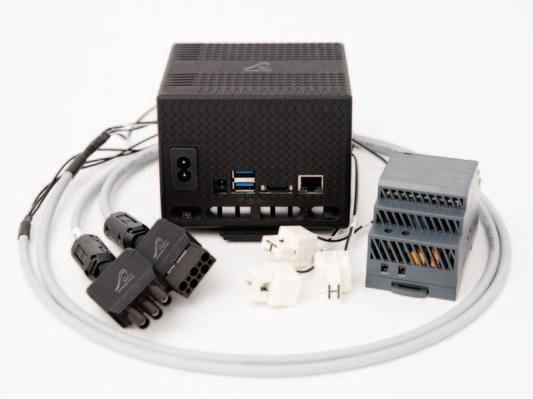
3 minute read
Submersible motor design considerations and advancements through the years?
Submersible motor design considerations and advancements through the years?
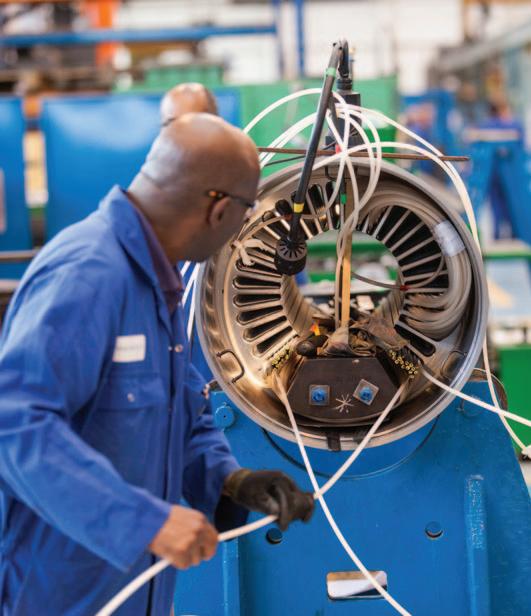
By: Tim Angs
Of
Hayward Tyler Ltd
The world’s first submersible motor was developed by Hayward Tyler in 1908 for a marine salvage application. Since its first invention, submersible motors have undergone gradual changes to meet the demand of various industries with international standards setting a precedent on design considerations.
Conventional air-cooled submersible motors appeared on the market as a form of marinised resin encapsulated ‘dry’ motors. Fluid filled, primarily oil-filled, submersible motors are also used as an alternative to the conventional air-cooled machines. However, the biggest draw-back of these designs are they are not tolerant against moisture and seawater ingress. The insulation used in the electrical windings and electrical joints are made of hygroscopic materials i.e. they tend to absorb moisture from the surroundings. This is obviously not desirable for an electrical motors as it could cause a short to ground. To satisfy the requirements of safety critical applications such as firewater pumps and to ensure trouble-free operation when installed in harsh environments, water-glycol submersible motors are the preferred choice for applications in the offshore oil and gas, desalination, renewables, mining, and defence industries.
Winding Insulation
The stator windings of a submersible motor need to be water resistant and operate under constant hydrostatic pressure at the design voltage for at least 20 years. Submersible motor design, initially used PVC insulated windings between the 1960s to 1990s. PVC even though water resistant has a comparatively(?) low dielectric breakdown strength and a lower temperature class rating compared to other waterresistant wires that were available at that time, which limited the lifespan of the windings. With ever increasingly challenging markets, to increase the lifetime of the stator windings, the wire insulation was then upgraded to Sioplas. However, Sioplas being chemically crosslinked, had its own disadvantages associated with storage conditions and splice manufacturing. Sioplas was eventually superseded by polyethylene crosslinked (XLPE) via irradiation in the 1990s. Irradiated XLPE creates an increased uniform and controlled insulation crosslinking, which has resulted in higher dielectric breakdown strength (70kV/mm), higher insulation thermal class rating (maximum 90oC continuous rating) and a significant improvement to the mechanical properties of the wire. Hayward Tyler only uses irradiated XLPE on submersible motors up to 13.8kV, for direct on-line and inverter duty application. Even though irradiated XLPE winding wires are more expensive than PVC and Sioplas, the benefits of using this technology results in longer wire life and a significant reduction in meantime-between-failure (MTBF). Longer life and reduction in MTBF is especially important in applications when lifting the motor out of the fluid (i.e. off shore) is very expensive and impacts the operability of the system.
Winding Wire
As well as the insulation system, equal emphasis should also be given to the overall winding wire design. The copper conductor of the winding wire are manufactured from high conductivity copper to increase the motor efficiency by reducing stator copper loss. For high voltage applications, it is important to use a semiconducting layer as the conductor screen. This semiconducting layer helps to smooth out surface irregularities and reduce electrical stresses, which is important to eliminate partial discharge activity within the wire. The insulation thickness of the wire varies depending on the operating voltage of the motor and the quality of supply voltage. Motor manufacturers need to ensure that inverter driven submersible motors are provided with adequate insulation thickness to withstand the voltage stresses at the output of the inverter. The winding wire outer sheath is covered by a film of polyamide to protect the winding wire against mechanical damage that can occur throughout the manufacturing process and during operation. These factors are important to prevent the formation of water-treeing within the winding insulation of a submersible motor. Finally, to ensure consistent quality, Hayward Tyler only uses approved cable manufacturers, which have undergone quality audits and stringent product testing in accordance with ISO 9001, ISO 14001, OHSAS 18001, IEC/EN 60811, IEC/EN 60034 standards.
To increase the reliability of a submersible motor, an adequate level of cleanliness is maintained, not only during the cable manufacturing process but also during the electrical joint manufacturing. The manufacturing facility is divided into several zones of cleanliness level, and the cleanliness level of the stator winding manufacturing is compliant with ISO Cleanroom standard 9. By adhering to a stringent cleanliness level, foreign object debris, which are known to initiate partial discharge activity within the electrical insulation, can be practically eliminated to ensure a highly reliable product.
(continued on page 32)