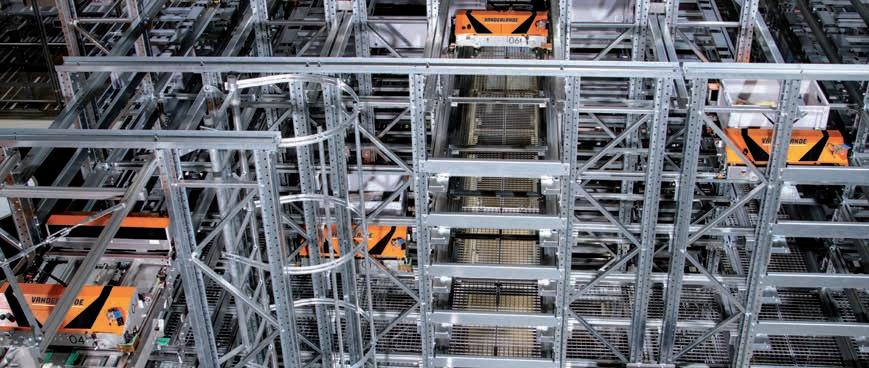
3 minute read
I De servicio mayorista a una preparación de pedidos unitaria
Instalación realizada con el sistema de roaming shuttles ADAPTO 3.0 de Vanderlande.
De servicio mayorista a una preparación de pedidos unitaria
Vanderlande entrega una solución tecnológica transformadora a De Bondt B.V.
La empresa holandesa De Bondt, mayorista mundial de artículos de mercería e hilados, cuenta con clientes en más de 70 países en todo el mundo. En 2020 Vanderlande recibió el encargo de idear un nuevo sistema de picking capaz de responder al alto crecimiento experimentado por la empresa en los últimos años.
La segunda generación de esta empresa familiar había comprendido que para mantener sus habituales altos niveles de servicio en todo el mundo, debía replantearse su estrategia y estructuras logísticas, haciéndolas a la vez más grandes y más flexibles a los distintos perfiles de pedidos. El primer paso fue tomar consciencia de que era preciso avanzar hacia estrategias producto a persona. Esto supuso sustituir el concepto existente de preparación con carritos y RFID, que implicaba largos recorridos por el almacén en busca de cada SKU y una verificación posterior para corregir los errores de un proceso manual. Por otro lado, era muy conveniente dar una solución.
Vanderlande como integrador
El proyecto integrado por Vanderlande se instaló en las fechas previstas y está en esto momentos en fase de ramp-up, añadiendo más y más referencias al sistema. De forma evidente, se ha aumentado la densidad de almacenaje (con más de 22.000 ubicaciones en doble profundidad), lo que también ayudará a ampliar el catálogo. La solución de almacenaje y secuenciación es el AS/RS ADAPTO de Vanderlande, un sistema flexible y escalable con características en 3D basado en roaming shuttles. Gracias a su capacidad multidireccional es muy fácil entregar los productos a la estación de preparación de pedidos en el orden correcto, “con lo que la preparación es mucho más eficiente y precisa que antes”, señalan desde Vanderlande. Esto facilita las entregas en el mismo día, una capacidad de respuesta que De Bondt recalca en su web.
La instalación extrae y envía la referencia precisa a la estación de picking, sin secuenciadores intermedios o bucles adicionales. El sistema permite a los operadores concentrarse en un solo pedido a la vez, en estaciones de trabajo que mejoran significativamente las condiciones de trabajo. La entrada/salida al sistema se ha diseñado como un circuito independiente, con líneas de reabastecimiento separadas en las que los contenedores vacíos pueden salir y entrar del sistema sin interferir el flujo de trabajo. El proceso de embalaje está automatizado con una formadora de cajas de cartón, insertadora de paquetes, cerradora y aplicador de etiquetas. Los operarios preparan directamente los pedidos en cajas de expedición, asegurando un proceso simple y productivo. Por último, las cajas de pedido se envían al clasificador de salidas para carga y expedición a cualquier sitio del mundo.
Pensando en el futuro
De entrada, la inversión en ADAPTO es la correcta para el escenario de diseño. Si el centro de distribución necesita cambiar en el futuro, su configuración adaptable y escalable le permite ir ampliándolo paso a paso. En este sentido, se pueden agregar pasillos y/o estaciones adicionales en la proporción que sea más apropiada en el momento, sin rigideces. De hecho, es posible hacer esta tarea mientras el sistema está funcionando.
En los momentos de máxima producción, se pueden agregar más shuttles de forma inmediata para ayudar a hacer frente a la demanda extra, que precisamente era algo muy necesario en el caso de De Bont. Este diseño modular ha permitido a De Bondt hacer un uso óptimo de todo el espacio existente en las instalaciones actuales, dejando las puertas abiertas a cualquier tipo de adaptación futura. Como señala Luis Escobedo, Branch Manager de Vanderlande para Iberia: “Todas las empresas requieren mayor flexibilidad y escalabilidad en sus procesos de almacén. La tecnología apropiada está disponible, de modo que se puede invertir lo justo hoy para beneficiarse de inmediato de una automatización de vanguardia”
EL SISTEMA IMPLANTADO,
PUNTO POR PUNTO
◗ Estanterías ADAPTO (22.176 posiciones) con almacenaje a doble profundidad. ◗ Sistema de roaming shuttles ADAPTO 3.0 para almacenamiento y recuperación automáticos (en secuencia estricta) de cubetas seccionadas, con dos ascensores y tres buffers en rack y 22 shuttles (820 DC/h). ◗ Dos puestos de trabajo ergonómicos GtP para preparación directa de pedidos. ◗ Puestos de trabajo multifuncionales para limpieza, picking, reabastecimiento y desfragmentación. ◗ Transportadores de reabastecimiento ADAP-
TO (dot.M), suministro automático y retirada de cajas de pedido, rutas de envío para almacenar el pedido, cajas de cartón y clasificación a tres destinos diferentes. ◗ Proceso de embalaje automatizado con una formadora de cajas de cartón, lista de paquetes, cerradora y aplicador de etiquetas. ◗ Software VISIÓN (HLC).