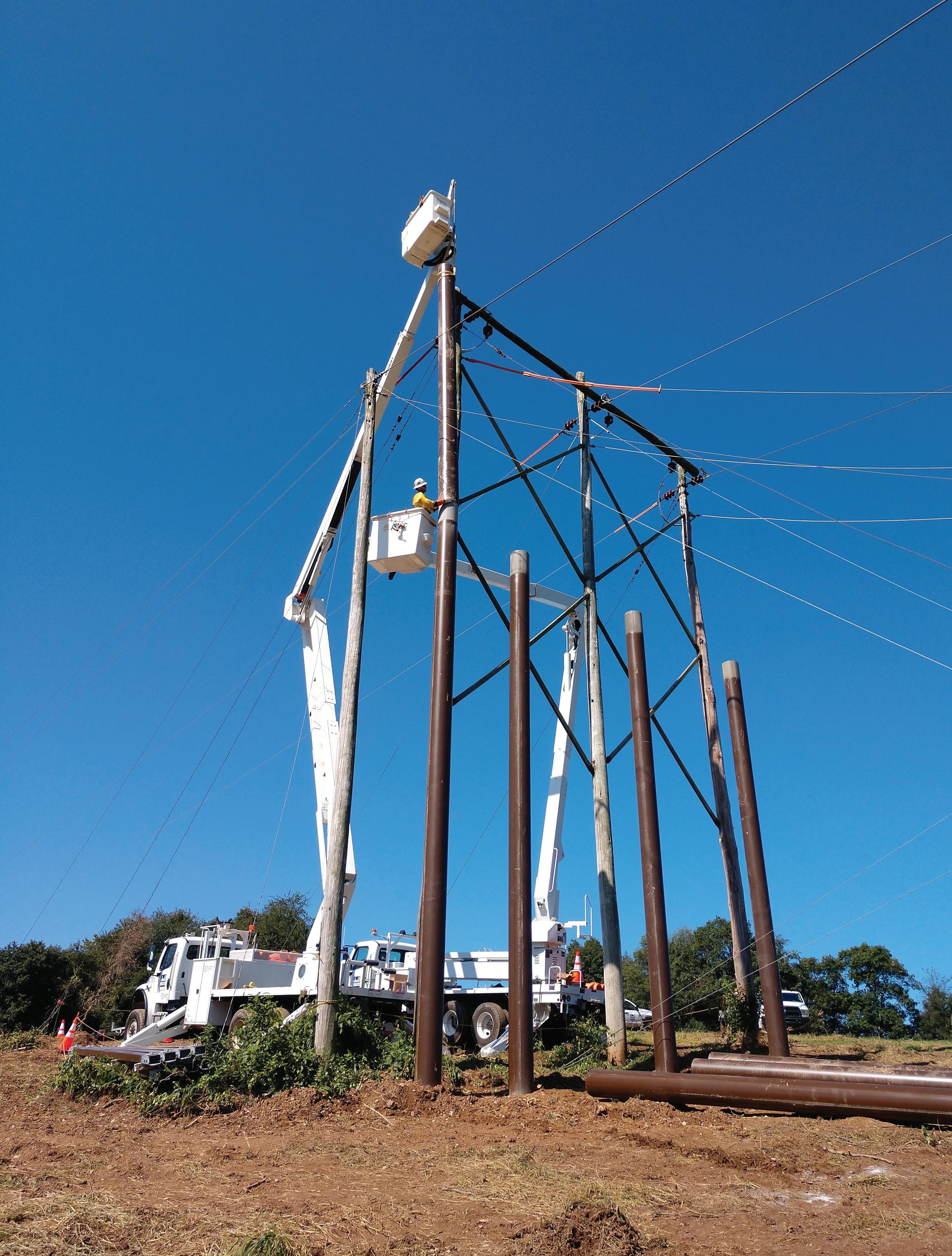
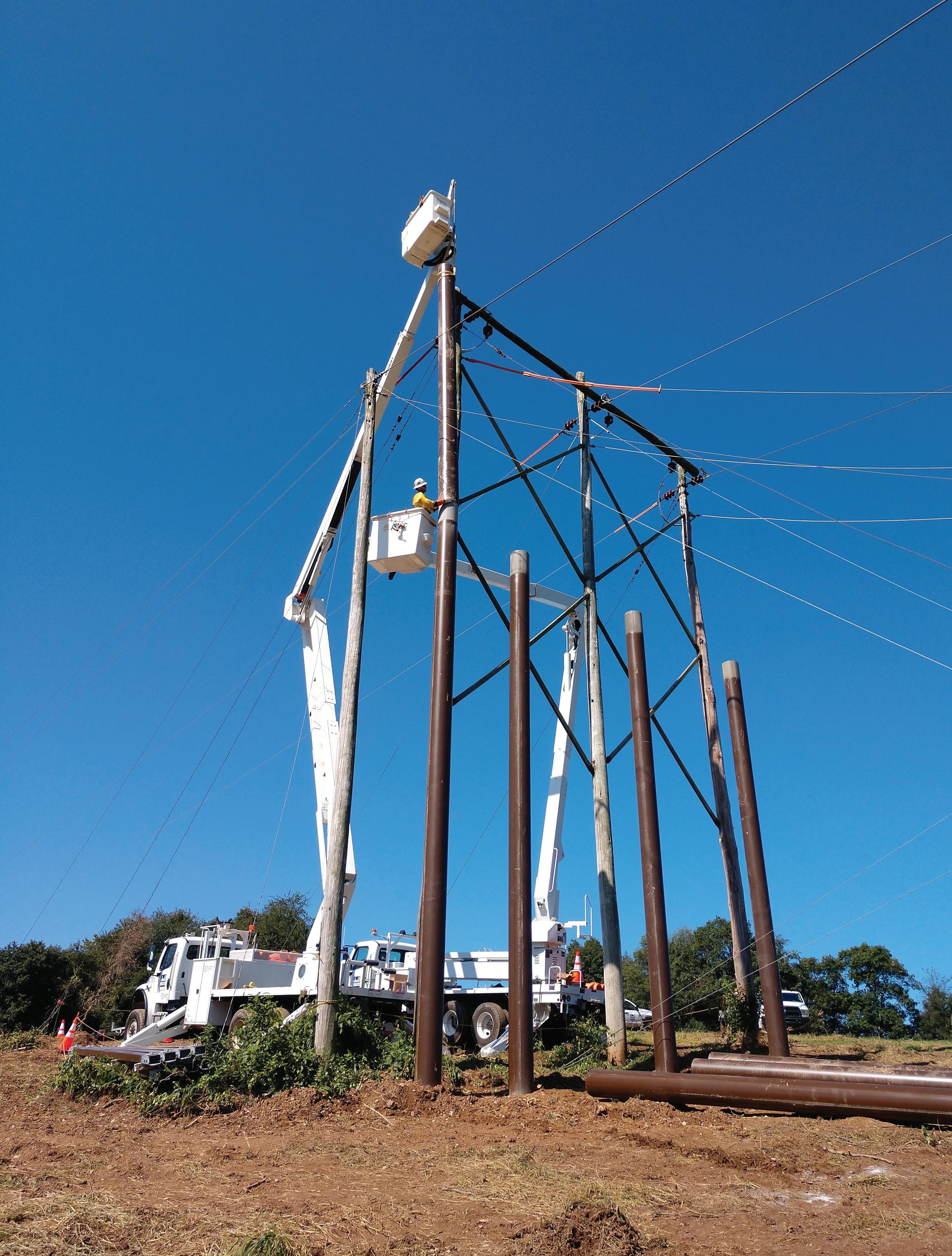
CompositesManufacturing
Let the Possibilities Reach New Heights with Composites One!
Expert Composite Materials and Process Professionals
Authorized Supply from Top Aerospace Material Providers
AS9120 Certified and Industry-Leading Capabilities
Extensive Product Selection, Including a Top-Tier Offering of Aerospace Specified Materials
Proprietary Reefer Trucks and Localized Freezer Storage for Fast Lead Times and Seamless Delivery
Cultivating Partnerships that Pave the Way for Innovative, Technical, and Supply Chain Solutions
Please contact 816-283-3330 to connect to a Composites One Aerospace expert.
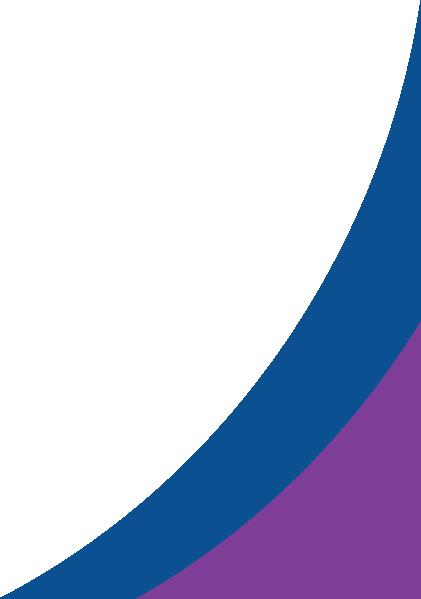
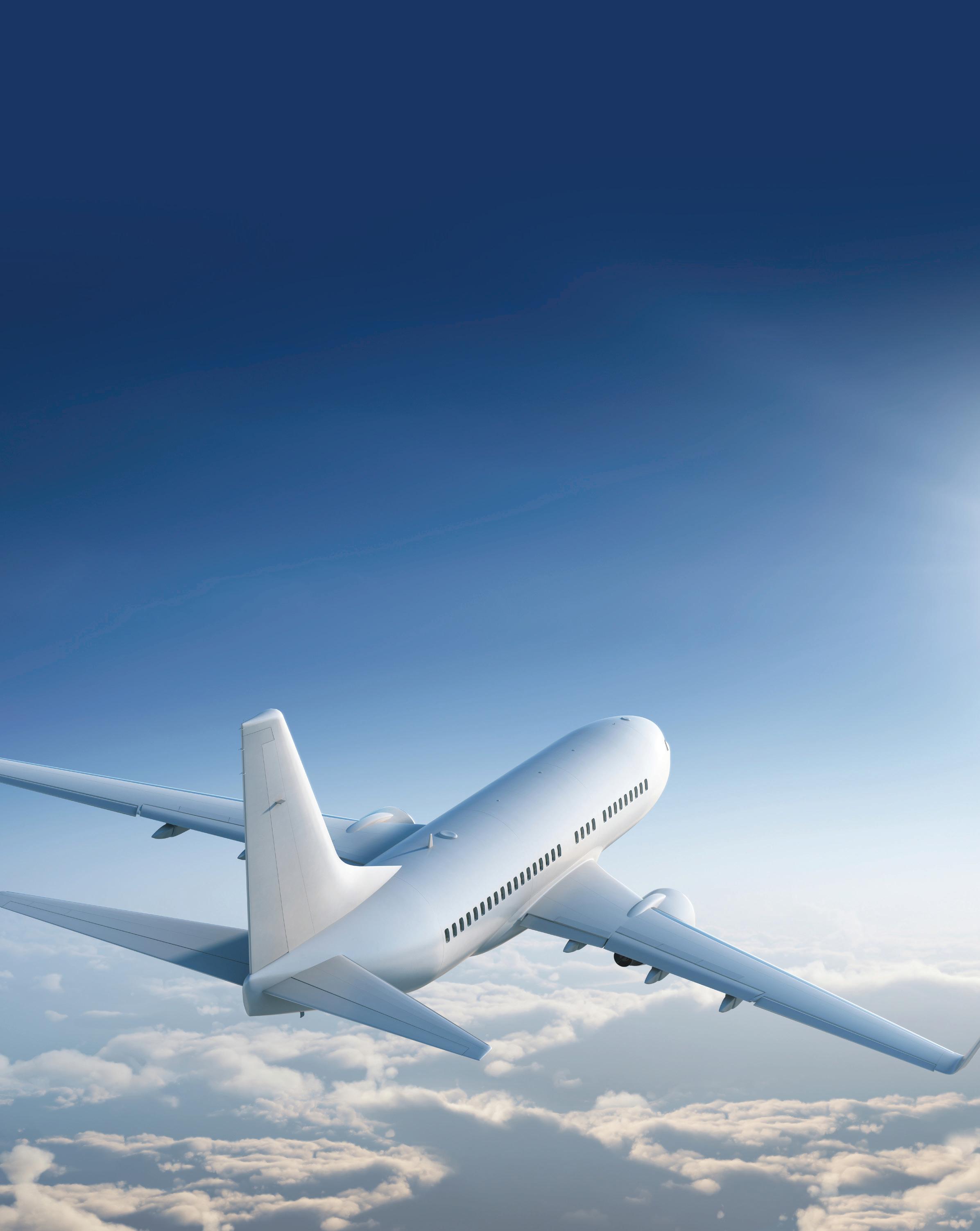
CompositesManufacturing
12 Strengthening the Power Grid
Utility companies and the federal government are searching for ways to build a more resilient power grid, and FRP poles and crossarms offer a solution.
By Mary Lou Jay
16 Building a Better Future
A consultant, structural engineer and former Department of Transportation administrator share ideas on how composites can become the sustainable material of choice in the infrastructure and construction market.
By Susan Keen Fynn
22 Robotics Aim for the Sky
Automated solutions, including robotic cells, can help the aerospace industry achieve high-rate manufacturing goals.
By Susan Keen Flynn
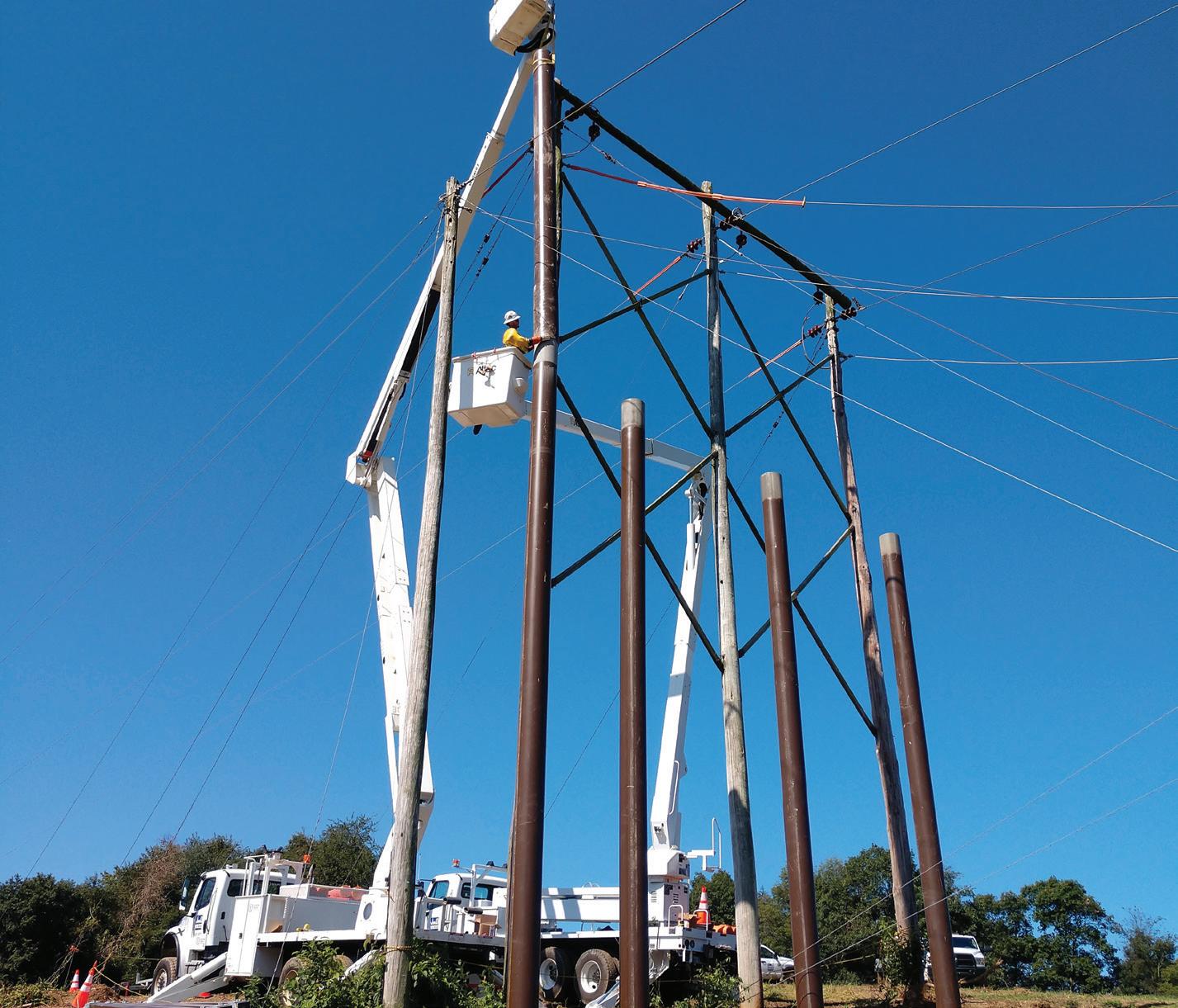
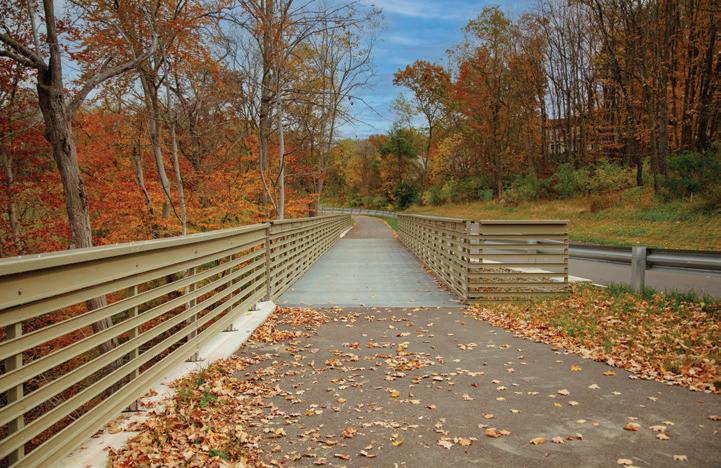
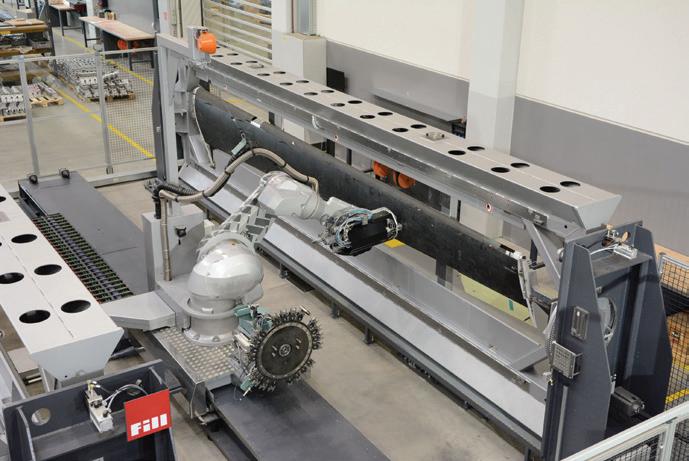
Photo Courtesy of Creative Composites Group
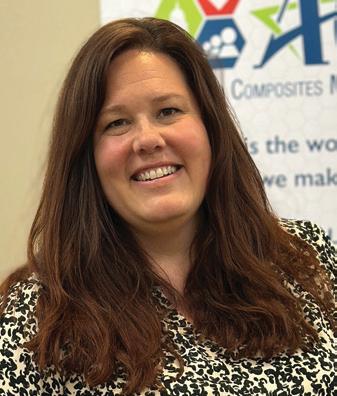
Staying Informed on Hot Industry Topics
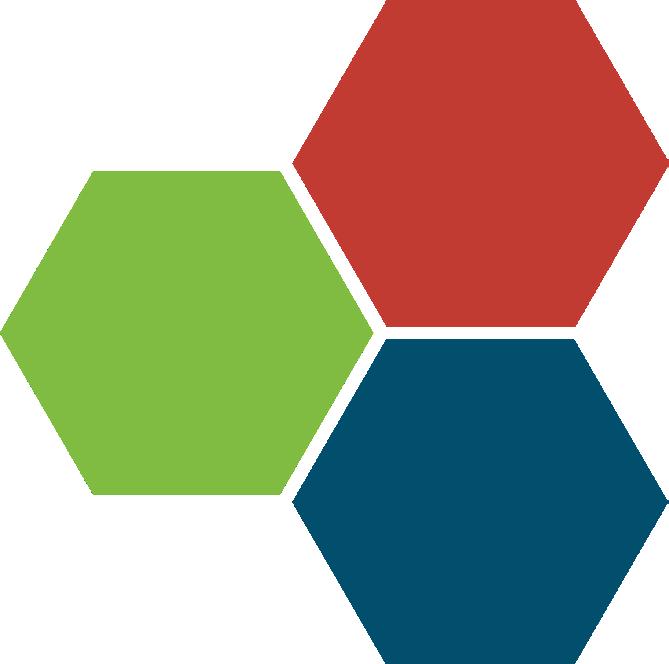
IN JUNE, two engineers from Bestbath attended ACMA’s Composites Sustainability Today event in Denver, where they learned about government policies, industry innovations, best practices and more. This information is invaluable not only because customers are increasingly asking questions about the sustainability of our custom FRP bathing products, but also because we want to ensure our manufacturing process is sustainable.
Our commitment to sustainable manufacturing means that we are looking to the future and taking care of our present. It includes everything from reducing our carbon footprint to increasing the comfort and safety of our employees. Thankfully, we are not alone in this. ACMA offers tools and resources to guide us. For example, ACMA and IACMI – The Composites Institute launched the CIRCLE Program to help composites manufacturers assess and reduce their cradle-to-gate environmental impacts and educate customers about the climate benefits of using composite products.
ACMA also provides education through its flagship publication, Composites Manufacturing magazine. Check out the article on page 16 for a look at how the sustainability movement is shaping the infrastructure and construction industry. It includes insight from speakers at Composites Sustainability Today.
Other articles in this issue discuss the role of composites in building a more resilient power grid (page 12) and the use of robotics to achieve highrate manufacturing in the aerospace industry (page 22).
The topic diversity within the pages of this magazine is indicative of the vast scope of our industry. To keep abreast of what’s new in the composites industry, I encourage you to attend CAMX in San Diego from Sept. 9–12, 2024. We have an amazing lineup of presentations and networking events, as well as exhibitions on the show floor.
I attended the predecessor to CAMX as a child with my father Gary Multanen, who started Bestbath and helped build ACMA. I am so proud to continue attending the conference every year and work with the board members and staff of ACMA and SAMPE to create the best possible experience for attendees. Every year I walk away with information and connections that positively impact my business. You can do the same. I urge you to register for CAMX today at thecamx.org/registration. I look forward to seeing you in sunny San Diego!
Sincerely,

Megan Multanen ACMA Chair of the Board
megan.multanen@bestbath.com
Composite s Manufacturing
Official Magazine of the American Composites Manufacturers Association
Publisher Cindy Squires csquires@acmanet.org
Editorial Managing Editor Susan Keen Flynn sflynn@keenconcepts.net
Director of Marketing & Communications Eliana White ewhite@acmanet.org
Editorial Design & Production 526 Media Group dkoenig@526mediagroup.com www.526mediagroup.com
Advertising Sales Director, Business Development John Catapano jcatapano@acmanet.org
All reprint requests should be directed to ewhite@acmanet.org
American Composites Manufacturers Association 2000 N. 15th Street, Ste. 250 Arlington, VA 22201 Phone: 703-525-0511 Fax: 703-525-0743 info@acmanet.org www.acmanet.org
Composites Manufacturing (ISSN 1084-841X) is published quarterly by the American Composites Manufacturers Association (ACMA), ACMA Headquarters, 2000 N. 15th Street, Ste. 250, Arlington, VA 22201 USA. Subscription rates: Free for members and non-members in the U.S., Canada and Mexico; $55 for international non-members. A free online subscription is available at cmmagazineonline. org. Periodical postage paid at Arlington, VA and additional mail offices.
POSTMASTER: Send address changes to Composites Manufacturing, ACMA Headquarters, 2000 N. 15th Street, Ste. 250, Arlington, VA 22201. The magazine is mailed to ACMA members and is also available by subscription. Canada Agreement number: PM40063731 Return Undeliverable Canadian Addresses to: Station A, PO Box 54, Windsor, ON N9A 6J5, Email: returnsil@imex. pb.com. Copyright© 2024 by ACMA. All rights reserved. No part of this publication may be reprinted without permission from the publisher. ACMA, a nonprofit organization representing the composites industry worldwide, publishes Composites Manufacturing, circulation 7,550, as a service to its members and other subscribers. Opinions or statements of authors and advertisers appearing in Composites Manufacturing are their own and don’t necessarily represent that of ACMA, its Board of Directors or its staff. Information is considered accurate at the time of publication, however accuracy is not warranted.
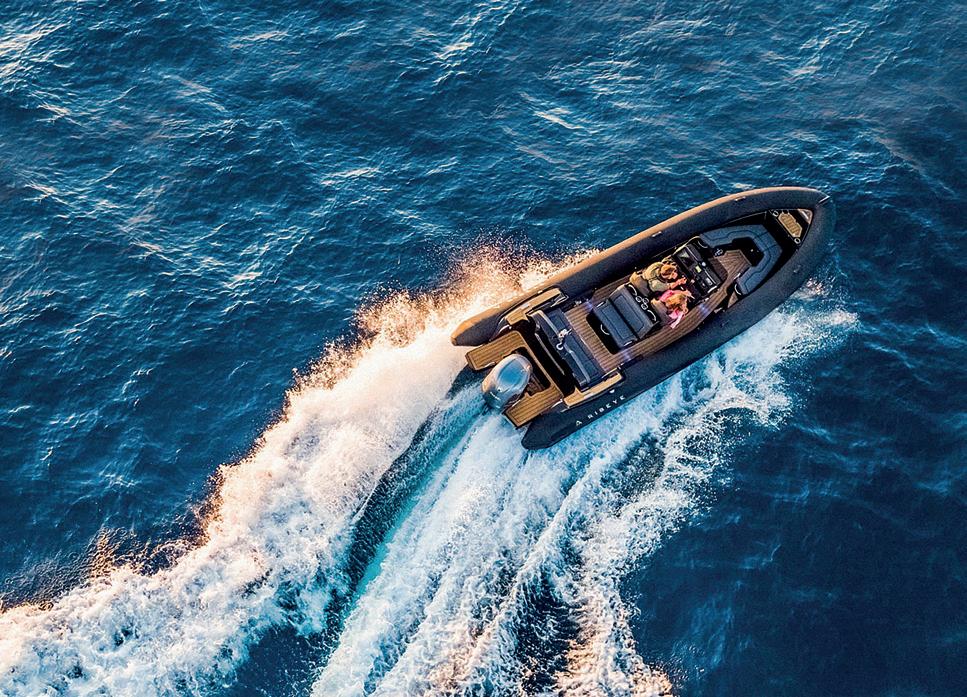
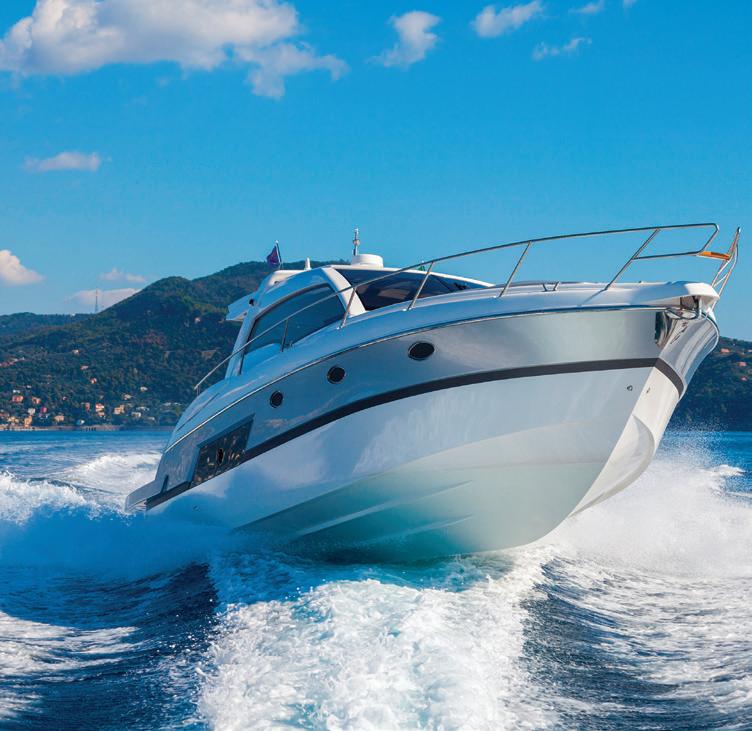
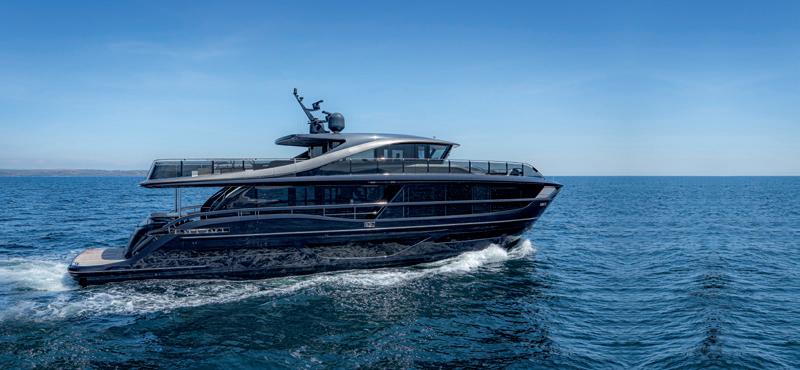


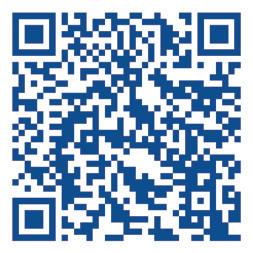
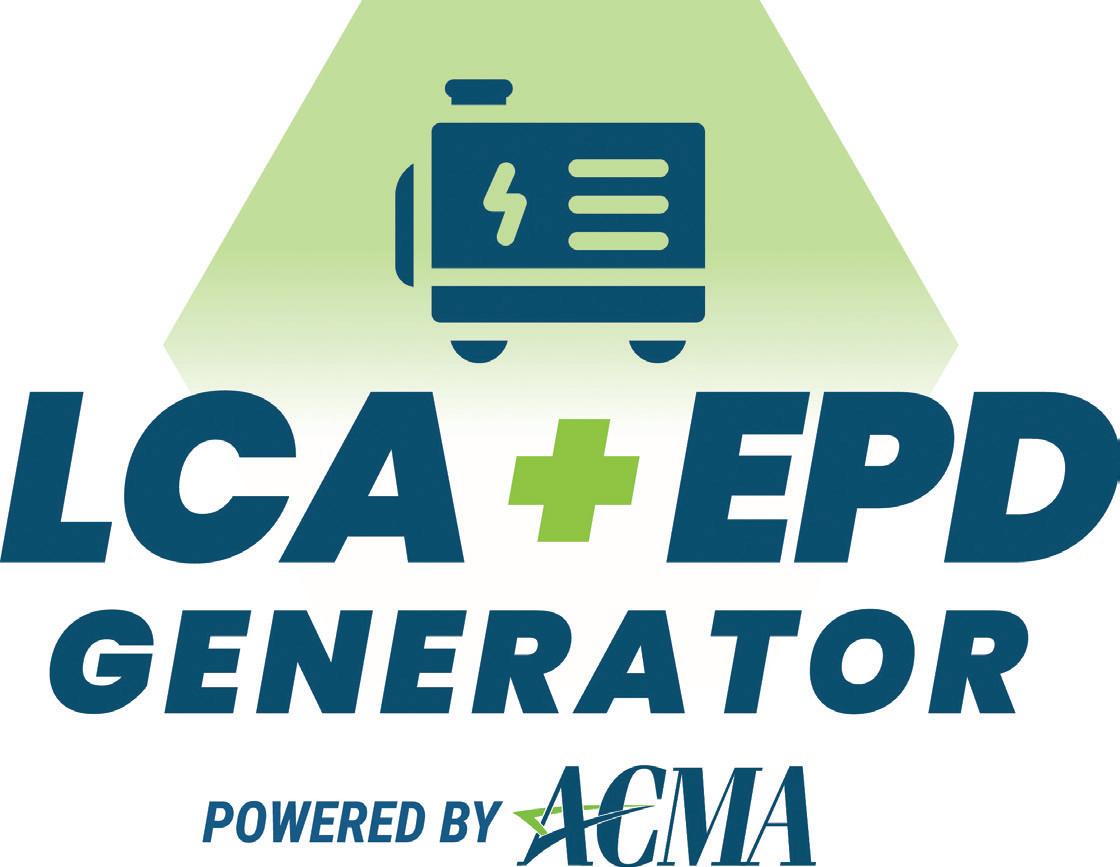
Report from the Field: Highway Sustainability
By John Schweitzer
THIS SUMMER, I’ve spent several days with groups of state DOT engineers, university faculty, trade association staff and Federal Highway Administration (FHWA) and Environmental Protection Administration (EPA) program managers, watching as they presented and discussed ideas for quantifying and reducing the climate impacts associated with the construction and use of transportation infrastructure. Possibly the most interesting takeaway from these meetings is that the state DOTs are fully committed.
Often, when Congress sets a policy regarding federally funded highways and then the FHWA promulgates an implementing regulation, the states find ways to work around the requirements and continue doing what they’ve always done. That’s not the case here.
State DOTs are investing heavily in the staff and tools needed to evaluate the lifecycle emissions of climate warming gases associated with alternative materials and construction practices. They are using the available data to evaluate climate impacts as they also look at cost and long-term performance when selecting design approaches and construction materials. States report they are ready to do more but are often frustrated by a lack of data. Environmental product declarations (EPDs) for
many products are either not available or lack data on impacts during the use and disposal phases of a product’s life cycle.
Notably, state DOTs are finding it easier to recruit engineers when sustainability is built into the job descriptions posted for open positions. The new engineering workforce is one that is oriented toward building a more sustainable infrastructure.
Several university civil engineering departments are taking leadership roles in collaborative efforts to reduce the emission of climate warming gases associated with construction and infrastructure. Some schools have multi-million-dollar grants from the EPA and FHWA for research on methods to evaluate the climate impact of highway construction materials and technologies. These academic departments are graduating engineers every year looking for career opportunities that include sustainability as a major objective in the work they will do for DOTs and highway design and construction companies.
The leading trade associations, including groups representing the asphalt, concrete and steel industries, have developed product category rules (PCRs) for construction products supplied by their association members, and they are rolling out webbased generators that will facilitate the preparation
ACMA WILL LAUNCH its LCA + EPD Generator later this year to provide robust EPDs for composite products at about one-third the typical cost to a company of preparing an EPD on its own.
of EPDs for these products. Encouragingly, ACMA is also focused on the development of PCRs and later this year will launch the LCA + EPD Generator for composite products.
That brings us to the EPA and FHWA. These agencies are implementing the sustainability programs described in the Bipartisan Infrastructure Law (BIL) and the Inflation Reduction Act (IRA), as well as executive orders issued by the Biden White House.
The IRA, for example, directs the EPA to use EPDs to identify construction products associated with emission of climate warming gases at levels less than the industry average of similar products. The EPA has released a draft approach for implementing its Label Program for Low Embodied Carbon Construction Materials, which will establish certain standards for the robust EPDs needed for valid comparison of the climate impacts associated with competing products.
And among other programs, the FHWA is advancing the use of EPDs to evaluate construction materials through its Every Day Counts initiative, a state-based model that aims to identify and rapidly deploy proven, yet underutilized innovations.
Lessons for the Composites Industry
It’s increasingly clear that composites manufacturers will need EPDs for their products to
be considered for construction and infrastructure projects. (ACMA wants every manufacturer of composite construction products to have at least one EPD by the end of 2026.)
And composites manufacturers will need to be “sustainability literate” to participate in discussions with designers, builders and owners of buildings, highways and other infrastructure. An EPD is not intended to convey and explain all the information that may be relevant to the sustainability of a construction project; it’s an instrument for providing information in a standardized format that will facilitate discussions between infrastructure builders and product suppliers.
Since our industry is just starting to develop programs in this area, we have an important opportunity to use PCRs and other guidance documents to ensure the EPDs for industry products are based on high-quality data and use transparent assessment methods. These data quality and transparency objectives will be built into the PCRs we develop and ACMA’s LCA + EPD Generator that will be launched later this year. CM
John Schweitzer is vice president of EH&S and sustainability at ACMA. Email comments to jschweitzer@acmanet.org.
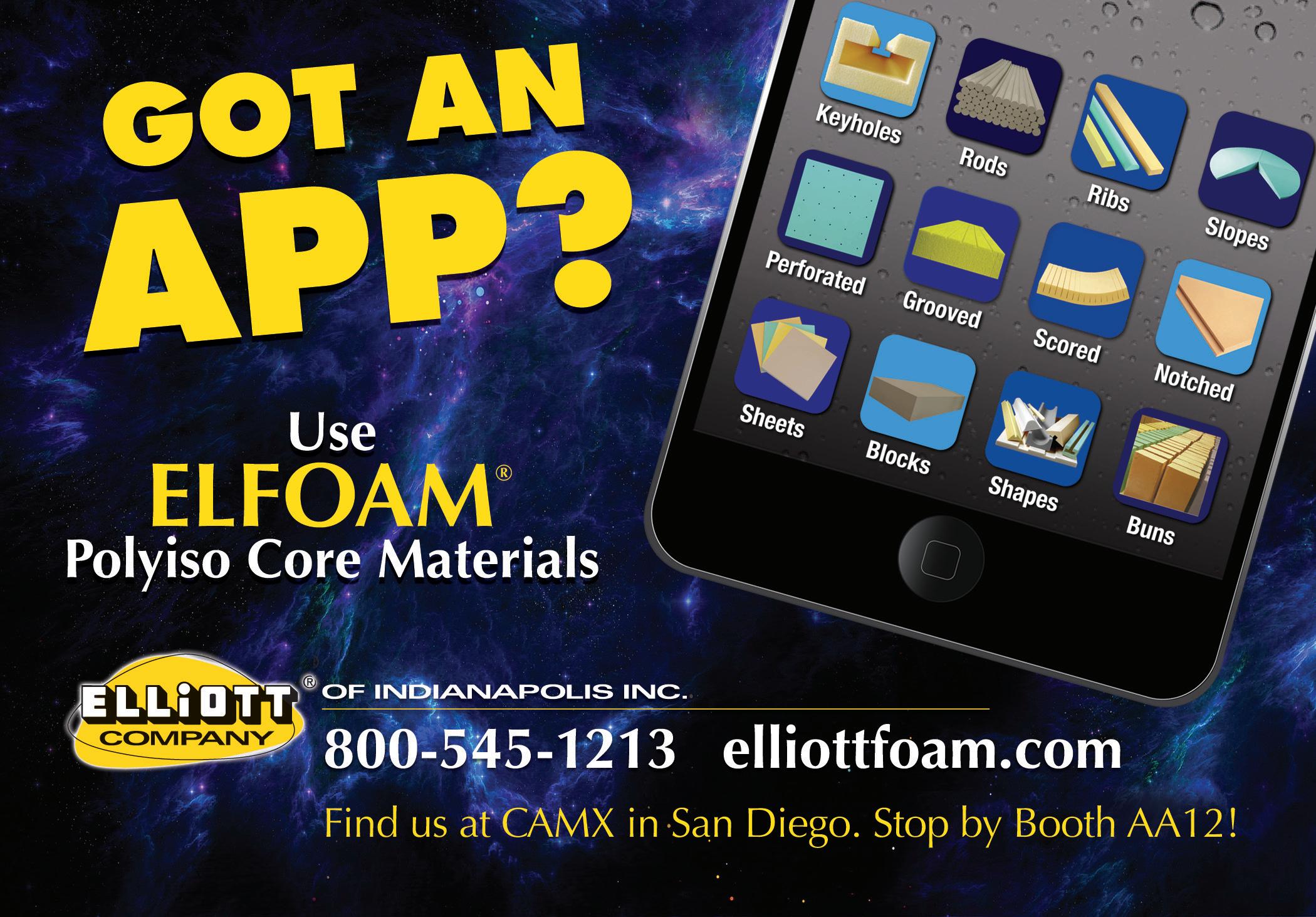
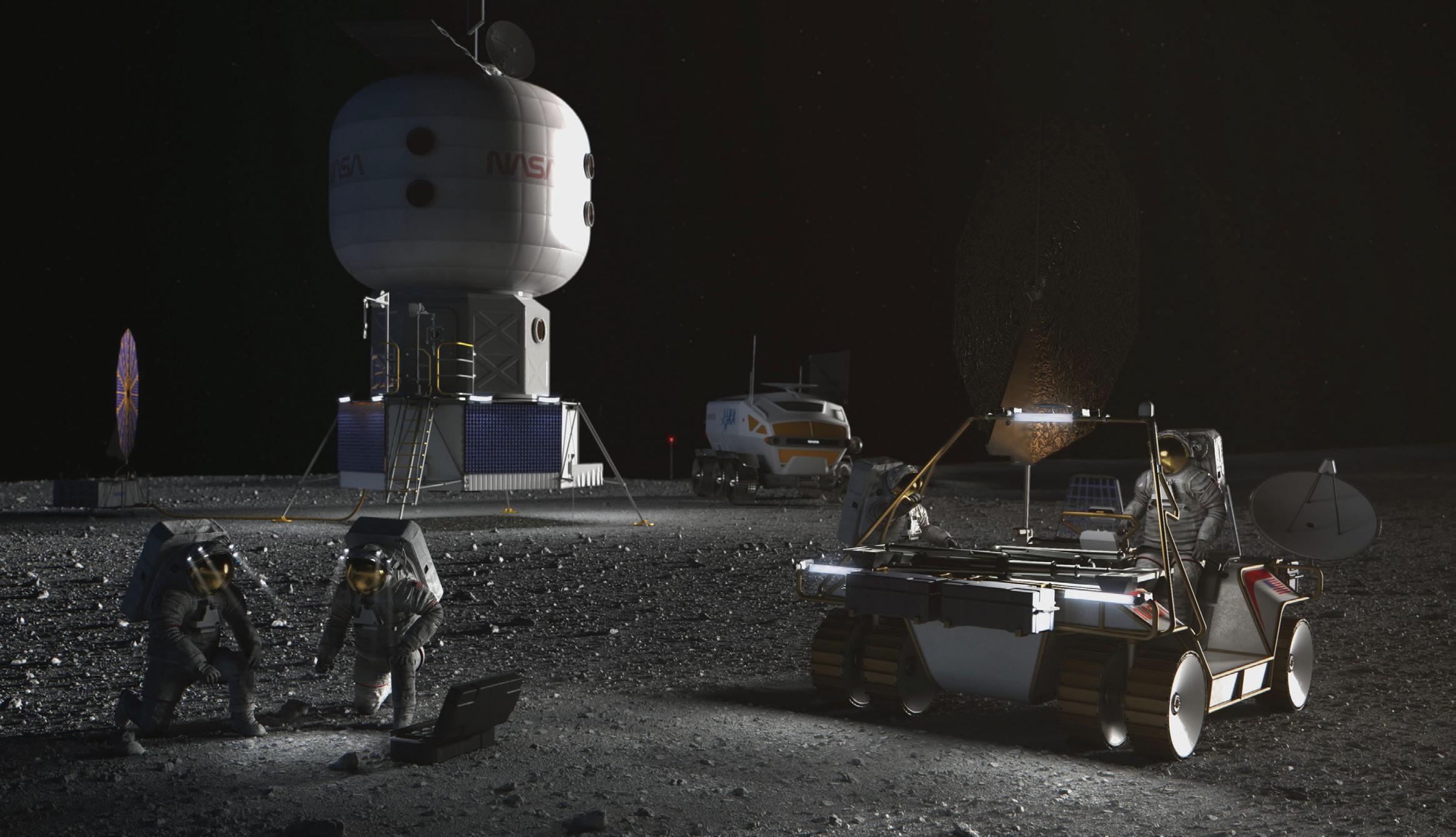
Strong Enough for Space
By Mary Lou Jay
A NASA RESEARCH team investigating methods of welding thermoplastic components could be opening up opportunities on the moon and in deep space for the composites industry.
The Thermoplastics Development for Exploration Applications (TDEA) team is funded through NASA’s Game Changing Development program. Researchers previously developed a bonding process for thermosets that will be used on the space agency’s new Space Launch System (SLS). Now they are looking into welding processes that could eliminate the need for heavy bolts typically used to join composite components. Potential applications include missions like the Roman Space Telescope (RST), which is an infrared telescope focused on studying dark energy, and the Tall Lunar Tower (TLT), a concept for elevating solar panels above the horizon to generate energy on the moon.
While the TDEA project is separate from the RST and TLT programs, the team has identified these structures as amenable to thermoplastic welding and established point designs based off the baseline designs and structural requirements of those programs.
The welding project, which began in 2021, has multiple components. The first step was reaching out to the composites industry, academia and other research organizations to determine state-of-theart practices in thermoplastics manufacturing and analysis. Researchers next evaluated five materials for their crystallization kinetics, including melting and crystallization temperatures, latent heat of crystallization and thermal conductivity relevant to welding.
Using all five materials, the team welded thermoplastic coupons using induction, resistance and ultrasonic techniques. “We evaluated their limitations with respect to materials and to the process,” says Sandi Miller, chemical engineer at NASA’s Glenn Research Center in Cleveland. The team also considered how easily each welding process could be used for in-space manufacturing processes. Induction welding, for example, might not be a viable choice since it requires auxiliary equipment for cooling.
NASA worked with three organizations — one for each type of welding — with an emphasis on the ultrasonic welding process from Agile Ultrasonics due to its promise of in-space operation. As of late
May, researchers were trying to optimize that process to reduce void content. “We have looked at process variables such as amplitude, pressure and dwell time, as well as the scan rate across the bond line,” says Miller. To reduce void formation in the bond region, they will also experiment with an energy director, which is placed at the interface of the bond and pulls the ultrasonic energy to the interface.
TDEA researchers are working simultaneously on two test applications. The Thermoplastic Terrestrial Point Design (TTPD) is adapted from the RST team’s design of a support beam assembly used to hold the telescope’s deployable aperture cover (DAC) blanket. The DAC closes over the telescope barrel during launch and then opens in orbit to help block sunlight from entering the aperture.
In the TDEA’s proposed design, the collar and beam assembly that helps open the DAC would become a single welded thermoplastic assembly, with the beam made from Toray’s Cetex® TC1200 PEEK and an additively manufactured carbon fiber reinforced PEEK with 30% fiber content for the collar area. This reduces the complexity, the part count and the mass of the assembly, according to William Mulhearn, aerospace materials engineer at NASA’s Goddard Space Flight Center in Greenbelt, Md.
“Because thermoplastics are relatively easy to manufacture, they’re opening up this new space of investigation for different applications.”
– Sandi Miller, NASA
The TDEA design for the TLT is known as the Thermoplastic In-Space Point Design (TSPD). The 50-meter tower, which might eventually be erected at the lunar South Pole, is intended to support solar arrays that will provide the United States’ moon base with power. Under the existing design, robots will connect the tower’s composite truss structure using metallic fittings and rivets. The TDEA team would like to improve upon that.
“We could make these truss structures out of thermoplastics and then have robots weld them through an end fitting. We would save all the weight of the rivets and also the management of the individual bolts,” Miller says. To test the feasibility of this approach, the researchers are building a small section of tower, which they call a repeating unit cell, with T700 carbon fiber and Cetex TC1225 low-melt PAEK from Toray. They will run tension and compression

tests on the welded joints in that cell.
The TDEA team plans to have the testing data for both point designs completed by the end of the government’s fiscal year on Sept. 30, 2024, but they hope to get additional funding to continue this work.
“There’s still quite a bit to do. We are trying to demonstrate the welding process in a vacuum chamber at cold temperatures, and we have plans to weld with a lunar dust simulant at the bond line,” Miller says. “There are also many unknowns when we’re trying to ultrasonically weld a large structure. For example, does the vibration from each subsequent weld affect the integrity of the previous weld? All the data that we collect will be useful in moving this work forward.”
Miller says thermoplastic composites could unlock other application possibilities — and potential research projects — for NASA, including high-rate manufacturing, in-situ consolidation and electric propulsion for aeronautics, as well as long-term cryogen storage on the lunar surface.
“Because thermoplastics are relatively easy to manufacture, they’re opening up this new space of investigation for different applications,” she adds. “There’s a lot of work that’s been done on thermoplastics, but I think there’s still a lot more that can be done.” CM
Mary Lou Jay is a freelance writer based in Timonium, Md. Email comments to mljay@comcast.net.
NASA’S THERMOPLASTICS Development for Exploration Applications (TDEA) team conducts research using Agile Ultrasonics’ welding system with a robotic end effector.
Photo Credit: Agile Ultrasonics Corp.
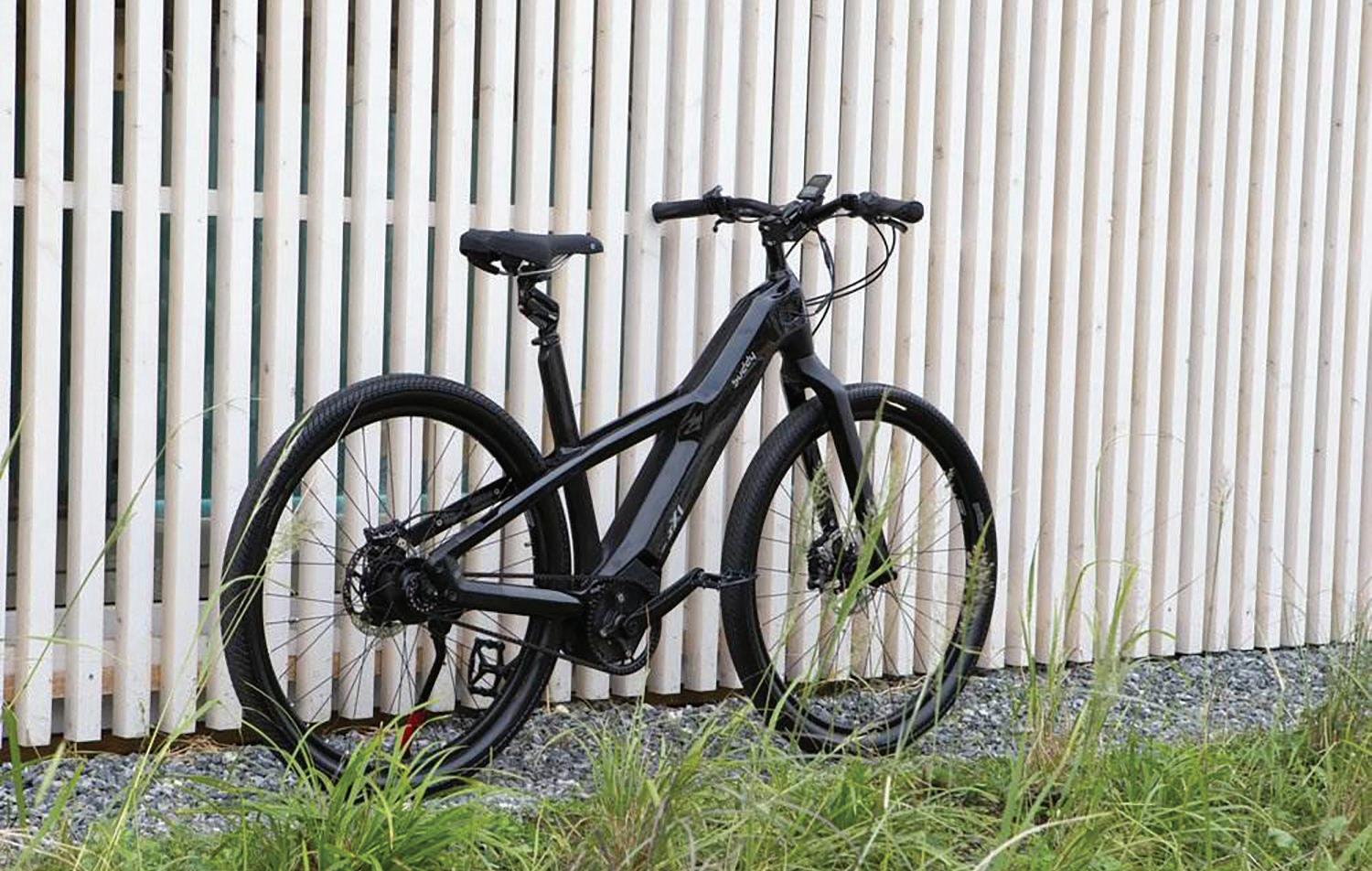
Elevating E-bike Frames
By Melissa O’Leary
AS THE MARKET for environmentally friendly electric bikes grows, V Frames of Saalfeld, Germany, is using water-assisted injection molding (WAIM) to produce carbon fiber reinforced thermoplastic (CFRTP) e-bike frames that break from the usual aluminum frames made in Asia and provide a 68% smaller carbon footprint.
The reduced environmental impact, which was documented in an independent life cycle analysis by Johannes Kepler University of Linz, results from a combination of factors. “It’s the elimination of transport from Asia. It’s using recycled fibers, then at the end of life being able to recycle them again,” says Michael Mueller, CEO of V Frames. “It’s really the complete life cycle.”
V Frames is a spin-off of ISOCO Plastics Technology, GmbH, a German firm that specializes in injection molded plastic containers and pallets. In 2014, Mueller and colleagues from ISOCO with years of experience in traditional injection molding began discussing how they might apply the lesser-known WAIM process to a highend product.
“Water-assisted injection molding is a niche technology that has been in the automotive industry for a long time, but nobody really knows about it,” says Mueller. Eventually, ISOCO decided to pursue CFRTP bicycle frames, a part that could benefit from the hollow tube geometry that WAIM can create. V Frames was founded in 2017 and began approaching e-bike OEMs to gauge interest in developing a CFRTP frame. “We didn’t get very far,” admits Mueller.
Accustomed to importing aluminum frames, the OEMs balked at the necessary investments in research,
development and injection molding machines — especially for a new, unproven material. “The toughest thing was to prove to the industry that it was possible to do it,” recalls Mueller.
V Frames decided to fund its own research and development and produce a CFRTP frame as proof of concept. The journey took nearly eight years as V Frames and, later, the engineering consultancy LZS GmbH conducted simulations to ensure the frame had the right stiffness for a smooth ride and impact resistance for safety. Mold engineering for the complex part was also laborious.
The long design and testing period was necessary, says Mueller. “The most critical thing is to simulate, to develop the product, because then you build the mold for half a million dollars or more and you cannot change it really,” he says. “If the product comes out and it’s not working, you have problems.”
Once the Ecobike One proof of concept frame was completed in 2021, V Frames began working with several European e-bike OEMs to develop water-assisted injection molded CFRTP frames. Today, Buddy Electric X1s and ADVANCED® RECO e-bikes feature V Frames. A third company, ISOCO Bikes, now distributes the technology globally and sells V Frames and e-bikes.
V Frames are produced using a custom water injection molding machine that heats recycled carbon fiber and nylon 6 thermoplastic pellets until they are liquified and shoots the molten material into the machine’s steel mold. The mold is then cooled from the outside so that the outer walls harden but the center remains liquefied.
THE BUDDY BIKE sX1 electric bike features a carbon fiber-reinforced thermoplastic frame, the 7th generation developed by V Frames. The company is currently seeking an OEM in the United States to introduce a white label X1. Photo Credit:

Next, water is injected into the part to push out the liquid center and create the hollow tube geometry.
The entire process takes just 90 seconds. Afterward, the frames are moved to a six-arm robot that drills holes for fasteners, cuts and polishes WAIM overflow channels and injection points, and mills the WAIM entry section. Depending on the design, the robot can also insert metal inlays and assemble additional parts onto the battery area.
The LEHVOSS Corporate Group in Germany and Pennsylvania-based R & M International Sales Corporation supply carbon fibers for the bike frames, 90% of which feature short fibers. However, R&M spent 13 months developing a recycled long carbon fiber and Aegis® nylon 6 pellets for V Frames, including a patented process to coat individual continuous fibers.
“Our pellets performed really well,” says Stephen Rawson, a partner at R&M. “They flowed well. They gave a really good finish to the bike. So, V Frames was able to use a recycled product without the loss of properties. It was a really big win.”
CFRTP frames provide several advantages over aluminum frames, including a 10% weight reduction, part-integration, higher impact resistance and a smoother ride, according to Mueller. The efficiency of WAIM offers another benefit. V Frames can produce 1,000 frames per day with a single machine and operator. Once a machine and mold have been developed for a customer, the company can manufacture on demand — a rarity in an industry still struggling with supply chain delays. “You have to order aluminum frames one year before you get them delivered from Asia,” says Mueller. “Let’s say the demand increases or decreases. You can do nothing!”
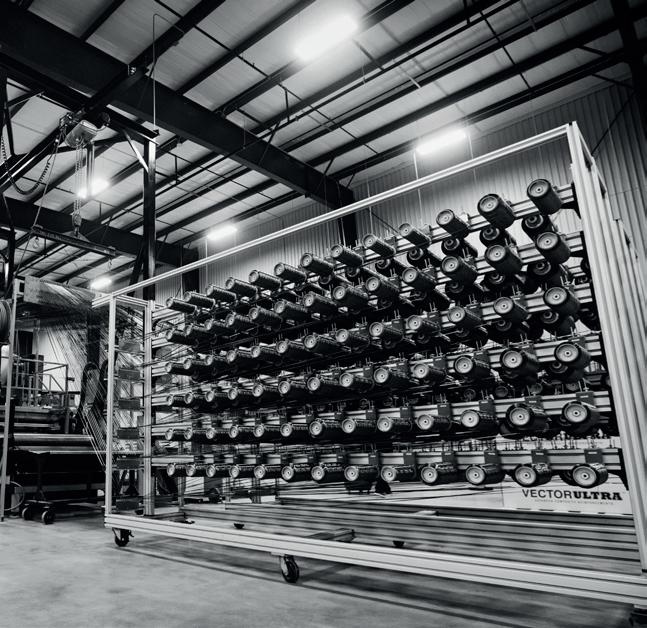
Unlimited Applications Unmatched Performance
Is it possible to increase strength and stiffness while reducing weight and cost? With Vectorply composite reinforcement fabrics it is! Our wide range of fiberglass, carbon and aramid fabrics, combined with industryleading technical services and support can take your product higher, farther, and faster with less weight and labor.
Giving your product the competitive edge is our business. Learn more at vectorply.com

But the biggest advantage may be the environmentally friendly production. Meuller says that V Frames are the first recyclable carbon fiber reinforced frame. “Most carbon fiber frames end up in a landfill. There’s no real technical solution,” he says. “This is simply another material. It can just be milled and reused.”
V Frames also produces water-assisted injection molded bicycle forks, cockpit components, mudguards, carriers and 28-inch wheels. In addition, the company is developing a wheelchair application.
Mueller believes that WAIM parts can be used for countless applications. With the ability to produce recyclable CFRTP products with complex, hollow tube geometries and integrated parts, the sky is the limit. CM
Melissa O’Leary is a freelance writer in Cleveland. Email comments to melissa@good4you.org.
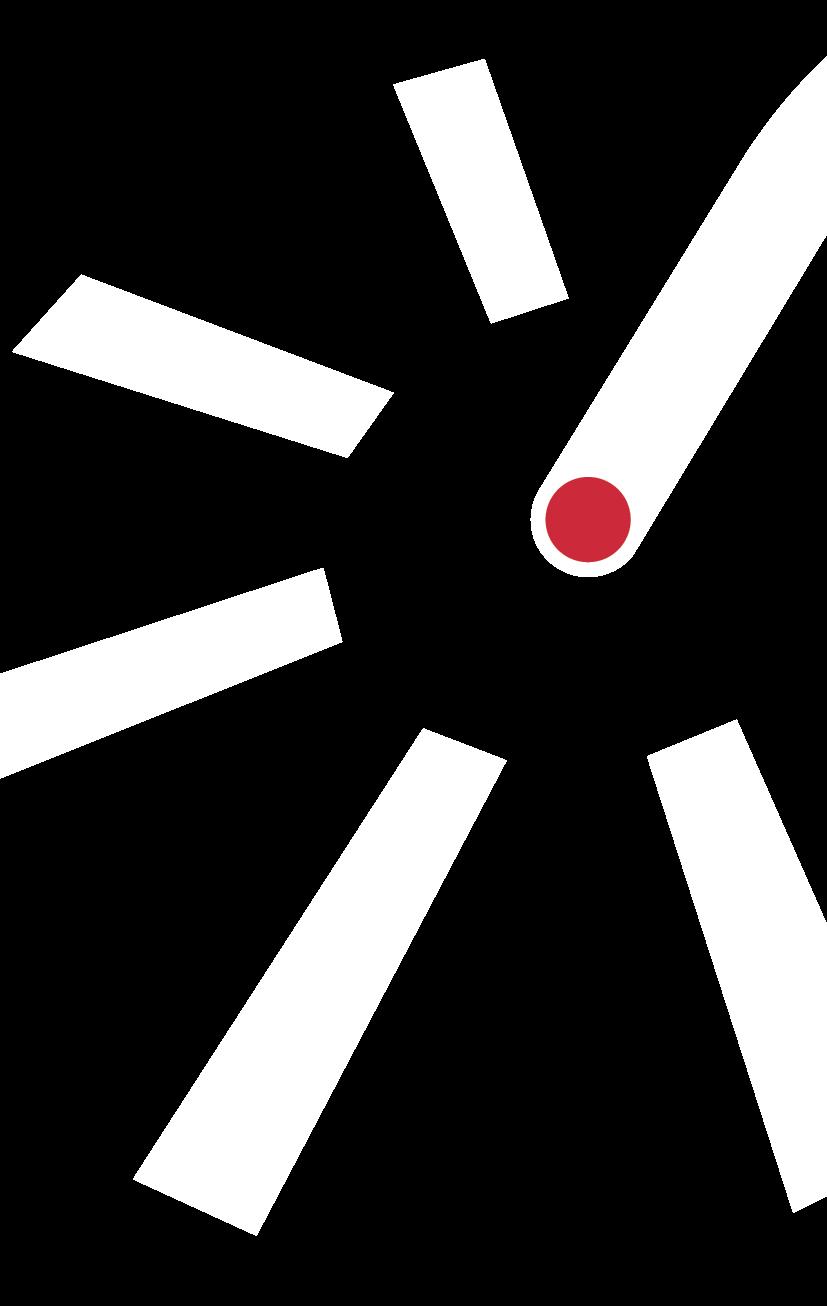
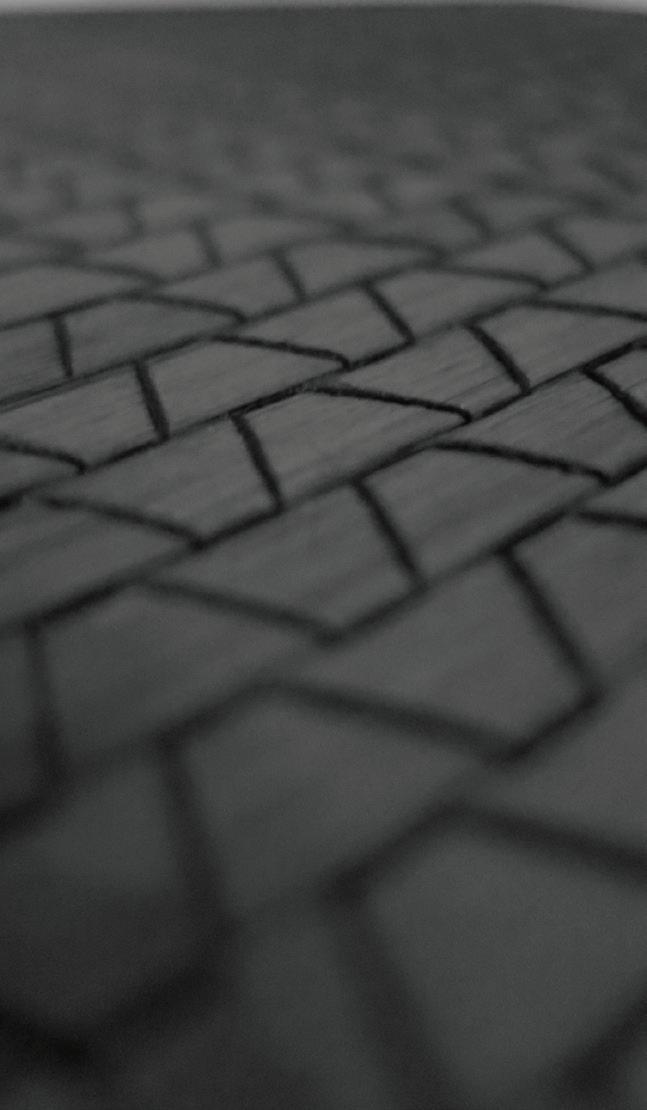
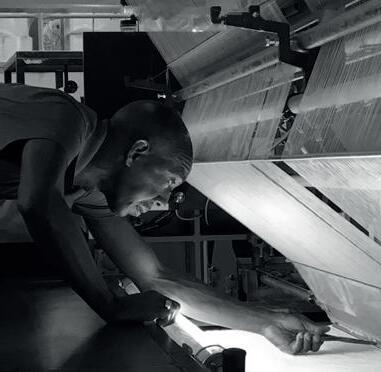
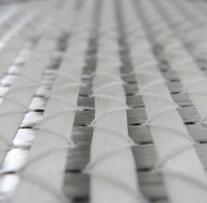
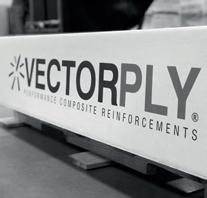
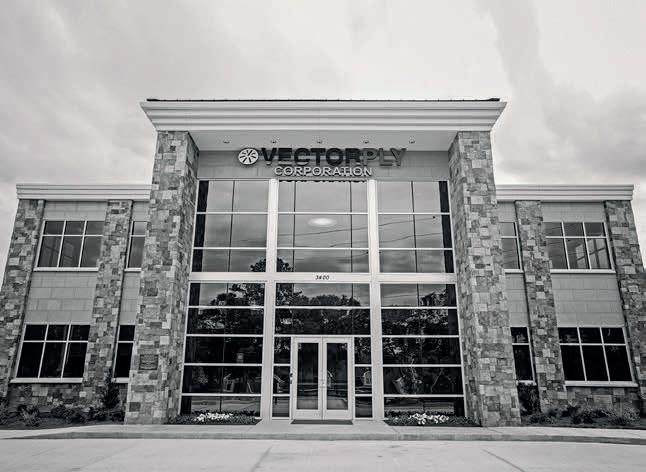
V FRAMES manufactures e-bike frames on water-assisted injection molding machines such as this one.
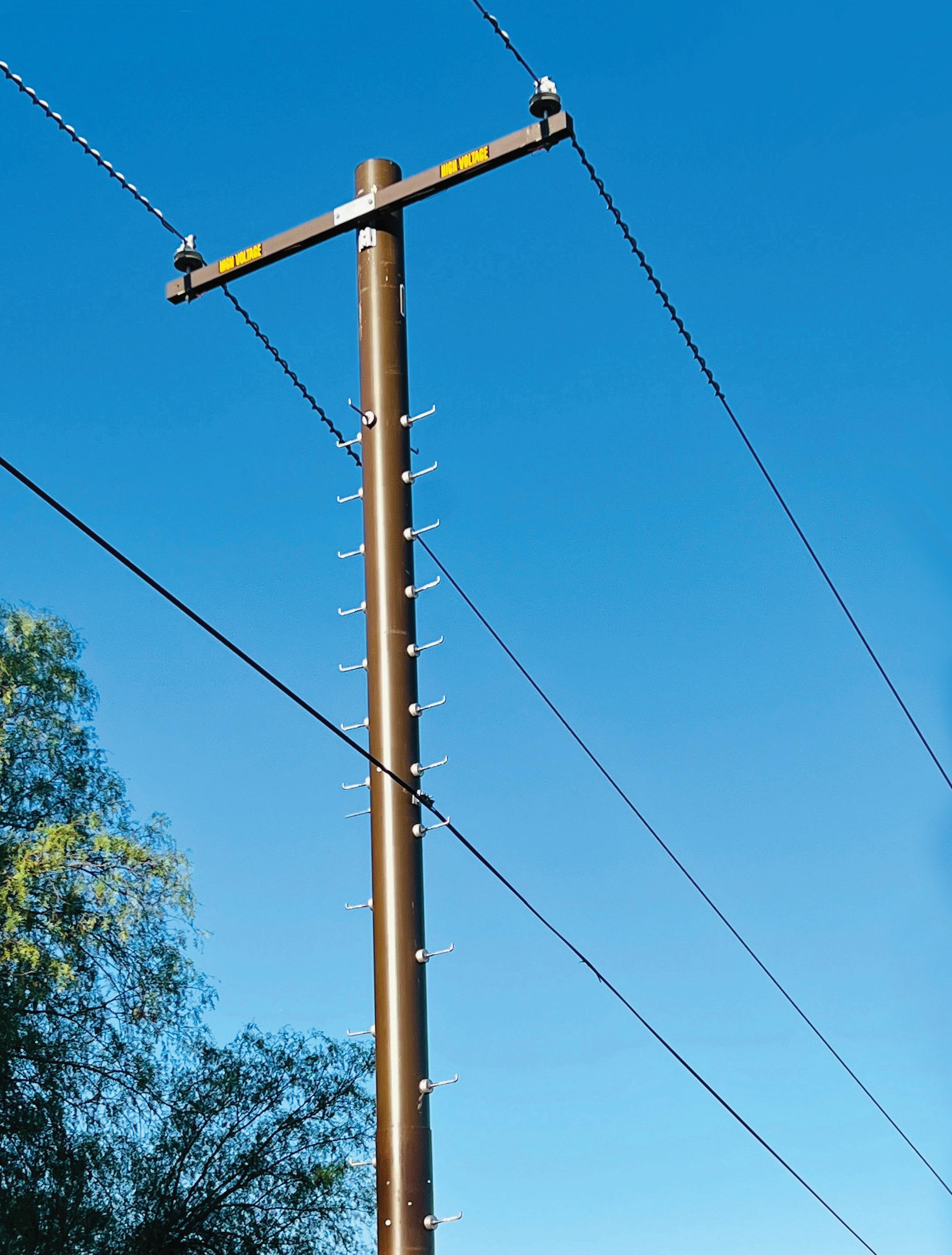
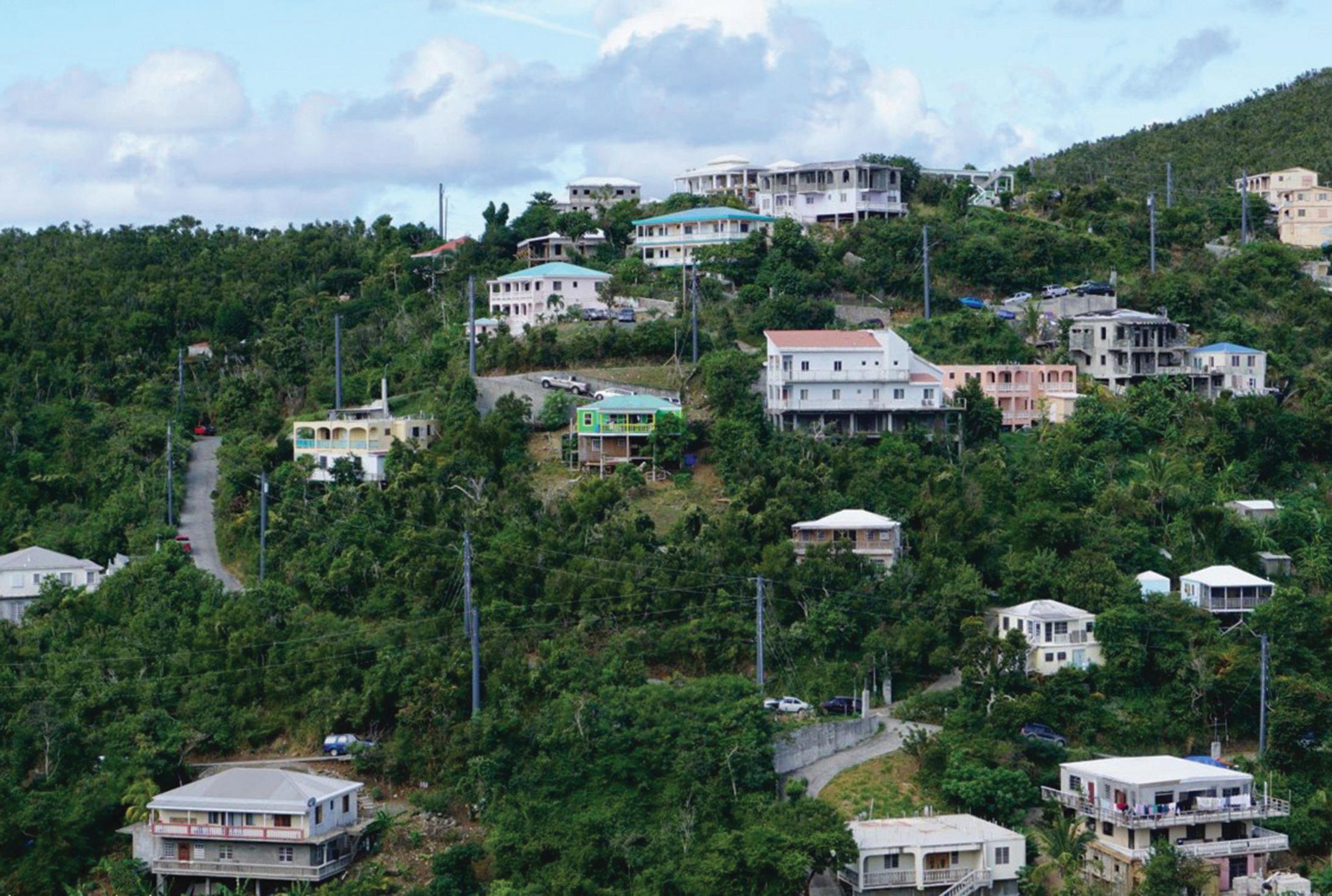
AFTER BACK-TO-BACK hurricanes took out the power grid in the U.S. Virgin Islands, the electric utility company improved resiliency by replacing broken wood poles, like those shown inset, with FRP poles.
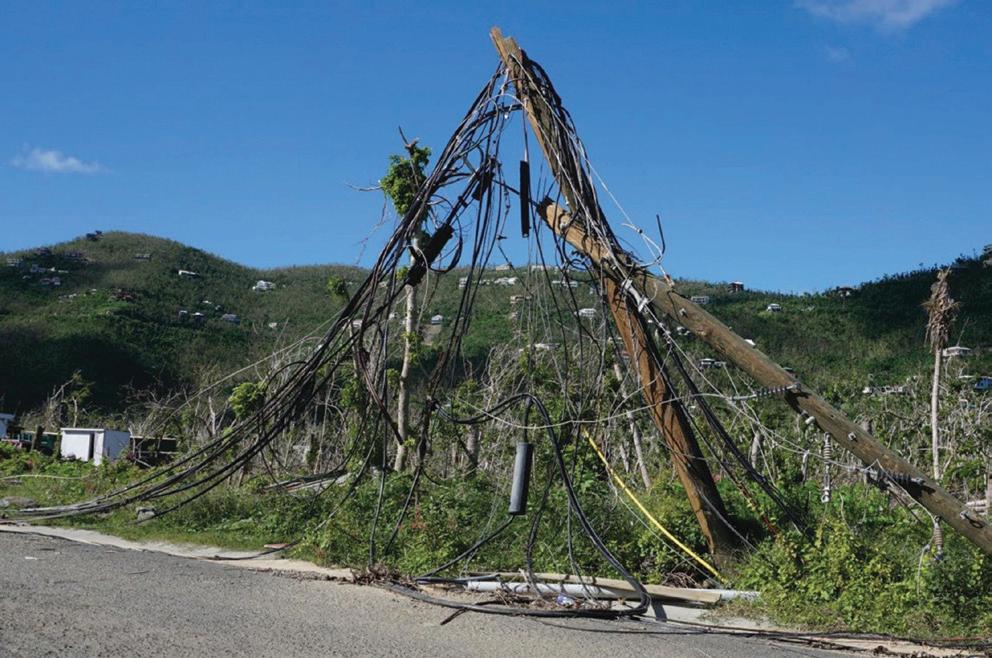
Strengthening the Power Grid
Composite poles and crossbars keep distribution and transmission lines up and operating under difficult conditions.
By Mary Lou Jay
THE U.S. POWER GRID is straining under the triple burden of increased demand, aging infrastructure and severe weather. Between 2011 and 2021, the country’s utility companies experienced 64% more major power outages than they had in the previous 10 years. The nonprofit Climate Central reports that 80% of those outages were caused by winter storms, hurricanes, tornadoes, wildfires and extreme heat.
Hardening and strengthening the grid is now a top priority for power providers and the federal government. The composites industry is part of the solution, providing FRP utility poles and crossarms that withstand weather events that routinely take out wooden ones.
Photo Credit: RS Technologies
Weather Tested
Composite electric poles have been around since the 1960s, but for years had only a small market share. During the last decade they have gained popularity because of technological improvements, as well as recognition among power companies of their effectiveness in reducing weather-related outages.
“Southern California Edison (SCE), the major electric utility in Southern California, went through a series of wildfires about six to seven years ago. They didn’t previously have any robust wildfire mitigation plans; however, subsequent to those wildfires, SCE developed an industryleading mitigation plan that has been successful in minimizing adverse effects of wildfires on its system,” says Clinton Char, formerly with SCE and now transmission engineering manager at E|2 Consulting Engineers.
Working with composites manufacturer RS Technologies, SCE tested different materials to determine which would have the best chance of surviving high temperatures and high winds. The utility chose FRP poles with a wraparound FRP shield, which protects the integrity of the pole itself. SCE has already installed thousands of composite poles in high-risk areas and will continue to use them to replace wood poles where necessary.
In May 2024, almost a million CenterPoint Energy customers in greater Houston lost power after derecho winds of more than 100 mph blasted through the area. In a LinkedIn post, Jason Ryan, CenterPoint’s executive vice president for regulatory services & government affairs, noted that the FRP poles the company had previously installed remained standing while wood poles did not. CenterPoint is now replacing hundreds of wood poles in this area with composite poles to avoid future outages.
In 2017, two major hurricanes took out most of the power grid in the U.S. Virgin Islands. In the following months, the territory’s Water and Power Authority (WAPA) convinced the Federal Emergency Management Agency (FEMA) to waive its usual “like for like” replacement policy, which enabled the utility to install approximately 9,000 more resilient FRP poles in place of wood poles. The composite poles have withstood other storms, meeting WAPA’s goal of providing residential customers and businesses a more dependable and resilient power supply.
Other utilities are taking notice. Scott Holmes, CTO of RS Technologies, says that some power companies hope to install FRP poles in their grids with money from the U.S. Department of Energy’s Grid Resilience and Innovative Partnerships (GRIP) program. The goal of the $10.5 billion program, funded as part of the Bipartisan Infrastructure Act,
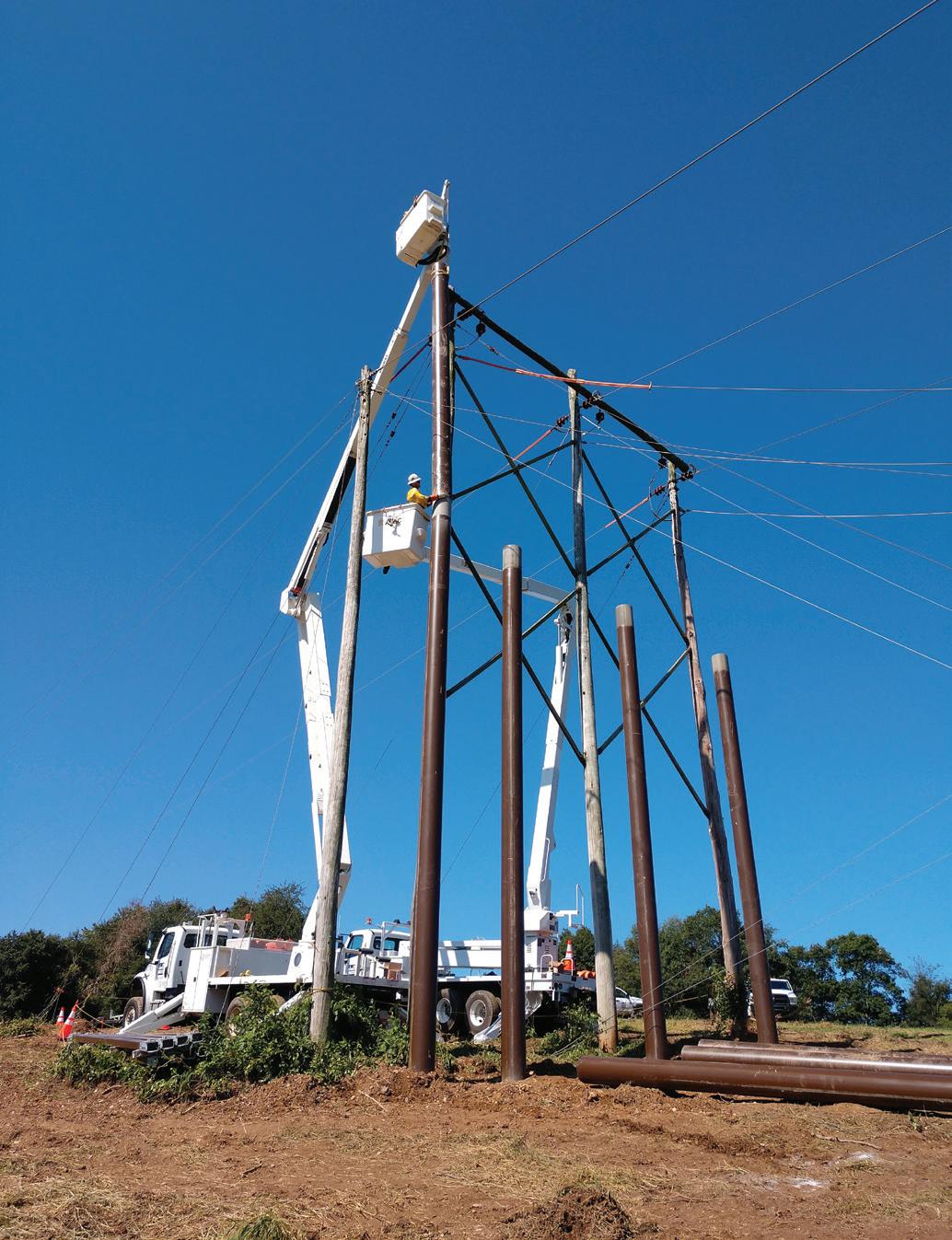
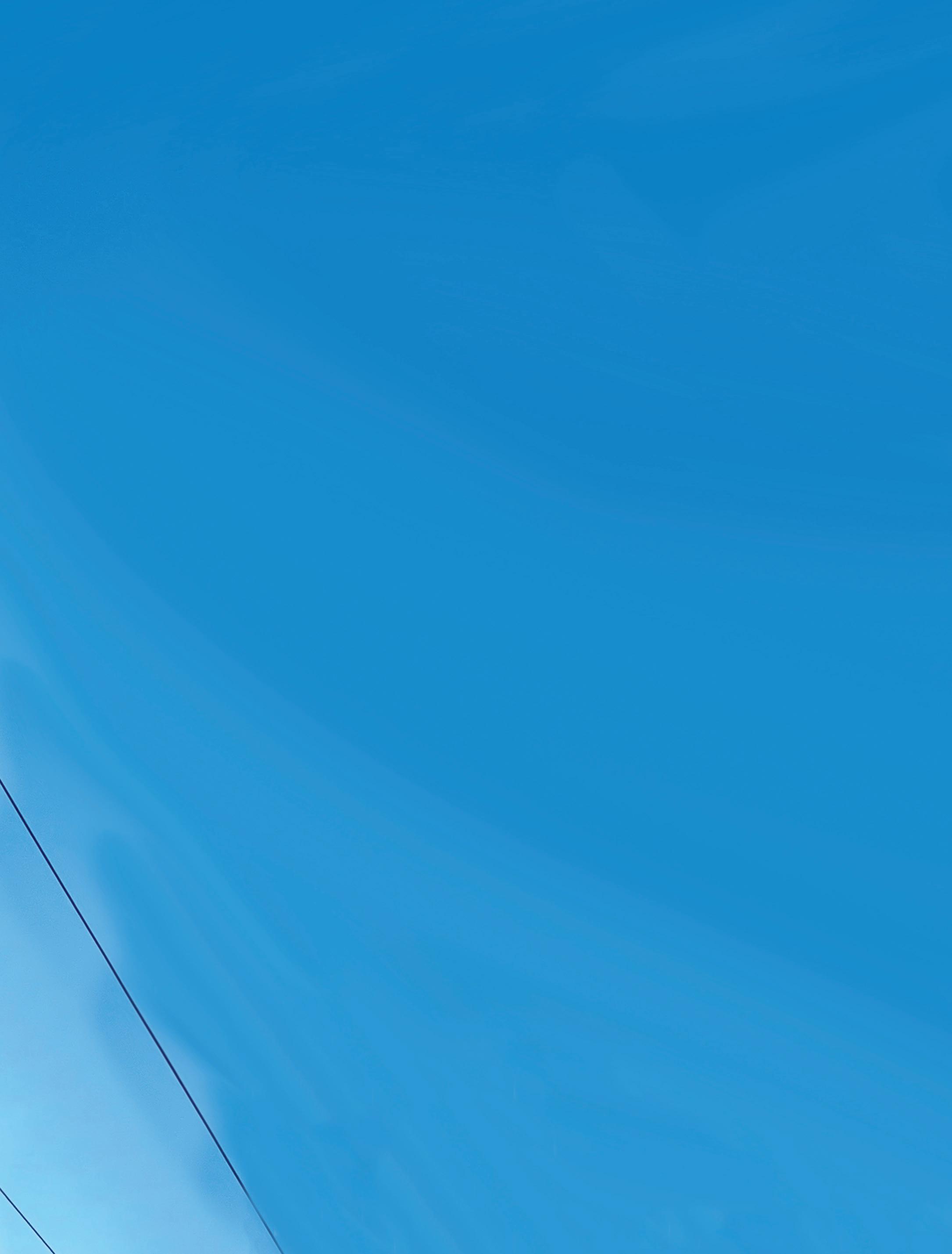
is to improve the resilience of the power system. On Nov. 14, 2023, the Biden Administration announced up to $3.9 billion available through a second round of funding for fiscal 2024 and 2025.
Composite Benefits
Composite utility products require minimal maintenance and are lightweight, reducing transportation and installation costs. FRP poles don’t attract insects or birds like woodpeckers, which can damage the structural integrity of wood poles.
Composite poles are inert, a big advantage over wood poles treated with preservatives that can be dangerous to humans and the environment. “In Maine, if a pole is going to be within 75 feet of a water source, one utility automatically earmarks that pole as a composite so it won’t leach anything into the environment like a wood pole would,” says Dustin Troutman, chief sales officer for Creative Composites Group.
FRP poles and crossarms are resilient under a variety of conditions. During winter storms they can bear much heavier ice loads than wood poles. In high winds that snap wood poles, FRP poles are flexible enough to bend.
RS Technologies manufactures all its FRP electric poles with a self-extinguishing polyurethane formulation that helps prevent the spread of fire. But for areas prone to wildfire, the company developed
COMPOSITE TRANSMISSION POLES are designed to carry larger and heavier wires and equipment than distribution poles.
the RS Fire Shield™ to encapsulate the lower portion of the FRP pole. The Fire Shield creates a sacrificial thermal barrier that helps maintain the pole’s structural integrity during a fire.
FireStrong™ power poles from Creative Composites Group are also built with an insulating FRP sleeve. “Once the temperature gets above 400 degrees, a chemical reaction takes place, and the sleeve will start to char and release some moisture. It actually cools the pole itself,” says Troutman. After a fire, utility crews can check the pole’s four temperature labels to determine the maximum temperature to which it was exposed. That enables utilities to determine if the pole retains enough strength to continue in service.
Horizontal crossarms on utility poles decay faster than poles because moisture accumulates on them and because their surface area is more exposed to the sun. Composite crossarms can alleviate those problems.
“One of the benefits of composites is that we can look at the material solution,” says John Higgins, CEO, RS Technologies. FRP crossarms designed with hydrophobic surfaces shed water and contaminants like road salt; UV-resistant resins in FRP crossarms provide additional protection from the sun.
Increasing Market Share
Although the price of composite poles has come down, they still cost two to four times as much as wood poles. But with the power industry’s increased focus on sustainability, composite pole manufacturers can make the case for their long-term cost effectiveness. Some utilities limit costs by replacing every fifth wood pole with a composite pole to reduce cascading failures. Others save money by using FRP poles when they need to handle heavy switches and other electric equipment.
Composite poles do face competition from concrete, steel and iron poles. But heavy concrete poles are harder and more expensive to transport, limiting their range, and steel and iron poles have long lead times. Wood poles may be in short supply as well. Electric companies want sturdier, largerdiameter poles to improve grid resiliency, and it takes longer for trees to reach this size. In addition, poles built from newer wood are often not as strong as those made decades ago with old-forest trees.
Composite pole manufacturers have responded to growing interest in their products by ramping up production. Last year, RS Technologies opened a new 400,000-square-foot pole and crossarm production facility in Houston. With this facility, the company was able to preposition product in Texas, so poles were readily available when CenterPoint needed them for storm remediation.
Creative Composites recently expanded its telecommunications and transmissions product line
and now offers poles with diameters ranging from 8 to 18 inches. “This enables FRP poles to be installed in broader applications while offering more sustainable, resilient solutions,” says Troutman.
To grow composites’ market share, the industry needs to continue to help develop codes and standards for these products and to promote case studies that communicate their successful deployment, Troutman says.
“We need more compelling evidence from utilities and their research partners that describe their experiences of FRP poles as compared to wood poles in hurricanes and other major weather-related events,” he says. “We also need to focus more on the installer, and to continue to develop how-to training programs so that linemen are familiar with our products when they finish school.”
Utility companies know that keeping the power on isn’t simply a matter of convenience; it’s vital to people’s health and to a region’s economy. FRP poles and crossarms can be key to maintaining that steady electric supply.
“There are absolutely places on the system where it just makes sense to use wood poles,” says Higgins. “But FRP poles are an excellent choice where you have critical circuits, where you have the real risk of weather-related disruptions, be that fire, storm, woodpeckers or other naturally induced disruptions. There are places where you want to be able to put in a pole and not have to go back and touch it again for a long time.”
CM
Mary Lou Jay is a freelance writer based in Timonium, Md. Email comments to mljay@comcast.net.
Setting New Standards
In 2019, ACMA released the NSI/ACMA Standard Specification for Fiber Reinforced Polymer Composites Utility Poles. Developed by ACMA’s Utility & Communications Structures Council, the standard covers the manufacturing, assembly and installation of FRP poles.
ACMA’s Utility & Communications Structures Council is currently undertaking the five-year, ANSI-mandated review of the standards. “The committee is working on upgrading the standards to do more to address resiliency, environmental sustainability and safety relative to handling and installing FRP utility poles,” says John Busel, vice president of ACMA’s Composites Growth Initiative. “It will present a major upgrade to the previous standard.”
After sending out the draft FRP utility pole standard for review by end users, asset owners, manufacturers, academics and suppliers, the ACMA committee will determine what edits to make. Busel says the committee hopes to publish the updated standards in about a year.
The committee is also working on draft specifications for fiberglass crossarms for distribution utility structures.
SCREW HOLDING. Able to hold at high PSI. High structural properties.
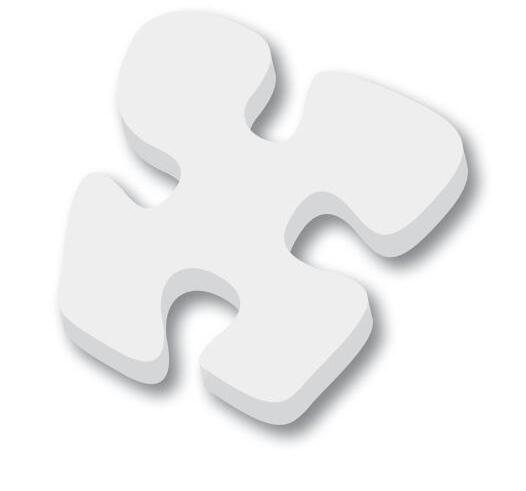

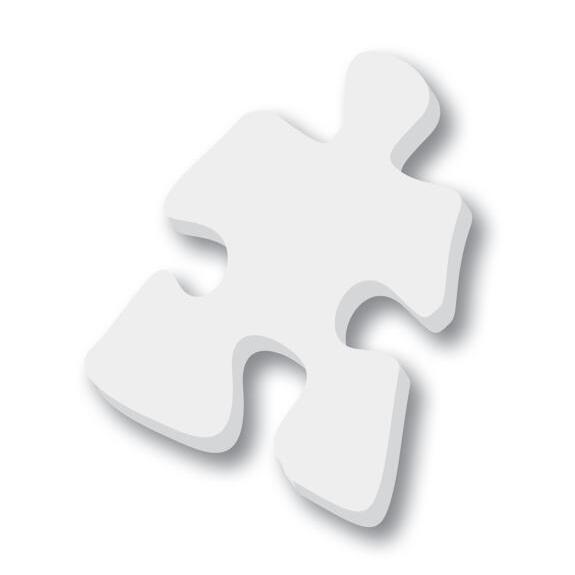
R VALUE. High insulation properties in a wide array of densities from 4 to 26-pound foam.
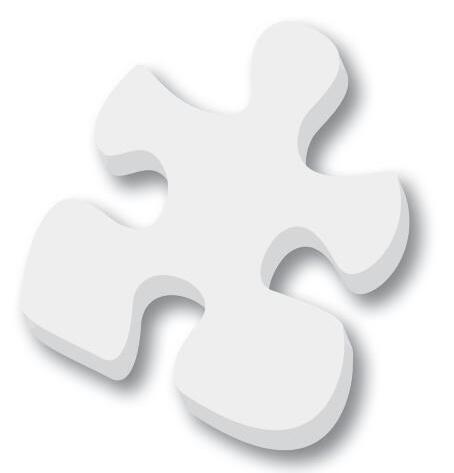
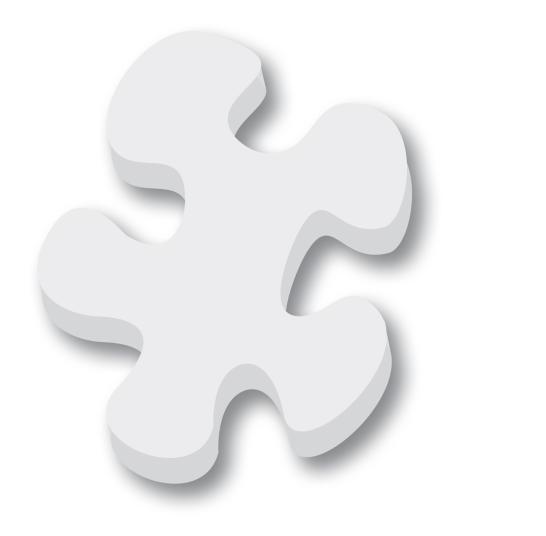
FIRE AND SMOKE PREVENTION.
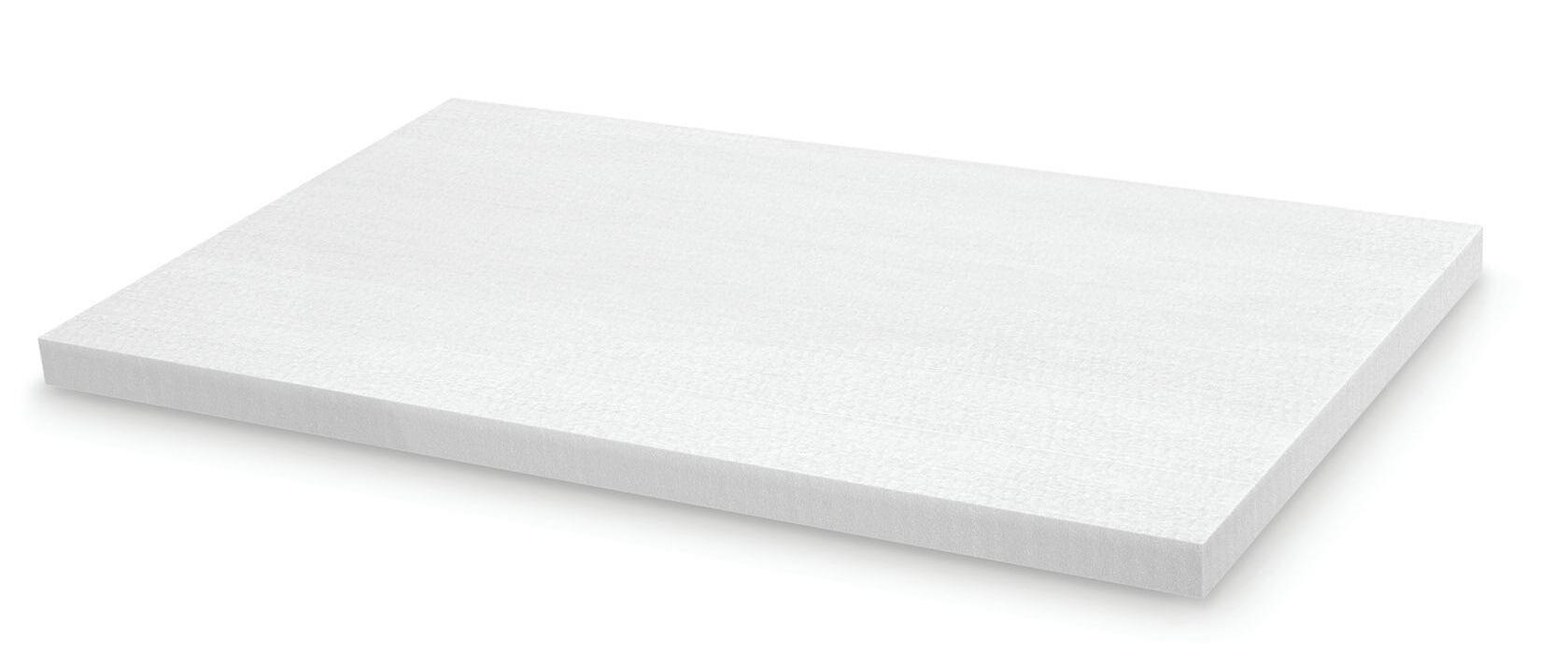
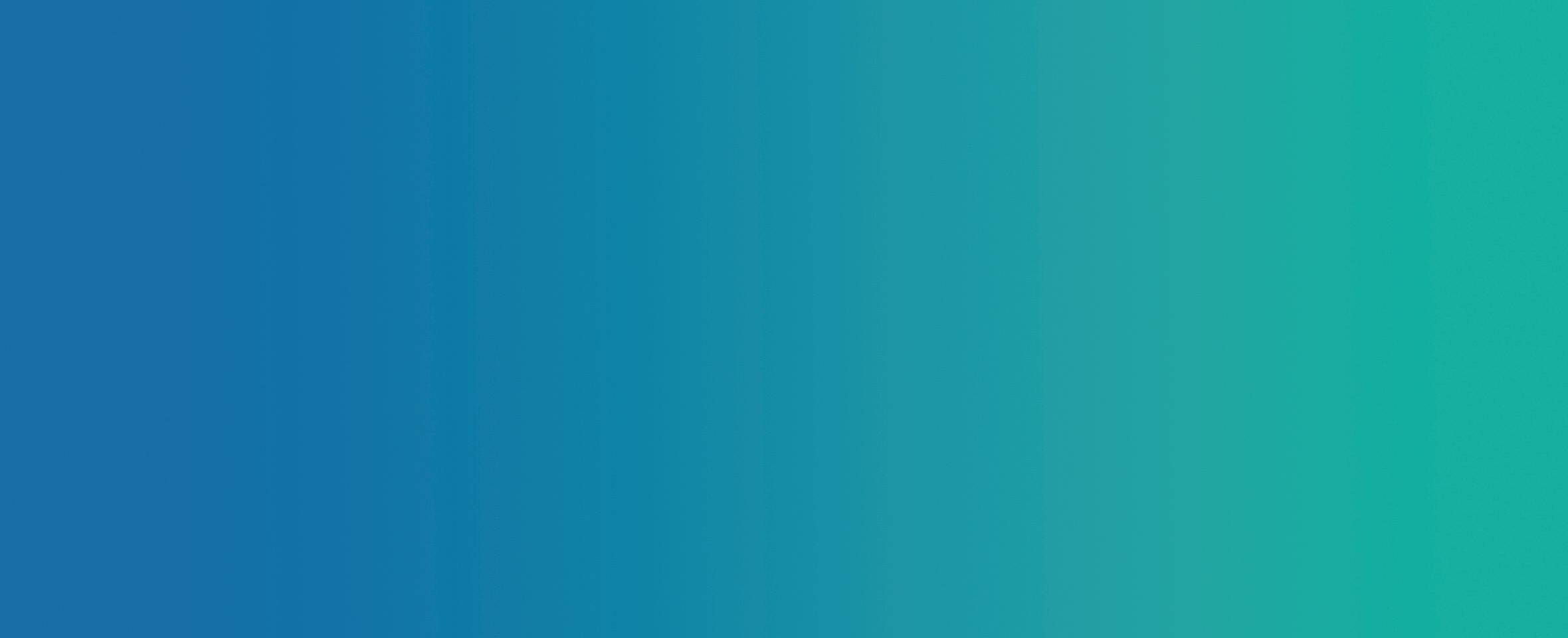
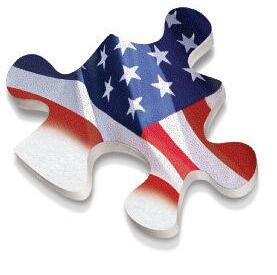
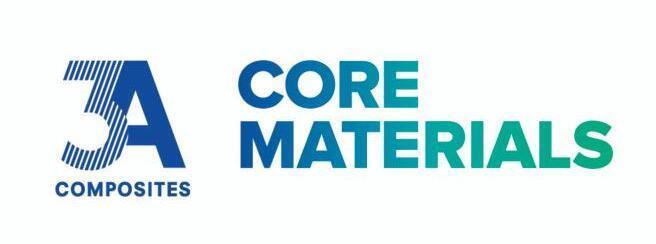
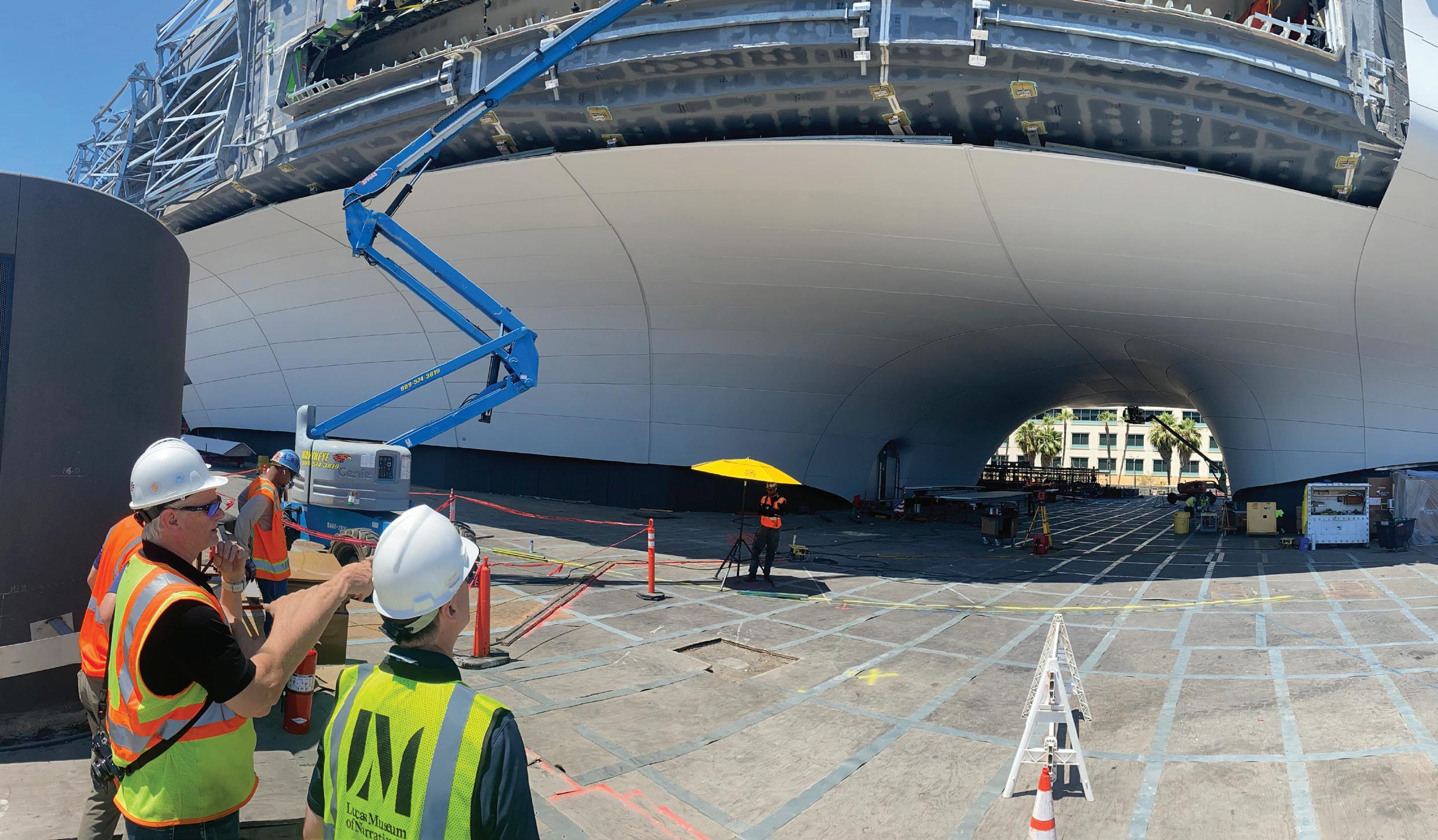
Building a Better Future
Sustainability initiatives in the infrastructure and construction markets aim to lower embodied carbon.
By Susan Keen Flynn
EARLY IN HIS ADMINISTRATION, President Biden launched the Federal Buy Clean Initiative to harness the nation’s purchasing power — more than $630 billion annually — while simultaneously investing in the country’s infrastructure. The initiative and the Buy Clean Task Force promote the use of low carbon, made in America construction materials.
“We are in the midst of a manufacturing boom here in America, and the Biden administration has made building the energy transition with American materials a top priority of that transition,” said John McAuliff, senior policy advisor for the Office of Clean Energy Innovation & Implementation at the White House, in his opening remarks at ACMA’s Composites Sustainability Today event in June. “The work you do this week and into the future will make a difference for your customers and our country.”
Composites Sustainability Today provided insight on how companies — and the composites industry as
a whole — can embrace the sustainability movement. The infrastructure and construction markets are front and center in this movement. The Inflation Reduction Act has six sections that address embodied carbon of construction materials, including:
• $100 million for the Environmental Protection Agency (EPA) to develop its Label Program for Low Embodied Carbon Construction Materials.
• $250 million to the EPA to create environmental product declarations (EPDs).
• $2 billion to the Department of Transportation (DOT) and Federal Highway Administration (FHWA) to reimburse and incentivize recipients for the use of construction materials and products with substantially lower embodied carbon.
“The sustainability movement is real and it’s significant,” says Gregory Nadeau, a former DOT/ FHWA administrator and publisher of the InfraTalk
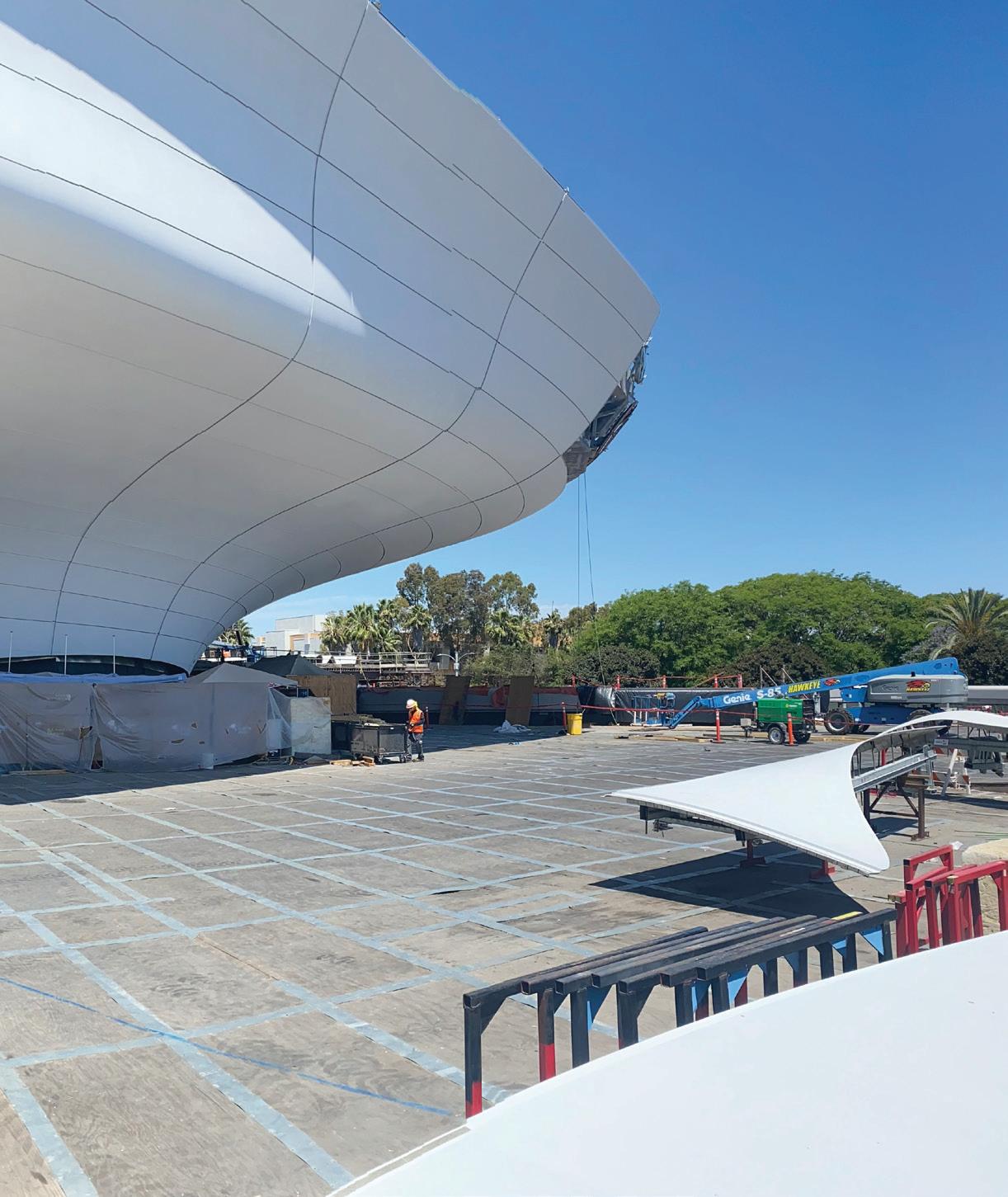
America multimedia platform. “Now is the time. We can’t continue to build infrastructure the way we have been when the opportunity to utilize newage technology that has been proven and tested is available to us.”
Making a Case for Composite Solutions
FRP is poised to help transform infrastructure and construction projects. ACMA and IACMI – The Composites Institute developed the CIRCLE Program to help composites manufacturers assess and reduce their cradle-to-gate environmental impacts and educate customers about the climate benefits of using composite products, of which there are many.
“FRP is clean energy enabling,” says Joe Fox, president of FX Consulting LLC and co-facilitator of IACMI’s Infrastructure & Construction Working Group. “FRP wind blades and towers facilitate sustainable wind energy on land and offshore.” Lightweight composites also require less energy to transport and install, a critical benefit for applications such as girders, rebar and bridge decks.
In addition, FRP can offer lifetime cost savings. “Durable FRP composites do not need to be repaired and replaced as frequently as other materials,” says
Fox. He cites the example of the Halls River Bridge construction in Homosassa, Fla., which used GFRP and CFRP in place of steel to reinforce the concrete. An article published in the journal Advances in Civil Engineering Materials in 2019 asserts that the bridge’s life cycle cost is 20% lower because of reduced maintenance and replacement costs associated with FRP materials.
Composites also contribute to decarbonization. “A life cycle assessment of the Halls River Bridge indicates the CO2 emissions are 26% lower with FRP than with steel,” says Fox.
These benefits should grab the attention of designers, engineers, contractors and owners within infrastructure and construction. But it will require education and marketing from the composites industry, something that Nadeau and Kirby Beegles, PE, SE, senior project engineer at Martin/Martin Inc., discussed during a panel discussion at Composites Sustainability Today.
Going After Government Projects
Nadeau is on a mission to unlock the market potential for government-funded infrastructure projects. He believes the key to doing so is achieving buy-in from state DOTs.
“The decision-making about what materials to use, what contract mechanisms to employ, whether or not to advance and accelerate the deployment of solutions — those decisions occur in 52 institutions across the country,” says Nadeau. “The federal role is to provide resources and incentives to be innovative, while the states principally deploy the FHWA programs at the local level.”
Approximately 650,000 bridges — half of the country’s inventory — are owned by local and county government, which have chronically underfunded maintenance programs, says Nadeau. “The operational reality is that when a steel bridge that’s rated to last 75 years hits about 35 or 40 years, we’re making a decision to replace it or spend more money maintaining it to last another 10 or 15 years,” he says. “The latter is a bad idea compared to building a new bridge with new materials that will last longer.”
Convincing local and county governments, as well as the engineers and contractors they work with, to consider FRP products first requires the backing of state DOTs. “Local governments are loathe to use materials that a state DOT has not blessed, sanctioned or adopted guidelines or specifications for,” says Nadeau.
He encourages the composites industry to campaign to DOTs in all 50 states, the District of
THE LUCAS MUSEUM of Narrative Arts, scheduled for completion in 2025, features FRP exterior cladding panels manufactured by Kreysler & Associates.
Photo Credit: Kreysler & Associates

Columbia and Puerto Rico to make a commitment to advanced materials. Sustainability is critical to that campaign.
“A bridge or structure built using non-corroding advanced materials would be a generational bridge,” says Nadeau. A durable bridge featuring FRP components that require minimal maintenance could become a cost-saving asset to the community, rather than a cost burden, he adds.
“If we can persuade state DOTs to incorporate FRP composites in their structures program, it’s like the Good Housekeeping Seal of approval for engineering services that go way beyond transportation infrastructure,” says Nadeau.
Targeting the Private Sector
Making the argument for a sustainable design in private construction requires buy-in from asset owners, which can be challenging.
“Some owners are very progressive and forwardthinking. For others, it’s strictly a business decision,” says Beegles. “They are not typically going to spend money on something that doesn’t bring any tangible value to them for that specific product.”
Engineers at Martin/Martin educate clients and asset owners on the importance of sustainable design and how to achieve it in their buildings. They are part of the Structural Engineering Institute’s SE 2050 Commitment.
“Data shows that about 37% of global warming emissions come from the building industry, and we think about 11% of that comes from the structural systems in buildings,” says Beegles. “We have voluntarily committed to reducing or eliminating embodied carbon in our designs by 2050.”
There are four components to the SE 2050 program: education, engagement, advocacy and reporting. For the latter, the Structural Engineering Institute collects data on embodied carbon impacts and trends on structural systems throughout the country. Martin/Martin reported on a handful of projects this year and plans to ramp up its reporting efforts.
“We perform a whole building life cycle analysis, taking all the components that go into a building’s structural system and evaluating what their global warming potential is based on the volume or weight of the material,” says Beegles.
THIS 80-FOOT-LONG truss bridge was installed in 2023 on the Morton Complex Perimeter Trail in Upper Saint Clair Township, Pa. It features Creative Composites Group’s SuperDeck® Lite FRP decking to meet H-5 loading and matching FRP handrailing.
Composite products can play a pivotal role in the move toward sustainability. Martin/Martin worked on the San Francisco Museum of Modern Art, which features 700 FRP exterior cladding panels designed and manufactured by Kreysler & Associates. Earlier this year, the composites manufacturer teamed up with ACMA and environmental consultancy Sustainable Solutions Corp. to develop a life cycle analysis and environmental product declaration for its composite panels. (Composites Manufacturing magazine featured an article on this process and other work by ACMA in its spring 2024 issue.)
“We love composite panels,” says Beegles. “The benefits that are really meaningful to what we do are the durability, the light weight and the long-term life cycle so the materials can withstand lots of elements for many years.”
Digging into the Data
Touting the benefits of FRP products isn’t enough for customers in the infrastructure and construction markets. They seek data to support claims of a product’s sustainability.
“For the government sector, it’s all about data, data, data,” says Nadeau. “The civil engineering community needs numbers to plug into their
What Is Embodied Carbon?
There’s lots of talk about reducing the embodied carbon of buildings and other structures, which represents a substantial percentage of global emissions. So, what is it?
Embodied carbon is the carbon dioxide or other greenhouse gas emissions, such as methane and nitric oxide, associated with the manufacture, transportation, installation, use, maintenance and disposal of materials or components used to construct a building or other structures. By contrast, operational carbon is the greenhouse gas emissions associated with the occupancy of a building, such as its heating and cooling.
“The Inflation Reduction Act provided funds for programs by the EPA and other agencies to reduce the embodied carbon associated with construction materials,” says ACMA’s sustainability leader John Schweitzer. “To remain competitive in these markets, manufacturers will need to demonstrate that use of their products reduces the embodied carbon of the built environment.”
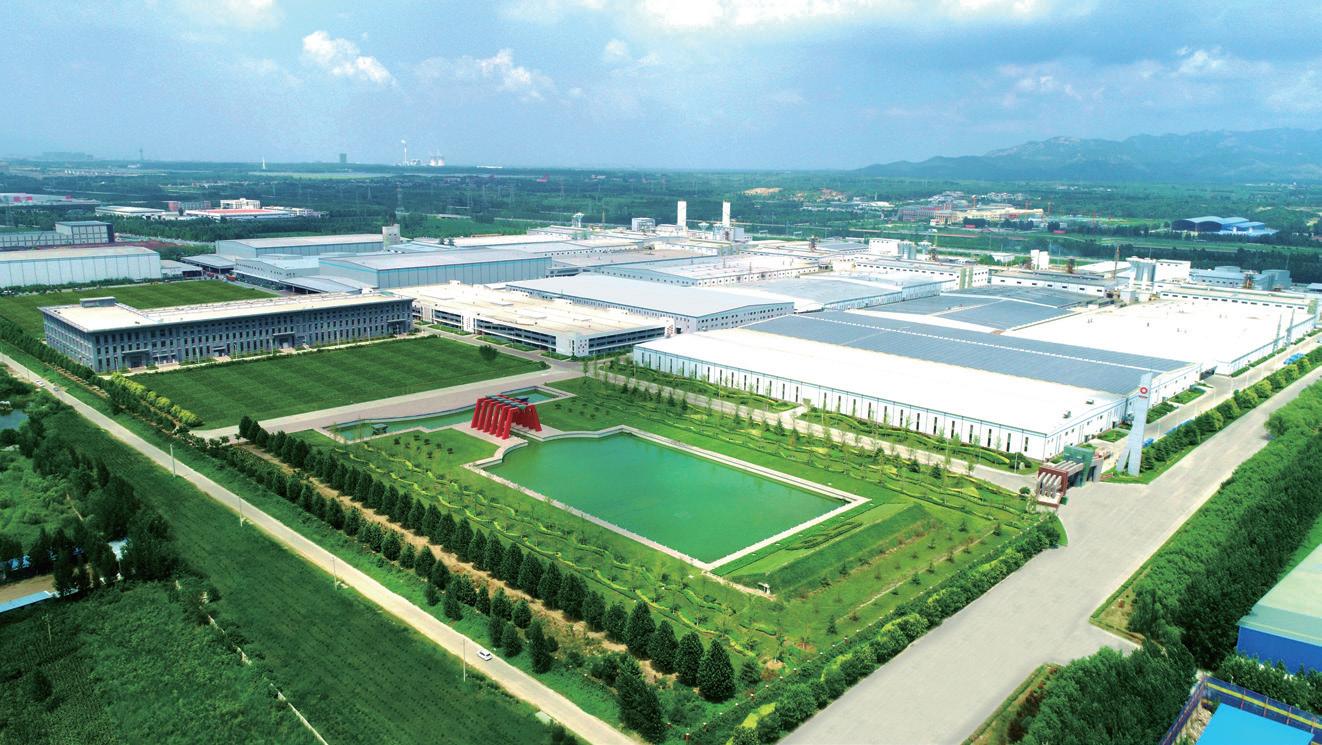
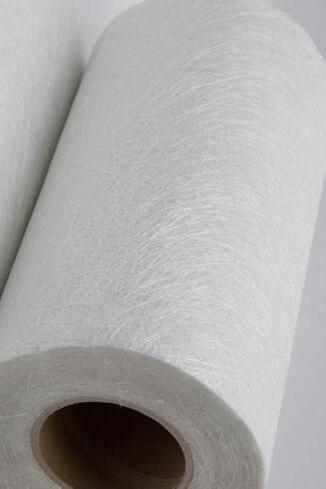
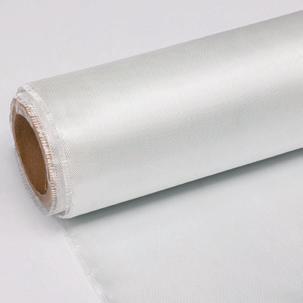
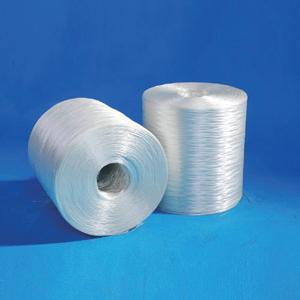
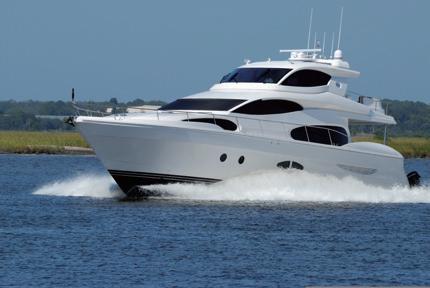
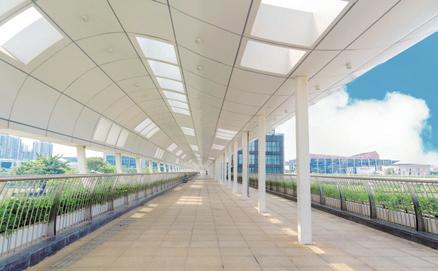
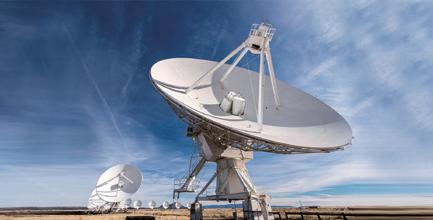
calculations. They need to depend on certifications and guide specifications, such as the one ACMA is driving with the American Association of State Highway and Transportation Officials (AASHTO).”
ACMA and its Transportation Structures Council collaborated with AASHTO’s Committee on Bridges and Structures to develop guide specifications for designing FRP pedestrian bridges. The second edition, renamed the LRFD Guide Specifications for the Design of FRP Pedestrian Bridges, was approved by state DOT bridge engineers in June.
Clients in the private sector are equally interested in data to comply with increasing legislation, as well as meet their own sustainability goals.
“Our building owners are asking, ‘Can you give me data to show exactly how much impact my building system has? Can you compare for me the decision I make to spend more money on a panel, finish or structural system that has a lower embodied carbon impact?’” says Beegles. “They want to be able to show that what they did made a difference.”
As engineering firms like Martin/Martin strive to offer more sustainable solutions – and contribute data to the SE 2050 Commitment database and others like it having transparent data to back up a product’s sustainability will be essential. The CIRCLE Program
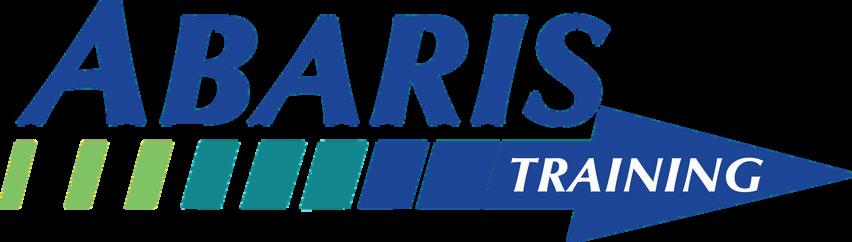
COMPOSITES ADVANCED TRAINING
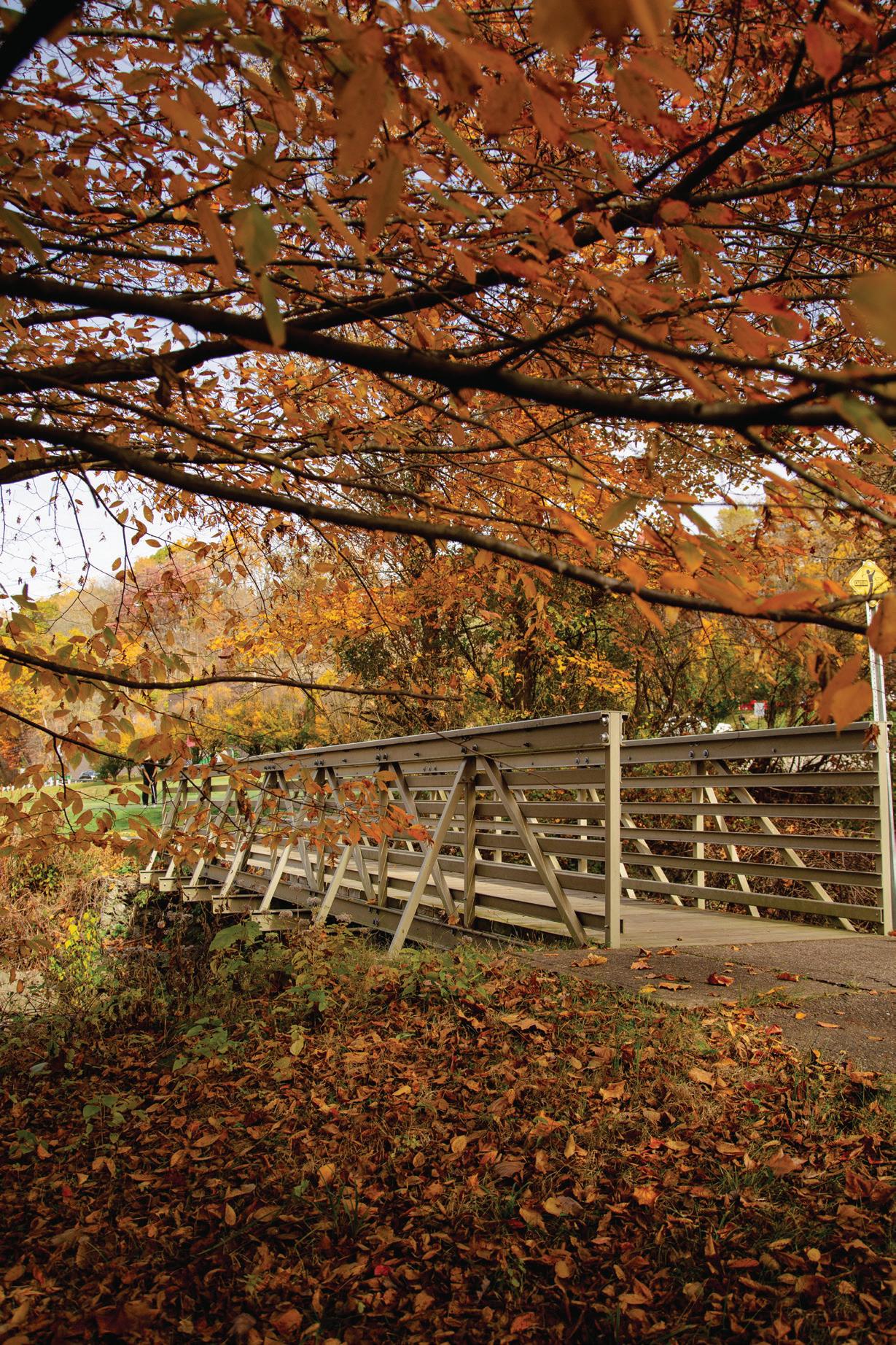
will help ACMA members generate that through its soon-to-be-released LCA-to-EPD generator.
“Having easy access to EPDs for your products is crucial for us as designers to be able to communicate to asset owners, architects and contractors the specific sustainable metrics associated with FRP panels and other composite products,” says Beegles.
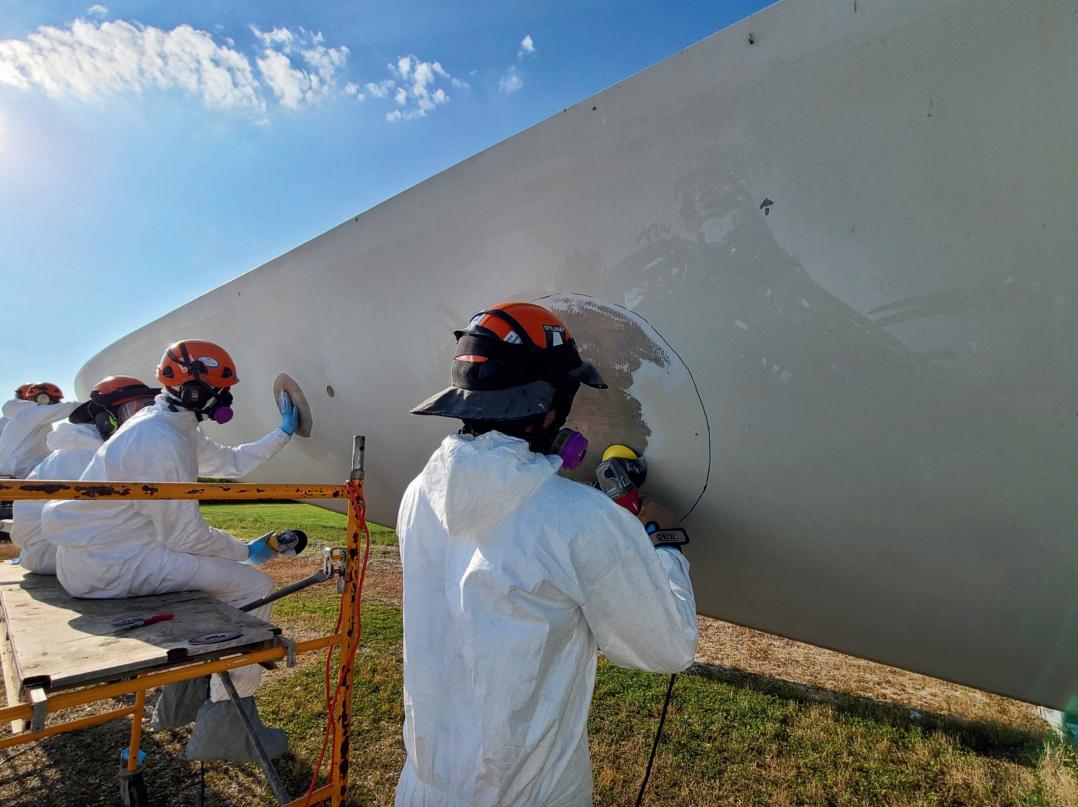
While data matters, the environmental impact is the ultimate aim.
“We want to see everybody working toward the same goal, which is creating materials that have a lower embodied carbon footprint,” says Beegles. CM
Susan Keen Flynn is managing editor of Composites Manufacturing magazine. Email comments to sflynn@ keenconcepts.net.
THIS E.T. TECHTONICS modular fiberglass pedestrian bridge was installed in rural Pennsylvania.
Photo Credit: Creative Composites Group
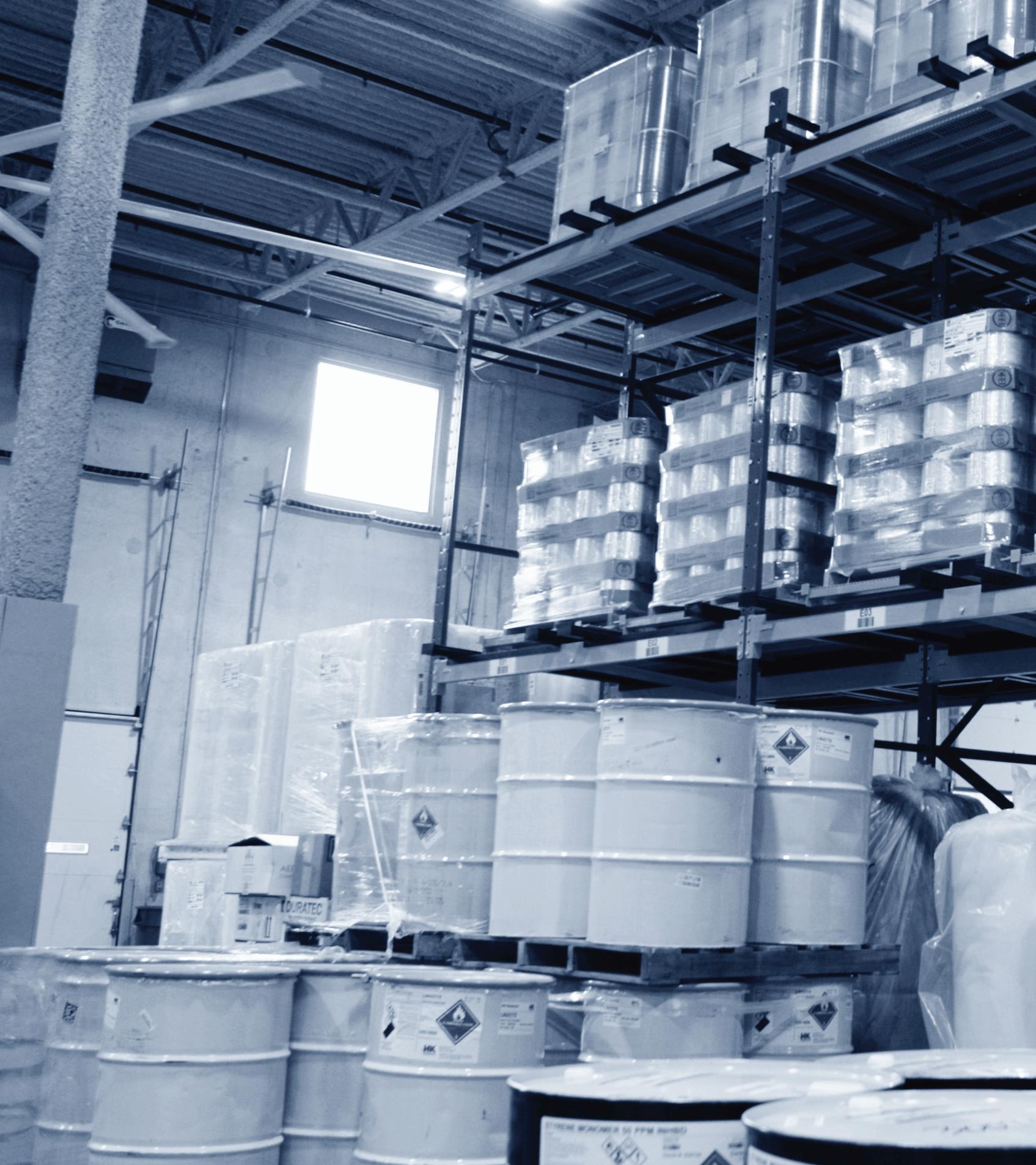
Innovative. Dependable. Results.
Why Choose Composites One?
• Extensive Inventory: Gain access to an unmatched range of high-quality composite materials and processing supplies.
• Expert Support: Access to material and process technical experts to help with efficient part manufacturing.
• Reliable Service: Ensuring the right product is in the right place at the right time.
• Unique Partnerships: Experience a partnership that’s designed to achieve your desired goals.
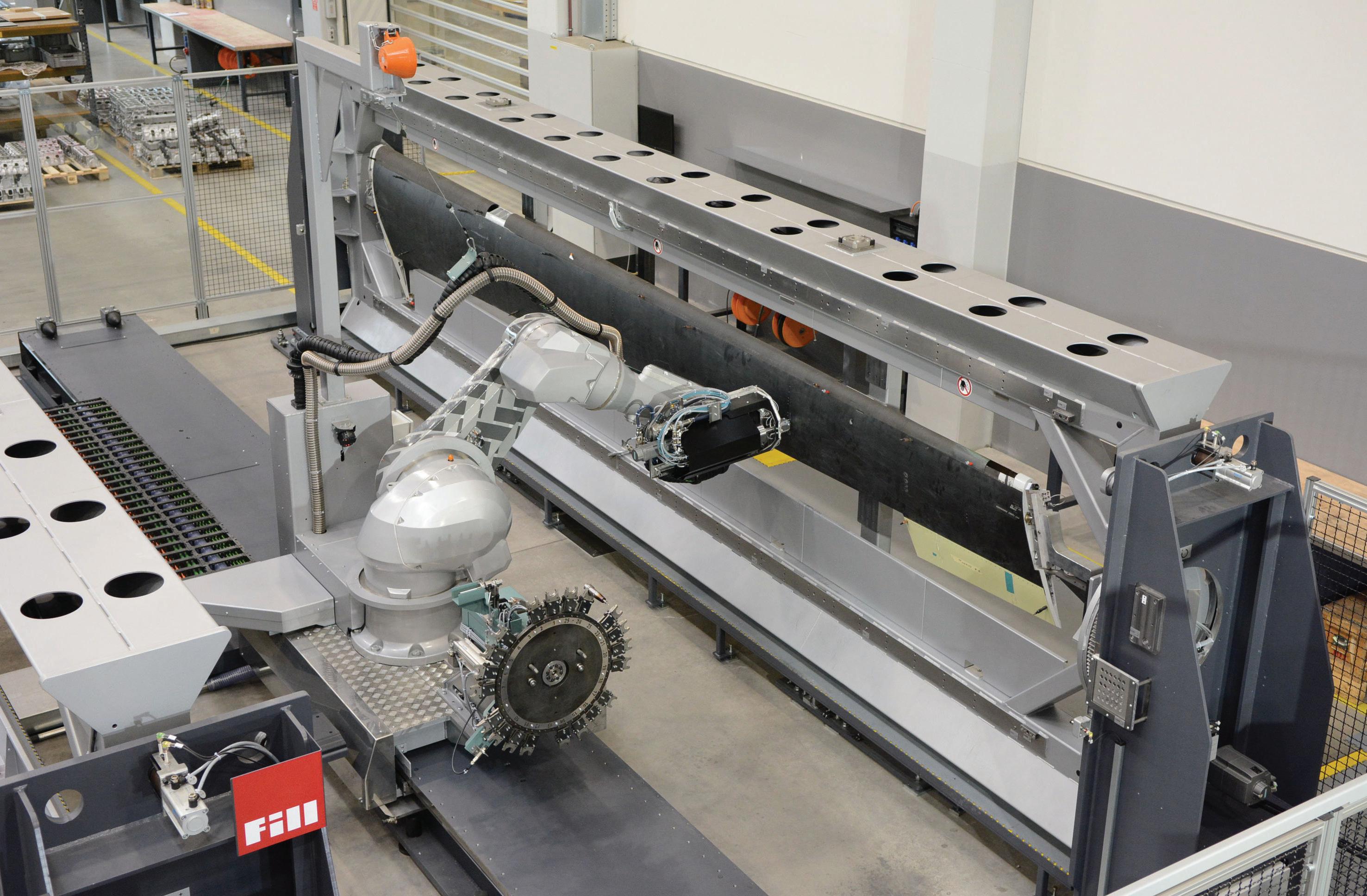
Robotics aim for the sky
Robots could help the aerospace industry achieve high-rate manufacturing goals.
By Susan Keen Flynn
THERE ARE NEARLY 26,000 aircraft in service worldwide, with aerospace OEMs anticipating more than 40,000 new passenger and cargo aircraft deliveries in the next 20 years. To meet that demand, current manufacturing rates will need to increase four to six times, according to Waruna Seneviratne, director of the Advanced Technologies Lab for Aerospace Systems at Wichita State University’s National Institute for Aviation Research (NIAR-ATLAS).
“Even with the most advanced automated equipment and technologies, it will be challenging to find enough trained technicians, engineers and designers to meet the high rates required by the aerospace industry,” says Seneviratne.
That’s where robotics come into play. A team at NIAR-ATLAS is working on a research project to demonstrate how technologies used for decades in high-rate automotive manufacturing could be used in aerospace. They are using hybrid overmolding to manufacture thermoplastic window plugs for cargo airplanes on a 450-ton Krauss Maffei injection molding machine equipped with two robotic cells.
“We can make a complete part every 90 seconds compared to two to three hours to machine the aluminum window plug it replaces,” says Senerviratne. And, thanks to automation and robotics, it only requires one person.
A Window of Opportunity
The thermoplastic window plug project represents a niche business in the aerospace industry –converting passenger planes into cargo haulers. Part of that process includes replacing acrylic windows with window plugs, currently made of aluminum.
Production of the demonstrator part at NIARATLAS begins with flat, oval-shaped organosheets made from VICTREX AE™ 250 low-melt PAEK that are heated in an infrared oven, then placed in a mold and thermoformed into the shape of the window plug. Afterward, they are injection molded with a PEEK material including approximately 30% chopped fiber.
The operation relies on two robots working simultaneously. The first robot places the blank organosheet in the oven, removes it once it’s
Photo Credit: Fiill
been heated and then puts it in the mold. After the overmolding is complete, the second robot removes the part from the mold and places it on a conveyor belt.
“While one robot pulls out the finished part, the other is transferring a new organosheet from a stack into the infrared oven,” says Seneviratne. “A bin at the end of the conveyor belt collects the finished parts that can then be picked up by a lab tech.”
Currently, the window plugs require surface preparation and painting. In the next phase of the project, NIAR-ATLAS hopes to add Krauss Maffei’s ColorForm technology to put polyurethane coating on the parts. The team is researching compatible materials.
In addition, the team is running thermal and mechanical testing on the thermoplastic window plugs to achieve FAA certification. When the certification paperwork is complete, Seneviratne is optimistic that the part will be integrated into the cargo plane conversion process. The advantages have caught the attention of aerospace OEMs.
“The thermoplastic window plug is 20% lighter than an aluminum one and faster and cheaper to produce,” he says. “While the mold is expensive, if you can make 40 parts in an hour — 300-plus parts a day — then you basically recover the entire cost of the mold within a few weeks.”
Applications Beyond Aerospace
While the ATLAS window plug project is a demonstrator, many commercial applications rely on
robotics. One example is front doors for houses.
“Instead of using wooden doors, one of our customers in the building industry makes door panels from fiber-reinforced composites via long fiber injection,” says Marc Perberschlager, general manager of Fill USA Inc., a machine engineering company. “They use Krauss Maffei and Fill technology to produce them at a high rate.”
WILL ROBOTS REPLACE WORKERS?
Robotic cells are taking over jobs in manufacturing plants, but that doesn’t mean employees on the plant floor are becoming obsolete.
“People sometimes tell us, ‘Your robots will take our jobs away.’ But it’s quite the opposite,” asserts Waruna Seneviratne, director at the ATLAS Lab at Wichita State University’s National Institute for Aviation Research. He notes that aerospace manufacturers can boost production significantly using automated equipment and robots — and create opportunities for workers.
“Instead of making five parts a month, now I’m making 20 parts a month,” says Seneviratne. “People still need to add the necessary wiring and electronics, paint the parts and so on. Now I need to find four times more employees to do those jobs.”
Andrew Pokelwaldt, owner of consultancy AWALDT LLC, adds that strategic use of robotics can improve job satisfaction and retention by freeing up employees to work on more meaningful tasks.
“When your hourly employees aren’t burdened with repetitive tasks that bore them, they can move on to things that bring value to your business,” he says. “This gives them a chance to focus on continuous improvement processes, quality assurance and other important areas.”
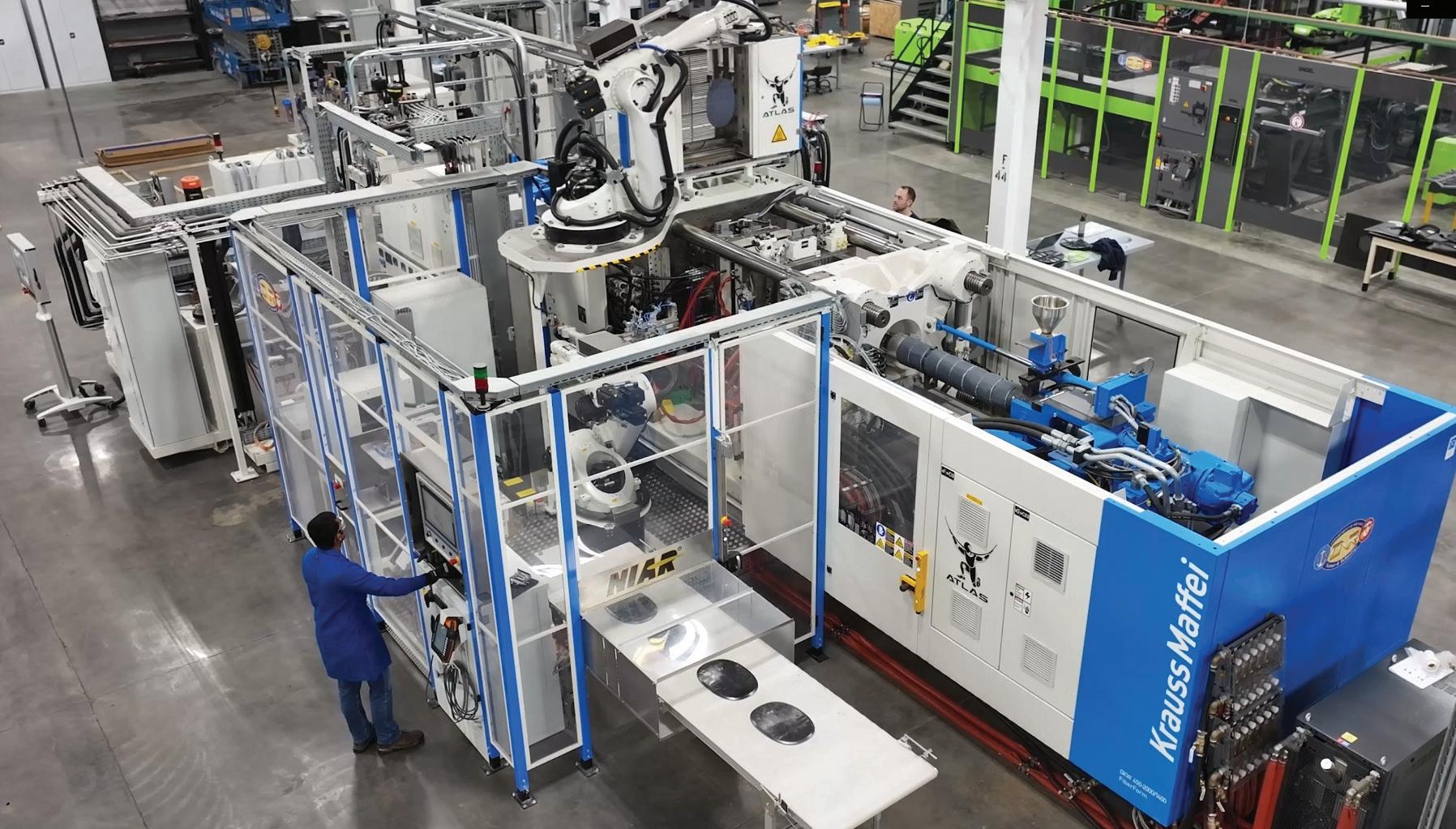
THE NATIONAL INSTITUTE for Aviation Research’s ATLAS lab can manufacture thermoplastic window plugs in 90 seconds on its Krauss Maffei injection molding machine equipped with two robotic cells. Photo
THE GRAYMATTER Scan&Sand™ system can sand a part up to four times faster than humans and catches more than 95% of sanding dust to enhance worker safety, according to the company.
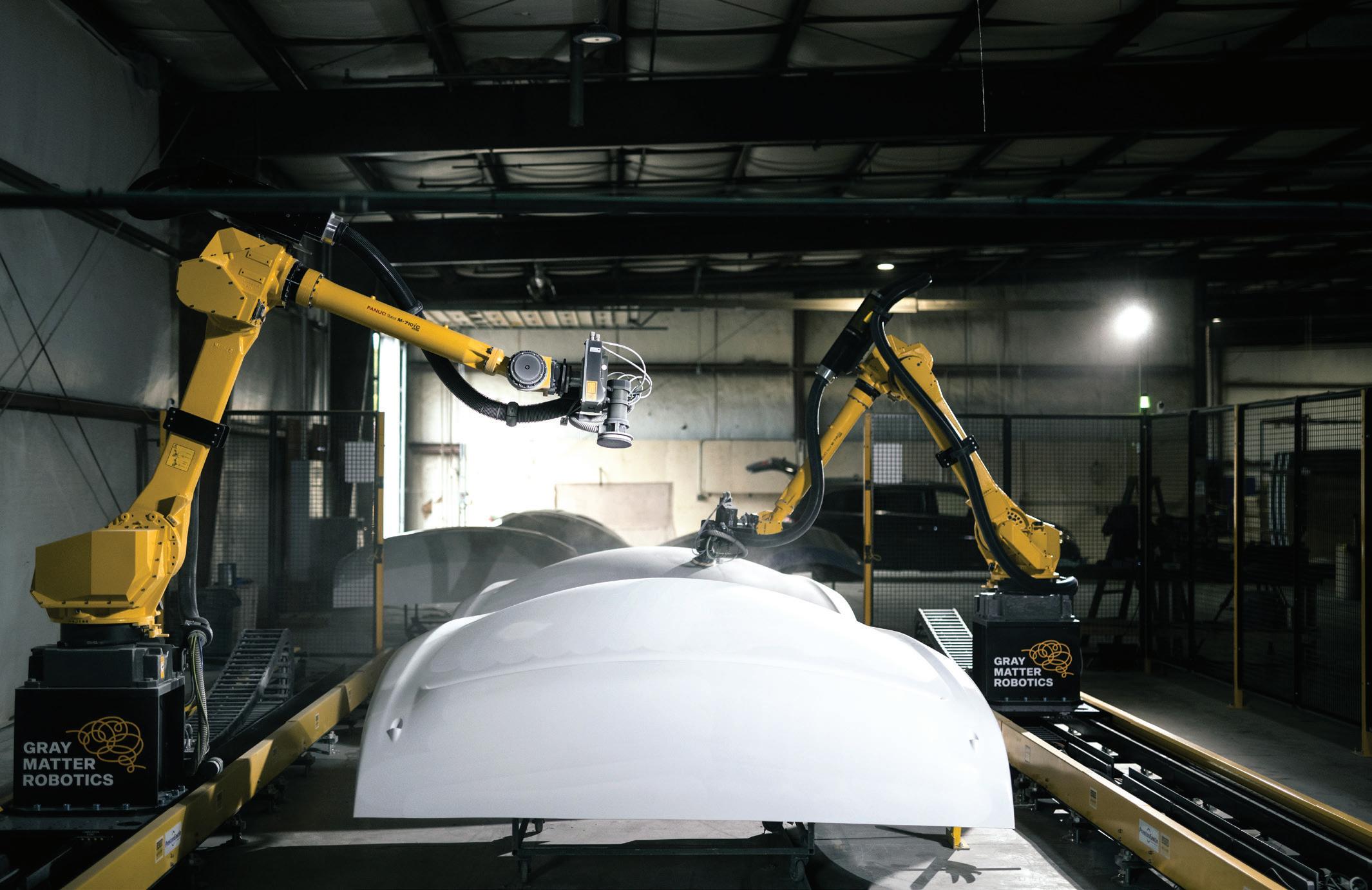
The manufacture of leaf springs for the Ford F-150 pickup truck also relies on robots to perform automated stack lay-up prior to high-pressure resin transfer molding.
“The robot stacks up the fiber layers and hands the stack over to the preform press, where it is consolidated under heat. Then the next robot takes the preform and puts it into the HP-RTM press, where the resin is injected,” says Perberschlager. “The leaf springs are also finished fully automatically using robots. Automation enables us to reduce the cycle time to less than one minute per part.”
Robotic cells are ideally suited to repetitive tasks, jobs that employees don’t want to do or work that presents safety hazards.
“Injection molders are using robotics to extract parts from machines, so people don’t have to handle them,” says Andrew Pokelwaldt, owner of consultancy AWALDT LLC, which offers automation training and education. “It’s dangerous and hot where the parts are coming out.”
GrayMatter Robotics built its business on providing automated solutions for tedious tasks. Its surface finishing and treatment robots perform sanding, polishing, buffing and grinding.
“People simply don’t want to do these tasks, and there is a lot of labor shortage in this area,” says Satyandra K. Gupta, co-founder and chief scientist at GrayMatter. “We needed to address this issue in the composites industry to avoid product delays and backlog.”
Among the challenges with automating these functions, however, are the high variability among parts and the need to avoid expensive custom fixtures to hold them. Gupta says GrayMatter’s robotic cells rapidly scan parts, then use automated planning software to build a model that ensures accurate placement and correct motion of the tool (grinder, sander, etc.). In addition, the system monitors the cell operation throughout the process to make sure it’s functioning properly.
“It provides complete traceability and quality assurance; therefore, you can produce higher quality products,” says Gupta.
Robotic Advancements
While robotic cells are well-suited for simple, repetitive tasks, suppliers continue to innovate.
Fill’s ACCUBOT multimodal robot system performs drilling, trimming and non-destructive testing.
Perberschlager says the equipment can perform five-dimensional operations with an accuracy of 0.1 millimeters. The ACCUBOT is equipped with an automatic tool changer to easily shift between functions.
Fill collaborated with an aerospace OEM to develop a vibration assisted drill spindle that can control parameters such as chip formation, temperature and revolutions per minute on the fly to drill through composite structures and metal parts. The technology causes significantly less fiber damage and eliminates the deburring and inspection
Photo Credit: GrayMatter Robotics
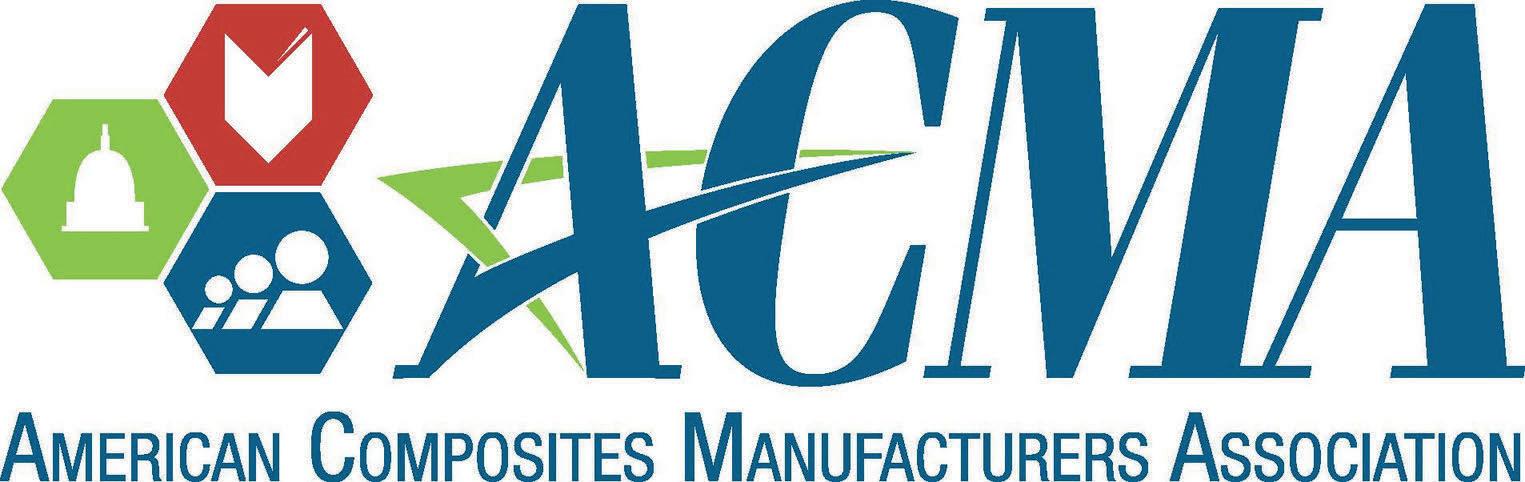
UPCOMING EVENTS 2024-25
Showcase your composite solutions, stay upto-date on industry trends, and expand your knowledge by attending ACMA events!
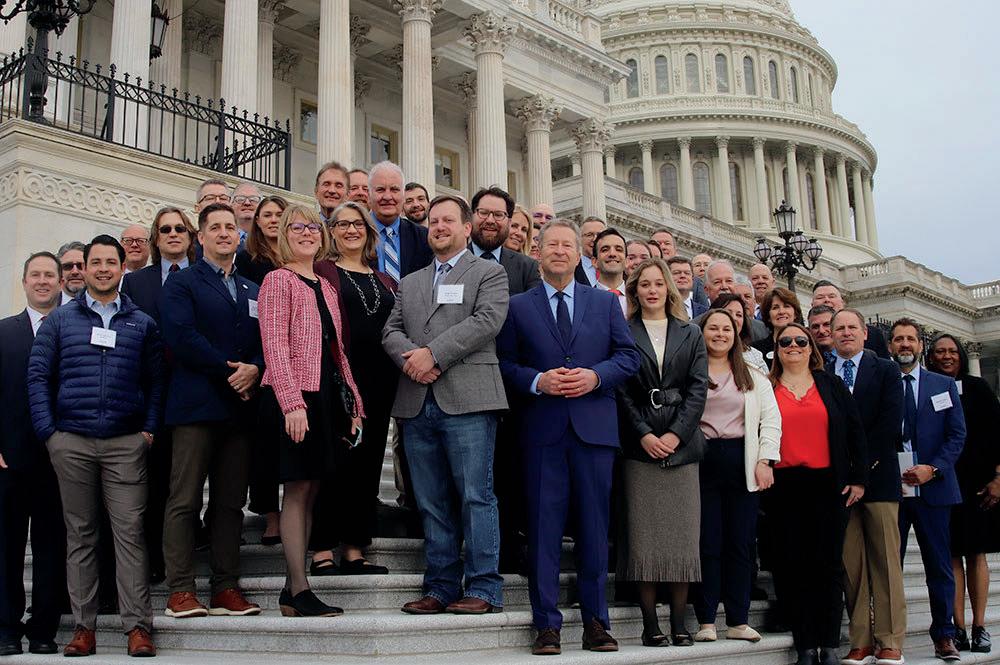

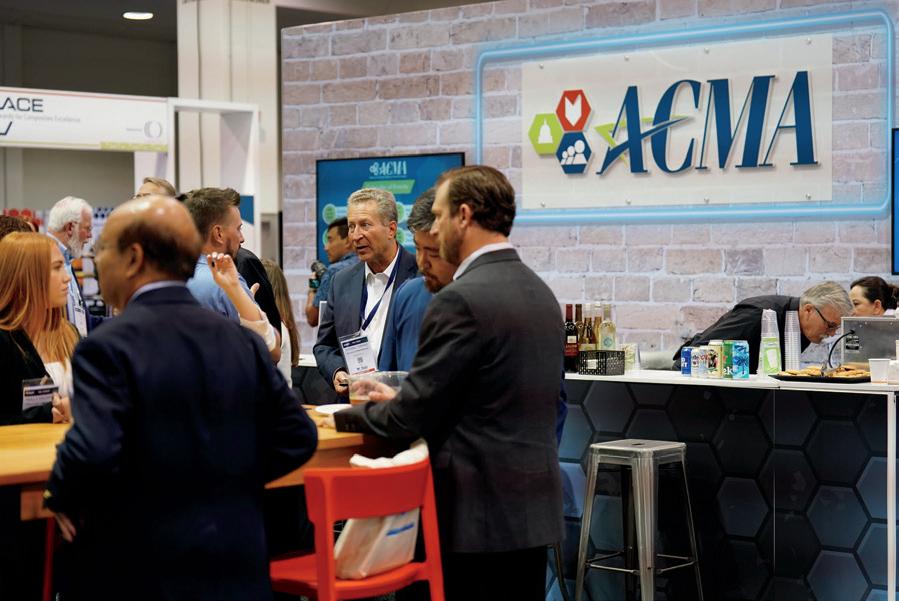
Get important updates on ACMA events by scanning the QR Code below.

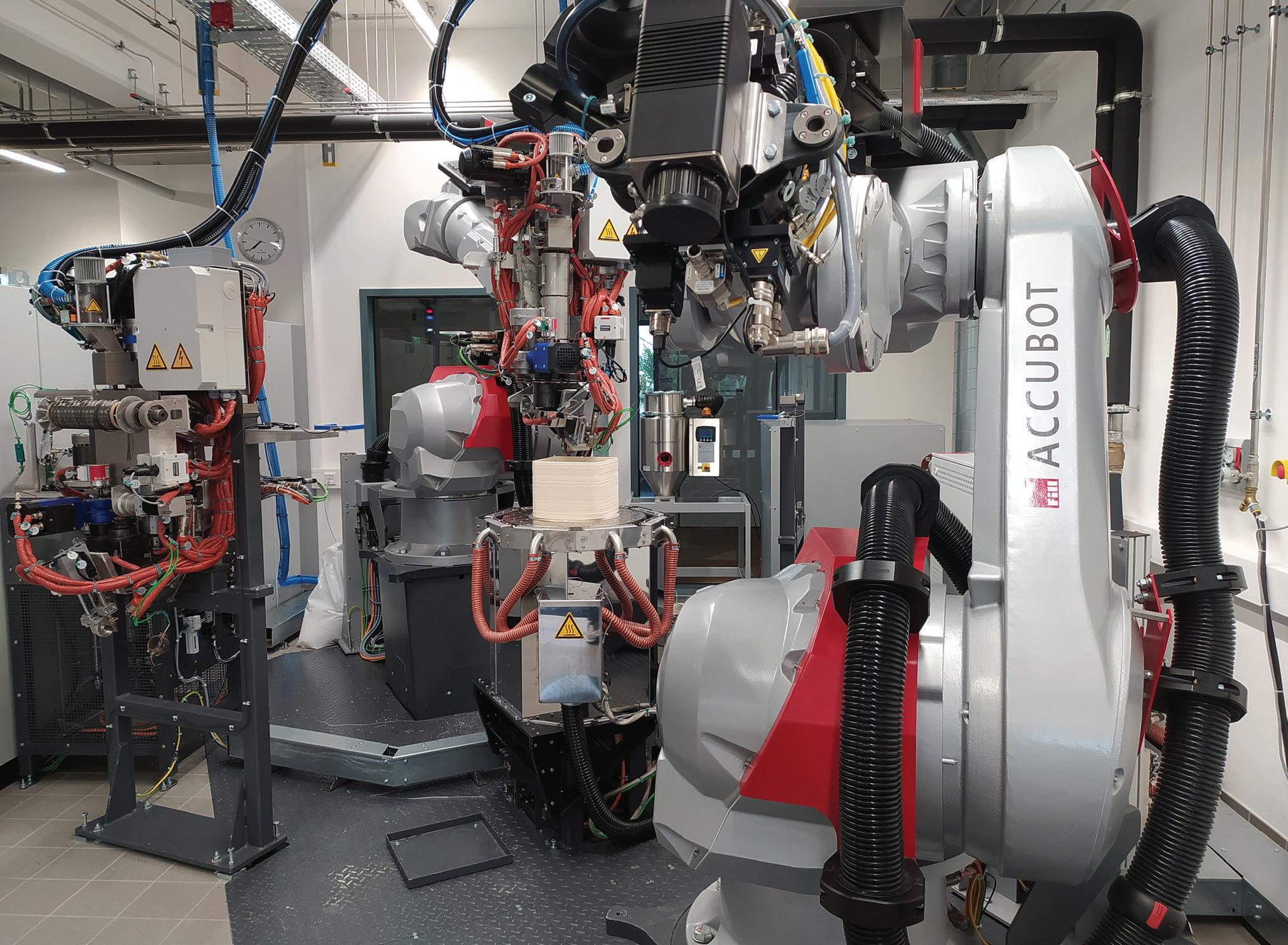
process, which saves time and tool costs in high-rate production, says Perberschlager.
“You don’t need to inspect the hole after drilling because the U.S. patented spindle acts as a sensor,” says Perberschlager. “If the real-time evaluated drilling parameters are off, the robot will flag that hole for inspection or even stop the operation to allow a human to assess the situation.”
Fill is currently teaming with Krauss Maffei on another project to create an additive manufacturing cell for fiber reinforced thermoplastics by placing an extruder on the ACCUBOT so customers can print, drill, trim and inspect a part in a single manufacturing cell. “Customers will be able to do very efficient, rapid prototyping with one machine,” says Perberschlager. “This solution is ideal for companies that don’t require high rates.”
Solutions for Everyone
Multifaceted automated systems may be out of reach for small companies, but turnkey solutions open the world of robotics to companies of all sizes. Some vendors offer a monthly or yearly service, so companies don’t have to make a large upfront capital investment.
“Even a small company can use our solution and get all the benefits of robotics without worrying about having robotics expertise to make it work,” says Gupta.
As technology advances, equipment and software are also becoming more user-friendly.
“I am not somebody that thinks in code, but I can get on a Fanuc collaborative robot now and it’s basically like working on an Android tablet putting together a program. There are some standardized templates that you feed into it, and the code is in the background,” says Pokelwaldt. “Eventually, you will have line workers setting things up because it’s not that hard to do.”
Employees and robots working in tandem can improve productivity, leading to sought-after high rates in the aerospace industry. For instance, the two-sided ACCUBOT drilling cell allows employees to manually load and unload a wing flap from the fixture, while the ACCUBOT simultaneously performs precision drilling and counter sinking on the previously loaded fixture.
“With robots, you can significantly cut back on hours of repetitive manual labor and reduce the risk of human error. You can build a very reliable process and allocate manpower to more challenging topics,” says Perberschlager. “Automating standard procedures with robots paves the way toward highrate manufacturing.” CM
Susan Keen Flynn is managing editor of Composites Manufacturing magazine. Email comments to sflynn@ keenconcepts.net.
FILL’S ACCUBOT (ACCUrate roBOT) system prints a fiberreinforced composite demonstrator part.

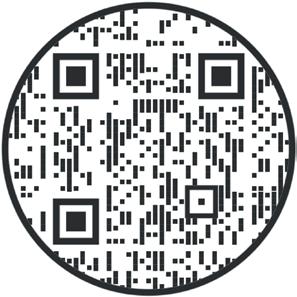
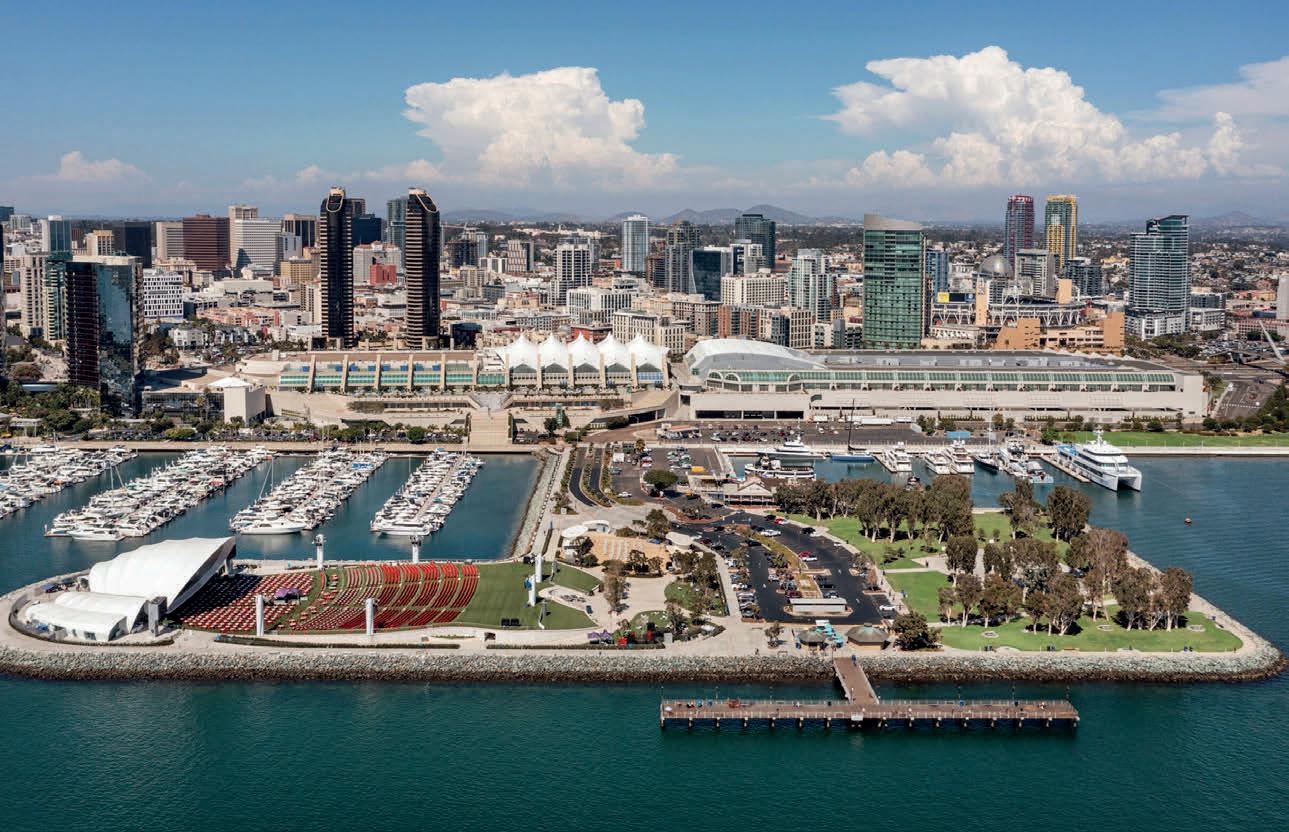
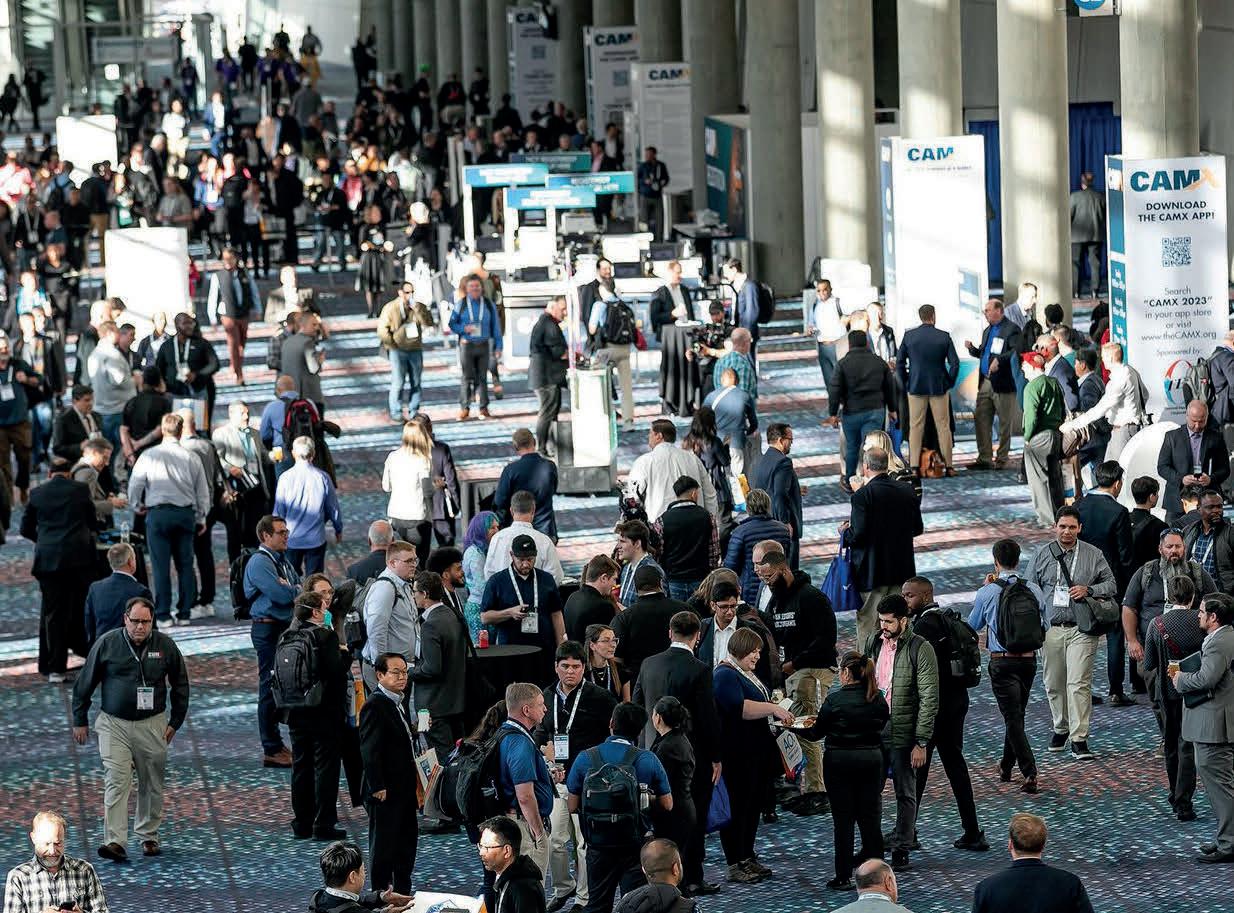
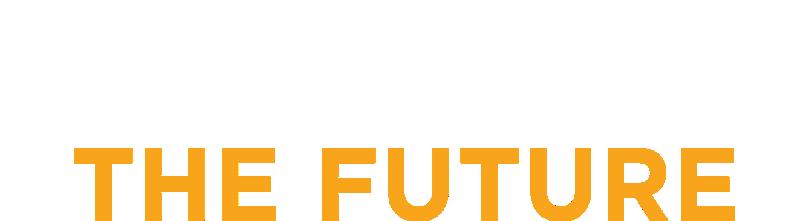
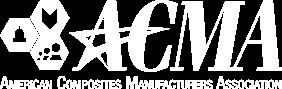

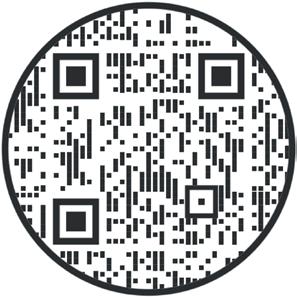
ACMA Targets Statistics Flaws
By Dan Neumann
ACMA HAS LAUNCHED a new initiative to update how the composites industry is counted. If successful, this initiative will help members quantify our benefit to the country and better track international supply chains. The ACMA government relations team, which is developing this program, is looking at inputs for composites manufacturing and products.
For more than a decade, ACMA has noted that U.S. trade statistics and U.S. Census economic data do not appropriately track composites. At its May meeting, the ACMA Board of Directors approved the creation of the Data Clarity Task Force to address this issue so that the composites industry more fully benefits from U.S. government statistical programs.
The work will be in two stages. First, ACMA will propose new 10-digit statistical reporting numbers, sometimes called 10-digit tariff codes, for several products. Interested parties, such as trade associations, can request these statistical reporting numbers through a process at the U.S. International Trade Commission twice a year, once in the fall and again in the spring.
Creating these codes will provide a better understanding of what is imported and exported for our industry. The products identified thus far as likely candidate are:
• Carbon fiber
• Chopped strand glass fiber
• Glass fiber rovings
• Unsaturated polyester resin
• Composite bathtubs and shower stalls
• Fiberglass rebar
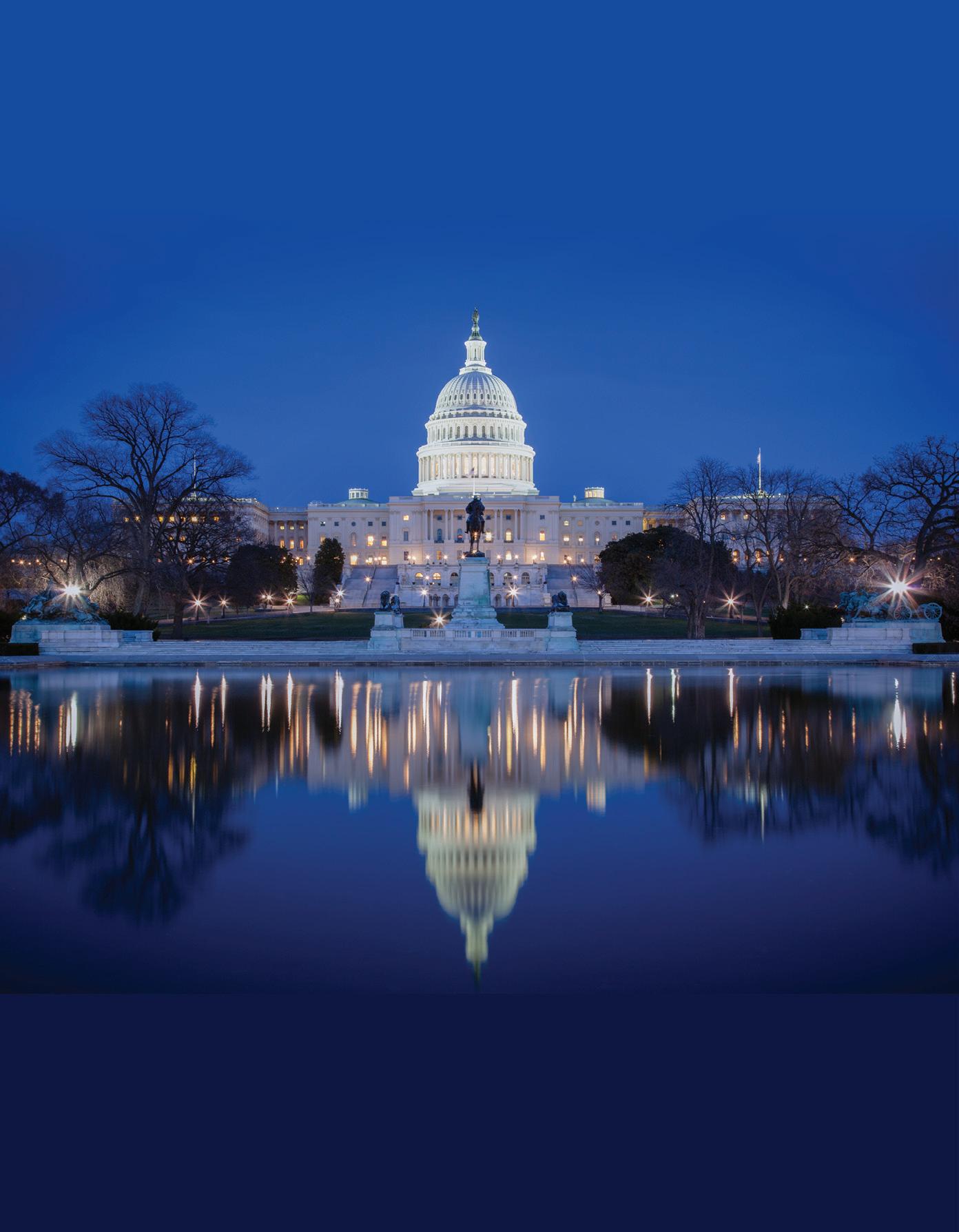
Trade data does not differentiate between different grades of carbon fiber. This makes it difficult to determine why imports may have significantly different prices per kilogram as capacity grows in other countries, such as China.
Similarly, glass fiber chopped strand and rovings can be further divided to make data clearer. By creating more specific categories, our industry will better understand our market.
Unsaturated polyester resin, bath and shower products and rebar all face a different challenge. These products are grouped with other products that are not related to the composites industry, making it impossible to accurately determine the amount of trade occurring. Unsaturated polyester resin is in a category with numerous other resin systems, and the finished products are grouped in with plastics, making the trade statistics uninformative. Creating a “breakout” — a category specific to the relevant composite materials — will provide more useful information.
meaning the economic data collected through the NAICS process does not provide meaningful insight into the U.S. composites industry. Similar to the process we have started with trade data, ACMA will work to create better categories under this program. Unfortunately, the next review of NAICS categories will not occur until 2027.
Latest in Additive Technology
Please do not hesitate to reach out to me if you have any questions or would like to participate on the task force. CM
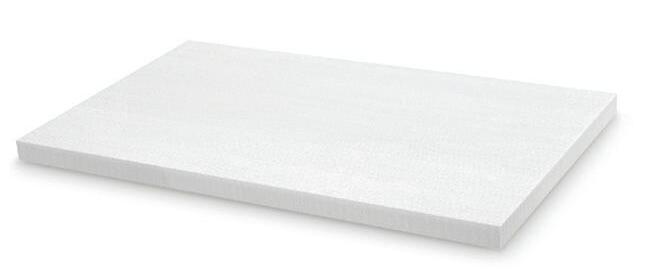
The second phase of this project will focus on statistics related to U.S. economic activity collected by the U.S. Census Bureau. The census groups U.S. manufacturers and other businesses into categories called the North American Industrial Classification System (NAICS).
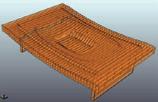
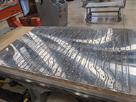
Like the situation with resins and fiberglass products, composites manufacturers are often grouped with single-use plastics or other materials,
Welcome Aboard! New ACMA Members
Dan Neumann is VP of government relations at dneumann@acmanet.org.
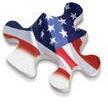
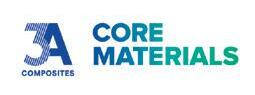
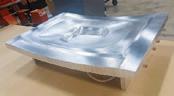
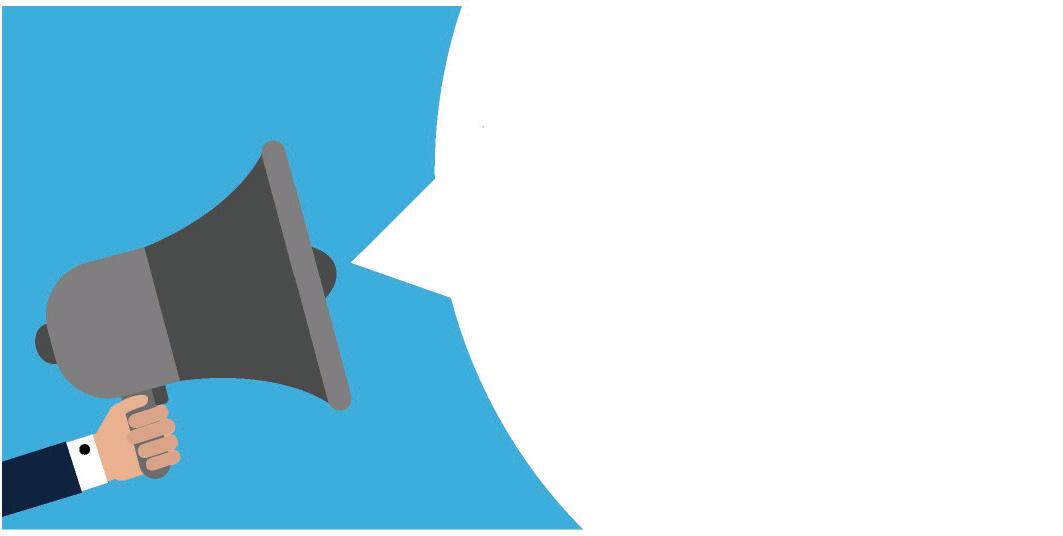
AIT COMPOSITES
Winterport, ME
GUILFORD TECHNICAL COMMUNITY COLLEGE Greensboro, NC
LUNA INNOVATIONS INC.
Blacksburg, VA
MARITIME TECHNICAL SERVICES LLC
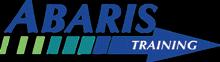
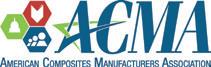
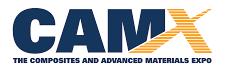
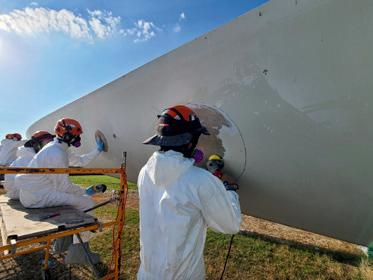

Harrisburg, NC
MISSISSIPPI STATE UNIVERSITY – ADVANCED COMPOSITES INSTITUTE
Starkville, MS
WAGNERS CFT USA Cresson, TX
San Rafael, CA MATEENBAR COMPOSITES REINFORCEMENTS LLC
For more information on becoming a member of ACMA, email membership@acmanet.org or call 703-525-0511.
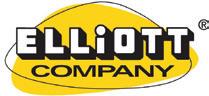
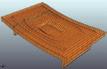

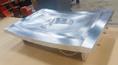

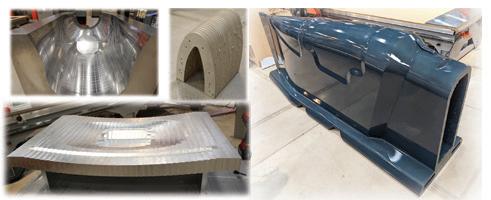
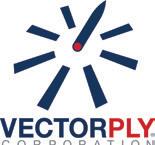
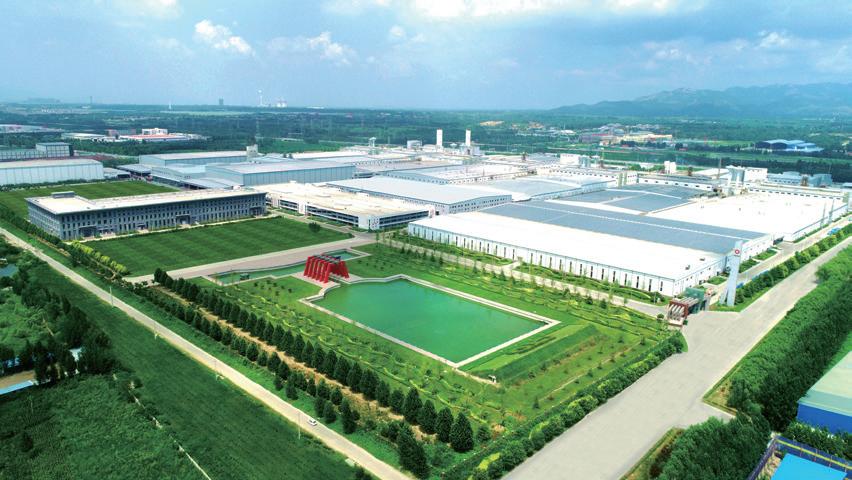
ACMA Thanks Its Board Members
As ACMA continues to grow and evolve, the association recognizes the invaluable contributions of departing board members and welcomes new appointees. Comprised of industry leaders, the ACMA board of directors plays a crucial role in steering the association’s mission and ensuring ongoing success.
“On behalf of ACMA, I extend our deepest gratitude to our departing board members. Their enduring commitment has been pivotal in shaping the future of the composites industry. We look forward to building upon this legacy as we welcome our new board members.”
–
Cindy Squires Esq., President & CEO of ACMA
With the dawn of its new fiscal year, ACMA will carry on its commitment to advancing the composites industry through innovation, education, collaboration and advocacy. The blend of seasoned expertise and fresh leadership will undoubtedly bring new energy and insights, fostering continued progress and success. ACMA is poised to reach new heights, championing the interests of its members and the broader industry.
Departing Board Members
• Eric Ball, Orenco Composites
• Kevin Barnett, United Fiberglass of America
• Tarik Basrawi, Saudi Aramco
• Fletcher Lindberg, AOC
• John O’Sullivan, Crane Composites, Inc.
• Chris Skinner, Owens Corning
Newly Appointed ACMA Board Members
• Tony Martin, North American Composites*
• Michael Rambo, Spirit AeroSystems*
• Goran Haag, Champion Fiberglass
• Mark Sickels, Superior Industrial Solutions
• Jane Thomas, Teijin Holdings USA*
• Harold Visser, Polynt Composites USA
• Ben Wiltsie, GEOTEK
* = Returning member assigned a new term or position
If you are interested in serving on an ACMA Board or other volunteer committees, contact Paige Patterson at ppatterson@acmanet.org.
Honoring ACMA Membership Award Winners
Join us on Sept. 9, 2024, from 5:30 p.m. to 7:30 p.m. at CAMX 2024 in San Diego, Calif., for the ACMA
Membership Awards Ceremony and Reception. This special evening is dedicated to celebrating the achievements of our award winners. Come and honor their exceptional work and contributions while networking with industry leaders and peers. Learn about the awards at acmanet.org/membership-awards.
Celebrate the ACE Award Winners
Stop by the ACE Pavilion at CAMX for the Awards for Composites Excellence (ACE) Ceremony on Sept. 10, 2024, at 2:00 p.m. Hosted by ACMA, this ceremony celebrates innovation in composites technology, manufacturing and product development. Six awards will be presented in three categories: Design, Manufacturing and Market Growth. Come congratulate the winners and hear about their innovations! Get more details at thecamx.org/awards
ACMA Hosts First Composites Sustainability Event
June’s Composites Sustainability Today event in Denver brought together industry leaders and sustainability advocates to explore the latest advancements in composites sustainability. Highlights included tours of Vartega’s recycling facility and the National Renewable Energy Laboratory, along with insightful presentations on policy, industry innovations and best practices. Get a full recap of the event at acma.today/CSTrecap and keep an eye out for future sustainability-related events at acmanet.org/ events.
Save the Date: 2025 North American Pultrusion Conference
Mark your calendars for the 2025 North American Pultrusion Conference, happening May 6-8. This premier education and networking event presented by ACMA in partnership with the European Pultrusion Technology Association will showcase the latest pultrusion applications and methods, highlight its use across various industries and enhance industry-wide knowledge of its benefits. The call for abstracts, exhibits and sponsorships, and registration will be announced soon. Check acmanet.org/events for updates.
Calendar of Events
CAMX – the Composites & Advanced Materials Expo
September 9-12, 2024
San Diego, CA thecamx.org
North American Pultrusion Conference
May 6-8, 2025
Chicago, IL
Smarter composites release systems.
TECHNOLOGY SOLUTIONS + IDEAS
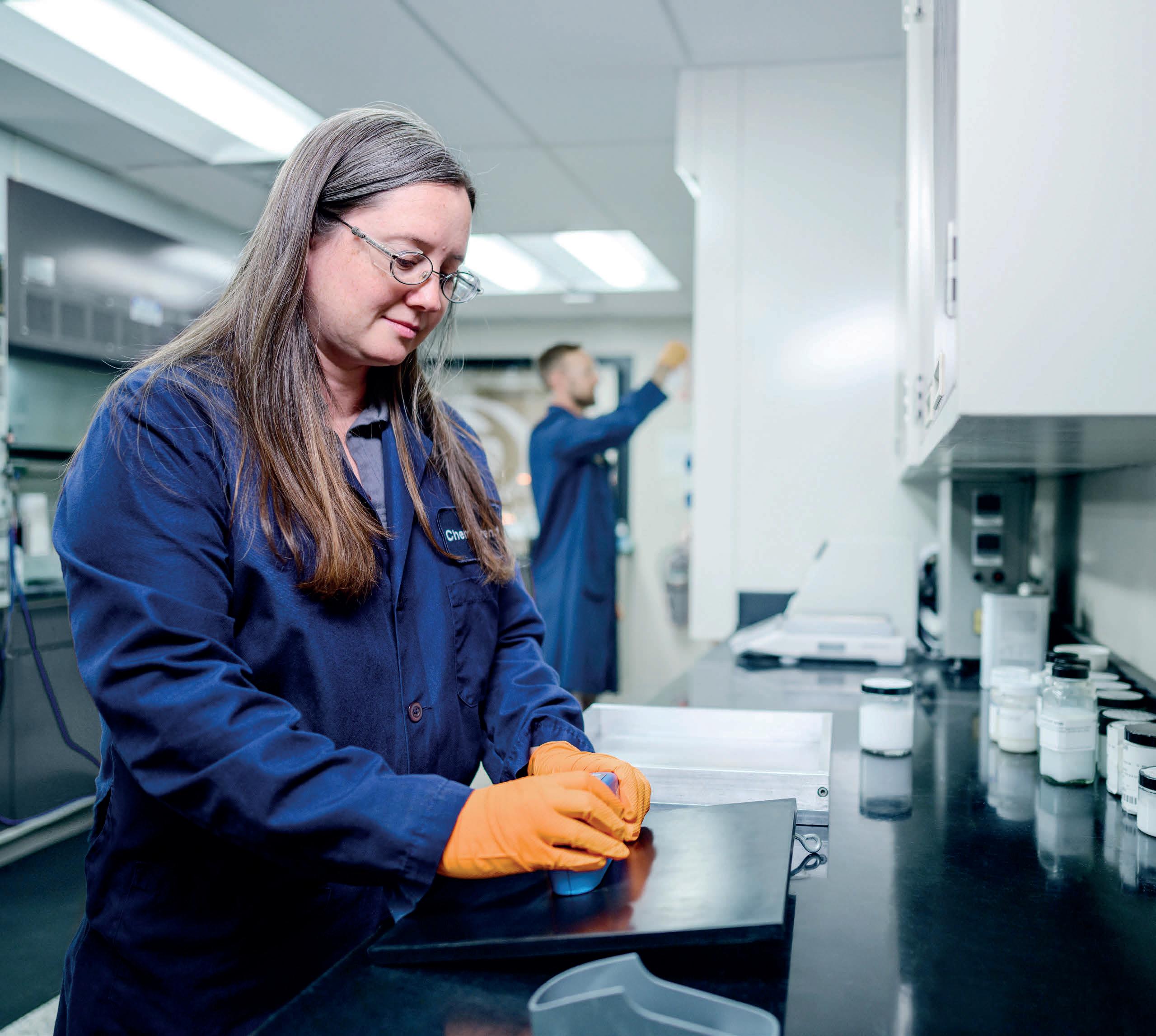
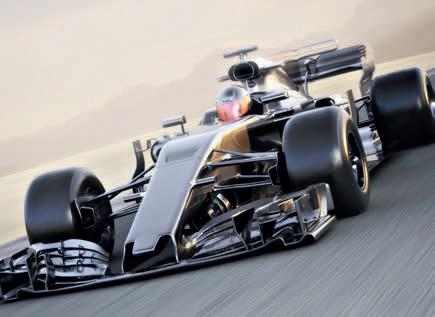
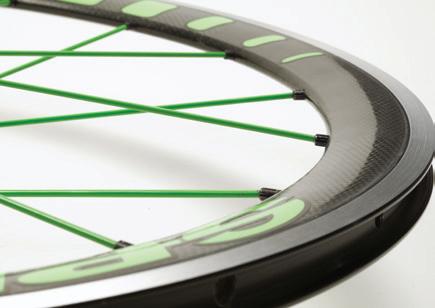

From the highly complex to the everyday, we provide custom solutions that bring consistency, dependability, and value, from aerospace applications to automotive, construction, marine, sporting goods, wind energy, and more. And we do so in a safe, sustainable fashion with a broad range of advanced water-based products. Whether it’s a cleaner, primer, sealer, release agent, or an entire system, we can deliver a solution fit for your specific application.
JOIN US IN SAN DIEGO CAMX
Booth FF41
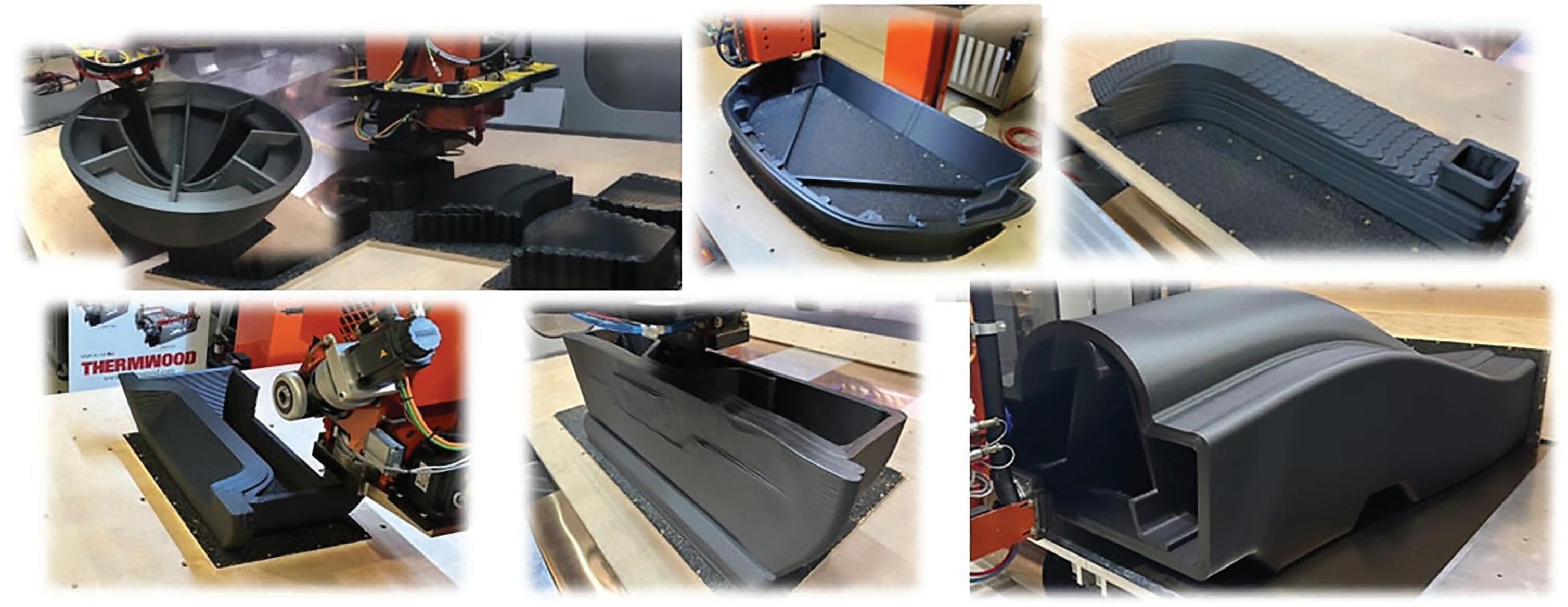
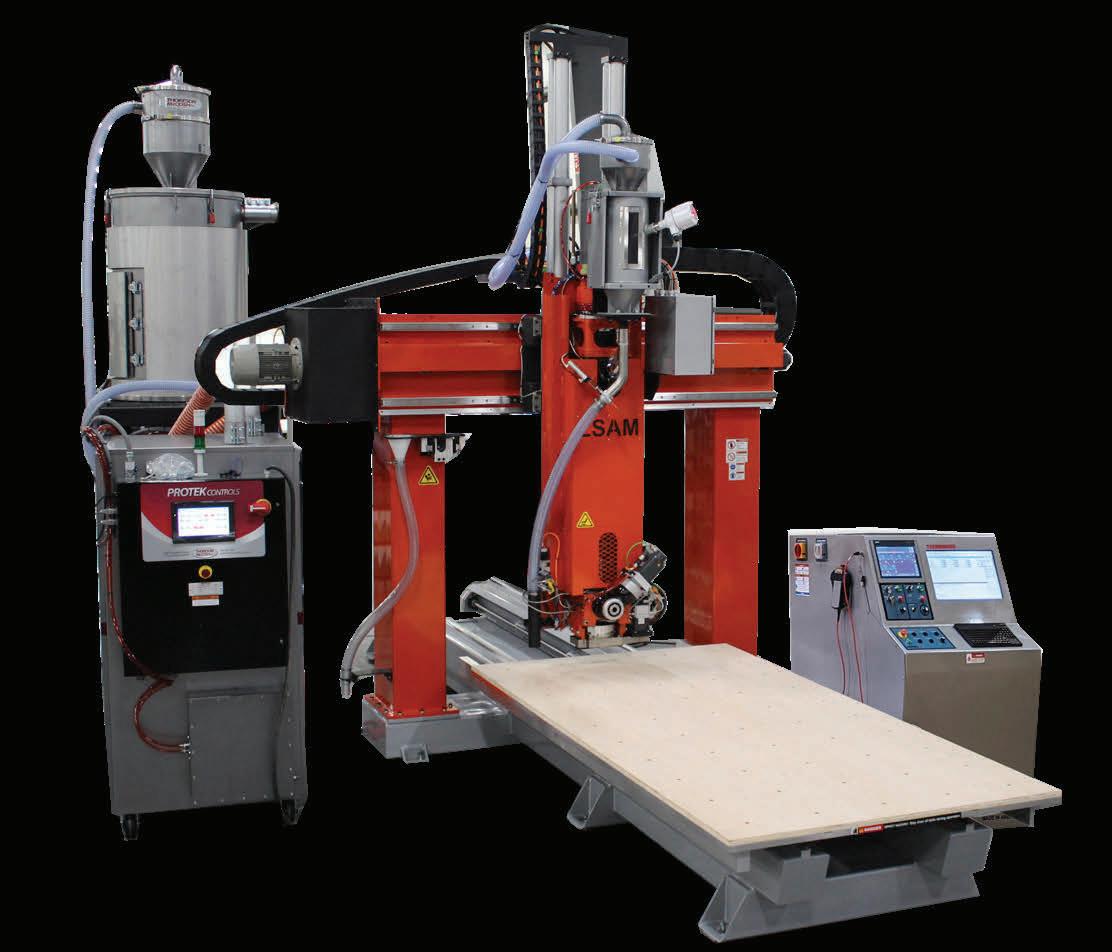

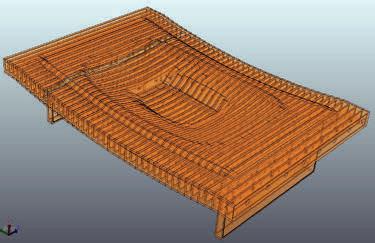
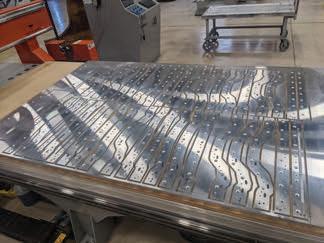
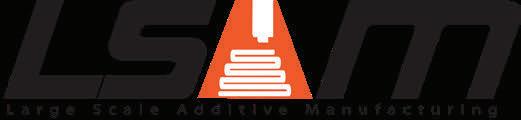
Fixtures
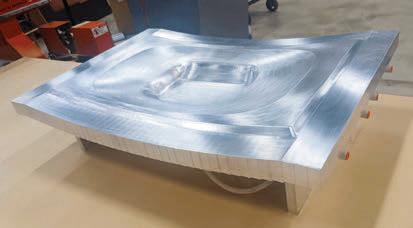
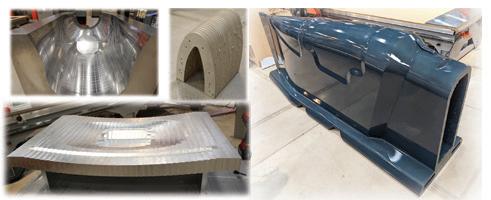
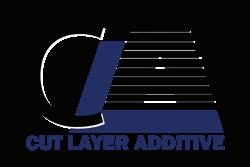
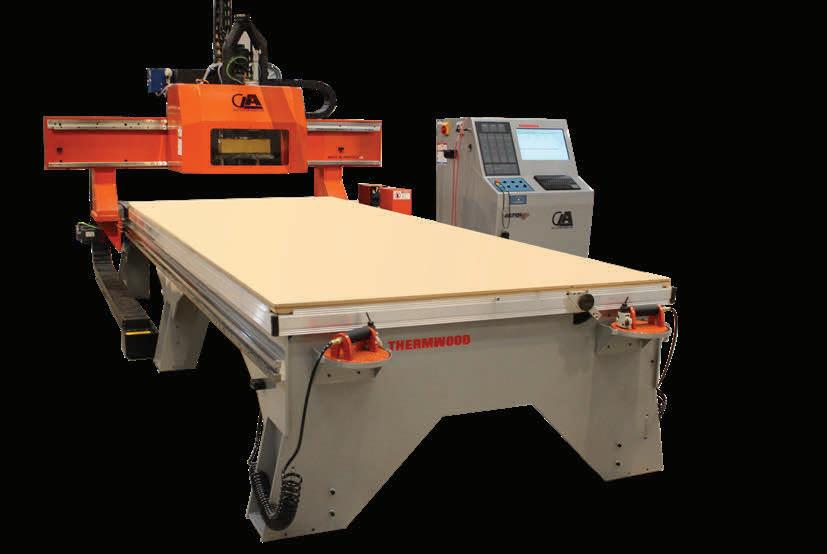
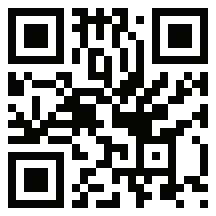
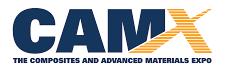