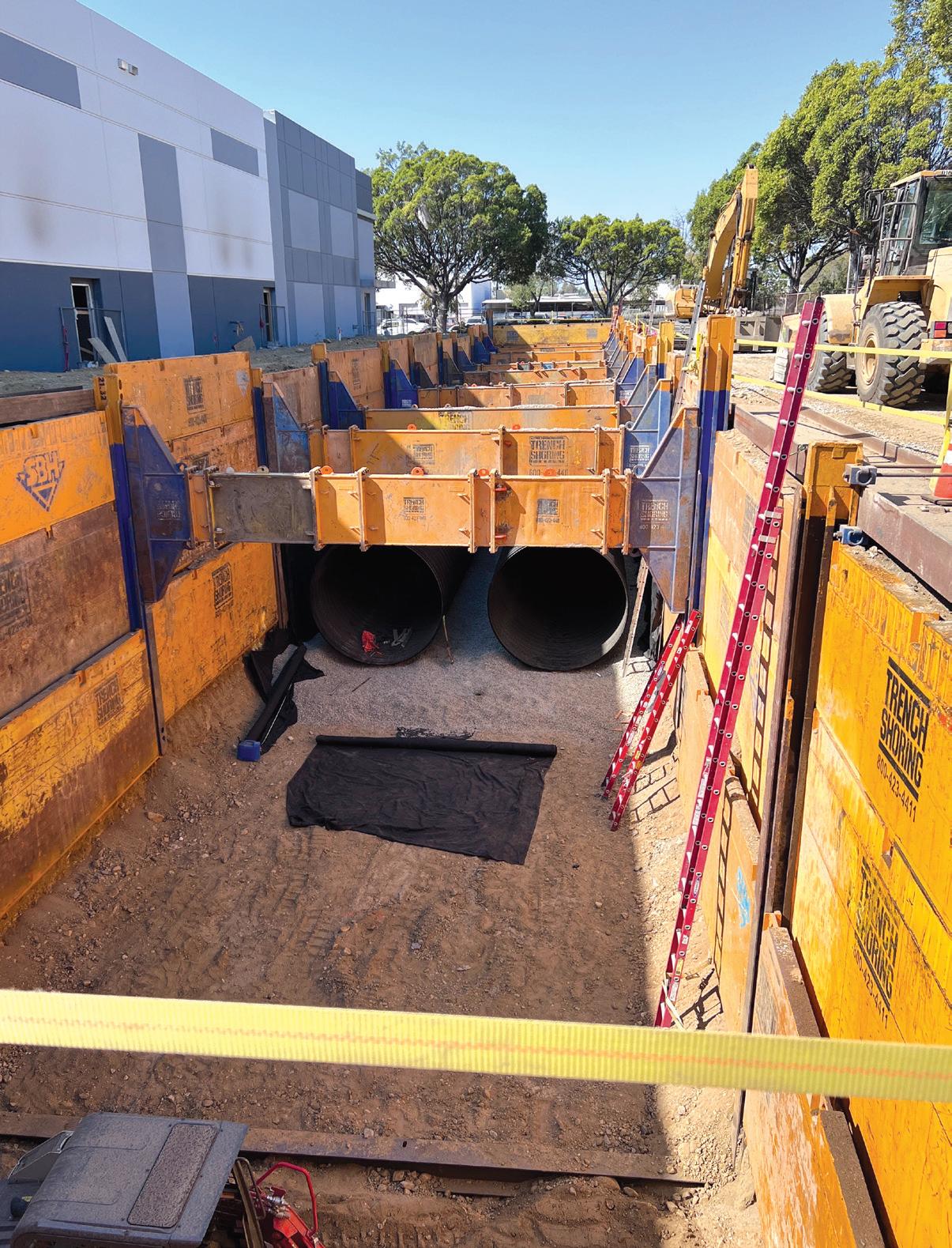
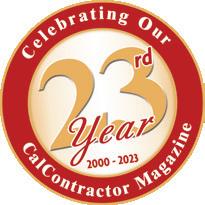
Returns your entire machine to good-as-new condition—or better-than-new condition with upgrades and enhancements
Restores like-new performance to your excavator’s hydraulic system
Restores everything from the radiator to the axles, bringing them back to new life
Maximizes the durability and performance of Cat ® commercial and industrial engines, including marine propulsion engines, generator sets, pumps, locomotives, and other power systems
Breathes new life into individual components like Cat machine engines, transmissions, torque converters, axle assemblies, or final drives
Let us prepare a Custom Rebuild tailored to the specific needs of your machine in specific applications. Restores your machine to like-new performance at a fraction the cost
We are so confident in the quality of our Certified Rebuilds, when you receive your machine back, it comes with a LIKE NEW WARRANTY. Contact your California Cat Dealer for more information.
SINCE 1956
hawthornecat.com
San Diego County 800-437-4228
SINCE 1919
quinncompany.com
Central & Southern California 888-842-2155
PUBLISHER: Kerry Hoover khoover@calcontractor.com
EDITOR: Brian Hoover, Senior Editor
GRAPHIC DESIGNER: Aldo Myftari
FOR ADVERTISING INFORMATION: Please call: (909) 772-3121
Bakersfield 9150 Golden State Hwy. Bakersfield, CA 93308
661.387.6090
Corona 22099 Knabe Rd. Corona, CA 92883 951.277.7620
Fresno 4501 E. Volvo Ave. Fresno, CA 93725
559.834.4420
Lakeside 12345 Mapleview St. Lakeside, CA 92040
619.441.3690
Redding 4963 Mountain Lakes Blvd. Redding, CA 96003
279.201.4869
Sacramento 8594 Fruitridge Rd. Sacramento, CA 95826 916.504.2300
San Leandro 1944 Marina Blvd. San Leandro, CA 94577 510.357.9131
Turlock
1275 Venture Ln. Turlock, CA 95380 209.410.6710
With high-performance equipment from Volvo Construction Equipment, you can tackle excavation, trenching and grading projects with ease. With powerful and reliable machinery on the ground, running pipelines, digging for utilities, and moving and grading the earth can be done more efficiently. Dig deeper and move more earth with Volvo.
Contact your local VCES location
• (72) SBH Slide Rail Panels
(30) 24.6’
(24) 16.4’
(12) 21.32’
(6) 27.9’
• (20) 21.3’ + 24.6’ MDSR SBH Slide Rail Posts
• (10) 24’ Distance Pieces
• (4) 21.32’ SBH MDSR Corner Posts
• (2) SBH 50’ Slide Rail Tie Back Beams
• (1) 28’ Waster Beam
• (1) SBH Tie Back Kit
• (1) SBH Rigging Kit
• (1) Standalone Davit Arm Fall Arrest/ Retrieval Device
• Miscellaneous Trench Plates
• (13) TSC Truckloads Delivered
• (12) TSC Truckloads Picked Up
• (5) Onsite Shoring Consultations
• (1) Week Of Onsite Instruction From Trench Shoring Company/SBH Slide Rail
Professionals
• (1) Engineered Shoring Design
Established in 1983, Paulus Engineering, Inc. is a general engineering contractor specializing in sewer, water, and storm drain installation throughout Southern California. With headquarters in Anaheim, the company is owned and operated by Jason Paulus, President. Recently, Paulus Engineering took on a project for American Fruits and Flavors out of Pacoima. This company specializes in the manufacturing of the finest fruit juices, concentrates and hundreds of unique fruit and flavor blends. American Fruits and Flavors uses propylene glycol in their manufacturing process and hired Paulus Engineering to install a 200,000-gallon overflow storage/ containment tank to help mitigate any emergency overflow issues.
Rory Campbell is the Vice President of Paulus Engineering, and he oversaw all aspects of the installation of the containment tank for American Fruits and Flavors. “We started the project in October 2022, and it went around five weeks, into December. We began by surveying the limits of excavation for the owner, followed
By Brian Hoover, Senior Editor / Photos provided by Paulus Engineering, Inc. Left: Paulus Engineering places 120” diameter SRPE (steel reinforced polyethylene) pipe within the engineered slide rail system from Trench Shoring Company.by multiple truckloads of shoring from Trench Shoring Company,” says Campbell. “We rented around 12 bays of fully engineered slide rail systems, from 16.4 to 27.9 feet in length. We self-performed the installation of all of the shoring as our crew excavated an area that was 240 feet in length, by 28 feet wide, by 20 feet in depth.”
According to Trench Shoring Company, the slide rail system provided to Paulus Engineering (Paulus) utilized 20-to-21-foot bays with re-brace systems to create six 40 foot clear span openings for the installation of the HDPE tank. Campbell explains that the installation of the shoring system started at the west end of the project site and was installed bay by bay as necessary. “We installed around 60 feet of slide rail shoring at a time and secured that area before moving on to the next section. Once each section was installed, we would begin to place
the 120-inch diameter by 40 feet long HDPE pipe,” says Campbell. “We also installed a 10-inch emergency drain system with two connections. If there is ever an issue with the Glyco system, the material will dump directly into the containment tank with double barrel pipe and two manholes at each end. Our crew then placed a ¾-inch rock base at the bottom of the pit before finally dropping the DuroMax tank in place.”
The project was originally designed for the use of multiple rebrace pits within the 240-foot run. However, the installing foreman for Paulus, John Powell, decided that leaving the struts in place would be a preferred method. Powell has years of experience and knowledge with the installation of slide rail shoring systems. “Leaving the struts in place eliminated the need for several waster beams that would be necessary for the rebraced
bays, saving both time and money in the process,” says Campbell. “Instead, we were able to move the 40-foot-long HDPE pipe joints using a single 43-foot-long rebraced bay. Our crew was then able to disconnect the rigging and reconnect on the other side of each brace spaced out at 24 feet and 16 feet apart. We had the entire shoring system installed in two weeks. The 120-inch SRPE (steel reinforced polyethylene) pipe installation took another week. This pipe is chemical resistant and a fusion bonded pipe, so once we were done with the installation and backfill, we fused the joints together. This took around one week, and then one more week for the removal of the shoring system.”
Campbell points out that the job presented several challenges, including the tight working space that was located just 22 feet off
Above Left: Paulus Engineering crew digging mass excavation to rough grade. Above Middle: Setting slide rail panel on the building side of the project.of a four-story building with an active public street on the other side. “Working within such a confined area meant that the numerous truckloads of slide rail panels, posts, beams, and other miscellaneous shoring equipment had to be carefully scheduled. We could only fit so many panels onsite at a time so that our six crew members and construction machines had room to maneuver,” continues Campbell. “In all, we excavated around 5,000 cubic yards of dirt to complete the installation of the entire system. We took out a lot of cobbly material that had to be exported.
We had a screening operation onsite to separate the oversized material from the backfill spoils. Once the shrinkage was evened up, the remaining material was, again, exported offsite.”
Campbell says that most of the work onsite was accomplished with a Cat 330D excavator, a Cat 950 wheel loader, a Cat 446 backhoe, and a Cat 262 skid steer loader. “The excavator was used primarily for digging the trench and for placing the piles and slide rails. The wheel loader moved the dirt from point A to B, while the backhoe helped with excavation and pipe placement,” says Campbell. “The skid steer
was used for making grade at the bottom of the pit. Our operators drove the skid steer in, and then we lifted it back out later with the excavator. Every movement was calculated as we, again, did not have much room to maneuver.”
Jason Paulus says that his company has been using Trench Shoring Company for their shoring needs for as far back as he can remember. “Trench Shoring Company has been our go-to shoring source for at least the past 25 years. They are always there for us, on call anytime for any specific need, including help with engineering. Jim White is our representative in Orange County
and Ken Slaughter takes care of our needs in LA County. In the event we have a project outside of these areas, we know that Trench Shoring Company has several locations and delivers anywhere in California and Nevada,” says Paulus. “Choosing your shoring company really all comes down to knowledge and service. We needed a massive amount of slide rail and other shoring for this storage tank installation project, and we knew that we could trust Trench Shoring Company to deliver. Other companies said they could handle it, but we go with the trusted leader because we know without question it will show up at the
jobsite on time and without any issues.”
For more information on Paulus Engineering, Inc., please visit www.paulusengineering.com or call their Anaheim headquarters at (714) 632-3975.
For more information on Trench Shoring Company, please visit www.trenchshoring.com or call the location nearest you in Compton (headquarters), Bakersfield, Banning, Corona, Fresno, Fullerton, Lake Forest, Moorpark, San Diego, San Leandro and Las Vegas, NV. Trench Shoring Company corporate office at (310) 327-5554. Cc
Above Left: Placing ¾-inch rock base in pipe zone. Above Right: Beginning a new slide rail bay installation. Left: Encapsulating rock backfill in filter fabric.SMALL
The WORKMASTER™ 25S sub-compact tractor is the perfect “first step” tractor for homeowners and AG-lifestylers who need a hard-working, versatile small tractor to handle the chores a garden tractor just can’t. it’s ready to take on your yard, landscape, gardening and property maintenance jobs. Its compact size makes it easy to operate and maneuver around obstacles and in confined spaces
Civil Construction, Inc. was founded in 2006 by Jim Lumm and Geoff Bohne after both men had worked for some well-known civil general engineering contractors for several years. They made the decision, 17 years ago, to pool their civil engineering degrees and more than 35 years of combined experience to start their own venture. Lumm remembers that LB Civil Construction’s first bid was submitted in January of 2007, just before the bottom seemed to fall out of construction in California and throughout the country. Lumm says that he remembers thinking to himself at the time, ‘what have we done,’ concerning starting a heavy civil construction business at what was eventually referred to as the
Great Recession. However, the two men remained laser focused and fully determined to make their vision a firm reality that would stand the test of any current or future economic challenge.
Now, in 2023, LB Civil Construction, Inc. (LB Civil) performs between $20 to $25 million in civil general engineering work annually. The company maintains between 35 to 40 employees, including operators, laborers, office staff and management personnel. LB Civil holds an A-General Engineering and B-General Building license and qualify as a Hub Zone contractor and Small Business Enterprise (SBE) on both the state and federal level. “We brought in several talented individuals that both Geoff and I have worked with
in the past before starting our company. We have also hired other very talented people that we believe can contribute to help us all achieve the level of excellence necessary to grow and succeed in this competitive business,” says Lumm. “An example of these individual team members are Lance Lawton, R.J. Columna and Mike Stewart. All three of these men are leading the effort in one of our newest projects, the H Street Storm Drain Replacement Project in Chula Vista. Lance Lawton is our General Superintendent, R.J. Columna is our Project Manager and Mike Stewart is the Superintendent, and these three are overseeing the daily operations of this challenging Caltrans emergency repair project.”
Lance Lawton (Lawton) is one of the LB Civil team members that Lumm worked with before starting the company. Lawton is also the General Superintendent in charge of the H Street Storm Drain Replacement Project. “We received a call and a request from Caltrans to look at two storm drain sections located 70 to 80 feet below H Street that were beginning to fail. After surveying the situation, our original thought or solution was to consider relining the existing pipe, but Caltrans did not want to shrink the existing storm drain, so tunneling became the next viable option,” says Lawton. “We bid the job and immediately began work a few days after winning the contract from Caltrans. The first order of business was to locate exactly
Above: LB Civil crew installing one of the massive W14x233 whalers while also welding it to chairs for support.where the existing storm drains were running so that we could plot out the new alignment of the new sections. This process required extensive potholing to depths as far down as 50 feet. The existing storm drains are not straight and have several radius’ and those had to be located. We officially began construction in April 2022 and hope to be finished by July 2023.”
Once the potholing and internal surveying procedures were complete, LB Civil’s next step was to plot out where the connecting pit would be located. The receiving pit location for the two new parallel lines that would connect to the existing storm drain system was determined to be within the Terra Nova Shopping Center parking lot on H Street located on the eastside of the 805 freeway. “One of the first things I noticed was that H
Street was another 20 foot higher than the parking lot area. The receiving pit is essentially 77 feet by 32 feet with a 20-foot step with wood lagging and a ladder and ramp from 40 feet to ground level. So, the pit goes from zero to negative 40 feet before it drops another 20 to 25 feet,” says Lawton. “We used a Cat 335 and Cat 308 excavator to do most of the excavation on the receiving pit. The Cat 308 worked out well as it fit right underneath the whalers where there is a 12-foot separation. We also used a smaller Cat 303 mini excavator to clean up around the edges and it was lowered and extracted from the pit with the onsite crane.”
In order to install the two new replacement storm drain sections, it would be necessary for LB Civil to excavate two separate launch
pits for tunneling back to the receiving pit in the shopping center parking lot. “We started excavation of Launch Pit 1 in June 2022 as our crew began cutting down the slope and installing shoring to support tunneling for the initial bore. We utilized our Cat 349 and 336 excavators and a Cat 966 wheel loader to dig down 30 feet for Launch Pit 1. This equipment was used to begin clearing out and boring the eventual 700-foot-long tunnel,” says Lawton. “However, we used a Cat underground mining loader to hog out the tunnel spoils that were then dumped into large buckets and raised out of the pit with a crane. We were down as far as 80 feet with the bore on H Street and came out at a depth of around 65 feet deep to the receiving pit in the parking lot.”
Lawton explains that his crews used old style tunnel lagging and metal rings to protect and support the long tunnel excavations. The tunneling work was subcontracted to Golden State Boring and Pipe Jacking out of Chino. “Our subcontractor utilized a hydraulic boring machine to dig into the open face. As the dirt was carved out, the Cat mining machine would scoop and back out the spoils and then the metal rings and wood lagging would be installed to support the tunnel,” says Lawton. “We just pulled the head out on Tunnel 1 on February 13. After Tunnel 1 was complete, the wood tunnel lagging and metal rings were grouted in place and a concrete false bottom was poured. At this point the new 84-inch RCP storm drain was installed with a 6-inch angular space left around the new pipe.”
According to Lawton, the pit for Tunnel 2 is now complete and tunneling operations began in the third week of February. “Tunnel 2 is being excavated just like Tunnel 1, but it is a bit longer at 800 feet
because it has a longer overall radius. Our crews are doing as much as 100 feet per week, or around 20 feet on a good day. Between both Tunnel 1 and 2, approximately 2,200 linear feet of RCP will be installed due to some open cut areas connecting to the existing pipe,” continues Lawton. “The tunneling operations will be complete by March, but there is additional work that needs to be done that will take us into July or August. This work will include final grading, base and concrete flatwork and some landscape restoration in and around the shopping center. There are multiple radiuses within both tunnels and that and other unforeseen challenges can always affect cost, productivity, and timing.”
Lawton points out that once both of the new storm drain sections make it to the existing vault at the receiving pit, his crews will need to finish the job by connecting the new pipe to the existing junction box. “We will need to break out one of the walls on the vault and extend it out to encompass and hold the new pipe sections. We will
then seal off the existing underground wastewater pipe sections and backfill, grade and add aggregate material before paving over the affected parking lot area.”
The H Street Storm Drain Replacement Project would of course not be possible without plenty of safe and reliable shoring. LB Civil hired D.H. Charles Engineering out of Cardiff to design the shoring plans and McMahon Construction out of Lakeside to drill the piles and place the massive beams and plates. Additionally, Coyote Steel Services out of Phoenix trucked in the steel beams from numerous locations and Super Mario Welding in Escondido helped LB Civil with all of the welding. “For our shoring needs, we rely on Trebor Shoring Rentals (TSR) who has always been there for us over the last decade. We work with Pat Burton and Dana Fredette at TSR and they went above and beyond to get us the plates and the entire slide rail system for this important emergency project,” says Lawton. “Dana is always there to supply
whatever we need for our shoring needs, and I have known Pat since we were kids, and he always treats us right. I called TSR at 4:00 p.m. last Friday and they had the additional plates we needed onsite by 5:30 p.m. TSR also made sure that we had the various sizes of plates we needed, even bringing them in from Los Angeles and Phoenix. In all, we will make use of around one million pounds of steel for the shoring between the plates and the beams. We can only push the plates to 40 feet, so our crews constructed wood lagging for everything below that point.”
LB Civil Construction, Inc. is a diverse civil general engineering firm that provides a long list of mostly self-performed services,
including underground construction, structural concrete, flatwork, wet and dry utilities, rough and fine grading, as well as shoring and other earthwork disciplines. “Geoff and I are always looking for the best possible team members to work here at LB Civil Construction. We won’t settle for anything less and that is why our crews and support staff are known for providing such consistent quality and excellence on every job, big or small. We are very proud of not only our crews, but also our subcontractors and everyone at Caltrans for doing such a great job on this important emergency storm drain project,” says Lumm. “We designed this job and structures on the fly and have worked closely with Caltrans to
continually determine the best course of action. John Hanson from Caltrans has been great to work with on this project. His attention to detail and ability to remain proactive has helped us to move along quickly and efficiently. It is just amazing to see that by everyone working together, we are able to bore a tunnel around 1,000 feet through twists and turns and have the boring machine head come up perfectly within the receiving pit.” For more information on LB Civil Construction, Inc., please visit www.lbcivil.com or call their Escondido headquarters at (760) 294-0974. Cc
Imagine being able to travel by rail from Azusa to Long Beach or from East Los Angeles to Santa Monica without transferring lines. Well in just a few short months, passengers in LA County will be able to do just that. The new Regional Connector is a 1.9mile underground double-track light rail transit line in downtown Los Angeles that will immediately improve and bring together the connections between the Metro L
(Gold), A (Blue), E (Expo), B (Red) and D (Purple) Lines at the 7th Street/Metro Center Station. The nearly completed project includes three new underground stations and extends from the L Line (Gold) in Little Tokyo and Arts District communities to the A (Blue ) and E (Expo Lines) at the 7th Street/Metro Center Station. Tunneling work and construction began in July 2014 and is expected to be completed and open to users by May 2023.
The Los Angeles County Metropolitan Transportation Authority (LACMTA) contracted Regional Connector Constructors,
a joint venture between Skanska USA Civil West California District, Inc. and Traylor Brothers Inc., to design and build the Regional Connector Transit Corridor Project. The $1.4 billion project will complete a 1.9-mile gap with three new stations to include Little Tokyo/Arts District (1st Street/Central Avenue), Historic Broadway (2nd Street/ Broadway), and Grand Avenue Arts/Bunker Hill (2nd Place/Hope Street) in downtown Los Angeles. The project began at the existing 7th Street/Metro Center Station as the new underground alignment extends north underground from the 7th Street/Metro Center Station following Flower Street, curving east under the 2nd Street roadway tunnel and 2nd Street, and continuing east under the intersection of 1st and Alameda Streets, surfacing to connect to the Metro Gold Line tracks within 1st Street at grade to the east and north of Temple Street toward Union Station. In all, around two miles of underground guideway tunnels were bored, along with substantial cut and cover to complete the three stations.
Justin Waguespack serves as VP of Operations for Skanska USA Civil West California District, Inc. Waguespack has been on the Regional Connector Transit Corridor Project since 2015,
representing several roles and responsibilities including Station Manager, Construction Manager, and now serving as Project Director overseeing all scopes of construction. “All three stations are substantially complete with around 98 percent of the architectural finishes and systems in place. We are currently in the final stage, referred to as testing and commissioning, where we have installed devices and systems throughout each station that allows for system integration testing,” says Waguespack. “We are in the home stretch as we report back to ROC (Metro Rail Operations Center) and send our testing results to CPUC (California Public Utilities Commission) to receive certificates of occupancy. We hope and expect to see everything up and running by mid-to-late May.” Waguespack further explains that the Regional Connectors Joint Venture’s current contract is scheduled to come in at between $1.25 to $1.3 billion, a number that does not include LACMTA’s portion.
Waguespack says that while Skanska USA is the majority and managing partner on this project, Traylor Bros., Inc. also brought a lot to the table.
“Traylor Bros. brings a long and successful history of underground construction and tunneling expertise. We felt that it was of utmost importance to partner with a company, like Traylor Bros., which has so much experience in this type of work. The joint venture purchased the Herrenknecht Tunnel Boring Machine (TBM) and self-performed all of the mining and maintenance,” says Waguespack. “Metro is running trains in both directions, so of course, it was necessary to mine twin tubes down the entire alignment. So, this was a 5,760-foot twin tunnel operation with an excavated diameter of 21.5 feet per tunnel. We first launched in one location and mined that entire alignment. Our crews then dismantled the TBM and brought it back to the start, where we once again began mining another tunnel immediately adjacent to the previously completed section. The tunnel depth ranged from 21 feet to 120 feet, with each underground station being around 400 feet in length.”
According to Waguespack, the construction of the Regional Connector Transit Corridor Project required careful coordination between both the TBM excavation and the cut-and-cover operations. “Our crews performed around
2,100 feet of cut-and-cover and retained cut guideway. We also used the sequential excavation method (SEM) to excavate a 300-foot-long cross-over cavern at the Historic Broadway Station. This required thoughtful engineering and monitoring during construction due to the inherent risks associated with this technique,” says Waguespack. “We would essentially push ahead five feet at a time with the TBM and then bring in five individual segments that would create an entire ring to support the tunnel walls. Each prefabricated segment included both inside and outside gaskets (double gaskets) that butted up against the previous section. Once in place, this is the final lining that will be viewed out the window by more than 88,000 users each day.”
Incursions from structural supports of highrise buildings along Flower Street was viewed as a potential challenge and obstacle. So, the decision was made to construct the tunnel via 1,400 linear feet of cut-and-cover. “They did not want mining with the TBM in this particular area on Flower Street as we tied into 7th Street. So, we instead excavated down 55 feet and at a width of around another 55 feet,” says Waguespack. “These giant holes had deck beams on top and concrete panels so the traffic could drive over the pit during construction. Our crews self-performed 100 percent of the beam and lagging, in addition to all of the pile work. We calculated that we utilized around 20 miles of I-beam piles if lined up end to end.”
Pressure balance tunneling utilizing a EPB (Earth Pressure Balance) TBM (Tunnel Boring Machine) turns the excavated material into a soil paste using soil conditioning that makes it possible to balance the soil pressure at the tunnel face. This allows the excavated soils to be used directly as a support medium. The soil enters the excavation chamber, where it mixes with the soil paste already in place. The pressure in the excavation chamber is continuously monitored using pressure sensors. “For stations construction, we worked within confined areas, and the excavation was primarily vertical. The
{ Continued on page 24 }
entire excavated sections were approximately 80 feet deep, 350 feet long, and 50 feet wide. That is like excavating an entire football field straight down,” continues Waguespack. “We utilized tiebacks, as well as struts, and as we excavated down, we relied primarily upon smaller excavators that fed the large Liebherr crane above with 5-yard muck buckets full of the slurry soil. Most of the spoils were trucked to places like Irwindale where the material was dumped and spread out in pits to dry before being compacted. Any non-contaminated dirt material was processed and stockpiled in a yard on Mission Avenue for later use as backfill.”
The Regional Connector Transit Corridor Project also called for the relocation of wet and dry utilities throughout the Downtown Los Angeles work area. “The wet and dry utilities located under this historic downtown Los Angeles area are some of the oldest in the entire region. The fragility of some
of these utilities made it more difficult to handle during excavation,” says Waguespack. “The relocation of utilities was more extensive than we first anticipated as much of the utility relocation scope was transferred to us from another existing contract. This required us to redesign, replace or relocate much of the underground infrastructure, which impacted both the schedule and budget.”
Waguespack makes it clear that as rewarding as this project was to everyone involved, it did not come without its challenges. “This was an extremely challenging project, and what looks good on paper can often be a different story when you get out into the field and begin construction. The top of Historic Broadway Station, for instance, has what we call a load transfer system, and it contains a tremendous amount of rebar and high-strength concrete. This called for mass concrete operations where our crews continuously monitored temperatures and utilized specialized blankets to ensure that the super hot concrete
was not going to flash off too quickly,” says Waguespack. “There were other challenges during the tunnel boring process, including areas with as little as 7 feet of clearance. Additionally, there were abrupt changes that required the need for a 4.5 percent downward mining grade into a 600-foot horizontal curve. Also, during the first reach of TBM tunneling, our crews ran into abandoned steel shoring piles from previous construction. The TBM is not designed to excavate through steel supports, but we were able to mine through these piles due to our skilled operators. We did, however, have stoppages to repair the cutting tools, but that time was more than made up on the following tunnel drive.”
Mining underneath the Red Line was also a major challenge for the Regional Connector Constructors Joint Venture. “We installed instrumentation within the existing Red Line tunnels so that all of the mining was constantly monitored for movement and unanticipated settlements. This is particularly important as the new tunnels pass within 6 feet below the
existing Red Line tunnels,” says Waguespack.
The Regional Connector is expected to attract nearly 17,000 new daily riders and will save passengers as much as 20 minutes off their daily commutes. “It is not an overstatement to say that it is a once-in-a-lifetime opportunity to be a part of a project like this Regional Connector Project. There is so much to be proud of, including everything from the
technicality of the entire scope of work to the amazing safety culture maintained throughout this multi-year project,” concludes Waguespack. “I want to thank everyone that contributed to the success of this massive endeavor and wish I could do that by name. I will, however, recognize and thank Paul Kennedy, our Superintendent, who has been here and done an amazing job almost from the very beginning.
I also want to recognize Jerry Mendoza and Mike Benton, our Safety Directors, who helped bring in a first for both the Metro and both Joint Venture partners. I am referring to almost 6.7 million work hours with zero lost time and a 0.72 recordable incident rate. That is just unheard of and there is never anything more important than safety.”
The total project cost under the Full Funding Grant Agreement (FFGA) is $1,402.93 million. The Section 5309 New Starts funding share is $669.90 million. The project is also partially funded by Measure R, the half-cent sales tax increase approved by Los Angeles County voters in 2008 and by a $670-million federal New Starts grant and $160-million federallybacked TIFIA loan. For more information about the Regional Connector project, visit metro.net/ projects/connector. Cc
Jack Massachi started working as a cable installer in 1985, during that time he took on a variety of roles for different companies within the telecommunications industry. He acquired his contractor’s license in 1989 and started doing some cable wiring work on the side for apartment builders and developers within the San Fernando Valley. During this time, Massachi began developing relationships with cable infrastructure contractors and decided to go out on his own in 1993 to begin operating as a subcontractor for these telecommunication companies. “I started with just one employee, and we did not have a lot of experience performing underground construction. So, I spent some time watching gas company crews using underground boring machines and eventually rented a machine and learned that way,” says Massachi. “We eventually decided to purchase our own Vermeer directional
drilling machines and several mini excavators and other equipment as we continued our growth and expansion.”
Massachi points out that as an immigrant, he always had the mentality that he wanted to learn a trade and have his own company one day. That day finally arrived 30 years ago, but it was far from easy. “It all started slowly with a lot of growing pains, and I had to wear numerous hats. As our workload increased, a few individuals that I had worked with at other companies decided to come on board,” says Massachi. “After a
year of struggling, the Northridge Earthquake hit in 1994, and our workload shot up dramatically to where we expanded into two crews and added aerial and underground construction capabilities. We continued our growth slowly and sustainably. Our next growth area will be in installing and maintaining EV charging stations to support the burgeoning electric vehicle revolution. The last 30 years have been challenging, gratifying and exciting, and we all look forward to what the next 30 years have in store.”
JM Utility Services is a telecommunications contractor that also performs other dry utility construction. “The majority of our work is for AT&T, installing fiber optic cable and other services. We have a vendor contract with AT&T in two specific regions in the San Fernando Valley. We started with this program around five years ago and are on call with AT&T 24 hours a day,” says Massachi. “A perfect example of this would be last Friday when we were called on an emergency project where
issues from recent rains caused 40 customers to lose service. We went out and worked on a Saturday to dig around 400 feet of trench to place new cable in the street. This is the lifeblood of our business right now, but we are also beginning to expand to be a preferred subcontractor to other companies that may need our underground utility expertise for telecommunications and other dry utilities. For instance, we perform a lot of electrical work and have sub-electricians working for us as needed.”
According to Massachi, JM Utility Services uses AT&T’s own platform to manage and complete construction projects for AT&T. “A typical job will come to us electronically. From there, we will call for someone to perform the USA (Underground Service Alert) markings on the job, do any initial construction prep, and schedule a preconstruction meeting with the city or agency. Once the preconstruction work is complete with the city inspector and we have the appropriate documents in hand, we schedule the job, review with the foreman, and then send out the proper equipment and crew to the jobsite,” says Massachi. “We may be on an AT&T job for a day, a week or several weeks. It all depends on the scope of work and what needs to be done. Once the work is complete, we notify AT&T that the job is ready for cable installation that may be performed by their crew or ours. We work all the way up to the point of entry at the side of a residential home if necessary. The last step is to get final inspection from the city or other agency.”
JM Utility Services also performs telecommunications and other dry utility work for builders and developers. “Our crews can do it all, including placing power conduits on the right-of-way and onsite for the developer, or setting
a vault and placing conduits for private construction companies,” continues Massachi. “No job is too large or too small. Today, for instance, we have eight crews working out in the field. One crew is replacing a deteriorated manhole, another is excavating to remove damage and blockage to conduit from tree roots and several other crews are excavating for new cable installations. We do it all, down to traffic control for AT&T if necessary. We are in the communications business, and to be the best in this business, it is really all about communication. Next to safety, this is the single most important aspect of dealing with each of our valued customers. We must always be accessible and treat our clients with the utmost
professionalism and respect. That is how and why our company will continue to grow and prosper.”
Massachi says that the work his company performs would not be possible without the equipment his crews rely on each day. “We were one of the first utility companies in Los Angeles to make the move from backhoes to mini excavators back in the 90s. Compact excavators are just a better solution to today’s tight working conditions,” says Massachi. “Today, we have an entire fleet of compact and midsized excavators from John Deere and Yanmar. We go with Case skid steer loaders, and our directional drilling machines are all Vermeer.
JM Utility Services has a reputation for being a family-
oriented company that respects and works well with co-workers and customers alike. The company has many long-term employees of 22 years and more. JM would not have grown to where it is today without its dedicated and key employees. It is clear that everyone at JM Utility Services loves working with and for Jack Massachi and his wife, Shannon, who works hard to manage the legal and other administrative duties. JM Utility Services works throughout Southern California with the bulk of their work in Los Angeles County, Ventura County, Orange County and the Inland Empire. For more information, please visit www.jmutility.com or call their Van Nuys headquarters at (818)901-9898. Cc
After five eventful days, ConExpo-Con/Agg came to an end on Saturday, March 18, 2023. More than 139,000 registered attendees from 133 countries made their way through this mega Las Vegas convention. There were also more than 2,400 exhibitors from 36 countries spread out over 3 million square feet of exhibit space, making ConExpo-Con/Agg the largest
single trade show in North American history.
Case
made a big splash at the ConExpo with a massive display that included several new machines. Leading from the theme, “The New CASE ,” the company showcased groundbreaking new equipment, exciting new partnerships, and a range of new solutions designed to help contractors get more work
done, easier, and more profitably than ever before.
Dozens of representatives from Sonsray Machinery were also on hand at the ConExpoCon/Agg show, as were many of their customers from Sonsray’s distribution areas in California, Washington, Oregon, Nevada, Arizona, New Jersey and New York. Sonsray Machinery treated their VIP customers to a very
special evening during ConExpo on Tuesday, March 14. Doing business with Sonsray Machinery and purchasing Case equipment can certainly have its advantages, as more than 200 Sonsray customers attended the Pre-Pardi Appreciation Event at the High Roller Wheel in Las Vegas.
Sonsray customers began showing up at 5:00 pm for cocktails at the Pre-Roll Event Space. The majority of the VIP clients were construction equipment customers, but there were also several agricultural and transportation buyers in attendance. 125 of these customers chose to take a ride on the High Roller Observation Wheel that soars 550 feet above the center of the Las Vegas Strip. Sonsray customers gathered 25 per cabin for a 30-minute rotation on the amazing High Roller Wheel that featured a full open bar. “The idea was to bring our valued customers into an event that would leave them with something to talk about after the show. We wanted to provide them with a unique experience that would also allow for some quiet, personal time to better build upon our relationships,” says Shawni Young, Director of Marketing for Sonsray. “We brought in 50 employees, from all territories and divisions, to support our customers, the
appreciation event, and the ConExpo convention. The High Roller Wheel cabins also allowed our account managers, project managers, and Sonsray executives to rotate throughout the numerous High Roller cars to meet and get to know our customers a little better. The last High Roller Wheel rotation was at 6:15, which allowed plenty of time to escort our customers across the street to the John Pardi Concert at the Brooklyn Bowl, sponsored by CASE Construction Equipment .”
Every Sonsray customer left the High Roller Event with VIP pins, Sonsray hats, and tickets to the John Pardi Concert sponsored by Case Construction Equipment. Each complimentary hat included a QR code with information on Sonsray, and two of these particular QR codes also featured a GOLD STAR, letting that lucky customer know that they had just won a YETI Roadie 24 Cooler. A great time was had by everyone, as the High Roller Wheel and John Pardi Concert may have just been the highlight of the ConExpo for many of the Sonsray customers. For more information on Sonsray Machinery, please visit www.sonsraymachinery.com or call 844-SONSRAY. Cc
1) Billy and team from 108 Excavating. 2) LGP Equipment Rentals out of Fontana with Sonsray General Manager Bryan Bernardino (far Right). 3) Greg Nordsiek and team from JP Excavation. 4) Rick and Juan from Fallbrook Equipment with Sonsray VP Richard Abbajay and Account Manager Crystal Vallombroso out of San Diego. 5) Cocktail reception at the Pre-Roll Event Space. 6) Anna McClendon (left), Executive Assistant to Sonsray CEO and Shawni M. Young, Director of Marketing.Effective April 1, 2023, Clairemont Equipment Company will be expanding its current Komatsu territory from San Diego north into the Los Angeles area, becoming the authorized sales and service provider of Komatsu construction equipment for all of southern California.
Specifically, Clairemont Equipment will be adding the southern California counties of Riverside, Orange, San Bernardino, Los Angeles, Ventura, Kern, Santa Barbara and San Luis Obispo to its existing territory of San Diego and Imperial counties. Clairemont’s headquarters will remain in San Diego, and they will service the new territory out of their existing facilities in Fontana and Indio, California, along with their other branches in Escondido and Imperial, California.
Clairemont inherits the sales and service of Komatsu construction equipment in this territory from Road Machinery. Road Machinery will continue serving as the authorized OEM distributor of
Komatsu mining-related equipment, parts and service in the territory.
About Komatsu
Komatsu develops and supplies technologies, equipment and services for the construction, mining, forklift, industrial and forestry markets. For a century, the company has been creating value for its customers through manufacturing and technology innovation, partnering with others to empower a sustainable future where people, business and the planet thrive together. Frontline industries worldwide use Komatsu solutions to develop modern infrastructure, extract fundamental minerals, maintain forests and create consumer products. The company’s global service and distributor networks support customer operations to enhance safety and productivity while optimizing performance. To learn more about Komatsu, visit https://www.komatsu.com/
About Clairemont Equipment
Clairemont Equipment company, a family business owned and operated by the Zagami family, has been providing best in class sales, service and rentals of heavy equipment to the southern California market since 1970. From its humble beginnings as a homeowner rent-to-rent business, brothers Ron and Jerry Zagami have grown the business to a full line heavy equipment dealer with six locations in southern California, and an impeccable reputation for unparalleled customer service.
Patrick Doheny from Australia won the final competition alongside other awards presented by Caterpillar during CONEXPO-CON/AGG 2023
More than 5,500 machine operators worldwide have been competing in the Caterpillar Global Operator Challenge since the spring of 2022, and today, one of them emerged as the “World Champion” – the best Cat construction machine operator on the planet.
On Tuesday, March 14, Patrick Doheny of Australia took the crown out of nine finalists from around the world who competed in the final round of the Global Operator Challenge in the Cat Operator Stadium in Las Vegas.
Caterpillar’s year-long Global Operator Challenge is one of the largest construction industry events, with operators from nearly three dozen countries participating. The Challenge highlights the amazing ways construction machine operators masterfully guide Cat machines and use the latest technologies to get the job done.
“Caterpillar created this competition to celebrate machine operators who build our world, advocate and drive awareness for their trade, and highlight solutions that address jobsite challenges,” said Jason Hurdis, Caterpillar
Lead and Global Market Professional. “All of the competitors – and especially our nine finalists – showed tremendous skills and abilities operating the latest Cat construction machines and technologies, maneuvering through some difficult challenges and showing the world the invaluable role they play in infrastructure creation.”
The Challenge kicked off in the spring of 2022 with more than 10,000 operators worldwide signing up to compete. After a prequalification phase, the first round featured 5,500 contestants competing in local events organized by 77 Cat dealers in 32 countries. The second round in the fall of 2022 consisted of four regional events held in the United States, Brazil, Spain, and Japan. These competitions included digging a trench, loading a precise amount of dirt, and hauling or maneuvering the machines through obstacles.
The third and final round this week in Las Vegas was the ultimate test of precision. Grouped into teams of three – Team Americas, Team Europe, and Team Asia – the
nine finalists competed individually and as teams, as they faced three challenges in a specially constructed stadium featuring stands, fans, big-screen TVs, and play-by-play announcers.
The finals kicked off with the “Fork ‘n Loader” challenge, where each operator used the Cat 950 wheel loader with Payload technology to load and move material through specified locations on the course. The “Backhoe Services” challenge had operators using both ends of the Cat 420 XE backhoe to open a small box and precisely place small objects inside. This challenge was designed by Jaus Neigum, the 2020 Caterpillar Global Operator Challenge World Champion, and highlighted Caterpillar’s Customer Value Agreements and services offerings. During the final “Trench Run” challenge, operators showed off their trenching skills using a Cat 315 excavator equipped with Grade technology.
Final scores were based on the operator’s skills, efficiency, and competence in executing a variety of tasks, with penalties imposed for
errors. Awards were given to the overall event champion, the individual with the lowest time in each skills challenge, and the team with the lowest combined score. The operators completed the challenges using Cat construction machines integrated with the latest machine-control and payload technologies, including Cat Payload, Grade and Command, Cat Grade Assist, rearview cameras, return to dig and return to carry.
Patrick Doheny from Australia was crowned the champion. Caterpillar awarded him with a trip for two to a location where Caterpillar has one of its worldwide production facilities.
“I am beyond thrilled to have earned the title of the best Caterpillar machine operator on the planet,” Doheny said. “Kudos to Caterpillar for hosting such an incredible event to highlight the importance of our profession. It is truly a dream come true to see your life’s passion be rewarded in such an amazing way.”
In second place was Matt Ferris from the United States, and third place was awarded to Łukasz Mokrzyński from Poland. Other awards presented were:
• “Fork ‘n Loader” challenge winner – Patrick Doheny from Australia
• “Backhoe Services” challenge winner – John Schiedeck from the United States
• “Trench Run” challenge winner – Łukasz Mokrzyński from Poland
• Team champion Team Americas (Fernando Do Nascimento from Brazil and Matt Ferris and John Schiedeck, both from the United States)
The Nine Finalists Representing Europe, Africa, and the Middle East:
• Sebastian Behr – Germany (placed third in the 2019/2020 Caterpillar Global Operator Challenge) with 35 years as an operator
• Pontus Ericksson – Sweden with 11 years as an operator
• Łukasz Mokrzyński – Poland with 15 years as an operator
Representing the Americas were:
• Fernando Do Nascimento –Brazil with 28 years as an operator
• Matt Ferris – United States (Arizona) with 20 years as an operator
• John Schiedeck – United States (Texas) with 16 years as an operator
Representing Asia-Pacific were:
• Patrick Doheny – Australia with 25 years as an operator
• Masato Imai – Japan with 20 years as an operator
• Nick Thompson – Australia with 15 years as an operator
For more information about the Caterpillar Global Operator Challenge, please visit www.cat.com/operatorchallenge.
From Commercial & Residential to Government & Municipality projects, we offer a large variety of industry-leading construction equipment solutions.
And we back our equipment with professional Service & Parts departments to ensure your machines are always hard at it!
The 300|AT features unmatched transportability, able to move its 162,000 maximum counterweight in only 4 over ow loads. Link-Belt’s newest AT offering maintains the great capacities, reliability and performance that’s it predecessors are known for. The 300|AT
Lifting Highlights
Featuring a seven-section, 46- to 238-foot pin and latch greaseless formed boom, the 300|AT has a 369-foot max boom tip height.
Under the Hood
The 300|AT is powered by a 554-horsepower Cummins X15 diesel engine with ZF Traxon automated manual transmission.
In the Cab
Like the 175|AT, the 300|AT has a two-person carrier cab with an air ride seat, a 10-inch touch display, automatic climate control, blue tooth radio, cellphone charging and LED lighting.
Other standout features of the 300|AT include:
• Wireless rigging remote (carrier function, upper function, fly erection)
• Tire pressure and temperature monitoring system
• SmartStack counterweight detection system
• 8’ Heavy Lift Jib for 2 line lifting applications
• 71' two-piece Link-Belt SmartFly