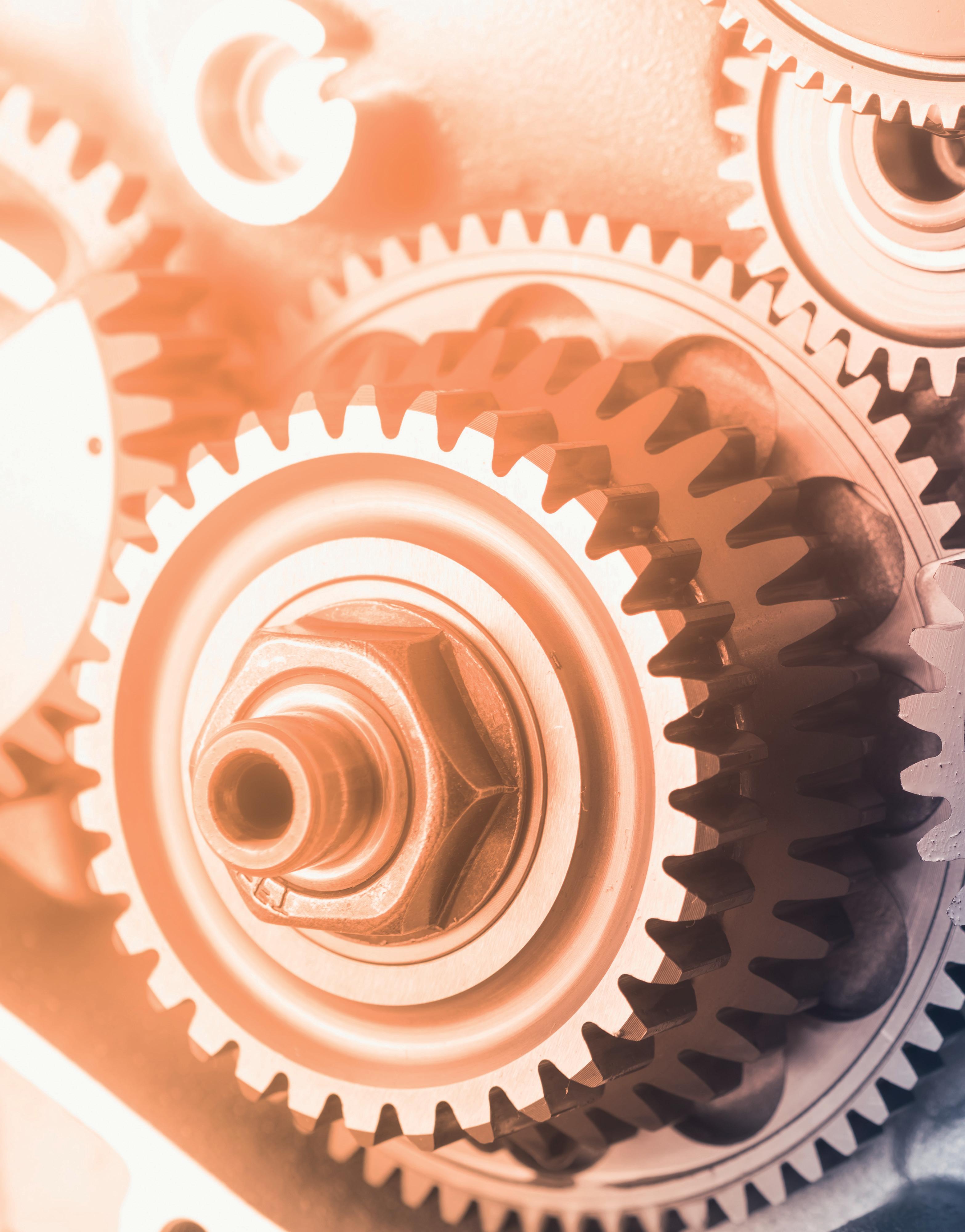
12 minute read
Uniformizar tarefas para ganhar qualidade
OTIMIZAÇÃO DE PROCESSOS DE FABRICO
STANDARDIZAÇÃO
UNIFORMIZAR TAREFAS PARA GANHAR QUALIDADE
Reduzir tempos de fabrico. Eliminar erros. Ganhar qualidade. A criação de uma linguagem uniforme e transversal a todo o processo de produção é a resposta para melhorar a eficiência das empresas e prepará-las para o futuro, num mercado cada vez mais exigente. Os produtores procuram criar standards que lhes permitam manter a qualidade, mas sem comprometer o preço e o prazo cada vez mais apertados.
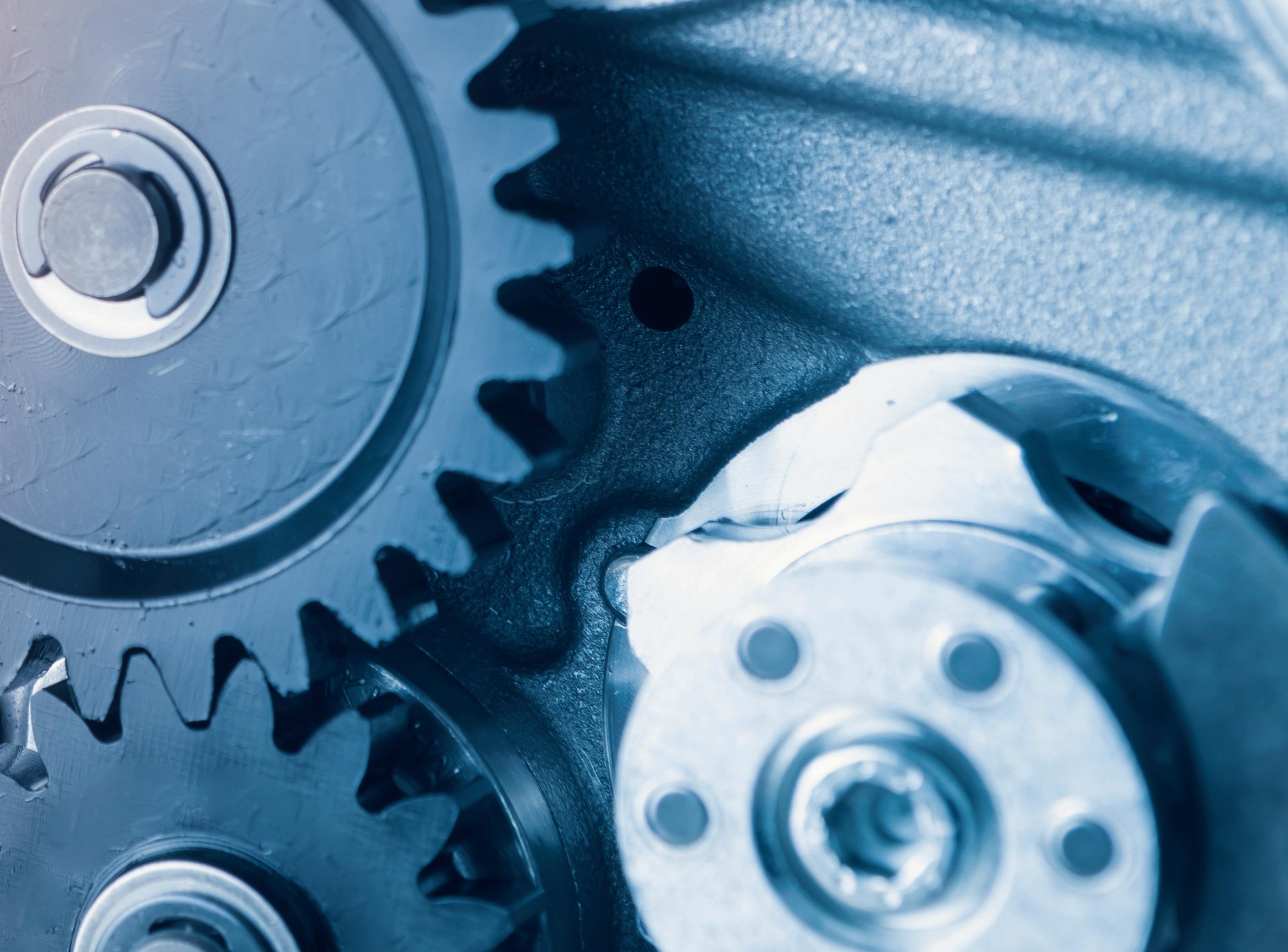
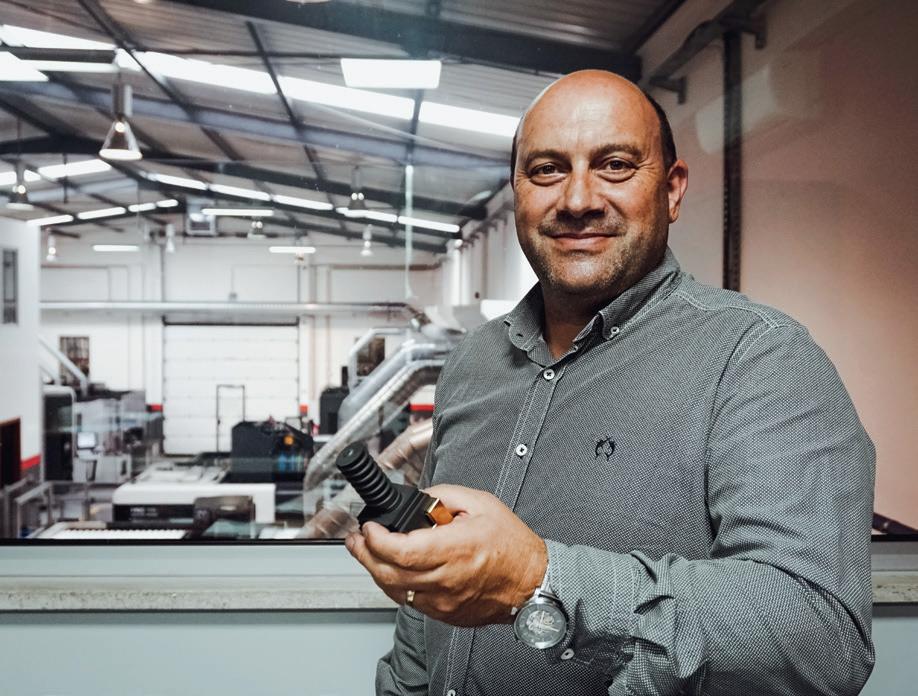
Joel Rodrigues – SM3D
Sistematizar procedimentos aproveitando as
potencialidades que as tecnologias oferecem, de forma a obter ganhos de produtividade. Joel Rodrigues, da SM3D, defende que a standardização é a resposta para tornar as empresas mais competitivas.
No caso da sua empresa, que desenvolve ferramentas em grafite para a indústria, esse foi o caminho que trilhou, considerando ter, neste momento, “um processo minimamente implementado em relação à standardização”. E, nestes 24 anos que a empresa leva de atividade, não se cansa de defender a necessidade de criar, para a indústria, uma ‘linguagem’ comum e transversal, que permita uma comunicação eficaz.
Exemplifica: “devia existir uma uniformização logo na migração de informação que vai de uns setores para os outros ou até de firmas para firmas”. E esta devia ser uma “variável identificável”, que permitisse que “todos falassem a mesma linguagem, de forma a facilitar os processos e a evitar os erros”.
Concretiza ainda melhor a sua ideia, contando que ao longo da sua atividade, “recebemos serviços das mais variadas empresas e tivemos, praticamente, de criar um tradutor para interpretar essa informação que é toda diferente, e transformá-la, de forma a conseguir manter um só método de produção na nossa empresa”. É que, defende, a criação desse método foi o que permitiu à sua empresa crescer. “Permite-nos trabalhar de forma rigorosa e automática. Ou seja, a Indústria 4.0 já é fisicamente visível no nosso chão de fábrica: temos tudo digitalizado”. Ter de interpretar cada informação que chega acaba por revelar-se “perda de tempo”.
Competitividade
O problema, considera, “é que ao longo dos anos, as empresas foram crescendo, foram adquirindo alguns sistemas e foram adaptando as suas maneiras de trabalhar e criaram os seus métodos próprios”. E, apesar de defender que “cada empresa deve fazer o que achar melhor, mais rentável e mais viável”, salienta que, por vezes, é preciso pedir trabalhos fora ou fazê-los para outras empresas. “E essa necessidade de se adaptar ao método do parceiro custa dinheiro e seria desnecessário se a indústria usasse uma linguagem que fosse mais universal”, explica.
Sendo certo que as empresas são constituídas por diferentes máquinas e linguagens, aquilo que preconiza é “um caminho que todos tentássemos percorrer, sem desvios muito acentuados”. Exemplifica que, no caso das aplicações para as células de produção, essa questão está a ser levada em conta pelos fornecedores. “Se não o fizessem, teriam de desenvolver um software à medida de cada empresa, o que seria inviável”, afirma.
Se esta ‘linguagem’ fosse adotada, o sector poderia, no seu entender, ser mais competitivo. E com isso, evitar-se-iam também os vários ritmos a que caminha a indústria. Como exemplo do efeito da linguagem uniforme, explica que na sua empresa, já está instalada a robotização de toda a produção. “Com um ‘clic’ do QR Code da peça, pode fazer-se todo o processo sem intervenção humana”, esclarece.
Melhoria
Foi em 2008 que, conta, começou o processo de automação da empresa. Foi nesse momento que “nos apercebemos do primeiro problema: a necessidade de criar uma interação entre os vários departamentos, softwares, robots”. Mas o mercado não tinha, então, soluções para responder a isso. “Nada do que existia dava resposta ao conceito que tínhamos”, adianta, relatando que foi necessário esperar até 2012, até que houvesse tecnologia capaz de permitir criar essa interação entre máquinas, robots e aplicação de software.
A partir daí, salienta, o processo de standardização caminhou mais célere. “Gastámos e despendemos recursos financeiros e humanos para conseguir automatizar e chegar onde estamos hoje. Temos dois pavilhões com células produtivas”, conta, sublinhando que “ainda não está a 100% porque este é um processo que está sempre a ser melhorado”.
Foi dada também resposta a uma dificuldade que sentiam, que se prendia com a qualidade da matéria-prima. Hoje, a empresa é representante de uma marca certificada de grafite. Com esta forma automatizada de trabalhar, adianta, “mais do que triplicámos a produção”. O método permitiu ganhos de tempo, mas também de qualidade.
Para garantir a eficácia, conta, foi necessário criar a figura do gestor de métodos e processos, que analisa a implementação das ideias e verifica o processo diariamente, percebendo as fragilidades e os pontos fortes. “É o fiel da balança para que as coisas funcionem e tem sido a chave para as tomadas de decisão”, acrescenta.
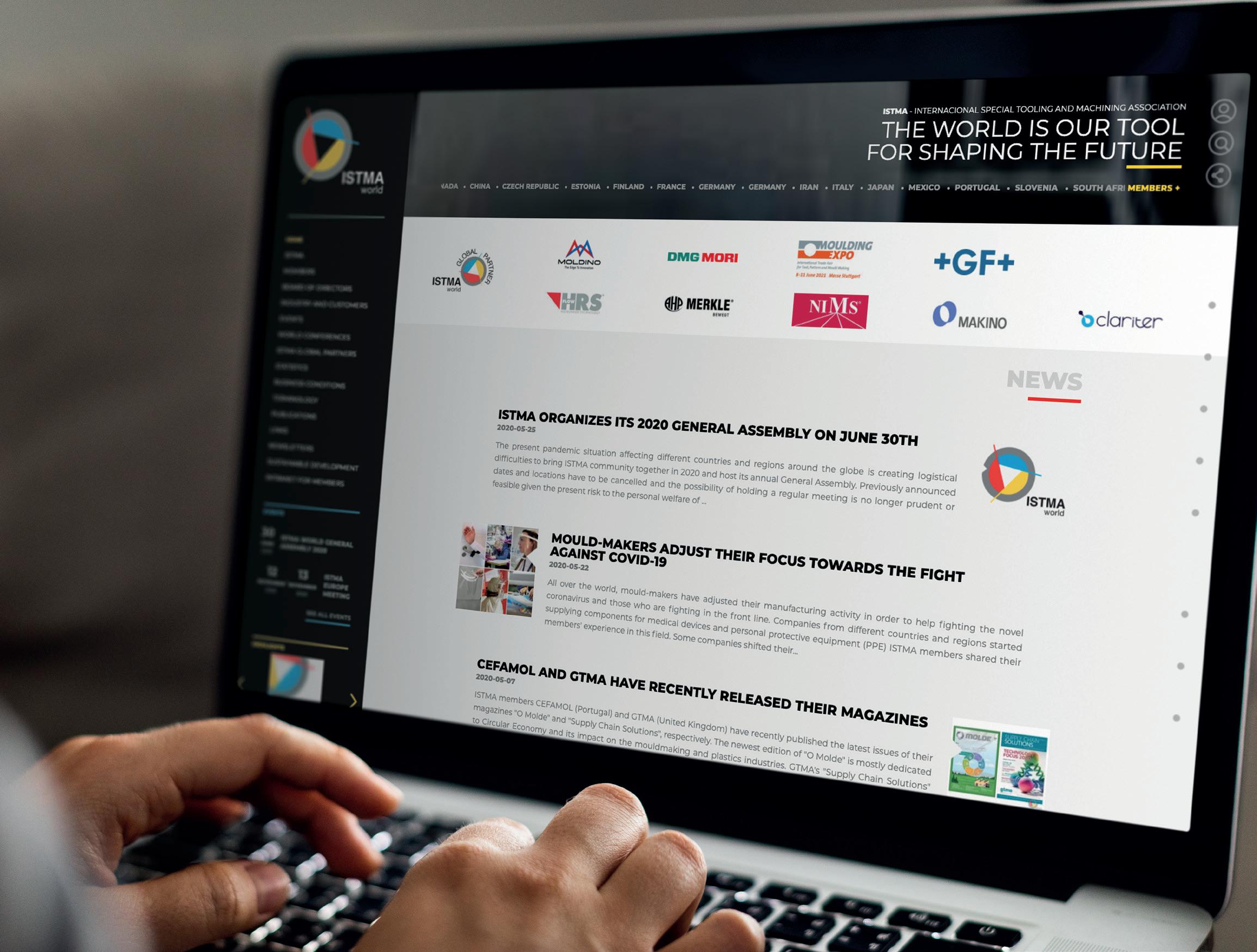
www.istma.org

Para Joel Rodrigues, as empresas que conseguirem abraçar o caminho da standardização vão conseguir manter-se competitivas o que, no atual momento de dificuldade por que passa a indústria, é fulcral para a sobrevivência. Mas manifesta sentir algum receio de que “com a descida dos preços, que seja o ‘salve-se quem puder’, e se esqueça o que se estava a fazer antes: o caminho da standardização”.
DRT: O digital como ferramenta de otimização
É através de um sistema que integra todas as áreas e departamentos das empresas do grupo, que a DRT assegura a uniformização da sua produção.
O passo que trouxe a empresa a este nível de otimização foi dado há 15 anos, conta Valdemar Duarte. “Quando fizemos a transformação digital da empresa, ou seja, conectar pessoas, coisas e processos, tivemos necessidade de trabalhar mais profundamente na standardização”, explica, lembrando que toda a indústria, até então, já trabalhava com alguns métodos standard, desde que, em 1983, foram sugeridas algumas medidas de uniformização, no decorrer do primeiro Congresso da Indústria de Moldes.
Hoje, os processos da DRT “estão numa forma digital, o que significa que quando se pretende fazer algo na empresa, isso seja feito de acordo com o fluxo de trabalho já definido (workflow)”.
Isto permite um controlo praticamente total sobre tudo o que se passa na empresa, em tempo real, o que auxilia na tomada de decisões e, logo, na rentabilidade do processo, adianta.
E este sistema, designado SBI (System Business Intelligence), assegura uma standardização com níveis de precisão muito elevados. Como exemplo, Valdemar Duarte aponta a recolha de dados em tempo real, através de sistemas de IOT (Internet das Coisas), usando data mining (mineração dos dados) para os estruturar e permitir que o próprio sistema vá aprendendo e vá progredindo.
“Quando analisamos os nossos indicadores, é preciso ter os dados muito bem estruturados para os conseguirmos obter e reorganizar na ‘família certa’, de forma que nos mostrem, com clareza, aquilo que precisamos de ver”, sustenta, considerando, numa analogia, que “a standardização é arrumar todo o armário de dados (big data)”.
Rastreabilidade
No seu entender, “quem quer entrar na era digital tem, obrigatoriamente, de fazer isto”. Os dados que, no passado, eram inseridos manualmente, são hoje geridos de forma automática e em tempo real, num fluxo onde as máquinas comunicam entre si e o papel das pessoas ficou reservado, sobretudo, a operações de criação e de controlo. “Desta forma, eliminamos erros e atrasos”, afirma.
Exemplifica: no caso da DRT, todos os processos estão ‘desenhados’ no sistema. Isto permite, por exemplo, que um funcionário recém-chegado à empresa, mesmo não conhecendo os procedimentos, não possa errar, uma vez que a sua tarefa está definida no sistema.
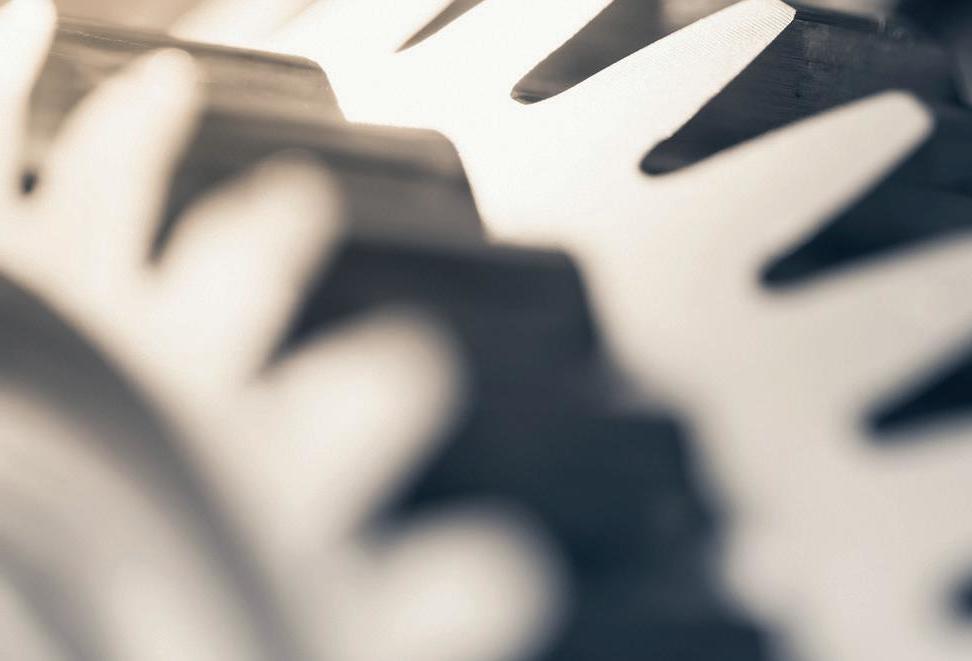
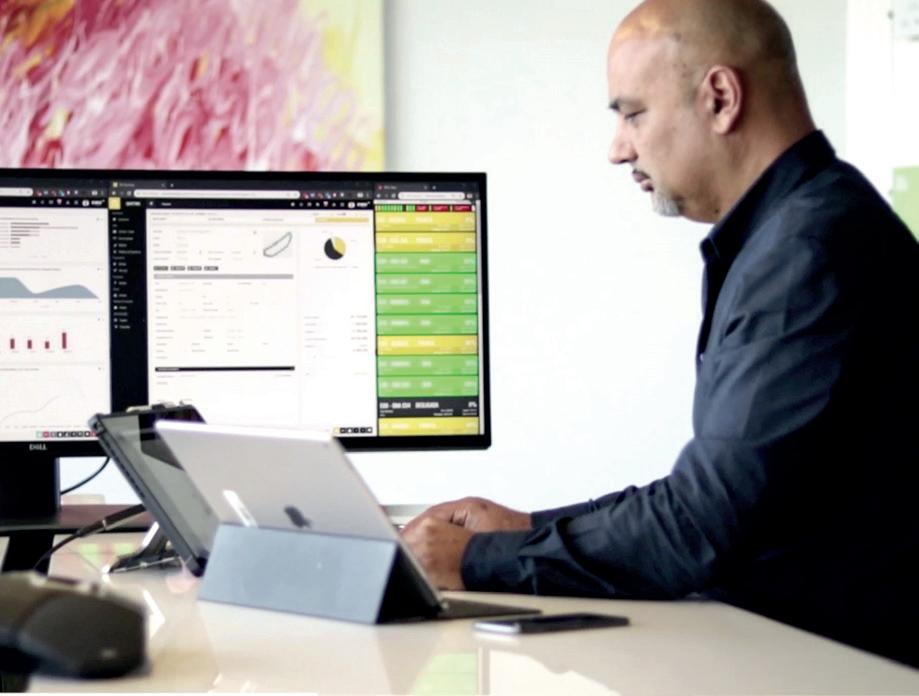
Valdemar Duarte – DRT
Num método mais tradicional, compara, o fluxo de trabalho está definido e plasmado no processo de qualidade, mas, apesar disso, se este não for digital não há forma de ter a certeza se está a ser bem executado.
“O sistema tradicional tem bastantes lacunas que, no nosso sistema, deixam de existir”, defende.
Uma das grandes vantagens que salienta é a possibilidade de rastrear tudo o que é feito porque o sistema cria um histórico que não desaparece. “Esta rastreabilidade, por exemplo de documentos, evita discussões e situações desconfortáveis que se vivem nas organizações. Desta forma, questões como ‘quem foi’, ‘quem fez’ são rapidamente esclarecidas pelo histórico que é gerado”, explica.
Da mesma forma, as tarefas estão contempladas e basta um clic para as despoletar. Volta a dar um exemplo. Quando é preciso embarcar um molde, há todo um conjunto de tarefas que são necessárias. Estão todas definidas no sistema, que comunica com os vários departamentos, de forma que, na data prevista, essa tarefa seja executada com sucesso. “Não há esquecimento de nenhum passo, nem enganos”, frisa. Integração

O sistema, tal como está, levou quase duas décadas a desenvolver. Mas, salienta, “está validado e testado, funcionando na perfeição há mais de oito anos, e numa evolução constante”. “Chegar aqui foi um salto grande, sobretudo o passo de ter tudo isto integrado em tempo real”, considera.
Apesar de parecer um sistema fechado, não é. Pelo contrário. É adaptável à realidade de qualquer empresa. “O software não dá procedimentos, tem de ser desenhado no sistema, em função das características de cada empresa”, esclarece.
Para Valdemar Duarte, a indústria de moldes está hoje num patamar em que a qualidade e a competitividade têm de ser asseguradas, sob pena da extinção de algumas organizações. “As empresas conseguem continuar a trabalhar, procurando adaptar o que têm, mas isso não é a solução porque fazê-lo vai provocar lacunas e, quando há uma avaria, por exemplo, nem sempre é fácil perceber onde e como reparar a situação. Por isso, a solução tem de ser um sistema integrado, com a mesma linguagem e as mesmas bases de dados”, defende, salientando que o objetivo é “trabalhar na prevenção e antecipação e não sobre o problema porque, nessa altura, já chegamos tarde”.
VSV: Empresas juntas pela equidade na standardização
As empresas deviam unir-se na busca de um processo de otimização que servisse para todo o sector de moldes, de forma a criar equidade na standardização. Quem o defende é Alberto Vinagre, da VSV, para quem uma grande parte dos processos “devia ser igual para todas as empresas”.
Para encontrar essa forma de trabalhar, considera que as organizações têm de falar e definir entre si o que pode ser feito e avançar. “Se todos contribuíssemos um bocadinho, no final ficaria um processo de qualidade, o que nos colocava a todos em patamares idênticos. Hoje, isso não acontece. Há empresas com os seus processos muito standardizados, e outras muito longe de lá chegar”, afirma.
Nos processos produtivos, considera, a standardização pode ser visível em soluções como a paletização, a maquinação contínua, ferramentas de aperto contínuo, ou as formas de desempenar ou centralizar a peça. “É o mais comum”, considera, adiantando que, depois, “há quem tenha outros procedimentos standardizados e é para aí que todos devemos caminhar”. E isto porque, no seu entender, a adoção do standard “permite reduzir erros, possibilita que os processos vão sendo encurtados e o tempo de fabricação acaba por ficar menor”.
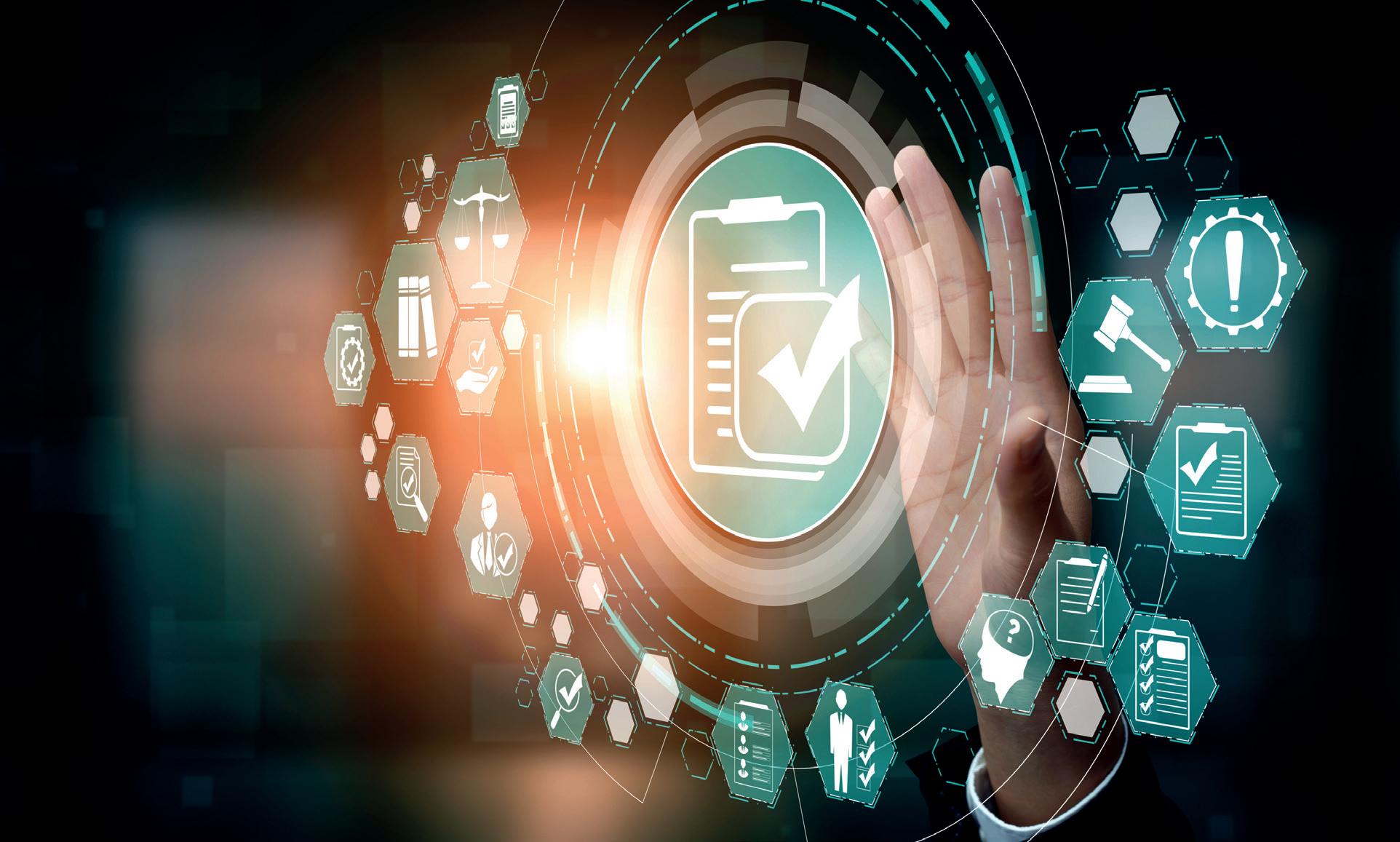
A standardização é, para si, “uma forma de combater os preços baixos”. Mas, adverte, “para avançar com o que é preciso as empresas precisam de capital para investir nas mudanças que necessitam”. E as organizações que entraram primeiro neste caminho, considera, “são hoje as mais avançadas, não apenas tecnologicamente, mas a nível de processos, de rapidez, de soluções”.
E isso é, no seu entender, fundamental para enfrentar situações complicadas como aquela que se vive atualmente, com a indefinição na indústria automóvel.
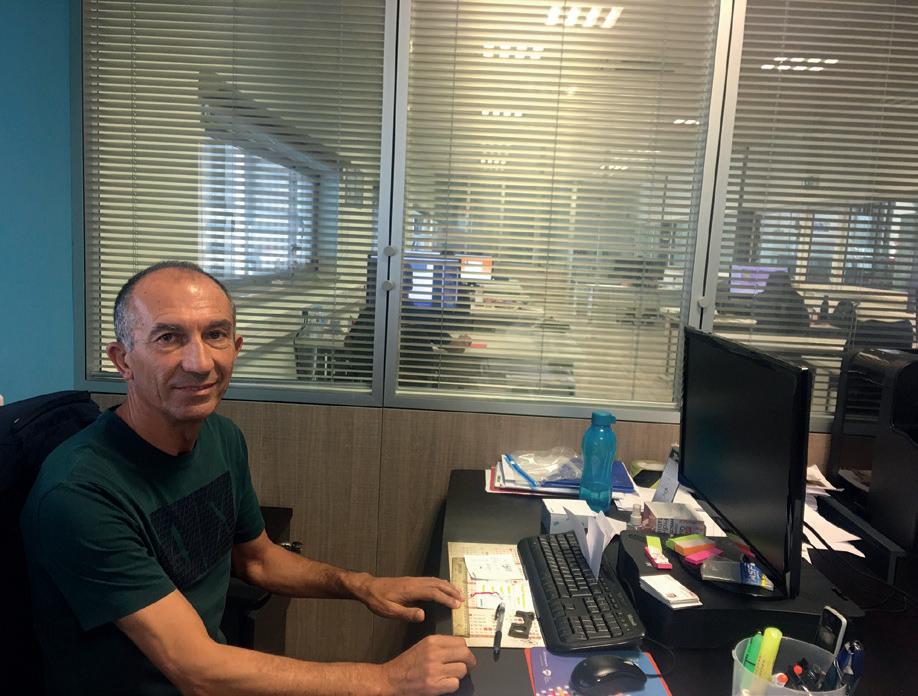
Alberto Vinagre – VSV
“Em momentos de crise, estas empresas são as que estão mais bem preparadas para os enfrentar porque têm os seus processos ‘oleados’. E em momentos de aperto, são aquelas que se vão salvar, uma vez que rapidez e eficiência são as armas contra as crises”, afirma. Para além destas duas características, também a especialização em determinado tipo de produtos é garantia de futuro para as empresas, no seu entender.
“Creio que daqui por seis anos, a indústria de moldes estará muito diferente do que é hoje. Vão salvar-se as empresas que fazem determinados trabalhos com maior especialização e um nível de tecnologia superior. E mais meia dúzia a fazer manutenções nos moldes. O resto, acredito que não conseguirá sobreviver”, afirma.
Desafios
Em relação à sua empresa, conta, “fomo-nos apercebendo, desde há alguns anos, da necessidade de mudar, de nos adaptarmos. Começamos pela centralização. Mas a paletização também é extremamente importante”. O objetivo, relata, foi “conseguir fazer o máximo num único trabalho, de forma a poupar tempo, energia e processos”.
Ao longo do fluxo produtivo, nas várias fases, “percebemos que íamos tendo repetição de trabalho e que isso podia ser evitado. E temos avançado por aí, diminuindo o trabalho e o tempo, reduzindo processos”. E a estratégia passa por ir avançando nesta standardização.
“Está em curso essa mudança na nossa empresa”, salienta, considerando é necessário aproveitar os mecanismos de apoio existentes e “mudar o que é necessário para sermos melhores e mais competitivos. O investimento não pode parar numa empresa, senão ela morre”, defende.
E quando se fala em investimento em tecnologias, Alberto Vinagre considera que se pensa também nas pessoas. Na sua qualificação. “É essa aposta na qualificação que nos vai permitir implementar essa mudança. Não são apenas as máquinas ou as tecnologias: as pessoas são fundamentais”, afirma.
“À medida que o tempo passa, os desafios vão sendo maiores, mais complexos”, defende. Mas os fabricantes portugueses têm conseguido, na sua opinião, evoluir ao mesmo ritmo das empresas europeias. A isso se deve bastante, no seu entender, o papel dos fornecedores de tecnologias, que “foram evoluindo e têm soluções excelentes à medida de cada empresa”. Por isso, mostra-se convicto de que “o caminho está definido, há soluções disponíveis” e compete a cada empresa “dar passos e otimizar o que conseguir, de forma a ganhar competitividade”.
C
M
Y
CM
MY
CY
CMY
K
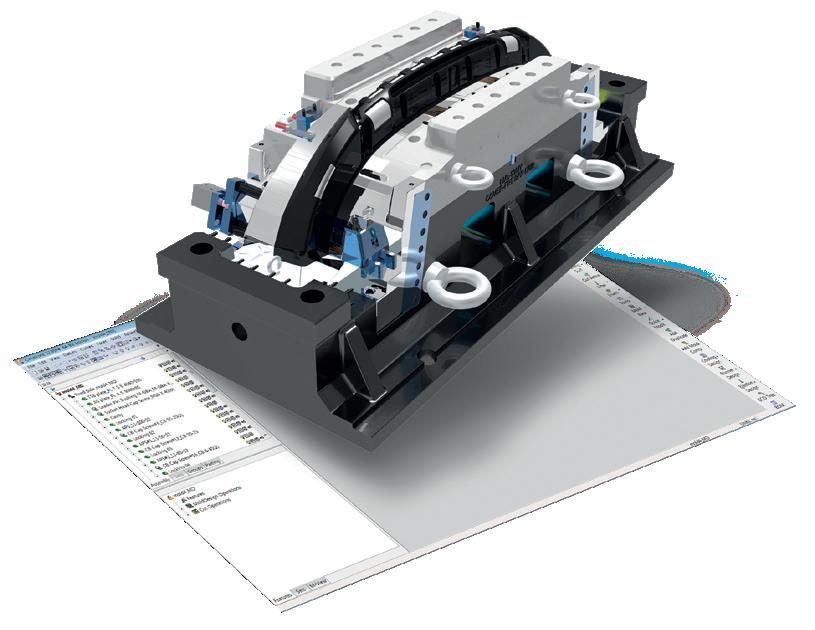
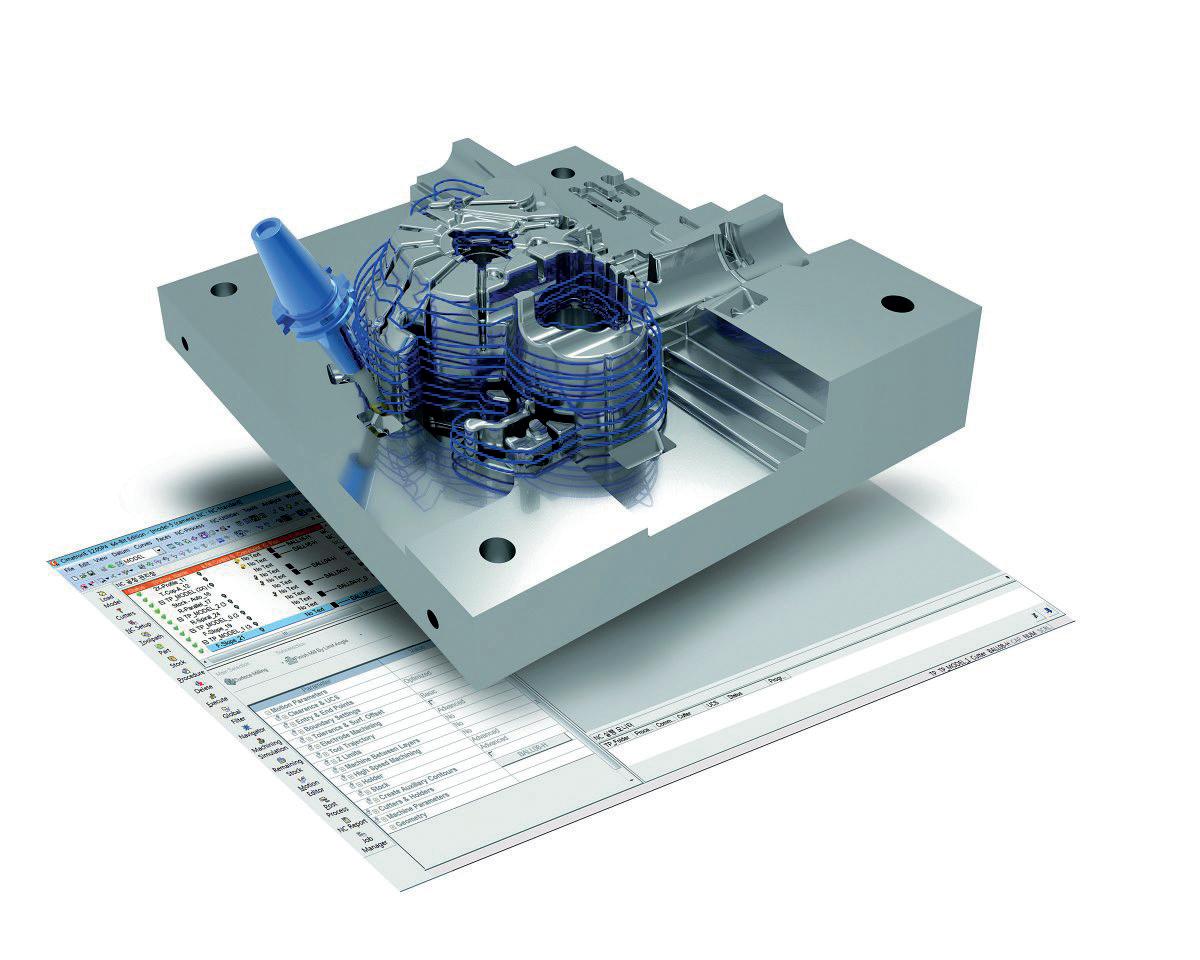