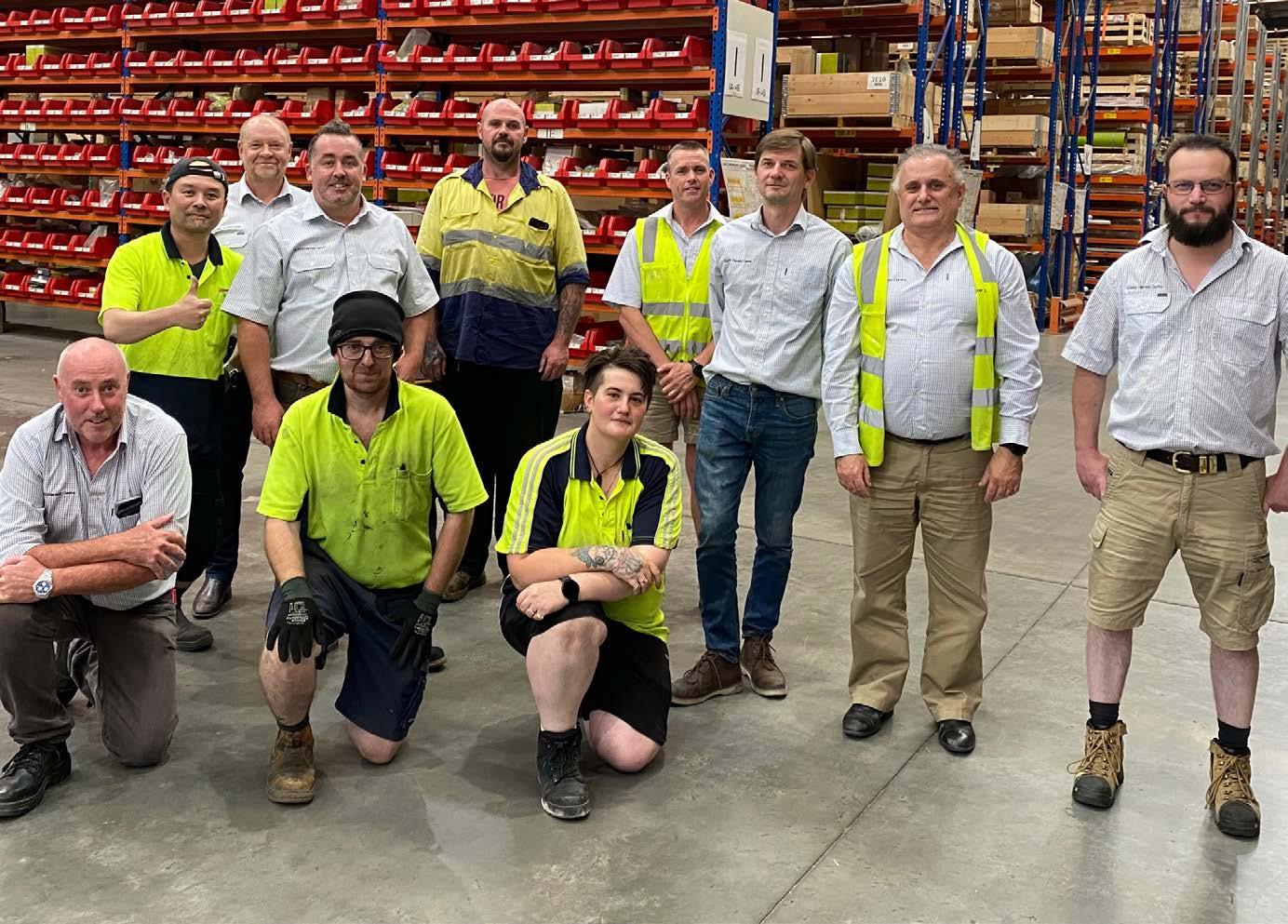
1 minute read
THEY PUT A RING ON IT
Led by New Zealand Warehouse Manager, Dave Cookson, the Christchurch team has been exploring technology to increase efficiency and minimise customer downtime by getting ordered parts out as quickly as possible.
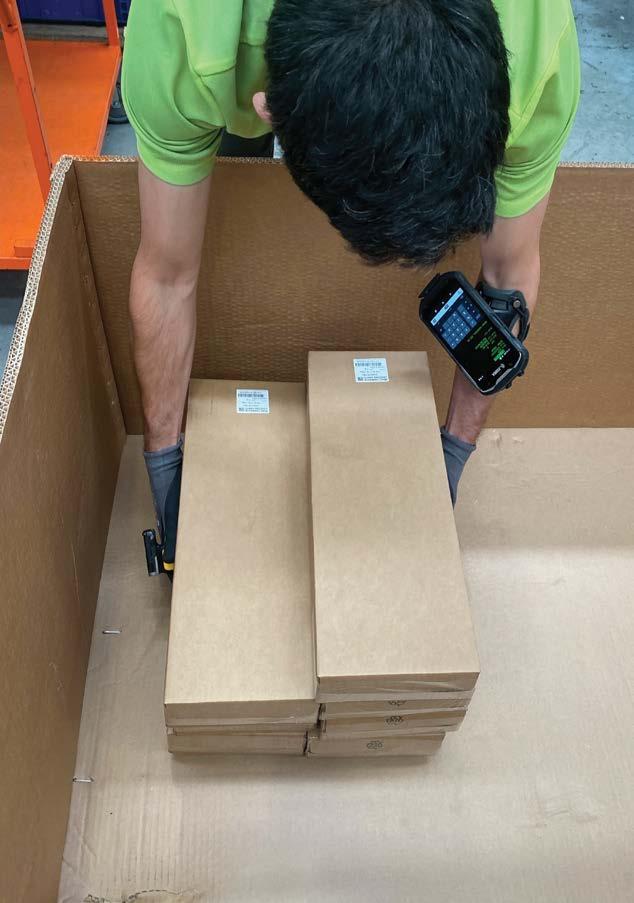
During harvest season, the team dispatches over 500 lines across 300 orders daily. Plus around 7,000 items are put on shelves each month. So any increase in efficiency, comfort, timesaving and safety is welcomed.
From Handheld to Ring Finger Solution? A new RF barcode ring scanner worn on a finger and paired with a wrist-mounted unit. Working with Zebra Technologies Dave says, “we trialed lots of new hardware but the TC52 with wrist strap paired RS5100 ring scanner were the clear winners”.
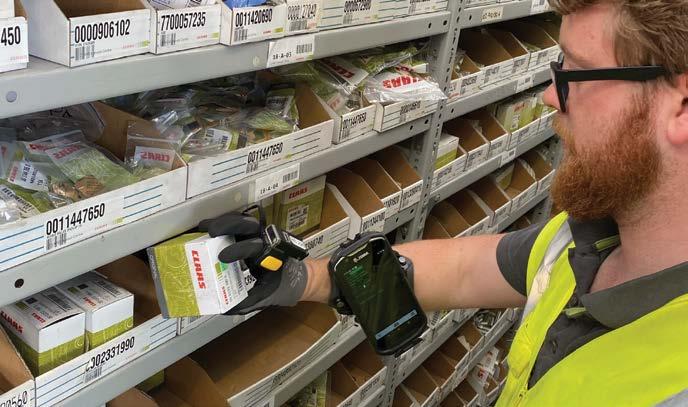
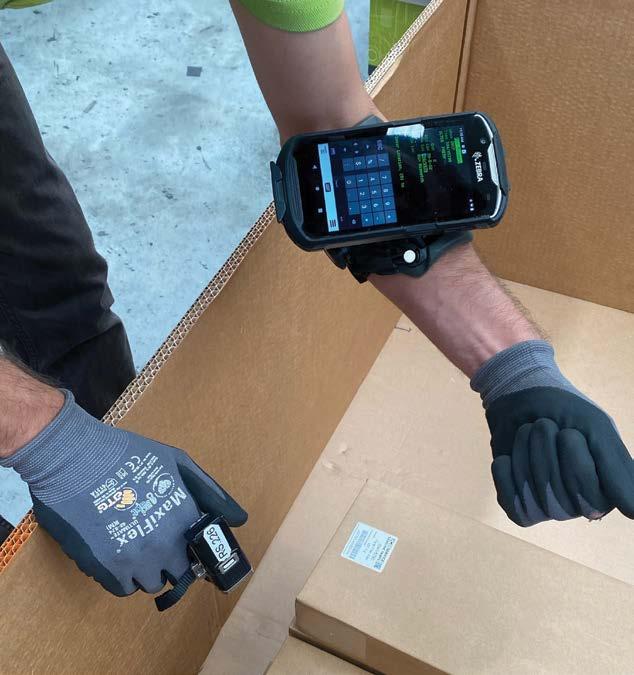
“This is a total hands-free package. It allows users to move freely and improves efficiency in all work where an RF scanner is required. As with most hardware upgrades the software needs to catch up for major benefits.”
What the team says
The selection and testing of these wearable devices involved the whole Christchurch team. And they wholeheartedly agree that having two hands free are better than one - especially in the busy season.
With two TC52 and four ring scanners in the Christchurch Parts Distribution Centre they’re seeing great efficiencies in despatch to inwards, stocktaking and relocating.
Following its successful implementation, Dave and crew look forward to sharing learnings across the Group.
QUIZ: THINK YOU KNOW YOUR PARTS?
1. What’s the most common part ordered at the Christchurch Warehouse?
2. And how many of that part has been ordered in the last three years?
3. How many stock lines are held in the Christchurch Warehouse?
4. Can you make a CLAAS machine from the parts stored in the Warehouse?
Answers on page 18.