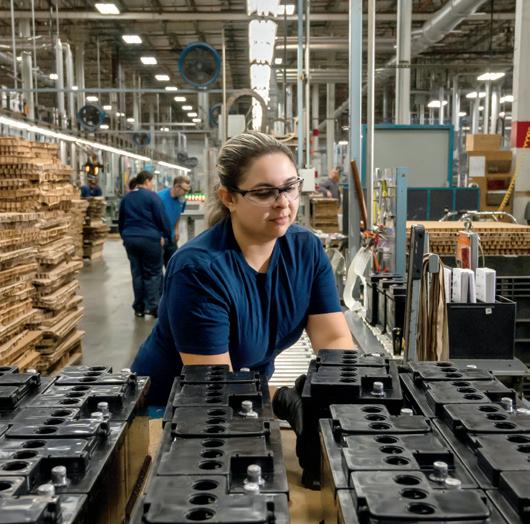
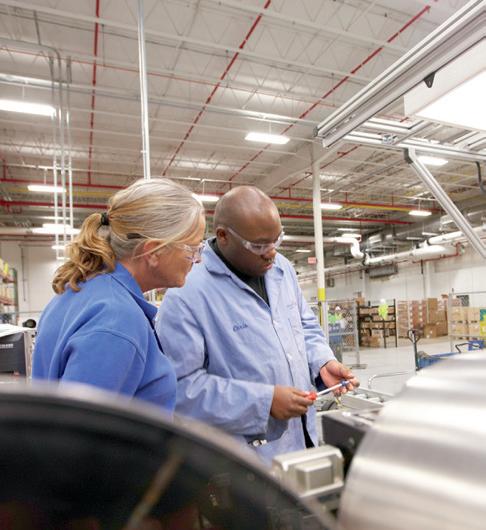
INTERNATIONAL
Special thanks to these BCI members for their financial support of this book.
“ Change is many things. It is inevitable, continuous, and at times unpredictable. But most of all, change is vital—though it presents us all with challenges, there is no way we would be able to grow without it. It is how we choose to work through and overcome these challenges that will make us stronger today and propel our industry into the future.
Right now, we are facing a world hungry for energy like never before. It’s going to take all of us working together to find solutions to help optimize it, conserve it, and sustainably store it. While in the past many of us have been more focused on one type of solution, the world is now challenging us to broaden our horizons and work with many types of solutions to meet our exponentially growing energy needs.
I strongly believe that BCI is the association confronting these challenges headon and leading the way with strategies that will help better prepare us all for the future. Together, united with one voice, we need to uphold the lead battery industry as a leader to other industries because we truly believe and know the great value it has to our society.”
—Chris Pruitt, CEO and President, East Penn Manufacturing Co. / BCI Chairman“When thinking of BCI’s many successes, one might think that an association of manufacturers might define success in terms of research and development, innovation, product development, and so on. What rises to the top for me is that BCI and its members created the most efficient and effective circular economy with lead batteries. By the collection, recycling, and reuse of lead battery materials, our industry minimizes waste and has established a means of continuing production for future generations in a sustainable and environmentally responsible manner. No other consumable product can make that claim. This story needs to be told more often and modeled by other industries—batteries or otherwise. With the advent of other battery chemistries, I hope those technologies can succeed as BCI and its members have.”
—Mark Kelley, Vice President, Industrial Products Group, Crown Battery“BCI has worked as a guiding force over the years to ensure that all domestic battery manufacturers are cognizant of the impact that the battery industry has on the environment. To that end, they have worked to build a better understanding of all the relative issues that government agencies are implementing as well as highlighting the proactive position that the battery industry has taken on its own to support the policies.
This forward-thinking approach has positioned the US lead battery industry well ahead of most restrictive governmental requirements. Working with the manufacturers, BCI efforts have improved working conditions within the industry as well as improving the surrounding environment. While many other industries are struggling with the tougher mandates, the lead battery industry continually meets or exceeds expectations. BCI is also working to bridge the thinking of legislative agencies regarding the feature benefits that the lead battery industry provides, such as the extremely high recyclability of lead batteries. Too often, the glitter of new technology can overshadow the benefits and future possibilities of current technologies. BCI has been the differentiator in creating a better global environment as well as minimizing the carbon footprint that the industry will leave as a legacy to our children and grandchildren.”
“Now is the golden age of the battery, with an increased focus on the need for energy storage in the transition to clean energy. However, there are three significant challenges the industry must overcome in the near- to mid-future.
Improvements need to be made in manufacturing processes to overcome workforce scarcity. Labor shortages will continue, so labor-intensive and ergonomically challenging processes will need to be automated to achieve operational efficiencies with fewer employees.
Recycling processes must be established to recover and reuse the critical minerals in lithium battery manufacturing. By establishing a circular economy for lithium batteries, a domestic supply chain for those components will be available to US battery manufacturers, lessening dependence on foreign suppliers.
Investments in research and development and domestic supply chain infrastructures will be essential to achieve energy security and energy independence. US battery manufacturers must continue investing in innovative battery technology through public and private research and development collaborations. Investments are also necessary to strengthen the domestic supply chain for battery components. Access to domestic suppliers for components, cells, electrolyte, grids, terminals, and injectionmolded polyethylene will enable US battery manufacturers to quickly respond to the growing market demands for energy storage systems.”
—Mike Judd, CEO and President, Stryten Energy“BCI has served a critical role defining and influencing the battery industry as we know it today. Among its many achievements, the most significant success has been advancing and promoting best practices in safety standards for the management of lead throughout the battery life cycle. BCI helped set global guiding principles for manufacturing and recycling to protect workers and the environment from the improper use of substandard operating practices.
A circular economy is critical for our future and everything we do must be done with a safety-first approach and never compromise the well-being of people or communities. From the recent setting of material stewardship guidelines to the employee blood lead reduction program implemented more than twenty years ago, BCI emphasizes the importance that organizations must always do the right thing and do things the right way.
As the industry continues to evolve with the introduction of lithium and other chemistries, prioritizing health and safety in manufacturing and recycling of these products will ensure a prosperous future through the energy transition and achieve the ultimate goal of making the world a better place.”
—David M. Shaffer, CEO and President, EnerSysCadillac introduced the first vehicle with an electric starter, necessitating the use of a battery.
In September, the first issue of the automotive electrical industry’s independent trade journal TheBatteryManis published, offering expert advice for members of the battery industry.
By now, nearly all new vehicles require an electric starter and reliable power supply, best delivered by a 6-volt battery.
On January 29, a small group of battery manufacturers gathers in Chicago to discuss forming a trade association. In March, the group becomes the National Battery Manufacturers Association (NBMA—now BCI) and officially launched with twenty-five members.
The first BCI convention is held on September 19 and 20 at the Hotel Clifton in Niagara Falls, New York.
One of the early conferences is held in Louisville, Kentucky, where dimension and productbuilding standards are proposed and approved. These are included in the National Recovery Administration’s Code of Fair Competition for the Electric Storage and Wet Primary Battery Industry.
NBMA changes its name to the Association of American Battery Manufacturers (AABM) to account for members from Canada, Mexico, and South America.
In 1946, the AABM creates a group-numbering system for lead batteries.
The first MethodforAssignmentof BatteryGroupandAssemblyNumbers is published (the foundation for today’s TechnicalManualBCIS-01).
BCI manufacturers and recyclers expand the sharing of best practices with competitors to tackle environmental and safety issues collaboratively.
Late 1980s— East Penn Manufacturing founder Delight Breidegam and his son, Dan, lead industry efforts to lobby in Washington on behalf of the industry to avoid a potential tax increase on lead.
The group-numbering system is updated as the auto industry shifts to the use of 12-volt batteries.
On January 20, the AABM changes its name to Battery Council International, recognizing its worldwide members’ focus on manufacturing issues and their global impact.
BCI publishes the BCI Model Battery Recycling Legislation, the first model legislation to protect the environment and to encourage recycling of batteries by promoting the industry-managed reverse-logistics system for the collection and recycling of batteries.
BCI data shows that recycling of end-of-life lead batteries in the United States exceeds 90 percent for the first time.
BCI begins hosting the national biannual Environmental Health & Safety Conference.
BCI promotes the adoption of the BCI Model Battery Recycling Legislation nationwide, with many states adopting the model within the first few years.
BCI develops instructions and model training documents regarding the proper transport of lead batteries, to assure limited environmental impact.
The digital version of the Battery Replacement Data Book is launched on CD-ROM.
The BCI Model State Bill is adopted by forty-two states—creating a closed-loop system to keep lead batteries out of landfills, so they can be used in perpetuity.
The first BCI Innovation Award is bestowed, honoring Sally Breidegam Miksiewicz, the late CEO of East Penn Manufacturing Co.
With BCI’s support, Congress passes the US MercuryContaining and Rechargeable Battery Management Act, establishing three chasing arrows as a universal label symbol for recyclable batteries.
BCI acquires the assets of the Independent Battery Manufacturers Association, and IBMA members are welcomed into BCI to form a single, powerful voice for the industry.
SourceBCI.com launches to provide web-based access to BCI’s batteryreplacement data.
BCI launches the Advancing Lead Batteries Communications Initiative (ALBCI) in North America.
The Essential Energy Everyday (EEE) website is launched to educate policy makers about the importance and sustainable nature of lead batteries.
The Lead-Acid Battery Recycling and Cleanup Fund is instituted after BCI’s collaboration with California legislators.
The Women in the Global Battery Industry (WGBI) Initiative is launched to promote the role of women in the industry.
The first Amplify Award is given to honor highly effective communications, marketing campaigns, and education.
BCI, the DOE’s Argonne National Laboratory, and DOE’s Office of Electricity hold a technical meeting to identify research priorities.
The first women’s networking reception is held at the BCI annual convention in Tucson, Arizona.
The California Department of Toxic Substances (DTSC) removes lead batteries from its Priority Product Work Plan, a decision supported by the education efforts of BCI.
The EEE website is rebranded.
BCI sets up the American Battery Research Group to encourage innovation and allow for collaboration among lead battery manufacturers.
BCI and the Department of Energy (DOE) create national lab partnerships and research collaborations as part of the DOE’s Energy Storage Grand Challenge.
Through BCI’s Energy Storage Systems Initiative (ESSI), BCI works with member companies and partner organizations to promote the use of batteries in future energy storage systems.
BCI’s membership consists of more than 125 companies worldwide.
BCI’s website is rebranded and a new logo is created as the association consolidates its messaging with the EEE brand to emphasize BCI’s powerful voice for the industry.
BCI forms the Flow Battery Industry Group to foster the newly forming flow battery sector.
In August, BCI’s ALBCI body of work since 2017 receives the prestigious dotCOMM Platinum Award for Team Achievement.
The Source BCI website is revamped with a mobileready interface, expanded functionality, faster load time, and increased ease of use.
In 1954, a new lead casting wheel was built at Doe Run’s refinery in Herculaneum, Missouri, for production of one-ton blocks or ingots of lead. Here, twenty-five-pound lead ingots are lifted out of the “link” mold using a vacuum head before swinging the finished lead onto a waiting wooden pallet.
It was the late 1980s, and Dan Breidegam was in Washington, DC, with his father, DeLight Breidegam Jr., founder and then-president of East Penn Manufacturing Company. The trip had been arranged by Battery Council International (BCI) so members of the association could discuss with lawmakers a proposed tax increase on lead of fifty cents per pound. The younger Breidegam, who joined the family business in 1974, watched as his father sat down in one senator’s office and asked a pivotal question: “Senator, don’t you sit on the Veterans Committee?”
“The senator perked up and said, ‘Veterans are very important to me,’” Dan Breidegam recalls. “My father replied, ‘When you go to the veterans hospitals and see those fellas riding around in electric wheelchairs, the batteries that run them are lead batteries. They’re making veterans mobile again.’”
The senator was genuinely surprised to hear that fact, and he quickly understood why the father and son were sitting in his office that day. He recognized the detrimental effects that a seemingly small tax would have on the lead battery industry and, ultimately, the veterans he proudly supported. Not long later, Breidegam reveals, “The whole damn thing went away.”
Providing battery manufacturers, recyclers, marketers, retailers, suppliers, and distributors across the lead battery industry with the opportunity to make their powerful voices heard has been one of BCI’s predominant goals since its founding back in 1924. Over the last century, the trade association has dedicated itself to a host of advocacy efforts, educating regulators and key policy makers about the broad role that lead batteries play in society on a daily basis. Today, BCI supports a membership of more than 125 companies
from around the world with a wide array of initiatives that not only give them the resources they need to tackle myriad challenges in an ever-changing market, but also to continually improve the industry itself. This includes overseeing one of the most impressive environmental success stories in history, with the lead battery being recognized as the world’s most-recycled consumer product. And BCI has done all of this while keeping an eye on the future, working diligently to anticipate what is around the curve and strategizing ways for its members to prepare themselves to thrive in an industry that serves the transportation, energy, and communications sectors, among many others.
This is the story of the groundbreaking efforts of Battery Council International, a dynamic trade association that has been instrumental in supporting the companies that have made the lead battery industry what it is today.
As President and Executive Director of Battery Council International, it is my honor to introduce this commemorative book honoring BCI’s centennial in 2024. For one hundred years, BCI has represented the interests of companies involved in every aspect of the battery industry. While the names and faces have changed over the decades, BCI’s mission remains the same: to support member companies as they manufacture, supply, distribute, and recycle the batteries that provide essential energy solutions worldwide.
It has been my deep privilege to serve BCI in various roles over the past fifteen years, working alongside visionary leaders and experts who understand the power of deliberate collaboration between fierce market competitors. By pooling their expertise, BCI members have revolutionized battery technologies and uses multiple times in the past century, pioneered groundbreaking recycling systems, and demonstrated an uncompromising commitment to environmental stewardship and employee safety. As stewards of an indispensable, ubiquitous, and profoundly sustainable technology, they have started the engines, powered the products, energized the workforce, and enabled the mobility of millions.
As we celebrate the BCI community’s achievements, the future shines brightly. With support from BCI, member companies continue to innovate boldly—exploring new technologies, applications, and chemistries, and embracing opportunities to expand the role of sustainable batteries in an electrified future. As the world transitions to more secure and renewable energy sources, wise product and environmental
stewardship remains imperative. BCI member companies are rising to meet these challenges with ingenuity, integrity, and vision.
Our first century of service exemplifies the dedication, grit, and achievement of the BCI members, BCI Board of Directors, and association staff. On behalf of the BCI Board of Directors and the entire BCI staff, I commit to you that BCI is embracing a second century of industry leadership with the same energy. We will continue to engage with stakeholders worldwide as a tireless champion on behalf of our incredible members, to advance the standards and data the industry needs, and to provide a forum for our members to work collaboratively to pioneer sustainable technologies for future generations. The best is yet to come.
On January 29, 1924, a small group of battery manufacturers gathered in Chicago, Illinois, to discuss the possibility of forming a trade association. The goal of the organization would be to discuss challenges and promote best practices among the companies that were producing the most predominant type of battery on the market at the time: the automotive battery. The demand for dependable car batteries had skyrocketed since Cadillac introduced the first vehicle equipped with an electric starter in 1912. By 1920, nearly all new vehicles on the road had an electric starter and needed a reliable power supply, which was best delivered by a
six-volt lead battery. The opportunities within the burgeoning market encouraged small battery manufacturers to open for business across the country. Most were family-owned mom-and-pop shops, and they often made batteries by hand in their garages. The fledgling companies included such now-iconic names as Voltmaster Company Inc., which was founded as Gibbs Battery Company by S.E. Gibbs in 1923; Trojan Battery Company, which dates back to 1925 when brothers-in-law George Godber and Carl Speer began manufacturing automotive batteries for commercial trucks; and Crown Battery Manufacturing Company, started in 1926 as a small battery-repair shop in Fremont, Ohio, by German immigrant William J. Koenig.
It did not take long for the emerging entrepreneurs to recognize the need for an entity that would bring a certain level of structure to an industry that showed no signs of slowing down. Therefore, in March of 1924, the National Battery Manufacturers Association (NBMA) officially launched and included twenty-five companies representing manufacturers and material suppliers. By the mid-1940s, the association changed its name to the Association of American Battery Manufacturers (AABM) to account for members from Canada, Mexico,
According to Harold “Hal” Hawk, who serves as chairman of BCI’s convention planning committee, attending the annual BCI Convention + Power Mart Expo has always been a prestigious opportunity, allowing association members to join together in one location for four days of networking, meeting with suppliers, participating in educational sessions, discussing the economics of the industry, and more. It is one of the main benefits of being a member of BCI.
“In the early days, if you were a member of BCI, it gave you a stamp of approval and showed that you were working with an industry that was sensitive to the lead battery business and also an advocate for the lead battery business,” Hawk says. “The convention offers a great opportunity to build relationships within the industry. And, in many cases, your competitors are also your friends; the convention gives us a spot to get together, have meetings, talk about the business, and learn more about the business.”
Today, the convention not only offers a host of both technical and marketing-based programming, but also access to BCI’s annual transportation forecast and a five-year industrial forecast. What’s more,
innovation takes center stage with the annual presentation of the BCI Innovation Award, which was named in honor of Sally Breidegam Miksiewicz, the late CEO of East Penn Manufacturing Co., who was renowned for her dedication to promoting cutting-edge advancements in the industry. The award recognizes innovation in packaging, technology, equipment, chemistry, and more. Also recognized each year is the winner of the Amplify Award, launched in 2022, which honors highly effective communications and marketing campaigns and programs that inform, educate, and promote the lead battery products, components, services, or industry as a whole.
As the battery manufacturing industry took off in the early 1920s, a small trade journal began circulating among those who worked in “the automobile storage battery and electrical field.”
The first issue of TheBatteryMan , an independent publication founded by Overton W. Pendergast Jr. and Al Hemberger, appeared in September of 1921. Every month until 2005, when The Battery Manceased publication, members of the industry received invaluable information, expert advice, and more in the pages of the periodical. For more than eight decades, it was recognized as a go-to resource that served the battery manufacturing industry worldwide.
“One of the original missions of the organization was to bring sanity to an unorganized way of making product across the industry.”
Roger Miksad President and Executive Director, BCI
and South America. The name changed for the final time on January 20, 1970, when member companies voted to call the association Battery Council International, or BCI, not only because of members’ facilities located in countries around the world, but also thanks to the organization’s focus on manufacturing issues that have a global impact. And while the name changed, the overriding goals of the association have remained intact for one hundred years.
“One of the original missions of the organization was to bring sanity to an unorganized way of making product across the industry,” notes Roger Miksad, president and executive director of BCI. “The battery manufacturers came together to bring some clarification in terms of product dimensions. They took a collaborative approach to product development.”
Indeed, creating standards for batteries across the industry was a core objective of the NBMA during its first decade. At one of the first industry conferences, held in Louisville, Kentucky, in 1933, member companies proposed specific dimension and product-building standards, which were approved
In 2018, BCI board member Julie McClure, chairman of MAC Engineering & Equipment Co. Inc., suggested that BCI hold a women’s reception during the annual convention in Tucson, Arizona. More women had become part of the industry, finding their way into positions both on the factory floor and in management, and she wanted to give them a chance to connect. The outstanding response to the event made the board of directors sit up and take notice.
“The board realized they needed to provide more diversification,” recalls Pam O’Brien, BCI’s recently retired senior vice president of operations, who, along with Donna Snyder, vice president of marketing and advertising for East Penn Manufacturing Co., decided to spearhead the development of the Women in the Global Battery Industry (WGBI) Initiative. The organization officially launched in 2019, and, according to O’Brien, its membership skyrocketed from zero to more than one hundred practically overnight.
“The mission is to promote women in the industry and make them more visible,” she adds. “It also strives to reach out to the
community to promote STEM and battery-industry-related educational opportunities for women from the college level all the way down to elementary school.” Members also have access to a quarterly webinar series, monthly conversations, and a newsletter. And battery manufacturers have supported their employees’ participation in the group. O’Brien states, “The companies know this is something that they should be engaged with. The WGBI has been a major milestone [for the industry].”
by then-board president E.D. Martin and included in the National Recovery Administration’s Code of Fair Competition for the Electric Storage and Wet Primary Battery Industry. In 1946, AABM took the effort a step further and created a group-numbering system for lead batteries to try and create consistency across the battery manufacturing sector. The system was updated in the 1950s as the automotive
industry shifted to the use of a twelve-volt battery for larger cars and engines, leading to the development of different shapes, sizes, and types of batteries. However, while the group-numbering system was in place, the method used to assign those numbers actually varied between companies and organizations.
continued on page 13
In a Banner Battery factory in 1958, molded book-casting grids were placed on a conveyor belt and pasted by applying a negative or positive mass. Paper was then applied by hand to prevent the paste from falling off.
In 1926, William J. Koenig, a seventeen-year-old German immigrant, founded a radiator and battery repair shop in Fremont, Ohio. As his business grew, he recognized a growing consumer demand for new batteries, so he began to produce car batteries, naming his thriving business Crown Battery Manufacturing Co., a nod to his last name’s German translation: “king.”
As sales of Crown batteries increased beyond Ohio’s
borders, Koenig’s family continually expanded its manufacturing facilities to produce them. In 1958, Crown joined the Independent Battery Manufacturers Association (IBMA) and Koenig’s son Lee served as the organization’s president on several occasions. Then, in 1998, he announced the sale of the company to a small group of loyal management employees.
Today, Crown Battery, still headquartered in Fremont, Ohio,
operates four wholly-owned subsidiaries in two countries and fourteen service centers in North America, serving more than one hundred markets in sixty countries.
Maintaining the highest level of quality is a top concern for the company, as the demand for electrification of new products and services expands exponentially. Meeting the need for highly efficient batteries dovetails with the company’s concern for environmental stewardship—batteries that last longer are replaced less often—a sustainability ripple-effect. Notably, Crown is the first battery company to be deemed a US Environmental Protection Agency (EPA) Green Power Partner, which recognizes efforts to reduce the negative
“No company could achieve this level of success without a great team. We’re proud of our entire team for embracing the challenges of manufacturing batteries that make the world a better place—raising the standards of living, health, and safety for the communities we serve.”
Harold F. Hawk Jr., CEO and President
health impacts of air emissions by using “green power.” In 2020, Crown switched to 100 percent solar and wind energy to minimize its carbon footprint while remaining cost efficient without reducing product quality. Its onsite water-recycling program saves more than 500,000 gallons of water per year.
Now, as Battery Council International celebrates its first century, Crown Battery, too, nears its first one hundred years in business. In that time, Crown has evolved from a small, successful repair shop to a large and growing company. Backed by a loyal customer base and more than 650 dedicated employees, the company has proved the name Crown was truly an appropriate choice.
Harold F. Hawk Jr., Crown Battery’s current CEO and president, sums up the company’s core values this way: “No company could achieve this level of success without a great team. We’re proud of our entire team for embracing the challenges of manufacturing batteries that make the world a better place—raising the standards of living, health, and safety for the communities we serve.”
“In the mid-1960s, there were at least five organizations that were assigning battery group numbers,” recalls Roger Winslow, who founded Voltmaster Corporation Inc. in 1964 and served as president of the BCI board of directors, a role now referred to as board chairman, from 1986 to 1988. “Those organizations were the AABM, the Society of Automotive Engineers (SAE), Delco, Autolite, and the Richardson Company. As new batteries were brought into the market, it was very confusing to have more than one distinct group number for the same battery.” While attending the AABM convention during that period, he stood up on the convention floor one day to encourage the association to take full control of assigning battery group numbers across the entire industry. “I said, ‘There ought to be a transparent method for assigning battery group numbers.’ It wasn’t very long before I found myself on that committee,” he continues. “In the end, [I helped] organize and publish the first formal MethodforAssignmentofBattery Group and Assembly Numbers . This original document provided the foundation for today’s TechnicalManualBCIS-01.”
The development of that time-honored technical manual served as just one illustration of the battery manufacturers’
“As new batteries were brought into the market, it was very confusing to have more than one distinct group number for the same battery.”
Roger Winslow Founder, Voltmaster Corporation Inc.
For more than eighty-five years, BCI has been the best source for information about battery fit and fitment for the more than 160,000 vehicles on the road. Today, BCI members can access critical data about 293 different battery types across six vehicle categories online thanks to Source BCI, a digital version of the Battery Replacement Data Book. The battery replacement database includes vintage data stretching to the present for all passenger cars, light trucks, vans and minivans, trucks, buses and coaches; farm equipment; industrial road and miscellaneous equipment; lawn and garden equipment; tractors; power sports including motorcycle, scooters, snowmobiles, and personal watercraft; utility vehicles; ATVs and go-carts; aerial lifts; and power scrubbers. The information is updated quarterly and also can be retrieved via the Source BCI website.
“These are the fiercest competitors in the marketplace, but they are incredibly committed to working together on issues of common concern.”
Roger Miksad President and Executive Director, BCI
willingness to come together for the good of the industry. “This is a very tight-knit industry,” Miksad observes. “These are the fiercest competitors in the marketplace, but they are incredibly committed to working together on issues of common concern, whether it’s a policy issue, a health and safety issue, or a social issue. You don’t see that in a lot of other industries, where the people are committed to being a community of competitors.”
That collaborative spirit became a hallmark for BCI as it entered uncharted territory in the early 1970s, when the reputation of lead took a tremendous downturn and association members realized that they had to move beyond product standards and find ways not only to prove the safety of the lead battery, but also to demonstrate its sustainability and promote its many benefits. Thus began a monumental undertaking that changed both the focus and the composition of the industry as it headed into an uncertain and often-challenging future.
When President Richard Nixon launched the US Environmental Protection Agency (EPA) in November of 1970 and the Occupational Safety and Health Administration (OSHA) in 1971, the
battery industry had its work cut out for it. For decades, lead had been used to manufacture all kinds of products, from glass and gasoline to paint, pipes, furniture, and toys—as well as car batteries. While there were rumblings over time about the potential dangers associated with lead exposure, the material remained omnipresent. Fifty years after the establishment of BCI, the EPA and OSHA were charged with overseeing a reduction in the amount of lead in both the environment and people’s bodies. This placed an onus on the battery manufacturing industry as it faced a great deal of prospective regulation directed at the manufacturing facilities and smelters at the heart of the trade.
“Our industry is highly regulated because we use a heavy metal. Lead has known toxic properties, and it was used so ubiquitously in the old days before people understood how dangerous it was,” notes David M. Shaffer, president and CEO of EnerSys. “It was used in gasoline, paint, and water pipes. And with the issues surrounding paint and water pipes in particular, lead became a four-letter word.”
The presence of the new federal agencies had a major impact as battery manufacturers scrambled to deal not only with new rules, but also the threat of major regulation across the board. “In the ’70s and ’80s, there were a lot of big-time changes in the industry. OSHA was a driver, and the EPA was a driver. You either complied with the regulations or you were going to be out of business,” Winslow reveals. “The smaller battery manufacturers didn’t have the horsepower, the technology, or the equipment to comply. A lot of people couldn’t afford to make the necessary changes, and they quit. In many cases, the larger manufacturers came in and purchased the smaller ones. So there was a lot of consolidation.”
In fact, the number of manufacturers in the industry has decreased dramatically since the late 1970s. According to Miksad, at that time there were approximately 180 companies and 250 manufacturing facilities across the United States; by late 2022, there were only 18 companies and 50 manufacturing
facilities. Howard M. Meyers, chairman of Quexco Inc. and previously the owner of one of the largest lead smelters in the United States, notes that the consolidation affected battery recyclers as well, with only a half-dozen smelters remaining out of the original sixty by the beginning of 2023. Miksad says, “You went from an era when you had numerous companies with between ten and fifty employees to having three or four very large companies with thousands of employees and several other smaller companies serving specific niche markets. So the industry definitely changed.”
Harold “Hal” Hawk, president of Crown Battery, attributes the change to a combination of the new regulatory environment and the fact that so many of the family-owned battery manufacturers did not have succession plans in place. While many boasted second-generation owners, as sons and sons-in-law assumed the businesses from their founders before the 1970s, making the leap to the third generation was more challenging. And as time marched on, some of the most renowned companies had owners who were simply aging out of the industry. Ultimately, the regulations placed on the industry virtually decimated the small, family-owned battery manufacturers. “You saw a lot of businesses look for answers by merging with other strategic partners in the battery business,” Hawk notes. “Suddenly, you had a company with an owner who was seventy years old and had no plans to pass the baton to someone else in the business. A lot of these guys were forced to sell.”
While the consolidation changed the dynamic of the industry stateside, the process actually opened the door for BCI to become a more internationally focused association, as many of the larger member companies had operations not only in Canada, Mexico, and South America, but also Europe and Asia. And as the number of actual members has decreased over the years due to industry consolidation, the size of those organizations has grown substantially, and the reach of the association has actually expanded. “Our membership spans the globe,”
“Suddenly, you had a company with an owner who was seventy years old and had no plans to pass the baton to someone else in the business.”
Harold “Hal” Hawk President, Crown Battery
Miksad states. “We look at global policies and have a global view in terms of the issues we are willing to take on and talk about.”
Of course, when it comes to major decisions about initiatives or campaigns implemented by BCI, there is a long-standing tradition of a steadfast decision-making process. Since the founding of the association, the underlying operating agreement states that voting members sitting on the board of directors must be chief executive officers or pinnacle decision makers for the North American, South American, or European companies that comprise it.
“One of the most significant reasons that BCI has been successful is the fact that the association insists on CEO membership on the board,” Shaffer asserts. “Having the top decision makers in the room makes a significant difference and allows us to get things done.”
“It’s a wonderful asset we have that, two times a year, we can get the CEOs of the major battery manufacturers around a table and agree to address those things that are very real and relevant to our industry,” adds Chris Pruitt, president and chief
executive officer of East Penn Manufacturing Co., who began serving as president of the BCI board in 2021 and now serves as chairman of the board. “We had a meeting in Washington, DC, and there were fifteen of us in a room. I realized that we represented the entire lead battery industry in North America. The meeting was cooperative, collegial, and respectful. There were no egos in that room. We gave great input, and we got great feedback. We were there trying to advance new ideas and better our industry.”
The unique aspect that has given competitors the space and opportunity to act as collaborators over the last one hundred years trickles down through the association, permeating all of the committees and working groups that gather regularly to brainstorm and problem solve. From the technical committee and marketing committee to the environmental health and safety committee, those who work in and serve the battery manufacturing industry come together as colleagues
Battery Council International strives to help its member companies be outstanding citizens within their communities and it recognizes the work the industry does in the charitable arena. From honoring battery manufacturers, recyclers, and suppliers that support families in need during the holiday season to sponsoring a mobile mammography unit, BCI and its member companies always find opportunities to give back. In 2022, the association took its efforts to a worldwide level, contributing to aid efforts for families displaced by the invasion of Ukraine. BCI member companies collected and donated more than $430,000 to groups working
to look at the bigger picture and provide solutions to a host of challenges. Their dedication keeps the industry moving forward and has allowed it to become what it is today.
“The battery manufacturing industry is the most well-situated, mature, and extensive industry in the United States,” says Dr. Matt Raiford, senior technical manager with the Consortium for Battery Innovation. “Lead batteries are everywhere. They’re used to start our cars. They’re used to back up our data centers. They’re used in our communications infrastructure and cell phone towers. They power warehouses and are found in floor scrubbers for schools. The military uses them for Humvees, personnel carriers, and submarines. Lead batteries fit the needs of products across more than eighty applications. You’re looking at an industry that has stewarded the technology well and is working on that stewardship all the time. The lead battery industry is the first of all great stewards.”
at the Ukrainian borders. In total, the association’s members donated $255,000 to UNICEF to support children and families displaced by the war and $175,000 to the International Red Cross, World Central Kitchen, Jesuit Refugee Service, and a variety of other charitable organizations.
In the 1990s, Johnson Controls introduced the Sears DieHard Gold battery with a pump system that produced more power and prolonged battery life.
At East Penn Manufacturing we often say, “we’re growing oak trees.” That’s because we know growing roots takes time. Time to gain strength, dive deeper into the soil and expand out, providing a powerful foundation for a towering and resilient tree. For seventy-seven years, East Penn and its incredible people have been planting deep roots and the company is still standing tall today.
It all started in 1946, when a father and son, DeLight Breidegam Sr. and DeLight Breidegam Jr., founded the enterprise. They worked out of a small, one-room creamery in the village of Bowers, Pennsylvania. Through hard work, ingenuity, and talented people, the company thrived and grew. By working hard, embracing change, and striving for innovation, the one-room operation with a handful of employees has transformed into what is now an expansive enterprise with over ten thousand employees and state-of-the-art operations around the world. Our product line has grown to 515 battery designs, meeting diverse energy needs including automotive, commercial, marine, motive power, UPS, and telecommunication markets.
What hasn’t changed is the company’s foundation, forged by DeLight and his father from the very beginning. Our family-driven values and people-centered culture are the core of who we are. We can truly say that people are the heart of East Penn, and we are wholly committed to supporting and empowering
enabling technology for carbon reduction, renewables, and promoting a circular economy.
East Penn hasn’t been alone throughout this journey. The energy storage industry is comprised of partnerships and associations that have led to incredible advancements in technology and sustainability. As we look to the exciting future, we sincerely value these relationships that encourage us all to continue to innovate and grow together with the expansion of changing energy needs.
As East Penn continues to grow, supported by our deep roots, solid foundation, and industry collaboration, we are ready to face and innovate through the challenges ahead, branching out to new heights.
employees, their families, and their communities as we work side-by-side to power the world around us.
Together, we build products with new innovations and advanced technologies that provide reliable power for vital energy needs and enhance our world’s sustainability goals. We are also focused on the future of energy storage by exploring untapped possibilities for lead battery technology. Our research includes enhancements to the performance of lead and revolutionizing the materials in lead batteries, new breakthroughs in process control, remarkable improvements in dynamic charge acceptance (DCA), and partnering with systems that incorporate lithium and other alternative battery technologies. These advances will not only meet the need of demanding future applications but be an