Inside Interviews with:
Yogesh Sarin, Director - Supply Chain, South Asia, Dell Technologies
Mayur Chhabra, Head – Supply Chain, White Cement and Paints Division, JK Cement
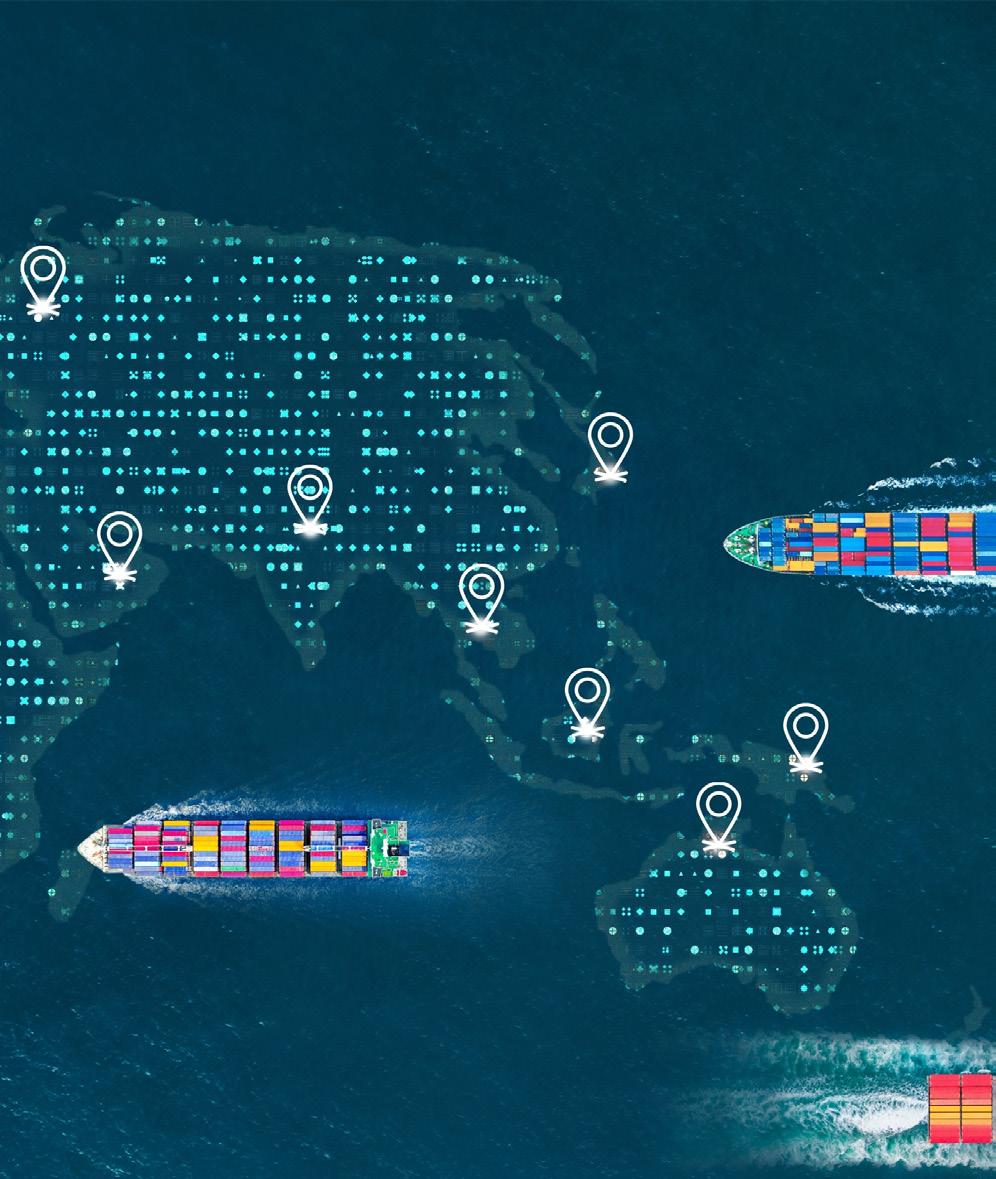
Inside Interviews with:
Yogesh Sarin, Director - Supply Chain, South Asia, Dell Technologies
Mayur Chhabra, Head – Supply Chain, White Cement and Paints Division, JK Cement
An Insightful Panorama of Leadership Traits to empower CSCOs climb the Success Ladder and Inspire Others
Dear Readers,
Welcome to our June 2024 issue. Our theme for this issue, “Leadership in the Supply Chain,” reflects the pivotal role of strong leadership in navigating the complexities and uncertainties that define the modern supply chain landscape.
We all know about the unprecedented challenges that supply chains have undergone – from pandemic to geo-political to technological disruptions and environmental concerns. These challenges have underscored the necessity for supply chain leaders who are not only strategic and innovative but also adaptable and forward-thinking.
While the key attributes of successful supply chain leadership align with those of leaders in other functions, navigating the complexities of supply chains during times of uncertainty demands a multifaceted approach. In this issue, we dedicate an entire section to articles and interviews from industry leaders, who share practical strategies and essential traits that supply chain professionals must adopt to steer their organizations successfully into the future. Their stories and strategies provide valuable lessons on the importance of leadership in achieving supply chain excellence.
As we continue to explore the evolving dynamics of supply chain management, we hope to inspire and equip our readers with the knowledge and tools needed to lead with confidence and resilience.
Thank you for joining us on this journey.
Warm Regards,
Charulata Bansal Publisher Charulata.bansal@celerityin.comwww.supplychaintribe.com
Edited by: Prerna Lodaya e-mail: prerna.lodaya@celerityin.com
Designed by: Lakshminarayanan G e-mail: lakshdesign@gmail.com
Printed by: Xposures, A 210, Byculla Service Industrial Estate, D K Cross Road, Byculla, Mumbai- 400027. Logistics Partner: Blue Dart Express Limited
14 Leading Supply Chains during Uncertainty
Rohit Menon, V G Venkatesh and Haripriya Vasudevan, emphasize that now more than ever is the time for leaders at every layer of the supply chain function to imbibe flexibility and out-of-the-box thinking.
Dr. Rakesh Sinha, Founder & CEO, Reflexive Supply Chain Solutions, asks a pertinent question - Are we solving the right Supply Chain problem?
Yogesh Sarin, Director - Supply Chain, South Asia, Dell Technologies, iterates, “Welcome uncertainty with passion as that is the only constant that would keep you inspired in everyday supply chain adventures.”
Mayur Chhabra, Head – Supply Chain, White Cement and Paints Division, JK Cement avows that in this constant pursuit of becoming a leader, one needs to lead by example, not necessarily all your tasks will be super hit.
Dirk Stolte, Supply Chain and Industry 4.0 expert, asserts that future-winning supply chains require forward-thinking supply chain executives to develop future-ready capabilities by cultivating new strengths and competencies.
In this this article, Sanjay Desai, General Manager – Asia, Supply Technologies, draws parallel between the qualities of great leaders and how these can be aligned with our personal and professional well-being.
08 FOCUS
The Sustainable Procurement Barometer benchmarks sustainable procurement practices across industries and explores how they adapt to this changing landscape.
Editor: Prerna LodayaDISCLAIMER: This magazine is being published on the condition and understanding that the information, comments and views it contains are merely for guidance and reference and must not be taken as having the authority of, or being binding in any way on, the author, editors, publishers who do not take any responsibility whatsoever for any loss, damage or distress to any person on account of any action taken or not taken on the basis of this publication. Despite all the care taken, errors or omissions may have crept inadvertently into this publication. The publisher shall be obliged if any such error or omission is brought to her notice for possible correction in the next edition.
The views expressed here are solely those of the author in his private/professional capacity and do not in any way represent the views of the publisher. All trademarks, products, pictures, copyrights, registered marks, patents, logos, holograms and names belong to the respective owners. The publication will entertain no claims on the above. No part of this publication can be reproduced or transmitted in any form or by any means, without prior permission of the publisher. All disputes are subject to the exclusive jurisdiction of competent courts and forums in Mumbai only.
“Welcome uncertainty with passion as that is the only constant that would keep you inspired in everyday supply chain adventures. It’s ok to fail but not ok to give up,” remarks Yogesh Sarin, Director - Supply Chain, South Asia, Dell Technologies, during this exclusive interview…
What are the leadership inflection points and personal growth that you have had in your career?
There were pivotal moments in career where significant changes occurred with moments of challenge, decision making on personal/ professional front. There were several inflection points, such as transitioning from individual contributor to team leader, navigating complex projects, exploring unchartered territories with new roles and increased responsibility. Each of these experiences have provided valuable lessons and opportunities for growth, helping to develop and refine approach to guiding in the supply chain domain.
How do you embrace change and continuous learning at the workplace?
Embracing change and continuous learning is crucial to staying adaptable in dynamic environment. Open mindedness & adaptability, proactive attitude to learn, welcoming feedback & focus on gaols are some ways that help.
What are the principles of success you’ve seen across different industries?
Across various industries, certain
principles of success tend to remain consistent:
d Clear Vision and Goals: Successful individuals and organizations often have a clear understanding of what they want to achieve and set specific, achievable goals to work towards.
d Continuous Learning and Adaptation: The ability to learn from experiences, stay updated with industry trends, and adapt to changes is crucial for long-term success.
d Effective Communication: Strong communication skills, both verbal and written, are essential for conveying ideas, building relationships, and resolving conflicts.
d Resilience and Perseverance: Overcoming setbacks, failures, and challenges is a common trait among successful individuals. They demonstrate resilience and perseverance in pursuing their goals.
d Innovation and Creativity: Successful organizations often innovate and think creatively to differentiate themselves from competitors and solve complex problems.
Sarin is an IMT Ghaziabad alumni with a BTech in Mechanical Engineering from University of Mysore. In over three decades of his illustrious career, he has established greenfield start-ups for consumer electronics and telecom products, developed agile supply chain operations for aftermarket services & manufacturing operations. Being the people’s leader, he has built & mentored crosscultural teams across multiple geographies, ensuring high standards of excellence & integrity to drive large diverse global collaborative engagements.
Embracing change and continuous learning is crucial to staying adaptable in dynamic environment. Open mindedness & adaptability, proactive attitude to learn, welcoming feedback & focus on gaols are some ways that help.
d Focus on Customer Satisfaction: Prioritizing customer needs, providing excellent service, and building long-term relationships are key drivers of success in many industries.
d Strong Work Ethic: Hard work, dedication, and commitment to excellence are fundamental to achieving success in any field.
d Effective Leadership: Strong leadership inspires and motivates teams, fosters a positive work environment, and drives the organization towards its goals.
d Embracing Diversity and Inclusion: Diversity in perspectives, backgrounds, and experiences fosters innovation and creativity, leading to greater success for organizations.
d Ethical Practices: Upholding high ethical standards and integrity in all dealings is critical for building trust and maintaining a positive reputation in the industry.
From your perspective, what are some of the toughest challenges that you see in operations and supply chain?
Many of operations and supply chain challenges stem from complexities of global market, technological advances, shorter product life cycles with evolving consumer demands. Cyber security risks, trade regulations, sustainability concerns and talent management add to the woes.
What are some of the principles and skills that no matter what happens will still be useful?
Certain principles are timeless and continue to be valuable regardless of changes in technologies, industry trends and economic conditions. These include critical thinking, communication skills to be clear & concise, creativity, emotional intelligence, resilience, Pareto principle to focus on most impactful option.
What are the biggest learnings you have as a leader? Is there a secret sauce to becoming a successful leader?
While there may be no one size that fit all,
some of the effective learnings include upholding integrity & ethics, agility to adapt & be resilient, clear communication towards strategic direction & vision, empowerment & delegation with sense of empathy & emotional intelligence.
What are the barriers to success when it comes to climb the corporate ladder for CSCOs?
Barriers can vary depending on individual circumstances, organizational culture, and industry dynamics. Some common barriers include complexity and volatility in supply chain operations, resistance to change, lack of integration, Tech disruptions, pressure to deliver quick results & availability of skilled talent.
Do you have any advice for young aspiring professionals?
Welcome uncertainty with passion as that is the only constant that would keep you inspired in everyday supply chain adventures. It’s ok to fail but not ok to give up!
Over the past few years, a unique confluence of forces has been reshaping the global business landscape. The Sustainable Procurement Barometer published and co-developed this year by EcoVadis and Accenture, benchmarks sustainable procurement practices across industries and explores how they adapt to this changing landscape. The report highlights trends around procurement priorities, sustainability monitoring tools, supplier engagement and internal process integration. Excerpts…
THE aftermath of the pandemic, combined with a series of geo-economic crises and the ever-increasing focus on ESG regulations, has propelled sustainable procurement to the forefront of the CEO agenda. Accenture’s earlier study with the United Nations Global Compact showed that more than half (54%) of CEOs are “strengthening visibility into the social impacts of their supply chain” and CEOs are also focused on “encouraging their suppliers to adopt sustainable behaviors,” with 33% of companies now incentivizing ESG outcomes for their supply chain.
However, a significant number of companies are still in the early stages of integrating sustainability practices into their procurement function. In many cases, CEO-led initiatives may not have fully trickled down to procurement or the function lacks the capabilities needed to effectively implement them. Financing these initiatives also remains a significant
challenge for many. Many companies are still merely attempting to incrementally improve existing frameworks by, for example, amplifying their compliance or risk management measures to enhance supplier transparency.
While these efforts are a step in the right direction, they often fail to deliver the same benefits as a more integrated and comprehensive approach. As the supply chain regulatory landscape continues to evolve, with reporting becoming increasingly stringent and focused on actions rather than commitments, companies will need to evolve too. The latest study from Ivalua and Procurious underscores this shift, revealing that 66% of procurement teams now see new sustainability expectations and regulations as a significant source of pressure. This ranks above even disruptions and shortages.
Sustainable procurement obstacles span
the key touchpoints of internal and external stakeholders, systems and data. These are:
Inadequate visibility into upstream supply chain ESG risks and performance: This lack of visibility often keeps procurement from prioritizing the right engagement investments. Roughly half of all companies have visibility into the sustainability practices of 50% or more of their Tier 1 suppliers – only 27% have visibility into 75%+ of their suppliers. Going deeper, half of companies have visibility into fewer than 5% of their Tier 2 suppliers. About a fifth of companies have visibility into more than 50% of Tier 2 – which drops to 15% for Tier 3.
Supplier engagement and collaboration practices are too limited: Fewer than 50% of mainstream programs engage suppliers with assessments or audits, and an even lower proportion engage in the four strategic activities
that are instrumental to improving performance and building a foundation for value creation: corrective or improvement action plans, GHG/ carbon emissions reduction programs, e-learning and training, and innovation programs.
primary obstacles slowing the adoption of best practices needed to deliver on the sustainable procurement agenda are:
Lack of ongoing C-suite engagement and buy-in: Making and expanding the business case to champion responsible procurement initiatives and allocate resources remains a persistent challenge for organizations. This hindering the development of more integrated procurement programs.
Immature sustainability skills and capabilities: Organizations need to build and maintain a workforce capable of executing responsible procurement strategies. Because procurement teams have not traditionally focused sustainability, new skills and capabilities are needed enable them to better embed it in their practices.
Low ESG integration into the procurement tech stack: vast majority of organizations are still struggling integrate sustainability data into advanced procurement technologies. Digitally embedding sustainability insights engagement, monitoring and analytics tools is key only for responding to evolving ESG regulations but for developing the level of performance management needed to build resilience across the value chain.
Integration of ESG data into procurement processes and touchpoints is not broad, deep or effective enough: On the transactional end, 63% fail to integrate ESG criteria into risk management systems, and 65% are lacking integration into RFx systems where, for example, the results of assessments or ratings can be used as weighted criteria in decision-making. Perhaps more critically, there is a clear deficiency in the integration of ESG into more strategic activities like supplier relationship management processes, with only 34% of companies currently doing so. That means that two-thirds of all companies surveyed are missing the opportunity to leverage this vital commercial engagement process for continuous performance improvement, which is fundamental for sustained value creation over time. Lastly, mainstream programs report that only 30% of their integrations are “very or extremely effective.”
Limited value chain visibility and engagement: Only about half of all companies surveyed have visibility the sustainability practices of 50% or more of their Tier suppliers – this drops sharply in the sub-tiers. Mainstream programs have been slow to adopt key supplier engagement activities like corrective action plans, Scope 3 carbon reduction strategies, e-learning and innovation programs. adoption rate of these activities ranges from 23 to 46%.
sustainable procurement best practices can prioritize to scale and accelerate their path toward sustainable value chain?
Cultivate executive sponsorship to drive internal stakeholder activation and mobilization.
70%
of programs say “delivering on corporate sustainability goals and commitments” is a top procurement driver.
of mainstream programs use integrated ESG data to “operationally inform” or “strategically engage” their executive stakeholders.
of companies have visibility into more than half of their Tier 1 suppliers – just a quarter have 50%+ visibility into Tier 2.
50–60%
integrate ESG data manually or digitally into procurement processes, only 30% of those integrations are reported as “Very” or “Extremely effective.”
Ongoing and action-oriented stakeholder engagement underpinned by ESG data – is crucial for changing behaviors and gaining buy-in for sustainable procurement initiatives. Leaders strategically engage their executive peers across Finance, Sustainability, Operations, Risk and Compliance with the results and outputs their programs. This helps facilitate collaboration capable of driving change and expanding the budget new initiatives.
Engage suppliers and industry partners more actively accelerate the adoption of sustainable practices. Through transparent and open communication with suppliers, organizations can foster collaboration jointly delivers on the sustainability agenda. This be done through, for example, carbon reduction programs, training and development, and industry coinnovation programs.
Missed opportunities to leverage data and technology: Digital technology can act as a catalyst for sustainable procurement, as many companies grapple with making data usable in procurement functions. “Digital integration” refers to plugging ESG KPIs and insights directly into procurement software (e.g., passing data directly via an API to procure-topay suites or standalone systems) for the processes noted above. It can put ESG data directly into the dashboards and supplier profiles that buyers use daily, accelerating decision-making and facilitating analysis and insights. Despite these benefits, digital integration remains low across all processes. Spend analytics is the process with the highest level of digital integration – adopted by 25% of companies. At the low end of integration are supplier relationship management (8%) and RFx systems (6%).
6% to 25%
of programs digitally integrate ESG into procurement processes. Only
9%
of leaders’ programs are driven by cost reduction (vs. 26% for non-leaders).
Programs with “high integration” are
3 to 4 times
more likely to have “strategic-level engagement” with C-suite stakeholders than those with “low integration.”
Building and scaling a successful sustainable procurement program hinges on engaging and mobilizing relevant stakeholders within the organization. In today’s world, effective engagement requires the ability to credibly present data-backed outputs across a wide range of procurement challenges, from risk mitigation to resilience building. Some are going even further by demonstrating how their sustainability efforts are enhancing brand value, driving revenue growth and reducing total cost of ownership. With this heightened data visibility, leaders can also build stronger cases for transitioning toward circular and low-carbon business models.
Organizational skill deficits: Developing talent with critical ESG knowledge and skills is essential to implementing sustainable procurement in practice. Leaders have been emphasizing green procurement skills and ESG for a few years – the rest of the respondents are now catching up. From another perspective, 43% of suppliers in our survey believe that their customers’ commitments to sustainability are “important to them only on paper.” This suggests a gap in trust, perception or consistency around the prioritization of ESG across all channels of interactions in the buyer-supplier commercial relationship. This finding echoes gaps and inconsistencies in the visibility, engagement, integration, digitization and talent development processes noted above.
Securing ongoing C-suite engagement and buy-in to support the sustainable procurement business case is a persistent challenge: Fewer than 50% of mainstream (non-leader) programs “strategically engage” or “operationally inform” their executive peers in Sustainability, Risk and Compliance or Operations with the outputs and results of their program. This figure drops to less than 40% for CFO/Finance, Product/Service Design and Marketing & Sales. Interestingly, this is an ongoing challenge: When asked to rank “critical factors needed to accelerate their programs,” leaders ranked “broader/
deeper buy-in and alignment from other business stakeholders” much higher than any other factor. This underscores that building an effective sustainable procurement program requires ongoing and effective engagement with executive stakeholder.
Value chain decarbonization remains a high priority for both leading and mainstream programs. Nearly 90% of leaders report that Scope 3 reductions and net-zero targets are a top-three driver of their program, compared to 60% of non-leaders. However, our findings reveal that more companies are realizing the imperative of expanding their program focus beyond carbon. Addressing social challenges in the value chain – encompassing everything from labor and human rights issues to diversity, equity and inclusion (DEI) –is now a top driver for more than 70% of mainstream programs and 80% of leaders. Other environmental impacts like biodiversity, nature-based solutions and circularity are emerging priorities for roughly a third of all surveyed organizations.
Today’s chief procurement officers (CPOs) have an unprecedented opportunity to leverage sustainability to place procurement at the heart of the corporate agenda. By using sustainability as a catalyst, CPOs can transform their procurement function from one focused on cost, efficiency and risk avoidance to a strategic partner capable of building enterprise resilience, achieving corporate
sustainability goals and driving value creation.
Building a sustainable procurement program capable of enhancing resilience and consistently delivering sustainable value across your organization does not happen overnight. The most successful procurement teams invest in advanced tools to gain visibility and deepen ESG engagement, integrate the resulting KPIs broadly across P2P processes, align team skills and incentives to outputs and leverage technology and data analytics to showcase their success within the company. This helps secure additional support from the business stakeholders and enables further expansion. As companies repeat this internal process and deepen their supplier engagement, they scale their value-creation potential.
Cultivate C-suite executive sponsorship to drive internal stakeholder activation and mobilization: Ongoing and actionoriented stakeholder engagement –underpinned by ESG data – is crucial for changing behaviours and gaining buy-in for sustainable procurement initiatives. Over 80% of leaders strategically engage or operationally inform their executive peers across Finance, Sustainability, Operations, and Risk and Compliance with the results and outputs of their programs. This level of engagement
helps expand the budget and facilitate collaboration capable of driving change.
Engage suppliers more deeply to accelerate the adoption of sustainable practices: Crucial for advancing an organization’s sustainable supply chain program, supplier engagement must go beyond mere disclosure and assessment. It should encompass collaboration on improvement and capacity building, foster a shared commitment to sustainability goals, promote enhanced and enriched transparency and encourage innovation in sustainable practices.
Almost twice the proportion of programs that use third-party ESG ratings combined with other disclosure tools follow through with strategic engagement
activities with an average of 2.8 vs.1.5 activities by those that do not combine those tools. These deeper activities (corrective action, carbon reduction, e-learning or innovation programs) drive supplier ESG improvement and produce richer data and insights.
Deeply integrate supplier sustainability data into your endto-end procurement approach: Unlocking the value of supplier ESG engagement efforts and the associated data throughout the procurement and supplier relationship workflow is crucial for CPOs and C-suite executives aiming to advance their sustainable value chain initiatives. Integrating ESG with a robust technological approach can not
only improve integration by automating transactional processes like sourcing and tenders but is also vital to extending this to strategic elements such as spend analytics.
This extension enables real-time data insights and integration with supplier relationship management systems, fostering ongoing improvement, collaboration and innovation with suppliers. This approach enhances the effectiveness and efficiency of sustainability efforts, accelerating mutual value creation.
Enhance ESG technology and digital capabilities to ensure reporting and improvement programs are built on a solid foundation: Reliable and
What
do the Sustainable Procurement Leaders in our study have in common?
These companies boast extensive engagement with their strategic and high-risk suppliers, using at least two of eight specified sustainable collaboration activities. This indicates a proactive approach to ensuring that sustainability is a shared priority throughout their value chain.
They have incorporated sustainability criteria into at least four of eight procurement processes, with a minimum of one process being digitally integrated. This indicates that sustainability is not an add-on –it is increasingly integrated into their procurement strategy.
These companies have visibility into at least 75% of their Tier 1 suppliers, 5075% of Tier 2 and 5-50% of Tier 3. This indicates a deep understanding and extensive monitoring of sustainability practices throughout their value chain.
The CFO and the CSO at these companies are at least strategically engaged.
These companies do not rank data accuracy as one of their top-three organizational challenges, indicating a relatively high level of confidence in the data underpinning their sustainability measures.
Leaders are placing much more emphasis on “net zero and Scope 3 emissions,” with 86% acknowledging it as a top-three driver compared to 60% of non-leaders. However, while this gap highlights leaders’ heightened focus on decarbonization, a study by Accenture found that just 7% of companies across global value chains are on track to meet their carbon reduction targets. This points to the scope of the challenges that lie ahead, even for companies with a relatively mature sustainable procurement program.
accurate data plays a pivotal role in propelling an organization’s sustainable procurement program forward. It facilitates informed decision-making, precise tracking of sustainability metrics and the identification of areas for improvement, ultimately driving more effective and impactful sustainability initiatives. It is also essential for building and maintaining a solid business case to ensure continued C-suite stakeholder support.
Invest in people and maintain regular engagement with internal stakeholders to integrate sustainability into everyday business processes: A skilled and motivated workforce is vital for implementing and managing sustainability initiatives, ensuring compliance and driving continuous improvement. Their expertise and commitment are crucial factors for the success of a sustainable supply chain program. Incorporate sustainability into job descriptions, promotions and compensation for roles such as buyers, category managers, supplier relationship managers and risk and compliance positions. This approach provides incentives for these individuals to adopt a more strategic approach to sustainability.
Use new tools and technologies to boost N-tier transparency and gain an understanding of supplier sustainability impacts and opportunities: Transparency provides a comprehensive view of the supplier footprint, highlighting both growth opportunities and potential pitfalls. This can be achieved through methods like predictive risk mapping and prioritizing
investments in building transparency, including supplier-specific disclosure and analysis. More than 70% of leaders are using risk and hotspot mapping tools to prioritize engagements, compared to just 47% of non-leaders. Tier-n transparency refers to transparency along the entire supply chain from the origin of raw materials to the consumer. Depending on the distance of one's own company, suppliers will be designated as Tier-1 to Tier-n. Crucial for advancing an organization’s sustainable supply chain program, N-tier transparency enables leaders to identify risks, inform engagement strategies and guide investments in responsible sourcing practices.
As the global community raises the bar on sustainability, the definition of “sustainability leadership” is also transforming. The journey is progressing from a mere compliance and “do no harm” approach to one that strives for net positive impact.
Today’s Sustainable Procurement Leaders, though ahead in many ways, are still constantly developing and evolving. They are actively broadening their focus across various ESG topics such as carbon, labor and human rights, DEI, biodiversity and more.
This expansion is extending across different regions and business units, encompassing more supplier types and sizes, and reaching deeper into the value chain.
As businesses transform, sustainable practices will become integral to business models, incorporated not merely as a function but also as a core business strategy. ESG standards will be ingrained
in product and service specifications, internal data and technology systems, and will be a staple in partnerships and customer interactions. They will also be reflected in job descriptions and training and woven into the fabric of targets and incentives – reaching every aspect of the organization.
The gradual transformation of the procurement function will also necessitate a foundational shift across industries – from manufacturing to retail to services – to ensure that ESG fundamentals are not only established but are digitally scalable. This entails building a solid foundation of policies, processes and skillsets that resonate with the digital age.
Looking ahead, the challenges and opportunities for procurement lie in bridging the gap between rhetoric and reality. Companies must foster a culture of sustainability that permeates all levels of operations and decisionmaking. By doing so, they can ensure that sustainability is not siloed in a given department but becomes a ubiquitous and defining element of an organization. The journey ahead will demand consistent efforts, strategic alignment and a commitment to adapt and grow in line with sustainable procurement principles. This approach will ensure that the practices of today contribute to shaping more equitable and sustainable value chains in the future.
The global business landscape navigates multiple boom and bust cycles marked by outliers. These events require business leaders to embrace bold decisions that pave the path for organizations to be either at the forefront or follow their peers. While often not in the limelight except during crises, the supply chain functions in organizations are essentially the backbone of their operations and are now rightly recognized even at the board levels. The frequency of black swan events in recent times has underpinned the need for supply chains to embrace VUCA (Volatility, Uncertainty, Complexity, and Ambiguity) as the new normal. Now more than ever is the time for leaders at every layer of the supply chain function to imbibe flexibility and out-of-the-box thinking, not just for them but also to encourage their larger teams to ensure that consumer and shareholder expectations are at the heart of every action in the face of adversity, write Rohit Menon, V G Venkatesh and Haripriya Vasudevan.
Rohit Menon
is a supply chain professional in the fast-moving consumer healthcare sector, currently based in Switzerland. He oversees the supply planning of multiple European site clusters for market-leading consumer brands. He holds an MBA in Operations Management from SIBM Pune and Mechanical Engineering from NIT Calicut and is an APICS-certified CSCP and CPIM professional. His geographic experience includes Europe, Middle East Africa, and the Indian subcontinent’s supply chain networks.
is a Professor at EM Normandie Business School, France. He brings more than two decades of combined experience in industry and academia across continents. He is a certified supply chain professional (CSCP) from APICS and a member of industry and research forums. Actively involved in the executive programs of reputable global companies, his teaching and research interests are in global business, strategic procurement, sustainability, logistics, warehousing and distribution, and digitalization.
BUSINESS leaders rely on recommendations from operational teams to ensure the right course of action is adopted to march ahead. It is a fact that global organizations work in a matrix format with multiple layers of data exchange from the point of occurrence to the moment of decisionmaking. As financial and operational planning teams are adept at scenario planning and forecasting, ensuring the latest guidance or intel is accounted for in their recommendations is of utmost importance. Multiple occasions draw attention to the fact that decisions taken are outpaced by a week or a month in the real market.
From sourcing at the best cost to leveraging the best available technology
in external supply partners, business revenue is highly exposed in the upstream and midstream segments of a supply chain outside one’s organization. Due to the limited real-time data integration across external supply partners, decisionmaking is exposed to data latency or unavailability.
With an increased focus on these gaps, supply leaders are making formal efforts to integrate financial and planning interfaces with external partners to ensure the availability of high-quality real-time data. With revenue-sharing models coming into the picture, we are seeing a gradual shift in the mindset of external supply networks towards collaborative growth strategies.
A recent case in point is how the maritime shipping chokepoints are vulnerable to geopolitical situations such as in the Suez Canal. Prominent global carriers were forced to increase
Haripriya Vasudevan
is a senior program management professional with more than two decades of experience in the IT industry. Having contributed to multinational corporations for a long time, she chose to be of service to other aspects of society. She is currently contributing to Education as a Professional Development Specialist in one of the popular chains of schools in Bengaluru, India.
their shipping lead times by choosing alternate routes across the horn of Africa, alongside spiking insurance and logistics costs. Organizations that could leverage real-time coordinates by using in-house control towers or technology-adept 4PL partners were at an advantage. Assessing the scale of their finished goods volume in the conflict region, they could make swift decisions to re-route their cargo to intermediate ports of call, disembark critical high-value goods, and further utilize airfreight modes.
A parallel issue that organizations with in-house manufacturing face during such a geopolitical crisis is – How long their factories can run efficiently until a production material shortage occurs? The planning teams should swiftly coordinate with site scheduling and value stream teams to activate contingency production plans in such material crises. The freshness and accuracy of information to its best
available detail during crisis also help companies minimize risk as complete risk mitigation may be infeasible. As nobody loves surprises, transparency in sharing with shareholders the adverse cost and cash exposure on their P&L during crisis management, holds the key to sustaining trust in an organization brand and its supply network.
The importance of the financial metric, Return on Assets (ROA), should not be overlooked. Prior to investing any further into newer technologies or interfaces to improve data agility, an E2E mapping of existing in-house technologies may expose cases of underutilization. Process improvements supported by adequate end-user refresher training on existing data systems alone may drive an intangible improvement in the company’s ROA.
While delving into improving data velocity and completeness, one has to acknowledge that a stable operating environment and a crisis are worlds apart. In a stable operating situation, a higher amount of data supports good decision-making, but in uncertain times, waiting for the perfect set of data may be ineffectual. It may risk delayed decisionmaking, and the competitor may leap ahead when time is of the essence.
The pandemic in the last years reminded
them of increased regional or local sourcing presence. The lockdowns globally had a detrimental impact on the smooth movement of goods irrespective of industries or regions. In some product categories, stockouts on shelves were mitigated in a few months, whereas in some extreme cases, increased global sourcing costs directly depleted product margins to the tipping point of their discontinuation. The pandemic was a stark reminder of how agility, flexibility, and scalability proved to be a boon for some companies, whereas a bane for the others that were averse to network change management.
It would be impossible to predict when and what the next black swan event could be. For supply, it would be shortsighted to completely move towards onshore manufacturing even though goods movement across global borders was impacted during COVID. In many supply organizations that responded with agility, the presence of their global dual production sources helped ensure product presence was alive on shelves or pharmacies. Specific to certain industries, such as consumer healthcare or pharma, regulatory approvals could be linked to the manufacturing site, country of origin, and qualified vendors for production materials. It is critical to maintain flexibility in regulatory filings that support multiple sources of manufacturing sites globally where
production technology allows for it. From a procurement perspective, a mapping of sole or single source hot spots up to the tier I or tier II vendors should be carried out, and the development of backup sources could prepare for any future adverse events. Disruptions are unavoidable. However, these strategies could enable leaders to swiftly decide to ramp up backup sources available in their supply network in the event of a natural calamity or geopolitical event.
Organizations are gradually inculcating the need for more generalists and restricting functional experts. This improves the flexibility across the management chain so that people can step up in crisis management. A compelling similarity in human resource management and manufacturing network strategy could be delved deeper into brownfield or greenfield investments if viewed from the lens of multivalent production line capabilities, which can complement the organization from a network strategy de-risking standpoint. The automobile industry was able to leverage the effective use of multivalent lines and modularity in product design. This brought a combined benefit of derisking and cost efficiencies.
The supply chain challenges today have multiple interdependent elements
A modular approach to continual improvement that can be easily adapted irrespective of variables globally should be ensured to support scalability of excellence programs. Global organizations sometimes underestimate how much learning a factory in one corner of the globe could pass onto another in terms of best-inclass practices. Processes improved through multiple cycles of trial & course correction could translate to significant benefits while expanding supply networks or production portfolios. Global centers of excellence in supply chain can help keep alive the crisis management playbook to ensure future leaders don’t have to traverse the entire lap right from the starting point.
internal and external to an organization. The situation is continually evolving, ranging from taxation, climate policies or regulatory changes requiring leaders to shift gears smartly. There will be multiple scenario recommendations and opinions from within an organization, however with no single correct answer. Consequently, some solutions emerge from a risk-based trial and course correction approach. An operationally flexible and agile team with a continuous improvement mindset needs to support this approach. Perfectionism may need to be compromised for the most optimal solution during a crisis or an uncertain situation.
From a product distribution standpoint, an approach that many consumer-packaged goods organizations followed during the pandemic was to curtail their sales portfolio. This was achieved by striking a balance between brand presence on shelves for their most strategic and consumer-sought products and the ability to maintain manufacturing lines running. Product sites globally were faced with increased levels of absenteeism and potential shortages in their production materials. This distribution strategy required cutting down the presence of wider brand extensions or different variants/
flavors among customers but ensuring the product was not in absolute stockout for extended periods across their channels. Not all the business markers on the scorecard may be positive during such a phase. The key was to strike the right balance between market share, top & bottom line, and business continuity with the long term in sight.
Panic buying trends were observed during the pandemic's initial phases, rendering statistical forecasting models ineffective. A low-data decision-making process backed by qualitative insights was essential to planning effectively for a crisis-limited product portfolio. It is a reality that business-supportive AI and machine learning models can succeed better with more supportive trends or data. However, unstable business environments may not present the luxury of having a wealth of information at our disposal. During these times, leaders need to recollect that low data decisionmaking helped humans thrive across millennia in the face of adversity, and not all boxes may be ticked prior to taking some key steps during uncertainty.
On various occasions, continuous
improvement initiatives are piloted in certain geographies within specific departments of supply chain organizations. Unlocking the long-term value of such initiatives relies in scaling up the operational excellence initiatives equally across the entire global supply network.
A modular approach to continual improvement that can be easily adapted irrespective of variables globally should be ensured to support scalability of excellence programs. Global organizations sometimes underestimate how much learning a factory in one corner of the globe could pass onto another in terms of best-in-class practices. Processes improved through multiple cycles of trial & course correction could translate to significant benefits while expanding supply networks or production portfolios. Global centers of excellence in supply chain can help keep alive the crisis management playbook to ensure future leaders don’t have to traverse the entire lap right from the starting point.
The leaders also may need to zoom out and share the learnings across regions with humility to ensure that failures in one part of an organization are not repeated in another corner of their global supply network.
Even though an internal race to the
podium may exist across sub-regions or functions in an organization, the shareholders win only when the entire global supply chain marches in rhythm and not with pockets of perfection.
While economic aims often overshadow social and environmental objectives in supply chains, today's leaders are keen on championing all three amidst challenges across different business verticals. This mission dances between participatory and transformative styles; each earning nods given the havoc wreaked by disruptions.
Take, for instance, social inclusivity in the supply chain, a participatory leadership style demands the fusion of diversity, equity, and inclusion strategies to forge sturdier, more flexible, and sustainable supply chains. Think of manufacturing giants embracing local talent or e-commerce firms like Amazon, Zomato, and Noon, enlisting individuals from diverse backgrounds and democratizing access to opportunities, resources, and benefits within the supply chain.
Some corporations undertake initiatives to upskill marginalized groups for supply chain roles, enriching the talent pool. These adaptive capacity-building endeavors nurture alliances and mitigate risks, fostering an empowering ecosystem primed for innovative solutions and approaches in the competitive corporate landscape. Leaders vouch for risk diversification across various nodes via the diversity, equity, and inclusion framework. An interdisciplinary mindset signals multiple perspectives, experiences, and problem-solving strategies, equipping teams to foresee and tackle unforeseen challenges in pivotal moments easily.
However, some organizations find it more challenging to manage them during uncertain times, as priorities shift and are influenced by other conditions, such as geopolitical requirements and supply disruptions. The growing demand for environmental actions and their associated results forces organizations to redraw their performance metrics,
Drawing insights from the ancient Indian treatise of Kautilya’s Artha Shastra, there must be an emphasis on the significance of foresight, organization, and dissemination of knowledge to prevent the recurrence of failures.
"Knowledge is the foundation of all enterprises. Therefore, acquire knowledge from all sources."
To implement these principles in global supply chain management, leaders may work on:
x Establish a Centralized Knowledge Repository to store historical data, including past failures and successful strategies across different regions of the supply chain network.
x Promote a Culture of Humility and Learning, leading everyone by example to adopt a humble mindset that acknowledges failures as opportunities for growth and a vulnerability to share their experiences and challenges openly, facilitating cross-regional learning through regular meetings or virtual conferences.
x Encourage collaboration and open dialogue to foster a sense of collective responsibility.
x Implement Continuous Improvement Mechanisms by utilizing insights from past failures to refine processes, update strategies, and implement preventive measures.
x Conduct periodic reviews and evaluations of the supply chain performance, analyzing trends, patterns, and areas for improvement to prevent similar failures from occurring in different parts of the organization.
Such a leadership mindset backed by a robust central data database can cultivate a resilient and adaptive supply chain network that learns from historical information how some operational crisis scenarios were navigated in prior instances and ensures their prevention across diverse regions.
especially after recent global disruptions. Leaders may need to communicate these changes effectively to their stakeholders. Such conditions also prompt leaders to steer transformative projects squarely to safeguard the business objectives.
It calls for Visionary Leadership to integrate sustainability into supply chain operations:
x Articulate vision effectively to inspire and mobilize stakeholders towards sustainable practices.
x Ensure Strategic Alignment with sustainability goals and initiatives.
x Foster Collaboration with suppliers, partners, and stakeholders to drive sustainability initiatives throughout the supply chain, building strong relationships based on trust and shared values to implement impactful changes.
x Leverage Technologies such as IoT, blockchain and AI to drive sustainability improvements in supply chain processes and enhance transparency, traceability, and efficiency.
x Encourage employees to Stay Updated on sustainability trends, best practices, and emerging technologies to drive innovation and adaptation.
x Promote transparency and accountability across the supply chain by setting clear sustainability metrics and targets and using effective reporting practices.
x Develop proactive Risk Management Strategies to conduct thorough risk assessments, identify potential vulnerabilities, and implement mitigation measures to enhance resilience.
x Engage and Empower employees at all levels to contribute to sustainability efforts. They should provide training, resources, and opportunities for involvement, fostering a sense of ownership and commitment to sustainability goals.
x Adopt a Long-Term perspective on sustainability, recognizing that investments in sustainable practices may require patience and persistence to yield significant results that deliver lasting benefits for the business, society, and the environment.
x Use their influence as leaders
to Advocate for sustainable practices within their industry, engage with policymakers, and champion sustainability initiatives to drive systemic change.
Uncertainty and ambiguity are not limited to operational supply situations but also affect long-term investment decisions in manufacturing, digitization, and automation technologies. There is always new technology on the block, which organizations may be vying for. It is important for leaders to ensure that a company doesn’t get into the rat race unless it translates into long-term value for shareholders and consumers.
As an example, the adoption of blockchain in supply chain networks caught the buzz a few years ago, and organizations are trying to invest in internal talent or leverage external partners to explore its use cases. Blockchain and distributed ledger technology are fit for purposes where transactions are carried out without central oversight in simplistic terms. Here in lies the question for organizations to ponder, across which segments of their supply network should blockchain technology be explored.
In a regulated consumer healthcare or pharma industry, downstream distribution of finished products
across multiple countries has track and trace technology embedded in their sellable packs. This enables consumers to understand the history of all the components that went into its production and the entire route the product traversed from the raw material stage to the consumer’s hands. For example, this area has a central reporting mechanism overseen by a country’s health authority, where investment into blockchain may seem redundant.
However, much upstream in the supply chain, where external supply partners are involved, there could be cases where the adoption of blockchain could help secure data integrity. From an ethical and sustainable sourcing standpoint, the blockchain model's traceability and tamper-resistant nature helps verify if the components are ethically sourced and from whereby external vendors. Recently, Walmart has explored the adoption of blockchain to trace the source of mangoes in the US, for example, to improve visibility and traceability. Another case in point is Maersk partnering with IBM to utilize blockchain technology. They aim to improve process efficiency in crossborder transactions involving multiple parties, a sector where reliance on manual paperwork is still prevalent.
Leaders need to consider that there is no ‘one size fits all’ approach when embracing newer and upcoming technologies in the supply chain
VUCA 2.0 - Vision, Understanding, Courage, Adaptability - With a clear Vision for their organizations, an in-depth understanding of their organization’s capabilities and strengths, stepping up with Courage to face challenges and risks that are posed by business dynamics, and being flexible and Adaptable to external changing circumstances, without altering strategic course, built on the principles of Ethical Value systems, leaders can ensure success even during the face of uncertainties. This new strategy of VUCA 2.0 seems more promising, practical, and sustainable in the years to come.
industry, as in any other. It is worth noting that leveraging internal process knowledge alongside credible industry benchmarking and insights is key to unlocking end consumer value.
Before pursuing any new technology, leaders should conduct thorough strategic planning and evaluation. This involves assessing how the technology aligns with the company's long-term goals, whether it adds value for shareholders and consumers and the potential risks and challenges involved. They should remain flexible and agile in investing in knowledge acquisition and learning to stay informed about emerging technologies and industry trends, adopt new technologies, and allow for course corrections and adjustments based on evolving market dynamics and feedback.
Leaders should also be open to diversifying investments across different technologies and innovation initiatives to mitigate risk and increase resilience. More importantly, they should ensure that technology adoption aligns with Ethical standards, corporate values, and Social Expectations to maintain trust.
“It is smart to be Ethical,” said a renowned leader.
In the intricate web of supply chain
management, ethics, and values serve as the guiding light, ensuring sustainable and responsible business practices. Genuine customer service, founded on honesty and transparency, not only fosters trust but also cultivates longterm relationships. In an era where profit margins often overshadow moral compasses, it is paramount for leaders to recognize that success is not solely measured by dominance over stakeholders. Rather, it lies in the integrity of actions and the commitment to ethical conduct. Misinformation and deception may yield short-term gains, but they erode the foundation of trust, ultimately leading to detrimental consequences for businesses and society. By embracing ethical principles and prioritizing authentic customer service, leaders uphold their moral obligation and pave the way for a more sustainable and prosperous future. Such values, once deeply ingrained in the system, would bring the most needed change and sustainable growth in the business world.
While, we have embraced VUCA (Volatility, Uncertainty, Complexity, and Ambiguity) as the new normal, it would be interesting to note that, a
management professor from Harvard has coined a new model, the VUCA 2.0, a strategy for steady leadership in an unsteady world.
VUCA 2.0 - Vision, Understanding, Courage, Adaptability - With a clear Vision for their organizations, an in-depth understanding of their organization’s capabilities and strengths, stepping up with Courage to face challenges and risks that are posed by business dynamics, and being flexible and Adaptable to external changing circumstances, without altering strategic course, built on the principles of Ethical Value systems, leaders can ensure success even during the face of uncertainties. This new strategy of VUCA 2.0 seems more promising, practical, and sustainable in the years to come.
A day in the supply chain doesn’t pass by without multiple reminders of how little influence we have on the level of change and uncertainty globally. Inculcating among the operational teams, a mindset to navigate this omnipresent change with agility and bold continuous improvement practices can help organizations compete and succeed in today’s ever evolving and uncertain business landscape.
Are we solving the right Supply Chain problem? Supply chain teams engage in solving a lot of customer problems, some of which pertain to major customers with significant revenue streams. It’s important that we first understand the actual customer problem, as experienced by the customer, highlights Dr. Rakesh Sinha, Founder & CEO, Reflexive Supply Chain Solutions. He emphasized this by giving an apt connotation that a sailing ship is most comfortable in steady sea waters. However, if it wants to reach the shore, it must embrace discomfort and pass through a bit of turbulence before reaching the destination and this is where it is pertinent to view Supply Chain Leadership from the consumers’ eyes…
THE question of Supply Chain Leadership has been debated for a long time. However, the concept remains ambiguous. How do we define and measure it? What should be the parameters? Should we benchmark the relevant parameters across various companies in an industry? How do we define an industry in the first place? I have been thinking about it for quite some time. In my opinion, supply chains exist to meet the needs of their
consumers, hence we must define leadership from their viewpoint. How are the brand owners and channels serving their primary needs? Who stands out as the leader in their eyes?
If we look at consumer goods, for example, the first and foremost parameter for consumers is the sheer availability of the product across channels. If a consumer goes to a store, be it a supermarket, hypermarket, or a kirana shop selling the product, will she find it on the shelf?
We know that stockout on shelves is a
Dr. Rakesh Sinha
significant reason for brand switch. If we want to build consumer loyalty through repeat purchases, a well-run supply chain ensuring consistent availability will surely help. The same holds true for new product launches, where consistent availability can help trials and contribute to the launch success. Many launches have suffered significantly on account of poor availability, either due to a demand surge or plain inefficiency of the supply chain.
If the consumer wants to buy it online, is it listed in the catalogue of her
Main area of expertise lies in designing and running agile supply chains to synchronise product supply with consumer demand on a dynamic basis. Dr. Sinha worked with Godrej Consumer Products for almost four decades with leading roles in Manufacturing, Projects, Supply Chain, Strategy, IT and Marketing. His experience spans across several countries including India, US, Indonesia, Africa, Argentina and Chile. He was the Global Head of Supply Chain, Manufacturing and IT before his superannuation. An alumnus of IIT, IIM and HBS, he holds the distinction of being the first doctorate in Supply Chain Management in India.
preferred e-commerce partner? If listed, is it available for immediate purchase or is it stocked out? All of us have experienced our favourite products getting stocked out often. What does it say about the brand’s supply chain? The same logic applies to the Quick Commerce channel as well, which is rapidly expanding across geographies and product offerings.
If a brand manages wide availability across stores and sites, coupled with consistent availability, its supply chain is seen as superior by the consumers. Consumers would also judge the channels on the same parameter.
Living up to the Freshness Quotient
The next important parameter in the eyes of consumers is the freshness of the product at the time of purchase. If you stand in the aisle of consumer goods in a self-service outlet, you will notice about half the shoppers turning the pack to check when it was manufactured. What is the remaining shelf life? If the consumer is considering alternate brands, she is likely to go with the one which is freshest.
The parameter of freshness is critical for products with a short shelf life, such as milk, bread, fruits, and vegetables. If their supply chain processes are not designed to ensure freshness on retail shelves, the brand may have to either collect the leftovers or pay for the writeoffs.
The freshness parameter is gaining traction even for products with long shelf life as consumers feel that fresher is better. In case of durables, they feel newer products are technically and aesthetically better. We have seen this phenomenon in cars where 2023 model sells at a significant discount to the 2024 model. TV, mobile and laptop brands strive to ensure that their products are fresher than their competitors.
Apart from availability and freshness, consumers care a lot for the product quality, which manifests at different times as a moment of truth. The first moment of truth is when the consumer interacts with the physical product for the first time, either on the retail shelf, or on opening the packet delivered at home. How is the outer packaging? Is it crumpled or dented? Is the printing clear or smudged? Can she read the grammage,
price and date of manufacturing clearly? Is the brand trying to display it properly or hide it by embossing instead of printing?
The second moment of truth is when the consumer uses the product. If it’s a soap, how is the lather, mushiness, and residue on the bathroom floor? In case of food products, how is the taste? The first usage creates perception of quality and imprints the effectiveness of the extended supply chain in her mind.
The third moment of truth is the post usage experience. Does the fragrance last for a long time? How does the skin feel? In case of food items, after-taste is an important parameter of quality in her mind.
Apart from availability, freshness, and quality, supply chains do play a major role in affordability of the product. Can she afford delivery fee for same day delivery or a 10 minute delivery? How does the product price compare with the other alternatives she has in mind? Channels can make the products affordable through a responsive and effective supply chain design, and through loyalty programs such as Amazon Prime or Zepto Pass. What’s important for the consumer is that she can buy across various channels at an affordable price.
The last in the list of parameters for consumers is the pride of ownership. Does she feel proud to tell her friends, relatives, and acquaintances that she is using this particular brand. The pride of ownership is governed by what the brand stands for. How does it affect the environment? Is it good for the society? Does the company follow sustainable practices in sourcing, manufacturing, and distribution?
Once a brand establishes pride of ownership with consumers, it benefits by word-of-mouth, which is useful in expanding its user base and is much more cost effective than mass media to get new triers in its fold. All the five parameters listed above, viz. availability, freshness, quality, affordability, and pride of ownership are important in the eyes of consumers.
These parameters are also influenced significantly by the supply chain design, policies, processes, and practices. Companies scoring well on these counts are seen by consumers as real supply chain leaders. Brands will do well to take cognizance of these vital parameters and set up a process of ongoing improvement to excel on these.
If a company wants to attain Supply Chain Leadership in its sphere of operations, what should it do to excel on these five parameters? Some companies take one parameter at a time, assess where they are vis-à-vis their competitors, and work out an action plan for improvement. Such an approach is unlikely to result in excellence across the spectrum of parameters, as improvement in one parameter often leads to deterioration in others.
Supply chains are complex systems with many inter-dependencies amongst its components. Moreover, there is inherent variability in many processes, which can’t be wished away. If we go back to Systems Theory, a complex system with inter-dependencies and inherent variability must be optimised as a whole, rather than improving its sub-systems, one at a time.
Supply Chain Leadership requires that we look at the fundamentals of supply chain in terms of its basic design. Is it designed for low cost operations, fast response, or continuous flow? These design options have a significant impact on how the supply chain will perform in the eyes of consumers.
I would recommend carrying out an initial assessment of your supply chain design and tweak it, if required, to facilitate continuous flow. It also means challenging the current policies, processes, and practices for flow improvement. Once the design is ready to support flow, further improvement requires working on the basic supply chain capabilities, viz. demand sensing, flexibility, and responsiveness. These capabilities can be improved significantly, no matter what the current state is. The improvement is endless as we can never arrive at the final destination.
Since we need to synchronize supplies
We know that stockout on shelves is a significant reason for brand switch. If we want to build consumer loyalty through repeat purchases, a well-run supply chain ensuring consistent availability will surely help. The same holds true for new product launches, where consistent availability can help trials and contribute to the launch success. Many launches have suffered significantly on account of poor availability, either due to a demand surge or plain inefficiency of the supply chain.
with demand, the starting point is an estimation of demand over the horizon of the Supply Lead Time. This lead time is different for the last mile customer service, production of finished goods, and procurement of input materials. Accordingly, we need demand estimate for these different time horizons.
There are two important design parameters if we want to excel in this area. The first parameter defines the granularity at which demand should be estimated, and the second parameter defines the frequency at which it should be refreshed as new data comes in.
Granularity of demand estimate is defined along the three dimensions of product, geography, and time. Should it be at the category level, product group level, brand level, or SKU level? Should it be at the national, regional, State, district, PIN code or distributor level? Should it be in monthly, weekly, or daily buckets? Supply Chain Leadership requires moving to more granular levels, so that the emerging demand patterns can be deciphered better. Some supply chain leaders have already moved to SKU-distributor-day level granularity for traditional channels and SKU-PIN codeday level granularity for direct sales to consumers through their website.
Frequency of refreshing demand estimate is important for supply responsiveness. It determines how quickly we notice a shift in demand pattern and incorporate it in our supply plans. Most traditional companies operate at monthly refresh of demand estimate, though some have now moved to weekly refresh. Since new demand data comes in
daily, Supply Chain Leadership requires that we refresh the granular demand estimates also daily. Since estimates are often based on Bayesian model, improving the frequency of refresh also leads to more accurate predictions.
Granular level demand estimate with daily refresh is at the heart of Demand Sensing, which is becoming a must for running effective supply chains and moving them to the leadership level.
The second capability required for Supply Chain Leadership is the flexibility in operations. Is our distribution network flexible? How flexible are our production lines and schedules? How flexible are our vendors for lead time and order quantity? Companies aiming for Supply Chain Leadership have moved significantly on making their entire endto-end operations flexible and they have put it on a continuous improvement path.
The third capability in Supply Chain Leadership is responsiveness. If there is a shift in consumer demand pattern at the granular level, how soon can the entire supply chain respond? How soon do companies sense this additional unusual demand and respond with higher supplies? Full response would, however, include expediting additional supplies to the affected area, modifying the production schedule to prioritize these items, and expediting the vendor delivery schedules for additional supply of the requisite input materials.
Where are we on these capabilities and what sort of disruptions can be managed by the supply chain without sacrificing product availability? We know
how companies suffered in Covid-19, which was a black swan event. Those with good demand sensing capabilities and a flexible, responsive back-end operations stood way above the rest in terms of their consistent product availability.
Supply Chain Leadership is not a cakewalk. It needs consumer focus, commitment, and capability development to be loved by the consumers and gain respect in their eyes. Supply Chain Leadership requires a razor-sharp focus on the key consumer needs of availability, freshness, quality, affordability, and pride of ownership. It also requires continuous development of key supply chain capabilities of demand sensing, flexibility, and responsiveness. This brings us to the important point. Can a company improve just its own operations and become the leader? It’s quite unlikely as effectiveness of the extended supply chain also depends on how the partners perform. We must work on developing an effective ecosystem comprising various partners such as vendors, distributors, transporters, agents, and channel partners for a coordinated response. Such an ecosystem is built on transparency and trust, with clearly understood roles and responsibilities for harmonious relations. It also requires someone orchestrating the overall response to create the symphony.
The future-winning supply chain requires forward-thinking Supply Chain Executives to build future-ready capabilities composed by new strengths and competencies, such as supply chain risk management, resilience, sustainability and agility. We continue to face turbulent times and the VUCA world has even become more challenging. Managing disruptions is both an old and new challenge. Additionally, the modern Supply Chain is undergoing a transformation like never before. The development from today’s linear supply chain to a dynamic, networked supply chain ecosystem requires to embrace industry 4.0 and digital supply chain technologies. How is the role of Supply Chain Leadership playing out here? The answer to that question is crystalclear: “Supply Chain Leadership is the differentiator that separates the winners from the rest of the crowd,” explains Supply Chain & Industry 4.0 expert Dirk Stolte, through this article…
Dirk Stolte
is a Supply Chain & Industry 4.0 expert based in Germany. As Interim Manager and Consultant, he supports companies with focus on Supply Chain Management, Operational Excellence and Industry 4.0 initiatives. With 20 years+ in Logistics & Supply Chain, he has held management roles in industry-leading companies, such as Honeywell, Federal-Mogul and Kennametal in Automotive, Metalworking and Technology businesses. Dirk holds an MBA from Liverpool John Moores University and is a certified Six Sigma Master Black Belt (ASQ®) and LEAN Master.
WHAT is the most successful Supply Chain Leadership approach for staying at the forefront of supply chain management? Effective supply chain leadership encompasses the orchestration of people, processes and technologies to enhance competitiveness
by optimizing the flow of goods from suppliers to customers. That includes setting the strategic direction, fostering supply chain collaboration, employing efficient supply chain risk management and for sure leveraging innovation to drive digital transformation. The functional areas covered here include all elements of the end-to-end (E2E) supply chain: planning, purchasing, procurement, manufacturing, logistics
and distribution.
By looking at classical leadership theories, leadership styles and supply chain leadership concepts, we can see that transformational leadership seems to be the best way to lead supply chain organizations. However, this alone doesn't fully answer the question. It's important to remember that this doesn't fully address the complexity of the matter, as it doesn't take into account the
challenges that the industry landscape, digital transformation and the supply chain face today.
To adequately answer what constitutes the most successful supply chain leadership approach, a more comprehensive statement and broader viewpoint are needed. This requires a deeper analysis and focus on the current challenges facing supply chains and the strategic and organizational frameworks that should be developed to address them. In other words, the focus should be more on the challenges that all supply chains currently face and the future strategies and organizational structures needed to stay at the forefront of supply chain management.
What are the challenges that Supply Chain Leaders facing in today's business environment?
The challenges supply chain leaders face today are multifaceted and complex. These challenges can be categorized into four main elements:
Globalization, regionalization, insourcing, outsourcing, offshoring or nearshoring? The search for the right strategy for today’s and future supply chain management is like the quest
for the holy grail in many corporations these days. Supply chain disruptions triggered by crises, wars, pandemics, inflation, stagflation, trade wars, shortages of raw materials, high freight prices and shortages of skilled workers are the topics that are currently omnipresent in all companies, often termed as the New Normal to be managed when the stormy times are gone.
But what is the new normal in supply chain management? The answer is quite simple with a certain level of complexity. There is no "new normal" in the meaning of a newly established status quo. Rather, companies and their supply chains must be prepared for the fact that supply chain disruptions caused by economic, political, and technological change will continue to be on the agenda in the future. Supply chain disruption is constant and impactful. Supply chain disruption is both omnipresent and unpredictable at the same time. The question to be addressed: Are we able to mitigate the next global supply chain disruption? Being able to deal with such shifts in the global economy including the associated risks and challenges has rather become a core competence for competitive supply chain management. Undoubtedly, this is a major challenge for all Supply Chain Leaders. Especially if they manage supply chain operations globally. In consequence, existing supply
chain designs, organizational structures and strategies need to be assessed and redefined.
But is that good enough to be futureready? For sure it is not. Being able to deal with the next global disruption that comes our way by employing resiliency and agility can be considered as the gold standard of today. The future supply chain leader is requested to go beyond the concept of resiliency. Being resilient means just to mitigate risks and minimize the impacts from disruptions in order to protect the supply chain and business. What is needed here is to lever it onto the next level - to create value from the uncertainty. Through the development of an antifragile supply chain - one that responds effectively to disruptions, adapts to changing conditions, learns, improves, and emerges stronger from adversity.
Traditionally, the functional teams in supply chain have operated in silos or functional segments such as sourcing, manufacturing, distribution and logistics, retail and aftersales service. The visibility across the functional areas was limited, data and information has been not shared and the interconnection between suppliers and customers could not be
Being able to deal with the next global disruption that comes our way by employing resiliency and agility can be considered as the gold standard of today. The future supply chain leader is required to go beyond the concept of resiliency. Being resilient means just to mitigate risks and minimize the impacts from disruptions in order to protect the supply chain and business. What is needed here is to lever it onto the next level - to create value from the uncertainty. Through the development of an antifragile supply chain - one that responds effectively to disruptions, adapts to changing conditions, learns, improves, and emerges stronger from adversity.
named as a network. That was resulting in unnecessary network disruptions and operational inefficiencies. But those days are gone. In today’s supply chain, it is crucial to understand how does each process step contribute to an end-to-end supply chain that maximize customer satisfaction, minimize operational costs and generate the competitive advantage. It requires effective coordination and collaboration among all stakeholders involved in the supply chain, from suppliers and manufacturers to logistics providers and retailers.
Does that sound simple? Not at all as it requires to manage complexity and to drive transformation leading to the new standard of an end-to-end supply chain to be established. The development from today's linear supply chain to a dynamic, networked supply chain ecosystem requires Supply Chain leaders of the future with a holistic mindset, understanding their roles as an embedded business function aligned with sales and marketing, research and development and suppliers and customers.
This requires a deep understanding of the business model, market dynamics, and business acumen, as competition has shifted from individual corporations to entire supply chains, making it a critical factor in gaining a competitive advantage or disadvantage. Orchestrating the endto-end supply chain, which includes all stakeholders and partners, necessitates a leadership style that aligns supply chain partner activities to achieve targeted and common goals for all stakeholders involved.
Supply chain management is undergoing a transformation like never before. The advances in technology, specifically in the context of digital transformation and industry 4.0 will change the landscape in Industry and Logistics. Digital supply chain networks and smart factories will define new standards. The development from today's linear supply chain to a dynamic, networked supply chain ecosystem warrants embracing industry 4.0 and digital supply chain technologies as the fundament for the digital supply chain of the future. Global Supply Chains, including all players like vendors, manufacturers, retailers, and customers, are part of this digital transformation. That will result in new breathtaking breakthroughs in terms of productivity, delivery performance and the way supply chain ecosystems are managed. The use of these new digital technologies - autonomous robots, artificial intelligence, machine learning, blockchain, digital twins, VR/AR and the Internet of Things (IoT) - will transform how supply chains operate.
The technology with most relevance for the entire supply chain is for the time being Artificial Intelligence (AI). Artificial intelligence (AI)-enabled supply chain management has the potential to supercharge demand forecasting, revolutionize end-to-end transparency and boost integrated business planning. 48% of companies
rate Artificial Intelligence (AI) as the game changer technology with significance for the digital supply chain of the future. Another technology with high level of relevance is the Digital Twin. Digital twins are used to simulate and optimize the performance of realworld objects and systems. They can be used to optimize production processes, predicting machine failures before they occur and identifying areas for improvement. They can also be used to simulate supply chain scenarios, helping companies to identify potential bottlenecks and optimize inventory levels. Combining digital twins with artificial intelligence (AI) will be the ultimate door opener for the future of supply chain planning processes.
Digital control towers are expected to play a significant role as well. They can provide a centralized, real-time view of the supply chain and enable companies to make more informed and agile decisions. The power of a networked supply chain ecosystems supported by digital control powers comes from the fact that all improvement initiatives will focus on the entire supply chain network and deliver results for all stakeholders and processes involved. This can be called as well as digital supply chain network where a digital core creates connectivity among traditionally unconnected links in the supply chain.
All of those aspects are part of the game and leading to a paradigm shift in industry and supply chain management. It’s clear that it’s time to engage digital supply chain management. In a first step
Supply chain leaders managing a successful transition into the future supply chain will need to assume the role of a Transformation Manager. They will be responsible for both optimizing current supply chain operations and transforming functions, organizational structures, and processes to build an end-to-end supply chain by incorporating digital supply chain and Industry 4.0 technologies. As a result, modern supply chain leadership entails assuming the role of a ‘Digital E2E Supply Chain Transformation Leader’.
first step, Supply Chain Leaders need to get an insight on what these mega trends and technologies are about. Which technologies should be prioritized while upgrading supply chain operations?
Therefore, supply chain leaders play the key role in leveraging digital supply chain technologies to drive improvements in their supply chain performance. The successful supply chain leaders need to acquire industry 4.0 expertise to understand the potential of these technologies and to set the right priorities.
Starting from the times of pandemic hybrid working models have become more common and supply chain leaders were requested to manage employee expectations. The learnings from that experience often resulted in a new way of thinking and flexible working policies. That has been just the starting point as in the meantime a move toward nontraditional work models such as gig work (short-term, temporary or independent contractors) and digital nomadism (work anywhere, workation) evolved. Especially the younger generation is striving here for greater flexibility how, when and where to work and that can be a game changer by dealing with the supply chain talent shortage. Following that it appears the need to redesign work experience by leveraging technology to enrich hybrid
and virtual work experiences.
Furthermore, the labor shortage on the shopfloor roles warrants incorporating more technology, advanced robotics and automation, especially for repetitive tasks and processes in factories, distribution centers and warehouses. That will contribute to improving the work environments by making them safer and reducing hard work.
Emerging technologies such as virtual (VR) and augmented reality (AR), digital twins, artificial intelligence (AI) and autonomous robots will open the door to a new world of working, resulting in better operational performance, customer service and higher profitability. That facilitates a new way of working where humans and robots interact in newly defined processes, striving for a new level of operational excellence. These human-robot interactions need to be designed to create or even reinvent the future work environments representing new industry standards.
Consequently, the human and digital coexistence comes up with the challenge to be build this new blended workforce aimed at becoming the excellence team of the future. That human and digital coexistence requires redefining and reinventing new roles and skills for supply chain professionals and leaders across all functionalities.
The challenge here comes with the fact that the workforce in place today at any time is not what will be needed in the future. That comes with a balancing act as both needs to be managed at the same
time: the workforce and organization as of today and simultaneously develop the workforce and organization of the future with new roles and skills needed for the coming years.
To summarize the outlined four challenges: Supply Chain leaders of the future require a holistic mindset with an excellent knowledge and expertise about the end-to-end Supply Chain (E2E Supply Chain) as the fundament to challenge the status quo. At the same time, they need to have more than just an insight of industry 4.0 & digital supply chain technology developments. Understanding when to invest in which technology requires a combination of Industry 4.0 expertise and strategic foresight.
The successful supply chain leader has the competence to deal with the fact that supply chain disruptions are omnipresent and unpredictable at the same time. Being able to deal with these shifts in the global economy has become a core competency for competitive supply chains. But the future supply chain leader is required to go beyond the concept of resiliency. What is needed here is to lever it onto the next level - to create value from the uncertainty. Through the development of an antifragile supply chain - one that responds effectively to disruptions, adapts to changing conditions, learns, improves, and emerges stronger from adversity.
To build a capable workforce of the future requires to take into account new working models composed by the employee expectations, hybrid working models, digital technologies and fact that labor shortages will continue being part of the game. As more and more technology such as advanced robotics, automation, digital twins and AI will play here, the human and digital coexistence will create a new working experience and environment by setting new industry standards.
Overall, the challenge for the Supply Chain Leader will be to simultaneously manage the current workforce, organizational structure and processes while also developing the function and structure for the future based on new technologies and processes by incorporating new roles and skills required in the coming years.
As a result, supply chain leaders managing a successful transition into the future supply chain will need to assume the role of a Transformation Manager. They will be responsible for both optimizing current supply chain operations and transforming functions, organizational structures, and processes to build an end-to-end supply chain by incorporating digital supply chain and Industry 4.0 technologies. As a result, modern supply chain leadership entails assuming the role of a ‘Digital E2E Supply Chain Transformation Leader’.
Does this sound challenging? Undoubtedly. In addition to the functional expertise and technical skills required to become a world-class supply chain leader as highlighted, there are also soft skills needed to perform the role. These include communication, collaboration, problemsolving, conflict resolution, influencing skills, customer focus, business acumen, negotiation skills, presentations and storytelling abilities, diplomacy and assertiveness, and the ability to influence internal and external stakeholders. And for sure, intercultural competencies are especially important for managing global supply chain operations. Indeed, that represents a comprehensive list of skills and competences required.
In consequence, effective leadership in supply chain management requires a high level of expertise, business acumen and the right skill. Many corporations have started to recognize that supply chain management is becoming an increasingly important board priority. Latest research shows that the bestin-class operations have supply chain expertise at the boardroom. The recommendation is clear: incorporating supply chain talent into the future board is one of the key success factors.
Developing a Vision and Roadmap:
Everything begins with developing a vision and roadmap for a digital endto-end supply chain organization aligned with business objectives. This process includes defining the required levels of supply chain and digital technology competencies. It also involves determining the skills needed for functional supply chain expertise areas such as strategy, demand planning and forecasting, inventory management, procurement, production planning, order management, and logistics and distribution. Most important here is to add to the requirements of traditional supply chain expertise the “new disciplines” such as advanced analytics, artificial intelligence, data management and scenario modeling. Evaluating leadership skills and soft skills is also a critical part of this process.
A maturity assessment is essential for understanding the current and future capabilities of the workforce, organizational structure and culture. This assessment serves as the foundation for identifying gaps, mismatches and areas that require improvement and change. Deciding on the optimal organizational design (centralized operating supply chain, decentralized supply chain, centralized strategic supply chain model, or platform) depends on various criteria such as business model and strategy, market trends and industry developments. Gaining a clear understanding of the operational design is a prerequisite to define roles and functions properly.
The most challenging aspect of the roadmap is developing a future-ready supply chain capability development initiative. This transformation initiative should encompass organizational development and a comprehensive supply chain development program composed by talent management, career paths, career progression plans, succession plans, mentoring and coaching programs, supply chain mastery level programs, center of excellence (CoE) concepts, and even an in-house supply chain academy.
To develop this supply chain capability transformation and the supply chain development program, it is recommended that a benchmarking exercise be conducted. While it is common for corporations to benchmark within their industry, it is advisable to extend benchmarking efforts beyond industry boundaries. By doing so, best practices and excellence standards from other industries can be adopted, especially if they appear with world-class supply chain performance.
Regardless of the roadmap or strategic concept employed, whether only the first steps have been taken or more extensive efforts have been made, it is now time to address the supply chain leadership challenge and develop futureready capabilities for Industry 4.0 and the digital supply chain.
Mahabharat is an ancient epic written during 500 BC. It reminds us of a historical narrative, which is timeless in its execution. Its teachings related to our value system, relationships, leadership, conflict resolution, and moral dilemmas are highly relevant to our lives today. The relevance of the Mahabharat today lies in its timeless teachings and insights into human nature and morality. Its lessons on ethics, the eternal struggle between good and bad continues to resonate with professionals from all walks of life. Through this article, Sanjay Desai, General Manager – Asia, Supply Technologies, draws parallel between some of the great Leaders’ qualities and how these can be aligned to our personal / professional well-being !!!
is an experienced commercial operation professional. Currently he is running Asia Commercial Vertical for Supply Technologies, USA as VP/GM based out of Singapore. In the past, he has been running profit & loss for over 500 million USD leading more than 2000 professionals located remotely across 30 international markets. He has led many Fortune100 multinationals in various segments like Pharma, FMCG, Oil & Gas, MedTech, IT/ Technology and Chemicals successfully for the last 40 years. Sanjay’s expertise lies in developing commercial & operational strategies, developing people’s skillset, and enabling market growth. He is a mentor for a couple of Start Up incubators. He sits as an advisory member on multiple start up and MSME organizations in SEA.
THE Mahabharat is not just a story but also contains philosophical and ethical teachings. It addresses complex and timeless themes such as duty (dharma), righteousness, the nature of life and death, and the concept of the self. Let’s dive into some of these leaders’ qualities that can be successfully imbibed in our lives as well to bring out the best…
Krishna is the central figure in The Mahabharat. His character is depicted as a role model, a guide, friend, and philosopher, not just to Arjun but to Kauravas and Pandavas both. He showcases how to live a righteous life and fulfill one's duties. He is a great mentor & possess huge inner strength. His actions and teaching aim to find right balance & justice.
In the current context, most genuine leaders are great mentors, they are role
models, and create young leaders. They do not force their way, instead they inspire others to follow them naturally. Modern day leaders define core principles, which include ethics and moral values. They practice these principles consistently during good as well as difficult times. This is where we can draw parallels between teaching of Lord Krishan with modern day leaders.
Dhritarashtra is portrayed as a tragic
figure who struggles with his desires and duties. His excessive attachment to his sons highlights the dangers of favouritism and a certain lack of direction and indecisiveness which was his undoing. He is aware of his shortcomings but is unable to overcome them, which ultimately leads to his downfall.
Dhritarashtra's behaviour towards his sons as well as towards Pandav’s highlights what happens when you allow your judgement to be impressed by personal attachments and favouritism. In reference to the modern times, his example highlights importance of genuine leadership, integrity, impartiality & ability to make decisions. At times, these decisions are uncomfortable to take but they are meant to do greater good to people and organization at large!!
Sanjay is the advisor and close confidante to blind King Dhritarashtra. Sanjay has (celestial sight) or ‘Divya Drishti’ to see events which are happening in far distance like the war in Kurukshetra. Sanjay's character embodies qualities such as foresight, communication, storytelling skills, emotional intelligence, sheer dedication, and love for the job.
In the current context, a leader must have a good vision and an ability to create the ‘Big Picture’. We can relate Sanjay’s character to the modern-day Consultant or The Therapist. These specialized professionals help corporate professionals to learn and upgrade their skills to steer through different business dynamics. And these are the similar traits that can help a modern day professional to navigate the complexities and lead with integrity and clarity.
Kauravas are depicted as antagonists to Pandavas. They are hungry for power. Their approach is confrontational, intimidating to achieve their goals anyhow. They emit negative energy with a destructive mindset with disregard for ethical and social values.
The current generation of leaders can derive several critical lessons from the failures of the Kauravas’ life. By
understanding and avoiding these pitfalls, leaders can foster an ethical, sustainable, and effective approach to leadership and cultivate a successful career path ahead. Effective leaders today adopt collaborative style to lean and leverage each other. They inspire and motivate their teams, fostering a positive and productive work environment.
Pandavas are portrayed as upholding ethical values, follow teachings of their guru. They display immense resilience in the face of adversity and stand up for their morale values. With their special skills, they also resonate with 5 senses (taste, hear, see, touch & smell).
Modern leaders strive hard to set high ethical standards, inspire trust, and promote a culture of integrity and accountability. They showcase and build a sense of equality and collaboration within their teams as well as across other functions. If we look at Pandavas’ individual prowess, we can resonate the diverse leadership in the current times. Modern day leaders exhibit a combination of these qualities which help them to scale greater achievements not just in their own career but others career as well.
Draupadi’s characterization is a symbol of strength, resilience, and purpose. She suffers humiliation in the Dice game in the Court. She has a single-minded purpose, which is to take revenge against Kauravas. She got all 5 brothers focused on this ‘Purpose’.
In today’s world, women face multiple challenges i.e. gender bias, glass ceiling, unequal opportunities. Despite these, women are increasingly asserting their rights, advocating for equal pay, and challenging discriminatory practices. They take on leadership roles and speak up against injustice and inequality. Draupadi’s character and behaviour inspire the current generation of women to have a purpose, stand up for their rights and go after their dreams!!!
King Karna is described as a noble warrior with strong sense of belonging to his duty. He stood up for what he believed is right. At the same time Mahabharat also shows his vulnerability. His undoing was his ego & misplaced loyalty in the bad company.
We can draw parallels between Lord Karna and modern-day professionals in terms of their hardships & struggles they face in their careers today. The modern professionals may have to navigate their way through favouritism, discrimination, and organizational biases. Like King Karna, modern day professionals also go out of their way to mentor others.
If we are able to imbibe some of these principles in our approach to lead, supply chain professionals will sure be able to turn the tides in their favours not only for their personal growth but also in building a highly resilient, strong and collaborative team that work together and bring out their respective best for the sustained organizational growth.
“It takes toll on your time & efforts to become a successful leader. In this constant pursuit of becoming a leader, one needs to lead by example, not necessarily all your tasks will be super hit. There will be some failures as well. Whatever be the reason, a true leader will never get impacted by failures, rather he will prepare in much better way / work on the shortcomings / learnings to make sure that failure is turned into grand success,” shares Mayur Chhabra, Head – Supply Chain, White Cement and Paints Division, JK Cement.
What are the leadership inflection points and personal growth you had in your career?
While I look back & deep dive into my professional journey of almost 22 years, there had been several incidences wherein self-confidence, critical thinking, resilience & agility played a pivotal role not only in managing the situation but also in succeeding & overcoming the situation. As we all know that we live in VUCA world, when it comes to supply chain as a function, it is evolving each passing day and therefore managing CHANGE, be it in demand pattern, customer expectations, speed to market have been the key to success. I cherish my memories of working with different companies starting from Beverages to FMCG, Health Care & Nutrition, Fresh Dairy, Perishables, canned fruits & vegetables and finally White Cement & decorative paints. By the god’s grace, I have had a successful career path with all these leading organizations because of the five traits I mentioned above.
How do you embrace change and continuous learning at the workplace?
As they say, ‘Change is the only constant’, I had been an admirer of this quote and hence have adopted this in my day-to-day
work life as well. No matter how old any organization would be, with the changing business dynamics, wherein factors such as the customers’ ever-evolving demands, e-commerce disrupting the value chain, geopolitical situation at the global level & the growing economy are making it almost next to impossible to think of working with the same old school of thought.
Our recent encounter with the pandemic such as the Covid 19 had made this crystal clear that one can’t even think of succeeding without embracing change & hence any seasoned supply chain professional always needs to have a plan B ready in case of any eventualities. Moreover, on the job training to the new joiners and exposure to different verticals of supply chain has today become a new normal. Just to mention a person managing DRP (Distribution requirement planning) in my value chain will also undergo handson exposure to production scheduling and MRP (Material resource planning) & vice versa.
What are the principles of success you’ve seen across different industries?
Self-Belief & confidence are one of the key ingredients for success, however
Mayur Chhabra is an astute supply chain professional with over 21 years of experience into streams of Supply Chain viz. Warehousing, Distribution, Demand & Supply planning, Network Optimization, etc. He has worked with reputed MNC FMCG companies such as Coca Cola, Nestle, Hindustan Unilever, Britannia, and Del Monte Foods. His academic qualifications include Post Graduate of commerce, Advance Program in Supply Chain Management from IIM Kolkata and MDP in Supply Chain from IIM Lucknow.
In my recent interactions with young professionals, the restlessness to grow at a fast pace in their career is something which comes out crystal clear but at the same time the acumen to master value chain and working on the shop floor seems to be diminishing. My advice is to deep dive into operations, go to Gemba, master the vertical & thereafter aspire to move ahead. This will definitely lead to SUSTAINABLE SUCCESS.
there is a very thin line of difference between Confidence & Over confidence. A confident person will try to learn new things but will be open to suggestions & inputs from his fellow colleagues, however in case someone is overconfident, the doors for improvement / inputs become minimal. While everyone is talking about Supply Chain 4.0, success rests on these key pillars – Resilience, Perseverance, Agility, Reflexiveness & most importantly keep updating as per the market demand /expectations.
Do you have any advice for young professionals who are aiming to reach the C-Suite level?
‘GOD lies in detailing’, my advice to the young professionals is to enrich the subject knowledge as much as one can imbibe, getting into thick of the things will not only help you understand the nitty-gritties of the task, but will also ensure that you will have complete control / confidence to handle any situation.
In my recent interactions with young professionals, the restlessness to grow at a fast pace in their career is something which comes out crystal clear but at the same time the acumen to master value chain and working on the shop floor seems to be diminishing. My advice is to deep dive into operations, go to Gemba, master the vertical & thereafter aspire to move ahead. This will lead to SUSTAINABLE SUCCESS.
From your perspective, what are some of the toughest challenges that you see in operations and supply chain?
Customer Service & Demand management are the most daunting tasks in operations & supply chain, which happen to be the backbone of any value chain & hence hold utmost importance.
Customer service: This includes the
customer experience in terms of Order to delivery (T.A.T), Quality & Packaging of the material when it gets delivered to the customer, availability of the stuff on the shelf, etc. We have witnessed a sea change in this aspect over the last decade wherein delivery times have been reducing every day & now there are some organizations who brag about 10 minutes delivery. We have also seen innovative packaging to deliver stuff in good quality irrespective of the distance being travelled. In a nutshell, we have been a witness to new initiatives by different organizations, which is actually a classic example of adapting to new ways of working.
Demand Management: As we know that we are in VUCA world & COVID-19 had actually tested nerves of the entire supply chain fraternity as almost all Algorithms, Logics, Demand / Supply planning tools actually FAILED Big time. While there was complete ambiguity on lead times / production/ demand, it was actually a situation wherein everything was out of syllabus, but as they say, ‘Requirement is the mother of all Inventions’, many organizations adapted DDMRP – Demand Driven Material Planning, which actually took cognizance of the open orders in system and used to trigger demand aggregation accordingly. Ever since the aftermath of Covid-19, the planning fraternity has evolved at a great pace and adapted themselves to be ready to any such disruptions wherein S&OP had now evolved to IBP & the use of AI & ML also started to cater to the uninterrupted supplies across the value chain with the minimum SLOB inventory (Slow-moving and obsolete inventory).
What are some of the principles and skills that no matter what happens will still be useful?
While I had mentioned five important
traits in my inputs earlier, if we need to follow / implement them in their entirety, the biggest behavioural trait is ‘Keeping Calm’. One should understand that whatever the situation may be, pressing the PANIC BUTTON is not the solution at all. While you press the PANIC BUTTON, the situation starts getting worse and the ability to think about the situation & chances to resolve the same keep decreasing. Therefore, it is advisable to keep a calm head, thoroughly understand the problem statement and thereafter adapt to DMAIC (Define, Measure, Analyse, Improve and Control) and 5W1H (A questioning technique used to gather information and understand a situation comprehensively) methods to get into thick of the things and find the most appropriate solution.
What are the biggest learnings you have as a leader? Is there a secret sauce to becoming a successful leader? ‘Success doesn’t come overnight’, it takes toll on your time & efforts to become a successful leader. No wonder how many sleepless nights had gone behind the success of an individual, but I see them as an investment for a bright future / career. In this constant pursuit of becoming a leader, one needs to lead by example, not necessarily all your tasks will be super hit. There will be some failures as well. Whatever be the reason, a true leader will never get impacted by failures, rather he will prepare in much better way / work on the shortcomings / learnings to make sure that failure is turned into grand success. Remember not everyone will like you, but one needs to understand that conflict is part of job & try to take everyone along. If any individual is able to follow the same, the transformation from an Individual to a successful leader will be seamless.
Email: tech@celerityin.com | Mobile: 79771 05913
Website: www.supplychaintribe.com www.supplychaintribe.events www.supplychaintribe.jobs