete in der Produktion, und betreffen nicht nur wie oben beschrieben die Energiewirtschaft, sondern können auch im Recycling, bzw. in der Kreislaufwirtschaft Einzug erhalten.
Global produzierenden Unternehmen steht ein Paradigmenwandel im Lieferkettenmanagement bevor: einerseits immer kürzere Zykluszeiten, Mass-Customization von Produkten und andererseits der wachende Druck der Kunden nach Nachhaltigkeit und Transparenz. Verschiedene Branchen, wie beispielsweise die Textilindustrie sind einerseits sehr schnelllebig und agil, hinken aber in Sachen Digitalisierung und Vernetzung stark hinterher.
Dazu kommt der Beschluss des Lieferkettengesetzes. Unternehmen müssen den Anforderungen der Gesetze und europäischen Regulierungsinitiativen gerecht werden. Die Textil- und Bekleidungsbranche muss jetzt Transparenz in den Lieferketten aufzeigen und dazu das Vertrauen zu Lieferanten und Händlern ausbauen. Partner zur Verifizierung von Qualitätszertifikaten, sowie Kontaktdaten der Subunternehmer sind in der Lieferkette nicht vorhanden
Die verschiedenen Akteure der textilen Wertschöpfungskette sind nicht transparent. Durch die Anwendung verschiedener individueller SoftwareTools zur Datenerfassung und Pflege der Daten der Zulieferer ist ein hoher Zeit-, Energie- und Kostenaufwand verbunden.
Durch datenbasierte Geschäftsmodelle und durch Transparenz in Produkten, Liefer- und Wertschöpfungsketten können auf kurze Sicht wichtige Impulse zur ressourceneffizienten Wirtschaft eingebracht werden
[8]. So wird am DCC Aachen neben der Nutzung von Recyclingmaterialien auch der Einsatz einer Blockchain gewinnbringend mit diesem Thema in Berührung gebracht.
Mit dem Einsatz von Distributed Ledger Technologien (konkret Blockchain) kann die Produktion des Armbandes und die Richtigkeit von Zertifikaten im DCC dargestellt werden.
Für eine erfolgreiche Weiterentwicklung und den Ausbau von Exzellenz im Bereich Lernfabriken in Deutschland, ist eine nationale und internationale Kooperation zwischen den Lernfabriken von hoher Bedeutung. Durch einen stetigen fachlichen Austausch und die Ausbildung von Fachkräften, können die Kooperationen im IALF Netzwerk sichergestellt werden.
Literatur:
[1] Christian Kille, Markus Meißner (2019) Logistik 2020 Struktur-und Wertewandel als Herausforderung. http://www.logistikweisen.de/wAssets/docs/ergebnisbericht-logistikweisen-2020.pdf Zugegriffen: 28. Juli 2021 [2]https://de.statista.com/statistik/daten/studie/204132/umfrage/volumendes-logistikmarktes-in-europa/ . Zugegriffen: 28. Juli 2021 [3] https://www.bito.com/de-de/fachwissen/artikel/zukunft-der-logistik/ . Zugegriffen: 28. Juli 2021 [4] Lackes R, Siepermann M (2018) Revision von Künstliche Intelligenz (KI). https://wirtschafts- lexikon.gabler. de/definition/kuenstliche-intelligenzki-40285/version-263673. Zugegriffen: 21. Okt. 2020 [5] Statistisches Bundesamt, Wiesbaden (2017) Gesamtverband der deutschen Textil- und Modeindustrie e. V, Berlin [6] Parish GJ, Reed CM (1980) Energy consumption and energy saving in the heat-setting and dye-fixation of textile fabrics on stenters. In: Strub AS, Ehringer H (Hrsg) New ways to save energy. Springer, Dordrecht [7] Greenpeace (2017). Konsumkollaps durch Fast Fashion. Textilwirtschaft 09/17. https://greenwire.greenpeace. de/system/files/2019-04/s01951_greenpeace_report_konsumkollaps_fast_fashion.pdf . Zugegriffen: 28. Juli 2021 [8] https://www.bmu.de/digitalagenda/ industrie-40-kreislaufwirtschaft/ . Zugegriffen: 28. Juli 2021
AutorInnen:
Sven Gores ist Mitarbeiter am Digital Capability Center in Aachen. Er studiert Maschinenbau an der RWTH Aachen mit dem Fokus der Produktionstechnik. Im Jahr 2019 hat er für Bosch in Stuttgart gearbeitet und war als Assistent des Managements im Bereich von Verlagerungsprojekten beteiligt. Am DCC Aachen führt er Entwicklungen im Rahmen von Augmented- und Virtual Reality Anwendungen sowie im Bereich Data Mining durch.
Gesine Köppe, M.Sc. ist Projektingenieurin für Digitalisierungslösungen in der ITA Academy GmbH, Aachen.
Seit 2017 ist sie Produktionsleiterin im Digital Capability Center Aachen, der Lernfabrik für Digitalisierung in der Produktion. Zwischen 2013 und 2015 arbeitete Sie in produzierenden Unternehmen im Bereich Produktentwicklung und technische Entwicklung für die Luftfahrt- und Automobilindustrie. Gesine Köppe schloss den Master of Science in Mönchengladbach mit dem Schwerpunkt Textile Produkte an der HSNR Hochschule Niederrhein ab. Nicolina Praß, MBA ist Geschäftsführerin der ITA Academy GmbH mit dem Digital Capability Center in Aachen. Sie studierte Textil- und Bekleidungstechnik und machte den Master of Business Administration an der Hochschule Niederrhein. Im Rahmen von Forschungs- und Entwicklungsprojekten mit dem ITA der RWTH Aachen war sie als Projektmanagerin tätig und übernahm den Aufbau der ITA Academy GmbH mit dem DCC Aachen im Jahr 2017. Als Geschäftsführerin verantwortet Sie die Digitalisierungsprojekte in Kooperation mit der produzierenden Industrie sowie den Technologiepartnern am DCC Aachen.
Univ.-Prof. Prof. h.c. (Moscow State Univ.) Dr.-Ing. Dipl.-Wirt.-Ing. Tho-
mas Gries ist Professor der RWTH Aachen für Textiltechnik/Textilmaschinenbau und Direktor des Instituts für Textiltechnik (ITA) der RWTH Aachen University.
Er studierte und promovierte an der RWTH Aachen im Bereich Maschinenbau. Als Leiter des Instituts für Textiltechnik der RWTH Aachen University entwickelt er seit 20 Jahren innovative Lösungen für die Textilindustrie und deren Lieferketten. Er ist in einigen Unternehmen als Aufsichtsrat tätig.
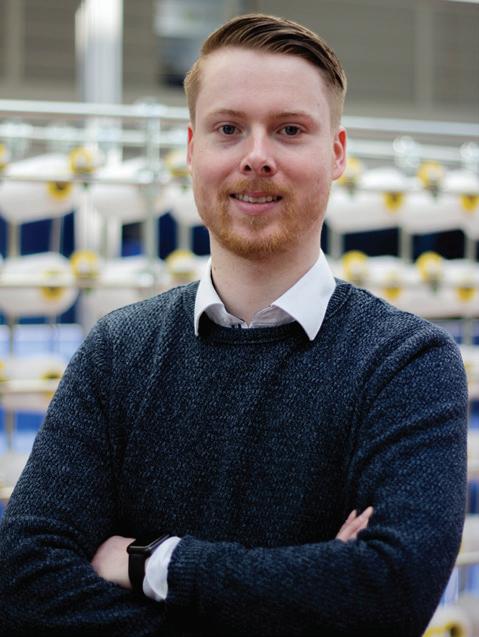
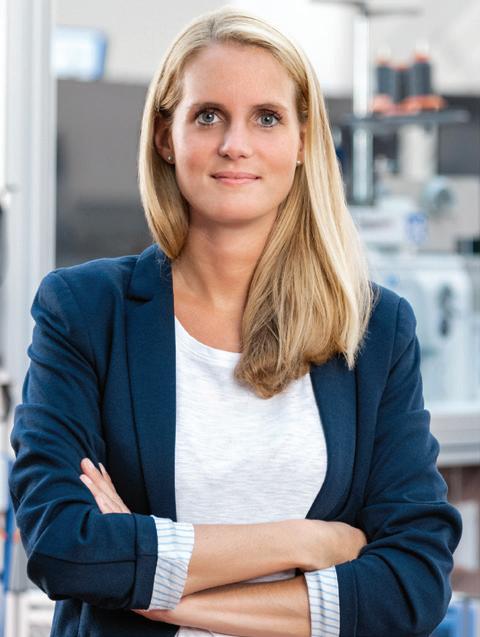
Sven Gores
Mitarbeiter am Digital Capability Center in Aachen
Nicolina Praß, MBA
Geschäftsführerin der ITA Academy GmbH mit dem Digital Capability Center in Aachen Gesine Köppe, M.Sc.
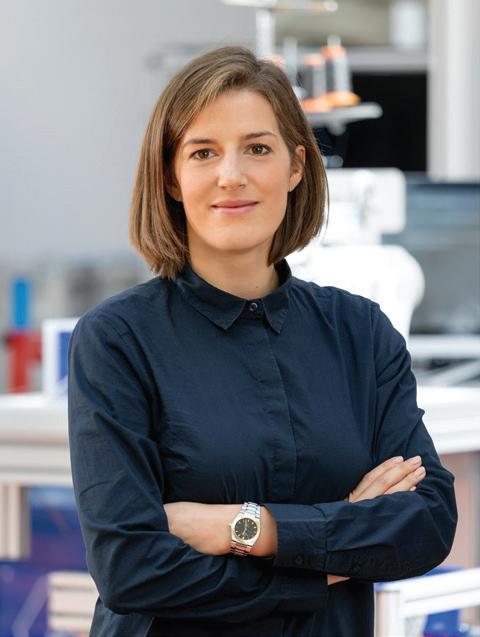
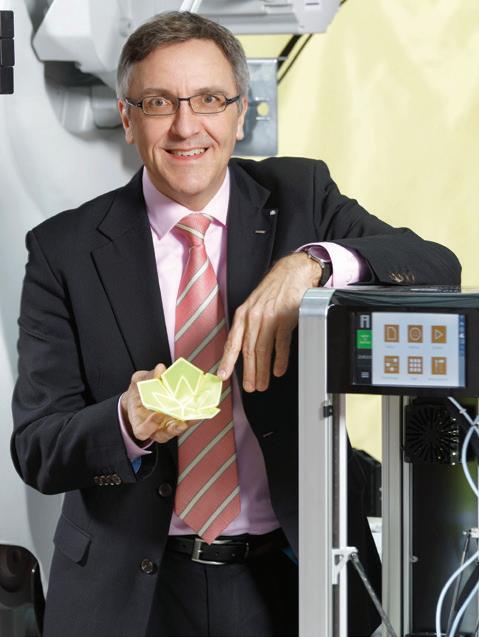