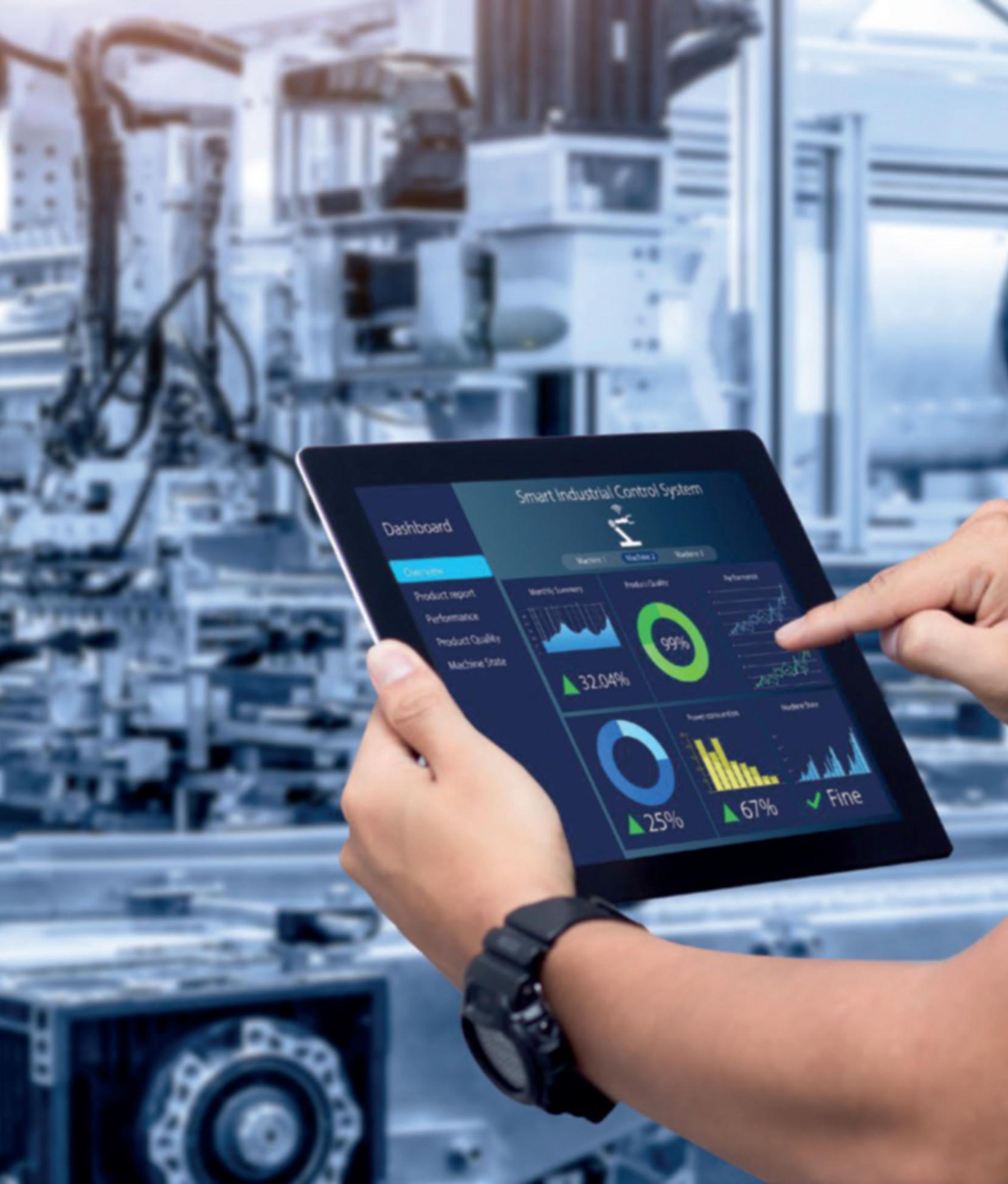
11 minute read
Organizar para ganhar tempo e qualidade
OTIMIZAÇÃO DA MAQUINAÇÃO
ORGANIZAR
PARA GANHAR TEMPO E QUALIDADE
Dos armários inteligentes, aos sistemas de aperto e de fabrico flexível. São variadas as opções que se colocam às empresas, no que toca a otimizar os processos de maquinação. Bem selecionados e integrados na produção, permitem rentabilizar o processo, com ganhos de tempo e qualidade.
Rapidez. Esta é, no entender de Ricardo Caseiro, da Moldata, uma das maiores vantagens da otimização quando aplicada ao processo produtivo. Hoje, em lugar de percorrer metros no chão de fábrica, “conseguimos ter toda a informação disponível através de um ‘clic’, carregando num botão”, explica, assegurando que a área produtiva da empresa registou melhorias significativas com a introdução das tecnologias. Desde armários inteligentes para ferramentas e peças até mil quilos, a sistemas de aperto: o investimento nestas soluções permitiu “reduzir tempo e ganhar eficiência”, adianta.
A diferença entre o antes e o depois “é grande”, no seu entender. E exemplifica: “Eliminámos algumas tarefas, como os pedidos. Ou seja, o armário faz automaticamente os pedidos em quantidades, diretamente para o fornecedor das ferramentas, em função das necessidades”. Para além disso, salienta, “conseguimos saber sempre onde está a peça que precisamos”. E com este sistema, essa peça é “acabada, verificada e colocada num armário, na prateleira respetiva do molde”.
Um outro exemplo que dá: “Hoje, em casa, consigo controlar as minhas máquinas, através do smartphone. Isto quer dizer que as tecnologias nos trouxeram qualidade de vida”. Uma parte significativa deste processo é automática e surge integrada na cadeia de produção. É um processo evolutivo, esclarece, adiantando que as soluções vão sendo introduzidas em função da estratégia definida pela empresa.
Dá ênfase a uma dessas soluções, os sistemas de aperto que, considera, permitiram “ganhos consideráveis de tempo”. “Ao colocar as peças na máquina, com estes sistemas, elas ficam praticamente 100% desempenadas e centradas”, explica.
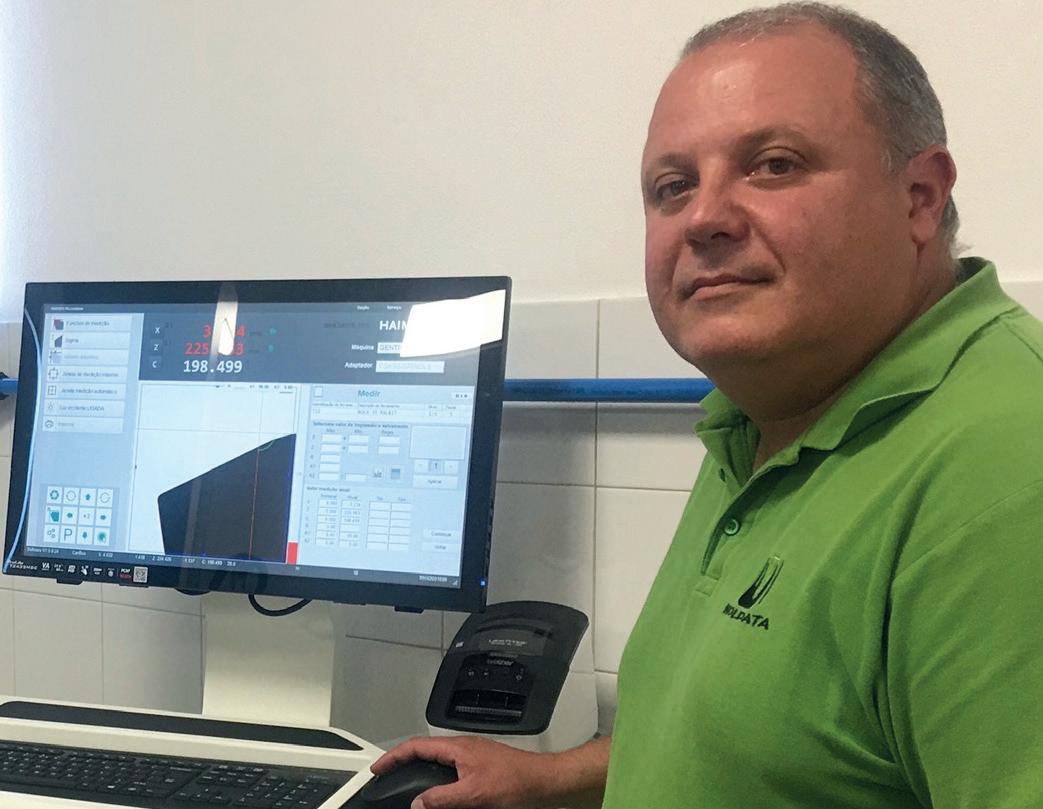
Ricardo Caseiro – MOLDATA Células
A tipologia de moldes a que a empresa se dedica – de grandes dimensões – foi uma das principais razões, conta, para ainda não ter avançado para outras soluções mais automatizadas, como as células de produção.
“Ainda não temos células, mas temos as máquinas que têm mesas que são colocadas por ponte rolante, atendendo a que se trata de peças consideráveis e com bastante peso”, esclarece. Mas não tem dúvidas de que o processo evoluirá para aí. Até porque, no seu entender, “as células permitem um grau enorme de otimização nesta fase da produção”.
É que, salienta Ricardo Caseiro, as células permitem “fazer tudo o que quisermos e necessitarmos que façam, desde o transporte das peças e, em alguns casos, até à sua lavagem”.
Por todas essas vantagens, as células são uma opção natural, em termos de futuro, para a empresa. Contudo, ressalva, há um conjunto de condições que é preciso criar para chegar aí. E é preciso grande ponderação antes de dar o passo, até porque o investimento “não é pequeno”.
“Não avançamos de imediato porque, neste momento, com a pandemia de Covid-19, há uma indefinição enorme nos mercados. Mas temos projetos pensados, sabemos para onde queremos ir, mas vamos com cautela”, afirma.
Está convicto de que as soluções existem. Aponta como exemplo o avanço tecnológico que, pouco antes da pandemia, teve oportunidade de observar numa visita ao Japão. Por isso, a aposta de melhoria passará pela aposta nas células.

O erro
Para Ricardo Caseiro, para além dos ganhos de tempo, uma das vantagens da otimização é a redução do erro no processo de fabrico. “O erro é a coisa mais cara da nossa indústria”, defende. Por outro lado, a otimização “também evita desperdícios”. Como exemplo, conta que, neste momento, a empresa está equipada com transportadores de limalhas em todo o chão de fábrica. “Saem diretamente das máquinas para os transportadores”, conta, adiantando que com estes sistemas “conseguimos poupar” e, no final, “poupar acaba por ser um ganho muito grande”.
Reduzindo o número de pessoas em algumas tarefas, será possível minimizar a possibilidade de errar. Mas as pessoas, sublinha, continuarão a ser “o mais importante da empresa”, contudo serão orientadas para “outras áreas onde o conhecimento humano é mais necessário”.
Considera que é inevitável que as empresas caminhem no sentido da adoção destas tecnologias. E que o futuro passará pelo incremento da robotização que, no seu entender, já se aplica em vários equipamentos, e também da inteligência artificial.
“As empresas de moldes têm de caminhar para este ponto, caso contrário dificilmente sobreviverão”, defende. Contudo, adverte que a otimização “requer um investimento grande, uma vez que as soluções que existem são todas muito caras”. Por isso, tem de ser bem ponderado. Para além disso, acrescenta, “não se rentabiliza rapidamente. Demora algum tempo. Mas fazemos mais trabalho com mais qualidade e mais rápido e, por isso, vai compensar mais tarde”. Tecnijusta: Otimizar pequenos procedimentos para ganhar no processo
Antes de chegar à máquina, qualquer processo de otimização, para ter sucesso “tem de passar pela formação das pessoas”. Quem o defende é Bruno Mendes, responsável pelas maquinações da Tecnijusta.
No seu entendimento, é fulcral sensibilizar cada trabalhador para “a importância dos pequenos procedimentos diários que nos permitirão ganhar mais à frente no processo”. Como exemplo, aponta a “auto-verificação, o controlo”. Ou seja, “se soubermos que a peça saiu da máquina em condições, sabemos que quando chegar à bancada está em condições”. Por isso, defende que “cinco minutos de verificação sistemática, significam horas no final do processo”.
E é por esta razão que considera de extrema importância a necessidade “ter um bom ambiente de trabalho, onde as pessoas se sintam bem e motivadas para integrar o processo, dando atenção a cada pormenor”.
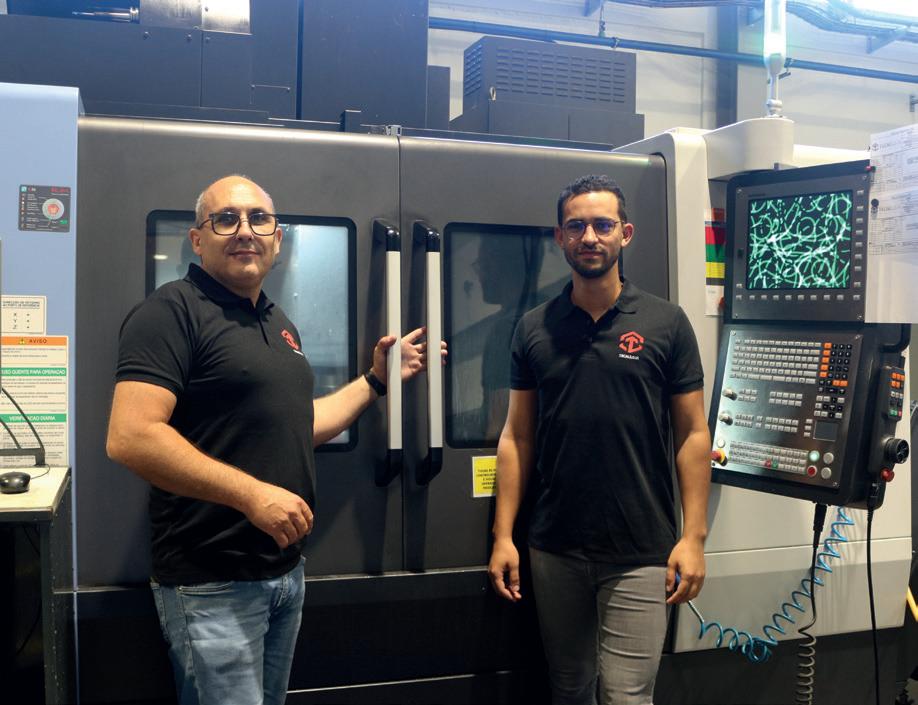
Pedro Mateus e Bruno Mendes – TECNIJUSTA
Bruno Mendes acrescenta ainda que, hoje, “já há ferramentas, a nível de software, que podem fazer essas verificações, mas se não partir do operador, não adianta”. Com isto, “conseguimos alcançar o objetivo que é chegar a um processo de fabrico fluido, porque foi feito e confirmado e passado ao operador seguinte”.
E o processo é fluído, no seu entender, quando “se consegue retirar rentabilidade e otimização, a nível de ferramentas e de processos”. Para isso, um dos passos é “elencar o número de horas para tudo o que se faça”.
Com isso, “conseguimos ter melhor perceção do trabalho que temos na empresa e onde podemos derrapar, mas também temos maior controlo, conseguindo sempre uma margem de manobra para os imprevistos”, explica, sublinhando que a partir daí, “encadeamos e colocamos no processo fluido, e sabemos se é viável executar esse processo no número de horas útil. Caso não seja possível, temos de começar a avançar com planos A, B ou C: ir buscar trabalho ao exterior, desfasamento de horário, o que for possível”. Implementar este sistema, admite, “não foi fácil inicialmente”. Mas hoje, “é uma questão de rotina”.
Este controlo horário é uma regra que nasceu da experiência do administrador, Pedro Mateus. “Sempre trabalhei com um objetivo. E aprendi a trabalhar à hora, apesar dos ‘plannings’ semanais. Uma semana tem muitas horas. Há máquinas que podem trabalhar fora de horas e, por isso, temos toda a vantagem em fazer esse controlo à hora”, explica.
Máquinas
Assegurado este procedimento, é tempo, então, de avançar para as máquinas, adianta Bruno Mendes. E aí a experiência é fulcral. “Temos de ter conhecimento do molde, em detalhe, de forma a saber quais as zonas onde nos vamos debruçar um bocadinho mais e as outras onde não é necessário esse excesso de zelo. Porque isso vai ter reflexos na montagem. E poupa-se tempo”, salienta. “E quando o molde chega às máquinas, chega da forma que, em equipa, achamos ser o mais correto”, acrescenta.
Esta otimização permite projetar o trabalho de forma mais vantajosa, definindo, por exemplo, quais as máquinas que irão trabalhar 24 horas. Essa organização do trabalho, que fica assim dividido entre tarefas com operador e tarefas só de máquina, “permite ganhar tempo e, com isso, ganhar rentabilidade”, explica Pedro Mateus. Dessa forma, a empresa consegue ser mais competitiva em períodos como o que a indústria vive atualmente, com os preços a serem “cada vez mais esmagados pelos clientes”.
“Estou convencido de que quem não conseguir trabalhar desta maneira terá tendência a desaparecer do mercado”, considera Pedro Mateus, defendendo que a ‘chave’ é a organização do trabalho. Lembra que “há outros países com mão de obra barata e que têm possibilidade de adquirir tecnologias e matéria-prima” e, por isso, “a nossa diferença tem de ser nesta sistematização do processo”. E isso deixa a empresa preparada para avançar para o passo seguinte da otimização que, explica Bruno Mendes, é a robotização.
Pedro Mateus admite que é fundamental, mas, no caso da sua empresa, é uma opção que necessita de ser bem ponderada, uma vez que “todos os dias, trabalhamos diferentes tipologias de moldes, de várias dimensões”. Estas tecnologias, considera, “representam um investimento avultado e que tem de ser rentabilizado”. “Sabemos que é o futuro, mas vamos adotá-lo como um investimento feito aos poucos, de forma gradual”, diz.
Bruno Mendes considera que à medida que a empresa vai evoluindo nos processos, a abertura para a robotização vai ficando mais preparada. “Temos a estrutura feita, na empresa, para um dia colocar isso em prática: as máquinas estão a evoluir, os softwares também”, conclui.
Moldoeste: Adotar a mudança de forma progressiva
A otimização é o resultado de uma constante evolução, assente em mudanças progressivas e transformadoras, com vista à melhoria da competitividade. Esta é, em resumo, a opinião de Celso Amaral, da Moldoeste. Desta forma, acrescenta, “a otimização é um processo que nunca acaba”, uma vez que “há sempre alguma coisa que se pode mudar e otimizar cada vez mais”. Porque, para a melhoria do processo produtivo, “a evolução das coisas é fundamental”.
Na Moldoeste, esta mudança tem vindo a acontecer de forma gradual, intensificando-se, sobretudo, nos últimos anos, com alterações aos processos, aplicação de novas metodologias de trabalho e de ferramentas. Como exemplo, explica que “alguns tipos de trabalho que não eram colocados em determinadas máquinas, eram feitos de outras formas, passaram agora a sê-lo”. Com isto, adianta, a produção “ganha tempo, produtividade e mais qualidade”.
Para que estas alterações se concretizem, Celso Amaral defende que é necessário existir, desde logo, “uma grande união entre as áreas de produção e de projeto, de forma a acertar as ‘extremidades’ dos processos”. Tal permite evitar que o projeto execute algumas peças que, uma vez chegadas à produção, “possam criar dificuldades no processo”.
“Esta união é importante para estudar metodologias e preparar o que fazer”, considera. Para além disso, esta ligação permanente entre os dois sectores permite “ir vendo sempre as melhorias a introduzir, tendo em conta os equipamentos que temos”. “Tem-se ganhado muito quando se trabalha em conjunto”, salienta.
Tecnologias
Esta metodologia é, no seu entender, fundamental antes de se avançar para a aquisição de máquinas e tecnologias. “Permite que consigamos perceber o que temos. E é fundamental que, primeiro, exploremos os recursos que temos, antes de avançar para outros”, explica, adiantando que “por vezes, as empresas têm muitos equipamentos e recursos disponíveis que não são explorados. E deviam ser. Esse devia ser o ponto de partida”.
Mas depois, acrescenta, é preciso apostar em tecnologias que permitam às empresas ir mais além. “Se queremos evoluir, temos de estar na linha da frente. Os softwares, as máquinas e as ferramentas são fundamentais para otimizar o processo e estar na linha da frente. Não se otimizam processos com equipamentos obsoletos, mas mesmo sem equipamentos de topo, é sempre possível otimizar o processo”, afirma. Celso Amaral – MOLDOESTE
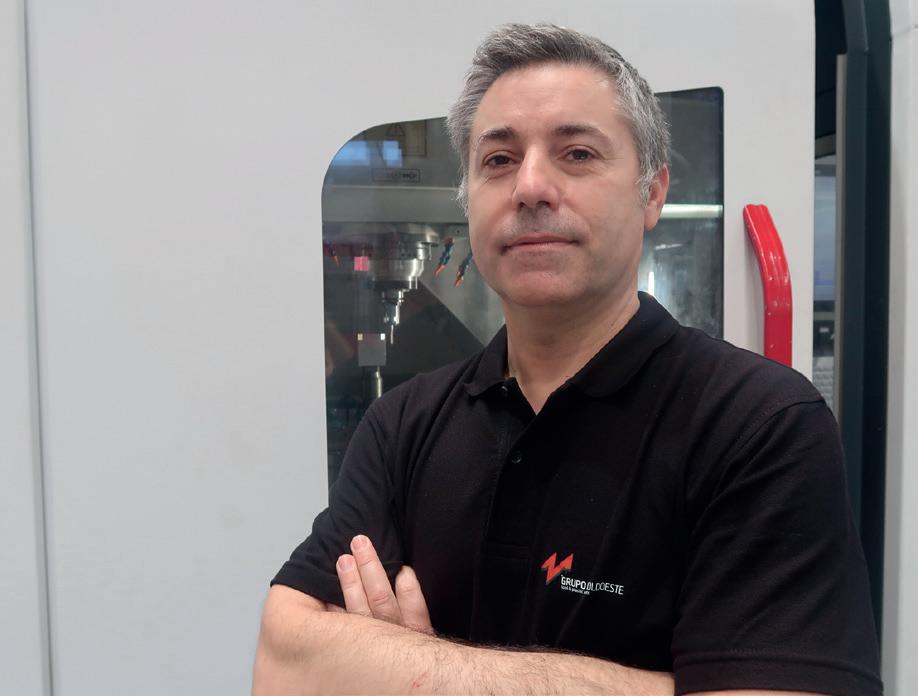
Contudo, enfatiza, o que acontece, por vezes, é que “as empresas se prendem aquela mentalidade do ‘sempre fizemos assim’ e, como têm muitos picos de trabalho, acabam por não ter tempo para parar e testar outras possibilidades”. Mas, defende, “é fundamental encontrar tempo. É preferível parar, mudar, porque depois vai-se ganhar mais à frente no processo”. Por isto, considera ser fundamental que as empresas apostem em pessoas dedicadas a acompanhar este processo de otimização, garantindo que a mudança acontece quando é necessário.
As tecnologias são, na sua opinião, de extrema relevância. “É importante fazer investimentos e automatizar processos, até para não depender tanto de recursos humanos e, ao mesmo tempo, melhorar a qualidade da produção e minorar os erros”, sustenta.
Nesse aspeto, considera, o mercado tem bastantes soluções disponíveis, mas têm, contudo, de “ser moldadas à necessidade de cada empresa, pois cada uma tem a sua maneira de trabalhar”. Mas os fornecedores são, no seu entender, mais do que vendedores, “transportadores de conhecimento que apoiam muito as empresas”. Por isso, adverte que é preciso ponderar antes de decidir. É que, salienta, “os tempos são cada vez mais reduzidos e é preciso fazer contas e perceber quais as melhores soluções”.