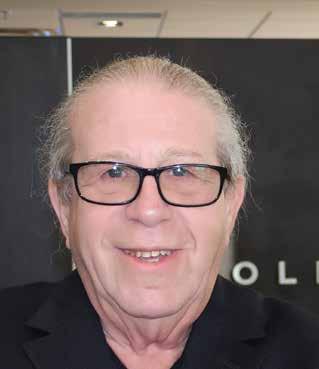
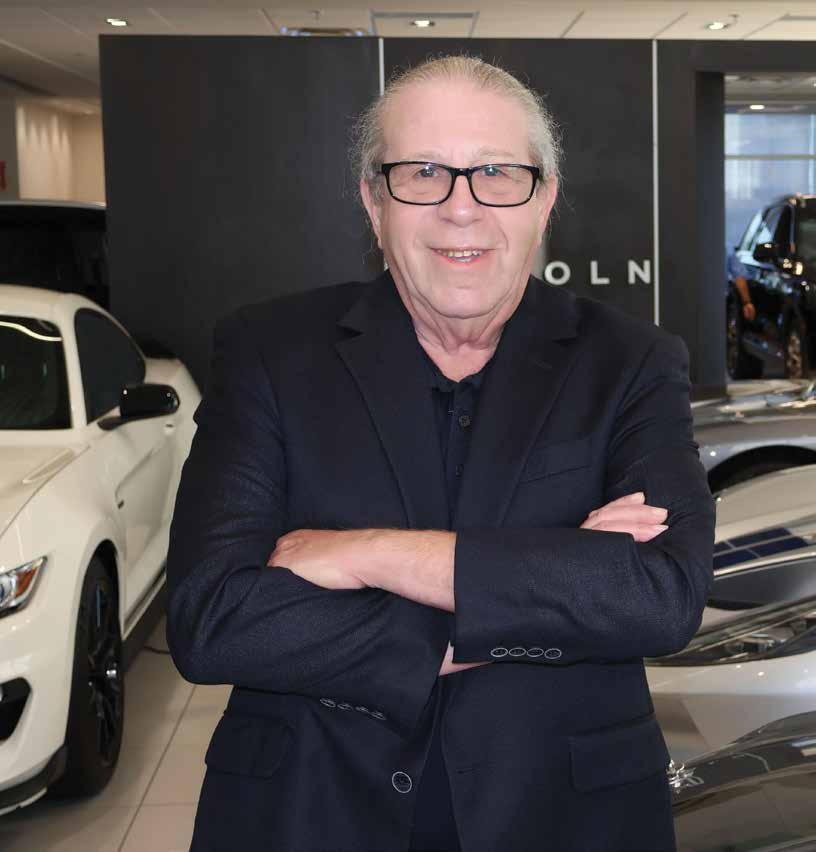
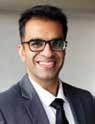

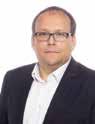
Simplify your body shop processes today.
The 3M OEM Match Family of seam sealing products are engineered to help technicians of all skill levels more easily replicate the appearance and function of a vehicle’s original factory seam sealer.
The system includes our line of seam sealer matching tips and the 2K 3M™ OEM Match Epoxy Seam Sealer in 4 colours –allowing you to replicate the most common OEM seams with one simple application.
With over 41 years in the collision repair industry, there isn’t much that Mark Silverman, fixed operations manager at Yonge Steeles Lincoln Ford, hasn’t seen. Overseeing services at the largest Ford dealership in Canada, Silverman has no intention of slowing down.
SIMPLICITY STEALS THE SHOW
Network hosts annual Growth Conference with a sustainable twist and exciting announcements.
ASSURED A GOOD TIME
Assured Automotive hosts its annual charity golf tournaments. Check out our paparazzi pics!
BIRDIES WITH BASF
BASF saw a record turnout of 300 golfers at its annual golf tournament at the Lionhead Golf Club and Conference Centre in Mississauga, Ontario.
Familiar faces, new roles!
NEWS-IN-BRIEF
Bite-sized updates from across the industry
Local news from coast to coast
PAGE By Darryl Simmons
TALES By Tom Bissonette
By Guarav (Rav) Mendriatta
By DARRYL SIMMONS
One of the most rewarding aspects of being the publisher of Collision Repair magazine is the opportunity to attend industry events and meet the extraordinary people who make this vital industry as exciting and influential as it is. There’s something special about the collision repair industry that keeps people energized, focused, and ready to tackle the challenges that come with ensuring the safety of drivers across Canada. Whether it’s restoring a vehicle after a major accident or handling the day-to-day demands of keeping operations running smoothly, the people who work in this industry do incredible things every day.
We often think about the collision repair industry as one that operates behind the scenes, but the truth is, it’s essential to the way we live and move. Without this industry, our roads would be filled with damaged, unsafe vehicles, and the peace of mind that drivers rely on after an accident would be near impossible to achieve. The work done by collision repair shops allows people to get back to their lives, confident that their vehicles have been restored to pre-accident condition—safe, reliable, and ready for the road again.
In each conversation, I am reminded of just how dynamic and forward-thinking this industry is. The challenges are many—whether it’s adapting to the latest vehicle technology, keeping up with training and certification requirements, or managing the rising costs of doing business. Yet, the resilience and ingenuity of the people in this industry never waver. Each event I attend reinforces the idea that the future of collision repair is in good hands because it’s driven by people who care deeply about what they do and who strive for excellence in every repair.
At Collision Repair magazine, we work hard to capture the essence of these events and share them with our readers. In every issue, you’ll find coverage of where our team has been, the people we’ve met, and the trends that are shaping the industry. I encourage you to check out our photo albums on the website, as we’re not always able to fit all the images from these events in the magazine itself. We want to ensure that even if
For me, the best part of this job is getting to meet the people who make all of this happen. Attending industry events is not just about hearing presentations or learning about new products— although those aspects are important—but it’s about connecting with the individuals who are at the forefront of the industry. These are the shop owners, technicians, suppliers, and innovators who keep the collision repair world moving forward. It’s truly an honour to shake hands, exchange stories, and hear about the passion and commitment that drives these professionals every day.
Recently, I had the privilege of attending several key events, including Automechanika in Germany, the Simplicity Conference in Montreal and the CIECA Conference in Detroit. Earlier this summer, I had the opportunity to meet many of you at the CARSTAR and Fix Network conferences. These gatherings offer a unique chance to learn about the latest trends and advancements in the collision repair industry, but what stands out to me most is the people. It’s the conversations in the hallways, the connections made over lunch, and the camaraderie that makes these events so memorable.
you can’t attend every event in person, you still get a sense of the energy, excitement and sense of community that make this industry so special. One thing is for sure: Collision Repair magazine will always be at the key events in this industry. And to us, every event is a key event. From shop openings and charity golf tournaments to major conferences and trade shows, we do our best to be there, capturing the moments that matter. We also love receiving invitations from our readers—if you have an event coming up, let us know. If we can’t attend in person, we’d be thrilled to include photos and details in our coverage. After all, this magazine is for you—the people who make this industry what it is—and we take that responsibility seriously.
Our next stop is SEMA, one of the industry’s most anticipated events. I’m looking forward to seeing many of you there, and I can’t wait to hear more about the amazing work you’re doing. Whether it’s at SEMA or somewhere else along the way, it’s always a pleasure to connect with the true champions of this industry. See you soon!
PUBLISHER
Darryl Simmons
publisher@collisionrepairmag.com
ASSOCIATE PUBLISHER
Orest Tkaczuk | orest@mediamatters.ca
EDITOR
Allison Rogers | allison@mediamatters.ca
ART DIRECTOR
Yvonne Maschke | yvonne@mediamatters.ca
ASSISTANT EDITOR
Sarah Perkins | sarah@mediamatters.ca
VP OF INDUSTRY RELATIONS & ADVERTISING
Gloria Mann 647.998.5677 | gd.mann@rogers.com
DIRECTOR OF BUSINESS SOLUTIONS
Ellen Smith 416.312.7446 | ellen@mediamatters.ca
INDUSTRY RELATIONS ASSISTANT
Wanja Mann 647.998.5677 wanjamann1@gmail.com
DIGITAL OPERATIONS MANAGER
Cassie Doyle | cassie@mediamatters.ca
AUDIENCE ENGAGEMENT MANAGER
William Simmons | william@mediamatters.ca
MEDIA PRODUCTION SPECIALIST
Dayna Dicuangco | dayna@mediamatters.ca
CONTRIBUTORS
Tom Bissonnette, Stefano Liessi, Jay Perry Gaurav (Rav) Mendiratta, Michael Vavaroutsos
SUBSCRIPTION
Single edition $7.99
One-year $39.95 ( 6 issues) Collision Repair ™ magazine is published bimonthly, and is dedicated to serving the business interests of the collision repair industry. It is published by Media Matters Inc. Material in Collision Repair™ magazine may not be reproduced in any form without written consent from the publisher. The publisher reserves the right to refuse any advertising and disclaims all responsibilities for claims or statements made by its advertisers or independent columnists. All facts, opinions and statements appearing in this publication have been compiled and included with the permission, though not necessarily the endorsement, of the editor, or of independent columnist contributors, and are in no way to be construed as those of the publisher, or as endorsements of them.
PRINTED IN CANADA ISSN 1707-6072
CANADA POST CANADIAN PUBLICATIONS MAIL SALES PRODUCT AGREEMENT No. 40841632
RETURN POSTAGE GUARANTEED
Send change of address notices and undeliverable copies to: 317 Reid St., Peterborough, ON K9J 3R2
“We acknowledge the financial support of the Government of Canada”
Collision Repair magazine is published by Media Matters Inc., publishers of:
Simplicity Car Care has appointed Shawn Wilson as the company’s new Chief Financial Officer. Wilson touts a career spanning more than two decades, and brings a wealth of experience and expertise in financial strategy, corporate governance and performance optimization across diverse industries. In his new role, Wilson will oversee Simplicity Car Care’s financial operations, providing strategic direction to support the company’s continued expansion and innovation in the automotive car industry.
Darrin Heise has been named Color Compass Corporation’s new General Manager for Eastern Canada. Heise brings 16 years of experience within the Color Compass organization, where he has been instrumental in managing the PBE Distribution business. In a release, Color Compass said Heise’s deep-rooted passion for the autobody collision industry, as well as his exceptional expertise in customer relations, vendor partnerships and a comprehensive knowledge of the Eastern Canada marketplace positions him uniquely for this new role.
Consolidated Collision Services (CCS), a division of Consolidated Dealers Co-Operative Inc. has announced that, going forward, Charles Aubry will assume the role of General Manager for the company, with Jason Arnott further assuming the role of Business and Operations Director for the West. Mike Beier, the outgoing General Manager is slated to take over Consolidated Dealers Co-Operative in 2025.
Efficiency, sustainability, and ease of use – these are just three of the reasons why PPG’s Envirobase High Performance waterborne paint system is the trusted choice for more than 40,000 body shops around the globe.
But the benefits don’t stop there. The Envirobase High Performance paint system supports fully digitalized repair processes and is compatible with every tool in the PPG LINQ™ digital ecosystem, making it the perfect solution for modern collision centers.
The refinish industry is always evolving. Our PPG experts continue to develop new products that enhance the core Envirobase High Performance waterborne system and help body shops meet changing demands and challenges.
As a long-time partner of CARSTAR Canada, Don Morton has transformed his business, offering a comprehensive range of services, supporting over 80 employees, uplifting the local community and leveraging CARSTAR’s core values to achieve remarkable success.
Story by ALLISON ROGERS
The builders of the earth’s first settlements were likely unaware they were crafting a village—something that would become an integral piece of groundwork for the social structures shaping human civilization.
Similarly, when Don Morton opened the doors to Don-Mor 45 years ago, he never envisioned that a single building would grow into a sprawling “repair village” set on 5.2 acres of land. Little did he know that his business would become a thriving hub for the auto repair needs of London and surrounding areas.
Despite all of this, Don understood the importance of adapting to the evolving demands of the automotive repair industry. As a CARSTAR Canada partner for nearly all of the company’s 30-year history, Don has elevated his business to not only offer a diverse range of services, but to embrace the latest and greatest of the industry—all while providing advanced training to his staff; adding services to the business; uplifting the local community with charitable support and so much more.
This partnership has allowed Don-Mor CARSTAR to thrive, turning a single facility into a complex where efficiency reigns—staff even use golf carts to navigate the campus, ensuring that precious minutes are saved on every repair order.
Plenty has changed since the facility’s Collision Repair magazine cover feature in 2017, from diversified services to varied community outreach efforts, training, taking on electric vehicles and more. As an I-CAR Gold Class facility, the company has made it paramount to show its commitment to quality, OEM-certified repairs and diversified services.
It’s been nose-to-the-grindstone for the Don-Mor CARSTAR team, who recently had their efforts recognized on a major scale as CARSTAR Canada’s 2024 Franchisee of the Year.
“It’s hard to put into words,” explained Don in the weeks following the win. “It’s an honour to be recognized at such a critical time at CARSTAR Canada, especially being part of Restore the Star. It’s truly an exciting time for everyone in the CARSTAR family.”
Launched in May 2024, CARSTAR Canada’s new initiative, Restore the Star, brings top-performing CARSTAR Canada franchisees together to address challenges facing collision repair centres. The plan is fixed on five key pillars: franchise profitability, safe and quality repairs, people and recruitment, world-class KPIs as well as addressing growth and subsequently, turnover.
“CARSTAR Canada has a legacy of being the original industry disruptor,” explained Jeff Brown, general manager of Don-Mor CARSTAR. “CARSTAR is consistently innovating and constantly pushing the standard a little higher. The network embodies the same values we’ve engrained into our business.”
After nearly 30 years with CARSTAR Canada and almost 50 years in the industry, Don has seen lots of change. When he looks at the current collision repair market, one major sentiment sums up his feelings: “Thank goodness we diversified.”
“We’ve added many innovations in recent years—our electric vehicle operations, OEM certifications with Tesla and VinFast, our new buildings, new fixture benches, electronic measuring and other state-of-the-art tools.
“You can see the hard work our team has put in, it is impressive,” said Don.
“Some business owners tend to stay stagnant,” said Jeff. “In the 45 years he’s owned his business, Don has never once let that happen.”
“Diversification has allowed us to skirt issues facing much of the industry,” added Jeff, referring specifically to profitability, skilled staff, repair cost and complexity.
“We’re seeing more consolidation due to these widespread issues,” Don commented.
Don-Mor CARSTAR staff sport their Humane Society of London-Middlesex shirts after committing $200k to the organization to help build the Don-Mor Auto Group & CARSTAR Community Engagement Centre and continue to be engaged in fundraising for CARSTAR’s CF commitments.
“Network support can offer a way to be more efficient and profitable—that is supported by scale.”
Yet another innovation at Don-Mor CARSTAR—the decision to open an ADAS-specific company, Precision ADAS, as well as a mechanical division on-campus.
“The goal of diversifying is to keep all work in-house. We believe it produces better KPIs—cycle time, specifically—to increase overall profitability and quality.”
“Plenty of collision repair centres today see clumps of volume versus nice, smooth, consistent production. We knew we needed to learn and adapt to achieve a more stable formula,” said Jeff.
One of the ambitious strategies involved cross-training staff to work across departments based on demand. This approach has proven to be transformative.
“We reallocate resources constantly,” Jeff explained. “We needed our team to be versatile
to achieve consistency. This adaptability has been key to achieving a steady production flow.
“When you have 80 to 100 employees at any given time and booking weeks out...that’s a very disturbing way to run a business,” said Don. “You need to have an even flow.”
Don-Mor may have more employees than your average shop, but it never lacks personalization. The incredibly diverse team is tight-knit and has plenty of committed employees. Dave Sutherland, production manager, just celebrated 40 years with the company. Diane Sutherland started as a frontline customer service representative and now leads day-to-day operations for the entire company.
“Diane has worked every role and sat at every desk in the company,” said Jeff. “Literally . And Dave is a shining example of Don-Mor Automotive Group’s core principles and values.”
Don-Mor has also brought on Director of Finance and Central Services, John Cabral, a CPA who touts extensive expertise in mergers and acquisitions. John has spent the last year and a half preparing each department for impending expansion.
The company is excited to announce its latest expansion: Don-Mor CARSTAR South, a brand-new location in a market they are exceedingly familiar with.
“We recognized there was an area of town that was lacking good collision repair
service,” said Don. “We’re always excited for growth—it’s a core theme of this business— and we think this is the first of lots to come in our future.”
“Re-entering that market, that area of London, is hugely important to us,” said Jeff.
The company had a location in the same area but had to close to due lease expiration last year.
The new location will open around the corner from a freshly-built Tesla Service Centre opening in 2025—likely
the only planned to serve the entire southwestern Ontario market, claims Don. Don-Mor CARSTAR South will also launch with an exciting AI estimating partner to increase efficiencies and turnaround time, he added.
This new location will include the same commitment to quality and service as its flagship store, so there’s only one question for the Don-Mor team: can they get the golf carts on the roads to drive there?!
“Don’t worry—we’ve got a permit.”
Auto Additive, a company that works to produce 3D auto parts, has announced the formation of its advisory council, featuring leaders from across the industry that are focused on the advancement of 3D printing in collision repair. Harold Sears, head of the council, said this group will “develop a roadmap for integrating 3D printing technology into repair processes, aiming to provide high-quality, OEMcompatible parts, tools and jigs to enhance efficiency and precision.” Promoting standardization of 3D-printed auto parts will be a key focus of the council. Auto Additive is also championing location-based printing for low-volume parts, which Sears says reduces waste and costs for OEMs or aftermarket providers. “By working alongside insurance companies, training bodies, OEMs and repair shops, Auto Additive is committed to helping the industry better understand the technology and adopt 3D-printed parts wherever possible,” said Sears.
Two of Canada’s largest railways—Canadian National and Canadian Pacific Kansas City—initiated strike action in late August, prompting fears widespread across industries that use freight as a method of transportation. According to Canada National’s website, the company transports more than two million finished vehicles on its rails annually. Meanwhile, CPKC handles about 90 percent of automotive assembly plants in Mexico. When speaking with Automotive News Canada, the Canadian Vehicle Manufacturers’ Association said the stoppage would have an immediate effect on the automotive industry. However, Val Kucherenko, director for Railway Education at Michigan State University, told Collision Repair mag that, in his opinion, the automotive industry impact seen from the Canadian railway strike would be ‘minimal,’ should the strike only last a few days. “Everyone was sort of aware and getting ready for the strike to happen,” he said, referring to the fact that collective bargaining talks had been ongoing for quite some time. “There was no certainty, but when you have something coming up and it’s not good for the supply, it can start working in plans B and C. From an automotive dealership perspective, there shouldn’t be any immediate impacts. I’m sure they were aware of it coming,” he said.
Kucherenko says that a combination of both large orders of the same part destined for assembly plants and general stock for dealerships or service centres are typically shipped via freight.
Orders can be placed now, product availability in the early new year.
It comes with a completely new nozzle concept and is available with new digital functionality. And a completely new shape - but one that is still characteristically SATA.
The jet X is available in four versions; jet X BASIC, jet X DIGITAL ready, jet X DIGITAL and jet X DIGITAL pro. The best paint spray gun that has ever left our factory. jet X. Works for you.
INFO www.sata.com/jetx
In Canada’s currently strong used vehicle market, collision repair is “key,” automotive market analyst Sam Fiorani told Collision Repair in August. J.D. Power’s recent Automotive Market Metrics for July 2024 indicated that the current new vehicle transaction price sat between $44,000 and $46,000 in July 2024, compared to new vehicle prices between $48,000 and $50,000. Fiorani said the current vehicle pricing trends “leave a lot of buyers out of the marketplace, making it much more important [for them] to maintain older vehicles.” The vice president of AutoForecast Solutions added that these rising prices—even if the increases are marginal—makes “used vehicles much more important in the marketplace.” J.D. Power’s data echoes Fiorani’s claims of economic struggle when it comes to affording cars. In the last 12 months, 50 percent of new vehicle transactions have been paid in loans. Twenty-five percent were leased and 25 percent were paid in cash. Comparatively, 53 percent of used vehicle transactions were paid by loans; 45 percent were paid in cash and two percent were leased.
Nearly two-thirds of American drivers would prefer to pay out of pocket and avoid using auto insurance in the event of an accident, according to a survey of 2,000 American consumers, conducted by LendingTree. Of those who did file a post-accident claim, 24 percent regret doing so. Thirty-nine percent of insured drivers said they had bypassed their auto insurance when they’ve experienced an accident or incident. Of those drivers, 59 percent said they bypassed insurance because the damage was minimal; 42 percent said it was because they didn’t want their insurance to increase, while 44 percent said it was because their deductible was higher than the repair cost. LendingTree’s results also note that 57 percent of drivers who have paid out of pocket for repairs did not disclose the incident to their insurer. The survey results also indicate that almost two-thirds of drivers would prefer to pay out of pocket for small repairs in case of a collision or incident, with men more likely to do so.
When considering size in terms of dollars, the overall Canadian light vehicle aftermarket grew significantly between 2021 and 2023, according to a new report from Desrosiers Automotive Consultants. From 2021 to 2023, DAC says the overall light vehicle aftermarket expanded from $22.5 billion in 2021 to $24.1 billion in 2023. Retail aftermarket parts saw an increase from $12.9 billion to $13.7 billion, while labour revenues rose from $9.6 billion to $10.4 billion during the same period. DAC also notes that, beneath this overall growth, there are “significant channel shifts” occurring in the aftermarket—particularly changing consumer maintenance patterns and the evolving structure of the vehicle fleet in terms of fuel types.
According to DAC Managing Partner Andrew King, “understanding [current market] shifts is critical” to forecast the future of the aftermarket and operations in new vehicle dealers, independent repairers and other auto businesses.
Hertz is accelerating its plan to sell 100,000+ Tesla units, the rental company said during its second-quarter earnings call in July. The company initially hoped to sell the units for as low as US$20,000 each, but prices have now been dropped further in an effort to clear out stock. Hertz originally announced it was selling a third of its Tesla fleet in January 2024, due to “weak demand” and high repair costs. Hertz anticipates the “fleet overhaul” to be complete by the end of 2025.
Chinese automaker BYD has penned a letter to the Federal Government of Canada announcing its intentions to enter the Canadian EV market, despite tariffs on Chinese-made EVs. Consultants working with BYD Canada Co. filed a notice with the federal registry of lobbyists in July, stating the OEM was in discussions with Ottawa to “advise the government of Canada of matters related to the expected market entry of BYD into Canada for the sale of passenger electric vehicles, and the establishment of a new business,” according to a report from the Globe and Mail. The filing also mentioned that BYD was seeking discussions regarding the implication of tariffs on Chinese-made EVs.
Advance Auto Parts has sold its Worldpac unit for US$1.5 billion as part of the company’s latest attempt to streamline operations. Worldpac will be sold to Carlyle Group, a private equity firm that formerly owned Axalta Coatings Systems, in a deal expected to close by the end of 2024. The announcement came hours before Advance Auto Parts’ webcast to discuss Q2 2024 financial results, and shares dropped more than 15 percent when the company cut its annual forecast on the call. Annual sales and profit forecasts were cut due to lower parts demand and future anticipated maintenance-related headwinds and lower discretionary spending.
The original award-winning flexible sheet & disc sanding system that cuts fast while delivering a shallow and uniform finish. Perfect for scuffing, blending, topcoat sanding and more...
ANTI-CLOGGING AGENT for Total DRY Sanding
Available in 3”, 5”, 6” Discs & Sheets K-2000 to K-3000
FLEXIBLE BONDING results in Extremely Uniform Scratches ULTRASHARP ABRASIVES results in Faster Cutting K-SYSTEM ABRASIVES CUT FASTER WITH A MORE UNIFORM FINISH BA SANDER 910-0202
Maximize efficiency with the premium Pneumatic BA Sander designed for Super Assilex and Super Buflex sheets
IT’S LIKE YOUR
IT’S LIKE YOUR Super Buflex Interface Pads
Available in 3”, 5”, 6” Discs & Sheets
Super Buflex is a revolutionary polish sanding system that works completely dry and delivers a more uniform finish while cutting faster. Leave the prep and mess of compound buffing behind and... reduce your buffing times by 50% or more!
When compared to equivalent grit abrasive papers, Super Buflex not only delivers a shallower scratch pattern, but also one that is more uniform.
By
Mercedes-Benz seized more than 1.6 million counterfeit parts in 2023. The parts were seized in more than 740 raids globally; a 20 percent increase in raids compared to previous years. More than 142,000 offers for counterfeit parts were removed as a result of the investigation. “The counterfeiting industry generates enormous margins and has the structures of organized crime,” said Renata Jungo Brungger, member of the Board of Management of Mercedes-Benz Group AG for Integrity, Governance and Sustainability. “By taking action against these highly criminal structures consistently with all legal means, we protect not only the reputation of our brand, but also our customers, other road users and ultimately all victims of the counterfeiting industry.”
Owners of General Motors-made SUVs have filed a class action lawsuit against the automaker, alleging a defective manufacturing process that led to paint peeling problems with its vehicles. The class action lawsuit, brought to the U.S. district court for the central district of California by an Alabama-based legal firm representing four people, states that the paint of affected vehicles is prone to defects. The suit alleges GM knew about the problem but continued with the faulty process anyway. Vehicles listed in the lawsuit include the Chevrolet Tahoe, Chevrolet Suburban and GMC Yukon XL, among others. Complaints related to these vehicles include peeling, cracking and delaminating paint, as well as clouding paint. Repair costs quoted in the suit are reportedly upwards of five figures. One Reddit user claims his repair was quoted at more than US$10,000.
paint suit stresses that “although the
knew or should have known of
Defendant continued to put the
INSURANCE NEWS
Accident Support Services International (ASSI) has launched “Start from Home,” an online service to allow drivers that have been in a collision to begin their own collision reports online, from home. The service can be accessed through reportacollision.com, and specifically allows drivers whose collision meets the threshold to report the event at a collision reporting centre to instead start an online report from their personal devices. The website allows drivers to provide a typed statement and capture several fields to complete an accident form. The goal of the new program is to reduce wait times at collision reporting centres. So far the service is available in Ontario, Alberta and P.E.I.
The Insurance Bureau of Canada (IBC) is warning that more auto insurers could be pushed out of Alberta following a record-breaking August hailstorm. Aaron Sutherland, IBC vice president for the Pacific and Western Canada region said the hailstorm resulted in $900 million in unexpected claims and comes “at a time when Alberta’s auto insurance system is in crisis due to the province’s rate cap.” He said that, under the rate cap, auto insurers are unable to recover from the growing cost of claims over the last two years. This has created a dire economic environment, he said, forcing several companies to leave Alberta’s auto insurance market. “Unless the rate cap is removed, the high number of new claims from the hailstorm will contribute to Alberta’s already tenuous market conditions, which may result in more insurance carriers making an exit from the market.”
Canadian Prime Minister Justin Trudeau announced that Canada will impose a 100 percent surtax on Chinese-made EVs, including hybrid vehicles, trucks and buses. The 100 percent surtax, applied to all Chinese-made EVs, will take effect October 1, 2024. A 25 percent surtax on imports of steel and aluminum products from China will also take effect October 15, 2024. The Prime Minister accused China of violating international trade rules and attempting to give itself an “unfair edge” in the emerging global EV market, adding that tariffs will “level the playing field for Canadian workers” and allow for competitive Canadian and North American industry. China rebutted by accusing Canada of protectionism.
The time has come. You are one step closer to seeing a Cybertruck in your repair bay. Tesla has officially launched the Cybertruck in Canada and has also confirmed that the electric truck will not be affected by the federal luxury tax. The federal luxury tax, which was introduced in 2022, is normally applicable to vehicles costing more than $100,000. According to the regulations, the amount taxed is either 10 percent of the taxable value of the vehicle or 20 percent of the amount that the vehicle’s price exceeds the $100,000 threshold, whichever is the lesser amount. As a result, for the Cybertruck, the 20 percent rule would have applied, meaning that the luxury tax would have added $8,173.20 for the all-wheel drive (AWD) variant and $13,773.20 for the tri-motor variant. However, Tesla has negotiated the removal of the tax by citing the fact that the vehicle’s weight—4,000 kg—makes it above the weight threshold for the luxury tax.
The Canadian federal government has released the ZEV Council Dashboard, which provides quarterly updates on Canada’s EV market share; data on incentive program uptake; information on the deployment on charging and hydrogen refuelling stations and federal investments in the ZEV space. Launched in partnership with Transport Canada and the ZEV Council, this online tool aims to show consumers and industry members data from several different sources across the country for EV adoption and charging station availability. The data on this new dashboard demonstrates that in Q1 2024, Quebec and British Columbia were in the lead in Canada in terms of EV adoption at 28.3 percent and 22.7 percent respectively.
Market penetration of light-duty EVs was high in the Yukon in Q1 2024 at 11.4 percent and was the third highest-adopting jurisdiction in Canada in the quarter. Following this, Prince Edward Island came in at 8.2 percent, with Ontario following at 7.9 percent.
The dashboard can be access via tc.canada.ca/en/roadtransportation/innovativetechnologies/zero-emissionvehicles/zev-council-dashboard.
BMW Group is now using humanoid robots in its vehicle production. The trial was conducted at the BMW Group Plant Spartanburg in South Carolina, United States. The humanoid is engineered by robotics company Figure and bears the name ‘Figure 02’. The robot was responsible for inserting sheet metal parts into specific fixtures assembled as part of the vehicles’ chassis. Milan Nedeljkoviv, member of the BMW AG Board of Management for Production said the “developments in the field of robotics are very promising.” He added that BMW is “now determining possible applications for humanoid robots” on the production floor.
CAN YOU BELIEVE THIS?!
Those who tuned in to coverage of the Paris 2024 Olympics may have noticed the gleaming hot air balloon that graced the city skyline each night, housing the Olympic flame. But did you know the vessel for the ancient fire bears a connection to our industry? Glasurit recently shared that its customer, Carrosserie Godot, located in Saône-et-Loire, France, had the honour of painting part of the structure that has graced the Paris skyline every evening of the Games. “Recognized as a reliable and highly qualified bodyshop in the region, Sébastien Godot had the incredible opportunity to paint the structure of the iconic flame,” said BASF Automotive Refinish Coatings in a social media post. The goal was to achieve a smooth and matte finish, said the coatings company. Godot finished the job using the waterborne basecoat from Glasurit 90 Line and clearcoat from AraClass.
You may have heard of it raining cats and dogs, but for one couple from Atlantic Highlands, New Jersey, it was raining fish when the windshield of their Tesla was shattered in one cod-filled caper. According to ABC7 News, Cynthia and Jeff Levine reportedly had their Tesla’s windshield smashed when a fish fell from the sky and landed on the vehicle. The vehicle was parked in the couple’s driveway at the time of the fishy situation. The pair told ABC7 News that they heard a crash outside of their home, located about two kilometres away from the nearest body of water. When the couple went to investigate, they found their Tesla’s windshield broken and covered in a mess “of fish and scales and blood.” The culprit? An eagle who failed to keep hold of his lunch.
Many vehicle drivers are dissatisfied with the artificial intelligence (AI) technology systems included in their vehicles, J.D. Power Report’s 2024 U.S. Tech Experience Index Study reveals. The study—which polled 81,926 owners of new 2024 model-year vehicles—found that while owners often offer praise for some advanced vehicle features, others are found to be lackluster. Specifically, the study reports that “New Artificial Intelligence-based technologies, like smart climate control, have quickly won popularity with those owners who have used it, yet recognition technologies such as facial recognition, fingerprint reader and interior gesture controls fall out of favour as they unsuccessfully try to solve problems.” The study also reports that drivers still prefer hands-on technology and don’t see value in passenger screens. J.D. Power noted many owners remain “indifferent” to the value of ADAS.
Recycled Transmissions and Engines are carefully removed from the vehicle in one of our state-of-the-art dismantling plants, inspected for damage, and inventoried with consistent descriptions and accurate donor vehicle mileage to ensure quality.
Remanufactured Transmissions and Engines go through a systematic process and are restored to “Like New” condition, meeting or exceeding OEM specs. Most LKQ Remanufactured Transmissions come with 3-Year Unlimited Mileage warranty, and most LKQ Remanufactured Engines come with a 4-Year Unlimited Mileage warranty.
Remtech’s Aristauto is here to offer collision repairers with advanced support
Remtech President Jamie Lapierre says it’s a “whole new world” when it comes to automotive calibrations. Luckily the precision diagnostics company is more than ready to offer online support so collision repair technicians can keep up with the technological demands of the modern vehicle.
With automotive OEMs requiring and expecting a specific variety of repairs for each vehicle, and with vehicles becoming more and more technologically advanced, it is becoming increasingly paramount that collision repair technicians have access to the most up-to-date information. This is where Remtech aims to combat the learning curve.
Remtech is a remote automotive diagnostics support team that gives users access to a network of master technicians and IT support specialists. The Remtech team walks a collision repairer through automotive calibrations and provides access to up-to-date information. The company is always synced with OEM data—Remtech’s services are available without the need for an appointment. The company
“Information is a tool, and with Remtech, our tools provide the information needed to stay upto-date on the latest repair and calibration requirements.”
— Jamie Lapierre, President of Remtech
strives to create a knowledge base with the information to correctly and safely get the job done, and the support to help a repairer through the process of bringing a vehicle back to OEM standards.
By providing their team with an online support platform that offers information at the source, bodyshops can in turn improve their cycle times by more easily performing calibrations in-house without having to facilitate sending vehicles to the dealership and then wait for their return. Remtech’s commitment is simple: providing top-notch auto diagnostic tools and unbeatable support, all wrapped up in an affordable monthly subscription.
On August 3, 2024 Remtech launched Aristauto—a website where repairers will be able to go for online support. Facing a challenge? Aristauto is here. The service specifically aims to extend Remtech’s message of community support by featuring a patient and meticulous team of experienced master technicians and tech specialists ready to offer
support so that repairers never miss a beat in providing top notch service.
“With advances in automotive technology happening so quickly, at Remtech, we recognize that knowledge is power and we want to put that power into the hands of repair professionals,” Lapierre commented. “We want to help accompany a technician as they grow and become increasingly skilled, and we see Remtech as a vital part of that journey.”
As National Automotive Service Task Force (NAST) and locksmith agents, Remtech is further able to provide customers with invaluable access to Manufacturer PIN codes. This unlocks the door to advanced diagnostics, repairs and expanded service offerings.
“Information is a tool, and with Remtech, our tools provide the information needed to stay up to date on the latest repair and calibration requirements,” said Lapierre.
Struggling to keep pace with the rapid advancements in automotive technology? Remtech and Aristauto are here for you. Reach out to info@remtechauto.com today.
Story by SARAH PERKINS
There isn’t much that Mark Silverman, fixed operations manager at Yonge Steeles Ford Lincoln in Thornhill, Ontario hasn’t seen in the past 41 years in the industry. Always sporting a neat ponytail, Mark, at 71, has no intention of slowing down—and as the head of one of the Greater Toronto Area’s leading dealership and repair facilities, Mark oversees a collision department that is never idle.
Since starting his own mechanic shop in the late 1970s in midtown Toronto, Mark has seen the automotive industry evolve through countless changes in repair methods, insurance relations and public perception. But for Mark, the key to success has never changed: it’s all about customer experience, and more specifically, about maintaining a work culture of honesty, transparency and empathy fit to turn any team into a family
and to ensure those in need of service feel right at home.
Silverman first began his career in the industry as an independent service centre before transitioning to working at a dealership.
“We were originally a Gulf station and then we ended up becoming a Petrol Canada station,” Mark said. “I had four mechanical repairers at the time. I was a mechanic myself back in the 70s, having written my license in 1974, and then I became the proprietor of the station. One of the partners wanted out and wanted to retire and they approached me to see if I wanted to buy into the business.”
As Mark puts it, from here, he “never looked back.” This venture lasted for about 12 years until the business was closed by the petrol company, seeing Mark turn his sights to working in a dealership.
“From there, I’ve been a fixed operations manager for 37 years,” Mark continued. “I’m still working at it. I don’t golf or play tennis, so I’d rather come to work than stay at home,” he joked. “I’ve gotten an extensive amount of experience in all facets of the industry. I’ve gotten experience that you can’t read in a book or buy in a store. You have to live it.”
And, in living and thriving in the industry, Mark has experienced everything from the traditional to the innovative.
In addition to traversing the traditional channels to become a mechanic, in the early 2000s, Mark regularly featured on a popular radio call-in show for the GTA, “Dave’s Corner Garage.” Hosted by Dave Redinger and Alan Gelman, the show focused on helping the public solve issues related to their vehicles.
“The show was on for many years, and I would be on two to three times a month. Dave
and Alan were good buddies of mine, and the show was also a great business opportunity. Every time I was on the air, business would show up the next day.”
Mark also did something that the Ford Motor Company had, at the time, never seen before and opened up a service centre in the Scarborough Town Centre. Opened under the name “Quick Lane,” the service centre offered customers the opportunity to stop in for a quick oil change and other mechanical help—or, as Mark puts it, and as was the slogan for the shop, the opportunity to “drop, shop and roll.”
“I was the only dealer at the time allowed to take the trade name Quick Lane and I had to lobby with Ford to use the name. I had the shop for two years before internal issues within the mall forced me to stop.”
“But I’ve always been that kind of guy,”
Mark told Collision Repair when asked about his capacity to innovate. “I’ve always been the kind of guy that wants to be involved and innovate within the industry.”
As a result, today, Mark oversees 92 employees across all services, including a small bodyshop. While the collision centre at Yonge Steeles Ford Lincoln is on the smaller side, it is an integral part of Mark’s overall plan for providing top notch customer service.
“We don’t have the largest collision repair facility in the area, but it’s certainly one of the best. We are obviously Ford certified and our customer base has been organically grown from our dealership. I kept the collision centre going because I wanted to be a one-stop shop for customers. I wanted customers to be able to buy the car here, get parts for the car here, get it serviced here and of course, if the unfortunate were to happen and a
“The industry, like any other industry, is evolving into something that’s totally different from when I started in the 70s, but there has always been an emphasis on looking after your customers.”
— Mark Silverman, Fixed Operations Manager at Yonge Steeles Ford Lincoln in Thornhill, Ontario
customer was in a collision, get your vehicle repaired here.”
As the largest Ford dealership in Canada, Yonge-Steeles Ford regularly services 200 cars a day.
“When it comes to the collision side of the shop, I don’t go looking for business,” Mark stressed. “Of course, if business comes my way, I take it. I also haven’t partnered with any insurance companies or banners. I think that they’re good programs, but I leave that side of things alone for the standalone guys who depend on that business to survive.”
“Ultimately,” Mark commented, “we’re not a big shop, but a healthy shop.”
In maintaining the health of the business, at its foundation is both an awareness of continually building work and customer culture as well as staying up to date with the latest technology.
“The industry, like any other industry, is evolving into something that’s totally different from when I started in the 70s, but there has always been an emphasis on looking after your customers—or as Ford calls them, guests. The other aspect of maintaining a business is upholding a culture of honesty, integrity and transparency. When I first started in the business, customers had less of an ability to fact check without the internet and so everything was word of mouth. It was important
to make sure that you were doing everything you could to make everyone feel welcome, and I still stand by that today.”
When asked what it takes to develop a community culture, Mark was quick to answer: “you work hard and you pay your employees what they deserve to be paid. You become a team and you work hard to have it become as close of a team and a family as you can.”
With the ongoing talent and labour shortage continuing to affect the industry, Mark further noted that “if you get a good bodyshop technician, you have to keep them.”
“When you have a happy team, this also translates to the customer. I’m the kind of manager that doesn’t make schedules. I let my advisors and team come up with schedules that work well for everyone. I trust my team; collision repair is full of skilled people and it’s an art.”
“If and when mistakes happen, I believe it’s important to keep a mindset of, ‘let’s take this as an opportunity to learn and then move onwards and upwards.’”
Moreover, when asked what Mark’s biggest challenge in the industry has been so far, he noted that it’s consistently been “keeping up with technology.”
However, with decades worth of experience in the industry, despite the consistent changes, Mark continues to stay versed in all the tools and tech that a modern bodyshop requires.
Equipped with a dedicated aluminum room, a state-of-the-art paint booth and a team of seasoned professionals, the facility has seen $80,000 in recent upgrades.
And, while Mark jokingly feels that his biggest achievement in the industry has been successfully getting up in the morning, in rising for the day, he also continues to rise to the challenges that the industry brings.
“I’ve gotten to the top and have developed my knowledge base. At the end of the day, it’s not all about the dollars and cents, it’s about having empathy. If you do everything correctly, the dollars and cents will follow. When you’re up to date with what you have to offer, you’ll get a whole variety of people
and if you’re traditional, you’ll only get traditional people.”
“Even at my age and my experience, there’s still things to learn every day about how to run a business and how to evolve and keep up with your customers’ expectations. If you start to slow down, then they’re not going to keep coming back.”
When asked about plans for the future, Mark says that he is content to maintain the success that he has built and the community connections that he has made. “The best advice I can offer collision centres is to partner with somebody. Vehicles are only going to become more technologically advanced as the years progress and so collision repair shops are going to increasingly need someone capable of handling the electronics in modern vehicles.”
As such, while Mark Silverman may have a decades long resume, with a diverse team that he loves and strong business foundations, he has no plans of retiring any time soon.
“I may be 71,” he concluded, “but I love my job and it keeps me young.”
Story by DARRYL SIMMONS
Simplicity Car Care recently held its annual Growth Conference at the iconic Rialto Theatre in Montreal. The network celebrated feats of this year, including advancing the Net Zero program of sustainability; Simplicity’s entry as a Top 500 Growing Corporation; surpassing 100 locations and the focus on capacity management and profitability. Check out the event highlights on the following pages.
Outlining Simplicity’s strategic growth and clearly stating objectives moving forward, Simplicity Car Care CEO Paul Prochilo delved into the company’s mission to lead the collision repair industry toward sustainability. He opened up the challenge not just to those present, but to all networks and auto claims economy partners.
“This is a sense of corporate responsibility that must be shared on a personal level. We all have a responsibility to ensure that future generations have a cleaner environment. For example, I want my three-year-old to know I did my best to leave the world a better place.”
Prochilo’s sentiments were echoed in a presentation by Alyssa Marchese, ESG manager at Simplicity, who stressed that small changes when made strategically, can make sweeping changes overall. She stressed that Simplicity’s sustainability and net-zero-centric business model will be something adopted across the industry in the years to come.
“Net zero is not just an environmental goal—it’s a direct path to profitability. Helping our earth also helps our bottom lines.”
In addition to sustainability, company President Domenic Ieraci said the path to continued success will see Simplicity leverage new technologies—such as capacity management tools, help desk support, loadlevelling solutions and virtual estimatics—to support franchisees in acquiring further OEM certifications and expanding brand
awareness. These are ultimately strategies in the company’s multi-pronged approach to enhancing profitability among its network members.
“Our strategy is to optimize business performance and revenue growth while ultimately providing our network with a better quality of life,” emphasized Ieraci. “At Simplicity, we are dedicated to raising the standards in the industry and are proud to boast a community of ambitious professionals.
Ieraci followed up on the stage with some big news– literally big news. Simplicity Truck Care is now open for business with an initial location in Cambridge. Focusing solely on heavy truck repair, the strategy is to cater to what is now an underserved market.
“We all have a responsibility to ensure that future generations have a cleaner environment. For example, I want my three-year-old to know I did my best to leave the world a better place.”
— Paul Prochilo, CEO, Simplicity Car Care
AWARD WINNERS
Simplicity Wow the Customer Award 2024: Simplicity Car Care Watford
Simplicity Sales Growth Award 2024: Simplicity Car Care Airdrie
Simplicity Best Cycle Time Award 2024: Simplicity Car Care Medicine Hat
Simplicity Highest Sales Per Square Foot 2024: Simplicity Car Care Ottawa Airport Simplicity Highest Sales Store 2024: Simplicity Car Care Edmonton South East
Simplicity Progress Award 2024: Simplicity Car Care Mississauga Central
Simplicity Engagement Award 2024: Peter Schalk, Simplicity Car Care Aylmer
Simplicity Brand Ambassador Award 2024: Simplicity Car Care Windsor Prix Simplicity 2024 pour excellent Leadership: Bassem Hijazi Montreal Nord
2024 SIMPLIFIER OF THE YEAR
MIKE NICHOL — SIMPLICITY CAR CARE AIRDRIE!
Congratulations to our 23#3 cover star, Mike Nichol and his team!
“At Simplicity, we are dedicated to raising the standards in the industry and are proud to boast a community of ambitious professionals.”
— Domenic Ieraci, President, Simplicity Car Care
Collision Repair magazine recently organized a tour of Lithion Technologies’ first commercial critical minerals extraction facility in Saint-Bruno-de-Montarville near Montreal, Quebec. The event was attended by 20 industry stakeholders including OEMs, collision centre personnel and automotive recycling industry representatives.
The day began with a safety briefing before attendees received information on battery recycling procedures and a history of Lithion Technologies by Marie-Line Paquet, external communications manager and Eva Carissimi, vice president and general manager. Following the brief, the group entered the plant and were greeted with another safety talk to emphasize the critical importance of safe practices around high-voltage technologies and extraction equipment.
Martin Archambault, operations director for Lithion Saint-Bruno showed the tour group where batteries are stored. Batteries and components are housed in individual solid compartments, and a 12-foot sprinkler system has been specially installed in the shelving unit to prevent any potential fires from spreading. Damaged batteries are kept
in a seperate, secure area for maximum safety.
The process of transforming used EV batteries into black mass, metal pellets and plastic flakes is quite complex. Lithion has designed a completely closed-circuit web shredding solution that allows the treatment of charged batteries, preventing thermal runaway reactions. The Solution adapts to all types of battery chemistry and recovers over 98 percent of the minerals contained in batteries and creates a black mass ready for hydrometallurgy processing.
Batteries are shredded to create a mixture of black mass, plastic flakes and metal pallets. Black mass is filtered from the mix, then pellets and flakes are efficiently separated and will also be recycled by dedicated partners.
Black mass will ultimately be processed in Lithion’s second phase of development, in its future hydrometallurgy plant, where batterygrade lithium carbonate, nickel sulphate and cobalt sulphate will be produced. All of these products would then be reintroduced into the battery value chain.
After the tour, attendees headed back to a boardroom for a Q&A session, answered by Nick Poupart, business development
manager, followed by a lunch, sponsored by Call2Recycle.
The group was enthralled with Lithion’s facilities and procedures. Many put forward questions about EV batteries in collision centres, given the sensitivity of these systems.
“It was fantastic to witness firsthand the progress being made in handling and recycling electric vehicle batteries—this has been a big concern as vehicle electrification continues,” commented Don Morton, owner of CARSTAR Don-Mor, which has OEM certifications with Tesla and VinFast. “We’re happy that recyclers are working with the collision repair industry and excited that we have somewhere to send our end-of-life or damaged batteries.”
“Meeting our clients and partners is essential for showcasing our recycling solutions and the technology that drives them,” said Poupart. “These conversations and exchanges are super valuable, helping us fine-tune our offerings and refine our knowledge of the market’s changing needs. We are in a new industry and we will build it together.”
For more information on Lithion Technologies, visit www.lithiontechnologies.com
On September 18, Collision Repair magazine’s EV Repair Tour, supported by Fix Network, continued its cross-Canada tour sharing electric vehicle repair information for the automotive aftermarket.
Dozens of Quebec-based repair professionals gathered at Fix Network’s state-of-the-art Blainville training centre, joining insurers, OEM representatives and EV battery experts to do their due diligence on the future of repairs. With more than 200,000 EVs and hybrid vehicles on Quebec roads, it is critical that all verticals of the industry be prepared for the new technologies inevitably entering their bays.
If you missed the event, fear not—we’ve compiled a bite-sized review of the day on the following pages.
Phillippe Bussières, senior advisor at Conseil provincial des comités paritaires de l’industrie des services automobiles (CPCPA) began the charging day of electric learning to deliver an overview of EV knowledge for safety and profitability.
He elaborated on the technological and voltage differences between hybrid vehicles, hydrogen fuel cell vehicles, extended-range electric vehicles (EREVs) and EVs.
A hybrid vehicle, Bussières pointed out, has a much smaller battery compared to an EREV or EV, due to its partial reliance on its internal combustion system.
The first step, said Bussières, is to prepare yourself for inevitable interaction with high-voltage technologies. That means acquiring PPE that protects your team against high-voltage harm: class-zero electrical insulating globes rated for 1,000 volts; CSA electrical (ohm) certified gloves and boots of the same quality. You also need to equip your team with tools to keep them safe from electrocution—insulated tools and lockout kits.
Bussières also advised installing a “security zone” in the EV repair area to ensure personnel that are not trained to handle high voltage technologies are made aware, as well as high-voltage warning stickers in potentially dangerous areas.
Bussières emphasized the effect of alternating and direct current. Where AC changes direction periodically and is commonly used to power homes and businesses, DC flows in one direction and is typically found in EVs.
He said the human body’s resistance is around 2,000 Ω (ohms), depending on certain factors. The voltage emitted by an EV can range between 400 volts and 800 volts—Ohm’s Law can be used to calculate just how much a human can stand.
Finally, Bussières stressed the “right-hand rule.” The right-hand rule is a mnemonic used in physics and electrical engineering to visualize the relationship between current, magnetic fields, and forces, particularly in electric vehicles.
By positioning your right thumb in the direction of conventional current and curling your fingers towards the magnetic field, you can predict motor rotation and component behaviour. This rule is essential for safely working with electrical systems in EVs, helping technicians understand electromagnetic interactions effectively.
Nick Poupart and Martin Archambault of Lithion Technologies were next to the stage to discuss the recycling of EV batteries in Quebec—something Lithion is highly involved in. They covered the company’s mission to repurpose the valuable metals used in EV batteries, like lithium, cobalt, nickel, manganese, aluminum and copper.
The pair discussed the process of mining to refining, and turning material to cathode and anode products. From there, these products are either turned to powdered cathode that are redirected to Lithion for reuse, or compacted into cells to be used in EVs.
These EV batteries still end up at Lithion at the end of their life, depending on the reason.
The duo also covered Lithion’s landmark opening of the Saint-Bruno recycling management site—a first-of-its-kind facility in
Quebec dedicated to the management of end-of-life EV batteries. The facility produces high-quality black mass, said Poupart, in an automatic process that ensures optimal efficiency. They added that 95 percent to 98 percent of battery “waste” processed through the Saint-Bruno plant is repurposed. See more about this facility on page 31.
Sebastian Menard from Call2Recycle Canada also discussed battery recycling. Since 1997, Call2Recycle has collected and recycled 50+ million kilograms of batteries and battery materials. The company does recycle more than just EV batteries; they recycle household batteries of up to five kilograms. The company operates on behalf of 400 different battery producers.
Batteries are collected by an authorized carrier and shipped to a Canadian sorting facility to be organized and sorted by type and chemical composition. Batteries are processed according to one of five trajectories: repair, manufacture, resale, reuse or recycling.
Ultimately, all paths for EV batteries end in recycling. Between 2016 and 2022, demand for lithium-ion batteries grew by nearly 1,500 percent, said Ménard.
With thank-you remarks to our gracious attendees and sponsors, Bisson ended the speaking portion of the event. A cocktail hour closed out the event, where everyone discussed the insights learned throughout the day.
You can read more about this landmark event in this year’s annual issue of EV Repair magazine—available now.
When you invest in a Fix Auto franchise, you invest in a business model with a proven track record in 12 countries around the world. You invest in a fully branded business with a roadmap for success. You invest in the same values and work ethic that grew your local business to what it is today.
Drive your business forward with:
• Solid performance-driven operational model and ongoing training.
• Full branding and marketing support for local awareness and promotion.
• Proven experience in winning insurance work.
• Established global supply and fleet arrangements.
Our owner started as a franchisee, and this inspires our commitment to the success of the local business owner.
In an era where electric vehicles (EVs) are speeding ahead and advanced driver assistance systems (ADAS) are setting new industry standards, collision repair shops stand at a pivotal moment. The key to staying competitive and relevant? Diversifying their services to embrace these technological advancements.
Picture a bustling repair shop that goes beyond merely addressing dents and scratches. Moreover, it skillfully handles the latest in EV technology and performs meticulous ADAS calibrations. Whether you need a cracked windshield replaced or a mechanical issue diagnosed alongside your collision repairs, this shop’s comprehensive service model means you can get everything sorted in one visit. You are thrilled with the convenience and efficiency, appreciating the peace of mind that comes from knowing your vehicle is getting top-tier care on all fronts.
Fix Network is at the forefront of this transformation, driving the evolution of automotive repair shops. The leading family of brands for collision, glass and mechanical repairs actively supports its franchise partners, empowering them to expand their service offerings to meet the needs of today’s vehicles and the demand of tomorrow.
With 86 percent of vehicles today requiring calibration and the expectation that this will soon reach 100 percent, the importance of being able to perform this process cannot be overstated. In a recent webinar hosted by Collision Repair magazine, titled “Shop of the Future,” Fix Network Canada President, Sylvain Seguin, alongside Vice President of Prime CarCare, Zakari Krieger, emphasized why the ‘Shop of the Future’ is already a reality for many, urging auto repair business owners to plan accordingly to remain relevant.
“New technology will reduce the frequency of accidents, so maximizing revenue on every vehicle becomes essential,” said Seguin.
Consequently, in-house calibration becomes a critical component for collision repair shops to reduce cycle times and improve customer service. Recognizing that not all shops have the physical space to accommodate calibration equipment, Seguin emphasized the importance of strategic planning, regardless of a shop’s constraints. Even if they cannot house the necessary equipment onsite, it’s crucial to have a solution in place for handling calibration services rather than relying on subcontractors.
One viable option is to manage these services at a separate location under their control. This approach ensures that shops maintain oversight over the quality and timeliness of the services provided.
Both Krieger and Seguin both emphasized the importance of understanding customer needs, highlighting that shops must maintain their ability to perform their original services while integrating new ones. Specifically, Krieger noted that it’s vital to not divert body technicians from their core roles to handle calibration and glass services, as this can negatively impact cycle times.
While mechanical shops already using scan technology may find introducing ADAS calibrations to be a natural addition to their offerings, it is different when incorporating these services into a collision repair shop. Having a separate windshield and calibration expert is crucial to maintaining efficiency and quality. By keeping specialized tasks in the hands of dedicated professionals, collision repair shops can ensure smoother operations and faster cycle times, ultimately delivering a superior service experience to customers.
Groupe Véronneau has redefined collision repair by incorporating windshield and mechanical services into their business portfolio, successfully establishing two Fix Network Supercentres in Coaticook and Sherbrooke East, Quebec. These innovative centres, featuring Fix Auto, NOVUS Glass and Speedy Auto Service, epitomize the ‘Shop of the Future’.
What motivated Groupe Véronneau to expand their services? According to President, Valérie Véronneau, the aim was to offer comprehensive solutions to their customers, fostering client loyalty. This holistic approach ensures that customers think of them immediately when faced with any automotive issues. Additionally, diversifying tasks enhanced her team’s motivation. After launching all three repair solutions together in 2019, the real purpose for their multi-service enterprises became clear: enhanced expertise and efficiency between these offerings, particularly with ADAS systems and alignments.
“The primary benefit has been the increased collaboration and knowledge sharing between our
various services. When technicians encounter mechanical issues, our on-site mechanics can quickly assist, avoiding delays and the need to involve subcontractors.
“Moreover, our NOVUS technicians, who are qualified in ADAS calibrations, share their expertise with the body shop team. This cross-pollination of knowledge facilitates new procedures that make reassembly more efficient when calibration is needed. This approach promotes a unified mission, ensuring our team provides all-encompassing support to our customers,” said Véronneau.
Groupe Véronneau recognizes the necessity of continuous learning for the safety of both technicians and drivers. As ADAS technologies evolve, they alter the nature of accidents. For instance, there has been a notable shift in damage repairs, with increasing instances of side damage rather than traditional front and rear collisions. This observation underscores the industry’s fluid nature and the imperative to master new technologies.
Groupe Véronneau has redefined collision repair by incorporating windshield and mechanical services into their business portfolio, successfully establishing two Fix Network Supercentres in Coaticook and Sherbrooke East, Quebec. These innovative centres, featuring Fix Auto, NOVUS Glass and Speedy Auto Service, epitomize the ‘Shop of the Future’.
The addition of glass and mechanical services to their business did not come without its challenges, particularly in achieving cohesion among the diverse offerings. Initially, personnel such as customer service representatives only needed to understand the bodywork repair process. The inclusion of mechanics and windshields presented new complexities with both insurers and consumers. For example, informing customers about brake wear during collision repairs often led to misunderstandings. The team had to learn to communicate more effectively, emphasizing that their goal extends beyond simply repairing accident damage to ensure the overall safety and maintenance of each vehicle. This strategic communication shift paid off, helping them meet modern customer expectations while fostering trust and loyalty.
What advice would they give to other body shop owners looking to diversify their services? Groupe Véronneau recommends surrounding yourself with experts in each service area. Success lies not in completing every imaginable training course, but in building a skilled team and encouraging collaboration. Achieving synergy between people and services is crucial to ensuring both flourish. Trust is the key to success, regardless of the business type. Innovation is ingrained in Groupe Véronneau’s DNA, and their Fix Network supercentres serve as a testament to their commitment to continous progress. They continually explore new technologies to enhance damage estimates and diagnostics and have plans to add car washes in the pipeline. Their most ambitious idea involves creating a workshop/school, dedicated to promoting the importance of continuous training and adaptability in the field. With plenty of concepts and projects in the works, their passion for evolution remains their driving force.
Groupe Vérronneau President, Valérie Vérronneau, with her husband Francis Boulange, general director of the group’s Supercentres.
Ultimately, diversification is about customer satisfaction, with Fix Network leadership underscoring the importance of providing a seamless process that stays ahead of consumer expectations. Moreover, the new generation of technicians seeks workplaces that offer the best training and equipment; a benefit Fix Network offers their franchises through their stateof-the-art training centres in Ontario, Quebec and Alberta. By embracing diversification, Groupe Véronneau and other visionary shops within Fix Network not only meet modern standards but also set new benchmarks in the collision repair industry. Their comprehensive approach ensures efficiency, customer satisfaction, and preparedness for the technology advanced vehicles of tomorrow.
Groupe Véronneau recommends surrounding yourself with experts in each service area. Success lies not in completing every imaginable training course, but in building a skilled team and encouraging collaboration. Achieving synergy between people and services is crucial to ensuring both flourish. Trust is the key to success, regardless of the business type.
To find out more about the ways in which we support our franchise owners or for information on joining our collision care network in Canada, please visit Fixnetwork.com
Assured Automotive hosted its 16th Annual Charity Golf Tournament on September 4, where more than 150 golfers met up for a day on the green and a post-tourney dinner. This year’s tournament was hosted once again at the Glen Abbey Golf Club in Oakville, Ontario, and raised funds for the Michael Pinball Clemons Foundation (MPCF).
“We are always so blessed to be able to host such an incredibly successful event every year here at Glen Abbey as we continue to celebrate and earn the trust and respect of each of our industry partners,” said Des Browne, vice president of sales and business development for Boyd Group Canada. “We are so thankful for their continued support as we come together to raise monies for such a wonderful charitable organization as the MPCF.”
Each year proceeds from the Assured Golf Tournament are re-directed to the company’s charity of choice, the Pinball Clemons Foundation, of which Assured touts a long history of support. The funds are put toward the Foundation’s well-balanced portfolio of both local and international initiatives.
As always, former football runningback and Pinball Clemons was in attendance to offer his thanks to the golfers. Clemons also spoke to attendees about the importance of the Foundation and events like the Assured Automotive Golf Tournament that operate in support of it.
Assured’s network partners all enjoyed the picturesque day on the green, as well as the camaraderie that followed. Check out our photos from the annual tourney!
Consolidated Collision Services (CCS), a division of Consolidated Dealers CoOperative, held its first of three events in its fall annual conference series, where 86 CCS network members and vendor partners witnessed plans for the network’s future and discussed initiatives to stay ‘On Target’.
Tom Langton, president and CEO at Consolidated Dealers, opened the event with an introductory speech in French, which received tremendous applause from the crowd. He went on to announce that the role of CCS General Manager will be passed to Charles Aubry as Mike Beier, current general manager, takes over Consolidated Dealers in January 2025.
Joined by Sandy Liguori, president of Consolidated Collision Services, Langton and Beier passed the ceremonial gavel to Aubry.
“The gavel is a symbol of leadership that has been part of Consolidated Dealers for more than 40 years,” explained Langton.
The appointment of Jason Arnott as Business Operations Director, West of Canada, was also announced and celebrated at the event.
“We are beyond excited to be able to promote from within our organization, and I couldn’t be more confident in our team and their vision for the future of CCS,” said Beier.
Aubry took the mic to speak on the conference’s central topic and theme—On Target. He spoke to the network’s plans for advancement and invited attendees to “find their targets.”
“Do you want to focus on managing WIP? Perhaps you want to turn your focus on parts—managing back orders, or wrong parts, or exceedingly high inventories?” he asked attendees to consider.
Marc Lambert, CCS business operations director for East of Canada, showed the crowd what a comprehensive action plan looks like. He stressed when the right time for a shop to create one may be; what it may include and why action plans are critical to achieving results. He said the goal of an action plan is to “standardize operations” across the business, ultimately achieving cohesive production and a smoother—and more profitable—overall operation.
Patrick Demers from Progi was next to the podium. He demonstrated new features of Progi’s product portfolio and showed how these new tools and features can be leveraged to achieve the very business goals outlined by the CCS executive team.
Jonathan Pilon, the new president of the
Corporation des carrossiers professionnels du Quebec (CCPQ), also delivered a compelling presentation on his vision for the organization, explaining the “360 shift” he plans for the organization. He stressed that the CCPQ mission will fall into three major areas: recognition of the industry, sustainability and technological innovation.
The event ended with closing remarks before attendees made their way to a networking reception.
“We’d like to thank all of our attendees for the positive feedback,” said Aubry. “The wonderful world of collision repair continues to get better and better. We at CCS are proud to help drive collective change for the industry while promoting profitability, growth and improvement among our network.”
CCS hosted its second annual conference event in Calgary, Alberta, in late September. The third event will be held in conjunction with the Automotive Conference and Expo in Niagara Falls, Ontario, on October 16 and 17.
You won’t find any chipping from BASF-affiliated bodyshops, but there was surely some chipping when BASF Canada hosted its annual golf tournament at the Lionhead Golf Club and Conference Centre in Mississauga, Ontario. The tournament has run for 30 years and, according to Mark Huisman, business manager, automotive refinish for BASF Canada, the tournament began as an event for BASF Canada’s automotive refinish team and partners.
“It’s now morphed into a bigger event,” he told Collision Repair. “The beauty if that the automotive refinish side is about half of the tournament. We had a record turnout—almost 300 golfers. This day is really a thank-you to our customers, for their loyalty—for their friendship. It’s really all about them.”
This year, the BASF Canada team collected non-perishable food items to be donated to a local food bank. Check out our photos from the day below.
From September 10 through 14, thousands of automotive aftermarket professionals were in Frankfurt, Germany, for the iconic Automechanika Frankfurt trade show. This year’s event highlighted significant trends in electric mobility, sustainability, and digitalization. Exhibitors presented a vast array of products, including advancements in electric vehicles; ADAS and other ultra-modern vehicle tech; smart repair technologies and more. Sustainability was
a key theme throughout the event, with many exhibitors showcasing eco-friendly practices and products. This focus reflected the automotive industry’s ongoing efforts to reduce its environmental impact and adapt to changing consumer demands.
Sustainable innovations underscored the industry’s commitment to a more sustainable and efficient future. Notably, several companies unveiled products designed to not only work with high voltage vehicle technologies, but
through the methods they are made and used. The atmosphere at Automechanika was electric. The event served as a vital hub for sharing ideas and driving innovation within the automotive community. Collision Repair magazine was on-site to capture all the exciting new product launches and demonstrations of industry-leading technology—plus catch up with all of our friends on the other side of the ocean.
SATA launched a series of products at Automechanika, including the jet X premium spray gun. The spray gun boasts a new look: what stands out is the simple, elegant exterior in matte black with red accents. According to SATA, the most important innovations are of a technical nature. An innovative nozzle technology is intended to set new standards in atomization. The labyrinth system invented by SATA guides the air in the nozzle so that it exits free of turbulence and pulsation. This ensures that the material is atomized extremely finely and homogeneously. The spray pattern is said to be particularly easy to control with optimized material distribution and clearly defined fade-out zones.
The jet X also has several other clever features, such as a trigger that can be removed in no time at all and without tools, with an integrated wrench for the fluid tip. The jet X is ergonomic and lighter weight than ever before. And with fewer components, the maintenance is said to be quick and easy.
SATA also launched LCS—the Liner Cup System at the event, which fits all SATA spray guns with a QCC cup connection–and without an adapter. This improves the weight and centre of gravity of the gun and makes cleaning easier, said the company.
Telwin launched its lineup of Smart Repair products at Automechanika designed to improve collision centre productivity, efficiency and speed while cutting costs and consumption.
The Telwin Smart Repair Battery Puller for the repair steel sheets features an interchangeable lithium-ion battery and smart battery status reporting. It has a cordless design and is able to quickly spot weld pins and washers for optimized productivity, says Telwin. This tool also offers digital control with synergic variation in welding parameters based on the type of work,and a 20mm sheet metal cleaning area.
The T-RACTION 250 smart straightening system for steel and aluminum uses compressed air to develop a vacuum effect that ensures optimal adhesion to the bodyshop floor, without any need for additional support or fixing points. The system has a manual hoist that develops a traction force of 250 kg, and it’s ideal for straightening thin sheets through slotted washers or glue systems.
Telwin’s new Smart Repair trolley complete workstation was also unveiled at Automechanika. This complete workstation offers six drawers and four swivel wheels, plus a complete set of more than 150 tools for repairs with both glue and spotter. Learn more about the tools at telwin.com, or reach out to the exclusive Canadian distributor of Telwin equipment, Crescent Industries, at rescentindustries.ca.
PPG won an Innovation Award at Automechanika Frankfurt for its Linq digital ecosystem. Judges selected the product for its ability to “enhance bodyshop efficiency and sustainability by digitizing and automating repair tasks.”
The PPQ LINQ digital ecosystem includes the PPG LINQ COLOR software; the PPG MAGICBOX bodyshop assistant; the PPG VISUALIZID software; the PPG DIGIMATCH Spectrophotometer and the award-winning PPG MOONWALK automated paint mixing system.
PPG says the entire LINQ portfolio features automated routine tasks and prioritizes optimized resource use. The company also insists it provides scalable solutions that can be customized to suit business size in addition to precise application and monitoring systems that reduce risk of errors and rework. Finally, the LINQ system is said to reduce material waste, energy consumption and process times, helping businesses reach their sustainability goals.
Jason Moseley, CEO of the International Bodyshop Industry Symposium (IBIS) and presenting juror at the Automechanika Innovation Awards ceremony explained why he and other judges selected the product as an award winner.
“The PPG LINQ digital ecosystem is really a complete digital solution in a market where optimizing the use of materials and efficiency are so important. That’s why we have chosen this new system as the winner.”
Eliminate failed calibrations due to uneven surfaces.
Ensure your workflow follows OEM-sourced procedures.
Reduce setup time by 6X versus mechanical measurements.
The IA700 is an advanced and versatile wheel alignment pre-check and ADAS calibration system engineered for both in-shop and mobile applications – move from bay to bay and shop to shop.
DISASSEMBLES IN LESS THAN 90 SECONDS FOR EASY TRANSPORT
BASF Coatings unveiled a first-of-its-kind technology at the recent Automechanika Frankfurt trade show with its launch of next-generation clearcoats manufactured from recycled tires.
The new product lines, which are projected to be available in Canada in early 2025, employ the company’s ChemCycling technology. They are marketed under BASF’s premium brands, Glasurit and R-M. By leveraging BASF’s ChemCycling technology, recycled feedstock derived from waste tires is used to create certified Ccycled® products, diverting them from landfills or incineration.
The recycled feedstock is attributed to the certified Ccycled clear coats through a mass balance approach: BASF Coatings’ Glasurit AraClass A-C-24 Eco Balance and R-M Race Finish-R eSense clearcoats are the first automotive refinish products that use this technology, according to Jane Niemi, head of global marketing for BASF Automotive Refinish who was on-site.
BASF claims these new clearcoats’ drying speeds allow for fast processing—the company says the coating dries in 20 minutes at 40 degrees Celsius.
“By reducing drying time, energy consumption is significantly lowered, resulting in improved efficiency and reduced environmental impact. This feature is particularly advantageous for electric vehicles as it minimizes their exposure to excessive heat,” according to the product announcement.
“At BASF Coatings, we’re always pushing what’s possible, empowering bodyshops to lead the change with sustainable technologies that are unique to the market,” said Chris Titmarsh, senior vice president of global automotive refinish coatings for BASF. “With our exclusive ChemCycling, our vision is to support a circular economy by reducing the use of fossil raw materials, minimizing waste and cutting CO2 emissions in the value chain.”
Axalta announced its latest innovation at Automechanika Frankfurt—and it has a Canadian twist.
The Axalta Nimbus global customer experience platform was unveiled on the first day of Automechanika Frankfurt in September. This new technology seamlessly connects customers to Axalta’s portfolio of tools and resources to improve efficiency, enhance productivity, boost performance and maximize profitability. Logan Macpherson, Axalta’s Ajax, Ontario-based director of customer experience and digital applications for global refinish led a global team to develop the system and bring it to fruition.
Set to go live in North America in early 2025, Axalta Nimbus is designed to provide a cohesive end-to-end experience for Axalta customers across the globe. The company operates in 120 countries with more than 80,000 customers globally.
“By working together in a single platform, comprehensive business insights provide actionable data that help owners and managers make informed decisions to increase profitability and performance,” said Patricia Morschel, vice president of marketing and commercial operations for Axalta global refinish, who demonstrated the new technology on the Automechanika show floor. “Axalta Nimbus is easy to use with an intuitive user interface for increased efficiency and customizable capabilities based on business needs.”
With Axalta Nimbus, customers can access Axalta Nimbus Color, Catalog, Stock, Store, Insights, Academy, and Support. Axalta Nimbus Color leverages proprietary algorithms to find, sort, and return accurate colour formulas and powers the Axalta Irus fully automated, digital colour management process.
Managers can review real-time consumption data and inventory management with Axalta Nimbus Stock and replenish inventory directly through the Axalta Nimbus Store. Axalta Nimbus Insights help refinish customers improve business performance using customizable dashboards and key performance indicators to drive informed business decisions. To learn more about Axalta Nimbus, visit www.refinish.axalta.eu/nimbus.
*Did you know that you can upgrade your existing i5 and i5s spot welders by installing a Retrofit kit with Ergo Lift Assist?
Story by ALLISON ROGERS
There are three major components of consideration when it comes to 3M™ RepairStack™ Performance Solutions benefits, according to Ryan Fuller, digital solutions marketing manager for 3M™.
“3M™ RepairStack™ was put together based on requests we received specifically from bodyshops. It all comes back to improving how you operate your business. We want to help collision centres run a better business, not just a better bodyshop,” Fuller told Collision Repair.
3M™RepairStack™ is more than an innovative storage cabinet. The technology tracks material usage and re-orders product when needed, which keeps your skilled repair personnel away from irrelevant tasks and on the specialized jobs where they’re really needed. The billables invoicing component allows collision centres to accurately document repairs and report materials to get paid appropriately for all the components used in that job. Data from materials, invoicing and sales can be compared for advanced visibility on gross profitability, efficiency, sales per estimator, sales per technician, use of material compared to labour hours and much more.
Fuller pointed out that, in 3M’s conversations with collision centres, the number-one problem is labour.
“It’s two different angles of the same problem: either they can’t get people at all, or there’s some people, but they don’t have exactly the right skills. 3M™ helps that problem by automating operations that can be automated; whether it’s integrations with bodyshop management systems, distributor management systems, integrations with paint portals, et cetera.
“By automating these operations, the skilled labourer can focus on the skilled projects they need to,” Fuller explained.
Precise material usage reports can provide far more information than you may think. Materials are categorized when staff remove them from inventory; the exact volume and dollar amount of that material will be recorded on the repair order and in your files.
“We want to help collision centres run a better business, not just a better bodyshop.”
—
“Say technician A goes through about $3 of abrasive per job, and you see via 3M™ RepairStack™ that an apprentice is using $6 of abrasives per job. We can look into it, figure out why that apprentice may be using more than they need, address the issue and ultimately use fewer materials, and save money,” explained Fuller.
“You can also compare dollar amounts per job; dollar amounts per labour hour and other data to track against yourself and compare over time.”
3M™RepairStack™ can be integrated with two different bodyshop management programs available to the Canadian market: BodyShop Connect and Axalta ProfitNet.
Solutions are customizable to the collision centre’s liking. If you seek the 3M™ RepairStack™program with built-in billable invoicing only, there’s an option for you.
Perhaps you have an organized space for your materials already and you don’t need the full 3M™ RepairStack™ cabinet, just the scanner. Or you can opt for the full suite of solutions—cabinets, software, scanner and all—to achieve your desired results.
Randy Weber and Brooklyn Brugess from Auto Reset Group in Ontario have been using 3M™ RepairStack™ at their CSN Walkerton location for more than year now. They first received the recommendation from Brown’s Auto Supply.
“The main selling feature for us was the ease of signing out products for our technicians, as well as the integration of 3M™ RepairStack™ Billables Invoicing,” Brooklyn, business deveopment manager for Auto Reset Group, told Collision Repair
“Introducing 3M™ RepairStack™ at two out of our three total facilities has been a very
“We would definitely recommend 3M™ RepairStack™. It has greatly increased our business’ efficiencies through the ease of signing out products, inventory reporting and claim-specific invoicing. We’re currently installing 3M™ RepairStack™ in our third facility.”
— Brooklyn Brugess Business development manager, Auto Reset Group
“The integration of 3M™ RepairStack™ Billables Invoicing allows us to invoice supplies to each specific claim. This has provided us with much more accurate reporting for each job and has had a direct impact on our shop and paint supply profitability.”
—
Randy
Weber Owner, Auto Reset Group
positive change, not only for our technicians signing the products out on the floor, but also for our administration team,” added Randy, owner and president of Auto Reset Group. “The integration of 3M™ RepairStack™ Billables Invoicing allows us to invoice supplies to each specific claim. This has provided us with much more accurate reporting for each job and has had a direct impact on our shop and paint supply profitability.”
“We’re setting 3M™RepairStack™ up at our third shop as we speak,” said Brooklyn.
CSN Walkerton was initially seeking a something that would counteract any instances of human error in material tracking and ordering.
“Challenges included a technician simply forgetting to write down a product they grabbed, or writing down an incorrect quantity for the amount of one item used. Intelligible writing also caused us to be charged and re-order products that weren’t necessarily the ones we used,” said Brooklyn.
“We would definitely recommend 3M™ RepairStack™. It has greatly increased our business’ efficiencies through the ease of signing out products, inventory reporting and claim-specific invoicing.”
For more information on 3M™RepairStack™Performance Solutions, visit 3M.ca/RepairStack or contact your local 3M sales representative today.
brandsandsizes(12to20feet),thedispenserfeatures
versatilesolutionforefficientplasticsheetingmanagement.
locationGluePullRepair.Thelightweightaluminumconstructionallowseasy accessorieschangeswithmobilityandsimplesetupinminutes.Theadded
220Vpowersupply.Multi-functionsynergicpowersource,basedonthe leadingedgeIGBTinvertertechnologywithfulldigitalcontrol,offering
MIGonallmaterial,especiallyaluminumandgalvanizedsteel.
technicianshavethetrainingandskillsneededforwelding.Theprogram satisfiesweldingcertificationrequirementsformostOEMCertification programs.Clientsgetthirdpartyoversightandonsitetrainingbycertified weldingspecialistsandenhancedcredibilityprovidedbyCWBAutomotive
CSAapprovedInverterPulseMIGwelders,Accuweld
andTheTECNAAutomaticSmartInverterResistanceSpotWelderModels3664P metals3680fromArslanAutomotivecanrecognizetypesandthicknessesof andsetallparametersautomatically.Thetoolfeatures
operation.Anewtouchscreenwithintuitivegraphicdesignletsyouchoose betweenAutomaticSmart+,QuickandFullmodes,whileanergonomic,
facility.Thisdeviceisalsowifienabledforfactoryupdatesanddiagnostics.
The asTech® All-In-One® is the most comprehensive and powerful repair device with the best
Display your product in both digital and printed formats through Collision Repair’s Buyers’ Guide and Business Directory!
Collision Repair’s Buyer’s Guide is an invaluable resource for the automotive repair sector, encompassing over 100 products and services tailored to this industry. Whether in print or online, this accessible tool equips the collision repair industry with vital information. With specialized categories including paint, alignment, tools, welding, glass repair, scanning, diagnostics, and more, the Buyers’ Guide places essential product details in the hands of your target audience. When it comes to connecting your product solution with the end user, Collision Repair’s Buyer’s Guide stands as the ultimate medium.
For additional details and to submit your products, visit buyersguide.collisionrepairmag.com.
www.axalta.com
Easy to mix. Easy to match. Easy to apply. Cromax® EZ is a waterborne basecoat system that makes life simpler-without compromising the integrity of your craft. It’s easy to mix. Easy to match. Easy to apply. With less material consumption and essentially no flash time between basecoat and clearcoat, Cromax® EZ is designed to deliver better coverage and speed than competitive waterborne systems. It’s not just better for your customers, it’s better for your bottom line.
Visit Axalta website: https://www.axalta.com/ca/en_CA.html
www.akzonobel.com
Sikkens Autowave® MM sets a new standard in waterborne basecoat performance with major advances in binder and pigment technology. It provides excellent coverage, metallic control and sprayability when duplicating OEM solid, metallic and pearl effect colors—with remarkable ease of use, first-time-right color reliability and reduced process time, Sikkens Autowave® MM is the right step in setting a solid foundation.
For more information on Sikkens products visit https://sikkensvr.com/us-en
www.autel.us
The Autel MaxiSYS IA700 is a versatile ADAS system for in-shop and mobile calibrations, featuring a modular calibration frame with wheel alignment pre-check and optical positioning. Compatible with MA600 and IA900 targets, patterns, and calibration components, it’s ideal for users seeking a mobile solution with optical positioning accuracy. Requires a MaxiSYS MS909, MS919, or MS Ultra tablet with an ADAS calibration software upgrade card. The frame includes robotic crossbar, six HD cameras, and disassembles for easy transport. Includes tire clamps, steering wheel lock, brake chocks, and more. Visit autel.us to learn more today!
CHC Paint and Body Shop Supplies are the proud new providers of PPG’s Moonwalk automated paint mixing technology.
CHC Paint and Body Shop Supplies is offering demonstrations of the Moonwalk paint mixing technology at its Markham, Ontario, location.
“We want people to see it in action,” said said Manny Pacheco, vice president of CHC Paint and Body Shop Supplies.
PPG’s Moonwalk automates the paint mixing process, allowing painters to leave the mixing to Moonwalk and complete other tasks in the meantime. The ultra-accurate technology is also designed to eliminate waste and mess. The easy-to-use, efficient mixing technology can save labour costs; streamline bodyshop processes and create greater workroom capacity.
Painters can select custom colours via Moonwalk or match with a sample from the included spectrophotometer. The system software analyzes the desired colour and provides the optimal formula to achieve it. The network of computerized paint dispensers precisely measure the required amounts of base, tints and other additives down to the very last drop, optimizing material usage. The mixed paint is analyzed by Moonwalk to ensure it meets the desired colour. Once verified, the painter is ready to remove their cup and start spraying.
CHC’s first install was in December 2023 at Tony Graham Automotive Group’s collision centre, in Ottawa, a large Toyota dealershipaffiliated facility.
“The installation of the PPG Moonwalk system has been the best decision we’ve made in years,” said Andy Ferguson, manager of the
Tony Graham Automotive Group Collision Centre. “It streamlines the paint mixing process and provides inventory control right down to the last drop. I highly recommend this fantastic technology.”
The system also offers error-proof technology; each toner bottle’s barcode is verified before dispensing. The ultra-precise moving scale is said to be 10 times more precise than a standard scale, allowing for an exact match every time.
“Moonwalk is the future of refinishing. As an independent company, CHC must continue investing in modern technologies to pass the benefits on to our customers and help them succeed,” Pacheco continued.
“The industry is on the cusp of technological change,” said Gabriel Chiappetta, operations manager at CHC Paint and Body Shop Supplies. “If we continue to provide our customers tools and materials to be on the forefront of that change, we need to align ourselves with future technologies like Moonwalk.”
With Moonwalk, the mixing process takes between three to five minutes. Many will argue that a technician could mix the paint faster—and they may be right. The purpose of Moonwalk is not to speed up the mixing process, but to free up the hands of the painter to save them time.
The PPG Moonwalk system comes complete with one Sartorius scale with 0.01 grams tolerance; one Kontron HDMI touch-screen; a Dell computer and a Brother label printer. Digi-match technology is also included, and users can add PPG 3D VisulizID, which eliminates the need to make sprayout test cards for colour confirmation, enabling effortless colour matching.
PPG also emphasizes that the use of Moonwalk keeps the production floor clean and that the self-contained solution has created to adapt to all sizes of mixing rooms.
CHC Paint and Body Shop Supplies is happy to invite anyone interested in witnessing the PPG Moonwalk technology to its facilities in Markham, Ontario, at 166 Bullock Drive, for a demonstration. Ottawa-area bodyshops may also inquire for an opportunity to witness PPG Moonwalk in action.
Story by SARAH PERKINS
Vehicles are packed with advanced technology—and as such, repair expenses climb higher and higher. These expenses apply pressure to various verticals of the industry. From the intricacies of new electronics to the rising price of specialized parts, collision repairers are facing an increasingly challenging landscape with costs passed down through the value chain.
Collision Repair reached out to members of the industry to learn how understanding these dynamics is essential for staying ahead and maintaining profitability in a rapidly evolving industry.
When speaking with Robbie Shreenan, owner and operator of Topcoat Automotive Collision repair in Halifax, Nova Scotia, he highlighted how increases in labour costs have contributed to the broader spectrum of rising costs in the industry.
“We are all short-staffed and keeping techs costs more. Despite this, insurance companies are still paying the same labour rates and margins are getting very tight,” he said.
Shreenan said price of material and shop supplies is another point of pressure.
“Small but essential things like rags, tip of the seam sealer and razor blades are rising every time I look, and these are not things we can easily bill to our customers. These costs hit our bottom line.”
“A third factor in rising costs is the need for a more diverse variety of tools and equipment. Scan tools, welders, rivet guns—every year, we need to add more and more to our toolbox. Repairing vehicles is becoming more and more technologically advanced.”
Technology-associated expenses are costly on multiple levels, he added.
“Technology affects us the most when it comes to time. We don’t always have the right scan tool or calibration tool. So, getting a dealer to scan the car is very time consuming. They are all booked for weeks. The cost of these scans are very expensive, and these costs translate to the customer.”
To navigate this changing environment and retain profitability, shop efficiency is paramount.
“At Topcoat Automotive Collision repair, we focus on techs, shop flow and making sure we are as efficient as possible. We need to be able to make each move and each minute count in the day. We can’t control the cost of things, but we can control how hard and smart we work.”
Jeff Labanovich, vice president of operations for Fix Network Canada, emphasized that near everything the automotive industry does has the potential to impact collision repairers later down the line.
“The global economy touches everything. From parts delays to issues in shipping, every aspect of the automotive industry creates a ripple effect for collision repairers,” said Labanovich.
“This is then further impacted by the increase in the complexity of individual parts. Take the headlamp for example. Before, a vehicle’s headlamps were just for lighting the road, but now, they serve multiple functions and feature complex technology like sensors and advanced driver assistance systems.”
“We need to be able to make each move and each minute count in the day. We can’t control the cost of things, but we can control how hard and smart we work.”
— Robbie Shreenan, owner and operator of Topcoat Automotive Collision repair
“The modern car has more parts than ever, but the collision repair industry continues to strive to be as efficient as possible.”
— Jeff Labanovich, Vice President of Operations, Fix Network Canada
“As a repairer, we are always focusing on how to reduce the cost of a repair and how to reduce cycle times. We believe that leveraging opportunities for repair versus replace as well as the inclusion of green parts in the estimatics process, not only helps reduce costs and cycle times, but also helps reduce carbon intensity—which is a massive win for all stakeholders and the planet.”
— Paul Prochilo, CEO of Simplicity Car Care
“It’s challenging, there’s no doubt about it. But every industry has its challenges. Our focus is not reducing the cost of repairs; its fixing the car right at the right cost, not a reduced or inflated cost. With the right tools, the right equipment, a focus on sustainability and delivering world class KPIs for our partners.”
— Michael Macaluso, Group President and EVP of the Paint, Collision and Glass segment, Driven Brands
In a time where cars have more complex parts than ever, the collision industry must strive for efficiency. Labanovich has some suggestions.
“I have seen shops make deals with suppliers and investing in equipment and training. New technology also offers opportunities for increased efficiency. Techniques like glue pull repair and other less invasive repairs help to increase repair time and reduce costs.”
A former shopowner himself, Labanovich believes the rise in repair costs and collision repair expenses has prompted an air of collaboration.
“I’ve seen certain insurers pay enhanced door rates for certifications. [Insurers] understand there’s a rise in cost and that it’s outside of the shop’s control. As such, insurers have also become more interested in having a branded facility and providing support to facilitate this kind of partnership.
“The collision repair industry has always been founded on community and collaboration, and the rising cost of repairs is one facet that is continuing to drive this. As the industry continues to change, so, too, will repairers continue to adjust to these changes.”
Prochilo, CEO of Simplicity Car Care reiterated that “costs in repairs are consistently rising based on a series of both micro and macro economic factors.”
As noted by Shreenan and Labanovich, this includes factors such as advanced vehicle technology in the form of vehicle sensors, cameras and advanced safety systems; labour costs; increased material costs, such as those for paint, adhesives and parts; and an increase in the complexity of repairs requiring more intricate and time-consuming repairs.
Prochilo further noted that the rising cost of repairs considerably impacts all stakeholders, specifically the consumer.
“As a repairer, we’ve doubled down on investments in technology and training to increase the percentage of repaired versus replaced panels. Obviously, OEM guidelines are always considered in the decisions, but we have identified that greater repair versus replace reduces costs to the customer and increases the profitability of a repairer, generating a win-win scenario for all parties involved.”
Prochilo also stressed that ADAS and other advanced safety technologies, as well as new vehicle substrates has impacted both repairability and costs.
“Plus,” he added, “the overall complexity of modern vehicles, with their interconnected systems and components, makes collision repair more intricate and time consuming which in turn, can lead to longer repair times and so higher costs.”
He said, at Simplicity, reducing repair costs and cycle times are a paramount goal.
“We believe that leveraging opportunities for repair versus replace as well as the inclusion of green parts in the estimatics process, not only helps reduce costs and cycle times, but also helps reduce carbon intensity—which is a massive win for all stakeholders and the planet.”
Michael Macaluso, group president and executive VP for the paint, collision and glass segment at Driven Brands, pointed out that repair expenses and complexity goes beyond things like ADAS or electric vehicle repairs—similar trends can be seen in refinishing.
“There is a steady rise in consumer demand
for complex colours and special effects, and these trends in advanced colour development will only continue to evolve. This includes more transparent colours, colours with unique metallics, increased frequency of three stage paint procedures and requirements for specialized ground coats resulting in four stage paint procedures. These were formerly custom offerings. Now it’s available on nearly every make and model of vehicle sold.”
Given the sheer breadth of complexity in modern repairs, Macaluso believes shops deserve to get compensated for their commitments to the future.
“Vehicles are now made with more technology, and that technology is more expensive to repair or replace. The cost of replacement part prices and materials, such as paint, have also increased substantially,” he pointed out.
“All of these factors drive up administrative cost of managing the claims process. At CARSTAR, we want to fix cars right and with the best customer experience. This requires investment in people, process and technology, and we need to be properly compensated for that.”
He acknowledges that balancing the scales is not an easy feat.
“It’s challenging, there’s no doubt about it, but every industry has its challenges. Our focus is on how we maximize the opportunities in the current market. We have these conversations more and more with our industry partners and this collaboration will continue to be essential to keep the total cost of repairs at a manageable level for insurers, but also allow us to meet the OEM requirements of a safe and quality repair on a modern vehicle.”
Get the training and welding qualification you need to stay ahead of the game.
Automotive Welding Qualification is a must-have for all technicians that repair and weld vehicles in your collision repair facility. To achieve the highest quality repair, utilize best practices, and ensure vehicles are properly and safely repaired, choose the CWB Automotive Repair Welding Qualification program for your team. For over 70 years, the CWB Group has provided training and testing services to companies across Canada seeking Certification and Welder Qualification.
CWB Automotive Welding Qualification Benefits
• Automotive Welding Training and Qualification at your own facility with your own equipment
• Ensure all your technicians have the training and skills needed for welding
• Increased skill levels = quality assurance for Collision Repair Facilities
• Satisfies welding certification requirements for most OEM Certification programs
• Third party oversight and onsite training by certified welding specialists
• Enhanced credibility provided by CWB Automotive welding certifications
• Savings when you register multiple technicians to participate
• Technicians receive CWB Automotive Welding accreditation after completing training and testing
Story by MICHAEL VAVAROUTSOS
Leadership is critical in our industry. Being properly trained and prepared for a role is one of the biggest contributing factors to ensure a shop’s success. Finding the right people to mentor and train staff is essential to any facility looking to ensure long-term profitability and viability.
Collision Repair magazine spoke with three mentors in the collision repair industry to see what it takes to become an effective mentor.
Jean-Marc Julien, collision repair instructor for the CWB Group’s Canadian Collision Repair Academy, believes that the key qualities or characteristics of an effective mentor in the collision repair industry can be summed up using just one word: Passion.
“If you’ve got somebody with passion for the industry and that wants to make a difference, that’s the key to being a good mentor.”
Julien made it very clear that being able to actively foster a positive learning environment for new hires or apprentices can’t be run independently. He said there has to be a set plan in place in which somebody can work with a technician for a certain amount of hours a day to learn on specific aspects of their repair process.
Rather than spending 10 to 15 minutes with an apprentice, Julien says that they should schedule a time in their day where they can spend time with an experienced technician.
“Apprentices don’t really learn like that. They should be able to spend an hour or two with an experienced technician to concentrate on the steps that they’re doing,” he said.
“They need to focus and concentrate.”
Julien became a mentor because he wanted to support the industry in the same way it supported him during his beginnings. He says that it is his passion.
“As a journeyperson, you do have to kind of put yourself in that mentorship role and allow them to oversee some of the work,” said Cecile Bukmeier. “It’s important to give them opportunities, but then also listen to them and understand their goals.”
“The industry has been very good to me in my career, and I love being able to help people. He added that there are some technicians out there that really don’t like to communicate with their apprentices. This is what makes an entry level person today so valuable to add to an experienced technician.
Agreeing with Julien, Bill Davidge, CARSTAR Director of Innovation and Technology, also plainly said some people aren’t meant to be mentors.
“The problem is that the shops think that they’re going to get their most experienced tech and he’s going to be able to teach him or her how to repair a vehicle. The thing is, the best technician isn’t always the best mentor.”
To be a good mentor, Davidge explained that your communication and listening skills have to be good, as well as being patient and understanding the generational gaps that may be in place.
“To be a good technician, you have to put yourself in their position. You have to help them understand the full picture, like what they are doing, why they are doing it.”
Cecile Bukmeier, the Chair of NAIT Auto Body Program, said a good mentor must be able to challenge the apprentice to be able to hone in on their skills, while also not letting them get complacent.
“You have to listen to them and watch them to see how they learn. Not everyone learns the same way, so getting to see the person that you’re training and seeing their learning styles and matching your mentorship to that is helpful for them,” Bukmeier said.
Bukmeier also says that giving them time is an important aspect towards success.
“Giving them space and opportunities to
develop is very important. As a journeyperson, you do have to kind of put yourself in that mentorship role and allow them to oversee some of the work. It’s important to give them opportunities, but then also listen to them and understand their goals,” she said.
The most important piece of advice that Bukmeier wanted to give to people trying to become a mentor is to try to get to know the people that you’re going to mentor. Seeing how your skills can be applied to give this person the best shot at success will allow them to have the best experience.
The structured format of an actual mentorship program is a much more effective method to train apprentices today. It helps to foster a smoother and faster learning experience for the employee into the job, while also making them feel more confident in their roles and allow them to learn new skills more quickly, which can contribute to safe collision repairs.
Both Bukmeier and Davidge brought up how colleges have mentorship programs and internships connected with collision repair shops. Davidge says that the best mentorship program they have now is in the network’s CARSTAR London Center, which has a relationship with Fanshawe College in London, Ontario.
“What makes this mentorship effective in comparison to other places is the disassembly and education,” Davidge said.
A mentorship program can also operate alongside a training program from sources like I-CAR Canada. This approach can strengthen the mentor’s skills development efforts and establish a solid foundation for the employee’s future roles.
Solera is on a journey to transform the collision claims process as we know it
The automotive industry is smackdab in the middle of some massive transformations. With challenges like vehicle electrification, rising repair complexity, diverse technologies facing the industry, Bill Brower, senior vice president of global industry relations and North American claims, believes the collision repair industry will experience more change in the next five years than it’s seen in the past 20 years.
As a global provider of claims technologies, Solera aims to lead the way in how the automotive industry navigates these factors. Two ways the company is forging new methods in the automotive industry: through its pursuit of sustainable collision claims and via the incorporation of advanced AI technologies in its Qapter estimating platform.
Collision Repair mag spoke to Brower to hear firsthand the various ways Solera is shaking things up for the benefit of bodyshops, insurance providers and consumers alike.
“When you think about collision claims, the question of sustainability is: how is this car being repaired? At Solera, we have been researching sustainability and working in this space for about three and a half years to create sustainable estimatics,” said Brower.
“In summary, sustainable estimatics measures the amount of carbon that’s generated in a collision repair. Sustainable estimatics provides guidance on how to lower emissions.”
When asked why a collision centre would be interested in pursuing sustainable claims, Brower said Solera’s advice for more sustainable practices—which includes strategies like using green recycled parts wherever possible, and repair over replace— can enable lower cycle times, length of rental and keep technicians happy.
“Plus consumers, in most cases, prefer to go for the eco-friendly collision repair,” he added.
As a global company that recognizes the collision industry’s carbon emissions contributions, Solera feels that sustainability is an area where the company can pave a way for the collision repair ecosystem.
Solera’s sustainable claims technology is ISO certified. It tracks a company’s emissions in the three scopes of carbon.
“Scope one is the carbon you produce in your own bodyshop, the emissions that you control. Scope two carbon emissions arise from the energy used in your shop. Your
shop may be powered by a local electric company; that could be run by solar power, hydroelectric, et cetera.”
“Scope three is the most difficult to track,” added Brower. “This would be the carbon created in the creation of parts that you, the collision centre, ultimately use in your repair. So, it’s all of the carbon emissions created in that process, from the gathering of raw materials to developing the part and shipping the part.”
The Solera sustainable claims score card tracks carbon emissions in the different scopes and presents that information to the business, along with strategies on how to reduce emissions contributions. The company put the technology and their sustainable mission as a whole on display for the industry at the first-ever Automotive Sustainability Summit, hosted by Solera and Simplicity Car Care, in June.
“We heard loud and clear from the insurance companies represented that this is a high priority and we must do more to drive sustainability in collision repair claims,” said Brower. “Our Sustainability Council is a way for Simplicity Car Care and Solera to bring the industry together to discuss strategies for sustainability. See what we can do together to move the needle toward a more sustainable industry, particularly in Canada.”
Sebastian Torres, president and owner of CARSTAR Torcam Group has used Solera’s AI estimating features in a recent capacity management overhaul. He’s raved about the technology’s abilities. In January, Torres’ Brantford store was about four to six weeks backlogged. By June, backlogs were down to one to two weeks. He told breakout session attendees that the results have been amazing.
“I can honestly say this work with Solera has
become the most rewarding partnership of my career,” said Torres, adding that he’s already seen significant increases in yearly sales.
Torres stressed that AI is a tool, not a magic wand. The technology can shave a 90-minute non-drive estimate down to a 20-minute job, but AI is no replacement for a human being.
“If you invest in a welder, or a frame rack, or in training for a technician, why would you not invest in AI? It’s a tool that can help your team work more productively. The estimate is 85 to 90 percent complete by the time the vehicle reaches disassembly.”
Solera’s AI tech is constantly learning from photos submitted to the system globally.
“AI is transformative for our industry— particularly for bodyshops,” said Brower. “If you think about running a bodyshop today, you want to be as efficient as can be. Personally, I’d like to be able to capture the damage through photographs, create an estimate electronically and speed up the process.”
With sustainable efforts and artificial intelligence-empowered estimatics, Solera is leading the way in transforming the claims industry for the benefit of the environment and businesses operating in the automotive repair sector.
“We feel that, in this era of transformation, Solera can help lead the automotive industry by sharing the message of sustainability and leveraging the power of new technologies.”
Scan the QR code to learn more about Solera’s endeavours in sustainable claims, artificial intelligence and more.
Fits
Story by ALLISON ROGERS
Original equipment manufacturer (OEM) certifications have been a widely discussed topic in recent years. With vehicle complexity con sistently on the rise, many argue that automakers are simply doing their due diligence to ensure these high-tech systems are repaired to proper functionality, by a technician that has had the proper OEM training to do so.
At the same time, some OE repair procedures, processes and, in some cases, parts are restricted, lest you carry a certification with the OEM. This has sparked debates like the Right to Repair bill that sits before Canada’s House of Commons, among countless other debacles behind closed doors and email firewalls.
We asked collision repair industry stakeholders to submit their opinions on the value of OEM certifications. See the following pages for their comments on benefits, drawbacks, importance of certifications and more.
WHAT ARE THE BENEFITS OF OEM CERTIFICATION PROGRAMS?
It gives confidence in maintaining Crash Safety Ratings during repair.
“None found so far.”
“Increased client confidence.”
“More DRP work.”
Implies to customers that you know how to repair their vehicles back to OE specs.
It creates a higher repair standard and a more competitive level, leaving behind those who don’t want to invest in getting better.
Ensuring a proper, safe repair, with pre-accident crashability. Without OEM procedures, you won’t get there.
Consumer trust, access to information, accountability, dealer warranty work.
Having 100 percent knowledge of how to repair properly, safely and efficiently.
Access to restricted parts, OEM training, OEM tooling and higher door rates.
Educated techs and more work driven to our door.
WHAT ARE THE DOWNFALLS OF OEM CERTIFICATION PROGRAMS?
I believe programs available to the industry are what we need to reference OEM repair procedures. These procedures should be standardized throughout the industry and should be taught at the time of apprenticeship programs.
High yearly cost with no payback from insurance partners.
[OEM certifications] are too expensive and have little flexibility.”
I would say the biggest downside is getting insurance partners to align with OEM policies.
Every OEM has different criteria to be certified. Plus, with cost, it’s more expensive every year. For example: we got two EV training programs from the same OEM, where the content was much of the same.
Q: DOES YOUR BUSINESS HOLD ANY OEM CERTIFICATIONS?
Yes, we hold multiple OEM certifications 68.2% Yes, we hold 1-2 OEM certifications 4.5%
Q: IF YOU HOLD OEM CERTIFICATIONS, DO YOU PLAN TO ACQUIRE MORE?
Yes 68.4% No 31.6%
Q: IN YOUR OPINION, HOW IMPORTANT IS IT THAT COLLISION CENTRES HAVE OEM CERTIFICATIONS?
1. Collision centres should have OEM certifications from any automaker they repair 43.5%
2. Collision centres should have OEM certifications, but they can operate without 39.1%
3. Collision centres don’t need OEM certifications 17.4%
There are some certifications that don’t require specific measuring or structural equipment, where others do. The standard seems low, in some instances.
Costly. Small shops can’t acquire them all.
The Insurance companies generally don’t recognize OEM repairs always a battle to get paid for what we do.
A blanket inspection seems inappropriate, and most do not require measure and structural equipment that is up to date, in my opinion.
It may limit access to vehicles for repair.
The goal of OEM certifications would be to get paid properly for OEM approved repairs.
Not currently but we’ve had OEM certifications that expired 6.8% No, we’ve never had any OEM certifications 20.5%
THE TOP 3 BENEFITS OF OEM CERTIFICATIONS according to respondents
Improved repair quality and safety 37.5%
Access to OEM repair procedures and technical information 21.9%
Increased customer trust 14.1%
Thecombinedweightofoccupantsandcargoshouldneverexceed
P265/70R17
P265/70R17
P265/70R17
TOAVOIDSERIOUSINJURYORDEATH: •Donotleanagainstthedoor. •Donotuseseatcoversthat Seeblocksideairbagdeployment. owner’smanualformoreinformation.POURÉVITERDESBLESSURES GRAVESOUMORTELLES: •Nevousappuyezpascontrelaporte. •N’utilizezpasuncouvre-siège quipeutbloquerledéploiementdu Voircoussingonflablelatéral.lemanuelduconducteurpour deplusamplesrenseignements.
GVWR 2200KG(4894LBS)
Conformstoregulations: 2015
Conformstoregulations:
U.S.EPAclass Californiaclass/stds: PC/ULEVqualified Group: FGMXV01.80111.2L
U.S.EPA:T2B4
Evap:SFI/HO2S/TWCFGMXR0095805
GAWRF 1155KG(2546LBS)P235/55R18
2.3L-Group:GFMXV02.3VJW Evap:GFMXR0125NBV Noadjustmentsneeded. FEDOBDII
Thecombinedweightofoccupantsandcargoshouldneverexceed352kgor776lbs.
VEHICLEEMISSIONCONTROLINFORMATION
Conformstoregulations:2016 MY California: Not for sale in states with California emissions standards. TWC/HO2S/WR-HO2S/CAC/TC/DFI
U.S. EPA:T2B4 LDV
2.3L-Group:GFMXV02.3VJW
Evap:GFMXR0125NBV Noadjustments FEDOBDII Fuel: Gasoline ABZ
A recap of SAAR’s latest event
Several years ago, Jessica Hill-Flaman of Saskatchewan Government Insurance (SGI) asked me why I was doing every single job at our conferences and running myself ragged. It took a while to get that thought through my brain, but eventually I started relying on other people to help carry the load.
I have had tremendous help from my lovely wife, Barb; my daughter, Lisa; Zac Chartrand from Henderson Insurance; Shane Goller from TBS in Prince Albert; Jessica Rust from Chuck’s Collision Centre in Assiniboia and Jeff Wildman from BASF.
Next, I want to thank all our suppliers for their generous sponsorship. There is no way we could put on an event like this without their support.
I also want to extend thanks to SGI for sending almost 20 people to our event to connect and communicate with Saskatchewan Association of Automotive Repairers’ (SAAR) members both on and off-stage. I cannot begin to tell you how important these relationships are—we may not be where we want to be but thank goodness we are not where we used to be in our working relationship with SGI. Let’s not take it for granted that we have a group
of insurance people that are willing to engage and work with our industry to make the claims process less stressful.
Our speakers were fantastic. Sharon Ashley and Jim Wraight of BodyshopConnect started things off, explaining new features to their existing program. The key thing is that every bodyshop should have a computerized management system to run their business. Trust me, you are missing out on time and money by not having one.
Mike Gilliland and Jenica Bennett from AutoHouse Technologies were next to the stage, explaining how their software program can take information from your computerized shop management system and filter data into bite-sized chunks to help you manage workflow. You’ve heard it a million times already and hopefully it’s getting through to you—you need to manage your work in process (WIP). Having too many vehicles on your lot and in your shop creates confusion and frustration for everyone involved.
A special panel discussion on attracting and retaining employees was well-received and appreciated by our audience. Janet Uchacz-Hart from the Saskatoon Industry and Education
TOM BISSONNETTE is the director of the Saskatchewan Association of Automotive Repairers (SAAR). Tom’s Tales is a series of Collision Repair magazine articles chronicling his journey through the collision industry, since 1982. Besides telling his story, Tom hopes that today’s shopowners and managers can learn from his victories— and his mistakes.
Council; Lori Gasper from the Sask Distance Learning Council; Scott Kucharyshen from Saskatchewan Polytechnic; Brayden Neufeld from Parr Auto Body, representing Skills Canada; Mark Edmonds from the Regina and District Industry and Education Council; Dave Flockhart from BETAG Innovation and Merv Armstrong from Swervin’ Mervin Mini Indy all shared how their organizations seek to attract and retain employees in their respective industry businesses. The key with these panellists—with the exception of BETAG—is that they are all working on behalf of SAAR members to direct young people to consider the autobody trade. Dave Flockhart made a great observation when he stated that it doesn’t feel like there is a shortage of young people coming into the trade—rather bodyshops have done a poor job of retaining them and demonstrating a career path.
Lisa McNab gave us a short presentation on Regen Replica Systems, which converts plastic waste like bumpers, grilles, headlamps, et cetera, to pellets. Then, using a 3-D printer, it repurposes this waste into usable products— even making hard-to-get parts for bodyshops.
Ryan Bast, executive director for the Motor
Safety Association (MSA), gave an overview of the services the association provides to our sector of the automotive industry—most of them free of charge! The MSA offers free support for a bodyshop to receive a Certificate of Recognition (COR) designation at no charge, among many other offerings.
Ciaran Downes, the manager of SGI appraisal services, gave an update on the public insurer’s digital transformation. He also shared insights on the industry’s performance over the past year, noting that SGI has seen continual increases in repaired claims since 2019. This has primarily been driven by labour costs as well as the ‘ad-
With asTech, you get more than just a technology provider, you get a true partner, invested in your success and dedicated to helping your shop become calibration experts. We provide the technology, tools, and training you’ll need to bring all calibrations in-house.
ditional costs’ category, which Ciaran said is mainly paint materials.
As stated, SGI brought a huge contingent of people to this event with the intent to create positive relationships and seek ways to improve the bodyshop experience with SGI at all levels.
Yanni Koutmos of Eagle MMS shared the innovative software his company has developed to help track paint and body materials on collision repairs. Koutmos and his team have created a program that captures all the paint and body materials for each specific job, based on the type of damage and the paint code of the vehicle.
Pat Quinney of Quickfalls Auto Body had a horrendous fire that destroyed his bodyshop this past spring. He shared his experience with SAAR attendees, explaining his dealings to date with his insurance company and various government agencies. The bottom line from Quinney—make sure you have a clear understanding of what your insurance coverage provides and what it does not. We at Parr Auto
Body recently had our insurance reviewed and we’ve made some major changes based on recommendations from a broker—decisions that potentially saved the shop and me, as the landlord, from some major headaches.
Pat added that his biggest headache of the many experienced was the disposal of “hazardous materials” due to the type of fire. He found his cleanup costs were exacerbated considerably due to asbestos and other chemical contamination. At the end of the day, the team hauled just shy of 500 tonnes of rubble to the dump, equalling a cost of $300,000—which you bet came off his rebuilding budget.
3M’s Andy Boyd from St. Paul, Minnesota, made the trip to Saskatoon again this year to educate us on the latest news with RepairStack, 3M’s materials management system. He also shared information on the 3M Collision Repair Academy and gave free admission to one lucky SAAR member—Brett Gareau from Advantage Collision.
LKQ Canada’s Marty Coonan and Dayle
Thys emphasized LKQ’s salvage division and a pending partnership with SGI to increase salvage parts usage in Saskatchewan. Car-Part Pro’s Tom Julius explained how his company’s software can bring real-time information on parts directly to bodyshops.
Finally, BGE Indoor Air Quality Solutions brought James Fast to the stage to explain how BGE can supply air filtration to practically any part of your bodyshop. They are a Canadian company with an office in Saskatoon—you can request an assessment for air quality at your shop.
Our recent conference was a testament to the power of collaboration and community within the automotive repair industry. It’s clear that, by leaning on one another we are not just improving our individual operations, but taking steps to elevate our entire sector.
Thank you once again to everyone who contributed to this successful fall conference. Your dedication, hard work and commitment to showing up is truly appreciated. See you all at our spring conference!
Column by GAURAV (RAV) MENDIRATTA
Artificial Intelligence (AI) isn’t just the stuff of sci-fi movies anymore. It’s here, it’s real, and it’s changing the game for industries everywhere, including ours in the collision world. If you’re still picturing robots taking over, don’t worry—it’s more about making our lives easier and our businesses smarter. Think of ChatGPT as a super-smart parrot. It can repeat and generate sentences based on what it has learned, but it doesn’t truly understand the world like we do.
This means it’s not going to take over your job or the world. Instead, think of AI as a powerful assistant that can handle repetitive tasks, give you creative suggestions, and make your workday smoother. As you learn the fundamentals of AI and GenAI this might become more evident, so let’s dive into it with a touch of humor and wit to keep things lively.
AI has been evolving for over 35 years, moving from simple rulebased systems to today’s sophisticated foundational models. Here’s a quick rundown:
• Traditional AI (Narrow AI or Weak AI) This type of AI is designed to perform specific tasks such as chess playing or making book recommendations. It is reactive and operates under fixed rules. Think of this as the basic trick-trained dog. It’s reactive, like when you throw a ball, and your dog fetches it without thinking twice.
• Machine Learning (ML) A subset of AI where computers learn from data to identify patterns and make decisions. Imagine a dog that learns new tricks by watching you. You don’t have to teach it every trick—it observes and learns. There are three main types of ML:
o Supervised Learning learns from labeled data, like a coach giving math problems with the answers (e.g., spam email filtering)
o Unsupervised Learning finds patterns on its own, like sorting puzzle pieces into groups (e.g. TikTok’s video recommendations)
o Reinforcement Learning learns by trial and error for example getting treats for good behaviour (e.g., AI-driven games, self-driving cars)
• Deep Learning A further subset of ML that uses neural networks to analyze various factors simultaneously. Continuing with the dog theme, this is the dog that not only performs tricks but also competes in dog shows, impressing everyone with its skills. It uses neural networks to analyze multiple factors simultaneously.
• Foundational Models and Generative AI: Here’s where it gets fun. Foundational Models are a subset of Deep Learning, and GenAI is built using Foundational Large Language models, like a dog inventing its own tricks—creating new content, like writing stories, generating art or composing music. It’s creativity unleashed!
Think of AI as a powerful assistant that can handle repetitive tasks, give you creative suggestions, and make your workday smoother.
Picture this: a customer has just been in a fender bender and is feeling stressed. An AI-driven virtual assistant steps in, offering real-time advice and ensuring all the necessary information is recorded accurately. No more fumbling for the right words—AI has got it covered.
Insurance companies and car rental services can tap into AI tools like Tractable, tCheck, and Altamira.ai. These tools analyze damage photos to provide accurate repair estimates faster than you can say “estimate,” while also sniffing out potential fraud. This means fewer headaches for estimators and more time for the tricky stuff.
AI is set to revolutionize every step of the customer journey in the collision industry. From accident reports to repair estimates and final settlements, AI tools will make processes faster, more accurate, and customer friendly. This transformation will also benefit related businesses, such as insurance companies and car rental services, creating a more efficient ecosystem.
By embracing AI, you not only enhance your operational efficiency but also position your business at the forefront of technological innovation. The future of the collision industry is bright with AI, and those who adapt early will reap the most significant benefits. So, dive in, experiment, and transform your business with AI today!
• Estimating Damage: AI tools can quickly analyze damage photos, generating AI repair estimates that are spot-on.
• Customer Service: AI virtual assistants handle inquiries, providing accurate and timely information.
Here’s how to get started:
• Explore AI Tools: Try out tools like ChatGPT, Fathom video, Perplexity, Gamma AI and see how they can improve your workflow.
• Attend Workshops and Seminars: Join AI workshops to gain deeper insights and practical knowledge.
• Collaborate and Share: Engage with peers and industry leaders to share experiences and learn from each other’s successes and challenges.
is a seasoned entrepreneur and CEO of SocioSquares, an AI software development and online marketing firm. With more than 15 years in digital marketing, internet technologies, Mendiratta has been the forefront of integrating AI into practical business solutions. He is recognized with “Top AI Voice” influencer badge on LinkedIn and has spoken at prestigious institutions the Warton School and Drexel University.
Column by STEFANO LIESSI
When you want to consider your return on investment (ROI)—and what better way to invest than buying the latest and greatest ‘Unicorn Fix-All 2000’?! It’s the answer to all of your problems.
Of course, you want to make sure you do your research on the item; use a reputable source to consult your purchase and, if you are purchasing at SEMA, make sure it is compatible with CSA requirements. If you do this, make sure it is also serviceable and maintainable through your supplier. All too often purchases are made, then never looked at or maintained again. Year after year I see the same story unfolding. As I go in and out of shops, it never ends.
Me: “What do you think of [INSERT PIECE OF EQUIPMENT HERE]?”
Tech: “Don’t know, haven’t used it.”
Me: “How come?”
Tech: “I dunno. Broken.”
I have already figured this out due to the load of dust on it and the fact it’s behind other items that also haven’t seen any love in ages. Let me clarify something: this scenario is far more common than not. Countless times over the years, I have been presented with a poorly maintained welder. Yes—of course the welder is needed for the course. Can you imagine my surprise? Actually, you can’t. I have become somewhat numb to these scenarios.
Here is where the training sessions begin to pay off. I am constantly hearing the same things: “I’ve been doing this for years. Why am I wasting my time?” “My guy is the best; he will pass this no problem.” “We need this for the OE Certification.” “Do you think we can get this wrapped up by noon?”
Now, on occasion, I get a tech with this mindset. However, while owners and managers often present this thought process, techs generally want to gain some new knowledge to better themselves;
Invest in the right things and get a quicker return on your investment. The right things are your techs and the maintenance of your equipment.
it’s tough to make a living. So, imagine a busy week and a course that needs to be completed. Here we are: a group of techs, a scheduled course and a broken welder. Now what?
As an instructor, I ask how many staff are familiar with the welding application we are testing that particular day. The general reply is, “I did it a few times, used to use it at my other shop.” My answer—“Great, then you will know how we can get around this situation.”
I have already concluded from the condition of the equipment that the experience is little to none; the welder is inoperable, with no backup welder. This is the hidden agenda with training ROI knowledge now; there is more to certification sessions than a plaque on the wall. A good, qualified technician will know when there is something wrong and know how to fix it or find an alternative to get through temporarily—not for two years.
Whenever I host a session, part of the day includes multiple discussions regarding processes, OE procedures, equipment usage, and maintenance. Understanding this is part of certification, the OE assumes and expects it. In this specific example, not all was lost; I was able to set them up and explain how to get around this temporarily, and hopefully, knowledge well retained.
It takes a genuine interest in a subject to retain the pertinent information to achieve constant success; this takes time and effort. It is a lot more than a 15-minute YouTube video. To be completely fair, if you have techs that don’t understand and don’t know the processes and how to use the equipment, and your equipment is inoperable or barely operable, then you are not fixing vehicles correctly or to OE standards… ergo you are not OE certified.
As an instructor or trainer, we can’t be responsible for what you do with the knowledge after the fact. All we can do is try to get you to see the relevance of the information and its relation to your day-to-day business. Consider the vehicle owner; that person has no idea, but we, as an industry, do. The customer relies on the state-of-the-art equipment your ads are touting. They trust you, and that’s why they are there.
What on earth does this have to do with ROI? Quite simply, I am telling you to invest in the right things and get a quicker return on your investment. The right things are your techs and the maintenance of your equipment. You maintain your car to rely on it; so do the same for your equipment; if the tech comes up front and tells you how much you need for a piece of equip-
STEFANO LIESSI
ment that will ultimately—if used correctly— will improve process, do not reply with, “Do we really need it?” Instead, ask for explanation and attempt to reach a mutual understanding.
In my opinion, and you are entitled to my opinion, the smaller investment into your techs and maintenance will prolong the life of the Unicorn Fix-All 2000 and pay back in dividends. You rely on your techs to keep the machine running; your techs rely on the equipment to keep things running; there is absolutely no use in acquiring a new Unicorn Fix-All 2000 if you don’t keep on top of maintaining your equipment and maintaining your techs. Take that investment and clean up your backyard; I bet you would make a way better ROI.
In this scenario, I imparted valuable information to these fine lads, giving them the information to keep the equipment up to par and having them realize that understanding the importance of maintaining the shop’s equipment is part of the value of good training. This will require some investment on the shop’s part, but it is well worth it. When you purchase another ‘Unicorn Fix-All 2000,’ it supplements your maintained equipment instead of replacing it.
is the Training and Curriculum coordinator for Color Compass Corporation. He is also a Red Seal technician and refinisher. Stefano enhances his 40 years of experience with 15 years of I-CAR instruction and a post-secondary degree. He also trains Skills Alberta students and has brought home 11 medals for the province, and taught high school students in the auto shop for six years.
He can be reached at sliessi@colorcompass.com.
Column by JAY PERRY
Hubris. The Webster Dictionary defines hubris as, “exaggerated pride or selfconfidence”. Now, there is a place for pride. It’s the exaggeration of pride that becomes the downfall of many. We should be proud of what we achieve throughout our careers. Many have run and/or built multimillion-dollar firms—not everyone can do that! It’s when people that have accomplished a great deal start believing that they have the secret to success or that they did it alone, this is when they have gone beyond the edge of hubris.
We have all met them, those that have that exaggerated sense of pride. They are not fun to be around. This can simply be part of how we are wired as humans. We all know there is a balance that we must maintain—proud but not too proud—if we are to capture the favour of the audience. It is why at times we see yesterday’s darling has turned into today’s pariah. We all abhor someone
There is a balance that we must maintain—proud but not too proud—if we are to capture the favour of the audience.
that is full of themselves. Maybe that’s part of why we like to root for the underdog so much!
One of the things in Ally Business Coaching’s coursework advises us to reflect on accomplishments and place them in a figurative trophy case— we have an exercise on this. This trophy-case should be visited every once-in-a-while. The success of the past is what gives us the courage to face the challenges of today. They are important to recognize and even celebrate!
It is when people adopt the attitude that there is no more to improve upon, that we have done it all and that we know best, that they are starting down a very slippery slope. People like this have abandoned the concept of continuous improvement. There is always something that can be improved upon. There is no arrival status when we truly embrace the concept. People seem to forget the continuous part of continuous improvement!
I’ve written about blind spots in the past. These are what allow us to think we have made it. We need others to help see through these spots and remember that the thinking that got you to where you are is not the thinking that will get you to where you want to be! We need a different perspective. Fortunately, there are many sources for that perspective, employees being the top of the list. Consultants, either independent or vested vendors like suppliers or professionals like accountants, lawyers, etc., can also be very useful.
Usually, we are emotionally involved with our businesses. After all, we built them from humble beginnings and nurtured them along the way to where they are today. Emotion is the driving force in the early days. To keep a creative spark going, get a different perspective. You don’t have to act on every piece of advice you get, but I’m betting you will find something that will help you stay the one who’s driving!
JAY PERRY
is the founder of Ally Business Coaching, a process improvement and leadership development firm, and co-author of the book Success Manifesto with Brian Tracy. Jay is also an education partner with California Coast University in Santa Ana, California. He can be reached at jayperryally@gmail.com
The Automotive Retailers’ Association (ARA) has announced significant updates to the Impound Lot Operators (ILO) program, as recently announced by Road Safety BC.
The new rates, as well as a revamped rate-setting methodology and other administrative changes, mark a major milestone for ILOs.
These updates specifically include the discontinuation of the order for release of vehicles impounded for 30 days and 60 days, and the discontinuation of the statutory declaration associated with disposals and refuse to issue applications.
The new updates represent part of a ten-year project that first began in 2014 when the ARA lobbied for new administrative fees to be applied to all impound vehicles, both claimed and unclaimed. More recently, in 2020, the provincial government ordered a comprehensive review of the ILO program—a direct result of ARA’s advocacy.
As a result, the ARA encourages non-members to consider joining the association to support ongoing advocacy efforts.
In the beginning of August, Uniparts O.E.M. welcomed both Preston Chevrolet and Coast Chrysler to the network as the newest dealerships in British Columbia.
In both instances for Uniparts O.E.M., these partnerships underscore the company’s commitment to providing exceptional service and high-quality automotive parts to collision centres across the B.C. region.
“Welcoming Preston Chevrolet, B.C., to our network is a significant step in strengthening our service offerings,” Territory Manager of UniParts O.E.M., Jason Whitbread said. “We are excited about the opportunities this collaboration brings to our valued clients.”
Fix Network Canada has announced a recent partnership with the Vancouver Bandits, having presented the team’s Fan Appreciation Game in July.
“We are thrilled to share the highlights of our recent partnership with the Vancouver Bandits for their Fan Appreciation game on July 18, proudly presented by Fix Auto.”
The social media post further noted that the game saw 4,205 fans in attendance, with a combined broadcast viewership of 18,000.
The game further saw the Bandits securing “an automatic berth to advance to the Western Conference Finals.”
Fix Network Canada concluded that “we are proud to support such vibrant community events and dynamically connect with fans. Thank you to everyone who attended and tuned in!”
CARSTAR Canada has partnered with the B.C. Lions, British Columbia’s Vancouverbased Canadian Football League (CFL) team to support community initiatives.
A recent press release notes that CARSTAR Canada will join the B.C through this partnership. Lions’ commitment to developing life skills for youth through amateur football. With this partnership, CARSTAR Canada has the opportunity to be involved in the B.C. Lions’ amateur football programs; Play with the Pros and Punt, Pass and Kick events.
In June of this year, CARSTAR Canada and the B.C. Lions also kicked off community camps, holding three Play with the Pros camps in Victoria, Kamloops and North Vancouver. Here, according to the press release, “B.C. Lions players were fully engaged in teaching and interacting with the kids, even after a tough game in Winnipeg.”
further
that “partnering
the
Lions represents more than just a collaboration; it’s a commitment to positively impacting our communities. This partnership allows us to extend our impact from the collision repair shop to the field, making a meaningful difference in the lives of young athletes and their communities.”
CARSTAR has announced the grand opening of CARSTAR Sunridge, formerly Sunridge Collision and Glass.
Kaizen Automotive Group, which owns and operates CARSTAR Fort McMurray, CARSTAR Strathmore, Carstar Calgary NE and CARSTAR Calgary Blackfoot (Shaw), will now be operating CARSTAR Calgary Sunridge.
CARSTAR Calgary Sunridge is a 1,486 sq. m. (16,000 sq. ft.) newly renovated facility, equipped to handle repairs for all vehicle types. The shop features two downdraft paint booths, accommodating all lightduty vehicles.
With a team of experienced staff and seasoned technicians, including 18 full-time employees in the centre, CARSTAR Sunridge aims to serve as an excellent training ground for new apprentices entering the trade. Additionally, the shop holds Ford and Nissan certifications and is working to obtain additional certifications in the future.
At the time of the signing announcement, the facility was undergoing renovations set to be complete in the fall.
On July 24, 2024, CSN Harold’s auto body shop in Edmonton revamped the truck of 18-year-old Carter Laframboise, a recent graduate of Sturgeon Composite High School who lives with cystic fibrosis.
The desire to have the truck refurbished was granted to Laframboise through the incredible efforts of Make-A-Wish Northern Alberta.
Bennett Douglas, co-owner of CSN Harold’s, expressed his appreciation to everyone who supported the event.
“Witnessing the joy and impact that Make-A-Wish brings to the lives of wish kids like Carter is truly heartwarming. We are honoured to have been involved with this project along with all the other supporters. It’s this community spirit that helps us make these dreams come true,” he said.
David Chester, technician and manager of a Speedy Glass service centre in Calgary, Alberta has become the first Canadian to win the Best of Belron Competition for auto glass repair and replacement.
The competition, which took place in Lisbon, Portugal from June 12 to 13, saw glass technicians from 30 countries competing in a variety of auto glass tasks.
Chester claimed the title of Best of Belron after excelling in windshield repair, windshield replacement, side-glass replacement and advanced driver safety assistance (ADAS) camera recalibration procedures.
During the competition, each of the four tasks performed by technicians was scored against a grid, including up to 95 steps, alongside measuring several key criteria, including work quality, customer service experience, respect to health and safety protocols and execution speed.
“Winning this title is the result of years of dedication and passion and would never have been possible without the incredible support from my colleagues and peers. It’s an honour to bring this recognition home and to inspire others in our extraordinary community to strive for excellence in their respective field or area of interest. Anything is possible when you set your eyes on a goal and work hard towards it, surrounded by the right people,” Chester concluded in a news release.
The competition, founded in 2002 is held every two years. To qualify for the global event, technicians must first qualify at a national level.
“We have proudly been a part of the CARSTAR team for over three years with reach across many different communities,” said Steve Billings, Director of Collision for the Kaizen Group. “In the time we have been a part of the network, we have felt the incredible support and guidance from the team and look forward to continuing our growth with the brand.”
In a statement, CSN Douglas Repair Groups said that they extend heartfelt thanks to everyone who made this event a success and are looking forward to many more occasions like this in the future. “Together, we can continue to make dreams come true and bring hope to those who need it most.”
Skills Canada has announced that the 2025 Skills Canada National Competition (SCNC) will be held in Saskatchewan for the second time since 2015.
The 2025 competition will specifically be held at the Regina Exhibition Association Limited (REAL) District from May 29 to May 31, 2025. There will be several events happening in conjunction with SCNC 2025. This includes the Skills Showcase featuring First Nations, Inuit and Métis skills, where links between Indigenous knowledge and skilled trades will be highlighted.
In addition, the event will also feature the Empowering Women in Trades (EWIT) space, where young women will be able to meet inspiring women who have pursued a career in the skilled trades.
The skilled trades events will take place over the course of the first two days of the competition with the closing ceremony, where the results of the competition will be announced, will take place on May 31. Here, a Winner’s Circle will also take place where the medalists will be professionally photographed and interviewed.
Shaun Thorson, Chief Executive Officer of Skills/Compétences Canada, commented that “we are pleased to be hosting the Skills Canada National Competition 2025, in Regina. SCNC provides an excellent opportunity to reach thousands of youths across Canada and promote the rewarding and lucrative careers that exist in the skilled trades and technologies.”
Members of the Motor Vehicle Industry of Manitoba were recently thanked by Surdinder Singh, the recipient of this year’s Board scholarship.
Surdinder came to Canada as an international student pursuing an associate arts degree. When Okanagan College introduced him to automotive repair and refinishing, Surdinder swapped programs.
Christine Stanley, manager at CARSTAR Winnipeg St. James, said Surdinder shows qualities beyond an apprentice level and has a strong ethic that accelerates his learning curve.
Allistar Houston, the lead technician at CARSTAR Winnipeg, recognizes Surdinder’s dedication, attention to detail, problem solving and keen ability to learn.
Surdinder Singh addresses members of the Motor Vehicle Industry of Manitoba Board.
Joe Saputo, CARSTAR MSO with now four facilities in the Ontario area, has recently announced the acquisition of CARSTAR Guelph and CARSTAR Oakville East.
Saputo, who was named the 2023 CARSTAR franchisee of the year, has had a longstanding career in the industry. Saputo’s parents, Sam and Rose, were in the first year of owning their own CARSTAR facility when they brought Joe to his first CARSTAR conference as a teenager in 1994. Following this, Saputo worked his way through the industry to owning his first location, CARSTAR Ancaster in Ancaster, Ontario.
“It has been exciting to work with both of the previous owners, Georg and Lorenzo, to understand how they ran their operations and learn more about their teams,” said Saputo. “It’s these exceptional team members that I’ve inherited, from detailers to estimators, that have been the most rewarding. I’m grateful to have received accolades throughout the years, but none of that is truly possible without these hard-working individuals behind the scenes and working so diligently for our customers. I strongly believe we have a tremendous senior and junior workforce at these locations and I’m very proud to now be a part of their teams.”
“It is incredible to see the continued legacy of excellence passed on from star owner-operators to the next generation,” said Dave Foster, SVP of Operations and Development for CARSTAR Canada. “Georg put this facility on the map, and I have no doubts that Joe and his team will continue to meet and exceed expectations. We wish Georg and Lorenzo the best in their next endeavours and can’t wait to follow the success of CARSTAR Guelph and CARSTAR Oakville East.”
The Financial Services Regulatory Authority of Ontario (FSRA) has implemented temporary measures to allow claims adjusters to process insurance claims more quickly, following flash floods that affected the Toronto area at the end of July.
Specifically, the FSRA is temporarily allowing licensed adjusting firms to use claims adjusters licensed outside of Ontario. The FSRA is also allowing Ontario insurers to use the services of employees of affiliated insurers.
Insurers and adjusting firms must also contact the FSRA to confirm the requirements of the temporary measures before proceeding with the changes.
These temporary measures will be in effect until October 31, 2024.
The rainfall that affected the Toronto area saw a month’s worth of water hit the city in 24 hours. Current reports list the effects caused by the storm as over one billion in insured damages.
Polytechnique Montreal students have won two races in the United States, the Solar Grand Prix and the American Solar Challenge, with their self-built solar-powered vehicle.
The vehicle, which took two-and-a-half years to build, specifically won the Electrek Formula Sun Grand Prix and the American Solar Challenge, both of which took place in July. Both races took place at the National Corvette Museum Motorsports Park in Bowling Green, Kentucky.
The Polytechnique Montreal students’ solar-powered vehicle, Esteban 11, is a two-seater with five square metres of solar panels and a battery capable of lasting up to 700 kilometres.
While the vehicle is not roadworthy, participating students see a bright future for the solar-powered tech.
Producing Esteban 11 was not a school project, and the students did not receive credits or compensation for the vehicle.
“The advantage [of a solar-powered vehicle] would be that the sun is always there, you don’t have to pay for it, and it’s always available from wherever you are,” said Polytechnique Montreal student Jalbert-Drouin. “It does feel different than a regular car. For example, there is no power steering, so all the steering needs to be from your arm.”
The Insurance Bureau of Canada (IBC) has released a “One-Year Update Following 2023 Nova Scotia Wildfires and Flooding” report that details that insured losses in the province are now approaching half a billion dollars.
The report specifically highlights the aftermath of two storms that affected the province in the late spring and early summer of 2023. Notably, from May 28 to June 4, 2023, a wildfire ripped through communities in the Halifax Regional Municipality. Then, on July 21, 2023, an atmospheric river event led to significant flooding in parts of Nova Scotia, including Halifax, East Hants, West Hants and Lunenburg and Queens. During this storm, more than 20 centimetres of rain fell in less than 24 hours.
The report further notes that the wildfire event saw a total of 150 automotive claims resulting in $2.28 million in total insured claims costs; with the average claims cost coming in at around $15,200.
Comparatively, when looking at the effects of the flooding, in total there were approximately 660 auto claims resulting in $12 million in total insured claims costs; with the average claim cost coming in at around $18,300.
The study concludes that ultimately, “we are now living in a world where large loss insurance events should be expected almost yearly,” and that despite the progress being made in Nova Scotia to recover from the 2023 storm events, extreme weather patterns in the area are expected to become more and more common.
Honda recently released a document outlining its 2024 environmental social governance (ESG) plans for increased recycling efforts for future products and parts. Honda claims it wants to “take on the challenge” in shifting to a recycling-oriented business that creates economic value while reducing the consumption of natural resources. The OEM said it is committed to creating a recycling-centric ecosystem which includes selecting materials suitable for recycling, easy disassembly and separation to enable the stable procurement of “high-quality recycled materials.” Honda has already taken steps to introduce recycled PET in the interior of its N-VAN light vehicles.
Alberta is expanding its recycling program with the long-term goal of recycling electric vehicle batteries. The updated recycling program, which will begin to be phased in April 2025, will start by accepting power tools, lawn and garden equipment, small appliances and household electronics. The Alberta Government made an announcement at the Edmonton Waste Management Centre detailing that it will further contribute a $250,000 investment to install an AI-powered X-ray system at the centre that will scan and identify material for hazardous waste, such as embedded batteries.
Trent Hardin has assumed executive directorship of the Alberta Automotive Recyclers and Dismantlers Association (AARDA) and will assume direct responsibility for AARDA members’ Canadian Auto Recyclers Environmental Code (CAREC) audits in Alberta. Hardin has spent 40 years in industrial operations in Alberta—starting with Syncrude in 1984 through computer chip manufacturing, industrial coatings, purchasing for major fabrication projects and rail transload. Along the way, Hardin has spent stints in retail, non-governmental organizations and service sectors, as well as some time as an infantry reservist. He is also a National Construction Safety Officer (NCSO) and has had extensive training in hazardous materials, from Workplace Hazardous Materials Information System (WHMIS), through TDG and HAZMAT response, to DG derailment response.
Australia’s federal government has been discussing the possibility of introducing a “passport” for EV batteries following concerns that the nation’s battery recycling industry may not be ready for an increase in battery waste. Battery passports are unique identification numbers linked to a vehicles’ VIN and could provide information like where the EV battery’s materials come from, who was involved in the power pack’s production throughout the supply chain, and more. According to a report from the Australian Associated Press, battery passports could allow for packs to be labelled for streamlining purposes and safe handling at the end of life. Representatives in Australia’s recycling and automotive industries have voiced their concerns about the situation, suggesting the federal government may have as little as six years before the issue of EV batteries and the end-of-life processing becomes a significant challenge. EVs account for about eight percent of new vehicle sales in Australia.
Tow operators in Northern Ontario have reported complications with the new industry requirements imposed on July 21, 2024, that require service testing not readily available in the region. The issue, according to Northern Ontario tow operators, is that there are currently only two authorized training providers in Ontario and one of them—CAA Club Group—only allows those in its contracted network to register for the course. These operators claim the training courses do not have the capacity to cover all of Ontario. Ontario’s Ministry of Transportation issued a statement that “this is an application-based program and currently no service providers located in the north have applied.” However, the Ministry expects that in future, more courses will become available as demand continues to increase.
In recognition and tribute to all those tow operators injured or lost their lives in the line of duty, the Professional Towing Association of Ontario (PTAO) held its second memorial scholarship procession on September 14, 2024, from 7 a.m. to 9 a.m. The event took place before the PTAO Tow Show opened for the day. The procession began at Guelph line and finished at the Bingemans Centre in Kitchener, Ontario. Following the procession, a formal dedication was made in addition to scholarship announcements meant to advance the training, education and professionalism in the towing industry.
By ALLISON ROGERS
What is accountability? I recently ran into a statistic online that suggested a startling 80 percent of people understand accountability in the workplace to be synonymous with punishment. Accountability, when you look up the definition of the word, is “the obligation or willingness to accept responsibility or to account for one’s actions.” That could sound ominous, to some. But to see that 80 percent of people believe accountability in the workplace to equal punishment suggests there’s something deeply flawed with everyone’s understanding of the word. Accountability is not a negative thing. Doesn’t it feel nice when you’re praised by someone for a job well done? That’s accountability; the complimenter gives the roses of accountability to
the kind of accountability that produces results. Creating a culture of open communication is essential. Feedback should be constructive and always aimed at behaviors and actions rather than personal criticism. Avoid pointing blame with statements like, “you always do this!” and instead address the action causing the problem. People need to understand their areas for improvement without feeling attacked to foster a willingness to improve, ultimately embracing accountability.
Mistakes must be viewed as learning opportunities. No one should ever be singled out for a mistake or made to feel stupid for not understanding. When individuals know they can learn from setbacks and won’t be made to feel silly for a screw-up or simple question, they’re more likely
the complimentee. But nowadays the small and medium-sized wins are so rarely appreciated that accountability has become a terrifying word—a word on a new employee contract promising you’ll be called out for every single thing you do wrong.
You can argue that the “big wins” are always celebrated. But when big wins become common, people will start to forget them. Many leaders are guilty of ignoring a win if it is even marginally smaller than the last. Every win must be grander if you want to ensure a pat on the back for your efforts.
That’s how accountability has become linked to blame, rather than constructive feedback, consistent betterment and praise. We’ve lost sight of true accountability—the type that inspires a team to work together to find solutions to any hiccups; to strive to be the best they can be, because they know they’re appreciated and that they will reap the rewards of their efforts. The type of accountability that acts as roots for positive work culture;
to engage in accountable behaviors without fear of punitive repercussions.
Most importantly—leaders play a vital role in shaping culture. By demonstrating accountability in their own actions—acknowledging mistakes and taking responsibility—leaders set a positive example for their teams. When leadership practices accountability, it encourages others to follow suit, reinforcing a shared commitment to personal responsibility.
In a culture where accountability is viewed positively, individuals are more likely to take initiative, learn from their mistakes and collaborate effectively. This shift not only enhances individual performance but ultimately drives organizational success. Worth a shot, right?!
As we move forward, let us commit to redefining accountability as a pathway to improvement, cultivation and excellence. In doing so, we can create workplaces that are not only productive but also enriching, where every individual feels empowered to own their journey.
With a waterborne basecoat that’s easy to mix, match and apply and that uses the same coat flash application you’ve already perfected, Cromax® EZ makes an exceptional finish feel effortless. Discover how easy an outstanding finish can be.
axalta.us/ez