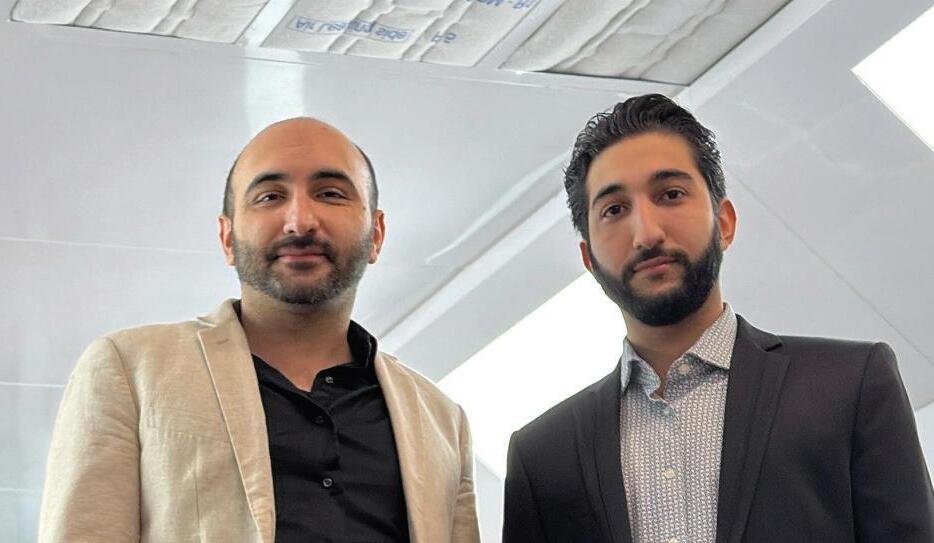
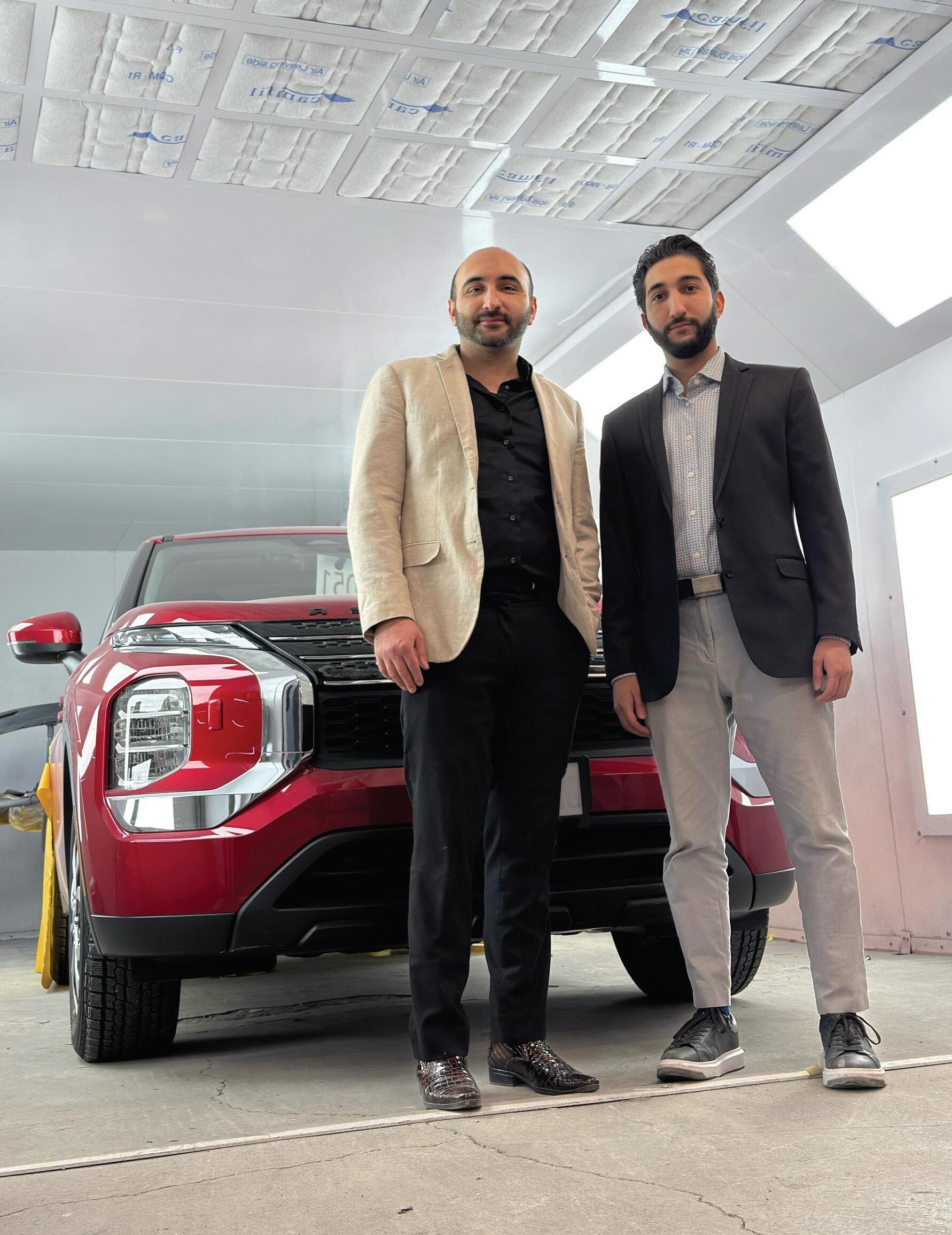
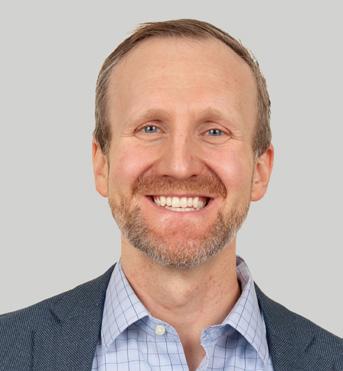

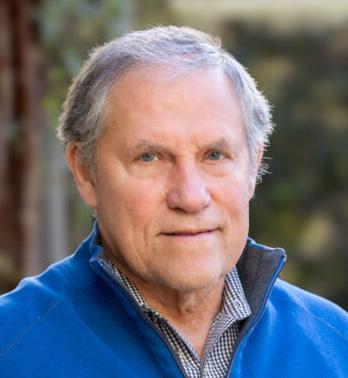
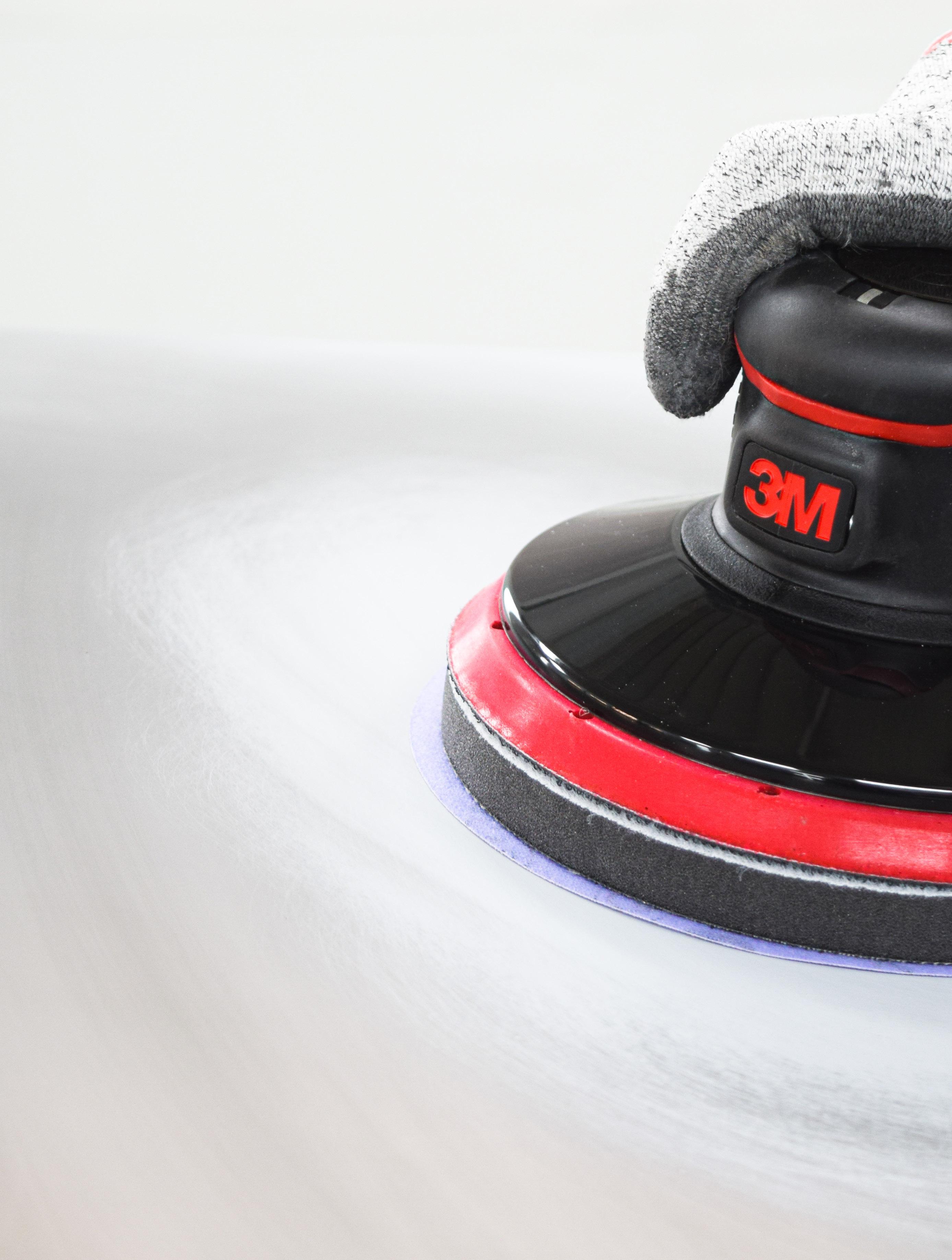
The 3M™ Clean Sanding System is a complete sanding solution that is:
Designed to reduce dust in the air from sanding for a cleaner workspace.
Helps shops boost productivity and efficiency by helping to reduce rework and cleanup time.
Compact and mobile. Designed for easy, flexible use around the shop.
Compatible with pneumatic and/or electric sanders.
Tech-friendly design including auto on/off, antistatic hose, rubber wheels, brake locks, and LED indicator lights.
BY DARRYL SIMMONS, PUBLISHER
With all the changes in technology, repair practices, and business operations, it is easy to lose sight of what makes this industry truly remarkable—the people who built it and the vital role collision repairers play in the lives of their customers.
Recently, I was reminded of this at a magazine publishers’ conference. During a focus group discussion, I pointed out that collision repair professionals are often not given the respect they deserve as highly skilled business owners and operators. Afterward, Paul Gatti, a successful publisher in the pharmaceutical media industry, approached me to say how much my comment resonated with him.
collisions and improve road safety. But they also present new challenges for repairers. Calibrating ADAS components properly after a repair is not just an added step—it is a crucial requirement to ensure vehicles function as intended. A misaligned camera or sensor can mean the difference between a system that works correctly and one that puts drivers at risk.
For shop owners and technicians, this means investing in training, equipment, and processes that keep pace with these evolving systems. It also means educating customers—and insurers—on why proper ADAS calibration is not optional. Unfortunately, too many still see these repairs as simple part replacements, rather than intricate
So, as we move forward, let’s keep two things in mind: honouring the legacy of those who built this industry and embracing the technology that is shaping its future.
Paul’s father had owned a collision repair shop after immigrating from Italy, and his first job was sweeping the floors. He told me that the lessons he learned from his father and the shop shaped his career. Today, he holds a PhD, is a nationally recognized scientist, and his publications guide medical professionals worldwide. Yet, it was in that repair shop that he first learned about hard work, integrity, and customer care—values that still guide him today.
This is a reminder to all of us: never forget the impact you have. You are the professionals who restore more than just vehicles—you restore confidence, security, and peace of mind for drivers during some of their most stressful moments. And beyond that, you are part of a legacy of hard work and innovation that has shaped this industry into what it is today.
That legacy, however, is not just about where we have been—it is also about where we are headed. The collision repair industry is in the midst of one of its most significant transitions, driven by rapid technological advancements. One of the most transformative changes we are seeing is the widespread adoption of Advanced Driver Assistance Systems (ADAS). That is why this issue of Collision Repair is titled All About ADAS—because its importance in the repair process today cannot be overstated.
ADAS has moved from being a luxury feature to a critical safety system found in nearly every new vehicle. Whether it is lane departure warnings, adaptive cruise control, or automatic emergency braking, these systems are designed to reduce
recalibrations that require precision and expertise.
As always, the responsibility falls on repairers to do the right thing. And that is what makes this industry exceptional. Collision repair professionals have always adapted, always innovated, and always put safety first. It is not easy. It requires continuous learning, advocacy, and sometimes, standing firm against pressures to cut corners. But it is what separates true professionals from those who simply fix dents and scratches.
So, as we move forward, let’s keep two things in mind: honouring the legacy of those who built this industry and embracing the technology that is shaping its future. The pioneers before us worked tirelessly to establish a profession built on skill, craftsmanship, and integrity. Today, it is our responsibility to uphold those values while mastering the complexities of modern vehicle technology.
ADAS is just one part of the bigger picture, but it represents the direction the industry is headed—toward smarter, safer, and more complex repairs. It is up to all of us to ensure that we are not just keeping up, but leading the way.
Thank you for the work you do. It matters more than you may ever know.
PUBLISHER
Darryl Simmons publisher@collisionrepairmag.com
ASSOCIATE PUBLISHER
Orest Tkaczuk | orest@mediamatters.ca
EDITOR
Allison Rogers | allison@mediamatters.ca
ART DIRECTOR
Yvonne Maschke | yvonne@mediamatters.ca
ASSISTANT EDITOR
Sarah Perkins | sarah@mediamatters.ca
VP OF INDUSTRY RELATIONS & ADVERTISING
Gloria Mann 647.998.5677 | gd.mann@rogers.com
INDUSTRY RELATIONS ASSISTANT Wanja Mann 647.998.5677 wanjamann1@gmail.com
DIGITAL OPERATIONS MANAGER
Cassie Doyle | cassie@mediamatters.ca
AUDIENCE ENGAGEMENT MANAGER
William Simmons | william@mediamatters.ca
MEDIA PRODUCTION SPECIALIST
Dayna Dicuangco | dayna@mediamatters.ca
CONTRIBUTORS
Jeff Brown, Greg Horn, Doug Kirk, Stefano Liessi, John Marlowe, Jay Perry
SUBSCRIPTION
Single edition $7.99 One-year $39.95 ( 6 issues) Collision Repair™ magazine is published bimonthly, and is dedicated to serving the business interests of the collision repair industry. It is published by Media Matters Inc. Material in Collision Repair™ magazine may not be reproduced in any form without written consent from the publisher. The publisher reserves the right to refuse any advertising and disclaims all responsibilities for claims or statements made by its advertisers or independent columnists. All facts, opinions and statements appearing in this publication have been compiled and included with the permission, though not necessarily the endorsement, of the editor, or of independent columnist contributors, and are in no way to be construed as those of the publisher, or as endorsements of them.
PRINTED IN CANADA ISSN 1707-6072
CANADA POST CANADIAN PUBLICATIONS MAIL
SALES PRODUCT AGREEMENT No. 40841632
RETURN POSTAGE GUARANTEED
Send change of address notices and undeliverable copies to: 317 Reid St., Peterborough, ON K9J 3R2
“We acknowledge the financial support of the Government of Canada”
Collision Repair magazine is published by Media Matters Inc., publishers of:
The ProColor PROcess is a winning formula.
A proven business model for 20 years, ProColor Collision provides an alternative to independent body shops that want to join one of the fastest growing networks in the world.
Local business owners are supported by a team of sales, operational and marketing professionals, and backed by proven tools and ongoing training programs.
ProColor Collision is committed to helping shop owners grow their business in their communities while leveraging strong established relationships with global insurers, suppliers and fleet companies.
Contact Amin Youssef at ayoussef@fixnetwork.com
Your Journey to Success Starts here
On January 22, 2025, Tim Bowes assumed the role as president of Global Industrial Coatings, Axalta, succeeding Shelley Bausch. Bowes most recently served as Axalta’s senior vice president and chief transformation officer. Before joining Axalta, he served as Senior Vice President and President of Electrification, Industrial, Aftermarket, Purchasing & Supply Chain for Meritor. Bowes has also served as Senior Vice President and President of the Casting business unit for American Axle & Manufacturing and CEO and President of Transtar Industries, an Industrial and Automotive Aftermarket company. He also held executive leadership roles at ITT Automotive and Internet.
Effective April 1, 2025, Wally Dingman will officially serve as ARC’s new Executive Director replacing Steve Fletcher in the role. Dingman has been a fixture in the auto recycling sector as the previous Chairman of the Ontario Automotive Recyclers Association (OARA) for 14 years and as the Chairman of ARC for 10 years, from 2011-2021. Fletcher will be stepping away from day-to-day activities after the OARA Convention & Trade Show in Niagara Falls in March. He will retain the international activities of ARC and work on important sector relationships and special projects with Dingman.
Bonner has been named 2025 Chair of the CIECA alongside a board of four other trustee officers. In his new role, Bonner will serve on CIECA’s executive committee, which oversees business matters throughout the year and plans the agenda for CIECA board meetings. Bonner has also served as the organization’s Vice President of Client Sales and Support, Safelite Solutions.
Fix Network has announced that Daryll O’Keefe has been promoted to the role of Vice President, Strategic Business Development of North America. In this new role, O’Keefe will focus on driving franchisee sales growth, expanding the network and enhancing the profitability of Fix Network’s collision brands across both the United States and Canada.
The Liner Cup System from SATA fits onto the QCC connection of your paint spray gun. The adapter is no longer required, and there are many additional advantages:
• More favourable centre of gravity
• Easier cleaning
• Low weight
• Particle-free: premium sieves
• Easy mixing: the SATA scale system
• 50 liners, lids and sieves. 1 hard cup and 20 caps per box
Leadership through collaboration is the IBIS 2025 theme
The International Bodyshop Industry Symposium (IBIS) Worldwide is thrilled to announce that registration is now open for the IBIS Global Summit 2025.
Set to take place from June 24th to the 26th at the Iconic Swissôtel The Bosphorus in Istanbul, the event aims to bring together industry leaders, innovators and decisionmakers from across the globe.
With a theme of “ Shaping The Future: Leadership Through Collaboration,” the 2025 summit will specifically focus on driving progress and transformation in the collision repair sector.
Additionally, the 2025 edition of the summit further aims to build on its annual legacy of networking opportunities.
Attendees can look forward to events such as: presentation and panel discussions featuring global experts addressing the most pressing challenges and opportunities in the collision repair industry; sessions exploring the latest technologies and best practices shaping the future of the sector; and all of the sites of Istanbul—a city where history meets modernity.
FOR MORE INFORMATION, OR TO REGISTER FOR THE EVENT, VISIT HTTPS://IBISWORLDWIDE.COM/IBIS-GLOBAL-SUMMIT-2025/REGISTRATION/. AND, FOR THE LATEST UPDATES ON UPCOMING EVENTS, VISIT WWW.IBISWORLDWIDE.COM OR FOLLOW IBIS WORLDWIDE ON LINKEDIN AND TWITTER (@IBISWORLDWIDE).
In its fourth-quarter report, Crash Course highlights the top trends that impacted the automotive and collision repair industry throughout 2024. According to the report, vehicles seven years or older now make up nearly 45 percent of all repairable claims, up from 35 percent in 2019.The report further notes that miles driven by consumers have increased 0.8 percent year-over-year through the third financial quarter, and up 0.6 percent compared to 2019.
Additionally, through Q3 2024, the average price per part is up 1.4 percent year-over-year following increases of two percent and 1.2 percent in the second and third quarters of 2024.
Canadian vehicle manufacturers and auto dealers met on Parliament Hill in Ottawa to formally call for the end of federal electric vehicle sales mandates previously brought into effect by the government in 2023.This call for action to end the mandates comes in the wake of the federal government ending electric vehicle incentives under the federal iZEV program, alongside continued insecurities over developing charging infrastructure. Attendees on Parliament Hill further highlighted the federal government’s failure to secure adequate funding for the transition to electrified transportation that was previously actively promoted by Canadian officials.
The Ontario government has announced that as of January 1, the province’s collision reporting threshold has been increased from $2,000 to $5,000. In a recent report highlighting the regulations and statutes in force for the new year, the government indicates that the motion is specifically intended to “help reduce the administrative burden on drivers, commercial vehicle operators and police services.”
In addition to the new Mercedes-Benz certification, CARSTAR Hamilton Gage also holds many other certifications, including: Audi Mixed Metals—where it is again one of two CARSTAR locations in Canada to hold this accreditation—Volkswagen, FCA (Fiat, Chrysler, Jeep, Dodge), Kia, Toyota, Nissan GTR, Nissan, CCIAP, Honda Pro First (Honda/Acura), Infiniti, Hyundai and Genesis.
CARSTAR Canada has announced that the first Canadian location, CARSTAR Hamilton Gage, owned by Adriano and Remo Mercanti, has officially earned Mercedes-Benz Elite certification. This achievement makes CARSTAR Hamilton Gage one of only 20 facilities in Canada with this certification.In response to the success of this certification, Remo Mercanti commented that “we are incredibly proud to carry on my late father’s legacy, Guerino Mercanti, in being the first and only CARSTAR facility to have earned the prestigious Mercedes-Benz certification. We have been serving the collision industry for over 65 years now, through three generations, with my son Adriano.”
Autel announced that its tablets have been certified by the Auto Authentication Authority (AutoAuth) to access Mercedes-Benz vehicles’ Security Gateway (SGW). As a result, tablet users can now access more vehicle brands’ secure gateways than any aftermarket tool using the authentication service. The company negotiated with Volkswagen/Audi Group to add SGW access capability to its diagnostics and service tablets, and earlier this year, Autel added the functionality to its tablets. Once Autel tablet owners register their tool for MercedesBenz vehicle SGW access with AutoAuth, they can perform restricted functions, including clearing codes, active tests, special functions, service resets, coding and adaptations, and Advanced Driver Assistance System (ADAS) calibrations.
According to a new study from Consumer Reports, which calculated predicted reliability ratings for vehicle brands, Subaru leads as the most reliable vehicle in North America. This year’s report specifically gathered data on more than 300,000 vehicles from the 2000 to 2024 model years, with a few 2025 models introduced early enough to be included. Subaru ranked number one with a score of 68 out of 100. On the opposite end of the spectrum, Rivian came in last place with a score of 14 out of 100. The study further notes that while internal combustion engine (ICE) vehicles have 17 potential trouble areas, EVs can have up to 12 trouble areas.
Manitoba Public Insurance (MPI) has reportedly countered the findings of a study shared by Preszler Injury Lawyers that originally stated that Manitoba recorded 85.4 percent more driving injuries than the national average. Using data from Transport Canada’s National Collision Databases, the study originally attributed the record number of injuries in the province to severe weather conditions as well as insufficient road safety measures. MPI spokesperson Tara Seel claimed the study overlooked Manitoba’s unique reporting methodology compared to other provinces: because the province is structured as a public insurer, Manitoba reports more injury and collision data than other provinces.
Hyundai Motor Company and Kia Corporation have announced the development of the Integrated Greenhouse Gas Information System (IGIS), a platform designed to monitor, quantity and manage carbon emissions throughout the entire vehicle lifecycle. By leveraging the Life Cycle Assessment (LCA) methodology, the automakers hope that the IGIS platform will provide detailed quantification and tracking of carbon emissions so that companies can ensure accurate and consistent data collection. The goal of the project is to anticipate future climate initiatives.
Volvo has released a position statement that updates technicians on the necessary precautions to take when welding the brand’s electric vehicles. The statement outlines that if the welding must be carried out in the immediate vicinity of an electronic unit/high-voltage battery, then the electronic unit/high-voltage battery must be removed. The position statement also offers safety details and suggestions, including remembering that “all batteries, 12V and over, are to be considered as highly dangerous,” as well as understanding that “no high-voltage-related components may be disassembled unless otherwise stated in VIDA.”
FOR SIA AND ARASH MOKHTARI, COLLISION REPAIR IS ALL ABOUT TURNING CHALLENGES INTO OPPORTUNITIES
BY SARAH PERKINS
“We are a performance-based MSO (Multi-Simplicity Owner) and we take that very seriously. From calibrations to ceramic coatings, you name it, we do it!”
— Sia Mokhtari, co-owner of Simplicity Car Care Windsor, Windsor East, and Windsor LaSalle.
Like so many who find themselves with a passion for the collision repair industry, co-owners of Simplicity Car Care Windsor, Windsor East, and Windsor LaSalle, brothers Sia and Arash Mokhtari grew up surrounded by cars in need of repairs.
Having spent a childhood working and learning in their father’s mechanical shop in the Windsor, Ontario area, the brothers gained an exposure to the industry that is familiar to many who continue to call the bodyshop a home away from home.
Sia and Arash would only build upon the foundations of their childhood after first taking a detour to work as engineers on the other side of the country.
“As kids, we were always around dad and in the shop. However, he originally didn’t want us to follow him into the industry. He wanted us to be either doctors or engineers,” said Sia. “I passed on being a doctor. So, I had to be an engineer.”
Arash and Sia both worked to get their degrees in civil engineering. They each spent
over a decade working on the oil sands in Alberta.
It later became obvious that their true goal in life was to continue building “another branch to the tree that was already planted.”
“We shared a vision to grow and expand the collision side of the business,” said Arash.
So, in 2015, the brothers purchased their first collision repair facility in Windsor and then in 2018, they joined the Simplicity Car Care network.
“With the help and guidance of the members of the Simplicity team, our insurance partners and our great clients, we were slowly able to add to our facilities one by one,” Sia said.
“The Simplicity leadership team is always open to sharing their knowledge of the industry and helping all franchisees grow. We felt that Simplicity would be a good fit for us because we share a similar view on the future of the industry and like them, we believe in the cornerstone of business being built on customer satisfaction.”
When asked about the transition from engineering and back to the automotive industry, the brothers say their degrees have imparted an ability to think analytically, but most of their knowledge of collision repair continues to be learned on the shop floor.
In continuing to work on gaining their own certifications, the brothers were quick to highlight how their current success comes from the team of approximately 30 membersthey have throughout their locations.
“We have a team of amazing certified technicians and we invest a lot of time into ensuring they have the proper training,” commented Sia. “We’re involved on a daily basis in every aspect of the business.”
“In our day to day, we always try to focus on customer service, retention and performance,” added Arash. “Our goal is to build lasting relationships with our clients and insurance partners by providing exceptional service and high-quality repairs. We’re committed to delivering the best performance in every job, ensuring that every client’s experience is
“Our goal is to build lasting relationships with our clients and insurance partners by providing exceptional service and high-quality repairs.”
“Sia and Arash have done an outstanding job at growing their business over the past several years. I’m most proud of their dedication to our customers and their willingness to learn and grow. They continue to lead by example and are always investing in the betterment of their business and people. Congratulations Sia and Arash on all your success, and I look forward to your continued growth.”
—
seamless and satisfying. We have invested in new paint booths, manufacturer-approved resistance spot welders, MIG welders and 3D computerized measuring systems which allow us to perform a quality repair more efficiently.”
When it comes to acquiring talent for their three facilities, the brothers believe that a lot hiring struggles come down to management styles. This is where Arash and Sia try to differentiate the business by being what they describe as “leaders in the industry, but not bosses.”
“I’ve learned a lot from my PMP certification on how to change both technicians’ and the general public’s perception of the industry,” commented Sia. “We’re trying to move away from the old school style of managing that was often more discipline focused. This style just doesn’t work these days. You have to keep people motivated and understand the psychology of each person.
It’s about knowing what motivates them, what keeps them happy and then taking this information and creating an environment that’s safe, free from hazards and negativity.”
These personable strategies were one of the shining lights guiding the brothers and their businesses through the challenges of the Covid-19 pandemic.
“Our proudest moment is also the efforts we took to navigate our locations through the pandemic,” said Arash. “There was an immense drop in volume during this time, but we also took that time to implement and improve the existing processes we had and perfect them for when volumes would rise again.”
Simplicity Windsor was even able to retain all staff.
“Our motto is always we’ll eat less, as long as everyone eats with us.”
This community mindset is something that the brothers feel helps set their busi-
ness apart from others in the area. And, by investing in top-of-the-line tools, training, certifications and in-house services, Arash and Sia are ready for the future.
“We’re open to acquiring more facilities and are always open for opportunities to grow and develop with Simplicity Car Care,” concluded Arash.
“We’re not the masters of anything,” added Sia, “but we do our best to learn and grow from others’ experiences and knowledge so that we can, day by day, better ourselves and our capabilities.”
“On behalf of our entire family and organization, we would like to thank all our loyal clients, insurance partners and everyone at the Simplicity Network for all the support we have received. We will continue to provide our existing cliental with great service and look forward to welcoming new cliental and insurance partners to our facilities across the market.”
BY JAY PERRY, ALLY BUSINESS CONSULTING
With so many things vying for our attention on a daily basis, it’s no wonder why we can get distracted from what matters. This applies in so many ways, such as understanding KPIs and working out plans to improve them, to helping our team members through struggles they face, to profitability issues, to customer service levels and feedback—think Google reviews—to so many more items that I could likely fill the column with listing just as the content.
That’s why one of the most important things we work to develop in our clients is the ability to slow down to speed up. You may have heard it before but what does it really mean and how can you develop a healthy usage of the practice?
To us it means recalibrating our thinking, not letting the frantic nature that surrounds us in business take over to the point that we find ourselves in a reactionary mode. The temptation is great and there is another axiom we should be mindful of: cooler heads prevail. Or, to use an abbreviated version of Rudyard Kipling’s turn of phrase: If you can keep your head when those about you are losing theirs, then you will be able to succeed.
This boils down to defining what matters, then doggedly pursuing and constantly evaluating your success in achieving these goals. The definition for some is the greatest challenge because their attention is so scattered. Hence, we have the first example of slowing down so we can speed up. You must take the time to list the things vying for your attention then prioritize that list in alignment with what truly matters to you.
This process is the same for all of us even though the answers will likely be unique to the individual. That’s another good reason why we next need to slow down and explain our vision to the others we work with. We all have a vision. Few take the time to articulate
If you can keep your head when those about you are losing theirs, then you will be able to succeed.
that vision and even fewer take the time to explain it to others and even fewer still take the time to create support from teammates by securing “buy-in” or in business-speak, engagement! For those that do take the time to execute these actions, the rewards are enormous!
Keep it simple in this step-by-step approach:
1. List the tings vying for your attention
2. Prioritize the list in alignment with what matters to you
3. Articulate the vision by writing it down in a way that others can understand
4. Engage with your team members and explain the details of the vision
5. Ask for their support in making it come into being
I have outlined a lot of work that will take time. It is only by taking this time—slowing down—and working on what matters in an organized approach that will help you succeed—speed up—and be the one who’s driving!
Smart Spot welder
Moving Parts, NO Lasers, NO Targets, NO Adaptors, NO Magnets Arms, NO Extensions, NO Wires, NO Wi-Fi, NO Bluetooth Calibration Needed, MITCHELL chassis data
Automatic setting of parameters
Water cooled for hi productivity
22 ft. long cable, No EMF emissions
Output 14,000 Amps, 450 daN or 700 daN
Input 50 Amps, 208-240V, 3 Phase
Approved by OEMs
3680 model wi-Fi, enabled for factory Updates and diagnostics
BY JEFF BROWN, CARSTAR DON-MOR AUTOMOTIVE
Our shop has been a Tesla Approved Collision Centre (TACC) since December of 2023. People often ask me how much capital we invested to become Tesla Certified, as if it’s a go or no-go mathematics equation only, but the answer isn’t that straightforward. Vehicle technology does not stop changing. Electrified vehicles are simply a result of progress and innovation in the auto manufacturing space. Repairing them requires us to think the same way OEMs are. We need to advance the technology and training in our facilities to repair any new vehicle properly–not just EVs. If you’re wondering if modern vehicle technology and EVs will make their way to your shop and if you’ll need to invest, I have some bad news: the train has already left the station. The good news is that pursuing the journey will make your business better, more sustainable, and more profitable than ever. The only question is if you’ll get out ahead of it now and embrace the change or be dragged behind it kicking and screaming.
Adding Tesla repairs to our portfolio has been one of the best strategic decisions we’ve made.
We’ve been busy incorporating an apprenticeship tool grant and training program into our business that has resulted in us hiring between five and eight new staff from local trade schools each year. Being ahead of the curve on EVs and repair technology means that staff tend to seek us out vs. us hunting for them because they’ll get to learn new skills and use new equipment to further their career. This isn’t rocket science. Investing in modern frame and fixturing racks, measuring systems, welders, and ADAS calibration equipment makes us ready to tackle whatever wrecks come our way in the most efficient way possible, electric or not. Here’s the punchline: if you’re fixing EVs or not, you’ll need most of these things anyway.
When it comes to employees, think about the basics. Employees are looking to work for a company that values their contributions and invests in their growth and efficiency. They’re looking for a career path and upward mobility. They’re looking for competitive pay based on what they bring to the table.
Do you have easy access to water and coffee in your facility? Do your staff have somewhere clean and comfortable to take a lunch break? Do you regularly provide opportunities for your staff to expand their skills through company-sponsored training? Do you offer a competitive benefits and retirement savings package to incentivize retention? Do you offer flexible hours and paid time off so parents can take
care of their family commitments?
Have you considered air conditioning your shop so you can maintain full productivity in the hot summer months?
It’s not a matter of if you can afford it—you can’t afford not to. These small but critical steps have made all the difference in our ability to deliver on our commitment to servicing insurers and customers in our market. Because of these investments our business has and continues to deliver exceptional financial and operational results.
If we get complacent or stray from this way of thinking, we won’t make it. It’s that simple. Any time we find ourselves struggling, I look back and realize it’s because we didn’t put people first.
APPROVED COLLISION
Adding Tesla repairs to our portfolio has been one of the best strategic decisions we’ve made. I was hesitant because of the unknown, our technicians were worried about change, and our estimators were concerned about all the rumors they had heard about less than stellar parts availability. It turns out these concerns were all unfounded.
Instead, we’ve found that our technicians appreciate the consistency of working on the same handful of vehicles, our estimators love working with the Tesla EPC Portal to find parts and OEM procedures, and I’m incredibly happy with finding a new and profitable additional revenue stream for our business. We’re a year in and Telsa already represents a significant portion of our collision repair revenue.
You’ll need a charging station, some specialty equipment from Tesla, and technician training, but if you’re up to date on equipment purchases in your facility, otherwise, the investment to get started can be surprisingly small.
The other benefit is that you’ll be ready for the other EVs that are likely to show up in your parking lot—Mustang Mach-Es, F150 Lightnings and Hummer EVs are gaining traction—and we’ve found ourselves ready to deal with the intricacies of these vehicles like battery disconnects and charging because of our Tesla journey.
If you haven’t seen an EV in your parking lot yet, you will soon. Before going all in and pursuing an OEM certification, there are some steps you can take to get ready.
• Enroll technicians in EV Safety Training and purchase basic safety equipment
• Create a process for EVs that arrive on your lot—in what circumstances will your staff need to de-energize the high voltage systems?
• Research the bake temperature of your spray booth and the requirements of different OEMs to avoid damage to EV battery packs
• Install an EV charging station. EVs require battery maintenance and unlike ICE vehicles, they consume energy even when idle. Maintaining the charge of customer’s vehicles is critical, especially if they’ re at your facility for a long time waiting for backordered parts.
• Take an EV for a spin—rent an electric car for the weekend and see what the hype is about. You’ll be better equipped to have a conversation with a potential customer or insurer after visiting a supercharger, using autopilot and experiencing the torque of an electric drive system!
My prediction—the collision repair industry is at a pivotal moment, and the new basics for staying relevant in 2025 will be all about embracing change rather than resisting it. Success in this new era requires more than just keeping up—it demands embracing change with enthusiasm, investing in people, and committing to continuous improvement.
I’m certain that the road ahead for us is boundless and full of opportunity and I can’t wait to see what happens next.
When spraying a catalyzed paint or waterborne paint product inside a spray booth or prep deck, the proper personal protection equipment is an air-supplied respirator. Air supplied respirators must be supplied with Grade “D” Breathable Air.
Quality Air Breathing Systems are designed to provide Grade “D” Breathable Air from your existing compressed air system, for compliance with current CSA Standards when using an air supplied respirator. Systems sized from one person to twelve persons at the same time. We offer complete systems, with proper filtration and carbon monoxide monitors, panel mounted, and ready to use. Available in belt mounted, wall mount, and portable versions.
In recent years, the automotive industry has undergone significant transformation, prompting Fix Network Canada’s leadership team to launch a strategic initiative aimed at strengthening its business verticals—Collision, Glass, Calibration, and Mechanical Services. The vision is clear: to create a more seamless, customer-centric repair model that eliminates inefficiencies, reduces cycle times, and enhances service quality. For many franchise partners, this meant embracing new business practices. However, for Johnny Soleas, owner of Fix Auto Fort McMurray, the “Shop of the Future” concept was something he had already started building long before the initiative was formally introduced, and something he continues to refine and expand as the industry evolves.
The vision is clear: to create a more seamless, customer-centric repair model that eliminates inefficiencies, reduces cycle times, and enhances service quality. For many franchise partners, this meant embracing new business practices.
Johnny’s journey toward a fully integrated repair model began in 2016 when he opened JHG Automotive, a mechanical shop named after him and his two brothers, Harry and George. The shop runs adjacent to his collision repair centre, which has been operating under the Fix Auto banner ever since he joined Fix Network’s family of premium automotive repair brands five years ago. Recognizing the need for an integrated approach, Johnny explains, “I was already repairing vehicles equipped with ADAS, and calibration was becoming necessary. I started subletting calibrations but delays and quality control issues made it clear that I needed to bring this service in-house.”
With a team of trained mechanics, many with dealership backgrounds, Johnny made the leap to invest in cutting-edge equipment. His latest acquisition? The Hunter Ultimate ADAS system—a state-of-the-art calibration machine that positions his shop ahead of even the local dealerships. “Now, we can even print proof of calibration, ensuring accuracy and compliance with industry standards,” he says. “It gives us control over cycle times and quality, something we never had when subletting.”
Having successfully integrated calibration, Johnny turned his attention on the next challenge: windshield repair and replacement. “Glass repair was another major sublet that held up cycle times,” he says. “We’d have vehicles ready for paint, but we were stuck waiting for glass technicians. That delay impacted everything.”
His solution? Co-branding with NOVUS Glass. By bringing glass repair in-house, Johnny aimed not only to improve efficiency but also to tap into the growing retail market. “Now, customers coming in for a windshield repair might later need mechanical or collision work. We’re the first shop that comes to mind for everything,” he says.
Furthermore, integrating glass repair services is a critical step in ensuring vehicle safety. Modern vehicles rely on ADAS features such as lane departure warnings, emergency braking, and adaptive cruise control, all of which require precise calibration after a windshield replacement. “If a windshield isn’t installed properly, and the ADAS sensors aren’t calibrated correctly, those safety features won’t function as they should. That puts drivers at risk,” Johnny explains.
As they prepare to officially launch with NOVUS Glass, Johnny is excited about the comprehensive training his
team will undergo. This training will ensure they are fully equipped to provide high-quality windshield repairs, seamlessly complementing his existing collision and mechanical services while prioritizing customer safety and vehicle integrity.
Executing a strategy like this would be challenging without the expertise, vendor relationships, and operational synergies within Fix Network. “From operational and training support to marketing initiatives, Fix Network has been instrumental in helping my business,” Johnny says.
“Johnny Soleas is a prime example of an entrepreneurial leader who operates a successful collision centre and independent mechanical facility,” says Zakari Krieger, Vice President of Prime CarCare brands at Fix Network. “By integrating calibration and retail glass services into his facilities, Johnny is positioning his business as a local leader in calibration expertise while tapping into the growing retail glass market. This kind of strategic expansion is exactly what we envisioned when we introduced the ‘Shop of the Future’ concept.”
Johnny’s career path has been anything but conventional. Born in Scarborough, Ontario, his family moved to Cyprus when he was a child, where he grew up working in his father’s auto body shop. After a stint in the military, Johnny returned to Canada where he pursued a different path—running a bar.
“I had Gene Simmons from KISS in my bar when the band played in Fort McMurray,” Johnny recalls. “We hit it off, and I ended up selling several bass guitars for him. He advertised my business on the radio and I even had the chance to borrow his motorhome from Family Jewels for a couple of days,” he laughs. “That was the peak of my bar career—It couldn’t get much better than that.”
Soon after, an opportunity arose to buy an auto body shop in town. Although the deal didn’t materialize, Johnny, with his family on board, found his way back to the industry. “At first, I was hesitant,” he admits. “I was already managing multiple businesses, but after my family looked into it and saw the potential, we decided to go for it—and we haven’t looked back.”
With calibration, glass, and mechanical services all under one roof, Johnny’s vision of a true one-stop-shop has become a reality. “We’re not just a collision centre anymore,” he says. “We’re an automotive repair facility—handling everything from diagnostics and mechanical work to ADAS calibration and windshield replacement.”
Supported by Fix Network Canada and its investments in training centres and strategic partnerships, Johnny sees the “Shop of the Future” as not just a concept but the new standard. “By eliminating sublets, controlling quality, and diversifying our services, we’re setting a new benchmark for efficiency and customer experience in collision repair. This is where the industry is headed, and we’re already there.”
For other shop owners considering a similar model, Johnny’s advice is simple: “Be willing to invest, be honest with your customers, and always look for ways to evolve. That’s how you stay ahead.”
“We’re an automotive repair facility—handling everything from diagnostics and mechanical work to ADAS calibration and windshield replacement.”
When you invest in a Fix Auto franchise, you invest in a business model with a globally proven track record. You invest in a fully branded business with a roadmap for success. You invest in the same values and work ethic that grew your local business to what it is today.
Drive your business forward with:
• Solid performance-driven operational model and ongoing training.
• Full branding and marketing support for local awareness and promotion.
• Proven experience in winning insurance work.
• Established global supply and fleet arrangements.
Our owner started as a franchisee, and this inspires our commitment to the success of the local business owner.
Make your first move!
BY STEFANO LIESSI
Before I begin, a plethora of people warrant a level of gratitude that words are not enough to express. I won’t name everyone here, to not leave anyone out. Though, to make it clear, SATA Canada and Color Compass Corporation are very fortunate to have some of the best people on the planet working for them, not to mention just being great companies overall. I am forever grateful to all that were there at that moment.
This thing happened to me on the way to work the other day. December 3, 2024, at 8 a.m., I was entering the offices of SATA Canada in Vaughan, Ontario, to set up for a workshop the following day. This workshop never happened, as I was granted the experience of having a heart attack as I walked through the door, a ‘widow maker’ as I was so elegantly informed by a smiling nurse later on.
For those of you in the industry, who, at times, I may offend with my opinions, let it be on the record that I am not done yet. When you are being whisked around the GTA in an ambulance between spurts of idle chit-chat with EMS attendants, you can’t help but think about collision repair and our processes and how they relate. Well, I can’t help it; it may be different for you. I know you’re asking what this has to do with anything ADAS-related because this Collision Repair magazine issue focuses on all things ADAS. Please work with me here.
As soon as the attack began, I was entered into a repair system, much like a vehicle getting towed to a shop. At this point, EVERYTHING was out of my hands. I decided not to question anything and let the system take its intended course of repair. After all, they are the profes-
sionals—who am I to question a medical expert with more student debt than the payroll for Manchester United?
First stop, triage—or repair planning. This is where they ask you a variety of questions, do a pre-scan and poke and prod at you to figure out what is damaged and what the repair plan will be. Now, this shop is swamped with a variety of claims, so it takes some time to get sorted. Due to volume, they have different levels of ‘estimating’ taking place. First, it is determined that I am a non-drive and will be staying. The team has created a repair plan involving some internal viewing, a ‘disassembly,’ so to speak; this will occur the following day due to scheduling, equipment, and technician availability. In just showing up, I will have an impact on their WIP.
A sublet is determined, and off I go; I need to be on the rack and get straightened out; some measurements take place showing the extent of the damages, they slide me into production, confirm the use of aftermarket parts—no OE available, discontinued—and voila, repairs underway. Once the sublet is complete, it’s back to the shop on file. At this point, everything is all good to go—or so I thought—but one more step: calibrations.
Yes, a post-scan is completed, verifying a few things. There are some historic codes and a few new ones. Based on the OE procedures available, some calibrations will be needed. Fifty-seven years without a scan and no MILs on the dash, who knew?
Now, this facility has state-of-the-art calibration equipment and access to information. It is a vital part of ensuring the repairs are completed up to the OE standards. My guess is they did a lot of research to find out which is most adaptable to their requirements. Would this equipment being used for cardiology be the same for neurology? Likely not. Is there a need for sublets? At times, most definitely; not every repair is the same. Some makes and models have different parameters. A little cleanup detail and final calibrations with a test drive complete, and I am on my way out the door: a seamless, successful repair.
This is where the collision industry and medical industry part ways. I entered this experience completely blind; it was not a planned service call. I felt very reassured and safe letting the medical system process my claim; they are professionals and I found comfort in their abilities; as I said, who am I to question
the approach, process, skillset and ability? What I noticed was the attention to time; it was noted that things had to progress quickly, but not so quickly as to cut corners, where confirmation and due diligence were required, the time was taken, and no questions asked. The skill set of each organization member was not to be questioned; they did what needed to be done and disregarded pressure from outside sources. The equipment was maintained and used for its intended purpose by someone who knew how to use it through constant training and professional development. All the OE procedures were followed and explained in detail.
In my opinion, and you are entitled to my opinion, I can write this article today because
these people did their job justice with high moral values, ethics, compassion, and professionalism. Now, I cannot account for what takes place behind the scenes or in the lunchroom of a hospital, what I do have is a lived experience. I have been calibrated and sent on my way in confidence after the repairs were completed. When it comes to ADAS calibrations in our industry, can we say the same? I want to take my vehicle to the place that places the same moral standards and values on their repair process as that hospital does. I want to drive away, knowing deep down all is good. I am not a medical professional, and your customer is not a collision repair professional, so it’s up to the professionals to set things right for the customer. Are we truly doing that?
When you are being whisked around the GTA in
between
you can’t help but think about
Stefano Liessi is the Training and Curriculum coordinator for Color Compass Corporation. He is also a Red Seal technician and refinisher. Stefano enhances his 40 years of experience with 15 years of I-CAR instruction and a post-secondary degree. He also trains Skills Alberta students and has brought home 11 medals for the province, and taught high school students in the auto shop for six years. He can be reached at sliessi@colorcompass.com.
Make the decision to sell your business a smart business decision.
When you’re ready to sell your collision repair business, the Boyd Group is ready for you. We’re the leading, scaled operator in Canada with a highly experienced team offering bestin-class performance, earned on a trusted reputation. Ensure continuity for your people and the communities you serve, reach out today!
BY GREG HORN, CHIEF INDUSTRY RELATIONS OFFICER, PARTSTRADER
When we hear the term advanced driver assistance systems (ADAS) today, cutting-edge technologies like cameras and LiDAR often come to mind. However, the origins of ADAS trace back much further than most people realize. In fact, the foundation of ADAS was first laid out in the 1950s with a simple but revolutionary feature: cruise control.
Cruise control made its debut in American luxury cars in the 1950s, offering drivers the ability to maintain a constant speed without pressing the accelerator. This mechanical system worked by holding the carburetor linkage in place and could be disengaged by pressing the brake pedal, thanks to a plunger mechanism.
In 1954, American engineer George Rashid took a leap forward with his patented “automatic vehicle control system,” capable of detecting an imminent collision and responding by slowing or stopping the vehicle. Unfortunately, due to high costs and reliability issues, his innovative system never reached mass production.
A few years later, Cadillac introduced the Cyclone concept car in 1959, which featured radar-based collision detection. Housed in futuristic, missile-shaped cones on the front of the car, the system warned drivers
of potential collisions but didn’t intervene to control the car.
Moving forwards, in the 1970s, Mercedes-Benz pioneered anti-lock braking systems (ABS), marking a significant milestone in electronic braking control. ABS ensured vehicles could maintain traction and avoid skidding during hard braking, paving the way for future ADAS technologies.
Throughout the 1980s, advancements in throttle and braking systems evolved inde-
pendently. The true breakthrough came with LiDAR (light detection and ranging), a sensor technology that uses laser pulses to measure distances. LiDAR provided a reliable means of identifying potential collisions, setting the stage for modern ADAS.
However, it wasn’t until 1992 when Mitsubishi introduced the first LiDAR-based distance detection system on the Japanese-market Debonair sedan. Marketed as “distance warning,” it alerted drivers of nearby obstacles but
didn’t interact with the vehicle’s throttle or brakes. By 1995, Mitsubishi enhanced the technology with the Diamante, which used “Preview Distance Control” to adjust speed via the accelerator and transmission but still lacked braking capability.
In 1997, Toyota introduced laser adaptive cruise control on its Japanese-market Celsior, which used throttle control and transmission adjustments to maintain speed but couldn’t apply brakes. Meanwhile, Mercedes-Benz brought adaptive cruise control to North America in 1999 with its Distronic system, which could slow the vehicle but not bring it to a full stop.
The first true Autonomous Emergency Braking (AEB) system debuted in 2003 when Honda released its Collision Mitigation Brake System on the Japan-exclusive Inspire. By 2005, Mercedes equipped the S-Class with Distronic Plus, which combined LiDAR with full braking capability, marking the first AEB system in North America.
By 2016, 40 percent of car models in North America offered AEB as an optional feature.
In 2021, consumer demand led six automakers to make city-speed AEB standard across all models, up from just two manufacturers in 2020. This shift reflects the growing recognition of AEB’s life-saving potential.
Today, studies reveal that AEB can reduce rear-end collisions by as much as 50 to 68
percent, particularly in crashes involving injuries. Recognizing these benefits, the National Highway Traffic Safety Administration (NHTSA) mandated AEB for all passenger vehicles in the United States. This regulation, expected to prevent at least 360 deaths and 24,000 injuries annually, highlights the profound impact of ADAS on road safety both today and continuing into the future.
Greg Horn is the chief industry relations officer at PartsTrader and writes collision industry articles and blogs, in addition to creating quarterly webinars for the industry. He is a frequent keynote speaker at collision repair conferences across North America. Horn previously served as Mitchell International’s vice president of industry relations and data analytics, where he published the company’s Industry Trends Report. A true ‘car guy’—he has owned more than 62 cars—Horn began in the industry working in Volkswagen and Porsche parts departments in high school and college. He began his auto claims career at Safeco and went on to hold senior leadership positions at many large insurance companies. He has also served on the I-CAR Education Foundation; the General Motors Safety Council and GM Fixed Operations Advisory Council. Horn also recently served two years as trustee with the Collision Industry Foundation. He studied at the University of Heidelberg in Germany as well as California State University, Long Beach, and holds degrees in Business Administration and German.
BY SARAH PERKINS
Ask those in the industry and they’ll be quick to tell you that with every passing year, vehicles become more integrated and more technologically complex.
From automatic systems and high-voltage features to the increasing inclusion of artificial intelligence, repairing today’s vehicles is not unlike rebuilding a computer—just with more panels and pieces involved.
And, as vehicles become increasingly equipped with Advanced Driver Assistance Systems (ADAS), the collision repair industry faces an ever-evolving challenge: ensuring the refinishing process doesn’t compromise the performance of these sophisticated systems.
While refinishing technology has long been a core competency in collision repair, the integration of ADAS presents a unique intersection of precision, technology and safety that demands new considerations.
Luckily, just as automotive repair continues to change, so too does the industry continue to rise to meet the learning curve, with repairers and companies alike more than ready to weigh-in on the present tech that makes the vehicles of today feel like ones from the future.
Notably, while “it’s no longer business as usual,” when it comes to today’s vehicles, the demand for quality and precision remains
the same, says Troy Knopik, 3M Automotive Aftermarket Application Engineer and Bill Suzuki, 3M Canada Automotive Aftermarket Application Engineer.
“At the 3M Skills Development Center training classes, we emphasize following OEM repair procedures, including paint specifications, to avoid any potential liabilities. When it comes to ADAS, proper
training is crucial, as incorrect refinishing can compromise the safety of both the driver and others on the road.”
“Calibrations are also vital to ensuring ADAS systems function correctly after repairs. Additionally, when refinishing components like bumpers, repairers should ensure that they pull the correct repair sheet every time,” Knopik and Suzuki further note.
And, when it comes to refinishing parts of a vehicle with ADAS components included, repairers “should first and foremost pay attention to paint mixtures and mil thickness requirements,” Knopik and Suzuki further stress.
“Excessive thickness can hinder sensor performance or calibration. To mitigate this, file handlers and blue printers should verify repair procedures during the planning phase.”
Similarly, for Brad Kruhlak, AkzoNobel Technical Manager, Canada, when it comes to refinishing vehicles with ADAS components, precision is the name of the game and repairs are all in the details.
Alongside concerns regarding paint thickness, “vehicle manufacturers have identified specific colours that may negatively impact radar performance when applied in a radar zone during refinishing operations.”
As a result of these potential pigment problems, “when requested by the OEM, paint manufacturers develop new formulas for these colours. These reformulated colours are then subjected to specialized testing by the OEM to ensure compatibility with the technology before receiving approval.”
However, Kruhlak further highlights that “colour formula approval and accurate mixing aren’t the only things to consider when
repairing vehicles with ADAS. A coating system’s film build is typically another critical consideration when dealing with radar systems.”
“Manufacturers often provide parameters for film build—even for specific paint system layers such as the undercoat, basecoat and clearcoat. Additionally, body fillers, putties, plastic welds and staples are all prohibited in radar zones. Even sanding and buffing procedures in these areas may need to be considered.”
Finally, it’s important to recognize the degree to which a vehicle component with ADAS features can be repaired or refinished, says Gordon Wry, Axalta Training Instructor at Axalta Refinishing Academy.
“Some manufacturers only allow a bumper, for instance, to be painted once,” notes Wry. “If over application [of paint] causes calibration issues, it renders that bumper useless and another will have to be ordered and refinished properly, potentially driving up the shop’s cost of repairs.”
Moreover, in ensuring that no mishaps lead to damaged or malfunctioning parts, repairers should ensure that there are “no plastics in Lidar transmission areas and to remain aware that scratches or overspray on the front or backside of ADAS features,
From automatic systems and highvoltage features to the increasing inclusion of artificial intelligence, repairing today’s vehicles is not unlike rebuilding a computer— just with more panels and pieces involved.
like the bumper, may affect transmission. So, masking the backside of the bumper in the transmission areas may be necessary to protect them.”
To help avoid overcoating, “use value shade primers or sealers to limit the number of basecoats,” suggests Wry and “always keep in mind that there are tinting restrictions.”
In this way, as the automotive coatings experts here emphasize, every detail—from paint thickness to calibration protocols—plays a crucial role in the success of the repair. The demand for quality remains as high as ever, and while the complexity of modern vehicles may present new challenges, it also opens the door to opportunities for those who are committed to ongoing learning and innovation.
As Wry succinctly puts it, at the end of the day, it all comes down “to being prepared to do your homework.”
The time to look for issues is before alignment, not during
If you’re not looking for something, will you find it anyway?
Sometimes. Maybe.
More likely, maybe not. When it comes to collision repair, that’s a problem. For the customer, and for the repair shop. Missing things that could or should have been caught results in inconvenience, extra cost and a very annoyed customer.
To uncover hidden problems, you’ve got to know where they might be hiding. The Collision Alignment System from Hunter Engineering shows technicians where to look.
This is often necessary, because what’s appropriate for a typical maintenance wheel alignment won’t always be enough for a collision scenario. Primary measurements, such as toe, camber and caster, only get you halfway to where you need to be. Possible hidden damage remains hidden.
The Collision Alignment System helps techs finish the job, thanks to specific collision workflow procedures that ensure they take essential in-depth measurements to uncover damage right away – rather than as a surprise during the alignment at the end of the repair process. Or worse: missing it altogether.
The five collision-specific diagnostic measurements are:
• Toe out on turn
• Maximum steer
• Ride height
• Suspension body dimension audit (SBDA)
• Symmetry and setback
Frequently, a vehicle can check out fine with the usual primary measurements. What the tech would not find without looking would be things like a damaged subframe or unibody, damaged lower control arms, shifted axles, bent spindles or other affected components that would slip under the radar.
Not only will the system provide a more complete blueprint of the necessary work, but it also makes the tech’s life easier by walking him or her through the process. Instead of hunting and pecking all over to find additional measurements, Hunter’s award-winning WinAlign® software guides the tech through the procedures step by step with minimal interaction.
Easily decipherable documentation also clearly communicates the nature of the work to be performed.
By finding hidden problems at the start of the process instead of the end, a complete estimate can be written that will require no later adjusting.
This means no extra cycle time and cost, saving time and money for both the customer and the collision shop. Not to mention missed items remaining dormant until they rear their heads months and many miles later, possibly in an unsafe manner.
For collision shops interested in doing ADAS work instead of subletting it, the system integrates with Hunter’s ADASLink® diagnostic scan tool, capable of guiding the technician through ADAS calibrations for millions of vehicles.
When you don’t know what you don’t know, it’s like walking around in the dark. The Collision Alignment System sheds light and allows you to retain your customers by maintaining your usual standard of quick and accurate service.
Top-of-the-line ADAS products at your fingertips
Discover the forefront of automotive technology with this top-of-the-line selection of ADAS products. Designed to enhance safety and efficiency, these innovative solutions are essential for anyone looking to elevate their vehicle’s capabilities. From advanced sensors that deliver real-time data to precision calibration tools that ensure optimal performance, each product is crafted to meet the evolving demands of the industry. Whether you’re a professional in collision repair or a vehicle owner seeking the latest in safety enhancements, these cutting-edge offerings provide the essential features needed for a smarter, safer driving experience. Embrace the future of automotive technology and explore the transformative potential of ADAS today!
www.level5drive.com
Level5Drive specializes in ADAS, providing essential calibration services to automotive businesses to ensure vehicles are calibrated safely, effectively and correctly, to OE standards. By partnering with Level5Drive, your business can provide expert calibration services, helping to improve customer safety and satisfaction while diversifying your revenue. With a focus on OEM procedures and tools as well as proper, documented calibrations, Level5Drive offers collision centres and other automotive businesses valuable resources and support, making it easier for you to integrate ADAS calibration into your operations. The company touts nine locations in Ontario; two sites in Saskatchewan and plenty more to come. Call 1-800-223-9608 for more information on a partnership.
The John Bean® Tru-Point™ advanced driver assistance system (ADAS) calibration tool evaluates ADAS-related wheel alignment values and meticulously monitors each phase of the setup process, ensuring compliance with OEM safety standards before any ADAS calibration is performed. Using advanced camera technology, it guarantees precise positioning and automatically adjusts based on the vehicle’s location. A detailed, userfriendly report documents the technician’s completion of all necessary steps for accurate calibration.
Auggie, developed by AirPro Diagnostics, is the automotive industry’s most advanced mobile Forward-Facing Camera (FFC) ADAS calibration solution. By leveraging machine learning and vision technology, Auggie ensures precise alignment for FFC ADAS calibrations that meet manufacturer specifications. This solution allows business owners to perform ADAS calibrations in-house, reducing cycle time and increasing profitability. Auggie’s FFC calibrations comply with NHTSA, IIHS, and Euro NCAP standards. For more information, reach out to https://airprodiagnostics. com/contact/
Hunter Engineering’s new ADAS Hub ADAS Learning Tool is a free, interactive training resource accessible via tablets and desktops. Designed for both counter workers and curious customers, the ADAS Learning Tool breaks ADAS procedures into four categories: camera, radar, ultrasound and internal. The tool includes colour-coded vehicle images that clearly explain functions and locations of components alongside calibration requirements. This tool by Hunter Engineering aims to clear confusion surrounding ADAS and system maintenance needs. Access the ADAS Learning Tool for free at www.hunter.com/media-center/adas-hub/ adas-learning-tool.
All systems health check, digital vehicle inspection, 3D wheel alignment, and step-by-step ADAS calibration instructions in a single system, investment, and workflow.
Specially designed for all-systems ADAS calibration, while providing safer and more efficient mechanical repair and wheel alignment in a single standard repair bay space.
BY JOHN MARLOWE, LEVEL5DRIVE
ADAS...this acronym spells out a great deal of confusion and misunderstanding in our industry.
One of the elements that is most often misunderstood is the “success report” produced by the scan tool. This includes reports from aftermarket and some OE tools, as well as screenshots of successful calibrations.
How can this be an area of confusion? Isn’t it proof of proper calibration you can be paid for? The confusing answer is yes, but Yes, the success report indicates a properly performed calibration, but only if all of the OE service manual requirements for environment, vehicle state, targeting, and driving/testing are meticulously followed. It is a very common belief that the system won’t allow a calibration to occur if any of the requirements are not met, therefore any success report must indicate that the systems will perform as intended. This is absolutely not true.
ADAS systems are complex networks that rely on precise calibration of their sensor suites to function properly. In many cases, a large part of the calibration process involves the vehicle being placed into a specific environment, with the vehicle set in a specific state; with sensors then exposed to specific targets or reflectors located in a specific place relative to some specific part of the vehicle.
We might consider this the zero point, or the condition from which all measurements will now be performed. This will include the vehicle calibration measurements, as well as all subsequent measurements performed by the vehicle systems (i.e., detecting things).
The calibration routines that are now performed will assume that the environment, vehicle, and targets or reflectors are all in the correct state, or at zero point.
Let’s consider the case of a vehicle requiring lane keep assist camera calibration following installation of a specific brand of aftermarket
It is a very common belief that the system won’t allow a calibration to occur if any of the requirements are not met, therefore any success report must indicate that the systems will perform as intended. This is absolutely not true.
windshield. The technician knows that a lane-keep assist camera calibration with this particular brand—and it could be any, I’m not referencing any glass manufacturer in particular here, just illustrating a common issue—means you must set the target 15 millimetres lower than it says in the repair manual in order to produce a success report.
Can we consider this ADAS system to now be properly calibrated, and relied upon to function correctly through all of it conditions it was designed for? Of course not. Yet, the technician has produced a success report. The technician, perhaps unknowingly, is exploiting the limitations inherent in the calibration software.
The term “success” doesn’t always mean that the system is properly aligned, calibrated and working as intended. Rather, it means that the required minimum threshold has been recognized by the software. As the software by necessity must assume that zero point is
correct, it will dutifully assess the calibration conditions and provide the calculated result.
In the case of the windshield technician adjusting the target height to accommodate an incorrectly positioned camera in an aftermarket windshield: every measurement performed by the lane-keep assist system will have some degree of error, even if all of the other factors comply with the procedures in the OE repair manual.
The confusion continues as ADAS systems are engineered to be robust and operate under a wide range of conditions. Thus, this system may seem to perform just fine under many conditions but may perform dangerously or not at all under some other conditions.
For example, operation during the daily commute might seem fine. Perhaps months go by and then the vehicle is used for a family camping trip. With a full tank of fuel, the whole family on board, and a weekend worth of camping supplies and food in the back, the system might fail to correctly locate the vehicle in the lane, perhaps even causing a crossover into a different lane. Or perhaps it fails to locate the lane marker at all during a moment when the driver is distracted and allows the vehicle to drift into the next lane.
Unfortunately, there is no reasonable way to test every vehicle under every operating condition. This is why it is so critical that every ADAS calibration is performed using OE compliant equipment, in the correct environment, with the vehicle in the correct state, faithfully adhering to the procedures in the OE repair manual.
It’s not only aftermarket windshields that can cause false-positive calibration results. These can easily happen when performing calibrations in an improper environment. Not enough space, floors not flat and level as specified by the vehicle manufacturer, lighting not controlled correctly, et cetera, or when the vehicle is not in the correct state; tire pressures/sizes incorrect, suspension modified, cargo inside vehicle. Or when using incorrect targeting, like resized targets to circumvent space requirements; measurements taken from the incorrect locations on the vehicle, target placement changed to suit incorrect sensor placement. Really, anything
that deviates from the OE repair manual can create a success report that doesn’t actually indicate a successful calibration.
The repair manual is loaded with statements that may seem unimportant. Especially since the calibration will proceed, apparently successfully, even when the technician ignores some or all of them. Blind spot sensor calibrations, for example, generally require that a minimum area be free of any metal or reflective objects. This is not a handy helpful hint from the vehicle manufacturer. It is a critical element in ensuring that the calibration can be performed without the sensor accidentally picking up a signal from some object other than the intended reflector. Many facilities don’t have such an area available and will perform the calibration with a frame rack, or a lift, or the wall of the building inside of this minimum area.
This, again, can result in a false-positive successful calibration report.
As with our previous false-positive windshield calibration, any improperly calibrated ADAS system may appear to function normally when test-driven. This is because of the very large range of conditions that the system is designed for. The error-driven
JOHN MARLOWE
system limitations may not be noticed until the vehicle enters an “edge case” condition, where the combination of imminent danger, an error-riddled ADAS system, and an unaware driver may cause a catastrophe, or may fail to prevent or mitigate a collision.
The mistaken notion that the scan tool’s success report definitively indicates a bonafide ADAS system calibration leads to a growing number of vehicles being calibrated using improper equipment, unsuitable environments, and an ever-increasing number of people selling devices specifically designed to cheat or defeat ADAS system calibration software with the sole purpose of producing a success report.
ADAS systems, when properly calibrated, can enhance road safety immediately and directly. Drivers quickly adapt to these systems and come to rely on them. ADAS systems, when improperly calibrated, may have limited or no safety value. Worse, some systems can take control of some vehicle functions and could directly cause damage, injury, or even death if they are not operating correctly.
If you’re performing ADAS calibrations, it is critical to not only ensure that you are faithfully adhering to the OEM procedures, but that you are also fully documenting this.
If you have an ADAS partner performing these operations for you, you really need to ensure that they are following the correct procedures and fully documenting that they have done so.
A success report from a scan tool isn’t going to save lives. Properly performed ADAS calibrations will.
The automotive landscape has been transformed by advanced driver assistance systems (ADAS). As a result, collision repair centres face an intricate challenge: how do you master this complex process that could put you in the hands of a driver’s life?
THE COMPLEX LANDSCAPE OF ADAS CALIBRATION
The rapid evolution of ADAS technologies in recent years has brought a diverse array of highly sensitive systems into vehicles today. This includes radar, cameras and LiDAR—light detection and ranging—which we all know are systems that have not existed in vehicles, at least to this degree, for most of the average repairers’ career.
Each of these systems have unique calibration requirements that vary significantly from one manufacturer to another. This complexity means even minor misalignments in calibration—or using the improper equipment—can lead to significant safety risks, impacting critical features that drivers rely on.
DID YOU KNOW?! The average driver of an ADAS-equipped vehicle is 100 percent reliant on lane-keep assist after just nine drives.
FACING
Technical expertise is required to perform calibrations, point blank. These calibrations cannot be correctly done without proper training and that cannot be overstated. Shops must use the latest technologies, tools and manufacturer specifications to ensure accurate calibrations.
Equipment is obviously a huge investment. Specialized tools and diagnostic equipment come with hefty price tags. For many facilities, this financial barrier is daunting, especially when you are trying to keep pace with the other fields of rapidly-changing technology.
Let’s talk about regulatory pressures and compliance. Sure, there’s no across-the-board standard for ADAS now, but it’s clear to the top ADAS players that adhering to manufacturer specifications for calibration is absolutely essential. Failure to do so, as we’ve covered, can result in liability issues and— obviously—jeopardize customer trust.
A recent adasThink report in Canada cites that more than 88 percent of ADAS calibrations are missed.
LEVEL5DRIVE—YOUR ESSENTIAL PARTNER
Does all of this seem a bit daunting? That’s a good thing—that means you are taking ADAS calibrations seriously.
Level5Drive is your trusted partner in comprehensive calibration services. With locations in Ontario and Saskatchewan—and more expansions planned—we are here to serve high-volume, low-volume and every complex job in between. We’ve spent years working on our ADAS expertise; our store managers and team can assist you with any ADAS challenge at the drop of a hat.
We at Level5Drive are committed to utilizing the latest calibration technology that always adheres to OEM recommendations. We take this seriously. Our procedures are proven to enhance a collision centre’s efficiency, accuracy and quality in ADAS calibrations. We also work alongside insurance companies and several big-name OEMs to enhance quality and specifications to ADAS calibrations.
Elevate your shop’s capabilities today. Your bottom line will see the impact. Partner with Level5Drive as your ADAS partner to navigate the complexities of this service with confidence and ease.
BY DOUG KIRK, GLOBAL COLLISION INDUSTRY ANALYST
When I read articles or overhear conversations about Advanced Driver Assistance System (ADAS) repairs, there’s one thought that immediately jumps to mind: liability.
Don’t get me wrong, I’m not concerned about the ability of my colleagues in the collision repair sector and their capacity to repair these systems. After all, they have spent huge amounts of money on specialist training and equipment to affect a safe repair.
No, the one thing that really worries me is liability. With repairers having spent huge amounts of money on specialist training and equipment, you would think that in every scenario they would be prepared and safe. Unfortunately, this is not always the case.
Before the humanoid robots take over complex tasks, artificial intelligence will be aiding us. Before the tech savvy raise up in arms and call for my head, let me say, I am not a luddite. I embrace technology, but the fact remains that we must sprinkle a little reality dust over some of the issues said technology brings.
It’s a repeated fact that vehicles fitted with ADAS features are not without their shortcomings. They can cause collisions due to system failures, resulting in injuries, even fatalities straight from the factory. Even a vehicle that is ‘factory fresh’ can suffer a technology malfunction and contribute to an accident.
In June 2022, the National Highway Traffic
Safety Administration (NHTSA) in the United States of America reported 392 crashes nationally involving Level 2 driver-assist systems, which include features like adaptive cruise control and lane-keeping assistance. Of these incidents, six resulted in fatalities, and by April 2024, a three-year NHTSA investigation into a single manufacturer system identified that it had contributed to at least 467 collisions, including 13 fatal accidents.
While we have no data to confirm if any of these vehicles had previously been involved in an accident and then repaired and re-instated into service, given the John Eagle case, I am confident that if there were any, we would have heard of about it.
My concerns about liability are not without foundation. Trust me, I love technology— especially technology that aids us to be optimal. I trust Waze to provide me with the most optimal route depending on my situation and the surrounding environment. But technology can fail, and if something fails, I expect it to fail to a safe state, not turn into oncoming traffic because it confused a shadow for a dog.
To return to my issue of liability, let us ask: when a vehicle is repaired and calibrated and certified, it is the same as when it came from the factory. So, if it fails, who is liable?
The ADAS discussions should not be about can I get paid for making an investment in space, equipment, training or any other specialist service I need to invest in? This should be a given, as my return on investment (ROI) should be built into my rate and not questioned by any ‘work provider’ or insurer as to why it costs what it costs. It costs what it costs, and so here is my repair execution proforma to validate it was done correctly.
The discussion should instead be who is liable in a few days, weeks or months if any of this vehicle’s components fail (as they have been seen to do when they are factory
fitted) and are complicit in the creation of a collision.
In the United Kingdom, the Automated Vehicles Act outlines how liability will be allocated when an automated vehicle commits a driving offence or is involved in an accident, and it makes for some very interesting reading.
There are six automation levels of vehicles, and their driving functions are described within the SAE international J3016-Standard.
• Level 0: No Driving Automation
• Level 1: Driver Assistance
• Level 2: Partial Driving Automation
• Level 3: Conditional Driving Automation
• Level 4: High Driving Automation
• Level 6: Full Driving Automation
According to an article for ZF in April of 2022, Fully Autonomous vehicles operating in mixed traffic will become established in the foreseeable future, but some experts suggest it is more than a few years away. Until then, we will have a menagerie of different levels of automation operating in harmony or otherwise on our roads, and I am sure this will add to the confusion of liability.
Here are just some of the issues that have been raised by risk management solicitors:
• Manufacturer liability: sensor malfunction, software glitches, inadequate cyber security measures, inadequate testing.
• Third party liability: software providers, bugs in updates etcetera.
• Service providers: connectivity issues from network providers, component providers, third party providers
• Driver liability: maintenance issues
• 3D printing: spurious of critical parts, counterfeit parts
• Hackers
Now add the repairer into the mix and where is the low hanging fruit?
This all being said—repairers, repair away. Get the right equipment, get the right training, but make sure you get in the right mindset and create the right documentation to support the coming changes. Go digital and record everything and keep it on file. Charge the right amount and make sure you get what you are worth. It is the only way you can continue to invest in this ever changing collision repair industry.
In early December, a group of Canadian collision repair professionals—including five technicians, two vocational tech instructors, and Collision Repair magazine’s own team member—traveled to St. Paul, Minnesota, for a transformative three-day experience at the 3M Skills Development Center (SDC). More than just a training session, this immersive program offered a glimpse into the philosophy and cutting-edge methods driving the future of collision repair.
The 3M Skills Development Center, which opened in October 2023, represents a milestone in technician education. Designed to address the collision repair industry’s growing demand for highly trained professionals, the
15,000-square-foot facility is equipped to provide hands-on, practical learning.
Approximately 70 percent of the center is dedicated to workshops, with areas like a 35-foot GFS XL paint booth and a welding section outfitted with advanced fume extraction systems. The remaining space is for classroom sessions, blending theory with practice. The facility’s philosophy centers on equipping technicians with not just the “how” but the “why” behind modern repair techniques.
From the outset, the training’s agenda reflected this philosophy. Participants dove into foundational body repair processes, each designed to ensure crashworthiness while also
adhering to OEM standards. Day one focused on the essentials: body repair tools and their proper usage. The instructors, seasoned experts with decades of experience, introduced products like the 3M™ Heavy-Bodied Seam Sealer, highlighting its ability to replicate OEM finishes and provide lasting corrosion protection.
The program’s hands-on approach was paired with discussions on the science of collision repair. Instructors emphasized the importance of moving beyond the “way it’s always been done” mindset. As one trainer put it, “every step we teach is grounded in restoring a vehicle to perform as designed— not just look repaired.”
Day two expanded into advanced techniques like aluminum substrate repair and dent methodology, using cutting-edge tools such as the Pro Spot i5s Smart Spot Welding System. This system’s adaptive technology, which adjusts to material properties in realtime, perfectly illustrated the modern collision repair philosophy: precision, adaptability, and a focus on safety.
The history of the center itself reinforced the importance of continuous education. The 3M SDC was conceived in response to a looming industry challenge: the significant shortage of trained collision repair technicians. Industry studies project a shortfall of over 100,000 professionals by 2026, creating an urgent
need for programs like this one. By offering hands-on courses tied directly to OEM repair documentation, the 3M Skills Development Center aims to close this gap and ensure vehicles are repaired to the highest safety and quality standards.
Beyond the technical sessions, participants enjoyed opportunities to connect and recharge.
A visit to the 3M Innovation Center provided a behind-the-scenes look at the company’s groundbreaking research and development. Later, an NHL game between the Minnesota Wild and the Vancouver Canucks brought some levity to the week, offering a chance to bond over a shared love of hockey and trade shop stories.
Approximately 70 percent of the centER is dedicated to workshops, with areas like a 35foot GFS XL paint booth and a welding section outfitted with advanced fume extraction systems.
Ultimately, the 3M Skills Development Center is more than a training hub. It is a response to the challenges of a rapidly changing industry.
The final day brought everything together with corrosion protection techniques. Seam sealing, a seemingly simple process, took on new significance as participants practiced achieving factory-quality finishes that safeguard vehicles from the elements. This attention to detail wasn’t just about aesthetics—it was about creating repairs that last, ensuring the safety and satisfaction of every driver.
For Collision Repair magazine, participating in the program underscored the industry’s urgent need to prioritize training. The SDC’s philosophy—rooted in collab-
oration, precision, and lifelong learning— sets a standard that the entire industry can aspire to.
Ultimately, the 3M Skills Development Center is more than a training hub. It is a response to the challenges of a rapidly changing industry, a commitment to equipping technicians with the skills they need and a testament to the importance of doing repairs the right way. For the attendees, the experience wasn’t just educational—it was transformative, instilling a renewed sense of purpose and pride in their craft.
Collision Repair magazine sat down with Benjamin Gervais, a senior business development manager with 3M Automotive Aftermarket Division, to learn more about the courses the 3M Skills Development Center offers and how Canadians can take advantage.
Collision Repair magazine: Why is a facility like the 3M Skills Development Center needed right now?
Benjamin Gervais: Firstly, there’s a technician shortage and it’s becoming more pronounced. The need for productive technicians is extremely important in the current market. Second, vehicles are becoming increasingly complex, with ADAS, aluminum considerations, EVs and so on. If bodyshops can’t understand how to properly consider all of the proper information for a quality, correct repair, that can have a great impact on their business.
It’s a vital decision to position oneself as a collision center that regularly improves and upgrades. We have received positive feedback about these courses for their effectiveness in addressing these challenges.
CR: Can you explain the courses offered through the 3M Skills Development Center?
BG: Certainly. We offer three courses from our 3M Skills Development Center: Body Repair; Paint, Prep & Refinish, and our new Front Office class.
Our body repair class takes students through the entire repair process. We go
through everything from panel sectioning and replacement; rivet bonding; welding; the proper application of fillers, glazes, foams and seam sealers. We cover topics like OEM recommendations and OEM replication, repair planning and corrosion protection considerations.
Our Paint, Prep & Refinish course features a significant amount of time spraying various coatings. Most students are preppers, painters, detailers or buffers that have the desire to transition into a more active painter role. It’s about honing the necessary skills in a low-risk environment and getting a ton of trigger time.
These two courses come with I-CAR credits, too.
Our new front office course is an interesting one because so many refer to it as an estimator course—which automatically brings the image of students sitting in a classroom, working on computers, to mind. Instead, we engage front office employees, including estimators, adjusters, and shop managers, in hands-on activities, which allows them to better engage with shop floor colleagues. They can write more accurate estimates; improve engagement with insurance companies and gain skills in the areas we believe will ultimately help administer higher quality repairs.
I would like to point out that all of our courses are very focused on the handson aspect. Approximately 80 percent of time is spent doing hands-on activities. We try to keep students out of the classroom environment and instead in an environment where they can complete hands-on, tactile activities.
Our training is process-focused. These are not courses about products where we preach the use of the latest and greatest 3M products. They are focused on the industry processes required to repair a modern vehicle back to pre-accident condition, with stress on OEM recommendations.
CR: Who are these courses designed for?
BG: The courses offered through the 3M Skills Development Center are not for somebody with no industry experience looking to use this as a shortcut in the field. We’re helping to accelerate the learnings of professionals in the field.
CR: How can Canadians take advantage of these courses?
BG: Each course runs approximately once per month. Everyone is invited, and we have a few different ways to attend. Whether it’s distributors sponsoring their shop customers; vocational instructors looking to upskill; independent collision centers and so on. Everyone has equal access to 3M Skills Development Center training.
There’s no barrier to access our courses—if a technician wanted to today, they can just go on our website with our calendar and sign up for one of the classes.
Contact a 3M representative today for the 3M Skills Development Center course schedule.
BY FOCUS ADVISORS
David Roberts, the founder and managing director of Focus Advisors Automotive M&A, presented the collision repair industry’s market update at last year’s MSO Symposium in early November in Las Vegas. Roberts addressed an audience of more than 400 attendees in his presentation titled “Scale and its Rewards: Industry Landscape and Market Dynamics”. He set the tone from the start, stating, “to succeed in an industry where complexity and access to repairable vehicles are ever more challenging, operators with scale will continue to grow and thrive.”
The industry seems to be normalizing more towards pre-COVID conditions. Meanwhile, vehicles have grown in complexity. Scale and specialization play pivotal roles for the operators that want to compete.
• Revenue Changes: The collision repair industry had softened revenues throughout 2024. Revenues are flat or down for many, and up only for a few exceptions. Single shops have seen their revenues decline most dramatically. WIP is down across the board, returning to more normal levels after the exceptional post-COVID period. In a similar trend, labor rate increases are returning to normal, and there are just fewer repairable vehicles, prompting shops to focus more on getting the work. While WIP and labor rate increases are normalizing, the average total cost of repair is still up 3.7 percent year-overyear, now exceeding US$4,600.
• Shop Numbers: Revenue slowdown and industry consolidation had resulted in a decline in single shops. Focus Advisors anticipates there were nearly 800 closures of
smaller, independent shops this year. Medium and large MSOs, meanwhile, are better poised to grow; Roberts said, “Independent MSOs with four to six shops—and especially those with seven or more—are not just surviving; they’re thriving,” The consolidators and larger independent MSOs are able to grow their market share by focusing on advanced repair technologies and operational efficiencies, which most often come from scale.
In his MSO presentation in 2023, Roberts introduced the “Fish Scale” that classifies the collision repairers in terms of their size. The “Whales” consist of the “Big Five” consolidators: Caliber, Crash Champions, Gerber, Classic Collision, and Joe Hudson’s. In 2024, their cumulative market share comprises 30 percent. Their collective footprint grew 13 percent, from 3,512 shops to 3,842 in 2024.
Caliber Collision stands apart within the “Whales”, with more than 1,800 shops and growing every day.
Two other “Whales”, Classic Collision and Joe Hudson’s, each grew their shop counts by north of 22 percent in 2024, almost exclusively through the acquisitions of single shops or MSOs. This growth is almost three times that of Caliber, Gerber and Crash Champions.
A more remarkable trend of 2024 has been the breakneck expansion of the “Sharks” cohort that Roberts introduced in 2023 as the seven fully—or newly launched MSOs with private equity sponsors. These seven are: Quality Collision Group, CollisionRight, Kaizen Collision, VIVE Collision, OpenRoad Collision, Puget Collision, and BrightPoint Auto Body. Collectively, they have almost three percent of the total market share across 376 shops. They’ve collectively added close to 100 shops this year, mostly through acquisitions.
The benefits of scale are seen northward in Canada. Some of the largest independent MSOs in Canada are the private equity-backed Lift Auto Group, Craftsman Collision and Kirmac Collision, all concentrated in British Columbia. Meanwhile, the Fix Auto
franchise has expanded with new franchise partners such as Fix Auto Halifax in Nova Scotia and Fix Auto North York in Ontario. CSN Collision Centers has been investing in training, equipment, and OEM certifications to support its growth and high standards. ProColor Collision has been actively expanding its presence in Canada in 2024. As of the end of the year, they have over 170 locations throughout Canada. In September 2024, the network launched a new location in Niagara Falls, Ontario led by industry veteran Justin Haars.
The CARSTAR franchise has grown its footprint in Canada, with approximately 320 locations. Another franchise, Simplicity Car Care, has grown from 60 locations in 2021 to 101 at the time of Roberts’s presentation, their geography focused mostly on Ontario and Quebec.
While the industry has consolidated a great deal in Canada and the average severity remains high, the major headwind that the Canadian collision industry faces is the technician shortage. According to the Romans Report, the latest data indicates the industry is still short by 30 percent to 40 percent of the number of technicians needed. While there have been efforts to implement a national auto body accreditation program that will generate more capable techs, this is still in development, aggravating the technician shortage. This will grow more significant as Canada makes way on its effort for 100 percent zero-emission car sales by 2035, as EVs require highly skilled techs.
Independent MSOs with seven or more shops now number 48, up from 43 last year. If one were to count all independent MSOs that are neither “Whales” nor “Sharks”, there are nearly 800. Collectively, they generate over US$8 billion in revenue, matching the total revenues of Caliber Collision.
Roberts emphasized the entrepreneurial vision driving their success, stating, “It really comes down to the vision of the entrepreneurs and the opportunities they see in their markets.” Each of the independent MSOs has its unique “playbook” of how it’s able to compete in its market. To name a few playbooks, some focus on OEM certifications, others on EVs or fleet work, while others either acquire distressed single-shops and turn them around, or alternatively, build their own shops from the ground up.
The collision repair industry remains highly attractive to private equity investors due to its strong existing returns and the tailwinds PE firms see in the collision industry. Roberts said that Focus Advisors had received inbound interest from over 50 PE firms in 2024 interested in the space. PE-backed consolidators are using acquisition strategies and operational improvements to achieve the end-goal of significant EBITDA growth and higher EBITDA multiples.
• PE’s Perspective: Roberts walked the audience through a typical PE strategy playbook to illustrate why there’s been so much interest.
i. Initial Acquisition: PE firm buys a collision repair platform for $48M, with $6M EBITDA at 8x multiple.
ii. Add-On Strategy: Plans to acquire 30 smaller shops, each with $500K EBITDA, for $75M total at 5x multiple.
iii. Total Investment: Combined investment reaches $123M.
iv. Growth Targets: Aims for 20 percent revenue growth and two percent EBITDA margin improvement over five years, targeting $30M EBITDA.
v. Re-Capitalization: Plans to re-capitalize at 10x EBITDA, valuing the business at $300M.
vi. Financial Gain: Expects $177M absolute gain (143 percent return).
vii. Leverage Impact: Return on equity amplified by typical three-to-one debt leverage ratio.
Roberts emphasized that this playbook is what has driven PE to continue to try to enter this space. While the financial structure is compelling, he also articulated some of the risks of this industry, citing: acquisitions cost more than expected; key management leaves; increases in labor costs and parts costs push down margins; industry revenues slow down and insurance companies apply downward pressures on margins.
Through specific case studies as well as the statistics on the bigger-picture of independent MSOs, it became clear that there are still many paths for the independent MSOs to compete against the national consolidators or PE-backed “Sharks”. By focusing on a specialized strategic playbook and their economies of scale, these independents can grow their market share and EBITDA margin. And with the increased interest by existing buyers and PE firms hoping to enter the industry, that higher EBITDA commands a higher EBITDA multiple—whether an owner of an independent MSO seeks growth capital or an exit.
Roberts concluded his presentation by providing some predictions for the collision repair industry. In the near-term, he foresees:
• Insurance companies will raise rates, deductibles, and squeeze collision repair providers.
• Vehicles will grow in complexity.
• OEMs will raise certification standards, training, equipment requirements, and they will limit access to parts.
• Consolidators will invest more in highly certified repair facilitators.
• Competition for highly trained technicians will become more fierce.
And over the next decade or so, he anticipates:
• There will continue to be conflict between OEMs and insurers, with more power going to dealers and OEMs.
• That will encourage MSOs to focus more on certifications and closer associations with dealerships.
• 1,000 or more shops will exit each year over the next five years.
• The retrenchment of electric vehicles is temporary and EVs will come back.
• Self-driving vehicles will proliferate in urban areas. They could disrupt repair volumes due to lower collision rates.
• The best repairers will become super-efficient while simultaneously becoming super capable.
• OEMs will increase their commitment to their own captive insurance companies.
• Consolidators will achieve more than 50 percent market share.
• Large regional MSOs will increase as more capital and more M&A will enable growth.
• There will be increased responsibility for settling claims at the MSO- and consolidator-level.
Roberts concluded with a reflection on the opportunities for collision repairers at scale: “The best repairers will need to be super-efficient. Consolidators and independent regional MSOs with a focus on the most advanced skill sets and certifications will dominate.”
ABOUT FOCUS ADVISORS:
Focus Advisors (www.focusadvisors.com) is the collision industry’s leading M&A advisory firm, partnering with independent MSOs between $10-100M in annual revenue, helping owners achieve maximum value through strategic growth and exits. Unlike traditional business brokers or large investment banks, Focus Advisors specializes exclusively in collision repair — giving owners unparalleled insight into value, interest, and opportunity timing. With over 25 years in the industry, Managing Director David Roberts has led more than 40 transactions totaling over $500 million in transaction value and more than 325 collision repair shops, including Tripp’s Collision, Pride Auto Body, Painter’s Collision, Mills Body Shops, and Master Collision.
www.car-o-liner.com
The Car-O-Liner® BenchRack™ Versa is the latest in-ground innovation in collision repair technology. It is easy and ergonomic to use, allowing for safe and fast vehicle lifting. It features high-strength steel and aluminum ramps that facilitate quick and proper vehicle lifting, providing full access for immediate work. The new short ramps enable lifting by the wheels, allowing technicians to quickly and securely position vehicles at an optimal working height.
www.akzonobel.com
Built on a proven track record of 165 years, Lesonal premium coatings deliver fast, efficient and consistent performance. Combined with marketleading technical expertise, Lesonal provides a comprehensive range of refinish products and systems, without compromising on quality. Basecoat WB is the Lesonal waterborne two-stage paint system. This cutting-edge waterborne basecoat technology ensures easy application, excellent colour match, consistent results, and meets most VOC limits.
To learn more visit: https://us.lesonal.com/en/contact-and-support
The 3M™ Clean Sanding System is a complete sanding solution for efficiently moving through your essential surface preparation and finishing work. The system includes our dust extractor, pneumatic and/or electric random orbital sanders, mobile workstation, wide selection of quality abrasives, and personal protective equipment. www.3mcanada.ca
www.accuvision-3D.com
QUICK - SIMPLE - ACCURATE. With no moving parts, lasers, targets, adaptors, magnets, arms, extensions, wires, Wi-Fi, or Bluetooth, there is also no calibration needed making it the “Quickest, simplest and most accurate 3D measuring system in the world.” The Accuvision 3D is durable, versatile, universal, mobile, and user friendly, saving you time and money. Everything you need for measuring and alignment can be done easily with the Accuvision 3D measuring system. Reserve now at 1-800-465-5875, info@arslanauto.com or accuvision-3D.com.
Seeblocksideairbagdeployment. owner’smanualformoreinformation.
POURÉVITERDESBLESSURES GRAVESOUMORTELLES: •Nevousappuyezpascontrelaporte. •N’utilizezpasuncouvre-siège quipeutbloquerledéploiementdu Voircoussingonflablelatéral.lemanuelduconducteurpour deplusamplesrenseignements. AVERTISSEMENT
AVERTISSEMENT
•Nevousappuyezpascontrelaporte. •N’utilizezpasuncouvre-siège quipeutbloquerledéploiementdu Voircoussingonflablelatéral.lemanuelduconducteurpour deplusamplesrenseignements.
Conformstoregulations:
Noadjustmentsneeded.
Whether
BY ALLISON ROGERS
Did you enjoy your school years? Elementary school, high school, postsecondary training, et cetera. Your default answer is likely no; but joke’s on you— as a member of the collision repair industry, you’ve proved you truly love learning.
We all know this industry changes in the blink of an eye. Keeping up with the changes is, more or less, like school. You’re looking up procedures, altering operations based on studies or practices you’ve read. Whether you’re diving into the latest repair techniques, exploring new materials, or adapting to evolving safety regulations, you
These informal interactions are a goldmine of information; you’re exchanging best practices, discussing trends and sharing solutions that can enhance your craft. This peer-to-peer learning is invaluable, reinforcing the idea that education doesn’t only happen in a structured environment.
Additionally, as technology advances, so too does the need for continuous education. Whether it’s mastering the latest diagnostic tools or understanding the intricacies of advanced driver assistance systems (ADAS), staying informed is essential. Online courses, webinars and industry conferences offer a wealth
Every day presents opportunities for learning, often disguised as routine tasks.
are engaging in a form of education that is just as critical as any formal classroom experience. Every day presents opportunities for learning, often disguised as routine tasks. When you troubleshoot a complex repair, you’re not just fixing a car—you’re applying problem-solving skills, drawing on past experiences perhaps even discovering a new approach that could streamline your processes. Each challenge faced is a lesson learned, adding to your repertoire of knowledge and skill.
Moreover, the collision repair industry thrives on collaboration. Conversations with colleagues, suppliers and even customers often yield insights that contribute to your professional growth.
of resources, ensuring that you’re always equipped with the latest knowledge.
In essence, every interaction you have—be it with a tool, a fellow technician, or a piece of literature—is part of your educational journey. Embrace this continuous learning mindset and recognize that you are, indeed, a lifelong learner. The skills and knowledge you acquire each day not only enhance your capabilities but also contribute to the overall growth of the industry.
So, if you have yet to browse through the pages of this issue, please know you should treat it as a mini-textbook. This is merely your intro to ADAS calibrations; grasp the tips we’ve provided you and thrive as a result.
With our single-visit application waterborne system, seamless data integration for optimized profitability, fully automated color matching, and eco-conscious solutions, enhancing your bottom line is our priority.
Experience the Quality, Performance, Conversion and Service of Axalta.
Spies Hecker – simply closer.