
31 minute read
Soluções Técnicas: Lucchini RS Group, voestalpine, Ramada, TEandM e Oerlikon Balzers Portugal
52 O PAPEL DOS AÇOS-FERRAMENTA NA INDÚSTRIA DE MOLDES PARA COMPONENTES PLÁSTICOS E FUNDIÇÃO INJETADA DE LIGAS LEVES
Departamento de Forja e Fundição - Lucchini RS Group
A Lucchini RS, pertencente ao grupo da família Lucchini, é especializada na conceção, produção, industrialização e comercialização de produtos siderúrgicos de alta tecnologia para uma ampla gama de sectores industriais. É líder nos mercados internacionais de produtos ferroviários, forjamento de lingotes, fundições de aço, forjados personalizados e aços-ferramenta e, graças à sua produção estratégica, a subsidiárias de venda e a uma ampla rede de distribuição, comercializa os seus produtos em todo o mundo.
Uma particularidade deste Grupo é poder realizar e controlar todas as etapas da cadeia produtiva do aço, desde a conceção, passando pelo fabrico até ao produto acabado. Cada aspeto é apoiado por pesquisa e desenvolvimento constantes, usando equipamentos sofisticados e pessoal altamente qualificado para fornecer materiais e produtos cada vez mais seguros e confiáveis e para desenvolver e industrializar novos produtos que atendam aos requisitos cada vez mais exigentes do mercado.
Após investimentos significativos desde o ano de 2010 nas instalações de produção, equipamentos e nas atividades de marketing e comercial para o sector ferroviário (que ainda estão em andamento), a partir de 2015 a Lucchini RS abriu uma nova temporada de mais investimentos no sector de forjados, do qual os aços-ferramenta são cada vez mais uma parte estratégica, confirmando o seu compromisso com o desenvolvimento contínuo de todas as linhas de negócio do Grupo.
Dois marcos do investimento referido foram, por um lado, a aquisição da empresa com sede em Cividate Camuno (Brescia, Itália) agora conhecida como Lucchini Mamé Forge, que permitiu ao Grupo aumentar significativamente a sua capacidade e gama de produtos forjados; por outro lado, a aquisição da empresa hoje conhecida como Lucchini Tool Steel, Centro de Serviços para aços-ferramenta localizado em Suisio (Bérgamo, Itália), que mais uma vez destaca o foco da Lucchini RS em desempenhar continuamente um papel de liderança nestes produtos por meio do fortalecimento e expandindo a sua posição em todos os principais mercados internacionais, um dos quais é certamente Portugal. A este respeito, importa referir que, para este mercado, a Lucchini RS pode contar com a experiência e a competência profissional de uma das suas mais antigas parceiras, a Ferrolmarinha - Comércio de Acessórios Industriais, Lda. (Marinha Grande, Portugal), que é o seu distribuidor exclusivo de aços-ferramenta em Portugal há mais de 15 anos.
Os critérios utilizados para avaliar o desempenho dos moldes de aços-ferramenta para componentes plásticos e para fundição injetada de ligas leves são muito diferentes daqueles aplicados a outros componentes fabricados por aços estruturais. Enquanto para os últimos, a vida presumida é igual à vida da máquina da qual são componentes, para os aços-ferramenta, quer para plástico, quer para aplicações de trabalho a quente, não há limite máximo de vida.
Quanto mais a ferramenta conseguir manter a sua forma, condição de superfície e características, mais será apreciada pelo seu utilizador, na medida em que a sua vida útil está geralmente ligada à rentabilidade dos próprios processos.
Portanto, as ferramentas ideais podem ser consideradas a base para um processo rentável, enquanto as ferramentas abaixo do ideal afetam negativamente a eficiência e o processo de produção rentável da melhor máquina.
Em geral, a vida do molde depende de muitos fatores: alguns deles estão relacionados com o processo ao qual o molde é submetido; outros podem ser direta ou indiretamente influenciados pelo produtor de aço, como o tipo de aço utilizado, a qualidade de fabrico, o processo de transformação a quente e o procedimento de tratamento térmico.
As características exigidas dos aços-ferramenta para fornecer o desempenho necessário para o fabrico de moldes ótimos são múltiplas e muitas vezes em contraste entre si, no sentido em que o aumento de uma propriedade pode levar à redução de outra, conforme mostrado na Figura 1, onde a referência é especificamente a família dos aços para ferramentas para trabalho a quente.
Além disso, os tipos de aço usados para moldes de componentes plásticos requerem simultaneamente muitas propriedades, em que algumas características estão em contraste entre si: alta dureza, maquinação, temperabilidade, alta tenacidade, resistência ao desgaste, resistência à corrosão de polímeros de substâncias agressivas, polimento, apta para fotogravura, soldabilidade.
Utilizados na produção de moldes para componentes plásticos, os aços diferenciam-se dos aços-ferramenta para trabalho a quente, pois não são submetidos a altas temperaturas, mas as suas condições de utilização devem atender a requisitos rigorosos e a elevados padrões de micro pureza e micro homogeneidade do aço.
Os tipos de aço para moldes de plástico podem ser divididos em três famílias principais, dependendo do processo de fabrico do molde: préendurecido, recozido, endurecido por precipitação.
Dentro de cada família de aços, podemos fazer uma distinção entre os que são resistentes apenas ao desgaste e os que também são resistentes à corrosão, que geralmente são tipos de aço inoxidável.
A Lucchini RS oferece aos seus clientes uma ampla e abrangente linha de aços para moldes de componentes plásticos para atender a todas as necessidades, mesmo as mais exigentes. Por exemplo, o Quadro 1 mostra a gama dos principais aços préendurecidos e aços recozidos para moldes para componentes plásticos oferecidos pela Lucchini RS.
No que se refere aos moldes para componentes plásticos, a categoria de classes mais utilizada é a dos aços pré-endurecidos, que são processados principalmente por maquinação e/ou maquinação por descarga elétrica (EDM).
Um dos pontos-chave para a utilização de aços pré-endurecidos é a necessidade de obtenção de propriedades homogéneas em blocos de grande porte, o que está relacionado com a temperabilidade do material, a espessura do bloco e o processo de tratamento térmico. A dificuldade de combinar todas estas características e procedimentos é agravada pela grande quantidade de material que deve ser retirado para chegar à forma do molde, que converte em limalhas a parte mais endurecida do forjamento.
Portanto, para atingir o melhor compromisso possível, é necessário visar o aumento das características “diretas”, ou seja, aquelas de interesse mais imediato, como a dureza e a resistência ao desgaste, ao mesmo tempo que se salvaguardam as características “indiretas” como a ductilidade e a tenacidade.
Lucchini RS principais Aços-ferramenta Pré-endurecidos Não-
Corrosivos Resistentes para Moldes de Componentes Plásticos KEYLOS®1730 Aço-carbono básico para moldes pequenos e protótipos. KEYLOS®1730M Aço-carbono especial para moldes pequenos e protótipos. KEYLOS®7225 Aço básico pré-endurecido para moldes pequenos.
KEYLOS®2311 Aço pioneiro para moldes pré-endurecido com boa maquinabilidade e bom para polimento. KEYLOS®2312 Aço pioneiro para moldes pré-endurecido com excelente maquinabilidade
KEYLOS®UP Aço especial e inovador pré-endurecido com bom endurecimento de penetração e maquinabilidade KEYLOS®2738 Aço pioneiro pré-endurecido para moldes grandes: homogeneidade muito boa de dureza e maquinabilidade. KEYLOS®PLUS Aço inovador pré-endurecido: dureza homogénea em toda a secção, boa maquinabilidade e fácil soldagem de reparo. KEYLOS®2738 Aço para moldes pré-endurecido: excelente MHH endurecimento ao longo do bloco, especificamente concebido para peças muito grandes. Melhor rácio entre dureza de núcleo e tenacidade KEYLOS®2002 Aço inovador pré-endurecido adequado para os moldes mais exigentes de médio/grande porte para componentes plásticos ESTÉTICOS ESKYLOS®2002 Versão ESR do KEYLOS®2002 com excelente capacidade para polimento.
BEYLOS®2711 Aço pré-endurecido concebido para moldes médios para componentes plásticos ESTÉTICOS KEYLOS®6959 Aço especial pré-endurecido para moldes de tamanho médio sujeitos a pressão a baixas e altas temperaturas que requerem grande tenacidade.
ESKYLOS®6959 Versão ESR do KEYLOS®6959
Lucchini RS principais Aços-ferramenta Recozidos Não-Corrosivos Resistentes para Moldes de Componentes Plásticos BEYLOS®2343 Aço recozido adequado para moldes para componentes plásticos ESTÉTICOS BEYLOS®2344 Aço recozido adequado para moldes para componentes plásticos ESTÉTICOS ESKYLOS®2343 Versão ESR do BEYLOS®2343 excelente para polimento. ESKYLOS®2344 Versão ESR do BEYLOS®2344 excelente para polimento. Com referência aos moldes para fundição injetada de ligas leves, é bem conhecido que o piro fissuramento e a fratura frágil são os dois principais mecanismos de dano que produzem o fim da vida útil da ferramenta.
A ocorrência de ambos os fenómenos de danos tem sido frequentemente relacionada com os níveis de ductilidade e tenacidade do material, pois estes parâmetros indiretos conferem ao material a capacidade de absorver e acumular deformações plásticas, sem fissurar.
Na verdade, estas duas características indiretas de um material dependem principalmente do tipo de aço: a escolha adequada de um aço-ferramenta específico, para plástico ou trabalho a quente, é parte integrante do projeto de um molde e deve envolver o conhecimento dos processos, características físicas e mecânicas e mecanismos de danos dos materiais.
Além disso, a ductilidade e a tenacidade, para o mesmo tipo de aço, são diretamente atribuíveis ao processo de fabrico de aço integrado, que tem a tarefa vital de garantir que os aços puros e isotrópicos sejam obtidos por meio de sistemas complexos de fusão e refinação “Super Clean” (metalurgia primária), complementado, se necessário, por processos especiais de refusão ESR (metalurgia secundária).
Deve-se prestar atenção especial aos processos subsequentes de forjamento e tratamento térmico, para fornecer ao aço a estrutura adequada na condição recozida.
Os aços-ferramenta para trabalho a quente mais comuns utilizados para moldes de fundição injetada são os aços martensíticos Cr-SiMo-V, que apresentam o fenómeno clássico de endurecimento secundário durante o processo de revenido.
Além disso, em relação a este sector específico, a Lucchini RS desenvolveu toda uma família de aços-ferramenta de trabalho a quente 5% Cr de MÁXIMA QUALIDADE, produzidos pelo processo ESR e cujo nome comercial é ESKYLOS®, a fim de atender a todos os complexos requisitos de qualidade do mercado atual de fundição injetada.
ESKYLOS®2343 DC - HDC
ESKYLOS®2344 DC - HDC
ESKYLOS®OptiMo
ESKYLOS®HiMo
/ / Quadro 2 O aço-ferramenta mais utilizado na indústria de fundição injetada na Europa pode ser usado para todas as matrizes de fundição injetada de Al/ Mg em todos os tamanhos. Graças ao seu bom equilíbrio químico pode ser produzido numa gama dimensional muito ampla. Excelente rácio resistência ao calor/ tenacidade. Favorável a tratamento térmico. Peças grandes podem ser tratadas termicamente em fornos de endurecimento a vácuo com riscos limitados de fissuras. O aço-ferramenta mais utilizado para moldes de fundição injetada de ligas leves em todo o mundo. Pode ser sempre utilizado em alternativa ao aço 1.2343. Devido ao seu conteúdo mais elevado de V, este aço beneficia particularmente do tratamento térmico. Temperaturas de endurecimento mais altas sem crescimento de grão, permitem utilizar o seu potencial em resistência a quente a 100%. Comparável a W. Nr. 1.2343, Combina melhor rigidez a quente com resistência a quente com excelente tenacidade. É recomendado para matrizes de longa tiragem e produção de peças Al-Mg que requerem superfícies lisas (para serem revestidas ou pintadas). Adequado também para matrizes grandes. Não recomendado para matrizes de curta tiragem (200-2000 peças). Não recomendado para matrizes não termoreguladas. Comparável a W. Nr. 1.2367, Resistência a quente similar por tenacidade melhorada. É recomendado para matrizes de longa tiragem produzindo peças de grande espessura e também de formas complexas. Adequado para matrizes de tamanho médio e grande (até 2 toneladas). Não recomendado para matrizes de curta tiragem (200-2000 peças). Não recomendado para matrizes não termoreguladas quer para peças de alumínio de espessura fina.
Os principais aços-ferramenta para trabalho a quente oferecidos pela Lucchini RS são mostrados no Quadro 2.
Ao lado dos graus tradicionais convencionais ESKYLOS®2343 DC-HDC, ESKYLOS®2344 DC-HDC, ESKYLOS®2340 DC-HDC e ESKYLOS®2367, a Lucchini RS desenvolveu um par de aços inovadores, chamados ESKYLOS®HiMo e ESKYLOS®OptiMo devido ao seu maior teor de molibdénio (Mo).
Na verdade, a adição de Mo aumenta a estabilidade de revenido, a dureza vermelha e a resistência ao desgaste. ESKYLOS®OptiMo foi desenvolvido a partir do experiente grau ESKYLOS®2340 (baixo Si), otimizando o conteúdo de Mo e adicionando elementos especiais de micro ligas.
ESKYLOS®HiMo foi desenvolvido a partir do experiente grau ESKYLOS® 2344, diminuindo o Si, aumentando o teor de Mo e adicionando elementos especiais de micro ligas.
O objetivo deste design de material estratégico é melhorar as características diretas de interesse imediato (alta resistência ao calor, baixa taxa de desgaste), mantendo ao mesmo tempo as características indiretas de Resistência à Fratura (Kv) e Resistência ao Impacto (Kvw).
Tratando-se de um aço de boa qualidade, fornecido no estado recozido, é importante ressalvar também que para atingir as melhores características é necessário realizar o tratamento térmico adequado, de acordo com as instruções do fornecedor, prestando especial atenção aos seguintes parâmetros principais: temperatura de austenização, tempo de imersão, taxa de arrefecimento e ciclos de têmpera.
Na verdade, a maioria das propriedades exigidas para o bom desempenho de uma matriz de fundição injetada são apenas potenciais no aço fornecido na condição recozida (após capacidade recozida). É o Tratamento Térmico de Qualidade que permite que elas se tornem reais (ver Figura 2).
Por esta razão, a Lucchini RS, nos últimos cinco anos, decidiu desenvolver uma parceria oficial com empresas de tratamento térmico de alto calibre profissional que trabalham de acordo com as suas especificações técnicas.
A otimização do “Custo do Ciclo de Vida Total” da matriz deve persuadir os clientes a escolherem fornecedores qualificados, preparados para fornecer não só aço, mas também uma gama de serviços, como suporte técnico de aplicação, capaz de sugerir a mais adequada solução de tratamento térmico e siderúrgico e assistência metalúrgica, capaz de investigar e esclarecer os principais mecanismos de avaria para cada aplicação específica.
Em relação ao sector de fundição injetada, apercebemo-nos de uma necessidade crescente de quantificar os benefícios gerais de produtividade de um molde. Graças ao feedback, entendemos que o impacto do custo do aço de maior qualidade no custo total do ciclo de vida do molde não é tão significativo, quase irrelevante e, de qualquer forma, bem pago pelo desempenho da produção.
Portanto, a alta qualidade dos aços e o suporte técnico do fabricante desempenham um papel fundamental na melhoria do desempenho do processo de fundição injetada.
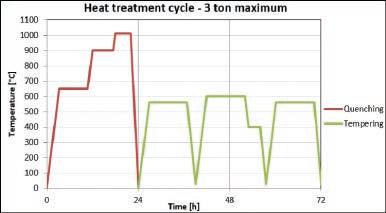
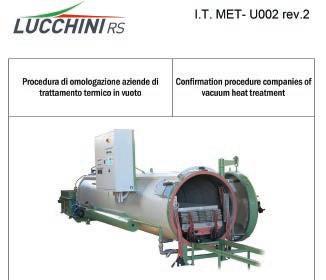

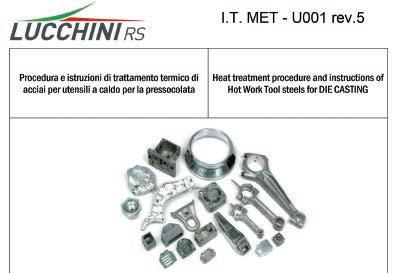
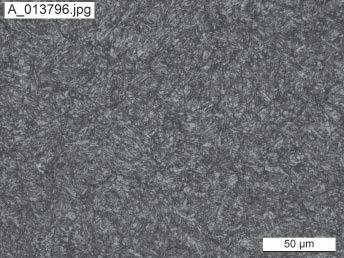
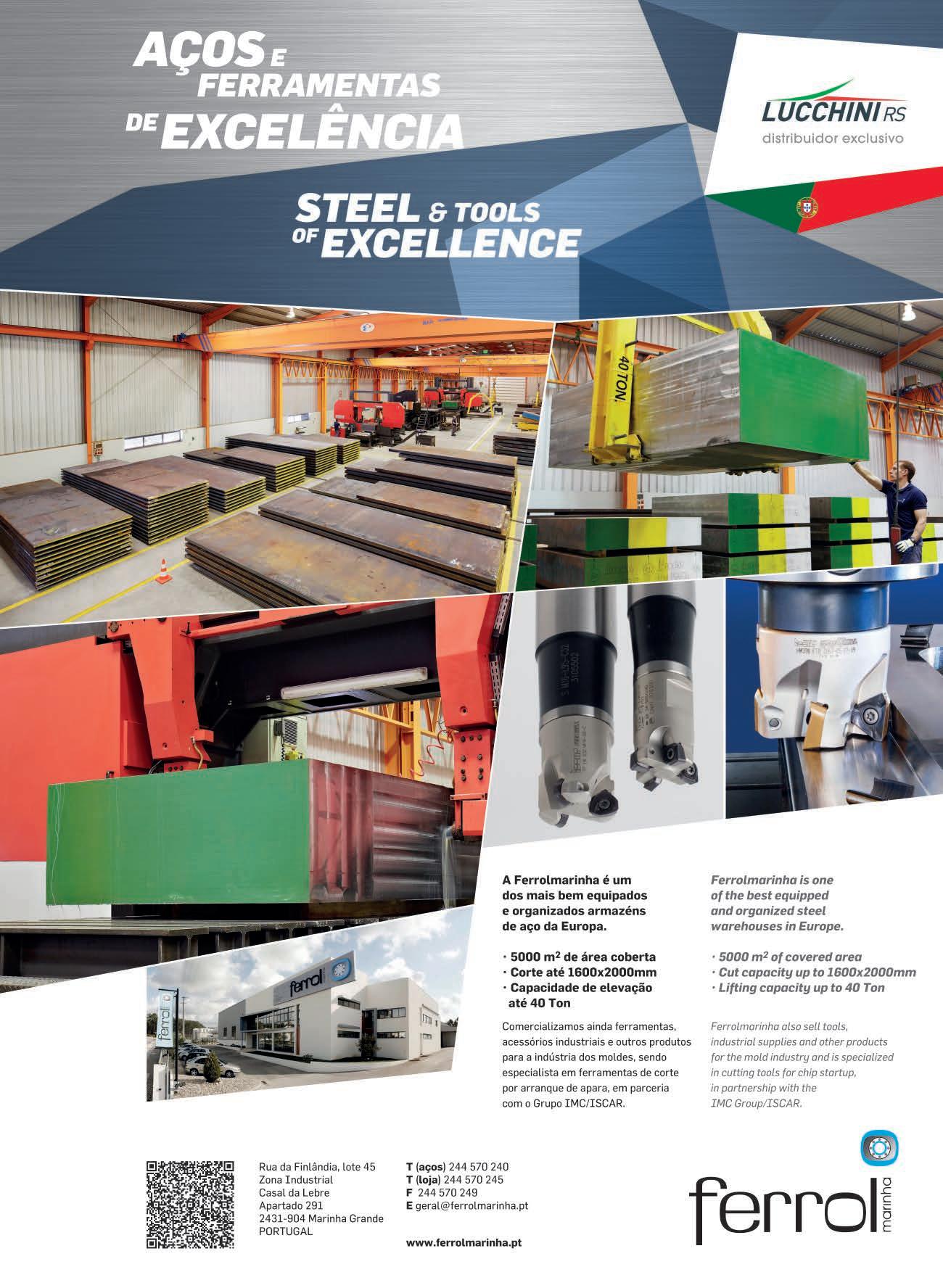
56 THRUHARD DIAMOND® “SUPREME PERFORMANCE STEEL” PARA MOLDES COM ACABAMENTO “ESPELHO“
Uma divisão da voestalpine High Performance Metals Portugal, Unipessoal, Lda.

Ver, tocar, desejar. Os aspetos óticos e hápticos dos nossos objetos do dia-a-dia são a chave para o desempenho das vendas. Compraria um anel de noivado de diamantes pela sua dureza?
Para moldes que requerem acabamentos de elevada exigência de polimento e texturas finas, a Buderus Edelstahl desenvolveu um produto de vanguarda para moldes de plástico, baseado na tecnologia de refundição (ESR - Electro-Slag Remelted).
A sua composição química foi otimizada para assegurar uma dureza constante, mesmo para secções transversais superiores a 900 mm, enquanto os processos ESR eliminam os eventuais efeitos prejudiciais das “segregações”. Moldes de lentes, por norma em aços como H11 (1.2343) ou H13 (1.2344), requerem endurecimento a vácuo após a pré-maquinação. O Thruhard Diamond® é utilizável em condições pré-endurecidas, permitindo reduzir custos, prazo de colocação no mercado e elimina o risco de distorção da peça ou de fissuras durante o tratamento térmico. Além disso, o teor de carbonetos é mantido a um nível mínimo (em comparação com H11/H13) o que facilita as etapas de maquinação, retificação e polimento.
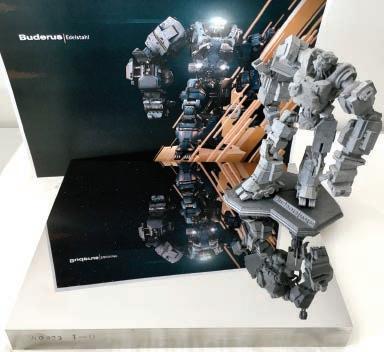
/ / Fig. 1: Placa com polimento “espelho”. O reflexo mantêm o paralelismo de linhas e proporções Em estado pré-tratado (temperado e revenido), com uma distribuição homogénea da dureza em toda a secção transversal, minimizamos as dificuldades de polimento inerentes às variações de dureza e a tão conhecida “casca de laranja“.

/ / Fig. 2: Gama de tamanhos disponíveis para blocos Thruhard Diamond®
O teor máximo de enxofre é de 10 ppm (partes por milhão) e o nível extremamente baixo de inclusões não metálicas (óxidos e sulfuretos) são a chave para um polimento sem poros ou picos.
O tempo de ciclo de injeção é altamente influenciado pela secção do artigo e pela capacidade do meio envolvente (aço) em dissipar o calor

do plástico injetado. O Thruhard Diamond®, com uma condutividade térmica incrementada até 45%, possibilita uma otimização da produtividade e uma boa relação custo-eficiência.
O Thruhard Diamond® permite alterações de desenho ou a fácil reparação de erros de maquinação durante a fabricação de moldes, utilizando o processo de solda.
Em conclusão, não importa se pretende superfícies brilhantes, espelhadas, transparentes ou funcionais, Thruhard Diamond® é o seu melhor aliado para obter a qualidade de superfície mais exigente.
Principais características: • Pureza extrema e uma Microestrutura de elevada homogeneidade • Capacidade de polimento até paste de diamante de 3 μm, Rmax=0.3 μm (Mirror-Surface Finish SPI-A1 / ISO 1302-N1). • Excelente capacidade de texturização mesmo para texturas extremamente delicadas. • Permite endurecimento a Laser, Nitruração, revestimentos Cromo-
Duro, PVD. • Condutividade térmica até 45% superior quando comparado com os aços ESR tipo H11/H13 ou 1.2083. • Melhor performance no processo de solda quando comparado com
H11/H13 ou 1.2083.
Estado de fornecimento: Temperado e Revenido com uma dureza superficial entre 360 e 405 HBW
APLICAÇÕES:
Moldes de injeção e compressão com elevadas exigências de acabamento superficial. - 2711. Para moldes sujeitos a elevados esforços mecânicos e choque térmico. - 2312. Fácil de maquinar e endurecer em profundidade. Para estruturas de moldes. - 2311. Fácil de maquinar, para polimento e revestimento cromo-duro. - 1730. Fácil de maquinar, permite endurecimento superficial.
A qualidade dos materiais é essencial para uma produção sem quebras de rendimento e assegurar a performance do produto final. Garantimos uma estabilidade nos materiais fornecidos, um enfoque na condutividade térmica do aço para otimização do tempo de arrefecimento e nas necessidades dos nossos clientes. Para informações adicionais contacte a Buderus Edelstahl Portugal.
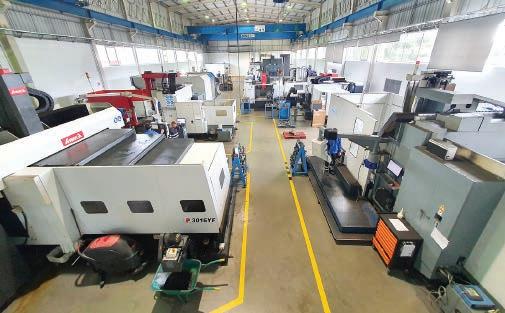
/ / Fig. 4: Divisão de maquinações, Moita- Marinha Grande
Em Estarreja - Portugal, a Buderus Edelstahl faz parte da voestalpine High Performance Portugal, Unipessoal, Lda.
Dispomos de uma gama de serviços completos: - Rastreabilidade total do aço, desde a fundição até ao produto acabado; - Vasto serviço de corte de serra, incluindo peças de grande dimensão; - Serviço de galgamento de aço e furos roscados para olhais em peças;
Além disso, dispomos de um serviço de fabrico de estruturas e suportes para moldes nas nossas instalações em Moita (Marinha Grande) com uma capacidade de maquinação de peças até 10 toneladas. Estamos capacitados para fornecer peças individuais, bem como, efetuar serviços de estruturas completas até 25 toneladas. - Serviços desbaste, maquinação CNC e furação profunda; - Serviços de retificação de chapas; - Controlo e rigor nos produtos fornecidos.
Para artigos transparentes como aplicações óticas (faróis), painéis de interior e painéis/grelhas de radiador.
Ideal para aplicações com alto polimento e superfícies com texturas extremamente finas.
A Buderus Edelstahl, como fabricante alemão de aços especiais, possui um portefólio de aços que permite satisfazer a procura dos fabricantes de moldes e ferramentas com os mais elevados padrões de exigência. Dispomos de aços que permitirão fazer frente a aspetos-chave como a resistência à corrosão, dureza, homogeneidade do produto, bom polimento e textura, entre outros. - Thruhard Supreme®. Qualidade premium da Buderus. Com maior dureza, apto a têmpera e boa condutividade térmica. - 2738. Para moldes de grandes dimensões, com mais de 400 mm de espessura.
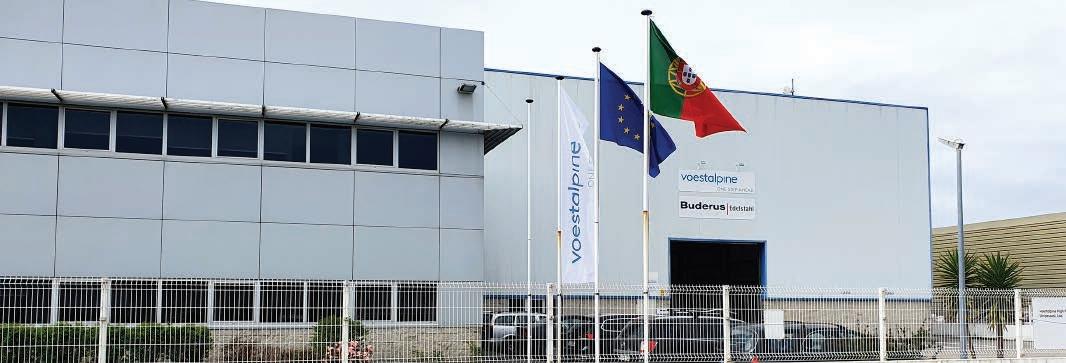
58 PERFORMANCE DO AÇO-FERRAMENTA: INFLUÊNCIA DA SELEÇÃO E TÉCNICAS DE FABRICO
Ângela Martins*, Vítor Fernandes *
Ramada
A injeção é um dos processos mais usados na produção em massa de peças plásticas. As indústrias da embalagem, médica, automóvel, entre outras, têm-se desenvolvido no sentido de usar, cada vez mais, plásticos reforçados (desde retardadores de chama, a biocompósitos e fibra de vidro), o que leva a um aumento da exigência do processo e, consequentemente, a uma melhor performance do aço-ferramenta.
De forma a assegurar a longevidade do molde é necessário garantir a seleção adequada do aço-ferramenta e do tratamento térmico, assim como o correto design do molde e técnicas de fabrico.
SELEÇÃO DO AÇO-FERRAMENTA
A correta seleção do aço-ferramenta torna-se fulcral para evitar a falha prematura do molde, diminuindo tempos de paragem e manutenção/reparação, ou, em casos mais extremos, a substituição da ferramenta. Conhecer o material a injetar (abrasivo e/ou corrosivo), o número de ciclos necessários, as dimensões do molde e o tipo de acabamento superficial (polimento de alto brilho, textura, revestimento ou nitruração, etc.) entre outros fatores, é de extrema relevância para determinar as propriedades necessárias ao aço.
Em caso de polímeros abrasivos e elevado número de ciclos, o uso de aços de têmpera pode tornar-se mais vantajoso para garantir maior resistência ao desgaste abrasivo, como é o caso do Vidar Superior, Orvar 2M, o Orvar Supreme e o Unimax. Dependendo das dimensões do molde, poderá ser mais viável o uso de aço pré-tratados de forma a garantir os níveis de tenacidade adequados: destacam-se os aços Nimax e MDXTRA SHH e o Nimax ESR, sendo este último a solução ideal para aplicações de polimento de alto brilho ou texturas de elevada exigência. Por fim, para aplicações em que o uso de aços inoxidáveis é um requisito, destacam-se os aços Stavax ESR, Mirrax ESR e Tyrax ESR (alia a melhor capacidade de polimento à elevada resistência ao desgaste abrasivo – 56 / 58 HRC). De ressalvar o Ramax HH e Royalloy, aços pré-tratados inoxidáveis com excelente maquinabilidade, tipicamente usados para as estruturas dos moldes.
TÉCNICAS DE FABRICO
Existem várias operações de maquinagem e vários processos para a produção de um molde que podem afetar o aço e levar a uma falha prematura da ferramenta. Dentro dos processos de maquinagem não convencional, no processo de eletro-erosão (EDM), devido às elevadas temperaturas atingidas, a superfície do material sofre alterações ao nível da microestrutura, dureza e até mesmo composição química. Esta camada, denominada por camada branca (Fig. 1), está repleta de concentrações de tensões e microfissuras, que tendem a propagar-se e a originar a fratura do material. Desta forma, é necessário assegurar que o último passo passa pelo EDM de acabamento, seguido de um polimento/remoção da camada branca. O uso de um revenido/alívio de tensões posterior (-25 °C do último revenido) também é altamente aconselhado, de forma a homogeneizar a distribuição de durezas geradas.
Na maquinagem convencional, como a fresagem, torneamento, furação e retificação, é importante assegurar que a geometria da peça produzida possui elevado rigor dimensional e qualidade no acabamento superficial, caso contrário será favorecido o aparecimento de zonas suscetíveis de apresentarem as indesejáveis concentrações de tensões (Fig. 2).

/ / Figura 1: Microfissuras na camada branca resultante do processo de EDM.
A correta seleção da geometria das ferramentas de corte, parâmetros de corte, método produtivo e controlo sobre as diversas etapas do processo de fabrico são fatores cruciais para a que a peça final obtida cumpra os requisitos para os quais foi projetada.
Um dos princípios técnicos que deve ser tido em consideração durante a produção do molde, é o da seleção de ferramentas de corte com raio de canto o mais elevado possível. Este princípio torna-se tanto mais relevante nos casos em que as peças a produzir sejam zonas moldantes, com execução de têmpera após operações de maquinação.
O processo de maquinação convencional mais presente na produção do molde é a fresagem, sendo que um dos parâmetros mais importantes a ter em consideração é a velocidade de corte (Vc), pelo facto de ser a variável que induz maior influência sobre a vida útil da ferramenta e, consequentemente, sobre a qualidade do acabamento superficial obtido, influenciando decisivamente a eficiência do corte durante todo o processo.

/ / Figura 2: Elevada rugosidade superficial após as operações de maquinagem.
Na maioria das aplicações de acabamento, devem ser consideradas velocidades de corte tendencialmente elevadas e pelo método de fresagem sincronizada, que conjugadas com o valor ideal de avanço por aresta, incremento axial e lateral, traduzem-se num processo de corte otimizado.
Por fim, o tratamento térmico é um processo complexo que envolve vários fatores que vão ditar, no caso da têmpera e do revenido, a relação entre a dureza e a tenacidade/ductilidade do material. Estas propriedades dependem de vários fatores, tais como a composição química e processo de fabrico do material, a quantidade de martensite revenida, o tipo, número e tamanho de carbonetos precipitados e a transformação da austenite residual em martensite.
O tratamento térmico também afeta o tipo de empenos e distorções que o material poderá sofrer. Assim, é sempre de relevância indicar as aplicações e durezas pretendidas para determinado material à equipa técnica dos tratamentos térmicos, para que possam ser avaliadas as melhores condições de tratamento para satisfazer os requisitos do projeto.
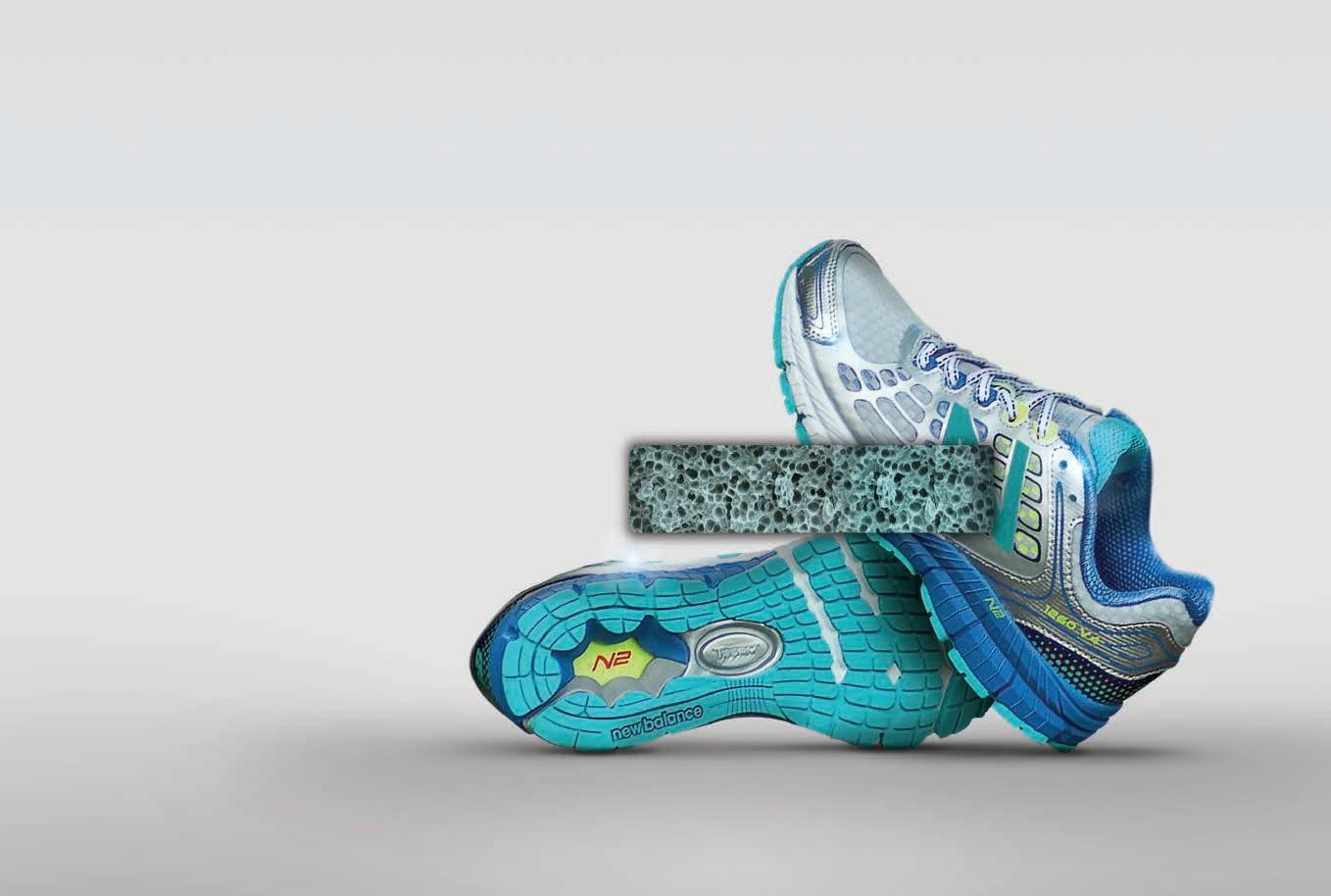
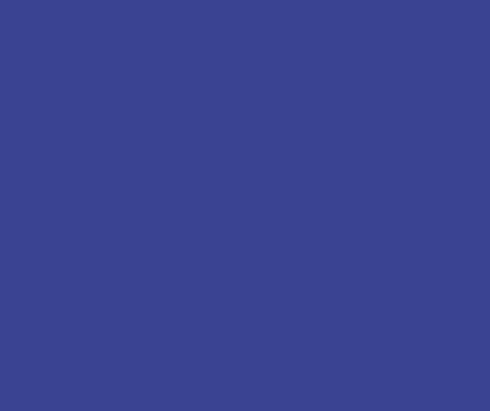

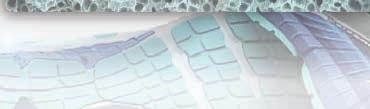
60 SOLUÇÕES PVD, LASER CLADDING E SUAS CAPACIDADES TÉCNICAS: O CASO PARTICULAR DOS MOLDES
Francisco Gonçalves *, Marta Sousa *
TEandM-Tecnologia e Engenharia de Materiais
TEandM - Tecnologia e Engenharia de Materiais, é uma empresa inovadora focada na produção de revestimentos técnicos em componentes para aplicações industriais. Dispõe das mais recentes tecnologias de engenharia de materiais, nomeadamente, revestimentos físicos em estado de vapor (PVD) e Laser Cladding. Com um esforço de investigação continuado, a empresa já introduziu no mercado mais de 50 produtos, registados em 27 marcas comerciais, constituindo uma geração de revestimentos nanoestruturados para a competitividade e alto desempenho da indústria de produção.
1 - INTRODUCÃO
A melhoria contínua da produtividade nas empresas é um facto relevante para se manterem competitivas e o aumento de vida útil das ferramentas, a redução dos tempos de ciclo e eliminação de paragens de produção são fundamentais. E porque a produtividade e a vida útil das ferramentas são aumentadas com a aplicação de revestimentos superficiais, é necessário oferecer aos clientes o melhor conhecimento científico e tecnológico, que permita desenvolver as melhores soluções para as necessidades dos clientes, melhorando desempenhos sem comprometer os processos.
Assim, a incorporação de uma camada de um material a outro, que localmente altera a estrutura química, com intenção de modificar o comportamento e as propriedades da superfície do material base, permite-nos obter sofisticadas nanoestruturas com propriedades mecânicas e tribológicas incomuns, como alta dureza, baixo coeficiente de atrito, elevada tenacidade e até mesmo comportamentos tribológicos de lubrificantes sólidos, diminuindo desta forma, ou até mesmo eliminando, o uso de lubrificantes durante os processos produtivos.
Problemas de desgaste associados às ferramentas, estampagem a frio e a quente, processos de produção na indústria dos moldes de injeção e ferramentas de corte utilizadas no processo por arranque de apara têm sido o alicerce para o desenvolvimento de produtos inovadores para dar resposta a estas necessidades. Contudo, a modificação de superfícies, através da utilização de revestimentos “duros” para prolongamento da vida útil, já não constitui uma novidade.
Um dos sectores industriais onde os fatores supra referidos assumem elevada importância, corresponde ao sector de produção de ferramentas moldantes, em particular, a produção de moldes para a injeção de plásticos de engenharia, que ainda apresenta novos desafios tecnológicos que são necessários ultrapassar. Problemas típicos como a corrosão e desgaste das superfícies moldantes, polidas ou texturizadas, elementos móveis, extratores, etc.; a gripagem dos elementos móveis; dificuldades de desmoldação e adesão do material injetado às superfícies moldantes têm-se revelado fundamentais, sendo a razão de aspeto das cavidades a preencher, a geração de calor devido a elevadas tensões de corte, o atrito e desgaste das superfícies moldantes, fatores que têm influência importante na funcionalidade e qualidade dos componentes a produzir e na durabilidade e performance do molde.
E é neste sentido que o portefólio de produtos oferecido pela TEandM consegue ultrapassar estes constrangimentos, oferecendo soluções de melhoria da resistência ao desgaste, facilitando a desmoldação, evitando fenómenos de gripagem, evitando a corrosão provocada por gases e outros compostos dos produtos orgânicos dos plásticos ou ligas leves com garantia de elevada durabilidade das soluções de revestimento.
2 - A TECNOLOGIA E SOLUÇÕES
2.1 - PVD O processo PVD é um processo de deposição atómica em que um material é transformado em vapor a partir de uma fonte sólida, transportado e depositado na superfície de um substrato, oferecendo maior resistência, durabilidade e qualidade superior, através de um revestimento extremamente fino e de elevada aderência. Dispõe-se de um leque alargado de soluções: HardSilK®; HardTiN®; DMold®; MoldLub ®; ULTRA Impact®e, ainda, as DLC’s, DiExtra®e Diaplus®, para satisfazer todas estas necessidades. São revestimentos que apresentam, na sua generalidade, dureza superior ao triplo de uma nitruração, baixo coeficiente de atrito e resistentes ao desgaste por adesão e abrasão.
2.2 LASER CLADDING Quanto à tecnologia de Laser Cladding, também utilizada na melhoria da superfície dos moldes e sua recuperação, consiste na deposição de camadas de material na superfície dos componentes, contudo, o material adicionado, agora sob a forma de pó, é injetado contra a superfície do componente a ser revestido. Em simultâneo um feixe de laser funde este material e a superfície da peça, formando-se uma camada de material com ligação metalúrgica ao substrato, que pode ter uma espessura entre 0,5 e dezenas de milímetros. É por isso considerada uma técnica de fabricação aditiva. É uma tecnologia semelhante aos processos de soldadura convencionais mas com as vantagens de se conseguir construir camadas com diluição controlada; baixa adição de calor, que resulta numa pequena zona termicamente afetada; baixa distorção dos componentes e porosidade nula ou negligenciável. Através deste processo é possível depositar materiais como aço 1.2344 que, devido às elevadas velocidades de arrefecimento do processo, apresenta uma dureza de 50-54 HRC após revestimento, aços inoxidáveis martensíticos e austeníticos, ligas à base de Níquel, Cobalto e materiais compósitos de matriz metálica com reforço cerâmico.
3 - CASO DE ESTUDO: OS MOLDES
No projeto de um molde de injeção, vários são os problemas típicos associados e, portanto, o seu correto dimensionamento envolve o conhecimento dos materiais plásticos, materiais utilizados no fabrico dos moldes, tratamentos térmicos, complexidade das peças plásticas e o controlo das variáveis do processo de injeção.
Um caso de estudo pertinente, refere-se à dificuldade de desmoldação onde é importante minimizar as forças de extração das peças plásticas processadas. Existe atrito entre a peça plástica e o material do molde, e o efeito de contração tem um efeito preponderante na força de atrito gerada entre a superfície moldante e o artigo injetado. Assim, o êxito desta fase está relacionado com parâmetros de processamento, ângulos de saída, acabamento, propriedades do material à temperatura de extração, dimensionamento do sistema de extração e do revestimento das superfícies moldantes.
Uma das mais notórias vantagens que se obtém ao aplicar este tipo de revestimentos é o aumento da resistência ao desgaste. Contudo, alguns materiais têm um comportamento abrasivo para com o aço no qual o molde é fabricado. Materiais como os plásticos reforçados com fibras são os casos mais críticos. A sua injeção, com percentagens entre 30-70% de fibra de vidro, apresenta desafios acrescidos de durabilidade das superfícies moldantes, especialmente quando há especificações de rugosidade, recorrendo-se ao polimento ou texturização das mesmas. O desgaste abrasivo severo, provocado durante a injeção, leva a paragens frequentes para manutenção dos moldes. Ultrapassar este problema foi um desafio que foi colocado à TEandM e que conduziu ao desenvolvimento de um revestimento PVD pela empresa, que se apresenta na linha da frente como uma das principais soluções para este problema da indústria da moldação por injeção: o Moldlub. Apresenta uma boa resistência ao desgaste funcionando como um “auto lubrificante sólido”, baixo coeficiente de atrito (reduz a força de extração em 300%) e dureza elevada (2000 HV), minimizando problemas de extração de componentes plásticos injetados.
Esta melhoria traduziu-se numa diminuição significativa da força de extração da peça processada, em carga e em vazio, enchimento mais rápido da peça plástica, menores pressões de injeção, diminuição da rugosidade decorrente do processo PVD e menor tempo de ciclo de moldação. Assim, a utilização deste tipo de solução com o recurso a revestimentos, melhora as condições de injeção e facilita o processo de extração.

/ / Figura 1: Figura esquemática da tecnologia PVD, Laser Clad-ding e correspondentes moldes revestidos.
62 BALITHERM PRIMEFORM: UM NOVO TRATAMENTO DE SUPERFÍCIE PARA MOLDES DE TODAS AS DIMENSÕES
Pedro Melo e Faro *
* Oerlikon Balzers Portugal
BALITHERM PRIMEFORM é o nome de um serviço concebido especificamente para o tratamento superficial de moldes de injeção de plástico. Oferece inúmeras vantagens: aumento significativo na dureza dos substratos das ferramentas; resistência ao desgaste e à corrosão; desmoldagem e proteção das superfícies polidas espelho. Pela primeira vez, estas vantagens podem ser realizadas em moldes de grande dimensão.
Este é um tratamento termoquímico de superfície ativado por plasma para produzir uma camada de difusão com um gradiente de dureza superficial. Os moldes de injeção de plástico, durante a sua vida útil, enfrentam diferentes problemas que reduzem a sua eficiência e geram elevados custos de manutenção. Com BALITHERM® PRIMEFORM, a Oerlikon Balzers está a oferecer uma solução única de redução de custos importantes e sustentáveis para os seus clientes. Estas reduções de custos provêm de:
• Resistência significativa ao desgaste – aumentando a dureza superficial do molde até 1400 HV; • Resistência aos riscos – reduzindo a sensibilidade do molde ao manuseamento;
• Propriedades melhoradas de polimento espelhado;
• Maior resistência à corrosão – melhor proteção contra aditivos agressivos e água condensada;
• Possibilidade de reparação por soldadura – as superfícies dos moldes podem ser soldadas a laser de boa qualidade e adequada para a maioria das aplicações.
As superfícies tratáveis dos moldes podem ter textura química ou laser, ser polidas ou com polimento espelho, fabricadas em aços que não sofram alterações dimensionais a temperaturas de 500°C. Independentemente do aço selecionado, ter sempre em mente a obrigatoriedade da Temperatura de Revenido do tratamento térmico ser superior à temperatura do revestimento a aplicar. Por exemplo, quando o tratamento BALITHERM® PRIMEFORM for executado à temperatura standard de 450°C, a Temperatura de Revenido do aço terá de ser superior a 500°C. No caso do tratamento BALITHERM PRIMEFORM ser aplicado à temperatura especial de 380°C, o aço terá de ter uma Temperatura de Revenido acima dos 410°C. Assim, não haverá qualquer possibilidade de deformação dimensional ou alteração das propriedades do aço.
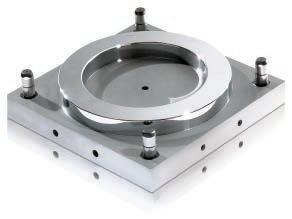
/ / Exemplo de Peça - BALITHERM® PRIMEFORM - O método de tratamento inovador para superfícies brilhantes
Isto aplica-se a todas as geometrias de moldes, exceto em zonas muito fechadas. Este processo ajuda a fornecer uma superfície mais resistente ao risco em moldes com um acabamento polido espelho, o que, por sua vez, facilitará eventuais polimentos posteriores. A maior qualidade das superfícies do molde simplifica a desmoldação e reduz a aderência e acumulação de depósitos. Além disso, as ferramentas tratadas com BALITHERM® PRIMEFORM podem ser facilmente reparadas por soldadura. Isto significa que ambos, o tempo de ciclo e os custos de manutenção, podem ser reduzidos.
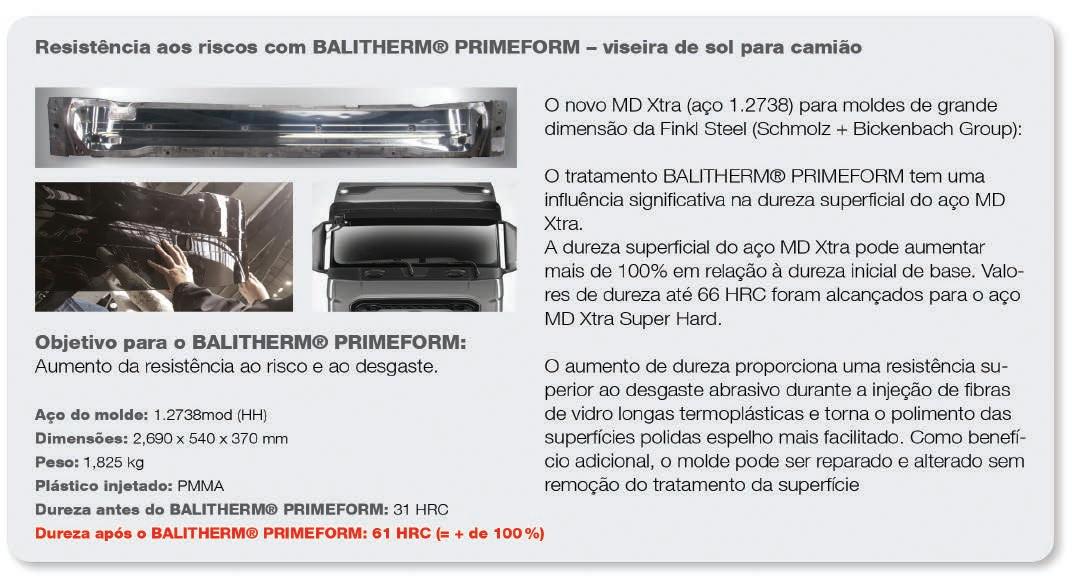
As superfícies das peças produzidas obtêm um excelente brilho; isto é especialmente verdade para peças transparentes. Como benefício, há menos correções e rejeições de peças. Os testes em várias indústrias, como o caso das indústrias elétrica, eletrónica e automóvel, já mostraram resultados convincentes.
Aplicações potenciais são encontradas na indústria automóvel na qual os moldes de injeção ou moldes de compressão (SMC) são usados para fabricar para-choques completos ou guarda-lamas para HGVs. Além disso, o tratamento também é adequado para o fabrico de cadeiras para estádios, cadeiras de restaurantes de fast food, assentos de plástico, banheiras de acrílico e bacias de duche. Este serviço é realizado em máquinas que estão entre as maiores do mundo no seu tipo.
Um molde revestido em funcionamento permitirá uma poupança significativa de custos operacionais e de manutenção. Os ganhos em produtividade e de qualidade das peças finais são também significativos.
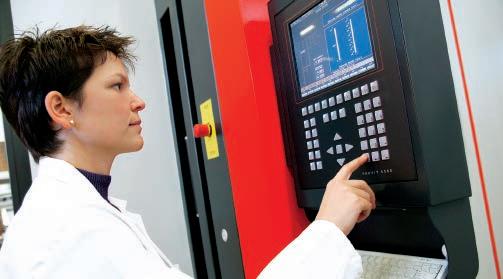
/ / Máquina BAI 1200 A Oerlikon Balzers desenvolveu soluções para todas as aplicações possíveis, qualquer que seja o tamanho do molde. Independentemente da superfície que tenha, proteja-a com a nova solução BALITHERM® PRIMEFORM.
Para os moldes de pequena dimensão (até Ø700x1000 mm) e baixo peso (até 700 Kg), temos disponível, no nosso centro produtivo em Portugal, a máquina BAI 1200.
Para moldes de grande dimensão (até Ø3x10 m) e peso elevado (até 40 Toneladas), utilizamos a máquina INAURA existente num dos nossos centros na Alemanha.
Os sistemas INAURA têm uma capacidade de carga de 10 x 3 metros e 40 toneladas. O processo totalmente automatizado garante um procedimento de tratamento de proteção de desgaste estável e controlado. A combinação de hidrogénio, azoto e eletricidade significa que a INAURA opera inteiramente sem gases ou produtos químicos venenosos.
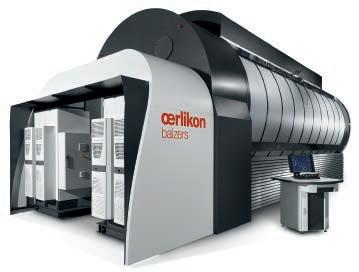
/ / Máquina iNAURA
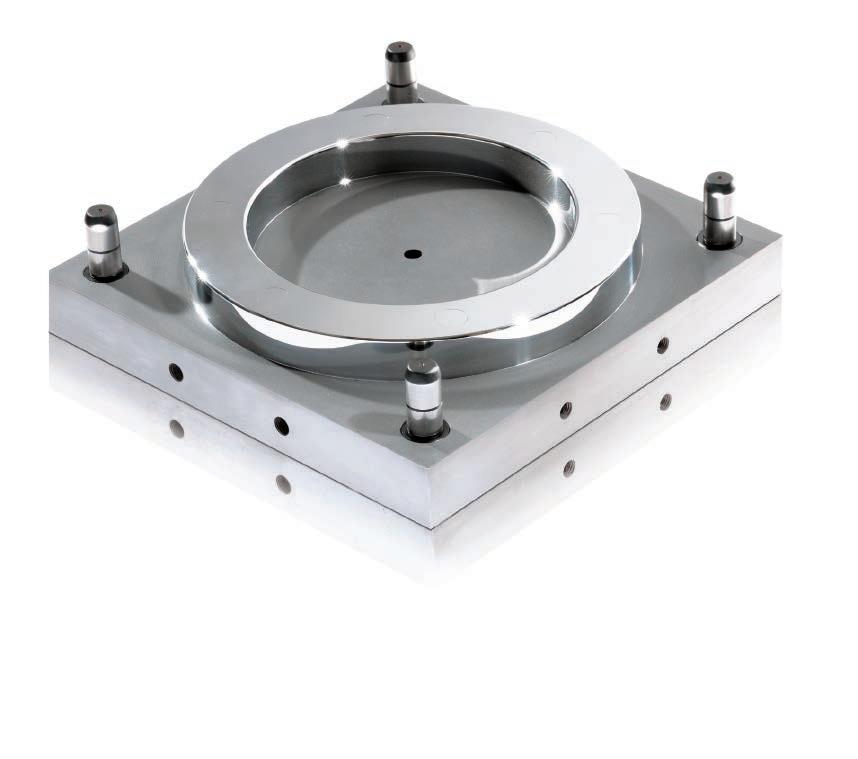
INOVAÇÃO
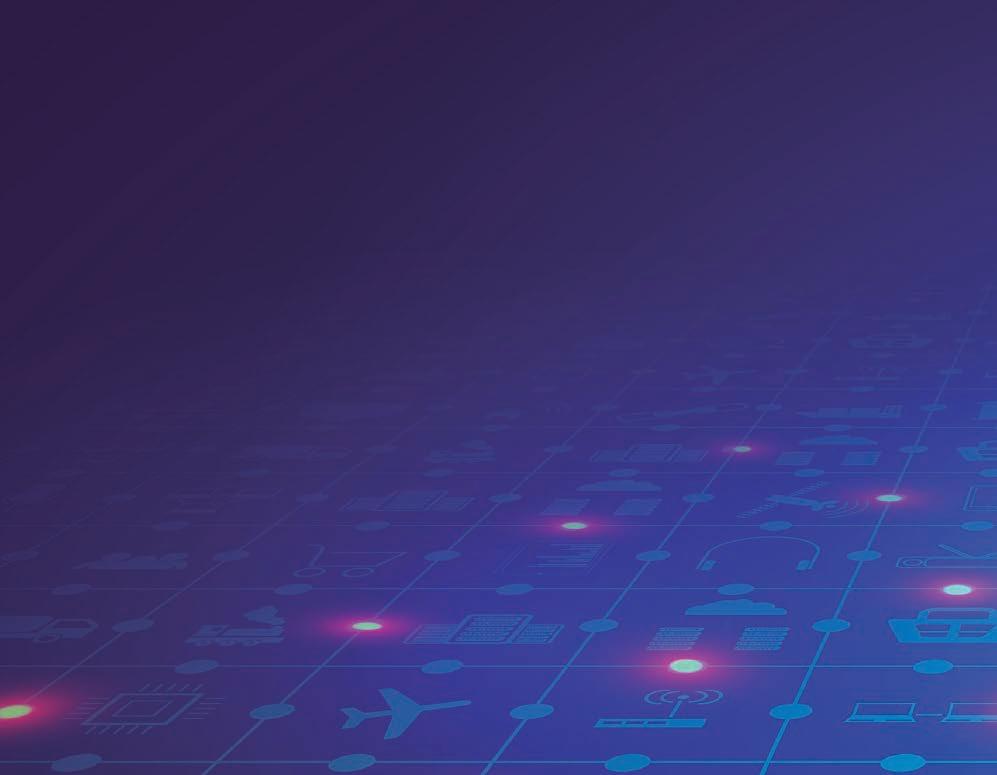
O QUE AS EMPRESAS CONCEBEM DE FORMA SINGULAR E INOVADORA
WHAT OUR COMPANIES CONCIEVE IN A SINGULAR AND INNOVATIVE WAY
GUIA RUMO À INDÚSTRIA 4.0
COMO IMPLEMENTAR UMA ESTRATÉGIA INTEGRAL DE DIGITALIZAÇÃO NOS MOLDES?
SISTEMA DE VALIDAÇÃO DA GARANTIA DE MOLDES
O MOLDE 4G – O MOLDE MULTIPROCESSO