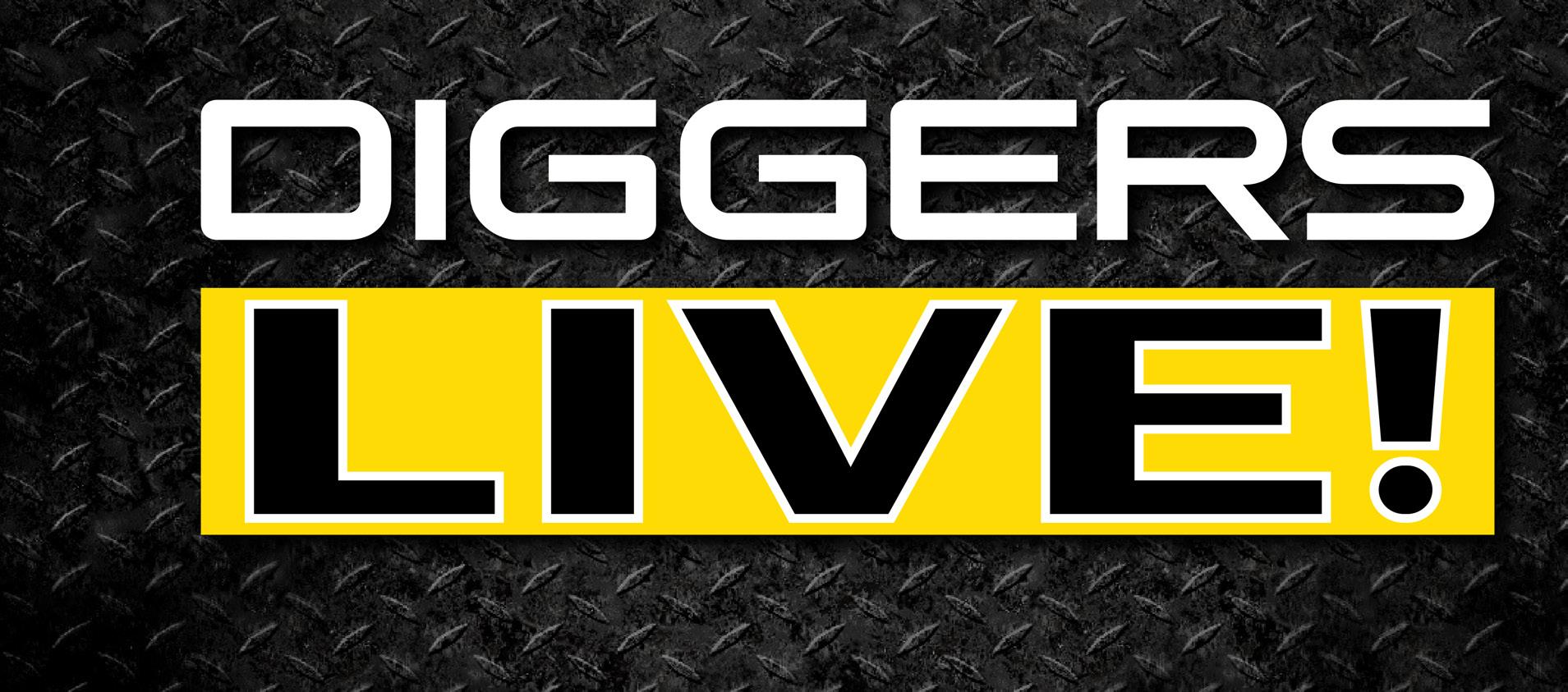






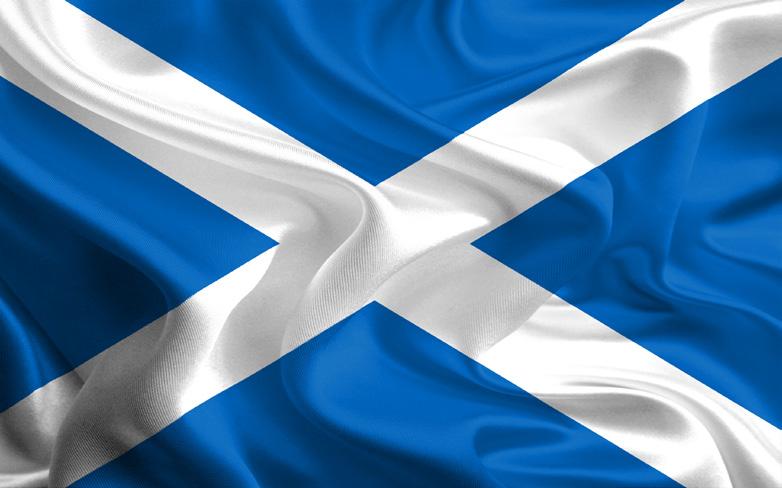
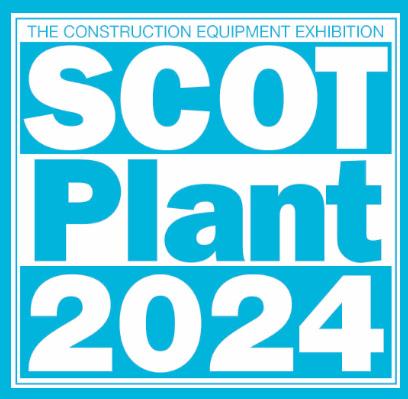
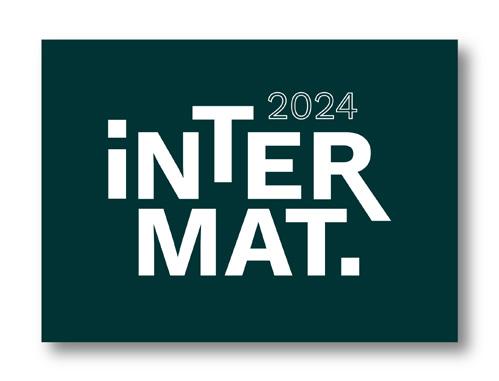


FROM 1.8 TO 95 TONNES THE ALL NEW F-SERIES BREAKS THE MOULD.
Well, that was an event-full couple of months for us at Diggers LIVE! Towers…
This issue’s regular BUSINESS INSIDER interview is with Joshua Copeland of Ulrich Attachments from page 10 and although conducted entirely by Toby, I was fortunate to be able to meet up with Josh and the Ulrich Attachments team at ScotPlant at the end of last month. What an engaging bunch they are, and all passionate about their brand.
Which leads me nicely on to the rest of the ScotPlant 2024 event, where I could quite easily make the same compliment to all the organisers, exhibitors and visitors I managed to cram in throughout the Friday.
ScotPlant was already embedded in my diary after a successful event a couple of years ago. It has leading OEMs exhibiting mixed in with British dealers and smaller manufacturers. It is in a great location and the team behind the event, Peebles Media Group and Project Plant Magazine, are a joy to deal with. Thanks Gary, Mark and Steph.
The one issue was that ScotPlant coincided with Intermat, held in Paris. I would have loved to have been at both, but the scheduling was impossible. Having to choose one I went with what I knew, in Edinburgh 700 miles to the north.
Speaking with those in the industry who did attend, I understand it was an incredible international affair and we have already been liaising with organiser Comexposium and its PR team at Promosalons as well as many of the exhibitors, postevent to bring you a comprehensive review of what went on.
In line with our mission to bring you original and engaging content, Toby conducted an exclusive interview with the event director Christophe Lecarpentier to run alongside our Intermat coverage. In the latter part of next year we will begin promotion with the hosts for the next Intermat. Thankfully in 2027 neither event will be missed.
International travel between issues had me off to San Antonio Texas and to Berlin both for our publishing house’s partnerships with global demolition associations, we have included a few snaps here, but all are covered more comprehensively in Demolition Hub Magazine issue #22.
Also in this edition the regular EQUIPMENT ENGAGEMENT interview is with General Sales Manager of Thwaites, Andrew Sabin from page six. From the shop floor in 1999 to General Sales Manager today, Andy tells us about the history of the business and why customers choose Thwaites.
We also have a double feature on crushers and screeners from page 70. Thank you to all those manufacturers and dealers that participated.
Channelling the industry events of the past month and the thoughts of our contributors and friends in the industry, we bring you the most comprehensive issue of Diggers LIVE! yet. Thank you all for your support.
Please do stay in touch: ben@globalnews.media |+44 (0)7803 844 806
With Andrew Sabin, General Sales Manager of Thwaites
With Joshua Copeland, Sales Director of Ulrich Attachments
16
• Ben Chambers visits ScotPlant
• DEVELON
• DIGGER GUARD
• Rokbak
• SANY
• An introduction to Hillhead
• Brokk
• CASE
• CDE
• DEVELON
• JCB
• SRL Traffic Systems
• Sunward Europe
• Tele Radio
• Wirtgen Group
• Toby Wilsdon speaks to Intermat Exhibition Director, Christophe Lecarpentier,
• Photo gallery
• Hitachi Construction Machinery (Europe)
• HCME with Xwatch Leica Geosystems
• Bobcat
• DEVELON
• Dynaset wins Gold at Intermat Innovation Awards
• Kobelco
• Kramer
• LiuGong
• MB Crusher
• Tele Radio
• Wacker Neuson
• Yanmar CE
• OilQuick
Future of Machine Control report from Topcon What’s in it for operators?
• Prodem screening buckets, supplied by BPH Attachments
• EDGE Innovate – EDGE SCREENPRO S18 scalping screen
• INMALO – Cutting-edge crushing attachments
• Finlay – Finlay 890 screener
• MB Crusher buckets – Recovering means monetising
• Rubble Master crushers, supplied by Red Knight 6
• Sandvik – QI353 mobile impact crusher
• Terex MPS, supplied by PowerX Equipment
• KEESTRACK, supplied by Warwick Ward
A first compact telehandler in the UK for Kubota Hebonilube – The slick choice for machinery lubrication
Diggers LIVE! and kicking – Ben and the team out promoting the industry between issues
Komatsu PC88MR-11 midi excavator
Xwatch Safety Solutions merges with Hexagon AB
Revealing the magic behind TVH: a haven for small earthmovers
Liebherr: 2023 marks yet another record revenue business year
Interviewee: Andrew Sabin
Role: General Sales Manager
Company: Thwaites
QTell us about the history, development and design principles of Thwaites Thwaites has been manufacturing on the same site in Leamington Spa since 1937, when our founder Basil Thwaites started manufacturing agricultural equipment. In 1941 the Thwaites Harvester was produced. The machine, towed by a tractor improved productivity and
Andy Sabin began his career at Thwaites in 1999, so this year he is celebrating 25 years with the business and in the industry. From the shop floor to General Sales Manager, Andy tells us about the history of the business and why customers choose Thwaites, in addition to what the next government needs to commit to, the importance of family and his passion for the Pittsburgh Steelers.
effectiveness at a critical time for the industry and country.
The post war rebuild saw Thwaites design its first piece of construction equipment, the Builders Hoist, making the job of building new homes safer and more efficient. In 1951 the post war boom was driving the need for new methodologies and machinery. Thwaites produced the first ever dumper, launching the three-wheel, 15 cwt (760 kg) reverse tip machine, which was an instant success.
With demand increasing, in 1953 we launched a four-wheel front tip machine that would go on to provide the template for all future dumper designs. Since this time, Thwaites has been a British privately owned manufacturer, solely focused on
dumper design, innovation and the safety of its stakeholders.
Every Thwaites dumper is manufactured in the factory, quite literally with steel coming in one door and a dumper going out of the other. Anyone who has toured the factory will have seen for themselves the blend of highly skilled, time served engineers and artisan crafts folk, working alongside the latest robotic welders and cutters.
We have a strict quality control system which minimises error, but errors do occur and when they do we quickly rectify and learn, before the machine passes through a comprehensive pre-despatch inspection.
Thwaites offers dumpers in a range of sizes from one to nine tonnes. The machines come, dependent on the
dumper, with a front tip or power swivel (tips to the side). The machines all comply with Stage V emissions and have a hydrostatic transmission, making the dumper more responsive for the operator.
We have recently shown our first allelectric dumper, a three-tonne forward tip, at the Executive Hire Show. We also have an exciting new product in the ninetonne category all lined up for this year’s Hillhead event, this dumper will further improve safety, efficiency and operational effectiveness.
We go to market through our network of distributors. The UK market has ten expert plant sales businesses that market, sell and service our products. Around the world Thwaites dumpers are available on five continents and in over 70 countries.
Q
Tell us about your team and the working culture. Is there a fundamental company philosophy?
The Thwaites team is genuinely dedicated to quality, enabling us to build and sell the very best dumper we can, while at the same time encouraging each member of the team to be the very best they can. While we are always on the lookout for the very best talent, we are keen to promote from within. Taking people from all backgrounds, immersing them in the business and exposing them to all aspects of the manufacturing process – it’s a sound grounding for future personal development.
QWhat can a customer expect when they buy Thwaites?
The Thwaites name is synonymous with the best quality dumpers on the market. When customers choose Thwaites, they are getting a reliable machine that will not let them down. They know the cost of ownership will be low, reliability high and when it’s time to sell or part exchange, the residuals will be the best in the business.
Q
How do you see the outlook for the plant industry and Thwaites in the medium term?
I am as confident as I can be about the medium-term outlook. We work in a resilient and creative industry, which I believe has a unique culture. There has been recent uncertainty in the market, but the lead indicators of downward interest rates and inflation encourage me that the second half of this year will see market improvement.
Whichever party wins the next election, we need to deliver the housing stock this country needs, along with investing the money “saved” from HS2 into our infrastructure.
QAnd how do you see the medium term future for Thwaites’ product development?
Thwaites has a great history and reputation for recognising next step product development and the market will see several exciting new products being launched later this year. This will include a new three-tonne electric drive machine that will be ideal on urban or high-rise developments where noise and fuel pollution have previously been a problem.
An exciting new concept product will be shown for the first time at this year’s Intermat in France. This product will give customers more choice when considering compliance with the new Manufacturing standard EN474 2022: part 6*, which comes into effect next March.
This standard states that these machines shall be provided with an additional means (for example cabs) to prevent the operator from being ejected from the overall dimensions of the machine in the event of a machine tip or roll over.
In addition, Thwaites will be launching a brand new nine-tonne cabbed dumper design at Hillhead that will further advantage the industry from both an operational, safety and compliance perspective.
QWhat is Thwaites doing with regard to sustainability and the net zero agenda?
We have invested heavily in the Thwaites factory to reduce waste and improve efficiency. The way we paint and bake our dumpers has had a significant impact on reducing our emissions as has the installation of state of the art cutting and welding machines.
Work has just begun on a new factory building that will encompass the latest design features such as solar capture, ultimately delivering a 33% reduction in our traditional energy costs and critically, further reducing emissions.
QAnd how about broader involvement in the community?
The Thwaites factory is located in a village called Cubbington, we have been here a long time and the local community has been and always will be important to us. We support many local initiatives by both donation and participation. Local schools, scout groups, charities and support groups are all important to us.
Many of the Thwaites team live in the local community, we also work hard to communicate with community groups about developments in and around our business. Engagement around the new factory build is so important to us, we have regular updates and newsletters to ensure the community knows exactly what is going on and how we will ensure the minimum of disruption at both the build and post commission phase.
Q
Tell us about one of Thwaites’ key products
As a dumper specialist all our products are key as they provide different solutions to different markets. From a landscape gardener using a one-tonne swivel skip on a tight job, to a housing contractor moving spoil away from site with a six-tonne dumper, to a ninetonne cabbed dumper working on a tier one contract – they are all equally important to us.
QOutline the key functions of the product
All Thwaites dumpers are built with hirers and contractors in mind, powered, dependent on the dumper size, by either a Yanmar or Deutz Tier 5 engine to give the maximum power and torque. Thwaites dumpers are all now fitted with hydrostatic transmissions to give the operator more control.
Cabbed machines are fitted with cameras giving 150° visibility all displayed on a five-inch dashboard screen. With a heater for the winter and air-con for the summer all to ensure the operator is comfortable and in control, improving safety, efficiency and performance.
QHow is this product critical for potential users?
We always say that when a customer buys a Thwaites dumper, they are safe, compliant and competitive. Built to last, customers notice and come back because of the low lifetime running costs and minimum downtime. Independent auction data consistently places Thwaites dumpers first for residual value, when compared to competitors’ machines from the same year of manufacture, hours worked and class.
Q
How will Thwaites be developing this product range in the near future?
Thwaites products are part of our continual improvement programme, updated and further improved regularly to help our customers with solutions they offer the latest technology and
manufacturing advancements.
Dumper development is advancing. The fact that operators can now rotate position and drive the dumpers with the skip in front of them or drive with the skip to the rear is further evidence of improving safety and operator performance. Look out for a new machine alert at Hillhead.
Q
How long have you been in the plant industry?
I joined the industry 25 years ago this year, so I guess this makes it my silver jubilee.
Q
What attracted you to the industry?
I live locally to Thwaites and love engineering and manufacturing. My family comes from a manufacturing background so this attracted me to both the industry and Thwaites.
QTell us about the different aspects of your work. What range of tasks do you undertake day to day?
As General Manager of Sales, I work with a team of distributor managers for both the UK and export markets. I am in regular contact with our distributors all to ensure we are playing our part so that each distributor can deliver the agreed plan and targets.
I also work closely with the engineering team on both product development and enhancements so that
Who would you be in an alternative life?
In an alternative life I would have wanted to be a professional footballer so I would be none other than Alan Shearer.
Who is your favourite artist?
It’s fair to say my musical taste is eclectic, from my early love of Motown to indie music, so artists as diverse as Marvin Gaye, Oasis, 50 Cent and Muse.
What would be your desert island (permanent exile) luxury?
Any device I can listen to my music on.
we can keep our distributor managers and distributors updated and aware of advancements and timings.
Another key area that we have developed and continue to improve is our external communications and marketing. We are a small but nimble team who, across social media and our website, produce and publish collateral that supports the sales ambition and target of both the business and our distribution network, not only here in the UK but around the world.
QWhat do you find most rewarding in work?
Helping people become the best they can be is the most rewarding part of my role. Seeing a new team member come into the business then grow and develop is so pleasing, as is the day they get given wider responsibilities or move to the next level.
Who do you most admire?
Pittsburgh Steelers Head Coach Mike Tomlin.
What gets you out of bed in the morning?
Providing the best life I can for my family.
When and where are you happiest?
Anywhere I am with family and friends.
What’s your bucket list activity?
To see the Pittsburgh Steelers win the Super Bowl.
Autumn, winter, spring or summer? Autumn.
What’s your favourite cuisine? Italian for me, every time.
What’s your tipple of choice?
You can never beat a cold beer.
Interviewee: Joshua Copeland
Role: Sales Director
Company: Ulrich Attachments
Employees: 12
Established: September 1998
Parent company: UTS Engineering Ltd
Acquired: May 2020
Associated brands: LCR Engineering Ltd
Geographic reach: Europe, Middle East
Prior roles: CNH Industrial Ltd (Case Construction), Ulrich Attachments, Filtermech Plant Sales Ltd. – Area Sales Manager, Sales & Accounts Manager, Parts Sales Manager
QTell us about how your career has developed to where it is today I’ve been within the construction industry since the age of 16, about 18 years now. It’s pretty much all I’ve known if I’m honest.
A family member of mine was the Business Director for the construction side of CNH Industrial – CASE, New Holland etc. The CASE side of the business has always been based in Doncaster so everybody has either had a parent or grandparent or great grandparent who worked for them. So I was at a barbecue and he asked if I’d be interested in starting in the sales
administration. I think like most 16-yearolds I didn’t know quite what direction to take so I joined up and got the bug for it. I started in sales admin, moved on to marketing, then selling parts and attachments and I was with CNH for 11 or 12 years.
At the time, Ulrich Attachments was one of our preferred suppliers, so we would deal with them on a weekly basis, supplying quotes and pricing for attachments for the CASE wheel loaders, etc. I built a good relationship, had a good understanding of the product and I was very impressed with the reputation of the company and the quality of the product. Then an opportunity arose to join them as Account Manager. All I’d known since leaving school was CASE Construction and I thought it would give me a great opportunity to broaden my horizons and see the wider construction world, dealing with Caterpillar, Volvo, JCB, etc.
After three and a half years as Account Manager and then Sales Manager, I had an opportunity to go elsewhere, selling machinery for a local Doosan dealer. This added to my experience selling directly on the front line, cold calling, door knocking, going to sites and speaking with people, looking at excavators, mini excavators, wheel loaders, dump trucks, dozers etc.
I’d been there two and a bit years and enjoyed it before I was approached to come back to Ulrich as they were making a few changes. The current MD had left, the previous director took a different role within the business and I was asked to take the role of Sales Director. It excited me and was an opportunity I couldn’t turn down.
I’m putting my own stamp on everything, getting the right team in place, understanding everybody’s role and getting feedback from the whole team.
QYou say you’re putting your own stamp on things. What is it you are trying to achieve?
I want to get back to basics, to get our social media, our website, marketing, admin, relationships with the factory etc running smoothly. I want to get the best processes in place to make everybody’s life easier within the company, which then passes on to the customers and gives us more focus on the industry. And I want to share the plans for the future – the targets,
where we want to expand what we want to achieve – with everybody within the team.
We’ve got people that have been with the company for more than 20 years, so I’m listening to feedback and trying to get everybody singing from the same hymn sheet and happy in their role. If I’m looking to change this product, expand into that area, or change a process, I’ll have discussed the pros and cons and I’ll have a reason why.
We want to expand into so many products and expand into different countries – longer term I want to double our turnover. I want to build our customer base, to sell direct from the website, we want part sales going through the roof. And I will lead by example, to be honest. I’ll never ask any staff to do anything I wouldn’t do.
QIs this way of working informed by your previous experience? When I was 16 years old I worked alongside some very experienced people who moulded me into the sort of person I am today, and I still speak to them on a regular basis.
CASE construction’s market share grew massively during my period in certain products aspects, down to the experience and relationships within the team. The team had a very good reputation and most of the people I worked with have now gone in other directions, but they still have a great reputation, still work the same way. It gave me a good background, which has helped me build my relationships within the industry.
QWhat would you say are the key skills for your job?
I think having the experience, contacts and knowledge of the industry is a key part of this role – understanding the industry and its needs, what you’re selling and who you’re selling to, who the main targets and key players are as well as having a personal touch. Because people buy from people.
You need your team to work in the same way. We want to be the first to answer the phone, the first to reply and the first to supply a price because it’s all about reputation. When business is tight and you’re chasing every deal you want quick, open and honest answers. In business relationships that always helps.
QHow do you think your colleagues see you, or you would like them to?
I would hope they see me as hard working, passionate about the industry and growing the business, and open to communication and very approachable. I’m always available, I always answer my phone, I wander around the office not just sit in my own room all day, I sit with colleagues and listen to ideas. I’m always on time, I’m always the last to leave. That’s just leading by example. I don’t do it for show.
QWould you ever consider doing a similar business role in an entirely different industry? Or are you wedded to construction?
I feel that the construction industry has given me the career and the opportunities that I’ve had. If you’d said 10 years ago, or even less, that I would be a sales director of the UK’s leading attachments manufacturer, I’d have snatched your hand off. I do not believe that in any other industry within the space of 10 to 15 years you’d go from administration to marketing to a sales director role. From the progress and the experience and the life it’s given me, I think I owe the industry that much.
So I would only really probably consider moving out of the industry if it was something that really excited me, but there’s nothing that springs to mind that excites me as much as this industry. It’s something different every day.
QTell us more about Ulrich Attachments
We’re probably the UK’s best kept secret in terms of attachments. We supply most if not all OEMs in the UK, dealers including Finning, SMT, all the JCB dealers, DEVELON, LiuGong etc. Our core business is the high tip buckets, but we can supply anything for a wheel loading shovel or a telehandler. As well as that we have a good aftersales department, we can do on-site repairs, on-site line boring. We offer up to five years warranty, which not a lot of our competitors do. We’re very quality focused and customer focused.
It started around 1998 as a management buyout of a company called Boughton, who do winches. The name Ulrich came from an American style of bucket – the Ulrich bucket, which we now
“ We can build anything standard or bespoke to fit your machine and load into whatever hopper or truck or bay size you require ”
call the Simplex bucket, but the name stuck.
They started supplying attachment including buckets, high tip buckets not just to the OEMs and the UK dealers, but to the Environment Agency, UK and US military, which we still do on the odd occasion. The overall product range expanded to match the need for higher sided trucks in the waste and recycling, agricultural, quarrying and demolition industries.
There won’t be many attachments in the past 26 years that we haven’t either built, been tempted to build, designed or had a look at within the UK market. We’ve done telescopic dippers and tree cutting equipment for the Environment Agency. We’ve worked with all sorts of government and military operations as well as the construction and agricultural industry. And previously, we’ve done structural building within our manufacturing facility, we did a lot of work on the Shard in London, for example.
We fill in the gaps around the standard buckets that come with machines – that’s where our experience and expertise come into play. We can build anything standard or bespoke to fit your machine and load into whatever hopper or truck or bay size you require.
If you’ve got a wheel loader and you want it to pick up potatoes or sugar beet or waste, we will ask you five or six questions and design a bucket depending on your needs. We will design that bucket based on the weight of the material, the density, the shape, how it flows. Grain, for example, flows like water.
Pretty much everything we do will be different – slightly wider, slightly taller, have a slightly different spill guard but in the waste industry there are very common sizes due to the tipping loads and due to the sizes of the wheel loading shovels. But everybody tries to squeeze that little bit extra out. If you’ve got an extra tonne of tipping load, you can go slightly bigger on the capacity of the bucket to load trailers and trucks more quickly, increasing productivity.
We’ll always work with the supplier or the OEM to get every last bit of productivity. Where a standard bucket is, say two and a half cubic metres, we could do the calculations to get five cubic
metres, which is double the size, double the productivity or half the time.
QAnd you manufacture as well?
Our parent company UTS Engineering Ltd, is owned by Shaun Sadler and he also owns LCR Engineering Limited over in Hull, which is our manufacturing facility. We work closely together and they are a dedicated manufacturing facility for Ulrich Attachments. I’m there regularly, I like to physically see the attachments, I’d rather they physically show me if we do come across any issues. So it’s a very open relationship and we’re all working towards the same goal.
QHow does the team dynamic at Ulrich work?
The people we have on the Ulrich side of the business are more sales and design focused – we have between 10 and 15 people and we’re looking to employ a couple more in the next month or so. We have a very good management team. We are very open and discuss ideas, with Roxanne Mercer (General and Finance Manager) being more accountant minded and Emma Pierce (National Sales Manager) commercially minded – we meet somewhere in the middle.
We’ve got three members of the design team and we potentially will have another for future products. Two of the lead design engineers have been with us for over 15 years, one of them almost 20. They’re predominantly office based, but we do send them to site on occasion, they’re happy to go out, take their own measurements so they fully understand the project. They’ve been doing this for a long time now but every day is still different.
Everything down to every crack and nut and weld is done on CAD (Computer Aided Design) using a package called SolidWorks. That is then sent off to the LCR Engineering manufacturing facility. We work closely with LCR, who work to employ the right machinists, engineers, welding team etc based in the factory in Hull. We’ve got a good team up there and they’re always looking to expand too.
We’ve had a couple of guys from college and university do their placements with us and one of them, Jack, joined us on the back of that. He wanted to be a design engineer but we’ve opened his role a little bit, we get him out seeing the
attachments on site, we get him into the factory doing his own checks.
We’ve had trainees three or four times over the last five or six years and it’s an option that we’re looking at the moment. The fourth designer that we bring in will be a work placement designer. We will train them, give them that experience and open the door for them to potentially come back like Jack did.
We’ve put employees through accounting training, we’ve put people through welding training, line boring training and we’ve just had some specific advanced training on SolidWorks. So we’re always looking to expand the team’s knowledge and give them that experience, which has helped us. That’s the way the opportunity came for me, so I can only say it’s worthwhile.
We’re attending some major exhibitions including ScotPlant in April, but we only booked it two weeks before. We had an open conversation with the team – do you think it’s worth it? What do you think we’ll get out of it? What is the return on investment? Who is going to be there?
At the end of the day I have to put my neck on the line for decisions I make, which is not a problem. But I listen to feedback from different departments with their different experience. If I’m going to attend these shows, if I’m going to invest in stock, if I’m going to invest in upgrading certain products, I’ve got to be
sure. I will sit back, put the pros and cons together in my head and discuss openly with my team.
QTell us about Ulrich’s involvement in the local community
Our parent company, UTS Engineering, is very involved and its owner Shaun has passed that on to us. He’s worked with all sorts of charities and he sponsors more football teams in this area than anybody else. We are looking for local sports teams to sponsor within the Aylesbury area – it’s not something that Ulrich itself has done previously but Shaun is very keen on us doing that.
QWhere do you see yourself in five or ten years?
I would like us to have a wide range of new attachments and services. I would like to have a bigger, wider customer base, not just in the UK but in Europe and the Middle East. We have a big presence worldwide with UTS and I would like to expand that with the Ulrich product. I want our customer service to be second to none. So that is where our five to ten-year plan would be based.
QAnd yourself personally?
Who is your favourite artist?
What do you do for fun?
Play golf and coach my son’s under sevens football team.
What’s the most expensive nonessential you’ve ever bought?
My honeymoon to Jamaica.
I would very much like to be part of that journey and would be very proud of that achievement if we were to do that.
What’s your bucket list activity?
To go to a World Cup final match.
James BluntExplore the full range of CASE products and services, tailored to meet your construction business needs
25-27 JUNE
Hillhead Quarry, Buxton, Derbyshire, UK
Stand X10
My domestic highlight of the year so far occurred between issues as I attended the returning ScotPlant event towards the end of April, a show I was really looking forward to and held in high regard following my first ScotPlant in 2022.
It was clearly evident that ScotPlant had surpassed the 2022 event’s footfall of 6,000 visitors, as confirmed to me by event organisers Peebles Media Group.
It was packed, stacked and all wrapped up together once again at the Royal Highland Centre, which is a perfect venue if ever there was one, being just three minutes’ drive from the airport with a perfect blend of outdoor and indoor exhibitors and plenty of space.
This year I met with perhaps a dozen brands that had until then either been on my contact to-do list, not approached us yet, or been names I had yet to discover.
At the show, I was invited to north America, was able to tie up advertising and enjoyed a laugh and industry chat with some very familiar faces.
Without a word of exaggeration, almost everybody was friendly and happy to be there, with the bright sunshine no doubt being a factor. I was only once met with a shoulder barge and an “Oh, they’ll let anyone in here,” – I assume he was joking.
The first ScotPlant exhibition was held in 1998 and the event has grown to over 200 exhibitors this year. ScotPlant’s assertion that it is the largest construction equipment show
in Scotland does it a disservice, as it certainly rivals other shows held across the UK and beyond.
Gary Moug, editor of Project Plant magazine, which is published by Peebles Media Group, had the following to say to Diggers LIVE!: “We are absolutely thrilled with the success of ScotPlant 2024. The exhibition cemented its status as the most important event on the calendar for the Scottish plant industry and the feedback we’ve had so far from both exhibitors and visitors has been nothing short of phenomenal.
“ScotPlant continues to grow with every event and it was particularly noticeable how many more construction equipment journalists/bloggers attended this year, reflecting both the enhanced reputation of the event and also the calibre of equipment and innovation on display. It was an incredible two days showcasing the very best of the Scottish and UK construction equipment sector and – for the third ScotPlant in succession – we were even blessed with glorious sunshine throughout! We can’t wait to do it all over again in 2026.”
Exhibitors and attendees alike were clearly echoing my sentiments and the activity on the socials post and particularly during the event were lit up with praise, deals done and why they were delighted to be in Edinburgh.
I cannot wait for ScotPlant 2026 and to once again be a part of an event attended by thousands of industry professionals that showcases the widest range of construction solutions.
Dumfries and Galloway-based James Gordon Ltd (Gordons), the Authorised Dealer for DEVELON for the whole of Scotland and the county of Cumbria in England, showed the DEVELON range for the first time at ScotPlant 2024. Gordons was established in 1865 and is a premier distributor of construction equipment in Scotland.
ScotPlant saw premieres on the Gordons stand not only for the DEVELON brand itself, but also the new DD130-7 15 3-tonne dozer and the latest version of the popular DX140LC7K 14.6-tonne crawler excavator.
These products were joined by a selection of DEVELON products from the smallest – 1 to 10-tonne mini-excavators and the DL80TL compact wheel loader – to some of the larger machines such as the 15.6-tonne DX140LCR-7, 23-tonne DX225LC-7 and 31.5-tonne DX300LC-7 crawler excavators and the DL380-7 wheel loader. The display also included a DEVELON DX235LCR-7 24.3-tonne crawler excavator specially adapted for scrapping vehicles.
DEVELON enters European dozer market
One of the biggest differences between the DD130-7 and other dozer brands is the visibility the DD130-7 provides of the machine’s dozer blade. To facilitate this, the front engine compartment offers a narrower design to make it easier for operators to see their work.
Other aspects of the DD130-7 that maximise visibility include:
• The precleaner is tucked away in the engine compartment,
• The electronic cooling system is relocated to the back of the dozer,
• The cab’s low profile front pillars provide maximum glass area,
• All glass doors provide a full view of the working environment.
A standard rear-view camera provides an additional view of the dozer’s surroundings, displayed on the full colour, 8-inch Smart Touch screen. Also standard are high illumination LED lights and four premium wiper blades.
New version of 14-tonne crawler excavator
The new DX140LC-7K has replaced DEVELON’s successful DX140LC-7 model. While the performance and working range are the same as the previous model, the new machine
incorporates many improvements that enhance safety and convenience both for the operator and for working on site, together with a better operator experience, particularly from a maintenance point of view.
Models on show include the 1-tonne DX10Z, 2-tonne DX20Z-7, 2.8-tonne DX27Z-7, 5.7-tonne DX55R-7, 6.2-tonne DX63-7 and 9.5-tonne DX85R-7 Stage V models. All these machines offer power and torque among the highest in their respective classes and cover many applications including heavy duty work.
The DX100W-7 10.7-tonne wheeled excavator offers a high performance solution for customers looking for a wheeled excavator designed primarily for urban and road maintenance applications. For this type of work the
DX100W-7 offers the best compromise between compactness and agility, complemented by excellent productivity and high-end comfort. It is very important that this type of machine can operate in very restricted areas so the DX100W-7 can be equipped with the option of four-wheel steering and a crabbing mode, with two-wheel steering as standard.
Like all the 11 models in the awardwinning DL-7 range of wheel loaders, the DL380-7 offers a state-of-the-art design, incorporating a powerful new Stage V engine and providing higher productivity, increased fuel efficiency and a low cost of ownership, coupled with a new cab offering a superb environment and experience for the operator.
The DL80TL is one of five compact wheel loaders from DEVELON that
also includes the DL60, DL65, DL80 and DL85-7 models, with operating weights from 3,500 to 5,000 kg. Just like the much heavier versions in the DEVELON range, these compact wheel loaders set the industry standard for productivity, flexibility, comfort, safety and reliability, with powerful Stage V engines, hydrostatic four-wheel drive, 100% differential lock on both axles and versatile and powerful hydraulics.
DIGGER GUARD demonstrated new features and improvements to its awardwinning Vandal Guard cab and windows protection kits, and the steel-surpassing capabilities of its Polymer Handrail systems.
The patented Vandal Guards have undergone a significant transformation achieving a further 27% weight reduction and now featuring premium stainless-steel fittings.
The show also saw the manufacturer launch its latest Vandal Guard innovation – an optional integrated beacon lighting system in its streamlined rooftop storage box. The weatherproof box is a secure storage solution for the panels when not in use.
DIGGER GUARD has redefined the standards for handrails with polymer versions that are 75% lighter than steel yet they exceed pull strength requirements. Surpassing steel’s limitations, these handrails are corrosion-resistant, selfcoloured, and don’t need to be coated or painted. International handrail patents are pending for DIGGER GUARD’s vibration dampening system that reduces part wear and replacement frequency.
Describing one competitive advantage is DIGGER GUARD’s slogan “robust and no rust” – it’s a unique selling point that now applies to both its Polymer Handrails and Vandal Guard systems that universally use stainless steel fittings.
Visitors to ScotPlant engaged with DIGGER GUARD’s expert team manning the stand and explored its product demonstrations first hand.
Scottish articulated hauler manufacturer Rokbak attended ScotPlant alongside its trusted dealer partner Molson Group. Rokbak travelled the short distance from its Motherwell factory to Edinburgh to showcase its RA30 and RA40 trucks in partnership with its UK dealer Molson Group.
Rokbak Regional Sales Manager EMEA Kenny Price said: “ScotPlant is our home show and we always enjoy promoting Rokbak within the local territory. Being part of Scotland’s premier plant event is an opportunity to catch up with our customers and
cultivate professional relationships with similarly home-grown brands and businesses.
“Rokbak ADTs remain proudly manufactured in Scotland, and ScotPlant is a great opportunity for people from Scotland and beyond to come and see how our trucks can help improve their operations.”
Quality to be proud of Attendees to the Molson Group stand were able to see the RA30 and RA40 trucks first-hand, sit in the ergonomically designed
Rokbak cab and talk face to face with Rokbak and Molson Group specialists.
Alistair Murdoch, Molson Scotland Sales Director said: “With Rokbak at ScotPlant, we are promoting something that’s built on the doorstep, that employs local people and puts back into the local economy. The journey that Rokbak has come on since it became part of the Volvo Group is incredible – both in build and product quality as well as reputation.
“Rokbak still maintains that
Scottish heritage but the evolution of the brand is one we’re proud to support. Molson as a company is expanding in Scotland and we want to build relationships across the country alongside Rokbak, which ScotPlant will help us to do.”
Developed with the support and investment of the Volvo Group, the 28-tonne RA30 articulated hauler has true independent front suspension as standard for more control and comfort for operators in applications including quarries, infrastructure developments and commercial construction projects.
The 38-tonne RA40 offers high capacity and performance for large-scale quarry, mine and construction jobs, delivering cost-effective productivity in the toughest conditions. Both machines feature the latest EU Stage V emissionscompliant engine, boasting up to a 7% improvement in fuel efficiency compared to the previous EU Stage IV models.
The Molson Group partnered with the Lighthouse Charity, which is dedicated to the emotional, physical and financial wellbeing of construction workers and their families, to host a series of mental health talks at ScotPlant.
Two presentations were held on the Molson stand each day, aiming to create comfortable and supportive industry environments, encouraging workers facing mental health challenges to reach out for the assistance they need.
SANY UK is delighted to have returned to the largest and most important event of the year for the Scottish construction equipment industry.
As part of an extensive lineup of more than 15 machines, SANY showcased its brand new telehandler series, which was displayed alongside a range excavators and mobile cranes.
The exhibition came hot on the heels of a series of telehandler roadshows that took place across the country in February and March aimed at showcasing SANY’s brand new range of telehandlers to the UK market. The STH1440 (14 m) and STH1840 (18 m) are the first machines to feature in the series, designed to offer the ultimate in safety, comfort and performance.
SANY also displayed a variety of excavators ranging from the zero tail-swing SY18U mini, the smallest machine in the SANY range at 1.8 tonnes, up to the larger 50-tonne SY500H machine with world renowned components such as a Cummins Stage V engine and Kawasaki hydraulics.
Commenting on the show, Brian McGrane, Senior Sales Manager for Scotland said: “The team are delighted to be exhibiting for a second time at
the ScotPlant event. Our first show here in April 2022 was a great success, we had a fantastic stand and it allowed us to showcase our full range of machines and meet a lot of potential new customers. Since then, SANY has grown considerably so it’s great to return to the show and have the opportunity to demonstrate how our product range is continuing to expand. It’s going to be an exciting event and we’re looking forward to meeting people, both old and new.”
The stand will also feature the SAC600E 60-tonne three axle all terrain crane launched to the UK market last year.
The SAC600E is powered by a
MTU OM470LA Stage V engine coupled with Allison transmission driven by Kessler axles. In addition it’s fitted with a 50-m main boom with the option of 16-m double folding jib and will travel with 13-t counterweight within UK STGO regulations.
SANY’s cranes are renowned for their reliability, performance and cutting-edge technology. The UK product range includes telescopic crawler cranes from 60 – 80-t with two larger models due later in 2024, and a range of lattice boom cranes from 60 –480 tonnes.
For those who felt like putting their operating skills to the test, SANY’s Operator Challenge was in full swing over the course of the two day event.
We have the largest central stockholding in the UK, which is supported by a finely tuned stock control program, a highly organised warehousing system and carefully selected logistics partners. This allows Astrak to have the undercarriage parts that you need available when you need them, minimising machine downtime.
Once it’s on the machine, our extended warranty is the most comprehensive in the market place. Each of our rubber tracks come with an extended 24 month warranty as standard.
All of our undercarriage and wear parts are manufactured in IS0 9001 and OEM approved production facilities with rigorous quality control procedures.
Place your order prior to 4.30pm and it will be despatched for delivery on the next working day.
Our wide range of heavy-duty components will keep your excavators, dozers and tracked machinery working harder, for longer. Every hour of machine downtime incurs avoidable costs! This is why you need a reliable partner you can rely on. Stocking the widest range from bucket teeth, cutting edges and OEM quality undercarriage components through to custom made wear parts. Astrak providing you complete undercarriage and wear part solutions. The right part, to the right place, at the right time!
Quarrying, Construction & Recycling
With ScotPlant and Intermat (both covered in this issue) over and done with, the attention of the construction plant industry moves to the next major event on its calendar – Hillhead 2024.
The event takes place from 25 to 27 June at Hillhead Quarry, near Buxton in Derbyshire. With more than 600 exhibitors, 20,000 visitors from around the world and four themed demonstration areas, Hillhead truly is the behemoth of UK construction plant events.
Innovations this year include an upgraded Showground Pavillion, which has been extended by almost a third to create a further 550 m2 of internal exhibitor space and the new Hillhead Cafe and networking area.
On the more practical side of things, there is a new viewing platform, more seating areas, additional welfare facilities and a new road linking the upper and
lower car parks. Shuttle buses will run between the Registration Pavilion and the car parks.
All those at Diggers LIVE! (and our sister publication Demolition Hub) are very much looking forward to attending the event, hoping to be blown away by the exhibits, if not quite literally by the live quarrying demonstrations themselves.
Here, we bring you a taster of what to expect from a select group of the 600 or so exhibitors – it’s just not possible to cover them all in our 100-odd-page magazine but we hope this will inspire any of you who are as yet undecided to attend – and perhaps meet with our team.
A full list of exhibitors, visitor registration portal, show guide booklet, and further practical details such as information about transport and accommodation are available at www.hillhead.com. See you there!
Among Brokk’s latest generation of industry-leading demolition robots are the Brokk 170 and Brokk 200+, which will be on show at Hillhead where attendees will discover how Brokk SmartPower+ and its many features offer significant improvements in endurance, operating experience, and intelligence.
Brokk’s new range of SmartPower+ robots offer unmatched endurance by increasing operational uptime with consistent power delivery over time, resulting in unmatched performance. Expertly engineered with rugged components, this newest generation is resistant to shock, temperature, and vibration – with all new robots and control boxes protected to an IP65 equivalent for outstanding reliability regardless of the work conditions.
Brokk’s SmartPower+ generation also includes a noteworthy 87% reduction in cables and connectors, reducing weak points while also facilitating servicing and troubleshooting.
Brokk SmartPower+, which revolutionises the operating experience for both seasoned professionals and new operators alike with more precision, better response times, and greater ease of operation, introduces a new and improved lightweight control box weighing less than 3 kg, which contributes to more enjoyable and comfortable work shifts.
The new ergonomically designed control box features tilted joysticks, easier-to-reach features and faster dual charging. The control box also includes the innovative Brokk QuickSwitch
and intuitive settings for an improved operating experience, making it easier than ever to operate a Brokk robot and, in turn, easier to find and train operators. With Brokk’s new range of SmartPower+ robots and state-of-theart features, operators can perform the demolition task at hand without shifting their gaze from the machine between commands, and as such, without compromising on performance or safety.
CEO of Brokk Group, Martin Krupicka said: “With nearly five decades of experience, Brokk understands the challenges many industry professionals face in finding skilled operators to get the job done right. This is precisely why we are committed to creating solutions for both seasoned professionals and new operators alike, setting a new benchmark in the demolition landscape.”
This new generation of robots elevates the operator-machine interaction, focusing on added intelligence for the benefit of the operator. Visual status updates through incremental light indicators allow the operator to focus their attention on the demolition work at hand while simultaneously monitoring the status of the machine. A two-way communication system communicates the status back to the operator in real time, while customised features enhance the operating experience.
Brokk’s SmartPower+ generation is much smarter too, alerting the operator about any unwanted power supply or machine statuses, further contributing to an increase in uptime and overall reliability. Moreover, Brokk SmartPower+ is enabled for future over-the-air upgrades to always be at the forefront of the industry. Fast and simple settings, an increase in sensors as well as the addition of individual tool presets all contribute toward a more user friendly and efficient operator interface.
Martin Krupicka said: “We are thrilled to introduce Brokk SmartPower+ and a new generation of demolition robots that redefine the demolition landscape. This innovative advancement reflects Brokk’s dedication to pushing the limits and providing operators cuttingedge machines that surpass expectations.
CASE will have a wide range of new and improved equipment on display at Hillhead, both static on the stand and working in the exhibition’s waste and recycling area, the secondary rock handling area and in Crusher Alley, where blasted rock will be processed.
Equipment on the working displays will include the CX250E and CX210E-S crawler excavators, along with the 651G, 821GXR and 1021G wheel loaders. Static machinery on the stand will include the latest CX15EV and CX25EV electric mini excavators, plus the electric compact wheel loader 12EV.
The battery-powered 12EV will join the company’s electric mini excavators in a growing zero emission CASE lineup, with the first CASE full electric compact shovel also on display.
Models from the latest mini and midi
excavator lineup, the larger crawler range, wheeled excavators, loaders and compact wheel loaders will also be represented.
Much of the focus will be on the new CX210E-S tracked excavator. This “essential” excavator retains all of the power and performance of the standard CX210E, yet boasts an increasingly competitive price point and a simplified list of options. Built with heavy-duty components throughout, the machine delivers all of the performance, operator comfort and productivity that customers expect.
Customers looking for a premium wheel loader will be drawn to the new 651G Evolution. Built to sit between the proven 621G and the 721G, the 651G boasts increased loading performance, thanks to reinforced front and rear chassis sections, plus heavy duty axles
as standard with a choice of locking differentials. Other wheel loaders will be on display, from the largest models to the latest compact loaders.
CASE’s equipment lines will be backed up by the full range of parts and service solutions, along with CNH Capital financing services, plus undercarriage products from CASE’s partner, Sampierana.
Product specialists will be able to walk you around CASE’s latest machinery, innovations and technologies answering all your questions, while keen operators may take part in the popular Operator Challenge, with a range of prizes throughout the exhibition.
Olivier Buschino, Business Director for the UK and Republic of Ireland said: “Hillhead provides a unique opportunity for our customers and the media to see our machinery in action and to take a closer look in detail on the stand.
“We look forward to welcoming customers old and new to the stand and having the opportunity to show the very latest technical innovation and engineering excellence on show from CASE Construction Equipment.”
The stage is set as CDE, a leading supplier of sand and aggregate wet processing solutions for the waste recycling and natural minerals processing sectors, announces its return to Hillhead with a major product showcase on the cards for 10.30 am on Tuesday 25 June, at the CDE stand.
The wet processing experts will shine a spotlight on equipment from the CDE product range, which is improving productivity and delivering consistent performance in the quarrying, construction and recycling industries.
The company will also debut its most efficient water management solution to date, which it says promises greater functionality, improved maintenance access and safety, speed, automation and material versatility to offer best value per tonne processed for operators.
Located at stand A11 beside the Registration Pavilion, CDE will present its AggMax 252SR scrubbing and classification system, which combines pre-screening, scrubbing, organics removal, sizing, stockpiling, fines recovery and filtrates removal on a compact chassis.
Also on display will be the latest generation of FreeFlow, the fully-mobile washing solution for aggregate and sand classification. Designed and built onto the bed of a semi-trailer for optimal mobility, the plant helps achieve maximum in-situ
material recovery and boasts integrated water storage and recycling.
Commenting on the company’s latest product reveal, CDE’s David Kinloch, Director of Business Development, UK & Ireland, said: “We see the world through our customers’ eyes and we engineer practical, scalable and proven solutions that address real-world problems, from the big picture issues concerning global sand shortages and the
industry’s waste burden, to the everyday needs of our customers.
“Our plans for Hillhead this year really reflect our commitment to innovation and our desire to elevate the industries and sectors we operate in. Alongside the AggMax – the backbone of the CDE process and the driving force behind countless natural processing and waste recycling solutions around the world – will be the latest generation of our FreeFlow and the global reveal of our newest product innovation.
“We look forward to sharing more information with the industry over the coming weeks and hosting the global product launch at the showground at 10:30 am on Tuesday 25 June.”
CDE will be joined at Hillhead by strategic partners Molson Washing, the specialist materials processing division of Molson Group, as well as Siemens Financial Services, to provide customers with expert guidance to support their investment in the latest wet processing technology.
You can request a meeting with the team in advance via the CDE website: cdegroup.com/hillhead.
The static display on DEVELON‘s stand will include the DX530LC-7 53-tonne crawler excavator, the DL420-7 wheel loader and the DA45-7 articulated dump truck (ADT). In the demonstration area, further products for the quarry face that will be showing their paces include the DX420LC-7 43.5-tonne crawler excavator, the DL550-7 wheel loader and the DA30-7 ADT.
Among new products being shown for the first time on the DEVELON stand are the new DX140RDM-7 22.5-tonne demolition excavator and the new
DD130-7 dozer. Compact equipment is another strong aspect, with the DX27Z-7 and DX55R-7 mini-excavators and DL85-7 compact wheel loader on show. The stand display will be completed by DEVELON‘s DX235LCR-7 24.3-tonne crawler excavator.
DX-7 range of crawler and wheeled excavators
The DX420LC-7 and DX530LC-7 are part of the range of large crawler excavators from DEVELON that also includes the DX800LC-7 80-tonne and
DX1000LC-7 100-tonne machines. Overall, all the models in the DX-7 range of crawler and wheeled excavators from 14 to 100 tonnes combine enhanced comfort with the latest features to boost fuel efficiency, uptime and return on investment, with a focus on increased power, robustness and agility.
The DL420-7 and DL550-7 are two of the four biggest standard models in the DL-7 range of wheel loaders from DEVELON, which also includes the DL480-7 and DL580-7 models. With redesigned buckets offering up to 7% more capacity, these DL-7 wheel loaders provide easier and faster loading with maximum bucket capacities from 4.5 to 6.4 m3. Altogether, the eleven DL-7 wheel loaders in the DEVELON range with bucket capacities starting at 2.0 m3 provide increased productivity for a very wide range of material-handling applications.
The market-leading DA30-7 and DA457 ADTs offer payloads of 28 tonnes and 41 tonnes, respectively. These models feature an articulation hinge positioned behind the turning ring to provide equal weight distribution to the front axle even during maximum steer articulation. This combined with a free-swinging rear tandem bogie ensures equal distribution of weight to each wheel and guarantees permanent six-wheel contact and drive for equal power distribution and excellent performance particularly on difficult terrains such as soft ground, uneven surfaces, very steep slopes, tight turns or a combination of all of these difficult conditions.
The DA30-7 and DA45-7 6x6 ADTs are now complemented by a new 4x4 version of the DA45-7 ADT intended to compete with rigid dump trucks (RDTs) in the 40-tonne class. In the new 4x4 ADT, the front truck and cab unit is the same as in the original 6x6 model, with modifications being made on the rear dumper unit only.
The DX140RDM-7 is the latest addition to the company’s successful range of demolition excavators and the only one of its type on the market. Like the larger models from 31 to 61 tonnes, this new 22.5-tonne excavator offers multiple configurations to choose from, providing the customer with a complete, flexible solution that allows them to use the same excavators for other applications on site as well as demolition.
In fact, the DX140RDM-7 offers even more choices, starting with a unique
Monolithic variant, only featuring a demolition arm without any possibility of interchangeability. Alternatively, like the larger machines, the DX140RDM-7 is also available in a dual format with a modular boom design and hydraulic lock mechanism allowing the user to change between different arms for demolition and digging using the same machine.
With the launch of the new DD130-7, DEVELON has entered the European dozer market. The wide range of features on the DD130-7 provides a productive
fine-grading solution for residential and light commercial construction projects. One of the biggest differences between the DD130-7 and other brands is the visibility it provides of the machine’s dozer blade. To facilitate this, the front engine compartment offers a narrower design and is combined with other features that make it easier for operators to see their work.
For further visibility and safety, a standard rear-view camera gives operators an additional view of their surroundings, displayed on the full-colour, 8-inch Smart Touch display. Also standard are high-illumination LED lights and four premium wiper blades. The DD130-7 offers a high level of comfort with a premium high-quality seat. The seat and joysticks move together via the air suspension system to absorb all vibrations.
The DX27Z-7 2.8-tonne and DX55R-7 5.7-tonne Stage V-compliant models are typical of the new DEVELON range of mini-excavators from 1 to 10 tonnes. The zero tail swing design of the DX27Z-7 and the reduced radius design of the DX55R-7 models make them ideal for confined space work.
The DX27Z-7 is powered by the D17 Stage V-compliant diesel engine providing 18.4 kW at 2,400 RPM. The DX55R-7 is powered by the D18 Stage V-compliant diesel engine providing 36.4 kW at 2,200 RPM. As a result, these models offer the highest power and torque in their respective classes and cover a wide range of applications including heavy duty work.
The DL85-7 is one of five compact wheel loaders from DEVELON, also including the DL60, DL65, DL80 and DL80TL models, with operating weights from 3,500 to 5,000 kg. Just like their much heavier cousins in the DEVELON range, these compact wheel loaders set the industry standard for productivity, flexibility, comfort, safety and reliability, with powerful Stage V engines, hydrostatic 4-wheel drive, 100% differential lock on both axles and powerful and versatile hydraulics.
At Hillhead 2024, JCB will showcase its biggest and most powerful X Series tracked excavator yet – the 370X.
Headlining on the JCB stand and in the demonstration area, the 370X is a heavy-duty earthmover that brings its industry leading productivity, durability and reliability to the 35-40 tonne sector.
Powered by a Stage V/T4F 240 kW diesel engine, the 370X can move 4.5 tonnes more material per litre of fuel than competitor models.
It features the new JCB UX user interface, with 10-inch colour touchscreen display and controls, increased hydraulic pressures boost performance in hard digging and extended service intervals for improved total cost of ownership.
The new model will be joined at the show by an extensive lineup of JCB machines for the quarrying, construction and recycling sectors, including JCB’s new Dual Drive
backhoe loader, new Hydradig with Raptor tiltrotator and the prototype backhoe loader powered by JCB’s hydrogen combustion engine.
Further products from the manufacturer’s Loadall telescopic handler, backhoe loader, tracked excavator, wheeled loading shovel, site dumper, compaction, power generation and compact equipment ranges will be shown across the stand, demonstration area and at the quarry face.
With enhanced cab comfort and visibility, plus improved fuel economy and digging performance, the new SV86 and SV100 improve your working day and build your business success.
SRL Traffic Systems, Europe’s largest manufacturer and supplier of mobile intelligent transport system (ITS) solutions to the traffic-management and construction industries, is expanding into the aggregates sector, making its Hillhead debut with the presentation of a portfolio of products designed to improve safety in quarries.
According to the Health and Safety Executive’s 2023 Vehicles and Edge Protection guidance, transport accounts for 40% of accidents and 60% of deaths in quarries. While quarry transport safety has long been an HSE priority, the organisation believes that it has yet to be effectively addressed by the industry.
SRL’s patented, award-winning Haul Route PLUS facilitates the safety of drivers at plant crossing points,
while promoting the efficient flow of traffic. The only plant crossing solution integrating adaptive detection technology, it incorporates traffic signals that respond to the actual flow of quarry vehicles rather than operating to timings set to accommodate the slowest plant. An all-red facility ensures that barriers remain open until plant is safely across the junction.
SRL this year incorporated the RiseMaster HE fully autonomous solarpowered automatic boom barrier into Haul Route PLUS to allow managers of longer-term projects to benefit from the solution. The robust, freestanding barrier features a continuous flanged post of high strength steel. Haul Route PLUS is also available with INSTABOOM protection barriers for shorter-term
deployments and can include variable message signs (VMS) and CCTV. All components are solar/hybrid.
Within quarry perimeters, barriers are used in conjunction with full-colour, high-resolution VMS, signals, CCTV and ANPR to promote on-site safety. Bespoke integrated solutions limit access to specific areas, such as tips and excavations, to authorised vehicles and separate visitor traffic from plant and pedestrians. They limit the quantity of vehicles on often narrow, single-lane haul routes, minimising risk of collision and the need for reversal. They also permit traffic management where HGVs and cars need to cross, where only one-way traffic is feasible and where pedestrians need to traverse haul routes.
Products may also be used in isolation. VMS alert drivers to speed limits and those of HGV vehicles to maximum height restrictions on routes with edge protections.
As well as promoting the safety of drivers, SRL solutions are designed to minimise the time that quarry staff and SRL maintenance teams need to spend in close proximity to live traffic lanes. Solar/hybrid equipment requires infrequent battery exchange, while Eurolight signals may be controlled remotely from a position of safety via the Euro Remote Control.
All products feature a robust design to guard against accidental damage and have been created to perform reliably even in harsh weather conditions.
SRL’s Business Development Director, Iain McDonald said: “SRL have been developing innovative solutions designed to promote the safety and efficiency of the UK and RoI’s road network and construction sites for over 25 years. Hillhead marks our official entry into the aggregates sector, where our goal is to enable quarry managers to improve safety and reduce accidents, safeguarding employees and visitors alike.”
SRL offers the industry’s largest distribution network of more than 30 depots and is the only ITS manufacturer available to customers on site 24 hours a day, seven days a week.
Merlo UK will be returning to the Hillhead’s Quarrying, Construction and Recycling exhibition in Buxton on the 25th to 27th of June for the UK’s largest construction equipment exhibition. Along with the ROTO50.30, on display will be an extensive collection of our Construction models. Visit us at stand A20 to find out more about our Construction Range.
Leading plant and equipment manufacturer Sunward Europe has announced its lineup for Hillhead 2024. Two excavators will make their UK debuts – the SWE 50UF mini and SWE 60UFED compact – lining up alongside models from the manufacturer’s bestselling ranges at the show.
The SWE 50UF mini and SWE 60UFED excavators will showcase Sunward’s static display of six machines, while the 21-tonne top-of-the-line medium excavator, the SWE 215F5A, will physically demonstrate the company’s unique mix of quality and value for money.
Sunward launched the SWE 50UF mini excavator at Intermat and the response justified the company’s claim that it is set to be a game changer, building as it is on the success of Sunward’s zero tail range, which earned an iF Design Award.
This five-tonne model, positioned between the SWE 35UF and SWE 60UF, features a zero-tail swing that makes it ideal for constrained spaces. Boasting a Kubota D1803-T engine, its user-friendly design ensures efficient control and easy maintenance.
Also new to Hillhead is Sunward’s SWE 60UFED, a six-tonne electric compact excavator that features a hightorque permanent magnet synchronous motor to ensure exceptional efficiency, and emission-free operation.
The demonstration SWE 215F-5A is the perfect fit for large construction, quarrying or demolition work. Designed to be versatile and durable, with a long lifetime, the SWE 215F’s masterful design, Cummins EU Stage V B6.7 engine and enhanced hydraulics system deliver power, smooth operation and high productivity.
Complementing Sunward’s static
display are the 2.5-tonne SWE 25UF mini excavator – the zero-tail version of the SWE 25F. Its unique zero-tail compact design makes it the perfect option for tight job sites where power is required and its light weight makes it exceptionally easy to transport.
Sunward’s nine-tonne SWE 90UF2PB compact excavator was launched at the end of 2021 and remains the shortest nine-tonne short-tail excavator on the market – by almost 20 cm. Developed especially for Europe, it combines a compact size with heavyduty performance. Its very short-tail swing and two-piece boom allow it to work in a wide variety of urban tasks, including operating in confined spaces and along walls.
Also on the stand will be Sunward’s 1.2-tonne SWTL 4538 compact track loader, which thanks to its suspended undercarriage system and tracks, offers excellent performance with outstanding drawbar power for operation on rough terrains like mulch, rock or dirt. It is also compact and versatile enough to be easily manoeuvrable in small spaces.
The other electric machine on Sunward’s stand is the two-tonne SWE 20FED – the first electric mini excavator from Sunward. Based on its bestseller in the European market, the SWE 20F, the cabbed/canopied SWE 20FED combines durability, reliability, performance and easy maintenance with exceptional value for money.
Sunward representatives will be on the stand to provide information on the manufacturer’s full range of equipment, warranties and competitive finance packages.
Tele Radio is one of the market leaders in the design and manufacture of radio remote-control solutions. Providing endto-end product solutions and services in the field of wireless equipment control and machine communication, its goal is to make products that add value to your business while providing impeccable support when required.
With a broad range of products, from small transmitters to big joystick platforms, Tele Radio offers a bespoke service to adapt products to suit the customer’s needs. The company’s experts
are dedicated to developing products that improve the way you work, with a central focus on building strong customer relations that extend beyond the sale.
Exhibiting at Hillhead for the first time in 2024, Tele Radio will be showcasing a range of products at the event from simple push-button controls to complex, customisable, proportional hydraulics and camera feedback systems. Tele Radio’s industrial remote controls are designed to improve efficiency and safety in the quarrying and construction industry, providing precise and easy-
to-use control for machinery and equipment.
One of the products on display will be the new SupraTEQ TW78 waist transmitter. With a much larger colour screen than the company’s other models and even smoother images, the SupraTEQ TW78 meets the increasing demand for better interaction when operating large machinery, installations, cranes, winches, etc. The SupraTEQ TW78 has been specially developed for demanding environments, where screen size is often important for showing detailed feedback information.
Also on display will be the Tele Radio Tiger remote control, capable of providing feedback from your machine, displayed on the transmitter’s LCD screen or alternatively using LEDs situated next to its function buttons. The lights on the transmitter are programmable, for instance to indicate whether a function is activated/not activated. Tiger offers maximum safety for complex industrial applications. It is Tele Radio’s strongest system and is independently certified to SIL3, PLe.
With safety as a central focus, Tele Radio puts great effort into making its products as safe as possible, ensuring that it meets the highest possible standards. The company’s products are not only safe, but also robust and can withstand rugged operations. Tele Radio cares about the environment and is certified according to the ISO 14001 standard.
Wirtgen Group will be exhibiting several products available for the first time in the UK from across its brands of Wirtgen, Vögele, Hamm, Kleemann, Benninghoven and John Deere.
These include the world’s first burner that can be fuelled exclusively with green hydrogen, from Benninghoven (pictured); two new Vögele Pavers – the Super 1900-5i Highway Class and Mini 500 Compact; and the MOBIREX MR 100(i) NEO/NEOe from Kleemann.
On the road to making the future of road construction more sustainable, the greatest leverage potential lies in the field of asphalt production. With the world’s first burner that can be fuelled exclusively with green hydrogen, Benninghoven presents a ground-breaking solution for the future that is already on the market. Alongside the latest generation of burners for use with alternative fuels, the special presentation on the stand will also be showcasing further technologies for sustainable asphalt production.
Thanks to its compact dimensions and low transport weight, the new Kleemann mobile impact crusher, MOBIREX MR 100(i) NEO/NEOe can be used flexibly, quickly and in a very wide variety of applications.
Operation in tight spaces on work sites or in frequently changing places of work is easily possible, while applications range from different recycling tasks, such as
the processing of concrete, rubble and asphalt, to the processing of soft to medium-hard natural stone. All-electric operation is possible with the Mobirex MR 100(i) NEOe variant.
In view of their intended project scenarios, the two Vögele road pavers could not be more different. On the one hand the MINI 500 compact paver, with a minimum paving width of only 0.25 m, is predestined for working in the tightest spaces on particularly small construction sites. On the other hand the new Dash 5 generation SUPER 1900-5(i) Highway Class paver, with paving widths of up to 11.5 m, is deployed primarily
on motorways or other large-scale infrastructure projects.
Visitors will also be able to discover more about the Wirtgen Group’s digital solutions. As a technological leader, it can offer customers mobile machine solutions for road construction and road rehabilitation as well as for the mining and processing of minerals.
Paul Holmes, Managing Director of the British Wirtgen Group subsidiary, Wirtgen Ltd said: “Digital assistance systems, telematics solutions, and the automation of processes will contribute to an increase in the efficiency and cost-effectiveness throughout the road construction process chain and simultaneously further reduce CO2 emissions.
“The Wirtgen Group have a roadmap for this and will play a decisive role in the advancement of the digital transformation as a driver of innovation in the road construction industry.”
Toby Wilsdon speaks to Intermat Exhibition Director Christophe Lecarpentier about the run up to the show, exhibitors, visitors and the new ideas for Intermat 2024
QSo, who is Intermat for?
In terms of exhibitors, it’s for the usual construction and road building industries, from machinery, equipment, attachments, but also digital solutions as well as the concrete sector. On top of these, we have a new technology and energy sector, which reflects the evolution of the construction world.
Regarding visitors, we have this historic profile of the people that visited the show, which are from the construction industry, people involved in the materials in the machines and equipment. So fleet managers, buyers, everybody in the various technical departments, but also design engineers, people from rental companies, their fleet managers and so on. Obviously, we have some of the CEOs and VPs of these companies.
What we also see more and more are people from health and safety departments and the sustainable development departments, digital transformation, BIM departments. So, I would say on top of the more traditional visitors that we had from the construction rental sector, it’s vast.
We have CEOs coming because they have to engage their company into a transition phase. And it goes beyond the fleet manager of the companies. And we’re using more and more digital tools to plan the sites to follow the machines on the site and so on.
QHow about the geographic reach? How far and wide do visitors come from?
Historically we have probably 80% French visitors and 20% international. We have people from everywhere from Europe, from Sweden, Norway, UK, Germany, Italy, Poland as well as Turkey. And then we have visitors from Francophone countries in Africa, where the links are quite strong. We have visitors from China and India and the US and Canada as well.
There’s a lot of students as well. We have groups of students from Holland, Portugal, Morocco and various other countries too. But we’re trying to attract not only students in our industry, but also people who haven’t made their career choices yet.
QTell us about this year’s theme
It is mainly a theme that has come from the industry but there is also more and more pressure from governments and from voters for reducing the carbon footprint of our industry.
The show needs to be useful to the industry and I think we need to make sure that the show is also valuable for the people attending. To be useful we need to bring solutions. So the first thing we did was to unite the various federations and discuss with them how we could make sure Intermat was responding to today’s needs. The word decarbonisation came pretty rapidly because from both the manufacturers and from the users’ points of view that’s obvious. We’re not going to resolve the situation in one day. But the innovations are moving very rapidly.
We have the EU CSRD (Corporate Sustainability Reporting Directive) being phased in from the financial year 2024.
The large construction companies that we talked to will all be measured against KPIs on CSRD soon. We also have cities, regions or communities that are raising their requirements to decarbonise machines when they do tenders. So all of this is going to push construction companies to move forward, but it’s not going to be about changing their fleet from diesel to electric in one day. It’s taking steps moving to low carbon diesel first, electric for some machinery, then potentially hydrogen.
It raises a lot of questions, not only about the machines, but also about how you generate and source the energy, how you bring the energy to the site, how you train your staff in these new forms of energy and so on. Changing energy is not only about the machines, it’s about a lot of other processes and that’s what we wanted the show to be.
What we hear from large construction
companies is that we need to move forward rapidly because 2030 is pretty soon and they have some strong commitments to reduce the carbon footprint on the sites [The UN 2030 built environment target requires that all new and refurbished buildings completed from 2030 should be net-zero carbon in operation].
There won’t be just one solution to decarbonisation and I think it’s important that we display the various options at the show. If we had done the show one year ago, we wouldn’t have had the same display. With the current technology, electric will be useful up to a certain size of machine. The electric machines that we have now can operate for at least a full day, the technology is moving rapidly and I think that’s the purpose of the show – to be a catalyst for these innovations.
The show is not only about the solutions that the exhibitors provide. It’s about the machines, but it’s also about the
infrastructure, it’s about changing the methods of working in the construction companies and it’s about the new generations and the training required. There are financial issues as well – you can design everything, but you need to make sure it’s sellable and usable on site.
Over the four days we had a full programme of talks and debates, to enlighten but also to work on the wider perspective. We had examples of infrastructure that is being developed to bring the energy to the sites, but also the hydrogen infrastructure. So we had people from Total Energy, for example, which has bio oil, it has electricity, it works in hydrogen.
QHow long have you been planning Intermat 2024?
I only joined the company in 2023, so just one year but I’ve been in this industry for 28 years; my first Intermat was in 1997 as an exhibitor. In terms of the organisation itself, when you prepare a show it really starts from the previous show with discussions with exhibitors and visitors, following their feedback, talking to the federations and representatives of the industry, so we can learn from the last show and see what needs to be improved. The last show was in 2018 so that work was done for Intermat 2021, which obviously didn’t happen due to Covid. In 2022, when things were a bit clearer about when we could do shows again, we started to set up what went into Intermat 2024.
Intermat 2018 was all about diesel but a lot of things have changed since then. The first thing was to unite the five federations (DLR, Evolis, Seimat, FFB and FNTP) around the show, give a theme and from that theme work on it. We couldn’t do a show about decarbonisation without asking what we could do ourselves. As you’ve seen, we reduced it from six days to four days. Exhibitors wanted to reduce the carbon footprint of the show as well so we changed the way we construct the show and we developed a special environmental chart so we can make sure we reduce our carbon footprint.
QWhat challenges did you face along the way?
The first exhibitor installed on 2 April and we were very happy with the way it turned out for the exhibitors.
We wanted to make sure that the format, the pricing and the duration of the event corresponded to our exhibitors. We were happy to see Monnoyeur, which represents Caterpillar in France and other European countries, coming back. Cat is back, Hitachi is back, we have Volvo, we have Komatsu. We were quite fortunate to have some key brands back but the richness of the show isn’t merely in the number of big brands. Obviously the big brands are important but we had more than 1,000 exhibitors and they make the show.
If you take the example of a fleet manager, he will go and see his current
suppliers and he will look at some of the big players as well. But what’s amazing is when you have buyers finding solutions that they haven’t thought about before coming to the show, whether they’re machines, materials, equipment, attachments or digital solutions. That’s what’s really useful to them.
To respond to your question, it was hard work to make sure we had a show that represented the big brands but was also rich in terms of its offer from a lot of countries as well as exhibitors. So we did a lot of promotion in various countries of Europe, in China and elsewhere so that people could see exhibitors that they couldn’t see anywhere else.
QTell us about the thought leadership programme
At the centre of the show was the Federations area. The presidents of the five federations signed a route to decarbonisation together – that’s more focused on France, but it does show the unity of the federations and how they work together to demonstrate this to the governments.
At the core of the Industry Forum we had a TV platform held by Emmanuel Lechypre and Raphaëlle Duchemin, well-known business journalists in France. During the four days we had various people from big construction companies, energy companies, politicians and European federations talking about decarbonisation, infrastructure and strategy, machinery, how we bring the energy to the site, how we train the people, how we attract the new generation.
We also had the Intermat Academy, which is based on employment and training. We have skills on this programme, different schools and so on. We had the startup forum, a new technology forum and we also had a conference about rebuilding Ukraine.
The CECE and various other organisations held meetings and there was also the World of Concrete forum, specifically about how we decarbonise the concrete sector.
When people come to the show they feel part of the community through the talks and that’s important because it’s when you meet face to face and discuss things that progress is made.
QWhich parts of the show excite you most?
Obviously, there’s the exhibitors with their stands and innovations and so on. They’re all important, from the 12-square metre stands to the 3,000 square metre ones. I think the richness of the exhibition is where these 12-metre stand companies and startups can display their innovations.
The Intermat demo area is important. We responded to exhibitor needs and had two zones of indoor demo – so it was live with a demonstration every 10 minutes. That’s an interesting part of the show.
And I think the TV platform with BFM business is another good part because it shows the unity of the five
federations. They’re all together on this TV platform where we had people from CEOs of companies to operators, fleet managers, infrastructure, mayors, MPs to talk about the challenges of decarbonisation for companies and how we can help the industry to transform.
I could mention many others. The Intermat Academy is important because our industry needs to attract new generations and to present the industry quite differently. When you talk about the construction industry, you think about noise, you think about machines blocking the roads and dirty work. That’s what the general public think of construction work. What we want to display to the new generations, but also to politicians and so on, is a more modern way, with decarbonisation and electric machines reducing the noise. So there’s lots of innovation, a lot of things happening in our industry that we want to show more positively.
QWhat’s the focus of the awards?
The jury wanted to give awards to real usable solutions, not prototypes that we’ll never see. So the awards are all about the challenges of our industry, highlighting true innovations that will make a difference in history.
We identified four industry challenges that are reflected in the awards:
• Site and machine organisation and efficiency,
• New technologies, materials and energy savings,
• Safety,
• Human resources.
QDo you have any innovations planned for Intermat 2027?
It’s too early to say. When you’ve talked to the visitors and exhibitors you can think about what needs to happen next time. What is true in my mind is that the show needs to remain useful to the industry and needs to stick to the industry challenges. So, yes, after the show we may have some thoughts about how we can change it and how we can improve things.
We’re in a world of challenges. Climate change is not going to go away so I think there will continue to be pressure on decarbonisation. But what I want to make sure is that the show really sticks
to the industry at the time the show is held. So yes, we may think about taking one direction, but what is important is for us to talk to federations, to users, to companies, exhibitors and visitors so that when we develop the show it will correspond to 2027.
Decarbonisation is key but things may change, you may have new legislation as well. So I think it’s important that more than ever, the show is useful to the visitors to find the solutions that meet their challenges.
Before Covid people were coming to the show to meet people to see new products and so on. But if I took a new excavator, it was an excavator with a new screen or a new diesel engine because there was a new standard. Everybody was moving from tier three to stage four, for example.
Now there are more questions about the energy that you use, people have less time so when they come to a show they need it to be valuable for themselves and for their company. So we need to make sure that the show sticks to the industry challenges and how we can respond to these challenges in 2027.
We’ll have some ideas a few weeks after Intermat 2024 when we’ve got feedback from exhibitors and visitors. But we have to stick to the content and do what’s useful for the visitors.
QSo do you have a holiday planned for May?
Actually, no because then we have Intermat India in Mumbai. I’m going there so I think my next holidays won’t be until August.
Hitachi Construction Machinery (Europe) NV (HCME) showcased the power of partnerships at Intermat. The theme of HCME’s +900m2 stand was Partner to Accelerate Change, highlighting the strong relationships it has with French dealers and its successful collaborations with industry leaders such as KTEG, Xwatch, Leica Geosystems, Trimble, and ShareMat.
Representatives from HCME Office France attended, along with delegates from regional Hitachi dealers including Hitachi Construction Machinery France (HCMF), Teramat, Prowimat, and ESMTP.
HCME President Francesco Quaranta said: “Following some changes within our dealer network last year, Intermat provides us with the perfect platform to support our partners and showcase our latest products and solutions together.”
Among the Hitachi excavators on display were the ZX390TC-7 special application excavator and ZE135 electric excavator, both of which were developed through a joint venture with KTEG. Additionally, the ZX225USLC-7 medium excavator and ZX135W-7 wheeled excavator featured factory-fitted machine control and safety systems from Xwatch and Leica Geosystems and Trimble, respectively.
Bill Drougkas, HCME Manager of Product Management and Solution Linkage said: “By offering solutions such as these to our customers, we
can combine the unrivalled control, precision and reliability of Hitachi excavators with the accuracy of 3D technology – helping them to further improve safety and efficiency on site.”
HCME also took the opportunity to promote Zaxis Finance, a comprehensive range of flexible finance solutions available for both new and used Zaxis excavators and ZW wheel loaders. This offering is made possible through a strategic partnership between HCME and BNP Paribas Lease Group SA, experts in asset finance solutions.
HCME has recently agreed a collaboration with ShareMat to provide cutting-edge telematics on excavators weighing three tonnes and above. This technology will allow customers in France to access operational data on their fleets, from every 24 hours to every ten minutes.
Commenting on this exciting new development, Mickaël Hammour, HCME Sales Support, said: “We are pleased to work with ShareMat to empower owners and operators of Hitachi construction machinery to enhance onsite performance.”
Hitachi Construction Machinery (Europe) presented its latest technology in construction machinery as a partner to accelerate change, emphasising, amongst other things, safety and efficiency on construction sites. One of the many highlights on the Hitachi stand was the Xwatch Leica Geosystems 3D Avoidance System on a ZX225USLC-7 2P excavator, demonstrating Hitachi’s commitment to advancing construction safety through innovation.
This partnership brings the Xwatch Leica Geosystems 3D System to Hitachi’s machinery, showcasing a direct application of cutting-edge safety assist technology in the company’s equipment range.
The Xwatch Leica 3D Collision Avoidance System is a pioneering safety assist solution developed through a
partnership between Xwatch Safety Solutions and Leica Geosystems. Designed to enhance construction site safety and efficiency, the system offers:
• Seamless integration: Works with Leica MC1 software to create and import 3D avoidance zones, enabling precise navigation around critical areas,
• Virtual wall functionality: Incorporates the XW5 system with height, slew, and Rated Capacity Indicator (RCI) functions, acting as a protective barrier around machinery,
• Automatic movement control: Automatically adjust an excavator’s movements (height, depth, slew) near avoidance zones, using proportional hydraulic control to prevent accidents,
• Environmental protection: Disables machinery movement in sensitive areas, safeguarding environmentally critical zones,
• Enhanced operational efficiency: Improves manoeuvring accuracy and safety, reducing the risk of accidents and ensuring project timelines and budgets are met.
This system represents a significant advancement in construction safety, combining technology and innovation to protect personnel, infrastructure, and the environment.
HCME’s stand focused on this ground breaking safety assist technology, highlighting the company’s range of equipment designed for sustainability and efficiency. The display covered the full spectrum of construction needs from the compact ZX26U-6 and ZX33U-6 mini excavators to the large ZX390TC-7 special application excavator and ZW310-7 wheel loader. Special attention was paid to electric models, the ZX55-6EB and ZE135-7EB, showcasing the company’s commitment to environmentally friendly construction solutions.
By featuring the Xwatch Leica 3D Avoidance System on the ZX225USLC-7 2P excavator, Hitachi demonstrated the potential of collaborative innovation in improving construction site safety and efficiency.
Bobcat showed the international construction community how it is accelerating towards a smarter, more sustainable and connected future with its innovative lineup of Bobcat construction, ground maintenance and material handling equipment displayed at the exhibition.
Bobcat used INTERMAT 2024 to debut several cutting-edge models, including its TL25.60e electric telehandler concept. It also showcased a range of other recently introduced products and innovations, including its M-Series S630 and S650 skidsteer loaders, PA12.7v compressor, hydrotreated vegetable oil (HVO) biofuel-compatible units, its updated range of rotary telehandlers for markets in Europe, the Middle East and Africa, and its collision warning and avoidance system.
The extensive lineup focused on safe, sustainable and cost-effective operations, with the aim of demonstrating how Bobcat innovations can help users accomplish more. Other product lines on display included mini-excavators,
skid-steer loaders, compact track loaders, backhoe loaders, compact wheel loaders, ground maintenance units, portable power models and material handling equipment.
Jan Moravec, Vice President of Product, Bobcat EMEA, said: “In line with Bobcat’s long-standing commitment to sustainable development, our team is continuing to develop products, attachments and services that exceed our customers’ expectations. The equipment we showcased at INTERMAT 2024 reflects our dedication to innovation, sustainability and customer-centricity, demonstrating that it is possible to shape a greener and more efficient future without compromising performance or productivity.”
Shining a spotlight on innovation INTERMAT 2024 provided the global launchpad for Bobcat’s TL25.60e electric telehandler concept. Powered by liquidcooled batteries that can operate in a range of weather conditions, the zeroemission machine has a rated operating capacity of 2.5 tonnes, equal to that of
the popular diesel-powered TL25.60 model.
With three separated electric motors designed to maximise efficiency, a hydrostatic transmission to boost performance, a top speed of 25 km/h and the same dimensions as its conventional counterpart, the TL25.60e also delivers low noise levels, minimal operating costs and impressive versatility, proving that industry-leading performance and environmentally friendly operations can go hand in hand.
Visitors to Bobcat’s INTERMAT 2024 stand also had an opportunity to experience Bobcat’s transparent OLED (T-OLED) screen technology, which has been incorporated into the righthand window of the TL25.60e concept. Developed in collaboration with LG and BSI Research, Bobcat’s T-OLED technology enables operators to access an array of functionality without taking their eyes off the worksite, offering unparalleled clarity, responsiveness and visibility. It also has the capacity to facilitate a range of more advanced applications, such as real-time virtual reality (VR) simulations for utility line mapping.
The Bobcat RogueX2 concept loader made its European debut at INTERMAT 2024. This autonomous, all-electric machine has been built as a proving ground for technologies developed as part of Bobcat’s innovation roadmap. The RogueX2 produces zero emissions thanks to its lithium-ion battery, electric drive system and electricactuated lift and tilt kinematics with no hydraulics. The machine features wheels instead of tracks to optimise electric battery runtime and its axial flux motors
deliver incredible tractive effort. With no cab, the fully autonomous RogueX2 offers a glimpse of how future generations of Bobcat loaders will facilitate an entirely new work experience for users.
Other innovations taking centre stage included Bobcat’s collision warning and avoidance system, which uses integrated radar sensors to enhance the situational awareness of skid-steer and compact track loader operators. The cutting-edge technology can be customised to suit sitespecific requirements, offering real-time obstacle and risk detection and a variety of response options.
In keeping with INTERMAT 2024’s focus on sustainability, Bobcat used the show to raise awareness of its green engine and fuel technology. The manufacturer’s stand featured the recently introduced M-Series S630 and S650 Stage V skid-steer loaders, which have been developed for use in European markets. The models’ D24 engines, which feature Bosch fuel-injection systems, deliver superior performance while adhering to strict emission regulations.
A new lineup of Bobcat rotary telehandlers featuring the manufacturer’s
patented panoramic cab was also on display in Paris. The latest range comprises nine Stage V models with lifting heights of between 18 and 39 metres designed for European markets, and four Stage IIIA machines with lifting
heights of 18 to 26 metres for use in the Middle East and Africa.
The Paris exhibition also provided a launchpad for Bobcat’s PG40 and PG50 generators. The units represent a leap forward in portable power solutions, offering a selection of advantages such as optional running gear for easy transportation and ‘Liquid Heat’, a low-load management system designed to reduce downtime and deliver peace of mind. Powered by Stage V Hyundai D24 engines, the eco-conscious models build on the success of their predecessors by delivering a combination of increased power and lower fuel consumption.
The Bobcat PA12.7v compressor also featured. The portable variable pressure compressor uses a FlexAir system that allows it to operate in the range of 5.5 to 12.1 bar, offering free air deliveries of 5.2 to 7 m3 per minute. As a result, the PA12.7v is suitable for a wide range of applications, making it one of the most versatile air compressors on the market.
With its electric and HVO powered machines as well as other innovations, Bobcat is demonstrating how its construction lineup is delivering even greater levels of sustainability.
DEVELON made its first appearance at the 2024 Intermat exhibition, making a big impact with an industry-leading display of state-of-the-art machine and digital technologies being seen for the first time.
This includes the first demonstration in Europe of DEVELON’s much-heralded Concept-X 2.0 remotely controlled (autonomous) construction equipment, with the leading edge DD100-CX autonomous dozer and DX225-CX autonomous crawler excavator being the stars of the show.
The stand was designed around four pillars – Carbon Reduction, Going Green, Compact and Innovation with the main focus centred around new innovative machines and technologies that support carbon reduction and wider sustainability to address the world climate crisis.
The DX20ZE Mini-Excavator is the first mass-produced electric-powered excavator manufactured by DEVELON. This two-tonne excavator combines low-noise and zero emissions with the features and
performance enhancements that are found on the next generation DX-7 Series family of mini-excavators.
Alongside the DX20ZE was the 14W-EREV electric concept vehicle, the most advanced, state-of-the-art machine of its kind. This electric wheeled excavator is designed with a regenerating drive system (eDrive), advanced swing system (eSwing) and eWorking systems to ensure maximum efficiency with zero emissions.
Completing this Future Energies Area of the display was the DL250-FCEV (Fuel Cell Electric Vehicle) which has a versatile, single platform design that allows it to be equipped with a fuel cell powerpack running on hydrogen, but offers the ability to transition to a BEV (Battery Electric Vehicle) by installing a battery pack.
DEVELON also showed a number of reduced emission solutions based on fuel saving technologies and the use of bio-fuels such as HVO and GTL.
The fuel-saving technologies included the first appearance of the company’s Concept-X 2.0 DD100-CX cabless dozer and DX225-CX cabless crawler excavator. Another fuel saving system on show was the 3D-control being used to operate the Concept-X 2.0 excavator and dozer and for the DD130-7 dozer and DX85R-7 mini-excavator.
Significant fuel savings are available via the CVT transmission in DEVELON’s DL420CVT-7 wheel loader shown off in the demonstration area, equipped with the unique Transparent Bucket safety system, also being shown at Intermat for the first time. The Transparent Bucket is the first safety system of its type address the danger of blind spots in front of the buckets of wheel loaders.
An additional fuel saving feature
offered by DEVELON is the Virtual Bleed Off (VBO) hydraulic system (D-ECOPOWER) shown on the latest version of the DX530LC-7K 53-tonne crawler excavator in the static display.
Another fuel saving solution on show was Full Electric Hydraulic (FEH) technology, which is similar to the D-ECOPOWER VBO system and is in effect, a VBO system without pilot pressure lines.
The Going Green pillar underpinning the DEVELON stand at Intermat showcases the company’s positioning as the industry’s green partner of choice for customers.
This is supported by the introduction of identification labels on machines, providing clear communication of their green credentials, such as HVO
compatibility; bio-oil filled, etc. It also encompasses Contamination Control offered by DEVELON with biologic/ organic oil provided from the assembly line.
Under the Going Green banner, the DEVELON stand demonstrates the compatibility of the company’s machinery for use with HVO and Gas To Liquid (GTL) diesel.
A large area of the static display section was dedicated to DEVELON’s new range of compact equipment, much of which was on show for the first time. This included the new DTL35-7, the company’s first compact track loader model. The DTL35-7 boasts impressive features that set it apart from its competitors. Visitors also saw
DEVELON’s new DD130-7 dozer model for the first time, offering a wide range of features providing a productive finegrading solution for residential and light commercial construction projects.
New DEVELON mini-excavators shown for the first time included the DX10Z-7 1.16-tonne, DX17Z-7 1.85-tonne, DX27Z-7 2.8-tonne and DX85R-7 8-tonne models. All the new models offer increased performance, optimum stability, additional versatility, enhanced operator comfort, controllability, durability, ease of maintenance and serviceability.
Other compact machines shown for the first time were the DX100WR-7 10.7-tonne wheeled mini-excavator equipped with a tiltrotator and the DL80TL-7 compact wheel loader, part of a five model 3.5 to 5 tonne range.
The Innovation theme covered new electric and hydrogen powered machines including the DX20ZE, DL250-FCEV and 14W-EREV and the innovative Transparent Bucket system. It also covered digital technologies displayed on screens and monitors in the main building such as the DEVELON Smart Quarry, DEVELON DXP digital platform and DEVELON Fleet Management systems.
The Smart Quarry Solution integrates all the business processes involved in running a quarry business, from order taking to sales using ICT technology to manage the site and increase productivity with minimal cost and time.
DEVELON also promoted the latest version of the company’s DEVELON Fleet Management state-of-art wireless fleet monitoring system, specifically designed for the DEVELON range. Providing comprehensive information about machine performance in a dual mode (satellite, mobile network), this telematics system offers a web-based fleet and asset management solution which is very useful for managing the performance and security of machines and promoting preventative maintenance.
Dynaset is thrilled to announce that the HRVB Hydraulic Recycling Vacuum Bucket has been awarded a gold medal in the Earthworks, Demolition and Transport category at the prestigious Intermat Innovation Awards 2024! The ceremony was held on the evening of 24 April, where Dynaset CEO Anni Karppinen and R&D Director Pasi YliKätkä proudly received the prize.
Anni Karppinen said: “This is a truly amazing feeling. We’re thrilled to pick up the gold medal in the Earthworks, Demolition and Transport category. It’s a wonderful recognition of our team’s incredible development and engineering efforts.
“The development of this product also involved a lot of valuable customer cooperation. We want to express our sincere gratitude to all the partners who participated. The HRVB Hydraulic Recycling Vacuum Bucket is a fantastic solution for material collection and recycling for anyone working in the demolition industry. Thanks to the increased recycling rate, waste management fees will also decrease. This product offers significant benefits for maintenance and cleaning operations in other industries as well.”
The competition was fierce. Steelwrist, a leading global manufacturer of tiltrotators, quick couplers and work tools for excavators, secured third place. Duratray, a renowned design, engineering, and manufacturing company for dump bodies used in haulage equipment, came in second.
With the HRVB Hydraulic Recycling Vacuum Bucket you can collect insulation materials on demolition sites. This particular bucket was used for collecting light expanded clay aggregate (LECA) insulation materials.
This recognition underscores the HRVB’s groundbreaking design and its potential to revolutionise waste management processes in the demolition, construction, and property management sectors.
A multifunctional marvel for waste management
The HRVB Hydraulic Recycling Vacuum Bucket is a true game changer. It combines the movability of a traditional excavator bucket with a powerful vacuum cleaner and an
air blower. This innovative attachment utilises the hydraulic power of compatible mobile machines to generate a strong vacuum for efficient waste sorting and debris collection.
Optimising waste handling and site cleanliness
The HRVB excels at separating smaller debris from rubble piles, streamlining waste sorting tasks and contributing to cleaner work sites. Its robust vacuum capabilities, with a negative air pressure of -8 kPA and a maximum airflow of 3.4 m³/sec, allow for the collection of various materials, including wood, wool, plastics, and even light expanded clay aggregate (LECA). This translates to improved waste treatment procedures and potential cost savings.
Dynaset Marketing Manager, Jyri Hartikainen, said: “HRVB Hydraulic Recycling Vacuum Bucket also improves work safety as the various materials can be collected without manual labour.”
With Intermat providing an ideal opportunity to reveal new machines to the public, centre stage on the KCME stand was taken by the all-new SK520LC-11E as it made its European debut. The Kobelco giant, which is best suited to general construction and quarrying, has a higher operating weight for improved stability, and increased bucket and arm force for better overall lifting performance.
Also in the heavy category, the SK350LC-11E was a popular attraction. Like all Kobelco’s Generation 11 machines, the SK350LC-11E follows the Performance x Design concept, boasting an excellent standard in cabin design, ergonomics, comfort and safety.
KCME’s 1,500m2 stand also featured an area dedicated to Kobelco’s Short Radius (SR) excavators, including the allnew SK380SRLC-7, the SK230SRLC-7 (two-piece boom), multipurpose
ED160BR-7 Blade Runner and SK140SRLC-7 Side Drain. SR machines are ideal for operators working on urban and residential jobsites as they benefit from a smaller working footprint, which means that they can access tighter areas.
Since their launch in 2019, Kobelco’s versatile midi excavators have been demonstrating their superior performance, greater efficiency and productivity on job sites all over the world, reinforcing their position as leaders in the mid-range category. The SK75SR-7 Side Drain and the SK85MSR-7 (twopiece boom) were both on display.
Frequently used for landscaping, utilities and small construction projects, mini excavators are key to Kobelco’s overall product lineup and are particularly popular due to increased demand for ongoing roadworks and utility maintenance. With this in mind, the KCME stand presented several mini
excavators, including the SK58SRX-7, recently released SK39SR-7, SK28SR-7 and SK26SR-7 models, plus the SK17SR-3E and SK10SR-2E.
KCME Managing Director, Makoto Kato, said: “We are excited to return to Intermat this year and we are proud to be able to support our dealers and customers by investing in this event for a third consecutive time. 2023 was also an important year for KCME as we celebrated our 10th anniversary in Europe and announced our expansion into new, larger purpose-built headquarters. Intermat 2024 kickstarts another busy year for Kobelco and further underlines our ongoing commitment to the whole region.”
Kramer presented the new generation 8-series wheel loaders, represented by the 8115, as well as the two zero emission products, electric wheel loader and electric telehandler.
Christian Stryffeler, Managing Director of Kramer-Werke GmbH said: “Intermat is an important platform for us. We are also looking forward to showcasing our new generation of 8-series wheel loaders and telescopic wheel loaders. With the intelligent travel drive, the operator can customise the machine to his individual needs and the corresponding application, thereby reducing his fuel consumption by between 10 and 15%.”
Zero emission – time for clean air. Electromobility is playing an increasingly important role in the construction industry. For low-noise work, for example in sensitive environments such as residential areas, city centres, parks, zoos and regions with a high proportion of tourism, the machines work very quietly and are completely free of CO2 emissions. Working indoors is also possible without restrictions.
Both zero emission machines, the 5065e wheel loader and 1445e telehandler, are fitted with a 96-Volt lithium-ion battery. The running times are up to four hours without intermediate charging. Four different
charging plug options are available for charging the machines. It therefore makes no difference whether you charge at a conventional household socket, an industrial socket, a wallbox or a public charging point. Charging power is limited by the type of charging plug and the charging power of the on-board charger.
New generation 8-series wheel loader –efficiency starts now Features, functions and comfort make
driving the premium series by Kramer a one-of-a-kind driving experience. Efficient, fuel-saving and modern – this is how the features of the new wheel and telescopic wheel loaders of the 8-series (8085, 8095, 8105, 8115, 8085T and 8095T) can be summarised. Depending on the model, the bucket tipping loads move within a range of 3,650 – 4,250 kg. As standard, all models have a 55 kW Deutz engine; with a 74.4 kW option for the models 8105, 8115 and 8095T.
The newly developed drive system provides four operating modes (Power, Eco, Road and CSD). Whether you are stacking, shovelling, moving, sweeping or milling – the right setting can be selected for any application to perform the work in the most efficient and fuel-saving manner.
The load-independent flow distribution (LUDV) ensures equal distribution of the hydraulic oil to the individual control circuits. As a result, several functions can be simultaneously performed independent of the load, e.g. lifting, extending and tipping out.
Even the cabin has been completely redesigned with two entries and exits on each cabin side. The fold-down armrest with a joystick and functional keys is mounted on the operator’s seat and can be comfortably adjusted to the operator’s needs in a longitudinal direction. The optional seven-inch display opens a new world of machine settings and assistance systems. The joystick sensitivity or the oil volume of the third control circuit can be adjusted using the jog dial.
The operator can reduce the required steering rotations for the maximum steering angle using Smart Steering. This means greater productivity and quick manoeuvring, above all when working in Y-cycle. There are two cabin versions available for all machines of the 8-series. With the standard cabin you can achieve a compact vehicle height of 2.49 metres (2.69 metres for models 8115 and 8095T). With the panoramic cabin visibility is extended upwards, which is especially practical for working with telescopic wheel loaders.
The innovative further development
of the familiar quickhitch plate to the fully hydraulic quickhitch system ‘Smart Attach’, now installed as standard in the 8-series, provides more productivity, efficiency and safety. Hydraulically driven attachments can be coupled with ‘Smart Attach’ without getting in and out of the vehicle, as connection with the hydraulic circuit is automatic.
Telehandler 2706 – Facelift for the bestseller
The height and width of the 2706 is below the two-metre limit – making it the ideal machine for confined spaces and low clearance heights. You also have a choice of cab height: just under two metres for maximum compactness of the vehicle or 2.10 metres for even better all-round visibility. The machine is also characterised by a payload of 2.7 tonnes and a 56 kW Kohler engine. A new feature is the optional travelling speed of 40 km/h, which allows increased productivity to be achieved when working over longer distances. An EC tractor licence is also available for the machine, which allows it to be used as a tractor on public roads.
A significant innovation is the cab design, which ensures increased operating comfort. An optional seveninch colour display with jog dial is now available for the 2706. In addition to the increased information content, the
display offers further optional functions. For example, the operator can adjust the joystick sensitivity and set and save the angle display for two attachments. This allows the operator to customise the machine to the requirements of the respective application, thereby increasing productivity.
The fully hydraulic Smart Attach quick-change system, which is now also available as an option for the 2706, also scores highly here. With Smart Attach, attachments with an additional hydraulic function, such as a sweeper or Power grab bucket, can be coupled and uncoupled in seconds without having to leave the cab.
LiuGong demonstrated its leadership in battery electric vehicle (BEV) technology at Intermat with an impressive lineup of four new electric machines and more than 40 new machines in the pipeline. LiuGong’s tour de force in electric is part of the company’s plan to be the number one in BEV technology in Europe by 2027.
Samuel Broillard, Head of LiuGong operations in France said: “Showcasing our world-class BEV capability at Intermat has surpassed our expectations. France is one of the largest markets in Europe and represents a significant opportunity for LiuGong.
“We know that French customers are increasingly looking for sustainable machine solutions, backed up by expert support and advice. We have had a great deal of interest from customers from across Europe this week.
“I think many people have been surprised at just how far advanced LiuGong is in BEV technology and how much credibility we actually have. We set out to show that we are leading the change to BEV in Europe, and I believe we have achieved that.”
Intermat was LiuGong’s first exhibition to showcase purely BEV machines. With their distinctive green livery, these machines share LiuGong’s Red Dot award-winning design DNA and put the operator at their heart. LiuGong is leading a revolution in BEV R&D and plans to launch over 40 BEV models by 2027, including new BEV excavators,
wheel loaders, telehandlers and access equipment.
0% finance
LiuGong’s Intermat lineup included four new BEV machines for the European market, two excavators, the 9027FE and 922FE, and two wheeled loaders, the 820TE and 856HE. As a show special, LiuGong’s electric machines are offered with 0% finance for a limited period.
This compact model takes LiuGong’s popular short tail swing 9027F and changes the power pack to a 20 kW LFP battery pack. The smallest of LiuGong’s new machines at Intermat, it has the power and performance you would expect enabling three to four hours of constant work and a rapid charging time of 90 minutes when using a fast charger.
Based on a 48V system, it is easy
and safe to service and maintain without needing high-voltage training.
Moving onto LiuGong’s high-voltage machines, the three launch models are powered with battery systems from CATL, LiuGong’s strategic partner and an industry leader in its own right.
The new 820TE
LiuGong’s first compact wheeled loader product, this machine has a spacious cabin, is capable of 40 km/h and is powered by a 70 kWh battery that can be recharged in 80 minutes. At a maximum height of 2.5 metres, and available with a fourth line auxiliary spool, this machine is excellent for agricultural and industrial applications.
The new 856HE
LiuGong’s third machine is its global best-selling EV product, the 856HE. A mid-class wheeled loader, the 856HE is powered by a 423 kWh battery pack and can work 10–12-hour shifts on a single charge, fully recharging in 90 minutes. Driven by two independent motors, one for the driving transmission and one for the hydraulic loader arms and auxiliary, the 856HE is an immensely powerful machine offering full drive traction from as little as 2 km/h.
The new 922FE
LiuGong’s fourth launch machine is the 922FE medium-class excavator. Powered by a 430 kW battery, this machine can work a full eight to 10-hour shift. This
is a high-performance machine with a motor delivering 140 kW, around 24 kW higher than a comparable diesel model and similar to a 26T class machine.
BEV expertise and support
Support is paramount and LiuGong’s European dealer network has either completed or is in the process of completing rigorous training to become “LiuGong BEV Certified”. Certification means dealers will have passed the necessary high-voltage training, CATL technical training and detailed service training. Certification also requires dealers to have mandatory spare parts and tooling before taking any machine into stock.
LiuGong’s electric family
LiuGong’s BEV pipeline extends over 40 electric machines, encompassing excavators and wheeled loaders up to access platforms, reach stackers, skid steers and motor graders. The company aims to be a full BEV solution provider. Beyond Intermat, LiuGong is launching two further battery electric machines perfectly matched to support each other in quarrying, mining and aggregates applications.
new 870HE
Equipped with a larger capacity loading shovel and supplied with a 4.7m3 bucket as standard, this high-performance wheeled loader is perfect for quarry and aggregate applications.
An industry first, the DR50CE is a 45-t capacity rigid mining truck featuring a direct drive electric motor, further reducing transmission losses and maintenance while increasing productivity and reliability. This is a unique machine with the ability to recharge itself when working on downhill operations greater than eight degrees. This rechargeability boosts productivity and reduces energy costs.
European Product Director, Harry Mellor, said: “Our new range of electric machines at Intermat clearly show our commitment to be the No. 1 for BEV machines in Europe, but they are only the start. As a company, we are on a mission to create a more sustainable future in the construction equipment industry and our continued investments in design, R&D and customer insight prove that we are leading the change.”
Key to supporting LiuGong’s BEV growth strategy in Europe is the extension and development of LiuGong’s dealer network. Alongside LiuGong’s investments in France, the company has also expanded its European operations with new regional offices in Germany, Italy and Turkey. Major expansion plans are also in place for the UK with a new R&D Centre, proving ground, test area and Customer Solutions Centre.
LiuGong Europe Chairman, Howard Dale, said: “Now is an exciting time to be considering the LiuGong brand. Significant investments have been made, not just in product development, but in future-proofing our business to be an even better partner for our customers. At Intermat we focused on our BEV products, but we will never forget that it’s relationships that really matter in our business. At LiuGong we are committed to listening to our customers and working with them to create a better future and success for everyone.”
Being independent on the job site is essential to be competitive. The solution is to optimise the sites by using the machines already there. All you need is a heavy machine, regardless of its weight, an operator, an MB Crusher attachment. For the first time, MB Crusher exhibited in full the range of equipment dedicated to compact machines at Intermat, reflecting the potential of the machines.
Crusher buckets, trommel and padding buckets, hydraulic cutters and sorting grapples: as the heavy line, the MB Crusher compact range does not change work habits: it improves them. Not just a complement to the carrier machine, as MB crusher attachments also expand their functionality and consequently enhance new job opportunities for companies.
Above all, Intermat 2024 was about sustainability and decarbonisation. And MB Crusher attachments mean sustainability because they allow waste to become a resource to be reused, they reduce emissions by avoiding the constant back and forth of trucks and they send a strong message that the valorisation of inert materials is the true wealth of all production.
Tele Radio shared a 40 m2 exhibit with sister company Åkerströms in Hall 5B, with the location specifically chosen because of its proximity to the area of the expo where cranes and hoists are showcased.
Ludovic Giroud, Managing Director of Tele Radio France said: “Cranes, lifting and hoisting is a big industry for us. However, besides cranes and winches, there are many more construction applications that we can offer remote controls for, including shovels, concrete trucks, water pumps, drilling equipment, aggregates, etc.”
Tele Radio and Åkerströms are both headquartered in Sweden and are part of the Allgon Group, having been acquired in 2018 and 2015 respectively. This was the first time that the business have had such an international presence at Intermat. Organisers report that one in three visitors attend from abroad; 160 countries are represented in the aisles; and 70% of the 1,000 exhibitors are from outside France.
The full Tele Radio range was on display during the show. Also on display was the latest Panther T29-12 handheld transmitter, which was launched last year. The 12-step PLd-certified push-
button hand transmitter can control a total of 24 different functions at a high security level.
Also on show were the TEQ waist transmitters. The TEQ line is available in two versions – Basic or Custom – and is targeted at the mobile vehicle sector including recovery, concrete pumping trucks, drilling, excavators, and earthmovers, lawn mowers and truck cranes.
The Basic line is equipped with standard components and specifications to serve a large portion of the market at an attractive price. For more exceptional applications, the line can be customised (Custom) to suit special requirements at the point of use.
As Intermat visitors discovered, several Tele Radio facilities in Europe now sell Åkerströms systems, including the Sesam 800 product line in Benelux, France, Ireland and the UK. Sesam transmitters and receivers complement Tele Radio’s own T20 / T60 products.
• Selected-used or refurbished parts
• All models catered for
• Export enquiries welcome
With Intermat 2024’s focus on sustainability it was the ideal opportunity for Wacker Neuson to present the extensive zero emission range with approximately 25 construction machines and equipment: from battery-powered rammers through to electric excavators.
François Escourrou, Managing Director of Wacker Neuson France said: “This trade fair is an excellent environment in which to present our newest innovations and to impress the visitors with our machines’ quality, efficiency, and ergonomics.”
The personal exchange and in-depth conversations with visitors about key areas like electrification, digitisation and innovation were the focus of this year’s presence by Wacker Neuson. Within approximately 500 m2, Wacker Neuson not only presented its zero emission portfolio, but also many other products and solutions that make every day working life easier on the construction site.
The emission-free site
As a pioneer in the field of batterypowered construction machines, Wacker Neuson has been continually expanding its portfolio since 2013 and, alongside the development of new products, is working on providing for the whole ecosystem of its customers – from the charging infrastructure through services, financial solutions and various exploitation models, to the life-cycle analysis of batteries.
An example of how Wacker Neuson is generating charging opportunities is the Charging Box CB250 – the powerbank for the construction site. The mobile energy store on the base of lithium-ion batteries enables a continual energy supply and was recently awarded in France with the Grand Prix Matériel in the category of construction equipment.
One of the newest members of the
Wacker Neuson zero emission family is the first all-electric telehandler TH412e, which enables working in confined spaces without any local exhaust emissions as a result of its compact design of under two by two metres. It can be used, for example, in an underground parking lot or warehouses. Even the new generation of the batterypowered rammer, tried and tested for 10 years, can be seen at the trade stand.
The rammer is powered by the same powerful Battery One batteries. The Battery One system is standardised and user friendly. It can not only be used in all Wacker Neuson battery-powered, electric equipment, but also in other manufacturers’ construction equipment. This saves on both investment and transportation costs, while clearly making construction operation easier.
EW100: a new era of wheeled excavators
Also on the stand was the Wacker Neuson EW100 wheeled excavator. The 10-tonne wheeled excavator is unique in its class and sets new benchmarks. Intelligent attachment management with tool recognition, a well thought-
out human-machine interface, and preparation for diverse assistance systems and interfaces are just a few examples. Operator friendliness and efficiency were a priority during development. As a result of the powerful drive hydraulics and high basic work performance of the EW100, it is possible to complete tasks for which a 14-tonne excavator would have to otherwise be used.
With the new model DV45, the electrohydraulic cabin can be rotated by 180° at the press of a button on the joystick. In the Multi-View mode (working with a laterally rotated cabin) the operator has optimal visibility of the lateral work area and can see precisely where they
are unloading the material or where the machine is moving along.
The automatic skip return automatically returns the cabin to the starting position at the press of a button, while the operator can concentrate on driving. The integrated hill-hold function, intelligent tilt monitoring and seatbelt monitoring with optional start release provide additional safety measures. Object monitoring “Active Sense Control” has recently been made available for the DV45 – where there is danger of a collision it automatically reduces the dumper’s speed, where necessary bringing it to a standstill. The system automatically calculates the route in combination with the speed and immediately activates when an obstacle appears on the collision course.
Yanmar CE has unveiled its most ambitious and cutting-edge range of compact machinery in decades, from all-electric loaders, excavator and tracked carriers, to the low-emission and justreleased SV86-7 and SV100-7 midi excavators.
Leading the charge
Demonstrating the company’s commitment to a carbon neutral future, Intermat made the perfect backdrop for Yanmar CE’s big reveal of its allelectric trio: the SV17e, V8e and C08e. Featuring an open-centre hydraulic system with load-sensing hydraulic pump, the SV17e mini excavator has been designed with operator experience in mind. Delivering 23.5 kWh gross electric power (19 kWh usable), the 48V air-cooled model provides impressive digging, lifting and carrying capability. And as its emissions are effectively nil, it easily meets all the world’s most demanding emission restrictions.
Meanwhile, the 4.5 tonne V8e electric wheel loader features an 800-litre
loading bucket and smooth hydrostatic drive and high-lifting capabilities, making it ideal for heavy lifting in allterrain applications – including tight job sites. It features powerful 11 kW charging in standard configuration and 22 kW in optional fast charging.
Completing the electric trio is Yanmar’s 555 kg C08e electric carrier, which combines compact dimensions with an 11.5 kWh battery and a capacity of 24V. Compact, capable and clean, it’s ready to navigate the narrowest of paths with ease, offering the power and manoeuvrability to excel in tight spaces.
With electric the theme running through the company’s presence at the show, the V7 and V7-HW are based on a new platform that can support both diesel and electric powertrains. Launched in diesel configuration, they fill a gap at the smaller end of the company’s compact wheel loader range. Some half tonne lighter than the next largest
machines in the Yanmar range, the V7 weighs 4,250 kg and has a standard bucket capacity of 0.7 m3, while the V7 H-W (Heavy Weight) – thanks to an additional 200 kg of ballast integrated into the machine – weighs 4,450 kg, with a bucket capacity of 0.8 m3
Also making their debut at a major show, Yanmar CE will unveil its nextgeneration midi-excavators – the SV86-7 and SV100-7. Its latest midi excavators set new standards of compactness and efficiency in the 8-10 tonne segment, as well as increased performance and operator-centric design. Despite being in the nine-tonne class SV86-7 and 10-tonne SV100-7 maintain a compact footprint associated with smaller machines. They feature a tight front swing radius and minimal rear turning radiuses. Coupled with minimal rear overhang, these machines are the tools to have if you find yourself in a tight spot.
As the product launches at Intermat clearly showed, Yanmar CE is adopting more sustainable practices and helping customers and users of its products do the same. The company, part of the Yanmar Group, is creating a sustainable future and along with its fellow Group companies, is committed to the environmental emission reduction targets of the Yanmar Green Challenge to help achieve this aim. The Challenge commits Yanmar CE to be free from greenhouse gas emissions by 2050.
To the historic backdrop of Paris, Yanmar CE dazzled with innovations that are shaping the future of utilities, construction and infrastructure.
OilQuick is a family owned modern industrial company focusing on development, manufacturing and sales. OilQuick is the world’s leading full line supplier for fully automatic attachment coupler systems for excavators, wheel loaders, forklift trucks, material handling machines and cranes. OilQuick also offers high quality tiltrotator systems for excavators.
OilQuick showcased its latest products and advancements in innovation at Intermat. Renowned for pushing the boundaries of excellence and quality, OilQuick has revolutionised efficiency and safety in the construction business for over three decades.
With its fully automatic quick coupler and tiltrotator systems, OilQuick has led the way in transforming the industry into a modern, effective and safe business.
Using its automatic couplers you can stay in the cab and do all the switching of hydraulic, electrical and mechanical tools and attachments with a push of a button. And OilQuick’s tiltrotators will transform your excavator into a highly versatile and effective machine.
OilQuick showcased its entire product range of fully automatic quick couplers for tool carrying machines, as well as its tiltrotator range for excavators.
There’s only one place you’ll find the heavy hitters of concrete and masonry this January: Vegas, baby — at World of Concrete 2025, the largest and only annual international event dedicated to your business. Be here to mix with industry giants. Get your hands on the latest technologies revolutionizing
EXHIBITS: JANUARY 21-23, 2025
EDUCATION: JANUARY 20-23
LAS VEGAS CONVENTION CENTER
The picture painted for the future of construction is uncertain and it’s now time for the sector to consider the ways it can guarantee stability and improve efficiencies to keep projects moving.
One of the most undeniable ways of doing that is by using machine control. The recent Future of Machine Control report from Topcon highlights the potential of using such technologies and how they can provide a solution to many of the challenges currently facing the construction sector.
As rising operational costs, the skills gap and labour shortage continue to impact jobs, investing in new technology may understandably not be a priority for many contractors. However, there are numerous benefits that machine control technology can offer to make life easier and improve project outcomes to support shortages, profitability and tight deadlines.
The struggle to find skilled workers
Today’s skills gap can be put down to an unfortunate combination of experienced workers coming to the end of their careers in the sector and a widespread failure to get young people excited about the construction industry. Ultimately, there’s a much smaller pool of current and future professionals.
One of the potential challenges for the construction industry recruiting young school and college leavers could be the assumption that construction and operating roles are often strenuous, wholly manual occupations. Without awareness of the cutting-edge projects that are rightly attractive to people, it can be difficult for those outside of the industry to get excited about what’s going on in the sector and want to be a part of it.
Embracing technology such as machine control could be one of the
first steps in tackling that. For example, if you put yourself in the shoes of a young person weighing up a career as an operator of an excavator or dozer, machine control vastly eases the training process and provides a leg up into much more complex and engaging work. At the other end of the scale, for the most experienced operators, machine control offers the opportunity to spend less time in the cab and more time supervising, even on complicated jobs.
Findings from Topcon’s Future of Machine Control report demonstrate that construction professionals are fully aware of their potential to change the sector’s image. Just under three quarters (73%) of respondents agree that technology like machine control would be key to attracting future talent into the industry. With this in mind, and with supply for operator jobs being higher than the number of jobseekers, the question must be asked – why wait to introduce machine control technology?
Automated machine control can play a huge role on site when it comes to improving accuracy and reducing reworks. In fact, of those already using machine control within their operations, both accuracy and efficiency were selected by a quarter (25%) of respondents as the main benefit of automation. The same proportion (26%) of construction managers reported that managing complex data in their projects was a major challenge, with this figure rising to 57% for those within the 25-34 age range.
But what does this look like for operators on site? Take Topcon’s MCMax solution for example. Using the most advanced and precise GPS positioning technology and sensors, the system allows operators to receive realtime, dynamic, on-screen bucket location and design views, meaning they can cut more accurately and check against complex designs in the cab, removing the need for someone to check the grade from the trench.
The technology also goes beyond providing operators with a visual guide to bucket or blade position – it moves the blade to grade by talking directly to the machine’s hydraulics. Unlike regular machine control, automated solutions use performance enhancing technology to determine accuracy and speed, meaning
projects can be completed significantly quicker. The need for reworks is also reduced due to less errors, cutting down on materials, products and labour, and avoiding unnecessary expense to improve profitability across projects.
With almost a quarter (24%) of respondents citing operator fatigue as a key concern, the need for machine control is clear and it’s up to construction management to invest in the technology so the benefits can be felt by all.
Besides enhancing speed, accuracy and efficiency, machine control plays its part in reducing carbon emissions. Industrywide sustainability goals are creeping closer and 67% of construction managers agree that the sector will be net zero by
2050, so it’s vital they see and utilise the far-reaching sustainability goals of machine control in supporting with the pressure facing operators on the ground to reduce carbon emissions across jobs.
An ever-growing focus on sustainability targets, coupled with the ongoing challenge of the skills gap means the benefits of technology can’t be ignored. Machine control offers an immediate solution and if construction is going to overcome the various challenges facing it, the technology can no longer be considered as a “nice to have”.
Download the full Future of Machine Control report here: www.topconpositioning.com/futuremachine-control-2023-report#
PRODEM rotary screening buckets offer a versatile approach for dealing with site material. Perfect for salvaging aggregates on construction and building renovation sites, selecting waste material on demolition sites, separating natural waste at landfill sites, loading containment cages, and concealing pipes in pipeline work.
The hydraulic rotary screening bucket features a four-piece interchangeable screening net available in a variety of sizes and easy to replace bolt-on wear edges that save downtime and maximise productivity.
Why
Rotary screening buckets are an excellent attachment for your excavator, especially in today’s construction, waste, groundworks and demolition landscape. They offer a versatile alternative to other screening options such as expensive screening plants that can take up a large amount of space on site. Operators can sort material
according to the removable screen net size, a 20 mm net will allows all material smaller than 20 mm to fall through while larger materials are retained in the bucket.
With an ever-increasing demand to increase efficiency while remaining sustainable, rotary screening buckets can help you to keep up. If you’re thinking about hiring or purchasing a screening bucket and can’t make your mind up, then this may help.
Main purposes of a rotary screening bucket
Re-use: A common use for a rotary screening bucket is preparing topsoil into a finer product which can then be used for landscaping or on site for padding and backfill for pipes and cables etc.
Salvaging: Rotary screening buckets simplify the process of salvaging aggregates from construction and building renovation sites by separating materials, allowing them to be identified and sorted properly. The salvaged materials can then be re-used for other purposes on and off-site.
Waste separation: Separating natural waste at landfill sites can be extremely time-consuming; however, the screening bucket speeds up the process by minimising manual intervention.
Screening: As their name suggests rotary screening buckets provide the ability to screen various materials from scrap to demolition and can help remove any contaminants prior to use in smaller materials such as sand.
With a rotary screening bucket operators can effectively and efficiently screen and sort materials on site for a low initial investment and operating costs. Having the option to sort and screen materials on site removes the need for them to be processed off site and reduces unnecessary costs. The fact that their size allows them to be used on almost any site, low costs and high efficiency makes it an attachment worth having.
As a leading supplier of excavator attachments for sale, hire or repairs, we cover the whole of the UK and offer next day delivery for in stock products. We’re known for providing high-quality products that are right for the customer. If you’re looking for a hydraulic excavator attachment, we’ve got it.
EDGE Innovate has expanded its offering with the EDGE SCREENPRO S18 heavy duty, tracked scalping screen, a product that delivers high production rates and precision screening.
The dynamic 5.4 x 1.75-m twodeck screen of the EDGE SCREENPRO S18 features interchangeable flip flow and conventional scalper screens, providing unprecedented flexibility. The SCREENPRO S18 is designed to process the most difficult and demanding of applications, including aggregate, construction waste, sand and gravel, soils and organic materials. With numerous screen media options and configurations available, the EDGE S18 can be used as a standalone unit or if needed, placed before or after a primary crusher.
Design features include a low-level feed hopper, two or three-way split configuration, hydraulic folding discharge conveyors to facilitate the quick transition from operation to transport and a fully integrated power unit with large service access. A user-friendly control system with sequential start/stop functionality provides exceptional operational performance and unit safety.
With the largest hopper capacity in its class, the EDGE SCREENPRO S18 encompasses a 1,400 mm-wide, variable speed feeder with forward / reverse functionality. A large feed opening ensures optimum flow of material to the scalping screen.
EDGE’s intelligent load management system constantly monitors conveyor load pressures and regulates feeder speed resulting in superior uptime by eliminating material overload and ensures optimum screening production at any
“With the largest hopper capacity in its class, the EDGE SCREENPRO S18 encompasses a 1,400 mm-wide variable speed feeder with forward / reverse functionality”
given time. Hydraulic folding hopper extensions allow for side loading while a folding hopper rear door provides even further loading flexibility.
At the heart of the SCREENPRO S18 is an EDGE-designed high-stroke scalping screen with a screening area of up to 18.3m² and a wide variable working angle to suit an array of applications. The aggressive high stroke action results in superior material separation and a generous screening area ensures precision fines separation. To ensure minimal downtime, the screenbox encompasses hydraulic lift-up functionality for a quick and efficient mesh exchange process, supported by full access walkways on both sides of the screen.
Customers can choose from a wide range of screen media options including woven mesh, punch plate, finger screens and bofor (grizzly) decks to achieve a variety of final grain sizes and to process different feed material.
Adding to the versatility of this new SCREENPRO range is its ability to interchange the highly aggressive scalping screen with EDGE Innovate’s award winning flip flow screen. This flexibility combined with numerous
screen media options and configurations allows the EDGE SCREENPRO S18 to process a wide range of materials and to tackle screening applications that other conventional screens cannot, such as incinerator slag or wet, damp and sticky material.
The side discharge conveyors offer market leading belt widths and discharge heights while setup takes a matter of minutes. Thanks to an intuitive design, the plant is fully customisable both in the field and from the factory with side conveyors that can be reversed or discharged on the same side or converted to a two-way split without any additional parts required. Unlike competing models, the SCREENPRO S18 can be road transported in these set up modes.
To meet the demands of recycling applications, the SCREENPRO S18 can be equipped with both over-band magnets and magnetic head drums for the extraction and recovery of ferrous metals.
The oversize discharge conveyor features a heavy duty 1,600-mm chevron belt as standard with a combination of impact bars and rollers absorbing the impact from loading material, prolonging the life of the conveyor belt. The oversize
discharge conveyor can be lowered to 5° to provide superior access to the lower screen deck and aids in the screen media exchange process.
The EDGE SCREENPRO S18 also offers added remote functionality for improved operator efficiency and safety. All major functions on the S18 including tracking, feed conveyor speed adjustment, sequential startup and hopper jacklegs can be remotely operated from a safe distance of up to 100 m or the comfort of the operator’s cabin.
Powered by either a Caterpillar or Cummins Stage V ACERT engine ensures the SCREENPRO S18 drive system provides a reliable, durable and efficient screening solution. An electric hybrid option further enhances cost savings and environmental benefits, combining the advantages of an electric power unit with traditional diesel/hydraulic power. Using a small onboard diesel engine for tracking and setup, operators can then connect to an external electricity supply once the machine is in position.
In the dynamic world of construction, demolition and waste, INMALO’s search for ever increasing efficiency and productivity for its customers reigns supreme.
INMALO’s choice of pioneering crushing and recovery attachments has ushered in a new era of quality performance attachments for waste, demolition and construction firms who demand significant return on investment.
Among these attachments are the MBI MCP-IP Fixed Pulveriser, GIDA HMG-T Scrap Magnet and Rock. Zone’s Crusher Bucket, which are now promising and delivering unparalleled benefits and maximising excavator efficiency for these industries.
Charles Polak, Director at INMALO said: “For customers, sustainability has become a key consideration. It has become vital to research and deploy practices and equipment that are compatible
with today’s values and standards. In the UK, INMALO understands customer needs, where every project demands precision, power and above all, reliability and service backup.”
MBI MCP-IP Fixed Pulveriser
Mantovanibenne’s MCP-IT Fixed Pulveriser is specifically designed for secondary demolition and concrete crushing, and its unique feature of nonrotation provides a substantial advantage. By eliminating rotation, it optimises more power, boasting a larger cylinder for enhanced crushing capabilities. This pulveriser also incorporates rebar cutters to increase scrap metal recovery.
With the addition of split double jaw plates that reduce wear part costs, a robust body ensuring longevity and a protected cylinder for durability, the MCP-IT Pulveriser is a testament to superior engineering. Furthermore, INMALO’s responsive service and support ensures seamless operations, reduced downtime and immediately available spares and service should you need them.
“Pioneering crushing and recovery attachments has ushered in a new era of quality performance attachments for waste, demolition and construction firms who demand significant return on investment”
The GIDA HMG-T Scrap Magnets have revolutionised metal separation with early adopters describing them as immensely powerful and an indispensable tool for scrap metal collection.
With a powerful magnet pickup and responsive release time, together with ground-raking teeth designed for effective metal separation within aggregates, they offer a quick return on investment. Their powerful and reliable hydraulically driven performance enables the rapid collection of scrap, running seamlessly from the breaker circuit.
Compatible with a variety of quick couplers, they ensure standardisation across excavators. Available for hire or purchase with INMALO service and support, they signify a transformative leap in recovering scrap metal from areas of concrete crushing activity.
Rock.Zone’s Crusher Bucket is a revolutionary solution for on-site crushing and recycling where concrete can be repurposed immediately to provide back fill and land stability aggregates. Profit optimisation by saving disposal costs and the need to import additional materials later underlines the value of this attachment.
The crusher bucket provides unique features mixed with unparalleled power and reliability. By crushing at the source, it significantly reduces transportation costs and saves valuable time. Its user-friendly setup, coupled with a reverse function that ejects jammed materials, ensures uninterrupted operations.
Moreover, the patented Quattro movement enhances performance, allowing for maximised profits by minimising transportation needs. Available for hire or purchase with immediate service and support, it symbolises efficiency and costeffectiveness on site.
The benefits offered by these three crushing and recovery products are manifold and undeniable. They elevate efficiency to unprecedented levels, facilitating the swift completion of projects while minimising downtime and provide tangible cost savings.
Finlay®, a leading global manufacturer of mobile crushing and screening equipment, proudly announces the successful production and launch of the new 890 – an aggressive, heavy duty two-deck scalping screener with a comprehensive variety of screen box media options and a variable screen angle.
Known for their high production capacity, efficiency and durability, the Finlay range of scalping screens offer robust and versatile solutions for a range of applications from fine screening to heavy scalping. The Finlay 890 is a welcome addition to the range, with the ability to process a high tonnage throughput of up to
700 tph, depending on mesh sizes and material type.
The aggressive screen box is engineered to deliver a high-quality screened product in secondary screening applications such as aggregates, topsoil, construction and demolition (C&D) waste, biomass, compost materials, overburden, foundry waste and processed ores and minerals. It has a modular configuration with a 6.1-m x 1.8-m top deck and 5.6-m x 1.8-m bottom deck screen and offers variety of media options including abrasion resistant punched plate, bofor bars, tines and a selection of heavy-duty mesh sizes. Equipped with a hydraulic raise screen box function, the Finlay 890 has convenient access to the bottom deck media for maintenance or replacement.
The discharge conveyors have individual variable speed controls, granting
operators the precision to tailor speeds for specific applications. Adaptability is further enhanced with the capability to interchange both side conveyors in the field, either on the same or opposite sides. Additionally, the Finlay 890 model can transition into a two-way split configuration, effectively ejecting oversized materials from both the top and bottom deck.
The fully self-contained plant can be hydraulically folded and ready for transport in less than 30 minutes, making it the ideal machine for large scale contract screening projects where a highly productive and dependable screen is paramount.
The Finlay 890 is available with hybrid technology consisting of onboard electrical motors permitting the flexibility to run the plant from an outside power supply or standard onboard engine.
Alan Witherow, Product and Applications Manager at Finlay, said:
“The Finlay 890 boasts advanced features and capabilities for operators seeking high-performance screening solutions. Its versatility ensures suitability across a wide range of applications, reinforcing Finlay’s commitment to engineering excellence and our dedication to providing our customers with cutting-edge equipment that meets and exceeds their expectations.”
There are materials some operators consider difficult to dispose of. These materials often pile up for years and take up space. Old light poles, columns, and concrete pipes, railway sleepers, vineyard poles with spring steel – these objects seem to be more complicated and expensive to recycle than others.
Construction sites that adopt MB Crusher units find an easy and inexpensive way to crush and recycle these types of inert material.
Four minutes flat
It’s not a riddle or an equation: it’s how long it takes MB’s crusher bucket to crush an eight-metre tall light pole. With the MB unit attached to the excavator on the construction, a
single operator can collect the pole, crush it and separate the iron from the concrete.
No drawbacks
Disposing of reinforced concrete poles in recycling centres is pricey, even if it’s just the cost of transporting the material. If a company wants to be autonomous and use a stationary crusher, the rebar in the concrete can easily cut the conveyor belt or jam the machine, which results in downtime, work stops and wasting time and money. Alternatively, some crush with demolition shears, but it is a slow process.
This doesn’t happen when using MB’s crushers: the iron comes out while the unit is crushing and can be separated from the processed material with the iron separator, which is installed on the MB unit and controlled by the operator from the cabin.
“Construction sites that adopt MB Crusher units find an easy and inexpensive way to crush and recycle inert material”
With the MB crusher bucket, it is easy to obtain different material output sizes. The excavator’s operator can do it directly on-site, by just unscrewing a few bolts, inserting or removing shims and adjusting the jaws according to his needs. Not only that but with MB’s crusher buckets, the resulting material is of good quality and ready to be reused or sold.
Earn from inert material and recovering iron
On two construction sites, one in France and the other in Bulgaria, the recovering of railway sleepers and reinforced concrete has become a new source of income.
Using MB’s crusher buckets and their excavator, the companies can collect poles and sleepers and crush them. During the crushing phase, the rebar is separated from the concrete and then removed from the crushed pile with an iron separator installed directly on the MB unit. The same crusher is used for crushing rocks. The material is quickly processed on-site with a single machine—a simple and fast operation.
Material recovered and immediately reused
Why throw it away when it can be recycled? This is what the administration of a Slovakian municipality thought when they found themselves handling several cubic metres of material from the demolition of pavements. The company that took charge of recovering the material created a real recycling centre with only
two attachments. A BF70.2 crusher bucket to crush the waste and an MB-S14 screening bucket to separate it. The material was then reused as a base for road work.
It had been a long time since a large Brazilian company had used the old light poles on a construction site. They used the MB crusher bucket to crush them, recover the iron and obtain excellent revenues from the resale.
This is what a company in the Czech Republic that deals with railways did. The problem was disposing of old sleepers that they kept in storage – renting a stationary crusher was too expensive and complicated. Bringing the material to a
recycling centre meant high hauling fees. The solution was under their noses: they used the BF70.2 crusher bucket attached to their operating machine and crushed the old sleepers on the spot, eliminating rental and transportation costs.
Sometimes, adopting new solutions to facilitate the workflow on the construction site is the answer. With MB Crusher units what was difficult and expensive to dispose of before becomes simple. There’s no longer a need for large storage areas. The waste is processed directly on the construction site and the iron is quickly separated from the concrete and piled on the side ready to be sold.
All of this work done on the job site with a single machine.
Crushing
Austrian based Rubble Master is leading the impact crushing world with its range of RM crushers, available from UK distributor Red Knight 6 Ltd. The range is led by the RM120X, delivering maximum efficiency and simplicity for use on a wide range of applications.
The RM120X features a range of solutions to make the life of the operator easier and safer, while also delivering cost benefits back to the business through intelligent management of the machine, based on the amount and type of material being crushed.
The RM Operations Assist and RM XSMART functions enable the operator to keep track of the machines performance from the excavator cab, with live updates on engine performance, fuel consumption and machines
performance all clearly visible via a lighting system on the outside of the machine.
Paul Donnelly, Managing Director of Red Knight 6 said: “The Rubble Master impact crushers are industry leading for a reason. Built to the most exacting standards, we’ve sold over 130 machines into the market in the last five years and those customers know they can trust the RM range to get the job done. The RM120X is the next evolution in the range. The largest of the impact crushers it also offers simplicity of use, maximum efficiency and safety for the operator via the Operations Assist,”
The Rubble Master range are highly mobile, versatile and powerful machines ideal for crushing natural rock (riverbed material, basalt, limestone, gypsum, granite) and for recycling rubble, asphalt, concrete, glass and production waste.
“Rubble Master impact crushers are industry leading for a reason –they are built to the most exacting standards”
Rubble Master has built its success on its market leading impact crushers, but its range of tracked scalping and sizing screens continues to gain traction in the market.
The range of scalping screens has four machines in total, from the incredibly compact but robust HS3500M through to the largest screen, the HS11000M. There is also an extensive range of sizing screens
of deals across both ranges and the feedback remains fantastic. Customers really see the quality of the machines, from build to operation and both ranges consistently exceeded expectations.
“Efficiency of operation is key but the ability to reduce fuel costs and have a positive environmental impact is crucial. We’ve seen a genuine improvement across both screening ranges and our customers are benefiting from that as well.”
A selection of the RM range of crushers and screens are available with hybrid or fully electric drive systems reducing your energy consumption and overall operating costs. As well as reducing costs, emissions will be limited, making them ideal for inner city operation as noise will also be reduced.
In addition the range is also equipped with X Smart, enabling even greater efficiency of operation.
with both two and three deck options, depending on your requirements. The MSC8500e also offers full hybrid drive capability, allowing you to limit fuel costs. It is something that has long been a feature of the crushing machines, but the same technology has been incorporated into the screeners, another example of the two sites working closely together for the benefit of customers.
Paul Donnelly, Managing Director at RK6 said: “We completed a number
Sandvik Mobile Crushers and Screens has launched its new QI353 mid-size impactor, the first of its new third generation 3-Series products. Designed in response to customer research, the QI353 has been built with more productivity, uptime, efficiency, flexibility, connectivity and safety at the forefront of its innovative design.
The QI353 features a ground-up new mid-size track platform and custom Prisec™ impact crusher. Targeted at quarry, recycling and contractor segments, the QI353 is the most
versatile, mid-sized mobile impactor available today, designed to provide more uptime than any other.
The QI353 offers a user-friendly mobile solution with controls and maintenance points located conveniently at ground level. A key highlight is the new automated control system featuring Optik™ intuitive user experience. With colour visual display, easy navigation, and total integration for troubleshooting, diagnostics and support.
The QI353 has been designed with productivity in mind and can process up to 400 tph. Its feed arrangement includes
a new hopper with curved heavy-duty sides for greater capacity and tapered feed arrangement to reduce blockages and ensure continuous crushing. It also features a new pan feeder with geared drive and a larger pre-screen with improved access to replace media. At the core of the QI353 is a new mid-size Prisec impact crusher, which boasts the largest feed opening 1,170 mm x 730 mm and largest rotor diameter 1,150 mm in its class. Adjustable apron curtains and tip speed ensure a wide range of product gradations can be achieved. Also, all plant conveyors have larger discharge heights for increased stockpiling capacity.
The QI353 features a free-flowing feed arrangement where all components in the flow path get wider for improved material flow; a load sensing system for feeder drive for continuous crushing; and a larger pre-screen for effective removal of fines, maximising throughput and reducing wear. In addition, the QI353 benefits from extended service intervals and larger onboard fuel storage to extend intervals between refuelling.
The QI353 has been designed to consume less energy, its double-deck pre-screen ensures maximum scalping capability and
prevents any undersize material passing through the impactor. This maximises crusher throughput, reduces wear costs and energy consumption. The machine requires 40% less hydraulic oil per service and benefits from extended hydraulic oil replacement intervals. When combined, this can be up to 64% less hydraulic oil consumed over 10,000 hours of machine usage (subject to oil sampling). The QI353 is also fitted with the latest emissionscompliant power pack for maximum performance and cost efficiency.
Boasting a high degree of flexibility to suit any application, the QI353 is particularly useful for contractors who change jobs frequently. The natural fines conveyor can be positioned for right or left-hand discharge with a three position bypass chute under the prescreen, allowing you to decide where to send your natural fines. The QI353 comes prepared to accept our new enhanced HS323 hanging screen module, offering the flexibility for the crusher to operate in open or closed circuit.
The HS323 enhancements include readiness to accept belt scales for tph monitoring on fines and stockpile conveyor belts; enhanced subframe for improved screen media access and tensioning; and an updated mid-size stockpile conveyor. The unique design enables setup in less than 30 minutes and can be fitted without the use of additional lifting equipment. The patent pending hanging screen option delivers multifunctionality as a one, two or three-way split screener.
The new automation system with Optik intuitive user experience, includes simplified operation controls and total integration with our My Fleet telematics solution. Diagnostic support, pre-installed guides for troubleshooting and real time information allows customers to know exactly how their equipment is being used. The optional belt scales fitted to the product conveyor enable productivity data to be displayed on the user interface and via My Fleet for tph monitoring.
“Designed in response to customer research,the QI353 has been built with more productivity, uptime, efficiency, flexibility, connectivity and safety at the forefront of its innovative design”
With operator safety paramount, it has a new access platform under the feeder and pre-screen and a spacious three-sided 270° platform for service and maintenance. A lifting beam, jib and tackle as well as the patented rotor turning device ensure operator safety when removing, rotating or installing hammers. A height adjustable overband magnet and all conveyors can be conveniently lowered for inspection and servicing purposes. Enhanced safety features are embedded within Optik intuitive user experience, including visual warnings and emergency stop locations.
Terex® MPS, a leading global provider of modular crushing, screening and conveying solutions, has successfully installed its first large modular plant in the United Kingdom.
The UK-based customer, a market leader in sustainable building materials, road contracting and building products was seeking a solution to reduce dust emissions and lower diesel costs. Terex MPS designed a fully electric modular setup, which included four modular plants: two Terex MPS MC320 cone modules and two Terex MPS MHS6203 screen modules.
Jake Wilson, Territory Sales Manager, Terex MPS said:
“The primary challenge of the design process was achieving a solution that reduced dust while maintaining material shape and throughput. We reduced dust content by having a lower initial reduction ratio while improving product shape through better stone on stone attrition and a more consistent crushing ratio. The solution we provided was a tailored solution to address customer needs and overcome
industry-specific hurdles.”
Blasted limestone is fed through a primary crusher at a rate of 450 tph and processed through an impactor and sizing screen. The 40-160 mm product enters the secondary crushing phase, a Terex MPS MC320 cone module, then to the Cedarapids MHS6203 modular screen. Finally, oversized material from the Cedarapids MHS6203 goes to the tertiary Terex MPS MC320 cone module before re-entering the MHS6203. The final output achieved is varied limestone aggregates including <4, 4-6, 6-10, 10-14 and 14-20 mm.
The plant was successfully sold through PowerX Equipment, trusted distribution partner of Terex MPS. Together Terex MPS and PowerX Equipment ensured reliable communication and support throughout the acquisition process.
Jake Wilson said: “From initial design discussions to the commissioning
phase, Terex MPS worked with PowerX Equipment to provide comprehensive support to the customer. The collaboration involved site visits, equipment training and fine-tuning during the commissioning process to ensure optimal plant performance.
“This installation marks the UK’s first large modular plant by Terex MPS and serves as a flagship project, demonstrating the positive impact that eco-conscious solutions can have in the quarrying and construction industry.”
To increase uptime, Keestrack decided to standardise the Long Life Grease on all scalpers (K-series) and classifiers (C-series) produced in its Czech factory. Due to great testing results since 2021, the manufacturer of mobile crushing and screening equipment decided in September last year to equip the K3, K4 and K5 standard with this system. Due to the gains on maintenance time, it decided to standardise the LLG-system to all screens in its product range.
Keestrack Long Life (LLG) grease contains anti-wear and anti-friction additives and is resistant to water and rust. It extends service intervals and lowers costs and downtime. It expands the lifetime of the bearings of the screen box and apron feeder by running at lower temperature. The LLG grease is resistant to high impact loads and vibrations and can handle an ambient temperature from -25°C to +145°C.
“Due to the LLG grease the service interval is 5 to 10 times longer, compared to standard EP2 grease”
Due to the LLG grease the service interval is 5 to 10 times longer, compared to standard EP2 grease. For example: greasing the screen box has been reduced from every 50 hours to every 500 hours.
The operating temperature of the bearings are much lower with LLG grease compared to standard EP2 grease. In one test, comparing the EP2 grease versus the LLG grease on the screen box of a K5, the bearings were running at an operating temperature up to 60°C with standard EP2 grease, while with LLG grease they were running at an operational temperature of 43°C, a significant difference.
The use of LLG grease has a huge positive effect on the lifespan of the bearings, resulting in more uptime, less downtime and lower costs.
To emphasise the unique characteristics of this grease the cartridges are branded under Keestrack private label.
The LLG grease is available in 400 ml tubes and can be easily applied by an ergonomic handpump. The cartridges are made with a screwable cap so they cannot be mixed up with other classic grease pumps. You can apply the grease by the handpump single handed or both handed.
The handpump is designed so you can always clearly identify the LLG grease. At the bottom it will stay clearly visible at all times.
Due to standardising the LLG grease, the central greasing option on the scalpers and classifiers will disappear, as this does not make sense anymore, as the bearings only have to be greased every 500 hours. The greasing nipples are well indicated by the green labels on the machine with clear instructions.
Kubota has unveiled a range of compact telehandlers, tracked dumpers and wheel loaders.
In a significant move the company has launched its first telehandler, as it seeks to provide a wider range of machinery solutions for construction and associated industries. Called the KTH4815-2, the compact machine boasts an overall width of 1.6 metres and an overall height of below 2 metres.
Model numbering is indicative of the telehandler’s lifting capability, with the KTH4815-2 capable of achieving a maximum lift height of 4.8 metres and a maximum lift capacity of 1.5 tonnes, depending on the variant. Hose burst check-valves and a load-moment sensor with forward over-turn protection meeting EN15000 certification, is also
part of the standard specification.
Four versions of the KTH4815-2 telehandler are available; two are canopy-equipped models with a curved front screen and two use fully glazed cabs with a two-piece door – the glazed upper section can be secured in the open position. The entry-level KTH4815-2 is supplied without a 170 kg rear counterweight and is shod on 10/75 x 15.3 narrow tyres, reducing both its cost and performance. A wider, 31/15.5 x 15 skid steer tyre option is available.
The KTH4815-2 offers a surprising amount of space in a stylish cab for a compact machine. The wide two-piece door allows for easy, safe access for operators of all shapes and sizes, with plenty of leg space from the seat to the
steering column and ample space behind the operator for storage. A generous shelf between the front window and steering wheel carries air vents, USB charging in addition to space for paperwork and site documentation.
Good ergonomics dictate that everything is in front of the operator and within reach. The fully glazed cab has a stylish screen curved from the wiper position to over the operator’s head, ensuring optimum visibility for safe and comfortable operation.
Finally, the machine has an inbuilt safety control system protecting the operator, people in the vicinity, the load and the machine.
The new compact telehandler is available now from the company’s 32-strong UK distributor network.
NO HOCUS-POCUS. JUST PARTS FOR SMALL EARTH-MOVERS.
When it comes to plant machinery, automatic lubrication systems are all about working smarter not harder and they don’t come better than the latest pumps and kits by Hebonilube.
Designed to lubricate while a vehicle is working, auto greasers apply the correct amount of grease required for the machine to operate efficiently and help to reduce unnecessary component wear. By avoiding maintenance downtime and the costs and safety risks associated with manual greasing, these systems can extend equipment life and even higher a machine’s residual value when trade in time comes around.
Available in 12 and 24V options and in a choice of sizes from two to eight kg, Hebonilube’s pumps are compatible with any EP2 grease and stand out from others on the market due to their IP67 rating.
Featuring quality, built to last components, these pumps include a two-year warranty (subject to terms and conditions).
To meet demand, Hebonilube has just developed a new range of full system kits to cover excavators, wheel loaders, articulated dump trucks and rigid trucks for popular machinery brands such as Caterpillar, DEVELON, JCB, John Deere, Komatsu, Liebherr and more. These handy kits comprise a grease pump, hose, distribution blocks, hose guard, valves, connectors and control module. Based around a simple design, a full system kit can be installed on an excavator or dozer in just a couple of days.
Hebonilube pumps and kits start from just £1,725 and are available to order with next day delivery to the UK and Ireland from AP Air Europe by calling 01453 891 320 or visiting www.apairltd.com.
Don’t settle for second best ENGINE 115 LIFT HEIGHT 16.6 LIFT CAPACITY
4.0 t
Developed to meet the specific needs of customers operating in the industrial, construction and infrastructure sector. Our Panoramic range guarantees exceptional performance and economic efficiency. This model portrays great versatility and can be offered in two versions that differ in their technical and configuration characteristics.
Ben and the team out promoting the industry between issues
The new Komatsu PC88MR-11 midi excavator builds on the solid foundations of the hugely successful PC88MR-10 to bring more unrivalled customer value to the midi excavator sector. The PC88MR11’s new features deliver a significant boost to productivity, reduced fuel consumption and faster work equipment speed.
The PC88MR-11 takes full advantage of Komatsu group know-how to offer ultimate versatility, ease of buying and increased efficiency with the factory-fitted Lehnhoff Powertilt option.
Environmental concerns are growing, and urban areas are becoming increasingly sensitive to emissions. The PC88MR-11’s low consumption and powerful 50.7 kW Stage V engine provides customers with the opportunity to participate in any tender, demonstrate environmental credentials and future-proof their investment.
A tight tail-swing lets the operator concentrate on the work at hand, with no worry about rear-swing impacts, helping to make the PC88MR-11 a
versatile solution, ideal even in confined areas.
The external design is also improved with an all-new MR-11 cutting edge styling. The new PC88MR-11 offers first class operator comfort, smart safety initiatives, intuitive ergonomics, huge advances in performance and controllability, easy serviceability, peace of mind through a proven Komatsu aftertreatment system, and the highest levels of standard specifications in the industry.
Operators will find improvements everywhere: a redesigned blade for better dozing, the repositioning of the low/high gear switch for better ergonomics, or an automatic change-over valve for higher comfort when changing attachments. This will be appreciated by current and new users alike.
Simone Reddi, Komatsu Europe Product Manager for midi excavators, said: “This is not just a simple model update. The PC88MR-11 introduces several improvements in digging performances and structure. The whole dig-loading cycle is improved, increasing production, giving the feeling of a faster machine. Last but not least, this latest Komatsu midi excavator features the European debut of the brand new 2.4-litre Stage V Komatsu engine with KDPF (no SCR needed). Enjoy lower fuel consumption, higher performances and unrivalled efficiency.”
PC88MR-11 – Features and benefits
• Modern, distinctive and desirable Komatsu MR-11 styling
• EU Stage V compliant engine with DPF and no need for SCR
• Net power increase vs. PC88MR-10
• Engine fan clutch system – low noise and fuel consumption reduction
• Productivity up 7% vs. PC88MR-10
• Fuel consumption on average, 6% lower than PC88MR-10
• Levelling speed 14% increase vs. PC88MR-10
• Attachment oil flow up 12% vs. PC88MR-10
• New blade shape for improved dozing operation
• Travel hi/lo switchable on blade lever intuitively positioned
• LED work lamps
• Bluetooth radio
• Air heated suspended seat
• Attachment flow setting
• Easy radiator cleaning thanks to the well placed dust net
• Large access doors
• Engine maintenance items all on one side and accessible from ground level
• Transport height reduced by 20 mm vs. PC88MR-10
• Automatic 2-way to 1-way to 2-way attachment switching
BMC
LARGE STOCK OF 1 - 22 TON BUCKETS AVAILABLE FOR NEXT
Xwatch Safety Solutions is pleased to announce its acquisition by Hexagon, a global leader in digital reality solutions. This acquisition represents a significant milestone in improving construction site safety through innovative technology.
The XW series has been leading the way in reducing risks on construction sites with features such as height control, slew control, and rated capacity indication (RCI) for construction plant and machinery. These technologies help operators establish safe working zones, significantly boosting safety measures around equipment.
This strategic move comes after Xwatch’s successful collaboration with Leica Geosystems, part of Hexagon, culminating in the innovative 3D Avoidance Zone system. This system represents a key step towards integrating its advanced safety solutions within Hexagon’s comprehensive suite of construction tools to enhance proactive risk management and decision-making processes for safer construction environments.
Dan Leaney, Director of Sales and Operations at Xwatch Safety Solutions Ltd said: “Joining Hexagon represents a transformative opportunity for us to push the boundaries of safety technology
in the construction industry. It allows us to leverage Hexagon’s global expertise and reach, bringing our cutting-edge safety solutions to a wider audience and significantly impacting worker safety worldwide.
“We are excited about the opportunities this acquisition brings to both our companies and the construction industry as a whole. Together, we are committed to driving innovation and embracing digital transformation to ensure safer, more efficient, and sustainable construction practices globally.
“Xwatch will continue to operate under its established brand and maintain strong partnerships with all our trusted dealers and installers. With the support of Hexagon, we will continue to deliver the high-quality service our customers expect, now with additional resources and support.”
Chris Fitzgerald, Xwatch founder and MD of Fitzgerald Plant Services, headquartered in Cwmbran, South Wales said: “This is a significant milestone in our company’s evolution and we eagerly anticipate the opportunities this transaction will bring. We look forward to utilising the strengths of Xwatch and Hexagon Group to expand our capabilities and enhance our customer experience.
Our commitment has always been to deliver the best customer experience and support our team members in doing so. Partnering with Hexagon Group is the perfect opportunity to continue achieving these goals.”
“We are excited about the opportunities this acquisition brings to both our companies and the construction industry as a whole”
In the world of small earthmovers where every movement counts and downtime is the nemesis, finding the right parts can often feel like searching for a needle in a haystack. But fear not, because TVH is the beacon of hope, offering a wealth of parts with no hocus pocus, just pure magic.
Step into the enchanting world of TVH, where more than five million well-known references await for all major makes and models, including Bobcat, JCB, Kubota, Volvo, Yanmar and many more. Tracks, undercarriages, windows, door panels, filters and countless accessories – you name it and TVH has it. With global delivery faster than the blink of an eye, your machines will be ready before you can say abracadabra.
But what really sets TVH apart is its in-house team of parts wizards, ready to help you find the perfect parts via email, phone or the online shop. Gone are the days of endless searching and guesswork; with TVH the right part is just a click away.
Joining TVH’s magic is as easy as waving a magic wand. With just three simple steps you can access its online shop, where you will find a host of parts to breathe new life into machines. From filling in the enquiry form to receiving your login, TVH provides a seamless journey into the world of quality parts.
So why settle for ordinary when it can be extraordinary? Let TVH be your missing magic touch, eliminating machine downtime and ensuring that every machine gets the care and attention it deserves.
Visit our website to find out more: www.tvh.com/no-hocus-pocus-justparts-for-sem
Liebherr’s revenue once again increased significantly compared with the previous year. The group increased revenues in 11 of its 13 product segments and surpassed its previous revenue record from 2022 by €1.5 bn. At €9.6 bn, revenue in the earthmoving, material handling technology, deep foundation machines, mobile and crawler cranes, tower cranes, concrete technology and mining product segments was 11.6 % higher than in the previous year. In the product segments of maritime cranes, aerospace and transportation systems, gear technology and automation systems, refrigerators and freezers, components and hotels, Liebherr achieved total revenues of €4.5 bn, an increase of 11.3 % compared with the previous year.
Business saw positive growth in virtually all regions. A satisfying revenue increase was registered in the EU, which has traditionally been the group’s strongest sales region. Revenues in Germany, France and Spain recorded particularly positive growth. The group recorded a slight decline in non-EU countries.
The business year was also extremely
encouraging in North America – driven by the USA and Mexico – as well as in Asia and Oceania. Revenue in the Africa, Near and Middle East region was also well above the previous year’s level. In Central and South America, revenue remained at the previous year’s level.
Furthermore, the number of employees grew once again in the 2023 business year. At the end of the year, Liebherr had a total of 53,659 employees worldwide, 2,338 more than in the previous year.
“ The demand for large cranes and raw materials is growing as numerous economies around the world undergo transformation processes ”
Economic conditions will remain challenging in 2024, however Liebherr has started the current business year with a very solid volume of orders. Although there are differing trends in the individual product segments, Liebherr will be able to compensate for this thanks to its decentralised, diversified structure and international positioning. The demand for large cranes and raw materials is growing as numerous economies around the world undergo transformation processes. This provides market opportunities for Liebherr. The Group anticipates growth in the USA and Australia, for instance.