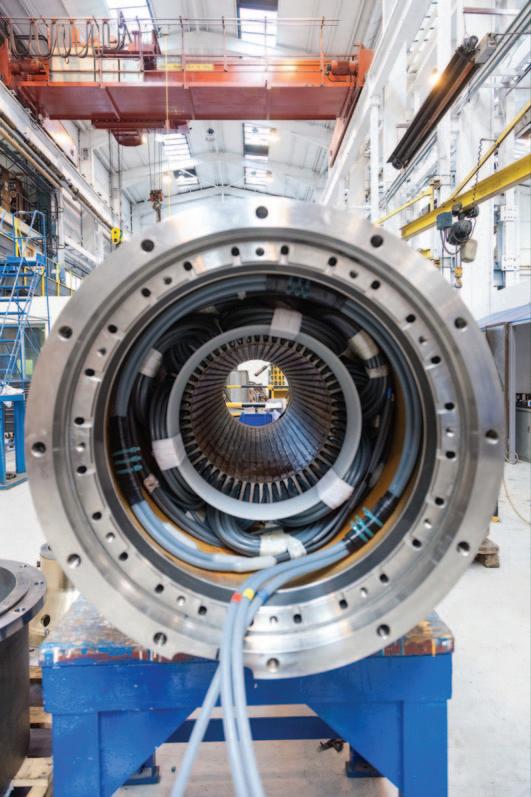
3 minute read
Submersible motor design considerations and advancements through the years?
Submersible motor design considerations... continued from page 31
Electrical Joints
The reliability of the electrical insulation system of a submersible motor lies in the integrity of the electrical joints. Submersible motors are 3 phase induction motors. Each phase can comprise of either a single length of cable or multiple bundles. To connect the individual cable lengths together electrical joints are needed. Additional joints are needed to connect the stator windings to the motor power cables. However, joints are inherently the weakest part of the motor insulation system therefore Hayward Tyler has undertaken extensive development work to maximise the reliability of our joints. Earlier generations of submersible motors used off-theshelf insulating tapes that were hand wrapped for the electrical connections within the stator. The effectiveness of these joints decreased with increasing pressure. Material compatibility between the insulating tapes and various types of water glycol was also an issue. As the demand for submersible motors to be installed in deeper waters grew, so did the need for more effective jointing methods that could withstand the increased pressure and voltage requirements. Initially handtaped XLPE joints were developed by Hayward Tyler in the 1990s that consisted of a homogenous electrical insulation system, offering a complete XLPE-insulated windings and joints. The nature of the XLPE is that upon proper manufacturing treatment the materials bond into one homogenous pieces with no boundary layers separating them. These XLPE handtaped joints, however, had its own disadvantages. Being a manual process, the technique is highly dependent on the skills of the operator especially in maintaining a uniform joint thickness. In 2010s, Hayward Tyler developed a novel moulded joint using a custom designed injection moulding machine. Hayward Tyler had developed a technique to create a solid XLPE-only insulation system that is void-free, water resistant and the ability to operate up to 400 bar up to 13.8kV that can retained all the benefits of the handtaped joints described above, but the process is automated and simple resulting in a more consistent joint. Having a complete XLPE homogeneity insulation system also ensures compatibility with a wide range of glycols used in various installations around the world. As part of the design and manufacturing process of cable and joint assemblies, Hayward Tyler employs the use of Finite Element Analysis (FEA) and physical product testing. The design of the cable-joint assemblies is verified using FEA to simulate the operating conditions. The cable-joint assemblies then undergo a series of qualification testing to the Subsea Electrical Power Stadardisation standard EPS SP-1001. Testing to other standards can also be carried out where required by customers or local requirements.. Examples of tests include high voltage tests insulation tests, partial discharge tests, pressure and temperature cycling tests, mechanical tests, and material tests. All of the tests are completed in the Hayward Tyler factory in Luton, UK. The results of the FEA and tests allows improvement to the design and qualify the product for use in the market. Thermal analysis is also performed on the whole motors to ensure the stator windings will operate within the thermal insulation class.
Condition Monitoring
As Hayward Tyler continues to strive for product improvements, a condition-based monitoring system was developed with the aim to help our customers plan for maintenance work, to reduce their production downtime with the aim of driving down the equipment cost of ownership. Hayward Tyler’s condition monitoring system is intended to be used where the equipment is located in a remote or inaccessible area and in hazardous or extreme environments where sensors cannot be fitted to the equipment. ■
For more info: Email: luton@haywardtyler.com Phone: +44 (0) 1582 731144 page 30
These factors are important considerations especially where onsite management of water impacts directly on local communities and consumers are increasingly proactive around environmental concerns. By adopting best-practices for wastewater treatment and identifying opportunities for water efficiencies at every stage of the process, sustainable practices can be implemented.
6. Make tangible efficiency gains
As an example of effective chemical dosing optimisation, the installation of a peristaltic dosing pump at the wastewater treatment plant serving the town of Hessisch-Lichtenau, Germany, has demonstrated that the deployment of accurate and reliable chemical dosing technologies has allowed the plant to meet strict environmental discharge limits efficiently. As a result of the pump installation, reliable ferric chloride sulphate dosing to treat wastewater has achieved a 97.5% reduction in phosphorus load over the first year since installation.
While the challenge of meeting regulatory standards, reducing capital expenditure, and striving for sustainability is complex, accurate chemical dosing can help wastewater treatment plants to continually drive efficiencies. The potential overall savings available by choosing the right dosing pump, and investing now to save later, should not be underestimated and will help utilities run operations with greater precision, efficiency, and cost control. ■
For more information, Phone: +44 (0) 1326 370 370 Email: sales.admin.uk@wmfts.com