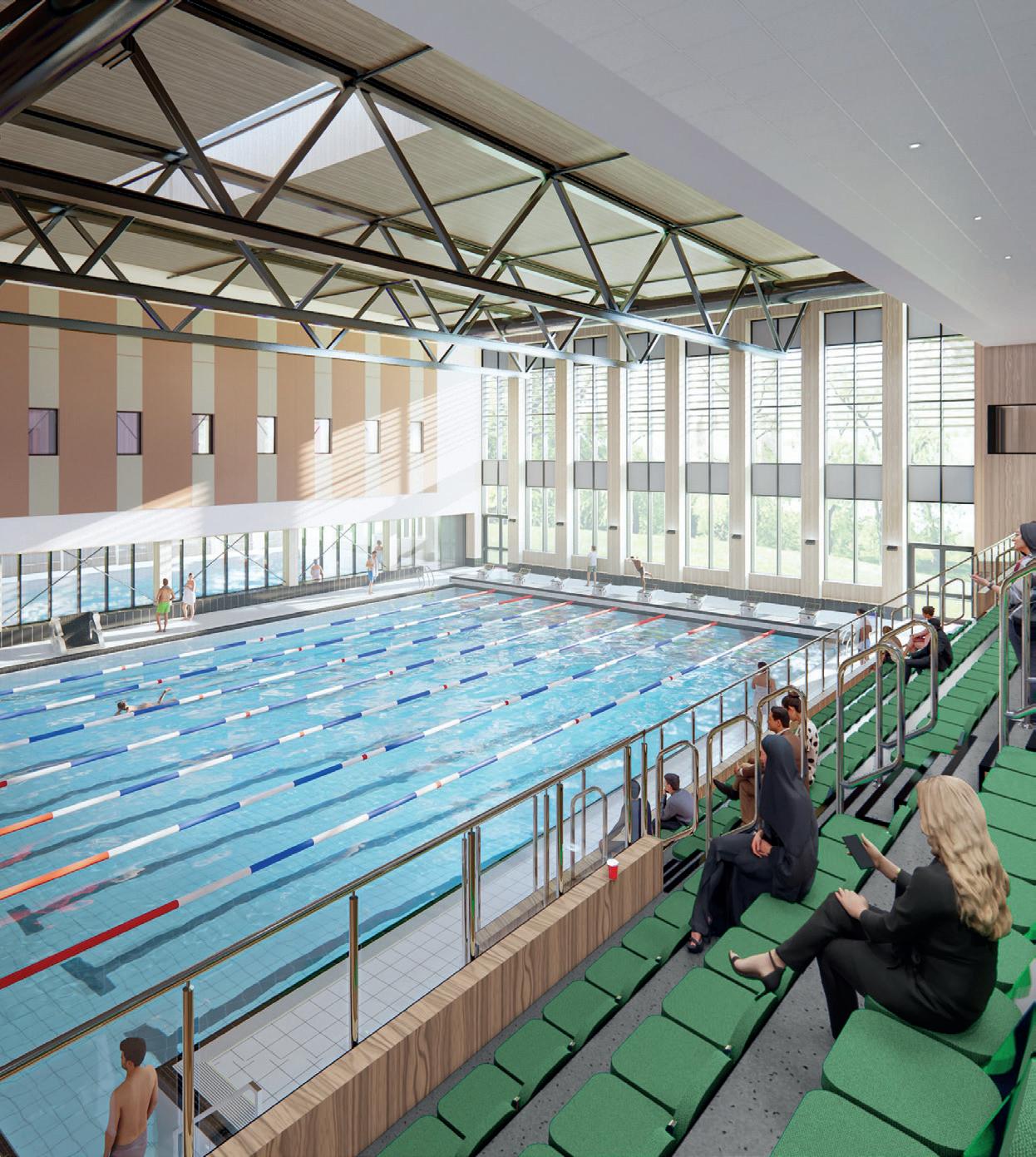
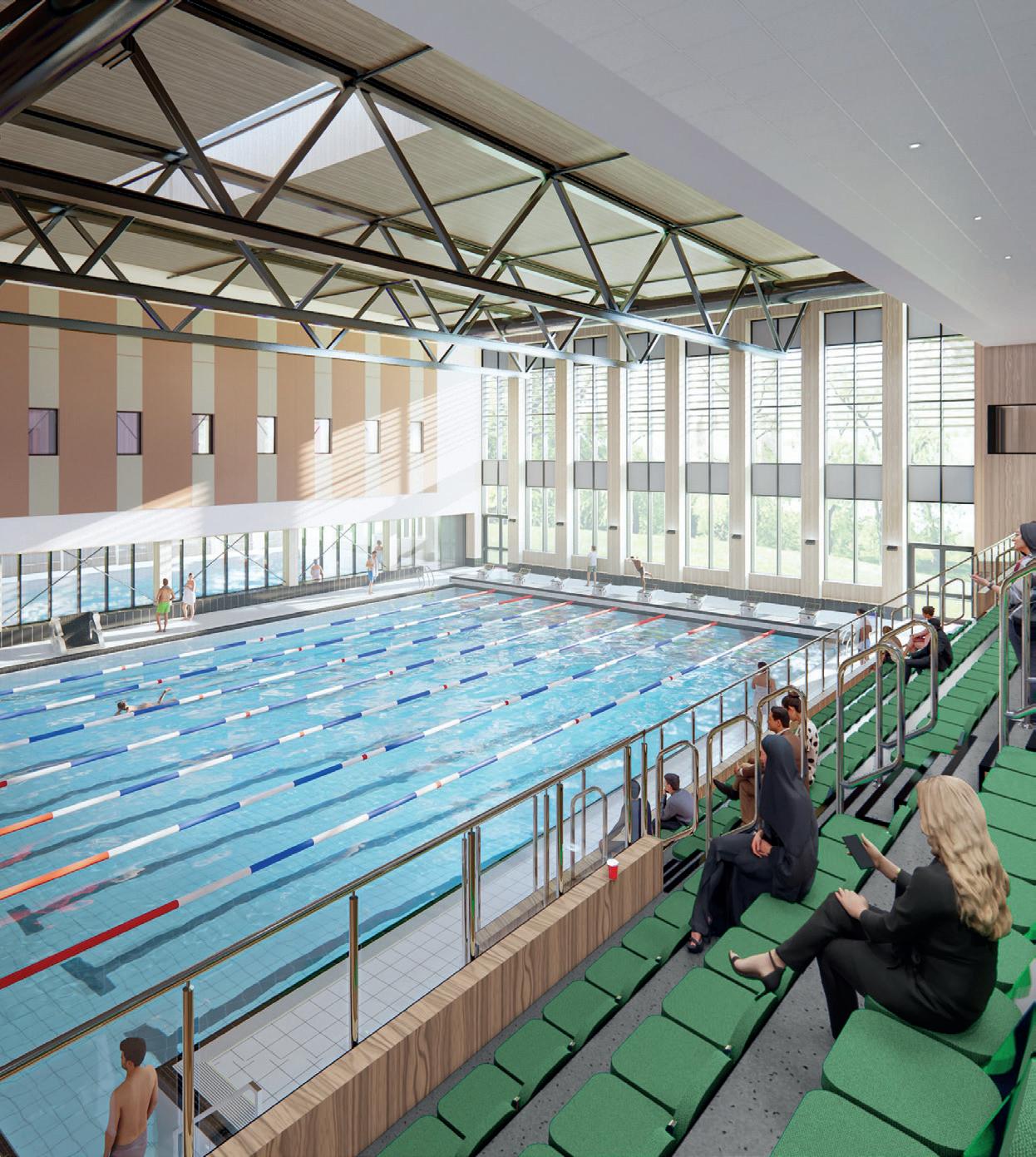
Flatroofs: fifthThefunctional façade
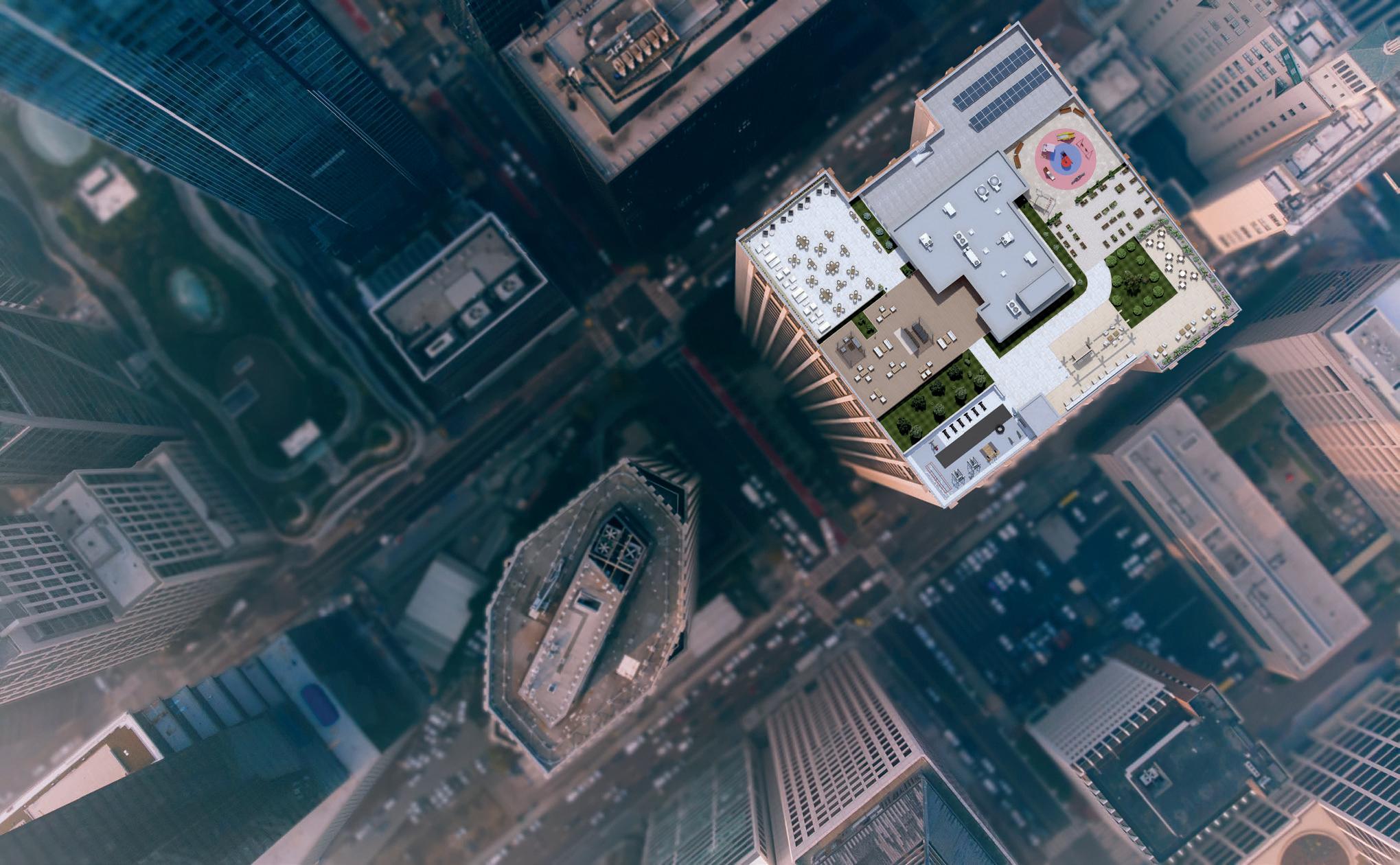
Mitigating fire risk above and below modern flat roofs.
Today's flat roofs are increasingly used as multifunctional spaces for social and practical applications, including solar energy installations.
This expanding remit, particularly in crowded urban areas, brings multifaceted challenges to specification and building design.
Learn to mitigate the risks.
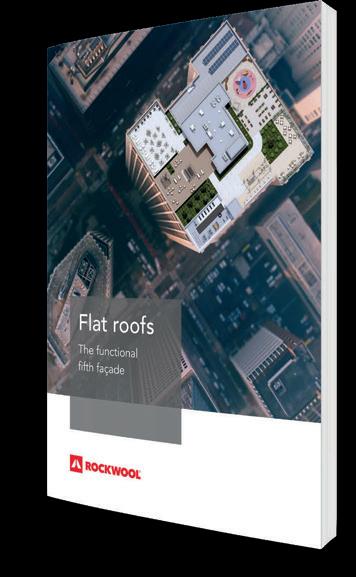
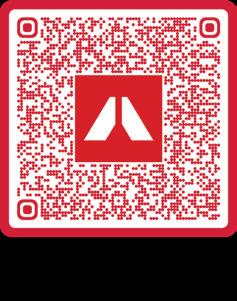
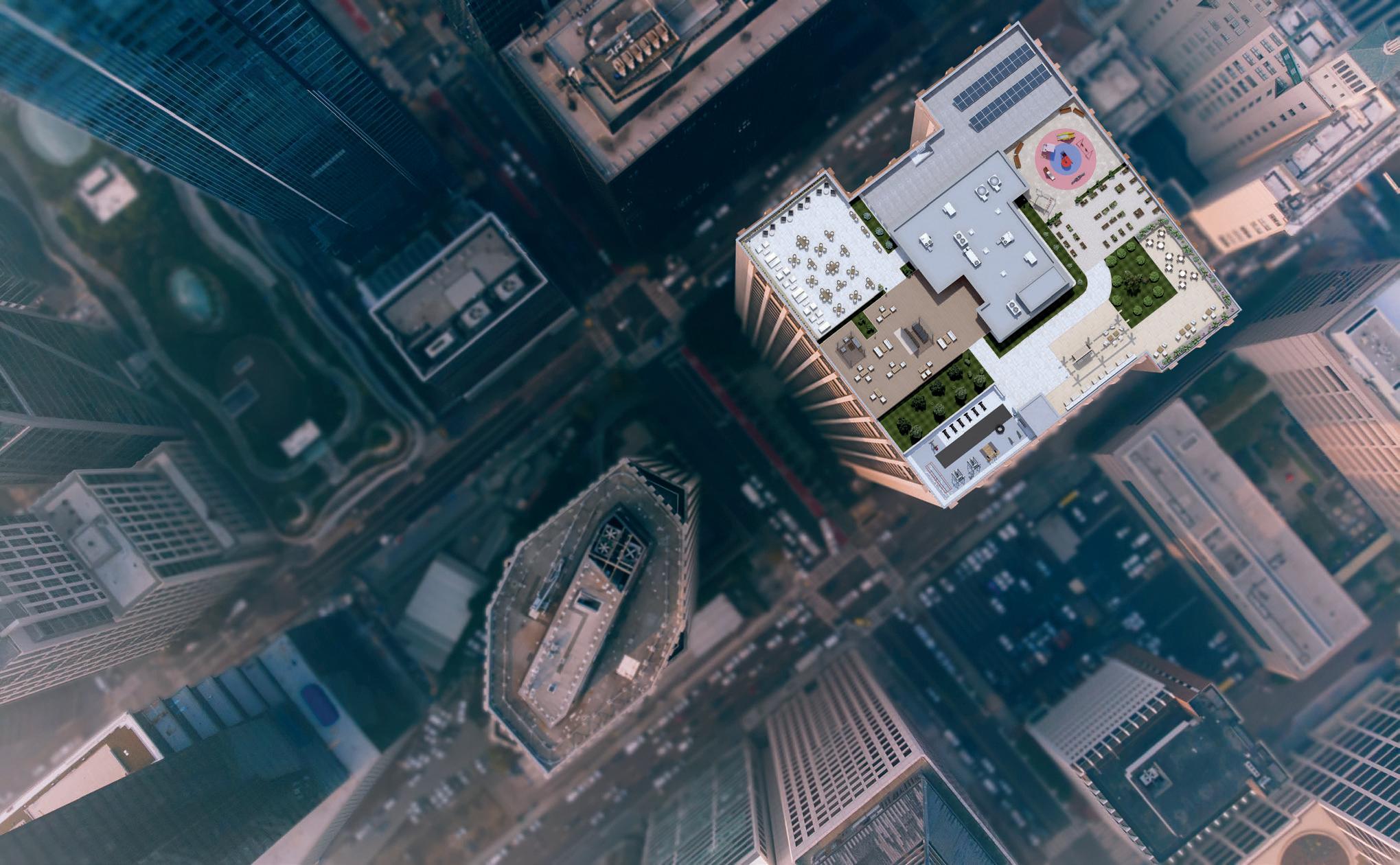
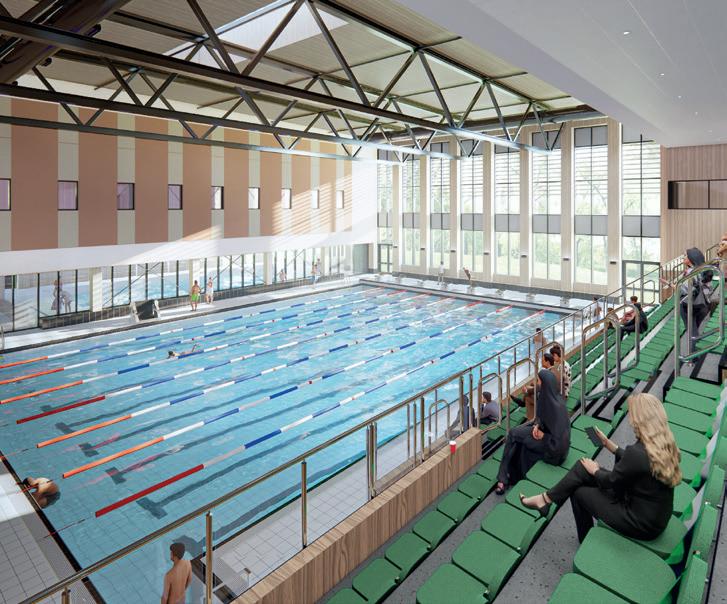
Welcome to the May issue of PSBJ...
In the construction industry, we’re acutely aware of the impact a skills shortage can have on the market, especially when operating within the public sector, where the pressure is magnified. STEM subjects have long been recognised for their potential to enhance national productivity, drive economic growth and play a crucial role in steering the UK towards its net-zero goals. As more companies start to invest in apprenticeship programmes and tailor their recruitment strategies to appeal to younger generations, we’re seeing a growing number of students choosing STEM subjects and expressing an interest in the field.
Consequently, there’s a noticeable increase in the development of state-of-the-art labs and facilities up and down the country designed specifically for these adept students to engage in pioneering research, fostering the next wave of innovations.
In this month’s issue, we delve into two cutting-edge medical facilities poised to nurture the next generation of scientific talent in the UK. The first, BIOS, is a £36.9m state-ofthe-art science, health and medical facility located at the heart of Teesside University’s Middlesbrough Campus. Delivered by Wates and Summers-Inman, this facility is set to revolutionise healthcare provision by providing top-tier training facilities for future healthcare professionals. Turn to page 08 for further details.
Elsewhere, we explore the expansion of a landmark facility at London’s King’s College for the Rayne Institute that houses the Gene Therapy Vector Facility (GTVF), which enables the delivery of the latest gene therapies into clinical production. This expansion, costing £5.8m, was undertaken in collaboration with Pick Everard, a multidisciplinary consultancy, to ensure the institute remains at the forefront of its field. Learn more about this facility and the creation of a new micro laboratory on page 12.

I hope you enjoy this issue. Don’t forget, you can also access the magazine’s features, product news and supplier information on PSBJ’s user-friendly and engaging website. Fully responsive, the website allows you to read all the latest stories on the go either on your smartphone or tablet. Simply visit www.psbjmagazine.com.
Rebecca
Rebecca Kemp • Editor • rebecca@redhutmedia.com06 News
A round up of the latest industry news, including charity events, awarded contracts, completed projects and much more.
08 Upfront
Delivered by Wates Group and the talented team at Summers-Inman, the cutting-edge £36.9m BIOS facility at Teesside University transforms healthcare education.
12 Education
King’s College London has completed its £5.8m expansion programme, enhancing the renowned Rayne Institute’s Gene Therapy Vector Facility in collaboration with Pick Everard.
14 Legal & Business
Duncan Osler, Partner at Morton Fraser MacRoberts, breaks down the UK Government’s post-Brexit public procurement reforms set to shake up the landscape.
16 Healthcare
Steve McSorley, Director at Perega, explores the complexities of RAAC in healthcare infrastructure.

18 Doors, Windows & Balustrades
Owen Jones from Distinction Doors, a trusted stockist and distributor of fds (fire door systems), offers valuable insights into the pivotal purpose these systems play in ensuring safety and compliance.
20 Leisure
Kevin Burns, Myrtha Pools’ UK Business Development Manager and former Olympic Swimmer, debunks myths hindering renovation progress in the leisure sector.
22 Facades & Rainscreen
From energy efficiency to structural health, dive into the advantages of external wall insulation (EWI) with Matthew Woodhams from Baumit.
24 HVAC
Discover how implementing innovative technologies like Hydromx has led to significant savings in both energy bills and carbon emissions for schools in Essex.
Specifying CFA members for your flooring projects means you’ll gain a wealth of experience from vetted contractors with the knowledge and products to fulfil your specification with a sustainability criteria.
CFA members are part of a supply chain that includes specialist contract flooring contractors, manufacturers and distributors, all promoting the highest standards and expertise.
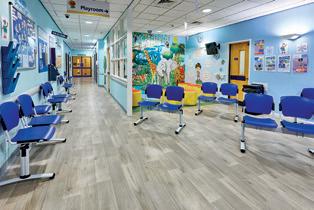
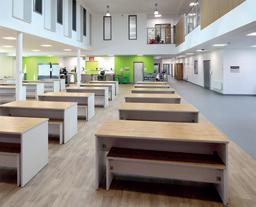
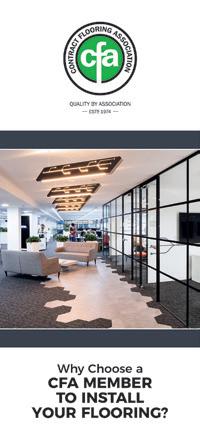
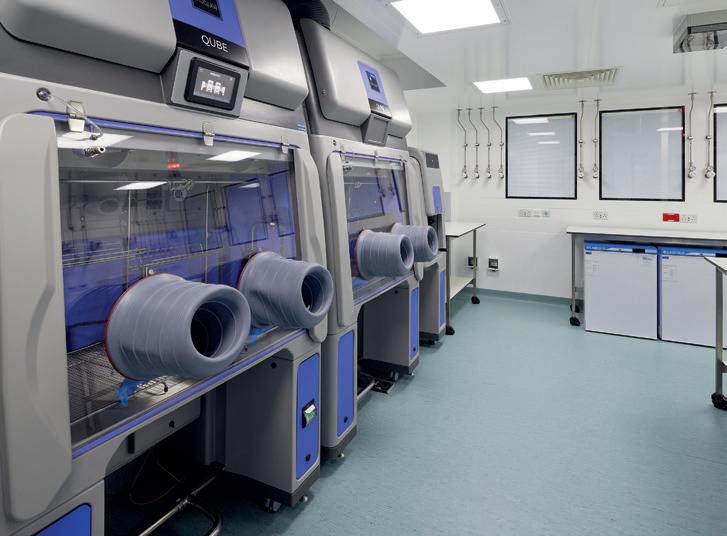
26 Housing
WestWood Liquid Technologies explores the world of BROOF(t4) certification and its pivotal function in setting roofing standards for social housing refurbishments.
28 Water Management
Brett Landscaping’s provision of 4000m2 of permeable paving is a vital component of the £23m flood resilience project in Hull, showcasing dedication to sustainable
30 Circularity
Debbie Huntley of PULSAR explores the growing demand for circular garment design in workwear and why it’s now more important than ever to balance comfort and functionality with durability.
32 Talking Point
Richard Murray, Director at Drees & Sommer UK, explains how educational institutions are leveraging capital funding to drive towards a
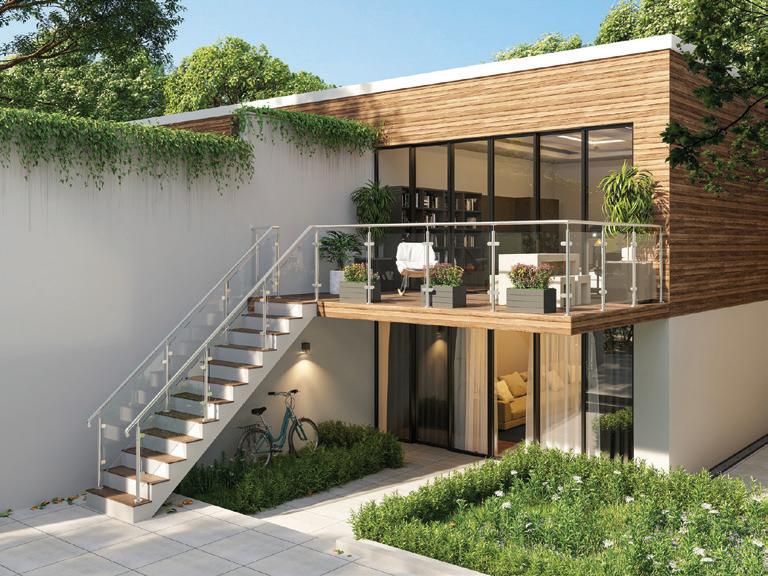
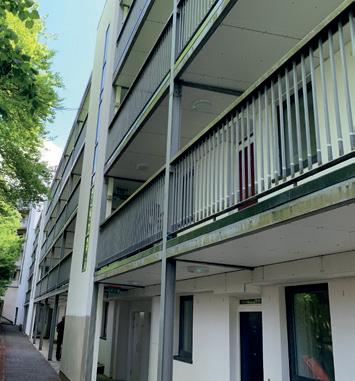
34 Technical Focus
John Duffin, Managing Director at Keyfix, emphasises the critical role specification plays throughout the construction process and why the built environment sector must continue to prioritise it.
36 UK Construction Week
UK Construction Week (UKCW) returns to London’s ExCeL from 7 to 9th May. Experience interactive demos, international pavilions and inspiring talks from industry leaders.
38 Product Guide
A dedicated focus of industry news, products and case studies to help specifiers and local authorities make informed decisions.
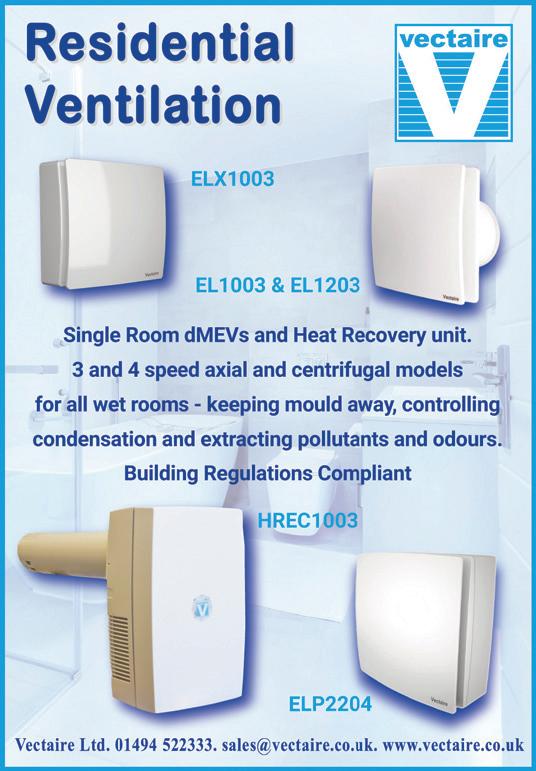
INDUSTRY UPDATES
Each month, PSBJ rounds up the latest public sector construction updates, from new contracts to industry awards.
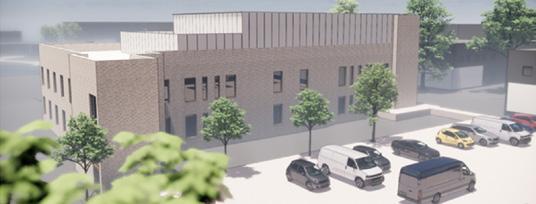
Morgan Sindall Construction appointed to develop Milton Keynes University Hospital’s new ward expansion
Morgan Sindall Construction’s Northern Home Counties business has been appointed to develop a £19.1m ward expansion on behalf of the Milton Keynes University Hospital (MKUH) NHS Foundation Trust. Procured via the Pagabo Framework, the project will create a new two-storey building, known as Oak Wards, as well as a link corridor to the existing A&E department in MKUH’s main building. These upgrades will enable the site to provide healthcare services to more people at a faster rate, helping meet the increased healthcare demands of Milton Keynes’ growing population. The project, the second that Morgan Sindall is currently delivering for the MKUH NHS Foundation Trust, is due to start on site in Q4 2024 and will be completed in late 2025. The new Oak Wards facility will increase MKUH’s ward capacity by providing two 24-bed wards, four of which will be five-bed bays and four single bedrooms, alongside ancillary space for storage, utility rooms, offices, a ward kitchen and staff areas. Both storeys will be laid out in a rectangular floor plan with a central nurse’s station and large bay windows to maximise the amount of natural light. This efficient floorplan mirrors an existing ward at the hospital and so will be familiar to staff from day one.
Sod-cutting ceremony marks the start of new Tamworth school
A new primary school is coming to Dunstall Park Estate in Tamworth and will be open to students for the start of the new school year in 2024/25. Construction works for Dunstall Park Primary School are being led by Midlands contractor, G F Tomlinson, on behalf of Staffordshire County Council and alongside project manager and concept architect, Entrust. The project was procured through the Constructing West Midlands (CWM) framework. Ideally located to accommodate a number of new housing developments in the area, the new one-form entry, two-storey school will open its doors in September, catering for 210 primary pupils and 26 nursery places. The school also has the capacity for expansion to 315 places in the future, which is in line with the demand for school places generated by further housing growth. The 1500m2 state-of-theart educational facility comprises seven classrooms, a separate nursery and practical area, an indoor school hall, staff offices and catering areas, alongside an outdoor space dedicated to a range of sporting activities. The school’s energy-efficient design prioritises daylight and natural ventilation into the building and, to ensure easy adjustment to temperature changes, high levels of insulation and thermal mass will be applied to walls and ceilings.
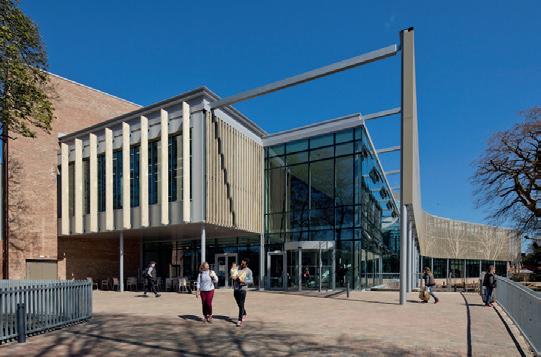
Morpeth Sport and Leisure Centre racks up industry award nominations
Since opening in April 2023, the new £21m Morpeth Sport and Leisure Centre has become a cornerstone of the community in the town. Continuing its huge success, it has been shortlisted for not one, but two construction industry awards. A sophisticated example of how well-designed facilities can strengthen social cohesion and inclusion in an aesthetically-pleasing hub, the centre has been shortlisted in the Public Sector Project and Community Benefit Project categories of this year’s RICS North East Awards. Commissioned and funded by Northumberland County Council and Advance Northumberland, this project was designed by leading firm GT3 Architects and constructed by Willmott Dixon. Located at the edge of the town-centre conservation area and sitting beside the River Wansbeck in Gas House Lane, the new facility acts as an exciting bookend to the existing high street. Along with the sporting facilities – including a six-lane swimming pool and spectator gallery, learner pool, spa and fitness suites, studio and multi-use sports hall – the centre incorporates a new community services hub. This includes a double-height community library, a customer service centre, a cafe and soft play with connections to a poetry garden and outdoor terraces, plus a brand-new adult learning facility with classrooms for a number of courses.
£18.5m contract awarded for new Whitecraig Primary School
The award-winning Durham-based architect, Howarth Litchfield, has been awarded the masterplanning contract for a project valued at circa £5m following a competitive bid through the North East Procurement Portal (NEPO) framework. Awarded by South Tyneside Council based on cost and experience, the project involves rationalising the council’s existing Middlefields Depot. This will enable the Howarth Litchfield team to draw on its recent experience gained on two similar projects. The first, at Morrison Busty Council Depot at Annfield Plain in County Durham, incorporated a three-megawatt solar farm to power the whole depot and reduce carbon emissions. Meanwhile, in Washington last year, the £9.1m redevelopment of Parsons Vehicle Workshop and Depot – which included a brand-new depot building with workshops, maintenance bays and charging points – has been designed to help drive Sunderland City Council’s aim to become a carbon-neutral city. In its role as lead consultant at Middlefields, Howarth Litchfield is responsible for appointing the remainder of the design team, which includes Hydrock, an integrated design, energy and sustainability consultancy – providing civil and structural engineering, highways work and mechanical and electrical engineering – planning consultant DPP, Ecosurv – an ecological consultancy – Apex – an acoustic consultancy – and landscape architect, Colour.
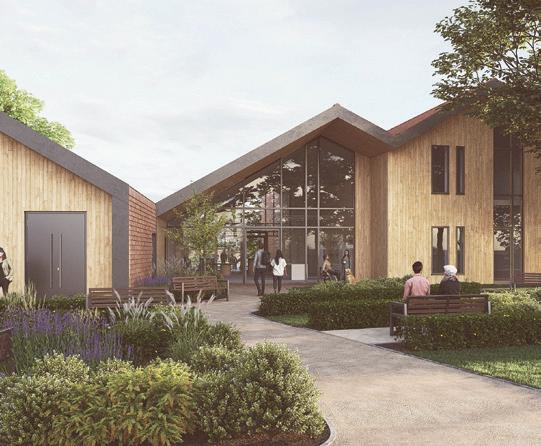
I&G to build new Rob Burrow Centre for Motor Neurone Disease
Yorkshire-based construction firm, I&G – part of the wider Sewell Group – has been appointed by Leeds Teaching Hospitals NHS Trust to build the new Rob Burrow Centre for Motor Neurone Disease; the first of its kind in the UK. The facility, which will be located on the Seacroft Hospital site, will bring a much-needed resource to the region and see all Motor Neurone Disease (MND) services housed under one roof for the first time. Named after rugby league legend Rob Burrow CBE, who campaigns for MND after being diagnosed with the condition in 2019, the new centre will be funded by Leeds Hospitals Charity, which has been fundraising to bring Rob’s vision to life. The building has been made possible through rigorous fundraising efforts across the UK and will be constructed using modern methods of construction, with structurally insulated panels (SIPs) being manufactured off site and erected in position, allowing a quicker, more efficient and more environmentallyfriendly process. The design is intended to create a sense of community and an environment that meets the needs of patients, families and staff. In addition to clinical areas and treatment rooms, it will include a central space where people can come together, along with reading and quiet spaces, as well as activity, dining and outdoor areas.
£2.5m regeneration scheme to reshape town-centre offering
A transformative town-centre regeneration project has been completed, revitalising the area for local businesses and residents and enhancing community space. Shepshed’s Market Place in Leicestershire is now a versatile and pedestrian-friendly environment, following work undertaken by multi-disciplinary consultancy Pick Everard. The improvements, which are set to boost trade and increase footfall in the region, include new carparking spaces, seating, bicycle-parking facilities and an array of trees and plantings. Pavements in Market Place and along nearby Brook Street have also been upgraded and expanded, with soft landscaping elements implemented to increase accessibility and reinforce visual identity in the town centre. The transformation forms part of a wider set of public realm works by Charnwood Borough Council, which will enable the town centre to host new events and market stalls. The work, which has been several years in the making, saw Pick Everard deliver project and cost management services via Perfect Circle and the SCAPE Consultancy direct award framework, designed to drive collaboration, efficiency, time and cost savings on construction projects.
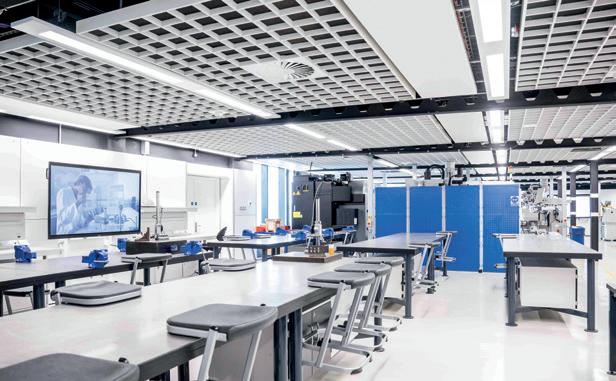
Stepnell completes multimillion-pound college revamp
The £3m refurbishment of the engineering and technology centre at Leicester College has been completed by award-winning complete construction partner Stepnell. Officially reopened by the deputy mayor of Leicester City Council, the facility on the Abbey Park Campus in the city’s centre will enable the college to provide industry-standard, technical training to students and employers across the region. Funded by Leicester College and the Department for Education (DfE), which provided more than £1m for the project with its T-Level capital grant, the project was delivered by Stepnell in close collaboration with Moss Architecture. The project involved the complete redesign of the facility’s internal space, including the installation of engineering laboratories and workshops to develop skills in robotics, programmable logic controllers, electronic circuits, electrical systems, mechanical systems and hydraulic and pneumatic systems. The facility also includes a range of mills, lathes, grinders, rigs, testing equipment and simulators. A new mechanical engineering workshop was also constructed to accommodate industry-standard lathes and milling machines. A specialist hand skills development and projects area, welding booths and a stateof-the-art grinding room have also been integrated to enhance student’s hands-on learning experience.
Wates Group set for Channel View regeneration scheme in Cardiff
Cardiff Council has appointed national developer, Wates Group, as the contractor to deliver its transformational redevelopment of the Channel View estate in Grangetown. The scheme is the largest and most exciting holistic estate redevelopment within the council’s development programme and will deliver up to 400 new highlyenergy-efficient, low-carbon mixed-tenure homes, including the replacement of the existing 180 council-managed properties. Wates already partners with the council on the Cardiff Living housing programme, which is delivering 1700 new homes, a mix of council homes and private homes to buy, across the city. Wates will deliver the entire Channel View project, commencing with the Phase-1 plans for older people’s accommodation to replace the existing tower block at the estate, as well as new communal facilities and a cafe. These accessible and adaptable apartments will promote independent living for older people. The redevelopment will provide better connectivity for the estate and the wider community to local facilities and transport links, improvements to the public open space at the Marl and the creation of well-managed, attractive public realm. Wates will also work with the council on the design development, consultation and planning of future phases of the redevelopment, the demolition of the existing housing stock and the construction of future phases, subject to viability.
CUTTING-EDGE £36.9M BIOS FACILITY PROVIDES STEP CHANGE FOR TEESSIDE UNIVERSITY
The newly-opened £36.9m BIOS, a stateof-the-art science, health and medical facility at the heart of Teesside University’s Middlesbrough campus, will transform the way healthcare provision is delivered.
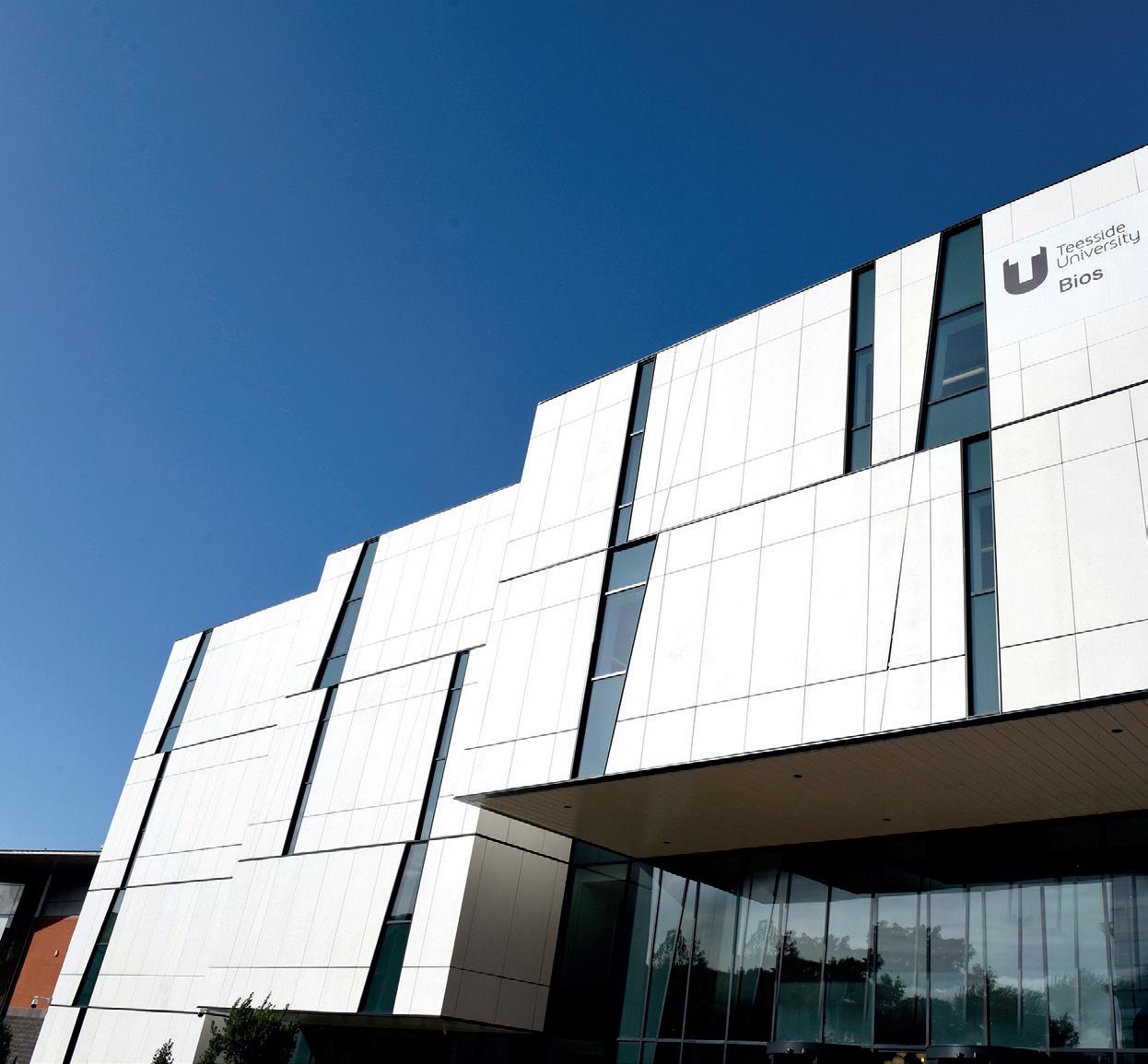
The building boasts immersive simulation suites, operating theatres and digital anatomy facilities, which have significantly enhanced the university’s teaching and learning environment.
Delivered by Wates and a first-class design team, award-winning project management and cost consultancy, Summers-Inman, provided project management and quantity surveying support from RIBA Stage 3 onwards, working on behalf of Teesside University.
It was the second project that SummersInman secured through the North East Universities Purchasing Consortium (NEUPC) framework, and it saw Wates and Summers-Inman working together again, hard on the heels of delivering the award-winning Cornell Quarter student accommodation building and Teesside University’s National Horizons Centre at its Darlington campus.
The future of healthcare training
BIOS is equipped with first-class facilities for the training of future healthcare professionals. Built over four floors with 5216m2 of bespoke teaching space, BIOS also contains an oral health research laboratory, a replica operating theatre and hospital ward, a biology suite and food science and food technology laboratories. Its fully-immersive simulation suite enables students to work in a range of settings, from hospitals to sports arenas. In between teaching, BIOS also has a pasta bar on the ground floor for the benefit of staff and students.
Summers-Inman’s Associate Director, Andy Rapmund, was responsible for working closely with Wates and managing the project successfully to conclusion. He said: “This was a challenging yet exciting project to be part of, given that we were working at the forefront of sustainable design with
a mandate to ensure the building achieved net-zero embodied carbon and a BREEAM ‘Outstanding’ certification.
Sustainable
design
“BIOS was designed with sustainability at its heart and incorporates a range of renewable energy systems such as PV panels, low-carbon building materials and energy-efficient equipment, systems and plant. Its attractive, high-quality and flexible environment has been designed to require minimal maintenance over its lifespan.
“Additionally, our appointment allowed us to draw on our extensive experience within the higher education sector and with the well-documented rising cost of materials, we were committed throughout to managing these fluctuations by early engagement with the supply chain supported by planned procurement to mitigate any delays to the construction programme.
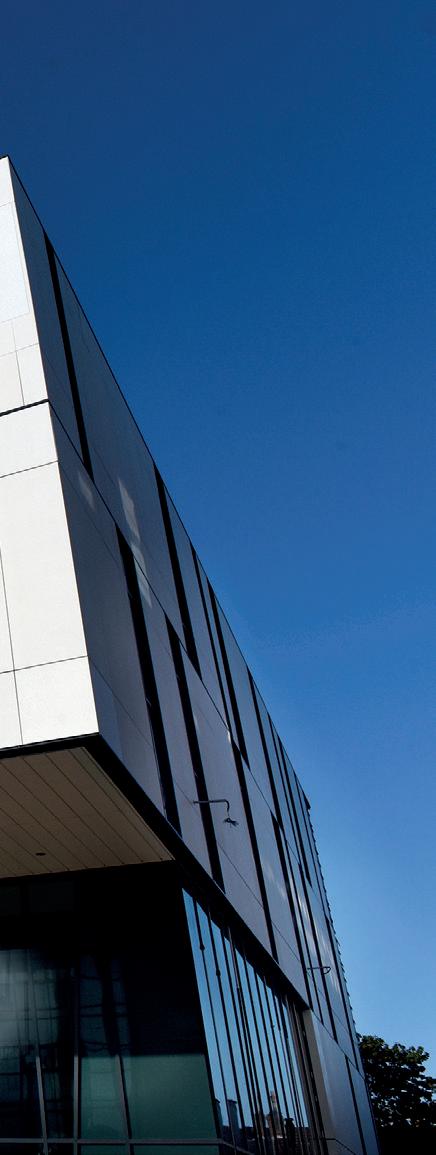
“We have very much enjoyed working again with Teesside University’s estates team and having the chance to further develop our professional relationship with Wates.”
A much-needed facility BIOS provides a bespoke new learning space for students in the university’s School of Health & Life Sciences.
Professor Tim Thompson, Dean of the School, said: “BIOS is more than just a building – it is a state-of the-art facility and a real game changer in terms of our health, medical and science provision.
“This was our ‘once-in-a-lifetime opportunity’ to provide a unique digital offer that will equip our students with the skills, experience and expertise to flourish within the sector.
“We are incredibly proud of what BIOS offers and delighted to see our students now taking advantage of the fantastic new facilities.”

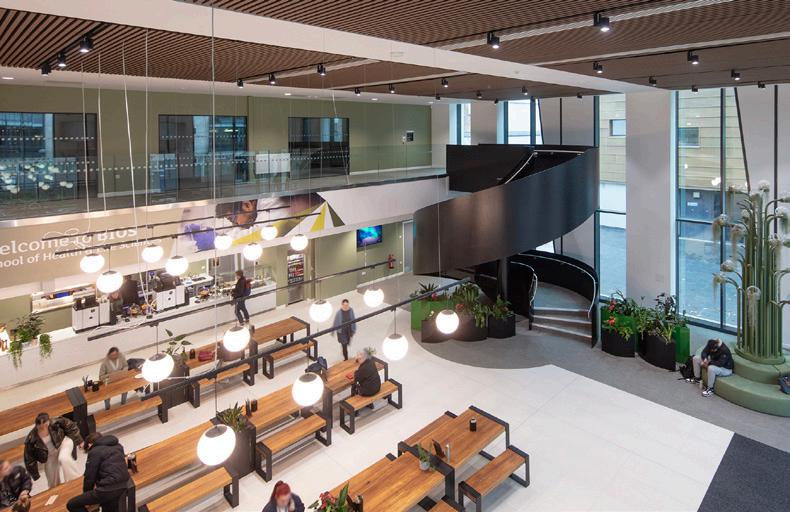

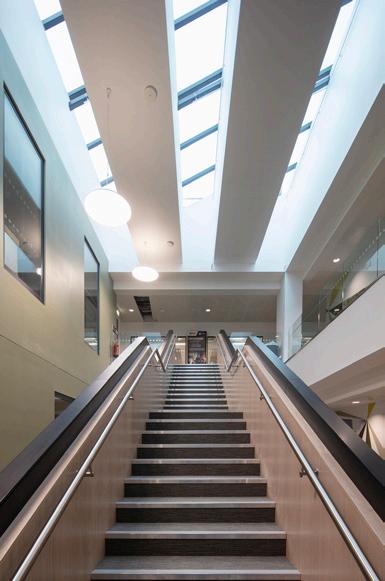
Social and sustainability KPIs
In delivering BIOS, Wates was keen to build not just an excellent building but a community as well. Commenting on the social value and sustainability elements of the project, David Wingfield, Regional Director for Yorkshire & North East Construction at Wates, said: “As the BIOS building developed, we were determined to have a directly beneficial, measurable effect on local people’s lives. That’s why we brought employment, training and educational opportunities to Middlesbrough people – from schoolchildren and students to the long-term unemployed with a particular focus on social enterprises.
“We used a local supply chain to assist with sustainability KPIs, resulting in 58% of the workforce living within a 40-mile radius of the site. We undertook an initial assessment with Mainers to understand the carbon requirements for the varying materials we would be procuring through the supply chain packages. Our target was to achieve <750 embodied carbon, which was achieved successfully.
“Working together with businesses and social enterprises across the Middlesbrough area, we leave a lasting legacy at Teesside University – a goal we strive to achieve at every site where we work.”
BIOS is the latest development to be completed as part of Teesside University’s ambitious campus masterplan, which has seen £280m invested in recent years to enhance the campus and facilities and provide the very best student and learning experience.
www.summers-inman.co.uk
FACT FILE:
PROFESSIONAL TEAM
PM/QS: Summers-Inman
Contractor: Wates
Architect: FaulknerBrowns
M&E services: Desco & Wilson Gray
C&S, transport: Curtins
Landscaping: One Environments
BREEAM/net-zero consultant: Mainer Associates
THE CONSTRUCTION PROCESS INCLUDED:
Steel-frame construction
Precast concrete planks to create spans of up to 15m
Internal fit-out (including lab fit-out)
Signature helical staircase
Double-height reception area with kitchen servery.
BIOS TARGETS
Local spend within 40 miles:
Target 75% | Actual 83.6%
SME supply chain engagement: Target 85% | Actual 87%
SME spend as percentage of construction contract value: Target 75% | Actual 77.4%
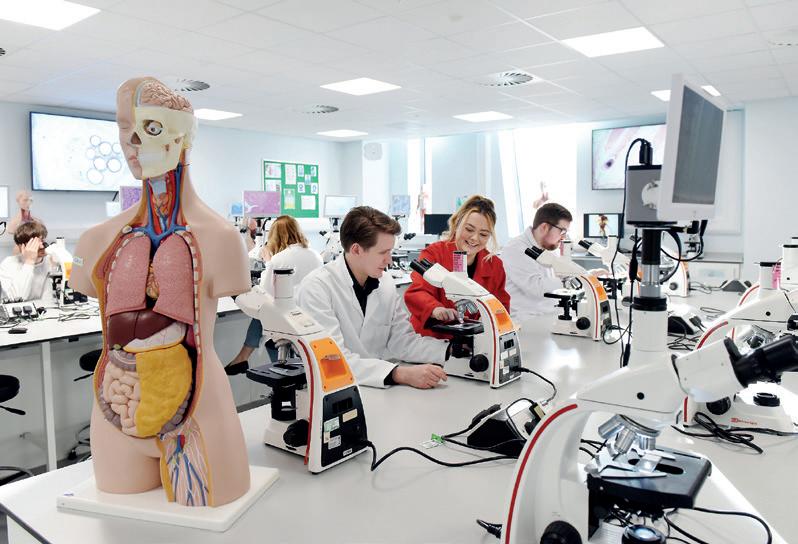
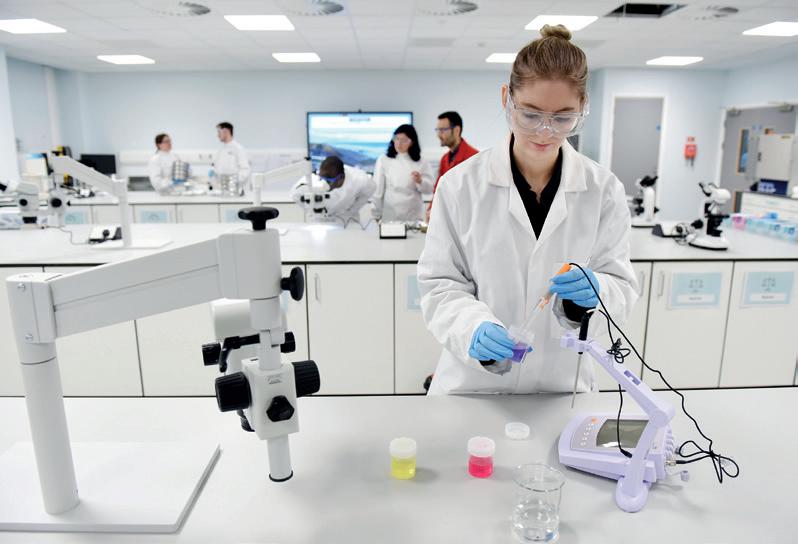
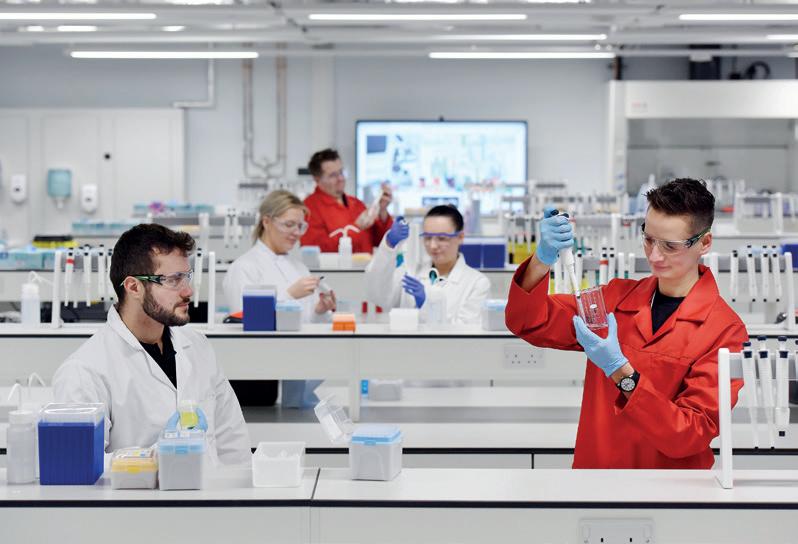
Fire rated glass
Steel Framed Fire doors and screens
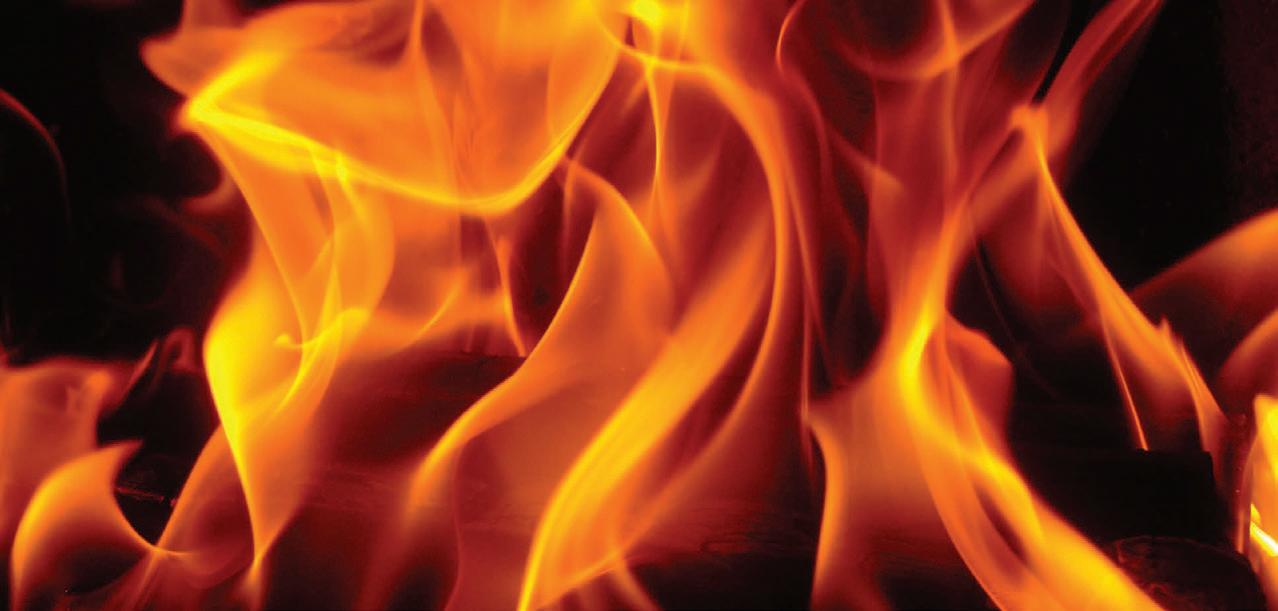
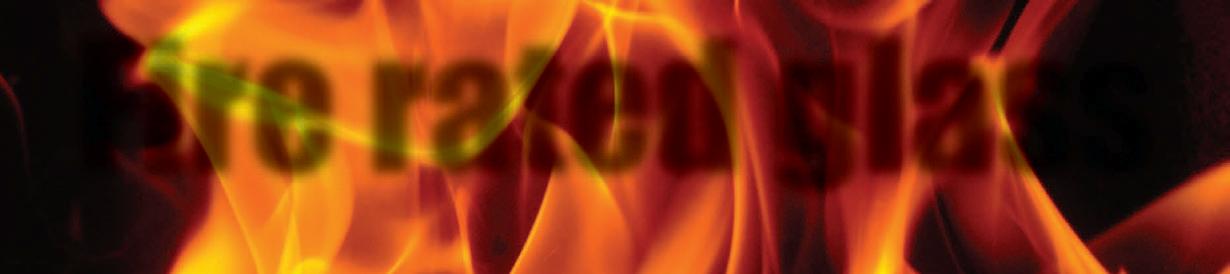
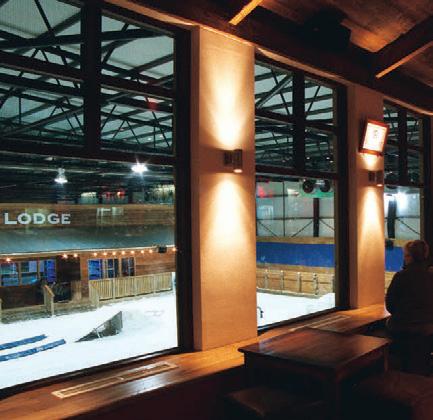
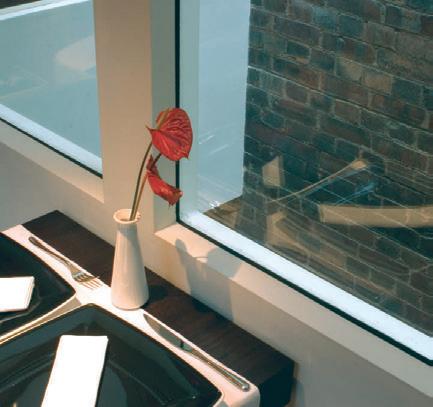
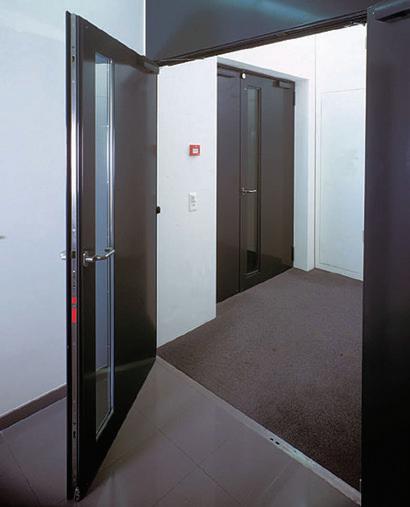
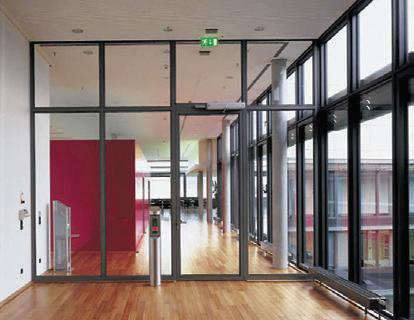
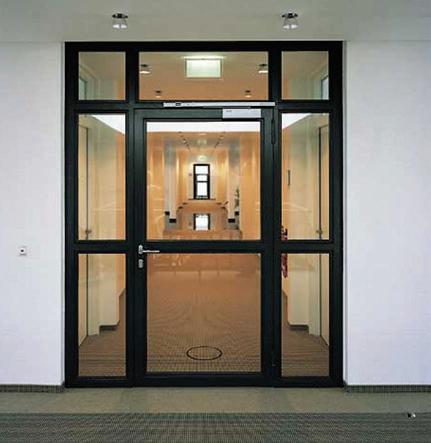

To further compliment our range of fireglass, Firman now offer complete steel framed fire doors and screens. Built to the most demanding specifications for commercial buildings, shop fronts, entrances, interior fire screen walls and virtually any other application.


Each system is designed specifically to suit the requirements of the particular application. Sections can be provided in mild steel, finished to any standard RAL colour, aluminium clad as well as our new range of stainless steel sections available in either a satin or bright polished finished.
Firman offer a full selection of fireglass, on either a supply only or a supply and install basis, providing fire protection from a basic 30 minute integrity only rating through to the highest levels of integrity and insulation.
To find out more about these products visit www.firmanglass.com Firman Glass,19 Bates Road, Harold Wood, Romford, Essex RM3 OJH Tel: 01708 374534 Fax: 01708 340511 Email: sales@firmanglass.com



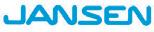
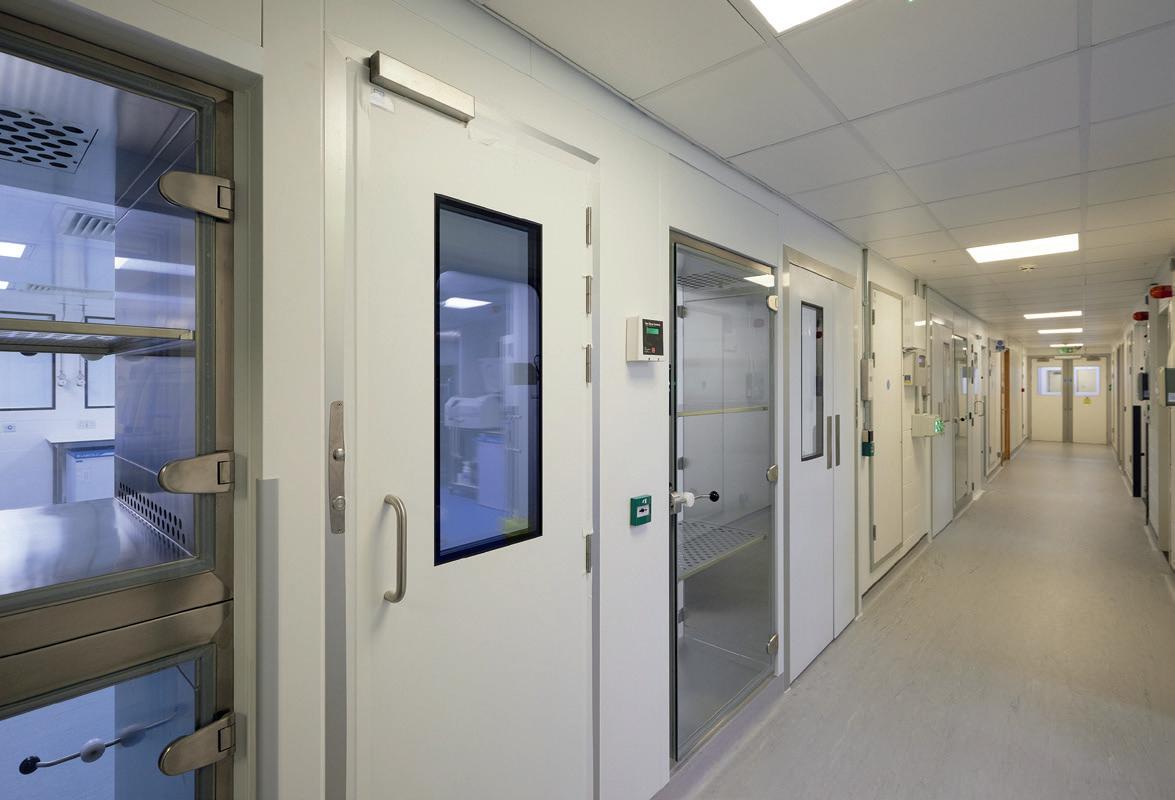
LANDMARK FACILITY EXPANSION PROGRAMME COMPLETED AT KING’S COLLEGE LONDON
King’s College London is one of the most established and respected universities in the world, with more than 33,000 students regularly undertaking studies from over 190 countries. At the heart of its operation is the Rayne Institute, a specialist medical research facility that supports industry advancement.
orking closely with the scientific community, it houses the Gene Therapy Vector Facility (GTVF), which enables the delivery of the latest gene therapies into clinical production.
Seeking to enhance and maintain its position at the forefront of medical and scientific discovery, it embarked on a £5.8m expansion programme with multidisciplinary property, infrastructure and construction consultancy Pick Everard to achieve its objectives.
A key part of the GTVF’s mission was to get projects into production at a greater pace of change, meaning it would need greater cohesion and integration of its teams and services in its current space, which has origins dating back to 2006. The project operated across a 140m2 space and was supported through funding from King’s College London and the EU’s European Regional Development Fund (ERDF), designed to encourage economic development and growth.
Pick Everard was responsible for managing and designing the project, providing mechanical, building, electrical, structural engineering and project management services. Sustainability and a green design were core to the project, with the facility targeting a BREEAM ‘Very Good’ rating.
Solution
A new micro laboratory was created, used for routine environmental monitoring activities and assessment of incoming microbiological media. Two laboratories on the second floor of the Rayne Institute were also fully stripped and fitted-out in order to create two Grade-C cleanrooms to support suites that manufacture viral vectors.
The project also included the consolidation of existing storage areas into one functioning suite, with a refurbishment changing area extended to accommodate the facility’s enhanced service capabilities. To achieve Grade-C status, the installation
of a new air handling unit to support filtration and humidity in the medical environments was necessary.
A key part of Pick Everard’s services also included regular assessment of the impact of its work within a live environment. A temporary scaffold was created to allow careful access for the contractor, which was separate from staff access, while noise impact reports were also a key part of preparatory work. Construction work, such as drilling, required careful coordination with everyday operations at the facility to minimise disruption.
Furthermore, any loss of power stemming from construction work could be hugely impactful to the critical scientific and medical work taking place. With this in mind, backup solutions and worst-case-scenario measures had to be accounted for, with solutions in place as part of a three-week lookahead programme that was verified with each project party, including the client.
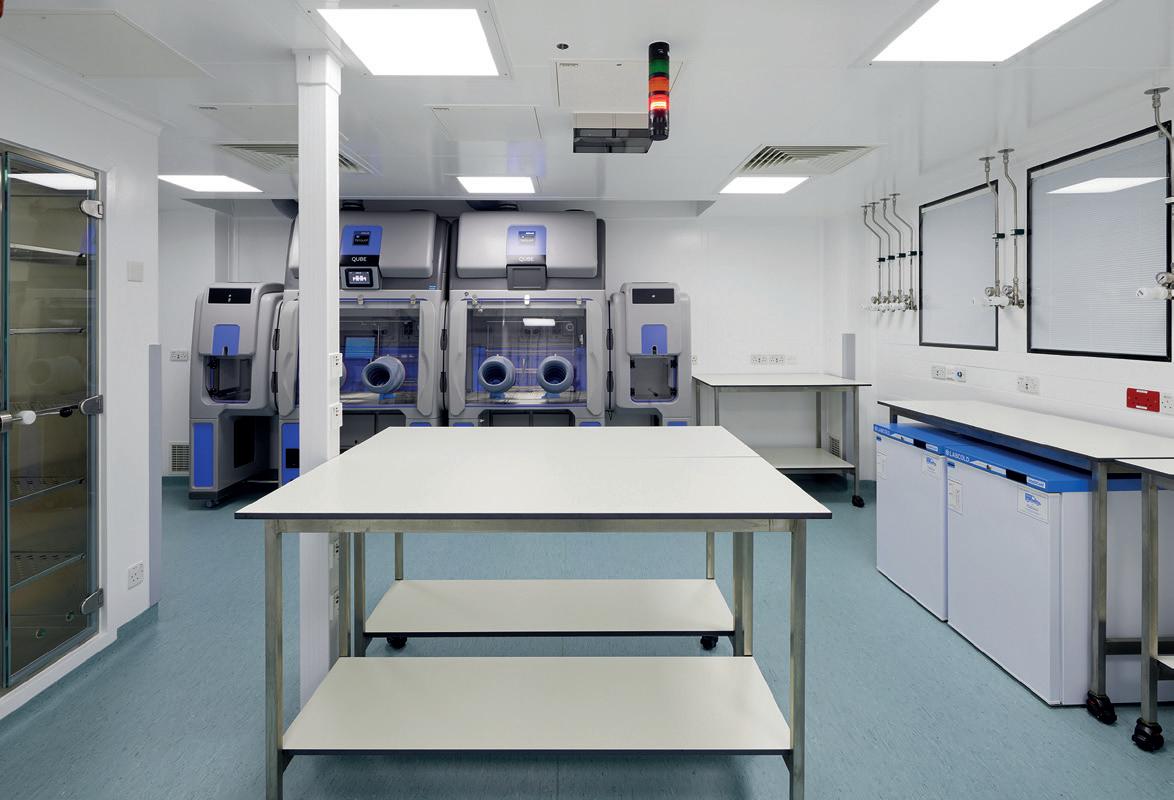
Operational qualification work, including testing of Building Management Systems (BMS) and other installed services, was also undertaken by Pick Everard ahead of project completion.
John Clarke, Director at Pick Everard, said: “This was a highlytechnical operation given the project’s nature and eventual end use. In turn, this presented a range of unique challenges for our design teams, which were carefully navigated through effective stakeholder engagement and ensuring close compliance with Medicines and Healthcare products Regulatory Agency (MHRA) and GMP regulations.
“Our work needed to ensure that it would not interfere with a live environment and the crucial work ongoing within the existing Rayne Institute. As well as undertaking weekly risk assessments, a rigorous preparation process was implemented to ensure no contaminants entered scientific and medical areas.”
Benefits
The GTVF is now one of the largest suppliers of GMP-grade viral vectors for clinical trials across Europe, offering lentiviral, retroviral and soon adeno-associated viral vector services. It can support academic and commercial clients via a team of 50 specialists, with a focus on early-stage clinical activity.
Specifically, the GTVF now has four active, fully-equipped production cleanrooms offering significant lab space. The GTVF is able to service a high volume of client projects, increasing the rate of production. Over the next 12 to 24 months, a further three brandnew, fully-equipped independent cleanrooms are set to be opened, which will further enhance available capacity for client projects.
Feedback
Simon Howell, Professor at King’s College London, says: “This new facility will help ensure that King’s College London and the UK maintain a Europe-leading position in the production of GMP-grade viral vectors for cell and gene therapy. Excellence in this important field of biomedicine will, in the long term, deliver both health and economic benefits for the UK and beyond.”
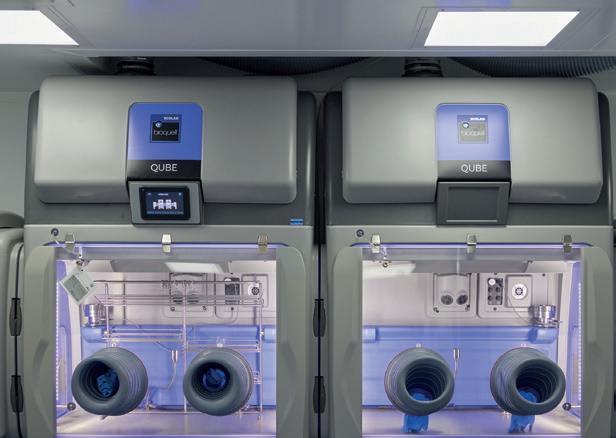
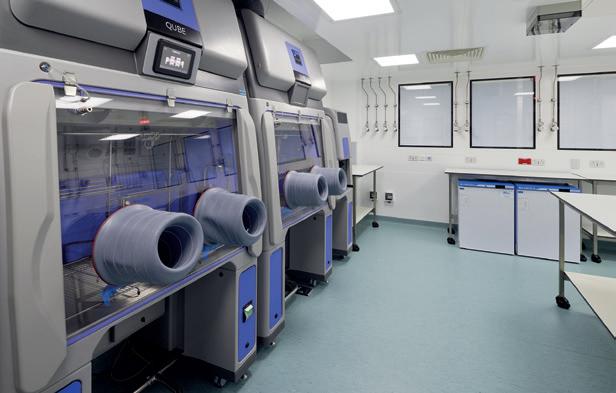

UK PUBLIC PROCUREMENT REGIME CHANGE
The UK Government’s post-Brexit public procurement reforms will take effect in October 2024, when the Procurement Act 2023 goes live. Here, Duncan Osler, Partner at Morton Fraser MacRoberts, explains what you need to know.
The UK Government aims to create a simpler, more flexible system, open public procurement opportunities for small businesses and social enterprises and embed transparency and spending scrutiny throughout the commercial lifecycle. But the new act falls short of revolutionary change, in part since the UK still needs to comply with international rules for procurement regimes. Nonetheless, the new regime is different, introducing a swathe of new terminology and some different approaches.
To encourage broader, more strategic public sector thinking about spending priorities, evaluation criteria must identify the “most advantageous tender” not the “most economicallyadvantageous tender”. Authorities must have regard to delivering value for money, maximising public benefit, transparency and acting with
integrity. There are important new rules on contract management covering payments to suppliers and performance reporting. There are extended transparency requirements; for example, a new published ‘debarment list’ of contractors excluded for serious misconduct and on other grounds.
The UK Cabinet Office is funding a learning and development package in the six-month implementation period through to October 2024 but six months is not a long time for busy authorities and bidders to get to grips with the new regime.
Importantly, the reforms are set to impact differently across the UK, but what will that mean for contracting authorities and bidders?
The new act reforms procurement in England and Wales and Northern Ireland, but “devolved Scottish authorities” are excluded. The Scottish Government
opted out of the reforms and current Scottish public procurement rules will stay in place. Scottish public authorities will continue to follow familiar EU-based procurement rules unless they are cross-border bodies or their functions are wholly reserved to Westminster. So, Scottish public bodies with activities extending crossborder will need to consider carefully whether they will be caught by the new act, or risk procurement non-compliance. UK procurement reforms still will be relevant for many public authorities governed by the Scottish regime. UK frameworks are widely used by public sector bodies, including in Scotland, to ‘call-off’ works, supplies and services. Scottish public authorities will need to understand and comply with the new regime when using UK-wide frameworks established under the new act. And delivery of UK investments in Scotland may

require the new act to be followed for supply chain procurements.
Of course, bidders wishing to compete UK-wide will need to engage under the Scottish and new UK regimes, calling for increased tendering capacity. Care will be needed to understand the differences, including when exercising bidder remedies: the new act limits automatic suspension of contract award to challenges initiated during the set standstill period (minimum eight working days), heightening current time pressures on raising litigation. It is too early to say how the courts may apply the new rules and how far case law on similar procurement situations will diverge.
Ultimately, these procurement reforms will impact differently UK wide. Get ready for regime change this October.
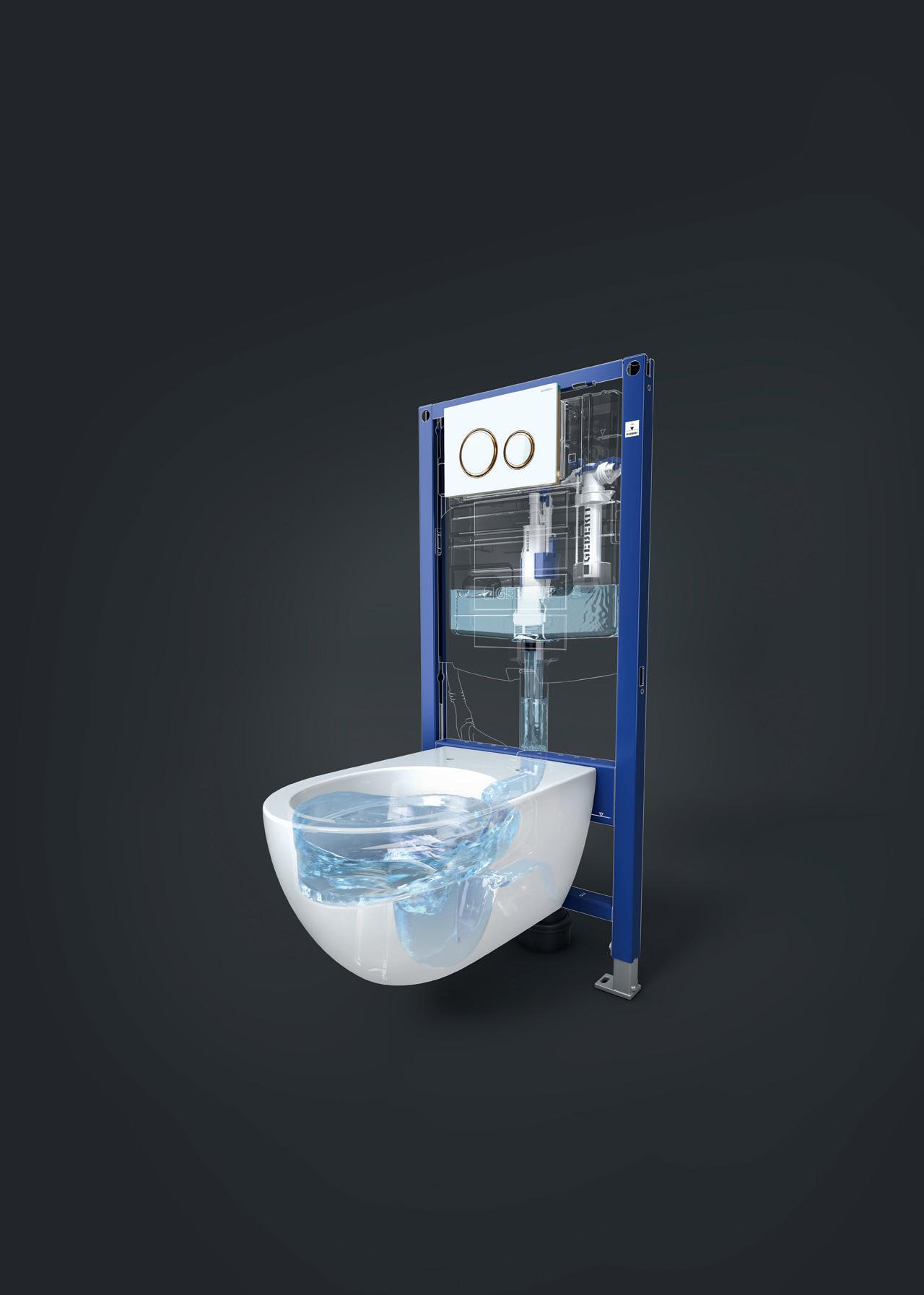
SUPERIOR FLUSH PERFORMANCE
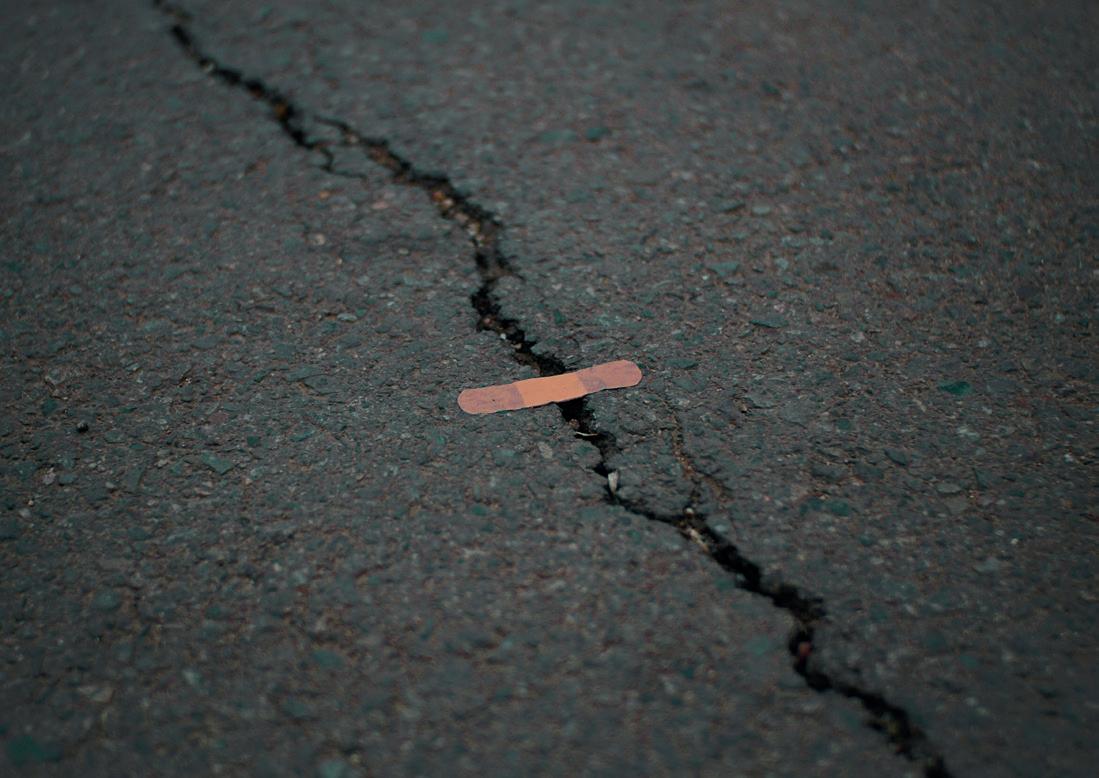
A TAKING THE TEMPERATURE OF RAAC IN THE HEALTHCARE SECTOR
The fairly extensive presence of RAAC across the UK’s healthcare infrastructure has been a thorny issue since the mid 90s when the construction industry came to realise the material’s limitations and lifespan. Yet the problem persists, and the stakes are high for healthcare facilities. If structural collapse occurs, it poses a risk to patients and personnel, and a major disruption to local public health, says Steve McSorley, Director at Perega.
s of February 2024, RAAC has been identified in 541 hospital sites, seven of which require a complete rebuild. It presents a real challenge, and one being taken very seriously, with the Government currently in the process of cataloguing RAAC in public buildings and a concerted effort being made by the NHS to eradicate the product within its estate. The Department of Health and Social Care (DHSC) is now committed to removing RAAC by 20352 and has pledged almost £700m from 2021 to 2025 to achieve this goal.
The silver lining in all this is that we possess the structural engineering knowledge to tackle RAAC head on and either remove it or reinforce buildings as required. However, to ensure this is achieved in as safe and nonintrusive a way as possible, healthcare estate managers need to know what they’re looking for and who to ask for help from. Here, I want to help readers make as informed a choice as possible. So, let’s take a closer look.
How did we get here?
RAAC’s widespread use, especially in NHS hospitals, was predominantly driven by its perception of being lightweight, cost effective and able to provide good thermal insulation. From the 1960s to the mid 1990s, it was used for many structural applications, including ceiling and roof support beams.
Unfortunately, the material possesses an inherent flaw: its vulnerability to water ingress. This results in the gradual corrosion of the product’s steel reinforcement, compromising RAAC’s structural integrity. The bearings of the planks on the structures that support them are also a matter of concern, as it is here that we have the potential for sudden failure. This means buildings with RAAC elements have become potentially dangerous to occupants. The risk is compounded by the difficulty in detecting its presence, as it may be concealed within the overall building fabric.
Historic RAAC installation adds further complexity, especially around the systems used to support it. The standard practice was to use a minimum 50mm bearing on supporting elements, however, new guidance from the Institution of Structural Engineers published in April 2023 recommends a minimum of 75mm, bringing it into line with other precast concrete elements. A larger bearing area can distribute the load more effectively, reducing stress on any single point and decreasing the risk of structural failure. Aligning with other precast concrete elements also helps to standardise construction practices.
Leaving no stone unturned
Luckily, the UK’s structural engineering community possesses some of the answers to this delicate matter. Initial identification, conducted by an IStructEaccredited professional, is often the first step. This involves technical
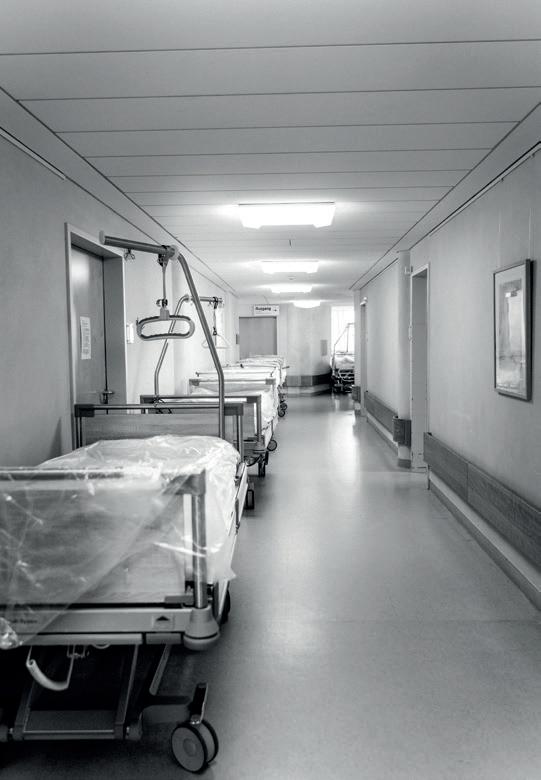
considerations, such as determining the structural condition of RAAC elements and selecting appropriate remediation strategies, along with operational concerns, such as managing the disruption to healthcare services during remediation works.
Full structural surveys are then carried out to identify RAAC’s presence and the extent of it, followed by mitigation and maintenance programmes to ensure staff, patient and visitor safety. Because RAAC can be difficult to identify, intrusive surveys may be required. A critical consideration here is the fragility of RAAC during this process. If work is done, with a lack of care and precision, it could cause collapse.
Depending on the condition of the RAAC, there are three ways of proceeding:
A. Leave it, with a monitoring regime, because it’s in good condition
B. Strengthen the planks where there are signs of degradation
C. Replace them where they are beyond remediation.
Each strategy comes with its own set of considerations. For instance, strengthening existing RAAC elements may involve the addition of support structures or the application of new materials to enhance durability and
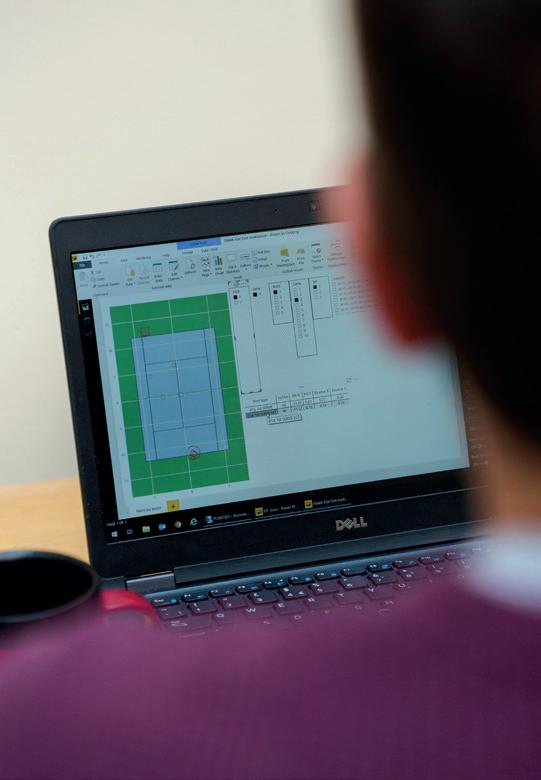
resistance to failure. Alternatively, replacing RAAC elements, especially in critical load-bearing applications, requires careful planning and execution to ensure the structural integrity of the building during and after the remediation process.
Building a safer future
Equally, it’s important to remember that whilst there’s much hype around this issue, buildings containing RAAC elements have been around for some time. In many cases, they’ve remained in place to this day without any signs of deterioration.
That doesn’t mean something won’t happen tomorrow. The construction industry must step up to deliver safe healthcare infrastructure by scrutinising their methods and processes. Fundamentally, we need to explore solutions that will help us build at pace and affordably without compromising safety.
So, in response to the challenges posed by RAAC, structural engineers are busy developing new standards and practices to ensure the safety and reliability of healthcare facilities. This includes the development of guidelines for the assessment and remediation of RAAC, as well as exploring materials and construction methods that deliver greater durability and resistance. It presents a great opportunity for the construction industry to demonstrate its commitment to safety and innovation.

Thankfully, there have not been many instances of RAAC failure so far, but why take the risk? I hope others will follow the example the NHS has set with its commitment to eradicate RAAC as soon as possible and explore the sustainable alternatives we can use to build the healthcare infrastructure of the future. Ultimately, we need to show that, whilst this is a big problem, it can be resolved with the right technical engineering support.
FOOTNOTES: 1National RAAC programme
2https://researchbriefings.files.parliament.uk/ documents/CBP-9917/CBP-9917.pdf
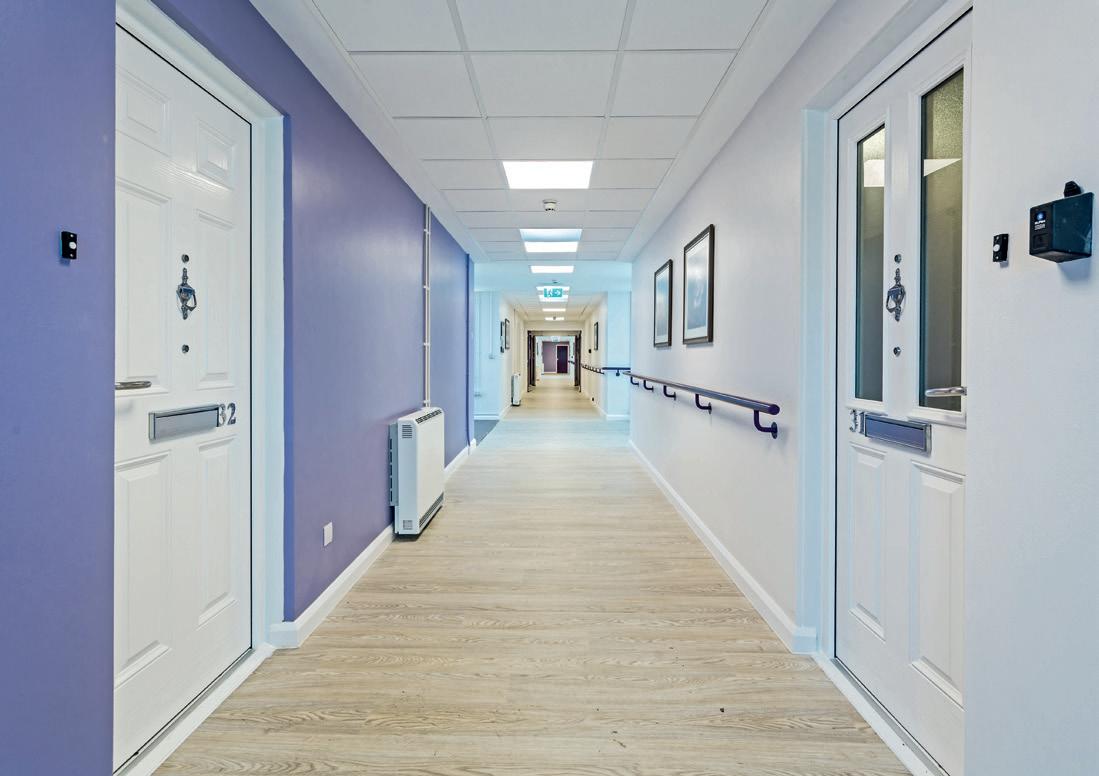
FIRE DOOR COMPLIANCE
With many councils facing a growing financial crisis, they are being forced to do more with less. Services are being scaled back with some being cut altogether. Amidst acute funding pressures, this creates undeniable challenges for those responsible for procuring products and services for property repair and maintenance and, indeed, new-build housing schemes.
They must have complete confidence in the products they are buying and whom they are buying them from,” comments Owen Jones, Technical Director at Distinction Doors, the stockist and distributor of the fds (fire door systems) fire door range. “They want to know they are investing in the best possible solution, and this is underpinned by robust and trustworthy service.”
Nowhere is this more apparent than in fire safety products.
“Understandably some people hesitate when it comes to specifying and installing fire protection. There have been, and continue to be, a lot of changes surrounding fire safety in the built environment, and this causes anxiety, not just for construction professionals but for the building occupants, too. In our experience, decision makers are looking to the supply chain for expertise and assurances, and we have a responsibility to deliver this at every stage of the process,” continues Owen.
Distinction Doors defines these stages as specification, procurement, manufacture, installation and maintenance.
“Fire doors are one product area that is still confounding, especially composite fire doors. As an industry, which includes members of the Association of Composite Door Manufacturers (ACDM), we are working tirelessly to educate and inform specifiers and decision makers of the significant advances, including robust testing, third-party certification and supply chain transparency. It is vital that we raise awareness of modern composite fire door capabilities to help solve the relentless demand for proven, compliant and consistent fire safety products.
Supporting specification and procurement
“Each stage presents its own challenges, but it is essential that specification is addressed appropriately because everything else follows. At a basic level, specifiers must seek confirmation of independent and verified test results, consistent performance, compliance and certified manufacturers and installers. Beyond this, there is now also the option to appoint GQA-accredited fire door inspectors, installers and maintainers. Only then can the scope of the product range be considered.
Certification and compliance
A high-performance composite fire doorset will be independently tested to British Standard BS 476-22:1987 and the more demanding European test method BS EN 1634-1:2014. This is denoted using FD30 and E30, respectively, proving a minimum of 30 minutes of integrity.
For internal applications, the fire doorset must also meet the demands of EN 1634-3:2004 (ambient smoke control). For external use, compliance with BS 6375 (weathertightness) is required.
Compliance with Approved Document L (thermal performance) is mandatory in either setting. Currently, PAS 24:2022 (security) is only mandatory for new-build projects; however, it is often required and specified for refurbishment projects, too. It can be strengthened by additional Secured by Design status, which independently verifies compliance with the Police Preferred Specification.

These tests must be conducted by a third party and certificated using an independent United Kingdom Accreditation Service (UKAS)-accredited test house and/ or certification body.
Supply chain confidence
“As with many building products, the fire door supply chain is onerous,” says Owen. “There are all the components associated with the complete fire doorset and their suppliers, and then there’s the doorset manufacturer, more commonly known as the fabricator, the installer – sometimes this service is also provided by the manufacturer, or it is outsourced. Some local authorities still command a fitting team, although this is rare nowadays. Once the doorset is installed, it’s over to the facilities and maintenance team of the associated council. Increasingly, fire door maintenance and inspections are also being outsourced.”
Voluntary audits
To combat the complexities, several composite fire door suppliers are taking control of their supply chain. This not only significantly reduces risk but also promotes stakeholder
confidence and goes some way to meet the demand for improved product traceability.
“We mandate our supply chain, auditing our manufacturing partners to meet the non-mandatory requirements of Q-Mark STD 170 and STD 050 under BM Trada. Being voluntary, this clearly demonstrates a commitment to quality and offers a strong competitive edge, with more tenders requesting third-party certification as awareness increases.
“This way, we can control all components associated with our fds fire door system, apart from the door closers and sealed units, which must match the tested specification and prevent dilution of the supply chain – a critical factor in the supply, installation and maintenance of fire doorsets.”
Fire door installation
While progress has been made in the supply chain, there is still the matter of competent installation and robust maintenance – both essential to consistent fire-resistant performance and critical in the lifecycle of these products.
“Some installation companies have recognised a demand for thirdparty certification and have taken steps to achieve this; something
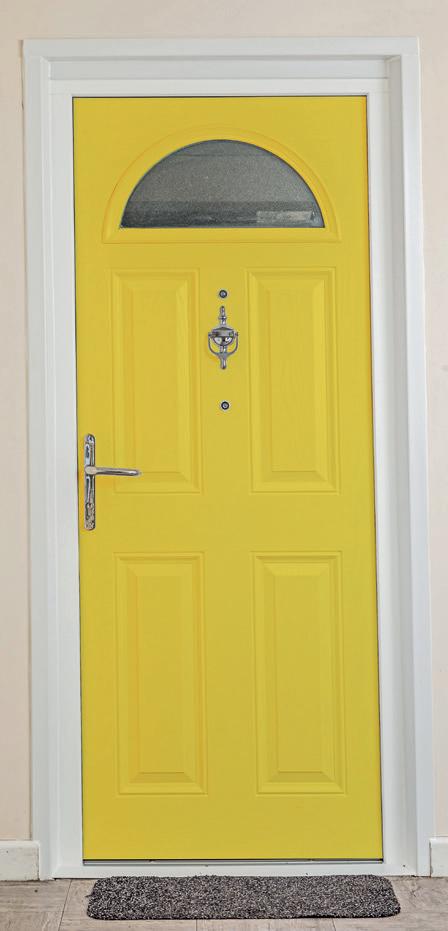
that we encourage. The BM TRADA Q-Mark Fire Door Installation scheme has been “…Designed to provide reassurance to specifiers, contractors and end users that the product they have chosen has been installed correctly and that it should perform as intended.”
“Local authorities would do well to seek installation companies that meet the requirements of Q-Mark STD 052 and demonstrate competence in the installation of fire doors. This can sometimes be the same supplier that fabricates the fire door – in reality, there is no one more competent.”
Door data tags
While voluntary, the increasing use of data tags in fire doorsets will likely drive manufacturers and installers to seek formal qualifications to ensure professional and compliant production, installation and maintenance of the fire doorset.
The data tags hold the ‘Golden Thread’ of information, which provides complete traceability for the doorset and proves effective management and a responsible approach to fire door compliance. Undoubtedly, this will give local authorities the confidence to choose composite fire doorsets for new-build and replacement projects.
www.firedoorsystems.co.uk
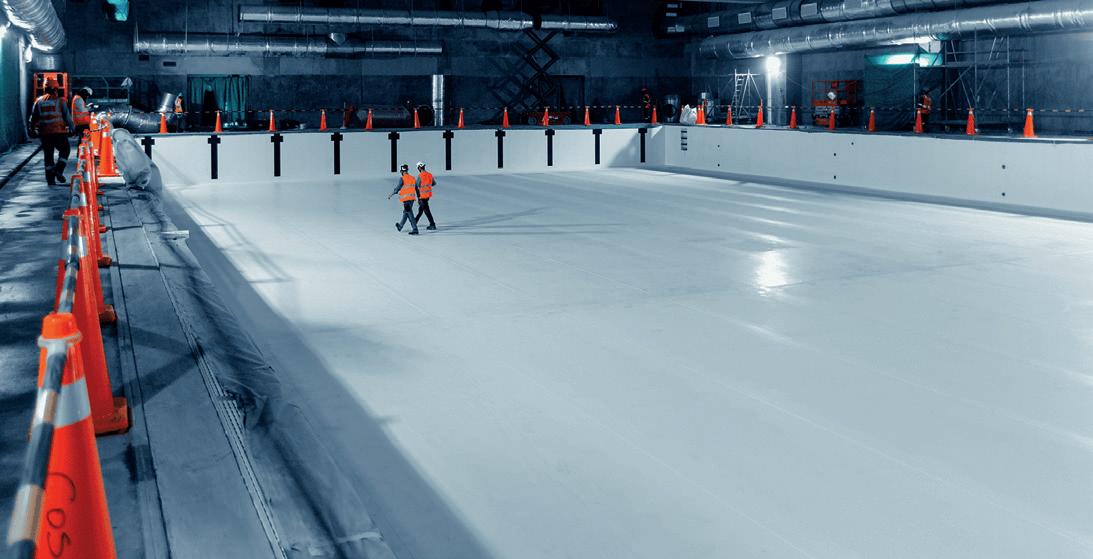
RENOVATION OVER REPLACEMENT: MYTH BUSTING
THE
UK LEISURE SECTOR
News of the Swimming Pool Support Fund has provided much-needed relief for local authorities in crisis mode –seeking to keep afloat the UK’s leisure stock. According to one modular pool provider, common misconceptions around updating facilities are costing leisure operators time, money and sustainable efficiency. Here, Myrtha Pools’ UK Business Development Manager and former Olympic Swimmer, Kevin Burns, discusses how modern methods of construction (MMC) are allowing renovation to come to the fore without the expensive new-build outlay.
Existing pools in the UK rarely meet today’s health code regulations and, therefore, need to adapt to become compliant. This was one of the key outcomes of Swim England’s Decade of Decline report two years ago, which revealed that almost 2000 pools will be lost by the end of the decade, without the intervention of vital funding in the sector. Now, leisure operators, relieved somewhat by the second round of Government funding, are fighting hard to meet modern standards, particularly with net zero at the core of sector-wide ambitions.
Replacing traditional concrete, gunite and shotcrete pools, however, is not just the answer. It has long been the modus operandi of local councils facing outdated pools – yet it’s a frustrating sticking point that we see too often as pool designers in this space, and it doesn’t have to be undertaken via a complete pool replacement.
Instead, renovation is breathing new life into creating affordable and sustainable pools for leisure operators, that are designed with the end goal of getting more people swimming in our regional communities. Here, we run through the most popular myths held by the leisure sector and the indecision that prevents it from delivering a profitable future for all.
Myth 1: I’ll lose vital profits by shutting down my pool for an extended period
Many leisure operators, already struggling to manage the day-to-day running of a pool, simply fear the costly outlay of shutting down their facilities and the losses this will incur until a new one is opened.
However, pioneering MMC techniques are allowing renovation practices to be undertaken in tightly-controlled production environments, with installation and delivery taking place at the very last moment – minimising disruption to site and allowing public pools to stay open longer than would be possible with a complete new build.
Operators through this methodology can completely reskin an existing pool to deliver several sustainable improvements, taking a pool out of operation for mere weeks, rather than months on end.
Pool reskinning as part of the renovation process is adaptable to its construction environment, whether that be on site or off. The steel/PVC materials used by experts like us is malleable and flexible, being millimetres thick and easily fused to the existing structure of a pool. It can be delivered in pre-manufactured rolls to site, ready to go and installed in a short period of time.
Myth 2: I’ll just be making ‘appearanceled’ improvements with no long-term gain The streamlined process of renovating a pool structure, along with the adaptability of the reskinning process, is beneficial to not only the cost and manpower associated with the project but also the carbon footprint. By taking the time to fix an old leaking pool with a watertight, insulated skin, pool authorities make incremental, sustainable gains that will, ultimately, have a long-lasting impact on the daily running cost of operating a pool.
At Myrtha, we estimate that a completely renovated pool can provide a 45% reduction in its carbon footprint, with 20% saved in running costs, against traditional construction methods that only use tile and concrete. It is these kinds of savings that allow operators to stand up and take note of how new ways of working can breed long-term benefits for their leisure facilities and sector wide.
Myth 3: I’ll have to completely change everything about my pool. I can’t just renovate individual areas. Far from just a simple reskin, the accessibility created by offsite construction allows for more than just a surface-level change. Improvements in both guttering and filtration can be achieved through renovation, delivering additional benefits to hygiene and water quality. While decisions

here may increase installation periods, many of the materials required for these processes can be pre-formed off site or, in some cases, adapted to existing concrete guttering.
We’ve worked with many operators that walk that difficult tightrope of budget, delivery and timeline estimations; balancing community need with planning for the future. It is really a case of working closely with all stakeholders in a project, determining their requirements and having early engagement as a core mantra, to ensure a streamlined interchange between old and new facilities, with minimal disruption to everyday programmes.
Myth 4: I won’t attract any new swimmers unless I make substantial new-build improvements It is important to highlight the depth and scale of just what can be achieved through renovation. While aspects such as floor depths and lengths of pools require longer-term adjustments, zero-entry or sloped entry options, for example, can still be achieved with any pool renovation – increasing swimmer accessibility in an age where inclusivity is so important. Swim England estimates that 1.88 million children are swimming every week in England, so it’s imperative that leisure operators increasingly look at ways of accommodating their needs in the most cost-efficient manner.
Myth 5: Safety improvements in the modern age will require a complete overhaul
The inclusion of soft-walk safety floors and added bubble systems to create an air safety cushion for divers are both practical and easy ways local councils can adapt their current pool stock to meet modern safety standards. The COVID-19 pandemic completely refocused efforts industry wide around safety, and not just in terms of hygiene and infection control. Operators must ensure that their pools can adapt to different market needs and age requirements and ensure safety systems tie in with this if they are to survive and increase their profits at times of rising inflation rates and spiralling operational costs. There are lots of innovative technology features offered on today’s market, that can be integrated into current stock, from ‘AngelEye’ safety systems that can help lifeguards in preventing incidents of drowning, to recessed steps and movable bulkheads, that can assist swimmers and cater for different swimming programmes.
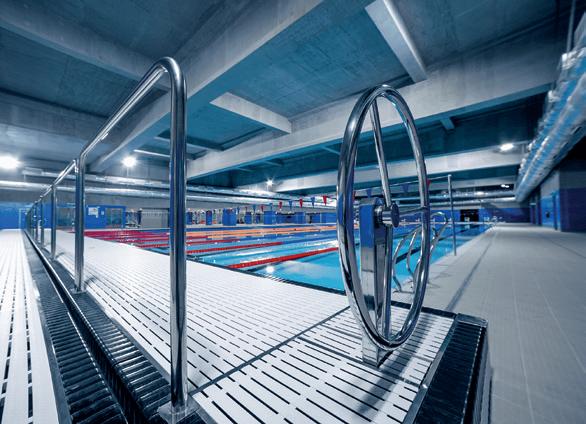


WHY CHOOSE BREATHABLE EWI?
Here, Matthew Woodhams, Technical Specification Manager at Baumit, looks at the advantages offered by breathable external wall insulation (EWI) for homes built with solid walls.
Solid wall is a common construction method for homes built in the Victorian era up to the early 20th century, but today’s requirements for energy efficiency, sustainability and better thermal performance mean local authorities need to upgrade them. For many, external wall insulation (EWI) is the preferred choice, and here we look at some of the reasons why.
Breathable EWI systems are designed to allow moisture in the building fabric
to travel through the structure to the outside. This relationship between moisture and insulation, particularly with solid walls, is essential for the structural health and performance of the building.
One of the primary concerns when it comes to solid wall insulation – both in new-build and refurbishment projects – is the risk of interstitial condensation. This happens when water vapour reaches a point that is 2 to 3° degrees cooler and condenses within the structure of the building.
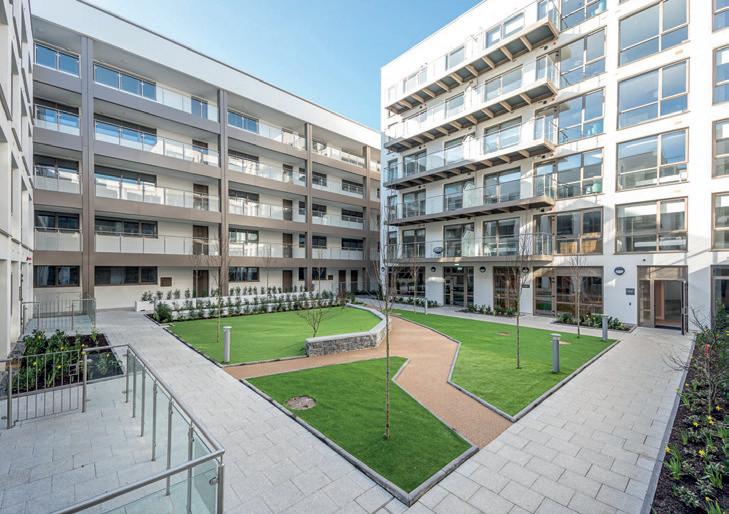
If insulation materials slow down the escape of moisture or are nonbreathable, they can inhibit the ability of moisture to escape. This can lead to serious issues with interstitial condensation, dampness, mould, rot and structural damage.
The importance of breathable wall insulation
When selecting EWI, the goal is to ensure that the temperature across the entirety of the insulation system remains higher than the dew-point temperature of the water vapour. This means keeping the walls warm enough to prevent condensation.
Breathable external wall insulation does this and offers an additional advantage in that it avoids trapping moisture internally. Vapour control layers can be installed on the warm side of the insulation to slow the rate of vapour entering.
It is also crucial to eliminate thermal bridging to avoid cold spots in the walls where condensation can gather. Additionally, a well-planned ventilation strategy and regular heating during colder weather are essential for maintaining warmer walls and avoiding condensation.
Natural, breathable insulation materials, such as wood fibre, are an excellent choice for EWI. This material can hold significant amounts of water vapour without compromising its thermal capabilities or structural integrity. It gradually releases any stored moisture as the external temperatures improve, creating a dry and healthy internal environment.
We’ve also developed EPS external wall insulation boards featuring our OpenAir technology. This ensures high vapour permeability, enabling it to be released externally. This creates a highly-breathable insulation system with all the installation advantages of standard EPS boards.
The aesthetic finish of the external wall insulation system is another important consideration. Lime-based renders are often recommended for their natural, eco-friendly and breathable properties.
The answer
Building owners and specifiers choose breathable external wall insulation systems because it provides long-term cost savings through reduced energy costs as well as enhanced weatherproofing, sound attenuation and better internal environment. That makes EWI an effective choice for the millions of existing buildings in the UK that have solid walls as well as new builds looking to access the benefits of breathable construction.
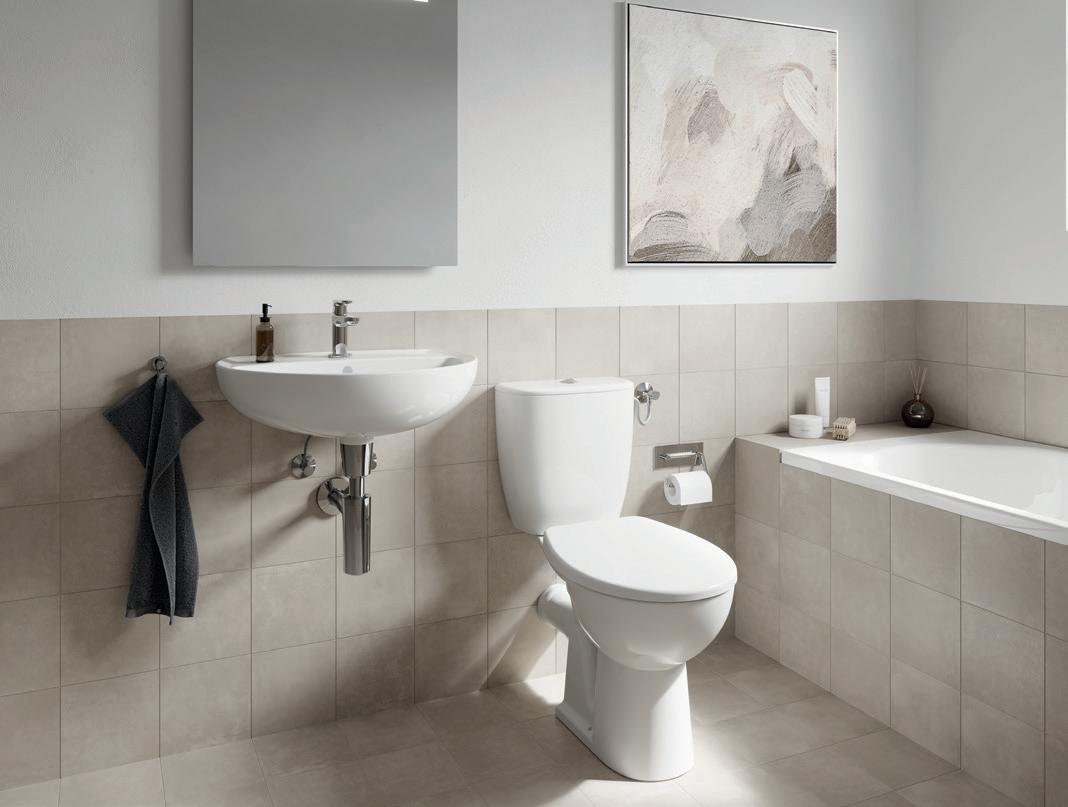
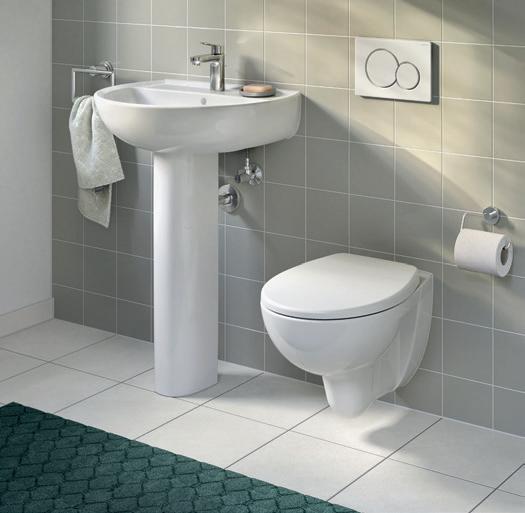
Made for professionals
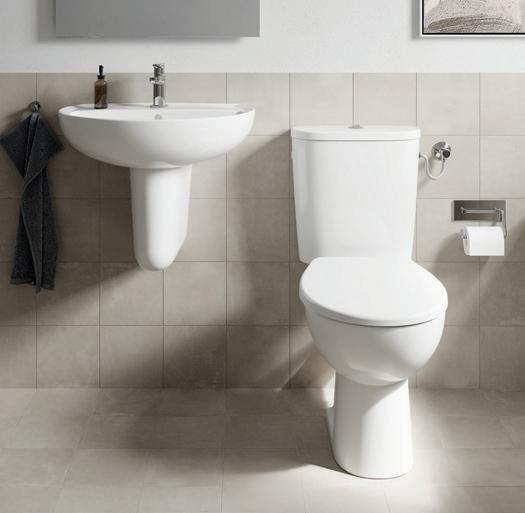
Twyford understand that product durability and stock continuity are key to fulfilling your housing targets and maintenance obligations. We also provide unrivalled logistical support, production, planning and installer training, advising on everything from bathroom safety to reliable pipework connections. This unique level of understanding, alongside delivering exceptional product choice and spare parts availability is the reason why today, we’re trusted by social housing providers all over the UK. For more information, download our Everything Affordable Housing brochure. Visit twyfordbathrooms.com
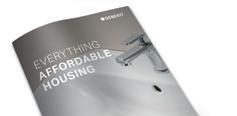
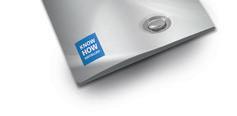
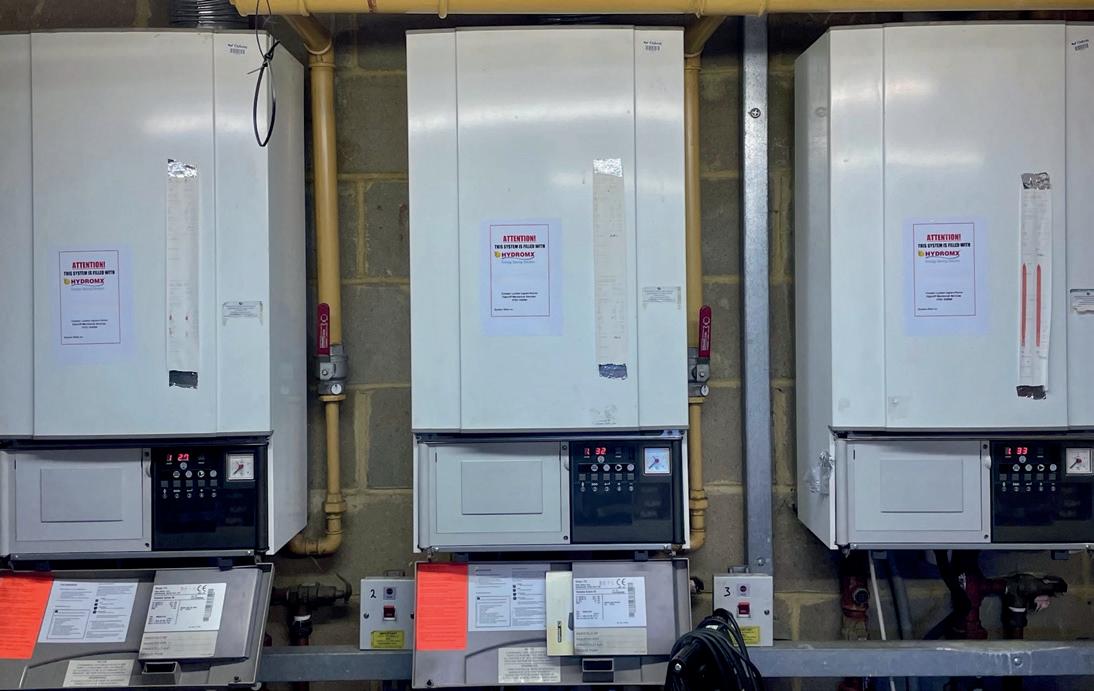
DIOCESE SCHOOLS BENEFIT FROM REDUCED HEATING BILLS
After staffing costs, energy bills are often the next biggest spend for schools. And with the demise of the Government’s Energy Bills Discount Scheme – with no replacement on the horizon – education budgets look set to be further squeezed, says Dominic Wish, HMX UK’s Technical Director.
Implementing energy-saving measures in primaries and secondaries is an ongoing focus for local authorities, academies and other organisations driving to hit net-zero targets and reduce energy bills in educational establishments.
Improved lighting, renewables, energy audits and upgrading heating systems are often starting points. An Environmental, Social, and Governance (ESG) strategy can also be a powerful tool not just to manage energy costs but also enhance a school’s reputation and deliver learning opportunities for pupils.
So with these established routes to better manage energy bills is there demand for another approach? We think so, as do our clients, who are benefitting from a relatively straightforward approach that has already delivered energy and cost savings of 35% and more for a group of schools in Essex.
Comfort levels
The Diocese of Chelmsford became the first in the country to adopt cutting-edge technology for the voluntary-aided primary
schools in its portfolio. The move saw it add a product called Hydromx to central heating systems in more than 30 schools with almost immediate effect, with heads reporting that hard-to-heat offices and other areas of their schools were far more comfortable heat wise. One said: “It’s such a great product. Everybody I have spoken to can’t quite believe how good it is.”
But while comfort levels are important, the real impact is in fuel bills and carbon emissions, with one school making a saving on its energy bill equivalent to its yearly book budget.
Prior to introducing Hydromx across its school portfolio, the Diocese – which is working towards a net-zero commitment – conducted a pilot project to assess the product’s performance, installing it in five schools. Of these, three recorded before and after energy usage statistics reveal gas consumption savings of between 37.5 and 47% from November 2022 to January 2023 when compared to the previous year (with an HDD – Heating Degree Day –calculation applied). ROI ranges from 1.42 years to 2.18 years. It should be noted that the schools fitted TRVs to manage
the heating and ensure optimum savings. There has also been a significant focus on energy saving within each, leading to these outstanding results. Reduction in carbon emissions of around seven tonnes per site per year are predicted.
Guaranteed
Hydromx is a cutting-edge heat transfer solution that improves the thermal conductivity of fluid within hydronic (water-based) heating and cooling systems. It is in use worldwide (New York’s Empire State Building has been benefitting from it for years, reducing chiller run time and cutting plant electricity bills by up to 50% in some cases) and is compatible with most HVAC systems. No major plant or system changes are required. The additive is noninvasive, inert, recyclable and guaranteed for 20 years. It performs the tasks of an inhibitor, protecting against calcification, corrosion, freezing, bacteria and algae growth. Depending upon the application and system characteristics, building operators and owners can expect carbon and cost savings of between 20 to 35%.
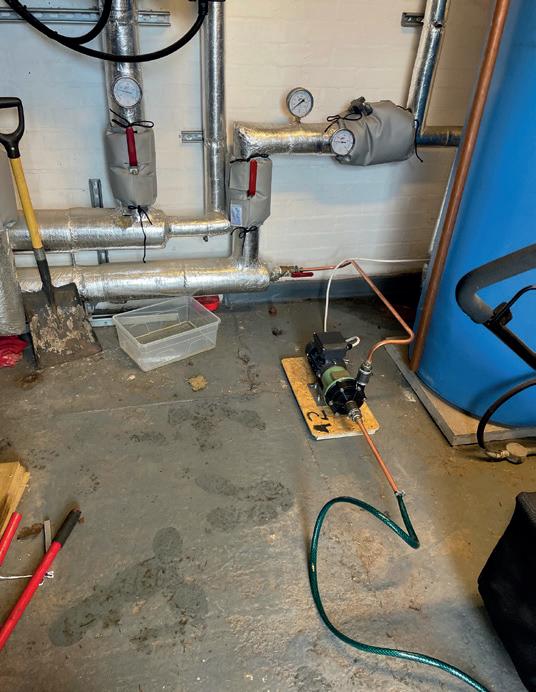
Installation
There are two key elements of installation – assessing system volume and ensuring it is clean (which usually means flushing to remove sludge and inhibitors. This process can also help ascertain volume if unknown). The heating/cooling system should be in good condition. Remedial work, if required (for example, the fitting of thermostat radiator valves), should be carried out prior to installation to ensure increased heat output can be managed. Boiler sequencing/thermostats will also need adjusting accordingly.
The Chelmsford Diocese school installations have all been carried out after school hours, over weekends or during holidays, with most taking less than a day. Once the heating system is confirmed as suitable (flushed, no leaks, TRVs fitted, remedial work completed etc.), it is drained down and refilled with a mix of water and Hydromx.
How it works
Economic and practical reasons have driven the use of water in central heating systems – it’s low cost and efficient. However, the development of Hydromx offers a new and far more efficient approach. At the heart of the product is nano-technology; it’s an accepted scientific principle that material properties change as size approaches the atomic scale, with the surface-area-to-volume ratio increasing. A cup of nanoparticles offers roughly the same surface area as almost two football pitches, and increased surface area equals increased heat transfer capability.
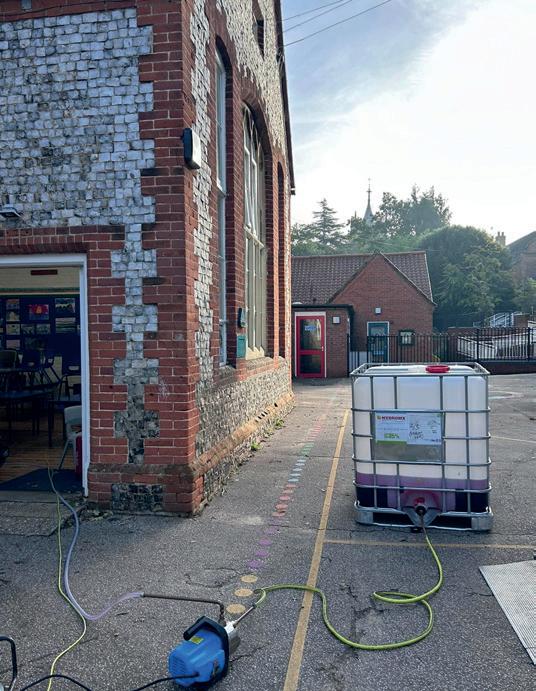

Nanoparticles are already an established technology delivering benefits in a variety of fields, from paints to glass, aerospace to medicine and even school uniform. Their use isn’t new within heating applications either but scientific advancements mean these tiny particles are now delivering substantial environmental and costsaving advantages. Sound scientific principles support their use and worldwide installations demonstrate results.
The approach is simple – replace water in hydronic systems with a fluid that has superior heat transfer properties. Not only does the heating or cooling system reach the desired temperature more
quickly (therefore, using less energy), but cycling is also reduced, offering the potential of increased equipment lifespan and lower maintenance requirements. It’s a win-win situation and can even negate the need for new plant if increased heating/cooling is required.
In many ways, it’s an obvious solution to make commercial HVAC systems work more efficiently. But applying fluid technology to this area has been largely overlooked until now and it’s challenging clients, specifiers and contractors to reconsider a fundamental element of HVAC systems.
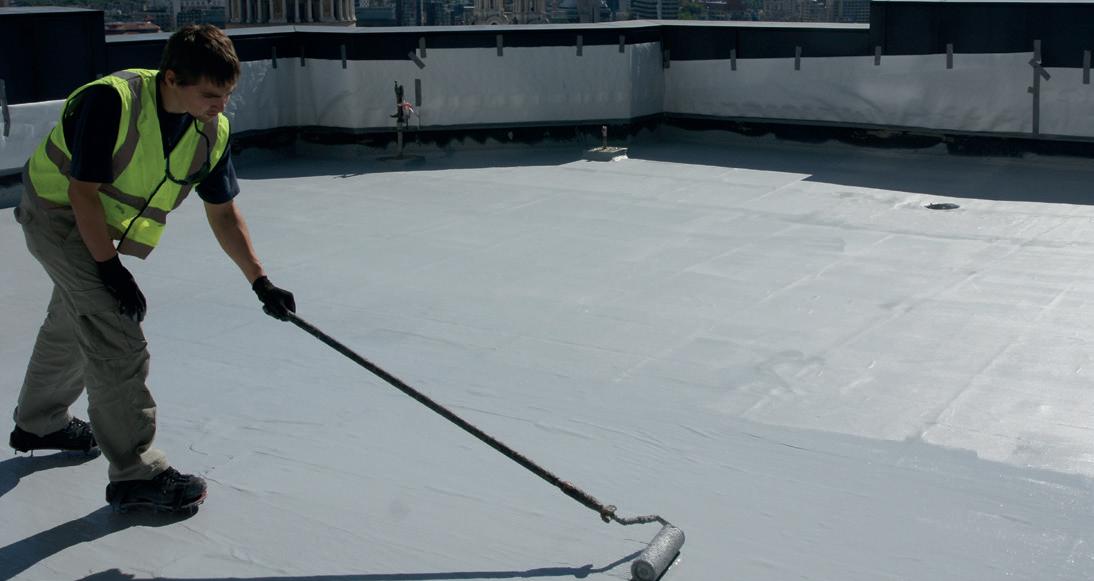
FLAT ROOFING: THE ROLE OF BROOF(T4) CERTIFICATION
In the dynamic realm of social housing refurbishment, Wayne Chissell, Technical Director at WestWood Liquid Technologies, highlights the importance for waterproofing manufacturers to surpass minimal requirements in health and safety protocols.
There is an emerging urgency to enhance roofing and waterproofing standards within the UK’s social housing landscape. With a rising demand for improved living conditions and heightened safety measures, there is a pressing call for manufacturers to exceed the minimum requirements in their products and how they deliver. The BROOF(t4) standard emerges as a pivotal benchmark, setting the baseline for roofing materials’ non-combustibility and ensuring robust fire safety measures in housing refurbishments.
Accountability matters
In discussing the evolving landscape of social housing, accountability takes centre stage. There are challenges posed by the current self-regulatory model in roofing and liquid waterproofing, emphasising the need for proactive measures to safeguard longevity and safety in housing association properties. By embracing standards like BROOF(t4), manufacturers demonstrate a commitment to accountability and quality assurance, mitigating risks and ensuring peace of mind for both residents and stakeholders.
What is BROOF(t4)?
BROOF(t4) classification, obtained through TS 1187 within the EN 13501-5 standard, evaluates roofing materials’ fire performance. It specifically measures their resistance to external fire exposure, crucial for preventing flame penetration and spread. BROOF(t4) compliance is integral, ensuring roofs meet stringent fire safety standards and bolsters safety of occupants by reducing the risk of flame spread. This regulation significantly influences specification, necessitating high-fire-resistance materials capable of enduring external fire exposure. Commonly-used system build ups meeting BROOF(t4) include liquid-applied membranes, and all of WestWood Liquid Technologies’ PMMA systems align with this regulation. During installation, manufacturer training and guidelines must be adhered to, which includes robust sealing, appropriate detailing at roof penetrations and integration with other fire safety measures like compartmentation and fire barriers.
Roofing professionals must prioritise regulatory compliance, seeking relevant training and certifications to demonstrate competence in designing, installing and maintaining firecompliant roofing systems. Compliance not only enhances industry reputation but also instils client confidence in buildings’ fire safety.
The demand for fire-compliant roofing solutions, such as those from WestWood, has surged due to stricter regulations in recent years – post Grenfell. Manufacturers are focusing on innovative products that offer improved fire-related performance while retaining other desirable properties such as durability, flexibility and offering a robust solution. Ultimately, investments in fire safety measures during construction yield long-term benefits by reducing fire-related damages and enhancing occupant safety.
Collaborative planning for success
Collaboration emerges as a cornerstone of success in complex housing refurbishments. Meticulous planning during social housing refurbishment is paramount; balancing budget constraints, time pressures and resident safety considerations must all be well thought out. With residents often remaining in situ during refurbishment, the need for seamless coordination, efficient execution and quick application becomes paramount –which is when the advantages of PMMA liquid technology come into their own. By fostering collaboration among stakeholders, from manufacturers to contractors and housing associations, projects can navigate challenges effectively while upholding the highest standards of safety and quality.
Unlocking the benefits of PMMA
Polymethyl methacrylate (PMMA) systems are not a new concept when it comes to public sector specification. In fact, PMMA technology is leading the way in terms of innovative and versatile solutions for housing associations, education, healthcare and local authorities. Quality PMMA systems, specified by a trusted and accredited manufacturer, will offer a durable, UV-stable, quick, easy and sound waterproofing solution.
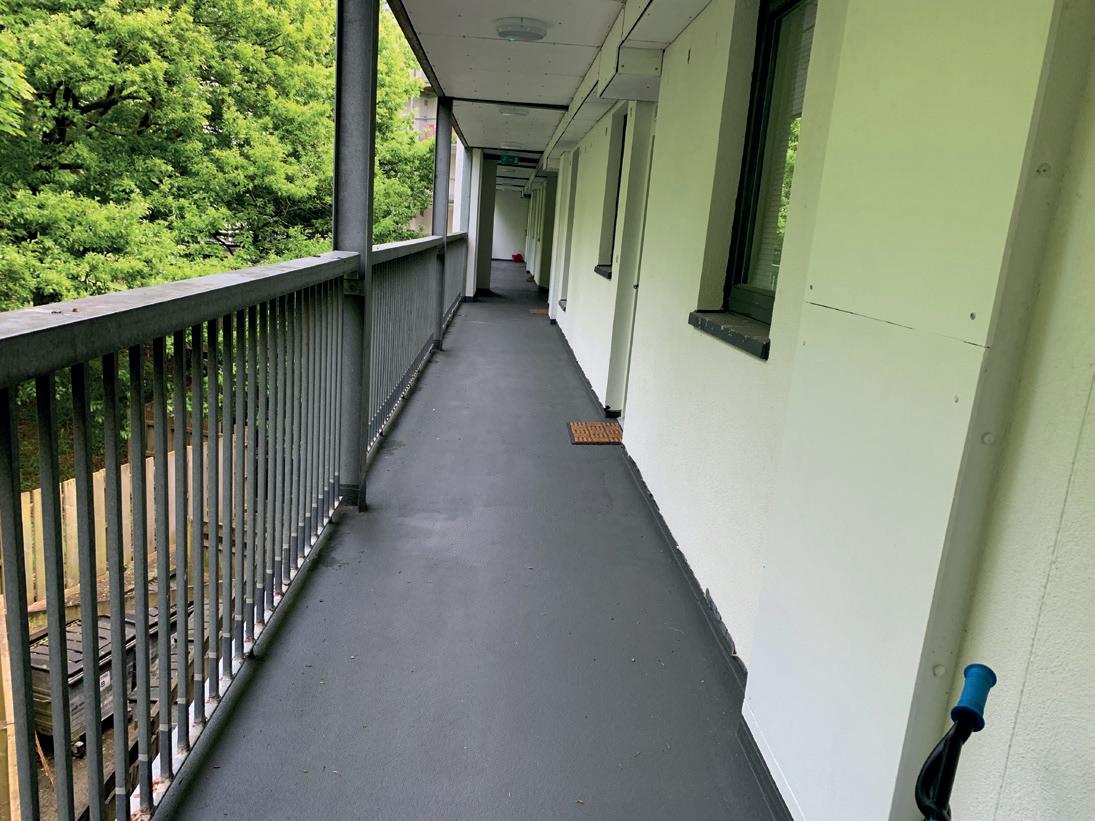
PMMA has benefitted the construction industry for decades. Thanks to ongoing research, development and investment, it is also a technology that has continuously evolved, making it a highlyversatile, safe and durable solution for applications including flat roofs, car parks, balconies as well as a multitude of other options.
Installation benefits
PMMA-based systems, which are solvent free and cold applied, tend to have a minimum of two components. The first being the resin and the second being a catalyst or activator. Contractors will mix the components together on site, starting an exothermic reaction to initiate the curing process.
The PMMA systems offered by WestWood, much like other manufacturers, provide a polyester reinforcing fleece that is first saturated within the waterproofing layer and bonds the membrane to the substrate as it is applied in its wet state. The surface layer is then applied onto the embedment coat whilst still wet, therefore, forming a single, seamless membrane of uniform thickness.
One of the reasons why PMMA is so successful is that it can rapidly cure – ideal for occupied housing blocks, for example. The liquid membrane can be cured in as little as 15 to 20 minutes, even at sub-zero temperatures. With variable amounts of catalyst added to the resin, the curing times can be controlled on site to suit the requirements of the installation team.
PMMA is an ideal solution for UK working due to the variable British weather. Certain systems, for example, can be applied in temperatures down to -15°C, meaning you don’t need to delay application if weather conditions worsen.
Safe and solvent free
A key advantage of using a PMMA system is that it does not require an open flame to install on site. This is a huge health and safety benefit for both the contractor, client and end user and useful for any projects that prohibit the use of a flame on site. To date, there have not been any incidents of fire recorded globally on a roof due to PMMA being installed.

As with any construction site work, there are always risks associated with building. At WestWood, our protocol is not to sell products to any contractor that hasn’t undertaken our mandatory contractor training. This is paramount to not only ensure the safe installation of our PMMA systems, but to guarantee a durable and robust solution for the customer.
Driving excellence
By prioritising safety, accountability and innovation, manufacturers can empower housing associations to deliver refurbishment projects that prioritise resident wellbeing and long-term sustainability. In the journey towards elevating roofing standards, BROOF(t4) stands as a beacon of quality assurance, ensuring that every refurbishment project meets the highest standards of safety and durability.
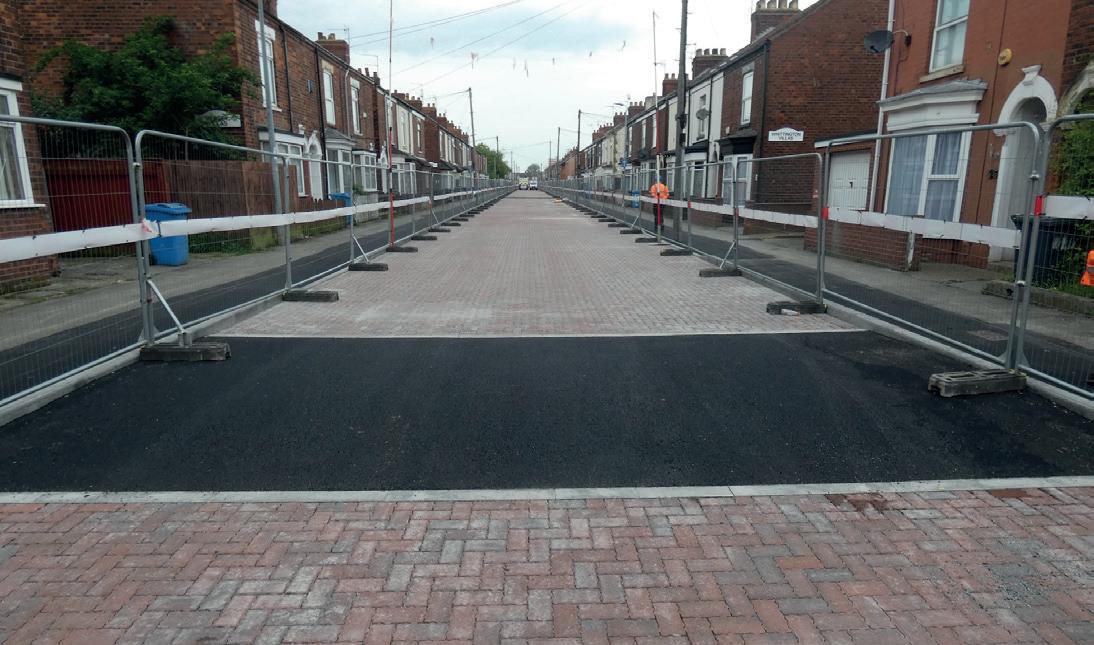
BRETT LANDSCAPING PROVIDES PERMEABLE PAVING TO £23M HULL FLOOD RESILIENCE PROJECT
The first part of a vital £23m project to alleviate the risk of flooding in Hull has been completed with product, design support and onsite assistance from Brett Landscaping.
Brett Landscaping has worked with contractor Morrison Water Services, civil engineer Alan Wood & Partners, Yorkshire Water and Hull City Council to retrofit Rosmead Street, a residential street vulnerable to surface water flooding, supplying 4000m2 of concrete block permeable paving.
The Rosmead Street scheme is the first part of a £23m investment in surface water management schemes planned across Hull and East Riding due to be completed over the next five years, coordinated by the Living With Water partnership.
Hull has always been a city susceptible to flooding due to its location on lowlying land alongside the Humber estuary and River Hull. Surface water from the surrounding area and the city itself has to flow through a series of drainage and sewer networks to discharge into the estuary. This system was challenged in 2007 when over 9000 properties were flooded. Since then, a number of partners have joined together to work on increasing the city’s resilience through awareness and engagement, alongside investment in the infrastructure.
The Living With Water partnership consists of Hull City Council, East Riding of Yorkshire, Environment Agency, Yorkshire Water and academic partner University of Hull with the objectives of raising awareness of flood risk in the region, educating and engagement with the community and look at ways to mitigate surface water flood risk in the area.
At Rosmead Street, the Living With Water team committed to a SuDS retrofit scheme that would help to mitigate any future serious rainfall incidents by removing the original Macadam roadway and using permeable paving to attenuate the water flow and ease pressure on the sewer systems.
Brett Landscaping supplied 4000m2 of its 80mm Omega Flow permeable paving. This rectangular block paving has a unique nib design that performs both structurally and hydraulically. It allows surface water through the joints between the blocks into the construction below while providing structural integrity to the pavement surface.
This form of SuDs is ideal for residential areas where the surface water needs to be managed whilst also providing a hard
trafficable pavement in areas where car parking is at a premium.
The Brett team supplied design services, sharing their experience and knowledge with Yorkshire Water on how the permeable paving systems would work in the future following installation.
By using Brett Landscaping’s PermCalc software, they were able to calculate the specific hydraulic and structural requirements for the design of the pavement at Rosmead Street.
Hull-based consulting civil and structural engineer Alan Wood & Partners worked extensively on the hydraulic and structural design for the retrofitting of the permeable pavement to Rosmead Street and needed to ensure that the system was both buildable and fit for purpose.
The technical team at Brett Landscaping was able to provide that detail on how to achieve compliance to BS 7533-13: 200 for a Type-C, fully-lined tanked system along the full length of the carriageway with a Dense Bituminous Macadam road base, to attenuate the surface water before it passes into the Yorkshire Water network of sewers.
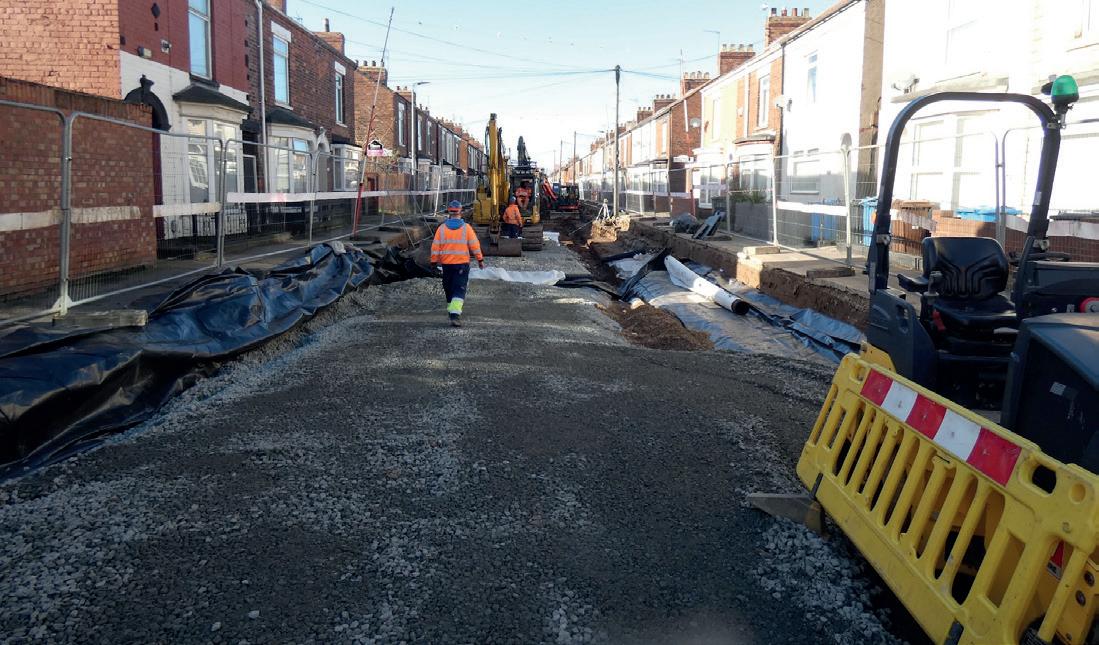
This would serve to ensure a long-term attenuation of stormwater while maintaining the strength and integrity of the permeable paving as it manages heavy traffic loads, with Brett Landscaping providing a maintenance programme to ensure the stabilisation of the paving joints and to mitigate the future clogging of the jointing material.
Finally, Brett Landscaping worked with Alan Wood & Partners to run CPDs on SuDS & The Role of Permeable Paving, providing information on compliance and how to use the Rosmead Street project as an active example of best practice.
Emma Brown, General Manager for Living With Water and Strategic Partnerships Manager at Yorkshire Water, said: “This is the first project of our Blue Green vision, which aims to increase flood resilience in the local area by managing surface water better during periods of heavy rain. We’ve engaged with the local community to understand what’s important to them and how we can work together to implement these measures in a way that works for them day to day.”
Ross Housley, Contract Director at Morrison Water Services, said: “Throughout the Living With Water programme, Morrison Water Services have integrated a supply chain ecosystem in order to deliver the very best outcomes for the partnership and the community in Hull.
“Brett Landscaping are the perfect example of this by supporting the design requirements set out by Morrison Water Services by supplying the Omega permeable paving. The team was not just a supplier of their product; they offered support throughout the project on several occasions. Partnership working at its best.”
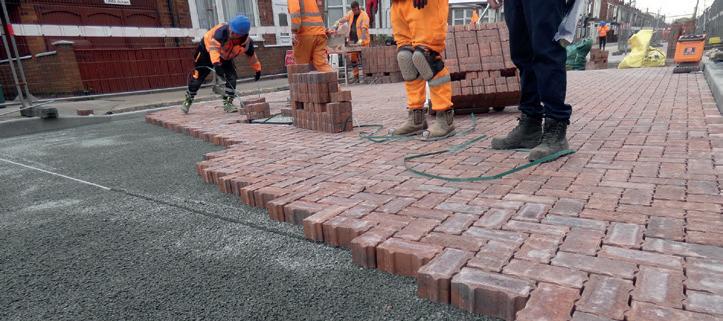
James Gibson, Director of Civil Engineering at Alan Wood & Partner, adds: “We have a good working relationship with Brett, who have previously provided us with CPD presentations on updates with permeable pavements and their compliance with British Standards.
“On this project, Brett Landscaping was able to help us with detailing of the pavements where the surface water needed to be attenuated and helped us to sense check the hydraulic and structural design of the pavements where a dense bituminous macadam has been used as the roadbase.”
Jamie Gledhill, Engineering Technical Manager at Brett Landscaping, said: “With the amendments in Government policy and Schedule 3 on SuDS coming into force in 2024, it is important that manufacturers step forward to provide active advice and assistance to these multipartner schemes as the industry adapts to the changing requirements.
“Brett Landscaping is now working on a range of schemes for water utility companies and local authorities that
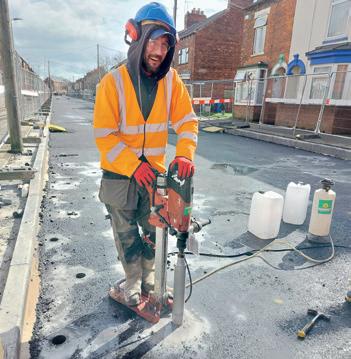
have been tasked by OFWAT to solve their localised problems of combined sewer overflow. The project at Rosmead Street is a strong example of multiagency cooperation and coordination with industry stakeholders to deliver a longterm solution to residents.”

ACCELERATING CHANGE: DESIGNS TO MAKE A DIFFERENCE
Debbie Huntley of PULSAR explores the growing demand for circular garment design in workwear and why it’s now more important than ever to balance comfort and functionality with durability.
Millions of working professionals are required to wear protective workwear and PPE items every day. From construction to the rail and highways sectors, employers and their staff rely on appropriate clothing that offers the technical protection, functionality and wearability needed to complete their respective specialist jobs.
At a basic level, protective clothing keeps individuals safe, secure and compliant in their professional setting. Such is its importance to the UK workforce, workwear and PPE markets are reportedly valued at over £8.6bn in the UK alone. Yet, despite accounting for less than 2% of the entire UK clothing market, end-of-life workwear remains a significant contributor to our planet’s waste. In fact, it’s said that approximately 90% of the UK’s used workwear and PPE is sent to landfills and incarcerated, adding to the 92 billion tonnes of global textile waste each year. These numbers make for dim reading, and while protective workwear may not share the same epidemic-level concerns
associated with fast fashion, it’s clear there’s a pressing issue that needs to be addressed. Simply put, without intervention, the professional clothing and wider textile industry will continue on a linear path and, conclusively, the ideologies of circular design must become more widely understood and practised.
Balancing act
Where sustainable practice is concerned, the same principles apply to most markets and their supply chains: buy durable and buy less. This is no different for those designing, procuring and operating in protective clothing, where the enhanced durability of a garment can help its wearer remain safe, secure and compliant over a longer period of time. It’s understood that by extending the active life of 50% of the UK’s clothing by nine months, carbon, water and waste footprints can be reduced by 4 to 10%. With greater significance being placed on the usable service life of garments, protective clothing design teams face a
balancing act, as they aim to provide multifunctional, technical and fitting garments that conform to strict regulatory standards while also delivering on environmental ingenuity. As a result, many conscious manufacturers are already taking positive steps, addressing responsible consumption by ensuring high-wear work garments retain their colour, fit and quality for up to 50 washes as standard.
Further than that, mindful decision teams are now looking to adopt a more circular approach to garment design as a way of reducing the waste generated in the workwear sector. Circular design is the practice of creating durable, reusable and recyclable products that generate zero waste. The model looks to move people away from the widely-performed ‘take-make-waste’ economy and aligns with the UN’s Sustainable Development Goal 12 (SDG 12), which encourages more sustainable consumption and production patterns and calls for a comprehensive set of actions from the supply chain to adapt to sustainable systems.
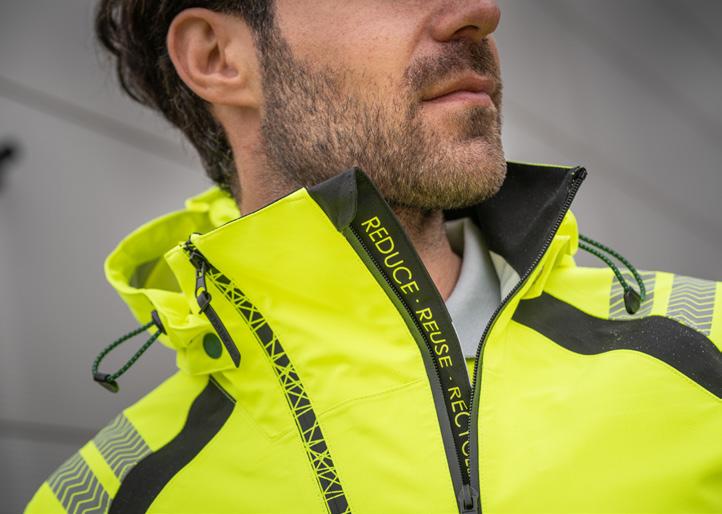
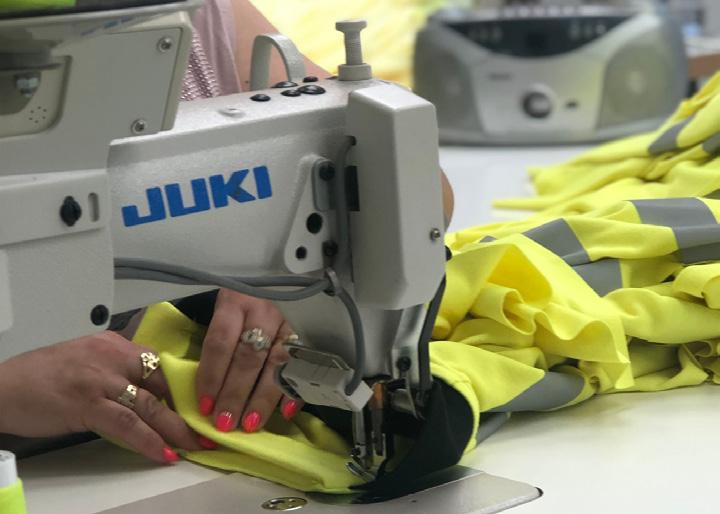
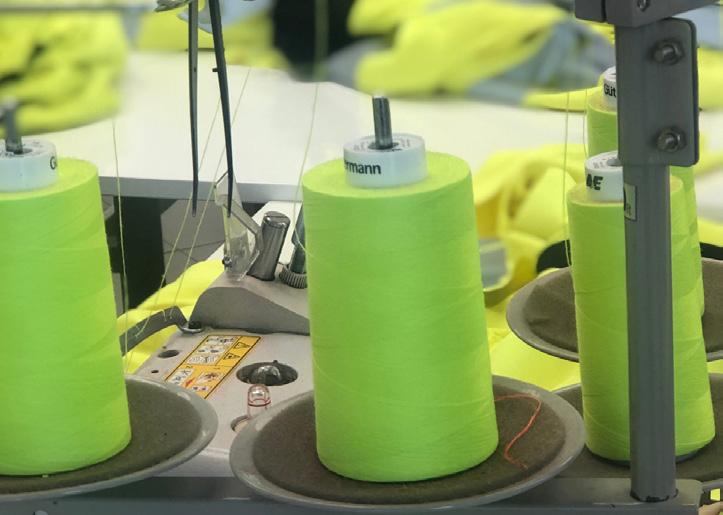
Collaborative action
Circular design can have a substantial positive impact on protective clothing and the planet, but its efficiency relies on collaboration. Currently, there is no industry standard that defines a ‘circular product’, as classification relies on a product’s design, circular business models, recycling infrastructure and disposal by end users.
As per the Extended Producer Responsibility (EPR), design teams are expected to conceptualise product designs that make use of environmentallyresponsible fabrics and degradable components to increase their recycling efficiency. In response, conscious design teams are adopting recycled fabrics and organic fibres throughout their protective clothing designs while also using reputable component partners for accessory items, such as zippers, buttons and labels. Furthermore, the transition from non-biodegradable materials, such as PFAS and PFOS, to natural water repellents – often classed as C-zero products –is revolutionising the approach to finishes and treatments for heavy-duty, waterproof garments and is another step forward for circular design.
While these design transformations are making an impact, there is also a call for greater transparency to help decision makers choose more suitable options when kitting out their workforces. When procuring protective workwear, employers are urged to seek out high-quality, durable gear that makes use of environmentally-responsible materials and naturally facilitates end-of-life reuse and recycling. In seeking out this information, decision makers can refer to wash care labels and the manufacturer’s product information, which can often be found online. By further improving education on circular design, decision makers will also better understand their role in the circular economy, ultimately, overcoming cost-based objectives in favour of the environment and all while making long-term gains by using longer-lasting garments.
Workwear and protective apparel will continue to evolve over time as they strive to meet the growing demands of their markets. While garment design teams have always strived to balance comfort and functionality with protection and safety, the pressing needs of our environment pose new questions that may only be answered by the widespread adoption of circular design.
www.aboutpulsar.com
SOURCES:
https://pciaw.org/the-circular-textiles-for-a-sustainable-future/ https://earth.org/statistics-about-fast-fashionwaste/#:~:text=92%20million%20tonnes%20of%20 textiles,on%20landfill%20sites%20every%20second. https://wrap.org.uk/sites/default/files/2020-10/WRAP-valuingour-clothes-the-cost-of-uk-fashion_WRAP.pdf https://sdgs.un.org/goals/goal12 https://wrap.org.uk/sites/default/files/2023-10/WRAP_Design_ for_Circularity_Toolkit.pdf
https://www.oecd.org/environment/extended-producerresponsibility.htm
https://consult.environment-agency.gov.uk/environment-andbusiness/challenges-and-choices/user_uploads/perfluorooctanesulfonate-and-related-substances-pressure-rbmp-2021.pdf

USING FUNDING AS A VEHICLE TO NET ZERO
In a time when the UK is working to improve and close its skills gap, it is important our education estates match the quality of professionals we hope to create. The UK’s ageing public estate needs to be upgraded if it hopes to create the next generation of leaders, says Richard Murray, Director at Drees & Sommer UK.
By undergoing refurbishment works, teaching experiences can be improved across a whole hosts of quality metrics, including sustainability. The UK Government has legislated to reduce emissions to be fully net zero by 2050 with an interim target of 68% by 2030. The education sector has its own target of 78% by 2035. Decarbonisation measures are no longer desired, but an essential piece of criteria for quality estate conditions. However, with college and school budgets under increasing pressure, longterm retrofitting plans are unsurprisingly falling down the agenda. It is capital funding that can be the key vehicle to unlocking the quality estates required to drive forward the UK’s skills economy but also its net-zero ambitions.
Routes to funding
The Department for Education (DfE) acknowledges its responsibility to improve conditions to bring education estates up to quality condition. Decarbonising will become a key byproduct of improving the quality of the overall estate and embedding decarbonisation and carbon reduction measures into how we view the future of the UK’s educational estate.
Knowing it is at the forefront of the Government’s objectives, various funding avenues have been opened by the Department of Education (DfE) and Department for Energy Security and Net Zero (DESNZ), for a broad range of sectors to apply for; education is no exception. These departments have deployed a range of capital funding options, including the Further Education Capital Transformation Fund (FECTF), T-Levels Capital Fund, The Condition Improvement Fund, Public Sector Decarbonisation Scheme (PSDS) and Low Carbon Skills Fund (LCSF). Alongside this, there are formula-based capital allocations such as the Schools Condition Allocations and the one-off £500m energy-efficiency upgrades funding for colleges and schools announced by DfE almost 12 months ago.
Launched in September 2020, the Public Sector Decarbonisation Scheme (PSDS) is one of the biggest fund allocations for public sector bodies, which looks to progress heat decarbonisation and the implementation of energy-efficiency measures. Phase 3 of the PSDS provided over £1.425bn of grant funding over the financial years 2022 to 2025. Phase 4, with an additional £1.17bn, is critical
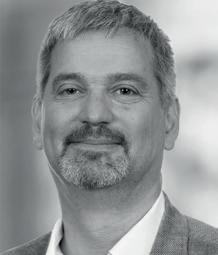
for unlocking this capital is critical for colleges, schools and other educational estates in meeting what can feel like an impossible deadline for net zero.
Unlocking net zero through capital funding
Drees & Sommer UK has been working with Calderdale College in West Yorkshire, where the school has received a green light to undergo a £7.5m transformation.
Scheduled to be complete in August 2024, the project would not have been possible without the £5.5m of capital funding granted from the DfE. The team at Drees & Sommer UK worked with the college from the outset, supporting it in securing the grant via the Further Education Condition Transformation Fund (FECTF).
The funding will be used to transform its facilities and significantly improve energy efficiency. As part of this, the Percival Whitley Centre will benefit from a new, thermally-insulated rendered finish, photovoltaics, LED and hot water upgrades. It will not only make the building warmer but secure the historic building’s long-term future by being more resilient and cost less to run.
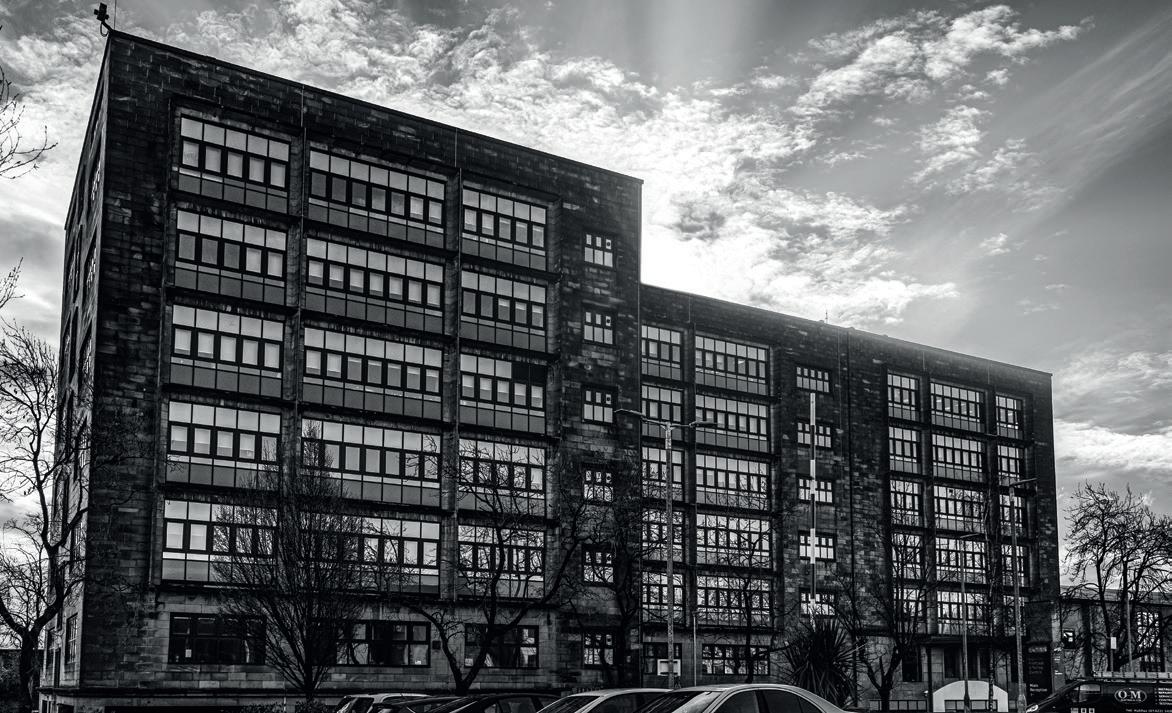
Currently, 51% of the district’s carbon emissions comes from its buildings. This project will contribute to Calderdale Council’s pledge to become net zero by 2038. It will also benefit more than 2000 young people, adults, apprentices and employees that the college welcomes each week.
Andrew Harrison, Vice Principal –Corporate Services at Calderdale College and Project Lead, said: “This funding has come at a critical time for the college, as the nation faces increased energy costs. The project will not only help to reduce rising energy bills, but it will also make a positive contribution to Calderdale’s sustainability agenda whilst also giving us a modern exterior that is in keeping with its original facade.”
Another example of unlocking decarbonisation through funding is Cheshire College South and West. Recent examples of the works undertaken at the college have been at the Crewe Campus, where Drees & Sommer UK provided multidisciplinary support, led by their specialist energy and sustainability team. The scheme, now completed, has reduced the Crewe Campus, carbon emissions by circa 60%. The project at Crewe Campus was supported by FECTF dealing with heating pipework and radiator issues which, by careful programming and specification, allowed a further PSDS (Phase 3A) decarbonisation scheme to be realised by replacing a large part of the gas boilers and installing air-source heat pumps. Combining funding streams in this way enabled a scheme that might otherwise have been unaffordable to be completed and helped the college transition towards a low-carbon future.
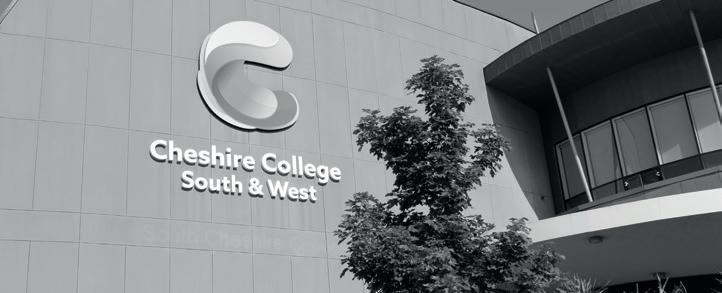

The PSDS has also been used on more than just Crewe Campus; funding has subsequently been secured for both the Chester (Phase 3B) and Ellesmere Port (Phase 3C) campuses, which are currently ongoing.
With education providers all over the country being under resourced to deal with their sub-standard buildings, the added pressure to meet net-zero targets means the various pots of UK
Government capital funding they’re entitled to bid for are valuable vehicles for sustainable development.
Opening up this funding can take away some of the headaches and allow colleges and schools to take their first steps in improving the quality and sustainability for today and tomorrow.
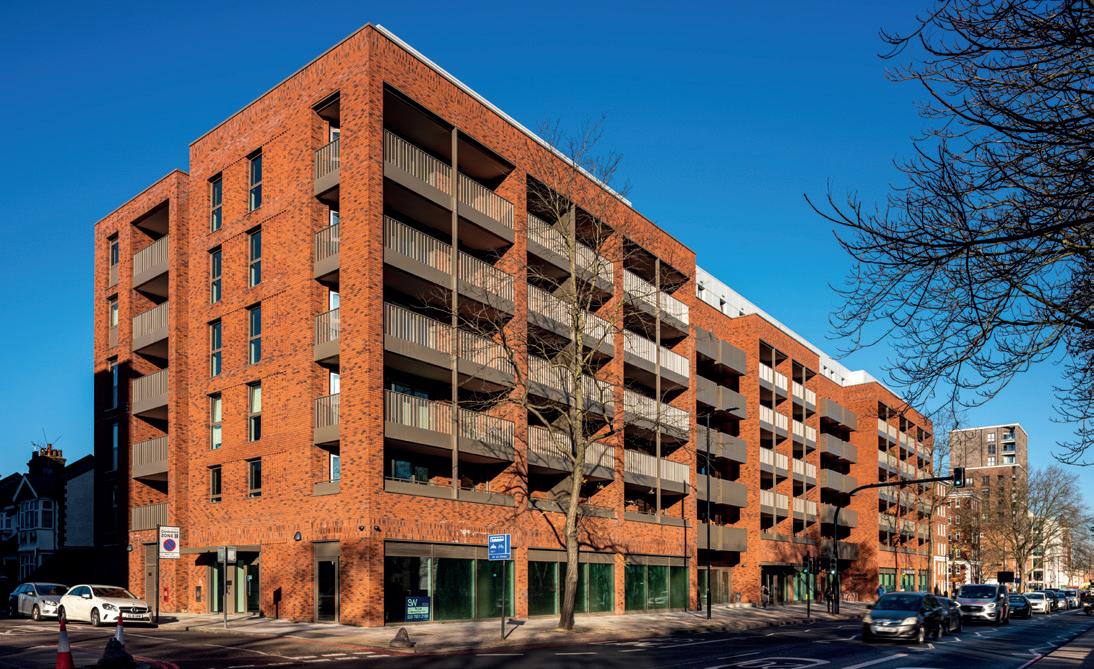
PROPER SPECIFICATION AND ITS VITAL ROLE IN THE CONSTRUCTION PROCESS
Proper specification is a fundamental element of construction quality, sustainability and safety in the UK. In an ever-evolving construction industry, this essential principle endures. John Duffin, Managing Director at Keyfix, emphasises the critical role specification plays throughout the construction process and why the built environment sector must continue to prioritise it.
Having a proper and comprehensive specification document is crucial to ensuring each project stays on track, is compliant with current regulatory requirements and, ultimately, allows everyone to work towards creating a successful build. This living document facilitates transparency throughout a project, providing all stakeholders with access to up-to-date and accurate data, from the initial conception right up to project completion.
In the modern built environment, best practice involves writing specifications as early as possible in the project lifecycle. By doing so, you can capture information from the client review and document what the client is trying to achieve on the project.
Before detailing just why proper specification is so important, it’s pertinent to understand exactly what specifications are and the role they play in the process.
What is a specification?
Put simply, a specification is the document that provides a detailed description of the materials, construction, workmanship and dimensions of work, either completed or
to be done, and is typically prepared by an engineer or architect.
The type of specification can often relate to either the project or the procurement route, whether that’s performance based, proprietary or prescriptive. This will depend on the project requirements.
Construction specifications usually cover:
Site establishment
Asset performance criteria
Contract type
Specific products to be used
Applicable standards and how they are executed
Systems and product quality.
Ensuring clear instructions and information are shared by all involved
Proper specification not only references any standards and quality that should be applied, but it also provides clear instructions on project intent, construction and performance. This lays the groundwork for an incredibly successful project with outstanding build quality, safety and sustainability.
Additionally, any materials and manufacturer products can be clearly defined from the outset, which enables the process to be as smooth and efficient as possible. While proper specification is typically provided at the beginning of a project, it also plays a vital role throughout the entirety of the construction. In fact, as a living document, it can be used by the complete project team throughout the construction phase.
Minimised project risk
Having a clear definition of all the materials involved and the dimensions needed throughout the project means the specification can form part of the contractual documents. As a result, project risk can be minimised and, should there be any legal disputes, support will be available. Indeed, as the specification is an essential part of the contract documentation, it will be legally binding in the event of any litigation or disputes. This is especially important given a report by Arcadis revealed the average construction dispute in the UK in 2020 was valued at £27.7m, an increase of 117% from 2019.
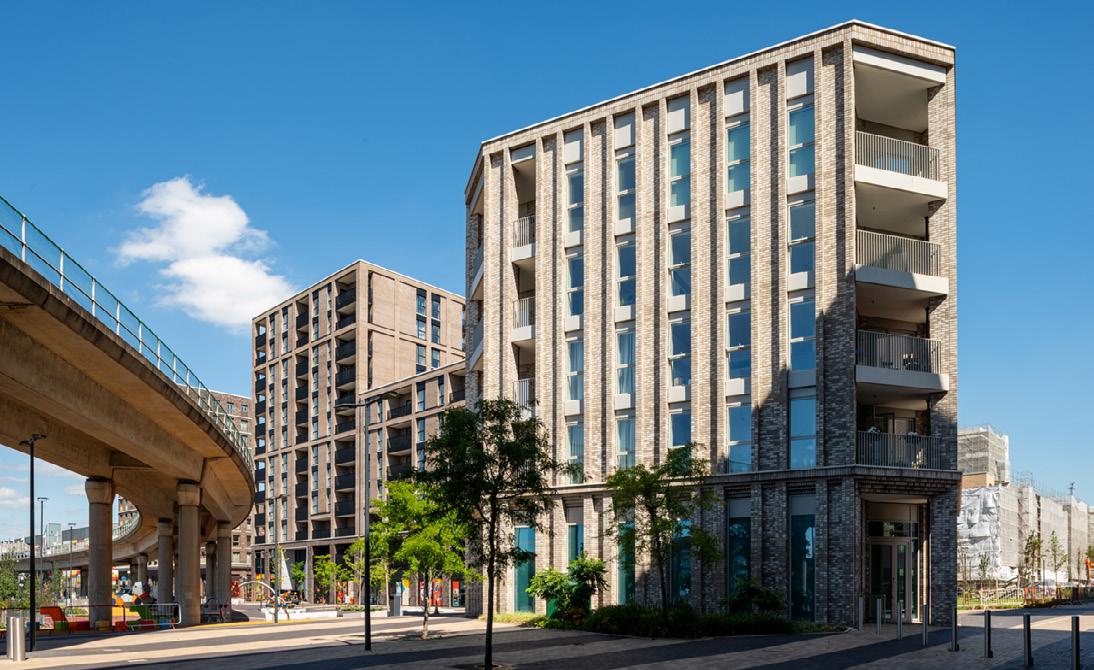
Furthermore, precise specifications will help to identify potential safety hazards and prevent accidents, both during construction and after completion.
Saving time and money
A new study by digital construction management specialist PlanRadar revealed building errors and the necessary rework amounted to 11% of total project costs for UK and EU constructions. Poor-quality materials and quality control were the two largest contributors to building errors and rework in the UK.
As a result, proper specification is absolutely vital. By providing clear, accurate and concise information, you will help to reduce the amount of rework required, saving precious time and money.
Additionally, specifications that are clear, extensive and information rich will provide answers to many onsite construction questions, further saving the contractor, project team and end client money and time.
Peace of mind for the client
While proper specification can make a huge difference to the quality and safety of a building, it can also provide the end user or client with the peace of mind of knowing that due diligence has been properly carried out throughout the project.
If something goes wrong with a project, it can often increase the amount of time taken to complete it or the amount of money it will cost to undertake amendments or repairs. An accurate and proper specification will ensure an audit trail for any project, giving any contractors and the end user easy and quick access to any relevant information.
As a company that prides itself on attention to detail and delivering exceptional quality, Keyfix understands the importance of proper specification and close collaboration between all members of a project. Working closely with clients from conception to completion, Keyfix specialises in the manufacture and supply of market-leading non-combustible cavity tray systems, ideal for any high-rise masonry UK construction project that requires Document B compliance.
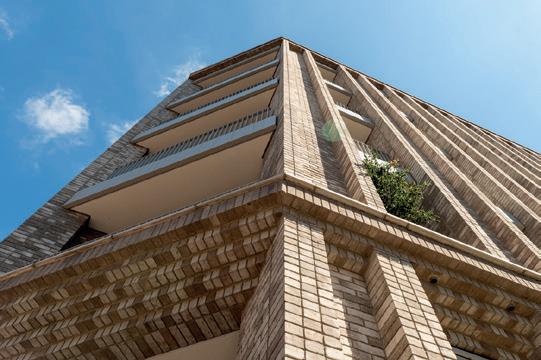
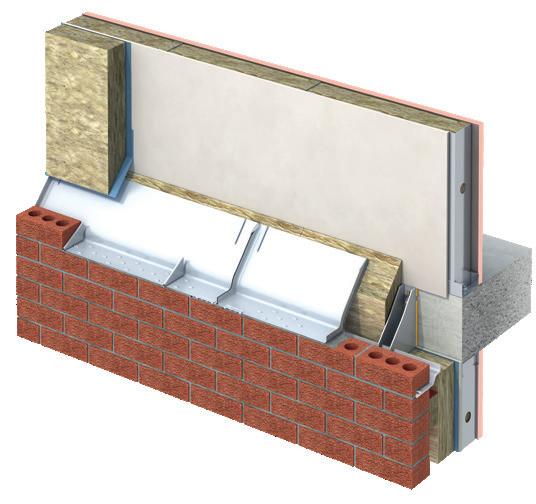

BUILT ENVIRONMENT EVENT RETURNS TO LONDON
One of the UK’s largest built environment events, UK Construction Week (UKCW), is returning to London’s ExCeL, from 7 to 9th May, with a host of new features including interactive demos, international pavilions and a list of prestigious speakers.
After being officially opened by Architect and TV Presenter, George Clarke, visitors can see the debut of a new Live Demo Theatre, Skills and Training Hub, a construction-specific Recruitment Zone and new C-Suite Summits to name but a few, as well as a host of international exhibitors housed in pavilions from India, China, Turkey, Italy, Czech, Poland and Latvia.
UKCW London is once again colocated with Concrete Expo and the
Offsite Show, as well as the UK’s premier event for the self-build sector, Grand Designs Live.
The construction show will host over 300 exhibitors, showcasing many products and services, from concrete and construction technology to safety services and alternative sustainable materials. Confirmed names include Creagh Concrete, FONN, Celsa UK, PlanRadar, Ford, O’Reilly, Clark Drain, CONTAINEX, Oracle and many more.
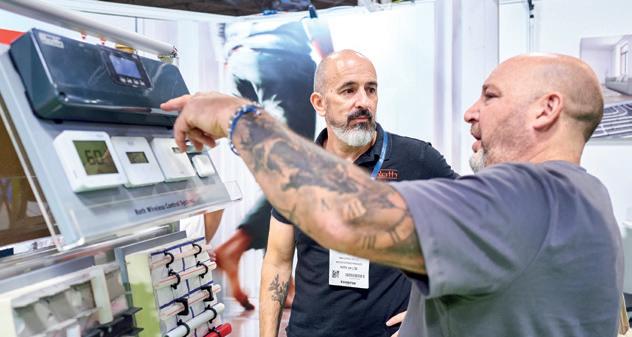
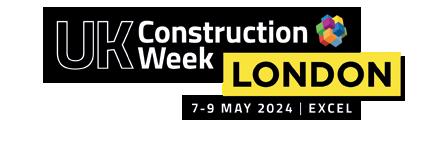
At this year’s exhibition, visitors can look forward to attending talks and panels hosted by key high-profile speakers, including former England international Footballer Trevor Steven and Andrew Lewer MP.
Trevor Steven, whose football career included 36 England caps, is now a Mental Health Ambassador at Causeway Technologies and will be speaking on day one of UKCW (7th May). Also in the line up is Andrew Lewer MP, Chair of the All-Party Parliamentary Group for SME housebuilders and LUHC Select Committee, who will discuss his plans for a ‘Builders’ Manifesto’.
Back for its seventh year running, the popular Role Models campaign will, for the first time ever, host three categories; Rising Star for Apprentices, Pioneer and Icon, to broaden its acknowledgments. Entries are now open, with the shortlist to be announced at the UKCW London show and the winner crowned at UKCW Birmingham (running from 1st to 3rd October).
The campaign welcomes anyone who works in the sector, including architecture, engineering, construction technology and property development, and is aimed at inspiring others to share their stories and career journeys.
What’s more, across the three days, visitors can also look forward to these new highlights, features and dedicated areas:
Skills: With an even larger emphasis at this year’s show on skills development, apprenticeships and training in the industry, new features include a live challenge featuring some of the world’s best in BIM digital construction; a new collaboration with the CITB (Construction Industry Training Board) and new show zones focused on skills, training, careers and recruitment.
Careers and Recruitment Zone: Another new area created in response to exhibitor and visitor feedback, this will not only be a focal point for all those working in recruitment, or simply looking for that next new role. Visitors will have face-to-face access to specialist recruiters from the construction sector, with discreet interview rooms allowing candidates to have onsite consultations.
Concrete Expo: Co-located with UKCW London, from 8 to 9th May, visitors can expect to see a Live BIM for Concrete Interactive Visitor Experience; technical advice clinic and a new dedicated area for testing, repair and reinforcement; the event will be showcasing an impressive selection of concrete products, equipment and services exhibitors.
To find out more about both shows and to register for UKCW London for free, visit the below website.
https://ukcw-london-2024.reg.buzz/cab-pr

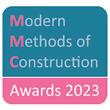
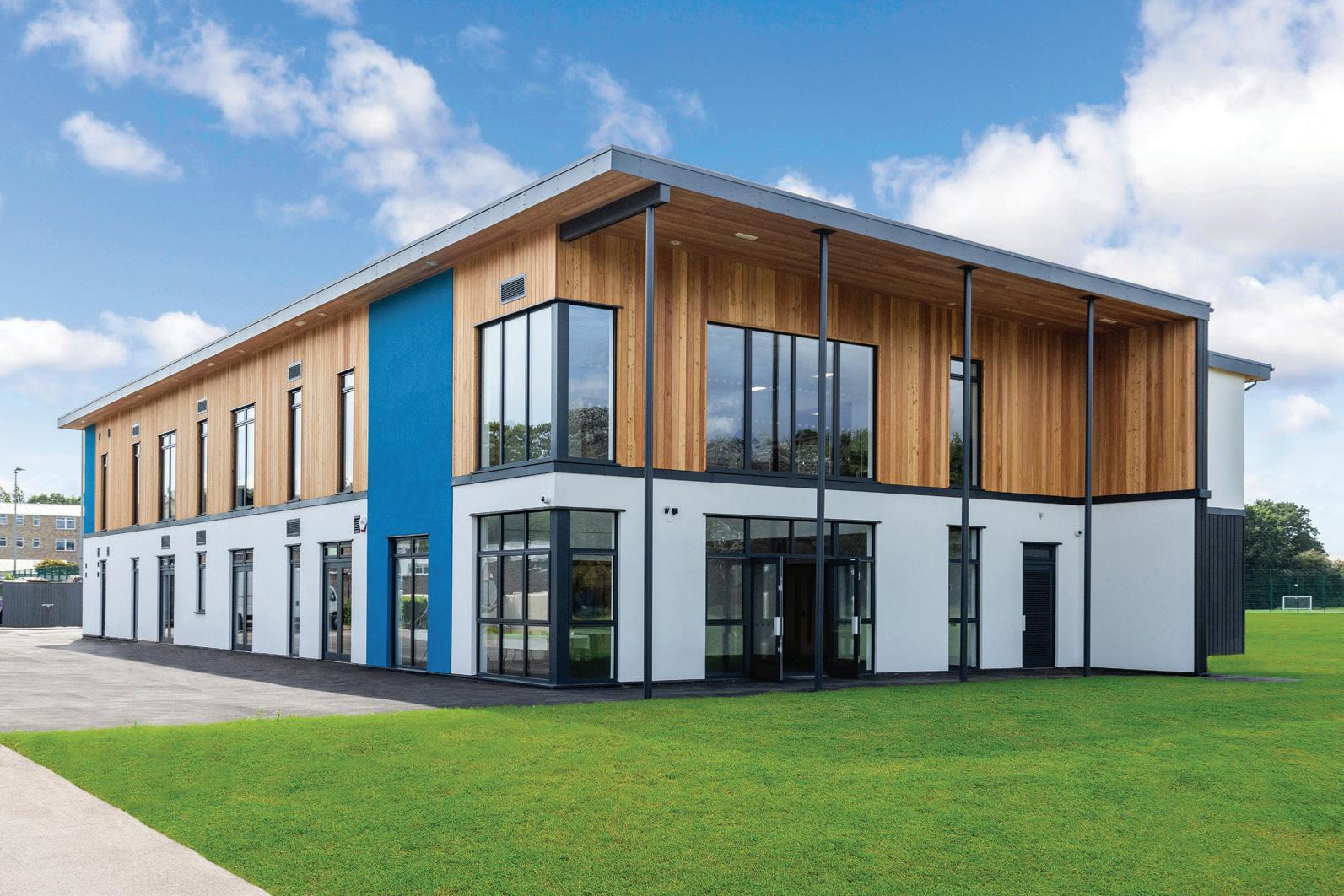

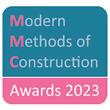
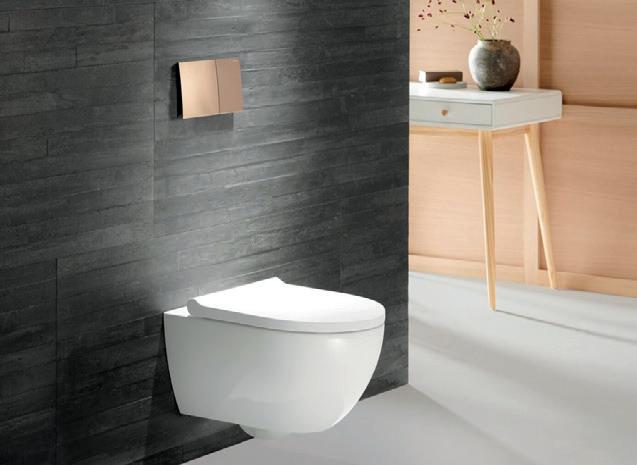
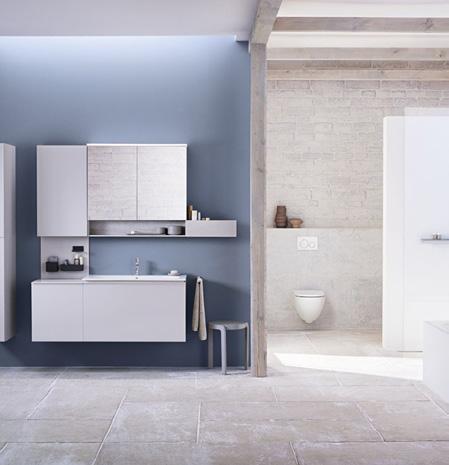
FLUSH TECHNOLOGY AND CERAMICS IN PERFECT HARMONY
The Geberit WC system scores points with its durability, fast and safe installation, decades of spare parts reliability, outstanding flushing performance and easy cleaning. Here, Sophie Weston, Head of Marketing at Geberit, shares its most important advantages.
The Geberit WC system, with Duofix, concealed cistern, Sigma70 actuator plate and Geberit Acanto WC, is more than the sum of its individual parts and offers the pinnacle of Geberit’s flushing technologies. The best performance is achieved by the individual elements working together: optimally coordinated, they meet the highest requirements of both installation specialists and bathroom users.
40% quicker installation than before * As part of the redesign process, developers have equipped the Geberit Acanto wall-hung WC with Easy Fast Fixing 3 (EEF3) installation technology, making installation of the ceramics even easier than before. Better yet, Geberit’s entire range of fullyshrouded, wall-hung pans now feature the EFF3 fixings – significantly reducing the possibility of installation error when opting for wall hung.
The toilet seat of the new Acanto WC is aligned and fixed from above utilising Geberit’s EasyMount fixing technology, ensuring that it can be fit in no time at all. This also makes maintenance work effortless and, as development continues, this feature will also be implemented into the wider series of Geberit ceramics to make installation easy across the range.
Guaranteed
spare parts availability for 50 years
The Geberit WC system is designed for decades of use and can be maintained without any problems, with the added benefit of 50 years’ spare parts availability ** for all replaceable mechanical parts of the concealed cistern.
Up
to 10 times better flush performance
At Geberit, we test our pans through 13 different performance tests; some are to ensure we meet local standards across the various markets in which we operate, and others are to ensure we meet the Geberit standard (which goes above and beyond local standards). In 2023, we tested nearly 500 pan and cistern combinations to ensure optimal performance and reduce water wastage.
Most recently, we have undertaken vigorous testing in line with EN 997; in one of these tests, we are required to flush 50 plastic balls. And, with the new technology in the Acanto pan, we are capable of exceeding this by 10 times the required amount.
Furthermore, the Acanto WC has gone through intensive rounds of testing – and the results speak for themselves. Instead of the 12 toilet paper balls required by the standard, the embedded TurboFlush technology effortlessly flushes away an impressive 60 balls.
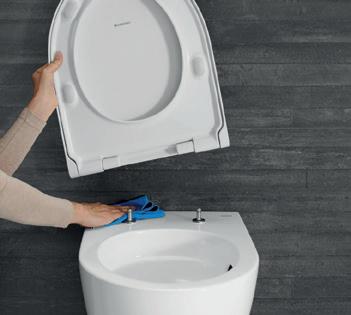
Powerful and gentle on water
The WC system achieves optimum flushing performance through the combination of the Geberit Acanto WC ceramic and the new type 212 flushing valve. The modified valve makes an important contribution to the resource-saving use of drinking water. With suitable ceramics, such as the Geberit Acanto WC, it ensures optimum flushing with minimum flush water volumes from 4l for the full flush volume and 2.6l for the partial flush volume.
Simply clean
Throughout the Geberit portfolio, our Rimfree and TurboFlush pans ensure easy cleaning is possible with no spaces for ‘bacteria’ or dirt to hide. Due to the faster (and quieter flush of TurboFlush) this also reduces the need for cleaning as the surfaces are cleaned with ease. Within our Geberit ONE and Xeno^2 ranges, we also have the additional surface coating KeraTect. KeraTect provides a virtually non-porous and extremely smooth surface so that the WC can be cleaned easily and efficiently.
*Than former fixing technology **Sigma and Omega only. Excludes electronic products.
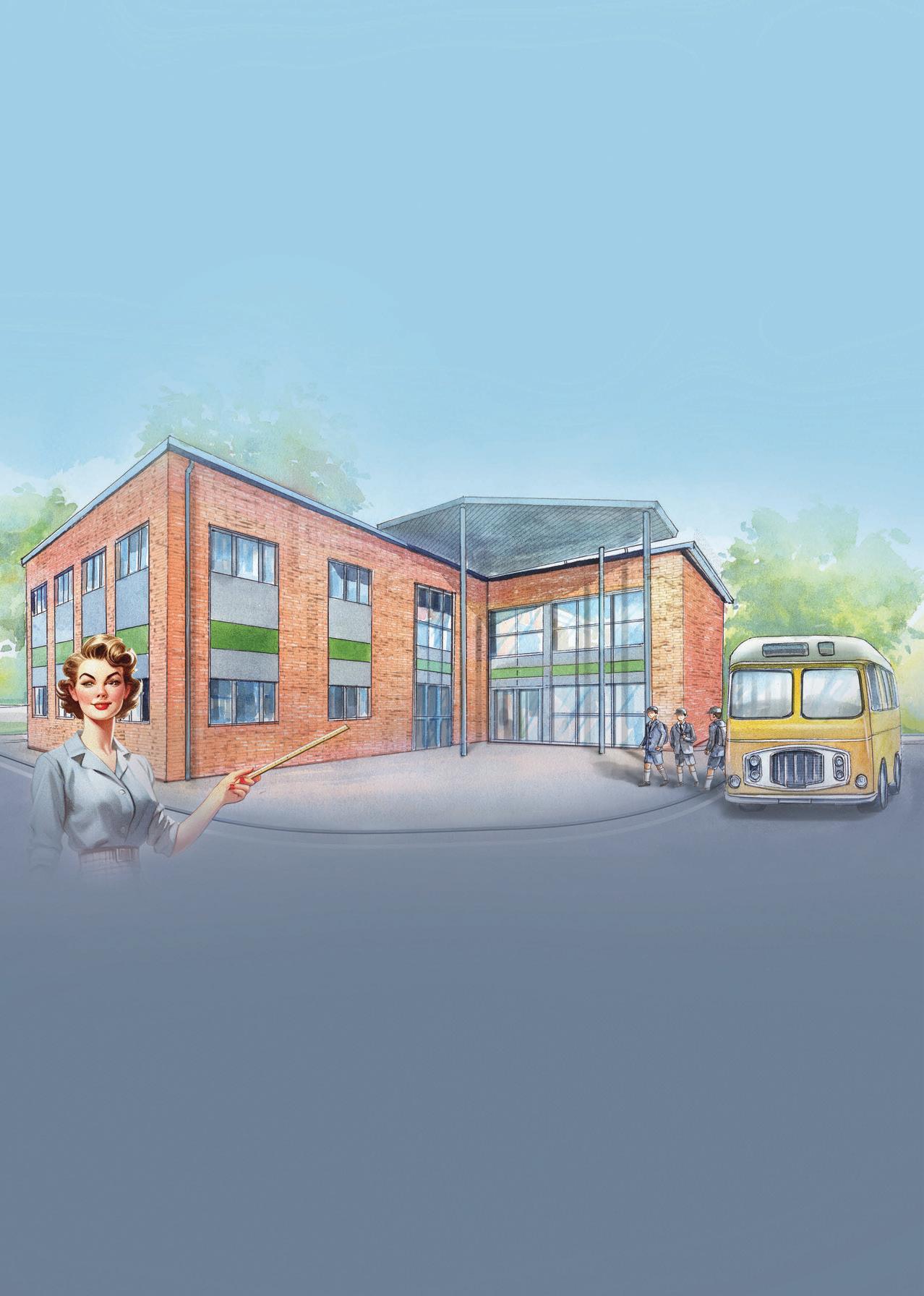
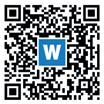
PROVIDING PRACTICAL SOLUTIONS FOR THE EDUCATION SECTOR
Modular construction stands out as an efficient method for creating contemporary and durable educational facilities. Choosing modular buildings over traditional construction brings numerous benefits, leading to a surge in modular schools nationwide. Whether it’s a single or multi-storey structure required, modular solutions offer adaptable designs, ensuring the creation of an ideal learning environment.
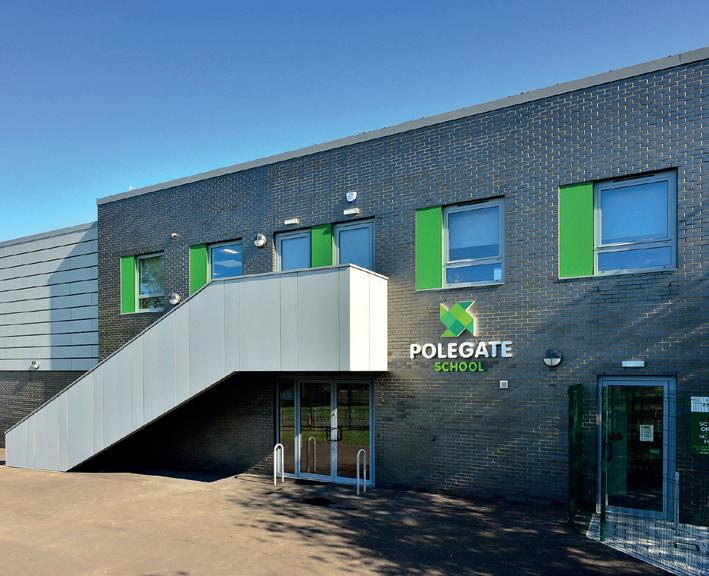
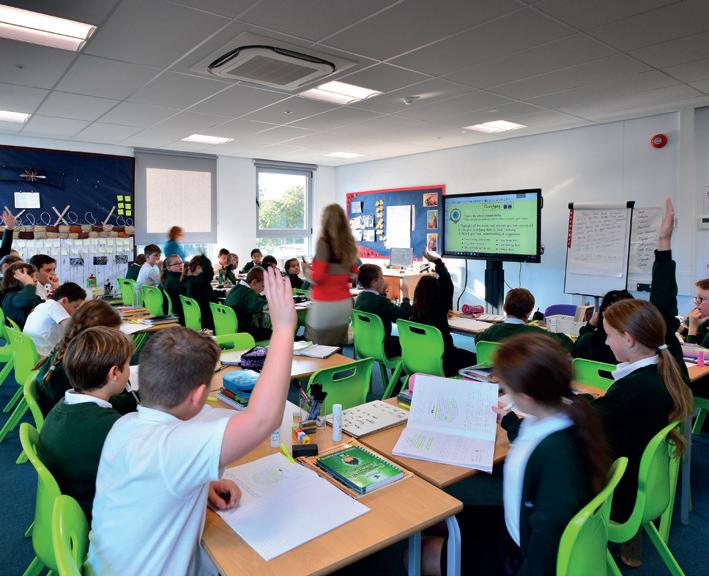
Wernick Buildings serves as a reliable partner for all your educational construction needs. From design and construction to swift installation, it delivers a comprehensive turnkey solution, providing fully-fitted buildings in significantly less time than traditional builds. Your project will be overseen by an experienced construction team, offering a smooth transition with inclusive training and thorough aftercare. Additionally, Wernick’s school buildings boast a remarkable 50-year design life.
Preparing for the next academic year
The modules are built in the company’s South Wales factory and either stored or delivered directly to clients, streamlining the construction process by up to 50% compared to traditional methods. It offers modern teaching equipment and features, maximising your space’s potential. As part of its turnkey service, Wernick extends support to groundwork and landscaping, encompassing car parks, multi-use game areas and playgrounds.
Embarking on a new educational development journey is always timely. Wernick building systems cater to a spectrum of educational levels, from nurseries to universities, emphasising aesthetic flexibility and enhanced building performance. Partnering with Wernick ensures your education facility is operational well before the next academic year, which showcases the company’s commitment to efficient and reliable solutions.
How to procure a modular building
Embarking on the journey to procure a modular school building with Wernick Buildings involves a wellstructured process designed for efficiency. The initial stage focuses on developing the building’s design and specifications, encompassing surveys, services and planning applications. Following this, the tender submission and evaluation phase includes project planning, tender submissions, client evaluations and transparent communication of feedback. Once the design is frozen, detailed planning ensues, and the project is strategically scheduled into the factory manufacturing programme. Detailed design covers everything from groundwork to structural, electrical and mechanical elements, ensuring a comprehensive approach.
Moving forward, the building warrant application is submitted, followed by clarification evaluations and considerations for factory work commencement. The subsequent stages involve manufacturing building modules in the factory, fitting doors, windows, plumbing and various systems. Concurrently, service applications for water, electricity and other necessities are addressed. Pre-mobilisation conditions, including approvals and permissions, are met before the mobilisation stage, which involves site preparation and community engagement.
Groundworks follow suit, preparing foundations, services, drainage and access. The installation phase sees the introduction of building modules and onsite fit out, ensuring seamless integration. Services such as power, water and data connections are established, leading to the commissioning, snagging and finishing stage, where thorough testing of various aspects is conducted. The final steps involve handover, including client training for building operations, key exchange and the sharing of certificates, manuals and reports.
www.wernick.co.uk
0800 112 4640
enquiries.buildings@wernickgroup.co.uk
AKW’S EXTENDED ONYX RANGE COMBINES STYLE AND SAFETY
AKW’s extended range of Onyx products now includes updated levelaccess shower trays and ramps, grab rails and shower seats alongside the cleverly-integrated mixer shower and grab rail.
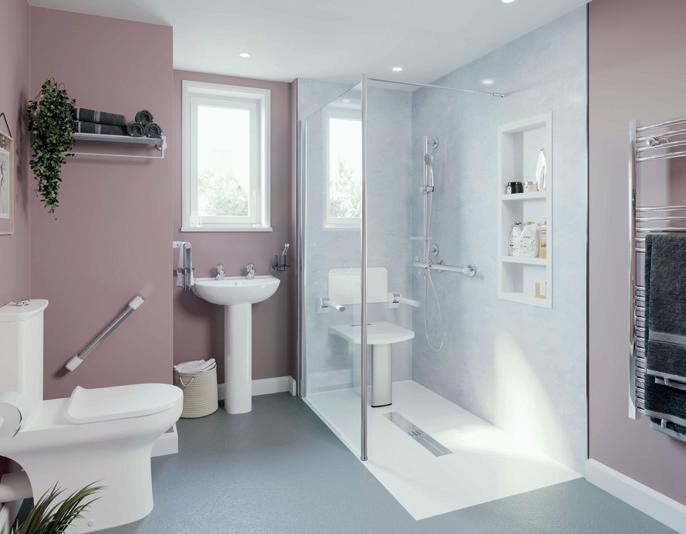
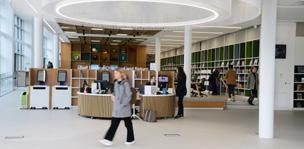
BY THE BOOK INSTALLATION
F. Ball products, including dual-purpose Stopgap Fill and Prime thixotropic primer and Stopgap 1200 smoothing compound, have been used to create a large-scale, high-performance flooring finish in the new Nottingham Central Library. Contractors used F. Ball’s Stopgap Fill and Prime and Stopgap 1200 smoothing compound to prepare metal raised access panels in all areas, creating a perfectly-smooth surface for floorcoverings. Once the primer had cured, F. Ball’s Stopgap 1200 smoothing compound was applied to create a smooth base for the installation of floorcoverings. Contractors then used F. Ball’s Styccobond F46 pressure-sensitive acrylic adhesive to install Gerflor safety flooring in all areas where subfloors had been prepared.
FUSING HEADLINE PERFORMANCE WITH MASSIVE RUNNING COST SAVINGS
AKW has launched the Onyx Linea shower tray and this includes a long, stainless-steel waste feature that allows for faster drainage for high-power showers. With a luxurious textured stone-effect finish that offers a high level of slip resistance, as well as a high-load capacity of 39st (247kg), this sleek shower tray is also suitable for wheelchair users or those with carers.
The AKW Onyx range has been extended to include the Onyx Exclusif shower tray and ramp and the Onyx Linea shower tray. The Onyx Exclusif shower tray provides a stylish yet strong showering solution, with a maximum capacity of 31.5st (200kg). Alongside this is the Onyx Exclusif Ramp has a 31.5st (200kg) weight capacity and is available in white to beautifully match the shower tray.
AKW’s Onyx Combo Mixer Shower brings safety and style to inclusive showering by incorporating two weight-loading grab rails into the L-shaped design. The rails extend from the cool-to-touch, TMV2-approved mixer valve via a vertical riser and horizontal grab rail, both of which can support users of up to 23.5st (150kg).
The Onyx Shower Seat and Grab Rails have also been updated to ensure a cohesive aesthetic. A seat back and arms option has been added, and these can either be purchased alongside the seat or separately. To complete the range, AKW’s new highly-contemporary Onyx 2 grab rails feature an ergonomic triangular rail that offers users greater ability to grip the rail.
www.akw-ltd.co.uk/types/onyx-range/
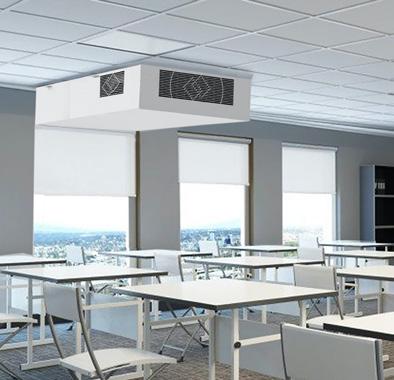
A new ventilation with heat recovery option can achieve performance better than anything else on the market, meaning massive savings on energy bills. Mistrale Fusion Deo is the concept of Gilberts Blackpool, which was instrumental in pioneering hybrid ventilation with its core Mistrale Fusion unit. The latest evolution achieves up to 65% heat recovery – significantly better than other similar-type systems. That outstanding performance means that, for a typical school, energy bills could be cut dramatically by recovering heat that would otherwise be wasted whilst ensuring an indoor air qualitycompliant, well-ventilated space. Gilberts’ dynamic Mistrale Fusion Deo will become, the company believes, the go-to solution for net-zero building services design, especially in educational establishments. The ventilation performance is compliant with BB101 and the DFE Output Specification. Further, it avoids overheating in the building, being TM52 comfort compliant. And it is quiet – meeting BB93 guidelines even for special educational needs. The MFS range attains air leakage better than legislative requirements – 3m3/HR/m2 – and a U-value of less than 1W/m2/°C. Being a standalone system, Mistrale Fusion is ideal for new-build or refurbishment/refit scenarios. The combined benefits of Gilberts’ Mistrale Fusion Deo performance contribute to low-/zero-carbon strategies, BREEAM and similar eco credentials.
www.gilbertsblackpool.com 01253 766911 info@gilbertsblackpool.com
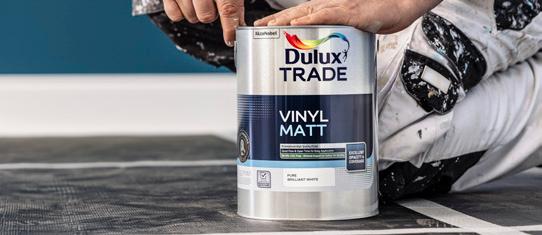
DULUX TRADE VINYL MATT: YOUR TESTED AND APPROVED, MORE SUSTAINABLE SOLUTION
Dulux Trade Vinyl Matt has been reformulated to provide specifiers and their clients with a more sustainable solution that is 99.9% VOC (volatile organic compound) free. The new product has also been tested and approved by professional decorators for added reassurance that it delivers the same great opacity and coverage as the previous formulation. Dulux Trade has reformulated its popular water-based Dulux Trade Vinyl Matt so that it is 99.9% VOC (volatile organic compound) free. This means that it has a reduced impact on indoor air quality and a lower carbon footprint when compared with the previous formulation. The enhanced sustainability benefits also make the new Dulux Trade Vinyl Matt perfect for projects that need to comply with the BREEAM and LEED accreditations – and IAC Gold certifications are also available. This can help specifiers to showcase carbon footprint reductions and deliver compliant projects with no compromise on product lifecycle or durability. Furthermore, whilst the sustainability credentials of the paint have been improved, Dulux Trade Vinyl Matt still delivers the same coverage and opacity to ensure a quality finish.
www.duluxtrade.co.uk/vinyl-matt
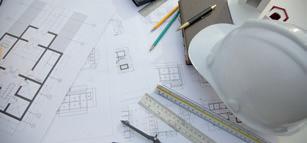
A HELPING HAND FOR SPECIFIERS FROM SFS
SFS Group enjoys excellent working relationships with a number of leading architectural practices, leading to the manufacturer’s involvement with a long list of landmark projects. In contrast to most competitors, which do not have staff fully dedicated to specifiers, SFS has two managers covering the North and South of the UK, who not only look to identify projects where they can directly add value but also liaise with the 12 regional technical sales managers along with other members of the technical team. From its unrivalled ConnectSuite online design tools to the delivery of half a dozen RIBA-certified CPD seminars and other types of support, SFS is committed to going above and beyond to help create standout structures.
uk.sfs.com
0330 055 5888
STOSILENT DIRECT SYSTEM BRINGS OXFORD COLLEGE ACOUSTICS UP TO DATE
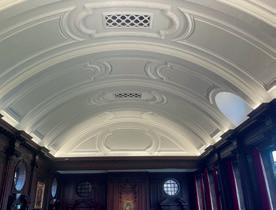
One of the leading Oxford University Colleges has significantly improved its acoustic performance thanks to the StoSilent Direct acoustic ceiling system. It has been installed at Somerville College as part of a major project to upgrade the acoustics and the lighting of the Grade II-Listed dining hall. “This was a complex project, where the aim was to create a much-improved acoustic environment in the hall,” explains Sto’s Acoustics Project Manager, James Gosling. “The hall is used both for dining and for formal events, so outstanding acoustic performance was a key requirement. The aim was to increase the amount of acoustic attenuation material within the moulded panels of the existing vaulted ceiling, but the chosen acoustic system also had to be sufficiently flexible to accommodate the new lighting system.” The StoSilent Direct system offers a particularly economical method of minimising reverberation times and reducing noise levels, as it can be applied directly to walls and ceilings without the need for a sub construction – a feature that also makes it quick and easy to install.
0330 024 2666
VENT-AXIA HELPS HILLINGDON COUNCIL WITH CARBON-FRIENDLY MAKEOVER
www.sto.co.uk
d.newton@sto.com

Vent-Axia has helped Hillingdon Council decarbonise its social housing properties by providing energy-efficient heat recovery ventilation for residents’ homes. Beginning in February 2022, heat recovery ventilation was installed in 150 properties in the first phase of upgrades. This is part of Hillingdon Council’s refurbishment rollout through the Government’s social housing decarbonisation programme. To provide the mechanical ventilation with heat recovery, Hillingdon Council opted for two products from Vent-Axia’s Heat Recovery Retrofit Solution, the Lo-Carbon Heat Save and the Lo-Carbon Tempra. The range has been designed to deliver decarbonisation to social housing providers, offering increased ventilation while minimising unnecessary heat loss through heat recovery technology.
www.vent-axia.com/heatrecoveryretrofitsolution
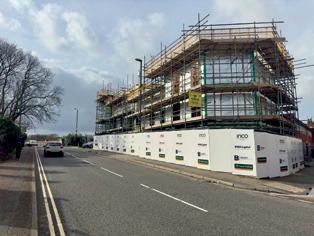
DEVELOPER CITES COMMERCIAL BENEFITS AS KEY TO SELECTING STERLINGOSB ZERO PRIMEDPLUS PANELS FOR CITY-CENTRE SCHEME
A multidisciplinary construction and property company based in the East Midlands has used SterlingOSB Zero PrimedPlus, from West Fraser, for the hoardings around one of its latest residential projects, close to Derby City Centre and its own head office. Aside from the practicalities of the ready-to-use panels offering time savings when erecting a safe and secure site hoarding, INCO Construction & Development Consultants (part of the Berry Group) cited the smart and professional appearance of West Fraser’s new product as being a primary reason for moving away from the use of standard OSB or plywood.
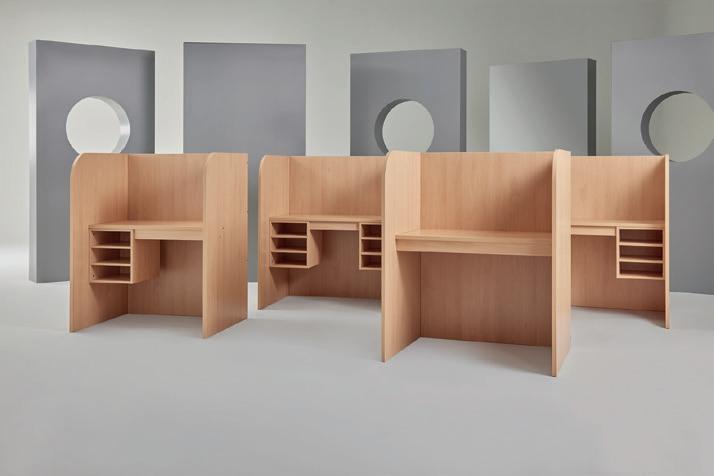
Depending on the requirements our Workstations come with a choice of full shelf storage, left or right units or no storage at all.
Our ToughSEN collection is specially designed for education facilities. Desks and Workstations help create individual secluded spaces, while seperation screens have a noise reduction feature which aims to keep the ambient noise down.
Learn more at https://www.toughfurniture.com/ product-category/toughsen/
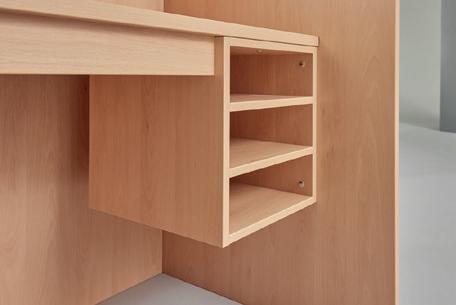

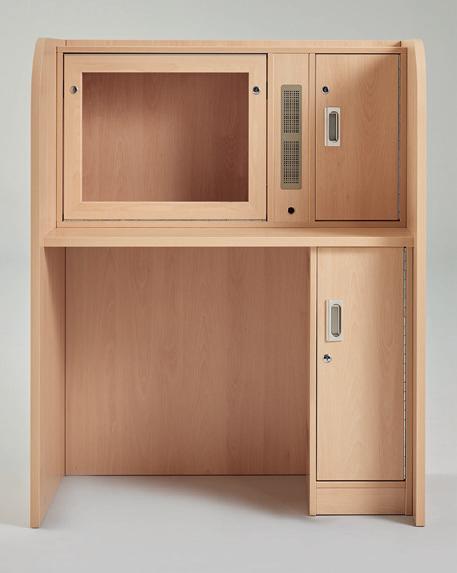
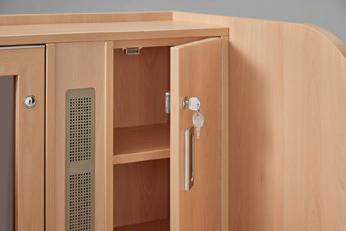
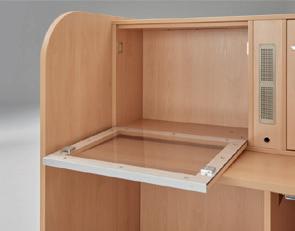
Fixed computer Workstations come fully lockable as standard with a choice of star key locks if preferred.
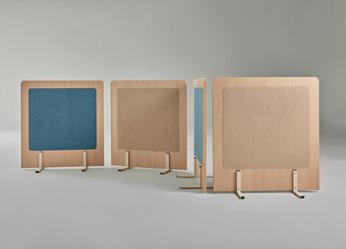
Classroom screens are designed to create secluded spaces and minimise distraction, while also keeping the noise down. Visit our website for more information.
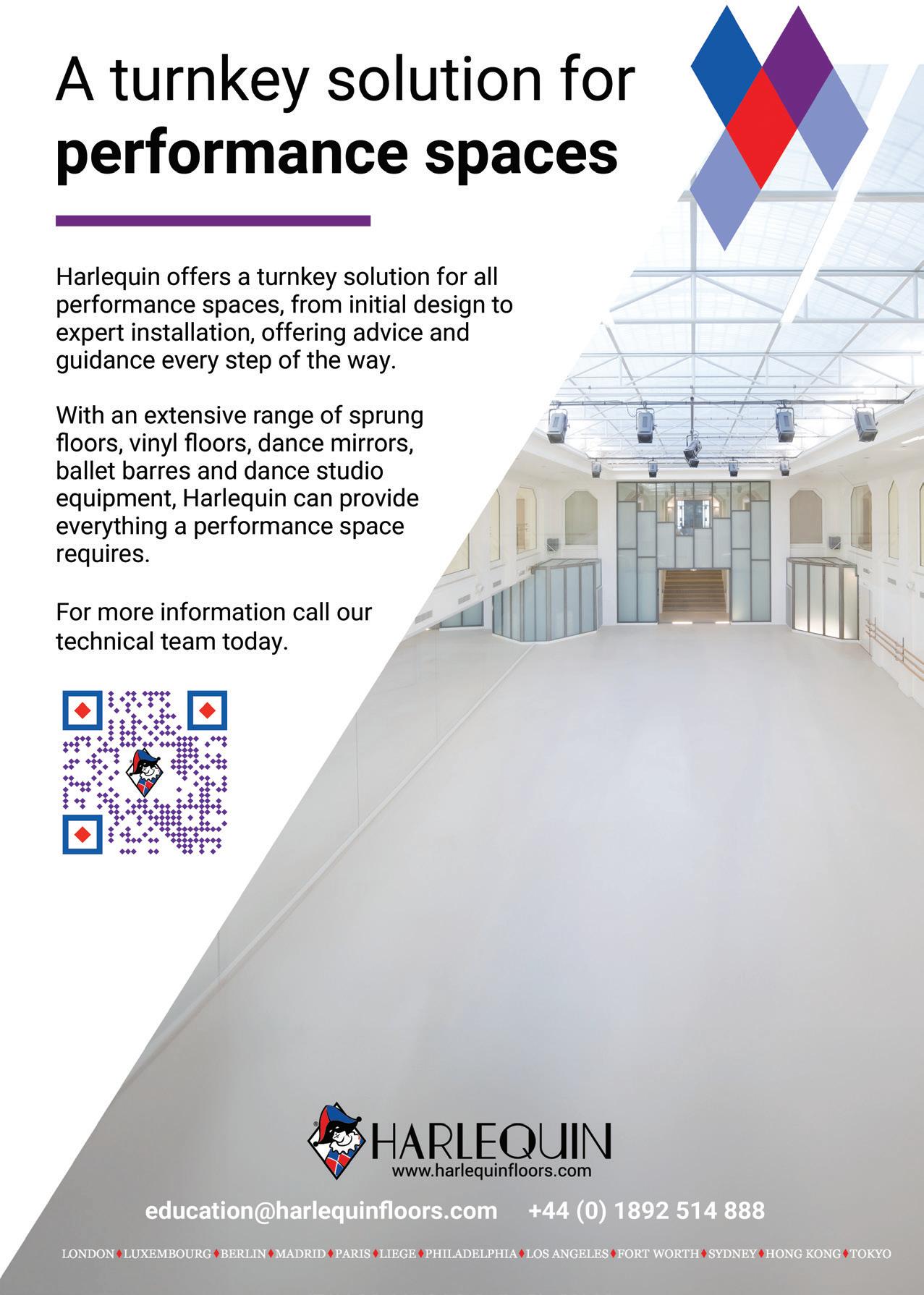