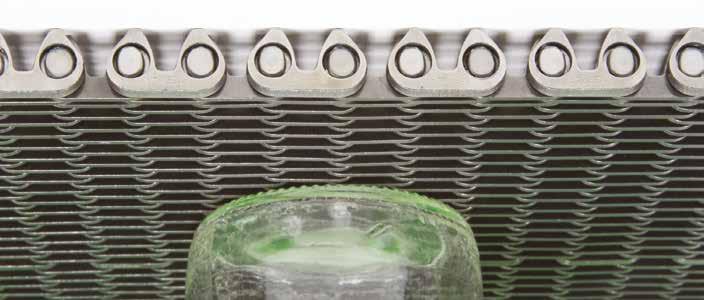
12 minute read
Batch
News Batch APB plans construction and awaits permits
United States // Borates
American Pacific Borates Ltd has enjoyed a productive December quarter and is ready to begin construction at its Fort Cady Borate Project in California once final permits have been approved.
The company is targeting increased sulphate of potash (SOP) production, which under the current plan will produce 108,000 tonnes per annum.
This increase in SOP production is expected to increase project internal rate of return (IRR) and net present value (NPV) as well as targeting US$345 million annual earnings before interest, tax, depreciation and amortisation (EBITDA) once in full production.
An enhanced DFS is expected to be released before April 30, 2020. During the December quarter the company began initial site works to prepare for the construction of the borate mine, which included improvement to roads, site clearing/clean-up and infrastructure improvements for construction activities.
A network gas contract has been signed and initial payment made to ensure network gas is available for first production at the site.
The company expects a final, positive permit to be awarded for the project over the coming months.
The ABR board believes there is an opportunity to increase production to take advantage of the fact that USA is a net importer of SOP and the only incumbent producer is a high-cost producer. The company will also have a very low cost of production relative to USA production and imported SOP.
Other potential advantages are: • The mine is on the West Coast, which is a major consuming area for SOP; • Growth rates for SOP consumption are stronger than USA GDP given the link to highvalue crops; and • The mine will have the required electricity and gas to power the additional Mannheim furnaces, as the mine has access to grid electricity and network gas The mine will also have access to a convenient logistics solution for increased production, with the process plant within four kilometres of a national rail network and a major interstate highway
On December 11, 2019, the company announced it had completed a placement of 11 million ordinary shares at 25 cents to raise A$2.75 million to three global institutional investors.
The placement included a five for six attaching option at 30 cents and funds will be used to progress construction related activities.
Discussions are ongoing with major Chinese state-owned enterprises (SOEs) with respect to boric acid and SOP offtake agreements.
The company has advised that it is not prepared to sign offtake agreements in the absence of prepayments to support construction or project level investment.
Chinese SOEs are expected to visit the site in March 2020.
China market share to continue falling?
World // Soda Ash
China’s share of the global soda ash market is set to continue declining amid new capacities in Turkey and inflow of US supplies to Asia.
In 2019, China exported less than 1.3m tonnes of soda ash, down 6.1% from the previous year.
The market outlook for 2020 is downbeat in view of ample supply on both the domestic and global fronts.
During the week ended 8 January 2020, dense grade soda ash prices fell $5/tonne to $200-210/tonne FOB (free on board) China; while prices of light grade soda ash fell $3/tonne to $200-207/tonne FOB China, ICIS data showed.
China’s import prices of dense grade material in northeast and southeast Asia likewise decreased, slipping $5-10/tonne, to $215-220/tonne CFR (cost and freight) NE (northeast) Asia and to $215-230/tonne CFR SE (southeast) Asia, respectively.
Spot prices were at their lowest levels since around October 2016, according to ICIS data.
Bulk lots from the US supplied under term contracts for delivery in the first two quarters of 2020 were available at lower prices.
This includes a 20,000- to 30,000-tonne lot of dense grade natural soda ash which is close to being settled at around $200/ tonne CFR SE Asia, according to market sources.
Term 2020 supplies from Turkey were being negotiated at around $200-210/tonne CFR SE Asia to as much as $220/tonne CFR NE Asia.
The US and Turkey enjoy lowcost manufacturing processes due to vast reserves of the trona mineral which is mined and refined into soda ash.
In China, two major producers – one from Jiangsu and the other from Shandong - foresee a 5% to 14% reduction in their export volumes for 2020.
“Last year, we exported 350,000 tonnes of dense and light grade soda ash and this year we [forecast] 300,000 to 350,000 tonnes,” a source from the Jiangsu-based producer said. In South Korea, the 2020 term import volumes are expected to be cut by 20% for dense grade soda ash due to depressed demand from a major downstream glass manufacturer as the country’s economy struggles with weak exports and construction investments.
China may see a consolidation of production bases in the long run given the lack of cost advantage of manufacturing soda ash through chemical processes. New soda ash projects are mostly located outside China.
Potential new soda ash capacity Company Capacity (tonnes/ year)
Tata Chemicals 900,000 (+ 250,000)
Yildirim Holding
Inner Mongolia Berun Group Sisecam Group & Ciner Group JV 400,000
5m
2.5m Location Status/Start-up schedule
Mithapur, Gujarat, India Received environmental clearance for capacity addition; targeted to come on stream in late 2021. Togyzkent village, Sarysu district, Zhambyl, Kazakhstan Construction scheduled to start in late 2019; no further update available. Inner Mongolia, China 2023 Green River, Wyoming, USA 2024
CIECH aims to get back to production
Romania // Soda Ash
CIECH Soda Romania, the Romanian subsidiary of Polich chemical group CIECH, has decided to take further measures to keep all its workers and managers at the Govora soda plant in Romania, hoping that the facility will soon resume production if steam supply is provided, the company said in a statement.
"It is a serious commitment from us and we hope that all discussions on finding a steam source for our factory will materialize with real support. We call on the authorities and we hope that all political statements on collaboration and solutions will be followed by concrete results," said Witold Urbanowski, the general director of CIECH Soda Romania.
The only soda ash factory in Romania is in stand-by mode since September 18, 2019, after the price of industrial the form of a partnership from the local administration.
steam requested by stateowned CET Govora in its last offer was over 75% higher than under the previous contract. The offer is far beyond the possibility of the company to cover these costs, CIECH managers commented. In exchange, CIECH proposed to build a new steam production facility - but asked support in At the end of October, CIECH prepared an offer for the Ramnicu Valcea City Council, energy producer CET Govora and other local partners, to build together a new thermal power plant in Ramnicu Valcea. “A cogeneration plant has several advantages, including energy efficiency, a reduced footprint on the environment and not least it can accomplish the needs of several industrial players. First of all, it must secure the delivery of steam at an optimal level, which means that it should meet certain conditions. At this moment we are considering different options. Of course, in the variant of a partnership with the authorities and the other economic agents, the problem of replacing the old, underperforming CET Govora could be solved, but this does not depend on us anymore,” Urbanowski said at that time.
ASIA... is one click away
AllSteel_HalfPagAd2_Asian Glass_Layout 1 7/29/2019 4:17 PM Page 1
RAMSEY ALL-STEEL. 100% STEEL. WILL NOT CRACK UNDER PRESSURE.
Ramsey All-Steel ® Wear Protected Conveying Chains are tough enough for the most demanding applications. Protected against lateral chain and pin head wear by 100% steel, hardened, alloy side links, the links in this chain will never crack under pressure.
Contact Ramsey at www.ramseychain.com, (704) 394-0322 sales@ramseychain.com
News Anaylsis
Glass: a soft target for
the climate lobby?
Glass is irreplaceable in buildings, making it a key part of the solution to unlock energy savings and help reach Europe’s decarbonisation targets. But it’s also an energy-intensive industry, for which no immediate clean energy alternative is available.
As a high-level group of CEOs, academics and politicians gathered in Brussels early this year, to discuss the future of the glass industry, they were well aware that glass was all around them. It was in the windows looking outside, on the table holding their beverages, even on their smartphone screens.
“Glass is everywhere,” noted Philippe Bastien, a regional president at AGC Glass Europe. “You cannot do anything without being in contact with glass. You wake up in the morning, you go to the window. You have glass in your shower, you have glass in your oven, and in the car or train you take to work.”
The reason glass is everywhere is because as a transparent material, it serves a unique function for which mankind has found no substitute. And this could make the sector a low-hanging fruit in lowering Europe’s emissions.
The dinner debate was an opportunity for industry association Glass Europe to present its vision for 2050, a manifesto for how flat glass can contribute to Ursula von der Leyen’s European Green Deal and 2050 decarbonisation target.
The industry sees an immediate opportunity, not in the production phase – at least not for now – but rather in the use phase.
Glass is an endlessly recyclable material, and right now most of that material lies locked in inefficient uses in buildings. 80% of glass goes to the buildings sector, and 85% of the glass in that sector is still inefficient, using either single glazing or inefficient double glazing.
These types of windows allow heating, one of the biggest contributors to emissions in Europe, to pour out of a building. The buildings sector alone is responsible for 36% of total EU emissions.
“For the glass industry, the net balance of the emissions remains highly positive,” said Bastien. The CO2 emitted to produce an energy efficient double-glazed window is offset within six to 20 months by its energy savings, according to industry calculations.
“I’m not looking for an excuse – it’s very important that we work on the production emissions side, and for sure we have to do that. But we still have room to do more good thanks to the use of our product.”
The industry is calling on the EU to enforce energy efficiency legislation that would require these windows to be replaced.
Maria Da Graça Carvalho, a centre-right Portuguese MEP who attended the dinner, was receptive to this idea. “There are certain sectors of the economy that are easier to decarbonise than others, so we should start with the sectors that are easier,” she said. “Of course the ones that are more difficult we need to start to find solutions. But for some sectors we can start immediately, like building and construction.”
The problem is that the EU has already legislated in this area, extensively. There has been an energy efficiency target in place since 2012, and there has been legislation requiring improved energy performance in buildings since 2010, revised in 2018. The EU will not meet its target of a 20% improvement in energy efficiency by 2020 because national governments have not correctly implemented the legislation.
“We have a lot of legislation already to get these goals, but also we have member states that are not doing their duty,” said Nicolás González Casares, a centre-left Spanish MEP who was also at the dinner.
“So the Commission has to push them. They have the instruments to tell these countries, you must do it. The Commission can’t only make new rules, they have to force the countries to implement the rules already there.”
Of course, it is in the glass industry’s economic interest that these renovations be forced by the EU. It would mean the availability of more glass stock from the recycled windows, and more demand for their products.
But the industry says without this increase in demand, they cannot make the investment needed to reduce emissions from their production processes. Despite building renovation and energy efficiency having been made EU policy priorities, glass demand is still below what it would take to make the needed investments.
“The technical challenge [in decarbonising production] for us is huge,” said Christian Quenett, head of architectural glass at NSG Group and chairman of Glass for Europe. “There is no solution on the horizon so far. Every company is doing some research work but we are all too small to find the solution.”
The glass production industry in Europe is small, and proportionately so is its emissions. There are 46 glass industrial installations subject to the EU’s emissions trading scheme in 12 countries, producing 10 million tonnes of glass each year. They primarily meet EU market demand. 85% of windows installed in the EU are made with European glass.
Those plants are powered chiefly by gas. 75% of the CO2 emissions from flat glass manufacturing derive from the use of natural gas to heat the melting furnace, while the remainder comes from the release of CO2 from raw materials carbonates.
The use of recycled glass, called “cullet”, can help tackle the raw material emissions. It also requires less energy to melt. Today it accounts for about a quarter of what goes into European flat glass furnaces. Advances in chemistry could also help reduce these material emissions.
But the gas fuel is proving harder to replace. Full-electric melting technology for flat glass not yet available. Hydrogen might be an interesting option, but it currently does not offer the necessary radiation for glass melting and high share of hydrogen causes technical problems to furnaces. It also would require new infrastructure to deliver.
“It’s really difficult to find the best compromise between hydrogen or electric energy, or a combination of that,” said Quenett. “That is something where I would hope support from the EU would help us in the next decade to revolutionise the process.”
Prepare for the future it’s less expensive than you think.
Monitoring
Smart Factory is approaching and, thanks to the YOUniverse, it has become far easier to prepare for. It’s also cost effective because the Tiama Hot-End Monitoring System is modular: you choose what you need and when you need it, building the YOUniverse that suits you.
TIAMA HOT MASS For gob weight control, gob shape and temperature monitoring
TIAMA HOT MOVE Article positioning management with early warning to avoid jam
TIAMA HOT EYE For critical defects detection and recognition, dimensional measurements
TIAMA HOT FORM For infrared radiation monitoring and real time statistics
… and they can take action autonimously – now that’s Smart! So, whatever your choice, it will improve your knowledge of the process and it is backed by our service, support and training, along with constant research. For more information visit youniverse.tiama.com.