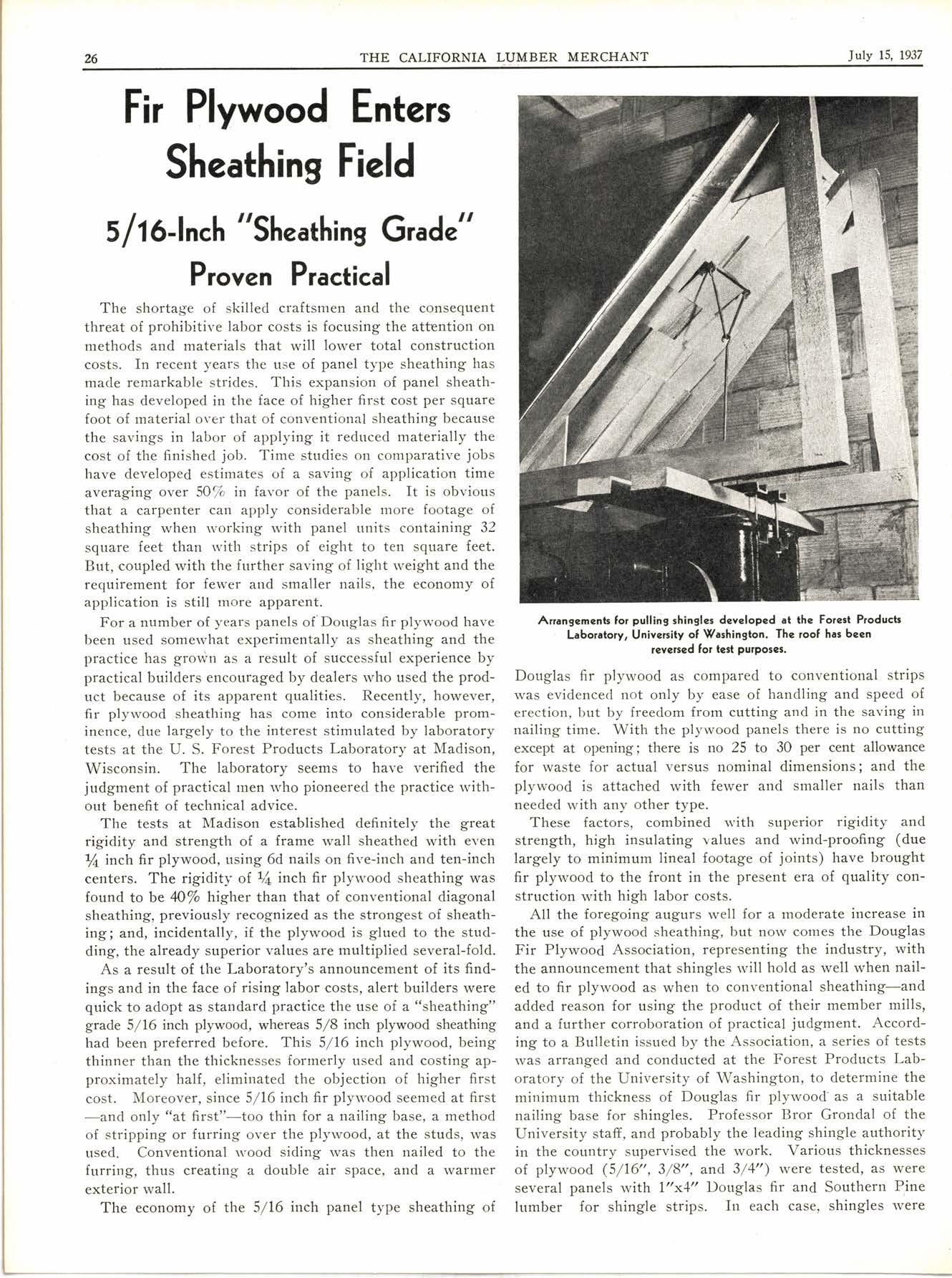
5 minute read
Gtade"
The shortage of skilled craftsmen and the consequent threat of prohibitive labor costs is focusing the attention on methods and materials that will lower total construction costs. In recent years the use of panel type sheathing has made remarkable strides. This expansion of panel sheathing has developed in the face of higher first cost per square foot of material over that of conventional sheathing because the savings in labor of applying it reduced materially the cost of the finished job. Time studies on comparative jobs have developed estimates of a saving of application time averaging over 5O7o in favor of the panels. It is obvious that a carpenter can apply considerable more footage of sheathing when rvorking with panel units containing 32 squa.re feet than rvith strips of eight to ten square feet. But, coupled with the further saving of light rveight and the requirement for fewer and smaller nails, the economy of application is still more apparent.
For a number of years panels of Douglas fir plywood have been used somervhat experimentally as sheathing and the practice has grown as a result of successful experience by practical builders encouraged by dealers who used the product because of its apparent qualities. Recently, however, fir plywood sheathing has come into considerable prominence, due largely to the interest stimulated by laboratory tests at the U. S. Forest Products Laboratory at Madison, Wisconsin. The laboratory seems to have verified the judgment of practical rnen u'ho pioneered the practice without benefit of technical advice.
The tests at Madison established definitely the great rigidity and strength of a frame wall sheathed with even la inch fir plywood, using 6d nails on five-inch and ten-inch centers. The rigiditl'of Va inch fir plywood sheathing was found to be 4A% higher than that of conventional diagonal sheathing, previously recognized as the strongest of sheathing; and, incidentally, if the plywood is glued to the studding, the already superior values are multiplied several-fold.
As a result of the Laboratory's announcement of its findings and in the face of rising labor'costs, alert builders were quick to adopt as standard practice the use of a "sheathing" grade 5/16 inch plywood, whereas 5/8 inch plywood sheathing had been preferred before. This 5/16 inch plywood, being thinner than the thicknesses forrnerly used and costing approximately half, eliminated the objection of higher first cost. Moreover, since 5/16 inch fir plyu.ood seemed at first -and only "at fi15f"-1eo thin for a nailing base, a method of stripping or furring over the plywood, at the studs, was used. Conventional wood siding was then nailed to the furring, thus creating a double air space, and a lvarmer exterior wall.
The economy of the 5/16 inch panel type sheathing of
Douglas fir plywood as compared to conventional strips was evidenced not only by ease of handling and speed of erection, but by freedom from cutting and in the saving in nailing time. With the plyrv'ood panels there is no cutting except at opening; there is no 25 to 30 per cent allowance for waste for actual versus nominal dimensions; and the plywood is attached with fewer and smaller nails than needed with any other type.
These factors, combined with superior rigidity and strength, high insulating values and wind-proofing (due largely to minimum lineal footage of joints) have brought fir plywood to the front in the present era of quality construction with high labor costs.
All the foregoing augurs well for a moderate increase in the use of plywood sheathing, but now c,omes the Douglas Fir Plywood Association, representing the industry, with the announcement that shingles s'ill hold as well when nailed to fir plywood as when to conventional sheathing-and added reason for using the product of their member mills, and a further corroboration of practical judgment. According to a Bulletin issued by the Association, a series of tests lvas arrang'ed and conducted at the Forest Products Laboratory of the University of Washington, to determine the minimum thickness of Douglas fir plywood'as a suitable nailing base for shingles. Professor Bror Grondal of the University stafi, and probably the leading shingle authority in the country supervised the work. Various thicknesses of plywood (5/16", 3/8", and 3/4") were tested, as were several panels with 1"x4" Douglas fir and Southern Pine lumber for shingle strips. In each case, shingles lvere applied in accordance with the standard specification of the Red Cedar Shingle Bureau, and the load applied to an eight-inch wide shingle in the center of the panel. The results, if somewhat surprising to the inexperienced, only substantiated the claims previously made by the carpenterbuilders who had used plywood after running simple tests. It is believed that these tests conducted at the University of Washington will open wide the market for plywood sheathing.
According to lthe Shingle Bureauhandbook of the Red Cedar
"To lift a shingle eight inches wide from a roof covered with No. 1, lGinch shingles laid with a S-inch exposure requires a pull of 85 pounds."
This authority referred to a one-inch lumber base. yet the University of Washington tests on 5/16 inch plywood "sheathing" developed a minimum pull of 85 pounds and a maximum of 115 p,ounds; and since an 85 pound pull on an eight-inch shingle with five-inch exposure is equivalent to 300 pounds per square foot, the home owner need have no worry about shingles nailed to plywood. Even a tornado doesn't exert half the lifting acti,on which the shingles withstood during the tests. Thus, the reasoning of the practical builders was fully proven and their judgment of generous safety margins supported.
One point is emphasi zed by the Association bulletin with respect to shingling over "tight decks." They caution the builder (and are supported by the Red Cedar Shingle Bureau) never to use a waterproof, saturated paper under shingles because such paper prevents "breathing', or the passage of water vapor.
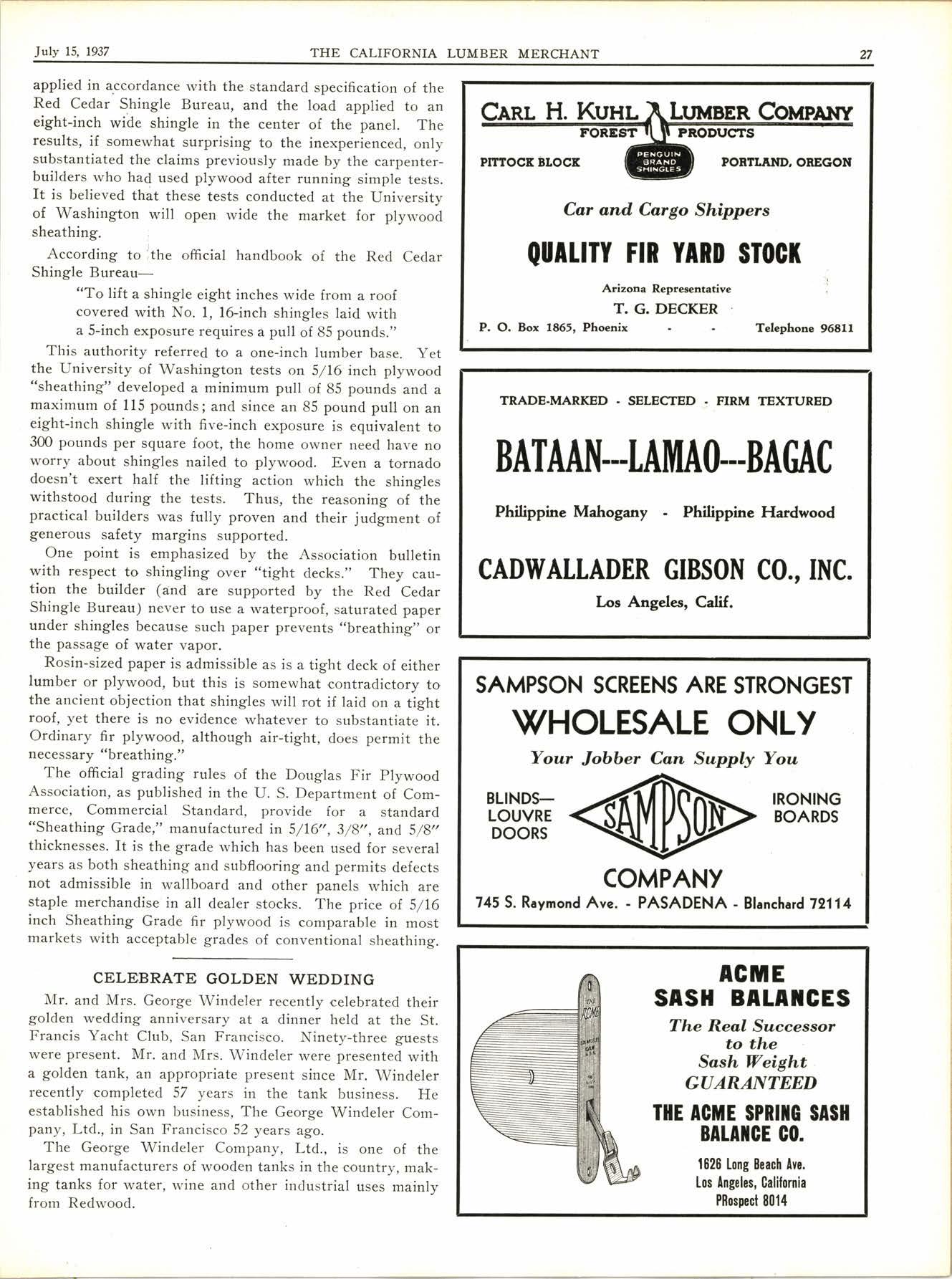
Rosin-sized paper is admissible as is a tight deck of either lumber or plywood, but this is somewhat ,contradictory to the ancient objection that shingles will rot if laid on a tight roof, yet there is no evidence whatever to substantiate it. Ordinary fir plywood, although air-tight, does permit the necessary "breathing."
The official grading rules of the Douglas Fir plywood Association, as published in the U. S. Department of Commerce, Commercial Standard, provide for a standard "Sheathing Grade," manufactured in 5/16,,, 3/8',, and 5/8r, thicknesses. It is the grade which has been used for several years as both sheathing and subflooring and permits defects not admissible in wallboard and other panels which are staple merchandise in all dealer stocks. The price of 5/16 inch Sheathing Grade fir plywood is comparable in most markets with acceptable grades of conventional sheathing.
Celebrate Golden Wedding
Mr. and Mrs. George Windeler recently celebrated their golden wedding anniversary at a dinner held at the St. Fran,cis Yacht Club, San Fran'cisco. Ninety-three guests were present. Mr. and Mrs. Windeler were presented with a golden tank, an appropriate present since Mr. Windeler recently completed 57 years in the tank business. He established his own business, The George Windeler Company, Ltd., in San Fran,cisco 52 years ago.
The George Windeler Company, Ltd., is one of the largest manufacturers of wooden tanks in the country, making tanks for water, wine and other industrial uses mainlv from Redwood.
TRADE.MARKED SELECTBD . FIRM TBXTURED
BATAAN...LAMA()...BAGAC
Philippine Mahogany Philippine Hardwood CADWATLADER