Interview with: Javier Cabeza, Vicepresident of Operations in Europe,

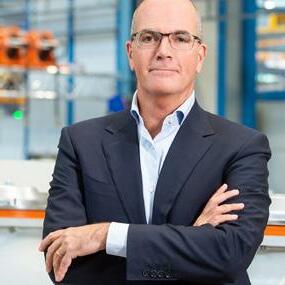

and Asia for Grupo
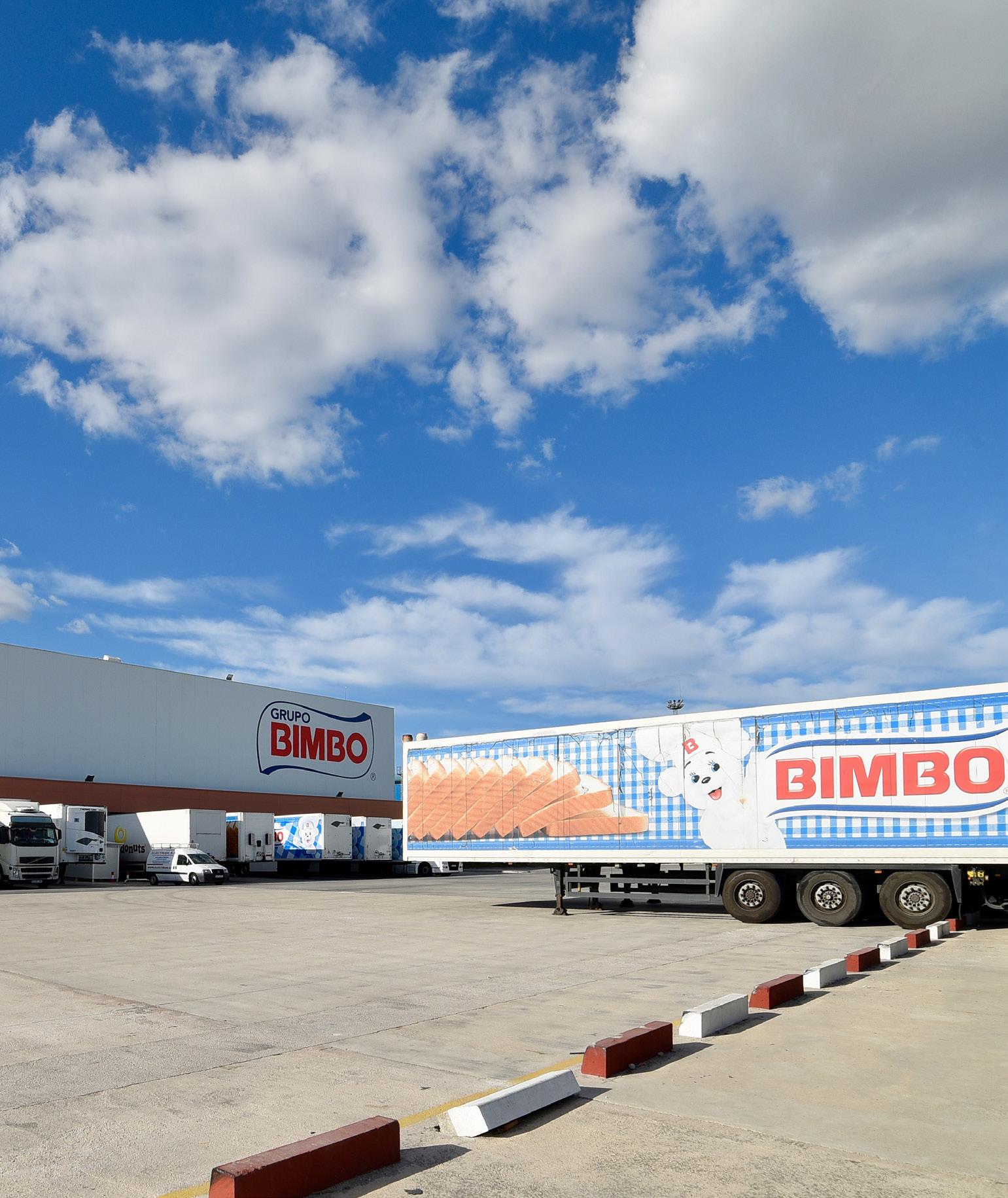
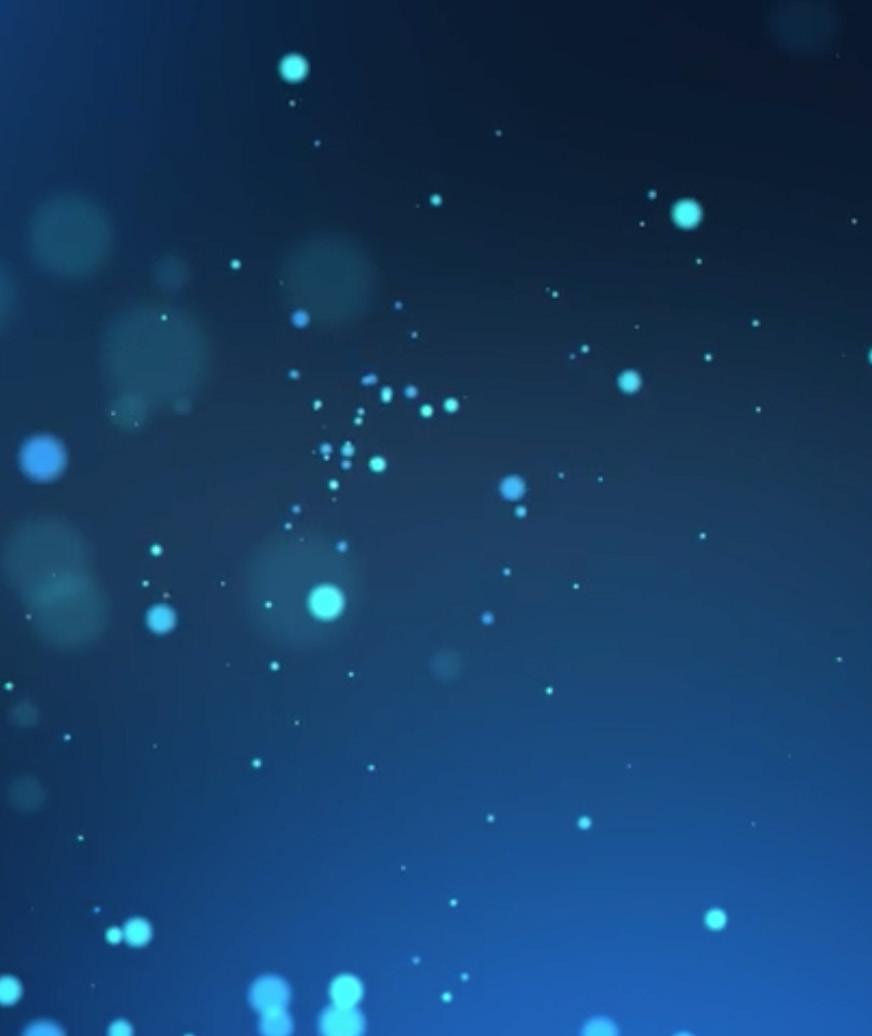
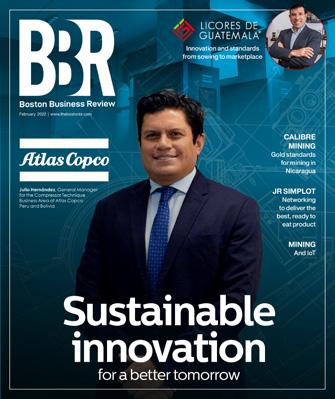
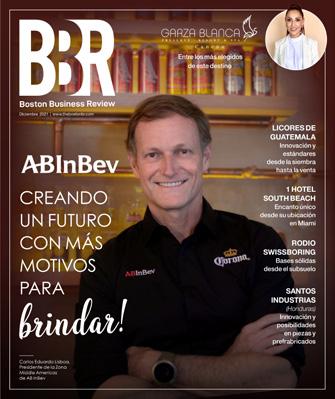

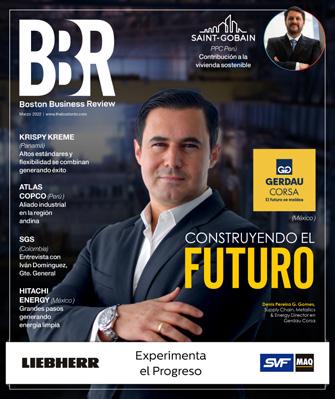

Interview with: Javier Cabeza, Vicepresident of Operations in Europe,
and Asia for Grupo
Special Edition We are pleased to know that once again you are enjoying the Boston Business Review. We are also happy that this month we are sharing some of the best features you’ve read here during the last year.
It was not that hard picking those operations that would stand out, as the Bimbo operation in Europe, Africa and Asia maintains steady growth after conquering the Americas. Also in places that may seem far from our radar, the AB InBev branch in Africa is bringing standards to make the most out of their local brands as well as their globally-
known heavyweights. We are proud to publish both operations scoped far from our radar’s regular findings.
Construction allies Saint Gobain PPC and Gerdau Corsa, Peru and Mexico, respectively, have also made a difference within their markets and have earned that place in this special issue. We even share with you a few places to wind down, relax and take a breath to face the rest of 2022.
Thanks for reading and sharing the Boston Business Review!
Editor in chief for The Boston Business Review
Email: rafael.tablado@thebostonbr.com
We wish to get to know more and more places around the world, including its unique and farthest corners. Let’s find out what to expect about the following destinations...
The top destination of the Mexican Caribbean offers attractions both for family vacations or couple getaways. Besides stunning beaches and nightclubs, Cancun also boasts unique shopping malls, museums, water parks and restaurants for any appetite. Cancun’s lodging offer also allows the city to become the base to explore vicinities within the Riviera Maya, such as Playa del Carmen and Tulum.
You should be reminded that each destination currently demands different conditions for admission due to the COVID-19 pandemic. We suggest you check this guide displaying each country’s requirements for admission, considering that such conditions are subject to change without notice.
Another option is enjoying a stay in the highest luxury all-inclusive environment of Garza Blanca Resort & Spa Cancun , part of the TAFER Hotels & Resorts chain, located in the Costa Mujeres area.
The inheritance of Celtic culture and mythology is imprinted throughout ancient buildings located in the green scenery resulting from the high volumes of rain falling in Ireland every year.
Ireland’s offer of attractions includes from the towering cliffs of Moher to urban environments, such as Dublin, strolling along Grafton Street, ideal for shopping and also to just relax and sit in any of its coffee shops, or maybe visiting Trinity College, Ireland’s oldest university, which
opened in the 16th century.
Other must-see locations in Ireland include the Blarney Stone (in Blarney Castle), located near Cork, as well as The Rock of Cashel, hosting buildings constructed between the 12th and 15th centuries.
For those who enjoy riding the road, the scenic ride along the Ring of Kerry is a must-see, as is nearby Killarney National Park, and the Wild Atlantic Way, on the west coast.
The “Land of the Rising Sun” blends nature, ancient sites depicting its culture and one-of-a-kind ultramodern city atmospheres that make it a unique destination.
Marvels from technology such as the Shinkansen (bullet train, able to reach more than 180 mph) allows people to get around the country’s territory faster, moving around to admire iconic landmarks such as Mount Fuji, the Chūbu-Sangaku National Park and the Japanese Alps.
Tokyo, the capital, offers every kind of attraction a city of its size can offer with landmarks such as the Imperial Palace with its gardens and different sanctuaries, museums, the tall Skytree tower and the older and slightly smaller Tokyo Tower.
This island nation in the Indian Ocean, just east of Africa, became independent of France during the latter half of the 20th century and hosts endemic wildlife which can be witnessed in large national parks such as Ranomafana -with its bamboo-fed lemures-, as well as the Masoala jungle and Andasibe park.
On its behalf, the two fishing villages comprising Ifaty are the starting point
to get into the ocean and dive or snorkel along a coral reef about 60 miles long.
Few landscapes worldwide can be as amazing as the Avenue of the Baobabs, a tree species able to live for centuries, as well as the Bemaraha limestone formations. Smaller islands Nosy Be and Saint Marie also offer beautiful beaches and sights.
This country on the northwest of Africa is one of the gateways to the continent, considering ship transit between Morocco and Spain. This was also a former French and Spanish colony in which Muslim culture can be witnessed along with remains from the Roman Empire -in Volubilis-, the beauty of its coastline in Chefchaouen, the solitude of the mountains in Rif, and dunes in Erg Chebbi and Erg Chigiga. Cities such as Fez and Marrakesh deliver a broad display of classic
Even though Tangier is no longer the debauchery playground of yore that appealed to writers, intellectuals and other artists during the 20th century, it still is worth visiting as Africa’s point of arrival for ships incoming from Spain and as Morocco’s most European city.
Muslim architecture through beautiful palaces and street markets, and Casablanca hosts the only mosque open to non-Muslims.These two islands in Oceania offer unique sites among snow-topped mountains and glaciers, lakes, bays and other landscapes and waterscapes.
The city of Auckland offers multiple attractions, such as its giant tower, besides being surrounded by wild trails for hiking, volcanos and black sand beaches. Queenstown, in the South Island, also offers ideal settings for
water sports and mountains for hiking, climbing and skiing.
Extremes meet at New Zealand, with glaciers to choose at Aoraki Park as well as in the South Island, in the Franz Josef and Fox glaciers at Westland Tai Poutini Park, while the Rotorua and Tongariro Park, in Maori territory, host high geothermal activity with volcanos, geysers and springs.
Located in the middle of the Balkans in a 180,262 sq. miles area, Serbia offers a blend of nature attractions as well as archaeological and historical sites. Preserved architecture from centuries past witnessed from streets of Belgrade enhance the road to Kalemegdan Park, whose gardens and landscapes are surrounded by a fortress.
Religion has had an imprint in Serbian history, as the St. Sava church
displays its majestic beauty, as does the monastery located in Studenica.
Recent history is honored in Skull Tower, a memorial located in Niš, created after centuries of Ottoman rule.
Nature draws attention through unique sites such as the Uvac Canyon and rock formations at the “Devil’s Town” in Đavolja Varoš. The Kopaonik mountains are also a sought-after place both during summer and winter, for skiing during the latter.
Sri Lanka’s place in history is heightened since the ancient Silk Road trading route, having been occupied by the Portuguese, Dutch and the British. It’s not difficult to understand why this island in the Indian Ocean just south of India was so coveted, hosting natural delights such as the Ravana Falls and the beaches on Arugam Bay, Mirissa and Weligama, ideal spots for surfing and other water sports with friendly
hotels and restaurants.
Worship sites have a very important place in Sri Lanka. With this in mind, the Dambulla Cave Temple opens a few days a week for tourists, and other places worthy of visiting are the Buddhist monastery atop Adam’s Peak and the Temple of the Tooth, which boasts a dental piece removed from Siddhartha Gautama immediately after his death.
The blend of modernity and nature offered by Thailand in its different locations is undoubtedly open to different vacations plans; from astonishing beaches in the Phi Phi and Koh Samui islands, besides Railay, where diving and other water sports can take place, to the peaceful mountains hosting worship sites such as Pai, near the Thai-Burmese border.
For close encounters with the local wildlife, the Khao Yai National Park offers elephant rides in their habitat, besides being home to exotic birds, monkeys and other tropical species, as well as to the Haew Narok and
Haew Suwat waterfalls. Cities in Thailand have busy commerce districts, with highlights such as the Sunday market in Chiang Mai and the must-see floating markets in Bangkok and vicinities; the country’s capital also hosts beautiful buildings and Buddhist temples such as the Grand Palace, hosting Wat Phra Kaeo (the Temple of the Emerald Buddha) and Wat Arun (Temple of the Dawn). For those into recent history, the Kanchanaburi Bridge is less than two hours from Bangkok, this is also known in cinematography as the bridge over the River Kwai.
This country in Africa’s East coast delivers all of those images coming to mind and more when mentioning the continent’s name. To begin with, northern Tanzania is the site of Mount Kilimanjaro, Africa’s highest point at more than 19,000 ft above sea level and just past 16,000 ft above its base; on the way to its peak there are farmlands, jungle, rainforest and a snow-covered top.
African wildlife spreads through thousands of sq. miles worth of national parks and conservation areas
such as Serengeti, Lake Manyara and Ruaha, where species such as hartebeests, buffalos, elephants, gazelles, giraffes, lions, zebras and many others are roaming free. Also, Tanzania is one of the few countries bordering Lake Victoria, the largest in Africa.
Beyond continental Africa, the Mafia, Pemba and Zanzibar islands, in the Indian Ocean, belong to Tanzania. White sand and crystal-clear water are the standard among its beaches, simply considered the best worldwide.
A
At Atlas Copco, our mission is to achieve a sustainable, profitable growth, seeking to empower our customers and drive society towards a better tomorrow
Interviewee Julio Hernández, General Manager for the Compressor Technique Business Area at Atlas Copco Peru and Bolivia
Produced by Jassen Pintado Art Direction Omar Rodríguez
Atlas Copco, worldwide group leader in compressed air, vacuum, energy, and industrial tool solutions, has operations in over 180 counties around the globe. Its customer center in Peru, that along with Bolivia are known as the Andean region, was the first office of the Group in Latin America and has been working in the development and execution of industrial projects since 1950. Julio Hernández, new General Manager for the Compressor Technique
Business Area at Atlas Copco Peru and Bolivia, tells us more about the vision and development plans for the division in the region.
During 2021, Atlas Copco experienced a growth in the demand of compressed air technologies for the
development of projects in different markets; from applications in new mining seams and expansions, to industrial installations for penumatic transport and wastewater treatment plants.
Aside from providing the latest in compressed air technological innovations, Atlas Copco advises its customers in the choice of the best solution from its wide equipment portfolio. “Our business is always focused on operational efficiency, sustainability and the responsible use of resources. Therefore, the correct choice of a compressor for an air installation is key for energy savings and the reduction of the carbon footprint at any operation” says Hernández. “We advise our customers about the difference between a 4-bar pressure blower, versus a 5 to 11 bar pressure compressor, and how with
- Julio Hernández, General Manager for the Compressor Technique Business Area at Atlas Copco Peru and Bolivia
the choice of the right equipment according to a particular application, they can get up to 50% of energy savings”. Usually, these low-pressure solutions are recommended due to its high efficiency and low energy consumption for wastewater treatment plants, flotation processes and pneumatic transport.
Atlas Copco always looks to
Machinery www.thebostonbr.com 31 Our business is always focused on operational efficiency, sustainability and the responsible use of resources
provide added value to its customer during their project development process. The accompaniment during the implementation of such projects goes beyond the installation itself, focused on prevention and energy efficiency. “We have seen growth in the awareness about the importance of preventive maintenance, which
goes hand in hand with energy efficiency. Keeping a machine in peak operational performance turns into energy savings. To achieve this, we have intelligent central controllers that regulate the demands and fluctuations of compressed air machines connected to our network, thus increasing their efficiency”.
The industry 4.0 and connectivity tools are not foreign to the compressed air world. Due to the confinement situation caused by COVID-19, remote monitoring platforms have been key for Atlas Copco customers to anticipate their maintenance needs. “All of our compressors come with remote monitoring technology or can be easily connected to our worldwide network through SMARTLINK. This tool supports us with preventive
maintenance since it helps reduce possible failures that may cause production losses to our customers. Also, it allows us to be proactive towards any alert sign the machine may send, which goes straight to our customer and our specialists”.
“Industrial innovations, like our third-generation variable speed drive technology VSDs and SMARTLINK for remote monitoring of compressed air installations, allows our customers to maximize their investment and
- Julio Hernández, General Manager for the Compressor Technique Business Area at Atlas Copco Peru and Bolivia
“Our mission is to achieve a sustainable, profitable growth, seeking to empower our customers and drive society towards a better tomorrow”Atlas Copco Perú
optimize the operational times at their installations in a responsible way with the environment”, says Julio.
Sustainability and innovation are key for the Atlas Copco Group. Its sustainability strategy is focused on providing its strategic partners with added value, not only through its products and services, but also through responsible actions with the
environment and society in general.
“At Atlas Copco, our mission is to achieve a sustainable, profitable growth, seeking to empower our customers and drive society towards a better tomorrow”, says Julio. And so, the Atlas Copco Group in Peru and Bolivia contributes with sustainable development through corporate projects aligned with the United Nations Sustainable Development Goals, and its
commitment with science-based targets. Julio tells us more about one of their initiatives: “Water for All is a corporate global initiative that develops projects to provide access to drinkable water in places where is needed. This initiative was born from a project promoted by our own staff, to later be adopted by the Group and executed worldwide through strategic partners and Atlas Copco volunteers in every country”.
For Julio, this 2022 arrives with several growth and project development opportunities that will need Atlas Copco solutions. “We are in a highly dynamic market that has increased its demand for products and services that, aside from having a
differential value from other offers, are sustainable, efficient and can generate saving in the short, medium and long term”. This year, an organic growth in the business volume is expected for the division in the region, based on tailor-made solutions for the customer and intelligent connectivity tools for service proactivity.
“Solutions based in innovation and advanced technology will be key this 2022, and at Atlas Copco we are more than ready to take on these new challenges the market has for us. With nearly 150 years of experience in compressed air technologies worldwide, our machines have proved to be efficient and sustainable no matter the industrial project they operate in”.
Atlasis taking
giant steps towards sustainable growth through well-developed strategies and its staff’s talent in different territories
The Bimbo group was created in Mexico in 1945 and is currently the best-known Mexican food brand worldwide. Its expansion within the Americas began during the 1980s as the brand began exporting to the United States and Central America, later venturing into South America during the 1990s.
Overseas, Bimbo first ventured into Spain when Mr. Jaime Jorba, one of the brand’s founders in Mexico, returned to his home country.
Bimbo Iberia was born from Bimbo’s operations in Spain and Portugal, working on its own until 2016.
Its evolution continued in 2019, when Gabino Gómez, CEO for Bimbo, pushed for the creation of an organization similar to the one he leads from Mexico -which supports the company’s operations in the United States and Latin America-, also incorporating Bimbo UK, China and the brand’s assets in India and Morocco,
thus becoming Bimbo.
“Bimbo was pretty set in the Americas and decided to grow in the continents where it lacked presence: Europe, Asia and Africa,” commented Javier Cabeza, Vice-president of Operations in Europe, Africa and Asia for Grupo Bimbo.
Javier Cabeza is near completion of his second decade of work for Bimbo, which means he was also part of the Bimbo company in Spain before being acquired by the Mexican business group in 2011.
Cabeza earned Bachelor degrees in
Business Engineering and Chemistry Engineering at the Technical University of Catalonia (in Barcelona, Spain). He also earned an MBA from the IESE Business School (also in Barcelona).
Among postgraduate studies, Cabeza obtained a Certificate as a Breadmaking Technologist from the American Institute of Baking and a Leadership program from the Harvard Business School.
Before joining Bimbo at 22, Cabeza worked for Synthesia Technology, a Spain-based leader in polyurethane solutions, and also for the Benetton clothing brand. Once in Bimbo, Cabeza has practically experienced every area
Javier Cabeza, Vice-president of Operations in Europe, Africa and Asia for Grupo Bimbo
“The company’s a heavyweight in Europe for its business in Spain, Portugal and now in Asia”
in the company from operations to technical positions. The deployment of lean manufacturing systems and continuous improvement processes highlight his tenure in the company. Besides his outstanding work in Spain, Bimbo also took Cabeza to Belgium, the United States and Netherlands, until being in charge of, probably, the most diverse of Grupo Bimbo’s operations, globally.
“I wanted to become part of an enterprise so big as to not know in which part of the world I would find myself the next day, and that’s why I like Bimbo a lot,” the executive declared.
Bimbo’s endeavors in Europe, Africa and Asia encompass 32 facilities -used both as corporate offices and as storage facilities-, involved in the production of 15 brands, operated by
approximately 16,000 workers serving more than 200,000 clients.
Bimbo’s UK business was added to the operations performed from Bimbo Iberia towards all of Europe. The UK branch’s business consisted mainly of bagel and croissant bread. In Africa, Bimbo arrived in Morocco by acquiring a small company, growing its presence from the initial four production facilities and also expanding its product portfolio.
“The company’s a heavyweight in Europe for its business in Spain, Portugal and now in Asia,” said Cabeza, who is familiar with the highly competitive European market which, sooner or later, ventures into Latin America.
Positioning Bimbo EAA as this clockwork operation able to replicate the model and reach of its parent company overseas is a very complex
• Inorganic growth. The group acquired companies in Spain, India, Morocco and the UK, which have resulted in a longer reach and a strengthened portfolio within the food market.
• Managerial structures deployment. These offer detail into the business alignment level obtained, and they also measure efficiency, capabilities, business contribution and adaptability.
• Investment in production capacity. This has implied great investments in every country, contributing to each territory’s growth.
• Implementation of Lean Manufacturing. This improvement system has been able to detect all contributing and non-contributing elements in bringing value to clients.
• Quality-focused operations. Quality has become the determining factor even for decision-making, from being a tactic to become a strategic factor. No matter how favorable aspects such as costs and revenue become, no decision is made if it affects the products’ quality.
• Talent detection and positioning. One of the most important strategies is getting to know the talent’s capabilities in every country, enabling them to develop the roles each territory requires, matching capable individuals with the tasks necessary to different countries, as well as to develop the company’s talent or sourcing enabled staff to fulfill areas in need.
“We do make a great difference by relying on staff from China, India, Morocco, Portugal, Spain and the UK, such variety provides a big contribution,” the vice-president pointed out.
Javier Cabeza, Vice-president of Operations in Europe, Africa and Asia for Grupo Bimbo
“We want to keep being a force in innovation. In every country we must fulfill the group’s philosophy: Feed better world”
Bimbo EAA makes the most from resources provided by Grupo Bimbo, especially those involving knowledge and products, as well as personnel, experience and contact with tech and raw materials suppliers, considering Bimbo has become the largest bakery company worldwide.
This network support has been key to take solid steps in relatively new territories such as India or Morocco.
“Grupo Bimbo is always at the top of our list, providing us with influence and knowledge,” Cabeza remarked.
An enterprise the size of Bimbo EAA
couldn’t be exempted from adapting to the consequences of the COVID-19 pandemic, deploying timely measures preventing the disease internally, reducing its spread to zero.
However, the company is aware that changes didn’t take place only within different companies, but also in consumer habits, becoming more conscious regarding the nutritional
value of products, plastic packaging and other trends previously detected, which simply took off as the pandemic began, such as online retail, to name one.
“We’ve learned to become more open, faster, to make the most out of business opportunities, to become leaner toward decision-making,” the executive said.
Taking Grupo Bimbo toward sustainable operations is a top priority, globally.
Up until now, Europe has been the ideal ground to reach different goals, considering the territory’s regulations, policies and culture, which allow for significant advance in purposes such as bringing CO2 emissions to net zero by 2050 and other intermediate goals related to the use of plastics in packaging, among other things. In countries such as Spain, Bimbo’s vehicle fleet boasts 20% of electric vehicles, an amount that will undoubtedly grow in the short term also in other countries. In Mexico, Bimbo has the largest electric vehicle fleets in Latin America.
The company offers different recyclable options for plastic packaging, including biodegradable solutions such as D2W. Also, Bimbo,
globally, has experienced progress in solar power.
In Europe, Bimbo is involved -along other brands, clients and distributorswith the Marcas Waste Warrior association, whose purpose is to eliminate food waste. The association created the Too Good To Go campaign, in which different brands offer attractive food packages near their expiration date at very low prices with the purpose of feeding more people instead of wasting food, aligning the company to reduce food waste in 50% in respect with their 2016 figures.
“Sustainability is one of the group’s strategies. These goals must be accomplished, it’s fundamental to our group, there are no excuses for unfulfillment,” Cabeza expressed.
If there’s a word describing the
Javier Cabeza, Vice-president of Operations in Europe, Africa and Asia for Grupo Bimbo
“Sustainability is one of the group’s strategies. It’s fundamental to our group”
future purposes of Bimbo EAA, it is undoubtedly “growth”. Asian territory is poised to become the grounds for such a purpose, specifically in India, where the company’s challenge is to reach more population.
In Africa, on its behalf, growth purposes also persist, but not in the short term. The market is evolving and it is very important to remain aware of its development.
The operation in Europe is consolidated, but the plan is to keep strengthening the company’s finances and enter categories yet to be explored by Bimbo.
Along with the brand’s efforts overseas, the company improves the fulfillment of its purpose to contribute to a better world by providing quality foods to a quantity of people that keeps growing.
“We want to keep being a force in innovation. In every country we must
Founded: 1945, in Mexico
Industry: Food & Beverage Employees: 16,000. Contact: www.grupobimbo.com atencionenlinea@grupobimbo.com
fulfill the group’s philosophy: Feed a better world,” finalized Javier Cabeza, Vice-president of Operations in Europe, Africa and Asia for Grupo Bimbo.
Alignment with best practices and global standards contribute to surpass different challenges faced across the territory, enabling a sustainable operation in brewing, completely invested in its surrounding communities
The origins of ABInBev in Africa go back to 1895, when the Castle Brewery was created by founder brewer Charles Glass in Johannesburg, South Africa (RSA). It only took two years before the company was listed on the Johannesburg stock exchange.
In 1950, the brewery’s corporate headquarters were moved from London to Johannesburg, with the purpose of achieving growth and expansion. Five years later, the Ohlsson’s and Chandler breweries were acquired by Castle, renaming the group as South African Breweries (SAB)
Besides arriving in Zimbabwe soon after, the most prominent expansion era for SAB took place during the
late 1990s, as the company grew into Mozambique, Tanzania and Zambia through different ventures.
After acquiring SABMiller in September 2016, ABInBev brought along global brands Budweiser, Corona and Stella Artois, now popular on the entire continent.
ABINBEV ACROSS AFRICA TODAY “ABInBev Africa represents one of the shining lights within ABInBev, globally.
There are so many achievements to be proud of”, stated Fernando Figiacone, Vice President of Supply in Africa for ABInBev.
ABInBev’s operations in Africa take place across eleven countries through three main territorial business units:
• The West territory encompasses Ghana and Nigeria. Focus brands in this area include Club, Hero, Trophy and Budweiser beers.
There are so many achievements to be proud of
• Botswana, Mozambique, Tanzania, Zambia and Uganda belong to the Southeast unit. Main brands in this territory include Kilimanjaro, Mosi, 2M, St Louis and Club.
• The South territory is formed by Eswatini, Lesotho, Namibia and South Africa. Brutal Fruit, Budweiser, Carling Black Label, Castle Lager, Castle Lite, Corona, Flying Fish (who recently created a flavored spritzer), Stella
Artois and Hansa are the key brands in the South.
In South Africa alone, the company provides 7,000 jobs, supporting a beer value chain from seed to sip of more than 250,000 individuals and ultimately contributing to over 1, 000, 000 livelihoods. With raw materials sourced from more than 1,200 farmers, SAB is able to produce a 30 million hL volume, exporting 14
brands into 28 different countries across Africa, besides exporting to countries in different continents.
Boosted by new breweries opened in Mozambique and Nigeria during the last three years, in 2021 the company reached a 50 million hL production across the continent.
Recent investments include a stateof-the-art malting facility in Zambia, and also investment in a takeover of a glass manufacturing facility in South
Africa, securing supplies for bottle production.
In the wake of economic uncertainty and the need for recovery, SAB recently reaffirmed its commitment to ignite the South African economy as it pledges to invest to R4.5bn – adding impact to an industry that already contributes 1.3% of the national GDP
During 2018, the brewery launched Brutal Fruit Ruby Apple Spritzer, which became the largest selling
innovation ever in the continent, growing total brand volume by 40% and driving double-digit growth.
“We ended a strong 2021 with growth in volume, revenue and EBITDA. We will continue to push for the same performance going forward,” the executive said.
A LONG TENURE IN BREWING PROVIDING LEADERSHIP Fernando Figiacone graduated from the Catholic University of Argentina as an Industrial Engineer. Figiacone also earned a postgraduate degree in Food & Beverage Marketing from the University of Belgrano (Argentina) and a Master in Company from the University of San Andrés (also in Argentina).
Other postgraduate studies taken by Figiacone include Supply Chain Training in MIT (Massachusetts Institute of Technology), Stanford
University and Darden University, all of these as part of ABInBev between 2015 and 2021.
UP TO GLOBAL STANDARDS
Operations in Africa bring along different challenges due to the infrastructure in some countries, as well as other factors such as commodity fluctuations and worsening currency exchange rates. To these common situations, the COVID-19 pandemic brought additional burdens to logistics and lead times.
“These are part of the challenges faced, but they are also what excites us and drives us to perform,” Figiacone explained.
The strong management systems in place across ABInBev Africa bring the company to the same level as all zones, globally. Constant training, adoption of best practices and KPI
tracking has enhanced its leadership, increasing autonomy across every team and successfully achieving benchmark levels. Notable areas which have become optimized include logistics, supply and the development of a returnable glass bottle system, among others.
THOROUGH INVOLVEMENT WITH LOCAL SUPPLIERS
As part of the historic merger conditions when ABInBev purchased SAB Miller, SAB committed to invest R1billion ($70m) into SA economy by the end of 2021 in three key areas of investment spend: Agricultural Development, Enterprise and Supplier Development, and Societal Upliftment initiatives.
Efforts have been consistent, as in the last five years the company invested more than $93.5 million in procurement with Black-owned
businesses. Also, 95% of procurement is spent through suppliers with significant ratings in respect to local business empowerment.
In 2020 alone, the company invested nearly $6.6 million and $5 million in Supplier and Enterprise Development Initiatives, respectively.
These programs have enabled the company to help develop and train nearly 1,000 emerging farmers, increasing the local barley, hops and corn production feeding the supply chain.
From 2017 to 2021, investments of more than $13 million have helped agricultural development programs.
The company’s commitment to enterprise and supplier development, local procurement and local businesses has allowed for the creation of programs such as the SAB Thrive Fund, not only becoming
a transformation factor within the company’s supply chain, but also providing much-needed jobs in local communities.
Support from ABInBev through global programs contribute to increasing
efficiency in the three business units forming ABInBev Africa. The Voyager Plant Optimization program deploys best practices and standardization of operations. The program evolves continuously, improving and certifying every process, leading to a safe, sustainable operation of every production plant.
Also, the Africa zone head office,
based in South Africa, oversees every business unit, playing an essential role of support regarding supply, logistics, procurement, finance and people management.
“We have been able to optimize our operations despite operating in hugely challenging environments,” said the executive.
Personnel working at ABInBev Africa develop unique skills after undergoing demanding training. The company can easily state that its staff is comprised of some of Africa’s finest, most brilliant individuals, whose sense of commitment and ownership drives them towards delivering excellence in execution despite any challenges
faced. Hence, the company strives to maintain a low turnover rate.
Along its tenure operating in Africa, ABInBev has found out that, as there are many resources that may
seem to provide an infinite supply of ingredients for brewing, the reality is that these coveted commodities must be managed wisely to ensure their availability for time to come.
One of the areas which has improved noticeably within the company’s drive to sustainability set to 2025 is the efficient management of
water resources, as during the last five years water usage has been reduced by 20%. The company, partnering with organizations such as the World Wildlife Fund has improved conditions of water availability in communities across the continent where it operates. One of the successful efforts is the borehole dug for the Caledon Maltings facility, reducing demand
from the municipality. The company set the goal of improving conditions with possible solutions to water restrictions challenging communities in Mozambique and Namibia.
On a related matter, the company has set a goal for 2025 to use 100% of returnable or recycled packaging. In Ghana and Nigeria possible solutions are being tested to increase recycled
content in PET. Tanzania is already experiencing PET-less bottling with brands such as Grand Malt being packaged in recyclable cans.
On its behalf, the Zambia branch created the Manja Pamodzi project, aimed to improve sanitation and hygiene through waste collection. The 815 collector program boasts 76% women, adding more than 14,000
tons of waste collected. Meanwhile, in South Africa, the EPR (Extended Producer Responsibility) program will allow an efficient management of single use and returnable products, thus implementing circular economy initiatives within communities.
Regarding the energy used to brew and bottle ABInBev products, the company set the goal of obtaining
100% of electricity from renewable sources, and enforcing a 25% reduction of carbon dioxide emissions across its value chain. This feat seems to be approached on time, as the seven Castle Lite breweries in South Africa already operate with solar power, and only in 2021 these generated more than
14 GWh of electric power, reducing CO2 emissions by 12,443 tons. And in Johannesburg, the Alrode brewery is powered by bio-gas. These results have prompted ABInBev into announcing the global goal of achieving net zero emissions across its value chain by 2040.
“Sustainable development is a massive focus for our business as it is for many other businesses,” Figiacone remarked.
ABInBev Africa has a ten-year plan in place to increase its capacity in different countries through different flexible projects. The goal for 2022 is reaching 500,000 hL of product exported across Africa.
“Our mission is to support Africa’s growth, by producing the best African
Beers with pride, through a highly engaged team, improving performance year over year. The focus is to further improve our performance reaching a very high utilization of our assets, and enabling our expansion capacity to support our zone and global growth strategy,” finalized Fernando Figiacone, Vice President of Supply Chain in Africa for ABInBev.
Hitachi Energy , today announced that it has achieved the first-step target set out in its Sustainability 2030 plan – the use of 100% fossilfree electricity in its own operations1. The company is driving towards being carbon-neutral in its own operations by 2030 2, in line with its Purpose, ‘Advancing a sustainable energy future for all’.
“By achieving 100% fossil-free electricity in our own operations, we have reduced our CO 2 equivalent emissions by over 50% compared to 2019,” says Claudio Facchin, CEO of Hitachi Energy. He continued, “The Net Zero challenge is global and it’s about acting now, innovating and collaborating across countries, industries and societies. Together
Notes:
1. The contract for its South Korea operations (equivalent to 0.4% total electricity usage) is expected to be signed in Special Edition retrospectively through green tariffs.
2. Discover more about Hitachi Energy’s approach to Sustainability 2030 here
with customers, partners, and all stakeholders, we are advancing the world’s energy system to be more sustainable, flexible and secure.”
The targeted 50% reduction achieved ahead of plan will amount to approximately 175 kilo tonnes of CO2e per year, equivalent to removing over 35,000 passenger cars off the road.
To achieve 100% fossil-free electricity in its own operations –and in support of the Hitachi Group’s carbon-neutrality goal 3 – the company has pursued a number of pathways including supporting projects to generate its own fossil-free electricity, such as installing solar roof panels combined with e-mesh TM digital solutions for distributed energy resources maximizing energy efficiency and minimizing CO 2
emissions. In its Zhongshan factory in China , the company is generating nearly 20% of its total energy consumption from solar panels. In its first year of operation, the power Instalación fotovoltaica, Zhongshan, China
Notes:
Hitachi Sustainability Report 2021
generated at the factory is expected to reach 1,510 megawatt hours (MWh), contributing to the reduction in annual carbon emissions by more than 1,000 tonnes.
To achieve 100% fossil-free electricity, Hitachi Energy has also
switched to green tariffs, bought Energy Attribute Certificates (EACs), and signed Power Purchase Agreements (PPAs) across its operations and facilities in 90 countries.
Looking ahead, Hitachi Energy is
continuing to invest in its journey towards carbon-neutrality by further increasing energy efficiency, as well as electrifying its own operations. In Ludvika, Sweden, the company is now using 100% renewable electricity generated from hydropower and from solar panels to support its operations. Ludvika, which is one of Hitachi Energy’s largest production facilities, has gone beyond tackling its electricity supply and is now close to removing the use of all fossil fuels from the whole of its operations. The company has a track record of implementing its own technologies in its operations to enable the integration of renewable energy. For example, in 2015 its South Africa operations installed a 750 kW rooftop photovoltaic plant and a 1 MVA/380 kWh battery-based PowerStoreTM for enhancing the use of renewables
and providing a continuous supply of power.
Through its Sustainability 2030 plan and targets, the company reinforces its commitment to accelerating actions driving business in a sustainable way. Based around four pillars – Planet, People, Peace, and Partnerships – the strategy draws from the UN’s Sustainable Development Goals (SDGs), with specific focus on the following eight: Good health and well-being, Quality education, Gender equality, Clean water and sanitation, Affordable and clean energy, Responsible consumption and production, Peace, justice and strong institutions; and Partnerships for the Goals. In line with these SDGs, each pillar has corresponding targets that drive the business to contribute social, environmental, and economic value.
Hitachi Energy is a global technology leader that is advancing a sustainable energy future for all. We serve customers in the utility, industry and infrastructure sectors with innovative solutions and services across the value chain. Together with customers and partners, we pioneer technologies and enable the digital transformation required to accelerate the energy transition towards a carbonneutral future. We are advancing the world’s energy system to become more sustainable, flexible and secure whilst balancing social, environmental and economic value. Hitachi Energy has a proven track record and
unparalleled installed base in more than 140 countries. Headquartered in Switzerland, we employ around 38,000 people in 90 countries and generate business volumes of approximately $10 billion USD.
ABOUT HITACHI, LTD.
Hitachi, Ltd. (TSE: 6501), headquartered in Tokyo, Japan, contributes to a sustainable society with a higher quality of life by driving innovation through data and technology as the Social Innovation Business. Hitachi is focused on strengthening its contribution to the Environment,
the Resilience of business and social infrastructure as well as comprehensive programs to enhance Security & Safety. Hitachi resolves the issues faced by customers and society across six domains: IT, Energy, Mobility, Industry, Smart Life and Automotive Systems through its proprietary Lumada solutions. The company’s consolidated revenues for fiscal year 2020 (ended March 31, 2021) totaled 8,729.1 billion yen ($78.6 billion), with 871 consolidated subsidiaries and approximately 350,000 employees worldwide. For more information on Hitachi, please visit the company’s website at www.hitachi.com
www.hitachienergy.com/mx/es
Over a century of prestige and growth make of Gerdau one of the main suppliers of long steel products in the Americas. This strength, strategic partnerships and sustainable management have consolidated Gerdau Corsa in MexicoTranslation by María Murgui
erdau’s history goes back to 1901 at the hands of German immigrants settled in Porto Alegre, in Southern Brazil. The nails factory started by Joao and Hugo Gerdau began its transformation in 1946, when Curt Johannpeter -Hugo’s son-in-law- took the reins of the company, thus spreading its business and operations.
The territorial growth began in the second half of the 20th century, and in 2007 the company arrived in Mexico.
The acquisitions and strategic partnerships have been a key factor for Gerdau’s consolidation in the Mexican market.
Upon its arrival in the country,
GGerdau purchased the totality of Siderúrgica Tultitlán (SIDERTUL steelmaker), which already had more than 50 years of experience in steel production.
A year later, Gerdau acquired 49% of the stocks of the Aceros Corsa company and its distributors’ network. After this strategic alliance, investments were planned to build the largest construction profiles plant in the country in Cuidad Sahagún, Hidalgo. These facilities started working in 2015, after a US$600M investment.
Their set-up capacity is of a million tons of liquid steel and 700,000 tons of laminated products.
“We are supported by 120 years of experience in the steel industry, we are one of the main long steel products manufacturers in America and one of the leading special steel suppliers in the world”, added Denis Gomes, Director of Supply Chain, Metal and Energy for Gerdau Corsa.
Gerdau- Denis Gomes, Director of Supply Chain, Metal and Energy for Gerdau Corsa
we are one of the main producers of long steel products in the world”
“We are supported by 120 years-experience,
PROVED LEADERSHIP ALL OVER THE CONTINENT Gomes graduated in Business Administration at the Federal University of Santa Maria (Brazil) and, afterwards, he earned an MBA with specialty in Finance at the Getulio Vargas Foundation, also in Brazil.
He also took updating courses during his years spent in Peru. In 2020 he finished his studies in the High Management Perfection Program, at the IPADE (PanAmerican Institute for High Business Management, in Mexico).
Also, Gomes took part in the Núcleo Preparatorio de Oficiales de la Reserva (Reserve Officer Preparatory Core), in the Brazilian Armed Forces.
Regarding his work, Denis Gomes started his career in Coca-Cola, working in the Finance, Accounting, Marketing and Strategic Planning departments. During his time in this company he earned the certification as Chief Auditor of the Coca-Cola Quality System and took part as Quality National Award Examining Board Auditor in Brazil.
After joining the Gerdau Bank, hecompleted the Trainees Program and later he became an integral part at Siderperu, being appointed Leader of Finance and Relationships with Investors, with the aim of achieving the Company’s financing reorganization; during that period he took part in the Global Comptrollers Training Program, and he got achievements such as the implementation of the financing area into the Shared Services Center (SSC) in 2012, thus centralizing the financing operations of six countries in Latin America.
In 2015 he took over the SSC General Management, thus incorporating part of the United States operations, and in 2018 he was appointed Finance Manager at Gerdau Corsa, where his main challenge was to optimize the financing and capital organization for the expansion and growth of the Company in Mexico. In December, 2020, Denis took over as Director of Supply Chain, Metal, Logistics, Energy and S&OP (sales and planning).
As well as for many other industries worldwide, matters such as logistics and the supply chain have meant a series of challenges for Gerdau Corsa since the COVID-19 pandemic broke out.
However, solutions to those problems through a digital mindset and the implementation of digital tools have allowed a quick and efficient performance. The use of Artificial Intelligence has been useful for the
automatic and remote classification for the recollection and processing of metal raw materials. Also, the implementation of the Gerdau Tracking System (GTS) for the Logistics area allows accurate monitoring of deliveries to each client.
“The most prepared companies, and those which reacted in a quick and efficient way were the ones to transform the supply chain’s basic functions”, the executive declared.
areas:
and Processing of
Raw
Sales and Planning (S&OP)
The latter is now in charge of managing and integrating the rest of the areas according to the market’s needs identified by the Business area, of the optimization of each of the resources with the aim of reaching maximum production capacity, as well
as guaranteeing the raw materials from a deep knowledge of the impact of the market’s prices and tendencies. The main purpose of this integration is to deliver the products to each client timely and in due form, customizing the work each of them may require. For that purpose, the Company is supported by the development of Business Intelligence programs, which allow the identification of prices, tendencies, raw materials demand and other factors. Also, a Supply Chain Innovation Day has been created, an event which gathers the whole supply chain and invites sector-related startups, besides giving recognition to best practices and implementations.
- Denis Gomes, Director of Supply Chain, Metal and Energy for Gerdau Corsa
“The most prepared companies, and those which reacted in a quick and efficient way were the ones to transform the supply chain’s basic functions”Special
Primetals Technologies Mexico located in Apodaca N.L. nearby the USA border, a services and products company part of the pioneer Primetals Technologies group, founded in 1994 focused on furnaces and recently for the past years giving specialized solutions for casters and mills.
Recently Primetals Technologies Mexico conditioned a third new workshop, some of the mention bellowed are part of the new equipment:
• CNC Table Type Horizontal Boring Mill 6”
• Gray CNC vertical mill 84”.
• Boring Mills, Vertical 56”.
• [2] Gantry machining centers.
• [2] Lathe 6T260L
• Lathe 5100LB
• Welder
• Conventional
• Milling
• [3] Laser trackers and a measuring Arm.
• Handyscan latest version.
• Nickel plating station. www.primetals.com contact@primtals.com
For further details please direct to:
• Alfredo Salazar (USA Account Manager) alfredo.salazar_cortes.ext@primetals.com
• Marco Rito (MX & SA Account Manager) marco.rito@primetals.com
• Luis Gamboa (VP & Sales Director) luisd.gamboa@primetals.com
Gerdau Corsa has created alternatives to funding programs for its supply chain along with different banks. These mechanisms have the purpose of developing and strengthen suppliers who are considered Business Partners for the Company by easing their access to credit, besides contributing to economic recovery.
All of the production output from Gerdau Corsa is made from millions of tons of recycled materials, making Gerdau the largest recyclers in Latin America.
Among other related efforts, the processes developed by Gerdau have allowed the company to reduce its carbon footprint, considering that per each ton of steel produced in the world, 1.89 CO2 tons are emitted (global average quantity within the steel industry) whereas the Company has reduced its average down to 0.93 CO2
Refractory products withstand extreme temperatures, enabling the production of steel, cement glass and many more materials essential to daily life.
Our 14,000 highly-skilled people are dedicated to delivering the best possible solutions for our customers, enhancing not only their operations but also their business performance.
Find out more at rhimagnesita.com
The first international company to offer products and services in refractories, insulation, passive fire proofing and heat treatments for the industry “TURNKEY” alfran.com Protect your coretones per each steel ton produced, besides assuming the commitment of reducing it to 0.83 CO2 tons until 2031.
Another remarkable effort was the sustainability agreement entered into with BBVA (Banco Bilbao Vizacaya
Argentaria) for the import of strap metal with an investment of US$60 million, positively affecting with this transaction the SDGs (Sustainable Development Goals), thus making sure to stock the company up with recycled raw materials and promoting the reuse of solid materials, and at the same time
- Denis Gomes, Director of Supply Chain, Metal and Energy for Gerdau Corsa
“We will continue working to update our industry and become a model to reach other 120 years and contribute to a more sustainable world”
contributing to Circular Economy.
“We are in continuous search for the improvement of environmental management which makes us become a leading company and a model within the industry”, Gomes explained.
For the future, Gerdau Corsa foresees a growth in the country which will keep present challenges related to logistics and energy, which are subject to each country’s regulation and policies.
There are plans for a markets
diversification beyond the iron and steel industry. The Company is also working in contributing to a more equitable community through diversity and inclusion policies and working in social projects related to education, environment and health which will allow it to contribute in neighboring communities.
“We will continue working to update our industry and become a model to reach other 120 years and contribute to a better world”, concluded Denis Gomes, Director of Supply Chain, Metal and Energy for Gerdau Corsa.
2007
Mexico
Produced by Jassen Pintado
Interviewee
Nicolás Pesaque, CEO for Saint-Gobain PPC Peru
Omar Rodríguez
Saint-Gobain has presence across 70 countries contributing to the construction sector. The company’s more than 350-year history began as a glass and mirror manufacturer for King Louis XIV, working in widely-known historical projects, such as the Palace of Versailles, in France. Besides its worldwide expansion, the company has also increased its specialized product portfolio for different tasks in construction and finishes. Saint-Gobain Productos para la Construcción (Saint-Gobain PPC, “products for construction”)
Saint-Gobain PPC is positioned in Peru, thrusted by its rapid growth to the leadership in the market for construction and finishings, besides taking a step forward toward sustainability in its operations and construction solutions, aligning this purpose through its value chain
arrived at Peru in 2013 through the launching of Weber mortars, which became a leading brand in 2019 after acquiring Pegamentos y Fraguas de Celima (Celima adhesives and forges). In 2021, Saint-Gobain acquired Soluciones Constructivas Volcán, a company established in Peru since 2011, specialized in manufacturing and marketing of the drywall system. And in late 2021, the company finished its acquisition of Z Aditivos, thus thrusting its way into the chemicals for construction industry.
Saint-Gobain PPC covers all of Peru directly and through strategic partnerships as well.
“We want to become a reference within the construction sector supported by the experience we bring to the market through our innovative products and solutions, with a high service level and a sustainable operation,” commented
Nicolás Pesaque, CEO for Saint-Gobain PPC Peru.
Nicolás Pesaque Roose leads the operation at Saint-Gobain PPC Peru. He earned a degree in Industrial Engineering at the Peruvian University of Applied Science, in Lima. Afterwards, Pesaque earned an MBA from the Macquarie Graduate School of Management, in Australia.
Pesaque’s career began in ASA Alimentos, a food production company commonly known for the “Negrita” brand. In ASA, Pesaque performed in the operations area. Afterwards, he joined Alicorp, becoming part of the company’s marketing team on an international level.
Pesaque entered the construction industry in 2016 as Business Manager for Soluciones Constructivas Volcán, taking over as General Manager for the
- Nicolás Pesaque, CEO for Saint-Gobain PPC Peru
company in 2018, and being named CEO for Saint-Gobain PPC Peru during early 2021.
The company supplies the construction and finishing works industry from five production facilities,
strategically located in Arequipa, Lima and Trujillo.
Saint-Gobain PPC Peru’s business units are:
• Weber and Weber-Celima mortars
• Drywall products from the Volcán and Placo brands
• Chemical products for construction from Weber and Z Aditivos
Atlas Copco, proud to be Saint-Gobain PPC strategic partner in their compressed air projects
Our air compressors, gas generators and air treatment products, provide our strategic partners, like Saint-Gobain PPC, innovative, efficient and sustainable industrial solutions. Working with the largest service network in the region, we are ready to help you wherever and whenever you need us.
Atlas Copco, Home of Industrial Ideas.
To the more than three-century experience and network support implied in Saint-Gobain’s global operation, other factors are added, contributing to a successful run for Saint-Gobain PPC Peru:
• Excellence in customer service
• The experience shared with customers and users
• The base of knowledge open to serve the market
• Permanent innovation in every product, solution and service platform
• Sustainable operation regarding resources and the development of neighboring communities
The Grow & Impact plan, from SaintGobain, is a global strategy designed to bring growth to the company through a wide array of solutions and its operation model, boosted by its performance on the marketplace.
This way, Saint-Gobain remains a leader in every market by developing sustainable products, resulting in a wide reduction of the carbon footprint, hence a better use of resources, relying on materials able to contribute to building better homes and buildings, answering to the company’s purpose of “Making the World a Better Home”. Saint-Gobain PPC Peru is focused in this program, sharing its premises
We will be summoning every player in the sector to achieve this”
- Nicolás Pesaque, CEO for Saint-Gobain PPC Peru
PSQ Argentina S.A. comprises different fields related to construction, painting and adhesives. It is worth highlighting the offer of waterproof and antifungal additives that help to preserve and extend lifecycles of buildings.
For further information, please contact us at: tecnica@psqargentina.com www.psqargentina.com
“A SYMBOL OF OUR WORK IS TO BE ONE STEP AHEAD OF THE MARKET NEEDS”.
throughout its supply chain, its own products and their life cycle.
“We want to become the global leader in light, sustainable construction, improving everyday life through high-performance solutions,” Pesaque added.
One of Saint-Gobain PPC advantages is working in Peru with many of the company’s global suppliers, which means goals and principles are aligned toward the same purposes, including in factors beyond the marketplace, as it is with reducing any environmental impact.
“It’s our duty to encourage decarbonizing in production processes. We will be summoning every player in the sector to achieve this, working like an ecosystem is the only way to become successful in the
implementation of this goal,” the executive said.
Company culture within SaintGobain PPC Peru is highlighted by its diversity and respect between the staff and inclusion. For key factors such as personnel development, three main subjects are considered:
• Strengthening an own management culture, supported on reliance, empowerment and collaboration.
• Obtaining tech skills able to increase agility in taking on innovation and its transference onto the market.
• Technical knowledge of every construction solution offered by the company.
The future ahead of Saint-Gobain PPC Peru is certainly shining, considering the company has every necessary element to deliver on set goals. As its main focus, the company is after an efficient integration of
businesses recently acquired, and afterwards thrust these into a sales volume resulting from a new value proposition and a strong portfolio. The company also foresees upcoming acquisitions with the purpose to increase the number of categories covered by the current portfolio,
thus becoming aligned to the plan of increasing Saint-Gobain’s leadership in Latin America.
To achieve all of these goals, new technology is to be deployed, enabled to increase production capacity in an efficient and sustainable manner.
In other matters, from within the
company, Comunidad Saint-Gobain (Saint-Gobain community) is being created with the purpose of improving the personnel’s housing conditions, and afterwards extending this collaborative effort to communities surrounding the Saint-Gobain PPC Peru operations.
the most important of which is to make sure every Peruvian has access to proper
housing”
- Nicolás Pesaque, CEO for Saint-Gobain PPC Peru
“We share endeavors and accomplishments along every country in the territory, the most important of which is to make sure every Peruvian has access to proper housing,” concluded Nicolás Pesaque Roose, CEO for Saint-Gobain PPC Peru.
NUMBER OF EMPLOYEES:
170,000+ (global)
FOUNDED: CONTACT:
www.saint-gobain.com nicolas.pesaque@saint-gobain.com
INDUSTRY: Construction
www.thebostonbr.com
109 1665, since 2013 in Peru