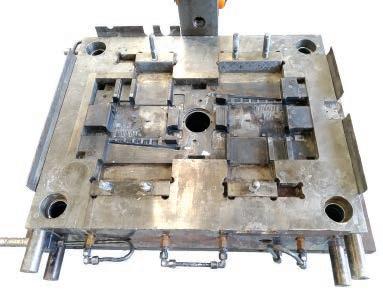
5 minute read
SEDLOM em projeto pioneiro de tecnologia Thixomolding
Helena Silva *
* Revista MOLDE
77
A Sedlom faz parte, há já dois anos, de um projeto pioneiro que desenvolve moldes para injeção através da tecnologia Thixomolding. Trata-se de um sistema que apresenta muitas semelhanças com os moldes para injeção de plásticos, mas que acaba por ser um ‘concorrente’ da fundição injetada, utilizando o magnésio e permitindo a criação de peças mais leves e mais finas, em particular para aplicações nas indústrias da eletrónica ou informática, mas também automóvel, entre outras.
Chama-se tecnologia tixotrópica ou Thixomolding, dado o estágio em que se encontra o material a injetar. Um método alternativo de fundição, que utiliza ‘aparas’ de liga de magnésio como matériaprima. Com algumas semelhanças com a injeção de plásticos, esta recente e inovadora tecnologia concorre de forma direta com a fundição injetada, mas apresenta algumas vantagens, desde logo, a criação de peças leves e de paredes mais finas. A Sedlom disponibiliza esta solução ao mercado, ao participar, juntamente com outra empresa nacional, num projeto pioneiro no nosso país. Jorge Silva, da Sedlom, conta que a empresa já fabricou vários moldes para o desenvolvimento de peças a partir desta tecnologia. A empresa parceira neste projeto, adianta, começou a
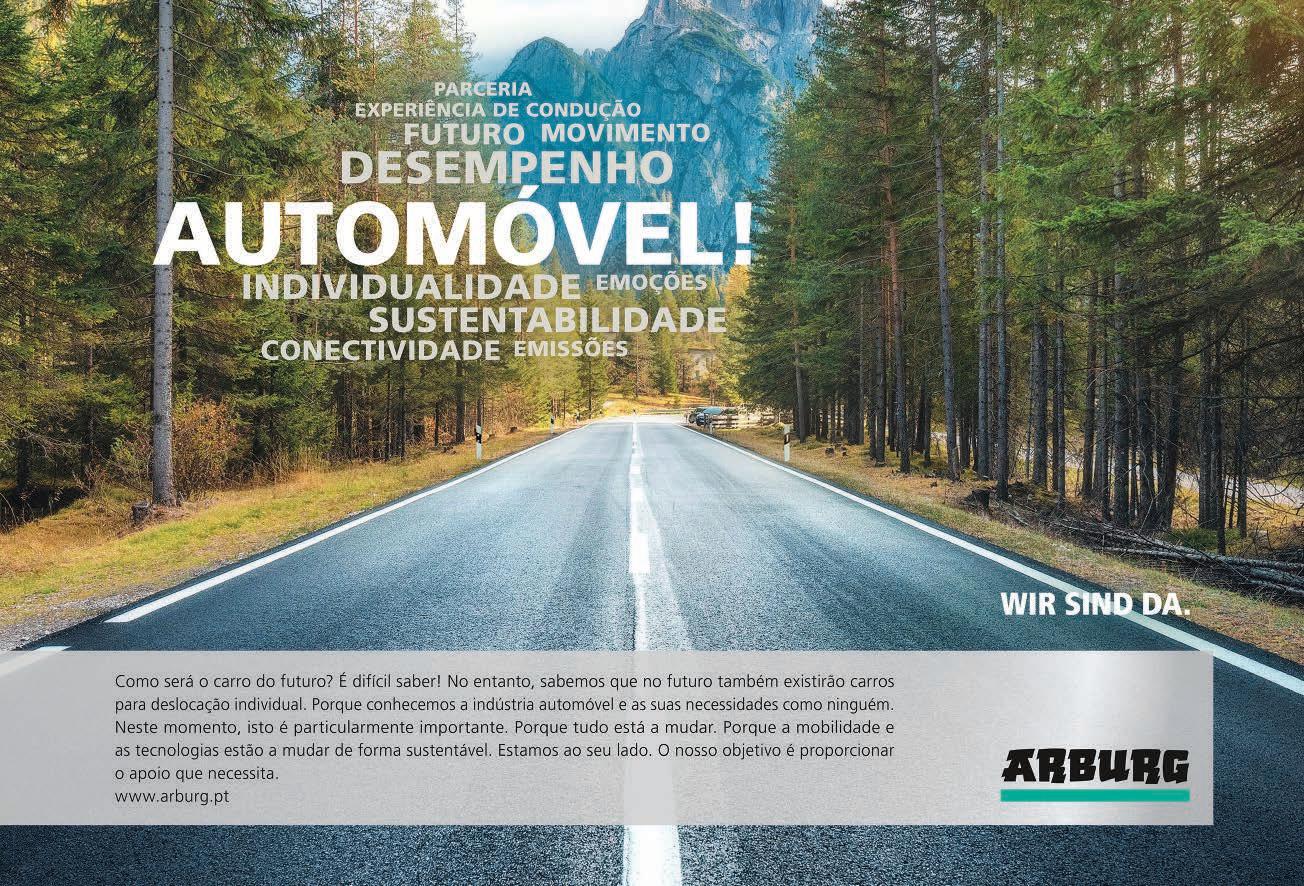
laboração, há quatro anos, com duas máquinas de injeção (que têm características específicas aplicadas ao Thixomolding, incluindo os periféricos) e, atualmente, já tem sete, sendo a maior empresa transformadora na Europa. Tanto a tecnologia ali aplicada, como a assistência técnica e formação são asseguradas pelo Japão, de onde são oriundas as máquinas.
Jorge Silva admite que o projeto foi iniciado “com algum receio”. No entanto, tem caminhado a bom ritmo, contribuindo para isso a experiência que as duas empresas têm, quer na injeção de plástico, quer na fundição injetada. É que, sublinha, este processo “utiliza o know-how de ambos os processos”.
O responsável adianta que, nesta fase, a tecnologia está em condições de ser adotada por outras empresas. Nesse sentido, apresentou, em 2019, o Thixomolding a um conjunto de professores e estudantes universitários. No seu entender, “este processo vai, num futuro muito próximo, reduzir a quantidade de peças feitas pela fundição injetada”.
O MAGNÉSIO
A matéria-prima deste processo, o magnésio, “representa uma opção interessante”, quando comparada a outros materiais, salienta Jorge Silva. Por um lado, apresenta uma condutibilidade térmica inferior à do alumínio, mas suficiente para estas aplicações, com uma densidade baixa (idêntica à peça de plástico) e com uma enorme resistência o que torna as peças muito atrativas para o ramo automóvel, uma vez que a redução de peso nos veículos é muito importante, de forma a reduzir consumos e aumento de autonomia nos elétricos. “A estabilidade dimensional é muito boa”, destaca, adiantando que “apesar de termos ciclos muito idênticos aos da injeção de plástico, não obtemos as mesmas deformações; asseguramos peças de maior resistência”.
E esta característica permite que a sua utilização seja um ganho, aplicada às mais variadas utilizações e transversal a vários sectores. Exemplifica com peças para computadores ou telemóveis, caixas para motores, máquinas fotográficas ou mesmo chassis de automóveis e até encaixes para mobiliário. A conceção dos moldes, frisa, não difere muito dos que se destinam à injeção de plástico.
Uma outra vantagem é que o magnésio é fácil de encontrar. Contudo, diz ter conhecimento de que apenas no Japão e China é trabalhado de forma a ser utilizado neste processo. Na Europa existem apenas duas fábricas a usar esta nova tecnologia: uma na Áustria e a do nosso parceiro em Portugal.
Nem tudo são vantagens, no entanto. O investimento inicial para adotar um processo deste tipo, adverte, é “bastante mais elevado do que o da injeção de plástico”, devido à necessidade de aquisição de máquinas e periféricos. E também os cuidados a ter com o processo e a matéria-prima têm grandes diferenças do plástico. Por isso, defende que uma empresa que pretenda iniciar-se neste processo deve rodear-se de algum apoio técnico, na fase inicial. Mas no seu entender, a curva de aprendizagem de um operador para uma máquina deste tipo é muito pequena, desde que tenha os conhecimentos de injeção de plástico. “Basta uma adaptação que não é difícil”, explica.
Em termos de rentabilização, considera que, neste momento, “há mercado e há compradores”. Trata-se de um processo que tem vindo a ser cada vez mais solicitado pelos clientes, muitos deles da indústria automóvel.
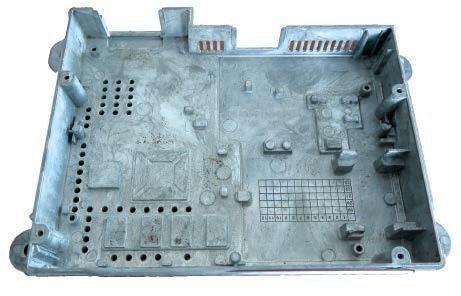
Em relação aos testes dos moldes, explica que não há empresas dedicadas a esses ensaios. Por isso, os moldes “têm de ser aprovados pelo fabricante, numa máquina de injeção, e validados uma segunda vez pelo cliente final, com uma máquina de Thixo”. Mas salienta que, com base na experiência da Sedlom, “os moldes nunca tiveram de retornar para nenhuma retificação de funcionamento”.
LIGAS ESPECIAIS
Os moldes para esta tecnologia são produzidos em aço, com ligas ligeiramente diferentes das utilizadas na injeção de plástico; mais próximas das de fundição injetada. No caso da Sedlom e no âmbito deste projeto, está a ser utilizada uma liga específica, indicada pelos técnicos japoneses. O Japão, enfatiza, tem uma experiência de mais de duas décadas neste tipo de processo.
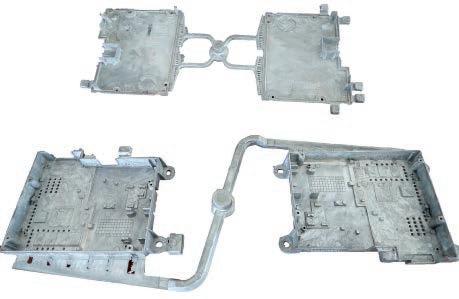
E a escolha desta liga tem uma razão de ser. É que o choque térmico é muito elevado. Explica que “as peças são injetadas com temperaturas próximas de 500 graus e depois numa fração de cerca de 20, 30 segundos, têm de baixar para uma temperatura na ordem dos 250 graus, que é a temperatura do molde”. Isto significa que os operadores não podem, de forma alguma, contactar com este material. As máquinas têm, por isso, de integrar células fechadas e manipuladas por robôs.
Sendo uma tecnologia em constante desenvolvimento, estão, também, a ser estudados e melhorados os vários tipos de magnésio utilizados como matéria-prima.
Jorge Silva destaca ainda que, através deste processo, são produzidas peças com densidade mais alta. “Enquanto que na fundição injetada conseguimos obter peças com aquilo a que na gíria chamamos chochos , que são bolsas de ar que no interior reduzem a resistência à própria peça, no processo de Thixomolding isso não existe. Há uma maior compactação que retira essas bolhas de ar”, explica. E o resultado são peças com maior resistência.
Chama ainda a atenção para um outro aspeto importante: este processo permite prolongar a vida útil dos moldes, aumentando a quantidade de ciclos efetuados.
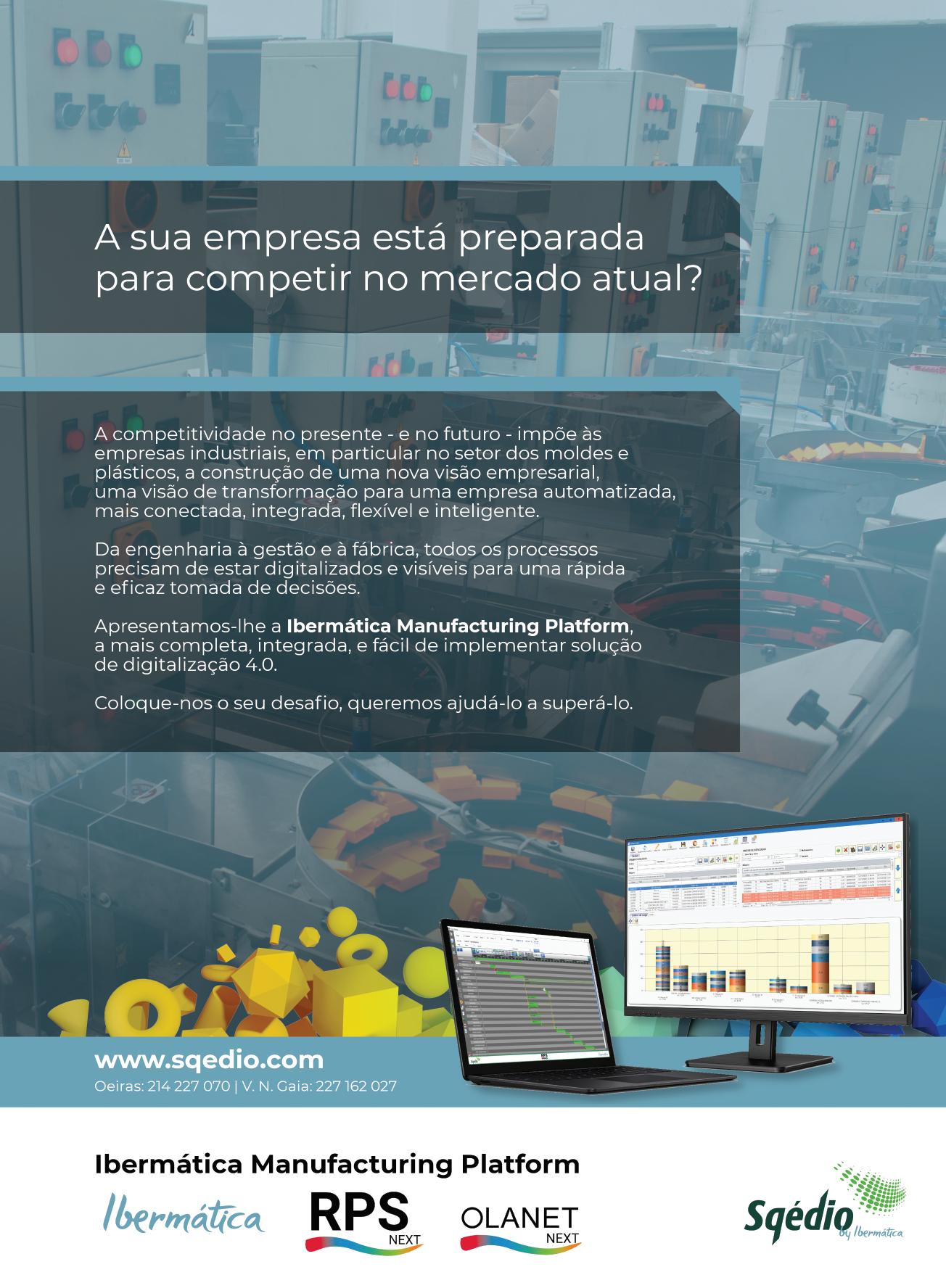