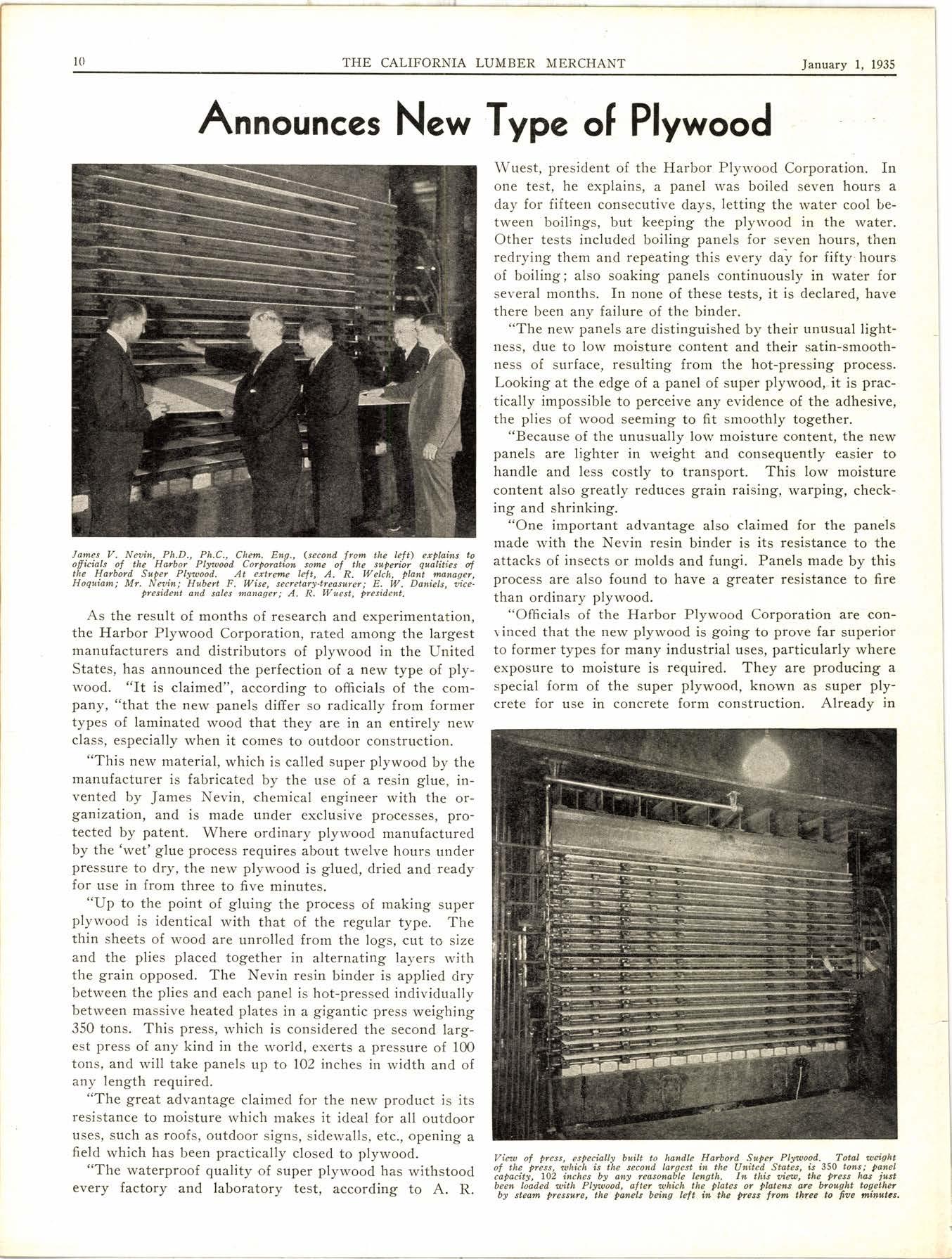
2 minute read
Announces New Typ" of Plywood
Wuest, president of the Harbor Plywood Corporation. In one test, he explains, a panel rvas boiled seven hours a day for fifteen consecutive days, letting the water cool between boilings, but keeping the plywood in the water. Other tests included boiling panels for seven hours, then redrying them and repeating this every day for fifty hours of boiling; also soaking panels continuously in water for several months. In none of these tests, it is declared, have there been any failure of the binder.
"The new panels are distinguished by their unusual lightness, due to low moisture content and their satin-smoothness of surface, resulting from the hot-pressing process. Looking at the edge of a panel of super plywood, it is practically impossible to perceive any evidence of the adhesive, the plies of wood seeming to fit smoothly together.
"Because of the unusually low moisture content, the new panels are lighter in weight and consequently easier to handle and less costly to transport. This low moisture content also greatly redu,ces grain raising, warping, checking and shrinking.
"One important advantage also claimed for the panels made rvith the Nevin resin binder is its resistance to the attacks of insects or molds and fungi. Panels made by this process are also found to have a greater resistance to fire than ordinary plywood.
As the result of months of research and experimentation, the Harbor Plywood Corporation, rated among the largest manufacturers and distributors of plywood in the United States, has announced the perfe'ction of a new type of plywood. "It is claimed", according to officials of the company, "that the new panels differ so radically from former types of laminated wood that they are in an entirely new class, especially when it comes to outdoor construction.
"This new material, which is called super plywood by the manufacturer is fabricated by the use of a resin glue, invented by James Nevin, chemical engineer with the organization, and is made under exclusive processes, protected by patent. Where ordinary plywood manufactured by the 'wet'glue process requires about twelve hours under pressure to dry, the new plywood is glued, dried and ready for use in from three to five minutes.
"Up to the point of gluing the process of making super plywood is identical with that of the regular type. The thin sheets of wood are unrolled from the logs, cut to size and the plies placed together in alternating layers with the grain opposed. The Nevin resin binder is applied dry between the plies and each panel is hot-pressed individually between massive heated plates in a gigantic press weighing 350 tons. This press, rvhich is considered the second largest press of any kind in the world, exerts a pressure of 100 tons, and will take panels up to 102 inches in width and of any length required.
"The great advantage claimed for the new product is its resistance to moisture which makes it ideal for all outdoor uses, such as roofs, outdoor signs, sidewalls, etc., opening a field which has been practically closed to plywood.
"The waterproof quality of super plywood has withstood every factory and laboratory test, according to A. R.
"Officials of the Harbor Plywood Corporation are .conrinced that the new plywood is going to prove far superior to former types for many industrial uses, particularly where exposure to moisture is required. They are producing a special form of the super plywood, known as super plycrete for use in concrete form construction. Already in many kinds of concrete construction where smooth surfaces are desired, plywood panels have been used advantageously for form material and the waterproof character of this new material will enable panels to be used over and over again, for many times, without the panels warping or the plies separating."