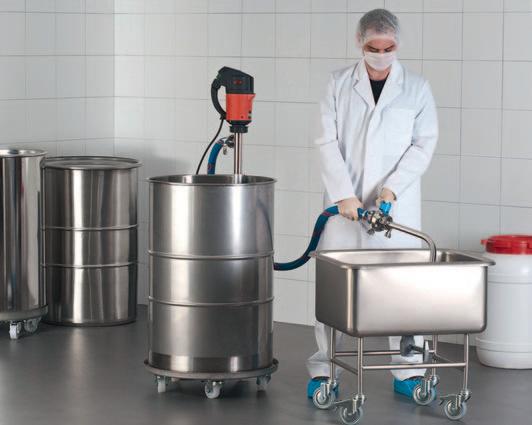
2 minute read
How to Select a Drum Pump
How to Select a Drum Pump
By: Russell Morgan of Flux Pumps International (UK) Ltd
Transporting liquids is an essential part of the manufacturing process for many businesses. Unlike solids, bulk liquids cannot simply be stacked and moved. Transferring liquid isn’t just a case of pouring from one vessel to another. Many factors play a part, such as time taken, the health and safety of workers, the size of storage containers and the application characteristics. That’s where a drum pump comes in. A drum pump is a portable pump used for transferring liquids from drums, barrels, IBC’s and tanks. They are also known as a barrel, stick or lance pumps. Drum pumps are also used for emptying sumps, filling smaller containers and filling mixing vessels. If you are considering this efficient solution, you may be wondering how to select a drum pump.
Using the wrong materials can cause the pump to fail. A mechanical seal extends pump life when abrasive media is being transferred. However, seal-less pumps have a long service-life with clean liquids and will tolerate periods of dry running.
• Delivery pressure and flow – Some applications require higher flow rates to empty larger IBCs or tanks, whereas others may need higher delivery pressure in order to transfer the liquid vertically higher, through additional pipework or for transferring more viscous fluids. Consult pump performance curves and use a pipe loss calculator to work out pipeline pressure drop.
• Density and viscosity – Fluid density and viscosity will influence pump type and motor power. Axial or semi-axial impellers are selected for liquids of different density. Progressive cavity pumps should be considered for high viscosity materials.
• Temperature – Temperature limits depend on pump construction and length. Hastelloy C is limited to 120 C, stainless steel and aluminium is 100 C, PVDF is 80 C and polypropylene is only 50 C. O-ring materials should also be considered.
• Power supply and motor approvals – Sites will have different motor preferences, for example, air driven vs electric. The location of the application is important. For example, an IP55 explosion-proof motor is required if the pump is used in a zoned area with concentrations of flammable vapours. If no power supply is available, a battery-powered motor may be a useful option.
Why should you select a drum pump?
To protect employees and the environment, liquids should be handled in a safe manner with the appropriate dispensing equipment. Too often, avoidable workplace accidents result from the mishandling of liquids. In addition, many businesses waste product by using the incorrect equipment. Drum pumps provide an efficient, safe and easy way to transfer fluids.
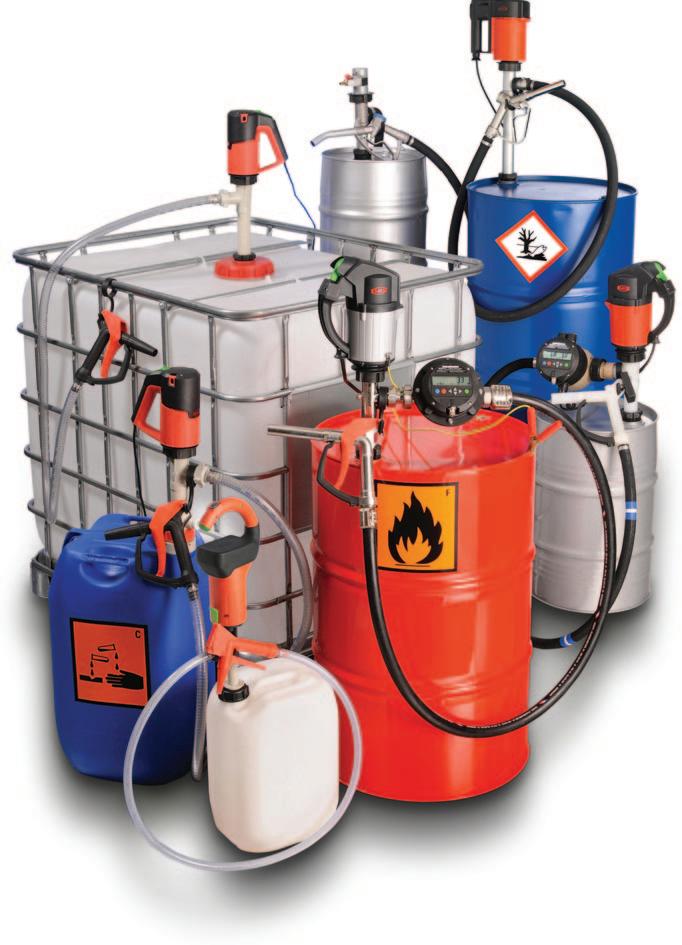
To ensure you have the right solution, there are many factors that should be considered. No two applications are the same and thus each may require a bespoke pump configuration. Below we will investigate how to select a drum pump, including key aspects you should consider before making your purchase. Selecting the incorrect pump will result in workflow disruption and unnecessary extra cost.
How to select a drum pump
Firstly, consider how and where the pump will be used and the application specifics. For example:
• Liquid characteristics – Drum pumps are manufactured in a range of key materials, such as PVDF, stainless steel, aluminium and polypropylene. Knowing the chemical will allow you to select suitable pump body and o-ring materials and approvals – especially important if the fluid is flammable or corrosive. Consult a resistance chart to check material compatibility.