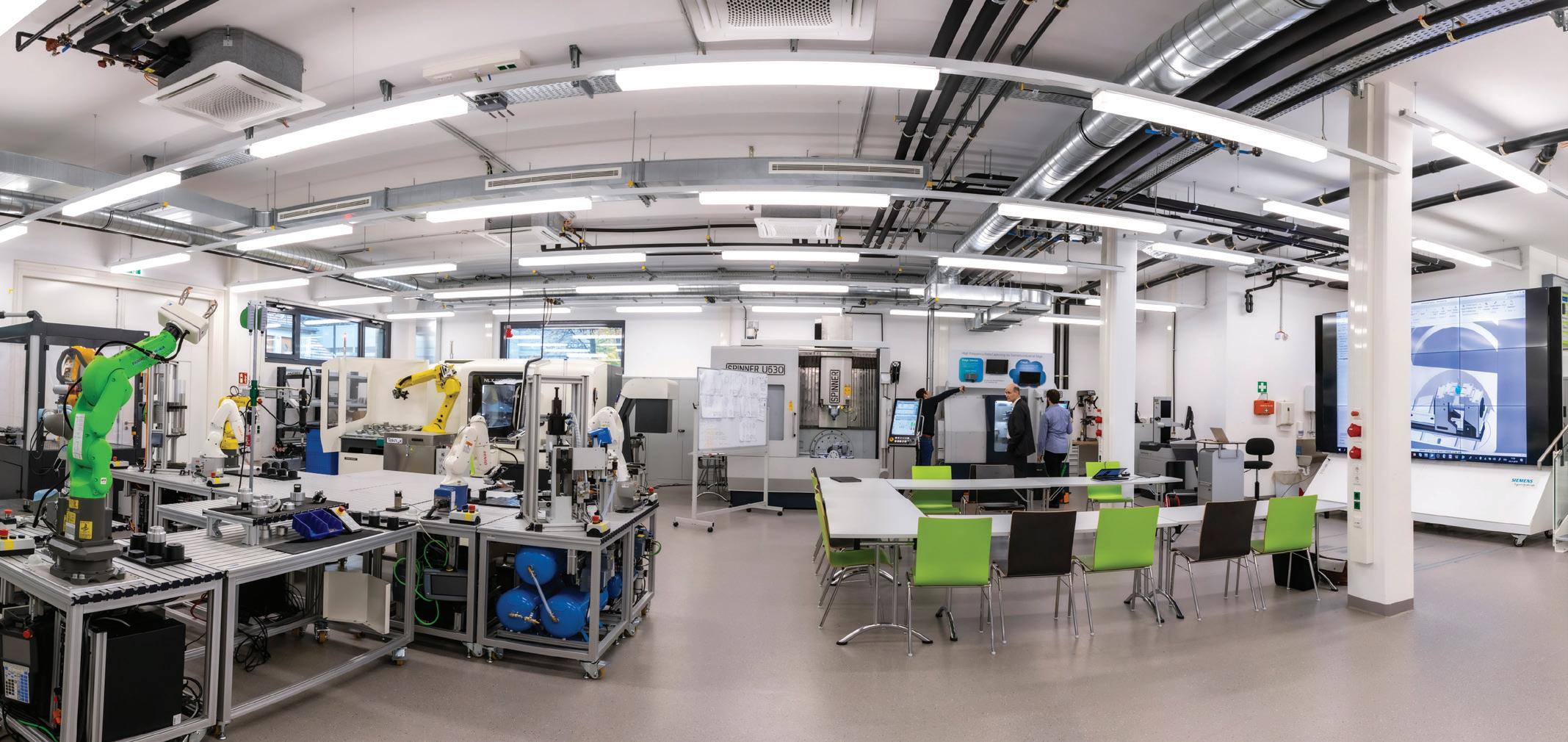
11 minute read
Das Angebot der TU Graz – Lernfabrik für Agilität und Datensicherheit
from WINGbusiness Heft 03 2021
by WING
Foto: Einblick in die smartfactory@tugraz; © Eigentum IFT
Rudolf Pichler
Advertisement
Es war 2015, als auch die TU Graz die strategische Entscheidung traf, als moderne und innovative Universität im Bereich der Forschung und Lehre rund um die Digitalisierung der Produktion eine Lernfabrik zu errichten, so wie dieses neue didaktische Format an einigen deutschen und amerikanischen Universitäten schon etwas zuvor eingezogen ist. Die zweite, nicht minder wichtige Entscheidung war die, Schwerpunktthemen für diese Lernfabrik zu finden, um nicht zu einer „one more of the same“ zu werden. Es galt also, für die Scientific Community und die interessierten Betriebe auch eine gewisse Einzigartigkeit zu schaffen. Im Zeitraum von 2017 bis 2021 wurde sodann am Institut für Fertigungstechnik höchst erfolgreich eine Lernfabrik für „Agile und Datensichere Fertigung“ aufgebaut. Und diese Fabrik, welche auch den brand name „smartfactory@tugraz“ trägt, sei hier mit ihren besonderen Merkmalen vorgestellt.
Grunsätzliche Merkmale
Viele der schon bestehenden Lernfabriken befassen sich vorrangig mit Montagevorgängen und decken damit nur einen Ausschnitt einer vollständigen Produktion dar. Für die smartfactory@tugraz war es wichtig, eine möglichst vollständige Wertschöpfungskette eines produzierenden Betriebs darzustellen, allein schon aus dem Grund, um als Institut für Fertigungstechnik das ureigene Kernforschungsgebiet der Fertigung einzubinden zu können. Somit wurden auch die zerspanende Produktion mittels moderner CNC-Anlagen und die metalladditive Fertigung Teil des Konzepts.
Wichtiges Gestaltungsmerkmal war auch die Entscheidung, nur Anlagen und Komponenten zu verwenden, wie sie tatsächlich auch von Industriebetrieben eingesetzt werden. Es wurde also sowohl im Fertigungs- wie auch Montagebereich darauf verzichtet, funktionstechnisch reduzierte Schulungsmaschinen anzuschaffen, sondern man wollte Standards und Funktionsumfänge haben, die ein industrielles Publikum ansprechen und auch für die Studierenden eine möglichst reale Produktionsumgebung schaffen.
Alle sichtbaren mechanischen, automatisierten und logistischen Einrichtungen der Lernfabrik wurden in ein Netzwerk aus vielfältigen und spezifischen Software-Lösungen eingebettet, wie es für eine modern organisierte Produktion nicht mehr verzichtbar ist. Letztlich geht es um die Darstellung einer „smarten“ Fabrik, insofern nehmen diese Installationen die eigentlich zentrale Rolle, um nicht zu sagen, das Kernelement der Lernfabrik ein. In dieser Hinsicht wurden nicht nur auf OT-Ebene, sondern gerade auch auf IT Ebene modernste Strukturen geschaffen, die letztlich ein Cyberphysikalisches Produktionssystem (CPPS) ausmachen. Auf der Feldebene wird die Infrastruktur von einem MES (Manufacturing Execution System) begleitet, auf IT-Ebene verfügt die smartfactory@tugraz über ein PLM- und ein ERP-System. Über diese informatorische Infrastruktur können Produkte konstruiert, Produktionsprozesse geplant, Produktionsaufträge generiert und durchgeführt und abschließend rückgemeldet werden. Einmal mehr zusammengefasst: Es ist alles verfügbar, was für eine glaubhaft echte und vollständige Produktion nötig ist. Und damit auch richtig produziert werden kann, hat man sich beim Demonstrator (Schauprodukt) für ein Produkt des Typs

„Wellgetriebe“ entschieden, welches für eine Variantenfertigung in 18 verschiedenen Ausführungen vorbereitet ist.
Die Forschungs-Infrastruktur für Agilität
Agilität ist die neue Antwort zur Bewältigung dynamischer und immer individueller ausgerichteter Märkte, ist damit also jene Fähigkeit, eine Produktion für solche neuen Produkte rasch umbauen bzw. adaptieren zu können. Agilität wird mittlerweile sehr oft als Lösung adressiert, wie jedoch konkrete physische Lösungen dazu aussehen können, fehlt in aller Regel. Darum hat es sich die smartfactory@tugraz zur Aufgabe gemacht, genau dafür entsprechende Umsetzungen zu entwickeln und darzustellen.
In einer Produktion agil sein heißt, dass die Elemente einer Wertschöpfungskette sehr universell einsetzbar und sehr leicht ortsveränderlich sein müssen. Auch wenn dies nicht für große Aggregate wie Öfen, Pressen, Werkzeugmaschinen, Lackieranlagen und dergleichen umsetzbar ist, bieten sich immer noch die Bereiche Montage, Vermessung, Reinigung, Prüfung, Kennzeichnung und Verpackung an, die der gesamten Fabrik zu einer agilen Aufstellung verhelfen können. In der smartfactory@tugraz hat man dies exemplarisch für die Montagelinie des besagten Wellgetriebes umgesetzt.
Agile Konzepte benötigen maximale Möglichkeiten für die rasche Rekonfiguration von Material- und Datenströmen, von Bearbeitungsfolgen und der dazugehörigen peripheren Prozesse. Die Realisierung in der Grazer Forschungs-und Lernfabrik im Bereich der Montage wurde über sogenannte „Mobile Arbeitsstationen (MAS)“ realisiert. Diese MAS bestehen aus einem für universelle Anwendungen standardisierten Grundgestell, das auf Rollen fahrbar gelagert ist und jeweils auf Arbeitshöhe eine Aufspannfläche von 700 mm x 700 mm mit Nutenprofilen bietet. Darauf werden die verfügbaren bzw. nötigen Funktionsbausteine einer Montage wie z.B. Handhaben und Positionieren über Roboter, Fügen von Bauteilen, Lager einpressen, Verschrauben, Kennzeichnen, etc. aufgebaut. Diese Art der Modularisierung soll später erlauben, über diese mobilen Einheiten für ein neues Produkt die entsprechend neu nötige Abfolge von wertschöpfenden Tätigkeiten rasch und einfach zu arrangieren. Wesentlich für einen unkomplizierten und schnellen Umbau ist dabei die Autarkie dieser MAS, d.h., es sollten für eine Reorganisation möglichst keine aufwändigen Entkopplungsarbeiten von zuvor verketteten und verkabelten MAS stattfinden müssen. Die Schaffung solch autarker MAS sah nun vor, dass z.B. die Energieversorgung (Strom, Druckluft) an Bord der MAS gebracht wurde, d.h., dass im konkreten Fall dafür Akkumulatoren bzw. Druckluftkessel im Unterbau des Grundgestells eingebaut wurden (siehe Abb. 1). Um auch im Rahmen der informatorischen Versorgung frei von kabelgebundenen Verbindungen (autark) zu sein, wurde auf WLAN- und 5G-basiserte Kommunikation gesetzt. In der smartfactory@tugraz wurden insgesamt 13 solcher autarken MAS aufgebaut.
Die dargestellte Autarkie stärkt auch die Agilität im Bereich des Austauschs von Aggregaten (im Schadensfall oder für die präventive Instandhaltung) als auch im Bereich der Skalierung von Montagelinien zur Erhöhung des Ausstoßes. Indem bei diesen MAS keine kabelgebundenen Versorgungsstränge abgekoppelt, bzw. nach Einfahren des Ersatz- oder
Erweiterungs-MAS aufwändig angeschlossen werden müssen, können die geplante Änderung bzw. Anpassung sehr rasch vollzogen und die Zeiten des Produktionsstopps sehr gering gehalten werden. Eine aktuelle Forschungsaufgabe besteht in der automatisierten, mannlosen Reorganisation von Montagelinien, in dem die MAS unter Zuhilfenahme eines flach bauenden Roboters Abb. 1: Ausführung von Mobilen Arbeitsstationen entkoppelt und gemäß der neuen (links: Akkumulator, rechts: Druckluftkessel) Konfiguration selbsttätig neu aufstellt werden. Die dahinterstehende Idee ist die, dass alle benötigten MAS für die Montagelinie eines neuen Produkts über Nacht neu aufgestellt werden können und durch die Mitarbeiter nur noch wenige Feinarbeiten vor dem Neustart durchgeführt werden müssen. Integrativer Bestandteil einer agilen Montage sind selbstverständlich auch die dazugehörigen logistischen Teilprozesse. Da der Einsatz von Förderbändern mit starren Längen und starrer Ausrichtung in einem agilen Konzept natürlich keine Berechtigung mehr haben, setzt man auf mobile Transportroboter (AGV + aufgesetzter kraftsensitiver Roboter), dies mit einem Produkt von incubedIT und einem von Evcocortex, womit auch zwei verschiedene Navigationssysteme vorgestellt werden können. Ein ganz besonderes Glanzstück der modernsten Intralogistik konnte aus dem Hause B&R implementiert werden. Das Produkt ACOPOStrak, ein modulares System aus Linearmotoren (siehe Abb. 3), erlaubt nicht nur ausgesprochen hohe Weitergabe-Geschwindigkeiten und Präzisionsstopps, sondern es kann in der vorliegenden Konfiguration auch Abb. 2: Intralogistik auf modernstem Standard, ACOPOStrak von B&R
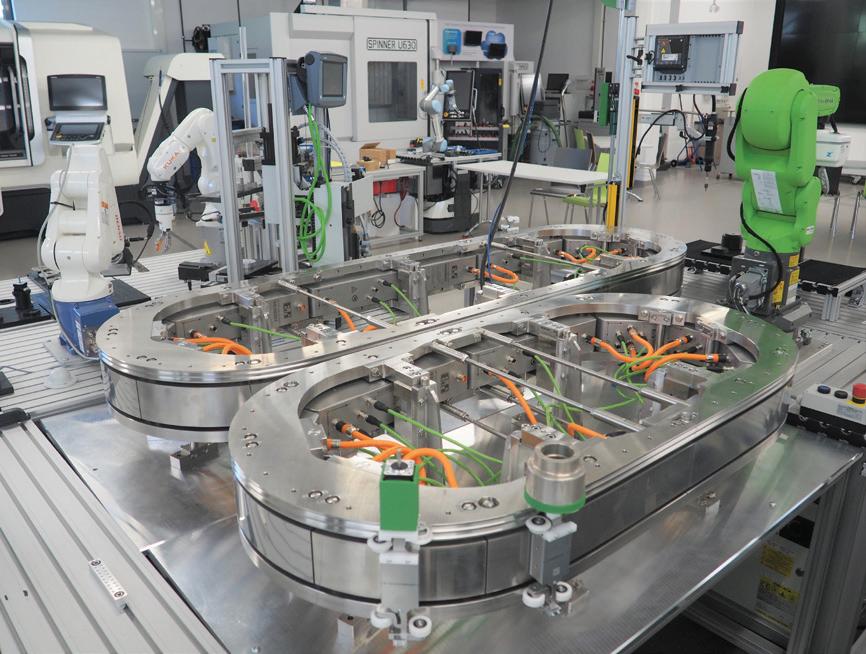
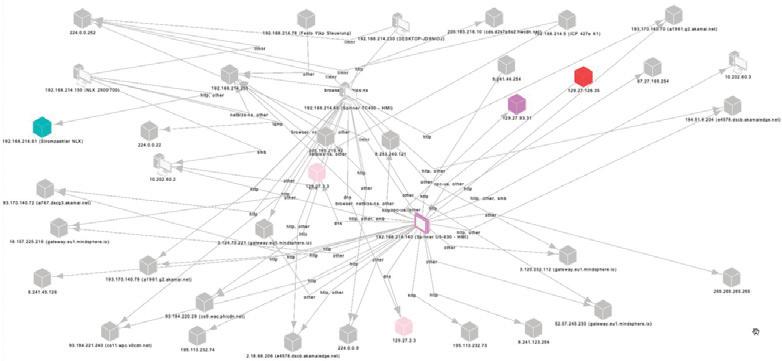
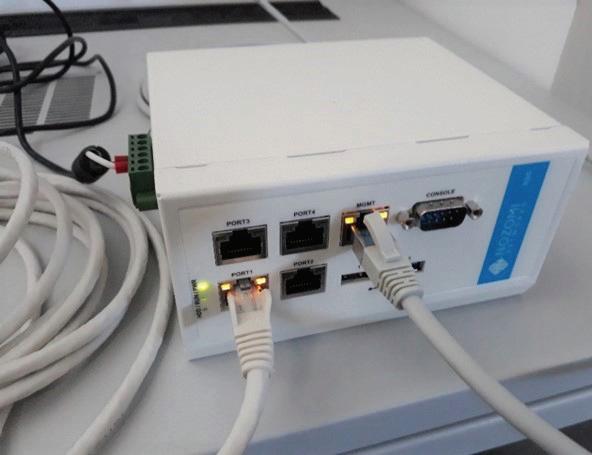
Abb. 3: Datenverkehrsüberwachung über Nozomi-Box
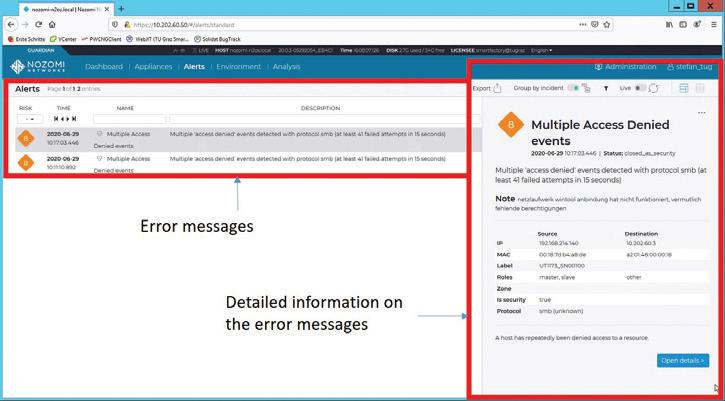
zum Ändern von Reihenfolgen und zum Puffern verwendet werden, also ein absolutes speedy highlight für die Ingenieure und die Agilität in der smartfactory@tugraz.
Die Forschungs-Infrastruktur für Datensicherheit
Indem in einer smarten Fabrik in hohem Maß mit den Diensten des Internet gearbeitet wird, muss diese gleichzeitige Exponiertheit auch entsprechend geschützt werden. Weltweit zeigen zahlreiche desaströse Beispiele aus der Industrie immer wieder die fatalen Konsequenzen, wenn die Infrastruktur einer vernetzten Fabrik nicht ausreichend geschützt ist. Somit war es auch beim Aufbau der smartfactory@tugraz die erklärte Aufgabe, dass hierfür moderne Lösungen angewendet und gezeigt werden. Nebst den sehr elementaren Grundsicherungen, dass nur mit gepatchten Schnittstellen und Firewalls gearbeitet wird, kommen in der smartfactory@tugraz genau 2 konzeptionelle Vorkehrungen für mehr Sicherheit im Sinn der Security zur Anwendung. Dies ist zum Einen die Segmentierung in Schutzzonen und zum Anderen die Datenstromüberwachung der gesamten Fabrik.
Um im Fall eines erfolgreichen Angriffs nicht die gesamte Fabrik betroffen zu machen, werden bei der Zonenbildung alle Einrichtungen (insbesondere Daten- und Programmserver) der smartfactory@tugraz in separaten Schutzzonen zusammengefasst, auf diese Weise differenziert verwaltet und somit besser geschützt. Man kann diese Vorgehensweise mit der Gliederung eines Bauobjekts in Brandschutzbereiche vergleichen.
Die genannte Datenstromüberwachung funktioniert über eine sogenannte „Nozomi-Box“ (siehe Abb 3). Das ist ein klein bauendes Gerät mit SW, welche sämtliche Datenflüsse der Fabrik auf Anomalien hin überprüft. Sollte ein Datensatz unüblich und aus der Norm sein, wird ein Alarm ausgelöst, der unmittelbar die Chance gibt, diese Informationsflüsse inhaltlich zu überprüfen und gegebenenfalls sofort Gegenmaßnahmen einzuleiten. Um diese Erkennung möglich zu machen, muss diese SW anfangs die für den Fabrikbetrieb typischen Datenströme kennen lernen, was im konkreten Fall nicht explizit getriggert werden muss, weil der Lernprozess sofort nach Aktivierung der Box umfassend startet.
Weitere technologische Themen in der Smart Factory
Wenngleich es um 2 Schwerpunkte in der smartfactory@tugraz geht, darf für das Forschungs- und Lehrangebot im Rahmen der digitalen Transformation in der Produktion eine Reihe von anderen technologischen Themen nicht fehlen.
In einem Nebenraum wird z.B. die Metalladditive Fertigung mit 2 Laserschmelzanlagen und der dazugehörigen Peripherie betrieben und steht damit ebenso als erlebbare disruptive Technologie zur Verfügung. Für die komplexen Vorplanungsprozesse wird auf Spezialsoftware zugegriffen und unter Einbeziehung der zur Verfügung stehenden Zerspanungsmaschinen kann der gesamte additive Prozess bestens verfolgt werden.
Im Bereich der Robotik wird die Interaktionsfähigkeit von Industrie-Robotern unterschiedlicher Hersteller gezeigt, welche über das TIA-Portal aus der Tecnomatix-Familie von Siemens realisiert wurde. Als Teil der Roboteranwendungen wurde auch ein kollaborativer Arbeitsbereich eingerichtet, um gerade auch das Thema Arbeitssicherheit, Risiko-Beurteilung und andere Anforderungen zu zeigen, die bei Nutzung dieser neuen Generation an Robotern zu berücksichtigen ist. Im Rahmen von Laborübungen arbeiten die Studierenden – aber auch angemeldete Besucher von externen Unternehmen - an und in diesem kollaborativen Arbeitssystem. Als weitere Einzigartigkeit muss auch die realisierte datentechnische Verbindung von PLM, ERP und MES in der smartfactory@tugraz erwähnt werden. Diese 3 Kernsysteme einer informatorischen Begleitung einer Produktion kommen in aller Regel von verschiedenen Herstellern und sind daher auch oft sehr isolierte Systeme, obwohl sie vielfach mit denselben Stammdaten arbeiten müssen. In der Pilotfabrik der TU Graz ist es gelungen, diese 3 Systeme über einen Enterprise-Service-Bus der Marke „PdM-Webconnector“ von TSystems durchgängig zu verbinden, d.h., Stammdaten die im Engineering (PLM) zu einem Produkt erzeugt wurden, stehen automatisch im ERP zur Verfügung, um damit Aufträge zu generieren, die die in der Folge ans MES weitergereicht werden können, obwohl dieser Datenfluss über Systeme von drei verschiedenen Herstellern läuft (siehe Abb. 4). Abb. 4: Datenintegration über Enterprise Service Bus auf IT-Ebene
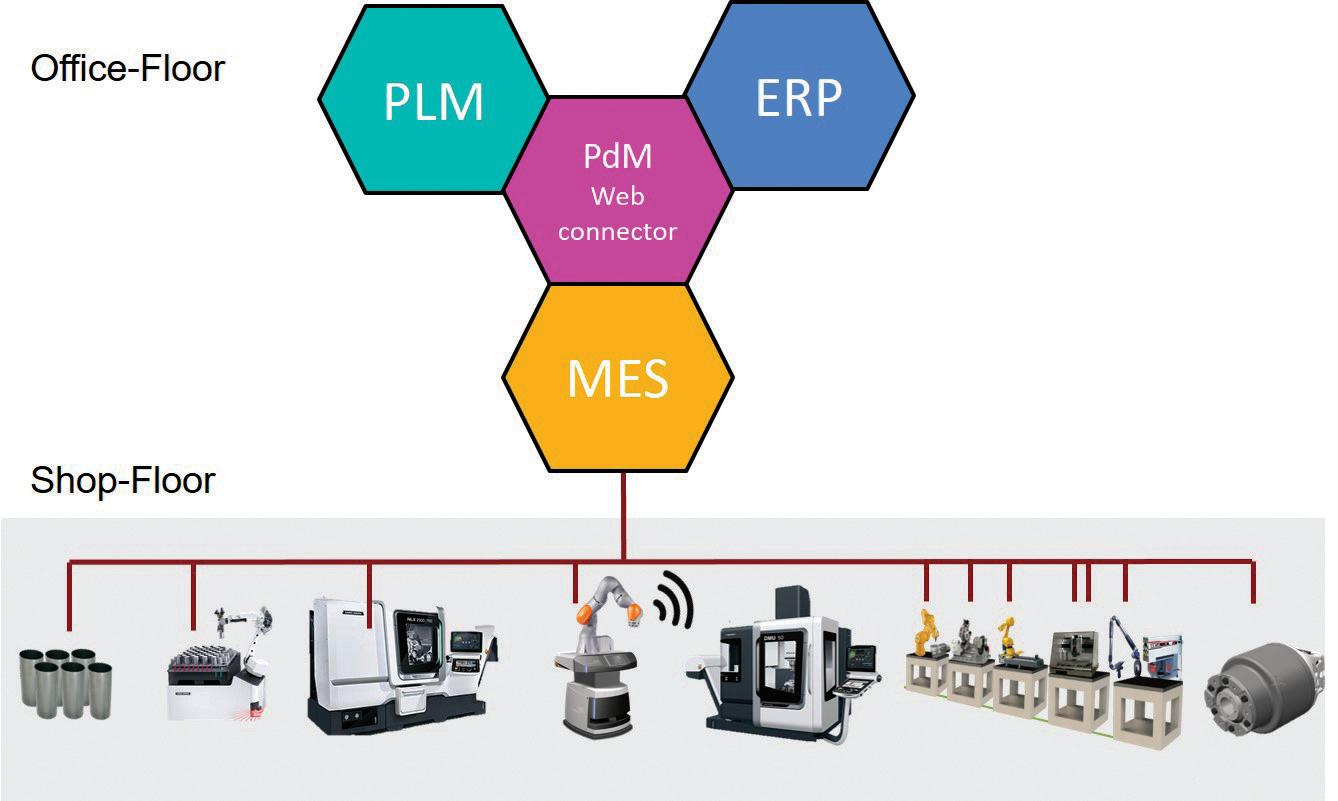
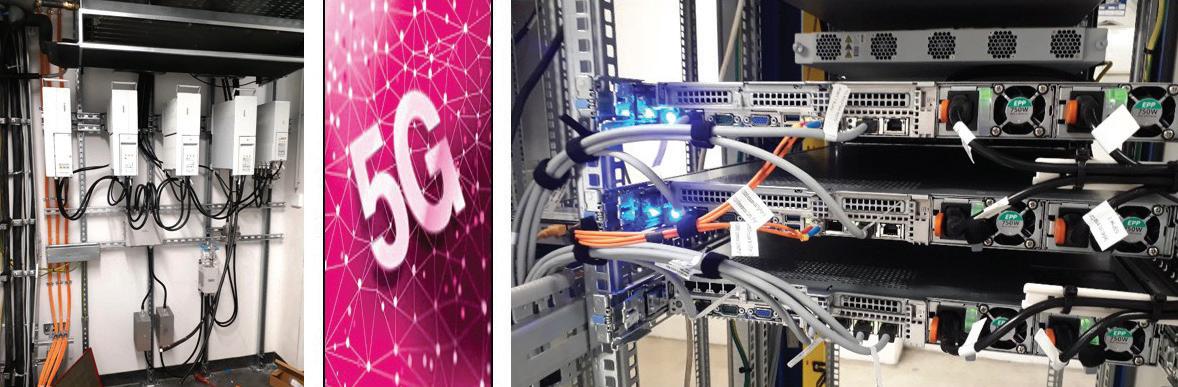
Abb. 5: 5G Infrastruktur
Die systematische Erfassung von Prozessdaten und deren Bereitstellung für Analysezwecke sind ein weiteres must-have einer smart-factory.
Diese Herausforderung wurde insofern gesteigert, als man bewusst auf eine hohe Heterogenität des Anlagenparks gesetzt hat, um zu zeigen, dass man auch von den Maschinen mit sehr unterschiedlichen Protokollen zu den gewünschten Datentransfers in diverse Data Lakes gelangt. Letztlich werden in der smartfactory@ tugraz Prozessdaten mit exotischeren Protokollen über Middleware in das Format OPC-UA transponiert, um der Data Analytics konsolidierte Daten in der Cloud bereitstellen zu können.
Als letztes Highlight der Grazer Forschungs- und Lernfabrik smartfactory@tugraz sei noch die installierte 5G-Campus-Lösung (siehe Abb. 5) vorgestellt, die für die Versuchsfläche im Ausmaß von ca. 300 m2 ein hochleistungsfähiges, abgesichertes Kommunikationsnetz für einen zeitsensiblen und datenintensiven Informationsaustausch nötig ist. Damit eröffnet sich ein zukunftsträchtiges Forschungsfeld, das viele zukunftsweisende, bildunterstützende und latenz-kritische Anwendungen testen und weiterentwickeln lässt.
Nutzungsformen
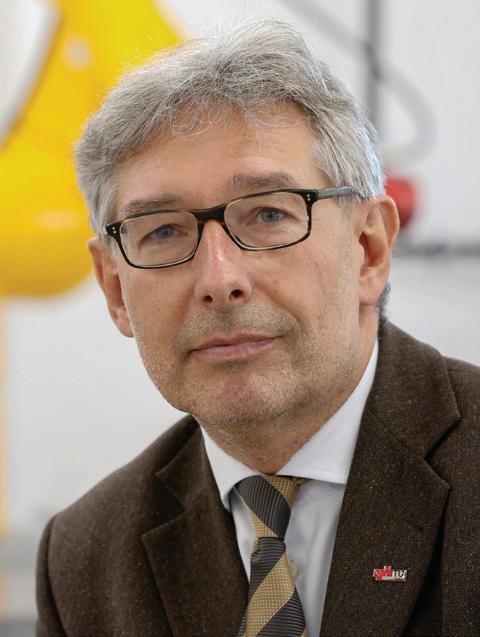
Die mit der smartfactory@tugraz aufgebaute Infrastruktur wird im Wesentlichen in drei Formen genutzt. Zum Ersten ist es eine Forschungsstätte für das Betreiber-Institut, das Institut für Fertigungstechnik, welches nun auf modernste Betriebsmittel und hochspezialisierte Software als Bestandteile eines Cyberphysikalischen Produktionssystems zugreifen kann. Aber auch andere Institute der TU Graz können dieses moderne Labor nutzen.
Zum Zweiten dient die smartfactory@tugraz der Lehre. Mittlerweile werden dort die „Laborübungen smart factory“ abgehalten, und auch Auszüge von facheinschlägigen Vorlesungen werden zur Veranschaulichung unmittelbar in dieser Umgebung durchgeführt.
Zum Dritten steht diese Forschungs- und Lernfabrik auch externen Betrieben aus Gewerbe und Industrie offen. Es ist die explizite Aufgabe der smartfactory@tugraz, dies auch als Auftrag des öffentlichen Fördergebers, dass die genannten Betriebe, hierin wieder ganz besonders die Klein- und Mittelbetriebe, diese Infrastruktur zur Weiterbildung und zur Platzierung von Auftragsforschung und Entwicklung im Kontext der digitalisierten Produktion nutzen sollen. Es ist die ideale Umgebung, um die digitale Transformation kennenlernen, exemplarisch testen und für die eigenen Zwecke vorbereiten zu können.
Finanzierung und Anerkennung
Das Projektvolumen des Aufbaus der smartfactory@tugraz beläuft sich auf ca. 4 Mio. €. Die Finanzierung dieser Summe wurde zur Hälfte aus Mitteln des damaligen Bundesministeriums für Verkehr, Infrastruktur und Technologie (bmvit) bestritten, die andere Hälfte stammt aus Sach- und Geldmitteln der folgenden Firmen: Siemens AG Österreich, T-Systems Austria GesmbH, proALPHA Software Austria GmbH, SoliDat Solutions in Data Processing GmbH, incubed IT GmbH, Know Center GmbH, TAGnology RFID GmbH, Anton Paar GmbH, AVL List GmbH, B&R Industrial Automation GmbH, DMG MORI Austria GmbH, FESTO GmbH, GGW Gruber & Co GmbH, NXP Semiconductors Austria GmbH, Infineon Technologies Austria AG, Magna Steyr Fahrzeugtechnik AG & Co KG, Magna Powertrain GmbH, TCM International Tool Consulting & Management GmbH, Voestalpine Stahl GmbH und Zoller Austria GmbH. An dieser Stelle sei einmal mehr der Dank an alle diese finanzierenden Organisationen ausgesprochen, ohne deren finanzieller und inhaltlicher Unterstützung die smartfactory@tugraz nie entstehen hätte können.
Autor:
Dipl.-Ing. Dr. techn. Rudolf Pichler
studierte Wirtschaftsingenieurwesen - Maschinenbau an der TU Graz und promovierte am Institut für Wirtschafts- und Betriebswissenschaften. Im Anschluss war er 20 Jahre lang immer in produktionsrelevanten Führungs-funktionen für Unternehmen wie Zumtobel AG, Umdasch AG, Siemens AG, TCM Tool Consulting und Management GmbH und im Anlagenbau tätig. Von 2015-2020 bekleidete Herr Pichler die Stiftungsprofessor für Advanced Manufacturing am Institut für Fertigungstechnik und baute dabei auch die Lernfabrik „smartfactory@tugraz“ auf, welche er nun als Senior Researcher leitet.