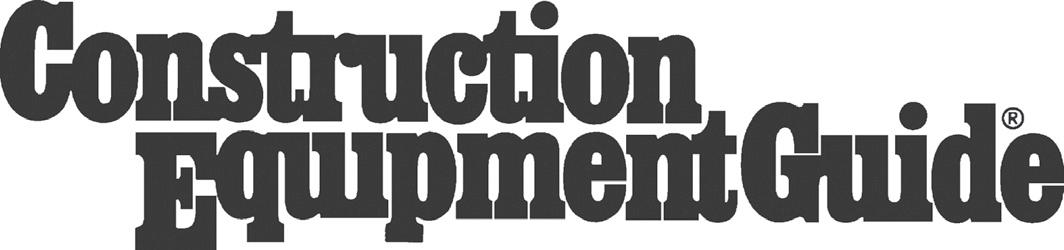
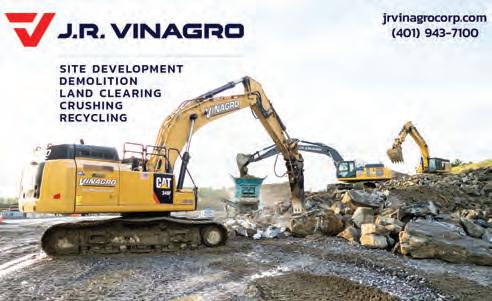
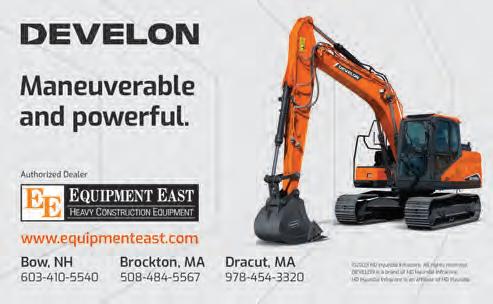
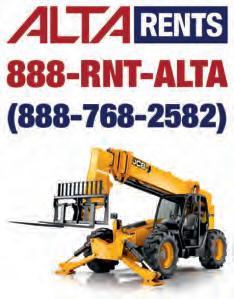
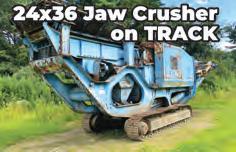
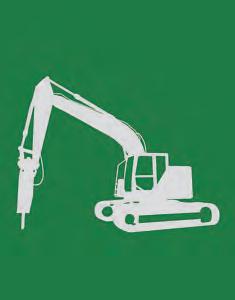
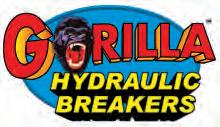

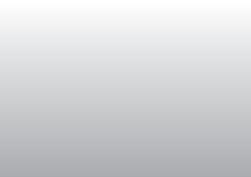

Fifteen years ago, in the town of Bradford, Vt., Adam Longto laid the foundation of what would become a thriving tree service company. Growing up with a natural affinity for hands-on work, Longto began his career in carpentry straight out of high school. However, it was his side hustle with his father — performing tree work on evenings and weekends — that planted the seed for what would later flourish as Longto Tree Service.
Longto’s decision to pursue tree work fulltime wasn’t immediate. Over time, the repetitive nature of carpentry began to wear on him, and the allure of the outdoors, combined with the satisfaction of tree work, became too strong to ignore. Taking a leap of faith, he set out on his own with minimal equipment, but an abundance of determination.
In the early days, Longto Tree Service was truly a grassroots operation. Longton relied on basic climbing gear and a simple dump trailer to handle jobs. Every branch, every log, was loaded by hand — a labor-intensive process that underscored his commitment to building the business from the ground up. There was no
Buildings cost a lot these days, but when concrete buildings are being constructed, there is another material that can make them less expensive: mud.
Researchers at the Massachusetts Institute of Technology (MIT) in Cambridge have developed a method to use lightly treated mud, including soil from a building site, as the “formwork” molds into which concrete is
poured. The technique deploys 3D printing and can replace the more costly method of building elaborate wood formworks for concrete construction.
“What we’ve demonstrated is that we can essentially take the ground we’re standing on, or waste soil from a construction site, and transform it into accurate, highly complex and flexible formwork for customized concrete
structures,” explained Sandy Curth, a PhD student in MIT’s Department of Architecture who has helped spearhead the project. He told MIT News that the approach could help concrete-based construction take place more quickly and efficiently, as well as reduce costs and carbon emissions.
“It has the potential for immediate
SENNEBOGEN, in kee philosophy to maxim created UPTIME Kits
eping with their mize uptime, has Whether you are a service technician i road, these kits have need for every service and PM task in one p created to save you t Managing hundreds o parts, from belts and and special tools bec single part number to n-house or on the everything you e, maintenance place. They were ime and money.
They are:
• Easy to order and ea t d t ockst asy to s l dow NO I th Norour intspar om c with omerscust
• Ideal for stocking se and trucks
Choose from the follo
• Central lubrication
• Preventive mainte
• O-Ring kits
• Electrical service k
• Hydraulic service k
Hydraulic service k : kits shops ols ervice owing kits system kits nance service kits its kits
And the best thing is in stock and ready to built to match your m and series. Count on
in-house. For more in UPTIME Kits, scan th
s that these kits, go, are custommachine model SENNEBOGEN nformation on he QR code.
e orf ) OCT(Ownership of
of related service d nuts to O-Rings omes easy with a o order and stock C OND YBE E H HE HIN T MA virtua lI entim lose llyt
xim ma ommitmentc h about e morad ontract Demolition C parepairtsinsthavether andvirtuinanothermachineI onttoback.If very e ctomehavea Theyechnician machine, wntim w American o-shiptady- of oriesinventplete orf uptime izes aftersale achine”M he yond “Beour ow , Bloomfield Hills, MI or theunitbackquickly. kIg losedonoSinctheey ally Ihaveasituation,[they]bringjust ogooverthroncougheamontht wntime… ock.get theSENNEBOGEN y-t t act OGEN f tor ained technicians tr ned tec cians components and too
The Maine Department of Transportation (MaineDOT) shifted westbound traffic on U.S. Highway 202/Western Avenue in Augusta to a temporary bridge on Jan. 25 as part of the ongoing work to replace the route’s former road bridge over Interstate 95.
The shift was done so that MaineDOT crews could demolish the existing structure and continue construction of a new bridge to carry Western Avenue traffic over I-95 at Exit 109. The state agency’s plan calls for vehicles to continue using the temporary structure until the new permanent bridge is fully built and opened.
As the project’s contractor, Reed & Reed Inc. in Woolwich, Maine, is allowed 11 months to complete the bridge construction. MaineDOT noted that the contract amount for the job is approximately $30 million.
As the project’s contractor, Reed & Reed Inc. in Woolwich, Maine, is allowed 11 months to complete the bridge construction. MaineDOT noted that the contract amount for the job is approximately $30 million.
Crews also will be closing the left-hand turn lane from Western Avenue onto Whitten Road at the intersection of the two streets. Westbound drivers who want to access Whitten Road can use the southbound interstate on-ramps to access the new connection between the interstate on-ramp and Whitten.
Traffic on Western Avenue will be narrowed to one eastbound lane and one westbound lane, with a third lane on the bridge specific to the westbound off-ramp traffic. Vehicles will continue to use the temporary bridge until the new permanent bridge is constructed and opened at the end of 2025.
At approximately 70 years old, the existing Western Avenue bridge, according to MaineDOT, is structurally deficient and has deteriorated to the point that the end of its useful life is near. It will be replaced by a new structure on a similar alignment with a two-span steel girder with a concrete bridge deck structure and concrete substructure units found on bedrock.
The state agency noted that the new overpass also will provide additional vertical clearance over I-95 to help avoid over-height vehicle strikes.
As part of the overall project, crews also will work to build new sidewalks, in addition to reconstructing old walkways — in all, approximately 1,350 ft. long — along Western Avenue and Whitten Road. By doing so, the state will achieve its goal of connecting pedestrian access along both sides of each respective roadway to create significantly safer access through the area.
On-site construction for the Augusta project first began in November 2023. MaineDOT has said that the entire Western Avenue corridor work is slated to be completed in June 2026.
A new Salmon Falls Bridge over the Saco River in Maine, on U.S. Highway 202 between Buxton and Hollis, is expected to be built in 2026.
Paul Merrill, a MaineDOT spokesperson, confirmed that the new bridge will be a full replacement. The current 26-ft.wide structure on the heavily traveled truck route was built 77 years ago.
“We’re planning to put the bridge replacement construction contract out to bid later this year — likely October,” Merrill said recently in an email to the American Journal, a weekly newspaper covering the Maine towns of Buxton, Gorham, Westbrook and the surrounding region south of Portland.
He expects the project to start and end during the 2026 construction season.
Julie Brask, a MaineDOT senior project manager, said in an email to the American Journal Jan. 22 that the rebuild would detour traffic from U.S. 202 to Maine Highway 4A through the village of Bar Mills.
“During the detour, temporary traffic signals will be in place at two locations along the detour route — one at the intersection of Route 4A and Route 117, and the other at the intersection of Route 4A and Route 112,” she noted.
The anticipated total cost of the replacement bridge has risen from $8 million last January to $10.4 million one year later, the Journal learned.
MaineDOT engineers determined that the Salmon Falls Bridge was determined in poor condition and too narrow for bicycle and pedestrian use.
Brask said plans for the new structure call for it be 32 ft. wide “curb-to-curb,” with two 11-ft. travel lanes and 5-ft. shoulders.
Devan Eaton, a former bridge project manager for MaineDOT, told the American Journal that the new design will be for a clear span without the need for piers in the river.
Additionally, he said its railings will be designed to be taller than the present 3-ft. height in part to discourage daredevil youth from jumping from the bridge to the water below.
A major educational building under construction in Portland draws inspiration from a nearby coastal Maine icon: the historic Cribstone Bridge between Orr’s and Bailey islands.
Northeastern University’s Roux Institute held a design contest for the Alfond Center on its new, $500 million Portland campus. The design needed to embody what is special about Maine, leading the CambridgeSeven architecture firm in Massachusetts to the historic span that connects the two islands near the small town of Harpswell.
Tim Mansfield, president of CambridgeSeven, told the Harpswell Anchor that his firm has known about the Cribstone Bridge for many years and felt inspired by the structure’s innovative design and its use of local materials, such as Yarmouth granite.
Built in 1928, the two-lane Cribstone Bridge — also known as the Bailey Island Bridge — carries traffic traveling north and south along Maine Highway 24 over Will’s Gut, a strait separating the two islands.
Its unique architecture employs an unusual cribwork of granite slabs to adapt to the conditions in the channel, allowing swift tidal currents to flow through the structure. The bridge is one of two of its kind ever constructed and the only one left in the world, the Anchor reported Feb. 1.
“The Cribstone Bridge is a wonderful icon in the state, and the fact that it has survived and performed beautifully over the years was very influential to us,” Mansfield said. “It embodied so much of what we were very interested in and cared about.”
David and Barbara Roux, founders of the Roux Institute, selected CambridgeSeven’s design as the winning submission. The Rouxs, who have a home in Harpswell, previously worked with the Cambridge, Mass.-based firm to design the Roux Center for the Environment at Bowdoin College.
Northeastern University’s main campus is located in Boston. Its Roux Institute is a graduate program created to “educate generations of local talent for the digital, artificial intelligence, and life sciences sectors, and drive sustained economic growth in northern New England,” according to Northeastern Global News.
When it opened in 2020, Portland’s Roux Institute leased space in the Wex building on Fore Street. The new campus will be on the site of the former B&M Baked Beans plant on the east side of the city.
Mansfield said the Cribstone Bridge’s influence will “come alive” in the design for the 245,000-sq.-ft. Alfond Center in both a physical and metaphorical way. The building borrows its name from the Harold Alfond Foundation, a major supporter of the project.
“We took the idea of the bridge metaphorically, as the institute is bridging technologies, bridging education, all the notions of bridging in that form,” he said.
One of the Alfond Center’s design features is an opening called “The Portal” that reflects the opening in the Cribstone
see ROUX page 8
Equipment East has = job the compact machine to ell do w one.
ork modes pl and w us one of the highest
ROUX from page 4
Bridge. In Portland, The Portal will become a gathering space with seating, as well as a place for lectures, conferences, meetings, and more.
In addition, Mansfield described the Alfond Center’s “curvilinear” design as “billowing out to Casco Bay.”
The building itself will include “computational academic spaces, life science labs, and advanced active-learning classrooms,” according to Boston Real Estate Times, and another structure will serve as an incubator for young companies, as well as a coastal path, parking garage, child care center, and green space.
Mansfield added that the Alfond Center will be all-electric, with power coming from geothermal wells, and said it is “absolutely paramount” that its design is sustainable.
To that end, the building will incorporate a three-story section built with mass timber, an emerging sustainable construction material. And, like the Cribstone Bridge, it will use Maine granite — in this case, Freshwater Pearl granite quarried in Frankfort, a town on the Penobscot River in Waldo County.
Construction broke ground at the Portland site this past September and is expected to be complete by Fall 2027.
The first step has been constructing the geothermal wells and the foundation, which is the hardest part, Mansfield said. Next, steel will begin to rise, and the building will take form.
“Portland is a vibrant, forward-looking city with this amazing history, [and] we don’t want to lose the history at all, but we also want to embrace the future,” he explained. “The Roux Institute is bridging that, which is another relationship to the Cribstone Bridge. We’re bridging the past to the future.”
CONCRETE from page 1
impact and doesn’t require changing the nature of the construction industry,” said Curth, who doubles as the director of the Programmable Mud Initiative.
He also has co-authored multiple papers about the method, most recently, “EarthWorks: Zero Waste 3D Printed Earthen Formwork for Shape-Optimized, Reinforced Concrete Construction,” published in the journal Construction and Building Materials. Curth wrote that paper with nine co-authors, including Natalie Pearl, Emily Wissemann, Tim Cousin, Latifa Alkhayat, Vincent Jackow, Keith Lee and Oliver Moldow, all MIT students; and Mohamed Ismail at the University of Virginia.
The study’s final two co-authors are Lawrence Sass, professor and chair of the Computation Group in MIT’s Department of Architecture, and Curth’s graduate advisor; and Caitlin Mueller, an associate professor at MIT in both the Department of Architecture and the Department of Civil and Environmental Engineering.
Constructing wooden formwork for a building is costly and time-consuming. There is a saying in the industry that concrete structures have to be built twice — once through the wooden formwork, then again in the concrete poured into the forms.
Using soil for the formwork could change that process, MIT News reported Jan. 24.
While it might seem like an unusual material compared to the solidity of wooden formwork, soil is firm enough to handle poured concrete. The EarthWorks method, as it is known, introduces some additive materials, such as straw, and a
wax-like coating for the soil material to prevent any water from draining out of the concrete. Using large-scale 3D printing, MIT researchers can take soil from a construction site and print it into a custom-designed formwork shape.
Beyond the low cost and ease of acquiring the materials, the method offers at least two other interrelated advantages.
One is environmental: Concrete construction accounts for as much as 8 percent of global carbon emissions, and this approach supports substantial emissions reductions, both through the formwork material itself and the ease of shaping the resulting concrete to only use what is structurally required.
Using a method called “shape optimization,” developed for reinforced concrete in previous research by Ismail and Mueller, it is possible to reduce the carbon emissions of concrete structural frames by more than 50 percent.
“The EarthWorks technique brings these complex, optimized structures much closer to reality by offering a lowcost, low-carbon fabrication technique for formwork that can be deployed anywhere in the world,” Mueller said in speaking with MIT News.
Curth added, “It’s an enabling technology to make reinforced concrete buildings much, much more materially efficient, which has a direct impact on global carbon emissions.”
More generally, the EarthWorks method allows architects and engineers to create customized concrete shapes more easily due to the flexibility of the formwork material. It is simpler to cast concrete in an unusual shape when molding it with soil, not wood.
As he noted, the projects developed by the Programmable
Mud group are highly collaborative.
Curth emphasized the roles played by both Sass, a leader in using computation to help develop low-cost housing; and Mueller, whose work also deploys new computational methods to assess innovative structural ideas in architecture.
“Concrete is a wonderful material when it is used thoughtfully and efficiently, which is inherently connected to how it is shaped,” noted Mueller. “However, the minimal forms that emerge from optimization are at odds with conventional construction logics. It is very exciting to advance a technique that subverts this supposed tradeoff, showing that performance-driven complexity can be achieved with low carbon emissions and low cost.”
While finishing his doctorate at MIT, Curth has also founded a company, FORMA Systems, through which he hopes to bring the EarthWorks method into the construction industry. Using this approach does mean builders would need to have a large 3D printer on-site; however, they would also save significantly on the costs of materials, he said.
Further into the future, Curth envisions a time when the method could be used not just for formworks, but — as an example — to construct templates for two-story residential buildings made entirely out of earth. Of course, some parts of the world, including the United States, extensively use adobe architecture already, but the idea here would be to systematize the production of such homes and make them inexpensive in the process.
The mud formwork project was supported in part by the Sidara Urban Research Seed Fund administered by MIT’s Leventhal Center for Advanced Urbanism.
Monroe Tractor has hired Robert (Rob) Willmore as its newest product support representative in southern Connecticut.
Willmore brings a wealth of experience in parts and service and a strong dedication to customer satisfaction. With seven years in the industry, he has helped many customers with his exceptional service and creative solutions. He looks forward to using his experience and insight to go above and beyond for Monroe Tractor customers, the company said.
“I am here to make sure every customer is beyond satisfied at the end of the day,” said Willmore. “I’m going to work hard to make your job easier.”
Willmore will cover Southern Connecticut — including Fairfield, New Haven, Middlesex and New London counties.
Matthew Denehey, branch manager, said “Rob’s extensive knowledge and hands-on experience in the indus-
try will be invaluable as he supports our customers with exceptional service and solutions. Rob’s commitment to excellence and his proactive approach
addition to
LONGTO from page 1
chipper in those first months; a stark contrast to the advanced equipment he would later acquire.
Despite these challenges, Longto’s dedication and work ethic began to pay off. Within the first year, he made his first significant investment — a farm tractor equipped with a winch and grapple. This marked the beginning of a series of upgrades that would not only enhance efficiency but also set the stage for Longto Tree Service to grow into a trusted name in the Northeast.
By the six-month mark, Longto added his first chipper to the arsenal, signaling a turning point for the company. Each year brought new equipment and capabilities, reflecting Longto’s philosophy of reinvesting in his business. From climbing trees manually to employing advanced hydraulics, the company evolved rapidly.
The journey wasn’t just about acquiring equipment; it was about refining the service model. Longto Tree Service expanded its offerings to include not just tree removal and trimming but also land clearing, field edge maintenance and more. The addition of tools like the CMC spider lift and miniexcavators further diversified the company's capabilities, enabling them to tackle both small, routine jobs and larger, more complex projects.
Throughout its growth, Longto Tree Service remained deeply connected to the local community. Operating primarily within a 30- to 40mi. radius of Bradford, Vt., the company became a trusted partner for homeowners and businesses alike. From Orange County to neighboring areas like Hanover and Lebanon, Longto and his team built their reputation on reliability, quality and a personal touch.
Today, Longto Tree Service runs with a dedicated crew of five.
Longto’s company now boasts a growing arsenal of machinery, including a mini-excavator with a grapple for daily tasks and a track lift for specialized trimming and removals. Recently, Longto turned to Robert Finke & Sons, a heavy equipment dealer who had just expanded from Selkirk, N.Y., and added a Colchester, Vt., location.
His first purchase from Finke was a Kobelco ED-160 BladeRunner, a machine equipped
with a six-way dozer blade, a larger undercarriage and various attachments, including a Rotobec grapple saw and an Indeco mulching head.
The Kobelco BladeRunner has become a cornerstone of Longto Tree Service’s operations. Its smooth hydraulics and
see LONGTO page 16
Each December, a poignant tradition takes place across the United States, bringing together communities to honor the men and women who have served in the military.
Wreaths Across America, an organization founded in 2007, has grown into a nationwide movement, placing wreaths at the graves of fallen soldiers to ensure they are remembered and celebrated for their sacrifice.
The story of Wreaths Across America began in 1992 when Morrill Worcester, owner of a wreath company in Maine, took an unexpected journey that would spark a movement. While visiting Arlington National Cemetery, he was struck by the sight of graves stretched out before him, each one holding a life lost in service to the nation. He immediately felt a connection and promised himself that he would find a way to honor them.
In 1992, Worcester sent a shipment of wreaths to Arlington, placing them at the headstones of the soldiers. The gesture was quiet and powerful, with no fanfare or media, just a simple act of remembrance. What began as a small personal tribute
quickly gained attention as others saw the meaningful symbol of respect that the wreaths represented. By 2007, the idea had grown into Wreaths Across America, a national initiative aimed at remembering, honoring and teaching about the sacrifices made by U.S. military personnel. The organization’s mission became clear: “Remember, Honor, Teach.”
Today, Wreaths Across America is a nationwide event that touches every corner of the country. Thousands of volunteers, families, veterans, active-duty military members and community members gather to place wreaths on veterans’ graves at more than 2,500 cemeteries across the United
Robert H Finke & Sons in Selkirk, N.Y., made a commitment to support Wreaths Across America by providing the services of its Kenworth T880 truck, which has a special paint job commemorating the horrific events of 9/11.
States. What started as a few wreaths going to Arlington National Cemetery has expanded to a heartfelt tribute in every state, with wreath-laying ceremonies in places like Florida, California, and even at overseas
military cemeteries.
This past December, Robert H Finke & Sons in Selkirk, N.Y., made a commitment to support Wreaths Across America by providing the services of its Kenworth T880 truck, which has a special paint job commemorating the horrific events of 9/11.
According to Don Fiacco, general manager of Robert H Finke & Sons, “On December 8 [2024], it was our honor to make available to Wreaths Across America our truck and the services of Richard Boice Jr, driver of MV911 with more than 20 years of service at Robert H. Finke & Sons. Rich traveled from our location in Selkirk to the Wreaths Across America facility in Columbia Falls, Maine, where he picked up 16 pallets and three boxes of wreaths, totaling 3,492 wreaths. We spent the following Tuesday delivering wreaths all across Connecticut.”
Robert H Finke & Sons has followed the Wreaths Across America mission for a number of years and have never been so honored as to have been a part of serving this nonprofit organization, the company said. (Photos courtesy of Robert H Finke & Sons.)
LONGTO from page 14
incredible pushing power make it suitable for diverse tasks, from clearing field edges and house lots to tackling land-clearing projects, Longto said, adding that he particularly appreciates the six-way blade, which allows for leveling uneven terrain — a crucial feature in the tree service industry where flat ground is rare.
The grapple saw, purchased from Finke, is another key tool. While it isn’t specifically designed to fell trees, Longto uses it to handle smaller trees, push over larger ones and separate stumps and logs for efficient processing. The saw’s rugged build allows it to withstand demanding tasks, making land clearing faster and easier.
The Indeco mulching head, an Italianmade attachment also acquired from Finke, complements the grapple saw. Designed to handle small trees and brush, it enables Longto’s team to mulch directly on-site, saving time and resources compared to chipping. Although not as common in the Northeast, mulching heads have proven to be a valuable addition to Longto Tree Service’s equipment lineup.
Longto’s experience with Robert Finke &
Sons began at the Northern Logger show, where he met Don Fiacco, general manager. Longto said working with Fiacco has been “an overwhelmingly positive experience.” From the initial purchase process to the customization of attachments, the team at Finke demonstrated exceptional dedication and attention to detail, he said.
For example, when setting up the grapple saw, Finke’s technicians spent many hours ensuring that every aspect — rotation, open/close mechanisms and other controls — aligned perfectly with Longto’ preferences. Their willingness to adapt and accommodate unique requests made the experience seamless, Longto said.
Longto values the reliability and performance of the equipment he purchased from Finke. The Kobelco BladeRunner, in particular, has exceeded expectations, offering a combination of power, versatility and operator comfort that simplifies daily operations. The equipment’s durability and functionality have not only improved efficiency but also reduced wear and tear on smaller machines, allowing Longto Tree Service to take on larger projects without compromising quality.
The service and support from Finke have
been equally remarkable. Longto praised its responsiveness, noting that any issues are addressed promptly and professionally. With its new Vermont facility just an hour and a half away, Finke has become an invaluable partner in Longto Tree Service’s continued success.
Longto has taken a significant step forward in safety and efficiency by incorporating the Mecanil 280 grapple saw into his operations. This advanced piece of equipment has transformed the way he and his team approach tree cutting and removal.
The Mecanil 280 grapple saw, mounted on a 2021 Western Star truck with a Copma 650 crane, boasts an impressive 112 ft. of reach. This setup allows Longto to perform high cuts and handle large trees with ease, all while operating the saw remotely from the ground using a radio remote control. This remote operation eliminates the need for climbers in trees or workers in buckets, significantly enhancing safety and efficiency.
Longto’s choice of the Mecanil 280 G2
model was driven by its superior capabilities. The grapple saw features a 25-in. bar, enabling it to cut through substantial tree limbs quickly and safely. The combination of a high-powered chainsaw and a robust grapple ensures that limbs can be lowered to the ground in a controlled manner, reducing the risk of accidents and damage.
The benefits of the Mecanil grapple saw extend beyond safety. Longto has found that the equipment allows his team to complete jobs faster and with greater ease. The grapple saw has become a primary tool for Longto Tree Service, enabling it to execute the same scope of work more efficiently. This increased productivity has not only improved job turnaround times but also expanded the range of services they can offer.
Longto’s investment in the Mecanil grapple saw, the Kobelco ED-160 BladeRunner and the Indeco mulching head reflects a broader trend in the tree service industry toward adopting advanced technology to enhance safety and efficiency.
For more information, visit www.longtotreeservice.com. CEG
(All photos courtesy of Longto Tree Service.)